H0FL-1200使用手册V1.3
FR1200用户手册V1.0

-5-
FR1200 用户手册 V1.0
验证流程如下图所示:
读头运行
获 取 指 纹 模 板 ,响 一 声 ,灭 灯 ,切 换
到4 8 5 任 务
是
提 示 :响3声, 亮红灯
是
获取控制器命令
是否超时 ?
否
是
判断是否是仅指
纹?
否
是
判断是否是指纹 or
卡?
否
否 判断是否已经获 取过卡号 ?
发送指纹模板
到控制器
其他未尽事宜,请参见安装指南、读头软件用户手册等相关资料。
-2-
3 设备操作
2 设备介绍
FR1200 读头既可连接门禁控制器的 Reader 接口作为 Wiegand 读头,也可 连接门禁控制器的扩展 485 接口,作为 inBIO 读头。操作过程以指示灯提示为 主,无屏显,无按键。本产品设计外观小巧、简洁大方,是一款新概念的 inBIO 指纹读头。
请不要将设备放在强光直射的地方,强光对指纹采集有着明显的影响,会 导致指纹验证无法通过。
1200安装使用说明书-22页文档资料

1200HⅡTE立式斜流泵安装使用说明书沈阳水泵股份有限公司2019年8月1 概述 (3)1.1 用途 (3)2 结构说明 (4)2.1 泵本体 (4)2.2 泵管路系统 (4)3 安装 (5)3.1 安装前的准备 (5)3.2 安装程序 (6)3.3 垫板的调整 (7)3.4 基础座的安装和初步调整 (8)3.5 泵本体的安装(参看图6安装拆卸示意图) (8)3.6 电机座的安装和调整 (8)3.7 垫铁的点焊 (9)3.8 电动机的安装和对中 (9)3.9 最后灌浆 (9)3.10 灌浆及灌浆注意事项 (9)3.11 排出管路的连接 (10)3.12 附属设备、辅助管路和导线的连接 (10)3.13 电动机预运转、定转向 (10)3.14 刚性联轴器的连接 (10)4 起动 (11)4.1 起动条件 (11)4.2 起动顺序 (11)4.3 起动时应注意事项 (12)5 运行 (12)5.1 运行前的准备 (12)5.2 运行中应注意事项 (13)6 停机 (14)6.1 停机顺序 (14)6.2 停机时应注意事项 (14)6.3 特殊停机 (14)7 维护 (15)7.1 作好运行日记 (15)7.2 检查 (15)7.2.1 外观检查 (15)7.2.2 拆卸检查 (16)7.3 检查周期 (18)7.3.1 每天的检查 (18)7.3.2 每半年检查 (18)7.3.3 每年检查 (18)7.4 仪表的使用 (18)7.5 长期停机时的维护 (18)8 拆卸与组装 (19)8.1 拆卸前的准备 (19)8.2 拆卸 (19)8.3 组装 (20)9 常见故障的原因及消除方法 (21)1 概述1.1 用途1200HⅡTE立式斜流泵是专为前湾电厂350MW级燃气-蒸汽联合循环发电机组输送循环冷却水设计的,也可用于其它工况相似的电厂及大型水利工程蓄水、排水,被输送液体温度不高于55℃。
2 结构说明2.1 泵本体整体结构见图1(1200HⅡTE-0000结构剖面图),简单介绍如下:a、泵本体由3个主要部分组成,即外壳、内壳和转子结合部。
Parker Hannifin Veriflo FRN1200高流量单阶铝合金压力减震器说明书

Contact Information:Parker Hannifin Corporation Veriflo Division 250 Canal BlvdRichmond, California 94804phone 510 235 9590*************************.com **************************.com /verifloMobile App: /verifloPrecise Control, High Flow PerformanceThe FRN1200 Series pressure reducing regulator offers high-flow capability with an inlet pressure up to 1700 psig and is an excellent choice for general point of use bulk gas applications.The large, tied Hastelloy C-22® diaphragm provides stable control over its full operational range while providing a robust seal for hazardous gas applications.High-Flow, Single Stage TiedDiaphragm Pressure Reducing RegulatorFRN1200 SeriesProduct Features:• 316L stainless steel body • Metal-to-metal diaphragm seal• High purity cleaned • Passivated• Hastelloy C-22® Tied diaphragm design • Integrated Filtration • F lows up to 1200 slpm (42 scfm)• Reliable leak tight performanceSafety Guide and Installation and Operating Instructions available at/veriflo0.020.040.060.080.0100.0120.0140.00200400600800100012001400O U T L E T P R E S S U R E (P S I G )FLOW (SLPM, N 2)(1200 psig inlet)(600 psig inlet)(250 psig inlet)FR1200 REGULATOR0.020.040.060.080.0100.0120.002004006005003001008001000700900O U T L E T P R E S S U R E (P S I G )FLOW (SLPM, N 2)(250 psig inlet)(150 psig inlet)(100 psig inlet)FR1200 REGULATORFRN1200 SeriesFlow CurvesAdditional flow curves available upon requestDimensional DrawingsAll dimensions in inches. Metric dimensions are for reference only.Porting ConfigurationsTop View3 P4 P2 P4 PBFlow Capacity 12 = 1.2 CvBuild an FRN1200 Series regulator by replacing the numbered symbols with an option from the corresponding tables below.Optional FeaturesThis section can have multiple optionsBlank = N onePM = Panel MountPort Style*4 = 1/4" NPT Female 6 = 3/8" NPT Female 8 = 1/2" NPT Female 4T = 1/4" A-LOK ® 6T = 3/8" A-LOK ®8T=1/2" A-LOK ®* 1/4" FNPT Gauge Ports are Standard Any other gauge port configuration may have an extended lead time.Inlet Gauge*X= No Gauge 01 = 0 - 100 psig 4 = 0 - 400 psig 10 = 0 - 1000 psig 20 = 0 - 2000 psig 30 = 0 - 3000 psig 40=0 - 4000 psig* Only include with “4P” body configuration.Basic SeriesFRN1203 = 1 - 30 psig FRN1206 = 5 - 60 psig FRN1210 = 10 - 100 psig FRN1215 =15 - 150 psig123457812345678910FRN1215 H S 12 K 4P X X 8 PMFRN1215HS12K4PXX8PMSample:Finished Order:9 10Body MaterialS = 316L SSSeat MaterialK = PCTFE V = PolyimidePorting*2P = 2 Ports 4P = 4 Ports 4PB = 4 Ports* R efer to the Regulator Porting Guide, 25000156, for additional porting6 Source Pressure RangeH = 0 - 1700 psig L = 0- 300 psig* F or low inlet pressure applications below 300 psig, specify “L” model for improved droop performance.Contact factory for most up to date lead time information.Blue = Configurations that have selections in blue will require a price quote and lead time from the factory.Outlet Gauge*X = No Gauge 03 = 0 - 30 psig OL = 0 - 60 psig 01 = 0 - 100 psig 2 = 0 - 200 psig 4=0 - 400 psig* Only include with “3P”, “4P”, or "4PB" body configurations.© 2017 Parker Hannifin CorporationOFFER OF SALE:The items described in this document are hereby offered for sale by Parker-Hannifin Corporation, its subsidiaries or its authorized distributors. This offer and its acceptance are governed by the provisions stated in the detailed “Offer of Sale” elsewhere in this document or available at /verifloWARNING USER RESPONSIBILITYFAILURE OR IMPROPER SELECTION OR IMPROPER USE OF THE PRODUCTS DESCRIBED HEREIN OR RELATED ITEMS CAN CAUSE DEATH, PERSONAL INJURY AND PROPERTY DAMAGE. THIS DOCUMENT IS FOR REFERENCE ONLY. PLEASE CONSULT FACTORY FOR LATEST PRODUCT DRAWINGS AND SPECIFICATIONSThis document and other information from Parker-Hannifin Corporation, its subsidiaries and authorized distributors provide product or system options for further investigation by users having technical expertise.The user, through its own analysis and testing, is solely responsible for making the final selection of the system and components and assuring that all performance, endurance, maintenance, safety and warning requirements of the application are met. The user must analyze all aspects of the application, follow applicable industry standards, and follow the information concerning the product in the current product catalog and in any other materials provided from Parker or its subsidiaries or authorized distributors.To the extent that Parker or its subsidiaries or authorized distributors provide component or system options based upon data or specifications provided by the user, the user is responsible for determining that such data and specifications are suitable and sufficient for all applications and reasonably foreseeable uses of the components or systems.The products described herein, including without limitation, product features, specifications, designs, availability and pricing are subject to change by Parker Hannifin Corp and it’s subsidiaries at any time without notice.Proposition 65 Warning: This product contains chemicals known to the state of California to cause cancer or birth defects or other reproductive harm.LitPN: 25000328Rev: ADate of Issue: 09/2022* Filter screen located within inlet port.A-LOK ® is a registered trademark of Parker Hannifin Corporation Hastelloy ® is a registered trademark of Haynes International, Inc.Inconel ® is a registered trademark of Special Metals CorporationAll specifications subject to change without notice.For additional information on materials of construction, functional performance and operating conditions, please refer to Veriflo report RI.EN.RP018 . 1. Internal volume includes end connections.2. P ressure rating based on nominal temperature conditions. Refer to Veriflo report RI.EN.RP018 for specific information regarding regulator performance at temperature.。
热处理炉 Hot Shot HS-1200 用户手册说明书

