圆形逆流提取器运行原理示意图
中药提取设备原理培训ppt课件

冷却水箱 的水
冷却水泵 抽出
水温下降 3-5度
热水经过 填料风冷
经过车间冷 凝器
送到楼顶 冷却塔
.
防爆区冷却水泵55KW
.
一般区冷却水泵90KW
.
冷却循环水箱300立方
.
冷却塔
.
冷却塔填料
.
冷却塔原理
冷却塔是利用空气同水的接触(直接或间接)来 冷却水的设备。是以水为循环冷却剂,从一系统 中吸收热量并排放至大气中,从而降低塔内循环 水的温度,随着冷却塔行业不断发展,越来越多 的行业和企业运用到了冷却塔,也有很多企业进 入到了冷却塔行业并发展。
板式加热器原理图
.
提取板式加热器
蒸 汽 进 热 水 出
进 水
.
冷凝器
冷 却 水 出
溶
剂
蒸
汽
.
冷
冷
却
凝
水
液
进
冷凝器
冷 冷 凝 液
冷 冻 水 出
热冷凝液
冷 冻 水 进
.
注意事项
.
双效浓缩器
.
双效浓缩器主要结构及性能
本设备主要由二个加热室、二个蒸发器、列管式冷凝器、集液器及工艺管道 所组成。采用了分别进料,加热室与蒸发室分开,循环管在外的自然循环方式。 加热室为列管式换热器,上管箱喷液管通过导流槽和蒸发室相连通,下管箱通 过循环管与蒸发室下部连通,供溶液在蒸发时循环。加热室上部为快开结构, 下部底盖也可开启,供清洗列管用。蒸发室上设有视镜,供操作者观察药液的 蒸发状况,顶部装有消泡器,二次蒸汽经消泡器,通过管道排出。真空表和温 度计安装在蒸发室正面,便于操作者观察。本设备也可作为单效浓缩器使用。
室正面,便于操作者观察。
常见泵结构和工作原理动态图

泵结构和工作原理动态图1、活塞泵基本原理借活塞在汽缸内的往复作用使缸内容积反复变化,以吸入和排出流体。
2、往复泵工作原理利用偏心轴的转动通过连杆装置带动活塞的运动,将轴的圆周转动转化为活塞的往复运动。
活塞不断往复运动,泵的吸水与压水过程就连续不断地交替进行。
特殊结构3、水环式真空泵工作原理水环式真空泵叶片的叶轮偏心地装在圆柱形泵壳内。
泵内注入一定量的水。
叶轮旋转时,将水甩至泵壳形成一个水环,环的内表面与叶轮轮毂相切。
由于泵壳与叶轮不同心,右半轮毂与水环间的进气空间4逐渐扩大,从而形成真空,使气体经进气管进入泵内进气空间。
随后气体进入左半部,由于毂环之间容积被逐渐压缩而增高了压强,于是气体经排气空间及排气管被排至泵外。
4、罗茨真空泵工作原理罗茨泵的工作原理与罗茨鼓风机相似。
由于转子的不断旋转,被抽气体从进气口吸入到转子与泵壳之间的空间v0内,再经排气口排出。
由于吸气后v0空间是全封闭状态,所以,在泵腔内气体没有压缩和膨胀。
但当转子顶部转过排气口边缘,v0空间与排气侧相通时,由于排气侧气体压强较高,则有一部分气体返冲到空间v0中去,使气体压强突然增高。
当转子继续转动时,气体排出泵外。
一般来说,罗茨泵具有以下特点:●在较宽的压强范围内有较大的抽速;●起动快,能立即工作;●对被抽气体中含有的灰尘和水蒸气不敏感;●转子不必润滑,泵腔内无油;●振动小,转子动平衡条件较好,没有排气阀;●驱动功率小,机械摩擦损失小;●结构紧凑,占地面积小;●运转维护费用低。
因此,罗茨泵在冶金、石油化工、造纸、食品、电子工业部门得到广泛的应用。
5、旋片式真空泵工作原理旋片式真空泵(简称旋片泵)是一种油封式机械真空泵。
其工作压强范围为101325~1.33×10-2(Pa)属于低真空泵。
它可以单独使用,也可以作为其它高真空泵或超高真空泵的前级泵。
它已广泛地应用于冶金、机械、军工、电子、化工、轻工、石油及医药等生产和科研部门。
提取罐工作原理

提取罐工作原理
提取罐是一种常见的化工设备,广泛应用于石油、化工、制药等行业。
它主要
用于从原料中提取特定的化合物或物质,是一种重要的分离设备。
提取罐的工作原理是基于物质在不同溶剂中的溶解度差异,利用溶剂对原料的选择性溶解,从而实现目标物质的分离和提取。
提取罐主要由罐体、进料口、出料口、溶剂加入口、搅拌装置、加热/冷却装
置等部分组成。
其工作原理可以分为以下几个步骤:
首先,将原料和溶剂加入提取罐中。
原料可以是固体、液体或气体,而溶剂则
根据需要选择。
在加入原料和溶剂后,搅拌装置开始工作,将原料和溶剂充分混合。
