uPG2214TB英文手册
M102用户手册 英文版
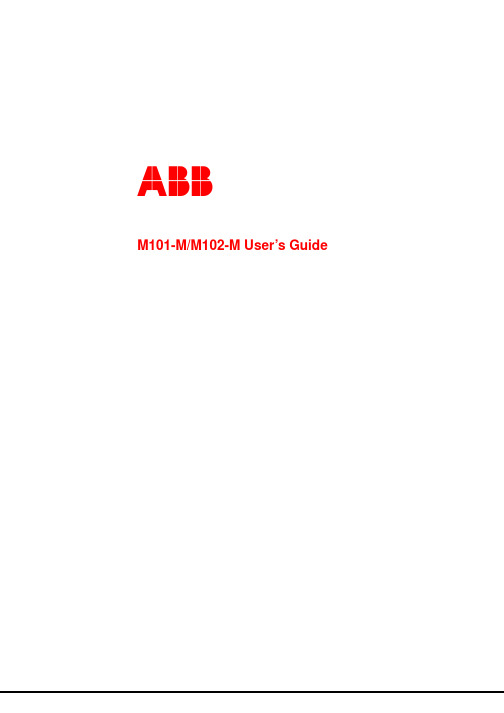
ABBM101-M/M102-M User’s GuideM101-M/M102-M User’s GuideTable of Contents1INTRODUCTION (3)1.1Objective (3)1.2Related Documentation (3)2PRODUCT OVERVIEW (3)2.1Introduction (3)2.2M101-M/M102-M’s Structure (4)3MOUNTING (4)3.1Mounting of M101-M/M102-M (4)4M101-M/M102-M INTERFACES (4)4.1Terminal Designations (5)4.2Typical diagram (9)5FUNCTIONALITY (10)5.1Starter Types (10)5.2Protection Function (21)5.3M101-M/M102-M Function and Supervision (34)6M101-M/M102-M COMMUNICATION INTERFACE (40)6.1Overview (40)6.2RS485 Interface Cable (40)6.3Function Description (40)7PARAMETERIZATION (40)7.1Overview (40)7.2Parameterization via MD2/MD3 (40)7.3Parameterization via MODBUS (40)M101-M/M102-M User’s Guide7.4M101-M/M102-M Parameters (40)8ACCESSORIES (40)8.1MD2/MD3 Operator Panel (40)8.2Parameterization Software: MCUsetup (44)9APPENDIX A TECHNICAL DATA (46)10APPENDIX B TYPE DESIGNATION (48)M101-M/M102-M User’s Guide1.1 ObjectiveThe objective of this users manual is to provide the technical information of M101-M/M102-M.This manual should be studied carefully before installing, parameterizing or operating the motor control unit. It is expected that the user has a basic knowledge of physical and electrical fundamentals, electrical wiring practices and electrical components.This document should be used along with M101-M/M102-M Parameter Description, which provides detailed information about parameters and their applications.1.2 RelatedDocumentation1TNC 911105 M0202 Parameter Description M101-M/M102-M1TNC 911505 M0203 Modbus Protocol Implementation for M101-M/M102-M2 ProductOverview2.1 IntroductionM101-M/M102-M is a motor protection and control device with a fieldbus interface.M101-M/M102-M is a microprocessor-based device. All motor protection and control functions are implemented with the microprocessor, as well as interlocking functions, the calculation of operating, diagnosis and statistical data and communication.Standard features simplify maintenance and plant expansion. One M101-M/M102-M is required for every starter unit in the MCC.Motor protection is included for the most common causes of failure to prevent costly shutdowns and rewinds. These include overload, stalled rotor, ground fault and phase failure etc.M101-M/M102-M with its redundant RS485 interface makes it possible to network upward with automation level in a high speed and reliable way. Any M101-M/M102-M may be interrogated on demand to determine both actual and operating parameters. Fast response time for alarm or trip status makes real time control of a complete process possible. Statistical recording of running hours andnumber of operations assists with predictive maintenance scheduling.fieldbus capacity: 32 nodescommunication connectionredundancy communication connectionPicture 1Network connection of M101-M/M102-MFor AC motor and the operated installation this means:• Reliable protection• Maximum utilization• Continuous supervision• FlexibilityM101-M/M102-M User’s Guide2.2 M101-M/M102-M’s StructureM101-M/M102-M consists of two parts: Main unitCurrent converter unitAs accessory of M101-M/M102-M: Operator panel MD2/MD3 Main unitThe Main unit is a unit contains the electronics of the motor control unit.Main unit is fixed to a mounting rail . Current converter unitThe Current converter unit contains the current transformers.It is fixed to the Main unit. Operator panel MD2/MD3The Operator panel is the user interface mounted onthe front door or drawer. With control buttons, LED,LCD module (MD2 only), MD2/MD3 provides thefunctions as motor control, supervision and parameterizing. M101-M/M102-M enclosure materialThe enclosure of the M101-M/M102-M is made of polycarbonate. Flammability rating of the material is UL 94 V-0 and material is halogen free. Colour of the enclosure is RAL 7012. Note: The details of MD2/MD3 please see the chapter 8 accessories.3 Mounting3.1Mounting of M101-M/M102-M• Basic dimension of M101-M/M102-M: WXHXD=110mmX140mmX75mm •Typical Installation ofM101-M/M102-M:DIN rail or installation to horizontal plane • Basic dimension of MD2: WXHXD=88mmX72mmX40mm • Mounting dimension of MD2: WXH=85mmX69mm• Basic dimension of MD3: WXHXD=88mmX50mmX28mm •Mounting dimension of MD3:WXH=84mmX46mmNote: The installation details of M101-M/M102-M and MD2/MD3please see the related documentation installation manual.4 M101-M/M102-M interfacesM101-M/M102-M has 4 I/O terminal blocks.I/O terminals located at the top of the main unit as shown in the following. The information of each port is described later. Picture 4 Terminals viewed from topPicture 2 M101-M/M102-MM101-M/M102-M User’s Guide4.1 TerminalDesignations Table 1 Device terminalsTerminal Block Terminal NumberDesignation…Plug/ContactsRemarkX1:1…X1:13 I/O block, switch inputX1X1:14…X1:16 PTC inputCross section 1.5mm2X2 X2:1…6 Interface for MD2/3 Cable with RJ11 is provided as standardX3:1…5 Fieldbus for external communicationX3:6,7 RCT inputX3X3:8…13 Voltage InputCross section 2.5mm2X4:1…9 Relay outputX4:10,11 24VDC SupplyX4X4:12 GroundCross section 2.5mm2L1-T1;L2-T2;L3-T3Let-through Current Measurement Φ10mm hole4.1.1 PowersupplyThe standard power supply is 24V DC preferably from a UPS.M101-M/M102-M User’s GuideTable 2 Power supply input terminalsTerminal No.Name Description4.1.1.1 X4:11 24VDC Power supply 24VDC + X4:10GNDPower supply 24VDC -4.1.2 Digital inputM101-M has 6 and M102-M has 13 digital inputs of the type 5mA/24VDC. Digital inputs are cyclically read. The contact is detected as closed if the input current is over 2.5mA and open if current is under 0.8mA. There are three programmable inputs included, which can be assigned to a defined function. Table 3 Digital input terminals and pins of M101-M. Terminal No. Name Description4.1.2.1 X1:1 IN_COM Digital input common terminal (DC24V-) X1:2 NC SpareX1:3 LOC/R Locate/remote control switch input X1:4 NC SpareX1:5 F_Ca Contactor control A feedback X1:6 NC SpareX1:7 F_Cb Contactor control B feedback X1:8 NC SpareX1:9 PROG_IN0 Programmable input 0 X1:10 NC SpareX1:11 PROG_IN1 Programmable input 1 X1:12 NCSpareX1:13 PROG_IN2Programmable input 2Table 4 Digital input terminals and pins of M102-M. Terminal No. Name Description4.1.2.2 X1:1 LIMIT1 Limit position switch 1 input X1:2 LIMIT2 Limit position switch 2 input X1:3 START1 Motor start 1 switch input X1:4 START2 Motor start 2 switch input X1:5 STOP Motor stop switch inputX1:6 LOC/R Locate/remote control switch input X1:7 F_Ca Contactor control A feedback X1:8 F_Cb Contactor control B feedback X1:9 F_Cc Contactor control C feedback X1:10 PROG_IN0 Programmable input 0 X1:11PROG_IN1Programmable input 1M101-M/M102-M User’s GuideX1:12 PROG_IN2 Programmable input 2X1:13 MCBAuxiliary contact from main switch4.1.3PTC input (only for M102-M)M102-M can utilize PTC sensor to follow the temperature of motor winding. The measuring principle is to use two identical current generators over a 3-wire Pt transmitter. PTC connector is located on the top of M102-M unit, terminal X1.Note: The M101-M hasn’t PTC input. Table 5 PTC input terminals. Terminal No. Name DescriptionX1:14 PTCA PTC measurement input A X1:15 PTCB PTC measurement input B X1:16PTCGPTC measurement input G4.1.4 Fieldbus interfaceThere are two RS485 communication interface integrated in M101-M/M102-M. The two communication ports are for redundancy design.Required bus cabling is shielded twisted pair (STP). Table 6 Fieldbus interface terminal . Terminal No. Name Description X3:1 2A Serial RS485 A X3:2 2B Serial RS485 B X3:3 SHIELD 485 shield X3:4 1A Serial RS485 A X3:5 1BSerial RS485 B4.1.5Residual current transformerM101-M/M102-M supports earth fault measurement through Residual Current Transformer ( RCT ). Table 7 Residual current transformer terminals Terminal No. Name DescriptionX3:6 Ioa Residual current transformer input A X3:7 IobResidual current transformer input BNote: The details of RCT please see the documentation of M101/M102 Ordering Guide.4.1.6Voltage measurement (only for M102-M)M102-M continuously measures three phase voltages. The voltage data is used for protection functions and power calculation.Note: The M102-M has voltage input only. Table 8 Voltage input terminals of M102-M only. Terminal No. Name DescriptionX3:9 Vc Phase C voltage input X3:11 Vb Phase B voltage input X3:13 Va Phase A voltage input X3:8NNeutral line inputM101-M/M102-M User’s Guide4.1.7 Current measurement terminalM101-M/M102-M measures continuously three motor phase currents. The phase current data will be used by the protection functions and is reported to the fieldbus. Phase currents are reported as relative value. Relative value is proportional to the motor nominal current In.Current wires are lead through current sensors from either side of the terminal.Direction can be either L->T or T->L considering that all currents must have the same direction.Motor nominal currents above 63A are not measured directly, but instead intermediate current transformer’s secondary side is connected through M101-M/M102-M current measurement terminal. Note: when one phase system is selected, current is measured only from phase A.4.1.8 Contactor control outputM101-M/M102-M supports several motor starter types. The control of the contactor is performed with internal relays (Output CCA, CCB, CCC) by the microprocessor.Internal relays CCA and CCB are hardwire-interlocked to prevent both contactors being closed at the same time.Note: M101-M has the relays CCA and CCB only.Table 9 Contactor control terminalsTerminal No. Name Description M101-MM102-MX4:6… CCLI Contactor control voltageinput√√X4:7 CCA Contactor control A √√X4:8 CCB Contactor control B √√X4:9 CCC Contactor control C √4.1.9 ProgrammableoutputM101-M/M102-M has two auxiliary programmable output relays. These two outputs can be assigned any of the functions defined in Clause 5.3.8.2.Table 10 Programmable output terminalsTerminal No. Name Description M101-MM102-M X4:1 GR1_AX4:2 GR1_B X4:3 GR1_C Programmable relay output 1 (NO+NC) √√X4:4 GR2_AX4:5 GR2_BProgrammable relay output 2 (NO) √4.1.10 Interface for MD2/MD3M101-M/M102-M has a RJ11 interface for operator panel MD2/MD3.Table 11 Operator panel interface terminalsTerminal No. Name DescriptionX2:1 RS485 BX2:2 RS485 ACommunication ports with operator panelX2:3 SHIELDX2:4 SHIELDShieldX2:5 Vcc Power supply for operator panelM101-M/M102-M User’s Guide4.1.11 GroundterminalTable 12 Ground terminalTerminal No. Name DescriptionX4:12 GROUND Ground safety and surgeThis is an additional ground terminal provided for dissipating transient signals and surges. This must be connected by a thick wire or braid to the system ground for reliable operation.diagram4.2 TypicalA typical wiring diagram is show belowPicture 5 typical wiring diagram for M101-MNote: I) The status of the relays is open when M101-M is power off, such as CCA, CCB, and programmable relay output1.ii) The GR1_A and GR1_C is the auxiliary contact of the programmable relay output1.iii) When M101-M is power on the status of the relays CCA,CCB depends on whether itreceives command or not.iv) When M101-M is power on the status of the relay programmable relay output1M101-M/M102-M User’s Guidedepends on the definition.Note: I) The status of the relays is open when M102-M is power off, such as CCA, CCB, and programmable relay output1/2.ii) The GR1_A, GR1_C, and GR2_A is the auxiliary contact of the programmable relaysoutput.iii) When M102-M is power on the status of the relays CCA, CCB and CCC depends onwhether it receives command or not.iv) When M102-M is power on the status of the relays programmable relay outputdepends on the definition.5 FunctionalityTypes5.1 StarterThe module offers several kinds of motor starting control modes via the control of relay output. It supervises the operating state of the contactor according to the feedback of auxiliary contact.The following starting control modes are offered:M101-M/M102-M User’s GuideTable 13 Starter types supported by M101-M/M102-M Starter type M101-MM102-MNR-DOL √ √ REV-DOL √ √ NR-DOL/RCU √ √ REV-DOL/RCU √ √ Actuator √ NR-S/D √ NR-2N√ Autotransformer √ NR_softstater √ REV_softstater√• NR_DOL: Non Reversing Direct Online • REV_DOL: Reversing Direct Online• NR_DOL/RCU: Non Reversing Direct Online with RCU • REV_DOL/RCU: Reversing Direct Online with RCU • Actuator: Actuator with limit switch input • NR_S/D: Non Reversing Star-Delta• NR_2N: Two speed driver for Non Reversing starter • Autotransformer: Autotransformer starter • NR_Softstarter: Non Reversing softstarter control •REV_Softstarter: Reversing softstarter controlStarter type is selected with a dedicated parameter to match the wiring for contactor and motor control circuits.5.1.1 NR-DOL STARTERNR_DOL starter is the basic starter type for driving motor to one direction. When start command has been received from field or local I/O, the contactor control output will be energized and remains this condition until stop command has been received or any protection function activated.Table 14 NR-DOL starter contactor control interface(for M101-M/M102-M) Name Pin DescriptionCCLI X4:6 Contactor control voltage input CCA X4:7 Contactor control ALOC/R X1:6 Local/remote control switch input F_Ca X1:7Contactor control A feedbackM101-M/M102-M User’s GuidePicture 7 Control circuit for NR-DOL starter (for M101-M/M102-M )5.1.2 NR-DOL STARTER (RCU )RCU (Remote Control Unit) is a starter type where contactors are directly controlled by a special RCU-switch located near the motor. This allows controlling the motor even if the M101-M/M102-M is not on duty.Table 15 NR-DOL starter contactor control interface (for M101-M/M102-M) Name Pin DescriptionRemark CCLI X4:6 Contactor control voltage input CCA X4:7 Contactor control AGR1_C X4:3 Programmable relay output Only for M101-M CCC X4:9 Contactor control CF_Ca X1:7 Contactor control A feedbackLOC/RX1:6Local/remote control switch inputPicture 8 Control circuit for NR-DOL/RCU starter(for M101-M)M101-M/M102-M User’s GuidePicture 9 Control circuit for NR-DOL/RCU starter(for M102-M)5.1.3 REV-DOL STARTERREV-DOL uses contactor control output A for controlling the contactor which drives motor to direction CW and correspondingly contactor control output B is used for direction CCW. When starting motor to either direction contactor will be energized and is stopped (not energized) by command (fieldbus or local I/O) or active protection function.Table 16 REV-DOL starter contactor control interface (for M101-M/M102-M) Name PinDescriptionCCLI X4:6 Contactor control voltage input CCA X4:7 Contactor control A CCB X4:8 Contactor control BF_Ca X1:7 Contactor control A feedback F_Cb X1:8 Contactor control B feedback LOC/R X1:6Local/remote control switch inputPicture 10 Control circuit for REV-DOL starter (for M101-M/M102-M)M101-M/M102-M User’s GuideSTARTERThe functionality of this starter type is according to NR-DOL/RCU starter with support for reversing use of motor.Table 17 REV-DOL starter contactor control interface (for M101-M/M102-M)Name Pin Description RemarkCCLI X4:6 Contactor control voltage inputCCA X4:7 Contactor control ACCB X4:8 Contactor control BGR1_C X4:3 Programmable relay output Only for M101-M CCC X4:9 Contactor control C Only for M102-M F_Ca X1:7 Contactor control A feedbackF_Cb X1:8 Contactor control B feedbackLOC/R X1:6 Local/remote control switch inputPicture 11 Control circuit for REV-DOL/RCU starter (for M101-M)M101-M/M102-M User’s GuidePicture 12 Control circuit for REV-DOL/RCU starter (for M102-M)5.1.5Actuator STARTER (for M102-M only)This starter type is for controlling valves and actuators by using limit switches. Table 18 Actuator starter contactor control interface NamePin DescriptionCCLI X4:6 Contactor control voltage input CCA X4:7 Contactor control A CCB X4:8 Contactor control B LIMIT1 X1:1 Limit position switch 1 input LIMIT2X1:2Limit position switch 2 inputM101-M/M102-M User’s GuidePROG_IN0 X1:10 Programmalbe input 0 (configured as Torque switch input) F_Ca X1:7 Contactor control A feedback F_Cb X1:8 Contactor control B feedback LOC/R X1:6Local/remote control switch inputPicture 13 Control circuit for Actuator starterLimit switch causes the motor to be stopped when activated. Event message is sent to the fieldbus according to activated limit switch and additionally start command is allowed only to reverse direction. Torque switch is selectable by parameterization and can be connected to programmable input 0. 5.1.6NR-S/D STARTER (for M102-M only)Motor start current is reduced in star connection to 1/3rdof the current in delta connection, with lower torque during the same time.Start to delta starting sequence is based on the presented control logic picture. The changeover condition is time.The following guideline applied for selecting parameter values Changeover time < Motor startup time Table 19 NR_S/D starter contactor control interface NamePin DescriptionCCLI X4:6 Contactor control voltage input CCA X4:7 Contactor control A CCB X4:8 Contactor control B CCC X4:9 Contactor control CF_Ca X1:7 Contactor control A feedback F_Cb X1:8 Contactor control B feedback F_Cc X1:9 Contactor control C feedback LOC/R X1:6Local/remote control switch inputM101-M/M102-M User’s GuidePicture 14 Control circuit for NR-S/D starter5.1.7NR-2N STARTER (for M102-M only)NR-2N/Dahlander uses three contactors control motor rotation speed, The motor contains a three phase winding. Rotation speed can be changed “on the fly” without stop command in between.Current measurement for NR-2N utilizes two external current transformers measuring current from motor main supply. External current transformers can be selected separately for both speeds. Table 20 NR-2N starter contactor control interface Name PinDescriptionCCLI X4:6 Contactor control voltage input CCA X4:7 Contactor control A CCB X4:8 Contactor control B CCC X4:9 Contactor control CF_Ca X1:7 Contactor control A feedback F_Cb X1:8 Contactor control B feedback F_Cc X1:9 Contactor control C feedback LOC/R X1:6Local/remote control switch inputPicture 15 Control circuit for NR_2N starter, DanlanderM101-M/M102-M User’s GuidePicture 16 Control circuit for NR_2N starter, separate windings5.1.8AUTOTRANSFORMER STARTER (for M102-M only)This starter type is used to control autotransformer unit in order to minimize the voltage drop during motor startup. Autotransformer starter with three contactors supports motor starting with reduced voltage thus providing reduced motor startup current. The starting torque will be reduced accordingly. The following guideline applied for selecting parameter values Changeover time < Motor startup timeTable 21 Autotransformer starter contactor control interface NamePin DescriptionCCLI X4:6 Contactor control voltage input CCA X4:7 Contactor control A CCB X4:8 Contactor control B CCC X4:9 Contactor control CF_CaX1:7Contactor control A feedbackM101-M/M102-M User’s GuideF_Cb X1:8 Contactor control B feedback F_Cc X1:9 Contactor control C feedback LOC/R X1:6Local/remote control switch inputPicture 17 Control circuit for Autotransformer starter5.1.9NR-SOFTSTARTER (for M102-M only)Softstarter applications are for controlling motor accessory softstarter device. M102-M gives start and stop commands to the softstarter unit. The softstarter is set for adjusting motor voltage with it’s own parameters. More information about softstarter can be found from softstarter’s manual.This starter type supports all protection functions during normal “Running” situation. For motor start and stop period some of the protection functions are disabled by these parameters. Table 22NR_Softstarter starter contactor control interface Name Pin DescriptionCCLI X4:6 Contactor control voltage input CCA X4:7 Contactor control AF_Ca X1:7 Contactor control A feedback LOC/R X1:6Local/remote control switch inputPicture 18 Control circuit for NR-softstarterM101-M/M102-M User’s Guide5.1.10REV-softstarter (for M102-M only)Functionality of this starter type is according to NR-softstarter starter with support for reversing use of motor.Table 23 REV-softstarter starter contactor control interface Name PinDescriptionCCLI X4:6 Contactor control voltage input CCA X4:7 Contactor control A CCB X4:8 Contactor control B CCC X4:9 Contactor control CF_Ca X1:7 Contactor control A feedback F_Cb X1:8 Contactor control B feedback LOC/R X1:6Local/remote control switch inputPicture 19 Control circuit for REV-SoftstarterM101-M/M102-M User’s Guide5.2 ProtectionFunctionThe module provides full protection for motor by supervising three phase voltages, three phase currents, earth fault current, PTC sensor, the state of contactors and the state of main switch.Functionality of protection functions is based on the parameters given by user. The operation of separate functions is independent thus protection functions can be active at the same time but the one which indicates the situation first will give a trip for motor.According to the application, all kinds of protection can be enabled, disabled by the upper level system or MCU setup tool, also the protection characteristics can be adjusted. Protection module offers the following protection and supervisory function.Table 24Protection supported by M101-M/M102-MProtection type M101-M M102-MThermal overload protection √√Stall protection √√Phase failure protection √√Unbalance protection √√Underload protection √√Noload protection √√Earth fault protection √√PTC protection √Undervoltage protection √Start limitation protection √√Note: M101-M can’t support EExe thermal model of thermal overload protection (TOL), support Standard thermal model only.5.2.1 Thermal overload protectionThermal overload protection (TOL) protects the motor against overheating. The motor thermal condition is simulated by a calculation. The result of the calculation is stored in a thermal register and can be reported via operator panel or fieldbus interface.Calculation is accomplished in a different motor operation conditions, principle presented below, thermal increase and decrease are simulated by TOL protection function for running and stopped motor. Picture 20 Principle picture of motor thermal simulationM101-M/M102-M User’s GuideM101-M/M102-M simulates thermal conditions in the motor for all operating modes ( Running or Stopped) . This permits maximum utilization of an installation and assures safe protection of the motor. Thermal overload protection simulation accounts for the temperature rise of both the stator winding and the iron mass of the motor, it gives thorough consideration on the effect of motor overheating due to three phase unbalance during the simulation calculation of motor thermal overload.There are two thermal models supported by M102-M: Standard or EEx e, but M101-M only supports Standard thermal model. The standard model makes use of parameters Trip class, t6 in thermal overload calculation. The protection of explosion proof three-phase motors with type of protection ‘increased safety’ EEx e is done with two special parameters, the Ia/In ratio ( stall/nominal current ratio ) and Te time.The following diagram offers the characteristic curve of overload protection, in which the character is adjusted by changing t6( trip time for current I Lmax =6×In from the cold state). Picture 21 Trip curve from cold conditionThe Maximum thermal capacity level is 100%. Maximum level is reached when motor as been running with a current 6xIn at the time t6 starting from the cold state in ambient temp. 40°C.M101-M/M102-M User’s GuideTrip class T610A 3-710 7-1220 10-2530 15-38In some applications it is beneficial to be able to bypass the TOL protection momentarily because of the process reasons. The lifetime of the motor will be shortened but it will be more costly to stop the process. TOL-bypass is a special command given through the fieldbus.There is a dedicated parameter to enable the execution of this command. TOL-bypass function is available only for TOL standard model, thus it cannot be enabled if TOL EEx e model is in use.When thermal level is above parameterised alarm level there is a possibility to send a bypass command to M101-M/M102-M. When bypass function is activated, the thermal image is allowed to rise to 200% level before a trip will occur.If motor is in overload condition, i.e. ILmax > 1,14 x TFLC (Thermal full load current multiplier reduced by motor ambient temperature), the Overload alarm is active to indicate overload, but time to trip is not updated if the thermal capacity level (θ) is not going to rise above 200% (I TOL < √2). If motor is stopped before trip and the thermal capacity decreases below TOL alarm level the bypass functionality is disabled. Bypass command is ignored when running under alarm level.Table 26 TOL protection parametersThermal modelSetting range 0=Standard model 1=EEX eDefault value 0Step value 1T6YSetting range 3-40sDefault value 6sStep value 1Ia/In ZSetting range 1.2-8.0Default value 5.0Step value 0.1Te ZSetting range 1-250sDefault value 5sStep value 1sCool coe.Setting range 1-10Default value 4Step value 1TOL Alarm LevelM101-M/M102-M User’s GuideSetting range 6 0-100% Default value 90% Step value 1%TOL Trip Level Setting range 70-100% Default value 100% Step value 1%TOL Reset Level Setting range 10-60% Default value 50% Step value 1%Trip Reset Mode Setting range 1=.Auto 2=Local 3=Remote 4=Remote&Local Default value 4 Step value 1TOL bypass Setting range 0=Disable 1=Enable Default value DisableY When Standard thermal model is selected Z When thermal models is selectedNote: M101-M can’t support the EExe thermal models. 5.2.2 Stall ProtectionStall protection is used to protect the driven mechanical system from jams and excessive overload. Stall protection function uses Imax as the criterion. There are other parameters to be determined as followed. Table 27 Stall protection parameters Function Enable/Disable Setting range 0=Disable 1=Enable 2=Trip only 3=Alarm only Default value 1 Step value 1Trip Level Setting range 120-800% Default value 400% Step value 1%Trip Delay Setting range 0.0-25.0s Default value 0.5s Step value 0.1s Trip Reset Mode Setting range1=Auto 2=Local 3=Remote 4=Remote&LocalM101-M/M102-M User’s GuideDefault value 4Step value 1Picture 22 Stall protectionI NILmaxStartup currentTrip LevelStall function activates after motor nominal startup time elapsed.The highest measured phase current (I Lmax) is compared against the Trip level. When I Lmax remains over the trip level at a time longer than Trip delay, a “Stall trip” alarm is issued and the contactor tripped.5.2.3 Phase failure protectionM101-M/M102-M protects the motor against phase current loss condition. Phase failure protection function uses I Lmin/I Lmax (the ratio of lowest I Lmin and highest measured phase value I Lmax ) as the criterion. Function is suppressed by parameters Motor startup time, Number of phases and Softstart ramp time. Table 28 Phase failure parametersFunction Enable/DisableSetting range 0=Disabled 1=EnabledDefault value DisabledStep value 1Alarm LevelSetting range 10-90%Default value 80%Step value 1%Trip LevelSetting range 5-90%Default value 70%Step value 1%Trip DelaySetting range 0-60sDefault value 10sStep value 1sTrip Reset ModeSetting range 2=Local 3=Remote 4=Remote&Local。
双牵引维护手册英文翻译

