注塑工艺应力的影响因素
注塑应力形成的原理及消除方案

如何检验塑胶件的应力?如何去除应力?A 、内应力产生的机理塑料内应力是指在塑料熔融加工过程中由于受到大分子链的取向和冷却收缩等因素而产生的一种内在应力。
内应力的本质为大分子链在熔融加工过程中形成的不平衡构象,这种不平衡构象在冷却固化时不能立刻恢复到与环境条件相适应的平衡构象,这种不均衡构象的实质为一种可逆的高弹形变,而冻结的高弹形变平时以位能情势储存在塑料制品中,在合适的条件下,这种被迫的不稳定的构象将向自在的稳固的构象转化,位能改变为动能而开释。
当大分子链间的作用力和相互缠结力蒙受不住这种动能时,内应力平衡即受到破坏,塑料制品就会产生应力开裂及翘曲变形等现象。
B、塑料内应力产生的起因(1)取向内应力取向内应力是塑料熔体在流动充模和保压补料过程中,大分子链沿流动方向排列定向构象被冻结而产生的一种内应力。
取向应力产生的详细过程为:近流道壁的熔体因冷却速度快而造成外层熔体粘度增高,从一而使熔体在型腔核心层流速远高于表层流速,导致熔体内部层与层之间受到剪切应力作用,产生沿流动方向的取向。
取向的大分子链解冻在塑料制品内也就象征着其中存在未松弛的可逆高弹形变,所以说取向应力就是大分子链从取向构象力求过渡到无取向构象的内力。
用热处理的方式,可降低或排除塑料制品内的取向应力。
塑料制品的取向内应力分布为从制品的表层到内层越来越小,并呈抛物线变化。
(2)冷却内应力冷却内应力是塑料制品在熔融加工过程中因冷却定型时收缩不均匀而产生的一种内应力。
尤其是对厚壁塑料制品,塑料制品的外层首先冷却凝固收缩,其内层可能仍是热熔体,这徉芯层就会限度表层的收缩,导致芯层处于压应力状况,而表层处于拉应力状态。
塑料制品冷却内应力的分布为从制品的表层到内层越来越大,并也呈抛物线变更.。
另外,带金属嵌件的塑料制品,因为金属与塑料的热胀系数相差较大,容易形成收缩不一平匀的内应力。
除上述两种重要内应力外,,还有以下多少种内应力:对结晶塑料制品而言,其制品内部各部位的结晶构造跟结晶度不同也会发生内应力。
影响注塑制件内应力的因素

影响注塑制件内应力的因素注塑制件是一种经济高效和具备多种形状及功能的重要制造技术,但是其内部应力却受到来自注塑工艺及其他外部因素的影响,使得注塑制件内应力产生变化,从而影响了其功能性能、使用寿命。
因此,探究影响注塑制件内部应力的因素和机理,对于改进注塑工艺及优化注塑制件的使用性能及使用寿命具有重要的意义。
首先,注塑参数是影响注塑制件内应力的重要因素之一。
注塑参数主要包括注塑温度、塑料填充量、熔料压力、射出速度等。
随着参数调整,注塑过程中塑料的塑形、熔料流动和成型性能以及塑料凝固动态特性发生明显变化,从而使得熔体在凝固过程中产生应力,由此导致注塑制件内部应力发生变化。
其次,注塑成型模具结构是影响注塑制件内应力的重要因素之二。
一般来说,注塑成型模具结构的设计会影响注塑的流植分布,而分布的不均衡会使得冷却水或空气在不同地方冷却速度不一,从而导致注塑件表面张力的不均匀,从而导致注塑制件内应力发生变化。
同时,模具中心热对流也会对注塑制件内应力产生影响。
此外,注塑材料也是影响注塑制件内应力的因素之一。
目前,注塑材料的选择一般是根据制件的用途来确定的,其受到多种因素的影响,例如熔点、熔体流动性、熔体弹性模量、收缩率等等。
这些因素的变化都会对注塑制件的内部应力产生影响。
另外,不良工艺及装配技术也是影响注塑制件内应力的因素之一。
如果在注塑过程中,采用了不合理的工艺操作,会使得塑料不均匀地冷却,而导致注塑制件内应力出现变化,从而影响制件的使用性能和使用寿命。
此外,注塑件装配时如果采用不正确的技术,也会导致注塑件内部应力发生变化。
综上所述,注塑参数、注塑模具结构、注塑材料、不良工艺及装配技术等多种因素都会影响注塑制件的内部应力,从而影响注塑制件的使用性能和使用寿命。
因此,在注塑工艺的设计和应用过程中,应该充分考虑这些因素,通过优化参数来改善注塑制件的内部应力,并采用合理的模具结构设计、优良的注塑材料,以及正确的装配技术,最大程度地降低注塑制件内部应力,提高其功能性能及使用寿命。
浅谈注塑工艺的影响因素
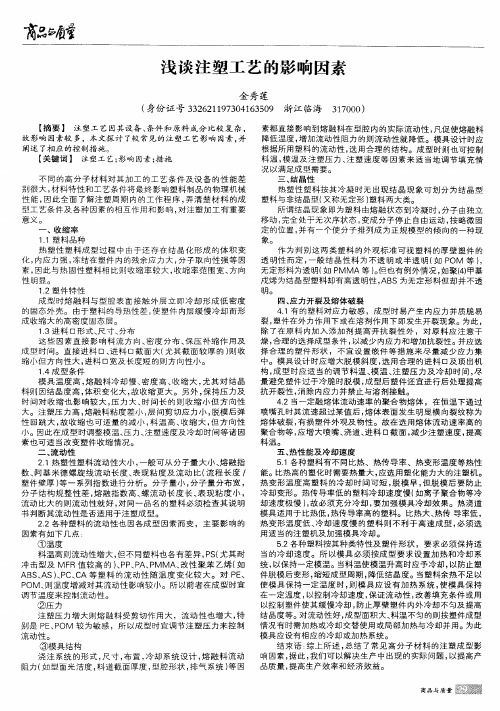
、
收 缩 率
11 料 品种 .塑 热 塑 性 塑 料 成 型 过 程 中 由 于 还 存 在 结 晶 化 形 成 的 体 积 变 化, 内应 力 强 , 结 在 塑件 内 的 残余 应 力 大 , 子 取 向性 强 等 因 冻 分 素, 因此 与 热 固 性 塑 料 相 比则 收 缩 率 较 大 , 缩 率 范 围 宽 、 向 收 方 性明显。 12塑 件 特 性 . 成 型 时 熔 融 料 与 型 腔 表 面 接 触 外 层 立 即冷 却 形 成 低 密 度 的 固 态外 壳 。 由于 塑 料 的导 热 性 差 , 塑 件 内层 缓 慢 冷 却 而 形 使 成 收缩 大 的 高 密度 固 态 层 。 1 . 料 口形 式 、 寸 、 布 3进 尺 分 这 些 因素 直 接 影 响料 流 方 向 、 度 分 布 、 压 补 缩 作 用 及 密 保 成 型 时 间 。直 接 进 料 口、 料 口截 面 大 ( 其 截 面 较 厚 的 ) 收 进 尤 则 缩 小 但 方 向性 大 , 料 口宽 及 长度 短 的 则 方 向 性 小 。 进 1 _ 型 条 件 4成 模 具 温 度 高 , 融 料 冷 却 慢 、 度 高 、 缩 大 , 其 对 结 晶 熔 密 收 尤 料则 因结 晶度 高 , 体积 变化大 , 故收缩更 大。另外 , 保持压力及 时 间 对 收 缩 也 影 响 较 大 , 力 大 、 间 长 的 则 收 缩 小 但 方 向性 压 时 大。 注 塑 压 力 高 , 融 料 粘 度 差 小 , 问剪 切 应 力 小 , 模 后 弹 熔 层 脱 性 回跳 大 , 收 缩 也 可 适 量 的减 小 , 温 高 、 缩 大 , 方 向 性 故 料 收 但 小 。因此 在 成 型 时 调 整 模 温 、 力 、 塑 速 度 及 冷 却 时 间 等 诸 因 压 注 素 也 可 适 当 改 变塑 件 收 缩 情 况 。
注塑成型过程中的影响因素

