经典:铝合金压铸技术
铝合金的铸造方法
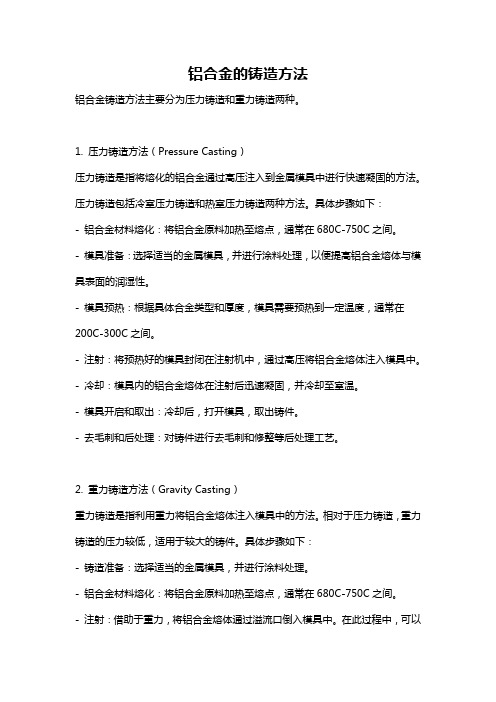
铝合金的铸造方法铝合金铸造方法主要分为压力铸造和重力铸造两种。
1. 压力铸造方法(Pressure Casting)压力铸造是指将熔化的铝合金通过高压注入到金属模具中进行快速凝固的方法。
压力铸造包括冷室压力铸造和热室压力铸造两种方法。
具体步骤如下:- 铝合金材料熔化:将铝合金原料加热至熔点,通常在680C-750C之间。
- 模具准备:选择适当的金属模具,并进行涂料处理,以便提高铝合金熔体与模具表面的润湿性。
- 模具预热:根据具体合金类型和厚度,模具需要预热到一定温度,通常在200C-300C之间。
- 注射:将预热好的模具封闭在注射机中,通过高压将铝合金熔体注入模具中。
- 冷却:模具内的铝合金熔体在注射后迅速凝固,并冷却至室温。
- 模具开启和取出:冷却后,打开模具,取出铸件。
- 去毛刺和后处理:对铸件进行去毛刺和修整等后处理工艺。
2. 重力铸造方法(Gravity Casting)重力铸造是指利用重力将铝合金熔体注入模具中的方法。
相对于压力铸造,重力铸造的压力较低,适用于较大的铸件。
具体步骤如下:- 铸造准备:选择适当的金属模具,并进行涂料处理。
- 铝合金材料熔化:将铝合金原料加热至熔点,通常在680C-750C之间。
- 注射:借助于重力,将铝合金熔体通过溢流口倒入模具中。
在此过程中,可以通过控制溢流口的大小和位置来控制铸件的形状和尺寸。
- 冷却:待铝合金熔体在模具中凝固,冷却至室温。
- 模具开启和取出:冷却后,打开模具,取出铸件。
- 去毛刺和后处理:对铸件进行去毛刺和修整等后处理工艺。
值得注意的是,上述方法仅列举了最常用和基本的铝合金铸造方法,实际生产中还有其他特殊的铸造方法,如砂芯铸造、低压铸造等。
具体方法的选择会根据铸件形状、尺寸和要求等因素进行灵活确定。
压铸铝工艺

压铸铝工艺
压铸铝工艺是一种常用的金属加工工艺,它使用压铸机将
铝合金熔融液体注入金属模具中,并加入压力进行压实和
冷却,最终得到所需的铝合金零件。
以下是压铸铝工艺的基本步骤:
1. 准备模具:根据产品设计要求制作铝合金的金属模具,
并确保模具表面平整且光滑。
2. 铝合金制备:根据产品要求选择合适的铝合金材料,并
将其加热至熔点,使其变为熔融液体。
3. 注入铝合金:将熔融的铝合金液体注入预热过的模具中,注入过程通常使用压铸机进行控制,以确保注液均匀。
4. 施加压力:在铝合金液体注入模具后,立即施加一定的
压力,以确保铝合金充分填充模具的空腔和形成所需形状。
5. 冷却和固化:在施加压力的同时,利用模具的冷却系统
冷却铝合金液体,使其快速凝固和固化。
6. 脱模:在冷却后,打开模具并取出固化的铝合金零件,
通常需要借助专用的脱模工具或脱模剂来辅助。
7. 表面处理:根据产品要求,对铝合金零件进行打磨、抛光、喷涂等表面处理,以达到所需的外观和质感。
压铸铝工艺具有高生产效率、制造精度高、产品表面平整
等优点,广泛应用于汽车、电子、通讯等领域的零件制造。
同时,压铸铝工艺还可以实现复杂形状和薄壁结构的铝合
金零件制造,提高了产品的设计自由度和功能性。
铝合金压铸技术要求
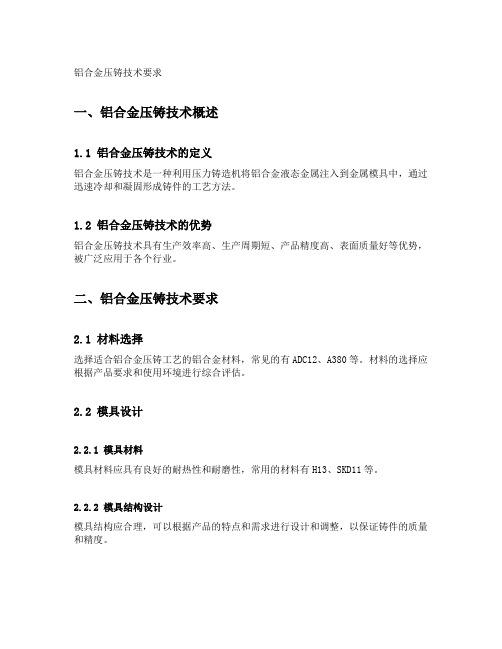
铝合金压铸技术要求一、铝合金压铸技术概述1.1 铝合金压铸技术的定义铝合金压铸技术是一种利用压力铸造机将铝合金液态金属注入到金属模具中,通过迅速冷却和凝固形成铸件的工艺方法。
1.2 铝合金压铸技术的优势铝合金压铸技术具有生产效率高、生产周期短、产品精度高、表面质量好等优势,被广泛应用于各个行业。
二、铝合金压铸技术要求2.1 材料选择选择适合铝合金压铸工艺的铝合金材料,常见的有ADC12、A380等。
材料的选择应根据产品要求和使用环境进行综合评估。
2.2 模具设计2.2.1 模具材料模具材料应具有良好的耐热性和耐磨性,常用的材料有H13、SKD11等。
2.2.2 模具结构设计模具结构应合理,可以根据产品的特点和需求进行设计和调整,以保证铸件的质量和精度。
2.3 注射设备2.3.1 压铸机选择根据产品的要求确定压铸机的型号和规格,包括锁力、注射压力等参数的选择。
2.3.2 注射系统注射系统包括注射缸、注射头、喷嘴等组成,其设计应合理,确保铝合金液态金属的注入和充填。
2.3.3 润滑系统润滑系统的设置对于铝合金压铸技术的稳定运行起着重要作用,应注意润滑剂的选择和使用。
2.4 工艺参数控制压铸工艺参数对于产品的质量和尺寸稳定性有很大的影响,应进行合理的控制和调整。
2.4.1 注射速度注射速度过快会导致铸件内部气孔、缺陷等问题,注射速度过慢会导致铝合金液态金属凝固不完全。
2.4.2 注射温度注射温度过高会导致铝合金液态金属粘度降低,流动性增强,但也会加快模具磨损。
注射温度过低则会导致液态金属凝固时间过长。
2.4.3 注射压力注射压力的控制对于铸件的密实性和表面质量有着重要影响,应根据产品要求进行精确控制。
2.4.4 注射时间注射时间应根据实际需要进行合理设置,以保证铝合金液态金属充填充实模腔。
2.5 热处理工艺铝合金压铸件在铸造成型后,经过热处理工艺可以改善其机械性能和物理性能,如固溶处理、时效处理等。
2.6 铸件表面处理铝合金压铸件的表面处理包括喷砂、喷涂、电镀等方法,以提高产品的外观质量和耐腐蚀性能。
铝合金压铸技术

铝合金熔解
1.冷室机:熔解温度630~650℃ 2.压铸铝合金的熔解温度(For ADC-12熔点为
516~582℃),另加高50~70℃以防热损.