SPECIFICATIONSMax Temperature Input Voltage HzAmp Circuit Required Power Controller VolumeInternal Dimensions Max Ambient Temperature2000°F (1093°C)240V 6020 Amp 4000WProgrammable PID 1200 in³10” wide x 10” tall x 12” deep95°F (35°C)alarm USB portThe Hot Shot 1200 Oven is a state of the art, table-top, heat treating oven capable of reaching and holding temperatures up 2000°F. Heat Treating Ovens can be used to heat such things as glass, cylinder heads, welded and carbon steel joints, pumps, various mechanical plates, ceramics, etc.HOT SHOT 1200 ELECTRICAL FEATURES• N ovus 480D programmable controller withfactory presets.• U SB port for programming.• F ailsafe overtemp manual reset thermostat.• 40 amp rated SSR with convection heat sink.• K iln type “K” thermocouple.• D oor limit switch.• E asy to read slant top control panel.• H eavy Duty cord with 20 amp plug.• F ully grounded control and oven shell.HOT SHOT 1200 MECHANICAL FEATURES• D ual layer air plenum for external heatmanagement and precise temperature control.• 20 Gauge 304 Stainless steel coreconstruction.• P owder coated exterior shell.• T wo-inch Kaowool insulation in door.• 16 Gauge Kanthal A-1 heating element.• 10H x 10W x 12D working chamber / 1200 cu-in.HOT SHOT 1200 PERFORMANCEPerformance Features• T he Hot Shot oven is equipped with Cool-Touch Technology (patent pending). Thisprovides a safe external temperature toallow for safer operation and protection of itssurroundings.• 240V 20-amp supply circuit required.• 4000-watt heating element/17 amp total ovenload.• 2000°F/1093°C max operating temperature.• A mbient to 2000°F/1093°C in as little as40 minutes (room temperature, empty oven).• M aximum ambient room temperature of 95°F - (35°C).Temperature ControllerProgramming Code:4912(Please keep with yourHot Shot Oven records)STARTING YOUR OVEN FOR THE FIRST TIME?Please carefully remove all packing material from the inside of your oven. Visually check that the element hasn’t been bumped or moved during shipping.• D O NOT block any vents.• K eep the back of the oven (fan unit) at least 3 inches away from a wall or other objects.• D O NOT attempt to duct the exhaust of the fan unless the exhaust has a power vent compatible with the cfm of the fan.Your temperature controller has been pre-programmed to outgas your oven automatically and anneal your heating element. Place oven on a level, non-combustible surface. Apply power.Control power = on. Heat enable = on. Door = closed. Press “P” once, e-prog = yes. Press “P” again, run = yes. Press “P” again to return to the main screen.Oven will start @ 400°F and will work its way up to 1800°F in timed segments, after 1800°F is reached, it will slowly cool down to ambient to anneal the heating element.Run command will automatically be removed at the end of the sequence. Do not open the door until the process has ended and the oven has cooled.If you are firing the oven for the first time, here’s what you can expect:Important: Do these steps in a well ventilated area or outdoors if possible.Note: The oven fan is regulated by the oven core temperature, therefore, it will not turn on immediately.• R un and heat soak for ½ hour @ 400°F - slight odor of burned anchor lube and assembly lubricants, small amount of smoke, kaowool board will turn chocolate brown and start outgassing.• R un and heat soak for 45 minutes @ 800°F - odor from the insulating board will really begin to stink, you will wonder if this is actually normal, don’t worry, it is. If you open the oven door, expect to see a fire show of outgassing contaminants & heavy smoke.• R un and soak for 1 hour @ 1200°F -• R un and soak for 1 hour @ 1600°F - your cooling fan should have kicked on by now, but the smell is still very strong, the inner insulating board of the oven is starting to cleanse itself and is turning white, there will be a brown ring around the door that will move away from the inner shell as temperature increases.• R un and soak for 1 hour @ 1800°F - all downhill from here, you have burned off most of the impurities from the insulating board. Inner oven should be chalk white. The brown ring around the door should be fading. 2nd and 3rd firings: slight odor will be present, decreasing with each subsequent firing.While it’s not necessary to run your oven all the way up to the max temperature for the outgassing process, holding at 1500°F for 1 hour will remove 90% of the contaminants from the insulation. You will see steam escaping from the seams and even water forming at the feet of the oven from trapped moisture being burned away from the inner (hot) layer and condensing when it gets to the outer (cooler) layer.Your heating element is made from Kanthal Ni-Chrome wire, allowing cold air to enter a hot oven will harden your element and make it become brittle. Never use compressed air or fans to force cool the oven, always close the door and let the oven cool on its own, this will keep your heating element annealed.Our cool touch technology, with the fan running, should keep the outer surface within 20°C of room ambient temperature.OVEN ON TEMP NOW?Here’s a few things to do after your oven has reached a stable operating temperature1. P ress and hold the “P” button until “ATUNE” appears, select yes and let your unit set its own PID’s. Autotune is complete when the “tune” light goes out on the main screen. Always auto tune +/- 200°F of your normal operating temperatures. Keep the door closed during this tuning; oven needs to be stable and have no cold air introduced during auto-tune.2. M ake certain that the cooling fan located in the back of your oven has engaged and the fans air movementis not impeded.SAFETY RECOMMENDATIONS1. Do not use an extension cord.2. Install on a 20 amp 240V circuit.3. Do not use the oven to cure paint or any other solvent borne products.4. Do not use the oven for powder coat.5. Use in a well ventilated area.6. Wear protective clothing and protect thyself from burns.7. Turn off the “heat enable” when loading/unloading parts.8. Do not unplug the unit till it has fully cooled down.9. Do not EVER put magnesium in the oven.10. Do not exceed 2000°F.11. Do not block any vents12. Keep the fan exhaust at least 3 inches from any wall or obstruction.13. I n the event the oven overheats, the oven will automatically shut down. Please contact our office at262-361-4912 to work with our team on resetting your oven if shut down occurs.READY TO PROGRAM YOUR CONTROLLER NOW?Novus 4 480D setting ramp and soak times, temps and events.The oven comes with a factory installed USB port for programming the controller via a computer. Note: Disconnect oven from power source before plugging in USB.Press and hold the “P” button till PTOL appears, the use the “P” button to scroll thru parameter group.Note: If any “PT” value is set to zero, the controller will stop and end the sequence at the point.rPT.P = number of times the controller will repeat the sequence (after the Pt9 has timed out, it will return to Pt1 and repeat the sequence)Running in manual set point mode.Press “P” once, E-prog = no press, press “P” again, run = yes, you can manually adjust the green temp set point and oven is in “run hold” mode with no timers. Use the “^-v” keys to change set point.N1030T controllers onlyFrom the main start up screen, press “P” to cycle through time and run-hold options.Press “P” once for timer display, twice for “T1” timer set, third time is run option.On the “run” screen select “yes” to run hold, “no” to remove run command or “F” to enable the function key.Once you have enable the “F” key, push and hold the F key for a 3 count, run command will applied and controller will run for the amount of time set on “T1”, when this timer reaches zero value, the run command is removed from the controller.。
微逻辑1200可编程控制器安装指南说明书
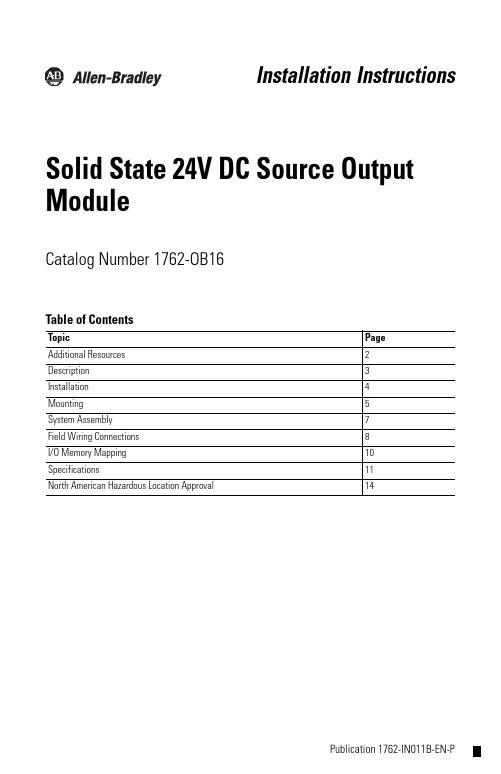
Publication 1762-IN011B-EN-PInstallation InstructionsSolid State 24V DC Source Output ModuleCatalog Number 1762-OB16Table of Contents Topic PageAdditional Resources 2Description 3Installation 4Mounting 5System Assembly 7Field Wiring Connections 8I/O Memory Mapping 10Specifications 11North American Hazardous Location Approval 142 Solid State 24V DC Source Output Module Publication 1762-IN011B-EN-P - June 2013Additional ResourcesIf you would like a manual, you can:•download a free electronic version from the Internet: •purchase a printed manual by contacting your local Allen-Bradley distributor or Rockwell Automation representative Publication DescriptionMicroLogix 1200 Programmable Controllers User Manual (Bulletin 1762 Controllers and Expansion I/O), publication rmation on installing, wiring, and operating a MicroLogix 1200 Programmable Controller.MicroLogix 1200 Programmable Controllers Installation Instructions, publication 1762-IN006.Installation guide for the MicroLogix 1200 Programmable Controller.Industrial Automation Wiring and Grounding Guidelines, publication 1770-4.1.More information on proper wiring and grounding techniques.Solid State 24V DC Source Output Module 3Publication 1762-IN011B-EN-P - June 2013Description Item Description Item Description1a upper panel mounting tab 5bus connector cover1b lower panel mounting tab 6flat ribbon cable with bus connector(female pins)2I/O diagnostic LEDs 7terminal block3module door with terminal identification label8DIN rail latch4bus connector with male pins 9pull loop1a64 Solid State 24V DC Source Output Module Publication 1762-IN011B-EN-P - June 2013Installation1762 I/O is suitable for use in an industrial environment when installed in accordance with these instructions. Specifically, this equipment is intended for use in clean, dry environments (Pollution degree 2(1)) and to circuits not exceeding Over Voltage Category II (2) (IEC 60664-1).