炉温曲线教材
炉温曲线设定
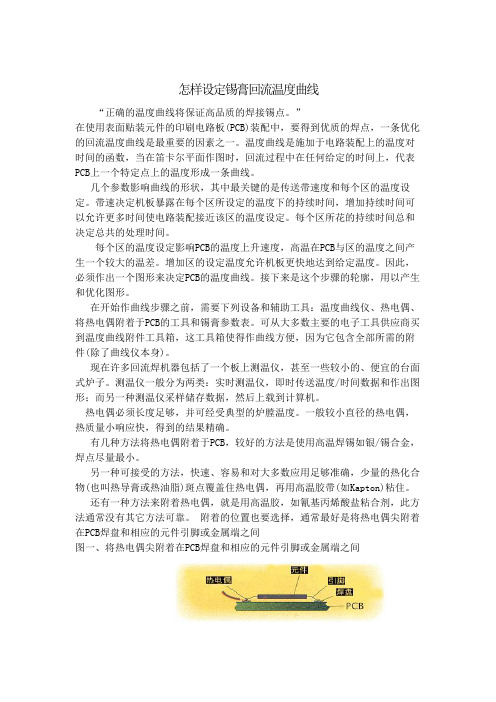
怎样设定锡膏回流温度曲线“正确的温度曲线将保证高品质的焊接锡点。
”在使用表面贴装元件的印刷电路板(PCB)装配中,要得到优质的焊点,一条优化的回流温度曲线是最重要的因素之一。
温度曲线是施加于电路装配上的温度对时间的函数,当在笛卡尔平面作图时,回流过程中在任何给定的时间上,代表PCB上一个特定点上的温度形成一条曲线。
几个参数影响曲线的形状,其中最关键的是传送带速度和每个区的温度设定。
带速决定机板暴露在每个区所设定的温度下的持续时间,增加持续时间可以允许更多时间使电路装配接近该区的温度设定。
每个区所花的持续时间总和决定总共的处理时间。
每个区的温度设定影响PCB的温度上升速度,高温在PCB与区的温度之间产生一个较大的温差。
增加区的设定温度允许机板更快地达到给定温度。
因此,必须作出一个图形来决定PCB的温度曲线。
接下来是这个步骤的轮廓,用以产生和优化图形。
在开始作曲线步骤之前,需要下列设备和辅助工具:温度曲线仪、热电偶、将热电偶附着于PCB的工具和锡膏参数表。
可从大多数主要的电子工具供应商买到温度曲线附件工具箱,这工具箱使得作曲线方便,因为它包含全部所需的附件(除了曲线仪本身)。
现在许多回流焊机器包括了一个板上测温仪,甚至一些较小的、便宜的台面式炉子。
测温仪一般分为两类:实时测温仪,即时传送温度/时间数据和作出图形;而另一种测温仪采样储存数据,然后上载到计算机。
热电偶必须长度足够,并可经受典型的炉膛温度。
一般较小直径的热电偶,热质量小响应快,得到的结果精确。
有几种方法将热电偶附着于PCB,较好的方法是使用高温焊锡如银/锡合金,焊点尽量最小。
另一种可接受的方法,快速、容易和对大多数应用足够准确,少量的热化合物(也叫热导膏或热油脂)斑点覆盖住热电偶,再用高温胶带(如Kapton)粘住。
还有一种方法来附着热电偶,就是用高温胶,如氰基丙烯酸盐粘合剂,此方法通常没有其它方法可靠。
附着的位置也要选择,通常最好是将热电偶尖附着在PCB焊盘和相应的元件引脚或金属端之间图一、将热电偶尖附着在PCB焊盘和相应的元件引脚或金属端之间锡膏特性参数表也是必要的,其包含的信息对温度曲线是至关重要的,如:所希望的温度曲线持续时间、锡膏活性温度、合金熔点和所希望的回流最高温度。
加热炉与热处理炉温度曲线的测试和优化PPT课件

通道数: 7或14通道; 采样周期: 1次/12秒- 1次/8小时; 数据记录仪工作条件:温度1400℃下 6 小时,在300℃
低温下工作可以达到30小时。
“黑匣子”开发过程中的热态测试
黑匣子的应用领域
金属加热和热处理 回流焊和波峰焊、钎焊 表面涂装和固化、不粘锅 陶瓷烧成 玻璃退火 食品烘焙
测试方法
在物料上打测温孔,将电偶热端紧紧插入物 料测温孔中,冷端的正负极与记录仪的正负 极一一对应相连接,同时记录下记录仪接口 的通道数所代表的物料测温孔的位置。
