SPC控制图的绘制方法及判断方法
SPC“控制图”的分析与判定
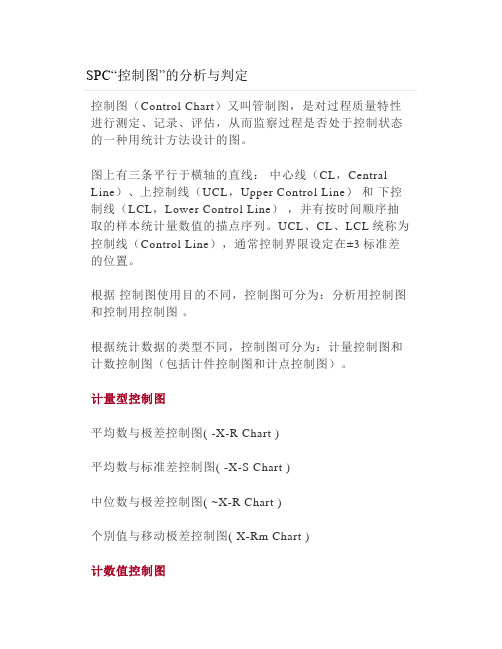
SPC“控制图”的分析与判定控制图(Control Chart)又叫管制图,是对过程质量特性进行测定、记录、评估,从而监察过程是否处于控制状态的一种用统计方法设计的图。
图上有三条平行于横轴的直线:中心线(CL,Central Line)、上控制线(UCL,Upper Control Line)和下控制线(LCL,Lower Control Line),并有按时间顺序抽取的样本统计量数值的描点序列。
UCL、CL、LCL统称为控制线(Control Line),通常控制界限设定在±3标准差的位置。
根据控制图使用目的不同,控制图可分为:分析用控制图和控制用控制图。
根据统计数据的类型不同,控制图可分为:计量控制图和计数控制图(包括计件控制图和计点控制图)。
计量型控制图平均数与极差控制图( -X-R Chart )平均数与标准差控制图( -X-S Chart )中位数与极差控制图( ~X-R Chart )个別值与移动极差控制图( X-Rm Chart )计数值控制图不良率控制图(P chart)不良数控制图(nP chart,又称 np chart 或 d chart)缺点数控制图(C chart)单位缺点数控制图(U chart)控制图种类及应用场合:控制图的分析与判定应用控制图的目的,就是要及时发现过程中出现的异常,判断异常的原则就是出现了“小概率事件”,为此,判断的准则有两类。
第一类:点子越出界限的概率为0.27% 。
准则1属于第一类。
第二类:点子虽在控制界限内,但是排列的形状有缺陷。
准则2-8属于第二类。
控制图八大判异准则(口诀)2/3A (连续3点中有2点在中心线同一侧的B区外<即A 区内>4/5C (连续5点中有4点在中心线同一侧的C区以外)6连串(连续6点递增或递减,即连成一串)8缺C (连续8点在中心线两侧,但没有一点在C区中)9单侧(连续9点落在中心线同一侧)14交替(连续14点相邻点上下交替)15全C (连续15点在C区中心线上下,即全部在C区内1界外(1点落在A区以外)▶2/3A (连续3点中有2点在中心线同一侧的B区外<即A区内>)判读:1 . 控制过严;2 . 材料品质有差异;3 . 检验设备或方法之大不相同;4 . 不同制程之资料绘于同一控制图上;5 . 不同品质材料混合使用。
SPC控制图判断标准

SPC控制图判断标准一:判稳准则在点子随机排列的情况下,符合下列个点之一就判稳:(1)连续25个点,界外点数d=0;(2)连续35个点,界外点数d≤1;(3)连续100个点,界外点数d≤2。
二:判异准则SPC的基准是稳态,如若过程出现显著偏离稳态则为异态。
异态出可分为异常好与异常坏两类。
判异准则:(1)点出界就判异;(2)界内点排列不随机判异。
2.1判异准则1一点落在A区以外。
出现该情况可能因素:计算错误、测量误差、原材料不合格、设备故障等。
点排布如下图2-1所示:图2-1 准则1判异图2.2判异准则2出现连续9点落在中心线一侧。
原因:分布的a减小。
点排布如下图2-2所示:图2-2 准则2判异图2.3判异准则3连续6点递增或递减。
产生趋势可能因素:工具逐渐磨损、维修水平逐渐降低、操作人员技能逐渐降低等。
点排布如下图2-3所示:图2-3 准则3判异图2.4判异准则4连续14点中相邻点上下交替。
产生趋势可能因素:轮流使用两台设备、两位人员轮流操作。
点排布如下图2-4所示:图2-4 准则4判异图2.5判异准则5连续3点落在中心线同一侧的B区以外。
产生趋势可能因素:参数u发生了变化。
点排布如下图2-5所示:图2-5准则5判异图2.6判异准则6连续5点中有4点落在中心线同一侧的C区以外。
表明参数u发生了变化。
点排布如下图2-6所示:图2-6准则6判异图2.7判异准则715点在C区中心线上下。
可能原因:①是否应用了假数据,弄虚作假;②是否数据分层不够。
