转炉炉渣喷溅的机理及预防措施共17页
转炉喷溅产生的原因及预防措施
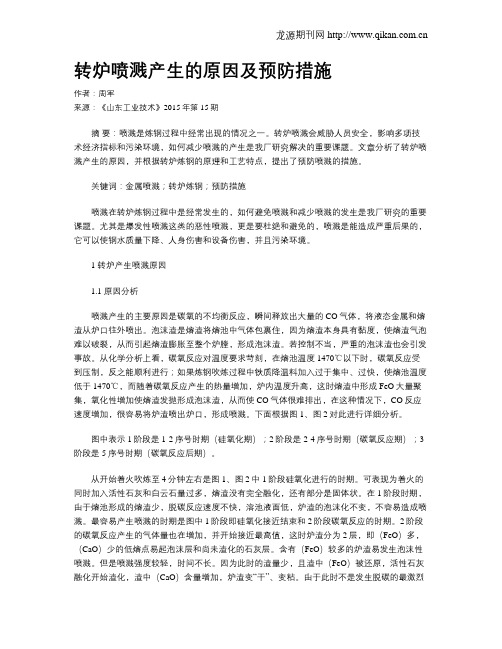
转炉喷溅产生的原因及预防措施作者:周军来源:《山东工业技术》2015年第15期摘要:喷溅是炼钢过程中经常出现的情况之一。
转炉喷溅会威胁人员安全,影响多项技术经济指标和污染环境,如何减少喷溅的产生是我厂研究解决的重要课题。
文章分析了转炉喷溅产生的原因,并根据转炉炼钢的原理和工艺特点,提出了预防喷溅的措施。
关键词:金属喷溅;转炉炼钢;预防措施喷溅在转炉炼钢过程中是经常发生的,如何避免喷溅和减少喷溅的发生是我厂研究的重要课题。
尤其是爆发性喷溅这类的恶性喷溅,更是要杜绝和避免的,喷溅是能造成严重后果的,它可以使钢水质量下降、人身伤害和设备伤害,并且污染环境。
1 转炉产生喷溅原因1.1 原因分析喷溅产生的主要原因是碳氧的不均衡反应,瞬间释放出大量的CO气体,将液态金属和熔渣从炉口往外喷出。
泡沫渣是熔渣将熔池中气体包裹住,因为熔渣本身具有黏度,使熔渣气泡难以破裂,从而引起熔渣膨胀至整个炉膛,形成泡沫渣。
若控制不当,严重的泡沫渣也会引发事故。
从化学分析上看,碳氧反应对温度要求苛刻,在熔池温度1470℃以下时,碳氧反应受到压制,反之能顺利进行;如果炼钢吹炼过程中铁质降温料加入过于集中、过快,使熔池温度低于1470℃,而随着碳氧反应产生的热量增加,炉内温度升高,这时熔渣中形成FeO大量聚集,氧化性增加使熔渣发抛形成泡沫渣,从而使CO气体很难排出,在这种情况下,CO反应速度增加,很容易将炉渣喷出炉口,形成喷溅。
下面根据图1、图2对此进行详细分析。
图中表示1阶段是1-2序号时期(硅氧化期);2阶段是2-4序号时期(碳氧反应期);3阶段是5序号时期(碳氧反应后期)。
从开始着火吹炼至4分钟左右是图1、图2中1阶段硅氧化进行的时期。
可表现为着火的同时加入活性石灰和白云石量过多,熔渣没有完全融化,还有部分是固体状。
在1阶段时期,由于熔池形成的熔渣少,脱碳反应速度不快,溶池液面低,炉渣的泡沫化不变,不容易造成喷溅。
最容易产生喷溅的时期是图中1阶段即硅氧化接近结束和2阶段碳氧反应的时期。
浅析转炉喷溅产生的原因
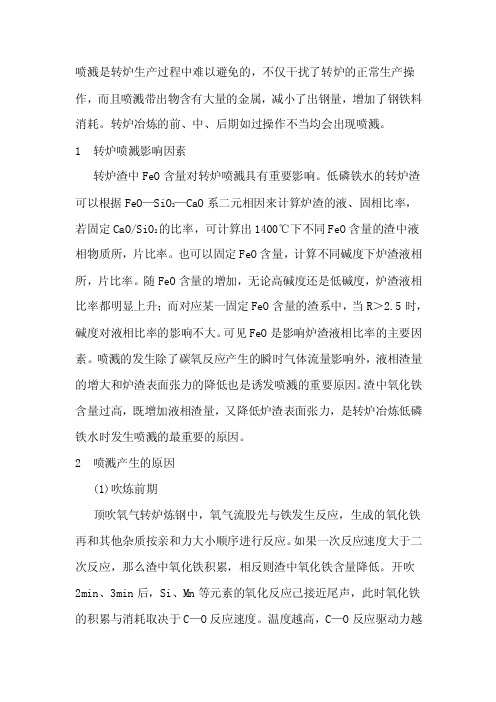
喷溅是转炉生产过程中难以避免的,不仅干扰了转炉的正常生产操作,而且喷溅带出物含有大量的金属,减小了出钢量,增加了钢铁料消耗。
转炉冶炼的前、中、后期如过操作不当均会出现喷溅。
1 转炉喷溅影响因素转炉渣中FeO含量对转炉喷溅具有重要影响。
低磷铁水的转炉渣可以根据FeO—SiO2—CaO系二元相因来计算炉渣的液、固相比率,若固定CaO/SiO2的比率,可计算出1400℃下不同FeO含量的渣中液相物质所,片比率。
也可以固定FeO含量,计算不同碱度下炉渣液相所,片比率。
随FeO含量的增加,无论高碱度还是低碱度,炉渣液相比率都明显上升;而对应某一固定FeO含量的渣系中,当R>2.5时,碱度对液相比率的影响不大。
可见FeO是影响炉渣液相比率的主要因素。
喷溅的发生除了碳氧反应产生的瞬时气体流量影响外,液相渣量的增大和炉渣表面张力的降低也是诱发喷溅的重要原因。
渣中氧化铁含量过高,既增加液相渣量,又降低炉渣表面张力,是转炉冶炼低磷铁水时发生喷溅的最重要的原因。
2 喷溅产生的原因(1)吹炼前期顶吹氧气转炉炼钢中,氧气流股先与铁发生反应,生成的氧化铁再和其他杂质按亲和力大小顺序进行反应。
如果一次反应速度大于二次反应,那么渣中氧化铁积累,相反则渣中氧化铁含量降低。
开吹2min、3min后,Si、Mn等元素的氧化反应己接近尾声,此时氧化铁的积累与消耗取决于C—O反应速度。
温度越高,C—O反应驱动力越大,渣中氧化铁不易累计,反之则易累计。
因此,前期温度偏低,C —O反应滞后,渣中积累氧化铁。
当熔池温度升高到C—O反应所需要的温度时,C开始强烈氧化,渣中积累的(FeO)给C—O反应提供了一个很大的附加供氧量,瞬间反应产生的气体流量猛增,而此时炉渣的碱度较低,很容易造成前期低温喷溅。
枪位较低时,氧气流股穿透深,具有较强的搅拌作用,生成的(FeO)容易与其他液相元素发生反应,且深吹流股在熔池内部产生气泡,形成了大量的C—O反应的成核点,促进了前期C—O反应的进行,因此,枪位较低时不利于渣中FeO的积累。
转炉炼钢喷溅产生的原因分析和预防措施标准版本

文件编号:RHD-QB-K1677 (解决方案范本系列)编辑:XXXXXX查核:XXXXXX时间:XXXXXX转炉炼钢喷溅产生的原因分析和预防措施标准版本转炉炼钢喷溅产生的原因分析和预防措施标准版本操作指导:该解决方案文件为日常单位或公司为保证的工作、生产能够安全稳定地有效运转而制定的,并由相关人员在办理业务或操作时进行更好的判断与管理。
