MAC3040中文资料
SF-3040资料

UHF 天线:TNC
COM1/USB:LEMO 7-pin
COM2:LEMO 6-pin
性能参数
跟踪新号(载波&相位)
GPS:L1 L2 L2C L5 载波;CA L1P L2P & L2C 码
GLONASS:G1 G2 载波;CA & P 码
Galileo:E1 E5a
SBAS:WAAS EGNOS MSAS & GAGAN
通讯 可选 UHF 电台:1W 403 – 473Hz 接口:2 个 RS232 接口;1 个 USB2.0 接口;蓝牙;Ethernet。 数据格式:NMEA0183:ALM,GBS,GGA,GLL,GRS,GSA,GST,GSV,RMC,RRE,
VTG,ZDA;Navcom NCT 数据格式。 差分改正:RTCM2.3,RTCM3.1,NTRIP,SBAS,StarFire RTK 差分:CMR/CMR+,RTCM2.3,RTCM3.1,NavCom UltraRTKTM 端口:2 个 RS232,1 个 USB 设备端口(与 COM1 共用),蓝牙端口 定位&原始数据输出频率:1Hz,5Hz,10Hz(可选) 内存:可移动 SD 卡
显示:3.5"" TFT LCD VGA (480 x 640)半穿反式阳光下可读显示屏 操作系统:正版 Windows Mobile® 6.1 Professional 通信接口:蓝牙 (v2.0+EDR Class 2),9 针串口 无线连接:802.11b/g,GSM/UMTS (HSDPA/EDGE) 电源:锂离子智能电池 (5600mAh)(最长 10 小时电池续航时间) 存储和内存:128MB MDDR,256MB NAND Flash 和 4GB iNAND 扩展插槽:SDIO / SDHC 卡槽(最大 16GB SDHC 存储卡) x 1 摄像头:300 万像素自动对焦摄像头带 LED 补光灯 工作温度:-30°C 至 60°C 储藏温度:-40°C 至 70°C 最大湿度:95% 相对湿度,无冷凝 强固特性:通过美军标 MIL-STD-810G 和 IP67 认证
REF3040AIDBZRG4中文资料

"
R30F
"
REF3033
"
SOT23-3
"
DBZ
"
–40°C to +125°C
"
R30D
"
REF3040
"
SOT23-3
"
DBZ
"
–40°C to +125°C
"
R30E
"
"
"
"
பைடு நூலகம்
"
NOTES: (1) For the most current package and ordering information, see the Package Option Addendum located at the end of this data sheet.
ELECTRICAL CHARACTERISTICS
Boldface limits apply over the specified temperature range, TA = –40°C to +125°C.
At TA = +25°C, ILOAD = 0mA, VIN = 5V, unless otherwise noted. REF30xx PARAMETER CONDITIONS MIN TYP MAX UNITS
APPLICATIONS
q PORTABLE, BATTERY-POWERED EQUIPMENT q DATA ACQUISITION SYSTEMS q MEDICAL EQUIPMENT q HAND-HELD TEST EQUIPMENT
龙雕3040 4040 4轴滚珠形丝杠雕刻机的使用说明书 mach3 2.63中文破解版

3040雕刻机使用说明2,本机是针对旋转轴比速1:6, 对刀块厚度为-26.2mm首先装好MACH3软件,根据以下说明设好参数,然后装上电气箱插上电源. 数据线和USB,如果软件装对,打开软件主轴不转,为正确.因为数据受控制, 如果打开软件主轴会转说明参数没设对或软件未装好.请客户认真仔细看以下说明.首先要看一下光盘的雕刻机接线图,步进电机从上往下最上是Z轴,中间是X轴,最下是Y轴(在这里特别要说明,长期使用要经常检验,步进电机线不能短路,控制板电源线不要接反,或路板。
机床发货时线都接好的,所以客户只要插上就可以用了,要6孔对6针,插对插正)新手使用时特注意:1.收到雕刻机后先看光盘资料。
2.然后需要一台25针的台式电脑,25针直接从主板上出来的台式机,先装MACH3软件,注意装时有360或杀毒软件的,先把360或杀毒软件的删了,再装MACH3,MACH3具体安装看下面说明。
3.装好后电脑重起,开机过程,先开电脑,后开软件,最后开电气箱,关机刚好相反。
先关电气箱后关软件,最后关电脑。
4.参数全部设好后,新手试机,看是否装对,能手动控制XYZ和主轴,说明装对了,先要学会手动操作,然后学会自动操,手动操作时注意这二处是绿灯才可进行5.平时加工时主轴开到最高速8000转加工,别低速加工。
6,特别注意点,电气箱通电后不要拔插步进电机接头,只有关机后才可以7.习惯,晚上不加工产品睡前把电气箱关了,哈哈,这是我自已的习惯8,XYZ的步进电机都是可以改变方向的,下面参数中有说到,这里我说一下,电机输出那里,6 74 52 3后面的钩和叉就是改变方向的,很多软件编程出来的Z轴方向刚好相反,客户在用时首先要确认Z轴方向正确了在进行,然后雕刻字时比如阴阳字雕刻也是改变步进电机方向得到的。
注意事项:1.机器使用前应该在滑道光轴和丝杠上滴一些机油,减少磨损延长磨损件的使用寿命。
2.由于该机器是电脑控制机械设备,电机都具有一定的力矩,具有伤害性。
GMR3040-2CKHSom

Congratulations on your purchase of the UnidenGMR3040-2CKHS (General Mobile Radio Service)radio. This lightweight, palm-sized radio is a state-of-the-art device, equipped with many valuablefeatures. Use it at sporting events, to stay incontact with family and friends, hiking, skiing,outdoors, or in a neighborhood watch for vitalcommunication.PACKAGE CONTENTSYour package contains two radios, two rechargeableNiMH battery packs, one AC adapter, one chargingcradle, two headset boom mics, two belt clips, 2carabiner clips and this reference guide. A NiMHbattery pack or 3 AAA alkaline batteries (not included)powers each unit. To order the following optionalaccessories, visit our web site at orcall 1-800-554-3988 during regular business hours.Use only Uniden accessories.• NiMH Battery Pack - #BT-1028 or BP-1028• Charging Cradle - #RC-1287• Headset - #ZA-133 or ZA-160• AC Adapter - #AD-0001• DC Adapter - #DC-1002• Carabiner Clip - # TSTD0720002GMRS LICENSEThe radio operates on the General Mobile RadioService (GMRS) frequencies when usingChannels 1-7 and channels 15-22. You musthave a GMRS license issued by the FederalCommunications Commission to legally usethese channels. For licensing information andapplication forms, visit the FCC online at: www./wtb/uls or call the FCC hotline at1-800-418-3676. If you have any questions, youcan contact the FCC direct at 1-888-225-5322.No license is required for operation on channels8-14 or operation on any channel in Canada.INSTALL THE BATTERYEach radio uses a supplied NiMH battery pack or3 AAA alkaline batteries (not included).To install the NiMH battery pack:1) Make sure your radio is OFF.2) Press the tab at the bottom of the batterycompartment door to remove the cover.3) Install the NiMH battery pack into the batterycompartment. Be certain to follow theinstructions written on the label on the batterypack. Installing the battery pack incorrectly willprevent the unit from operating.4) Replace the battery compartment door.BATTERY LEVEL AND LOWBATTERY ALERTThis unit has a battery level meter on the display toindicate the status of the batteries. When thebattery in the unit is low, the battery level metericon flashes. Recharge the NiMH batterypack immediately or if you are using alkalinebatteries, you must replace the alkaline batteries inorder to continue using the radio.Warning! To avoid the risk of personal injury orproperty damage from fire or electrical shock, onlyuse the Uniden accessories specifically designatedfor this product.CHARGING THE RADIOIf you use the rechargeable NiMH battery pack, tworadios can be charged directly or by using thesupplied charging cradle.USING The RadIo1) Connect the optional DC adapter (#DC-1002) toDC 9V jack of the radio and to a cigarette lighterport.2) Charge the battery pack for 16 hours until thebattery indicator stops flashing.USING The ChaRGING CRadle1) Connect the AC adapter (#AD-0001) to DC 9Vjack and to a standard 120V AC wall outlet.2) Set the charging cradle on the desk or tabletop,and place the radio in the charging cradle withthe keypad facing forward.3) Make sure that the LED illuminates. Charge thebattery pack for 16 hours and remove the radiofrom the charging cradle after charging.Note:• For charging batteries directly without the cradle,use only the #DC-1002 Cigarette Lighter Adaptercord, available from . Otherpower cords could damage your radio.• DC 9V jack of the radio is for charging only.Be sure to install the battery before charging.• Use only the supplied battery and AC adapter orapproved accessories from Uniden.• Charge time may vary depending on the batterylife remaining.• Do not recharge alkaline batteries. Doing so cancreate a safety hazard or damage the radio.• For fastest charging, turn off the radio beforecharging.• The battery must be installed for the unit tooperate, even if the unit is also connected toexternal power.TalKING oN YoUR RadIoTo talk to others using the radio:1) Press and hold the PTT button and speak in aclear, normal voice about 2-3 inches away fromthe microphone. While you are transmitting, theicon appears on the display. To avoid cuttingoff the first part of your transmission, pauseslightly after pressing the PTT button before youstart talking.2) When you have finished speaking, release thePTT button. You can now receive incomingcalls. While receiving, displays.MoNIToR Mode FeaTUReYour radio allows you to listen for weak signals onthe current channel at the press of a key.To turn ON Monitor mode:• Press and hold WX/MON for 2 seconds until twobeeps sound. The receiver circuit stays open,and both noise and weak signals can be heard.To turn OFF Monitor mode:• Press and hold WX/MON for 2 seconds to returnto "Normal" mode; the icon stops blinkingand disappears.adVaNCed FUNCTIoNS (MeNUS)Use MENU/1) Press2) Additional presses ofoperating mode.3) Other methods of exiting the Menu function are:a. Press and holdb. Press any key except CH ▲ / CH ▼ or VOL ▲/ VOL ▼ and wait 10 seconds until the unitreturns to “Normal” mode.Sub CodeEach of the channels 1-22 may have any one ofthe codes, OFF, or 1-121 selected. Code oF (OFF)indicates no Sub code selected and your radio canreceive a signal regardless of the code settings ofthe transmitting radio.1) Press Menu mode. The2) Press CH ▲ / CH ▼ key to increase orthrough the speaker but will not be transmitted.Cycle through these tones and stay on the toneyou want to select.3) Exit Call Tone to set the selected tone.KeY loCKTo lock the keypad:1) Press and hold CALL/LOCK; displays.These functions are not affected by Key Lock:• Volume adjust• Call tone transmission• Enter monitor mode• PTT transmission• Power offTo unlock the keypad:1) Press and hold CALL/LOCK again;disappears.aUToMaTIC poWeR SaVeYour radio has a circuit designed to dramaticallyextend the life of the batteries. If there is notransmission or an incoming call within 3 seconds,your radio switches to Power Save mode. The radiois still able to receive transmissions in this mode.lCd BaCKlIGhTThe LCD Backlight automatically turns ON when anykey (except the PTT button) is pressed. The LCDdisplay illuminates for 10 seconds before turningOFF.RoGeR BeepRoger Beep is a BEEP that is sent to notify the end oftransmission (both PTT and VOX transmission).Roger Beep can be heard through the speaker whenboth Roger Beep and Key Beep are set to ON. WhenRoger Beep is set to ON and Key Beep is set to OFF,Roger Beep will not be heard from the speaker but itwill be transmitted to your party. When Roger Beep isset to OFF, Roger Beep will neither be heard nortransmitted.To change Roger Beep setting:Press and hold VOL ▲ while turning the radio on andoff. If Roger Beep is ON, it will be turned off; if it isOFF, it will be turned on.decrease the code number displayed. You(OFF) at this stage.3) Press4) Press any key other than CH ▲ / CH ▼ orVOL ▲ / VOL ▼ and the radio returns toIdle mode in 10 seconds.ScanYour radio has a channel scan feature thatallows you to easily scan all 22 channels.When an active channel is detected, the radiopauses on that channel until the channel isclear. Then, after a 2 second delay, the radiocontinues scanning. Pressing the PTT buttonwhile the scan is paused on a channel allowsyou to transmit on that channel.To turn ON channel scan:1) Press scan...icon and oF blink.2. Press CH ▲ / to select Scan modeand pressTo turn OFF channel scan:1) PressoF.2) Press any key other than CH ▲ / CH ▼ orVOL ▲ / VOL ▼ to turn channel scan off in10 seconds.Voice Operated TransmissionYour radio is equipped with a user selectableVoice Operated Transmitter (VOX) that can beused for automatic voice transmissions. TheVOX feature is designed to be used with orwithout a headset with a microphone.Transmission is initiated by speaking into themicrophone instead of pressing PTT.To select VOX level:1) Press vox(OFF, 1-5)blink.2) Press CH ▲ / CH ▼ to change the VOXsensitivity levels. Use level 1 for increasedsensitivity to voice in normally quietenvironments, and use a higher level toreduce undesired activation in very noisyenvironments.Call ToneYour radio is equipped with 10 selectable calltones that are transmitted when CALL/LOCK ispressed.To select a call tone:1) Press CALLicon and start to blink on thedisplay.2) Press CH ▲ / CH ▼ to move through theavailable call tones. Each tone will be heard U1UT63ZZA()EnglishChannels 15 GMRS/7 FRS/7 Weather Sub Codes 38 Sub-Audible Tones83 DCS Codes Operating FrequencyGMRS/FRS: 462.5500 - 467.7125 MHz WX: 162.4000 - 162.5500 MHz Power Source NiMH Battery Pack (BT-1028 or BP-1028) or3 AAA Alkaline Batteries Range Channel 1-7 up to 30 miles Channel 8-14 up to5 milesChannel 15-22 up to 30 miles Battery Life 10 Hours typ. - NiMH Battery Pack(5/5/90 duty cycle)Frequency Chart Ch. Freq. Cross Ref. Ch. Freq. Cross Ref.1 462.5625 FRS & GMRS 1 12 467.6625 FRS 122 462.5875 FRS & GMRS 2 13 467.6875 FRS 133 462.6125 FRS & GMRS 3 14 467.7125 FRS 144 462.6375 FRS & GMRS 4 15 462.5500 GMRS 115 462.6625 FRS & GMRS 5 16 462.5750 GMRS 86 462.6875 FRS & GMRS 6 17 462.6000 GMRS 127 462.7125 FRS & GMRS 7 18 462.6250 GMRS 98 467.5625 FRS 8 19 462.6500 GMRS 139 467.5875 FRS 9 20 462.6750 GMRS 1010 467.6125 FRS 10 21 462.7000 GMRS 1411 467.6375FRS 1122 462.7250GMRS 15Important: Evidence of original purchase is required for warranty service.WARRANTOR: UNIDEN AMERICA CORPORATION ("Uniden")ELEMENTS OF WARRANTY: Uniden warrants, for three years, to the original retail owner, this Uniden Product to be free from defects in materials and craftsmanship with only the limitations or exclusions set out below.WARRANTY DURATION: This warranty to the original user shall terminate and be of no further effect 36 months after the date of original retail sale. The warranty is invalid if the Product is: (A) damaged or not maintained as reasonable or necessary, (B) modified, altered, or used as part of any conversion kits, sub-assemblies, or any configurations not sold by Uniden, (C) improperly installed, (D) serviced or repaired by someone other than an authorized Uniden service center for a defect or malfunction covered by this warranty, (E) used in any conjunction with equipment or parts or as part of any system not manufactured by Uniden, or (F) installed or programmed by anyone other than as detailed by the owner’s manual for this product.STATEMENT OF REMEDY: In the event that the product does not conform to this warranty at any time while this warranty is in effect, warrantor will either, at its option, repair or replace the defective unit and return it to you without charge for parts, service, or any other cost (except shipping and handling) incurred by warrantor or itsrepresentatives in connection with the performance of this warranty. Warrantor, at its option, may replace the unit with a new or refurbished unit. THE LIMITED WARRANTY SET FORTH ABOVE IS THE SOLE AND ENTIRE WARRANTYPERTAINING TO THE PRODUCT AND IS IN LIEU OF AND EXCLUDES ALL OTHER WARRANTIES OF ANY NATURE WHATSOEVER, WHETHER EXPRESS, IMPLIED OR ARISING BYOPERATION OF LAW, INCLUDING, BUT NOT LIMITED TO ANY IMPLIED WARRANTIES OF MERCHANTABILITY OR FITNESS FOR APARTICULAR PURPOSE.THIS WARRANTY DOES NOT COVER OR PROVIDE FOR THE REIMBURSEMENT OVERPAYMENT OFINCIDENTAL OR CONSEQUENTIAL DAMAGES. Some states do not allow this exclusion or limitation of incidental or consequential damages so the above limitation or exclusion may not apply to you.LEGAL REMEDIES: This warranty gives you specific legal rights, and you may also have other rights which vary from state to state. This warranty is void outside the United States of America and Canada.PROCEDURE FOR OBTAINING PERFORMANCE OF WARRANTY: If, after following the instructions in the owner’s manual you are certain that the Product is defective, pack the Product carefully (preferably in its original packaging). Disconnect the battery from the Product and separately secure the battery in its own separate packaging within the shipping carton. The Product should include all parts and accessories originally packaged with the Product. Include evidence of original purchase and a note describing the defect that has caused you to return it.The Product should be shipped freight prepaid, by traceable means, to warrantor at:THREE YEAR LIMITED WARRANTYUniden America Service4700 Amon Carter Blvd. Fort Worth, TX 76155(800) 297-1023 during regular business hours (CST)(See for current hours of operation.)© 2012 Uniden America Corporation All rights reserved. Printed in Vietnam.SPECIFICATIONSREGULATORY INFORMATIONWaRNING! Read this information before using the radio. In August 1996 the FederalCommunications Commission (FCC) of the United States with its action in Report and Order FCC 96-326 adopted an updated safety standard for human exposure to radio frequencyelectromagnetic energy emitted by FCC regulated transmitters.Those guidelines are consistent with the safety standard previously set by both U.S. andinternational standards bodies. The design of the radio complies with the FCC guidelines and these international standards.Never allow children to operate the radio without adult supervision and the knowledge of the following guidelines.WaRNING! It is up to the user to properly operate this radio transmitter to insure safe operation. Please adhere to the following:Use only the supplied or an approved antenna. Unauthorized antennas, modifications, orattachments could impair call quality, damage the radio, or result in violation of FCC regulations.Do not use the radio with a damaged antenna. If a damaged antenna comes into contact with the skin, a minor burn may result. Please contact your local dealer for a replacement antenna.hand-held operation (held-to-Face)This device was evaluated for typical hand-held (held-to-face) operations with a 1 inch spacing from the front of the radio. For hand-held operation, the radio should be held 1 inch from the user's face in order to comply with FCC RF exposure requirements.Body-worn operationThis device was evaluated for body-worn operations with the supplied belt-clip accessory. (All necessary accessories are included in the package; anyRF EXPOSURE INFORMATIONThis device complies with Part 15 of the FCC Rules. Operation is subject to the following two conditions:(1) This device may not cause harmful interference.