气缸组合式自动吊具改进技术
解放了起重机改进的方案
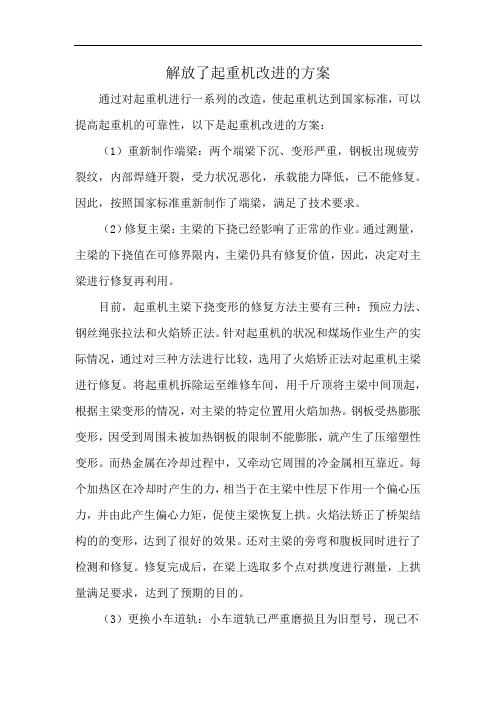
解放了起重机改进的方案通过对起重机进行一系列的改造,使起重机达到国家标准,可以提高起重机的可靠性,以下是起重机改进的方案:(1)重新制作端梁:两个端梁下沉、变形严重,钢板出现疲劳裂纹,内部焊缝开裂,受力状况恶化,承载能力降低,已不能修复。
因此,按照国家标准重新制作了端梁,满足了技术要求。
(2)修复主梁:主梁的下挠已经影响了正常的作业。
通过测量,主梁的下挠值在可修界限内,主梁仍具有修复价值,因此,决定对主梁进行修复再利用。
目前,起重机主梁下挠变形的修复方法主要有三种:预应力法、钢丝绳张拉法和火焰矫正法。
针对起重机的状况和煤场作业生产的实际情况,通过对三种方法进行比较,选用了火焰矫正法对起重机主梁进行修复。
将起重机拆除运至维修车间,用千斤顶将主梁中间顶起,根据主梁变形的情况,对主梁的特定位置用火焰加热。
钢板受热膨胀变形,因受到周围未被加热钢板的限制不能膨胀,就产生了压缩塑性变形。
而热金属在冷却过程中,又牵动它周围的冷金属相互靠近。
每个加热区在冷却时产生的力,相当于在主梁中性层下作用一个偏心压力,并由此产生偏心力矩,促使主梁恢复上拱。
火焰法矫正了桥架结构的的变形,达到了很好的效果。
还对主梁的旁弯和腹板同时进行了检测和修复。
修复完成后,在梁上选取多个点对拱度进行测量,上拱量满足要求,达到了预期的目的。
(3)更换小车道轨:小车道轨已严重磨损且为旧型号,现已不生产,针对这种情况,根据小车车轮的尺寸,通过计算,将道轨规格改为24kg/m,增大了可靠性。
(4)更新驾驶室:因使用年限长,驾驶室已经不能使用。
按国家标准重新制作了驾驶室,有利于操作和维护。
(5)更换缓冲器和止挡:将原有的缓冲器底座进行改进,采用了无反弹、缓冲力恒定、能吸收能量、缓冲行程短、外形尺寸小的液压缓冲器,使之更加安全可靠。
重新制作轨道端部止挡,确保安全。
(6)完善安全附件:对起重机上所有的安全附件进行更换、维修,达到国家标准。
(7)更换电气元件:对老化的电气元件进行更换、完善,保证了起重机的运行正常。
用于双燃料柴油机气缸体的吊运工装和方法[发明专利]
![用于双燃料柴油机气缸体的吊运工装和方法[发明专利]](https://img.taocdn.com/s3/m/46d8df2f5fbfc77da369b11b.png)
专利名称:用于双燃料柴油机气缸体的吊运工装和方法专利类型:发明专利
发明人:范红健,沈治东,张伟,蒋立国,武勇
申请号:CN202010593807.6
申请日:20200628
公开号:CN111704023A
公开日:
20200925
专利内容由知识产权出版社提供