,其中条款可根据自己现实基础上调整,请仔细浏览后进行编辑与保存。
一、产生原因转炉常见喷溅主要分为爆发性喷溅、泡沫性喷溅和金属喷溅。
1 爆发性喷溅产生的原因熔池内碳氧反应不均衡发展,瞬时产生大量的CO气体,这是发生爆发性喷溅的根本原因。
碳氧反应:[C]+(FeO)={CO}+[Fe]是吸热反应,反应速度受熔池碳含量、渣中(TFe)含量和温度的共同影响。
由于操作上的原因,熔池骤然受到冷却,抑制了正在激烈进行的碳氧反应;供人的氧气生成了大量(FeO)并聚积;当熔池温度再度升高到一定程度(一般在1470℃以上),(FeO)聚积到20%以上时,碳氧反应重新以更猛烈的速度进行,瞬间排出大量具有巨大能量的CO气体从炉口排出,同时还挟带着一定量的钢水和熔渣,形成了较大的喷溅。
在熔渣氧化性过高,熔池温度突然冷却后又升高的情况下,就有可能发生爆发性喷溅。
2 泡沫性喷溅产生的原因除了碳的氧化不均衡外,还有如炉容比、渣量、炉渣泡沫化程度等因素也会引起喷溅。
在铁水Si、P含量较高时,渣中SiO2、P2O5含量也高,渣量较大,再加上熔渣中TFe含量较高,其表面张力降低,阻碍着CO气体通畅排出,因而渣层膨胀增厚,严重时能够上涨到炉口。
此时只要有一个不大的推力,熔渣就会从炉口喷出,熔渣所夹带的金属液也随之而出,形成喷溅。
同时泡沫渣对熔池液面覆盖良好,对气体的排出有阻碍作用。
严重的泡沫渣可能导致炉口溢渣。
显然,渣量大时,比较容易产生喷溅;炉容比大的转炉,炉膛空间也大,相对而言发生较大喷溅的可能性小些。
转炉钢包喷溅机理及安全预防对策
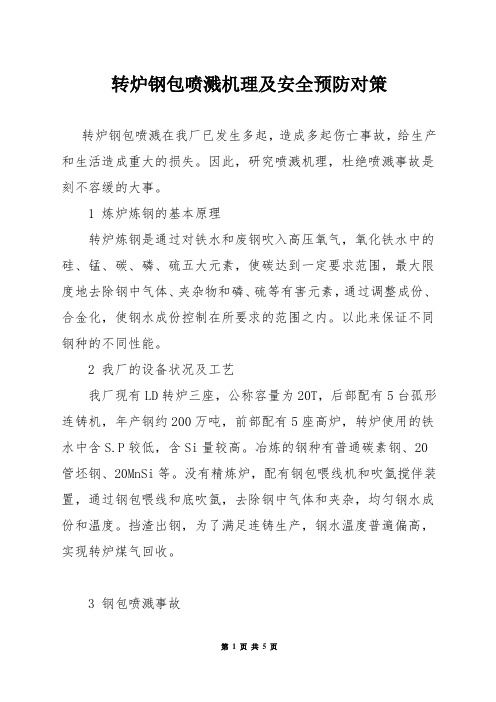
转炉钢包喷溅机理及安全预防对策转炉钢包喷溅在我厂已发生多起,造成多起伤亡事故,给生产和生活造成重大的损失。
因此,研究喷溅机理,杜绝喷溅事故是刻不容缓的大事。
1 炼炉炼钢的基本原理转炉炼钢是通过对铁水和废钢吹入高压氧气,氧化铁水中的硅、锰、碳、磷、硫五大元素,使碳达到一定要求范围,最大限度地去除钢中气体、夹杂物和磷、硫等有害元素,通过调整成份、合金化,使钢水成份控制在所要求的范围之内。
以此来保证不同钢种的不同性能。
2 我厂的设备状况及工艺我厂现有LD转炉三座,公称容量为20T,后部配有5台孤形连铸机,年产钢约200万吨,前部配有5座高炉,转炉使用的铁水中含S.P较低,含Si量较高。
冶炼的钢种有普通碳素钢、20管坯钢、20MnSi等。
没有精炼炉,配有钢包喂线机和吹氩搅伴装置,通过钢包喂线和底吹氩,去除钢中气体和夹杂,均匀钢水成份和温度。
挡渣出钢,为了满足连铸生产,钢水温度普遍偏高,实现转炉煤气回收。
3 钢包喷溅事故我厂自连铸投产以来,多次发生钢包喷溅事故,导致死亡和群伤事故多起,特别是4#连铸机1998年4月15日发生钢包喷溅事故,死亡3人,烧伤7人,经济损失惨重,为此,集团公司和有关部门非常重视,成立了事故调查组,专访了有关部门,查对了有关资料。
本炉钢的冶炼经过如下:3点零9分,5#炉开始冶炼第19炉钢,炉号为5—11307,兑入铁水23t,废钢2.3t,吹炼12min,提枪倒炉,测温1737℃,班长指挥出钢,该包包号为81#,包令41次,红包,钢包底部有渣壳,使用合金流槽出钢,先加合金,然后加入SiC6袋,约60kg,补加硅铝钡两锹约5kg,两锹锰铁,半锹硅铁,锰铁加入约180kg,硅铁加入约85kg,快出完钢时加挡渣球,出完钢后,吹氩,时间为2分零6秒,底吹,吹氩压力0.3Mpa,翻花,约2分钟后取样,取样时仍然在吹氩,成份没回来就指挥吊车将钢包吊起到连铸准备开机,平台温度1659℃,冶炼钢种为Q235炉前取样成份为:C0.10% Mn0.49% Si0.17% P0.021% S0.033%复验C0.09% Mn0.51% Si0.18% P0.021% S0.032%本炉钢吊运连铸平台镇静十分钟,连铸准备开浇,由于大包水口打不开。
炼钢转炉喷溅事故的原因和预防措施

炼钢转炉喷溅事故的原因和预防措施前言转炉是炼钢过程中的一种重要设备,主要用于高炉生铁除渣、除硫和合金化等工艺。
但在使用过程中,经常发生喷溅事故,给生产带来严重的威胁。
本文将从原因和预防措施两个方面来分析和探讨炼钢转炉喷溅事故。
喷溅事故的原因1. 转炉操作不规范炼钢转炉具有高温高压等特点,操作不规范会导致炉料溢出、热态反应失控等现象的发生。
比如说在加入炉料时没有及时开放炉门,炉料积压过多,导致热态反应失控,引起喷溅事故。
2. 转炉内壁破损炼钢转炉的内壁经常受到高温高压的冲击,长期使用后容易出现裂缝、缺陷等问题。
尤其在高炉煤气、生铁、镁砂等各种物料的强冲击下更容易造成内壁破损,从而引起钢水、炉料等的喷溅。
3. 炉料粒度不均炉料的粒度对喷溅事故的发生也有一定影响。
