MAX400CSA+中文资料
Tracer UC400程序可编程控制器产品数据手册说明书

T racer™ UC400 Programmable ControllerOrdering Number: BMUC400AAA0100011BAS-PRC033-E4The Tracer™UC400 controller is a multi-purpose, programmable,wireless sensor support device. This field- or factory-installed deviceis designed to control the following equipment:•Single- and dual-duct variable-air-volume (VAV) units •Fan coils •Unit ventilators •Blower coils •Water-source heat pumps (WSHP)•Small air handlersFeatures and Benefits Feature Benefit BACnet MS/TPAn open standard building automation communications protocol which enables connections to other BAS systems and controllersConfigurable and fully programmable•Factory programs available through quick configuration for lowest setup time•Programmable for flexibility to meet unique sequence or hardware needs Total of 23 I/O points built inMeets most terminal unit needs with extra built-in I/O available to network oradditional programming on controllerExpandable to 55 points Flexibility to meet additional equipment needs Data logging—25,000 samplesEasier investigation of equipment, zone, or building problems Factory and field mounting optionsOptions to best meet job schedule and bidding processRemovable connectors, DIN rail mounting, multiple service tool connectionsEase of installation and serviceController Specifications and Agency ComplianceController dimensions StorageTemperature:-48°F to 203°F (-55°C to 95°C)Relative humidity:Between 5% to 95% (noncondensing)OperatingTemperature:-40°F to 158°F (-40°C to 70°C)Humidity:Between 5% to 95% (noncondensing)Power:20.4–27.6 Vac (24 Vac, ±15% nominal) 50–60 Hz 24 VA (24 VA plus binary output loads for a maximum of 12 VA for each binary output)Mounting weight of controller:Mounting surface must support .80 lb. (.364 kg)Environmental rating (enclosure):NEMA 1Altitude:6,500 ft maximum (1,981 m)Installation:UL 840: Category 3Pollution UL 840: Degree 2Wiring/Transformer16 AWG (recommended) copper wire•UL Listed, Class 2 power transformer 20.4–27.6 Vac (24 Vac, ±15% nominal)•The transformer must be sized to provide adequate power to the UC400 controller (12 VA) and outputs (maximum 12 VA per binary output)Agency Compliance•UL916 PAZX- Open Energy Management Equipment •UL94-5V Flammability •CE Marked •FCC Part 15, Subpart B, Class B Limit •AS/NZS CISPR 22:2006•VCCI V-3/2008.04•ICES-003, Issue 4:2004•Communications BACnet MS/TP , supports BACnet protocol ASHRAE 135-2004 and meets BACnet Testing Laboratory (BTL) as an Application Specific Controller (ASC) profile deviceDevice ConnectionsT able 1.Device connections Connection Quantity TypesRange Notes *Analog input (AI1 to AI5)5Temperature10 k Ω thermistor Setpoint0 Ω to 1,000 ΩResistive200 Ω to 20 k ΩTypically used for fan speed switch Universal input (UI1 and UI2)2Linear0–20 mA These inputs may be configured to be thermistor inputs, 0–10 Vdc inputs, or 4–20 mA inputs. Linear0–10 Vdc Resistive* Refer to analog input connection for ranges and types above BinarySolid state open collector Pulse Solid state open collector Minimum dwell time is 10 milliseconds (ms) ON and 10 milliseconds OFF .Binary input (a)(BI1 to BI3)(a)Binary Inputs, Binary Outputs, and TRIACs: For safety precautions, do not mix Class 1 and Class 2 voltages in an enclosure or on a controller without a physical barrier between these units.324 Vac detectThe UC400 controller provides the 24 Vac that is required to drive the binary inputs when using the recommended connections.Binary output (a)(BO1 to BO3)3Relay 2.88 A @24 Vac pilot duty (For further power ratings, refer to the Tracer UC400 Installation, Operation, and Maintenance Manual [BAS-SVX20]).Power needs to be wired to the binary output. All outputs are isolated from each other and from ground or power . Ranges given are per contact .Binary output (a)(BO4 to BO9)6TRIAC 0.5 A max @24-277 Vac, resistive and pilot duty (For further power ratings, refer to the Tracer UC400 Installation, Operation, and Maintenance Manual [BAS-SVX20]).Use for modulating TRIAC. User determines whether closing high side (providing voltage to the grounded load) or low side (providing ground to the power load). Ranges given are per contact and power comes from TRIAC SUPPLY circuit .Analog output/binary input (AO1/BI4 and AO2/BI5)2Linear output 0–20 mAEach termination must be configured as either an analog output or binary input.Linear output 0–10 VdcBinary input Dry contact Pressure inputs (PI1 and PI2)23-wire 0–5 in H 2O Pressure inputs supplied with 5 volts of power . Designed for Kavlico™ pressure transducers.Overall Point Total 23Trane optimizes the performance of homes and buildings around the world. A business of Ingersoll Rand, the leader in creating and sustaining saf e, comf ortable and energy ef f icient environments, Trane of f ers a broad portf olio of advanced controls and HVAC systems, comprehensive building services, and parts.For more information, visit .Trane has a policy of continuous product and product data improvement and reserves the right to change design and specifications without notice.© 2010 Trane All rights reserved BAS-PRC033-E4 April 2011Produced with paper that uses fewer trees and chemicals, less energy, and environmentally friendly print practices that reduce waste.。
赛米控丹佛斯 SEMITRANS IGBT模块 SKM400GB07E3 数据表

Rev. 3.0–20.04.20201SEMITRANS ®3GBTrench IGBT ModulesSKM400GB07E3Features*•V CE(sat) with positive temperature coefficient•High short circuit capability, self limiting to 6 x I cnom•Fast & soft switching inverse CAL diodes•Insulated copper baseplate using DCB Technology (Direct Copper Bonding) •With integrated gate resistorTypical Applications•AC inverter drives •UPS•Electronic weldersRemarks•Case temperature limited to T c = 125°C max.•Recommended T op = -40 ... +150°C •Product reliability results valid for T j = 150°C•Use of soft R G necessaryAbsolute Maximum Ratings SymbolConditions Values UnitIGBT V CES T j =25°C 650V I C T j =175°CT c =25°C 506A T c =80°C381A I Cnom 400A I CRMI CRM = 3 x I Cnom 1200A V GES -20 (20)V t psc V CC =360V V GE ≤ 15V V CES ≤ 650 V T j =150°C6µs T j -40...175°C Inverse diodeV RRM T j =25°C 650V I F T j =175°CT c =25°C 447A T c =80°C324A I Fnom 400A I FRM I FRM = 2 x I Fnom800A I FSM t p =10ms, sin 180°, T j =25°C2646A T j -40...175°C Module I t(RMS)500A T stg module without TIM -40...125°C V isolAC sinus 50 Hz, t =1min4000VCharacteristics SymbolConditionsmin.typ.max.UnitIGBT V CE(sat)I C =400A V GE =15V chiplevel T j =25°C 1.45 1.92V T j =150°C 1.70 2.10V V CE0chiplevel T j =25°C 0.90 1.00V T j =150°C 0.820.90V r CE V GE =15V chiplevelT j =25°C 1.38 2.3m ΩT j =150°C2.23.0m ΩV GE(th)V GE =V CE , I C =6.4mA5.1 5.86.4V I CES V GE =0V,V CE =650V, T j =25°C 0.8mA C ies V CE =25V V GE =0Vf =1MHz 24.7nF C oes f =1MHz 1.54nF C res f =1MHz0.73nF Q G V GE =- 8 V...+ 15 V 3200nC R Gint T j =25°C 1.0Ωt d(on)V CC =300V I C =400AV GE =+15/-7.5V R G on =1ΩR G off =4.2Ωdi/dt on =7000A/µs di/dt off =5000A/µs dv/dt =2200V/µs L s =18nH T j =150°C 190ns t r T j =150°C 60ns E on T j =150°C 4mJ t d(off)T j =150°C 850ns t f T j =150°C 50ns E off T j =150°C 17mJR th(j-c)per IGBT0.12K/W R th(c-s)per IGBT (λgrease =0.81 W/(m*K))0.04K/W R th(c-s)per IGBT, pre-applied phase change material0.033K/W2Rev. 3.0–20.04.2020© by SEMIKRONSEMITRANS ®3GBTrench IGBT ModulesSKM400GB07E3Features*•V CE(sat) with positive temperature coefficient•High short circuit capability, self limiting to 6 x I cnom•Fast & soft switching inverse CAL diodes•Insulated copper baseplate using DCB Technology (Direct Copper Bonding) •With integrated gate resistorTypical Applications•AC inverter drives •UPS•Electronic weldersRemarks•Case temperature limited to T c = 125°C max.•Recommended T op = -40 ... +150°C •Product reliability results valid for T j = 150°C•Use of soft R G necessaryCharacteristics SymbolConditionsmin.typ.max.UnitInverse diodeV F = V EC I F =400AV GE =0V chiplevelT j =25°C 1.39 1.75V T j =150°C 1.38 1.76V V F0chiplevel T j =25°C 1.04 1.24V T j =150°C 0.850.99V r FchiplevelT j =25°C 0.88 1.30m ΩT j =150°C1.32 1.93m ΩI RRM I F =400A di/dt off =7000A/µs V GE =-7.5VV CC =300VT j =150°C 459A Q rr T j=150°C61µC E rr T j =150°C 12mJR th(j-c)per diode0.191K/W R th(c-s)per diode (λgrease =0.81 W/(m*K))0.041K/W R th(c-s)per diode, pre-applied phase change material0.036K/W Module L CE 15nH R CC'+EE'measured per switchT C =25°C 0.55m ΩT C =125°C0.85m ΩR th(c-s)1calculated without thermal coupling (λgrease =0.81 W/(m*K))0.0101K/W R th(c-s)2including thermal coupling, T s underneath module (λgrease =0.81 W/(m*K))0.017K/W R th(c-s)2including thermal coupling,T s underneath module, pre-applied phase change material 0.014K/WM s to heat sink M635Nm M t to terminals M62.55Nm Nm w325g© by SEMIKRON Rev. 3.0–20.04.20203Fig. 10: Typ. CAL diode forward charact., incl. R4Rev. 3.0–20.04.2020© by SEMIKRON© by SEMIKRON Rev. 3.0–20.04.20205GBThis is an electrostatic discharge sensitive device (ESDS), international standard IEC 60747-1, chapter IX.*IMPORTANT INFORMATION AND WARNINGSThe specifications of SEMIKRON products may not be considered as guarantee or assurance of product characteristics ("Beschaffenheitsgarantie"). The specifications of SEMIKRON products describe only the usual characteristics of products to be expected in typical applications, which may still vary depending on the specific application. Therefore, products must be tested for the respective application in advance. Application adjustments may be necessary. The user of SEMIKRON products is responsible for the safety of their applications embedding SEMIKRON products and must take adequate safety measures to prevent the applications from causing a physical injury, fire or other problem if any of SEMIKRON products become faulty. The user is responsible to make sure that the application design is compliant with all applicable laws, regulations, norms and standards. Except as otherwise explicitly approved by SEMIKRON in a written document signed by authorized representatives of SEMIKRON, SEMIKRON products may not be used in any applications where a failure of the product or any consequences of the use thereof can reasonably be expected to result in personal injury. No representation or warranty is given and no liability is assumed with respect to the accuracy, completeness and/or use of any information herein, including without limitation, warranties of non-infringement of intellectual property rights of any third party. SEMIKRON does not assume any liability arising out of the applications or use of any product; neither does it convey any license under its patent rights, copyrights, trade secrets or other intellectual property rights, nor the rights of others. SEMIKRON makes no representation or warranty of non-infringement or alleged non-infringement of intellectual property rights of any third party which may arise from applications. Due to technical requirements our products may contain dangerous substances. For information on the types in question please contact the nearest SEMIKRON sales office. This document supersedes and replaces all information previously supplied and may be superseded by updates. SEMIKRON reserves the right to make changes.6。
clearone常用产品技术说明
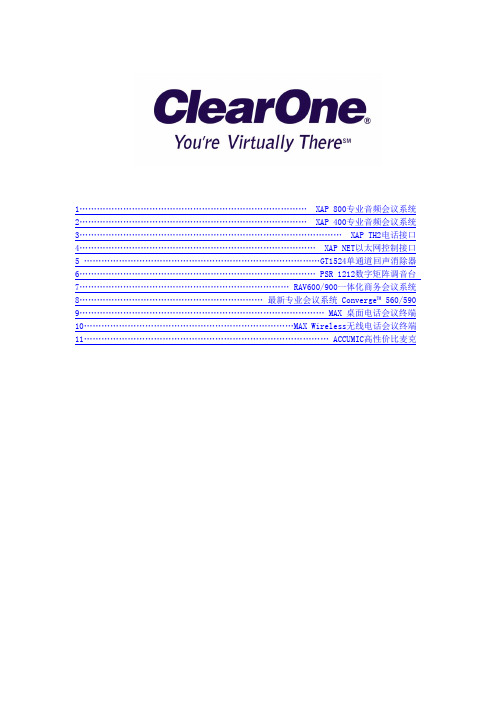
1…………………………………………………………………… XAP 800专业音频会议系统2…………………………………………………………………… XAP 400专业音频会议系统3……………………………………………………………………………… XAP TH2电话接口4……………………………………………………………………… XAP NET以太网控制接口5 ………………………………………………………………………GT1524单通道回声消除器6……………………………………………………………………… PSR 1212数字矩阵调音台7……………………………………………………………… RAV600/900一体化商务会议系统8………………………………………………………最新专业会议系统 Converge™ 560/590 9………………………………………………………………………… MAX 桌面电话会议终端10………………………………………………………………MAX Wireless无线电话会议终端11………………………………………………………………………… ACCUMIC高性价比麦克XAP 800专业音频会议系统市场上功能最齐全、最成熟的音频会议系统。
XAP 800以其独一无二的音频处理能力,引领了音频会议系统的新标准!产品特点出众的音频性能分布式回声消除——更有效地消除回声噪音抑制——抑制来自风扇或HVAC 系统的背景噪音全双工——使与会者在同一时间不用切入切出就可以互相交流第一麦克优先——通过只激活最靠近说话人的麦克来消除中空“隧道”声8路麦克/线路输入,4 路纯线路输入12 路输出20Hz 到20kHz带宽,提供完整的音频响应自动电平控制和自动增益控制八个独立的音频处理模块,每个都包含有15 段滤波器灵活的配置可扩展-连接多个XAP 设备(XAP 400,XAP800,XAP TH2),提供多达64路麦克输入和16 路电话接入32x32 音频矩阵,每个交叉点具有电平控制功能多种系统控制功能选项:遥控、音量控制、选择控制、第三方控制系统,如AMX、Cresstron 通过G-Ware软件、RS-323端口进行配置控制12 路双向音频线路的增强型扩展总线来连接其他的XAP 产品1U机架式安装简单地操作和控制所有输入、输出、宏和预置的标识都保存在设备里前面板可以实现增益和静音控制在会议进行中可以执行32 个预置选择而不会影响正在进行的操作宏脚本语言和宏记录器简化了宏的创建RAMP 串行命令通过增益调节进行控制,无需外部音量卡会议容量XAP TH2 和XAP400具有电话会议功能连接多达16个XAP TH2获得16 方电话会议的能力技术参数音频性能:条件:除非另外指定,所有的测量都限制在一个22Hz—22KHz 带宽范围内进行(没有额外开销);频率响应:20Hz—20KHz ±1dB;噪音(EIN):-126dB,20KHz BW,最大增益,阻抗=150Ω;总谐波失真:<0.02%;信噪比:80dBre0dBu(A-weighted);动态范围:100dB(A-weighted) ;串音<-91dB re;20dBu@20KHz 通道到通道矩阵混音参数:32x32 矩阵;12 路逻辑输入/输出;12 路扩展线路输入/输出;8路可指定的音频处理模块输入/输出自动混音器参数:打开麦克风数量(NOM);PA适应模式;第一麦克优先模式;最后麦克模式;最大麦克数量模式;环境电平;选通率;衰减量;保持时间;收敛率可指定的处理模块:滤波器:全通、低通、高通、低曲柄型响应、高曲柄型响应、参量均衡、梳形滤波、CD Horn;旁通: Bessel 、Butterworth 、Linkwitz-Riely;压缩器;延迟可调节至500ms麦克输入配置:输入增益调节;麦克或线路电平;幻象电源开/关;回声消除开/关;噪音抑制开/关;滤波器:全通、低通、高通、梳形滤波、参量均衡;静音开/关;主席优先开/关;自动增益控制(AGC)开/关;语音平衡器开/关;自动gate/手工gate;自适应环境电平开/关麦克/线路输入1—8:桥接平衡按压式接线排;阻抗:5 KΩ;正常电平:可调整-55dBu,-25dBu,0dBu;最大电平:-35dBu,-5dBu,+20dBu;回声消除:130ms 尾音时间(房间增益12dB);噪音抑制:衰减6—15dB;幻象电源;24V,可选择线路输入9—12:桥接平衡按压式接线排;阻抗:>10 KΩ;正常电平:0dBu;最大电平:20dBu输出1—12:平衡按压式接线排;阻抗:50Ω;正常电平:0dBu ;最大电平:20dBu 扩展总线输入/输出:专有网络,RJ-45(2)接口, 115.2kbps ,110K;五类双绞线,任何两个XAP800、XAP400或PSR1212之间连接最长可达24 米RS-232串口:DB-9 接口(母头),波特率9600/19200/38400(缺省)/57600;8 位数据位,1 位停止位,无奇偶校验位,硬件流量控制开(缺省)/关控制/状态:DB-25 接口(母头)A/B(2);输入A/B:activelow(接地);输出A/B:open collector,最大40VDC,每个40mA;+5VDC 管脚(300mA过流保护)远程面板A/B:4 管脚按压式接线排;RS-485 专用协议;五类双绞线,一对数据,一对电源和地;+15VDC(300mA过流保护)认证:FCC,CSA,IC,CE,NOM,ACA,SABS,JATE体积(长x宽x 高):43.8x26x4.5厘米重量:净重3.2公斤,装箱5.5公斤设置软件:G-WareXAP 400专业音频会议系统成熟、专业的音频会议系统,包含了最完善的音频技术。
MAX320-MAX322中文资料

ELECTRICAL CHARACTERISTICS
(V+ = +5V ±10%, V- = -5V ±10%, VINH = 3.5V, VINL = 2.5V, TA = TMIN to TMAX, unless otherwise noted.)