(2) This device must accept any interference received, including interference that may cause undesired operation.Important: Any changes or modifications not expressly approved by the party responsible for compliance could void the user's authority tooperate this device. Your radio is set up to transmit a regulated signal on an assigned frequency. It is against the law to alter or adjust the settings inside the radio to exceed those limitations. Any adjustments to your radio must be made by qualified technicians.To be safe and sure:• Never open your radio’s case.• Never change or replace anything in your radio except the batteries.Your radio might cause TV or radio interference even when it is operating properly. To determine whether your radio is causing the interference, turn it off. If the interference goes away, your radio is causing it. Try to eliminate the interference by moving your radio away from the receiver. If you cannot eliminate the interference, the FCC requires that you stop using the radio.hazardous environments: Do not operate the radio in hazardous environments. Explosion or fire may result. Do not operate the radio near unshielded electrical blasting caps.Under certain conditions, radios can interfere with blasting operations and may cause an explosion. Turn your radio OFF to prevent accidental transmission when in a blasting area or in areas posted: "Turn off two-way radio." Construction crews often use remote control RF devices to setT one octal No. Code 39 023 40 025 41 026 42 031 43 032 44 043 45 047 46 051 47 054 48 065 49 071 50 072 51 073 52 074 53 114 54 115 55 116 56 125 57 131 58 132 59 134 60 143 61 152 62 155 63 156 64 162 65 165 66172T one octal No. Code 95 445 96 464 97 465 98 466 99 503 100 506 101 516 102 532 103 546 104 565 105 606 106 612 107 624 108 627 109 631 110 632 111 654 112 662 113 664 114 703 115 712 116 723 117 731 118 732 119 734 120 743 121 754RBRC INFORMATIONadditional or optional accessories are not required for compliance with the guidelines.) Third partyaccessories (unless approved by the manufacturer) should be avoided as these might not comply with FCC RF exposure guidelines.For more information about RF exposure, please visit the FCC web site at .off explosives.Care and Safety: To clean the radio, use a soft cloth dampened with water. Do not use cleaners or solvents because they can harm the body of the unit and leak inside, causing permanent damage. Use a dry, lint-free cloth to clean the batterycontacts. Do not submerge the unit in water. If the unit gets wet, turn it off and remove the batteries immediately.Dry the battery compartment with a soft cloth to minimize potential water damage. Leave the battery compartment cover off overnight to ensurecomplete drying. Do not use the radio until the unit is completely dry.As part of our commitment to protect the environment and conserve natural resources, Uniden voluntarily participates in an RBRC ® industry program to collect and recycle used Ni-MH batteries within the US.Please call 1-800-8-BATTERY for information on Ni-MH battery recycling in your area. (RBRC ® is a registered trademark of the Rechargeable BatteryRecycling Corporation.)CTCSS Chart (hz)Code Freq. Code Freq.oF oFF 20 131.81 67.0 21 136.52 71.9 22 141.33 74.4 23 146.24 77.0 24 151.45 79.7 25 156.76 82.5 26 162.27 85.4 27 167.98 88.5 28 173.89 91.5 29 179.910 94.8 30 186.211 97.4 31 192.812 100.0 32 203.513 103.5 33 210.714 107.2 34 218.115 110.9 35 225.716 114.8 36 233.617 118.8 37 241.818 123.0 38250.319127.3dCS Code list USING THE WEATHER RADIOYour radio can receive weather broadcasts from the NOAA National Weather Service. While using the Weather Radio, you are not able to receive GMRS communications.press WX/MON . The icon appears.2) Press CH ▲ / CH ▼to increase or decrease the number to the desired Weather Channel.WX/MON NOAA Weather Radio Frequency ListChannel 1 162.550 MHz Channel 5 162.450 MHz Channel 2 162.400 MHz Channel 6 162.500 MHz Channel 3 162.475 MHz Channel 7 162.525 MHz Channel 4 162.425 MHz。
MAC6中文说明书
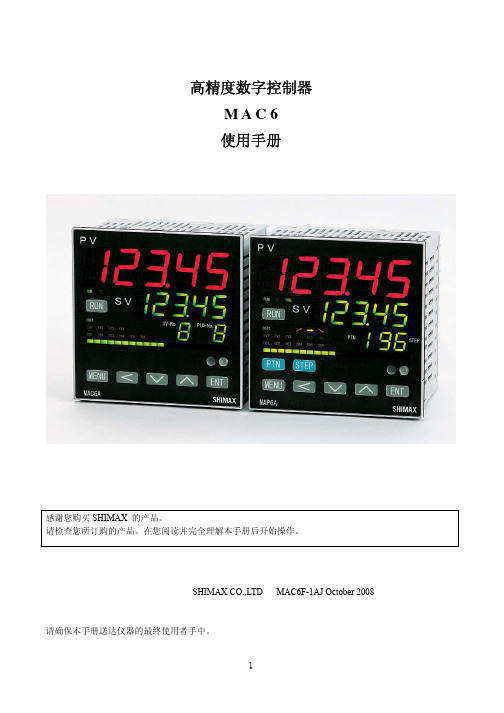
3-3 订货信息
项目 型号 输入
代码 MAC6A-
调节输出 1
电源
规格 96×96mm 5 位数字显示高精度字控制器 M 自由输入、TC、RTD、mV、V、mA
C 继电器接点 1a 240V AC 2A( 阻性负载 ) S 固态继电器(SSR)驱动 12V DC 最大20mA I 电流 4-20mA DC 负载电阻最大500Ω V 电压 0-10V DC 负载电流最大2mA Y 控制电机 (伺服控制输出)接点容量1C 240V AC 2A X 控制电机 (伺服控制输出)SSR 240V AC 2A
3
生电磁干扰。请在采取有效措施后使用。 ● 仪器具有用于散热的通风口,并且确保金属不会进入通风口中,否则会引起故障或者火灾。 ● 不要阻塞通风口或者使尘埃和其他类似物附着在上面,温度升高或者绝缘失效都会缩短产品寿命并
引起火灾。 ● 应该注意在重复性极限值(如电压、噪声、浪涌)实验时可能会损坏设备。 ● 禁止使用者改型和不正当使用。 3 简介 3-1 使用前的检查
在使用 MAC6 前请检查型号代码、外观和附件。确认没有错误、损坏和丢失。 确认型号代码,检查与订货的产品一致。根据下述代码表检查机壳上的型号代码。 检查附件 「注」 如果您有任何问题请联系我们的代理商或者营业本部。我们欢迎任何询问,例如,产品缺
陷、附件丢失等。
「 注意 」
3-2 使用注意事项 ●不要用硬的、尖的物体操作前面板。不要用指甲尖触碰按键。 ●当清洁仪器时,用干布轻擦。不要使用溶剂,如,稀释剂。
7. 功能的补充说明・・・・・・・・・・・・・・・・・・・・・・・・・・・・・・・・・・・・・・・・・・・・・・・・・・・・・・・・・・・・・・・60
7-1 自动返回功能・・・・・・・・・・・・・・・・・・・・・・・・・・・・・・・・・・・・・・・・・・・・・・・・・・・・・・・・・・・・・60 7-2 输出软启动功能・・・・・・・・・・・・・・・・・・・・・・・・・・・・・・・・・・・・・・・・・・・・・・・・・・・・・・・・・・・60 7-3 事件报警方式・・・・・・・・・・・・・・・・・・・・・・・・・・・・・・・・・・・・・・・・・・・・・・・・・・・・・・・・・・・・・60 7-4 AT(自整定)・・・・・・・・・・・・・・・・・・・・・・・・・・・・・・・・・・・・・・・・・・・・・・・・・・・・・・・・・・・・・60
MUR3040中文资料

4
3
2 dc 1 IN FREE AIR WITH NO HEATSINK 0 0 20 40 60 80 100 120 140 160 TA, AMBIENT TEMPERATURE (°C) 180 200
Figure 3. Current Derating, Case
Figure 4. Current Derating, Ambient
1 4 3
1 3
4
CASE 340E–02, STYLE 1
MAXIMUM RATINGS
Rating Peak Repetitive Reverse Voltage Working Peak Reverse Voltage DC Blocking Voltage Average Rectified Forward Current TC = 70°C Peak Repetitive Forward Current (Rated VR, Square Wave, 20 kHz) TC = 150°C Non Repetitive Peak Surge Current (Surge applied at rated load conditions halfwave, single phase, 60 Hz) Operating Junction Temperature and Storage Temperature Symbol VRRM VRWM VR IF(AV) IFRM IFSM TJ, Tstg Max 400 Unit Volts
30 30 300 – 65 to +175
Amps Amps Amps °C
THERMAL CHARACTERISTICS
Thermal Resistance, Junction to Case RθJC 1.0 °C/W
.3040AN40;.3040S20;.3040AN30;.3040AN;.3040A;中文规格书,Datasheet资料

Power OutputIndustrial VRS Magnetic Speed SensorsDESCRIPTIONPower Output VRS sensors are designed for driving lowresistance loads at large air gaps in applications where larger actuators may be used.Passive VRS (Variable Reluctance Speed) Magnetic Speed sensors are simple, rugged devices that do not require an external voltage source for operation.A permanent magnet in the sensor establishes a fixedmagnetic field. The approach and passing of a ferrous metal target near the sensor’s pole piece (sensing area) changes the flux lines of the magnetic field, dynamically changing its strength. This change in magnetic field strength induces a current into a coil winding which is attached to the output terminals.The output signal of a VRS sensor is an ac voltage that varies in amplitude and wave frequency as the speed of themonitored device changes, and is usually expressed in peak to peak voltage (Vp-p).One complete waveform (cycle) occurs as each target passes the sensor’s pole piece. If a standard gear were used as a target, this output signal would resemble a sine wave if viewed on an oscilloscope.Honeywell also offers VRS sensors for general purpose, high output, high resolution, high temperature and hazardous location applications, as well as low-cost molded versions.FEATURES• Self-powered operation• Direct conversion of actuator speed to output frequency • Simple installation • No moving parts• Designed for use over a wide range of speeds • Adaptable to a wide variety of configurations• Customized VRS products for unique speed sensingapplications• Housing diameter: 5/8 in (M16)• Housing material/style: stainless steel threaded • Terminations: MS3106 connector, preleaded • Output voltage: 70 Vp-pPOTENTIAL APPLICATIONS• Engine RPM (revolutions per minute) measurement onaircraft, automobiles, boats, buses, trucks and rail vehicles• Motor RPM measurement on drills, grinders, lathes andautomatic screw machines• Motor RPM measurement on precision camera, taperecording and motion picture equipment• Process speed measurement on food, textile, paper,woodworking, printing, tobacco and pharmaceutical industry machinery• Motor speed measurement of electrical generatingequipment• Speed measurement of pumps, blowers, mixers, exhaustand ventilating fans• Flow measurement on turbine meters• Wheel-slip measurement on autos and locomotives • Gear speed measurementPower Output2 /sensing5/8 INCH (M16*) SENSORS (All dimensions for reference only. mm/[in]) *Contact Honeywell for availability of metric mounting thread versions.General SpecificationsTest Condition SpecificationsParameter Characteristic Parameter Characteristic Parameter Characteristic Min. output voltage 70 Vp-p Inductance 85 mH max. Surface speed 25 m/s[1000 in/s]Coil resistance 120 Ohm to 162 Ohm Gear pitch range 12 DP (module 2.11) or coarser Gear 8 DP(module 3.17)Pole piece diameter 4,75 mm [0.187 in] Optimum actuator 8 DP (module 3.17) ferrous metal gear Air gap 0,127 mm[0.005 in]Min. surface speed0,38 m/s [15 in/s] typ. Max. operating frequency40 kHz typ. Operating temp. range-55 ºC to 120 ºC [-67 ºF to 250 ºF] Vibration Mil-Std 202FMethod 204DMounting thread 5/8-18 UNF-2ATermination MS3106 connectorLoadresistance 1.25 kOhmGeneral SpecificationsTest Condition SpecificationsParameter Characteristic Parameter Characteristic Parameter Characteristic Min. output voltage 70 Vp-p Inductance 85 mH max. Surface speed 25 m/s[1000 in/s]Coil resistance 120 Ohm to 162 Ohm Gear pitch range 12 DP (module 2.11) or coarser Gear 8 DP(module 3.17)Pole piece diameter 4,75 mm [0.187 in] Optimum actuator 8 DP (module 3.17) ferrous metal gear Air gap 0,127 mm[0.005 in]Min. surface speed0,38 m/s [15 in/s] typ. Max. operatingfrequency40 kHz typ. Operating temp. range-55 ºC to 120 ºC [-67 ºF to 250 ºF] Vibration Mil-Std 202FMethod 204DMounting Thread 5/8-18 UNF-2ATermination 20 AWG Teflon-insulated leadsLoadresistance 1.25 kOhmIndustrial VRS Magnetic Speed SensorsHoneywell Sensing and Control35/8 INCH (M16*) SENSORS CONTINUED (All dimensions for reference only. mm/[in]) *Contact Honeywell for availability of metric mounting thread versions.General SpecificationsTest Condition SpecificationsParameter Characteristic Parameter Characteristic Parameter Characteristic Min. output voltage 70 Vp-p Inductance 85 mH max. Surface speed 25 m/s[1000 in/s]Coil resistance 120 Ohm to 162 Ohm Gear pitch range 12 DP (module 2.11) or coarser Gear 8 DP(module 3.17)Pole piece diameter 4,75 mm [0.187 in] Optimum actuator 8 DP (module 3.17) ferrous metal gear Air gap 0,127 mm [0.005 in]Min. surface speed 0,38 m/s [15 in/s] typ. Max. operating frequency 40 kHz typ. Operating temp.range-55 ºC to 120 ºC [-67 ºF to 250 ºF] Vibration Mil-Std 202F Method 204DMounting thread5/8-18UNF-2ATermination 20 AWG Teflon-insulated leads, conduitmountLoadresistance 1.25 kOhm General SpecificationsTest Condition SpecificationsParameter Characteristic Parameter Characteristic Parameter Characteristic Min. output voltage 70 Vp-p Inductance 85 mH max. Surface speed 25 m/s[1000 in/s]Coil resistance 120 Ohm to 162 Ohm Gear pitch range 12 DP (module 2.11) or coarser Gear 8 DP(module 3.17)Pole piece diameter 4,75 mm [0.187 in] Optimum actuator 8 DP (module 3.17) ferrous metal gear Air gap 0,127 mm [0.005 in] Min. surface speed 0,38 m/s [15 in/s] typ. Max. operating frequency 40 kHz typ. Operating temp. range-55 ºC to 120 ºC [-67 ºF to 250 ºF] Vibration Mil-Std 202F Method 204DMounting thread 5/8-18 UNF-2ATerminationMS3106 connectorLoad resistance1.25 kOhmAutomation and Control Solutions Sensing and Control Honeywell1985 Douglas Drive North Minneapolis, MN 55422 /sensing 005880-1-EN IL50 GLO Printed in USA March 2007Copyright © 2007Honeywell International Inc. All rights reserved.WARNINGPERSONAL INJURYDO NOT USE these products as safety or emergency stop devices or in any other application where failure of the product could result in personal injury.Failure to comply with these instructions could result in death or serious injury.WARRANTY/REMEDYHoneywell warrants goods of its manufacture as being free of defective materials and faulty workmanship. Honeywell’sstandard product warranty applies unless agreed to otherwise by Honeywell in writing; please refer to your orderacknowledgement or consult your local sales office for specific warranty details. If warranted goods are returned to Honeywell during the period of coverage, Honeywell will repair or replace, at its option, without charge those items it finds defective. The foregoing is buyer’s sole remedy and is in lieu of all other warranties, expressed or implied, including those ofmerchantability and fitness for a particular purpose. In no event shall Honeywell be liable for consequential, special, or indirect damages.While we provide application assistance personally, through our literature and the Honeywell web site, it is up to the customer to determine the suitability of the product in the application.Specifications may change without notice. The information we supply is believed to be accurate and reliable as of thisprinting. However, we assume no responsibility for its use.WARNINGMISUSE OF DOCUMENTATION• The information presented in this product sheet is forreference only. Do not use this document as a product installation guide.• Complete installation, operation, and maintenanceinformation is provided in the instructions supplied with each product.Failure to comply with these instructions could result in death or serious injury.SALES AND SERVICEHoneywell serves its customers through a worldwide network of sales offices, representatives and distributors. Forapplication assistance, current specifications, pricing or name of the nearest Authorized Distributor, contact your local sales office or:E-mail: info.sc@Internet: /sensingPhone and Fax: Asia Pacific +65 6355-2828 +65 6445-3033 Fax Europe +44 (0) 1698 481481 +44 (0) 1698 481676 Fax Latin America +1-305-805-8188 +1-305-883-8257 Fax USA/Canada +1-800-537-6945 +1-815-235-6847 +1-815-235-6545 Fax分销商库存信息:HONEYWELL.3040AN40.3040S20.3040AN30 .3040AN.3040A.3040AN25 .3040A25.3040AN50。
BKAD2A234MAC40101资料

