高效率的整体刀具自动制造单元
数控机床刀具选择和应用

数控机床刀具选择和应用数控机床刀具选择和应用数控机床刀具选择和应用摘要:数控机床取代传统的普通机床进行大量机械加工,普通机械逐渐被数控机械所代替。
数控机床的刀具材料选择和近几年来在刀具材料,创新科技领域的现状及发展趋势。
拉削、滚压、搓挤刀具和复合(组合)孔加工数控刀具和集成刀具材料及特种数控机床领域的创新科技成果不断产生制造业新兴经济增长点。
关键词:数控机床;刀具材料;选择及应用机械制造产业应用数控机床(CNC)加工中心(MC)柔性制造单元(FMC)和柔性制造(FMS)作为自动化制造工程组成部分,成配套数控机床选择合适的刀具材料与刀具,在数控机床加工生产中是核心重要问题。
正确设计与合理使用数控机床对应材料的刀具,对数控机床高效率自动化流程作业进程有提高生产效率和提升工件表面加工精度的重要意义。
数控机床应用刀具为两大类。
模块化刀具为主流,以前常用普通机床配置的常规刀具。
目前数控机床模块化刀具在数控加工制造业占比重越来越高,数控机床模块化刀具可以缩短换到时间、缩短数控机床停机时间、单位时间内增加工件的产成率、将数控机床的夹具对应配套刀具配置与换刀时间大幅缩短,使单位时间内生产效率提升,提高性价比和经济效益。
数控加工刀具执行科学合理与标准化配置,提高了刀具使用率。
按照模块化刀具系统,数控加工刀具分配为车削加工刀具、钻削加工刀具、镗铣加工刀具。
加工逆螺纹刀具、复合机床刀具应用于特别的数控机床加工工件,为特殊加工刀具。
可转位与不可转位机床夹具由加工刀具的刀体结构决定归类为机架式刀具和焊接式刀具,即为镶嵌式加工刀具。
加工复杂体工型件转速较高及材料硬度较高毛坯件时,需加工刀具刀柄有良好减震措施,即为减震式加工刀具。
加工高硬度、高强度材料毛坯件造成高热高温需降温润滑,由加工刀具的中空体内部精细通孔将切削冷却润滑液注射至随机刀刃切削刃位置起到冷却润滑和带走切削屑的作用,此为冷却式加工刀具。
切削工字钢及YT类可锻铸铁为P型,切削合金铸铁及高含量锰钢和不锈钢奥氏体及铸铁为YW类属于M型,切削钛金属及高温合金属于M-S型,切削非钛金属、低温强硬铸铁、铸铁属于K类即YG型,切削非铁合金、镁铝金属属于K-N 型,切削淬火硬化合金属于K-H型。
数控机床自动换刀装置
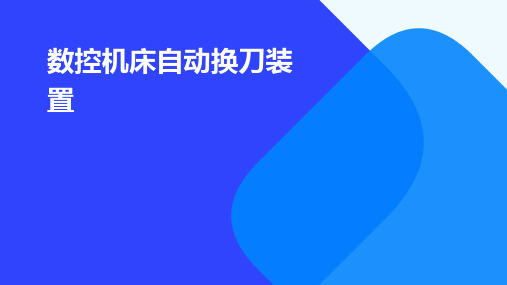
02
数控机床自动换刀装置 的结构与设计
刀库设计
刀库容量
根据数控机床的加工需求, 合理设计刀库容量,确保 能够存放足够数量的刀具。
刀具存放方式
采用合适的刀具存放方式, 如刀具架、刀具套等,以 便于刀具的存取和管理。
刀库布局
根据数控机床的整体布局 和加工要求,合理布置刀 库的位置和方向,以提高 换刀效率和加工精度。
例如,在发动机缸体的加工中,需要使用不同种类的刀具进行粗加工、半精加工和精加工。数控机床 自动换刀装置可以在加工过程中自动识别需要更换的刀具,并快速、准确地完成换刀操作,保证了加 工过程的连续性和稳定性。
应用案例二:航空航天业
航空航天业对零部件的加工精度和效率要求极高,数控机床自动换刀装置在航空 航天业中也有着广泛的应用。例如,在飞机机身和机翼的制造中,需要使用大型 五轴数控机床进行加工,而大型五轴数控机床的换刀时间较长,影响了加工效率 。
数控机床自动换刀装置的应用,可以大大缩短换刀时间,提高加工效率。同时, 由于航空航天业对零部件的加工精度要求极高,数控机床自动换刀装置的精确性 和稳定性也得到了充分验证,为航空航天业的发展提供了有力支持。
应用案例三:模具制造业
模具制造业是数控机床自动换刀装置的重要应用领域 之一。在模具的制造过程中,需要使用不同种类的刀 具进行粗加工、半精加工和精加工。数控机床自动换 刀装置的应用,可以大大提高模具的加工效率和精度 。
分类与比较
按换刀方式分类
数控机床自动换刀装置可分为机械手换刀和机器人换刀两种 方式。机械手换刀方式具有结构简单、成本低等优点,但换 刀速度较慢;机器人换刀方式具有换刀速度快、精度高等优 点,但结构复杂、成本较高。
按刀库类型分类
数控机床自动换刀装置可分为固定刀库和旋转刀库两种类型 。固定刀库具有容量大、换刀速度快等优点,但结构复杂、 成本较高;旋转刀库具有结构简单、成本低等优点,但容量 较小、换刀速度较慢。
先进制造技术课后作业

第三章课后习题3-2 有哪几类零件成形方法?列举这些成形方法各自工艺内容。
答:依据材料成形学观点,从物质组成方式可把机械零件成形方式分为如下三类型: ① 受迫成形:利用材料的可成形性,在特定的边界和外力约束条件下的成形方法。
② 去除成形:运用分离的办法,把一部分材料(裕量材料)有序地从基体中分离出去而成形的办法。
③ 堆积成形:它是运用合并与连接的办法,把材料(气、液、固相)有序地合并堆积起来的成形方法。
3-5 什么是超塑性?目前金属超塑性主要有哪两种工艺手段获得?答:超塑性是指材料在一定的内部组织条件(如晶粒形状及尺寸、相变等)和外部环境条件(如温度、应变速率等)下,呈现出异常低的流变抗力、异常高的流变性能的现象。
超塑性的特点有大延伸率,无缩颈,小应力, 易成形。
金属的超塑性主要有两种类型:1)细晶超塑性,又称组织超塑性恒温超塑性,其超塑性产生的内在条件是具有均匀、稳定的等轴细晶组织,晶粒尺寸常小于10μm ;外在条件是每种超塑性材料应在特地的温度及速度下变形,一般应变速率在154min 10~10---范围内,要比普通金属应变速率至少低一个数量级。
2)相变超塑性,又称环境超塑性,是指在材料相变点上下进行温度变化循环的同时对式样加载,经多次循环式样得到积累的大变形。
3-6 目前在高分子材料注射成形工艺中有哪些先进技术?答: 目前在高分子材料注射成形工艺中的先进技术有:以组合惰性气体为特征的气辅成型、微发泡成型等;以组合压缩过程为特征的注射压缩成形、注射压制成形、表面贴合成形等;以组合模具移动或加热等过程为特征的自切浇口成形、模具滑合成形、热流道模具成形等; 以组合取向或延伸过程为特征的剪切场控制取向成形、磁场成形等。
3-11 在怎样的速度范围下进行加工属于高速加工?分析高速切削加工所需解决的关键技术。
答:超高速加工技术是指采用超硬材料刀具磨具和能可靠地实现高速运动的高精度、高自动化、高柔性的制造设备,以极大地提高切削速度来达到提高材料切除率、加工精度和加工质量的现代制造加工技术。
CAPP在数控加工中的应用

