重整装置反应器壁超温原因分析及处理措施
煤基甲醇装置co变换超温原因及对策
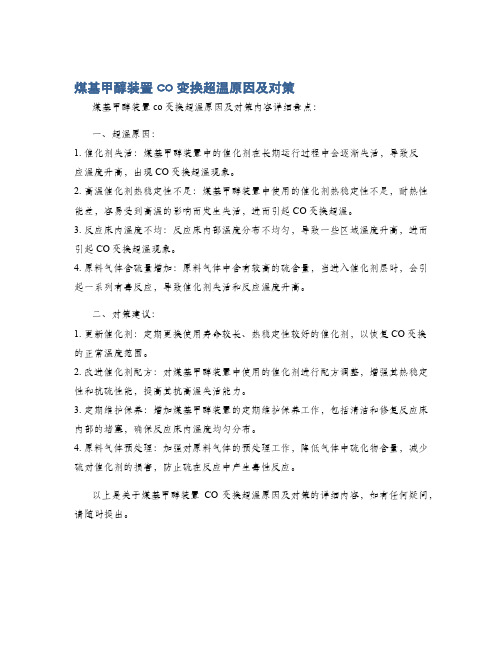
煤基甲醇装置co变换超温原因及对策
煤基甲醇装置co变换超温原因及对策内容详细盘点:
一、超温原因:
1. 催化剂失活:煤基甲醇装置中的催化剂在长期运行过程中会逐渐失活,导致反
应温度升高,出现CO变换超温现象。
2. 高温催化剂热稳定性不足:煤基甲醇装置中使用的催化剂热稳定性不足,耐热性能差,容易受到高温的影响而发生失活,进而引起CO变换超温。
3. 反应床内温度不均:反应床内部温度分布不均匀,导致一些区域温度升高,进而引起CO变换超温现象。
4. 原料气体含硫量增加:原料气体中含有较高的硫含量,当进入催化剂层时,会引起一系列有毒反应,导致催化剂失活和反应温度升高。
二、对策建议:
1. 更新催化剂:定期更换使用寿命较长、热稳定性较好的催化剂,以恢复CO变换的正常温度范围。
2. 改进催化剂配方:对煤基甲醇装置中使用的催化剂进行配方调整,增强其热稳定性和抗硫性能,提高其抗高温失活能力。
3. 定期维护保养:增加煤基甲醇装置的定期维护保养工作,包括清洁和修复反应床内部的堵塞,确保反应床内温度均匀分布。
4. 原料气体预处理:加强对原料气体的预处理工作,降低气体中硫化物含量,减少硫对催化剂的损害,防止硫在反应中产生毒性反应。
以上是关于煤基甲醇装置CO变换超温原因及对策的详细内容,如有任何疑问,请随时提出。
连续重整装置异常运行的分析与处理

图2 脱戊烷塔参数2 原因分析2.1 板换运行效果差分析2.1.1 生产波动查询生产记录,2013年大检修前出现因循环机停机、还原段催化剂跑损、晃电等原因造成的紧急停工,停工过程进料、产物、循环氢等流量大幅波动,板换出现温度、压力骤变甚至物料倒流的异常情况,可能引起板束的变形。
大幅波动易导致管线内附着物脱落进入板换,造成压降升高、换热效率下降等情况。
2.1.2 扩能改造扩能后未对进料管路、换热器及反应器等相关设备进行改动,各压降相应升高,影响进料量的提高。
随着进出物料的流量、流速和温度等发生变化,板换换热效率改变甚至超过其换热负荷,是导致热端温差过高、一反进料加热炉负荷过大的主要原因。
2.1.3 过滤器及入口喷淋棒堵塞引罐区精制油直接做为重整进料、蒸发塔波动以及加裂重石波动,可能带入管路杂质使过滤器压差过高;过滤器后管路存在杂质或者过滤器损坏导致杂质通过,进料中过高的氮、氯、烯烃、重组分等于板换入口产生结焦、结盐现象,均可能堵塞入口喷淋棒孔眼,导致压降过高、处理量达不到控制值和换热效果差等问题。
2.2 脱戊烷塔波动分析用精密压力表测量塔盘总压降约44kPa ,较正常运行的30kPa 偏高,结合运行情况,初步判断塔盘结盐。
为进一步了解塔内气液相分布情况,2015年11月利用γ射线扫描检测技术对塔的运行工况进行检测,结果1~39层塔盘正常,40层塔盘存在液泛,液层高度约1m ,表明塔盘或其降液管存在堵塞情况[1]。
塔内上升气体或者下降液体流动不畅,某一时刻出现大量气体上0 引言某连续重整装置2006年建成投产,采用UOP 公司CycleMax工艺,由中石化工程建设公司设计建造,加工能力1.2Mt/a ,催化剂为UOP 公司R274,再生能力为908Kg/h 。
2013年全厂总流程调整以及经济效益方面的考虑,扩能至1.44Mt/a ,再生部分未做调整,改用中石化PS-Ⅵ催化剂,并由汽油型转换为芳烃型重整。
重整二反压降过高的原因及整改措施
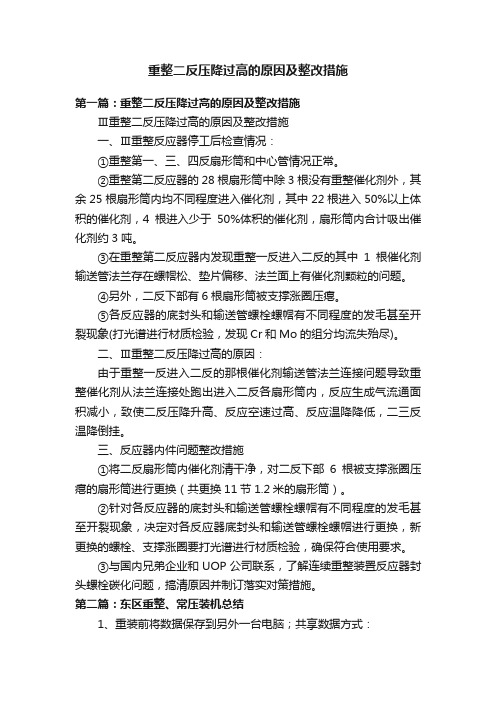
重整二反压降过高的原因及整改措施第一篇:重整二反压降过高的原因及整改措施Ⅲ重整二反压降过高的原因及整改措施一、Ⅲ重整反应器停工后检查情况:①重整第一、三、四反扇形筒和中心管情况正常。
②重整第二反应器的28根扇形筒中除3根没有重整催化剂外,其余25根扇形筒内均不同程度进入催化剂,其中22根进入50%以上体积的催化剂,4根进入少于50%体积的催化剂,扇形筒内合计吸出催化剂约3吨。
③在重整第二反应器内发现重整一反进入二反的其中1根催化剂输送管法兰存在螺帽松、垫片偏移、法兰面上有催化剂颗粒的问题。
④另外,二反下部有6根扇形筒被支撑涨圈压瘪。
⑤各反应器的底封头和输送管螺栓螺帽有不同程度的发毛甚至开裂现象(打光谱进行材质检验,发现Cr和Mo的组分均流失殆尽)。
二、Ⅲ重整二反压降过高的原因:由于重整一反进入二反的那根催化剂输送管法兰连接问题导致重整催化剂从法兰连接处跑出进入二反各扇形筒内,反应生成气流通面积减小,致使二反压降升高、反应空速过高、反应温降降低,二三反温降倒挂。
三、反应器内件问题整改措施①将二反扇形筒内催化剂清干净,对二反下部6根被支撑涨圈压瘪的扇形筒进行更换(共更换11节1.2米的扇形筒)。
②针对各反应器的底封头和输送管螺栓螺帽有不同程度的发毛甚至开裂现象,决定对各反应器底封头和输送管螺栓螺帽进行更换,新更换的螺栓、支撑涨圈要打光谱进行材质检验,确保符合使用要求。
