注水管道结垢腐蚀影响因素及防护措施
油田注水管道的腐蚀因素及防腐措施

油田注水管道的腐蚀因素及防腐措施油田注水管道是向石油储层注入水以增加油田产能的重要设备之一,其正常运行对于油田开发和经济效益的发挥非常重要。
但是,由于注水管道长期处于极端环境中,遭受了复杂的腐蚀作用,从而导致了管道的老化和失效。
因此,对注水管道的腐蚀因素进行认真研究,采取有效的防腐措施对于提高管道的使用寿命和安全性能至关重要。
注水管道的腐蚀因素主要包括以下几个方面:1. 环境因素。
由于管道它经常处于开采工地或平原或沙漠环境,表面的腐蚀物质也会因为化学抑制等防腐措施更难逐步去除。
而在注水管道内部,含有的化学物质如氧气、水等容易在管道的表面形成一个薄膜,形成电池电位差进而加剧腐蚀。
2. 构造因素。
注水管道因为要承受压力和各种力的作用,需要采用厚重的钢材,这样容易在管道中形成缺陷,比如气孔、裂纹和焊接缺陷等。
这些缺陷是管道遭受腐蚀的重点,因此注水管道的各个部位,比如焊接处和弯头区域,在施工的时候都需要特殊的注意。
3. 材质因素。
注水管道的材质可以是钢材、铸铁、铜等材料。
不同的材料受腐蚀的性质也不同,其中钢管是最常见的,也是最常见的腐蚀材料。
由于其材料成分不同,其防腐措施也需要进行不同的调整。
针对以上腐蚀因素,注水管道需要采取下列防腐措施来保证管道的使用寿命和安全性能:1. 防护涂料。
将注水管道表面喷涂上合适的防腐涂料,在管道外表形成一个保护膜,以减少接触和吸附腐蚀物质的机会,从而有效地延缓了管道的老化和腐蚀速度。
2. 电化学防腐。
电化学防腐就是在管道外表面覆盖上一层有电阻的铸铁板,这样可以形成一个电化学反应,并且在管道表面形成一层稳定的氧化层从而有效的甚至腐蚀的发生。
3. 浸涂防腐。
采用浸渍法将防腐油或其他化学品渗透到注水管道的表面,以形成一层均匀的防腐层,并且可以将其深入到管道内部以实现更多的腐蚀防护。
总之,注水管道是油田开采和生产的重要设备之一,其腐蚀和老化问题需要从多个方面进行有效的防治。
以上所述防腐措施只是其中的一部分。
油田注水系统腐蚀原因及对策

油田注水系统腐蚀原因及对策油田注水系统是一种非常重要的设备,它可以有效地提高油田的产能和延长油田的寿命。
在使用过程中,油田注水系统会面临腐蚀的问题,这不仅会影响系统的正常运行,还会给系统带来安全隐患。
了解油田注水系统腐蚀的原因及对策是非常重要的。
本文将深入探讨油田注水系统腐蚀的原因,并提出相应的对策。
一、腐蚀原因1. 水质腐蚀水质是影响油田注水系统腐蚀的主要因素之一。
当水中含有氧、二氧化碳、硫化物等易腐蚀物质时,会促进金属表面的腐蚀。
特别是当水中的溶解氧含量较高时,会加剧金属的腐蚀速度。
2. 流体速度腐蚀流体速度是导致油田注水系统腐蚀的另一个重要因素。
当流体速度过大时,会增加金属表面的携砂磨损和冲刷力,从而加剧金属的腐蚀程度。
4. 金属成分和结构金属的成分和结构也会影响油田注水系统的腐蚀情况。
当金属中含有易腐蚀的成分时,会加剧金属的腐蚀速度。
金属的结构也会影响腐蚀的程度,例如金属的表面粗糙度、表面处理等都会对腐蚀产生影响。
二、腐蚀对策1. 选择合适的材料针对水质腐蚀问题,可以选择抗腐蚀性能较好的材料,例如不锈钢、镍基合金等材料。
这些材料具有较好的耐腐蚀性能,可以有效地延长系统的使用寿命。
针对流体速度腐蚀问题,可以通过控制流体速度来减缓金属的腐蚀速度。
可以采取加装节流装置,控制管道内的流体速度,从而减少金属的腐蚀程度。
3. 控制温度4. 表面处理针对金属成分和结构问题,可以采取表面处理的措施,例如对金属表面进行研磨、镀层等处理,从而提高金属的耐腐蚀性能。
5. 定期检查和维护定期检查和维护是预防腐蚀问题的重要措施。
可以定期对系统进行检查,及时发现和处理系统内的腐蚀问题,从而减少腐蚀对系统的影响。
油田注水系统腐蚀问题是一个复杂的工程问题,需要综合考虑材料、流体速度、温度等因素,并采取相应的对策来预防和减少腐蚀的发生。
只有在综合考虑系统的使用环境和条件,针对性地采取相应的措施,才能有效地延长系统的使用寿命,提高系统的安全性和稳定性。
油田注水管道的腐蚀因素及防腐措施
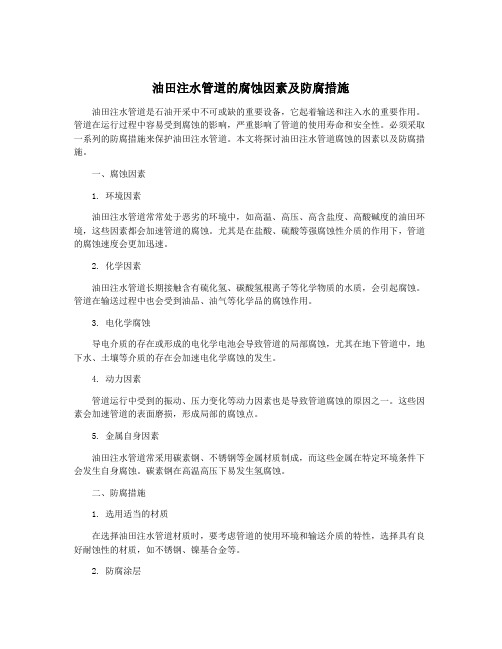
油田注水管道的腐蚀因素及防腐措施油田注水管道是石油开采中不可或缺的重要设备,它起着输送和注入水的重要作用。
管道在运行过程中容易受到腐蚀的影响,严重影响了管道的使用寿命和安全性。
必须采取一系列的防腐措施来保护油田注水管道。
本文将探讨油田注水管道腐蚀的因素以及防腐措施。
一、腐蚀因素1. 环境因素油田注水管道常常处于恶劣的环境中,如高温、高压、高含盐度、高酸碱度的油田环境,这些因素都会加速管道的腐蚀。
尤其是在盐酸、硫酸等强腐蚀性介质的作用下,管道的腐蚀速度会更加迅速。
2. 化学因素油田注水管道长期接触含有硫化氢、碳酸氢根离子等化学物质的水质,会引起腐蚀。
管道在输送过程中也会受到油品、油气等化学品的腐蚀作用。
3. 电化学腐蚀导电介质的存在或形成的电化学电池会导致管道的局部腐蚀,尤其在地下管道中,地下水、土壤等介质的存在会加速电化学腐蚀的发生。
