Format of Final Project
工程职称英语试题及答案

工程职称英语试题及答案一、选择题(每题1分,共10分)1. The term "engineering" refers to:A. A type of professionB. A specific disciplineC. A method of constructionD. A type of technology答案:A2. Which of the following is not a characteristic of engineering?A. SystematicB. PracticalC. CreativeD. Static答案:D3. The basic elements of engineering include:A. Materials, energy, and informationB. Money, manpower, and materialsC. Information, technology, and moneyD. Energy, manpower, and technology答案:A4. The primary goal of engineering is to:A. Solve practical problemsB. Pursue scientific truthC. Achieve artistic expressionD. Maximize economic benefits答案:A5. The role of engineering in society includes:A. Enhancing the quality of lifeB. Promoting social progressC. Protecting the environmentD. All of the above答案:D6. The engineering design process generally includes the following stages except:A. Problem identificationB. Conceptual designC. FabricationD. Market research答案:D7. Which of the following is not a common method of engineering analysis?A. Mathematical modelingB. Experimental researchC. Literature reviewD. Computer simulation答案:C8. In engineering, the concept of "sustainability" refers to:A. Economic sustainabilityB. Environmental sustainabilityC. Social sustainabilityD. All of the above答案:D9. The "Internet of Things" (IoT) is related to engineering because it:A. Enhances communication capabilitiesB. Facilitates remote monitoring and controlC. Reduces the need for human laborD. B and C only答案:B10. The acronym "CAD" stands for:A. Computer-Aided DesignB. Computer-Aided DraftingC. Computer-Aided DevelopmentD. Computer-Aided Diagnostics答案:A二、填空题(每空1分,共10分)11. The ________ of an engineering project refers to its ability to meet the needs of the users.答案:functionality12. In engineering, the term "feasibility study" is used to evaluate the ________ and practicality of a project.答案:viability13. The process of converting raw materials into finished products is known as ________.答案:manufacturing14. The use of renewable energy sources is an example of engineering efforts to achieve ________.答案:sustainability15. A ________ is a tool that engineers use to createdetailed drawings of their designs.答案:CAD software16. The ________ of a structure refers to its ability to withstand loads without breaking or deforming excessively.答案:stability17. In the context of engineering, "innovation" often involves the development of new ________ or processes.答案:products18. The ________ of a project refers to the total cost of all the resources required to complete it.答案:budget19. Environmental impact assessments are conducted to evaluate the potential ________ of a project on the naturalsurroundings.答案:effects20. The term "mechatronics" combines elements of mechanical engineering, electronics, and ________.答案:computer engineering三、简答题(每题5分,共20分)21. What are the key factors that engineers consider when designing a bridge?答案:Key factors include the bridge's intended load capacity, the materials to be used, the environmental conditions it will be subjected to, and the overall cost of construction.22. Explain the difference between "prototype" and "final product" in the context of engineering.答案:A prototype is an early sample or model of aproject used to test concepts and processes. The finalproduct is the completed, polished version that is ready for use or distribution.23. What is the significance of "risk assessment" in engineering projects?答案:Risk assessment is significant as it helps identify potential hazards and assess their likelihood and impact.This allows engineers to take preventive measures and ensure the safety and success of the project.24. Describe the role of "project management" in engineering.答案:Project management in engineering involves planning,organizing, and controlling resources to achieve specific project goals. It includes scheduling, budgeting, and coordinating the efforts of the team to ensure timely completion and adherence to quality standards.四、论述题。
托福听力conversation总结

Conversation题目简单语速快(point易漏)记下所有的提问学生问答、自问自答必考评论必考例子必考废话必考把所有重复的记下话题一、教授1、作业A、选题(选题换题目):老师引导你去想tough decisionB、材料:哪儿可能有(研究材料性质:文章、评论、tap);更常考:材料不存在->补充材料supplemental (老师诱导去找其他的补充材料)ask for source material for his paperC、写到一半时,知识点残缺(interview然后结果不一样:原因:1、学生的理解有问题(解决:老师再讲一遍课上讲的东西,“孩子,加油”);2、学生的数据有问题(老师讲如何正确收集数据,为什么错了,“没关系,我再给你讲一遍”)D、最后都写完了,拿给老师做最后审查①正常情况:“你写的不错,哪儿好,但是several problem”,老师举现实生活中的例子(experience)作解释;②(常考)写的特别好,老师感兴趣的点,“你是如何想到去采访这个人?详细说明”,“你能不能再把它写长点,把project做大,投稿/在课上做个presentation)submit a piece of writing for publicationGeneral or casual idea 大致的想法An increase in the quantity of certain gases in Earth's atmosphereget a position as reporter/2、课上问题开头废话:“下周有个quiz,但我第三章有问题”,老师说“这个东西不考”但会给予讲解,考试前去问老师。
开始讲:一般围绕某一个词(词义,理论是怎么回事儿),都是解释性的。
3、志愿者主动找老师作志愿者:为什么找他(experience,resume);讨论有没有pay(food);是否可以帮忙(拍马屁):1、事情是什么2、有什么意义(重要信息:时间fit into my schedule(评论:是否available,考虑是否太长太短;地点,考虑是否便利)3、目的(为了加分:extra credit,credit is awarded(一般没有加分,“目前没有,但报的同学比较少,为吸引人报名可能会有加分”)老师来找学生(好处)Invite the student to work on a committee二、图书馆1、找不到书:为什么找不到(连书名都不知道,要找一个评论但不知道去哪儿找,管理员会告诉你在哪儿,还可能进行讨论(“我曾经看过,还有video tape”))类别地点(第一个地儿如果没有就去另一个地儿找)通过什么方式找(computer,啊我都不知道,怎么上网找,回家找,找不到,还是在这儿找吧)2、漏洞bug:过期书催还(解决办法:借别的书,复印,….)To find out if he needs to immediately return a book3、介绍图书馆(不怎么考了已经,因为过简单):介绍parking,怎么停车,怎么拿parking card三、注册中心registration office要选课:sign up for the courseOptional classa、手动选课:为什么要选这个课(大四了;是其他课的先修课;非常感兴趣)为什么没选上(不在场别人帮、(最常见)这课需要别的先修课但我没有修-)会看其他课类似课是否有修,我还有经验资质)选上课但没有上(原因:没有收到cancel通知email问题,我没通知inform学校)d、毕不了业(解决:继续上;给出qualifications证明自己能力经验)新托福听力场景汇总之CONVERSATION篇1. 课程相关事务场景➢场景特点:主要涉及到一些和课程相关事项的解决方法。
2019年工程造价工程师资格考试建筑工程专业英语历年真题解析
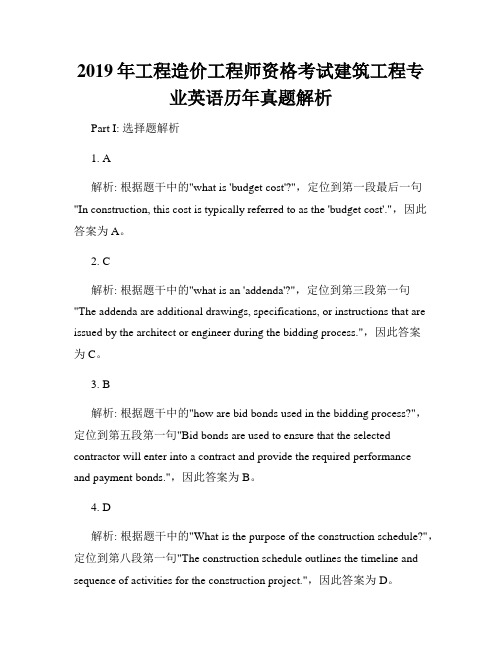
2019年工程造价工程师资格考试建筑工程专业英语历年真题解析Part I: 选择题解析1. A解析: 根据题干中的"what is 'budget cost'?",定位到第一段最后一句"In construction, this cost is typically referred to as the 'budget cost'.",因此答案为A。
2. C解析: 根据题干中的"what is an 'addenda'?",定位到第三段第一句"The addenda are additional drawings, specifications, or instructions that are issued by the architect or engineer during the bidding process.",因此答案为C。
3. B解析: 根据题干中的"how are bid bonds used in the bidding process?",定位到第五段第一句"Bid bonds are used to ensure that the selected contractor will enter into a contract and provide the required performanceand payment bonds.",因此答案为B。
4. D解析: 根据题干中的"What is the purpose of the construction schedule?",定位到第八段第一句"The construction schedule outlines the timeline and sequence of activities for the construction project.",因此答案为D。
FRP-FINAL PROJECT

1.IntroductionThe design outcomes may not be the optimized solutions. However, the intention of this project is to extensively research all the retrofitting techniques that we learnt in the course. Thus it is able to identify the feasibility of these techniques, and compare various retrofitting options. This report consists of three main sections which represent the three design problems respectively. In section 2, it is aimed to design an un-plated beam section which can support the apply load for a general office building; In section 3, many retrofitting techniques and design options are discussed with respect to the ability of strengthening beam’s critical sections; In section 4, the feasibility of different retrofitting options will be discussed again but in relation to the influence on the capacity of moment redistribution of the beam.2.Part I - Design of beam2.1Load and DimensionsThe reinforced concrete weighs in the order of 25 KN per cubic meter. In the design, It is assumed that any concentrated of loads are ignored for simplification reason. The slab design is only based on the preliminary design guideline; no further iteration has been done as it is not the focus of this project. The load and dimensions of slab and beam are tabulated in table 2.1 and table 2.2 respectively.Table 2.1 Design Load Table 2.2 Dimensions2.1.1 Live LoadDue to structure being an office building, according to AS 1170.1, , an uniformly distributed live load of 3 KPa is assumed. Additional 1KPa live load is applied to allow for the weight of non-structural items such as ceilings and services.2.1.2 Dimension & Load of SlabAs the slabs are continuous at both ends, for the load of 1 + 3 KPa, a span/depth ratio of 29 is selected. At this stage, I assume a rectangular beam with beam width of 300 mm. Therefore, the clear span is 6000 – 300 = 5700 mm. It is worth noting that, a more advanced beam system could potentially optimize the design. For instance, band beam system reduces the span/depth ratio to 11 which greatly decreases the size of beams. However, considering the retrofitting capacity, a larger dimension is desirable for higher ductility at this stage. The slab depth is computed as 5700 / 29 = 196.55 mm, it is then rounded up to 200 mm for the ease of design and construction. Thereafter the dead load of slab is calculated as 5 KPa.2.1.3 Dimension & Load of BeamThere are three cases that are of particular interest for beam design. They are:1.The maximum As (steel area) which will minimize beam dimension.2.The minimum As which will maximize beam dimension.`1/63. The maximum As which will minimize beam dimension and for which the stiffness will increase, thereforethe moment redistribution capacity will be minimized. Although moment redistribution will cause higher beam deflection which might not be desirable in some cases, the intention of our design is to allow moment redistribution. Therefore the beam section is carefully designed so that full moment redistribution can achieve, that is M hog = M sag . As we do not consider any safety factor, the suggested span/depth ratio in the literature will be over-estimated. Thus the dimension of beam is defined by trails, which is tabulated in table 2.2. 2.2 Beam DetailingThe concrete stress strain property is designed to follow the Popovic ’s model, and the steel is simplified to have a bi -linear elastic to hardening behaviour with the fracture stress at 700 Mpa. The value of concrete cover in this design is quite high, it is aimed to encounter any fire events, and more importantly, it is to allow better feasibility of Near Surface Mounted (NSM) plate to be added in later stages. A summary of material properties and reinforce arrangement is tabulated in table 2.3. Table 2.3: Beam Details2.3 Design Capacities and AnalysisSectional Analysis is only taken place at critical sections, which are at the end and mid-span. Detailed reinforcement design, such as steel bar development length, is ignored as it is not the focus of the design. Details of the design moment and sectional capacities are shown in table 2.4. Table 2.4The beam section is designed that can allow full moment redistribution; therefore the static moment can be equally distributed to the end and mid-span. It is found that, based on the Ku approach, the MR capacity is directed affected by the neutral axis depth. Owing to the high flexural rigidity (EI) of large neutral axis section, the MR capacity is low; smaller neutral axis depthresults to higher ductility, and therefore higher MR capacity. For example, for 5 bar arrangement, the EI is 173 x 1011 with a MR capacity of 14.6%. For 4 bar arrangement, it has smaller EI of 1.41 x 1011where the MR capacity is 30%. However, when the neutral axis depth is small, it leads to an over-sized or poorly reinforced section. Hence, as can be seen in table 2.4, the Ku value is altered to be smaller but very close to 0.2, therefore the section can have full MR capacity while maintains some economical design.3. Part II – Moment-CurvatureIn this part, different retrofitting techniques and plating options will be compared, consequently a recommended retrofitting arrangement will be selected and used to strengthen the beam