汽车前车门内饰板设计方法
浅谈汽车门内饰板设计

浅谈汽车门内饰板设计摘要:随着汽车行业发展,汽车市场对内饰造型的要求越来越高,如何快速、准确、有根据的让人赏心悦目、引人入胜的内饰尤为重要。
不仅在外观上,在功能上、互动方面,市场对装修都提出了更高的要求,这也可以成为我们设计装修的依据,汽车门内饰板设计需要考虑的东西越来越多,从美学到科技,在艺术设计和工程方面也是大有可为的在保证正确方法的基础上,我们要优化现有装修,不断改良,制造具有国际竞争力的中国汽车内饰。
基于此,本文主要探讨了汽车门内饰板设计。
关键词:门内饰板;定位策略;设计;刚度中图分类号:U463文献标志码:A引言国民经济水平的提高带动了汽车行业的发展。
现阶段,汽车工业的发展受到越来越多国家和地区的重视。
人们在追求高品质生活的同时,对健康、安全意识的关注度也在不断提高,对汽车内饰美感、功能的关注点逐渐下降,而对汽车内饰的舒适性、环保性能的关注度则呈逐年上升趋势。
针对门内饰板中乘客经常接触的区域进行分析,并对门饰板进行刚度分析,可为后续相应车型提供参考。
1门内饰板的成型工艺门内饰板分为硬质内饰板和软质内饰板两种。
常用的成型工艺有注塑成型、手工包覆成型、阳模真空吸附成型以及阴模真空吸附成型、软质门内饰板成本较高,以前一般用于高端车型上。
目前随着汽车市场竞争日益激烈,为了让自身开发的车型能够在市场上竞争力更大,各大主机厂大量使用软质内饰板的设计,而硬质门内饰板由于成本较低,目前主要用于较低端的商用车上。
2内饰板设计概述汽车门内饰板占据了驾驶室内左右两个侧面,是汽车内饰中重要的功能件和装饰件,使用十分频繁,门内饰板上装有门锁内开手柄、门锁开启按钮、玻璃升降器开关、扶手、杂物袋、扬声器等,并对驾乘人员肘部活动空间有直接影响。
汽车门内饰板一般设计流程为:产品技术路线规划(产品材料、工艺、储物功能规划)→门内饰板造型硬点确定(边界条件、安装点确认)→造型CAS确认(确认各电器件边界信息/确认与钣金件边界条件、门槛、仪表板、玻璃、密封条等周边件)→造型可行性分析(人机/总布置、主断面设计)→产品设计(详细结构设计、CAE分析)。
前车门布置设计流程讲义
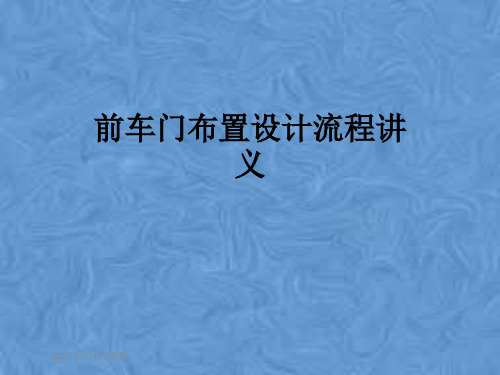
后视镜 间隙 后视镜 座 成型条
手柄 锁& 连 杆 铰链& 限位器 挡水条
升降器
玻璃
窗框
面板
车门组 件
基本要求
OOO
O
车门长度, 铰链的强度
OOO
OOO
车门扭转强度
OO
OOOOO
手柄固定座的强度
OOO
O
O O O O 车门扭转强度
OOOOOOO
车门扭转强度
OOO
O
OO
窗框的精度
OOOOO
OOO
OOO
5. 密封
掀拉式
旋转式
车门组
7. Door Lock System
件
E. 安全锁杆护套 : 设计考虑
1. 结构上要防止杆运动时干涉
2. 低摩擦材料 : 乙酰 / ABS
3. 厚度
护套
车门组
7. 门锁系统
件
F. 内手柄
1. 开闭耐久性试验
2. 喷涂材料 : 压铸件镀锌 /聚乙烯-乙酰 / 碳酸聚乙烯
前期设计时期的布置检查 1. 影响门洞线的因素: 阶段
截面尺寸越大, 门洞线越小 H. 顶盖侧边梁尺寸 I. 侧围下边梁高度 : 与上车有关 J. 侧围下边梁截面尺寸
顶盖侧边梁
上述三点与上车方便性及感觉有关
侧围下边梁
前期设计时期的布置检查 1. 影响门洞线的因素 阶段
K. 车轮中心和直径 : 轮罩 L. 前、后悬大小 M. 防撞垫的正切向尺寸
窗框