PARAMETER ANALOG SWITCH Analog Signal Range
For equivalent devices specified for single-supply operation, see the MAX323/MAX324/MAX325 data sheet. For quad versions of these switches, see the MAX391/MAX392/MAX393 data sheet.
Plastic DIP (derate 9.09mW/°C above +70°C) .............727mW Narrow SO (derate 5.88mW/°C above +70°C) .............471mW
µMAX (derate 4.10mW/°C above +70°C) .....................330mW CERDIP (derate 8.00mW/°C above +70°C) ..................640mW Operating Temperature Ranges MAX32_C_ _ ........................................................0°C to +70°C MAX32_E_ _......................................................-40°C to +85°C MAX32_MJA ...................................................-55°C to +125°C Storage Temperature Range .............................-65°C to +150°C Lead Temperature (soldering, 10sec) .............................+300°C
MAX1487CSA中文资料

For pricing, delivery, and ordering information,please contact Maxim/Dallas Direct!at 1-888-629-4642, or visit Maxim’s website at .General DescriptionThe MAX481, MAX483, MAX485, MAX487–MAX491, and MAX1487 are low-power transceivers for RS-485 and RS-422 communication. Each part contains one driver and one receiver. The MAX483, MAX487, MAX488, and MAX489feature reduced slew-rate drivers that minimize EMI and reduce reflections caused by improperly terminated cables,thus allowing error-free data transmission up to 250kbps.The driver slew rates of the MAX481, MAX485, MAX490,MAX491, and MAX1487 are not limited, allowing them to transmit up to 2.5Mbps.These transceivers draw between 120µA and 500µA of supply current when unloaded or fully loaded with disabled drivers. Additionally, the MAX481, MAX483, and MAX487have a low-current shutdown mode in which they consume only 0.1µA. All parts operate from a single 5V supply.Drivers are short-circuit current limited and are protected against excessive power dissipation by thermal shutdown circuitry that places the driver outputs into a high-imped-ance state. The receiver input has a fail-safe feature that guarantees a logic-high output if the input is open circuit.The MAX487 and MAX1487 feature quarter-unit-load receiver input impedance, allowing up to 128 MAX487/MAX1487 transceivers on the bus. Full-duplex communi-cations are obtained using the MAX488–MAX491, while the MAX481, MAX483, MAX485, MAX487, and MAX1487are designed for half-duplex applications.________________________ApplicationsLow-Power RS-485 Transceivers Low-Power RS-422 Transceivers Level TranslatorsTransceivers for EMI-Sensitive Applications Industrial-Control Local Area Networks__Next Generation Device Features♦For Fault-Tolerant ApplicationsMAX3430: ±80V Fault-Protected, Fail-Safe, 1/4Unit Load, +3.3V, RS-485 TransceiverMAX3440E–MAX3444E: ±15kV ESD-Protected,±60V Fault-Protected, 10Mbps, Fail-Safe, RS-485/J1708 Transceivers♦For Space-Constrained ApplicationsMAX3460–MAX3464: +5V, Fail-Safe, 20Mbps,Profibus RS-485/RS-422 TransceiversMAX3362: +3.3V, High-Speed, RS-485/RS-422Transceiver in a SOT23 PackageMAX3280E–MAX3284E: ±15kV ESD-Protected,52Mbps, +3V to +5.5V, SOT23, RS-485/RS-422,True Fail-Safe ReceiversMAX3293/MAX3294/MAX3295: 20Mbps, +3.3V,SOT23, RS-855/RS-422 Transmitters ♦For Multiple Transceiver ApplicationsMAX3030E–MAX3033E: ±15kV ESD-Protected,+3.3V, Quad RS-422 Transmitters ♦For Fail-Safe ApplicationsMAX3080–MAX3089: Fail-Safe, High-Speed (10Mbps), Slew-Rate-Limited RS-485/RS-422Transceivers♦For Low-Voltage ApplicationsMAX3483E/MAX3485E/MAX3486E/MAX3488E/MAX3490E/MAX3491E: +3.3V Powered, ±15kV ESD-Protected, 12Mbps, Slew-Rate-Limited,True RS-485/RS-422 TransceiversMAX481/MAX483/MAX485/MAX487–MAX491/MAX1487Low-Power, Slew-Rate-Limited RS-485/RS-422 Transceivers______________________________________________________________Selection Table19-0122; Rev 8; 10/03Ordering Information appears at end of data sheet.M A X 481/M A X 483/M A X 485/M A X 487–M A X 491/M A X 1487Low-Power, Slew-Rate-Limited RS-485/RS-422 Transceivers 2_______________________________________________________________________________________ABSOLUTE MAXIMUM RATINGSSupply Voltage (V CC ).............................................................12V Control Input Voltage (RE , DE)...................-0.5V to (V CC + 0.5V)Driver Input Voltage (DI).............................-0.5V to (V CC + 0.5V)Driver Output Voltage (A, B)...................................-8V to +12.5V Receiver Input Voltage (A, B).................................-8V to +12.5V Receiver Output Voltage (RO).....................-0.5V to (V CC +0.5V)Continuous Power Dissipation (T A = +70°C)8-Pin Plastic DIP (derate 9.09mW/°C above +70°C)....727mW 14-Pin Plastic DIP (derate 10.00mW/°C above +70°C)..800mW 8-Pin SO (derate 5.88mW/°C above +70°C).................471mW14-Pin SO (derate 8.33mW/°C above +70°C)...............667mW 8-Pin µMAX (derate 4.1mW/°C above +70°C)..............830mW 8-Pin CERDIP (derate 8.00mW/°C above +70°C).........640mW 14-Pin CERDIP (derate 9.09mW/°C above +70°C).......727mW Operating Temperature RangesMAX4_ _C_ _/MAX1487C_ A...............................0°C to +70°C MAX4__E_ _/MAX1487E_ A.............................-40°C to +85°C MAX4__MJ_/MAX1487MJA...........................-55°C to +125°C Storage Temperature Range.............................-65°C to +160°C Lead Temperature (soldering, 10sec).............................+300°CDC ELECTRICAL CHARACTERISTICS(V CC = 5V ±5%, T A = T MIN to T MAX , unless otherwise noted.) (Notes 1, 2)Stresses beyond those listed under “Absolute Maximum Ratings” may cause permanent damage to the device. These are stress ratings only, and functional operation of the device at these or any other conditions beyond those indicated in the operational sections of the specifications is not implied. Exposure to absolute maximum rating conditions for extended periods may affect device reliability.V V IN = -7VV IN = 12V V IN = -7V V IN = 12V Input Current (A, B)I IN2V TH k Ω48-7V ≤V CM ≤12V, MAX487/MAX1487R INReceiver Input Resistance -7V ≤V CM ≤12V, all devices except MAX487/MAX1487R = 27Ω(RS-485), Figure 40.4V ≤V O ≤2.4VR = 50Ω(RS-422)I O = 4mA, V ID = -200mV I O = -4mA, V ID = 200mV V CM = 0V-7V ≤V CM ≤12V DE, DI, RE DE, DI, RE MAX487/MAX1487,DE = 0V, V CC = 0V or 5.25VDE, DI, RE R = 27Ωor 50Ω, Figure 4R = 27Ωor 50Ω, Figure 4R = 27Ωor 50Ω, Figure 4DE = 0V;V CC = 0V or 5.25V,all devices except MAX487/MAX1487CONDITIONSk Ω12µA ±1I OZRThree-State (high impedance)Output Current at ReceiverV 0.4V OL Receiver Output Low Voltage 3.5V OH Receiver Output High Voltage mV 70∆V TH Receiver Input Hysteresis V -0.20.2Receiver Differential Threshold Voltage-0.2mA 0.25mA-0.81.01.55V OD2Differential Driver Output (with load)V 2V 5V OD1Differential Driver Output (no load)µA±2I IN1Input CurrentV 0.8V IL Input Low Voltage V 2.0V IH Input High Voltage V 0.2∆V OD Change in Magnitude of Driver Common-Mode Output Voltage for Complementary Output States V 0.2∆V OD Change in Magnitude of Driver Differential Output Voltage for Complementary Output States V 3V OC Driver Common-Mode Output VoltageUNITS MINTYPMAX SYMBOL PARAMETERMAX481/MAX483/MAX485/MAX487–MAX491/MAX1487Low-Power, Slew-Rate-Limited RS-485/RS-422 Transceivers_______________________________________________________________________________________3SWITCHING CHARACTERISTICS—MAX481/MAX485, MAX490/MAX491, MAX1487(V CC = 5V ±5%, T A = T MIN to T MAX , unless otherwise noted.) (Notes 1, 2)DC ELECTRICAL CHARACTERISTICS (continued)(V CC = 5V ±5%, T A = T MIN to T MAX , unless otherwise noted.) (Notes 1, 2)ns 103060t PHLDriver Rise or Fall Time Figures 6 and 8, R DIFF = 54Ω, C L1= C L2= 100pF ns MAX490M, MAX491M MAX490C/E, MAX491C/E2090150MAX481, MAX485, MAX1487MAX490M, MAX491MMAX490C/E, MAX491C/E MAX481, MAX485, MAX1487Figures 6 and 8, R DIFF = 54Ω,C L1= C L2= 100pF MAX481 (Note 5)Figures 5 and 11, C RL = 15pF, S2 closedFigures 5 and 11, C RL = 15pF, S1 closed Figures 5 and 11, C RL = 15pF, S2 closed Figures 5 and 11, C RL = 15pF, S1 closed Figures 6 and 10, R DIFF = 54Ω,C L1= C L2= 100pFFigures 6 and 8,R DIFF = 54Ω,C L1= C L2= 100pF Figures 6 and 10,R DIFF = 54Ω,C L1= C L2= 100pF CONDITIONS ns 510t SKEW ns50200600t SHDNTime to ShutdownMbps 2.5f MAX Maximum Data Rate ns 2050t HZ Receiver Disable Time from High ns 103060t PLH 2050t LZ Receiver Disable Time from Low ns 2050t ZH Driver Input to Output Receiver Enable to Output High ns 2050t ZL Receiver Enable to Output Low 2090200ns ns 134070t HZ t SKD Driver Disable Time from High |t PLH - t PHL |DifferentialReceiver Skewns 4070t LZ Driver Disable Time from Low ns 4070t ZL Driver Enable to Output Low 31540ns51525ns 31540t R , t F 2090200Driver Output Skew to Output t PLH , t PHL Receiver Input to Output4070t ZH Driver Enable to Output High UNITS MIN TYP MAX SYMBOL PARAMETERFigures 7 and 9, C L = 100pF, S2 closed Figures 7 and 9, C L = 100pF, S1 closed Figures 7 and 9, C L = 15pF, S1 closed Figures 7 and 9, C L = 15pF, S2 closedM A X 481/M A X 483/M A X 485/M A X 487–M A X 491/M A X 1487Low-Power, Slew-Rate-Limited RS-485/RS-422 Transceivers 4_______________________________________________________________________________________SWITCHING CHARACTERISTICS—MAX483, MAX487/MAX488/MAX489(V CC = 5V ±5%, T A = T MIN to T MAX , unless otherwise noted.) (Notes 1, 2)SWITCHING CHARACTERISTICS—MAX481/MAX485, MAX490/MAX491, MAX1487 (continued)(V CC = 5V ±5%, T A = T MIN to T MAX , unless otherwise noted.) (Notes 1, 2)3001000Figures 7 and 9, C L = 100pF, S2 closed Figures 7 and 9, C L = 100pF, S1 closed Figures 5 and 11, C L = 15pF, S2 closed,A - B = 2VCONDITIONSns 40100t ZH(SHDN)Driver Enable from Shutdown toOutput High (MAX481)nsFigures 5 and 11, C L = 15pF, S1 closed,B - A = 2Vt ZL(SHDN)Receiver Enable from Shutdownto Output Low (MAX481)ns 40100t ZL(SHDN)Driver Enable from Shutdown toOutput Low (MAX481)ns 3001000t ZH(SHDN)Receiver Enable from Shutdownto Output High (MAX481)UNITS MINTYP MAX SYMBOLPARAMETERt PLH t SKEW Figures 6 and 8, R DIFF = 54Ω,C L1= C L2= 100pFt PHL Figures 6 and 8, R DIFF = 54Ω,C L1= C L2= 100pFDriver Input to Output Driver Output Skew to Output ns 100800ns ns 2000MAX483/MAX487, Figures 7 and 9,C L = 100pF, S2 closedt ZH(SHDN)Driver Enable from Shutdown to Output High2502000ns2500MAX483/MAX487, Figures 5 and 11,C L = 15pF, S1 closedt ZL(SHDN)Receiver Enable from Shutdown to Output Lowns 2500MAX483/MAX487, Figures 5 and 11,C L = 15pF, S2 closedt ZH(SHDN)Receiver Enable from Shutdown to Output Highns 2000MAX483/MAX487, Figures 7 and 9,C L = 100pF, S1 closedt ZL(SHDN)Driver Enable from Shutdown to Output Lowns 50200600MAX483/MAX487 (Note 5) t SHDN Time to Shutdownt PHL t PLH , t PHL < 50% of data period Figures 5 and 11, C RL = 15pF, S2 closed Figures 5 and 11, C RL = 15pF, S1 closed Figures 5 and 11, C RL = 15pF, S2 closed Figures 5 and 11, C RL = 15pF, S1 closed Figures 7 and 9, C L = 15pF, S2 closed Figures 6 and 10, R DIFF = 54Ω,C L1= C L2= 100pFFigures 7 and 9, C L = 15pF, S1 closed Figures 7 and 9, C L = 100pF, S1 closed Figures 7 and 9, C L = 100pF, S2 closed CONDITIONSkbps 250f MAX 2508002000Maximum Data Rate ns 2050t HZ Receiver Disable Time from High ns 25080020002050t LZ Receiver Disable Time from Low ns 2050t ZH Receiver Enable to Output High ns 2050t ZL Receiver Enable to Output Low ns ns 1003003000t HZ t SKD Driver Disable Time from High I t PLH - t PHL I DifferentialReceiver SkewFigures 6 and 10, R DIFF = 54Ω,C L1= C L2= 100pFns 3003000t LZ Driver Disable Time from Low ns 2502000t ZL Driver Enable to Output Low ns Figures 6 and 8, R DIFF = 54Ω,C L1= C L2= 100pFns 2502000t R , t F 2502000Driver Rise or Fall Time ns t PLH Receiver Input to Output2502000t ZH Driver Enable to Output High UNITS MIN TYP MAX SYMBOL PARAMETERMAX481/MAX483/MAX485/MAX487–MAX491/MAX1487Low-Power, Slew-Rate-Limited RS-485/RS-422 Transceivers_______________________________________________________________________________________530002.5OUTPUT CURRENT vs.RECEIVER OUTPUT LOW VOLTAGE525M A X 481-01OUTPUT LOW VOLTAGE (V)O U T P U T C U R R E N T (m A )1.515100.51.02.0203540450.90.1-50-252575RECEIVER OUTPUT LOW VOLTAGE vs.TEMPERATURE0.30.7TEMPERATURE (°C)O U T P U TL O W V O L T A G E (V )500.50.80.20.60.40100125-20-41.5 2.0 3.0 5.0OUTPUT CURRENT vs.RECEIVER OUTPUT HIGH VOLTAGE-8-16M A X 481-02OUTPUT HIGH VOLTAGE (V)O U T P U T C U R R E N T (m A )2.5 4.0-12-18-6-14-10-203.54.5 4.83.2-50-252575RECEIVER OUTPUT HIGH VOLTAGE vs.TEMPERATURE3.64.4TEMPERATURE (°C)O U T P UT H I G H V O L T A G E (V )0504.04.63.44.23.83.01001259000 1.0 3.0 4.5DRIVER OUTPUT CURRENT vs.DIFFERENTIAL OUTPUT VOLTAGE1070M A X 481-05DIFFERENTIAL OUTPUT VOLTAGE (V)O U T P U T C U R R E N T (m A )2.0 4.05030806040200.5 1.5 2.53.5 2.31.5-50-2525125DRIVER DIFFERENTIAL OUTPUT VOLTAGEvs. TEMPERATURE1.72.1TEMPERATURE (°C)D I F FE R E N T I A L O U T P U T V O L T A G E (V )751.92.21.62.01.8100502.4__________________________________________Typical Operating Characteristics(V CC = 5V, T A = +25°C, unless otherwise noted.)NOTES FOR ELECTRICAL/SWITCHING CHARACTERISTICSNote 1:All currents into device pins are positive; all currents out of device pins are negative. All voltages are referenced to deviceground unless otherwise specified.Note 2:All typical specifications are given for V CC = 5V and T A = +25°C.Note 3:Supply current specification is valid for loaded transmitters when DE = 0V.Note 4:Applies to peak current. See Typical Operating Characteristics.Note 5:The MAX481/MAX483/MAX487 are put into shutdown by bringing RE high and DE low. If the inputs are in this state for lessthan 50ns, the parts are guaranteed not to enter shutdown. If the inputs are in this state for at least 600ns, the parts are guaranteed to have entered shutdown. See Low-Power Shutdown Mode section.M A X 481/M A X 483/M A X 485/M A X 487–M A X 491/M A X 1487Low-Power, Slew-Rate-Limited RS-485/RS-422 Transceivers 6___________________________________________________________________________________________________________________Typical Operating Characteristics (continued)(V CC = 5V, T A = +25°C, unless otherwise noted.)120008OUTPUT CURRENT vs.DRIVER OUTPUT LOW VOLTAGE20100M A X 481-07OUTPUT LOW VOLTAGE (V)O U T P U T C U R R E N T (m A )6604024801012140-1200-7-5-15OUTPUT CURRENT vs.DRIVER OUTPUT HIGH VOLTAGE-20-80M A X 481-08OUTPUT HIGH VOLTAGE (V)O U T P U T C U R R E N T (m A )-31-603-6-4-2024-100-40100-40-60-2040100120MAX1487SUPPLY CURRENT vs. TEMPERATURE300TEMPERATURE (°C)S U P P L Y C U R R E N T (µA )20608050020060040000140100-50-2550100MAX481/MAX485/MAX490/MAX491SUPPLY CURRENT vs. TEMPERATURE300TEMPERATURE (°C)S U P P L Y C U R R E N T (µA )257550020060040000125100-50-2550100MAX483/MAX487–MAX489SUPPLY CURRENT vs. TEMPERATURE300TEMPERATURE (°C)S U P P L Y C U R R E N T (µA )257550020060040000125MAX481/MAX483/MAX485/MAX487–MAX491/MAX1487Low-Power, Slew-Rate-Limited RS-485/RS-422 Transceivers_______________________________________________________________________________________7______________________________________________________________Pin DescriptionFigure 1. MAX481/MAX483/MAX485/MAX487/MAX1487 Pin Configuration and Typical Operating CircuitM A X 481/M A X 483/M A X 485/M A X 487–M A X 491/M A X 1487__________Applications InformationThe MAX481/MAX483/MAX485/MAX487–MAX491 and MAX1487 are low-power transceivers for RS-485 and RS-422 communications. The MAX481, MAX485, MAX490,MAX491, and MAX1487 can transmit and receive at data rates up to 2.5Mbps, while the MAX483, MAX487,MAX488, and MAX489 are specified for data rates up to 250kbps. The MAX488–MAX491 are full-duplex trans-ceivers while the MAX481, MAX483, MAX485, MAX487,and MAX1487 are half-duplex. In addition, Driver Enable (DE) and Receiver Enable (RE) pins are included on the MAX481, MAX483, MAX485, MAX487, MAX489,MAX491, and MAX1487. When disabled, the driver and receiver outputs are high impedance.MAX487/MAX1487:128 Transceivers on the BusThe 48k Ω, 1/4-unit-load receiver input impedance of the MAX487 and MAX1487 allows up to 128 transceivers on a bus, compared to the 1-unit load (12k Ωinput impedance) of standard RS-485 drivers (32 trans-ceivers maximum). Any combination of MAX487/MAX1487 and other RS-485 transceivers with a total of 32 unit loads or less can be put on the bus. The MAX481/MAX483/MAX485 and MAX488–MAX491 have standard 12k ΩReceiver Input impedance.Low-Power, Slew-Rate-Limited RS-485/RS-422 Transceivers 8_______________________________________________________________________________________Figure 2. MAX488/MAX490 Pin Configuration and Typical Operating CircuitFigure 3. MAX489/MAX491 Pin Configuration and Typical Operating CircuitMAX483/MAX487/MAX488/MAX489:Reduced EMI and ReflectionsThe MAX483 and MAX487–MAX489 are slew-rate limit-ed, minimizing EMI and reducing reflections caused by improperly terminated cables. Figure 12 shows the dri-ver output waveform and its Fourier analysis of a 150kHz signal transmitted by a MAX481, MAX485,MAX490, MAX491, or MAX1487. High-frequency har-monics with large