高剪切反应器对乙炔二聚液相催化反应的影响
传热学试题(附答案)
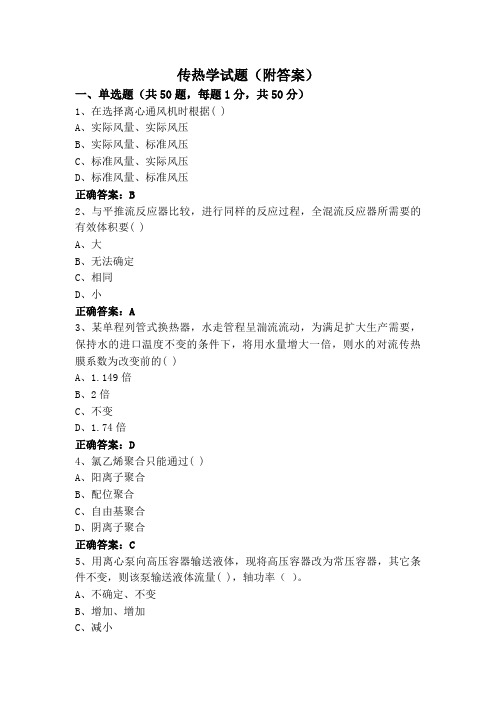
传热学试题(附答案)一、单选题(共50题,每题1分,共50分)1、在选择离心通风机时根据( )A、实际风量、实际风压B、实际风量、标准风压C、标准风量、实际风压D、标准风量、标准风压正确答案:B2、与平推流反应器比较,进行同样的反应过程,全混流反应器所需要的有效体积要( )A、大B、无法确定C、相同D、小正确答案:A3、某单程列管式换热器,水走管程呈湍流流动,为满足扩大生产需要,保持水的进口温度不变的条件下,将用水量增大一倍,则水的对流传热膜系数为改变前的( )A、1.149倍B、2倍C、不变D、1.74倍正确答案:D4、氯乙烯聚合只能通过( )A、阳离子聚合B、配位聚合C、自由基聚合D、阴离子聚合正确答案:C5、用离心泵向高压容器输送液体,现将高压容器改为常压容器,其它条件不变,则该泵输送液体流量( ),轴功率()。
A、不确定、不变B、增加、增加C、减小D、增加正确答案:B6、列管换热器中下列流体宜走壳程的是( )A、腐蚀性的流体B、压力高的流体C、被冷却的流体D、不洁净或易结垢的流体正确答案:C7、某并流操作的间壁式换热气中,热流体的进出口温度为90℃和50℃,冷流体的进出口温度为20℃和40℃,此时传热平均温度差△tm=( )。
A、40℃B、30.8℃C、39.2℃正确答案:B8、工业上甲醇氧化生产甲醛所用的反应器为( )A、釜式反应器B、具换热式固定床反应器C、流化床反应器D、绝热式固定床反应器正确答案:D9、离心泵最常用的调节方法是 ( )A、安装回流支路,改变循环量的大小B、改变出口管路中阀门开度C、改变吸入管路中阀门开度D、车削离心泵的叶轮正确答案:B10、当壳体和管速之间温度大于50℃时,考虑热补偿,列管换热器应选用( )A、固定管板式B、套管式C、浮头式正确答案:C11、下面关于裂解气分离流程说法正确的是( )A、一套乙烯装置分离收率和分离流程顺序关系很大,顺序分离流程和前脱乙烷流程、前脱丙烷流程相比乙烯收率最高。
乙炔含量超标对低密度聚乙烯生产的影响

乙炔含量超标对低密度聚乙烯生产的影响摘要:从生产实际出发,对生产过程中因原料乙烯中乙炔含量超标对聚合反应、连续生产、产品质量的影响进行深入的分析研究:详细分析了随着超标乙炔参与聚合反应而出现的聚合反应异常、生产波动较大、产品质量发生明显差异,特别是对产生的灰料进行深入的分析,得出乙烯中乙炔含量超标对低密度聚乙烯生产造成的影响,并提出了预防和优化措施。
关键词:低密度聚乙烯乙炔含量超标影响中国石油天然气股份有限公司大庆市石化分公司高压聚乙烯一套装置以乙烯为主要原料,以氧气为引发剂,丁烯、丙烯为调整剂,采用高压管式法反应器技术。
生产过程中乙烯中乙炔含量超标,造成生产波动,操作困难,产生过渡料。
本文分析了乙炔含量高对聚合反应的影响和对装置连续生产的影响,并提出了预防和调整措施。
1 原料乙烯中乙炔含量超标对低密度聚乙烯生产的影响1.1 乙炔来源通常来自裂解乙烯,由于碳二加氢单元出现异常,造成除炔不彻底,乙烯中含有微量乙炔,原料乙烯质量指标要求乙炔小于10mL/m3。
而通过对原料乙烯进行取样分析,得到的乙烯中乙炔含量的数据高达70mL/m3,乙烯中乙炔含量已明显超标。
随着超标乙炔加入到反应器参与聚合反应,反应器温度、峰形、挤压机模头压力、熔融指数等参数均产生波动,随后在振动筛采样中发现灰料。
本文对这些现象进行原因分析和总结。
1.2 乙烯中乙炔超标对聚合反应的影响1.2.1 聚合反应温度异常上升,反应放热量增大随着超标乙炔加入反应器参与聚合反应,乙炔代替乙烯与初期自由基引发剂——氧作用生成单体自由基,反应式如下:但由于该自由基比乙烯单体自由基活泼,在反应中能迅速完成链增长,加快整个反应器的反应速度,造成放热量增大,在反应器换热量恒定不变的情况下,导致温峰异常上升。
1.2.2 反应温峰峰形不稳定随着超标乙炔加入反应器参与聚合反应,形成的乙炔自由基具有延长聚合诱导期、延长聚合周期的性质,导致整个反应温峰后移,温峰最高点向后移动,为了稳定温峰,需要调整反应器各冷流注入量配比和各温峰分氧量,这些参数的频繁调整都会破坏聚合反应的热平衡,导致各峰出现周期性波动,影响峰形的整体稳定。
聚合物合成工艺学思考题及 其答案
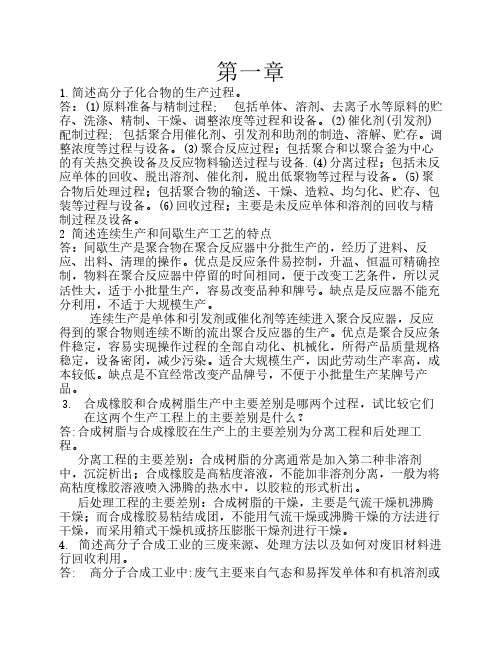
第一章1.简述高分子化合物的生产过程。
答:(1)原料准备与精制过程; 包括单体、溶剂、去离子水等原料的贮存、洗涤、精制、干燥、调整浓度等过程和设备。
(2)催化剂(引发剂)配制过程; 包括聚合用催化剂、引发剂和助剂的制造、溶解、贮存。
调整浓度等过程与设备。
(3)聚合反应过程;包括聚合和以聚合釜为中心的有关热交换设备及反应物料输送过程与设备.(4)分离过程;包括未反应单体的回收、脱出溶剂、催化剂,脱出低聚物等过程与设备。
(5)聚合物后处理过程;包括聚合物的输送、干燥、造粒、均匀化、贮存、包装等过程与设备。
(6)回收过程;主要是未反应单体和溶剂的回收与精制过程及设备。
2 简述连续生产和间歇生产工艺的特点答:间歇生产是聚合物在聚合反应器中分批生产的,经历了进料、反应、出料、清理的操作。
优点是反应条件易控制,升温、恒温可精确控制,物料在聚合反应器中停留的时间相同,便于改变工艺条件,所以灵活性大,适于小批量生产,容易改变品种和牌号。
缺点是反应器不能充分利用,不适于大规模生产。
连续生产是单体和引发剂或催化剂等连续进入聚合反应器,反应得到的聚合物则连续不断的流出聚合反应器的生产。
优点是聚合反应条件稳定,容易实现操作过程的全部自动化、机械化,所得产品质量规格稳定,设备密闭,减少污染。
适合大规模生产,因此劳动生产率高,成本较低。
缺点是不宜经常改变产品牌号,不便于小批量生产某牌号产品。
3. 合成橡胶和合成树脂生产中主要差别是哪两个过程,试比较它们在这两个生产工程上的主要差别是什么?答:合成树脂与合成橡胶在生产上的主要差别为分离工程和后处理工程。
分离工程的主要差别:合成树脂的分离通常是加入第二种非溶剂中,沉淀析出;合成橡胶是高粘度溶液,不能加非溶剂分离,一般为将高粘度橡胶溶液喷入沸腾的热水中,以胶粒的形式析出。
后处理工程的主要差别:合成树脂的干燥,主要是气流干燥机沸腾干燥;而合成橡胶易粘结成团,不能用气流干燥或沸腾干燥的方法进行干燥,而采用箱式干燥机或挤压膨胀干燥剂进行干燥。
(完整word版)高聚物合成工艺课后题答案
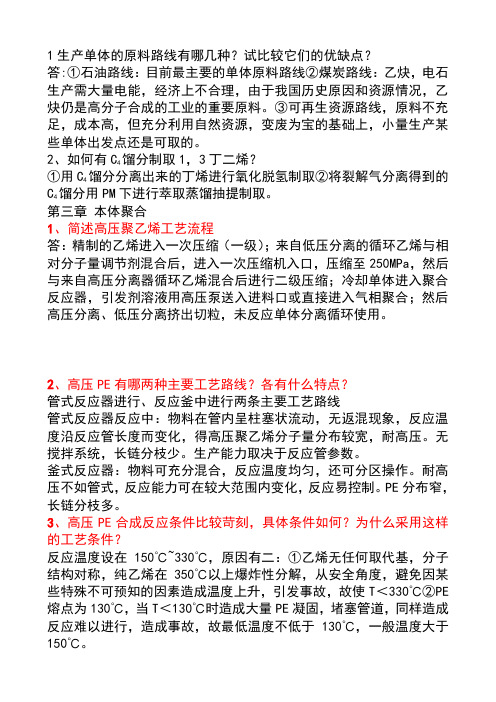
1生产单体的原料路线有哪几种?试比较它们的优缺点?答:①石油路线:目前最主要的单体原料路线②煤炭路线:乙炔,电石生产需大量电能,经济上不合理,由于我国历史原因和资源情况,乙炔仍是高分子合成的工业的重要原料。
③可再生资源路线,原料不充足,成本高,但充分利用自然资源,变废为宝的基础上,小量生产某些单体出发点还是可取的。
2、如何有C4馏分制取1,3丁二烯?①用C4馏分分离出来的丁烯进行氧化脱氢制取②将裂解气分离得到的C4馏分用PM下进行萃取蒸馏抽提制取。
第三章本体聚合1、简述高压聚乙烯工艺流程答:精制的乙烯进入一次压缩(一级);来自低压分离的循环乙烯与相对分子量调节剂混合后,进入一次压缩机入口,压缩至250MPa,然后与来自高压分离器循环乙烯混合后进行二级压缩;冷却单体进入聚合反应器,引发剂溶液用高压泵送入进料口或直接进入气相聚合;然后高压分离、低压分离挤出切粒,未反应单体分离循环使用。
2、高压PE有哪两种主要工艺路线?各有什么特点?管式反应器进行、反应釜中进行两条主要工艺路线管式反应器反应中:物料在管内呈柱塞状流动,无返混现象,反应温度沿反应管长度而变化,得高压聚乙烯分子量分布较宽,耐高压。
无搅拌系统,长链分枝少。
生产能力取决于反应管参数。
釜式反应器:物料可充分混合,反应温度均匀,还可分区操作。
耐高压不如管式,反应能力可在较大范围内变化,反应易控制。
PE分布窄,长链分枝多。
3、高压PE合成反应条件比较苛刻,具体条件如何?为什么采用这样的工艺条件?反应温度设在150℃~330℃,原因有二:①乙烯无任何取代基,分子结构对称,纯乙烯在350℃以上爆炸性分解,从安全角度,避免因某些特殊不可预知的因素造成温度上升,引发事故,故使T<330℃②PE 熔点为130℃,当T<130℃时造成大量PE凝固,堵塞管道,同样造成反应难以进行,造成事故,故最低温度不低于130℃,一般温度大于150℃。
反应在低压下进行,原因:乙烯常压下位气体,分子间距离远,不易反应,压缩后,分子间距离显著缩短,极大增加了自由基与单体分子之间碰撞几率,易反应,在100~300MPa下,C2H4接近液态烃,近似不可压缩状态,其次T上升,需压力也增加,才能使PE与单体形成均相状态,保持反应顺利进行。
剪切作用对PP_EPDM共混物性能的影响

剪切作用对PP/EPDM共混物性能的影响杨 其 黄亚江 毛益民 曾邦禄 王鹏驹(四川大学高分子科学与工程学院,成都 610065) 摘要 研究了聚丙烯/(乙烯/丙烯/二烯)共聚物(PP/EPDM)共混物动态硫化过程中,剪切作用对其力学性能的影响。