注塑成型过程中的影响因素注塑成型是一门工程技术,它所涉及的内容是将塑料变化为有用并能保持原有性能的制品。
注射成型的紧要工艺条件是影响塑化流动和冷却的温度,压力和相应的各个作用时间。
一、温度掌控1、料筒温度注射模塑过程需要掌控的温度有料筒温度、喷嘴温度和模具温度等。
前两个温度重要影响塑料的塑化和流动,而后一种温度重要是影响塑料的流动和冷却。
每一种塑料都具有不同的流动温度,同一种塑料,由于来源或牌号不同,其流动温度及分解温度是有差别的,这是由于平均分子量和分子量分布不同所致,塑料在不同类型的注射机内的塑化过程也是不同的,因而选择料筒温度也不相同。
2、喷嘴温度喷嘴温度通常是略低于料筒zui高温度的,这是为了防止熔料在直通式喷嘴可能发生的“流涎现象”。
喷嘴温度也不能过低,否则将会造成熔料的早凝而将喷嘴堵死,或者由于早凝料注入模腔而影响制品的性能。
3、模具温度模具温度对制品的内在性能和表观质量影响很大。
模具温度的高处与低处决议于塑料结晶性的有无、制品的尺寸与结构、性能要求,以及其它工艺条件(熔料温度、注射速度及注射压力、模塑周期等)。
二、压力掌控注塑过程中压力包括塑化压力和注射压力两种,并直接影响塑料的塑化和制品质量。
1、塑化压力(背压)采纳螺杆式注射机时,螺杆顶部熔料在螺杆转动后退时所受到的压力称为塑化压力,亦称背压。
这种压力的大小是可以通过液压系统中的溢流阀来调整的。
在注射中,塑化压力的大小是随螺杆的转速都不变,则加添塑化压力时即会提高熔体的温度,但会减小塑化的速度。
此外,加添塑化压力常能使熔体的温度均匀,色料的混合均匀和排出熔体中的气体。
一般操作中,塑化压力的决议应在保证制品质量优良的前提下越低越好,其实在数值是随所用的塑料的品种而异的,但通常很少超过20公斤/厘米。
2、注射压力在当前生产中,几乎全部的注射机的注射压力都是以柱塞或螺杆顶部对塑料所施的压力(由油路压力换算来的)为准的。
注射压力在注塑成型中所起的作用是,克服塑料从料筒流向型腔的流动阻力,予以熔料充模的速率以及对熔料进行压实。
塑胶件 内应力

1 内应力产生在注塑制品中,各处局部应力状态是不同的,制品变形程度将决定于应力分布。
如果制品在冷却时。
存在温度梯度,则这类应力会发展,所以这类应力又称为“成型应力”。
注塑制品的内应力包两种:一种是注塑制品成型应力,另一种是温度应力。
当熔体进入温度较低的模具时,靠近模腔壁的熔体讯速地冷却而固化,于是分子链段被“冻结”。
由于凝固的聚合物层,导热性很差,在制品厚度方向上产生较大的温度梯度。
制品心部凝固相当缓慢,以致于当浇口封闭时,制品中心的熔体单元还未凝固,这时注塑机又无法对冷却收缩进行补料。
这样制品内部收缩作用与硬皮层作用方向是相反的;心部处于静态拉伸而表层则处于静态压缩。
在熔体充模流动时,除了有体积收缩效应引起的应力外。
还有因流道,浇口出口的膨胀效应而引起的应力;前一种效应引起的应力与熔体流动方向有关,后者由于出口膨胀效应将引起在垂直于流动方向应力作用。
2 影响愉应力的工艺因素(1)向应力的影响在速冷条件下,取向会导致聚合物内应力的形成。
由于聚合物熔体的粘度高,内应力不能很快松驰,影响制品的物理性能和尺寸稳定性。
各参数对取向应力的影响a熔体温度,熔体温度高,粘度低,剪切应力降低取向度减小;另一方面由于熔体温度高会使应力松驰加快,促使解取向能力加强。
可是在不改变注塑机压力的情况下,模腔压力会增大,强剪切作用又导致取向应力的提高。
b在喷嘴封闭以前,延长保压时间,会导致取向应力增加。
c提高注射压力或保压压力,会增大取向应力,d模具温度高可保证制品缓慢冷却,起到解取向作用。
e增加制品厚度使取向应力降低,因为厚壁制品冷却时慢,粘度提高慢,应力松驰过程的时间长,所以取向应力小。
(2)对温度应力的影响如上所述由于在充模时熔体和型壁之间温度梯度很大,先凝固的外层熔体要助止后凝固的内层熔体的收缩,结果在外层产生压应力(收缩应力),内层产生拉应力(取向应力)。
如果充模后又在保压压力的作用下持续较长时间,聚合物熔体又补入模腔中,使模腔压力提高,此压力会改变由于温度不均而产生的内应力。
塑料件应力开裂原因分析及检测方法简述