记录仪随物料一同进入炉内,经过加热、热 处理或烧成后,从炉子出口拿出。
出炉后,待箱体温度下降后,取出记录仪, 通过与计算机相连,将记录仪中保存的数据 传输到计算机中,用excel进行数据处理,绘 制出物料升温曲线和炉温沿炉长方向的变化 曲线。
黑匣子应用解决的问题
加热炉投产验收 加热工艺数字化 热处理工艺数字化 加热温度和段面温差、钢坯长度方向的温差 氧化烧损 水管黑印 数学模型参数提取、数学模型验证等
加热温度曲线的分析
钢坯是放置在实底床上。钢坯的中心温度和下表面 温度是基本一致的。
钢坯加热到750℃时,钢坯的相变区因为相变吸热升 温速率变小。
钢坯出炉温度1320℃,出炉钢坯上中温差8℃, 上 下温差为13℃。
加热168分钟后钢坯温度达到1300℃,此时上下温差 30℃。
钢坯的加热温度过高是引起穿管孔洞的原因之一。 加热温度过高的原因的炉顶热电偶的安装位置不合 适,没有真正反映炉内温度水平,测试后对炉温热 电偶的位置进行了调整,使测得温度真正反映炉内 温度。
炉温曲线图 精品
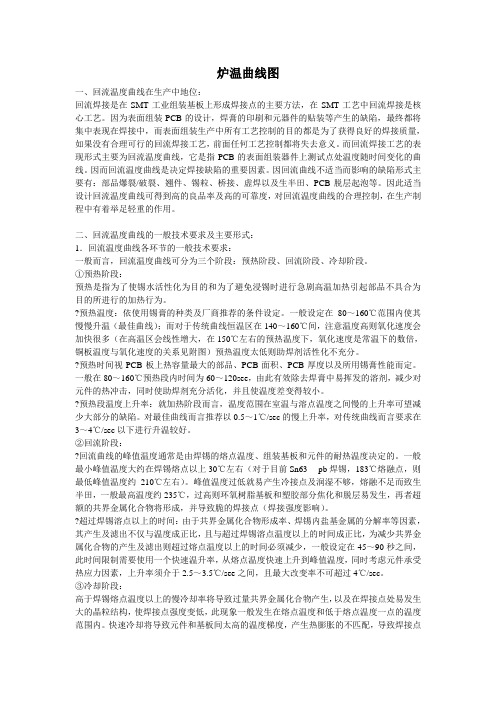
炉温曲线图一、回流温度曲线在生产中地位:回流焊接是在SMT工业组装基板上形成焊接点的主要方法,在SMT工艺中回流焊接是核心工艺。
因为表面组装PCB的设计,焊膏的印刷和元器件的贴装等产生的缺陷,最终都将集中表现在焊接中,而表面组装生产中所有工艺控制的目的都是为了获得良好的焊接质量,如果没有合理可行的回流焊接工艺,前面任何工艺控制都将失去意义。
而回流焊接工艺的表现形式主要为回流温度曲线,它是指PCB的表面组装器件上测试点处温度随时间变化的曲线。
因而回流温度曲线是决定焊接缺陷的重要因素。
因回流曲线不适当而影响的缺陷形式主要有:部品爆裂/破裂、翘件、锡粒、桥接、虚焊以及生半田、PCB脱层起泡等。
因此适当设计回流温度曲线可得到高的良品率及高的可靠度,对回流温度曲线的合理控制,在生产制程中有着举足轻重的作用。
二、回流温度曲线的一般技术要求及主要形式:1.回流温度曲线各环节的一般技术要求:一般而言,回流温度曲线可分为三个阶段:预热阶段、回流阶段、冷却阶段。
①预热阶段:预热是指为了使锡水活性化为目的和为了避免浸锡时进行急剧高温加热引起部品不具合为目的所进行的加热行为。
?预热温度:依使用锡膏的种类及厂商推荐的条件设定。
一般设定在80~160℃范围内使其慢慢升温(最佳曲线);而对于传统曲线恒温区在140~160℃间,注意温度高则氧化速度会加快很多(在高温区会线性增大,在150℃左右的预热温度下,氧化速度是常温下的数倍,铜板温度与氧化速度的关系见附图)预热温度太低则助焊剂活性化不充分。
?预热时间视PCB板上热容量最大的部品、PCB面积、PCB厚度以及所用锡膏性能而定。
一般在80~160℃预热段内时间为60~120see,由此有效除去焊膏中易挥发的溶剂,减少对元件的热冲击,同时使助焊剂充分活化,并且使温度差变得较小。
