氧化膜连续性测试
ISO 7599-1983 铝和铝合金的阳极氧化铝的阳极氧化膜的一般规范

国际标准ISO7599铝和铝合金的阳极氧化铝的阳极氧化膜的一般规范第一版— 1983-09-15前言ISO(国际标准化组织)是一个国家标准机构(ISO成员组织)的世界联盟。
国际标准的起草准备工作通常由ISO的技术委员会进行。
任何对技术委员会所起草标准主题感兴趣的组织成员,与ISO有关的国际组织,政府或非政府性均有权利加入该技术委员会。
由技术委员会起草的国际标准草案在ISO委员会接受其为国际标准前要分发给各成员组织进行表决。
ISO7599是由ISO/TC 79技术委员会起草准备。
轻金属和其合金,在1982年3月分发到各成员。
已被以下成员国家批准通过:澳大利亚伊拉克沙特阿拉伯奥地利爱尔兰南非中国日本西班牙捷克斯洛伐克韩国瑞典埃及墨西哥瑞士法国挪威大不列颠联合王国匈牙利波兰美国印度罗马尼亚苏联以下成员国家对技术领域的文件表示不赞同:意大利荷兰铝和铝合金的阳极氧化铝的阳极氧化膜的一般规范1 范围本国际标准描述阳极氧化铝的阳极氧化膜的一般规范。
它定义了阳极氧化铝的阳极氧化膜的特性,列出了检查特性的检测方法,说明了最低检测要求,提供了适合阳极氧化的铝的等级的信息,并且描述了为了保证所要求的外观或修整的表面而做的预处理的重要性。
2 适用领域本国际标准主要适用阳极氧化铝的氧化膜,这种氧化膜在铝的表层,通过一个铝作正极的电解氧化过程而形成。
其不适用:a)阻挡层类型的非多孔渗水的阳极氧化膜;b)只为准备同时产生的有机氧化膜或金属电解底层的阳极氧化膜;c)硬质阳极氧化膜,主要用于工程用途,该阳极氧化膜的主要特点是耐磨损性。
3 参考ISO1463,金属和阳极氧化膜—氧化膜厚度的测量—精微方法。
ISO2064,金属和其它非有机氧化膜—关于厚度测量的定义和惯例。
ISO2079,表面处理和金属氧化膜—术语的通常分类。
ISO2085,铝和其合金的阳极氧化处理—薄阳极氧化膜的连续性的检查—硫酸铜测试。
ISO2106,铝和其合金的阳极氧化处理—单位面积(表面密度)阳极氧化膜的质量的确定—重量分析法。
电镀锡薄钢板氧化膜和钝化膜的分析检测方法

电镀锡薄钢板氧化膜和钝化膜的分析检测方法V_o1.29No.11电镀锡薄钢板氧化膜和钝化膜的分析检测方法曾林,李宁术,黎德育(哈尔滨工业大学化工学院应用化学系,黑龙江哈尔滨150001)摘要:介绍了电镀锡薄钢板氧化膜和钝化膜的分析检测方法,包括传统的化学分析方法,电化学分析方法和现代表面分析技术,如x射线光电子能谱(xPs),俄歇电子能谱(AES),辉光放电光谱(GDS)以及电子探针微区分析(EPMA)等.关键词:镀锡钢板;X射线光电子能谱;俄歇电子能谱;辉光放电光谱;电子探针微区分析中图分类号:TQ153.13文献标志码:A文章编号:1004—227X(2010)1l一0041—05 Detectionandanalysismethodsforoxidefilmandpassivefilmontinplate//ZENGLin,LINing,LIDe—yuAbstract:Thedetectionandanalysismethodsforoxidefilm andpassivefilmontinplatedsteelsheetincludingthe traditionalchemicalanalysis,electrochemicalanalysisand modemsurfaceanalysistechnologiessuchasX—ray photoelectronspectroscopy(xes),Augerelectronspectroscopy(AES),glowdischargespectrometry(GDS)andelectronicprobemicro.analysis(EPMA)wereintroduced.Keywords:tinplate;X—rayphotoelectronspectroscopy; augerelectronspectroscopy;glowdischargespectrometry; electronicprobemicro—analysisFirst-author'saddress:DepartmentofAppliedChemistry. SchoolofChemicalEngineering&Technology.Harbin InstituteofTechnology.Harbin150001.China1前言镀锡板是在低碳薄钢板表面电镀纯锡而成,由于锡金属显着的成型性,可焊性以及无毒性,因此镀锡板在食品包装行业得到了广泛的应用n].虽然目前电镀锡钢板受到了铝,玻璃,塑料等替代材料的挑战,但是电镀锡板仍然在包装行业占有很大的份额.现代化的高速电镀锡生产线能快速地生产高质量的电镀锡卷材和片材,满足食品包装行业的使用需求【2_3】.电镀锡薄钢板成品组成比较复杂,其基本组成示意图如图1[4-5].收稿日期:201O_06_09作者简介:曾林(1985一),男,湖南岳阳人,硕士,研究方向为电镀和表面处理.通讯作者:李宁,教授,博士生导师,(E—mail)lininghit@.图1镀锡钢板组成示意图Figure1Schematicdiagramofcompositionoftinplatedsteelsheet一般镀锡板浅表层指的是自由锡层顶层及其以上部分,即镀锡板表面20~50nm范围内,包括钝化膜,氧化膜以及自由锡层.由于镀锡层是一个阴极型镀层,镀锡板浅表层的构成会影响到镀锡板的外观,耐蚀性能,涂漆性能以及钎焊性能等l6J,因此镀锡板浅表层的构成对镀锡板的质量至关重要.本文总结了电镀锡薄钢板氧化膜和钝化膜的分析检测方法.这些方法能够较好地了解镀锡板氧化膜和钝化膜的信息,为镀锡板质量问题的解决以及镀锡板质量的改进提供帮助.2氧化膜和钝化膜的组成电镀锡薄钢板表面的氧化膜主要成分为SnO2和SnO.电镀锡薄钢板在储存过程中,表层的自由锡与空气接触会部分氧化形成SnO2.SnO是锡的高温氧化物, 主要形成于电镀锡工艺中软熔工艺段.如果软熔温度控制不当,形成大量SnO,镀锡板质量将会受到较大的影响.在实际检测过程中,锡元素的检测既有锡氧化物的检测,也包括自由锡的检测.《镀锡板指南》[7j指出,应将锡氧化物控制在较低的含量,锡氧化物含量过高会对镀锡板质量造成不利影响.与氧化膜相比,钝化膜比较薄,且组成复杂(不同的钝化工艺对钝化膜组成的影响很大).研究表明,钝化膜的组成包括Cr,Cr(OH)3或者Cr(OH)3"nH2O,Cr203 和残留的cr(VI).对化学钝化而言,铬总含量较低,为1~3mg/m,主要为Cr(OH)3以及残留的Cr(VI).