射出速度
射出依柱塞的运动速度可分为两个阶段:
>第一个阶段,柱塞是以低速前进将熔汤充满 料管到浇口的空间.
>第二个阶段,柱塞是以高速前进,以便将熔汤 高速射入模穴.
熔汤在料管中的流动
1.柱塞速度小于临界速度料管的空气排不出 2.柱塞速度大于临界速度料管的空气包卷 3.柱塞速度等于临界速度料管的空气能排出
慢射阶段的临界速度( in/sec )
料 管 直 径 ( in )
1.00 1.25 1.50 1.75 2.00 2.25 2.50
50 11.3 12.6 13.8 15.0 16.0 17.0 17.9
1.3max 1.3max
0.5max 0.5max
ቤተ መጻሕፍቲ ባይዱ
0.5max 0.5max
0.3max 其余 0.3max 其余
1.3max 0.3max 0.3max 0.3max 其余
压铸概论
压铸机分冷室压铸机和热室压铸机二种: 1.冷室压铸机适合:铝合金和铜合金. 2.热室压铸机适合:锌合金,镁合金和锡铅合金.
铝合金压铸制程
铝合金压铸的过程首先将铝合金锭熔解, 然后将熔汤送至压铸机内,再将熔汤射入模穴 内,待铸件成形冷却后,开模,顶出铸件并取出, 然后对模具喷离型剂,合模后等待射出即完成 一个循环.
压铸制程特性
>高速充填 >充填时间很短 >高压 >熔汤和冷却速度快
铝合金压铸制程流程
1.合金熔解 2.将熔汤送至压铸机→射出→成形→开模→顶
铝合金压铸工艺

铝合金压铸工艺简介铝合金压铸是一种常见的金属成形工艺,通常用于制造各种铝合金零件。
其原理是将熔融的铝合金注入到模具中,并在一定的压力下冷却和凝固,最终得到所需的铝合金零件。
本文将介绍铝合金压铸的工艺流程以及相关的工艺参数。
工艺流程铝合金压铸的工艺流程主要包括模具准备、铝合金液态处理、注液和凝固、零件脱模和表面处理等几个主要步骤。
下面将详细介绍每个步骤的内容。
1. 模具准备在铝合金压铸工艺中,模具是非常重要的一部分。
首先需要根据所需零件的形状和尺寸设计制作模具。
模具通常由两部分构成,一部分是固定模,另一部分是活动模。
固定模固定在压铸机上,而活动模则与固定模相连,在注液和凝固过程中参与零件的成形。
模具内部还需要加工一些通道和排气口,以便铝合金的顺利注入和冷却。
在使用模具之前,还需要对其进行表面处理,以确保零件的顺利脱模。
2. 铝合金液态处理铝合金压铸需要使用熔融的铝合金作为原料。
在铝合金的制备过程中,需要控制好温度和成分的配比。
通常采用电炉或燃气炉加热铝合金,直到其达到液态状态。
同时,在熔炼过程中还需要添加一些合适的轻质合金元素,以提高铝合金的流动性和强度。
3. 注液和凝固当铝合金达到液态后,可以开始注入模具中进行成型。
首先将模具合拢,并在一定的压力下将铝合金注入到模具的腔室中。
在注液的过程中,铝合金要通过模具内部的通道和排气口,以确保零件填充完全且没有气泡。
注液的时间和压力应根据零件的大小和形状进行调整。
当铝合金填充完毕后,需要保持一定的压力,直到零件完全凝固。
4. 零件脱模在铝合金凝固后,需要将零件从模具中取出,这个过程称为脱模。
脱模的方法有很多种,可以通过机械力或气动力来推动零件从模具中顺利脱离。
在脱模之前,需要注意保护零件的表面,以免在脱模过程中造成刮擦或其他损坏。
5. 表面处理铝合金压铸零件脱模后,通常还需要进行一些表面处理工艺,以提高零件的外观和性能。
常见的表面处理方法包括机械抛光、电镀、喷涂、阳极氧化等。
铝合金压铸技术要求

1、范围本标准规定了铝合金压铸件的技术要求、试验方法、检验规那么、交货条件等。
本标准适用于汽车发电机铝合金端盖压铸件。
2、引用标准GB6414铸件尺寸公差铝及铝合金化学分析方法GB288-87金属拉力试验法GB/T13822-92 压铸有色合金试样GB6060.5 外表粗造度比拟样块抛(喷)丸、喷吵加工外表3、技术要求3.1 压铸铝合金的牌号压铸铝合金采用UNS-A03800〔美国,日本ADC10〕可选用材料UNS-A03830 〔美国,日本ADC12〕化学成份见表1表1供给商可选择上述四种牌号的任何一种,如在生产过程中更换其它牌号,需重新进展样件鉴定。
一级回炉料:浇道、化学成份合格的废铸件,后加工次品等不含水分和油污。
二级回炉料:集渣包、坩埚底部剩料、退货废品、存放时间长〔超过10天〕的一级回炉料。
三级回炉料:飞边、溅屑、细小的碎料、带有油污的渣料、因化学成份报废的铸件、从铝渣中捡出的铝粒。