CAUTECHMaintenance ma nualDouble-rail Double-head automatic pullerCompany name:Foshan Autech Engineering CO.,LtdAddress:Area B, Shishan Science& Technology Industrial Area, Nanhai, Foshan, Guangdong, ChinaTel:+86-0757-******** Fax:+86-0757-********Warning Cautions✓✓✓✓✓✓✓✓AttentionAttentionAttentionAttentionAttentionAttentionAttentionAttentionThink twice before operationWearing eye protection equipmentObserving the content in the machine operationDisconnect and lock the power supply before maintenanceRead the instructions carefully before operationEnsure the protective facilities installed in placeEnsure the cutting tools installed firmlyPay attention to other matters within the region beforestarting the machineProhibited items ✓ Prohibited✓✓✓✓✓ProhibitedProhibitedProhibitedProhibitedProhibitedPutting hand or other body parts into machine or cuttingregion before disconnect and lock the powerOperating before the protective facilities installed inplaceOpening the protection door before the machine is fullystoppedOperating the machine without trainingAway from the operator position when machine is runningWearing loose clothes, gloves or jewelryC Warning NAUTECH maintenance bulletinCleaning procedures for double-head puller’s conductive railThe low voltage part of the conductive rail must be cleaned every once in a while, it’s length of time interval varies according to factory condition. When collecting boots wear and conductive rail have dirt, the communication system of extrusion puller is prone to errors. Communication failures for some of the phenomenon: (1) false extrusion puller failures; (2) Multiplexing com fault; (3) wrong or needless move of the extrusion puller.You can operate in accordance with the following procedure if you have doubt about the communication failure of conductive rail :.1.Pull the disconnect handle on the main control board, disconnect all power.2.Break the lock a ccording to the operation manual of “equipment lock”.3.Inspecting the electric boots of per extrusion puller, check up its side and slidingsurface uneven wear. Repairing collector boots by file, or replacing it when it is necessary.4.Cleaning the power rail contactor by volatile solvents which won’t be leaving residual.After cleaning, rub the rail dry by clean and lint-free cloth.5.After cleaning, validation set whether electric boots is embed in the right conductiveslot.AUTECH maintenance bulletinMaintenance procedures for double-head pullerDaily maintenance content:1.Check up all shields and safety facilities, it’s forbidden to start the equipment if shieldis not all installed in office or safety facilities isn’t all in the normal operation. 2. Clean the debris in the debris slot and guide area.Weekly maintenance content:1. Check the running state of the upper and lower rollers on extrusion puller.2. Check the flying saw blade, if necessary, to replace or sharpening it.3. Clean the filter of motor cooling fan (if applicable).4. Check the scraps appliance of rail, adjustments if necessary.Monthly maintenance content:1. Inject grease to all bearing.2. Check the hydraulic system of the extrusion puller, check the sampling of the hydraulicoil, check up whether it is leak, to oil the fuel reservoir again if necessary. Check the mobile speed, adjust the flow and pressure if necessary. If the hydraulic oil Changes, the oil filter on oil suction side should be also replaced.3. Check the operating height of extrusion puller, to adjust it if necessary.4. Check the installation and strong degree of all sensors (encoder, approach switch, etc.)5. Adjust the friction compensation value of guide rail.6. Check the transmission chain tensioning device, adjust the hydraulic pump and regulatorif necessary, check the drawings for reference, to verify the operation of the valve.7.Check the electrical panel to confirm whether all internal components are installed firmly.Maintenance content every six months:1. Check the oil level of the gear transmission, filling lubricating oil if necessary. Changethe lubricating oil, according to its service life which manufacturer recommends.2. Check the electric boots, to replace or sharpening it if necessary.3. Check the oil filter of hydraulic unit brush, to replace it if necessary.4. Check the teeth of extrusion jaws, to clean up and lubrication if necessary.5. Check whether the brake friction surface was worn and correctly adjusted. To view themanufacturer files as a guide.Annual maintenance content:1. According to motor manufacturers specifications, add grease filling to the bearing.2.Inspect the sprocket of the tension side and gear transmission side for position alignment,firm, worn, adjust or change it as needed.3. Inspect the drive motor and gearbox coupling for worn, firm shaft, calibrate or replace it as needed.AUTECH maintenance bulletinchain tension device adjustment procedures for double-head pullerRemove part of the transmission chain periodically to keep the appropriate tension of transmission chain. After the first week operation, check the bearing condition of the tension side, and readjust it (remove some links). This is by reason of the transmission chain elongated. After the first cutting, the transmission chain will remain stable. After the first week, check the bearing condition of tension side periodically, making it as a maintenance content component. Please refer to the feature size of tension device assembly drawing.Procedure:1.Close the air supply to pressure multiplier on the lock valve, and open the globe valveof the adjusted side to release the tension of the transmission chain. So the pressure of the hydraulic cylinder can be released.2.Manual return the slip component of the sprocket.3.Remove the excess links of the transmission chain, or unload the faulty transmission chain.4.Close the globe valve.5.Open the air supply to pressure multiplier.6.Check the oil level of the storage tank.7.Verify the transmission chain is under tension.AUTECH maintenance bulletinHydraulic device and hydraulic oil(recommended)1.Long stick hot shear and hot saw:Recommended:At 100℉, viscosity range between 150 and 220 SSU fire resistance of Polyol Ester type hydraulic oil(32 to 45 cSt).2. Heat oven pusher:(no hot shear)Recommended:At 100℉, viscosity range between 150 and 220 SSU oil type hydraulic oil (32 to 45 cSt).3.Profile puller:Recommended:At 100℉, viscosity range between 140 and 163 SSU oil type hydraulic oil (30 to 35 cSt).4.Elevating conveyer with hydrostatic transmission:Recommended:At 100℉, viscosity range between 150 and 220 SSU oil type hydraulic oil (32 to 45 cSt).5.Puller or cutting feed conveyor up/down:Recommended:At 100℉, viscosity range between 150 and 220 SSU oil type hydraulic oi l (32 to 45 cSt).6.Stretcher:Recommended:At 100℉, viscosity range between 150 and 220 SSU oil type hydraulic oi l (32 to 45 cSt).7.Profile cutting saw and cold saw:Recommended:At 100℉, viscosity range between 140 and 163 SSU oil type hydraulic oil (30 to 35 cSt).AUTECH maintenance bulletinThe hydraulic unit maintenance bulletin1. As separate installed system for oil pump and motor, you should have to check the motor shaft and the oil pump for axis alignment before the power unit accessed, adjust it if necessary. Oil pump axis unaligned will greatly shorten the service life of pump.2. The hydraulic oil injected in the fuel tank has to reach the viscosity index of 90 or above. If the pressure rise to 600 PSI, the temperature reach 130 ℉ occasions, we can use the hydraulic oil with 150 SSU viscosity when its temperature reach 110 ℉. If you want to reach a higher pressure and temperature, using a temperature of 110 ℉ with 225 to 325 SSU viscosity hydraulic oil which will provide the biggest oil pump life.3. Oil level of hydraulic oil should remain within the scope of the oil level gauge of license.4. After the first week operation, inhaled oil filter should be removed and cleaned. So we can remove the foreign matter in the storage tank brought by oil from external pipeline system.5. After the initial phase of the cleanup, normally we just need to clean oil filter once every six months. But this time limit length should be along with the environmental conditions and application type. If the hydraulic oil is dirty, we should empty the storage tank and fill with clean hydraulic oil.6. Cleanliness is the most important factor to keep the service life of pump and other devices. The top of the power unit should be kept clean. Be careful in the process of filling the oil, prevent dust from entering the oil storage tank.7. The noise of pump or sound “click-crack” was mostly caused by the air in the inlet pipe of the oil pump. Screw into the tubing connector, this kind of phenomenon can be removed.8. 130℉was regarded as the highest working temperature of the majority of applications.When the temperature is higher, the life of the components will be decreased.The quality of hydraulic oil will drop at the same time, and there are potentially dangerous to the operator.9. Keep the system pressure in the low post as much as possible, prevent the hydraulicoil unnecessary heat up.10. Before starting the oil pump, inject oil to pump box, then start the motor of theoil pump, check the pump rotation direction. Exchange the connect position of the two leads on the motor to change the direction of the motor rotation.AUTECH maintenance bulletinOverhead cooling pipe maintenance planDaily maintenance content:1、Check over all shields and safety facilities. It is strictly prohibited to start the equipmentwhen the shields are not all in place and not all the safety facilities are in the normal operation.Weekly maintenance content:1、Check whether the fan drive belt tension is normal. Replace the worn belt if necessary;2、Check the shock absorber connecting and fastening for normal. To ensure that the shockabsorber can move freely.Maintenance content every six months:1、Add lubricating oil to all bearing;2、Check the bearing for leaks;3、Check fan installation bolt for fastening.AUTECH maintenance bulletinHigh pressure jet water quench maintenance planDaily maintenance content:1. Check over all shields and safety facilities. It is strictly prohibited to start theequipment when the shields are not all in place and not all the safety facilities are in the normal operation.2. Remove and clean the filter of pressure pipeline.Weekly maintenance content:1. Inspect the water tank inlet for blocked, cleaning as needed.Monthly maintenance content:1. Inspect the spray head for blocked, to remove and clean it as needed.2. Add grease to all bearing and screw jack.Maintenance content every six months:1. Check the hose and coupling clamp for wear, if necessary, to replace it.2. Check the graphite plate (if any) for crack or wear, if necessary, to replace it.3.Check whether the fasteners on the pump and motor is loose, tighten again if necessary.Annually maintenance content:1. Check input shaft seal of pump (refer to the pump manufacturer's maintenance files asa guide), to replace it if necessary.。
超热电源平板系统消耗材料指南说明书
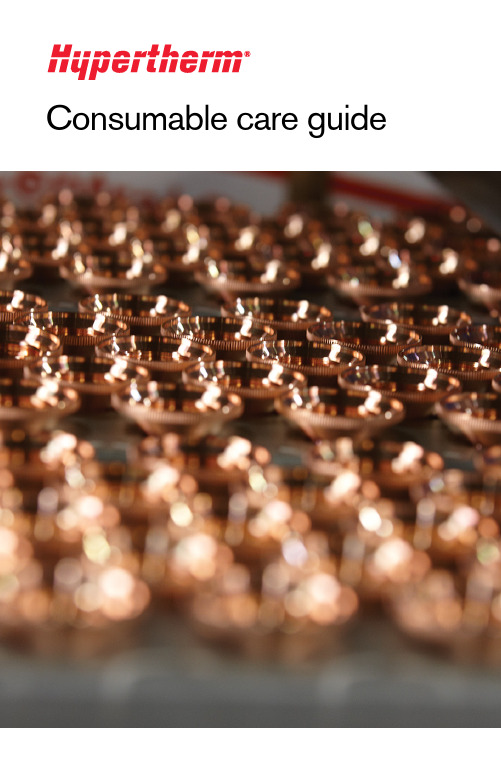
Consumable care guideOverviewA plasma system is only as good as the consumable parts in thetorch. While changing consumables frequently will ensure exceptional cut quality, changing consumables before the end of their life is costly. That’s why understanding how consumables work is a necessary first step to optimizing their performance.This guide will help you:• Identify different consumable types, their features, and identify consumable wear• Find all of the relevant consumable information to properly assemble any Hypertherm torch• Establish common practices and daily maintenance routines and accurately evaluate and track consumable performanceContents1 The torch body2 The electrode3 The nozzle4 The swirl ring5 The shield6 Inner retaining cap7 Outer retaining cap8 Consumable installation8Tracking and evaluating performanceWater tubeThe water tube is crucial for effective electrode cooling.ElectrodeThe primary function of theelectrode is to provide power to the plasma arc. It is the starting point and electrical contact point of the plasma arc.Swirl ringThe main function of the swirl ring is to control the swirling action of the plasma gas flow around the electrode in order to center the cutting arc on the electrode and through the nozzle, and to constrict the cutting arc for faster cut speeds and thicker cut capability.NozzleThe primary function of the nozzle is to shape, direct, and constrict the plasma arc.Nozzle capThe inner retaining cap’s primary function is to hold the nozzle and swirl ring in place while directing coolant flow to the exterior of the nozzle.ShieldThe main function of the shield is to protect and cool the other consumables, especially the nozzle from molten splatter. In some cases, the shield also contributes to theswirling action of the plasma gas.Shield capThe outer retaining cap holds the shield in place over the nozzle (or inner retaining cap, if applicable) and directs secondary gas or shield gas to the shield.The torch bodyThe base of your consumable stack‑up is the torch body. The torch body is a precision manufactured device that serves as the working end of the plasma cutting system. Among other things, the torch body:• Holds the consumable parts in perfect alignment• Provides pre‑flow, plasma gas, and shield gas to the consumables• Delivers the cutting current to the electrodeThe key to long torch body life is cleanliness. Dirt and/ o r greaseon the inner parts of the torchcan eventually cause internal arcing, misfires, and possible torch failure.Use a clean cloth to clean the inside of the torch and use compressed air at a low pressure to blow debris off the threads.You will want to inspect the o‑rings found in your torch for any cracks or tears and replace if needed. When re‑installing or replacing the o‑rings, you may find it helpful to use a silicone lubricant. Put a small amount on your index finger and then rub it together with your thumb. Now apply the thinfilm to all the o‑rings. Youwant the o‑ring to look wetor shiny. If you can see a physical build‑up of siliconeleft behind, you haveapplied too much. Siliconecan clog or plug ports andfor that reason you needto be especially carefulwith its application around the swirl ring so that the gas flow will work properly. Silicone lubricant, part number 027055, is available through Hypertherm’s network of partners. Hypertherm does not recommend the use of substitutes, like petroleum‑based lubricants, as they can cause fires within the torch. If you have a liquid cooled torch you will find a removable cylindrical component called a water tube.The water tube is crucial foreffective electrode cooling.It is an important componentthat should be checkedduring regularly scheduledmaintenance. If your watertube is damaged and needsto be replaced, rememberto lubricate the small o‑ringfound on the base of the tube.1The electrodeThe primary function of the electrode in any plasma cutting torch is to provide power to the plasma arc. It is the starting point and electrical contact point of the plasma arc. One of the main features ofthe electrode is the plasma arc attachment point. The attachment point is a small cylindrical insert in the tip of the electrode made of an element with a very high melting point such as tungsten or hafnium.This insert must withstand the extreme heat of the plasma arc. Normal electrode wear can be observed by examining the insert.As electrodes are used, the insert will slowly erode, forming a small pit on the top of the electrode. For most of our systems, our recommendation is to change out your electrode when the pit depth gets to 1 mm (0.040") if using a standard copper electrode and twice that, to 2 mm (0.080"), if using a silver electrode. Still, since every plasma system is different, itis important to read your owner’s manual for recommended pit depth measurements. For example, if you are using an XPR™ system you can go to 1.25 mm (0.050") if cutting between 130 and 300 amps, and to 1.5 mm (0.060") if cutting at 300 amps. Electrode pit depth can simply and accurately be measured using a dial indicator. Regularly checking pit depth will help you maximize theuseful life of your electrodes.Normal wear Excessive wear Excessive electrode wear reduces cut quality and increases the risk of catastrophic electrode failure that may damage other consumables and/ or the torch.Premature electrode wear is commonly caused by:• Mismatching torch parts• Incorrect gas flow settings• Insufficient coolant flow (if using a liquid‑cooled torch)• Gas leaks or restrictions, such as kinked or split hoses• Build‑up of moisture and contaminates in the plasma gasTo avoid buildup of contaminates, always make sure that the pressurized gas or shop air you are using is clean and dry.2The nozzleA new nozzle has a perfectly round orifice with sharp inside and outside edges, ensuring excellent cut quality. The most common issue affecting nozzle performance is the incorrect match‑up of consumables. Nozzles can also be damaged by the following:• Piercing and cutting too close to the work piece• Piercing metal thicker than the maximum recommended thickness • Incorrect gas settings• Amperage or current that is too high • Using the electrode beyond its life • A pierce delay that is too short or long when mechanized cuttingTo ensure the best cut quality, operators should replace the nozzle if the orifice:• Is nicked or notched• Is out‑of‑round or oval• Has rounded edgesWe recommend changing the nozzle and electrode as a set to ensure thebest cut quality.3The swirl ringThe main function of the swirl ring is to control the swirling action of the plasma gas flow around the electrode. It does this in order to:• Center the cutting arc on the electrode and through the nozzle • Constrict the cutting arc for faster cut speeds and thicker cut capability The swirl ring has small angled holes and, on certain models, one or more o‑ring seals typically made of ceramic or thermoplastic. Ceramic swirl rings are fragile. Accidentally dropping one on the floor may cause a chip or crack, requiring replacement.During each consumable change, check the swirl ring holes to ensure they are clear of dirt and o‑ring lubricant. Clogged swirl holes will decrease cut quality and shorten electrode and nozzle life.When treated properly, swirl rings will last through several electrodeand nozzle changes.4The shieldThe shield has several important functions.• The shield protects the other consumables, especially the nozzle from molten splatter• It helps cool the nozzle• It contributes to good cut quality and fast cut speeds• When using a hand torch, the shield enables drag‑cuttingThe shield has a main orifice that aligns with the nozzle orifice and may have additional vent holes around the center. The most common issues associated with the shield are damage to the main orifice or clogging of the vent holes. Both issues can cause performance problems.The shield may be wearing when you spot signs of dross aroundthe orifice. This indicates that the workpiece may have been pierced with the torch too close to the plate. Sometimes you can easily pick or brush the dross off the shield with a wire brush. If the orifice is still perfectly round then the shield can still be used. If not, the shield shouldbe replaced.5Inner retaining cap Some larger plasma systems, such as HyPerformance® andX‑Definition® plasma systems,use an inner retaining cap in the consumable stack‑up. The inner retaining cap’s primary function is to hold the nozzle and swirl ring in place while directing coolant flow to the exterior of the nozzle.The most common feature of the inner retaining cap are the vent holes.It is essential to keep the threads clean. Dirt or grease on the ring can burn the cap. Dirt will damage threads over time, requiring the cap to be replaced prematurely.When treated with care, the inner retaining cap can last through several electrode and nozzlechange‑outs.6Outer retaining cap The outer retaining cap holds the shield in place over the nozzle(or inner retaining cap, if applicable) and directs secondary gas or shield gas to the shield.The outer retaining cap should be inspected where the shield seals to ensure that the threads and o‑rings are in good shape. Make sure threads are free of dirt to prevent thread damage. The outer retaining cap can last through several sets of electrode andnozzle replacements.78Tracking and evaluating performanceTracking and evaluating performance is an important and critical process that helps you determine if you are getting the life your consumables are designed to deliver.Consumable life is driven by many factors, including:• Cut speeds • Metal thickness • Duration of each cut • Amperage settingsWe recommend tracking the number of starts and arc‑on time for each consumable change to gaugeconsumable life over time. For a true comparison, try to compare similar jobs in which you are cutting the same metal thickness at the same amperage for the same cut duration. Hypertherm provides plasma cut data collection sheets to assist you with tracking performance.Tracking consumable life will allow you to measure how efficiently you are using your consumables so they don’t prematurely end up in the scrap bucket.Consumable installationUsing the correct consumables and matching them togetherappropriately is critical to achieving optimal cutting performance. Proper installation of your consumables involves:• Using the correct consumable part numbers• Making sure parts are not over‑tightened• Using o‑ring lubricant on the consumable and torch o‑rings • Keeping all consumable surfaces clean of dust and dirtConsumables are specific to amperage, the material you are cutting, and application.People commonly use the wrong consumables so be sure to confirm that the consumables you are installing match the part numbers shown in your owner's manual. Hypertherm laser marks each consumable with its part number to make this easy to do. Also, make sure you install consumables in the right order. Again, your owner's manual is a great resource.If you’ve lost your manual, you can download a new one at . You can also download a catalog with torch and consumable part numbers. Choose the About consumables section underneath the Products tab.9Hypertherm is a trademark of Hypertherm, Inc. and may be registered in the United States and/or other countries. All other trademarks are the property of their respective owners.Environmental stewardship is one of Hypertherm’s core values, and it is critical to oursuccess and our customers’ success. We are striving to reduce the environmental impact of everything we do. For more information: /environment.© 6/2020 Hypertherm, Inc. Revision 2895540For more information on how to optimize your cutting operations, visit: P L A S MA |L A S E R |W A T E R J E T |A U T O MA T I O N |S O F T W A R E |C O N S U MA B L E S。
美好暖和的商品说明书:美国好曼晟制造公司RP-658B维修部件

REPAIR PARTSRP-658BThis manual is to be used by qualified technicians only.This manual replaces RP-658A.© 2011-2013 Goodman Manufacturing Company, L.P. ◊ 5151 San Felipe, Suite 500 ◊ Houston, TX 77056August 2013*PD14 Dual Fuel Package UnitsAPD1424070M41AA APD1424070M41BA APD1430090M41AA APD1430090M41BA APD1436090M41AA APD1436090M41BA APD1437090M41AA APD1442115M41AA APD1442115M41BA APD1448115M41AA APD1448115M41BA GPD1424070M41AA GPD1424070M41BA GPD1430090M41AA GPD1430090M41BA GPD1436090M41AA GPD1436090M41BA GPD1437090M41AA GPD1442115M41AA GPD1442115M41BA GPD1448115M41AA GPD1448115M41BAImportant Information For assistance within the U.S.A. contact:Goodman Company, L.P.For assistance outside the U.S.A. contact:IndexFunctional Parts List Rev B: Addition of 3 Ton models with increased efficiencyIllustration and Parts......................................................................................................................................................................................................Views shown are for parts illustrations only, not servicing procedures.AR - As Required NA - Not Available NS - Not Shown00000000 - See NoteQTY - Quantity Example (QTY 3) (If Quantity not shown, Quantity = 1)M - Model Example (M1) (If M Code not shown, then part is used on all Models)Text Codes:ExampleM1 - Model#1 M2 - Model#2 M3 - Model#3Expanded Model Nomenclature:Goodman Manufacturing Company, L.P. is not responsible for personal injury or property damage resulting from improper service. Review all service information before beginning repairs.Warranty service must be performed by an authorized technician, using authorized factory parts. If service is required after the warranty expires, Goodman Manufacturing Company, L.P. also recommends contacting an authorized technician and using authorized factory parts.Goodman Manufacturing Company, L.P. reserves the right to discontinue, or change at any time, specifications or designs without notice or without incurring obligations. 2Consumer Affairs DepartmentGoodman Manufacturing Company, L.P.7401 Security Way Houston, Texas 77040877-254-4729-Telephone 713-863-2382-FacsimileInternational DivisionGoodman Manufacturing Company, L.P.7401 Security Way Houston, Texas 77040713-861-2500-Telephone 713-863-2382-Facsimileg g 4 - 153RP-658BFunctional Parts PartNo:Description:0130M0002524V RELAY10735102BECKETT BURNER (QTY A/R)D6723303S BLOWER WHEEL (M3, M4, M5, M6, M7, M14,M15, M16, M17, M18)B1368058BLOWER WHEEL 10 X 8 (M1, M2, M12, M13) B1368000BLOWER WHEEL 11 X 10 (M8, M9, M10, M11,M19, M20, M21, M22)CAP050400440RT CAPACITOR 5/40/440V (M1, M2, M3, M4, M12,M13, M14, M15)CAP050450440RT CAPACITOR 5/45/440V (M5, M6, M7, M8, M9,M10, M11, M16, M17, M18, M19, M20, M21,M22)ZP21K5EPFV130COMP,21300,208/230/60/1 (M1, M2, M12, M13) ZP34K5EPFV130COMP,34500,208/230/60/1 (M8, M9, M19, M20) ZP25K5EPFV130COMPRESSOR 25200, 208/230/60/1 (M3, M4,M14, M15)ZP29K5EPFV130COMPRESSOR 29000, 208/230/60/1 (M7, M18) ZP31K5EPFV130COMPRESSOR 31100, 208/230/60/1 (M5, M6,M16, M17)ZP39K5EPFV130COMPRESSOR 39000, 208/230/60/1 (M10,M11, M21, M22)0131M00429COND MOTOR 1/4 HP, 1 SP, 6 PL (M8, M9,M10, M11, M19, M20, M21, M22)0131M00061COND MOTOR 1/4 HP, 1 SP, 8 PL (M3, M4,M5, M6, M7, M14, M15, M16, M17, M18)0131M00009P COND MOTOR 1/6 HP, 1 SP, 8 PL (M1, M2,M12, M13)CONT1P025024V CONTACTOR 25 AMP, 1P, 24V (M1, M2, M3,M4, M5, M6, M7, M12, M13, M14, M15, M16,M17, M18)CONT1P030024V CONTACTOR 30 AMP, 1P, 24V (M8, M9, M10,M11, M19, M20, M21, M22)0230G00005CRANKCASE HEATER SWITCH (M8, M9,M19, M20)B1086773FAN BLADE 22" (M1, M2, M12, M13)0150G00003FAN BLADE SWEPT-WING (M8, M9, M10,M11, M19, M20, M21, M22)0150G00002FAN BLADE SWEPT-WING (M3, M4, M5, M6,M7, M14, M15, M16, M17, M18)0130F00010FLAME SENSOR0151F00000P GAS VALVE - WHITE-RODGERS 2-STAGE 0163R00003HEATER, CRANKCASE 230V 40W (M8, M9,M19, M20)0130M00074HIGH PRESSURE SWITCH0130F00014IGNITOR10728344LIMIT SWITCH (M8, M9, M10, M11, M19, M20,M21, M22)10728343LIMIT SWITCH (M1, M2, M3, M4, M5, M6, M7,M12, M13, M14, M15, M16, M17, M18)0130M00075LOW PRESSURE SWITCH10123529MANUAL RESET LIMIT0131M00361MOTOR - 3/4 HP PROGRAMMED SELE (M10,M21)0131M00351MOTOR - 3/4 HP PROGRAMMED SELE (M8,M19)0131M00379MOTOR-1/2 HP PROGRAMMED SELEC (M3,M14)0131M00378MOTOR-1/2 HP PROGRAMMED SELEC (M5,M16)0131M00364MOTOR-1/2 HP PROGRAMMED SELEC (M1,M12)PCBDM133PCB, DEFROST CONTROLPCBAG127PCB, IGNITION, DSI, 2 STG 11112501PRESSURE SWITCH0131M00594PROGRAMMED MOTOR (M7, M18)0131M00434PROGRAMMED MOTOR (M2, M13)0131M00435PROGRAMMED MOTOR (M4, M15)0131M00436PROGRAMMED MOTOR (M6, M17)0131M00441PROGRAMMED MOTOR (M11, M22)0131M00440PROGRAMMED MOTOR (M9, M20)0151M00019REVERSING VALVE (M1, M2, M3, M4, M7,M12, M13, M14, M15, M18)0151M00021REVERSING VALVE (M5, M6, M8, M9, M10,M11, M16, M17, M19, M20, M21, M22)0130M00138TRANSFORMER, 208/230, 24VExpanded Model NomenclatureM1 - APD1424070M41AAM2 - APD1424070M41BAM3 - APD1430090M41AAM4 - APD1430090M41BAM5 - APD1436090M41AAM6 - APD1436090M41BAM7 - APD1437090M41AAM8 - APD1442115M41AAM9 - APD1442115M41BAM10 - APD1448115M41AAM11 - APD1448115M41BAM12 - GPD1424070M41AAM13 - GPD1424070M41BAM14 - GPD1430090M41AAM15 - GPD1430090M41BAM16 - GPD1436090M41AAM17 - GPD1436090M41BAM18 - GPD1437090M41AAM19 - GPD1442115M41AAM20 - GPD1442115M41BAM21 - GPD1448115M41AAM22 - GPD1448115M41BA3RP-658B Top Panel/Fan/Cabinet 4RP-658BTop Panel/Fan/CabinetRef.No:Part No:Description:Ref.No:Part No:Description:Image 1:FAN BLADE 22" (M1, M2, M12, M13)B108677311FAN BLADE SWEPT-WING (M3, M4, M5, M6, M7, M14, M15, M16, M17, M18)0150G0000211FAN BLADE SWEPT-WING (M8, M9, M10, M11, M19, M20, M21, M22)0150G0000311COND MOTOR 1/4 HP, 1 SP, 6 PL (M8, M9, M10, M11, M19, M20, M21, M22)0131M0042921COND MOTOR 1/4 HP, 1 SP, 8 PL (M3, M4, M5, M6, M7, M14, M15, M16, M17, M18)0131M0006121COND MOTOR 1/6 HP, 1 SP, 8 PL (M1, M2, M12, M13)0131M00009P 21GRILLE-FAN 0152G0000231PNL, TOP, PNT 0121G00156PDG 41SMALL SCREW (QTY 6)M022181751ACORN NUT 5/16 HEX BLACK (QTY 4)0163M00006P 61BLOWER DOOR 32" (M1, M2, M3, M4, M5, M6, M7, M12, M13, M14, M15, M16, M17, M18)20464801PDG 71BLOWER DOOR 40" (M8, M9, M10, M11, M19, M20, M21, M22)20464806PDG 71DOOR-EVAP/CONTROL 32 W/PAINT (M1, M2, M3, M4, M5, M6, M7, M12, M13, M14, M15, M16, M17, M18)20464802PDG81EVAP/CONTROL DOOR 40" (M8, M9, M10, M11, M19, M20, M21, M22)20464807PDG 81DOOR-HT EXCHANGE 32 (M1, M2, M3, M4, M5, M6, M7, M12, M13, M14, M15, M16, M17, M18)0121G00526DG 91DOOR-HT EXCHANGE 38 (M8, M9, M10, M11, M19, M20, M21, M22)0121G00527DG 91DOOR-COMPRESSOR 32 W/PAINT (M1, M2, M3, M4, M5, M6, M7, M12, M13, M14, M15, M16, M17, M18)20464804PDG101DOOR-COMPRESSOR 40 W/PAINT (M8, M9, M10, M11, M19, M20, M21, M22)20464809PDG 101LOUVERED PANEL, COND SIDE 32" (M12, M13, M14, M15, M16, M17, M18)20467701PDG 111LOUVERED PANEL, COND SIDE 32" (M1, M2, M3, M4, M5, M6, M7)20467701PLG 111LOUVERED PANEL, COND SIDE 40" (M19, M20, M21, M22)20467702PDG 111LOUVERED PANEL, COND SIDE 40" (M8, M9, M10, M11)20467702PLG 111UTILITY PANEL 32" (M1, M2, M3, M4, M5, M6, M7, M12, M13, M14, M15, M16, M17, M18)20466101PDG 121UTILITY PANEL 40" (M8, M9, M10, M11, M19, M20, M21, M22)20466102PDG 121PNL, DUCT, GAS 32.5" (M1, M2, M3, M4, M5, M6, M7, M12, M13, M14, M15, M16, M17, M18)0121G00442DG 131PNL, DUCT, GAS 40" (M8, M9, M10, M11, M19, M20, M21, M22)0121G00443DG 131SUPPORT POST 32" (M1, M2, M3, M4, M5, M6, M7, M12, M13, M14, M15, M16, M17, M18)0121G00460141SUPPORT POST 40" (M8, M9, M10, M11, M19, M20, M21, M22)0121G00462141LOUVERED PANEL, COND SIDE 32" (M12, M13, M14, M15, M16, M17, M18)20464401PDG 161LOUVERED PANEL, COND SIDE 32" (M1, M2, M3, M4, M5, M6, M7)20464401PLG 161LOUVERED PANEL, COND SIDE 40" (M19, M20, M21, M22)20464402PDG 161LOUVERED PANEL, COND SIDE 40" (M8, M9, M10, M11)20464402PLG 161BASE PAN RAIL (QTY 2)0121G00290181CORNER POST-COMP END 32" (M1, M2, M3, M4, M5, M6, M7, M12, M13, M14, M15, M16, M17, M18)20464201PDG251Image 1:CORNER POST-COMP END 40" (M8, M9, M10, M11, M19, M20, M21, M22)20464202PDG 251CORNER POST-HAIRPIN END 32" (M1, M2, M3, M4, M5, M6, M7, M12, M13, M14, M15, M16, M17, M18)20464301PDG261CORNER POST-HAIRPIN END 40" (M8, M9, M10, M11, M19, M20, M21, M22)20464302PDG 261FLUE HOOD (QTY 2)0121G00323271FLUE HOOD-LOWER 0121G00190281SCREEN-FLUE HOOD 20472601291GAS LINE GROMMET B1910012301ACCESS FITTING (QTY 2)B1373315NS CAP WITH O-RING (QTY 2)0163M00175NS FLUE HOOD ASSY 0270G00070NS PVC CONDUIT 8.25"177********F NS WASHER, BLACK (.50 OD .218ID) (QTY 4)0163M00005P NS WIRE HARNESS, FAN MOTOR (M1, M2, M8, M9, M10, M11, M12, M13, M19, M20, M21, M22)0259G00106NS WIRE HARNESS, FAN MOTOR (M3, M4, M5, M6, M7, M14, M15, M16, M17, M18)0259G00107NSExpanded Model Nomenclature M1 - APD1424070M41AA M2 - APD1424070M41BA M3 - APD1430090M41AA M4 - APD1430090M41BA M5 - APD1436090M41AA M6 - APD1436090M41BA M7 - APD1437090M41AA M8 - APD1442115M41AA M9 - APD1442115M41BA M10 - APD1448115M41AA M11 - APD1448115M41BA M12 - GPD1424070M41AA M13 - GPD1424070M41BA M14 - GPD1430090M41AA M15 - GPD1430090M41BA M16 - GPD1436090M41AA M17 - GPD1436090M41BA M18 - GPD1437090M41AA M19 - GPD1442115M41AA M20 - GPD1442115M41BA M21 - GPD1448115M41AA M22 - GPD1448115M41BA5RP-658B Partition Panels 6RP-658BPartition PanelsRef.No:Part No:Description:Ref.No:Part No:Description:Image 1:BLOWER DIVIDER (M1, M2, M12, M13)2046530571BLOWER DIVIDER 32" 10 X 9 (M3, M4, M5, M6, M7, M14, M15, M16, M17, M18)2046530471BLOWER DIVIDER 38" (M8, M9, M10, M11, M19, M20, M21, M22)0121G0017771FILLER PANEL, HEAT EXCHANGER 32" (M1, M2, M3, M4, M5, M6, M7, M12, M13, M14, M15, M16, M17, M18)20465201101FILLER PANEL, HEAT EXCHANGER 40" (M8, M9, M10, M11, M19, M20, M21, M22)20465202101PNL, PTN, 32.5" (M1, M2, M3, M4, M5, M6, M7, M12, M13, M14, M15, M16, M17, M18)0121G00360111PNL, PTN, 40" (M8, M9, M10, M11, M19, M20, M21, M22)0121G00361111EVAP/HEAT EXCHANGER DIVIDER 32" (M1, M2, M3, M4, M5, M6, M7, M12, M13, M14, M15, M16, M17, M18)20465501121EVAP/HEAT EXCHANGER DIVIDER 38" (M8, M9, M10, M11, M19, M20, M21, M22)20465502121FAN PARTITION SHELF20465701131FAN SURROUND 32" (M1, M2, M3, M4, M5, M6, M7, M12, M13, M14, M15, M16, M17, M18)20465801141SHIELD, HEAT EXCHANGER TUBES 20472501151DRAIN CHANNEL, SUCTION TUBE20496801161EVAP/BASEPAN BLOCK 32" (M1, M2, M3, M4, M5, M6, M7, M12, M13, M14, M15, M16, M17, M18)20463802221EVAP/BASEPAN BLOCK 40" (M8, M9, M10, M11, M19, M20, M21, M22)20463801221Effective July 2008 (serial codes 0807), single phase units will no longer be factory shipped with horizontal duct covers.For downshot applications, contact your local Goodman distributor.Expanded Model Nomenclature M1 - APD1424070M41AA M2 - APD1424070M41BA M3 - APD1430090M41AA M4 - APD1430090M41BA M5 - APD1436090M41AA M6 - APD1436090M41BA M7 - APD1437090M41AA M8 - APD1442115M41AA M9 - APD1442115M41BA M10 - APD1448115M41AA M11 - APD1448115M41BA M12 - GPD1424070M41AA M13 - GPD1424070M41BA M14 - GPD1430090M41AA M15 - GPD1430090M41BA M16 - GPD1436090M41AA M17 - GPD1436090M41BA M18 - GPD1437090M41AA M19 - GPD1442115M41AA M20 - GPD1442115M41BA M21 - GPD1448115M41AA M22 - GPD1448115M41BA7RP-658BBasepan/Blower Assembly 8RP-658BBasepan/Blower AssemblyRef.No:Part No:Description:Ref.No:Part No:Description:Image 1:TC SCREW 1.25" (QTY 3)M025056511MOTOR MOUNT BAND 0121M0003821MOTOR MOUNT ARM (QTY 3)B137685731BLOWER WHEEL (M3, M4, M5, M6, M7, M14, M15, M16, M17, M18)D6723303S 41BLOWER WHEEL 10 X 8 (M1, M2, M12, M13)B136805841BLOWER WHEEL 11 X 10 (M8, M9, M10, M11, M19, M20, M21, M22)B136800041MACHINE SCREW HWH 1/4-20 X 1-1/2 BZ B139332361BASEPAN, PACKAGE0121G0044471SINGLE COVER, DOWN DISCHARGE (QTY 2)0121G0014891LOCKNUT, NYLON, INSERT 1/4, 20B1393800101MOTOR - 3/4 HP PROGRAMMED SELE (M8, M19)0131M00351121MOTOR - 3/4 HP PROGRAMMED SELE (M10, M21)0131M00361121MOTOR-1/2 HP PROGRAMMED SELEC (M1, M12)0131M00364121MOTOR-1/2 HP PROGRAMMED SELEC (M5, M16)0131M00378121MOTOR-1/2 HP PROGRAMMED SELEC (M3, M14)0131M00379121PROGRAMMED MOTOR (M2, M13)0131M00434121PROGRAMMED MOTOR (M4, M15)0131M00435121PROGRAMMED MOTOR (M6, M17)0131M00436121PROGRAMMED MOTOR (M9, M20)0131M00440121PROGRAMMED MOTOR (M11, M22)0131M00441121PROGRAMMED MOTOR (M7, M18)0131M00594121AUXILIARY LIMIT, AUTO RESET20269903131BLOWER BLOCK-OFF (M3, M4, M5, M6, M7, M14, M15, M16, M17, M18)764742141BLOWER BLOCK-OFF 10 X 8 (M1, M2, M12, M13)764740141BLOWER CUT-OFF (M8, M9, M10, M11, M19, M20, M21, M22)1864703F 141AUXILIARY LIMIT BRACKET2509503F 151BLOWER HOUSING ASSY (11X10) (M8, M9, M10, M11, M19, M20, M21, M22)2539309161BLOWER HOUSING ASSY 10 X 8 (M1, M2, M12, M13)0271F00001P 161BLOWER HOUSING ASSY 10 X 9 (M3, M4, M5, M6, M7, M14, M15, M16, M17, M18)0271G0002416111 X 10 BLOWER MOUNTING (M8, M9, M10, M11, M19, M20, M21, M22)20463701171Expanded Model Nomenclature M1 - APD1424070M41AA M2 - APD1424070M41BA M3 - APD1430090M41AA M4 - APD1430090M41BA M5 - APD1436090M41AA M6 - APD1436090M41BA M7 - APD1437090M41AA M8 - APD1442115M41AA M9 - APD1442115M41BA M10 - APD1448115M41AA M11 - APD1448115M41BA M12 - GPD1424070M41AA M13 - GPD1424070M41BA M14 - GPD1430090M41AA M15 - GPD1430090M41BA M16 - GPD1436090M41AA M17 - GPD1436090M41BA M18 - GPD1437090M41AA M19 - GPD1442115M41AA M20 - GPD1442115M41BA M21 - GPD1448115M41AA M22 - GPD1448115M41BA9RP-658B Compresor/Tubing Assembly 10RP-658BCompresor/Tubing AssemblyRef.No:Part No:Description:Ref.No:Part No:Description:Image 1:COMP,21300,208/230/60/1 (M1, M2, M12, M13)ZP21K5EPFV13011COMP,34500,208/230/60/1 (M8, M9, M19, M20)ZP34K5EPFV13011COMPRESSOR 25200, 208/230/60/1 (M3, M4, M14, M15)ZP25K5EPFV13011COMPRESSOR 29000, 208/230/60/1 (M7, M18)ZP29K5EPFV13011COMPRESSOR 31100, 208/230/60/1 (M5, M6, M16, M17)ZP31K5EPFV13011COMPRESSOR 39000, 208/230/60/1 (M10, M11, M21, M22)ZP39K5EPFV13011TF SHOULDER SCREW (QTY 4)M022164131TUBING ASSY, EVAP COIL (M10, M11, M21, M22)0202G0028261TUBING ASSY, EVAP COIL (M1, M2, M12, M13)0202G0028361TUBING ASSY, EVAP COIL (M3, M4, M7, M14, M15, M18)0202G0031561TUBING ASSY, EVAP COIL (M8, M9, M19, M20)0202G0031661TUBING ASSY, EVAP COIL (M5, M6, M16, M17)1262643 61COND COIL TUBING ASSY (M1, M2, M3, M4, M5, M6, M7, M12, M13, M14, M15, M16, M17, M18)0201G0016491COND COIL TUBING ASSY (M8, M9, M19, M20)0201G0024291COND COIL TUBING ASSY (M10, M11, M21, M22)0201G0026091REVERSING VALVE (M1, M2, M3, M4, M7, M12, M13, M14, M15, M18)0151M00019111REVERSING VALVE (M5, M6, M8, M9, M10, M11, M16, M17, M19, M20, M21, M22)0151M00021111HIGH PRESSURE SWITCH0130M00074141HEATER, CRANKCASE 230V 40W (M8, M9, M19, M20)0163R00003171ACCUMULATOR (M1, M2, M3, M4, M7, M12, M13, M14, M15, M18)B1226206211ACCUMULATOR .875 (M5, M6, M8, M9, M10, M11, M16, M17, M19, M20, M21, M22)B1226207211BI-FLOW FILTER DRIER20485201241COMPRESSOR GROMMET (QTY 4)B1339533NS COMPRESSOR SCROLL HARNESS (M1, M2, M3, M4, M5, M6, M7, M12, M13, M14, M15, M16, M17, M18)0159G00002NSCOMPRESSOR SCROLL HARNESS (M8, M9, M10, M11, M19, M20, M21, M22)0159G00006NS CONTROL, DEFROST (M1, M2, M3, M4, M5, M6, M7, M12, M13, M14, M15, M16, M17, M18)0130M00099NS CONTROL, DEFROST (M8, M9, M10, M11, M19, M20, M21, M22)0130M00102NS CRANKCASE HEATER SWITCH (M8, M9, M19, M20)0230G00005NS DRAIN PAN-EVAP COIL 20464901DF NS DRAIN PAN-EVAP COIL 20464901DF NS EVAP DRAIN FITTING 20513001NS EVAP DRIP SHIELD 0121G00324NS LOW PRESSURE SWITCH 0130M00075NS SOLENOID COIL B1225022NS WIRE ASSY-9 CIRCUIT0259G00029NSExpanded Model Nomenclature M1 - APD1424070M41AA M2 - APD1424070M41BA M3 - APD1430090M41AA M4 - APD1430090M41BA M5 - APD1436090M41AA M6 - APD1436090M41BA M7 - APD1437090M41AA M8 - APD1442115M41AA M9 - APD1442115M41BA M10 - APD1448115M41AA M11 - APD1448115M41BA M12 - GPD1424070M41AA M13 - GPD1424070M41BA M14 - GPD1430090M41AA M15 - GPD1430090M41BA M16 - GPD1436090M41AA M17 - GPD1436090M41BA M18 - GPD1437090M41AA M19 - GPD1442115M41AA M20 - GPD1442115M41BA M21 - GPD1448115M41AA M22 - GPD1448115M41BAHeat Exchanger/Manifold/Gas ValveHeat Exchanger/Manifold/Gas ValveRef.No:Part No:Description:Ref.No:Part No:Description:Image 1:ID BLOWER0131G0000121ID BLOWER PLATE LRG 5 BRNR (M8, M9, M10, M11, M19, M20, M21, M22)0121G0021831ID BLOWER PLATE SML 3 BRNR (M1, M2, M12, M13)2046310231ID BLOWER PLATE SML 4 BRNR (M3, M4, M5, M6, M7, M14, M15, M16, M17, M18)2046310331PRESSURE SWITCH1111250141PART/TUBE ASSY 3B (M12, M13)2049070751PART/TUBE ASSY 3B (M1, M2)2049071051PART/TUBE ASSY 4B (M14, M15, M16, M17, M18)2049070351PART/TUBE ASSY 4B (M3, M4, M5, M6, M7)2049071151PART/TUBE ASSY 5B (M19, M20, M21, M22)2049070551PART/TUBE ASSY 5B (M8, M9, M10, M11)2049071351IGNITOR0130F0001471GAS VALVE - WHITE-RODGERS 2-STAGE 0151F00000P 81FLAME SENSOR0130F0001091MANIFOLD - 3 BRNR (M1, M2, M12, M13)20493103101MANIFOLD - 4 BRNR (M3, M4, M5, M6, M7, M14, M15, M16, M17, M18)20493104101MANIFOLD - 5 BRNR (M8, M9, M10, M11, M19, M20, M21, M22)20493106101BECKETT BURNER (QTY A/R)10735102111BURNER BRACKET 3B (M1, M2, M12, M13)20190411121BURNER BRACKET 4B (M3, M4, M5, M6, M7, M14, M15, M16, M17, M18)20190412121BURNER BRACKET 5B (M8, M9, M10, M11, M19, M20, M21, M22)20190413121MANUAL RESET LIMIT 10123529131ELBOW-FLUE LEFT 20484401141ELBOW-FLUE RIGHT20484402141ORIFICE SHIELD (M1, M2, M12, M13)11072202151ORIFICE SHIELD (M3, M4, M5, M6, M7, M14, M15, M16, M17, M18)11072203151ORIFICE SHIELD (M8, M9, M10, M11, M19, M20, M21, M22)11072204151SMALL SCREW (QTY 25)M022*******ID BLOWER PLATE GASKET LRG (M8, M9, M10, M11, M19, M20, M21, M22)20463001NS ID BLOWER PLATE GASKET SML (M1, M2, M3, M4, M5, M6, M7, M12, M13, M14, M15, M16, M17, M18)20462801NSORIFICE (QTY A/R)10716003NS Expanded Model Nomenclature M1 - APD1424070M41AA M2 - APD1424070M41BA M3 - APD1430090M41AA M4 - APD1430090M41BA M5 - APD1436090M41AA M6 - APD1436090M41BA M7 - APD1437090M41AA M8 - APD1442115M41AA M9 - APD1442115M41BA M10 - APD1448115M41AA M11 - APD1448115M41BA M12 - GPD1424070M41AA M13 - GPD1424070M41BA M14 - GPD1430090M41AA M15 - GPD1430090M41BA M16 - GPD1436090M41AA M17 - GPD1436090M41BA M18 - GPD1437090M41AA M19 - GPD1442115M41AA M20 - GPD1442115M41BA M21 - GPD1448115M41AA M22 - GPD1448115M41BAControl PanelControl PanelRef.No:Part No:Description:Ref.No:Part No:Description:Image 1:LIMIT SWITCH (M1, M2, M3, M4, M5, M6, M7, M12, M13, M14, M15, M16, M17, M18)1072834341LIMIT SWITCH (M8, M9, M10, M11, M19, M20, M21, M22)1072834441PCB, IGNITION, DSI, 2 STG PCBAG12751TRANSFORMER, 208/230, 24V0130M0013861CAPACITOR 5/40/440V (M1, M2, M3, M4, M12, M13, M14, M15)CAP050400440RT 71CAPACITOR 5/45/440V (M5, M6, M7, M8, M9, M10, M11, M16, M17, M18, M19, M20, M21, M22)CAP050450440RT 71CONTACTOR 25 AMP, 1P, 24V (M1, M2, M3, M4, M5, M6, M7, M12, M13, M14, M15, M16, M17, M18)CONT1P025024V 81CONTACTOR 30 AMP, 1P, 24V (M8, M9, M10, M11, M19, M20, M21, M22)CONT1P030024V 81PCB, DEFROST CONTROL PCBDM1339124V RELAY0130M00025111CAPACITOR STRAP 20520901NS WIRE HARNESS ASSY 0259G00101NS WIRE HARNESS ASSY 0259G00102NS WIRE HARNESS ASSY0259G00103NS WIRE HARNESS ASSY (M1, M2, M3, M4, M5, M6, M7, M12, M13, M14, M15, M16, M17, M18)0259G00104NS WIRE HARNESS ASSY (M8, M9, M10, M11, M19, M20, M21, M22)0259G00105NS WIRE HARNESS ASSY (M1, M2, M3, M4, M5, M6, M7, M12, M13, M14, M15, M16, M17, M18)0259G00108NS WIRE HARNESS ASSY (M8, M9, M10, M11, M19, M20, M21, M22)0259G00109NS WIRE HARNESS, 6 CIRCUIT 0259G00098NS WIRE HARNESS, 9 CIRCUIT 0259G00110NS WIRE HARNESS, ECONO0259G00099NS WIRE HARNESS, OUTDOOR THERMO0259G00100NSExpanded Model Nomenclature M1 - APD1424070M41AA M2 - APD1424070M41BA M3 - APD1430090M41AA M4 - APD1430090M41BA M5 - APD1436090M41AA M6 - APD1436090M41BA M7 - APD1437090M41AA M8 - APD1442115M41AA M9 - APD1442115M41BA M10 - APD1448115M41AA M11 - APD1448115M41BA M12 - GPD1424070M41AA M13 - GPD1424070M41BA M14 - GPD1430090M41AA M15 - GPD1430090M41BA M16 - GPD1436090M41AA M17 - GPD1436090M41BA M18 - GPD1437090M41AA M19 - GPD1442115M41AA M20 - GPD1442115M41BA M21 - GPD1448115M41AA M22 - GPD1448115M41BA。
油管英文版说明书DOC

Manual of BAODA Oil Well PipeChapter 1 IntroductionWuxi Baoda Tubular Goods Producing Co., Ltd. founded in March 2001, presently has three lines of producing Oil well pipes and casing .It mainly processes oil well pipes, coupling and pup-joint in all size and several grades with ou tside diameter from Φ60.3~Φ339.7mm. Annual capacity is up to 80,000 tons. The company carries out management according to ISO9001: 2000 and API Q1 standards. The strength of several experienced specific technologists provides our products with powerful technology support.Oil well pipes of BAODA are widely used in the exploration of land oil field and pipe convey, being the safe and durable products. To acknowledge the support to WUXI BAODA from petroleum industry and mass users for years, make the products have best performance in uses and help oil field technicians know the products deeply; we compile the BAODA Manual in particular. Users are advised to read the manual carefully when choose, transport, load and unload, store, inspect and repair our oil well pipes.Oil well pipes made by BAODA are mostly used in the process of oil field development for the task purposes of oil extraction, fracturing, acidification, affuse, gas injection and well workover. The body stocks of oil well pipe of BAODA adopt the technologies of electric steel making, vacuum degassing, secondary steel making processes, which make products with equal component and good metallurgy quality. Roller trio skew rolling and 12- frame tension reducing technology can guarantee the good shape, high precision dimension and nice mechanical properties; finishing and nondestructive technology (ultrasonic and eddy current testing) can assure the excellent exterior and interior quality; moreover, the parameter of screw thread made by high precision numerical control lathe is 30% stricter than API standard, which leaves the properties of anti-thread gluing, anti-slipping and sealability up to set values of API standard.The oil well pipe products of BAODA cooperate with SHANGHAI W.M Precision Thread Manufactures Co., Ltd., which are well sold in both domestic and foreign market. The oil well pipes are widely used in Yanchang, Shengli Oil and exported to Canada, Middle East regions.For the operation instruction of BAODA thread oil well pipe, see this manual, and see also API RP 5C1Care and Use Of Casing and Tubing、ISO10405 Petroleum and natural gas industries--Care and Use of Casing and Tubing. Contact the manufacturer directly for the BAODA thread oil well pipe that needs to return for repair.Chapter 2 Guidance to Oil Well Pipe Selection1.1IntroductionOil well pipe, the sole channel for oil extraction and gas production hold a significant position in the exploitation of oil field. For recent years, we have established product standard, rules or technological conditions for order supplement when employ API standard. All the standards are to guarantee the production, inspection, transport and quality control in use. However, there is no standard recommended operation for the choosing of oil well pipe serving diverse well depth, pressure, temperature, and purpose. Some oil well pipes up to API standard may have accident usually. It’s far from satisfaction that the product merely meet API standard. With the constant development of our oil and gas exploitation, there will be plenty of complex working condition of water injection well、gas injection well、thermal recovery well、deep well、ultra-deep well、high pressure oil and gas field as well as fracturing, acidification, polymer. In these harsh working conditions, proper choose of oil well pipe is much more important, which will directly influence the production and benefit of oil and gas well. Because of thread gluing、surge、leakage、break、corrosion、fatigue fracture by selecting the improper oil well pipe, the loss of them is quite big.This chapter is compiled according to API standard and the field use, offering the general principle and recommended operation for the choosing of BAODA oil well pipe in oil exploitation. However, as to the specific conditions of well, there cannot be forcing choosing of the oil well pipe. Technicians must make deeper and more specific analysis to the working condition when reading this chapter, so as to better choose and use BAODA oil well pipe.2.2LengthLength Range Grade 1 Length Grade 2 Length 6.10~7.32m(20~24ft)8.53~9.75m(28~32ft)100% Carload Length Range:Allowed Max. Length Variation……0.61m(2ft)0.61m(2ft)Min. Allowed Length…………… 6.10m(20ft)8.53m(28ft)2.3 Basic Parameter of BAODA Oil Well PipeAPI Non-Upset Round Thread Oil Well PipeAPI Non-Upset Round Thread Oil Well PipeAPI Upset Round Thread Oil Well Pipeternal Diameter——73.03mm (2 7/8〞)第 5 页共23 页第 6 页共23 页2.4 BAODA Oil Well Pipe VarietiesBAODA oil well pipe and thread tie-in are API series in major.2.5 Choosing of Well DepthAs to the oil well pipes of diverse external diameter wall thickness, make the choice according to the strength level of different range. Upset oil pipe is recommended for the horizontal well with the depth over 3000m or vertical well over 3500m deep.Table 2.5 gives out the recommended selection of BAODA oil well pipes in diverse well depths.Table 2.5 Oil Pipe Recommended for Diverse Well Depth2、Commonly, the oil well pipes used on the sea are one level higher than that of thesame well depth used on the land.2.6 Pressure ConditionChoose the suitable oil well pipe according to the oil, gas well and working condition in different well mouth pressure.API Round Thread or API Round thread + special thread seal grease are recommended forthe gas well with the well mouth pressure less than 28Mpa.Chapter 3 Transport, Load & Unload and Store3.1 IntroductionGenerally, threads of oil pipe are precisely made, so load and unload both the old and new ones carefully. For both the new or old oil well pipe, wear them thread protector during the process of transport, load and unload, and store, place them on the stand without stone, sand or dirt (except slurry in well field), the wood plate or mental plate. If the oil well pipe is accidentally dragged into the dirt, clean the thread once again and reuse after the required treatment.3.2 Transport3.2.1 Water transport3.2.1.1 Arrange special people to supervise during the loading and unloading of pipe;3.2.1.2 Avoid the movement of pipes owing to the improper underlay or insufficient support when the ship inclines;3.2.1.3 Avoid putting the oil well pipes to the places with sewage, poisonous chemicals or other corrosive material;3.2.1.4 Avoid heaping, dragging and pulling the oil well pipes along the pipe;3.2.1.5 Avoid hook coupling or thread protector, or strike to the edge of hatch, guardrail and hull of ship.3.2.1.6 No heavy goods are allowed if the lading reaches some height.3.2.2 Land transport3.2.2.1 Oil well pipe should be placed on the stow-wood and packed tightly. For the long pipes (L>9m), fastness in middle part is suggested;3.2.2.2 Coupling end of all pipes should be placed in the same end of the carriage, and cannot place beyond the vehicle end by more than 1.2m; see the picture 1;Picture 13.3.2.3 Load and unload with care, pack tightly, Avoid abrasion and collision between pipe ends;3.2.2.4 Over load and over high pile of casings on a same vehicle is not safe. If there is abnormal evidence, unload or repack them midway;3.2.2.5 After the moving for certain distance, repack the goods tightly in case that it looses;3.2.2.6 Pack fastness for small amount transport of oil well pipe is recommended.3.2.3 Railway transport3.2.3.1 Horizontally place crosstie at the bottom of the truck in order to support the pipe and provide space for lifting, keep ventilated at the bottom part and not be polluted;3.2.3.2 Level up the bottom of truck and keep the same plane of the pile of pipes;3.2.3.3 Coupling and upset part of oil well pipe should not be placed on the crosstie;3.2.3.4 Oil well pipe should be fixed and avoid move3.3 Load and unload3.3.1 All casings(new or old)must wear thread protector , screw down to the original position, and thread protector must be clean and in good condition;3.3.2 Avoid injuring of the oil well pipe, avoid load and unload in haste, don’t drag and hit on the ground;3.3.3 Load and unload each pipe with rope or steel wire, the quantity of each loading and unloading depends on whether you can fully control the them;3.3.4 Don’t bind the pipe just at one end and lift it, don’t throw the oil pipe from the transport vehicle such as truck and rain;3.3.5 When oil pipes chute, pipes should roll paralleling with pipe pile. Mass rolling down of pipe and striking on the end are not allowed;3.3.6 Before the sliding pipe reach the front one, push it to proper position with hand.3.3.7 Use wood board or other underlay for pipe piles.3.4 Store3.4.1 Store the oil pipe on the dry and ventilated rack above 0.5m high. The rack foundation should be firm and leveled;3.4.2 3~4m span between pipe rack, ensure at least three support points for each pipe, align the stow-wood , and line them vertically with the pipe body;3.4.3 Oil pipe should be put according to category; inside and outside thread respectively align ina direction so as to facilitate lifting;3.4.4 Align each layer of pipe, crisscro dispose of up and down layers, stagger about one coupling length;3.4.5Heigh of stock pipes cannot be higher than 3m, pipes pile at the well site cannot be more than 5 layers;3.4.6 During store, oil well pipe should be prevented from rust and corrosion regularly, not accumulate water, slurry or oil dirt, dust sand in the inner wall of pipe;3.4.7 There shouldn’t be heavy, acid and alkaline chemical in the stored place of pipes, and no electrical and gas-soldering operations is allowed neither;3.4.8 Carry out 1~2 times thread inspection each year and coat the store grease for long term store.Chapter 4 Inspection4.1 IntroductionInspection involves that of arrived product, of repaired product (include the inspection of working procedure), and of class production before tripping. Users can carry out inspections aiming at diverse situation. Besides the prescribed sampling inspection rate、items, method and measure for inspection, classification of reused and repaired oil well pipe are needed for the inspection result, so as to determine the application of them.Inspection of oil well pipe commodity and finished product should be done according to product standard and supplementary technology condition of order by special personnel. Production inspection and grade of oil well pipe are done by the professional workers from the manufacturer.4.2 PreparationLine the oil well pipe on the rack in case the thread tie-in has dirt, sand or dust, leave enough space and allow each pipe can roll in all direct for the inspection and cleaning of thread.Use the steel rope or special rope for lifting the oil well pipe, do not use pipe hook、pipe tongs、pipe grabber and etc.. When remove the thread protector at both ends, don’t use tools that may injure inner wall of pipe as well as the thread, Pay more attention to the inner coating layer.Use the compressed air to clean the inner surface (from blow from coupling inside thread to the outside one), in order the clean out the mud and residue in pipe. Clear away the accumulated grease on the thread surface in order to clean out the mud and residue. When clear away the accumulated grease on the surface or thread seal grease, small pressure equipment is recommended, and non-mental brush, saw powder or oil solvent. Fully dry the thread after cleaning, steel wire brush cannot be used.Clean thread protector, throw away the bad thread protector.Clean organic solvent again at the tie-in. When the environment is lower than zero, check the ice residue at the bottom and tooth of inner thread.4.3 New Oil Well Pipe InspectionThere will be sample inspection and nearly 5%~10%of the arrived goods will be checked according to API SPEC 5CT、API STD 5B、API RP 5B1 standard and relating technological conditions of the order. Newly recommended Inspection items are listed in table 4.1Table 4.1 Inspection Items of New Oil Well PipeCrack DetectionMaterial4.4 Inspection of Reused Oil Well PipeAs to the used BAODA oil well pipe , inspect the recycled or repaired casing via visual method、mechanical measure method、Crack Detection(include Electromagnetism Crack Detection、Ultrasonic Crack Detection、Whirlpool Crack Detection or Radial Crack Detection).The inspections are limited to confirm the crack, pit and the place of defect on the surface including: corrosion damage of casing surface; internal and external transverse crack; inside surface steel rope pull (lengthways); inside surface sucker rod abrasion and inside and outside big tongs slips damage.4.4.1 Pipe Body InspectionUse wall thickness micrometer or ultrasonic thickness tester(with error less than 2%) to measure pipe body wall thickness. The measurement will be classified according to the min residual wall thickness (see table 4.2) and work out the application scope of reused oil well pipe according to the residual strength estimated by min. wall thickness.Reused oil well pipes are graded according to the measured min. residual wall thickness.Table 4.2 Category of Thickness Measure for Reused Oil Well Pipecategory are new ones.4.4.2 Thread Tie-in InspectionInspection of reused oil well pipe thread includes API round thread distortion in length、thread gluing, fatigue crack by final thread jiggle and thread appearance.If the pitch at the joggle enlarges, it shows the thread has been lengthened, and serving load exceeds the yield strength of tie-in. They may work next time, but the property of connecting and sealing won’t be so well, not suitable for reuse.Thread gluing is the frequent failure of oil pipe break-up. If the thread tooth shape doesn’t change greatly, the influence to connecting and sealing won’t be large. However, to thread gluing with serious adhesive abrasion, metal surface of thread tooth has trails, or even with the obvious change of buckle shape, depose or repair them, for thread gluing is often the inducement of leakage.Alternate tension of oil pipe string often lead to fatigue crack, low carrying capacity, or failures in next use. Repair the buckle until it can be used.Judge the quality of reused oil pipe according to the serious grade of thread distortion, injury, thread gluing, piercing, worn crack.Chapter 5 Process of Oil Well Pipe Tripping and Requirement5.1 Preparation of oil well pipe trip5.1.1 Check if the equipment, tools, materials can meet the list of operation.5.1.2 Examine the equipment, tools, materials in accordance with relating operation regulations and see whether the specification、property and quality can reach the requirement of operation. If not, revise them in time. Main inspection items include:5.1.2.1Hydraulic power tongs(include model、tongs mouth size、length of connecting-rod, oil well pipe with coupling, main and back tongs, connecting-rod Length 230mm,extreme-line or narrow clearance coupling oil pipe, main and back tongs connecting-rod Length≥500mm);5.1.2.2 Hydraulic driver;5.1.2.3 Hydraulic line;5.1.2.4 Stabbing board;5.1.2.5 Elevator and slips;5.1.2.6 Torsion gage and sensor;5.1.2.7 Spring hanger and hydraulic expansion joint;5.1.2.8 Rig tools;5.1.2.9 Power tongs tail rope and connecting fittings;5.1.2.10 Fast removal of thread protector.5.2 Tripping of Oil Well Pipe5.2.1 Lift with balance and suspend with even speed, lift, forbid the sudden fierce operations.5.2.2 When use hydraulic tongs for operation ,extreme-line oil well pipe and narrow clearance coupling oil pipe, break-up operation back tongs are not allowed to chuck coupling (See picture 2b).a bPicture 2Make-up Break-up Make and breakMain Tongs Main Tongs Main TongsNon-Upset Back Tongs Extreme-line TypeUpsetBack Tongs Back Tongs5.2.3 Remove the oil pipe、pup joint、tools of tripping out, clean the inside and outside thread .5.2.4 Check if the inside and outside surface, airproof side and shoulder have serious distortion, nick and mar. Find out the unqualified oil well pipes.5.2.5 Screw on the thread protector for the qualified oil well pipe after inspection, and put them in the proper place.5.3 Preparation of oil pipe tripping5.3.1 Check if the equipment, tools, materials can meet the list of operation.5.3.2 Examine the equipment, tools, materials in accordance with relating operation regulations and see whether the specification、property and quality can reach the requirement of operation. If not, revise them in time. The major inspection items include:5.3.2.1Hydraulic power tongs(include model、bite size、connecting-rod length≥500mm);5.3.2.2 Hydraulic driver、hydraulic line;5.3.2.3 Stabbing board、elevator and slips;5.3.2.4 Torsion gage and sensor;5.3.2.5 Spring hanger and hydraulic expansion joint;5.3.2.6 Rig tools;5.3.2.7 Accessories、pup joints for all sorts of oil well pipes;5.3.2.8 Power tongs tail rope and connecting fittings;5.3.2.9 Thread compound;5.3.2.10 Check the centering of lift equipment and the well mouth, prevent the stabbing and cross threading during tripping.5.3.3 Examine that if the steel grade、specification、quantity、pipe end form, and make and break of tripping pipe are up to engineering standard.5.3.4 Check the oil pipe of trip and the thread, replace the damaged pipe immediately.5.3.5 Number the oil pip, measure the length, and examine the diameter.5.4 Tripping of oil pipe5.4.1 Lift the oil pipe, remove the thread protector, and coat the thread compound.5.4.2 Center the oil pipe, and spin-up speed≤25r/min.5.4.3 Do the tightening operation of API Thread tie-in according to the recommended torque values in table 5.1.5.4.4When use hydraulic tongs to operate, for the flat oil well pipe、upset oil well pipe or extreme-line oil pipe, back tongs can not chuck coupling ,but the pipe body(See picture 2).5.4.5 Choose the right hydraulic tongs and hydraulic driver according to the steel grade, specification and recommended torque range of the oil well pipe. To the hydraulic tongs with pressure limiting valve and without torquemeter, you can know the spin-up pressure and torque via the adjustment of auxiliary valve.5.4.6 For the homemade hydraulic tongs without torquemeter and pressure limiting valve, do choose the low rating torque and big tongs according to the steel grade and specification of the oil well pipe.5.4.7 Spin-up torque curve in the field is not agree with recommended picture, break-up, check inside and outside thread, and replace the damaged oil pipe.5.4.8 Oil pipe Tightening reaches the prescribed torque, spin-up position can be decided by the residual 1~2 buckles.5.4.9 When use pneumatic slips, brake first and then turn off slips, and remove the elevator. Never turn off the pneumatic slips during tripping.5.4.10 Do the tripping of oil pipe as the design requirements. When near to Inflexion, seal section and design position, going-in speed should not exceed 5m/min, Normal going-in speed should not exceed 25 pieces/h. Recommended tightening torque refers to Table 5.1.Table 5.1 Recommended Torque for Oil Well Pipe TighteningTorque Unit Conversion Factor:1ft-Ib=1.355818J.Chapter 6 Operation Process with Import Hydraulic Tongs and Requirements6.1 Choose the bite size of hydraulic tongs、make and break torque and spindle speeds according to oil pipe steel grade、specification、pipe end and tie-in form.6.2 Hydraulic tongs spin-up、break-up chucking operation according to picture 2 .6.3 When make and break the pipe body with back tongs, string must use the slips fixed position, when use back tongs for coupling break-up, string can use seat elevator operation.6.4 Set the recommended torque value by pipe manufacturer in the torsion gauge or torque monitoring system.6.5 Operate according to the operator.6.6 When work at the well mouth, take strict precautions against the stuff dropping down to the well.6.7 Make and break operation can refer to API RP 5C1.6.8 Precisely record the running of tongs、hydraulic driver、torque monitoring system, including rotate speed of diesel engine、oil pressure、oil(water) temperature、air pressure; hydraulic pump oil temperature、displacement; oil pipe tongs spin-up max. torque of 、back tongs、pressure、oil pipe specification, size, quantity; torque setting value of torque monitoring system and etc.Chapter 7 Operation Process with Homemade Hydraulic Tongs and Requirement7.1 Choose the bite size of hydraulic tongs、make and break torque and spindle speeds according to oil pipe steel grade、specification、pipe end and tie-in form.7.2 Choose hydraulic tongs according to the recommended torque value in table 5.1 and application range in table 7.1.7.3 When install the hydraulic tongs of torquemeter and pressure limiting valve, refer to Chapter 5.Table 7.1 Application Range for Homemade Hydraulic Tongs7.4 Hydraulic tongs without torquemeter and pressure limiting valve must operate as follows:7.4.1Operate strictly according to 7.2 section, choose the proper oil pipe hydraulic tongs and corresponding hydraulic source system.7.4.2 Connecting Rod between main tongs and back tongs ≥500mm, chuck pipe body, make and break according to picture 2.7.4.3 Lift oil pipe、coat thread compound ,center the thread ,rotate speed≤25r/min for two circles spin-up, and then spin-up to the prescribed torque place, and max. 1~2 buckles are allowed outside.7.4.4 Control with the operation of flat buckle is not allowed..7.4.5Generally back tongs are not allowed to hold the upper end of coupling..7.4.6 When work at the well mouth, take strict precautions against the stuff dropping down to the well.7.5 For hydraulic tongs without torquemeter and pressure limiting valve, the distance of connecting rod between back tongs and main tongs cannot be lengthened, that is operation of picture 2 is not applicable to it, so the make and break must do as follows:7.5.1 Operate strictly according to 6.2 section, choose the right hydraulic tongs and corresponding hydraulic source system.7.5.2 Lift oil well pipe, coat thread compound, centering thread, spin-up with manual tool, and spin up for two rings at the low torque .(in spin-up, try to use the back tongs at the below end).7.5.3 After tightening 1~2buckles are allowed outside.7.5.4 To avoid cross threading, hydraulic tongs are not allowed to stabbing directly and spin-up continuously.7.5.5 Control with the operation of flat buckle is not allowed.7.5.6 When work at the well mouth, take strict precautions against the stuff dropping down to the well.Chapter 8 Causes of Invalid Oil Will Pipe8.1 Causes of Thread Gluing of the Tie-in8.1.1 Incomplete inspection of oil well pipe before trip, improper control land maintenance in store, rusty thread surface;8.1.2 Careless load and unload, and transport, or injured thread owing to thread protector loosing, coupling distortion;8.1.3 Not operate in accordance with the instruction in the trip, the spin-up speed is too fast (over 25r/min), torque is over big (exceed those in table 5.1), over hammer to coupling, over holding force, coupling and pipe body distorts;8.1.4 If the thread surface of coupling is, replace the worn coupling with non standard one;8.1.5 Unclean thread, thread compound foreign body left on the thread;8.1.6 Improper tolerance of processed thread of repaired oil well pipe, thread fastener has burr; 8.1.7 Use the unqualified hydraulic tongs;8.1.8 Cross threading spin-up.8.2 Causes of oil well pipe surge、break8.2.1 Improper choose of strength and use, especially when there is need of upset oil pipe butnon-Upset oil pipe is used;8.2.2 Use the worn and mismatching equipment, chuck、big tongs、tongs tooth and pipe wrench. When tripping out the oil pipe, there is lack of spin-up torque (or no torque control), external thread doesn’t reach the set position, or spin-up torque of outside thread is too large and go beyond the coupling midline;8.2.3 Surface fatigue caused by the final thread joggle, which has no effective remedy measures. Use the upset oil well pipe instead of non-upset oil pipe and delay the failure occurrence.8.2.4 improper installation of well mouth、christmas tree、pumping unit(non-concentric),oil pipe string thread tie-in declines;8.2.5 Because of thread gluing or fatigue source by processing tool, the fatigue stress in oil extraction causes the crack expands and breaks;8.2.6 Oil well pipe with serious thread gluing.8.3 Causes of the Tie-in Leaking8.3.1 Improper selection or use of the thread compound, thread compound is diluted or quality is inferior;8.3.2 Corrosion and rusting owing to the dirty thread or the use of antisepsis material;8.3.3 Thread is not tightened or over tightened; and coupling is distorted by hammering and beating;8.3.4 Thread abrasion caused by dirt and other staff、cross threading、thread gluing、injury, improper grinding in field repair of thread;8.3.5 Sudden lift and pull of pipe or much repeating trips;5.3.6 Oil well pipe with serious thread gluing.8.4 Causes of corrosion8.4.1 Improper material choosing of pipe, cannot select the suitable anti-corrosion oil pipe aiming at the serving environment;8.4.2 Not use the pipe inner coating for the strong corrosive well of H2S+CO2;8.4.3 Not use well on the beam and gas-lift well, not use the corrosion inhibitor to fill in the annulus between casing and oil well pipe, not use packer to jam the annulus room in flowing well;8.4.4 Charge of water injection well hasn’t been deoxidized;8.4.5 Corrosion by complex factors, uncertain influences;8.5 Causes of Pipe Body Break8.5.1 Coupling abrasion and abrasion of sucker rod to pipe inner wall;8.5.2 Sucker rod is seriously damaged;8.5.3 Inner wall of pipe body corrosion or the inner surface-folding defect that hasn’t beendetected;8.5.4 Improper sort selection of reused oil pipe and use the left oil well pipe with too small wall thickness;8.5.5 Wrong selection of steel grade and specification for the broken oil well pipeChapter 9 RepairOil well pipe that is injured by use or misuse can be reused after repair. The repair must do in accordance with API SPEC 5CT and API STD 5B standard, and the usability of repaired product can be confirmed after the inspection of 5.4 section in this manual.Appendix: Table of Oil Well Pipe Basic Parameter in British System API Non-Upset Round Thread Oil Well PipeAPI Non-Upset Round Thread Oil Well PipeManual of BAODA Oil Well Pipe第21 页共23 页API Upset Round Thread Oil Well Pipexternal Diameter——2 7/8〞第22 页共23 页xternal Diameter——4〞xternal Diameter——4 1/2〞第23 页共23 页。
