APQP五阶段输入输出汇编
APQP输入输出
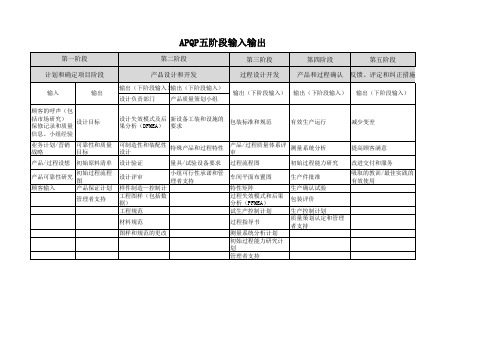
设计失效模式及后 新设备工装和设施的 果分析(DFMEA) 要求 可制造性和装配性 特殊产品和过程特性 设计 设计验证 设计评审 样件制造—控制计 划 工程图样(包括数 据) 工程规范 材料规范 图样和规范的更改 量具/试验设备要求 小组可行性承诺和管 理者支持
包装标准和规范
有效生产运行
减少变差
产品/过程质量体系评 测量系统分析 审 过程流程图 车间平面布置图 特性矩阵 过程失效模式和后果 分析(PFMEA) 试生产控制计划 过程指导书 测量系统分析计划 初始过程能力研究计 划 管理者支持 初始过程能力研究 生产件批准 生产确认试验 包装评价 生产控制计划 质量策划认定和管理 者支持
可制造性和装配性 量具/试验设备清单 设计报告 设计验证和评审报 项目可行性分析报告 告 样件控制计划 小组可行性承诺报告
会议记录
成本分析报告
控制计划检查清单
场地平面布置图检查 清单
汽车产品客户调 查问卷
产品图纸 生产作业规范 材料规范 材料测试报告 工程变更书
特殊矩阵图 PFMEA PFMEA检查清单 试生产控制计划 控制计划检查清单 各工序操作指引 测量系统分析计划 初始过程能力研究计 划
APQP五阶段输入输出
第一阶段 计划和确定项目阶段
输入 输出
第二阶段 产品设计和开发
输出(下阶段输入) 输出(下阶段输入) 设计负责部门 产品质量策划小组
第三阶段 过程设计开发
输出(下阶段输入)
第四阶段 产品和过程确认
输出(下阶段输入)
第五阶段 反馈、评定和纠正措施
输出(下阶段输入)
顾客的呼声(包 括市场研究) 设计目标 保修记录和质量 信息、小组经验 业务计划/营销 战略 产品/过程设想 产品可靠性研究 顾客输入 可靠性和质量 目标 初始原料清单 初始过程流程 图 产品保证计划 管理者支持
最新APQP五个阶段的输入和输出过程流程图及所有表单名称

五 反 馈 评 定 和 纠 正 措 施
4.11管理者支持
3.12量具/试验设备要求
3.13 小组可行性承诺和 管理者支持
所用表单和文件
立项表 试作通知书 试作品方案策划表 顾客图纸\样品 产品质量先期策划进度 表 会议记录 汽车产品客户调查问卷
所用表单和文件
设计目标 产品可靠性和质量目标 报告 初始材料清单 初始过程流程图 产品和过程特殊特性初 始清单 产品保证计划 成本分析报告
2.7管理者支持
3.7工程规范
4.7试生产控制计划
5.7生产控制计划指导书
5.8质量策划认定和管理 者支持
1.6顾客输入
3.9图样和规范的更改
4.9测量系统分析计划
3.10新设备\工装和设施 需求 3.11 产品和过程特殊特 性
4.10 初始过程能力研究 计划
所用表单和文件
DFMEA DFMEA检查清单(参考) 可制造和装配设计报告 设计验证和评审报告 样件控制计划 控制计划检查清单(参 考) 产品图纸 生产作业规范 材料规范 材料测试报告 工程变更书 新设备/工装和设施清单 产品/过程特殊特性清单 量具/试验设备清单 项目可行行分析报告 小组可行性承诺报告
所用表单和文件
产品包装作业指导书 产品/过程质量体系评审 表 过程流程图 过程流程图检查清单 场地平面布置图 场地平面布置图检查清 单 特性矩阵图 PFMEA PFMEA检查清单 试生产控制计划 控制计划检查清单 各工序操作指引 测量系统的分析计划 初始过程能力研究计划
所用表单和文件
试生产制造计划 生产运行鉴定表 生产效率测算表 MSA分析报告 初始过程能力研究报告 PPAP清单 产品全尺寸检测报告 产品性能测试报告 包装评价报告 生产控制计划 控制计划检查清单 产品质量策划总结/认定 PSW(零件提交保证书)
IATF16949-2016最新APQP产品质量先期策划五个阶段的输入和输出