如果炉料的粒度不均匀,松紧程度不同,就会导致在加入新料时出现热态反应失控或部分炉料被抛出转炉的情况。
从而引起钢水、热风、渣等物料的喷溅。
喷溅事故的预防措施1. 做好安全防护在炼钢转炉使用过程中,必须严格执行操作规程和操作规范,保持注意力高度集中,特别是在加料、出钢水、冶炼合金等重要步骤时。
同时应做好防护措施,如安装可调式盖罩、定期检测转炉内壁等。
2. 均匀加料为防止粉尘喷溅,要求将物料加入转炉时应注意保持物料的均匀与抗溅性能。
机加工料和原料的混合、充堆、热敏年脆等理化状态的因素都会对加料的均匀性起到重要影响。
3. 定期检修定期检查和维护炼钢转炉的内壁和相关设备,以确保其完好无损,可正常运行。
同时,在检查转炉内壁之前,还应先通风、放空、冷却、卸料等步骤,确保操作人员的安全。
结论炼钢转炉是冶金生产线中重要的设备,发生喷溅事故有可能给生产带来不良影响。
为了保证炼钢生产的连续性和稳定性,必须制定出有效的技术维修方案和操作规程,以保证转炉的正常运转。
在生产中,我们还要加强对喷溅事故的风险评估和瓶颈监控,及时发现隐患并采取措施消除,以确保生产线的整体安全性和稳定性。
炼钢转炉喷溅现象的成因分析和预防措施
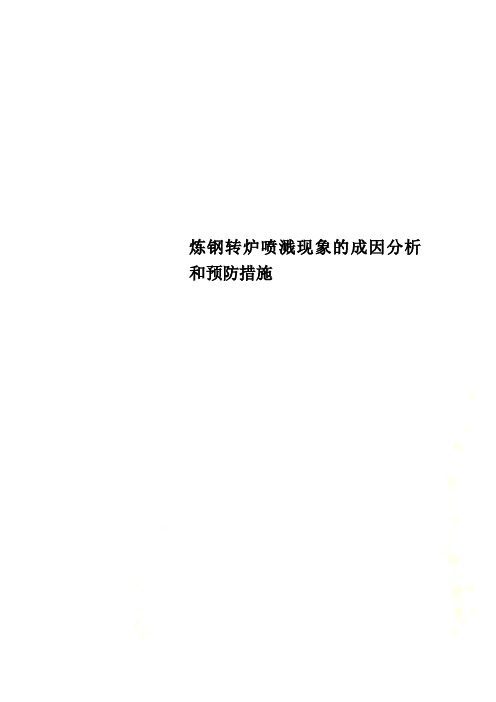
炼钢转炉喷溅现象的成因分析和预防措施河北冶金高级技工学校毕业论文2007冶金炼钢专业作者:刘紫昊题目:炼钢转炉喷溅现象的成因分析和预防措施概述:喷溅是顶吹转炉吹炼过程中经常见到的一种现象,喷溅造渣中必然的过程,生产当中喷溅的控制,减少金属损失是转炉生产的一项重要课题。
本文通过接近现实的笔触,试述了这一课题。
并且将喷溅的形式做了分类,从生产实践的角度归纳了一些控制转炉喷溅的方法。
关键词:转炉、喷溅、危害、控制正文:1、喷溅产生原因转炉常见喷溅主要分为爆发性喷溅、泡沫性喷溅和金属喷溅。
1.1、爆发性喷溅产生的原因熔池内碳氧反应不均衡发展,瞬时产生大量的CO气体,这是发生爆发性喷溅的根本原因。
碳氧反应:[C]+(FeO)={CO}+[Fe]是吸热反应,反应速度受熔池碳含量、渣中(TFe)含量和温度的共同影响。
由于操作上的原因,熔池骤然受到冷却,抑制了正在激烈进行的碳氧反应;供人的氧气生成了大量(FeO)并聚积;当熔池温度再度升高到一定程度(一般在1470℃以上),(FeO)聚积到20%以上时,碳氧反应重新以更猛烈的速度进行,瞬间排出大量具有巨大能量的CO气体从炉口排出,同时还挟带着一定量的钢水和熔渣,形成了较大的喷溅。
在熔渣氧化性过高,熔池温度突然冷却后又升高的情况下,就有可能发生爆发性喷溅。
1.2、泡沫性喷溅产生的原因除了碳的氧化不均衡外,还有如炉容比、渣量、炉渣泡沫化程度等因素也会引起喷溅。
在铁水Si、P含量较高时,渣中SiO2、P2O5含量也高,渣量较大,再加上熔渣中TFe含量较高,其表面张力降低,阻碍着CO气体通畅排出,因而渣层膨胀增厚,严重时能够上涨到炉口。
此时只要有一个不大的推力,熔渣就会从炉口喷出,熔渣所夹带的金属液也随之而出,形成喷溅。
同时泡沫渣对熔池液面覆盖良好,对气体的排出有阻碍作用。
严重的泡沫渣可能导致炉口溢渣。
显然,渣量大时,比较容易产生喷溅;炉容比大的转炉,炉膛空间也大,相对而言发生较大喷溅的可能性小些。
浅析转炉喷溅的形成原因
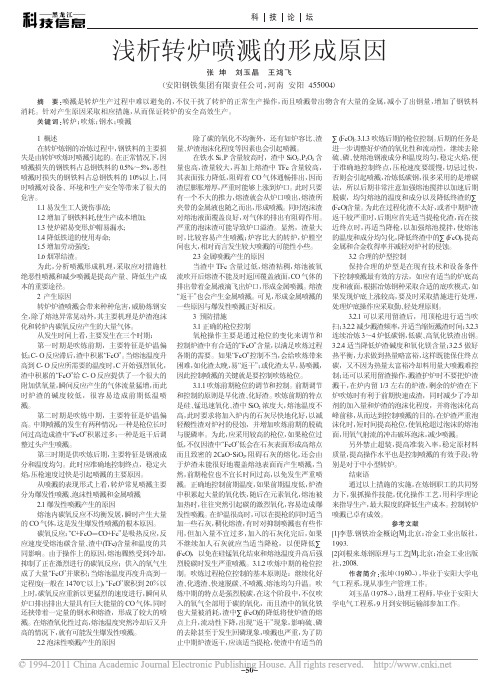
渣中积累的“FeO”给 C- O 反应提供了一个很大的 因此控制喷溅的关键就是要控制吹炼枪位。
制;还可以采用留渣操作,溅渣护炉时不要把炉渣
附加供氧量,瞬间反应产生的气体流量猛增,而此
3.1.1 吹炼前期枪位的调节和控制。前期调节 溅干,在炉内留 1/3 左右的炉渣,剩余的炉渣在下
时炉渣的碱度较低,很容易造成前期低温喷 和控制的原则是早化渣、化好渣。吹炼前期的特点 炉吹炼时有利于前期快速成渣,同时减少了冷却
分和温度均匀。此时应准确地控制终点,稳定火 于炉渣未能很好地覆盖熔池表面而产生喷溅,当 别是对于中小型转炉。
焰,压枪速度过快是引起喷溅的主要原因。
然,前期枪位也不常见喷溅主要 溅。正确地控制前期温度,如果前期温度低,炉渣
通过以上措施的实施,在炼钢职工的共同努
1.3 使炉裙易变形,炉帽易漏水;
严重的泡沫渣可能导致炉口溢渣。显然,渣量大 近终点时,再适当降枪,以加强熔池搅拌,使熔池
1.4 降低铁道的使用寿命;
时,比较容易产生喷溅;炉容比大的转炉,炉膛空 的温度和成分均匀化,降低终渣中的∑(FeO),提高
1.5 增加劳动强度;
间也大,相对而言发生较大喷溅的可能性小些。 金属和合金收得率并减轻对炉衬的侵蚀。
科技论坛
浅析转炉喷溅的形成原因
张 坤 刘玉晶 王鸿飞 (安阳钢铁集团有限责任公司,河南 安阳 455004)
