加工中心上镗孔加工的刀具技术
加工中心的镗孔加工的加工技术

加工中心的镗孔加工的加工技术加工中心的镗孔加工的加工技术1、绪言所谓镗孔加工(Boring)就是指将工件上原有的孔进行扩大或精化。
它的特征是修正下孔的偏心、获得精确的孔的位置,取得高精度的圆度、圆柱度和表面光洁度。
所以,镗孔加工作为一种高精度加工法往往被使用在最后的工序上。
例如,各种机器的轴承孔以及各种发动机的箱体、箱盖的加工等。
和其它机械加工相比,镗孔加工是属一种较难的加工。
它只靠调节一枚刀片(或刀片座) 要加工出象H7、H 6这样的微米级的孔。
随着加工中心(Machining center)的普及,现在的镗孔加工只需要进行编程、按扭操作等。
正因为这样,就需要有更简单、更方便、更精密的刀具来保证产品的质量。
这里主要从工具技术的角度来分析加工中心的镗孔加工。
2、加工中心的镗孔加工的特点2.1工具转动和车床加工不同,加工中心加工时由于工具转动,便不可能在加工中及时掌握刀尖的情况来调节进刀量等。
也不可能象数控车床那样可以只调节数控按扭就可以改变加工直径。
这便成了完全自动化加工的一个很大的障碍。
也正因为加工中心不具有自动加工直径调节机能(附有U 轴机能的除外) ,就要求镗刀必须具有微调机构或自动补偿机能,特别是在精镗时根据公差要求有时必须在微米级调节。
另外,加工中心镗孔时由于切屑的流出方向在不断地改变,所以刀尖、工件的冷却以及切屑的排出都要比车床加工时难的多。
特别是用纵型加工中心进行钢的盲孔粗镗加工时,至今这个问题还没得到完全解决。
2.2颤振(Chatter)镗孔加工时最常出现的、也是最令人头疼问题是颤振。
在加工中心上发生颤振的原因主要有以下几点①工具系统的刚性(Rigidity):包括刀柄、镗杆、镗头以及中间连接部分的刚性。
因为是悬臂加工(Stub Boring)所以特别是小孔、深孔及硬质工件的加工时,工具系统的刚性尤为重要。
②工具系统的动平衡(Balance):相对于工具系统的转动轴心,工具自身如有一不平衡质量,在转动时因不平衡的离心力的作用而导致颤振的发生。
镗孔加工的加工技术

镗孔加工的加工技术所谓镗孔加工(Boring)就是指将工件上原有的孔进行扩大或精化。
它的特征是修正下孔的偏心、获得精确的孔的位置,取得高精度的圆度、圆柱度和表面光洁度。
所以,镗孔加工作为一种高精度加工法往往被使用在最后的工序上。
例如,各种机器的轴承孔以及各种发动机的箱体、箱盖的加工等。
和其它机械加工相比,镗孔加工是属一种较难的加工。
它只靠调节一枚刀片(或刀片座)要加工出象H7、H6这样的微米级的孔。
随着加工中心(Machining center)的普及,现在的镗孔加工只需要进行编程、按扭操作等。
正因为这样,就需要有更简单、更方便、更精密的刀具来保证产品的质量。
这里主要从工具技术的角度来分析加工中心的镗孔加工。
1、加工中心的镗孔加工的特点1.1工具转动和车床加工不同,加工中心加工时由于工具转动,便不可能在加工中及时掌握刀尖的情况来调节进刀量等。
也不可能象数控车床那样可以只调节数控按扭就可以改变加工直径。
这便成了完全自动化加工的一个很大的障碍。
也正因为加工中心不具有自动加工直径调节机能(附有U轴机能的除外),就要求镗刀必须具有微调机构或自动补偿机能,特别是在精镗时根据公差要求有时必须在微米级调节。
另外,加工中心镗孔时由于切屑的流出方向在不断地改变,所以刀尖、工件的冷却以及切屑的排出都要比车床加工时难的多。
特别是用纵型加工中心进行钢的盲孔粗镗加工时,至今这个问题还没得到完全解决。
1.2颤振(Chatter)镗孔加工时最常出现的、也是最令人头疼问题是颤振。
在加工中心上发生颤振的原因主要有以下几点①工具系统的刚性(Rigidity):包括刀柄、镗杆、镗头以及中间连接部分的刚性。
因为是悬臂加工(Stub Boring)所以特别是小孔、深孔及硬质工件的加工时,工具系统的刚性尤为重要。
②工具系统的动平衡(Balance):相对于工具系统的转动轴心,工具自身如有一不平衡质量,在转动时因不平衡的离心力的作用而导致颤振的发生。
数控加工中心反镗孔刀具与程序设计
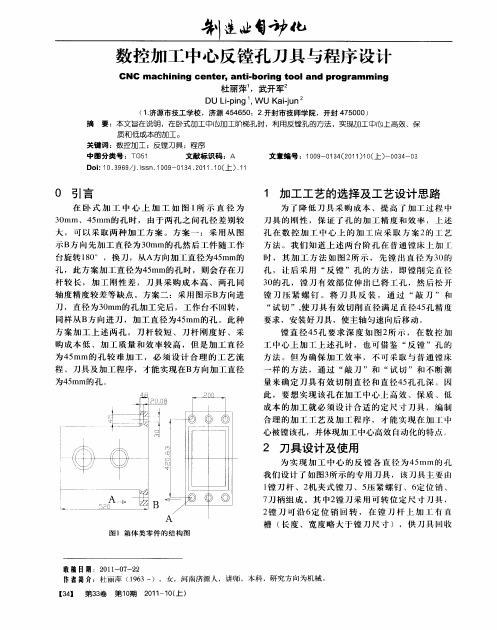
收 稿 日 期 :2 1- 7 2 0 1 0 -2 作 者 简 介 :杜 丽 萍 ( 9 3一) ,女 ,河 南 济 源 人 ,讲 师 , 本 科 ,研 究 方 向为 机 械 。 16 【 4 第 3 卷 3】 3 第 1期 0 2 1— 0 上 ) 01 1 (
( . 源市技工学校 ,济源 4 4 5 ;2开封 市技 师学院 ,开封 4 5 0 ) 1济 560 . 7 0 0
摘