3.12量具/试验设备要求
3.13小组可行性承诺和管理者支持
所用表单和文件
DFMEA
DFMEA检查清单(参考)
可制造和装配设计报告
设计验证和评审报告
样件控制计划
控制计划检查清单(参考)产图纸生产作业规范材料规范
材料测试报告
工程变更书
新设备/工装和设施清单
产品/过程特殊特性清单
产品和过程特殊特性初始清单
产品保证计划
成本分析报告
第三阶段: 过程设计和开发
3.1设计失效模式及后果分析(DFMEA)
3.2可制造性和装配设计
3.3设计验证
3.4设计评审
3.5样件制造——控制计划
3.6工程图样(包括数学数据)
3.7工程规范
3.8材料规范
3.9图样和规范的更改
3.10新设备\工装和设施需求
5.2测量系统评价
5.3初始过程能力研究
5.4生产件批准
5.5生产确认试验
5.6包装评价
5.7生产控制计划
5.8质量策划认定和管理者支持
所用表单和文件
试生产制造计划
生产运行鉴定表
生产效率测算表
MSA分析报告
初始过程能力研究报告
PPAP清单
产品全尺寸检测报告
产品性能测试报告
包装评价报告
生产控制计划
控制计划检查清单
顾客图纸\样品
产品质量先期策划进度表
会议记录
汽车产品客户调查问卷
第二阶段:产品设计和开发
2.1设计目标
2.2可靠性和质量目标
2.3初始材料清单
2.4初始过程流程图
2.5产品和过程的特殊性的初始清单
APQP五阶段输入输出一览表

1.设计目标(设计任务书) 2.可靠性和质量目标 3.初始材料清单 4.初始过程流程图 5.特殊产品和过程特性清单 6.产品保证计划 7.管理者支持
1.项目进度计划 2.成本目标 3.产能计划 4.风险评估 5.合同/可行性评审 6.主要联系人名单
第 二 阶 段
产品设计和开发
1.制定设计的功能和特 性 第一阶段的输出 2.着重审查功能要求 3.评估可能的加工问题 4.评估产品安全性
1.对输出进行评价 第四阶段的输出 2.SPC的应用进行评估
APQP第一阶段:计划与确定项目,对应的是PPAP资料识别; 第二、三阶段产品、过程设计开发与验证,对应的是PPAP启动及PPAP资料准备与评审; 第四阶段:产品与过程确认,对应的是PPAP交付物提交; 而SOP(批量生产)对应的是PPAP的批准。
APQP五阶段输入输出一览表
阶段 阶段名称 目的 主要输入
1.顾客的呼声 —市场调研 —保修记录和质量信息 —小组经验 2.业务计划/营销策略 3.产品/过程指标 4.产品/过程设想 5. 产品可靠性研究 6.顾客输入(技术协议/合 同)
主要输出
附客需要 2.策划一个战略项目
1.设计FMEA小组的输出 —设计FMEA —设计验证计划和报告 —样件制造——模拟生产 —图纸和规范 2.APQP小组的输出 1.设备清单 —新设备工装和设施要求 2.工装图纸 —在关键/重要产品和过程 3.工装清单 特性上取得一致 —量具/实验设备要求 —样件控制计划 —小组可行性承诺 —管理者支持 1.包装标准(内) 2.产品/过程质量体系评审 3.过程流程图 4.场地平面布置图 5.特性清单/特性矩阵图 6.过程FMEA 7.试生产控制计划 8.过程作业指导书 9.测量系统分析计划 10.初始过程能力研究计划 11.包装规范(外) 1.试生产 2.测量系统评价 3.初始过程能力研究 4.生产件批准 5.生产确认试验 6.包装评价 7.生产控制计划 8.质量策划认定 9.管理者支持 1.减少变差 2.顾客满意 3.交付和服务
APQP各阶段关键输入输出

APQP各阶段关键输⼊输出APQP五⼤阶段⼀计划和确定项⽬输⼊顾客的呼声:市场研究,保修记录和质量信息,⼩组经验业务计划/营销战略:务计划可将限制性要求施加给⼩组(诸如进度、成本、投资、产品定位、研究与开发(R&D)资源)⽽影响其执⾏⽅向。