摘 要:喷溅是转炉生产过程中难以避免的,不仅干扰了转炉的正常生产操作,而且喷溅带出物含有大量的金属,减小了出钢量,增加了钢铁料 消耗。针对产生原因采取相应措施,从而保证转炉的安全高效生产。
关 键 词 :转炉;吹炼;钢水;喷溅
同影响。由于操作上的原因,熔池骤然受到冷却, (FeO),以免在硅锰氧化结束和熔池温度升高后强 [2]刘根来.炼钢原理与工艺[M].北京:冶金工业出版
转炉炉渣喷溅的机理及预防措施

图3:喷溅临界(FeO)含量与[C]关系
2.易发生转炉炉渣喷溅的几种情况与分析
2.1炉容比过小的转炉,易发生炉渣喷溅
一般认为,在供氧强度为3.0~4.0(Nm3/t· min)的 情况下,中小型转炉(<100t)的炉容比应为0.80~ 0.90[4],当炉容比V/T≤0.80的都易发生炉渣喷溅(见 表1)。
2.2铁水[Si]高,易在冶炼前中期 发生低温炉渣喷溅
2.2.1随铁水[Si]提高,渣 量大大增加
表1:铁水[Si]提高相应增加的渣量
铁水[Si]提高 /% 渣量增加
0.1
0.2
0.3
/kg/t 10.2 20.5 30.7
图4:CaO-SiO2-FeO渣系的表面张力 ——Kowai._____ Kazakevitch 初期炉渣成分区
图1: 炉渣碱度和炉渣易起泡程度的关系
在1500℃左右,当R≥1.27 就会析出C2S,使炉渣表观粘 度增加。导致炉渣中的气体 被较长时间阻滞在渣层之中, 炉渣泡沫性增大。但碱度过 高会使炉渣进入熔点比C2S 低的C3S(2070℃)占优势的 区域,反而使炉渣粘度下降, 使泡沫性减小。而转炉开吹 4~6分时,炉渣碱度提高 到1.7左右,所以炉渣的泡 沫性达到了最大值。
3.转炉炉渣喷溅的防止措施
3.1避免转炉超装,确保炉容比Vw/T≥0.80。 3.2一旦发现“喷溅” 前兆,采取相应压喷措施
3.2.1采用专门的“压喷剂”或石灰石、生白云石、轻烧白云 石,进行压喷操作:宝钢、马钢采用专门“压喷剂”的实践表 明,使用量1~2kg/t钢,压渣成功率90%以上。我国北方某钢厂, 采用后一种炉料进行压喷操作,喷溅率相对下降70%。 3.2.2采用调节氧枪枪位进行压喷操作 在冶炼前中期在熔池温度偏低的情况下,若发现喷溅预兆时, 一般适当降枪进行压喷操作;在冶炼中后期熔池温度偏高情况 下,若发现喷溅预兆时,可适情提枪压喷。 3.2.3提高底部供气强度,防止喷溅发生
浅谈转炉炉渣喷溅的机理与预防措施
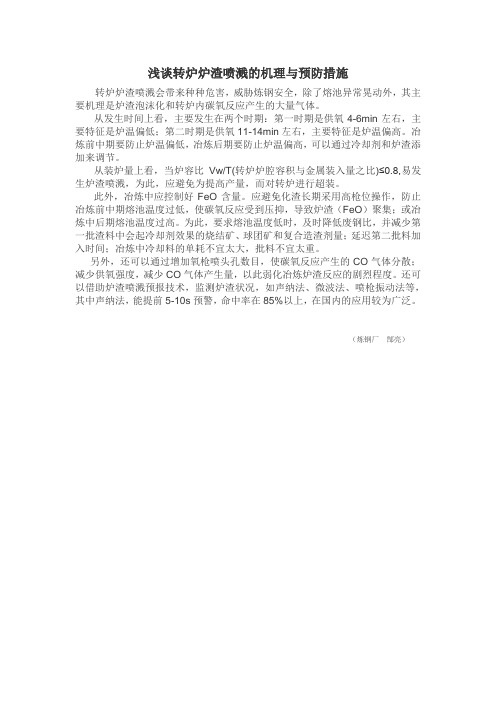
浅谈转炉炉渣喷溅的机理与预防措施
转炉炉渣喷溅会带来种种危害,威胁炼钢安全,除了熔池异常晃动外,其主要机理是炉渣泡沫化和转炉内碳氧反应产生的大量气体。
从发生时间上看,主要发生在两个时期:第一时期是供氧4-6min左右,主要特征是炉温偏低;第二时期是供氧11-14min左右,主要特征是炉温偏高。
冶炼前中期要防止炉温偏低,冶炼后期要防止炉温偏高,可以通过冷却剂和炉渣添加来调节。
从装炉量上看,当炉容比Vw/T(转炉炉腔容积与金属装入量之比)≤0.8,易发生炉渣喷溅,为此,应避免为提高产量,而对转炉进行超装。
此外,冶炼中应控制好FeO含量。
应避免化渣长期采用高枪位操作,防止冶炼前中期熔池温度过低,使碳氧反应受到压抑,导致炉渣(FeO)聚集;或冶炼中后期熔池温度过高。
为此,要求熔池温度低时,及时降低废钢比,并减少第一批渣料中会起冷却剂效果的烧结矿、球团矿和复合造渣剂量;延迟第二批料加入时间;冶炼中冷却料的单耗不宜太大,批料不宜太重。
另外,还可以通过增加氧枪喷头孔数目,使碳氧反应产生的CO气体分散;减少供氧强度,减少CO气体产生量,以此弱化冶炼炉渣反应的剧烈程度。
还可以借助炉渣喷溅预报技术,监测炉渣状况,如声纳法、微波法、喷枪振动法等,其中声纳法,能提前5-10s预警,命中率在85%以上,在国内的应用较为广泛。
(炼钢厂郜亮)。
转炉炉渣喷溅的机理及预防措施
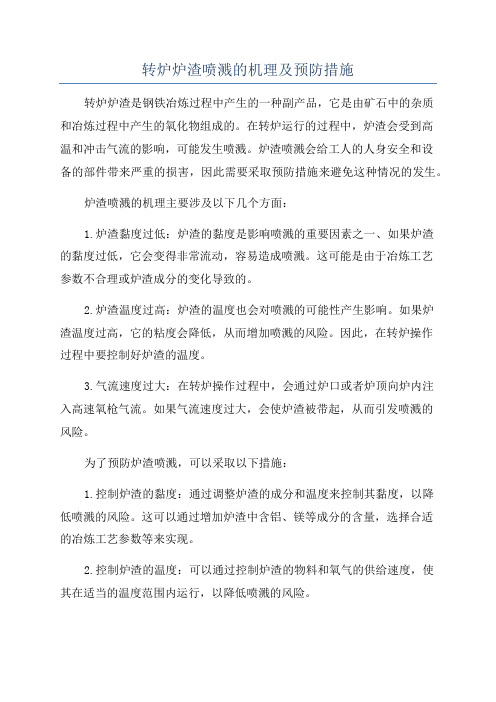
转炉炉渣喷溅的机理及预防措施转炉炉渣是钢铁冶炼过程中产生的一种副产品,它是由矿石中的杂质和冶炼过程中产生的氧化物组成的。
在转炉运行的过程中,炉渣会受到高温和冲击气流的影响,可能发生喷溅。
炉渣喷溅会给工人的人身安全和设备的部件带来严重的损害,因此需要采取预防措施来避免这种情况的发生。
炉渣喷溅的机理主要涉及以下几个方面:1.炉渣黏度过低:炉渣的黏度是影响喷溅的重要因素之一、如果炉渣的黏度过低,它会变得非常流动,容易造成喷溅。
这可能是由于冶炼工艺参数不合理或炉渣成分的变化导致的。
2.炉渣温度过高:炉渣的温度也会对喷溅的可能性产生影响。
如果炉渣温度过高,它的粘度会降低,从而增加喷溅的风险。
