PCB 裂纹改善报告
pcb维修工作总结报告

pcb维修工作总结报告
《PCB维修工作总结报告》。
近期,我在进行了一系列PCB维修工作后,特此总结报告,以便对工作进行
回顾和总结,为今后的工作提供参考和借鉴。
在进行PCB维修工作中,我发现了一些常见的故障现象和解决方法。
首先,
常见的故障现象包括焊点断裂、元器件损坏、电路板烧坏等。
针对这些问题,我采取了一系列有效的解决方法,包括重新焊接焊点、更换损坏的元器件、修复烧坏的电路板等。
通过这些方法,我成功地解决了许多PCB维修工作中遇到的问题,为
客户提供了高效的维修服务。
其次,我在PCB维修工作中还总结了一些经验和技巧。
例如,我发现在进行
焊接工作时,要特别注意焊接温度和时间,以免造成元器件损坏或电路板烧坏。
此外,我还总结了一些常见的维修工具和设备的使用技巧,以提高维修效率和质量。
最后,我在PCB维修工作中还发现了一些问题和不足之处。
例如,我发现在
一些复杂的维修工作中,需要更多的专业知识和技能,以提高维修的成功率和质量。
因此,我决定在今后的工作中,加强学习和提升自己的专业能力,以更好地应对各种PCB维修工作。
总的来说,通过这次PCB维修工作总结报告,我对自己的工作进行了回顾和
总结,发现了一些问题和不足之处,也总结了一些经验和技巧。
我相信在今后的工作中,我会更加努力地提高自己的维修能力,为客户提供更好的维修服务。
裂纹原因分析报告

裂纹原因分析报告1. 引言本报告旨在对裂纹产生的原因进行分析和解释。
通过对裂纹的形成机制、材料特性、工艺参数等方面的研究,对裂纹的产生原因进行归纳总结,并提供相应的解决方案。
2. 裂纹的定义裂纹是指材料中的断裂缝隙,通常由于外部力、热膨胀或其他因素引起。
裂纹的存在对材料的性能和使用寿命都会产生重大影响,因此对裂纹的原因进行深入研究具有重要意义。
3. 裂纹的分类根据裂纹的形态和产生原因,裂纹可以分为以下几种类型:3.1 表面裂纹表面裂纹是指在材料表面形成的裂纹,通常由于外部力或疲劳等因素引起。
表面裂纹的主要特点是易被观察到,并且对材料的疲劳寿命影响较大。
3.2 内部裂纹内部裂纹是指在材料内部形成的裂纹,通常由于材料内部的缺陷或应力集中等因素引起。
内部裂纹的存在对材料的强度和韧性产生较大影响。
3.3 焊接裂纹焊接裂纹是指在焊接过程中产生的裂纹,通常由于焊接材料和基材的热膨胀系数不匹配或焊接过程中的应力集中等因素引起。
焊接裂纹的存在对焊接接头的强度和密封性产生重要影响。
4. 裂纹产生的原因裂纹产生的原因复杂多样,以下列举了几个常见的原因:4.1 材料特性材料的特性是裂纹产生的重要原因之一。
例如,材料的强度、韧性、热膨胀系数等特性会直接影响裂纹的形成和扩展。
如果材料强度较低或韧性较差,则裂纹很容易形成并扩展。
4.2 外部力外部力是裂纹产生的常见原因之一。
当材料受到外部力的作用时,会产生应力集中,从而导致裂纹的形成。
例如,弯曲、拉伸、压缩等外部力都可能引起裂纹的产生。
4.3 工艺参数工艺参数是影响裂纹产生的重要因素之一。
例如,焊接过程中的温度、焊接速度、焊接压力等参数都会对焊接接头的质量产生重要影响。
如果工艺参数设置不当,就会导致焊接裂纹的产生。
4.4 环境条件环境条件是裂纹产生的重要因素之一。
例如,温度变化、湿度变化等环境条件的改变都可能引起材料的热膨胀或收缩,从而导致裂纹的形成。
此外,化学腐蚀等环境因素也会加速裂纹的扩展。
PCB品质改善报告
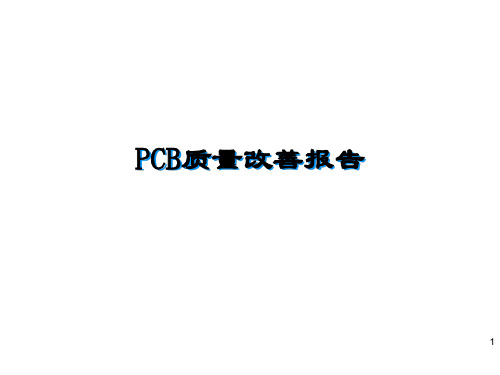
现场作业员不规范的 检板方式,检板时板 角与板面摩擦碰撞,
造成刮伤。
放板框内摆放凌乱, 且珍珠棉未完全填满 空隙,造成搬运时板 倒刮伤。
改善作业方式,将待 检板放在L架上,取板 时,呈“V”型拿取。
放板框内的板子需正确摆 放,珍珠棉必须填满框内剩 余空隙,防止板倒刮伤。
作业员将盖板在基板 上拖动,导致板面刮 伤。
对位时有用目镜 确认
OK
20
不良原因
可能原因 Item
底片定位胶带没有粘 性
7
底片上的Pin没有套 入板子,人员赶气会 导致偏移 8
确认结果
描述
判定
人员有按要求每 20片更换一次 胶带的动作
OK
人员没有在套 pin后进行再次 确认
NG
21
流出分析
不良现象不明显,FQC作业员的漏失导致不良流出
22
电测
无铅OSP
成品检验
包装
30
改善对策
FQC电视屏幕上播放近期客诉,增加检验员对此不良的重视。对检验员进行教育倡导,检查此 曝偏不良。
31
Thank – You!
32
上盖板先对准(以防呆 PIN为水平线的)三个 孔,然后垂直放下板子.