4. 动力因素管道运行中受到的振动、压力变化等动力因素也是导致管道腐蚀的原因之一。
这些因素会加速管道的表面磨损,形成局部的腐蚀点。
5. 金属自身因素油田注水管道常采用碳素钢、不锈钢等金属材质制成,而这些金属在特定环境条件下会发生自身腐蚀。
碳素钢在高温高压下易发生氢腐蚀。
二、防腐措施1. 选用适当的材质在选择油田注水管道材质时,要考虑管道的使用环境和输送介质的特性,选择具有良好耐蚀性的材质,如不锈钢、镍基合金等。
2. 防腐涂层对于碳素钢管道,喷涂或浸渍防腐涂层是一种有效的防腐措施。
常用的防腐涂层有环氧树脂涂层、聚氨酯涂层等,可以有效隔离管道与外界介质的直接接触,减缓腐蚀速度。
3. 牺牲阳极保护在管道上安装牺牲阳极是一种有效的防腐措施。
牺牲阳极的工作原理是将一种相对活泼的金属置于被保护的金属表面,通过阳极的自身腐蚀来减轻被保护金属的腐蚀。
4. 电化学防腐通过外加电场来改变管道金属表面的电化学腐蚀状况,是一种新型的防腐措施。
这种防腐方法能够有效减少管道的腐蚀,提高管道的使用寿命。
塔中四油田注水管线结垢腐蚀影响因素分析

的硫化物 、 氯 离子 , 呈 酸性 , 存 在极 大 的腐蚀 风 险 。
2 注 水 管 线 结 垢 影 响 因 素 研 究
对 塔 中 四油 田 回注水 管线 水 质 和垢 样 成 分 分 析
内流速低 , 剪 切力 小 , 悬 浮物 质 易沉 积在 管 道 内壁 , 成 为结 晶核 , 为结 垢 创 造 了条 件 。此 外 , 水 中含 有 较 多
Cl 一
食 熏
( 4 。 2 ~7 . 5 ) ×1 0
S O4 。 ~
3 8 4 ~6 9 0
阴离 子 总 量
( 2 . 7 ~7 . 6 2 ) ×1 0
C a + 鞋 i § ℃ 璧
《 3 。 2 " - 5 . 8 ) ×l 0 ‘ 2 . 黾 2 — 2 篙
最高, 混塔 中 6 3 C的碳 酸根 离子 最高 。通 过油 田无机
p H 值 等 因素对 注水 管 线结垢 的影 响l _ 2 | 3 l 。
2 . 1 疰遗 和 的影 响
结垢 预测 软 件 得 到 塔 中 四 的结 垢 趋 势 。 ] , 以及 与最 高钙 离子 水 和最高 碳酸 根离 子水 1:1 混 合后 结 垢趋 势, 见图 1 。预 测 结 果 显 示 , 塔 中 四采 出水 饱 和 指 数 为2 . 7 8 , 有 结垢 趋势 , 外 围 作业 区最 高钙 离 子水 和最 高碳 酸根 离子 水 1:1混 合 后 , 饱和指数增加到 3 . 8 以上 , 结垢 趋 势 显 著增 大 。 因此 , 可 以考 虑 修建 调 蓄
油 气 田 环 境 保 护
・
2 2 ・2 O1 4年 6月
油田注水系统腐蚀原因及对策
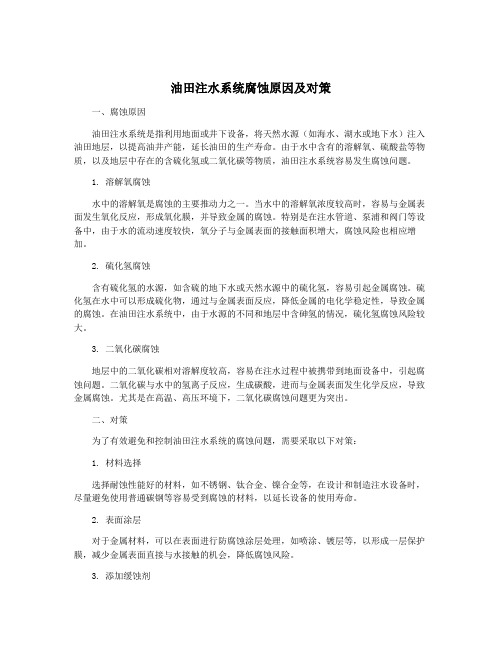
油田注水系统腐蚀原因及对策一、腐蚀原因油田注水系统是指利用地面或井下设备,将天然水源(如海水、湖水或地下水)注入油田地层,以提高油井产能,延长油田的生产寿命。
由于水中含有的溶解氧、硫酸盐等物质,以及地层中存在的含硫化氢或二氧化碳等物质,油田注水系统容易发生腐蚀问题。
1. 溶解氧腐蚀水中的溶解氧是腐蚀的主要推动力之一。
当水中的溶解氧浓度较高时,容易与金属表面发生氧化反应,形成氧化膜,并导致金属的腐蚀。
特别是在注水管道、泵浦和阀门等设备中,由于水的流动速度较快,氧分子与金属表面的接触面积增大,腐蚀风险也相应增加。
2. 硫化氢腐蚀含有硫化氢的水源,如含硫的地下水或天然水源中的硫化氢,容易引起金属腐蚀。
硫化氢在水中可以形成硫化物,通过与金属表面反应,降低金属的电化学稳定性,导致金属的腐蚀。
在油田注水系统中,由于水源的不同和地层中含砷氢的情况,硫化氢腐蚀风险较大。
3. 二氧化碳腐蚀地层中的二氧化碳相对溶解度较高,容易在注水过程中被携带到地面设备中,引起腐蚀问题。
二氧化碳与水中的氢离子反应,生成碳酸,进而与金属表面发生化学反应,导致金属腐蚀。
尤其是在高温、高压环境下,二氧化碳腐蚀问题更为突出。
二、对策为了有效避免和控制油田注水系统的腐蚀问题,需要采取以下对策:1. 材料选择选择耐蚀性能好的材料,如不锈钢、钛合金、镍合金等,在设计和制造注水设备时,尽量避免使用普通碳钢等容易受到腐蚀的材料,以延长设备的使用寿命。
2. 表面涂层对于金属材料,可以在表面进行防腐蚀涂层处理,如喷涂、镀层等,以形成一层保护膜,减少金属表面直接与水接触的机会,降低腐蚀风险。
3. 添加缓蚀剂在注水系统中添加合适的缓蚀剂,可以有效减少腐蚀的发生。
缓蚀剂可以形成一层保护膜,阻断金属与水接触,减缓腐蚀的速度。
4. 控制水质定期监测和改善注水水源的水质,合理控制含氧量、硫化氢含量、二氧化碳含量等指标,降低腐蚀的风险。
5. 优化运行合理设计注水系统的运行参数,如流速、压力等,避免过高的流速和压力对金属构件造成冲刷和损伤,降低腐蚀风险。
油田注水管道的腐蚀因素及防腐措施
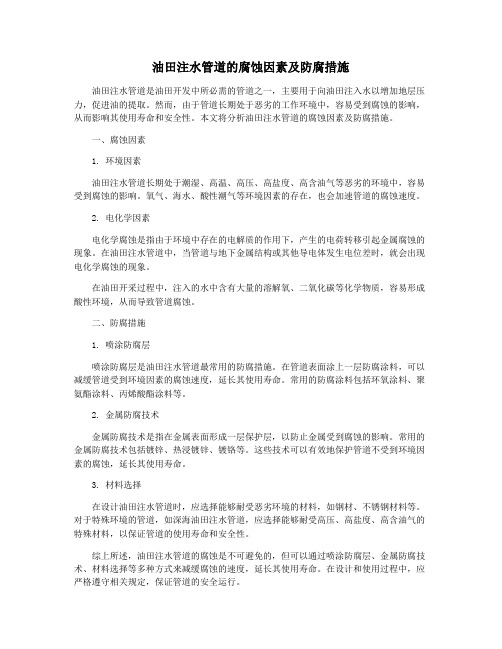
油田注水管道的腐蚀因素及防腐措施油田注水管道是油田开发中所必需的管道之一,主要用于向油田注入水以增加地层压力,促进油的提取。