ARINC 600 BKAD/E/F Low insertion force contacts.Both environmental and non- environmentalversions.Polarizing posts that are removable from themating face.Field replaceable inserts for size 22 andpower contacts.Up to 800 size 22 contacts in one connector.Crimp, coax, power, printed circuit and wirewrappable post style contacts.Uses standard DPX crimp, insertion/extractiontooling.Waveguide connections available.BKAD/EBKAD/E connectors represent a major milestones in presenting a new rack and panel connector for support of the air transportation market.Several important design concerns have been ad-dressed and solved in this new series. High mating forces of pluggable modules in a rack have been reduced by approximately two-thirds.The low insertion force contacts are also inter-changeable with the contacts used in the DPX series and permit retrofit of existing equipment.BKAFThis new connector is totally intermateable and intermountable with ARINC 600 connectors now in the field.The BKAF permits the user to easily replace a contact in case of problems, rather than disas-semble the entire connector--it is available with size 22 contacts in wrap post or solder-tail ver-sions. The system maintains the advantages of low insertion force technology incorporated in all ARINC 600 connectors.Rear Release/Rear Removable Size 12, 16, 20, 22 Crimp Contacts Front Release/Front RemovableSize 22 Solder Tail and Wrap Post ContactsPos-Aline Connector Construction FeatureMaterial Specifications In the ARINC 600 connector series, Size 22 con-tacts are the only size that utilize this designfeature. The hooded socket extends from its in-sulator while the pin contacts are shrouded by itsfront insulator.All other contacts used in this series employ stan-dard contact design.The result is that the complement of contacts forthe plug connectors will consist of pin contacts forsize 22 and socket contacts for all others. Thereceptacle contacts will be just the reverse, socketcontact for size 22 and pin contacts for thebalance.Shell & WaveguideBKAD BKAE BKAF SpecificationsInsulatorContactsGrommets/Seals O-Ring FinishMaterialMaterialMaterialFinishTerminationMaterialMaterial1200AlodineThermosetAluminum alloyCopper alloyGold over NickelCrimpN/AN/A1200AlodineThermosetAluminum alloyCopper alloyGold over NickelCrimpSilicone-based ElastomerSilicone-based Elastomer1200AlodineThermosetAluminum alloyCopper alloyGold over NickelP.C./Wrap PostN/AN/AMIL-C-5541N/AQQ A-591/A380QQ-C-533MIL-G-45204N/AN/AN/A* = For Polarizing Position greater then 99, add third digit. ARINC 600 BKAD/E/FCONNECTOR SERIES CLASS SHELL SIZECONNECTOR LAYOUT DESCRIPTION SIZE 1 COAX INSERT MODIFIER BOEING COAX MODIFIER SHELL STYLECONNECTOR MOUNTING MODIFIER POLARIZING POSITIONMODIFIER (Contact, Finish, Material)How to OrderBKA D 2 A234 M * 3 00 01 * F0CONNECTOR SERIESBOEING COAX MODIFIERSHELL STYLECONNECTOR MOUNTING MODIFIERCLASSNon-environmental (rear release, crimp contacts)Environmental (rear release, crimp con-tacts)Non-environmental (front release, solder and wrap post #22 contact, rear release all others)Same as E, except uses BKAD shells, and Less 0 rings on plug side.Environmental (0-ring is used to seal between connector shell and insulators)with rear release, crimp contacts.Non-environmental connector using fil-tered contacts (reference Cannon Phoe-nix)Max. contact capacity - 125Max. contact capacity - 400Max. contact capacity - 800Connector contains modified 71W1 or 2W2 insert (four MTG screw hole loca-tions and coaxial contact used in this insert are interchangeable between dif-ferent manufacturersPlug (rack side)Receptacle (box side)Standard design, .148 dia. holesWith #6-32 ESNA (#12 NCFMA2-62) clinch nuts (see chart)Size 1 receptacle only - less 3 printed circuit board mounting lugsWith #4-40 ESNA (#22 NCFMA2-40) clinch nuts (see chart)Size 2 and 3 plug and receptacle only - with #4-40 ESNA (#22 NCFMA2-40) clinch nuts (all mounting holes)Size 2 and 3 plug and receptacle only - with #6-32 ESNA (#12 NCFMA2-62) clinch nuts (all mounting holes)Same as - 00 mounting modification except with nickel finished shells .0008 - .0012 thick with EMI grounding spring for plug shells and supplied with non-environmental inserts.Same as - 00 mounting modification except with nickel finished shells .0008 - .0012 thick with EMI grounding spring for plug shells and supplied with environmental inserts not potted into shell.With floating eyelets (.048 min. radial float)4 corner holes per connector.Consult factory if other modifications are requiredSHELL SIZECONNECTOR LAYOUT DESCRIPTIONSIZE 1 COAX INSERT MODIFIERNOTE: A dash must be inserted whenever code does not apply.D BKA (Per ARINC 600)E FC ST 3 -4 -00 -01 -02 -03 -08 -09 -16 -17 -23 -M123(See page 4)----------Boeing Coax Code Connector Size1234484610Number of Clinch Nuts Plug ReceptacleITTC Code Plug Connector Receptacle Connector ITTC Coax Contacts SuppliedAA AB AC AD AE AFBlank B C D E FNo Coax Supplied 349-0013-000 349-0015-000 349-0013-000 349-0017-000 349-0015-000 349-0018-000 349-0015-000 349-0017-000No Coax Supplied 349-0014-000 349-0016-000 349-0014-000 349-0002-000 349-0016-000 349-0004-000 349-0016-000 349-0002-000AR INC 600 B K AD/E/FHow to Order (Continued)CONNECTOR LAYOUT DESCRIPTION NOTE. ANY OTHER COMBINATION OF INSERTS WITHIN A SPECIFIC SHELL IS AVAILABLE UPON REQUESTPOLARIZING POSITIONMODIFIER (Contact, Finish, Material)01 thru 99 (per ARINC 600)Blank-Polarizing posts or keys not installed but supplied with connectorBlank -SC -WC -WD -SD -WA -WB -Rear release, crimp, signal and powercontacts supplied with connector (when applicable)Contacts not supplied with connector (FO not stamped on connector)Less contacts and waveguide (FOO notstamped on connector)Front release .025(0.63) D. x .150(3.81) solder post and crimp, rear re-lease power contacts (when applica-ble) supplied with connectorFront release .025(0.63) D. x .250(6.35) solder post and crimp, rear re-lease power contacts (when applica-ble) supplied with connectorFront release .025(0.63) D. x .375(9.53) solder post and crimp, rear re-lease power contacts (when applica-ble) supplied with connectorFront release .025(0.63) D. x .500(12.7) solder post and crimp, rear re-lease power contacts (when applica-ble) supplied with connectorFront release .025(0.63) Sq. x .250(6.35) (1 wrap) wrap post and crimp,rear release power contacts (when ap-plicable) supplied with connector Front release .025(0.63 Sq. x .375(9.53) (2 wraps) wrap post and crimp,rear relase power contacts (when ap-plicable) supplied with connectorFront release .025(0.63) Sq. x 500(12.7) (3 wraps) wrap post and crimp,rear release power contacts (when ap-plicable) supplied with connector Front release .025 (0.64) Sq. x 641(16.28) (3 wraps) wrap post and crimp, rear release power contacts (when applicable) supplied with con-nectorNOTE: COAXIAL CONTACTS TO BE ORDERED SEPARATELYFO -FOO -SA -SB -Layout included in the following ARINC configurations 702, 710, 711, 712, 714, 715, 716, yout included in the following ARINC configurations 707, 718 & 730.Layout included in the following ARINC configurations 701, 702, 703, 704, 705, 706, 724, yout included in the following ARINC configurations 701, 717, 726, 729.Note: All layouts with "OPEN' insert cavity are not supplied with an insulator. If a Blank insert is required please consult factory.Shell Dimensions - Size 1PlugRetainer Plate *This dimension indicates distance from centerline of retaining screw to the centerline of first contact cavity.For further information, refer to ARINC 600 specification or consult factory.Size 1 Receptacle Panel CutoutRetainer Plate Size 1 Plug Panel CutoutReceptacleFor further information, refer to ARINC 600 specification or consult factory.* This dimension indicates distance from centerline of retaining screw to the centerline of first contact cavity.BKAE SERIES 1.550 (39.37) MAXCBABKAE SERIES 1.670 (42.42)Shell Dimensions - Size 2 Plug11550 (39.37) MAXBKAE SERIES130 (3.30.120 (3.05)1.317 (33.45).355 (9.02)1.5301.670 (42.42)Retainer Plate*This dimension indicates distance from centerline of retaining screw to the centerline of first contact cavity.For further information, refer to ARINC 600 specification or consult factory.Size 2 Receptacle Panel Cutout Retainer Plate Size 2 Plug Panel Cutout ReceptacleFor further information, refer to ARINC 600 specification or consult factory.* This dimension indicates distance from centerline of retaining screw to the centerline of first contact cavity.Shell Dimensions - Size 3BKAE SERIES 1.550 (39.37) MAX1.670 (42.42 )MAXRetainer Plate ReceptaclePlugSize 3 Plug Panel Cutout* This dimension indicates distance form centerline of retaining screw to the centerline of first contact cavity.For furter information, refer to ARINC 600 specification or consult factory.Retainer Plate Size 3 Plug Panel Cutout* This dimension indicates distance form centerline of retaining screw to the centerline of first contact cavity.For furter information, refer to ARINC 600 specification or consult factory.Contact Arrangements - Shell Size 1Contact Arrangements - Shell Sizes 2 and 3BKAD/BKAE (Plug Rear face shown)BKAD/BKAE (Plug Rear face shown)REAR SURFACE WHITE ON BLUE TO INDICATE REAR RELEASE REAR REMOVAL CONTACTS ENGAGING END SURFACE WHITE ON RED TO INDICATE FRONT RELEASE FRONT REMOVAL CONTACTS**Pending ARINC release.NOTE: In layouts using #22 contacts mixed with any other contact size (20HD, 16, 12), the size #22 contact type (pin or socket) determines the insulator as a pin insert or a socket insert.(For Contact Cavity Location and Contact Cavity Identification refer to ARINC 600 or consult factory)REAR SURFACE WHITE ON BLUE TO INDICATE REAR RELEASE, REAR REMOVAL CONTACTS FOR INSERTS CONTAINING STANDARD SIGNAL & POWER CONTACTS(For Contact Cavity Location and Contact Cavity Identification refer to ARINC 600 or consult factory)30T228 #222 #8 TWINAX/COAX (#8 Grounded toShell)6060 #226**6 #86T6**6 #8(Metallic Insert)13W24 #20, 4 #12, 3 #162 #5 COAX24T4**20 #20, 4 #8100100 #228580 #22, 4 #20, 1 #1659**50 #22, 5 #16, 4 #1234**24 #20, 10 #1844 #125W21 #122 #162 #5 COAX4040 #226060 #225W21 #122 #162 #5 COAXBKAF - Available Receptacle Shell Only (Front Release)Shell Cavity A or BShell Cavity C or FShell CavityCShell CavityCShell CavityA or BContact Arrangements - Shell Sizes 2 and 3BKAD/BKAE (Plug Rear face shown)Shell Cavity A,B,D,E2W22 #1 COAX4W44 Modified #1 COAX (Metallic Insert)10T10**10 #8 TRIAX/COAX (#8 Grounded to Shell)(Metallic Insert)24**24 #1271W170 #221 #1 COAX 71W1B 70 #221 #1 COAX60**60 #2049T2**47 #202 #8110**100 #225 #12 & 5 #20** Pending ARINC release.(For Contact Cavity Location and Contact Cavity Identification refer to ARINC 600 or consult factory)REAR SURFACE WHITE ON BLUE TO INDICATE REAR RELEASE. REAR REMOVAL CONTACTS FOR INSERTS CONTAINING STANDARD SIGNAL & POWER CONTACTS150150 #22120T2 **118 #222 #8 TWINAX/COAX (#8 Grounded to Shell)121**110 #225 #166 #20Contact Arrangements - Shell Sizes 2 and 3BKAF - Available Receptacle Shell ONLY (Front Release)SHELL CAVITY A, B, D, E,BKAF - Available Receptacle Shell ONLY (Front Release)SHELL CAVITY C, F** Pending ARINC release.NOTE #22 CONTACTS ARE SOCKETS, 20HD,16, 12 ARE PIN CONTACTS.(For Contacts Cavity Location and Contact Cavity Identification refer to ARINC 600 or Consult Factory)ENGAGING END SURFACE WHITE ON RED TO INDICATE FRONT RELEASE FRONT REMOVAL CONTACTS FOR INSERTS CONTAINING STANDARD SIGNAL & POWER CONTACTSENGAGING END SURFACE WHITE ON RED TO INDICATE FRONT RELEASE, FRONT REMOVAL CONTACTS FOR INSERTS CONTAINING STANDARD SIGNAL & POWER CONTACTS71W170 #22150150 #226T6**6 #813W24 #203 #164 #122 #5 COAX100100 #2271W1B 70 #2210T10**10 #8121F**110 #22 6 #205 #16Waveguide ConnectionsPolarization (Engaging End)WAVEGUIDE DETAIL SHOWN FULLY ENGAGEDFULLYCENTERPOSTRIGHTPOSTLEFTPOSTCENTERPOSTRIGHTPOSTLEFTPOST INSULATOR ANDWAVEGUIDE RETAININGPLATEPlugBKA*1PLUG RECEPTACLE PLUG RECEPTACLEBKA*2BKA*3ReceptaclePolarizing PositionsPOSTDark area represents postPositionPositionLeft PostCenter PostRight PostLeft PostCenter PostRight PostPositionLeft PostCenter PostRight PostPositionLeft PostCenter PostRight PostPositionLeft PostCenter PostRight PostPositionLeft PostCenter PostRight PostPlug ShellReceptacle ShellKEYKit P/N 320-1067-000Kit P/N 320-1067-0030102030405060708091011121314151617181920212223242526272829303132333435363738394041424344454647484950515253545556575859606162636465666768697071727374750102030405060708091011121314151617181920212223242526272829303132333435363738394041424344454647484950515253545556575859606162636465666768697071727374751234561234561234561234561234561234561234561234561234561234561234561234561231111111111111111111111111111111111112222222222222222222222222222222222223331111116666665 55555444444333333222222111111666666555555444444333333222222111456123456123456123456123456123456123 456123456123456123456123456123456123456444444555555666666111111222222333333444444555555666666111111222222333333444444444444444444444444444444444444444333333333333333333333333333333333333222432165432165432165432165432165432165432165432165432165432165432165432165432444555555666666111111222222333333444444555555666666111111222222333333444444222222222222222222222222222222222111111111111111111111111111111111111666666165432165432165432165432165432165432165432165432165432165432165432165432165333333333333333333333333333333333444444444444444444444444444444444444555555111666666555555444444333333222222111111666666555555444444333333222222111111123456123456123456123456123456123456123456123456123456123456123456555555555555555555555555555555666666666666666666666666666666666666666666555555444444333333222222111111666666555555444444333333222222555555666666111111222222333333444444555555666666111111222222333333666666666666666666666666666666555555555555555555555555555555555555432165432165432165432165432165432165432165432165432165432165432165151152153154155156157158159160161162163164165166167168169170171172173174175176177178179180181182183184185186187188189190191192193194195196197198199200201202203204205206207208209210211212213214215216151152153154155156157158159160161162163164165166167168169170171172173174175176177178179180181182183184185186187188189190191192193194195196197198199200201202203204205206207208209210211212213214215216767778798081828384858687888990919293949596979899100101102103104105106107108109110111112113114115116117118119120121122123124125126127128129130131132133134135136137138139140141142143144145146147148149150767778798081828384858687888990919293949596979899100101102103104105106107108109110111112113114115116117118119120121122123124125126127128129130131132133134135136137138139140141142143144145146147148149150Contact and Termination Tooling DataBKA* (LIF) Crimp ContactsBKAF-ARINC 600 Size 22 Wrap Post Socket Contacts With .025(6.35) Square Wire-Wrappable Tails-Receptacle Only.BKA* Thermocouple ContactsBKAF Printed Circuit Solder Post Socket Contacts Size 22 with .025(6.35) Dia. Printed Circuit Tails-Receptacle Only.The new low insertion force, front-insertable, front-removable #22 socket contacts with .025(6.35) dia., PC tails are now availble for use in the BKAF non-environmental receptacle version only.These contacts can be sold separately or they can be supplied with a connector (see How to Order). Use part numbers shown in the table on the right when ordering separately.BKAD/F Solder Post, Power Pin Contacts (Captive)-Receptacle Only.Contacts are captivated between two unbonded insulator halves.BKAF Solder Post Pin Contact Front ReleaseFront Release Pin Contacts Size 20 and 16The new low insertion force, front-insertable, front-removable #22 socketcontacts with .025(6.35) square wire wrappable tails are now available for use in the BKAF non-enviornmental receptacle version only.These contacts can be sold separately or they can be supplied with a connector (see How to Order). Use part numbers shown in the table on the right when ordering separately.*Applies to BKAF 13W2 and 5W2 inserts only*Consult facotry for other available lengthsSize 5 Coax Contact (Rear insertable/removable)Size 12 Shielded Contact (Rear insertable/removable)Size 1 Modified Coaxial Contacts (4W4 Layout Only)Crimp Center Contact-Conforming to ARINC 600Part Number Style Solder Type Replacement Termination KitsCrimpType CoaxCoaxReplacement Termination KitsCable AccommodationPart Number Style Solder Type CrimpType Cable AccommodationRG316 DS RG142Various349-1051-002349-1044-000349-1042-000Straight Straight SMA Adapter320-1066-008320-1066-007N/A N/A RG214AA-5886RG393ECS 311201AA-5887AA-5888RG142Various349-1043-001349-1048-000349-1051-000349-1046-000349-1049-000349-1050-000349-1047-000349-1047-001Straight Straight Straight Straight Straight Straight Straight TNC Adapter320-1066-000320-1066-002320-1066-003320-1066-001320-1066-004320-1066-005320-1066-006320-1066-016320-1066-018320-1066-019320-1066-017320-1066-013320-1066-014320-1066-015----Plug ConnectorCustomer Use Drawings:All Coax contacts (except 349-1047-001) customer use drawing #349-0000-305Crimp termination kits: Customer use drawing #320-0000-305Solder termination kits: Customer use drawing #320-0000-304Receptacle ConnectorCustomer Use Drawings:Coax contacts 349-1051-002 and 349-1044-000 are located on cusomter use drawing #349-0000-304Coax contacts 349-1042-000 is located on cusomter use drawing #320-1042-000Sizes 1 Coax Contacts (71W1 layout only)Sizes 1 Coax Contacts (To be used with connectors containing 71W1A, 71W1B and 2W2 insert modifier-"M")Same standard coax contacts as used in ITT Cannon's DPX (ARINC 404) connector series.Designed to be interchangeable with contacts made by other manufacturers.Receptacle ConnectorPlug ConnectorSize 8 Coaxial ContactsSize 8 Twinax ContactsSize 8 Ground ContactsPlug ConnectorReceptacle ConnectorPlug ConnectorReceptacle ConnectorReceptacle ConnectorPlug ConnectorContact Type Socket Part Number *Engagement**TerminationShort Long Crimp RR-RR X -----349-1087-000-----349-1087-001349-1084-000349-1084-001349-1084-002349-1084-003349-1086-000349-1086-001349-1006-000349-1081-000----X X349-1007-000349-1080-000349-1080-001349-1080-002349-1080-003349-1082-000349-1082-001349-1088-000031-3300-000--X8, 10 AWG030-3306-000030-3306-001030-3676-000---X X8, 10 AWG 8, 10 AWG 8, 10 AWGX X -X-X -X -X ----X X X-X X X-X X XXXXXX X XX X XX X XX XX Crimp FR-RRSolder .250 (6.35)FR-FR .375 (9.52)RF Cable NumberContact Type Socket Part Number *Engagement**TerminationShort Long Crimp RR-RRCrimp FR-RRFR-FR .250 (6.35)Solder .375 (9.52)RF Cable NumberContact Type Socket Part Number *Engagement**TerminationShort Long Crimp RR-RR Crimp FR-RRSolder .250 (6.35)FR-FR .375 (9.52)RF Cable Number Contact Type Socket Part Number *Engagement**TerminationShortLong Crimp RR-RR Crimp FR-RRSolder .250 (6.35)FR-FR .375 (9.52)RF Cable Number Contact Type Socket Part Number * The electrical engagement of "Long" contacts is .150 (3.81) greater than the electrical engagement of "Short" contact.