氨合成
氨的合成化学方程式

氨的合成化学方程式
摘要:
1.氨的合成反应方程式
2.氨的合成反应的原理
3.氨的合成反应的实际应用
正文:
氨的合成化学方程式为:N2 + 3H2 -> 2NH3。
这个方程式表示,在适当的条件下,两个氮原子(N2)和三个氢原子(H2)可以结合成为两个氨分子(NH3)。
氨的合成反应的原理是,氮气和氢气在高温、高压和催化剂的作用下,发生化学反应生成氨。
这个反应过程通常采用铁触媒作为催化剂,其活性高、稳定性好、成本低,是氨合成反应的理想催化剂。
氨的合成反应的实际应用非常广泛。
氨是制造肥料的重要原料,是生产氮肥的主要成分。
此外,氨还是制造塑料、树脂、染料、药品、炸药等的重要原料。
合成氨工作原理

1.氨合成的基本原理氨是由气态氢和氮在氨触媒的作用下反应生成的,其反应式为:3H2+N2=2NH3+热量这是一个可逆、放热、体积缩小的反应,对其反应机理存在着不同的观点,一般认为:氮在铁催化剂上被活性吸附,离解为氮原子,然后逐步加氢,连续生成NH、NH2和NH3。
即:N2(扩散)→2N(吸附)→2NH(吸附)→2NH2(吸附)→2NH3(脱附)→2NH3(扩散到气相)由质量作用定律和平衡移动原理可知:1.温度升高,不利于反应平衡而有利于反应速度。
2.压力愈高愈有利于反应平衡和速度。
3.氢氮气(比例3:1)含量越高越有利于反应和速度。
4.触媒不影响反应平衡,但可以加快反应速度。
2、温度对氨合成反应的影响氨合成反应是一个可逆放热反应。
当反应温度升高时,平衡向着氨的分解方向移动;温度降低反应向着氨的生成方向移动。
因此,从平衡观点来看,要使氨的平衡产率高,应该采取较低的反应温度。
但是从化学反应速度的观点来看,提高温度总能使反应的速度加快,这是因为温度升高分子的运动加快,分子间碰撞的机率增加,同时又使化合时分子克服阻力的能力加大,从而增加分子有效结合的机率。
总之,温度低时,反应有利于向合成氨的方向进行,但是氨合成的反应速度较低;提高温度不利于向氨的合成方向移动,但反应速度可以增加。
在实际生产中反应温度的选择主要决定于氨合成催化剂的性能。
3.压力对氨合成反应的影响氨的合成反应是一个分子的氮与三个分子的氢结合生成两个分子的氨,即氨合成反应是分子数目减少、体积缩小的反应,提高压力,可使反应向着生成氨的方向进行。
对于氨合成反应来说,提高压力就是提高反应气体的浓度,从而增加反应分子间碰撞的机会,加快了反应的速率。
总之,增加压力对氨的合成反应是有利的,既能增大平衡转化率,又能加快反应速率。
但压力也不宜过高,否则,不仅增加动力的消耗,而且对设备和材料的要求也较高。
根据我国具体情况,目前在小型合成氨厂,设计压力一般为31.4MPa。
第二章(3):氨的合成

3 H2 2 NH 3
p k2 p
2 NH 3 3 H2
1
式中k1、k2分别为正逆反应的速率常数, rNH3为过程的瞬 时速率;为实验常数,视催化剂性质及反应条件而异, 工业条件下对工业铁催化剂一般 0.5。
17
1.4.2.2 反应机理与动力学方程
p1.5 H2 r k1 pN 2 pNH 3 pNH 3 k2 p1.5 H2
(1.4.12)
上式只适用于压力较低的的接近平衡的情况,压力较高时,
要用实验得出的速率常数与压力的关系加以校正。另外,当 反应远离平衡时上式不成立,例如pNH30时r 。捷姆金 还推出了远离平衡时的动力学方程:
16
1.4.2.2 反应机理与动力学方程
1939年捷姆金和佩热夫根据上述机理,提出几点假设: ①氮的活性吸附是反应速率的控制步骤;②催化剂表面很 不均匀;③吸附态主要是氮,吸附遮盖度中等;④气体为 理想气体,反应距平衡不很远。由此推导出本征动力学方 程式为:由此机理导出的动力学方程为
p r k1 pN 2 p
实际生产不可能无限增加空速,空速大系统阻力大,功耗 增大。另外,新鲜气量一定时,空速增大只能通过增加循 环气量来实现,循环气量过大,除了上述功耗原因外,还 使单位循环气产氨量下降,从而使气体温升下降,产生不 能维持“自热”的问题。一般空速值为:30MPa 2000030000h-1 15MPa 10000h-1
第八节 氨的合成
一、基本原理 二、氨合成催化剂 三、工艺条件选择 四、氨的分离 五、氨合成塔 六、生产总流程 七、我国合成氨生产装臵现状
1
一、基本原理
1.4.1 氨合成反应的热力学基础 1.4.1.1 化学平衡 氨合成反应如下: 1.5H2(g) + 0.5 N2(g) = NH3(g) +46.22kJ/mol 该反应为放热反应,其平衡常数为
合成氨生产工艺流程

博健软件
二、氨合成工艺流程
由于压缩机型式、操作压力、氨分离折 冷凝级 数、热能回收形式以及各部分相对位置的差异, 氨合成工艺流程也水相同。操作压力在 600~100MPa称高压法,在20~40MPa称中压法。 大10MPa左右称低压法。中压法氨合成的工艺 流程,在技术和泾济上都比较优越,因此目前 国内外普遍采用中压法。