接着,通过加热或冷却装置对提取罐中的混合物进行温度控制。
温度的选择可
以根据目标物质的溶解度特性来确定,有时也需要根据反应热力学条件来调节温度。
随后,原料中的目标物质会根据其在不同溶剂中的溶解度被选择性地溶解到溶
剂中,而其他杂质则会保持在原料中或沉淀出来。
这一步骤是提取罐实现分离的关键。
最后,通过出料口将溶解了目标物质的溶液从提取罐中抽出,经过后续的处理
步骤,如蒸馏、结晶、浓缩等,就可以得到纯净的目标物质。
提取罐的工作原理基于溶解度差异的分离原理,因此在实际应用中需要根据目
标物质的特性、原料的性质、溶剂的选择等因素来合理设计提取工艺,以达到最佳的分离效果。
总的来说,提取罐通过溶剂对原料的选择性溶解,实现了目标物质的分离和提取。
它在化工生产中起着重要作用,为我们生活中的化工产品提供了可靠的分离技术支持。
圆形逆流式工业冷却水塔设备工艺原理

圆形逆流式工业冷却水塔设备工艺原理引言工业冷却水塔是为了解决工业生产中需大量使用水的问题而专门设计制造的一种高效节能、省水降温设备。
目前较为常见的冷却水塔类型包括:直冷式、交叉流式、逆流式和交叉逆流式水塔等,本文将重点介绍逆流式水塔。
工艺原理逆流式水塔处理冷却水的方式是将冷却水由上往下喷淋到水塔中,同时在水塔内的填料层内由下往上将空气吹送至塔顶,使冷却水在接触填料的过程中和上下逆向空气之间交换热量,从而达到降温的目的。
具体工艺原理如下:喷淋层冷却水首先从进口管道进入水塔,通过喷头均匀喷洒到喷淋层中,形成水膜,将热量传递到周围空气中。
其喷淋层通常采用的是卡式式喷喷淋头,可根据需要进行增加或减少数量来控制冷却水的喷淋量。
填料层水塔填料层是冷却水和空气热量交换的主要场所。
填料可分为整体式、拼装式和卡式三类。
整体式填料一般采用铝、铜、镀锌铁等金属材料制成,其具有导热、强度高、寿命长等优点,同时还能防止虫害、腐蚀和磨损。
拼装式和卡式填料属于模块式填料,组装方便,而且也容易对填料进行清洗和更换维护。
风机层在水塔内下面的风机层,风机通过叶片将外部风气引入塔内,并向塔内吹送冷却空气。
风机通常有轴流和离心两类。
轴流风机主要适用于中小型水塔,其能耗低,但风量不大;离心风机适用于大中型水塔,风量大,但较为耗能。
底部水池在水塔的下方是一个底部水池,其主要作用是收集冷却水以及净化剂,防止因短时间内水量过大而影响冷却效果。
底部水池还能起到缓冲、稳定水塔水位的作用,同时为设备维护提供方便。
结论圆形逆流式工业冷却水塔具有结构简单、操作灵活、降温效果明显等优点,已被广泛应用于各种工业生产领域。
通过了解逆流式水塔的工艺原理,我们可以更好的理解水塔的工作原理,有效掌握其使用方法和性能特点。
十二级旋流洗涤管工作原理及使用

十二级旋流洗涤管工作原理及使用用于悬浮液中的固体相与混合液相的分离,悬浮液体靠在锥体壁筒高速旋转的条件下进行分离,经常用于含有可沉降固体相与混合液相·的悬浮液的固液分离,不同密度物相分离是在双锥筒内10m/秒线速度的情况下,在离心场内以3500~12000倍地心重力加速度进行的。
比重轻的液体相聚集在转筒的中央,转重的固体相被自身重力旋压在双锥筒的周边。
在不断加入的重力固体相的不断推动下,向锥口集中并不断排出锥体,为使悬浮液体混合物能有最佳分离效果,相界层必须处在上升通道区,而且上升通道位置必须调整与相分离比率相适应(依据介质性质条件进行计算)。
双锥筒离心分离的典型应用范围是将尺寸在0.2~10微米,最小密度差别30~300公斤/米的悬浮液固相体分离开来,以及20~400公斤/米的密度差,经过洗涤或萃取得来的混合液体分离,这种双锥筒适宜加工较高浓液的悬浮液(按体积比约为≥25%)。
旋流洗涤精制工艺本工艺采用多级旋流分离器去除粗淀粉乳的杂质。
工艺原理流程如下图所示:图2-4-2 旋流洗涤精制流程由于精制的淀粉乳经过淀粉与麸质分离机和旋流分离器的洗涤,所以该工艺俗称为分离机加旋流器淀粉提取工艺。
用于淀粉乳洗涤精制的旋流器称为洗涤旋流器。
由于一般常采用旋流洗涤级数为12级,该工艺常称12级旋流洗涤。
在12级旋流洗涤中采用逆流洗涤原理,一次新鲜水从末级(第12级)进入洗涤系统,旋流器溢流逐级返回做为前一级的洗涤水,首级旋器的溢流进入淀粉与麸质分离机进行再分离,洗涤去除的杂质进入麸质水从分享机溢流排出。
