成形技术review
材料成形技术基础
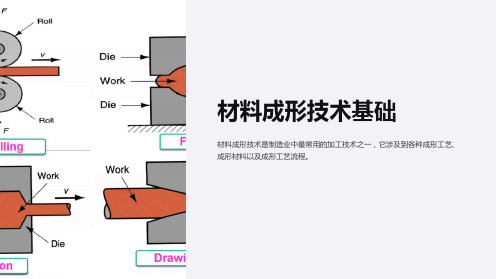
电子制造
材料成形技术在电子设备的封装和连接中起着重要 作用。
航空航天
艺术雕塑
材料成形技术用于制造航空航天部件和航天器结构。 材料成形技术被艺术家用于创作各种雕塑作品。
材料成形技术的挑战与发展趋势
1 高性能材料
随着科技的进步,材料成形技术需要适应高性能材料的特性和要求。
材料成形技术基础
材料成形技术是制造业中最常用的加工技术之一,它涉及到各种成形工艺、 成形材料以及成形工艺流程。
成形技术定义
成形技术是通过施加力或应用热量将原始材料转化为所需形状和尺寸的加工方法。
主要成形技术分类
1 压力成形技术
将材料置于模具中,并施加压力使其变形, 如冲压、铸造等。
2 热成形技术
2 节能环保
开发符合节能环保要求的成形工艺和材料,减少资源消耗和环境污染。
3 数字化制造
利用数字化技术实现材料成形过程的自动化和智能化。
3
成形操作
按照成形工艺要求进行操作,施加力或应用热量使材料变形。
常见的成形材料
金属
如铝、钢等,用于制造汽车零部件、电子设备等。
塑料
如聚乙烯、聚丙烯等,广泛用于塑料制品的生产。
陶瓷
如瓷器、陶器等,用于制作装饰品、器皿等。
复合材料
如碳纤维增强复合材料,用于制造航空航天部件。
材料成形技术的应用领域
汽车制造
通过加热材料使其变软或熔化,然后形成所 需形状,如热压、热挤压等。
3 凝固成形技术
通过材料凝固过程中的相变来实现成形,如 注射成型、凝胶成型等。
4 仿生如3D打印、 模具复制等。
成形工艺流程
1
有关快速成型技术论文
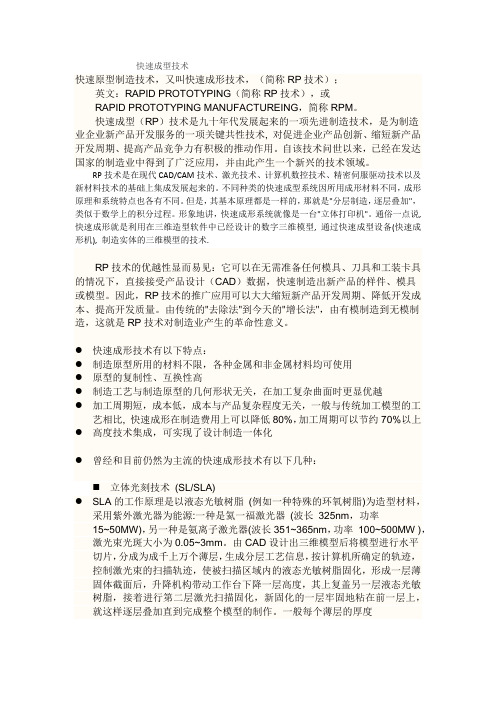
快速成型技术快速原型制造技术,又叫快速成形技术,(简称RP技术);英文:RAPID PROTOTYPING(简称RP技术),或RAPID PROTOTYPING MANUFACTUREING,简称RPM。
快速成型(RP)技术是九十年代发展起来的一项先进制造技术,是为制造业企业新产品开发服务的一项关键共性技术, 对促进企业产品创新、缩短新产品开发周期、提高产品竞争力有积极的推动作用。
自该技术问世以来,已经在发达国家的制造业中得到了广泛应用,并由此产生一个新兴的技术领域。
RP技术是在现代CAD/CAM技术、激光技术、计算机数控技术、精密伺服驱动技术以及新材料技术的基础上集成发展起来的。
不同种类的快速成型系统因所用成形材料不同,成形原理和系统特点也各有不同。
但是,其基本原理都是一样的,那就是"分层制造,逐层叠加",类似于数学上的积分过程。
形象地讲,快速成形系统就像是一台"立体打印机"。
通俗一点说, 快速成形就是利用在三维造型软件中已经设计的数字三维模型, 通过快速成型设备(快速成形机), 制造实体的三维模型的技术.RP技术的优越性显而易见:它可以在无需准备任何模具、刀具和工装卡具的情况下,直接接受产品设计(CAD)数据,快速制造出新产品的样件、模具或模型。
因此,RP技术的推广应用可以大大缩短新产品开发周期、降低开发成本、提高开发质量。
由传统的"去除法"到今天的"增长法",由有模制造到无模制造,这就是RP技术对制造业产生的革命性意义。
●快速成形技术有以下特点:●制造原型所用的材料不限,各种金属和非金属材料均可使用●原型的复制性、互换性高●制造工艺与制造原型的几何形状无关,在加工复杂曲面时更显优越●加工周期短,成本低,成本与产品复杂程度无关,一般与传统加工模型的工艺相比, 快速成形在制造费用上可以降低80%,加工周期可以节约70%以上●高度技术集成,可实现了设计制造一体化●曾经和目前仍然为主流的快速成形技术有以下几种:⏹立体光刻技术(SL/SLA)●SLA的工作原理是以液态光敏树脂(例如一种特殊的环氧树脂)为造型材料,采用紫外激光器为能源:一种是氦一福激光器(波长325nm,功率15~50MW),另一种是氨离子激光器(波长351~365nm,功率100~500MW ),激光束光斑大小为0.05~3mm。
先进金属复合材料成形技术

先进金属复合材料成形技术
先进金属复合材料成形技术是指利用先进的工艺和设备对金属复合材料进行成形加工的技术。
金属复合材料是由金属基体和增强材料(如纤维增强材料)组成的复合材料。
相比于传统的单一金属材料,金属复合材料具有更高的强度、刚度和耐热性能。
然而,由于其复杂的结构和成分,金属复合材料的成形加工相对困难。
先进金属复合材料成形技术主要包括以下几个方面:
1. 粉末冶金成形技术:通过将金属粉末与增强材料混合,然后经过高温和高压的成形过程,使其熔合并固化成型。
这种成形技术适用于复杂形状和大尺寸的金属复合材料制品。
2. 金属复合材料锻造技术:利用锻机对金属复合材料进行锻造成型。
锻造可以改变材料的内部组织结构和形状,从而提高其力学性能和耐热性能。
3. 金属复合材料挤压技术:通过在金属复合材料中施加高压,使其通过模具的通道流动并成形。
挤压成形技术适用于长条形的金属复合材料制品。
4. 金属复合材料注射成型技术:利用注射机将金属复合材料融化后注入模具中进行成型。
注射成型技术可以制造出高精度和复杂形状的金属复合材料制品。
以上是几种常见的先进金属复合材料成形技术,通过这些技术的应用,可以制造出更高性能、更复杂的金属复合材料制品,满足不同领域对于材料强度和耐热性能的要求。
材料成型工艺基础部分中英文词汇对照

材料成型工艺基础部分中英文词汇对照材料成型工艺基础部分0 绪论金属材料:metal material (MR)高分子材料:high-molecular material陶瓷材料:ceramic material复合材料:composition material成形工艺:formation technology1 铸造铸造工艺:casting technique铸件:foundry goods (casting)机器零件:machine part毛坯:blank力学性能:mechanical property砂型铸造:sand casting process型砂:foundry sand1.1 铸件成形理论基础合金:alloy铸造性能:casting property工艺性能:processing property 收缩性:constringency偏析性:aliquation氧化性:oxidizability吸气性:inspiratory铸件结构:casting structure 使用性能:service performance 浇不足:misrun冷隔:cold shut夹渣:cinder inclusion粘砂:sand fusion缺陷:flaw, defect, falling流动性:flowing power铸型:cast (foundry mold)蓄热系数:thermal storage capacity浇注:pouring凝固:freezing收缩性:constringency逐层凝固:layer-by-layer freezing糊状凝固:mushy freezing结晶:crystal缩孔:shrinkage void缩松:shrinkage porosity顺序凝固:progressive solidification冷铁:iron chill补缩:feeding等温线法:constant temperature line method内接圆法:inscribed circle method 铸造应力:casting stress 变形:deforming裂纹:crack机械应力:mechanical stress热应力:heat stress相变应力:transformation stress 气孔:blow hole铸铁:ingot铸钢:cast steel非铁合金:nonferrous alloy灰铸铁:gray cast-iorn孕育处理:inoculation球墨铸铁:spheroidal球化处理:sheroidisation可锻铸铁:ductile cast iron石墨:graphite蠕墨铸铁:vermicular cast iron 热处理:heat processing铝合金:Al-alloy熔炼:fusion metallurgy铜合金:copper alloy氢脆:hydrogen brittleness1.2 铸造方法(casting method)手工造型:hand moulding机器造型:machine moulding金属型:metal mold casting金属模:permanent mould压力铸造:press casting熔模铸造:investment moulding蜡膜:cere离心铸造:centrifugal casting低压铸造:casting under low pressure 差压铸造:counter-pressure casting 陶瓷型铸造:shaw process1.3 铸造工艺设计浇注位置:pouring position分型面:mould joint活块:loose piece起模:patter drawing型芯:core型芯撑:chaplet工艺参数:processing parameter下芯:core setting合型:mould assembly冒口:casting head尺寸公差:dimensional tolerance 尺寸公差带:tolerance zone 机械加工余量:machining allowance 铸孔:core hole非标准:nonstandard label收缩率:rate of contraction线收缩:linear contraction体收缩:volume contraction起模斜度:pattern draft铸造圆角:curving of castings芯头:core register芯头间隙:clearance芯座:core print seat分型线:joint line分模线:die parting line 1.4 铸造结构工艺性加强筋:rib reinforcement 撒砂:stuccoing内腔:entocoele2 金属塑性加工塑性加工:plastic working 塑性:plastic property锻造:forge work冲压:punching轧制:rolling拉拔:drawing挤压:extruding细化晶粒:grain refinement 热锻:hit-forging2.1 金属塑性加工理论基础塑性变形:plastic yield加工硬化:work-hardening韧性:ductility回复温度:return temperature 再结晶:recrystallize 再结晶退火:full annealing 冷变形:cold deformation 热变性:heat denaturation锻造比:forging ratio镦粗:upset拔长:pull out纤维组织:fibrous tissue锻造性能:forging property变形抗力:resistance of deformation化学成分:chemical constitution热脆性:hot brittleness冷脆性:cold-shortness变形速度:deformation velocity应力状态:stress condition变形温度:deformation temperature过热:overheating过烧:burning脱碳:carbon elimination始锻温度:initiation forging temperature 终锻温度:final forging temperature2.2 金属塑性加工方法自由锻:flat-die hammer弯曲:bend弯曲半径:bending radius切割:cut扭转:twist rotation错移:offsetting锻接:percussion基本工序:basic process辅助工序:auxiliary process精整工序:finishing process模锻:contour forging锻模:forging die胎膜锻:fetal membrane forging 剪床:shearing machine冲床:backing-out punch弹性变形:elastic distortion塑性变形:plastic yield剪切变形:shearing deformation最小弯曲半径:minimum bending radius 曲率:angularity弯裂:rupture回弹:rebound辊轧:roll forming辊锻:roll forging斜轧:oblique rolling横轧:transverse rolling辗压:tamping drum挤压:extruding拉拔:draft2.3 塑性加工工艺设计工艺规程:process specification 锻件图:forging drawing敷料:dressing锻件余量:forging allowance锻件公差:forging tolerance工夹具:clamping apparatus加热设备:firing equipment加热规范:heating schedule冷却规范:cooling schedule后续处理:after treatment分模面:die parting face冲孔连皮:punching the wad模锻斜度:draft angle圆角半径:radius of corner圆饼类锻件:circumcresent cake-like forging 长轴类锻件:long axis-like forging2.4 锻件结构工艺性锥体:cone斜面:cant空间曲线:curve in space粗糙度:degree of roughness2.5 冲压件结构工艺性3 焊接焊接:welding铆接:riverting熔焊:fusion welding压焊:press welding钎焊:braze welding3.1 焊接理论基础冶金:metallurgy电弧焊:arc welding气焊:acetylene welding电渣焊:electro-slag welding高能束焊:high energy welding电子焊:electronic welding激光焊:laser welding等离子焊:plasma welding电弧:electric arc阳极区:anode region阴极区:negative polarity弧柱区:arc stream正接法:electrode negative method 反接法:opposition method脱氧剂:deoxidizing agent焊缝:welded seam焊缝区:weld zone熔合区:fusion area热影响区:heat-affected zone脆性断裂:brittle fracture过热区:overheated zone正火区:normalized zone相变区:phase change zone焊接应力:welding stress收缩变形:contraction distortion角变形:angular deformation弯曲变形:bend deformation扭曲变形:warping deformation波浪变形:wave transformation反变形法:reversible deformation method刚性固定法:rigid fixing method预热:warming-up缓冷:slow cool焊后热处理:postweld heat treatment矫形处理:shape-righting3.2 焊接方法埋弧焊:hidden arc welding气体保护焊:gas shielded arc welding氩弧焊:argon welding熔化极氩弧焊:consumable electrode argon welding 钨极氩弧焊:argon tungsten-arc weldinggas shielded arc welding 二氧化碳气体保护焊:CO2碳弧焊:carbon arc welding碳弧气刨:carbon arc air gouging电渣焊:electro-slag welding高能焊:high grade energy welding等离子弧切割:plasma arc cutting (PAC)堆焊:bead weld电阻焊:resistance welding电焊:electric welding缝焊:seam welding压焊:press welding多点凸焊:multiple projection welding 对焊:welding neck 摩擦焊:friction welding扩散焊:diffusion welding硬钎料:brazing alloy软钎料:soft solder3.3 常用金属材料的焊接焊接性:weldability焊接方法:welding method焊接材料:welding material 焊条:electrode焊剂:flux material碳素钢:carbon steel低碳钢:low carbon steel中碳钢:medium carbon steel 高碳钢:high carbon steel 低合金钢:lean alloy steel 不锈钢:non-corrosive steel 有色金属:nonferrous metal 3.4 焊接工艺设计型材:sectional bar药皮:coating焊丝:soldering wire。
材料成形技术基础知识总结