将某种催化剂在一定成产条件下具有最高氨生 成率的温度称为最适宜的温度。
最适宜温度还和空间速度、压力等有关 经生产实践得出氨合成操作温度控制在
470~520度较为适宜。 三、空间速度 当操作压力、温度及进塔气组成一定时,空速
增加,氨净值降低。由于氨净值降低的程度比 空间速度的增大倍数少,所以空间速度增加时 氨合成生产强度有所提高及氨产量有所增加。
第博健软一件 节 氨合成的基本理论
一、氨合成反应的特点
3H2+N2=2NH3+Q
(1)是可逆反应。即在氢气和氮气反应生成氨的
同时,氨也分解成氢气和氮气。
(2)是放热反应。在生成氨的同时放出热量,反 应热与温度、压力有关。源自 (3)是体积缩小的反应。
(4)反应需要有催化剂才能较快的进行 。
博健软件
博健软件
(三)催化剂
可以作氨合成催化剂的物质 很多,如铁、铂、锰、钨和铀 等。但由于以铁为主体的催化 剂具有原料来原广,价格低廉, 在低温下有较好的活性抗毒能 力强,使用寿命长等优点 、 广泛采用。
博健1软. 件催化剂的预还原 为了使合成氨系统在短时间内投入
生产,将铁催化剂在合成塔外预先 进行还原,即所谓催化剂的预还原。
(6)为内扩散过程; (3)、 (4)和(5)总称为化学动力学 的过程。
氨合成反应原理

结论:根据平衡移动规律可知,降低温度,提高压力, 有利于平衡向生成氨的方向移动。
氨合成影响因素
平衡氨含量:
(2)平衡氨含量 反应达到平衡时氨在混合气体中的百分含量。
1· 温度和压力的影响
温度/℃
350 380 420 460 500 550
压力/MPa
0.101 0.84% 0.54% 0.31% 0.19% 0.12% 0.07% 10.13 37.86% 29.95% 21.36% 15.00% 10.51% 6.82% 15.20 46.21% 37.89% 28.25% 20.60% 14.87% 9.90% 20.26 52.46% 44.08% 33.93% 25.45% 18.81% 12.82% 30.39 61.61% 53.50% 43.04% 33.66% 25.80% 18.23% 40.52 68.23% 60.59% 50.25% 40.49% 31.90% 23.20%
(4)惰性气体的影响 惰性气体含量增加,总反应速率下降。
总结
小结
• 什么是合成氨?(定义)
• 为什么要合成氨?(地位· 作用)
合成氨是重要的无机化工产品
由氮和氢在高温高压和催化剂存在下直接合成的氨
• 怎么合成氨?(原理) • 什么影响氨合成?(影响因素)
温度 压力 氢氮比 惰性气体
合成氨用途
合成氨是重要的无机化工产品
氨主要用于制造氮肥和复合肥料,例如尿素、 硝酸铵、磷酸铵、氯化铵以及各种含氮复合 肥,都是以氨为原料的。
氨合成的基本原理
氨是由气态氢和氮在氨触媒的作用下反应生成的 其反应式为:
可逆 放热 体积减小
氨合成影响因素
平衡常数:
P(的分压
合成氨工艺

合成氨工艺————————————————————————————————作者:————————————————————————————————日期:合成氨工艺流程(1)原料气制备将煤和天然气等原料制成含氢和氮的粗原料气。
对于固体原料煤和焦炭,通常采用气化的方法制取合成气;渣油可采用非催化部分氧化的方法获得合成气;对气态烃类和石脑油,工业中利用二段蒸汽转化法制取合成气。
(2)净化对粗原料气进行净化处理,除去氢气和氮气以外的杂质,主要包括变换过程、脱硫脱碳过程以及气体精制过程。
①一氧化碳变换过程在合成氨生产中,各种方法制取的原料气都含有CO,其体积分数一般为12%~40%。
合成氨需要的两种组分是H2和N2,因此需要除去合成气中的CO。
变换反应如下:CO+H2OH→2+CO2 =-41.2kJ/mol 0298HΔ由于CO变换过程是强放热过程,必须分段进行以利于回收反应热,并控制变换段出口残余CO含量。
第一步是高温变换,使大部分CO转变为CO2和H2;第二步是低温变换,将CO含量降至0.3%左右。
因此,CO变换反应既是原料气制造的继续,又是净化的过程,为后续脱碳过程创造条件。
②脱硫脱碳过程各种原料制取的粗原料气,都含有一些硫和碳的氧化物,为了防止合成氨生产过程催化剂的中毒,必须在氨合成工序前加以脱除,以天然气为原料的蒸汽转化法,第一道工序是脱硫,用以保护转化催化剂,以重油和煤为原料的部分氧化法,根据一氧化碳变换是否采用耐硫的催化剂而确定脱硫的位置。
工业脱硫方法种类很多,通常是采用物理或化学吸收的方法,常用的有低温甲醇洗法(Rectisol)、聚乙二醇二甲醚法(Selexol)等。
粗原料气经CO变换以后,变换气中除H2外,还有CO2、CO和CH4等组分,其中以CO2含量最多。