**RR-RR indicates rear release, rear removal. FR-RR indicates front release, rear removal. FR-FR indicates front release, front removal.*Engagement**TerminationShortLong Crimp RR-RRCrimp FR-RRSolder .250 (6.35)FR-FR .375 (9.52)Wire Size Contact Type Socket Part Number *Engagement**TerminationShortLong Crimp RR-RRCrimp FR-RRSolder .250 (6.35)FR-FR .375 (9.52)Wire Size Adams-Russell Co. Inc.FC11Z Adams-Russell Co. Inc.FC14ZAdams-Russell Co. Inc.FC11Z Adams-Russell Co. Inc.FC14ZM17/176-00002Tensolite Co.24463/9 B017X-2 (LD)Tensolite Co.24463/9 B017X-2 (LD)Tensolite Co.24463/9 B017X-2 (LD)Tensolite Co.24463/9 B017X-2 (LD)M17/176-00002Sealing Plugs-BKAE Environmental Connnectors OnlyFiller Plugs-BKAD Non-Environmental Connectors OnlyCavity ReducerDust CapsPart Number Contact Size Color A B C Part Number #5 Coax to #12 ContactCavity reducers are available when additional circuits are required for siz 12 power contacts. These reducers, having the internal configuration of size 12 power contact, are inserted into the size 5 coaxial insulator cavity to create size 12 power contact cavity.225-0094-000225-1013-000225-0070-000225-0071-000225-0072-000225-0090-000225-0095-000225-0096-000225-0097-000225-0098-000225-0099-000025-1121-001025-1122-001025-1123-001025-1124-001PinP/N 021-8756-000SocketP/N 021-8757-000Note: Supplied as standard for BKA product line only.BKAD 1-A & B-Plug BKAD 1-C-Plug BKAD 2&3-A & B-Plug BKAD 2&3-C-Plug025-1155-001025-1156-001025-1157-001025-1158-001BKAD 1-A&B-Receptacle BKAD 1-C-Receptacle BKAD 2&3-A & B-Receptacle BKAD 2&3-C-Receptacle22201612#5 Coax (Pin)22201612#5 and #9 Coax#5 and #9 Coax(Socket)Black Red Blue Yellow White Black Red Blue Yellow White.063 (1.6).085 (2.2).115 (2.9).171 (4.3).365 (9.3).040 (1.0).065 (1.6).075 (1.9).121 (3.1).287 (7.3).469 (11.9).469 (11.9).469 (11.9).564 (14.3).835 (21.2)White.069 (1.7).083 (2.1).131 (3.3).187 (4.7).275 (7.0).275 (7.0).051 (1.3).069 (1.7).108 (2.7).156 (4.0).251 (6.4).251 (6.4).420 (10.7).350 (8.9).320 (8.1).320 (8.1).450 (11.4)1.061 (26.9)Part Number Part Number Description Description Contact Size Color A B C P/N 225-0090-000Material: Teflon(All others thermoplastic)P/N 225-0099-000Material: Teflon(All others thermoplastic)BKAF P/N 225-1058-000(Size 22 - Black)(See Customer Use Drawing for details)Conductive dust caps protect against static electricity.AAAABBBBCCCCReplaceable InsertsPart NumberSocket AssemblyPin AssemblyClassBKAD BKAE BKAE BKAD BKAE BKAD BKAE BKAF BKAE BKAD BKAE BKAF BKAD BKAE BKAD BKAE BKAF BKAD BKAE BKAD BKAE BKAE BKAE BKAE BKAD BKAE BKAF BKAD BKAE BKAF BKAD BKAE BKAF BKAD BKAE BKAF BKAD BKAE BKAF BKAD BKAE BKAF BKAE BKAD BKAE BKAF BKAD BKAE BKAD BKAE BKAF 144-2944-000144-2944-000143-1156-001177-1000-002177-1000-002143-1912-000143-1912-001143-1141-000143-1154-001228-1026-002228-1026-001N/A228-1027-002228-1027-001143-1908-000143-1908-001143-1142-000143-1173-000143-1173-001143-1159-001143-1097-005143-1171-001143-1167-001143-3714-003143-1910-000143-1910-001N/A143-1958-000143-1958-002N/A143-2085-001143-2085-000N/A143-1113-000143-114-000N/A143-3877-000143-3879-000N/A143-2015-000143-2015-001N/A143-1182-000N/A143-1165-001N/A143-1150-002143-1150-001143-1906-000143-1906-001N/A144-2945-000144-2945-000143-1157-001177-1001-004177-1001-004143-1913-000143-1913-001N/A143-1155-001228-1012-003228-1012-001228-1015-001N/A228-1014-002143-1909-000143-1909-001N/A143-1174-000143-1174-001N/A143-1098-005143-1172-001143-1170-001143-3715-003143-1911-000143-1911-001143-2065-000143-1960-000143-1960-002143-2090-000143-2086-001143-2086-000143-2066-000143-1111-000143-1112-000143-1118-000143-3878-000143-3880-000143-1178-000143-2016-000143-2016-001143-2067-000143-1183-000143-1166-002143-1166-001143-1177-000143-1158-002143-1158-001143-1907-000143-1907-001143-2068-000Layout2W2**A4W4**5W266T610T1013W230T2344059*60-#20**60-#22**71W171W1A*71W1B85100110120T2121150Consult factory for Insert Part Numbers not listed.*Modified 71W1 insert to be used with connectors containing 71W1 insert modifier "M"**"Pin Inserts' accept receptacle coax contacts. "Socket Inserts" accept plug coax contacts.AR INC 600 R ack and Panel Connectors B K AD/E/FCross Reference-Part Number/Customer-Use DrawingCOMPONENT PART NUMBER CUSTOMER USE DRAWING NUMBERCOMPONENT PART NUMBER CUSTOMER USE DRAWING NUMBERCOMPONENT PART NUMBERCUSTOMER USE DRAWING NUMBER030-1975-009030-1975-010030-2259-000030-2273-000030-2280-000030-2286-000030-2356-000030-2357-000030-2358-000031-1113-009031-1113-010031-1287-000031-1302-000031-1303-000031-1308-000031-1351-000031-1351-001031-1351-002031-1351-003031-1352-000031-1252-000031-1252-002031-1352-003143-1908-000143-1908-001143-1909-000143-1909-001143-1910-000143-1910-001143-1911-000143-1911-001143-1912-000143-1912-001143-1913-000143-1913-001143-1958-000143-1958-002143-1960-000143-1960-002143-2015-000143-2015-001143-2016-000143-2016-001143-2065-000143-2066-000143-2067-000143-2068-000143-2085-000143-2085-001143-2086-000143-2086-001249-1521-002249-1522-009249-1522-010249-1554-002249-1604-003249-1604-004249-2201-000249-2202-000249-5027-013249-5027-015249-5027-016320-0051-000320-1066-000320-1066-001320-1066-002320-1066-003320-1066-004320-1066-005320-1066-006249-1521-002249-1522-010249-1522-010249-1554-002249-1604-003249-1604-004249-1521-002249-1522-010249-5027-013249-5027-007249-5027-0161250Y320-000-305025-1121-001025-1122-001025-1123-001025-1124-001025-1155-001025-1156-001025-1157-001025-1158-001025-0000-054(Conductive Only)025-0000-055(Conductive Only)225-0000-014225-0094-000225-0095-000225-0096-000225-0097-000225-0098-000225-0099-000225-1058-000225-0072-000225-0090-000225-1013-000225-1014-000225-1015-000225-0000-006225-0090-000225-0000-008143-0000-081143-0000-077143-0000-080143-0000-079143-0000-0781247Y 143-0000-079249-1521-000249-1522-000249-1522-002249-1554-000249-1604-000249-1604-001249-5027-008249-5027-017249-5027-000249-5027-007349-0000-306249-1521-000249-1522-000249-1522-002249-1554-000249-1604-000249-1604-001249-1604-002249-1882-000249-1882-002249-1885-002249-5027-008249-5027-017249-5123-000249-5123-001349-1053-000349-1053-001349-1053-002349-1053-003349-1053-0043491053-005349-1053-006349-1053-007349-1053-008349-1053-009030-1975-009030-1975-010030-2259-000030-2273-000030-2280-000030-2286-000030-2356-000030-2357-000030-2358-000031-1113-009031-1113-010031-1287-000031-1302-000031-1303-000031-1308-000031-0000-343031-0000-344021-0144-000021-0144-001021-0144-002021-0144-003021-0144-004021-0144-006021-0144-008021-0144-011021-0144-000021-0144-001021-0144-002021-0144-003021-0144-004021-0144-006021-0144-008021-0144-011349-0013-000349-0014-000349-0015-000349-0016-000349-1003-000349-1009-000349-0000-000349-0000-001349-0000-002349-0000-001349-000-301249-1767-000249-1767-001249-1768-000249-2203-000249-1767-000249-1767-001249-1768-000249-2203-000143-1906-000143-1906-001143-1907-001143-1907-001143-0000-079ContactsReplacement Coax Termination KitDust CapsFiller PlugsSealing PlugsReplacement Coax Body AssemblySize #1 Coax ContactsSize #5 Coax ContactsSize #12 Shielded ContactReplaceable InsertsFor part numbers not listed, consult ITT Cannon for applicalbe customer-use drawing.。
MOC3040中文资料

MIN TYP MAX UNITS 1.2 1.4 10 500 400 3.0 V µA nA V V V/µs
TEST CONDITION IF = 20mA VR = 6V VDRM = 400V (note 1 ) IDRM = 500nA ITM = 100mA ( peak )
Output
'X' SPECIFICATION APPROVALS
l
2.54 7.0 6.0 1.2
Dimensions in mm 1 2 3 6 5 4
VDE 0884 in 3 available lead form : - STD - G form
- SMD approved to CECC 00802 DESCRIPTION The MOC304_ Series are optically coupled isolators consisting of a Gallium Arsenide infrared emitting diode coupled with a monolithic silicon detector performing the functions of a zero crossing bilateral triac mounted in a standard 6 pin dual-in-line package. FEATURES l Options :10mm lead spread - add G after part no. Surface mount - add SM after part no. Tape&reel - add SMT&R after part no. l High Isolation Voltage (5.3kVRMS ,7.5kVPK ) l Zero Voltage Crossing l 400V Peak Blocking Voltage l All electrical parameters 100% tested l Custom electrical selections available
FGD3040G2;中文规格书,Datasheet资料
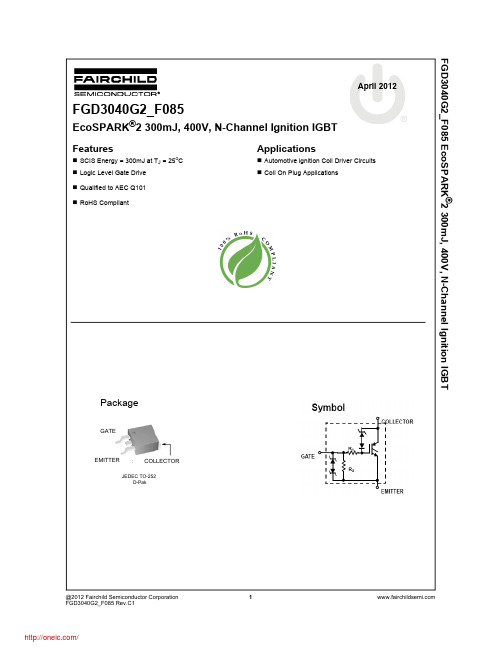
2
FGD3040G2_F085 Rev.C1
/
FGD3040G2_F085 EcoSPARK®2 300mJ, 400V, N-Channel Ignition IGBT
Electrical Characteristics TA = 25°C unless otherwise noted
FGD3040G2 FGD3040G2_F085
Package TO252
Reel Size 330mm
Ratings 400 28 300 170 41 25.6 ±10 150 1
-55 to +175 -55 to +175
300 260
4 2
Units V V mJ mJ A A V W
W/oC oC oC
Symbol
Parameter
Test Conditions
Min Typ Max Units
Dynamic Characteristics
QG(ON) Gate Charge VGE(TH) Gate to Emitter Threshold Voltage VGEP Gate to Emitter Plateau Voltage
390 420 450 V
28 -
-
V
±12 ±14 -
V
-
- 25 μA
-
-
1 mA
-
-
1
mA
-
- 40
- 120 - Ω
10K - 30K Ω
- 1.15 1.25 V - 1.35 1.50 V - 1.68 1.85 V
-
- 300 mJ
@2012 Fairchild Semiconductor Corporation
IPAM-4050 数字量非隔离输入输出模块 用户手册
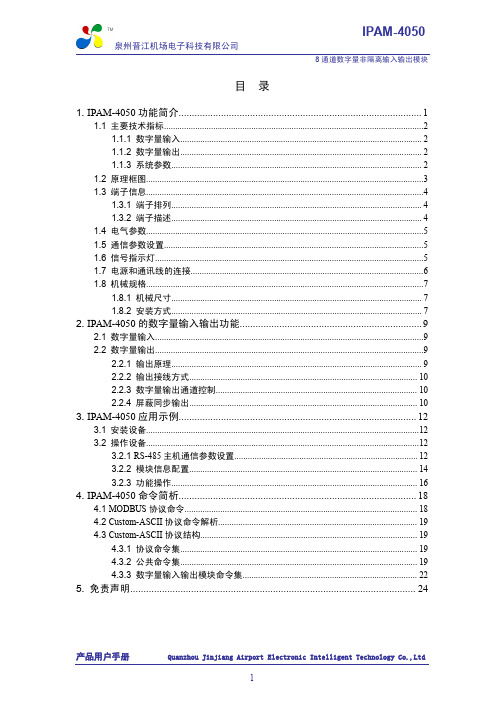
5. 免责声明............................................................................................................ 24
产品用户手册
Quanzhou Jinjiang Airport Electronic Intelligent Technology Co.,Ltd
4. IPAM-4050 命令简析.......................................................................................... 18
4.1 MODBUS 协议命令........................................................................................................ 18 4.2 Custom-ASCII 协议命令解析......................................................................................... 19 4.3 Custom-ASCII 协议结构................................................................................................. 19 4.3.1 协议命令集.......................................................................................................... 19 4.3.2 公共命令集.......................................................................................................... 19 4.3.3 数字量输入输出模块命令集.............................................................................. 22
OptiPlex 3040M 用户手册说明书

OptiPlex 3040M 用户手册管制型号: D10U管制类型: D10U001注、小心和警告注: “注”表示可以帮助您更好地使用计算机的重要信息。
小心: “小心”表示可能会损坏硬件或导致数据丢失,并说明如何避免此类问题。
警告: “警告”表示可能会造成财产损失、人身伤害甚至死亡。
版权所有© 2015 Dell Inc. 保留所有权利。
本产品受美国、国际版权和知识产权法律保护。
Dell™和 Dell 徽标是 Dell Inc. 在美国和 / 或其他管辖区域的商标。
所有此处提及的其他商标和产品名称可能是其各自所属公司的商标。
2015 - 11Rev. A00目录1 拆装计算机内部组件 (5)拆装计算机内部组件之前 (5)关闭计算机 (6)拆装计算机内部组件之后 (6)2 卸下和安装组件 (7)建议工具 (7)卸下护盖 (7)安装护盖 (8)卸下硬盘驱动器部件 (8)将硬盘驱动器从硬盘驱动器支架卸下 (8)将硬盘驱动器安装到硬盘驱动器支架中 (9)安装硬盘驱动器部件 (9)卸下 VGA 板 (9)安装 VGA 板 (10)卸下系统风扇 (10)安装系统风扇 (11)卸下内存模块 (12)安装内存模块 (12)卸下散热器 (12)安装散热器 (13)卸下处理器 (13)安装处理器 (14)卸下扬声器 (14)安装扬声器 (15)卸下币形电池 (15)安装币形电池 (16)卸下系统板 (16)安装系统板 (17)系统板布局 (18)3 排除计算机故障 (20)诊断电源 LED 代码 (20)诊断错误消息 (21)系统错误消息 (24)4 系统设置程序 (26)Boot Sequence (26)3导航键 (26)系统设置程序概览 (27)访问系统设置程序 (27)系统设置程序选项 (27)更新 BIOS (34)系统密码和设置密码 (35)分配系统密码和设置密码 (35)删除或更改现有系统密码和/或设置密码 (36)5 规格 (37)6 联系 Dell (41)41拆装计算机内部组件拆装计算机内部组件之前遵循以下安全原则有助于防止您的计算机受到潜在损坏,并有助于确保您的人身安全。
MAX3043CUE+中文资料

General DescriptionThe MAX3040–MAX3045 is a family of 5V quad RS-485/RS-422 transmitters designed for digital data trans-mission over twisted-pair balanced lines. All transmitter outputs are protected to ±10kV using the Human Body Model. In addition the MAX3040–MAX3045 withstand ±4kV per IEC 1000-4-4 Electrical Fast Transient/Burst Stressing. The MAX3040/MAX3043 (250kbps) and the MAX3041/MAX3044 (2.5Mbps) are slew-rate limited transmitters that minimize EMI and reduce reflections caused by improperly terminated cables, thus allowing error-free transmission.The MAX3040–MAX3045 feature a hot-swap capability*that eliminates false transitions on the data cable during power-up or hot insertion. The MAX3042B/MAX3045B are optimized for data transfer rates up to 20Mbps, the MAX3041/MAX3044 for data rates up to 2.5Mbps, and the MAX3040/MAX3043 for data rates up to 250kbps.The MAX3040–MAX3045 offer optimum performance when used with the MAX3093E or MAX3095 5V quad differential line receivers or MAX3094E/MAX3096 3V quad differential line receivers.The MAX3040–MAX3045 are ESD-protected pin-compat-ible, low-power upgrades to the industry-standard ‘SN75174 and ‘DS26LS31C. They are available in space-saving TSSOP, narrow SO, and wide SO packages.*Patent pendingApplicationsTelecommunications Equipment Industrial Motor ControlTransmitter for ESD-Sensitive Applications Hand-Held Equipment Industrial PLCs NetworkingFeatureso ESD Protection: ±10kV—Human Body Model o Single +5V Operationo Guaranteed Device-to-Device Skew(MAX3040/MAX3041/MAX3043/MAX3044)o Pin-Compatible with ‘SN75174, ‘26LS31C and LTC487o Hot-Swappable for Telecom Applications o Up to 20Mbps Data Rate (MAX3042B/MAX3045B)o Slew-Rate Limited (Data Rates at 2.5Mbps and 250kbps)o 2nA Low-Power Shutdown Mode o 1mA Operating Supply Currento ±4kV EFT Fast Transient Burst Immunity per IEC 1000-4-4o Level 2 Surge Immunity per IEC 1000-4-5,Unshielded Cable Model o Ultra-Small 16-Pin TSSOP, 16-Pin Narrow SO, and Wide 16-Pin SOMAX3040–MAX3045±10kV ESD-Protected, Quad 5V RS-485/RS-422Transmitters________________________________________________________________Maxim Integrated Products1Pin ConfigurationsSelector GuideOrdering Information19-2143; Rev 1; 12/01Ordering Information continued at end of data sheet.For pricing, delivery, and ordering information,please contact Maxim/Dallas Direct!at 1-888-629-4642, or visit Maxim’s website at .M A X 3040–M A X 3045±10kV ESD-Protected, Quad 5V RS-485/RS-422TransmittersABSOLUTE MAXIMUM RATINGSELECTRICAL CHARACTERISTICSStresses beyond those listed under “Absolute Maximum Ratings” may cause permanent damage to the device. These are stress ratings only, and functional operation of the device at these or any other conditions beyond those indicated in the operational sections of the specifications is not implied. Exposure to absolute maximum rating conditions for extended periods may affect device reliability.All voltages referenced to ground (GND).Supply Voltage (V CC ).............................................................+7V Control Input Voltage (EN, EN , EN_) .........-0.3V to (V CC + 0.3V)Driver Input Voltage (T_IN).........................-0.3V to (V CC + 0.3V)Driver Output Voltage (Y_, Z_)(Driver Disabled).............................................-7.5V to +12.5V Driver Output Voltage (Y_, Z_)(Driver Enabled).................................................-7.5V to +10V Continuous Power Dissipation (T A = +70°C)16-Pin TSSOP (derate 9.4mW/°C above +70°C)..........755mW16-Pin Narrow SO (derate 8.70mW/°C above +70°C)..696mW 16-Pin Wide SO (derate 9.52mW/°C above +70°C).....762mW Operating Temperature RangeMAX304_C_E.......................................................0°C to +70°C MAX304_E_E....................................................-40°C to +85°C Maximum Junction Temperature.....................................+150°C Storage Temperature Range.............................-65°C to +150°C Lead Temperature (soldering, 10s).................................