使用单一某级回炉料:一级回炉料最大使用量50%,二级回炉料最大使用量40%。
一级、二级回炉料混合使用:回炉料总量不超过40%,其中二级回炉料最大使用量20%。
三级回炉料:不能直接使用,必须经过重熔、精炼且化学成份分析合格后才能使用,其最大使用量10%,仅与铝锭混合使用。
小颗粒回炉料大块回炉料铝锭,如此循环。
3.2 力学性能采用单铸拉力试样检验,其力学性能应满足抗拉强度≥240Mpa,伸长率≥1%,HB85〔5/250/30〕。
试样尺寸及形状应符合GB/T 13822-92?压铸有色合金试样?的规定。
3.3 压铸件尺寸压铸件的几何形状和尺寸应符合铸件图的规定。
3.4 待加工外表用符号“〞标明,尖头指向被加工面。
例:0.5 表示该外表留有加工余量3.5 外表质量3.5.1 铸件清理后的外表质量铸件的浇口、飞边、溢流口、隔皮等应清理干净,但允许留有清理痕迹。
在不影响使用的情况下,因去除浇口、溢流口时所形成的缺肉或高出均不得超过壁厚的四分之一,并且不得超过1.5 mm。
铝合金真空压铸技术

铝合金真空压铸技术铝合金真空压铸技术是一种高效、精密的铝合金铸造工艺,通过在真空环境中进行压铸,可以有效避免铸件表面氧化、气孔等缺陷,提高铸件的质量和性能。
以下是关于铝合金真空压铸技术的详细介绍,包括其工艺流程、优势、应用领域等方面。
一、铝合金真空压铸技术概述铝合金真空压铸技术是一种在真空环境下进行的高压铸造工艺。
其主要步骤包括:模具封闭,抽真空,充填铝液,施加高压,保压定型,冷却固化,开模取件。
整个过程在真空条件下进行,以确保铸件表面无气孔、氧化等缺陷,同时通过高压实现铝液的充分充填,提高铸件的密度和机械性能。
二、铝合金真空压铸技术的工艺流程模具设计和制造:根据产品的形状和尺寸,设计并制造合适的压铸模具,确保模具具有足够的强度和耐磨性。
模具封闭:将设计好的模具封闭,形成一个密封的腔室,以准备进行真空铸造。
真空抽气:在模腔封闭后,通过真空泵将模腔内的空气抽出,创造真空环境。
真空状态有助于减少铝液中气体的溶解,防止气孔的生成。
铝液充填:在真空状态下,将预热至一定温度的铝液注入模腔,确保铝液在模腔中均匀充填。
施加高压:在铝液充填后,施加高压,使铝液充分充填模腔,提高铸件的密度和机械性能。
保压定型:在高压作用下,保持一段时间,使铝液定型成型。
冷却固化:在定型后,通过冷却系统将模腔内的铝液迅速冷却,固化成为铝合金铸件。
开模取件:冷却固化后,打开模具,取出成型的铝合金铸件,进行后续的处理和加工。
三、铝合金真空压铸技术的优势减少氧化和气孔:在真空环境下进行铸造可以有效减少铸件表面的氧化,同时通过真空抽气减少气体的溶解,避免气孔的生成,提高铸件的表面质量。
提高密度和机械性能:高压充填和保压定型能够使铝液充分充填模腔,提高铝合金铸件的密度和机械性能。
精密铸造:铝合金真空压铸技术可以实现更精密的铸造,适用于复杂形状、高精度要求的铝合金零件生产。
高生产效率:由于真空压铸工艺的高压和高速度,可以实现较短的充填时间和较快的冷却速度,提高生产效率。
压铸铝技术参数
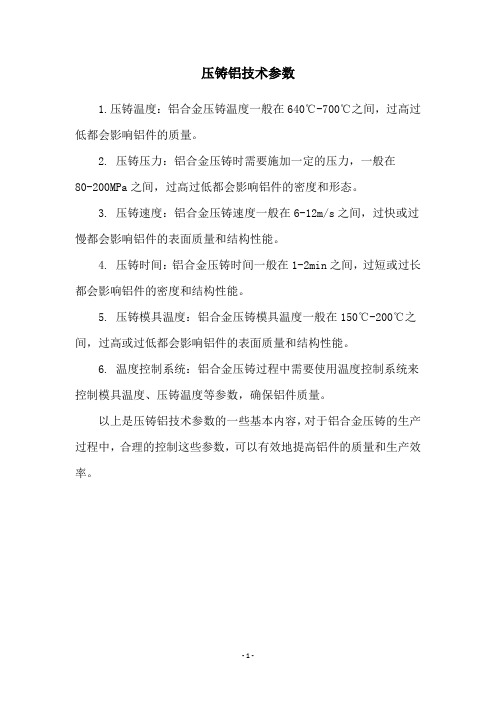
压铸铝技术参数
1.压铸温度:铝合金压铸温度一般在640℃-700℃之间,过高过低都会影响铝件的质量。
2. 压铸压力:铝合金压铸时需要施加一定的压力,一般在
80-200MPa之间,过高过低都会影响铝件的密度和形态。
3. 压铸速度:铝合金压铸速度一般在6-12m/s之间,过快或过慢都会影响铝件的表面质量和结构性能。
4. 压铸时间:铝合金压铸时间一般在1-2min之间,过短或过长都会影响铝件的密度和结构性能。
5. 压铸模具温度:铝合金压铸模具温度一般在150℃-200℃之间,过高或过低都会影响铝件的表面质量和结构性能。
6. 温度控制系统:铝合金压铸过程中需要使用温度控制系统来控制模具温度、压铸温度等参数,确保铝件质量。
以上是压铸铝技术参数的一些基本内容,对于铝合金压铸的生产过程中,合理的控制这些参数,可以有效地提高铝件的质量和生产效率。
- 1 -。
铝压铸工艺流程

铝压铸工艺流程
《铝压铸工艺流程》
铝压铸工艺是一种常用的金属加工工艺,适用于生产各种铝合金零件。
铝压铸工艺流程包括模具设计、铝合金熔化、压铸成型、去毛刺、处理和检验等步骤。
首先是模具设计。
根据零件的形状和尺寸设计出合适的模具,模具设计的质量直接影响到最终产品的质量。
接下来是铝合金熔化。