玻璃导槽 尼龙绒
A型
窗框 玻璃导槽
涂层Biblioteka B型9. 挡水条车门组 件
▪ 设计考虑 :
1) 要求. : 水密性, 隔音, 吸冲击, 防震 2) 材料 : EPDM 三元乙丙橡胶 (乙丙海绵橡胶带涂层)
门内饰板总成设计指南

模板编号: JN-0047-V1 汽车工程技术规范文件前门内饰板总成设计指南Front Door trim Shield Design guide目录1.范围 (1)2.设计指南引用文件 (1)3.定义 (1)4.设计指南内容 (2)4.1组成结构、安装方式、常用材料和常用生产工艺 (2)4.1.1组成结构 (2)4.1.2安装方式 (3)4.1.3前门内饰板常用材料 (3)4.1.4门内饰板常用工艺 (4)4.2前门内饰板设计关重项 (4)4.3前门内饰板定位及安装点布置原则 (4)4.4零部件设计 (5)4.4.1内开手柄盒 (5)4.4.2摇机手柄 (5)4.4.3肘靠(平扶手面板) (6)4.4.4喇叭孔(罩) (7)4.4.5喇叭与面罩的安装距离; (9)4.4.6玻璃升降器开关面板 (10)4.4.7扶手盒 (11)4.4.8立扶手 (12)4.4.9储物盒(地图带) (13)4.4.10吸音棉 (14)4.4.11吸能块 (15)4.4.12内开手柄布置要求: (16)4.4.13门内饰板设计边界要求: (17)4.4.14门内饰板密封条 (18)4.4.15扶手包覆 (18)4.4.16与内夹条搭接方式 (19)4.4.17与车门钣金搭接方式 (20)4.4.18与仪表板搭接方式 (20)4.4.19与门槛配合方式 (21)4.4.20与密封条配合方式 (22)4.4.21与门灯配合方式 (22)4.4.22防水薄膜 (23)4.5模块化结构 (23)4.5.1卡座模块化结构 (23)4.5.2BOSS柱模块化结构 (24)4.5.3焊接模块化结构 (25)4.6常用标件 (26)4.7前门内饰板性能指标 (26)4.8前门内饰板常见问题 (26)前门内饰板总成设计指南1.范围本规范规定了轿车车门内饰板在开发设计过程中应遵守一些要求和标准,规定了车门内饰板开发的一般过程、材料的选择、车门内饰板的分块、结构等。
(整理)7-前门系统结构设计

第八章前车门系统结构设计第一节概述1.前车门系统零部件结构组成:一般情况下,前车门系统零部件包括:车门钣金焊接总成、车门铰链、车门玻璃、玻璃呢槽、玻璃升降器总成、玻璃导轨、内外挡水条、门锁总成(含锁体、锁扣、锁芯、内外把手等)、车门限位器总成、车门内饰板等。
如图1所示。
图1 前车门系统零部件组成车门钣金焊接总成是车门系统各零部件的安装载体,因此车门的结构布置设计是否合理、车门的结构刚性和结构强度是否能够满足车门系统各零部件的功能实现就成了车门系统设计的主要内容。
车门钣金焊接总成组成零件:车门外板、车门内板、车门防撞梁、车门玻璃导轨、车门锁安装加强件、车门铰链安装加强件、外后视镜安装加强件及其它局部加强件等。
如图2所示。
图2 车门钣金焊接总成零部件组成2.车门系统设计的基本技术要求:(1)车门开启时应保证乘员上下车的方便性,要合理确定车门数,车门的开口位置,设计车门的开口大小和形状,并且车门要能够停留在最大开度的位置上。
(2)车门在开启过程中不应和车身的其它部位发生干涉。
(3)车门关闭后,要锁止可靠、安全,行车中车门不会自动打开。
(4)车门机构操纵要方便,包括车门开关自如,玻璃升降轻便等。
(5)车门应具有良好的密封性能。
