涂装线验证工作及标准参数表
油漆-涂装线前质量检验标准
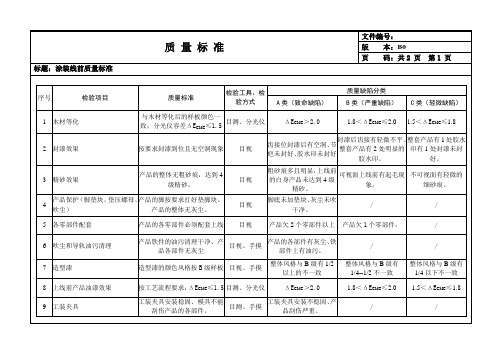
/
7
造型漆
造型漆的颜色风格按B级样板
目视、手摸
整体风格与B级有1/2以上的不一致
整体风格与B级有1/4--1/2不一致
整体风格与B级有1/4以下不一致
8
上线前产品油漆效果
按工艺流程要求;ΔECMC≤1.5
目测、分光仪
ΔECMC>2.0
1.8<ΔECMC≤2.0
1.5<ΔECMC≤1.8
9
工装夹具
工装夹具安装稳固、模不能刮伤产品的各部件。
4
产品保护(脚垫块、垫压螺母、吹尘)
产品的脚按要求打好垫脚块、产品的整体无灰尘。
目视
脚底未加垫块、灰尘未吹干净。
/
/
5
各零部件配套
产品的各零部件必须配套上线
目视
产品欠2个零部件以上
产品欠1个零部件。
/
6
吹尘和导轨油污清理
产品铁件的油污清理干净、产品各部件无灰尘
目视、手摸
产品的各部件有灰尘、铁部件上有油污。
编制
审核
批准
质量标准
文件编号:
版本:B0
页码:共2页第1页
标题:涂装线前质量标准
序号
检验项目
质量标准
检验工具、检验方式
质量缺陷分类
A类(致命缺陷)
B类(严重缺陷)
C类(轻微缺陷)
1
木材等化
与木材等化后的样板颜色一致;分光仪容差ΔECMC≤1.5
目测、分光仪
ΔECMC>2.0
1.8<ΔECMC≤2.0
1.5<ΔECMC≤1.8
2
封漆效果
按要求封漆到位且无空洞现象
目视
齿接位封漆后有空洞、节疤未封好、胶水印未封好
涂行业各类检验标准汇总
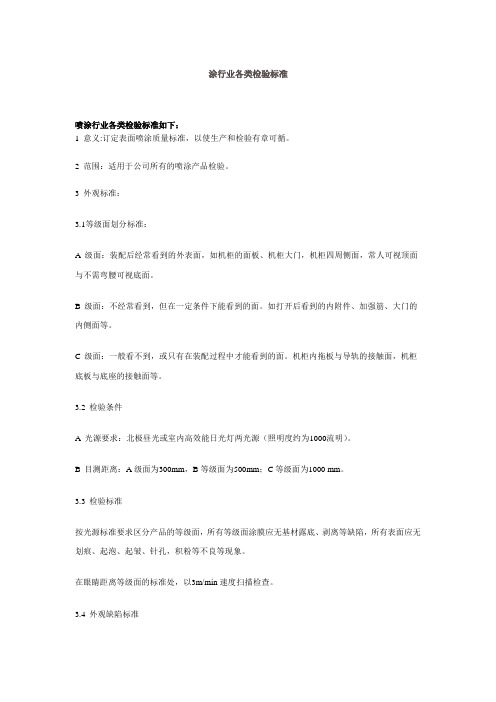
涂行业各类检验标准喷涂行业各类检验标准如下:1 意义:订定表面喷涂质量标准,以使生产和检验有章可循。
2 范围:适用于公司所有的喷涂产品检验。
3 外观标准:3.1等级面划分标准:A级面:装配后经常看到的外表面,如机柜的面板、机柜大门,机柜四周侧面,常人可视顶面与不需弯腰可视底面。
B级面:不经常看到,但在一定条件下能看到的面。
如打开后看到的内附件、加强筋、大门的内侧面等。
C级面:一般看不到,或只有在装配过程中才能看到的面。
机柜内拖板与导轨的接触面,机柜底板与底座的接触面等。
3.2检验条件A光源要求:北极昼光或室内高效能日光灯两光源(照明度约为1000流明)。
B目测距离:A级面为300mm,B等级面为500mm;C等级面为1000 mm。
3.3检验标准按光源标准要求区分产品的等级面,所有等级面涂膜应无基材露底、剥离等缺陷,所有表面应无划痕、起泡、起皱、针孔,积粉等不良等现象。
在眼睛距离等级面的标准处,以3m/min速度扫描检查。
3.4外观缺陷标准判定标准见附表一。
4 尺寸标准附表一:表面缺陷判定标准:5性能标准5.1喷涂色板制作A、在烘烤时,每一炉均需制作2件色板,以备性能测试需要。
取与制品同材质的金属板,尺寸80×120,与产品正常条件下加工,出炉后标识好粉号、固化条件、日期与时间,并由QE签名经确认后编号命名登记管理。
一件测试用,一件存档。
B、制程喷粉色板有效期限为二年,保存在室温下,保存温湿度为70±15%,保存环境为无任何光线照射。
5.2 非破坏性检验检验项目光泽:使用光泽计来判定,入射角度60°,±5%误差为检验合格。
色泽:颜色须符合设计图纸或与色板比较无明显差异,使用色差仪进行检测,推荐HP-200精密色差仪5.3破坏性检验5.3.1附着力测试:百格试验法:喷涂后,取一随炉色板,在涂膜面上,按间隔1mm纵横平行刻画11道,以适当的力度(划痕以露出基体为准)在喷涂面划成100个方格,再用强力透明胶覆盖按紧,呈45度角,然后突然撕掉,此时检查方格内之物是否掉落,1格为百分之一,验收标准为5级,即脱落数量为不超过5个方格为合格。
涂装过程检验记录表

涂装过程检验记录表---1. 检验概述本文档记录了涂装过程中的检验记录,旨在确保涂装工序的质量和合规性。
---2. 检验内容2.1 涂装前准备- 检查涂装设备是否完好并运作正常。
- 检查涂料是否符合要求,包括颜色、粘度、干燥时间等。
- 检查工件的表面处理是否完备。
2.2 涂装过程- 检查涂装人员是否佩戴防护设施,如手套、眼镜、防护服等。
- 检查涂料的搅拌情况,确保颜料分散均匀。
- 涂装过程中定期检查喷枪、喷嘴等设备的清洁和磨损情况。
- 检查涂装过程中的湿度和温度是否符合要求。
2.3 涂装后处理- 检查涂装表面的质量,如有无气泡、流挂、起皱等缺陷。
- 检查涂装层厚度是否符合要求。
- 检查涂装工件的标识和编号是否清晰可见。
- 检查涂装过程产生的废料的处理情况。
---3. 检验记录---4. 检验结果分析根据上述检验记录,总体来看,涂装过程中的准备工作基本符合要求,涂装过程也较为顺利。