第一章绪论1. 现代制造过程的分类:质量增加、质量不变、质量减少2. 质量增加过程:渗碳,渗氮,氰化处理,电镀3. 质量减少过程:切削,切割,电解,落料,冲孔,剪切4. 质量不变过程:锻造,轧制第二章液态材料铸造成形技术过程1. 充型能力:液态金属充满铸型型腔,获得形状完整、轮廓清晰的铸件的能力。
表征方式:最小壁厚2. 充型能力弱:产生浇不足,冷隔,气孔,夹杂,缩孔,热裂等缺陷3. 充型能力取决于:金属自身的流动能力(主要),铸型性质(速度,热交换强度,蓄热系数),浇筑条件(速度温度),铸型结构(折算厚度)4. 金属的流动性:1. 定义:液态金属自身的流动能力2. 测量方法:将金属液浇入螺旋型试样铸型中,表征方式:螺旋线试样长度5. 收缩铸件在液态,凝固和固态冷却过程中所产生的体积和尺寸减小的现象6. 收缩的三个阶段1. 液态凝固阶段表现:腔内液面降低2. 凝固收缩阶段3. 固态收缩阶段表现:铸件外形尺寸减少;是产生拉力、变形、裂纹等缺陷的基本原因凝固:逐层凝固,体积凝固,中间凝固。
7. 铸件的实际收缩1. 铸型表面的摩擦阻力2. 热阻力(壁厚均匀则无3. 机械阻力只受到1,自由收缩否则为受阻收缩8. 缩孔:凝固过程,大而密集的孔洞形成条件:金属在恒温/很窄的温度范围结晶,铸件由表及里逐层凝固原因:金属的液态收缩和凝固收缩值大于固态收缩值,且得不到补偿形成部位:铸件最后凝固区域9. 缩松:凝固过程小而分散的孔洞形成条件:结晶温度范围较宽,体积凝固原因:金属的液态收缩和凝固收缩大于固态收缩形成部位:铸件壁中心区域厚大部位10. 防止方法:1. 采用顺序凝固即a.合理设计内浇口位置和浇注工艺b.合理应用冒口、冷铁和补贴等技术措施2. 加压补缩11. 铸造应力:铸件在凝固和随后的冷却过程中,固态收缩受到阻碍而引起的内应力分类:热应力【薄壁、细小部位:冷的快,受压应力(凸出);厚壁、粗大部位:冷得慢,受拉应力(凹进)】,相变应力,机械阻碍应力12.减少措施:选弹性模量,收缩系数小;同时凝固;浇冒口,缓冷;选退让性好的砂芯13. 热裂:形状特征:裂缝短,缝隙宽,形状曲折,缝内呈氧化颜色防止措施:改善型砂退让性冷裂:形状特征:裂纹细小,呈连续直线状,缝内有金属光泽或轻微氧化色14. 吸气性:金属在熔炼过程中会溶解气体(主要H2、N2、O2)15. 吸气过程:气分子撞击金属液表面,高温而离解为原子,吸附在金属表面,扩散到内部16. 偏析:铸件凝固后,截面上不同部位,以至于晶粒内部产生化学成分不均匀的现象宏观偏析:成分不均匀现象表现在较大尺寸范围,分类:正偏析(k>1),逆偏析(k<1)k:溶质平衡分配系数(固相溶质/液相溶质)微观偏析:微小范围内的化学成分不均匀,分类:晶内偏析(消除:扩散退火,均匀化退火)和晶界偏析(细化晶粒)17. 气孔分类:侵入气孔:砂型或型芯中的挥发物挥发生成析出气孔:溶解于金属液的气体因溶解度下降析出反应气孔:化学反应产生的气体18. 浇注系统结构和功能1. 结构:浇口杯,直浇道,横浇道,内浇道2. 功能:连接型腔浇包,平稳导入液态金属;挡渣及排除腔中气体;调节温度分布控制凝固顺序;合理地充满铸型19. 冒口定义:储存金属液补偿铸件收缩,防止缩松缩孔。
燃料电池金属双极板设计与成形技术综述

第14卷 第3期 精 密 成 形 工 程2022年3月JOURNAL OF NETSHAPE FORMING ENGINEERING25收稿日期:2020-06-02基金项目:江苏省前沿引领技术基础研究专项(SBK2019050036);国防基础科研项目(JCKY2020203B056);江苏省高等学校自然科学研究重大项目(20KJA460003);江苏省“六大人才高峰”高层次人才项目(GDZB-069) 作者简介:华日升(1996—),男,硕士生,主要研究方向为金属极板精密成形技术。
通讯作者:王春举(1978—),男,博士,教授,主要研究方向为金属微结构智能制造与系统应用。
燃料电池金属双极板设计与成形技术综述华日升a ,张文泉a ,程利冬b ,王春举a(苏州大学 a. 机电工程学院 机器人与微系统研究中心;b. 档案馆,江苏 苏州 215325) 摘要:氢燃料电池具有清洁、高效等诸多优点,受到了世界各国的高度关注,极板是其重要部件之一。
综述了质子交换膜氢燃料电池金属双极板设计、成形等方向的研究和应用进展。
在金属双极板设计方向,从极板平面流场分布设计、3D 流场设计、考虑电堆结构的极板流场设计以及微流道尺寸优化设计等方面进行综述;在金属极板成形方向,从刚模冲压成形、软模冲压成形以及成形质量与电池性能相关性等方面进行综述。
最后,结合笔者对行业的调研和理解,对未来金属极板的方向发展进行了展望。
关键词:氢燃料电池;金属双极板;流场设计;冲压成形;工艺与性能相关性 DOI :10.3969/j.issn.1674-6457.2022.03.004中图分类号:TG386 文献标识码:A 文章编号:1674-6457(2022)03-0025-09Review on Design and Forming Technology of Metallic Bipolar Plates for Fuel CellsHUA Ri-sheng a , ZHANG Wen-quan a , CHENG Li-dong b , WANG Chun-ju a(a. Robotics and Microsystems Center, School of Mechanical and Electrical Engineering; b. Archives,Soochow University, Suzhou 215325, China)ABSTRACT: Hydrogen fuel cell has attracted great attention from all over the world due to the advantages such as cleanliness, high efficiency, etc., and polar plate is one of its important components. The research and application progress in the design and forming of metallic bipolar plates of proton exchange membrane hydrogen fuel cells were reviewed. In the design direction of metallic bipolar plate, the design of planar flow field distribution, 3D flow field design, flow field design of bipolar plate con-sidering stack structure and optimization design of microchannel size were summarized. In the forming direction of metallic po-lar plate, the rigid die stamping forming, soft die stamping forming and the correlation between forming quality and battery per-formance were overviewed. Finally, combined with the author's research and understanding of the industry, the future develop-ment of metallic polar plate was prospected.KEY WORDS: hydrogen fuel cells; metallic bipolar plates; design of flow field; stamping forming; correlation between process and performance人类赖以生存的传统化石燃料日渐枯竭,世界各国政府纷纷出台传统能源车禁售时间表,氢能作为国际公认的清洁、高效能源,受到各国政府和产业的高度重视。
钢板成形技术

