生产线平衡公式
生产线平衡

生产线平衡率的计算方法
平衡率是评价一条产线的重要指标,平衡率高就表示在同等 条件下平衡损失就少,也就是说平衡率高的产线人均产能就 高。
目的:通过平衡生产线提高生产效率同时使生产现场更 加容易理解“一个流”的必要性及对于真正实现“OPF”进 而导入“cell production”的重要意义。
平衡生产线的意义
游戏时间
平衡生产线的意义
通过Line balancing我们可以达到以下几个目的:
有效减少工时损失进而提高作业员及设备工装的工作效率; 减少产品的C/T和pitch time,最终导致Takt time 的减少,提高productivity. 提高OEE & OME. 减少WIP,更容易真正实现“OPF”。 在Line balancing 基础上,实现单元生产,提高了生产对柔性化市场的应变能 力。
Line balance rate = ∑Standard time/(bottleneck time*person qty) = ∑ Standard time/(Pitch time*person qty)
Line imbalance rate =1-Line balance rate
Remark: Pitch time 是指生产线每产出一个batch产品所消耗 的时间,这里我们定义batch size 为1pcs, 所以pitch time=bottleneck time, 理想情况下pitch time=Takt time.
1.不同产品的特性差异
生产线平衡-答案

《生产线平衡》试题姓名工号成绩 , 一﹑填空﹕(12*4=分)1.ECRS原则具体是指﹕Eliminate﹑Combine﹑Rearrange﹑Simple。
2.生产力是指每人每小时生产台数。
3.生产线平衡公式=各工站工时之和÷(瓶颈工站工时×工站总数) ×100%。
4.6M分析改善法﹐分别是指人员方面﹑机器设备方面﹑材料方面﹑作业方法﹑环境评量工具、仪器。
二﹑问答题和应用题﹕1.N客户要求H公司的交期是:110天(已扣除假期及双休日);交货量为:1210万PCS;现H公司有11条冲压生产线,预估良率为98%,稼动率为85% (每日作业时间是20小时)。
请问单线节拍至少为多少秒时才不会延误交期? ( 20分)解﹕单线日产能=12,100,000/(110*11)=10,000 PCS/(日*线)考虑良率及稼动率的影响,其实际产能应为:10000/0.98/0.85=12005 PCS/(日*线)Tact Time =3600*20/12005= 6.0 (秒)2.某条生产线有5个工站﹐工时分别为:9s,11s,8s,12,10s﹐请计算出线平衡率? ( 12分)解﹕线平衡=各工站工时之和÷(瓶颈工站工时×工站总数) ×100%==(9+11+8+12+10)/(12*5)*100%=83%3. ( 20分)请写出生产线平衡改善的八大步骤( 20分)解﹕第一步:平衡前的数据收集整理与分析第二步:消除生产的浪费第三步:利用方法研究进行改善第四步: 山积表平衡第五步:建立新的生产流程第六表:实施后的效果确认第七步:改善后的总结报告第八步:标准化。
工序平衡率计算公式
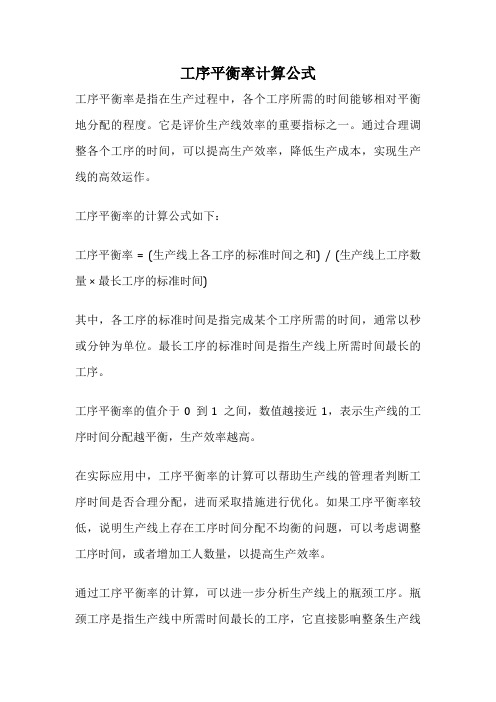
工序平衡率计算公式
工序平衡率是指在生产过程中,各个工序所需的时间能够相对平衡地分配的程度。
它是评价生产线效率的重要指标之一。
通过合理调整各个工序的时间,可以提高生产效率,降低生产成本,实现生产线的高效运作。
工序平衡率的计算公式如下:
工序平衡率= (生产线上各工序的标准时间之和) / (生产线上工序数量 × 最长工序的标准时间)
其中,各工序的标准时间是指完成某个工序所需的时间,通常以秒或分钟为单位。
