GMC Manual 2010 CN
GMCW 冷藏柜说明书

Countertop RefrigeratorsOperator ManualModels CTR2.68LD, CTR3.75 and CTR3.75T©2015 GMCWPrinted in China0415 Form # CW-311-03Part # NR68AGMCW4003 Collins Lane, Louisville, KY 40245 USA Phone: 502.425.4776 Toll Free: 800.695.4500Fax: 502.425.4664Web:Email:*************Model CTR2.68LDModel CTR3.75Specifications...........................2Installation...............................4Operation................................4Cleaning & Maintenance.. (5)Troubleshooting Guide...........6Parts List ..................................7Graphic Template.. (8)Thank you for purchasing this quality refrigerator. For your safety and the safety of others, read all warnings and the operator’s manual before installing or using the product. Properly instruct all operators.Keep training records.Table of ContentsModel CTR3.75TGMCW provides the industry’s BEST warranty. Visit for warranty terms and conditions.SpecificationsSafety InformationImportant Safety InformationThis is the safety alert symbol. It is used to alert you to potential personal injury hazards. Obey all safety messages that follow this symbol to avoid possible injury or death.For your safety and the safety of others, read all warnings and the operator’s manual before installing or using the product.DANGER:This term warns the user of imminent hazard that will result in serious injury or death.WARNING:This term refers to a potential hazard or unsafe practice, which could result in serious injury or death.CAUTION:This term refers to a potential hazard or unsafe practice, which could result in minor or moderate injury.NOTICE:This term refers to information that needs special attention or must be fully understood.WARNINGModel CTR3.75 and CTR3.75TCTR2.68LD Refrigerator with illuminated header.2.7 cubic ft., 4 shelves.C-ETL-US, ETL Sanitation Certification 1/8120V / 240 W / 2A / 1 Ph CTR3.75Refrigerator. 3.8 cubic ft., 5 shelves.C-ETL-US, ETL Sanitation Certification 1/8120V / 240 W / 2A / 1 PhCTR3.75T Refrigerator with exterior themometer.3.8 cubic ft., 5 shelves.C-ETL-US, ETL Sanitation Certification1/8120V / 240 W / 2A / 1 PhCAUTIONSafety Information (continued)WARNINGInstallationNOTICE:For most efficient operation, install the unit in a place which is well ventilated.Please read this manual before installing the refrigerator.1. Carefully remove package, tape, and other shipping materials and leave door open to ventilate.2. Level unit by adjusting the feet.3. The unit is cleaned before shipment.However, clean the compartment interior once after delivery.4. Insert plug into a dedicated wall outlet. Do not use an extension cord.5. Allow the unit to operate about 1 hour to cool the compartment before placing items in the refrigerator.If you need help, call Grindmaster Cecilware Technical Service Department for help, (502) 425-4776 or (800)695-4500 (USA & Canada only) 8 AM - 6 PM EST.Prior authorization must be obtained from GMCW for all warranty claims.OperationYour new refrigerator is easy to operate and maintain.Before you place it in service,please have all personnel familiarize themselves with these instructions. Keep this manual in a convenient place for ready reference.Temperature AdjustmentThe temperature can be adjusted between approximately 34° F and 45° F .1. Adjust the storage temperature through the temperature controller.2. The temperature adjustable capacity is from “1”-“5”. Adjust the storage temperature by turning the temperature controllerclockwise. The “5” setting is for colder storage temperature. The knob can turn freely but can't turn clockwise from “5”to“1”. Factory setting position is on “3”position.3. Check if the knob is on the appropriate position before using. Frequent adjustments are not necessary.4. To turn unit off, turn dial to position “0”.Notice:After the unit is turned off, wait 30minutes before restarting. Restarting immediately after it has been turned off may cause fuses to blow and activate the circuit breaker; the compressor may be overloaded, and/or other damge may occur.5. Excessive refrigeration will cause increased,unnecessary electricity consumption.Shelf Height AdjustmentThe shelf height can be adjusted. Arrange the shelves in accordance with the dimensions of the items to be placed in the cooler.Helpful HintsTo prevent cold air from escaping, open and close the door quickly.Power FailureIn case of power failure, keep opening and closing of door to minimum and avoid placing new items in the refrigerator as this will raise the temperature inside the compartment.Moving the unitKeep the unit vertical when carrying the unit. The •angle to the horizontal line should not be over 50°,otherwise it will damage the compressor and affect normal operation of the e care not to damage feet.•Do not allow feet to damge power cord. Inspect •cord before plugging into outlet.Level the unit using adjustment on the feet.•After moving the unit, let it stand for 30 minutes •before switching it on.If the unit was previously running: Close the door •and connect the power. Turn on the light switch.The temperature should be suitable for normal use after half hour.f the unit was not previously running: After •connecting the power, the unit should be kept empty for one hour.4Cecilware ®Countertop Refrigerators®5Cleaning & MaintenanceCleaning InstructionsWARNING Disconnect the power supply beforeperforming maintenance on the refrigerator.WARNING Never splash water directly onto theproduct or wash with water as electrical shock could result.NOTICE:Never use polishing powder, soap powder,benzine, oil, or hot water as these will damage the painted and plastic components.Clean regularly:Wipe with a soft, dry cloth. I f very soiled, wipe •with a cloth that has been moistened with a mild detergent. Then wipe with a damp cloth moistened with water. Dry with a soft cloth to prevent rust.Do not use a hard brush to clean the case.To keep the door gasket clean, remove it from the •door and wash it. Dry and replace the seal. Putting some talcum powder on the magnetic surface would prolong its service life.MaintenanceTo ensure safety, perform the following checks after cleaning:Confirm the power plug is firmly inserted into a •dedicated wall outlet.Check the power cord for cracks and damage. If •damage is observed, a new power cord is required.Contact the dealer from whom the unit was purchased or our customer service department.To replace the light bulb:Remove the top cover, take out the light, and •replace with a new bulb of same wattage. DefrostingDefrosting is performed automatically and drain water is collected in the drip tray.StorageWARNING Affix item such as piece of woodbetween door and compartment to prevent complete closing of the door. Should a child enter the compartment and the door is closed, the child may not be able to open the door from inside the unit and could suffocate.Prolonged StorageIf the unit will not be used for a long time, remove items from refrigerator, disconnect the power, and clean it by following the above steps. Then clean the inside of the case with a soft cloth. Discard the water in the drip tray. To prevent mold formation or foul smell, leave door open to dry the compartment completely.Troubleshooting GuideBefore you call for help, please read the following:WARNING Unplug power cord from outlet before cleaning or servicing your unit.If you still need help, call GMCW Technical Service Department, (502) 425-4776 or (800) 695-4500 (USA & Canada only) (Monday through Friday 8 AM - 6 PM EST). Please have the model and serial number ready so that accurate information can be given.Prior authorization must be obtained from GMCW for all warranty claims.GMCW provides the industry’s BEST warranty. Visit our website at for warranty terms and conditions.6®No refrigerationPower cord disconnected from wall outlet.Check power cord.Circuit breaker activated.Check breaker box for tripped circuit breaker or blown fuse.Poor refrigerationTemperature setting incorrect.Adjust temperature control knob to colder setting.Items obstructing the cold air inlet or suction outlet.Move items away from air inlet and outlets.Stored items packed too tightly.Redistribute items or reduce quantity.Door left open or opened and closed frequently.Limit amount of time door opened.Condenser clogged.Remove dust and debris with air or have professionally cleaned.Excessive noiseNot all feet touching floor.Adjust feet.Rear panel contacting wall or other objects.Move unit away from wall or items away from unit.Condensation on cooler exteriorCondensation may form on the exterior of the door during hot and humid days or depending on the place of installation. This occurs when thehumidity is high and water particles in the air contact cold surfaces.This is normal. Wipe away condensation with a dry cloth.Parts ListCountertop Refrigerators Cecilware ®7Big Foot08711L 08711L 08711L08703L08703L08703Lx = not applicableIlluminated Header Transparency。
GMCC往复式压缩机产品手册说明书

RECIP COMPRESSOR 2020 Array往复式压缩机产品手册12144749我们的企业CompanyGREEN MILE 绿色里程1995年09月 公司成立Sep 1995, Company establishment 1996年10月X1C、X2C系列压缩机开始投产Oct 1996,X1C,X2C seriesrotary comp.2004年03月顺德容桂基地正式投产Mar 2004, Ronggui plant wentinto production2007年11月高效G1系列产品量产成功Nov 2007,High-efficiencyG1 series comp.2008年11月安徽合肥制冷基地投产2008年12月R410A冷媒双缸直流变频产品实现量产Dec 2008, R410A DCinverter twin cylinder comp.2000年10月交流变频机种研发成功实现量产Oct 2000, AC invertercomp.2003年09月R410A直流变频压缩机研发成功实现量产Sep 2003, R410A DCinverter comp.Nov 2008, Hefei plantwent into production2009年12月R134a热泵热水器专用压缩机投放市场Dec 2009, Special comp. forHP water heater in R134a2011年10月安徽芜湖空压基地投产Oct 2011, Wuhu plantwas put into production2011年11月2010年01月卧式系列冷冻压缩机研发成功,投入市场Jan 2010, Horizontalrefrigerating comp.2010年05月CO 热泵热水器专用压缩机研发成功May 2010, Comp. for HPwater heater in CO2010年06月第一亿台旋转式压缩机下线June 2010, The 100 millionthA/C compressor roll-out2010年10月双缸变容压缩机研发成功投入市场Oct 2010, Twin cylindervariable capacity comp.2012年07月2013年09月喷气增焓旋转式变频压缩机研发成功Sep 2013, Gas-injectioninverter comp.2013年09月第2亿台空调压缩机下线Sep 2013, The 200 millionthA/C compressor offline2014年全球市场占有率达30%In 2014, Market shareup to 30%2015年荣获2015年度广东省政府质量奖In 2015, Won theGuangdong QualityAward2016年11月独立压缩机研发成功并正式发布Nov 2016,I-CCC comp.2016年荣获2016年度安徽省质量奖In 2016, Won the AnhuiQuality Award2017年05月欧洲研发中心成立May 2017,EuropeanR&D centerestablishment签约为联合国蒙特利尔R290压缩机示范线Nov 2011, The UN MontrealR290 compressordemonstration line第3000万台变频压缩机下线July 2012,The 30 millionthDC inverter compressorroll-out2018年4月喷气变频热泵采暖专用压缩机正式发布Apr 2018,Heat pump heatingcomp. with EVI.2018年10月“V致能”小型变频空调压缩机研发成功并发布Oct 2018Miniaturized DCinverter comp.日本研发中心成立Japan R&D centerestablishment2019年第五亿台空调压缩机下线The 500 millionthA/C compressorroll-out0405在绿色节能大潮流下,冰箱压缩机行业呈现出高效化、小型化和节能化等技术发展趋势。
精选-久其GMC集团财务产品用户手册-实物资产系统
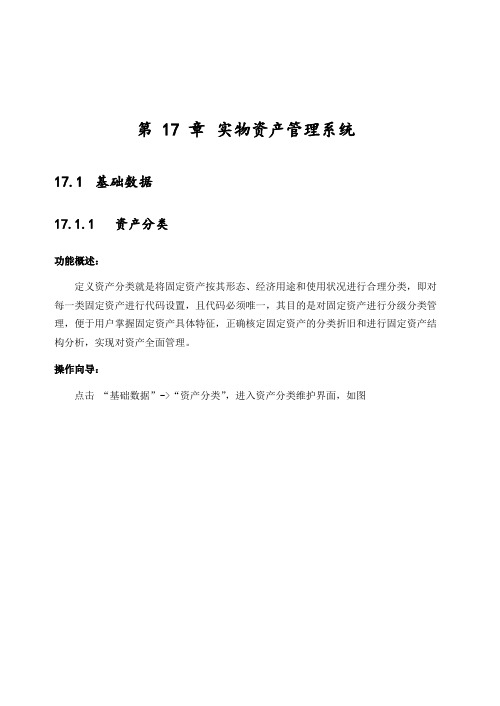
第 17 章实物资产管理系统17.1基础数据17.1.1资产分类功能概述:定义资产分类就是将固定资产按其形态、经济用途和使用状况进行合理分类,即对每一类固定资产进行代码设置,且代码必须唯一,其目的是对固定资产进行分级分类管理,便于用户掌握固定资产具体特征,正确核定固定资产的分类折旧和进行固定资产结构分析,实现对资产全面管理。
操作向导:点击“基础数据”->“资产分类”,进入资产分类维护界面,如图图17.1-1资产分类维护界面特别提示:✐资产分类支持级次管理。
✐资产分类代码不能重复。
✐已经引用过的资产分类不能修改、删除操作。
✐已经引用过的资产分类不能增加明细类。
✐资产分类使用状态若不打勾,则在建立时无法选择到该资产分类。
17.1.2存放地点功能概述:每一项固定资产均有其存放的地点,设置固定资产的存放地点,可以考察每一地点资产的状态及使用情况,便于资产清点盘存,有利于用户对资产进行全面管理。
操作向导:点击“基础数据”->“存放地点”,进入存放地点维护界面,如图:2图17.1-2存放地点维护界面特别提示:✐存放地点的代码不能重复。
✐存放地点的名称不能重复。
✐已经引用过的存放地点不能修改、删除操作。
17.1.3计量单位功能概述:此功能主要设置企业业务中用到的计量单位的基本信息。
操作向导:1、点击“固定资产管理”->“基础数据维护”->“计量单位”,进入“计量单位”维护界面,如图3图 17.1-3 计量单位维护界面2、点击工具栏新建按钮,输入计量单位代码和计量单位名称,输入完之后点击保存按钮。
3、如需修改计量单位信息,选择需要修改的计量单位点击修改按钮进入编辑状态。
4、如需删除计量单位信息,选择需要删除的计量单位点击删除按钮即可。
特别提示:✐已使用的计量单位不能删除。
✐在同一组织机构网络操作中,可能同时有多个操作员在同时增加记录,可以单击刷新按钮,即可查看到当前最新记录情况。
✐计量单位的基础数组织管理若设置为共享,当其它组织机构同时也在增加记录时,可以单击刷新按钮,即可查看到当前最新记录情况,即包括其它组织机构增加的记录。
2010版GMP英文版