塑料件应力开裂原因分析及检测方法简述1.材料本身的问题:塑料材料选择不当、材料质量不过关或添加剂使用不当等都可能导致塑料件的应力开裂。
例如,在高温环境下,一些塑料材料会发生老化或失去强度,容易出现应力开裂。
2.设计不合理:塑料件的设计不合理也是应力开裂的常见原因之一、例如,墙厚过薄、变截面和过小的毛胚等都可能导致塑料件的应力集中,进而导致开裂。
3.加工工艺问题:塑料件在加工过程中如果没有采取适当的工艺措施,例如注塑温度过高、注塑压力过大、注塑速度过快等都可能导致应力集中和应力开裂。
1.观察外观:通过目测可以检测到塑料件的开裂情况。
开裂通常是由于应力集中导致的,因此在塑料件表面或边缘会出现明显的裂纹。
2.断面观察:将塑料件进行切割,观察其断面的结构和裂纹情况。
这种方法可以更直观地了解塑料件的应力分布情况,从而确定是否存在应力开裂。
3.拉伸试验:通过进行拉伸试验,可以测试塑料件的断裂强度和断裂伸长率。
如果塑料件的强度较低或伸长率较小,说明存在应力开裂的风险。
4.光散射检测:利用光散射原理,通过照射塑料件表面,观察光的散射情况来判断塑料件的应力状态。
应力集中的区域通常会散射更多的光。
5.应力测量:通过应力分析仪等设备对塑料件进行应力测试。
可以直接测量塑料件内部的应力分布,从而判断是否存在应力开裂的潜在风险。
总之,塑料件应力开裂的原因和检测方法多种多样,需要综合考虑材料、设计、加工和使用等方面的因素。
合理选择材料、优化设计、控制加工工艺以及进行适当的检测,可以降低应力开裂的风险,提高塑料件的使用寿命和可靠性。
注塑件内应力的产生及解决对策

注塑件内应力的产生及解决对策注塑件内应力的产生是由于注塑过程中的热胀冷缩效应引起的。
具体而言,注塑过程中,塑料在高温下进入模具中,然后在冷却过程中,塑料会收缩并形成注塑件。
然而,由于注塑过程中塑料的不均匀收缩,以及与模具之间的附着力,注塑件内部会形成应力。
1.外观缺陷:注塑件可能会出现翘曲、扭曲、脱模或开缺等问题,从而影响其外观质量。
2.尺寸变化:由于应力会导致塑料变形,从而导致注塑件的尺寸变化。
3.力学性能下降:注塑件的内应力可能导致其力学性能下降,使得产品更容易断裂或失效。
以下是一些解决注塑件内应力的对策:1.优化模具设计:合理的模具设计可以减少内应力的产生。
例如,通过增加模具冷却通道和增加射胶点的数量和位置等方式,可以加快注塑件的冷却速度,减少应力的产生。
2.优化材料选择:选择合适的塑料材料也可以减少内应力的产生。
一些塑料材料具有更低的热胀冷缩系数,可以减少注塑件的收缩程度和应力水平。
3.控制注塑工艺参数:合理控制注塑工艺参数也可以减少内应力的产生。
例如,调整注射速度、保压时间和冷却时间等,可以减少塑料的不均匀收缩,并减少应力的产生。
4.使用预应力技术:预应力技术可以在注塑过程中施加一定的压力,以减小注塑件形成后的应力水平。
这可以通过在注塑模具上加装压力缸或在模具关闭之前施加辅助压力等方式实现。
5.热处理和退火:对于内应力较高的注塑件,可以通过热处理或退火等热处理方法,来减小或消除部分内应力。
总之,在注塑件生产中,必须重视注塑件内应力的产生和解决。
通过合理的模具设计、优化材料选择、控制工艺参数、使用预应力技术以及热处理和退火等方法,可以有效减少内应力的产生,并优化注塑件的性能和外观质量。
注塑制品内应力的分析及控制

注塑制品内应力的分析及控制注塑成型是一种常见的塑料制品成型方法,其特点是成型周期短、生产效率高、成型精度高等。
然而,注塑制品在生产过程中往往会产生内应力,如果不及时进行分析和控制,会对产品的质量和性能造成不利影响。
本文将从注塑制品内应力的分析和控制两个方面进行详细探讨。
一、注塑制品内应力分析1.内应力形成原因:注塑制品在注塑过程中,由于塑料材料的热胀冷缩、固化收缩以及注塑工艺参数的变化等原因,会产生一定的内应力。
内应力存在的主要原因包括材料性能、注塑工艺参数、产品几何形态等。
2.内应力对产品的影响:内应力会直接影响注塑制品的力学性能、外观质量和尺寸稳定性。
例如,内应力过大会导致产品变形、开裂,甚至影响产品的使用寿命。
因此,分析注塑制品内应力,对产品质量的控制至关重要。
二、注塑制品内应力的控制1.材料选择:合理选择适合注塑成型的塑料材料,具有良好的流动性、热稳定性和机械性能。
材料的选择与产品的使用环境及要求有关,同时要考虑到产品的成本控制。
2.工艺参数控制:合理调整注塑工艺参数,包括注塑温度、注塑压力、注射速度等。
通过优化工艺参数,可以减小注塑过程中的温度梯度和压力差,减少内应力的产生。
3.产品设计优化:在注塑制品的产品设计阶段,考虑使用适当的加强件、结构设计等手段,使得产品的应力分布更加均匀,减少应力集中的区域。
4.合理模具设计:模具结构的设计对于控制注塑制品的内应力也非常重要。
合理的模具结构可以减小内应力的产生,减轻产品变形的风险。
5.后处理措施:包括产品的冷却、固化和放松等过程,都可以对内应力进行控制。
通过合理的冷却方式和固化条件,可以使注塑制品内部的应力得到释放和均衡。
6.检测与调整:对于关键零件和高要求的注塑制品,可以采用应力检测等方法,及时发现问题,进行调整和优化。
综上所述,注塑制品内应力的分析和控制对于改善产品质量、提高生产效率至关重要。
通过合理的材料选择、工艺参数控制、产品设计优化、模具设计、后处理措施以及检测和调整等综合手段,可以降低内应力的产生,保证产品的力学性能和外观质量。
塑胶件应力形成的原因