将铝合金原料投入熔炉中融化,熔化后的铝合金需要在一定的温度和时间内维持液态状态,以保证良好的流动性。
再之后是压铸成型。
将熔化的铝合金倒入注塑机中,通过高压将铝液注入模具中,快速冷却凝固成型。
铸出的零件表面光滑,尺寸精确。
接着是去毛刺。
将铸件去除表面毛刺,使其外观更加美观,同时也减少对下一道工序的干扰。
然后是处理。
处理工艺包括去除零件表面的氧化层,增加零件的强度和硬度,提高表面光洁度等。
最后是检验。
对成品进行严格的检验,包括外观质量、尺寸精度、力学性能等方面的测试。
铝压铸工艺流程的每个环节都是非常重要的,只有严格控制每个环节,确保每个步骤的质量,才能生产出高质量的铝合金零件。
同时,铝压铸工艺也需要不断的技术创新和提升,以适应不断变化的市场需求,满足客户的要求。
铝合金压铸技术要求
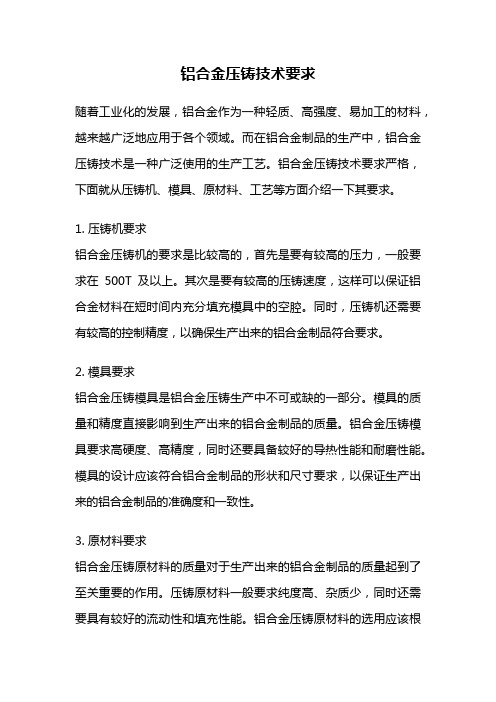
铝合金压铸技术要求随着工业化的发展,铝合金作为一种轻质、高强度、易加工的材料,越来越广泛地应用于各个领域。
而在铝合金制品的生产中,铝合金压铸技术是一种广泛使用的生产工艺。
铝合金压铸技术要求严格,下面就从压铸机、模具、原材料、工艺等方面介绍一下其要求。
1. 压铸机要求铝合金压铸机的要求是比较高的,首先是要有较高的压力,一般要求在500T及以上。
其次是要有较高的压铸速度,这样可以保证铝合金材料在短时间内充分填充模具中的空腔。
同时,压铸机还需要有较高的控制精度,以确保生产出来的铝合金制品符合要求。
2. 模具要求铝合金压铸模具是铝合金压铸生产中不可或缺的一部分。
模具的质量和精度直接影响到生产出来的铝合金制品的质量。
铝合金压铸模具要求高硬度、高精度,同时还要具备较好的导热性能和耐磨性能。
模具的设计应该符合铝合金制品的形状和尺寸要求,以保证生产出来的铝合金制品的准确度和一致性。
3. 原材料要求铝合金压铸原材料的质量对于生产出来的铝合金制品的质量起到了至关重要的作用。
压铸原材料一般要求纯度高、杂质少,同时还需要具有较好的流动性和填充性能。
铝合金压铸原材料的选用应该根据铝合金制品的要求和生产工艺来进行选择。
4. 工艺要求铝合金压铸技术的工艺要求主要包括模具温度、压铸温度、压铸速度等。
模具温度一般要求在200℃以上,以保证铝合金材料充分流动。
压铸温度要求控制在合适的范围内,过高会导致铝合金材料产生气孔,过低则会导致铝合金材料填充不充分。
压铸速度也要根据铝合金制品的要求和生产工艺来进行调整。
铝合金压铸技术要求严格,需要从多个方面考虑,才能生产出符合要求和标准的铝合金制品。
同时,压铸技术的不断创新和完善,也为铝合金制品的生产提供了更好的技术支持。
铝合金压铸的介绍

铝合金压铸的介绍铝合金压铸是一种用于生产复杂形状铝合金零件的工艺。
压铸是指将铝合金熔融后注入到特殊的铸造模具中,利用模具的压力将熔融铝合金充填到模具腔内,随后冷却固化形成所需零件。
铝合金压铸具有以下特点:1.复杂形状:铝合金压铸能够生产出复杂形状的零件,如薄壁结构、内腔、槽形等。
这得益于压铸模具能够精确复制设计图纸的形状,使铝合金在固化后能够保持原有的细节和精度。
2.高精度:铝合金压铸具有较高的尺寸精度和表面质量,能够满足对精度要求较高的零件生产。
这是由于压铸过程中,熔融铝合金通过模具的压力充填到腔内,形成接近模具表面的铸件。
3.高效生产:铝合金压铸是一种高效的生产工艺,可实现大批量、连续、自动化的生产。
这使得铝合金压铸成为一种经济实用的生产方式,能够满足工业生产对大规模生产的需求。
4.材料性能优越:铝合金具有低密度、优良的导热性能和机械性能,使得压铸的铝合金零件具有较好的强度和刚性。
此外,铝合金还具有良好的耐腐蚀性和可靠的耐用性。
5.可加工性强:铝合金容易加工,可进行切削、冲压、焊接等工艺。
这为铝合金压铸零件的二次加工提供了便利,例如孔加工、表面处理、组装等。
铝合金压铸广泛应用于各行业,如汽车、航空航天、电子、建筑等。
其中,汽车行业是铝合金压铸的主要应用领域,利用铝合金压铸可以生产轻量化的零部件,提高汽车的燃油效率和性能。
而航空航天行业也广泛使用铝合金压铸零件,以满足轻质化、高强度和高精度的要求。
总的来说,铝合金压铸是一种重要的铝合金加工工艺,具有复杂形状、高精度、高效生产等优点,广泛应用于各个领域。
通过铝合金压铸,可以生产出高质量、高性能的铝合金零件,推动各行业的发展与进步。
铝合金压铸

铝合金压铸1. 引言铝合金压铸是一种广泛应用于制造业的铝合金加工方法。