SDA Order #79Order by Ministry of Health of the People’s Republic of ChinaPublished on February 12, 2011No. 79Good Manufacturing Practice for Pharmaceutical Products (Amended in 2010) has passed by Affairs Meeting on October 19, 2010. This Regulation is now published and shall be effective from March 1, 2011.Director Zhu CHENJanuary 17, 2011Chapter 1 General ProvisionsArticle 1 In order to standardize good manufacturing for pharmaceutical products, this Regulation is enacted in accordance with the “Drug Administration Law of the People’s Republic of China” and “The Regulation on the Implementation of Drug Administration Law of the People’s Republic of China”.Article 2 A p harmaceutical enterprise shall establish pharmaceutical goods’ quality control system. The system shall contain all factors which may affect the quality of pharmaceutical goods, including all organized and planned activities ensuring pharmaceutical goods’ quality in accordance with intending purpose.Article 3 This Regulation is part of quality control system, is basic requirement for manufacturing and quality control of pharmaceutical products. This Regulation aims to reduce the risks in pharmaceutical g oods’ manufacturing process at its maximum, such as pollution,cross pollution and confusion, mistake, ensure for continuous stably manufacturing pharmaceutical goods in accordance with intending purpose and registered requirements.Article 4 The enterprise shall obey this Regulation strictly, insist on honesty and keep faith, prohibit any ostensible and spurious activities.Chapter 2 Quality ControlSection 1 PrincipleArticle 5 The enterprise shall establish quality target in accordance with pharmaceutical goods’ quality control requirements, carry out all requirements related to safety, effective and quality control into the process of pharmaceutical goods’ manufacturing, control and products’ discharging, storag e, delivering, ensure all pharmaceutical goods are produced in accordance with intending purpose and registered requirements.Article 6 Senior administrator in enterprise shall ensure the achievement of intending quality target. Personnel in different levels and provider, dealer shall participate in and take each responsibility.Article 7 The enterprise shall equip adequate personnel, workshop, establishment and equipment in accordance with requirements, and provide essential condition for achieving quality target.Section 2 Quality GuaranteeArticle 8 Quality guarantee is a part of quality control system. The enterprise must establish quality guarantee system, and establish integrate document system at the same time, in order to ensure the system’s e ffective running.Article 9 Quality guarantee system shall ensure the following:I. Represent the requirements of this Regulation in pharmaceutical goods’ design anddevelopment.II. In accordance with the requirements of this Regulation in manufacturing management and quality control activities;III. Specific management responsibility;IV. Exact stocked and used raw material and wrapper;V. Effective control in semifinished product;VI. Implement of confirmation and validation;VII. Manufacture, examine, inspect and double examined according to rules strictly; VIII. Each batch of products shall only discharge after quality authorizing person’s approval;IX. Applicable measures to ensure pharmaceutical goods’ quality during the process of storage, delivering and all succedent operation process;X. According to self-examine rules, examine and evaluate the validity and applicability of the quality guarantee system quality.Article 10 Basic requirements of pharmaceutical goods’ manufacture quality management: I. Frame manufacturing technique, systemic review and demonstrate it couldcontinuous stably manufacturing products in accordance with requirements;II. Manufacturing technique and its important changes shall be validated;III. Equip all required resources, include, but not limited the following:1. Hold applicable qualification and the eligible trained personnel;2. Adequate workshop and space;3. Applicable equipment and maintain guarantee;4. Accurate raw material, wrapper and label;5. Approved technique rules and operate rules;6. Applicable storage and freight condition.IV. Use accurate and easy understand language to frame operate rules;V. The operate person could accurate operate according to operate rules after training;VI. The whole manufacture process shall be recorded. The windage shall be researched and be recorded;VII. Batch record and delivering record shall be traced back to the whole history of the batch of products, and the records shall be saved appropriately and be easy consult; VIII. Reduce the quality risk during the pharmaceutical goods’ delivering process;IX. Establish pharmaceutical goods’recall system, and ensure any batch delivered and sold products could be recalled;X. Survey the reasons leading to pharmaceutical goods’complaints and quality objections, take measures to prevent similar quality objections.Section 3 Quality ControlArticle 11 Quality control includes corresponding organization, document system and sampling, test and so on, to ensure material or products finish necessary examination before delivering, and to verify its quality is in accordance with the requirements.Article 12 Basic requirements of quality control:I. Equip applicable establishment, equipment, instrument and trained personnel to effective and reliable finish all related quality control activities;II. Have approved operate rules, which used to sampling, examine, inspect raw material, wrapper, semifinished product, bulk product and finished product and products’stability, monitor environment when necessary, to ensure the products is in accordance with the requirements of this Regulation;III. Authorized person shall sampling to raw material, wrapper, semifinished product, bulk product and finished product according to stated methods;IV. Inspect methods shall be confirmed and validated;V. Sampling, check, inspect shall be recorded, the windage shall be researched and be recorded;VI. Material, semifinished product, bulk product and finished product shall be checked and inspected according to quality standard and be recorded;VII. Material and packaged finished product shall have enough reserved samples so that necessary check or inspect shall be taken; except the finished product with too large package container, the reserved sample s’package shall be the same with the final package of the finished product.Section 4 Quality Risk ManagementArticle 13 Quality risk management is evaluate, control, communicate, audit system process to quality risk during the whole product life period, via the manner of foresee or review.Article 14 Quality risk shall evaluate according to science knowledge and experience in order to ensure products’ quality.Article 15 The method, measure, form take during the quality risk management process and the documents formed in the said process shall accommodate to the level of the existent risk.Chapter 3 Organization and PersonnelSection 1 PrincipleArticle 16 An enterprise shall establish management organization which accommodate to the pharmaceutical goods’ product and have its organization framework chart.The enterprise shall set up independent quality management department, which carries out the responsibilities of quality guarantee and quality control. The quality management department could set up quality guarantee department and quality control department respectively.Article 17 Quality management department shall take part in all activities relating to quality, and take responsibility to audit all documents relating to this Regulation. The personnel inquality management department shall not relegate his responsibility to the personnel in other department.Article 18 The enterprise shall be staffed by an appropriate number of management and technical personnel with appropriate qualification (including education background, training and practice experience), and the responsibilities of each department and each station shall be clarified. Station’s responsibility shall not be missed and cross responsibility shall be prescribed specifically. Responsibility taken by each person shall not be overfull.Every person shall clear and understand his own responsibilities, be familiar with the requirements related to his responsibilities, and accept necessary training, including pre-job training and on-job training.Article 19 Generally, one shall not relegate his responsibility to other person. If the responsibilities do need to be relegated, the one should relegate his responsibility to the designated person who has equivalent qualification.Section 2 Important PersonArticle 20 The important person shall be the full-time person of the enterprise, at least including the director of the enterprise, director of manufacturing management, director of quality management and authorized person of quality.Director of quality management and director of manufacturing management shall be independent of each other. Director of quality management and authorized person of quality shall not be independent of each other. Operation proceduress shall be established so that authorized person of quality could take his responsibility independently, with no interference from director of enterprise and other person.Article 21 Director of enterpriseDirector of enterprise is the main responsible person of pharmaceutical goods’ quality, who comprehensive responsible to the daily management of the enterprise. In order to ensure theenterprise complete quality target and manufacture pharmaceutical goods according to this Regulation, the director of enterprise shall take responsible for providing necessary resources, reasonable plan, organize and correspond to ensure the quality management department could take its responsibility independently.Article 22 Director of manufacturing managementI. Qualification:Director of manufacturing management shall at least have pharmacology or related specialty undergraduate education background (or secondary professional technical title or licensed pharmacist qualification), have at least three years’ pharmaceutical goods’ manufacturing and quality management experience, including at least one year’s pharmaceutical goods’manufacturing management experience, have taken part in professional knowledge training related to manufacturing products.II. Main responsibility:1. Manufacture and storage the pharmaceutical goods according to approvedtechnology procedure in order to ensure the quality of the pharmaceutical goods;2. Ensure every operation proceduress related to manufacturing operation areperformed strictly;3. Ensure batch production record and batch package record are audited by designatedperson and submitted to quality management department;4. Ensure the maintenance of workshop and equipment in order to preserve its goodworking condition;5. Ensure all kind of necessary validation work is completed;6. Ensure person related to manufacturing have been trained by pre-job training andon-job training, adjust training content according to actual demands.Article 23 Director of quality managementI. Qualification:Director of quality management shall at least have pharmacology or related specialty undergraduate education background (or secondary professional technical title or licensedpharmacist qualification), have at least five years’ pharmaceutical goods’ manufacturing and quality management experience, including at least one year’s pharmaceutical goods’ quality management experience, have taken part in professional knowledge training related to manufacturing products.II. Main responsibility:1. Ensure the raw material, wrapper, semifinished product, bulk product and finishedproduct are in accordance with the registered approved requirements and quality standard;2. Ensure the products are audited to batch record before delivering;3. Ensure necessary inspection is finished;4. Approve quality standard, sampling method, inspection method and other operationproceduress of quality management;5. Audit and approve all changes related to quality;6. Ensure all important windage and exceed criterion inspection results have beenresearched and been dealt with in time;7. Approve and supervise consigned inspection;8. Supervise the maintenance of workshop and equipment in order to maintain its goodworking condition;9. Ensure to finish every necessary confirmation and validation work, checking andapproving confirmation or validation scheme and report;10. Ensure to finish self-check;11. Evaluate and approve material supplier;12. Ensure all complaints related to product quality have been researched, and have beendealt with in time and accurately;13. Ensure to finish products’persistent stability review plan, provide the data ofpersistent stability review;14. Ensure to finish product quality review analysis;15. Ensure quality control and quality guarantee person have been trained by pre-jobtraining and on-job training, adjust training content according to actual demands.Article 24 Director of manufacturing management and director of quality management often have the following common responsibility:I. Audit and approve the documents of products’technology procedure, operation proceduress;II. Supervise the sanitation condition of factory;III. Ensure the key equipment have been confirmed;IV. Ensure to finish the validation of production technology;V. Ensure all related person in enterprise been trained by pre-job training and on-job training, adjust training content according to actual demands;VI. Approve and supervise consigned manufacture;VII. Ensure and monitor the storage condition of material and goods;VIII. Save the record;IX. Supervise the implement condition of this Regulation;X. Monitor the factors influence the quality of the products.Article 25 Authorized person of qualityI. Qualification:Authorized person of quality shall at least have pharmacology or related specialty undergraduate education background (or secondary professional technical title or licensed pharmacist qualification), have at least five years’ pharmaceutical goods’ manufacturing and quality management experience, have the experience of manufacturing process control and quality check work.Authorized person of quality shall have necessary professional theory knowledge, have taken part in the train about product delivering, and could take his responsibility independently.II. Main responsibility:1. Take part in the establishment of enterprise quality system, interior self-check,exterior quality audit, validate and pharmaceutical goods’bad reaction report, product recall and other quality management activities;2. Take the responsibility of product delivering, to ensure the manufacturing, checkingof every batch of delivered products are all in accordance with corresponding code, pharmaceutical goods’ registered requirements and quality standard;3. Before delivering the products, authorized person of quality must issue productdelivering audit record according to the said item 2 and bring it into batch record.Section 3 TrainingArticle 26 The enterprise shall designate department or person to take responsible for training management work, and shall have the training scheme or plan audited or approved by director of manufacture management or director of quality management. The training record shall be preserved.Article 27 All personnel related to pharmaceutical goods’manufacturing, quality shall be trained, the training content shall accommodate to the post. Except the training of theory and practice of this Regulation, responsibility, skill training about the related code, relevant post