7、板后变化趋势
初始板厚1mm
钢板成形技术
目录
1、概述 2、钢板成形技术介绍 3、拉深成形技术介绍 4、拉深成形中对成形质量影响的工艺参数
1、概述
汽车产品
航天产品
航空产品
家用产品
2、钢板成形技术介绍
二. 板材成形极限及影响因素 (1)提高伸长类成形极限的措施
1)提高材料塑性 2)减小变形不均匀程度(提高塑性变形稳定性) 3)消除引起局部应力集中的因素
3、压边力
在成形过程中施加的压边力对材料成形也有巨大影响,材料的压边力过 大会出现材料表面起皱现象,但是如果材料的压边力过大又会导致材料的成 形后出现破裂现象。
4、压边间隙
在成形过程中压边间隙也是影响成形质量的重要因素,压边间隙过小, 材料在成形过程中很难流动,而如果压边间隙过大材料快速进入成形模内, 材料就会在短时间大量堆积,出现表面起皱破裂等现象。
(2)提高压缩类成形极限的措施 1)提高传力区的承载能力,降低变形区的变形抗力及摩擦力 2)阻止毛坯变形区失稳起皱 3)以降低变形区的变形抗力为主要目的的退火
3、拉深成形技术介绍
在凸模作用下,原直径为D0的毛坯, 在凹模和压边圈之间的缝隙中变形, 并被拉进凸,凹模的间隙中形成空间 零件的直壁
拉深的成形方式有很多,如普通拉深,多道次拉深,软模拉深,
拉深成形一般在室温下进行,因此材料硬化 性能对变形有较大影响,材料的成形性已为材料 性能的研究重点,其主要失效形式是破裂和起皱。
在板材成形时,把变形毛坯分成变形区和不变形区。 板料主要出现失稳出现在传力区
快速成型技术论文(2)

快速成型技术论文(2)快速成型技术论文篇二快速成型技术及其在微机械制造中的应用【摘要】速成型技术它全方位的提供了一种可测量,可触摸的手段,是设计者,制造者与用户之间的新媒体,在集成制造及微机制造中应用广泛,大大缩短了新产品制造以及成本的费用,受到国内外的广泛关注。
本文概述了快速成型技术的基本原理以及在集成制造:产品设计、制模、铸造等方面的应用及其快速成型技术在微机制造中的应用。
【关键字】快速成型技术,微机制造,应用中图分类号: TH16 文献标识码: A 文章编号:一.前言快速成形技术又称快速原型制造(Rapid Prototyping Manufacturing,简称RPM)技术,诞生于20世纪80年代后期,是基于材料堆积法的一种高新制造技术。
快速成形技术与虚拟制造技术一起,被称为未来制造行业的两大支柱制造技术,它全方位的提供了一种可测量,可触摸的手段,是设计者、制造者与用户之间的新媒体,其核心是基于数字化得新形成型制造技术,可以自动、直接、快速、精确地将设计思想转变为具有一定功能的原型或直接制造零件。
快速成形技术就是利用三维CAD的数据,通过快速成型机,将一层层的材料堆积成实体原型,被称为是近20年来制造技术领域的一次重大突破。
二.快速成型的基本工作原理快速成型能根据零件的形状,将制作成的一个个微小厚度和特定形状的截面逐层粘结起来,然后得到了所需制造的立体的零件。
与传统的成型加工方法不同,利用RPMM加工零件,可以不需要刀具和模具,利用光热电等方式,通过物理作用,完成从液粉末态到实体状态的过程,当然,如果成形材料不一样,RPMM系统的工作原理也会有些不同,但基本原理都是一样的,那就是“分层制造、逐层叠加”。
这种工艺可以形象地叫做“增长法”或“加法”。
每个截面数据相当于医学上的一张CT像片;整个制造过程可以比喻为一个“积分”的过程(见图1)。
图1 快速成型系统工作原理分析图快速成形制造技术综合采用CAD技术,数控技术,激光加工技术和材料技术实现从零件设计到三维实体原型制造一体化的系统技术,它采用软件离散,材料堆积的原理实现零件的成形,具体制造过程为;构造三维实体模型;近似处理三维模型生成;选择成形方向;处理切片;三维产品样件;表面处理。
成形工艺技术

成形工艺技术成形工艺技术是一门工程技术学科,通过对工件的成型过程及其技术性能的研究,设计出成型方法和工艺流程,实现对原材料的加工和转化。
成形工艺技术广泛应用于制造业各个领域,包括金属加工、塑料加工、陶瓷加工等。
成形工艺技术的基本理论是原材料形变和流变性能的研究。
通过研究材料的流动行为,可以设计出合适的成型设备和工艺参数,实现对原材料的精确控制。
成形工艺技术还研究了原材料的热力学性质、机械性能、物理性能等,为工艺设计提供了基础。
成形工艺技术的一大特点是可以大规模生产相同的零部件。
通过模具制造和成型设备的使用,可以在短时间内批量生产大量的相同产品。
与传统的手工制造相比,成形工艺技术大大提高了生产效率,降低了人力成本。
成形工艺技术的应用非常广泛,其中最常见的就是金属成形技术。
金属成形技术包括锻造、压力成型、铸造等。
锻造是将金属材料加热至一定温度后,利用力使其发生塑性变形,从而得到所需形状的工艺。
压力成型是通过施加压力使金属原材料变形,从而得到所需形状的工艺。
铸造是将金属熔化后,倒入模具中进行冷却凝固,最终得到所需形状的工艺。
除了金属成形技术,塑料成形技术也是成形工艺技术的重要组成部分。
塑料成形技术包括注塑成型、挤出成型、吹塑成型等。
注塑成型是将塑料原料加热熔融后,通过注射装置将其注入模具中,在模具中冷却硬化,最终得到所需形状的工艺。
挤出成型是将塑料原料加热熔融后,通过挤出机将其从模具中挤出,最终得到所需形状的工艺。
吹塑成型是将塑料原料加热熔融后,通过吹塑机在模具中进行吹塑,最终得到所需形状的工艺。
另外,成形工艺技术还涉及到陶瓷成形技术、橡胶成形技术等。
陶瓷成形技术包括注浆成型、挤出成型、压制成型等。
橡胶成形技术包括压制成型、挤出成型、注射成型等。
这些成形技术在陶瓷制造和橡胶制造领域得到了广泛应用。
总之,成形工艺技术在制造业中发挥了重要作用。
通过成形工艺技术,可以实现对原材料的精确控制,大规模生产相同的零部件,提高生产效率和降低成本。
先进塑性成形技术

先进塑性成形技术先进塑性成形技术简介一、微成型技术(Microform)微成型技术是一种仅有十几年历史的新兴技术,它是指以塑性加工的方法生产至少在二维方向上尺寸处于亚毫米级的零件或结构技术。
典型的微成型技术工艺有微挤压、微钣金、微模锻工艺等。
它是一种可以进行重复的批量生产复杂而有精密微细结构塑件的制造技术。
在微成形技术中,最突出的特点是微尺度效应。
1、微成型技术的特点及应用微成型技术继承了传统塑性加工技术生产效率高、材料利用率高、力学性能好等优点, 可以采用各种塑性加工方法, 如冲裁、拉伸、挤压和弯曲等, 精密成形各种复杂形状的微型零件, 广泛运用于电子和微机械产品中, 如集成电路引线框和紧固件。
微成型技术用于航空航天领域时可以大幅减少航天器的重量,如果把一颗人造地球卫星上的素有零部件都采用微成型技术加工成微观尺寸的话其重量将会变得非常轻,发射航天器所需的燃料也会相应地减少很多,这样就能使航空航天成本降低,另外,大部分航天器都属于一次性产品,减小其尺寸后可节省更多珍稀材料;微成型技术也可用于医疗卫生方向,比如人体微血管在被血液垃圾堵塞后容易导致脑淤血、冠心病等危险的发生,传统的治疗方法是采用搭桥等大手术,这样的手术本身就很危险而且会留下术后各种不适,对人体造成很大伤害。
采用微成型技术制造尺寸极为细小的机器人将其导入人体血管后用其自带的微型道具便可以疏通血管减少病人的痛苦。
2、现阶段微成型技术领域微成型技术是一种只有十几年历史的新兴技术,其理论基础和制造技术还很不完善。
现有的生产方法可以生产三维的单晶硅、纯金属和一些二元合金等微型部件, 在研究室中可以做出尺寸在微米级的齿轮等细小零部件,然而实际应用却并不多,并且多数情况下生产成本是非常高的, 且难以做到批量生产。
但是由于这一技术的诸多优势和广泛的应用领域,许多世界工业发达国家,如美国、日本及欧洲各国投入了大量资金资助相关研究。
美国国会把微电子机械系统作为21世纪重点发展的学科之一;日本政府和许多知名企业如Olympus等在微成型机械与微成型研究方面投入大量资金;德国研究技术部将微型机械系统列为新开发的重点项目,德国的CIRP成员也致力于微成型领域的研究。
钛合金热成形技术_概述及解释说明

钛合金热成形技术概述及解释说明1. 引言1.1 概述钛合金热成形技术是一种利用高温和压力对钛合金进行塑性变形的方法。
通过在特定温度下将钛合金加热到其塑性区域,然后施加压力来实现成形。
这种技术在航空航天、汽车制造、医疗器械等领域中得到广泛应用,并且在近年来取得了显著的发展和突破。
1.2 文章结构本文将从几个方面对钛合金热成形技术进行全面介绍和解释说明。
首先,我们将概述该技术的定义、原理以及其历史发展情况。
然后,我们将详细介绍该技术在不同领域的应用,并探讨其在实际生产中的工艺流程。
接下来,我们将深入分析钛合金热成形技术的优势,并提出当前面临的挑战以及相应的解决方法。
最后,我们将总结主要观点并对该技术未来发展进行展望。
1.3 目的本文旨在全面介绍和解释钛合金热成形技术,并分析其优势和挑战。
通过对该技术的准确理解,读者可以更好地了解钛合金热成形技术在工业生产中的应用和潜力,并为相关领域的研究和实践提供参考依据。
2. 钛合金热成形技术概述2.1 定义和原理钛合金热成形技术是一种通过将钛合金材料加热至其塑性变形温度,然后进行成型的制造工艺。
它基于钛合金在高温下具有良好的塑性和可变形性的特点,通过控制温度和应力来实现对钛合金材料的可控变形。
该技术主要依靠热胀冷缩原理,即在加热过程中,钛合金材料会膨胀并变软,使其容易成形;而在冷却过程中,由于收缩效应,材料会保持所需的形状。
通过精确控制加热、保温、成形和冷却阶段的参数和时间,可以实现对钛合金材料复杂三维几何形状的成型。
2.2 历史发展钛合金热成形技术起源于20世纪50年代。
当时,在航空航天工业领域对功能强大、轻量化及高机械性能要求极高的部件需求推动了该技术的发展。
最初的试验主要集中在单晶和多晶钛合金的热加工方面,通过探索适宜的加热温度和形变速率以及工艺参数的优化,成功实现了钛合金材料的热成形。
随着技术的不断进步和先进材料的开发,钛合金热成形技术得到了广泛应用。
如今,它已在航空、航天、汽车、医疗器械等领域得到广泛应用,并为这些领域带来了许多新的设计可能性和解决方案。
成形基础知识(成形)课件
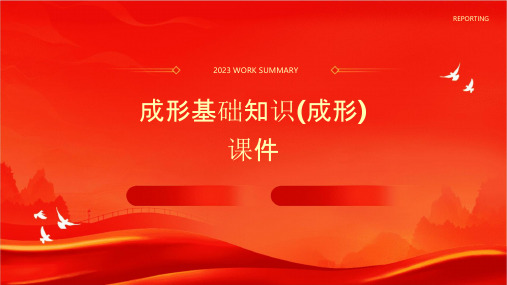
行业标准
特定行业内的质量标准, 用于规范行业内的产品质量。
2023 WORK SUMMARY
THANKS
感谢观看
REPORTING
02
固态成形原理主要包括材料的弹塑性行为、断裂准则和热变形等,这 些原理用于描述材料在固态成形过程中的行为。
03
常见的固态成形工艺包括切削加工、激光切割、3D打印等,这些工 艺广泛应用于各种材料的加工。
04
固态成形原理的应用有助于优化工艺参数、提高加工精度和降低生产 成本。
PART 03
成形工艺方法
等离子切割机
利用高温等离子气体对金属板 材进行切割的设备。
水切割机
利用高压水射流对非金属材料 进行切割的设备。
冲压机
利用模具和冲头对金属板材进 行冲压成形的设备。
PART 05
成形工艺质量控制
质量控制原理
预防原则
标准化原则
预防潜在的质量问题,而非单纯依赖 检验。
制定和执行标准操作程序,确保稳定 的生产过程。
PART 04
成形工艺设备
塑性成形设备
锻造设备
用于将金属坯料通过压 力和摩擦力进行塑性变 形,以形成所需形状的
设备。
挤压机
利用压力将金属坯料通 过模具挤压成形的设备。
轧制机
拉拔机
通过两个旋转轧辊之间 的压力将金属坯料轧制
成所需形状的设备。
通过拉伸力将金属坯料 拉制成所需形状的设备。
液态成形设备
总结词
利用固态材料的物理或化学变化,通过改变材料的内部结构 和性质,以获得所需形状和尺寸的零件的工艺方法。
详细描述
固态成形工艺方法主要包括焊接、热处理、粉末冶金等,这 些方法能够通过改变材料的内部结构和性质来控制零件的形 状和尺寸。固态成形工艺具有较低的生产成本和较高的灵活 性,适用于不同材料和形状的零件生产。
射出成形技术名词说明