营销战略将确定⽬标顾客、主要的销售点和主要的竞争者。
产品/过程基准数据:识别合适的基准;了解你⽬前状况和基准之间产⽣差距的原因;制定缩⼩与基准差距、符合基准或超过基准的计划。
产品/过程设想:设想产品具有某些特性\某种设计和过程概论。
产品可靠性研究:这⼀类型的数据考虑了在⼀规定时间内零件修理和更换的频率,以及长期可⾏性/耐久性试验的结果。
顾客输⼊:产品的后续顾客可提供与他们的需要和期望有关的有价值信息。
输出(作为第⼆章的输⼊)设计⽬标:顾客的呼声转化为初步和可度量的设计⽬标。
可靠性和质量⽬标:⽆安全问题和可维修性,质量⽬标如零件/百万(PPM)、缺陷⽔平或废品降低率。
产品和过程特殊特性的初始清单:与FMEA分析紧密相关产品保证计划:将设计⽬标转化为设计要求;概述项⽬要求;确定可靠性、耐久性和分配⽬标和/或要求;评定新技术、复杂性、材料、应⽤、环境、包装、服务和制造要求或其它任何会给项⽬带来风险的因素;进⾏失效模式分析(FMEA )(参见附录 H );制定初始⼯程标准要求。
管理者⽀持:包括项⽬时间,资源的策划及⽀持产能的⼈员策划(通过表明已满⾜所有的策划要求和/或关注问题已写⼊⽂件列⼊解决的⽬标来保持管理者的⽀持,包括项⽬时间、资源策划及⽀持产能的⼈员策划。
⼆产品设计和开发⼀个可⾏的设计应能满⾜⽣产量、⼯期和⼯程要求的能⼒,并满⾜质量、可靠性、投资成本、重量、单件成本和进度⽬标等。
在这⼀过程阶段,要进⾏初始可⾏性分析,以评定在制造过程中可能发⽣的潜在问题。
输⼊(源于第⼀章的输出)· 设计⽬标;· 可靠性和质量⽬标;· 初始材料清单;· 初始过程流程图;· 产品和过程特殊特性的初始清单;· 产品保证计划;· 管理者⽀持。
APQP五大过程输入和输出

产品/过程特殊特性清单 量具/试验设备清单 项目可行行分析报告 小组可行性承诺报告
阶段的输入和输出
4.1 包装标准和规格
四 5.1 有效生产运行
4.2 产品/过程4.3 过程流程图
5.3 初始过程能力研究
产 5.4 生产件批准
4.4 车间平面布置图
品 5.5 生产确认试验
4.5 4.6
特性矩阵图 过程失效模式和后果分
和
5.6 5.7
包装评价 生产控制计划
析(PFMEA)
过 5.8 质量策划认定和管理
4.7 试生产控制计划 4.8 过程指导书 4.9 测量系统分析计划
程 者支持 确
4.10 初始过程能力研究计 认
划
4.11 管理者支持
五 6.1 减少变差
(DFMEA)
2.3 初始材料清单
3.2 可制造性和装配设计
计 2.4 初始过程流程图
产 3.3 设计验证
过
划 2.5 产品和过程的特殊性 品 3.4 设计评审
程
和
的初始清单 2.6 产品保证计划
设
3.5 3.6
样件制造一一控制计划 工程图样(包括数学数据)
设
确 2.7 管理者支持
计 3.7 工程规范
计
定
和
3.8 3.9
材料规范 图样和规范的更改
和
项
幵 3.10 新设备\工装和设施需求 开
目
发 3.11 产品和过程特殊特性
发
3.12 量具/试验设备要求
3.13 小组可行性承诺和管理者
支持
所用表单和文件
立项表 试作通知书 试作品方案策划表 顾客图纸\样品
APQP的三个准备工作及五个阶段之目标和输出

APQP的三个准备工作及五个阶段之目标和输出APQP的三个准备工作1、成立跨功能小组(或APQP小组),小组成员职责分工。
成员一般来自工程、制造、材料控制、采购、现场服务、分包方、质量、顾客(适用时)。
坚强的组织是做好一切工作的保证。
2、运用关键路径法拟定《APQP项目进度控制总表》——甘特表。
3、最高管理者的支持和项目人财物资源保证。
APQP五个阶段的目标和输出1、计划和项目的确定————第一阶段目标:确定客户需求,策划一个新产品质量保证项目(立项)。
输入:客户的呼声、一线市场调查的结果、质量标准的分析、过去的产品资料信息、过去的产品质量信息。