然而,由于管道长期处于恶劣的工作环境中,容易受到腐蚀的影响,从而影响其使用寿命和安全性。
本文将分析油田注水管道的腐蚀因素及防腐措施。
一、腐蚀因素1. 环境因素油田注水管道长期处于潮湿、高温、高压、高盐度、高含油气等恶劣的环境中,容易受到腐蚀的影响。
氧气、海水、酸性潮气等环境因素的存在,也会加速管道的腐蚀速度。
2. 电化学因素电化学腐蚀是指由于环境中存在的电解质的作用下,产生的电荷转移引起金属腐蚀的现象。
在油田注水管道中,当管道与地下金属结构或其他导电体发生电位差时,就会出现电化学腐蚀的现象。
在油田开采过程中,注入的水中含有大量的溶解氧、二氧化碳等化学物质,容易形成酸性环境,从而导致管道腐蚀。
二、防腐措施1. 喷涂防腐层喷涂防腐层是油田注水管道最常用的防腐措施。
在管道表面涂上一层防腐涂料,可以减缓管道受到环境因素的腐蚀速度,延长其使用寿命。
常用的防腐涂料包括环氧涂料、聚氨酯涂料、丙烯酸酯涂料等。
2. 金属防腐技术金属防腐技术是指在金属表面形成一层保护层,以防止金属受到腐蚀的影响。
常用的金属防腐技术包括镀锌、热浸镀锌、镀铬等。
这些技术可以有效地保护管道不受到环境因素的腐蚀,延长其使用寿命。
3. 材料选择在设计油田注水管道时,应选择能够耐受恶劣环境的材料,如钢材、不锈钢材料等。
对于特殊环境的管道,如深海油田注水管道,应选择能够耐受高压、高盐度、高含油气的特殊材料,以保证管道的使用寿命和安全性。
综上所述,油田注水管道的腐蚀是不可避免的,但可以通过喷涂防腐层、金属防腐技术、材料选择等多种方式来减缓腐蚀的速度,延长其使用寿命。
在设计和使用过程中,应严格遵守相关规定,保证管道的安全运行。
油田注水管道的腐蚀因素及防腐措施

油田注水管道的腐蚀因素及防腐措施油田注水管道的腐蚀因素主要包括以下几个方面:1. 氧腐蚀:在注水过程中,管道中存在氧气,与金属管道发生氧化反应,导致管道腐蚀。
氧腐蚀主要通过两个途径进行:氧化腐蚀和流动腐蚀。
在管道的接触部分,氧化腐蚀是介质、金属和氧的三者共同发生的一种形式,而在管道的大部分空间中,腐蚀是氧化腐蚀和流动腐蚀并行的。
2. 酸性腐蚀:酸性溶液中的酸性离子与金属发生化学反应,产生酸性腐蚀。
这种腐蚀主要是由于酸性溶液中的酸性离子导致的管道表面的腐蚀。
3. 硫腐蚀:在注水过程中,硫含量较高的水泉或者油井注水会引起硫腐蚀。
硫腐蚀主要是由于水中硫氢酸、硫酸或者亚硫酸铵等溶液中的硫离子与金属发生反应,产生硫酸盐沉积。
4. 细菌腐蚀:水中存在的细菌或微生物会分解有机物质,生成酸性物质,导致管道的腐蚀。
细菌腐蚀是由于水泉中的微生物在无氧环境中分解有机物质,产生了酸性物质,从而引起了管道的腐蚀。
1. 选择耐腐蚀材料:在设计和选择管道材料时,应选用具有较好耐腐蚀性能的材料,如不锈钢、高合金钢等。
2. 阳极保护:通过在管道表面设立阳极,利用阳极的自身溶解来保护管道不受腐蚀。
常用的阳极保护方法有牺牲阳极保护和外加电流保护等。
3. 防腐涂层:在管道表面涂覆特殊的防腐涂层,形成一层致密的障碍物,防止介质与金属表面直接接触,从而起到保护管道的作用。
4. 清洁维护:定期对管道进行清洁和维护,去除管道表面的污垢和腐蚀产物,保持管道表面的光滑和清洁。
5. 控制水质:通过控制注水水质、控制水中含氧量、控制硫含量等方法,来减少水中的腐蚀物质,降低管道腐蚀的风险。
针对油田注水管道的腐蚀问题,可以通过选用耐腐蚀材料、采取阳极保护、涂层防护、定期清洁维护和控制水质等多种措施来进行防腐。
不同的管道材料、介质和工况需要采取相应的措施,以达到延长管道使用寿命、确保管道安全运行的目标。
油田注水管道的腐蚀因素及防腐措施

油田注水管道的腐蚀因素及防腐措施
油田注水管道的腐蚀问题对于油田开发和注水作业的安全和长期稳定运行具有很大的影响。
腐蚀的主要原因包括化学腐蚀、电化学腐蚀和物理腐蚀等因素。
为了避免腐蚀问题对油田注水管道的影响,需要采取一系列的防腐措施。
化学腐蚀是由管道内介质的成分和性质引起的,主要包括酸性物质、碱性物质和盐类物质。
这些介质的腐蚀作用导致管道内壁的金属材料被腐蚀、破坏。
为了防止化学腐蚀,可以采用选用耐腐蚀材料制造管道,例如不锈钢、塑料等材料。
还可以在管道内壁涂覆一层耐酸碱的保护涂层,以增加管道的抗腐蚀性能。
电化学腐蚀是由于管道金属与介质之间的电位差而引起的。
在油田注水作业中,通常会使用不同电位的金属材料,例如钢管和铜管。
这种不同金属之间的电位差容易导致电化学腐蚀。
为了防止电化学腐蚀,可以采用以下方法:尽量减小金属之间的电位差,例如在接触面涂覆一层电绝缘涂料或垫片;使用金属缓冲层来降低电位差,例如在接触面添加一层金属缓冲层;采用电化学保护方法,例如阴极保护和阳极保护。
物理腐蚀是由于管道内流体的流动状态引起的。
在油田注水作业中,流体的高速流动容易导致管道内壁的磨损和腐蚀。
为了减少物理腐蚀,可以采取以下措施:采用平滑的管道内壁和适当的管道截面形状,以减小流体的流动阻力和速度;使用耐磨损的材料制造管道,例如高硬度的合金钢;定期进行管道的检查和维修,及时修补和更换受损的管道。
浅谈注水系统结垢腐蚀影响因素及其对策