改善前
相关图片
改善后
12
13
问题描述
P/N
Defect Name
防焊曝偏
1-887-459-21 1-887-460-21
对地短路 对地短路
对地短路
Defect photo
Failure D/C 200721
200810 200924 201005
改善对策
短期措施
将底片对位的开窗从6个改为8个,增加底片与板子的粘合度,避免底片偏移造成防焊曝偏
pcb维修工作总结报告

pcb维修工作总结报告《PCB维修工作总结报告》。
近年来,随着电子产品的普及和更新换代的速度加快,PCB(Printed Circuit Board)维修工作变得越发重要。
作为电子产品的核心部件,PCB的维修工作不仅关乎产品的质量和性能,也直接影响到用户的体验和满意度。
在过去的一段时间里,我们团队在PCB维修工作方面取得了一定的成绩,现就此进行总结报告。
首先,我们团队在PCB维修工作中加强了对技术的学习和研究。
针对不同类型的PCB板,我们深入学习了其原理和结构,掌握了各类维修工具和设备的使用方法,提高了维修工作的效率和准确性。
同时,我们还不断学习新的维修技术和方法,保持对行业最新发展的敏感度,以确保我们的维修工作始终处于领先地位。
其次,我们团队在PCB维修工作中加强了对质量的控制和管理。
我们建立了严格的维修标准和流程,对每一道工序都进行了详细的规范和要求,确保维修工作的质量和稳定性。
同时,我们还加强了对维修过程中可能出现的问题和风险的预判和控制,以最大限度地保障维修工作的顺利进行和成功完成。
最后,我们团队在PCB维修工作中加强了对客户需求的理解和满足。
我们深入了解客户的需求和期望,及时响应客户的问题和反馈,保持与客户的沟通和互动,以提供更加个性化和专业化的维修服务。
我们还不断改进和优化我们的服务流程和方式,以提高客户的满意度和忠诚度。
总的来说,我们团队在PCB维修工作中取得了一定的成绩,但也意识到还有许多地方需要进一步改进和提升。
我们将继续努力,不断学习和提高自身的维修技术和能力,以提供更加优质和专业的PCB维修服务,为客户创造更大的价值和满意度。
PCB质量改善项目总结
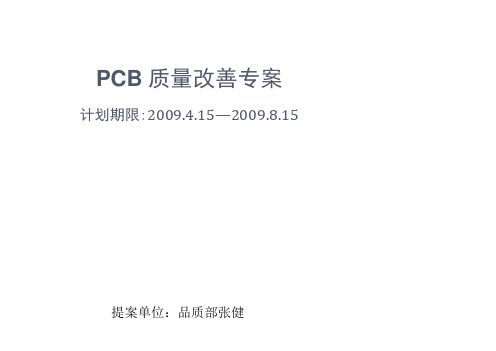
PCB质量改善专案计划期限:2009.4.15—2009.8.15提案单位:品质部张健项目进程说明Define阶段Measure 阶段Analyze 阶段Improve 阶段Contro I 阶段课题选择(现状调查[设定目标要因分析确定要因.制定对策对策实施效果确认标准化下步计划课题类型问题解决型—目标值类型自选取目标值型课题选定丿1状调查设定LI标要因分析确定要因制定对策对策实施效果确认标准化下步计划项目背景PCB来料外观不良较高,严重影响了直通率,且挑选不良品耗费产线人员的工时,报废的PCBA增加后工序拆零负担,且成品的报废对供应商也是一笔较大的费用。
针对PCB外观不良,成立PCB品质改善项目小组,对PCB夕卜观不良作重点改善。
课题选定观状调查设定LI标要因分析确定要因制定对策对策实施效果确认标准化下步il•划项目组织架构“"1/课题选定观状调查设定LI标要因分析确定要因制定对策对策实施效果确认标准化下步il•划项目小组职责课题选定现状调查设定LI标要因分析确定要因制定对策对策实施效果确认标准化下步计划项目小组职责-项目沟通:每两周召开一次项目例会,遇到关键问题可临时组织会议。
-项目监控:以达成目标为准则,以计划为依据。
每周例会汇报,对重点工作需增加监控。
项目组公约Ki •VR4MwE KK-X©・・,》>. g・.負4•- «KKRVk*・ H«X. 介貝■AM*•n JlftAi •/; t.tAi Z.-A.'» « <F ♦T* tL • • • •V* 1 1 • ■Lm"W«¥s IA4-11 i « DMflil«. rr*KV 1ht 口・W«V 4« «•••• J ••••WQ・•"・•- Ulf .. ...... ... ... ...................* UiS *・-te ■<・■•・••0 ■!:•・•・・项目推进计划PCB质量改善项目推进图任务名称项目计划Kick off meeting确定人选,成立庇AM匸作小组PCB历史品质数据分析利用统计工具找岀影响产品质虽的儿大不良完成项目计划书在线挑选来料问题分析控制制定在线挑选不RDPPM值LI标建立來料不良验证机制供应商audit/visit厂商提出前几大來料不良问题的改善措施改善落实宀线挑迟不IW屈妆腳攵集效果确认PCB功能问题分析与控制制定改善目标收集不良数据,查找不良原因针对集中性问题制定对策验证可行性改善落实效果确认完成参数优化,操作方式变更等相关文件总结项目,完成总结报告项目呈现四月五月W20W21W22W23六月W24W25W26七月W27W28主导人张健张健张健张健张健张健李铭山.张健张健供应商供应商.