因此,在转炉操作过程中要控制好炉渣的温度。
3.气流速度过大:在转炉操作过程中,会通过炉口或者炉顶向炉内注入高速氧枪气流。
如果气流速度过大,会使炉渣被带起,从而引发喷溅的风险。
为了预防炉渣喷溅,可以采取以下措施:1.控制炉渣的黏度:通过调整炉渣的成分和温度来控制其黏度,以降低喷溅的风险。
这可以通过增加炉渣中含铝、镁等成分的含量,选择合适的冶炼工艺参数等来实现。
2.控制炉渣的温度:可以通过控制炉渣的物料和氧气的供给速度,使其在适当的温度范围内运行,以降低喷溅的风险。
3.控制气流的速度:应合理设计炉内氧气的供应方式和参数,以控制气流速度,减少炉渣被带起的可能性。
这可以通过增加氧气的喷吹角度、减小喷嘴口径等方法来实现。
4.定期检查和维护设备:定期对转炉设备进行检查和维护,确保设备正常运行。
及时更换磨损严重的喷嘴和其它设备,以保证其正常运行,减少炉渣喷溅的机会。
5.加强操作员的培训和防护用具的配备:提高操作员的安全意识,加强对炉渣喷溅风险的认识和预防措施的培训。
同时,应配备好防护用具,如防火服、护目镜等,以保护操作人员的安全。
总之,炉渣喷溅是钢铁冶炼过程中一种常见但危险的现象,可以通过控制炉渣的黏度、温度和气流速度等措施来预防。
转炉炼钢喷溅产生的原因分析和预防措施
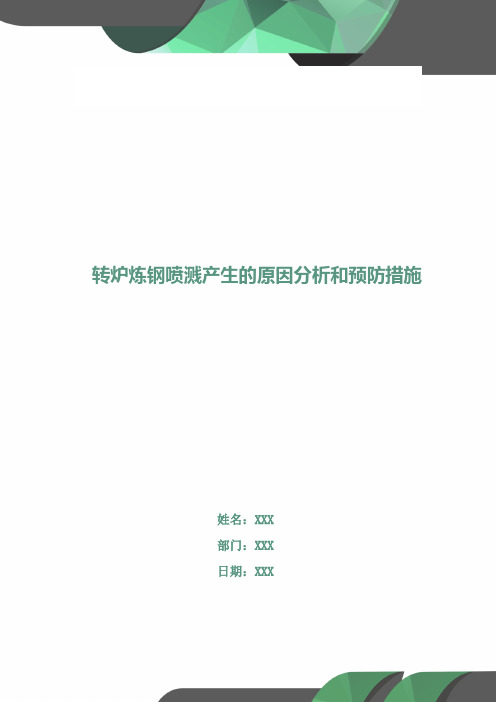
转炉炼钢喷溅产生的原因分析和预防措施姓名:XXX部门:XXX日期:XXX转炉炼钢喷溅产生的原因分析和预防措施一、产生原因转炉常见喷溅主要分为爆发性喷溅、泡沫性喷溅和金属喷溅。
1爆发性喷溅产生的原因熔池内碳氧反应不均衡发展,瞬时产生大量的CO气体,这是发生爆发性喷溅的根本原因。
碳氧反应:[C]+(FeO)={CO}+[Fe]是吸热反应,反应速度受熔池碳含量、渣中(TFe)含量和温度的共同影响。
由于操作上的原因,熔池骤然受到冷却,抑制了正在激烈进行的碳氧反应;供人的氧气生成了大量(FeO)并聚积;当熔池温度再度升高到一定程度(一般在1470℃以上),(FeO)聚积到20%以上时,碳氧反应重新以更猛烈的速度进行,瞬间排出大量具有巨大能量的CO气体从炉口排出,同时还挟带着一定量的钢水和熔渣,形成了较大的喷溅。
在熔渣氧化性过高,熔池温度突然冷却后又升高的情况下,就有可能发生爆发性喷溅。
2泡沫性喷溅产生的原因除了碳的氧化不均衡外,还有如炉容比、渣量、炉渣泡沫化程度等因素也会引起喷溅。
在铁水Si、P含量较高时,渣中SiO2、P2O5含量也高,渣量较大,再加上熔渣中TFe含量较高,其表面张力降低,阻碍着CO气体通畅排出,因而渣层膨胀增厚,严重时能够上涨到炉口。
此时只要有一个不大的推力,熔渣就会从炉口喷出,熔渣所夹带的金属液也随之而出,形成喷溅。
同时泡沫渣对熔池液面覆盖良好,对气体的排出有阻碍作用。
严重的泡沫渣可能导致炉口溢渣。
显然,渣量大时,比较容易产生喷溅;第 2 页共 6 页炉容比大的转炉,炉膛空间也大,相对而言发生较大喷溅的可能性小些。
3金属喷溅产生的原因当渣中TFe含量过低,熔渣粘稠,熔池被氧流吹开后熔渣不能及时返回覆盖液面,CO气体的排出带着金属液滴飞出炉口,形成金属喷溅。
熔渣“返干”也会产生金属喷溅。
可见,形成金属喷溅的一些原因与爆发性喷溅正好相反。
二、预防措施1正确的枪位控制在某种程度上复吹转炉炼钢的氧枪操作主要是通过枪位的变化来调节和控制炉渣中有合适的(FeO)含量,以满足吹炼过程各期的需要。
转炉喷溅产生的原因及预防措施
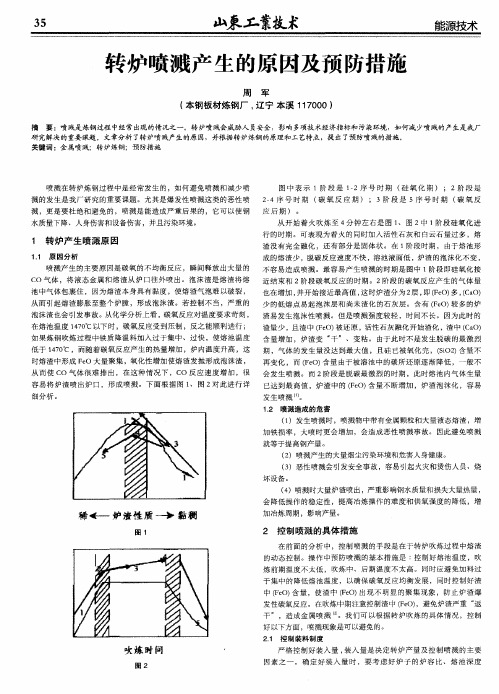
得 了极 高 的蠕 变 断裂 强度 ,S u p e r 3 0 4 H 钢许 用应 力在 6 0 0 ℃- 6 5 0 ℃ 较T P 3 4 7 H钢 高 2 2 0 % 以上。该钢 的组织 和力学性 能稳 定 ,高温抗 氧 化 性能 突出 ,且价格 便宜 ,是超 超临界 锅炉过 热器 、再 热器 热段 用
中的Z , ( F e O) 含 量过 低 , 熔渣 变 “ 干 , 熔渣 不 能覆盖 住钢 液表 面上 ,
强 烈 的氧 气 流股 带 着 钢液 蹦 出炉 口 ,形 成 金属 性 喷 溅 。这 时应 及
时提 高枪 位和 适 当的 减少供 氧 强度 ,增 加渣 中 ∑( F e O)含量 ,使 熔
成 恶性 喷 溅 。这 时应 及 时 降低 枪 位和 适 当 的减 少 供氧 强 度 ,减 少 力 的保证 。
渣中 Z ( F e O ) 含 量 ,使 熔渣 变干 。 因此 ,必须 正确 适 当的调 整枪 位 和 供 氧强度 。
2 . 3 控制好造渣制度 参考文献 :
[ 1 ]王 世 杰 . 《 企业科技与发展》 [ M ] . 2 0 0 9 .