要 :本文 旨在说明 ,在 卧式加工中心加工 阶梯孔 时 ,利用反 镗孔的方法 ,实现加工中心上 高效 、保 质和 低成 本的加工。
关键 词 :数控加工 ;反镗 刀具 ;程序
为4 mm的 孔 。 5
样 的 方 法 ,通 过 “ 刀 ”和 “ 切 ”和 不 断 测 敲 试
量 来 确 定 刀 具 有 效切 削 直 径 和 直 径4 ; : 深 。 因 5 LL ff 此 , 要 想 实 现 该 孔 在 加 工 中心 上 高效 、 保 质 、低 成本 的加 工 就 必 须设 计 合 适 的 定 尺 寸 刀 具 ,编 制
、 I
匐 化
பைடு நூலகம்
1 刀杆 2 刀 3 J 镗 镗 Y 片夹紧螺钉 4 夹式刀片 机
5压 紧 螺钉 6定位 销 7 J ]柄
图 3 刀 具 打 开 状 态 示 意 图
— —
1 紧 螺钥 2晋 通 镗 刀 3工 件 4刀 具 压
/\ ll \ /\\\\
/
图2在普通镗床上加工该孔示意 图
1 加工工艺的选择及工艺设计思路
为 了降 低 刀具 采 购 成 本 、 提 高 l 工 过 程 中 『加
刀 具 的 刚 性 ,保 证 了孔 的 加 工 精 度 和 效 率 , 上述
加工中心镗刀完整的使用方法

加工中心镗刀完整的使用方法加工中心镗刀是一种常见的切削工具,用于加工金属零件的精确孔径。
以下是它完整的使用方法:
1.确定加工要求:在使用加工中心镗刀前,必须先确定所需孔的直径、深度及其精度等加工要求。
2.安装:将加工中心镗刀插入加工中心的主轴中,紧固并夹紧,调整刀具偏心。
3.编程:根据加工要求编写程序。
4.预设切削参数:预设切削参数,如切削速度、进给速度和切削深度等。
5.加工:将工件放置在加工中心上,启动机床并开始加工。
6.精确测量:在加工完成后,使用合适的测量工具,如千分尺、游标卡尺等进行精确的测量,判断加工效果是否达到要求。
7.刀具保养:及时清理刀具、夹具等部件,保证其正常运转。
8.如有异常现象,如振动、噪音等,需要立即停止机床,进行检查和调整。
以上是加工中心镗刀完整的使用方法,使用时需要注意安全,保证加工效果和刀具寿命,同时也需要定期维护和保养,以便更好地发挥其功能。
CNC机床加工中的镗削刀具的选择与应用
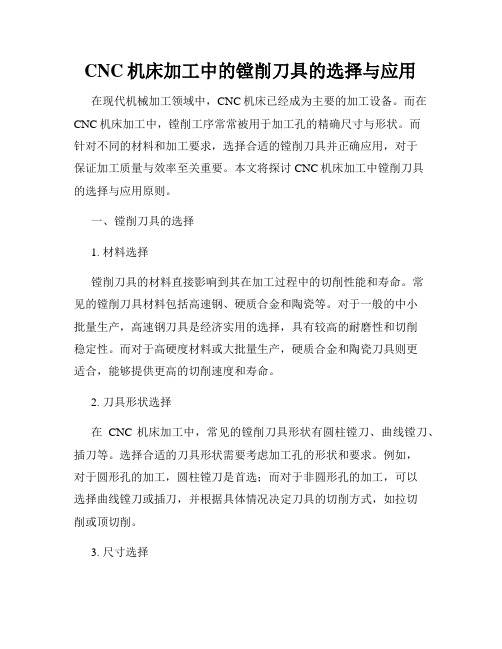
CNC机床加工中的镗削刀具的选择与应用在现代机械加工领域中,CNC机床已经成为主要的加工设备。
而在CNC机床加工中,镗削工序常常被用于加工孔的精确尺寸与形状。
而针对不同的材料和加工要求,选择合适的镗削刀具并正确应用,对于保证加工质量与效率至关重要。
本文将探讨CNC机床加工中镗削刀具的选择与应用原则。
一、镗削刀具的选择1. 材料选择镗削刀具的材料直接影响到其在加工过程中的切削性能和寿命。
常见的镗削刀具材料包括高速钢、硬质合金和陶瓷等。
对于一般的中小批量生产,高速钢刀具是经济实用的选择,具有较高的耐磨性和切削稳定性。
而对于高硬度材料或大批量生产,硬质合金和陶瓷刀具则更适合,能够提供更高的切削速度和寿命。
2. 刀具形状选择在CNC机床加工中,常见的镗削刀具形状有圆柱镗刀、曲线镗刀、插刀等。
选择合适的刀具形状需要考虑加工孔的形状和要求。
例如,对于圆形孔的加工,圆柱镗刀是首选;而对于非圆形孔的加工,可以选择曲线镗刀或插刀,并根据具体情况决定刀具的切削方式,如拉切削或顶切削。
3. 尺寸选择刀具尺寸的选择需要根据加工孔的直径和深度来确定。
刀具的直径应略大于加工孔直径以保证加工余量,并根据要求选择合适的刀具长度和孔深比。
二、镗削刀具的应用原则1. 加工参数选择在进行CNC机床加工时,合理选择加工参数是确保镗削刀具正常运行和保证加工质量的关键。
主要的加工参数包括切削速度、进给速度和切削深度。
切削速度应根据镗削刀具材料、工件材料和加工要求进行选择,过高的切削速度容易造成刀具磨损和热变形,而过低的切削速度则影响加工效率。
进给速度应根据加工目标、切削稳定性和切屑排除等因素来选择。
切削深度的选取应结合刀具和工件的刚度来确定,以避免过大或过小的切削深度引起刀具断裂或加工精度下降。
2. 切削液的应用在CNC机床加工中,镗削刀具与工件之间产生的热量需要得到有效地排除,以保持加工的稳定性和刀具的寿命。
此时,切削液的应用变得尤为重要。
镗孔技巧
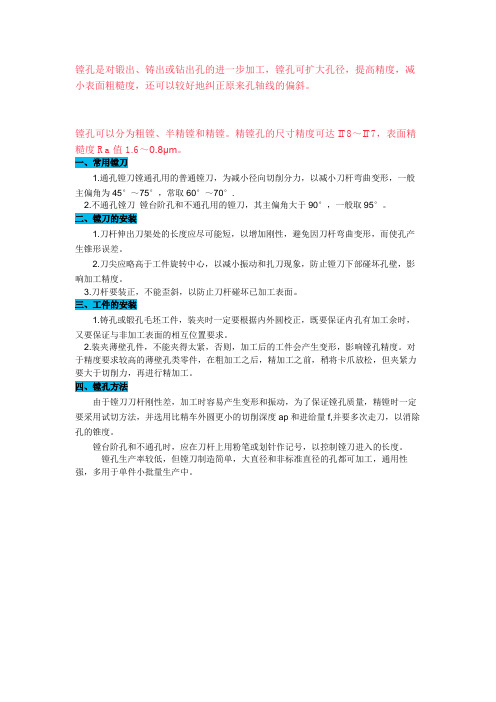
镗孔是对锻出、铸出或钻出孔的进一步加工,镗孔可扩大孔径,提高精度,减小表面粗糙度,还可以较好地纠正原来孔轴线的偏斜。
镗孔可以分为粗镗、半精镗和精镗。
精镗孔的尺寸精度可达IT8~IT7,表面精糙度Ra值1.6~0.8μm。
一、常用镗刀
1.通孔镗刀镗通孔用的普通镗刀,为减小径向切削分力,以减小刀杆弯曲变形,一般主偏角为45°~75°,常取60°~70°.
