特殊钢精炼技术-冶金学
钢铁冶金学(炼铁部分)
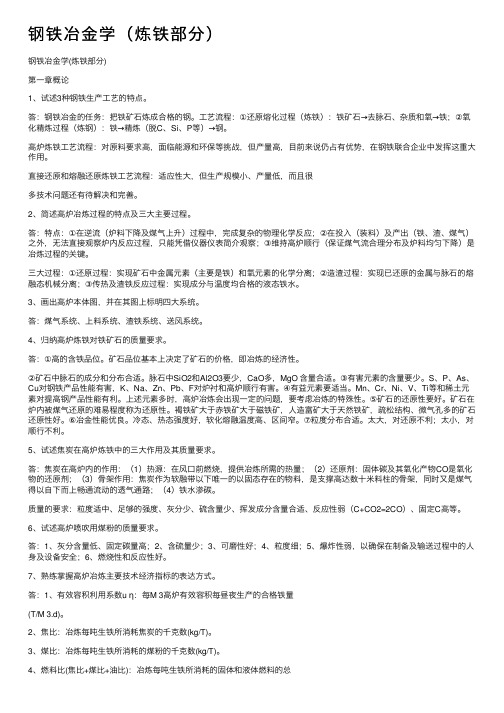
钢铁冶⾦学(炼铁部分)钢铁冶⾦学(炼铁部分)第⼀章概论1、试述3种钢铁⽣产⼯艺的特点。
答:钢铁冶⾦的任务:把铁矿⽯炼成合格的钢。
⼯艺流程:①还原熔化过程(炼铁):铁矿⽯→去脉⽯、杂质和氧→铁;②氧化精炼过程(炼钢):铁→精炼(脱C、Si、P等)→钢。
⾼炉炼铁⼯艺流程:对原料要求⾼,⾯临能源和环保等挑战,但产量⾼,⽬前来说仍占有优势,在钢铁联合企业中发挥这重⼤作⽤。
直接还原和熔融还原炼铁⼯艺流程:适应性⼤,但⽣产规模⼩、产量低,⽽且很多技术问题还有待解决和完善。
2、简述⾼炉冶炼过程的特点及三⼤主要过程。
答:特点:①在逆流(炉料下降及煤⽓上升)过程中,完成复杂的物理化学反应;②在投⼊(装料)及产出(铁、渣、煤⽓)之外,⽆法直接观察炉内反应过程,只能凭借仪器仪表简介观察;③维持⾼炉顺⾏(保证煤⽓流合理分布及炉料均匀下降)是冶炼过程的关键。
三⼤过程:①还原过程:实现矿⽯中⾦属元素(主要是铁)和氧元素的化学分离;②造渣过程:实现已还原的⾦属与脉⽯的熔融态机械分离;③传热及渣铁反应过程:实现成分与温度均合格的液态铁⽔。
3、画出⾼炉本体图,并在其图上标明四⼤系统。
答:煤⽓系统、上料系统、渣铁系统、送风系统。
4、归纳⾼炉炼铁对铁矿⽯的质量要求。
答:①⾼的含铁品位。
矿⽯品位基本上决定了矿⽯的价格,即冶炼的经济性。
②矿⽯中脉⽯的成分和分布合适。
脉⽯中SiO2和Al2O3要少,CaO多,MgO 含量合适。
③有害元素的含量要少。
S、P、As、Cu对钢铁产品性能有害,K、Na、Zn、Pb、F对炉衬和⾼炉顺⾏有害。
④有益元素要适当。
Mn、Cr、Ni、V、Ti等和稀⼟元素对提⾼钢产品性能有利。
上述元素多时,⾼炉冶炼会出现⼀定的问题,要考虑冶炼的特殊性。
⑤矿⽯的还原性要好。
矿⽯在炉内被煤⽓还原的难易程度称为还原性。
褐铁矿⼤于⾚铁矿⼤于磁铁矿,⼈造富矿⼤于天然铁矿,疏松结构、微⽓孔多的矿⽯还原性好。
⑥冶⾦性能优良。
冷态、热态强度好,软化熔融温度⾼、区间窄。
钢铁冶金学炼钢部分

炼钢学复习题第二章一.思考题1.炼钢的任务。
1)脱碳:含碳量是决定铁与钢定义的元素,同时也是控制性能最主要的元素,一般来用向钢中供养,利于碳氧反应去除。
2)脱硫脱磷:对绝大多数钢种来说,硫磷为有害元素,硫则引起钢的热脆,而磷将引起钢的冷脆,因此要求炼钢过程尽量去除。
3)脱氧:在炼钢中,用氧去除钢中的杂质后,必然残留大量氧,给钢的生产和性能带来危害,必须脱除,减少钢中含氧量叫做脱氧。
(合金脱氧,真空脱氧)4)去除气体和非金属夹杂物:钢中气体主要指溶解在钢中的氢和氮,非金属夹杂物包括氧化物,硫化物以及其他化合物,一般采用CO气泡沸腾和真空处理手段。
5)升温:炼钢过程必须在一定高温下才能进行,同时为保证钢水能浇成合格的钢锭,也要求钢水有一定的温度,铁水最温度很低,1300摄氏度左右 Q215钢熔点1515摄氏度6)合金化:为使钢有必要的性能,必须根据钢中要求加适量的合金元素。
7)浇成良锭:液态钢水必须浇铸成一定形状的固体铸坯,采用作为轧材的原料,同时要求质量良好,一般有模铸和连铸两种方式。
2.S的危害原因和控制方式。
(1)产生热脆。
(硫的最大危害)(2)形成夹杂:S在固体钢中基本上是以硫化物夹杂的形式存在。
降低塑性,危害各向同性(采用Mn抑制S的热脆),影响深冲性能和疲劳性能,夹杂物的评级,强度(S对钢的影响不大)(3)改善切削性能(这是硫的唯一有用用途)(2)控制措施有两种方法:(1)提高Mn含量:Mn/S高则晶界处形成的MnS量多、FeS量生成量少,提高了钢的热塑性,减少了钢裂纹倾向。
(2)降低S含量:过高的S会产生较多的MnS夹杂,影响钢的性能。
3.Mn控制S的危害的原理,要求值。
Mn影响S的原理:钢中的Mn在凝固过程中同样产生选分结晶,在晶界处与S反应生产MnS。
Mns的熔点高,在轧制和连铸过程中仍处于固态,因此消除了低熔点FeS引起的热脆现象。
Mn\S:Mn对S的控制力,一般用Mn和S的质量百分数的比值表示,称为“锰硫比”。
钢铁冶炼与冶金工艺培训ppt

04
工作环境改善
优化工作环境,降低噪声和振动 的影响,为员工创造一个良好的
工作条件。
06
实践操作与案例分析
钢铁冶炼实践操作
钢铁原料准备
了解和掌握各种钢铁原料的 性质、用途和加工方法,以 及合理配比和优化原料的实 践操作。
高炉炼铁工艺
通过实践操作掌握高炉炼铁 的工艺流程、技术参数和操 作要点,包括原料加工、烧 结、高炉炼铁等环节。
无缝钢管轧制技术
无缝钢管轧制技术是生产无缝钢管的主要方法,通过精确 控制轧制温度、压力和变形量得到高质量的无缝钢管。
04
钢铁冶炼环境保护与节能 减排
钢铁冶炼的环境影响
01
02
03
空气污染
钢铁冶炼过程中会产生大 量的烟尘和有害气体,如 硫化物、氮氧化物等,对 空气质量造成严重影响。
水污染
钢铁冶炼过程中产生的废 水含有多种有害物质,如 重金属离子、酸碱物质等 ,对水体造成严重污染。
电炉炼钢技术
电炉炼钢技术是一种节能环保的炼钢方法,通过电能将废钢或生铁熔 化,再加入合金元素来得到不同品质的钢。
炉外精炼技术
炉外精炼技术是在传统的炼钢工艺基础上发展起来的一种新型技术, 通过在钢包中加入各种精炼剂来进一步优化钢的成分和性能。
连铸技术的发展
传统连铸技术
传统的连铸技术是将液态钢倒 入固定模子中,形成钢坯后进 行切割和轧制。
影响。
安全管理与操作规程
建立健全安全管理制度
制定并执行安全生产责任制、安全检查 制度等,确保各项安全工作有序开展。