③与国内兄弟企业和UOP公司联系,了解连续重整装置反应器封头螺栓碳化问题,搞清原因并制订落实对策措施。
第二篇:东区重整、常压装机总结1、重装前将数据保存到另外一台电脑;共享数据方式:a.在控制面板,管理工具里本地安全策略里,安全选项里:本地帐户的共享和安全模式改为经典模式,使用空白密码的本地帐户停用,来宾帐户状态启用。
b.用户权利指派中将拒绝从网络访问这台计算机Guest账户删除。
在运行里输入D0op52F$。
或E盘,D盘,就可打开。
c.共享的两台电脑Administrator取消密码。
连续重整装置典型问题及处理
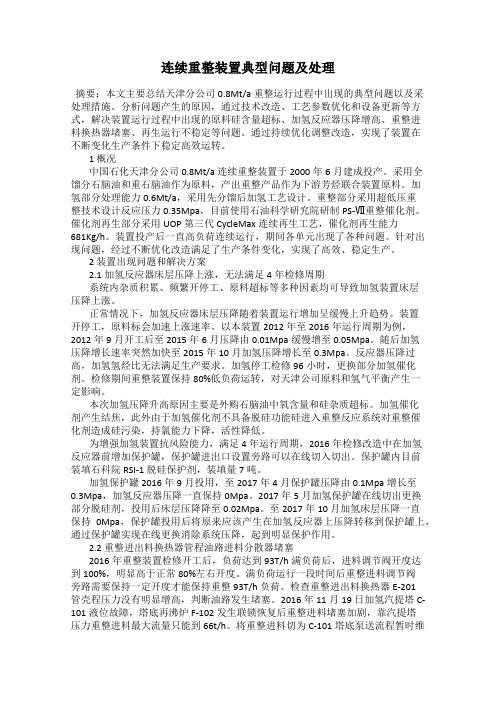
连续重整装置典型问题及处理摘要:本文主要总结天津分公司0.8Mt/a重整运行过程中出现的典型问题以及采处理措施。
分析问题产生的原因,通过技术改造、工艺参数优化和设备更新等方式,解决装置运行过程中出现的原料硅含量超标、加氢反应器压降增高、重整进料换热器堵塞、再生运行不稳定等问题。
通过持续优化调整改造,实现了装置在不断变化生产条件下稳定高效运转。
1 概况中国石化天津分公司0.8Mt/a连续重整装置于2000年6月建成投产。
采用全馏分石脑油和重石脑油作为原料,产出重整产品作为下游芳烃联合装置原料。
加氢部分处理能力0.6Mt/a,采用先分馏后加氢工艺设计。
重整部分采用超低压重整技术设计反应压力0.35Mpa,目前使用石油科学研究院研制PS-Ⅶ重整催化剂。
催化剂再生部分采用UOP第三代CycleMax连续再生工艺,催化剂再生能力681Kg/h。
装置投产后一直高负荷连续运行,期间各单元出现了各种问题。
针对出现问题,经过不断优化改造满足了生产条件变化,实现了高效、稳定生产。
2 装置出现问题和解决方案2.1加氢反应器床层压降上涨,无法满足4年检修周期系统内杂质积累、频繁开停工、原料超标等多种因素均可导致加氢装置床层压降上涨。
正常情况下,加氢反应器床层压降随着装置运行增加呈缓慢上升趋势。
装置开停工,原料标会加速上涨速率。
以本装置2012年至2016年运行周期为例,2012年9月开工后至2015年6月压降由0.01Mpa缓慢增至0.05Mpa。
随后加氢压降增长速率突然加快至2015年10月加氢压降增长至0.3Mpa。
反应器压降过高,加氢氢烃比无法满足生产要求。
加氢停工检修96小时,更换部分加氢催化剂。
检修期间重整装置保持80%低负荷运转,对天津公司原料和氢气平衡产生一定影响。
本次加氢压降升高原因主要是外购石脑油中氧含量和硅杂质超标。
加氢催化剂产生结焦,此外由于加氢催化剂不具备脱硅功能硅进入重整反应系统对重整催化剂造成硅污染,持氯能力下降,活性降低。
反应器超温的处理
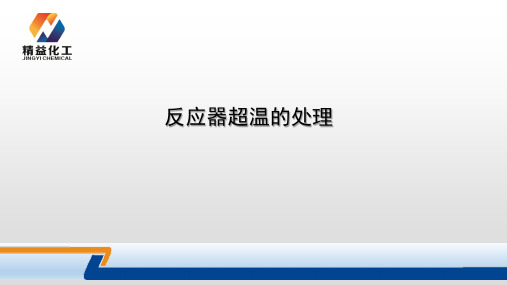
轻烃回收岗位: 1. 联系调度,重整C5馏分油去脱丁烷塔切出。吸收石脑油会逐渐减少。 2. 待分馏系统塔底循环后,吸收石脑油会减少至0,逐渐切出1208-T-103、1208-T-102停注
缓蚀剂,维持各塔顶回流罐界位。 3. 分馏改小循环后,塔底重沸器没有热源,1208-T-101、1208-T-102塔底温度会快速下降,
口电动阀,停注硫泵、阻垢剂泵,关闭注硫泵、阻垢剂泵出口手阀,并关闭注硫、阻垢 剂注入点手阀。投泵出口冲洗氢。 4. 若新氢压缩机停机,联系沸腾床岗位关闭新氢机出口手阀。联系主操开大新氢机入口放 火炬,严防高压串低压事故发生、新氢机入口安全阀及各级出口安全阀超压起跳。
5. 配合主操分馏改分馏小循环,反应改至E-204后不合格线去罐区。 6. 配合主操对照高低分液界位。 7. 配合主操低分气改放火炬。 8. 现场巡检检查有无泄漏、冒烟情况。
20202调节阀,维持V-201液位,关小PV-20101,维持V-201压力。 7. 随着F-201进料温度降低,分馏塔降温后,关小FV-20802、FV-10803外送阀,关小侧线
塔抽出阀FV-20901,平衡侧线塔液位。 8. 关小分馏塔顶回流罐塔顶回流调节阀,适当开大泵出口至回流罐小流量线手阀,保证
整维持其稳定。 12. 待T-201、T-202、T-203塔底温度降至200时,各塔顶温度会降至100℃,各塔顶回流
已无法建立塔顶回流故切出,停P-201、P-203、P-206、P-207。 13. 当温度降至200~250℃时,侧线塔抽出将减少至0,此时切出T-203,停P-205。 14. 建立T-201、T-202塔底分馏自身循环。
4. 开大脱H2S汽提塔底泵至F-201调节阀FV-20401、FV-20402,以增大E-103管程循环油量 来带走反应生成的多余热。
连续重整装置再生器压降升高原因分析及解决措施
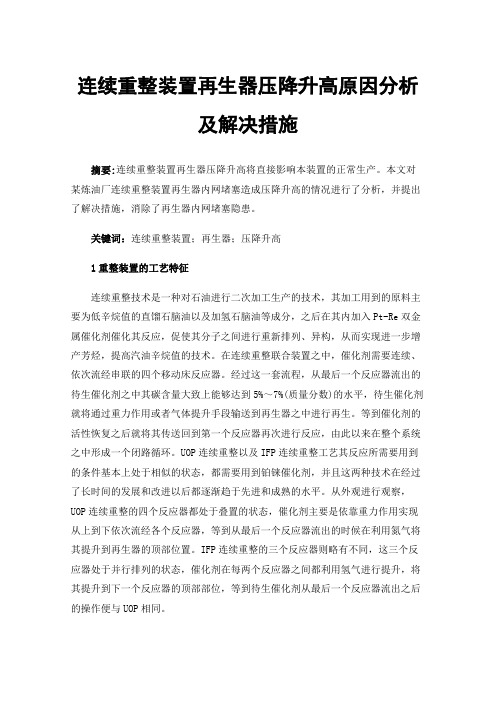
连续重整装置再生器压降升高原因分析及解决措施摘要:连续重整装置再生器压降升高将直接影响本装置的正常生产。
本文对某炼油厂连续重整装置再生器内网堵塞造成压降升高的情况进行了分析,并提出了解决措施,消除了再生器内网堵塞隐患。