通过改变密炼机转子转速,得到了一系列PP/EPDM共混物,采用扫描电子显微镜、小角激光散射技术对试样进行微观分析。
结果表明,不同转子转速对应于不同形态结构;剪切作用有一最佳值,对应于EPDM增韧PP的效果最佳;剪切作用对其拉伸强度影响不大。
关键词 聚丙烯 (乙烯/丙烯/二烯)共聚物 剪切 动态硫化 力学性能 动态硫化聚丙烯(PP)/(乙烯/丙烯/二烯)共聚物(EPDM)共混物是增韧PP最成功的范例,具有韧性好、质量轻、价格低、综合性能优良及易成型加工等优点[1~3]。
所谓“动态硫化”是指在PP与EPDM共混过程中加入硫化剂,在高温、高剪切作用下完成硫化。
在动态硫化过程中,EPDM中的二烯上的双键被化学交联剂打开,形成具有反应活性的EPDM链自由基,这些自由基再进行链增长反应,形成交联的EPDM,并在高温、高剪切作用下不断地被剪碎、拉断,形成较小的颗粒分散于PP连续相中[4,5]。
PP/EPDM共混物的动态硫化是一个集物理熔融共混、化学引发交联和剪切细化分散为一体的复杂过程,高分子材料的性能除取决于组成、组分性能和化学交联体系外,还与加工工艺有关[6]。
但现有的研究中绝大多数集中在组分配比、组分的相互影响、硫化体系、第三组分(如填料等)等方面[7~10],而研究工艺条件却很少见[11~13]。
对聚合物共混物而言,在聚合物组分选定之后,其在加工中形成并保留(冻结)在制品中的相结构将决定着制品的使用性能。
剪切是影响聚合物共混物相结构的最主要因素之一,因此开展剪切条件下聚合物熔体(流体)相结构形态及其对制品性能影响的研究,掌握其变化和控制规律及其对制品性能影响的关系,是实现高分子材料性能设计、充分发挥材料潜在性能的必要条件,也是开发新的成型方法和理论的基础[14,15]。
化学反应工程基础

幂函数形式:rA = -
1 V
nd A
dt
=
kCAα
1
CBα
2
k: 反应速率常数 α1,α2:实验测定常数
总级数 n=α1+α2
对基元反应: α1=a α2=b
复杂反应: n需实验测定
k遵循Arrehnies方程:
k = A0e-E/RT lnk =lnA0 – E/RT dlnk/dT = E/RT2
釜式、塔式 釜式、塔式 固定床、流化床、移动
床 釜式、塔式
回转筒式 固定床、流化床
(2) 按反应器的结构型式分类
结构型式
适用的相态
反应釜(包括 液相、气-液相、液-液
多釜串联)
相、液-固相
管式
气相、液相
鼓泡塔 固定床
流化床 回转筒式 喷雾式
气-液相、气-液-固(催 化剂)相
气-固(催化或非催化) 相
A+B
S
rA =
dCA dt
=kCACB
因为A,B等摩尔消耗,所以CA0xA = CB0xB 令M=CB0/CA0
(1)M=1 即 CA0=CB0 CA=CB
rA = kCA2 =
kt = 1
1
dCA dt
=
1
xA
CA CA0 CA0 1-xA
(2)M≠1 即 CA0≠CB0 CA≠CB
rA = kCA20 (1-xA)(M-xA)
t
半连续反应器
B
A
半连续反应器特点:
1、某些反应物料一次
加入,其余物料连续加
入,或者将某种产物连
续取出。
C
2、非稳态操作。 t
0
CO2与环氧化物耦合制备环状碳酸酯的多相催化体系研究进展

化工进展Chemical Industry and Engineering Progress2024 年第 43 卷第 3 期CO 2与环氧化物耦合制备环状碳酸酯的多相催化体系研究进展刘方旺1,韩艺1,张佳佳1,步红红1,王兴鹏1,于传峰1,刘猛帅2(1 潍坊职业学院化学工程学院,山东 潍坊 262737;2 青岛科技大学化工学院,山东 青岛 266045)摘要:作为最主要的温室气体,二氧化碳(CO 2)的过度排放已导致了严重的环境问题。
同时,CO 2也属于储量丰富、廉价、安全和可再生利用的C 1资源,被认为是有机合成的理想碳材料。
高效且绿色的化学固定CO 2耦合制备具有高沸点、高极性、低挥发性和可生物降解性等优点的环状碳酸酯是CO 2资源化利用的有效方式,已引起社会各界的广泛关注。
本文首先简述了目前合成环状碳酸酯的现有反应路径。
然后,以CO 2和环氧化物的耦合反应为出发点,着重分析了该反应发生所涉及的反应机理以及催化该反应时多相催化体系的设计思路和当前研究进展。
同时,综合比较了不同多相催化体系的催化条件、催化活性及循环使用性等催化参数的优缺点。
最后,基于上述分析,本文总结了不同多相催化体系的应用前景并建议其后续发展应与均相催化体系相结合,利用两者的优势高效活化CO 2与环氧化物,以实现温和条件下催化耦合反应。
关键词:二氧化碳;催化剂;环氧化物;催化作用;耦合反应;环状碳酸酯中图分类号:TQ203.2 文献标志码:A 文章编号:1000-6613(2024)03-1252-14Research advance of heterogeneous catalytic system for the couplingbetween CO 2 and epoxide into propylene carbonateLIU Fangwang 1,HAN Yi 1,ZHANG Jiajia 1,BU Honghong 1,WANG Xingpeng 1,YU Chuanfeng 1,LIU Mengshuai 2(1 College of Chemical Engineering, Weifang Vocational College, Weifang 262737, Shandong, China; 2 College of ChemicalEngineering, Qingdao University of Science and Technology, Qingdao 266042, Shandong, China)Abstract: As the most important greenhouse gas, carbon dioxide (CO 2) has caused serious environmentalproblems by excessive emission. On the other hand, CO 2 is an abundant, cheap, safe and renewable C 1 resource, and thus is considered as an ideal carbon material in organic synthesis. Efficient and green chemical fixing CO 2 to prepare cyclic carbonate with high boiling, high polarity, low volatility and biological degradability is an effective way of CO 2 resource utilization, which has attracted wide attention. In this paper, the existing reaction pathways for the synthesis of cyclic carbonate are briefly described. Then, staring with the coupling reaction of CO 2 with epoxides, we emphatically analyze the reaction mechanism, and the design ideas and current research advance of the heterogeneous catalytic system. Meanwhile, the advantages and disadvantages of the catalytic parameters such as catalytic conditions,catalytic activity and recyclability, of different heterogeneous catalytic systems are comprehensively compared. Finally, the application and development prospects of different heterogeneous catalytic systems综述与专论DOI :10.16085/j.issn.1000-6613.2023-0351收稿日期:2023-03-08;修改稿日期:2023-06-13。
Reppe生产工艺

Reppe生产工艺Reppe法工艺包括传统法、改良法、Linde法、BASF/Du Pont法四种。
1.1 Reppe传统法Reppe法是30年代由德国I.G法本公司(BASF公司的前身)Reppe等人开发成功,也称炔醛法、甲醛炔化法等。