CAPP在数控加工中的应用数控加工是一种利用计算机操控数控设备自动加工零件的技术,已经成为了现代制造业中不可或缺的一部分。
而CAPP (计算机辅助加工工艺)则是其中重要的一环,它通过计算机模拟和优化加工工艺,帮助制定高效的生产工艺,提高加工精度和效率。
本文将介绍CAPP在数控加工中的应用。
一、CAPP的定义和功能CAPP是一种计算机辅助制造技术,它通过计算机模拟、优化加工工艺流程,帮助制定高效的工艺方案,提高零件加工效率和质量。
它通常包括以下功能:1. 工艺规划。
根据零件的几何特征、材料、加工工艺和机床设备的性能,自动生成加工工艺方案。
2. 刀具路径规划和优化。
根据零件的几何形状和刀具特征,计算出最优的刀具路径,以尽可能避免冲突、减小干涉并提高切削性能。
3. 刀具选择。
根据零件的材料和加工要求,自动选择最适合的刀具,以确保高效加工和良好表面质量。
4. 加工参数优化。
根据加工条件、切削参数和刀具特征等因素,优化加工参数,提高加工效率和加工质量。
二、CAPP在数控加工中的应用CAPP在数控加工中的应用主要有以下几个方面:1. 数控编程优化:CAPP可以通过计算机模拟、验证和优化加工工艺流程,辅助数控编程人员快速编写高效的数控加工程序,减少编程时间和错误。
2. 刀具路径优化:CAPP可以通过计算机模拟和优化刀具路径,以实现最优的切削效果和加工精度,避免冲突和干涉,减少切削时间,提高生产效率。
3. 刀具选择:CAPP可以根据材料和加工要求自动选择最适合的刀具,以保证高效加工和优质表面质量。
4. 加工参数优化:CAPP可以根据加工条件和材料特性,自动优化加工参数,达到最佳的生产效率和加工质量。
5. 零件成本优化:CAPP可利用数据分析和工艺规划,辅助企业制定全面的加工工艺方案,实现零件成本的降低,提高企业生产效益和市场竞争力。
三、CAPP的优点和局限CAPP在数控加工中有以下优点:1. 自动化程度高:CAPP通过计算机辅助制造技术,自动化完成工艺规划、刀具路径规划、刀具选择和加工参数优化等工作,提高效率。
高速切削技术研究
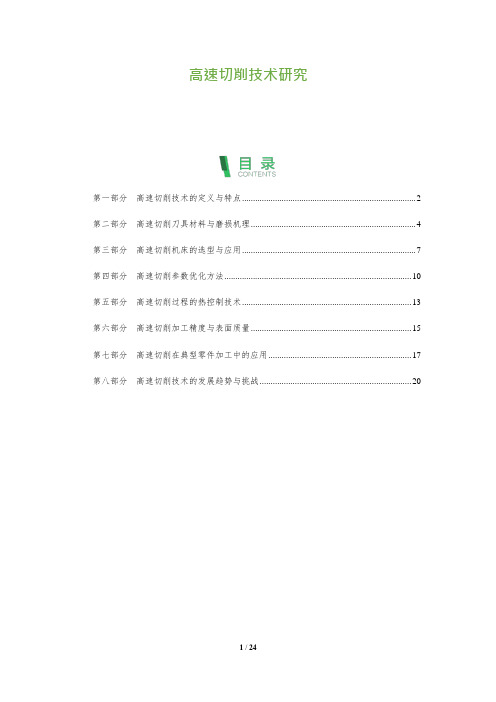
高速切削技术研究第一部分高速切削技术的定义与特点 (2)第二部分高速切削刀具材料与磨损机理 (4)第三部分高速切削机床的选型与应用 (7)第四部分高速切削参数优化方法 (10)第五部分高速切削过程的热控制技术 (13)第六部分高速切削加工精度与表面质量 (15)第七部分高速切削在典型零件加工中的应用 (17)第八部分高速切削技术的发展趋势与挑战 (20)第一部分高速切削技术的定义与特点高速切削技术是一种先进的制造工艺,它通过使用高转速的刀具和优化的切削参数来提高材料去除率、加工精度和表面质量。
该技术的核心在于实现高效率、高质量和高精度的加工过程。
在高速切削过程中,刀具以极高的速度旋转(通常超过每分钟数千转),同时进给速度也相应提高。
这种高速旋转产生的离心力有助于减小切削力和切削热,从而延长刀具寿命并减少工件的热变形。
此外,由于切削力的降低,高速切削还可以减少振动,进一步提高加工精度。
高速切削技术的优势主要体现在以下几个方面:1.高效率:与传统切削相比,高速切削可以显著提高材料去除率,缩短加工时间。
研究表明,高速切削可以提高生产效率达 30%至50%。
2.高精度:高速切削过程中的低切削力可以减少工件的振动,从而提高加工精度。
此外,由于切削热的影响较小,工件的热变形也得到了控制。
3.高质量表面:高速切削产生的切削热较低,这有助于减少工件的烧伤和裂纹,从而获得更好的表面质量。
4.刀具寿命延长:高速切削可以降低切削力,减少刀具磨损,从而延长刀具的使用寿命。
5.节能减排:高速切削技术可以实现更高的材料去除率,从而减少能源消耗和碳排放。
然而,高速切削技术也存在一些挑战,如刀具成本较高、对机床性能要求较高等。
因此,在实际应用中,需要根据具体加工需求和技术条件,合理选择切削参数和刀具,以确保高速切削技术的有效性和经济性。
总之,高速切削技术作为一种先进的制造工艺,具有高效率、高精度、高质量表面等优势,但在实际应用中需充分考虑其成本和设备要求。
数控机床的基本构造及工作原理