?预热段温度上升率:就加热阶段而言,温度范围在室温与溶点温度之间慢的上升率可望减少大部分的缺陷。
对最佳曲线而言推荐以0.5~1℃/sec的慢上升率,对传统曲线而言要求在3~4℃/sec以下进行升温较好。
低温锡膏的炉温曲线

低温锡膏的炉温曲线
低温锡膏是一种常用于电子元器件表面贴装的焊接材料,其熔点较低,通常在100℃左右,因此需要在较低的温度下进行热处理。
炉温曲线
是指在热处理过程中,炉温随时间的变化曲线。
下面将介绍低温锡膏
的炉温曲线。
低温锡膏的炉温曲线通常分为三个阶段:预热阶段、焊接阶段和冷却
阶段。
预热阶段:在这个阶段,炉温逐渐升高,以达到锡膏的熔点。
预热的
目的是使锡膏中的挥发性成分挥发掉,以避免在焊接过程中产生气泡
和其他缺陷。
预热温度通常在50℃到100℃之间,时间为5分钟到
10分钟。
焊接阶段:在预热阶段结束后,炉温会进一步升高,以达到焊接温度。
焊接温度通常在100℃到150℃之间,时间为1分钟到3分钟。
在这
个阶段,锡膏会熔化,与电子元器件表面形成焊点。
焊接完成后,需
要保持焊点温度一段时间,以确保焊点充分固化。
冷却阶段:在焊接完成后,炉温会逐渐降低,以使焊点冷却。
冷却温
度通常在50℃到100℃之间,时间为5分钟到10分钟。
在这个阶段,
需要避免焊点过快冷却,以避免产生应力和其他缺陷。
总的来说,低温锡膏的炉温曲线需要根据具体的焊接材料和电子元器件进行调整。
在热处理过程中,需要注意控制炉温和时间,以确保焊点质量和电子元器件的安全性。
回焊炉温度曲线设定方法

回焊炉温度曲线设定方法(总5页)--本页仅作为文档封面,使用时请直接删除即可----内页可以根据需求调整合适字体及大小--回焊炉温度曲线设定方法(一)“正确的温度曲线将保证高质量的焊接锡点。
”约翰 . 希罗与约翰 . 马尔波尤夫 ( 美 )在使用表面贴装组件的印刷电路板 (PCB) 装配中,要得到优质的焊点,一条优化的回流温度曲线是最重要的因素之一。
温度曲线是施加于电路装配上的温度对时间的函数,当在笛卡尔平面作图时,回流过程中在任何给定的时间上,代表 PCB 上一个特定点上的温度形成一条曲线。
几个参数影响曲线的形状,其中最关键的是传送带速度和每个区的温度设定。
带速决定机板暴露在每个区所设定的温度下的持续时间,增加持续时间可以允许更多时间使电路装配接近该区的温度设定。
每个区所花的持续时间总和决定总共的处理时间。
每个区的温度设定影响 PCB 的温度上升速度,高温在 PCB 与区的温度之间产生一个较大的温差。
增加区的设定温度允许机板更快地达到给定温度。
因此,必须作出一个图形来决定 PCB 的温度曲线。
接下来是这个步骤的轮廓,用以产生和优化图形。
在开始作曲线步骤之前,需要下列设备和辅助工具:温度曲线仪、热电偶、将热电偶附着于 PCB 的工具和锡膏参数表。
可从大多数主要的电子工具供货商买到温度曲线附件工具箱,这工具箱使得作曲线方便,因为它包含全部所需的附件 ( 除了曲线仪本身 ) 。