摘要:一种用于双燃料柴油机气缸体的吊运工装及方法,该气缸体设有格兰孔,所述吊运工装包括轴、支架、吊耳、弹簧、钢球和螺母;其中,支架设有支承面、定位面和圆锥形导向面,该支架上设有圆弧导轨凹槽,该圆弧导轨凹槽的中央和两侧端各设有一半球面凹槽,轴套外侧面设有圆柱盲孔,轴和螺母将支架与吊耳可相对旋转地铰接在一起,弹簧和钢球设置于该圆柱盲孔内,在弹簧的作用下,钢球分别突入三个半球面凹槽中,将支架与吊耳分别锁定于三个不同相对位置上;支架的导向面引导定位面进入格兰孔内且达到自动定心,支承面贴合格兰孔的端面,从而吊运工装和钢丝绳与气缸体的重心处在同一垂线上,实现气缸体的自动定位和平稳吊运。
本发明具有自动定心和自锁功能,提高了生产效率,消除了安全隐患,改善了作业条件。
申请人:上海中船三井造船柴油机有限公司
地址:201306 上海市浦东新区临港新城新元南路6号
国籍:CN
代理机构:上海恒慧知识产权代理事务所(特殊普通合伙)
代理人:祖志翔
更多信息请下载全文后查看。
柴油机气缸盖配件调整螺钉组组装夹具的改进

柴油机气缸盖配件调整螺钉组组装夹具的改进葛成荣【摘要】本文采用静载荷装配,有效减小了装配应力;通过车床横向进给,解决了因人为敲击产生的应力集中和受力不均匀的问题,消除了球座开裂和卡滞现象。
此种改进方法有效解决了困扰已久的装配问题,节约了成本,保证了产品质量。
【期刊名称】《金属加工:冷加工》【年(卷),期】2016(000)004【总页数】2页(P41-42)【作者】葛成荣【作者单位】常州铁道高等职业技术学校江苏 213011【正文语种】中文图1所示的调整螺钉组为某大功率机车柴油机气缸盖配件的重要零部件,由调整螺钉和球座(见图2)组成,其作用是调节气阀间歇。
该零件组是配气机构的运动部件,需不断上下运动,特别是列车高速运转时,其运动速度更快,因此其承受着不小的冲击力,为解决其在运动过程中由角度变化而引起的力变化,需要其与轴线在20°~25°的范围内关节转动灵活,水平转动球座一周,不发生螺钉跟带现象。
由调整螺钉组装配要求可知,其难点主要是如何将球座均匀包裹在调整螺钉上,并使其在与轴线20°~25°范围内灵活转动。
于是借鉴原国产机车相似零部件的装配方法,采用如图3所示的装配辅具,将调整螺钉套在辅具内,使球座的17°角外圆面与辅具的36°角内圆面相贴合,用铁锤从上方敲击,使球座包裹在调整螺钉的SR10mm球面上,从而完成装配。
但该产品装车半年以来,从机务段反映的情况来看,已交车的机车陆续出现不同程度的开裂(见图4),导致返工车辆达25辆左右,直接经济损失达到20多万元,为此被迫暂时采购进口调整螺钉组,大大增加了采购成本。
将开裂的球座送至检测中心做裂纹分析,经过详细分析,发现裂纹撕裂起始点为球座17°倒角处,即从装配部位开始开裂。
对于这一问题,我们发现在装配过程中,球座受到了瞬间冲击力,几何形状发生突变,产生应力集中,在调整螺钉组运动的交变应力作用下,裂纹发生并发展,造成了最后的开裂。
发动机厂产品吊具的管理及改进优化

作者: 陈剑峰
作者机构: 江铃汽车股份有限公司发动机厂,江西南昌330001
出版物刊名: 科技资讯
页码: 76-77页
年卷期: 2015年 第26期
主题词: 起重机械 产品吊具 管理及应用 改进优化