电镀锡薄钢板氧化膜和钝化膜的分析检测方法而现在常用的阴极钝化工艺所得钝化膜中铬的总含量较高,为5~12mg/m2,其中包括上面提到的所有成分.虽然六价铬有毒,但是经重铬酸盐钝化后得到的钝化膜能提高镀锡板的耐氧化能力,抗硫化斑能力和涂漆附着力,因此铬酸盐钝化工艺仍在沿用.表l总结了铬及其化合物的各种分析方法.表1铬及其化合物的分析方法Table1AnalysismethodsforchromiumanditscompoundsCr(OH)3碱性可溶,在电化学检测时不能够被阳极氧化;Cr203碱性不可溶,在电化学检测中能够被阳极氧化【】们.这些差别导致化学方法和电化学方法无法完全检测镀锡板钝化后的表面铬含量,更无法分析铬元素的种类,只有现代表面分析技术才能胜任.3化学检测方法3.1钝化膜的化学检测美国测试材料协会标准ASTMA623—77详细描述了通过化学方法分析镀锡板钝化膜含铬量的方法,具体的测试过程如下:将电镀锡板放入1mol/LNaOH和W=5%的Na3PO混合溶液中煮沸约1.5min,然后将碱液转移至新容器中,向原来的烧杯和试样加入25mL H2So4溶液,加热至沸点,然后滴加1~2滴KMnO4使溶液呈粉红色,煮沸3~4min使铬氧化,再加入5滴盐酸=1.19g/mL),继续煮沸直至粉红色消失为止.加入指示剂二苯卡巴肼并定容,用分光光度计测定在540nln处的光密度.该检测过程实际上是将钝化膜氧化并检测溶液中Cr(VI),因此这个方法的缺点是无法检测到表面残留六价铬的量.3.2氧化膜的化学检测氧化膜层的检测比较麻烦.一般而言,无法单独通过化学方法测定锡氧化膜的含量,但是,锡氧化膜和自由锡层可以一起溶解之后检测出来.例如将镀锡板浸入50g/LNaOH和l0LKIO3的混合溶液中,直到自由锡层完全去除,然后采用化学滴定法测试溶液中锡元素的含量,从而得到镀层中锡的含量.不过由于溶解自由锡层的终点不容易判定,因此这种测量方法误差比较大.?2-4电化学检测电化学检测钝化膜和氧化膜含量在现代化的电镀锡生产线现场检测中得到了广泛应用.其基本原理是施加恒定的电流,记录电位一时间曲线,通过电位一时问曲线中的电势变化来分析氧化膜和钝化膜的含量. 这种检测方法简单易行,并且精确度较高.4.1氧化膜的电化学检测在一种不含氧且与锡的氧化物不反应的溶液(如lmmol/L的氢溴酸)中,用一定的微小电流使镀锡板试片表面的锡氧化物还原,记录电位一时间曲线,锡氧化物的量可用氧化物完全还原所消耗的电量来度量.由于表层锡氧化物含量少,还原所需的电量较小,因此阴极还原电流不宜过大,合适的电流密度为25Hl2.测试过程中,溶液中的溶解氧对测试结果影响很大, 因此氢溴酸溶液在使用之前需严格除氧【17'¨】. 图2是典型的锡氧化物还原的电位一时间曲线.t/S图2锡氧化物还原的电位一时间曲线Figure2PotentialVS.timecurveforthereductionoftinoxide 通过做切线的方法可以求得锡氧化膜还原所需的时问,从而计算出还原所需要的电量.锡氧化物的组成不是固定的,因此实际上通常是将氧化物量记录为以mC/cm表示的还原电量值.对新电镀锡板而言,所测得的还原电量值通常小于1mC/cm2.4.2钝化膜的电化学检测前面已经提到,电化学方法无法完全检测出钝化膜的铬含量,但是可以通过化学分析法对照而标定出对应的换算关系,这种方法仍然能够得到很好的应用. 由于简单易行,电化学检测钝化膜的方法能够满足大多数常规性检测'川J.测试原理是通过施加阳极电流使钝化膜中可被阳极氧化的部分氧化成可溶性的六价铬.由于被氧化的铬价态不相同,不能简单按照Cr~氧化成Cr+的氧化反应通过的电量计算铬的理论含量.测试溶液一般选择pH为6.0~8.5的磷酸型缓冲溶液,电流密度通常采用25,A/era2.钝化膜阳极氧化典型的曲线如图3所示. 该测量法的关键在于确定钝化膜溶解的起始时间(图3 电镀锡薄钢板氧化膜和钝化膜的分析检测方法中的A点)和结束时间(图3中的B点).确定钝化膜溶解时间之后,乘以通过的电流就可以确定溶解所需的电量.换算关系为:1mC/cm相当于O.1pg/cm表面铬量.这是一种近似的测定值,其准确性取决于同化学分析结果相对而进行的标定.图3电镀锡板钝化膜电化学检测的电位一时间曲线Figure3Potential.timecurveofelectrochemicalanalysis forpassivefilmontinplate5现代表面分析技术检测随着现代现场技术和各种谱学技术的发展,许多新型的现代科学分析设备被应用于表面分析中.各种表面分析仪器和测试技术的出现,为精确和完整了解表面的各种信息提供了有力的保证【12-14].现代电镀锡行业中也广泛采用这些分析技术,以便了解电镀锡板表面的信息,分析和解决技术故障以及改进电镀工艺.以下简要介绍几种常用于镀锡板表面的分析技术,这些方法大部分已获得了实际应用.5.1X射线光电子谱(xes)待测物受x光照射后,内部电子吸收光能而脱离待测物表面形成光电子,不同元素形成的光电子是不同的,因此,通过对光电子能量的分析可了解待测物的组成.应用XPS能够分析表面元素组成和化学组成,原子的价态以及表面能态分布.该方法可用于定性和定量分析.镀锡板表面XPS测试中常见元素的特征谱线见表2.表2镀锡板表面元素主要的XPS特征谱线Table2MainXPScharacteristicspectrallinesofelementson thesurfaceoftinplate元素特征谱线及其结合能Sn3d5/2484.9eV;SnO486.3eV;SnO2487.3eV;SnSn3d/2493.3eV:Sn497.2eV;Sn3p3/2714.6eV;Sn3p1/2756.2eV:Sn3s885.2eVCr2p3/2574.3eV:Cr2p575.0eV.Cr203575.6eV;CrCrO3579.5eV:Cr574.3eV:Cr(OH)3577~577.8eV!旦!鱼:二Z:!!212!!:=!OO2s23.1eV;Ols531.8eV;金属氧化物528.1~531eVFe2p3/2706.7eV;FeS2707.2eV.FeO709.8eVFe7-Fe203710.4eV:c【一Fe203710.8eV;FeOOH711.5eV:Fe2pl/2719.9eVCC1S285.0eV注:数据来源于XPSInternationa1.1nc.网站以及Perkin.Elmer公司的XPS数据手册.对比特征谱线可以定性分析镀锡板表面元素的组成.对比实际测量的谱线和特征谱线的结合能,了解元素的化学位移,可以了解元素所处的化学环境以及所处的化学形态.同样,XPS也能够进行定量的分析,通过和标准样品谱峰相比较即所谓的标样法来进行分析,精确度可达98%~99%.XPS分析中采用A溅射.