输出:设计目标、可靠性目标、产品保证计划、BOM(初始材料清单)、初始过程流程图、初始特殊特性清单,项目状态报告和查核清单,合同评审/可行性评审报告(对有产品设计职责的供应商此项工作在设计和开发阶段之前完成,对无产品设计职责的供应商此项工作在过程开发阶段之前完成)2、产品设计和开发————第二阶段目标:制定设计的功能和特性,着重审查工程要求,评估可能存在的加工问题,评估产品安全性。
设计开发部的输出:设计失效模式及后果分析(DFMEA)、可制造性和装配设计、设计验证计划和报告(DVPR)、设计评审计划和报告、样件制造——模拟生产、样件控制计划、工程图样、材料规范、图样和规范的更改记录。
APQP小组的输出:新设备、工装和设施要求、特殊(产品和过程)特性取得一致、量具和试验设备要求、小组可行性承诺书报告。
3、过程设计和开发————第三阶段目标:开发完整而有效的的制造系统,保证制造系统满足客户要求。
输出:包装标准(内部)、产品/过程质量体系审核指导书、场地平面布置图、过程流程图、特性矩阵图、PFMEA、试生产控制计划、试产作业指导书、MSA测量系统评估计划、初始过程能力研究计划、包装规范(外部)。
4、产品和过程确认开发————第四阶段目标:制造过程确认,产品定型确认,确保满足客户期望,确定附加事项。
APQP各阶段的输入及输出
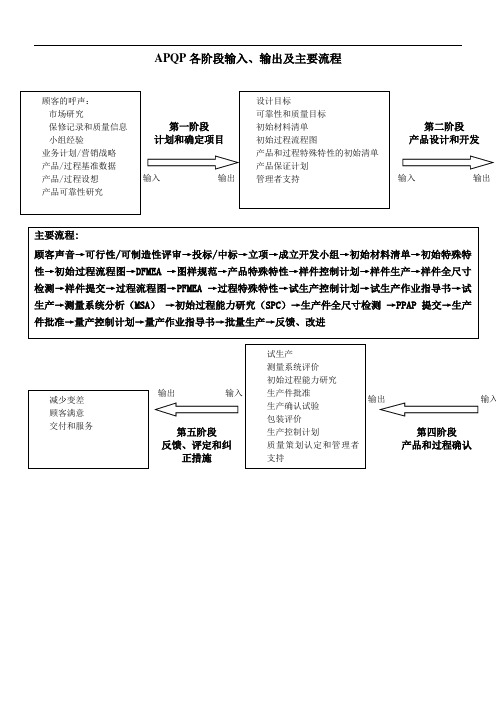
APQP 各阶段输入、输出及主要流程
顾客的呼声: 市场研究
保修记录和质量信息 小组经验
业务计划/营销战略 产品/过程基准数据 产品/过程设想 产品可靠性研究
设计目标
可靠性和质量目标 初始材料清单 初始过程流程图
产品和过程特殊特性的初始清单
产品保证计划
管理者支持
试生产
测量系统评价
初始过程能力研究 生产件批准
生产确认试验
包装评价 生产控制计划
质量策划认定和管理者支持
减少变差 顾客满意
交付和服务
第二阶段 产品设计和开发
第四阶段 产品和过程确认
第五阶段 反馈、评定和纠
正措施
输入 输出 输入
输出
输入。
APQP各阶段输入及输出流程图(含输出资料清单)

4.8
产品质量先期策划认定
产品质量策划总结和认定报告
管理者支持
管理者支持
五、反馈/评定和纠正措施
批量生产
生产计划表
5.1
减小变差
Xbar-R控制图
5.2
顾客满意
顾客满意度指标统计
顾客满意度调查表
5.3
交付和服务
产品交付绩效统计表/顾客服务反馈记录表
持续改进
3.3
过程流程图
过程流程图
过程流程图检查表
3.4
车间平面布局图
车间平面布置图
车间平面布置检查表
3.5
特性矩阵图
特性矩阵图
3.6
PFMEA
过程失效模式及后果分析
PFMEA检查表
3.7
试生产控制计划
(试生产)控制计划
控制计划检查表
3.8
作业指导书编制
作业指导书
3.9
测量系统分析计划
测量系统分析计划
3.10
工程规范
2.8
材料规范编制
材料规范
2.2
可制造性和可装配性设计
可制造性和可装配性设计
2.5
制订样件控制计划
样件控制计划
样件控制计划检查表
编制样件制造计划
样件制造计划
样件制造及确认
样件检验和确认记录表
2.3
产品设计验证
设计验证记录
2.4
产品设计评审
设计开发评审表
工程图样确认
工程图样确认表
工程规范确认
工程规范确认表
初始过程能力研究计划
初始过程能力研究计划
制定生产线平衡分析计划
生产线平衡分析计划
指定生产过程确认计划
APQP摘要及各阶段输入输出汇总表

产品开发
产品开发
产品开发
质量 项目经理
运行维护 项目经理 项目经理
项目经理 项目经理 项目经理 项目经理 项目经理 项目经理
1 DFMEA
DFMEA 检查表
样件PFMEA 样件PFMEA 检查表
2 可制造性和装配设计 DFAM