但在涂装后处理阶段发现了涂装表面有缺陷的情况,需要进一步分析原因并采取相应的改进措施。
同时,其他方面的检验结果基本符合要求,反映了涂装工序的整体质量较好。
---5. 改进建议- 对涂装后处理过程进行审查,分析缺陷产生的原因,并制定改进方案。
- 加强涂装人员防护设施的宣传和培训,确保其正确佩戴和使用。
- 定期对涂装设备进行维护和保养,确保其运作正常。
- 强化废料处理的管理,确保涂装过程的环保合规。
---该文档仅作为涂装过程检验的参考记录,未来可根据实际情况进行补充和修改。
同时,检验结果和改进建议也需要根据具体需求进行调整。
以上所述仅供参考,具体操作请根据实际情况进行。
希望以上内容能帮到您,如有任何问题或需要进一步帮助,请随时告知。
涂装工作检查评分表

涂装工作检查评分表
1. 项目背景
本评分表旨在帮助检查员对涂装工作进行全面评估,确保工作质量符合标准要求。
通过准确评分,可以及时发现问题,及早进行调整和改进。
2. 评分标准
2.1 外观质量
2.2 工艺标准
3. 检查步骤
1. 根据评分表的评分项,逐一检查涂装工作的质量。
2. 对每一项进行评分,根据实际情况给予相应的分值。
3. 累计各项评分得到总分,并根据总分进行等级评定。
4. 等级评定
- 总分在85分及以上,评定为优秀。
- 总分在70分至84分之间,评定为良好。
- 总分在60分至69分之间,评定为合格。
- 总分在0分至59分之间,评定为不合格。
5. 结论
根据涂装工作检查评分表的评分结果,及时发现问题,采取必要的改进措施,以确保涂装工作质量符合标准要求,并达到优秀的水平。
所有评分和评定应基于客观的实际检查结果,并准确记录在评分表中。
本文档仅为参考,请根据实际需要进行修改和调整。
涂装检验标准及检验方法

用一个200mm长的Scotch610胶带粘在切割面上,停顿90秒的时 间,然后撕下胶带,并用橡皮去擦胶带粘过的地方。
胶带法判定:
没有可视的氧化皮粘在胶带上视为合格,否则视为不合格。
基体检验标准及方法
9、焊接形成的硅沉积物
A、图例
B、目标要求 A1
A2 AC AF B C
C、检验方法:目视
油漆检验标准及方法
9、硬度
A、图例
B、目标要求 A1
A2 ≥HB
B C
C、检验方法:铅笔硬度仪
油漆检验标准及方法
10、针孔
A、图例
B、目标要求 A1
不允许 A2 B 3,直径≤1mm,无聚集 C 5,直径≤1mm,无聚集
C、检验方法:目视
D、针孔分析
可能原因 施工温度太高,溶剂挥发太快
被涂表面存在水分、油分 油漆温度过低(冬天易出现)
C、检验方法:目视
不允许 如果不是在装配位置可见,则可接受 均匀的图形深度不超过0.5mm,则接受 均匀的图形深度不超过0.5mm,则接受 如果不是在装配位置可见,则可接受 如果不是在装配位置可见,则可接受
基体检验标准及方法
3、划痕
A、图例
B、目标要求 A1 A2 AC AF B C
不允许
不超过3个,长度不超过20mm 不超过3个,长度不超过20mm 不超过3个,长度不超过20mm 不超过3个,长度不超过30mm 不超过3个,长度不超过30mm
AC 不超过3个,直径≤5mm,深度≤2mm
AF 不超过3个,直径≤5mm,深度≤2mm
B
不超过5个,直径不超过7mm
C
不超过5个,直径不超过7mm
C、检验方法:目视,钢板尺
喷涂生产线检验表1
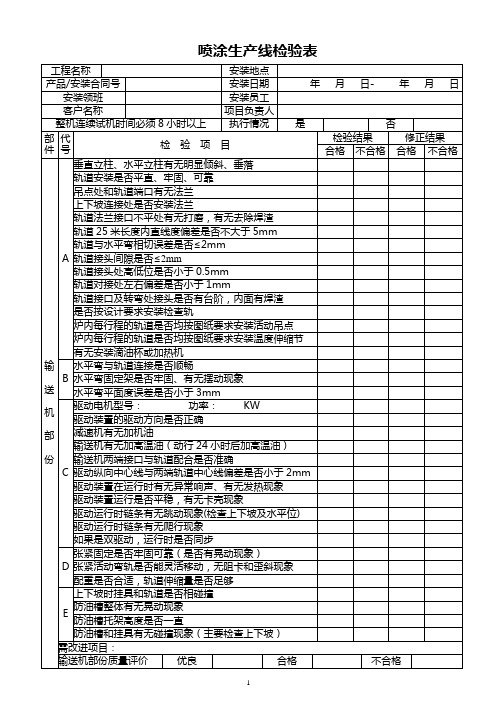
风管直出房顶时,房顶是否漏雨
几条排风支管同出一条主管时,各支管有无加装碟阀
需改进项目:
喷漆系统质量评价
优良
合格
不合格
部件
代号
检验项目
检验结果
修正结果
合格
不合格
合格
不合格
油
箱
水
箱
S
油箱所有管件有无渗漏现象
水箱所有管件有无漏水现象
水冷风机冷热水循环管长度是否适中
水箱、油箱上是否有液位显示管
优良
合格
不合格
完工
检验
整体完工后,是否钉上公司铭牌
整体完工后,是否清洁施工现场
整体质量评价
优良
合格
不合格
验
收
部
门
意
见
技术部:
年 月 日
工程部:
年 月 日
售后服务部:
年 月 日
现场施工领班:
年月日
经理助理:
年 月 日
总经理:
年 月 日
风机轴承有无加高温油
I
皮带有无磨擦皮带罩
风叶运行是否正常
风机有无异常噪音及发热现象
J
加热器火筒是否能配燃烧机火筒
火筒轴线与炉膛筒轴线有无向上或向下倾斜
加长热风风管和加热室连接处有无上法兰加棉毡
热风风管有无漏风现象
热风风管外包是否合格
加热室和炉体连接部位有无漏气现象
炉内散热排管对接处有无漏气现象
风机与风管连接处有无加密封垫,是否有漏气现象
热风循环风机水箱有无热水回流
热风循环风机管路是否畅通
水箱进出口安装是否正确