amplitudes are evident. Figure 13shows the same information displayed for a MAX483,MAX487, MAX488, or MAX489 transmitting under the same conditions. Figure 13’s high-frequency harmonics have much lower amplitudes, and the potential for EMI is significantly reduced.MAX481/MAX483/MAX485/MAX487–MAX491/MAX1487Low-Power, Slew-Rate-Limited RS-485/RS-422 Transceivers_______________________________________________________________________________________9_________________________________________________________________Test CircuitsFigure 4. Driver DC Test Load Figure 5. Receiver Timing Test LoadFigure 6. Driver/Receiver Timing Test Circuit Figure 7. Driver Timing Test LoadM A X 481/M A X 483/M A X 485/M A X 487–M A X 491/M A X 1487Low-Power, Slew-Rate-Limited RS-485/RS-422 Transceivers 10_______________________________________________________Switching Waveforms_________________Function Tables (MAX481/MAX483/MAX485/MAX487/MAX1487)Figure 8. Driver Propagation DelaysFigure 9. Driver Enable and Disable Times (except MAX488 and MAX490)Figure 10. Receiver Propagation DelaysFigure 11. Receiver Enable and Disable Times (except MAX488and MAX490)Table 1. TransmittingTable 2. ReceivingLow-Power Shutdown Mode (MAX481/MAX483/MAX487)A low-power shutdown mode is initiated by bringing both RE high and DE low. The devices will not shut down unless both the driver and receiver are disabled.In shutdown, the devices typically draw only 0.1µA of supply current.RE and DE may be driven simultaneously; the parts are guaranteed not to enter shutdown if RE is high and DE is low for less than 50ns. If the inputs are in this state for at least 600ns, the parts are guaranteed to enter shutdown.For the MAX481, MAX483, and MAX487, the t ZH and t ZL enable times assume the part was not in the low-power shutdown state (the MAX485/MAX488–MAX491and MAX1487 can not be shut down). The t ZH(SHDN)and t ZL(SHDN)enable times assume the parts were shut down (see Electrical Characteristics ).It takes the drivers and receivers longer to become enabled from the low-power shutdown state (t ZH(SHDN ), t ZL(SHDN)) than from the operating mode (t ZH , t ZL ). (The parts are in operating mode if the –R —E –,DE inputs equal a logical 0,1 or 1,1 or 0, 0.)Driver Output ProtectionExcessive output current and power dissipation caused by faults or by bus contention are prevented by two mechanisms. A foldback current limit on the output stage provides immediate protection against short cir-cuits over the whole common-mode voltage range (see Typical Operating Characteristics ). In addition, a ther-mal shutdown circuit forces the driver outputs into a high-impedance state if the die temperature rises excessively.Propagation DelayMany digital encoding schemes depend on the differ-ence between the driver and receiver propagation delay times. Typical propagation delays are shown in Figures 15–18 using Figure 14’s test circuit.The difference in receiver delay times, | t PLH - t PHL |, is typically under 13ns for the MAX481, MAX485,MAX490, MAX491, and MAX1487 and is typically less than 100ns for the MAX483 and MAX487–MAX489.The driver skew times are typically 5ns (10ns max) for the MAX481, MAX485, MAX490, MAX491, and MAX1487, and are typically 100ns (800ns max) for the MAX483 and MAX487–MAX489.MAX481/MAX483/MAX485/MAX487–MAX491/MAX1487Low-Power, Slew-Rate-Limited RS-485/RS-422 Transceivers______________________________________________________________________________________1110dB/div0Hz5MHz500kHz/div10dB/div0Hz5MHz500kHz/divFigure 12. Driver Output Waveform and FFT Plot of MAX481/MAX485/MAX490/MAX491/MAX1487 Transmitting a 150kHz SignalFigure 13. Driver Output Waveform and FFT Plot of MAX483/MAX487–MAX489 Transmitting a 150kHz SignalM A X 481/M A X 483/M A X 485/M A X 487–M A X 491/M A X 1487Low-Power, Slew-Rate-Limited RS-485/RS-422 Transceivers 12______________________________________________________________________________________V CC = 5V T A = +25°CV CC = 5V T A = +25°CV CC = 5V T A = +25°CV CC = 5V T A = +25°CFigure 14. Receiver Propagation Delay Test CircuitFigure 15. MAX481/MAX485/MAX490/MAX491/MAX1487Receiver t PHLFigure 16. MAX481/MAX485/MAX490/MAX491/MAX1487Receiver t PLHPHL Figure 18. MAX483, MAX487–MAX489 Receiver t PLHLine Length vs. Data RateThe RS-485/RS-422 standard covers line lengths up to 4000 feet. For line lengths greater than 4000 feet, see Figure 23.Figures 19 and 20 show the system differential voltage for the parts driving 4000 feet of 26AWG twisted-pair wire at 110kHz into 120Ωloads.Typical ApplicationsThe MAX481, MAX483, MAX485, MAX487–MAX491, and MAX1487 transceivers are designed for bidirectional data communications on multipoint bus transmission lines.Figures 21 and 22 show typical network applications circuits. These parts can also be used as line repeaters, with cable lengths longer than 4000 feet, as shown in Figure 23.To minimize reflections, the line should be terminated at both ends in its characteristic impedance, and stub lengths off the main line should be kept as short as possi-ble. The slew-rate-limited MAX483 and MAX487–MAX489are more tolerant of imperfect termination.MAX481/MAX483/MAX485/MAX487–MAX491/MAX1487Low-Power, Slew-Rate-Limited RS-485/RS-422 Transceivers______________________________________________________________________________________13DIV Y -V ZRO5V 0V1V0V -1V5V 0V2µs/divFigure 19. MAX481/MAX485/MAX490/MAX491/MAX1487 System Differential Voltage at 110kHz Driving 4000ft of Cable Figure 20. MAX483, MAX487–MAX489 System Differential Voltage at 110kHz Driving 4000ft of CableFigure 21. MAX481/MAX483/MAX485/MAX487/MAX1487 Typical Half-Duplex RS-485 NetworkM A X 481/M A X 483/M A X 485/M A X 487–M A X 491/M A X 1487Low-Power, Slew-Rate-Limited RS-485/RS-422 Transceivers 14______________________________________________________________________________________Figure 22. MAX488–MAX491 Full-Duplex RS-485 NetworkFigure 23. Line Repeater for MAX488–MAX491Isolated RS-485For isolated RS-485 applications, see the MAX253 and MAX1480 data sheets.MAX481/MAX483/MAX485/MAX487–MAX491/MAX1487Low-Power, Slew-Rate-Limited RS-485/RS-422 Transceivers______________________________________________________________________________________15_______________Ordering Information_________________Chip TopographiesMAX481/MAX483/MAX485/MAX487/MAX1487N.C. RO 0.054"(1.372mm)0.080"(2.032mm)DE DIGND B N.C.V CCARE * Contact factory for dice specifications.__Ordering Information (continued)M A X 481/M A X 483/M A X 485/M A X 487–M A X 491/M A X 1487Low-Power, Slew-Rate-Limited RS-485/RS-422 Transceivers 16______________________________________________________________________________________TRANSISTOR COUNT: 248SUBSTRATE CONNECTED TO GNDMAX488/MAX490B RO 0.054"(1.372mm)0.080"(2.032mm)N.C. DIGND Z A V CCYN.C._____________________________________________Chip Topographies (continued)MAX489/MAX491B RO 0.054"(1.372mm)0.080"(2.032mm)DE DIGND Z A V CCYREMAX481/MAX483/MAX485/MAX487–MAX491/MAX1487Low-Power, Slew-Rate-Limited RS-485/RS-422 Transceivers______________________________________________________________________________________17Package Information(The package drawing(s) in this data sheet may not reflect the most current specifications. For the latest package outline information go to /packages .)S O I C N .E P SM A X 481/M A X 483/M A X 485/M A X 487–M A X 491/M A X 1487Low-Power, Slew-Rate-Limited RS-485/RS-422 Transceivers 18______________________________________________________________________________________Package Information (continued)(The package drawing(s) in this data sheet may not reflect the most current specifications. For the latest package outline information go to /packages .)MAX481/MAX483/MAX485/MAX487–MAX491Low-Power, Slew-Rate-Limited RS-485/RS-422 TransceiversMaxim cannot assume responsibility for use of any circuitry other than circuitry entirely embodied in a Maxim product. No circuit patent licenses are implied. Maxim reserves the right to change the circuitry and specifications without notice at any time.Maxim Integrated Products, 120 San Gabriel Drive, Sunnyvale, CA 94086 408-737-7600 ____________________19©2003 Maxim Integrated ProductsPrinted USAis a registered trademark of Maxim Integrated Products.M A X 481/M A X 483/M A X 485/M A X 487–M A X 491/M A X 1487P D I P N .E PSPackage Information (continued)(The package drawing(s) in this data sheet may not reflect the most current specifications. For the latest package outline information go to /packages .)。
TI美信芯片命名规则.

AXIM前缀是“MAX”。
DALLAS则是以“DS”开头。
MAX×××或MAX××××说明:1后缀CSA、CWA 其中C表示普通级,S表示表贴,W表示宽体表贴。
2 后缀CWI表示宽体表贴,EEWI宽体工业级表贴,后缀MJA或883为军级。
3 CPA、BCPI、BCPP、CPP、CCPP、CPE、CPD、ACPA后缀均为普通双列直插。
举例MAX202CPE、CPE普通ECPE普通带抗静电保护MAX202EEPE 工业级抗静电保护(-45℃-85℃说明 E指抗静电保护MAXIM数字排列分类1字头模拟器 2字头滤波器 3字头多路开关4字头放大器 5字头数模转换器 6字头电压基准7字头电压转换 8字头复位器 9字头比较器三字母后缀:例如:MAX358CPDC = 温度范围P = 封装类型D = 管脚数温度范围:C = 0℃至70℃(商业级I = -20℃至+85℃ (工业级E = -40℃至+85℃ (扩展工业级A = -40℃至+85℃ (航空级M = -55℃至+125℃ (军品级封装类型:A SSOP(缩小外型封装B CERQUADC TO-220, TQFP(薄型四方扁平封装D 陶瓷铜顶封装E 四分之一大的小外型封装F 陶瓷扁平封装H 模块封装, SBGA(超级球式栅格阵列, 5x5 TQFP J CERDIP (陶瓷双列直插K TO-3 塑料接脚栅格阵列L LCC (无引线芯片承载封装M MQFP (公制四方扁平封装N 窄体塑封双列直插P 塑封双列直插Q PLCC (塑料式引线芯片承载封装R 窄体陶瓷双列直插封装(300milS 小外型封装T TO5,TO-99,TO-100U TSSOP,μMAX,SOTW 宽体小外型封装(300milX SC-70(3脚,5脚,6脚Y 窄体铜顶封装Z TO-92,MQUAD/D 裸片/PR 增强型塑封/W 晶圆1、 MAXIM 更多资料请参考 MAXIM前缀是“MAX”。
CSA Mark 认证商品说明书 - Siemens AG 产品

Certificate of ComplianceCertificate:2494434Master Contract:165071Project:2682820Date Issued:December 5, 2013Issued to:Siemens AGI IA CE CP R&D-VI 4Werner-von-Siemens-Strasse 48Amberg, 92220GermanyAttention: Mr. Michael SchröckThe products listed below are eligible to bear the CSA Mark shownJ.-C. ChowIssued by:J.-C. ChowPRODUCTS CLASS 3211 04- INDUSTRIAL CONTROL EQUIPMENT - Motor Controllers - Magnetic CLASS 3211 24- INDUSTRIAL CONTROL EQUIPMENT - Motor Controllers-Magnetic CLASS 3211 37- INDUSTRIAL CONTROL EQUIPMENT - Sub-Assemblies - ComponentsPart-A (Class 3211-04)Magnetic motor controllers, direct-on-line or reversing, Types 3RA2, open type assemblies including Certified manual motor controllers and magnetic contactors, with following ratings:Main Contacts (lesser rating of Certified manual motor controller and contactor assemblies):•Type 3RA2.1: lesser rating of Types 3RT201 and 3RV2•Type 3RA2.2: lesser rating of Types 3RT202 and 3RV2Short-circuit ratings (RMS symmetrical amperes):Type Contactor or ReversingMMC 3RV2Short-Circuit V oltage 3RA2.13RT201 or 3RA231,Size S00Max 16 A65 kA 480 V 3RA2.13RT201 or 3RA231,Size S00Max 12.5 A(seeNotes 2, 3)30 kA 600 V 3RA2.23RT2024 or 3RA2324, Size S0Max 12.5 A65 kA 480 V 3RA2.23RT2025 or 3RA2325, Size S0Max 16 A(see Note4)65 kA 480 V 3RA2.265 kA480 VCertificate:2494434Master Contract:165071Project:2682820Date Issued:December 5, 20133RT2026 or3RA2326, Size S0Max 25 A(see Note 4)3RA2.23RT2027 or3RA2327, Size S0Max 32 A(see Notes 1, 4)50 kA 480 V 3RA2.23RT202 or 3RA232,Size S0Max 12.5 A(see Notes 2, 3)30 kA 600 VCoil Ratings: 24 through 600 Vac; or 12 through 250 Vdc.Notes:1) These open type assemblies are rated for use in an ambient temperature of 40°C max, except for assemblies provided with 32 A MMC 3RV2 is rated for use in a surrounding air temperature rating of 40°C max.2) For 600V short-circuit rating, the assembly with MMC 3RV2 is to be installed with Branch Circuit Protective Device, Max Fuse 50 A Class J.3) For 600V short-circuit rating, the screw-mounting assembly is to be installed with an isolation between the assembly and enclosure, according to test conducted with mounting adapter Type 3RA2922-1A; the isolation may be achieved by mounting adapter, Type 8US1. For device assembly mounted on Din rail, no isolation is necessary.4) For specified 480V short-circuit rating, the screw-mounting device assembly is to be installed with an isolation between the assembly and enclosure, according to test conducted with mounting adapter Type3RA2922-1A; the isolation may be achieved by mounting adapter, Type 8US1. For device assembly mounted on Din rail with minimum 15 mm spacing to enclosure, no isolation is necessary.Part-B (Class 3211-24)Combination motor controllers Type F, direct-on-line or reversing, Types 3RA2, open type assemblies including Certified self-protected (Type E manual) combination motor controllers and magnetic contactors, with following ratings:Main Contacts (lesser rating of Certified self-protected combination motor controller and contactor assemblies):•Type 3RA2.1: lesser rating of Types 3RT201 and 3RV2•Type 3RA2.2: lesser rating of Types 3RT202 and 3RV2Short-circuit ratings (RMS symmetrical amperes):Type Contactor or ReversingCMC 3RV2Short-Circuit V oltage3RA2.13RT201 or 3RA231,Size S00Max 16 A65 kA 480Y/277 V , 240 V 3RA2.13RT201 or 3RA231,Size S00Max 12.5 A(seeNotes 3, 5)or, Max 10 A(seeNote 2)30 kA600Y/347 VCertificate:2494434Master Contract:165071 Project:2682820Date Issued:December 5, 20133RA2.23RT2024 or3RA2324, Size S0Max 12.5 A65 kA480Y/277 V, 240 V3RA2.23RT2025 or3RA2325, Size S0Max 16 A(see Note4)65 kA480Y/277 V, 240 V3RA2.23RT2026 or3RA2326, Size S0Max 25 A(see Note4)65 kA480Y/277 V, 240 V3RA2.23RT2027 or3RA2327, Size S0Max 32 A(see Note4)50 kA480Y/277 V, 240 V3RA2.23RT202 or 3RA232,Size S0Max 12.5 A(seeNotes 3, 5)or, Max 10 A(seeNote 2)30 kA600Y/347 VCoil Ratings: 24 through 600 Vac; or 12 through 250 Vdc.Notes:1) These open type assemblies are rated for use in an ambient temperature of 40°C max, except for assemblies provided with 32 A CMC 3RV2 is rated for use in a surrounding air temperature rating of 40°C max.2) For specified 600V short-circuit rating, the device assembly installed on Fastbus system is to be mounted with terminal adapter Type 3RV2928-1K for CMC 3RV2.3) For specified 600V short-circuit rating, the screw-mounting device assembly is to be installed with an isolation provided between the assembly and enclosure, according to test conducted with mounting adapter Type 3RA2922-1A; the isolation may be achieved by mounting adapter, Type 8US1. For device assembly mounted on Din rail with minimum 15 mm spacing to enclosure, no isolation is necessary.4) For specified 480V short-circuit rating, the screw-mounting device assembly is to be installed with an isolation between the assembly and enclosure, according to test conducted with mounting adapter Type3RA2922-1A; the isolation may be achieved by mounting adapter, Type 8US1. For device assembly mounted on Din rail, no isolation is necessary.5) For specified 600V short-circuit rating, the device assembly installed without Fastbus system is tobe mounted with terminal adapter Type 3RV2928-1K for CMC 3RV2, or with terminal adapter kit Type3RV2928-1H for CMC 3RV2.Part-C (Class 3211-37)Accessories:•Link modules to connect manual/combination motor controller 3RV20 to contactor 3RT2: Types3RA1921-1D, 3RA2911-2A, 3RA2911-2F, 3RA2921-1A, 3RA2921-2A, 3RA2921-2F•Link module to connect manual/combination motor controller 3RV20 to contactor 3RT2; or to solid-state motor controllers 3RW301, 3RW302, 3RW402, 3RF24, 3RF34: Type 3RA2921-1B•Mounting adapter for standard Din rail: Type 3RA2922-1A, may be followed by additional numbers and/or lettersCertificate:2494434Master Contract:165071 Project:2682820Date Issued:December 5, 2013•Spacer module for AC-contactors with spring terminals: Type 3RA2911-1C, may be followed by additional numbers and/or lettersGeneral Notes:1. The type designation may be completed with suffixes indicating shape of contacts, terminal design, mounting, etc.2. Open-type device assemblies are Certified only for use in complete assemblies where the suitability of the combination is subject to further investigation.3. The auxiliary contacts are available as contact blocks Type 3RH29 (side or top mounted to contactor 3RT2), integrated auxiliary contacts (contactor 3RT2), and/or contact blocks Type 3RV29.Nomenclature Breakdown3RA2110-0B A150-…I II III IV V VI VII VIII IXI Controller designation3RA2 Basic deviceII Controller type1 Direct-on-line contactor2 Reversing contactorIII Size of controller and contactor Type1 Size S00 and contactor Type 3RT2.12 Size S0 and contactor Type 3RT2.2IV Auxiliary contact arrangements of the 3RV200 None provided1 1 normally open and 1 normally closed, side mounted2 2 normally open, side mounted3 2 normally closed, side mounted4 1 changeover contact, top mounted5 1 normally open and 1 normally closed, top mountedCertificate:2494434Master Contract:165071 Project:2682820Date Issued:December 5, 20136 1 normally open and 1 normally closed with spring terminals, top mounted (only for versions A, Band D according VI of the Nomenclature Breakdown)V Current setting range of 3RV20Suffix from to (A)0A0.110.160B0.140.20C0.180.250D0.220.320E0.280.40F0.350.50G0.450.630H0.550.80J0.710K0.9 1.251A 1.1 1.61B 1.421C 1.8 2.51D 2.2 3.21E 2.841F 3.551G 4.5 6.31H 5.581J7101K912.54A11164B14204C17224D20254N23284E2732VI Mounting and type of terminalsA Without Mounting rail adapter, screw terminalsB With Mounting rail adapter (only for reversing Size S0), screw terminalsD With Fastbus adapter, screw terminalsE Without Mounting rail adapter, spring terminalsF With Mounting rail adapter (only for reversing Size S0), spring terminals (not for “Part-B”)H With Fastbus adapter (Size S00 and S0), spring terminals (not for “Part-B”)Certificate:2494434Master Contract:165071 Project:2682820Date Issued:December 5, 2013S With Fastbus adapter (Size S00), spring terminals (not for “Part-B”)VII Type of contactor or reversing contactor15 Type 3RT2015 contactor or 3RA2315 reversing contactor16 Type 3RT2016 contactor or 3RA2316 reversing contactor17 Type 3RT2017 contactor or 3RA2317 reversing contactor18 Type 3RT2018 contactor or 3RA2318 reversing contactor24 Type 3RT2024 contactor or 3RA2324 reversing contactor25 Type 3RT2025 contactor or 3RA2325 reversing contactor26 Type 3RT2026 contactor or 3RA2326 reversing contactor27 Type 3RT2027 contactor or 3RA2327 reversing contactorVIII Auxiliary contact arrangement0 With 1 NO + 1 NC for Size S01 With 1 NO for Size S00 only2 With 1 NC for Size S00 onlyIX Indicates coil voltage and optional external overvoltage protectionX Manufacturers IdentificationAPPLICABLE REQUIREMENTSCSA-C22.2 No. 14-13 - Industrial Control EquipmentCAN/CSA-C22.2 No 60947-1-07 - Low-V oltage Switchgear and Controlgear - Part 1 : General rulesCAN/CSA-C22.2 No 60947-4-1-07 - Low-V oltage Switchgear and Controlgear - Part 4-1: Contactors and motor-starters - Electromechanical contactors and motor-starters。