最长工序的标准时间是指生产线上所需时间最长的工序。
工序平衡率的值介于0到1之间,数值越接近1,表示生产线的工序时间分配越平衡,生产效率越高。
在实际应用中,工序平衡率的计算可以帮助生产线的管理者判断工序时间是否合理分配,进而采取措施进行优化。
如果工序平衡率较低,说明生产线上存在工序时间分配不均衡的问题,可以考虑调整工序时间,或者增加工人数量,以提高生产效率。
通过工序平衡率的计算,可以进一步分析生产线上的瓶颈工序。
瓶颈工序是指生产线中所需时间最长的工序,它直接影响整条生产线
的效率。
通过优化瓶颈工序,可以进一步提高生产效率,减少生产成本。
除了工序平衡率,还有一些其他指标可以用来评估生产线的效率,例如生产效率、生产能力利用率等。
这些指标可以相互配合,全面评估生产线的运作情况。
工序平衡率是评价生产线效率的重要指标之一。
通过合理调整各个工序的时间,可以提高生产效率,降低生产成本。
因此,在生产线管理中,我们应该重视工序平衡率的计算和优化,以实现生产线的高效运作。
生产线平衡

什么是生产线平衡(line balance)?一、“节拍”、“瓶颈”、“空闲时间”、“工艺平衡”的定义流程的“节拍”(Cycle time)是指连续完成相同的两个产品(或两次服务,或两批产品)之间的间隔时间。
换句话说,即指完成一个产品所需的平均时间。
节拍通常只是用于定义一个流程中某一具体工序或环节的单位产出时间。
如果产品必须是成批制作的,则节拍指两批产品之间的间隔时间。
在流程设计中,如果预先给定了一个流程每天(或其它单位时间段)必须的产出,首先需要考虑的是流程的节拍。
而通常把一个流程中生产节拍最慢的环节叫做“瓶颈“(Bottleneck)。
流程中存在的瓶颈不仅限制了一个流程的产出速度,而且影响了其它环节生产能力的发挥。
更广义地讲,所谓瓶颈是指整个流程中制约产出的各种因素。
例如,在有些情况下,可能利用的人力不足、原材料不能及时到位、某环节设备发生故障、信息流阻滞等,都有可能成为瓶颈。
正如“瓶颈”的字面含义,一个瓶子瓶口大小决定着液体从中流出的速度,生产运作流程中的瓶颈则制约着整个流程的产出速度。
瓶颈还有可能“漂移”,取决于在特定时间段内生产的产品或使用的人力和设备。
因此在流程设计中和日后的日常生产运作中都需要引起足够的重视。
与节拍和瓶颈相关联的另一个概念是流程中的“空闲时间”(idle time)。
空闲时间是指工作时间内没有执行有效工作任务的那段时间,可以指设备或人的时间。
当一个流程中各个工序的节拍不一致时,瓶颈工序以外的其它工序就会产生空闲时间。
这就需要对生产工艺进行平衡。
制造业的生产线多半是在进行了细分之后的多工序流水化连续作业生产线,此时由于分工作业,简化了作业难度,使作业熟练度容易提高,从而提高了作业效率。
然而经过了这样的作业细分化之后,各工序的作业时间在理论上,现实上都不能完全相同,这就势必存在工序间节拍不一致出现瓶颈的现象。
除了造成的无谓的工时损失外,还造成大量的工序堆积即存滞品发生,严重的还会造成生产的中止。
生产线平衡的技巧

4.合并相关工序,重新排布生产工序(作业内容相对较多的情况下
易拉平衡)。 5.分解时间较短的工序,将该工序安排到其他工序中。
作业分析
问题主要原因的四M要素: 1.机械(Machine) 2.材料(Material) 3.作业人员(Man) 4.作业方 法(Method) 1.机械(Machine) 活动的重点(细部的主要原因): 1>.机械的哪一部份会影响到所谓的特性呢?(如:品质、运转率 等). 2>.开始作业时和日常处理(检查、上油). 3>.发现毛闰病以及处理(保全). 4>.机械应改善的事项(故障率). 5>.开始作业时的整理、整顿(环境).