GPG
49
10. 頂出力
說明
頂出梢要將成品平順的從公模頂出, 就必須 分布很均勻才行, 否則成品會破裂變形凸起 等缺點發生.
GPG
50
10. 頂出力
頂出力大小的應用依:
a. 成品設計 b. 模具設計 c. 模具精密度
等而定.
GPG
51
三. 行程
GPG
40
7. 鎖模力
說明
鎖模力是用來將模具緊緊的關閉, 並且用來 對抗射出壓力, 維持壓力的力量, 以使完成 品完美, 沒有毛邊.
GPG
41
7. 鎖模力
鎖模力大小的應用依: a. 成品設計 b. 原料種類
等而定.
GPG
42
8. 模具保護壓力
定義 在模具的關閉過程中, 為了防止模具夾傷而 設定的低壓力關模, 叫模具保護壓力.
說明 一般油壓錶所測得的射出壓力是射出油壓
缸內的壓力, 要再將螺桿截面積與油壓缸 截面積比換算後才是當時的射出壓力. 因 此, 當射出油壓缸的壓力固定時, 所使用 螺桿愈小, 則射出壓力愈大.一般原料說明 書所談的, 所需"射出壓力"是指換算後的 真正射出壓力.
GPG
26
1. 射出壓力
射出壓力大小的應用依下列而定:
GPG
4. 維持壓力墊距離
定義 射出動作完成時, 螺桿尖端的位置與螺桿尖 端可能最前面的位置間的距離, 叫維持壓力 墊距離.
GPG
4. 維持壓力墊距離
說明 維持壓力墊距離只是檢知確保維持壓力而 已. 若沒有維持壓力墊距離, 則沒有正確的 維持壓力. 若維持壓力墊距離太長, 又怕原 料過熱分解. 一般為5~10mm. 在閘門冷凝 之前, 螺桿要位於維持壓力墊的距離. 維持 壓力墊距離沒辦法單獨調整, 只能從料量行 程減去射出量行程, 剩下來的就是維持壓力 墊距離了.
成形制造技术介绍

成形制造技术介绍成形制造技术是一种以材料为基础,通过特定的加工方法,将材料加工成特定形状和尺寸的技术。
成形制造技术在工业生产中占有重要地位,广泛应用于汽车制造、航空航天、电子设备等领域。
本文将介绍成形制造技术的基本原理和常见的成形加工方法,以及其在工业生产中的应用。
成形制造技术的基本原理是通过施加力量对材料进行加工,使材料的形状和尺寸发生变化。
成形制造技术主要分为塑性成形、压力成形和去除成形三类。
首先介绍塑性成形技术。
塑性成形技术是利用材料在一定温度和应力条件下的塑性变形特性进行加工,常见的塑性成形工艺包括锻造、压铸和挤压等。
其中锻造是将金属材料放在模具中,通过施加压力使其产生塑性变形,最终得到所需的形状和尺寸。
压铸是将熔化的金属注入模具中,等待其凝固后取出成品。
挤压是将金属材料置于挤压机中,通过挤压力使其变形成所需形状的工艺。
这些塑性成形工艺在制造行业中广泛应用,可以高效地生产出各种零部件和产品。
其次介绍压力成形技术。
压力成形技术是通过加压对材料进行加工,使其填充模具腔室并形成所需形状的加工方法。
压力成形技术主要包括冷冲压、热冲压和深冲压等。
冷冲压是利用冲床对金属材料进行加工,常用于生产汽车车身零部件等。
热冲压则是在一定温度下对金属材料进行加工,以提高金属的塑性变形能力。
深冲压是将金属材料冲压成深层次的形状,常用于生产各种金属容器和零部件。
这些压力成形工艺能够高效地生产出各种金属零部件,具有高精度和高效率的特点。
最后介绍去除成形技术。
去除成形技术是通过去除材料使其形成所需的形状和尺寸的加工方法,主要包括数控加工、激光切割和电火花加工等。
数控加工是利用数控机床对材料进行精细加工,能够生产出高精度的零部件。
激光切割是利用激光对金属材料进行切割,具有高速、高效的特点。
电火花加工是利用电脉冲在导电材料上进行加工,常用于加工复杂零部件和模具。
这些去除成形工艺能够满足对零部件形状和尺寸精度要求高的需求,具有高精度和复杂形状加工的优势。
成形技术review

熔化极氩弧焊 埋弧自动焊 电渣焊 点焊 缝焊
<25 6~60 30~500 <4 <3
各种批量 批量 单件和批量 单件和批量 单件和批量
可全方位焊接、质量好、成本高 只可平焊,20mm以下不开坡口,焊缝>1m 立焊,需焊后热处理 搭接,密封性差 搭接,密封性好
第
页
焊接方法选择
焊接方法 电阻对焊 闪光对焊 摩擦焊 搅拌摩擦焊 材料尺寸 mm <20 各种 各种 长焊缝 批量 批量 批量 批量 各种批量 说明 对接,表面清理要求高,15%以下差 对接,表面无需清理, 15%以下差 不适合焊非圆截面工件 铝合金
6、挤压
挤压的方式:正挤压、反挤压、复合挤压和径向挤压。 热挤压:氧气瓶挤压:热挤压-拔深-收口
第
页
7、冷镦 螺栓,冷镦加搓丝。 8、超塑成形 金属及合金在特定的组织条件、温度条件及变形速度下进行 变形时,可呈现出异乎寻常的塑性(延伸率可超过100%,甚至 1000%以上),而变形抗力则大大降低(常态的1/5左右,甚至 更低),这种现象称为超塑性。超塑性分为细晶超塑性(又称恒 温超塑性)和相变超塑性(又称动态超塑性)等。
第
页
2009年材料及成形技术(二)
复
考试时间
习
答疑时间
材料成形(二)复习要点: 铸造
第
页
1.铸造工艺图: 造型方法、浇注位置、分型面、分模面、工艺 参数(余量、斜度、收缩率、孔、浇注系统)
2.定向凝固(顺序凝固)和同时凝固: 浇口、冒口、冷铁的设置,目的及应用场合。
3.铸造应力和变形分析: 热应力和机械应力、自由收缩和受阻收缩 4.铸件的结构工艺性(不合理结构的修改)
材料:15钢 1万件 焊接方法:埋弧自动焊
华工成型技术重点第三部分总结