Maxstar 400和800电缸TIG焊接机说明书

Maxstar ®Issued March 2021 • Index No. DC/24.5Power source is warrantied for three years, parts and labor.Maxstar 400 Wireless CompleteMaxstar 400 machine onlyAllows for any input voltage hookup (208–575 V) with no manual linking, providing convenience in any job setting. Ideal solution for digital meters to be calibrated dedicated-use receptacle for feature operates the auxiliary cooling power source cooling system operates only when needed, reducing noise, energy use and the amount of contaminants pulled though the machine.Auto-postflow adjusts the length of postflow time based on the amperage setting, shielding your tungsten and eliminating the need to set the postflow time.Lift-Arc ™ provides DC arc initiation without the use of high frequency.Blue Lightning ™ high-frequency (HF) arc starter for non-contact arc initiation. Provides more consistent arc starts and greater reliability compared to traditional HF arc starters.TIG/Stick WeldingPower SourceMiller Electric Mfg. LLCAn ITW Welding Company 1635 West Spencer Street P.O. Box 1079Appleton, WI 54912-1079 USAEquipment Sales US and CanadaPhone: 866-931-9730 FAX: 800-637-2315International Phone: 920-735-4554 International FAX: 920-735-41252Performance Data*Sense voltage for low OCV stick and Lift-Arc ™ TIG.All CE models conform to the applicable parts of the IEC 60974 series of standards.Certified by Canadian Standards Association to both the Canadian and U.S. Standards.Tech Menu (Hold Gas and Amperage buttons five seconds.)332101141513671289Maxstar ®400 and 800 Control Panel(9 DC TIG) (9 DC stick) 2.Memory Display 3.Voltmeter Display 4.Ammeter Display5.Process/Arc Starting TIG: HF impulse, Lift-ArcSTICK: Adaptive Hot Start 6.Output Control Standard remote,2T trigger hold, Output on 7.Pulser ControlPulses per Second* DC: 0.1–5,000 pps Peak Time* 5–95% Background Amps* 5–95%*Pro-Set parameter selectable.9.Activity Indicator 10.Encoder Control 11.Amperage Button12.Gas/DIGPreflow Off–25.0 seconds Postflow Auto/Off–50 seconds DIG* Off–100% 13.Sequencer ControlInitial Amps 3–400 A/5–800 A Initial Time Off–25.0 seconds Initial Slope Off–50.0 seconds Weld Time Off–999 seconds Final Slope Off–50.0 seconds Final Amps 3–400 A/5–800 A Final Time Off–25.0 seconds1. Tungsten Size 400 = .020–3/16 in./GEN or 0.5–4.8 mm 800 = .040–1/4 in./GEN or 1.0–6.4 mm2. Remote Trigger = 2T/3T/4T/4TL/4TE/4Tm3. Stick Hot Start = ON/OFF1. Arc Time 0.0–9,999 hours 0.0–59 minutes 0–999,999 cycles Resettable2. Error Log = Error event recorder3. Stick Stuc = OFF/ON4. OCV = LOW/NORM5. Weld Timers = OFF/ON6. Cooler Power = AUTO/ON/OFF7. Locks = OFF/1–48. Meter Display9. External Pulse Control = OFF/ON 10. Machine Reset 11. Software Number 12. Serial Number13. Slave (with Modbus ®Address = 1–247 automation expansion)Baudrate = 9600/19.2K Parity = EVEN/ODD/NONEUser Menu (Press Gas and Amperage buttons.)Pulsed TIG Controls4Maxstar ®400 and 800 Models/Packages5907716001 package shown.951874package shown.907716 and 907718models shown.301580 remote shown.301268 kit shown.907716001 Maxstar 400TIGRunner ® shown with four bottles of 043810Low-Conductivity Coolant.Build aWater-Cooled PackageSelect desired stock number for each step.Machines and Preconfigured Water-Cooled PackagesOrder machine only or use a single stock number to order a complete preconfigured system.6Water-Cooled TIG Torch Connector 195377 For Dynasty ® and Maxstar ® 400.50 mm Dinse-style with water return line. For use with all Weldcraft ™ water-cooled torches.Water-Cooled TIG Torch Connector 225028 For Dynasty and Maxstar 800.50 mm thread-lock with water return line. For use with all Weldcraft ™ water-cooled torches.Runner™ Cart300244Designed toaccommodate Dynasty or Maxstar 400 or 800 power sources and a Coolmate ™ 3.5 Cooler. Cart features single cylinder rack, foot pedal holder, three cable/torchholders, and two TIG electrode filler holders.Coolmate ™3.5 300245Designed to integrate with the Dynasty and Maxstar 400 and 800 power sources. For use with water-cooled torches rated up to 600 amps. 3.5-gallon capacity.Low-Conductivity TIG Coolant 043810Sold in multiples of four in one-gallon recyclable plastic bottles. Millercoolants contains a base of ethyleneglycol and deionized water to protect against freezing to -37° Fahrenheit (-38°C) or boiling to 227° Fahrenheit (108°C).Automation Interface Connection Kit 278161 FieldProvides control of power source welding parameters through a 28-pin receptacle. The 28-pin receptacle replaces the standard 14-pin receptacle and requires a PLC controller to operate the power source. Ideal for automated equipment integration.Weld Current Sensor 300179 FieldDetects when work clamp is not connected and prevents expensive damage to disconnectdevices and input power cord and wiring.Water-Cooled Torch KitsW-280 Torch Kit 300990Weldcraft ™ W-280 25-foot (7.6 m) TIG torch with Dinse-style connector Torch cable coverWork clamp with 15-foot (4.6 m) 1/0 cable and Dinse-style connector Flowmeter regulatorGas hose (regulator to machine)AK4GL torch accessory kit includes short back cap, nozzles, gas lenses, collets and 2% ceriated tungsten electrodes (1/16, 3/32 and 1/8 inch)W-375 Torch Kit 301268Recommended for Maxstar 400Weldcraft ™ W-375 25-foot (7.6 m) TIG torch with Dinse-style connector Torch cable coverWork clamp with 15-foot (4.6 m) 1/0 cable and Dinse-style connector Flowmeter regulatorGas hose (regulator to machine)AK4GL torch accessory kit includes short back cap, nozzles, gas lenses, collets and 2% ceriated tungsten electrodes (1/16, 3/32 and 1/8 inch)W-400 (WP-18SC) Torch Kit 300186 Recommended for Maxstar 800Weldcraft ™ W-400 (WP-18SC) 25-foot (7.6 m) TIG torch with thread-lock connector Torch cable coverWork clamp with 12-foot (3.7 m) 4/0 cable with thread-lock connector Flowmeter regulatorGas hose (regulator to machine)AK18C torch accessory kit includes short back cap, nozzles, collets, collet bodies and 2% ceriated tungsten electrodes (3/32, 1/8 and 5/32 inch)Genuine Miller ®AccessoriesGenuine Miller® Accessories (Continued)into the 14-pin receptacle of Miller machine.Includes 20-foot (6 m) cord and 14-pin plug.Tungsten7Ordering InformationEquipment and Options Stock No. Description Qty. Price Maxstar® 400907716 Auto-Line™ 208–575 V, 50/60 Hz, CSA. 8 ft. power cordMaxstar® 400 International 907716002 Auto-Line™ 380–575 V, 50/60 Hz, CE. 8 ft. power cordMaxstar® 400 TIGRunner®907716001 Auto-Line™ 208–575 V, 50/60 Hz, CSA. 8 ft. power cord. Requires coolantMaxstar® 400 Wireless Complete 951874 Auto-Line™ 208–575 V, 50/60 Hz, CSA. 8 ft. power cordMaxstar® 400 Complete 951692 Auto-Line™ 208–575 V, 50/60 Hz, CSA. 8 ft. power cordMaxstar® 800907718 Auto-Line™ 208–575 V, 50/60 Hz, CSAMaxstar® 800 International907718002 Auto-Line™ 380–575 V, 50/60 Hz, CETIG Torches, Kits and ConnectorsWater-Cooled Torch Kits300990 W-280(see page 6 for contents)301268 W-375 (recommended for Maxstar 400)300186 W-400 (WP-18SC) (recommended for Maxstar 800)Water-Cooled TIG Torch Connectors 195377 Connects Weldcraft™ water-cooled torches to Dinse-style connector225028 Connects Weldcraft™ water-cooled torches to Maxstar 800(thread-lock connector included with 800 models)Tungsten See page 7Remote ControlsWireless Remote Foot Control 301580 Foot control with wireless 90 ft. (27.4 m) operating rangeWireless Remote Hand Control301582 Hand control with wireless 300 ft. (91.4 m) operating rangeRCCS-14043688 North/south fingertip controlRCC-14 151086 East/west fingertip controlRFCS-14 HD194744 Heavy-duty foot controlRHC-14242211020 Hand controlRMLS-14 129337 Momentary/maintained rocker switchRMS-14 187208 Momentary rubber dome switchExtension Cables See page 7AccessoriesRunner™ Cart 300244 See page 6Coolmate™ 3.5300245 120 V, 50/60 Hz, CE.Requires coolantTIG Coolant 043810 1-gallon plastic bottle. Protects against freezing to -37° Fahrenheit (-38°C)(must be ordered in quantities of four) or boiling to 227° Fahrenheit (108°C)Automation Interface Kit 278161 Field installation required. Provides 28-pin automation connectionsWeld Current Sensor300179 Field installation required. Detects when work clamp is not connectedDinse-Style Connector 50 mm (1 male) 042418 Used to connect weld cable to Dinse terminal machineThread-Lock Connectors (2 male) 225029 Used to connect weld cable to Dynasty 800 or Maxstar 800Dinse-Style Connector 50 mm 042419 Used to extend weld cables(1 male, 1 female)Dinse/Tweco® Adapter042465 Male Dinse to female TwecoDinse/Cam-Lok Adapter042466 Male Dinse to female Cam-LokTIG Welding Gloves See page 7Memory Cards 301151 14-Pin automation expansion301152 14-Pin Modbus® expansion301080 BlankGas Tungsten Arc Welding (TIG) Publication250833Date: Total Quoted Price:Distributed by:©2021 Miller Electric Mfg. LLC。
ARCO 400 一体化测试设备用于重闭器控制器说明书

ARCO 400Universal test set for recloser controlsSmart and rugged testing solution forCoping with modern recloser functionsTechnology has significantly improved overhead distribution networks by reducing customer-minutes of interruptions through the use of modern reclosers.While the latest control technology brings advancedfunctionality, including distribution automation capabilities, testing all settings to ensure proper operation has become a challenge.What if controller testing can be done in only a few minutes?ARCO 400, the lightweight and easy to use test set, is the universal solution for all types of recloser controls. Con-necting the test set to the recloser control has never been easier: A single plug on the test set combined with intel-ligent recloser-specific ARCO 400 smart controller adapters allow a flawless connection within seconds. This saves timeand avoids faulty wiring during the test setup.Safe and touch-proof combined test interface:3 x 12.5 A6 x 8 V (6 x 150 V optional)6 binary inputs 9 binary outputsLEDs indicating breaker positions for each phaseChangeable dust filtersUSB and Ethernet interfacesYour benefi ts> >weather conditions > >distribution scheme tests >training requiredall types of recloser controlsSimple plug-and-play functionality checksARCO 400 provides the fastest and easiest way to perform simple trip/close checks. Every smart controller adapter includes a chip through which ARCO 400 automatically recognizes the specific adapter and, once connected, con-figures itself for the test procedure. This allows immediate basic trip and close functionality checks via the controller's push buttons – without the use of any software.All recloser control functions coveredARCO 400 is specifically designed to simulate the complete primary recloser component for the testing process. Itenables three-phase testing of all types of recloser controls in both laboratory and field environments.High testing fl exibilityThe accurate 3-phase 12.5 A current amplifiers enable both testing at very low amplitudes and the testing of functions with high fault values.Conventional potential transformers or capacitive and resis-tive voltage sensors are simulated by the 6-phase voltage amplifiers and are available in either an 8 V or 150 V range. This allows testing of any voltage based function. The test set is equipped with six binary inputs and nine binary outputs to measure trip and close commands and simulate circuit breaker auxiliary contacts.Software based control for more functionalityARCO 400 is operated by the ARCO Control software which can be used for simple SCADA metering checks or for the testing of any protection function, including frequency based protection functions used for load-shedding.With the ReCoPlan software, testing procedures are standardized by creating test plans, which also reduce testing time and enable comprehensive reporting.The wireless connection between ARCO 400 and a control-ling laptop or tablet allows remote flexible operation of thetest set.Push buttons to change recloser OPEN/CLOSE statusOMICRON Smart ConnectRugged enclosure for field use 10 kg (22 lbs)200 x 350 x 455 mm (7.9 x 13.8 x 17.9 in)Designed to fit specific requirementsManual control and test templatesSpecific recloser and sectionalizer test modules in the ARCO Control softwareallow the convenient testing of any controller function. To meet your company’stest requirements, ARCO 400 also enables manual testing of the controller. Thesetests are performed through either the given test modules or by executing a testplan predefined in ReCoPlan, which saves time and reduces complexity duringsite testing.Distributed scheme testingSeveral ARCO 400s can be time-synchronized to GPS and controlled simultane-ously with RelaySimTest. This enables complete testing, including communicationchannels, by performing distribution automation scheme tests.Rugged design for outdoor usageTesting in the field demands the test set to be rugged and usable in harshweather conditions. ARCO 400's robust enclosure makes it the ideal test set forany bucket truck. Special shock absorbing material lining the enclosure protectsthe float mounted main unit from many types of vibrations, shocks, or drops.Shock absorbing materialFloat mounted main unitRugged enclosuredisconnect 1connect2test3ARCO ControlEasy testing of controllersARCO Control, specifically designed for testing recloser and sectionalizer controls, is an easy to use software for ARCO 400. Commissioning and maintenance tests are easily performed through the software's comprehensive test tools.The software is configured to allow quick testing of recloser and sectionalizer controls in the field. The navigation menu guides you through each test sequence with step by step instructions. The test results are obtained quickly and reliably, and can then be exported for reporting purposes.ARCO Control runs on a Windows Laptop/PC or Android tablet.Test tools provide a wide range of functions:Analog Output Check allows the output of analog test quantities to perform simplewiring checks.The Pick-Up tool is used to test the thresholdsof recloser and sectionalizer control functions.The Direct tool enables individual manipula-tion of magnitudes, phase angle and fre-quency of all ARCO 400 outputs for manualtesting, troubleshooting, and diagnostics.The Trip Time Characteristics tool checks the operating characteristics and the switchinglogic between a fast and slow curve.The Restoration tool allows testing of voltage controlled functions used in automated distribution restoration schemes.The Tripping Sequence tool tests the func-tionality of the device by simulating a full sequence to lockout, a successful reclose orcoordination with a downstream device.The Test Plan Mode allows the execution oftest plans created via ReCoPlan software.Plug-and-play start up procedureStarting a new test is both easy and intuitive. Simply connect an ARCO 400 smart controller adapter and extension cable to ARCO 400 and the hardware will configure itself by reading the configuration associated with the smart adapter. After selecting the controller to be tested, the user has the option to input specific test data such as location, tester's name and report informa-tion. Tests can then be started right away by selecting the desired test tool.Plug in adapterThe software recognizes the smart controller adapter once it is connected. Only the control-ler to be tested has to be selected from the provided list.Hardware configurationARCO 400 amplifiers and information such as CT ratio are automatically set in the software