张健SMTSMT、张健张健、陈质陈质、张健、供应商供应商、张健、陈质供应商陈质、张健张健、供应瀚课题选现状调入设定LI标要因分析确定要因制定对策对策实施效果确认标准化下步计划入库课题选定〉现状调査设定LI标要因分析确定要因制定对策对策实施效果确认标准化下步计划/现状调查设定□标要因分析确定要因制定对策对策实施效果确认标准化下步计划PCB供应商ETON,对来料不良贡献,问题TOP3:露铜&绿油不均、板变形、金手指划伤各项不良比例如下:................................... “"1/课题选总:要因分析确定要因制定对策对策实施效果确认标准化下步讣划PCB供应商E&E,对来料不良贡献,问题T0P3:擦花绿油、金手指擦花、金手指颜色不良各项不良比例如下:.................................... “"1/课题选定现状调查设定LI慘夷因分析确定要因制定对策对策实施效果确认标准化下步计划项目目标:、焊i 发黑、残橡皮屑)为重点,建立PCB质量改善方法;将PCB在线挑选的不良由目前的0. 83%降至0. 3%,并逐步取消人工在线挑选; .......................................................................................................................................以解决PCB外观不良问题(露铜&绿油不均、板变形、金手指划伤课题选定现状调查设定LI标定要因制定对策对策实施效果确认标准化下步讣划图片收集:)>要因分析露铜1露铜2课题选定现状调查设定LI标〉要因分歩定要因制定对策对策实施效果确认标准化下步计划油薄露铜1甩油露铜2课题选定现状调查 设定LI 标 定要因 制定对策 对策实施 效果确认 标准化下步讣划,要因分析 SAYAl JUXT ■*玖 I V f ■ 。
PCB质量改善项目报告
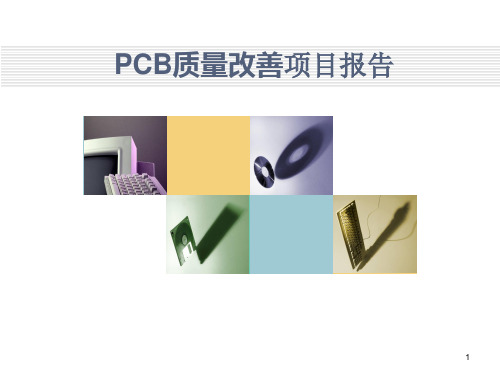
主导拟定改善对策
5
课题选定 现状调查 设定目标 要因分析 确定要因 制定对策 对策实施 效果确认 标准化 下步计划
项目小组职责
Name
Ministry
YANG Shou Sheng E&E PE Sr. Director
Title Member
Responsibility 主导拟定改善对策
项目推进计划
任务名称
项目计划 Kick off meeting 确定人选,成立TEAM工作小组 PCB历史品质数据分析 利用统计工具找出影响产品质量的几大不良 完成项目计划书 在线挑选来料问题分析控制 制定在线挑选不良DPPM值目标 建立来料不良验证机制 供应商audit/visit 厂商提出前几大来料不良问题的改善措施 改善落实 在线挑选不良每周数据收集 效果确认 PCB功能问题分析与控制 制定改善目标 收集不良数据,查找不良原因 针对集中性问题制定对策验证可行性 改善落实 效果确认 完成参数优化,操作方式变更等相关文件 总结项目,完成总结报告 项目呈现
中山依顿
贾大合
审核
参会人员 (敬称略)
品质:张健、李铭山 制造:郭季方、张辉、陈质、曾杰敏 依顿:蔡金华、贾大合、余前军
项次 1
2
项目介绍
决议事项 决议内容
针对此品质项目,依顿完全配合宝龙达的项目计划,并安排专人进行项 目跟进;
责任人 张健
贾大合
3
每两周由依顿项目负责人员参加宝龙达的项目例会(可电话会议);
Responsibility 領导项目Team,push改善进度
郭幼颖
VP
Sponsor
项目方向性把握和资源支持
张志威
PCB裂纹改善报告PPT课件

区分
数量
天津 SI 不良试料
6EA
高新进口检查 不良试料
11EA
表面确认 裂纹确认 裂纹确认
断面确认 Ni层为止裂纹 Ni层为止 裂纹
镀金厚度
Au(㎛)
0.06 ~
0.07 0.05
~ 0.09
Ni(㎛)
1.56 ~
2.16 1.69
~ 1.98
2. 检讨意见 2.1 裂纹 现象 : Ni层为止 裂纹发生 2.2 按现检查方法(显微镜 40倍-MAX)不能检出 2.3 和1次裂纹发生的现象统一但(Ni层为止 裂纹), 裂纹形态相异
制品 1回
上,下反复回数
5回
10回
20回
SGHF480 5M
裂纹发生 無
裂纹 1EA发生
裂纹 2EA发生
裂纹 1EA发生
他社制品 裂纹发生 無
裂纹发生 無
裂纹发生 無
裂纹发生 無 6
Ⅳ. 原因分析
■ 得出7个潜在原因,线路 裂纹 不良 再现检证
不良 现象 线路 裂纹
发生 可能 原因
潜在原因 1. 超声波大小 (安培)
变更前
变更后
D/F COATING
E/T投入 10
Ⅴ. 对策方案
变更前 印刷
2. 邀请事项 :线路宽补强(和PAD宽统一)
变更前 线路形状
变更后 变更后
11
Ⅵ. 选别进行结果
1. 检查方法(临时对策) : 显微镜 200倍 检查
显微镜全景
检查倍率(× 200)
检查部位(Hot-Bar部线路)
2. SI FLEX 在库,在工 : 显微镜 200倍 检查(4/13 现在)
7
Ⅳ. 原因分析
pcb维修工作总结报告
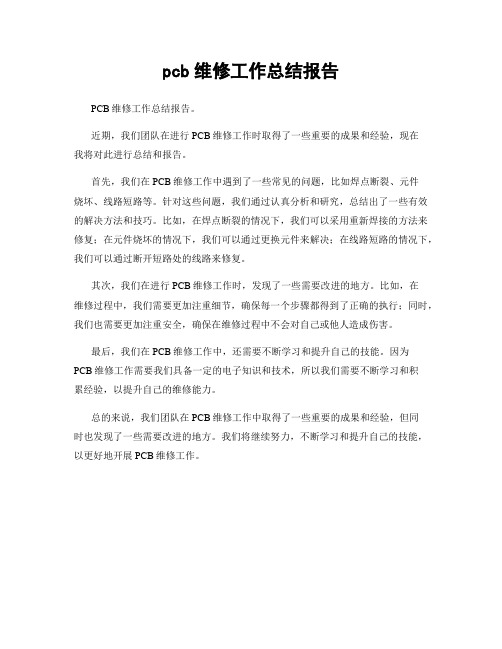
pcb维修工作总结报告
PCB维修工作总结报告。
近期,我们团队在进行PCB维修工作时取得了一些重要的成果和经验,现在
我将对此进行总结和报告。
首先,我们在PCB维修工作中遇到了一些常见的问题,比如焊点断裂、元件
烧坏、线路短路等。
针对这些问题,我们通过认真分析和研究,总结出了一些有效的解决方法和技巧。
比如,在焊点断裂的情况下,我们可以采用重新焊接的方法来修复;在元件烧坏的情况下,我们可以通过更换元件来解决;在线路短路的情况下,我们可以通过断开短路处的线路来修复。
其次,我们在进行PCB维修工作时,发现了一些需要改进的地方。