关键词:连续重整装置;再生器;压降升高1重整装置的工艺特征连续重整技术是一种对石油进行二次加工生产的技术,其加工用到的原料主要为低辛烷值的直馏石脑油以及加氢石脑油等成分,之后在其内加入Pt-Re双金属催化剂催化其反应,促使其分子之间进行重新排列、异构,从而实现进一步增产芳烃,提高汽油辛烷值的技术。
在连续重整联合装置之中,催化剂需要连续、依次流经串联的四个移动床反应器。
经过这一套流程,从最后一个反应器流出的待生催化剂之中其碳含量大致上能够达到5%~7%(质量分数)的水平,待生催化剂就将通过重力作用或者气体提升手段输送到再生器之中进行再生。
等到催化剂的活性恢复之后就将其传送回到第一个反应器再次进行反应,由此以来在整个系统之中形成一个闭路循环。
UOP连续重整以及IFP连续重整工艺其反应所需要用到的条件基本上处于相似的状态,都需要用到铂铼催化剂,并且这两种技术在经过了长时间的发展和改进以后都逐渐趋于先进和成熟的水平。
从外观进行观察,UOP连续重整的四个反应器都处于叠置的状态,催化剂主要是依靠重力作用实现从上到下依次流经各个反应器,等到从最后一个反应器流出的时候在利用氮气将其提升到再生器的顶部位置。
IFP连续重整的三个反应器则略有不同,这三个反应器处于并行排列的状态,催化剂在每两个反应器之间都利用氢气进行提升,将其提升到下一个反应器的顶部部位,等到待生催化剂从最后一个反应器流出之后的操作便与UOP相同。
2连续重整装置再生器压降升高原因分析某炼油厂1.0Mt/a连续重整装置(简称2号重整)于2020年3月16日建成投产。
反应物料的流动方向与催化剂的流动方向相反。
催化剂再生单元规模1000kg/h,再生循环气体回路采用干冷循环形式,再生循环气、氧氯化放空气分别流经固体脱氯罐,以去除其中的氯化物。
十二、反应器超温超压现场处置方案

十二、反应器超温超压现场处置方案1、事故特征1.1危险性分析,可能发生的事故类型反应器超温超压,会造成催化剂损坏,系统压力超高会引起系统安全阀起跳,甚至会引起阀门,法兰泄漏等。
1.2 事故发生的区域、地点或装置的名称高温高压的场所,反应器系统1.3事故可能发生的时机和造成的危害程度事故可能发生的时机:原料处理量突然加大或处理烯烃含量高的时候或操作不当超温;造成的危害程度:反应器超温超压如处理不当,极易引起法兰泄漏,从而引起中毒,火灾或发生爆炸;1.4事故前的可能出现的征兆反应器床层温度大幅度上升,系统压力快速上涨2、应急组织与职责2.1 现场自救小组及人员构成情况应急自救小组组长:当班装置班长应急自救小组成员:装置外操人员、装置内操人员、机动部值班人员2.2职责2.2.1应急自救小组组长的职责a)根据事故现场的情况,确保应急资源配备投入到位,组织现场应急救援工作;b)同援助部门紧密合作,共同处理好事故,如果事故有扩大、发展趋势,应及时报请公司应急指挥部,启动公司专项应急预案。
c) 组织编制现场处置方案,组织搞好培训和演练;d)负责现场应急处置,落实应急行动,根据险情发展,提出改进措施;e)组织做好善后工作。
2.2.2事故第一发现人职责a) 发生事故后立即通知部门领导及现场人员;b)采取应急处置措施,及时控制住当前局势,防止事故继续恶化c)及时疏散现场无关人员撤离现场。
3、应急处置3.1应急处置程序3.1.1事故第一发现人立即以大声呼叫方式向现场人员报警,并马上通知当班装置班长,报告事故发生地点、种类、事故危害程度等。
3.1.2当班装置班长接报后立即报告部门领导,并迅速赶赴现场,组织协调处理事故,并宣布启动事故现场处置方案,按事故现场处置方案及相关程序、方法组织事故应急救援。
3.1.3当无法有效处置事故或者超过公司救援能力范围时,由部门领导报告公司总指挥部,启动公司级响应,总指挥应根据公司应急预案立即成立事故救援小组,制定详细的救援计划,并由单位负责人报请政府及有关部门支援。
反应器温度波动原因分析及解决方案

第 6 期
石
油
化
工
自 动
化
Vo 1 . 5 2,No . 6
De c e mb e r ,2 0 1 6
2 0 1 6年 1 2月
AUT0M ATI ON I N PETRO- CH E MI CAL I NDU S TRY
反 应 器 温 度 波 动 原 因分 析 及 解 决 方 案
温水 阀 ( TV 4 0 0 1 —2 4 A, TV4 0 0 1 — 2 6 B ) 。反 应 器
全密度 聚 乙烯 反 应 系 统 由 聚合 反 应 器 、 循 环气冷却器 、 离 心式 压缩 机 、 2套催 化 剂加 料 器 和产 品排料 系统 组成 。反应循 环气体 在 离心式 压缩机 的作 用 下 , 连 续 通过 流 化 的树 脂 床 层 和 循环气冷 却器 , 这 样 循 环 气 流 既 流 化 床 层 又 移 走反应 生成 的热 量 。在循 环 气 冷却 器 中 , 调 温 水将循环气 移 出的反 应 热带 走 , 在调 温 水 冷却 器 中, 这部 分反 应 热 由冷 却 水撤 除。调 温水 系
一
定 的 周期定 时 采 样 , 与设 定 值 进 行 比较 后 , 按 照