designed in Part I. The option matrix is presented in Figure 3.1 and outlined in table 3.1 (Detail excel spreadsheet can be seen in Appendix.1). This testing scheme allows for the largest possible variation in plating options available in the course. Option one acts as a control and was designed to compare directly to all options by varying an individual parameter.The plate used in the design has same cross sectional dimension of 20 mm x 2 mm, For FRP plate, the Young’s Modulus is selected to be 200 GPa with a fracture strain 0.02, and the steel properties are same as in part I.Figure 3.1: Testing Scheme3.1Efficiency of EB and NSMOption 1 and 2 are used to investigate the efficiency of EB and NSM. As can be seen from the results, for both plating arrangement, the failure is governed by plate debonding. Thus higher cohesive performance is expected to carry out better performance. This is proved by the moment at failure. NSM plate obtained 25% more moment compared to EB plate. In addition, when comparing the load at debonding (P IC), EB plate has 21.24 KN which is only 13.275% of the load of FRP fracture. In the case of NSM plate, the load at debonding is 98 KN, which occupies 61.25% of the maximum load of FRP plate at fracture. Hence, NSM technique is much moreefficient than EB when considering the strength state. One of the drawback of NSM plate is that it requires more formwork, and the depth of NSM plate is constrained by the existing concrete cover. Thus, with manageable retrofitting conditions, NSM is recommended to be more effective than EB.3.1 Location of Platting (Tension Face vs. Side Face)Option 1 and 4 are constructed to identify the influence of the location of plate on the sectional behaviour. It should be note that the amount of FRP plate is very low comparing to the size of the beam. Therefore, it is observed that, for tension face plating, the failure is governed by the FRP plate debonding, and the concrete strain at compression fibre is only 0.00235. When moving the FRP plate towards the compression fibre, as the debonding strain of FRP plate does not change, the debonding of FRP plate is delayed and the strain at concrete compression fibre is enlarged. In option 4, when the FRP plate move to 485 mm away from the compression fibre, the FRP plate debonds at the same time of concrete crushing. Thus, option 4 produces 440 KN.m moment which is higher than option 1 (426 KN.m). In summary, for certain bottom plate retrofitting arrangement, if the concrete crush does not govern the failure, it is more appropriate to move the strengthening plate towards the neutral axis by using side plate to maximize the moment capacity (allow concrete crush to govern the failure).3.2Platting Material (FRP vs. Steel)It is known that steel can achieve similar Young’s modulus as FRP before yielding. Thus, I have decided to define the steel and FRP to have same E, only except after steel yields. It is to observe the performance of different plating material, typically, what is the influence when steel yielding happens. As pointed out in section 3.2, the plating arrangement of option 1 is not sufficient to obtain maximum M* as a result of FRP debonds before concrete crushing. In the case of steel plate, because of hardening behaviour of steel plate, it is expected that steel plate will produce greater elongation to allow concrete crushing. Thus it has the potential to increase the maximum moment M*. This `hypothesis is proved by option 5. For option 5, the steel plate has extremely large debonding strain (0.08 in this case), and FRP plate only holds 0.012. The steel plate allows the concrete crushing to govern the failure and the maximum moment M* is increased to 427 KN.m. To sum up, retrofitting with steel plate can allow the concrete to reach its crushing strain more easily than FRP plate, due to the elastic to plastic behaviour. However, with proper design of FRP plating, such that concrete crushing governs the failure, FRP plating will be more effective due to its high strength and linear elastic behaviour. This is also evidenced by the FRP side plate example: option 4, which has 440 KN.m ultimate moment.3.3Multiple Plates Arrangement (Group Debonding)When incorporating the group debonding effect, it is observed group debonding load is always smaller than no group debonding. That is when adding more plates, the efficiency of individual plate is decrease, however, the total debonding load does increase. The most important finding of my observation is that, when adding more plates, the failure tends to change from group debonding to concrete crushing. At the time that concrete crushing governs the failure, the maximum moment is actually equal to the case which does not consider group debonding. For instance, in option 3, 6 FRP plates were used. When do not consider group debonding, the maximum moment is 593 KN.m and concrete crushes first. For same arrangement, but including group debonding, the maximum moment is also 593 KN.m. Hence, my observation is when the tension plate is strong enough to allow concrete crushing to govern the failure, the plate group achieves maximum efficiency.3.4Compression face platingThe last design option is to add compression plate. It is observed that, in this project compression plate is more appropriate after the amount of tension plate reaches the threshold which allows concrete crushing governs the failure. Compression plate is not effective when the concrete crushing does not govern the failure, as a result that extra compression plate will accelerate the debonding of tension plates. However, when the tension platesare strong enough or even over reinforced, by adding compression plate can suppress concrete crushing, thus to improve the beam performance. For instance, in option 6, 1 compression FRP plate is added to beam in option 3. The compression FRP plate generates additional strength for concrete, which results in 2.3% increase in maximum moment. In summary, compression face plating is an idea technique to retrofit the beam when the tension face passes the threshold. With proper compression plating, it is able to delay the concrete crush by reinforcing the compression strength, thus to allow more tension reinforcement to be developed.3.5RetrofittingAs the un-plated sectional moment capacity is 423 KN.m, option 6 is used to retrofit the hogging section to 607 KN.m. Thus the applied load has been increased from 50.76 KN.m to 72.84 KN.m, and the termination is 2 meter from both ends. It should be noted that, as the mid-span has the same sectional design, even with this retrofitting arrangement, the moment at mid-span does not reach its moment capacity. More compression plates can be added to enhance the moment capacity at both ends. Consequently, it can be twice of the moment capacity of mid span.4.Part III - Moment-Rotation AnalysisIn this section, Moment-rotation method will be used to observe the influence and effectiveness of various retrofitting techniques and plating options on the moment redistribution capacity. Firstly, it is important to understand the difference between moment-rotation and moment-curvature method. Therefore, the un-plated section is again analyzed by using moment-rotation method and then the result is compared with moment-curvature method, as shown in table 4.1. As the plating options, such as side plating and compression plating, have been discussed in part 2, in this section, I will be mainly focusing on identifying the difference between these two major plating techniques: EB and NSM. Detailed testing arrangement is tabulated in table 4.2.4.1Moment-Rotation methodIn the previous moment-curvature analysis in part I, the curvature approach is a simple 2-dimensional analysis, which cannot cope with 3-dimensional crack widening which contributes to the majority of the rotation. The failure mode in moment-curvature analysis is also simply defined as concrete crushing at a fixed strain point, which does not take into account the softening effect after crushing, and any other failure modes, such as steel fracture and bar sliding. Thus, a more advanced technique moment-rotation analysis is utilized in this part. As can been seen in table 4.1, because the concrete is allowed to go beyond crushing (defined in part I), the sectional moment capacity has been increased due to the strain hardening in steel and more concrete has been incorporated. It is also interesting to note that, for this particle section arrangement, when using momentrotation analysis, the failure mode has changed from concrete failure to steel bar fracture failure. Lastly, in part III, a more comprehensive identification of the capacity of moment redistribution can be achieved.4.2EB Plate vs. NSM PlateIt is observed in part II, due to the brittle bond behavior of EB plate, pre-mature failure of plate debonding has occurred, as can be seen in option 2. In contrast, NSM plates have greater bond strength, which provides higher moment capacity. It also debonds at higher slip so that greater rotation at failure can be achieved, and therefore increases the moment redistribution capacity. As shown in table 4.2, with the same amount of FRP plate, NSM technique produces twice the moment and increase the MR capacity dramatically. Although one NSM plate is not sufficient to allow moderate retrofitting, it has shown that NSM plate is more appropriate when retrofitting members with ductility requirements.4.3 Multiple Plate ArrangementIt is observed that, when plating is not sufficient, the failure is always governed by the failure of retrofitting component. Furthermore, as being discussed in part II, it is more appropriate to split one large retrofitting plate into small strips so as to increase the resistance to debonding. This is particularly true for FRP plates as it has high fracture strength and elastic behaviour. Thus multiple NSM plates have been used to retrofit the beam. As shown in option 3 to 7, the increase in FRP plates results in higher tension force, which enlarges the depth of softening zone. Also, as the amount of FRP increases, the moment redistribution capacity is increased, as well as the rotation. This observation appears in contrast to the ku approach which suggests lower reinforcement produces higher moment redistribution capacity. This is because more failure modes have been incorporated in the beam system. Ultimately, a limitation of the amount of FRP can be added is defined by the sliding capacity of concrete. For instance, in option 7, 6 FRP is strong enough to allow concrete wedge slip to govern the failure. Therefore, after reaching the threshold, extra FRP plates will be ineffective.4.3Design LimitationsIn the design, steel component has been the most challenging part and involves many limitations. Firstly, when using moment rotation technique, the slip and fracture of steel bar become to be the factors that can govern the failure. That is smaller steel diameter will provide higher bond transfer capacity, but it is more likely to fracture. For instance, as the steel diameter is defined earlier in part I, the slip and fracture displacement are computed to be 15 mm and 7.2 mm. In addition, when adding more FRP plates, it is found that, due to the increase in concrete softening zone, the neutral axis is moving towards the steel fibre, which decreases the strength in steel. In order to come up with efficient design, it is more desirable to have steel staying beyond yielding. And lastly, for simplification reasons, the effect of transverse reinforcement is ignored in the design.4.4RetrofittingConsidering the cost efficient design, hogging to sagging is more desirable. However, as the moment redistribution capacity is determined in hogging section, which only has 25%, in this case, the mid span does not require any retrofitting. Thus, I planned to retrofit the hogging region to allow moment transfer from sagging to hogging region. To maximize the moment capacity, 6 NSM plates are used which will allow concrete slip to govern the failure, and it increases the moment capacity from 646 KN.m to 870KN.m at hogging region. Thus the applied load has been increased from 77.52 KN.m to 104 KN.m. With this retrofitting arrangement, the moment at mid-span still does not reach its moment capacity. Adding compression plates could be one hypothesis to further increase the moment at both ends. However, with concrete softening at compression face, the bonding capacity might be decreased. With current knowledge, it is not able to define this problem.。