浅谈注水系统结垢腐蚀影响因素及其对策本文结合青西采油厂采油队注水系统的现状,阐述了影响注水系统结垢腐蚀的因素,并对影响原因队部注水系统结垢腐蚀的原因进行了分析,提出了防治对策,以求在进一步的工作中能适当缓解和减轻注水系统结垢和腐蚀程度,提高注水效率。
标签:结垢腐蚀;影响因素;防治对策1 前言油田进入中后期开发后,普遍采用注水采油的方式,为消除环境污染,也会采取回注处理。
在上述生产中,由于压力、温度、水热力学不稳定性、化学相溶性等条件,往往会造成注水地层、油套管、井下、地面设备及管线出现结垢腐蚀。
2 注水系统结垢腐蚀的危害性地面注水管线、注水泵站等注水系统结垢,会导致管道漏失甚至穿孔,既会增加管线维护成本,又为SRB细菌的繁殖提供了有利条件,若不及时控制,会导致管线大面积的损害;此外,发生垢堵塞时,垢物和污物、盐类、氧化铁等粘结在一起,会造成注水压力上升,降低整个注水系统的流量和效率,既增加了能耗,又增加了清洗费用和停产检修的时间。
3 注水系统结垢腐蚀影响因素3.1溶解度过饱和在地层压力、温度、PH值、盐度合适的条件下,一些矿物溶解于水中达到最大浓度,随着水注入地层或进入井筒,温度、压力逐渐下降,使其平衡条件发生变化,水溶解矿物的能力下降,出现了饱和现象,导致沉淀而生成了水垢。
3.2温度温度的变化,会影响细菌的繁殖速度、钢铁电化学反应的速率,从而影响腐蚀垢的生成速率,同时随着温度升高,盐类垢更容易析出沉淀。
不同温度的水,腐蚀速率不同,因此高矿化度的注入水在较高的运行温度下,腐蚀性很强。
3.3 PH值的影响提高溶液的pH 值,碳酸盐溶解将迅速结晶,会促进污垢的生长,但PH值若太低,会加大腐蚀,引起腐蚀垢;水质在酸性范围内或PH〉8后,腐蚀速率都极高,所以推荐合适的PH值为7.0-8.0之间。
3.4 压力的影响压力降低,促进结垢。
在管线输送中,压力一般都是降低的,因此结垢呈上升的趋势。
3.5 流速、液流流态水的流动越缓和,成垢核心生长的环境越稳定,垢越易生成,水的流速越小,结垢趋势越大。
油田注水管道的腐蚀因素及防腐措施

油田注水管道的腐蚀因素及防腐措施随着全球能源需求的不断增长,油田注水成为一种常见的油田开采方式。
在油田注水过程中,注水管道的安全和可靠性显得尤为重要。
油田注水管道在长期运行中容易受到腐蚀的影响,导致管道漏损、破裂等安全隐患。
了解油田注水管道的腐蚀因素,并采取相应的防腐措施,对确保油田注水管道的安全运行至关重要。
一、油田注水管道腐蚀因素1. 地下水和土壤成分:地下水和土壤中的盐分、二氧化碳、硫化物等化学物质对注水管道的腐蚀起着重要作用。
地下水中的盐分和二氧化碳会加速金属的腐蚀速度,使得管道的厚度不断减小。
土壤中的硫化物也会加速管道的腐蚀速度,对注水管道的安全性构成严重威胁。
2. 油田注水中的化学物质:油田注水中可能携带有各种化学物质,如硫酸盐、氯化物等。
这些化学物质在接触管道金属时,会引发电化学腐蚀反应,加速管道的腐蚀速度,从而降低管道的承载能力。
3. 流体运输过程中的机械磨损:流体在注水管道中运输的过程中,会对管道内壁造成机械磨损,使得管道金属暴露在外界,增加腐蚀的可能性。
4. 温度和湿度:环境中的温度和湿度对管道的腐蚀速度有着重要的影响。
高温和高湿度环境下,注水管道容易发生腐蚀,缩短了管道的使用寿命。
1. 选择合适的材料:在设计和选择注水管道材料时,应考虑到地下水和土壤中的腐蚀性物质,选择能够抵抗腐蚀的材料。
常见的防腐蚀材料包括不锈钢、镀锌钢、聚乙烯等。
2. 表面处理:对注水管道进行合适的表面处理,如喷涂防腐漆、涂覆防腐膜等,能够有效地阻止化学物质对管道金属的直接接触,延缓管道的腐蚀速度。
3. 阴极保护:采用阴极保护技术,给注水管道表面施加一定的电流,使得管道表面形成一层保护膜,阻止腐蚀性物质对金属的进一步侵蚀。
4. 材料选择和油品成分调整:调整油田注水的成分,减少其中的腐蚀性物质含量,同时选择抗腐蚀性能好的管道材料,能够有效地减缓注水管道的腐蚀速度。
5. 定期维护和检查:对注水管道进行定期的维护和检查是预防腐蚀的有效手段。
油田注水管道的腐蚀因素及防腐措施

油田注水管道的腐蚀因素及防腐措施随着石油勘探开发的不断深入和油田开采规模的逐渐扩大,油田注水管道的重要性日益凸显。
由于油田注水管道长期处于恶劣的工作环境中,其往往容易受到腐蚀的影响,严重影响管道的使用寿命和正常运行,甚至造成安全事故。
了解油田注水管道的腐蚀因素及有效的防腐措施对于保障油田注水管道的安全运行具有重要意义。
一、油田注水管道的腐蚀因素1. 化学腐蚀油田注水管道在工作过程中会受到包括水、二氧化碳、硫化氢等在内的多种化学物质的腐蚀影响。
水腐蚀是油田注水管道中最主要的腐蚀形式之一,水中可溶解的氧、二氧化碳和碱度等因素都会对管道材料产生腐蚀作用,造成管壁的损害。
而二氧化碳和硫化氢则会在水的存在下形成酸性物质,对管道材料产生腐蚀作用。
2. 电化学腐蚀在油田注水管道中,由于存在电解质和金属等材料的联系,就会出现电化学腐蚀的现象。
当管道表面出现损伤或缺陷时,电化学腐蚀会更加严重,导致管道腐蚀加速。
3. 生物腐蚀在一些油田注水管道中,由于水源的不洁净或者其他原因,容易滋生大量微生物,这些微生物会产生酸性物质,对管道材料产生腐蚀作用,加速管道的老化破损。
