CNC与PLC的区别
数控系统中的PLC控制

上一页 下一页 返回
第一节 数控系统中的PLC
由图5 -9可见,独立型PLC的CNC系统中不但要进行机床 侧的I/O连接,而且还要进行CNC装置侧的I/O连接,CNC和 PLC均具有各自的I/O接口电路。独立型PLC一般采用模块化 结构,装在插板式机笼内,I/O点数和规模可通过I/O模块的
增减灵活配置。对于数控车床、数控铣床和加工中心等单台
的各种变量转换成标准的逻辑电平信号,送入CPU处理。
上一页 下一页 返回
第一节 数控系统中的PLC
2. PLC的软件结构 在可编程控制器中,PLC的软件分为两大部分: · 系统监控程序:用于控制可编程控制器本身的运行,主要 由管理程序、用户指令解释程序和标准程序模块,系统调用;
.用户程序:它是由可编程控制器的使用者编制的,用于控
上一页 下一页 返回
第一节 数控系统中的PLC
(3)编程器编程器是用于用户程序的编制、编辑、调试、监 视以及运行应用程序的特殊工具,一般由键盘、显示屏、智 能处理器、外部设备(如硬盘/软盘驱动器等)组成,它通过通 信接口与PLC相连,完成人一机对话功能。
编程器分为简易型和智能型两种。简易型编程器只能在线
设备,选用微型或小型PLC;对于FMC、FMS、FA、CIMS 等大型数控系统,则需要选用中型或大型PLC。其存储容量随着PLC类别或规模的
不同而改变。
上一页 下一页 返回
第一节 数控系统中的PLC
(5)输入/输出(I/O)模块I/O模块是PLC与现场I/O装置或其他 外部设备之间进行信息交换的桥梁。其任务是将CPU处理产 生的控制信号输出传送到被控设备或生产现场,驱动各种执 行机构动作,实现实时控制;同时将被控对象或被控生产过程
如何理解华中数控系统的PLC

如何理解华中数控系统的PLC所谓PLC就是Programmable Logic Controller,即可编程逻辑控制器。
如果做个比方的话,PLC好比就是连接在计算机数控系统(CNC)与机床之间的一道桥梁。
数控机床用PLC一般分为两类:一类是将CNC和PLC综合起来设计,称为内装型(或集成型)PLC,内装型PLC是CNC装置的一部分;另一类是以独立专业化的PLC生产厂家产品来实现顺序控制功能,称为独立型(或外装型)PLC。
华中数控铣削数控系统的PLC为内装型(或称为内置式)PLC。
一、怎样查看PLC执行文件所在的位置在DOS系统下面,首先进入铣床软件所安装的目录(如C:\HCNC2000),然后在提示符下敲入:type ncbios.cfg您将会清晰地看到屏幕上出现如下的内容(具体内容因机床的不同而异,分号后面是我们这里添加的注释):DEVICE=C:\HCNC2000\bin\sv_step.drv ;步进电机伺服驱动DEVICE=C:\HCNC2000\bin\hc5904.drv ;5904驱动程序DEVICE=C:\HCNC2000\plc\ ;PLC程序PARMPATH=C:\HCNC2000\PARM ;系统参数所在目录DATAPATH=C:\HCNC2000\DATA ;系统数据所在目录PROGPATH=C:\HCNC2000\PROG ;数控程序所在目录DISKPATH=A: ;软盘BINPATH=C:\HCNC2000\bin ;系统BIN目录TMPPATH=C:\HCNC2000 ;临时文件所在目录NETPATH=X: ;网络目录在第三行用粗体突出的就是一个PLC路径设置的实例。
二、PLC源程序的识别和编译华中数控系统的PLC源程序都是以.cld为后缀的文件。
如:PLC_FX2.CLD、PLC_BYJN.CLD、KBD_PLC1.CLD等等。
怎样编译一个已经编好的CLD文件呢?首先,您手头上必须拥有华中数控公司所提供的PLC编译软件包。
CNC与PLC的区别

PLC在数控机床中的控制功能:
(1)、操作面板的控制。
操作面板分为系统操作面板和机床操作面板。
系统操作面板的控制信号先是进入NC,然后由NC送到PLC,控制数控机床的运行。
机床操作面板控制信号,直接进入PLC,控制机床的运行。
(2)、机床外部开关输入信号。
将机床侧的开关信号输入到送入PLC,进行逻辑运算。
这些开关信号,包括很多检测元件信号(如:行程开关、接近开关、模式选择开关等等)
(3)、输出信号控制:PLC输出信号经外围控制电路中的继电器、接触器、电磁阀等输出给控制对象。
(4)、T功能实现。
系统送出T指令给PLC,经过译码,在数据表内检索,找到T代码指定的刀号,并与主轴刀号进行比较。
如果不符,发出换刀指令,刀具换刀,换刀完成后,系统发出完成信号。
(5)、M功能实现。
系统送出M指令给PLC,经过译码,输出控制信号,控制主轴正反转和启动停止等等。
M指令完成,系统发出完成信号。