shall also be trained, and actual effect shall be periodic evaluated.Article 28 The working person in high risk operating area (such as: manufacture area of high activity, high toxic, infective, high sensitive material) shall take expert training.Section 4 Personnel SanitationArticle 29 All personnel shall take sanitation requirements training, the enterprise shall establish personnel sanitation operation proceduress, so that to reduce the pollution risk to pharmaceutical goods taken by person at its maximum.Article 30 Personnel sanitation operation procedures shall include the content related to health, sanitation practice and personnel dress. Personnel in manufacturing area and quality control area shall correctly understand related personnel sanitation operation procedures. Theenterprise shall take measures to ensure the implement of personnel sanitation operation procedures.Article 31 The enterprise shall manage personnel’s health and establish health file. The manufacture personnel contact pharmaceutical goods directly shall receive physical check, and take at least one physical check per year.Article 32 The enterprise shall take appropriate measure to avoid the person have wound in body surface, have infection disease or other person may pollute pharmaceutical goods to take the manufacture work which directly contact pharmaceutical goods.Article 33 Visiting person and untrained person shall not enter manufacture area and quality control area, if the persons need to enter in special conditions, the items of their individual sanitation, clothes changing and so on shall be instructed.Article 34 Any person enters into manufacturing area shall change clothes according to prescription. The material, style and dressing method of work clothes shall be accommodate to the work engaged and the level of air clean degree.Article 35 The person enters into clean manufacturing area shall not make up and adorn with accouterment.Article 36 Manufacturing area, storage area shall forbid smoking and having meals, forbid to store food, beverage, cigarette and individual pharmaceutical goods and other non-manufacturing goods.Article 37 Operation person shall avoid to touch the surface of pharmaceutical goods, wrapper material contact pharmaceutical goods directly and equipment by hand.Chapter 4 Workshop and EstablishmentSection 1 PrincipleArticle 38 The workshop location’s choice, design, overall arrangement, construct, reconstruct and maintenance must in accordance with the pharmaceutical goods’manufacturing requirements, which may avoid pollution, cross pollution, confusion and mistake at its maximum, and may convenient for clean, operate and maintenance.Article 39 The workshop’s location shall consider according to the workshop and manufacturing safety measures. The environment of the workshop shall reduce the pollution risk to material or products at its maximum.Article 40 The enterprise shall have tidy manufacturing environment. The floor, road surface of the workshop and transport shall not pollute the pharmaceutical goods’manufacturing. The overall arrangement of the manufacturing area, administration area, living area and assistant area shall be reasonable arranged and do not interfere each other. Stream of people and material in factory area and workshop shall reasonable.Article 41 The workshop shall take appropriate maintenance, and ensure the maintenance activity may not influence the quality of pharmaceutical goods. Clean or take necessary sterilization to workshop according to detailed written operation procedures.Article 42 The workshop shall have appropriate illumination, temperature, humidity and aeration, to ensure the quality of produced and reserved products and the performance of related equipment shall not be influenced directly or indirectly.Article 43 The design and installation of workshop, establishment shall effective prevent insect or other animal to enter in. Necessary measures shall be taken to prevent of using raticide, insecticide, smoke fumigant and so on which may pollute equipment, material, goods.Article 44 Necessary measures shall be taken to prevent unauthorized person to enter in. Manufacturing, storage and quality control area shall not be the direct gate for staffs not in this area.Article 45 Complete drawing of constructed or reconstructed workshop, public service, fixed pipeline shall be saved.Section 2 Manufacturing AreaArticle 46 In order to reduce pollution and cross pollution risk, workshop, manufacturing establishment and equipment shall reasonable designed, overall arranged and used according to the characteristic, technique process and corresponding clean level, and in accordance with the following requirements:I. Comprehensive considering the pharmaceutical goods’ characteristic, technique andintending purpose and other factors, to confirm feasibility of using workshop, manufacturing establishment and equipment together, and hing related evaluating report;II. Special and independent workshop, manufacturing establishment and equipment must be used when manufacturing special character pharmaceutical goods, such as high sensitive pharmaceutical goods (i.e. Penicillin) or biologics goods (i.e. bcg vaccine or other pharmaceutical goods prepared by active microorganism). The operating area with large quantity of dust forpenicillin species pharmaceutical goods shall keep comparatively negative pressure, the exhaust gas discharged to outdoor shall carry cleanse management and make it be up to the mustard. Air outlet shall be away from air inlet of other air cleanse system;III. Special establishment (i.e. independent air cleanse system) and equipment must be used when manufacturing β-lactam structure species pharmaceutical goods, sexhormone species prophylactic pharmaceutical goods, and shall be detached with other pharmaceutical goods’ manufacturing area strictly;IV. Special establishment (i.e. independent air cleanse system) and equipment shall be used when manufacturing some hormone species, cell toxicity species, high active chemical pharmaceutical goods; under special circumstance, if necessary validation shall be take before taking special protection measures, the above said pharmaceutical goods preparation could use the same establishment and equipment via manufacturing modes in different phases;V. Ventilation of air cleanse system in the above said item II, III, IV shall take cleanse management;VI. Pharmaceutical goods’ m anufacturing workshop shall not used for manufacturing non-officinal used products which may have bad influence to pharmaceutical goods’ quality.Article 47 Manufacturing area and storage area shall have enough space to ensure equipment, material, semifinished product, bulk product and finished product could storage in order, to prevent the confusion, cross pollution of different products or material, to prevent missing or mistake during the operation of manufacturing or quality control.Article 48 Air condition cleanse system shall be equipped according to pharmaceutical goods’variety, manufacturing operation’s requirement and exterior environment condition which let the manufacturing area can effective aeration, and have temperature, humidity control and atmosphere cleanse filtration, to ensure the manufacturing environment of pharmaceutical goods is in accordance with the requirements.The pressure difference between clean area and non-clean area, clean areas in different level shall not lower than 10Pascal. When necessary, appropriate pressure difference grads shall also be kept in different functional areas (operation area) with same clean level.Exposure working procedure area for oral liquid and solid preparation, chamber use pharmaceutical goods (including rectal pharmaceutical goods), surface external use pharmaceutical goods and other non-asepsis preparation manufacturing and exposureworking procedure area for wrapper material directly contact pharmaceutical goods shall equip according to the requirements of “Asepsis Pharmaceutical Goods” D level clean area in Annex. The enterprise could take appropriate microorganism monitor measures according to product s’ standard and characteristic.Article 49 Inner surface of clean area (wall, floor, sunshade) shall be slick, non-crack, narrow joint, non granule fell off, prevent stored dust, convenient for effective clean, and take sterilization when necessary.Article 50 The design and installation of every kind of pipeline, lighting establishment, place with a draught and other public establishment shall prevent having the part of not easy to clean, and shall try best to maintain outside the manufacturing area.Article 51 Sewerage shall have appropriate size and install the device of reversing flow. Try best to prevent drain in clear channel, if it is inevitably, the clear channel shall be flat so that it is convenient to clean and sterilize.Article 52 Quantify of preparation’s raw material often carry on in the metage room special designed.Article 53 Operation rooms which produce dust (such as sampling, metage, mix, package of dry material or products rooms and other operation rooms) shall keep comparatively negative pressure or take special measure, so as to prevent the diffusion of powder dust, avoid cross pollution and easy to keep clean.Article 54 Pharmaceutical goods’packaging workshop or area shall be reasonable designed and arranged, to prevent confusion or cross pollution. If there are several packaging lines in one area, isolation measures shall be taken.Article 55 Manufacturing area shall have appropriate light, the light in contact manufacturing area shall satisfy the operation requirements.Article 56 Manufacturing area could set middle control area. However, middle control operation shall not bring quality risk to pharmaceutical goods.Section 3 Storage AreaArticle 57 Storage area shall have enough space, which ensure the under-examined, qualified, disqualified, withdrew or recalled raw material, wrapper, semifinished product, bulk product and finished product and all kinds of material and products could store in order.Article 58 The design and construct of storage area shall ensure good storage condition, and have aeration and lighting establishment. Storage area shall satisfy material or products’storage condition (such as temperature, humidity, avoid of light) and safety storage requirements, and check and monitor shall be taken.Article 59 High active material or product and printing package material shall storage in safe area.Article 60 Receiving, extending and delivering area shall protect material, product out of influence of weather outside (such as rain, snow). The arrangement and establishment of receiving area shall ensure taking necessary cleaning to the received material’s outside packaging.Article 61 If the under-examined material is stored in separate isolate area, the under-examine area shall have distinct mark, and only authorized person could in and out. Disqualified, withdrew or recalled material or product shall be stored isolated.If other method is used for replacing physics isolation, this method shall have equal security.Article 62 Separate material sampling area is often set up. Air cleaning level of sampling area is the same with the manufacturing requirements. If sample is taken in other area or use other method, pollution or cross pollution shall prevent.Section 4 Quality Control AreaArticle 63 Quality control laboratory is often divided from manufacturing area. Biology examine, microorganism and radioactivity isotope laboratory shall also divided from each other.Article 64 The design of laboratory shall ensure for applying it’s intending purpose, and prevent confusion and cross pollution, enough area shall have for disposing samples, reserved samples and samples for reviewing stability and keeping the records.Article 65 When necessary, set a special instrument room to prevent static, shaking, humid or other outside factors’ disturbance to instrument with high sensitivity.Article 66 The laboratory disposing special goods such as biology samples or radioactivity samples shall in accordance with the related requirements of the country.Article 67 Experiment animal room shall be strictly divided from other area. Its design, construct shall in accordance with the related requirements of the country and have independent air disposing establishment and animal’s special channel.Section 5 Assistant AreaArticle 68 Retiring room shall not take bad influence to manufacturing area, storage area and quality control area.。
群体品牌GMC资格评审须知

群体品牌GMC 资格评审须知所有申请群体品牌GMC 标志的制造商都必须接受环球市场集团委托的第三方国际认证/审核机构的现场审核,并提供相关证明文件和声明需承担其举证责任,以确认其真正具备GMC 标准规定的出口实力。
符合指标要求的制造商才能获得群体品牌GMC 标志。
备注:1)带有§符号的标准,为群体品牌GMC 制造商的主要评审标准。
这五项标准必须通过审核机构的评审达标,环球市场集团方可颁发相关级别认证、标志使用。
没有配带符号的标准,为群体品牌GMC 制造商的参考评审标准。
这三项参考标准必须同时没有出现严重的违反行为,并通过审核机构的评审达标。
2)审核申请方与接受GMC 审核的主体的权属关系,必须符合如下5种关系中的任何一种,审核机构才接受群体品牌GMC 资格评审申请。
□ 1. 客户本身即审核工厂□ 2. 客户全资自有工厂□ 3. 客户控股工厂 (客户是工厂最大股东,有控股权,包括绝对控股和相对控股)□ 4. 客户参股工厂30%以上 (客户非控股股东,则必须拥有30%以上的股权)□ 5. 客户是品牌制造商(以自主品牌的产品出口)(仅限品牌制造商)这个权属关系包含:如果客户是进出口公司、贸易商,但有控股工厂或者参股工厂;不包含:没有股份关系,纯合作形式的国际贸易合作伙伴 ,如供货商,代工厂等。
3) 现场评审地点:仅限一家生产工厂;或品牌制造商的办公场所。
环球市场保留对群体品牌GMC 资格评审标准修改或调整的权利。
V e r s i o n 2010_05群体品牌GMC资格审核文件清单第三方审核机构_________审核组受“GMC审核委员会”委派,执行编号为____________________的审核。
以便于贵公司获得或持续保持在环球市场的群体品牌GMC标识的使用权,并充分展现贵司的能力。
本次审核主要通过对1、企业概况类;(如:营业执照;或持有商标注册,品牌发展计划,自主出口权等)2、企业产品质量控制类;(如:质量管理体系;合作制造商管理以及提供优质产品能力等)3、企业经营信息类;(如:产能,或品牌产品出口额等)4、企业外贸研发类;(如:外贸和研发人员名单等)5、企业社会责任类;(如:环保,安全,商誉等)五类的文件审核以及现场审核,综合评定贵司是否具备群体品牌GMC优质制造商的资格。
ManBWKMEC主机操作系统说明书

Tuning of P,comp is made by adding an offset to the Compression Ratio here
A demand for additional balancing when running low load is supplied here.