铝合金以其低密度、高强度和良好的耐腐蚀性能,在汽车、电子、航空航天等领域中得到了广泛的应用。
压铸技术可以高效地生产出复杂形状的铝合金零件,因此在铝合金加工中占据重要地位。
本文将介绍铝合金压铸的工艺流程、优势和应用领域,并讨论一些常见问题。
2. 工艺流程铝合金压铸的工艺流程主要包括模具设计、合金熔炼、注射成形、冷却和处理。
2.1 模具设计模具设计是铝合金压铸的第一步。
模具需要根据所需零件的形状和尺寸进行设计,包括模具的结构、内腔和冷却系统。
模具设计要考虑到零件的收缩率和变形,以确保最终产品的质量。
2.2 合金熔炼铝合金压铸所使用的合金通常是从铝锭中熔化得到的。
合金的成分可以根据具体应用需求进行调整。
在熔化过程中,需要控制合金的温度、气氛和熔化时间,以确保合金的纯度和一致性。
2.3 注射成形熔化的铝合金被注入到预先设计好的模具中。
注射时需要控制注射速度和压力,以防止产生气体孔洞或缺陷。
注射成形后,需要等待一段时间,让注入的铝合金在模具中冷却和凝固。
2.4 冷却和处理冷却过程包括模具内外的冷却系,以确保铝合金零件能够迅速冷却并保持其形状稳定。
在冷却后,铝合金零件需要进行一些处理,如去除模具的挂钩和余震,修整边缘和表面处理等。
3. 优势铝合金压铸相比其他加工方法具有以下优势:3.1 快速生产铝合金压铸能够实现高效快速的生产。
模具的设计和制造时间相对较短,而且铝合金的注射成形过程也比较迅速。
这意味着铝合金压铸可以满足紧急需求或大批量生产的要求。
3.2 复杂零件制造铝合金压铸可以生产出形状复杂的零件,包括薄壁结构、凹凸面和细节部分等。
这使得铝合金压铸在汽车、电子和航空航天等领域中得到广泛应用。
3.3 成本效益相比其他铝合金加工方法,铝合金压铸具有较低的成本。
模具的制造成本相对较低,并且可以在多次使用中平摊成本。
此外,铝合金的重量轻,材料成本较低。
铝合金一体化压铸技术

铝合金一体化压铸技术【摘要】铝合金一体化压铸技术是一种高效的金属加工技术,通过压铸设备将铝合金熔融液注入模具中,经过高压铸造成型,实现一次成型并得到零件产品。
这种技术在汽车、航空航天、电子产品等领域有广泛的应用,其优势主要体现在生产效率高、产品质量好、设计自由度大等方面。
随着科技的不断发展,铝合金一体化压铸技术的工艺流程越来越完善,未来的发展趋势将更加智能化和自动化。
铝合金一体化压铸技术的未来发展具有重要意义,不仅可以提高生产效率,降低生产成本,还可以推动金属加工行业的发展。
铝合金一体化压铸技术的经济效益和重要性不言而喻。
随着技术的不断改进和应用领域的扩大,铝合金一体化压铸技术必将在未来发展出更广阔的市场。
【关键词】铝合金、一体化、压铸技术、原理、应用领域、优势、发展趋势、工艺流程、未来发展、重要性、经济效益1. 引言1.1 铝合金一体化压铸技术概述铝合金一体化压铸技术是一种先进的压铸工艺,将铝合金和其他金属或非金属材料一次性压制成型,实现了多种工艺的一体化,具有高效、省时、省力的特点。
该技术在制造业中被广泛应用,可用于汽车零部件、航空航天设备、通讯设备等领域。
铝合金一体化压铸技术的优势主要包括生产效率高、成本低、产品质量稳定等。
随着科技的不断进步和市场需求的变化,铝合金一体化压铸技术不断发展壮大,未来的发展趋势将更加智能化、自动化。
该技术的工艺流程主要包括模具设计、铸造工艺、静态与动态模具等环节。
铝合金一体化压铸技术在未来的发展中将发挥越来越重要的作用,不仅在经济上带来效益,而且在技术发展上也有着重要意义。
2. 正文2.1 铝合金一体化压铸技术的原理铝合金一体化压铸技术的原理是指将铝合金材料经过精密的合金配比,加热至一定温度后,通过高压注射成型,使铝合金在模具中快速冷却凝固,形成具有一定形状和尺寸的铝合金零件。
这一过程主要包括以下几个步骤:1. 铝合金材料处理:首先需要对铝合金进行合适的合金配比,以确保零件具有良好的力学性能和耐蚀性。
电力金具铝合金压铸工艺流程简述
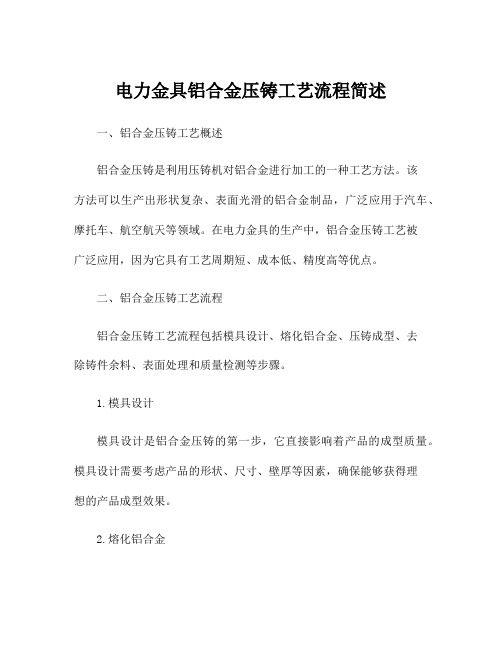
电力金具铝合金压铸工艺流程简述一、铝合金压铸工艺概述铝合金压铸是利用压铸机对铝合金进行加工的一种工艺方法。
该方法可以生产出形状复杂、表面光滑的铝合金制品,广泛应用于汽车、摩托车、航空航天等领域。
在电力金具的生产中,铝合金压铸工艺被广泛应用,因为它具有工艺周期短、成本低、精度高等优点。
二、铝合金压铸工艺流程铝合金压铸工艺流程包括模具设计、熔化铝合金、压铸成型、去除铸件余料、表面处理和质量检测等步骤。