based on the controller selection. Pre-set nomi-nal values can be altered if required. General data can be added in the Report Information section (e.g. tester, location).Starting a testSelect the desired test tool in the main menu totest the functions in the controller.123ARCO Control test examplesTripping Sequence test toolWith this test tool, the functionality of recloser and sectionalizer controls is easily ascertained for full sequence, lockout, and automatic reclosing sequences. Sectionalizer testing simulates the trip-close sequence of an upstream device. The proper timing of the recloser or sectionalizer control ismeasured and included in the report.Application modeThere are two different applications that can be tested with the Tripping Sequence test tool (recloser or sectionalizer). When selecting the DUT (device under test), the software also determines which additional units will be involved in testing. For example, the test of a recloser with a simulated downstream recloser is selected.ConfigurationThe type of test sequence is defined in theconfiguration menu. Selectable options are Full Sequence to Lockout, Successful Reclose and Co-ordination with Downstream Recloser.Test screenAll configured test parameters are summarized and clearly displayed. The test results are automatically assessed once the test has finished.123Trip Time Characteristics test toolThe Trip Time Characteristics test tool checks both the operating characteristics of the recloser control and the switch logic between the fast and slow curve which occurs when a fuse-savingscheme is applied. For this, a complete test sequence is executed up to the lock out of the controller. To test the tripping behavior of a single curve only, repeated test shots can be sent to the controllerin the Trip Only mode.CurvesThe following parameters are set in this menu: >The two curves to be tested >The optional time additions>The number of test shots on the fast curve >The current pickup valueSequenceThe test is performed as a sequence. A test sequence consists of a fixed number of shots with pre-defined currents to test the timing of the curve at different points.Test screenOnce the sequence is completed with all test shots, a graphic displays the shots recorded and compares them to the nominal trip times. Actual trip times are displayed for comparison and an assessment is automatically made basedon defined tolerances.123ReCoPlanGuided testing workfl owStandardized testing procedures can easily be developed through test plans which specify a pre d efined workflow of tests for recloser and sectionalizer controls.Our PC-based software ReCoPlan allows you to create test plans using the available tools ofARCO Control. One additional feature with ReCoPlan is the Instruction Command which provides additional or specific information to the tester on what the test plan is to accomplish or whether an interaction is needed from the tester to complete the test procedure.After designing the test plan in ReCoPlan, it can be saved and executed using the ARCO Control software.Your ReCoPlan benefi ts>Fast and easy creation of test plans including pre-defined test values >Standardize testing procedures >Reduce test time>Include working instructions >One combined reportDistribute test plan or directlyexecute it from ReCoPlan ** If this is on a different computer, send the test plan file via email or transfer it via SD card toARCO ControlExecute in ARCO Control Run tests by selecting the pre-defined test tools.2Compliance requirementsThe new NERC PRC-005-6 standardIn North America, the NERC defines test and maintenance requirements for protection systems.The new PRC-005-6 reliability standard requires the devel-opment of a comprehensive protection system including maintenance and testing processes, replacing PRC-005-5. To be technically valid, maintenance programs requiredocumentation showing how the verified protection system segments overlap so that no segment is left unverified.Focus on documentation requirementsThe new standard alters the process of documentation of monitoring, testing, and maintaining distribution systems, underfrequency load-shedding systems and undervoltage load-shedding systems. This includes protection systems, such as automatic reclosing and sudden pressure relaying, which affect the reliably of the Bulk Electric System (BES). ARCO 400 provides functionality that supports all PRC-005-6 requirements.Grid operators all over the world need to meet national compliance requirements for maintenance and documentation of the protection system. One of the hardest standards is the NERC (North American Electric Reliability Corporation) PRC-005-6.Comply with documentation requirementsOffering user-friendly access to all information and docu-mentation, the ADMO database software enables central planning and management of testing and maintenance activities for protection systems in the power industry. With this database you can manage the following protec-tion system components: auto-reclosers, protective relays, communication systems, control circuitry, current andvoltage transformers, circuit breakers, station DC supplies, and energy meters.Exchange your documents with various platformsADMO supports the storing and management ofARCO 400 data and testing results, as well as third-party test documents and documents individually created in Microsoft Excel, Microsoft Word or Adobe Acrobat (PDF) file formats. Graphic files can also be attached (e.g. photosof the test set-up, screenshots).ADMO is an easy-to-use database software for central planning and management of all testing and maintenance activities for protection systems in the power industryDistribution automation scheme testingTesting protection and communicationWith the increase of distribution automation schemes being implemented due to Smart Grid requirements, modern auto-reclosers must use complex algorithms to adapt to the network and failures. Simple function tests of single controllers are not sufficient for testing the automation functionality. Instead, synchronized injection into thecontrollers involved in the automation scheme is required to test not only the switching logic, but also the communica-tion channels which are an essential part of the scheme.Benefi t from a novel testing approachRelaySimTest is a unique software for system-based,distributed protection testing in the field that covers these new demands. Its unique approach can reveal failures in the logic of the switching scheme as well as communication issues, requiring only a minimum amount of test steps. System-based testing does not depend on recloser type, manufacturer, or the detailed parameters of a singlecontroller. The correct tripping and closing behavior is the only variable that is of concern.Ordering options6 x 150 VCannot find the adapter you are looking for? Please check our website or contact us. We are constantly expanding the range of smart controller adapters to provide you with a suitable adapter for your recloser or sectionalizer control.ARCO 400 smart controller adaptersARCO 400 smart controller adapters with OMCRON Smart Connect technology are offered for testing of recloser andsectionalizer controls with 10, 14, 19, 24, 26, 32, and 42 pin interfaces. This enables testing of the widest range of controllers including:Pin CountSwitch/Breaker typeSuitable for controllers such asAdapterOrder No.10G&W Viper SPT&B Elastimold MVR SEL 351RS KestrelRVP2 1VEHZ118414Cooper NOVA G&W Viper ST&B Elastimold MVR Eaton/Cooper Form 4C, 4D, 5, 6SEL 351R, 651R, 651RARST2 1VEHZ117119Cooper NOVA G&W Viper SEaton/Cooper Form 4C, 4D, 5, 6SEL 651RRCP2 1VEHZ117224Arteche smART RC Arteche smART P500RAR2VEHZ118024ABB GridShield ABB RER620RGS2 1VEHZ118124Schneider N-/U-/RL-/W-SeriesSchneider ADVC Nu-Lec PTCC RNU2VEHZ117524ABB OVR/VR3S ABB PCD 2SEL 651R ROV2 1VEHZ118224S&C ScadaMate S&C 5801S&C 6801RSM2VEHZ118326Cooper NOVA-TS/STS Eaton/Cooper TS/STS Eaton/Cooper Form 5, 6SEL 651R RCS2 1VEHZ117332NOJA OSM-xx-3xx NOJA RC 10RNO2VEHZ117732Tavrida OSMNOJA OSM-xx-2xx Tavrida RC 05NOJA RC-01RTA2VEHZ117832Tavrida OSM Al_2SEL 651R RTO2VEHZ117632G&W Viper ST/LT T&B Elastimold MVR SEL 651R RVT2 1VEHZ117442G&W Viper ST/LT T&B Elastimold MVR Tavrida OSM Al_4SEL 651R RMI2VEHZ11791 Requires RVO2 Voltage Generator Combination Cable (see page 14) if controller is equipped with a separate voltage input connector 2Version without block close function from yellow handle (69 switch) supported onlyTechnical data ARCO 400Amplifier specificationsCurrent amplifierNumber of outputs3Ranges Range I: 0 ... 1.25 ARange II: 0 ... 12.5 ARange III: 0 ... 8 VFrequency Range0 ... 599 HzAmplitude accuracyError typical Error guaranteed AC accuracy50/60 Hz< 0.04 % of rd.1+ 0.01 % of rg.1< 0.08 % of rd. + 0.02 % of rg.≤ 599 Hz< 0.25 % of rd.+ 0.05 % of rg.THD+N at 50/60Hz< 0.1 %< 0.25 % Phase error50/60 Hz< 0.05°< 0.2°DC offset1.25 A range< 30 μA< 300 μA 12.5 A range< 300 μA< 3 mAOutput powerCompliance voltage> 12 V (RMS)> 18 V (DC)Output power AC 3 × 100 Wat 8 … 12.5 A Voltage amplifierNumber of outputs6Ranges Range I: 0 ... 8 VRange II 2: 0 ... 150 VFrequency Range0 ... 599 HzAmplitude accuracyError typical Error guaranteed AC accuracy50/60 Hz< 0.04 % of rd.+ 0.01 % of rg.< 0.08 % of rd.+ 0.02 % of rg.≤ 599 Hz< 0.25 % of rd.+ 0.05 % of rg.THD+N at 50/60Hz< 0.1 %< 0.25 %Phase error50/60 Hz< 0.05°< 0.2°DC offset150 V range< 10 mV< 20 mV8 V range< 500 μV< 1 mVOutput powerPer channel (Range II)250 mA (AC)350 mA (DC)Output power AC 3 × 15 W / 6 × 10 Wat 57 ... 150 VARCO 4001 rd. = reading, rg. = range2 Hardware optionBinary inputsNumber of binary inputs6Number of potential groups6Type WetSampling frequency10 kHzTime resolution100 μsRated input voltage250 V CAT IIIResolution 1 VThreshold voltage range 5 ... 250 VInput impedance ConfigurableInsulation 6 galvanically isolated binary inputs Binary output relaysNumber of binary outputs9Number of potential groups3Type Potential-free contacts, NOContact rating250 V / 0.5 ATotal make time< 6 msTotal break time< 3 msAll input / output values are guaranteed for one year within an ambient temperature of 23 °C ± 5 °C / 73 °F ± 10 °F.Accuracy values indicate that the error is smaller than ± [(read value x reading error) + (range setting x range error)].Environmental conditionsOperatingtemperature-10 °C ... +50 °C / +14 °F ... +122 °F-10 °C (+14 °F) – 16 h (IEC 60068-2-1)+50 °C (+122 °F) – 16 h (IEC 60068-2-2) Storage andtransportation-25 °C ... +70 °C / -13 °F ... +158 °FMaximum altitudeOperating 4 000 m / 13 000 ftNon-operating15 000 m / 49 000 ftHumidity 5 % … 95 % relative humidity; no condensation Equipment reliabilityEMC IEC 61326-1, CISPR 22,FCC Subpart B of Part 15 Class AShock30 g (11 ms half sine) according to IEC 68-2-27 Vibration 5 g (10 Hz – 2000 Hz) according to IEC 68-2-64 Drop test 2 drops (transport position) 0.5 m / 1.6 ftIEC 60068-2-31Power supply and mechanical dataSingle-phase,nominal100 ... 240 VACSingle-phase,permissible85 ... 264 VACCurrent, nominal 1 A max. at < 170 V10 A max. at > 170 VFrequency, nominal50/60 HzWeight10 kg / 22 lbsDimensions(W × H × D)200 × 350 × 455 mm / 7.9 × 13.8 × 17.9 in CertificationsWelcome to the teamAt OMICRON you can always depend on an experienced team that actively sup-ports you and an infrastructure that you can rely on. We always listen attentively in order to understand your needs so that we can off er you the best possible solutions. We strive for lasting partnerships and ensure that you can continue to rely on your product long after you've purchased it. In order to do this, we focus on quality, the transfer of knowledge and unique customer support.Aditya, David and Fabian are able to tell you about the services we have available for you and why it pays to be part of the team.A strong and safe connectionAditya TanejaApplication SpecialistAppSolutions you can rely on...... developed with experience, passion and an innovative approach that we use to continually set groundbreaking standards in our industry sector.We invest more than 15 % of the total turnover in research and development so that we can even guarantee the reliable use of the latest technology and methods in the future.Our comprehensive product care concept also guarantees that your investment in our solutions – like free software updates – pays offin the long term.we use tose toDavid Negron OMICRON AcademyFabian KolbTechnical SupportWe share our knowledge...… by maintaining a constant dialogue with users and experts. Some examples of this are our customer events and conferences that take place all over the world and our collaboration with numerous standardization committees. We also make our knowledge available to you in the customer section of our website in the form of application reports, specialized articles and articles in the discussion forum. With the OMICRON Academy, we also provide a wide spectrum of training possibilities and assist you with Start-up training and freeWhen rapid assistance is required...… our excellent level of support is always appreciated. You can reach the highly-qualified and committed technicians in our customer support department 24 hours a day, seven days a week – and it's completely free. We deal with repair services and service features in a fair and non-bureaucratic manner.We can help minimize your downtime by lending you equipment from a readily avail-able plant at one of our service centers in your area. A comprehensive off er of services for consulting, testing and diagnostics completes our range of services.We share… by mainof this areworld andWe also mwebsite in the discus spectrumwebinars.webthe spe webRelaySimTest ADMO Testing Solutions for Recloser ControlsOMICRON is an international company serving the electrical power industry with innovative testing and diagnostic solutions. The application of OMICRON products allows users to assess the condition of the primary and secondary equipment on their systems with complete confidence. Services offered in the area of consulting, commissioning, testing, diagnosis and training make the product range complete.Customers in more than 150 countries rely on the company’s ability to supply leading-edge technology of excellent quality. Service centers on all continents provide a broad base of knowledge and extraordinary customer support. All of this together with our strong network of sales partners is what has made our company a market leader in the electrical power industry.。
MAX4003EVKIT+中文资料