比如,在
维修过程中,我们需要更加注重细节,确保每一个步骤都得到了正确的执行;同时,我们也需要更加注重安全,确保在维修过程中不会对自己或他人造成伤害。
最后,我们在PCB维修工作中,还需要不断学习和提升自己的技能。
因为
PCB维修工作需要我们具备一定的电子知识和技术,所以我们需要不断学习和积
累经验,以提升自己的维修能力。
总的来说,我们团队在PCB维修工作中取得了一些重要的成果和经验,但同
时也发现了一些需要改进的地方。
我们将继续努力,不断学习和提升自己的技能,以更好地开展PCB维修工作。
pcb品质改善报告范文

pcb品质改善报告范文一、前言。
大家好!咱们今天来唠唠咱PCB(印刷电路板)的品质改善这档子事儿。
PCB这玩意儿就像是电子产品的骨架和神经系统,要是它出了岔子,那整个电子产品都得跟着闹脾气。
最近咱在这方面遇到了些问题,不过别担心,咱们已经在努力改善啦。
二、问题描述。
# (一)短路问题。
1. 现象。
就像电路里突然来了两个调皮的小鬼,不该搭在一起的线路,它们偏偏凑一块儿了,这就造成了短路。
在我们检查的一批PCB板中,有好几块都出现了这种短路的情况,有的是在小元件之间的线路短路,有的则是在大的线路网络之间出了问题。
2. 影响。
这短路可不得了啊,就像交通堵塞一样,电流本来应该规规矩矩地在自己的线路上跑,这一短路,整个电路就乱套了。
导致用了这些PCB板的产品要么开不了机,要么就出现各种奇怪的故障,像屏幕乱闪啊,功能错乱之类的。
# (二)开路问题。
1. 现象。
跟短路相反,这开路就像是道路中间突然断了一截,电流走到这儿就没路可走了。
在一些PCB板的边缘或者是经过一些过孔的地方,线路就这么莫名其妙地断开了。
2. 影响。
这就好比快递员(电流)送包裹(电信号),半路上遇到个断桥,包裹送不到目的地,那产品的某些功能就没法正常工作了。
比如说,本来应该有声音输出的,结果因为开路,就成了个哑巴产品。
# (三)焊接不良。
1. 现象。
你看那焊接点,就像是建筑的根基,要是根基不牢,房子就摇摇欲坠。
我们发现有些焊点就像没吃饱饭似的,锡量少得可怜,有的则像是得了肥胖症,锡堆得太多,还有些焊点就像是歪瓜裂枣,形状不规则,歪歪扭扭的。
2. 影响。
焊接不良的话,元件就不能很好地和PCB板连接起来。
就像人和人之间拉手,如果拉得松松垮垮的,肯定不能齐心协力干事儿。
在电子产品里,这就会导致元件松动,接触不良,信号传输不稳定,产品性能大打折扣。
三、原因分析。
# (一)设计方面。
1. 线路布局有时候就像城市规划一样,要是规划得不合理,就容易出乱子。
裂纹原因分析报告
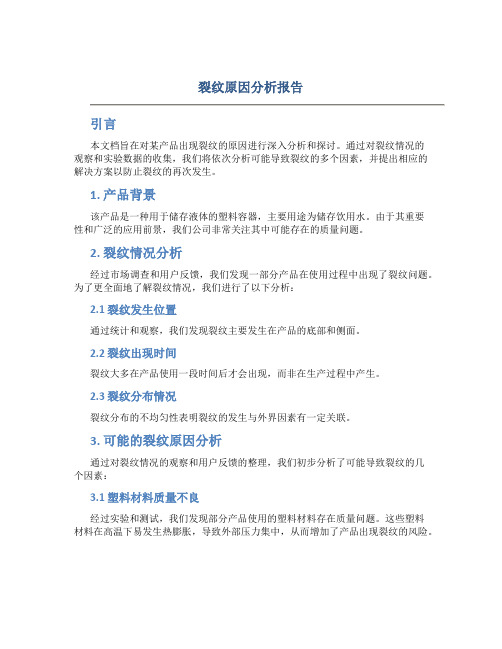
裂纹原因分析报告引言本文档旨在对某产品出现裂纹的原因进行深入分析和探讨。
通过对裂纹情况的观察和实验数据的收集,我们将依次分析可能导致裂纹的多个因素,并提出相应的解决方案以防止裂纹的再次发生。
1. 产品背景该产品是一种用于储存液体的塑料容器,主要用途为储存饮用水。
由于其重要性和广泛的应用前景,我们公司非常关注其中可能存在的质量问题。
2. 裂纹情况分析经过市场调查和用户反馈,我们发现一部分产品在使用过程中出现了裂纹问题。
为了更全面地了解裂纹情况,我们进行了以下分析:2.1 裂纹发生位置通过统计和观察,我们发现裂纹主要发生在产品的底部和侧面。
2.2 裂纹出现时间裂纹大多在产品使用一段时间后才会出现,而非在生产过程中产生。
2.3 裂纹分布情况裂纹分布的不均匀性表明裂纹的发生与外界因素有一定关联。
3. 可能的裂纹原因分析通过对裂纹情况的观察和用户反馈的整理,我们初步分析了可能导致裂纹的几个因素:3.1 塑料材料质量不良经过实验和测试,我们发现部分产品使用的塑料材料存在质量问题。
这些塑料材料在高温下易发生热膨胀,导致外部压力集中,从而增加了产品出现裂纹的风险。
3.2 产品设计缺陷部分产品的设计存在一些缺陷,例如底部加工面积过小、侧面强度不足等。
这些设计缺陷使得容器在承受外界压力时容易发生变形和产生应力集中,从而导致裂纹的产生。
3.3 使用环境不合适部分用户在使用容器时选择了不适宜的环境,例如高温或低温环境。
过高的温度会增加塑料的膨胀系数,造成裂纹;而过低的温度则会导致塑料变脆,易于发生破裂。
4. 解决方案基于以上分析,我们提出以下解决方案以预防和减少产品裂纹问题的发生:4.1 优化材料选择选择质量更好的塑料材料,具有较低的热膨胀系数,以减少塑料在高温条件下的变形和裂纹问题。
4.2 改进产品设计在产品设计中考虑底部和侧面的加工面积和强度,确保其能够承受外界压力,减少应力集中的发生。
4.3 提供使用指导向用户提供使用指导,明确容器的适用温度范围,并强调不宜将容器长时间置于极端温度环境中。
PCB生产过程中产生变形的原因及改善

PCB生产过程中产生变形的原因及改善PCB(Printed Circuit Board,印刷电路板)是电子产品中常见的基础组件之一,用于连接电子器件及传导信号和电能。
在PCB的生产过程中,常常会出现变形现象,这会对产品性能和可靠性产生负面影响。
下面将分析PCB产生变形的原因,并提出相应的改善措施。
首先,PCB产生变形的原因主要有以下几点:1.热应力:在PCB的生产过程中,可能会有焊接、印刷等步骤,这些步骤会带来温度的变化,从而产生热应力。
过大的热应力会导致PCB变形,尤其是对于较薄的PCB来说。