(6)具有大的透光面,满足侧向视野要求。
(7)门体应具有足够的强度和刚度,保证车门工作可靠,减小车门部分振动,提高车辆侧向碰撞的安全。
(8)车门应具有足够的安装刚度,防止车门下沉。
(9)车门应具有良好的制造工艺。
(10)车门造型上应与整车协调一致,包括外表面形状,覆盖件的分块,门缝的设计和内饰。
3.车门系统设计的原则:(1)车门系统设计的总原则:由外而内、先外板后内板、先断面再数模、先周边再内部的而过程。
(2)车门结构设计原则:零件的结构设计尽可能简单,便于制造;零件之间的搭接结构合理,便于装配操作;零件的分块尽可能过合理,减少废料的产生,减低成本;在制造可行的前提下,零件的数量和分块尽可能少。
门内饰板设计规范

门内饰板总成设计规范R&D-CS-6102-001-2010门内饰板总成设计规范1 范围1.1 本规范适用于车门内饰板总成设计。
1.2 本规范适用于所有车。
2 规范性引用文件下列文件中的条款通过本规范的引用而成为本规范的条款。
凡是注日期的引用文件,其随后所有的修改单(不包括勘误的内容)或修订版均不适用于本规范,然而,鼓励根据本规范达成协议的各方研究是否可使用这些文件的最新版本。
凡是不注日期的引用文件,其最新版本适用于本规范。
GB 8410-2006 汽车内饰材料燃烧特性GB 11552-1999 轿车内部凸出物3 术语PP:聚已稀PVC:聚氯乙烯PU:聚氨酯4目标性能4.1门内饰板的主要功能是包覆金属门板,提供优美外观,并满足人机工程、舒适性、功能性和方便性等要求;为满足更多的储物功能,设置地图袋、卡片夹、烟灰盒等;在侧撞时提供适当的吸能保护,对车外噪声提供屏蔽作用;4.2符合GB 8410-2006汽车内材料的燃烧特性;4.3满足GB 11552-1999轿车内部凸出物法规要求5门内饰板总成组成门内饰板本体、上饰板、嵌饰条、储物袋、扶肘、拉手盒(盖)、门脚灯盖板及吸音绵等6 设计方法6.1 结构设计6.1.1门内饰板本体本体又称基板或门饰板骨架,是联接和安装门内饰板系统中其他功能件和装饰件的载体,应设计有定位和紧固系统使整个门饰板安装到钣金上。
本体要有足够的强度和刚度保持门饰板的形状,需有布置合理R&D-CS-6102-001-2010的紧固点位置和设计合理的紧固件使安装时插入力小而拔出力大,还必须留有一定的变形空间起到以达到乘员保护的目的。
6.1.2上饰板有硬质和软质两类。
硬质上饰板可单独分块,无造型或材料特殊要求也可与本体合为一个零件;软质上饰板通常由表皮、发泡层和骨架三部分组成。
上饰板与骨架通过孔销定位,用焊接或螺钉方式连接。
6.1.3嵌饰板嵌饰板用以提供手肘倚靠,以软质为多,分层结构由表皮(面料、革或真皮)、发泡层和骨架三部分组成。
汽车车门内板冲压成形工艺分析

缺陷检测ห้องสมุดไป่ตู้针对常见的冲压成形缺陷,采用特定的检测方法和技术手段,及时发现并处理缺 陷,避免批量质量问题。
质量追溯:建立完善的质量追溯体系,对每个环节进行记录和追踪,确保产品质量可追溯, 便于问题排查和解决。
冲压成形中的应力应变分析:板料在冲压过程中,会发生应力应变,其分布和大小对成形质量 有重要影响。
冲压成形中的缺陷分析:如起皱、开裂、回弹等,与材料性质、模具设计、工艺参数等因素有 关。
材料在冲压过程中的流动与变形规律 材料的应力应变行为 材料屈服准则和本构方程 材料硬化特性对冲压成形的影响
冲压速度:根据 材料厚度和成形 要求选择合适的 冲压速度,以保 证成形质量和效