这样在淀粉乳精制过程中,可充分回收淀粉,提高淀粉收率,同时减少一次新鲜水的用量。
目前国内玉米湿磨提取淀粉的工厂,大都采用分离机加12级洗涤旋流器工艺。
3、12级旋流洗涤工艺的发展从12级旋流洗涤流程中,不难看出首级旋流器溢流返回再进淀粉麸质分离机,相应增加了分离处理量,同时还会降低分离机进料浓度。
目前国内大多数玉米淀粉生产工厂(特别生产规模大的工厂)都将首级旋流器的溢流进行浓缩,而分离出大量的澄清过程中。
常见泵结构和工作原理动态图

泵结构和工作原理动态图1、活塞泵基本原理借活塞在汽缸内的往复作用使缸内容积反复变化,以吸入和排出流体。
2、往复泵工作原理利用偏心轴的转动通过连杆装置带动活塞的运动,将轴的圆周转动转化为活塞的往复运动。
活塞不断往复运动,泵的吸水与压水过程就连续不断地交替进行。
特殊结构3、水环式真空泵工作原理水环式真空泵叶片的叶轮偏心地装在圆柱形泵壳内。
泵内注入一定量的水。
叶轮旋转时,将水甩至泵壳形成一个水环,环的内表面与叶轮轮毂相切。
由于泵壳与叶轮不同心,右半轮毂与水环间的进气空间4逐渐扩大,从而形成真空,使气体经进气管进入泵内进气空间。
随后气体进入左半部,由于毂环之间容积被逐渐压缩而增高了压强,于是气体经排气空间与排气管被排至泵外。
4、罗茨真空泵工作原理罗茨泵的工作原理与罗茨鼓风机相似。
由于转子的不断旋转,被抽气体从进气口吸入到转子与泵壳之间的空间v0内,再经排气口排出。
由于吸气后v0空间是全封闭状态,所以,在泵腔内气体没有压缩和膨胀。
但当转子顶部转过排气口边缘,v0空间与排气侧相通时,由于排气侧气体压强较高,则有一部分气体返冲到空间v0中去,使气体压强突然增高。
当转子继续转动时,气体排出泵外。
一般来说,罗茨泵具有以下特点:●在较宽的压强范围内有较大的抽速;●起动快,能立即工作;●对被抽气体中含有的灰尘和水蒸气不敏感;●转子不必润滑,泵腔内无油;●振动小,转子动平衡条件较好,没有排气阀;●驱动功率小,机械摩擦损失小;●结构紧凑,占地面积小;●运转维护费用低。
因此,罗茨泵在冶金、石油化工、造纸、食品、电子工业部门得到广泛的应用。
5、旋片式真空泵工作原理旋片式真空泵(简称旋片泵)是一种油封式机械真空泵。
其工作压强范围为101325~1.33×10-2(Pa)属于低真空泵。
它可以单独使用,也可以作为其它高真空泵或超高真空泵的前级泵。
它已广泛地应用于冶金、机械、军工、电子、化工、轻工、石油与医药等生产和科研部门。
各种过滤设备工作原理及结构分析(动画演示)

由许多块带凹凸纹路的滤板与滤框交替排列组装于机构成。
主要包括滤板、滤框、夹紧机构、机架等组成。
滤板:凹凸不平的表⾯,凸部⽤来⽀撑滤布,凹槽是滤液的流道。
滤板右上⾓的圆孔,是滤浆通道;左上⾓的圆孔,是洗⽔通道。
洗涤板:左上⾓的洗⽔通道与两侧表⾯的凹槽相通,使洗⽔流进凹槽;⾮洗涤板:洗⽔通道与两侧表⾯的凹槽不相通。
滤框:滤浆通道:滤框右上⾓的圆孔洗⽔通道:滤框左上⾓的圆孔为了避免这两种板和框的安装次序有错,在铸造时常在板与框的外侧⾯分别铸有⼀个、两个或三个⼩钮。
⾮洗涤板为⼀钮板,框带两个钮,洗涤板为三钮板。
板框压滤机为间歇操作,每个操作循环由装合、过滤、洗涤、卸饼、清理5个阶段组成。
装合:将板与框按 1-2-3-2-1-2-3的顺序,滤板的两侧表⾯放上滤布,然后⽤⼿动的或机动的压紧装置固定,使板与框紧密接触。
过滤:悬浮液在指定压强下送进滤浆通道,由通道流进每个滤框⾥;滤液分别穿过滤框两侧的滤布,沿滤板板⾯的沟道⾄滤液出⼝排出;颗粒被滤布截留⽽沉积在滤布上,待滤饼充满全框后,停⽌过滤。
根据滤液排出⽅式分为:明流和暗流。
洗涤:洗涤⽔经洗⽔通路从洗涤板上的孔道进⼊各个洗涤板的两侧,洗涤⽔在压差(洗涤板上的滤液出⼝关闭形成)的推动⼒下先穿过⼀层滤布及整个框厚的滤饼,然后再穿过⼀层滤布,最后沿滤板(⼀钮板)板⾯沟道⾄滤液出⼝排出。
这种操作⽅式称为横穿洗涤法。
洗涤⽔穿过的途径正好是过滤终了时滤液穿过途径的⼆倍,流通⾯积是过滤⾯积的⼀半。
卸渣、整理:打开板框,卸出滤饼,洗涤滤布及板、框。