数控机床中PLC实现的功能

数控机床中PLC实现的功能
1.M、S、T功能
M、S、T功能可以由数控加工程序来指定,也可以在机床的操作面板上进行掌握。
plc依据不同的M功能,可掌握主轴的正转、反转和停止,主轴准停,冷却液的开、关,卡盘的夹紧、松开及换刀机械手的取刀、归刀等动作。
S功能在PLC中可以简单地用四位代码直接指定转速。
CNC送出S代码值到PLC,PLC将十进制数转换为二进制数后送到D/A转换器,转换成相对应的输出电压,作为转速指令来掌握主轴的转速。
数控机床通过PLC可管理刀库,进行刀具的自动交换。
处理的信息包括刀库选刀方式、刀具累计使用次数、刀具剩余寿命和刀具刃磨次数等。
2.机床外部开关量信号掌握功能
机床的开关量有各类掌握开关、行程开关、接近开关、压力开关和温控开关等,将各开关量信号送入PLC,经规律运算后,输出给掌握对象。
3.输出信号掌握功能
PLC输出的信号经强电柜中的继电器、接触器,通过机床侧的液压或气动电磁阀,对刀库、机械手和回转工作台等装置进行掌握,另外还对冷却泵电动机、润滑泵电动机及电磁制动器等进行掌握。
4.伺服掌握功能
通过驱动装置,驱动主轴电动机、伺服进给电动机和刀库电动机等。
5.报警处理功能
PLC收集强电柜、机床侧和伺服驱动装置的故障信号,将报警标志区中的相应报警标志位置位,数控系统便发出报警信号或显示报警文本以便利故障诊断。
6.其它介质输入装置互联掌握
有些数控机床用计算机软盘读入数控加工程序,通过掌握软盘驱动装置,实现与数控系统进行零件程序、机床参数和刀具补偿等数据的传输。
FANUC 0i mate C 数控铣床电气控制系统及PLC控制设计

Abstract Can be
CNC milling machine is a common milling machine used digital control system the control of the program code accurately for milling machining
Key words :FANUC 0i mate C;CNC milling machine; Frequency conversion governor; PLC;Servo drive
FANUC 0i mate C 数控铣床电气控制系统及 PLC 控制设计
目录
引言.....................................................................1 1 FANUC 0i mate C 系统构成...............................................2 1.1 FANUC 0i mate C 系统组成及功能....................................2 1.2 FANUC 0i mate C 系统的配置........................................3 1.3 FANUC 0i mate C 系统的功能连接....................................6 2 系统硬件配置............................................................8 2.1 主轴电机的选型.....................................................8 2.2 交流异步电动机的调速方法...........................................8 2.3 变频调速器工作原理和基本构成......................................10 2.4 变频调速器的选择..................................................12 2.5 变频调速器的参数设置..............................................13 2.6 CNC 变频调速器的连接框图..........................................16 2.7 数控机床进给伺服系统的组成和功能特点..............................16 2.8 伺服电机的选型....................................................19 2.9 进给伺服单元的选型................................................24 3 电气控制系统电路图设计.................................................26 3.1 主轴控制原理图....................................................26 3.2 供电原理图.......................................................26 3.3 CNC 主板............................ ............................27