修造船舶实用英语手册.doc

第一章专业词汇第一节:船体部分A居住舱室:Accommodation调整:Adjust调节阀:Adjust valve艉垂线:Aft perpendicular艉尖舱:Aft peak tank艉尖舱壁:Aft peak bulkhead空气扩散器:Air diffuser通风孔:Air hole进气口:Air intake航空母舰:Aircraft carrier气动水泵:Air-driven water pump 找中、找对:Align确定,探知:Ascertain装配,组装:Assemble向岸地,在岸上地:Ashore锚:Anchor锚臂:Anchor arm锚链:Anchor chain锚冠:Anchor crown锚爪:Anchor fluke链环:Anchor link锚唇:Anchor mouth锚穴:Anchor recess锚卸扣:Anchor shackle锚杆:Anchor stock角钢:Angle bar退火:Anneal斜角甲板:Angled deck天线:Antenna防腐油漆:Anti-corrosive paint减摇水舱:Anti-rolling tank自动喷水器:Automatic sprinkler自动通风筒:Automatic ventilator辅机机座:Auxiliary engine seating调节水舱:Auxiliary tank施加:ApplyB叶背:Back of blade挡板,隔板:Baffle行李舱:Baggage room烘:Bake平衡锤:Balance weight平衡舵:Balanced rudder滚珠轴承,球型布司:Ball bearing球阀:Ball valve压载舱:Ballast tank圆筒:Barrel垫块:Base block长条护板:Batten横梁:Beam横梁肘板:Beam knee横梁肘板:Beam bracket轴承:Bearing轴承座:Bearing seat轴承外壳:Bearing shell基座纵桁:Bed-plate girder锚链筒喇叭口:Bell-mouth of hawspipe 软垫床:Berth两色灯:Bi-colored light舭肘板:Bilge bracket舭龙骨:Bilge keel舭肘板:Bilge plating舭部边舱水深探管:Bilge sounding pipe 舭列板:Bilge strake舱底水:Bilge water单柱系缆桩:Bitt双柱系缆桩:Bitts (螺旋桨)桨叶:Blade叶面:Blade face叶根:Blade root叶梢:Blade tip闷住:Blind阻塞:Block堵塞:Blockage吊艇架:Boat davit艇甲板:Boat deck吊艇索:Boat fall艇吊钩,(舢板)挽钩:Boat hook 帆缆库:Boatswain’s store room首斜桅拉索:Bobstay锅炉:Boiler锅炉基座:Boiler bearer系缆桩:Bollard螺栓:Bolt插销锁:Bolt lock书柜:Book case舱室:Booth镗:Bore(螺旋桨)轴毂:Boss轴包架,轴毂:Bossing帆缆库:Bosun store舱底铺板:Bottom ceiling中底桁:Bottom center girder船底肋骨:Bottom frame船底垫板:Bottom grating船底板:Bottom plate旁底桁:Bottom side girder感谢您的观看底边舱:Bottom side tank底肋板(纵骨架式结构):Bottom transverse 艏门(滚装船):Bow door(帆船)艏斜桅:Bowsprit艏端结构:Bow structure艏侧推:Bow thruster艏锚:Bower anchor箱型龙骨:Box keel转帆索:Brace肘板,三角板:Bracket框架肋板:Bracket floor制动装置,刹车:Brake制动带,刹车带:Brake band(lining)制动曲柄:Brake crank arm制动液压缸:Brake hydraulic cylinder刹车卷筒:Brake drum刹车液压管:Brake hydraulic pipe艏肘板:Breast hook船宽:Breadth桥楼,驾驶台:Bridge驾驶室集中操作台:Bridge console stand主机遥控柜:Bridge panel of engine remote control 刷:Brush缓冲弹簧:Buffer spring堆焊:Build-up by welding球扁钢:Bulb plate球鼻艏:Bulbous bow散货船:Bulk cargo carrier舱壁:Bulkhead舱壁甲板:Bulkhead deck舷墙:Bulwark舷墙板:Bulwark plate舷墙支撑:Bulwark stay浮筒:Buoy航标船:Buoy tender浮力舱:Buoyancy tank浮箱:Buoyant box蝶形螺帽:Butterfly screw capC船舱:Cabin电缆,缆索:Cable导缆钳:Cable chock缆索卷筒:Cable drum弃链器:Cable releaser钢索绞车:Cable winch起货机操纵室:Cage校准:Calibrate梁拱:Camber取消:Cancel斜横梁:Cant beam斜肋骨:Cant frame悬臂梁:Cantilever beam船长:Captain船长室:Captain room碳化物:Carbide货物:Cargo货物护板条:Cargo battens吊货滑车:Cargo block吊杆:Cargo boom吊货短链:Cargo chain吊货索:Cargo fall, cargo runner货舱口:Cargo hatch吊钩:Cargo hook吊货钩卸扣:Cargo hook shackle吊钩转环:Cargo hook swivel货油软管:Cargo hose吊货索导向滑轮:Cargo runner lead block 起货绞车:Cargo winch进行,执行:Carry out铸:Cast铸钢艏柱:Cast steel stem post步桥(油船),栈道:Cat walk高速双体船:Catamaran室顶板:Ceiling吊灯:Ceiling lamp 水泥:Cement水泥流水沟:Cement draining中纵桁:Center girder中内龙骨:Center keelson中纵舱壁:Centerline bulkhead导缆钳:Chock圆形导缆孔:Circular mooring pipe倒角:Chamfer链轮轴:Chain axle制链钳:Chain clamp导链滚轮:Chain cable fairlead制链器:Chain cable stopper制链器:Chain controller锚链环:Chain link锚链舱:Chain locker链轮:Chain wheel链轮轴:Chain wheel shaft龟裂:Chap海图:Chart海图灯:Chart light海图室:Chart room海图桌:Chart table轮机长室:Chief engineer’s room削:Chip镀铬:Chrominum-plate旋回视窗:Clear view screen通焊孔:Clearance hole系缆扣:Cleat羊角系缆桩:Cleat post夹扣:Clip飞剪型船艏:Clipper bow闭室导缆钳:Closed mooring chock离合器:Clutch离合器手轮:Clutch hand wheel二氧化碳灭火器:CO2 fire extinguisher 涂(漆):Coat感谢您的观看衣帽钩:Coat and hat hook空隔舱:Cofferdam防撞舱壁:Collision bulkhead立柱:Column主机轮换实验:Continuous survey of the main engine 普通链环:Common link连通管:Communicating pipe连通水柜:Communicating tank交通船:Commuter罗经:Compass罗经甲板:Compass deck压缩空气瓶:Compressed air bottle冷凝器:Condenser导管:Conductor tube连接水柜:Connecting tank吊钩梁:Connecting traverse集装箱:Container集装箱船:Container ship (liner, vessel)操纵台:Control desk轮机控制台:Control console of main engine控制阀:Control valve软木,软塞:Cork使腐蚀,侵蚀:Corrode 槽型舱壁:Corrugated bulkhead接头(考贝令):Coupling盖板:Cover plate头巾型通风筒:Cowl head ventilator 软垫:Cushion裂纹:Crack克令吊、起重机:Crane曲柄:Crank船员:Crew普通船员寝室:Crew’s bed room船员餐厅:Crew’s mess room桅杆了望台:Crow’s nest船员居住区:Crew’s quarters船员厕所:Crew’s W.C十字头:Crosshead双十字系缆桩:Cruciform bitts单十字系缆桩:Cruciform post bollard 巡洋舰:Cruiser巡洋舰式船尾:Cruiser stern球窝关节:Cup and ball joint窗帘:Curtain直叶推进器:Cycloidal propeller缸体、圆柱体:CylinderD缓冲器:Damper吊臂(吊艇架):Davit arm吊艇钩:Davit hook起居室:Day room(舷窗的)风暴盖:Deadlight甲板中心线:Deck centerline甲板骨架:Deck framing甲板锚链孔凸缘:Deck flange of hawse pipe 甲板纵桁:Deck girder甲板室:Deck house甲板纵骨:Deck longitudinal甲板边线:Deck side line甲板边板:Deck stringer强横梁(纵骨架式结构):Deck transverse 深潜器:Deep sea vehicle深舱:Deep tank变形:Deform除霜:Defrost棘爪、制链器:Detent (stopper) 起重机,吊杆:Derrick吊杆:Derrick boom吊杆索:Derrick fall吊杆柱:Derrick post吊杆装置:Derrick rig去锈:Derusting台灯:Desk lamp驱逐舰:Destroyer脱落:Detach散合式连接卸扣:Detachable shackle 检查:Detect链式制链器:Devil’s claw斜置加强筋:Diagonal stiffener柴油机:Diesel engine方位测定器:Direction finder测向仪天线:Direction finder antenna 解体:Disassemble排出、卸下:Discharge脱开:Disconnect拆卸:Dismantle卸下:Dismount调度中心:Dispatch center医务室:Dispensary排水量:Displacement排水型船:Displacement type vessel 张索:Distance line蒸馏:Distil船坞:Dock球形舱壁:Domed bulkhead门帘:Door curtain门框:Door frame门把:Door handle 门钩:Door hook门板:Door plate出入门:Doorway双层底:Double bottom双层底舱:Double bottom tank山字钩:Double hook双滚轮式导缆钳:Double roller chock 复合板,加强板:Doubling plate降帆索:Down halyard吃水:Draft吃水线:Draft line水尺:Draft mark拉索:Dragline感谢您的观看感谢你的观看感谢您的观看流水孔、污水孔:Drain hole 污水井:Drain well 拉(拔出):Draw 抽屉:Drawer抽屉把手:Drawer handle 修饰:Dress up 挖泥船:Dredger 钻孔法:Drilling 钻井船:Drill ship传动轴系:Driving shaft system下降:Drop 卷筒:Drum卷筒凸缘:Drum flange 干电池:Dry cell干粉容器:Dry power container干粉灭火器:Dry power fire extinguisher 干燥剂:Drying agent着色探伤:Dye-penetration test动力支撑型船舶:Dynamic supported craftE接地:Earth偏心轮:Eccentric wheel偏心起升滚轮装置:Eccentric roller jacking device 回声测深仪:Echo-sounder电动机、电马达:Electric motor 电动舵机:Electric rudder gear电动回转式起重机:Electric revolving crane 电动锚机:Electric motor windlass 升降机装置:Elevating system elevator 椭圆形导缆孔:Elliptical mooring pipe 椭圆形船尾:Elliptical stern 登乘甲板:Embarkation deck 紧急出口:Emergency exit封闭式救生艇:Enclosed lifeboat 末端链环:End open link 末端卸扣:End shackle 口齿合:Engage主机、发动机:Engine发动机进气口:Engine air inlet 机舱棚:Engine casing机座:Engine foundation 机舱:Engine room机舱口:Engine room opening 机舱肋骨:Engine room frame机舱口端梁:Engine room hatch end beam 机舱口纵桁:Engine room hatch girder 车钟:Engine telegraph 加大链环:Enlarged link(集装箱格栅)入口导承:Enter guider 基本结构图:Essential structure plan 仔细检查:Examine(发动机)排气管:Exhaust pipe 排气阀:Exhaust valve延伸肘板:Expanded bracket 伸缩接头:Expansion joint 膨胀井:Expansion trunk 拔出:Extract 眼板:Eye plateF制作:Fabricate 面板:Face plate 平顺:Fair up 导缆器:Fairlead 鼓风机:Fan鼓风机排气口:Fan vent 高速船舶:Fast craft 护舷材:Fender 轮渡:Ferry 锉:File过滤器:Filter 鳍:Fin鳍角反馈装置:Fin angle feedback set 鳍箱:Fin box 鳍轴:Fin shaft减摇鳍:Fin stabilizer 加工、完成:Finish消防船:Fire boat (fire fighting ship) 灭火剂:Fire extinguishing agent 消防枪:Fire fighting gun 消防水管:Fire hose消防栓:Fire hydrant (fire plug) 安装:Fit拂刮:Fit and scrape固定式水灭火器:Fixed water fire extinguisher折边、法兰:Flange (flange edge) 折板(滚装船艏艉跳板):Flap 襟翼舵:Flap-type rudder 扁钢:Flat steel plate 浮吊:Floating crane浮船坞:Floating dock 槽型水舱:Flume tank 冲洗:Flush冲水阀:Flush valve 纱窗:Fly net 步桥(油船):Flying passage泡沫液容器:Foam concentrate container泡沫灭火器:Foam fire extinguisher 折叠式舱盖:Folding hatch cover 脚踏刹车:Foot brake 地令:Foot ring 根缆:Footrope前后拉索:Fore and aft stay前下中桅帆:Fore lower topsail感谢你的观看感谢您的观看前上中桅帆:Fore upper topsail 艏楼:Forecastle艏楼甲板:Forecastle deck 艏尖舱:Fore peak艏垂线:Fore perpendicular 锻:Forge锻钢艏柱:Forged steel stem船艏吃水:Forward draft mark 打断:Fracture 骨架:Framing干舷:Freeboard 排水口:Freeing port氟里昂系统:Freon system淡水载重线:Fresh water load line 淡水柜:Fresh water tank 燃油箱:Fuel box 燃油舱:Fuel oil tank满载水线:Full load waterline 烟囱:FunnelG纵帆斜桁:Gaff前桅主帆:Gaff foresail 主帆:Gaff mainsail 镀锌:Galvanize 舷梯:Gangway(船上)厨房:Galley 气管阀:Gas line valve 垫圈:Gasket汽油箱:Gasoline tank 量表:Gauge 小齿轮:Gear大齿轮:Gearwheel杂货船:General cargo ship 基座纵桁:Girder of foundation 门型桅(柱):Goalpost前进和后退:Go-ahead and go-back 磨平:Ground smooth防滑格子,格兰丁:Grating重力式吊艇架:Gravity type boat davit 保证,担保:Guarantee 导轨:Guide rail导向滚轮:Guide roller 研磨:Grind 冲砂:Grit blast 船舷上缘:Gunwale舷边角钢:Gunwale angle舷边圆弧后板:Gunwale rounded thick strake 菱形板:Gusset plate 稳索:Guy定位索:Guyline 链轮(锚机上的):Gypsy自动操舵操纵台:Gyro-pilot steering indicator 回转仪:GyroscopeH半梁:Half beam半深纵骨:Half depth girder半圆扁钢:Half rounded flat plate 半圆钢:Half round steel bar 手摇柄:Hand crank 手栏杆:Handrail 手轮:Hand wheel 把手:Handle 舱口:Hatch舱口梁座:Hatch beam sockets 舱口围:Hatch coaming 舱盖:Hatch cover舱口盖板隔架:Hatch cover rack 舱口端横梁:Hatch end beam 舱口悬臂梁:Hatch side cantilever 舱口纵桁:Hatch side girder 舱口:Hatchway 锚链孔:Hawsehole 锚链筒:Hawse pipe 艏缆:Head rope 艉柱根:Heel piece 直升机:Helicopter直升机甲板:Helicopter deck高压软管:High-pressure soft pipe 铰链:Hinge铰链舱盖:Hinged hatch cover 艉部吊门(滚装船):Hinged stern door 中拱弯曲:Hogging 货舱:Hold货舱梯子:Hold ladder 货舱内支柱:Hold pillar 搪磨:Hone 钩:Hook钩头螺栓:Hook bolt 水平桁:Horizontal girder水平扶强材:Horizontal stiffener 船壳:Hull船壳板:Hull plank 船壳板:Hull plate液压油缸:Hydraulic cylinder 液压泵:Hydraulic pump液压回转式起重机:Hydraulic revolving crane 水翼:Hydrofoil水翼船:Hydrofoil craftI破冰船:Icebreaker破冰型船艏:Icebreaker bow浸透:Impregnate倾斜:Incline独立舱柜:Independent tank气胀式救生筏:Inflatable liferaft 充气阀:Inflation valve内底板:Inner bottom plate内门(滚装船):Inner door内平板龙骨:Inner plate keel整体舱柜:Integral tank中间肋骨:Intermediate frame内燃机组:Internal combustion engine set出具:IssueJ船首旗:Jack船首旗杆:Jack staff自升式钻井平台:Jack up drilling platform 咬住:Jam喷筒:Jet泡沫灭火枪:Jet foam ejector喷管:Jet pipe首帆,起重机的臂:Jib支架:Jig接头:Joint连接卸扣:Joint shackle K龙骨:Keel双半式连接链环:Kenter shackle主柱:King post肘板:KneeL梯子:Ladder步梯:Ladder way车床:Lathe下水:Launch洗手间:Lavatory导向滑车:Lead block导索槽轮:Lead sheave导边(螺旋桨叶):Leading edge 漏泄:Leakage闸刀式制链器:Lever chain stopper 船长:Length船总长:Length overall救生艇:Lifeboat救生艇吊柱:Lifeboat davit救生圈:Lifebuoy救生衣:Lifejacket救生筏:Liferaft吊:Lift out艇吊钩:Lifting hook灯泡:Light bulb轻型吊杆:Light derrick空舱:Light hold空载吃水:Light load waterline减轻孔:Lightening hole舭部污水道顶板:Limbers board联动把手:Linkage handle液体散货船:Liquid bulk cargo carrier液体化学品船:Liquid chemical tanker液化天然气船:Liquefied natural gas carrier液化石油气船:Liquefied petroleum gas carrier吊重实验:Load test载重线:Loadline局部强度:Local strength立柜:Locker纵骨:Longitudinal纵舱壁:Longitudinal bulkhead总纵弯曲:Longitudinal bending总纵强度:Longitudinally framed system扩音器:Loud speaker下甲板:Lower deck下底墩:Lower stool加滑油:Lubricate变幅绞车:Luffing winchM车(光车):Machine主肋骨:Main frame主机:Main engine主桅:Main mast磁粉探伤:Magnetic particle testing 人孔:Manhole人孔盖:Manhole cover边板:Margin plate桅:Mast桅杆天线:Mast antenna桅座:Mast clutch 桅灯:Masthead light桅屋:Mast house床垫:Mattress最大宽度:Maximum breadth商船:Merchant ship餐桌:Mess table用金属扣合法修理:Metalock 中剖面图:Mid-ship section plan 铣:Mill混合器:Mixer型宽:Molded breadth感谢您的观看型深:Molded depth船舶型尺度:Molded dimension系泊实验和航行实验:Mooring and sea trial 系缆孔:Mooring hole系缆桩:Mooring post滚柱导缆器:Multi-angle fairlead多用途船:Multi-purpose carrier菇形通风筒:Mushroom ventilator N航区:Navigation area驾驶台:Navigation bridge 航海甲板:Navigation deck 航行灯:Navigation light航海雷达:Navigation radar 氮瓶:Nitrogen bottle失压实验:No-voltage test止回阀:Non-return valve螺旋桨整流帽:Nose cone切口:Notch喷嘴:Nozzle螺母:NutO桨:Oar斜式双柱系缆桩:Oblique bitts 驾驶员:Officer加油点:Oil filler进油管:Oil intake pipe油船:Oil tanker栅栏杆:Open rail开口:Opening矿砂船:Ore carrier舷外机:Outboard motor外首帆:Outer jib舾装:Outfitting检查:Overhaul舷外吊杆叉头:Outrigger P桨:Paddle油漆:Paint强胸结构、抗拍击结构:Panting arrangement 强胸横梁、抗拍击横梁:Panting beam隔板:Partition人行通道:Passage堵漏板:Patch board堵漏螺杆:Patch bolt补:Patch up支柱:Pillar销子:Pin螺距:Pitch活塞:Piston活塞杆:Piston rod刨:Plane平面舱壁:Plane bulkhead平板:Plate平板龙骨:Plate keel平台:Platform抛光:Polish箱形舱盖:Pontoon hatch cover艉楼:Poop左舷:Port左舷灯:Port light手提泡沫灭火器:Portable foam fire extinguisher龙门架式起货机:Portal frame crane限位器:Position stop压力表:Pressure gauge探照灯:Project探照灯吊杆:Project davit螺旋桨:Propeller桨穴:Propeller cave螺旋桨柱:Propeller post艉轴架:Propeller shaft bracket食物储藏室:Provision stores软垫:Pudding(护舷)碰垫:Pudding fender泵:Pump泵房:Pump roomPVC泡沫塑料:PVC foamed plasticQ舵柄:Quadrant居住区:Quarter舱内侧梁柱:Quarter pillar淬火:Quench报价:Quote R雷达:Radar雷达指示器:Radar indicator 旋臂吊艇架:Radial davit 筏:Raft栏杆、轨道:Rail前倾型船艏:Raked bow平放:Range 后桅灯,距离灯:Range light 跳板,滑道:Ramp后门:Rear door校正:Rectify减速箱:Reduction gear box (绞车)主卷筒:Reeling drum 重新装:Refit感谢您的观看冷藏室:Refrigerated room注册港:Registered port浇铅:Remetal换新:Renew填(填料):Repack内底横骨:Reverse frame逆功率实验:Reverse power test重焊:Reweld重绕:Rewind锁具,钻井平台:Rig直角舷边:Right angle gunwale转出:Roll out滚轮,滚柱:Roller滚柱轴承:Roller bearing滚轮导缆器:Roller fairlead缆绳:Rope回转底盘(克令吊):Rotating chassis 回转平台:Rotating platform回转式螺旋推进器:Rotary screw propeller滚装船:Ro-Ro ship排(电线):Route橡胶,橡皮:Rubber橡胶填料、橡皮条:Rubber packing舵:Rudder舵承:Rudder bearing舵叶:Rudder blade操舵杆:Rudder control rod舵销孔:rudder pintle舵板:Rudder plate舵柱:Rudder post舵轴:Rudder spindle舵杆:Rudder stock舵杆围阱:Rudder trunk铁锈:RustS安全阀:Safety valve沙箱:Sand box清洁用水柜:Sanitary tank帆:Sail托盘:Salver (tray)舢板:Sampan结垢:Scaled铲刮:Scrape轻型舱壁:Screen bulkhead螺旋桨、螺钉、螺杆:Screw螺旋式制链器:Screw compressor螺旋桨:Screw propeller拉毛:Scuff排水孔:Scupper舷窗:Scuttle密封:Seal密封圈:Seal ring边接缝:Seam探照灯:Search light咬住:Seize半平衡舵:Semi-balanced rudder半潜式钻井平台:Semi-submersible rilling platform 伺服系统:Servo system污水:Sewage轴毂:Shaft bossing连轴节:Shaft coupling轴隧:Shaft tunnel (passage)滑车轮、槽轮:Sheave舷弧:Sheer舷顶列板:Sheer strake帆脚索:Sheet船壳:Shell船壳外板:Shell plate船厂:Shipyard艉柱踵材:Shoe piece半梁:Short beam桅牵索:Shroud 舷边:Side舷侧肋骨:Side frame旁内龙骨:Side keelson舷灯:Side light舷侧外板:Side plate舷窗:Side scuttle甲板边板:Side stringer签字:Sign信号钟:Signal bell消音器:Silencer单底:Single bottom单柱式导缆钳:Single cylindrical roller chock平板舵:Single plate rudder图纸:Sketch光洁:Skim up天窗:Skylight衬套:Sleeve摆动稳索:Slewing guy回转液压马达:Slewing hydraulic motor斜坡板:Slope board顶边舱斜底板:Sloping bottom plate of topside tank底边舱斜顶板:Sloping top plate of bottom side tank沙发:Sofa软梯:Soft ladder焊(锡焊):Solder悬挂舵:Spade rudder杆,心轴:Spindle备件:Spare parts测速仪:Speedometer舷伸甲板:Sponson deck喷漆:Spray喷枪:Spray gun稳性:Stability扶梯:Stairway支柱:Stanchion感谢您的观看准备:Stand-by右舷:Starboard定期的,规定的:Stated钢结构:Steel structure舵机:Steering gear方向盘、舵轮:Steering wheel 船首:Stem艏锚:Stem anchor船艉:Stern艉锚:Stern anchor艉跳板:Stern ramp尾轴:Stern shaft尾轴管:Stern shaft tube艉封板:Stern transom plate加强筋:Stiffener蓄电池:Storage battery备用柜:Store box船底板:Strake强力甲板:Strengthen deck填料:Stuffing夏季载重线:Summer loadline上层建筑:Superstructure提供:Supply牙筋板:Swage plate止荡板、防波板:Swash plate配电板:Switch board转环(锚链):Swivel link T尾翼式锚:Tail-stabilizer anchor 取(测取):Take货油舱盖:Tank lid货舱阀(油船):Tank valve油船:TankerT型材:T-bar工艺员:Technician回火:Temper实验:Test舵柄:Tiller木材运输船:Timber carrier节流阀:Throttle valve侧推器:Thruster推力轴承:Thruster bearing上紧:Tighten公差:Tolerance工具箱:Tool box顶边舱:Top side tank千斤索:Topping lift (line)千斤滑车:Topping lift block顶边舱:Topside tank扭转:Torsion补漆:Touch up随边(螺旋桨叶):Trailing edge转、驳:Transfer横舱壁:Transverse bulkhead处理:Treat修整(毛刺等):Trim拖轮:Tug轴隧:Tunnel可转动桨叶:Turnable blade回转指示器:Turning indicator甲板间舱:Tweendeck cargo space双桨:Tween screwU超声仪探测:Ultrasonic instrument U形水舱:U sharp tank万向导缆器:Universal fairlead拧开:Unscrew放松:Untighten上甲板:Upper deck V真空实验:Vacuum test蒸汽:Vapor蒸汽管子:Vapor pipe阀:V alve阀座:Valve seat可变螺距螺旋桨:Variable pitch screw propeller 浸漆,上凡立水:Varnish开V型槽:Vee out通风筒:V entilator通风管道:Ventilator duct风路:Ventilation trunk证实:Verify垂直型船首:V ertical bow竖桁:Vertical girder垂直传动轴:V ertical shaft反光镜:Viewfinder旋转视窗:View screen W腰带:Waist band系缆滚筒:Warping drum 系缆绞车:Warping winch 战舰、军舰:Warship洗脸盆:Wash basin 开水锅炉:Water boiler 抽水马桶:Water closet 水过滤器:Water filter 水密:Watertight水密门:Watertight door感谢您的观看感谢你的观看感谢您的观看水密肋板:Watertight floor 水密填料:Watertight stuffing 磨损:Wear露天甲板:Weather deck 腹板:Web强横梁:Web beam 强肋骨:Web frame 焊:Weld焊缝:Welding seam 车轮:Wheel 汽笛:Whistle 绞车:Winch 绕:Wind锚机:Windlass起锚机卷筒:Windlass gipsy 窗帘:Window certain 挡风玻璃:Windshield 翅龙骨:Wing-keel 两翼甲板:Wing deck 边舱:Wing tank 钢索:Wire rope滑车钢丝绳:Wire rope fall 无线电天线:Wireless antenna 退出,拔出:Withdraw 木结构:Wooden structure 蜗杆:Worm蜗轮:Worm wheelY游艇:Yacht 船厂:Yard第二节:轮机部分A驱动器:Adapter活动扳手:Adjustable wrench 调整环:Adjusting ring调节螺钉:Adjusting screw 调节阀:Adjusting valve 调节垫圈:Adjusting washer空气调节螺钉:Air adjust screw 进气阀:Air admission valve 空气瓶:Air bottle进气冷却器:Air charge cooler 充气阀:Air charge valve 空气滤清器:Air cleaner 空气压缩机:Air compressor 空气冷却器:Air cooler空气冷却器壳体:Air cooler frame 空调:Air conditioner空气分配器:Air distributor 排气阀:Air escape valve 空气过滤器:Air filter 空气叶轮:Air impeller 进气阀:Air induction valve 进气阀:Air inlet valve 空气马达:Air motor 排气阀:Air outlet valve 空气管:Air pipe 空气活塞:Air piston 空气泵:Air pump空气净化器:Air purifier空气减压阀:Air reducing valve 空调制冷装置:Air refrigerated plant 放气阀:Air release valve 气封:Air seal空气弹簧:Air spring空气启动装置:Air starting device 空气开关:Air switch 气密门:Air tight door 交流发电机:Alternator 铝块保护:Aluminum anode锚链设备:Anchor and chain gear 锚链:Anchor chain锚链拉力器:Anchor chain meter 角杆:Angle lever抗蚀牛油:Anti-corrosive grease多用途喷嘴接头:Applicator for all purpose nozzle 螺母套:Assembling nut 连接螺栓:Attachment bolt 自动报警:Automatic alarm自动调节器:Automatic regulator 自动制动阀:Automatic stop valve 自动开关:Automatic switch 轴箱:Axle box 轴套:Axle bush 轴键:Axle key 轴套:Axle sleeveB平衡衬套:Balance bush 平衡舵:Balance rudder 平衡阀:Balance valve 飞轮:Balance wheel 滚珠轴承:Ball bearing卡圈:Band带扣螺丝管夹:Banding screw buckle 底座:Base轴承套:Bearing bush 轴承盖:Bearing cover轴瓦:Bearing shell轴承压盖:Bearing stopper下轴承:Bearing, lower part上轴承:Bearing, upper part泄放螺丝:Bleeder screw盲法兰:Blind flange封闭接头:Blind joint螺帽:Blind nut截断阀:Block valve放气阀:Blow-off pipe本体:Body本体填料:Body packing锅炉附件:Boiler accessories锅炉报警:Boiler alarm锅炉座:Boiler bedding锅炉排污管:Boiler blow-out pipeline 锅炉给水泵:Boiler feed pump锅炉附件:Boiler fittings锅炉平台:Boiler flat锅炉炉膛:Boiler furnace螺栓:Bolt螺栓拉力测量仪:Bolt tension machine 管帽:Bonnet轮毂:Boss底盖:Bottom cover底部法兰:Bottom flange支架、三角板:Bracket制动器、刹车:Brake铜管帽:Brass cap十字型铜接:Brass cross黄铜弯头:Brass elbow黄铜六角外螺丝:Brass hexagon nipple黄铜针阀:Brass needle valve黄铜异径套管:Brass reducing socket黄铜短外螺丝:Brass short nipple安全螺栓:Breaker bolt通气阀:Breather valve海水管:Brine pipe缓冲器:Buffer毛刺:Burr安全板:Bursting plate布司(轴承):Bush滚轮导套衬套:Bushing for roller guide蝶形螺栓、元宝螺栓:Butterfly bolt蝶形螺母:Butterfly nut蝶阀:Butterfly valveC室内温度器:Cabin thermometer电缆:Cable电缆衬套:Cable bushing电缆剪:Cable cutter凸轮:Cam凸轮间隙:Cam clearance凸轮驱动:Cam driven凸轮滚柱:Cam roller凸轮轴:Cam shaft盖头四角颈螺栓:Cap head square neck bolt二氧化碳灭火器:Carbon dioxide fire extinguisher 石棉填料:Carbon-cotton packing油石:Carborundum oil stone箱子:Case铸造合金:Cast alloy铸造黄铜:Cast brass铸造青铜:Cast bronze铸铜合金:Cast copper alloy铸锭:Cast ingot铸铁:Cast iron铸管:Cast pipe铸钢:Cast steel中心轴:Centering shaft链条葫芦:Chain block链传动及导杆:Chain drive and guide bar链环:Chain link链传动轮:Chain wheel增压空气管:Charge air pipe挡板:Check plate止动销:Check pin固定螺丝:Check screw 止回阀:Check valve止回阀本体:Check valve body止回阀壳体:Check valve case夹具、马脚:Clamp夹紧螺丝:Clamp screw夹具垫圈:Clamp washer夹臂:Clamp arm夹件:Clamping piece清洁管:Cleaning pipe清洗阀:Cleaning valve离合器体:Clutch body离合器:Clutch coupling离合器盖:Clutch cover离合器齿轮:Clutch gear离合器接头:Clutch joint离合器销:Clutch pin离合器拉杆:Clutch rod离合器轴:Clutch shaft线圈:Coil海水/空气混合喷射泵:Combined brine/air ejector 可燃气体检测器:Combustible gas detector平衡阀:Compensation valve压缩环:Compression ring圆锥体:Cone锥孔:Conical bore锥形阀:Conical valve接头:Connection定距螺旋桨:Constant pitch propeller定速调速器:Constant speed governor控制手柄:Control handle操纵杆:Control lever感谢您的观看散热片、冷却片:Cooling fin淡水冷却泵:Cooling fresh water pump 冷却水套:Cooling jacket冷却油管路:Cooling oil pipe冷却系统:Cooling system冷却水接头:Cooling water connection 铜管:Copper pipe开口销:Cotter pin联轴节、考必令:Coupling连接法兰:Coupling flange盖板:Cover plate曲轴销轴瓦:Crank pin bearing shell 曲轴齿轮:Crank shaft gear曲轴臂:Crank web曲轴箱:Crankcase曲轴箱盖:Crankcase cover曲轴销轴承盖:Crankpin bearing cap 曲轴:Crankshaft曲轴拐挡表:Crankshaft distortion dial gauge十字槽螺钉:Cross machine screw十字头:Crosshead十字头轴承盖:Crosshead bearing cap十字头轴瓦:Crosshead bearing shell卡环:Crump band挡水环:Cut ring气缸:Cylinder气缸体:Cylinder block气缸体:Cylinder body气缸内径:Cylinder bore气缸盖:Cylinder cap气缸盖:Cylinder cover气缸盖:Cylinder head气缸盖螺栓:Cylinder head bolt气缸衬套:Cylinder liner气缸销:Cylinder pin圆柱形销:Cylinder ring pinD减震器:Damper止点:Dead center定位螺钉:Deflector除湿:Dehumidify去雾器:Demister深度测微器:Depth micrometer 测微器:Dial gauge隔膜:Diaphragm膜片阀:Diaphragm valve柴油:Diesel oil圆盘:Disc圆盘阀:Disc valve排出阀:Discharge valve定距套:Distance bushing定距盘:Distance disc定距环:Distance ring分配器壳体:Distributing cover 分配板:Distributing plate配电盘:Distributor disc配电板:Distributor plate进料环:Dosing ring双向推力轴承:Double direction thrust ball bearing双头开口扳手:Double open end wrench放残管:Drain tube放残阀:Drain valve传动链:Drive chain主动齿轮:Drive gear主动齿轮箱:Drive gear box驱动螺杆:Drive screw从动齿轮:Driven gear从动轴:Driven shaft传动键:Driving key压销:Driving pin传动轴:Driving shaft传动轮:Driving wheel防尘罩:Dust cap吸尘器:Dust catcher防尘罩:Dust cover防尘密封:Dust seal除尘器:Dust removerE偏心轮:Eccentric喷射嘴:Ejector nozzle喷射管:Ejector pipe弹性离合器:Elastic clutch弯头:Elbow弯头接头:Elbow joint弯管:Elbow pipe电弧:Electric arc电刷:Electrical brush电子式调速器:Electrical governor电工用螺丝起子:Electrician screwdriver 滤器滤心:Element for filter砂布:Emery cloth端盖:End cover端盖:End cap 端盖:End housing尾销:End pin端板:End plate端环:End ring机座:Engine base机座:Engine bed机架安全阀:Engine frame safety valve 助燃剂:Engine igniter功率指示器:Engine indicator爆发压力示功器:Engine peak indicator 蒸发器:Evaporator废气锅炉:Exhaust boiler排气凸轮:Exhaust cam排气管:Exhaust pipe排气阀:Exhaust valve感谢您的观看插销:Extension bolt受拉弹簧:Extension spring吊环螺栓:Eye boltF鼓风机:Fan通风机:Fan blower风室:Fan house风轮:Fan wheel给水管系:Feed piping给水阀:Feed valve塞尺:Feeler过滤器:Filter滤筒:Filter bowl滤筒:Filter drum滤网:Filter net散热片:Fin消防皮龙箱:Fire hose box消防皮龙喷嘴:Fire hose nozzle 一级齿轮:First stage gear连接法兰:Fitting flange垫板:Fitting plate固定螺钉:Fixing bolt定位销:Fixing pin固定板:Fixing plate法兰:Flange法兰螺母:Flange nut平键:Flat key柔性管:Flexible hose浮子:Float浮子开关:Float switch浮阀:Float valve流量计:Flow meter流量开关:Flow switch飞轮:Fly wheel摩擦块:Friction block前盖:Front cover高压油管:Fuel oil injection pipe高压油泵:Fuel oil injection pump支点:FulcrumG进气口:Gas inlet port排气口:Gas outlet密封垫:Gasket汽油:Gasoline (petrol)表:Gauge齿轮:Gear齿轮离合器:Gear clutch齿轮泵:Gear pump齿轮组:Gear train压盖:Gland填料函:Gland box填料压盖:Gland cover填料函:Gland housing密封填料:Gland packing密封填料:Gland seal调速器:Governor调速器本体:Governor body调速箱:Governor box box调速器从动齿轮:Governor driven gear调速器传动齿轮:Governor driving gear调速手柄:Governor handle调速杆:Governor lever调速杆:Governor rod调速轴:Governor shaft格栅:Grate重力盘:Gravity disk牛油枪:Grease gun牛油咀:Grease nipple牛油:Grease oil槽:Groove十字头销:Gudgeon pin导板:Guide导向叶片:Guide blade导块:Guide block导套:Guide bushing导向凸轮:Guide camH手柄:Handle止动杆:Handle stopper手轮:Hand wheel前盖:Head cover冷凝气热交换器:Heat exchanger condenser蒸发器:Heat exchanger evaporator强力油泵:Heavy duty pump oiler六角衬套:Hexagon bushing六角法兰螺帽:Hexagon flange nut内六角盖头螺钉:Hexagon socket head cap screw 铰链:Hinge 铰链接头:Hinge joint铰链销:Hinge pin定位环:Holder ring软管接头:Hose nipple软管:Hose line液压调速器:Hydraulic governor液压千斤顶:Hydraulic jack液压泵:Hydraulic pump水(压密)封:Hydraulic seal轻油用比重计:Hydrometers for light oil感谢您的观看感谢你的观看感谢您的观看I发火装置:Ignition叶轮:Impeller叶轮箱:Impeller casing叶轮键:Impeller key叶轮螺母:Impeller nut叶轮泵:Impeller pump叶轮轴:Impeller shaft指示器:Indicator指示器凸轮:Indicator cam 示功阀:Indicator valve叶轮:Inducer导风轮键:Inducer key进口弯头:Inlet elbow进口管:Inlet pipe进口阀:Inlet valve内套:Inner case内链环:Inner link内环:Inner ring主动轴:Input shaft观察镜:Inspection glass绝缘接头:Insulating joint绝缘板:Insulating disc绝缘端盖:Insulation cover中间轴承:Intermediate bearing中间轴端盖:Intermediate shaft cover铁块:Iron blockJ气缸套冷却水:Jacket cooling water 气缸套冷却水进口:Jacket water inlet 接头:Joint接头螺母:Joint nut连接件:Joint piece连接座:Joint seat连接块:Junction block接线盒:Junction box连接螺栓:Junction bolt连接管:Junction pipe连接板:Junction plate K煤油:Kerosene 键:Key键槽:Key slot旋钮:Knob止动销:Knock L润滑油:L. O. (lubricate oil)滑油喷嘴:L.O.nozzle滑油泵本体:L.O.pump body滑油泵端盖:L.O.pump cover滑油泵从动齿轮:L.O.pump driven gear 滑油泵主动齿轮:L.O.pump driving gear 挡油板:L.O.cut plate刮油环薄片:Lamella for scraper ring 杆:Lever盖:Lid救生艇磁罗经:Lifeboat compass吊环:Lifting bolt吊环:Lifting eye支撑轴:Lifting stud衬套:Liner阀杆导套衬套:Liner for spindle guide连接环:Link活动连接:Link joint连杆销:Link pin连杆:Link rod锁:Lock固定销:Lock pin锁紧垫圈:Lock washer止动爪:Locking claw锁紧环:Locking ring锁紧丝:Locking wire防松螺丝:Locknut润滑油泵:Lub oil pump润滑油管:Lubrication pipe主油器:LubricatorM机床:Machine tool三角锉刀:Machinist file主轴承:Main bearing主轴瓦:Main bearing shell主轴承双头螺栓:Main bearing stud 主传动齿轮:Main driving gear 主弹簧:Main spring外螺十字接头:Male cross 外螺纹弯头:Male elbow 人孔盖:Manhole cover总管:Manifold压力计:Manometer。
全自动订书机英文说明书

CB5000 Vehicular Baler Operation InstructionSafety Tips1、Please read this specification carefully before operation.2、Lowered cab should cover door closed when stop the machine, meanwhile steel grasp machine is placed on the bracket, and cut off all the power.3、Equipment shall not be maintained in the process of work. Also the worker should not stand on the fuselage and should not hand foot and other parts of body must not be placed in the door between the cover and the box body.4、If you need in packaging case for cleaning or maintenance, the device should be in a state of downtime, and the door covers is fixed in the fully open position, cut off the equipment power rear can be carried out. When piping system leak or failure occurs, please stop immediately, to run after trouble shooting. Equipment of diseased or overload operation is prohibited5、Remove the hydraulic valve replacement seals and check the pipeline, the pressure in the system, please state, avoid when remove the high pressure oil made hydraulic valve and pipeline damage in the body.6、The hydraulic nonprofessionals should not adjust the hydraulic system of hydraulic valve, avoid the equipment cannot run normally or damage to the hydraulic valves .7、When equipment running , it shall not live without operator in front of he operation stage .8、According to using frequency , you should often check the oil cylinder installation area and other connection key parts , may not have a screw loose or pin off accident hidden trouble.9、When it in work state, you must raise cab.10、If you can’t solve the problems, lease contact our nearest office, also can find our after-sales service department directly .Catalogue1. Usage and features------------------------------------------------------------ 42. General structure and working principle ---------------------------------- 43. Mainly technical specification------------------------------------------------ 64. General breakdown and solution ------------------------------------------- 75. Maintenance and serving ----------------------------------------------------- 86. Overall drawing ------------------------------------------------------------------ 91. Usage and features1) UsageThe equipment is mainly for baling low-carbon light and life scrap steel; scrap cars; light metal structural parts with steel material to bales for furnace. It is an ideal machine for steel factories; non-ferrous metal smelting industry; precision casting industry and raw materials factories.2)Features1、This machine with big volume; large open areas; amount of feeding capacity; high efficiency. It is very convenient for processing large shape materials, especially in gather feeding and capture scrap.2、Hydromechatronics control, easy to learning, and intuitive operation and convenient.3、PLC control, high reliability and easy for maintenance.4、Hydraulic drive; working smooth; high efficiency.2. General structure and working principle1). General structureMainly composed of mechanical systems (main machine), power systems, hydraulic systems. (see schematic layout)〈1〉、Mechanical systemBe composed of press box; hydraulic press cylinder and other assistant component. (see main machine structure diagram)1.Press boxBe made up of material body; level 1 lid; level 2 lid; main cylinder components. Material body is composed of pedestal, level 1 lid, level 2 lid, there are ware plates on it. Part of ware plates are import DILLINDUR which made by Germany. Compressed scrap material by wrapped work of level 1 lid and lever 2 lid so that increase density. After that, two main press cylinder will continues to compress scraps into blocks.2. Hydraulic cylinder is made up of main press cylinder; level 1 lid cylinder; lever 2 lid cylinder. Mainly turn hydraulic power into mechanical power, the cylinder mainly drive all parts of action, in order to complete compression and pressed actions.(1) Main press cylinders, totally two sets which installed on the bottom of press box. Piston rod connection with head of press plates to compress scraps inside by advance and forward of main press cylinders.(2). Level 1 lid cylinders, totally 3 sets which installed on the side of press box to compress scraps by piston rod advance action when scraps to be packaged.(3). Level 2 lid cylinder, totally 3 sets which installed on the other side of press box to complete open and close action for press lid by piston rod advance action and back action.The above are double acting single piston rod structure, and the liner with piston and seals, the cylinder body to form two oil chambers and small cavity. When the high pressure oil of the front chamber or the rear chamber, the push rod and piston within the cylinder for reciprocating liner motion, thereby driving the workpiece movements. Cylinder brim with guide sleeve, the above is also equipped with a ring, as the piston rod supporting, guiding and sealing.<2> The power system is composed of main engine circuit, engine start/stop control circuit and the PLC input and output control circuit, external line,pressing stroke control device, external stroke control system etc..<3> The hydraulic system, is composed of a hydraulic oil tank, hydraulic pump, valve, hydraulic station pipeline system, is the host of the central control system.<4> Pipeline system is connected to the host (Mechanical Systems) and between the hydraulic system, hydraulic oil for transfer.2). working principle and attention(1) working principle and processThe two main oil cylinders backhaul in place, the first and second level pressing door r\ opening, the operator use the grab machine to package materials into the pressing box in the cab. The first level pressing door close, the second level pressing door close , forming clips action, two main pressing oil cylinder forward, the material to the middle pressed into blocks. Then return in place, the first and second level pressing door open, the operator remove the bale by the grab, equipment repeat the above action until the end of the work.(2) attention1.The scrap’s density and rigidity greatly is not allowed to add too much, otherwise it will make the first and second pressing door is not in place, thus affecting the machine, or even destroy the machine.2.Mixed with pressure vessel, flammable items are not allowed in the waste3.This machine belongs to the hydraulic equipment, prolong the service life of hydraulic components, please ensure the cleanliness of the system.Technical ParametersGeneral failures and exclusionDuring shearing time,If abnormal situation be founded,you should stop working,After waiting for troubleshooting to continue shear, in use process may be the cause of theProblems in the practical work, may be caused by many factors, so in the event of a failure, should be carefully observed and carefully analyze the causes, and then start out.MaintenanceThe correct use of machinery and equipment, seriously implement the system of maintenance and strictly abide by rules of safe operation, is extending the service life of the machine, improve production efficiency and ensure the necessary conditions for production. Therefore, recommend that users establish a maintenance and safe operating procedures, operating personnel in addition to the machine should be familiar with the structure and operating procedures, also must pay attention to the following points:1.The oil in oil tank should pass strict filtering, and often should keep enough oil.2.Once every half a year should clean and replace the oil , but the first oil change time should be no more than three months, the oil can pass strict filtered using it again.3.Lubricating oil lubrication each machine should be according to the requirements listed. Before work and after work every day need to inspect again to check whether the machine is normal.4.Without learning, don't understand the machine structure, performance and operatingrules cannot do STH without authorization to start the machine.5.When the machine appear serious leak or abnormal phenomena occurred during work, you should immediately stop, analysis of causes and troubleshooting, shall not be forced to run .6.Machine in the process of operation or packaging, shall not carry out repair or touch themoving parts by hand , it is forbidden to use hands or feet press materials in feed box. 7.To adjust the valve, pressure gauge, must be conducted by experienced technical workers, in case of malfunctioning of a pressure gauge, should immediately check the repair or replacement of the new table.8.Sealing element should be changed regularly, if any, should be replaced immediately.。