水箱进水口位置是否低于顶部200mm
涂装外观 检验 标准

内容页次1.目的 2 2.范围 2 3.优先原则 2 4.外观 2 5.表面划分 4 6.塑料件 4 7.金属板金件 5 8.铸造件8 9.油漆和喷涂件9 10.产品标识101.0.目的该程序是为了建立和描述用来判定零件、装配件、产品外观质量合格与否的准则2.0.范围2.1凡本公司所生产的和供应商提供的所有产品,包括零件、装配件和成品。
如客户有特定要求和规范,应以要求的规范为准。
2.2本规范适用于所有的塑料件、金属板金件、丝印和喷涂件及产品的标识。
3.0.优先原则在发生矛盾时,采用以下优先原则:3.1.文件应与特别规定的适用性上保持一致,如零件的公差。
3.2.采购合同或专门条款。
3.3.现用的图纸或要求。
3.4.本外观标准。
4.0.外观4.1.总体要求在本标准的各个部分中,外观检查使用时间和距离来描述。
该标准可用于员工培训,任何加工过程的外观表面质量控制以及判定产品合格与否。
4.2.观察条件所有检查都应在正常灯光下,独立的标准的观察条件下进行。
检查中,仅肉眼检查之为准。
零件表面检查不需任何放大帮助,45°观察角下进行。
A级表面在检查时,可旋转表面,利用最强的反射。
B级、C级则不需要。
5.0.表面划分A级(装饰表面):用户经常看到的表面。
例如底座,面板表面等等。
B级(适当装饰表面):不翻动时偶然才会看到的表面。
例如架式底盘的两侧和顶部,后面等等。
C级(非装饰表面):翻动才会看到的表面。
例如底盘的外部和内部零件等6.0.塑料件6.1.接受标准6.1.1. 可接受的A、B、C级缺陷都应不影响产品的装配或功能,如有影响就应自动拒收。
6.1.2. 检查要求和观察条件参考第4部分(外观标准/检验要求)6.1.3. 公差表中是指50平方英寸(约320cm2)范围内允许存在缺陷的数量,超过50平方英寸其缺陷数按比例增加,如同时存在2种以上的缺陷应拒收。
6.3. 缺陷定义6.3.1. 突起:表面上局部高出(如水泡,肿块,山脊状)6.3.2. 变色:与原色不同,或在同一零件中颜色不一致6.3.3. 流痕:表面呈波纹、条纹状6.3.4. 雾状:透明件中呈现云雾状6.3.5. 凹坑:零件表面的小弹坑6.3.6. 斑点:粘在表面上的细小颗粒6.3.7. 划伤:表面上的线状浅槽6.3.8. 缩水:表面局部下陷6.3.9. 溶接线:流料溶接处形成的可见线6.3.10.色泽差:表面光泽不一致6.3.11.分型线/飞边:零件在模具接合点处形成的可见线或突出线6.3.12.质地变化:对于同一取样零件切片上有明显的质地结构变化6.3.13.脱模:喷射润滑油,易于零件脱模6.3.14.色差:零件颜色与色板不同6.4. 公差表(塑胶件)每个表面的缺陷数量不得超过可接受的限度,此表可用于检验人员的培训和判定产品的拒收。
涂装自动线工艺参数表[空白模板]
![涂装自动线工艺参数表[空白模板]](https://img.taocdn.com/s3/m/80ea0089168884868662d6e1.png)
位置 喷枪喷距cm 喷枪高度 喷枪气压kg
版本:V02
记录保管期限:5年
制作:
审核:
核准:
批量生产烘烤时间
底漆喷枪 喷枪一 喷枪二 喷枪三 喷枪四 喷枪五 喷枪六 喷枪七 喷枪八
位置
PU/橡胶漆 喷枪喷距cm
PU/3.H 注意:
喷枪高度
喷枪气压 kg
中漆枪数 喷枪一 喷枪二 喷枪三 喷枪四 喷枪五 喷枪六 喷枪七 喷枪八
位置
备注: 1.膜厚达标后才能进行小批量试产,小批量试产成功后必须要先填写参数表方可上线. 2.产品头部,侧边,底部,表面,都必须贴膜厚,并都要达到规定膜厚。 2.uv能量上中下最低保证在1000mj/CM²±200mj。
线别/粘度
膜厚 滤网目数
文件编码
产 品 示 图
壳体名称 版次
泵浦压力 (KG)
UV能量
顶灯 侧灯 低灯
第一组灯 强光 中光 弱光
强光
第二组灯
中光
弱光
UV能量控制范围:
加油房 卫生状
况
喷房/喷枪 卫生状况 (OK/KG)
喷房温度 (℃)
喷房湿度 (%)
线体链速(m/min)
喷枪喷距cm
喷枪高度 喷枪气压kg 面漆喷枪 喷枪一 喷枪二 喷枪三 喷枪四 喷枪五 喷枪六 喷枪七 喷枪八
线体:
涂装自动线工艺参数表
日期:
客户 素材颜色
涂层
油漆编号
油漆颜色
机型名称 喷涂颜色 供应商 开油比例
底漆
固化剂
助剂
底漆稀释剂
中漆
固化剂
中漆稀释剂
助剂
面漆光油
面漆哑油
固化剂
喷涂参数要求

槽液 PH 值:7.5-9
磷化
游离酸度
1-2Pt(手动)
0.8-1.5Pt(自 动)
槽液总酸度:25-40 点
促进剂浓度:2pt-5pt
电泳
12-16%(手动) 槽液固体份
12-14%(自动)