数控机床PLC控制基础知识
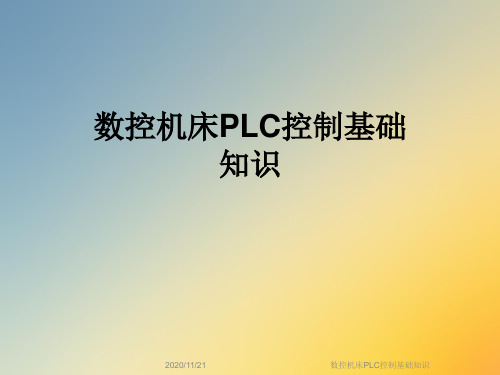
数控机床PLC控制基础知识
具有内装型PLC的CNC系统
数控机床PLC控制基础知识
子程序必须在第二级程序 后指定。
数控机床PLC控制基础知识
FANUC系统PMC的分类:
PMC—L/M:用于FANUC—OC/OD系统 PMC—SA1:用于FANUC—O i系统/O i Mate系统 PMC—SA3:用于FANUC—O i A系统 PMC—SB7:用于FANUC—16i/18i/21i及O i B/O i C系统 PMC—RB5/RB6:用于FANUC—16/18系统
数控机床PLC控制基础知识
3、CNC至PLC
• CNC至机床的信息主要是M、S、T、F等功能代码。 S功能是指用几位代码指定主轴转速,在PLC中通 过转换输出主轴转速控制指令;T功能是通过PLC 管理刀库,进行自动刀具交换;M功能是辅助功能, 根据不同的M代码,可控制主轴的正、反转和停止, 主轴齿轮箱的换档变速,切削液的开、关,卡盘 的夹紧、松开及换刀机械手的取刀、归刀等动作; F功能是通过PLC控制伺服系统完成坐标轴进给率 的输出。
数控机床PLC控制基础 知识
2020/11/21
数控机床PLC控制基础知识
5.1.1 数控机床PMC概述
PLC用于数控机床通常称之为可编程序机床控制器 PMC(Programmable Machine Controller)。 ❖数控机床的控制,由CNC和PMC协调配合共同完成。 ☺CNC主要完成哪些功能? ☺PMC主要完成哪些功能? CNC完成插补运算、译码、位置伺服控制等。 PMC完成工件的装夹、刀具的更换、冷却液的开关等一 些辅助动作;它还接受机床操作面板的指令,一方面直 接控制机床的动作,另一方面将一部分指令送往CNC用 于加工过程的控制。
PLC和NC的关系

一、PLC和NC的关系PLC用于通用设备的自动控制,称为可编程控制器。
PLC用于数控机床的外围辅助电气的控制,称为可编程序机床控制器。
因此,在很多数控系统中将其称之为PMC。
数控系统有两大部分,一是NC、二是PLC,这两者在数控机床所起的作用范围是不相同的。
可以这样来划分NC和PLC的作用范围:1、实现刀具相对于工件各坐标轴几何运动规律的数字控制。
这个任务是由NC来完成;2、机床辅助设备的控制是由PLC来完成。
它是在数控机床运行过程中,根据CNC内部标志以及机床的各控制开关、检测元件、运行部件的状态,按照程序设定的控制逻辑对诸如刀库运动、换刀机构、冷却液等的运行进行控制。
在数控机床中这两种控制任务,是密不可分的,它们按照上面的原则进行了分工,同时也按照一定的方式进行连接。
NC和PLC的接口方式遵循国际标准“ISSO 4336-1981(E)机床数字控制-数控装置和数控机床电气设备之间的接口规范”的规定,接口分为四种类型:1、与驱动命令有关的连接电路;2、数控装置与测量系统和测量传感器间的连接电路;3、电源及保护电路;4、通断信号及代码信号连接电路;从接口分类的标准来看,第一类、第二类连接电路传送的是数控装置与伺服单元、伺服电机、位置检测以及数据检测装置之间控制信息。
第三类是由数控机床强电电路中的电源控制控制电路构成。
通常由电源变压器、控制变压器、各种断路器、保护开关、继电器、接触器等等构成。
为其他电机、电磁阀、电磁铁等执行元件供电。
这些相对于数控系统来讲,属于强电回路。
这些强电回路是不能够和控制系统的弱电回路,直接相连接的,只能够通过中间继电器等电子元器件转换成直流低压下工作的开关信号,才能够成为PLC或继电器逻辑控制电路的可接受的电信号。
反之,PLC或继电器逻辑控制来的控制信号,也必须经过中间继电器或转换电路变成能连接到强电线路的信号,再由强电回路驱动执行元件工作。
第四类信号是数控装置向外部传送的输入输出控制信号。
数控系统中的PLC

PLC控制对象
➢ 第一个环:是操作系统,用
它来管理PLC的硬件资源;
PLC
硬件
➢ 第二个环:是编译系统,这
两 个环构成了的PLC软件系
统。
➢ 第三个环:是实现用户要求 的应用程序。
二. 可编程控制器的结构和编程方法
PLC 的硬件原理框图
编程器
电池 RAM
EEPROM 用户程序
EPROM 系统软件