溅射速率一定时,通过控制溅射时间可以精确地刻蚀掉镀锡板表面一定的厚度(纳米级),实现对镀锡板表层的逐层分析.XPS分析的另外一个应用是可以进行小角度分析,其原理如图4所示.(a)大角度分析(a)Analysisinlargeanglefb)小角度分析(b)Analysisinsmallangleb/eV(c1XPS小角度分析镀锡板表面Sn,O和Cr元素(c)Sn,OandCranalysisbyXPSinsmallangleonthesurfaceoftinplate 图4XPS分析镀锡板表面元素Figure4XPSanalysisofelementsonthesurfaceoftinplate图4a中检测器和样品的角度为90.,接收到的光电子信号为镀层深层元素的信号;图4b中检测器和样品的角度较小,接收到的光电子信号为镀层浅表层元素的信号.通过不断调整检测角的大小,可以实现对镀锡板表面元素的逐层分析,能够很好地表征镀锡板表面钝化膜以及氧化膜的分布情况.图4c是对某种镀锡板表面的检测结果,可以看到随着检测角度的增大(即检测深度的增加),表层的Sn氧化物含量降低,而自由锡的含量上升;检测角小时表层检测不到Cr单质的信号,而检测角增加时,表层出现Cr单质的信号,这说明镀锡板进行阴极钝化时首先在自由锡顶层沉积一层Cr单质,然后才会出现Cr的化合物.这可用来探讨阴极钝化的成膜机理【1].??电镀锡溥铜板氧化膜和钝化膜的分析检测方法图5是本课题组对某镀锡板XPS分析的结果.{/L\——————————/\//~}\,——————————L~/,厂\\//\\———一/LLJu496492488484480Eb/eV图5镀锡板sn元素的XPS谱图Figure5XPSpatternofSnintinplate图5中黑色的竖线是Sn的3d5/2和3d3/2特征谱线.正常板溅射前出现2个峰,说明表面存在单质锡以及氧化锡.溅射300S(Ar+刻蚀速率为0.03nm/s,刻蚀深度约为10nm)后,只存在一个单质锡的峰,说明正常板表面存在一个氧化膜层,且该氧化膜较薄.溅射10nm之后基本上为纯锡的信号峰,说明氧化膜的厚度约为10nm.有缺陷的镀锡板表层基本上没有锡单质的信号峰,结合能向高处移动,说明表面形成了锡的氧化物,自由锡层已经全部被氧化.溅射600S(刻蚀深度约为20nm)后才有纯锡的信号峰,说明其表层的氧化膜较厚.同时,与特征谱线对比,缺陷板溅射600S后的峰形和特征谱线仍然有一定的化学位移,说明镀锡板表面锡氧化态多样且不唯一.5.2俄歇电子能谱(AES)俄歇电子能谱和XPS相似,也是基于"激励一响应" 机制,不同的是俄歇电子能谱仪采用高能电子束,内层电子受到激发后,在退激发时使较外层电子激发成为自由电子(被称为俄歇电子),通过检测这些俄歇电子可以表征镀锡板的组成.俄歇电子测试也应用于镀锡板表面成分的检测.一般而言,俄歇电子应用于镀锡板表面定性检测的结果较好,因为轰击的电子能量高,基本上镀层中的所有元素都能够产生信号,对于一些微量元素的检测效果较好.但是,俄歇电子测试的定量分析精度不高,只能做半定量分析(精度仅为30%左右).但如果能够正确估计俄歇电子的有效深度,那么精度可提高不少. 图6是阴极钝化之后电镀锡板表面的俄歇电子能谱.5.3辉光放电光谱(GDS)辉光放电光谱的基本原理与其他发射光谱类似,即利用一种光源使被测样品元素处于受激状态,样品元素外层电子从高能态回到低能态时发射出特征光谱,根据元素发射出的特征光谱分析出样品中含有的元素.●-●..nl/-●Ieh…-Sn0(1002003004删300删700800900l000l100/eV图6电镀锡板的俄歇电子能谱图Figure6Augerelectronspectrumoftinplate辉光放电光谱应用于镀锡板表面元素分析具有很多优点:(1)镀锡板可以直接检测,加上辉光放电的温度不高,基本上可以认为是原位检测;(2)检出限低; (3)可对样品表面进行逐层检测;(4)检测速度陕,一次能够给出十几个元素含量的信息【l6_"】.与XPS相比, GDS能够进行深度剖析,即从最外层的钝化膜开始进行逐层的分析,直到铁基体,而这是XPS做不到的.辉光放电应用于镀锡板表面的钝化膜和氧化膜的检测已经有一些研究结果.借助于GDS的深度剖析,能够比较全面地了解钝化膜和氧化膜的组成,以及Cr, Sn,0等元素随镀层厚度的变化,同时也可以用于定量分析.5.4电子探针微区分析(EPMA)EPMA是利用聚焦电子束与试样微米至亚微米尺度的区域相互作用,用x射线谱仪对电子激发体积内的元素进行分析的技术.与扫描电子显微镜(SEM)相比,EPMA可在样品微米领域进行高灵敏度的无损元素分析.配备波谱仪(WDS)及能谱仪(EDS)的电子探针仪能够对镀锡板表面进行点分析,线分析,可在1~2gm范围内得到定量分析结果.同时,电子探针仪还能够进行面分析,可对镀锡板表面进行三维空间分析, 结合镀锡板试样的微观图像,得出镀锡板表面元素分布及其含量的信息.图7是本课题组对一种缺陷镀锡板进行EPMA面分析的结果.图7a是背散射图像,从中可以看到镀锡板表面存在条状的缺陷.图7b是Sn元素面分析的结果.从图7b中可以看出,产生这些缺陷的地方,Sn元素的信号峰弱,说明这些缺陷区域表层的锡层已经被破坏.从图7中的标尺可以看出,EPMA能够对镀锡板表层的微小区域(微米级)进行分析.EPMA分析的缺点是定量分析较差,一些轻元素峰重叠和峰干扰比较强;但是,可以采用定量修正的方法对测试结果进行修正,国家标准也对这种方法进。
铝及铝合金阳极氧化膜检测方法
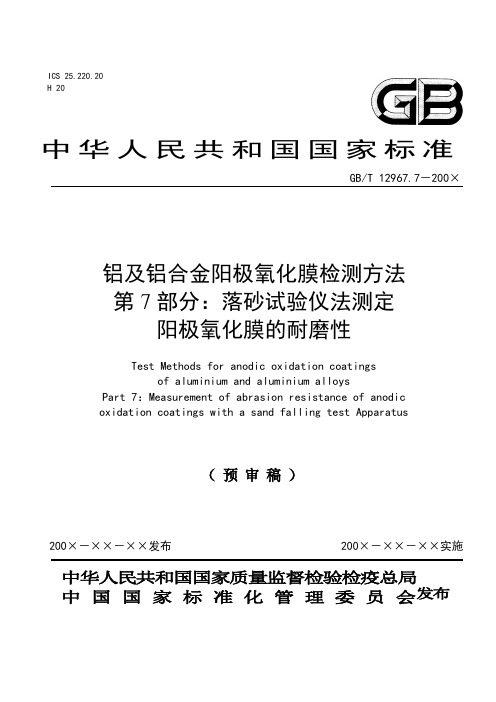
ICS 25.220.20 ArrayH 20中华人民共和国国家标准GB/T 12967.7-200×铝及铝合金阳极氧化膜检测方法第7部分:落砂试验仪法测定阳极氧化膜的耐磨性Test Methods for anodic oxidation coatingsof aluminium and aluminium alloysPart 7:Measurement of abrasion resistance of anodicoxidation coatings with a sand falling test Apparatus(预审稿)200×-××-××发布 200×-××-××实施中华人民共和国国家质量监督检验检疫总局中国国家标准化管理委员会发布GB/T 12967.7-200×前言GB/T 12967《铝及铝合金阳极氧化膜检测方法》分为7个部分:——第1部分用喷磨试验仪测定阳极氧化膜的平均耐磨性——第2部分用轮式磨损试验仪测定阳极氧化膜的耐磨性和耐磨系数——第3部分铜加速乙酸盐雾试验(CASS试验)——第4部分着色阳极氧化膜耐紫外光性能的测定——第5部分用变形法评定阳极氧化膜的抗破裂性——第6部分目视观察法检验着色阳极氧化膜色差和外观质量——第7部分用落砂试验仪测定阳极氧化膜的耐磨性本部分为GB/T 12967的第7部分。