+300°CMAX3040–MAX3045±10kV ESD-Protected, Quad 5V RS-485/RS-422TransmittersSWITCHING CHARACTERISTICS —MAX3040/MAX3043SWITCHING CHARACTERISTICS —MAX3041/MAX3044M A X 3040–M A X 3045±10kV ESD-Protected, Quad 5V RS-485/RS-422Transmitters 4_______________________________________________________________________________________Note 2:∆V OD and ∆V OC are the changes in V OD and V OC , respectively, when the transmitter input changes state.Note 3:This input current level is for the hot-swap enable (EN_, EN, EN ) inputs and is present until the first transition only. After thefirst transition the input reverts to a standard high-impedance CMOS input with input current I IN . For the first 20µs the input current may be as high as 1mA. During this period the input is disabled.Note 4:Maximum current level applies to peak current just prior to foldback-current limiting. Minimum current level applies duringcurrent limiting.SWITCHING CHARACTERISTICS —MAX3041/MAX3044 (continued)(V CC = +5V ±5%, T A = T MIN to T MAX , unless otherwise noted. Typical values are at V CC = +5V and T A = +25°C.)OUTPUT LOW VOLTAGE (V)O U T P U T C U R R E N T (m A )54-6-5-4-2-1012-3310203040506070800-76OUTPUT CURRENT vs. TRANSMITTEROUTPUT HIGH VOLTAGE0.70.81.00.91.11.220103040506070SUPPLY CURRENT vs. TEMPERATURETEMPERATURE (°C)S U P P L Y C U RR E N T (m A )10010000105152025353040450.1110MAX3040/MAX3043SUPPLY CURRENT vs. DATA RATEDATA RATE (kbps)S U P P L Y C U R R E N T (m A )4000.1110100100010,000MAX3041/MAX3044SUPPLY CURRENT vs. DATA RATEDATA RATE (kbps)S U P P L Y C U R R E N T (m A )1052015353025MAX3042B/MAX3045BSUPPLY CURRENT vs. DATA RATEDATA RATE (kbps)0.1100100010,000110100,000S U P P L Y C U R R E N T (m A )60010203050400201040306050700426810OUTPUT CURRENT vs. TRANSMITTEROUTPUT LOW VOLTAGEOUTPUT LOW VOLTAGE (V)O U T P U T C U R R E N T (m A )MAX3040–MAX3045±10kV ESD-Protected, Quad 5V RS-485/RS-422Transmitters_______________________________________________________________________________________5Typical Operating Characteristics(V CC = +5V, T A = +25°C, unless otherwise noted.)020104030605070021345OUTPUT CURRENTvs. DIFFERENTIAL OUTPUT VOLTAGEM A X 3040 t oc 07DIFFERENTIAL OUTPUT VOLTAGE (V)O U T P U T C U R R E N T (m A )2.102.202.152.352.302.252.502.452.402.5520301040506070TRANSMITTER DIFFERENTIAL OUTPUTVOLTAGE vs. TEMPERATURETEMPERATURE (°C)D I F FE R E N T I A L O U T P U T V O L T A G E (V )M A X 3040–M A X 3045±10kV ESD-Protected, Quad 5V RS-485/RS-422Transmitters 6_______________________________________________________________________________________MAX3040–MAX3045±10kV ESD-Protected, Quad 5V RS-485/RS-422Transmitters7Detailed DescriptionThe MAX3040–MAX3045 are quad RS-485/RS-422 trans-mitters. They operate from a single +5V power supply and are designed to give optimum performance when used with the MAX3093E/MAX3095 5V quad RS-485/RS-422 receivers or MAX3094E/MAX3096 3V quad RS-485/RS-422 receivers. The MAX3040–MAX3045 only need 1mA of operating supply current and consume 2nA when they enter a low-power shutdown mode. The MAX3040–MAX3045 also feature a hot-swap capability allowing line insertion without erroneous data transfer.The MAX3042B/MAX3045B are capable of transferring data up to 20Mbps, the MAX3041/MAX3044 for data rates up to 2.5Mbps, and the MAX3040/MAX3043 for data rates up to 250kbps. All transmitter outputs are pro-tected to ±10kV using the Human Body Model.±10kV ESD ProtectionAs with all Maxim devices, ESD-protection structures are incorporated on all pins to protect against electro-static discharges (ESD) encountered during handling and assembly. The MAX3040–MAX3045 transmitter outputs have extra protection against electrostatic dis-charges found in normal operation. Maxim ’s engineers have developed state-of-the-art structures to protect these pins against the application of ±10kV ESD (Human Body Model), without damage.ESD Test ConditionsESD performance depends on a number of conditions.Contact Maxim for a reliability report that documents test setup, methodology, and results.Human Body ModelFigure 6a shows the Human Body Model, and Figure 6b shows the current waveform it generates when dis-charged into low impedance. This model consists of a 100pF capacitor charged to the ESD voltage of interest,which is then discharged into the device through a 1.5k Ωresistor.Machine ModelThe Machine Model for ESD testing uses a 200pF stor-age capacitor and zero-discharge resistance. It mimics the stress caused by handling during manufacturing and assembly. Of course, all pins (not just RS-485inputs) require this protection during manufacturing.Therefore, the Machine Model is less relevant to the I/O ports than are the Human Body Model.±4kV Electrical Fast Transient/Burst Testing(IEC 1000-4-4)IEC 1000-4-4 Electrical Fast Transient/Burst (EFT/B) is an immunity test for the evaluation of electrical and electronic systems during operating conditions. The test was adapted for evaluation of integrated circuits with power applied. Repetitive fast transients with severe pulsed EMI were applied to signal and control ports. Over 15,000 distinct discharges per minute are sent to each interface port of the IC or equipment under test (EUT) simultaneously with a minimum test duration time of one minute. This simulates stress due to dis-placement current from electrical transients on AC mains, or other telecommunication lines in close prox-imity. Short rise times and very specific repetition rates are essential to the validity of the test.Stress placed on the EUT is severe. In addition to the controlled individual discharges placed on the EUT,extraneous noise and ringing on the transmission line can multiply the number of discharges as well as increase the magnitude of each discharge. All cabling was left unterminated to simulate worst-case reflections.The MAX3040–MAX3045 were setup as specified in IEC 1000-4-4 and the Typical Operating Circuit of this data sheet. The amplitude, pulse rise time, pulse dura-tion, pulse repetition period, burst duration, and burst period (Figure 8)of the burst generator were all verified with a digital oscilloscope according to the specifica-tions in IEC 1000-4-4 sections 6.1.1 and 6.1.2. A simpli-fied diagram of the EFT/B generator is shown in Figure 7. The burst stresses were applied to Y1–Y4 and Z1–Z4simultaneously.IEC 1000-4-4 provides several levels of test severity (see Table 1). The MAX3040–MAX3045 pass the 4000V stress, a special category “X ” beyond the highest level for severe (transient) industrial environments for telecommunication lines.M A X 3040–M A X 3045±10kV ESD-Protected, Quad 5V RS-485/RS-422Transmitters 8_______________________________________________________________________________________MAX3040–MAX3045±10kV ESD-Protected, Quad 5V RS-485/RS-422Transmitters_______________________________________________________________________________________9IEC 1000-4-4 Burst/Electrical FastTransient Test Levels (For Communication Lines)The stresses are applied while the MAX3040–MAX3045are powered up. Test results are reported as:1)Normal performance within the specification limits.2)Temporary degradation or loss of function or perfor-mance which is self-recoverable.3)Temporary degradation, loss of function or perfor-mance requiring operator intervention, such as sys-tem reset.4)Degradation or loss of function not recoverable due to damage.The MAX3040–MAX3045 meets classification 2 listed above. Additionally, the MAX3040–MAX3045 will not latchup during the IEC burst stress events.Hot-Swap CapabilityHot-Swap InputsWhen circuit boards are plugged into a “hot ” back-plane, there can be disturbances to the differential sig-nal levels that could be detected by receivers connected to the transmission line. This erroneous data could cause data errors to an RS-485/RS-422 system.To avoid this, the MAX3040–MAX3045 have hot-swap capable inputs.When a circuit board is plugged into a “hot ” backplane there is an interval during which the processor is going through its power-up sequence. During this time, the processor ’s output drivers are high impedance and will be unable to drive the enable inputs of the MAX3040–MAX3045 (EN, EN , EN_) to defined logic lev-els. Leakage currents from these high impedance dri-vers, of as much as 10µA, could cause the enable inputs of the MAX3040–MAX3045 to drift high or low.Additionally, parasitic capacitance of the circuit board could cause capacitive coupling of the enable inputs to either G ND or V CC . These factors could cause the enable inputs of the MAX3040–MAX3045 to drift to lev-els that may enable the transmitter outputs (Y_ and Z_).To avoid this problem, the hot-swap input provides a method of holding the enable inputs of the MAX3040–MAX3045 in the disabled state as V CC ramps up. This hot-swap input is able to overcome the leakage currents and parasitic capacitances that may pull the enable inputs to the enabled state.Hot-Swap Input CircuitryIn the MAX3040–MAX3045 the enable inputs feature hot-swap capability. At the input there are two NMOSdevices, Q1 and Q2 (Figure 9). When V CC is ramping up from 0, an internal 10µs timer turns on Q2 and sets the SR latch, which also turns on Q1. Transistors Q2, a 700µA current sink, and Q1, an 85µA current sink, pull EN to GND through a 5.6k Ωresistor. Q2 is designed to pull the EN input to the disabled state against an exter-nal parasitic capacitance of up to 100pF that is trying to enable the EN input. After 10µs, the timer turns Q2 off and Q1 remains on, holding the EN input low against three-state output leakages that might enable EN. Q1remains on until an external source overcomes theM A X 3040–M A X 3045required input current. At this time the SR latch resets and Q1 turns off. When Q1 turns off, EN reverts to a standard, high-impedance CMOS input. Whenever V CC drops below 1V, the hot-swap input is reset.The EN12 and EN34 input structures are identical to the EN input. For the EN input, there is a complimentary cir-cuit employing two PMOS devices pulling the EN input to V CC .Hot-Swap Line TransientThe circuit of Figure 10 shows a typical offset termina-tion used to guarantee a greater than 200mV offset when a line is not driven. The 50pF represents the mini-mum parasitic capacitance which would exist in a typi-cal application. In most cases, more capacitance exists in the system and will reduce the magnitude of the glitch. During a “hot-swap ” event when the driver is connected to the line and is powered up, the driver must not cause the differential signal to drop below 200mV. Figures 11 and 12 show the results of the MAX3040–MAX3045 during power-up for two different V CC ramp rates (0.1V/µs and 1V/µs). The photos show the V CC ramp, the single-ended signal on each side of the 100Ωtermination, the differential signal across the termination, and shows the hot-swap line transient stays above the 200mV RS-485 specification.Operation of Enable PinsThe MAX3040–MAX3045 family has two enable-func-tional versions:The MAX3040/MAX3041/MAX3042B have two transmit-ter enable inputs EN12 and EN34. EN12 controls the transmitters 1 and 2, and EN34 controls transmitters 3and 4. EN12 and EN34 are active-high and the part will enter the low-power shutdown mode when both are pulled low. The transmitter outputs are high impedance when disabled (Table 2).The MAX3043/MAX3044/MAX3045B have two transmit-ter enable inputs EN and EN , which are active-high and active-low, respectively. When EN is logic high or EN is logic low all transmitters are active. When EN is pulled low and EN is driven high, all transmitters are disabled and the part enters the low-power shutdown mode. The transmitter outputs are high impedance when disabled (Table 3).Applications InformationTypical ApplicationsThe MAX3040–MAX3045 offer optimum performance when used with the MAX3093E/MAX3095 5V quad receivers or MAX3094E/MAX3096 3V quad differential line receivers. Figure 13 shows a typical RS-485 con-nection for transmitting and receiving data and Figure 14 shows a typical multi-point connection.±10kV ESD-Protected, Quad 5V RS-485/RS-422Transmitters 10______________________________________________________________________________________Figure 9. Simplified Structure of the Driver Enable Pin (EN)MAX3040–MAX3045±10kV ESD-Protected, Quad 5V RS-485/RS-422Transmitters______________________________________________________________________________________11V CC 2V/div Y-Z(20mV/div)238mVY200mV/div Z200mV/div Figure 11. Differential Power-Up Glitch (0.1V/µs)V CC 2V/div Y-Z(5mV/div)238mVY50mV/div Z50mV/div 1µs/divFigure 12. Differential Power-Up Glitch (1V/µs)Figure 10. Differential Power-Up Glitch (Hot Swap)M A X 3040–M A X 3045±10kV ESD-Protected, Quad 5V RS-485/RS-422Transmitters 12______________________________________________________________________________________Typical Multiple-Point ConnectionFigure 14 shows a typical multiple-point connection for the MAX3040–MAX3045 with the MAX3095. Because of the high frequencies and the distances involved, high attention must be paid to transmission-line effects while using termination resistors. A terminating resistor (RT)is simply a resistor that should be placed at the extreme ends of the cable to match the characteristic impedance of the cable. When the termination resis-tance is not the same value as the characteristic impedance of the cable, reflections will occur as the signal is traveling down the cable. Although some reflections are inevitable due to the cable and resistor tolerances, large mismatches can cause significant reflections resulting in errors in the data. With this in mind, it is very important to match the terminating resis-tance and the characteristic impedance as closely as possible. As a general rule in a multi-drop system, termi-nation resistors should always be placed at both ends of the cable.Figure 13. Typical Connection of a Quad Transmitter and a Quad Receiver as a PairMAX3040–MAX3045±10kV ESD-Protected, Quad 5V RS-485/RS-422Transmitters13Pin Configurations (continued)Figure 12. Typical Connection for Multiple-Point RS-485 BusChip InformationTRANSISTOR COUNT: 545PROCESS: CMOSOrdering Information (continued)M A X 3040–M A X 3045±10kV ESD-Protected, Quad 5V RS-485/422Transmitters 14______________________________________________________________________________________Ordering Information (continued)Pin Configurations (continued)MAX3040–MAX3045±10kV ESD-Protected, Quad 5V RS-485/RS-422TransmittersM axim cannot assume responsibility for use of any circuitry other than circuitry entirely embodied in a M axim product. No circuit patent licenses are implied. Maxim reserves the right to change the circuitry and specifications without notice at any time.Maxim Integrated Products, 120 San Gabriel Drive, Sunnyvale, CA 94086 408-737-7600 ____________________15©2001 Maxim Integrated ProductsPrinted USAis a registered trademark of Maxim Integrated Products.Package Information (continued)。
H3C MSR 系列路由器 配置指导13-WLAN配置指导

H3C、
、H3CS、H3CIE、H3CNE、Aolynk、
、H3Care、
、IRF、NetPilot、
Netflow、SecEngine、SecPath、SecCenter、SecBlade、Comware、ITCMM、HUASAN、华三 均为杭州华三通信技术有限公司的商标。对于本手册中出现的其它公司的商标、产品标识及商品名
i
1 WLAN接口
适用款型
本手册所描述的内容适用于 MSR 系列路由器中的如下款型:
款型
MSR 900
MSR 900 MSR 920 MSR 930
MSR 930-GU
MSR 930
MSR 930-GT
MSR 930-DG
MSR 930-SA
MSR 20-10
MSR 20-10E
MSR 20-1X
MSR 20-11 MSR 20-12
MSR 30 路由器安装指导
硬件描述与安装
MSR 20-2X[40] 路由器安装指导 MSR 20-1X 路由器安装指导
MSR 900 路由器安装指导
MSR 系列路由器接口模块手册
业务配置
MSR 系列路由器 配置指导(V5)
内容介绍
帮助您了解产品的主要规格参数及亮点
帮助您详细了解设备硬件规格和安装方法,指导 您对设备进行安装 帮助您详细了解单板的硬件规格 帮助您掌握设备软件功能的配置方法及配置步骤
称,由各自权利人拥有。
由于产品版本升级或其他原因,本手册内容有可能变更。H3C 保留在没有任何通知或者提示的情况 下对本手册的内容进行修改的权利。本手册仅作为使用指导,H3C 尽全力在本手册中提供准确的信 息,但是 H3C 并不确保手册内容完全没有错误,本手册中的所有陈述、信息和建议也不构成任何 明示或暗示的担保。
KYOCERA ECOSYS M3040dn ECOSYS M3540dn 黑白多功能打印机说明书
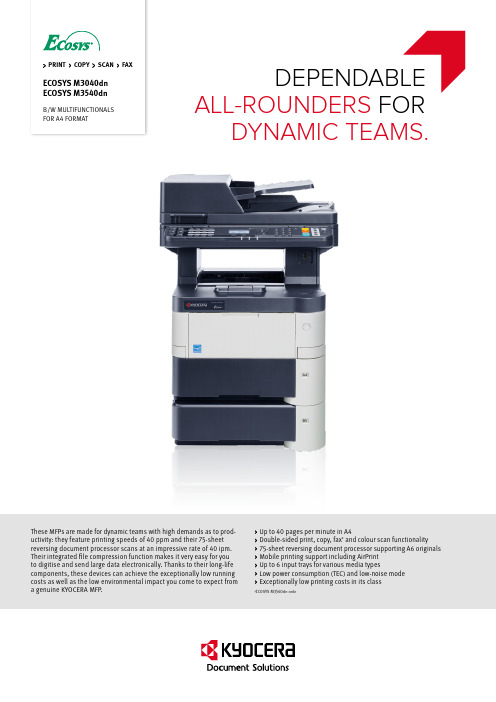