造 渣是 炼钢 的一项 重要操 作 ,前期采 用小 批量 、多批次 的加 入 方法 ,以保证 活性 石灰 融化 ,快速 形成熔 渣 ,并 控制 熔渣活 度在 合
能 比T P 3 0 0 系列 奥 氏体 钢 都更 为优 良,所 以 ,当 T P 3 4 7 H钢乃 至新
型 奥 氏体耐 热钢 S u p e r 3 0 4 H钢不 能满 足 向火侧抗 烟气 腐蚀和 内壁 抗
蒸 汽 氧 化 的工 况 下 ,应 选 用 HR 3 C钢 。
转炉高温液体渣喷溅事故的危害分析与防范措施
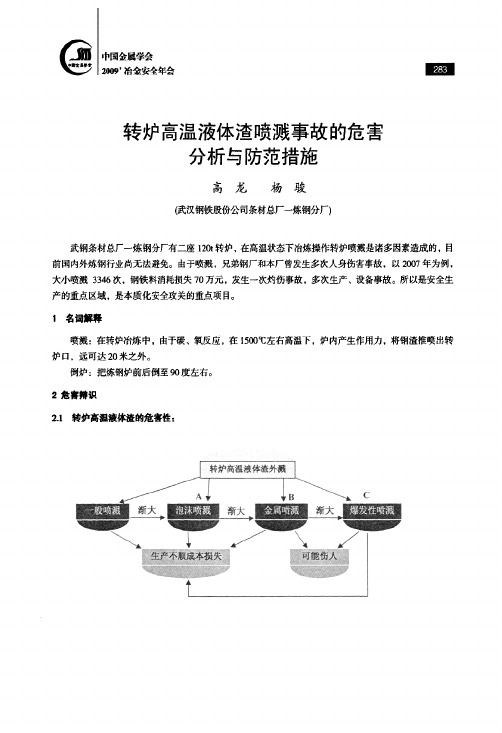
.一r州P钾孵端硝《辩F矾毋掣耶啊滞帮碍碍礴熟席髓§‰。 通过现场分析观察,按躁冶炼时间与持位控倒对姝探作.
正常情况下不会产生喷藏,但是转炉零位发生变化时或渣 性干、稀时就会产生喷藏。
““蛐黼黼黼黼幽‰∞mⅫ幽汹蹦妇幽“
验证结论:氧樯艳位控制不合适是要因,需要攻美;~‘、。。.
验证六
工艺操作不台理
本厂转炉工艺是成静工艺,虽然与先进转炉 比设宵副枪测温取样,需用人工进行测温取样, 但是,操作工均在转炉停止吹炼后。按‘取样安全 操作规程》到炉前铡温取样。
丰13
l 3‘14 14’15 15、16 16
Q195、MIO、M8等低碳钢
1280、1300
>】300
>1320
(3)优化护炉模式,保持炉形正常炉形正常时过程温度控制足关键作用,通过研究,确定了标准 ①冶炼操作:加料之前垫石灰,冶炼自口期就配镁,碳温协调早化渣 ②溅渣护炉操作_|仓位控制台理分三段进行溅渣倒炉角度适中.保证溅渣量不干不稀。 ③补炉操作勤补薄唼,护好渣线与耳轴。
\\圈素
位级\
1 2 3
石灰量A(Kg)
400(1) 450(2) 500(3)
精炼渣量B(Kg)
150(1) 200(2) 250(3)
萤石量C(Kg)
\
80(1) 100(2) 120(3)
不考虑交互效应,按L9(33)表安排并进行试验,制定试验计划且每一次试验选取16炉作为样本, 成分温度合格率见下表: 表15:正交试验条件及试验结果表
2月15日共调查跟踪 460炉,按现场观察与计 算机上数据统计,摇炉 速度均在标准速度范围 内。(四个电机0.85~ 0.75转/分)
WO-1
08.2.25
转炉喷溅机理及预防措施
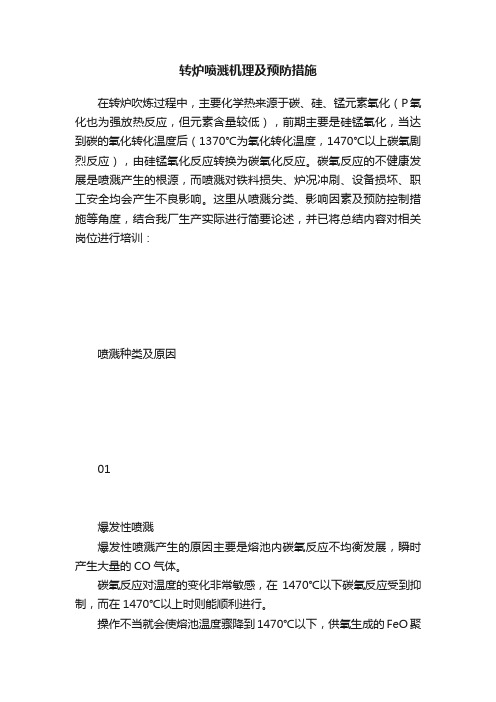
转炉喷溅机理及预防措施在转炉吹炼过程中,主要化学热来源于碳、硅、锰元素氧化(P氧化也为强放热反应,但元素含量较低),前期主要是硅锰氧化,当达到碳的氧化转化温度后(1370℃为氧化转化温度,1470℃以上碳氧剧烈反应),由硅锰氧化反应转换为碳氧化反应。
碳氧反应的不健康发展是喷溅产生的根源,而喷溅对铁料损失、炉况冲刷、设备损坏、职工安全均会产生不良影响。
这里从喷溅分类、影响因素及预防控制措施等角度,结合我厂生产实际进行简要论述,并已将总结内容对相关岗位进行培训:喷溅种类及原因01爆发性喷溅爆发性喷溅产生的原因主要是熔池内碳氧反应不均衡发展,瞬时产生大量的CO气体。
碳氧反应对温度的变化非常敏感,在1470℃以下碳氧反应受到抑制,而在1470℃以上时则能顺利进行。
操作不当就会使熔池温度骤降到1470℃以下,供氧生成的FeO聚积,而后随着温度升高至1470℃以上,则会发生激烈的碳氧反应,从而造成喷溅。
02泡沫渣喷溅泡沫性喷溅产生的原因主要是炉渣泡沫化严重时,使渣层变厚,阻碍CO气体顺畅排出而造成。
除了碳氧反应不均衡外,还与炉容比的大小、渣量多少及熔渣泡沫化程度等有关。
03金属喷溅金属喷溅产生的原因主要是渣中TFe过低,熔渣流动性不好,氧气流直接接触金属液面,碳氧反应生成的CO气体排出时带动金属液滴飞出炉外而形成。
金属喷溅也往往与操作不当有很大关系,如:长时间枪位过低、二批料加入过早、炉渣未化透就急于降枪脱碳等,都有可能产生金属喷溅。
影响喷溅的因素1、炉容比:炉容比V/T≤0.80的都易发生炉渣喷溅。
2、当生铁块加入过多时,转炉炼钢出现熔池温度低、石灰不易熔化、炉口溢渣、金属消耗增加、脱磷困难、终点命中率降低等问题。
(一般要求生铁加入量≤总装入量的10%)3、熔池温度低,金属的粘度加大,废钢熔化困难。
熔池温度降低100℃,金属的粘度增加0.18 Pa ·s。
金属粘度高降低了熔池传热、传质速度。
4、枪位控制:(1)、枪位较高时(即软吹),有利于渣中氧化铁积累,尤其当加入了过多轻废钢或生铁块,前期熔池温度偏低时。
转炉喷溅产生的原因及预防措施
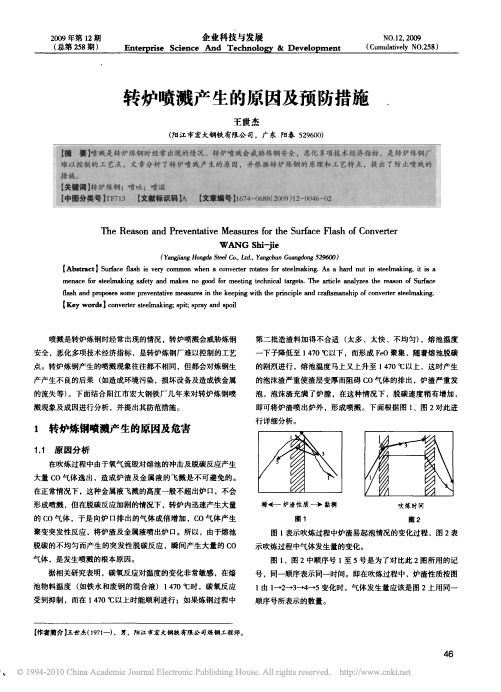
3吞汤 的金属 , 小喷溅将损失约 1. 左右的金属 2%
(2 ) 磷 的去除
发生大 喷溅 时 , 炉 内渣量减少 , 影 响吹炼过程 中硫 &
. 26
. 27
防止 下料 摘卡料 , 避 免石 灰在 熔 池 中结 沱
尽可 能做 到不 留渣 & 不 留钢操 作
留渣 & 留钢操作对兑铁水有影响, 会导致产生大喷爆发性
[K ey w r山1 onver r st o e t eelm 砍i # vit pr a d spoi n :, a n r l
喷溅是转炉炼钢 时经 常出现的情况 , 转 炉喷溅会 威胁炼 钢 安全 , 恶化 多项技术经济指 标 , 是转炉炼钢 厂难以控 制的工艺 点 转炉炼钢产生 的喷溅现象往往都不相的质.