安全设施配备
配备齐全的安全设施,如防护罩、防 护栏、报警装置等,确保员工在工作
过程中得到有效保护。
操作规程培训
钢铁冶金学(炼钢学)
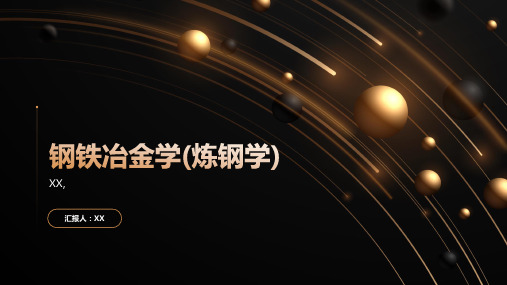
脱氧和脱硫反应 的平衡:在炼钢 过程中,需要控 制脱氧和脱硫反 应的平衡,以保 证钢的质量和性 能。
脱氧和脱硫反应 的影响因素:温 度、时间、钢的 成分等会影响脱 氧和脱硫反应的 效果。
转炉:用于炼钢的主要设备,具有容量大、生产率高、操作方便等特点。 电炉:用于炼钢的辅助设备,具有节能环保、操作简单等特点。 炉外精炼设备:用于提高钢的质量和性能,具有高效、节能、环保等特点。 连铸设备:用于将钢水连续铸造成钢坯,具有高效、节能、环保等特点。 轧钢设备:用于将钢坯轧制成各种钢材,具有高效、节能、环保等特点。
按化学成分分类:碳钢、合金钢、不锈钢等 按生产工艺分类:转炉钢、电炉钢、平炉钢等 按用途分类:建筑用钢、机械用钢、汽车用钢等 性能要求:强度、硬度、韧性、塑性、焊接性能等 标准:国家标准、行业标准、企业标准等
碳钢:含碳量在0.25%-2.11%之间,硬度高,耐磨性好,适用于制造机械零件、工具等。
XX,
汇报人:XX
钢铁冶金学:研究钢铁生产工艺、 原理和设备的科学
定义:包括炼铁、炼钢、轧钢等过 程
重要性:钢铁是现代工业的基础材 料,广泛应用于建筑、机械、汽车、 船舶等领域
发展历程:从早期的土法炼铁到现 代的高炉炼铁、转炉炼钢等技术, 不断提高钢铁质量和生产效率
古代冶金:青铜器、铁器等金属制品的出现 近代冶金:18世纪末,高炉炼铁、转炉炼钢等技术的出现 现代冶金:20世纪初,电炉炼钢、氧气顶吹转炉炼钢等技术的发展 现代冶金:21世纪初,绿色冶金、智能制造等技术的兴起和发展
操作技术:包括设备启 动、运行、停机等步骤, 以及操作注意事项和常 见故障处理方法
维护技术:包括设备日 常维护、定期检查、维 修和更换部件等,以及 维护注意事项和常见故 障处理方法
钢铁冶金学(炼钢部分).
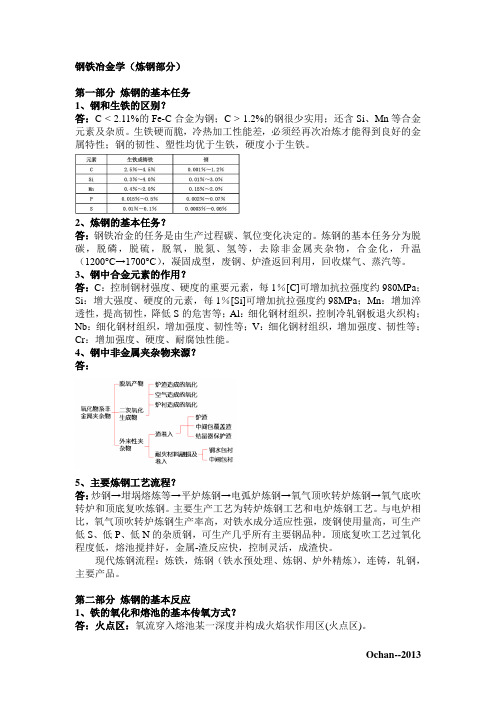
钢铁冶金学(炼钢部分)第一部分炼钢的基本任务1、钢和生铁的区别?答:C < 2.11%的Fe-C合金为钢;C > 1.2%的钢很少实用;还含Si、Mn等合金元素及杂质。
生铁硬而脆,冷热加工性能差,必须经再次冶炼才能得到良好的金属特性;钢的韧性、塑性均优于生铁,硬度小于生铁。
2、炼钢的基本任务?答:钢铁冶金的任务是由生产过程碳、氧位变化决定的。
炼钢的基本任务分为脱碳,脱磷,脱硫,脱氧,脱氮、氢等,去除非金属夹杂物,合金化,升温(1200°C→1700°C),凝固成型,废钢、炉渣返回利用,回收煤气、蒸汽等。
3、钢中合金元素的作用?答:C:控制钢材强度、硬度的重要元素,每1%[C]可增加抗拉强度约980MPa;Si:增大强度、硬度的元素,每1%[Si]可增加抗拉强度约98MPa;Mn:增加淬透性,提高韧性,降低S的危害等;Al:细化钢材组织,控制冷轧钢板退火织构;Nb:细化钢材组织,增加强度、韧性等;V:细化钢材组织,增加强度、韧性等;Cr:增加强度、硬度、耐腐蚀性能。
4、钢中非金属夹杂物来源?答:5、主要炼钢工艺流程?答:炒钢→坩埚熔炼等→平炉炼钢→电弧炉炼钢→氧气顶吹转炉炼钢→氧气底吹转炉和顶底复吹炼钢。
主要生产工艺为转炉炼钢工艺和电炉炼钢工艺。
与电炉相比,氧气顶吹转炉炼钢生产率高,对铁水成分适应性强,废钢使用量高,可生产低S、低P、低N的杂质钢,可生产几乎所有主要钢品种。
顶底复吹工艺过氧化程度低,熔池搅拌好,金属-渣反应快,控制灵活,成渣快。
现代炼钢流程:炼铁,炼钢(铁水预处理、炼钢、炉外精炼),连铸,轧钢,主要产品。
第二部分炼钢的基本反应1、铁的氧化和熔池的基本传氧方式?答:火点区:氧流穿入熔池某一深度并构成火焰状作用区(火点区)。
吹氧炼钢的特点:熔池在氧流作用下形成的强烈运动和高度弥散的气体-熔渣-金属乳化相,是吹氧炼钢的特点。
乳化可以极大地增加渣-铁间接触面积,因而可以加快渣-铁间反应。
LF精炼技术
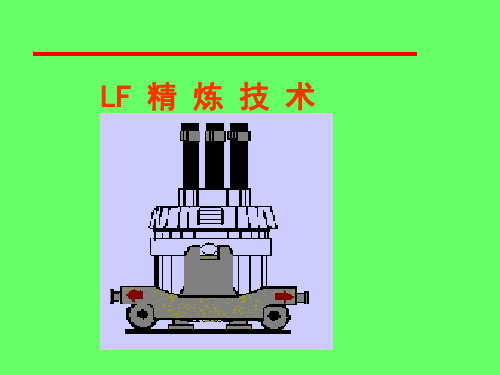
1 LF精炼目的
• 钢水温度满足连铸工艺要求; • 处理时间满足多炉连浇要求; • 成份微调能保证产品具有合格的成份及
实现最低成本控制; • 钢水纯净度能满足产品质量要求; • 均衡物流的手段; • 取消电炉还原期。
2 LF精炼工艺
• 电炉或转炉出钢→ 去渣→ 脱氧(加还原渣、加 脱氧剂)→ 加热(加合金、取样)→ 浇注
代入式(1)、(2)计算可得:
对 40t 钢液引起的钢液温降为 0.0075℃/min;
对 60t 钢液引起的钢液温降为 0.005℃/min;
对 80t 钢液引起的钢液温降为 0.0037℃/min。
由此可见,氩气吸热对钢液温降的影响完全可以忽略不计。
5.3.2 吹氩搅拌引起钢液温降分析
• 钢包包衬的蓄热
。
浇注温度
工艺要求:正常条件下,保护浇注温度为±5℃ ,浇注工可根据条件改变。
浇注过程中的成分偏差
工艺要求:成分最大偏差满足以下要求:C 0.03%;Mn 0.12%,Si 0.1% CEQ 0.03%。
存在问题:如果钢成分不在成分偏差的最大范围,钢质量降级。
•N
精炼结束后,钢包吊往连铸。
• 工艺过程中应注意
规程。操作者应该能生产规定的所有钢种。
6 控制设备 测温枪、定氧仪、合金称量设备及喂线机被控制并按计划校准。
3 LF工艺过程操作要点
• 根据钢液中酸溶铝的要求及钢液中溶解氧控制加铝 量的喂铝线操作;