标书中英文翻译样本及常用词汇

标书中英文翻译样本及常用词汇1. 投标书Tender1.1 投标人应完整地填写招标文件中提供的商务投标书、技术投标书、投标一览表和投标报价表(包括投标报价汇总表和分项报价表)。
价格表(表中项目除价格数字外都要填写)及报价说明三份(一正二副)和投标人银行保函应分别单独密封,随投标文件一同递交。
Among the tender documents, tenderers shall fill out completely the Business Tender, Technical Tender, Tender List and Tender Quotation. The Quotation (all items in the Quotation shall be filled out except for the prices) and three copies (one Original and two Duplicates) of the Instructions to Quotations as well as the letter of guarantee from the bank of tenderers must be sealed separately, and be submitted together with the tender documents.1.2 在投标文件澄清后提交的附件6价格表部分正、副本应用信封单独密封,封面上注明项目名称、招标编号、投标人名址、“正本”“副本”字样及“分项价格”和“保密”字样。
同时提供单独密封的价格表电子版本一份(WORD格式)。
The Attachment 6 to be submitted after the tender documents have been clarified the Original and Duplicate copies of the Quotation must be sealed separately in different envelops, on which the item names, tender codes, tenderer addresses, words of ‘Original’, ‘Duplicate’ and ‘Item Price’ and ‘Confidential’ must be written. An e-version of the Quotation (in WORD format) that is separately sealed must be furnished at the same time.2. 投标报价Tender Offers2.1 投标人应在投标报价汇总表和投标分项报价表上标明本合同拟提供货物的单价(如适用)和总价。
CRM_Guidelines for Final Project_2012

3
EXHIBIT 6.2 PICTURING THE CUSTOMER LIFE CYCLE
Acquisition Suspect Prospect Customer : 1st transaction Retention Loyal advocate Repeat customer Inactive regular customer Winback
10
Suggested Reading
1. Berman, B. (2006). Developing an Effective Loyalty Program, California Management Review, 49, pp. 123-148. 2. Blattberg, R. C., Kim, B.D. and Neslin, S. A. (2008). Database Marketing: Analyzing and Managing Customers. New York, NY: Springer, chapters 22 and 23. 3. Dorotic, M., Fok, D., Verhoef, P.C. and Bijmolt, T.H.A. (2010). Do Vendors Benefit from Promotions in a Multi-vendor Loyalty Program?, Marketing Letters, (OnlineFirst 2 November 2010), pp. 1-16. 4. Leenheer, J., Van Heerde, H.J., Bijmolt, T.H.A. and Smidts, A. (2007). Do Loyalty Programs Really Enhance Behavioral Loyalty? An Empirical Analysis Accounting For Self-Selecting Members, International Journal of Research in Marketing, 24, pp. 31-47. 5. Liu, Y. (2007). The Long-Term Impact of Loyalty Programs on Consumer Purchase Behavior and Loyalty, Journal of Marketing, 71, pp. 19–35. 6. Nunes, J.C. and Dreze, X. (2006a). Your Loyalty Program is Betraying You, Harvard Business Review, 84, pp. 124-31. 7. Taylor, G.A. and Neslin, S.A. (2003). The Current and Future Sales Impact of a Retail Frequency Reward Program, Journal of Retailing, 81, pp. 293-305. 8. Wansink, B. (2003). Developing a Cost-effective Brand Loyalty Program, Journal of Advertising Research, 43, pp. 301-309. 9. Dorotic,M., Bijmolt, T.H.A., Verhoef, P.C. (2012). Loyalty Programmes: Current Knowledge and Research Directions, International Journal of Management Reviews, 14, pp. 217–237 11
ProjectTemplateSuggestedFormat
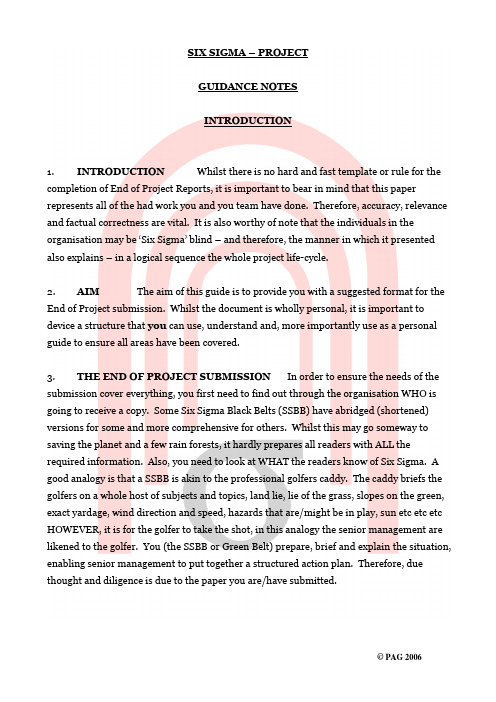
SIX SIGMA – PROJECTGUIDANCE NOTESINTRODUCTION1. INTRODUCTION Whilst there is no hard and fast template or rule for the completion of End of Project Reports, it is important to bear in mind that this paper represents all of the had work you and you team have done. Therefore, accuracy, relevance and factual correctness are vital. It is also worthy of note that the individuals in the organisation may be ‘Six Sigma’ blind – and therefore, the manner in which it presented also explains – in a logical sequence the whole project life-cycle.2. AIM The aim of this guide is to provide you with a suggested format for the End of Project submission. Whilst the document is wholly personal, it is important to device a structure that you can use, understand and, more importantly use as a personal guide to ensure all areas have been covered.3. THE END OF PROJECT SUBMISSION In order to ensure the needs of the submission cover everything, you first need to find out through the organisation WHO is going to receive a copy. Some Six Sigma Black Belts (SSBB) have abridged (shortened) versions for some and more comprehensive for others. Whilst this may go someway to saving the planet and a few rain forests, it hardly prepares all readers with ALL the required information. Also, you need to look at WHAT the readers know of Six Sigma. A good analogy is that a SSBB is akin to the professional golfers caddy. The caddy briefs the golfers on a whole host of subjects and topics, land lie, lie of the grass, slopes on the green, exact yardage, wind direction and speed, hazards that are/might be in play, sun etc etc etc HOWEVER, it is for the golfer to take the shot, in this analogy the senior management are likened to the golfer. You (the SSBB or Green Belt) prepare, brief and explain the situation, enabling senior management to put together a structured action plan. Therefore, due thought and diligence is due to the paper you are/have submitted.4. LAYOUT OF THE DOCUMENT As explained in paragraph 1 there is no formal/template layout for a SS Submission paper but it does need to be conclusive. Attached at Annex A is my suggestion for the layout and degree of detail required.5. SUPPORTING INFORMATION It is a good plan to have supporting information, charts, nominal rolls (participants in the project) financial information, scope details etc put together as a document, either formally bound (comb binder) or contained within a tidy (preferably new!) binder. Again, it is worth bearing in mind that if the submission is delivered in a tardy fashion, it will be assumed that the information contained within it will also be of equal tardiness! Therefore, programme sufficient time into the closedown of the project to allow you an ‘administrative window’ to close properly and professionally. It is all too common in Six Sigma and Project Management that submissions are used a coffee mats because that’s what they look like they should be used for. So, TOP TIP of the day, plan the closedown, allow sufficient time and present the document so that the main people think WOW!6. INFORMATION TECHNOLOGY As important as the hard (Paper) copies is the IT copy. Make sure this is delivered to key people properly and neatly presented so that if they are bored on the journey home they can load the information onto their laptop and view with pleasure. This ideally should be contained within a CD pocket with the hard copy. A big MUST is that a copy of the CD is archived with the Project Management Office (or similar) for auditable, reference, historic purposes. Also, in case all of the copies get lost –if this sounds a little far fetched, wait until you’ve been doing it a few years!7. CONCLUSION If you stick to the same template that you have devised you can’t, in the long term get lost. If anything, it will act as a reminder and/or activate action. This way, you are more likely to produce an outstanding piece of work to reflect the project and omit nothing – a comprehensive report, that covers everything is critical. You get one opportunity to submit the report, miss things out and the project loses value – ALSO, you’re unlikely to go much further in the industry.Good Luck.ANNEX ATO SIX SIGMA PROJECTSUGGESTED TEMPLATE FOR THE SUBMISSION OFTHE FINAL PROJECT REPORTPART ONEIndex (of Submission Paperwork) Page 1 > Project Charter (Ensure this is complete and signed) Page 2 > Overview of the Project Definition Page 3 > What?When?Where?Why?How?Composition of the Team Page 4 >Key Personnel’s backgr ound Page 5 > ChampionMaster Black BeltBlack BeltGreen/Yellow BeltsOverview of the Project Allowances Page 6 > Scope (Quality)Cost (Amount Allocated)Time (Allocated to the Project)Overview of the Project Desired Outcomes Page 7 > Method/overlay of Project Management Page 8>Printout of MS Project1 (or similar)Or, Sequence of eventsProcesses, such asReportingSeeking Approval/AuthorityPART TWODefine the Project Requirements2 in more detail Page 9 > What?Why?When?Where?How?Identify what measurements3 you are going to take Page 10 > Pose Immediate Questions Page 11 > Again,What?Why?When?Where?How?Describe your questioning Processes Page 12 > Who/WhyWhat information do you wish to gain etc.PART THREEMeasure the Existing System Page 13 > MetricsCharts n, np, x, etcBar ChartsTime/Motion etc1 IF MS Project is used present a printout – if not elaborate on the project timetable with critical path or route taken to achieve end state2D MAIC – Define the goals of the improvement Activity3Attributes of good metricsExplain the charts – in lay speak so that all understand Page 14 > Label ChartsHighlight and explain key featuresDraw attention to critical informationProduce ‘at a glance’ where we are versus where we could be charts Page 15 > Produce Six Sigma Calculations Page 16 > Use the one prepared and available on the attached excel fileProduce RAW data Page 17 > Such as orders, demands, sales, etcPART FOURAnalyse the system to identify ways to eliminate the gap between Page 18 > Current performance of the system or process and the desired goal Page 19 > Provide ChartsProvide GraphsEnsure accuracy of calculations and that everything is labelledIf necessary, break the organisation – consider everything!SupplierQualityCostTimeetcInputChanges/modifications requiredStorageInventory etcProcessTimeScopeCostStaff TrainingOutputTimeCostScope etcConsumer/CustomerSatisfactionVoice of the Customer (VOC)Their perception of service level ….. etcShow you understand the implications and explain in terms for allto understandPART FIVEImprove the System Page 20 > Make RecommendationsIf?What?When?Where?Who?How? Etc etcDescribe the General Business Situation –Current Page 21 > Describe the Business Situation - Future Page 22 > Be sure to offer comparisonBe sure to deliver the information simplifiedDescribe effects IF improvements are implemented Page 23 > How?When?Where?Who?How?Explain Quality Assurances – impact etc Page 24 >PART SIXCONTROL the new systemGive a General Understanding/explanation of what control is Page 25 > Detail and explain control measures Page 26 > ManpowerEquipmentRegistersUpper/Lower Control Limits etc etcUse Charts/Graphs to demonstrate the processes Page 27 >PART SEVENCONCLUSION Page 28 > Cover pertinent pointRe-amplify critical requirementsGive a brief Synopsis of the Organisation Page 29 > TodayTomorrowIf changes acceptedIf changed declined。
VW_01014 大众图纸图框及字体规范
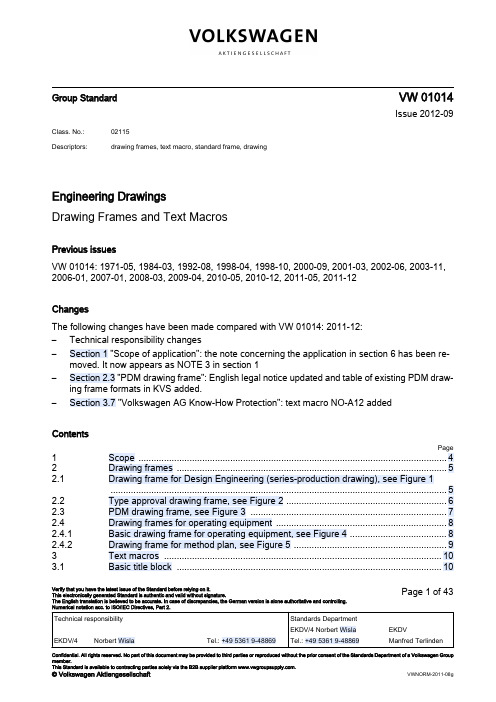