该法是1,4-丁二醇的经典生产工艺,应用该法生产的1,4-丁二醇曾经占世界总产量的85%以上。
它主要以乙炔和甲醛为主要原料,分两步进行:第一步在以SiO2为载体的氧化铜催化剂条件下进行反应,为了抑制铜聚反应,需要加入少量的氧化钛作助催化剂的,由乙炔和甲醛(37wt%)反应先生成丁炔二醇,反应条件为:乙炔分压0.49MPa,反应温度90~100℃,甲醛转化率在95%左右;第二步是丁炔二醇经催化加氢制得1,4-丁二醇,催化剂为载于含硅载体上15%Ni-5%-0.7Mn,反应条件是:压力29.4MPa,反应温度70~140℃,1,4-丁二醇的收率为95%。
主要化学反应式如下:该法催化剂与产品无需分离,操作费用低,由于一直缺乏经济的替代工艺,该工艺垄断1,4-丁二醇生产长达40年之久。
但因操作压力高进行,特别是乙炔分压较高,只能采用滴流床(也有人称为涓流床)反应器在液相中连续反应,以避免因乙炔气体的不断积累而引起爆炸。
同时反应器设计安全系数高达12~20倍,致使反应装置庞大,设备造价昂贵,投资高。
另外,乙炔聚合会生成的聚乙炔,易导致催化剂失活,聚乙炔也会堵塞管道,从而缩短生产周期,降低生产能力。
由于Reppe工艺的诸多缺点,国外许多大公司和学者对该工艺进行了大量改进,形成了许多改良工艺,改良后的Reppe法基本上采用常压工艺,主要改进大多集中在对催化剂的改进上,有的催化剂呈浆态,有的催化剂呈悬浮态等,主要代表工艺有BASF、Du Pont公司的悬浮床工艺和GAF的淤桨床工艺。
雷佩法生产过程不太复杂,生产成本取决于原料乙炔的生产工艺或价格。
1.2改良法(GAF法)美国通用苯胺和胶片公司(GAF)首先对传统的Reppe工艺的催化剂进行了改进,催化剂主要由硝酸铜和硝酸铋组成,制作方法简述如下:将硝酸铜和硝酸铋浸渍在硅酸镁载体上,经焙烧后,制成Cu 12%、Bi 2%的催化剂。
乙炔制醋酸乙烯酯概述

(4)醋酐旳生成:
2CH3COOH→(CH3CO)2O+H2O CH3CH(OCOCH3)2→(CH3CO)2O+CH3CHO Zn(OCOCH3)2→(CH3CO)2O+ZnO
醋酸乙烯合成反应是在一定温度范围内进行旳。因为醋酸锌-活性炭触媒对乙炔 发生化学吸附起始温度为160℃,而且缔合为双分子旳醋酸在160℃以上开始离 解为单分子醋酸,才干 与乙炔反应。所以, 反应温度不得低于160℃。
当反应温度升高时,反应速度加紧,醋酸单程转化率升高,使空时收率增长。但 反应温度过高,触媒中毒系数增大,选择性降低,付反应增多,使反应液中丙酮、 丁烯醛、二乙烯基乙炔等有害杂质增多,影响产品质量,故反应温度一般不应超 出210℃。
概述
醋酸乙烯合成生产工艺技术概况
⑵天然气乙炔法 以天然气为原料,部分氧化裂解制得乙炔 采用固定床反应器气相催化合成醋酸乙烯旳天然气 乙炔法。 目前国内四川川维引进有生产装置。
概述
醋酸乙烯合成生产工艺技术概况
⑶电石乙炔法
用水与电石生产乙炔
采用沸腾床反应器气相催化合成醋酸乙烯旳电石乙 炔法是最早实现工业化旳一种生产措施。
C2H2+H2O→CH3CHO CH2CHOCOCH3+H2O→CH3CHO+CH3COOH CH3CH(OCOCH3)2→CH3CHO+(CH3CO)2O
(2)丁烯醛旳生成:
2CH3CHO→CH3CH=CHCHO+H2O HC≡CH+CH3CHO→CH3CH=CHCHO
聚合物合成工艺学思考题及其答案
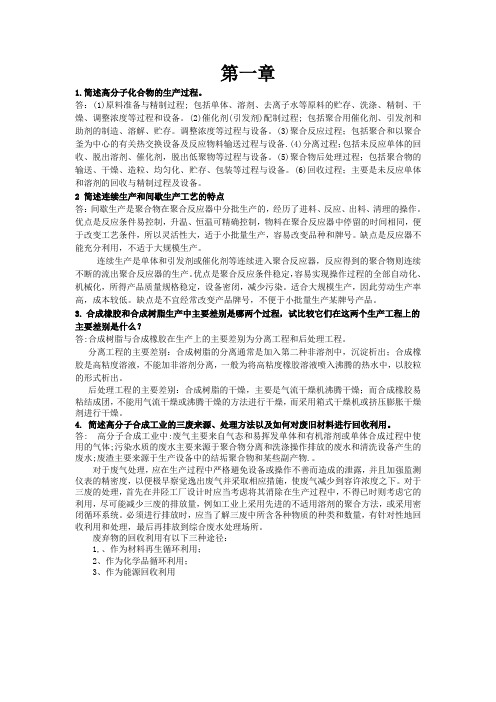
第一章1.简述高分子化合物的生产过程。
答:(1)原料准备与精制过程; 包括单体、溶剂、去离子水等原料的贮存、洗涤、精制、干燥、调整浓度等过程和设备。
(2)催化剂(引发剂)配制过程; 包括聚合用催化剂、引发剂和助剂的制造、溶解、贮存。
调整浓度等过程与设备。
(3)聚合反应过程;包括聚合和以聚合釜为中心的有关热交换设备及反应物料输送过程与设备.(4)分离过程;包括未反应单体的回收、脱出溶剂、催化剂,脱出低聚物等过程与设备。
(5)聚合物后处理过程;包括聚合物的输送、干燥、造粒、均匀化、贮存、包装等过程与设备。
(6)回收过程;主要是未反应单体和溶剂的回收与精制过程及设备。
2 简述连续生产和间歇生产工艺的特点答:间歇生产是聚合物在聚合反应器中分批生产的,经历了进料、反应、出料、清理的操作。
优点是反应条件易控制,升温、恒温可精确控制,物料在聚合反应器中停留的时间相同,便于改变工艺条件,所以灵活性大,适于小批量生产,容易改变品种和牌号。
缺点是反应器不能充分利用,不适于大规模生产。
连续生产是单体和引发剂或催化剂等连续进入聚合反应器,反应得到的聚合物则连续不断的流出聚合反应器的生产。
优点是聚合反应条件稳定,容易实现操作过程的全部自动化、机械化,所得产品质量规格稳定,设备密闭,减少污染。
适合大规模生产,因此劳动生产率高,成本较低。
缺点是不宜经常改变产品牌号,不便于小批量生产某牌号产品。
3.合成橡胶和合成树脂生产中主要差别是哪两个过程,试比较它们在这两个生产工程上的主要差别是什么?答:合成树脂与合成橡胶在生产上的主要差别为分离工程和后处理工程。
分离工程的主要差别:合成树脂的分离通常是加入第二种非溶剂中,沉淀析出;合成橡胶是高粘度溶液,不能加非溶剂分离,一般为将高粘度橡胶溶液喷入沸腾的热水中,以胶粒的形式析出。
后处理工程的主要差别:合成树脂的干燥,主要是气流干燥机沸腾干燥;而合成橡胶易粘结成团,不能用气流干燥或沸腾干燥的方法进行干燥,而采用箱式干燥机或挤压膨胀干燥剂进行干燥。
两级式流化床反应器中乙炔氢氯化的气相催化反应
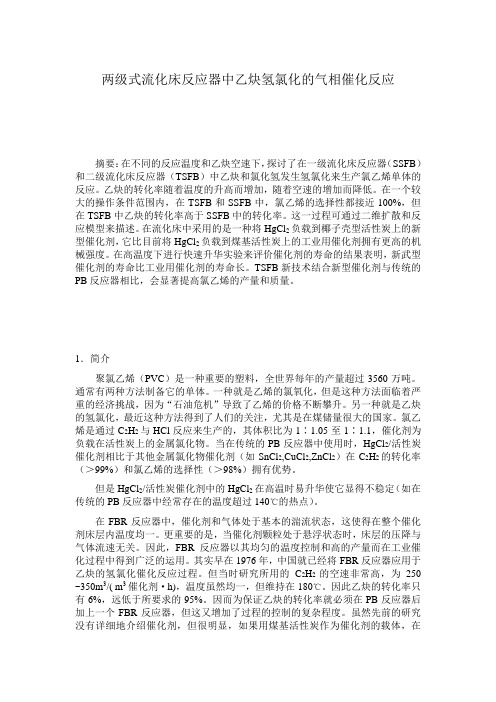
两级式流化床反应器中乙炔氢氯化的气相催化反应摘要:在不同的反应温度和乙炔空速下,探讨了在一级流化床反应器(SSFB)和二级流化床反应器(TSFB)中乙炔和氯化氢发生氢氯化来生产氯乙烯单体的反应。
乙炔的转化率随着温度的升高而增加,随着空速的增加而降低。
在一个较大的操作条件范围内,在TSFB和SSFB中,氯乙烯的选择性都接近100%,但在TSFB中乙炔的转化率高于SSFB中的转化率。
这一过程可通过二维扩散和反应模型来描述。
在流化床中采用的是一种将HgCl2负载到椰子壳型活性炭上的新型催化剂,它比目前将HgCl2负载到煤基活性炭上的工业用催化剂拥有更高的机械强度。
在高温度下进行快速升华实验来评价催化剂的寿命的结果表明,新武型催化剂的寿命比工业用催化剂的寿命长。
TSFB新技术结合新型催化剂与传统的PB反应器相比,会显著提高氯乙烯的产量和质量。
1.简介聚氯乙烯(PVC)是一种重要的塑料,全世界每年的产量超过3560万吨。
通常有两种方法制备它的单体。
一种就是乙烯的氯氧化,但是这种方法面临着严重的经济挑战,因为“石油危机”导致了乙烯的价格不断攀升。
另一种就是乙炔的氢氯化,最近这种方法得到了人们的关注,尤其是在煤储量很大的国家。
氯乙烯是通过C2H2与HCl反应来生产的,其体积比为1∶1.05至1∶1.1,催化剂为负载在活性炭上的金属氯化物。
当在传统的PB反应器中使用时,HgCl2/活性炭催化剂相比于其他金属氯化物催化剂(如SnCl2,CuCl2,ZnCl2)在C2H2的转化率(>99%)和氯乙烯的选择性(>98%)拥有优势。
但是HgCl2/活性炭催化剂中的HgCl2在高温时易升华使它显得不稳定(如在传统的PB反应器中经常存在的温度超过140℃的热点)。
在FBR反应器中,催化剂和气体处于基本的湍流状态,这使得在整个催化剂床层内温度均一。
更重要的是,当催化剂颗粒处于悬浮状态时,床层的压降与气体流速无关。
因此,FBR反应器以其均匀的温度控制和高的产量而在工业催化过程中得到广泛的运用。
化工工艺学习题与答案

化工工艺学试题1一、填空:每空1分共10分1. 目前工业上对、间二甲苯的分离方法有----------------------------、------------------------------和-----------------------------------三种;2. 