l
T T 4 0 0 1 — 2 6
P I D A
l
C M : T I C 一 4 0 0 1 — 2 6
温度 ( T T4 0 0 1 —2 6 ) 通 过 反 应 器 人 口循 环 气 温 度
( T T 4 0 0 卜4 6 ) 的设 置来 控制冷却水 及部 分旁 通
调温 水 的 流 量 , 反应器 温度控制器 ( T I C 4 0 0 1 —
连续重整装置反应器结焦问题原因分析及对策

1201 发现结焦的经过某连续重整装置第一周期按计划停工检修,检修期间,对反应器和再生器的内件进行检查(再生器卸剂,反应器没卸剂),扇形筒、内构件没有发现变形,再生器内外网无过热现象。
检修开工一年后,出现待生催化剂提升不畅,停再生,拆开待生”L”阀组后,在”L”阀组弯头处发现有碳块,清理后再生恢复正常。
对于碳块的出现,车间高度重视,马上对重整注硫进行了调整,由0.1~0.2ppm调整为按0.3~0.4ppm注。
同时将碳样寄送北京石科院做碳型分析。
在离第2周期检修前3个月,催化剂再生系统的提升开始频繁出现问题,主要是有碳块带到下部提升线,造成催化剂无法提升。
重整注硫由0.3~0.4ppm调整为0.4~0.5ppm注,也将碳样寄送北京石科院做碳型分析。
3月车间在收集器出口至待生催化剂“L”阀组处增设临时过滤网,减少了停车的次数。
连续重整装置第2周期按计划停工检修,重整反应器、再生开始卸剂,利用大概2天时间4台反应器初步清焦完毕。
2 反应器及炉管的检查情况2.1 重整第一反应器重整第一反应器底死区、扇形筒与器壁拐角部位有结炭,有块状结炭,个别扇形筒内有结炭,设备内构件没有损坏。
2.2 重整第二反应器重整第二反应器扇形筒底部死区拐角部位结炭严重,扇形筒支撑板严重变形,共8根扇形筒有不同程度的变形,2根扇形筒下部已变形裂开约有20cm,扇形筒内、扇形筒间隙、支撑圈、输送管及反应器器壁等均有不同程度的结碳现象,催化剂输送管已堵塞了约三分之二。
2.3 重整第三反应器重整第三反应器底死区、扇形筒与器壁拐角部位有结炭,有块状结炭,个别扇形筒内有结炭,设备内构件没有损坏。
2.4 重整第四反应器重整第四反应器底部、中心管、扇形筒内无明显结炭,设备内构件没有损坏。
2.5 重整四合一炉集合管重整第一、二、四反应器出口炉管有微量的碳粉,无明显结炭出现。
3 装置积碳原因分析装置出现炭块后,及时将收集到的炭块送至石科院进行了物化分析,并由此分析炭块形成的初步可能原因,并及时采取了相应的措施。
连续重整装置再生器飞温原因分析及对策
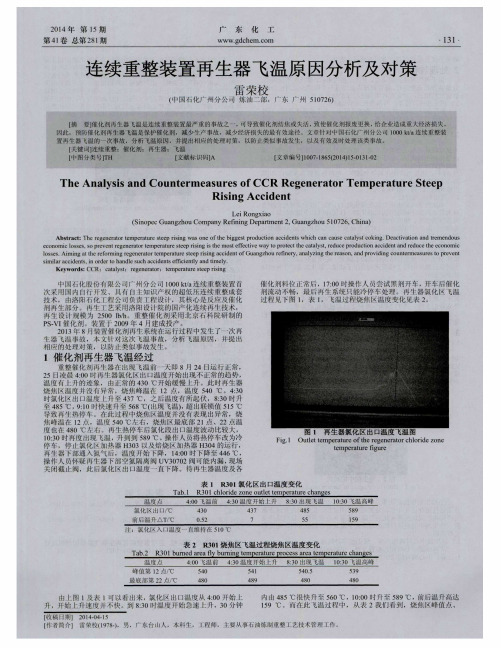
( S i n o p e c Gu a n g z h o u C o mp a n y R e f i n i n g De p a r t me n t 2 , Gu a n g z h o u 5 1 0 7 2 6 , C h i n a )
Abs t r a c t :T h e r e g e n e r a t o r t e mp e r a t u r e s t e e p r i s i n g wa s o n e o f t h e b i g g e s t p r o d u c t i o n a c c i d e n t s whi c h c a n c a u s e c a t a l ys t c o k i n g . De a c t i v a t i o n a n d t r e me n d o u s
l o s s e s Ai mi n g a t t h e r e f o r mi n g r e g e n e r a t o r t e mp e r a t u r e s t e e p r i s i n g a c c i d e n t o f Gu a n g z h o u r e i f n e r y , a n a l y z i n g t h e r e a s o n , a n d p r o v i di n g c o u n t e m e r a s u r e s t o p r e v e n t
, 器 1 { - 黼 故, 小义钏‘ 刈这 次 1 { l 温 事 故,分 析 乜 温原 , 并提 相戍 的处 理对 策 ,以防 J 类 似 事故发 , 。
s i mi l a r a c c i d e n t s . i n o r d e r t o h a n d l e s u c h a c c i d e n t s e f i f c i e n t l y a n d t i me l y . Ke y wor d s : CCR : c a t a l y s t :r e g e n e r a t o r :t e mp e r a t u r e s t e e p r i s i n g
导致反应器温度升高的因素与处理措施-化工论文-化学论文