工写斯特 工位中心 产品说明书
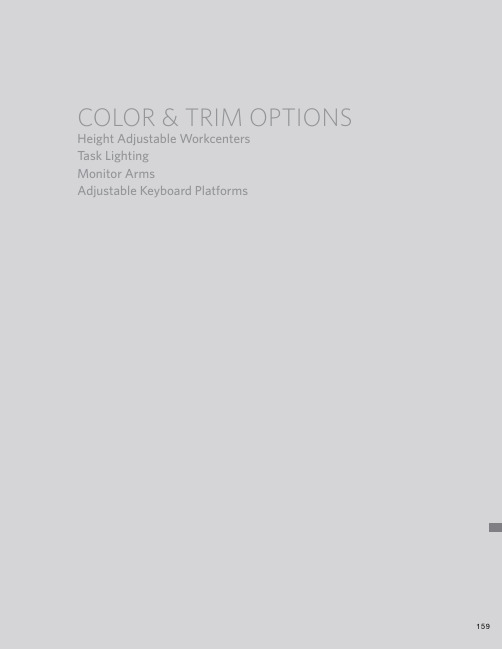
color & trIm oPtIonsHeight Adjustable WorkcentersT ask LightingMonitor ArmsAdjustable Keyboard Platforms159159Color & Trim Options160Silhouette Edge ProfilesErgoS1BlockS2CraftS3Height Adjustable Workcenters: Laminate ColorsClassic Collection–Workrite Sierra HX, HXL and ProliftixFolkstone GraySG241Opti GraySG213BlackSE101Ice FishinWF181White SpectrumAW785Gateway to the FutureAV100Cavalcade SouthAT650Tropical GetawayAV110Summer Heat WaveAO360IL Palio PapelAV981Coriander FiberAT981Leave LikatreWP120Looks LikatreWP110Appears LikatreWP115Seems LikatreWP125Hardrock MapleWM791PearwoodWX031Shaker CherryWC521Oiled CherryWC421Jewel MahoganyWY351Black AshwoodSZ101Silhouette Collection–Workrite Sierra HX & HXLHardrock Maplewith brown coreWM791Appears Likatrewith brown coreWP115Seems Likatrewith brown coreWP125Oiled Cherrywith brown coreWC421Folkstone Graywith black coreSG241White Spectrumwith black coreAW785Looks Likatrewith black coreWP110Blackwith black coreSE101All Silhouette worksurfaces are made of GREENGUARD® certified material.Color & Trim Options161 800.959.9675Note: Due to printing limitations, colors are not guaranteed to be accurately reproduced. For best results, refer to actual finish samples available from your Workrite sales representativeor by calling 1.800.959.9675Lead Times:Classic Collection: 10 working days for quantity 20 or less.Designer Collection: 20 working days for quantity 10 or less.Silhouette Collection: 10 working days for quantity 10 or less.Height Adjustable Workcenters: Metal Finishes & Trim OptionsMetal FinishesSierra HX and HXLProliftixSierra Silver SCharcoal CEdge Treatments for Classic & Designer LaminatesStandardWedgeRippleBlack 07Height Adjustable Workcenters: Laminate Colors (cont.)Designer Collection–Workrite Sierra HX and HXLSpa White S740T Almond ST655Putty Gray SG209Taupe ST606Sage SV720Cubicle Papel AG561Gray Santos AG291Negotiating in Geneva PFA60Beige Crepe AT251Opti Gray Crepe AG341Vanilla Fiber AW871Wheat Fiber AT991Oatmeal Fiber AT101Thyme Fiber AV721Pepper Fiber AG581Manila Linen AT231Gridlock in LA PFA51Travlin Light AT680Gold Pannin AT710Passin Through AV250Blue Sandstone AB191Caramel Crepe AT111Amber Raffia II AO355Brick by Brick AR350Anigre WX041Millwork Cherry WC431Honey Maple WM951Yorkshire Cherry WC411Moroccan Fresco AT121Sipping Seattle Java PFA48Color & Trim Options162Adjustable Keyboard PlatformsGlide 2All OthersPlatform Palm Support PlatformPalm SupportCharcoalCCool GrayGCharcoal11Cool Gray12BLight GrayG25Dove Gray26Monitor ArmsWillowWorkrite Poise, SwingArm & SteadyArmSilverSGraphiteBSilverSTask LightingDazz—SL Fino, Verano & AstraLincolnD1N1N2G1G2G4W1CSterlingS WSilverSNote: Due to printing limitations, colors arenot guaranteed to be accurately reproduced.For best results, refer to actual finish samplesavailable from your Workrite sales representativeor by calling 1.800.959.9675 Height Adjustable Workcenters: Sierra Modesty PanelFabric ColorSierra HX, HXL and ProliftixWhite01Pearl02Bronze03Dove04Linen05Pewter06Charcoal07。
ORTEC 142IH 前放说明书

Model 142IHPreamplifierOperating and Service ManualPrinted in U.S.A. ORTEC® Part No. 717590 1202Manual Revision CAdvanced Measurement Technology, Inc.a/k/a/ ORTEC®, a subsidiary of AMETEK®, Inc.WARRANTYORTEC* warrants that the items will be delivered free from defects in material or workmanship. ORTEC makes no other warranties, express or implied, and specifically NO WARRANTY OF MERCHANTABILITY OR FITNESS FOR A PARTICULAR PURPOSE.ORTEC’s exclusive liability is limited to repairing or replacing at ORTEC’s option, items found by ORTEC to be defective in workmanship or materials within one year from the date of delivery. ORTEC’s liability on any claim of any kind, including negligence, loss, or damages arising out of, connected with, or from the performance or breach thereof, or from the manufacture, sale, delivery, resale, repair, or use of any item or services covered by this agreement or purchase order, shall in no case exceed the price allocable to the item or service furnished or any part thereof that gives rise to the claim. In the event ORTEC fails to manufacture or deliver items called for in this agreement or purchase order, ORTEC’s exclusive liability and buyer’s exclusive remedy shall be release of the buyer from the obligation to pay the purchase price. In no event shall ORTEC be liable for special or consequential damages.Quality ControlBefore being approved for shipment, each ORTEC instrument must pass a stringent set of quality control tests designed to expose any flaws in materials or workmanship. Permanent records of these tests are maintained for use in warranty repair and as a source of statistical information for design improvements.Repair ServiceIf it becomes necessary to return this instrument for repair, it is essential that Customer Services be contacted in advance of its return so that a Return Authorization Number can be assigned to the unit. Also, ORTEC must be informed, either in writing, by telephone [(865) 482-4411] or by facsimile transmission [(865) 483-2133], of the nature of the fault of the instrument being returned and of the model, serial, and revision ("Rev" on rear panel) numbers. Failure to do so may cause unnecessary delays in getting the unit repaired. The ORTEC standard procedure requires that instruments returned for repair pass the same quality control tests that are used for new-production instruments. Instruments that are returned should be packed so that they will withstand normal transit handling and must be shipped PREPAID via Air Parcel Post or United Parcel Service to the designated ORTEC repair center. The address label and the package should include the Return Authorization Number assigned. Instruments being returned that are damaged in transit due to inadequate packing will be repaired at the sender's expense, and it will be the sender's responsibility to make claim with the shipper. Instruments not in warranty should follow the same procedure and ORTEC will provide a quotation.Damage in TransitShipments should be examined immediately upon receipt for evidence of external or concealed damage. The carrier making delivery should be notified immediately of any such damage, since the carrier is normally liable for damage in shipment. Packing materials, waybills, and other such documentation should be preserved in order to establish claims. After such notification to the carrier, please notify ORTEC of the circumstances so that assistance can be provided in making damage claims and in providing replacement equipment, if necessary.Copyright © 2002, Advanced Measurement Technology, Inc. All rights reserved.*ORTEC® is a registered trademark of Advanced Measurement Technology, Inc. All other trademarks used herein are the property of their respective owners.CONTENTS WARRANTY (ii)SAFETY INSTRUCTIONS AND SYMBOLS (iv)SAFETY WARNINGS AND CLEANING INSTRUCTIONS (v)1.DESCRIPTION (2)2. SPECIFICATIONS (3)2.1.PERFORMANCE (3)2.2.INPUTS (3)2.3.OUTPUTS (3)2.4.CONNECTORS (3)2.5.ELECTRICAL AND MECHANICAL (3)3.INSTALLATION (3)3.1.CONNECTION TO DETECTOR (3)3.2.CONNECTION TO AMPLIFIERS (4)3.3.INPUT POWER (4)3.4.TEST PULSE (4)3.5.DETECTOR BIAS INPUT (4)4.OPERATION (5)4.1.GENERAL (5)4.2.DETECTOR BIAS (6)4.3.ENERGY OUTPUT (6)4.4.TIMING OUTPUT (6)4.5.INPUT PROTECTION (6)5. MAINTENANCE INSTRUCTIONS (7)5.1.TESTING PERFORMANCE (7)5.2. FACTORY REPAIR (8)SAFETY INSTRUCTIONS AND SYMBOLSThis manual contains up to three levels of safety instructions that must be observed in order to avoid personal injury and/or damage to equipment or other property. These are:DANGER Indicates a hazard that could result in death or serious bodily harm if the safety instruction is not observed.WARNING Indicates a hazard that could result in bodily harm if the safety instruction is not observed. CAUTION Indicates a hazard that could result in property damage if the safety instruction is not observed.Please read all safety instructions carefully and make sure you understand them fully before attempting to use this product.In addition, the following symbol may appear on the product:ATTENTION – Refer to ManualDANGER – High VoltagePlease read all safety instructions carefully and make sure you understand them fully before attempting to use this product.DANGEROpening the cover of this instrument is likely to expose dangerous voltages. Disconnect the instrument from all voltage sources while it is being opened.WARNING Using this instrument in a manner not specified by the manufacturer may impair theprotection provided by the instrument.CAUTION To prevent moisture inside of the instrument during external cleaning, use only enough liquidto dampen the cloth or applicator.SAFETY WARNINGS AND CLEANING INSTRUCTIONSCleaning InstructionsTo clean the instrument exterior:!Unplug the instrument from the ac power supply.!Remove loose dust on the outside of the instrument with a lint-free cloth.!Remove remaining dirt with a lint-free cloth dampened in a general-purpose detergent and watersolution. Do not use abrasive cleaners.!Allow the instrument to dry completely before reconnecting it to the power source.NOTICEThis preamplifier has been shipped to you with its protection circuit connected into the input circuit. The protection circuit prevents destruction of the input FET due to large transients that may occur during abnormal operating conditions and serves as an impedance matching termination for the input cable from the detector. The presence of the protection circuit imposes only a slight resolution degradation. With the protection circuit installed, the preamplifier is immune to almost anything the operator is likely to do that causes transients at either the detector input or the bias input connector. The protection circuit does not protect the detector, but even if the detector breaks down as a result of overvoltage, the preamplifier will survive the resulting large transients if the protection circuit is in. This, of course, would not be true if the protection circuit were taken out, in which case the input FET is very susceptible to destruction by transients at the input connector on the preamplifier.If the input protection circuit must be taken out for any reason, this involves disconnecting one transistor lead and installing a jumper across a 51S series resistor. The Warranty of the 142IH is void if the protection circuit is taken out unless all of the following precautions are taken:1. COMPLETELY DISCHARGE the bias circuitry before connecting a low impedance, a cable, or any other capacitive device to the Input connector on the preamplifier.2. Discharge the bias circuitry before making any connections to the Input connector and before disconnecting the preamplifier from the detector.3. To discharge the bias circuitry, connect a low impedance (shorting cap is preferred) for at least one minute across the Bias connector on the preamplifier.The input circuit will be destroyed if the Input connector is shorted while the bias components are charged, and the quality of these capacitors is such that they will retain a charge through a long period of time. Such a short could result from connecting a detector, cable, or other capacitive device such as a voltmeter probe. A short circuit, either short term or continuous, will cause the applied bias (stored on C2) to be coupled directly to the input transistor, causing a catastrophic breakdown.If a variable bias supply is used, merely turn down the voltage control to zero and leave it for at least one minute. This will suffice since the bias circuitry can discharge itself through the output of the bias supply.Sometimes it is necessary to simply disconnect the bias supply, such as is the case when using batteries for bias. This situation leaves no discharge path, so a path must be provided by placing a short circuit or low impedance across the Bias connector on the rear panel of the preamplifier. DO NOT SHORT THE INPUT CONNECTOR on the front panel of the instrument unless the input circuitry has been completely discharged.ORTEC 142IH PREAMPLIFIER1. DESCRIPTIONThe ORTEC 142IH charge-sensitive Preamplifier is designed as a minimum-cost general-purpose unit. It is intended for use in systems where the detector, rather that the preamplifier, is the major noise source in the system or in systems where the ultimate in performance is not required and the cost of the system must be minimized. It can be used with semiconductor detectors, proportional counters, scintillation counters, ionization chambers, etc.A bias circuit is included to accept the operating voltage required by the detector and to furnish this bias out to the detector through the signal input cable. The bias input circuit in the 142IH Preamplifier includes a 100-M S load resistor, R4, and any detector leakage current will have to pass through this resistance as well as through R1, 1.5 M S, in series. A considerable voltage drop will be expected across this 100-M S resistor for a detector with high leakage, and resistor R3 (shipped as an accessory) can be installed in parallel with R4; R3 has a value of only 10 M S.An input protection circuit is built into the preamplifier. It protects the input FET from any large transient voltages that would otherwise damage the transistor. This is discussed in the Notice inside the front cover. The protection circuit also provides a damping resistance on the input so that relatively long cable lengths can be used between the detector and the preamplifier without disrupting the system stability.A Test Pulse connector with built-in charge terminator is provided for use with a pulse generator such as the ORTEC 419, 448, or 480 to simulate the signal from the detector. This allows a check of the system performance while an experiment is in progress.The 142IH will accommodate up to ±3000 V for the detector. The output pulse polarity is the same as the applied bias polarity. The 142IH Preamplifier output can be connected to a shaping main amplifier such as the ORTEC 451, 485, or 572 for energy spectroscopy or to a timing filter amplifier such as the ORTEC 474 for time spectroscopy. Output connectors are provided so that both types of analysis can be operated simultaneously.If it is necessary to open the case for any reason, observe the following instructions carefully to prevent serious injury to yourself and/or damage to the instrument.Observe the steps that are included in the Notice at the front of the manual to discharge the high voltage and prevent shock; the voltage levels that can be used are lethal and the capacitors are very high quality so they retain a charge much longer than normally expected.Do not touch the high-megohm resistors, R4 and R7, with your bare fingers; the presence of skin oil can reduce the resistance of the component and alter operating characteristics. See Section 4 for instructions that involve the protection circuit.2. SPECIFICATIONS2.1. PERFORMANCENOISE Increases with increasing input capacitance. Typical performance values, based on silicon equivalent of , = 3.6 eV at J = 2µs, are 1.9 keV at 0 pF; these degrade to 4.6 keV at 100 pF and to 35 keV at 1000 pF.RISETIME Based on a +0.5 V signal through either output into a 93S circuit and measured from 10% to 90% of peak amplitude; 20 ns at 0 pF and 50 ns at 100 pF.SENSITIVITY Nominal, measured through either output, 45 mV/MeV Si.ENERGY RANGE 0 to 100 MeV Si.ENERGY RATE 3 X 105 MeV/s.DYNAMIC INPUT CAPACITANCE 10,000 pF.INTEGRAL NONLINEARITY #0.05% for 0 to ±7 V open circuit, or ±3.5 V terminated in 93S. TEMPERATURE INSTABILITY #±100 ppm/°, 273 to 323 K (0 to 50°C).DETECTOR BIAS ISOLATION ±3000 V.OPEN LOOP GAIN $40,000.2.2. INPUTSINPUT Accepts input signal from a detector and extends operating bias to the detector.BIAS Accepts the bias voltage for the detector from a bias supply.TEST PULSE Accepts input voltage pulses from apulse generator for instrument and system check and calibration; Rin= 93S.2.3. OUTPUTSE AND T (for Energy and Timing) Two connectors furnish identical signals through two output paths; either or both outputs can be used as required, andthey are interchangeable; R= 93S through each connector and the output polarity is opposite from the input pulse polarity (output pulse polarity is the same as bias polarity).2.4. CONNECTORSINPUT and BIAS Type SHV.TEST PULSE, E, and T Type BNC.POWER CABLE 10-ft (3 m) captive power cable, ORTEC 121-C1; longer lengths available from ORTEC on special order.2.5. ELECTRICAL AND MECHANICAL POWER REQUIRED Furnished from NIM bin and power supply through any ORTEC main amplifier, or from an ORTEC 114 Preamplifier Power Supply; built-in captive cable is compatible with either source.+24 V, 30 mA; -24 V, 10 mA; +12 V, 15 mA;-12 V, 15 mA.DIMENSIONS 1.5 x 2.4 x 4.5 in., plus 10-ft cable (38 x 61 x 114 mm, plus 3 m cable).3. INSTALLATION3.1. CONNECTION TO DETECTORA direct connection with shielded cable should be made between the detector and the Input SHV connector on the preamplifier. The performance of the 142IH Preamplifier, like that of all similar instruments, is degraded as the capacity at the input increases. Therefore it is important that the length of coaxial cable used between the detector and the preamplifier be kept at the minimum length that is necessary. Also it is preferable to use 93S or 100S characteristic impedance cable rather than 75S or 50S cable because the capacity per foot is less for the cable with the higher characteristic impedance. Type RG-62/U cable is recommended; this has a 93S impedance and a capacitance of 13.5 pF/ft (40.1 pF/m). An AMP 51426-2 connector mates with the SHV connector on the 142I Preamplifier.Once the input cable installation has been made, the electronic noise performance of the 142IH can be predicted by calculating the cable capacity from the above information and adding the capacity expected from the detector.3.2. CONNECTION TO AMPLIFIERS Either or both the E and T outputs of the 142IH can be connected to an amplifier input for further processing. The output impedance through either of these connectors is 93S, providing a series termination for 93S cable so that long cable lengthscan be driven easily. Although the outputs are marked E (for Energy) and T (for Timing), the pulse characteristics are identical and the circuits are interchangeable.In an energy spectroscopy system, the preamplifier output is furnished into a shaping main amplifier. In a timing spectrometer system, the preamplifier output is furnished into a timing filter amplifier. With the dual output connections on the 142IH, the signals can be furnished simultaneously to both types of spectrometer systems. If either the E or T output connector is not being used, it should simply be left open-circuited (unterminated).3.3. INPUT POWERPower for the 142IH is supplied through the Power Cable that is captive through the rear panel of the unit. The normal connection for this power cable is included on the rear panel of the mating ORTEC amplifier, furnishing ±12 V and ±24 V from the bin and power supply in which the amplifier is operated. If this facility is not available or if such a connection would increase the loading on the bin and power supply beyond its maximum rated capacity, use an ORTEC 114 Preamplifier Power Supply to furnish the operating power requirements through the captive cable. The ORTEC 114 can furnish power for two ORTEC preamplifiers simultaneously if desired.3.4. TEST PULSEA voltage test pulse for energy calibration can be accepted through the Test Pulse input connector on the 142IH without the use of an external charge terminator. The test input of the preamplifier has an input impedance of 93S and its circuitry provides charge injection to the preamplifier input. The shape of this pulse should be a fast risetime (less than 40 ns) followed by a slow exponential decay back to the baseline (200 to 400 µs). While the test pulses are being furnished, connect either the detector (with bias applied) or the equivalent capacitance (without bias applied) to the Input connector on the 142IH.The Test Pulse input may be used in conjunction with the output of a pulser such as the ORTEC 419 or 448 to calibrate the preamplifier E output amplitude in terms of energy for calibration of a multichannel analyzer. However, due to stray coupling between the test circuit and other portions of the preamplifier circuitry, the transient performance of the preamplifier is best determined by connecting the actual detector signal through the Input connector instead of using the pulse generator output signals for this calibration.A voltage test pulse for transient response in the 142IH can be accepted through a charge terminator and into the Input connector on the 142IH. If external capacitance is to be included for these tests, an SHV tee can be inserted between the Input connector and the charge terminator, and this will then accommodate the test capacitances. Do not furnish any bias during these tests.3.5. DETECTOR BIAS INPUT Operating bias for the detector is supplied to the Bias connector on the 142IH and, through a filter and a large bias resistance, to the Input signal connector. From there it is furnished out through the signal input cable to the detector.Connect a cable from the detector bias supply (ORTEC 428 or 459 is typical) to the Bias connector on the 142IH. Type SHV connectors are used in this high-voltage circuit and the mating cable should be furnished with the bias supply module.Fig. 4.1. Simplified Block Diagram of the 142IH Preamplifier.4. OPERATION4.1. GENERALWhen the 142IH is installed according to the appropriate information in Section 3, it operates at all times when power is applied from the power source. The power is furnished from either the bin and power supply through a mating amplifier or from an ORTEC 114 Preamplifier Power Supply.Figure 4.1 is a simplified block diagram of the circuits in the 142IH Preamplifier. The completecircuit is shown in schematic 142IH-0201-S1,included at the back of the manual. When the protection circuit is in, the diode clamp to ground from a point in the input circuit will protect the input FET transistor from large transients, which are not a part of the input pulse information. When the protection circuit is out, there is no clamp to ground and a series input resistor is shorted by a jumper.4.2. DETECTOR BIASThe amount of bias required to operate the detector is specified in the data furnished with the detector. The bias that is accepted into the preamplifier through the SHV Bias connector is furnished through the load resistance (about 100 M S) to the Input SHV connector of the preamplifier. If the leakage current through the detector is appreciable, a notable voltage drop will occur across the series load resistance in the preamplifier, and this must be added to the detector requirement when the bias supply level is adjusted.With the protection circuit in, the input cable can be removed and reconnected without catastrophic damage to the preamplifier even with bias applied to the circuit; but the user must be very cautious to prevent touching the interior of the connector with anything other than a good insulator because potentially lethal high voltage can be present on the center pin of the Input connector under these conditions.With the protection circuit out, the operating bias level must be reduced gradually to zero before the detector is either connected to or disconnected from the Input connector on the 142IH.4.3. ENERGY OUTPUTThe charge-sensitive loop is essentially an operational amplifier with a capacitive feedback through a 1-pF capacitor. The conversion gain is approximately 45 mV/MeV (Si equivalent). A dc feedback is applied through a 100-M S resistor. The energy signal from the preamplifier is a fast risetime voltage step with an exponential return to the baseline with a time constant of 100 µs. The polarity of signals through the E output is inverted from the signal polarity at the output of the detector. When a positive bias polarity is used for the detector, its output pulses are negative and so the E output of the preamplifier is positive.The risetime of the charge-sensitive loop increases as the external capacity increases. External capacity is a function of the detector and its cabled connection to the preamplifier Input.4.4. TIMING OUTPUTThe T output connector provides an alternate path for the same output pulses that are furnished through the E output connector. The intent is to provide both connections for convenience when the 142IH Preamplifier is used to drive two systems -one for energy spectroscopy and the other for timing spectroscopy.4.5. INPUT PROTECTIONA provision is built into the preamplifier to protect the input FET from damage when there are high-voltage transients at its input. These transients can result from any one or more of many causes including detector breakdown, moisture condensation on the Input connector, short circuits or uncharged capacitance connected across the input while bias is applied, or disconnection of a bias voltage without first reducing it gradually to zero.The protection circuit is installed in the preamplifier when the unit is shipped from the factory. Although it offers protection to the FET, it also causes a slight degradation of the noise performance of the preamplifier and this increases as detector capacity increases.With the protection circuit in, the emitter lead of Q11 is attached to the junction between resistor R5 and the FET input. Transistor Q11 is connected as a diode, with both the base and the collector tied to ground through R8. This prevents the voltage in the input circuit from rising beyond the safe limit for the FET input. To take the protection circuit out, simply remove the emitter lead of Q11 from its circuit connection and install a wire jumper across R5.In order to take full advantage of the risetime capabilities of the 142IH for timing experiments (typical risetimes of 20 to 300 ns for input capacitances from 1 to 500 pF), the total cable length should be kept as short as possible. Due to vagaries in the system installation - ground loops, stray inductances, etc. - and since the maximum cable length is a factor in the input capacitance of the preamplifier, it is not possible to give absolute numbers. In general, it is desirable to keep the length of the input cable less than two feet so that the risetime performance with low capacity detectors will not be degraded significantly.5. MAINTENANCE INSTRUCTIONS5.1. TESTING PERFORMANCEAs ordinarily used in a counting or spectroscopy system, the preamplifier is one part of a series system involving the source of particles to be analyzed, the detector, the preamplifier, the main amplifier, and the pulse height analyzer. When the proper results are not being obtained and tests for proper performance of the preamplifier and the other components are indicated, it is important to realize that rapid and logical testing is possible only when the individual components are separated from the system. In proving the performance of the preamplifier, it should be removed from the system and be dealt with alone by providing known electrical signals through the input and testing for the proper output signals with an oscilloscope as specified in the following steps:1. Furnish a voltage pulse to the Test Pulse connector as outlined in Section 3.4. The polarity of the test pulse signal should agree with the expected signal input polarity from a detector.2. Using a calibrated pulser, the 142IH output, either E or T, should be inverted from the input and have a nominal scale factor of 45 mV per 1 MeV equivalent energy (Si).3. The noise contribution of the preamplifier may be verified by two basic methods. In either case, the normal capacity of the detector and associated cables should be replaced by a capacity of equal value placed across the Input connector, and no bias should be applied. This is necessary because the noise contribution of the preamplifier is dependent upon input capacity. The only meaningful statement of the noise level is one that relates to the spread caused by the noise in actual spectra. This can be measured and expressed in terms of the full width at half maximum (FWHM) of a monoenergetic signal after passing through the preamplifier and the main amplifier in the system.The noise performance referenced in the Specifications in Section 2 is stated in these terms, and verification methods will be described. If desired, the preamplifier can be tested with no external capacity on the Input connector, in which case the noise width should be approximately that shown for zero external capacity. In any case, the Input connector and capacitors, when used, should be completely shielded electrically. A wrapping of aluminum foil around the Input connector or a shielding cap attached to the connector will sufficefor testing at zero capacity.4. The preamplifier must be tested in conjunction with an associated main amplifier that provides the required pulse shaping. The typical noise performance given in Section 2 is obtained using an ORTEC 572 Spectroscopy Amplifier on which 2-µs time constants have been selected as specified. For comparison of these tabulated values, it is preferable to test the preamplifier under identical pulse-shaping conditions. It is also important to ensure that the noise level of the input stage of the associated main amplifier does not contribute materially to the total noise. This is usually no problem provided that the input attenuator, if any, on the main amplifier is set for minimum attenuation.5. If a multichannel analyzer is used to measure the main amplifier output pulses, testing of the noise performance can be accomplished by merely using a calibrated test pulse generator with a charge terminator. With only the charge terminator connected to the 142IH Input, the spread of the pulser peak thus analyzed will be due to only the noise contribution of the preamplifier and the main amplifier. The analyzer can be calibrated in terms of keV per channel by observing two different pulser peaks of known energy, and the FWHM of a peak can be computed directly from the analyzer readout.6. It is also possible to determine the noise performance of the preamplifier by use of a wide bandwidth rms ac voltmeter such as the Hewlett-Packard 3400A, reading the main amplifier output noise level and correlating it with expected pulse amplitudes per keV of signal through the input under the same conditions. Again, a calibrated pulse generator is required for an accurate measurement.In this method the preamplifier and main amplifier are set up as they would be used normally, but with a dummy capacitor (or no capacity) in the Input connector of the 142IH, and with the ac voltmeter connected to the main amplifier output. The noise level indicated on the voltmeter, designated Erms, is then read and noted. Then a test pulse of knownenergy, Ein(in keV), is applied to the input and the。