CPU
1.0 120.1 1.2 1.3 120.1 1.4 1.5 120.2
二. 可编程控制器的结构和编程方法
高级语言编程法(如C语言等); 随着数控技术的发展,可编程控制器控制的设备
已由单机扩展到FMS、CIMS等。可编程控制器处理 的信息除开关量信号、模拟量信号、交流信号外,还 需要完成与上位机或下位机的信息交换。某些信息的 处理已不能采用顺序执行的方式,而必须采用高速实 时处理方式。基于这些原因,计算机所用的高级语言 便逐步被引用到PC的应用程序中来。
三. PC的工作过程及其特点
操作维护容易 可编程控制器信息通过总线或数据传送线与
主机相连,调试和操作方便。可编程控制器采用 模块化结构,如有损坏,即可更换。
四. 数控机床的PLC功能
1. CNC、PLC、机床之间的信号处理过程 CNC装置和机床之间的信号传送处理两个过程:
CNC装置→机床: ➢ CNC装置CNC装置的RAM PLC的RAM中。 ➢ PLC 软件对其RAM中的数据进行逻辑运算处理。 ➢ 处理后的数据仍在PLC的RAM中, ✓ 对内装型PLC,PLC将已处理好的数据通过 CNC的输出接口送至机床; ✓ 对独立型PLC,其RAM中已处理好的数据通过 PLC的输出接口送至机床。
数控机床基本知识
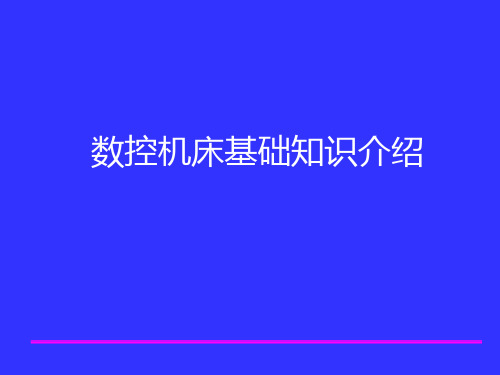
数控机床的认识
数控机床一般指那些只能完成车、铣、镗、磨、钻 等单一工序的数控机床。
在类型上可分为: • 数控车床(CNC车床) • 数控铣床 • 数控镗床 • 数控磨床 • 数控钻床等等。
CNC加工中心
NC加工中心其实就 是内装计算机、备有 自动换刀装置的数控 机床,其控制系统能 控制机床自动换刀, 连续地按一定程序对 各个加工面自动地完 成铣削、镗削、钻孔、 攻丝等多工序加工的 数控机床。
数控机床的优点
• 适应性强
• 对于同一批零件,由于 使用同一机床和刀具及
• 加工质量稳 定
同一加工程序,刀具的 运动轨迹完全相同,且 数控机床是根据数控程
• 生产效率高 • 加工精度高
序自动进行加工,可以 避免人为的误差,这就 保证了零件加工的一致
• 减轻劳动强度 性好且质量稳定。
数控机床的优点
数控机床的优点
• 适应性强 • 加工质量稳定 • 生产效率高 • 加工精度高 • 减轻劳动强度
• 在输入程序并启动后, 就自动地连续加工,直 至零件加工完毕。简化 了工人地操作,使劳动 强度大大降低。
数控机床的缺点
• 成本高 • 要求管理和操作人员素质高
数控机床的认识
NC是Numerical Control(数值控制装置)的缩写。 是自动地控制机床的工作台,刀架 号等位置和速 度的装置。NC以前是由晶体管、IC等电子元件构 成的。随着微型计算机的出现,由它组成了NC并 进一步商品化,把这种NC称为CNC (Computerized Numerical Control)。CNC的第 一个C是内装计算机的意思。
数控机床基础知识介绍
数控机床的认识
• 什么是数控机床
用专业术语来说,数控机床即“数字程序控制 机床”(Numerically Controlled Machine Tool), 是用数字和字母形式来表达工件的形状和尺寸 等技术要求及加工工艺要求,经过数控装置运 算,用数字代码信息(程序指令)控制刀具按给定 的工作程序、运动速度和轨迹进行自动加工的 机床。
第二章 计算机数控系统CNC与控制原理总结

速度处理要做的工作是根据合成速度来计算各运动坐标 的 分速度。 开环系统:通过控制向步进电机输出脉冲的频率来实现。
速度计算的方法是根据程编的F值来确定该频率值。 半闭环和闭环系统:采用数据采样方法进行插补加工,速度
计算是根据程编的F值,将轮廓曲线分割为采样周期的轮 廓步长。
可以实现较复杂的系统功能。容错能力强,在某模块出 故障后,通过系统重组仍可断继续工作。
12
2.2 CNC装置的硬件结构
结构形式:可分:分布式、主从式、总线式。
分布式:各CPU独立、完整,通过外部通信链路连接起来,
数据交换和资源共享通过网络技术实现。
主从式:主控CPU、从控CPU,主控CPU才能控制和访问总
第二章 计算机数控系统CNC与控制原理
本章主要内容
第一节 概述 第二节 CNC装置的硬件结构 第三节 CNC装置的软件结构
第四节 可编程控制器(PLC)
第五节 典型的CNC系统简介
2
2.1概述
1. CNC系统?
从自动控制的角度来看,CNC系统是一种位置、速 度
(还包括电流)控制系统,其本质上是以多执行部件(各运 动轴)的位移量、速度为控制对象并使其协调运动的自动控 制系统,是一种配有专用操作系统的计算机控制系统。 从外部特征来看,CNC系统是由硬件(通用硬件和专 用硬件)和软件(专用)两大部分组成的。