DEPENDABLEALL-ROUNDERS FOR DYNAMIC TEAMS.PRINT COPY SCAN FAXECOSYS M3040dn ECOSYS M3540dnB/W MULTIFUNCTIONALS FOR A4 FORMATThese MFPs are made for dynamic teams with high demands as to productivity: they feature printing speeds of 40 ppm and their 75sheet reversing document processor scans at an impressive rate of 40 ipm. Their integrated file compression function makes it very easy for you to digitise and send large data electronically. Thanks to their longlife components, these devices can achieve the exceptionally low running costs as well as the low environmental impact you come to expect from a genuine KYOCERA MFP.Up to 40 pages per minute in A4Doublesided print, copy, fax * and colour scan functionality 75sheet reversing document processor supporting A6 originals Mobile printing support including AirPrint Up to 6 input trays for various media typesLow power consumption (TEC) and lownoise mode Exceptionally low printing costs in its classECOSYS M3540dn only1403D S E C O S Y S M 3540D N S E R I E S /E M CYOUR KYOCERA BUSINESS PARTNERKYOCERA Document Solutions Europe B.V. – Branch Office Germany OttoHahnStraße 12 – 40670 Meerbusch – Germany Tel +49 (0) 2159 928500 – Fax +49 (0) 2159 918100www.kyoceradocumentsolutions.eu–****************.comKYOCERA Document Solutions Inc. – 228, 1Chome – TamatsukuriChuoKu – Osaka 5408585 – Japan – KYOCERA Document Solutions does not warrant that any specifications mentioned will be errorfree. Specifications are subject to change without notice. Information is correct at time of going to press. All other brand and product names may be registered trademarks or trademarks of their respective holders and are hereby acknowledged.Depending on the countryECOSYS M3040dn | ECOSYS M3540dn GENERALTechnology: KYOCERA ECOSYS Laser Control panel display: 5 lines LCD display Engine speed: Up to 40 pages A4 per minute Resolution: 1,200 dpi quality (1,800 x 600, print), 600 x 600 dpi, 256 greyscales (scan / copy) Duty cycle: Max. 150,000 pages per month Warm-up time: Approx. 21 seconds or less Time to first print / copy: Approx. 9 seconds or less CPU: PowerPC 465S / 667 MHzMemory: Standard 512 MB, max. 1,536 MBStandard interface: USB 2.0 (HiSpeed), 2 x USB Host 2.0, GigaBit Ethernet (10BaseT / 100BaseTX / 1000BaseT), slot for optional internal interface or SSD hard disc, slot for optional S D / S DHC ® cardIntegrated accounting: 100 department codes Dimensions (W x D x H): 475 x 455 x 575 mm Weight: Approx. 21,5 kgPower source: AC 220 ~ 240 V, 50 / 60 Hz Power consumption ECOSYS M3040dn ECOSYS M3540dnCopying / Printing: 679 W 680 W Ready mode: 53.7 W 54.7 W Lowpower mode: 28.7 W 29.7 W Sleepmode: 2.6 W2.6 WNoise (Sound pressure level): ISO 7779 / ISO 9296): ECOSYS M3040dn ECOSYS M3540dn Ready mode: 26.8 dB (A) LpA 26.5 dB (A) LpA Copying / Printing: 51.4 dB (A) LpA 51.1 dB (A) LpA Quiet mode: 48.9 dB (A) LpA 48.9 dB (A) LpA Typical Electricity Consumption (TEC): 2.2 KWh / week Safety standards: TÜV / GS, CEThis unit is manufactured according to ISO 9001 quality standard and ISO 14001 environmental standard. PAPER HANDLINGAll paper capacities quoted are based on a paper thickness of max. 0.11 mm. Please use paper recommended by KYOCERA under normal environmental conditions.Input capacity: 100sheet multipurpose tray; 60 – 220 g/m 2; A4, A5, A6, B5, Letter, Legal, Custom (70 x 148 – 216 x 356 mm) 500sheet universal paper cassette, 60 – 120 g/m 2; A4, A5, B5, Letter, Legal, Custom (140 x 210 – 216 x356 mm) Max. input capacity incl. options: 2,600 sheets Duplex unit: Duplex as standard supports A4, A5, B5, Letter, Legal, Custom (140 x 210 mm – 216 x 356 mm), 60–120 g/m 2Reversing document processor: 75sheet, 50–120 g/m 2, A4, A5, A6, B5, Letter, Legal, Custom (105 x 148 to 216 x 356 mm)Output capacity: 250sheetfacedown with paper full sensorPRINT FUNCTIONSController language: PRESCRIBE IIeEmulations: PCL 6 (5c / XL), KPDL 3 (PostScript 3compatible), Line Printer, IBM Proprinter X24E, Epson LQ850, PDF Direct Print 1.7, XPS Direct PrintOperating systems: All current Windows operating systems, MAC OS X version 10.5 or higher, Unix, Linux as well as other operating systems on requestFonts / barcodes: 93 outline fonts (PCL 6, KPDL 3) + 8 (Windows Vista), 1 bitmap font, 45 types of onedimensional barcodes, 1 type of twodimensional barcode (PDF417)Features: AirPrint, Encrypted PDF Direct Print, IPP printing, Email printing, WSD print, Secure printing via SSL, IPsec, HTTPS, SNMPv3, IPPS, POP over SSL, SMTP over SSL, FTP over SSL, Private Print, Toner save mode COPY FUNCTIONS Max. original size: A4 / Legal Continuous copying: 1 – 999 Zoom range: 25 – 400 % in 1 % stepsPreset magnification ratios: 7 reductions / 5 enlargements Exposure mode: Auto, manual: 9 stepsImage adjustments: Text + photo, text, photo, graphic/map Features: Scanoncecopymany, electronic sort, 2in1, 4in1, IDcard copy, job reserve, priority print, program, auto duplex copy, split copy, continuous scan, auto cassette change, copy density control SCAN FUNCTIONSFunctionality: Scantoemail, ScantoFTP , ScantoSMB, Scan to USB Host, TWAIN scan (USB, network), WSD (WIA) scan (USB, network)Scan speed: 40 ipm (300 dpi, A4, b/w), 30 ipm (600 dpi, A4, b/w, 300 dpi, A4, colour)Scan resolution: 600, 400, 300, 200 dpi (256 greyscales) Max. scan size: A4, LegalOriginal recognition: Text, photo, text + photo, for OCR File types: PDF (high compression, encrypted, PDF/A), JPEG, TIFF, XPSCompression method : MMR / JPEGFeatures: Colour scan, integrated address book, Active Directory support, encrypted data transfer, multisend (email, fax, SMB / FTP folder, print) at once FAX FUNCTIONS (ECOSYS M3540dn only)Compatibility: ITU T Super G3 Modem speed: Max. 33.6 kbpsTransmission speed: Less than 3 seconds Scanning speed: 2.5 seconds One-touch dial: 22 numbers Address book: 100 entriesScanning density Normal: 200 x 100 dpi Fine: 200 x 200 dpiSuperfine: 200 x 400 dpi Ultrafine: 400 x 400 dpi Halftone: 256 greyscales Maximum original size: A4, Legal Compression method: JBIG, MMR, MR, MH Memory reception: 256 sheets or moreFeatures: Network fax, duplex transmission and reception, encrypted transmission and reception, polling transmission and reception, broadcast OPTIONSPaper handlingPF-320 Paper feeder (max. 4 units): Max. 500 sheets; 60 – 120 g/m2; A4, A5, B5, Letter, Legal, Custom (148 x 210 mm – 216 x 356 mm) Memory upgradeMDDR3-1GB: 1,024 MBHD-6 SSD hard disc: 32 GB for easy document management HD-7 SSD hard disc: 128 GB for easy document management Data security kit (E): in line with security level EAL3UG-33: ThinPrint supportUSB IC Card Reader + Card Authentication Kit (B) Support for various authentication keys available Optional interfacesIB-50 Gigabit Ethernet: 10BaseT / 100BaseTX / 1000BaseT IB-51 Wireless LAN: 802.11b / g / nCB-360 Cabinet: Wooden desk with storage capacity CONSUMABLESAverage continuous toner yield in accordance with ISO / IEC 19752TK-3100 Toner-Kit: Microfine toner for 12,500 pages A4 Capacity of starter toner is 6,000 pages A4 WARRANTY1year warranty * as standard. Kyocera guarantees the drum and developer for 3 years or 300,000 pages (whichever occurs sooner), provided each device is used and cleaned in accordance with the service instructions.Up to 5year onsite warranty extensions available for printerand options.ECOSYS stands for ECOlogy, ECOnomy and SYStem printing. With their longlife components, ECOSYS devices are designed to maximise durability and minimise theconcept allows you to add workflowenhancing functions as required. Integrated system software provides longterm crossnetwork compatibility.。
KyOCERa KM-2540 KM-3040 说明书

附带的手册本机附带以下手册。
请根据需要参考合适的手册。
操作手册(本手册)说明如何装入纸张、基本复印操作以及故障排除。
高级操作手册详细介绍复印功能以及默认设定。
快速参考指南列出并简要介绍机器的复印功能。
i本手册中使用的安全规范使用本机前请阅读操作手册。
请将其放置在机器附近以便查阅。
本手册章节以及本机上标识的符号为安全警告,旨在保护用户、他人与周围的物体,并确保机器的使用正确、安全。
这些符号及其含义如下。
符号符号表示相关内容含有安全警告信息。
具体注意要点在符号内标出。
符号表示相关内容含有禁止操作的信息。
具体禁止操作内容在符号内标出。
z 符号表示相关部位含有必须操作的信息。
具体要求操作内容在符号内标出。
若操作手册的安全警告无法辨识,或操作手册遗失,请与维修服务人员联系,向其索要更换。
(付费)警告:表示若对相关要点不引起充分重视或不正确执行,则可能会导致严重人身伤害,甚至死亡。
小心:表示若对相关要点不引起充分重视或不正确执行,则可能会导致人身伤害,或机械损坏。
....[一般警告]....[触电危险警告]....[高温警告]....[禁止操作警告]....[禁止拆解]....[要求操作警示]....[拔下电源插头]....[本机务必使用有接地连接的插座]内容法律信息和规范 (ix)1部件名称 ..................................................................................................1-1主机 ..........................................................................................................1-2操作面板 ..................................................................................................1-5触摸面板 ..................................................................................................1-62使用准备 ..................................................................................................2-1装纸 ..........................................................................................................2-2设定纸盒和手送纸盘中的纸张类型和尺寸 ..........................................2-7装入原稿 ................................................................................................2-14语言 ........................................................................................................2-183基本操作 ..................................................................................................3-1基本复印步骤 ..........................................................................................3-2选择原稿模式 ..........................................................................................3-4调节浓度 ..................................................................................................3-5缩小/放大 ..............................................................................................3-6双面模式 ................................................................................................3-10分割模式 ................................................................................................3-13分页模式 ................................................................................................3-15插印 ........................................................................................................3-16节能模式 ................................................................................................3-17睡眠模式 ................................................................................................3-174选购设备 ..................................................................................................4-1选购设备概述 ..........................................................................................4-2送稿器 ......................................................................................................4-3供纸盒 ......................................................................................................4-3内置装订器 ..............................................................................................4-3装订器 ......................................................................................................4-6作业分离器 ..............................................................................................4-6打印组件 ..................................................................................................4-7传真组件 ..................................................................................................4-75保养 ..........................................................................................................5-1清洁 ..........................................................................................................5-2更换墨粉盒和废粉盒 ..............................................................................5-76故障排除 ..................................................................................................6-1解决故障 ..................................................................................................6-2针对错误信息的解决措施 ......................................................................6-4清除卡纸 ..................................................................................................6-87附录 ..........................................................................................................7-1在触摸面板上输入字符 ..........................................................................7-2纸张 ..........................................................................................................7-5规格 ..........................................................................................................7-6索引 ................................................................................................. 索引-1 ii小心/警告标签出于安全考虑,本机以下位置贴有小心标识。
AMMC-3040-W10资料

Note: These devices are ESD sensitive. The following precautions are strongly recommended:Ensure that an ESD approved carrier is used when dice are transported from one destination to another.Personal grounding is to be worn at all times when handling these devices.Agilent AMMC-304018-36 GHz Double-Balanced Mixer with Integrated LO Amplifier/MultiplierData SheetDescriptionThe AMMC-3040 is a broadbandDouble-Balanced M ixer (DBM ) with an integrated high-gain LO amplifier. This M M IC can be used as either an up converter or down converter in microwave or millimeter wave applications. If desired, the LO amplifier can be biased to function as a frequency multiplier to enable second harmonic mixing of the LO input. The mixer section ofthe AM M C-3040 is fabricated using a suspended metal system to create a unique, broadside-coupled balun structure (patent pending) to achieve exceptional bandwidth. The M M IC provides repeatable conversion losswithout tuning, making it highly suitable for automated assembly processes.Chip Size:2520 x 760 µm (99.2 x 29.9 mils)Chip Size Tolerance:± 10 µm (± 0.4 mils)Chip Thickness:100 ± 10 µm (4 ± 0.4 mils)Pad Dimensions:75 x 75 µm (3 ± 0.4 mils)AMMC-3040 Absolute Maximum Ratings [1]SymbolParameters/ConditionsUnits Min.Max.V D1, 2, 3, 4Positive Drain Voltage V 5V G1, 2, 3, 4Gate Voltage V -3.00.5I dd Total Drain Current mA 550T ch Operating Channel Temp.°C +160T b Operating Backside Temp.°C -55T stg Storage Case Temp.°C-65+165T maxMaximum Assembly Temp (60 sec max)°C+300Note:1.Operation in excess of any one of these conditions may result in permanent damage to this device.Features•High IIP3 : +23 dBm •Wide Bandwidth •RF: 18-36 GHz •LO: 18-36 GHz•IF: DC-3 GHz•Fundamental or Sub-Harmonic Mixing•Up or Down Converter •Conversion Loss: 9.5dB •P1dB : +17 dBm•Low LO Drive Power: + 2 dBm•Usable to 42 GHz Applications•Point-to-Point Radio •LMDS •SATCOM2AMMC-3040 DC Specifications/Physical Properties [1]AMMC-3040 RF SpecificationsZo=50 Ω, Tb = 25°C, IF Output = 2 GHz, LO Input Power = +2 dBm, RF Input Power = -20 dBm, except as noted.Symbol Parameters and Test Conditions Units Min.Typ.Max.V D1, 2, 3, 4 Drain Supply Operating Voltage V 23.55I d1First Stage Drain Supply Current V dd = 3.5 V, V g1 = −0.5 VmA 50I D2, 3, 4Total Drain Supply Current for Stages 2, 3 and 4(V dd = 3.5 V, V gg = −0.5 V)mA 225V G1, 2, 3, 4Gate Supply Operating Voltages (I dd = 250 mA)V -0.5V p Pinch-off Voltage (V dd = 3.5 V, I dd < 10 mA V -1.5θch-bThermal Resistance [2] (Backside Temp. T b = 25°C)°C/W49Notes:1.Measured in wafer form with T chuck = 25°C. (Except θch-bs.)2.Channel-to-backside Thermal Resistance (θch-b)=58°C/Ω at Tchannel (Tc)=150 °C as measured using the liquid crystal method. Thermal Resistance at backside temperature (T b )=25 °C calculated from measured data.Symbol Parameters and Test Conditions UnitsV dd =3.5 V,I dd =250 mA V dd =4.5 V,I dd =150 mA Typ.Max.Typ.Lc Conversion Loss, Down Conversion [1]dB 9.51210Lc Conversion Loss, Up Conversion [2]dB 1010.5ISOL L-R LO - RF Isolation at RF Frequency = 22 GHz [3]dB 3132P −1 dB Input Power at 1 dB Conversion Loss Compression, Down ConversiondBm 1717IIP3Input 3rd Order Intercept Point,Down Conversion at RF Frequency = 22 GHz [4]dBm2322Notes:1.100% on-wafer RF testing is done at RF frequency = 18, 22, and 32 GHz.2.IF Input = 2 GHz, IF Input Power = -20 dBm, RF freq = LO + IF3.Does not include LO amplifier gain of ~20 dB.4.∆f = 2 MHz, RF Input Power = -5 dBm.AMMC-3040 Typical PerformanceZo=50 Ω, Tb = 25°C, IF = 2 GHz, LO Input Power = +2 dBm, RF Input Power = -20 dBm, except as noted.Figure 1. Conversion Loss, UpConversion. V d = 3.5 V, I d = 250 mA, LO freq = RF - IF.Figure 2. Conversion Loss, Down Conversion.V d = 3.5 V, I d = 250 mA, LO freq = RF - IF.Figure 3. Conversion Loss, Up Conversion.V d = 4.5 V, I d = 150 mA, LO freq = RF + IF.Figure 4. Conversion Loss, Down Conversion. V d = 4.5 V, I d = 150 mA, LO freq = RF + IF.Figure 5. Conversion Loss Vs. LO Input Power, UpConversion. V d = 3.5 V, I d = 250 mA, LO freq = RF- IF.Figure 6. Conversion Loss Vs. LO Input Power,Down Conversion. V d = 3.5 V, I d = 250 mA, LOfreq = RF - IF.Figure 7. Input Power at 1 dB Conversion Loss Compression, Down Conversion.V d = 3.5 V, I d = 250 mA, LO freq = RF + IF.Figure 8. Input Power at 1 dB Conversion LossCompression, Up Conversion.V d = 3.5 V, I d = 250 mA, LO freq = RF + IF.Figure 9. Input Power at 1 dB Conversion LossCompression, Down Conversion.V d = 4.5 V, I d = 150 mA, LO freq = RF + IF.34AMMC-3040 Typical Performance(cont.)Figure 10. Input Power at 1 dB Conversion Loss Compression, Up Conversion.V d = 4.5 V, I d = 150 mA, LO freq = RF + IF.Figure 11. Input 3rd Order Intercept Point,, Down Conversion. V d = 3.5 V, I d = 250 mA, LO freq = RF - IF.Figure 12. Input 3rd Order Intercept Point, Down Conversion. V d = 4.5 V, I d = 150 mA, LO freq = RF - IF.Figure 13. LO-RF Isolation, Down Conversion.V d = 3.5 V, I d = 250 mA. Note: Does not include LO Buffer amplifier gain of ~20 dB, LO freq = RF - IF. Figure 14. LO-RF Isolation, Down Conversion.V d = 4.5 V, I d = 150 mA. Note: Does not include LO Buffer amplifier gain of ~18 dB, LO freq = RF - IF.Figure 15. AMMC-3040 Bond Pad Locations, dimensions in microns.RFV IFV d4V d3V d2V g2V d15Biasing for Fundamental Mixing The recommended DC bias condition for the AM M C-3040 LO amplifier when used as a fundamental frequency mixer is with all four drains connected to a single 3.5 to 4.5V supply and all four gates connected to an adjustable negative supply voltage as shown in Figure 16 (a). The gate voltage is adjusted for a total drain supply current of typically 150 to 250 mA.The second, third, and fourth stage DC drain bias lines are connected internally andtherefore require only a single bond wire. A separate bond wire is needed for the first stage DC drain bias, V d1.The third and fourth stage DC gate bias lines are connected internally. A total of three DC gate bond wires are required: one for V g1, one for V g2, and one for the V g3 / V g4 connection. The internal matching circuitry at the RF input creates a 50-ohm DC and RF path to ground. Any DC voltage applied to the RF input must be maintained below 1 volt, otherwise, a blocking capacitor should be used. The RF output is AC coupled.