作业分析
◎ 作业人员按规定作业时,仍然会产生不良产品(必须修改作业 指导书,变更作业方法). 5>.作业人员的工作态度(协调性、积极性、士气). 4.作业方法(Method) 活动的重点(细部的主要原因): 1>.作业方法的哪一点会影响到特性(工程质量能力、作业准备). 2>.作业的顺序保持现状好呢?或者按作业指导书进行(作业顺序、 进行方法). 3>.是否在没有使用作业指导书之下进行作业. 4>.对于变更作业指导书的处置(作业的进行方法). 5>.作业指示图是否应,改善以及是否有不适当之处. 6>.作业人员的安全之确保(安全纲). 7>.作业场所的配置有否缺陷?
改善方向
2.合并 (1)把必須突然改变方向的各个小动作结合成一个连续的曲线动 作。 (2)合并各种工具,使成为多用途。 (3)合并可能的作业。 (4)合并可能同时进行的动作。 3.重排 (1)使工作平均分配于兩手,兩手之同时动作,最好呈对称性。 (2)组作业时,应把工作平均分配于各成員。 (3)把工作安排成清晰的直线順序。
IE的定义及公式计算

I E的定义及公式计算------------------------------------------作者xxxx------------------------------------------日期xxxxIE培训技术资料IE的定义:IE(Industrial Enginccring)即工业工程与现场改善。
生产线平衡率(编程率)=各站标准工时之和/瓶颈时间*站数*100%平衡时间 = 60分*60秒*8H*(8H)产能/(1+宽放率)标准工时= 60分*8H*(站数)/产能(8H)標準工時簡稱「標時」。
在傳統產業,尤其是勞力密集的產業中是一種重要的標準。
舉凡每日標準的工作量衡量、計件工資、生產獎勵辦法的指標設定、加工成本的估算、員額設定、‧‧等等都以標時為基準。
正常工時─以一個正常效能的工人,在無干擾的正常情況下完成一項指定作業所需要的工作時間。
標準工時─以一個正常效能的工人,在考量某些無法免除的正常因素下完成一項指定作業所需要的工作時間。
─上述所謂「無法免除的正常因素」是指在現行的管理體制下和現有工作環境及設備、方法條件下從事長期的相同且重覆性工作。
其平均完成一項指定作業所需要的工作時間。
在標準工時計算公式中,一般稱之為「寬放」。
一般工業測定標準工時之方法大概採用兩種方式,其一為預測法;另一種則為實測法。
這兩種方式通常都會交叉採用,相互印證。
預測法─以預定動作時間訂定時間標準預測法在工業工程專門學科中叫做「PTS法」─其全名稱為Predetermined Time Standard ─中文譯為「預定時間標準法」。
最早的PTS法又以MTM法─Method Time Measurement 、WF法─Work Factor 為最早發展完成且係最佳的兩種方式。
PTS法係將工人之操作動作拍成影片,然後詳細分析其動作和條件。
分析後發現工人之作業皆由若干基本動作和若干條件所構成。
於是在確立各種基本動作和條件因素後再求出以正常合格工人實施各種基本動作所需要的時間,最後將這些確定的時間值整理成「數據卡」。
生产线平衡改善案例
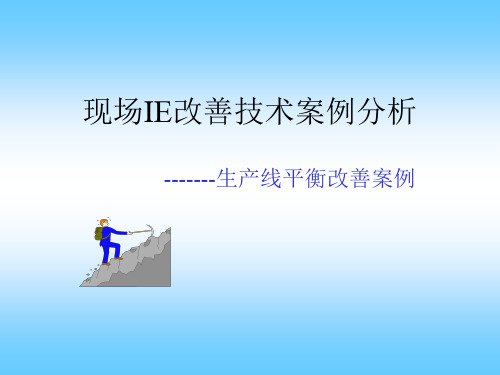
24.7 28