摘要:发动机厂的机加工、装配生产中需使用的产品吊具(以下简称吊具)有其特殊的要求,通常按产品和作业环境要求设计制作专用吊具,吊具又属于特种安全机构,需保证吊装产品的定位可靠;吊具使用环境复杂,危险因素较多,安全风险较大,如果使用不当或管理不善,极易发生事故和人员伤害,因此对吊具管理、使用、维护有很高的要求;该文主要结合发动机厂多年对吊具管理应用和经验论述了发动机厂产品吊具的日常管理和应用实例为今后规划新发动机厂的产品吊具管理提供参考。
- 1、下载文档前请自行甄别文档内容的完整性,平台不提供额外的编辑、内容补充、找答案等附加服务。
- 2、"仅部分预览"的文档,不可在线预览部分如存在完整性等问题,可反馈申请退款(可完整预览的文档不适用该条件!)。
- 3、如文档侵犯您的权益,请联系客服反馈,我们会尽快为您处理(人工客服工作时间:9:00-18:30)。
气缸组合式自动吊具改进技术
作者:上汽通用五菱汽车股份有限公司臧宏霍炳武唐煜
摘要:介绍了该团队对原白车身前地板转运装置进行工艺改造和设备改造的情况,技术改造后装置能力达到了设计要求,很好地解决了生产中存在的问题。
关键词:气缸;挂钩;技改
一、技术改造前的描述
1、工艺流程简述
汽车白车身前地板在生产主线线旁拼台组合焊接后,经两名操作工人由焊接拼台抬到上料口,等待自行小车下降到固定点时开始挂装前地板,自行小车为固定周期循环。
经挂装完成后,操作工人按下手柄开关按钮“工作完成”键小车自然过料至生产主线进一步拼装焊接。
2、主要设备
(1)铰链挂钩
铰链挂钩的主要成分是铁,有少量的碳等元素,常温下很容易氧化,且使用频次高后极易磨损。
(2)控制按钮开关
控制按钮由外壳、急停开关及多按钮开关组合而成。
外壳采用ABS塑料压注成型。
按钮头采用明显的功能指示标记,不易磨损。
触点采用标准银触头,导电性能好。
急停开关需旋转或指动后复位,操纵按钮为自动复位。
(3)小车架上有3个挂钩,生产主线及前地板焊装拼台共两个控制按钮合。
3、设备安装完毕后,运行较长一段时间,运行期间生产运行效率低,人力、物力消耗大,主要存在以下问题。
(1)人机工程损伤
因为该小车采用人工挂料,也就是在前地板与拼台之间加需通过人工取料,等待运料小车下降至挂料点,等待过程无形中加重了操作工人的做功时间,不仅增加了操作工人的手臂做功,也加重了前地板变形现象,给操作工人带来了积累性的人机工程损伤。
生产中需要不断送料挂钩,既浪费人力,也使生产不能连续正常进行,运料过程摩擦大还影响了铰链挂钩的运行寿命。
(2)影响生产节拍
操作工人取料、挂料难以控制在固定时间内,在挂料过程中难以将铰链挂钩准确挂进零件孔,只好采用人工反复多挂,挂好后再将小车送至主线拼装工序。
到主线拼装时,再由两名操作工人将前地板脱钩取料,使得在整个操作周期无法控制,得不到固定的时间周期,间接影响生产节拍18″。
(3)影响产品质量
由于前地板运料的挂钩工艺比较落后,采用人工自制的挂钩,不仅使零件与挂钩有干涉,而且在运料过程中晃动也很大,严重影响了前地板安装定位孔的精确性。
生产过程中问题不断暴露,尤其是装配不到位,不能达到预期生产能力,浪费了大量的人力物力,严重制约前地板与白车声车架的组合。
为此,对现有设备和工艺进行技术革新,取得了比较理想的效果。