ME Engine - PMI (January 2010)
© MAN Diesel
2010/01/01
Adjustment of maximum pressure
P,comp tuning is done by entering a Compression Ratio Offset:
C,Ratio=P,Comp / P,Scav.
C, = Ratio Offset
-1,1 / 3,62 = -0,3
(Reading from P.scav sensor is corrected to Absolute value by adding athmospheric pressure, 1 bar)
PrimeServ-Academy Copenhagen The purpose is to follow alterations in: the combustion conditions, the general cylinder condition, the general engine condition in order to discover any operational disturbances.
GMC电量仪表说明书
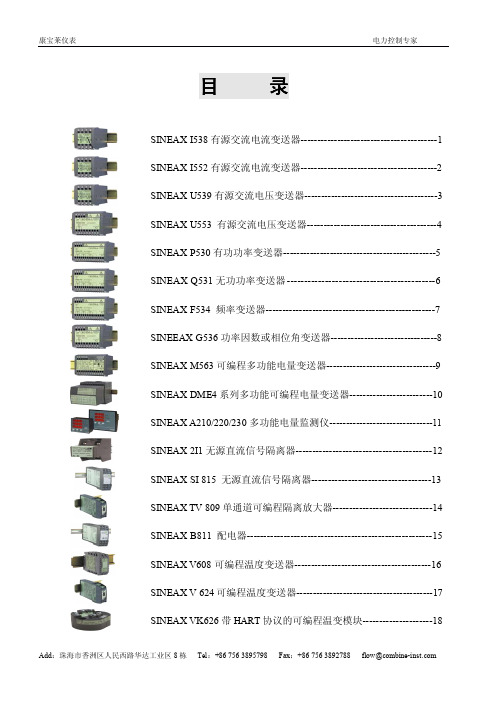
2×UN
测量输出:直流电流或直流电压 输出电流余波:≤1%p.p. 设定时间: 精 ≤300ms 0.2 级 度:符合 DIN/IEC688-1)
1) 230VAC 2) 24VDC 3) 二线制 24VDC
保护等级:Ⅱ(隔离保护) 防污等级: 2 外壳防护等级: IP IP 过压等级:Ⅲ 40 外壳 20 端子
特
�
性:
测量输入:交流电流、正弦波形 测量范围 0…50 到 0…500V
型号规格及选型表
SINEAX U5391.测量范围 1) 0~100V 2) 0~250V 3) 0~500V 4) 非标:0~50 至 0~500V 2.输出信号 1 2 5 F 4 1 □ □ □
测量变量 AC 电流 � � � �
B C D E F G
耗: ≤5mv/a( 输入上限值时)
过载能力: 测量值 过载次数 一次过载 持续时间
1.22×UN
0~<20mA;0.2~1 至<(4~20mA) 两次 过载 之间间隔 … 10s 5) 0…10V,Rext≥1KΩ 6 ) 非 标 : 0~1 至
… 10
持续 1s
0~<10V;0.2~1 至 2~10V 3.供 电 7 8 9
Add:珠海市香洲区人民西路华达工业区 8 栋
Tel :+86 756 3895798
Fax:+86 756 3892788
flow@
康宝莱仪表
电力控制专家
SINEAX U553 有源交流电压变送器
应 用
该变送器适用于纯正或叠加畸变波形的正弦波交流 电压测量, 将交流电压输入按正比例转换成相对应的直 流电流或电压信号输出. 显著特点: 适用于 50/60HZ 或 400HZ 频率的叠加 畸变波形的正弦波.) (安装在 35mm 滑轨上的带 p8/35q 外壳的电压变送器)
典藏-久其GMC集团财务产品用户手册-总账系统
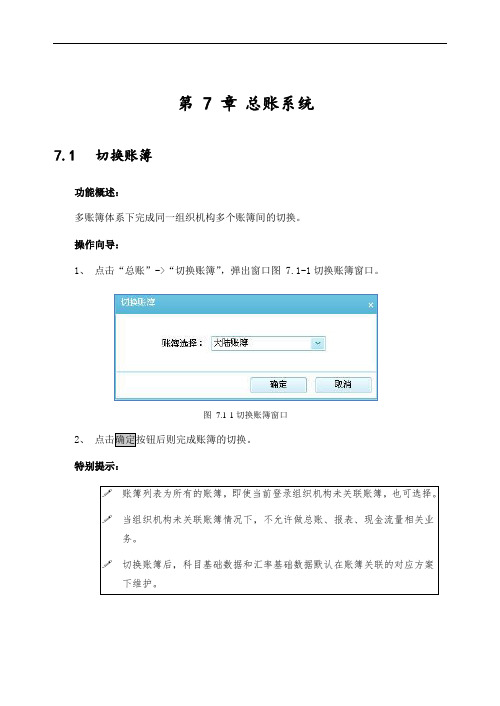
第 7 章总账系统7.1切换账簿功能概述:多账簿体系下完成同一组织机构多个账簿间的切换。
操作向导:1、点击“总账”->“切换账簿”,弹出窗口图 7.1-1切换账簿窗口。
图7.1-1切换账簿窗口2、点击确定按钮后则完成账簿的切换。
特别提示:✐账簿列表为所有的账簿,即使当前登录组织机构未关联账簿,也可选择。
✐当组织机构未关联账簿情况下,不允许做总账、报表、现金流量相关业务。
✐切换账簿后,科目基础数据和汇率基础数据默认在账簿关联的对应方案下维护。
7.2总账初始功能概述:总账初始是指对账簿的科目数据进行初始化,将原有的财务数据“移植”到久其VA 集中核算系统中。
初始数据包括:科目初始数据、往来单位初始数据、部门核算初始数据及其他辅助核算初始数据。
对于涉及辅助核算的多级初始,不需要将这些数据逐级录入,用户可以只录入到明细层次,由系统自动向上汇总。
例如:A企业2013年4月开始启用总账系统,那么应将该企业2013年的年初余额与1-3月份的累计发生额整理出来录入到系统中。
说明:只有明细组织机构才可使用此功能,非明细组织机构无法使用,弹出提示信息框,如图。
图7.2-1提示信息7.2.1科目初始功能概述:科目初始功能录入科目的年初余额、期初借累、期初贷累,系统自动计算出此科目的期初余额。
科目初始数据录入完成后,系统自动检查录入数据借贷平衡关系,包括年初数借\贷是否平衡,借方累计\贷方累计借贷是否平衡。
科目初始时,只能对最明细科目进行操作,由系统自动汇总到上级非明细科目。
操作向导:1、单击“总账”->“初始”->“科目初始”,进入科目初始界面:2图7.2-2 科目初始2、单击录入框,进行数据录入。
对于本位币核算科目,可以直拉录入本位币值;对于外币核算科目,单击此科目所在行,会自动展开成外币模式;对于数量核算科目,会自动展开成数量核算模式。
用户可以直接录入外币值或数量金额值,系统根据自动计算本位币值或金额值并进行填充。
96000 Series RF Reference Source 操作员手册说明书

May 2014 (Simplified Chinese) © 2014 Fluke Corporation. All rights reserved. Specifications are subject to change without notice. All product names are trademarks of their respective companies.96000 SeriesRF Reference Source操作员手册有限担保及责任范围Fluke 公司保证其每一个Fluke的产品在正常使用及维护情形下,其用料和做工都是毫无瑕疵的。
保证期限是一年并从产品寄运日起开始计算。
零件、产品修理及服务的保证期是 90 天。
本保证只提供给从Fluke 授权经销商处购买的原购买者或最终用户, 且不包括保险丝、电池以及因误用、改变、疏忽、或非正常情况下的使用或搬运而损坏(根据 Fluke 的意见而定)的产品。
Fluke 保证在 90 天之内,软件会根据其功能指标运行,同时软件已经正确地被记录在没有损坏的媒介上。
Fluke 不能保证其软件没有错误或者在运行时不会中断。
Fluke 仅授权经销商将本保证提供给购买新的、未曾使用过的产品的最终用户。
经销商无权以 Fluke 的名义来给予其它任何担保。
保修服务仅限于从 Fluke 授权销售处所购买的产品,或购买者已付出适当的Fluke国际价格。
在某一国家购买而需要在另一国家维修的产品,Fluke 保留向购买者征收维修/更换零件进口费用的权利。
Fluke 的保证是有限的,在保用期间退回 Fluke 授权服务中心的损坏产品,Fluke有权决定采用退款、免费维修或把产品更换的方式处理。
欲取得保证服务,请和您附近的Fluke服务中心联系,或把产品寄到最靠近您的Fluke服务中心(请说明故障所在,预付邮资和保险费用,并以 FOB 目的地方式寄送)。
GMC数据手册V
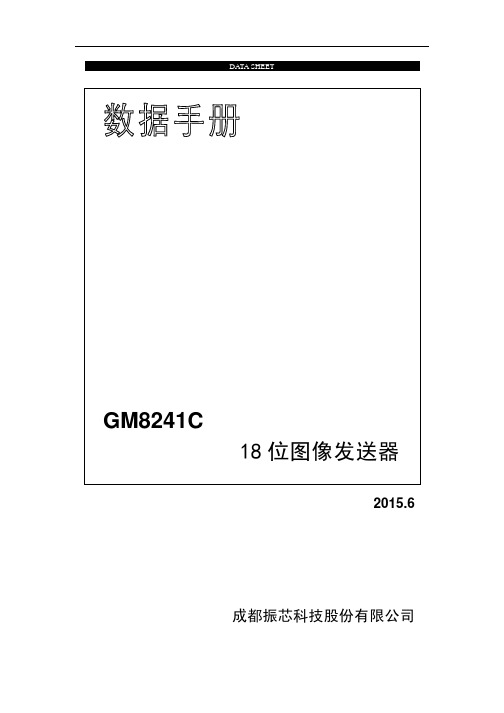
2015.6 成都振芯科技股份有限公司18位图像发送器GM8241C GM8241C版本记录:1.1 当前版本时间:2015年6月新旧版本改动比较:旧版文档页数当前版本文档页数主题(和旧版本相比的主要变化)6 6 修改封装和管脚定义如果您有技术、交付或价格方面的任何问题,请联系成都振芯科技股份有限公司的相关办公室或当地的代理商,或访问官方网站:谢谢!编制时间:2015年6月由成都振芯科技股份有限公司发布发布地点:成都成都振芯科技股份有限公司版权所有1概述GM8241C型18位图像发送器,其主要功能是实现将并行的18bit的RGB数据以及3位控制信号(HS/VS/DE)转换为1路高速差分信号输出。
芯片内部集成终端电阻,支持power down模式。
芯片core电源V DDn为1.8V,IO电源V DDIO可支持3.3V和1.8V两种电压。
该芯片的主要应用领域是视频图像的高速传输,采用1对差分传输线缆即可实现视频信号传输,极大提高了视频图像传输系统的集成度。
2特征a)工作温度范围:-40℃~85℃;b)电源电压V DDn:1.8V;c)电源电压V DDIO:3.3V或1.8V;d)封装形式:QFN48;e)器件等级:工业级。
3封装及引脚功能说明本器件采用48引线的方形扁平无引脚封装(QFN48),引脚排序如下所示。
管脚名序号类型描述LVCMOS 并行接口B[5:0] 2, 1, 48, 47, 46, 45,I, LVCMOSw/ pull-downBLUE并行数据输入端(MSB = 5, LSB = 0)HS 3I, LVCMOSw/ pull-downHorizontal Sync数据输入端VS 4I, LVCMOSw/ pull-downVertical Sync 数据输入端DE 5I, LVCMOSw/ pull-downData Enable 数据输入端PCLK 10I, LVCMOSw/ pull-downPixel Clock 数据输入端采样关系通过RFB 管脚配置控制配置接口PDB 21I, LVCMOSw/ pull-downPower-down Mode 控制输入端PDB = 1, 芯片正常工作;PDB = 0, 芯片关断。
GMC资料
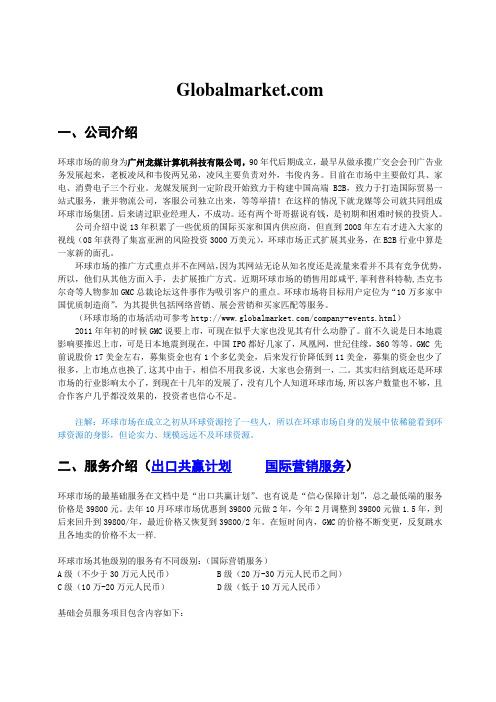
一、公司介绍环球市场的前身为广州龙媒计算机科技有限公司,90年代后期成立,最早从做承揽广交会会刊广告业务发展起来,老板凌风和韦俊两兄弟,凌风主要负责对外,韦俊内务。
目前在市场中主要做灯具、家电、消费电子三个行业。
龙媒发展到一定阶段开始致力于构建中国高端B2B,致力于打造国际贸易一站式服务,兼并物流公司,客服公司独立出来,等等举措!在这样的情况下就龙媒等公司就共同组成环球市场集团。
后来请过职业经理人,不成功。
还有两个哥哥据说有钱,是初期和困难时候的投资人。
公司介绍中说13年积累了一些优质的国际买家和国内供应商,但直到2008年左右才进入大家的视线(08年获得了集富亚洲的风险投资3000万美元),环球市场正式扩展其业务,在B2B行业中算是一家新的面孔。
环球市场的推广方式重点并不在网站,因为其网站无论从知名度还是流量来看并不具有竞争优势,所以,他们从其他方面入手,去扩展推广方式。
近期环球市场的销售用郎咸平,菲利普科特勒,杰克韦尔奇等人物参加GMC总裁论坛这件事作为吸引客户的重点。
环球市场将目标用户定位为“10万多家中国优质制造商”,为其提供包括网络营销、展会营销和买家匹配等服务。
(环球市场的市场活动可参考/company-events.html)2011年年初的时候GMC说要上市,可现在似乎大家也没见其有什么动静了。
前不久说是日本地震影响要推迟上市,可是日本地震到现在,中国IPO都好几家了,凤凰网,世纪佳缘,360等等。
GMC 先前说股价17美金左右,募集资金也有1个多亿美金,后来发行价降低到11美金,募集的资金也少了很多,上市地点也换了,这其中由于,相信不用我多说,大家也会猜到一,二。
其实归结到底还是环球市场的行业影响太小了,到现在十几年的发展了,没有几个人知道环球市场,所以客户数量也不够,且合作客户几乎都没效果的,投资者也信心不足。
注解:环球市场在成立之初从环球资源挖了一些人,所以在环球市场自身的发展中依稀能看到环球资源的身影,但论实力、规模远远不及环球资源。
中国优质制造商GMC认证流程-龙为科技

GMC(中国优质供应商)认证申请与审核流程全球权威的审核机构“德国莱茵TÜV”受环球市场GMC审核委员会委托,对中国制造商进行审核。
GMC标准是根据百万海外买家在采购中国产品,对中国制造商筛选时最关注的八大模块,集合国际权威认证、买家验厂机构的智慧,制定出来的“优质制造商标准”,助您迅速获得百万买家关注,赢取国际买家信任,获取优质买家询盘。
审核准备工作:1.审核日期前准备齐全附件《GMC审核文件清单》中列示的审核资料,确保在审核中充分展现贵司实力。
其中★号项为核心的审核文件,将影响审核结论,请重点准备妥当。
现场审核时,须将原件供审核员检查,复印件提交审核员;2.建议由外贸经理或以上职位的人员作为审厂负责人,以便能有效调配资源配合审厂;由各部门负责人,如生产部/内审员或品管部负责人/外贸部/销售部/财务部/研发部的负责人组成高效的审厂准备小组,有助于全面做好审厂准备,呈现工厂最佳状态;3.在审厂当天,审核资料提供人、审厂负责人需全程在现场协调;且研发人员、外贸人员、内销人员需重点配合访谈,非常关键!*实地验厂流程审核时间一般为1个工作日如因不可调剂的原因(如生产线无法运行)可延期审核,至少提前2个工作日通知审核部门。
中国优质制造商GMC-惠州龙为科技有限公司证书附件:全球权威的审核机构“德国莱茵TÜV ”受环球市场GMC 审核委员会委托,对中国制造商进行审核。
GMC 标准是根据百万海外买家在采购中国产品,对中国制造商筛选时最关注的八大模块,集合国际权威认证、买家验厂机构的智慧,制定出来的“优质制造商标准”,助您迅速获得百万买家关注,赢取国际买家信任,获取优质买家询盘。
以下审核资料是贵司向全球买家的实力展现,赢取百万商机的基础,敬请迅速妥善准备!二、资料提供情况符号★:表示核心的审核文件。
请按企业平时实际运行的情况尽量完整提供,否则,资料不完整可能影响最终评审结果。
符号☆:表示选择性提供的资料。
GMC 泡棉资料

Gredmann公司介绍台湾格雷蒙集团,总公司成立于1978年7月,目前在美国、泰国、韩国、香港、上海、广州、 深圳、北京皆设有分公司,在台湾、韩国、广东及广西拥有五个全资及控股工厂。
台湾格雷蒙 (伟斯企业)于台湾中华征信所( 大服务)评为 位大企业 天下杂志( 大服务业)评为 (伟斯企业)于台湾中华征信所(500大服务)评为234位大企业、天下杂志(500大服务业)评为 第212位大企业,在2010年于贸易产业中被评为第12位。
作为集团的子公司之一,韩国格雷蒙已设立多条高密度聚氨酯泡棉生产线。
为全球客户提 供最优质的泡棉产品。
GMC高密度聚氨酯泡棉1,均匀吸收震动 2 压缩负荷承受力强 2, 3,极好的密封性能GM CELL是一种密度均匀 ,表面精度精确, 吸震和内部缓冲以及密封性能出色的高密度微孔 高密度微孔 聚氨酯泡綿GMC应用领域GMC型号GMC 品牌厚度 系列 0.15 0.2 0.3 0.4 0.5 0.6 0.7 0.8 0.9 1.0 1.2 1.5 1.7 2.0 2.5 3.0 3.5 4.0 R ◎ ⊙ ⊙ ⊙ ⊙ ⊙ ⊙ ⊙ ◎ ⊙ ⊙ ⊙ ⊙ ⊙ ⊙ ⊙ ◎ ⊙050 厚度S / ◎ ⊙ ⊙ ⊙ ◎ ⊙ ⊙ ⊙ ⊙ ◎ ⊙ ◎ ⊙ ◎ ◎ ◎ ◎ SR / ⊙ ⊙ ⊙ ⊙ ⊙ ⊙ ⊙ ◎ ⊙ ◎ ⊙ ◎ ⊙ ◎ ⊙ ◎ ◎R 特性SSR / / / / ⊙ ⊙ ⊙ ⊙ ◎ ⊙ ◎ ⊙ ◎ ⊙ ◎ ⊙ / / M / / ⊙ ◎ ⊙ ◎ ⊙ ⊙ ◎ ⊙ ◎ ⊙ ◎ ⊙ ◎ ⊙ ◎ ◎ OM / / ⊙ ◎ ⊙ ◎ ⊙ ⊙ ◎ ⊙ ◎ ⊙ ◎ ⊙ ◎ ⊙ ◎ ◎ O / / ⊙ ◎ ⊙ ◎ ⊙ ⊙ ◎ ⊙ ◎ ⊙ ◎ ⊙ ◎ ⊙ ◎ ◎ T / ⊙ ⊙ ◎ ⊙ ◎ ⊙ ⊙ ◎ ⊙ ◎ ⊙ ◎ ⊙ ◎ ⊙ ◎ ◎ UT / ⊙ ⊙ ⊙ ⊙ ◎ ⊙ ⊙ ◎ ⊙ ◎ ⊙ ◎ ⊙ ◎ ⊙ ◎ ◎ ST / / ⊙ ◎ ⊙ ◎ ◎ ◎ ◎ ⊙ ◎ ⊙ ◎ ⊙ ◎ ⊙ ◎ ◎ MH60 / / ⊙ ◎ ⊙ ◎ ◎ ◎ ◎ ⊙ ◎ ⊙ ◎ ⊙ ◎ ⊙ ◎ ◎ MH70 / / ⊙ ◎ ⊙ ◎ ◎ ◎ ◎ ⊙ ◎ ⊙ ◎ ⊙ ◎ ⊙ ◎ ◎⊙标准品◎非标品 非标品*其他厚度产品请联络销售人员 其他厚度产品请联络销售人员GMC物性测试 环境测试 GMC物性测试-环境测试H Heavy M Metals t lTest Items Cadmium (Cd) Lead (Pb) Mercury (Hg) (Cr Ⅵ) ) Hexavalent chromium ( Unit mg/kg mg/kg mg/kg mg/kg g/ g MDL *1) 0.5 5 2 1 Results N.D. *2) N.D. N.D. N.D.Halogen ContentsTest Items Bromine (Br) Chlorine (Cl) Fluorine (F) Iodine (I)*1) Method Detection Limit *2) Not Detected ( < MDL )Unit mg/kg mg/kg mg/kg mg/kgMDL 0.5 5 2 1Results N.D. N.D. N.D. N.D.GMC物性测试 回弹测试 GMC物性测试-回弹测试35 30 25 20(% )15 10 5 0 Without GM-CELL GM-CELLTest Method : JIS K 6401 将直径6 钢球从460 高度自由落体来测定回弹高度 将直径6mm钢球从460mm高度自由落体来测定回弹高度。
MANAGEMENT MANUAL

CONTENTSPart I INTRODUCTION 6 Part II FITTING-OUT GUIDE 72.1 Handing-over of Premises 8 2.2 Owner/Tenant Contact Information 8 2.3 Fitting-out Works by Owner/Tenant 82.3.1 Approval of Fitting-out Plans 9 2.3.2 Preparation of Fitting-out Plans/Drawings 10 2.3.3 M&E Installation102.3.4 Submission Of Fitting-out Plans/Drawings 11 2.3.5 Fitting-out Works by Developer’s Nominated Contractor 11 2.3.6 Fitting-out Garbage Removal Charge & Decoration Deposit 12 2.3.7 Temporary Electricity Supply 12 2.3.8 Inspection on Tenant Decoration 12 2.3.9 Special Notes for Fitting-out Work 132.4 Summary of Fitting-out Process 14PART III FITTING-OUT RULES 153.1 Confirmation of Fitting-out Works 16 3.2 List of Fitting-out Works Supervisors 16 3.3 Transportation of Materials &Removal of Decoration Garbage 16 3.5 Damage Resulting from Fitting-out Works163.6 Fitting-out Actives to be confined inside Premises163.7 Security of Materials & Tools Array173.8 Re-instatement of Fixtures/Fittings 173.9 Supply of Water & Electricity 173.10 Fitting-out Time and Name List 173.11 Works at Common Area 173.12 Safety Measures 183.13 Behavior of Contractors 183.14 Erection of Hoarding 183.15 Area Passage 183.16 Observance of Regulations 18PART IV MANAGEMENT SERVICES 194.1 Introduction of Management Work 204.2 Location for Paymentof Management Fee 204.3 Notes for Payment 20PART V NOTES ON MOVING IN & HOUSE RULES 215.1 Notes On Moving In 225.1.1 Prior Booking for Service Lift 225.1.2 Trolley of Rubber/Plastic Castors tobe used 225.1.3 Staff to be Employed to OverseeMoving In 225.1.4 Handling of Debris 