两个以上任务处理。
♦ 并行处理的实现方式: ☆ 资源分时共享(单CPU)
☆ 资源重叠流水处理(多CPU)
34
Have a Rest!
2.3 CNC系统的软件
资源分时共享并行处理(对单一资源的系统)
♦ 在单CPU结构的CNC系统中,可采用 “资源分时共
第五章 数控系统中的PLC控制汇总

序号
1 2 3 4 5 6 7 8 9 10 11
公司名称
FANUC FANUC FANUC FANUC FANUC FANUC SIEMENS SIEMENS SIEMENS SIEMENS SIEMENS
CNC系统型号
System 0 System 0 Mate System 3 System 6 System 10/11 System 15/16/18 SINUMERIK 820 SINUMERIK 3 SINUMERIK 8 SINUMERIK 850 SINUMERIK 880
第二节 数控系统中的PLC
一、PLC的结构、特点及其工作过程 (一)PLC的基本结构
PLC的种类型号很多,大、中、小型PLC的功能不尽相同, 其结构也各不相同,但它们的基本结构形式大体上是相同的,都 是由中央处理单元(CPU)、存储器(RAM/ROM)、输入/输 出单元(I/O)、编程器、电源模块和外部设备等组成,并且内 部采用总线结构。
刀具更换、工件及工作台交换、液动与气动以及润滑等辅助功能进 行顺序控制。
二、概念 可编程序控制器PC(Programmable Controller)是一种数
字运算系统,专为工业环境下的设备运行与控制而设计。
在数控系 统信息流 通中PLC 控制的辅 助功能 (M、S、 T等)信 息
图7-1 数控系统内部信息流
图7-4 PLC的扫描过程
图7-5 PLC的工作过程
二、数控系统中的PLC分类 数控系统中的PLC可分为“内装型”(Built-in-Type)PLC
和“独立型”(Stand-alone-Type)PLC两种类型。 1.内装型PLC 内装型PLC是指PLC内置于CNC装置内,从属于CNC装置,与 CNC装置集于一体
数控机床电气控制与PLC10.0数控机床PLC编程基础
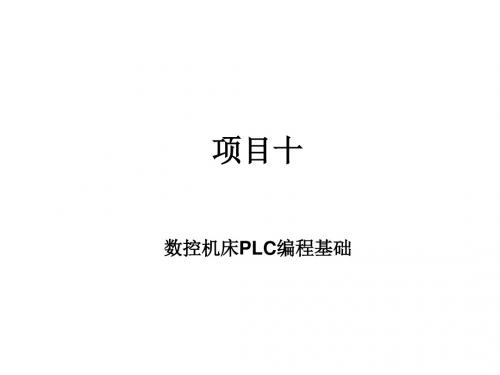
数控机床PLC编程基础
主要内容
数控机床PLC控制系统
结构
作用
FANUC数控PMC编程方法
一、数控机床PLC控制系统
PLC(Programmable Logical Controller,可 编程控制器),以微处理器为核心,能实现顺序 控制、数字运算、软件编程等功能的一种新型控 制元件。它的出现使继电器接触器控制线路得到 极大地简化,PLC被列为工业生产自动化技术的 支柱之一。 数控机床是装有数控系统的自动化机床。数控 技术的产生对机床控制技术的发展产生了革命性 影响。 FANUC 和 SIEMENS 是全球最著名的数控 系统制造商,他们都是将可编程控制器集成于数 控系统中。 可编程控制器(PLC)与数控系统一起完成机 床的复杂逻辑运算、信号交换等功能。
(一)数控机床控制系统结构
数控机床控制系统从功能上看包括两大部分:
1. CNC控制部分: 以机床工作台(或刀架)的运动轨迹控制为显 著特点,通常只用来进行复杂轨迹、精确定位等 高精度、高速度加工设备的定位与运动的控制, 其使用范围单一,但对轨迹的准确性和位置精度 控制要求非常高 。
2. PLC控制部分:
操作面板
PLC
(二)PLC在数控机床中的作用 及应用形式
1. 作用
(1)实现机床操作面板的控制。 (2) 将机床侧的开关信号送入到PLC,进行 逻辑运算。 (3) 将信号输出到继电器、接触器、电磁铁 等元件,以控制其运行。
作用
(4)将信号输出到系统侧,以改变系统的工 作方式、进给倍率、主轴停止、紧急停止等。 (5)实现数控机床辅助功能,如:自动换刀、 工件冷却、机床润滑、机床照明等。
为两侧 的工作状态、系统 参数、译码信息等 指示灯、电磁阀等输 以PLC为中心 出信号
《机床数控系统》试题6
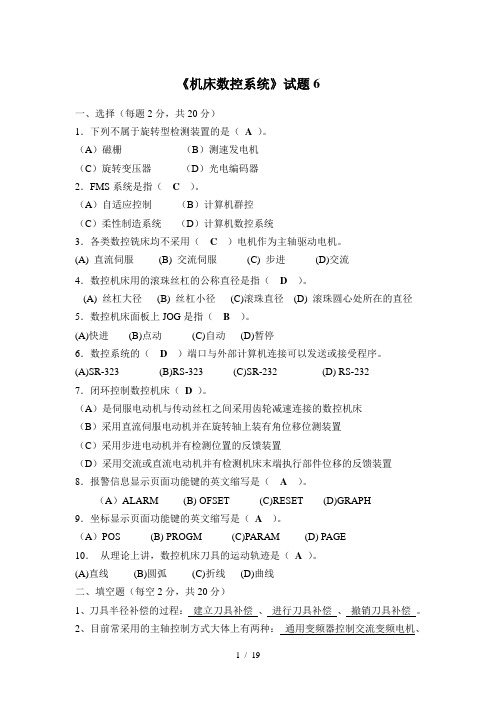
《机床数控系统》试题6一、选择(每题2分,共20分)1.下列不属于旋转型检测装置的是(A)。
(A)磁栅(B)测速发电机(C)旋转变压器(D)光电编码器2.FMS系统是指(C)。
(A)自适应控制(B)计算机群控(C)柔性制造系统(D)计算机数控系统3.各类数控铣床均不采用(C)电机作为主轴驱动电机。
(A) 直流伺服(B) 交流伺服(C) 步进(D)交流4.数控机床用的滚珠丝杠的公称直径是指(D)。
(A) 丝杠大径(B) 丝杠小径(C)滚珠直径(D) 滚珠圆心处所在的直径5.数控机床面板上JOG是指(B)。