本部分参照了JIS H 8682-3:1999《铝及铝合金阳极氧化膜耐磨性试验方法-第3部分:落砂磨损试验方法》。
本部分的附录A是规范性附录。
本部分由中国有色金属工业协会提出。
本部分由全国有色金属标准化技术委员会归口。
本部分负责起草单位:国家有色金属质量监督检验中心、本部分参加起草单位:本部分主要起草人:ⅠGB/T 12967.7-200×铝及铝合金阳极氧化膜检测方法第7部分:用落砂试验仪测定阳极氧化膜的耐磨性1 范围1.1本部分规定了采用落砂试验仪测定阳极氧化膜耐磨性的方法。
阳极氧化相关标准
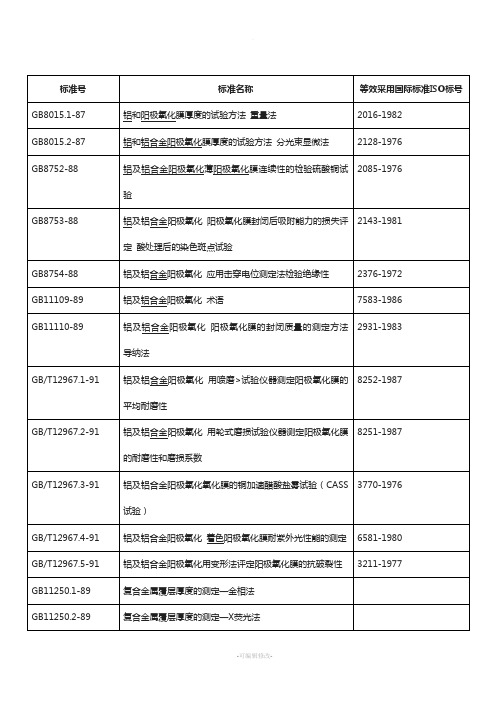
复合金属覆层厚度的测定—容量法
GB11250.4-89
复合金属覆层厚度的测定—重量法
GB/T13322-91
金属覆盖层 低氢脆镉钛电镀层
GB/T13346-92
金属覆盖层钢铁上镉电镀层
2082-1986
JB/T5067-91
钢铁制件镀锌
JB/T5068-91
金属覆盖层厚度测量 X射线光谱测量方法
铝和铝合金阳极氧化行业检测标准一览
铝及铝合金阳极氧化 阳极氧化膜封闭后吸附能力的损失评定 酸处理后的染色斑点试验
2143-1981
GB8754-88
铝及铝合金阳极氧化 应用击穿电位测定法检验绝缘性
2376-1972
GB11109-89
铝及铝合金阳极氧化 术语
7583-1986
GB11110-89
铝及铝合金阳极氧化 阳极氧化膜的封闭质量的测定方法 导纳法
2931-1983
GB/T12967.1-91
铝及铝合金阳极氧化 用喷磨>试验仪器测定阳极氧化膜的平均耐磨性
8252-1987
GB/T12967.2-91
铝及铝合金阳极氧化 用轮式磨损试验仪器测定阳极氧化膜的耐磨性和磨损系数
8251-1987
GB/T12967.3-91
铝及铝合金阳极氧化氧化膜的铜加速醋酸盐雾试验(CASS试验)
标准号
标准名称
等效采用国际标准ISO标号
GB8015.1-87
铝和阳极氧化膜厚度的试验方法 重量法
2016-1982
GB8015.2-87
铝和铝合金阳极氧化膜厚度的试验方法 分光束显微法
2128-1976
GB8752-88
阳极氧化uv测试标准

阳极氧化uv测试标准绪论阳极氧化是一种将金属表面形成氧化膜的电化学过程,常用于提高金属材料的耐腐蚀性、硬度和装饰性。
然而,阳极氧化膜的质量和性能往往受到外界环境和紫外光(UV)辐射的影响。
因此,为了保证阳极氧化膜的质量和使用寿命,制定一套可行的阳极氧化UV测试标准是必要的。
一、测试设备在进行阳极氧化UV测试之前,需要准备以下设备:1. 紫外线辐射室:用于暴露测试样品在紫外光下,常见的有Xenon 氙灯、Mercury汞灯等。
2. 温湿度控制装置:用于控制测试环境的温度和湿度,确保测试条件的稳定性。
3. 光照度检测仪:用于测量测试室内的光照强度。
4. 试样支架和固定装置:用于将测试样品固定在紫外线辐射室中,保持稳定的测试位置。
二、测试方法阳极氧化UV测试的方法主要包括以下几个步骤:1. 样品准备:将需要测试的阳极氧化膜样品按照一定规格和要求制备好,保证样品质量和尺寸的一致性。
2. 曝晒测试:将样品放置在紫外线辐射室内,暴露在设定的紫外光照射下。
测试时间可以根据实际需要确定,一般建议至少持续100小时以上。
3. 温湿度控制:在测试过程中,通过温湿度控制装置,调节测试环境的温度和湿度,使其保持稳定。
常见的测试条件为30°C下,相对湿度60%。
4. 光照度检测:在测试过程中,使用光照度检测仪测量测试室内的光照强度,确保测试条件的一致性。
5. 质量评估:测试结束后,对测试样品进行质量评估。
一般可以通过测量阳极氧化膜的厚度、硬度、耐腐蚀性等指标来评估阳极氧化膜质量的变化情况。
6. 数据分析:对测试结果进行数据分析和统计,得出阳极氧化膜在紫外光辐射下的性能变化规律。
三、测试标准为了较为准确地评估阳极氧化膜在紫外光辐射下的性能,可参考以下测试标准:1. ASTM G155 - Standard Practice for Operating Xenon Arc Light Apparatus for Exposure of Non-Metallic Materials。
铝合金阳极氧化检验规范标准
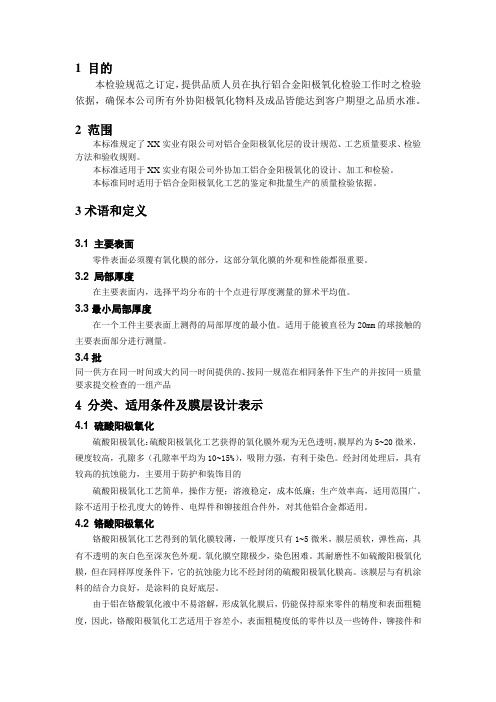
1 目的本检验规范之订定,提供品质人员在执行铝合金阳极氧化检验工作时之检验依据,确保本公司所有外协阳极氧化物料及成品皆能达到客户期望之品质水准。
2 范围本标准规定了XX实业有限公司对铝合金阳极氧化层的设计规范、工艺质量要求、检验方法和验收规则。
本标准适用于XX实业有限公司外协加工铝合金阳极氧化的设计、加工和检验。
本标准同时适用于铝合金阳极氧化工艺的鉴定和批量生产的质量检验依据。
3术语和定义3.1 主要表面零件表面必须覆有氧化膜的部分,这部分氧化膜的外观和性能都很重要。
3.2 局部厚度在主要表面内,选择平均分布的十个点进行厚度测量的算术平均值。
3.3最小局部厚度在一个工件主要表面上测得的局部厚度的最小值。
适用于能被直径为20mm的球接触的主要表面部分进行测量。
3.4批同一供方在同一时间或大约同一时间提供的、按同一规范在相同条件下生产的并按同一质量要求提交检查的一组产品4 分类、适用条件及膜层设计表示4.1 硫酸阳极氧化硫酸阳极氧化:硫酸阳极氧化工艺获得的氧化膜外观为无色透明,膜厚约为5~20微米,硬度较高,孔隙多(孔隙率平均为10~15%),吸附力强,有利于染色。
经封闭处理后,具有较高的抗蚀能力,主要用于防护和装饰目的硫酸阳极氧化工艺简单,操作方便;溶液稳定,成本低廉;生产效率高,适用范围广。
除不适用于松孔度大的铸件、电焊件和铆接组合件外,对其他铝合金都适用。
4.2 铬酸阳极氧化铬酸阳极氧化工艺得到的氧化膜较薄,一般厚度只有1~5微米,膜层质软,弹性高,具有不透明的灰白色至深灰色外观。
氧化膜空隙极少,染色困难。
其耐磨性不如硫酸阳极氧化膜,但在同样厚度条件下,它的抗蚀能力比不经封闭的硫酸阳极氧化膜高。
该膜层与有机涂料的结合力良好,是涂料的良好底层。
由于铝在铬酸氧化液中不易溶解,形成氧化膜后,仍能保持原来零件的精度和表面粗糙度,因此,铬酸阳极氧化工艺适用于容差小,表面粗糙度低的零件以及一些铸件,铆接件和电焊件等。
阳极氧化膜各检测项目检测方法各国标准
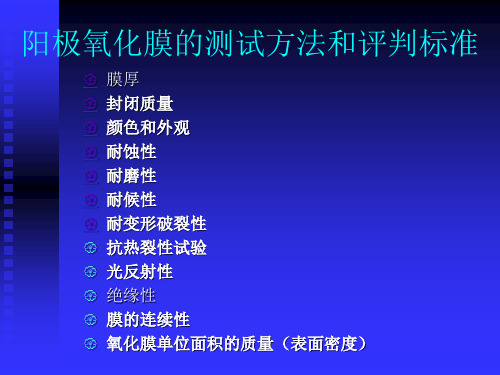