2.不通孔镗刀镗台阶孔和不通孔用的镗刀,其主偏角大于90°,一般取95°。
二、镗刀的安装
1.刀杆伸出刀架处的长度应尽可能短,以增加刚性,避免因刀杆弯曲变形,而使孔产生锥形误差。
2.刀尖应略高于工件旋转中心,以减小振动和扎刀现象,防止镗刀下部碰坏孔壁,影响加工精度。
3.刀杆要装正,不能歪斜,以防止刀杆碰坏已加工表面。
三、工件的安装
1.铸孔或锻孔毛坯工件,装夹时一定要根据内外圆校正,既要保证内孔有加工余时,又要保证与非加工表面的相互位置要求。
2.装夹薄壁孔件,不能夹得太紧,否则,加工后的工件会产生变形,影响镗孔精度。
对于精度要求较高的薄壁孔类零件,在粗加工之后,精加工之前,稍将卡爪放松,但夹紧力要大于切削力,再进行精加工。
四、镗孔方法
由于镗刀刀杆刚性差,加工时容易产生变形和振动,为了保证镗孔质量,精镗时一定要采用试切方法,并选用比精车外圆更小的切削深度ap和进给量f,并要多次走刀,以消除孔的锥度。
镗台阶孔和不通孔时,应在刀杆上用粉笔或划针作记号,以控制镗刀进入的长度。
镗孔生产率较低,但镗刀制造简单,大直径和非标准直径的孔都可加工,通用性强,多用于单件小批量生产中。
CNC机床加工中的镗削加工技术与策略

CNC机床加工中的镗削加工技术与策略镗削加工作为CNC机床加工中的一种常见工艺,广泛应用于模具制造、航空航天、汽车制造等领域。
本文将探讨CNC机床加工中的镗削加工技术与策略,以帮助读者更好地理解和应用这一技术。
一、镗削加工的概述镗削加工是一种利用旋转刀具将工件内孔进行加工的工艺。
相比于传统的铰削和扩孔工艺,镗削加工具有加工质量高、效率高、加工尺寸稳定等优点。
在CNC机床加工中,镗削加工通常由电脑控制系统控制刀具的移动和进给,实现高精度和高效率的加工。
二、镗削加工的技术要点1. 刀具的选择在镗削加工中,刀具的选择对加工质量和效率起着重要作用。
通常情况下,采用硬质合金材料制成的刀具能够满足大部分的加工需求。
根据具体加工要求,选择合适的刀具类型,如精密镗刀、微小孔径镗刀等。
2. 切削参数的确定切削参数的确定直接影响到加工效果。
在镗削加工中,切削速度、进给速度和切削深度是关键参数。
合理的切削速度可以保证刀具寿命和加工质量,进给速度要控制在一个合适的范围内,切削深度要根据工件材料和加工要求进行合理选择。
3. 刀架的调整刀架的调整对加工质量和效率也有一定影响。
在镗削加工中,刀架的调整应使刀具与工件轴线保持一致,并注意刀具的张紧力度,以确保稳定和精确的加工。
三、镗削加工的策略1. 初次进刀策略镗削加工中,初次进刀对于保证加工质量尤为关键。
在初次进刀时,应减小进给量,以防止刀具摆动和工件断裂的风险。
根据工件的材料和孔的特点,控制进给量,逐渐增加进给速度和切削深度,最终达到稳定的加工状态。
2. 切削轨迹策略切削轨迹的选择是保证加工效果的重要因素。
在镗削加工中,常见的切削轨迹有圆周切削、螺旋切削和横向切削等。
根据工件的形状和加工要求,选择合适的切削轨迹,确保加工质量和效率。
3. 切削润滑策略切削润滑对于镗削加工的顺利进行起着至关重要的作用。
良好的切削润滑可以减少摩擦阻力、降低切削温度、延长刀具寿命等。
根据工件材料和加工情况,选择合适的切削润滑方式,如清洗液、切削液等。
第二节镗孔加工

第六章 孔系加工
二、镗孔刀具
镗刀由刀柄和刀具组成,具有一个或两个切削 部分,专门用于对已有的孔进行粗加工、半精加 工或精加工的刀具,如下图所示。镗刀可在镗床、 车床或铣床上使用。因装夹方式的不同,镗刀柄 部有方柄、莫氏锥柄和7:24锥柄等多种形式。在 数控铣床上一般采用7:24锥柄镗刀。
第六章 孔系加工
(3)刀具安装后进行动态跳动检查。动态跳动检 查是一个综合指标,它反映机床主轴精度、刀具精度 以及刀具与机床的连接精度。这个精度如果超过被加 工孔要求的精度的 1/2 或 2/3 就不能进行加工,需 找出原因并消除后才能进行。这一点操作者必须牢记, 并严格执行,否则加工出来的孔不能符合要求。
第六章 孔系加工
格式: G85 X__Y__Z__R__ F__; G86 X__Y__Z__R__ P__F__;
第六章 孔系加工
式中 G85─镗孔循环在孔底时主轴不停转,然后快速退
刀;如下图a所示。 G86─镗孔循环在孔底时主轴停止,然后快速退刀;
如下图b所示。
图6-13 粗镗孔动作图
a)G98 G85动作
b)G98 G86动作
第六章 孔系加工
(2)G76/G87程序段中Q代表刀具在轴反向位移增量。 (3)G87指令编程时,注意刀具进给切削方向是从工件的 下方到工件的上方。 (4)为了提高加工效率,在指令固定循环前,应先使主轴 旋转。 (5)由于固定循环是模态指令,因此,在固定循环有效期
镗孔粗糙度走刀计算公式