改善前生产线平衡率=(39+74+48+72+103)/(28*14)*100%=85.7% 改善前生产线各工位平衡图:
改善前生产线各工位平衡图
35.0 30.0 25.0 20.0 15.0 10.0 5.0 0.0 测中肉1 测中肉2 点滴1 点滴2 点滴3 接合1 接合2 涂边1 涂边2 涂边3 检查包装1 检查包装2 检查包装3 检查包装4
1
测中肉
2
点滴
3
接合
4
涂边
5
检查包装
改善前分析
生产线各工位的分析如下:
测中肉 工序 测中肉1 测中肉2 点滴1 工位 39 时间 2 工人数 各工位时间 19.5 19.5 24.7 节拍 28 28 28 点滴 点滴2 74 3 24.7 28 点滴3 接合 接合1 接合2 48 2 24.0 24.0 28 28 涂边 检查包装 涂边1 涂边2 涂边3 检查包装1 检查包装2 检查包装3 检查包装4 72 103 3 4 24.0 24.0 24.0 25.8 25.8 25.8 25.8 28 28 28 28 28 28 28
节拍=28秒
24.0 24.0 25.8 25.8 25.8 25.8
24.7 19.5 19.5
24.7
24.7
24.0
24.0
24.0
改善前分析
序号 工序 1 测中肉 作业内容 调整机器 到指定点取镜头 测中肉 镜头整理 搬运镜头给下工位 小计 检查 点滴 整理工装夹具 小计 到上一工位取镜头 调整机器 紫外线接合 搬运镜头到硬化炉 小计 到硬化炉取镜头 搅伴墨水 调整机器 涂边 检查 整理托盘等 小计 搬运镜头到硬化炉 检查 包装 取包装材料 整理台面等 搬运镜头至仓库 小计 节拍时间=28秒 时间(秒) 工人数 6 8 15 2 6 4 39 12 56 3 6 74 5 6 2 25 12 48 11 3 5 3 35 10 8 72 15 32 15 4 6 7 28 103
生产线平衡的测定及目标

平衡率=450(S)*100%=86%
25*21(S)
5.2生产线平衡目标的设定:
5.2.1 MP初期要求60%(MP第一个月);
5.2.2 MP第二个月要求70%以上;
5.2.3 MP第三个月要求80%以上;
6.管理方法
版本
B
生产线平衡测定方法
编制
页数
3
审核
日期
文件编号:
批准
日期
版本
条款
更改内容
2012.9.15
B
5.1.2
产线平衡率计算
2012.9.15
B
6.2.3
平衡率不达标,参与改善的责任部门
1.定义﹕
对生产线各工序进行平均化,调整各工序的作业负荷,以使各作业时间尽可能相近。
2.目的﹕
建立生产效率极大化生产体系
2、不良率的管控,指导作业员正确操作;
3、跟进产线的生产进度,改善产线不良现象。
ME:1、负责测试、组装夹具的制作、修改;
2、负责设备的维修、保养;
3、负责辅助治具的修理;
生产:1、员工由生产部讲师专人培训,考核作业能力,确认员工的操作水平;
2、产线需按标准SOP作业,完全掌握作业内容;
3、正常生产,产线发现问题,需及时知会管理人员(领班、PIE等);
6.1 MP初期IE需每周测定计算出生产线平衡率;并评估临时标准产能;
6.2 MP 3个月后生产线平衡率需达85%以上.每月需测定1次随时对生产线平衡进行监控;
6.3根据生产平衡管理的目标,针对未达标的拉线,IE需组织PE和生产单位进行数据分析,找出造