3 设计验证
DVP&R
4 设计评审
设计评审
责任部门
物料
质量 制造工程 制造工程
制造工程 制造工程 产品开发/制造工程 制造工程 制造工程
质量 质量
制造工程
质量 质量 制造工程 项目经理/制造工程 项目经理/制造工程 项目经理/制造工程 项目经理/制造工程
项目经理/制造工程 制造工程
项目经理/制造工程
项目经理/制造工程 制造工程 运行维护
产品开发/制造工程 产品开发/制造工程
3 初始材料清单
4 初始过程流程图
5
产品和过程特殊 特性的初始清单
6 产品保证计划
管理者支持 (包括项目时 7 间,资源的策划 及支持产能的人 员策划)
输入
递交物 设计目标
APQP 阶段2—产品设计开发
责任部门 产品开发
序号 APQP建议输出
输出
递交物 DFMEA
质量目标
质量
初始材料清单 (BOM) 初始过程流程图 产品和过程特殊特 性的 初始清单 产品保证计划 项目进度计划 环评、安全、消防 报告 APQP清单 SDT清单/资源计划 项目启动会,人员 职责 项目阶段评审 项目状态报告
APQP 阶段1—计划和确定项目
输入
序号
APQP建议输入
递交物梳理 市场调查报告 项目可行性分析报 技术可行性分析报
APQP五个阶段输入程输出(49项)

APQP五个阶段输入程输出(49项)
APQP五个阶段
计划和确定项目产品设计和开发过程设计和开发产品程过程确认反馈,评定和纠正措施
输入
1.顾客的呼声
2.经营计划程营销战略
3.产品/过程基准数据
4.产品过程设想
5.产品可靠性研究
6.顾客输入
输出
1.设计目标
2.可靠性和质量指标
3.初始材料清单
4.初始过程流程图
5.产品和过程特殊特性的初始清单
6.产品保证计划
7.管理者支持输出
1.DFMEA
2.可制造性和可装配性设计
3.设计验证
4.设计评审
5.样件制造
6.技术图样
7.枝术标准
8.材料标准
9.图样和标准的更改
10.新设备,工装,和设施要求
11.产品和过程的特殊特性
12.量具/试验设务的要求
13.小组可行性承诺和管理者的支持输出
1.包装标准和规范
2.产品/过程质量体系的评审
3.过程流程图
4.车间平面布置图
5.特性矩阵图
6.PDFMEA
7.试生产控制计划
8.过程指导书
9.测量系统分析计划
10.初始过程能力研究计划
11.管理者支持
输出
1.试生产(有效生产)
2.测量系统分析
3.初始过程能力研究
4.生产件批准
5.生产确认试验
6.包装评价
7.生产控制计划
8.质量策划认定和管理者支持
输出
1.减少变差
2.提高顾客满意度
3.提高交付和服务水平
4.总结经验教训。
APQP各阶段的输入及输出(中英文版)

输出 产品和过程特殊特性的初始清单 产品保证计划
管理者支持
第二阶段 产品设计和开发
输入
输出
设计部门输出: 设计失效模式和后果分析(DFMEA) 可制造性和装配设计 设计验证 设计评审 制造样件—控制计划 工程图样(包括数学数据) 工程规范 材料规范 图样和规范的更改
Phase One Plan and Define
Program
Reliability and Quality Goals Preliminary Bill of Material Preliminary Process Flow Chart Preliminary Listing of Special Product and
Packaging Evaluation Production Control Plan Quality Planning Sign – Off and
Management Support
Phase Four Product and Process Validation
Design Outputs:
Reduced Variation Improved Customer Satisfaction Improved Delivery and Service Effective Use of Lessons Learn/
Best Practices
Outputs
Inputs
Phase Five Feedback, Assessment and Corrective Action
APQP Every Phase Inputs, Outputs and Main Process
APQP五大阶段输入输出
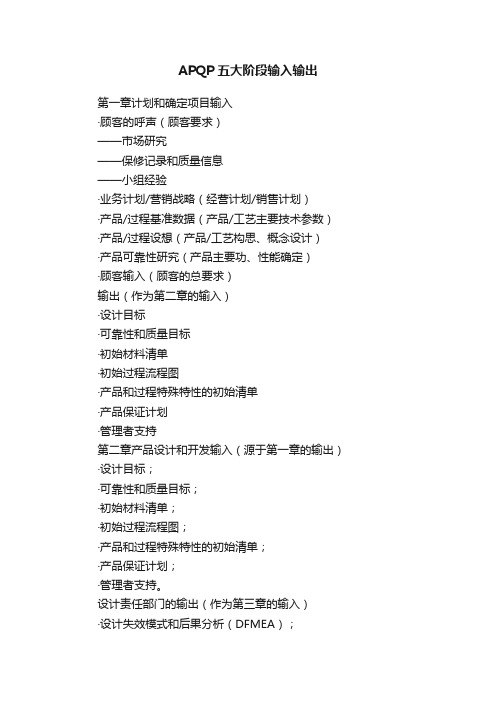
APQP五大阶段输入输出第一章计划和确定项目输入·顾客的呼声(顾客要求)——市场研究——保修记录和质量信息——小组经验·业务计划/营销战略(经营计划/销售计划)·产品/过程基准数据(产品/工艺主要技术参数)·产品/过程设想(产品/工艺构思、概念设计)·产品可靠性研究(产品主要功、性能确定)·顾客输入(顾客的总要求)输出(作为第二章的输入)·设计目标·可靠性和质量目标·初始材料清单·初始过程流程图·产品和过程特殊特性的初始清单·产品保证计划·管理者支持第二章产品设计和开发输入(源于第一章的输出)·设计目标;·可靠性和质量目标;·初始材料清单;·初始过程流程图;·产品和过程特殊特性的初始清单;·产品保证计划;·管理者支持。
设计责任部门的输出(作为第三章的输入)·设计失效模式和后果分析(DFMEA);·可制造性和装配设计;·设计验证;·设计评审;·制造样件控制计划;·工程图样(包括数学数据);·工程规范;·材料规范;·图样和规范更改。
第三章过程设计与开发输入(源于第二章中的输出)·设计失效模式及后果分析(DFMEA);·可制造性和装配设计;·设计评审;·样件制造控制计划;·工程图样(包括数学数据);·工程规范;·材料规范;·图样和规范的更改;·新设备、工装和设施要求;·产品和过程特殊特性;·量具/试验设备要求;·小组可行性承诺和管理者支持。
输出(作为第四章的输入)·包装标准;·产品/过程质量体系评审;·过程流程图;·车间平面布置图;·特性矩阵图;·过程失效模式及后果分析(PFMEA);·试生产控制计划;·过程指导书;·测量系统分析计划;·初始过程能力研究计划;·包装规范;·管理者支持。
APQP五个阶段输入与输出

APQP五阶段输入输出表阶段内容目的主要输入主要输出附加输出一·计划和项目确定·确定顾客需要·策划一个质量项目·顾客的呼声—市场调研—保修记录和质量信息—小组经验·业务计划/营销策略·产品/过程指标·产品/过程设想·产品可靠性研究·顾客输入(技术协议/合同)·设计目标(设计任务书)·可靠性和质量目标·初始材料清单·初始过程流程图·特殊产品和过程特性清单·产品保证计划·管理者支持·项目进度计划·成本目标·产能计划·风险评估·合同/可行性评审·主要联系人名单二·产品设计和开发·制定设计的功能和特性·着重审查功能要求·评估可能的加工问题·评估产品安全性第一阶段的输出■设计FMEA小组的输出·设计FMEA·设计验证计划和报告·样件制造—模拟生产·图纸和规范■APQP小组的输出·新设备工装和设施要求·在关键/重要产品和过程特性上取得一致·量具/试验设备要求·样件控制计划·小组可行性承诺·管理者支持·设备清单·工装图纸·工装清单三·过程设计和开发·开发完整而有效的制造体系·保证制造系统满足顾客要求第二阶段的输出·包装标准(内)·产品/过程质量体系评审·过程流程图·场地平面布置图·特性清单/特性矩阵图·过程FMEA·试生产控制计划·过程作业指导书·测量系统分析计划·初始过程能力研究计划·包装规范(外)·工艺作业指导卡·特殊特性清单·特性矩阵图四·产品和过程确任·确认制造过程·确保满足顾客需要·确定附加事项第三阶段的输出·试生产·测量系统评价·初始过程能力研究·生产件批准·生产确认试验·包装评价·生产控制计划·质量策划认定·管理者支持·MSA分析·试验报告五·过程评价和持续改进·对输出进行评价·SPC的应用进行评估第四阶段的输出·减少变差·顾客满意·交付和服务。