PSS 21H-2Y14 B4 I A Series 扩展字段总线模块说明书

PSS 21H-2Y14 B4I/A Series ® HARDWAREProduct SpecificationsFEM100 Fieldbus Expansion ModuleThe Fieldbus Expansion Module (FEM100) provides four Expanded Fieldbuses to the Field Control Processor 270 (FCP270). Each of the four Expanded Fieldbuses can accommodate up to thirty-two 200Series Fieldbus Modules (FBMs).FEATURESFor typical control usage enables a FCP270 tocommunicate with up to 128 of the 200Series FBMs, over four Expanded FieldbusesRedundancy minimizes communicationinterruption from Expanded Fieldbus 1 through 4Two-Slot and Four-Slot FEM100 ExpansionBaseplates both support the 2Mbps Module Fieldbus for 200 Series (or equivalent) FBMsTwo-slot Expansion Baseplate accommodatesFEM100 modules only, used to upgrade existing FCP270 installationsFour-slot Expansion Baseplate accommodatestwo FCP270 control processors and their fiber optic splitter/combiners, plus two FEM100 modules, for new installations.Harsh (Class G3 - ISA S71.04) contaminationprotection.PSS 21H-2Y14 B4Page 2OVERVIEWThe FEM100 module provides four ExpandedFieldbuses to an I/A Series FCP270 to increase the number of 200Series (or equivalent) FBMssupported by the FCP270 modules. The FEM100 module supports the 2Mbps HDLC module Fieldbus for communication between the I/A Series® FCP270 and the 200Series FBMs (see Figure 3 on page 5).The FEM100s are installed in a DIN rail mounted Modular Two-Slot or Four-Slot Expansion Baseplate for 2Mbps communication between the FBMs and FCP270 modules (see Figure1 and Figure 2).Figure 1. Redundant FEM100 Modules on DIN Rail Mounted Modular Two-Slot Expansion BaseplateTwo-Slot Expansion Baseplate Vertical Mounted OnlyDIN RailTo/From Expanded Fieldbuses 1-4To/From Field Control Processor FEM100 Module RedundantTerminated WithTerminator P0916RBPSS 21H-2Y14 B4Page 3Figure 2. Redundant FEM100 Modules on DIN Rail Mounted Modular Four-Slot Expansion BaseplateFEM100 MODULE DESIGNFEM100 modules have a compact design, with a rugged extruded aluminum exterior for physical protection of the electronics. Enclosures specially designed for mounting of DIN rail mounted Fieldbus equipment provide various levels of environmental protection for the FEM100 modules, up to harsh environments per ISA Standard S71.04.The FEM100 can be removed/replaced from an Expansion Baseplate without removing power. Light-emitting diodes (LEDs) incorporated into the front of the FEM100 indicate module Fieldbuscommunications activity and module status.The FEM100 communicates to the FCP270 over the 2Mbps HDLC Fieldbus, as shown in Figure 3 on page 5.Four-Slot Expansion BaseplateVertical Mounted OnlyFEM100Module (Bus A)FCP270 Fault-TolerantModule PairSplitter/Combiner To/From Control Network Ethernet Fiber Switch 1/2PairTo/From Expanded Fieldbuses 3-4FEM100Module (Bus B)To/From Expanded Fieldbuses 1-2Terminated100 Mbps Orange Fiber CablesPSS 21H-2Y14 B4 Page 4HIGH AVAILABILITYA pair of FEM100 modules provides redundancy for the Extended Fieldbuses to maintain very high subsystem availability. When both modules are active, the FCP270 sends and receives communications across both A andB buses. In the case of a FEM100 module failure, the FCP270 switches all traffic to the bus with the availableFEM100 module until the failed module is replaced.Either module may be replaced without upsetting input or output communications to the other module.EXPANSION BASEPLATE MOUNTINGThe FEM100 modules mount on either the Two-Slot or Four-Slot Expansion Baseplate. These baseplates are DIN rail mounted and vertically oriented only. These baseplates include signal connectors for the FEM100s, redundant independent dc power connections, and four cable connections to the2Mbps HDLC Expanded Fieldbuses.The Two-Slot Expansion Baseplate includes a redundant I/O cable connection to the FCP270s. One connector supports both A and B buses, while the other is terminated. Alternatively, both connectors can be used in conjunction with a FieldbusSplitter/Terminator (P0926KW).The Four-Slot Expansion Baseplate includes two slots for mounting a fault-tolerant pair of FCP270s and their fiber optic splitter/combiners.For more information on these baseplates, refer to DIN Rail Mounted Modular Baseplates(PSS 21H-2W6 B4).MODULE FIELDBUS COMMUNICATIONThe Expansion Baseplates support the 2Mbps module Fieldbus. They connect to the 2Mbps module Fieldbus for communication to all 200Series DIN I/O FBMs, the Siemens APACS+™ and Westinghouse competitive migration modules (see “Devices Supported” on page7).The 2Mbps module Fieldbus is redundant and all 200Series modules can receive/transmit messages over both A and B buses.PSS 21H-2Y14 B4Page 5Figure 3. Typical Expanded Fieldbus Network Configuration (Simplified) With Four Expanded Baseplate GroupsEXPANDED FIELDBUS 1EXPANDED FIELDBUS 2EXPANDED FIELDBUS 3EXPANDED FIELDBUS 4NOTE: First and Last Fieldbus Connector in each Chain must be terminated (P0916RB).PSS 21H-2Y14 B4 Page 6EXPANDED FIELDBUS EXTENSION VIAFCM2F2/FCM2F4/FCM2F10 FIELDBUS COMMUNICATIONS MODULESThe FCM2F2/FCM2F4/FCM2F10 Fieldbus Communications Modules provide baseplate-to-baseplate fiber optic extension of the Expanded Fieldbuses. This allows DIN rail mounted Fieldbus Modules (FBMs) to be locally, or remotely distributed in multiple enclosures for strategic placement of input/output points.The three versions of the FCM2Fs – FCM2F2,FCM2F4, and FCM2F10 – offer three different maximum baseplate-to-baseplate fiber optic cabling distances: up to 2 km (1.24 mi), up to 4 km (2.48 mi), and up to 10 km (6.2 mi), respectively. FCM2F2 and FCM2F4 are used with multimode graded-index fiber cable, and FCM2F10 is used with single-mode fiber cable.The FCM2Fs are mounted on any baseplate which accepts both FCMs and FBMs. For the Expanded Fieldbuses, FCM2Fs must be installed redundant, one on each end of one of the “A” and “B” cables of the Expanded Fieldbuses (four FCM2Fs total).The FCM2Fs can extend any of the Expanded Fieldbuses between the FEM100 baseplate and the FBM baseplates. The redundant FCM2F pair on the baseplate-side of the fiber optic extension may be installed on the first FBM baseplate in the chain, or on a separate baseplate, such as an FCM/FBM 2-position baseplate. Keeping the FCM2F pair on a separate baseplate allows the baseplate chain to use all 32 possible slots for FBMs, while including the FCM2F pair on the first baseplate in the chain leaves 30 slots for FBMs. Figure4 illustrates this configuration for the first Expanded Fieldbus.PSS 21H-2Y14 B4Page 7Figure 4. FCM2F2/FCM2F4/FCM2F10 Fieldbus Communications Modules on Expanded FieldbusDEVICES SUPPORTEDThe FEM100 supports the following devices on the 2Mbps module Expanded Fieldbus:All 200 Series DIN rail mounted FBMs (FBM201,FBM202, and so forth)Fieldbus Communications Modules,FCM2F2/FCM2F4/FCM2F10, for remote FieldbusesField Device Systems Integrator (FDSI) modules DCS Fieldbus Modules for Siemens APACS+systemsDCS Fieldbus Modules for WestinghouseWPDF® systems.2 Mbps HDLC Expanded Module Fieldbus (Shielded Twisted Pair Cables)FCP270 Control Processor F C P 270F E M 100F E M 1002 Mbps HDLC Module Fieldbus (Shielded Twisted Pair Cables) Includes Fieldbus A and BFEM100s (Redundant)Redundant Fieldbus F B MEXPANDED FIELDBUS 1F B MF B MIncludes Fieldbus A and B F C P 270(Fault-Tolerant)F C M 2FF C M 2FTo Next Baseplate in Chain(Chain has up to four Baseplates,32 FBMs total)F C M 2FF C M 2FF C M 2FF C M 2FABORBA (Similar for Expanded Fieldbuses 2-4)Redundant Fieldbus F B MEXPANDED FIELDBUS 1To Next Baseplate in Chain(Chain has up to four Baseplates,30 FBMs total)(Similar for Expanded Fieldbuses 2-4)FCM2F2/4/10s (Redundant) InFCM2F2/4/10s (Redundant) InF C M 2FF C M 2FFiber Optic Cables (A and B)Fiber Optic Cables (A and B)Shielded Twisted Pair Cables FCM/FBM 2-Position BaseplateFCM/FBM 2-Position BaseplateFirst FCM/FBM Baseplate In ChainFirst FCM/FBM Baseplate In Chain(Four Expanded Fieldbuses)(A and B)PSS 21H-2Y14 B4Page 8NOTEExisting 200Series FBMs must be upgraded with I/A Series system 8.3 release IOM files to support the Expanded Fieldbus.LED INDICATORSLight-emitting diodes (LEDs) on the front of the FEM100 module provide visual indication of the:FEM100 operational status - power and watchdog timerHDLC transmit/receive - for Field Control ProcessorsHDLC transmit/receive - for Expanded Fieldbuses 1-4FUNCTIONAL SPECIFICATIONSProcess I/O CommunicationsMODULE FIELDBUS COMMUNICATIONSTransmission Rate2 Mbps for 200 Series DIN FBMsProcess I/O Capacity (2 Mbps Fieldbus)CABLE LENGTHFCP270 Fieldbus and Expanded Fieldbuses (1-4) without FCM2FsThe cable length of the Fieldbus cannot exceed 60m (198ft) (see Figure 5)Figure 5. Expanded Fieldbus Cable Length RestrictionsFCP270 Fieldbus and Expanded Fieldbuses (1-4) with FCM2FsThe cable (not counting the fiber optic cabling provided by the FCM2F2/4/10 modules) cannot exceed 60m (198ft) (see Figure 6)Figure 6. Expanded Fieldbus Cable Length Restrictionsw/FCM2FsFirstLast in Chain FCP FCP FEMFEMBase PlateFBM Base PlateFBM Base PlateFBM Base PlateFBM 60 m (198 ft)FirstLast in Chain FCP FCP FEMFEMBase PlateFBM Base PlateFBM Base PlateFBM Base PlateFBM 60 m (198 ft)60 m (198 ft)FCP/FEM Baseplate FCPBaseplate FEMBaseplate FirstLast in Chain60 m (198 ft)10 km*(6.2 mi)Chain 60 m (198 ft)60 m (198 ft)10 km*(6.2 mi)FCP/FEM Baseplate FCPFEMthe use of four pairs of FCM2F10s.PSS 21H-2Y14 B4Page 9 FUNCTIONAL SPECIFICATIONS (CONTINUED)200 SERIES FBMS32 (maximum) Fieldbus Modules per ExpandedFieldbus (four per FEM100 pair).Up to 128 FBMs for typical control usage.Number of FBMs depends on control processor sizing constraints (refer to FCP270 SizingGuidelines (B0700AV)).Power RequirementsINPUT VOLTAGE RANGE21 to 26 V dcCONSUMPTION2.2 W (maximum)Regulatory ComplianceELECTROMAGNETIC COMPATIBILITY (EMC) European EMC Directive 89/336/EECMeets: EN 50081-2 Emission standardEN 50082-2 Immunity standardEN 61326 Annex A (Industrial Levels)CISPR 11, Industrial Scientific and Medical(ISM) Radio-frequency Equipment -Electromagnetic Disturbance Characteristics- Limits and Methods of MeasurementMeets:Class A LimitsIEC 61000-4-2 ESD Immunity6 kV current dischargeIEC 61000-4-3 Radiated Field Immunity10 V/m at 26 to 1000 MHzIEC 61000-4-4 Electrical FastTransient/Burst Immunity2 kV on I/O, dc power and communicationlinesIEC 61000-4-5 Surge Immunity2kV on ac and dc power lines; 1kV on I/Oand communications linesIEC 61000-4-6 Immunity to ConductedDisturbances Induced by Radio-frequencyFields10 V (rms) at 150 kHz to 80 MHz on I/O,dc power and communication linesELECTROMAGNETIC COMPATIBILITY (EMC)(CONT.)IEC 61000-4-8 Power Frequency MagneticField Immunity30 A/m at 50 and 60 HzPRODUCT SAFETYUnderwriters Laboratories (UL) for U.S. andCanadaUL/UL-C listed as suitable for use inUL/UL-C listed Class 1, Groups A-D;Division 2; temperature code T5 enclosurebased systems. These modules are also ULand UL-C listed as associated apparatus forsupplying non-incendive communicationcircuits for Class 1, Groups A-D hazardouslocations when connected to specifiedI/A Series processor modules as describedin the I/A Series DIN Rail MountedSubsystem User’s Guide (B0400FA).Communications circuits also meet therequirements for Class2 as defined inArticle725 of the National Electrical Code(NFPA No.70) and Section 16 of theCanadian Electrical Code (CSA C22.1).Conditions for use are as specified in theI/A Series DIN Rail Mounted SubsystemUser’s Guide (B0400FA).European Low Voltage Directive 73/23/EECand Explosive Atmospheres (ATEX) directive94/9/ECCENELEC (DEMKO) certified as EEx nA IICT4 for use in CENELEC certified Zone 2enclosure certified as associated apparatusfor supplying non-incendive field circuits forZone 2, Group IIC, potentially explosiveatmospheres when connected to specifiedI/A Series processor modules as describedin the I/A Series DIN Rail MountedSubsystem User’s Guide (B0400FA). Calibration RequirementsCalibration of the module is not required.PSS 21H-2Y14 B4Page 10ENVIRONMENTAL SPECIFICATIONS(1)OperatingTEMPERATURE-20 to +70°C (-4 to +158°F)RELATIVE HUMIDITY5 to 95% (noncondensing)ALTITUDE-300 to +3,000 m (-1,000 to +10,000 ft) StorageTEMPERATURE-40 to +85°C (-40 to +185°F)RELATIVE HUMIDITY5 to 95% (noncondensing)ALTITUDE-300 to +12,000 m (-1,000 to +40,000 ft) ContaminationSuitable for Class G3 (Harsh) environments as defined in ISA Standard S71.04, based on exposure testing according to EIA Standard 364-65, Class III. Vibration0.75 g from 5 to 500 HzPHYSICAL SPECIFICATIONSMountingThe redundant installation consists of two modules. A single module can also be used.FEM100 mounts on a Two-Slot (P0973CG) orFour-Slot (P0973CN) Expansion Baseplate. These baseplates can be mounted on a vertical DIN rail. Refer to PSS21H-2W6 B4 for details.Mass0.6 kg (1.3 lb) approximate (each module)Part NumberP0973CA DimensionsHEIGHT99 mm (3.9 in)114 mm (4.5 in) including mounting lugs WIDTH44.6 mm (1.75 in)DEPTH105 mm (4.12 in)(1)The environmental limits of this module may be enhanced by the type of enclosure containing the module. Refer to the applicableProduct Specification Sheet (PSS) which describes the specific type of enclosure that is to be used.PSS 21H-2Y14 B4Page 11FOR MORE INFORMATIONFor more information refer to the following ProductSpecification Sheets (PSS):PSS Number DescriptionPSS 21H-1B9 B3Field Control Processor 270 (FCP270)PSS 21H-2W1 B3DIN Rail Mounted Subsystem OverviewPSS 21H-2W6 B4DIN Rail Mounted Modular BaseplatesPSS 21H-2Y3 B3Fieldbus Communications Module,FCM2F2/FCM2F4/FCM2F10PSS 21H-2Y14 B4 Page 12Invensys Operations Management5601 Granite Parkway Suite 1000 Plano, TX 75024United States of AmericaGlobal Customer SupportInside U.S.:1-866-746-6477Outside U.S.:1-508-549-2424 or contact your local Invensys representative. Website: Invensys, Foxboro, I/A Series, Iand the Invensys logo are trademarks of Invensys plc, its subsidiaries, and affiliates. All other brands and product names may be the trademarks of their respective owners.Copyright 2005-2011 Invensys Systems, Inc. All rights reserved. Unauthorized duplication or distribution is strictly prohibited.MB 21A1111。
悉尼自由行 2 英寸接驳架说明书
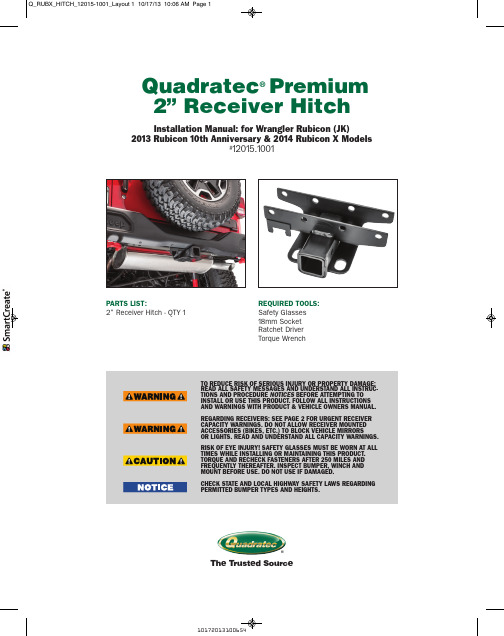
The Trusted Source®Quadratec ®Premium 2” Receiver Hitch TO REDUCE RISK OF SERIOUS INJURY OR PROPERTY DAMAGE:READ ALL SAFETY MESSAGES AND UNDERSTAND ALL INSTRUC-TIONS AND PROCEDURE NOTICES BEFORE ATTEMPTING TO INSTALL OR USE THIS PRODUCT. FOLLOW ALL INSTRUCTIONS AND WARNINGS WITH PRODUCT & VEHICLE OWNERS MANUAL.REGARDING RECEIVERS: SEE PAGE 2 FOR URGENT RECEIVER CAPACITY WARNINGS. DO NOT ALLOW RECEIVER MOUNTED ACCESSORIES (BIKES, ETC.) TO BLOCK VEHICLE MIRRORS OR LIGHTS. READ AND UNDERSTAND ALL CAPACITY WARNINGS.RISK OF EYE INJURY! SAFETY GLASSES MUST BE WORN AT ALL TIMES WHILE INSTALLING OR MAINTAINING THIS PRODUCT.TORQUE AND RECHECK FASTENERS AFTER 250 MILES AND FREQUENTLY THEREAFTER. INSPECT BUMPER, WINCH AND MOUNT BEFORE USE. DO NOT USE IF DAMAGED.CHECK STATE AND LOCAL HIGHWAY SAFETY LAWS REGARDING PERMITTED BUMPER TYPES AND HEIGHTS.Installation Manual: for Wrangler Rubicon (JK)2013 Rubicon 10th Anniversary & 2014 Rubicon X Models#12015.1001PARTS LIST:2” Receiver Hitch - QTY 1REQUIRED TOOLS: Safety Glasses18mm SocketRatchet DriverTorque WrenchTHIS CLASS II RECEIVER: 4 DOOR JK: MAX TOW WEIGHT 3500 LBS. MAX TONGUE WT. 300 LBS.4 DOOR JK: MAX TOW WEIGHT 2000 LBS. MAX TONGUE WT. 200 LBS.TO REDUCE RISK OF SERIOUS INJURY OR PROPERTY DAMAGE:INSTALL ACCORDING TO INSTRUCTIONS. TORQUE AND RECHECK FASTENERS AFTER 250 MILES AND FREQUENTLY THEREAFTER.INSPECT AND DO NOT USE RECEIVER/BUMPER IF DAMAGED.CONSULT & NEVER EXCEED LESSER OF VEHICLE, RECEIVER OR TRAILER MAXIMUM TOW OR WEIGHT RATINGS. CONSULT AND FOLLOW ALL LIMITATIONS & WARNINGS IN YOUR VEHICLE OWNERS MANUAL AND SAFE TOWING SUPPLEMENT.CHECK STATE AND LOCAL HIGHWAY SAFETY LAWS REGARDING PERMITTED BUMPER TYPES AND HEIGHTS.The Trusted Source®Before You Begin Installation: Congratulations on your purchase of the Quadratec Premium 2” Receiver Hitch for (2013 to current) 10th AnniversaryRubicon and Rubicon X Wrangler JK Vehicles. This version is specifically designed for this original equipment fac-tory bumper.When unpacking, check to make sure all parts are included and not damaged due to shipping.If any part is missing or broken, please call Customer Service at 800-745-6037as soon as possible.As tow hitches tend to be heavy, we suggest you get help for steps involving lifting, locating or holding the hitch dur-ing installation.Thank you again for your purchaseand let’s start the installation process.a hazardous situation which, if not avoided, could result in death or serious injury. You CAN be KILLED or SERIOUSLY HURT if you don’t follow instructions.a hazardous situation which, if not avoided, could result in minor or moderate injury. You CAN be moderately HURT and also may suffer property damage if you don’t follow instructions.Careful attention is required to this instruction or operation but does generally not relate to personal injury. Damage to your Quadratec ®product or other property may result if you don’t follow instructions. A Few Words About Product Safety: Your Receiver Hitch is intended toenhance the utility and enjoyment of your off road capable vehicle. Before installation, please take a moment to review the following safety information and installation instructions. Important safety information is generally preceded by one of three signal words indicating the relative risk of injury.The signal words mean:The Trusted Source®Hitch Installation:Install the hitch over the rear cross member, then reinstall the 4 factory bolts through the hitch and rear cross member and thread them intothe factory bumper. As shown in Fig. 4Torque the bolts to 80 ft.lbs. using an 18mm socket and a torque wrench. Put on safety glasses. Remove the 4factory bolts on the rear cross member of the vehicle using an 18mm wrench or socket. Be careful, the spacer plate may fall out of the bumper when removing the bolts. Remove and discard the fac-tory spacer plate and retaining washers.These will not be needed when in-stalling the Quadratec Premium 2”Receiver Hitch.Figure 1Figure 2Figure 3Figure 4The Trusted Source®Quadratec ® Exclusive Three Year Limited Warranty Your Quadratec ®branded accessories are covered by the following Limited Warranty provided exclusively by Quadratec, Inc., 1028Saunders Lane, West Chester PA 19380.This Limited Warranty is the only warranty made in connection with your purchase.Quadratec neither assumes nor authorizes any vendor, retailer or other person or entity to as-sume for it any other obligation or liability inconnection with this product or Limited War-ranty . This Limited Warranty does not apply and is not cumulative to any accessory or part distributed by Quadratec for which the Manu-facturer provides a separate written warranty. What is Covered: Subject to the terms, exclu-sions and limitations herein and with respect only to Quadratec branded accessories first sold in the United States, Quadratec warrants to the initial retail purchaser only that your Quadratec accessory shall be free of defects inmaterial and workmanship: for a period of three (3) years from date of retail purchase.This Limited Warranty is not assignable and shall terminate upon sale of the vehicle upon which the Quadratec accessory is installed or other transfer third persons.All other warranties are hereby disclaimed, ex-cept to the extent prohibited by applicable law in which case any implied warranty of mer-chantability or fitness for a particular purposeon this product is limited to 3 year from date of initial retail sale. Quadratec reserves the rights to: (a.) require invoice or other proof your ac-cessory is within the terms of this Limited Warranty as a condition of warranty service and, (b.) make future revisions to this product and Limited Warranty without prior notice or obligation to upgrade your product.What is Not Covered:Your Quadratec Limited Warranty does not cover products or parts Quadratec determinesto have been damaged by or subjected to:(a.) installation damage, alteration, modifica-tion, combination with other parts, failure to maintain or improper repair or service, (b.) nor-mal wear & tear, cosmetic damage or damagefrom moisture or water immersion, (c.) Acts ofGod, accidents, misuse, negligence, inadequate mounting or impact with vehicle(s), obstacles or other aspects of the environment, (d.) theft,vandalism or other intentional damage.Remedy Limited to Repair/Replacement:The exclusive remedy provided hereunder shall,upon Quadratec inspection and at Q uadratec’s option, be either repair or replacement of prod-uct or parts (new or refurbished) covered underthis Limited Warranty.Customers requestingwarranty consideration should first contact Quadratec to obtain a RGA number (610-701-3336). All labor, removal, shipping and installation costs are customer’s responsibility.Other Limitations - Exclusion of Damages -Your Rights Under State Law:In consideration of the purchase price paid, nei-ther Quadratec nor any independent Quadratec distributor/licensee are responsible for any time loss, rental costs, or for any incidental, conse-quential, punitive or other damages you mayhave or incur in connection with any part orproduct purchased. Your exclusive remedy hereunder for covered parts is repair/replace-ment as described above.This Limited Warranty gives you specific rights.You may also have other rights that vary from state to state. For example, some states do not allow limitations of how long an implied war-ranty lasts and /or do not allow the exclusion or limitation of incidental or consequential damages, so the limitations and exclusions herein may not apply to you.©Quadratec, Inc. 2013. All Rights Reserved.10.17.13 LTR Version Part #12999.3008。
星制造国际有限公司产品说明书 - GR14系列
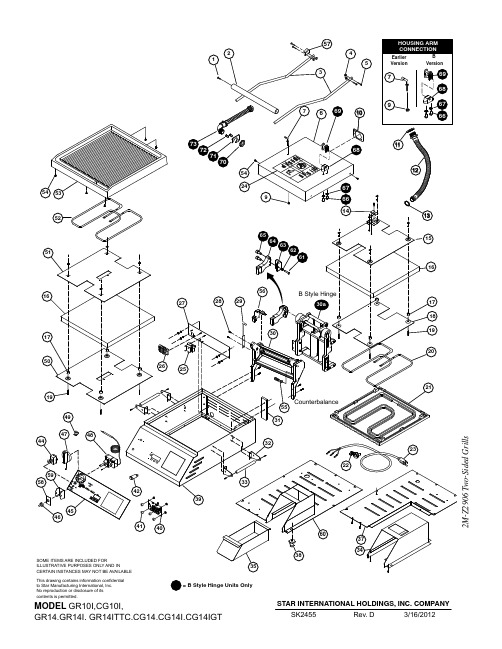
This drawing contains information confidential to Star Manufacturing International, Inc.IMPORTANT: WHEN ORDERING, SPECIFY VOLTAGE OR TYPE DESIREDPAGE 1 INCLUDE MODEL AND SERIAL NUMBER OF 4MODELPARTS LISTMarch 21, 2014, Rev. O14' TWO SIDED GRILLSFig. NoPart NoQtyDescriptionApplication12C-Z29922SCREW, HANDLE 22V-Z113951HANDLE, B-STYLE HINGECG142TB, CG14B, CG14E, CG14IB, CG14IGTB,CG14ITB, CG14ITGTB240, CG14ITLB, CG14ITSC,CG14TB, GR14B, GR14E, GR14IB, GR14ITB, GR14SNB, GR14TB2V-Z2989HANDLE - 14”, COUNTERBALANCE 2V-Z3413HANDLE - 14” S.S.GR14, GR14T, SER. # GRC00112 - 00138, GRC00778 - 00858, GRC00864 - 0125632B-Z113912ARM 14” SPT GR14SNB2B-Z2987ARM - 14”CG14EA, CG14IEA, GR14EA, GR14IEA, GR14C, CG14I, CG14IGT, CG14IT, CG14ITGT, GR14, GR14I, GR14IT 2B-Z3336ARMGR14SN2B-Z14019ARM, STANDARD 45 DEG.CG14DTB, CG14B, CG14E, CG14IB, CG14IT, GR14B, GR14E, GR14IB, GR14ITB42C-406374NUT 1/4-20 ACORN CAP MS ALL EXCEPT GR14SNB MODELS2C-08-07-0262WASHER52C-Z29924SCREW, ARM TO BRACKET2C-15234SCREW, .250-20UNC X .75 LG RHP B SERIES COUNTERBALANCE2C-08-07-0262LCKWSHR, .250 INTERLOCK TOOTH 6D9-Z20361HOUSING-TOP-14”D9-Z140201TOP HOUSING, LEFT, 14”CG142TB, CG14B, CG14E, CG14IB, CG14IGTB, CG14ITB, CG14ITGTB240, CG14ITLB, CG14ITSC,CG14TB, GR14B, GR14E, GR14IB, GR14ITB, GR14SNB, GR14TB72C-Z32002PIN - TOP HOUSING 82C-Z28552RETAINER RING92C-08-07-004021/4” NUT, USE PART NUMBER 2C-Z2820102A-Z38271PLATE, STAMPING - CONDUIT 112C-Z37802CONDUIT RETAINER 122E-Z28981CONDUIT ASSY. - PTFE 132E-Z37681CONDUIT LOCKNUT 14D9-04-GR-01661WIRE MOUNT15D9-GR00791TOP RETAINING PLATE AY/1416D9-Z28882INSULATION - 14”172A-Z66048SPACER - INSULATED PLATE 18D9-Z20751TOP ELEMENT/INS. PLATE/14192C-08-07-02858SCREW, ELEMENT RET. PLATE 20PS-Z19801ELEMNT REPL. KIT, 800W/120V CG14, CG14T, GR14, GR14IB GR14T, CG14IT-120V PS-Z2021ELEMNT REPL. KIT, 800W/240V CG14, CG14T, GR14, GR14TD9-GR0535ELEM\NT ASSY 800W/240V CG/GR14E-230V, CG/GR14E-240VPS-Z2391ELEMNT REPL, KIT, 1800W/240GR14I, GR14IT, CG14IGT, CG14ITGT, CG14I, CG14IT D9-GR0514ELEMENT, TOPCG14E-120V, GR14E-120V, GR14IE2M -Z 2906 T w o -S i d e d G r i l l sIMPORTANT: WHEN ORDERING, SPECIFY VOLTAGE OR TYPE DESIREDPAGE INCLUDE MODEL AND SERIAL NUMBEROF25MODELPARTS LISTMarch 21, 2014, Rev. O14' TWO SIDED GRILLS2M -Z 2906 T w o -S i d e d G r i l l sIMPORTANT: WHEN ORDERING, SPECIFY VOLTAGE OR TYPE DESIREDPAGEINCLUDE MODEL AND SERIAL NUMBER OF35MODELPARTS LISTMarch 21, 2014, Rev. O14' TWO SIDED GRILLSFig. NoPart NoQtyDescriptionApplication382A-Z14854FOOT, 1” ADJUSTABLE, 1/4” STUD CERTAIN APPLICATIONS 2A-Z11501FOOT, 1” SOLID RUBBER, 1/4” STUD ALLUMINUM PLATES2A-Z0314-1BASE, FOOT 4” CAST W/RUBBER FOOTCG14IB, CG14IGTB, CG14ITB, CG14ITLB, CG14ITSC, GR14IB, GR14ITB2A-Z12980 2.5” FOOT BASE, 3/8” STUD GR14I, GR14IT, CG14I, CG14IT, CG14IGT, CG14ITGT 2A-Z12946BASE, FOOT, NON-SKID CG14I, CG14IB, CG14IE, CG14IEGT, CG14IGTB, GR14I GR14IB, GR14IE, GR14ITB, (mfg after 4-2010) 39D9-GR00611BODY ASSY. - 14”D9-GR0184BODY ASSY GR14SN402J-Z18361TIMER CONTROL CG14T, CG14IT, CG14IGT, GR14T, GR14IT412K-Z19714SPACERCG14T, CG14IT, CG14IGT, CG14E, GR14T, GR14IT, GR14E,422J-Y66891PILOT LIGHT, 120V CG14, GR14 (120V MODELS)2J-Y6690PILOT LIGHT, 240V GR14I, CG14IGT, CG14I, CG14, GR14 (240V)44PS-GR02241RKER SWITCH RPL 14” KIT CG14T-120V W/SERIAL NO BELOW CGC25308CG14IT-120V W/SERIAL NO BELOW CGC24701GR14T-120V W/SERIAL NO BELOW GRC23789CG14IT-240V W/SERIAL NO BELOW CGC245592E-Z6863SWITCH 3 POS, DPDT CG14T, CG14IT, CG14IGT, GR14T, GR14IT 2E-Z3808SWITCH - 30A@120V CG14E-120V, GR14E-120V452M-Z30501OVERLAY - 14” NO TIMERGR14I, CG14IGT, CG14I, CG14, CG14B, GR14, GR14B, CG14GTB 2M-Z3816OVERLAY - 14” w/2 MANUAL TIMERS CG14-2T2M-Z3929OVERLAY, CHIPOTLE GR14SN, GR14SNB2M-Z6870OVERLAY - 14” w/TIMER GR14IT, CG14ITGT, CG14IT, CG14T, GR14T, GR14TB 2M-Z12002OVERLAYCG14E, GR14E 2M-Z18461LABEL ON & OFFCG14E, GR14E462I-05-07-00131RUBBER BOOT, SWITCH 472R-Z18541KNOB-CONTROL482T-64471THERMOSTAT 118V-236V 492A-Z30261HALF CLIP50D9-Z133381BTM. INSULATION RET. PLT. 14”51D9-Z133381BTM ELEMENT RET. PLATE 14”522N-Z19811BTM ELEMENT, HEATING, 1000W/120CG14, CG14T, GR14, GR14IB, GR14T, CG14IT-120V 2N-Z2022BTM ELEMENT, HEATING, 1000W/240CG14, CG14T, GR14, GR14T D9-GR0534BTM ELEMENT ASSY, 1000W/240GR14E-240V2N-Z2392BTM ELEMENT, HTG, 1800W/240V GR14I, GR14IT, CG14IGT, CG14ITGT, CG14I, CG14IT D9-GR0513BTM ELEMENT ASSYCG14E-120V, GR14E-120V, GR14IE 532F-Z19451CASTING, SM. BOT., ALUM.-14”GR14, GR14T, CG14GTB 2F-Z1947CASTING, GR. BOT., ALUM.-14”CG14, CG14T2F-Z1949CASTING, SM. BOT., IRON-14”GR14I, GR14IT, CG14IGT, CG14ITGT 2F-Z1951CASTING, GR. BOT., IRON-14”CG14I, CG14IT542C-Z58838SCREW 10-24X1/2 FZA 55PS-GR1342ROLLER BEARING KIT2M -Z 2906 T w o -S i d e d G r i l l sIMPORTANT: WHEN ORDERING, SPECIFY VOLTAGE OR TYPE DESIREDPAGE INCLUDE MODEL AND SERIAL NUMBEROF45MODELPARTS LISTMarch 21, 2014, Rev. O14' TWO SIDED GRILLS2M -Z 2906 T w o -S i d e d G r i l l sIMPORTANT: WHEN ORDERING, SPECIFY VOLTAGE OR TYPE DESIREDPAGE INCLUDE MODEL AND SERIAL NUMBEROF55MODELPARTS LISTMarch 21, 2014, Rev. O14' TWO SIDED GRILLSFig. NoPart NoQtyDescriptionApplicationNI 2R-09-WB-00062KNOB-BLACK (NOT SHOWN)CG14-2TNI2V-Z30272CROSS SUPPORT (NOT SHOWN)GR14I, GR14IT, CG14I, CG14IT, CG14IGT, CG14ITGT NI D9-GR01081FACEPLATE ASSY. - 14” NO TIMER GR14I, CG14IGT, CG14I, CG14, GR14NI D9-GR01781FACEPLATE ASSY. - 14” 2 TIMERS CG14-2T NI D9-GR01851FACEPLATE ASSY, - 14”GR14SNNI D9-GR02101FACEPLATE ASSY. - 14” w/TIMER GR14IT, CG14ITGT, CG14IT, CG14T, GR14T NI D9-Z120271PROBE BRACKET - BOTTOM CG14E, GR14ENI D9-Z30281SIDE SUPPORT (NOT SHOWN)GR14I, GR14IT, CG14I, CG14IT, CG14IGT, CG14ITGT NI D9-Z30291PART SUPPORT (NOT SHOWN)GR14I, GR14IT, CG14I, CG14IT, CG14IGT, CG14ITGT NIZ1-70-07-03431SWITCH GUARDCG14E, GR14E2M -Z 2906 T w o -S i d e d G r i l l s。