Engineering DrawingsDrawing Frames and Text MacrosPrevious issuesVW 01014: 1971-05, 1984-03, 1992-08, 1998-04, 1998-10, 2000-09, 2001-03, 2002-06, 2003-11,2006-01, 2007-01, 2008-03, 2009-04, 2010-05, 2010-12, 2011-05, 2011-12ChangesThe following changes have been made compared with VW 01014: 2011-12:–Technical responsibility changes–Section 1 "Scope of application": the note concerning the application in section 6 has been re‐moved. It now appears as NOTE 3 in section 1–Section 2.3 "PDM drawing frame": English legal notice updated and table of existing PDM draw‐ing frame formats in KVS added.–Section 3.7 "Volkswagen AG Know-How Protection": text macro NO-A12 added ContentsPageScope .........................................................................................................................4Drawing frames ..........................................................................................................5Drawing frame for Design Engineering (series-production drawing), see Figure 1....................................................................................................................................5Type approval drawing frame, see Figure 2 ...............................................................6PDM drawing frame, see Figure 3 .............................................................................7Drawing frames for operating equipment ...................................................................8Basic drawing frame for operating equipment, see Figure 4 ......................................8Drawing frame for method plan, see Figure 5 ............................................................9Text macros .............................................................................................................10Basic title block .. (10)122.12.22.32.42.4.12.4.233.1Group StandardVW 01014Issue 2012-09Class. No.:02115Descriptors:drawing frames, text macro, standard frame, drawingVerify that you have the latest issue of the Standard before relying on it.This electronically generated Standard is authentic and valid without signature.The English translation is believed to be accurate. In case of discrepancies, the German version is alone authoritative and controlling.Page 1 of 43Confidential. All rights reserved. No part of this document may be provided to third parties or reproduced without the prior consent of the Standards Department of a Volkswagen Group member.This Standard is available to contracting parties solely via the B2B supplier platform .© Volkswagen AktiengesellschaftVWNORM-2011-08gTitle blocks for drawings with restrictions on use .....................................................11Title block for layout drawings (ENT) > A0 ...............................................................12Symbol for European projection method ..................................................................13Change block for formats > A0 .................................................................................13Tolerancing principle as per VW 01054 ...................................................................13Volkswagen Group know-how protection .................................................................13Drawing field ............................................................................................................14Lower left corner of drawing for formats > A0 ..........................................................14Left drawing edge for formats > A0 ..........................................................................14Explanation of parenthesized dimensions for formats > A0 (lower left corner ofdrawing field) ............................................................................................................14References for formats > A0 ....................................................................................15Migration from CATIA V4 to CATIA V5 ....................................................................15Parts marking ...........................................................................................................15Part number assignment drawn / symmetrically opposite ........................................15Note on utilization of scrap material .........................................................................16NO-F1 Drawings with multiple sheets ......................................................................16Repeating and unchanging notes, mostly on body components ..............................16Drawing only for the company stated .......................................................................16Note on parts which are subject to build sample approval (BMG) ...........................17Notes on testing as per Technical Supply Specifications (TL) .................................17Note on type approval ..............................................................................................17Note on undimensioned design models in the data record ......................................17Note on open-air weathering ....................................................................................17Note on model approval ...........................................................................................17Note on master model ..............................................................................................18Note on second original, font size 7 mm ..................................................................18Note on second original, font size 3,5 mm ...............................................................18Note on heavy-duty component ...............................................................................18Note on mandatory type approval ............................................................................19Note on avoidance of hazardous substances ..........................................................19Note on other relevant drawings ..............................................................................19Note on undimensioned bend and trim radii ............................................................19Note on simplified representation .............................................................................19Note on flawless condition of surfaces .....................................................................19Note on material for form tool in grain area ..............................................................20Table for RPS ...........................................................................................................20Note on emission behavior .......................................................................................20Note on length dimensions to be measured up to relevant functional datum plane ..................................................................................................................................20Note on related tolerances for nominal dimension ranges up to relevant functional datum plane .............................................................................................................21Note on tolerances of surfaces as compared to the data record and defined RPS..................................................................................................................................21Note on tolerances of marked surfaces as compared to the data record anddefined RPS .............................................................................................................21Note on tolerances of marked and limited surfaces as compared to the datarecord and defined RPS ...........................................................................................21Note on tolerances of marked edges as compared to the data record and defined RPS ..........................................................................................................................21Note on alternative materials and surface protection types .....................................22Note on color and grain .. (22)3.23.33.43.53.63.744.14.24.34.44.54.64.74.84.94.104.114.124.134.144.154.164.174.184.194.204.214.224.234.244.254.264.274.284.294.304.314.324.334.344.354.364.374.38Page 2VW 01014: 2012-09Note on temperature resistance ...............................................................................22Note on color consistency ........................................................................................22Note on lightfastness ................................................................................................22Note on fixing, clamping and contact surface ..........................................................23Note on related finished part drawing ......................................................................23Note on material specifications, complete ................................................................23Note on material specifications, subdivided .............................................................24Note on optional welding technology .......................................................................24Note on flammability features ...................................................................................24Note on table containing gear tooth data .................................................................25Note on weight indication .........................................................................................25Note on amine emission of foam parts .....................................................................25Note on cleanliness requirements for engine components ......................................25Countersinks for internal threads .............................................................................26Testing of rolled bushings ........................................................................................26Table for limit dimensions ........................................................................................26Detail drawing for radius under screw head, mostly for standard part drawings (27)Test specification for disk wheels .............................................................................27Test specification for brake drums ...........................................................................28General tolerances for castings ...............................................................................28General tolerances for forgings ................................................................................29Coordinate dimensioning for tubes and bars ...........................................................30Bill of materials for layout drawings (ENT) ...............................................................30Distribution list for layout drawings (ENT) ................................................................31Text macros for operating equipment ......................................................................31Title block for individual part .....................................................................................31Note on pass direction, left .......................................................................................32Note on pass direction, right ....................................................................................32Title block for operating equipment label .................................................................32General tolerances for nominal dimensions without tolerance specification ............32Note on simplified drawing specifications on surface roughnesses .........................33Permissible deviations for nominal sizes without tolerance specification onweldments ................................................................................................................33Permissible deviations for nominal dimensions without tolerance specificationson flame-cut parts ....................................................................................................33Note on parts used ...................................................................................................34Note on rolled flame-cutting template plots ..............................................................34Note on "Add ½ kerf" ................................................................................................34Note on "designed" and "symmetrical opposite" ......................................................34Text macros for the "3D drawingless process" (3DZP – German abbreviation) ......35VW copyright ............................................................................................................35Note on restriction on use ........................................................................................35Note on type approval documentation and type approval number ...........................35Draft number ............................................................................................................36Note on engineering project number ........................................................................36Note on safety documentation .................................................................................36Recycling requirements as per VW 91102 ...............................................................36All dimensions apply to the finished part including surface protection .....................36Surface roughness as per VW 13705 and VDA 2005 ..............................................36Surface roughness as per VW 13705 and VDA 2005 (reference without symbol) (37)4.394.404.414.424.434.444.454.464.474.484.494.504.514.524.534.544.554.564.574.584.594.604.614.6255.15.25.35.45.55.65.75.85.95.105.115.1266.16.26.36.46.56.66.76.86.96.9.1Page 3VW 01014: 2012-09Surface roughness as per VW 13705 and VDA 2005 (reference with symbol) .......37Surface roughness as per VW 13705 and VDA 2005 (reference with symbol,collective specification 1) .........................................................................................38Surface roughness as per VW 13705 and VDA 2005 (reference with symbol,collective specification 2) .........................................................................................39Workpiece edges as per VW 01088 .........................................................................39Workpiece edges as per VW 01088 (reference without symbol) .............................40Workpiece edges as per VW 01088 (reference with symbol) ..................................40Workpiece edges as per VW 01088 (reference with symbol, collectivespecification 1) .........................................................................................................41Workpiece edges as per VW 01088 (reference with symbol, collectivespecification 2) .........................................................................................................42Applicable documents ..............................................................................................426.9.26.9.36.9.46.106.10.16.10.26.10.36.10.47ScopeThis standard applies to the computer-aided graphical representation and presentation of drawing templates, standard frames and text macros for drawings within the Volkswagen Group.NOTE 1 The standardized text macros are subject to drawing standard regulations and are centrally managed by the "Virtual Systems and Standardization" department.NOTE 2 All drawing frames and text macros shown here are available in the appropriate standard system environment of the CAD systems CATIA and Creo Elements/Pro (formerly PRO/E). The PDM drawing frames are also available as IsoDraw and Excel templates in the KVS, and also as Catia V5templates.NOTE 3 The text macros shown in section 6 are for the drawingless process only. The creator and the user of the data must agree whether their process chain allows for the use of documents as per the 3DZP method, and whether this is permissible.1Page 4VW 01014: 2012-09Drawing framesDrawing frame for Design Engineering (series-production drawing), see Figure 1Figure 1 – Drawing frame for Design Engineering (series-production drawing)2 2.1Page 5VW 01014: 2012-09Type approval drawing frame, see Figure 2Figure 2 – Type approval drawing frame2.2 Page 6VW 01014: 2012-09PDM drawing frame, see Figure 3Figure 3 – PDM drawing frame2.3 Page 7VW 01014: 2012-09Drawing frames for operating equipmentBasic drawing frame for operating equipment, see Figure 4Figure 4 – Basic drawing frame for operating equipment2.4 2.4.1Page 8VW 01014: 2012-09Drawing frame for method plan, see Figure 5Figure 5 – Drawing frame for method plan2.4.2 Page 9VW 01014: 2012-09Text macrosBasic title blockFigure 6 – Code no: NO-A1Basic title block for formats > A03 3.1Page 10VW 01014: 2012-09Title blocks for drawings with restrictions on useFigure 7 – Code no: NO-A7 A3The title block may only be used if supplier original drawings are used as modified finished part drawings.Notes on the usage of these title blocks see VW 01058.3.2Title block for layout drawings (ENT) > A0Figure 8 – Code no: NO-A3ENT = Draft3.3Symbol for European projection methodFigure 9 – Code no: NO-A5Change block for formats > A0Figure 10 – Code no: NO-A6Tolerancing principle as per VW 01054Figure 11 – Code no: NO-A11Volkswagen Group know-how protectionFigure 12 – Code no: NO-A123.4 3.5 3.6 3.7Drawing fieldLower left corner of drawing for formats > A0Figure 13 – Code no: NO-B1Left drawing edge for formats > A0Figure 14 – Code no: NO-B3Explanation of parenthesized dimensions for formats > A0 (lower left corner of drawingfield)Figure 15 – Code no: NO-B644.1 4.2 4.3References for formats > A0Figure 16 – Code no: NO-B7Migration from CATIA V4 to CATIA V5Figure 17 – Code no: NO-B8Parts markingFigure 18 – Code no: NO-E2Part number assignment drawn / symmetrically oppositeFigure 19 – Code no: NO-E54.4 4.5 4.6 4.7Note on utilization of scrap materialFigure 20 – Code no.:NO-F1 Drawings with multiple sheetsFigure 21 – Code no: NO-F2Repeating and unchanging notes, mostly on body componentsFigure 22 – Code no: NO-F3Drawing only for the company statedFigure 23 – Code no: NO-F4 (do not use for new designs!)4.8 4.9 4.10 4.11Note on parts which are subject to build sample approval (BMG)Figure 24 – Code no: NO-F5Notes on testing as per Technical Supply Specifications (TL)Figure 25 – Code no: NO-F6Note on type approvalFigure 26 – Code no: NO-F7Note on undimensioned design models in the data recordFigure 27 – Code no: NO-F8Note on open-air weatheringFigure 28 – Code no: NO-F9Note on model approvalFigure 29 – Code no: NO-F104.12 4.13 4.14 4.15 4.16 4.17Note on master modelFigure 30 – Code no: NO-F11Note on second original, font size 7 mmFigure 31 – Code no: NO-F12Note on second original, font size 3,5 mmFigure 32 – Code no: NO-F13Note on heavy-duty componentFigure 33 – Code no: NO-F144.18 4.19 4.20 4.21Note on mandatory type approvalFigure 34 – Code no: NO-F15Note on avoidance of hazardous substancesFigure 35 – Code no: NO-F16Note on other relevant drawingsFigure 36 – Code no: NO-F17Note on undimensioned bend and trim radiiFigure 37 – Code no: NO-F18Note on simplified representationFigure 38 – Code no: NO-F19Note on flawless condition of surfacesFigure 39 – Code no: NO-F204.22 4.23 4.24 4.25 4.26 4.27Note on material for form tool in grain areaFigure 40 – Code no: NO-F22Table for RPSFigure 41 – Code no: NO-F23Note on emission behaviorFigure 42 – Code no: NO-F24Note on length dimensions to be measured up to relevant functional datum planeFigure 43 – Code no: NO-F254.28 4.29 4.30 4.31Note on related tolerances for nominal dimension ranges up to relevant functional datumplaneFigure 44 – Code no: NO-F26Note on tolerances of surfaces as compared to the data record and defined RPSFigure 45 – Code no: NO-F27Note on tolerances of marked surfaces as compared to the data record and defined RPSFigure 46 – Code no: NO-F28Note on tolerances of marked and limited surfaces as compared to the data record anddefined RPSFigure 47 – Code no: NO-F29Note on tolerances of marked edges as compared to the data record and defined RPSFigure 48 – Code no: NO-F304.32 4.33 4.34 4.35 4.36Note on alternative materials and surface protection typesFigure 49 – Code no: NO-F31Note on color and grainFigure 50 – Code no: NO-F32Note on temperature resistanceFigure 51 – Code no: NO-F33Note on color consistencyFigure 52 – Code no: NO-F35Note on lightfastnessFigure 53 – Code no: NO-F364.37 4.38 4.39 4.40 4.41Note on fixing, clamping and contact surfaceFigure 54 – Code no: NO-F37Note on related finished part drawingFigure 55 – Code no: NO-F38Note on material specifications, completeFigure 56 – Code no: NO-F394.42 4.43 4.44Note on material specifications, subdividedFigure 57 – Code no: NO-F40Note on optional welding technologyFigure 58 – Code no: NO-F41Note on flammability featuresFigure 59 – Code no: NO-F424.45 4.46 4.47Note on table containing gear tooth dataFigure 60 – Code no: NO-F43Note on weight indicationFigure 61 – Code no: NO-F44Note on amine emission of foam partsFigure 62 – Code no: NO-F45Note on cleanliness requirements for engine componentsFigure 63 – Code no: NO-F464.48 4.49 4.50 4.51Countersinks for internal threadsFigure 64 – Code no: NO-G0Testing of rolled bushingsFigure 65 – Code no: NO-G1Table for limit dimensionsFigure 66 – Code no: NO-G24.52 4.53 4.54Detail drawing for radius under screw head, mostly for standard part drawingsFigure 67 – Code no: NO-G4Test specification for disk wheelsFigure 68 – Code no: NO-G64.55 4.56Test specification for brake drumsFigure 69 – Code no: NO-G7General tolerances for castingsFigure 70 – Code no: NO-G84.57 4.58General tolerances for forgingsFigure 71 – Code no: NO-G94.59Coordinate dimensioning for tubes and barsFigure 72 – Code no: NO-G10Bill of materials for layout drawings (ENT)Figure 73 – Code no: NO-H14.60 4.61Distribution list for layout drawings (ENT)Figure 74 – Code no: NO-H2Text macros for operating equipmentTitle block for individual partFigure 75 – Code no: R001 individual part4.62 55.1Note on pass direction, leftFigure 76 – Code no: R002 pass direction, leftNote on pass direction, rightFigure 77 – Code no: R003 pass direction, rightTitle block for operating equipment labelFigure 78 – Code no: R004 operating equipment labelGeneral tolerances for nominal dimensions without tolerance specificationFigure 79 – Code no: R005 machining operation5.2 5.35.45.5Note on simplified drawing specifications on surface roughnessesFigure 80 – Code no: R006 surfacesPermissible deviations for nominal sizes without tolerance specification on weldmentsFigure 81 – Code no: R007 welded partsPermissible deviations for nominal dimensions without tolerance specifications on flame-cut partsFigure 82 – Code no: R008 flame-cut parts5.6 5.75.8Note on parts usedFigure 83 – Code no: R009 parts usedNote on rolled flame-cutting template plotsFigure 84 – Code no: R010 flame-cutting templateNote on "Add ½ kerf"Figure 85 – Code no: R011 kerfNote on "designed" and "symmetrical opposite"Figure 86 – Code no: R012 symmetrical opposite5.9 5.105.115.12Text macros for the "3D drawingless process" (3DZP – German abbreviation)The following text macros are not created in CAD systems, but only in the PDM system KVS.The design engineer must add the necessary parameters to the text macros.VW copyrightFigure 87 – Code no: NOZ-01Note on restriction on useLegend P01Company nameFigure 88 – Code no: NOZ-02Note on type approval documentation and type approval numberLegend P01Type approval doc. and type approval numberFigure 89 – Code no: NOZ-036 6.16.26.3Draft numberLegend P01Draft numberFigure 90 – Code no: NOZ-04Note on engineering project numberLegend P01Engineering project numberFigure 91 – Code no: NOZ-05Note on safety documentationLegend P01TLD number (technical guideline for documentation – German abbreviation)Figure 92 – Code no: NOZ-06Recycling requirements as per VW 91102Figure 93 – Code no: NOZ-07All dimensions apply to the finished part including surface protectionFigure 94 – Code no: NOZ-08Surface roughness as per VW 13705 and VDA 2005The design engineer must add the required parameters to the symbols shown here (e.g., Rz value).Two types of text macros (with and without graphical representation) have been defined. Variant NOZ-09 is a reference to Standard VW 13705, additional information possible, but restricted. Variants NOZ-09-01 a to f are reserved for the main surface roughness value. Due to system restrictions,identical symbols cannot be used more than once. For this reason, the symbols in section 6.9.3 and6.4 6.56.66.76.86.9section 6.9.4 must be used for cases of multiple use. If surface roughness values are added as a note, the text macros are placed beneath each other instead of beside each other. This deviating representation has been released for the 3DZP drawingless process.Surface roughness as per VW 13705 and VDA 2005 (reference without symbol)Figure 95 – Code no: NOZ-09Surface roughness as per VW 13705 and VDA 2005 (reference with symbol)Figure 96 – Code no: NOZ-09-01-aFigure 97 – Code no: NOZ-09-01-bFigure 98 – Code no.: NOZ-09-01-cLegend P01Machining allowance (numerical value in mm)P02Production processP03Surface parameter and numerical valueP04if applicable, additional requirement as per VDA 2005P05if applicable, additional requirement as per VDA 2005P06if applicable, second requirement on surface texture (surface parameter,numerical value)P07Specification of the surface groovesLegend P01Letter for simplified drawing specification. Method defined in section "simplified specifi‐cation" in VDA 2005Figure 99 – Code no: NOZ-09-01-d6.9.16.9.2Figure 100 – Code no: NOZ-09-01-e Figure 101 – Code no: NOZ-09-01-fSurface roughness as per VW 13705 and VDA 2005 (reference with symbol, collectivespecification 1)Figure 102 – Code no: NOZ-09-02-aFigure 103 – Code no: NOZ-09-02-bFigure 104 – Code no: NOZ-09-02-cLegend P01Machining allowance (numerical value in mm)P02Production processP03Surface parameter and numerical valueP04if applicable, additional requirement as per VDA 2005P05if applicable, additional requirement as per VDA 2005P06if applicable, second requirement onsurface texture (surface parameter,numerical value) P07Specifica‐tion of thesurface groovesCode no.:Legend P01Letter for simplified drawing specification. Method defined in section "simplified specifi‐cation" in VDA 2005Figure 105 – NOZ-09-02-dFigure 106 – Code no: NOZ-09-02-e Figure 107 – Code no: NOZ-09-02-f6.9.3。
Three Body Problem (English Introduction)
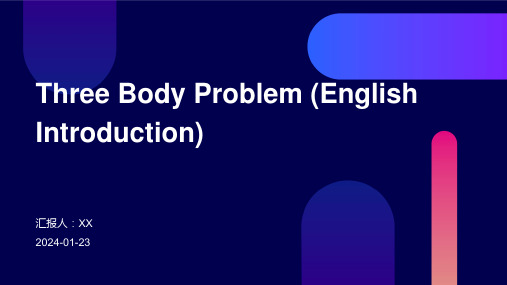
03
Luo Ji's intelligence, maturity, and determination drive the narrative forward as he strives to understand and combat the lien threat
Cheng Xin
A female aerospace engineer who benefits a key figure in the resistance against the Trisolaran invasion
the attention of potential predictors
03
Predator and pre dynamics
The Dark Forest Law suggestions that the universe is a
dangerous place where predictors consistently seek out and
• Description of the Trisolaran invasion and the subsequence human resistance • Introduction of Cheng Xin, the new Wallace, and her plan to save humanity • Conclusion of the story with the revision of the ultimate fate of the human race and the universe • Note: The above points are a brief overview of the plot and do not include detailed spoilers The
意大利美院毕设流程
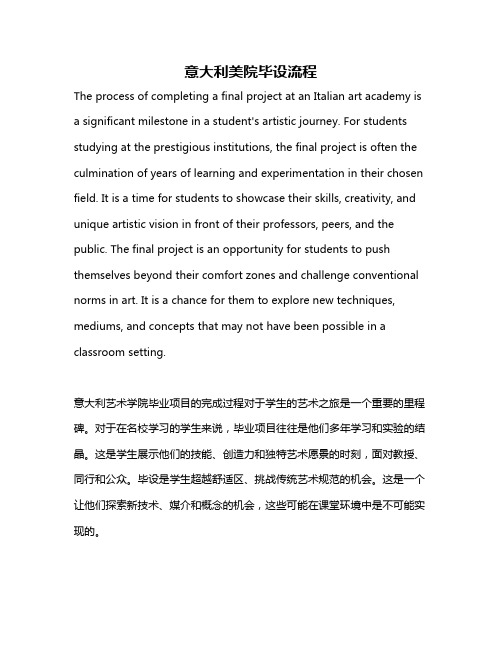
意大利美院毕设流程The process of completing a final project at an Italian art academy is a significant milestone in a student's artistic journey. For students studying at the prestigious institutions, the final project is often the culmination of years of learning and experimentation in their chosen field. It is a time for students to showcase their skills, creativity, and unique artistic vision in front of their professors, peers, and the public. The final project is an opportunity for students to push themselves beyond their comfort zones and challenge conventional norms in art. It is a chance for them to explore new techniques, mediums, and concepts that may not have been possible in a classroom setting.意大利艺术学院毕业项目的完成过程对于学生的艺术之旅是一个重要的里程碑。
对于在名校学习的学生来说,毕业项目往往是他们多年学习和实验的结晶。
这是学生展示他们的技能、创造力和独特艺术愿景的时刻,面对教授、同行和公众。
腰椎间盘突出毕业设计任务书
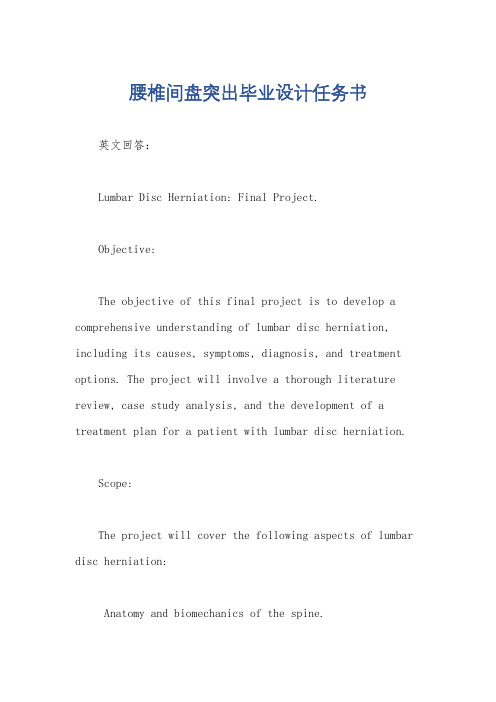
腰椎间盘突出毕业设计任务书英文回答:Lumbar Disc Herniation: Final Project.Objective:The objective of this final project is to develop a comprehensive understanding of lumbar disc herniation, including its causes, symptoms, diagnosis, and treatment options. The project will involve a thorough literature review, case study analysis, and the development of a treatment plan for a patient with lumbar disc herniation.Scope:The project will cover the following aspects of lumbar disc herniation:Anatomy and biomechanics of the spine.Causes and risk factors for lumbar disc herniation.Clinical signs and symptoms of lumbar disc herniation.Diagnostic tests and imaging techniques.Conservative and surgical treatment options.Rehabilitation and prevention strategies.Methodology:The project will utilize a combination of qualitative and quantitative research methods, including:Literature review of peer-reviewed articles, textbooks, and clinical guidelines.Case study analysis of a patient with lumbar disc herniation.Development of a comprehensive treatment plan based on the literature review and case study analysis.Expected Outcomes:Upon completion of this project, the student will be able to:Describe the anatomy and biomechanics of the spine.Identify the causes and risk factors for lumbar disc herniation.Diagnose and differentiate lumbar disc herniation from other conditions.Develop a comprehensive treatment plan for a patient with lumbar disc herniation.Evaluate the effectiveness of treatment and recommend appropriate modifications.Timeline:The project will be completed over a period of 8 weeks, with the following milestones:Week 1: Literature review and case study selection.Week 2: Case study analysis and treatment plan development.Week 3-8: Treatment implementation and evaluation.Reporting:The project findings will be presented in a final report that includes the following sections:Introduction.Literature review.Case study analysis.Treatment plan.Evaluation and discussion.Conclusion.Supervision:The project will be supervised by a faculty member with expertise in spinal disorders.Assessment:The project will be assessed based on the following criteria:Depth of understanding of the subject matter.Quality of literature review and case study analysis.Comprehensiveness and effectiveness of the treatmentplan.Clarity and organization of the final report.中文回答:腰椎间盘突出毕业设计任务书。
transform project final phase翻译

transform project final phase翻译transform project final phase的翻译是转变项目的最终阶段。
该短语用于描述一个项目的末尾阶段,指一系列的转变或变化。
双语例句:1. We are now entering the transform project final phase, where we will implement all the changes planned for the organization.我们现在进入了转变项目的最终阶段,在这个阶段我们将实施为组织计划的所有变化。
2. The transform project final phase focuses on transitioning the company's workflow to a more efficient and streamlined process.转变项目的最终阶段注重将公司的工作流程转变为更高效和流畅的过程。
3. In the transform project final phase, we will evaluate the results of our previous efforts and make any necessary adjustments.在转变项目的最终阶段,我们将评估之前努力的结果,并进行必要的调整。
4. The transform project final phase involves trainingour employees to adapt to the new systems and processes.转变项目的最终阶段涉及培训我们的员工以适应新的系统和流程。
5. The success of the transform project final phaserelies on effective communication and collaboration among all stakeholders.转变项目的最终阶段的成功依赖于所有利益相关者之间的有效沟通和合作。
招标文件英文模板

[Company Name][Company Address][City, State, Zip Code][Country][Phone Number][Email Address][Website]Date: [Insert Date]TO:[Potential Bidders’ Name][Company Name][Company Address][City, State, Zip Code][Country]SUBJECT: Invitation to Bid for [Project/Service Name]1. Introduction[Company Name] hereby invites sealed bids from qualified contractors/ vendors for the supply and installation of [specify the goods/services required] as per the specifications and terms and conditions set forth in this bid document. The project is located at [Project Location] andis scheduled to commence on [Start Date] and be completed by [Completion Date].2. Scope of WorkThe scope of work includes but is not limited to the following:- Detailed description of the project, including the nature of the goods/services required.- List of specific tasks or deliverables to be performed.- Any special requirements or considerations to be taken into account.3. Bidders EligibilityTo be eligible to submit a bid, the bidder must:- Be a legally registered and operating business entity.- Have a minimum of [number] years of experience in the relevant field.- Possess the necessary licenses, permits, and insurance to perform the work.- Provide a current certificate of good standing from the appropriate licensing authority.- Demonstrate financial stability and capability to undertake the project.4. Bid Submission RequirementsAll bids must be submitted in a sealed envelope marked with thefollowing information:- Bidder’s Name and Contact Information- Project/Service Name- Date of Submission- The bid must be submitted to [Address for Submission] by [Closing Date and Time].5. Bid FormatThe bid should be prepared in the following format:- Cover Page: Provide the bidder’s name, contact information, and a clear statement of the bid amount.- Technical Proposal: Detail the methodology, approach, and resourcesthat will be used to complete the project.- Financial Proposal: Include a detailed breakdown of the costs,including labor, materials, equipment, and any other expenses.- References: Provide a list of at least [number] references fromprevious similar projects.- Insurance Certificates: Attach copies of current liability and workers’ compensation insurance certificates.- Warranty Information: Outline the warranty period and terms for the goods/services provided.6. Evaluation CriteriaBids will be evaluated based on the following criteria:- Compliance with the bid document requirements.- Technical expertise and proposed methodology.- Financial proposal and cost-effectiveness.- Past performance and references.- Ability to meet the project schedule and deadlines.7. Bid Opening and AwardBids will be opened at [Time and Date of Bid Opening] in the presence of bidders or their authorized representatives. The award will be made tothe bidder whose bid is determined to be the most advantageous to [Company Name], considering the evaluation criteria.8. Contract Terms and ConditionsThe successful bidder will be required to enter into a contract with [Company Name] that includes the following terms and conditions:- Detailed project scope and specifications.- Payment terms and schedule.- Delivery or performance schedule.- Quality assurance and control measures.- Liability and indemnification provisions.- Termination clause.9. Contact InformationFor any questions or clarifications regarding this bid document, please contact:[Name][Title][Company Name][Phone Number][Email Address]10. Submission of BidsBids must be submitted in a sealed envelope and marked as follows:FOR: [Project/Service Name] Bid SubmissionFROM: [Bidder’s Name][Date of Submission][Closing Date and Time]11. Disposal of BidsAll bids received will be publicly opened and read aloud at the specified bid opening time and date. Unsuccessful bids will be disposed of in accordance with applicable laws and regulations.12. Instructions to Bidders- Bidders are responsible for reading and understanding all terms and conditions contained in this bid document.- Bidders are required to provide all necessary information as requested in the bid document.- Bidders must ensure that their bid is received by the closing date and time.- Bidders are responsible for any costs associated with the preparation and submission of their bid.13. Final Notes[Company Name] reserves the right to reject any or all bids, to cancel the bid process, or to negotiate with bidders if deemed necessary in the best interest of the project.[Company Name][Signature of Authorized Representative][Title of Authorized Representative][Date]---Please note that this is a template and should be customized to fit the specific requirements of the project or service being bid. It is also important to consult with legal counsel to ensure that all documents comply with local laws and regulations.。