(A)快进(B)点动(C)自动(D)暂停6.数控系统的(D)端口与外部计算机连接可以发送或接受程序。
(A)SR-323 (B)RS-323 (C)SR-232 (D) RS-2327.闭环控制数控机床(D)。
(A)是伺服电动机与传动丝杠之间采用齿轮减速连接的数控机床(B)采用直流伺服电动机并在旋转轴上装有角位移位测装置(C)采用步进电动机并有检测位置的反馈装置(D)采用交流或直流电动机并有检测机床末端执行部件位移的反馈装置8.报警信息显示页面功能键的英文缩写是(A)。
(A)ALARM (B) OFSET (C)RESET (D)GRAPH9.坐标显示页面功能键的英文缩写是(A )。
(A)POS (B) PROGM (C)PARAM (D) PAGE10.从理论上讲,数控机床刀具的运动轨迹是(A)。
(A)直线(B)圆弧(C)折线(D)曲线二、填空题(每空2分,共20分)1、刀具半径补偿的过程:建立刀具补偿、进行刀具补偿、撤销刀具补偿。
2、目前常采用的主轴控制方式大体上有两种:通用变频器控制交流变频电机、采用伺服驱动控制交流伺服电动机。
3、数控装置可通过三种方式控制主轴驱动转速:模拟电压指定,12位二进制指定、2位BCD码指定。
4、目前常用的主轴自动换档的方法有两种,分别是液压拨叉换挡、电磁离合器换挡。
数控机床知识点
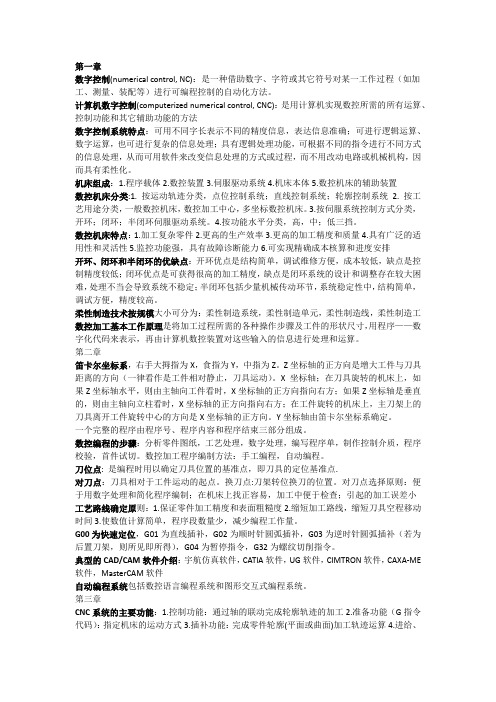
第一章数字控制(numerical control, NC):是一种借助数字、字符或其它符号对某一工作过程(如加工、测量、装配等)进行可编程控制的自动化方法。
计算机数字控制(computerized numerical control, CNC):是用计算机实现数控所需的所有运算、控制功能和其它辅助功能的方法数字控制系统特点:可用不同字长表示不同的精度信息,表达信息准确;可进行逻辑运算、数字运算,也可进行复杂的信息处理;具有逻辑处理功能,可根据不同的指令进行不同方式的信息处理,从而可用软件来改变信息处理的方式或过程,而不用改动电路或机械机构,因而具有柔性化。
机床组成:1.程序载体2.数控装置3.伺服驱动系统4.机床本体5.数控机床的辅助装置数控机床分类:1. 按运动轨迹分类,点位控制系统;直线控制系统;轮廓控制系统2. 按工艺用途分类,一般数控机床,数控加工中心,多坐标数控机床。
3.按伺服系统控制方式分类,开环;闭环;半闭环伺服驱动系统。
4.按功能水平分类,高,中;低三挡。
数控机床特点:1.加工复杂零件2.更高的生产效率3.更高的加工精度和质量4.具有广泛的适用性和灵活性5.监控功能强,具有故障诊断能力6.可实现精确成本核算和进度安排开环、闭环和半闭环的优缺点:开环优点是结构简单,调试维修方便,成本较低,缺点是控制精度较低;闭环优点是可获得很高的加工精度,缺点是闭环系统的设计和调整存在较大困难,处理不当会导致系统不稳定;半闭环包括少量机械传动环节,系统稳定性中,结构简单,调试方便,精度较高。
柔性制造技术按规模大小可分为:柔性制造系统,柔性制造单元,柔性制造线,柔性制造工数控加工基本工作原理是将加工过程所需的各种操作步骤及工件的形状尺寸,用程序——数字化代码来表示,再由计算机数控装置对这些输入的信息进行处理和运算。
第二章笛卡尔坐标系,右手大拇指为X,食指为Y,中指为Z。
Z坐标轴的正方向是增大工件与刀具距离的方向(一律看作是工件相对静止,刀具运动)。
- 1、下载文档前请自行甄别文档内容的完整性,平台不提供额外的编辑、内容补充、找答案等附加服务。
- 2、"仅部分预览"的文档,不可在线预览部分如存在完整性等问题,可反馈申请退款(可完整预览的文档不适用该条件!)。
- 3、如文档侵犯您的权益,请联系客服反馈,我们会尽快为您处理(人工客服工作时间:9:00-18:30)。
CNC与PLC的区别首先,很少能找到既精通CNC,又精通PLC的人,就像金庸武侠小说里的武林高手,同在一个江湖却分属不同的门派,CNC就像少林派,有本派的72绝技,每练一项都要穷尽毕生精力去练习。
而PLC更像道家的内功,各种呼吸吐纳的法门,内功深厚才能将武功施展的淋漓极致。
《天龙八部》中的武学奇才吐蕃法师鸠摩智,也曾用道家内功催动少林72绝技,还是被虚竹看出破绽不是纯正的少林武功,虽然能打败几个少林高僧,但鸠摩智自己最终落得个走火入魔,武功尽失的下场。
那么现实中CNC也有这么多的独门绝技吗?每种绝技都是做什么的呢,下面列举几个典型CNC应用3.图1:CNC典型应用如此众多的绝技要练好还真不容易,而PLC的内功也不是那么好练的,不但产品众多而且编程软件也是各有各的特色。
既然要想想知道两者的区别和关系,先要搞清楚CNC和PLC都是什么,怎么发展来的。
CNC和PLC的定义和发展历史CNC(数控机床)是计算机数字控制机床(Computer numerical control)的简称,是一种由程序控制的自动化机床。