塑胶件应力形成的原因引言:塑胶件是指通过塑料材料加工而成的各种形状的产品,广泛应用于日常生活和工业生产中。
塑胶件在加工过程中,往往会出现应力现象,这种应力可能对产品的使用性能和寿命产生不良影响。
本文将从塑胶件的材料特性、加工工艺以及产品设计等方面探讨塑胶件应力形成的原因。
一、材料特性:1.1塑料材料的流变性:塑料具有可塑性和可压性的特性,容易受外力作用而发生变形。
在塑胶件加工过程中,由于注塑或挤出等成型工艺的复杂性,塑料材料会经历多次变形和冷却,使得材料内部产生残余应力。
这种残余应力会导致塑胶件在使用过程中产生应力集中和应力松弛现象。
1.2材料粘度和分子结构:塑料材料的粘度和分子结构也会对塑胶件的应力形成产生影响。
粘度较高的塑料流动性差,容易产生应力积累现象;而分子结构复杂的塑料,如聚合物材料,由于分子链的交联和纠缠,容易导致塑胶件产生内应力。
二、加工工艺:2.1成型工艺参数:塑料件的成型工艺参数,如温度、压力和速度等,对于塑胶件的应力形成有重要影响。
温度过高或过低、压力过大或过小、注射速度过快或过慢等都可能引起应力集中和应力积累现象。
例如,温度过高会导致材料熔化不充分,形成含气孔的塑胶件,从而产生内应力。
2.2成型工艺选择:不同的成型工艺对塑胶件的应力形成也有不同的影响。
常见的成型工艺有注塑、挤出、吹塑等,每种工艺的特点和应用领域不同,其应力形成的机理也不同。
例如,注塑工艺易于产生内应力,而挤出工艺易于产生表面应力。
2.3产品尺寸和形状:塑胶件的尺寸和形状设计是影响应力形成的重要因素之一、当塑胶件的尺寸较大或形状复杂时,由于塑料材料的热胀冷缩和冷却不均匀等原因,易导致内部应力集中。
此外,塑胶件的壁厚也会对应力形成产生影响,过大或过小的壁厚都可能引起应力积累现象。
三、产品设计:3.1断面形状:塑胶件的断面形状对于应力形成具有重要影响。
常见的塑胶件断面形状有矩形、圆形、梯形等,不同形状的断面对应力分布有不同的影响。
注塑件的应力变形分析及解决对策
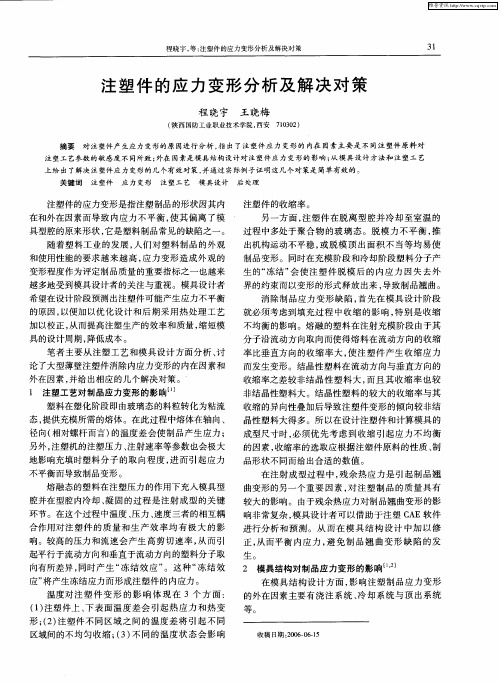
2 模 具结 构 对制 品应 力 变 形的 影 响 ¨ 在模 具 结 构 设 计 方 面 , 响注 塑 制 品应 力 变形 影
的外在因素主要有浇注系统 、 冷却 系统与顶 出系统
等。
收稿 日期 :0 6 0 -5 2 0 -61
形 ;2 注塑件不 同区域之间 的温度差将 引起不 同 ()
关 键 词 注 塑件 应 力 变 形 注 塑 工 艺 模 具设 计 后 处 理
注塑件 的应 力 变形 是指 注 塑制 品 的形 状 因其 内
注塑件 的收缩率。 另一方面 , 注塑件在脱离型腔并 冷却至室温的 过程中多处于聚合物的玻璃态。脱 模力不平衡 , 推 出机构运动不平稳 , 或脱模顶 出面积不 当等均易使 制品变形。同时在充模阶段和冷却阶段塑料分子产
较大的影响。由于残余热应力对制品翘 曲变形的影 响非常复杂 , 模具设计者可以借助于注塑 C E软件 A 进行分析和 预测。从 而在模 具结构 设计 中加 以修 正, 从而平衡 内应 力 , 避免制 品翘 曲变形缺 陷 的发
生。
腔并在型腔内冷却 、 固的过程是注射成型的关键 凝 环节 。在 这个过 程 中温 度 、 压力 、 速度 三 者 的相互 耦 合作用对注塑件 的质 量和生 产效率均 有极大 的影 响。较高的压力和流速会产生 高剪切速率 , 从而引
外在因素 , 并给出相应的几个解决对策。 1 注 塑工 艺对 制 品应力 变 形的 影响 …
塑 料 在塑化 阶段 即 由玻 璃态 的料 粒转 化 为粘 流 态 , 充模 所需 的熔体 。在此 过程 中熔 体在 轴 向 、 提供 径 向( 相对 螺杆 而言 ) 的温 度 差会 使 制 品产 生 应力 ;
变形 程度 作为评 定 制 品质量 的重要指 标之 一 也越 来 越多地 受 到模具 设 计者 的关 注与 重视 。模 具设 计者 希望在 设计 阶段 预 测 出注塑 件可 能产 生 应力不 平衡 的原 因 , 以便加 以优 化设 计 和 后 期 采 用 热 处 理 工 艺
塑胶产品应力痕原因

注塑加工生产时为什么会产生应力痕
注塑加工
在注塑加工生产的成品上,常见的ABS、PP、PC,我们会看到成型的产品表面会有发白、发亮的应力痕出现,也就是常称“光印、骨影”,这些就是内应力造成的结果,顶针应力痕、镶件应力痕、肉厚差应力痕,这些缺陷在放置一段时间后会有所消减。
但我们需要从源头看下究竟是什么样的原因造成了应力痕的出现。
1.成型产品的结构
(1)产品肉厚胶位的突然变化,而且壁厚相差过大,都会导致内应力的产生。
2、塑料注塑模具
(1)塑料注塑模具浇口附近会出现不规则应力痕,而顶针、斜顶应力痕形成的因素会更为多一点;
(2)镶件配合不紧,在高压的环境下填充时间过长,会导致镶件的松动,会产生应力;
(3)模具变形或模具装配问题,如注塑过程中顶针板变形,顶针、顶块稍微后退等,都有可能造成应力痕
(4)模具部分过热,冷却不均匀,冷却水道离应力痕产生部位太远。
3.成型工艺和使用材料
(1)随着保压压力和保压时间的增加,最先开始的是肉厚差应力痕、顶针斜顶应力痕、然后是肉厚差应力痕,最后是浇口附近不规则的应力痕;
(2)外观平面或弧面形成明显的应力痕,胶厚突变,致使塑胶件薄壁在冷却的过程中由于有从外到的冷却过程,使得冷却速率不一致,冷却的塑胶对先冷却的产生各种各样的作用应力;
(3)保压压力太高、模温太低、料温太低。
摘要 分析影响注塑制件内应力的主要因素