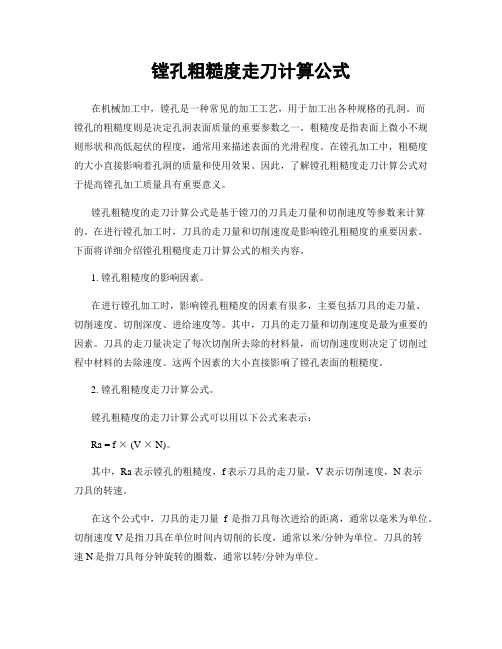
镗孔粗糙度走刀计算公式在机械加工中,镗孔是一种常见的加工工艺,用于加工出各种规格的孔洞。
而镗孔的粗糙度则是决定孔洞表面质量的重要参数之一。
粗糙度是指表面上微小不规则形状和高低起伏的程度,通常用来描述表面的光滑程度。
在镗孔加工中,粗糙度的大小直接影响着孔洞的质量和使用效果。
因此,了解镗孔粗糙度走刀计算公式对于提高镗孔加工质量具有重要意义。
镗孔粗糙度的走刀计算公式是基于镗刀的刀具走刀量和切削速度等参数来计算的。
在进行镗孔加工时,刀具的走刀量和切削速度是影响镗孔粗糙度的重要因素。
下面将详细介绍镗孔粗糙度走刀计算公式的相关内容。
1. 镗孔粗糙度的影响因素。
在进行镗孔加工时,影响镗孔粗糙度的因素有很多,主要包括刀具的走刀量、切削速度、切削深度、进给速度等。
其中,刀具的走刀量和切削速度是最为重要的因素。
刀具的走刀量决定了每次切削所去除的材料量,而切削速度则决定了切削过程中材料的去除速度。
这两个因素的大小直接影响了镗孔表面的粗糙度。
2. 镗孔粗糙度走刀计算公式。
镗孔粗糙度的走刀计算公式可以用以下公式来表示:Ra = f × (V × N)。
其中,Ra表示镗孔的粗糙度,f表示刀具的走刀量,V表示切削速度,N表示刀具的转速。
在这个公式中,刀具的走刀量f是指刀具每次进给的距离,通常以毫米为单位。
切削速度V是指刀具在单位时间内切削的长度,通常以米/分钟为单位。
刀具的转速N是指刀具每分钟旋转的圈数,通常以转/分钟为单位。
通过这个公式,我们可以清楚地看到镗孔粗糙度与刀具的走刀量和切削速度之间的关系。
当刀具的走刀量增大或切削速度增大时,镗孔的粗糙度也会随之增大。
因此,在实际的镗孔加工中,我们需要根据具体的工件材料和加工要求来确定合适的刀具走刀量和切削速度,以控制镗孔的粗糙度。
3. 镗孔粗糙度走刀计算公式的应用。
镗孔粗糙度走刀计算公式的应用对于提高镗孔加工质量具有重要意义。
在实际的镗孔加工中,我们可以根据工件材料的硬度、切削性能等因素,选择合适的刀具走刀量和切削速度,以控制镗孔的粗糙度。
镗削和镗刀
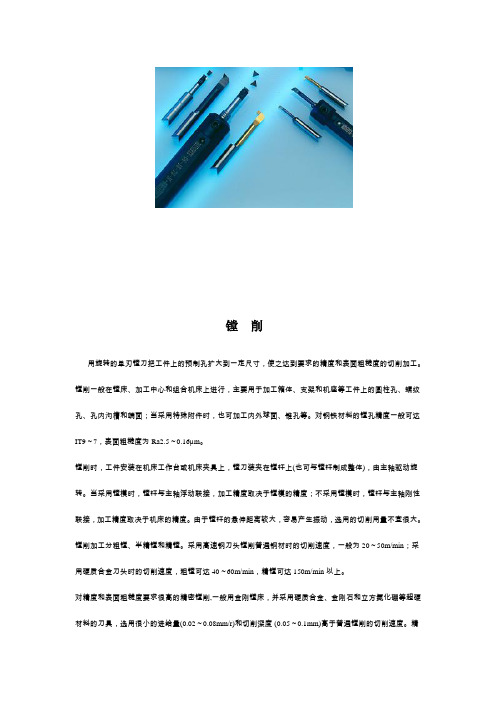
镗削用旋转的单刃镗刀把工件上的预制孔扩大到一定尺寸,使之达到要求的精度和表面粗糙度的切削加工。
镗削一般在镗床、加工中心和组合机床上进行,主要用于加工箱体、支架和机座等工件上的圆柱孔、螺纹孔、孔内沟槽和端面;当采用特殊附件时,也可加工内外球面、锥孔等。
对钢铁材料的镗孔精度一般可达IT9~7,表面粗糙度为Ra2.5~0.16µm。
镗削时,工件安装在机床工作台或机床夹具上,镗刀装夹在镗杆上(也可与镗杆制成整体),由主轴驱动旋转。
当采用镗模时,镗杆与主轴浮动联接,加工精度取决于镗模的精度;不采用镗模时,镗杆与主轴刚性联接,加工精度取决于机床的精度。
由于镗杆的悬伸距离较大,容易产生振动,选用的切削用量不宜很大。
镗削加工分粗镗、半精镗和精镗。
采用高速钢刀头镗削普通钢材时的切削速度,一般为20~50m/min;采用硬质合金刀头时的切削速度,粗镗可达40~60m/min,精镗可达150m/min以上。
对精度和表面粗糙度要求很高的精密镗削,一般用金刚镗床,并采用硬质合金、金刚石和立方氮化硼等超硬材料的刀具,选用很小的进给量(0.02~0.08mm/r)和切削深度 (0.05~0.1mm)高于普通镗削的切削速度。
精密镗削的加工精度能达到IT7~6,表面粗糙度为Ra0.63~0.08µm。
精密镗孔以前,预制孔要经过粗镗、半精镗和精镗工序,为精密镗孔留下很薄而均匀的加工余量。
镗刀具有一个或两个切削部分、专门用于对已有的孔进行粗加工、半精加工或精加工的刀具。
镗刀可在镗床、车床或铣床上使用。
因装夹方式的不同,镗刀柄部有方柄、莫氏锥柄和7:24锥柄等多种形式。
单刃镗刀切削部分的形状与车刀相似。
为了使孔获得高的尺寸精度,精加工用镗刀的尺寸需要准确地调整。
微调镗刀可以在机床上精确地调节镗孔尺寸,它有一个精密游标刻线的指示盘,指示盘同装有镗刀头的心杆组成一对精密丝杆螺母副机构。
当转动螺母时,装有刀头的心杆即可沿定向键作直线移动,藉助游标刻度读数精度可达0.001mm。
基于FANUC系统的加工中心镗孔加工初探

单刃镗刀一般做成可以调节尺寸的形式,根据加工的
用途可分为通孔镗刀、阶梯孔镗刀和盲孔镗刀。 由于单刃
镗 刀 装 夹 在 刀 杆 上 ,靠 紧 固 螺 栓 锁 紧 ,刚 性 较 差 ,容易振
动 ,应选择较大的主偏角,以减少刀杆受到的径向力。单刃
镗刀调节时由于不带刻度,需要在对刀仪或采用打表的方 式进行调节,效率 较低,由于结构简单,成 本 较 低 ,在小批