导致反应器温度升高的因素与处理措施-化工论文-化学论文——文章均为WORD文档,下载后可直接编辑使用亦可打印——1 前言中石化武汉分公司乙烯装置是针对抗冲共聚物和R-TPONEWCON 的产品结构进行设计的,其生产能力为20 万吨/ 年,年运行时间为8,000 小时。
该专利许可装置还能够生产各种均聚物和无规共聚物,预期的生产能力能够达到30吨/小时。
专利许可产品的牌号总共有98 个,是针对各种产品应用领域而设计的,包括汽车和家用电器等行业,而制造出来的产品形式则包括注塑或成型产品、板材、薄膜、纤维或者其他。
2 导致反应器温度升高的因素2.1 散热不足(1)催化剂进料流量突然增加,发生过度聚合反应。
(2)急冷液泵故障急冷液泵是输送急冷液至反应器车热的关键设备,若急冷液泵发生故障直接会导致急冷液中断,那么几分钟之内就会飞温,导致停车。
(3)急冷液喷嘴堵塞急冷液喷嘴堵塞会导致急冷液不能形成良好的喷射状态打入反应器,从而容易造成局部温度过高,此时要切换至备用喷嘴,导致极冷喷嘴堵塞有几个原因:①急冷液泵的入口或是压力低,泵不上量;②急冷液的最小回流线的管线堵塞,③催化剂配置不合格,导致反应生成大量的细粉。
④,反应器料位太高⑤旋风分离器效果不好,D-201 中沉积得粉料太多⑥急冷液泵的出口压力和反应器的压差过小。
(4)反应器温度控制的急冷液控制阀故障急冷液控制阀发生故障,不能准确的调节进入反应器的急冷液的流量,若急冷液流量过小就会导致温度升高。
(5)反应器压力升高反应器压力升高,导致发生过度聚合反应,热量则俩不急撤走,导致温度升高。
(6)在生产无规共聚物产品期间,乙烯进料过量乙烯尽量过量会导致发生过度导聚合反应,聚合热来不及撤走,导致反应器温度上升。
2.2 温度指示器故障温度指示器故障时,不能正确显示反应器温度。
当反应器内实际反应温度超温时,温度指示器故障不能反应,从而没有及时采取措施解决温度过高问题,会导致粉料熔融,结块,严重时会导致飞温引起停工。
重整装置预处理单元运行瓶颈问题分析及措施

重整装置预处理单元运行瓶颈问题分析及措施摘要:中国石油辽河石化公司 600 kt /a 连续重整装置预加氢单元自2012年开工以来第一个运行周期内生产正常,但从2015年大检修后,多次出现反应器床层压降高问题,导致预加氢单元进料困难,限制了加工负荷,被迫停工撇头。
预加氢单元加工负荷受限,加热炉负荷过大,存在炉膛超温风险;通过模型分析预加氢进料量对换热器负荷、换后温度及加热炉负荷的影响,分析进料换热器E1101A可能存在管束结垢问题,造成换热器效果不好,限制了加工负荷,采取措施是在大检修中对管束进行清理检查,保障预加氢加工处理量的满负荷运行效能。
关键词:运行瓶颈热负荷结垢1 前言中国石油辽河石化公司 600 kt /a 连续重整装置预加氢单元主要流程是由装置外来的混合石脑油经预加氢进料泵P-1104送至预加氢进料缓冲罐D-1101,由预加氢进料泵P-1101升压后与从预加氢循环氢压缩机K-1101来的H2混合,经预加氢进料换热器E1101AB与预加氢产物换热,由加热炉F-1101加热至反应温度后依次进入预加氢反应器R-1101和脱氯反应器R-1102。
2问题描述重整装置预加氢单元自2012年开工在第一个运行周期内生产正常,但从2015年大检修后,多次出现反应器床层压降高问题,导致预加氢单元进料困难,限制了加工负荷,被迫停工撇头。
从历史数据看出,装置从2017年5月份开始预加氢进料换热器E1101换后温度有明显下降,进料加热炉炉膛温度升高,燃料气消耗量增加。
在2018年大检修期间对E1101A/B管束进行了清理,但因管束密集,内部污垢难以清理干净,开工后仍存在换后温度偏低问题,装置在43t/h处理量下,进料加热炉炉膛温度达到690℃,燃料气流量超程。
在2020年3月份对E1101B管束进行更换,换后温度有一定升高,但与第一个运行周期相比,差距仍然较大。
目前预加氢单元加工负荷受限,加热炉负荷过大,存在炉膛超温风险。
反应釜超温现场处置方案
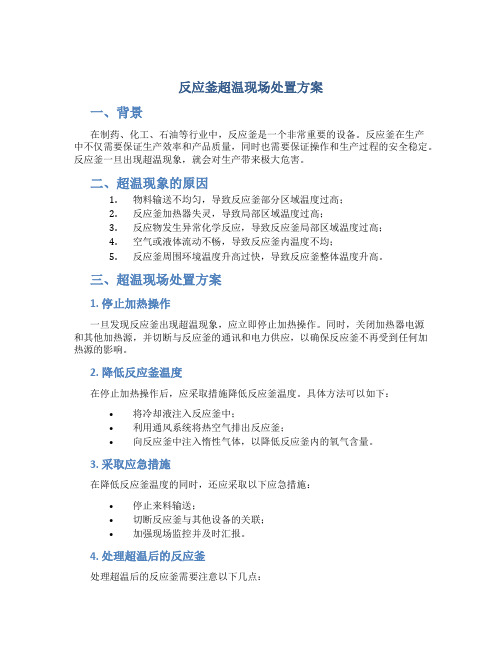
反应釜超温现场处置方案一、背景在制药、化工、石油等行业中,反应釜是一个非常重要的设备。
反应釜在生产中不仅需要保证生产效率和产品质量,同时也需要保证操作和生产过程的安全稳定。
反应釜一旦出现超温现象,就会对生产带来极大危害。
二、超温现象的原因1.物料输送不均匀,导致反应釜部分区域温度过高;2.反应釜加热器失灵,导致局部区域温度过高;3.反应物发生异常化学反应,导致反应釜局部区域温度过高;4.空气或液体流动不畅,导致反应釜内温度不均;5.反应釜周围环境温度升高过快,导致反应釜整体温度升高。
三、超温现场处置方案1. 停止加热操作一旦发现反应釜出现超温现象,应立即停止加热操作。
同时,关闭加热器电源和其他加热源,并切断与反应釜的通讯和电力供应,以确保反应釜不再受到任何加热源的影响。
2. 降低反应釜温度在停止加热操作后,应采取措施降低反应釜温度。
具体方法可以如下:•将冷却液注入反应釜中;•利用通风系统将热空气排出反应釜;•向反应釜中注入惰性气体,以降低反应釜内的氧气含量。