Part III 成形(型)部分Forming and Shaping Processes and Equipment13 Rolling of Metal (轧制)13.1、IntroductionRolling(轧制):is the process of reducing the thickness (or changing the cross-section) of a long workpiece by compressive forces applied through a set of rollsPlate(厚板):which are generally regards as having a thickness greater than 6 mm, are used for structural applications Sheet(薄板):having a thickness less than 6 mm thick; are provided to manufacturing facilities as flat pieces or as strip in coils for further processing into various products.Plate厚板作为结构件,Sheet薄板作为半成品13.2、Flat Rolling(平扎)Flat Rolling(平扎):A strip (带料/ 条料)of thickness ho enters the roll gap (辊缝/ 辊隙/ 辊间距离)and is reduced to thickness hf by a pair of rotating rolls, each roll being powered through its own shaft by electric motors (电动机)Vr: The surface speed of the rolls(轧辊的速度)V0: The velocity of the strip at the entrance(板材入口处的速度)Vf: The velocity of the strip at the exit(板材出口处的速度)neutral point(中性点)or no-slip point(无滑动点) :one point along thecontact length where the velocity of the strip is the same as that of theroll.由于速度在中性点前后不一致引起摩擦力的方向在中性点两侧不一致(1) Frictional Forces(摩擦力-平扎中材料前行的驱动力)The rolls pull the material into the roll gap through a net frictional force(净摩擦力)on the material.摩擦力的危害:1) energy is dissipated in overcoming friction;2) high friction could damage the surfaceof the rolled productThe maximum possible draft(压下量), defined as the difference between the initial and finalthicknesses, (ho-hf), is a function of the coefficient of friction,μ,and the roll radius, R: ho-hf =ūRThus, the higher the friction and the larger the roll radius, the grater the maximum possible draft (and reduction in thickness) becomes.(2) Roll Force(轧制力):F= L W Yavg减少轧制力的措施:1)reducing friction; 2)using smaller-diameter rolls ;3)taking smaller reductions per pass;4)rolling at elevated temperatures(3)Spreading现象:对于有高宽厚比的厚板或者薄板的轧制,材料的宽度在轧制过程中基本保持不变,但对于宽厚比较小的厚板或薄板的轧制,材料的宽度在轧制的过程中增加的现象叫做Spreading现象;从左图中Top view俯视图可以看出轧制后宽度变大13.3、Flat Rolling Practice(平扎工艺)(1)Hot rolling(热轧) and Cold rolling(冷轧):Hot rolling: carried out above the recrystallization temperature(再结晶温度) of the metal.The initial breaking down of an ingot or of a continuously cast slab is done by hot rolling. (为什么要用热轧对铸件进行初始的压碎?)1)reduce grain size in metals; 2)breaking up of brittle grain boundaries and the closing up of internal defects, especially porosity;3)improve strength and ductilityCold rolling: carried out at room temperatureCompared to hot rolling, Cold rolling produces sheet and strip with1) much better surface finish (because of lack of scale); 2) much better dimensional tolerances; 3) much better mechanical properties ( because of strain hardening).(2)Cast structure(铸造结构) and Wrought structure(锻造结构):cast structure:1) typically dendritic (树枝状的);2) includes coarse(粗糙的) and nonuniform(不均匀的)grains;3) usually brittle (易碎的) and porous(多孔的)wrought structure:1) finer grains size(细小的晶粒尺寸);2) enhanced strength and ductility(增强的强度和延展性)(3)The product of the hot rolling(热轧产品):Slab :a slab is usually rectangular in cross-section. slabs are rolled into plates and sheets later.Slab通常是具有长方形截面的厚板或者薄板Bloom:Bloom usually has a square cross-section, at least 150mm on the side. Blooms are processed further, by shaping rolling, into structure shapes, such as I-beams and railroad rails.Bloom通常是具有边长大于150mm的正方形截面的结构件,例如I字梁或者铁轨Billets:billets are usually square, with a cross-section area smaller than blooms; they are later rolled into various shapes, such as round rods and bars by the use of shaped rolls.Billets通常是具有边长小于150mm的正方形截面的圆棒或者方棒(4)Scale(热轧中的氧化皮):Scale is conditioned by various means. Such as:1)use of a torch(火炬)or scaring (火焰表面清理);2) by pickling with acids (acid etching酸洗) ;3) by such mechanical means as blasting with water (水爆);4) grinding(研磨)(5)Packing rolling(叠板轧制):Pack rolling is a flat-rolling operation in which two or more layers of metal are rolled together; this process can improve productivity (记住Packing rolling的目的在于提高生产效率)(6)Defects in Rolled Plates and Sheets(轧制过程中的缺陷):Undesirable(不利)- Degrade surface appearance(降低表面外观); Adversely affect the strength(影响强度)Sheet metal defects include:1) scale(绣皮)rust(氧化皮)scratches(擦伤). gouges(槽)pits(坑)2) Cracks (裂纹)—May be caused by impurities and inclusions4) Alligatoring ( 皱裂,鳄纹)——complex phenomenon图(a)是波浪形边缘;图(b)是中心裂纹;图(c)是拉链式边缘裂纹;图(d)是皱裂13.5、Shape-Rolling OperationsStraight and long structure shapes, such as solid bars,channels, I-beams, and railroad rails, are rolled by passing the stock (原料) through a set of specially designed rolls(特制的轧辊)—型轧与平轧的主要区别在于型轧使用特制的轧辊(1) Ring rolling(圆环轧制):In the ring-rolling process, a thick ring is expanded into a large diameter ring with a reduced cross-section. The ring is placed between two rolls, one of which is driven ,and its thickness is reduced by bringing the rolls closer together as they rotate.Since the volume of the ring remains constant during deformation, the reduction in thickness is compensated (补偿)by an increase in the ring’s diameter.The advantages of this process are 1)short production times, 2)material saving, 3)close dimensional tolerances(精确的尺寸公差)4)favorable(良好的)grain flow(晶粒流线)in the product.(2)Thread-Rolling(螺纹轧制):The thread rolling process is a cold-forming process by which straight or tapered threads are formed on round rods by passing them between dies.The thread-rolling process has advantages such as 1)without any loss of material (scrap) ;2) with a good strength (due to cold working);3)The surface finish is very smooth;4)induces(诱发)compressive residual stresses(残余压应力)on the workpiece surfaces;5)at high rates of production;6) Thread rolling is superior( 更好的)to the other methods of manufacturing threadsFigure 13.16 (a) Features of a machined or rolledthread. (b) Grain flow in machined and rolled threads.Unlike machining, which cuts through the grains ofthe metal, the rolling of threads causes improvedstrength, because of cold working and favorable grainflow.机加工螺纹内部组织被切断,而轧制螺纹由于冷成型加工而保持良好的晶粒流线Review:1. Rolling is the process of reducing the thickness (or changing the cross-section) of a long workpiece by forces applied through a set of rolls. The rolls pull the material into the roll gap through forces on the material.a) compressive b) tensile c) shear d) frictional2. Which one is NOT the characteristic of a cast structure?a) dendritic b) finer grains size c) brittle d) porous3. Which one is the characteristic of a wrough structure?a) dendritic b) finer grains size c) brittle d) porous4.Which one of the following is NOT the product of the hot rolling process?a) billet b) ingot c) slab d) bloom5. Although friction is necessary for rolling materials, energy is dissipated in overcoming friction; thus, increasing friction means increasing forces and power requirements. Furthermore, high friction could damage the surface of the rolled product.A compromise has to be made, one which includes low coefficients of friction by using effective lubrication. ( )6.In the flat rolling products, sheets are generally regarded as having a thickness greater then 6mm. ( )SUMMARY1、Rolling is the process of reducing the thickness or changing the cross-section of a long workpiece by compressive forces applied through a set of rolls.In addition to flat rolling, shape rolling is used to make products with various cross-sections.Products made by rolling include: plate, sheet, foil, rod, seamless pipe(无缝钢管), and tubing; shaped-rolled products,such as I-beams and structural shapes; and bars of various cross-section.Other rolling operation include ring rolling and thread rolling.2、Rolling may be carried out at room temperature (cold rolling) or at elevated temperatures (hot rolling).The process involves several material and process variables, including roll diameter (relative to material thickness),reduction per pass, speed, lubrication, and temperature.3、Continuous casting and rolling of ferrous and of nonferrous metals(黑色和有色金属)into semifinished products have become a common practice because of its economic benefits.Question:1、What is the definition of the rolling?2、How to classify rolling process?3、What is the flat rolling?4、What is the difference between a plate and a sheet?5、Give some examples of the application of the plates and sheets.6、Explain the relationship of the velocity between the strip and rolls.7、Explain the advantages and disadvantages of the friction during the rolling.8、Define (a) roll gap, (b) neutral point, ( c )draft9、Describe the difference between a bloom, a slab , and a billet.10、List the defects commonly observed after flat rolling11、What is the hot rolling and cold rolling?12、What is the difference between cast structure and wrought structure?13、What is the difference between hot rolling and cold rolling??14、What is scale?15、How to remove the scale ?16、What is the shape rolling?17、Make a list of some parts that can be made by shape rolling.18、Describe types of products that can be made by thread rolling19、What is the advantages of the rolling process ?14 Forging of Metal(锻造)14.1 、Introduction(1)Forging is a process in which a workpiece is shaped (formed) by compressive forces applied through various dies(模具) and tools(工具). Most forgings, however, require a set of dies and such equipment as a press (压力机) or a forging hammer(锻锤).Characteristics of forged part: Metal flow and grain structure can be controlled, Forged parts have good strength and toughness. They can be used reliably for stressed and critical(关键的) application.Typical forged products: Bolts(螺栓)、Rivets(铆钉)、Connecting rods(连杆)、Gears(齿轮)、Shaft(轴)、Hand tool(手工具)、Structural components(结构组件)铸造件(Casting)有不可避免的缺陷,如晶粒粗大、结构疏松、具有多孔,其组织和性能均较差切削件(Maching)的内部晶粒大小和结构不改变,且其金属纤维组织被切断了,使得零件强度下降锻造件(Forging)在经受了塑性变形和再结晶,粗大的树枝状结晶组织被破碎,疏松和孔隙被压实、焊合,内部组织和性能都得到了提高(2)Classification of ForgingA、depending on temperature–cold forging(冷锻):at room temperature–hot forging(热锻):above recrystallization temperature–warm forging(温锻):between room temperature and recrystallization temperatureB、depending on tools–Open-Die Forging(自由锻造)–Impression-Die Forging(模锻)–Closed-Die Forging (闭式模锻)–Preicison Forging(精密锻造)(3)Comparison of Cold Forging to Hot ForgingCold forging: 1) requires greater forces, 2) workpiece materials must have sufficient ductility at room temperature.3) Cold-forged parts have good surface finish and dimensional accuracy.Hot forging: 1)Hot forging requires smaller forces, 2)but it produces dimensional accuracy and surface finish that are not as good14.2 、Open-Die Forging(1)Open-die forging is the simplest forging process. It can be depicted(描述)by a solid workpiece placed between two flat dies and reduced in height by compressing it. Open-die forging is also called upsetting(顶锻,镦粗)or flat- die forging(平模锻造)(2)Barrel(鼓形现象产生原因及减小措施):Friction(摩擦的原因):Barreling is caused primarily by frictional force at the die-workpiece interfaces that oppose the outward flow of the materials at these interfaces.措施:Barreling caused by friction can be minimized if an effective lubricant is used.使用润滑剂Temperature difference(温度差的原因):Barreling can also occur in upsetting hot workpiece between cold dies. The material at and near interfaces cools rapidly, while the rest of the workpiece remains relatively hot. Thus, the material at the ends of the workpiece has higher resistance to deformation than the material at its center. the central portion of the workpiece expands laterally to a greater extent than do its ends.措施:Barreling from thermal effects can be reduced or eliminated by using heated dies.加热模具(3)Cogging (开坯或者拔长), also called drawing out, isbasically an open-die forging operation in which the thickness of abar is reduced by successive(连续的)forging steps at specificintervals(时间间隔). Because the contact area per stroke is small, along section of a bar can be reduced in thickness without requiringlarge forces or machinery.14.3 、Impression Die (开模锻)and Closed-Die Forging(闭模锻)(1)In impression-die forging, the workpiece acquires the shape of the die cavities (impressions) while being forged between two shaped dies(Fig. 14.6).Flash(飞边)的作用:Because the thin flash cools rapidly and has higher frictional resistance than die cavity, it subjects the material in the die cavity to high pressures, thereby encouraging the filling of the die cavity.连杆的开模锻过程:1) Preparing blan(备料):(a) cutting or cropping from anextruded or drawn bar stock.(从一根挤出或者拉伸棒料上剪切) (b) a preform in operations such as powder metallurgy.用粉末冶金之类的操作方法预成形) (c) casting.(铸造)(d) a preform blank in aprior forging operation.(用预锻造操作预成形坯料)2)Preforming processes(预成形):Preforming processes, suchas fullering(压槽)and edging(切边,修边)(Fig. 14.7band c), are used to distribute the material into various regionsof the blank.fullering-排料,edging-聚料In fullering, material is distributed away from an area. Inedging, material is gathered into a localized area3) blocking(粗模锻):After preform processes, the part is thenformed into the rough shape of a connecting rod by a processcalled blocking (粗模锻), using blocker dies.4)finishing forging(精模锻)5)trimming operation(剪切)(2)Closed-die forging(闭式模锻):The example shown in Figs. 14.6 and 14.7 are also referred to as closed-die forgings. However, in true closed-die or flashless forging, flash does not form and the workpiece completely fills the die cavity. Accurate control of the volume of material and proper die design are essential in order to obtain a closed –die forging of the desired dimensions and tolerances: Undersize(不足的) blanks prevent the complete filling of the die cavity; conversely, oversize(过多的) blanks generate excessive pressures and may cause dies to fail prematurely or to jam.(3)闭式模锻应用之一精密锻造(Precision Forging )Forging generally require additional finishing operations, such as heat treating(热处理), to modify properties, and then machining(机加工)to obtain accurate finished dimension. These operations can be minimized by precision forging, which is an important example of the trend toward net-shape or near-net shape forming(净成形或近净成形)processes. This trend significantly reduces the number of operations required, and hence the manufacturing cost to make the final product.