APQP各阶段输入、输出及效益出线
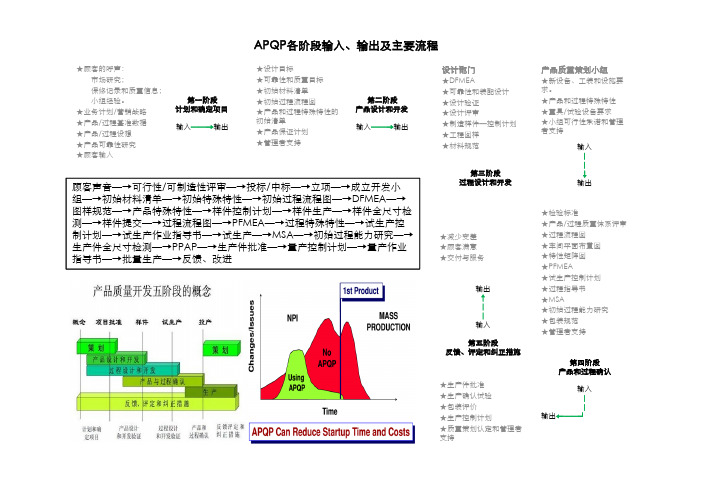
APQP各阶段输入、输出及主要流程
★设计目标
★可靠性和质量目标
★初始材料清单
★初始过程流程图
★产品和过程特殊特性的初始清单
★产品保证计划
★管理者支持第二阶段产品设计和开发
输入——→输出设计部门★DFMEA ★可靠性和装配设计★设计验证★设计评审★制造样件—控制计划★工程图样★材料规范第三阶段过程设计和开发产品质量策划小组★新设备、工装和设施要求。
★产品和过程特殊特性★量具/试验设备要求★小组可行性承诺和管理者支持输入||↓输出★检验标准★产品/过程质量体系评审★过程流程图★车间平面布置图★特性矩阵图★PFMEA ★试生产控制计划★过程指导书★MSA ★初始过程能力研究★包装规范★管理者支持第四阶段产品和过程确认输入||输出←━━┛★生产件批准
★生产确认试验
★包装评价
★生产控制计划
★质量策划认定和管理者支持输出↑|
|
输入第五阶段
反馈、评定和纠正措施★减少变差★顾客满意
★交付与服务
第一阶段计划和确定项目输入——→输出★顾客的呼声:市场研究;保修记录和质量信息;小组经验。
★业务计划/营销战略★产品/过程基准数据★产品/过程设想★产品可靠性研究★顾客输入
顾客声音—→可行性/可制造性评审—→投标/中标—→立项—→成立开发小组—→初始材料清单—→初始特殊特性—→初始过程流程图—→DFMEA—→图样规范—→产品特殊特性—→样件控制计划—→样件生产—→样件全尺寸检测—→样件提交—→过程流程图—→PFMEA—→过程特殊特性—→试生产控制计划—→试生产作业指导书—→试生产—→MSA—→初始过程能力研究—→生产件全尺寸检测—→PPAP—→生产件批准—→量产控制计划—→量产作业指导书—→批量生产—→反馈、改进。
APQP各阶段输入与输出内容详解
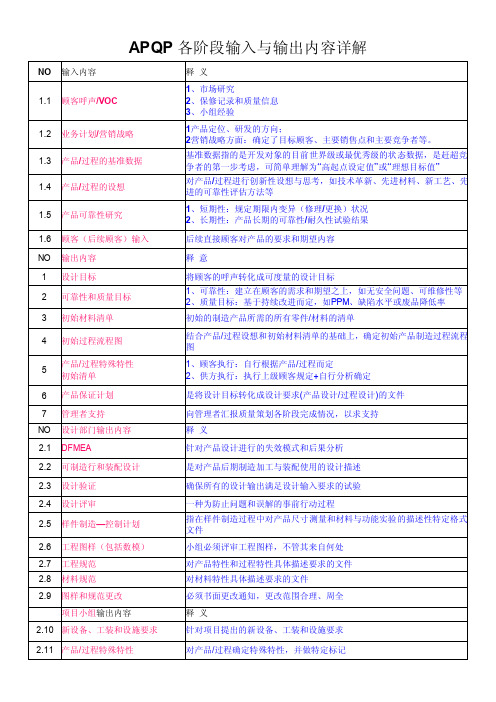
测量系统自身性能的有效性分析评价 初始过程的能力情况评价 按顾客规定的批准方式提交顾客批准
对正式生产工装和过程制造出来的产品是否满足工程标 准进行的工程试验
产品包装在正常和异常状态时对产品的保护能力的评价 正式生产阶段,对制造过程和产品特性的控制描述 通过对制造过程和产品特性控制 情况的评价来进行策划 认定,并把情况汇 报给管理者,以得到支持和肯定 释义 通过一定技术方法来减少变异和变差 始终达到和超越顾客的要求 长期的提供合格产品和优质服务
2.12 量具/试验设备要求
针对项目提出的量具/试验设备的要求
2.13 小组可行性承诺和管理者支持 针对产品设计和开发阶段内容进行的多方论证评议,并提交管理者审批
NO 输出内容 3.1 包装标准 3.2 产品/过程质量体系评审 3.3 过程流程图 3.4 车间平面布置图 3.5 特性矩阵图
3.6 PFMEA
6 产品保证计划 7 管理者支持 NO 设计部门输出内容 2.1 DFMEA
2.2 可制造行和装配设计
2.3 设计验证 2.4 设计评审
2.5 样件制造—控制计划
2.6 工程图样(包括数模) 2.7 工程规范 2.8 材料规范 2.9 图样和规范更改
项目小组输出内容 2.10 新设备、工装和设施要求
3.8 过程指导书 3.9 测量系统分析计划 3.10 初始过程能力研究计划 3.11 包装规范 3.12 管理者支持 NO 输出内容
对试生产阶段进行的尺寸测量和材料、功能试验的控制描述
指导过程正确操作的规定性文件 测量系统能力的分析计划 试生产期间过程性能短期能力的研究 产品包装形式的规定性文件 管理者了解、评价、支持此阶段工作 释义