结构简单,价格低廉,占地⾯积⼩,过滤⾯积⼤。
可根据需要增减滤板的数量,调节过滤能⼒。
对物料的适应能⼒较强,由于操作压⼒较⾼(3~10kg/cm2),对颗粒细⼩⽽液体粘度较⼤的滤浆,也能适⽤。
间歇操作,⽣产能⼒低,卸渣清洗和组装阶段需⽤⼈⼒操作,劳动强度⼤,所以它只适⽤于⼩规模⽣产。
叶滤机由许多不同宽度的长⽅形滤叶装合⽽成。
滤叶由⾦属丝⽹制造,内部具有空间,外罩滤布。
离心机工作原理及结构示意图
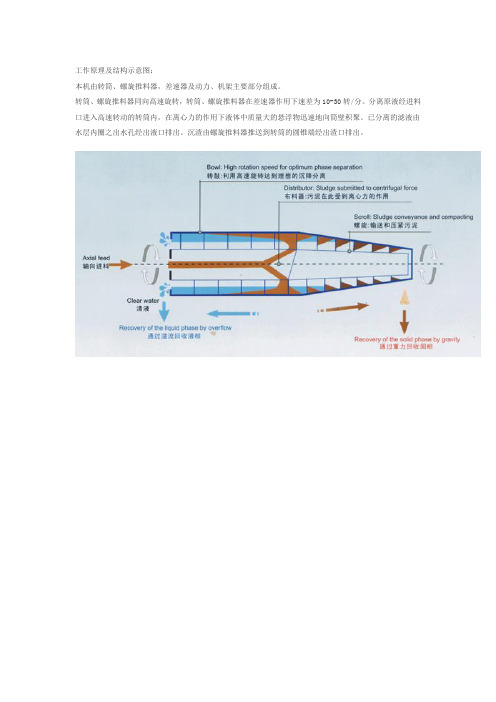
工作原理及结构示意图:本机由转筒、螺旋推料器,差速器及动力、机架主要部分组成。
转筒、螺旋推料器同向高速旋转,转筒、螺旋推料器在差速器作用下速差为10-30转/分。
分离原液经进料口进入高速转动的转筒内,在离心力的作用下液体中质量大的悬浮物迅速地向筒壁积聚。
已分离的滤液由水层内圈之出水孔经出液口排出。
沉渣由螺旋推料器推送到转筒的圆锥端经出渣口排出。
污水处理工艺流程是用于某种污水处理的工艺方法的组合。
通常根据污水的水质和水量,回收的经济价值,排放标准及其他社会、经济条件,经过分析和比较,必要时,还需要进行试验研究,决定所采用的处理流程。
一般原则是:改革工艺,减少污染,回收利用,综合防治,技术先进,经济合理等。
在流程选择时应注重整体最优,而不只是追求某一环节的最优。
现代污水处理技术,按处理程度划分,可分为一级、二级和三级处理。
一级处理,主要去除污水中呈悬浮状态的固体污染物质,物理处理法大部分只能完成一级处理的要求。
经过一级处理的污水,BOD一般可去除30%左右,达不到排放标准。
一级处理属于二级处理的预处理。
二级处理,主要去除污水中呈胶体和溶解状态的有机污染物质(BOD,COD物质),去除率可达90%以上,使有机污染物达到排放标准。
三级处理,进一步处理难降解的有机物、氮和磷等能够导致水体富营养化的可溶性无机物等。
主要方法有生物脱氮除磷法,混凝沉淀法,砂率法,活性炭吸附法,离子交换法和电渗分析法等。
整个过程为通过粗格删的原污水经过污水提升泵提升后,经过格删或者筛率器,之后进入沉砂池,经过砂水分离的污水进入初次沉淀池,以上为一级处理(即物理处理),初沉池的出水进入生物处理设备,有活性污泥法和生物膜法,(其中活性污泥法的反应器有曝气池,氧化沟等,生物膜法包括生物滤池、生物转盘、生物接触氧化法和生物流化床),生物处理设备的出水进入二次沉淀池,二沉池的出水经过消毒排放或者进入三级处理,一级处理结束到此为二级处理,三级处理包括生物脱氮除磷法,混凝沉淀法,砂滤法,活性炭吸附法,离子交换法和电渗析法。
《中药提取设备》演示PPT
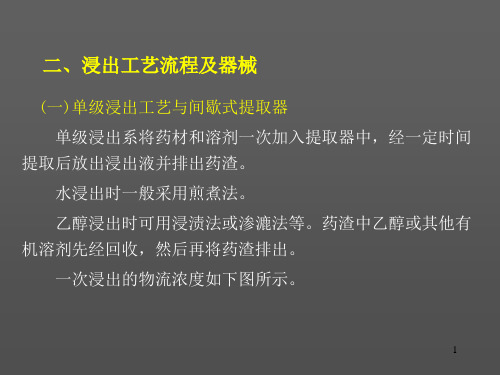
提取操作根据不同需要采取不同方式
①加热方式 用水提取时通入蒸气加热,当温度达到提取温度后停止
向罐内而改向夹层通蒸气进行间接加热,以维持罐内温度在 规定范围内。
如用醇提取,则全部用夹层通蒸气进行间接加热。 ②强制循环
在提取过程中,用泵对药液进行强制性循环,即从罐体 下部放液口放出浸出液,经管道滤过器滤过,再用水泵打回 罐体内。
一次浸出浸出速度变化情况图
4
单级浸出工艺比较简单,常用于小批量生产。缺点是漫 出时间长,药渣能吸收一定量浸出液,可溶性成分的浸出率 低,浸出液的浓度亦较低,浓缩时消耗热量大。
单级浸出工艺常用间歇式提取器。这类提取器型式较多。 下页为表示多能提取器的工艺流程图。
可提供药材水提取、醇提取、挥发油提取并可回收药渣 中的溶剂,也能用于渗漉、温浸、回流、循环浸渍、加压或 减压浸出等多种漫出工艺,因此也称为多能提取器。
21
SJN型三效节能浓缩器 1.加热室;2.蒸发室
二次 蒸汽
蒸 汽
料液 出口
冷凝 水出 口
料液进口 22
23
2. 醇沉淀设备
浸出液经浓缩后进行醇沉,使淀粉、树胶、 蛋白质、果胶、多糖、粘液质、色素等醇不溶物 析出沉淀,藉此除去杂质,提高浸膏质量。
醇沉前,浸出液经浓缩至密度在1.15~1.25 g/cm3之间。
(1)真空干燥器 适用于热敏性物料的低温干燥,并可回收物料中的溶剂。
有一部分可通直接蒸汽用于低压灭菌(105~115℃ )。 真空干燥器有方形及圆筒形两种。