特点:1) Precision forging produces parts having greater accuracies than those from impression-die forging and requiring much less machining. 2) The process requires higher capacity equipment, because of the greater forces required to obtain fine details on the part. 3) Precision forging requires special and more complex dies, precision control of th e billet’s volume and shape, accurate positioning of the billets in the die cavity, and hence higher investment. .4) Less material is wasted, and much less subsequent machining is required, because the part is closer to the final desired shape应用:1)Because of the relatively low forging loads and temperatures that they require, aluminum and magnesium alloys are particularly suitable for precision forging; 2) Typical precision-forged products are gears , connecting rods, housings, and turbine blades.3) The choice between conventional forging and precision forging requires an economic analysis, particularly in regard to the production volume.(4)闭式模锻工艺应用之二—压印(Coining)Coining essentially is a closed-die forging process typically used in minting coins,medallions and jewelry. The pressures required can be as high as five or six times the strength of the material. Lubricants cannot be applied in coining.14.4、Related Forging OperationsHeading(镦头) is essentially an upsetting operation, usually performed at the end of round rod or wire in order to produce a larger cross-section. The typical parts are the Bolts(螺钉), screws(螺杆), rivets(铆钉), nails(钉子), and other fasteners (紧固件).Piercing(冲孔) is a process of indenting (压窝)the surface of a workpiece with a punch (but not breaking through) in order to produce a cavity or an impression14.7 、Die Materials and Lubrication(锻造材料要求和润滑剂的作用)(1)General requirements for die materials therefore are: 1) strength and toughness at elevated temperature;2) hardenability(淬硬性)and ability to harden uniformly; 3) resistance to abrasive wear, because of the presence of scale in hot forging.(2)Lubricants 1)greatly influence friction and wear, they affect the forces required and the flow of the metal in die cavities;2)They can act as a thermal barrier between the hot workpiece and the relatively cool dies, slowing the rate of cooling of the workpiece and improving metal flow. 3) Lubricants serve as a parting agent (脱模剂)which inhibits(抑制)the forging form sticking to the dies and helps in its release from the die.14.8 、ForgeabilityForgeability is generally defined as the capability of a material to undergo deformation without cracking.锻造性通常被定义为一种材料经受变形而不开裂的能力Review1 Forging is a process in which the workpiece is shaped by forces applied through various dies and tools. In the impression-die forging, some of the material flows outward and forms a _____, which has a significant role in the flow of material in impression-die forging.2. and are used to distribute the material into various regions of the forging workpiece.3、Pack rolling is a flat-rolling operation in which two or more layers of metal are rolled together; this process improves .3、flat rolling, or simply rolling, where the rolled products are flat and .4、Which process is was first used to make jewelry, coins, and various implements by hammering metal with tools made of stone before 4000B.C.A. StampingB. RollingC. ForgingD. Extrusion5. Which operation in the following options is not forging processes?A. pancakingB. PiercingC. punchD. Heading1.The die surfaces in open-die forging always is flat. [ ].2.In plastic forming process, the volume of workpiece maintains constant. [ ]3.Barreling is caused primarily by frictional force at the die- workpiece interfaces that oppose the outward flow of the materials at these interfaces. [ ]4.The flash is excess metal that is subsequently trimmed off, so it is necessary to avoid flash in forging process. [ ] 5.In impression-die forging, the workpiece acquires the shape of the die cavities, while being forged between two shaped dies. ()SUMMARY1)Forging is carried out by compressive forces applied through a set of dies.2)Forging is capable of producing a wide variety of structural parts with favorable characteristics such as strength, toughness, dimensional accuracy, and reliability in service.3)The forging process can be carried out at room, warm, or high temperatures (above the recrystallization temperature).4)Workpiece material behavior during deformation, friction, heat transfer, and material-flow characteristics in the die cavity are important considerations.Question1、What is forging process ?2、What is the difference between rolling and forging ??3、What do the typical forged products include?4、What are the advantages of the forging parts ??5、What is the difference between cast parts, cutting parts and forging parts ?6、How to decide the production method of a component ?7、How to distinguish cold forging and hot forging ?8、What is the difference between cold forging and hot forging?9、What is the open-die forging ?Review and Question10、What is the difference between ideal forging and actual forging ?11、How is the barreling caused in forging ?12、How to minimize the barreling?13、What is the cogging operation ?14、What is the difference between open-die forging and impression-die forging ?15、What is the flash ? 16、How to form the flash ? 17、What is the significance of the flash? 18、What does the complete forging process include?19、How is the blank to be forged prepared ?20、How is the blank to be forged prepared ?21、What is the result of Preforming processes ?22、What is the difference between fullering and edging?23、What do the conditions include which are essential in order to obtain a closed-die forging of the desired dimensions and tolerances ?24、What is the net-shape forging or near-net shape ?25、Why is the trend in forging toward greater precision forging ?26、Describe the Characteristic of the Precision Forging.27、What is Heading operation ?28、What is the typical products of heading operation ?29、Describe the Characteristic of Heading 30、What is piercing ? 31、What are general requirements for die materials ? 32、How to select the proper die materials ? 33、What is the significance of lubrication to the forging process ? 34、How to Apply lubricants in forging ? 35、What is the forgeability ? 36、How to quantify forgeability of materials ? 37、What do the Forging defects include ? 38、What is the difference between piercing and punching ? 39、Explain the difference between fullering, edging, and blocking ?15 Extrusion and Drawing Metals (挤压和拉拔)15.1 、IntroductionExtrusion is a process where a billet(generally round) is forced through a die, in a manner similar to squeezing toothpaste from a tube.Extrusion is a semicontinuous(半连续)process.Parts have constant cross-section.类型一:型材类Typical products made by extrusion are railings for sliding doors, tubing having various cross-section, structural and architectural shapes, and door and window frames.类型二:重要零部件Extrusion is often combined with forging operations, in which case it is generally known as cold extrusion (冷挤压). It has numerous important applications, including fasteners and components for automobiles, bicycles, motorcycles, heavy machinery, and transportation equipment.15.2 、The Extrusion Process(1)Direct Extrusio(直接挤压,正挤压)Direct also is called forward extrusion,a round billet is placed in a chamber(container) (容器/料筒)and forcedthrough a die opening by ahydraulically-driven(液压驱动)ram(冲击) or pressing stem(压力阀杆).The direction the metal flows issame with that the pressing stem moves toward.(棒料金属流动方向和压力阀杆运动方向一致)(2)Indirect Extrusion(间接挤压,反挤压)In indirect extrusion (reverse, inverted,or backward extrusion), the die movestoward the billet. Unlike in directextrusion, there is no friction toovercome along the container walls.(反挤压的摩擦力小)The direction the metal flow is oppositeto that the pressing stem moves toward.(棒料金属流动方向和压力阀杆运动方向相反)(3)Hydrostatic Extrusion(静水压挤压)In hydrostatic extrusion the billet is smallerin diameter than the chamber, which isfilled with a fluid, and the pressure istransmitted to the billet by a ram. Unlike indirect extrusion, there is no friction toovercome along the container walls.(静水压挤压无摩擦力,可提高材料的塑形)特点:The pressure required for extrusion is supplied through and incompressible fluid medium surrounding the billetUsually carried at room temperature, typically using vegetable oils as the fluidBrittle materials are extruded generally by this methodIt increases ductility of the materialIt has complex nature of the tooling(4) lateral Extrusion(侧向挤压/轴向挤压)Another type of extrusion is lateral, or side extrusion.15.3、Important parameters of extrusion process(挤压工艺中的重要工艺参数)1) The die angle, α(模具角)2) Extrusion Ratio(挤压比):the ratio of thecross-sectional area of the billet to the cross-sectional areaof extruded product. Ao/Af3) extrusion speed(挤压速度)4) billet temperature(棒料温度)5) lubrication(润滑剂的使用)(6) CCD-Circumscribing-circle diameter (外接圆直径),abbreviated CCD, is a parameter describing the shape ofthe extruded product. It is the diameter of the smallestcircle into which the extruded cross-section will fit .Thusthe CCD for a square cross-section is its diagonal(对角线)dimension(7)Shape Factor (形状因子):The shape factor is used to describe the complexity of an extrusion.The complexity of an extrusion is a function of the ratio of the perimeter(周长)of the extruded product to its cross-sectional area, known as the shape factor. Obviously, a solid round extrusion has the smallest shape factor.(周长与截面积之比,圆形的形状因子最简单)(8)Extrusion Force(挤压力):F = AokIn(Ao/Af) (k-extrusion constant ,Ao, Af billet and extruded product areas)(9)摩擦力对挤压变形的影响:(a)Flow pattern obtained at low friction,or in indirect extrusion;(b)Flow Pattern obtained at high friction at the billet-chamber interfaces; (c)Flow Pattern obtained at high friction, or with cooling of the outer regions of the billet in the chamber15.3 、Hot ExtrusionExtrusion is carried out at elevated temperatures-for metals and alloys that do not have sufficient ductility at room temperature, or in order to reduce the forces required.热挤压中的常见问题及对策:Question 1: die wear can be excessive,and cooling of the hot billet in the chamber can be a problem which results in highly nonuniform deformation(模具磨损厉害)Method1:Using extrusion dies preheated to reduce cooling of the billet and to prolong die life, as is done in hot forging operations.Question 2: The billet may develop an oxide film (氧化膜unless heated in an inert-atmosphere(惰性气氛).(产生氧化皮)Method2: Using the dummy block(挤压垫)made a little smaller in diameter than the container and placed ahead of the ram to avoid the formation of oxide films on the hot extruded product.15.4 、Cold ExtrusionCombination of operations, such as direct and indirect extrusion and forging.Advantages:Improved mechanical properties;Good control of dimensional tolerances ;Improved surface finish ;Elimination of the need for billet heating;15.5 、The Drawing Process(拉拔)In this process the cross section of a round rod or wire is typically reduced or changed by pulling it through a die15.6 、Drawing PracticeBundle drawing-捆绑拉拔-目的提高生产效率Review1. Compared to casting and machining, forging can produce parts with .a. low costb. good surface finishc. tight dimensional tolerancesd. good strength and toughness2. Which one of the following does NOT describe the characteristic of upsetting?a. Lubrication is important for high quality.b. The billet is reduced in height by compressive forces applied through two flat dies.c. The workpiece is deformed uniformly in actual operations.d. The forged part may develop a barrel shape.3. In _____________ extrusion, the die moves toward the billet, and the direction of metal flowing is opposite to that of the pressing stem moving.a. directb. indirectc. hydrostaticd. lateralSUMMARYExtrusion is the process of forcing a billet through a die, to reduce its cross-section or to produce a wide range of solid or hollow cross- sections.The process is generally carried out at elevated temperatures, to reduce forces and to improve the ductility of the material. Important factors in extrusion are die design, extrusion ratio, billet temperature, lubrication, and extrusion speed.Although the term cold extrusion applies to extrusion at room temperature, it is also the name for a process which is combination of extrusion and forging operations.Cold extrusion is capable of economically producing discrete parts in various shapes, with good mechanical properties and dimensional tolerances.Rod, wire, and tube drawing basically involve the process of pulling the material through a die (or a set of dies in tandem). Although the cross-section of most drawn products are round, other shapes can also be drawn.Drawing tubular products, to reduce either their diameter or their thickness, usually requires internal mandrels.The die design, the reduction in cross-sectional area per pass, and the selection of die materials and lubricants are all important parameters in obtaining drawn products of high quality and of good surface finish.Both external defects and internal defects (chevron cracking) can develop both in extrusion and in drawing; their minimization depends principally on the die angle, the reduction per pass, and the quality of the workpiece material.16 Sheet-Metal Forming Processes (板材成形/ 冲压)板料成形(sheet metal forming)是利用安装在压力机上的冲模对金属板材施加压力,使金属产生分离或者塑性变形从而获得所需要的零件的一种加工法.因为它们一般是在常温下进行的,所以称之为冷冲压(cold stamping)16.1. Introduction板材成形的特点:Compared to those made by casting and by forging, sheet-metal parts offer the many advantages. 1)High production efficiency;2)Saving rough material;3)Easy to implement mechanization and automatization;4)Low cost in mass production;5)light weight;6)versatile shape板料成形的分类:Shearing deformation(剪切变形) and Plasticdeformation(成形工艺)16.2. Shearing(1)The sheet is cut by subjecting sheet metal to shear stresses,typically ones developed between a punch(凸模) and a die(凹模) . Shearing usually starts with the formation of cracks onboth the top and bottom edges of the workpiece (A ,B, C andD in Fig. 16.2a). These cracks eventually meet each other andseparation occurs.(2)剪切边的特征:1)In fact , the sheared edges are not smooth, and they are notperpendicular to the plane of the sheet.。
模具外文翻译--冲压成形的研究方法-其他专业