数控机床的基本构造及工作原理数控机床是一种利用计算机控制的自动化机械设备。
它是在传统机床的基础上发展而来,具有高精度、高效率和多功能特点。
下面将对数控机床的基本构造和工作原理进行详细介绍。
一、数控机床的基本构造1.机床主体部分:机床主体通常由床身、立柱、横梁和工作台等组成。
床身是整个机床的基础,用于安装和支撑其他各个部件。
立柱起支撑和导向作用,横梁用于支撑和传递载荷,工作台用于支撑工件。
2.传动系统:传动系统将电机产生的动力传递给刀具或工件,实现切削加工。
常见的传动方式包括电机驱动螺杆、齿轮传动和皮带传动等。
3.控制系统:控制系统是数控机床的核心部分,用于实现机床的自动化操作。
它由计算机、数控装置、伺服控制器和编码器等组成。
计算机是控制系统的主控部分,负责接收和处理指令。
数控装置将计算机的指令转化为电信号,控制伺服控制器和驱动器工作。
伺服控制器接收数控装置的信号,输出相应的电流给驱动器,驱动刀具或工件运动。
4.动力系统:动力系统提供机床的驱动力,通常由电机提供动力。
根据不同的切削工况和需求,可以采用不同类型的电机,如交流伺服电机、直流伺服电机和步进电机等。
5.刀具或工件换刀系统:刀具或工件换刀系统用于实现自动化换刀操作,提高生产效率。
根据不同的切削任务和工艺要求,可以配置不同的换刀方式,如手动换刀、自动换刀和带刀库的换刀等。
二、数控机床的工作原理1.编程:要进行数控加工,首先需要编写加工程序。
加工程序是由一系列指令组成的文本文件,用于描述切削路径、刀具换向、进给速度、切削深度等参数。
2.坐标系转换:在编写加工程序时,需要定义一个坐标系,用于描述刀具或工件的位置和运动。
通常使用直角坐标系或极坐标系。
在实际运行时,数控系统会将编程坐标转换为机床坐标,以控制机床的运动。
3.运动控制:数控系统根据加工程序生成的指令,通过伺服控制器控制电机运动,实现刀具或工件在空间中的运动。
伺服控制器接收数控装置发出的指令,输出相应的电流给驱动器,驱动电机旋转。
数控车床的基本组成和工作原理

数控车床的基本组成和工作原理数控车床是一种通过计算机程序控制刀具移动和工件旋转等运动的机床,能够精确加工各类轴对称的零部件。
它是现代制造业中重要的加工设备,具有高精度、高效率、灵活性强等优点。
下面将介绍数控车床的基本组成和工作原理。
一、基本组成1.床身:数控车床的床身是整个机床的基础架构,承载整个机床的各个部件和组件。
床身一般由铸铁制成,具有高强度和抗振性能。
2.主轴箱:主轴箱安装在床身上,负责驱动工件的旋转运动。
主轴由电机驱动,在主轴箱内通过轴承支撑和转动。
3.刀架:刀架负责调节和控制刀具的位置和运动。
数控车床一般配备多个刀架,用于安装不同类型和规格的刀具。
刀架配有电动或液压驱动装置,可以实现刀具的快速切换和自动换刀。
4.工作台:工作台是放置和夹持工件的平台。
数控车床的工作台可以实现不同方向的移动和旋转,以便于刀具的切削和工件的加工。
5.伺服系统:伺服系统由数控装置、伺服电机和测量装置等组成,用于控制刀具和工件的运动。
数控装置是数控车床的大脑,根据预先编写的切削程序计算和控制刀具运动轨迹、进给速度和加工参数等。
6.冷却系统:冷却系统用于为数控车床提供冷却液,以冷却工件和刀具,减少摩擦和热量的产生,保护工件和刀具不受损坏。
二、工作原理1.切削程序编写:在进行切削之前,需要先编写切削程序。
切削程序是指通过计算机软件编写的程序,包含了刀具运动轨迹、进给速度、切削深度等加工参数的信息。
2.加工设备准备:在进行数控加工之前,需要进行刀具的安装和工件夹持。
安装刀具时,需要选择合适的刀具规格和类型,并进行刀具刀柄的装夹。
工件夹持时,需要使用合适的夹具将工件固定在工作台上。
3.参数设置:设置数控装置的各项参数,包括切削深度、进给速度、切削速度、加工路径等。
这些参数的设置根据切削程序和工件的要求进行调整。
4.启动加工:当设置完成后,启动数控装置,数控装置根据切削程序的要求,计算刀具的运动轨迹和运动速度,控制伺服系统的动作。
数控的工作总结(6篇万能)
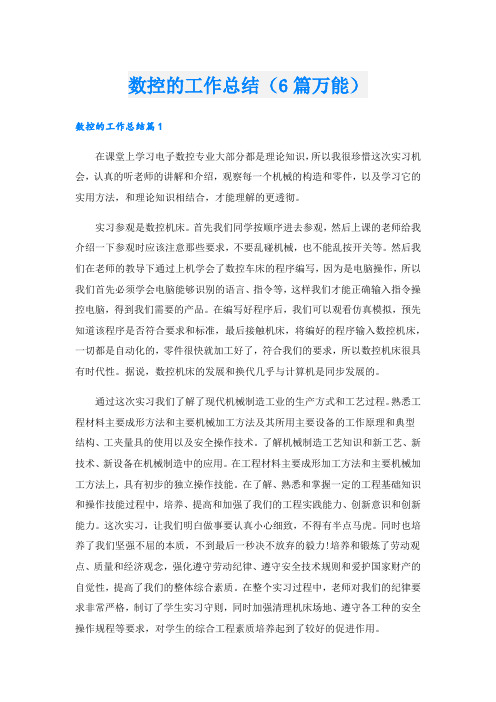
数控的工作总结(6篇万能)数控的工作总结篇1在课堂上学习电子数控专业大部分都是理论知识,所以我很珍惜这次实习机会,认真的听老师的讲解和介绍,观察每一个机械的构造和零件,以及学习它的实用方法,和理论知识相结合,才能理解的更透彻。
实习参观是数控机床。
首先我们同学按顺序进去参观,然后上课的老师给我介绍一下参观时应该注意那些要求,不要乱碰机械,也不能乱按开关等。
然后我们在老师的教导下通过上机学会了数控车床的程序编写,因为是电脑操作,所以我们首先必须学会电脑能够识别的语言、指令等,这样我们才能正确输入指令操控电脑,得到我们需要的产品。
在编写好程序后,我们可以观看仿真模拟,预先知道该程序是否符合要求和标准,最后接触机床,将编好的程序输入数控机床,一切都是自动化的,零件很快就加工好了,符合我们的要求,所以数控机床很具有时代性。
据说,数控机床的发展和换代几乎与计算机是同步发展的。
通过这次实习我们了解了现代机械制造工业的生产方式和工艺过程。
熟悉工程材料主要成形方法和主要机械加工方法及其所用主要设备的工作原理和典型结构、工夹量具的使用以及安全操作技术。
了解机械制造工艺知识和新工艺、新技术、新设备在机械制造中的应用。
在工程材料主要成形加工方法和主要机械加工方法上,具有初步的独立操作技能。
在了解、熟悉和掌握一定的工程基础知识和操作技能过程中,培养、提高和加强了我们的工程实践能力、创新意识和创新能力。
这次实习,让我们明白做事要认真小心细致,不得有半点马虎。
同时也培养了我们坚强不屈的本质,不到最后一秒决不放弃的毅力!培养和锻炼了劳动观点、质量和经济观念,强化遵守劳动纪律、遵守安全技术规则和爱护国家财产的自觉性,提高了我们的整体综合素质。
在整个实习过程中,老师对我们的纪律要求非常严格,制订了学生实习守则,同时加强清理机床场地、遵守各工种的安全操作规程等要求,对学生的综合工程素质培养起到了较好的促进作用。
生平第一次有种“学以致用”的感觉,内心很有成就感,也真切的体会到真理必须要用实践去检验,不亲自去动手试验一下。
刀具自动化