CO2既是氨合成催化剂的毒物,又是制造尿素、碳酸氢铵等氮肥的重要原料。
因此变换气中CO2的脱除必须兼顾这两方面的要求。
一般采用溶液吸收法脱除CO2。
第七章__合成氨
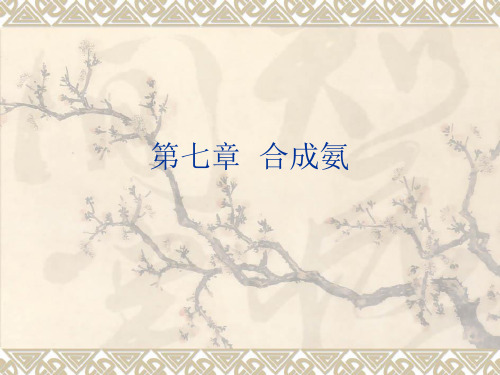
❖ 确 一定方还面原是条还件原的生原成则 的一铁方结面晶是不使因重Fe结3O晶4充而分长还大原,为以α保-F证e,有另最 大的比表面积和更多的活性中心。为此,宜选取合适的还原 温度、压力、空速和还原气组成。
❖ 提高还原温度能加快还原反应速率,但必须按不同的阶段, 逐渐升温,才能保证活化质量,还原温度不超过正常使用温 度;还原压力宜控制在比正常的操作压力低一些的条件下进 行;还原的起始空速可选择在3000~5000h-1或略高一些; 同时采用正常操作时的氢氮混合气作还原气。
年在德国奥堡建成世界上第一个合成氨厂,生产能 力为日产30t氨。氨合成方法的研究成功,不仅为获
取化合态氮开辟了广阔的道路,而且也促进了许多
相关科学技术(如高压技术、低温技术、催化、特
殊金属材料、固体燃料汽化、烃类燃料的合理利用 等)的发展。
❖ 中国的合成氨工业,虽早在20世纪30年代南京和大 连就已建有氨厂,但直到解放,全国仍只有这两个 厂,生产能力每年不过几万吨氨。建国以后,合成 氨工业得到很大发展。20世纪末期已经拥有多种原 料,不同流程的大、中、小型合成氨厂1000多个, 其中大、中型企业达137个,而年产30万吨合成氨 的引进装置就有21个。年产量进入了世界的前列 (年产量达近亿吨),而且有了一支从事合成氨生 产的科研、设计、制造与施工的技术队伍。
❖ 合成塔需用高镍优质合金钢制造,即使这样,也会 产生破裂。高压法管理比较复杂,特别是由于合成 率高,催化剂层内的反应热不易排除而使催化剂长 期处于高温下操作,容易失去活性。
❖ 中压法 操作压力为20~35MPa的称为中压法,操 作温度为450~550℃。中压法的优缺点介于高压法 与低压法之间,但从经济效果来看,设备投资费用 和生产费用都比较低。
第三章 氨的合成
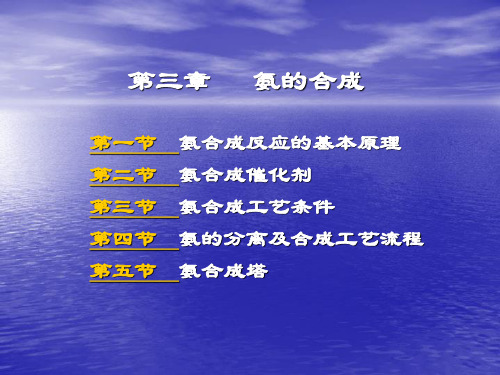
不同温度、压力时平衡氨摩尔分数的数据见表3-3
氢氮比为3时一些温度、压力下平衡氨含量的值
P/MPa T/℃ 10 15 20 43.00 33.00 24.71 18.24 12.62 32 54.00 43.60 34.24 30.90 18.99 60 80
360
384 424 464 504 552
又 ∵
yH 2 yN2
r
y NH 3 y H 2
yH 2 r
yi 1
∴
pN 2 PyN 2 P(1 y NH 3 yi ) / 1 r
1 r yH 2 ( ) 1 y NH 3 yi r r pH 2 PyH 2 P (1 y NH 3 yi ) 1 r
(控制步骤, 慢 )
2Nσ + 3H2 = 2NH3 + 2σ (快,达到平衡)
根据氮在催化剂表面上的活性吸附是氨合成过程的控制步骤、氮
在催化剂表面呈中等覆盖度、吸附表面很不均匀等条件,捷姆金和佩 热夫导得的速度方程式如下:
在铁催化剂上:
rNH 3 k1 p N 2
p1.5 H2 p NH 3
作条件下,合成反应能达到的最大限度。
平衡氨含量的计算: 设:进口氢氮比为r,总压为P, 达到平衡时混合气中NH3的平衡组成为yNH3, 惰性气体组成为yi,
平衡氨含量的计算:
以1kmol为计算基准:则有
y NH 3 yH 2 y N 2 yi 1
即 yH 2 r y N 2
⑷ 温度对反应速率的影响
化学反应速度,随着温度的升高而显著加快。这是因为 温度升高,反应物运动的速度加快,分子间碰撞次数增 加,从而增加了分子有效接触的机会。对于氨合成反应 也是同样的道理,温度升高,加速了氮的活性吸附,同 时又增加了吸附氮与氢的接触机会,使氨合成反应速度 加快。 但升高温度对平衡氨产率始终不利。起初在远离平衡的 情况下,反应速度是随着温度的升高而增大的,达到最 大值;以后再升高,由于受平衡的影响,以后反应速度 又趋于下降,从反应机理来看,因为这时逆反应速度增 加得更快了。
合成氨原理

合成氨原理合成氨是一种重要的化学原料,广泛用于生产化肥等工业过程。
其原理是通过哈柏过程或奥斯特华尔德过程来实现。
哈柏过程(哈柏氨合成法)是最常用的合成氨工业方法之一。
该过程将氮气和氢气在高温高压条件下通过一个铁催化剂进行催化反应。
具体步骤如下:1. 氮气的制备:氮气在空气中占绝大部分,可以通过空分设备将空气中的氧气和其他杂质分离出来,得到纯净的氮气。
2. 氢气的制备:氢气可以通过蒸汽重整、部分氧化、水电解等方法来制备。
3. 氮气和氢气混合:经过精确的配比,将纯净的氮气和氢气按一定比例混合。
4. 催化反应器:将混合气送入一个催化反应器中,其中催化剂通常采用铁(Fe)。