Schneider Electric ТеSys GV2设备手册说明书

T h e i n f o r m a t i o n p r o v i d e d i n t h i s d o c u m e n t a t i o n c o n t a i n s g e n e r a l d e s c r i p t i o n s a n d /o r t e c h n i c a l c h a r a c t e r i s t i c s o f t h e p e r f o r m a n c e o f t h e p r o d u c t s c o n t a i n e d h e r e i n .T h i s d o c u m e n t a t i o n i s n o t i n t e n d e d a s a s u b s t i t u t e f o r a n d i s n o t t o b e u s e d f o r d e t e r m i n i n g s u i t a b i l i t y o r r e l i a b i l i t y o f t h e s e p r o d u c t s f o r s p e c i f i c u s e r a p p l i c a t i o n s .I t i s t h e d u t y o f a n y s u c h u s e r o r i n t e g r a t o r t o p e r f o r m t h e a p p r o p r i a t e a n d c o m p l e t e r i s k a n a l y s i s , e v a l u a t i o n a n d t e s t i n g o f t h e p r o d u c t s w i t h r e s p e c t t o t h e r e l e v a n t s p e c i f i c a p p l i c a t i o n o r u s e t h e r e o f .N e i t h e r S c h n e i d e r E l e c t r i c I n d u s t r i e s S A S n o r a n y o f i t s a f f i l i a t e s o r s u b s i d i a r i e s s h a l l b e r e s p o n s i b l e o r l i a b l e f o r m i s u s e o f t h e i n f o r m a t i o n c o n t a i n e d h e r e i n .Product data sheetCharacteristicsGV2ME08TeSys GV2 Manual Starter and Protector,thermal magnetic circuit protector, pushbuttons, 2.5 to 4 A, screw clampProduct availability: Stock - Normally stocked in distribution facilityMainRange TeSys Product name TeSys GV2Device short name GV2ME Device application MotorTrip unit technologyThermal-magneticComplementaryPoles description 3P Network type ACUtilisation category AC-3 IEC 60947-4-1Category A IEC 60947-2Network frequency 50/60 Hz IEC 60947-4-1Fixing mode 35 mm symmetrical DIN rail clipped Panel screwed with adaptor plate)Operating position Any positionMotor power kW1.1 KW 400/415 V AC 50/60 Hz 1.5 KW 400/415 V AC 50/60 Hz 1.5 KW 500 V AC 50/60 Hz 3 KW 690 V AC 50/60 Hz2.2 KW 500 V AC 50/60 Hz 2.2 kW 690 V AC 50/60 HzBreaking capacity100 KA Icu 230/240 V AC 50/60 Hz IEC 60947-2100 KA Icu 400/415 V AC 50/60 Hz IEC 60947-2100 KA Icu 440 V AC 50/60 Hz IEC 60947-2100 KA Icu 500 V AC 50/60 Hz IEC 60947-23 kA Icu 690 V AC 50/60 Hz IEC 60947-2[Ics] rated service short-circuit breaking capacity100 % 500 V AC 50/60 Hz IEC 60947-2100 % 230/240 V AC 50/60 Hz IEC 60947-2100 % 440 V AC 50/60 Hz IEC 60947-2100 % 400/415 V AC 50/60 Hz IEC 60947-275 % 690 V AC 50/60 Hz IEC 60947-2Control type Push-button Line Rated Current4 A Thermal protection adjustment range 2.5…4 A Magnetic tripping current 51 A[Ue] rated operational voltage 690 V AC 50/60 Hz IEC 60947-2[Ui] rated insulation voltage690 V AC 50/60 Hz IEC 60947-2[Ith] conventional free air thermal current 4 A IEC 60947-4-1[Uimp] rated impulse withstand voltage 6 kV IEC 60947-2Power dissipation per pole 2.5 W Mechanical durability 100000 cyclesElectrical durability 100000 cycles AC-3 440 V Maximum operating rate25 cyc/hRated duty Continuous IEC 60947-4-1Connections - terminals Screw clamp terminals 2 0.00…0.01 in² (1…6 mm²) solidScrew clamp terminals 2 0.00…0.01 in² (1.5…6 mm²) flexible without cable endScrew clamp terminals 2 0.00…0.01 in² (1…4 mm²) flexible with cable end Tightening torque15.05 lbf.in (1.7 N.m) screw clamp terminalsSuitability for isolation Yes IEC 60947-1Phase failure sensitivity Yes IEC 60947-4-1Height 3.50 in (89 mm)Width 1.77 in (45 mm)Depth 3.09 in (78.5 mm)Net weight0.57 lb(US) (0.26 kg)EnvironmentStandards EN/IEC 60947-2EN/IEC 60947-4-1CSA C22.2 No 60947-4-1UL 60947-4-1Product certifications IECEE CB SchemeULCSACCCEACATEXBVLROS (Lloyds register of shipping)DNV-GLRINAProtective treatment THIP degree of protection IP20 IEC 60529IK degree of protection IK04Ambient air temperature for operation-4…140 °F (-20…60 °C)Ambient air temperature for storage-40…176 °F (-40…80 °C)Fire resistance1760 °F (960 °C) IEC 60695-2-1Operating altitude6561.68 ft (2000 m)Ordering and shipping detailsCategory22367 - MANUAL STR PROTECTOR - GV2Discount Schedule I11GTIN00785901211952Package weight(Lbs)0.26 kg (0.58 lb(US))Returnability YesCountry of origin THOffer SustainabilitySustainable offer status Green Premium productREACh Regulation REACh DeclarationEU RoHS Directive Compliant EU RoHS DeclarationMercury free YesRoHS exemption information YesChina RoHS Regulation China RoHS DeclarationEnvironmental Disclosure Product Environmental ProfileCircularity Profile No need of specific recycling operationsWEEE The product must be disposed on European Union markets following specificwaste collection and never end up in rubbish bins.Contractual warrantyWarranty18 monthsProduct data sheetPerformance CurvesGV2ME08Thermal-Magnetic Tripping Curves for GV2ME and GV2PAverage Operating Times at 20 °C Related to Multiples of the Setting Current1 3 poles from cold state2 2 poles from cold state3 3 poles from hot stateCurrent Limitation on Short-Circuit for GV2ME and GV2P (3-Phase 400/415 V))Dynamic StressI peak = f (prospective Isc) at 1.05 Ue = 435 V1Maximum peak current224-32 A320-25 A417-23 A513-18 A69-14 A76-10 A84-6.3 A9 2.5-4 A10 1.6-2.5 A111-1.6 A12Limit of rated ultimate breaking capacity on short-circuit of GV2ME (14, 18, 23, and 25 A ratings).Thermal Limit on Short-Circuit for GV2METhermal Limit in kA2s in the Magnetic Operating ZoneSum of I2dt = f (prospective Isc) at 1.05 Ue = 435 V124-32 A 220-25 A 317-23 A 413-18 A 59-14 A 66-10 A 74-6.3 A8 2.5-4 A9 1.6-2.5 A 101-1.6 AProduct data sheetDimensions DrawingsGV2ME08DimensionGV2ME(1)MaximumMountingGV2ME On 35 mm railc = 78.5 on AM1 DP200 (35 x 7.5)c = 86 on AM1 DE200, ED200 (35 x 15)On panel with adapter plate GV2AF02On pre-slotted plate AM1 PAOn rails DZ5 MB201GV2AF01Combination GV2ME + TeSys k contactorGV2AF3Combination GV2ME + TeSys d contactorGV2AF4 + LAD311Combination GV2ME + TeSys d contactorGV2ME + GV1L3 (Current Limiter)X1 = 10 mm for Ue = 230 V or 30 mm for 230 V < Ue ≤ 690 VProduct data sheetGV2ME08 Connections and SchemaGV2ME•• and GV2RTConnection of Undervoltage Trip for Dangerous Machines (Conforming to INRS) on GV2ME Only。
More time on the road AT-1202 August 2014 部件清单说明书

More time on the road®Illustrated Parts List AT-1202August 2014ContentsHow To Use The Illustrated Parts List (3)AIR SHIFT ASSY (4)CASE (AUX) (6)CASE (FRONT) (8)COUNTERSHAFT ASSY (10)INPUT SHAFT & DRIVE GEAR (11)KITS & ASSEMBLIES (13)MAINSHAFT ASSY (14)MECHANICAL SHIFT ASSY (15)MISCELLANEOUS (16)2How To Use The Illustrated Parts ListThe information contained in this document is subject to frequent updates. Therefore, for the latest information available, please visit the interactive Electronic Parts Catalog at /epc.Model Designation or Nomenclature•For information regarding Model Designation and Nomenclature, visit .Kits and Assemblies (K/A's)•Kits and Assemblies contain groups of individual or assembled parts developed for optimal replacement or repair of a service problem.•Kits and Assemblies are shown with applicable parts groupings in the parts listings.Identifying Kits and AssembliesA- Part numbers beginning with the letter 'A' are pre-assembled Production AssembliesK- Part numbers beginning with the letter 'K' are kits that are not assembledS- Part numbers beginning with the letter 'S' are pre-assembled Service Assemblies•Note: Some Production Assemblies do not begin with a letter prefix (Midrange only).Illustrations•Illustrations show parts in assembly groups.•Item numbers on illustrations correspond with parts listings on pages adjacent to the illustration.•Notes are included on illustrations where additional information is needed.Parts ListingParts listings are defined by parts groupings and are broken down by service assemblies. Parts listings identify a part for servicing with the following categories•Item Number - corresponding with numbers on illlustrations for part identification.•Current Part - indentifies part as it is available for service.•Description - specifies part name or description.•Replaced Part - quantity quantity required for assembly.•Quantity - defines unique characteristics or requirements.•Notes - indicates Kits or Assemblies that contain a particular part.•Kits/Assy's Where Used34Group: AIR SHIFT ASSYAIR SHIFT ASSYItemCurrent PartDescription Replaced Part Qty. NotesKits/Assys WhereNeeded 1 14644 -O- RING1 K-1552 2 17413 SHIFT CYLINDER1 3 S-1265 SHIFT PISTON ASSY 17417 1 4 17418 -O- RING 1 K-1552 5 62518 ROLL PIN 1 S-1265 6 14621 -O- RING 1 K-1552 7 18542 YOKE BAR 1 8 17414 CYLINDER COVER 1 9 17415 GASKET 1 10 X-3-600 LOCKWASHER 4 3/8"11 X-8-679 CAPSCREW 4 3/8"-16X1-3/4" 49 17411SHIFT YOKE111Item CurrentPart Description ReplacedPartQty.Notes Kits/Assys WhereNeeded50 3220 LOCKSCREW 151 14347 GASKET 1 K-147961 12845 ELBOW 3 1/8"64 18634 AIR VALVE 1 USE W/O NEUTRAL SWITCH64 4305767 AIR VALVE 18554 1 USE W/NEUTRAL SWITCH65 18555 VALVE PLATE 1 USE W/NEUTRAL SWITCH65 18633 NO LONGER AVAILABLE 1 USE W/O NEUTRAL SWITCH5Group: CASE (AUX) CASE (AUX)Item CurrentPart Description ReplacedPartQty.Notes Kits/Assys WhereNeeded28 S-1347 REAR HOUSING ASSY 17548 ,18736 ,18757,18784 ,19100129 14335 GASKET 1 K-147930 X-8L-602 CAPSCREW 16 3/8"-16X1-1/2"30 X-8L-605 CAPSCREW 1 3/8"-16X3"30 X-8L-614 CAPSCREW 2 3/8"-16X2"31 16784 GASKET 2 K-147932 16770 REAR BEARING COVER 233 X-8L-602 CAPSCREW 8 3/8"-16X1-1/2"35 15532 GASKET 1 K-1479,K-2256,K-2262,S-2119,S-21516Item CurrentPart Description ReplacedPartQty.Notes Kits/Assys WhereNeeded36 S-2119 REAR BRG COVER ASSY 20048 ,22045,4302009 ,4302031 ,S- 1558 S - 15601 EXTENDED36 S-2151 REAR BRG COVER ASSY S - 1429 138 X-8L-605 CAPSCREW 5 3/8"-16X3", USE W/S-2151 COVER38 X-8L-611 CAPSCREW 5 3/8"-16X3-1/4", USE W/S-2119COVER39 7992 BUSHING 1 S-2119,S-215142 X-8-682 CAPSCREW 1 3/8"-16X3"43 20920 OIL SEAL 15087 1 3-1/2" I.D.43 K-2256 OIL SEAL KIT 19109, 21036 157 4304602 BREATHER 23605 1 1/4"NPT58 X-12-404 PIPE PLUG 1 1/4" NPT67 20224 PLUG-MAGNETIC 2 S-2119,S-215168 13679 -O-RING 1 USE W/OEM SUPPLIEDADJUSTABLE SPEEDOMETERSENSOR NOT TO BE USED WITH4301954 SEAL68 20225 -O-RING 2 USE W/20224 PLUG OR OEMSUPPLIED NON-ADJUSTABLESPEEDOMETER SENSOR NOT TOBE USED WITH 4301954 SEAL68 4301954 SENSOR SEAL 2 O-RING NOT REQUIRED S-2119,S-215169 17106 GASKET 1 K-2256,K-2262,S-2119,S-215170 20815 LIFTINGEYE 17105 171 X-8L-609 CAPSCREW 1 3/8"-16X1-3/4"73 19709 COLLAR 1 K-2256,K-2262,S-2119,S-215175 14142 -O-RING 1 S-2119,S-215176 20226 PLUG-MECHANICAL 2237 1 S-2119,S-215180 K-2262 OIL SEAL W/SLINGER 20807, 20808 1 "FOR MECHANICAL COVER"82 K-3651 OIL SEAL TOOL KIT 17Group: CASE (FRONT) CASE (FRONT)Item CurrentPart Description ReplacedPartQty.Notes Kits/Assys WhereNeeded1 S-1264 CASE ASSY 17400 ,18545 12 X-8-686 CAPSCREW 6 3/8"-16X3/4"3 4305309 GASKET 1684 1 K-14794 14575 PTOCOVER 4302254 15 4305310 GASKET 4302810 1 K-14796 4302809 PTOCOVER 16596 18 X-8-725 CAPSCREW X 8 724 8 7/16"-14X7/8"9 X-12-1207 PIPE PLUG X12 1202 ,X12 1206 1 3/4" MAGNETIC10 X-1-1012 HEXNUT X-1-1005 4 .625-1811 X-10-1005 WASHER X 3 1000 ,X10 1000,X10 1004 4 1.23 X 6.60108Item CurrentPart Description ReplacedPartQty.Notes Kits/Assys WhereNeeded12 14554 STUD 1632 ,6579 4 5/8" X 2-3/16"13 X-1-800 NUT 6 1/2"-2014 X-3-801 LOCKWASHER 6 1/2"15 23592 STUD 12022 616 14373 MAGNET 1 S-126417 7935 BREATHER 117 X-12-208 PIPE PLUG 1 1/8" NPT18 X-12-2007 PIPE PLUG X12 2006 119 X-12-802 PIPE PLUG X12 800 1 1/2"22 18128 PIN 223 17423 SEAL 1 USE W/MANUAL SHIFT24 17422 OIL SEAL 1 USE W/MANUAL SHIFT25 X-8L-600 CAPSCREW 8 3/8"-16X1"26 4881 COVER 227 4886 GASKET 2 K-147959 4303655 PLUG 17178 1 S-126460 17179 GASKET 1 USE W/MANUAL SHIFT S-126461 22941 NEUTRAL LIGHT SWITCH 12639 1 SWITCH NORMALLY OPEN USEW/AIR SHIFT62 15899 PIN 1 USE W/AIR SHIFT63 13359 EXPANSION PLUG 1 USE W/AIR SHIFT70 20815 LIFTINGEYE 17105 172 X-8L-604 CAPSCREW 1 3/8"-16X1-1/4"910 Group: COUNTERSHAFT ASSYCOUNTERSHAFT ASSYItemCurrent PartDescription Replaced Part Qty. NotesKits/Assys WhereNeeded 24 6488 BEARING 2 25 A-4286 WELDEDCOUNTERSHAFT ASSY2C/S 17408 - D/G 1740926 81012 BEARING 2 27 11364 SNAP RING22425262710362-7-95Group: INPUT SHAFT & DRIVE GEARINPUT SHAFT & DRIVE GEARItem CurrentPart Description ReplacedPartQty.Notes Kits/Assys WhereNeeded1 22254 NUT 11956 13 17425 OILSEAL 1 3-1/2"I.D.3 18408 OILSEAL 1 3-3/4"I.D.4 15241 SNAPRING 15 4303920 BEARING 81042 16 S-1005 HOUSINGASSY 17401 17 17395 INPUTSHAFT 18 17396 MAINSHAFT 19 X-7-650 CAPSCREW 110 81559 BEARING 111 17397 SNAPRING 1Item CurrentPart Description ReplacedPartQty.Notes Kits/Assys WhereNeeded12 17398 DRIVEGEAR 113 17399 SNAPRING 114 17505 PLUG 1 S-100515 17402 GASKET 1 K-1479KITS & ASSEMBLIESItem CurrentPart Description ReplacedPartQty.Notes Kits/Assys WhereNeededK-1479 GASKETKIT 1K-1552 -O- RING KIT 1 FOR AIR SHIFT ASSYK-2256 OIL SEAL KIT 14337 ,19109 ,21036 1K-2262 OIL SEAL W/SLINGER 20807, 20808 1 "FOR MECHANICAL COVER"K-3651 OIL SEAL TOOL KIT 1S-1005 HOUSINGASSY 17401 1S-1264 CASE ASSY 17400 ,18545 1S-1265 SHIFTPISTONASSY 17417 1S-1347 REAR HOUSING ASSY 17548 ,18736 ,18757,18784 ,191001S-2119 REAR BRG COVER ASSY 20048 ,22045,4302009 ,4302031 ,S- 1558 S - 15601 EXTENDEDS-2151 REAR BRG COVER ASSY S - 1429 1Group: MAINSHAFT ASSY MAINSHAFT ASSYItem CurrentPart Description ReplacedPartQty.Notes Kits/Assys WhereNeeded16 18543 SLIDINGCLUTCH 17404 117 17403 MAINSHAFT 118 17405 REDUCTIONGEAR 119 17406 BEARING 120 17410 SNAPRING 1 21 17407 WASHER 123 22254 NUT 11956 124 15260 BEARING 125 20191 ROTOR 1Group: MECHANICAL SHIFT ASSY MECHANICAL SHIFT ASSYItem CurrentPart Description ReplacedPartQty.Notes Kits/Assys WhereNeeded45 1884 EYE ROD END 146 X-1-700 NUT 1 7/16"-2047 18635 YOKEBAR 17420 148 17421 SPACER 149 17411 SHIFTYOKE 150 3220 LOCKSCREW 151 14347 GASKET 1 K-147952 17419 SHIFTCYLINDER 153 17412 PLUG 154 X-8L-604 CAPSCREW 4 3/8"-16X1-1/4"55 15918 SPRING 156 X-14-800 STEELBALL 1 1/2"84 4696 NLA-SPACER 1 TO BLOCK OUT LOW ANDNEUTRALMISCELLANEOUSItem CurrentPart Description ReplacedPartQty.Notes Kits/Assys WhereNeeded18457 WARNINGLABEL 118524 WARNINGLABEL 118544 WARNINGLABEL 171203 SILICONE LUBE 1 8 OZ (236.59 CC)-FLEET SIZE71204 ADHESIVESEALANT 1 0.5 CC (SINGLE APPLICATIONSIZE)71205 SEALANT 1 2 CC (SINGLE APPLICATION SIZE)71206 SILICONE LUBE 1 4 CC (SINGLE APPLICATION SIZE) K-1552。
亚し 美国双层保护管道系统产品说明书

Double ContainmentPiping SystemsDuo-Pro®• Poly-Flo®• Pro-Lock™Leak Detection • Welding EquipmentWebsite:Email:*********************************************Why Use Double Containment?Protecting our environment is everyone’s responsibility.Asahi/America pioneered thermoplastic double containment piping systems with precisely this in mind. Our systems are engineered to protect our eco-system from the dangers of exposed aggressive chemicals.Additionally, the Environmental Protection Agency (EPA) has directed the underground transport of hazardous materials be protected from release into the environment in its Standard 40 CFR, Part 280 & 281. In order to be in compliance, systems must:- Be Double Contained- Have Automated Leak Detection for Pressurized Systems - Have at least Manual Leak Detection for Drainage Systems- Have Outer Containment able to retain Media Transport for a minimum of 30 daysDouble containment should be specified for more applications than regulated by the EPA. Hazardous chemicals should be protected from escape in areas where there are chemicals transported above work stations, or any other potential safety hazards due to exposure to the media.Asahi/America, Leadership in Double ContainmentAsahi/America has been the industry leader in engineered thermoplastic double contained piping systems for decades. Our systems have been successfully installed with confidence across a broad range of industries.We offer the broadest range of quality thermoplastic double contained piping systems available. Ranging in sizes from 1x2 to 16x20 and above, choosing Asahi/America provides maximum flexibility in system engineering and design. Materials of construction by standard size andsystem include:Duo-ProAvailable Sizes: 1x3 thru 16x20Materials: Polypropylene, PVDF and E-CTFE (HALAR)Ratings: 150 psi and DrainagePoly-FloAvailable Sizes: 1x2 thru 4x6Materials: Black Polypropylene & High Density Polyethylene Ratings: 100 psi and DrainagePro-LockAvailable Sizes: 1/2x2 thru 4x8Materials: PVC and C-PVCRatings: Schedule 40x40, 80x40 and 80x80Asahi/America, 35 Green St, P .O. Box 653, Malden, MA 02148 Tel: 800-343-3618; 781-321-5409, Fax 800-426-7058ManualLeak Detection PortEngineered DesignAll of Asahi/America’s Double Contained Systems are thoroughly designed and engineered for rigorous and demanding applications. Our stringent engineering review process ensures proper installation application and design. Applying our expertise in thermoplastics, we engineer systems that provide security and reliability.Asahi/America offers a variety of quality leakrequirements.minimal repair excavation.switches.available to assist with proper selection,systems based on your application requirement.Website:Email:*********************************************Duo-Pro ®PP, PVDF & E-CTFE Double ContainmentThe premier double containment piping system offered on the market today, Duo-Pro has been successfully installed in Fortune 500 insemiconductor, pharmaceutical and chemical Duo-Pro has been created to solve all the previously encountered problems in double containment piping.-The system uses proven, highly corrosion resistant materialssuch as Copolymer Polypropylene, Super Proline PVDF and-Fluids can be pumped through the carrier pipe up to 150 psi -Can be assembled using simultaneous butt or staggered butt fusion -Leak detection cable can be easily installed in sizes 3x6 and higher® Halar is a registered trademark of Solvay SolexisE-CTFE/Halar ®Asahi/America, 35 Green St, P .O. Box 653, Malden, MA 02148 Tel: 800-343-3618; 781-321-5409, Fax 800-426-7058Poly-Flo ®PP & HDPEDouble ContainmentUnique continuous support in both fittings and pipe provide inherent system restraint against system expansion forces.Poly-Flo ® Engineered DesignWhy Specify Poly-Flo ® SystemsPoly-Flo’s unique unitary construction saves time and labor on each project. Low cost and easy installation makes Poly-Flo the ideal system for drainage systems, pressurized transfer lines and industrial applications needing up to 4” carrier pipe.Typical installations are in waste treatment, carrying sulfuric acid or caustic soda, in chemical processing applications, for bulk storage chemicals such as sodium hydroxide and aluminum nitrite, and in semiconductor plants, handling sulfuric, nitric, andhydrofluoric acids for wet stations.The Poly-Flo System is a unique dual extruded and molded system. All other double containment systems are made from single wall components and then assembled into a double wall configuration. The Poly-Flo System thereby reduces fabrication resulting in significant cost savings. Asahi/America’s patented extrusion process locks the pipe together by use of continuous support ribs. This unique process is applied to molding fittings as well. The continuous support provides inherent restraint to expansion forces thus eliminating the requirement of Dogbone fittings in the Poly-Flo System.Poly-Flo’s patented double O-ring flanges allow systems to be efficiently pre-assembled then easily bolted into place in the field.The Poly-Flo system is available with manual and low point leak detectionsensors only. The use of leak detection cable is not possible due to limited annular space.Website:Email:*********************************************Pro-Lock TMPVC & C-PVCDouble ContainmentPro-Lock systems by Asahi-Americacombine engineering design with cost effective materials.The result is reliable double contained piping systems for a variety of applications. Pro-Lock exceeds the requirements of EPA Standard 40 CFR, Part 280 & 281 for underground transport of hazardous chemicals.Annular space sufficient for low-point leak detection and continuous cable systems.Pro-Lock TM Engineered DesignWhy Specify Pro-Lock TM SystemsPro-Lock is ideally suited for use in water and wastewater treatment applications and anywhere sodium hypochlorite is used.Pro-Lock system’s design consists of a centralizing support disk inside the containment pipe & fitting, minimizing carrier pipe deflection & extending the system’s life. Fittings are made of the same resin as the pipe and are available in a variety of configurations for pressureapplications. Fittings are supplied from the factory dual contained and locked together ready for installation.Pro-Lock is assembled in the field using staggered or simultaneous joining methods. Joining cements are recommended based on your application. Pro-Lock fittings and pipe are NSF-61 certified and IAPMO approved.Asahi/America, 35 Green St, P .O. Box 653, Malden, MA 02148 Tel: 800-343-3618; 781-321-5409, Fax 800-426-7058-Gain quick and easy access to your system. Provides -Manual or automatic solutions to determe if the system has a -Protect your valves with a corrosion resistantAllow Asahi/America’s team of professionals to prefabricate your double wall system in our factory. Most systems can be prefabricated in our factory, minimizing field installation requirement; saving time and installation costs.Prior to assembly our engineering staff will work with you to ensure the system structural integrity through theirinvolvement with overall system design and project layouts,pressure rating review, stress analysis, takeoffs, support The type of material and system will dictate the welding method and tool selection. On all Asahi/America double wall systems, butt fusion is the recommended system offered due to its ideal functionality. Be certain not to weld in the rain, as rain willdamage equipment and improperly influence the weld. In addition, high winds and cold temperature below 40 F will negatively influence the welding process. Please consult Asahi-America’s chart on page F-46 in Asahi/America’s Engineering Design Guide for tool selection recommendations.Tools Available:Asahi/America has a wide array of welding machines available for purchase or rent.We offer industrial tools to fit almost every application installation. From manual tools that can be modfied for use in tight space constraints, to trench tools that can weld in adverse site conditions, to tools than can weld in difficult positions, we are poised to supply the tool that meets your job’s unique demands.W4400 Trench 6W2500 Shop 12Website:Email:*********************************************DoubleContainment Size RangesDuo-Pro ®Double Containment Supply RangeAsahi/********************************************************:800-343-3618;781-321-5409,Fax800-426-705Pro-Lock TMFittingsPP PVDF E-CTFE PP HDPE PVC CPVC Pipe 1x3 to 16x201x3 to 12x161x3 to 4x81x2 to 4x61x2 to 4x61/2x2 to 4x81/2x2 to 4x8901x3 to 16x201x3 to 12x161x3 to 4x81x2 to 4x61x2 to 4x61/2x2 to 4x81/2x2 to 4x8Tee 1x3 to 16x201x3 to 12x161x3 to 4x81x2 to 4x61x2 to 4x61/2x2 to 4x81/2x2 to 4x8451x3 to 16x201x3 to 12x161x3 to 4x81x2 to 4x61x2 to 4x61/2x2 to 4x81/2x2 to 4x8Reducer-Concentric(3x1) (6x3) to (14x12) (18x16)(3x1) (6x3) to (10x4) (14x8)(3x1) (6x3) to (4x3) (8x6)(2x1) (3x2) to (4x22) (6x3)(2x1) (3x2) to (4x22) (6x3)1/2x2 to 4x81/2x2 to 4x8Dogbone1x3 to 16x201x3 to 12x161x3 to 4x8Not Needed Not Needed 1/2x2 to 4x81/2x2 to 4x8Restraint Dogbone1x3 to 16x201x3 to 12x161x3 to 4x81x2 to 4x61x2 to 4x61/2x2 to 4x81/2x2 to 4x8End Termination1x3 to 16x201x3 to 12x161x3 to 4x81x2 to 4x61x2 to 4x61/2x2 to 4x81/2x2 to 4x82 PC End TerminationNot AvailableNot Available Not Available Not Available Not Available 1/2x2 to 4x81/2x2 to 4x8Reducer-Eccentric(3x1) (6x3) to (10x4)(14x18)Not Available Not Available Not Available Not Available C.F. C.F.Low Point Station1x3 to 12x161x3 to 12x161x3 to 4x81x2 to 4x61x2 to 4x61/2x2 to 4x81/2x2 to 4x8Access Tee1x3 to 12x161x3 to 12x161x3 to 4x8Not Needed Not Needed Not Available Not Available Cap1x3 to 16x201x3 to 8x121x3 to 4x81x2 to 4x61x2 to 4x6Not Available Not Available Dw Flange 1x3 to 16x20 C.F.Not Available 1x2 to 4x61x2 to 4x6Not Available Not Available Lateral1x3 to 16x201x3 to 8x12 C.F.2x3 to 4x62x3 to 4x6Not Available Not Available Lateral w/ 1/8 Bend1x3 to 16x201x3 to 8x12 C.F.2x3 to 4x62x3 to 4x6Not Available Not Available P Trap 1x3 to 16x201x3 to 8x121x3 to 4x81x2 to 4x61x2 to 4x6Not Available Not Available Floor Drain2x4 to 6x102x4 to 4x8 C.F.2x3 to 4x62x3 to 4x6Not Available Not Available Clean Out1x3 to 16x201x3 to 6x10 C.F.1x2 to 4x61x2 to 4x61/2x2 to 4x81/2x24x6Sanitary Tee1x3 to 16x201x3 to 8x12C.F.Not AvailableNot AvailableNot AvailableNot AvailablePoly-Flo®Duo-Pro ®Poly-Flo ®Pro-Lock TMPoly-Flo DPP HDPEPP Pro150 x 150 Pro150 x 45 Pro45 x 45PVDF PVDF x Pro150 PVDF x Pro45 PVDF x PVDF E-CTFE Halar x Halar Halar x Pro150 Halar x Pro45Pro-Lock PVC 40 x 40 PVC 80 x 40 PVC 80 x 80 CPVC 80 x 80 CPVC x PVC 80/40 CPVC x PVC 80/80。
2GIG-DW10-345 细胚门窗联系器安装说明书
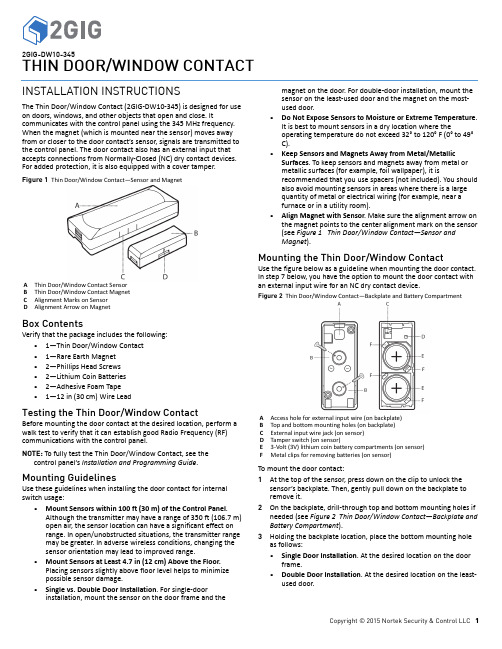
Copyright © 2015 Nortek Security & Control LLC 12GIG-DW10-345THIN DOOR/WINDOW CONTACTINSTALLATION INSTRUCTIONSThe Thin Door/Window Contact (2GIG ‐DW10‐345) is designed for use on doors, windows, and other objects that open and close. Itcommunicates with the control panel using the 345 MHz frequency. When the magnet (which is mounted near the sensor) moves away from or closer to the door contact’s sensor, signals are transmitted to the control panel. The door contact also has an external input that accepts connections from Normally ‐Closed (NC) dry contact devices. For added protection, it is also equipped with a cover tamper.Figure 1 ThinDoor/Window Contact—Sensor and MagnetBox ContentsVerify that the package includes the following:•1—Thin Door/Window Contact •1—Rare Earth Magnet •2—Phillips Head Screws •2—Lithium Coin Batteries •2—Adhesive Foam Tape •1—12 in (30 cm) Wire LeadTesting the Thin Door/Window ContactBefore mounting the door contact at the desired location, perform awalk test to verify that it can establish good Radio Frequency (RF) communications with the control panel.NOTE: To fully test the Thin Door/Window Contact, see thecontrol panel’s Installation and Programming Guide .Mounting GuidelinesUse these guidelines when installing the door contact for internal switch usage:•Mount Sensors within 100 ft (30 m) of the Control Panel .Although the transmitter may have a range of 350 ft (106.7 m) open air, the sensor location can have a significant effect on range. In open/unobstructed situations, the transmitter range may be greater. In adverse wireless conditions, changing the sensor orientation may lead to improved range.•Mount Sensors at Least 4.7 in (12 cm) Above the Floor.Placing sensors slightly above floor level helps to minimize possible sensor damage.•Single vs. Double Door Installation . For single ‐doorinstallation, mount the sensor on the door frame and themagnet on the door. For double ‐door installation, mount the sensor on the least ‐used door and the magnet on the most ‐used door.•Do Not Expose Sensors to Moisture or Extreme Temperature . It is best to mount sensors in a dry location where theoperating temperature do not exceed 32° to 120° F (0° to 49° C).•Keep Sensors and Magnets Away from Metal/Metallic Surfaces . To keep sensors and magnets away from metal or metallic surfaces (for example, foil wallpaper), it isrecommended that you use spacers (not included). You should also avoid mounting sensors in areas where there is a large quantity of metal or electrical wiring (for example, near a furnace or in a utility room).•Align Magnet with Sensor . Make sure the alignment arrow on the magnet points to the center alignment mark on the sensor (see Figure 1 Thin Door/Window Contact—Sensor and Magnet ).Mounting the Thin Door/Window ContactUse the figure below as a guideline when mounting the door contact. In step 7 below, you have the option to mount the door contact with an external input wire for an NC dry contact device.Figure 2 Thin Door/Window Contact—Backplate and Battery CompartmentTo mount the door contact:1At the top of the sensor, press down on the clip to unlock thesensor’s backplate. Then, gently pull down on the backplate to remove it.2On the backplate, drill ‐through top and bottom mounting holes ifneeded (see Figure 2 Thin Door/Window Contact—Backplate and Battery Compartment ).3Holding the backplate location, place the bottom mounting holeas follows:•Single Door Installation . At the desired location on the doorframe.•Double Door Installation . At the desired location on the least ‐used door.A Thin Door/Window Contact SensorB Thin Door/Window Contact MagnetC Alignment Marks on Sensor DAlignment Arrow on MagnetA Access hole for external input wire (on backplate)B Top and bottom mounting holes (on backplate)C External input wire jack (on sensor)D Tamper switch (on sensor)E 3‐Volt (3V) lithium coin battery compartments (on sensor)F Metal clips for removing batteries (on sensor)Thin Door/Window Contact | Installation InstructionsIMPORTANT: To minimize the risk of potential sensor damage, always mount the sensor at a minimum height of 4.7 in (12cm) from the floor.4Using the two (2) Phillip Head Screws (provided), secure the backplate the door (or door frame).5Ensure that the alignment arrow on the magnet is lined up with the middle mark on the sensor (see Figure 1 Thin Door/Window Contact—Sensor and Magnet).6Use the adhesive (provided) to secure the magnet as follows:•Single Door Installation. On the door.