精益生产节拍与平衡率的快速计算方法

产品的节拍T/T即瓶颈工时B/T
(T/CT)/工位 为10秒,求这条生产线的平衡
数*T/T*100% 率? 该条生产线的平衡率:
50秒/10工站*10秒=50%
备注
客人每天的需求是6000件产
节拍T/T=付 出工时/客人 需求
品,求客人需求的节拍也就是 生产节拍? 生产节拍计 算:11小时*3600秒/6000件 =6.6秒,即这条生产线必须每6
秒钟产出1件产品才能满足客人
需求。
一条生产线有10个工站,生产
平衡率L/B= 的产品总工时T/CT为50秒,该
总工时
精益生产节拍与平衡率快速计算公式
评估类型
生产节拍 (T/T)
平衡率 (L/B)
需要获取的参数
一个时间段 一条生产线需
内的客户需 要投入的工作
求
时间
各工站的工
一条生产线
时/CT,汇总 节拍或瓶颈工 的工站数,
成的总工时 时,T/T或B/T 即有多少个
/T/CT。
工位。
计算公式
举例说明
一条生产线每天工作11小时,
生产线平衡
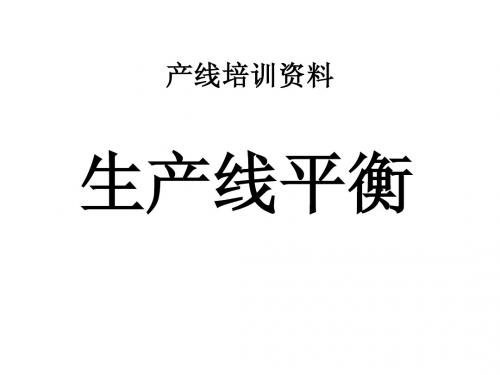
3.平衡改善过程中应注意事项
七、平衡改善的实施步骤
八、案例分析
问题:假定每天10H要装配电风扇143台,周期 时间应是多少? 回答:
问题:理论上的最少工位数是多少? 回答:
四、瓶颈
五、影响生产线平衡的因素
1.工艺编排; 2.不良品; 3.人员安排; 4.新人加入; 5.作业不标准; 6.设备; 7.治工具设计; 8.产线布局; 9.人员心情; ……
六、平衡改善法则与注意事项
1.平衡改善法则—ECRS法则
2-1.平衡改善的基本原则与方法
2-2.平衡改善的基本原则与方法
产线培训资料
或改为震动 请把心带来
请充份讨论与分享 请带空杯来,装点水回去
请思考:
一条正常运作的生产线产 量的高低由那个工序决定?
一、木桶定律
二、生产线平衡与木桶定律的关系
三、生产线平衡的定义
三、提升生产线平衡的意义
三、生产线平衡的相关术语
1.节拍(Pitch Time):指在规定时间内完成预定产量, 各工序完成单位成品所需的时间。计算公式:节拍=有 效出勤时间/(生产计划量*(1+不良率)); 2.传送带速度(CV):流水线皮带传送的速度; 3.瓶颈工时:指生产线所有工序中所用人均工时最长的 工序,通常指一道工序,有时也指几道工序; 4.总瓶颈工时:指瓶颈站工时*生产线作业人数的总和; 5.周程时间:指单个产品从前到后所有工序所费时间的 总和; 6.平衡率:平衡率=生产线各工序时间总和/总瓶颈工时;
三、生产线平衡的相关术语
7.平衡损失:平衡损失=1-平衡率; 8.平衡损失时间:计算公式=∑(瓶颈工时-工位工时); 9.稼动损失时间:计算公式=(节拍-瓶颈工时)*总人 数; 10.稼动损失率:计算公式=稼动损失时间/(节拍*总人 数)*100%。 平衡损失时间与稼动损失时间是两个不同的概念, 平衡损失时间是指瓶颈工时与各工位工时时间差的总和, 而稼动损失时间是指工序生产节拍与瓶颈工时时间差的 总和,他们的关系如下图所示:
生产线平衡率
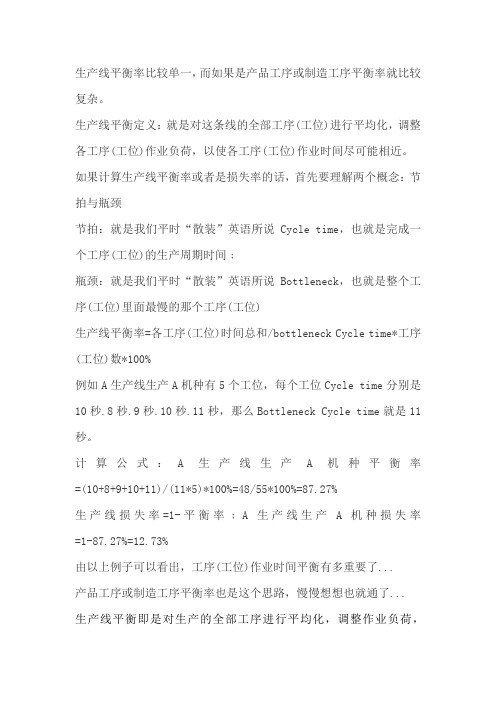
生产线平衡率比较单一,而如果是产品工序或制造工序平衡率就比较复杂。
生产线平衡定义:就是对这条线的全部工序(工位)进行平均化,调整各工序(工位)作业负荷,以使各工序(工位)作业时间尽可能相近。