轻量化材料:如高强度钢、铝合金等,可有效降低车身重量,提高燃油经济性和 动力性能。
新型成形工艺:如热冲压、温冲压等,可提高材料成形极限和零件强度,降低生 产成本。
复合材料:如碳纤维复合材料,具有高强度、轻量化和可设计性等优点,是未来 汽车车门内板冲压成形工艺的重要发展方向。
智能化技术:如人工智能、大数据等,可实现冲压成形工艺的智能化控制和优化, 提高生产效率和产品质量。
模具刚度与强度:确保模具在冲压 过程中具有足够的刚度和强度,避 免变形和损坏。
添加标题
添加标题
添加标题
添加标题
模具结构设计:采用易于加工、装 配和维修的结构,降低制造成本。
模具冷却系统:优化冷却系统设计, 提高冷却效果,减少模具温度波动 和热疲劳损伤。
研发背景:传统冲压成形工艺存在局限性,新型工艺应运而生 主要技术:激光冲压成形、热冲压成形等 应用领域:汽车制造、航空航天等 优势与效果:提高材料利用率、减少生产成本、提高产品性能等
汽车白车身前门内板结构设计
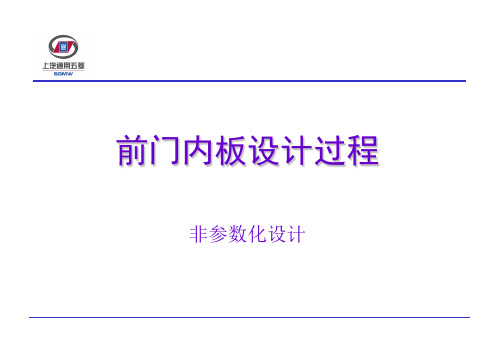
1
2
Page 30
B柱内板的设 计相对比较简单,
1
前门和中门的密封
胶条边定下来后, 中间结构按断面来 确定,要注意的两 处地方是:1,上端 与上边梁内板的搭 接过渡。2,与下B
2
柱内板的搭接过渡 (此处要考e 31
上边梁外挡板与中上边梁外板除了考虑模具制造和焊装问题进行 分块外,还要考虑 1处与导轨有一定的间隙而且要均匀。2处与上边梁
Page 22
A柱内板
为了 便于仪 表盘的 安装, 在此处 A柱内 板在X 方向上 必须保 证没有 负角。
Page 23
A柱内板
A柱 内板应与 侧围上边 梁内板保 持一直性。
Page 24
U0阶段对基本的结构方案确定以后,T1阶段就是对U0模 型的细化,对U0阶段考虑不周的地方,(如;各总成之间的搭 接、配合,各零件之间的搭接、配合问题,零件的制造、生产 线上的焊接、装配问题,再就是对整车的强度、刚度、安全性 方面的问题)进行方案的优化和细节的修改。
1
2
Page 28
1
A柱内板 的修改主要是
2
保证1处与顶
盖的距离要保 证15mm以上, 2处三层板的 圆角之间要保 证焊装间隙。 3处与前横梁 的焊接处应顺 滑,与顶盖的 间隙距离应均 匀。
3
Page 29
A柱加强板的修 改主要考虑1处:由 于材料与前侧围外板 不一样,成型时材料 的流动性变差而导致 的成型困难的问题。 3 2处:解决避免(前侧 围外板、A柱加强板、 侧板、前轮罩)4层板 的焊接,而又要保证 加强板与侧围焊接的 问题。3处的结构主 要是起到加强作用。
Page 18
前侧围外板
前门和中门的胶条边由前门和 中门所确定的密封线来确定。这里 要注意的是:在构建内板和加强板 时,由于内板和加强板的胶条边界 比外板的要短1mm,而胶条边是 由曲面组成,如果内板加强板是由 这条密封线偏置后裁剪再加厚,就 可能出现外板边界和内板加强板的 边界之间的1mm偏差有不均匀的 现象,此处可以由外板加厚后的边 界面偏置1mm后去裁剪。
车门内饰板设计规范

编号代替密级商密×级▲汽车工程研究院设计技术规范车门内饰板设计规范2005-01-22制订 2005-11-22发布前言汽车的自主开发是中国汽车业健康发展的必经之路。
在汽车自主开发设计中,内外饰设计占有及其重要的位置,特别是车门内饰板设计。
在此,特编写此规范——《车门内饰板设计规范》,希望对坚持走自主开发之路的新生力量的快速成长能起到一定帮助,也希望对各位设计人员能有一定帮助。