槽液电导率:1200± 300us/cm
PH 值:6-6.5
烘干
老线烘干温度:170°-180° 新线烘干温度:170°-200°
1、检查记录表 2、查看是否按照工艺规 定进行倒槽。
1、检查记录表
广范试纸进行测试对比 2、查看是否按照工艺规定 进行倒槽。
3 酸洗 4 表调
婆梅氏比重:13-17 表调槽液 PH 值:7.5-9
婆梅氏比重计对比 PH 试纸对比
检查记录表 1、检查记录表 2、查看是否按照工艺规定 进行倒槽。
1、槽液游离酸度(FA):1-2 点(手
1、检查记录表
动线)/0.8-2Pt(自动线); 5 磷化★
2、促进剂浓度 2pt-5pt; 3、槽液总酸度:25-40 点。
利用酚酞、酚蓝滴定测 2、查看是否按照工艺规定
试
进行倒槽。
1、槽液固体份:12-16%(手动线)
1、检查记录表
/12-14%(自动线); 6 电泳★
烤箱、电导率仪、PH 仪 2、查看是否按照工艺规定
品控课:
车 间:
注:整改措施现场不能确定的,相应课室须明确后续的得出时间,否则视为 1 个工作日内完成。
5
10-13 秒(冬季)
泳后漆膜厚度 漆膜厚度 中涂漆膜厚度
成品漆膜厚度
附着力应达到 1 级
成品质量
硬度达到 1H
光泽度:≥50Gs
空压系统压力:0.6-0.8MPa
涂装检验标准
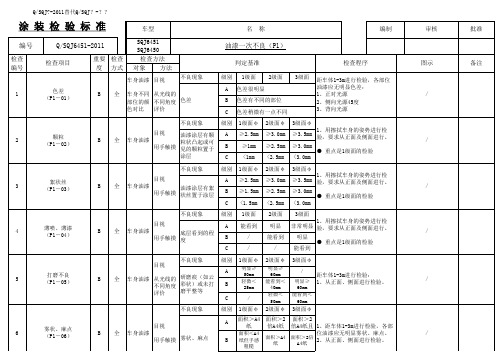
/
1级面φ
2级面φ
3级面φ
6
雾状、麻点 (P1-06)
B
全
车身油漆 用手触摸 雾状、麻点
面积>A4 面积>2 面积>2 纸 倍A4纸 倍A4纸且 1、距车体1-3m进行检验,各部 粗糙 位油漆应无明显雾状、麻点。 面积<A4 面积>A4 面积>2倍 纸但手感 2、从正面、侧面进行检验。
粗糙 纸 A4纸
/ 明显≥ 60mm 能看到< 60mm
2
颗粒 (P1-02)
B
全
油漆涂层有颗 车身油漆 粒状凸起或可 用手触摸 见的颗粒置于 涂层 不良现象
目视
/
● 重点是1级面的检验
3
絮状丝 (P1-03)
目视 B 全 车身油漆 油漆涂层有絮 用手触摸 状丝置于涂层 不良现象
/
● 重点是1级面的检验
级别 A B C
非常明显 明显 能清楚看到
符号
年月日 2007.9 2008.4 2010.12
修 订 记 录 第一版 第二版 第三版
编 制
审 核
批 准
符号
年月日
修 订 记 录
编 制
审 核
批 准
四川汽车工业集团有限公司
质量部
2010年12月 编制
页码共 4 页Fra bibliotek1级面能看到 看到一点 /
2级面
清楚看到 能看到 看到一点
3级面 用擦拭车身的姿势进行检验, 要求从正面及侧面进行,从正 清楚看到 面、侧面进行检验。
/ 能看到
/
1级面
明显 能清楚看 到 /
2级面
非常明显 明显 能清楚看 到
17
油漆分线不良 (P1-17)
涂装检验规范

涂装质量检验规范1 目的为有效控制涂装作业的正常生产,确保产品质量,提高效益,防止因涂装不当导致结构件的防腐保护失效。
2 范围本标准规定了对涂装进行质量检验时应遵循的基本原则和控制内容。
本标准适用于涂装的质量控制,工艺纪律管理(基本要求、主要内容及考核办法)。
3 引用标准下列标准所包含的条文,通过在本标准中引用而构成为本标准的条文。
本标准出版时,所示版本均为有效。
所有标准都会被修订,使用本标准的各方应探讨使用下列标准最新版本的可能性。
GB/T 10300.5 质量管理和质量体系要素指南JB/Z 220 工序质量控制通则GB/T 19023 质量管理体系文件指南Q/XZ 200-2008 质量手册GB/T 15498 企业标准体系JB/T 5059-1991 特殊工序质量控制导则4涂装检验的基本原则4.1 涂装过程在整个工作期间易受操作者差错或有害环境的影响。
另外,要通过检查已完成的工作发现存在何种问题通常较为困难。
因此,在工作完成后再进行质量控制就不是一件容易的事。
检查人员(或任何质量控制人员)必须在工作进行过程中位于现场,并且对其进行始终如一的观察评价,才能对涂装过程作出准确判断。
4.2 操作人员、检验人员要经过技术培训和资格认证。
4.3 应对工作环境(杂质、温度、湿度、露点等)进行控制,以满足工艺文件的要求,必要时应加以验证。
4.4 检验和施工应严格遵循技术规范和质量管理等文件的要求,严格控制工艺参数及影响参数波动的各种因素,使涂装过程处于受控状态。
同时加强工艺方法的试验验证和反馈。
4.5 所用工艺材料、被加工物资应实行严格控制,必要时应进行复检。
4.6 必须使用经确认合格的模具、工装、设备和计量器具,并积极采用先进的检测技术和控制手段,对影响质量特性的主要因素进行快速、准确的检测和调整,减少质量波动。