4. 机械腐蚀除了化学腐蚀、电化学腐蚀和生物腐蚀外,油田注水管道还可能受到外部机械力的作用,例如振动、磨擦等,导致管道的磨损和腐蚀,影响管道的使用寿命。
以上种种腐蚀因素使得油田注水管道的寿命大大降低,一旦管道发生泄漏或损坏,将给油田注水运行安全带来严重危害。
针对油田注水管道腐蚀问题,必须采取有效的防腐措施。
1. 选用抗腐蚀材料为了减少管道的腐蚀程度,首先需要对油田注水管道的材质进行选择。
一般来说,不锈钢、镍基合金、钛合金、聚四氟乙烯等抗腐蚀材料能够起到很好的防护作用,可以有效降低管道的腐蚀速度,延长使用寿命。
2. 表面处理对于普通的碳钢管道,常用的防腐蚀措施是对其进行表面处理。
比如喷涂防腐漆、热浸镀锌、喷涂耐蚀涂料等措施,可以有效降低管道的腐蚀速度,提高抗腐蚀性能。
油田注水管道的腐蚀因素及防腐措施

油田注水管道的腐蚀因素及防腐措施
油田注水管道在运行过程中,会面临着多种不同的腐蚀因素,包括物理腐蚀、化学腐
蚀和生物腐蚀等。
为了保护管道的安全运行,需要采取一系列的防腐措施。
物理腐蚀是腐蚀因素中的一种,在注水过程中,高速流动的水会对管道内壁产生磨损,导致管道腐蚀。
为了减少物理腐蚀,可以采用内衬材料,如耐磨橡胶、陶瓷等,来增加内
壁的防护层,减少磨损。
化学腐蚀是指注水中存在的一些化学物质对管道材料产生的腐蚀作用。
常见的化学腐
蚀因素包括酸性物质、盐和硫化物等。
对于酸性物质,可以选择耐酸材料来制造管道,如
不锈钢等。
对于盐和硫化物,可以采用防腐涂料,如环氧涂料、涂层等,来在管道表面形
成一个保护膜,阻挡化学物质的侵蚀。
生物腐蚀是指在注水过程中,一些微生物会在管道内壁生长,形成生物膜,并产生腐
蚀性物质。
为了防止生物腐蚀,可以采用生物阻垢剂,来阻止微生物生长和繁殖,减少管
道内壁的腐蚀。
除了采取上述的防腐措施外,还可以定期进行管道的维护和保养,及时清除管道内的
沉积物和腐蚀产物,防止其对管道的进一步腐蚀。
注水管道的设计和施工也是防腐的重要
环节,应考虑管道材料的选择、管道的防护层厚度以及管道的排水等因素,以提高管道的
防腐性能。
油田注水管道的腐蚀因素包括物理腐蚀、化学腐蚀和生物腐蚀等,为了保护管道的安
全运行,需要采取相应的防腐措施,包括增加防护层、选择耐蚀材料、使用防腐涂料、阻
止微生物繁殖等,同时定期进行管道的维护和保养,以延长管道的使用寿命。
油田注水管道的腐蚀因素及防腐措施

油田注水管道的腐蚀因素及防腐措施油田注水管道是油田生产过程中不可或缺的重要设备,其负责输送注水,维持油田压力,提高原油产量。
在长期使用过程中,管道常常会出现腐蚀现象,给油田生产带来不良影响。
对油田注水管道的腐蚀因素进行深入分析,制定有效的防腐措施势在必行。
一、油田注水管道的腐蚀因素1.化学腐蚀油田注水管道在输送注水的过程中,常受到水中溶解的盐类、硫化物、碳酸盐等化学物质的侵蚀,导致管道金属表面产生腐蚀。
而且随着油田开采程度的加深,油藏中含有的硫化氢、二氧化碳等腐蚀性物质也会增加,加剧了管道的化学腐蚀程度。
2.电化学腐蚀在油田注水管道中,金属管壁和管道表面上的任何局部细小缺陷、损伤或结垢都可能成为电化学腐蚀的起点。
当介质中存在氧气和水时,金属管道表面就会发生阳极和阴极的电化学反应,从而引发腐蚀过程。
3.微生物腐蚀在油田注水管道中,部分地区的地下水含有微生物,这些微生物对金属管道具有很强的生物腐蚀作用。
微生物产生有害代谢产物,附着在管道表面形成生物膜,导致管道表面的腐蚀。
4.机械磨损油田注水管道在使用过程中,由于介质流动或管道振动等原因,金属管道的表面会产生机械磨损,从而加速管道的腐蚀速度。
二、油田注水管道腐蚀防腐措施1.选用抗腐蚀材料在油田注水管道的选材方面,应尽可能选用抗腐蚀能力较强的材料,如耐腐蚀钢、双相不锈钢等,以提高管道的抗腐蚀性能。
2.表面处理油田注水管道在使用前应进行表面防腐处理,包括喷涂耐腐蚀涂层、热浸镀锌、喷涂环氧涂层等,增加管道表面的防腐蚀能力。
3.定期检测定期对油田注水管道进行检测和监控,及时发现管道表面的腐蚀情况,采取相应的防腐修复措施。
4.阴极保护通过给管道表面施加电流,使管道的金属表面成为阴极,形成保护层,阻断腐蚀过程,从而实现阴极保护的作用。
5.选择合适的防腐胶带在油田注水管道上使用防腐胶带可以很好地防止外部介质直接对管道金属表面进行腐蚀,提高了管道的耐腐蚀能力。
6.消除局部腐蚀针对已出现的管道局部腐蚀部位,可采取局部修复措施,如填充焊、喷涂防腐涂层等,延长管道的使用寿命。
油田注水系统腐蚀原因及对策

油田注水系统腐蚀原因及对策随着石油工业的发展,油田注水系统已成为一种重要的提高油田采收率、保持油田压力稳定的技术手段。
油田注水系统由井口设备、输送管道、水处理设备、储水池等组成,其中输送管道是重要的组成部分之一。
然而,输送管道的腐蚀问题也是油田注水系统面临的严重挑战之一。
本文将分析油田注水系统腐蚀的原因,并提出相应的对策。
一、腐蚀原因1.1 金属本身材质问题输送管道常用的材质有钢铁、玻璃钢等,然而这些金属材料本身的缺陷、不良质量也是管道腐蚀的直接原因之一。