摘要分析影响注塑制件内应力的主要因素,针对造型设计、注塑机选用、机械加工、注射成型工艺条件给出了相应的解决办法,并指出热处理是降低或消除注塑制件残余内应力,使其内部结构加速达到稳定状态的一个有效措施。
关键词注塑制件内应力因素成型工艺热处理塑料由于具有质量轻、比强度高、耐磨损、消间减振、电性能好及便于成型加工等优点,在许多领域得到了广泛应用。
但注塑制件有一个普遍存在的缺点,即内应力。
内应力的存在不权会引起制件翘曲变形甚至开裂,也会影响注塑件的光学性能、电学性能、物理力学性能和表现质量,因此找出各种成型因素对注塑制件内应力影响的规律性,以便采取有效措施减小制件的内应力,并使其在注塑制件断面尽可能均匀地分布,这对提高注塑制件的质量具有重要意义。
特别是注塑制件在使用条件下要承受热、有机溶剂和其它能加速其开裂的腐蚀介质时,减小注塑制件的内应力对保证其正常具有更加重要的意义。
1影响注塑制件内应力的因素分析注塑制件的造型设计不合理、模具设计不合理、成型工艺条件不正确、注塑机选用不当等都会使注塑制件内存在比较大的内应力。
影响注塑制件内应力的因素很多,也很复杂,主要影响因素如图1所示。
1.1造型设计(1)圆角注塑制件除了使用上要求采用尖角外,各表面相交处应尽可能采用圆弧过渡。
由于注塑制件形状和截面变化易使注射过程中溶料在尖角处的流态发生急剧变化而产生大的应力,并残留在尖角处,在有载荷或受冲击时会发生破裂,甚至在脱模过程中由于模塑内应力而开裂,特别是注塑制件的内角处更易开裂。
通常,采用R0.5mm的圆角就能使注塑制件的强度大为增加。
理想的内圆角半径应有壁厚的1/4以上,外圆角半径可取壁厚的1.5倍。
采用圆弧过渡既可以减小应力集中,还可大大改善塑料的充模特性,避免在转角处因受冲击而形成波纹或弃不满模腔。
注塑制件设计成圆角,使得模具型腔对应部位也呈圆角,这样增加了模具的坚固性,注塑制件的外圆角对应着型腔的内圆角,它使模具在淬炎或使用时不致因应力集中而开裂,提高了模具的使用寿命。
塑胶件应力形成的原因

塑胶件应力形成的原因
注塑件成型过程中冷却的不均匀和过多的保压压力残余等,都会产生内应力,注塑件在一定环境条件的配合下,就会产生内应力塑性变形。
内应力塑性变形有很明显的特征:①变形常带有明显的方向性②内应力塑性变形通常不会改变注塑件的体积大小,只改变零件的外形结构和形状。
按应力产生的根源和表现特征的不同,分为热应力塑性变形(冷却的不均匀)和组织应力塑性(过多的保压压力残余)变形。
?
注塑件应力产生的一个主要原因是在成型过程中,由于制件表里冷却速度不同,表面物料接触温度较低的模壁,迅速冷却固化成一层硬壳,而内部物料还处于熔融状态,随着它的冷却收缩,使得制件内部产生内应力,还有一个因素就是为了注塑件的可靠充填,在注塑工艺调节上使用一定的保压压力,压力通过熔融状态的料流传递到未冷却的制件部位,使注塑件过度压缩产生应力。
注塑件后天应力开裂过程可归结为以下几种情况:化学键破坏;分子间滑脱;范德华力或氢键破坏。
通过对这三种破坏情况的断裂强度理论分析表明:由于实际高分子链的长度是有限的,同时分子链也总会或多或少存在着未取向的部分,因此高聚物正常破坏时,首先将发生在未取向部分的氢键或范德华力的破坏,随后应力集中到取向的主链上,尽管共价键的强度比分子间作用力大10~20倍,但是由于直接承受外力的取向主链数目少,最终还是会有化学键的断裂。
注塑制件内应力影响因素分析

注塑制件内应力影响因素分析文章详细对注塑制件内应力的产生因素进行了分析,并针对其不同的影响因素提出了针对性的解决措施,从实践中证实热处理对于消除或降低注塑制件内应力的有效性,通过该种方式有效稳定热塑制件内部结构,从而保证热塑制件结构质量。
标签:注塑制件;内应力;因素;成型工艺;热处理塑料的加工成型特点优良,因而在加工行业得到了广泛的使用,其最主要的优势在于比强度高、电性能好、质量相对较强,且相比其他材料塑料耐磨性良好,能够消音减震,最重要的是加工方便。
但是注塑制件仍旧存在一个无法避免的缺陷——内应力。
热塑制件会因为内应力而出现翘曲变形现象,严重者会导致制件开裂,另外还会对制件的光学、电学、物理学等性能造成影响,表观质量也同样会受到内应力的影响。
所以寻找对热塑制件内应力影响因素,从而针对性的提出解决措施,是保证热塑制件质量的重要前提,通过有效措施使得热塑制件内应力能够均匀分布。
尤其在使用热塑制件时环境恶劣,例如需要直接接触高热、有机溶剂以及其他腐蚀性介质时,降低内应力可以保证热塑制件结构的稳定性。
1 影响因素分析影响注塑制件内应力大小的因素有很多,具体分析包括以下几点。
1.1 造型设计1.1.1 圆角。
注塑制件其表面相交之处应当采用圆弧进行过度,而其使用上则要求使用尖角。
这是因为注塑制件在注塑过程中截面、形状发生变化的过程中在尖角的位置容易产生极大的应力,并始终无法消除,一旦受到外界的冲击以及超出其能够承受的荷载时就会生生破裂,有些在脱膜过程中就会由于其内应力而出现开裂现象,特别在内角位置。
该类问题可以通过尖角改圆角的方式予以消除,采用0.5mm圆角就能够改善应力集中现象消除内应力的产生,从而改善制件的结构特性,避免由于冲击造成材料不满模腔或形成波纹等问题。
将注塑制件过度位置设计成圆角,那么模型内部也呈圆角,因而磨具也同样具有坚固特性。
由于制件圆角对应模型圆角,因而在热塑过程中不会造成应力过于几种,不但提高了制件的质量,还提升了模具的使用寿命。
塑胶件应力形成的原因