• 考虑埋弧加热、脱硫、吸附夹杂物的造渣操作;
• 考虑防止吸气、卷渣以及加快夹杂物去除的最佳搅 拌模型控制的吹氩搅拌处理;
•C
钢包到钢包炉等待位置后,钢包炉处吹氩接通,吹 氩时保证不裸露钢液面,但当要从料仓加料时,增加 氩气流量,吹开渣面,料加到裸露的钢液面上。
钢铁冶金学炼钢部分总结
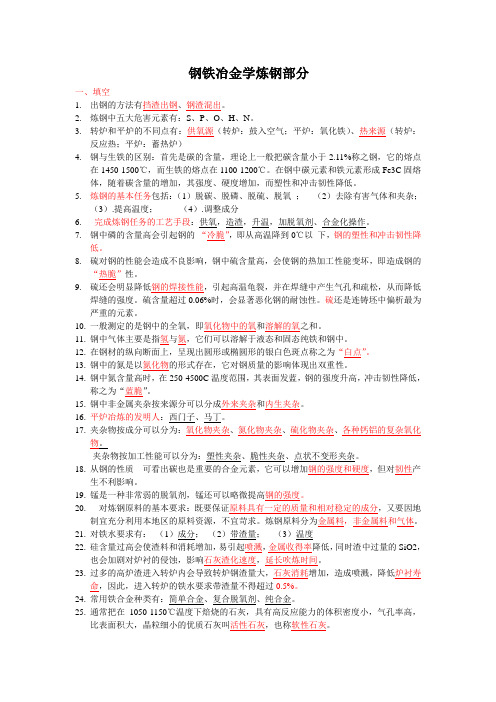
钢铁冶金学炼钢部分一、填空1.出钢的方法有挡渣出钢、钢渣混出。
2.炼钢中五大危害元素有:S、P、O、H、N。
3.转炉和平炉的不同点有:供氧源(转炉:鼓入空气;平炉:氧化铁)、热来源(转炉:反应热;平炉:蓄热炉)4.钢与生铁的区别:首先是碳的含量,理论上一般把碳含量小于2.11%称之钢,它的熔点在1450-1500℃,而生铁的熔点在1100-1200℃。
在钢中碳元素和铁元素形成Fe3C固熔体,随着碳含量的增加,其强度、硬度增加,而塑性和冲击韧性降低。
5.炼钢的基本任务包括:(1)脱碳、脱磷、脱硫、脱氧;(2)去除有害气体和夹杂;(3).提高温度;(4).调整成分6.完成炼钢任务的工艺手段:供氧,造渣,升温,加脱氧剂、合金化操作。
7.钢中磷的含量高会引起钢的“冷脆”,即从高温降到0℃以下,钢的塑性和冲击韧性降低。
8.硫对钢的性能会造成不良影响,钢中硫含量高,会使钢的热加工性能变坏,即造成钢的“热脆”性。
9.硫还会明显降低钢的焊接性能,引起高温龟裂,并在焊缝中产生气孔和疏松,从而降低焊缝的强度。
硫含量超过0.06%时,会显著恶化钢的耐蚀性。
硫还是连铸坯中偏析最为严重的元素。
10.一般测定的是钢中的全氧,即氧化物中的氧和溶解的氧之和。
11.钢中气体主要是指氢与氮,它们可以溶解于液态和固态纯铁和钢中。
12.在钢材的纵向断面上,呈现出圆形或椭圆形的银白色斑点称之为“白点”。
13.钢中的氮是以氮化物的形式存在,它对钢质量的影响体现出双重性。
14.钢中氮含量高时,在250-4500C温度范围,其表面发蓝,钢的强度升高,冲击韧性降低,称之为“蓝脆”。
15.钢中非金属夹杂按来源分可以分成外来夹杂和内生夹杂。
16.平炉冶炼的发明人:西门子、马丁。
17.夹杂物按成分可以分为:氧化物夹杂、氮化物夹杂、硫化物夹杂、各种钙铝的复杂氧化物。
夹杂物按加工性能可以分为:塑性夹杂、脆性夹杂、点状不变形夹杂。
18.从钢的性质可看出碳也是重要的合金元素,它可以增加钢的强度和硬度,但对韧性产生不利影响。
钢铁冶金学(炼钢学)
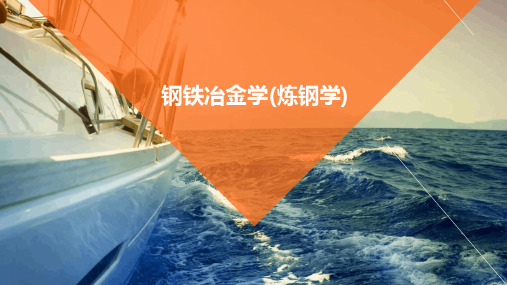
02 炼钢原料及预处理
炼钢原料种类及性质
A
铁矿石
主要含铁矿物,分为磁铁矿、赤铁矿等,是炼 钢的主要原料之一。
废钢
来自报废的汽车、建筑、机器等,是炼钢 的重要原料之一,具有可回收性和环保性。
B
C
熔剂
如石灰石、白云石等,用于造渣和脱硫,保 证钢的质量。
合金元素
如铬、镍、钨等,用于提高钢的力学性能和 耐腐蚀性。
特点
钢铁冶金学是一门综合性很强的 技术科学,它涉及地质、采矿、 选矿、冶炼、金属加工和金属材 料性能等多方面的知识。
炼钢学发展历史及现状
发展历史
炼钢学的发展经历了漫长的岁月,从 古代的铁匠铺到现代的钢铁联合企业 ,炼钢技术不断得到改进和完善。
现状
目前,炼钢学已经成为一门高度自动 化的技术科学,采用了许多先进的工 艺和设备,如高炉炼铁、转炉炼钢、 电炉炼钢等。
钢铁冶金学(炼钢学)
目录
• 绪论 • 炼钢原料及预处理 • 炼钢工艺过程及设备 • 炉外精炼技术与应用 • 连铸技术与发展趋势 • 节能环保与资源综合利用 • 课程总结与展望
01
绪论
钢铁冶金学定义与特点
定义
钢铁冶金学是研究从矿石中提取 金属,并用各种加工方法制成具 有一定性能的金属材料的学科。
01
02
03
04
高炉
用于将铁矿石还原成生铁的主 要设备,具有高温、高压、高
还原性的特点。
转炉
用于将生铁和废钢转化为钢水 的重要设备,通过吹氧和加入 造渣剂去除杂质和调整成分。
电炉
利用电能加热原料进行熔炼的 设备,具有灵活性高、环保性
好的优点。
连铸机
将钢水连续浇铸成坯或板的设 备,提高了生产效率和产品质
冶金学

冶金学:是一门研究如何经济地从矿石或其它原料中提取金属或金属化合物,并用一定加工方法制成具有一定性能的金属材料的科学。
由于矿石性能不同,提取金属的原理、工艺过程和设备不同,从而形成专门的冶金学科。
提取冶金的分类:按所冶炼金属类型分:有色冶金钢铁冶金按冶金工艺过程不同分:火法冶金湿法冶金电冶金火法冶金主要过程:干燥:去水,温度为400~600℃。
焙烧:以驱除其中的挥发性组分,改变原料组成为目的、在低于矿石熔点温度下、在特定气氛中进行的冶金过程。
煅烧:在空气中以去CO2 、水、NOx为目的的冶金过程。
烧结与球团:以获得特定矿物组成、结构及性能的造块。
熔炼:还原氧化物,提取粗金属。
精炼:氧化杂质,获得纯金属。
铸造:液态金属凝固成固态。
生铁:是含碳量大于2.0%的铁碳合金,工业生铁含碳量一般在2.5%-4%,并含C、Si、Mn、S、P等元素,是用铁矿石经高炉冶炼的产品生铁性能:生铁坚硬、耐磨、铸造性好,但生铁脆,不能锻压钢:指含碳量0.2-2%的铁碳合金。
根据成分不同,又可分为碳素钢和合金钢,根据性能和用途不同,又可分为结构钢、工具钢和特殊性能钢高强高韧是钢的重要特征炒钢:向熔化的生铁鼓风,同时进行搅拌促使生铁中的碳氧化。
再经过渗碳锻打成钢。
也可有控制地把生铁含碳量炒到需要的程度,再锻制成钢制品。