5. 反应条件:反应需要在高温(约400-500摄氏度)和高压(约100-250atm)的条件下进行。
6. 催化反应:在催化剂的作用下,氮气和氢气发生氮氢化反应,生成氨气。
7. 分离氨气:将反应产物经过冷却处理,得到氨气。
奥斯特华尔德过程(奥斯特华尔德氨合成法)是另一种常用的合成氨方法。
该过程在低温低压条件下进行,适用于小规模的合成氨生产。
具体步骤如下:1. 原料气体准备:氮气和氢气经过压缩、净化等处理,得到纯净的原料气体。
2. 催化剂床层:将催化剂(通常为铁-铝合金)放置在反应器中形成床层。
3. 缓冲层:在催化剂床层上方加入缓冲床层,用于分离反应床和冷凝器。
4. 过热器:将原料气体加热至适宜的反应温度(通常为400-550摄氏度)。
5. 反应器:通过加热后的原料气体对催化剂进行反应,生成氨气。
6. 冷凝器:将反应产生的氨气进行冷却,使其凝结为液体。
7. 分离氨液:将凝结的氨液体与剩余的气体进行分离,得到纯净的合成氨。
这些合成氨的过程可用于工业生产中,以满足各种应用的需求。
氨的合成方法

氨的合成方法
1.氨气与氢气的直接合成:常见的直接合成氨的方法是通过气态氮气和氢气在高温高压条件下催化反应制得。
这种方法需要使用特殊的催化剂,如铁钾催化剂或铁锆催化剂,反应温度通常在400500摄氏度,压力在100200大气压。
这个方法广泛应用于工业生产中。
2.氧化铵法:氧化铵法是一种将铵盐经过催化剂催化氧化产生氨的方法。
具体步骤为首先将铵盐(如尿素或氨盐)与气态空气或氧气在高温下催化燃烧,生成一氧化氮和水蒸气,然后将一氧化氮与过量的氢气在催化剂的作用下反应生成氨。
这种方法的优点是反应条件较为温和,使用方便,但产氨量一般较低。
3.超临界氮气合成法:超临界氮气合成法是一种新的氨合成方法,可以在常压下实现氮气与氢气的合成。
该方法利用氢气和氮气在超临界条件下(如高温高压或低温低压)直接反应,产生氨。
这种方法具有操作简单、环境友好、能源消耗低等优点,但目前仍处于实验研究阶段。
4.微生物发酵法:微生物发酵法是通过利用氮固定菌,如植物根际中的根瘤菌或土壤中的氮固定细菌,将大气中的氮气固定成氨。
这种方法需要种植植物或在土壤中添加适当的菌种,通过微生物代谢过程产生氨。
这种方法在农业中广泛应用,可提供植物生长所需的氮源,促进作物生长。
氨合成

第三节 氨合成催化剂
二、催化剂的还原与保持
氨合成催化剂的主要活性组分是Fe3O4 ,必须经过 还原后才有活性,该活性不仅与还原前的化学组成和 结构有关,而且与制备方法及还原条件有很大关系。
第二节 氨的合成反应动力学
第二节 氨的合成反应动力学
第二节 氨的合成反应动力学 一、动力学方程 氮和氢在催化剂上的反应,一般认为是氮被催化剂活化吸 附离解为氮原子,然后逐步生成NH、NH2、NH3;
氨合成反应历程 (1)气体反应物扩散到催化剂外表面; (2)反应物扩散到催化剂毛细孔内表面; (3)气体被催化剂内表面活性吸咐; (4)反应气体在催化剂表面上进行化学反应,生成一系列中 间化合物,形成吸附态的氨
为统一物料基准,采用氨分解基流量表示
混合气体流量以氨分解基流量表示公式
N
1
N0 y( NH 3 )
V0
22.41 y( NH 3 )
第二节 氨的合成反应动力学
影响氨合成反应速度的因素:
(1)压力:提高压力,使一定质量的气体体积相应减小,单位 体积中气体分子数增加,因而缩短了分子间距离,分子碰撞 的机会增多,促使反应速度加快.正反应速度与压力成1.5次 方关系,而逆反应速度与压力成0.5次方关系,所以提高压力 明显有利于氨合成反应速度.
F 38338.9 0.23131
T
T3
p
22.3864T 10.57 104T 2 7.0828 106T 3k J / k mol
实际上由于混合时吸热,其热效应小于以上计算值.
合成氨技术

合成氨技术合成氨指由氮和氢在高温高压和催化剂存在下直接合成的氨,为一种基本无机化工流程。
现代化学工业中,氨是化肥工业和基本有机化工的主要原料。
合成氨工业在20世纪初期形成,开始用氨作火炸药工业的原料,为战争服务,第一次世界大战结束后,转向为农业、工业服务。
随着科学技术的发展,对氨的需要量日益增长。
催化机理热力学计算表明,低温、高压对合成氨反应是有利的,但无催化剂时,反应的活化能很高,反应几乎不发生。
当采用铁催化剂时,由于改变了反应历程,降低了反应的活化能,使反应以显著的速率进行。
合成氨反应的机理,首先是氮分子在铁催化剂表面上进行化学吸附,使氮原子间的化学键减弱。
接着是化学吸附的氢原子不断地跟表面上的氮分子作用,在催化剂表面上逐步生成—NH、—NH2和NH3,最后氨分子在表面上脱吸而生成气态的氨。
上述反应途径可简单地表示为:xFe+N2→FexNFexN+[H]吸→FexNHFexNH+[H]吸→FexNH2FexNH2+[H]吸FexNH3xFe+NH3在无催化剂时,氨的合成反应的活化能很高,大约335kJ/mol。