MAX4003EVKIT+中文资料General DescriptionThe MAX4003 evaluation kit (EV kit) is a fully assembled and tested surface-mount circuit board that evaluates the MAX4003 RF detector in an 8-pin μMAX ?package.The MAX4003 EV kit includes an on-board shutdown control as well as quasi-measurement mode circuitry to provide an easy method to evaluate the MAX4000/MAX4001/MAX4002. The RF input utilizes a 50ΩSMA connector for convenient connection to test equipment.The MAX4003 EV kit can also be used to evaluate the MAX4000/MAX4001/MAX4002 RF-detecting controllers.Features2.7V to 5.5V Single-Supply Operation50ΩSMA Connector on RF InputOn-Board Quasi-Measurement Mode Circuitry ?On-Board Shutdown ControlFully Assembled and Tested Surface-Mount BoardEvaluates: MAX4000–MAX4003MAX4003 Evaluation Kit________________________________________________________________ Maxim Integrated Products 119-0635; Rev 0; 8/06Component ListFor pricing, delivery, and ordering information,please contact Maxim/Dallas Direct!at 1-888-629-4642, or visit Maxim’s website at .Ordering Information+Denotes a lead-free and RoHS-compliant EV kit.Note:T o evaluate the MAX4000, MAX4001, or MAX4002,request a MAX4000EUA, MAX4001EUA, or MAX4002EUA free sample with the MAX4003 EV kit.μMAX is a registered trademark of Maxim Integrated Products, Inc.Component SupplierE v a l u a t e s : M A X 4000–M A X 4003MAX4003 Evaluation Kit 2___________________________________________________________________ ____________________Quick StartRecommended EquipmentOne variable DC power supply capable of supplying between 2.7V and 5.5V at 50mA ?One signal generator capable of delivering -45dBm to 0dBm at frequencies between 100MHz and 2.5GHz ?One voltmeterProcedureThe MAX4003 EV kit is fully assembled and tested. Follow the steps below to verify board operation. Do not turn on the power supply until all connections are completed.1)Set the variable DC power supply to 3V.2)Ensure that the variable DC power supply isturned off.3)Connect the positive terminal of the variable DC power supply to the VCC pad. Connect the ground return of the variable DC power supply to the GND pad.4)Set the signal generator to produce an output signalof 0dBm at a frequency of 100MHz.5)Ensure that the signal generator is turned off.6)Connect the signal generator to the PC edge-mountSMA connector marked RFIN.7)Connect the positive terminal of the voltmeter to theOUT pad. Connect the ground return of the volt-meter to the GND pad.8)Ensure that shunts are removed from jumper JU2.9)Ensure that a shunt is placed across pins 1-2 ofjumper JU3.10)Ensure that a shunt is placed across pins 1-2 ofjumper JU1.11)Turn on the variable DC power supply.12)Turn on/enable the output of the signal generator.13)Verify with the voltmeter that an output voltage of1.46V (±5%) is produced between both the OUT and GND pads.Detailed DescriptionThe MAX4003 EV kit is a fully assembled and tested surface-mount circuit board that evaluates the MAX4003 RF detector. The MAX4003 EV kit can also be used to evaluate the MAX4000/MAX4001/MAX4002RF-detecting controllers. The MAX4003 EV kit includes an on-board shutdown control as well as quasi-mea-surement mode circuitry to provide an easy method to evaluate the MAX4000/MAX4001/MAX4002. The RF input utilizes a 50ΩSMA connector for convenient con-nection to test equipment.Evaluating the MAX4003By default a MAX4003 is installed on the MAX4003 EV kit. To evaluate the MAX4003, remove the shunt on JU2to disconnect the quasi-measurement mode circuitry from the MAX4003. Place the shunt on pins 1-2 of JU1to connect pin 3 of the MAX4003 to ground. The volt-age on the OUT pad reflects the power level of the RF input signal.Evaluating theMAX4000/MAX4001/MAX4002Evaluating the MAX4000The MAX4003 can be replaced with the MAX4000 to allow an input range of -45dBm to 0dBm into 50Ω. The modifications required are as follows:1)Replace U1 with a MAX4000EUA.Evaluating the MAX4001 or MAX4002The MAX4003 can be replaced with the MAX4001 to allow an input range of -35dBm to +10dBm in 50Ω, or with the MAX4002 to allow an input range of -30dBm to +15dBm in 50Ω. The modifications required are as follows:1)Replace U1 with a MAX4001EUA or MAX4002EUA.2)Replace R9 with a 33pF (0402) capacitor.MAX4000/MAX4001/MAX4002 Controller Mode For operation in controller mode, both JU1 and JU2 should be removed. Use a DAC or external precision voltage supply to apply the set-point voltage to the SET pad. RFIN is connected to the RF source—power amplifier (PA) output through a directional coupler—and the OUT pad is connected to the gain-control pin of the PA. When used in controller mode, a capacitor must be installed in C4 for loop stability (see the Filter Capacitor Selection section).MAX4000/MAX4001/MAX4002 AutomaticGain Control To simulate an automatic gain-control (AGC) loop, a quasi-measurement mode can be implemented where the MAX4000/MAX4001/MAX4002 deliver an output voltage that is proportional to the log of the input signal (see the Quasi-Measurement Mode section). To estab-lish the transfer function of the log amp, the RF input power level should be swept while the voltage at the SET pad is measured. This is the simplest method to validate operation of the evaluation board.Filter Capacitor Selection When functioning as a PA controller, the MAX4000/ MAX4001/MAX4002 require some capacitance tomain-tain loop stability. Global system for mobile (GSM) appli-cations require a control-loop bandwidth of at least 150kHz. Install a 2200pF capacitor at the location desig-nated by C4 (located on the board’s component side) to obtain this control-loop bandwidth. Refer to Figure 3 of the MAX4000/MAX4001/MAX4002 data sheet for alterna-tive capacitor values.Quasi-Measurement Mode In the quasi-measurement mode, the MAX4003 EV kit works as a log detector. This mode allows for easy measurement of RFIN versus the SET voltage and these measurements can then be used to find the inter-cept and slope required for the given application. Place a shunt on pins 2-3 of JU1 and install a shunt across JU2 to enable the quasi-measurement mode, which connects the OUT voltage through an inverting op amp to the SET pin. The quasi-measurement mode yields a nominal relationship between RFIN and SET. See Table 1 for quasi-measurement mode shunt positions.Shutdown Controlpin (SHDN) of the MAX4003, which disables the MAX4003. Removing the shunt from JU3 allows the SHDN pin to be driven with an external signal source connected to the SHDN pad. See Table 2 for shutdown shunt positions.Layout Considerationsguide for board layout using the MAX4000–MAX4003. Keep traces carrying RF signals as short as possible to minimize radiation and insertion loss due to the PC board. Each VCC node on the PC board should have its own decoupling capacitor. This minimizes supply coupling from one section of the PC board to another. Using a star topology for the supply layout, in which each VCC node in the circuit has a separate connec-tion to the central VCC node, can further minimize cou-pling between sections of the PC board. Evaluates: MAX4000–MAX4003MAX4003 Evaluation Kit________________________________________________________________ _______________________3E v a l u a t e s : M A X 4000–M A X 4003MAX4003 Evaluation Kit 4___________________________________________________________________ ____________________Figure 1. MAX4003 EV Kit SchematicEvaluates: MAX4000–MAX4003MAX4003 Evaluation Kit________________________________________________________________ _______________________5Figure 2. MAX4003 EV Kit Component Placement Guide—Component SideFigure 3. MAX4003 EV Kit PC Board Layout—Component SideFigure 4a. MAX4003 EV Kit PC Board Layout—Ground PlaneLayer 2Figure 4b. MAX4003 EV Kit PC Board Layout—Ground Plane Layer 3Maxim cannot assume responsibility for use of any circuitry other than circuitry entirely embodied in a Maxim product. No circuit patent licenses are implied. Maxim reserves the right to change the circuitry and specifications without notice at any time.6_____________________Maxim Integrated Products, 120 San Gabriel Drive, Sunnyvale, CA 94086 408-737-7600?2006 Maxim Integrated Productsis a registered trademark of Maxim Integrated Products, Inc.E v a l u a t e s : M A X 4000–M A X 4003MAX4003 Evaluation KitFigure 5. MAX4003 EV Kit PC Board Layout—Solder Side。
Ametek Sorensen SG Series高功率可编程直流电源说明书

SG Series : Product SpecificationsCommonRemote SenseTerminals are provided to sense output voltage at point of load. Maximum line drop 5% of rated voltage per line for 40-100V models, line drop 1V of rated voltage per line for 10-20V models, 1.5V for 30V models, 2% of rated voltage per line for models 160V and greater. (Greater line drop is allowed, but output regulation specifications no longer apply).Parallel OperationUp to 5 units may be paralleled for additional current within the power supply single-unit specifications, with exception of the DC output current set accuracy. Additional paralleled SG units will add 0.3% inaccuracy per unit. To parallel more than 5 units, contact factory.Series OperationUp to 2 units (see Output Float Voltage)InputNominal Voltage3 phase, 3 wire + ground 208/220 VAC (operating range 187 - 242 VAC)380/400 VAC (operating range 342 - 440 VAC)440/480 VAC (operating range 396 - 528 VAC)Frequency 47 – 63Hz , 400Hz ( 400Hz @ 208VAC, for 6U units is optional modification and does not carry CE, UL or CSA markings )Power Factor>0.9 typical for 10V - 30V, 50V, 1000V and other models with optional “PF” modification.>0.75 typical for 208/220 VAC input (40V, 60V - 800V models, 0.9 available with modification “PF”)>0.72 typical for 380/480 VAC input (40V, 60V - 800V models, 0.9 available with modification “PF”)>0.69 typical for 440/480 VAC input (40V, 60V - 800V models, 0.9 available with modification “PF”)Protection ( typical )½ cycle ride-though , typical, on all three phases, 3 cycle ride through on single phase; missing phase shutdown ( 800V model 6.4 msec on all 3 phases )Physical3U Models (10V-30V)3U Models (40V-1000V)6U Models (60V-600V)Width 19.00 in (48.3 cm)19.00 in (48.3 cm)19.00 in (48.3 cm)Depth 28.09 in (71.35 cm)26.4 in (67.1 cm)27.18 in (69.04 cm)Height 5.25 in (13.3 cm)5.25 in (13.3 cm)10.5 in (26.7 cm)Weight(4kW, 10V 15V) ≈<65 lbs (29 kg)(5kW, 20V 30V) ≈<65 lbs (29 kg)(8kW, 10V 15V) ≈<85 lbs (39 kg)(10kW, 20V 30V) ≈<85 lbs (39 kg)(12kW, 10V 15V) ≈<110 lbs (50 kg)(15kW, 20V 30V) ≈<110 lbs (50 kg)(5kW) ≈ 40 lbs (18 kg)(10kW) ≈ 60 lbs (27 kg)(15kW) ≈ 80 lbs (36 kg)(20kW) ≈ 120 lbs (54 kg)(25kW) ≈ 140 lbs (64 kg)(30kW) ≈ 160 lbs (73 kg)Shipping Weight Contact factory for more product & shipping weightsProgramming & Read-back Specifications ( with sense wires used )Programming Read-Back / Monitoring AccuracyResolutionAccuracyResolutionFront panel DisplaySGA: +/- (0.5%fs + 1 digit)SGI (40-1000V) +/- 0.1% of voltage at full scaleSGI (40-1000V) +/- 0.4% of current at full scale SGA: 3.5 digits SGI: 4.0 digitsSGA: +/- (0.5%fs + 1 digit)SGI, Voltage: +/- 0.1% of full scale SGI, Current: +/- 0.4% of full scaleSGA: 3.5 digits SGI: 4.0 digitsKnob control & Display read-backSGI (10-30V) 0.1% of actual +0.15% voltage ratingSGI (10-30V) 0.1% of set point +0.1% of voltage rating SGI (10-30V) 0.1% of set point +0.4% of current ratingRemote Analog InterfaceVoltage +/-0.25% of full scale Current (40-1000V) 0.8% of full scale , (10-30V) 1.0% of full scaleNA(40-1000V) +/-1.0% of full scale NA 25-pin D-sub connector (0~5 V or 0~10 V)(10-30V) +/-0.5% of full scaleRemote Digital Interface Voltage: +/- 0.1% of full scale, Current: +/- 0.4% of full scale+/-0.002% of full scale Voltage: +/- 0.1% of full scale Current: +/- 0.4% of full scale +/-0.002% of full scaleRS-232C (Standard on SGI), Optional IEEE-488.2 and Optional LXICompliant 10/100 base-T Ethernet (see Options)OVP +/- 1% of full scale+/-0.002% of full scaleProgramming range: 5-110% Configured from front panel, remote analog or via optional digital inputsUser I/O Disconnect & Polarity-reversal relay control ( Only available with Ethernet Option )Digital 10-pin Molex type connector See SoftwareIVI & CVI drivers available under SUPPORT at: 68858.458.0223sales.ppd@ Output: Voltage and Current Ranges3U6U Ripple & NoisePower 4/5 kW 8/10 kW 12/15 kW 16/20 kW 20/25 kW 24/30 kW rms(20 Hz-300 kHz)p-p(20 Hz-20 MHz)Voltage Current1040080012001600*2000*2400*20 mV 50 mV 152675348011068*1335*1602*20 mV 50 mV 202505007501000*1250*1500*20 mV 60 mV 30167334501668*835*1002*20 mV 60 mV 40125250375500*625*750*20 mV 75 mV 50100200300400*500*600*20 mV 75 mV 608316725033341750020 mV 75 mV 806312518825031337520 mV 100 mV 1005010015020025030020 mV 100 mV 16031639412515618825 mV 150 mV 20025507510012515025 mV 175 mV 2502040608010012030 mV 200 mV 33015304561769130 mV 200 mV 40012253850637530 mV 300 mV 50010203040506050mV 350mV 6008172533425060 mV 350 mV 800 6.212.518.725*31.2*37.5*80 mV 500 mV 10005101520*25*30*100 mV650 mV* By way of paralleling 3U suppliesOutputRipple & Noise (Voltage Mode, Typical)See Output: Voltage & Current Ranges Chart below. Ripple and noise specified at full load, nominal AC input. Noise measured with 6 ft. cable, 1μf at loadRipple (Current Mode)<+/- 0.04% of full scale rms currentOutput Voltage Rise Time (40-1000V)≈< 100 ms 10-90% of full scale typical - full resistive load (Contact factory for model specific slew rates)Output Voltage Rise Time (10-30V)Rise Time, ms, max Condition10Measured from 10% to 90% of the output voltage change - resistive load, typicalOutput Voltage Fall Time (10-30V)Fall Time, ms maxConditionNo Load 1100% CC Load100% CR LoadMeasured from 90% to 10% of the output voltage change. - resistive load, typical501010Output Current Rise Time (10-30V)Rise Time, ms max Condition20Measured from 10% to 90% of the output current change - resistive load, typical Output Current Fall Time (10-30V)Fall Time, ms max Condition10Measured from 90% to 10% of the output current change - resistive load, typical DC Current Slew Rate45A / ms typical - resistive loadLine Regulation ( with sense wires used )(±10% of nominal AC input, constant load)Voltage Mode: +/- 0.01% of full scale (40-800V) Current Mode: +/- 0.05% of full scale (40-800V)Voltage Mode and Current Mode: +/- 0.05% of full scale (10-30V)Load Regulation (with sense wires used)(no load to full load, nominal AC input)Voltage Mode: +/- 0.02% of full scale (40-800V) Current Mode: +/- 0.1% of full scaleVoltage Mode: +/- 0.05% of full scale (10-30V)Load Transient Response Recovers within 1ms to +/-0.75% of full-scale of steadystate output for a 50% to 100% or 100% to 50% load change Efficiency 87% typical at nominal line and max loadStability±0.05% of set point after 30 minute warm-up and over 8 hours at fixed line, load and temperature, typical Temperature Coefficient 0.02%/ C of maximum output voltage rating for voltage set point, typical 0.03%/ C of maximum output current rating for current set point, typicalOutput Float VoltageNegative terminal within +/- 300 V of chassis potential. ( We recommend the use of optional isolated analog Interface (IAI). ) Supplies in “series” have a system current limit of the lowest current supply in the system.4-150 kWSG Series : Product Specifications69SG Series : Product Diagram1.6241.2Top View173.22.3323.906.82607.1.121.634.19106.5Rear View16.90429.3Front View5.22132.519.00482.63U Case (10-30V)1.6241.23U Case (40-1000V)Front View19.00482.65.22132.5Rear View16.90429.3Top View2.3323.90 .12607.12.5063.51.631.6241.26U Case (60-600V)Rear View17.03432.5Top View23.031.0426.5585.15432.5 4.0017.03 .12Front View10.47265.919.00482.670858.458.0223sales.ppd@ SG SeriesSGI / SGA Comparison Chart FeatureSGASGIModular Design ••Fast Load Transient ••Parallelable••Analog & Digital Summing Optional•Direct Front Panel V/I Control ••3½ Digit LED Readout •Graphics Display •Sequencing •Save/Recall Setups •System Power Readouts •Constant Power Mode •IEEE-488.2/RS-232C Optional RS-232C Std, IEEE-488.2 Optional LXI Class C Ethernet/ RS-232OptionalRS-232C Std, Ethernet OptionalFront Panel Dust FilterOptional (3U unit only)Optional (3U unit only)Advanced Power SimulationSGI model provides constant power mode allowing independent setting of the max voltage, current and power4–150 kWEnvironmentalOperating Temperature 0 to 50º C Storage Temperature -25º C to 65º CHumidity Range Relative humidity up to 95% non-condensing, 0º C – 50º CAltitude Operating full power available up to 5,000 ft. (~1,500 m), derate 10% of full power for every 1,000 feet higher; non-operating to 40,000 ft. (~12,000 m)Cooling Front and side air inlet, rear exhaust. Temperature controlled, variable speed fans. Units may be stacked without spacing.RegulatoryCertified to UL/CSA 61010 and IEC/EN 61010-1 by a NRTL, CE Compliant, Semi-F47 Compliant.LVD Categories: Installation Category II: Pollution Degree 2; Class II Equipment: for Indoor Use Only, back panel not user accessible (see user manual for installation instructions)EMC Directive, EN 61326:1998Front Panel Dust Filter30 PPI (Pores Per Inch) - must ensure adequate airflow and / or derate max. temperature. 3U unit only.71SG Series-A SGControl Designation100Voltage 1A AA Remote Control OptionsProcess Options 100X CurrentC Input Voltage OptionsA = Analog I = Intelligent4 - 15kW = “ X ”20 - 30kW = “ / ”AAModifications(For units with greater than 3 digits, Voltage/Current is represented in numeric format, e.g., above “100” represents 100A.For units at 1000 and above, the voltage is represented by the format “XKX”, e.g, 1K2 = 1200V and 1K0 = 1000V)Options and Accessories Control OptionsA: Analog I: IntelligentInput OptionsC: Input Voltage 187 / 242VAC, 3 Phase D: Input Voltage 342 / 440VAC, 3 Phase E: Input Voltage 396 / 528VAC, 3 PhaseRemote Control Options0A: No Option1A: IEEE-488.2 + RS-232C (Note: SGI comes standard with RS-232C)1C: Ethernet + RS-232C 1D: Isolated Analog Control 1E: Shaft Locks (SGA series only)2A: Combined Options 1A+1D2C: Combined Options 1A+1E (SGA Only)2G: Combined Options 1C+1D2H: Combined Options 1C+1E (SGA Only)2J: Combined Options 1D+1E (SGA Only)3C: Combined Options 1A+1D+1E (SGA Only)3G: Combined Options 1C+1D+1E (SGA Only)Process Options AA: No optionAB: Certificate of Calibration to ANSI / NCSL Z540-1 (includes Test Data)ModificationsAJ: Front panel dust filter - factory installed - 3U unit onlyCV: 400Hz AC input @ 208 VAC ( does not carry CE, CSA or UL marks ) ( 6U only ) STD on 3UPF: Passive power factor correction to 0.9 (Only applicable to 40V, 60V to 800V. Included in 10V-30V, 50V and 1000V.)Accessories890-453-03: Paralleling Cable (for up to 5 units, requires one cable per unit placed in parallel)K550212-01: 3U Rack Slides (for 5kW, 10kW and 15kW models)K550213-01: 6U Rack Slides (for 20kW, 25kW and 30kW models)5550568-01: Front panel dust filter - field installation kit - 3U unit only 5551082-01: Optional AC input cover kit - 3U unit onlyContact factory for other combinations72© 2013 AMETEK Programmable Power All rights reserved. AMETEK Programmable Power is the trademark of AMETEK Inc., registered in the U.S. and other countries. Elgar, Sorensen, California Instruments, and Power Ten are trademarks of AMETEK Inc., registered in the U.S.。
CSA 认证证书说明书

(*1) These devices are intended to be used in Combination with this manufacturer (Siemens) Certified overload relays Type 3RU. or 3RB.