平炉时代优势:可以炼废钢,原料适用广,质量提高缺陷:生产率低,环境污染大氧气转炉时代产量高,质量好,无需外热源,投资低,建设快钢铁生产的典型工艺(长流程)块状区:主要特征:焦与炭呈交替分布状,皆为固体状态。
主要反应:矿石间接还原,碳酸盐分解。
软熔区:主要特征:矿石呈软熔状,对煤气阻力大。
主要反应:矿石的直接还原、渗碳和焦炭的气化反应。
滴落区:主要特征:焦炭下降,其间夹杂渣铁液滴。
主要反应:非铁元素还原、脱硫、渗碳、焦炭的气化反应。
焦炭回旋区:主要特征:焦炭作回旋运动。
主要反应:鼓风中的氧和蒸汽与焦炭及喷入的辅助燃料发生燃烧反应。
钢铁冶金学(炼钢学)PPT课件

36
1.3.4 钢中的气体
钢液中的气体会显著降低钢的性能,而且容易 造成钢的许多缺陷。钢中气体主要是指氢与氮, 它们可以溶解于液态和固态纯铁和钢中。 氢在固态钢中溶解度很小,在钢水凝固和冷却 过 程 中 , 氢 会 和 CO 、 N2 等 气 体 一 起 析 出 , 形 成皮下气泡中心缩孔、疏松、造成白点和发纹。
完整编辑ppt
11
炼 钢 方 法(6)
瑞典人罗伯特·杜勒首先进行了氧气顶吹 转炉炼钢的试验,并获得了成功。1952 年奥地利的林茨城(Linz)和多纳维兹城 (Donawitz)先后建成了30吨的氧气顶吹 转炉车间并投入生产,所以此法也称为
LD法。美国称为BOF法(Basic Oxygen Furnace)或BOP法。
完整编辑ppt
23
1.3.1 钢中的磷
对于绝大多数钢种来说磷是有害元素。钢中磷的 含量高会引起钢的 “冷脆”,即从高温降到0℃ 以下,钢的塑性和冲击韧性降低,并使钢的焊接 性能与冷弯性能变差。
磷是降低钢的表面张力的元素,随着磷含量的增 加,钢液的表面张力降低显著,从而降低了钢的 抗裂性能。
完整编辑ppt
完整编辑ppt
39
钢中加入适量的铝,可生成稳定的AlN,能够 压抑Fe4N生成和析出,不仅改善钢的时效性, 还可以阻止奥氏体晶粒的长大。氮可以作为合 金元素起到细化晶粒的作用.在冶炼铬钢,镍铬 系钢或铬锰系等高合金钢时,加入适量的氮, 能够改善塑性和高温加工性能。
完整编辑ppt
40
1.3.5 钢中的夹杂
完整编辑ppt
16
LD- Q- BOP
完整编辑ppt
17
炼 钢 方 法(9)
我国首先在 1972-1973 年 在沈阳第一炼钢 厂成功开发了全 氧侧吹转炉炼钢 工艺。并在唐钢 等企业推广应用。
钢铁冶金学 炼铁部分习题

1、冶金的方法及其特点是什么提取冶金工艺方法:火法冶金、湿法冶金、电冶金、卤化冶金、羰基冶金等。
(1) 火法冶金:在高温下利用各种冶金炉从矿石或其它原料中进行金属提取的冶金工艺过程。
操作单元包括:干燥、煅烧、焙烧(烧结)、熔炼、精炼。
(2) 湿法冶金:在水溶液中对矿石和精矿中的金属进行提取和回收的冶金过程。
操作单元包括:浸取(出)、富(3) 电冶金:利用电能提取金属的冶金过程,包括电热冶金和电化学冶金。
电热冶金:利用电能转变为热能进行金属冶炼,实质上属火法冶金。
电化学冶金:利用电化学反应使金属从含金属盐类的溶液或熔体中析出。
如:①水溶液电解:如Cu、Pb、Zn等。
可列入湿法冶金。
②熔盐电解:如Al、Mg、Ca、Na等。
可列入火法冶金。
钢铁冶金:火法、电热冶金)有色冶金:火法、湿法、电化学冶金。
通常为“火法+湿法”联合。
集(净化和浓缩)、提取(金属或金属化合物)等2、钢与生铁有何区别都是以铁为基底元素,并含少量C、Si、Mn、P、S——铁碳合金。
(1) 生铁:硬而脆,不能锻造。
用途:①炼钢生铁;②铸造生铁,占10%。
用于铸造零、部件,如电机外壳、机架等。
(2) 钢:有较好的综合机械性能,如机械强度高、韧性好、可加工成钢材和制品;能铸造、锻造和焊接;还可加工成不同性能的特殊钢种。
3、钢铁冶炼的任务及基本冶炼工艺是什么把铁矿石冶炼成合格的钢:铁矿石:铁氧化物,脉石杂质。
·炼铁:去除铁矿石中的氧及大部分杂质,形成铁水和炉渣并使其分离。
炼钢:把铁水进一步去除杂质,进行氧化精炼。
铁矿石→去脉石、杂质和氧→铁铁→精炼(脱C、Si、P等)→钢4、试述3种钢铁生产工艺及其特点。
传统流程:间接炼钢法:高炉炼铁+ 转炉炼钢。
优点:工艺成熟,生产率高,成本低缺点:流程工序多,反复氧化还原,环保差短流程:直接炼钢法:直接还原炉+ 电炉,将铁矿石一步炼成钢。
优点:避免反复氧化还原!缺点:铁回收率低,要求高品位矿,能耗高,技术尚存在一定问题。
炼钢-精炼工艺介绍
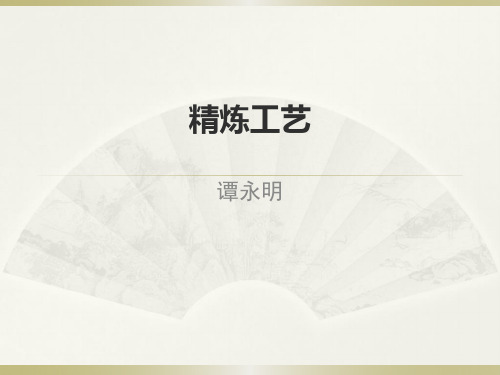
1、精炼过程用原料
1.4常用气体 1.4.1惰性气体 氮气、氩气等为冶金用惰性气体。主要用于二次钢水的保
护与隔离,以及对钢水精炼时的搅拌、吸气、去杂质等。 对人体的危害表现为窒息性伤害,浓度达到25g/m3时有危 险。 要求:干燥、干净、无杂质、水分<1%、纯度≥99.9%、 氧气<6PPm、氮气<20PPm、氧气+氮气≯20PPm 1.5钢包炉用材料 1.5.1冶金石灰: 采用转炉炼钢用活性石灰,保存期不得大于10天。
1.5.3埋弧渣:
化学指标 物理指标
CaO% 40~60
SiO2% 3~7
熔点(℃)
≥1320
杂质总和% ≤3.0
MgO% 4~10
Al2O3% ≤5
灼减(%)
≥35
粒度mm 10~50
S%
H2O%
≤0.1
≤1.0
粒度(mm)
≥3
1、精炼过程用原料
1.5.4电极
1#LF炉:Φ450mm高功率石墨电极(长度1800±100 mm)
转炉挡渣出钢 钢包内渣层过厚回对CAS处理带来不良影响:底吹排渣效
果差甚至无法裸露出钢液面,从而造成浸罩内残留渣量多 甚至无法进行CAS处理;成份调节时,合金元素收得率降 低;钢水脱氧效果差甚至出现钢水回鳞现象等。对于CAS 处理最好将钢包钢水顶渣厚度控制在≤50mm。