27
28
(2)喷雾干燥
喷雾干燥是用雾化器将溶液喷成雾滴分散于热气流中, 使水分迅速蒸发直接获得干燥产品的设备 。
通常雾滴直径10~60µm,每1L溶液具有100~600m2 的蒸发面积,因此干燥时间很短,约3~10s。
简易热回流浸提装置

简易热回流浸提装置热回流浸提技术是提取中药有效成分的一种较好的方法。
对于药厂和企业来说,购买或定制成套的设备是没有问题的,但是对于心痒也想弄一弄的小伙伴们来说,动辄几万、几十万一套的设备,确实是不能承受之重。
本文介绍的就是一种业余的玩法,希望对大家有所帮助和启发。
一、原理简介:利用“罐中罐”,将大罐中的酒精进行蒸馏,然后通过动力泵回流系统将冷凝的酒精送入提取罐(小罐)的底部,酒精自下而上与物料接触,产生浸提作用;提取罐内的浸提液溢满后,通过带滤网的上口流入大罐中,其中的酒精继续参与蒸发,提取的成分则留在大罐中。
如此循环往复,就可以提取物料(中药等)的大部分有效成分。
二、器材的准备1、一套敞口不锈钢蒸馏设备。
我现在用的是直径30cm、容量35升的葡萄酒发酵桶(自带冷凝器,可蒸馏)。
蒸馏罐需要开2个接口(出口),一个是引出蒸汽,另一个是引入回流液。
我的蒸馏罐就是在盖子上加钻了一个小孔,装上高压锅的气嘴作为接口。
接口的外侧接蠕动泵,内侧通过硅胶管接到提取罐的底部接口。
下图就是我用的这款蒸馏罐。
2、一个5升以上的阔口玻璃瓶或者不锈钢瓶。
需要在瓶的侧面距离底部约3cm处钻一个10mm左右的孔,制作(买也可以)一根长4-5cm 的螺纹管,插入所打的孔中,内外用螺母、硅胶垫等拧紧、密封,螺纹管的外露部分磨去螺纹、打磨光滑,作为回流管的接口。
下图是我做的第一个提取罐,第二次使用的过程中爆裂了,主要是我用的滤网太密,还有蠕动泵流速调得太大,这个大家要注意,有条件最好是用不锈钢的。
3、动力泵。
购买一个每分钟最大流量500毫升以上的可调速蠕动泵。
隔膜泵不建议使用,因为在回流的过程中管道经常是带有空气的,隔膜泵由于空气进入,经常会失去作用;同时,蠕动泵起到单向阀的作用,可防止逆流。
4、接液缓冲瓶(罐)。
这个罐的作用是:①接取蒸馏出的冷凝溶剂②开一个出气口与外界相通(这样蒸汽才能流出并被冷凝)③将冷凝的溶剂转送给蠕动泵。
分离器结构及工作原理ppt课件
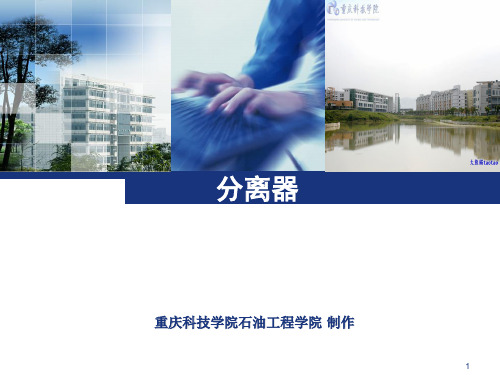
1.5 2
1 0.8 0.6 0.5 0.4 0.3 0.2 0.15
1.5 2
3 4 5 6 8 10
10 8 6 5 4 3 2 1.5
1.5 2
1.5 2 3 4 5 6 8 10.00
3 4 5 6 8 10
颗粒直径 Dm, μm
3 4 5 6 8 10.00 1 5
10 20
w
0.153d1.14 L g 0.43 0.29
g
g 0.71 0.71
3. 当颗粒直径大于(300~800)10-6m,且雷诺数500<Re<1500时, CD=0.44,则以上方程变为下列式:
0.5
d w 1.74
L g g
g
将以上公式制为图表便可得下图,通过此图,可查得在不同压力下,水 滴的沉降速度w与其直径d的关系。
CQUST
2.6 分离器外壳及主要内部构件 2.6.1 外壳
内部承压的容器,为圆形筒 体,其内径、长度尺寸根据气体 处理量以及操作参数设计确定, 两端是椭球形或球形的封头。
CQUST
2.6 分离器外壳及主要内部构件 2.6.2 内部构件
进口转向器
导流档板:快速变化液流方向和速度; 旋风式进口:应用离心力分离时采用。
CQUST
2.1 两相分离器
2.1.2.立式两相分离器基本结构及工作过程
气液混合流体经气液进 口进入分离器进行基本相分 离,气体进入气体通道向上 流动通过重力沉降分离出液 滴,液体进入液体空间向下 流动,同时分离出气泡。气 体在离开分离器之前经捕雾 器除去小液滴后从出气口流 出,液体从出液口流出。
K 0.5cm3 / m3气 S 0.05cm3 / m3液
《多级逆流萃取》PPT课件
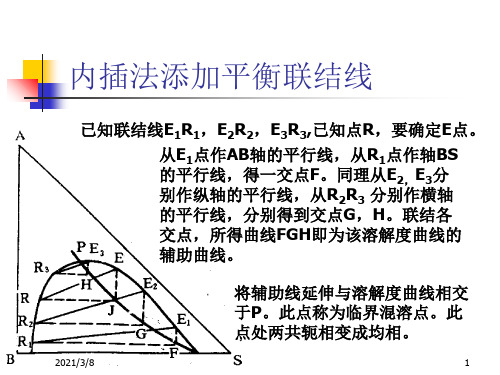
2021/3/8
18
超临界流体的性质
气体、液体和超临界流体的性质