阵 、三 维 机 器 误 差 模 型 的 构 建 模 式 ,希 望 可 以 为 数 控 加 工 中心位置误差补偿模型领域的发展提供参考,提升数控加 工中心位置误差补偿效果。
参考文献: [1]范晋伟,李伟,李云,蒙顺政,雒驼,罗建平.运用分步式矢 量方法的立式数控加工中心误差分离的研究「J1.机械设计与制
G86、G88、G76、G87 等六种。
指 令 格 式 :G_ X_Y _Z_R_Q_P_ F_ ,其 中 G 为循环指
令 代 码 ,X Y 为 孔 的坐 标 值 ,Z 为 镗 孔 的 最终 深 度,R 为镗
孔的 参考高度,Q 在底孔时镗刀的回退距离(mm), 为孔
有广泛的应用。
2 镗孔加工方法
3.2 镗刀
镗孔加工分为粗镗、半精镗、精镗削刃个数分为单刃镗刀和双刃镗刀。 3.2.1单刃镗刀
粗镗是镗孔加工的重要前期工艺,对工件钻削后的内 孔进行预先的加工,为以后的半精镗精镗奠定基础。粗镗 预 留 单 边 2耀3 毫米作为半精镗、精镗的加工余量。在粗镗 过程中为了提高加工效率,使用 较大 的切削 用量 ,造成切 削 力 较 大 、切 削 温 度 较 高 ,刀 具 磨 损 较 严 重 ,因此粗镗刀必 须具有较高的强度和抗冲击能力。
作者简介:许清海(1976-)男,福建晋江人,机械机电部主任,机 孔长径比较小时,选用刀尖半径大的刀片。
镗孔步骤
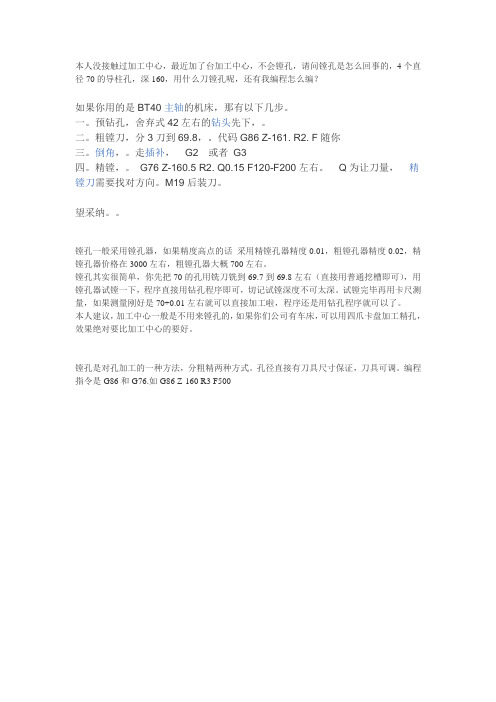
本人没接触过加工中心,最近加了台加工中心,不会镗孔,请问镗孔是怎么回事的,4个直径70的导柱孔,深160,用什么刀镗孔呢,还有我编程怎么编?
如果你用的是BT40主轴的机床,那有以下几步。
一。
预钻孔,舍弃式42左右的钻头先下,。
二。
粗镗刀,分3刀到69.8,。
代码G86 Z-161. R2. F随你
三。
倒角,。
走插补,G2 或者G3
四。
精镗,。
G76 Z-160.5 R2. Q0.15 F120-F200左右。
Q为让刀量,精镗刀需要找对方向。
M19后装刀。
望采纳。
镗孔一般采用镗孔器,如果精度高点的话采用精镗孔器精度0.01,粗镗孔器精度0.02,精镗孔器价格在3000左右,粗镗孔器大概700左右。
镗孔其实很简单,你先把70的孔用铣刀铣到69.7到69.8左右(直接用普通挖槽即可),用镗孔器试镗一下,程序直接用钻孔程序即可,切记试镗深度不可太深。
试镗完毕再用卡尺测量,如果测量刚好是70+0.01左右就可以直接加工啦,程序还是用钻孔程序就可以了。
本人建议,加工中心一般是不用来镗孔的,如果你们公司有车床,可以用四爪卡盘加工精孔,效果绝对要比加工中心的要好。
镗孔是对孔加工的一种方法,分粗精两种方式。
孔径直接有刀具尺寸保证,刀具可调。
编程指令是G86和G76.如G86 Z-160 R3 F500。
数控刀具之孔加工刀具
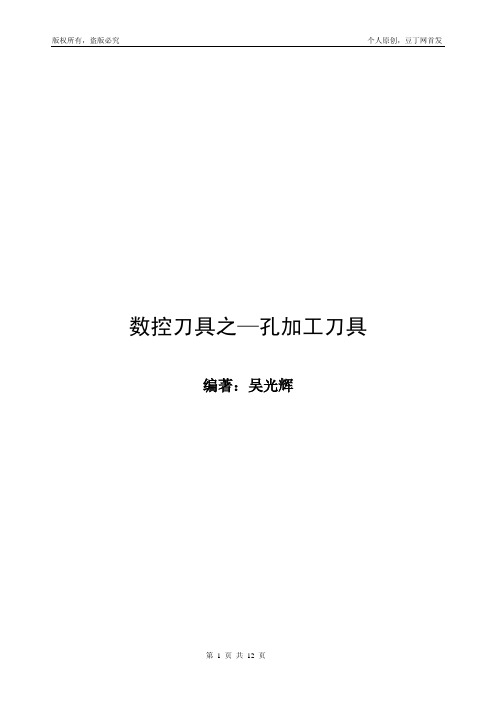
被切屑材料过软切削外排性不好 改换钻头或加工方法
钻柄部有损伤或缺陷引起打滑 消除损伤或缺陷
扁尾折断 过度套有磨损或损伤
更换或修复过渡套
刃磨精度不好(切削阻力大) 重新刃磨校正
发生振动音
后角大 钻头刚性不足
重新刃磨校正 提高钻头刚性
切屑缠绕 切屑过长,切削滞留
重新考虑加工方法,切削条件及钻头选型
顶尖与轴心不重合(车床 ) 钻头单侧磨损
等因素进行研究,根据其各自的切削环
境制作不同形状和材质的刀片,结果大
大提升了快速钻的实际切削性能,而且
与以往的一些快速钻产品相比,可以有
效的提高孔的加工精度。
可转位刀片钻头的选择:确定孔的直径、深度和质量要求——选择钻头类型——选择刀片的牌号
——选择刀片的槽型——选择钻头柄的类型
使用块速钻头尽量使用高压中心出水,以增加刀片寿命及排屑的良好 注 使用 CNC 车床时刀具中心点和机床中心点尽量平行;
第 4 页 共 12 页
版权所有,盗版必究
个人原创,豆丁网首发
制成 60°锥度,保护锥制成 120°锥度。
复合中心钻工作部分的外圆须经斜向铲磨,才能保证锪孔部与钻孔 部的过渡部分具有后角。
(2)定心钻
定心钻(见图 4.2.2b)主要用于进行钻孔前的中心定位和孔口倒角加
工。中心定位加工可提高孔的位置精度,倒角加工可防止攻丝时的在端面
第 3 页 共 12 页
版权所有,盗版必究
后角过大
重新刃磨校正
个人原创,豆丁网首发
钻头材质不合适
改换钻头材质
已超过重磨期
及时刃磨,缩短刃磨周期
顶尖与轴心不重合(车床 )
加工前仔细调整
刃口肩部异常 切削速度过高
镗孔]
![镗孔]](https://img.taocdn.com/s3/m/a1f7625677232f60ddcca1a3.png)
6.7 镗孔工艺、编程6.7.1 镗孔加工概述1.镗孔加工要求镗孔是加工中心的主要加工内容之一,它能精确地保证孔系的尺寸精度和形位精度,并纠正上道工序的误差。