由于材质不佳,原材料生产不规范等问题,导致管道表面粗糙度大,存在缺口、气泡、夹杂物等缺陷,使水洗过程中泥沙等杂质在管道表面产生磨蚀,形成局部腐蚀,最终导致管道失效。
1.2 介质腐蚀注水过程中,注入的水不光是清洁的淡水,其中含有酸性、碱性等不同性质的介质,这些介质会引起管道的化学腐蚀。
酸性介质可使金属表面腐蚀、产生氢气、破坏金属晶界;碱性介质则能使金属表面受到腐蚀,形成金属氢化物,导致管道材料的脆化,速度快。
1.3 电化学腐蚀水和金属之间存在一定的电化学反应。
在管道内部,水与管道材料之间的电化学反应形成电池,通过电子转移发生腐蚀。
在水中,经常存在各种离子,如氯离子、硫酸根离子、碳酸根离子、钠离子、钙离子等,它们与金属表面发生反应,形成附着物,阻碍正常的输送。
1.4 环境腐蚀在自然环境条件下,管道也容易被腐蚀。
特别是在具有强酸性、强碱性、强氧化性等环境中,金属更容易因氧化等原因退化,导致管道失效。
二、对策2.1 表面处理为了减少因金属本身材质问题引起的腐蚀,可以通过表面处理来提高管道表面质量。
表面处理可以包括喷丸处理、酸洗处理、化学转化膜、电解均匀处理等,可以有效的改善管道表面缺陷,提高抗腐蚀性能。
2.2 选用合适的材料合理选择管道的材料也是避免腐蚀的重要手段之一。
应根据具体环境条件和使用要求,选用质量好、抗应力腐蚀、抗软化腐蚀、抗点蚀的材料。
2.3 防腐措施对于不可避免的管道腐蚀问题,可以通过防腐措施来防止管道腐蚀。
油田注水管道的腐蚀因素及防腐措施

油田注水管道的腐蚀因素及防腐措施
油田注水管道是输送水的管道系统,它的腐蚀问题一直是油田技术人员关注的重点。
腐蚀是指物质与环境中的氧气、水等发生化学反应,导致物质的损耗和器件的损坏。
油田注水管道腐蚀的因素主要有化学因素和电化学因素两方面,下面分别介绍防腐蚀的措施。
一、化学因素
1.注水液中的溶解物:注水液中的溶解物如盐、水垢等都会对管道产生腐蚀作用。
为了防止这些溶解物沉积在管道内,可以采取过滤、沉淀等手段进行处理。
2.注水液的氧含量:氧气是腐蚀物质的“催化剂”,在含氧量高的注水液中,容易发生电化学腐蚀。
可以通过减少注水液中的氧含量,例如采用脱氧剂进行处理,来降低腐蚀的发生。
二、电化学因素
1.金属电位差异:油田注水管道由不同金属材料构成时,金属之间存在电位差异,容易产生电化学腐蚀。
可以采取两种金属之间的电连接方法,如使用金属连接器或焊接来减小电位差异。
2.缺陷和材料:油田注水管道的生产和安装过程中可能会出现缺陷,如焊接缺陷、材料脆性等。
这些缺陷会在使用过程中形成电化学腐蚀的“热点”,需要及时修复或更换。
3.防腐涂层:给油田注水管道涂上抗腐蚀的涂层是一种常用的防腐措施。
抗腐蚀涂层可以屏蔽氧气和水等物质与金属接触,起到阻止电化学腐蚀的作用。
油田注水管道的腐蚀因素主要包括化学因素和电化学因素。
防腐措施可以从注水液的处理、金属材料的选择和连接、缺陷和材料的处理以及防腐涂层等方面入手来减少腐蚀的发生,从而延长管道的使用寿命,提高油田注水的效率。
油田注水管道的腐蚀因素及防腐措施
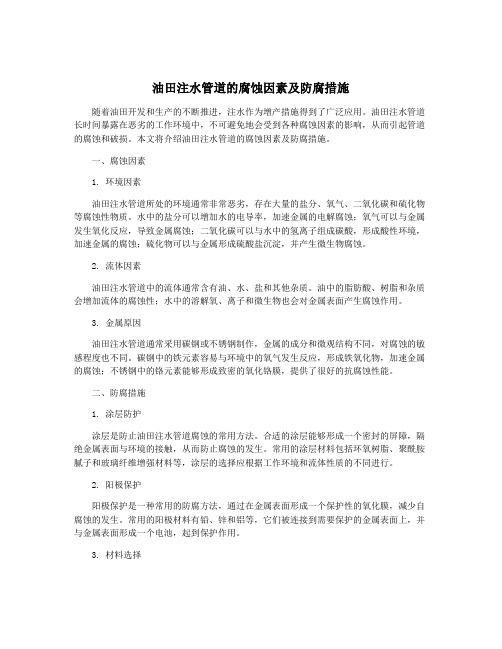
油田注水管道的腐蚀因素及防腐措施随着油田开发和生产的不断推进,注水作为增产措施得到了广泛应用。
油田注水管道长时间暴露在恶劣的工作环境中,不可避免地会受到各种腐蚀因素的影响,从而引起管道的腐蚀和破损。
本文将介绍油田注水管道的腐蚀因素及防腐措施。
一、腐蚀因素1. 环境因素油田注水管道所处的环境通常非常恶劣,存在大量的盐分、氧气、二氧化碳和硫化物等腐蚀性物质。
水中的盐分可以增加水的电导率,加速金属的电解腐蚀;氧气可以与金属发生氧化反应,导致金属腐蚀;二氧化碳可以与水中的氢离子组成碳酸,形成酸性环境,加速金属的腐蚀;硫化物可以与金属形成硫酸盐沉淀,并产生微生物腐蚀。
2. 流体因素油田注水管道中的流体通常含有油、水、盐和其他杂质。
油中的脂肪酸、树脂和杂质会增加流体的腐蚀性;水中的溶解氧、离子和微生物也会对金属表面产生腐蚀作用。
3. 金属原因油田注水管道通常采用碳钢或不锈钢制作,金属的成分和微观结构不同,对腐蚀的敏感程度也不同。
碳钢中的铁元素容易与环境中的氧气发生反应,形成铁氧化物,加速金属的腐蚀;不锈钢中的铬元素能够形成致密的氧化铬膜,提供了很好的抗腐蚀性能。
二、防腐措施1. 涂层防护涂层是防止油田注水管道腐蚀的常用方法。
合适的涂层能够形成一个密封的屏障,隔绝金属表面与环境的接触,从而防止腐蚀的发生。
常用的涂层材料包括环氧树脂、聚酰胺腻子和玻璃纤维增强材料等,涂层的选择应根据工作环境和流体性质的不同进行。
2. 阳极保护阳极保护是一种常用的防腐方法,通过在金属表面形成一个保护性的氧化膜,减少自腐蚀的发生。
常用的阳极材料有铅、锌和铝等,它们被连接到需要保护的金属表面上,并与金属表面形成一个电池,起到保护作用。
3. 材料选择在设计和选择油田注水管道时,应根据工作环境和流体性质的不同,选择具有较好抗腐蚀性能的材料。
常用的材料有不锈钢、合金钢、钻具涂层和塑料管道等,具有高耐蚀性和耐久性,能够减少腐蚀问题的发生。