加入铁催化剂后,反应以生成氮化物和氮氢化物两个阶段进行。
第一阶段的反应活化能为126kJ/mol~167kJ/mol,第二阶段的反应活化能为13kJ/mol。
由于反应途径的改变(生成不稳定的中间化合物),降低了反应的活化能,因而反应速率加快了。
催化剂的催化能力一般称为催化活性。
有人认为:由于催化剂在反应前后的化学性质和质量不变,一旦制成一批催化剂之后,便可以永远使用下去。
实际上许多催化剂在使用过程中,其活性从小到大,逐渐达到正常水平,这就是催化剂的成熟期。
接着,催化剂活性在一段时间里保持稳定,然后再下降,一直到衰老而不能再使用。
活性保持稳定的时间即为催化剂的寿命,其长短因催化剂的制备方法和使用条件而异。
催化剂在稳定活性期间,往往因接触少量的杂质而使活性明显下降甚至被破坏,这种现象称为催化剂的中毒。
合成氨
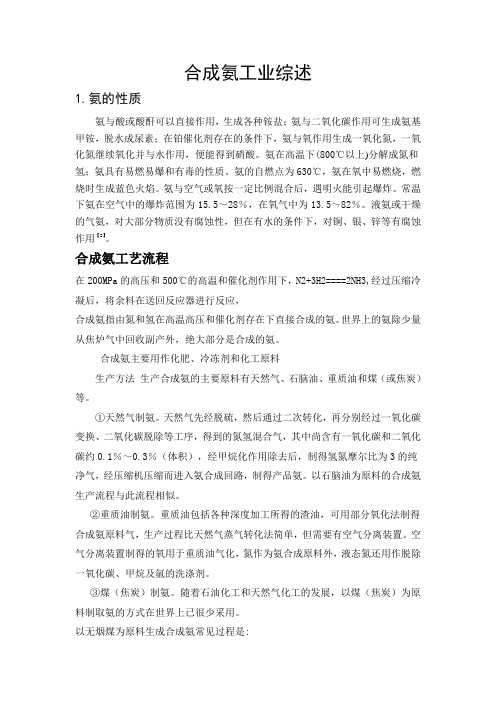
合成氨工业综述1.氨的性质氨与酸或酸酐可以直接作用,生成各种铵盐;氨与二氧化碳作用可生成氨基甲铵,脱水成尿素;在铂催化剂存在的条件下,氨与氧作用生成一氧化氮,一氧化氮继续氧化并与水作用,便能得到硝酸。
氨在高温下(800℃以上)分解成氮和氢;氨具有易燃易爆和有毒的性质。
氨的自燃点为630℃,氨在氧中易燃烧,燃烧时生成蓝色火焰。
氨与空气或氧按一定比例混合后,遇明火能引起爆炸。
常温下氨在空气中的爆炸范围为15.5~28%,在氧气中为13.5~82%。
液氨或干燥的气氨,对大部分物质没有腐蚀性,但在有水的条件下,对铜、银、锌等有腐蚀作用【2】。
合成氨工艺流程在200MPa的高压和500℃的高温和催化剂作用下,N2+3H2====2NH3,经过压缩冷凝后,将余料在送回反应器进行反应,合成氨指由氮和氢在高温高压和催化剂存在下直接合成的氨。
世界上的氨除少量从焦炉气中回收副产外,绝大部分是合成的氨。
合成氨主要用作化肥、冷冻剂和化工原料生产方法生产合成氨的主要原料有天然气、石脑油、重质油和煤(或焦炭)等。
①天然气制氨。
天然气先经脱硫,然后通过二次转化,再分别经过一氧化碳变换、二氧化碳脱除等工序,得到的氮氢混合气,其中尚含有一氧化碳和二氧化碳约0.1%~0.3%(体积),经甲烷化作用除去后,制得氢氮摩尔比为3的纯净气,经压缩机压缩而进入氨合成回路,制得产品氨。
以石脑油为原料的合成氨生产流程与此流程相似。
②重质油制氨。
重质油包括各种深度加工所得的渣油,可用部分氧化法制得合成氨原料气,生产过程比天然气蒸气转化法简单,但需要有空气分离装置。
空气分离装置制得的氧用于重质油气化,氮作为氨合成原料外,液态氮还用作脱除一氧化碳、甲烷及氩的洗涤剂。
③煤(焦炭)制氨。
随着石油化工和天然气化工的发展,以煤(焦炭)为原料制取氨的方式在世界上已很少采用。
以无烟煤为原料生成合成氨常见过程是:造气 -> 半水煤气脱硫 -> 压缩机1,2工段 -> 变换 -> 变换气脱硫 ->压缩机3段 -> 脱硫 ->压缩机4,5工段 -> 铜洗 -> 压缩机6段 -> 氨合成 -> 产品NH3采用甲烷化法脱硫除原料气中CO. CO2 时, 合成氨工艺流程图如下: 造气 ->半水煤气脱硫 ->压缩机1,2段 ->变换 -> 变换气脱硫 -> 压缩机3段 ->脱碳 -> 精脱硫 ->甲烷化 ->压缩机4,5,6段 ->氨合成 ->产品NH32.合成氨工艺2.1依据合成条件—压力的不同的几种合成方法氨的合成是合成氨生产的最后一道工序,其任务是将经过精制的氢氮混合气在催化剂的作用下多快好省地合成为氨。
氨的合成

氨的合成1.概念:氨的合成是整个合成氨流程的最后一道工序,是合成氨的核心部分。
合成氨工业有近八十年的历史,基本方法没有原则性的改变,氨合成过程属于气固相催化反应过程,通常是在高温(300-550)、高压(10-100)及熔铁催化剂作用下将氢、氮气合成为氨的。
由于氢、氮气一次通过合成熔的反应过程只有少部分合成氨,反应后的混合气中氨含量一般为10-20,因此反应后的气体混合物经分离氨后循环使用。
常温常压下,氨是一种具有强烈刺激性气味的气体,极易溶于水,醇类、丙醇、三氮甲烷、笨等,且易燃易爆,其主要物理化学性质如下表1:常温常压下,1升水中约可溶解700升氨,氨溶于水时放出大量的热:生成的氢氧根离子呈碱性,通常向除氧器出口的锅炉化学清洗液及工厂排污水中添加氨,以调节PH值。
氨水(溶液)的比重和冰点均随氨浓度而变化。
图1给出了不同浓度氨水的冰点。
从图中可以看出。
随氨含量升高,氨水的冰点迅速下降,在氨水浓度约33%时,冰点最低(约-107)氨含量继续上升,氨水的冰点,反而提高。
此性质被用于在氨合成系统停车后再开车时,向合成回路和合成压缩机段间注氨,防止水汽冻结堵塞,氨也可以溶解于盐类水溶液和各种有机溶液如乙醇等。
氨在高温下可分解为氢和氮、氮或空气与氨的混合物遇火会爆炸,遇热放出氮及氮氧化物的有毒烟雾。