(3)Prevent Electrostatic Discharge Remove Power(1)Pollution Degree 2 is an environment where, normally, only non-conductive pollution occurs except that occasionally a temporary conductivity caused by condensation shall be expected.(2)Over Voltage Category II is the load level section of the electrical distribution system. At this level transient voltages are controlled and do not exceed the impulse voltage capability of the product’s insulation.(3)Pollution Degree 2 and Over Voltage Category II are International Electrotechnical Commission (IEC) designations.Electrostatic discharge can damage integrated circuits or semiconductors if you touch bus connector pins. Follow these guidelines when you handle the module:•T ouch a grounded object to discharge static potential.•W ear an approved wrist-strap grounding device.•Do not touch the bus connector or connector pins.•Do not touch circuit components inside the module.•If available, use a static-safe work station.•When not in use, keep the module in its static-shield box.Remove power before removing or installing this module. When you remove or install a module with power applied, an electrical arc may occur. An electrical arc can cause personal injury or property damage by:•sending an erroneous signal to your system’s field devices, causing unintended machine motion•causing an explosion in a hazardous environment•causing permanent damage to the module’s circuitryElectrical arcing causes excessive wear to contacts on both the module and its mating connector. W orn contacts may create electrical resistance.Solid State 24V DC Source Output Module 5Publication 1762-IN011B-EN-P - June 2013Mounting Minimum Spacing Maintain spacing from enclosure walls, wireways, adjacent equipment, etc. Allow 50.8 mm (2 in.) of space on all sides for adequate ventilation, as shown:Do not remove protective debris strip until after the module and all other equipment near the module is mounted and wiring is complete. Once wiring is complete and the module is free of debris, carefully remove protective debris strip. Failure to remove strip before operating can cause overheating.1762 expansion I/O may be mounted horizontally only.During panel or DIN rail mounting of all devices, be sure that all debris (metal chips, wire strands, etc.) are kept from falling into the module. Debris that fall into the module could cause damage when power is applied to the module.6 Solid State 24V DC Source Output Module Publication 1762-IN011B-EN-P - June 2013DIN Rail MountingThe module can be mounted using the following DIN rails: 35 x 7.5 mm(EN 50 022 - 35 x 7.5) or 35 x 15 mm (EN 50 022 - 35 x 15).Before mounting the module on a DIN rail, close the DIN rail latch. Press the DIN rail mounting area of the module against the DIN rail. The latch will momentarily open and lock into place.Use DIN rail end anchors (Allen-Bradley part number 1492-EA35 or 1492-EAH35) for vibration or shock environments.Panel MountingUse the dimensional template shown below to mount the module. The preferred mounting method is to use two M4 or #8 panhead screws per module. M3.5 or #6 panhead screws may also be used, but a washer may be needed to ensure a good mechanical contact. Mounting screws are required on every module.For environments with greater vibration and shock concerns, use the panelmounting method described below, instead of DIN rail mounting.For more than 2 modules: (number of modules - 1) x 40 mm (1.58 in.)NOTE: All dimensions are in mm (inches). Hole spacing tolerance: ±0.4 mm (0.016 in.).Solid State 24V DC Source Output Module 7Publication 1762-IN011B-EN-P - June 2013System AssemblyThe expansion I/O module is attached to the controller or another I/O module by means of a flat ribbon cable after mounting as shown below.TIP Use the pull loop on the connector to disconnect modules. Do not pull on the ribbon cable.EXPLOSION HAZARD•In Class I, Division 2 applications, the bus connector must be fully seated and the bus connector cover must be snapped in place.•In Class I, Division 2 applications, all modules must be mounted in direct contact with each other as shown on Page 6. If DIN rail mounting is used, an end stop must be installed ahead of the controllerand after the last 1762 I/O module.8 Solid State 24V DC Source Output Module Publication 1762-IN011B-EN-P - June 2013Field Wiring ConnectionsGrounding the ModuleThis product is intended to be mounted to a well-grounded mounting surface such as a metal panel. Refer to Industrial Automation Wiring and Grounding Guidelines, Allen-Bradley publication 1770-4.1, for additional information.Output WiringBasic wiring (1) of the 1762-OB16 is shown below.A write-on label is provided with the module. Mark the identification of each terminal with permanent ink, and slide the label back into the door.(1)Surge Suppression – Connecting surge suppressors across your external inductive load will extend the life of the relay contacts. For additional details, refer to Industrial Automation Wiring and Grounding Guidelines , Allen-Bradley publication 1770-4.1.Be careful when stripping wires. Wire fragments that fall into a module could cause damage when power is applied. Once wiring is complete, ensure the module is free of all metal fragments.Solid State 24V DC Source Output Module 9Publication 1762-IN011B-EN-P - June 2013Wiring the Finger-Safe Terminal BlockWhen wiring the terminal block, keep the finger-safe cover in place.1.Route the wire under the terminal pressure plate. Y ou can use the stripped end of the wire or aspade lug. The terminals will accept a 6.35 mm (0.25 in.) spade lug.2.Tighten the terminal screw making sure the pressure plate secures the wire. Recommended torque when tightening terminal screws is 0.90 Nm(8 lb-in.).Miswiring of the module to an AC power source will damage the module.Finger-safe cover not shown for clarity.If you need to remove the finger-safe cover, insert a screw driver into one of the square wiring holes and gently pry the cover off. If you wire the terminal block with the finger-safe cover removed, you will not be able toput it back on the terminal block because the wires will be in the way.10 Solid State 24V DC Source Output Module Publication 1762-IN011B-EN-P - June 2013Wire Size and Terminal Screw TorqueEach terminal accepts up to two wires with the following restrictions:I/O Memory MappingOutput Data FileFor each output module, the output data file contains the controller-directed state of the discrete output points. Bit positions 0…15 correspond to output terminals 0…15.w = write onlyA ddressing The addressing scheme for 1762 Expansion I/O is shown below.(1)I/O located on the controller (embedded I/O) is slot 0. I/O added to the controller (expansion I/O) begins with slot 1.Wire Type Wire Size Terminal Screw Torque Solid Cu-90 °C (194 °F)#14…22 AWG 0.90 Nm (8 lb-in.)Stranded Cu-90 °C (194 °F)#16…22 AWG 0.90 Nm (8 lb-in.)W o rd Bit Position 15141312111098765432100w w w w w w w w w w w w w w w w O0:x.0/0OutputData File Slot Number (1)Word (always zero for this module)Bit (0…15)Bit DelimiterWord DelimiterSlot DelimiterSolid State 24V DC Source Output Module 11Publication 1762-IN011B-EN-P - June 2013SpecificationsGeneral Specifications Specification ValueDimensions, HxWxD 90 x 40.4 x 87 mm (height including mounting tabs is 110 mm)3.54 x 1.59 x 3.43 in. (height including mounting tabs is4.33 in.)Approximate Shipping Weight (with carton)235 g (0.52 lbs.)Temperature, nonoperating -40…85 °C (-40…185 °F)Temperature, operating 0…55 °C (32…131 °F)Humidity, operating 5…95% non-condensingAltitude, operating 2000 m (6561 ft)Vibration, operating 10…500 Hz, 5 g, 0.030 in. max. peak-to-peak, 2 hours per axis Shock Operating: 30 g panel mounted, 3 pulses per axisNon-Operating: 50 g panel mounted, 3 pulses per axis (40 g DIN Rail mounted)Hazardous Environment Class Class I, Division 2, Hazardous Location, Groups A, B, C, D ISA/ANSI 12.12.01(C-UL under CSA C22.2 No. 213)Radiated and Conducted Emissions EN50081-2 Class AESD Immunity (IEC1000-4-2) 4 kV contact, 8 kV air, 4 kV indirectRadiated Immunity (IEC1000-4-3)10 V/m, 80…1000 MHz, 80% amplitude modulation, +900 MHz keyed carrierFast Transient Burst (IEC1000-4-4) 2 kV, 5 kHzSurge Immunity (IEC1000-4-5) 2 kV common mode, 1 kV differential modeConducted Immunity (IEC1000-4-6)10V, 0.15…80 MHz (1)(1)Conducted Immunity frequency range may be 150 kHz…30 MHz if the Radiated Immunity frequency range is 30…1000 MHz.12 Solid State 24V DC Source Output Module Publication 1762-IN011B-EN-P - June 2013Sourcing Output - Source describes the current flow between the I/O module and the field device. Sourcing output circuits supply (source) current to sinking field devices. Field devices connected to the negative side (DC Common) of the field power supply are sinking field devices. Field devices connected to the positive side (+V) of the field supply are sourcing field devices.Typical Loading Resistor - T o limit the effects of leakage current through solid-state outputs, a loading resistor can be connected in parallel with your load. Use a 5.6k ohm, 1/4 W resistor for transistor outputs, 24V DC operation.Recommended Surge Suppression - Use a 1N4004 diode reverse-wired across the load for transistor outputs switching 24V DC inductive loads. For additional information, refer to Industrial Automation Wiring and Grounding Guidelines, Allen-Bradley publication 1770-4.1.Output Specifications Specification ValueVoltage Category 24V DCOperating Voltage Range 20.4…26.4V DCNumber of Outputs 16Bus Current Draw, max 175 mA @ 5V DC (0.88 W)Heat Dissipation max 2.9 total Watts @ 30 °C (86°F)2.1 total Watts @ 55 °C (131 °F)Signal Delay (max.) – resistive load turn-on = 0.1 msturn-off = 1.0 msOff-State Leakage max 1.0 mAOn-State Current (min.) 1.0 mAOn-State Voltage Drop, max 1.0V DCContinuous Current per Point, max 0.5A @ 55 °C (131 °F)1.0A @ 30 °C (86 °F)Continuous Current per Module, max 4.0A @ 55 °C (131 °F)8.0A @ 30 °C (86 °F)Surge Current, max 2.0 A (Repeatability is once every 2 s @ 55 °C (131 °F), once every second @ 30 °C (86 °F) for a duration of 10 ms.)Power Supply Distance Rating 6 (The module may not be more than 6 modules away from the power supply.)Isolated Groups Group 1: Outputs 0 (15)Output Group to Backplane Isolation Verified by one of the following dielectric tests: 1200V AC for 1 s or 1697V DC for 1 s.75V DC working voltage (IEC Class 2 reinforced insulation)Vendor I.D. Code 1Product Type Code 7Product Code 103Solid State 24V DC Source Output Module 13Publication 1762-IN011B-EN-P - June 2013Certifications Certification (when product is marked)(1)(1)See product certification link at /products/certification for Declaration of Conformity, Certificates, and other certification details.Valuec-UL-us UL Listed Industrial Control Equipment, certified for US andCanada.UL Listed for Class I, Division 2 Group A,B,C,D HazardousLocations, certified for U.S and Canada.See UL File E334470.CE European Union 2004/108/EC EMC Directive, compliant with:EN 61326-1; Meas./Control/Lab., Industrial RequirementsEN 61000-6-2; Industrial ImmunityEN 61000-6-4; Industrial EmissionsEN 61131-2; Programmable Controllers (Clause 8, Zone A & B)C-Tick Autralian Rediocommunications Act, compliant with:AS/NZS CISPR 11; Industrial EmissionsKC Korean Registration of Broadcasting and CommunicationsEquipment, compliant with:Article 58-2 of Radio Waves Act, Clause 314 Solid State 24V DC Source Output Module Publication 1762-IN011B-EN-P - June 2013North American Hazardous Location Approval This equipment is suitable for use in Class I, Division 2, Groups A, B, C, D or non-hazardous locations only.The following W ARNING statement applies to use in hazardous locations.The following information applies when operating this equipment in hazardous locations:Informations sur l’utilisation de cet équipement en environnements dangereux:Products marked "CL I, DIV 2, GP A, B, C, D" are suitable for use in Class I Division 2 Groups A, B, C, D, Hazardous Locations and nonhazardous locations only. Each product is supplied with markings on the rating nameplate indicating the hazardous location temperature code. When combining products within a system, the most adverse temperature code (lowest "T" number) may be used to help determine the overall temperature code of the system. Combinations of equipment in your system are subject to investigation by the local Authority Having Jurisdiction at the time of installation.Les produits marqués "CL I, DIV 2, GP A, B, C, D" ne conviennent qu'à une utilisation en environnements de Classe I Division 2 Groupes A, B, C, D dangereux et non dangereux. Chaque produit est livré avec des marquages sur sa plaque d'identification qui indiquent le code de température pour les environnements dangereux. Lorsque plusieurs produits sont combinés dans un système, le code de température le plus défavorable (code de température le plus faible) peut être utilisé pour déterminer le code de température global du système. Les combinaisons d'équipements dans le système sont sujettes à inspection par les autorités locales qualifiées au moment de l'installation.EXPLOSION HAZARD •Substitution of components may impair suitability for Class I, Division 2.•Do not replace components or disconnect equipment unless power has been switched off.•Do not connect or disconnect components unless power has been switched off.•This product must be installed in an enclosure.•In Class I, Division 2 applications, the bus connector must be fully seated and the bus connector cover must be snapped in place.•In Class I, Division 2 applications, all modules must be mounted in direct contact with each other as shown on Page 6. If DIN rail mounting is used, an end stop must be installed ahead of the controller and after the last 1762 I/O module.•All wiring must comply with N.E.C. article 501-4(b).•The interior of the enclosure must be accessible only by the use of a tool.•For applicable equipment (relay modules, etc.), exposure to some chemicals may degrade the sealing properties of materials used in the following devices: Relays, Epoxy. It is recommended that the User periodically inspect these devices for any degradation of properties and replace the module if degradation is found.RISQUE D’EXPLOSION•La substitution de composants peut rendre cet équipement impropre à une utilisation en environnement de Classe 1, Division 2. •Ne pas remplacer de composants ou déconnecter l'équipement sans s'être assuré que l'alimentation est coupée. •Ne pas connecter ou déconnecter des composants sans s'être assuré que l'alimentation est coupée. •Ce produit doit être installé dans une armoire. •Pour les applications de Classe I, Division 2, le connecteur de bus doit être correctement installé et son couvercle enclenché. •Pour les applications de Classe 1, Division 2, tous les modules doivent être installés en contact direct les uns avec les autres, comme indiqué page 6. Si on utilise le montage sur rail DIN, une butée doit être placée à l'avant de l'automate et après la dernière unité d'E/S 1762.Solid State 24V DC Source Output Module 15 Notes:Publication 1762-IN011B-EN-P - June 2013Rockwell Automation SupportRockwell Automation provides technical information on the Web to assist you in using its products. At /support/, you can find technical manuals, a knowledge base of FAQs, technical and application notes, sample code and links to software service packs, and a MySupport feature that you can customize to make the best use of these tools.For an additional level of technical phone support for installation, configuration and troubleshooting, we offer TechConnect support programs. For more information, contact your local distributor or Rockwell Automation representative, or visit /support/.Installation AssistanceIf you experience a problem within the first 24 hours of installation, please review the information that's contained in this manual. You can also contact a special Customer Support number for initial help in getting your product up and running .New Product Satisfaction ReturnRockwell Automation tests all of its products to ensure that they are fully operational when shipped from the manufacturing facility. However, if your product is not functioning and needs to be returned, follow these procedures.Documentation FeedbackYour comments will help us serve your documentation needs better. If you have any suggestions on how to improve this document, complete this form, publication RA-DU002, available at /literature/.United States or Canada 1.440.646.3434Outside United States or Canada Use theWorldwide Locator at/support/americas/phone_en.html , orcontact your local Rockwell Automation representative.United States Contact your distributor. You must provide a Customer Support case number (call the phone number above to obtain one) to your distributor to complete the return process.Outside United States Please contact your local Rockwell Automation representative for the return procedure.Allen-Bradley, Rockwell Automation, MicroLogix, and T echConnect are trademarks of Rockwell Automation, Inc.Trademarks not belonging to Rockwell Automation are property of their respective companies.Publication 1762-IN011B-EN-P - June 2013Supersedes Publication 1762-IN011A-EN-P - July 2000Copyright © 2013 Rockwell Automation, Inc. All rights reserved.。