此外,在实际使用中,电子器件也会产生热量,进一步加剧热应力。
2.材料挠度:PCB的主要材料是玻璃纤维增强树脂,其在加工、静态负载和动态负载下都会产生一定的挠度。
此外,玻璃纤维增强树脂本身也有热膨胀系数,受温度变化的影响,容易产生挠曲。
3.相邻材料性能差异:在PCB中,不同材料的热膨胀系数和刚性等性能可能不同,这就意味着在温度变化下,不同材料的热胀冷缩程度也不同。
这种差异可能导致PCB产生变形,尤其是在温度变化较大的环境下。
基于以上变形原因,可以采取以下改善措施:1.控制热应力:在PCB的制造过程中,应尽量减少或控制产生热应力的步骤。
对于焊接工艺,可以采用较低的温度进行焊接,或者采用无铅焊料等低温焊接材料。
此外,对于PCB板材的选型,可以选择具有较低热膨胀系数的材料,减少热应力的影响。
2.优化设计:通过合理的PCB设计,可以减少PCB的变形。
例如,在布局设计时,可以减少电子器件的集中放置,减少热量的集中释放。
另外,对于PCB板材的选择,可以选择厚度较大的板材,增加PCB的刚度,从而减小变形的可能性。
3.优化材料选择:在PCB的制造过程中,可以选择热膨胀系数较小的材料,以减少材料差异引起的变形。
此外,可以在PCB板材的复合结构中添加补强层或填充层,以增加PCB的刚性,减少挠度。
4.引入支撑结构:在一些特殊情况下,可以考虑在PCB的设计中引入支撑结构,以增加PCB的刚度,减小变形的可能性。
金手指裂纹报告

FPC在钢琴盖下 方且相互接触
补强板容易受力向前,进 入钢琴盖下方,再向上抬 起时造成折伤。
前力后进入钢琴盖下方。
方且相互接触
钢琴盖打开后FPC自然状
钢琴盖打开后FPC自然状
2.钢琴 盖拨开 后FPC 自然状 态说明
侧上视图
FPC(补强+金手指)
FPC与档块不接触 侧后视图
小耳朵 挡块
FPC不在钢琴盖 下方且不相互接
FPC不在钢琴盖 下方且不相互接
FPC自然状态验证说明: *方法----钢琴盖扣合后再打开 为一次 *次数:30次 CN基座 *结果:补强板均未在钢琴盖下 面
After
:抬起钢琴盖
拿取FPC向后上方拔
步骤2:拿取FPC直接向后 上方拔取。
四、改善方案
Before
受力方向说
明:向前后 再向上
上
2
步骤1:抬起钢琴盖
前
1
拿取补强板把手向上抬 后拔取
步骤2:拿取补强板把手取 出FPC. 风险:拿取补强板时,补 强板容易受力向前,进入 钢琴盖下方,再向上抬起 时造成折伤。
步骤1:抬起钢琴盖
补强板外观: sample1
补强板外观: sample2
压接位置前 部补强板向 上翘起
Sample4
小耳朵OK
OK Sample
遗留确认项目: FPC金手指的厚度或其他特性参 数是否正常-----*****
补强板插入钢琴盖下方 时
金手指)
钢琴盖
遗留确认项目:车载与工控CN 规格尺寸是否一致。
FPC在钢琴盖下 方且相互接触
CN基座
方且相互接触
金手指)
钢琴盖
步骤3:压接位置下 方位置发生断裂
线材开裂整改报告
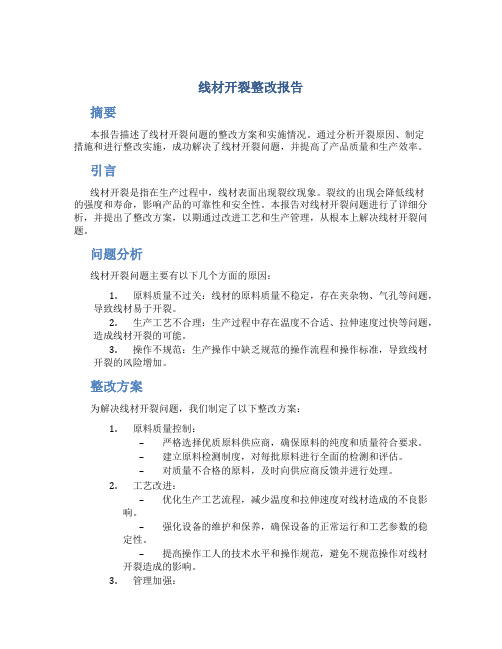
线材开裂整改报告摘要本报告描述了线材开裂问题的整改方案和实施情况。
通过分析开裂原因、制定措施和进行整改实施,成功解决了线材开裂问题,并提高了产品质量和生产效率。
引言线材开裂是指在生产过程中,线材表面出现裂纹现象。
裂纹的出现会降低线材的强度和寿命,影响产品的可靠性和安全性。
本报告对线材开裂问题进行了详细分析,并提出了整改方案,以期通过改进工艺和生产管理,从根本上解决线材开裂问题。
问题分析线材开裂问题主要有以下几个方面的原因:1.原料质量不过关:线材的原料质量不稳定,存在夹杂物、气孔等问题,导致线材易于开裂。
2.生产工艺不合理:生产过程中存在温度不合适、拉伸速度过快等问题,造成线材开裂的可能。
3.操作不规范:生产操作中缺乏规范的操作流程和操作标准,导致线材开裂的风险增加。
整改方案为解决线材开裂问题,我们制定了以下整改方案:1.原料质量控制:–严格选择优质原料供应商,确保原料的纯度和质量符合要求。
–建立原料检测制度,对每批原料进行全面的检测和评估。
–对质量不合格的原料,及时向供应商反馈并进行处理。
2.工艺改进:–优化生产工艺流程,减少温度和拉伸速度对线材造成的不良影响。
–强化设备的维护和保养,确保设备的正常运行和工艺参数的稳定性。
–提高操作工人的技术水平和操作规范,避免不规范操作对线材开裂造成的影响。
3.管理加强:–建立质量管理体系,落实质量目标和责任,确保产品质量的稳定和可靠性。
–加强对生产过程的监控和控制,及时发现并解决线材开裂的问题。
–对每批产品进行抽样检测,确保产品质量符合标准要求。
整改实施我们按照上述整改方案,进行了以下整改实施:1.建立了原料检测制度,对每批原料进行全面检测,确保原料质量达标。
2.对生产工艺流程进行了优化,调整了温度和拉伸速度,提高线材的生产质量。
3.对操作工人进行了培训和规范化管理,确保操作过程规范,减少线材开裂的风险。
4.加强了质量管理体系的建立和运行,建立了生产过程监控和抽样检测机制。
PCB孔铜断裂分析报告

孔铜断裂通常表现为电气连接失 效,可能引发电路故障或产品性 能下降。
断裂原因与影响
原因
孔铜断裂可能由多种因素引起,包括 制造过程中的缺陷、材料问题、环境 因素等。
影响
孔铜断裂可能导致电路板功能失效, 增加产品故障率,降低产品质量和可 靠性。
断裂分析的重要性