刀具自动化刀具自动化⒈引言刀具自动化是指利用自动化技术,对刀具加工进行自动化控制,提高生产效率和产品质量的方法。
本文档旨在详细介绍刀具自动化的相关内容,包括刀具自动化的定义、原理、应用领域、技术要点以及可能涉及到的法律名词及其注释。
⒉刀具自动化的定义刀具自动化是指通过自动化设备和系统,对刀具进行自动化控制和操作。
它包括对刀具的自动上下料、自动校准、自动磨损检测、自动切削参数调整等操作。
⒊刀具自动化的原理刀具自动化的基本原理是通过传感器、控制系统和执行器的协调作用,实现对刀具的自动操作。
传感器用于感知刀具的位置、状态和工作情况,控制系统根据传感器反馈的信息进行决策和控制,执行器负责实施具体的刀具操作。
⒋刀具自动化的应用领域刀具自动化广泛应用于机械加工、汽车制造、航空航天等领域。
在机械加工中,刀具自动化可以提高加工效率和产品质量,减少人工干预。
在汽车制造中,刀具自动化可以实现高速、高精度的切削操作,提高汽车生产线的效率和稳定性。
在航空航天中,刀具自动化可以实现对复杂零件的高精度加工,确保飞行器的安全性和可靠性。
⒌刀具自动化的技术要点刀具自动化的技术要点包括传感技术、控制技术、执行技术等。
传感技术主要用于刀具位置、状态和磨损等信息的感知。
控制技术主要用于刀具操作的决策和控制。
执行技术主要用于刀具操作的实施和控制。
⒍法律名词及注释⑴知识产权知识产权是指人们通过智力创造所得到的用于经济和社会发展的权利。
包括专利权、商标权、著作权等。
⑵专利权专利权是指国家授予发明家的一项独占权,享有对发明所作的独占权利,防止他人在授权有效期内制造、使用、销售该发明。
⑶商标权商标权是指商标注册人对其商标享有的排他性使用权,包括商标的使用、转让和许可等权利。
⒎结尾本文档涉及附件,请参阅附件内容以获取更详细的信息。
本文所涉及的法律名词及注释:知识产权是指人们通过智力创造所得到的用于经济和社会发展的权利,包括专利权、商标权、著作权等。
FMS的构成与功能

柔性制造系统(FMS)柔性制造系统( Flexible Manufacturing System, FMS)是由统一的控制系统和物料输送系统联接起来的一组加工设备,能在不停机的情况下实现多品种工件的加工,并且具有一定管理功能的制造系统。
作为当代最先进的制造系统之一, FMS集高效率、高精度、高柔性于一体,使多品种小批量生产的生产过程也像大量生产一样实现了自动化。
其柔性主要体现在两个方面:一是能在同一时间内加工不同种类零件的不同工序;一是能选择不同的工艺路线加工一种零件的一组工序。
由于上述工艺上的高柔性,使FMS的设备利用率大大提高。
有资料表明,一般数控机床的切削时间约占一个工作班时间的10~30% ,而柔性生产系统的切削时间所占比例能达到50~90% 。
FMS的技术功能和生产能力在系统设计之初已经确定和保证,但实际中能否充分发挥它的能力,确保柔性的真正实现,则取决于投产后的作业调度与安排。
只有合理地安排工艺作业顺序、制定计划,才能合理有效地使用FMS系统。
1. FMS的组成典型的FMS按其功能, 由数控加工系统、物流系统和信息流系统。
(1)数控加工系统。
数控加工系统的功能是以任意顺序自动加工各种工件,并能自动地更换工件和刀具。
主要采用加工中心和数控车床,前者用于加工箱体类和板类零件,后者则用于加工轴类和盘类零件。
中、大批量少品种生产中所用的FMS,常采用可更换主轴箱的加工中心,以获得更高的生产效率。
加工系统的设备种类和数量取决于加工对象的工艺要求。
FMS的加工对象一般为回转体和非回转体两大类。
回转体类零件采用车削加工中心。
非回转体类零件比如箱体类、立方体类等则采用镗铣加工中心。
除此,一般还配备一定数量的数控机床或经过数控化改装的机床。
(2)物流系统在FMS中工件、工具流统称为物流系统,物流系统即物料贮运系统,是柔性制造系统中的一个重要组成部分。
一个工件从毛坯到成品的生产过程中,很大一部分时间都消耗于物料贮运系统中,合理的选择FMS的物料贮运系统,可以大大提高整个制造系统的柔性和效率。
机械制造基础第二版贾振元课后答案