•Double Door Installation. On the most‐used door. IMPORTANT: The magnet must be no more than 0.4 in (1 cm) away from the sensor.NOTE: If you are not using an external input wire, skip step 7 and continue with step 8.7If you are using an external input wire, do the following: 7a Thread the external input wire through the base.7b Insert the two‐pin connector into the external input wire jack on the (see Part C in Figure 2 Thin Door/WindowContact—Backplate and Battery Compartment) cover.8Replace the sensor backplate. If applicable, ensure that the external input wire is connected to the NC dry contact device. NOTE: To learn how to program a sensor into the Control Panel, see the Control Panel’s Installation & Programming Guide. Inserting and Replacing the BatteriesTo insert or replace the batteries:1At the top of the sensor, push down the clip to unlock the sensor’s backplate. Then, gently pull down on the backplate to remove it.2Place a small flathead screwdriver in the slot between the metal clip and battery (see Part F in Figure 2 Thin Door/WindowContact—Backplate and Battery Compartment).3Holding down the raised plastic edge in the battery compartment, gently twist the screwdriver to pop out eachbattery.IMPORTANT: Always dispose and/or recycle used batteries in accordance with the hazardous waste recovery andrecycling regulations for your location. Your city, state, orcountry may also require you to comply with additionalhandling, recycling, and disposal requirements.4Insert the replacement batteries in the compartment. The plus (+) sign of both batteries should be facing up and the minus (‐) side facing down.WARNING: Failure to follow these warnings and instructions can lead to heat generation, rupture, leakage, explosion,fire, or other injury, or damage. Do not insert the batteryinto the compartment in the wrong direction. Alwaysreplace the battery with the same or equivalent type (seeSpecifications on page 2). Never recharge or disassemblethe battery. Never place the battery in fire or water. Alwayskeep batteries away from small children. If batteries areswallowed, promptly see a doctor. SPECIFICATIONSWireless Signal Range350 ft (106.7 m), open air, with WirelessControl PanelCode Outputs Alarm; Alarm Restore; Supervisory; LowBattery; External Alarm; External Restore;Tamper; Tamper RestoreTransmitter Frequency345.00 MHz (crystal controlled)Unique ID Codes Over one (1) million different codecombinationsSupervisory Interval70 minutesExternal Input Accepts N/C dry contact devicesMagnet Dimensions (L x W x H) 1.3 x 0.435 x 0.312 in (3.3 x 1.1 x 0.79 cm) Magnet Type Rare EarthSensor Dimensions (D x H) 2.59 x 1.03 x 0.49 in (6.58 x 2.62 x 1.24 cm) Weight (including battery & magnet)1.1 oz (31.2 g)Housing Material ABS PlasticColor WhiteOperating Temperature32°‐120° F (0° ‐ 49° C)Relative Humidity5‐90% Non‐CondensingBattery (included)Two (2) CR 2013 or equivalent LithiumbatteriesCertification Anatel, ETL, FCC, IC, and NOM REGULATORY INFORMATIONFCC NoticeThis device complies with Part 15 of the FCC's Rules. Operation is subject to the following two conditions:1This device may not cause harmful interference, and2This device must accept any interference received, including interference that may cause undesired operation.This equipment has been tested and found to comply with the limits for a Class B digital device, pursuant to Part 15 of the FCC Rules. These limits are designed to provide reasonable protection against harmful interference in a residential installation.This equipment generates, uses and can radiate radio frequency energy and, if not installed and used in accordance with the instructions, may cause harmful interference to radio communications. However, there is no guarantee that interference will not occur in a particular installation. If this equipment does cause harmful interference to radio or television reception, which can be determined by turning the equipment off and on, the user is encouraged to try to correct the interference by one or more of the following measures:•Reorient or relocate the receiving antenna.•Increase the separation between the equipment and receiver.•Connect the equipment into an outlet on a circuit different from that to which the receiver is connected.•Consult the dealer or an experienced radio/TV technician for help.This product complies with FCC radiation exposure limits for an uncontrolled environment. Avoid operating this product at a distance less than 20 cm from the user.2 Copyright © 2015 Nortek Security & Control LLCCAUTION: Any changed or modifications not expressly approved by the party responsible for compliance could void the user'sauthority to operate this equipment.Industry Canada (IC) ComplianceThis device complies with Industry Canada license‐exempt RSS standard(s). Operation is subject to the following two conditions: (1) this device may not cause interference, and (2) this device must accept any interference, including interference that may cause undesired operation of the device.Repairs to certified equipment should be made by an authorized Canadian maintenance facility designated by the supplier. Any repairs or alterations made by the user to this equipment, or equipment malfunctions, may give the telecommunications company cause to request the user to disconnect the equipment.Users should ensure for their own protection that the electrical ground connections of the power utility, telephone lines and internal metallic water pipe system, if present, are connected together. This precaution may be particularly important in rural areas.Users should not attempt to make such connections themselves, but should contact the appropriate electric inspection authority, or electrician, as appropriate.LIMITED WARRANTYThis Nortek Security & Control LLC product is warranted against defects in material and workmanship for two (2) years. This warranty extends only to wholesale customers who buy direct from Nortek Security & Control LLC or through Nortek Security & Control LLC’s normal distribution channels. Nortek Security & Control LLC does not warrant this product to consumers. Consumers should inquire from their selling dealer as to the nature of the dealer’s warranty, if any. There are no obligations or liabilities on the part of Nortek Security & Control LLC for consequential damages arising out of or in connection with use or performance of this product or other indirect damages with respect to loss of property, revenue, or profit, or cost of removal, installation, or reinstallation. All implied warranties for functionality, are valid only until the warranty expires. This Nortek Security & Control LLC Warranty is in lieu of all other warranties expressed or implied.2GIG1950 Camino Vida Roble, Suite 150Carlsbad, CA 92008 USAFor technical support in the USA and Canada:855‐2GIG‐TECH (855‐244‐4832)Email: ******************************Visit web site for technical support hours of operationFor technical support outside of the USA and Canada:Contact your regional distributorVisit for a list of distributors in yourregion77‐000015‐001 Rev. CCopyright © 2015 Nortek Security & Control LLC 3。
MB Quilted Soft-Top Cover 安裝指示说明书

Parts List:ShadeMaker Mesh Fabric Bimini Topor Bimini Top Plus - QTY 1Required Tools:Safety GlassesShadeMaker™ Freedom Mesh Bimini, Bimini PlusTops for 2007-2018 Jeep ®Wrangler JK VehiclesItems #142013XX, #142213XX and #142214XX2Important Safety informationYour MasterTop ®ShadeMaker™ Bimini Top, Bimini Top Plus are intended to increase the fair weather enjoyment of your off-road capable vehicle. Before installation, please take a moment to review the following safety information and installation instructions. Important safety information is generally preceded by one of three signal words indicating the relative risk of injury. The signal words mean:Attaching Quick Release Buckles:Throughout the installation you will need to attach several buckles around the sport bar of your Jeep. The MasterTop quick release buckles are designed for easy on-off installation. To buckle, simply insert the buckle pins into the Buckle box until it “clicks” shut. To disengage, squeeze the sides of the buckle box until the pins unclip. To tighten the strap,simply pull the exposed webbing “tab” located where the strap is threaded through the buckle.Before you begin Installation:We are excited that you have chosen the MasterTop ShadeMaker Freedom Mesh Bimini Top/Bimini Top Plus!These high quality tops are designed to enhance your fair weather driving pleasure while providing needed shade while driving in the hot sun while allowing you to keep the mesh top on when you put your hard or complete soft top back on your Jeep. Please note that it is important that you become familiar with the installation process of this top by reading the following instruction sheet and warnings thoroughly. Though we have used only the finest materials in creating this top, any product that is exposed to the elements requires some general maintenance to keep it looking like new. Please see page 7 for these important maintenance tips. Please also note that it is normal for the mesh fabric to contract and wrinkle when stored in the shipping carton. In a few days the fabric will relax and wrinkles will disappear.When unpacking, check to make sure all parts are included. If any part is missing or broken, please call MasterTop customer service at 720-575-5440.Installing the MasterTop ShadeMaker Freedom Mesh tops entails the wrapping of nylon webbing around several locations on your factory installed sport bar. In order to simplify the installation process, the following instructions show the general location of these straps and may not match exactly to the model you purchased. In all cases, the straps are to be wrapped around the sport bar and not around the door surround hardware unless noted.IMPORTANT Instruction Sheet Strap Installation Note: (all versions)Insert pins into buckle box to engage.To disengage,squeeze sides.Step 1: Attach to Windshield (all versions)Put on safety glasses. After removing/folding down your hard top Freedom Panels or soft top, drape the mesh fabric over the top of your Jeep with the snap straps facing forward. Thread the snap strap through the center windshield footman hoop and snap together to the snap that is closest to the snap head. Note that the Strap may fit somewhat sideways through the center footman loop depending on the model year of your Jeep. See Figs 1 & 1AThe ShadeMaker Freedom Mesh Concept:The MasterTop ShadeMaker Mesh Bimini top series are designed as an easy-on, easy off sun shade for your Jeep.The tight mesh weave is specially designed to block the heat caused by the sun while letting light and air to flow freely. The installation of these products is easy and requires no tools or windshield header, and allows this product to be left on while you run your hard or your soft top. Enjoy the shade and thank you for purchasing from MasterTop!Step 2: Front Side Snap MountOn 07-17 models it is required to attach the frontsnap straps to the larger side factory D-rings mountson the windshield. Line up the snap straps with thelarge D-rings and snap closed. See Fig 2.For Bimini Top Plus Installation, skip to page 5.FIG 2Installation of ShadeMaker Mesh Bimini and Bimini Plus Tops:Step 3: for Bimini Top onlySecure Side StrapsAfter securing the front of the Bimini Top to the frontFootman loops, wrap the front side corner strapsaround the horizontal sport bars located over the frontportion of the door and connect the buckles. Repeatthis strap install around the sport bar. Buckle strapstogether and tighten straps on each side evenly whilemaking sure the top is centered on the vehicle. Wesuggest you tighten from front to back, left side firstthen right side so top is centered. Then repeat until topis fairly tight. You will tighten top completely after step 4. See Fig 3 for side strap location on the sport Bar.FIG 3Installation of ShadeMaker Freedom Mesh Bimini Top:Step 4: for Bimini Top onlySecure Rear and Corner StrapsLocate the 2 rear straps and wrap the strap around thesound bar or center support and the center hoop of thesport bar. Attach straps to buckles and cinch tight. SeeFig 4.Locate the rear corner straps and wrap the strapsaround the corner “B-Pillar” as shown in Fig 5.Note how the corner strap fits under the seat belt mountas shown in Fig 6. Tighten all straps.For 07-18 JK 2 Door Vehicles, installation ofShadeMaker Freedom Mesh Bimini Top is complete.FIG 5FIG 6Step 4: for Bimini Top Plus: Secure Rear StrapsLocate the rear straps (Fig 9 & 10) and note how the corner strap fits under the seatbelt mount as shown in Fig 6. Attach and tighten straps while making sure the top iscentered on the vehicle. Tighten all straps after attaching to buckles.For 07-18 Wrangler Vehicles, installation of yourShadeMaker Mesh Bimini Top Plus is complete.Step 3: for Bimini Top Plus: Secure Side & B-Pillar StrapsAfter securing the front of the Bimini Top Plus to the front footman loops, wrap the sidestraps around the horizontal Sport Bars over the door(s) of the vehicle and attachbuckle pins into the buckles. See Figs 7 & 8 for strap location.Notice in Fig 8A how the center straps attach to the “B pillar” on 4 Door JK Wrangler.Tighten the straps while making sure the top is centered on the vehicle. We suggestyou tighten from front to back, left side first then right side so top is centered. Then repeat until top is fairly tight. You will tighten top completely after step 4.Make sure the rear tension straps DO NOTinterfere with rear seatbelt operation.FIG 7Plus for 2Door FIG 8Plus for 4Door Installation of ShadeMaker Mesh Bimini Top Plus:FIG 8AFIG 9Plus for 2 Door FIG 10Plus for 4 DoorFIG 66For Hardtop or Soft Top: Installation with Mesh Top “in place”:Un-snap all three front snaps from the windshield footman loops. Take each snap strap and snap it back to the snap stud outside the footman loop. This will keep the snap straps from hanging down. Loosen or disconnect the front two side straps near the roll bar so the Freedom panel latches can move freely. Latch the soft top or freedom panels to the front of the windshield. Re-connect/Tighten the front two side straps to tighten the front of the mesh top. See Fig 11 & 12. FIG 11FIG 12Using your ShadeMaker Freedom Mesh Top with your Hardtop or Soft Top Installed:Your Shade Maker Freedom Mesh top is designed to work with your hard top or original equipment soft top installed.Regardless of which top you have, each ShadeMaker top will need to be disconnected from the windshield footman loops so you can attach your top header or freedom panels to the windshield. If your front side straps are tight, this disconnection should not cause any unsightly drooping of the fabric.Fig 11 shows all three snap straps un-snapped and header latches closed on outside footman loops Front side straps need to be loosened or disconnected to allow your Freedom Panel latch to close. Re-connect/tighten straps once latches are closed.Freedom Panel Installation with Mesh Top “in place”:Your Freedom Mesh Top has cutouts for attaching the factory Freedom Top panels back on the vehicle. As shownabove in Fig 13 after placing the Freedom Top panels on the vehicle, slip your hand through the cutouts to secure the Freedom panels to the vehicle. Note that for the outside Freedom panel latches it may be easier to reach around the fabric to install the panels. For Bimini Plus models, the two rear “screw knobs” fit through the Freedom panel cut-outs above the sound bar as shown in Fig 14.FIG 11FIG 127Your MasterTop ShadeMaker Bimini Top or Bimini Top Plus is made of the finest materials available but to keep it looking new and for the maximum possible wear, it will need periodic cleaning and basic maintenance. The main threat to your soft top is pollutants, dirt and grime. By keeping your top clean you will prolong the life of your top.We recommend the following to keep your top like new:Washing:The top fabric should be washed often using a mild soap, warm water and a soft bristle brush. You can also use spe-cial soft top cleaners available on our Distributors websites. Make sure that after cleaning you rinse with clear water to remove all traces of soap to avoid residue. Hang to dry, do not put a ShadeMaker Top in a clothes dryer.For more information on MasterTop:This and other helpful product information is available on Please visit our website frequently for product updates and exciting news.Care and Maintenance of your MasterTopShadeMaker™ Bimini, Bimini Plus Tops:07-18 JK 4 Door Wranglerwith ShadeMaker FreedomBimini Plus shown installed.Your MasterTop®accessory is covered by the following Limited Warranty provided exclusively by MasterTop, Inc., 420 J Corporate Circle, Golden, CO 80401.This Limited Warranty is the only warranty made in connection with your purchase. MasterTop neither assumes nor authorizes any vendor, retailer or other person or entity to assume for it any other obligation or liability in connection with this product or Limited Warranty. This Limited Warranty does not apply and is not cumulative to any accessory or part distributed by any MasterTop distributor for which the Manufacturer provides a separate written warranty.What is Covered:Subject to the terms, exclusions and limitations herein and with respect only to MasterTop branded accessories first sold in the United States, MasterTop warrants to the initial retail purchaser only that your MasterTop accessory shall be free of defects in material and workmanship; for a period of 3 years from date of initial retail sale.All other warranties are hereby disclaimed, except to the extent prohibited by applicable law in which case any implied warranty of merchantability or fitness for a particular purpose on this product is limited to 3 years from date of initial retail sale. MasterTop reserves the rights to: (a.) require invoice or other proof your product is within the terms of this Limited Warranty as a condition of warranty service and, (b.) make future revisions to this product and Limited Warranty without prior notice or obligation to upgrade your product.What is Not Covered:Your MasterTop Limited Warranty does not cover products or parts MasterTop determines to have been damaged by or subjected to: (a.) installation damage, alteration, modification, failure to maintain or attempted repair or service by anyone not authorized by MasterTop, (b.) normal wearand tear, cosmetic damage or damage from water immersion, (c.) Acts of God, accidents, misuse, negligence, inadequate mounting or impact with vehicle(s), obstacles or other aspects of the environment, (d.) theft, vandalism or other intentional damage, (e.) fleet, rental or commercial use, (f.) use in competition or racing.Remedy Limited to Repair/Replacement: The exclusive remedy provided hereunder shall, upon MasterTop inspection and at MasterTop’s option, be either repair or replacement of product or parts (new or refurbished) covered under this Limited Warranty. Customers requesting warranty consideration on MasterTop Products should first contact MasterTop to obtain a RGA number (720-575-5440). All labor, removal, shipping and installation costs are customer’s responsibility.Other Limitations - Exclusion of Damages- Your Rights Under State Law:In consideration of the purchase price paid, neither MasterTop nor any independent MasterTop distributor /licensee are responsible for any time loss, rental costs, or for any incidental, consequential, punitive or other damages you may have or incur in connection with any part or product purchased. Your exclusive remedy hereunder for covered parts is repair/replacement as described above.This Limited Warranty gives you specific rights. You may also have other rights that vary from state to state. For example, some states do not allow limitations of how long an implied warranty lasts and/or do not allow the exclusion or limitation of incidental or consequential damages, so the limitations and exclusions herein may not apply to you.©MasterTop, Inc. 2017. All Rights Reserved. The term MasterTop®is a Registered Trademark of MasterTop Incorporated, Registered in U.S. Patent and Trademark Office.Part #941018.01 Version 12.14.17 LTR。
潘基电工具梯架产品说明书

7 PARTS MANUAL 7.1 LIFT ASSEMBLY7.2 PARTS LISTITEM QTY. DESCRIPTION PART #1 1 POWER PACK, 230V/1PH//60HZ. 6-19361 POWER PACK, 230V/3PH//60HZ. 6-11652 1 POWER POST WELDING (L.S.) 4-04293 2 SAFETY RACK WELDMENT (REAR) 3-04874 1 ALIGNMENT DECK WELDMENT (LEFT SIDE) 4-06791 SERVICE DECK WELDMENT (LEFT SIDE) 4-10245 1 FRONT CROSSMEMBER WELDMENT (LEFT SIDE) 4-03666 2 FRONT WHEEL STOP WELDMENT 2-09987 22 HEX NUT, 3/4"-10UNC 6-07378 30 F LAT WASHER, 3/4" I.D. 6-07389 22 WEDGE ANCHOR, 3/4"-10UNC X 5 1/2"LG. 6-137910 14 HEX HD. BOLT, 3/8"-16UNC X 1"LG. GR.8 6-066811 16 LOCKWASHER, 3/8" I.D. 6-005812 6 FLAT WASHER, 3/8" I.D. 6-062513 4 HEX HD. BOLT, 5/16"-18UNC X 1"LG. 6-029314 4 LOCKWASHER, 5/16" I.D. 6-067415 16LOCKWASHER,1/2"I.D. 6-005916 6 HEX HD. BOLT, 1/2"-13UNC X 1"LG. 6-004517 24LOCKWASHER,1/4"I.D. 6-005618 8 HEX HD. BOLT, 1/4"-20UNC X 3/4"LG. 6-017819 4RETAININGBAR 2-139120 8 FLAT WASHER 2"O.D X 13/32I.D. X 3/32 6-042621 8 SHOULDER BOLT 3/8" X 5/8"LG. 6-006922 2 REAR SLIP PLATE (FULL FLOATING) 3-019723 2BEARINGCAGE 3-019624 1 SET 1/4" BALL BEARING 6-082925 8GLIDEBEARING 2-077226 11SHEAVEASSEMBLY 2-055727 21 NYLON THRUST WASHER 1-075728 1 REAR CROSSMEMBER (WELDING) 4-037129 4 LOCKING PIN ASSEMBLY 2-063730 4 SELF TAP SCREW #10 X ½"LG. 6-050531 4 R AMP PIN 1-097832 4 C OTTER PIN, 1/8" X 1 1/2" LG. 6-097833 1 POST WELDING (FRONT - R.S) 4-043034 4 HEX NUT, 5/16UNC GR.5 6-029435 8 FLAT WASHER, 5/16" I.D. 6-029536 2APPROACHRAMP 3-028537 2 REAR POST WELDING 3-034738 1 ALIGNMENT DECK WELDMENT, (RIGHT SIDE) 4-06801 SERVICE DECK WELDMENT, (RIGHT SIDE) 4-102539 1 SHEAVE-SPACER 2 1/2"LG. 1-079840 1 SHEAVE-SPACER 1 1/4"LG. 1-078841 4 DECK SHEAVE PIN 2-100842 2 SHOULDER BOLT 3/8"DIA. X 1"LG. 6-020643 6 SHOULDER BOLT 3/8" DIA. X 5/8"LG. 6-006944 4 LOCK SAFETY PIN (WELDING) 1-123445 4CABLEROLLER 1-0766464748 848TENSION SPRINGCROSSMEMBER SHEAVE PINSHEAVE SPACER, 3/8” LG1-07681-07711-0786ITEM QTY. DESCRIPTION PART #49 4 SAFETY SHOE WELDMENT 2-099050 4 HEX. NYLON LOCKNUT, 1/4"-28UNF 6-156351 4COMPRESSIONSPRING 1-076752 4 HEX. NUT, 5/8"-18UNF 6-066253 4 INTERNAL TOOTH LOCKWASHER, 5/8" I.D. 6-066354 4 AIR CYLINDER (CLIPPARD #SRR-12-2-SP; 5 1/2" ROD EXT.) 6-065155 11 LOCK-SAFETY LSLOCK SAFETY RS2-05672-147556 4PLASTICBRACKET 1-0775 57 4PLASTICGUIDE 1-077658 8 HEX NUT, 5/8"-11UNC, GR.8 6-067359 2 SHEAVE-SPACER 1 3/4"LG. 1-079960 8 SET SCREW, 1/2"-13UNC X 1" LG. GR.8 6-072661 2 SHEAVE-SPACER 2 "LG. 1-094362 16 FLAT WASHER, ¼”ID X ¾”OD, PLATED 6-006063 1 HYDRAULIC CYLINDER 3.5" 4-018764 2 SAFETY RACK WELDMENT 3-058165 1 WEAR RING 3/8" WIDE X 1/8"THK. X 3 1/2"O.D. 6-000466 1PISTON 2-056467 1 "O" RING 1 1/8"O.D. X 1/8" C/S 6-065668 1 PISTON SEAL 3 1/2"O.D. X 3"I.D. X 3/8" 6-000369 1 PISTON SEAL KIT 0-016970 1 PISTON ROD (MACHINED) 2-056571 2 HEX NUT 1"-14UNF-2A 6-066472 1CABLEFLANGE 2-056173 1 HOSE CLAMP 4 1/2"DIA. 6-066574 2 HEX. BOLT 3/8"-16UNC-1 1/4"LG. GR.8 6-066675 1RODWIPER 6-0653 76 1RODSEAL 6-0654 77 1GLAND 3-034878 1 "O" RING 3 1/2"O.D. X 1/8" C/S 6-065579 1 GLAND SEAL KIT 0-017080 4 HEX HD. BOLT 3/8"-16UNC X 3"LG. 6-138681 4SHEAVECOVER 2-0997 82 1SERIALTAG 6-1115 83 1"ALI"PLATE 6-098884 1 FRONT CROSSMEMBER WELDMENT (RIGHT SIDE) 4-036885 1 DECAL SET, ALI/WL 200 6-098888 11 LOCK SAFETY LSLOCK SAFETY RS2-09802-142789 1 "CAUTION" TAPE, (40" LG.) 6-112590 2 HEX HD. BOLT, 1/2"-13UNC x 3"LG. 6-138191 16 HEX HD. BOLT, 1/4"-20UNC x 1 1/4"LG. 6-002792 10 HEX HD. BOLT, 1/2"-13UNC x 2"LG. 6-076993 20 FLAT WASHER, 1/2"I.D. SAE 6-024894 10 HEX NUT, 1/2"-13UNC 6-003595 2TOPPLATE 2-112596 1 LOCK NUT, 7/8”-14UNF 6-116097 1“ATTENTION”DECAL 6-16377.3 HYDRAULICS AND AIR KITS ASSEMBLY7.4 HYDRAULIC AND AIR KITSITEM QTY. DESCRIPTION PART#1 9 90° ELBOW, 1/8"NPT X 1/4"POLY TUBE 6-07092 4 AIR CYLINDER 6-06513 1 1/4" DIA. POLY TUBE (50’ LG.) 6-07064 3 ADAPTER, 3/8" POLY TUBE X 1/4"NPT 6-07105 2 TERMINAL BOLT, 3/4" 6-07136 2 PLUG, 1/4"NPT 6-02827 3 1/4" NPT STREET TEE 6-00148 1 1/4" NPT STREET ELBOW 6-00159 1 3/8" DIA. POLY TUBE (25’ LG.) 6-070710 1 90° ELBOW, 3/8"JIC M X 9/16"SAE M 6-080411 1 HOSE GUARD (4’ LG.) 6-071412 1 POWER PACK 230V/1 PH/60 HZ. 6-19361 POWER PACK 230V/3 PH/60 HZ. 6-116513 1 HYD.HOSE ASS'Y, 3/8"JIC-F, 16FT LG. 6-169214 3 CABLE TIE 6-073115 1 AIR VALVE & FILTER ASS’Y 2-139416 1 ADAPTER, 3/8"NPT M X 3/8"JIC M 6-034517 1 FLOW CONTROL 6-193718 1 3-WAY AIR VALVE 6-177519 1 90° ELBOW, 1/4"NPT M X 3/8"NPT F 6-079620 3 ADAPTER, 1/4" POLY TUBE X 1/8"NPT 6-070821 1 AIR VALVE PUSHBUTTON KIT 6-177722 1 AIR FILTER ASSEMBLY 6-07721 AIR FILTER ELEMENT, (REPLACEMENT) 6-018023 1 AIR VALVE FITTING KIT 0-040524 1 VELOCITY FUSE 6-168425 1 PLUG, 1/8" NPT 6-018226 2 MANIFOLD 1-105727 4 HEX HD.CAP SCREW, 1/4"-20UNC X 2"LG. 6-017728 4 HEX NUT, 1/4"-20UNC 6-003229 4 LOCKWASHER, 1/4"I.D. 6-005630 2 1/4” POLYTUBE ADAPTER 6-074732 1 "LIFT OPERATION" DECAL 6-059333 1 ADAPTER, 1/8"NPT M X 1/4"JIC M 6-028034 1 ADAPTER, 3/8"NPT M X 3/8"JIC F, SWIVEL 6-07977.5 CABLE ROUTING DIAGRAM7.6 CABLE ROUTINGITEM QTY. DESCRIPTION PART#1 1 CABLE ASSEMBLY, 404.5”LG. (LEFT-FRONT) 2-15042 1 CABLE ASSEMBLY, 157.75"LG. (LEFT-REAR) 2-15053 1 CABLE ASSEMBLY, 213.75"LG. (RIGHT-REAR) 2-15064 1 CABLE ASSEMBLY, 459.5”LG. (RIGHT-FRONT) 2-15075 8 HEX NUT, 7/8"-14UNF, GR.8 6-07246 4 CABLE SPACER, 2"LG. 1-08007 4 FLAT WASHER, 7/8" I.D. 6-07258 4 CABLE SPACER, 1"LG. 1-08017.7 POWER PACK7.8 POWER PACK PARTS LIST:#6-1936 (AB-1400) 208-230V/1PH/60Hz#6-1165 (AD-1044) 208-230V/3PH/60Hz# DESCRIPTIONPART ITEMQTY.6-1087CHECKCARTRIDGE1 1 VALVE6-2136AUTOHOIST2 1 LABELINSTALLATIONBLADDER&6-1376CAP4 1 BREATHER6 1 MOTOR AC 208-230V. 2HP/1PH/60Hz, BLK 6-21391 MOTOR AC 208-230V. 2HP/3PH/60Hz, BLK 6-1079AUTOHOIST 6-2149WARNING7 1 LABEL9 1 SPRING 0.480” x 0.063” x 0.42” COMP 6-215110 1 RETURN HOSE 3/8” OD x 21.5” 6-2152NUT6-2153TUBE11 1 COMPRESSIONSLEEVE6-2154TUBE12 1 COMPRESSIONAUTOHOIST6-2155UNIVERSAL13 1 ENDHEAD14 1 PUMPASSY 3.1 CC/REV. SHORT SPLINE 6-168815 1 RELIEF ASSEMBLY FIXED 170 BAR 6-131716 1 VALVE CARTRIDGE RELEASE MANUAL 6-088017 1 WIRING ASSEMBLY AC 1PH FENNER 6-2156FENNER6-09183PHASSEMBLY1 WIRINGAC18 2 BOLT 5/16”-24 x 3.00” TORX G8 6-10901.260”6-07749T-20/40SAE19 1 COUPLING6-21579/16”SAEPLUG20 1 PLUMBING21 1 SEAL SHAFT 0.500” x 1.00” x 0.25” 6-215822 1 WASHER 0.338” x 0.625” x 0.060” STEEL 6-21596-2161NPT3/8”24 1 PLUMBINGPLUG6-2162 25 1 PLUMBINGMAGNET27 2 SCREW TAPTITE M6 x 1.0 12MM TORX 6-216428 1 COVERSUCTION 6-2165ASSY29 1 PLUMBING CLAMP HOSE ADJ. INLET 6-21661.00”6-1392SHCS30 1 BOLT5/16”-18x31 1 NUT ¾”-16 x 1” HEX x 0.250” STEEL 6-216732 1 WASHER ¾” INT. TOOTH LOCK 6-216833 1 BRACKET – HANDLE ASSY REL BLACK 6-077634 4 BOLT M6 x 1.0 35MM SOC HD 6-2169HI-COLLAR 6-2170LOCK35 4 WASHER¼”37 4 BOLT #12-24 x 0.50’ HEX WSHRHD 6-109138 1 PLUMBING ASSY INLET 17.24 (3) 6-0786ASSEMBLY 6-1089CAP39 1 RELIEFVALVE40 1 TANK PLASTIC 6.7 OS 22.50” BLK 6-1399WHITE6-1846LONG8”41 1 CABLETIE6-0875BUNA42 1 O-RING2-348CAUTIONALL SAFETY LADDERS USED ON 4-POST LIFTS ARE PRELOADED.REMOVING THE BOLT HOLDING THE BOTTOM PORTION OF THE SAFETY LADDER WITHOUT PROPER PRECAUTIONS CAN RESULT IN INJURY. PLEASE CONTACT CUSTOMER SERVICE FOR PROPER REMOVAL INSTRUCTIONS.33。
- 1、下载文档前请自行甄别文档内容的完整性,平台不提供额外的编辑、内容补充、找答案等附加服务。
- 2、"仅部分预览"的文档,不可在线预览部分如存在完整性等问题,可反馈申请退款(可完整预览的文档不适用该条件!)。
- 3、如文档侵犯您的权益,请联系客服反馈,我们会尽快为您处理(人工客服工作时间:9:00-18:30)。
Note Vcont1 − Vcont2 ≤ 6.0 V
RECOMMENDED OPERATING RANGE (TA = +25°C, unless otherwise specified)
Symbol Vcont (H) Vcont (L) MIN. 1.8 −0.2 TYP. 3.0 0 MAX. 5.3 0.2 Unit V V
•
• •
APPLICATIONS
• L, S-band digital cellular or cordless telephone TM • W-LAN, WLL and Bluetooth etc.
ORDERING INFORMATION
Part Number Package 6-pin super minimold (2012) Marking G4J Supplying Form • Embossed tape 8 mm wide • Pin 4, 5, 6 face the perforation side of the tape • Qty 3 kpcs/reel
Note 3
Pin (1 dB)
f = 0.5 to 3.0 GHz
2nd Harmonics
2f0
f = 2.0 GHz, Pin = +15 dBm f = 2.5 GHz, Pin = +15 dBm
dBc dBc dBc dBc dBm
3rd Harmonics
3f0
f = 2.0 GHz, Pin = +15 dBm f = 2.5 GHz, Pin = +15 dBm
µPG2214TB
PIN CONNECTIONS AND INTERNAL BLOCK DIAGRAM
(Top View)
1 6 1
(Top View)
6 6
(Bottom View)
1
Pin No. 1 2 3 4
Pin Name OUTPUT1 GND OUTPUT2 Vcont2 INPUT Vcont1
MAX. 0.45 0.45 0.50 0.55 0.60 − − − − − − − − − − − − −47 −47 −47 −47 −
Unit dB dB dB dB dB dB dB dB dB dB dB dB dB dB dBm dBm dBm
1 dB Loss Compression Input Power
G4J
Vcont1 Low High Low Parameter Parameter
2
5 2
5 5
2
3
4 3
4 4
3
5 6
TRUTH TABLE
Vcont2 High INPUT−OUTPUT1 ON OFF INPUT−OUTPUT2 OFF ON
ABSOLUTE MAXIMUM RATINGS (TA = +25°C, unless otherwise specified)
Note 1 Note 1 Note 1 Note 1
MIN. − − − − − 29 25 24 23 21 15 15 15 15 +21.0 − − − − − − − −
TYP. 0.25 0.25 0.30 0.35 0.35 32 28 27 26 24 20 20 20 20 +23.0 +23.0 +27.0 −55 −55 −55 −55 +58
Intermodulation Intercept Point
IIP3
f = 0.5 to 3.0 GHz, 2 tone, Pin = +16 dBm, 5 MHz spicing
Switch Control Current Switch Control Speed
Parameter Insertion Loss 1 Insertion Loss 2 Insertion Loss 3 Insertion Loss 4 Insertion Loss 5 Isolation 1 Isolation 2 Isolation 3 Isolation 4 Isolation 5 Input Return Loss 1 Input Return Loss 2 Output Return Loss 1 Output Return Loss 2 0.1 dB Loss Compression Input Power
Note 2
Symbol Lins1 Lins2 Lins3 Lins4 Lins5 ISL1 ISL2 ISL3 ISL4 ISL5 RLin1 RLin2 RLout1 RLout2 Pin (0.1 dB)
Test Conditions f = 0.05 to 0.5 GHz f = 0.5 to 1.0 GHz f = 1.0 to 2.0 GHz f = 2.0 to 2.5 GHz f = 2.5 to 3.0 GHz f = 0.05 to 0.5 GHz f = 0.5 to 1.0 GHz f = 1.0 to 2.0 GHz f = 2.0 to 2.5 GHz f = 2.5 to 3.0 GHz f = 0.05 to 0.5 GHz f = 0.5 to 3.0 GHz f = 0.05 to 0.5 GHz f = 0.5 to 3.0 GHz f = 2.0/2.5 GHz f = 0.5 to 3.0 GHz
Document No. PG10477EJ03V0DS (3rd edition) Date Published October 2004 CP(K) Printed in Japan
The mark shows major revised points. NEC Compound Semiconductor Devices, Ltd. 2004
µPG2214TB-E4
Remark To order evaluation samples, contact your nearby sales office. Part number for sample order: µPG2214TB
Caution Observe precautions when handling because these devices are sensitive to electrostatic discharge.
Symbol Vcont Pin TA Tstg Ratings +6.0
Note
Unit V dBm °C °C
Switch Control Voltage Input Power Operating Ambient Temperature Storage Temperature
+30 −45 to +85 −55 to +150
The information in this document is subject to change without notice. Before using this document, please confirm that this is the latest version.
Not all devices/types available in every country. Please check with local NEC Compound Semiconductor Devices representative for availability and additional information.
FEATURES
• Switch control voltage • : Vcont (H) = 1.8 to 5.3 V (3.0 V TYP.) : Vcont (L) = −0.2 to +0.2 V (0 V TYP.) Low insertion loss : Lins1 = 0.25 dB TYP. @ f = 0.05 to 0.5 GHz, Vcont (H) = 3.0 V, Vcont (L) = 0 V : Lins2 = 0.25 dB TYP. @ f = 0.5 to 1.0 GHz, Vcont (H) = 3.0 V, Vcont (L) = 0 V : Lins3 = 0.30 dB TYP. @ f = 1.0 to 2.0 GHz, Vcont (H) = 3.0 V, Vcont (L) = 0 V : Lins4 = 0.35 dB TYP. @ f = 2.0 to 2.5 GHz, Vcont (H) = 3.0 V, Vcont (L) = 0 V : Lins5 = 0.35 dB TYP. @ f = 2.5 to 3.0 GHz, Vcont (H) = 3.0 V, Vcont (L) = 0 V High isolation : ISL1 = 32 dB TYP. @ f = 0.05 to 0.5 GHz, Vcont (H) = 3.0 V, Vcont (L) = 0 V : ISL2 = 28 dB TYP. @ f = 0.5 to 1.0 GHz, Vcont (H) = 3.0 V, Vcont (L) = 0 V : ISL3 = 27 dB TYP. @ f = 1.0 to 2.0 GHz, Vcont (H) = 3.0 V, Vcont (L) = 0 V : ISL4 = 26 dB TYP. @ f = 2.0 to 2.5 GHz, Vcont (H) = 3.0 V, Vcont (L) = 0 V : ISL5 = 24 dB TYP. @ f = 2.5 to 3.0 GHz, Vcont (H) = 3.0 V, Vcont (L) = 0 V Handling power : Pin (1 dB) = +27.0 dBm TYP. @ f = 0.5 to 3.0 GHz, Vcont (H) = 3.0 V, Vcont (L) = 0 V : Pin (1 dB) = +20.0 dBm TYP. @ f = 0.5 to 3.0 GHz, Vcont (H) = 1.8 V, Vcont (L) = 0 V High-density surface mounting : 6-pin super minimold package (2.0 × 1.25 × 0.9 mm)