4.7 检验员应检查涂装施工的整个过程,检查重点应放在表面处理和涂装施工的起始,以加强过程控制为主,辅以必要的多频次的工序检查,检查人员与质量保证人员对现场操作负有监督的责任和权限。
涂装工艺及验收技术标准
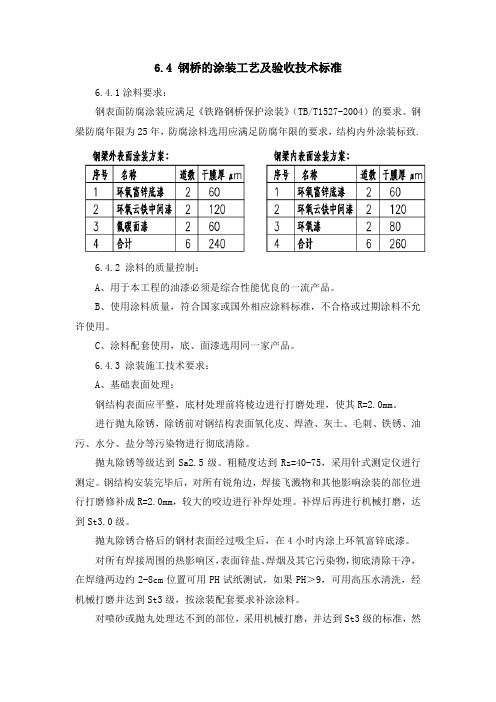
6.4 钢桥的涂装工艺及验收技术标准6.4.1涂料要求:钢表面防腐涂装应满足《铁路钢桥保护涂装》(TB/T1527-2004)的要求。
钢梁防腐年限为25年,防腐涂料选用应满足防腐年限的要求,结构内外涂装标致.6.4.2 涂料的质量控制:A、用于本工程的油漆必须是综合性能优良的一流产品。
B、使用涂料质量,符合国家或国外相应涂料标准,不合格或过期涂料不允许使用。
C、涂料配套使用,底、面漆选用同一家产品。
6.4.3 涂装施工技术要求:A、基础表面处理:钢结构表面应平整,底材处理前将棱边进行打磨处理,使其R=2.0mm。
进行抛丸除锈,除锈前对钢结构表面氧化皮、焊渣、灰土、毛刺、铁锈、油污、水分、盐分等污染物进行彻底清除。
抛丸除锈等级达到Sa2.5级。
粗糙度达到Rz=40-75,采用针式测定仪进行测定。
钢结构安装完毕后,对所有锐角边,焊接飞溅物和其他影响涂装的部位进行打磨修补成R=2.0mm,较大的咬边进行补焊处理。
补焊后再进行机械打磨,达到St3.0级。
抛丸除锈合格后的钢材表面经过吸尘后,在4小时内涂上环氧富锌底漆。
对所有焊接周围的热影响区,表面锌盐、焊烟及其它污染物,彻底清除干净,在焊缝两边约2-8cm位置可用PH试纸测试,如果PH>9,可用高压水清洗,经机械打磨并达到St3级,按涂装配套要求补涂涂料。
对喷砂或抛丸处理达不到的部位,采用机械打磨,并达到St3级的标准,然后按涂装配套要求补涂涂料。
B、涂装工艺:涂装方法:本工程制作安装采取刷涂、滚涂、有气喷涂及高压无气喷涂的多种方法涂装。
每道漆涂装时,先用板刷将边角、缝隙等处涂刷一遍,再采用滚涂或喷涂进行大面积涂撞。
常温下每道漆的涂装间隔时间为24小时。
如果因某些原因没按规定时间涂覆下道漆,并且间隔时间较长时,进行拉毛处理后再进行下道漆涂装。
再进行下道漆前要测定前道漆得干膜厚度,如达不到要求,需要进行补涂。
在整个涂装过程中,所用的各种涂料必须严格按规定的配制比例配漆,使用各自配套的专用稀释剂,配好后的涂料必须在规定时间内用完,否则失效。
涂装质量检查及标准
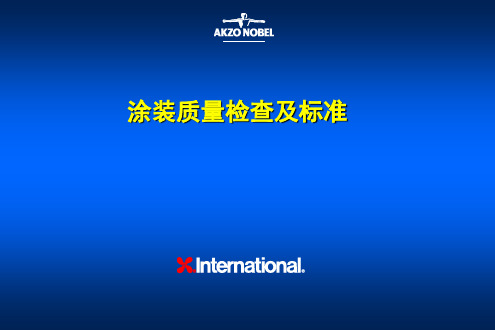
涂装检查
湿膜厚度(WFT)检测
破坏性检查(可以是非破坏性的) 过程检查 控制喷涂施工有效且实用的方法 不精确 不作为最终检查标准
Protective Coatings
涂装检查 湿膜厚度与干膜厚度的关系
不加稀释剂时 干膜厚度(DFT) 体积固体份(VS)% 加稀释剂时 干膜厚度 (1 +稀释剂体积%) 湿膜厚度(WFT)
涂装检查
表面清洁度检查
氧化皮的定性试验 –将硫酸铜酸性溶液涂在喷砂清理过的表面上 ,清洁的钢板上会出现闪亮的铜,但在氧化 皮上则呈现黑色
Protective Coatings
涂装检查
表面清洁度检查 可溶性铁的定量试验 –Merckoquant试验提供了反应水中所溶解的 铁量的指示试纸。为了表明该过程的定量特 性,必须使用控制的洗涤或揩拭技术 –一份已称量的蒸馏水(22.5毫升)用来洗涤15 厘米x15厘米(225平方厘米)见方的喷砂清理 过的表面。重复洗涤表面直至大多数污物- 如有的话,从表面洗下并保留。水样用指示 试纸测试,根据可溶铁的量,颜色发生变化 –该试验不决定氯化物,硫酸盐或其他特殊盐 类的量,只测定可溶性铁,以Fe++或Fe+++ 离子的形式呈现
Protective Coatings
涂装检查
表面清洁度检查
可溶性氯化物的定性试验 –试纸用硝酸银溶液(2%重量)湿润,然后压在 钢表面上,约20秒钟后剥下,用不含氯化物 的水彻底清洗。任何形成的氯化银留在试纸 上,再浸入照相显影液,都会被检测出来。 在有氯化物的地方呈现棕黑色。
Protective Coatings
干膜厚度总平均值:__________ 最低干膜厚度:________ 最高干膜厚度:__________ 符合配套情况,是 /否? :___________
整机涂装工艺规程及检验标准

涂装工艺、检验标准、质量要求一、工艺流程及技术要求油漆涂装工艺流程:1、铸件、结构件→抛丸室→手动抛丸→清理→人工打磨→喷底漆→自然干燥。
2、滑块部件:高性能及其变形产品系列产品,L36系列、L31系列、E36系列、E31系列等整体闭式半闭式单双点产品,JF36系列、JK36系列机床,F75G 系列、VH系列、SH系列机床-滑块、连杆(含连杆盖)在机加工完成后,转油漆工序按成品油漆标准进行涂装(不含滑块斑马线),转装配总装后不再油漆。