机械制造基础第二版贾振元课后答案1、什么是机械加工工艺过程?答:用机械的加工方法(包括钳工的手工操作)按规定的顺序把毛坯(包括轧制材料)变成零件的全部过程。
2、工艺过程的基本单元是什么?如何划分?答:工序是工艺过程的基本单元。
工艺过程可分为工序、安装、工位、工步和走刀。
3、什么是工序、安装、工步、工位和走刀?答: 1、工序指的是一个工人(或一组工人)在一个工作地点(一般是指一台机床)对一个工件(对多轴机床来说是同时对几个工件)所连续完成的那一部分工艺过程。
2、一个工序有时在零件的几次装夹下完成,这时在零件每装夹一次下所完成的那部分工作称为一次安装。
3、在多轴机床上或在带有转位夹具的机床上加工时,工件在机床上所占有的一个位置上所完成的那部分工作称为一个工位。
4、在加工表面、切削刀具和切削用量(对车削来说,指主轴转速和车刀进给量,不包括切深,对其他加工也类似)都不变的情况下所连续完成的那一部分工作。
5、刀具在加工表面上对工件每一次切削所完成的那一部分工作称为一次走刀。
4、机械加工工艺规程制订的指导思想?答:保证质量、提高效率、降低成本。
三者关系是,在保证质量的前提下,最大限度的提高生产率,满足生产量要求;尽可能地节约耗费、减少投资、降低制造成本。
5、不同生产类型的工艺过程的特点是什么?答:企业生产专业化程度的分类称为生产类型,机械制造业一般有三种生产类型,即大量生产、成批生产和单件生产。
单件小批生产中,要能适应各种经常变化的加工对象,广泛使用万能机床、通用夹具通用刀具和万能量具,一般采用较低精度的毛坯。
大批大量生产下,广泛使用各种高效率的、自动化程度高、专用的机床、夹具、刀具和量具,一般尽可能使用精度较高的毛坯。
6、什么是机械加工工艺规程﹖它的作用是什么﹖工艺规程的设计的原则和步骤有哪些?答:将合理的工艺过程和操作方法,按照一定的格式写成文件,用来指导生产,这个工艺文件就叫做加工工艺规程。
工艺规程的作用:(1)工艺规程是组织生产的指导性文件。
简述数控机床的结构及组成
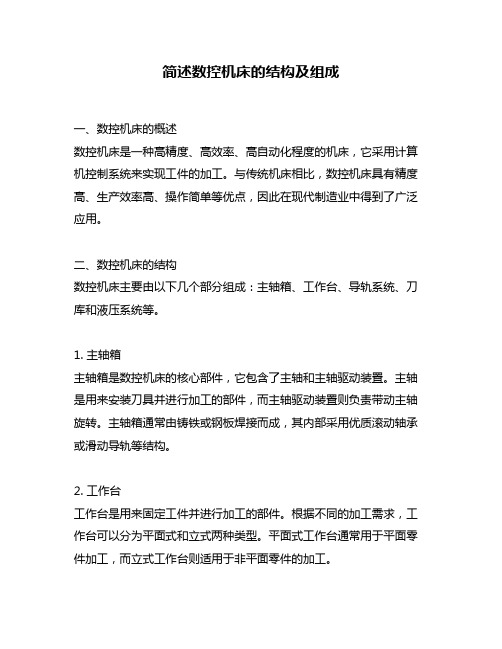
简述数控机床的结构及组成一、数控机床的概述数控机床是一种高精度、高效率、高自动化程度的机床,它采用计算机控制系统来实现工件的加工。
与传统机床相比,数控机床具有精度高、生产效率高、操作简单等优点,因此在现代制造业中得到了广泛应用。
二、数控机床的结构数控机床主要由以下几个部分组成:主轴箱、工作台、导轨系统、刀库和液压系统等。
1. 主轴箱主轴箱是数控机床的核心部件,它包含了主轴和主轴驱动装置。
主轴是用来安装刀具并进行加工的部件,而主轴驱动装置则负责带动主轴旋转。
主轴箱通常由铸铁或钢板焊接而成,其内部采用优质滚动轴承或滑动导轨等结构。
2. 工作台工作台是用来固定工件并进行加工的部件。
根据不同的加工需求,工作台可以分为平面式和立式两种类型。
平面式工作台通常用于平面零件加工,而立式工作台则适用于非平面零件的加工。
3. 导轨系统导轨系统是数控机床的重要组成部分,它负责支撑和定位主轴箱、工作台等部件。
导轨系统通常由滚珠丝杠、直线导轨等组成,其精度和刚度直接影响到机床的加工精度和稳定性。
4. 刀库刀库是用来存放刀具的部件,它通常由多个刀柄和一个转盘组成。
不同类型的刀具可以根据需要进行更换,以满足不同的加工需求。
5. 液压系统液压系统是数控机床的动力源,它负责驱动各种液压元件来完成机床各项功能。
液压系统通常包括油泵、油箱、油管等部件,其性能直接影响到机床的运行效率和稳定性。
三、数控机床的组成数控机床由以下几个主要组成部分构成:1. 数控装置数控装置是数控机床最重要的组成部分之一,它负责对加工过程进行监测和控制。
数控装置通常由计算机、数字信号处理器、编码器等组成,可以实现加工参数的自动调整和控制。
2. 伺服系统伺服系统是数控机床的关键部分之一,它负责驱动主轴箱、工作台等部件进行运动。
伺服系统通常由电机、减速器、编码器等组成,其性能直接影响到机床的加工精度和效率。
3. 控制面板控制面板是数控机床的人机交互界面,它负责向操作员提供操作界面和参数设置功能。
第三章数控刀具的选用