3. 采取应急措施在降低反应釜温度的同时,还应采取以下应急措施:•停止来料输送;•切断反应釜与其他设备的关联;•加强现场监控并及时汇报。
4. 处理超温后的反应釜处理超温后的反应釜需要注意以下几点:•禁止立即进行任何操作,等待反应釜恢复正常温度后再进行操作;•确保反应釜内的反应物已全部冷却,确保安全;•清理反应釜内部,以排除可能的残留物和气体。
四、超温事故的预防预防超温事故的发生,需要注意以下几点:•建立完善的安全操作规程;•加强对操作人员的培训和交流;•定期对设备进行检修和维护;•在反应釜周围设置温度和压力传感器,及时监测反应釜的温度和压力变化。
五、结论反应釜超温现场处置方案是保证反应釜安全稳定运行的重要措施。
在处理超温现象时,需要迅速采取应急措施,并降低反应釜温度。
预防超温事故的发生,则需要加强安全意识和培训,并保证设备正常维护。
催节匕重整预加氢反应器压降过高的原因分析及对策

催节匕重整预加氢反应器压降过高的原因分析及对策催节匕重整预加氢反应器压降过高是指反应器内部的压力降低得过大,超出正常范围。
这个问题可能影响到催化催化剂的活性和选择性,甚至可能引起整个催化过程的中断。
因此,对于催节匕重整预加氢反应器压降过高,需要进行原因分析并采取相应的对策。
1.反应器进料流量超过设计范围:当反应器进料流量超过设计范围时,会导致反应器内部压力下降过大。
这种情况下,可以考虑调整进料流量,使其在设计范围内运行。
2.反应器床层饱和:当反应器床层的活性组分过多,床层中的床层活性组分积聚过多,会导致反应器的压降升高。
这种情况下,可以定期清洗和更换床层,以保持床层的活性。
3.催化剂活性下降:催化剂活性的下降也是导致压降升高的一个重要原因。
可以考虑定期更换催化剂或者采取逆洗、再生等方法来恢复催化剂的活性。
4.反应物质积聚:在反应器中,反应物质的积聚也会导致反应器压降升高。
可以通过增加反应物的流动速度或者调整反应器的布局,以减少反应物质的积聚。
5.缓慢的传质过程:在反应器中,缓慢的传质过程也会增加反应器的压降。
可以采用增加传质表面积、调整传质方式等方法来改善传质过程,从而减少压降。
6.温度和压力的变化:温度和压力的变化也会导致反应器压降的变化。
可以通过调整温度和压力的控制参数,使其保持在正常范围内,从而减少压降。
在对策方面,可以采取以下措施来应对催节匕重整预加氢反应器压降过高的问题:1.定期检查和清洗反应器:定期检查和清洗反应器,包括床层、传质设备等,以确保反应器内部的清洁和良好的运行状态。
2.更换催化剂:在催化剂活性下降的情况下,及时更换催化剂,以保证反应器的正常运行。
3.优化反应器布局:针对反应物积聚和传质不良等问题,可以优化反应器的布局,增加反应物的流动速度和反应物的接触面积,以改善反应器的传质性能。
4.调整温度和压力:根据反应器的实际情况,合理地调整温度和压力的控制参数,使其保持在正常范围内,从而减少压降的发生。
超温治理方案

超温治理方案1. 引言随着科技的不断进步和社会的发展,能源的需求也越来越大。
然而,能源的过度消耗也导致了能源的有限性和环境的恶化。
超温现象是能源消耗过度的一种典型表现,不仅造成资源的浪费,还对环境造成了严重的污染。
因此,制定一套完善的超温治理方案,对保护环境、节约能源具有重要意义。
2. 超温的原因分析超温是指物体或系统内部温度超过了正常运行范围。
其原因主要包括以下几点:•不合理的设计或制造,导致散热不畅或散热面积不足;•长时间高负荷运行,导致机械设施的温度升高;•不当的使用方式,如长时间不关机或在高温环境中使用设备等。
3. 超温治理方案为了有效治理超温现象,可以采取以下方案:3.1 合理的设计与制造在设计与制造过程中,应充分考虑设备散热问题。
合理配置散热装置,如风扇、散热片等,以增加散热面积;合理设置通风孔,提高空气对设备的对流散热效果。
3.2 定期维护与检查对于长时间运行的设备,应建立起定期的维护和检查制度。
检查和清洁设备的散热孔、散热器等重要部位,确保散热效果良好。
及时更换老化的散热装置,保持设备的正常散热功能。
3.3 合理使用与操作在使用设备时,要遵循正确的使用方式和操作规范。
避免长时间高负荷运行,合理分配设备的工作时间和休息时间。
在设备工作的过程中,注意设备周围的通风情况,避免设备在密闭环境中运行。
3.4 温度监控系统建立温度监控系统是治理超温的重要手段。
通过安装温度传感器,实时监测设备的温度变化。
当温度超过设定阈值时,系统可以及时报警并采取措施,例如自动降低设备的负荷或自动停机,以避免超温。
3.5 提升人员意识高温是超温现象的一个重要标志,因此提高人员的意识,加强对超温的认识和理解,是超温治理的关键。
通过加强培训和教育,让人员了解超温的危害和治理方法,提高他们在工作中的防范意识。
4. 结论超温现象的治理对保护环境和节约能源具有重要意义。
通过合理的设计与制造、定期维护与检查、合理使用与操作、温度监控系统以及提升人员意识等措施,可以有效预防和治理超温问题。
中过超温总结分析及防范措施