1.模具设计模具设计是铝合金压铸的第一步,它直接影响着产品的成型质量。
模具设计需要考虑产品的形状、尺寸、壁厚等因素,确保能够获得理想的产品成型效果。
2.熔化铝合金在铝合金压铸工艺中,首先需要将铝合金加热熔化成液态,以便后续的压铸成型。
熔化铝合金需要控制好温度和成分,确保合金液的质量符合要求。
3.压铸成型熔化铝合金之后,将其注入压铸机的射出室,并闭合模具,将熔化的铝合金注入到模具腔中,压铸成型。
4.去除铸件余料在压铸成型后,铝合金铸件上会残留有一些余料,需要进行去除,以便后续的加工和表面处理。
5.表面处理铝合金铸件的表面处理包括除渣、粗磨、抛光等步骤,以获得平整光滑的表面,符合产品要求。
6.质量检测最后,对铝合金铸件进行质量检测,包括外形尺寸检测、化学成分分析、力学性能测试等,确保产品的质量符合标准要求。
三、铝合金压铸工艺的优势铝合金压铸工艺相比传统的铸造工艺具有以下优势:1.精度高:铝合金压铸工艺可以生产出形状复杂、精度高的铝合金制品,适用于电力金具的生产。
2.工艺周期短:铝合金压铸工艺生产效率高,工艺周期短,能够满足大批量生产的需求。
3.成本低:铝合金压铸工艺不仅可以节约原材料,而且可以减少加工工序和能源消耗,成本较低。
4.表面光滑:铝合金压铸成型的产品表面光滑,不需要二次加工,提高了生产效率。
综上所述,铝合金压铸工艺是电力金具生产中一种重要的工艺方法,它具有精度高、工艺周期短、成本低、表面光滑等优点。
铝合金压铸工艺流程

铝合金压铸工艺流程铝合金压铸工艺是一种常见的金属加工工艺,它通过将铝合金加热至液态状态,然后注入模具中进行压铸,最终得到所需形状的铝合金制品。
在工业生产中,铝合金压铸工艺被广泛应用于汽车零部件、航空航天零部件、通讯设备外壳等领域。
下面将详细介绍铝合金压铸工艺的流程。
首先,铝合金压铸工艺的第一步是原料准备。
在进行压铸之前,需要准备好所需的铝合金材料,这些材料通常是铝合金锭。
在选择铝合金材料时,需要考虑其成分和性能,以确保最终制品的质量和性能符合要求。
接下来是模具设计和制造。
模具是铝合金压铸工艺中至关重要的一环,它直接影响着最终产品的形状和尺寸精度。
模具设计需要根据最终产品的形状和尺寸要求进行,然后制造出相应的模具。
模具制造的精度和质量对于铝合金压铸工艺的成功至关重要。
第三步是熔炼和注射。
在进行铝合金压铸之前,需要将铝合金锭加热至一定温度使其熔化,然后通过注射机将熔化的铝合金注入模具中。
在注射过程中,需要控制注射速度和压力,以确保铝合金充填模具的每一个角落,避免产生气孔和缺陷。
接着是冷却和固化。
一旦铝合金充填模具完成,就需要进行冷却和固化,使铝合金在模具中逐渐冷却凝固。
在这个过程中,需要控制冷却速度和温度,以确保最终产品的组织结构和性能达到要求。
最后是脱模和后处理。
当铝合金在模具中完全固化后,就需要将其从模具中取出,这个过程称为脱模。
脱模后的铝合金制品通常还需要进行去闪、修磨、喷漆等后处理工艺,以提高其表面质量和精度。
总的来说,铝合金压铸工艺流程包括原料准备、模具设计和制造、熔炼和注射、冷却和固化、脱模和后处理等几个关键步骤。
每个步骤都需要严格控制和操作,以确保最终产品的质量和性能达到要求。
铝合金压铸工艺在现代制造业中具有重要的地位,它为各种工业制品的生产提供了高效、精密的加工方法。
纯铝压铸工艺及压铸模技术要点总结
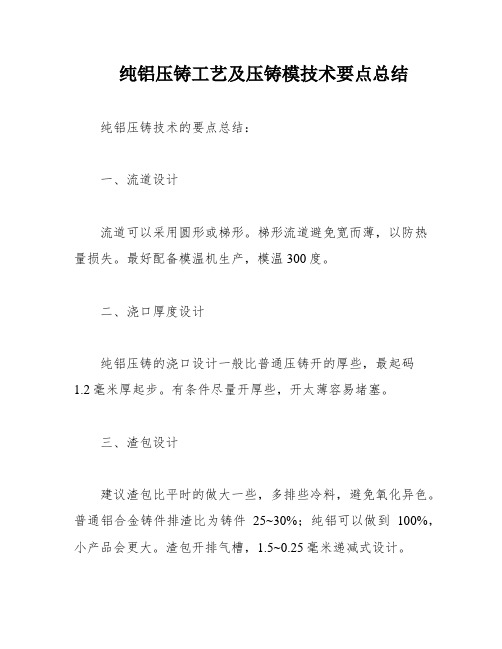
纯铝压铸工艺及压铸模技术要点总结
纯铝压铸技术的要点总结:
一、流道设计
流道可以采用圆形或梯形。
梯形流道避免宽而薄,以防热量损失。
最好配备模温机生产,模温300度。
二、浇口厚度设计
纯铝压铸的浇口设计一般比普通压铸开的厚些,最起码
1.2毫米厚起步。
有条件尽量开厚些,开太薄容易堵塞。
三、渣包设计
建议渣包比平时的做大一些,多排些冷料,避免氧化异色。
普通铝合金铸件排渣比为铸件25~30%;纯铝可以做到100%,小产品会更大。
渣包开排气槽,1.5~0.25毫米递减式设计。
四、顶针孔间隙设计
间隙比普通铝压铸模放大1.5~2.0倍,不会跑料。
五、钢材及热处理
可选用国产8418.热处理:48~50HRC比较合理。
模芯大的更低些,镶针镶件硬度可以高些,易断的部件降低点热处理硬度。
六、铝液温度
保持铝液的稳定性,一般生产在700~730度,也可以高于730度,最高不高于750度,最低不低于700.