英文资料Methods to study stamping formingThe objective of the stamping forming research is to realize and apply the principles to solve various engineering problems through study on the stamping forming procedure. Recently, the research on stamping has been carried out in wide range with various methods. The research can be summed up substantially into following types.The double line arrows in the picture denote the procedure of formal theoretical research. In such research, the actions of the equipment and die are decomposed into micro-ingredients of the force and applied on the microstructure of the metal according to the multi-crystal microstructure of the deformation metal, the deformation of the metal microstructure is then investigated and the deformation of the microstructure to macro-deformation of the sheet metal is summed up. This scientific method is perfect, but current development in mechanics and metallurgy cannot meet such demand, therefore this kind of formal theoretical research is still in burgeoning, and is not applicable in practice.Since the formal theoretical research method encounters formidable difficulty, a kind of simplified theoretical method appears in the research field of the stamping forming. The characteristic of this kind of research method is denoted by continuous line in the picture, which is the main trend of the recent research. This research assumes metal as the ideal homogeneous solid and simplifies the property parameters, the boundary conditions and the blank geometrical parameters of the metal, the stamping process and principle are analyzed and described by mathematical method. Naturally, the assumptions adopted in the analysis would induce some deviation between the real stamping process and its simulation. The result is certainly approximate and does not reflect the real stamping process completely. Especially in analyzing complex stamping forming, this theory is not so valid. In recent years, due to the development of the finite element method and computer technology, this kind of theoretical method has greatly progressed, it shows applicable prospect even in analyzing complex stamping forming. The application of this kind of theoretical method mainly focuses on some special stamping deformation investigation, and it is expected that more achievements can be obtained in the fundamental principle of stamping forming. On the other hand, due to the simplification and assumptions, experiments are indispensable to test the validity of this theory.The third method to study stamping forming is shown by dashed dotted line in the picture. The characteristic of this method is that ignoring the deformation process of the blank under the action of the load during stamping forming conditions (including the structure of the die, the geometrical parameters of the die working portion and the properties of the stamping equipment) with the final results of the stamping forming. It is a rational empirical method, and widely used in stamping technology filed in recent years. This method is intuitional, simple and easy to be adopted by engineers, but it cannot be used to reveal the real procedure of the stamping deformation, so it is not the radical method to investigate the principles of the stamping forming more thoroughly and its usage is strictly limited.The fourth method to study stamping forming is denoted by dashed line in thepicture. Based on the fundamental knowledge of the mechanics and metallurgy, the essential characteristics and principle of the stamping forming are investigated to solve the practical problems in stamping process. In comparison with other plastic processes, the characteristics of the stamping forming, the principles of the sheet metal deformation are unique. So this method has definitely aim and the analysis results can be used directly to solve different problems in stamping forming. The characteristics and effects of this research of this research of this research method are illustrated by following examples.(1)The sequence of the stamping process can be decided by the trend rule of the stamping deformation.(2)According to the rule of uniform velocity distribution in the outer flange of the deformation zone during multi-pass deep drawing for the box parts, the shape and dimension of the blank during process sequence can be calculated. Therefore the calculation the for deep box parts of the multi-pass deep drawing technology is based on scientific foundation to improve the technique level of stamping forming.(3)According to the research on the wrinkle during the sheet metal forming caused by non-uniform tensile and shearing force, a new research field is developed beyond the traditional compressive instability theory. The results obtained offer an effective measure to cope directly with wrinkle during stamping forming.(4)The theory of sorting stamping forming based on the characteristics of the stamping deformation and mechanics and mechanics is an easy approach to systematize of the stamping forming, and can be used to deepen the investigation on stamping forming limit, to point out a clear and definite direction for improve the stamping forming limit.Above examples indicate that this method is closely relevant to the real stamping forming process. It can be used to analyze and solve the stamping forming problems effectively. Although this method is in the junior stage, mainly focusing on the qualitative analysis for stamping forming now . With the constant progress of this method and combined with modern mechanics, the breakthrough of this method isexpected to further enhance stamping forming technology.Structural design of blanking diel. Principle and general procedure of die designingThe steps of die designing include collecting necessary data, determining the structure scheme based on sufficient analysis and investigation, drawing the working principle diagram, the final assembly diagram, and then drawing the part diagram of the die according to the final assembly diagram.The necessary data to be collected include: the parts drawing of the product, the productive batch of the product, the process chart, the process specification and the die design program. The manufacture datum of each operation, the types of the die structural (simple die, progressive die or compound die) , the capacity of the press, the quality of the blanking work piece and other necessary items should be record in the process chart and the process specification.The detailed structure and dimension of the die are determined according to the production batch and work piece demand, etc. For the small batch production, the structure of die should be simple, the manufacture period should be short, and the cost should be as low as possible. For the large batch, the perfect structure, high productivity and long working life should be pursued.Furthermore, the structure measures to adjust, utilize, maintain, transport and deposit the dies should be taken into account.2. Determination of the pressure center of dieThe acting point of the resultant force in blanking is called the pressure center of die. In order to guarantee the die to work smoothly, the pressure center of die should align with the axes of shank and the center line of the slide block of press, to prevent the deflection of die during working, which would result in non-uniform clearance and wearing. Usually, the pressure center of die is laid on its symmetrical center point. The determination of the pressure center of die is mainly for the complex, multi-punch punching and progressive dies.For the work piece with complex shape, it can be divided into straight-linesection (the pressure center of die is situated at the middle of the straight) and arc section, and then to calculate its pressure center.The method to find the resultant force of the parallel force system is usually adopted to obtain the pressure center of die. The procedure to obtain the pressure center of die for multi-punch blanking by analytic method is showns chematically in .(1) Draw the outline of the working portion of punch proportionally.(2) Select the co-ordinate X-Y. The selection of the co-ordinate should simplify the calculation.(3)calculate the perimeter of each graphic outline (or linear section)L1,L2,L3,L4,..., L n(representing the blanking force), and the distance of gravity center in each graphic outline to the coordinate axes x1, x2, x3, x4, ...,x n and y1,y2,y3,y4,...,y n.(4) According to the mechanic principle that "the moment of the resultant force to a certain axis is equal to the sum of the moment of each component to the same axis", the calculation equation of the distance from the die pressure center to the axes of X and Y can be obtained:x0=L1x1+L2x2+L3x3+⋯+L n x n(3-20)L1+L2+L3+⋯+L n(3-21) y0=L1y1+L2y2+L3y3+⋯+L n y nL1+L2+L3+⋯+L nThe determination of the pressure center of die can also be obtained graphically by the linear polygon method.3. Determination of the shut height of dieThe outline dimension of die should fit with the selected example,the lower die of the blanking should be able to install in the working table of the press,the dimension of the shank should be consistent with that of the hole in the slide block,the ejecting pin of the ejecting device in the lower die should be able to penetrate through the bolster hole of press. The shut height of die should be consistent with that of the press.The shut height of die refers to the distance H between the top surface of the upper bolster and bottom surface of the lower bolster when the die is in the lowest working position. The shut height of press refers to the distance between the lower surface of the slide block and the upper surface of the bolster installed in the working bable when the slide block is in the lower dead point. The height when the length of the connecting rod is adjusted to the shortest, is called the maximum shut height H max; the height when the length of the connecting rod is adjusted to the longest, is called the minimum shut height H min, as shown schematically in . The shut height of die is between the maximum and minimum shut height of press, usually:If the shut height of die is larger than the maximum height of press, the die cannot be used in this press; oppositely, if the shut height of die is less than the minimum height, the die can be used by adding a bolster.中文翻译冲压成形的研究方法冲压成形的研究工作,就是在正确而深入地了解冲压成形过程的基础上,认识冲压成形过程中的各种规律性的内容,并把它运用于解决冲压生产中出现的各种实际问题。
成型技术的总结