确定断裂原因
优化制ቤተ መጻሕፍቲ ባይዱ工艺
通过对孔铜断裂进行分析,可以确定 导致断裂的具体原因,为后续的改进 和预防措施提供依据。
对PCB的布局和布线进 行优化,尽量减少应力 集中区域,特别是通孔 连接处的设计。可以考 虑增加过孔的直径或优 化过孔的排布来降低应 力水平。
加强质量检测与 可靠性评估
在PCB生产和组装过程 中,增加对通孔质量的 检测环节,确保无缺陷 产品流入市场。同时, 对已生产和在役的PCB 进行可靠性评估,特别 是针对可能承受较大应 力的区域进行重点检查 。
工艺优化与改进
总结词
优化和改进制造工艺可以有效降低PCB孔铜 断裂的风险。
详细描述
通过改进钻孔、电镀和焊接等工艺过程,可 以增强PCB的机械性能和耐久性。例如,优 化钻孔参数可以减少孔内缺陷和应力,提高 孔壁的附着力和强度。
环境因素控制
要点一
总结词
环境因素对PCB孔铜断裂具有重要影响,需严格控制。
切片分析
深入观察
通过将PCB切片,可以更深入地观察孔铜内部的断裂情况。 切片分析可以揭示断裂的起始点、扩展方向以及断裂面的微 观结构。
扫描电镜分析
高倍观察
扫描电镜可以提供高倍率的观察,帮助分析孔铜断裂的具 体细节。通过扫描电镜,可以观察到断裂面的微观形貌、 晶体结构和元素分布,为后续分析提供依据。
盲孔底部开裂改善DOE

第一阶段改善试验-试验因子筛选表
小要因
控制力
技术力
因子代码
压板固化度
√
+
A
激光能量
√
+
B
凹蚀速率
√
+
C
微蚀速率
√
+
D
电镀前酸洗
√
+
E
沉铜速率
√
+
F
沉铜厚度
√
+
G
①属于母数之小要因打“√”,否则打“X”; ②技术力筛选强“+”、中“∆”、弱“-”; ③不考虑因子间的交互作用。
PDF 文件使用 "pdfFactory Pro" 试用版本创建
试验水平说明
因子
1(低水平)
2(中水平) 3(高水平)
B(激光能量) 3shot,8,2,1 3shot,8,4,2 3shot,8,6,4
D(微蚀速率)
1.0um
1.6um
2.2um
PDF 文件使用 "pdfFactory Pro" 试用版本创建
取样说明
1.分别于测试前、高温烘烤后测试网络电阻值,取10个样,两面共20个数据, 取样位置为如下图,测试工具为万用表;
速率
洗
率
度 电阻变化率
D
E
F
G
1
1
112
2
2
1 16.95%
2
2
121
2
1
1 18.14%
3
1
211
2
1
2 15.28%
4
2
222
2
2
pcb裂纹报告
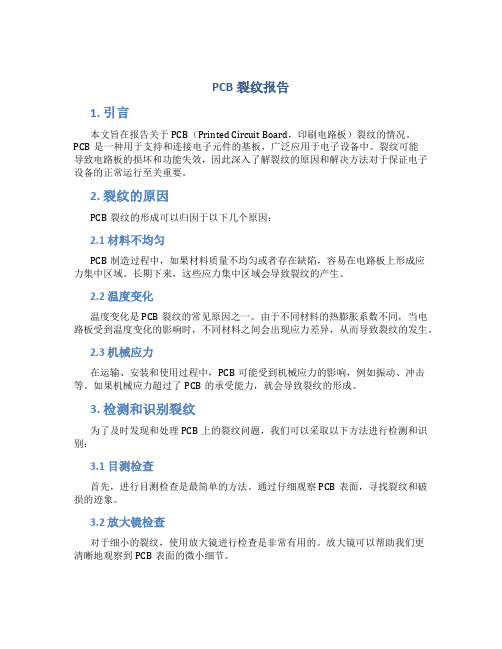
PCB裂纹报告1. 引言本文旨在报告关于PCB(Printed Circuit Board,印刷电路板)裂纹的情况。
PCB是一种用于支持和连接电子元件的基板,广泛应用于电子设备中。
裂纹可能导致电路板的损坏和功能失效,因此深入了解裂纹的原因和解决方法对于保证电子设备的正常运行至关重要。
2. 裂纹的原因PCB裂纹的形成可以归因于以下几个原因:2.1 材料不均匀PCB制造过程中,如果材料质量不均匀或者存在缺陷,容易在电路板上形成应力集中区域。
长期下来,这些应力集中区域会导致裂纹的产生。
2.2 温度变化温度变化是PCB裂纹的常见原因之一。
由于不同材料的热膨胀系数不同,当电路板受到温度变化的影响时,不同材料之间会出现应力差异,从而导致裂纹的发生。
2.3 机械应力在运输、安装和使用过程中,PCB可能受到机械应力的影响,例如振动、冲击等。
如果机械应力超过了PCB的承受能力,就会导致裂纹的形成。
3. 检测和识别裂纹为了及时发现和处理PCB上的裂纹问题,我们可以采取以下方法进行检测和识别:3.1 目测检查首先,进行目测检查是最简单的方法。
通过仔细观察PCB表面,寻找裂纹和破损的迹象。
3.2 放大镜检查对于细小的裂纹,使用放大镜进行检查是非常有用的。
放大镜可以帮助我们更清晰地观察到PCB表面的微小细节。
3.3 瑕疵检测设备使用专业的瑕疵检测设备,如X射线检测仪、红外线热成像仪等,可以更准确地检测和识别PCB上的裂纹。
4. 解决方案一旦发现PCB上存在裂纹,我们需要采取相应的解决方案来修复或预防进一步损坏。
4.1 修复裂纹对于小型裂纹,可以使用导电胶或裂纹填充剂进行修复。
这些材料可以填充裂纹,并具有导电性,以保证电路板的正常功能。
4.2 替换受损元件如果裂纹严重影响了PCB上的元件连接,我们可能需要替换受损的元件。
这需要重新焊接或更换新的元件。
4.3 加强PCB设计和制造过程为了预防裂纹的发生,我们还可以在PCB设计和制造过程中采取一些措施。
pcb维修工作总结报告
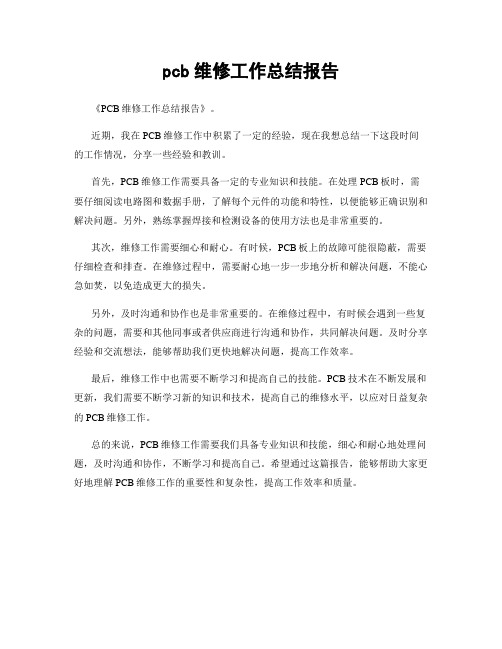
pcb维修工作总结报告
《PCB维修工作总结报告》。
近期,我在PCB维修工作中积累了一定的经验,现在我想总结一下这段时间的工作情况,分享一些经验和教训。
首先,PCB维修工作需要具备一定的专业知识和技能。
在处理PCB板时,需要仔细阅读电路图和数据手册,了解每个元件的功能和特性,以便能够正确识别和解决问题。
另外,熟练掌握焊接和检测设备的使用方法也是非常重要的。
其次,维修工作需要细心和耐心。
有时候,PCB板上的故障可能很隐蔽,需要仔细检查和排查。
在维修过程中,需要耐心地一步一步地分析和解决问题,不能心急如焚,以免造成更大的损失。
另外,及时沟通和协作也是非常重要的。