现在许多回流焊机器包括了一个板上测温仪,甚至一些较小的、便宜的台面式炉子。
测温仪一般分为两类:实时测温仪,实时传送温度 / 时间数据和作出图形;而另一种测温仪采样储存数据,然后上载到计算机。
热电偶必须长度足够,并可经受典型的炉膛温度。
一般较小直径的热电偶,热质量小响应快,得到的结果精确。
有几种方法将热电偶附着于 PCB ,较好的方法是使用高温焊锡如银 / 锡合金,焊点尽量最小。
另一种可接受的方法,快速、容易和对大多数应用足够准确,少量的热化合物 ( 也叫热导膏或热油脂 ) 斑点覆盖住热电偶,再用高温胶带 ( 如 Kapton) 粘住。
炉温曲线图

炉温曲线图一、回流温度曲线在生产中地位:回流焊接是在SMT工业组装基板上形成焊接点的主要方法,在SMT工艺中回流焊接是核心工艺。
因为表面组装PCB的设计,焊膏的印刷和元器件的贴装等产生的缺陷,最终都将集中表现在焊接中,而表面组装生产中所有工艺控制的目的都是为了获得良好的焊接质量,如果没有合理可行的回流焊接工艺,前面任何工艺控制都将失去意义。
而回流焊接工艺的表现形式主要为回流温度曲线,它是指PCB的表面组装器件上测试点处温度随时间变化的曲线。
因而回流温度曲线是决定焊接缺陷的重要因素。
因回流曲线不适当而影响的缺陷形式主要有:部品爆裂/破裂、翘件、锡粒、桥接、虚焊以及生半田、PCB脱层起泡等。
因此适当设计回流温度曲线可得到高的良品率及高的可靠度,对回流温度曲线的合理控制,在生产制程中有着举足轻重的作用。
二、回流温度曲线的一般技术要求及主要形式:1.回流温度曲线各环节的一般技术要求:一般而言,回流温度曲线可分为三个阶段:预热阶段、回流阶段、冷却阶段。
①预热阶段:预热是指为了使锡水活性化为目的和为了避免浸锡时进行急剧高温加热引起部品不具合为目的所进行的加热行为。
?预热温度:依使用锡膏的种类及厂商推荐的条件设定。
一般设定在80~160℃范围内使其慢慢升温(最佳曲线);而对于传统曲线恒温区在140~160℃间,注意温度高则氧化速度会加快很多(在高温区会线性增大,在150℃左右的预热温度下,氧化速度是常温下的数倍,铜板温度与氧化速度的关系见附图)预热温度太低则助焊剂活性化不充分。
?预热时间视PCB板上热容量最大的部品、PCB面积、PCB厚度以及所用锡膏性能而定。
一般在80~160℃预热段内时间为60~120see,由此有效除去焊膏中易挥发的溶剂,减少对元件的热冲击,同时使助焊剂充分活化,并且使温度差变得较小。
?预热段温度上升率:就加热阶段而言,温度范围在室温与溶点温度之间慢的上升率可望减少大部分的缺陷。
对最佳曲线而言推荐以0.5~1℃/sec的慢上升率,对传统曲线而言要求在3~4℃/sec以下进行升温较好。
炉温曲线教材

PCB bending After Soaking 由於PP的軟化溫度點為140 ℃,故如可考慮縮短Over 140 ℃的時間來改善空焊,此為一嶄新觀念,其實這種方法在實踐 中被証明是有效的.