4.1 试生产
使用正式的工装、设备、环境、人员、设施和循环时间,进行的试生产
APQP各阶段的输入及输出(中英文版)

顾客的呼声: ¾ 市场研究 ¾ 保修记录和质量信息 ¾ 小组经验
业务计划/营销战略 产品/过程基准数据 产品/过程设想 产品可靠性研究 顾客输入
第一阶段 计划和确定项目
设计目标 可靠性和质量目标 初始材料清单
初始过程流程图
输入
Voice of Customer → Feasibility/Manufacturability Review → Bid/Win the biding → Define Program → Organize the development team → Preliminary Bill of Material → Preliminary Listing of Special Product and Process characteristic → Preliminary Process Flow Chart → DFMEA → Drawing Specification → Product and Process Characteristic → Prototype Control Plan → Prototype Trail Run → Prototype Full Dimension →Submit Prototype → Process Flow Chart → PFMEA → Special Process Characteristic → Pre-Launch Control Plan → Pre-Launch WI → Pre-Launch → Measurement System Analysis(MSA) → Preliminary Process Capability Study(SPC)→ Production Parts Full Dimension Check →Submit PPAP→ Production Part Approval → Production CP → Production WI → Master Production → Feedback, Improvement
- 1、下载文档前请自行甄别文档内容的完整性,平台不提供额外的编辑、内容补充、找答案等附加服务。
- 2、"仅部分预览"的文档,不可在线预览部分如存在完整性等问题,可反馈申请退款(可完整预览的文档不适用该条件!)。
- 3、如文档侵犯您的权益,请联系客服反馈,我们会尽快为您处理(人工客服工作时间:9:00-18:30)。
第三阶段第四阶段第五阶段过程设计开发
产品和过程确认
反馈、评定和纠正
措施
输出(下阶段输
入)输出(下阶段输
入)设计负责部门
产品质量策划小组
顾客的呼声(包括市
场研究、
保修记录和质量信息
、小组经验)设计目标DFMEA
新设备工装和设施
的要求
包装标准和规范有效生产运行减少变差
业务计划/营销战略可靠性和质量目标DFM/DFA (可制造性和装配性设计)特殊产品和过程特性产品/过程质量体系评审
测量系统分析提高顾客满意产品/过程基准数据初始材料清单设计验证量具/试验设备要求
过程流程图
初始过程能力研究改进交付和服务产品/过程设想初始过程流程图设计评审小组可行性承诺和
管理者支持
车间平面布置图
生产件批准吸取的教训/最佳实践的有效使用
产品可靠性研究产品和过程特殊特性
的初始清单样件制造特性矩阵生产确认试验顾客输入
产品保证计划工程图样PFMEA 包装评价管理者支持
工程规范试生产控制计划生产控制计划材料规范过程指导书质量策划认定和管理
者支持
图样和规范的更改
测量系统分析计划初始过程能力研究计
划管理者支持
第一阶段第二阶段计划和确定项目阶段产品设计和开发
输入
输出(下阶段输入)
输出(下阶段输入)输出(下阶段输入)
输出。