1200安装使用说明书

1200HⅡTE立式斜流泵安装使用说明书沈阳水泵股份有限公司2005年8月1 概述 (4)1.1 用途 (4)2 结构说明 (4)2.1 泵本体 (4)2.2 泵管路系统 (5)3 安装 (6)3.1 安装前的准备 (6)3.2 安装程序 (6)3.3 垫板的调整 (8)3.4 基础座的安装和初步调整 (8)3.5 泵本体的安装(参看图6安装拆卸示意图) (9)3.6 电机座的安装和调整 (9)3.7 垫铁的点焊 (9)3.8 电动机的安装和对中 (9)3.9 最后灌浆 (10)3.10 灌浆及灌浆注意事项 (10)3.11 排出管路的连接 (10)3.12 附属设备、辅助管路和导线的连接 (11)3.13 电动机预运转、定转向 (11)3.14 刚性联轴器的连接 (11)4 起动 (11)4.1 起动条件 (11)4.2 起动顺序 (12)4.3 起动时应注意事项 (12)5 运行 (13)5.1 运行前的准备 (13)5.2 运行中应注意事项 (14)6 停机 (14)6.1 停机顺序 (14)6.2 停机时应注意事项 (15)6.3 特殊停机 (15)7 维护 (15)7.1 作好运行日记 (15)7.2 检查 (16)7.2.1 外观检查 (16)7.2.2 拆卸检查 (17)7.3 检查周期 (18)7.3.1 每天的检查 (18)7.3.2 每半年检查 (18)7.3.3 每年检查 (18)7.4 仪表的使用 (19)7.5 长期停机时的维护 (19)8 拆卸与组装 (19)8.1 拆卸前的准备 (19)8.2 拆卸 (20)8.3 组装 (20)9 常见故障的原因及消除方法 (22)1 概述1.1 用途1200HⅡTE立式斜流泵是专为前湾电厂350MW级燃气-蒸汽联合循环发电机组输送循环冷却水设计的,也可用于其它工况相似的电厂及大型水利工程蓄水、排水,被输送液体温度不高于55℃。
2 结构说明2.1 泵本体整体结构见图1(1200HⅡTE-0000结构剖面图),简单介绍如下:a、泵本体由3个主要部分组成,即外壳、内壳和转子结合部。
菲博电子芯片有限公司 CUBE 1200可重充电锂离子电池用户手册说明书

Features• A high-capacity, high-load on-ground battery with integrated charger • 1172 Wh – 81,6 Ah• Multivoltage (5,0V - 14,4Vnom - 24,0V - 48,0V) • For cinematography cameras and lighting •RecellableSafety Instructions• Only for professional use! Keep batteries out of reach of children and personnel that has not been instructed concerning the use of high-capacity Lithium-Ion batteries! • Use only with integrated charger.• Keep the battery dry and do not immerse in water. • Never open the case of the battery.• Do not expose the battery to temperatures over 60°C.• Do not expose the battery to fire! May explode if thrown into fire! • Maximum load 500W.•Handle with care! Do not throw! Do not drop!CUBE 1200 rechargeable Li-Ion Battery USER MANUALWE STRONGLY RECOMMEND THAT YOU READ THIS INSTRUCTION BEFORE USING YOUR CUBE 1200 BATTERY! PLEASE KEEP THIS MANUAL FOR FUTURE REFERENCECharging•Never load unattended•Wait 30 Minutes after discharge before charging your battery.•The bebob CUBE 1200 battery can be charged via the internal charger.•Charging time ~ 8,5h•Approximate charging time may vary depending on charger and temperature.•For optimal performance, the bebob CUBE 1200 should be charged in ambienttemperature around 10°C - 30°C.•The bebob CUBE 1200 can be recharged in any state of charge.•Charger input: AC IN 90-240V – 50-60Hz•Input fuse: 1x5AT – 1 spare fuse•Charging current 10A internalAC Adapter•The bebob CUBE 1200 battery can be used as an 150W AC adapter when plugged into AC.•When the device powered needs more than 150W, the overload gets compensated through the battery until the battery is empty.•When the device powered needs less than 150W, the free power will be charged into the battery.•When the AC Adapter is on, the Status led will light greenDischarging•5,0V: 2x USB.1x 2A self-resetting fuse•12V (unreg 12 to 16,8V)): 2x XLR4 10A, 1x Twist D-Tap 10A, electronic fuses•24V (28,0V+/- 5V adjustable): 2x XLR3 16A, electronic fuses•48V (48,0V +/- 3V adjustable): 1x XLR10 10A electronic fuse•The battery can be used in ambient temperature of - 20°C to + 55°C.Status LED•Status LED lights up for 3 seconds after switch off:-- green: full capacity over 80%- yellow: between 60% and 80%- red: under 60%•Status LED lights green when the CUBE is plugged into AC.Fuel Gauge•Five-step LED power indicator•Flashes while charging•Lights up while discharging•Last LED (20%) flashes when the capacity comes under 10%.Outputs LED´s•12V/24V LED light up green when the CUBE is switched ON at 24V.•12V/48V LED light up green when the CUBE is switched ON at 48V.•12V/24V/48V LED are off when the CUBE is switched OFF.•12V/24V/48V LED turn first yellow and then red after 5s when overloaded (more than 10A).The output is locked. Remove or reduce load!•24V/48V LED flash red when the internal temperature of the CUBE reaches 90°C.24V/48V output is locked. Remove or reduce load!Storage•Storage temperature range is - 20°C to + 35°C (<85% humidity).•To store the battery for a long period (longer than 4 weeks), the battery should be charged between 50% and 75%. The battery should be recharged every 4 weeks.•After storage some self-discharge will occur. Before re-use it is advisable to fully recharge the battery.Warranty•The CUBE 1200 is covered by a 2 years unconditional warranty on all parts, except the cells.•The cells are covered by a 2 year warranty, for 80% of the original capacity.•For warranty issues, or if you have any additional questions, please contact the appropriate bebob distributor listed at .Voltage Selection•Main Switch on Position OFF: No Voltages available•Main Switch on Position 24V: 5, 12 and 24V Voltage available•Main Switch on Position 48V: 5, 12 and 48V availableVoltage SettingDisposal•The CUBE 1200 battery has to be disposed within a dedicated collection container for used device batteries. Please be aware that only empty batteries are allowed for disposal incollection containers. In case the battery is not completely discharged, precautions againsta potential short-circuit have to be taken.SpecificationsModel CUBE 1200Capacity 1172 Wh – 81,6 AhVoltage 5,0V DC14,4V DC (12,0V to 16,8V unreg.) 28,0V DC (adjustable +/-5V) 48,0V DC (adjustable +/-3V)Cells Lithium-Ion Trimix HL made in Japan Max. Discharge Power 500WFuel Gauge 5-Step LEDStatus Green: Full Capacity over 80%Yellow: Full Capacity between 60 and 80%Red: Full Capacity under 60%Weight 8,95 KgDimensions (WXHXD) 208x356x167mmCharger IntegratedCharging time 8,5 HoursOperating Temp. Range Charge: + 10°C ~ + 30°C recommendedDischarge:- 20°C ~ + 55°CStorage:- 20°C ~ + 35°C (<85% RH )Transport as of April 1st 2016•This summary reflects our current knowledge.1. Transport by Commercial Airline / Carry-on Luggage•The CUBE 1200 is forbidden in your carry-on luggage.2. Transport by Commercial Airline / Checked-in Luggage•The CUBE 1200 is forbidden in your checked-in luggage.3. Transport as air-, road- and sea-freight•Li-Ion batteries, including the bebob CUBE 1200, when shipped by air, road or sea are classified as dangerous goods class 9 and subject to special UN certified packaging.•Air transport authority training and authorisation (PK 1/ PK 2) are required for packing the CUBE 1200 for an air cargo shipment.•Li-Ion batteries for air cargo must have a state-of-charge of no more than 30% for shipping – meaning only one out of the five fuel gauge LED lights up.•We recommend that you confirm with your carrier of choice to determine any further restriction or local policies before travelling. You will find the actual regulations ofyour carrier of choice in the bebob transport information system www.fly-.。
FL-1200系列高流速旋钢管流量表说明书

Displacement Transducers, Dynamic Measurement Force Sensors, Instrumentation for Pressure and Strain Measurements, Load Cells, Pressure Gauges, Pressure Reference Section, Pressure Switches, Pressure Transducers, Proximity Transducers, Regulators, Pressure Transmitters, Strain Gauges, Torque Transducers, Valves
HIGH FLOW RATE PURGE ROTAMETERS
CAPACITIES: 0.08 to 5.0 GPM for Water,
0.34 to 15.0 SCFM for Air
B
FL-1200 Series
$670
wFiosthreecootphrareegrleafltBui-oi7dn.s,
ߜ 316 SS and Brass Construction Available
ߜ Shielded for Use in Pressurized Systems
ߜ Easy-to-Read 65 mm (2.6") Scale
Dimensions: mm (in)
The FL-1200 flowmeters provide a low-cost means of flow rate indication. They are designed for applications where precise accuracy requirements for metering are not imperative. These meters are ideal for purge service, sealed oil systems, bearing lubrication, cooling water indication, and other associated applications.
Agilent 1200 Infinity 系列产品介绍说明书
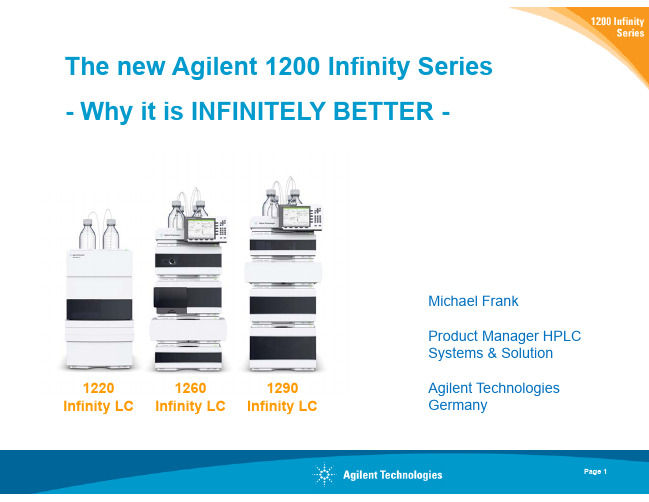
• Pump: New next generation inlet valves for better performance • Detectors: Next generation 1290 Infinity DAD technology • HiP Autosampler: leveraging of many parts of the 1290 Infinity
• 30 % Price Reduction by March 1st, attractive upfront contracts • Based on
– proven robustness – 2x higher than 1100 Series at introduction – Increased parts lifetime / longer maintenance intervalls – new design-for-supportability technology for faster maintenance,
1260 Infinity Quat./Iso LC 1220 Infinity LC
6
8
10 flow
Page 6
1260 Quaternary LC and 1220 Gradient LC
RRLC Performance for EVERY LAB!