氨属于剧毒类物质,短期内吸入大量氨气后,会出现咽痛,声音嘶哑,胸闷,呼吸困难等,并伴有头痛,恶心,呕吐等症状,严重可出现紫绀,咽部充血水肿或呼吸窘迫综合症,支气管粘膜坏死脱落,窒息,眼部结膜充血,灼伤皮肤,含氨0.5%时,在很短的时间内就能使人窒息而死。
空气中允许浓度为0.03氨合成反应的理论基础氨合成反应是在高温高压下进行的气固相催化反应,化学反应方程式如下:从上式可以看出,氨合成反应是一个放热和体积(分子数)减少的可逆反应。
一、化学平衡常数KP说明(1)常压(低压)下的平衡常数在低压下,平衡常数只是温度的函数,经验式如下:(2)加压下的化学平衡常数在加压条件下,化学平衡常数KP不仅与温度有关,而且与压力和气体组成有关,需改用度表示,A.将系统看成真实气体的理想溶液1.各组分的度系数R值可取各“纯”组分在相同温度及总压下的度系数,可从普遍化度系数图查得。
第六章合成氨方案

工业合成氨原料: 1、固体原料:焦炭和煤 2、气体原料:天然气、油田气、焦炉气等 3、液体原料:石脑油、重油、原油等。
五、合成氨发展的三个典型特点:
1.原料构成: 基本完成了从煤、焦炭到油(石脑油、 重油)、天然气的转变。
2.生产规模单系列大型化。 1000~1500T/日
3.能量的合理利用。 用过程余热自产蒸汽推动 蒸汽机供动 力,基本不用电能。
第一节 概述
一、氨的用途
• 85%的氨用来制化学肥料,其余作为生产其 他化工产品的原料。
• 氨除了主要用作化学肥料的原料外,还是生 产染料、炸药、医药、有机合成、塑料、合 成纤维、石油化工等的重要原料。
氨的其他工业用途也十分广泛,例如:在制
冰、空调、冷藏等系统的致冷剂。
二、氨的物理性质
标准状态下是无色气体,具有特殊的刺激性臭味。 20℃下将氨气加压0.8MPa时,液化为无色的液体。
加热措施:开车时采用电加热,正常 生产时氢氮混合气被反应后的高温气体 加热。
氨合成中的反应热进行回收,副产蒸 汽。
(3)氨的分离
a、冷凝法
冷却含氨混合气,气氨冷凝为液氨,经气液分离 设备将液氨从混合气中分离。
理论依据——拉尔逊公式:具体见教材。由拉尔 逊公式可看出,提高压力、降低温度有利于氨 的冷凝分离。
2、合成氨的工艺流程
工艺流程图讲解。 看课本讲解
2.4
蒸汽 精炼气至压缩工段
12 MPa
压 缩 机 来 氢 氨 混 合 气
气氨至冷冻工段 液氨至冷冻工段 再生气去回收
冷却水
12 MPa
Hale Waihona Puke 去废铜液地下槽空气来自空压机
气氨来自液氨计量瓶
铜氨液吸收和再生流程
合成氨工艺流程简述

合成氨工艺流程简述合成氨是一种重要的工业原料,广泛应用于化肥、制药和塑料等领域。
下面将简述合成氨的工艺流程。
合成氨的工艺流程主要包括空气分离、合成气制备、氨合成和氨分离四个步骤。
首先是空气分离。
空气中主要是78%的氮气和21%的氧气,其余是稀有气体和水蒸气。
为了获得高纯度的氢气和氮气,需要进行空气分离。
常用的方法是利用分子筛吸附剂将水蒸气去除后,通过等温膜分离或低温分馏将氧气和氮气分离。
接下来是合成气制备。
合成气主要是一氧化碳和氢气的混合气体。
合成气可以由多种原料制备,常用的方法是通过燃烧天然气或煤气产生一氧化碳和二氧化碳,然后通过水蒸气重整反应将一氧化碳转化为二氧化碳和氢气,再通过变换反应将二氧化碳还原为一氧化碳和氢气。
另外,也可以利用生物质或石油等原料通过气化反应产生合成气。
然后是氨合成。
氨合成是将合成气经过一系列催化反应转化为氨气的过程。
通常采用的是哈-布斯法,即在一定的温度和压力下,将合成气经过催化剂床层,催化剂通常是铁或铑以及促进剂,使一氧化碳和氢气发生反应生成氨气。
该反应是一个放热反应,需要控制温度和压力使反应达到最佳状态。
最后是氨分离。
氨合成反应产生的氨气通常含有一定的氮气和水蒸气等杂质,需要经过分离和净化处理。
常用的方法是通过冷凝和吸附等手段将气相中的水蒸气和杂质去除,得到高纯度的氨气。
以上是合成氨的工艺流程简述。
合成氨工艺需要密切控制各个步骤的条件,如温度、压力和催化剂等,以提高氨气的产率和纯度。
合成氨工艺的发展不仅推动了化肥领域的进步,也对其他相关行业的发展产生了积极的推动作用。
合成氨的反应原理

合成氨的反应原理合成氨是一种重要的化学工业反应,其原理是将氢气和氮气在一定的条件下进行结合反应,生成氨气。
合成氨的反应原理是依据哈柏法的原理。
哈柏法是由德国化学家哈柏于1905年提出的,该法以铁为催化剂,将氮气和氢气在高温高压下进行反应,生成氨气。
在反应中,氢气和氮气的物质性质发生了变化。
氢气是无色无味的气体,在常温下为不活泼的分子气体,由两个氢原子组成。
氮气是一种无色无味的气体,也是不活泼的分子气体,由两个氮原子组成。
合成氨的反应物为氮气和氢气,反应物中氢气和氮气的化学键发生了断裂和形成的过程。