期末作品总结英文
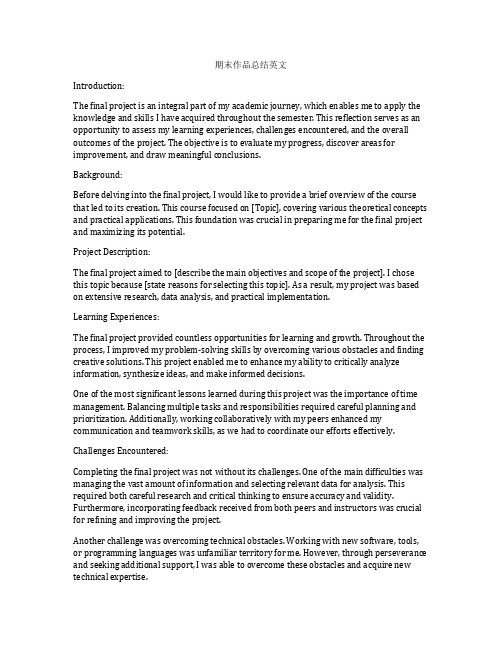
期末作品总结英文Introduction:The final project is an integral part of my academic journey, which enables me to apply the knowledge and skills I have acquired throughout the semester. This reflection serves as an opportunity to assess my learning experiences, challenges encountered, and the overall outcomes of the project. The objective is to evaluate my progress, discover areas for improvement, and draw meaningful conclusions.Background:Before delving into the final project, I would like to provide a brief overview of the course that led to its creation. This course focused on [Topic], covering various theoretical concepts and practical applications. This foundation was crucial in preparing me for the final project and maximizing its potential.Project Description:The final project aimed to [describe the main objectives and scope of the project]. I chose this topic because [state reasons for selecting this topic]. As a result, my project was based on extensive research, data analysis, and practical implementation.Learning Experiences:The final project provided countless opportunities for learning and growth. Throughout the process, I improved my problem-solving skills by overcoming various obstacles and finding creative solutions. This project enabled me to enhance my ability to critically analyze information, synthesize ideas, and make informed decisions.One of the most significant lessons learned during this project was the importance of time management. Balancing multiple tasks and responsibilities required careful planning and prioritization. Additionally, working collaboratively with my peers enhanced my communication and teamwork skills, as we had to coordinate our efforts effectively.Challenges Encountered:Completing the final project was not without its challenges. One of the main difficulties was managing the vast amount of information and selecting relevant data for analysis. This required both careful research and critical thinking to ensure accuracy and validity. Furthermore, incorporating feedback received from both peers and instructors was crucial for refining and improving the project.Another challenge was overcoming technical obstacles. Working with new software, tools, or programming languages was unfamiliar territory for me. However, through perseverance and seeking additional support, I was able to overcome these obstacles and acquire new technical expertise.Outcomes and Achievements:The final project yielded significant outcomes and achievements. Firstly, it allowed me to deepen my understanding of the course material by applying it to real-world scenarios. Secondly, it provided me with an opportunity to showcase my acquired skills and abilities, reinforcing my confidence in my capabilities. Additionally, the project encouraged increased self-motivation and perseverance in completing tasks, contributing to personal growth and development.Conclusion:In conclusion, the final project has been an invaluable experience that has not only enabled me to put theory into practice but also fostered personal growth and development. The project has enhanced my problem-solving, critical thinking, and time management skills, while also teaching me the importance of effective communication and collaboration. I am grateful for the opportunity to work on this project and am confident that the skills and knowledge gained will be beneficial in my future academic and professional pursuits. Overall, the final project has been a fulfilling and rewarding experience.。
英文设计合同
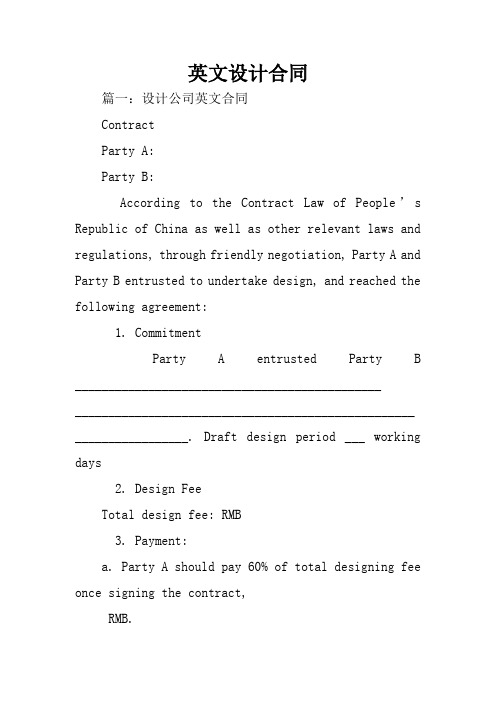
英文设计合同篇一:设计公司英文合同ContractParty A:Party B:According to the Contract Law of People’s Republic of China as well as other relevant laws and regulations, through friendly negotiation, Party A and Party B entrusted to undertake design, and reached the following agreement:1. CommitmentParty A entrusted Party B _________________________________________________________________________________________________ _________________. Draft design period ___ working days2. Design FeeTotal design fee: RMB3. Payment:a. Party A should pay 60% of total designing fee once signing the contract,RMB.b. After confirming the designing schedule and style, and when in need ofadjusting on electric designs, Party A should pay 30% of total design fee, RMBc. After fixing the complete designing schedule, Party A should pay thebalance of the design fee, RMB, Party B should hand over the printing CD after receiving the balance of payment.4. Period and means of delivery of the design plan.a. Party B must complete the draft of design within the time agreed by thetwo parties. If party B can not complete on time due to reduplicative changes from Party A, the delivery time can be put off. To ensure the smooth cooperation, Party A must confirm or make suggestion within three working days after receipt of the design from Party B, Party B should not exceed five working days to feedback the suggestion.b. Party A should supply the necessary designing information within 20working days after signing of the contract. AsParty A (not supply complete information and so on) make the design delayed, if delayed time more than three months (subject to the date of contract), Party A should pay the balance design fee, Party B will carry on making the design. If more than six months, this contract will automatically be terminated. Party B will supply the original CD. If Party A still need Party B to make the design, Party A should pay anther palette and design fee.c. After the final confirmation of the design, Party B should supply thecolored prints and electronic documents.d. Party A should bear the actual cost if needs the printing sample.5. Intellectual Property.a. Before Party A pay off all the design fee, Party B own the copyright,Party A can not use this design, and have no any right of this works.b. Party A have the right to sign the Copyright Transfer Contract, to havethe proprietary rights, rights of use andalterations after paying off the payment. Copyright of design not used by Party A still belongs to Party B, Party A do not have any right for this.c. After the final confirmation by Party A, if as the changes of Party A’scompany name or commodity name to change the design plan or have all different idea with the original plan, it should be as new plan, and PartyA should pay the balance fee, and sign new contract, PartyB will make new design plan.d. After paying off, Party B can not alter the design and give any othercompany.6. Responsibility and authoritya. Responsibility of Party A(1) Party A should try their best to supply the information for thisdesign.(2) Once finding the mistake, oversight or disagreement with thecontract, Party A should inform Party B in writing timely, and PartyB should make amendment in time.(3) Party A should abide by the payment terms in the contract.(4) Party A should make the confirmation for all the documents andthings that need confirmed timely.(5) Party A have the right to give a suggestion for Party B’s design andmake the works accords with the enterprise culture.b. Responsibility of Party B(1) Party B must make the plan and creative design according to therequirement in the contract made by Party A, and make full use ofspecialized knowledge and experience, to supply first design andservice to Party A.(2) Party B should supply all the design documents, making sizes anddesigns of every period according to the all requirement of thecontract and appendix, and complete the design.(3) Party B should make the design according to the things thatconfirmed by Party A critically.(4) Party B should make the design creation as the requirement of PartyA and supply the satisfied works.7. Breach of Dutya. Party A to terminate the contract before draft design completed, Party Bwill not return the deposit. Party A to terminate the contract after the final design, they should pay all the fees.b. Party B to terminate the contract without cause, to return all the fees toParty A.8. The two copies of the both signed contract, the two sides an armed, andhave the equal legal effect.The design time begins after the contract signed and received the deposit.Party A Signature (seal):Party B Signature (seal):Address: Address:Tel:Date:Tel: Date篇二:项目设计合同(中英文对照)项目设计合同(中英文对照)(上) (XX-6-17 18:57:52) 分类:合同范本标签:房产项目项目设计房产设计景观设计别墅设计会所设计概念设计初步设计设计合同合同范本 |PROJECT DESIGN AGREEMENT项目设计合同Agreement made as of:×××协议签订日期:××××年××月×日Between The Client: ×××(PARTY A) 业主:上海××开发有限公司(“甲方”)And The Design Consultant: ×××(PARTY B)设计顾问:×××(“乙方”)For the following project: ×××PROJECT (the Project)项目名称:×××项目(“项目”)Project Description:项目概况:×××Project (“the Project”) consists of 3 land Zones with ×××m2 Zone A, ×××m2 Zone B and ×××m2 Zone D which are located on West Side to ×××Road, Shanghai City, China. Zone A will be developed as a luxury residential area, Zone B will be developed as beach-front luxury commercial properties such as shops and restaurants , and Zone D will be a club house, a golf driving range and landscaped garden. In addition, ×××m2 Zone C may be used for the further development of the Project. The details are shown in attachment 1 of the Agreement.×××项目(“项目”)由坐落于中国上海市×××路的×××平方米的A区、×××平方米的B区以及×××平方米的D区三个区域组成。
材导final project----材料四面体之高频基板

上海交通大學高頻基板之材料四面体所別材料科學與工程學院學號5130519142姓名李韋志指導教授韓秀君西元2014年 6 月目錄摘要(abstract)1.前言2.高頻材料四面体2-1高頻基板的表現(performance)2-2高頻基板的結構設計與特性(structure & properties) 2-3高頻基板的制備及其難點(synthesis)3.高頻基板的展望與應用4.結束語參考文獻圖目錄<圖1>數位通訊科技演進與面臨問題<圖2>高頻基板當前應用產品與規格需求<圖3>材料四面体<圖4>傳輸訊號損失計算公式<圖5>柔性高頻基板技術發展藍圖<圖6>剛性高頻基板技術發展藍圖<圖7>樹脂材料結構設計<圖8>LCP薄膜與PI薄膜介電特性<圖9>剛性基板制備流程圖<圖10>含浸示意圖<圖11>有膠式柔性基板制備流程圖<圖12>高溫壓合設備示意圖<圖13>集膚效應<圖14>銅箔基板粗糙度與信號損失關係圖<圖15>柔性高頻基板未來發展規則摘要隨著信息處理需求的增大,具有高速信息處理的電子用品已經成為了人們日常生活不可或缺的一部分。
在信號傳輸速度上,預測將在今後五十年內增長10倍以上,實現這種高速化技術已經成為印刷電路板及覆蓋銅板產業的當前最重要任務。
*[1]因為高介電常數(Dk)會使傳輸速度變慢,而高散失因子(Df)則會使信號部分轉化為熱能損失使信號強度減弱。
降低Dk & Df已經成為PCB(印刷電路板)業者們的共同目標,各式新型也一一湧出。
本文以材料四面体(Material tetrahedron)為主體,參考諸多相關論文、期刊與廠商報告。
就高頻基板(substrate)中的特性、結構設計與制備及表現一一介紹以研究基板材料高速化、高頻化的理論及特性。
scope_statement

.
Product Characteristics and Requirements:
er submissions: User will be encouraged to email files with sample templates and tools to the Webmasters, The Webmasters will forward the files to the appropriate person for review and then post the files to the social website, if desired.
Scope Statement (Version xx)
Project Title:Talking social website
Date:4.10Prepared by:HuanLi,YaTingWei,JiaYiLiang,QiZhao,QianNiu
Project Justification:
Aldrich,sponsorofforce team, requested this project to assist the company in meeting its strategic goals. To help people build social network of Internet application services. It will also help reduce website costs and improve profitability by providing standard tools, techniques, templates, and project management knowledge to all website consultants. The budget for the project is 1,000,000 Yuan. An additional 300,000 Yuan per year will be required for operational expenses after the project is completed. Estimated benefits are 2,000,000 Yuan each year. It is important to focus on the system paying for itself within one year.