10x productivity increase and improved data quality!
Conventional 4.6x150, 5µm Resolution peak 5 = 4.20 Run time 11 min
双通道、3 MHz、1200 mA降压稳压器ADP5034——用户手册说明书
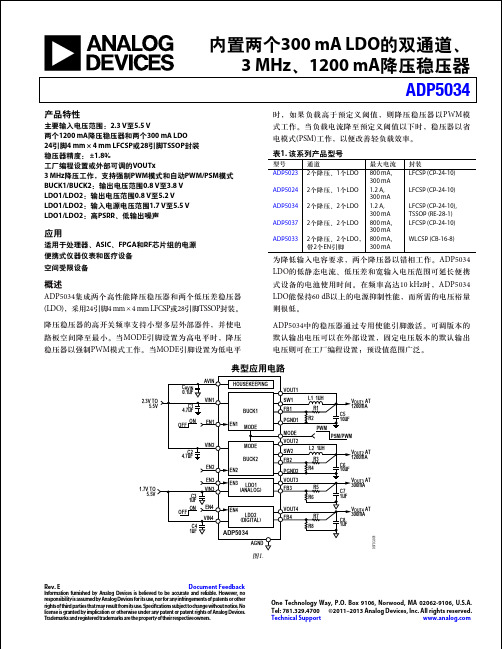
内置两个300 mA LDO 的双通道、3 MHz 、1200 mA 降压稳压器ADP5034Rev. EDocument FeedbackInformation furnished by Analog Devices is believed to be accurate and reliable. However , no responsibility is assumed by Analog Devices for its use, nor for any infringements of patents or other rights of third parties that may result from its use. Speci cations subject to change wit hout notice. No license is granted by implication or otherwise under any patent or patent rights of Analog Devices. T rademarks and registered trademarks are the property of their respective owners.One Technology Way, P.O. Box 9106, Norwood, MA 02062-9106, U.S.A. Tel: 781.329.4700 ©2011–2013 Analog Devices, Inc. All rights reserved. Technical Support 表1. 该系列产品型号型号通道最大电流封装ADP5023 2个降压、1个LDO800 mA, 300 mA LFCSP (CP-24-10) ADP5024 2个降压、1个LDO1.2 A, 300 mA LFCSP (CP-24-10) ADP5034 2个降压、2个LDO1.2 A, 300 mA LFCSP (CP-24-10), TSSOP (RE-28-1) ADP5037 2个降压、2个LDO800 mA, 300 mALFCSP (CP-24-10) ADP50332个降压、2个LDO ,带2个EN 引脚800 mA,300 mA WLCSP (CB-16-8)典型应用电路09703-001VIN1VIN3EN1PWMPSM/PWM2.3V TO5.5VSW1FB1R2R1VOUT1PGND1MODEC510µFV OUT1 AT 1200mAV OUT2 AT 1200mAV OUT3 AT 300mA V OUT4 AT 300mAL1 1µH EN1BUCK1MODEC31µF C24.7µFC14.7µF AVINC AVIN 0.1µFC41µFVIN2EN2AGNDEN2BUCK2MODE EN31.7V TO5.5VEN4VIN4ONOFFONOFFEN3LDO1(ANALOG)ADP5034HOUSEKEEPINGSW2FB2R4R3VOUT2PGND2C610µFL2 1µH FB3R6R5VOUT3C71µFFB4R8R7VOUT4C81µFEN4LDO2(DIGITAL)图1.产品特性主要输入电压范围:2.3 V 至5.5 V两个1200 mA 降压稳压器和两个300 mA LDO 24引脚4 mm × 4 mm LFCSP 或28引脚TSSOP 封装 稳压器精度: ±1.8%工厂编程设置或外部可调的VOUTx3 MHz 降压工作,支持强制PWM 模式和自动PWM/PSM 模式 BUCK1/BUCK2:输出电压范围0.8 V 至3.8 V LDO1/LDO2:输出电压范围0.8 V 至5.2 V LDO1/LDO2:输入电源电压范围1.7 V 至5.5 V LDO1/LDO2:高PSRR 、低输出噪声应用适用于处理器、ASIC 、FPGA 和RF 芯片组的电源 便携式仪器仪表和医疗设备 空间受限设备概述ADP5034集成两个高性能降压稳压器和两个低压差稳压器(LDO),采用24引脚4 mm × 4 mm LFCSP 或28引脚TSSOP 封装。
OF1200x使用说明书

OF1200x使用说明书1、有机热载炉内、外部的检查和准备,包括:有机热载炉内部残存水已放尽、吹干;炉膛内杂物清除干净;各检查孔、人孔等都已密闭,使用填料符合热载体炉介质要求。
安全附件和保护装置的检查1) 压力表弯管前端的针形阀或截止阀处全开状态。
压力表精度、量程、表盘直径符合要求,无压力时指针回零。
2) 液位计放油管阀门处关闭状态,放液管已与储存罐正确联接。
3) 温度计及自动记录仪表已校验合格;超温超压报警、自动连锁保护装置已投入,电器控制各接点无异常。
4) 燃烧通风设备检查,无异常。
2.介质化验及冷态循环有机热载炉使用的热传导液质量合格,对热载体锅炉安全运行关系极大,所以,应先对使用的热传导液取样化验或有供应方的相关质量证明,应明确:1) 热传导液最高使用温度是否与有机热载体炉供热条件一致。
炉出口温度至少应比热传导液允许使用温度低30~40℃,否则热传导液在使用中会很快分解变质,提前失效。
2) 抽样化验,测定热传导液的外观质量、闪点、粘度、酸值、残炭和水分,与热传导液生产厂提供的质量证明书是否相符,同时也为今后运行中介质质量变化监测提供依据。
装油将化验合格的热传导液用加油泵往炉内和膨胀器内注入热传导液。
在加油泵向系统注热传导液时,应再检查一遍炉体、用热设备、管道系统的排污阀、放油阀是否关好,以免热传导液流失。
同时将管道和炉体上的排汽阀逐一打开,排除空气,直至有油流出时关闭。
当膨胀器液位计上出现油位时停止注热传导液,然后启动循环泵,进行冷态循环。
冷态循环冷态循环的目的是试验整个供热系统是否有滞阻现象,设备、管路、阀门等处有无渗漏,循环泵的流量和扬程能否满足生产要求。
由于冷油粘度较高,故热载体炉进出口压力差比较大,管路系统的流动阻力也较大,每台循环泵应轮流启动、试车,使冷油在系统内循环6~8小时。
冷态循环中,还要经常打开放气阀门排放残存空气,观察并记录各点压力表、温度表、电流表等显示情况,注意记录循环泵电流、进出口压差、循环泵出口压力、有机热载体炉进出口压差等数据,并检查油泵运行是否平稳,轴承密封是否良好。
FS-1200A称重仪表面板操作说明书

FS-1200A称重仪表面板操作说明书一、产品概述二、安全注意事项1.请保持称重仪表的工作环境干燥。
2.避免在震动强烈的环境中使用称重仪表,以免影响称重结果。
3.在使用称重仪表前,请确认所称量的物体不超过仪表的最大承重范围。
4.在操作称重仪表时,请注意避免猛烈碰撞仪表,以免损坏。
5.请按要求使用仪表所配备的电源,不要随意更换电源。
三、面板功能介绍1.电源按钮:用于开启或关闭仪表电源。
2.显示屏:用于显示称重结果。
3.单位选择按钮:用于切换称重单位,例如千克、克等。
4.归零按钮:用于将称重仪表归零,以便于再次称量。
5.清零按钮:用于清除显示屏上的称重结果。
6.确认按钮:用于确认所称量物体的重量。
四、正常操作流程1.开启仪表电源,待仪表显示屏显示正常后,即可开始操作。
2.将待称物体放置于称重仪表上,确保物体均匀受力。
3.若需要调整称重单位,请按下单位选择按钮,直到显示屏上显示所需单位。
4.若需要将仪表归零,请按下归零按钮,待显示屏上的数值全部清零后,即可继续操作。
5.若需要清除显示屏上的称重结果,请按下清零按钮,待显示屏上的数值清零后,即可继续操作。
6.若需要确认称量结果,请按下确认按钮,称重结果将被保存并显示于显示屏上。
五、故障排除1.若显示屏无法正常显示,请检查电源是否接触良好,是否已开启仪表电源。
2.若称重结果异常,请确认称重物体的均匀受力,以及没有超过仪表的最大承重范围。
3.若仪表无法归零,请检查是否按下了归零按钮,或是否有物体干扰导致无法归零。
六、维护保养1.定期清洁仪表表面,以保持仪表的正常工作。
2.不要将其他物体放置在仪表上,以免损坏或干扰仪表的正常工作。
3.在长时间不使用时,应关闭仪表电源,并妥善存放。
霍利斯LED1200罐装照明系统用户手册说明书

LED1200 - Canister Light SystemLED1200 Canister Light SystemDocument Control#HO.11.01.001Hollis1540 North 2200 WestSalt Lake City, UT 84116 USAToll-Free: 1-888-270-8595TABLE OF CONTENTS PAGE3Introduction4WarningsStarted5GettingInformation5Charging5Pre-Dive6Post-Dive/TransportSpecifications6Technical7Records8Notes/Service9ContactIntroductionThank you for choosing the Hollis LED1200 Canister Light System. To help ensure its high performance and reliability, please take the time to review and understand this manual.This User’s Guide describes the unique functions and features of the Hollis LED1200 Canister Light System. The more acquainted that you become with your new light, the more you will enjoy your diving experience. By following the instructions in this guide, you will understand how your light works allowing the best use of its features. It is very important to first read the entire contents of this manual before attempting to use your new light.The LED1200 is designed manufactured with pride in the USA. All Hollis products are tested for function and water integrity before leaving the factory. Hollis products are constructed with the highest quality materials and utilize the latest computer aided design and manufacturing techniques to ensure their highest performance and reliability.CAUTION: This denotes instances that if not handled properly could result indamage to the equipment.NOTE: Represents important information.CAUTION:•It is essential that the diver read this guide to familiarize themselves with the proper setup, care, and use of any Hollis LED1200 Canister Light System. If the instructions given in this guide are not understood and followed; seriousdamage to the light can occur.•DO NOT interchange NiMh and Li-Ion batteries and/or chargers. The electronics on each model are designed specifically for that model’s intendedbattery type. Using the wrong battery may cause combustion and injury.•Avoid exposing the light to heat exceeding 100˚F (37.7˚C), such as in the trunk of a car, furnace rooms, engine rooms, etc. Prolonged exposure to heat will shorten the life of the batteries and possibly damage them.