22 5.2 House Rules 225.2.1 Emergency Contact 225.2.2 Installation and Alteration 225.2.3 Sign 225.2.4 Erection of Aerial 225.2.5 Loading and Unloading 23 Array5.2.6 Use of Service Lift 235.2.7 Use of Toilet 235.2.8 Use of Premises 235.2.9 No Sleeping or Domestic Use 235.2.10 No Preparation of Food and Cooking 235.2.11 Normal Business hours 245.2.12 Keep Premises Open 245.2.13 Keep Shop Front and Sign Lighting 245.2.14 No Encroachment at Common Area 245.2.15 Cleaning 245.2.16 Refuse and Garbage Removal 245.2.17 Touting 245.2.18 Nuisance 245.2.19 Animal and Pet 255.2.20 Dangerous Goods 255.2.21 Obstruction in Staircase or Passage 255.2.22 Access to Premises after NormalBusiness hours 255.2.23 Works outside Opening Hours ofthe Plaza 255.2.24 Rules Amendment 255.2.25 Compliance of Regulations 25 PART VI FIRE EV ACUATION 266.1 Fire Order for Display 276.1.1 If You See A Fire, Remain Calm 276.1.2 If You Hear a Fire Alarm, Remain Calm 276.1.3 How To Use The Hose Reel 276.2 Instruction for Evacuation 286.2.1 While Awaiting Instructions 286.2.2 If Evacuation Is Ordered,Remain Calm 286.3 Warning System 286.3.1 Fire Alarm 286.3.2 Additional Equipment 296.3.3 Public Address System 296.3.4 Emergency Light 296.4 Fire Precautions 29PART VII APPENDIX 307.1 Charges for Decoration GarbageRemoval & Decoration Deposit 317.2 Temporary Electricity SupplyCharge Rate 317.3 The Premium Amount for Contractor'sAll Risks Insurance 327.4 Opening Hours of The Management Office& Contact No.327.5 Operation Time of Passenger& Service Lifts in Office Tower 327.6 Central Air-Conditioning Supply forOffice Tower 337.7 Operation Time of Passenger& Service Lifts in Shopping Arcade 337.8 Central Air-Conditioning Supplyfor Shopping Arcade 33 7.9 Charges of Non-Office-HourAir-Conditioning Supply 33 7.10 Useful Telephone Numbers 33PART 1INTRODUCTONShanghai New World Property Management Company Limited welcomes you as an office owner / shop owner / office tenant of Hong Kong New World Tower and wishes you prosperous business for many years to come.This Handbook aims at providing an overall guidance to the understanding by commercial owners / tenants with general information on the procedures and requirement of commercial premises, the management services to be provided, house rules and regulations to be observed, etc. It is of an advisory nature only and should be read subject to the Deed of Mutual Covenant and Management Agreement. It is also for information only and should not be relied upon to the exclusion of any legal documentation concerning a tenancy and Deed of Mutual Covenant. We hope that you will find this Handbook informative and useful. Please feel free to contact the local management staff who are always ready to assist you if you require further information.We take this opportunity to assure you of our best service at all times.Shanghai New World Property Management Company LimitedDirector & General ManagerPART 2FITTING-OUT GUIDEPART 22.1 Handing-over of Premisesmanagement fees, a notification letter of premises taking-over andrequirement of premises taking-over will be issued by theDeveloper's leasing sector. Keys of the premises are then allocatedby the Hong Kong New World Management Office on production ofleasing sector notification letter at a specific date which shall benotified in writing by the Registered Owner / Tenant under normalcircumstances. An official company seal / chop must be brought inwhile taking over the premises. On receipt of the keys, you will beaccompanied by our management staff to inspect on the condition ofthe provided fixture and fittings, which are ready to be taken over inthe premises.Subject to the provision of the Deed of Mutual Covenant andManagement Agreement, owners / tenants are responsible for the up-keeping, including maintenance and repair, of all the items handedover. If you appoint your agent or representative to take over thepremises, an authorization letter must be presented to theManagement Office.2.2Owner / Tenant Contact InformationOwner / Tenant shall complete and return a contact information formupon taking over the premises which will be used for the purpose ofday-to-day communication and emergency contact.2.3Fitting-out Works by Owner / TenantThe owners / tenants are responsible at their own expenses for all fitting-out words, including alterations or additions to the Developer’s provided fittings or fixtures, within the premises. It is for the owner's / tenants' benefit tosubmit plans before the intending date of hand-over, which shallPART2construction concerning the Electricity Engineering will be arranged by the contractor nominated by the Developer while the additional charges will be at tenants' expenses. Fitting-out works, including theremoval of any Developer fixtures or fittings, should NOT be carried outbefore approval is obtained from the Management Office.2.3.1 Approval of Fitting-out PlansOwners / Tenants must submit the fitting-out plans to the Management Office for written approval prior to the commencement of any fitting-out works. The following plans are generally required depending on the extent of alteration / additional works.2.3.1.1 Floor plan with clear indication of the internalpartitions with detailed description / specifications of Fitting-outmaterial to be used;2.3.1.2 Elevation / section of floor plan with details ofshop front / shop sign;2.3.1.3 Drop-ceiling and lighting plans;2.3.1.4 Drainage layout plan;2.3.1.5 Fire control equipment and smoke-detectorsprinkler system layout plan;2.3.1.6 Air-conditioning steel duct system layout planwith details;2.3.1.7 High-voltage line electricity supply layout plan2.3.1.8 High-voltage line electricity plane layout plan(lighting power)2.3.1.9 Low-voltage line systemFITTING-OUT GUIDE2.3.1.10 Low-voltage line plane layout.(telephone,computer lines layout plan)2.3.1.11 Thermo-control layout plan2.3.1.12 Instructions of other decoration design2.3.2 Fitting-out Plans / DrawingsIn your submission of fitting-out plans / drawings, you should take noteof the following in order to avoid delay:2.3.2.1 All plans / drawings should be in metric scale sand properlynumbered;2.3.2.2 All technical information should be in metric units;2.3.2.3 Correct levels and dimension should be marked on submittedplans / drawings. In all cases, dimensions should be verified bysite measurement;2.3.2.4 Construction details, specification of materials and method offixing should be shown on drawings;2.3.2.5 Plants / equipment should be shown on drawings;2.3.2.6 Any alteration to the building's structure is prohibited.2.3.3 M & E InstallationMajor modification and / or alteration of the building services is notpermitted. Owners / tenants who intend to have minor alteration andadditional works to the building services must submit applications to theManagement Office with all plans and drawings concerned. Theapplication with plans will be vetted by the M & E Consultant. Noadditional or alteration works to the building services shall becommenced without prior approval of the Management Office.FITTING-OUT GUIDEIf you want to connect electrical cable to the building main switchroom control panel, prior application in specified form should becompleted and returned to the Management Office 3 days before theworks. During the decoration period, immediate application would notbe entertained. All the works has to execute after 23:00 hours. You areheld solely liable for any loss, damage and claim arising therefrom ifManagement Office's approval has not been obtained.2.3.4 Submission of Fitting-out Plans / DrawingsOwners / tenants can submit the plans / drawings to the ManagementOffice for approval. The following are the addresses:2.3.4.1 Shanghai New World Property Management Co., LtdHong Kong New World Tower Management Office: No.300Huai Hai Road (M), Floor, Shanghai..2.3.4.2 Owners / tenants can request a meeting with the ManagementOffice to discuss the proposed fitting-out word, if considerednecessary.2.3.5 Owners' / Tenants' Works by Developer’s Nominated Contractors Toensure safety to the public & proper functioning of the building servicessystem during owner's / tenants' fitting-out period as well as futureoperation, the following works must be done by Developer’s NominatedContractors at owner's / tenant's cost:2.3.5.1 Additional / Alteration Works on Air-conditioningInstallation (including fan reel, air-adjustment machine)no matter such works involves the owners’/tenants’ areaor common area must be done by the Developer’snominated contractors.2.3.5.2 Additional/Alteration Works on Water Supply andDrainage System no matter such works involve commonarea or the owners’/ tenants’ premises must be done bythe Developer’s nominated contractor..FITTING-OUT GUIDE2.3.5.3 Additional / Alteration Works on Fire Fighting Installation(including sprinklers, fire alarm.) The Developer’snominated contractor must be appointed to do all suchalteration / additional word no matter