审查部 • 其具体的审批过程与QUALANOD类似。
国标的阳极氧化膜厚度与欧盟、日本等标准接近一致,为中国铝合金建 筑型材的国际贸易提供了技术支持,消除了我国阳极氧化型材在国际贸 易中的技术壁垒问题。与美国标准AAMA611存在差异性,原因如下:
不适用于测特殊膜(如:深色氧化膜)、试 样基底粗糙的膜。通常可测10μm以上的膜。 表面平滑时也可测5~20μm的膜。 仪器:专用分光束显微镜 步骤: 1. 供需双方商定测量表面,在考察区域内
至少取10点进行测量。 2. 计算出膜厚的算术平均值。(异常值须
舍去)
原理
e——氧化膜的真实厚度,μm e’——仪器侧量的厚度,μm n——氧化膜折射率(1.59~1.62)
在阳极氧化型材的国际贸易中,很少采用美国标准AAMA611,常采用 日本标准JISH8601、欧盟标准QUALANOD或者国家标准GB5237.2,在技 术要求中很少要求氧化膜的表观密度和氧化膜质量要求。
氧化膜的表观密度和氧化膜质量要求一般适用于功能性氧化膜,对于 装饰用铝合金建筑型材氧化膜,常使用平均膜厚和局部膜厚来确定氧 化膜厚度的均匀性,不要求氧化膜的表观密度和氧化膜质量要求。
计算:
表面密度 A
m1
m2 A
ρA——表面密度(氧化膜单位面积上的质量),g/mm2; m1——氧化膜溶解前的试样质量,g
m2——氧化膜溶解后的试样质量,g A ——覆有氧化膜的面积,mm2
平均膜厚 A 106
δ——平均膜厚,μm
ρA——表面密度(单位面积上氧化膜的质量),g/mm2; ρ——密度,g/cm3 (正常情况下2.3~3g/cm3,不含铜的铝及
GB8013.1-2007-T 铝及铝合金阳极氧化膜与有机聚合物膜 第1部分 阳极氧化膜

ICS 25.220.01 H 60GB/T 8013.1—200X代替 GB/T 8013-1987铝及铝合金阳极氧化膜与有机聚合物膜第1部分: 阳极氧化膜Anodic oxide coatings and organic polymer coatings on aluminium and its alloysPart 1: Anodic oxide coatings(报批稿)200X —XX —XX 发布 200X —XX —XX 实施GB/T 8013.1-200×中华人民共和国国家标准中华人民共和国国家质量监督检验检疫总局中 国 国 家 标 准 化 管 理 委 员 会发布前言GB/T 8013《铝及铝合金阳极氧化膜与有机聚合物膜》分为三部分:——第1部分:阳极氧化膜——第2部分:阳极氧化复合膜——第3部分:有机聚合物喷涂膜本部分为GB/T 8013的第1部分。
本部分代替GB/T 8013-1987《铝及铝合金阳极氧化阳极氧化膜的总规范》。
本部分与GB/T 8013-1987相比,主要变化如下:——本部分全面更改了标准的结构,将原第4章~第16章变化为第4章性能要求和第5章试验方法。
各项性能要求归并入 4.1~4.13,而相应的试验方法列入 5.1~5.13。
——本部分增加了以下性能要求和试验方法:(1) 增加了“4.4.1.2 硝酸预浸的磷铬酸试验”;(2) 增加了“4.5.1耐盐雾腐蚀性”和“4.5.2耐碱性”,并规定了各种级别的CASS和耐碱性的性能要求;(3) 增加了“4.8抗热裂性”;(4) 增加了“4.9.2 自然耐候性”、“4.9.3 加速耐候性”、并且将4.9.3分为“4.9.3.1 耐人造光”和“4.9.3.2 耐紫外光”。
相应章节增加了试验方法。
——本部分撤销了原标准“7.2.2 交替式耐酸试验”及“12 耐晒度及紫外辐射性”。
——本部分撤销了原标准“13 光的反射性能”,增加了“5.10 光反射性测量方法”,分别按照新国标GB/T 20503-2006,GB/T 20504-2006,GB/T 20505-2006,GB/T20506-2006执行。
阳极氧化膜性能测试及国家标准
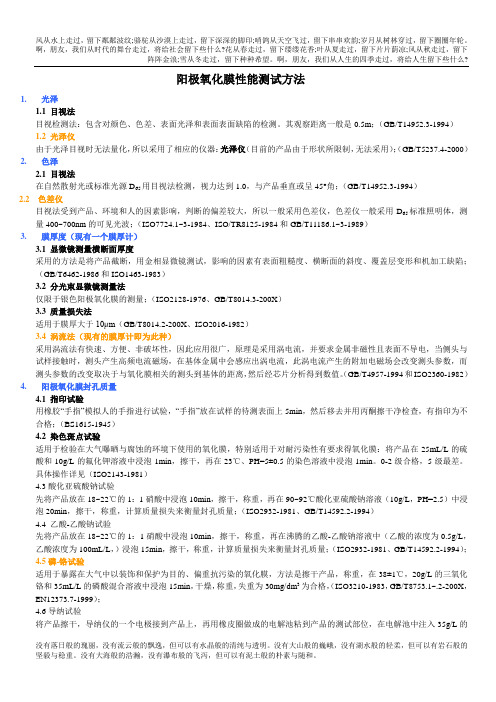
阳极氧化膜性能测试方法1. 光泽1.1 目视法目视检测法:包含对颜色、色差、表面光泽和表面表面缺陷的检测。
其观察距离一般是0.5m;(GB/T14952.3-1994)1.2 光泽仪由于光泽目视时无法量化,所以采用了相应的仪器:光泽仪(目前的产品由于形状所限制,无法采用);(GB/T5237.4-2000)2. 色泽2.1 目视法在自然散射光或标准光源D65用目视法检测,视力达到1.0,与产品垂直或呈45°角;(GB/T14952.3-1994)2.2 色差仪目视法受到产品、环境和人的因素影响,判断的偏差较大,所以一般采用色差仪,色差仪一般采用D65标准照明体,测量400~700nm的可见光波;(ISO7724.1~3-1984、ISO/TR8125-1984和GB/T11186.1~3-1989)3. 膜厚度(现有一个膜厚计)3.1 显微镜测量横断面厚度采用的方法是将产品截断,用金相显微镜测试,影响的因素有表面粗糙度、横断面的斜度、覆盖层变形和机加工缺陷;(GB/T6462-1986和ISO1463-1983)3.2 分光束显微镜测量法仅限于银色阳极氧化膜的测量;(ISO2128-1976、GB/T8014.3-200X)3.3 质量损失法适用于膜厚大于10μm(GB/T8014.2-200X、ISO2016-1982)3.4 涡流法(现有的膜厚计即为此种)采用涡流法有快速、方便、非破坏性,因此应用很广,原理是采用涡电流,并要求金属非磁性且表面不导电,当侧头与试样接触时,测头产生高频电流磁场,在基体金属中会感应出涡电流,此涡电流产生的附加电磁场会改变测头参数,而测头参数的改变取决于与氧化膜相关的测头到基体的距离,然后经芯片分析得到数值。
(GB/T4957-1994和ISO2360-1982)4. 阳极氧化膜封孔质量4.1 指印试验用橡胶“手指”模拟人的手指进行试验,“手指”放在试样的待测表面上5min,然后移去并用丙酮擦干净检查,有指印为不合格;(BS1615-1945)4.2 染色斑点试验适用于检验在大气曝晒与腐蚀的环境下使用的氧化膜,特别适用于对耐污染性有要求得氧化膜:将产品在25mL/L的硫酸和10g/L的氟化钾溶液中浸泡1min,擦干,再在23℃、PH=5±0.5的染色溶液中浸泡1min。
氧化膜封孔质量试验指导书

氧化膜封孔质量试验指导书
1:仪器
分析天平感量为0.1㎎
2:试剂
2.1 预浸溶液:移取650ml硝酸于1000ml容量瓶中,用水稀释至刻度。
2.2磷-铬酸溶液:溶解20㎎三氧化铬和35ml磷酸于500ml水中,移入1000ml容量瓶,
以水稀释至刻度,混匀。
3:取样