本规范尚有许多不足之处,需要我们在实际操作中进一步完善和补充,希望大家能给予指正。
本规范由汽车工程研究院车身所负责起草;本规范由汽车工程研究院项目处进行管理和解释;本规范主要起草人员:编制:校核:审定:批准:本规范的版本记录和版本号变动及修订记录车门内饰板设计规范一、适用范围本规范规定了轿车车门内饰板在开发设计过程中应遵守一些要求和标准,规定了车门内饰板开发的一般过程、材料的选择、车门内饰板的分块、结构等。
本规范适用于M1、N1类车辆。
二、专业术语三维坐标系:指汽车制造厂在最初设计阶段确定的由三个正交的基准平面组成的系统。
三个基准平面如下:X基准平面——垂直于Y基准平面的铅垂面,通常规定通过左右前轮中心;Y基准平面——汽车纵向对称平面;Z基准平面——垂直于Y和X基准平面的水平面。
R点:汽车制造厂规定的基准点,该点具有及车辆结构相关的固定的坐标,对应于驾驶员座位在正常的最低及最后位置时的躯干和大腿旋转点(H点)的理论位置,或各座位在车辆制造厂规定的使用位置时的H点理论位置。
三、车门内饰板总成的组成车门内饰板总成通用组成件见表一,根据造形的不同、所开发车的档次不同和所选用的生产工艺的不同等,车门内饰板总成组成会有所不同,车门内饰板总成各部件间主要是采用焊接、螺钉或者卡接结构连接成整体。
表一:下图是以本公司前车门内饰板总成为例介绍门的组成:车门锁止按钮套圈车门内开手柄总成六、车门内饰板总成各部件设计要求 :1、吸能块设计要求此件根据法规要求而设计(法规需要),多采用热熔胶及门板本粘接,一般情况下为、发泡,发泡倍数协商;以下是其设计及周边配合要求: 编号 内 容 基准值 备注① 及车窗玻璃的间隙 10 ② 及车门内板表面的间隙 5 ③ 及车门内板孔的间隙 10 ④及车门内饰的间隙2门内饰杂物盒(包含扬声器孔盖) 车门内拉手(包含车门控制开关)门内饰板主体(包含扶手)门内饰板上部装饰板杂物盒盖板2、内开扳手框的设计要求内开扳手框,是一个覆盖于门板上、套在内开扳手的装饰件,多采用材料加工;它在门板总成上的位置随内开扳手而确定,一般采用螺钉联接及卡挂在内开扳手座上两种方式固定(均需要设计相的卡挂结构及门板本体固定),下表是其设计的边界要求:⑨编号内容基准值备注①扣手度<685最大限度760②从开始的位置>480最小限度420③及竖立把手开始位置120~1402④内开扳手框周围及对手件的间隙(前后方向)⑤内开扳手框周围及对手件的3搭接量(前后方向)⑥内开扳手框周围及对手件的1间隙(上下方向)3、摇窗机手柄设计要求摇窗机手柄总长度一般设计为120左右,多数情况下借用参考车件,需配合升降玻璃扭矩校核;下表是其设计的边界要求:⑦及座椅垫的距离参照图B手柄臂背面及门板距7⑧离0.3手柄臂背面及门板平⑨行度要求4、电动控制钮的布置设计要求编号内容基准值备注625~715①电动控制钮前端布置及人体模型肩部转点要求②从把手开始的距离>140③从把手开始的角度<18°④前后倾斜角0~10°前面提升至10°⑤左右倾斜角0~5°扶手表面⑥及内饰表面的距离≥255、肘靠的设计要求⑴肘靠也叫扶手,分独立加工和及门板本体一体加工两种方式,独立加工件分纯注塑、覆表皮或面料(低压注塑或包覆)、塘塑、聚胺脂发泡等类型;及门板一体成型多采用压制和低压注塑两种成型方式,这两种均需要覆面料或表皮,同时需在肘靠处表皮下增加泡沫垫或成型软垫。
乘用车门内饰板3D建模方法概述
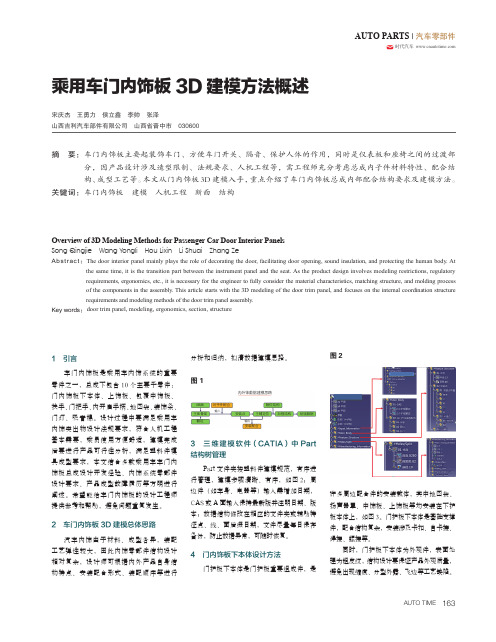