(使用带防护吊具,生产全过程注意油漆面防护)3、机身部件:(1)高性能等整体机身机床(不含VH系列、SH系列),机身在机加工完成后,转油漆工序,其内腔按成品油漆标准进行涂装,侧面安装电箱部位喷成机床主色;机床在完成传动部分装配(不再需翻身)后,机床立放进行成品油漆。
(使用带防护吊具,生产全过程注意油漆面防护)(2)其余分体机床的上横梁、立柱、底座及VH系列、SH系列机床机身,在机加工完成后转油漆工序,外表面及内腔均按成品油漆标准进行涂装;机床装配完成后不再油漆。
(使用带防护吊具,生产全过程注意油漆面防护)4、其他部件(导轨、工作台板除外):钣金件、走台围栏、蜗轮箱、大齿轮(刷黄漆)、管路等需油漆的机床所有的其他部件,转油漆工序完成成品油漆后进行装配。
(使用带防护吊具,生产全过程注意油漆面防护)5、导轨、工作台板、滑块斑马线:所有机床的导轨、工作台板、滑块斑马线在完成性能交验合格后进行成品油漆。
(使用帆布带吊绳、台板起吊专用工装安装工作台板)二、结构件(铸件)涂装工艺规程及检验标准1、抛丸1.1对转入抛丸工序的工件进行核实确认,并规范填写《抛丸工序记录表》,保证产品的可追溯性。
1.2操作前首先检查风机、管路输送等设备是否运转正常;喷丸服、视镜是否完好、输气管是否通畅,确认合格后方可经行抛丸工序的操作。
1.3经抛丸后的工件应达到表面无锈点、氧化皮、污垢。
要求达到瑞典分级表Sa2.5级,钢面呈均匀银白色金属光泽。
涂装检查员检验方法及标准
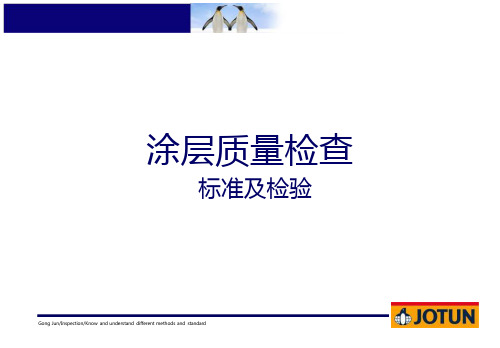
决定锈蚀等级的标准
ISO 8501
锈蚀等级A、B、C和D
Gong Jun/Inspection/Know and understand different methods and standard
10 15
46
20 50
8 20
Gong Jun/Inspection/Know and understand different methods and standard
污染物 – 油脂
• 表面油脂的检测并无标准方 法。
• 通常可采用三种经验方法测 定表面是否含有油脂:
– 表面淋水。 – 粉笔画线。
– 紫外光照射。
Gong Jun/Inspection/Know and understand different methods and standard
表面处理 – ISO 8501 / 1
• 表面清洁度的目测评估标准
• 未施工油漆的钢材表面锈蚀等级和处理 等级
• 采用不同磨料喷砂清洁后的钢材照片样 板
Gong Jun/Inspection/Know and understand different methods and standard
ISO 8502: 施工油漆或相似产品前钢材表面 处理 – 测试和评估表面清洁度
第六部分
* 第九部分
第十部分
油漆施工前表面可溶性杂质的取样 。Bresle方法
– 交点(4): 向上得到空气中 5 的水汽含量1克/公斤
– 交点(5): 露点温度- 15摄氏
度
涂装检验标准书
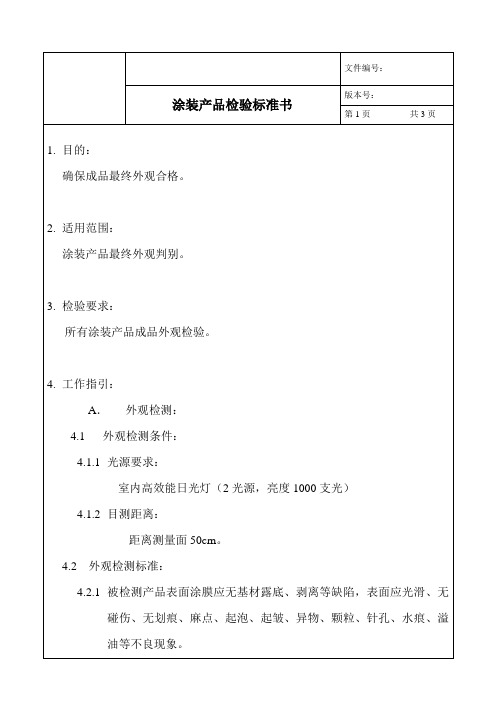
文件编号:涂装产品检验标准书版本号:第1页共3页1.目的:确保成品最终外观合格。
2.适用范围:涂装产品最终外观判别。
3.检验要求:所有涂装产品成品外观检验。
4.工作指引:A.外观检测:4.1 外观检测条件:4.1.1光源要求:室内高效能日光灯(2光源,亮度1000支光)4.1.2目测距离:距离测量面50cm。
4.2外观检测标准:4.2.1被检测产品表面涂膜应无基材露底、剥离等缺陷,表面应光滑、无碰伤、无划痕、麻点、起泡、起皱、异物、颗粒、针孔、水痕、溢油等不良现象。
4.2.2被检测产品表面色泽、光泽的要求:目测状态下与标准色板或样品基本一致,无色泽和光泽存在不均现象。
B.附着力测试:(百格测试法)4.3测试条件:4.3.1测试工具:刀片、强力透明胶。
4.3.2测试方法:在测试工件表面以间隔1mm纵横平行刻画11道,切割深度以将涂层切断至基体面为准,再用强力透明胶带贴紧覆盖方格面,呈45度角快速撕开然后检验方格内涂层是否剥离,验收合格标准为5%,即脱落涂层不超过5个方格数量为合格。
C.硬度测试:4.4测试条件:4.4.1测试工具:2H铅笔4.4.2测试方法:用削尖的2H铅笔与工件表面呈45度夹角,沿直尺方向推划15mm,用橡皮擦拭划痕后检查涂层表面无明显痕迹。
D.其他检验方法:(有耐腐蚀性测试:按照相关测试技术要求进行)4.5.对检验后产品的处理方法:4.5.1对检验合格后的产品应参照作业标准按不同要求进行包装、装箱,以保证产品表面保持清洁及在包装、运输过程中不因互相碰撞、摩擦造成不良。