(a) Fundamental LO. Single drain and single gate supply assembly for using the LO amplifier in fundamental frequency mixer applications.(b) Sub-harmonic LO. Separate first-stage gate bias supply to use the LO amplifier as a multiplier for application as a sub-harmonic mixer. (Note: To assure stable operation bias supply feeds should be bypassed to ground with a capacitor, Cb > 100 pF typical)Figure 16. AMMC-3040 Assembly diagram.No ground bond wires are needed since the groundconnection is made by means of plated through via holes to the backside of the chip.Biasing for Sub-Harmonic Mixing The LO amplifier in the AM M C-3040 can also be used as a frequency doubler. Optimum conversion efficiency as a doubler is obtained with an input power level of 3 to 8 dBm.Frequency multiplication is achieved by reducing the bias on the first stage FET toefficiently generate harmonics. The remaining three stages are then used to provide amplification.While many bias methods could be used to generate and amplify the desired harmonics within the AM M C-3040’s LO amplifier, the following information is suggested as a starting point for sub-harmonic mixing applications.Frequency doubling isaccomplished by biasing the first stage FET at pinch-off by setting V g1 = V p ≈ –1.1 volts. The remaining three stages are biased for normal amplification, e.g., V gg is adjusted such that I d2 + I d3 + I d4 ≈ 250 mA. The drain voltage, Vdd, for all four stages should be 3.5 to 4.5 volts. The assembly diagram shown in Figure 16 (b) can be used as a guideline.In all cases, Cb > 100 pF to assure stability.IF Output PortThe IF output port is located near the middle of the die, allowing this connection to be made from either side of the chip for maximum layout flexibility.The LO and RF signals arereflectively terminating at the IF port by connecting a 20-mil (500 um) long bond wire from the IF output pad on the M M IC to a shunt 0.6 pF chip capacitor mounted off-chip as indicated in Figure 16./semiconductorsFor product information and a complete list of distributors, please go to our web site.Data subject to change.Copyright 2004 Agilent Technologies, Inc.February 12, 20045989-0528ENAssembly TechniquesThe backside of the AMMC-3040 chip is RF ground. Formicrostripline applications, the chip should be attached directly to the ground plane (e.g., circuit carrier or heatsink) usingelectrically conductive epoxy [1]. For best performance, thetopside of the M M IC should be brought up to the same height as the circuit surrounding it. This can be accomplished by mounting a gold plated metal shim (same length and width as the M M IC) under the chip, which is of the correctthickness to make the chip and adjacent circuit coplanar.The amount of epoxy used for chip and or shim attachment should be just enough toprovide a thin fillet around the bottom perimeter of the chip or shim. The ground plane should be free of any residue that may jeopardize electrical or mechanical attachment.For use on coplanar circuits, the chip can be mounteddirectly on the topside ground plane of the circuit as long as care is taken to ensureadequate heat sinking. M ultiple vias underneath the chip will significantly improve heat conduction.The location of the RF, LO, and IF bond pads is shown in Figure 15. Note that all RFinput and output ports are in a Ground-Signal-Groundconfiguration. The IF port is located near the middle of the die, which allows for maximum layout flexibility since the IF connection can be made from either side of the chip.RF connections should be kept as short as reasonable to minimize performance degradation due to seriesinductance. A single bond wire is sufficient for all signal connections. However, double-bonding with 0.7 mil gold wire or the use of gold mesh [2] is recommended for bestperformance, especially near the high end of the frequency range. Thermosonic wedge bonding is the preferred method for wire attachment to the bond pads. Gold mesh can be attached using a 2 mil round tracking tool and a tool force ofapproximately 22 grams with an ultrasonic power of roughly 55 dB for a duration of 76 ± 8 mS. A guided wedge at an ultrasonic power level of 64 dB can be used for the 0.7 mil wire. The recommended wire bond stage temperature is 150 ± 2° C.Caution should be taken to not exceed the Absolute M aximum Ratings for assembly temperature and time.The chip is 100 µm thick and should be handled with care. This M M IC has exposed air bridges on the top surface and should be handled by the edges or with a custom collet (do not pick up die with vacuum on die center.)This M M IC is also static sensitive and ESD handling precautions should be taken.Notes:1.Ablebond 84-1 LM1 silver epoxy is recommended.2.Buckbee-Mears Corporation, St. Paul, MN, 800-262-3824Ordering Information:AMMC-3040-W10 = waffle pack, 10 devices per trayAMMC-3040-W50 = waffle pack, 50 devices per tray。
ADNS-3040资料

DescriptionThe ADNS-3040 is an ultra low-power optical navigation sensor. It has a new, low-power architecture and auto-matic power management modes, making it ideal for battery-and power-sensitive applications such as cordless input devices.The ADNS-3040 is capable of high-speed motion detec-tion – up to 20 ips and 8G. In addition, it has an on-chip oscillator and LED driver to minimize external compo-nents.The ADNS-3040 along with the ADNS-3120-001 lens, ADNS-2220 clip and HLMP-ED80-PS000 LED form a complete and compact mouse tracking system. There are no moving parts, which means high reliability and less maintenance for the end user. In addition, precision optical alignment is not required, facilitating high volume assembly.The sensor is programmed via registers through a four-wire serial port. It is packaged in a 20-pin DIP .ADNS-3040Ultra Low-Power Optical Mouse SensorData SheetFeatures• Low power architecture• Self-adjusting power-saving modes for longest bat-tery life • High speed motion detection up to 20 ips and 8G • SmartSpeed self-adjusting frame rate for optimum performance • Motion detect pin output• Internal oscillator – no clock input needed • Selectable 400 and 800 cpi resolution • Wide operating voltage: 2.6V-3.6V nominal • Four wire serial port• Minimal number of passive componentsApplications• Optical Mice • Optical trackballs • Integrated input devices • Battery-powered input devicesFigure 1. Package outline drawing (top view)AGND NCNCS MISO SCLK VDD LED GNDGND AGND GND GND XY_LED NC MOTION NC MOSI NCPINOUTAVDD AGND Pin Name Description1NCS Chip select (active low input)MISO Serial data output (Master In/Slave Out)3SCLK Serial clock input4MOSI Serial data input (Master Out/Slave In)5MOTION Motion Detect (active low output)6XY_LED LED control7LED_GND Ground for LED current 8NC No connection 9AGND Analog Ground10SHTDWN Shutdown (active high input)11AVDD Analog Supply Voltage 1 GND Ground 13GND Ground 14AGND Analog Ground 15VDD Supply Voltage 16GND Ground 17NC No connection 18NC No connection 19AGND Analog Ground 0NCNo connectionTheory of OperationThe ADNS-3040 is based on Optical Navigation Technol-ogy, which measures changes in position by optically acquiring sequential surface images (frames) and math-ematically determining the direction and magnitude of movement.The ADNS-3040 contains an Image Acquisition System (IAS), a Digital Signal Processor (DSP), and a four wire serial port.The IAS acquires microscopic surface images via the lensand illumination system. These images are processed by the DSP to determine the direction and distance of mo-tion. The DSP calculates the ∆x and ∆y relative displace-ment values.An external microcontroller reads the ∆x and ∆y informa-tion from the sensor serial port. The microcontroller then translates the data into PS2, USB, or RF signals before sending them to the host PC or game console.Pinout of ADNS-3040 Optical Mouse SensorFigure 2. Package outline drawingLead OffsetφNotes:1. Dimension in millimeters(inches). . Dimension tolerence of ± 0.1mm.3. Coplanarity of leads: 0.01mm.4. Lead pitch toleronce: ± 0.15mm.5. Cummulative pitch tolerance: ±0.15mm.6. Angular tolerance: ±3.0˚.7. Maximum flash + 0. mm8. Chamfer ( 5˚ x ) on the taper side of the lead.Dimensions in millimeters / inchesFigure 3. Recommended PCB mechanical cutouts and spacingOverview of Optical Mouse Sensor AssemblyAvago Technologies provides an IGES file drawing de-scribing the base plate molding features for lens and PCB alignment.The components interlock as they are mounted onto defined features on the base plate.The ADNS-3040 sensor is designed for mounting on a through-hole PCB, looking down. There is an aperture stop and features on the package that align to the lens.The ADNS-3120-001 lens provides optics for the imaging of the surface as well as illumination of the surface at theoptimum angle. Features on the lens align it to the sen-sor, base plate, and clip with the LED.The ADNS-2220 clip holds the LED in relation to the lens. The LED must be inserted into the clip and the LED’s leads formed prior to loading on the PCB. The clip inter-locks the sensor to the lens, and through the lens to the alignment features on the base plate.The HLMP-ED80-PS000 LED is recommended for illumi-nation.to top of PCBFigure 4. 2D Assembly drawing of ADNS-3040 (top and side view)HLMP-ED80-PS000 (LED)ADNS-2220 (Clip)ADNS-3040 (Sensor)Customer supplied PCBADNS-3120-001 (Lens)Customer supplied baseplate with recommendedalignment features perIGES drawingFigure 5. Exploded viewSurfaceFigure 7. Sectional view of PCB assembly highlighting optical mouse componentsNCS MOSI MISO MOTIONVDD XY_LEDGND SHTDWNAVDDAGND Figure 6. Block diagram of ADNS-3040 optical mouse sensorPCB Assembly Considerations1. Insert the sensor and all other electrical components into PCB.2. Insert the LED into the assembly clip and bend the leads 90 degrees.3. Insert the LED/clip assembly into PCB.4. Wave Solder the entire assembly in a no-wash solder process utilizing solder fixture. The solder fixture is needed to protect the sensor during the solder pro-cess. It also sets the correct sensor-to-PCB distance as the lead shoulders do not normally rest on the PCB surface. The fixture should be designed to expose the sensor leads to solder while shielding the optical aperture from direct solder contact.5. Place the lens onto the base plate.6. Remove the protective kapton tape from optical aperture of the sensor. Care must be taken to keepNotethat the lens material is polycarbonate and therefore, cyanoacrylate based adhesives or other adhesives that may damage the lens should NOT be used.Typical Distance Millimeters Creepage 16.0 Clearance.1contaminants from entering the aperture. Recom-mend not to place the PCB facing up during the entire mouse assembly process. Recommend to hold the PCB first vertically for the kapton removal process.7. Insert PCB assembly over the lens onto the base plate aligning post to retain PCB assembly. The sensor ap-erture ring should self-align to the lens. 8. The optical position reference for the PCB is set by the base plate and lens. Note that the PCB motion due to button presses must be minimized to maintain optical alignment.9. Install mouse top case. There MUST be a feature in the top case to press down onto the clip to ensure all components are interlocked to the correct vertical height.Design considerations for improved ESD PerformanceFor improved electrostatic discharge performance, typical creepage and clearance distance are shown in the table below. Assumption: base plate construction as per the Avago Technologies supplied IGES file and ADNS-3120-001 lens.N o t e s T h e s u p p l y a n d g r o u n d p a t h s s h o u l d b e l a i d o u t u s i n g a s t a r t o p o l o g y .F i g u r e 8. S c h e m a t i c D i a g r a m f o r I n t e r f a c e b e t w e e n A D N S -3040 a n d m i c r o c o n t r o l l e rAbsolute Maximum RatingsRegulatory Requirements• Passes FCC B and worldwide analogous emission limits when assembled into a mouse with shielded cable and following Avago Technologies recommen-dations. • Passes IEC-1000-4-3 radiated susceptibility level when assembled into a mouse with shielded cable and fol-lowing Avago Technologies recommendations.• Passes EN61000-4-4/IEC801-4 EFT tests when assem-bled into a mouse with shielded cable and following Avago Technologies recommendations.• UL flammability level UL94 V-0.• Provides sufficient ESD creepage/clearance distance to avoid discharge up to 15kV when assembled into amouse according to usage instructions above.Figure 9. Distance from lens reference plane to surfaceParameterSymbolMin.Max.UnitsNotesStorage Temperature T S-4085°C Lead Solder Temp 60°C For 10 seconds, 1.6mm below seating plane.Supply Voltage V DD-0.53.7V ESD kV All pins, human body model MIL 883 Method 3015Input Voltage V IN -0.5V DD +0.5V All Pins Latchup CurrentI OUTmAAll PinsParameterSymbolMin.Typ.Max.UnitsNotesOperating Temperature T A 040°C Power supply voltage- for HLMP-ED80-PS000 LED *V DD .6 3.6Volts Including noise. Power supply rise time V RT 0.001100ms 0 to .6V Supply noise(Sinusoidal)V NA 100mV p-p 10kHz-50MHzSerial Port Clock Frequency f SCLK 1MHz Active drive, 50% duty cycle.Distance from lens reference plane to surface Z .45 .55 .65mm Results in 0. mm DOF, See drawing belowSpeed S 0in/sec AccelerationA8GLoad CapacitanceC OUT100pF MOTION, MISORecommended Operating ConditionsAC Electrical SpecificationsElectrical Characteristics over recommended operating conditions. Typical values at 25 °C, V DD3=2.6V. Parameter Symbol Min.Typ.Max.Units NotesMotion delay after reset t MOT-RST 3ms From SW_RESET register write to valid motion,assuming motion is presentShutdown t STDWN50ms From STDWN pin active to low currentWake from shutdown t WAKEUP1s From STDWN pin inactive to valid motion.Notes: A RESET must be asserted after a shut-down. Refer to section “Notes on Shutdownand Forced Rest”, also note t MOT-RSTForced Rest enable t REST-EN1s From RESTEN bits set to low currentWake from Forced Rest t REST-DIS1s From RESTEN bits cleared to valid motionMISO rise time t r-MISO150300ns C L = 100pFMISO fall time t f-MISO150300ns C L = 100pFMISO delay after SCLK t DLY-MISO1 0ns From SCLK falling edge to MISO data valid, noload conditionsMISO hold time t HOLD-MISO0.51/f SCLKµs Data held until next falling SCLK edgeMOSI hold time t HOLD-MOSI 00ns Amount of time data is valid after SCLK risingedgeMOSI setup time t SETUP-MOSI1 0ns From data valid to SCLK rising edgeSPI time between write commands t SWW30m s From rising SCLK for last bit of the first databyte, to rising SCLK for last bit of the seconddata byte.SPI time between write and read commands t SWR 0m s From rising SCLK for last bit of the first databyte, to rising SCLK for last bit of the secondaddress byte.SPI time between read and subsequent commands t SRW t SRR500ns From rising SCLK for last bit of the first databyte, to falling SCLK for the first bit of the ad-dress byte of the next command.SPI read address-data delay t SRAD4m s From rising SCLK for last bit of the addressbyte, to falling SCLK for first bit of data beingread.NCS inactive after motion burst t BEXIT500ns Minimum NCS inactive time after motion burstbefore next SPI usageNCS to SCLK active t NCS-SCLK1 0ns From NCS falling edge to first SCLK rising edgeSCLK to NCS inactive (for read operation)t SCLK-NCS1 0ns From last SCLK rising edge to NCS rising edge,for valid MISO data transferSCLK to NCS inactive (for write operation)t SCLK-NCS 0us From last SCLK rising edge to NCS rising edge,for valid MOSI data transferNCS to MISO high-Z t NCS-MISO500ns From NCS rising edge to MISO high-Z stateMOTION rise time t r-MOTION150300ns C L = 100pFMOTION fall time tf-MOTION150300ns C L = 100pFSHTDWN pulse width t P-STDWN1sTransient Supply Current I DDT45mA Max supply current during a V DD ramp from 0to .6VDC Electrical SpecificationsElectrical Characteristics over recommended operating conditions. Typical values at 25 °C, V DD=2.6 V. Parameter Symbol Min.Typ.Max.Units NotesDC Supply Current in various modes I DD_RUNI DD_REST1I DD_RESTI DD_REST3.90.50.10.03101.80.40.15mA Average current, including LED current. Noload on MISO, MOTION.Peak Supply Current40mA Peak current in 100kHz bandwidth, includingLED current.Shutdown Supply Current I DDSTDWN11 m A SCLK, MOSI and NCS must be within 300mVof GND or V DD. STDWN must be within300mV of V DD.Input Low Voltage V IL0.6V SCLK, MOSI, NCS, STDWNInput High Voltage V IH VDD - 0.6V SCLK, MOSI, NCS, STDWNInput hysteresis V I_HYS100mV SCLK, MOSI, NCS, STDWNInput leakage current I leak±1±10m A Vin=VDD-0.6V, SCLK, MOSI, NCS, STDWNXY_LED Current I LED13 5mA XY_LED pin voltage should be greater than0.15V and less than 1.4V. XY_LED current ispulsed, so average value is much lowerOutput Low Voltage V OL0.7V Iout=1mA, MISO, MOTIONOutput High Voltage V OH VDD-0.7V Iout=-1mA, MISO, MOTIONInput Capacitance C in10pF MOSI, NCS, SCLK, STDWNTypical Performance Characteristics01002003004005006001.71.81.922.12.22.32.42.52.62.72.82.933.13.23.33.4Z-height (mm, 2.55=nominal focus)R e s o l u t i o n (c p i )Typical Path DeviationLargest Single Perpendicular Deviation From A Straight Line At 45 DegreesPath Length = 4 inches; Speed = 6 ips ; Resolution = 500 cpi102030405060Distance From Lens Reference Plane To Navigation Surface (2.55mm)M a x i m u m d i s t a n c e (m o u s e c o u n t )Relative Responsivity for ADNS-30400.00.10. 