在维修过程中,有时候会遇到一些复杂的问题,需要和其他同事或者供应商进行沟通和协作,共同解决问题。
及时分享经验和交流想法,能够帮助我们更快地解决问题,提高工作效率。
最后,维修工作中也需要不断学习和提高自己的技能。
PCB技术在不断发展和更新,我们需要不断学习新的知识和技术,提高自己的维修水平,以应对日益复杂的PCB维修工作。
总的来说,PCB维修工作需要我们具备专业知识和技能,细心和耐心地处理问题,及时沟通和协作,不断学习和提高自己。
希望通过这篇报告,能够帮助大家更好地理解PCB维修工作的重要性和复杂性,提高工作效率和质量。
详谈pcb钻孔孔壁镀铜开裂问题及解决方案-豆丁
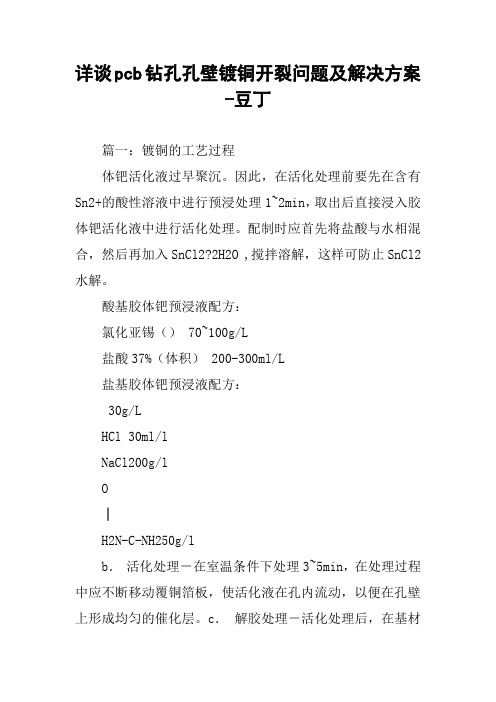
详谈pcb钻孔孔壁镀铜开裂问题及解决方案-豆丁篇一:镀铜的工艺过程体钯活化液过早聚沉。
因此,在活化处理前要先在含有Sn2+的酸性溶液中进行预浸处理1~2min,取出后直接浸入胶体钯活化液中进行活化处理。
配制时应首先将盐酸与水相混合,然后再加入SnCl2?2H2O ,搅拌溶解,这样可防止SnCl2水解。
酸基胶体钯预浸液配方:氯化亚锡() 70~100g/L盐酸37%(体积) 200-300ml/L盐基胶体钯预浸液配方:30g/LHCl 30ml/lNaCl200g/lO║H2N-C-NH250g/lb.活化处理-在室温条件下处理3~5min,在处理过程中应不断移动覆铜箔板,使活化液在孔内流动,以便在孔壁上形成均匀的催化层。
c.解胶处理-活化处理后,在基材表面吸附着以钯粒子为核心,在钯核的周围,具有碱式锡酸盐的胶体化合物。
在化学镀铜前,应将碱式锡酸盐去除,使活性的钯晶核充分暴露出来,从而使钯晶核具有非常强而均匀的活性。
经过解胶处理再进行化学镀铜,不但提高了胶体钯的活性,而且也显著提高化学镀铜层与基材间的结合强度。
常用的解胶处理液是5%的氢氧化钠水溶液或1%氟硼酸水溶液。
解胶处理在室温条件下处理1~2min,水洗后进行化学镀铜。
d.胶体铜活化液简介:明胶 2g/l/lDMAB(二甲胺基硼烷)5g/l水合肼 10 g/l钯20ppm配制过程:首先分别将明胶和硫酸铜用温水(40度C)溶解后将明胶加入至硫酸铜的溶液中,用25%H2SO4将PH值调至2..5当温度为45度C时,将溶解后DMAB在搅拌条件下缓慢加入上述的混合溶液中,并加入去离子稀释至1升,保温40~45度C,并搅拌至反应开始(约5~10分钟)溶液的颜色由蓝再变成绿色。
放置24小时颜色变成红黑色后加入水合肼。
篇二:PCB线路板镀铜表面粗糙问题原因分析PCB线路板镀銅表面粗糙问题原因分析可能原因如下:镀铜槽本身的问题1、阳极问题:成分含量不当导致产生杂质2、光泽剂问题(分解等)3、电流密度不当导致铜面不均匀4、槽液成分失调或杂质污染5、设备设计或组装不当导致电流分布太差…………当然作为镀铜本身来讲;以上问题导致粗糙的可能性不大前制程问题PTH制程带入其他杂质:1、活化成分失调钯浓度太高或者预浸盐残留板面2、速化失调板面镀铜是残有锡离子3、化学铜失调板面沉铜不均4、镀铜前酸洗不当导致板面残留杂质………………黑孔制程:微蚀不净导致残碳抗氧化不当导致板面不良烘干不良导致微蚀无法将板面碳剥除导致残碳电流输入输出不当导致板面不良…………篇三:化学镀铜常见故障和纠正方法-PCB工艺论文,SMT 技术文章-SMT专家网化学镀铜常见故障和纠正方法◎化学镀铜常见故障和纠正方法故障发生原因纠正方法化学镀铜空洞①钻孔粉尘,孔化后脱落①检查吸尘器,钻头质量,转速/进给等②加强去毛刺的高压水冲洗钻孔后孔壁裂缝或内层间分离检查钻头质量,转速/进给,以及层压板厚材料和层压工艺条件③除钻污过度,造成树脂变成海绵状,引起水洗不良和镀层脱落检查除钻污法工艺,适当降低去钻污强度④除钻污后中和处理不充分,残留Mn残渣检查中和处理工艺⑤清洁调整不足,影响Pd的吸附检查清洗调整处理工艺(如浓度、温度、时间)及副产物是否过量⑥活化液浓度偏低影响Pd吸附检查活化处理工艺补充活化剂⑦加速处理过度,在去除Sn的同时Pd也被除掉检查加速处理工艺条件(温度/时间/浓度)如降低加速剂浓度或浸板时间⑧水洗不充分,使各槽位的药水相互污染检查水洗能力,水量/水洗时间⑨孔内有气泡加设摇摆、震动等⑩化学镀铜液的活性差检查NaOH、HCHO、Cu2+的浓度以及溶液温度等⑾反应过程中产生气体无法及时逸出加强移动、振动和空气搅拌等。
- 1、下载文档前请自行甄别文档内容的完整性,平台不提供额外的编辑、内容补充、找答案等附加服务。
- 2、"仅部分预览"的文档,不可在线预览部分如存在完整性等问题,可反馈申请退款(可完整预览的文档不适用该条件!)。
- 3、如文档侵犯您的权益,请联系客服反馈,我们会尽快为您处理(人工客服工作时间:9:00-18:30)。
)
SGH-F480 5M 急喊搬苞
检查数 工厂 工厂 896EA 882EA 1,778EA
处 0.22% 0.68% 0.45% 试 4EA ▶ Ni层为 纹进
TOTAL
3. 检查
较(高
进口检查 & SI FLEX)
高 进口检查 200 显 镜检查 (SPL) 显 镜连 各工 : 2 G-Ⅱ适 / SI FLEX 200 显 器, 显 器检查 12 口检查 : G-Ⅱ SPL
没 Burr 去 没
■对 声
声
, JET研 : 3/12 :线 纹
对 ,适 业开 没 ,去
:1
纹发
时,得
.