包装产品在装板待运状态下应以缠绕膜进行包裹固定。
4.5.2 对检验出不合格的产品应按照不良品处理流程进行标示并分类放置,以便进行不良品修复工作。
4.5.3 对每批次产生的不良品应进行详细记录,并汇合生产部门查找原因,如情况严重品检员可要求停止生产进行查找,直至查明原因方可恢复生产修改记录年月日年月日修改码更改通知单号。
油漆涂装工艺与检验标准
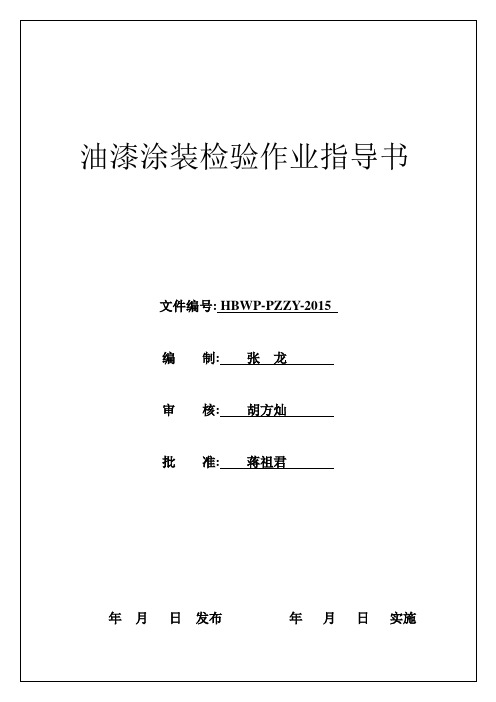
油漆涂装检验作业指导书文件编号: HBWP-PZZY-2015编制: 张龙审核: 胡方灿批准: 蒋祖君年月日发布年月日实施油漆质量检验作业指导书1 主要内容与适用范围本检验作业指导书规定了汽车零部件及总成产品的油漆涂层的检验内容与技术要求。
本检验作业指导书适用于河北王派车业有限公司自制件及所有外委、外协制品的油漆涂装质量检验。
2 引用标准下列标准包括的条文,通过在本检验作业指导书中的引用而构成本检验作业指导书的条文,在本检验作业指导书发布时,所示版本均为有效,所有标准都会被修订,使用本检验作业指导书的各方应探讨使用下列标准最新版本的可能性。
Q/LQB Y-4-2011 《汽车涂成标准》GB/T13452.2-2008 《色漆和清漆漆膜厚度的测定》GB/T 6739-2006 《硬度铅笔测试法》GB/T 9286-1998 《漆和清漆漆膜的规格实验》《自然耐候性试验标准》3 检验标准3.1 检验环境检验在生产现场的检验工位进行,当异地检验存在争议时,选用的检验场地应符合下列条件:3.1.1 环境整洁、空气清新、不应有明显影响检验作业的热气、湿气、烟尘。
3.1.2 检验场地长度和宽度至少应超出被检产品3m,地面和墙壁均为白色,且不应反光炫目。
3.1.3 采用日光灯照明,日光灯的影响,在垂直涂面呈上下方向,在水平涂面呈左右方向。
油漆质量检验作业指导书3.2 检验人员检验人员辨色力正常,视力在0.8以上(含校正后),检验人员应经过培训并得到授权。
3.3 检验仪器及量检具3.3.1 检验仪器:漆膜测厚仪。
3.3.1 量检具:钢板尺、中华牌高级绘图铅笔(H、HB、B三种规格),单面刀片等。
3.3.3 所有仪器及量检具应符合计量检定要求,并在有效的检定周期内。
4 检验内容4.1 表面油漆涂层质量表面油漆(包括装饰性面漆和防护性底漆)涂层质量检验包括:缺漆(露底)、颗粒、流痕、缩孔、起皱、桔皮、杂漆发花、擦伤划痕、砂纸纹、补漆雾圈、生锈、气泡、坑包、开裂脱落、涂层不干、底材凹凸等外观缺陷。
- 1、下载文档前请自行甄别文档内容的完整性,平台不提供额外的编辑、内容补充、找答案等附加服务。
- 2、"仅部分预览"的文档,不可在线预览部分如存在完整性等问题,可反馈申请退款(可完整预览的文档不适用该条件!)。
- 3、如文档侵犯您的权益,请联系客服反馈,我们会尽快为您处理(人工客服工作时间:9:00-18:30)。
一、 生产制程工艺数据
A.设备参数
序号 工艺名 喷淋 清洗 1 表面 前处理 11 清洗 槽数 设备总 h/纯 h/自来水 水切炉温 功率 水耗量 耗量 ℃ kw 2T 5T 110-150 设备参数 炉长m 干燥方式 H耗量/m3 燃烧机 台数 线速 烘烤时间h挂点数量 m/mi n 0.5 1660 2
无
无
无
无
补充水<10u 电导率仪 室温
N次
4H/次
管理核准:
文件审核:
工程作成:
ห้องสมุดไป่ตู้
4
水洗
自来水
0
2
0.8~1.5 1-2min
清洗工件 表面碱液
无
无
无
无
< 室温 1000us 电导率仪 /cm
1班/次
根据自来 水喷淋消 耗按照目 测进行补 充 取10ml试样与250ml锥 形杯 中,加入50ml去 离子水,在滴入5-8滴 指示剂(溴酚蓝)。 用0.1N的NaOH溶液滴 定至样品由蓝色。用 去0.1N的NaOH溶液的 毫升数即为游离酸的 点数。
7
水洗
自来水
0
2
0.8~1.5 1-2min
清洗工件 表面酸液
无
无
无
无
电导率仪 室温 <200us/cm
1班/次
4H/次
根据自来 水喷淋消 耗按照目 测进行补 充 1.用移液管取10ml的 0.042N的KMn4标准溶 液到150ml的锥形烧杯 中,加入50ml去离子 水稀释,再加入5ml的 50%的硫酸溶液 2. 用Bonderite4595槽 液以每秒3-4滴的速度 滴定至紫色退为淡黄 色
6
水洗
自来水
0
2
0.8~1.5 1-2min
清洗工件 表面酸液
无
无
无
无
电导率仪 室温 <300us/cm
1班/次
4H/次
根据自来 水喷淋消 耗按照目 测进行补 充