such worksinvolves common or owner's / tenant’s area.2.3.5.4 Alteration / Additional Work on CABD Installation. Suchwork no matter involve co mmon or owner’s/tenant’sarea must be done by the Developer’s nominatedcontractor .2.3.5.5 Alteration / Additional Works on the Building Structureno matter involve common or owner’s/tenant’s area mustbe done by the Developer’s nominated contractor.2.3.6 Decoration Garbage Removal Charge and Decoration DepositThe Management Office will designate a garbage collection stationfor disposal of garbage during the fitting-out period. Owners /tenants are requested to put all their decoration garbage at theaforesaid station. Details of dumping charge please refer toAppendix 7.1. The garbage removal charges include the expenseof transporting the garbage from collection station to the certaingarbage zone set up by the government Garbage removal charge &decoration deposit should reach the Management Office beforecommencement of work. In case of the debris dumping at thecommon area, additional garbage removal charge will be debutedfrom the decoration deposit (appendix 7.1).2.3.7 Temporary Electricity SupplyOwner / Tenants can directly send application to ask for temporaryelectricity supply by completing and returning the specified formfor approval. Owners/Tenants are requested to pay the temporaryelectricity supply charges (appendix 7.2) which will be deductedfrom decoration deposit. The fixing and lease of the temporaryelectricity must be done by the Developer’s nominated contractor.FITTING-OUT GUIDEThe applicants are responsible for all damages or consequencescaused by the electricity supply. The balance of decoration depositwill be refunded without interest upon completion of decorationwork and deduction of temporary electricity supply charges2.3.8.Inspection on Interior DecorationManagement staff will inspect on your decoration work during thefitting-out period in order to ensure that all the work have beendone in accordance with approved plans/drawings. Uponcompletion of the work ,owners/tenants are requested to inform theManagement Office for final inspection. Besides, owners/tenantsare also requested to notify the date of business opening. Aspecified form to record the same should be signed byowners/tenants for our information and follow up action.2.3.9 Special Notes for Fitting-out Work2.3.9.1 Owners/Tenants should ensure that their designer orcontractor is aware of the necessity for theinstallations/design to comply with all statutoryrequirements of the government authorities and utilitiescompanies concerned. The fitting-out plans/drawingsapproved by the Management Office do not guarantee theissue of licenses from the appropriate authorities.2.3.9.2 Owners/Tenants should try to avoid conflicts in theirdesign with locations of services in their premises. Thecost of each relocation or alteration is borne by theowners/tenants. Therefore, the owners/tenants are advisedto consult the Management Office beforehand or requestfor the supply of relevant plans for reference.2.3.9.2PRIOR approval must be obtained form the ManagementOffice before commencement of any fitting-out works.Particularly, no cutting into columns, walls, beams orslabs is permitted without PRIOR written consent of theManagement Office. Sufficient loading should be ensuredFITTING-OUT GUIDEbefore installation of any machines/plants.2.4Summery of Fitting-out Process2.4.1Taking-over of premises and Management Manual;2.4.2Inspection of finishes /fittings, etc. in the premises and reporting ofdefects to the Management Office;2.4.3Application for installation of meters for supply of water andelectricity;2.4.4Submission of fitting-out plans/drawings to the Management Office.Owners/Tenants are advised to submit the plans/drawings beforehandover of the premises;2.4.5Arrangement of meeting with the Management Office to discussabout the proposed fitting-out works, if considered necessary;2.4.6All the proposed fitting-out works can only commence uponobtaining the approval from the Government Fire FightingDepartment and Quality Control Department;2.4.7All the decoration works can only commence upon obtaining theapproval of the Management Office;2.4.8Commencement of fitting-out works and briefing to the contractorsof the following:-і) Fitting-out rules;ii)Contact telephone numbers of the Security Control Office incase of emergency;iii)Submission of copies of insurance certificate to theManagement Office and arrange for the debris removal chargeand decoration deposit.iv)Electrical cable connecting to the building's electricity controlpanel, prior approval must be obtained 3 days beforecommencement of the work.2.4.9Notification to the Management Office upon completion offitting-out works to facilitate the final inspection and thefitting-out work is completed only after the government firefighting department and quality control department hasapproved.PART 3FITTING-OUT RULESPART 3 FITTING-OUT RULES3.1Confirmation of Fitting-out WorksIf the owners/tenants wish to authorize the designers, architects orcontractors to contact the Management Office director in respect of thefitting-out works, the owners/tenants should confirm the arrangement inwriting.3.2List of fitting-out Works SupervisorsThe Management Office should be provided with a list of supervisors ofeach contractor responsible for the fitting-out works for the purpose ofliaison during the fitting-out period and in case of emergency after officehours.3.3InsuranceOwners/Tenants should arrange for workmen's compensation insurance,fire insurance, water damage insurance and third party liability insuranceagainst damage to properties and injury to persons during the fitting-outperiod. Copies of insurance document have to be sent to the managementOffice before commencement of fitting-out work. Details of the premiumamount please refer to Appendix 7.3.3.4Transportation of Materials and Removal of Decoration GarbageAll materials and decoration garbage should be transported to and fromthe premises by carts or trolleys on nylon or rubber wheels via designatedloading bays, goods elevators and passage ways. Passenger lifts andescalators should NOT be used for transportation of materials andgarbage.3.5Damage Resulting form Fitting-out WorksAny damage to the finishes and facilities, fittings of the Building duringfitting-out works should be reinstated to the Management Office'ssatisfaction. The Management Office reserves the right to make good thedamage on the owners'/tenants' behalf and at the owners'/tenants'expenses.3.6Fitting -out Activities to be Confined Inside PremisesAll the fitting-out works must be confined within the premises. All tools,PART 3 FITTING-OUT RULESmaterials are not allowed to be kept at the common area. Otherwise, theManagement Office will have them removed without prior notice. Theremoving charges plus 15% administration cost incurred will be recoveredfrom the owner/tenant by deduction of the fitting-out deposit and demandthe balance if the deposit is not sufficient to cover the cost.3.7Security of Materials & ToolsThe contractors of the owners/tenants are responsible for the security oftheir tools and materials.3.8Re-installment of Fixtures/FittingsIf the owner/tenant remove any fixtures and fittings installed in theirpromises, prior approval must be obtained form the Management Office inwriting.3.9Supply of Water & ElectricityOwners/Tenant can make their own arrangements for the supply ofwater/electricity for decoration form the supply authorities.3.10Fitting-out Time and Workers’ Name ListThe decoration time is scheduled from 06:00 p.m. to 01:00 a.m. in thebuilding. However, the Management Office may request certain works,which may cause nuisance to other occupiers, to be carried out during aspecified time. In case of extending the working hours or entering thecommon area i.e. common corridor, meter room, etc., working permit hasto be obtained at the Management Office before carrying out any works.In order to avoid the irrelevant personnel disturbing, owners/tenants arerequested to hand in the name list and I.D. card number of workers ONEweek before the commencement of the decoration work. Moreover, thesame procedure will be required for daytime works by the contractors.3.11Works at Common AreaShould the contractors want to carry out any work at the common area,prior application in specified form should be made to the ManagementOffice and works should NOT be carried out until obtaining the approval,which indicate the time and the date of the commencement of the work.Before the commencement of the work, workers should obtain andPART 3 FITTING-OUT RULESregistered the work permit at the bui lding’s security department. Workersare requested to wear the working permit during the fitting-out work.Working permit has to be returned to the Office on the same day afterwork. Failure to return the working permit and administration charge willbe levied.3.12Safety