•DO NOT use any chargers other than an authorized Hollis charger to recharge your light. Doing so may cause severe damage to the battery, andwill void the warranty.•DO NOT expose the charger to moisture, salt air, sand, or dust. Keep it clean and dry at all times.•Prior to storage for any length of time, it is critical to ensure that the power leads have been disconnected.•Avoid storing the light with the housing assembled. Allow the housing to vent by setting in place but not securing it onto the canister body.•If moisture has entered the canister, DO NOT attempt to operate or store it with the housing assembled. Take the canister top off to dry. If moisture hasentered the light head or internal canister, return to your Authorized HollisDealer immediately, where it should receive a factory authorized service andinspection.•DO NOT store the light in a discharged state, or with the light head connected to the battery.•Carry a cutting device and be prepared to free yourself from the light if necessary.•DO NOT use any aerosols on the inside of the canister; as it could damage internal components or cause a fire hazard.Getting StartedPlease take the time to get familiarized with your new light. Included inside the box will be the light head connected to the canister lid, Canister body/ sealed battery and charger assembly.Charging Information1.Remove canister lid from body exposing the canister/battery connection2.Attach the battery to the charger – Red to Red and Black to Black3.Plug charger into wall outlet – Universal Li-Ion Smart Charger automaticallyadjusts to 110/220V current and 50/60Hz frequency.4.Always ensure the charger is not covered and is not in direct sunlight.5.Charge for 5 hours and disconnect after a full charge (the LED will display green)–DO NOT leave the charger attached to the battery for a prolonged period oftime beyond the charging cycle as this could damage the battery and/or charger. 6.NOTE: The included 5.2-A/h(Li-Ion) rechargeable battery has a high energydensity, very good cycle life and is environmentally friendly. Li-Ion batteries can be stored for several months without significantly losing charge. However,Unlike NiMh batteries, after use it is suggested to store in a partially chargedstate – but never fully charged as this could shorten the battery life or damage the batteryPre - Dive1.Confirm your battery pack has been charged for a full 5 hours or until green andremove from charger.2.Inspect the O-ring on canister lid and seat on canister body. Confirm the O-ring isin place and free of any contaminants.3.Be sure to position the banana plugs on canister lid in contact with thecanister/battery connection4.Press canister lid onto the body and seal using the locking latches on both sidese of LED lamp out of water is not suggested for more than 30 seconds,howeveris suggested for Pre-Dive inspection. If used out of water for more than 5minutes the LED can build excessive heat and will switch to a lower setting. This setting can be reset by switching the light off, then back on.6.Take this time to inspect the glass surface and LED for any visible damage orloose particles. Do not look directly into light!Post – Dive / Transport1.Remove canister lid from the body and wipe with clean towel – This will helpremove any possible gases and/or moisture. If any excessive moisture is present,recheck the O-ring.2.Detach the light head from battery canister for transport to help avoid accidentallyturning the light on/off possibly damaging the switch, battery and/or LED.Technical SpecificationsThe LED1200 C anister S ystem offers the power of HID with the reliability,durability and efficiency of LED technology. This system offers a concentratedbeam that is preferred for exploration diving including underwater signaling.Powered with a Lithium-ion r echargeable battery, the LED1200 burns at 1200lumens of brightness for 5 hours. This single LED offers the advantage of a verylong 20,000 hour life and a concentrated 6° beam.LightHead Aluminum housing w/Osram LED Weight 2lbsinwater/4lbsabovewater BeamDegree 6DegreeBurnTime Approx.4hoursOutput 1200 LumensBulbLife 20,000hourlifeChargingTime Approx.5hoursServiceInterval Visuallyinspecto-ringbeforeandBattery after every d iveLithium Ion - 5.2A/h / 57.5W/hMaximum Operating Depth 500 Feet / 152 MetersRecordsDate of Purchase:Hollis Dealer:Dealer Phone No.:Inspections & ServiceDate Service Performed Dealer / TechnicianNotesMANUFACTURER WARRANTY – 3 Year LimitedFor details, refer to the Product Warranty section on the Hollis web site.SERVICE – For details, refer to the service section on the Hollis websiteCOPYRIGHT NOTICE - This user’s guide is copyrighted, all rights are reserved. It may not, in whole or in part, be copied, photocopied, reproduced, translated, orreduced to any electronic medium or machine readable format without prior consent in writing from Hollis.LED1200 Canister Light System Document Control #HO.11.01.001Hollis 1540 North 2200 West Salt Lake City, UT 84116 USA Toll-Free: 1-888-270-8595 TRADEMARK NOTICEHollis and the Hollis logo are registered or unregistered trademarks of Hollis. All rights are reserved.。
Aeroflex IRS1200 自动惯性参考测试系统用户指南说明书

Two Configurations Automated: 2-Axis Tilt Table Optional: Manual Tilt Table Fully Automated Configuration Unattended Test Operation Multiple Unattended NAV Runs Comprehensive Turnkey ATE System Includes Tilt Table Power Supplies Measurement Resources Test Unit Adapters (TUA) Test Program Sets ARINC Databus Resources Test Control Computer w/ Test Exec. Software Spares Kit Software Revision Service Capable Field Application Engineering staff can provide in-depth training (factory or on-site), installation and expert technical support.