在背景条件下,铁催化剂有助于降低反应的活化能,促进氮气与氢气发生相互作用。
反应物中的氮气与氢气经过一系列的反应过程,最终会转化为氨气。
合成氨的反应需要在高温高压的条件下进行。
通常情况下,反应温度为400-500,压力约为150-200atm。
高温高压的条件对于将氢气和氮气转化为氨气非常重要,可以提高反应速率和产率。
此外,配合性的铁催化剂也是合成氨反应的关键。
反应中,氢气和氮气发生反应生成氨气的过程可以用以下化学方程式表示:N2 + 3H2 > 2NH3在这个方程式中,氮气与氢气的反应生成了氨气。
根据化学方程式可以看出,氮气和氢气的消耗是按照比例的。
每一摩尔的氮气需要消耗3摩尔的氢气才能生成2摩尔的氨气。
合成氨的反应发生在一个封闭的反应器中。
反应器内部有很强的耐压性,以承受高温高压条件下的反应过程。
反应器内的铁催化剂可以促进反应的进行,提高反应速率和产率。
同时,反应器内要保持一定的温度和压力条件,以便使反应物充分反应,生成氨气。
合成氨是一种重要的化学反应,广泛应用于化学工业的领域。
氨气是一种重要的化学原料,用于制造肥料、塑料等化学产品。
合成氨的反应原理和条件对于合成氨的产量和质量有着重要的影响,因此需要掌握合成氨的反应原理和工艺条件。
- 1、下载文档前请自行甄别文档内容的完整性,平台不提供额外的编辑、内容补充、找答案等附加服务。
- 2、"仅部分预览"的文档,不可在线预览部分如存在完整性等问题,可反馈申请退款(可完整预览的文档不适用该条件!)。
- 3、如文档侵犯您的权益,请联系客服反馈,我们会尽快为您处理(人工客服工作时间:9:00-18:30)。
压力:10-20MPa 还原空速:10000h-1
还原气体组成:75%氢气和水蒸汽0.72.0g/m3
(四)、催化剂的还原阶段 1 2 3 4 升温阶段: 还原初期: 还原主期: 还原末期:
5 轻负荷期:
理论出水量的计算
G=W * [
H 2O FeO * a% + 3H2O 2Fe2O3 * b% ]
T/°C 360 384 424 464 504 552
10 35.10 29.00 20.63 14.48 10.15 6.71
32 60.43 54.00 43.60 34.24 30.90 18.99
60 75.32 69.94 60.35 50.62 41.44 31.81
80 81.80 77.24 68.68 59.42 50.13 39.78
从上表也可看出,温度升高平衡氨含量下降;压力增加,平衡氨含 量增加。这是由反应本身为放热反应和反应减少分子数决定的。
四、影响平衡氨含量的因素
平衡氨含量是温度、压力、气体组成的函数
a.压力和温度的影响 温度越低,压力越高,平 衡常数Kp越大,平衡氨含量y*NH3越高。
结论:反应热不仅与温度有关,还与压力和组成有关。
六、氨合成催化剂 p208
(一)、催化剂的组成和作用
外观:黑色,有金属光泽,带磁性,不规则 主要成分:Fe2O3、FeO 重点掌握催化剂中各组分的作用 促进剂:K2O,提高活性;CaO, 增强抗毒能力;Al2O3, 与Fe3O4形成共溶体,增加催化剂对气体的吸附作用, 加速反应。 型号:A106,A109,A110,A201,A301。后三种为 低温型催化剂,其还原温度和使用温度比前两种低20度。
⑴ ⑵
⑶ ⑷ ⑸ cAS
⑹ ⑺ B
A (g)
B(g)
氮、氢气在催化剂表面反应过程的机理,可表示为: N2(g)+Cate —→2N(Cate)
H2(g)+Cate —→2H(Cate)
N(Cate) + H(Cate) —→NH(Cate) NH(Cate) + H(Cate) —→NH2(Cate) NH2(Cate) + H(Cate) —→NH3(Cate)
氨合成反应过程中,物料的总摩尔数随反应进行而 减小,实际计算过程中为便于计算,令y0惰为氨分 解基惰性气含量,y0惰= y惰/(1+yNH3).
结论: y*氨随压力升高、温度降低、惰气含量而增大。
五、氨合成反应的热效应
34734 .4 1.89963 1010 H F 38338 .9 [22.5304 ] p 22.3864 T 10.5717 10 4 T 2 7.08281 10 6 T 3 3 T T
Kf f NH 3
* 1/ 2 * * 3/ 2
( f N2 ) ( f H 2 )
PNH 3 NH 3
*
( PN 2 N 2 ) ( PH 2 H 2 )
* 1/ 2 *
3/ 2
K P K
式中:f和y为各平衡组分的逸度和逸度系数。 若已知各平衡组分的逸度系数y,由上式 可计算加压下的Kp值。 Kr P206
c. 惰性气体含量的影响
y0惰为氨分解基惰性气含量,y0惰= y惰/(1+yNH3).
近似公式
y0NH3 * =(y0NH3) * /b=(y0NH3)* (1 -y0惰) /(1 +y0惰).