钢包渣改质
4、CAS工艺
求如何确定? 2、各类材料、介质等对钢水作用?在使用中应注意哪些事项?
2、钢包吹氩工艺
2.1钢包吹氩主要工艺参数 钢包吹氩应根据钢种性质、钢水状态、精炼目的,来选择合适
钢铁冶金导论--冶金的分类
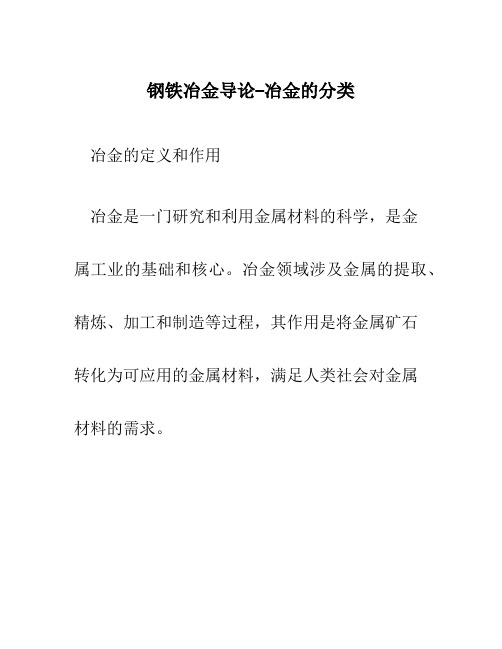
钢铁冶金导论–冶金的分类冶金的定义和作用冶金是一门研究和利用金属材料的科学,是金属工业的基础和核心。
冶金领域涉及金属的提取、精炼、加工和制造等过程,其作用是将金属矿石转化为可应用的金属材料,满足人类社会对金属材料的需求。
冶金的分类1. 原料冶金原料冶金是指将矿石作为原料,经过提取、精炼等过程,将金属元素从矿石中分离出来的冶金学科。
原料冶金是冶金学的基础,也是其他冶金学科的前提。
1.1 矿石的分类矿石是指含有金属元素的矿石矿物,根据其组成和成分的不同,可以分为金属矿石、非金属矿石和贵金属矿石等。
1.1.1 金属矿石金属矿石是指含有大量金属元素的矿石,如铁矿石、铜矿石、铝矿石等。
金属矿石是原料冶金的主要对象,通过提炼和精炼,将其中的金属元素分离出来,得到可用于制造金属材料的金属。
1.1.2 非金属矿石非金属矿石是指不含有金属元素或含有很少金属元素的矿石,如硫矿石、石灰石、石墨等。
非金属矿石主要用于非金属工业,如建材、化工等领域。
1.1.3 贵金属矿石贵金属矿石是指含有贵金属元素的矿石,如金、银、铂等。
贵金属矿石具有很高的价值,主要用于珠宝、电子等领域。
1.2 原料冶金的工艺过程原料冶金包括矿石的选矿、矿石的破碎、矿石的浸出、金属元素的精炼等工艺过程。
这些过程涉及到化学、物理等知识,通过这些过程将矿石中的金属元素提取出来。
2. 冶金材料学冶金材料学是研究金属材料的科学,涉及金属材料的性能、组织结构和工艺等方面。
冶金材料学主要包括金属的相变规律、组织结构的变化、力学性能的改善等。
2.1 金属材料的分类金属材料可以根据其成分和性质的不同,进行不同的分类。
常见的金属材料分类包括钢铁、有色金属、合金等。
钢铁是指以铁为主要成分,添加一定数量的碳和其他合金元素而成的金属材料。
钢铁具有高强度、良好的可塑性和可焊性等特点,广泛应用于建筑、机械制造等领域。
2.1.2 有色金属有色金属是指除铁、钢以外的金属材料,如铜、铝、锌、镍等。
冶金学3炼钢的基本任务
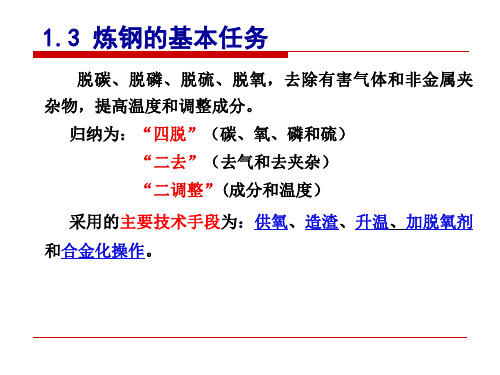
[Mn]/[S]比对低碳钢热延展性的影响
硫还会明显降低钢的焊接性能,引起高温龟裂,并在焊缝中产生气孔和疏松, 从而降低焊缝的强度。硫含量超过0.06%时,会显著恶化钢的耐蚀Байду номын сангаас。硫还 是连铸坯中偏析最为严重的元素。
不同钢种对硫含量有严格的规定: ●非合金钢中普通质量级钢[S]≤0.045%; ●优质级钢[S]≤0.035%; ●特殊质量级钢[S]≤0.025%; ●有的钢种要求如管线钢[S]≤0.005%。 有些钢种,如易切削钢硫则作为合金元素加入,要求 [S]=0.08%-0.20%。
钢中的氧
在吹炼过程中,向熔池供入了大量的氧气,到吹炼终点时,钢水中含有过量的 氧,即钢中实际氧含量高于平均值。如不脱氧,在出钢、浇铸中,温度降低, 氧溶解度降低,促使碳氧反应,钢液剧烈沸腾,使浇铸困难,得不到正确凝固 组织结构的连铸坯。
钢中大部分内生夹杂是在脱氧和凝固过程中产生的。 由于夹杂对钢的性能产生严重的影响,因此在炼钢、精炼和连铸过程应
最大限度地降低钢液中夹杂物的含量,控制其形状、尺寸。
根据成分不同,夹杂物可分为:
氧化物夹杂,即 FeO、MnO、SiO2、Al2O3 、Cr2O3等简单氧化物; FeO-Fe2O3 、FeO-Al2O3、MgO-Al2O3等尖晶石类和各种钙铝的复杂氧化物; 2FeO-SiO2,、2MnO-SiO2、 3MnO-Al2O3-2SiO2等硅酸盐;
131钢中的磷磷是仅次于硫在钢的连铸坯中偏析度高的元素而且在铁固熔体中扩散速率很小因而磷的偏析很难消除从而严重影响钢的性能所以脱磷是炼钢过程的重要任务之一
冶金学课程教学大纲

冶金学课程教学大纲课程编号:110100101课程性质:专业必修课适用专业:冶金工程先修课程:冶金物理化学后续课程:专业课一、教学目的与要求本课程是冶金工程专业学生钢铁冶金、有色冶金方向的重要专业课,为必修课。
通过本课程的学习,使学生了解钢铁及常用有色金属的性质、用途以及冶炼工艺的发展动态;掌握钢铁及常用有色金属的冶炼工艺、原理、主体设备的构造和技术经济指标控制。
二、课程内容及学时分配1.绪论(建议学时数:1学时)目的要求:本部分讲解冶金基本概念,钢铁在国民经济中的地位,现代高炉生产工艺及冶炼过程概述,我国钢铁冶金的发展,国外钢铁生产发展状况和趋势,高炉冶炼产品及主要技术经济指标,炼钢生产的主要技术经济指标。
教学内容:我国及国外钢铁生产发展状况和趋势。
2.炼铁部分(建议学时数:17学时)目的要求:本部分讲解炼铁的基本概念,包括高炉炼铁过程、高炉与高炉附属系统,炼铁产品与技术经济指标;高炉炼铁原料与质量评价指标,烧结与球团生产工艺及设备;高炉冶炼基础理论,高炉内煤气与炉料运动,高炉调剂原理;非高炉炼铁工艺的发展。
让学生掌握炼铁的相关理论与知识。