废钢 块度 合适 , 减 少轻 型废 钢 (如压 块 & 散料 废 钢等 ) 做到优 质废 钢 (如机 械零部 件 & 切 头 & 废 锭 & 汤 道等 ) 另外 , 废钢 比例的大 小也影 响到
与轻 型废钢合理搭 配使用
溅的一个因素
吹炼前 期的低温滋 渣等现 象 , 所 以废钢单 耗合理 也是控 制喷
示吹炼过程 中气体发生量的变化
图 1 & 图 2 中顺序号 I 至 5 号是 为了对 比此 2 图所用的记
气体 , 是发生喷溅的根本原 因 据相 关研究表明 , 碳氧反应对温度的变化非常敏感 , 在熔 池物料温度 (如铁水 和废 钢的混合液 ) 1470 % 时 , 碳 氧反应 受到抑制 , 而在 1 4 0 % 以上时能顺利进行 ; 如果炼 钢过程 中 7
期 表现 为点火 同时加人石 灰过 多且未化好 , 有部分渣料还是
转炉炉渣喷溅的机理及预防措施

转炉炉渣喷溅的机理及预防措施
铸锭转炉炉渣喷溅的机理及预防措施
一、转炉炉渣喷溅的机理
1、转炉内温差大:转炉正常生产过程中,最高温点和最低温点较大,
温差较大,温度变化大,内坩埚上有自然对流,温差过大可能会影响
炉渣的表面张力,从而导致炉渣喷溅。
2、渣层出现不同层次:由于熔炉温升太快,会形成多层炉渣,其中有
的渣层分析品种比较稳定,部分渣层会有熔点比较低的物质。
随着熔
炉温度的升高,这部分比较低熔点的渣层开始发生了变化,导致熔炉
渣易于喷溅。
3、炉壁出现裂缝:由于转炉熔炉温升太快,可能使炉壁外表面产生张力,比内壁张力大,炉体发热量太大可能也会导致炉壁出现裂缝,炉
渣通过裂缝喷溅出来了。
二、转炉炉渣喷溅的预防措施
1、降低熔炉温度:通过降低熔炉温度,均匀更好的冷却熔炉的内壁,
防止熔炉温度差大,从而避免熔炉渣喷溅。
2、控制加料速度:让加料过程比较缓慢,既可以节约原料,又能防止
熔炉温度太快升温,有利于控制熔炉温差大导致熔炉渣喷溅。
3、配置球墨铸铁制品:当合金在熔化过程中,其表面受到足够的冷却,就可以降低温度过快造成的炉渣喷溅现象。
4、检查炉壁:定期检查炉壁,及时更换不合格炉壁,及时修复炉壁的破损部位,避免熔炉温度高造成的炉渣喷溅。
5、加装保护板:加装熔炉保护板,可以在正常加料过程中,延缓温度变化过快,从而防止熔炉渣受到温度激起喷溅。
转炉炼钢喷溅产生的原因分析和预防措施正式样本

文件编号:TP-AR-L1677In Terms Of Organization Management, It Is Necessary To Form A Certain Guiding And Planning Executable Plan, So As To Help Decision-Makers To Carry Out Better Production And Management From Multiple Perspectives.(示范文本)编制:_______________审核:_______________单位:_______________转炉炼钢喷溅产生的原因分析和预防措施正式样本转炉炼钢喷溅产生的原因分析和预防措施正式样本使用注意:该解决方案资料可用在组织/机构/单位管理上,形成一定的具有指导性,规划性的可执行计划,从而实现多角度地帮助决策人员进行更好的生产与管理。
材料内容可根据实际情况作相应修改,请在使用时认真阅读。
一、产生原因转炉常见喷溅主要分为爆发性喷溅、泡沫性喷溅和金属喷溅。
1 爆发性喷溅产生的原因熔池内碳氧反应不均衡发展,瞬时产生大量的CO气体,这是发生爆发性喷溅的根本原因。
碳氧反应:[C]+(FeO)={CO}+[Fe]是吸热反应,反应速度受熔池碳含量、渣中(TFe)含量和温度的共同影响。
由于操作上的原因,熔池骤然受到冷却,抑制了正在激烈进行的碳氧反应;供人的氧气生成了大量(FeO)并聚积;当熔池温度再度升高到一定程度(一般在1470℃以上),(FeO)聚积到20%以上时,碳氧反应重新以更猛烈的速度进行,瞬间排出大量具有巨大能量的CO气体从炉口排出,同时还挟带着一定量的钢水和熔渣,形成了较大的喷溅。
在熔渣氧化性过高,熔池温度突然冷却后又升高的情况下,就有可能发生爆发性喷溅。
2 泡沫性喷溅产生的原因除了碳的氧化不均衡外,还有如炉容比、渣量、炉渣泡沫化程度等因素也会引起喷溅。
喷溅产生的原因
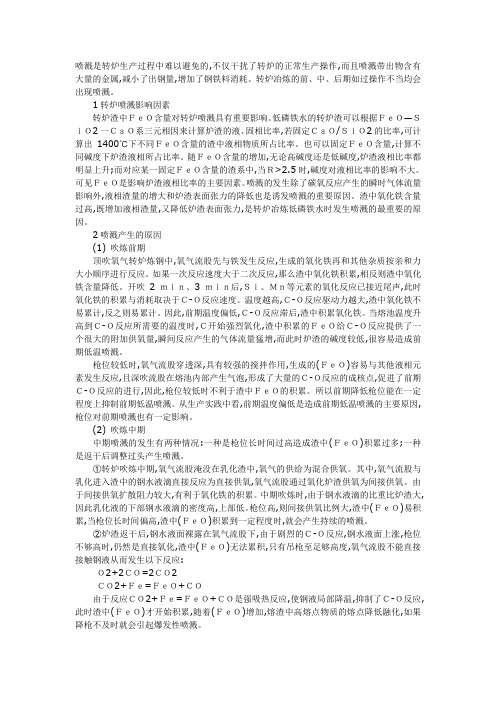
喷溅是转炉生产过程中难以避免的,不仅干扰了转炉的正常生产操作,而且喷溅带出物含有大量的金属,减小了出钢量,增加了钢铁料消耗。
转炉冶炼的前、中、后期如过操作不当均会出现喷溅。
1转炉喷溅影响因素转炉渣中FeO含量对转炉喷溅具有重要影响。
低磷铁水的转炉渣可以根据FeO—SiO2一CaO系三元相因来计算炉渣的液、固相比率,若固定CaO/SiO2的比率,可计算出1400℃下不同FeO含量的渣中液相物质所占比率。
也可以固定FeO含量,计算不同碱度下炉渣液相所占比率。