AUTO TIME163AUTO PARTS | 汽车零部件时代汽车 乘用车门内饰板3D 建模方法概述宋庆杰 王勇力 侯立鑫 李帅 张泽山西吉利汽车部件有限公司 山西省晋中市 030600摘 要: 车门内饰板主要起装饰车门、方便车门开关、隔音、保护人体的作用,同时是仪表板和座椅之间的过渡部分,因产品设计涉及造型限制、法规要求、人机工程等,需工程师充分考虑总成内子件材料特性、配合结构、成型工艺等。
本文从门内饰板3D 建模入手,重点介绍了车门内饰板总成内部配合结构要求及建模方法。
关键词:车门内饰板 建模 人机工程 断面 结构1 引言车门内饰板是乘用车内饰系统的重要零件之一,总成下包含10个主要子零件:门内饰板下本体、上饰板、包覆中饰板、扶手、门把手、内开启手柄、地图袋、装饰条、门灯、吸音棉。
设计过程中要满足乘用车内饰突出物设计法规要求,符合人机工程基本需要,乘员使用方便舒适,建模完成后要进行产品可行性分析,满足塑料件模具成型要求,本文结合多款乘用车车门内饰板总成设计开发经验、内饰系统零部件设计要求、产品成型故障履历等方明进行阐述。
希望能给车门内饰板的设计工程师提供参考和帮助,避免问题重复发生。
2 车门内饰板3D 建模总体思路汽车内饰由于材料、成型各异,装配工艺弹性较大,因此内饰零部件结构设计相对复杂,设计师可根据内外产品自身结构特点、安装配合形式、装配顺序等进行分析和归纳,拟清数据建模思路。
图1内外饰数据建模思路AB面主体骨架对手件配合安装点主辅定位安装配合限位结构加强结构初版数据输入输出翻边3 三维建模软件(CATIA)中Part 结构树管理Part 文件夹按塑料件建模规范,有序进行管理,建模步骤清晰、有序,如图2;周边件(如车身、电器等)输入需增加日期,CAS 或A 面输入保持最新版并注明日期、版本;数据结构修改在相应的文件夹或辅助特征点、线、面后缀日期,文件尽量每日保存备份,防止数据异常,可随时恢复。
车门内板冲压工艺设计与成形分析
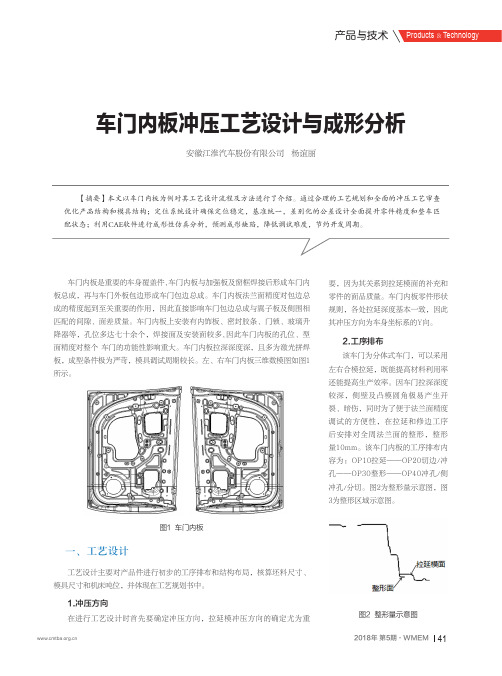
412018年 第5期·WMEM产品与技术车门内板冲压工艺设计与成形分析安徽江淮汽车股份有限公司 杨谊丽【摘要】本文以车门内板为例对其工艺设计流程及方法进行了介绍。
通过合理的工艺规划和全面的冲压工艺审查优化产品结构和模具结构;定位系统设计确保定位稳定,基准统一,差别化的公差设计全面提升零件精度和整车匹配状态;利用CAE软件进行成形性仿真分析,预测成形缺陷,降低调试难度,节约开发周期。
车门内板是重要的车身覆盖件,车门内板与加强板及窗框焊接后形成车门内板总成,再与车门外板包边形成车门包边总成。
车门内板法兰面精度对包边总成的精度起到至关重要的作用,因此直接影响车门包边总成与翼子板及侧围相匹配的间隙、面差质量。
车门内板上安装有内饰板、密封胶条、门锁、玻璃升降器等,孔位多达七十余个,焊接面及安装面较多,因此车门内板的孔位、型面精度对整个 车门的功能性影响重大。
车门内板拉深深度深,且多为激光拼焊板,成型条件极为严苛,模具调试周期较长。
左、右车门内板三维数模图如图1所示。
图1 车门内板图2 整形量示意图一、工艺设计工艺设计主要对产品件进行初步的工序排布和结构布局,核算坯料尺寸、模具尺寸和机床吨位,并体现在工艺规划书中。
1.冲压方向在进行工艺设计时首先要确定冲压方向,拉延模冲压方向的确定尤为重要,因为其关系到拉延模面的补充和零件的面品质量。
车门内板零件形状规则,各处拉延深度基本一致,因此其冲压方向为车身坐标系的Y向。