Soaking Zone :
*Homologous heating (PCB, Components and solder paste) 溫度達到一致(機板,零件,錫膏) *Solder paste viscosity control 錫膏黏性控制 *Solder wetting and wicking begin. 錫膏浸潤開始 *Surface solder balls melting. 表面焊料金屬熔融 Plastic BGA substrate (Tg :1750C)
Soaking Zone
PCB bending
Parameter setting :
1 2 3
2 Lead > 1 Body > 3 Pad
Normal soldering
Wicking Bridge by wicking
Less heat from the top
2 Lead > 1 Body > 3 Pad
*三元晶相圖
*黏度隨溫度,時間的變化圖
END
針對Intel RG82845 BGA soak zone time:50~65sec;
Preheating Zone :
*Solder Pastes’ Viscosity 錫膏黏度: 1.Solvent evaporation cause viscosity higher. 溶劑揮發使黏度變大 2.Heating solvent will cause viscosity down. 加熱溶劑會使黏度降低 Viscosity
加热炉与热处理炉温度曲线的测试和优化PPT课件

环形加热炉加热温度曲线的测试
测试应用 - 环型加热炉
氧化铁皮厚。生 成的氧化铁有时 很难去除,不仅 造成氧化烧损大 ,而且影响管坯 表面质量;
管坯加热温度不 均匀。
轧制节奏快时, 管坯与炉底接触 面附近发暗。
宝钢钢管环形炉黑匣子测试Φ179
宝钢环型炉
黑匣子安装在管坯上
天津钢管环形炉加热温度曲线
测试点的安装
鞍钢热轧加热炉黑匣子出炉
宝钢厚板B炉黑匣子出炉
宝钢厚板C炉黑匣子出炉
黑匣子安装在管坯上
“黑匣子”安装在测试钢坯上
马钢热处理黑匣子进炉
车轮热处理出炉
钎焊接炉温度均匀性测焊温度曲线
铝车轮固熔温度曲线测试
炉温跟踪仪器出固熔炉
铝合金固熔温度曲线1:545℃下13h
炉气温度和管坯平均温度
炉气温度曲线的分析
炉内热电偶只能测试安装位置点的炉温。采用这种 实验方法把炉气温度曲线测试出来。如果在钢坯的 长度方向安装多支热电偶,就可以测得全炉炉气温 度的分布。为炉型结构、烧嘴位置布置、供热调节 和操作改进提供依据。
通过测试,发现在钢坯的出口有一个炉气温度低于 钢坯温度的一个区,在这里钢坯温度会降低,是由 于布置反向烧嘴造成的。
管坯得断面温差
加热温差的分析
钢坯的温差在相变时因为导热系数降低,温 差最大, 最大温差达到213℃。
加热168分钟后钢坯温度达到1300℃,此时 上下温差30℃。
出炉时断面温差达到8℃。 钢坯出炉后表面温度降约为40℃/min, 从出炉
到开轧需要一分钟左右,出炉表面与中心的 温差在30℃是可行的。
热回收段
预热段 95
加热 I段 122
加热II段 157
均热段 194
LF炉温度控制曲线

LF炉温度控制曲线LF Furnace temperature control curve二.LF钢包精炼炉工艺流程及作业周期(min)Second. LF Ladle refining furnace process and operation cycle(min)1 工艺流程图1 Process flow diagram2 作业周期(min)2 Operation cycle (min)三.LF-90t精炼炉工艺操作描述Third. LF-90t Finer furnace process operation description1 LF炉精炼阶段1LF Furnace refining stage电弧炉出钢,根据生产工艺确定精炼包钢水装入量,通过冶炼浇铸跨行车吊包座包于90tLF炉钢包车上,人工接通氩气管,钢包车载包运行至加热工位(定位精度±5mm),水冷炉盖下降封闭钢包,三相电极下降,送电加热。
送电过程中使用正常的吹氩氩量进行搅拌,通过加料系统补加渣料。
由于热平衡,送电初期钢液温度继续下降,3~4min开始升温。
精炼期加还原剂还原,分批加入,少批量,多批次撒匀。
同时将试样速送至化验室进行快速分析。