性 质
密 度 (g/ml) 粘 度 (g/cm s) 扩 散 系 数 (cm2/s)
气 体
超 临 界 流 体
1atm,15~30oC Tc,pc (0.6~2)10-3 0.2~0.5
Tc,4pc 0.4~0.9
(1~3)10-4 (1~3)10-4 (3~9)10-4
分子之间的相互作用随分子尺 寸的增大而增加。因此在大分 子系统中占主导地位。
因此一种聚合物分子周围将聚 集同种分子而排斥异种分子。 达到平衡时,即形成富含不同 聚合物的两相。
26
双水相系统
常用的双水相系统有聚合物-聚合物和聚合物盐两大类。
常用的聚合物体系有聚乙二醇(PEG)/葡聚糖 (DEX)、聚丙二醇/聚乙二醇和甲基纤维素/ 葡聚糖等
2021/3/8
1
多级逆流萃取
第一级物料衡算: FE2R1E1 第一、二级间物料衡算: FE3R2E1 第一级到第n级间衡算: FSRnE1
FE1R1E2 FE1R2E3 FE1RnS
F E 1 R 1 E 2 R 2 E 3 R n 1 E n R n S
2021/3/8
早期采用啤酒花直接酿酒, -酸只能利用25%,
后改用有机溶剂萃取,利用率提高60~80%。 用超临界CO2萃取, -酸萃取率可达95%以上。
2021/3/8
23
脱尼古丁
2021/3/8
24
双水相萃取(Aqueous two-phase extraction)
双水相萃取现象最早是1896年由Beijerinck在 琼脂和可溶性淀粉或明胶混合时发现的。这种 现象被称为是聚合物的“不相溶性”。
萃取设备 错流萃取 逆流萃取幻灯片

溶剂回收装置 (如蒸馏塔)
31
工业上的萃取过程按操作方式分类,可 分为: 单级萃取: 多级萃取:又可分为错流萃取和逆流萃取。
32
(一)单级萃取
33
一个混合器、 一个分离器
34
使用一个混合器和一个分离器的萃取操作:
料液F与萃取剂S一起加入混合器内搅拌混合萃取; 达到平衡后的溶液送到分离器内分离得到萃取相L和萃余相R; 萃取相送到回收器,萃余相R为废液; 在回收器内产物与溶剂分离(如蒸馏、反萃取等),溶剂则 可循环使用。
1
100%
99.32%
44
由此可见,当萃取剂用量相同时,二级萃取收 率比单级萃取收率要高。也就是说,在萃取剂 用量一定的情况下,萃取次数越多,则萃取越 完全。
多级错流萃取流程的特点:每级均加新鲜溶剂, 故溶剂消耗量大,得到的萃取液产物平均浓度 较稀,但萃取较完全。
45
(三)多级逆流萃取
必须是稀溶液 溶质对溶剂的互溶度没有影响 溶质在两相中必须是同一种分子类型,
即不发生缔合或离解。
③萃取工艺操作方式
单级萃取 多级错流萃取 多级萃取 多级逆流萃取
6
2、液-液萃取的分类
(2)化学萃取
在萃取过程中常伴随有化学反应,包括相内 反应与相界面上的反应。这类萃取统称为化 学萃取(反应萃取)。
S
萃取器
分离器
回收器
F
R
P(产物)
35
萃取因素E为:
E
萃取相中溶质总量 萃余相中溶质总量
C1VS C 2VF
K
VS VF
K
1 m
式中 :VF—料液体积;Vs—萃取剂的体积; C1—溶质在萃取液的浓度; C2—溶质在萃余相的浓度; K—表观分配系数; m—浓缩倍数
罐组式动态逆流提取的原理

罐组式动态逆流提取的原理罐组式动态逆流提取是一种常见的物质分离方法,它利用了物质在不同溶剂中的溶解度差异,通过连续循环的方式将目标物质从原始溶液中提取出来。
下面将详细介绍该方法的原理。
罐组式动态逆流提取是以液液均质传质方式进行的,它是在由多个逆流提取单元组成的罐组中进行。
每个逆流提取单元包括一个提取罐和一个萃取罐,二者通过一个计量泵和一段输送管道连接。
在进行罐组式动态逆流提取时,首先将原始溶液和萃取剂分别加入提取罐和萃取罐中,然后以一定速率通过计量泵和管道将两者进行连续循环。
这样就形成了液液传质的逆流过程。
在物质传质的过程中,溶质从原始溶液中通过界面传递到萃取剂中,进而实现提取的目的。
这主要是因为物质在两种溶剂中的溶解度不同,原始溶液中的溶质可以更好地溶解于萃取剂中。
在提取罐中,物质从原始溶液中溶解到萃取剂中。
这是因为在提取罐中,原始溶液和萃取剂在界面附近发生接触,物质分子会向着溶度的较大方向进行扩散,从而从原始溶液中转移到萃取剂中。