塑胶件应力形成的原因首先,塑料材料的性质是形成塑胶件应力的重要原因之一、塑料材料通常具有一定的粘弹性,即在受力的过程中会发生一定的流变行为。
当外力作用于塑胶件时,塑料会发生变形,而这种变形会引起内部分子链的移动和重排,从而产生应力。
不同种类的塑料材料对外力的响应也会有所不同,因此塑胶件在受力时会出现不同的应力形式。
其次,塑胶件应力形成还与塑料加工过程中的力学效应有关。
塑料加工过程中常常需要通过注塑、挤出、吹塑等方式对塑料进行加工和成型。
在这些过程中,塑料会受到外力的作用,从而引起塑胶件产生应力。
例如,在注塑过程中,塑料在注射机的高压下进入模具腔体,此时会形成模内应力;而在挤出过程中,塑料通过模具的孔口挤出时,会因其速度和流动性而产生不均匀的应力分布。
此外,塑胶件的尺寸和形状也会对应力形成产生影响。
由于塑料本身的收缩性,塑胶件在冷却过程中会出现尺寸的变化,从而产生应力。
尤其在大型厚壁塑胶件中,收缩不均会导致在内部和外部形成不同的应力分布。
另外,塑胶件在使用过程中还会受到外界力的作用,如挤压、撞击、拉伸等,这些外界力也会导致塑胶件产生应力。
在受到这些外界力的作用下,塑胶件会发生形变和应力分布的变化,进而影响其性能和寿命。
为了降低塑胶件应力的产生,可以采取一些措施。
首先,在塑料成型过程中,可以通过合理的模具设计和工艺参数控制,减少应力的集中和不均匀分布。
其次,在塑胶件的设计中尽量避免出现过大的厚度变化和急剧的角度,从而减少应力的集中。
此外,对于在使用过程中易受外界力作用的塑胶件,可以采取增加支撑结构、增加材料刚性等手段来提高其抗应力的能力。
综上所述,塑胶件应力形成是多方面因素共同作用的结果,包括塑料材料的性质、塑料加工过程中的力学效应、塑胶件的尺寸和形状以及外界力的作用等。
了解和控制这些原因,可以有效降低塑胶件应力的产生,并提高其性能和寿命。
注塑件 残余应力
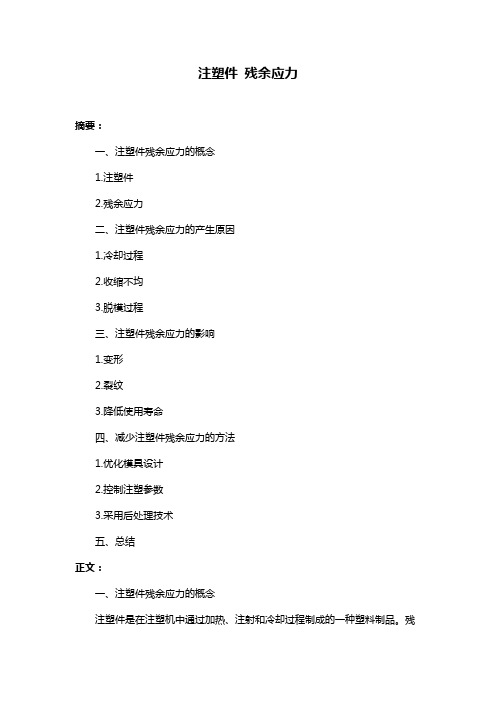
注塑件残余应力摘要:一、注塑件残余应力的概念1.注塑件2.残余应力二、注塑件残余应力的产生原因1.冷却过程2.收缩不均3.脱模过程三、注塑件残余应力的影响1.变形2.裂纹3.降低使用寿命四、减少注塑件残余应力的方法1.优化模具设计2.控制注塑参数3.采用后处理技术五、总结正文:一、注塑件残余应力的概念注塑件是在注塑机中通过加热、注射和冷却过程制成的一种塑料制品。
残余应力是指在注塑件生产过程中,由于冷却收缩、脱模等外力作用,使得塑料内部产生的一种潜在的应力。
这种应力在制品内部形成一个平衡状态,但如果受到外部因素的影响,可能会引发制品变形、裂纹等问题。
二、注塑件残余应力的产生原因1.冷却过程:在注塑件冷却过程中,由于塑料的热膨胀系数和冷却速度不同,容易产生收缩不均,从而导致内部应力的产生。
2.收缩不均:由于模具设计不合理、浇口位置不当等原因,使得塑料在冷却过程中收缩不均,从而形成残余应力。
3.脱模过程:在脱模过程中,如果脱模力过大或过小,都可能导致制品内部产生应力。
三、注塑件残余应力的影响1.变形:残余应力使制品在存放、使用过程中容易发生变形,影响制品的外观和使用性能。
2.裂纹:当残余应力超过制品的强度极限时,容易在制品表面形成裂纹,导致制品报废。
3.降低使用寿命:残余应力会降低制品的使用寿命,严重时可能导致制品在使用过程中突然损坏。
四、减少注塑件残余应力的方法1.优化模具设计:合理设置模具冷却水道,确保冷却速度均匀;选择合适的模具材料,提高模具刚性;合理设置浇口位置,减小收缩变形。
2.控制注塑参数:合理选择注射速度、压力、时间和温度等注塑参数,降低残余应力的产生。
3.采用后处理技术:通过热处理、时效处理等方法,消除或减小残余应力,提高制品的稳定性和使用寿命。
综上所述,注塑件残余应力对制品的质量、使用寿命和性能具有重要影响。
要减少残余应力,需要从模具设计、注塑参数控制和后处理技术等方面进行优化。
塑料加工中的变形和应力分析
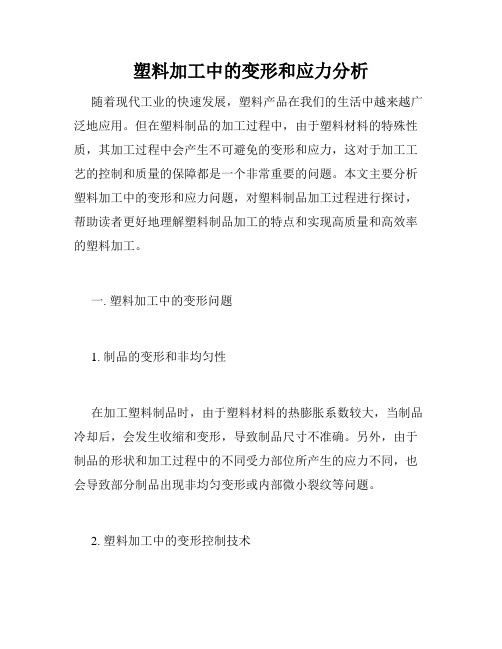
塑料加工中的变形和应力分析随着现代工业的快速发展,塑料产品在我们的生活中越来越广泛地应用。
但在塑料制品的加工过程中,由于塑料材料的特殊性质,其加工过程中会产生不可避免的变形和应力,这对于加工工艺的控制和质量的保障都是一个非常重要的问题。
本文主要分析塑料加工中的变形和应力问题,对塑料制品加工过程进行探讨,帮助读者更好地理解塑料制品加工的特点和实现高质量和高效率的塑料加工。
一. 塑料加工中的变形问题1. 制品的变形和非均匀性在加工塑料制品时,由于塑料材料的热膨胀系数较大,当制品冷却后,会发生收缩和变形,导致制品尺寸不准确。
另外,由于制品的形状和加工过程中的不同受力部位所产生的应力不同,也会导致部分制品出现非均匀变形或内部微小裂纹等问题。
2. 塑料加工中的变形控制技术为解决塑料加工中的变形问题,一般采用以下技术:①优化注塑工艺:可以通过优化注塑工艺,对制品尺寸、厚度和形状进行控制,降低制品的变形程度。
②改善模具结构:改善模具结构可以使制品的应力分布更加均匀,从而减缓制品的变形过程。
③控制材料特性:在加工前,通过改变材料的成分、熔指和注射温度等参数,对材料的变形性进行控制,从根本上减少制品的变形问题。
二. 塑料加工中的应力问题1. 塑料制品中的塑性流变在塑料制品加工过程中,由于塑料材料的特殊性质,其产生的应力和变形是不可避免的。
当塑料材料在加工过程中受到外力时,其分子链会发生流动,这种塑性流变会导致塑料产生应力。
2. 塑料制品中的应力分析为了确保制品质量,需要对塑料制品中的应力进行分析和计算。
应力分析可以通过数学模型进行计算,包括材料的弹性模量、切变模量、泊松比等参数,以及制品的形状和加工过程中受力部位等因素。
通过应力分析,可以确定制品结构和加工工艺的合理性,并对加工工艺进行优化和改进,以减少制品产生的应力。
3. 应力控制和优化技术为了控制和优化塑料制品中的应力,可以采用以下技术:①适当降低注射温度:合理降低注射温度可以减少塑料在注射过程中发生流变的机会,减少制品产生的应力。
注塑件应力痕的原因及解决方法