乙苯催化脱氢合成苯乙烯时脱氢部分常用-----------------------和-----------------------两种类型反应器;3、催化加氢反应所用的催化剂以催化剂的形态分有-------------------------、-----------------------------、-----------------------------、-------------------------------、-------------------------五种1、低温结晶分离法、络合分离法和模拟移动床吸附法三种;3、金属催化剂、骨架催化剂、金属氧化物、金属硫化物、金属络合物;二、简答每题5分,共90分1、煤的干馏和煤的气化的定义;答:将煤隔绝空气加热,随着温度的升高,煤中有机物逐渐开始分解,其中挥发性物质呈气态逸出,残留下不挥物性产物主是焦炭或半焦,这种加工方法称煤的干馏;煤、焦或半焦在高温常压或加压条件下,与气化剂反应转化为一氧化碳、氢等可燃性气体的过程,称为煤的气化;2、什么叫烃类热裂解答:烃类热裂解法是将石油系烃类原料天然气、炼厂气、轻油、柴油、重油等经高温作用,使烃类分子发生碳链断裂或脱氢反应,生成分子量较小的烯烃、烷烃和其它分子量不同的轻质和重质烃类;3、烃类热裂解的原料有哪些答:4、烃类热裂解过程有何特点答:①强吸热反应,且须在高温下进行,反应温度一般在750K以上;②存在二次反应,为了避免二次反应,停留时间很短,烃的分压要低;③反应产物是一复杂的混合物,除了气态烃和液态烃外,尚有固态焦的生成;5、烃类热裂解制乙烯的分离过程中,裂解气为什么要进行压缩为什么要分段压缩答:裂解气中许多组分在常压下都是气体,沸点很底,为了使分离温度不太底,可以适当提高分离压力;多段压缩有如下好处:节省压缩功;段与段中间可以进行降温,避免温度太高引起二烯烃的聚合;段与段中间也可便于进行净化和分离;6、烃类裂解制乙烯的过程中,为什么要对裂解气进行脱酸性气体怎样进行脱除答:酸性气体主要是指二氧化碳和硫化氢,另外还含有少量有机硫化物,这些酸性气体过多会对分离过程带来危害:例如硫化氢会腐蚀管道和设备,使加氢脱炔催化剂中毒,使干燥用的分子筛寿命缩短,二氧化碳会结成干冰,会堵塞管道,他们对产物的进一步利用也有危害,所以必须脱除;用碱洗法脱除;酸性气体量多时可以先用乙醇胺脱除,再用碱洗法彻底除去;7、脱甲烷塔高压法和低压法有何优缺点答:低压法分离效果好,乙烯收率高,能量消耗低;低压法也有不利之处,如需要耐低温钢材、多一套甲烷制冷系统、流程比较复杂;高压法的脱甲烷塔顶温度为—96℃左右,不必采用甲烷制冷系统,只需用液态乙烯冷剂即可,比甲烷冷冻系统简单;此外提高压力可缩小精馏塔的容积,所以从投资和材质要求来看,高压法是有利的;但高压法因乙烯与甲烷相对挥发度接近而不易分离,运行能耗要高于低压法;8、为了节省能量和简化流程,乙烯塔作了哪两项改进答:用中间再沸器的办法来回收冷量;不设第二脱甲烷塔,在乙烯塔塔顶脱甲烷,在精馏段侧线出产品乙烯,一个塔起两个塔的作用;9、写出在裂解气分离中低压脱甲烷塔的塔顶需要-1400C左右的冷量,说明或画图说明如何获得这一级别的冷量答:可采用甲烷、乙烯、丙烯三元复迭制冷循环,通过两个复迭换热器,使冷水向丙烯供冷,丙烯向乙烯供冷,乙烯向甲烷供冷,甲烷就可向低于-140℃的冷量用户供冷;10、芳烃烷基化反应中,工业生产上无水AlCl3催化剂应该怎样处理才具有活性答:纯的无水AlCl3无催化活性,必须有助催化剂HCl或RCl同时存在,使其转化为络合物,工业生产上使用的AlCl3络合物是将无水AlCl3溶于芳烃中,并同时通入HCl或加入少量水,使少量AlCl3水解产生HCl配置而成芳烃·H+·AlCl4-的复合体;AlCl3络合物催化剂活性甚高,可使反应在100℃左右进行,还具有使多烷基苯与苯发生烷基转移的作用;但其呈强酸性,对设备、管道具有强腐蚀性;11、分别写出由合成气制备甲醇、丙烯氨氧化制备丙烯腈以及过氧化氢异丙苯发生酸解的反应方程式; 答:CO+2H2CH3OHC3H6+NH3+3/2O2 → CH2=CH-CN g+3H2O g12、简要回答以苯和乙烯为原料,我们怎样才能合成出苯乙烯;以及苯乙烯在储存时应注意那些事项答:包括两步:第一步苯与乙烯烷基化合成乙苯;第二步乙苯催化脱氢合成苯乙烯;因苯乙烯活性高,容易聚合,因此贮存的苯乙烯要放在干燥而清洁的贮槽中,必须加阻聚剂,环境温度不宜高,保持期也不宜过长;13、炔烃和烯烃在同一催化剂上加氢时,单独加氢和共同加氢时反应速度有何不同,为什么答:同一催化剂上当单独加氢是烯烃速度大于炔烃,但当共同加烃时炔烃速度大于烯烃,这是因为共同存在时发生了吸附竞争,乙炔吸附能力最强,大部分活性中心被乙炔所覆盖,所以乙炔加氢速度快;14、举例说明芳烃之间转化的主要反应有哪几种;答:异构化反应:歧化反应:烷基化反应:烷基转移反应:脱烷基化反应:15、氯醇法生产环氧丙烷分哪两步进行有何优缺点答:优点是生产过程比较简单,主要缺点是生产成本高,氯消耗量大,有大量含氯化钙污水需要处理;16、简要回答丙烯腈生产过程中的含腈废水是怎样进行处理的;答:1 水量少而HCN和有机腈化合物含量高的废水例如急冷塔排出的废水,一般是经过滤除去固体杂质后,可采用燃烧法处理,以空气作氧化剂,将废水直接喷入或用碱水处理后再喷入烧却炉,用中压水蒸气雾化并加入辅助燃料,进行烧却处理;2 当废水量较大氰化物包括有机腈化物含量较低时,则可用生化方法处理;最常用的法是曝气池活性污泥法或生物转盘法;17、以化学方程式表示在醋酸锰催化剂的存在下乙醛催化自氧化合成醋酸的反应机理答:18、液相均相催化氧化在工艺上有哪些优缺点答:优越性: 1 反应条件比较缓和,有较高的选择性,并可采用溶剂以缓和反应的进行和提高选择性;2 反应热的除去比较方便,有些氧化过程可方便地利用反应物或溶剂的蒸发以移走反应热;3 反应温度比较容易控制,温度分布比较均匀; 4 反应设备结构简单,生产能力较高;不足:反应介质的腐蚀性往往比较严重;有些反应,主要是络合催化氧化,需用贵金属盐作催化剂,必须解决催化剂的回收问题;化工工艺学2一、填空:每空1分,共10分1、衡量水质污染程度常用的指标是化学耗氧量和生物耗氧量;2. 烃类裂解制乙烯时,工业上采用吸附方式对裂解气脱水,用分子筛、活性氧化铝或硅胶作吸附剂;3、目前工业上对、间二甲苯的分离方法有低温结晶分离法、络合分离法和模拟移动床吸附法三种;4、工业上常用的芳烃烷基化的烷基化剂主要有烯烃和卤代烷烃--------两种,另外醇、醛、酮也可作为烷基化剂;二、简答每题5分,共90分1、烃类热裂解制乙烯的过程中,管式裂解炉的辐射管为什么用变径管前细后粗比用均径管有好处答:反应初期用小管径有利于强化传热,使原料迅速升温,缩短停留时间;裂解管后部管径变粗,有利于减小烃分压,减少二次反应,而且也不会因二次反应生成的焦很快堵塞管道,因而延长了操作周期,提高了乙烯收率;2、炔烃和烯烃在同一催化剂上加氢时,单独加氢和共同加氢时反应速度有何不同,为什么答:同一催化剂上当单独加氢是烯烃速度大于炔烃,但当共同加烃时炔烃速度大于烯烃,这是因为共同存存在时发生了吸附竞争,乙炔吸附能力最强,大部分活性中心被乙炔所覆盖,所以乙炔加氢速度快;3、烃类热裂解制乙烯的分离过程中,裂解气为什么要进行压缩为什么要分段压缩答:裂解气中许多组分在常压下都是气体,沸点很底,为了使分离温度不太底,可以适当提高分离压力;多段压缩有如下好处:节省压缩功;段间进行降温,避免温度太高引起二烯烃聚合;段间可便于进行净化和分离;4、工业上苯的来源主要有哪5种答:从炼焦副产粗笨中获取,从裂解汽油中获取,从重整汽油中获取,从甲苯岐化获取或甲苯加氢脱甲基获取5、芳烃脱烷基化有哪几种方法甲苯脱甲基工业化的是哪一种答:①、烷基芳烃催化裂化脱烷基;②、烷基芳烃催化氧化脱烷基;③、烷基芳烃的加氢脱烷基;④、烷基苯的水蒸气脱烷基法;甲苯脱甲基工业化的是第③种;6、乙烯钯盐络合催化氧化过程中,由哪三个基本反应组成,写出方程式;答:乙烯钯盐的络合:钯的氧化:氧化亚铜的氧化:7、工业上获取丁二烯有哪三种方法目前主要是哪2种答:1、从烃类热裂解制乙烯的联产物碳四馏分分离得到;2、由丁烷或丁烯催化脱氢法制取;3、由丁烯氧化脱氢法制取;目前主要是第一和第三种;8、烃类热裂解制乙烯的过程中,为什么要对裂解气进行脱炔怎样进行脱除答:9、应当采取哪些措施,才能使多级循环制冷的能量得到合理利用答:1 尽可能使各段引出的不同温度的蒸气,作不同温度级位的热剂,供工艺中相应温度级位的热量用户如再沸器的需要;2 尽可能使各段分出的不同温度的液体,作不同温度级位的冷剂,供工艺中相应温度级位的冷量用户如冷凝器之需要;3 尽可能组织热交换,把液态冷剂进行过冷,在过冷状态下进行节流膨胀,能多获得供冷的低温液态冷剂,少产生气相冷剂,使节流膨胀后的气化率降低,以提高制冷能力;10、芳烃烷基化反应中,工业生产上无水AlCl3催化剂应该怎样处理才具有活性这种催化剂有何优缺点答:纯的无水AlCl3无催化活性,必须有助催化剂HCl或RCl同时存在,使其转化为络合物,工业生产上使用的AlCl3络合物是将无水AlCl3溶于芳烃中,并同时通入HCl或加入少量水,使少量AlCl3水解产生HCl配置而成芳烃·H+·AlCl-的复合体;11、烃类热裂解过程中为什么常用水蒸气做稀释剂答:水蒸气除了能降低烃分压外,还有如下优点:热容大,能稳定炉温,保护炉管;易于分离,便宜易得;可以抑制原料中的硫对合金钢裂解管的腐蚀作用;水蒸气在高温下有清焦作用;水蒸气的氧化性使金属表面的铁、镍形成氧化薄膜,减轻了铁和镍对烃类气体分解生碳的催化作用;12、烃类热裂解制乙烯的过程中,结焦和生炭的机理有何不同答:结焦是在较低的温度下〈1200K〉通过芳烃缩合而成;生碳是在较高的温度下1200K通过生成乙炔的中间阶段,脱氢为稠合的碳原子13、烃类热裂解过程有那些工艺特点答:①强吸热反应,且须在高温下进行,反应温度一般在750K以上;②存在二次反应,为了避免二次反应,停留时间很短,烃的分压要低;③反应产物是一复杂的混合物,除了气态烃和液态烃外,尚有固态焦的生成14、氧化脱氢法与催化脱氢法相比有哪些优点;答:15、氢气的来源有哪些答:电解水,炼油厂重整装置等的炼厂气分离,烃类热烈解装置也副产氢气,焦炉煤气经变压吸附分离,及工业上常用的烃类水蒸气转化或部分氧化法制氢;16、在丙烯氨氧化合成丙烯腈的工艺中含氰废水是怎样进行处理的答:1 