每天每批取2根型材,在型材封孔完毕120h后各切取1个试样,其有效表面积约10000㎜²(最小5000㎜²),质量不超过200g。
4:试验步骤
4.1 测量试样的有效面积,用干布擦去试样表面霜斑。
4.2 在室温下,将试样在适当的有机溶剂中搅拌30s或擦洗脱脂。
4.3 对试样进行干燥处理:首先,试样在室温空干5min,再直立放入预热至60℃的干燥箱
内,干燥15min,然后在密封的干燥器内置于硅胶上方冷却30min。
4.4 立即称重试样,精确至0.1㎎。
4.5 将试样直立浸入温度为19℃±1℃的预浸溶液中,保持10min。
4.6 将试样从预浸溶液取出,先用自来水再用蒸馏水彻底洗净。
4.7 将试样直立的完全浸入预先加热至38℃±1℃的磷-铬酸溶液中,浸泡15min。
4.8 从溶液中取出试样,先用自来水,然后用去离子水或蒸馏水清洗。
按4.3的方法称重,精确到0.1㎎。
4.9 在所有操作过程中,禁止用手接触试样。
5:试验结果
按照公式计算出结果,并填写《检测报告》。
质检部
2012年11月20日。
阳极氧化膜性能测试及国家标准
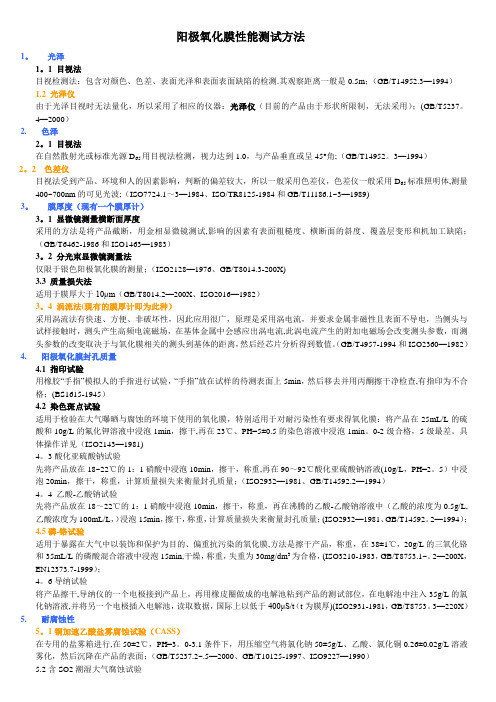
阳极氧化膜性能测试方法1。
光泽1。
1 目视法目视检测法:包含对颜色、色差、表面光泽和表面表面缺陷的检测.其观察距离一般是0.5m;(GB/T14952.3—1994)1.2 光泽仪由于光泽目视时无法量化,所以采用了相应的仪器:光泽仪(目前的产品由于形状所限制,无法采用);(GB/T5237。
4—2000)2. 色泽2。
1 目视法在自然散射光或标准光源D65用目视法检测,视力达到1.0,与产品垂直或呈45°角;(GB/T14952。
3—1994)2。
2 色差仪目视法受到产品、环境和人的因素影响,判断的偏差较大,所以一般采用色差仪,色差仪一般采用D65标准照明体,测量400~700nm的可见光波;(ISO7724.1~3—1984、ISO/TR8125-1984和GB/T11186.1~3—1989)3。
膜厚度(现有一个膜厚计)3。
1 显微镜测量横断面厚度采用的方法是将产品截断,用金相显微镜测试,影响的因素有表面粗糙度、横断面的斜度、覆盖层变形和机加工缺陷;(GB/T6462-1986和ISO1463—1983)3。
2 分光束显微镜测量法仅限于银色阳极氧化膜的测量;(ISO2128—1976、GB/T8014.3-200X)3.3 质量损失法适用于膜厚大于10μm(GB/T8014.2—200X、ISO2016—1982)3。
4 涡流法(现有的膜厚计即为此种)采用涡流法有快速、方便、非破坏性,因此应用很广,原理是采用涡电流,并要求金属非磁性且表面不导电,当侧头与试样接触时,测头产生高频电流磁场,在基体金属中会感应出涡电流,此涡电流产生的附加电磁场会改变测头参数,而测头参数的改变取决于与氧化膜相关的测头到基体的距离,然后经芯片分析得到数值。
(GB/T4957-1994和ISO2360—1982)4. 阳极氧化膜封孔质量4.1 指印试验用橡胶“手指”模拟人的手指进行试验,“手指”放在试样的待测表面上5min,然后移去并用丙酮擦干净检查,有指印为不合格;(BS1615-1945)4.2 染色斑点试验适用于检验在大气曝晒与腐蚀的环境下使用的氧化膜,特别适用于对耐污染性有要求得氧化膜:将产品在25mL/L的硫酸和10g/L的氟化钾溶液中浸泡1min,擦干,再在23℃、PH=5±0.5的染色溶液中浸泡1min。
检测报告 氧化膜 解释说明以及概述

检测报告氧化膜解释说明以及概述1. 引言1.1 概述本文将讨论氧化膜的检测报告,深入介绍氧化膜的定义、检测方法和技术,并对其重要性进行探讨。
同时,文章还将解释说明形成氧化膜的原因和过程,并探讨氧化膜对材料性能的影响与应用领域。
最后,我们将分享加强氧化膜控制的方法和策略。
通过本文的研究,读者将了解到在材料科学与工程领域中,氧化膜作为一个关键指标在质量控制和性能优化中扮演者重要角色。
1.2 文章结构本文分为四个主要部分:引言、氧化膜的检测报告、氧化膜的解释说明以及结论。
以下将依次介绍每个部分的内容。
1.3 目的本文旨在全面介绍氧化膜相关概念及其检测方法,并深入探讨其形成原因、对材料性能的影响以及加强控制方法。
通过阅读本文,读者可以了解到如何准确评估材料表面是否存在氧化膜,并且明确理解氧化膜的作用和重要性。
最终,希望本文能为氧化膜检测研究提供有益的展望与建议。
2. 氧化膜的检测报告:2.1 定义和描述氧化膜:氧化膜是指金属表面在与氧气接触时形成的一种氧化物薄膜。
它常见于各种金属材料,如铁、铝、锌等。
氧化膜往往具有不同的颜色和特性,这取决于金属的类型以及氧化反应的条件。
它可以是一种保护性薄膜,也可以是一种缺陷或污染物表达的标志。
2.2 氧化膜检测的重要性:检测和评估氧化膜对于了解金属材料的性能、表面质量以及预测其寿命至关重要。
准确地了解和掌握氧化膜的形成情况和属性可以帮助我们判断材料是否符合特定要求,并决定是否需要采取进一步处理措施。
此外,通过对氧化膜进行分析和测试,我们可以检测出可能存在的缺陷或污染物,从而避免因为这些问题导致材料失效。
2.3 氧化膜检测方法和技术概述:目前,有多种方法和技术可用于检测氧化膜,每种方法都有其特定的优势和应用场景。
以下是一些常见的氧化膜检测方法:1. 光学显微镜观察:使用光学显微镜对金属表面进行观察,通过观察氧化膜的颜色、形态以及分布来评估其质量和均匀性。
2. 扫描电子显微镜(SEM):SEM能够提供更高分辨率的金属表面图像,从而可以更直观地观察氧化膜,并通过能谱分析等技术来确定其成分。
氧化膜厚硬度测试方法

氧化膜厚硬度测试方法一、引言氧化膜是由金属表面与氧化剂接触产生的一层氧化物薄膜,在金属材料的应用中具有重要的作用。
氧化膜的硬度是评估其质量的重要指标之一,因此需要进行硬度测试。
本文将介绍几种常用的氧化膜厚硬度测试方法。
二、电化学测试法电化学测试法是一种常用的氧化膜厚硬度测试方法,它基于电化学原理,通过测量氧化膜在电场中的电流和电压变化来评估其硬度。
该方法具有非破坏性、快速、准确的特点,适用于各种金属材料的氧化膜硬度测试。
三、微硬度测试法微硬度测试法是一种通过在氧化膜表面施加一定压力,然后测量压痕的大小来评估氧化膜硬度的方法。
该方法可以测量氧化膜表面和内部的硬度,并且可以在不同位置进行测试,对于评估氧化膜的均匀性具有重要意义。
四、纳米硬度测试法纳米硬度测试法是一种利用纳米硬度计对氧化膜进行硬度测试的方法。
该方法具有高分辨率、高精度的特点,可以测量氧化膜表面的硬度,并且可以对不同区域进行测试,对于评估氧化膜的质量具有重要意义。
五、厚度测试法氧化膜的厚度对其硬度具有重要影响,因此可以通过测量氧化膜的厚度来间接评估其硬度。