七、根据压铸件氧化的颜色需求选择合适的铝含量成份
氧化黑色,建议用铝含量低的铝锭,可以用ADC10.氧化灰色,比如铁灰色,建议铝含量在95~97%的铝锭。
铝的一体化压铸

铝的一体化压铸全文共四篇示例,供读者参考第一篇示例:铝的一体化压铸是一种先进的工艺技术,它将铸造和成型两个环节整合在一起,使得生产效率大大提高,产品质量也更加稳定。
一体化压铸技术在工业生产中得到了广泛应用,特别是在汽车零部件、电子产品、建筑材料等行业中发展迅猛。
本文将从技术原理、应用领域、发展趋势等方面介绍铝的一体化压铸技术。
一体化压铸技术是将铝及其合金加热熔化后,通过高压注射模具形成产品的工艺。
相比传统的压铸工艺,一体化压铸技术不仅可以将产品生产周期缩短,还可以减少成本、提高产品质量。
这是因为一体化压铸技术可以有效避免铸造过程中的气孔、热裂纹等缺陷,确保产品的一致性和稳定性。
一体化压铸技术还可以实现对产品结构和形状的精确控制,满足不同客户的需求。
铝的一体化压铸技术在汽车零部件、电子产品、建筑材料等行业中得到广泛应用。
在汽车行业中,一体化压铸技术可以制造轻量化、高强度的零部件,提高汽车的燃油效率和安全性。
在电子产品领域,一体化压铸技术可以生产小型、高精度的零部件,满足电子产品对轻量化和高性能的要求。
在建筑材料领域,一体化压铸技术可以制造形状复杂的构件,提高建筑物的整体性和美观性。
随着工业技术的不断进步,铝的一体化压铸技术也在不断创新和发展。
未来,一体化压铸技术将更加智能化、自动化,进一步提高产品的生产效率和质量。
一体化压铸技术还将广泛应用于更多的行业,为工业制造带来更大的变革和提升。
第二篇示例:铝的一体化压铸是一种先进的生产技术,能够将铝合金材料一次性压制成特定形状的工件。
通过一体化压铸技术,不仅可以降低生产成本,提高生产效率,而且可以提高产品质量,满足客户的需求。
本文将重点介绍铝的一体化压铸技术的工艺流程、特点及应用。
一、铝的一体化压铸技术的工艺流程铝的一体化压铸技术是指将铝合金材料加热至一定温度,然后注入模具中,通过高压铸造技术将铝液压制成特定形状的工件。
其工艺流程主要包括以下几个步骤:1. 材料准备:首先需要选用适合的铝合金材料,将其进行加热处理,以确保铝合金材料在一定温度下可流动性良好。
铝压铸成型技术
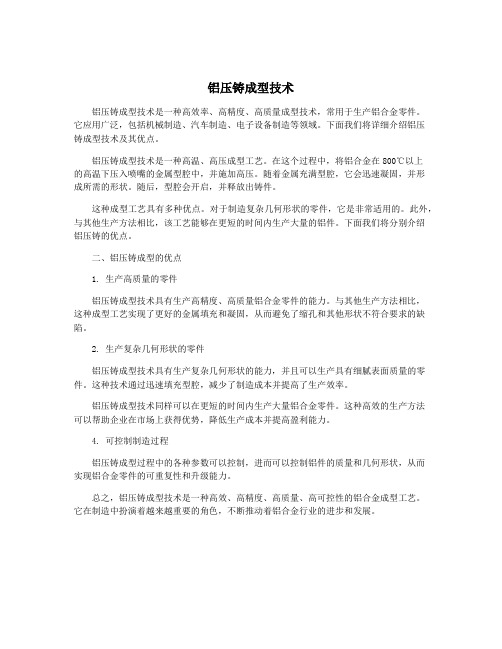
铝压铸成型技术铝压铸成型技术是一种高效率、高精度、高质量成型技术,常用于生产铝合金零件。
它应用广泛,包括机械制造、汽车制造、电子设备制造等领域。
下面我们将详细介绍铝压铸成型技术及其优点。
铝压铸成型技术是一种高温、高压成型工艺。
在这个过程中,将铝合金在800℃以上的高温下压入喷嘴的金属型腔中,并施加高压。
随着金属充满型腔,它会迅速凝固,并形成所需的形状。
随后,型腔会开启,并释放出铸件。
这种成型工艺具有多种优点。
对于制造复杂几何形状的零件,它是非常适用的。
此外,与其他生产方法相比,该工艺能够在更短的时间内生产大量的铝件。
下面我们将分别介绍铝压铸的优点。
二、铝压铸成型的优点1. 生产高质量的零件铝压铸成型技术具有生产高精度、高质量铝合金零件的能力。
与其他生产方法相比,这种成型工艺实现了更好的金属填充和凝固,从而避免了缩孔和其他形状不符合要求的缺陷。
2. 生产复杂几何形状的零件铝压铸成型技术具有生产复杂几何形状的能力,并且可以生产具有细腻表面质量的零件。
这种技术通过迅速填充型腔,减少了制造成本并提高了生产效率。
铝压铸成型技术同样可以在更短的时间内生产大量铝合金零件。
这种高效的生产方法可以帮助企业在市场上获得优势,降低生产成本并提高盈利能力。
4. 可控制制造过程铝压铸成型过程中的各种参数可以控制,进而可以控制铝件的质量和几何形状,从而实现铝合金零件的可重复性和升级能力。
总之,铝压铸成型技术是一种高效、高精度、高质量、高可控性的铝合金成型工艺。
它在制造中扮演着越来越重要的角色,不断推动着铝合金行业的进步和发展。
铝压铸成型技术

铝压铸成型技术
铝压铸成型技术是一种高效、精密的铸造工艺,它采用高压下将铝合金液态金属注入模具中,经过冷却凝固后得到所需的铝合金零件。
这种技术具有成本低、生产效率高、产品质量稳定等优点,因此在汽车、航空航天、电子、机械等领域得到广泛应用。
铝压铸成型技术的优点之一是生产效率高。
相比传统的铸造工艺,铝压铸成型技术可以在短时间内完成大批量的生产,而且生产过程中不需要额外的加工工序,可以直接得到所需的零件。
这不仅提高了生产效率,还降低了生产成本。
另一个优点是产品质量稳定。
铝压铸成型技术可以制造出高精度、高强度、高密度的铝合金零件,这些零件具有良好的表面质量和尺寸精度,可以满足各种复杂零件的要求。
同时,铝压铸成型技术还可以避免铝合金零件在生产过程中出现气孔、缩孔等缺陷,从而提高了产品的质量稳定性。
铝压铸成型技术还具有成本低的优点。
相比其他铸造工艺,铝压铸成型技术的生产成本较低,因为它可以在短时间内完成大批量的生产,而且生产过程中不需要额外的加工工序。
这使得铝压铸成型技术在大批量生产铝合金零件时具有明显的优势。
铝压铸成型技术是一种高效、精密的铸造工艺,它具有成本低、生产效率高、产品质量稳定等优点,因此在各种领域得到广泛应用。
未来,随着科技的不断发展,铝压铸成型技术将会更加完善,为各行各业提供更好的服务。
- 1、下载文档前请自行甄别文档内容的完整性,平台不提供额外的编辑、内容补充、找答案等附加服务。
- 2、"仅部分预览"的文档,不可在线预览部分如存在完整性等问题,可反馈申请退款(可完整预览的文档不适用该条件!)。
- 3、如文档侵犯您的权益,请联系客服反馈,我们会尽快为您处理(人工客服工作时间:9:00-18:30)。
GD-AlSi12(Cu) GD-AlSi10Mg GD-AlMg9 ----GD-AlSi9Cu3 GD-AlSi9Cu3 -------------
6
压铸铝合金材料成份规范
编号
ADC-1
Cu
1.0
ADC-3 0.6max
ADC-5 0.2max
ADC-6 0.1max
ADC-10 2.0~4.0
8
铝合金压铸制程
铝合金压铸的过程首先将铝合金锭熔解, 然后将熔汤送至压铸机内,再将熔汤射入模穴 内,待铸件成形冷却后,开模,顶出铸件并取出, 然后对模具喷离型剂,合模后等待射出即完成 一个循环.