水量少而HCN 和有机腈化合物含量高的废水,一般是经过滤除去固体杂质后,可采用燃烧法处理,以空气作氧化剂,将废水直接喷入或用碱水处理后再喷入烧却炉,用中压水蒸气雾化并加入辅助燃料,进行烧却处理; 2 当废水量较大氰化物包括有机腈化物含量较低时,则可用生化方法处理;17、 石油加工方法中,什么是催化裂化、催化重整和加氢裂化答:催化裂化目的是将不能用作轻质燃料的常减压馏分油,加工成辛烷值较高的汽油等轻质燃料;催化重整是使原油常压蒸馏所得的轻汽油馏分经过化学加工转变成富含芳烃的高辛烷值汽油的过程,现在该法不仅用于生产高辛烷值汽油,且已成为生产芳烃的一个重要方法;加氢裂化是炼油工业中增产航空喷气燃料和优质轻柴油常采用的一种方法,所用的原料是不容易处理的一些重质油品;18、 烃类热裂解制乙烯的反应中,烷烃、环烷烃和芳烃各有什么反应规律答:化工工艺学考试题31、 写出合成气制甲醇、甲烷化法脱CO 、丙烯氨氧化制丙烯腈的化学方程式;答:CO+2H 2 CH 3OH 1分2、 描述如何实现低压脱甲烷塔塔顶-140℃的低温,注:用丙烯、乙烯和甲烷三种制冷剂;答:可采用甲烷、乙烯、丙烯三元复迭制冷循环,通过两个复迭换热器,使冷水向丙烯供冷,丙烯向乙烯供冷,乙烯向甲烷供冷,甲烷就可向低于-140℃的冷量用户供冷;3分 或:3、 说明催化裂化和烃类热裂解的异同点;答:相同点:都是主要发生脱氢和断链反应;不同点:①催化裂化温度低,裂解程度底,而烃类热裂解裂解程度高,②催化裂化主要目的是生产高辛烷值汽油,而烃类热裂解主要目的是准备乙烯、丙烯并联产丁二烯等,③催化裂化需要催化剂,烃类热裂解不需要催化剂;注:其他合理异同点也可;O H CH H CO O Al Ni MPa 24/,0.32323+−−−−−→−+4、烃类热裂解中,为何要加入水蒸气答:水蒸汽优点:1降低烃分压,有利于一次反应,抑制二次反应;2 水蒸气的热容较大,水蒸气升温时虽然耗热较多,但能对炉管温度起稳定作用,在一定程度上保护了炉管;3 易于从裂解产物中分离,对裂解气的质量无影响,且水蒸气便宜易得;4 可以抑制原料中的硫对合金钢裂解管的腐蚀作用; 水蒸气在高温下与裂解管中沉积的焦碳发生如下反应C+H2O=H2+CO实际上起了对炉管的清焦作用;5 水蒸气对金属表面起一定的氧化作用,使金属表面的铁、镍形成氧化薄膜,减轻了铁和镍对烃类气体分解生碳的催化作用;5、高压和低压脱甲烷塔的优缺点;答:低压法分离效果好,乙烯收率高,能量消耗低;低压法也有不利之处,如需要耐低温钢材、多一套甲烷制冷系统、流程比较复杂;高压法的脱甲烷塔顶温度为-96℃左右,不必采用甲烷制冷系统,只需用液态乙烯冷剂即可,比甲烷冷冻系统简单;此外提高压力可缩小精馏塔的容积,所以从投资和材质要求来看,高压法是有利的,但高压法的能耗要高;6、描述烃类热裂解中,链烷烃、环烷烃、芳烃和烯烃的裂解规律;答:烷烃——正构烷烃最利于生成乙烯、丙烯,分子量愈小则烯烃的总收率愈高;异构烷烃的烯烃总收率低于同碳原子数的正构烷烃;随着分子量增大,这种差别就减小;环烷烃——在通常裂解条件下,环烷烃生成芳烃的反应优于生成单烯烃的反应;含环烷烃较多的原料,其丁二烯、芳烃的收率较高,乙烯的收率较低;芳烃——无侧链的芳烃基本上不易裂解为烯烃;有侧链的芳烃,主要是侧链逐步断裂及脱氢;芳环倾向于脱氢缩合生成稠环芳烃,直至结焦;烯烃——大分子的烯烃能裂解为乙烯和丙烯等低级烯烃,但烯烃会发生二次反应,最后生成焦和碳;所以含烯烃的原料如二次加工产品作为裂解原料不好;7、写出“三烯”和“三苯”的主要来源;答:“三烯”主要来源:炼厂气分离,烃类热裂解制备;“三苯”主要来源:从炼焦副产粗笨中获取,从裂解汽油中获取,从重整汽油中获取;8、芳烃的脱烷基化有哪四种方式甲苯脱甲基常用哪种方式答:①烷基芳烃催化裂化脱烷基,②烷基芳烃的催化氧化脱烷基 ,③烷基芳烃的加氢脱烷基,④烷基苯的水蒸气脱烷基法;⑤甲苯脱甲基常用第三种9、催化加氢反应用的催化剂,写出在150℃以下、150℃~200℃之间、高于250℃以及防止硫中毒各分别通常用哪一种或几种催化剂答:通常反应温度在150℃以下,多用Pt、Pd等贵金属催化剂,以及用活性很高的骨架镍催化剂;而在150~200℃的反应温度区间,用Ni、Cu以及它们的合金催化剂;在温度高于250℃时,多用金属及金属氧化物催化剂;为防止硫中毒则用金属硫化物催化剂,通常都是在高温下进行加氢;10、工业上苯乙烯的主要来源有哪三种储存苯乙烯时有哪些注意事项答:烃类裂解制乙烯所得副产裂解汽油中分离;乙苯脱氢法制得;以乙苯和丙烯为原料联产苯乙烯和环氧丙烷的新工艺,称为哈尔康Halcon法;贮存的苯乙烯要放在干燥而清洁的贮槽中,必须加阻聚剂,环境温度不宜高,保持期也不宜过长;11、氯醇法生产环氧乙烷分哪两步进行有何优缺点目前环氧乙烷的主要生产方法什么答:1分该法优点对乙烯纯度要求不高,反应条件较缓和,其主要缺点是要消耗大量氯气和石灰,反应介质有强腐蚀性,且有大量含氯化钙的污水要排放处理;目前环氧乙烷的主要生产方法乙烯直接环氧化制备环氧乙烷;12、简要回答以石脑油为原料,我们怎样才能合成出苯酚和丙酮;答:原油常减压蒸馏得到石脑油,石脑油热裂解并分离得到苯和丙烯,苯和丙烯烷基化得到异丙苯,异丙苯催化自氧化得到过氧化氢异丙苯,过氧化氢异丙苯酸性条件下分解得到苯酚和丙酮;13、什么是一碳化学试简要分析我国目前一碳化学的发展;答:所谓一碳化学技术,就是将含有一个碳原子的化合物主要是一氧化碳和甲醇为原料,通过化学加工合成含有两个或两个以上碳原子的基本有机化工产品的技术;14、、烃类热裂解制乙烯的过程中,管式裂解炉的辐射管为什么用变径管前细后粗比用均径管有好处答:反应初期用小管有利于强化传热,使原料迅速升温,缩短停留时间;裂解管后部管径变粗,有利于减小烃分压,减少二次反应,而且也不会因二次反应生成的焦很快堵塞管道,因而延长了操作周期,提高了乙烯收率.15、烃类热裂解制乙烯的过程中,能量回收主要有哪三个途径答:异构化反应,例如:间二甲苯异构化生成对二甲苯的反应;歧化反应,例如:甲苯歧化生成苯和二甲苯的反应;烷基化反应,例如:苯和乙烯烷基化化生成乙苯的反应;烷基转移反应,例如:三甲苯和甲苯发生烷基转移反应生成二甲苯的反应;脱烷基化反应,例如:甲苯脱烷基化反应生成苯的反应或写方程式也可16、举例说明芳烃转化反应主要有哪几类答:从烃类热裂解制乙烯的联产物碳四馏分分离得到;由丁烷或丁烯催化脱氢法制取;由丁烯氧化脱氢法制取;目前第一和第三种方法最主要;17、工业上获取丁二烯有哪三种方法目前哪两种方法最主要答:由于过氧醋酸是一不稳定的具有爆炸性的化合物,其浓度积累到一定程度后会导致突然分解而发生爆炸;常用的催化剂是醋酸锰于催化剂醋酸锰能加速中间复合物的形成和分解,从而使反应系统中过氧醋酸的浓度达到很低程度,不致发生突发性分解;18、乙醛催化自氧化合成醋酸的反应机理是什么,为何要用醋酸锰作催化剂答:19、乙苯催化脱氢合成苯乙烯工艺中脱氢部分用哪两种类型的反应器,各有什么优缺点;答:分为:1等温反应器和 2绝热反应器;等温反应器优点是出口温度高于进口,对动力学、热力学有利:采用等温反应器脱氢,乙苯转化率选择性都好,另外水仅作为稀释,用量为绝热的1/2,缺点是结构复杂,成本高;绝热反应器优点是简单,生产能力大,成本低;缺点:出口温度低于进口影响转化率,因此绝热反应器脱氢,不仅转化率较低,选择性也较低;20、烃类裂解制乙烯的过程中,为什么要对裂解气进行脱水怎样进行脱除答:裂解气分离是在-100℃以下进行的,在低温下水能冻结成冰;在一定的温度压力下,水能和烃类形成白色结晶水合物,与冰雪相似,这些水合物,在高压低温下是稳定的冰和水合物结在管壁上,轻则增大动力消耗,重则使管道堵塞,影响正常生产;工业上是采用吸附方法脱水,用分子筛、活性氧化铝或硅胶作吸附剂;化工工艺学考试题41.基本有机化学工业的主要任务是什么答:基本有机化学工业的主要任务是利用自然界中大量存在的天然资源煤、石油、天然气及生物质等通过各种化学加工的方法,制成一系列重要的基本有机化工产品;2.写出由煤制乙炔的方程式,说明其缺点;答:电石制取:CaO+3C→CaC2+CO电石生产乙炔:CaC2+2H2O→C2H2+CaOH2缺点:电石生产乙炔耗电量大;3.简要写出几种由生物质制备的化学品至少5种;答:例如:农副产品废渣的水解是工业生产糠醛的唯一路线,富含淀粉的谷类、薯类、植物果实等发酵制乙醇、甲醇和丙酮,以淀粉类物质为原料制麦芽糖和葡萄糖,以木屑、稻草和玉米芯等为原料制木糖和木糖醇,此外由某些植物提取香精、染料、药材等;4.什么叫烃类的热裂解答:烃类热裂解法是将石油系烃类原料天然气、炼厂气、石脑油、柴油、重油等经高温作用,使烃类分子发生碳链断裂或脱氢反应,生成分子量较小的烯烃、烷烃和其他分子量不同的轻质和重质烃类;5.