现代成形技术第一章快速成形技术1.1成形方式分类快速成形技术是基于离散—堆积成形原理的成形方法。
在研究离散—堆积成形原理前,有必要回顾一下成形原理和方法,根据现代成形学的观点,从物质的组织方式上,可把成形方式分为以下四类:(1)去除成形:去除成形是运用分离的方法,把一部分材料(裕量材料)有序地从基体上分离出去而成形的方法。
传统的车、铣、刨、磨等加工方法均属于于去除成形,现代的电火花加工、激光切割、打孔等也是去除成形。
去除成形最先实现了数字化控制,是目前主要的成形方式o(2)堆积成形;堆积成形是运用合并与连接的方法,把材料(气、液、固相)有序地合并堆积起来的成形方法。
RP即属于堆积成形。
堆积成形是在计算机控制下完成的,其最大特点是不受成形零件复杂程度的限制。
从广义讲,焊接也属堆积成形范畴。
(3)受迫成形:受迫成形是利用材料的可成形性(如塑性等)在特定外围约束(边界约束或外力约束)下成形的方法。
传统的锻压、铸造和粉末冶金等均属于受迫成形。
目前受迫成形还未完全实现计算机控制,多用于毛坯成形、特种材料成形等。
(4)生长成形:生长成形是利用材料的活性进行成形的方法,自然界中生物个体发育均同于生长成形,“克隆”技术是产生在人为系统中的生长成形方式。
随着活性材料、仿生学、生物化学、生命科学的发展,这种成形方式将会得到很大发展。
1.2快速成形原理与过程快速成形技术是由CAD模型直接驱动,快速制造任意复杂形状的三维物理实体的技术。
其核心是由CAD模型直接驱动,其基本过程如图1.1所示:首先由是由CAD软件设计出所需零件的计算机三维曲面或实体模型,即数字模型或称电子模型;然后根据工艺要求,按照一定的规则将该模型离散为一系列有序的单元,通常在Z向将其按一定厚度进行离散(习惯称为分层或切片),把三维电子模型变成一系列的二维层片;再根据每个层片的轮廓信息,进行工艺规划,选择合适的加工参数自动生成数控代码;最后由成形机接受控制指令制造一系列层片并自动将它们联接起来,得到一个三维物理实体。
- 1、下载文档前请自行甄别文档内容的完整性,平台不提供额外的编辑、内容补充、找答案等附加服务。
- 2、"仅部分预览"的文档,不可在线预览部分如存在完整性等问题,可反馈申请退款(可完整预览的文档不适用该条件!)。
- 3、如文档侵犯您的权益,请联系客服反馈,我们会尽快为您处理(人工客服工作时间:9:00-18:30)。
第
页
零件4-螺栓:属于标准件,采用碳素结构钢 (如Q235)经冷镦加搓丝成形。 零件5-挡油盘:单件时用Q235圆棒直接下料 切削而成,大批量时采用08钢 薄板冲压而成。 零件6-滚动轴承:由内、外套圈、滚珠和保 持架组成,属于标准件。内、 外套圈用滚动轴承钢(如GCr15) 经扩孔或辗环轧制而成。滚珠 用滚动轴承钢经螺旋斜轧而成, 保持架则用08钢薄板冲压成形。
2、各种焊接方法的特点 重点:埋弧自动焊、钨极氩弧焊
第
页
第
页
第
页
第
页
第
页
( 1 )焊接方法
用埋弧自动焊焊筒身及封头,输入
和输出管用手工电弧焊焊接。焊环缝时焊件转动,焊 接小车不动。焊接接头用对接,不开坡口。
( 2 )焊缝位置
为了避免应力集中,对容器的圆弧
部分或焊件壁厚相差大于 3mm 的地方,需要作相应的 过渡措施,同时要避免焊缝密集。
第
页
锻压
1.塑性变形后的组织与性能变化: 加工硬化、回复、再结晶、锻造流线 2.模锻分模面及模锻件图 3.简单模、连续模、复合模的结构简图和应用场 合及刃口尺寸计算 4.模锻件、冲压件的结构工艺性(修改不合理结构)
第
页
第三章 锻压
3.1金属的塑性变形
3.1.1塑性变形概念:滑移、位错、孪生变形
第
材料:15钢 1万件 焊接方法:埋弧自动焊
材料:20钢
1000件
材料:45钢、孔径40
1万件
成形方法:正挤压
成形方法:平锻机上模锻
第
页
三、单项选择题(每题1分,共10分)
1. 今有青铜仿古铜像须按普通人尺寸的十分之一大小进行仿形铸造,应采用 ( 3 ) (1) 金属型铸造 (2) 压力铸造 (3) 熔模铸造 (4) 普通砂型铸造 2. 对于高熔点合金精密铸件的成批生产,常采用 (1) 压力铸造 (2) 低压铸造 (3) 熔模铸造 (4) 金属型铸造 3. 助动车发动机缸体,材料ZL202,100万件,其毛坯成形工艺为 (1) 低压铸造 (2) 压力铸造 (3) 离心铸造 (4) 熔模铸造 4. 下列模锻设备中最适宜进行拔长工步的是 (1) 模锻锤 (2) 机械锻压机 (3) 摩擦压力机 (4) 平锻机 (3 )
第
页
第
页
2.1.2 砂型铸造工艺分析 1、浇注位置与分型面的确定 浇注位置选定原则:5点;分型面选定原则8点 P88~89 2、工艺参数 不铸孔尺寸、加工余量、铸造收缩率、起模斜度 3、铸造工艺图制定
第
页
第
页
2.1.3 砂型铸造方法
1、气动微震压实造型 2、高压造型 多触头高压造型,垂直分型无箱造型 3、消失模造型
1、 剃 齿 刀 10件 材料: ZGW18Cr4V 2、 气 罐 3、 冲 压 管 接 头 1000件 材料: 08钢 10万件 4、 拖 拉 机 轮 壳 材料: HT250 10万件
材料: ZG400
成形方法:熔模铸造
5、螺栓
成形方法:机器砂型铸造
6、阀体
成形方法:涨型
7、包角块
成形方法:机器砂型铸造
页
3.1.2 冷变形对金属性能的影响
加工硬化 硬度、强度上升,塑性韧性下降 加工硬化产生的原因:晶粒拉长、晶格扭曲、产生碎晶 纤维组织 各向异性
3.1.3 回复和再结晶
T回=0.25~0.3T熔 T再=0.4T熔
3.1.4 冷变形和热变形 3.1.5 合金的锻造性 塑性、变形抗力
金属本质 变形条件 化学成分、组织结构 变形温度、变形速度、应力状态 锻锤结构、分模面选择、模锻件图
SHANGHAI UNIVERSITY
第
页
1
第2章 铸造成形
2.1 本章重点
2.1.1铸件形成理论基础 1、金属的充型 影响充型能力的因素和原因(表2-2) 2、金属的凝固 三种凝固方式
第
页
3、影响凝固方式的因素:结晶温度范围、温度梯度 4、影响温度梯度的因素:合金性质、铸型蓄热能力、浇注温度 5、合金的收缩: 三种收缩方式,液态收缩、凝固收缩、固态收缩 影响收缩因素,化学成分、浇注温度,铸件结构和铸型条件 缩孔及缩松 产生缩孔的原因: 液态和凝固收缩大、气体多 6、应力与变形:热应力和收缩应力、变形趋势
第
页
第7章 零件的毛坯选择
7.1 毛坯选择原则 1、工艺性原则 2、适应性原则 3、生产条件兼顾原则 4、经济性原则 7.2 毛坯成形方法的比较 1、铸造 2、锻造 3、焊接 7.3 常用零件的成形方法 1、轴杆类零件 2、盘套类零件
3、机架箱体类零件
第
页
§7-4 毛坯成形方法选择实例
第
页
零件1-箱体:HT150、HT200等灰铸铁,单件 小批用手工砂型铸造,大批量 用机器砂型铸造。 零件2-齿轮:45、40Cr等中碳钢,单件小批 自由锻,大批量模锻或热轧。 零件3-窥视孔盖:单件小批用Q235A钢板直接 下料或灰铸铁(HT150)手工砂 型铸造;大批量时用优质碳素 结构钢板(10~30)冲压或用灰 铸铁机器砂型铸造。
第
页
1、改错题(将下表不合适结构改为合适结构,并写出改进理由;每题2分, 共20分。)
不合适结构
1.铸件
改进后结构
改进理由 凸台仿碍起模,将凸台延长
2.铸件
避免交叉及收缩受阻
3. 铸件
侧凹铸件不利于大批生产
第
页
不合适结构 4.自由锻件
改进后结构
改进理由
相贯线无法锻出,避免两圆 柱体垂直相交
锤 上 模 锻 件 6. 拉 深 件
中心孔未垂直于分型面,孔 无法锻出
底部圆角半径必须大于2t,凸 缘圆角半径必须大于(3~4)t
7. 手 弧 焊
手弧焊焊接结构必须能运条
第
页
不合适结构
8.点焊
改进后结构
改进理由 点焊焊接结构必须能放入电 极
9. 手 弧 焊
焊缝处尽量远离加工表面
10. 拼 焊 顺 序
拼板焊接要避免收缩受阻
第
页
2、工艺填空题:根据下表已给的条件,在指定的空格中填入合适的毛坯 成形或连接方法。(每空1分)
第
页
拉深模与冲裁模的区别 ①模具间隙较大。 ②模具无刃口,呈圆角。
第
页
3.3.2 冲压模具
1、简单模 简单模是指在一次冲压行程中,只完成一个工序的冲模。 简单模有落料模、冲孔模、切变模、弯曲模、拉深模、翻边模 等。 2、连续模 (级进模、跳步模) 压力机在一次行程中,依次在几个不同的位置上同时完成 多道工序的冲模。 3、复合模
第
页
零件7-端盖:单件小批时用灰铸铁(HT150) 手工砂型铸造或用Q235圆钢直 接下料车削而成;大批时用灰 铸铁机器砂型铸造。 零件8-箱盖:HT150、HT200等灰铸铁,单件 小批用手工砂型铸造,大批量用 机器砂型铸造。 零件9和10-齿轮轴和轴:45、40Cr等中碳钢, 单件小批自由锻,大批量模锻。 零件11-螺母:属于标准件,通常采用碳素结 构钢(如Q235)经冷镦而成。
6、挤压
挤压的方式:正挤压、反挤压、复合挤压和径向挤压。 热挤压:氧气瓶挤压:热挤压-拔深-收口
第
页
7、冷镦 螺栓,冷镦加搓丝。 8、超塑成形 金属及合金在特定的组织条件、温度条件及变形速度下进行 变形时,可呈现出异乎寻常的塑性(延伸率可超过100%,甚至 100超塑性。超塑性分为细晶超塑性(又称恒 温超塑性)和相变超塑性(又称动态超塑性)等。
第
页
2009年材料及成形技术(二)
复
考试时间
习
答疑时间
材料成形(二)复习要点: 铸造
第
页
1.铸造工艺图: 造型方法、浇注位置、分型面、分模面、工艺 参数(余量、斜度、收缩率、孔、浇注系统)
2.定向凝固(顺序凝固)和同时凝固: 浇口、冒口、冷铁的设置,目的及应用场合。
3.铸造应力和变形分析: 热应力和机械应力、自由收缩和受阻收缩 4.铸件的结构工艺性(不合理结构的修改)
2.1.4 特种铸造
1、离心铸造 2、压力铸造 3、低压铸造 4、熔模铸造 5、陶瓷型铸造 6、壳型铸造
铸造回转体铸件,可镶嵌金属 铸造薄壁大批生产铸件,可镶嵌金属 铸造致密性好的铸件 精密铸造 精密铸造 常用于制芯 发动机缸体、活塞等
刀具、叶片、高熔点金属的零件 模具为主
2.1.5 铸造方法选择
根据材料、形状、批量选择铸造方法
8、加强筋焊接
材料:Q235 成形方法:冷镦+搓丝 9、大口径 管焊接
材料:KTH330-08 1万件 成形方法:机器砂型铸造 10、 轿车 车壳 焊接 材料:轿车车壳板材 焊接方法:细丝CO2焊
材料:08钢
10万件
材料:15钢
100件
成形方法:冲孔、落料、翻边 11、 隔 套
焊接方法:手工电弧焊 12、 双 联 齿 轮
复合模是指压力机在一次行程中,在同一中心位置上,同 时完成几道工序的冲模。由于复合模在同一中心位置上完成几 道工序,因此它必须在同一中心位置上布置几套凸、凹模。
第
页
3.4 锻压新技术
1、辊锻 2、横轧 3、纵轧 4、斜轧
第
页
5、碾环 环形毛坯在旋转的轧辊中受压变形而使厚度变薄直径扩大的 锻压方法称为碾环。
剪切、冲孔、落料、切断、切边、剖切
拉深、弯曲、涨型、翻边、收口、压筋等
第
页
3、冲裁模尺寸计算 落料:
凹 D凹=(Dmax x)0
D凸=( D凹-Z min ) 0 凸
凹 d凹=(d凸+Z min ) 0
冲孔:
d凸=(d min x) 0 凸
式中:D凹、D凸——落料凹模、凸模基本尺寸; d凸、d凹——冲孔凸模、凹模基本尺寸; Dmax ——落料件的最大极限尺寸; dmin ——冲孔件的最小极限尺寸; △ ——冲裁件的公差; x ——磨损系数,与冲裁件的精度有关