教学内容:第2章高炉炼铁概述(2学时)2.1高炉炼铁过程2.2高炉与高炉附属系统2.3炼铁产品与技术经济指标第3章高炉炼铁原料(5学时)3.1铁矿石种类3.2矿石质量评价3.3燃料与熔剂3.4烧结矿质量指标与生产3.5烧结矿固结机理3.6球团矿质量指标与生产3.7球团矿生产设备第4章高炉冶炼基础(4学时)4.1高炉内还原反应4.2直接还原度计算及还原动力学4.3渗碳与生铁形成4.4高炉炉渣形成过程4.5炉渣的成分与性质4.6造渣与脱硫第5章高炉调剂原理(4学时)5.1高炉炉缸反应5.2下部调剂原理5.3高炉炉料与煤气运动5.4上部调剂原理第6章非高炉炼铁(2学时)6.1概述6.2直接还原6.3熔融还原2.炼钢部分(建议学时数:31学时)目的要求:本部分讲解炼钢的基本概念,包括炼钢的基本任务、炼钢基础理论,炼钢所使用的原材料。
RH、LF和VD炉外精炼技术

通电时,采用小流量吹 Ar,均匀温度又不引起大的 液面波动.
28
③造渣制度
目 的:
脱S、脱O、去夹杂; 提高炉衬寿命; 防止钢水二次氧化,提高合 金收得率。
基本制度:
渣料加入量8-10Kg/t; 分 批 加 入 , 出 钢 过 程 加 4050%,其余待化渣后分2-3次加入; 炉渣过稠加CaF2,炉渣过稀加 CaO.
4
2.炉外精炼的发展
• 20世纪30年代 • 20世纪40年代 • 20世纪50年代 • 20世纪60,70年代 • 20世纪80年代
多的R(理包HD有(种精-HO循C形炼)BA环使渣高式)大泵真炉,S在钢理合在V,真发钢用C进,,问抽空;金低水O提真A空真展水高行D微S世速法真进升空处-空,质碱O调脱理真,蒸 用吹空 行、B广脱D量及度S)(空H氩度 脱泛汽 于温气;以合V,R、L处脱应度下 气基A喷 钢HF成提D理,处氧用R钢对 处础射 水H上、,
7
4.炉外精炼方法的共同特点
• ①理想的精炼气氛条件,通常应用真空、 惰性气氛或还原气氛;
• ②搅动钢水,采用电磁力、惰性气体或机 械搅拌的方法;
• ③为补偿精炼过程的钢水温度损失,采用 加热设施有电弧加热、等离子加热或增加 钢水中的化学热等。
8
二.RH、LF及VD法简介
RH 法 LF 法 VD 法
34
④事故搅拌装置
作 用:
在透气砖不能工作情况 下,惰性气体通过顶枪吹入 钢包,进行事故搅拌;
结 构:
顶枪安装在支撑框架上, 支撑框架安装在炉盖侧面, 顶枪通过电动机和卷筒实现 上下;
参 数:
顶枪压力:0.6-1.6MPa; 流量(max):600NL/min
LF炉精炼研究总结(2)
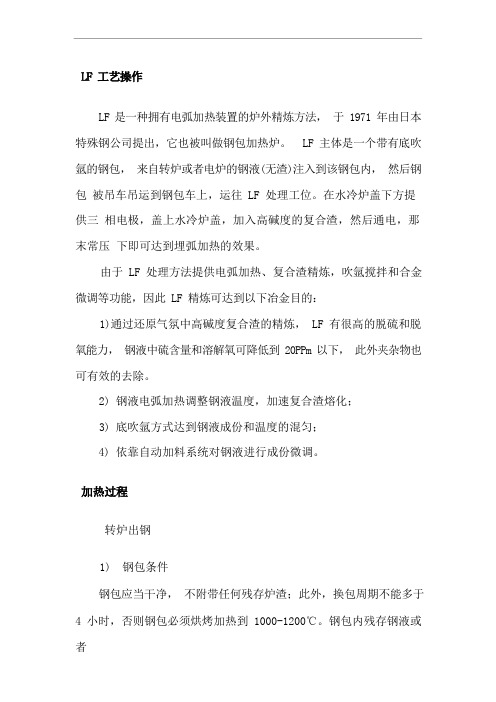
LF 是一种拥有电弧加热装置的炉外精炼方法,于 1971 年由日本特殊钢公司提出,它也被叫做钢包加热炉。
LF 主体是一个带有底吹氩的钢包,来自转炉或者电炉的钢液(无渣)注入到该钢包内,然后钢包被吊车吊运到钢包车上,运往 LF 处理工位。
在水冷炉盖下方提供三相电极,盖上水冷炉盖,加入高碱度的复合渣,然后通电,那末常压下即可达到埋弧加热的效果。
由于 LF 处理方法提供电弧加热、复合渣精炼,吹氩搅拌和合金微调等功能,因此 LF 精炼可达到以下冶金目的:1)通过还原气氛中高碱度复合渣的精炼, LF 有很高的脱硫和脱氧能力,钢液中硫含量和溶解氧可降低到 20PPm 以下,此外夹杂物也可有效的去除。
2) 钢液电弧加热调整钢液温度,加速复合渣熔化;3) 底吹氩方式达到钢液成份和温度的混匀;4) 依靠自动加料系统对钢液进行成份微调。
转炉出钢1) 钢包条件钢包应当干净,不附带任何残存炉渣;此外,换包周期不能多于4 小时,否则钢包必须烘烤加热到 1000-1200℃。
钢包内残存钢液或者炉渣会引起钢包温降,失去的热量需 LF 处理补偿,这些因素在 LF 电脑模型中都需要考虑进去。
2) 挡渣转炉出钢需要进行挡渣,众所周知转炉顶吹终点,钢液中存在一定含量的溶解氧,它与渣中氧保持平衡。
渣中FeO 和 P O 含量很高。
2 5当还原剂加入钢包钢液中溶解氧含量降低,钢渣间的氧平衡被打破,渣中 FeO 含量减小。
因为炉渣的氧化性降低,发生回磷现象。
因此为了阻挠钢液回磷和保证稳定的 LF 加热过程,转炉出钢要求挡渣。
3)合金和造渣剂的添加为保证钢液成份,出钢过程中需加入合金和还原剂。
LF 加热过程钢包精炼工艺包括几个过程,彼此间相互关联。
对于不同钢种,加热操作不尽相同,且处理过程参数均有相关的标准计算模型。
步骤 A:搅拌当钢包抵达 LF 处理位,接通自动快换接头向钢包提供氩气,根据钢种选择不同的吹氩模式。
a) 吹氩量: 150~300Nl/min步骤 B:混匀依据钢种提供不同的混匀方法a) 吹氩量: 300~600Nl/minb) 还原剂:硅铁,铝丸不同混匀模式中,还原剂用量是一定的 (~TS).这个步骤分为两个加热阶段,第一阶段持续 1 分钟,加热速度越慢越好,温度上升大约3℃/min,这是起弧阶段。
冶金行业VOD精炼法详解

(以18-8型低碳不锈钢的炉外精炼为例,详解VOD法)
目录: • 1、VOD法 • 2、VOD法设备 • 3、工艺流程图解 • 4、操作工艺 • 5、真空氧气脱碳精炼工艺分析 • 6、VOD工艺效果及存在问题 • 7、AOD法与VOD法比较
• 一种在真空条件下吹氧脱碳并吹氩搅拌生产高铬不锈
终点控制仪表
氧浓差电池控制吹炼过程的原理是:
• 一般采用氧浓差电池为主,废气温度和真空计为辅的废气检测系统。
• 式中R为气体常数,8.315J/mol•℃;T为绝对温度,K;F为法拉