9
压铸制程特性
>高速充填 >充填时间很短 >高压 >熔汤和冷却速度快
10
铝合金压铸制程流程
1.合金熔解 2.将熔汤送至压铸机→射出→成形→开模→顶
13
熔汤在料管中的流动
1.柱塞速度小于临界速度料管的空气排不出 2.柱塞速度大于临界速度料管的空气包卷 3.柱塞速度等于临界速度料管的空气能排出
14
慢射阶段的临界速度( in/sec )
料 管 直 径 ( in )
1.00 1.25 1.50 1.75 2.00 2.25 2.50
50 11.3 12.6 13.8 15.0 16.0 17.0 17.9
份 Zn
0.5max 0.5max 0.1max 0.4max 1.0max 3.0max
9.6~12.0 9.6~12.0
0.3max 0.3max
1.0max 3.0max
16.0~18.0 0.45~0.65 1.5max
Fe
1.3max 1.3max 1.8max 0.8max 1.3max 1.3max
16
铝合金熔解
1.冷室机:熔解温度630~650℃ 2.压铸铝合金的熔解温度(For ADC-12熔点为
516~582℃),另加高50~70℃以防热损.
17
射出速度
射出依柱塞的运动速度可分为两个阶段:
>第一个阶段,柱塞是以低速前进将熔汤充满 料管到浇口的空间.
>第二个阶段,柱塞是以高速前进,以便将熔汤 高速射入模穴.
1.3max 1.3max
0.5max 0.5max
0.5max 0.5max
0.3max 其余 0.3max 其余
1.3max 0.3max 0.3max 0.3max 其余
7Байду номын сангаас
压铸概论
压铸机分冷室压铸机和热室压铸机二种: 1.冷室压铸机适合:铝合金和铜合金. 2.热室压铸机适合:锌合金,镁合金和锡铅合金.
铝合金压铸技术
整理: 陈达福
1
课程内容
>压铸概论与压铸铝合金 >压铸制程条件与设定 >模具方案设计 >实例研讨
2
压铸铝合金
压铸用铝合金全世界超过3000种型号
3
压铸铝合金的基本要求
1.流动性好 2.收缩率.龟裂倾向小 3.等温凝固比率大,如此方可产生致密之表面化铸
肌,避免缩孔之危害 4.有一定之高温强度,顶出时才不致变形 5.常温下有足够强度,以利生产薄壁件 6.不易与模具起化学或物理反应,否则粘模,影响量
18
浇口速度:熔汤通过浇口的速度
厚铸件 >5mm
浇口速度(m/sec) 15~20
一般铸件 2~5mm
20~30
薄铸件 1~2mm
30~40
柱塞的高速速度值计算: Vp=VgAg/Ap
其中:Vp柱塞速度; Vg浇口速度; Ag浇口面积; Ap柱塞面积
超薄件 <1mm
7.0 7.5
8.1
8.5 9.0
% 80 4.6 5.2
5.7 6.1
6.6
7.0 7.3
85 3.6 4.0
4.4 4.7
5.0
5.4 5.6
90 2.5 2.8
3.0 3.3
3.5
3.7 3.9
95 1.3 1.5
1.6 1.8
1.9
2.0 2.1
15
压铸制程条件
>合金熔解
>射出速度 >高速切换位置 >铸造压力 >温度控制
出铸件并取出→洒离型剂→合模→(进入下 一循环) 3.从时间上看,制程流程为:a.充填;b.凝固; c.铸件 取出;d.开模等待
11
压铸制程熔汤的流动方式
低速流动是连续性的 中速流动是断续的呈粗颗粒状 压铸是高速流动,进入型腔是呈雾状喷入
12
熔汤在模穴中的流动
1.熔汤通过浇口 2.高速喷入反弹 3.回包卷气
ADC10Z
ADC-12
2.0~4.0 1.5~3.5
ADC12Z
ADC-14
1.5~3.5 4.0~5.0
化 Si
11.0~13.0 9.0~10.0 0.3max 1.0max 7.5~9.5 7.5~9.5
学成 Mg
0.3max 0.4~0.6 4.0~8.5 2.5~4.0 0.3max 0.3max
产 7.良好的被加工性和抗腐蚀性
4
压铸铝合金的种类
Al-Si合金 调质,高温强度,机械性质,耐蚀性 Al-Cu合金 热处理,精度要求 Al-Mg合金 机械性质,耐蚀性,机械加工,延性 Al-Si-Cu合金 Al-Si-Mg合金
5
各国压铸铝合金材料规范对照表
合金系
Al-Si系 Al-Si-Mg系 Al-Mg系 Al-Mg系 Al-Si-Cu系 Al-Si-Cu系 Al-Si-Cu系 Al-Si-Cu系 Al-Si-Cu系
55 10.1 11.3 12.4 13.4 14.3 15.2 16.0
起 60 9.0 10.0 11.0 11.9 12.7 13.5 14.2
始 65 7.8
8.8
9.6 10.4 11.1 11.8 12.4
充
填 70 6.8
7.6
8.3 9.0
9.6
10.2 10.7
率 75 5.7 6.4
CNS编号 JIS编号(H5302) AA/ASTM(1984) DIN1725(1986)
1种 3种 5种 6种 10种 10种Z 12种 12种Z 14种Z
ADC-1 ADC-3 ADC-5 ADC-6 ADC-10 ADC-10Z ADC-12 ADC-12Z ADC-14
A413 A360.0 518.0 515.0 B380.0 A380.0 383.0 383.0 B390.0
Mn
0.3max 0.3max 0.3max 0.4~0.6 0.5max 0.5max
Ni
0.5max 0.5max 0.1max 0.1max 0.5max 0.5max
Sn Al
0.1max 其余 0.1max 其余 0.1max 其余 0.3max 其余 0.3max 其余 0.3max 其余