4. 定期检测和维护油田注水管道的定期检测和维护是确保其正常运行和延长使用寿命的重要手段。
油田注水管道的腐蚀因素及防腐措施

油田注水管道的腐蚀因素及防腐措施随着石油资源的逐渐枯竭,油田注水成为提高石油产量的重要手段之一。
注水管道作为输送水质的关键设施,其安全稳定运行直接关系到油田的生产效率和安全生产。
注水管道在使用过程中容易受到腐蚀的影响,了解腐蚀因素并采取防腐措施显得至关重要。
本文将从腐蚀的原因和防腐的措施两方面进行探讨。
一、腐蚀的原因1.化学腐蚀注水管道在输送水质的过程中,水质中的溶解氧、二氧化碳、硫化氢等物质会引起金属表面的化学腐蚀。
特别是硫化氢对管道的腐蚀作用非常严重,容易形成硫化物覆盖层,导致金属材料的腐蚀损坏。
2.电化学腐蚀在地下油田环境中,由于土壤和水的存在,管道的金属材料会产生电位差,形成电化学腐蚀。
而在注水管道中,由于管道与土壤、水质之间的电位差,会引起管道金属表面的阳极或阴极部分腐蚀。
3.微生物腐蚀微生物腐蚀是注水管道的另一种常见腐蚀形式。
在油田地下环境中,微生物会以金属表面的水和水膜中的微量氧化物为营养源,在金属表面形成腐蚀区域。
特别是在高温高压下,微生物腐蚀的速度更加迅速。
4.机械磨损在注水管道的运行过程中,受到泵送液体的冲击和管道内部介质的摩擦,会形成机械磨损。
这种磨损也会加速管道金属材料的腐蚀,导致管道的损坏。
二、防腐措施1.选择合适的材料在注水管道的选材中,应该优先选择能够抵抗化学和电化学腐蚀的金属材料,例如不锈钢、耐腐蚀钢等。
还可以加工涂层或添加合金元素来提高金属材料的抗腐蚀能力。
2.防腐涂层在注水管道的表面涂覆防腐蚀涂层,可以有效阻隔管道与介质之间的腐蚀作用。
常用的涂层材料有环氧树脂、聚乙烯、聚氨酯等,可以选择根据实际使用环境来进行涂层的选择。
3.阴极保护采用阴极保护技术是一种有效的防腐措施。
通过在注水管道上设置阳极材料,使得管道成为阴极,从而降低管道金属表面的腐蚀速度。
4.监控与维护定期对注水管道进行腐蚀监测和维护是保障管道安全运行的重要环节。
定期使用超声波测厚仪进行管道壁厚度的监测,及时对管道进行维护和修复,可以有效延长管道的使用寿命。
油田注水管道的腐蚀因素及防腐措施

油田注水管道的腐蚀因素及防腐措施随着石油需求的不断增长,油田开采量逐年上升,对注水管道的使用需求也越来越大。
然而,注水管道的使用环境通常十分恶劣,腐蚀问题也十分严重,严重影响了管道的使用寿命和安全性。
在此,我们将分析油田注水管道的腐蚀因素及防腐措施,以期为实际生产提供指导。
(一)水质问题油田地下水含有大量的杂质和盐分,经过处理之后再用于注水管道中,其化学成分不稳定,导致腐蚀问题日益凸显。
一般情况下,水中盐分含量越高,管道腐蚀的速率越快。
在运输和使用过程中,水会与管道中的空气和金属离子发生反应,形成电化学反应,导致管道腐蚀。
(二)氧化问题油田注水管道的使用过程中也会遇到氧化问题,由于管道在输送过程中接触空气,管道内的铁元素会和氧气发生反应,形成氧化物,导致管道腐蚀。
此外,在管道内部的垃圾和其他杂质也会促进氧化反应的发生,从而增加了管道腐蚀的风险。
(三)细菌问题油田注水管道中的细菌会促进腐蚀的发生,这种腐蚀通常被称为微生物腐蚀。
细菌是在水中繁殖的,当注水管道内的水质不稳定或存放时间过长时,细菌数量可能会增加,导致细菌腐蚀的发生。
这种类型的腐蚀很难检测,并且难以处理,一旦发生,就会影响注水管道的使用寿命和安全性。
(一)外涂防腐层外涂防腐层是一种常见的防腐措施,可以有效地保护注水管道,防止腐蚀的发生。
外涂防腐层可以对管道表面进行涂覆,形成一层防腐隔离层,隔离管道与外界环境的接触,从而减少腐蚀的风险。
(二)选用合适的材料注水管道的选材也直接关乎其防腐效果。
合适的材料可以降低管道腐蚀的风险,延长其使用寿命。
一般来说,经过表面涂防腐处理的铁管、镀锌钢管、不锈钢管等都可以作为注水管道的材料。
(三)加强管道的清洁与维护加强管道清洁维护也是非常重要的一项措施。
要定期清洗管道内的污垢和其他杂质,保持管道内的水质清洁。
另外,要修补管道表面的破损或锈蚀处,防止污水侵入,影响管道质量。
总之,油田注水管道的防腐工作极为重要,减少腐蚀的风险,可以保证管道的正常使用,提高其安全性和使用寿命。
- 1、下载文档前请自行甄别文档内容的完整性,平台不提供额外的编辑、内容补充、找答案等附加服务。
- 2、"仅部分预览"的文档,不可在线预览部分如存在完整性等问题,可反馈申请退款(可完整预览的文档不适用该条件!)。
- 3、如文档侵犯您的权益,请联系客服反馈,我们会尽快为您处理(人工客服工作时间:9:00-18:30)。
浅析注水管道结垢腐蚀影响因素及防护措施
【摘要】本文介绍了注水系统管道腐蚀结垢的影响因素,得出了结垢因素有水质、温度、压力等,腐蚀因素有溶解氧、co2、微生物等。
根据管道腐蚀结垢特点筛选出了imc - 97缓蚀剂、f21阻垢剂、杀菌剂。
针对注水系统管道外腐蚀现象提出了对管道阴极保护的措施。
【关键词】结垢腐蚀阴极保护器
自进入高含水开发阶段以来,随着注水水质的不断恶化,油田井下管柱和输油管线的腐蚀及结垢问题,一直是困扰油气开采和输送的顽症。
因此有必要了解水质条件,分析结垢并提出切实有效的防护措施。