第常数,96500C/mol;E为固体电池的电势,1000mV。根据上式, 废气中氧的分压PO2(废)愈低,则电池电势E愈大;PO2(废)愈高, 则电池电势愈小,当PO2(废)=0.021MPa时,E就变为零(因为 PO2(空)=0.021MPa)、PO2(废)>0.021MPa时,E变为负值。由 于吹氧过程中产生大量CO会改变PO2(废),脱碳激烈时PO2(废)极小, E增大;脱碳微弱时,CO很少,E会趋近于零,因此根据氧浓差电势 的开始上升,在一定E值下波动和趋近于零,即可确定吹氧脱碳的 起点、正常进行和终点。氧浓差电池只适用于控制趋低碳(C<0.03 %)钢的终点,对中、高碳钢及极低碳钢(含C在10-6级),则需要用 质谱仪来控制。
5、真空氧气脱碳精炼工艺分析
• A 影响真空脱碳的因素
影响真空脱碳的因素有: • ①临界含碳量:临界含碳量是指在一定温度下,脱碳速 度vc与钢中碳含量无关的高碳区和vc随[%C]降低而减 小的低碳区之间的交界含碳量。临界含碳量越低,脱碳 越容易进行。临界含碳量的值与钢液中含铬量、冶炼真 空度和温度,以及是否吹氩等因素有关,通常冶炼真空 度及温度越高,临界含碳量就越低。对于18-8型不锈 钢而言,VOD法精炼时的临界含碳量波动在0.02%~ 0.06%之间,而电弧炉返回吹氧法的临界含碳量大于 0.15%。例如:国内某厂吹氧平均真空度为6.67~ 13.33KPa,采用水冷拉瓦尔喷枪深坑硬吹,采用氩气搅 拌,其临界含碳量为0.02%~0.03%。可见,在VOD精 炼条件下,冶炼含碳量小于0.03%的超低碳不锈钢是十 分有利的。
- 1、下载文档前请自行甄别文档内容的完整性,平台不提供额外的编辑、内容补充、找答案等附加服务。
- 2、"仅部分预览"的文档,不可在线预览部分如存在完整性等问题,可反馈申请退款(可完整预览的文档不适用该条件!)。
- 3、如文档侵犯您的权益,请联系客服反馈,我们会尽快为您处理(人工客服工作时间:9:00-18:30)。
2 炉外精炼方法分类及发展
2.1 炉外精炼方法分类
•(1) •(2) •(3) •(4) •(5) •(6) 钢包沸腾法 真空处理方法 电弧加热法 不锈钢精炼方法 喷粉精炼法 喂丝精炼法
AB精炼法、SAB精炼法、CAB精炼法、CAS精炼法、CAS-OB精炼法 RH法、RH-OB精炼法、RH-KTB精炼法、RH-喷射法、VOD精炼法 ASEA-SKF精炼法、VAD精炼法、LF(V)精炼法 VOD精炼法、AOD精炼法 TN精炼法、SL精炼法
特殊钢厂冶炼工艺路线
VD 精炼 废钢 生铁 DRI/HBI UHP 电炉 LF 精炼 RH 精炼 大方 坯连 铸 轴承钢 轴承钢 齿轮钢 齿轮钢 优质弹簧钢 优质弹簧钢 硬线钢 硬线钢 帘线钢 帘线钢 石油套管 石油套管
铁水 脱硅 脱磷
转炉 复吹
AOD
SS-V OD
大板 坯连 铸
不锈钢
RHOB/ KTB
增大反应界面(1)增加吹人熔池的气体 量,特别是惰性气体量;(2)在气体量 相同条件下,弥散而细小的气泡有利; 加强熔池搅拌 提高真空度或稀释气体比例,降低平衡 CO分压
钢水深脱碳技术(2)
提高RH脱碳速度的措施:
• 增大环流量:增大吸嘴内径,改圆形吸嘴为椭圆形
• 增大驱动氩气流量 • 增大泵的抽气能力,其中采用水环泵和蒸气泵联用可提高 泵的抽气能力,降低RH能耗和水耗 • 向驱动氩气中掺入氢气,在碳含量小于20×10-6时可使脱碳 速率增加一倍 • 在真空侧墙安装氩气喷嘴,在增大反应面积 • 减少真空室的法兰盘数可提高真空度,减少漏气
短流程钢厂冶炼工艺路线
铁水 脱硫 转炉 CASOB 小方坯 连铸 废钢 电炉 LF 炉 各类建材 普碳钢 普通低合金钢 机械工程用钢 易切削钢
废钢 生铁 DRI/HBI
UHP 电炉
LF 精炼
薄板坯 连铸
普通热轧板 冷轧板 镀层板
1 前言
炉外精炼:钢液的炉外精炼是把一般炼钢炉(平、转、电) 中要完成的精炼转移到炉外的“钢包”或专用容器中进行。如 脱S、脱O、去气、去夹杂、调整成分和温度等。 这样就把原来的炼钢工艺分成两步: 第一步 在一般炼钢炉中熔化和初炼,称初炼炉; 第二步 在“钢包”或专用容器中进行精炼, 这些“钢包”或专用容器称为精炼炉。 炉外精炼的目的:“四脱、二去、二调整” (1)脱碳、脱氧、脱硫、脱磷 (2)去气(N、H、O)、去除非金属夹杂物 (3)调整钢液成分、调整钢液温度
(7)真空吹氧脱碳VOD (Vacuum Oxygen Decarburigation)
Witten-Standar Messo 威腾公司和梅索标 准公司1967年开发
(8)RH-OB和KTB等 Kawatetsu Top Blowing Method
(9)桶炉 ASEA-SKF
2.2 各种炉外精炼设备的冶金功能比较
真空处理装置
(1)真空浇注
(2)真空钢流脱气(Bochumer Verein)
(3)真空吸上脱气DH
(4)钢包真空脱气VD (Vacuum Degassing)
(5)真空循环脱气RH (Ruhrstahl A.G-C.Heraeus)
(6)真空电弧加热VAD(Vacuum Arc Degassing)
钢铁冶金硕士生专业课
特殊钢材料学及冶金原理
第二讲 特殊钢精炼技术
姜周华 钢铁冶金研究所 2006年3月
大型联合企业冶炼工艺流程
产品
CAS-OB 板坯连铸 热轧钢板 冷轧深冲钢板 镀层板,涂层板 锅炉板、桥梁板 造船板
铁水脱硫
转炉复吹
LF
产品
RH/KTB/PB 板坯连铸 IF 钢 电工用钢 石油管线钢 低温用钢 超深冲钢
生产 调节 ●● ○ ●● ○ ●● ○ ●
● ○ ●● ●● ● ● ● ●● — ● ● ●● —不具备
不同冶炼方法可达到的钢的洁净度