山特维克可乐满车刀的夹紧方式选择
22
第三章 数控刀具的选用
刀片形状的选择
可 正型(前角)刀片:
转 对于内轮廓加工,小 型机床加工,工艺系
位 统刚性较差和工件结
车 刀
构形状较复杂应优先 选择正型刀片。 负型(前角)刀片:
的 选
对于外圆加工,金属 切除率高和加工条件 较差时应优先选择负
用 型刀片。
23
则宜大些
28
第三章 数控刀具的选用
刃倾角是前刀面
倾斜的角度。重
切削时,切削开
始点的刀尖上要
承受很大的冲击
刃
力,为防止刀尖 受此力而发生脆
倾
性损伤,故需有
角 的
刃倾角。推荐车 削时为3°~5°; 铣削时10°~15°
刃倾角的影响
作 用
刃倾角为负时,切屑流向工件;为正 时,反向排出 刃倾角为负时,切削刃强度增大,但切 削背向力也增加,易产生振动
第三章 数控刀具的选用
刀片形状的选择
可
一般外圆车削常用80°
转
凸三角形、四方形和
位
80 °菱形刀片;仿形 加工常用55 °、35 °
车
菱形和圆形刀片;
刀
在机床刚性、功率允 许的条件下,大余量、
的
粗加工应选择刀尖角
选
较大的刀片,反之选 择刀尖角较小的刀片。
用
根据加工轮廓 选择刀片形状
24
第三章 数控刀具的选用
合金工具代替。
12
第三章 数控刀具的选用
硬质合金刀具
新型硬质合金 刀具加工实例
普通
数
硬质
控 刀 具
合金
超细晶粒 硬质合金
粒径在1μm以下,这种材料具有 硬度高、韧性好、切削刀可靠性 高等优异性能
2024年PCBN刀具市场前景分析
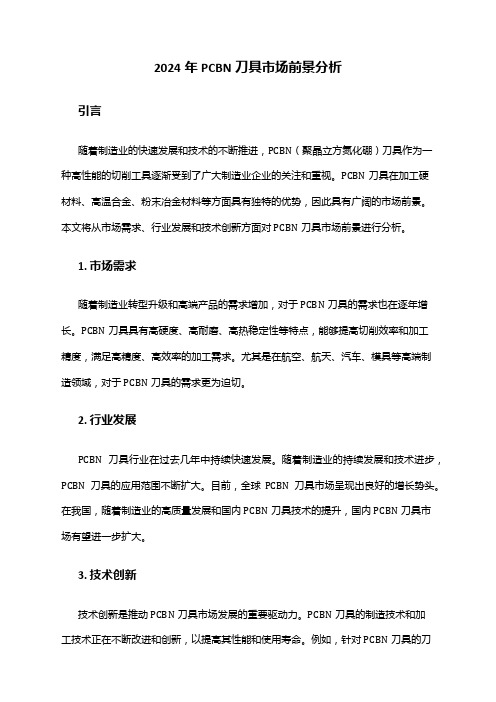
2024年PCBN刀具市场前景分析引言随着制造业的快速发展和技术的不断推进,PCBN(聚晶立方氮化硼)刀具作为一种高性能的切削工具逐渐受到了广大制造业企业的关注和重视。
PCBN刀具在加工硬材料、高温合金、粉末冶金材料等方面具有独特的优势,因此具有广阔的市场前景。
本文将从市场需求、行业发展和技术创新方面对PCBN刀具市场前景进行分析。
1. 市场需求随着制造业转型升级和高端产品的需求增加,对于PCBN刀具的需求也在逐年增长。
PCBN刀具具有高硬度、高耐磨、高热稳定性等特点,能够提高切削效率和加工精度,满足高精度、高效率的加工需求。
尤其是在航空、航天、汽车、模具等高端制造领域,对于PCBN刀具的需求更为迫切。
2. 行业发展PCBN刀具行业在过去几年中持续快速发展。
随着制造业的持续发展和技术进步,PCBN刀具的应用范围不断扩大。
目前,全球PCBN刀具市场呈现出良好的增长势头。
在我国,随着制造业的高质量发展和国内PCBN刀具技术的提升,国内PCBN刀具市场有望进一步扩大。
3. 技术创新技术创新是推动PCBN刀具市场发展的重要驱动力。
PCBN刀具的制造技术和加工技术正在不断改进和创新,以提高其性能和使用寿命。
例如,针对PCBN刀具的刀具涂层技术不断提升,能够进一步提高刀具的耐磨性和切削效率。
此外,PCBN刀具的设计和制造技术也在不断改进,以提高其稳定性和精密度。
结论PCBN刀具作为一种高性能的切削工具,具有广阔的市场前景。
随着制造业的发展和技术的推进,PCBN刀具的市场需求将进一步增长。
行业发展和技术创新将推动PCBN刀具市场的健康发展。
因此,在PCBN刀具市场上投资和发展具有良好的前景,需要企业和相关机构密切关注市场动态,加强技术研发,提高产品质量,以满足市场需求并取得竞争优势。
(字数:1500字)。
数控常用刀具及功能

数控常用刀具及功能一、整体介绍数控(Numerical Control)是一种通过计算机控制的自动化加工技术,其应用广泛,尤其在制造业中。
在数控加工过程中,刀具起着至关重要的作用,不同的刀具具有不同的功能和特点,本文将为大家介绍数控常用刀具及其功能。
二、常用刀具及功能1. 铣刀铣刀是数控加工中最常用的刀具之一,其主要用于平面、曲面的铣削加工。
铣刀通常由刀柄和刀片组成,刀片可以更换,以适应不同的加工需求。
铣刀具有高速切削、高精度、高效率等特点,广泛应用于汽车制造、航空航天等领域。
2. 钻头钻头是用于钻孔的刀具,可分为直柄钻头和螺旋钻头。
直柄钻头适用于钻孔直径较小的情况,而螺旋钻头则适用于钻孔直径较大的情况。
钻头具有高效、精度高、加工质量好等特点,广泛应用于金属加工、木工等领域。
3. 刀片刀片是数控加工中不可或缺的刀具之一,广泛应用于铣削、车削、钻孔等加工过程中。
刀片的种类繁多,根据不同的加工需求,可以选择不同形状、材质和刀片角度的刀片。
刀片具有高硬度、耐磨损、切削力小等特点,能够提高加工效率和加工质量。
4. 镗刀镗刀是用于加工孔的刀具,其主要功能是将加工孔的精度和表面质量提高到一定的要求。
镗刀由刀柄和刀具组成,刀具可以更换以适应不同尺寸的孔加工。
镗刀具有高精度、高效率、高稳定性等特点,广泛应用于汽车发动机缸体、气缸套等零部件的加工。
5. 锯片锯片是用于切割材料的刀具,其主要用途是将工件切割成所需的尺寸和形状。
锯片通常由金属或合金制成,具有高硬度、耐磨损、切削效率高等特点。
锯片广泛应用于金属加工、木工、建筑等领域。
6. 车刀车刀是用于车削加工的刀具,其主要功能是将工件上的材料去除,使其达到所需的形状和尺寸。
车刀通常由刀柄和刀片组成,刀片可以更换以适应不同的加工需求。
车刀具有高效、精度高、加工质量好等特点,广泛应用于汽车制造、航空航天等领域。
7. 刀具夹具刀具夹具是用于夹持刀具的装置,其主要功能是确保刀具的稳定性和精度,从而保证加工质量。
自动化名词解释与简答

1. 机械化:执行制造过程的基本动作是由机器(机械)代替人力劳动来完成的。
2. 自学习控制系统:如果计算机能够不断地根据受控对象运行结果积累经验,自行改变和完善控制规律,使控制效果愈来愈好,这样的系统即为自学习控制系统。
3. AGV:一种有蓄电池驱动,装有非接触导向装置,在计算机控制下,自动完成运输任务的物料运载工具。
4. 在线测量:指在设备运行,生产不停顿的情况下,对设备和加工过程运行状态的信息数据进行采集的方式。
5. 自动化制造系统:在较少人工直接或间接干预下,将原料加工成零件并组装成产品,在加工过程和装配过程中实现工艺过程自动化。
6. 系统:由相互联系,相互作用和相互制约的各个要素组成且具有一定功能的整体。
7. FMS:在计算机统一控制下,有自动装卸与运输系统将若干台数控机床或加工中心连接起来构成的一种适合多品种,多小批量生产的先进制造系统。
8. 物流系统:对工件、工具和配套装置及材料进行与存储的系统,主要完成物料的存储、输送、装卸、管理等功能。
9. 制造过程检测自动化:利用各种自动化检测装置,自动检测被测量对象的有关参数,不断提供各种有价值的信息和数据。
10. 结构工艺性:指产品和零件在保证使用的前提下,力求能够采用生产率高,劳动量小,材料消耗少和生产成本低的方法制造处理。
1.什么叫工艺过程自动化?答:一个工艺过程通常包括若干个工序,如果不仅每一个工序都自动化了,并且把他们有机地联系起来,使得整个工艺过程都自动进行,而工人只是对这一整个工艺过程做总的操纵和监督,从而形成了某一加工工艺的自动生产线。
2.为什么说加工设备的自动化是实现零件加工自动化的基础?答:加工设备是机械制造的基本生产手段和主要组成单元,单台机床或加工设备的自动化,能满足零件加工过程中某个或几个工序的加工半自动化和自动化的需要,为多机床管理创造了条件,是建立自动生产线和过渡到全盘自动化的必要前提。
3.简述一下车削中心与数控卧式车床的主要区别?答:车削中心的转塔刀架上带有能使刀具旋转的动力刀座;车削中心的主轴具有按轮廓成型要求的连续(不等速回转)运动和进行连续精确分度的C轴功能,并能与X轴或Z轴联动;车削中心可发展出车磨中心、车铣中心等多工序复合加工的机床。
双主轴数控排刀机实现高效的刀具排列和自动换刀操作