通过镗削上加工的圆柱孔,大多数是机器零件中的主要配合孔或支承孔,所以有较高的尺寸精度要求。
一般配合孔的尺寸精度要求控制在IT7~IT8,机床主轴箱体孔的尺寸精度为IT6,精度要求较低的孔一般控制在IT11。
对于精度要求较高的支架类、套类零件的孔以及箱体类零件的重要孔,其形状精度应控制在孔径公差的1/2~1/3。
镗孔的孔距间误差一般控制在±0.025~0.06 mm,两孔轴心线平行度误差控制在0.03~0.10 mm。
镗削表面粗糙度,一般是Ra1.6~0.4 μm。
2.镗孔加工方法孔的镗削加工往往要经过粗镗、半精镗、精镗工序的过程。
粗镗、半精镗、精镗工序的选择,决定于所镗孔的精度要求、工件的材质及工件的具体结构等因素。
⑴粗镗粗镗是圆柱孔镗削加工的重要工艺过程,它主要是对工件的毛坯孔(铸、锻孔)或对钻、扩后的孔进行预加工,为下一步半精镗、精镗加工达到要求奠定基础,并能及时发现毛坯的缺陷(裂纹、夹砂、砂眼等)。
粗镗后一般留单边2~3 mm作为半精镗和精镗的余量。
对于精密的箱体类工件,一般粗镗后还应安排回火或时效处理,以消除粗镗时所产生的内应力,最后再进行精镗。
由于在粗镗中采用较大的切削用量,故在粗镗中产生的切削力大、切削温度高,刀具磨损严重。
为了保证粗镗的生产率及一定的镗削精度,因此要求粗镗刀应有足够的强度,能承受较大的切削力,并有良好的抗冲击性能;粗镗要求镗刀有合适的几何角度,以减小切削力,并有利于镗刀的散热。
⑵半精镗半精镗是精镗的预备工序,主要是解决粗镗时残留下来的余量不均部分。
对精度要求高的孔,半精镗一般分两次进行:第一次主要是去掉粗镗时留下的余量不均匀的部分;第二次是镗削余下的余量,以提高孔的尺寸精度、形状精度及减小表面粗糙度。
数控加工中心反镗孔刀具及程序设计
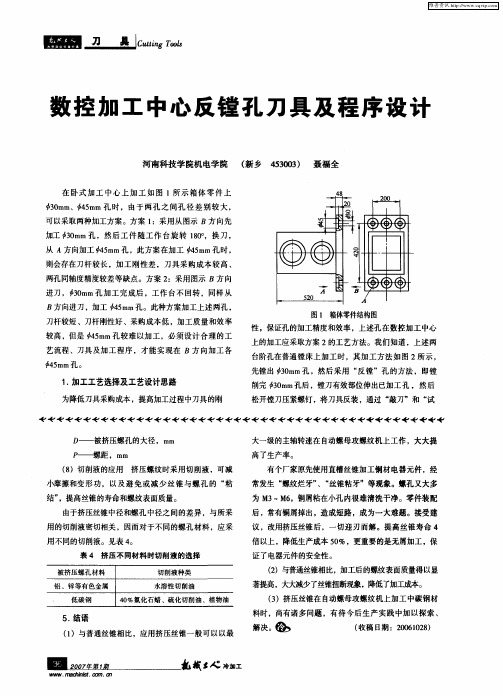
刀杆较短、刀杆刚性好 、 采购成本低 ,加工质量和效率 较高,但是  ̄5 m孔较难以加工,必须设计合理的工 4m 艺流程、刀具及加工程序,才能实现在 曰方向加工各
 ̄5 4 mm孔 。
图 l 箱体零件结构图
性, 保证孔的加工精度和效率 ,上述孔在 数控加工 中心 上的加工应采取方案 2 的工 艺方法。我们知道 ,上述两
下 宜采用涂层硬质合金刀片 ; 线速度 30 50 / i 0 — 0 m mn以
内可采用 陶瓷刀片 ;50 / i 0 m mn以上 ,就应采 用 C N刀 B
2 。在数控加工 中心 )
上加工上述孔 时,也
可借鉴 “ 反镗”孔的 图2 在普通镗床上加工该孔示意图 方法进行 , 为确 保 但 1 压紧螺钉 2 普通镗刀 . .
K" - -K '
K ' -K ' -K ' -K ' -K ' -K ' - -K ' -K ' -K ' -K ' -K" - -K ' -K ' -K" -K ' -K" -K ' -K ' -K ' -K ' - " -K ' -K" -K" ' -K ' -K" -K ' -K ' -K ' ' -K" - ' -K ' - ' -K ' - ' - K K K K K K
为 M M , 3 6 铜屑粘在小孔内很难清洗干净。零件装配
后, 常有铜屑掉出, 造成短路,成为一大难题。接受建
议, 改用挤压丝锥后,一切迎刃而解。提高丝锥寿命 4 倍以上,降低生产成本 5 %,更重要的是无屑加工,保 0
证了电器元件 的安全性 。
()与普通丝锥相 比,加工后 的螺纹 表面质量得 以显 2
结” ,提高丝锥的寿命和螺纹表面质量。 由于挤压丝锥中径和螺孔中径之间的差异,与所采
镗刀刀具知识
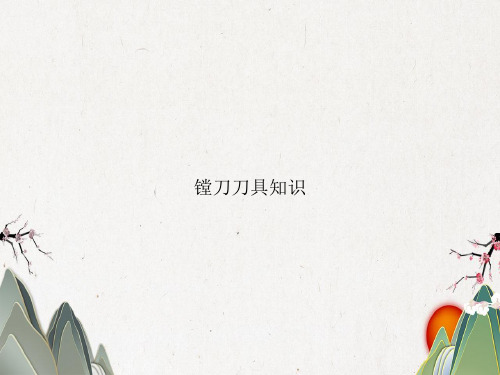
同一镗头
既可用于正镗→
也可用于反镗→
二、精镗刀具 3、模块式精镗安装示意
延长器
减径器
根据不同的孔径,孔深及型状选配刀具。
二、精镗刀具
3、模块式精镗切削参数 Vc=80-300,进给F=0.05-0.1,切深ap=0.1-0.3
三、精镗注意事项
1、精镗加工步骤 2
1.对刀
3
5
4 调整
6 7
试切 测量 试切 测量 加工
消除齿隙?
三、精镗注意事项
5、表面光洁度与进给及刀尖半径的关系
进给增大
刀尖半径增大
r1 Ry1
进给f1
r1 R
进给f2
r2 Ry3
进给f1
f2 Ry =
8r
三、精镗注意事项
5、振动的发生&解决办法
发生振动的原因很复杂但主要是: · 工具系统的刚性 · 工具系统的平衡性 · 工件自身的刚性和工件的固定刚性 · 刀片(刀尖半径前角、后角、断屑槽) · 切削条件(速度、进给、切削量、冷却液) · 主轴系统(刚性、精度、连接刚性)
四、对刀仪
1、电子式
2、光学感应式
(经济 适用) (功能丰富)
五、考考你???