随FeO含量的增加,无论高碱度还是低碱度,炉渣液相比率都明显上升;而对应某一固定FeO含量的渣系中,当R>2.5时,碱度对液相比率的影响不大。
可见FeO是影响炉渣液相比率的主要因素。
喷溅的发生除了碳氧反应产生的瞬时气体流量影响外,液相渣量的增大和炉渣表面张力的降低也是诱发喷溅的重要原因。
渣中氧化铁含量过高,既增加液相渣量,又降低炉渣表面张力,是转炉冶炼低磷铁水时发生喷溅的最重要的原因。
2喷溅产生的原因(1) 吹炼前期顶吹氧气转炉炼钢中,氧气流股先与铁发生反应,生成的氧化铁再和其他杂质按亲和力大小顺序进行反应。
如果一次反应速度大于二次反应,那么渣中氧化铁积累,相反则渣中氧化铁含量降低。
开吹2 min、3 min后,Si、Mn等元素的氧化反应已接近尾声,此时氧化铁的积累与消耗取决于C-O反应速度。
温度越高,C-O反应驱动力越大,渣中氧化铁不易累计,反之则易累计。
因此,前期温度偏低,C-O反应滞后,渣中积累氧化铁。
当熔池温度升高到C-O反应所需要的温度时,C开始强烈氧化,渣中积累的FeO给C-O反应提供了一个很大的附加供氧量,瞬间反应产生的气体流量猛增,而此时炉渣的碱度较低,很容易造成前期低温喷溅。
枪位较低时,氧气流股穿透深,具有较强的搅拌作用,生成的(FeO)容易与其他液相元素发生反应,且深吹流股在熔池内部产生气泡,形成了大量的C-O反应的成核点,促进了前期C-O反应的进行,因此,枪位较低时不利于渣中FeO的积累。
喷溅及预防
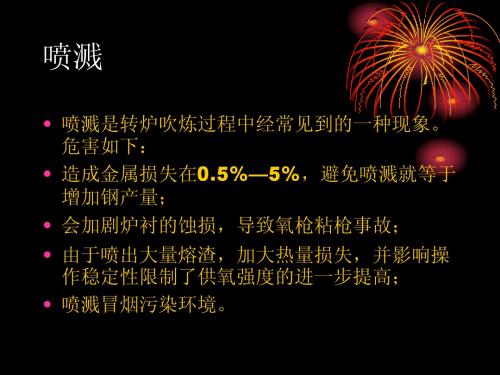
泡沫性喷溅
• 泡沫性喷溅产生的原因 • 有时各炉吹炼情况差不多,碳的氧化速度也不相上下。但有的炉 次大喷,有的就没有,说明除了碳的氧化不均衡外还有其它原因 引起喷溅,如炉容比的大小、渣量多少、炉渣泡沫化程度等。 • 炉内有大量泡沫渣存在,说明熔渣中滞留了大量的气体。 • 铁水Si和P较高时,渣中SiO2、P2O5含量也高,渣量大,再加 上熔渣中TFe含量较高,熔渣表面张力降低,熔渣大泡,阻碍着 CO气体通畅排出,当渣面上涨接近炉口时只要有一个不大的推 力,熔渣就会从炉口喷出,熔渣所夹带的金属液也随之而出,形 成喷溅。泡沫渣对熔池液面覆盖良好,对气体排出有阻碍作用, 因此严重的泡沫渣就是造成泡沫性喷溅的主要原因。 • 渣量大比较容易产生喷溅;炉容比大的转炉,气体排出通畅,发 生较大喷溅的可能性小些。 • 泡沫性喷溅渣中TFe较高,往往伴随着爆发性喷溅。
• ②渣返干后,钢水液面裸露在氧气流股下,由于剧烈 剧烈的C—O反应,钢水液面上涨,枪位不够高时,仍 然是直接氧化,渣中(FeO)无法累积,只有吊枪至足 够高度,氧气流股不能直接接触钢液从而发生以下反 应: • O2+2CO= 2CO2 • CO2+ Fe= FO+CO • 由于反应CO2+ Fe= FeO + CO是强吸热反应, 使钢液局部降温,抑制了C—O反应,此时渣中(FeO) 才开始积累,随着(FeO)增加,熔渣中高熔点物质的 熔点降低融化,如果降枪不及时就会引起爆发性喷溅。
泡沫性喷溅的预防和处理
• 根据泡沫性喷溅产生的原因,预防措施有: • (1)控制好铁水中的si、p含量, • (2)控制好TFe含量不出现积聚,以免熔渣过分发泡。
• 当渣中TFe含量过低,析出高熔点化合物,熔渣变得粘稠,熔池 被氧流吹开后熔渣不能及时覆盖液面,由于碳氧反应生成CO气 体的排出,带动金属液滴飞出炉口,形成金属喷溅。飞溅的金属 液滴粘附在氧枪喷头上,严重恶化了喷头冷却条件,同时铁与铜 形成低熔点共晶,降低了喷头熔点导致喷头损坏。熔渣“返干” 就会产生金属喷溅。可见,形成金属喷溅的原因与爆发性喷溅正 好相反。 • 当长时间低枪位操作、二批料加入过早、炉渣未化透就急于降枪 脱碳以及炉内液面上涨而没有及时调整枪位,都有可能产生金属 喷溅。
- 1、下载文档前请自行甄别文档内容的完整性,平台不提供额外的编辑、内容补充、找答案等附加服务。
- 2、"仅部分预览"的文档,不可在线预览部分如存在完整性等问题,可反馈申请退款(可完整预览的文档不适用该条件!)。
- 3、如文档侵犯您的权益,请联系客服反馈,我们会尽快为您处理(人工客服工作时间:9:00-18:30)。
41、学问是异常珍贵的东西,从任何源泉吸 收都不可耻。——阿卜·日·法拉兹
42、只有在人群中间,才能认识自 己。——德国
43、重复别人所说的话,只需要教育; 而要挑战别人所说的话,则需要头脑。—— 玛丽·佩蒂博恩·普尔
44、卓越的人一ቤተ መጻሕፍቲ ባይዱ优点是:在不利与艰 难的遭遇里百折不饶。——贝多芬
转炉炉渣喷溅的机理及预防措施
56、极端的法规,就是极端的不公。 ——西 塞罗 57、法律一旦成为人们的需要,人们 就不再 配享受 自由了 。—— 毕达哥 拉斯 58、法律规定的惩罚不是为了私人的 利益, 而是为 了公共 的利益 ;一部 分靠有 害的强 制,一 部分靠 榜样的 效力。 ——格 老秀斯 59、假如没有法律他们会更快乐的话 ,那么 法律作 为一件 无用之 物自己 就会消 灭。— —洛克
45、自己的饭量自己知道。——苏联