如果计算生产线平衡率或者是损失率的话,首先要理解两个概念:节拍与瓶颈节拍:就是我们平时“散装”英语所说Cycle time,也就是完成一个工序(工位)的生产周期时间﹔瓶颈:就是我们平时“散装”英语所说Bottleneck,也就是整个工序(工位)里面最慢的那个工序(工位)生产线平衡率=各工序(工位)时间总和/bottleneck Cycle time*工序(工位)数*100%例如A生产线生产A机种有5个工位,每个工位Cycle time分别是10秒.8秒.9秒.10秒.11秒,那么Bottleneck Cycle time就是11秒。
计算公式:A生产线生产A机种平衡率=(10+8+9+10+11)/(11*5)*100%=48/55*100%=87.27%生产线损失率=1-平衡率﹔A生产线生产A机种损失率=1-87.27%=12.73%由以上例子可以看出,工序(工位)作业时间平衡有多重要了...产品工序或制造工序平衡率也是这个思路,慢慢想想也就通了... 生产线平衡即是对生产的全部工序进行平均化,调整作业负荷,以使各作业时间尽可能相近的技术手段与方法。
目的是消除作业间不平衡的效率损失以及生产过剩。
生产线平衡是一门很大的学问,生产线平衡直接关系到生产线的正常使用。
生产线平衡指南主要包括生产线平衡的相关定义、生产线平衡的意义、工艺平衡率的计算、生产线平衡的改善原则和方法。
(Line Balancing)如何指派工作予工作站的决策过程,及使各个工作站负荷一样,便称之为生产线平衡。
Line Balancing (LB), is the problem of assigning operations to workstations along an assembly line, in such a way that the assignment be optimal in some sense.节拍、瓶颈、空闲时间、工艺平衡的定义流程的“节拍”(Cycle time)是指连续完成相同的两个产品(或两次服务,或两批产品)之间的间隔时间。
产线平衡率标准
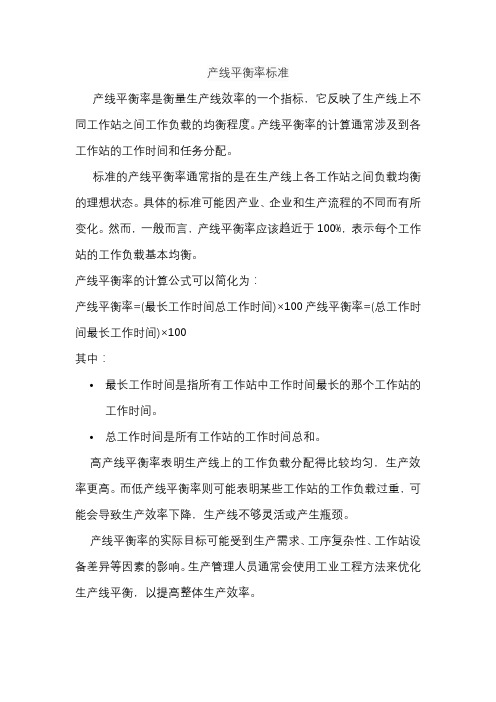
产线平衡率标准
产线平衡率是衡量生产线效率的一个指标,它反映了生产线上不同工作站之间工作负载的均衡程度。
产线平衡率的计算通常涉及到各工作站的工作时间和任务分配。
标准的产线平衡率通常指的是在生产线上各工作站之间负载均衡的理想状态。
具体的标准可能因产业、企业和生产流程的不同而有所变化。
然而,一般而言,产线平衡率应该趋近于100%,表示每个工作站的工作负载基本均衡。
产线平衡率的计算公式可以简化为:
产线平衡率=(最长工作时间总工作时间)×100产线平衡率=(总工作时间最长工作时间)×100
其中:
•最长工作时间是指所有工作站中工作时间最长的那个工作站的工作时间。
•总工作时间是所有工作站的工作时间总和。
高产线平衡率表明生产线上的工作负载分配得比较均匀,生产效率更高。
而低产线平衡率则可能表明某些工作站的工作负载过重,可能会导致生产效率下降,生产线不够灵活或产生瓶颈。
产线平衡率的实际目标可能受到生产需求、工序复杂性、工作站设备差异等因素的影响。
生产管理人员通常会使用工业工程方法来优化生产线平衡,以提高整体生产效率。