二、技术改造和改造后运行效果
1、改变挂钩工艺
根据生产过程中操作工人难挂钩、主线难取料的情况,将原铰链挂钩取消,用气缸组合式挂吊工艺,也就是采用4*4的方钢为原材料,根据前地板的轮罩外观模型,制作出具体挂装点的模型,通过气缸收缩行程作用,将挂钩与气缸组合,即为自动式挂料,这不仅使小车在运料过程消除晃动的情况,而且还保证前地板的零件质量。
物料缓冲架通过固定在地面,操作工人在从拼台取料至挂料过程,可以将前地板放置在缓冲架,无形之中降低了人机工程损伤。
2、将挂料方式改为自动
既然挂钩已经与气缸是组合式联动机构,挂料控制存在偶然性,同时对工人的操作要求较高,劳动强度加大。
现采用滚轮杠杆式阀RS-3-1\8安装在挂钩上作为零件触点开关,当自行小车下降到固定点时,滚轮杠杆与零件接触,此时气路为开,气缸通气后带动挂钩联动机构,此时较好地控制了挂钩自动准确将零件挂装好,操作工人只需按确认键即完成整个操作周期。
待小车运料至主线下料口后,主线拼装台取料的操作工人只需按下控制按钮,就可以直接将前地板放下。
这减轻了生产强度及工人的劳动强度,为生产节拍提供良好的保障。
三、成果验证
通过一系列技术改造,目前气缸组合式自动吊具与原生产挂装运料工艺相比有了显著的改善和提高,具体表现如下:
1、白车身前地板及主线该焊接工序生产节拍能力显著提高,由原来的112″降低到98″以下,消除瓶颈工序,满足了生产要求。
2、操作工人劳动强度明显降低。
3、运料周期时间缩短。
由于采用了新的挂装及取料工艺,分别经控制按钮、滚轮杠杆式阀完成前地板自动装料、卸料,大大降低了操作工人挂料及取料的时间,消除了反复多次挂料现象的发生,降低挂料时间,提高了设备的运行能力,延长了挂钩的使用寿命,使生产的连续性得以保证。
4、产品质量受控。
用原铰链挂钩进行挂装前地板定位孔不便控制,运料过程中存在晃动较大,安装定位孔往往变形,既造成前地板与白车身车架利空、错位等,也造成了零件返修的浪费。
改用气缸自动挂料,将挂的方式改为固定夹、构的方式后,很好地控制小车在运料过程中的稳定性,既不存在安装孔变形的现象,也为主线拼装工序提供了合格的前地板,消除了前地板零件返修的浪费。
四、推广价值
该运料技术工艺结构均可在各生产线分组装的情况下使用,以压缩空气作为原动力,不仅设计巧妙,操作方便,便于维护,且原材料成本低。
五、结论
通过一系列的技术改造,既降低了操作工人的劳动强度,也降低了生产成本,提高了生产效率,为公司创造了更多的经济效益。
因此在企业生产管理过程中,要充分调动广大职工的积极性和能动性,大胆进行技术革新,充分采纳员工的合理化建议,充分挖掘设备的最大潜能,为企业创造更多的经济效益。
维护的重点是气缸联动机构、滚轮杠杆式阀。
通过长期观察,对所运行设备的完好周期有个大致的估算,定期处理。
对气缸联动机构半月加1次黄油,无需更换联动轴承,滚轮杠杆式阀1月加一次润滑油。
有计划更换滚轮杠杆式阀与气管相连的直通接头及PU高压气管,保持其在密封状态。
实践证明这种定期维护的办法很有效,防患未然,减少了由停机造成生产停线的损失。
(end)。