Arc furnace tapping, according to the production process to identify refining steel water loading, through smelting casting crane packets packets to cross 90tLF furnace steel car, artificial trachea on argon ladle car package, running to the heating station ( positioning accuracy of 5mm ), water-cooling furnace cover sealing ladle drop, three-phase electrode decreases, send electric heating. Transmission process using normal argon blowing argon stirring volume, by adding slag material feeding system. The heat balance of power transmission, initial temperature of molten steel continued to decline, 3 ~ 4min began to heat up. Refining period is reduced by adding reducing agent, batch addition, little batch, batch sprinkle. At the same time samples will be sent to the laboratory for rapid analysis speed.根据化验分析值与钢种目标值之间的差值,计算出需要加入合金的种类和物料质量,在规定时间内将规定牌号和数量的合金料经称量送至LF炉受料斗,启动受料斗闸门,合金料即可加入钢包,达到合金调整之目的。
2020炉温曲线原题

2020炉温曲线原题?
答:2020年炉温曲线原题如下:
题目:在集成电路板等电子产品生产中,需要将安装有各种电子元件的印刷电路板放置在回焊炉中,通过加热,将电子元件自动焊接到电路板上。
在这个生产过程中,让回焊炉的各部分保持工艺要求的温度,对产品质量至关重要。
目前,这方面的许多工作是通过实验测试来进行控制和调整的。
本题旨在通过机理模型来进行分析研究。
问题描述:回焊炉内部设置若干个小温区,它们从功能上可分成4个大温区:预热区、恒温区、回流区、冷却区。
另外,生产车间的温度保持在25℃。
在设定各温区的温度和传送带的过炉速度后,可以通过温度传感器测试某些位置上焊接区域中心的温度,称之为炉温曲线(即焊接区域中心温度曲线)。
附件是某次实验中炉温曲线的数据,各温区设定的温度分别为175℃(小温区1-5)、195℃(小温区6)、235℃(小温区7)、255℃(小温区8-9)及25℃(小温区10~11);传送带的过炉速度为70 cm/min;焊接区域的厚度为0.15 mm。
请回答下列问题:
1.请对焊接区域的温度变化规律建立数学模型。
- 1、下载文档前请自行甄别文档内容的完整性,平台不提供额外的编辑、内容补充、找答案等附加服务。
- 2、"仅部分预览"的文档,不可在线预览部分如存在完整性等问题,可反馈申请退款(可完整预览的文档不适用该条件!)。
- 3、如文档侵犯您的权益,请联系客服反馈,我们会尽快为您处理(人工客服工作时间:9:00-18:30)。
T1 + T2 =T3
T1 + T2 >T3
T3
d T1 T2
Partial melting
Peak Zone :
*Peak temperature and Reflow time should be controlled 焊接與回流焊溫度應被控制 *The flowing ability(surface tension) of solder (High Good)
錫膏的表面張力由變高
*Void formation 空洞構成 *Component and / or board damage 零件或機板受損 *N2 concentration 氮氣濃度
銲接區
當我們將液態的免洗助銲劑滴入液態的 Rework錫槽內,您將發現助銲劑極速的 去除錫面上的氧化物。同理可證:在 Reflow的狀態中,當松香和銲錫皆為液 態時,銲錫性最佳,去氧化物的效果最 好,並產生介面合金層接合零件及銲點。 各種錫膏的活性表現亦在此時獲得比較。
Before Soaking
After Soaking
恆溫區
恆溫區其目的再於使PCB上所有的零件溫 度達到均溫,簡少零件熱衝擊,恆溫區 的長度則取決於PCB面積的大小。 此時錫膏內劑不斷揮發,活性劑持續作 用去氧化,松香軟化並披覆在銲點上, 具有熱保護及熱傳媒的作用。
恆溫區
*Plastic BGA
*Flux softness point :
Flux softness point will decrease solder paste viscosity. 助焊劑(松香)軟化會降低錫膏黏性 Viscosity Very low heating rate Low heating rate High heating rate
Plastic BGA
PCB bending After Soaking 由於PP的軟化溫度點為140 ℃,故如可考慮縮短Over 140 ℃的時間來改善空焊,此為一嶄新觀念,其實這種方法在實踐 中被証明是有效的.