双主轴数控排刀机实现高效的刀具排列和自动换刀操作双主轴数控排刀机是一种先进的切削加工设备,具备两个独立的主轴和多个刀位,可以实现高效的刀具排列和自动换刀操作。
采纳先进的数控技术和机械传动系统,通过双主轴的联动工作实现多个刀具的同时加工。
每个刀位都有独立的主轴,并通过掌控系统进行精准明确的调度和运行。
其工作流程重要包括程序编程、主轴运转和自动换刀三个步骤。
首先,通过编程软件编写加工程序,确定刀具排列和加工路径。
然后,掌控系统将指令发送给双主轴,使它们依照预定的次序开始运转。
最后,在切削过程中,当需要换刀时,自动换刀装置会自动将待用刀具送到主轴上,实现快速换刀操作。
1、高效性:排刀机能够同时进行多个刀具的加工,提高了生产效率。
通过合理的刀具排列和充分利用主轴的运转时间,大大缩短了加工周期,提高了加工效率。
2、快捷性:排刀机具有良好的刀具排列和调度本领,可以依据不同的加工需求进行快捷配置。
它可以依据加工程序的要求自动选择合适的刀具,实现不同类型的加工任务,充足多样化的生产需求。
3、精度性:排刀机具备高精度的切削本领,可以实现精准明确的切削加工。
通过先进的掌控系统和传感器技术,可以监测和调整刀具的位置和状态,保证加工精度和质量。
4、自动化:排刀机具备自动换刀功能,可以实现快速、精准的刀具更换。
自动换刀装置能够自主感知刀具磨损情形,并在需要时进行换刀操作,削减了人工干预,提高了生产效率和安全性。
双主轴数控排刀机作为一种智能刀具排列解决方案,具备高效、快捷、精度高、自动化等特点,对于提升生产效率和质量具有紧要意义。
它在汽车制造、机械制造、航空航天和刀具制造等领域的应用,为工业生产供给了牢靠的技术支持和创新解决方案。
1、汽车制造业:排刀机广泛应用于汽车零部件的加工和制造中。
它可以同时进行多个刀具的加工,充足汽车零部件的大批量生产需求,提高生产效率和质量。
2、机械制造业:排刀机在机械制造业中被广泛应用于各类金属零部件的加工。
《数控机床》作业参考答案

《数控机床》作业参考答案(一)第一章数控机床简介一、填空题1、控制介质、数控系统、伺服系统、机床本体、反馈装置2、数字控制3、并联4、自适应控制(AC)二、单选题1、C2、D3、A4、D5、B三、判断题1、×2、√3、×4、√5、√四、简答题1、简述数控机床的发展趋势。
答:(1)高速度与高精度化:为实现这一指标,主要采取以下的措施:①数控系统采用位数、频率更高的微处理器;②采用全数字交流伺服系统,大大提高了系统的定位精度、进给速度;③机床静、动摩擦的非线性补偿技术;④应用高速大功率电主轴;⑤配置高速、功能强的内装式可编程控制器;⑥采用高性能和可靠的新型功能部件—电滚珠丝杠;(2)多功能化:数控机床采用一机多能;数控机床具有前台加工、后台编辑的前后台功能;数控机床除具有通讯口、DNC功能外,还具有网络功能;(3)智能化:数控机床引进自适应控制技术;采用故障自诊断、自修复功能;具有刀具寿命自动检测和自动换刀功能;数控机床引进模式识别技术;(4)高的可靠性:为实现这一指标,主要采取以下的措施:①提高系统的硬件质量;②采用硬件结构模块化、标准化、通用化方式;③增强故障自诊断、自恢复和保护功能。
2、简述数控机床各组成部分的作用。
答:数控机床一般由以下几个部分组成:(1)控制介质:控制介质是将零件加工信息传送到数控装置中去的信息载体,是人与数控机床之间联系的中间媒介物质,反映了数控加工中的全部信息。
常见的控制介质有穿孔纸带、穿孔卡、磁盘、磁带等。
(2)数控系统:数控系统是机床实现自动加工的核心,是整个数控机床的灵魂所在,主要由输入装置、监视器、主控制系统、可编程控制器、各种输入/输出接口等组成。
主控制系统主要由CPU、存储器、控制器等组成,是数控系统的核心,一般称它为数控装置(CNC装置)。
(3)伺服系统:是数控系统和机床本体之间的电传动联系环节,主要由伺服电机、伺服驱动控制器组成。
伺服电机是系统的执行元件,驱动控制系统则是伺服电机的动力源。
一种柔性数控加工智能制造单元的设计与应用

一种柔性数控加工智能制造单元的设计与应用发布时间:2023-05-22T03:18:34.434Z 来源:《科技潮》2023年7期作者:何树洋[导读] 传统的机床需要繁重的体力劳动,并且对人员的操作技能水平极高,而数控机床作为工作母机,数控技术不仅赋予机床一个大脑,使机床变得越来越“聪明”。
广州数控设备有限公司广州 510530摘要:介绍了一种柔性切削加工智能制造单元的设计与实现。
首先通过数控加工技术的特点以及现状,以某校办工厂企业设备改造升级需求为案例,对某轴类和端盖类小批量零件加工基本工艺流程进行分析,介绍柔性数控加工智能制造单元的设计和应用,并对系统的控制原理进行详细阐述,深入分析工业机器人、加工设备、PLC控制器、MES计算机之间的通讯结构和通讯方式。
然后详细介绍工业机器人主程序、料仓取放料程序、机床上下料程序的基本控制流程。
最后证明智能制造单元可通过网络协同方式实现柔性制造。
关键词:柔性加工;智能制造;工业机器人引言传统的机床需要繁重的体力劳动,并且对人员的操作技能水平极高,而数控机床作为工作母机,数控技术不仅赋予机床一个大脑,使机床变得越来越“聪明”。
数控技术也已经从被动执行运动指令发展到能够“感知”机床的温度、振动、能耗等工况并加以调整和控制,通过配套传感技术以及检测系统可以实现在线测量工件尺寸、刀具破损和预测刀具寿命,以及防止刀具和运动部件干涉,甚至为操作者进行语音导航或发送短消息。
数控机床具备智能化功能可以保证机床自动适应加工环境的变化,从而使机床操作更加便利,精度更加稳定,效率更加提升。
显而易见,设备数字化、网络化、智能化具有极为重要的现实意义。
1数控加工技术的特点以及现状1.1数控加工技术的特点数控加工技术是一种以软件编程技术为核心的自动化控制加工生产技术[1]。
首先,数控加工技术可以加工各种形状的零件,即使是一些带有不规则斜角的零件或形状更复杂的零件,也可以采用数控加工技术完成精密加工。
pqart数控加工单元介绍