你A
该
选
择 谁
B
?
d1
L1
L2
d2
d1
L2 L1
五、考考你???
你
A
该
选
择B
谁
?
五、考考你???
A
Φ39
你该选择谁?
B
Φ50
41-54 例:Φ53 52-70
五、考考你???
A
Φ50
52-70
数控机床镗削加工技巧分享

数控机床镗削加工技巧分享数控机床镗削加工是现代制造业中的一种非常重要的加工方式。
与传统的手动和半自动加工相比,数控机床镗削具有高效性、精度高、可靠性强等优点。
本文将分享一些数控机床镗削加工的技巧,希望对读者在实际应用中有所帮助。
首先,正确选择刀具是数控机床镗削加工的关键。
刀具的选择应根据工件的材质、形状和加工要求来确定。
常用的刀具材料有硬质合金、高速钢和陶瓷等,而刀具的设计要根据具体的加工要求来确定。
在选择刀具时,应注意刀具的强度、刚性和耐磨性等因素,并且要根据工件的尺寸和形状来选择合适的刀具长度。
其次,合理设置加工参数也是数控机床镗削加工的重要一环。
加工参数的设置直接影响到加工效果和加工质量。
在设置切削速度时,应根据工件材料和刀具材料来确定,通常可以通过试切试验来确定最佳的切削速度。
切削进给量的选择要根据切削力的大小和刀具的刃长来确定,切削过大容易导致切削力过大,从而影响加工质量。
此外,还要注意切削液的选择和使用,切削液可以有效降低切削温度、延长刀具寿命和提高加工质量。
另外,精确测量工件尺寸是数控机床镗削加工中不可或缺的一步。
在加工结束后,应通过合适的测量工具来测量工件的尺寸,并与设计尺寸进行对比。
常用的测量工具有千分尺、千分表和高度规等。
同时,在测量过程中要注意保持测量工具的准确度和稳定性,并进行合理的修整和调整。
此外,刀具磨损的检查和更换也是数控机床镗削加工中的重要环节。
刀具的磨损会直接影响加工精度和加工质量,因此应定期检查刀具的磨损情况,并及时更换。
通常可以通过目测和测量刀具的刃口长度等来判断刀具的磨损情况。
一旦发现刀具磨损严重,应立即更换刀具,以保证加工质量。
最后,合理设计夹具和工装也是数控机床镗削加工中的重要一环。
夹具和工装的设计直接影响到工件的稳定性和加工精度。
在设计夹具和工装时,应考虑工件的形状、尺寸和加工要求,并确保夹具和工装能够牢固地夹紧工件,同时又不会对工件造成损坏。
此外,还要注意夹具和工装的刚性和稳定性,避免在加工过程中产生振动和变形。
镗孔工作原理
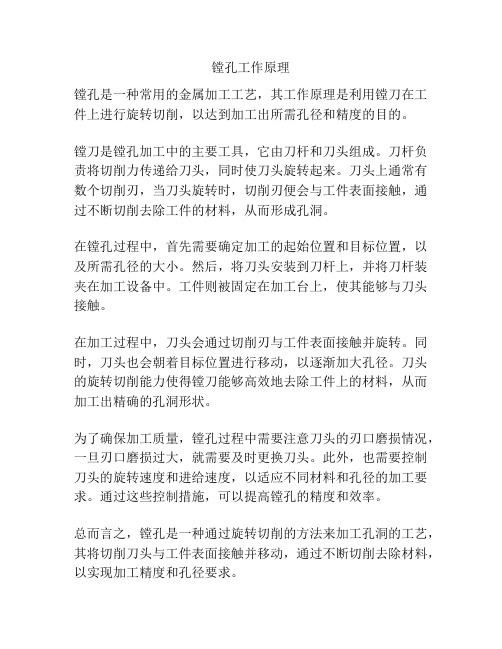
镗孔工作原理
镗孔是一种常用的金属加工工艺,其工作原理是利用镗刀在工件上进行旋转切削,以达到加工出所需孔径和精度的目的。
镗刀是镗孔加工中的主要工具,它由刀杆和刀头组成。
刀杆负责将切削力传递给刀头,同时使刀头旋转起来。
刀头上通常有数个切削刃,当刀头旋转时,切削刃便会与工件表面接触,通过不断切削去除工件的材料,从而形成孔洞。
在镗孔过程中,首先需要确定加工的起始位置和目标位置,以及所需孔径的大小。
然后,将刀头安装到刀杆上,并将刀杆装夹在加工设备中。
工件则被固定在加工台上,使其能够与刀头接触。
在加工过程中,刀头会通过切削刃与工件表面接触并旋转。
同时,刀头也会朝着目标位置进行移动,以逐渐加大孔径。
刀头的旋转切削能力使得镗刀能够高效地去除工件上的材料,从而加工出精确的孔洞形状。
为了确保加工质量,镗孔过程中需要注意刀头的刃口磨损情况,一旦刃口磨损过大,就需要及时更换刀头。
此外,也需要控制刀头的旋转速度和进给速度,以适应不同材料和孔径的加工要求。
通过这些控制措施,可以提高镗孔的精度和效率。
总而言之,镗孔是一种通过旋转切削的方法来加工孔洞的工艺,其将切削刀头与工件表面接触并移动,通过不断切削去除材料,以实现加工精度和孔径要求。
立式加工中心镗削工艺的加工步骤及注意事项

立式加工中心镗削工艺的加工步骤及注意事项立式加工中心镗削步骤及注意事项:镗刀安装安装镗刀工作部是很重要的,特别是针对采用偏心原理的工作调整,安装镗孔刀后一定要注意观察镗刀的主刀刃上平面,是否与镗刀头的进给方向在同一水平面上?安装在同一水平面上才能保证几个切屑刃是在正常的加工切削角度。
镗削步骤及注意事项镗刀试镗孔镗刀按工艺制造要求调整预留0.3~0.5mm余量,扩镗、配镗孔按初孔余量调整粗镗余量≤0.5mm,必须保证满足后续精镗加工余量。
镗刀安装借出后,需开展试镗验证镗刀调试是否满足粗镗要求。
镗削步骤及注意事项镗孔要求镗削加工前仔细检查工装、工件的定位基准、各定位元件是否稳定可靠。
用卡尺检测待加工初孔的直径是多少?测算现在还有多少预留加工余量?镗孔加工前检查设备(主轴)重复定位精度、动态平衡精度是否满足工艺加工制造要求。
卧加镗孔试镗过程中须检查镗杆重力悬伸动态跳动值,合理修正切削参数减少加工离心剪切振动影响。
按粗镗、半精镗、精镗步骤合理分配层镗削余量,粗镗余量约0.5mm为宜;半精镗、精镗余量约0.15mm,防止半精镗因余量过大产生让刀现象影响精镗余量调整精度。
难加工材料、高精度镗孔(容差≤0.02mm)可增加精细镗加工步骤,镗削余量不小于0.05mm防止加工面弹性让刀。
刀对刀过程中,须注意防止镗刀工作部(刀片和刀座)与对刀块发生冲击,损坏刀片及刀座导向槽使镗刀调整值发生变化影响孔径加工精度。
镗削加工过程中注意保持冷却充分,增加加工部位的润滑效果以减少切削力。
各加工步骤中严格排屑,防止切屑参与二次切削影响孔径加工精度与表面质量。
镗削加工过程中随时检查刀具(刀片)磨损程度,及时更换以保证孔径加工质量;精镗步骤严禁更换刀片防止误差;每步骤加工后须严格执行过程质量控制要求,仔细检测实际加工孔径并做好记录,便于分析、调整完善镗孔加工。