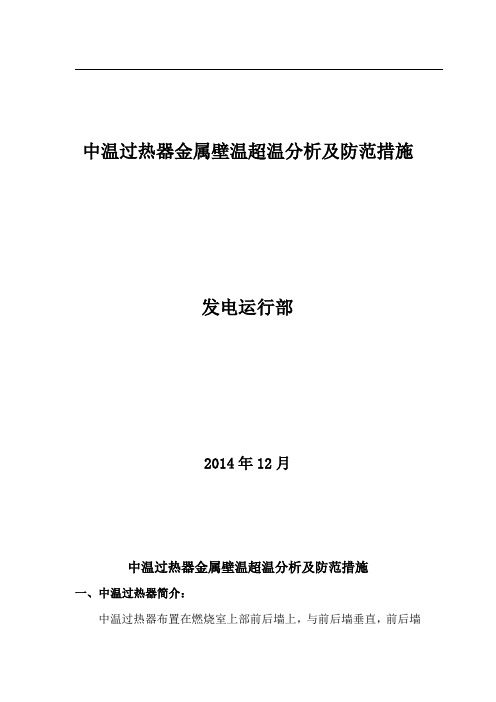
中温过热器金属壁温超温分析及防范措施发电运行部2014年12月中温过热器金属壁温超温分析及防范措施一、中温过热器简介:中温过热器布置在燃烧室上部前后墙上,与前后墙垂直,前后墙各布置8片,每片中温过热器屏由37根管子组成,管子直径为Φ51×7mm,材料12Cr1MoVG和SA-213T91。
中温过热器为膜式管屏,节距70mm,鳍片材料12Cr1MoV 。
中温过热器下部表面覆盖有耐磨浇注料。
入口汇集集箱Φ406×57mm,每片屏的进口集箱为Φ219×28mm,出口集箱均为Φ219×28mm,集箱材料为12Cr1MoVG。
二、汽温调节方式:过热蒸汽温度的调节采用二级喷水减温器,分别位于低温过热器与屏式过热器之间的管道上,屏式过热器和高温过热器之间的管道上。
喷水水源来自给水泵出口和高加前,减温器采用笛形管式。
(#1炉2012年A修中加了三级减水温水。
)在设计煤种B-MCR工况下,Ⅰ级减温器喷水量为20.16吨/时,将蒸汽温度从378℃降至371℃,Ⅱ级减温器喷水量为13.32吨/时,将蒸汽温度从475℃降至462℃。
三、超温情况:1、超温规定:低过管壁520℃为超温;中过Ⅰ管壁510℃为超温;中过Ⅱ管壁550℃为超温;低再管壁530℃为超温;高再管壁610℃为超温;高过管壁565℃为超温。
2、机组异常工况或机组启动过程中,中过管壁容易发生超温。
四、主要超温时段:1、机组冷态启动时汽轮机冲转、发电机并网及并网后,负荷在50MW-130 MW之间,包括给水旁路切主路时,发生中温过热器管壁超温。
2、机组单台一次风机或单台引风机运行,负荷在120MW以下时中温过热器管壁超温。
3、机组热态启动时汽轮机冲转、发电机并网及并网后,负荷在50 MW -130 MW之间,发生中温过热器管壁超温。
4、锅炉发生翻床或大量甩负荷后,机组重新升负荷至50 MW -130 MW之间时,发生中温过热器管壁超温。
超温处置方案

超温处置方案随着时代的发展,科技的进步和生产力的提升,产能不断增加,人们的生活水平也得到了提高。
但这一切的发展和进步也给环境带来了极大的压力,大气污染、水资源短缺、垃圾固废等问题日益突出。
其中,超温问题是大气污染以及生活垃圾处理面临的难题之一。
超温含义超温指的是在环保设备内或者堆体中,处于可燃状态,控制条件无法控制氧化反应速率,产生大量的过热气体,造成大面积的自燃和有害气体的排放。
超温严重影响到处理工艺和处理效果,同时对环境和人类的健康造成威胁。
超温处置方案1.了解和把握规律超温产生的原因和规律是多样的,对于不同的超温原因和类型,需要有不同的处置方法。
对于环保行业工作者而言,通过对不同超温规律的了解掌握,才能科学有效地制定超温处置方案。
例如,生活垃圾焚烧设备的超温多发于垃圾生热峰期,那么就需要对垃圾实时监测,把握生热高峰期,及时采取调控措施。
2.提高运维能力提高超温处置的运维能力是解决超温问题的重要保障。
保持稳定的生产操作,定期检查和维护环保设备,及时处理隐患问题等都是运维的关键。
对于高风险的环境和设备,建立相应的应急预案,及时采取措施,有效应对不同的超温情景。
3.创新技术超温处置技术不断创新是环保行业向前发展的必要条件。
例如,利用智能监测系统,智能预测超温问题,自动调控环境设备;建立温度和气体浓度的模型,针对不同的超温情况,给出相应的处置建议等等。
4.环保人员素质提升环境保护设备的稳定运行和超温问题的有效处置需要有专业的运营和管理人员。
提高环保人员的技能和素质,才能够更加贴近生产实际,深度了解环保设备的应用和运维等知识,更好地发挥专业作用,提高超温处置的效率和质量。
结论超温问题的产生不仅影响到生产效率和处理效果,还严重威胁着环境和人类的健康。
因此,制定超温处置方案也需要针对具体情况,采取不同的措施。
在逐步提高环保设备的技术和运维提供质量的同时,还需要注重环保人员的培训和提高素质,以保证超温问题得到高效和可靠的解决。
- 1、下载文档前请自行甄别文档内容的完整性,平台不提供额外的编辑、内容补充、找答案等附加服务。
- 2、"仅部分预览"的文档,不可在线预览部分如存在完整性等问题,可反馈申请退款(可完整预览的文档不适用该条件!)。
- 3、如文档侵犯您的权益,请联系客服反馈,我们会尽快为您处理(人工客服工作时间:9:00-18:30)。
() 5 设立 了分子筛 干燥循环气系统 ;
收稿 日期 :0 6 1 — 0 20-0 2
作者简介 : 喻朝善( 9 9 ) , 16 一 男 四川南充人 , 硕士 , , 讲师 主要从事石油化工教学 与科研工作。
73
维普资讯
设计温度 设计 压力 氢油比( 体积 比 )
空速 Biblioteka 1 冽2 1
确、 迅速的制订检修方案, 在故障处理后保证平稳操作。20 05 年8 月车间对重整装置第 二反应器 R 0 壁 超温故 障 的原 因 22 分析 以及处理为今后 的工作 积累了经验 , 也为今后反应器的使
用 提出了新 的要求。
21反应器壁超温故障特征 .