这个过程被称为物质的反向挤压。
在萃取罐中,物质从萃取剂中再次分配到原始溶液中,这个过程被称为物质的正向挤压。
这是因为在萃取罐中,原始溶液和萃取剂再次发生接触,物质分子会向着溶度的较小方向进行扩散,从而从萃取剂中转移到原始溶液中。
通过这两个步骤的交替进行,物质可以在原始溶液和萃取剂之间进行连续传递,逐渐从原始溶液中提取出来。
这就是罐组式动态逆流提取的基本原理。
在实际操作中,为了增加物质传质的速率和效果,可以通过增大界面积、加强搅拌、调整溶液浓度和温度等方式进行优化。
同时,还可以采用连续逆流提取的方式,将多个逆流提取单元串联起来,进一步增强提取效果。
总结起来,罐组式动态逆流提取是一种利用溶质在两种溶剂中溶解度差异的物质分离方法。
通过逆流传质的方式,原始溶液中的目标物质可以被提取到萃取剂中。
通过连续循环和优化操作条件,可以实现高效的物质提取。
RO机工作原理解剖图-

RO机工作原理解剖图
一般灰尘50微米细菌0.5微米
过滤性病毒0.02微米重金属离子0.005微米
RO膜孔径0.0001微米
纯水机各种零配件的功能简介
★低压开关:自来水停水、水压太低(≤0.05MPa)、PPF 滤芯堵塞等原因,造成水泵吸空时,低压开关(常开触点)提供电信号给制水系统,机器报警并停止制水。
★高压开关:当压力储水桶水满时,储水桶内水压达到0.25Mpa,高压开关(常闭触点)在水压作用下切断系统电源,停止制水。
★冲洗、废水组合电磁阀:在制水系统每次开始制水时自动打开18秒,让水快速流过RO膜表面,将RO膜表面冲洗干净,避免RO膜堵塞,延长RO膜寿命。
★进水电磁阀:在系统停止制水时,切断系统水源,防止在自来水压力作用下,水慢慢透过RO膜,造成机器废水流不停。
★废水比例器:为RO膜需要建立大于渗透压的压力而起到阻止作用。
★高压泵:为RO膜提供反渗透压力
★微电脑盒:控制主机制停水,显示机器工作状态主要技术参数。
逆流提取机组使用说明书

目录一、装置简介 (3)1、逆流提取设备主要用途 (3)2、逆流提取设备工作原理 (3)3、逆流提取设备结构和特点 (3)4、逆流提取设备工作方式 (3)二、装置技术参数 (3)三、操作规程 (4)1、上岗人员的技能培训 (4)2、开机前的准备 (4)3、操作流程 (4)4、清洗 (4)四、操作注意事项 (4)五、常见故障与解决方法 (5)六、设备的安全操作与保养 (6)一、装置简介1、逆流提取设备主要用途逆流提取机用于天然中草药的有效成分和色素等提取,在医疗、化工、保健食品各行业有极其广泛用途。
2、逆流提取设备工作原理逆流法是:药材与溶剂在浸出容器中沿相反方向运动,连续而充分地进行接触提取的一种方法。
设备为高效连续动态逆流提取机,其提取原理是:可以利用微波穿透力强的加热方式,也可以采用夹套蒸汽加热,使提取更为快捷方便。
连续逆流提取设备是动态提取、逆流提取、煎煮提取工艺的结合,在保留多种传统工艺优点的同时,创造了这些传统工艺所无法达到的诸多优点:提取速度快、有效成分提取充分、提取收得率高、溶剂耗量少、药液浓度高、减少了蒸发浓缩等后续处理艺、滚筒内药材颗粒移动速度可调节,从而可根据药材特点调节提取时间的长短、药材在温和的动态环境下进行提取,加热温度较低、有效成分破坏较少,使药液中杂质含量少,属于连续式生产,处理能力大。
3、逆流提取设备结构和特点该逆流提取:由投料斗、内带螺旋输送装置的提取筒、出渣螺旋输送器、过滤器、挤榨机等组成。
原料经粗粉碎、浸润后从投料斗投入,提取筒轴旋转,固定在轴的螺旋带将物料从机组前端向后缓慢推进,同时提取溶剂从机组末端的进液管进入过滤器,由筒后端穿过移动的物料向前端流动,固液两相物质在这种逆向运动中充分接触,从而将药材中有效成分提取出来。
药渣经出渣螺旋输送器强制推动至出挤榨机而排出,出渣螺旋同时对药渣进行挤压,将药渣申残留药液挤出药材组织,减少药渣申残留药液含量。
4、逆流提取设备工作方式正向进料、反向进水,物料与水的流动为逆向连续动态流动,使药材和溶媒能保持相对运动,使料液浓度扩散更新持续作用,进而保证了料液浸出速度快。
收藏 !12种塔器工作原理与流程图,温故知新