什么叫烃类热裂解过程的一次反应和二次反应;答:烃类热裂解过程中生成目的产物乙烯、丙烯等低级烯烃为主的反应称为一次反应;一次反应生成的乙烯、丙烯继续反应并转化为炔烃、二烯烃、芳烃直至生碳或结焦的反应成为二次反应;6.什么叫停留时间,停留时间对裂解产物分布有何影响答:物料从反应开始到达某一转化率时,在反应器中经历的时间叫停留时间;停留时间的选择除与裂解温度有关外,也与裂解原料和裂解工艺技术等有关:在一定的反应温度下,每一种裂解原料,都有它最适宜的停留时间,如裂解原料较重,则停留时间应短一些,原料较轻则可选择稍长一些;7.为什么要对裂解气急冷,急冷有哪两种哪种方式更好答:8.管式裂解炉结焦的现象有哪些,如何清焦答:裂解炉辐射盘管管壁温度或急冷锅炉出口温度超过规定值;或裂解炉辐射段入口压力增加值或急冷锅炉进出口压差超过规定值;清焦方法有停炉清焦法和不停炉清焦法也称在线清焦法;9.什么是裂解气深冷分离答:裂解气分离是在-100℃左右的低温下,将裂解气中除了氢和甲烷以外的其它烃类全部冷凝下来;然后利用裂解气中各种烃类的相对挥发度不同,以精馏的方法将各组分分离开来,达到分离的目的;实际上,此法为冷凝精馏过程; 因为这种分离方法采用了-100℃以下的冷冻系统,故称为深度冷冻分离,简称深冷分离;10.什么叫前加氢流程什么叫后加氢流程各有什么优缺点答:前加氢:脱甲烷塔前进行的加氢脱炔;前加氢由于氢气自给,故流程简单,能量消耗低;缺点:加氢选择性较差,乙烯损失量多;同时副反应的剧烈发生,不仅造成乙烯、丙烯加氢遭受损失,而且可能导致反应温度的失控,乃至出现催化剂床层温度飞速上升;此外裂解气中较重组分的存在,对加氢催化剂性能有较大的影响,使催化剂寿命缩短;后加氢:脱甲烷塔后进行的加氢脱炔;后加氢其优点有:一是因为是在脱甲烷塔之后进行,氢气已分出,加氢所用氢气按比例加入,加氢选择性高,乙烯几乎没有损失;二是加氢产品质量稳定,加氢原料中所含乙炔、丙炔和丙二烯的脱除均能达到指标要求;三是加氢原料气体中杂质少,催化剂使用周期长,产品纯度也高;不足之处:为了保证乙烯的纯度,加氢后还需要将氢气带入的甲烷和剩余的氢脱除,因此,需设第二脱甲烷塔,导致流程复杂,设备费用高;11.什么是冷箱,冷箱有什么作用;答:冷箱是在-100摄氏度~-160摄氏度下操作的低温设备;它的原理是用节流膨胀阀来获得低温,它的用途是依靠低温来回收乙烯,制取富含氢气和富含甲烷的馏分;12.应当采取哪些措施,才能使多级循环制冷的能量得到合理利用答:13.写出二甲苯异构化的反应图式和乙苯异构化的反应方程式;答:二甲苯的异构化图式:2分乙苯异构化的反应方程式:。
《化学反应过程与设备》课程标准
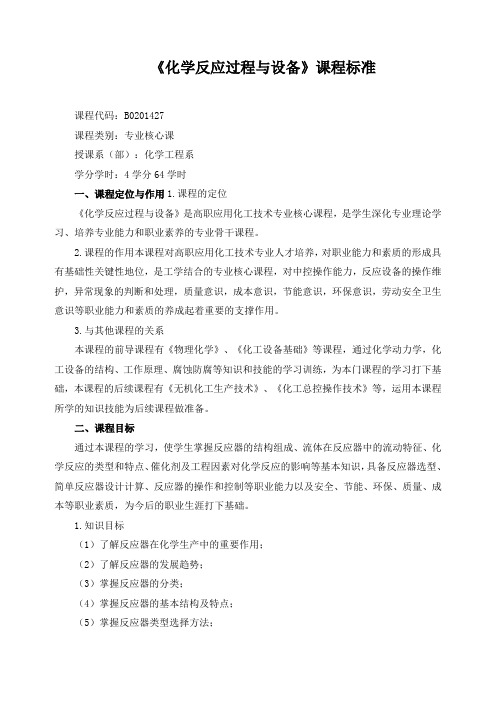
《化学反应过程与设备》课程标准课程代码:B0201427课程类别:专业核心课授课系(部):化学工程系学分学时:4学分64学时一、课程定位与作用1.课程的定位《化学反应过程与设备》是高职应用化工技术专业核心课程,是学生深化专业理论学习、培养专业能力和职业素养的专业骨干课程。
2.课程的作用本课程对高职应用化工技术专业人才培养,对职业能力和素质的形成具有基础性关键性地位,是工学结合的专业核心课程,对中控操作能力,反应设备的操作维护,异常现象的判断和处理,质量意识,成本意识,节能意识,环保意识,劳动安全卫生意识等职业能力和素质的养成起着重要的支撑作用。
3.与其他课程的关系本课程的前导课程有《物理化学》、《化工设备基础》等课程,通过化学动力学,化工设备的结构、工作原理、腐蚀防腐等知识和技能的学习训练,为本门课程的学习打下基础,本课程的后续课程有《无机化工生产技术》、《化工总控操作技术》等,运用本课程所学的知识技能为后续课程做准备。
二、课程目标通过本课程的学习,使学生掌握反应器的结构组成、流体在反应器中的流动特征、化学反应的类型和特点、催化剂及工程因素对化学反应的影响等基本知识,具备反应器选型、简单反应器设计计算、反应器的操作和控制等职业能力以及安全、节能、环保、质量、成本等职业素质,为今后的职业生涯打下基础。
1.知识目标(1)了解反应器在化学生产中的重要作用;(2)了解反应器的发展趋势;(3)掌握反应器的分类;(4)掌握反应器的基本结构及特点;(5)掌握反应器类型选择方法;(6)掌握均相、非均相反应动力学基本概念;(7)掌握理想流动模型的特点及造成非理想流动的原因;(8)掌握降低反应器返混程度的措施;(9)掌握催化剂基本概念;(10)掌握反应器设计的简单计算;(11)掌握反应器操作工艺参数的控制方法。
2、能力目标(1)能根据反应特点和工艺要求选择反应器类型;(2)能对反应器的设计与操作进行简单的优化或改进;(3)能按生产操作规程操作反应单元;(4)能对反应器进行操作参数调节控制;(5)能分析和处理操作反应器过程中出现的常见故障;3、素质目标(1)具有较强的口头与书面表达能力、人际沟通能力;(2)具有团队意识和合作精神;(3)具有良好的心理素质和克服困难的能力;(4)具有自主学习新知识、新技术的能力;(5)具有通过各种媒体资源查找所需信息的能力(6)具有独立制订工作计划并实施的能力;(7)具有规范操作、文明操作意识;(8)具有分析问题和解决问题的能力;(9)具有科学思维方法;(10)具有劳动保护与安全生产意识;(11)具有节能减排意识;(12)具有经济成本意识;(13)具有化工生产职业道德;(14)具有“6S”管理意识。
乙烯氧氯化制氯乙烯

⼄烯氧氯化制氯⼄烯⼄烯氧氯化制氯⼄烯氯⼄烯是最重要的单体之⼀,主要⽤于⽣产聚氯⼄烯。
就产量⽽⾔,在⼄烯系列⾼聚物中聚氯⼄烯仅次于聚⼄烯居第2位。
氯⼄烯也能与1-1-⼆氯⼄烯、醋酸⼄烯、丙烯酸甲酯、丁⼆烯和丙烯腈等共聚。
此外,氯⼄烯还⽤作冷冻剂。
1. 氯⼄烯⽣产⽅法评述在氯⼄烯⽣产历史上,曾出现过以下4种⽣产⽅法。
(1)⼄炔法这是20世纪50年代前氯⼄烯的主要⽣产⽅法,中国⾄今还有⼀些化⼯企业仍采⽤本法⽣产氯⼄烯。
⼄炔转化率97%~98%,氯⼄烯产率80%~95%,主要的副产物是1-1-⼆氯⼄烷,它是由氯⼄烯与过量的氯化氢经加成反应⽣成的。
反应中为保证催化剂HgCl2不被⼄炔还原成低价汞盐Hg2Cl2或⾦属汞,氯化氢是过量的,过量以不超过15%为宜。
⼄炔法技术成熟,反应条件缓和,设备简单,副产物少,产率⾼。
因为⽤氯化氢作原料,适合在以氯化氢为副产物的企业(例如电化⼚)组织⽣产。
本法的主要缺点是⼄炔价贵,催化剂含汞有毒,不仅损害⼯⼈⾝体健康,还会污染环境。
(2)⼄烯法这是20世纪50年代后发展起来的⽣产⽅法。
⼄烯与氯经加成反应⽣成⼆氯⼄烷:⼆氯⼄烷再在500~550摄⽒度下热裂解或在1.0MPa,140~145摄⽒度下经碱分解制得氯⼄烯:⼄烯已能由⽯油烃热裂解⼤量制造出来,价格⽐⼄炔便宜,催化剂毒害⽐氯化汞⼩得多。
但氯的利⽤率只有50%,另⼀半氯以氯化氢的形式从热裂解⽓中分离出来后,由于含有有机杂质,⾊泽和纯度都达不到国家标准,它的销售和利⽤问题就成为⼯⼚必须解决的技术经济问题,虽然也可⽤空⽓或氧把氯化氢氧化成氯⽓重新使⽤,但设备费和操作费均较⾼,导致氯⼄烯⽣产成本提⾼。
(3)联合法是上述两法的改良。
⽬的是⽤⼄炔来消耗⼄烯法副产的氯化氢。
本法等于在⼯⼚中并⾏建⽴两套⽣产氯⼄烯的装臵,基建投资和操作费⽤会明显增加,有⼀半烃进料是价格较贵的⼄炔,致使⽣产总成本上升,⼄炔法的引⼊仍会带来汞的污染问题。
因此,本法也不甚理想。
乙炔的二聚反应方程式

乙炔的二聚反应1. 乙炔的二聚反应原理和概念乙炔的二聚反应是一种有机反应,涉及乙炔分子的两个分子通过加成反应结合成乙烯和丙炔。
该反应是乙炔加成的典型例子,通常在特定的条件下进行。
2. 反应条件与催化剂的作用乙炔的二聚反应通常在高温高压条件下进行,并需要催化剂来加速反应。
常用的催化剂包括氯化汞、氯化亚铜等金属氯化物,以及有机金属化合物如二茂铁等。
这些催化剂可以降低反应的活化能,提高反应速率。
3. 生成产物乙烯和丙炔的化学方程式表示乙炔的二聚反应可以表示为:CH≡CH+CH≡CH →CH2=CH-CH=CH2+H2其中,CH≡CH表示乙炔,CH2=CH-CH=CH2表示乙烯和丙炔的混合物,H2表示氢气。
4. 二聚反应历程与机制乙炔的二聚反应通常经历以下步骤:首先,乙炔分子在催化剂的作用下形成活性中间体;然后,两个活性中间体通过加成反应形成乙烯和丙炔;最后,生成的乙烯和丙炔可能进一步发生后续反应。
5. 相关实验现象和实验条件要求在进行乙炔的二聚反应实验时,观察到的现象包括产生乙烯和丙炔的混合物,以及释放氢气。
实验条件包括高温高压、催化剂的存在以及适当的溶剂。
实验过程中需要注意安全,因为乙炔是一种易燃易爆的气体。
6. 二聚反应在有机合成中的应用实例分析乙炔的二聚反应在有机合成中具有广泛的应用。
例如,可以通过该反应合成含有多个双键的有机化合物,这些化合物在合成材料、药物等领域具有广泛的应用。
此外,乙炔的二聚反应还可以用于合成多种含碳官能团的有机化合物。
7. 对环境因素和工程实践的影响乙炔的二聚反应产生的废气中可能含有有害物质,如催化剂的残留物、未完全反应的乙炔等。
因此,在进行实验和工业生产过程中需要采取有效的措施来处理这些废气,以减少对环境的影响。