注塑件应力痕的原因及解决方法嘿,咱今儿就来唠唠注塑件应力痕这档子事儿。
你说这应力痕啊,就像是注塑件上的一个小捣蛋鬼,时不时就冒出来给咱添乱。
先说说这应力痕出现的原因吧。
就好比咱走路,走着走着碰到个石头绊了一下,这注塑过程中也会有各种“绊脚石”呢。
材料的选择就是一块很重要的“石头”呀,如果选的材料不合适,那可就容易出问题啦。
还有注塑工艺呢,温度啦、压力啦、速度啦,这些没把握好,那不就相当于走路没走好,摔了一跤嘛,应力痕就出来啦。
模具设计不合理也是个大问题呀,就像给人穿了一双不合脚的鞋,能舒服吗?能不留下点痕迹吗?那咱咋解决这讨厌的应力痕呢?嘿嘿,这可得有点小妙招。
咱先从材料下手,精挑细选,找那最合适的,就像找对象似的,得找个合得来的呀。
注塑工艺呢,那可得小心翼翼地调整,温度别太高也别太低,压力和速度都得恰到好处,这可得有点耐心和细心哟。
模具设计也得改改呀,让它更合理,更适合注塑件的“成长”,这不就相当于给它一个舒适的“家”嘛。
你想想,要是注塑件都没了应力痕,那得多漂亮呀,多让人喜欢呀!就像一个人脸上没了痘痘,那得多精神呀!咱不能让这应力痕坏了咱的好事呀,对不对?所以呀,咱得重视起来,把这个小捣蛋鬼给赶跑咯!咱得让注塑件都漂漂亮亮、光光滑滑的,这样用起来才舒心呀,你说是不是这个理儿?而且呀,解决了应力痕问题,不只是看着好看,它的质量也会更好呀。
就好比一个人,不仅外表好看,内在也很优秀,那多棒呀!这样的注塑件用起来才更放心,更长久呢。
总之呢,注塑件应力痕可不是个小问题,咱得认真对待,找对原因,用对方法,把它彻底解决掉。
让咱的注塑件都能完美无瑕,为我们的生活和工作添彩呀!别小瞧了这小小的应力痕,处理好了那可是大功劳呢!。
注塑机热应力计算公式