目前常用的氧化膜厚度测试方法主要包括光学显微镜观察、扫描电子显微镜观察等。
六、X射线衍射测试法X射线衍射测试法是一种通过测量氧化膜的晶体结构来评估其硬度的方法。
该方法利用X射线的特性,通过测量X射线的衍射角度和强度来确定氧化膜的晶体结构和硬度。
七、总结氧化膜厚硬度测试是评估氧化膜质量的重要手段之一。
本文介绍了几种常用的氧化膜厚硬度测试方法,包括电化学测试法、微硬度测试法、纳米硬度测试法、厚度测试法和X射线衍射测试法。
这些方法各具特点,可以相互补充,从不同角度评估氧化膜的硬度。
在实际应用中,可以根据具体情况选择适合的方法进行测试,以确保氧化膜的质量和性能。
氧化膜厚硬度测试方法

氧化膜厚硬度测试方法以氧化膜厚硬度测试方法为标题,本文将介绍氧化膜厚度测试的目的、常用的测试方法以及测试过程中需要注意的事项。
一、测试目的氧化膜厚度是评估金属表面质量和性能的重要指标,对于保护金属材料、延长其使用寿命具有重要意义。
通过测试氧化膜的厚度,可以了解材料表面的保护层是否达到要求,从而判断材料的耐腐蚀性和耐磨性等性能。
二、常用测试方法1. 金相显微镜法金相显微镜法是一种常用且有效的测试方法。
通过显微镜观察金属材料表面的氧化膜,根据观察结果可以大致判断氧化膜的厚度。
此方法操作简单、直观,但只能得到氧化膜的相对厚度,并不能精确测量厚度数值。
2. 电子显微镜法电子显微镜法是一种高分辨率的测试方法,可以用来观察氧化膜的形貌和测量其厚度。
通过在电子显微镜下对样品进行观察,利用显微镜的测量功能可以准确测量氧化膜的厚度。
但此方法设备昂贵,操作要求高,适用于实验室等专业场所。
3. X射线衍射法X射线衍射法是一种无损的测试方法,可以精确测量氧化膜的厚度。
通过射线的衍射和干涉原理,结合计算方法,可以得到氧化膜的厚度数值。
此方法准确性高,适用于工业生产中对氧化膜厚度的精确要求较高的场合。
三、测试过程与注意事项1. 样品的制备:在进行氧化膜厚度测试之前,需要对样品进行制备。
首先,确保样品表面平整干净,无油污、氧化物等杂质。
然后,根据测试方法的要求,进行必要的样品处理,例如去除氧化膜、修整样品尺寸等。
2. 测试仪器的选择:根据测试要求和样品特点,选择合适的测试仪器。
例如,金相显微镜适用于观察氧化膜的相对厚度;电子显微镜适用于观察氧化膜形貌和测量厚度;X射线衍射仪适用于精确测量氧化膜厚度。
3. 测试条件的控制:在进行氧化膜厚度测试时,需要控制好测试条件。
例如,对于金相显微镜法,需要选择合适的放大倍数、光源亮度等参数;对于电子显微镜法,需要调整好电子束的加速电压和聚焦等参数;对于X射线衍射法,需要确定好测量角度和X射线的能量等。
实验1 硅片氧化层性能测试

实验1 硅片氧化层性能测试●氧化层性能测试1质量要求: 二氧化硅薄膜质量好坏,对器件的成品率和性能影响很大。
因此要求薄膜表面无斑点、裂纹、白雾、发花和针孔等缺陷。
厚度达到规定指标并保持均匀,结构致密。
对薄膜中可动带电离子,特别是钠离子的含量要有明确的要求。
2检验方法●厚度的检查测量二氧化硅薄膜厚度的方法很多。
如精度不高的比色法,腐蚀法,京都要求稍高的双光干涉法,电容电压法,还有精度高达10埃的椭圆偏振光法等。
1)比色法利用不同厚度氧化膜,在白色垂直照射下会呈现出不同颜色的干涉色彩这一现象,用金相显微镜观察并对照标准的比色样品,直接从颜色的比较来得出氧化层的厚度。
其相应的关系如下表所示:2)双光干涉法[测试仪器与装置][实验原理]干涉显微镜可用来检测经过精加工后工件的表面粗糙度,也可用来检测薄膜厚度。
精加工后,工件表面的微观不平度很小,实际上工件表面存在许多极细的“沟槽”。
检测时,首先通过显微系统将“沟槽”放大,然后利用干涉原理再将微观不平度显示出来。
常用的干涉显微镜是以迈克耳逊干涉仪为原型的双物镜干涉显微镜系统。
它的典型光路如上图所示。
光源1(白织灯)由聚光镜2成象在孔径光阑16上,插入滤光片3可以获得单色光。
视场光阑17位于准直物镜4的前焦面上。
由物镜4射出的平行光束在分光板5处分为两部分:一束向上反射,经显微镜7会聚在被测工件表面M 2上,M 2与显微镜7的焦面重合。
由M 2返回的光束依次通过显微物镜7、分光板5后被辅助物镜9会聚在测微目镜12的分划板11处,分划板11与物镜9的焦平面重合。
利用测微目镜12可以看到被测表面M 2清晰的象。
另一束光通过分光板5,补偿板6,由显微镜8会聚在参考反射镜M 1上,M 1与显微物镜81—白织灯 2—聚光镜 3—滤光片 4—准直物镜 5—分光板 6—补偿板7、8—显微物镜 M 2—被测工件 M 1—参考反射镜 9—辅助物镜 10、14—反射镜 11—分划板 12—测微目镜 13—摄影物镜 15—照相底版或观察屏 16—孔径光阑 17—视场光阑的焦平面重合。
- 1、下载文档前请自行甄别文档内容的完整性,平台不提供额外的编辑、内容补充、找答案等附加服务。
- 2、"仅部分预览"的文档,不可在线预览部分如存在完整性等问题,可反馈申请退款(可完整预览的文档不适用该条件!)。
- 3、如文档侵犯您的权益,请联系客服反馈,我们会尽快为您处理(人工客服工作时间:9:00-18:30)。
阳极氧化膜连续性测试方法
阳极氧化膜的连续性测试(大孔性)(本测试用于评定铝合金阳极氧化膜连续性)要求:将20克的硫酸铜CuSO4溶解到1升去离子水中,并搅拌均匀。
往此溶液中添加20cc的盐酸溶液,并继续搅拌均匀。
将此混合溶液滴到产品表面任意四个位置。
如果有必要,可以用纸巾将产品表面清除干净,以确保表面有污点存在。
暴露五分钟后,如果产品表面没有暗点,则可判定产品可以通过氧化膜连续性测试。
本试验至少测3件样本(注意:在产品封孔性及连续性测试时,只要溶液滴在不同位置上,即封孔性及连续性测试可以在同一件产品上做测试)。
求助:黑色不能过,不锈钢色可以过
阳极氧化膜性能测试方法
1.光泽
1.1目视法
目视检测法:包含对颜色、色差、表面光泽和表面表面缺陷的检测。
其观察距离一般是
0.5m;(GB/T14952.3-1994)
1.2光泽仪
由于光泽目视时无法量化,所以采用了相应的仪器:光泽仪(目前的产品由于形状所限制,无法采用);(GB/T5237.4-2000)
2.色泽
2.1目视法
在自然散射光或标准光源D65用目视法检测,视力达到1.0,与产品垂直或呈45°角;
(GB/T14952.3-1994)
2.2色差仪
目视法受到产品、环境和人的因素影响,判断的偏差较大,所以一般采用色差仪,色差仪一般采用D65标准照明体,测量400~700nm的可见光波;(ISO7724.1~3-1984、ISO/TR8125-1984和GB/T11186.1~3-1989)
3.膜厚度(现有一个膜厚计)
3.1显微镜测量横断面厚度