Attachment 3 Sample TOR for Project Management Sup

INDICATIVE TERMS OF REFERENCE FOR CONSULTINGSERVICES FORPACKAGE CS-05: PROJECT MANAGEMENT SUPPORTA. Introduction1. This document sets out indicative terms of reference for consulting services needed toensure the smooth implementation of the Guizhou Rocky Desertification Area Water Management Project. The direct client of the consulting services is the project management office (PMO). The PMO is under Guizhou Provincial Water Resources Bureau and physically located in Guizhou Water Resources Investment Company Limited (GWIC) wholly-owned by the Guizhou provincial government (executing agency of the project). The consulting services will be also provided to two project implementation units (PIUs). One is physically located in Pingqiao Reservoir Company Limited which belongs to Anlong County Water Resources Bureau; and another PIU is physically located in Pingshan Reservoir Management Office which belongs to Nayong County Water Resources Bureau.B. Implementation Arrangements2. The consulting services for project management support will be carried out by a team ofconsultants through a firm. A total of 71.0 person-months of national consulting services will be required. The consulting services will be financed by Asian Development Bank (ADB) and the consultants will be recruited by the PMO according to ADB’s Guidelines on the Use of Consultants (2013, as amended from time to time). The consulting firm will be selected by (i) inviting simplified technical proposals; and (ii) using the quality- and cost-based selection method, with a quality–cost ratio of 80:20. The consulting services are expected to start in 8 January 2018 until 31 December 2023.C. Reporting Requirements3. The consultant team will produce (i) an inception report within 4 weeks of the start of theconsulting services, (ii) an annual report by the end of each year during 2017−2022, (iii) draft project completion report (PCR) by 31 October 2023, and (iv) a final PCR by 31 December 2023. The inception and annual reports and draft PCR will be subject to tripartite reviews by ADB, PMO, and consultants. All reports are to be written in English and translated into Chinese. One soft and three hard copies of each report are to be submitted to ADB (English version only) and the PMO (both Chinese and English versions).4. The inception report will present an approach for the consulting services, including a workplan and an implementation schedule. The annual reports will present activities conducted by the consultants, effects of the consulting services, issues encountered, and recommendations to improve project management. The draft and final PCRs will include summary and evaluation of project implementation; environmental management; land acquisition and resettlement; ethnic minority development; implementation of ethnic minority and social development plans (EMSDPs), and gender action plan (GAP);compliance to the loan and project covenants; and achievements of the project impact, outcome, and outputs; as well as lesson learned from the project implementation and follow-up actions recommended.D. Other Requirements5. The consultant team will provide a fully qualified interpreter to work with the consultantson a full-time basis and support the ADB missions.E. Scope of Services and Consultants’ Inputs6. For each of the national consultant positions, (i) possession of a related degree,qualification, memberships of related academic societies, and/or participation in related training courses, (ii) experience in similar positions for projects or technical assistances, and (iii) experience in working with international organizations and consultants, will be highly evaluated.1. Project Management Specialist/Team Leader (national, 14.0 person-months[pm])7. The specialist will (i) coordinate all project management support activities as team leader;(ii) finalize approaches for project management support; (iii) prepare the inception report, interim reports, annual reports, draft PCR, and final PCR; (iv) assist the PMO in implementing, monitoring, and evaluating the overall project and subprojects; (v) assist the PMO in preparing quarterly project progress reports in a format provided by ADB; (vi) assess needs for capacity development for staff of the PMO, PIUs, and others, and plan, design, organize, and implement seminars, workshops, and/or training for project management; financial management; disbursement arrangements, implementation, monitoring; and evaluation of resettlement, gender development, and environmental management, and project monitoring and evaluation [M&E]), if necessary;1 (vii) monitor compliance with the loan covenants, assess key implementation issues, and make recommendations for improvement; and (viii) conduct any other necessary work for smooth and appropriate implementation of the project.2. Procurement and Contract Management Specialist (national, 14.0 pm)8. The specialist will (i) monitor procurement activities under the project and assist the PMOin updating and implementing the procurement plan; (ii) assist the PMO in conducting management of contracts for civil works, goods, and consulting services, including, but not limited to, supervision and inspection of activities under contracts; payments to contractors, suppliers, and consultants; preparation of withdrawal applications;improvement of fund flow efficiency by streamlining the preparation of withdrawal applications; and contract variations; (iii) assist the project management specialist/team leader in monitoring compliance with the loan covenants, assess key implementation issues, and make recommendations for improvement, from procurement and contract management viewpoint; (iv) provide the PMO with support for the preparation of procurement and contract management aspects of quarterly progress reports; (v) provide support to the project management specialist/team leader for assessing needs for capacity development, and planning, designing, organizing, and implementing seminars, workshops, and/or training for procurement and contract management; (vi) provide support to the project management specialist/team leader for preparing the inception report, annual reports, draft PCR, and final PCR; and (vii) conduct any other necessary work for procurement and contract management assigned by the project management specialist/team leader.1Costs for seminars, workshops, and training excluding consulting services (costs for venues, printing, accommodation and transport for participants, etc.) will be funded from ADB loan under the project separately from the contract for the consulting services.3. Environmental Specialist (national, 17.0 pm)9. The specialist will (i) assist the PMO and design institute in updating the environmentalimpact assessment (EIA) report and environmental management plan (EMP) approved by ADB for the project, in ADB format and based on the detailed designs; and obtain ADB’s approval of them;2 (ii) assist the PMO, PIUs, Pingqiao Reservoir Company Limited, and Pingshan Reservoir Management Office in constructing, operating, maintaining, and monitoring the project facilities in strict conformity with all applicable laws and regulations, including national and local regulations and standards for environmental protection, health, labor, and occupational safety; and ADB’s Safeguard Policy Statement (2009),3 and the EIA report and EMP; (iii) assist the PMO in preparing and submitting to ADB semiannual environmental monitoring reports in a format acceptable to ADB during construction and implementation of the project; (iv) monitor compliance with the EIA report and EMP, assess the degree of impacts and key implementation issues, explain key issues to the PMO and PIUs, and assist them in conducting follow-up actions to address the key issues;(v) provide the PMO with support for the preparation of environmental aspects of quarterly progress reports; (vi) provide supports to the project management specialist/team leader for assessing needs for capacity development, and planning, designing, organizing, and implementing seminars, workshops, and/or training for environmental management; (vii) provide support to the project management specialist/team leader for preparing the inception report, annual reports, draft PCR, and final PCR; and (viii) undertake any other necessary work assigned by the project management specialist/ team leader.4. Resettlement Specialist (national 8.0 pm)10. The specialist will (i) assist the PMO, PIUs, and design institute in updating theresettlement plans approved by ADB , in ADB format and based on the detailed designs;disclose them to th e affected persons prior to ADB’s approval; and obtain ADB’s approval of them; as necessary; (ii) assist the PMO, PIUs, Pingqiao Reservoir Company Limited, and Pingshan Reservoir Management Office in implementing land acquisition and resettlement in accordance with the resettlement plans, (iii) assist the PIUs, Pingqiao Reservoir Company Limited, and Pingshan Reservoir Management Office in supervising contractors to ensure compliance with requirements of the resettlement plans, applicable laws and regulatio ns, and ADB’s Safeguard Policy Statement; (iv) assist the PMO, PIUs, Pingqiao Reservoir Company Limited, and Pingshan Reservoir Management Office in supervising the processes of resettlement by collecting and updating basic data, and closely coordinating between the PMO, PIUs, Pingqiao Reservoir Company Limited, Pingshan Reservoir Management Office, and an external resettlement monitor; (v) follow up with the Anlong and Nayong county governments for post resettlement subsidies to be provided to households displaced by the construction of Pingiqiao and Pingshan reservoirs; affected; (vi) review external M&E reports prepared by the external resettlement monitor and ADB’s comments on the reports, monitor compliance with the resettlement plans, assess the degree of impacts and key implementation issues, explain key issues to the PMO, PIUs, Pingqiao Reservoir Company Limited, and Pingshan Reservoir Management Office, and assist them in conducting follow-up actions to address the key issues; (vii) assist the PMO to monitor compliance with the resettlement plans, assess key implementation issues, formulate remedial measures, and assist them in 2The EMP is included in the EIA report.3 Available at: /documents/safeguard-policy-statementconducting follow-up actions; (viii) provide the PMO with support for the preparation of resettlement aspects, including semiannual internal resettlement monitoring of quarterly progress reports; (ix) provide support to the project management specialist/team leader for assessing needs for capacity development, and planning, designing, organizing, and implementing seminars, workshops, and/or training for implementation and M&E of land acquisition and resettlement; (x) provide support to the project management specialist/team leader for preparing the inception report, annual reports, draft PCR, and final PCR; and (xi) undertake any other necessary work assigned by the project management specialist/team leader.5. Social Development and Gender Specialist (national, 8.0 pm)11. The specialist will (i) if there is a change in the project scope, assist the PMO, PIUs, anddesign institute in updating the EMSDPs approved by ADB, in ADB format and based on the change; and obtain ADB’s approval of it; (ii) assist the PMO and PIUs in implementing the EMSDPs and GAP prepared during project preparation; (iii) assist the PMO, PIUs, Pingqiao Reservoir Company Limited, and Pingshan Reservoir Management Office in supervising contractors to ensure compliance with requirements of the EMSDPs and GAP, and applicable laws and regulations; (iv) monitor compliance with the EMSDPs and GAP;assess the degree of impacts and key implementation issues; explain key issues to the PMO and PIUs; and assist them in conducting follow-up actions to address the key issues;(v) provide the PMO with support for the preparation of social aspects of quarterly progress reports, including semiannual internal social monitoring reports; (vi) provide support to the project management specialist/team leader for assessing needs for capacity development, and planning, designing, organizing, and implementing seminars, workshops, and/or training for implementation and M&E of the EMSDPs and GAP; (vii) provide support to the project management specialist/team leader for preparing the inception report, annual reports, draft PCR, and final PCR; and (viii) undertake any other necessary work assigned by the project management specialist/team leader.6. Economist (national, 4.0 pm)12. The specialist will (i) review background documents, including the economic analysis ofthe project undertaken during project preparation; (ii) conduct economic analyses of the overall project and each subproject to determine economic internal rate of return of the overall project and each subproject at the midterm of project implementation (in 2020), and at physical completion of the project; (iii) provide support to the project management specialist/team leader for assessing needs for capacity development; and planning, designing, organizing, and implementing seminars, workshops, and/or training for economic analysis, as necessary; (iv) provide support to the project management specialist/team leader for preparing the inception report, annual reports, draft PCR, and final PCR; and (v) undertake any other necessary work assigned by the project management specialist/team leader.7. Financial Specialist (national, 6.0 pm)13. The specialist will (i) review background documents, including the financial analysis of theproject undertaken during project preparation; (ii) conduct financial analysis at the midterm of project implementation (in 2020), and at physical completion of the project, including (a) financial sustainability analysis to assess the fiscal sustainability debt repayment capacity of the GWIC as a whole; and (b) an assessment of the financial viability of the revenue-generating components, i.e., water supply; (iii) assist the GWIC, PMO, Pingqiao Reservoir Company Limited, Pingshan Reservoir Management Office, and PIUs in establishing and implementing a financial management system; (iv) assist the Guizhou Provincial Government including GWIC and PMO, and Anlong and Nayong county governments including Pingqiao Reservoir Company Limited, Pingshan Reservoir Management Office, and PIUs in preparing withdrawal applications and streamlining the preparation of withdrawal applications; (v) assist the Guizhou Provincial Finance Department, Guizhou Provincial Audit Office, PMO, and PIUs in meeting requirements of the financial management action plan (Table V-1, project administration manual); (vi) provide support to the project management specialist/team leader for assessing needs for capacity development; and planning, designing, organizing, and implementing seminars, workshops, and/or training for financial analysis, as necessary; (vii) provide support to the project management specialist/team leader for preparing the inception report, annual reports, draft PCR, and final PCR; and (ix) undertake any other necessary work assigned by the project management specialist/team leader.F. Cost EstimateTable A2.5: Cost EstimateItem Total Cost ($'000)1. Consultantsa. Remuneration and per diemNational consultants (71.0 person-months) 579.3b. Local travel 64.5c. Reports and communications 2.02. Surveys3.03. Miscellaneous administration and support costs e4.04. Contingencies 34.2Total 687.0 Source: Asian Development Bank estimates.。
Extended Project Performance Overview说明书
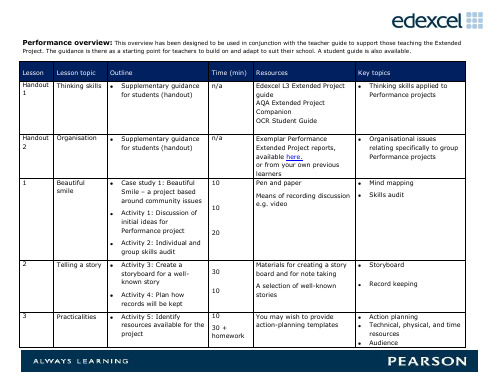
4-7
Hot dog
Lesson
Handout 1
Lesson topic Thinking skills
Outline
Supplementary guidance for students (handout)
Time (min) n/a
Resources
Edexcel L3 Extended Project guide AQA Extended Project Companion OCR Student Guide
Acknowledgments: These free resources were originally published on the Edexcel Level 3 Extended Project Teacher Resource Disc (Heinemann 2009). They have been slightly adapted and updated by the coordinating editors for free dissemination on this website.
Case study 1: Beautiful
10
Smile – a project based
around community issues 10
Activity 1: Discussion of
initial ideas for