镗削加工主要问题刀具磨损在镗削加工中,刀具连续切削,易出现磨损和破损现象,降低孔加工的尺寸精度,使表面粗糙度值增大;同时,微调进给单元标定出现异常,导致调整误差使加工孔径出现偏差甚至引发产品质量故障。
- 1、下载文档前请自行甄别文档内容的完整性,平台不提供额外的编辑、内容补充、找答案等附加服务。
- 2、"仅部分预览"的文档,不可在线预览部分如存在完整性等问题,可反馈申请退款(可完整预览的文档不适用该条件!)。
- 3、如文档侵犯您的权益,请联系客服反馈,我们会尽快为您处理(人工客服工作时间:9:00-18:30)。
加工中心上镗孔加工的刀具技术
1 机床润滑系统的特点和分类
机床润滑系统在机床整机中占有十分重要的位置,其设计、调试和维修保养,对于提高机床加工精度、延长机床使用寿命等都有着十分重要的作用。
现代机床导轨、丝杆等滑动副的润滑,基本上都是采用集中润滑系统。
集中润滑系统是由一个液压泵提供一定排量、一定压力的润滑油,为系统中所有的主、次油路上的分流器供油,而由分流器将油按所需油量分配到各润滑点:同时,由控制器完成润滑时间、次数的监控和故障报警以及停机等功能,以实现自动润滑的目的。
集中润滑系统的特点是定时、定量、准确、效率高,使用方便可靠,有利于提高机器寿命,保障使用性能。
集中润滑系统按使用的润滑元件可分为阻尼式润滑系统、递进式润滑系统和容积式润滑系统。
2 单线阻尼式润滑系统
此系统适合于机床润滑点需油量相对较少,并需周期供油的场合。
它是利用阻尼式分配器,把泵打出的油按一定比例分配到润滑点。
一般用于循环系统,也可以用于开放系统,可通过时间的控制,以控制润滑点的油量。
该润滑系统非常灵活,多一个润滑点或少一个都可以,并可由用户安装,且当某一点发生阻塞时,不影响其他点的使用,故应用十分广泛。
3 递进式润滑系统
递进式润滑系统主要由泵站、递进片式分流器组成,并可附有控制装置加以监控。
其特点是能对任一润滑点的堵塞进行报警并终止运行,以保护设备;定量准确、压力高,不但可以使用稀油,而且还适用于使用油脂润滑的情况。
润滑点可达100个,压力可达21MPa。
递进式分流器由一块底板、一块端板及最少三块中间板组成。
一组阀最多可有8块中间板,可润滑18个点。
其工作原理是由中间板中的柱塞从一定位置起依次动作供油,若某一点产生堵塞,则下一个出油口就不会动作,因而整个分流器停止供油。
堵塞指示器可以指示堵塞位置,便于维修。
4 容积式润滑系统
该系统以定量阀为分配器向润滑点供油,在系统中配有压力继电器,使得系统油压达到预定值后发讯,使电动机延时停止,润滑油从定量分配器供给,系统通过换向阀卸荷,并保持一个最低压力,使定量阀分配器补充润滑油,电动机再次起动,重复这一过程,直至达到规定润滑时间。
该系统压力一般在50MPa以下,润滑点可达几百个,其应用范围广、性能可靠,但不能作为连续润滑系统。
定量阀的结构原理是:由上下两个油腔组成,在系统的高压下将油打到润滑点,在低压时,靠自身弹簧复位和碗形密封将存于下腔的油压入位于上腔的排油腔,排量为0.1~1.6mL,并可按实际需要进行组合。
5 润滑系统故障维修4例
加工表面粗糙度不理想的故障维修
故障现象:某数控龙门铣床,用右面垂直刀架铣产品机架平面时,发现工件表面粗糙度达不到预定的精度要求。
分析及处理过程:这一故障产生以后,把查找故障的注意力集中在检查右垂直刀架主轴箱内的各部滚动轴承(尤其是主轴的前后轴承)的精度上,但出乎意料的
是各部滚动轴承均正常;后来经过研究分析及细致的检查发现:为工作台蜗杆及固定在工作台下部的螺母条这一传动副提供润滑油的四根管基本上都不供油。
经调节布置在床身上的控制这四根油管出油量的四个针形节流阀,使润滑油管流量正常后,故障消失。
润滑油损耗大的故障维修
故障现象:TH5640立式加工中心,集中润滑站的润滑油损耗大,隔1天就要向润滑站加油,切削液中明显混入大量润滑油。
分析及处理过程:TH5640立式加工中心采用容积式润滑系统。
这一故障产生以后,开始认为是润滑时间间隔太短,润滑电动机起动频繁,润滑过多,导致集中润滑站的润滑油损耗大。
将润滑电动机起动时间间隔由12min改为30min后,集中润滑站的润滑油损耗有所改善但是油损耗仍很大。
故又集中注意力查找润滑管路问题,润滑管路完好并无漏油,但发现Y轴丝杠螺母润滑油特别多,拧下Y轴丝杠螺母润滑计量件,检查发现计量件中的Y形密封圈破损。
换上新的润滑计量件后,故障排除。
导轨润滑不足的故障维修
故障现象:TH6363卧式加工中心,Y轴导轨润滑不足。
分析及处理过程:TH6363卧式加工中心采用单线阻尼式润滑系统。
故障产生以后,开始认为是润滑时间间隔太长,导致Y轴润滑不足。
将润滑电动机起动时间间隔由15min改为10min,Y轴导轨润滑有所改善但是油量仍不理想。
故又集中注意力查找润滑管路问题,润滑管路完好;拧下Y轴导轨润滑计量件,检查发现计量件中的小孔堵塞。
清洗后,故障排除。
润滑系统压力不能建立的故障维修
故障现象:TH68125卧式加工中心,润滑系统压力不能建立。
分析及处理过程:TH68125卧式加工中心组装后,进行润滑试验。
该卧式加工中心采用容积式润滑系统。
通电后润滑电动机旋转,但是润滑系统压力始终上不去。
检查润滑泵工作正常,润滑站出油口有压力油:检查润滑管路完好;检查X 轴滚珠丝杠轴承润滑,发现大量润滑油从轴承里面漏出;检查该计量件,型号为ASA-5Y,查计量件生产公司润滑手册,发现ASA-5Y为单线阻尼式润滑系统的计量件,而该机床采用的是容积式润滑系统,两种润滑系统的计量件不能混装。
更换容积式润滑系统计量件ZSAM-20T后,故障排除。