1 注水系统管道结垢原因
某厂注水水源有两种,一是地下水,也称清水;另一种是经过净化的油田采出水,即回注污水。
我们在几个采油区的注水系统中有选择性地采集了水样,并在正在使用的钢管内壁选取垢样。
垢样分析结果表明,两种水混注时产生的垢的主要成分是碳酸盐,而单注清水或污水时生成的垢主要为铁化合物。
1.1 注水水质的影响
1.1.1 注水管线中碳酸盐结垢分析
采用stiff和davis的饱和指数法计算注水的结垢因子si,得出所有水样的si值均大于0,即所有水样都有碳酸钙结垢倾向。
1.1.2 注水管线中铁化合物结垢分析
该厂注水体系中存在大量的碳酸氢根离子,这样的水进入管线后,必然形成feco3垢沉积在金属表面。
同时feco3溶解度随温度升高而降低,这正是我们在注水管线中检测到feco3垢的原因。
1.2 其它影响因素1.2.1 温度的影响
该厂注水水温分别为7℃(清水)和40℃(回注污水),清水的水温较低,caco3的溶解性好,结垢倾向小。
而回注污水水温较高,caco3的溶解性差,结垢倾向也大。
1.2.2 压力的影响
压力升高可使caco3在水中的溶解度增加,不易结垢。
1.3 清水污水混注时结垢原因分析
采用清水和污水混注技术,实践中发现混注时caco3结垢明显加重。
采用stiff和davis的饱和指数法,得出任何比例的混合水的碳酸钙结垢倾向均大于单一的清水和污水。
这正是混注时更易结垢的原因。
2 注水系统管道腐蚀原因
(1)溶解氧引起的腐蚀:o2会产生很强的腐蚀性,在套管的局部生成4fe(oh) 3,产生很深的腐蚀坑,长期作用,套管即被腐蚀穿孔。
(2)co2的腐蚀作用:当水中的co2越多,形成的h2co3就越多,h2co3电离后生成极化剂h+越多,地下水对油水井套管的氢去极化腐蚀就越强。
(3)微生物腐蚀作用:光谱分析发现,套管的腐蚀产物中含有
部分fes,fe(oh)2,说明硫酸盐还原菌对套管有一定的腐蚀作用。
3 注水系统结垢腐蚀防护措施
3.1 注水系统管道内侧腐蚀结垢防护措施3.1.1 缓蚀阻垢剂评
选
为了找出能普遍适用于该厂各区块的缓蚀剂,挑选了七种缓蚀剂进行初选,浓度均为100mg/ l。
通过试验结果得出,imc - 97在浓度为20 mg/ l~50 mg/ l 时,缓蚀率的变化不大,但均大于60 %,为此选用imc -97 进入现场试验。
3.1.2 阻垢剂的评选
(1)对硫酸钙垢的阻垢率,实验结果表明f21、f02等两种阻垢剂防硫酸钙垢的能力均较强。
(2)对硫酸钡垢的阻垢率,试验表明,f21 有较好的防硫酸钡垢效果。
(3)对硫酸钙和碳酸钙混合垢的阻垢率,f21 对硫酸钙和碳酸钙混合垢有较好的阻垢能力,并且适用于防多种垢,我们把f21带入现场。
3.1.3 缓蚀剂与阻垢剂的配伍性评价
通过试验得出,阻垢剂f21和f02与缓蚀剂混合后,药剂之间的溶解性很好,由此确定缓蚀阻垢剂配方为:f21+imc-97。
3.1.4 杀菌剂的评选
所选的杀菌剂与上述所选的缓蚀剂和阻垢剂配伍性好,互不影响各自的性能。
cyd1021b的最低有效杀菌浓度为70mg/ l 。
因此优
先选用cyd1021b杀菌剂。
3.2 现场实施效果的分析
我们在该厂进行了现场投加缓蚀剂试验,试验前该系统现场挂片腐蚀速率为1.0mm/a以上,试片表面结垢严重,附着生长一层坚硬的黑色垢质,酸洗后试片坑蚀严重。
而投加缓蚀剂imc-97后,现场腐蚀速率仅为0.0163mm/a,缓蚀速率高达88.4%,试片光滑,使得注水系统腐蚀结垢问题得到了彻底解决。
再投加缓蚀剂6个月时,对现场观察管进行了取样观察分析,投加缓蚀剂前,管线结垢严重,厚度在1.5cm左右,而投加缓蚀剂后,管线内壁光滑,无明显结垢。
3.3 大庆注水系统管道外侧腐蚀防护措施
针对套管的腐蚀问题,提出了油水井套管腐蚀的防护措施—油管阴极保护器。
其原理是利用比管道电极电位更低的金属材料与管道相连,构成一个新的宏电池,根据电化学理论,电位相对较低的金属材料成为阳极,管道成为阴极。
由于国内油田在外加电流阴极保护上存在的主要问题是管理不善,且维护费用高、运行时率低,对边远井、无电源气井都很难实施。
牺牲阳极保护在本质上与外加电流阴极保护等同,只是在给被保护体提供电流的方式上不同。
它具有简单、不需地面设施、不需日常管理的优点,并且还适合于外部环境较差的边远井、无电源井的保护。
因此,根据国内外在这一技术领域的发展动态和大庆油田浅表层套管腐蚀的实际情况,采用经济、实用可靠的自生电流免维护防腐
工艺是符合我国国情的。
4 结论
(1)针对注水系统管线内的腐蚀和结垢问题,通过实验筛选出了20mg/ l的imc -97缓蚀剂、20mg/ l的f21+imc-97阻垢剂。
通过现场试验验证了所选的药剂适合现场应用效果理想。
(2)针对套管的腐蚀问题,提出了油管阴极保护器的防护措施。
参考文献
[1] 李福军,等.油水井套管的腐蚀及防护理论、实验与应用—油水井套管的腐蚀与防护.大庆石油学院学报2000,23(5): 80-85 作者简介
陈丽鹤(1986.10-),女,吉林辽源市人,2009年毕业于东北石油大学,现从事机采综合分析工作。