Capacitive Switching 3RT5647
400 A max -
-
(*5) CSA Certified, Type E (self-protected) Combination motor controller (Class 3211 08) manufactured by
Siemens, Type 3RV504 (size S3, refer to report 165071-1997985).
Horsepower 3RT5046(*1)
Voltage
1-ph
115 V
10 hp
200/208 V
15 hp
230/240 V
20 hp
460/480 V
-
575/600 V
-
3-ph 30 hp 30 hp 75 hp 100 hp
FLA 100 A 92 A 80 A 96 A 99 A
LRA 776 A 674 A 773 A 749 A
LRA 500 A 435 A 543 A 580 A
Horsepower 3RT5446(*1)) (3 NO Main Contacts)
Voltage
3-ph
FLA
230/240 V
15 hp
42 A
460/480 V
30 hp
40 A
575/600 V
MAX803SEXR中文资料

MAX803SEXRRev. ARELIABILITY REPORTFORMAX803SEXRPLASTIC ENCAPSULATED DEVICESAugust 3, 2006MAXIM INTEGRATED PRODUCTS120 SAN GABRIEL DR.SUNNYVALE, CA 94086byWrittenPedicordJimQualityAssuranceManager, Reliability LabConclusionThe MAX803 successfully meets the quality and reliability standards required of all Maxim products. In addition, Maxim’s continuous reliability monitoring program ensures that all outgoing product will continue to meet Maxim’s quality and reliability standards.Table of ContentsI. ........Device Description V. ........Quality Assurance InformationII. ........Manufacturing Information VI. .......Reliability EvaluationIII. .......Packaging Information IV. .......Die Information.....AttachmentsI. Device DescriptionA. GeneralThe MAX803 is a microprocessor (µP) supervisory circuit used to monitor the power supplies in µP and digital systems. It provides excellent circuit reliability and low cost by eliminating externalcomponents and adjustments when used with +5V, +3.3V, +3.0V, or +2.5V powered circuits.This circuit performs a single function: it asserts a reset signal whenever the V CC supply voltage declines below a preset threshold, keeping it asserted for at least 140ms after V CC has risen above the reset threshold. Reset thresholds suitable for operation with a variety of supply voltages are available.The MAX803 has an open-drain output stage. The MAX803's open-drain RESET-bar output requiresa pull-up resistor that can be connected to a voltage higher than V CC. The MAX803 has an active-low RESET-bar output. The reset comparator is designed to ignore fast transients on V CC, and the outputs are guaranteed to be in the correct logic state for V CC down to 1V.Low supply current makes the MAX803 ideal for use in portable equipment. The MAX803 isavailable in a 3-pin SC70 package.B. Absolute Maximum RatingsItem RatingTerminal Voltage (with respect to GND)VCC -0.3V to +6.0VRESET, RESET (push-pull) -0.3V to (VCC + 0.3V)to-0.3V+6.0VRESETdrain)(open20mAVCCInputCurrent,Output Current, RESET, RESET 20mAVCC 100V/µsRateRise,ofContinuous Power Dissipation (TA = +70°C)3-Pin SC70 (derate 2.17mW/°C above +70°C) 174mW3-Pin SOT23 (derate 4mW/°C above +70°C) 320mWOperating Temperature Range+125°Cto-40°C3-PinSC70+105°Cto3-Pin-40°CSOT23Storage Temperature Range -65°C to +150°CLead Temperature (soldering, 10s) +300°CII. Manufacturing InformationA. Description/Function: 3-Pin Microprocessor Reset CircuitsB. Process: B8 (Standard 0.8 micron silicon gate CMOS)C. Number of Device Transistors: 380D. Fabrication Location: California, USAE. Assembly Location: MalaysiaF. Date of Initial Production: January, 2000III. Packaging InformationSC70-3A. Package Type: 3-PinB. Lead Frame: Alloy 42C. Lead Finish: Solder Plate or 100% Matte TinD. Die Attach: Nonconductive EpoxyE. Bondwire: Gold (1 mil dia.)F. Mold Material: Epoxy with silica fillerG. Assembly Diagram: # 05-1601-0082H. Flammability Rating: Class UL94-V0I. Classification of Moisture Sensitivityper JEDEC standard J-STD-020-C: Level 1IV. Die InformationA. Dimensions: 30 x 30 milsPassivation: Si3N4/SiO2 (Silicon nitride/ Silicon dioxide)B.C. Interconnect: Aluminum/Si (Si = 1%)D. Backside Metallization: NoneE. Minimum Metal Width: 0.8 microns (as drawn)F. Minimum Metal Spacing: 0.8 microns (as drawn)G. Bondpad Dimensions: 5 mil. Sq.H. Isolation Dielectric: SiO2I. Die Separation Method: Wafer SawV. Quality Assurance InformationA. Quality Assurance Contacts: Jim Pedicord (Manager, Reliability Operations)Bryan Preeshl (Managing Director of QA)B. Outgoing Inspection Level: 0.1% for all electrical parameters guaranteed by the Datasheet.0.1% For all Visual Defects.C. Observed Outgoing Defect Rate: < 50 ppmD. Sampling Plan: Mil-Std-105DVI. Reliability EvaluationA. Accelerated Life TestThe results of the 135°C biased (static) life test are shown in Table 1. Using these results, the Failure Rate (λ) is calculated as follows:λ = 1 = 1.83 (Chi square value for MTTF upper limit)MTTFλ = 6.87 x 10-9λ = 6.87 F.I.T. (60% confidence level @ 25°C)This low failure rate represents data collected from Maxim’s reliability monitor program. In addition to routine production Burn-In, Maxim pulls a sample from every fabrication process three times per week and subjects it to an extended Burn-In prior to shipment to ensure its reliability. The reliability control level for each lot to be shipped as standard product is 59 F.I.T. at a 60% confidence level, which equates to 3 failures in an 80 piece sample. Attached Burn-In Schematic (Spec. #06-5033) shows the static Burn-In circuit. Maxim performs failure analysis on any lot that exceeds this reliability control level. Maxim also performs quarterly 1000 hour life test monitors. This data is published in the Product Reliability Report (RR-1N). Current monitor data for the B8/S8 Process results in a FIT rate of 0.17 @ 25°C and 2.92 @ 55°C (eV = 0.8, UCL = 60%).B. Moisture Resistance TestsMaxim pulls pressure pot samples from every assembly process three times per week. Each lot sample must meet an LTPD = 20 or less before shipment as standard product. Additionally, the industry standard 85°C/85%RH testing is done per generic device/package family once a quarter.C. E.S.D. and Latch-Up TestingThe MS42 die type has been found to have all pins able to withstand a transient pulse of ±2500V, per Mil-Std-883 Method 3015 (reference attached ESD Test Circuit). Latch-Up testing has shown that this device withstands a current of ±250mA.Table 1Reliability Evaluation Test ResultsMAX803S EXRTEST ITEM TEST CONDITION FAILURE SAMPLE NUMBER OFSIZEFAILURES IDENTIFICATION PACKAGEStatic Life Test (Note 1)160DCParametersTa = 135°CBiased & functionalityTime = 192 hrs.Moisture Testing (Note 2)77SC70ParametersPressure Pot Ta = 121°CDCP = 15 psi. & functionality100%RH=Time = 168hrs.77ParametersTa85°C DC85/85=85% &functionality=RHBiased1000hrs.=TimeMechanical Stress (Note 2)77 0ParametersTemperature -65°C/150°CDCfunctionalityCycles&1000Cycle1010MethodNote 1: Life Test Data may represent plastic DIP qualification lots.Note 2: Generic Package/Process dataAttachment #1TABLE II. Pin combination to be tested. 1/ 2/1/ Table II is restated in narrative form in 3.4 below. 2/ No connects are not to be tested. 3/ Repeat pin combination I for each named Power supply and for ground (e.g., where V PS1 is V DD , V CC , V SS , V BB , GND, +V S, -V S , V REF , etc). 3.4 Pin combinations to be tested. a.Each pin individually connected to terminal A with respect to the device ground pin(s) connected to terminal B. All pins except the one being tested and the ground pin(s) shall be open. b. Each pin individually connected to terminal A with respect to each different set of a combination of all named power supply pins (e.g., V SS1, or V SS2 or V SS3 or V CC1, or V CC2) connected to terminal B. All pins except the one being tested and the power supply pin or set of pins shall be open.c.Each input and each output individually connected to terminal A with respect to a combination of all the other input and output pins connected to terminal B. All pins except the input or output pin being tested and the combination of all the other input and output pins shall be open.Terminal A (Each pin individually connected to terminal A with the other floating) Terminal B (The common combination of all like-named pins connected to terminal B) 1. All pins except V PS1 3/ All V PS1 pins 2. All input and output pinsAll other input-output pinsMil Std 883DMethod 3015.7Notice 8 TERMINAL BTERMINAL APROBE (NOTE 6) R = 1.5k ΩC = 100pf。
MAX202CSE中文资料
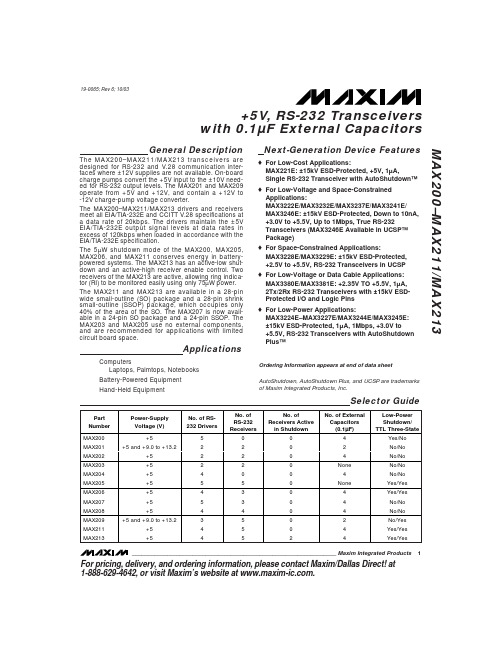
General DescriptionThe MAX200–MAX211/MAX213 transceivers are designed for RS-232 and V.28 communication inter-faces where ±12V supplies are not available. On-board charge pumps convert the +5V input to the ±10V need-ed for RS-232 output levels. The MAX201 and MAX209operate from +5V and +12V, and contain a +12V to -12V charge-pump voltage converter.The MAX200–MAX211/MAX213 drivers and receivers meet all EIA/TIA-232E and CCITT V.28 specifications at a data rate of 20kbps. The drivers maintain the ±5V EIA/TIA-232E output signal levels at data rates in excess of 120kbps when loaded in accordance with the EIA/TIA-232E specification.The 5µW shutdown mode of the MAX200, MAX205,MAX206, and MAX211 conserves energy in battery-powered systems. The MAX213 has an active-low shut-down and an active-high receiver enable control. Two receivers of the MAX213 are active, allowing ring indica-tor (RI) to be monitored easily using only 75µW power.The MAX211 and MAX213 are available in a 28-pin wide small-outline (SO) package and a 28-pin shrink small-outline (SSOP) package, which occupies only 40% of the area of the SO. The MAX207 is now avail-able in a 24-pin SO package and a 24-pin SSOP. The MAX203 and MAX205 use no external components,and are recommended for applications with limited circuit board space.ApplicationsComputersLaptops, Palmtops, Notebooks Battery-Powered Equipment Hand-Held Equipment Next-Generation Device Features ♦For Low-Cost Applications:MAX221E: ±15kV ESD-Protected, +5V, 1µA, Single RS-232 Transceiver with AutoShutdown™♦For Low-Voltage and Space-Constrained Applications:MAX3222E/MAX3232E/MAX3237E/MAX3241E/MAX3246E: ±15kV ESD-Protected, Down to 10nA,+3.0V to +5.5V, Up to 1Mbps, True RS-232Transceivers (MAX3246E Available in UCSP™Package)♦For Space-Constrained Applications:MAX3228E/MAX3229E: ±15kV ESD-Protected,+2.5V to +5.5V, RS-232 Transceivers in UCSP ♦For Low-Voltage or Data Cable Applications:MAX3380E/MAX3381E: +2.35V TO +5.5V, 1µA,2Tx/2Rx RS-232 Transceivers with ±15kV ESD-Protected I/O and Logic Pins ♦For Low-Power Applications:MAX3224E–MAX3227E/MAX3244E/MAX3245E:±15kV ESD-Protected, 1µA, 1Mbps, +3.0V to+5.5V, RS-232 Transceivers with AutoShutdown Plus™MAX200–MAX211/MAX213+5V , RS-232 Transceivers with 0.1µF External Capacitors ________________________________________________________________Maxim Integrated Products 119-0065; Rev 6; 10/03For pricing, delivery, and ordering information,please contact Maxim/Dallas Direct!at 1-888-629-4642, or visit Maxim’s website at .Ordering Information appears at end of data sheetAutoShutdown, AutoShutdown Plus, and UCSP are trademarks of Maxim Integrated Products, Inc.MAX200–MAX211/MAX213+5V , RS-232 Transceiverswith 0.1µF External Capacitors______________________________________________________________________________________19Ordering Information*Contact factory for dice specifications.M A X 200–M A X 211/M A X 213+5V , RS-232 Transceiverswith 0.1µF External Capacitors Maxim cannot assume responsibility for use of any circuitry other than circuitry entirely embodied in a Maxim product. No circuit patent licenses are implied. Maxim reserves the right to change the circuitry and specifications without notice at any time.20____________________Maxim Integrated Products, 120 San Gabriel Drive, Sunnyvale, CA 94086 408-737-7600©2003 Maxim Integrated ProductsPrinted USAis a registered trademark of Maxim Integrated Products.Package Information(The package drawing(s) in this data sheet may not reflect the most current specifications. For the latest package outline information,go to /packages .)。
施耐德 Symmetra PX 48、96和160 kW 400 V 100 kW 208 V说明书

寿命周期监控 (LCM) .................................................................................26 部件更换 ..................................................................................................26
概述 ...............................................................................................................7
用户界面 ....................................................................................................7 显示界面 ....................................................................................................7
危险
危险表示危险状况,如不避免,将导致人员死亡或严重伤害。 未按说明操作将导致人身伤亡等严重严重伤害。 未按说明操作可能导致人身伤亡或设备损坏等严重后果。
小心
小心表示危险状况,如不避免,可能会导致轻度或中度人身伤害。 不遵循上述说明可能导致人身伤害或设备损坏。
EXTECH 400Amp AC Clamp Meter + NCV Model MA410 说明书
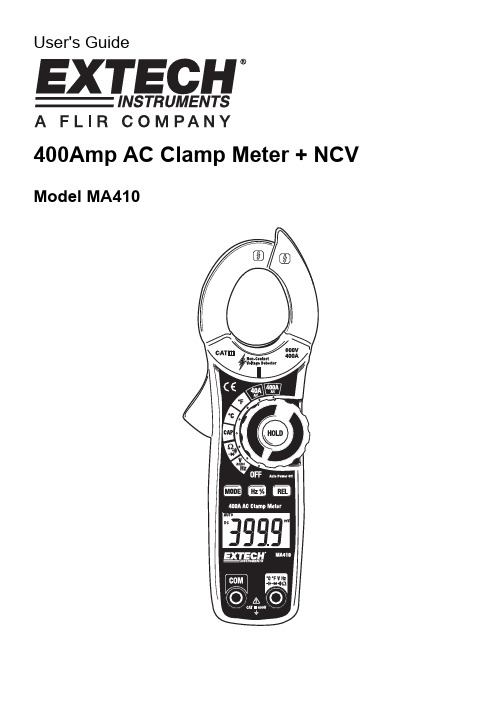
User's Guide400Amp AC Clamp Meter + NCV Model MA410IntroductionCongratulations on your purchase of this Extech MA410 Clamp Meter. This meter measures ACCurrent, AC/DC Voltage, Resistance, Capacitance, Frequency, Diode Test, Duty Cycle and Continuity. Special features include Thermocouple Temperature and Non-Contact Voltage detection. The double molded case is designed for heavy duty use. This meter is shipped fully tested and calibrated and, with proper use, will provide years of reliable service.SafetyInternational Safety SymbolsThis symbol, adjacent to another symbol or terminal, indicates the user must refer to the manual for further information.This symbol, adjacent to a terminal, indicates that, under normal use, hazardous voltages may be presentDouble insulationThis WARNING symbol indicates a potentially hazardous situation, which if not avoided, could result in death or serious injury.This CAUTION symbol indicates a potentially hazardous situation, which if not avoided, may result damage to the product.PER IEC1010 OVERVOLTAGE INSTALLATION CATEGORYOVERVOLTAGE CATEGORY IEquipment of OVERVOLTAGE CATEGORY I is equipment for connection to circuits in which measures are taken to limit the transient overvoltages to an appropriate low level. Note – Examples include protected electronic circuits.OVERVOLTAGE CATEGORY IIEquipment of OVERVOLTAGE CATEGORY II is energy-consuming equipment to be supplied from the fixed installation.Note – Examples include household, office, and laboratory appliances.OVERVOLTAGE CATEGORY IIIEquipment of OVERVOLTAGE CATEGORY III is equipment in fixed installations.Note – Examples include switches in the fixed installation and some equipment for industrial use with permanent connection to the fixed installation.OVERVOLTAGE CATEGORY IVEquipment of OVERVOLTAGE CATEGORY IV is for use at the origin of the installation. Note – Examples include electricity meters and primary over-current protection equipmentSAFETY NOTES•Do not exceed the maximum allowable input range of any function.•Do not apply voltage to meter when resistance function is selected.•Set the function switch OFF when the meter is not in use.•Remove the battery if meter is to be stored for longer than 60 days.WARNINGS•Set function switch to the appropriate position before measuring.•When measuring volts do not switch to current/resistance modes.•Do not measure current on a circuit whose voltage exceeds 600V.•When changing ranges always disconnect the test leads from the circuit under test.CAUTIONS•Improper use of this meter can cause damage, shock, injury or death. Read and understandthis user manual before operating the meter.•Always remove the test leads before replacing the battery or fuses.•Inspect the condition of the test leads and the meter itself for any damage before operating the meter. Repair or replace any damage before use.•Use great care when making measurements if the voltages are greater than 25VAC rms or35VDC. These voltages are considered a shock hazard.•Always discharge capacitors and remove power from the device under test before performingDiode, Resistance or Continuity tests.•Voltage checks on electrical outlets can be difficult and misleading because of the uncertaintyof connection to the recessed electrical contacts. Other means should be used to ensure thatthe terminals are not "live".