收藏!12种塔器工作原理与流程图,温故知新塔设备是石油化工行业最显著的设备,在塔设备内可进行气液或液液两相间的充分接触,实施相间传质,因此在生产过程中常用塔设备进行精馏、吸收、解吸、气体的增湿及冷却等单元操作过程。
1.填料吸收塔填料吸收塔介绍:填料塔是以塔内的填料作为气液两相间接触构件的传质设备。
填料塔塔身是一直立式圆筒,底部装有填料支承板,填料以乱堆或整砌的方式放置在支撑板上。
填料的上方安装填料压板,以防被上升气流吹动。
液体从塔顶经液体分布器喷淋到填料上,并沿填料表面流下。
气体从塔底送入,经气体分布装置(小直径塔一般不设气体分布装置)分布后,与液体呈逆流连续通过填料层的空隙,在填料表面上,气液两相密切接触进行传质。
填料塔属于连续接触式气液传质设备,两相组成沿塔高连续变化,在正常操作状态下,气相为连续相,液相为分散相。
优点:生产能力大,分离效率高,压降小,持液量小,操作弹性大等。
缺点:填料造价高;当液体负荷较小时不能有效地润湿填料表面,使传质效率降低;不能直接用于有悬浮物或容易聚合的物料;对侧线进料和出料等复杂精馏不太适合等。
2.板式精馏塔板式精馏塔板式精馏塔内部流动情况板式塔为逐级接触式气液传质设备,它主要由圆柱形壳体、塔板、溢流堰、降液管及受液盘等部件构成。
原理:液体依靠重力作用,由上层塔板的降液管流到下层塔板的受液盘,然后横向流过塔板,从另一侧的降液管流至下一层塔板。
溢流堰的作用是使塔板上保持一定厚度的液层。
气体则在压力差的推动下,自下而上穿过各层塔板的气体通道(泡罩、筛孔或浮阀等),分散成小股气流,鼓泡通过各层塔板的液层。
在塔板上,气液两相密切接触,进行热量和质量的交换。
在板式塔中,气液两相逐级接触,两相的组成沿塔高呈阶梯式变化,在正常操作下,液相为连续相,气相为分散相。
3.气体冷却塔气体冷却塔冷却塔作用:工业生产过程中产生的废热,一般要用冷却水来带走。
冷却塔的作用就是将挟带废热的冷却水在塔内与空气进行热交换,使废热传输给空气并散入大气中。
史上最全的反应器结构及工作原理图解!

史上最全的反应器结构及工作原理图解!这里给大家介绍一下常用的反应器设备,主要有以下类型:①管式反应器。
由长径比较大的空管或填充管构成,可用于实现气相反应和液相反应。
②釜式反应器。
由长径比较小的圆筒形容器构成,常装有机械搅拌或气流搅拌装置,可用于液相单相反应过程和液液相、气液相、气液固相等多相反应过程。
用于气液相反应过程的称为鼓泡搅拌釜(见鼓泡反应器);用于气液固相反应过程的称为搅拌釜式浆态反应器。
③有固体颗粒床层的反应器。
气体或(和)液体通过固定的或运动的固体颗粒床层以实现多相反应过程,包括固定床反应器、流化床反应器、移动床反应器、涓流床反应器等。
④塔式反应器。
用于实现气液相或液液相反应过程的塔式设备,包括填充塔、板式塔、鼓泡塔等(见彩图)。
一、管式反应器一种呈管状、长径比很大的连续操作反应器。
这种反应器可以很长,如丙烯二聚的反应器管长以公里计。
反应器的结构可以是单管,也可以是多管并联;可以是空管,如管式裂解炉,也可以是在管内填充颗粒状催化剂的填充管,以进行多相催化反应,如列管式固定床反应器。
通常,反应物流处于湍流状态时,空管的长径比大于50;填充段长与粒径之比大于100(气体)或200(液体),物料的流动可近似地视为平推流。
分类:1、水平管式反应器由无缝钢管与U形管连接而成。
这种结构易于加工制造和检修。
高压反应管道的连接采用标准槽对焊钢法兰,可承受1600-10000kPa 压力。
如用透镜面钢法兰,承受压力可达10000-20000kPa。
2、立管式反应器立管式反应器被应用于液相氨化反应、液相加氢反应、液相氧化反应等工艺中。
3、盘管式反应器将管式反应器做成盘管的形式,设备紧凑,节省空间。
但检修和清刷管道比较困难。
4、U形管式反应器U形管式反应器的管内设有多孔挡板或搅拌装置,以强化传热与传质过程。
U形管的直径大,物料停留时间增长,可应用于反应速率较慢的反应。
5、多管并联管式反应器多管并联结构的管式反应器一般用于气固相反应,例如气相氯化氢和乙炔在多管并联装有固相催化剂的反应器中反应制氯乙烯,气相氮和氢混合物在多管并联装有固相铁催化剂的反应器中合成氨。