点排布如下图2-7所示:图2-7准则7判异图2.8判异准则88点在中心线两侧,但无一在C区中。
原因:数据分层不够。
点排布如下图2-8所示:图2-8准则8判异图。
SPC(质量管理与控制)

1.在质量诊断方面,可以用来度量过程的稳定性,即过程是否处于统计控制状态; 2.在质量控制方面,可以用来确定什么时候需要对过程加以调整,而什么时候则需使过程保持相应的稳定状态; 3.在质量改进方面,可以用来确认某过程是否得到了改进。 应用步骤如下: 1.选择控制图拟控制的质量特性,如重量、不合格品数等; 2.选用合适的控制图种类; 3.确定样本容量和抽样间隔; 4.收集并记录至少20~ 25个样本的数据,或使用以前所记录的数据; 5.计算各个样本的统计量,如样本平均值、样本极差、样本标准差等; 6.计算各统计量的控制界限; 7.画控制图并标出各样本的统计量; 8.研究在控制线以外的点子和在控制线内排列有缺陷的点子以及标明异常(特殊)原因的状态; 9.决定下一步的行动。 应用控制图的常见错误: 1.在5M1E因素未加控制、工序处于不稳定状态时就使用控制图管理工作; 2.在工序能力不足时,即在CP< 1的情况下,就使用控制图管理工作; 3.用公差线代替控制线,或用压缩的公差线代替控制线; 4.仅打“点”而不做分析判断,失去控制图的报警作用; 5.不及时打“点”,因而不能及时发现工序异常; 6.当“5M1E”发生变化时,未及时调整控制线; 7.画法不规范或不完整; 8.在研究分析控制图时,对已弄清有异常原因的异常点,在原因消除后,未剔除异常点数据。
1) 异常变动
过程中变动因素是不在统计管理状态下的非随机性原因,由于异常因素不是过程所固有,固不难除去,一般情况现场人员对异常因素的消除可以自行决定采取措施,而不必要请示更高级的管理人员,所以也称之为减少变动的局部措施。
2)偶然变动
过程中的变动因素是统计管理的状态下,其产品的特性有固定的分布,即分布位置、分布及分布形状三种,由于偶然因素是过程所固有的,难于消除,要消除偶然因素必须涉及到人、机、料、法、环境等整个系统的改造问题,需要投入大量的资金,故不是现场人员所能决定的,而必须经过深入的调查研究和做出全面的可行性报告后,再经高层领导做最后的定夺,所以称之为减少变动的系统措施。 特殊原因 一种间断性的,不可预计的,不稳定的变差来源。有时被称为可查明原因,存在它的信号是:存在超过控制线的点或存在在控制线之内的链或其他非随机性的情形。 普通原因 造成变差的一个原因,它影响被研究过程输出的所有单值;在控制图分析中,它表现为随机过程变差的一部分。 合理使用控制图的益处 ? 供正在进行过程控制的操作者使用 ? 有助于过程在质量上和成本上能持续的、可预测的保持下去 ? 使过程达到: ? 更高的质量 ? 更低的单件成本 ? 更高的有效能力 ? 为讨论过程的性能提供共同的语言 ? 区分变差的特殊原因和普通原因,作为采取局部措施或对系统采取措施的指南 在实际应用中,当各组容量与其平均值相差不超过正负25%时,可用平均样本容量( )来计算控制限. 在什么条件下分析阶段确定的控制限可以转入控制阶段使用: ? 控制图是受控的 ? 过程能力能够满足生产要求 控制图是根据稳定状态下的条件(人员、设备、原材料、工艺方法、测量系统、环境)来制定的。如果上述条件变化,则必须重新计算控制限,例如: ? 操作人员经过培训,操作水平显著提高; ? 设备更新、经过修理、更换零件; ? 改变工艺参数或采用新工艺; ? 改变测量方法或测量仪器; ? 采用新型原材料或其他原材料; ? 环境变化。 使用一段时间后检验控制图还是否适用,控制限是否过宽或过窄,否则需要重新收集数据计算控制限; 过程能力值有大的变化时,需要重新收集数据计算控制限。 对于p,np图, 过程能力是通过过程平均不合格品率 来表示,当所有点都受控后才计算该值. 当Cpk指数值降低代表要增加: ? 控制 ? 检查 ? 返工及报废, 在这种情况下,成本会增加,品质也会降低, 生产能力可能不足。 当Cpk指数值增大,不良品减少,最重要是产品/零件接近我们的“理想设计数值/目标”,给予顾客最大满足感。 