MeasuresWarning signs reminding the public that fitting-out work in progressshould be put at observable areas in accordance with the instructionsgiven by the Management Office3.13Behaviour of ContractorsGambling, sleeping overnight, preparation of food or other inappropriatebehaviour may create nuisance to other owners/tenants or visitors arestrictly prohibited within the building. Otherwise, fitting-out works wouldbe stopped immediately by the Management Office without giving priornotice.3.14Erection Of HoardingsOwners/Tenants should erect hoarding surrounding the premises tomitigate potential risk, noise or air pollution arising form the work. Allentrances should always be kept closed during the fitting-out period.Otherwise, fitting-out works would be stopped immediately by theManagement Office without giving prior notice.3.15Work Site AccessEither premises within Developer's construction site access of premisesvia the site area, the owners/tenants and their contractors should strictlycomply with the fitting-out rules given by the Management Office so as tominimize contravention among all parties involved.3.16Observance of RegulationsThe owners'/tenants' contractors and their employees when working insidethe site area should observe strictly any other regulations of the buildingas laid down by Management Office. from time to time.PART 4PART 4MANAGEMENT SERVICES4.1 Introduction of Management ServicesSecurity: To provide 24 hours security services for safeguarding theinterest of both the Owners & TenantsCleaning: To provide a series of high quality cleaning services inmaintaining a comfortable working and shopping environmentof the building with a view to pursue the image as a high classcommercial center.Maintenance: To provide comprehensive maintenance schemes to ensurethat all building services system and facilities are in normaloperation.Promotion: To provide intensive promotion activities to attract visitorswhich will indirectly boost owners'/tenants' business.For the opening hours of the Management office, please refer toaaAppendix7.4. Details regarding the operation time of passenger &service lifts and central air-conditioning supply timing for office Tower,please refer to Appendix 7.5 and 7.6 respectively. Besides, data on theoperation time of passenger & service lifts and central air-conditioningsupply timing for shopping arcade will be found on Appendix 7.7 and 7.8respectively.If NON-OFFICE-HOUR air-conditioning supply is required, please contactthe Management Office for such arrangement. Details ofNON-OFFICE-HOUR air-conditioning charges will be found on Appendix7.9.4.2Location for payment of Management FeeOwners/Tenants can settle the payment wither by mailing to or directlyapproaching the following address:No.300 Huai Hai Road (M) Floor , Hong Kong New World TowerManagement Office4.3Notes for Payment4.3.1Owners/Tenants can directly settle payment by approaching theManagement Office in person during office hours.4.3.2All payment of management fee must be made by "Cross Cheque"payable to "New World Property Management Limited ". Pleasewrite your company name with address and demand of note numberon the back of the cheque.4.3.3Management fee must be paid in advance on the first day of eachcalendar month.4.3.4Office receipt will be issued upon the payment credited to theBuilding AccountPART 5NOTES ON MOVING IN & HOUSE RULESPART 5 NOTES ON MOVING IN & HOUSE RULES5.1Notes On Moving In5.1.1 Prior Booking for Service LiftOwners/tenants must inform the Management Office one week priorto moving in. Reservation of the service lift for transportation mustbe made in writing to notify the Management Office.5.1.2Trolley of Rubber/Plastic Carts to be usedOwners/tenants must use the rubber wheeled carts to transport thefurniture/cargo to avoid damage to the floor surface.5.1.3Staff to be Developed to Oversee Moving inOwners/Tenants must be designate a person to oversee the movingin process and inform the Management Office with contacttelephone numbers of the designated person.5.1.4Handling of GarbageNo waste materials and garbage are allowed to be left at commoncorridor, staircase and public area. All the waste materials must betransported to the designated garbage collection station.5.2House Rules5.2.1 Emergency ContactTo provide the names and telephone numbers of contact person incase of emergency or activation of burglary alarm after office hours.5.2.2 Installation and alterationPlease refer to Part II of this Manual for any alteration /additionalworks you may propose.5.2.3 SignUnless with the written consent of the Management Office,owner/tenant shall not exhibit or display on or affix to the exteriorof the shop front or external walls of the premises any writing sign,signboard abutting any public corridors or areas.5.2.4 Erection of AerialUnless with the written consent of the Management Office, noaerials shall be erected in or upon the building.NOTES ON MOVING IN & HOUSE RULES5.2.5 Loading and UnloadingLoading and unloading of goods shall be carried out in designatedbays in a proper manner and during such time period as from timesto time stipulated by the Management Office.5.2.6 Use of Service LiftNo the Owner's /Tenant's servants, employees, agents, invitees ordeliverer shall bring into any passenger lift of the building anybulky parcels, tools, food trays, carriers or other space-occupyingand hazardous items. Owner/Tenant must ensure that all such itemsare restricted to the designated service lift only. No hydraulic trolleyis allowed to be used in the public area of the building.5.2.7 Use of ToiletOwners'/tenants' must use exclusive toilets in a proper manner andnot to cause any damage to the sanitary fitting therein while the thedaily sanitary goods are at owners’/tenants’ expense.5.1.8 User RightUnder no circumstances should the premises be used for anypurpose other than those specified in the Lease Covenant.Owners/Tenants should not use their premises for any immoral orillegal purposes.5.1.9 No Sleeping or Domestic UseOwners /tenants should neither permit their staff or third parties toremain overnight in their premises, nor permit any hiring ofsleeping accommodation within their premises.5.1.10 No Preparation of cooking of FoodNo preparation or cooking of food is allowed within the premises,unless as otherwise obtained prior approval form the ManagementOffice.5.1.11 Normal business HoursNormal Business hours are defined asOffice Tower: Monday to Friday 08:00 to 18:00Saturday (Except public holidays) 08:00 to 13:00Sunday and Public Holiday NON-OPEN HOURSShopping Arcade: Daily 10:00 to 22:00。
美国汽车零售商 - 恒达汽车辅助服务指南说明书

Honda dealership personnel are trained professionals. They should be able to answer all your questions.If you encounter a problem that your dealership does not solve to your satisfaction, please discuss it with the dealership’s management. The service manager or general manager can help. Almost all problems are solved in this way.If you are dissatisfied with the decision made by the dealership’s management, contact your Honda Customer Service Office.U.S. Owners:Canadian Owners:In Puerto Rico and the U.S. Virgin Islands:When you call or write, please give us this information:Vehicle Identification Number (see page )Name and address of the dealer who services your vehicle Date of purchase Mileage on your vehicle Your name,address,and tele-phone numberA detailed description of the problemName of the dealer who sold the vehicle to you421Customer Service Information438CUSTOMER RELATIONSRELATIONS AVEC LA CLIENTÉLE American Honda Motor Co.,Inc.Automobile Customer Service Mail Stop 500-2N-7A1919Torrance BoulevardTorrance,California 90501-2746Tel:(800)999-1009Honda Canada Inc.715Milner Avenue Toronto,ON M1B 2K8Tel:1-888-9-HONDA-9Fax:Toll-free 1-877-939-0909Toronto (416)287-4776Vortex Motor Corp.Bella International P.O.Box 190816San Juan,PR 00919-0816Tel:(787)620-7546Your new vehicle is covered by these warranties:covers your new vehicle,except for the battery,emissions control systems,and accessories,against defects in materials and workmanship.these twowarranties cover your vehicle’s emissions control systems.Time,mileage,and coverage are conditional.Please read your warranty booklet for exact information.providescoverage for as long as the pur-chaser of the muffler owns the vehicle.provides proratedcoverage for a replacement battery purchased from your dealer.this warranty gives upto 100%credit toward a replacement battery.a seatbelt that fails to function properly is covered by a limited warranty.Please read your warranty booklet for details.Restrictions and exclusions apply to all these warranties.Please read the 2007Honda warranty information booklet that came with your vehicle for precise information on warranty coverages.Your vehicle’s original tires are covered by their manufacturer.Tire warrantyinformation is in a separate booklet.Please refer to the 2007warranty manual that came with your