Soaking Zone :
*Homologous heating (PCB, Components and solder paste) 溫度達到一致(機板,零件,錫膏) *Solder paste viscosity control 錫膏黏性控制 *Solder wetting and wicking begin. 錫膏浸潤開始 *Surface solder balls melting. 表面焊料金屬熔融 Plastic BGA substrate (Tg :1750C)
Peak: Solder balls melt, wetting and wicking begin.&
Solder melting completes, surface tension takes over. 錫
球熔化,浸潤開始,焊接進行,表面張力起作用
Cooling : Cool down phase. 快速冷卻階段
Temperature
Soaking Zone :
1.Solvent evaporate completely 溶劑完全揮發 2.Flux activation and oxidation 助焊劑被激活並去氧化
3. Soaking time and temperature
3.1 For N2 oven the Soaking time can be longer. 3.2 For Air oven the Soaking time should shorter than N2 oven 4. PCB board bending control PCB板彎控制 PCB PCB
*三元晶相圖
*黏度隨溫度,時間的變化圖
END
錫膏Reflow的溫度曲線
ቤተ መጻሕፍቲ ባይዱ
現在我們來討論為甚麼“馬鞍型溫度曲線”被廣泛使用的理由,主要是因為透過 強迫性對流流焊製程的協助,有恆溫區的加溫曲線可達到類似在汽相流焊製程中 的最高流焊區極上熱平衡分佈的結果。 我們認為要達到最佳的產品產出率,在考慮如何決定流焊的溫度曲線時,因此考 慮各種不同零件的吸熱情況以及底材PCB的特性而不必太在乎加熱製程中錫膏的 表現。 例如,當我們測量兩個不同零件,chip capacitor和B.G.A的焊接點溫度時,這兩個 零件間最高點溫度差的差異會最大,因為每一個零件熱含量不同,導致每個零件 的溫升速率不同。 請注意,使用鞍狀流焊溫度曲線的目的在於確保得到良好的銲接點品質,而不必 掛感零件尺寸大小和熱含量多寡,廠商也已研發出特殊的抗垂流劑,可確保即使 在很陡的溫升段情況下仍可得到很好的抗塌陷性,同時可以使用高沸點的溶劑來 延長錫膏在鋼版上的使用時間及粘滯時間,這種新抗垂流劑已經在KOKI SE4M953i及SE4-M1000等系統上大量使用。 新助焊劑組成的發展,己經成功地使銲錫膏愈來愈不受溫度曲線的影響,並使得 焊接製程的限制大大地減少 (process window放寬很多)
3 Pad> 2 Lead > 1 Body
More heat from the bottom
Tombstoning :
T3 d T1 T2
Condition which causes tombstoning shall be : T1 + T2 >T3
In order to overcome the problem, the momentum relation must become as below ;
Cooling Zone :
*Cooling down speed Cool Down ≦3℃/sec =1.5 ℃/sec is best. •N2 concentration
錫膏Reflow的溫度曲線