声 发电机 工 维
7
- JET研
Ⅳ.
1. 1.1 为 纹 电 金镀金 ~ 现: 及问题 发工 间 各工 拿 , 纹发 现TEST结果 参 :参
变更 问题
2. 各工 别拿
D/F COATING
拿 可能 •A纹
, 发
弯曲 可能
拿 , E/T 可能 •A纹 发
弯曲 可能
8
Ⅳ.
变更 问题
两 R,
拿 纹发 可能
1. 发
线
宽
发
发
: 发 弯曲时 废 间 没 空间, 张 响 : 纹发 2. 发 : 发 弯曲时 废 间 空间 张 响
9
Ⅴ. 对
1. 1.1 电 金镀金 ~ 拿 两 发工 拿 为 : , 拿 为 改 :参 纹.
『2
纹
』
SGH-F480 5M
• 机种 • SIFLEX :线 质 证
纹
纹 ’颜
结果
: SGH-F480 5M
SI FLEX 품질그룹
1
Ⅰ Ⅱ Ⅲ Ⅳ Ⅴ Ⅵ
顾客 VOC 现况 现 现 TEST
对 选别进 结果
2
Ⅰ. 顾客 VOC 现况
1. 发 2. 发 3. 发 4. 发 5. 场 期 : 2009년 04월 08일(SI FLEX : )→2 发 检查 ,检 . 电机 高 工厂 进口检查 – 显 镜 200
镀金 区 数 认 断 认 Au(㎛) SI 试 6EA 纹 认 Ni层为 纹 0.06 ~ 0.07 0.05 ~ 0.09 Ni(㎛) 1.56 ~ 2.16 1.69 ~ 1.98 度 线 宽 (㎛) 77.9 ~ 84.7 74.9 ~ 84.0
资
玫柳SI 阂樊矫丰 盒籍
高
进口检查 试
11EA
变更
弯曲,曲 发
变更
D/F COATING
E/T
10
Ⅴ. 对
变更 变更
2.
请
项 :线
宽补强( PAD宽统
变更
)
变更
线
状
11
Ⅵ. 选别进 结果
1. 检查 (临时对
显 镜 景
):显
镜 200
检查
检查 (×200) 检查 (Hot-Bar 线 )
2. SI FLEX
区
库,
工:显
镜 200
检查(4/13 现
显 镜 检查 检查数
SHEET状态 状态, ▣ SHEET状态, 为拿
工 内 电 金镀金 ~ 发 工
响
结 论 ~20 )
秒鞭钎霖(困秦) 秒鞭钎霖(玫柳)
据 拿 检证 1. 对 SGH-F480 5M 发 , BENDING TEST实 1.1 TEST : SHEET状态 , 复 BENDING(1 1.2 TEST结果 : 参 ▶ 发 : 从5 BENDING开 ,线 发 纹 ▶ 发 : 20 为 发 纹 现
, 1 5
复 数 10 20
内
SGHF480 5M 线 宽 : 0.1 纹发 纹 1EA发 纹 2EA发 纹 1EA发
线
宽 : 0.2
纹发
纹发
纹发
纹发
结果
根据线
宽
度,
纹
(线
宽
, 为拿
发
纹
)
14
机种 : SGH-F480 5M 数 现 : 11EA / 70EA (15.7%) : HOT-BAR
现 1
线
纹
现 2 现 3 现 4
1 (3월9일)
2 (4월8일)
▶1 ▶2
试 试
: :
纹 纹
线 态发 ( 为
击发
) )
3
态发 ( 为拿 发
Ⅱ.
1. 1.1 对 试 高
现
结果 进口检查, SI 检 试 , 结果.
纹
认
Ni层为
纹
绊脚荐八 阂樊矫丰 盒籍
2. 检讨 2.1 2.2 2.3
见 : Ni层为 纹发
纹现 现检查 1
(显 镜 40 -MAX) 能检 现 统 但(Ni层为 纹), 纹 态 异
纹发
4
Ⅲ.
1. 同 现 1.1 为 1.2 1.3 同 现
现TEST
现TEST(SI 检, :抓 工厂) 张状态拿 , 线 复进 发 适当 TEST. 10 (参 纹.(Ni层为 图 ) 纹)
TEST结果
纹发 : 2EA
现 TEST
现 TEST结果 : ACF压缩
TEST
SGHF480 5M
,
10
复
纹
能发 能发
5
Ⅲ.
2.1 2.2 随 , ,
现TEST
拿 认, 发 数 TEST结果 纹 认:参 结果 , 纹 . 复 数别
2. SGH-F480 5M &
BENDING 复
加, SGH-F480 5M
, 复 数
1
5
10
20
SGHF480 5M
纹发
纹 1EA发
纹 2EA发
纹 1EA发
纹发
纹发
纹发
纹发 6
Ⅳ.
■ 得 7个
现 发
,线
可能
纹
现检证
结果 备
1. 声 2. 3. 线 纹 JET研
声 大 声 时间 声 数
(
) 去 异
1. 喷 压 2. 컨베어 속도 감소 拿 线 现 1. 拿 1. 线 宽 ( 发 SHEET状态)
(
,
)
, 1 5
复 数 10 20
内
发 纹 1EA发 纹 1EA发 纹 1EA发 纹 2EA发
发 纹发 纹发 纹发 纹发
结果
根据
拿
度(BENDING)
纹
13
ACF压缩 ▣ ACF压缩
工 内 设计
为宽
响
结 论 ~20 ) ( , )
ACF压缩 据线 宽 度, 检证 1. SGH-F480 5M & BENDING TEST进 1.1 TEST : SHEET状态 , 复 BENDING(1 1.2ห้องสมุดไป่ตู้TEST结果 : 参 ▶ SGH-F480 5M : 5 BENDING开 线 发 纹 ▶ : 20 为 发 纹。 线 现