2.工序排布该车门为分体式车门,可以采用左右合模拉延,既能提高材料利用率还能提高生产效率。
因车门拉深深度较深,侧壁及凸模圆角极易产生开裂、暗伤,同时为了便于法兰面精度调试的方便性,在拉延和修边工序后安排对全周法兰面的整形,整形量10mm。
该车门内板的工序排布内容为:OP10拉延——OP20切边/冲孔——OP30整形——OP40冲孔/侧冲孔/分切。
图2为整形量示意图,图3为整形区域示意图。
42WMEM·2018年 第5期图3 整形区域示意图3. 坯料尺寸在零件的长度和宽度方向上分别选取线长最长的截面,如图4所示,测量A 、B 、C 值,并按照如下公式计算坯料的长度和宽度:L (W )=A +B +C +E +D +20其中E =5m m ~7m m ,D =20mm~30mm;图4图5 ECR测量零件的长、宽、高尺寸后预估坯料尺寸,长度1020mm,宽度770mm,高度90mm。
汽车车门内板冲压成形工艺分析

汽车车门内板冲压成形工艺分析•该文分析了某轿车车门内板的成形工艺及易产生的缺陷,并据此制定了其合理的冲压工艺方案。
文章通过对拉延成形过程的模拟与分析,得出了合理的工艺方案,目的是为类似零件工艺方案的制定提供参考。
汽车覆盖件具有尺寸大、相对厚度小、形状复杂等特点,决定了在冲压成形中板料变形的复杂性,变形规律不易被掌握,不能定量地对主要工艺参数和模具参数进行计算,在工程实践中还主要运用经验类比来进行冲压工艺设计。
一、冲压工艺制定1.零件工艺分析图1所示为某轿车车门内板零件图,材料为St14,料厚0.8mm。
从图可以看出,该零件形状复杂,高差较大,局部成形较多,板料的变形不是单纯的拉延成形,而是存在一定程度的胀形变形,是典型的汽车覆盖件。
图1中的a和b处,由于窗框部分进行内工艺补充后,形成了零件的反成形形状,这部分形状的成形一般不能靠外部材料进行补充,只能靠该部分板料的胀形成形来实现,胀形成形深度较深,a和b处大约有20mm左右,且转角部R较小,因此在拉延成形过程中很容易出现破裂。
在零件的c处,存在大约12mm高的台阶,此部分若在第一次拉延过程中直接成形,则压料面可能有以下两种分法:(1)将c部分作为压边面的一部分,即将分模线分在零件侧壁圆角处,这样由于台阶对板料的进料阻力较大,易导致零件在拉延过程中可能产生破裂;(2)将c部分作为凸模的一部分,即将分模线分在c部分外侧的法兰上,则在拉延过程中该区域的板料是悬空的,在径向拉应力和切向压应力的作用下,材料集中收缩到此处,可能导致零件的该部分起皱,甚至有迭料的可能。
由上面的工艺分析可知,该覆盖件成形难度大,成形工艺较复杂。
图1 某轿车车门内板零件图2.工艺方案的制定产品冲压成形工艺的确定过程,就是分析和预测板料在变形过程中可能产生的缺陷,并采取一定的措施,以消除和防止冲压缺陷,同时考虑制造能力、冲压设备、投资成本等因素。
根据本零件的工艺性和本身的结构特点,结合实际生产情况,车门内板的工艺过程如下:拉延+切角;二次拉延+切边+冲孔;切边+冲孔;侧切+侧冲孔翻孔+冲孔+整形;整形+冲孔。
车门内板的设计

车门内板的设计过程研究汽车车门的介绍:汽车车身属于汽车的3大总成之一,在汽车设计中占有极其重要的地位。
车门作为汽车的重要组成部分,是车身侧面最富变化和最受人关注的对象。
一方面,车门作为车身结构中的重要组成部分,其造型风格、强度、刚度、可靠性及工艺性等必需满足车身整体性能的要求;另一方面,车门结构自身的视野性、安全性、密封等性能,既对整个车身结构性能影响较大,也是车门功能要求的重要部分。