采用的方法是将产品截断,用金相显微镜测试,影响的因素有表面粗糙度、横断面的斜度、覆盖层变形和机加工缺陷;(GB/T6462-1986和ISO1463-1983)
3.2分光束显微镜测量法
仅限于银色阳极氧化膜的测量;(ISO2128-1976、GB/T8014.3-200X)
3.3质量损失法
适用于膜厚大于10μm(GB/T8014.2-200X、ISO2016-1982)
3.4涡流法(现有的膜厚计即为此种)
采用涡流法有快速、方便、非破坏性,因此应用很广,原理是采用涡电流,并要求金属非磁性且表面不导电,当侧头与试样接触时,测头产生高频电流磁场,在基体金属中会感应出涡电流,此涡电流产生的附加电磁场会改变测头参数,而测头参数的改变取决于与氧化膜相关的测头到基体的距离,然后经芯片分析得到数值。
(GB/T4957-1994和ISO2360-1982)
4.阳极氧化膜封孔质量
4.1指印试验
用橡胶“手指”模拟人的手指进行试验,“手指”放在试样的待测表面上5min,然后移去并用丙酮擦干净检查,有指印为不合格;(BS1615-1945)
4.2染色斑点试验
适用于检验在大气曝晒与腐蚀的环境下使用的氧化膜,特别适用于对耐污染性有要求得氧化膜:将产品在25mL/L的硫酸和10g/L的氟化钾溶液中浸泡1min,擦干,再在23℃、PH=5±0.5的染色溶液中浸泡1min。
0-2级合格,5级最差。
具体操作详见(ISO2143-1981)
4.3酸化亚硫酸钠试验
先将产品放在18~22℃的1:1硝酸中浸泡10min,擦干,称重,再在90~92℃酸化亚硫酸钠溶液(10g/L,PH=2.5)中浸泡20min,擦干,称重,计算质量损失来衡量封孔质量;
(ISO2932-1981、GB/T14592.2-1994)
4.4 乙酸-乙酸钠试验
先将产品放在18~22℃的1:1硝酸中浸泡10min,擦干,称重,再在沸腾的乙酸-乙酸钠溶液中(乙酸的浓度为0.5g/L,乙酸浓度为100mL/L,)浸泡15min,擦干,称重,计算质量损失来衡量封孔质量;(ISO2932-1981、GB/T14592.2-1994);
4.5磷-铬试验
适用于暴露在大气中以装饰和保护为目的、偏重抗污染的氧化膜,方法是擦干产品,称重,在38±1℃,20g/L的三氧化铬和35mL/L的磷酸混合溶液中浸泡15min,干燥,称重,
失重为30mg/dm3为合格,(ISO3210-1983,GB/T8753.1~.2-200X,EN12373.7-1999);
4.6导纳试验
将产品擦干,导纳仪的一个电极接到产品上,再用橡皮圈做成的电解池粘到产品的测试部位,在电解池中注入35g/L的氯化钠溶液,并将另一个电极插入电解池,读取数据,国际上以低于400μS/t(t为膜厚)(ISO2931-1981,GB/T8753.3-220X)
5.耐腐蚀性
5.1铜加速乙酸盐雾腐蚀试验(CASS)
在专用的盐雾箱进行,在50±2℃,PH=3.0-3.1条件下,用压缩空气将氯化钠50±5g/L、乙酸、氯化铜0.26±0.02g/L溶液雾化,然后沉降在产品的表面;(GB/T5237.2~.5-2000、GB/T10125-1997、ISO9227-1990)
5.2含SO2潮湿大气腐蚀试验
先将产品在外观面用刀划深至基体的交叉线,再放入含有2L SO2、2L CO2的300±10L的气密箱中,温度控制在40±3℃。
(GB/T9789-1988、ISO3231-1997)
5.3马丘腐蚀试验
主要检测铝合金型材涂层产品的耐丝状腐蚀性能,为加速腐蚀,马丘试验的溶液成分为氯化钠50g/L、冰醋酸10g/L、30%的过氧化氢5mL/L、PH为3.0~3.3,温度为37±1℃,试验时间48h,试验前先画深至基体的交叉线,实验后要求0.5mm以外不能有腐蚀现象。
(Qualicoat-2000)
5.4 滴碱腐蚀试验
在35±1℃下,将10mg、100g/L的氢氧化钠溶液滴在产品表面,目视观察滴处产生气泡,计算时间,(JIS H 8601-1992)
6.耐化学稳定性
6.1耐酸试验
A、盐酸试验
10滴10%(体积)的盐酸滴在产品表面,用表面皿盖住,在18~27℃的温度下放置15min,然后洗干净,无气泡和其他明显变化为合格(美国建筑生产商协会AAMA2603~2605)
B、硝酸试验
,产品放在有半瓶70%的硝酸的宽口瓶的瓶口,测试面朝下,30min后冲洗干净,放置1h 后,有无变化。
6.2耐碱试验
(JIS H 8601-1992)
6.3耐灰浆试验
(美国建筑生产商协会AAMA2603~2605)
6.4耐洗涤剂试验
(美国建筑生产商协会AAMA2603~2605)
7.耐候性(产品的使用寿命)
7.1自然暴晒耐候试验
选择合适的环境,将产品露天放置,测试面的底边离地面0.8m高,以月或年为检查周期,投试一年后,三个月为周期,检查变化情况。
(ISO2810)
7.2人工加速耐候试验
我国主要采用荧光紫外灯人工加速耐候试验和氙弧灯人工加速耐候试验,日本、美国AAMA2603、韩国只是采用了碳弧灯人工加速耐候试验,英国Qualicoat只采用氙弧灯人工加速耐候试验,三个试验相似之处在于都是模拟自然气候,但是不同的环境材料的选择将导致试验的结果相处很大。
荧光紫外灯人工加速是一套冷凝系统模拟雨露现象,荧光紫外灯模拟太阳紫外光照射和自动温度控制系统;氙弧灯人工加速采用氙弧灯辐射耐候仪模拟自然气候或在玻璃遮盖下的试验;碳弧灯人工加速采用了模拟和强化自然气候的设备,由开放式碳弧灯光源、滤光、控温、控湿和喷水系统。
8.硬度
8.1压痕硬度试验
采用巴克霍尔兹压痕仪检测,适用于膜厚要求较高的产品,温度23±2℃,相对湿度在50±5%;(GB/T9275-1988)
8.2铅笔硬度试验
(GB/T6739-1996)
8.3显微硬度试验
采用显微硬度计测定,以规定的试验力,有一定形状的金刚石以适当的速度垂直压入待测层,保持规定的时间卸除试验力,然后测量压痕对角线的长度,由公式计算维氏和努氏硬度;(GB9790-1988、ISO4516-1980E)
9.耐磨性
9.1喷磨试验(GB/T12967.1-1991、ISO8252-1987)
9.2轮式磨损试验(GB/T12967.2-1991、ISO8251-1987)
9.3落砂试验
10.阳极氧化膜绝缘性
(GB/T8754-200X、ISO2376-1976)
11.抗变形破裂性
(GB/T12967.5-1991)
12.氧化膜的连续性
(GB/T8752-200X、ISO2085-1976)
13.附着力
13.1附着力划格试验(GB/T5237-2000、GB/T9286-1998、ISO2409-1992)13.2附着力仪器试验(GB/T1720-1979)。