此外,在工业生产中需要选择合适的催化剂和工艺条件以提高反应效率和产物的纯度。
8. 类似反应的区别与联系与乙炔的二聚反应类似的反应包括烯烃的加成反应、炔烃的加成反应等。
乙烯装置乙炔加氢反应器稳定运行的探讨

乙烯装置乙炔加氢反应器稳定运行的探讨中文摘要乙炔加氢反应器是乙烯装置的核心装置,关系到产品质量与装置的稳定运行。
在前脱丙烷前加氢流程中,对加氢反应器催化剂活性的影响因素有很多。
对于采取该流程的兰州石化46万吨/年乙烯装置来说,加氢反应器的稳定运行一直是制约装置长周期稳定运行的瓶颈。
在装置2016年至2019年运行周期内乙炔加氢反应器三次飞温,造成了催化剂性能的严重劣化,给装置的长周期稳定运行带来了极大的困难与挑战。
通过对乙炔加氢反应器301D三次飞温经过及原因分析,运行状况的探讨,发现了空速、CO浓度、炔烃含量、床层除炔量分布、C4组分含量以及催化剂毒物等因素对加氢反应器稳定运行的影响。
最终通过优化裂解炉操作、控制裂解深度使CO浓度及炔烃在合适的范围内、优化高压脱丙烷塔操作降低反应器进料中C4组分含量、合理分配各床层除炔量、变更催化剂填装方式减少催化剂毒物等措施后,乙炔加氢反应器各床层除炔率达到生产工艺要求,反应器各床层温升稳定,入口温度控制在合理范围,最终反应器稳定运行11个月,有效提高了乙烯装置的经济效益。
通过以上分析及研究,最终推断出针对前脱丙烷前加氢流程提升乙炔加氢反应器稳定运行的优化操作的建议。
关键词:乙烯装置,乙炔加氢反应器,飞温,CO浓度,C4组分,除炔率。
Discussion on stable operation of acetylene hydrogenationreactor in ethylene plantAbstractAcetylene hydrogenation reactor is the core unit of ethylene plant, which is related to product quality and stable operation of the plant. In the process of pre depropanization and hydrogenation, there are many factors affecting the catalyst activity. The 460000 T / a ethylene plant of Lanzhou Petrochemical Co., Ltd. experienced three temperature jumps during the operation period from 2016 to 2019, which caused serious deterioration of catalyst performance and brought great difficulties and challenges to the long-term stable operation of the unit. Based on the analysis of the causes and the operation of the reactor 301D in the 460000 T / a ethylene plant of Lanzhou Petrochemical Co., Ltd., it was found that the influence of space velocity, CO concentration, alkyne content, bed deacetylene distribution, C4 component content and catalyst poison on the stable operation of the hydrogenation reactor was found. After optimizing the operation of cracking furnace, controlling the cracking depth to make CO concentration and alkynes in the appropriate range, optimizing the operation of high pressure depropanizer to reduce the content of C4 component, reasonably distributing the amount of acetylene in each bed, changing the loading mode of catalyst and reducing the poison of catalyst, the results show that the acetylene removal rate of each bed of acetylene hydrogenation reactor meets the process requirements, the temperature rise of each bed is stable, and the inlet temperature is controlled within a reasonable range. Finally, the reactor runs stably for 11 months, which effectively improves the economic benefits of ethylene plant. Based on the above analysis and research, the optimal operation of acetylene hydrogenation reactor was concluded.Key words:Ethylene plant,Acetylene hydrogenation reactor, Temperature run away, CO concentration, C4 component,Acetylene removal rate.目 录中文摘要 (I)Abstract (II)第一章前言 (4)1.1引言 (4)1.2常用的脱炔流程 (4)1.3乙炔加氢反应原理 (5)1.4 加氢脱炔催化剂 (6)1.4.1催化剂的组成 (6)1.4.2 催化反应机理 (6)1.4.3催化剂毒物 (7)1.4.4 影响催化剂活性的因素 (8)第二章乙炔加氢反应器运行分析 (10)2.1前加氢脱炔流程简介 (10)2.2 46万吨/年乙烯装置乙炔加氢反应器简介 (10)2.2.1乙炔加氢反应器301D流程介绍 (10)2.2.2乙炔加氢反应器301D床层催化剂KL7741B-T5 (11)2.3 乙炔加氢反应器301D目前存在的问题 (13)2.4乙炔加氢反应器301D运行状况分析 (14)2.4.1反应床催化剂飞温原理 (14)2.4.2反应床301D的三次飞温经过及原因分析 (15)2.4.3 反应床301D三次飞温前后运行状况分析 (20)2.5 结论及优化措施 (29)2.6 实验效果 (35)第三章结论与展望 (40)3.1乙炔加氢反应器优化操作 (40)3.2 展望 (40)参考文献 (41)致 谢 (42)第一章 前言1.1引言乙烯原料是一种非常重要的化工原料,其应用量大且广泛,横跨高分子材料和精细化工领域。
BDO装置乙炔升压及循环系统异常现况及处理

BDO装置乙炔升压及循环系统异常现况及处理摘要:BDO装置乙炔升压及循环系统是由乙炔循环压缩机将新鲜乙炔源源不断送入BYD反应器进行反应的系统,由于洗涤塔内部工艺物料的性质导致了塔内易出现聚合物将填料堵塞、液体发泡的情况,本文对其异常现象及处理措施进行分析探讨。
关键词:洗涤塔;填料;乙炔循环压缩机;液泛发泡1 概述BDO装置炔化反应是由乙炔与甲醛在乙炔铜催化剂的作用下反应合成丁炔二醇(BYD),而新鲜乙炔需要升压到100KPa并且在系统内不断循环冷却才能进入BYD反应器,同时提供铜铋催化剂颗粒悬浮与搅拌的动力。
乙炔升压及循环系统是将界区新鲜乙炔通过液环式压缩机压缩后经过洗涤冷却进入BYD反应器,而未反应完毕的气体通过出口洗涤塔洗涤冷却后进入压缩机再次一并压缩后送入反应器,洗涤塔洗涤后循环气量中的部分甲醛不断累积,需要置换后送入后端进行回收甲醛原料的系统。
由于甲醛在一定温度/压力下容易聚合的特点,洗涤塔容易出现填料堵塞,甲醛达到一定浓度后液体发泡,会导致塔内液位/压力波动,影响乙炔循环压缩机的安全稳定运行。
2 入口洗涤塔两次异常现象(1)2016年7月8日,BYD系统建立乙炔氮气循环运行期间,入口洗涤塔压力波动较大,同时伴随着液位波动较大、压缩机出口/入口压力波动较大、循环气流量波动较大;由于系统处于前期开车准备阶段,故相关联锁均未投用,避免了压缩机跳车情况的出现。
此时经过车间领导协商后,采取降低循环气流量、降低入口洗涤塔压力设定值以便同时使压缩机出口压力得以降低,在洗涤塔处于低液位的情况下,系统才得以稳定下来。