该控制系统能够逻辑地处理具有控制编码或其他符号指令规定的程序,通过计算机将其译码,从而使机床执行规定好了的动作,通过刀具切削将毛坯料加工成半成品成品零件。
--引用自《百度百科》说简单点就是计算机控制的机电一体品,主要用于机加工。
PLC(Programmable Logic Controller)可编程逻辑控制器,是一种专门为在工业环境下应用而设计的数字运算操作的电子装置。
它采用可以编制程序的存储器,用来在其内部存储执行逻辑运算、顺序运算、计时、计数和算术运算等操作的指令,并能通过数字式或模拟式的输入和输出,控制各种类型的机械或生产过程,在运动控制、过程控制等领域也发挥着十分重要的作用。
--引用自《百度百科》针对具体的应用行业,分类也很多,从小型单体PLC到多个PLC组成大型复杂系统。
小型单体可实现对某一个设备,或者工业过程的控制,比如:西门子小型S7-200 SMART PLC中大型PLC由于计算能力,通讯能力以及编程软件功能的增强,可以实现更复杂的功能。
可用单机的形式工作,控制对象可以是一台设备,也可以是一个工艺过程;也可以组成复杂的系统,举例如下,1500 PLC向下通过PROFINET或者PROFIBUS网络与现场层的分布式 ET 200远程站相连,ET 200远程IO站再连接传感器执行器等信号。
1500 PLC向上还可以和监控软件,MES软件等相连,实现生产管理的功能。
同时1500 PLC还可以横向和其他的PLC通讯,实现复杂的控制功能,或者与其他的系统交换数据。
>图2:西门子中大型S7-1500 PLC所以追本溯源,看看CNC和PLC的历史。
首先CNC属于机械数控加工范畴。
要进行精确的加工,需要控制的通常是位置、角度、速度等机械量和与机械能量流向有关的开关量。
数控的产生依赖于数据载体和二进制形式数据运算的出现。
看一下数控技术的几个时间点:1908年,穿孔的金属薄片互换式数据载体问世;19世纪末,以纸为数据载体并具有辅助功能的控制系统被发明;1938年,香农在美国麻省理工学院进行了数据快速运算和传输,奠定了现代计算机,包括计算机数字控制系统的基础。
1952年,第一台数控机床问世(由帕森斯和麻省理工学院合作)--引用自《百度百科》数控技术是与机床控制密切结合发展起来的。
第一台数控机床问世这成为世界机械工业史上最重要的一个里程碑,注意这是机械工业的里程碑,与PLC相比早出现了很多年。
再看一下PLC发展的几个时间点:1968年,美国通用汽车公司提出取代继电器控制装置的要求;1969年,美国数字设备公司研制出第一台可编程控制器PDP-14;1971年,日本研制出第一台DCS-8;1973年,德国研制出第一台PLC;1975年,西门子公司SIMATIC S3系列PLC发布。
--引用自《百度百科》从时间上也可以直观的看出PLC的发展是滞后于数控技术的发展的,在两种技术同时出现之后,就出现了相互学习,相互融合的过程。
看看西门子是如何融合数控和PLC技术的:1960-1964,西门子的工业数控系统在市场上出现。
这一代的西门子数控系统以继电器控制为基础,主要以模拟量控制和绝对编码器为基础。
1965-1972,西门子以上一代的数控系统为基础,推出用于车床,铣床,和磨床的基于晶体管技术的硬件。
1973-1981,西门子推出在SINUMERIK 550系统。
这一代系统开始应用微型计算机和微处理器。
在此系统中,PLC集成到控制器。
--引用自《百度百科》当数控机床出现的时候工厂还在用继电器呢,最初数控机床的辅助控制里用的也都是传统继电器还没有PLC的身影。
数控机床首先解决了精确的机加工问题,而PLC最初就是为了取代传统继电器控制而出现的高性价比控制器。
90年代初,我在机械加工厂实习,机床师傅就已经能用数控机床在钢板上刻画加工米老鼠的卡通形象了,而整个生产线上还都是各自独立,没有流程没有用上PLC,完成一个联合动作要几十上百个大型继电器不停吸合,场面可以用壮观来形容。
而要更改一个生产逻辑对电气工程师来说简直就是噩梦。
如今的大部分生产线都用上了PLC,通过梯形图,语句表,顺控等等电脑上动动手指就实现了逻辑的更改,而且还能仿真模拟运行,真的是方便了很多,并且PLC也不再局限于逻辑控制,在运动控制、过程控制等领域也发挥着十分重要的作用。
CNC和PLC的当前现状题主的疑问也是在PLC取得的长足发展的基础上出现的,在CNC的体系中把一部分辅助功能交给了PLC来处理,而PLC也得到了施展才华的机会,除了辅助功能之外,还实现了复杂的运动控制功能。