生产线平衡计算范文
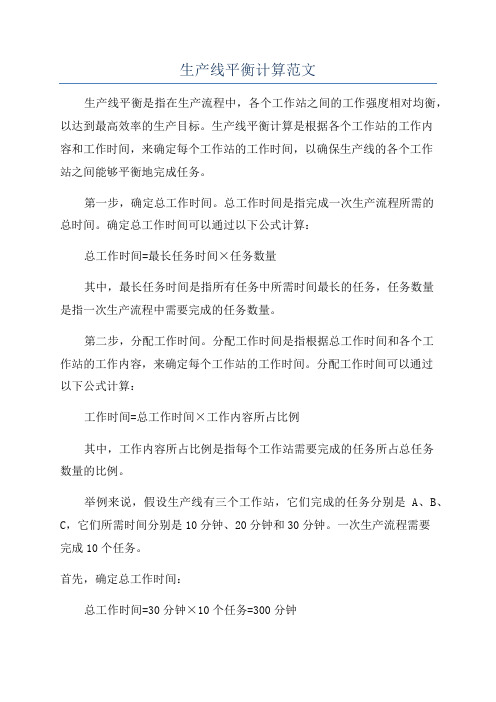
生产线平衡计算范文生产线平衡是指在生产流程中,各个工作站之间的工作强度相对均衡,以达到最高效率的生产目标。
生产线平衡计算是根据各个工作站的工作内容和工作时间,来确定每个工作站的工作时间,以确保生产线的各个工作站之间能够平衡地完成任务。
第一步,确定总工作时间。
总工作时间是指完成一次生产流程所需的总时间。
确定总工作时间可以通过以下公式计算:总工作时间=最长任务时间×任务数量其中,最长任务时间是指所有任务中所需时间最长的任务,任务数量是指一次生产流程中需要完成的任务数量。
第二步,分配工作时间。
分配工作时间是指根据总工作时间和各个工作站的工作内容,来确定每个工作站的工作时间。
分配工作时间可以通过以下公式计算:工作时间=总工作时间×工作内容所占比例其中,工作内容所占比例是指每个工作站需要完成的任务所占总任务数量的比例。
举例来说,假设生产线有三个工作站,它们完成的任务分别是A、B、C,它们所需时间分别是10分钟、20分钟和30分钟。
一次生产流程需要完成10个任务。
首先,确定总工作时间:总工作时间=30分钟×10个任务=300分钟然后,分配工作时间:工作站A的工作时间=300分钟×(10/30)=100分钟工作站B的工作时间=300分钟×(20/30)=200分钟工作站C的工作时间=300分钟×(30/30)=300分钟通过以上计算,可以确定每个工作站的工作时间,以确保生产线的各个工作站之间能够平衡地完成任务。
生产线平衡计算的目标是使得各个工作站的工作强度相对均衡,以避免一些工作站出现工作过多或过少的情况。
如果一些工作站的工作强度过大,可能会导致工作站的效率降低、出现瓶颈;如果一些工作站的工作强度过小,可能会导致其他工作站的等待时间增加、生产效率下降。
生产线平衡计算在实际生产中非常重要,它可以帮助企业合理安排各个工作站的工作时间,提高生产线的效率和产能。
- 1、下载文档前请自行甄别文档内容的完整性,平台不提供额外的编辑、内容补充、找答案等附加服务。
- 2、"仅部分预览"的文档,不可在线预览部分如存在完整性等问题,可反馈申请退款(可完整预览的文档不适用该条件!)。
- 3、如文档侵犯您的权益,请联系客服反馈,我们会尽快为您处理(人工客服工作时间:9:00-18:30)。
生产线平衡的定义
一、“节拍”、“瓶颈”、“空闲时间”、“工艺平衡”的定义
流程的“节拍”(Cycle time)是指连续完成相同的两个产品(或两次服务,或两批产品)之间的间隔时间。换句话说,即指完成一个产品所需的平均
时间。节拍通常只是用于定义一个流程中某一具体工序或环节的单位产出时间。如果产品必须是成批制作的,则节拍指两批产品之间的间隔时间。在流
程设计中,如果预先给定了一个流程每天(或其它单位时间段)必须的产出,首先需要考虑的是流程的节拍。
而通常把一个流程中生产节拍最慢的环节叫做“瓶颈“(Bottleneck)。流程中存在的瓶颈不仅限制了一个流程的产出速度,而且影响了其它环节生产能力
的发挥。更广义地讲,所谓瓶颈是指整个流程中制约产出的各种因素。例如,在有些情况下,可能利用的人力不足、原材料不能及时到位、某环节设备
发生故障、信息流阻滞等,都有可能成为瓶颈。正如“瓶颈”的字面含义,一个瓶子瓶口大小决定着液体从中流出的速度,生产运作流程中的瓶颈则制