注塑机热应力计算公式引言。
注塑机是一种用于生产塑料制品的设备,它通过将塑料加热至熔化状态,然后将熔融塑料注入模具中,最终形成所需的塑料制品。
在注塑过程中,熔融塑料会受到热应力的影响,这会对最终的产品质量产生影响。
因此,热应力的计算对于注塑机的运行和产品质量具有重要意义。
热应力的定义。
热应力是指材料在受热或冷却时由于温度变化引起的内部应力。
在注塑机中,熔融塑料在加热和冷却过程中会受到热应力的影响,这会导致产品的变形和内部应力的积累。
因此,了解和计算热应力是非常重要的。
热应力的计算公式。
热应力的计算公式可以通过材料的热膨胀系数和温度变化来进行计算。
在注塑机中,常用的热应力计算公式如下:σ = E αΔT。
其中,σ表示热应力,E表示杨氏模量,α表示热膨胀系数,ΔT表示温度变化。
在这个公式中,杨氏模量是材料的一种力学性质,它反映了材料在受力时的变形能力。
热膨胀系数则是材料在温度变化时的膨胀程度,它反映了材料对温度变化的敏感程度。
通过这个公式,我们可以计算出在注塑过程中熔融塑料所受到的热应力。
热应力的影响因素。
在注塑机中,热应力的大小受到多种因素的影响,包括材料的性质、注塑过程中的温度变化、注射速度和压力等。
其中,材料的性质是影响热应力的关键因素之一。
不同的塑料材料具有不同的热膨胀系数和杨氏模量,因此它们在注塑过程中所受到的热应力也会有所不同。
此外,注塑过程中的温度变化也会对热应力产生影响。
在注塑过程中,熔融塑料会经历加热和冷却的过程,这会导致温度的变化,从而产生热应力。
注射速度和压力也会对热应力产生影响,过快的注射速度和过大的压力会导致熔融塑料受到更大的热应力。
热应力的控制方法。
为了减小热应力对注塑产品的影响,可以采取一些控制方法。
首先,可以通过选择合适的塑料材料来降低热应力的大小。
不同的塑料材料具有不同的热膨胀系数和杨氏模量,因此选择合适的塑料材料可以降低热应力的大小。
其次,可以通过控制注塑过程中的温度变化来减小热应力。
注塑时减少应力集中的方法
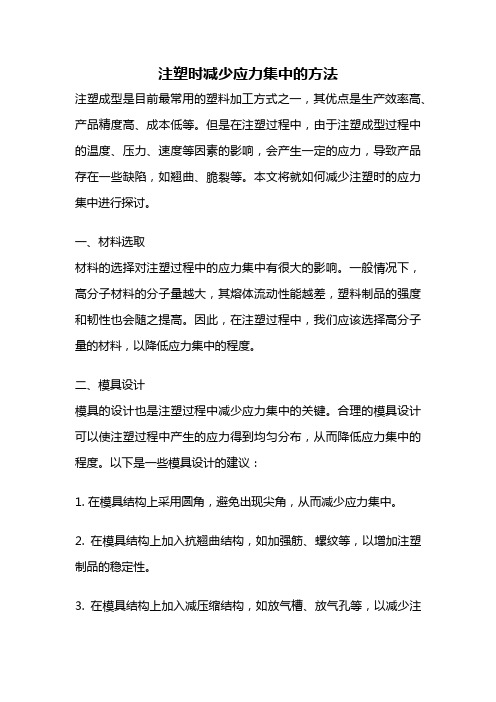
注塑时减少应力集中的方法注塑成型是目前最常用的塑料加工方式之一,其优点是生产效率高、产品精度高、成本低等。
但是在注塑过程中,由于注塑成型过程中的温度、压力、速度等因素的影响,会产生一定的应力,导致产品存在一些缺陷,如翘曲、脆裂等。
本文将就如何减少注塑时的应力集中进行探讨。
一、材料选取材料的选择对注塑过程中的应力集中有很大的影响。
一般情况下,高分子材料的分子量越大,其熔体流动性能越差,塑料制品的强度和韧性也会随之提高。
因此,在注塑过程中,我们应该选择高分子量的材料,以降低应力集中的程度。
二、模具设计模具的设计也是注塑过程中减少应力集中的关键。
合理的模具设计可以使注塑过程中产生的应力得到均匀分布,从而降低应力集中的程度。
以下是一些模具设计的建议:1. 在模具结构上采用圆角,避免出现尖角,从而减少应力集中。
2. 在模具结构上加入抗翘曲结构,如加强筋、螺纹等,以增加注塑制品的稳定性。
3. 在模具结构上加入减压缩结构,如放气槽、放气孔等,以减少注塑制品的内部应力。
4. 在模具结构上加入冷却结构,如冷却水路、冷却器等,以加速制品冷却,减少内部应力。
三、注塑工艺参数的控制在注塑过程中,控制注塑工艺参数也是减少应力集中的重要方法。
以下是一些注塑工艺参数的控制建议:1. 控制注塑温度。
注塑温度过高会导致熔体流动性能变差,注塑制品的强度和韧性也会随之下降。
2. 控制注塑压力。
注塑压力过大会使熔体内部应力增大,从而导致应力集中的程度加大。
3. 控制注塑速度。
注塑速度过快会导致熔体流动不均,注塑制品的强度和韧性也会随之下降。
4. 控制射胶量。
射胶量过大会导致注塑制品的尺寸不稳定,从而导致应力集中的程度加大。
5. 控制模具温度。
模具温度过高会导致注塑制品的内部应力增大,从而导致应力集中的程度加大。
四、注塑制品的后处理注塑制品的后处理也是减少应力集中的重要方法。
以下是一些注塑制品后处理的建议:1. 在注塑制品冷却后,应立即取出制品,并进行冷却处理。
- 1、下载文档前请自行甄别文档内容的完整性,平台不提供额外的编辑、内容补充、找答案等附加服务。
- 2、"仅部分预览"的文档,不可在线预览部分如存在完整性等问题,可反馈申请退款(可完整预览的文档不适用该条件!)。
- 3、如文档侵犯您的权益,请联系客服反馈,我们会尽快为您处理(人工客服工作时间:9:00-18:30)。
注射工艺的影响的三大因素
时间:2013-07-24来源:环球塑化资讯网
摘要:影响注射工艺有三大因素,它的正确制订是为了保证塑料熔体良好的塑化,并且顺利地充模、冷却于定型,以便生产出质量合乎要求的制品;在注射工艺中最重要的工艺参数是温度(料温、喷嘴温度、模具温度)、压力(塑化压力、注塑压力、型腔压力)和相对应的各个作用时间(注射时间、保证时间、冷却时间)等。
下面仅讨论主要的工艺参数及相互影响。
影响注射工艺有三大因素,它的正确制订是为了保证塑料熔体良好的塑化,并且顺利地充模、冷却于定型,以便生产出质量合乎要求的制品;在注射工艺中最重要的工艺参数是温度(料温、喷嘴温度、模具温度)、压力(塑化压力、注塑压力、型腔压力)和相对应的各个作用时间(注射时间、保证时间、冷却时间)等。
下面仅讨论主要的工艺参数及相互影响。
一、温度的影响
1.料温
塑料的加工温度是由注射机料筒来控制的。
料筒温度的正确选择关系到塑料的塑化质量,其原则是能保证顺利地注射成型而又不引起塑料局部降解。
通常,料筒末端最高温度应高于塑料的流动温度(或熔融温度),但低于塑料的分解温度。
在生产中除了要严格控制注射机料筒的最高温度外,还应控制塑料熔体在料筒中的停留时间。
在确定料筒温度时,还应考虑制品和模具的结构特点。
当成型薄壁或形状复杂的制品时,流动阻力大,提高料筒温度有助于改善熔体的流动性。
通常控制喷嘴的最高温度稍低于料筒的最高温度,以防止熔体在喷嘴口发生流延现象。
2.模具温度
在注射成型过程中模具温度是由冷却介质(一般为水)控制的,它决定了塑料熔体的冷却速度。
模具温度越低,冷却速度越快,熔体温度降低得越迅速,造成熔体粘度增大、注射压力损失增加,严重时甚至于引起充模不足。
随着模具温度的增加,熔体流动性增加,所需充模压力减小,制品表面质量提高;但由于冷却时间增长,制品的生产率下降,制品的成型收缩率增大。
对于结晶形塑料,由于较高温度有利于结晶,所以升高模具温度能提高制品的密度或结构晶度。
在较高的模温下制品中聚合物大分子松弛过程较快,分子取向作用和内应力都会降低。
二、压力的影响
注射成型过程中的压力包括塑化压力、注射压力和型腔压力。
塑化压力又称背压,是指注射机螺杆顶部的熔体在螺杆转动后退时所受到的压力,是通过调节注射液压缸的回油阻力来控制的。
塑化压力增加了熔体的内压力,加强了剪切效果,由于塑料的剪切发热,因此提高了熔体的温度。
塑化压力的增加使螺杆退回速度减慢,延长了塑料在螺杆中的受热时间,塑化质量可以得到改善;但过大的塑化压力还增加料筒计量室内熔体的反流和漏流,降低了熔体的输送能力,减少了塑化量,增加了功率消耗,并且过高塑化压力会使剪切发热或切应力过大,熔体易发生降解。
注射压力是指注射时在螺杆头部产生的熔体压强。
在选择注射压力时,首先应考虑注塑机所允许的注塑压力,只有在注射压力过低回导致型腔压力不足,熔体不能顺利充满型腔;反之,注射压力过大,不仅会造成制品溢漏,还会造成制品变形,甚至于系统过载。
在注射过程中注射压力与熔体温度是相互制约的。
料温高时所需注射压力和料温的组合下才会获得满意的结果。
型腔压力是指注塑压力经过喷嘴、流道贺浇口的压力损失后在模具型腔内产生的熔体压强。
三、注射成型周期和注射速度
完成一次注塑成型所需的时间称为注射成型周期,它包括加料、加热、充模、保压、冷却时间,以及开模、脱模、闭模及辅助作业等时间。
在整个注射成型周期中,注射速度和冷却时间对制品的性能有着决定性的影响。
注射速度主要影响熔体在型腔内德流动行为。
通常随着注射速度的增大,熔体流速增加,剪切作用加强;熔体温度因剪切发热而升高,粘度降低,所以有利于充模。
并且制品各部分的熔合纹强度也得以增加。
但是,由于注射速度增大,可能使熔体从层流体状态变为流,严重时会引起熔体在模内喷射而造成模内空气无法排出,这部分空气在高压下被压缩速度升温,会引起制品局部烧焦或分解。
在实际生产中,注射速度通常是经过试验来确认的。
一般先以低压慢速度注射,然后根据制品的成型情况而调整注射速度。
现代的注射机已实现了多级注射技术,即在一个注射过程中,当注射机螺杆推动熔体注入模具时,可以根据不同的需要实现对在不同位置上有不同注射速度和不同注射压力等工艺参数的控制。
多级注射工艺应根据不同品种的塑料和不同的制品进行拟定和选择。