第一,对使用方便性来说,要求:开关方便性:灵活、轻便、自如,有最大、中间两档开度,并能可靠限位;上下车方便性:开度应足够,一般不低于60°或开度不小于650mm。
第二,对视野性来说,要求:尽量加大车门窗口及玻璃尺寸,并合理布置三角窗位置、大小、形状。
第三,对可靠性安全性来说,要求:足够的强度、刚度,不允许因变形、下沉而影响车门开关可靠性;车门开关时不允许有振动噪声;部件性能可靠、不干涉;撞翻车时不能自行开门,以确保乘员安全;满足侧撞时对乘员的保护要求。
第四,对密封性来说,要求:雨、雪、尘不能进入车内,应具备良好的气密封性。
第五,对工艺性维修性来说,要求:易于生产制造,拆装方便。
车门的结构类型多种多样。
按开启方式可分为旋转门、拉门、折叠门和外摆式车门;按车门结构可分为整体式车门和分开式车门;按有无窗框可分为有窗框和无窗框式车门;按旋转方向可分为顺开门、逆开门和上开门。
而在本次的设计中我们设计的是比较普通的车门是由壳体、附件和内饰盖板组成。
壳体按其结构可分为整体式或框架式。
整体式车门的玻璃窗框是与门内、外板一体冲压的,框架式车门的玻璃窗框是用螺丝钉固定或焊接在门体上的。
车门壳体是由厚度0.8- 1 0 mm 的钢板冲压的外板和内板等焊接而成。
外板外型与整车协调,外板包着内板,沿着门的边缘形成一刚性箍。
内板是车门的主要零件,在内板上冲有各种形状的窝穴、加强筋和孔洞,以便安装附件在安装完附件之后,用内饰板将其遮盖。
汽车门内饰板嵌饰板制造工艺分析及质量控制

汽车门内饰板嵌饰板制造工艺分析及质量控制汽车门内饰板是车门内部的装饰板,通常由塑料制成,用于美化车门内部环境和提升车内舒适度和豪华感。
门内饰板的制造工艺和质量控制对于确保它的美观、耐用和安全性能至关重要。
下面将对汽车门内饰板的制造工艺和质量控制进行分析。
第一,模具制造。
汽车门内饰板的制造首先需要制作适应其形状和尺寸的模具,通常采用金属材料制作。
制作模具过程中需要考虑到内饰板的曲线和空间要求,确保模具的精度和可靠性。
同时,模具制造也需要合理安排冷却系统,以确保塑料注塑过程中的均匀冷却和收缩。
第二,塑料注塑。
制造汽车门内饰板通常采用塑料注塑工艺。
注塑过程中,需要选择适合内饰板的塑料材料,并通过控制注塑温度、注塑压力和注塑时间等参数,确保内饰板的成型质量。
此外,还需要考虑塑料流动路径设计,避免产生破损、缩孔、热胀冷缩等缺陷。
第三,表面处理。
汽车门内饰板的表面需要经过处理以提升其质感和耐用性。
常见的表面处理方法包括喷涂和贴膜。
喷涂过程需要注意底漆和面漆的选择和涂装工艺的控制,确保饰板的颜色、光泽和附着力。
贴膜过程则需要注意膜的选择和贴合工艺的控制,确保膜的平整度和附着力。
第四,装配过程。
制造完成的汽车门内饰板需要进行装配到车门上。
在进行装配过程中,需要确保饰板与车门的尺寸和形状完全匹配,同时需要注意装配零件的固定和连接方法,确保饰板的安全性和稳定性。
以上是汽车门内饰板制造工艺的基本分析,下面将对其质量控制进行讨论。
首先,原材料的质量控制。
选择合适的塑料材料,并进行合格供应商的认证和质量检测,确保原材料的可靠性和符合相关标准。
其次,注塑成型工艺的质量控制。
通过在线监测和离线检测等手段,对注塑过程中的温度、压力和时间等参数进行监控和调整,确保内饰板的成型质量和一致性。
第三,表面处理的质量控制。
对表面处理过程中的涂装或贴膜工艺进行监测和调整,确保饰板的颜色、光泽和质感符合要求,并进行耐候性和耐磨性的测试和评估。