约着整个流程的产出速度。瓶颈还有可能“漂移”,取决于在特定时间段内生产的产品或使用的人力和设备。因此在流程设计中和日后的日常生产运作中
都需要引起足够的重视。
与节拍和瓶颈相关联的另一个概念是流程中的“空闲时间”(idle time)。空闲时间是指工作时间内没有执行有效工作任务的那段时间,可以指设备或人
的时间。当一个流程中各个工序的节拍不一致时,瓶颈工序以外的其它工序就会产生空闲时间。
这就需要对生产工艺进行平衡。制造业的生产线多半是在进行了细分之后的多工序流水化连续作业生产线,此时由于分工作业,简化了作业难度,使作
业熟练度容易提高,从而提高了作业效率。然而经过了这样的作业细分化之后,各工序的作业时间在理论上,现实上都不能完全相同,这就势必存在工
序间节拍不一致出现瓶颈的现象。除了造成的无谓的工时损失外,还造成大量的工序堆积即存滞品发生,严重的还会造成生产的中止。为了解决以上问
题就必须对各工序的作业时间平均化,同时对作业进行标准化,以使生产线能顺畅活动。
“生产线工艺平衡”即是对生产的全部工序进行平均化,调整各作业负荷,以使各作业时间尽可能相近。是生产流程设计与作业标准化必须考虑的最重
要的问题。生产线工艺平衡的目的是通过平衡生产线使用现场更加容易理解“一个流”的必要性及“小单元生产”(Cell production)的编制方法,它是
一切新理论新方法的基础。
二、平衡生产线的意义
通过平衡生产线可以达到以下几个目的:
1、提高作业员及设备工装的工作效率;
2、减少单件产品的工时消耗,降低成本(等同于提高人均产量);
3、减少工序的在制品,真正实现“一个流”;
4、在平衡的生产线基础上实现单元生产,提高生产应变能力,对应市场变化,实现柔性生产系统;
5、通过平衡生产线可以综合应用到程序分析、动作分析、规划(Layout)分析、搬运分析、时间分析等全部IE手法,提高全员综合素质。
三、工艺平衡率的计算
要衡量工艺总平衡状态的好坏,我们必须设定一个定量值来表示,即生产线平衡率或平衡损失率,以百分率表示。
首先,要明确一点,虽然各工序的工序时间长短不同,但如前所述,决定生产线的作业周期的工序时间只有一个,即最长工序时间Pitch time,也就是说
Pitch time等于节拍(cycle time)。另外一种计算方法同样可以得到cycle time,即由每小时平均产量,求得一个产品的CT(Q,每小时产量)。
cycle time(CT)=Pitch time=3600/Q
1、生产线的平衡计算公式
平衡率=(各工序时间总和/(工位数*CT))*100=(∑ti/(工位数*CT))*100
2、生产线的平衡损失率计算公式
平衡损失率=1-平衡率
四、生产线工艺平衡的改善原则方法
平衡率改善的基本原则是通过调整工序的作业内容来使各工序作业时间接近或减少这一偏差。实施时可遵循以下方法:
1、首先应考虑对瓶颈工序进行作业改善,作业改善的方法,可参照程序分析的改善方法及动作分析、工装自动化等IE方法与手段;
2、将瓶颈工序的作业内容分担给其它工序;
3、增加各作业员,只要平衡率提高了,人均产量就等于提高了,单位产品成本也随之下降;
4、合并相关工序,重新排布生产工序,相对来讲在作业内容较多的情况下容易拉平衡;
6、分解作业时间较短的工序,把该工序安排到其它工序当中去。