那么既然CNC的几个重要组成部分序列器、插补器、伺服控制器、逻辑控制器和人机控制接口,都能通过PLC集成其他组件和设备来实现,是不是可以用PLC来代替CNC,实现更优的性价比呢?现实情况又是怎样的呢?现实中虽然完全可以用PLC搭建自己的CNC系统,DIY一个自己的机加工中心也是可行的,西门子的s7-1500T系列加私服电机配合TIA软件集成运动控制和人机界面,需要全面的一体机开发经验,没有一个整体团队是完成不了的。
所以等你开发完发现西门子本身就有成体系的数控机床系统840D,集成度更好,功能更完善。
看一下西门子的全集成自动化大图中,数控和控制器的位置,红框是数控系统,黑框是控制器部分,数控系统中的辅助功能都是PLC来控制>图3:西门子数控和PLC的整体位置CNC和PLC的编程软件区别CNC 操作界面是这样的,SINUMERIK Operate 操作软件。
/>>图4:SINUMERIK Operate 操作软件SINUMERIK Operate 操作软件,集成了带动画功能的 Program GUIDE 的文本编辑器能够完美支持零件程序编程。
Program GUIDE 融合了 G 代码编程和循环支持功能。
如此就能确保最大的灵活度和较短的加工时间,非常适合用于中、大批量加工。
集成了带动画功能的 Program GUIDE 的文本编辑器能够完美支持零件程序编程。
>图5:CNC 仿真功能PLC的操作界面是这样的,更注重编程。
>图6:Step7 编程软件>图7:PCS7编程软件CFC界面TIA 软件PID自调>图8:TIA编程界面西门子的808D和828D,都是集成了PLC的 S7-200的控制器的。
(S7-200和S7-300编程软件是完全不同的,而且最新的博途软件编程工具也不支持S7-200 PLC,本次介绍略过S7-200 部分)>图9:SINUMERIK 840D slSINUMERIK 840D sl 中集成了 PLC S7-300系列的控制器。
咱们主要介绍一下840D中的PLC 是个什么样的角色,内容偏具体,有不明白的可以网上查一下。
在 SINUMERIK 840D sl 中,自动化系统 S7-300 的 CPU 被用作 PLC完成一些基本动作和数据交互。
使用 SINUMERIK 840D sl 时,NCU 中集成的 PLC 支持直接通过一个 Dual-Port-RAM(双端口 RAM)在 NC 和 PLC 间进行信号交换。
>图10:SINUMERIK 840D sl中与s7-300 PLC 接口示意图SINUMERIK 840D sl 上的 NC-PLC 连接NC 和 PLC 之间的数据交换由 PLC 通过基本程序组织。
由 NC 保存在 NC/PLC 接口中的状态信息(例如“程序运行中”)通过基本程序在循环开始处(OB1)复制到数据块,之后便可在用户程序中访问该信息(用户接口)。
由用户输入到接口 DB 的、发送至 NC 的控制信号(例如“NC 启动”)同样在循环开始处传输至针对 NC 的内部 DPR。
基于工件程序传输至PLC 的辅助功能首先会由基本程序在报警控制下进行分析,之后在OB1 的开始处传输至用户接口。
若相关程序段中包含了需要中断 NC 处理的辅助功能(例如用于换刀的 M06),那么基本程序的 NC 程序段解码会先停止一个 PLC 循环的时间。
之后用户可通过接口信号“读取禁止”一直停止解码,直至换刀完成。
与之相反,若相关NC 程序段中只包含不需要中断解码的辅助功能(例如M08“冷却剂ON”)。
PLC辅助功能具体实现辅助功能的传输会直接在 OB40 中应答,这样一来向 PLC 的传输只会对解码造成较小影响。
由 NC 传输的 G 指令同样会在报警控制下接受检测和应答,不过之后会直接传输至用户接口。
若在 PLC 程序中的多个位置检测一个 G 指令,那么一个 PLC 循环内 G 指令的信息可能会出现差异。
对于由 PLC 触发和参数设置的 NC 动作(例如运行并行轴),触发和设置不通过接口 DB进行,而是通过 FC 和 FB 进行。
从属于 NC 动作的 FC 会和基本程序一起提供。
所需的FC 和 FB 必须由用户载入,并在机床制造商的 PLC 程序(机床程序)中调用。
除了 PLC和 NC 间的默认信号外,根据需要系统还会生成一个用于编译循环的接口数据块(DB9)。
基于编译循环的相应信号在 OB1 的开始处循环传输。
传输通过基本程序以从低到高的地址顺序进行。
首先会从 PLC 向 NC 传输信号,之后再从 NC 向 PLC 传输信号。
用户必须在 NC 和PLC 间执行必要的同步(例如通过信号量)。
信号传输在 NC 和 PLC间异步进行。
此时,通过 PLC 进行的已开始的 NC 数据传输可能会中断。
这样一来数据有时会不统一。
PLC更适用于通用控制任务CNC更专注加工普通PLC的控制精度没有CNC那么高,而带运动控制的高端PLC整体解决方案又比CNC的总成本高,尽管普通PLC成本更低。