pqart数控加工单元介绍【数控加工单元介绍】一、数控加工单元的概念与分类数控加工单元是机械加工和自动化技术的综合应用,集加工设备、工艺装备、自动控制系统和信息处理技术于一体的综合性技术工艺单元。
数控加工单元可用于金属加工、塑料加工、玻璃加工等领域。
按照功能和用途的不同,数控加工单元可以分为:铣削单元、镗削单元、钻削单元、磨削单元、车削单元、切削单元等。
二、数控加工单元的结构与工作原理1. 结构:数控加工单元的主要组成部分包括:机床、数控装置、执行元件和机床附件。
- 机床:数控加工单元可使用各种类型的机床,如铣床、车床、钻床等。
- 数控装置:数控装置是控制整个加工过程的核心部分,可采用CNC控制器、PLC控制器等。
- 执行元件:执行元件包括伺服电机、伺服驱动器等,用于实现机床各轴的运动。
- 机床附件:机床附件包括刀库、刀具、工件夹紧装置等。
2. 工作原理:数控加工单元通过数控装置对机床进行编程控制,实现加工工艺的自动化。
具体的工作流程分为以下几个步骤:- 设计加工工艺:根据产品的要求,设计出相应的加工工艺方案,包括刀具的选择、切削参数的确定等。
- 编写控制程序:根据加工工艺方案,编写相应的数控程序,定义机床各轴的运动轨迹、速度、加速度等参数。
- 加工准备:将编写好的控制程序转换成数控装置能够识别的代码,并加载到数控装置中。
同时,安装好刀具、调整好工件夹紧装置等。
- 运行加工:启动数控装置,开始运行编好的控制程序。
数控装置将根据程序中设定的参数,控制机床按照要求进行加工。
- 检查加工质量:加工完成后,进行质量检查,判断是否符合设计要求。
三、数控加工单元的特点和优势1. 精度高:数控加工单元采用计算机控制,能够精确控制加工过程中的各项参数,提高加工精度和稳定性。
2. 生产效率高:数控加工单元具备自动化、高速、连续运转等特点,能够大幅度提高生产效率。
3. 工艺灵活:数控加工单元可根据产品要求进行灵活的工艺参数调整,适应不同的加工需求。
- 1、下载文档前请自行甄别文档内容的完整性,平台不提供额外的编辑、内容补充、找答案等附加服务。
- 2、"仅部分预览"的文档,不可在线预览部分如存在完整性等问题,可反馈申请退款(可完整预览的文档不适用该条件!)。
- 3、如文档侵犯您的权益,请联系客服反馈,我们会尽快为您处理(人工客服工作时间:9:00-18:30)。
高效率的整体刀具自动制造单元
作者:瓦尔特(无锡)有限公司舒智勇
在加工效率不断提高的情况下,数控加工设备的参数设置(刀具测量及设置/编程)时间就越来越成为制约生产效率的瓶颈,这个瓶颈在数控刀具磨床上尤其突出。
这是因为刀具产品品种繁多,各种类型刀具的尺寸和角度复杂,使得砂轮测量、编程和调整时间较长。
德国瓦尔特公司为此推出了一个一揽子解决方案——高效率的刀具自动制造单元(Automated Tool Room)。
该单元由刀具磨床、刀具测量机和刀具虚拟磨削软件(Cybergrinding)三部分组成(如图所示),可将刀具磨削参数的设置时间减少50%以上,其实现步骤分以下三步。
第一步:虚拟磨削软件的应用
将本该输入到机床的全套刀具几何参数和磨削工艺参数输入到虚拟磨削软件(Cybergrinding),该软件就可以对机床的磨削过程、刀具磨削后的状态进行仿真。
用户不但可以停留在磨削过程中的任何一点对整个机床或刀具进行多视角、近距离的观察,而且可以自动检测在刀具磨削的制造过程中是否产生干涉。
如果结果满意,该程序可以直接输入到机床上立即进行加工,其真实的加工状况和模拟的理论上没有任何差别。
这种方法避免了试加工所带来的诸如占用机时长、砂轮消耗甚至破损、浪费棒料等等许多问题。
据统计,虚拟磨削软件的使用可减少编程调试时间通常在30%以上。
第二步:用刀具测量机对砂轮和刀具进行自动测量
标准的测量程序存储在刀具测量机中,只要调用就可以对砂轮和刀具进行无接触、全自动地测量。
其测量精度可达±0.001mm,平均测量的时间为6分钟,其测量结果可打印输出为自行设计的格式。
第一步和第二步结合可减少机床设置时间达40%以上。
投影光、反射光和聚焦测距原理的应用、先进的计算机图像处理和数字控制技术实现了“无接触”和“程序化”的测量,才使得机床具备这样高的精度和效率。
没有砂轮的准确测量,虚拟磨削软件的仿真效果也难达到完美的地步。
第三步:构成制造单元的局域网络
最后将运行虚拟磨削软件的工作站、刀具磨床和刀具测量机构成一个局域网络,可将机床设置时间减少达50%以上。
这是因为刀具设置参数、砂轮参数通过网络可以在三者之间共享,用户不用手持软盘在它们之间奔忙,而是通过网络将数据从一台电脑发送到另外一台电脑的相应菜单中,即节省了时间又避免了人工输入所带来的误操作。
在线刀具补偿(Online Tool Compensation)可将刀具测量机上测量的结果发送到刀具磨床上,在下一次的修整磨削中补偿由于砂轮磨损、温度变化或其他因素所带来的刀具制造误差。
除了刀具磨床和刀具测量机外,如果您有一台作为文件服务器的电脑、一个光纤集线器和每台电脑具有网卡、只要增加相应的软件就可以轻松组建一个整体刀具自动制造单元。
这种低廉的投资回报是:不但机床的设置时间大幅度减少;而且您可以坐在舒适的办公室的电脑前将您想象中刀具编好程序,进行模拟加工,而此时机床正在夜以继日地加工刀具。
(end。