0.30.40.50.60.70.80.91.04005006007008009001000Wavelength (nm)R e l a t i v e R e s p o n s i v i t yFigure 12. Relative ResponsivityFigure 11. Average error vs. distance (mm)Figure 10. Mean Resolution vs. Z (White Paper).Power management modesThe ADNS-3040 has three power-saving modes. Each mode has a different motion detection period, affecting response time to mouse motion (Response Time). The sensor automatically changes to the appropriate mode, depending on the time since the last reported motion (Downshift Time). The parameters of each mode are shown in the following table.Motion Pin TimingThe motion pin is a level-sensitive output that signals the micro-controller when motion has occurred. The motion pin is lowered whenever the motion bit is set; in other words, whenever there is data in the Delta_X or Delta_Y registers. Clearing the motion bit (by reading Delta_Y and Delta_X, or writing to the Motion register) will put the motion pin high.LED ModeFor power savings, the LED will not be continuously on. ADNS-3040 will flash the LED only when needed. Synchronous Serial PortThe synchronous serial port is used to set and read pa-rameters in the ADNS-3040, and to read out the motion information.The port is a four wire serial port. The host micro-con-troller always initiates communication; the ADNS-3040 never initiates data transfers. SCLK, MOSI, and NCS may be driven directly by a micro-controller. The port pins may be shared with other SPI slave devices. When the NCS pin is high, the inputs are ignored and the output is tri-stated.Mode Response Time(nominal)Downshift Time(nominal)Rest 116.5 ms 37 ms Rest 28 ms8.4 s Rest 3410 ms504 s The lines that comprise the SPI port:SCLK:Clock input. It is always generated by the master (the mi-cro-controller).MOSI:Input data. (Master Out/Slave In)MISO:Output data. (Master In/Slave Out)NCS:Chip select input (active low). NCS needs to be low to activate the serial port; otherwise, MISO will be high Z, and MOSI & SCLK will be ignored. NCS can also be used to reset the serial port in case of an error.Chip Select OperationThe serial port is activated after NCS goes low. If NCS is raised during a transaction, the entire transaction is aborted and the serial port will be reset. This is true for all transactions. After a transaction is aborted, the nor-mal address-to-data or transaction-to-transaction delay is still required before beginning the next transaction. To improve communication reliability, all serial transac-tions should be framed by NCS. In other words, the port should not remain enabled during periods of non-use because ESD and EFT/B events could be interpreted as serial communication and put the chip into an unknown state. In addition, NCS must be raised after each burst-mode transaction is complete to terminate burst-mode. The port is not available for further use until burst-mode is terminated.MOSI Driven by Micro ControllerNCSFigure 13. Write OperationFigure 14. MOSI Setup and Hold TimeSCLKSCLK MOSIMISONCS Figure 16. MISO Delay and Hold TimeSCLKMOSIsetup,MOSISCLK MISOt Write OperationWrite operation, defined as data going from the micro-controller to the ADNS-3040, is always initiated by the micro-controller and consists of two bytes. The first byte contains the address (seven bits) and has a “1” as its MSB to indicate data direction. The second byte contains the data. The ADNS-3040 reads MOSI on rising edges of SCLK.Read OperationA read operation, defined as data going from the ADNS-3040 to the micro-controller, is always initiated by the micro-controller and consists of two bytes. The first byte contains the address, is sent by the micro-controller over MOSI, and has a “0” as its MSB to indicate data direction. The second byte contains the data and is driven by theADNS-3040 over MISO. The sensor outputs MISO bits on falling edges of SCLK and samples MOSI bits on every rising edge of SCLK.NOTE:The 0.5/f SCLK minimum high state of SCLK is also the minimum MISO data hold time of the ADNS-3040. Since the falling edge of SCLK is actually the start of the next read or write command, the ADNS-3040 will hold the state of data on MISO until the falling edge of SCLK.SCLKFigure 17. Timing between two write commandsWrite OperationNext Read OperationSCLKFigure 18. Timing between write and read commandsNext Read or Write OperationRead Operationt & tSCLKFigure 19. Timing between read and either write or subsequent read commandsRequired timing between Read and Write CommandsThere are minimum timing requirements between read and write commands on the serial port.If the rising edge of the SCLK for the last data bit of the second write command occurs before the required delay (t SWW ), then the first write command may not complete correctly.If the rising edge of SCLK for the last address bit of the read command occurs before the required delay (t SWR ), the write command may not complete correctly.During a read operation SCLK should be delayed at least t SRAD after the last address data bit to ensure that the ADNS-3040 has time to prepare the requested data. The falling edge of SCLK for the first address bit of either the read or write command must be at least t SRR or t SRW after the last SCLK rising edge of the last data bit of the previ-ous read operation.Burst Mode OperationBurst mode is a special serial port operation mode that may be used to reduce the serial transaction time for a motion read. The speed improvement is achieved by continuous data clocking from multiple registers with-out the need to specify the register address, and by not requiring the normal delay period between data bytes. Burst mode is activated by reading the Motion_Burst register. The ADNS-3040 will respond with the contents of the Motion, Delta_Y, Delta_X, SQUAL, Shutter_Upper, Shutter_Lower and Maximum_Pixel registers in that order. The burst transaction can be terminated after the first 3 bytes of the sequence are read by bringing the NCS pin high. After sending the register address, the micro-controller must wait t SRAD and then begin reading data. All data bits can be read with no delay between bytes by driving SCLK at the normal rate. The data is latched into the output buffer after the last address bit is received. After the burst transmission is complete, the micro-controller must raise the NCS line for at least t BEXIT to terminate burst mode. The serial port is not available for use until it is reset with NCS, even for a second burst transmission.Notes on Shutdown and Forced RestThe ADNS-3040 can be set to Rest mode through the Configuration_Bits register (0x11). This is to allow for further power savings in applications where the sensor does not need to operate all the time.The ADNS-3040 can be set to Shutdown mode by assert-ing the SHTDWN pin. For proper operation, SHTDWN pulse width must be at least t STDWN . Shorter pulse widths may cause the chip to enter an undefined state. In addition, the SPI port should not be accessed when SHTDWN is asserted. (Other ICs on the same SPI bus can be accessed, as long as the sensor’s NCS pin is not as-serted.) The table below shows the state of various pins during shutdown. After deasserting SHTDWN, a full reset must be initiated. Wait t WAKEUP before accessing the SPI port, then write 0x5A to the POWER_UP_RESET register. Any register settings must then be reloaded.* NCS pin must be held to 1 (high) if SPI bus is shared with other devices. It can be in either state if the sensor is the only device in addi-tionto the microcontroller.Note:There are long wakeup times from shutdown and forced Rest. These features should not beused for power management during normal mouse motion.Notes on Power-upThe ADNS-3040 does not perform an internal power up self-reset; the POWER_UP_RESET register must be written every time power is applied. The appropriate sequence is as follows:1. Apply power2. Drive NCS high, then low to reset the SPI port3. Write 0x5a to register 0x3a4. Read from registers 0x02, 0x03 and 0x04 (or read these same 3 bytes from burst motionregister 0x42) one time regardless the state of the motion pin.During power-up there will be a period of time after the power supply is high but before any clocks are available. The table below shows the state of the various pins dur-ing power-up and reset.Pin On Power-Up NCS high before reset NCS Low before reset After Reset NCS functional high low functional MISO undefined undefined functional dependson NCS SCLK ignored ignored functional dependson NCS MOSI ignored ignored functional dependson NCS XY_LED undefined undefined undefined functional MOTION undefined undefined undefined functional SHT-DWNmust be lowmust belowmust be lowfunctionalState of Signal Pins After VDD is ValidPin SHTDWN active NCS Functional* MISO Undefined SCLK Undefined MOSI Undefined XY_LED Low current MOTIONUndefinedSCLKt SRADFigure 20. Motion Burst TimingRegistersThe ADNS-3040 registers are accessible via the serial port. The registers are used to read motion data and status as well as to set the device configuration.Address Register Read/Write Default Value0x00Product_ID R0x0D0x01Revision_ID R0x00x0 Motion R/W0x000x03Delta_Y R Any0x04Delta_X R Any0x05SQUAL R Any0x06Shutter_Upper R Any0x07Shutter_Lower R Any0x08Maximum_Pixel R Any0x09Pixel_Sum R Any0x0a Minimum_Pixel R Any0x0b Pixel_Grab R/W Any0x0c CRC0R Any0x0d CRC1R Any0x0e CRC R Any0x0f CRC3R Any0x10Self_Test W0x11Configuration_Bits R/W0x030x1 -0x d Reserved0x e Observation R/W Any0x f-0x38Reserved0x3a POWER_UP_RESET W0x3b-0x3d Reserved0x3e Inverse_Revision_ID R0xFD0x3f Inverse_Product_ID R0xF0x4 Motion_Burst R AnyProduct ID Address: 0x00Access: Read Reset Value: 0x0DBit76543210Field PID7PID6PID5PID4PID3PID PID1PID0Data Type: 8-Bit unsigned integerUSAGE: This register contains a unique identification assigned to the ADNS-3040. The value in this register does not change; it can be used to verify that the serial communications link is functional.Revision ID Address: 0x01Access: Read Reset Value: 0x02Bit76543210Field RID7RID6RID5RID4RID3RID RID1RID0 Data Type: 8-Bit unsigned integerUSAGE: This register contains the IC revision. It is subject to change when new IC versions are released.Motion Address: 0x02Access: Read/Write Reset Value: 0x00Bit76543210Field MOT PIXRDY PIXFIRST OVF Reserved Reserved Reserved ReservedData Type: Bit field.USAGE: Register 0x02 allows the user to determine if motion has occurred since the last time it was read. If the MOT bit is set, then the user should read registers 0x03 and 0x04 to get the accumulated motion. Read this register before reading the Delta_Y and Delta_X registers.Writing anything to this register clears the MOT and OVF bits, Delta_Y and Delta_X registers. The written data byte is not saved.Internal buffers can accumulate more than eight bits of motion for X or Y. If either one of the internal buffers overflows, then absolute path data is lost and the OVF bit is set. This bit is cleared once some motion has been read from the Delta_X and Delta_Y registers, and if the buffers are not at full scale. Since more data is present in the buffers, the cycle of reading the Motion, Delta_X and Delta_Y registers should be repeated until the motion bit (MOT) is cleared. Until MOT is cleared, either the Delta_X or Delta_Y registers will read either positive or negative full scale. If the motion register has not been read for long time, at 400 cpi it may take up to 16 read cycles to clear the buffers, at 800 cpi, up to 32 cycles. To clear an overflow, write anything to this register.The PIXRDY bit will be set whenever a valid pixel data byte is available in the Pixel_Dump register. Check that this bit is set before reading from Pixel_Dump. To ensure that the Pixel_Grab pointer has been reset to pixel 0,0 on the initial write to Pixel_Grab, check to see if PIXFIRST is set to high.Field Name DescriptionMOT Motion since last report0 = No motion1 = Motion occurred, data ready for reading in Delta_X and Delta_Y registersPIXRDY Pixel Dump data byte is available in Pixel_Dump register0 = data not available1 = data availablePIXFIRST This bit is set when the Pixel_Grab register is written to or when the complete pixel array has been read, initiating an increment to pixel 0,0.0 = Pixel_Grab data not from pixel 0,01 = Pixel_Grab data is from pixel 0,0OVF Motion overflow, ∆Y and/or ∆X buffer has overflowed since last report0 = no overflow1 = Overflow has occurredDelta Y Address: 0x03access: ReadReset Value: UndefinedBit76543210X 7X 6X 5X 4X 3XX 1X 0Data Type: Eight bit 2’s complement number.USAGE: Y movement is counts since last report. Absolute value is determined by resolution. Reading clears the reg-ister.00010 7E 7F+1 7+1 6+1+ FFFE 81800-1- -1 7-1 8MotionDelta_Y NOTES: Avago Technologies RECOMMENDS that registers 0x03 and 0x04 be read sequentially.Delta X Address: 0x04Access: ReadReset Values: UndefinedBit7654321Data Type: Eight bit 2’s complement number.USAGE: X movement is counts since last report. Absolute value is determined by resolution. Reading clears the reg-ister.00010 7E 7F+1 7+1 6+1+FFFE 81800-1--1 7-1 8MotionDelta_XNOTES: Avago Technologies RECOMMENDS that registers 0x03 and 0x04 be read sequentially.SQUAL Address: 0x05Access: ReadReset Value: UndefinedBit76543210SQ 7SQ 6SQ 5SQ 4SQ 3SQSQ 1SQ 0Data Type: Upper 8 bits of a 9-bit unsigned integer.USAGE: SQUAL (Surface Quality) is a measure of the number of valid features visible by the sensor in the current frame.The maximum SQUAL register value is 167. Since small changes in the current frame can result in changes in SQUAL, variations in SQUAL when looking at a surface are expected. The graph below shows 500 sequentially acquired SQUAL values, while a sensor was moved slowly over white paper. SQUAL is nearly equal to zero, if there is no surface below the sensor. SQUAL is typically maximized when the navigation surface is at the optimum distance from the imaging lens (the nominal Z-height).Figure 21. SQUAL values (white paper)Mean SQUAL vs Z (white paper)102030405060 1.61.822.2 2.4 2.6 2.833.2Delta from Nominal Focus (2.55mm)S q u a l V a l u e (c o u n t )Figure 22. Mean SQUAL vs. Z (white paper)14791 141619 1 4 6 83133363840434548CountS q u a l v a l u e。
016 铬酐安全技术说明书(MSDS)
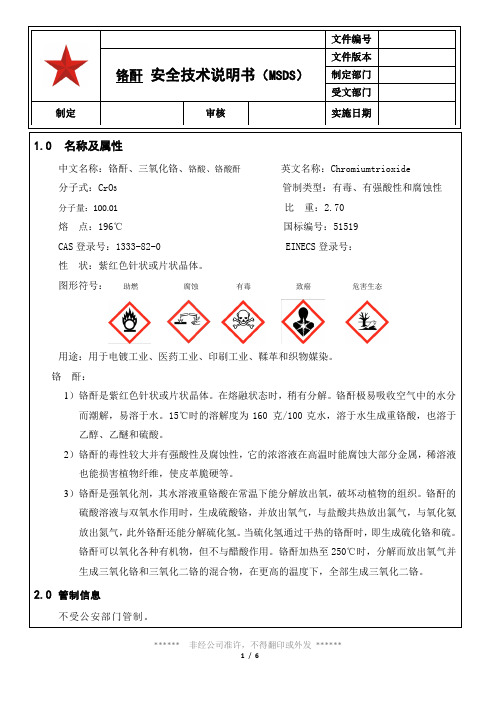
1.0名称及属性
中文名称:铬酐、三氧化铬、铬酸、铬酸酐英文名称:Chromiumtrioxide
分子式:CrO3管制类型:有毒、有强酸性和腐蚀性
分子量:100.01 比重:2.70
熔点:196℃国标编号:51519
CAS登录号:1333-82-0 EINECS登录号:
性状:紫红色针状或片状晶体。
图形符号:助燃腐蚀有毒致癌危害生态
用途:用于电镀工业、医药工业、印刷工业、鞣革和织物媒染。
铬酐:
1)铬酐是紫红色针状或片状晶体。
在熔融状态时,稍有分解。
铬酐极易吸收空气中的水分而潮解,易溶于水。
15℃时的溶解度为160 克/100克水,溶于水生成重铬酸,也溶于
乙醇、乙醚和硫酸。
2)铬酐的毒性较大并有强酸性及腐蚀性,它的浓溶液在高温时能腐蚀大部分金属,稀溶液也能损害植物纤维,使皮革脆硬等。
3)铬酐是强氧化剂,其水溶液重铬酸在常温下能分解放出氧,破坏动植物的组织。
铬酐的硫酸溶液与双氧水作用时,生成硫酸铬,并放出氧气,与盐酸共热放出氯气,与氧化氨
放出氮气,此外铬酐还能分解硫化氢。
当硫化氢通过干热的铬酐时,即生成硫化铬和硫。
铬酐可以氧化各种有机物,但不与醋酸作用。
铬酐加热至250℃时,分解而放出氧气并
生成三氧化铬和三氧化二铬的混合物,在更高的温度下,全部生成三氧化二铬。
2.0管制信息
不受公安部门管制。