在討論溫度曲線之前,讓我們先討論一下傳統的溫度曲線:馬鞍狀的溫度曲線,恆 溫區在140~160OC之間。 最早開始使用表面粘裝零件(SMT components)流焊組裝製程時SMT零件在PCB上的 分佈密度並不高,而且零件間的熱含量差異相當小,這種簡單的P.C板結構容許應 用“和緩溫昇,無恆溫區”的溫度曲線,而不會有任何問題。 由於業界對P.C板輕溥短小的設計的改進,SMT零件的分佈密度愈趨緊密,加速了 高熱含量零件封裝體的應用,例如IC和QFP。因為各種不同大小零件間的熱含量增 加,使得在使用傳統的遠紅線(far IR)流焊爐時,因為熱量分佈不均,再加上使用 “和緩溫昇型”的溫昇曲線(甚至於“馬鞍狀,恆溫型溫度曲線”),很難在零件間 達到熱平衡。 為了解決熱平衡不佳的問題,人們開始考慮使用汽相流焊製程(Vapor phase reflow process),但是因為急挺的熱量提升造成的零件裂開及墓碑效應、溶劑的毒性、 CFC溶劑的禁用等問題,汽相流焊很快就不受歡迎了。 後來研發的強迫空氣對流流焊製程(forced air convection reflow process)因此比遠 紅外線流焊的熱分佈均勻性好很多而大受歡迎。
Profile
Curve
REFIOW形式(HEATER分佈)
Peak
183 oC
170oC
140oC
Soaking Preheating
Cooling
Preheating : Solvent evaporation 溶劑揮發 Soaking :Flux reduces and Metal oxides 助焊劑還原金屬氧化物
錫膏Reflow的溫度曲線
應用廠商建議的「和緩加溫」或「鞍狀加溫」的溫度曲線,只要能確保流焊爐的熱量 足夠讓所有溶劑揮發,但是,廠商的建議是所應用的溫度曲線的決定必需全盤考量 PCB底材和零件的熱平衡以確保每個零件焊接點的品質,而不必太考慮錫膏在流焊製 程中的表現。事實上,許多工廠都在持續使用鞍狀溫度曲線而沒有任何焊錫問題。 根據以往的經驗,如何設計鋼版開口尺寸對防止焊錫不良,例如邊球和錫橋,會比改 變溫度曲線來得更有實質上的效果。 從焊錫膏的觀點來看,當溫度升高時,焊錫膏傾向如果第一段溫度升太陡或助焊劑組 成不適當時,焊錫膏傾向於變軟並且可能造成塌陷(slumping)產生邊球、錫橋和其他 焊接缺點。 較慢的溫升(ramp-up)段,會讓溶劑揮發時,松香及抗垂流劑變軟的速度較慢,有助 於減少solder beads(邊球),錫橋(bridging)和其他缺點. 較陡的溫升段會造成錫膏粘度較快速的下降,因此,廠商已經針對錫膏成份設計出較 低沸點的溶劑,使得大部份的溶劑在松香和其他固形物達到較化點之前就已經揮發來 減少造成slump和solder beads的機會,但是,可能因此使得錫膏在鋼版的應用時間 和粘滯力維持的時間縮短。
Reflow的製程條件
ASUS 規範:
1.1 First Ramp-up : Ø 3J /sec(Intel) ¡ ¢ 0.8¢ /sec¡ X¡ 2¢ /sec(SIS) J Ø Ø J 1.2 Soak Zone : 140 ã 170J for 50ã 90sec ¡ ¢ ¡ 1.3 Peak Temp : (1) 205 Ø BGA Ø 225J (BGA Substrate) ¡ ¡ ¢ (2) 205Ø BGA Ø 220J (BGA Bottom) ¡ ¡ ¢ (3) 205Ø QFPØ 225J (QFP Lead¾ ¨ ¥ ½ à ) ¡ ¡ ¢ a ñ i Õ ä (4) 200Ø QFPØ 220J (QFP Lead¾ ¨ § § à ) ¡ ¡ ¢ a ñ T w ä (5)205Ø BGA Ø 225J (CPU Socket) ¡ ¡ ¢ 1.4 Over 183J (1)³ IC¹ ¥ : 45ã 90sec ¢ ¦ s ó ¡ (2)³ IC¹ ¥ : 10sec(R.L.C¾ ¨ § § ä ) ¦ s ó a ñ T w à 1.5 Cool Down Ø 3J /sec ¡ ¢