() 1为防止第 一反应器内催化剂再 次进入第二反应器 , 将
第一反应器内催化剂卸 出重新过筛 , 出体积较小的催化剂 ; 取
() 2同时为抑制第一反应器 内催化剂进入第二反应器 内 , 第一反应 器中心管加高 4e ; 0r a () 3为第一反应器 内催化剂受高速流动的油气气流 冲击造 成催化剂 的塌 陷。 将第一反应器顶部盖板加长 lo Om裙边 ; ( ) 证反应 的充分、 4为保 平稳 。 将第二反应器 内催化剂过筛 重装 , 对第一反应器补充新 的催化剂到规定装填数量。 并
维普资讯
《 装备制造技术)0 7 20 年第 1 期
重 整 装 置 反 应 器 壁 超 温 原 因 分 析 及 处 理 措 袍
喻朝 善
( 克拉玛依职业技术学院石油化工系, 新疆 独山子 830 ) 36o
摘要 : 重整装置的棱心反应主要是在四个反应 器中进行 , 每一个反应 器的正常运行都与产品质量的稳 定密切相 关。因此 , 必须要保证每
催 化剂名称
P T C铂铼催化剂 R— 反应器规格 ( 直径 高 厚 ) 1 0 9 5 4 24 2 80
反应器主体 材质 备注
S —14 B A : Gr 0
直立、 径向璧冷
1 重整 装置概 况
11重整反应基本原理 . 重整装置 以蒸馏车间的低辛烷值直馏 汽油为原料 ( 属于燃
为3 2万吨 , 2 0 年。 0 0年装置进行了 4 5万吨 , 年配套项 目的部
项 目
流程编号 反应介质
指 标
R-2 02
汽油、 氢气
52 5 ℃
2I M Pa 78
分改造现加工能力为 4 万 吨 , 0 年。装置核心部分——重整反 应系统为共 四炉 四反 ,反应 器壁超温会造成催化剂结焦失活 , 影 响产品质量 。 时会造成器壁破裂 , 严重 引发事故 。 因此必须 准
斯、 拔头油等。 12 重整第二反应器 R 2 . 20 的剖面 图及主要参数指标 重 整反应 器为 轴 向冷壁 式反应 器 ,催化 剂装填 在 反应
反应。重整反应系统工艺流程如图 2所示 。
F 2 1 F 2 2 F 2 3 F 2 4 —.t - 、 - 、 - 、 - 0 . 】 整第一、 0 0 0 第二 、 第三 、 四加热炉 第 R 2 1 R 2 2 R 2 3 R 2 ——重 整第一 、 一 0 、 — 0 、一 , -倒 0 第二 、 第三、 四反应器 第 图 2 重整反应系统工艺流程
13 重整反应系统工艺流程( . 原则流程) 预加 氢来 的精 制油经 重整原 料泵 P 2 1 / - 0 AB升压 后 与重 整循环机 C 2 1 的氢气混合, -0 来 然后进人原料换热器 E 21 一0 管 程 与 重 整 反 应 产 物 换 热 到 4 0C左 右 ,依 次 经 过 F 2 1 2o -0 ,
14重整装置主要技术特点 . () 1 重整采用 P T C P T D铂铼催化剂 , 四炉 四反 ; R - 、R - 共
() 2 重整加热炉 为四合一加热炉 , 对流室设废热锅炉 回收系统
用 于 自产蒸汽 ;
() 3为缩短重整催化剂烧焦时间 , 再生采用两段 高压烧焦 ;
() 4 为防止硫对重整催化剂的污染设立了脱硫保护床;
E u p n n f cr g e h oo yNO. , 0 7 q i me t Ma u a t n c n lg i T 12 0
() 6 没有预分馏系统。
找到故障原 因后 , 车间技术攻关小组立 即进行讨论 、 算 计
并迅速制定 出了以下处理方案 :
2反应器壁超温故障特征及原因分析
R 2 1F 2 2 R 22 F 2 3 R 2 3F 2 4 R 2 完 成 重 整 - 0 ,- 0 , 一 0 ,- 0 , 一 0 , 一 0 , 一 0 4
料类型为 8 O~1 0C 10 ,化工 型装置 为 7 7  ̄或 8 ℃ 0~1 0 , 4 ℃)经
重整催化剂 的作用 ( 催化剂装填为 C 一 、B 7 B 6C 一 两段 混装 )并 , 在氢气保护和一定 的反应条件 下 ,发生芳构化反应和其它反 应, 使原来含少量芳烃 的原料 分子结构的重排 , 而成为 富含芳 烃和异构烷烃的生成物。这种产物经进一 步加工处理 , 可获得 高纯度的芳烃或高辛烷值的汽油 ,副产品有氢气 、液态烃、 瓦
一
个反应嚣操作 的平稳。通过对重整装王反应器壁超温原因进行科 学、 客观的分析 , 出故障原 因, 找 制订正 确的检修 方案, 时的采取 及
了处理措 施 。 失降到 了最低 。 把损 开工后 实现 了平稳操作 , 从根本上 消除 了事故 隐患。
关键词 : 重整: 器壁; 温; 因; 反应 超 原 措施
中图分类号 :E9 T 6
文献标识码 : A
文章编号 :6 2- 520 )1 07 - 2 17 -4 (0 70 - 03 0 5 表 1 反应器相关技术特性 参数
中国石油独 山子石化 分公 司重整芳 烃车 间重整装置为 引 进 比利时雪夫隆炼油厂的二 手设备 , 原投产于 17 年 , 90 设计生 产能力为 加 万吨 , 年。引进后由独山子石化公 司设计 院设计