冶炼方法 氧气转炉 电弧炉 铁水喷粉 ≤10-150 脱硫 50-150 100-200 预处理喷粉脱磷硫 铁水 Si≤0.15% CaO 系/Ca-Si 喷粉法 〈50-100 钢水脱硫 10-50 Ca-Si 包芯线 喂丝法 10-50 脱硫法 造渣搅拌或喷粉 LF 精炼 20-50 脱磷法 加 FeO 换渣加热 10-50 真空 20-50 常规法 RH OB 或 KTB 吹氧炼超低碳钢喷粉 <20 10~50 20-50 PB 法 喷粉 [C] 钢水未处理,钢包中 300 50 钢包中 条件 可达到的纯度/ppm [S] [P] [O] [H] [N] 150 100 80-200 3-5 40-60 100 150 80-200 4-6 50-70
(3) 增大渣钢反应面积。 对各种炉外精炼设备均采用各种搅拌或喷粉 工艺,造成钢渣乳化、颗粒气泡上浮、碰撞、聚合 等现象,显著增加渣钢反应面积,提高反应速度。 •(4) 精确控制反应条件,均匀钢水成分、温度。 多数炉外精炼设备,配备了各种不同的加热功 能,可以精确控制反应温度。同时,通过搅拌均匀 钢水成分,精确调整成分,实现成分微调。精确控 制化学反应条件,使各种冶金反应更趋近平衡。 •(5) 健全在线检测设施,对精炼过程实现计算机智 能化控制。 保证精炼终点的命中率和控制精度,提高产品 质量的稳定性。
精炼功能 工艺 CASOB 非真 CAB 空处 LF 理 AOD RH 真空 VD 处理 VOD ●●强 ●一般 搅拌 ●● ○ ●● ●● ●● ● ● ○较弱 升温 ●● 合金 化 ●● 脱气 — — ○ ○ ●● ●● ●● 脱碳 — — — ●● ●● ○ ●● 渣洗 ○ ○ ●● ○ ○ ● ● 喷粉 — — — — ●● — ● 夹杂物 处理 ● ○ ●● ● ● ● ●
(4) 喷射冶金: 通过载气将固体颗粒反应物喷入熔池 深处,造成熔池的强烈搅拌并增大反应面 积。固体颗粒上浮过程中发生熔化、溶 解,完成固—液反应,显著提高精炼效果。 (5)加热与控温: 为了精确控制反应温度与终点钢水温 度,多炉炉外精炼设备采用了各种不同的 加热功能,避免精炼过程温降。主要的加 热方法有:电弧加热、化学加热和脱碳二 次燃烧加热。
1) 2)
Melting period: in EAF or similar metallurgy unit Refining period: how to pCO ? by vacuum by dilution Vacuum Oxygen Decarburization (VOD) Argon Oxygen Decarburization (AOD)
年份
3 特殊钢精炼理论与工艺
——杂质元素及夹杂物 控制技术
3.1 超低碳钢
碳含量:<20~30ppm(碳钢); <50~100ppm(不锈钢)
钢水深脱碳技术(1)
深脱碳用精炼设备
• AOD • VOD,SS-VOD,VOD-PB • VCR(Vacccum Converter Refiner) • RH, RH-OB, RH-KTB
炉外精炼的冶金功能
各种炉外精炼设备的冶金功能主要包括: (1) 熔池搅拌功能,均匀钢水成分和温度,保 证钢材质量均匀; (2) 提纯精炼功能,通过钢渣反应、真空冶 炼; (3) 钢水升温和控温功能,实现成分微调; (4) 生产调节功能,均衡炼钢—连铸生产。
为实现上述冶金功能,各种炉外精炼设备一般 均采用以下精炼方法: (1) 渣洗精炼:精确控制炉渣成分,通过渣钢反应 实现对钢水的提纯精炼。主要用于钢水脱氧、脱硫 和去除夹杂物等方面。 (2) 真空精炼:在真空条件下实现钢水的提纯精炼。 通常工作压力≥ 50Pa,适用于对钢液脱气、脱碳和 用碳脱氧等反应过程。 (3) 熔池搅拌:通常是向反应体系提供一定的能 量,促使该系统内的熔体产生流动。通过对流加速 熔体内传热、传质过程,达到混匀的效果。搅拌的 方法主要有气体搅拌、电磁搅拌和机械搅拌三种方 法。
lgfN =∑
e
j [%j] N
lgfN,T =
3280 ( − 0.75)∑ T
e
j [%j] N ,1873
0.5
C
B Te
0.0
As O Zr Ti
Se Al
S P Si
Co,Ni Sb,Cu Sn W Mn Ta Cr Mo
logf N
-0.5
j
Nb
V
-1.0 0 2 4 6 8 10
合 元 素 j的 重 量 百 分 数 金
2
3
脱碳保铬的措施
(2) (1)
Pco=1 Pco< 1
ΔG
Tf
2C + O2 = 2CO 4/3Cr +O2 = 2/3Cr2O3
T
(1) (2)
提高温度: 但耐火材料寿命降低 降低CO分压
Cr-C equilibrium as a function of temperature and partial pressure of CO
炉外精炼的冶金特点
各种炉外精炼设备都具备高效精炼的特点,适 宜冶炼各类洁净钢、超洁净钢。其原因在于各种炉 外精炼设备的工艺与设备设计能满足以下 冶金特点 : •(1) 改善冶金化学反应的热力学条件。如炼钢中脱碳、 脱气反应,反应产物为气体。降低气相压力,提高 真空度,有利于反应继续进行。 •(2) 加速熔池传质速度。对于多数冶金反应,液相传 质是反应速度的限制环节。各种精炼设备采用不同 的搅拌方式,强化熔池搅拌,加速混匀过程,提高 化学反应速度。
(1)钢包吹氩(顶吹和底吹) GAZAL
(2)钢包加盖吹氩 CAB(Cap Argon Bubbling)
(3)钢包小盖吹氩CAS和CAS-OB (Composition Adjustment by Sealed Argon Bubbling)
(4)钢包加热——底吹氩LF (5)氩氧脱碳AOD (Argon Oxygen Decarburigation (Ladle Furnace)