vehicle.covers all Honda replacement parts against defects in materials and workmanship.Honda accessories are covered under this warranty.Time andmileage limits depend on the type of accessory and other factors.Please read your warranty booklet for details.all exterior body panels are covered for rust-through from the inside for the specified time period with no mileage limit.Warranty CoveragesU.S.OwnersCanadian OwnersNew Vehicle Limited Warranty Emissions Control Systems Defects Warranty and EmissionsPerformance Warranty Replacement Muffler Lifetime Limited Warranty Replacement Battery Limited Warranty Original Equipment Battery Limited Warranty Seat Belt Limited Warranty Replacement Parts Limited Warranty Accessory Limited Warranty Rust Perforation Limited WarrantyWarranty and Customer Relations439If you believe that your vehicle has a defect which could cause a crash or could cause injury or death,you should immediately inform the National Highway Traffic Safety Administration (NHTSA)in addition to notifying American Honda Motor Co.,Inc.If NHTSA receives similar com-plaints,it may open an investigation,and if it finds that a safety defect exists in a group of vehicles,it may order a recall and remedy campaign.However,NHTSA cannot become involved in individual problems between you,your dealer,or American Honda Motor Co.,Inc.To contact NHTSA,you may call the Vehicle Safety Hotline toll-free at 1-888-327-4236(TTY:1-800-424-9153);go to;or write to:Administrator,NHTSA,400Seventh Street,SW.,Washington,DC 20590.You can also obtain otherinformation about motor vehicle safety from .Reporting Safety Defects (U.S.Vehicles)440http://www.saf http://www.safAuthorized ManualsAuthorized Manuals441This manual covers maintenance and recommended procedures for repair to engine and chassis components.It is written for the journeyman mechanic,but is simple enough for most mechanically-inclined owners to under-stand.This manual complements the service manual byproviding in-depth troubleshooting information for each electrical circuit in your vehicle.This manual describes the procedures involved in the replacement of damaged body parts.Authorized ManualsService Manual:Electrical Troubleshooting Manual:Body Repair Manual:442P.O.BOX 07280·DETROIT,MICHIGAN 48207·1-800-782-4356These Publications cannot be returned for credit without receiving advance authorization within 14days of delivery.On returns,a restocking fee may be applied against the originalorder.。
GMC大赛2014手册(中文版)

国际企业管理挑战赛参赛手册2014版国际企业管理挑战赛中国赛区组织委员会北京新世界中心北办公楼7层电话:(8610) /传真: (8610)邮箱: info@官网: 本中文版手册译自英文版,仅供参考2014/9/15目录第一部分前言............................................................................................................ 错误!未定义书签。
简介................................................................................................................... 错误!未定义书签。
参赛队的任务 .................................................................................................... 错误!未定义书签。
如何参赛决策 .................................................................................................... 错误!未定义书签。
几个重要的基本概念 ......................................................................................... 错误!未定义书签。
如何使用《参赛手册》...................................................................................... 错误!未定义书签。
第二部分经营环境 .................................................................................................. 错误!未定义书签。
精选-久其GMC集团财务产品用户手册-应收账款管理
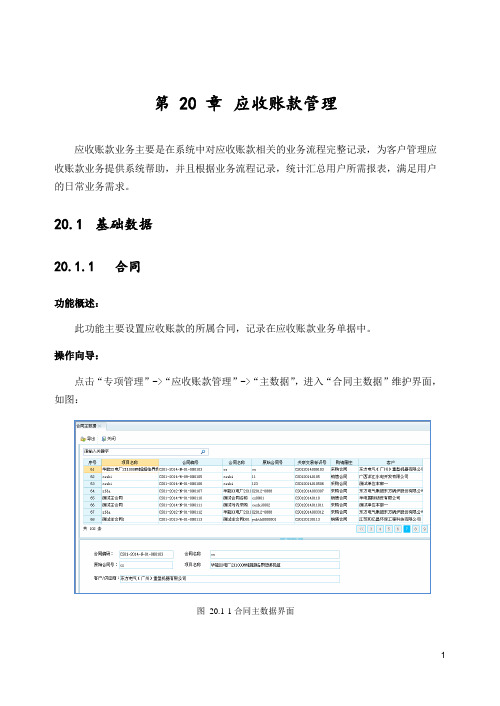
第 20 章应收账款管理应收账款业务主要是在系统中对应收账款相关的业务流程完整记录,为客户管理应收账款业务提供系统帮助,并且根据业务流程记录,统计汇总用户所需报表,满足用户的日常业务需求。
20.1基础数据20.1.1合同功能概述:此功能主要设置应收账款的所属合同,记录在应收账款业务单据中。
操作向导:点击“专项管理”->“应收账款管理”->“主数据”,进入“合同主数据”维护界面,如图:图20.1-1合同主数据界面20.1.2板块功能概述:此功能主要定义合同所属板块,关联合同基础数据。
操作向导:点击“专项管理”->“应收账款管理”->“主数据”,进入“板块”维护界面,如图:图20.1-2板块维护界面特别提示:✐资产分类支持级次管理。
✐资产分类代码不能重复。
✐已经引用过的资产分类不能修改、删除操作。
✐已经引用过的资产分类不能增加明细类。
✐资产分类使用状态若不打勾,则在建立时无法选择到该资产分类。
20.1.3款项性质功能概述:此功能主要设置应收账款的款项性质。
操作向导:点击“专项管理”->“应收账款管理”->“主数据”,进入“款项性质”维护界面,如图:图20.1-3款项性质维护界面特别提示:✐存放地点的代码不能重复。
✐存放地点的名称不能重复。
✐已经引用过的存放地点不能修改、删除操作。
20.1.4是否达到收款条件功能概述:此功能主要设置应收账款是否达到收款条件,用于业务人员记录到应收账款单据中。
操作向导:点击“专项管理”->“应收账款管理”->“主数据”,进入“是否达到收款条件”维护界面,如图:图 20.1-4 是否达到收款条件维护界面20.1.5未达收款条件原因功能概述:此功能主要用于未达收款条件时的原因,用于业务人员记录在应收账款单据中。
操作向导:点击“专项管理”->“应收账款管理”->“主数据”,进入“未达收款条件原因”维护界面,如图:图20.1-5未达收款条件原因20.1.6逾期原因功能概述:此功能主要设置逾期原因类别,用于业务人员记录在应收账款单据中。
- 1、下载文档前请自行甄别文档内容的完整性,平台不提供额外的编辑、内容补充、找答案等附加服务。
- 2、"仅部分预览"的文档,不可在线预览部分如存在完整性等问题,可反馈申请退款(可完整预览的文档不适用该条件!)。
- 3、如文档侵犯您的权益,请联系客服反馈,我们会尽快为您处理(人工客服工作时间:9:00-18:30)。
GMC国际企业管理挑战赛目 录第一部分前言 (3)第二部分经营环境与经济背景 (5)经济类型 (5)国际重大事件的影响 (6)市场营销 (7)定价 (9)产品质量 (9)研究与开发 (10)广告宣传 (11)销售活动 (12)产品的供货保证 (14)市场营销管理 (14)生产与运输 (15)机加工 (15)机器维修 (16)组装 (16)生产进度安排 (16)保修与质量 (17)运输,仓储与分销 (18)原材料采购和仓储 (18)信息技术 (19)生产管理 (20)人力资源管理 (20)劳动力供给 (21)工资待遇 (23)财务、资产与会计 (24)股息 (25)投资 (25)借贷-中期贷款 (25)借贷-透支 (25)借贷-无抵押贷款 (25)固定资产-不动产 (26)固定资产-机器 (26)会计惯例 (27)保险政策 (28)第三部分《管理报告》 (29)资源的合理利用 (29)原材料 (30)GMC国际企业管理挑战赛人力资源管理 (31)代理商和经销商 (31)信息技术 (32)产品 (32)财务帐目 (34)一般管理费用 (34)利润和亏损 (36)资产负债表 (37)现金流量 (39)商业信息 (40)经济信息 (41)第四部分《决策单》 (41)管理参数附1 (42)决策参量表附2 (49)管理参数经济信息表格1-----------------------------------------------------------------------------------------42表格2-----------------------------------------------------------------------------------42市场营销成本表格3---------------43国内市场代理商、北美自由贸易区分销商、国际互联网分销商成本表格4--------------------------------------------------------------------------------43国际互联网费用表格5-----------------------------------------------------------------------------------43制造活动参数表格6-----------------------------------------------------------------------------------------43维修成本表格7-----------------------------------------43各种轮班制下每季度每台机器的最大工作时间表格8-----------------------------------------------------------------------44不合格产品的废品价格表格9-----------------------------------------------------------------------------------44保修服务费用表格 10-----------------------------------------------------------------------------------44生产成本表格 11--------------------------------------------------------------------------------44集装箱容量表格 12-----------------------------------------------------------------------------------44运输成本表格 13--------------------------------------------------------------------------------44仓储与采购表格 14--------------------------------------------45平均季度储备、贷款及投资的计算方法表格 15-----------------------------------------------------------------------45人力资源部门成本表格 16-----------------------45每个生产工人每季度的最大工作时数及相应的报酬补贴表格 17--------------------------------------------------------------45最低工作时数和最低工资表格 18-----------------------------------------------------------------------------------46机器成本表格 19-----------------------------------------------------------46从银行透支上限的计算方法表格 20-----------------------------------------------------------------------------------46财务参数表格 21-----------------------------------------------------------------47库存产品和原材料价值表格 22-----------------------------------------------------------------------------------47保险方案表格 23--------------------------------------------------------------------47债务人付款时间指标表格 24--------------------------------------------------------------48向债权人支付的时间安排表格 25-----------------------------------------------------------------------------------48网站容量GMC国际企业管理挑战赛第一部分 前言国际企业管理挑战赛,即战略和管理模拟系统是以真实经营环境为基础,参赛各队分别代表不同的虚拟公司,在相同的经营环境中彼此竞争。
比赛将使用一个精密的综合性计算机模型模拟每个公司内各个部门之间的相互作用、各公司间的竞争关系以及经济背景与环境。
各参赛队所面临的任务是经营一家虚构的公司,并把它当作真实的公司进行管理。
本手册旨在介绍如何参加比赛、竞赛的具体方法、各队必须做的工作、这家虚构的公司是如何运作的以及如何与其它各队所管理的公司发生联系的。
本手册共分为四个部分:∙ 前言∙ 经营环境说明公司的内部职能以及公司与市场之间的相互作用∙《管理报告》说明计算机输出的模拟结果∙《决策单》说明参赛队如何填写决策单以便输入计算机由模拟系统进行评定你所管理的公司是一个有机的整体,尽管总体结构很容易理解,但其运作方式却有许多微妙之处。
手册的第二部分描述了你所经营公司的结构。
其着眼点放在营销,生产、人力资源管理和财务四个主要管理职能上,说明这些职能如何发挥作用并重点解释它们之间的相互联系。
比赛的主要目的之一是说明这些相互联系,并且证明在管理公司的过程中,职能部门间的良好配合是取得成功的关键,而这靠的是团队精神、良好的组织工作和有效的沟通。
各参赛队自行设计其组织结构分派队员职位,以便履行公司的高层管理职责。
至于如何自我组织则由各队自己来决定。
可以按照职能进行组织,每人负责管理企业的一个方面。
也可以设立一个董事长,把每个人的意见归纳起来以形成一个总体看法。
还可以成立一个更松散的委员会,让每人都成为其中的一员。
比赛对参赛队所使用的辅助工具没有任何限制。
假如你想设计自己的“电子数据表”模型,手册第三部分的详细定义会对你有所帮助。
您对公司的决策控制,通过下列两个文件完成操作的:(A)由模拟系统形成的季度《管理报告》,展示你的公司在刚刚过去的一段时间的绩效。
(B)《决策单》用以记录您对您所管理的公司所做的有关下一个时期如何经营的决策,以便输入模拟系统。
为了使您确切地知道经营状况,有必要对公司的运作方式进行详细的描述,这使手册看GMC国际企业管理挑战赛上去非常复杂,不过,这一活动的总体结构却比较简单。
要想获胜,你只需设法使您的公司具备最佳前景即可。
这样,在比赛结束时,你的股票价格将是最高的。
这意味着要确定一个战略,指导您去实现这一长期目标。
制定了战略之后,还要制定使其得以实施的经营策略(如果发现你的公司有了麻烦,可以对公司战略进行修正,使之能够实现)。
在营销方面,可先对市场进行通盘考虑,然后据此制定市场营销计划。
这样做必然意味着要预测出可能达到的销售额。
在生产方面,只要拥有必需的劳动力和设备资源,就能生产出这一数量的产品并运往销售地点。
人力资源管理部门必须关注这一点,因为市场营销部门与生产部门所作出的决策,将会影响到工人的收入和工作状况。
最后,财务部门应始终整个过程进行审查,以确保公司盈利并拥有足够的财力开展经营活动。
综上所述,参赛队需要以团队精神为基础,相互协作,寻求一个不仅能适应公司短期策略,而且能适应更为长期的战略的最佳公司决策。
为了使您对公司的情况有一个初步了解,您会得到一份包括赛前最近一个时期经营情况在内的简要公司资料及造成这一状况的决策内容(《公司历史》)。
在阅读这本手册时,用这些资料来说明所讨论的问题是很有用的。
由于所有公司都是从同一起点开始的,因此所有参赛队得到的资料(《公司历史》)是完全相同的。
手册的第三部分将对《管理报告》的内容进行详细描述。
比赛中的各种关系,有许多是用纯数字表示的(如财务信息),其余的则属于那类即使在现实生活中也无法确切得出的关系(如:你可能得到多少定单,设备养护的效果如何,等等)。
为了有效地进行经营,在比赛进程中,有必要对这些不确定的因素进行探索和估计,测试其敏感性并且了解其对你公司经营情况的影响。
在制定某些具体决策时,这类分析将有助您对可能发生的事情得出一个大概的结论。
对情况作出判断并决定了所要采取的行动之后,请按照比赛时间表的规定填好第一份《决策单》,送交组委会计算机进行处理。
然后,你将收到下一份《管理报告》,告诉你所做的决策对公司的经营产生了什么结果。