•If the equipment is used in a manner not specified by the manufacturer, the protection provided by the equipment may be impaired.Input Function MaximumA AC, 400AV DC, V AC 600V DC/ACResistance, Capacitance, Frequency, Diode250V DC/ACTest, Continuity, Temperatureclamp1. Current2. NCV LED indicator3. Clamp opening trigger4. MODE button5. HZ/%buttonDisplay6. LCD7. Negative input jack8. Non-Contact Voltage Detectorbutton9. HOLD10. Function switch11. Relative Button12. Battery compartment (rear)13. Positive input jackDisplay icons DescriptionHoldHOLD DataAUTO AutorangingDC Direct CurrentCurrentAC AlternatingbatteryLowREL Relative(Voltage)V VoltsΩ Ohms(Resistance)A Amperes(Current)F Farad(Capacitance)(Frequency)Hz Hertz% DutyRatioo F and o C Fahrenheit and Celsius units (Temperature)n, m, μ, M, k Unit of measure prefixes: nano, milli, micro, mega, and kilotest•))) ContinuityDiode testNOTES: Read and understand all Warning and Caution statements in this operation manual prior to using this meter. Set the function select switch to the OFF position when the meter is not in use. Non-Contact Voltage DetectorWARNING: Risk of Electrocution. Before use, always test the Voltage Detector on a known live circuit to verify proper operation.1. Rotate the Function switch to any measurement position.2. Place the detector probe tip on the conductor to be tested.3. If AC voltage is present, the NCV detector light will turn on witha steady red light.NOTE: The conductors in electrical cord sets are often twisted. Forbest results, move the probe tip along a length of the cord toassure placing the tip in close proximity to the liveconductor.NOTE: The detector is designed with high sensitivity. Staticelectricity or other sources of energy may randomly trip the sensor. This is normal operation.AC Current MeasurementsWARNING: Disconnect the test leads before making clamp measurements.1. Rotate the Function switch to the 400A position2. Press the trigger to open jaw. Fully encloseonly one conductor.3. Read the current value in the display.4. If the value is less than 40A, rotate the functionswitch to the 40A position to improveresolution.AC/DC Voltage, Frequency, Duty Cycle MeasurementsCAUTION: Do not measure voltages if a motor on the circuit is being switched ON or OFF. Large voltage surges may occur that can damage the meter.1. Rotate the function switch to the V position.2. Press the MODE button to select AC or DC Voltage.3.Insert the black test lead banana plug into the negative COM jack.Insert the red test lead banana plug into the positive V jack.4. Touch the black test probe tip to the negative side of the circuit.Touch the red test probe tip to the positive side of the circuit. 5. Read the voltage value in the display. 6. Press the Hz % button to display Frequency 7. Press the Hz % button to display Duty CycleResistance, Diode, Continuity MeasurementsNote: Remove power from the device under test before making resistance measurements1. Set the function switch to the Ω position.2. Insert the black test lead banana plug into the negative COM jack.Insert the red test lead banana plug into the positive V jack. 3. Touch the black test probe tip to one side of the device. Touch the red test probe tip to the other side of the device. 4.Read the resistance value in the display.5. Press the MODE button to select the DIODE mode. The Diode symbol willappear in the display. 6. Press the MODE button to select the Continuity mode. The continuity symbolwill appear in the display. If the resistance is <150 ohms the tone will sound.Capacitance MeasurementsRelativePress the REL button (REL will appear in the display) to zero the reading and create a reference point. All future reading will be the difference between the actual reading and the stored “REL”reading. In the REL mode, autoranging is disabled and measurements are limited to the range active when the REL button was pressed. Press the REL button to exit the mode.Note: Relative does not function in Frequency or Duty Cycle mode.Automatic Power OffIn order to conserve battery life, the meter will automatically turn off after approximately 30 minutes.To turn the meter on again, change the position of the function switch.Low battery indicationWhen the icon appears in the display, the battery should be replaced. Refer to the batteryreplacement procedure in the maintenance section.MaintenanceWARNING: To avoid electrical shock, disconnect the meter from any circuit, remove the test leads from the input terminals, and turn OFF the meter before opening the case. Do not operate the meter with an open case.Cleaning and StoragePeriodically wipe the case with a damp cloth and mild detergent; do not use abrasives orsolvents. If the meter is not to be used for 60 days or more, remove the battery and store itseparately.Battery Replacement1. Remove the 2 Phillips head screws that secures the rear battery cover2. Open the battery compartment3. Replace the 2 AAA batteries.4. Secure the battery compartment doorBattery ordinance) to return all used batteriesdisposal in the household garbage is prohibited!Follow the valid legal stipulations in respect of the disposal of the device at the end of its lifecycleSpecificationsFunction Range ResolutionAccuracy(% of reading + digits)40.00 AAC 0.01A ±(2.5% + 8 digits) AC Current50/60Hz400.0 AAC 0.1A ±(2.8% + 8 digits)4.000 VAC 0.001V40.00 VAC 0.01V 400.0 VAC 0.1V ±(1.8% + 8 digits)AC Voltage50 to 400Hz600 VAC 1V ±(2.5% + 8 digits)400.0 mVDC 0.1mV ±(0.8% + 2 digits)4.000 VDC 0.001V40.00 VDC 0.01V 400.0 VDC 0.1V ±(1.5% + 2 digits)DC Voltage600 VDC 1V ±(2.0% + 2 digits)400.0Ω 0.1Ω±(1.0% + 4 digits)4.000kΩ 0.001kΩ40.00kΩ 0.01kΩ400.0kΩ 0.1kΩ±(1.5% + 2 digits)4.000MΩ 0.001MΩ±(2.5% + 3 digits) Resistance40.00MΩ 0.01MΩ±(3.5% + 5 digits)40.00nF 0.01nF ±(4.0% + 20 digits)400.0nF 0.1nF40.00µF 0.01µF Capacitance100.0µF 0.1µF±(3.0% + 5 digits)10 to 10kHz 0.01Hz ±(1.5% + 2 digits) FrequencySensitivity: 15V rms0.5% to 99.0% 0.1% ±(1.2% + 2 digits) Duty CyclePulse width: 100μs to 100ms, Frequency: 10Hz to 10kHz-4.0 to 1400°F -20 to 760°C 0.1° <400°1° >400°±(3% + 9°F/5°C)TemperatureType KSpecification does not include probe accuracy. Range of supplied probe is -4 to482°F (-20 to 250°C).General SpecificationsClamp jaw opening 30mm (1.18") approx.Display 4,000 count LCDContinuity check Threshold <150Ω; Test current < 0.5mADiode test Test current of 0.3mA typical;Open circuit voltage [ 1.5VDC typicalLow Battery indication Battery symbol is displayedOver-range indication ‘OL’displayMeasurement rate 2 readings per second, nominalThermocouple sensor Type K thermocouple requiredInput Impedance 10MΩ (VDC and VAC)AC bandwidth 50 to 400Hz (VAC)AC response Average respondingOperating Temperature5°C to 40°C (41°F to 104°F)Storage Temperature -20°C to 60°C (-4°F to 140°F)Operating Humidity Max 80% up to 31°C (87°F) decreasing linearly to 50% at 40°C(104°F)Storage Humidity <80%Operating Altitude 2000meters (7000ft) maximum.Battery Two “AAA” 1.5V batteriesAuto power OFF After approx. 30 minutesDimensions & Weight200x66x37mm (7.9x2.6x1.5”); 205g (7.23oz)Safety For indoor use and in accordance with the requirements for doubleinsulation to IEC1010-1 (2001): EN61010-1 (2001) OvervoltageCategory III 600V, Pollution Degree 2.Approvals CE,Copyright © 2012 Extech Instruments Corporation (a FLIR company) All rights reserved including the right of reproduction in whole or in part in any form.。
GEA SmartPacker SX CX400产品说明书

GEA Food Solutions Weert B.V. P.O. Box 296, 6000 AGDe Fuus 8, 6006 RV Weert The Netherlands Tel. +31 (0)495 457 777Fax +31 (0)495 524 125/contactB6.3.25EN_3219©GEAFoodSolutionsTheinformationcontainedinthisbrochuremerelyservesasanon-bindingdescriptionofourproductsandiswithoutguarantee.Bindinginformation,inparticularrelatingtocapacitydataandsuitabilityforspecificapplications,canonlybeprovidedwithintheframeworkofconcreteinquiries.Subjecttomodification.Residual air reduction without compromising in speed Cost-e cient production in the frozen food application not only includes reliable equipment but also removing residual air from the bag.With the GEA SmartPacker we supply our customers a varietyof solutions to ful ll the need for less residual air in the bag. Concentrating on the exact needs, speci cations and designof the bag GEA o ers 3 di erent solutions.Visual perforationPerforation is applied to the bag by means of puncturing or delicately creating small holes in the lm. For example, perforation by needles, by perforation knife or a high speed puncturing unit.Non-visual perforationPerforations, which are not detectable by the eye, are applied in the cross seal of the bag. By interrupting the cross seal on several spots in combination with standard air expellers decreases the volume of the bag by expelling residual air out of the bag.Shape absorbing air reduction systemTo produce bags without perforations of any kind, GEA developed an air-expeller which, by absorbing the shape of the product, expels even more residual air from the top of the bag without compromising in speed. As a result, the bag has just enough air left to evenly divide the product before entering the casepacker and maximize the number of bags in a box.ITC-sealing system for PE film materialGEA has used its experience and inspired engineering to design an induction welding system which gives you all the bene ts of its proven PTC-sealing system and even more. The GEA SmartPacker comes with a variety of sealing systems which ful ll the needs of the industry. Building on the experience we have with our current sealing systems, i.e. heatseal, ultrasonic sealing and PTC sealing we have developed a new method of sealing, using induction to heat the sealing surface.GEA SmartPacker is taking uptime to the next levelWhen developing the ITC-Sealing system we kept two subjects in mind, uptime and reliability. Being able to click on the ITC system and using as little wires, components and connectors as possible further improves on the uptime of our sealing system. This contributes to the high standard of reliability you come to know from GEA SmartPackers.Cost savingWith our ITC system you will be able to use thinner lm types in comparison to other systems in the market, following the market trend and resulting in reduced material cost. Next to that, ITC uses a fraction of the energy compared to conventional sealing systems for PE- lm material, without losing speed in heating-up, even heating up faster.Summary• Improvement of uptime and reliability by using minimal amount of parts• Reduction of product loss from downtime• Easy to install and exchange• Cost savings in lm and energy usage• Accurate and fast temperature controlReference DataGEA SmartPacker CX400GEA SmartPacker SX400Bag length (max.)550 mm550 mmBag width (min./max.)80/400 mm80/400 mmDimension H x W x D2020 x 1280 x 2185 mm2020 x 1280 x 2185 mmMaximum Speed (bags/min.)*120100Core diameter film reel (min. max.)70/77 mm70/77 mmOuter diameter film reel. (max.)500 mm500 mm* Without stripping. Depending on product, film and dosing equipment.Pillow bag Blockbottom bag EasyDoy bag。
- 1、下载文档前请自行甄别文档内容的完整性,平台不提供额外的编辑、内容补充、找答案等附加服务。
- 2、"仅部分预览"的文档,不可在线预览部分如存在完整性等问题,可反馈申请退款(可完整预览的文档不适用该条件!)。
- 3、如文档侵犯您的权益,请联系客服反馈,我们会尽快为您处理(人工客服工作时间:9:00-18:30)。
Not Recommended for New DesignsThis product was manufactured for Maxim by an outside wafer foundry using a process that is no longer available. It is not recommended for new designs. The data sheet remains available for existing users.A Maxim replacement or an industry second-source may be available. Please see the QuickView data sheet for this part or contact technical support for assistance.For further information, contact Maxim’s Applications Tech Support.General DescriptionThe MAX400 guaranteed maximum 10µV offset error is the lowest input offset voltage of any commercially avail-able (nonchopper) monolithic amplifier. The M AX400represents a 2.5 times improvement over the highest grade OP07 (the OP07A), and a 5 times improvement over the best commercial temperature range device (OP07E). The offset voltage drift is guaranteed to be a maximum of 0.3µV/°C which is also an improvement over the OP07 family.For the ultimate in DC performance (5µV maximum offset voltage and 0.05µV/°C maximum offset voltage drift) the MAX420 and MAX430 series of ±15V monolithic,chopper-stabilized amplifiers should be consulted.ApplicationsPrecision Amplifiers Thermocouple Amplifiers Low-Level Signal Processing Medical Instrumentation Strain Gauge Amplifiers High-Accuracy Data AcquisitionFeatures♦Ultra-Low Offset Voltage: 10µV (max)♦Ultra-Low Offset Voltage Drift: 0.2µV/°C ♦Ultra Stable vs. Time: 0.2µV/month ♦Ultra-Low Noise: 0.35µV P-P ♦Wide Supply Voltage: ±3V to ±18V ♦High Common-Mode Input: ±14V ♦No External Components Required ♦Fits OP07, AD510, 725, 108A/308A SocketsMAX400Ultra-Low OffsetVoltage Operational Amplifier________________________________________________________________Maxim Integrated Products 1Pin ConfigurationOrdering InformationTypical Operating Circuit19-3001; Rev 1; 10/05For pricing, delivery, and ordering information,please contact Maxim/Dallas Direct!at 1-888-629-4642, or visit Maxim’s website at .M A X 400Ultra-Low OffsetVoltage Operational Amplifier 2_______________________________________________________________________________________ABSOLUTE MAXIMUM RATINGSELECTRICAL CHARACTERISTICSStresses beyond those listed under “Absolute Maximum Ratings” may cause permanent damage to the device. These are stress ratings only, and functional operation of the device at these or any other conditions beyond those indicated in the operational sections of the specifications is not implied. Exposure to absolute maximum rating conditions for extended periods may affect device reliability.Total Supply Voltage (V+ to V-)...........................................±22V Internal Power Dissipation.................................................500mV TO-99 (T) (derate at 7.1mW/ above +80°C)Hermatic Dip (J) (derate 6.7mW/°C above +75°C)Plastic Dip (P) (derate 5.6mW/°C above +36°C)Differential Input Voltage .....................................................±30V Input Voltage (Note 1)..........................................................±22V Storage Temperature Range.............................-65°C to +150°COperating Temperature RangeMAX400M......................................................-55°C to +125°C MAX400E.........................................................-40°C to +85°C MAX400C............................................................0°C to +70°C Lead Temperature (soldering, 10s).................................+300°C Duration of Output Short Circuit....................................Indefinite Junction Temperature (T J ).................................-65°C to +160°CNote 1:For supply voltages less than ±22V, the absolute maximum input voltage is equal to the supply voltage.MAX400Ultra-Low OffsetVoltage Operational Amplifier_______________________________________________________________________________________3ELECTRICAL CHARACTERISTICS (continued)Note 3:Long-term Input Offset Voltage Stability refers to the average trend line of V OS vs. Time over extended periods after the first30 days of operation. Excluding the initial hour of operation, changes in V OS during the first 30 operating days are typically 2.5µV – refer to typical performance curves.Note 4:Guaranteed by design.ELECTRICAL CHARACTERISTICS(V S = ±15V, T A = full operating temperature range , unless otherwise noted.)Note 6:100% tested.M A X 400Ultra-Low OffsetVoltage Operational Amplifier 4_______________________________________________________________________________________Typical Operating CharacteristicsMAXIMUM OUTPUT SWINGvs. FREQUENCYFREQUENCY (Hz)P E A K -T O -P E A K A M P L I T U D E (V )4812162024280LOW-FREQUENCY NOISEMAX400 toc02TOTAL INPUT NOISE VOLTAGEvs. FREQUENCYFREQUENCY (Hz)I N P U T N O I S E V O L T A G E (n V H z )10100101001000111kFigure 1. Optional Offset Nulling Circuit Figure 2. Low-Frequency Noise Test CircuitMAX400Ultra-Low OffsetVoltage Operational AmplifierMaxi m cannot assume responsi bi li ty for use of any ci rcui try other than ci rcui try enti rely embodi ed i n a Maxi m product. No ci rcui t patent li censes are implied. Maxim reserves the right to change the circuitry and specifications without notice at any time.Maxim Integrated Products, 120 San Gabriel Drive, Sunnyvale, CA 94086 408-737-7600 _____________________5©2005 Maxim Integrated ProductsPrinted USAis a registered trademark of Maxim Integrated Products, Inc.CMRR vs. FREQUENCYM A X 400 t o c 04FREQUENCY (Hz)C M R R (d B )10k1k10010708090100110120130601100kPSRR vs. FREQUENCYM A X 400 t o c 05FREQUENCY (Hz)1k100101.060708090100110120500.110kOPEN-LOOP FREQUENCY RESPONSEFREQUENCY (Hz)O P E N L O O P G A I N (d B )1M 100k 1101001k10k 04080120-400.110MOFFSET VOLTAGE CHANGE DUE TO THERMAL SHOCKTIME (s)A B S O L U T E C H A N G E I N I N P U T O F F S E T V O L T A G E (µV )80602040510152025300-20100INPUT BIAS CURRENT vs. TEMPERATURETEMPERATURE (°C)I N P U T B I A S C U R RE N T (n A )1234INPUT BIAS CURRENTvs. DIFFERENTIAL INPUT VOLTAGEDIFFERENTIAL INPUT VOLTAGE (V)N O N I N V E R T I N G I N P U T B I A S C U R R E N T (m A )2010-20-10-20-100102030-30-3030Typical Operating Characteristics (continued)。