增加惰性气体含量相当于降低了反应物的分压,对平衡不 利。理论上是惰性气体越少越好,但实际上这是不现实的 。要确定一个合理的惰性气体含量范围,还需大量计算, 综合各种操作因素作图比较分析得出。
解得 r=3.进料氢氮比为化学计量比时,平衡氨含量最大。但实际考 虑到其它因素,平衡氨含量不为3。实际上在压力为10~100MPa, 氢氮比的适宜值为2.9~3.0。
若不考虑R对Kp 的影响,解得
R=3时,yNH3 为最大值;高压
下,气体偏离理想状态,Kp将
随R而变,所以具有最大yNH3 时 的 R 略 小 于 3 , 约 在 2.68 ~ 2.90之间,如图所示。
实际生产不可能无限增加空速,空速大系统阻力大,功 耗增大。另外,新鲜气量一定时,空速增大只能通过增 加循环气量来实现,循环气量过大,除了上述功耗原因 外,还使单位循环气产氨量下降,从而使气体温升下降 ,产生不能维持“自热”的问题。一般空速值为:
30MPa
1
20000-30000-
NH3(Cate)—→NH3(g) + (Cate)
实验结果证明,N2活性吸附是最慢的一步,即为表面 反应过程的控制步骤。
对整个气固相催化反应过程,是表面反应控制还
是扩散控制,取决于实际操作条件。低温时可能
是动力学控制,高温时可能是内扩散控制;
大颗粒的催化剂内扩散路径长,小颗粒的路径 短,所以在同样温度下大颗粒可能是内扩散控制 ,小颗粒可能是化学动力学控制。
b.氢氮比的影响
若氢氮比不为3,则平衡常数表达式为:
y NH 3 (1 y NH 3 r 1.5 K 0 P / p0 p yi ) 2 (1 r ) 2
其它条件不变,改变氢氮比使平衡氨含量最大时,可对上式求导,并 令其为零得
1.5r 0.5 (1 r ) 2 2r 1.5 (1 r ) 0 4 (1 r )
点呀!
1 可逆反应,转化率的问题 2 放热反应,反应热及时移走,温度控制 3 体积缩小,反应压力 4 催化剂加速,选择问题,寿命问题 5 平衡氨含量随压力升高 、温度降低、惰 性气含量减少而增大。
二、化学平衡及平衡常数
氨合成是放热和摩尔数减少的可逆反应:
高压下气体不能看做理想 气体 加压下的化学平衡常数Kp不仅与温度有关, 而且与压力和气体组成有关,需改用逸度 表示。Kp与Kf之间的关系为;
(五)、催化剂的毒物 暂时毒物 氧及含氧的化合物 硫及其化合物 毒物 永久毒物 氯及其化合物 磷及其化合物
CO、CO2、H2O
砷及其化合物
五、合成氨反应的动力学
了解
①动力学过程 氨合成为气固相催 化反应,它的宏观动力学过程包 括以下几个步骤。
气固相催化反应宏观过程
氮氢气体从气流主体扩散到催化 剂颗粒的外表面----外扩散 反应物从外表面向催化剂的孔道 内部扩散----内扩散 反应物被催化剂吸附----吸附 在催化剂内部孔道内组成的内表 面上进行催化反应----化学反应 产物从催化剂表面脱附----脱附 产物从催化剂内表面扩散到外表 面----内扩散 产物从外表面扩散到气流主体---外扩散
三、平衡 氨含量
将各分压带入平衡常数公式,得
进气组成已知时,yi可确定,此式为一元二次方程
无困难
,求解
。
氢氮比为3时一些温度压力下平衡氨含量的值如表1.10. P/MPa 15 20 43.35 49.62 36.84 43.00 27.39 33.00 19.94 24.71 14.39 18.24 9.75 12.62
图 1.31
局部温度过高,以破坏催化剂。
(二)、压力对出口氨含量的影响
1.从化学平衡和化学反应速率的角度看,提高操作压力有利。 2. 生产能力随压力提高而增加,氨分离流程可以简化。 3. 选择操作压力的主要依据:能量消耗、原料费用、设备投 资。 能量消耗:原料气压缩功、循环气压缩功和氨分离的冷 冻功。
n1 y NH 3 1 y2, NH 3
再将上式中的流量换成空速,得出生产能力的公式
G 17V0 s y NH 3 22.4(1 y1, NH 3 )(1 y2, NH 3 ) 17Vs1y NH 3 22.4(1 y2, NH 3 ) 17Vs 2 y NH 3 22.4(1 y1, NH 3 )
Ai
Bi
Ci /104
N2 H2 NH3 CH4 Ar
0.1975 1.3445 2.3930 2.2769 1.2907
0.02096 0.05046 0.03415
0.054 4.20 476.87
实际计算时,由于组成不知,必须用迭代法。用计算机编程计算 比较方便。也有许多便于实际少量计算的逸度系数图可查。 一个不计算逸度系数,直接计算氨合成反应平衡常数的经验公式 如下:
2. 温度
正如在变换反应所讨论的那样,氨合成反应也存在一个最佳温度。
图 1.30
3. 压力
从速度方程可看出,提高压力可使正反应速度增加大于 逆反应速度增加,所以一般选择较高压力。同时必须在 较高压力下才有可观的速度。但现代设计并不盲目高压 力,而是综合考虑全厂经济效益,选择压力比以前有所 降低。
各国催化剂的组成和型号:表1-4-5
(二)、催化剂的还原和使用
Fe3O4 4 H 2 3Fe 4 H 2O
确定还原条件的原则:
使四氧化三铁充分还原为α-Fe, 使还原生成的铁结晶不因重结晶而长大,以保证有 最大的比表面积和更多的活性中心。
(三)、影响还原质量的因素
还原温度:不同还原时期有不同温度
氨合成
重点 掌握氨合成原理及反应特点 掌握主要工艺条件 了解氨合成塔分类、结构形式及其特点 知道节能型合成工艺的热回收形式 掌握催化剂型号及主要成分和作用
第—节 热力学基础
一、氨的合成及其反应特点
反应原理一定要记住!
3H 2 N 2 2 NH3 Cat
420-450
反应特点:是本章的重