通过分析对洗涤塔内液体分析数据得知甲醛浓度仅仅为0.5%,由于公司开车进度在即,暂未分析得出此次异常现象的原因。
(2)2016年8月4日,压缩机B跳车。
原因分析过程中发现是由于B出口压力高联锁出现所致,同时发现入口压力、出口压力、气体循环量、洗涤塔液位、洗涤塔压力以及压缩机电流均出现较大波动,洗涤塔压差由之前的0.5KPa上涨到3.5KPa。
【有机】华南理工祝诗发课题组Chem.Sci.:以乙炔作为C2砌块合成烯丙醇类化合物

【有机】华南理工祝诗发课题组Chem.Sci.:以乙炔作为C2砌块合成烯丙醇类化合物烯丙醇是一类重要的有机合成骨架,传统的合成方法通常需要有机金属试剂或预制备的反应前体。
近日,华南理工大学化学与化工学院祝诗发教授课题组通过镍催化乙炔、醛和硅烷的三组分反应实现了烯丙醇类化合物的高效合成,相关成果以“Synthesis of Vinyl-Substituted Alcohols Using Acetylene as C2 Building Block”为题发表在Chemical Science(DOI: 10.1039/D2SC06400F)。
在该反应中,乙炔作为C2砌块,是产物烯丙醇分子中乙烯基的来源。
同时,作者通过一系列机理实验证明了由醛和乙炔环金属化生成的五元镍氧环是反应的关键中间体,该中间体进而被Si-H介导的σ-复分解开环得到烯基镍氢物种,最后再经历还原消除得到目标产物。
作为一类重要的有机合成骨架,烯丙醇为官能团的修饰、引入以及复杂分子结构的构建提供了不胜枚举的机会。
由此,化学家们已经发展了许多实用的方法来合成该类骨架。
其中,醛与乙烯基金属试剂的烯基化反应是最为常见得到烯丙醇的策略之一(图一A,path a),但该策略需要使用当量敏感的有机金属试剂。
类似地,利用丙烯醛与有机金属试剂的1,2-加成也可以合成烯丙醇分子(path b),但是1,2-和1,4-加成的竞争使该反应失去实用性。
除了金属试剂的亲核加成,过渡金属催化下氧亲核试剂的烯丙基化反应则是另外一种得到烯丙醇的重要途径(path c),但该方法受制于反应的区域选择性及需要预先制备烯丙基前体。
总的来说,当前策略受限于对水和空气敏感的金属试剂或是烯丙基前体。
因此,以简单易得的原料出发,开发温和高效的替代方法实现烯丙醇类化合物的合成是十分必要的。
图一. 烯丙醇类化合物的合成策略(来源:Chem. Sci.)作为最简单的炔烃,乙炔十分廉价易得,且产量巨大,常作为大宗含乙烯基聚合物单体的生产原料在化学工业中得到广泛使用。
- 1、下载文档前请自行甄别文档内容的完整性,平台不提供额外的编辑、内容补充、找答案等附加服务。
- 2、"仅部分预览"的文档,不可在线预览部分如存在完整性等问题,可反馈申请退款(可完整预览的文档不适用该条件!)。
- 3、如文档侵犯您的权益,请联系客服反馈,我们会尽快为您处理(人工客服工作时间:9:00-18:30)。
高剪切反应器对乙炔二聚液相催化反应的影响
张启霞 1 袁游延贺 1 袁谢建伟 1 袁代斌 1 袁张金利 2
渊1 石河子大学化学化工学院袁新疆石河子 832003曰2 天津大学化工学院袁天津 30035冤
摘要:乙烯基乙炔作为乙炔的下游产品袁 是生产氯丁橡胶和胶黏剂的重要原料袁 传统生产方法是由乙炔在纽兰德
Zhang Qixia1袁You Yanhe1袁Xie Jianwei1袁Dai Bin1袁Zhang Jinli2
(1 School of Chemistry and Chemical Engineering袁Shihezi University袁Shihezi袁Xinjiang 832003 China曰 2 School of Chemical Engineering and Technology袁Tianjin University袁Tianjin 300350袁China)
Abstract院As a downstream product of acetylene袁monovinyl acetylene (MVA) is an important raw material for the production of chloroprene and adhesive.The traditional catalyst for acetylene dimerization is the Nieuwland catalyst袁and the reaction is generally performed in a bubble column reactor.However袁because of low gas-liquid mass transfer袁the drawbacks of this catalytic system include low acetylene conversion rates and low MVA selectivity.In this paper袁high-speed shear reactor was implied to gas-liquid acetylene dimerization reaction.The results show that under the conditions of the traditional Nieuwland catalyst and bubble column reactor袁the acetylene conversion is 25.5% with 76.1% yield of MVAselectivity.To our delight袁under the condition of high shear reactor that the catalyst solution and reaction gas are fully contacted due to its high shear rate袁the one-way conversion rate of acetylene is significantly increased to 43.2% 袁and the selectivity of MVA remains relatively unchanged.For ligand-modified Nieuwland catalyst袁the conversation of acetylene increased slightly with the yield of 45.7% (L1-NC) and 50.9%(L2-NC)袁respectively. Similarly袁the effect of the MVA selectivity is not obvious. Key words院high-speed shear reactor曰acetylene dimerization曰monovinyl acetylene曰bubble column reactor
影响不大遥
关 键 词 :高 剪 切 反 应 器 曰 乙 炔 二 聚 曰 乙 烯 基 乙 炔 曰 鼓 泡 床 反 应 器
中图分类号:T Q 027 . 1
文 献 标 志 码 :A
Effect of high-speed shear reactor in liquid phase catalytic reaction of acetylene di h lorop ren e ru b b er袁C R 冤 作 为 七 大 合 成橡胶之一袁是在生产生活的各个领域具有广泛应 用前景 的一种 合成高 分子材 料遥 基于 我国野 富 煤尧贫 油 尧 少 气 冶 的 现 状 袁 乙 炔 法渊 乙 炔 二 聚 生 成 乙 烯 基 乙
而在高剪切反应器条件下袁由于其高剪切速率袁使得催化剂溶液和反应气充分接触袁乙炔的单程转化率显著提高袁达
到 43. 2 % 袁而乙烯基乙炔的选择性相对保持不变遥 对于配体改性的 N ieuwland 催化剂袁高剪切反应器对乙炔单程转化
率的提升幅度小一些袁但乙炔单程转化率也分别达到 4 5 . 7 %渊 L 1 - N C冤 和 50 . 9 %渊 L 2- N C 冤 袁同样袁对乙烯基乙炔的选择性
第 37 卷 第 1 期 2019 年 2 月
石河子大学学报渊自然科学版冤 Journal of Shihezi University渊Natural Science冤
Vol.37 No.1 Feb. 2019
DOI:10.13880/ki.65-1174/n.2019.01.010
文章编号:1007-7383(2019)01-0067-06
渊 N ieuwland冤 催化剂下发生二聚反应制得袁反应器为鼓泡床反应器为主袁但由于其气液传质传热效率相对较低袁该反应
中乙炔单程转化率和乙烯基乙炔的选择性较低遥 基于此袁本文研究将高剪切反应器应用于乙炔二聚气液反应袁结果表
明院在传统的 N ieuwland 催化剂和鼓泡床反应器条件下袁乙炔的单程转化率为 25.5% 袁乙烯基乙炔的选择性为 76.1 % 曰