MD-90, F100, RJ
HG1050BX
A300-600, A310
HG1150BX
MD-11
CG1XXX
IRMP, ISDU, MSU, CDU - All Aircraft
The ADIRU expansion to the system is required to test the IRU as well as all ADIRUs, giving the system the ability to test these additional Honeywell part numbers:
FW1200螺杆式冷水机组通用型微电脑控制器说明书

在默认设置状态下(四段调载、间歇电磁阀 ON 为 1 秒,间隙电磁阀 OFF 为 5 秒, 启动方式为“分绕组”启动)
系统上电 3 秒且无故障,当系统收到启动信号后机组运行指示灯亮,同时打开机组 冷冻水泵且机组加载电磁阀工作在脉冲方式。冷冻水泵开启 15 秒后开冷却水泵,冷却 水泵开启(热模式同时打开四通阀)15 秒后,打开螺杆机组启动端和螺杆机组卸载阀并 延时 0.5 秒后开启螺杆机组运行端,运行端开启后延时 5 秒(或系统低压压力值小于开 启压力值)开螺杆机组液路阀、延时 15 秒开启螺杆机关闭螺杆机组卸载阀开螺杆机组 50%电磁阀;60 秒后关 50%电磁阀同时打开 75%电磁阀;90 秒后关 75%电磁阀系统进入 100%运行模式。
1.2 技术特点
¾ 采用开关电源供电,电压适应范围广,可以在开闭压缩机的瞬间都保证正常的供电。 ¾ 通过多层次高低频滤波,有效过滤复杂电磁环境中的电流或者电磁干扰。 ¾ 主机和控制面板采用差分带校验的通讯方式,被动接收和主动查询的方式相互结合,使
主机和控制面板保持高度一致,使通讯非常稳定可靠。 ¾ 所有输入和输出点均采用稳压 5V 控制,有效避免电压波动引起的误动作。 ¾ RS485 通讯接口,可在线升级和远程控制,抗干扰能力强。
系统卸载:开启压缩机卸载电磁阀 15 秒后;液路阀在压缩机运行端关闭前 5 秒钟 关闭(或低压压力小于关闭压力值)。系统运行待机时,卸载阀常开,以保证下次启动处 于最小负载;若有关机信号:冷却水泵和冷冻水泵要在压缩机卸载电磁阀关闭后延时 15 分钟后才可以关闭或冷冻进出水温度大于关闭温度、冷却进出水温度小于可关闭温 度并持续 3S 后关闭冷冻水泵、冷却水泵并停机。
范围 5~50 5~50 0=制冷,1=制热 -20~20 -20~20 -20~20 -20~20 -20~20 -20~20
FC-1200频率计使用教程

FC-1200频率计使用教程1.频率计分为3个部分,显示屏,输入端口和按键功能区,想要使用就必须知道每个部分功能是做什么的。
2.POWER电源开关。
按下按钮电源打开,仪器进入工作状态,释放则关闭整机电源。
HOLD保持功能键。
按钮按下后仪器将锁定在当前的工作状态,显示也将保持不变。
按钮释放后仪器进入正常工作状态。
O.O1s闸门时间0.01s选择键。
按钮按下测量结果将显示六位。
RESET复位键,将数据清零复位3.0.01s闸门时间0.01s选择键。
按钮按下测量结果将显示六位,0.1s闸门时间0.1s选择键。
按钮按下测量结果将显示七位。
1s闸门1s选择键。
按钮按下测量结果将显示八位。
4.CHECK检查键,检查频率计是否正常APERA通道周期测量选择键。
按钮按下并且选择闸门时间键按下,就可以从A通道进行周期测量了ATOT计数功能键。
计数时只能对A通道进行计数。
计数键按下后,计数器开始工计数,并将计数结果实时显示出来。
按下TOLD键(保持功能键)计数显示将保持不变,此时计数器仍在计数。
释放HOLD键后计数显示则与计数同步。
当计数功能键释放时计数显示将保持,再次按下计数功能键计数器将清零并从零开始计数。
5.FA通道频率测量选择键。
按钮按下并且选择闸门时间键按下,就可从A通道进行频率测量了。
FB通道频率测量选择键。
B通道只能进行频率测量,按钮按下并且选择闸门时间键按下,就可以从B通道进行频率测量X20衰减功能键。
此按钮只在A通道测量时使用,按钮按下后输入信号被衰减20倍。
6.A通道输入端。
被测信号频率为10Hz一100MHz接入此通道进行测量。
B通道输入端。
被测信号频率为100MHz一1GHz接入此通道进行测量。
7.根据测试需要选择A,B通道,接上探笔,选择频率范围和GATE time,按下开关,打开频率计将探笔置于需要测试的晶振上,读出数值,按下hold键。
H-1200 Fast Flow Fluid Warmer 与集成空气检测器 锁阀说明书

H-1200 Fast Flow Fluid Warmerwith integrated Air Detector/Clamp Temperature Management Solutions for improved patient outcomesAutomated Pressure Chambers• Mounted pressure chambers allow fast and easy bag changes • Accommodate standard blood and crystalloid bags • On/Off toggle switch automatically pressurizes chambers to a constant pressure of 300 mmHgHeat Exchanger• Aluminum heat exchanger transfers heat 1000 times faster than plastic 1 • Counter-current recirculating solution at 42°C provides effective and stable heatingBuilt-in Safety Features• Displays reservoir set point • Monitors reservoir temperature to prevent overheating • Audible and visual alarms if reservoir temperature reaches 43.9°C • Audible and visual alarms if disposable is not correctly inserted into the fluid warmer • Audible and visual alarms ifrecirculating solution in reservoir is below the minimum desired level • Meets all AABB standards for blood warming 2• Level 1® Air Detector/Clamp detects air in the I.V. line and stops flow of fluid if air is presentTHESTANDARD OF CARE FOR RAPID INFUSIONWarmRecirculatingHeat ExchangerWhen lives are at stake from significant blood loss due to trauma or major surgery, the Level 1® Fast Flow Fluid Warmer provides a rapid flow ofnormothermic blood and I.V. fluids. Even a small drop in body temperature can be detrimental–delaying recovery or allowing infection to set in. Level 1® H-1200 Fast Flow Fluid Warmers allow rapid infusion of warm fluids while providing the extra level of protection of an integrated Air Detector/Clamp. Upon detection of air in the line, the flow of blood and crystalloid is automatically stopped,allowing quick removal of air and restoration of flow without disconnecting from the patient or changing disposable administration sets. Different disposable sets are available for a variety of clinical applications.Level 1® H-31B Air Detector/ClampLevel 1® H-31B Air Detector/Clamp• Operating Mode indicator lights green when the fluid warmer is ON, thedisposable is properly inserted, and the Air Detector/Clamp door is closed • Check Tubing Mode indicator lights yellow and a medium priority alarm beeps when the tubing has not been placed properly into the Air Detector/Clamp slot and/or when the Clamp Slot door is not closed correctly • Air Detector/Clamped Mode indicator lights red and a high priority alarm beeps when air is detected in the Gas Vent/Filter Assembly – the patient line is automatically clamped preventing fluid going into the patient – itautomatically unclamps and resumes operation once all air is removed through the Gas Vent • Air is detected in the fluid path and removed through the Gas Vent without disconnecting from the patient • Upgrade your Level 1® H-1025 Fast Flow Fluid Warmer with the newLevel 1® H-31B Air Detector/Clamp to provide the benefits of air detection and automatic clampingEasy To Use• Disposables are simple to insert and remove • Gas Vent/Filter Assembly * can be changed without replacing the entire disposable • Durable surface makes it easy to clean • Large roller wheels on base make iteasy to transport within your facility* G as Vent/Filter Assembly (F-10 and F-30) need replacing every three hours, when filter becomes clogged, or when flow rate slows down.DI-100 Disposable Administration SetFull Range of DisposableAdministration Sets and AccessoriesPRODUCT(S) DESCRIBED MAY NOT BE LICENSED OR AVAILABLE FOR SALE IN CANADA AND OTHER COUNTRIESSmiths Medical India Private Limited 508/509, Western Edge-2, W.E. Highway, Borivali (E), Mumbai - 66, India.T: + 99 22 28705210 F: +91 22 28705211E:*************************FIND YOUR LOCAL CONTACT INFORMATION AT: /CUSTOMER-SUPPORTSmiths Medical is part of the global technology business Smiths Group plc. Please see the Instructions for Use/Operator’s Manual for a complete listing of the indications, contraindications,warnings and precautions. Level 1 and Temperature Management Solutions and the Smiths Medical and design marks are trademarks of Smiths Medical. The symbol ® indicates the trademark is registered in the U.S. Patent and Trademark Office and certain other countries. All other names and marks mentioned are the trademarks or service marks of their respective owners. ©2019 Smiths Medical. All rights reserved. TM194805GBIN-092019MPAUCA-1806For more information visit our website at Product Code DescriptionUnits/Case H-1200-EN-230V-CELevel 1® Fast Flow Fluid Warmer with integrated Air Detector/Clamp1Product Code DescriptionUnits/Case DI-60HL Maximum normothermic flow rate: 530 mL/min 10DI-100Maximum normothermic flow rate: 950 mL/min 10DI-300Maximum normothermic flow rate: 1400 mL/min10NOTE: D-60HL rates based on using crystalloid, 300 mmHg with 14g catheter. DI-100 and DI-300 flow rates based on using crystalloid, 300 mmHg with 8.5Fr catheter. (data on file)Product Code DescriptionUnits/Case F-10Gas Vent/Filter Assembly (Replacement for D-60HL, D-70, D-100)20F-30Gas Vent/Filter Assembly (Replacement for D-300)20PF-1Fast Flow Pre-Filter (use one per unit of blood)6080-04-003O-Ring Kit1References1. F lancbaum L et al. Evaluation of blood-warming devices with the apparent thermal clearance. Ann Emer Med. 1989;18:355-9.2. Guidelines for the use of Blood Warming Devices. AABB. 2002.High Performance Disposable Administration Sets and AccessoriesSmiths Medical offers a full line of disposable administration sets and accessories for use with the Level 1® Fast Flow Fluid Warmer. Fast flow disposable administration sets and accessories offer:• Latex-free • Sterile fluid path• Designed for single patient useOrdering Information。
- 1、下载文档前请自行甄别文档内容的完整性,平台不提供额外的编辑、内容补充、找答案等附加服务。
- 2、"仅部分预览"的文档,不可在线预览部分如存在完整性等问题,可反馈申请退款(可完整预览的文档不适用该条件!)。
- 3、如文档侵犯您的权益,请联系客服反馈,我们会尽快为您处理(人工客服工作时间:9:00-18:30)。
H0FL-1200双以太网光纤收发器使用手册
H0FL-1200双以太网光纤收发器通过一对或一根光纤可提供
两个100M以太网通道,容量相当于两台普通的光纤收发器。
两个100M通道之间物理隔离,适用于不同业务网合并传输的场合,例如内部办公网和因特网的接入。
●光传输距离说明
双纤传输:35 km(标配);单纤传输:10 km(标配)
若需要更长距离传输可选用大功率光收发模块,详情请咨询华环公司。
●注意事项
自协商模式下以太网接口可以自动检测所接网线的收发线序并适配,所以无论所接的以太网口是MDI或MDI-X接口,无论所用的网线是交叉或非交叉线都可以使用,但强制模式下不支持该自动交叉反线功能。
H0FL-1200双以太网光纤收发器
使用手册
北京华环电子股份有限公司产品名称:H0FL-1200双以太网光纤收发器
手册版本:1.3
发表日期:2008年2月
北京华环电子股份有限公司
BEIJING HUAHUAN ELECTRONICS Co., LTD.
联络资讯
地址:北京市海淀区上地六街26号(100085)
业务电话:(8610)62981998
售后服务:(8610)62988820
技术支持:(8610)62960985
传真:(8610)82899801
网址:, E-mail: support@。