每班更换一次槽 液,每三天清洗 一次槽壁,每天 检测循环管口及 时发现阻塞并清 理 每班更换一次槽 液,每三天清洗 一次槽壁,每天 检测循环管口及 时发现阻塞并清 理
每班更换一次槽 液,每三天清洗 一次槽壁,每天 检测循环管口及 时发现阻塞并清 理 每班更换一次槽 液,每周清洗一 次槽壁,每天检 测循环管口及时 发现阻塞并清理 每班更换一次槽 液,每周清洗一 次槽壁,每天检 测循环管口及时 发现阻塞并清理 每月保养设备
10
纯水
纯水
0
2
0.8~1.5 1-2min
8
钝化EPP 纯水
0
5
0.8~1.5 1-2min
钝化增强 涂料与铝 Bonderit 机体的附 eM-NT 着力,增 4595 强涂层防 腐性能
40-50
初配槽: 无色酸性 添加12KG的 液体,能 4595 在铝合金 补充:加 表面产生 4595按照 薄的耐腐 0.25KG提升 性能 1点
室温
试管 烧杯 电导率仪
1月/次
2H/次
一个月更换一次 根据槽液 槽液,每天至少 喷淋消耗 检查一次槽内循 按照时段 环过滤管口状 进行补充 况,及时发现阻 塞并清理正常。
9
水洗
自来水
0
2
0.8~1.5 1-2min
清洗工件 表面酸液
无
无
无
无
≤150us/cm 电导率仪 室温
1班/次
根据自来 水喷淋消 耗按照目 测进行补 充 根据自来 水喷淋消 使用电导率测试仪取 耗按照目 样进行检测 测进行补 充 根据自来 水喷淋消 使用电导率测试仪取 耗按照目 样进行检测 测进行补 充 使用电导率测试仪取 按时点检 样进行检测 开启设备
去离子水 清洗
无
无
无
无
室温
槽液< 试管 30us 烧杯 补充水 电导率仪 <10us 槽液< 试管 30us 烧杯 补充水 电导率仪 <10us
1班/次
4H/次
11
纯水
纯水
0
2
0.8~1.5 1-2min
去离子水 清洗
无
无
无
无
室温
1班/次
4H/次
12
直喷
纯水
0
2
0.8~1.5 1-2min
去离子水 冲洗
2
主脱
自来水 55±10
5
0.8~1.5 1-2min
初配槽: 添加30KG*6 不含硅酸 除油及表 Bonderit 游离碱5桶 盐的浓缩 面氧化层 e212 7 点 补充:加药 型清洗剂 45L增加一 个点
试管 烧杯
1月/次
2H/次
一个月更换一次 根据槽液 槽液,每天至少 喷淋消耗 检查一次槽内循 按照时段 环过滤管口状 进行补充 况,及时发现阻 塞并清理正常。
40
GAS气体
14
B.工艺流程
制程指引→:上件---预脱脂---主脱---水洗1---水洗2---表调---水洗3---水洗4---无铬化---水洗5---纯水1---纯水2---纯水直喷---水切炉干燥
C.化学药剂
序号 槽名 水体 水温℃ 容积T 喷淋压力 m3/Mpa 化学品 喷淋时间 槽液作用 药剂 配槽浓度 药剂性能 配槽用量 水文标准 PH值 温度 电导率 检测设备 使用周期 测试 时间 槽液分析法 取10ml试样与250ml锥 形杯 中,加入50ml去 离子水,在滴入3-5滴 指示剂(酚酞)。用 0.1N的盐酸溶液滴定 至由紫红色变为无色 为终点。用去0.1N盐 酸溶液的毫升数即为 游离碱的点数。 取10ml试样与250ml锥 形杯 中,加入50ml去 离子水,在滴入3-5滴 指示剂(酚酞)。用 0.1N的盐酸溶液滴定 至由紫红色变为无色 为终点。用去0.1N盐 酸溶液的毫升数即为 游离碱的点数。 槽液调整 方式 注意事项
3
水洗
自来水
0
2
0.8~1.5 1-2min
清洗工件 表面碱液
无
无
无
无
<8 室温
电导率仪
1班/次
根据自来 水喷淋消 耗按照目 测进行补 充
每班更换一次槽 液,每三天清洗 一次槽壁,每天 检测循环管口及 时发现阻塞并清 理 每班更换一次槽 液,每三天清洗 一次槽壁,每天 检测循环管口及 时发现阻塞并清 理
5
表调
自来水
0
2
0.8~1.5 1-2min
用于铝合 初配槽: 去除工件 Bonderit 金表面出 添加12L 表面的氧 eM-NT 游离酸9-12光和控制 补充:加药 化膜 2040 侵蚀的浓 1.2L增加一 缩性液体 个点
室温
电导率仪
1月/次
2H/次
一个月更换一次 根据槽液 槽液,每天至少 喷淋消耗 检查一次槽内循 按照时段 环过滤管口状 进行补充 况,及时发现阻 塞并清理正常。
1
预脱
自来水 55±10
2.5
0.8~1.5 1-2min
初配槽: 添加30KG*4 不含硅酸 除油及表 Bonderit 游离碱5桶 盐的浓缩 面氧化层 e212 7 点 补充:加药 型清洗剂 30L增加一 个点
试管 烧杯
1月/次
2H/次
一个月更换一次 根据槽液 槽液,每天至少 喷淋消耗 检查一次槽内循 按照时段 环过滤管口状 进行补充 况,及时发现阻 塞并清理正常。