当Cpk指数值开始到达1.33或更高时对检验工作可以减少,减少我们对运作审查成本。 ? 普通原因变差 ? 影响过程中每个单位 ? 在控制图上表现为随机性 ? 没有明确的图案 ? 但遵循一个分布 ? 是由所有不可分派的小变差源组成 ? 通常需要采取系统措施来减小 ? 特殊原因变差 ? 间断的,偶然的,通常是不可预测的和不稳定的变差 ? 在控制图上表现为超出控制限的点或链或趋势 ? 非随机的图案 ? 是由可分派的变差源造成该变差源可以被纠正 ? 工业经验建议为: ? 只有过程变差的15%是特殊的可以通过与操作直接有关的人员纠正 ? 大部分 (其余的85%) 是管理人员通过对系统采取措施可纠正的 ? 控制图可以区分出普通原因变差和特殊原因变差 ? 特殊原因变差要求立即采取措施 ? 减少普通原因变差需要改变产品或过程的设计 控制图 - 过程的声音 ? 试图通过持续调整过程参数来固定住普通原因变差,称为过度调整,结果会导致更大的过程变差造成客户满意度下降 ? 试图通过改变设计来减小特殊原因变差可能解决不了问题,会造成时间和金钱的浪费 ? 控制图可以给我们提供出出现了哪种类型的变差的线索,供我们采取相应的措施 ? 能力指数的计算基于以下假设条件: ? 过程处于统计稳定状态 ? 每个测量单值遵循正态分布 ? 规格的上、下限是基于客户的要求 ? 测量系统能力充分 ? 如果理解关满足了这些假设后,能力指数的数值越大,潜在的客户满意度越高 过程能力分析的用途 -设计部门可参考目前之制程能力,以设计出可制 造的产品 -评估人员、设备、材料与工作方法的适当性 -根据规格公差设定设备的管制界限 -决定最经济的作业方式 过程控制和过程能力 ◎目标:过程控制系统目标,是对影响过程的措 施作出经济合理的决定, 避免过度控制 与控制不足 ◎过程能力讨论:必需注意二个观念 ○由造成变差的普通原因来确定 ○内外部顾客开心过程的输出及与他 们的要求的关系如何。 SPC就是利用统计方法去: 1.分析过程的输出并指出其特性. 2.使过程在统计控制情况下成功地进行和维持. 3.有系统地减少该过程主要输出特性的变异. 统计制程管制 (SPC) 它可用统计管制图及时监督与控制线场作业 . . 它可用统计计算制程能力及规格 . . 它可防止制程的偏差去影响产品的良率与品质 / 可靠性. . 它可消除非机率原因的变异来改善制程. SPC 就是依据 统计 的逻辑 来判断 制程 是否正常 及应否采取改善对策的一套 控制系统 ? 对的问题比对的答案更重要
SPC的基本做法及步骤
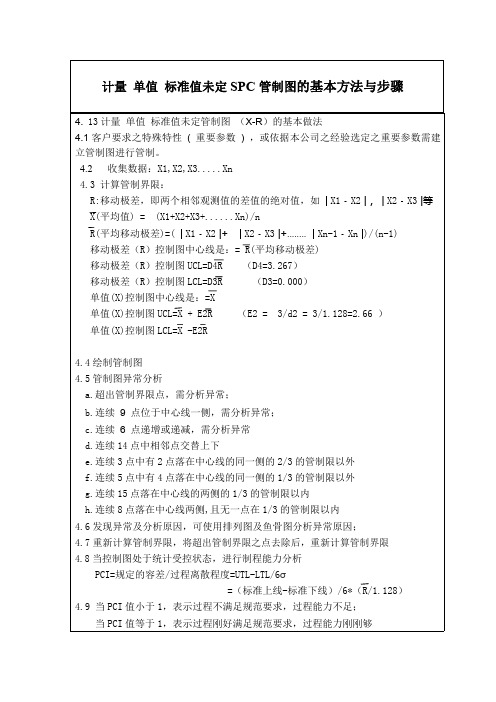
PCI=规定的容差/过程离散程度=UTL-LTL/6σ =(标准上线-标准下线)/6*(R/1.128)
4.9 当 PCI 值小于 1,表示过程不满足规范要求,过程能力不足; 当 PCI 值等于 1,表示过程刚好满足规范要求,过程能力刚刚够
在实际工作中,通常取 PCI=1.33 为最小可接受值 4.10 当 PCI 值小于 1,表示过程不满足规范要求,需改善:相关分析人员根据结果, 对不能接受的情况从人员、机器、物料、方法、环境等方面进行分析
移动极差(R)控制图 LCL=D3R
(D3=0.000)
单值(X)控制图中心线是:=X
Hale Waihona Puke 单值(X)控制图 UCL=X + E2R (E2 = 3/d2 = 3/1.128=2.66 )
单值(X)控制图 LCL=X -E2R
4.4 绘制管制图 4.5 管制图异常分析
a.超出管制界限点,需分析异常; b.连续 9 点位于中心线一侧,需分析异常; c.连续 6 点递增或递减,需分析异常 d.连续 14 点中相邻点交替上下 e.连续 3 点中有 2 点落在中心线的同一侧的 2/3 的管制限以外 f.连续 5 点中有 4 点落在中心线的同一侧的 1/3 的管制限以外 g.连续 15 点落在中心线的两侧的 1/3 的管制限以内 h.连续 8 点落在中心线两侧,且无一点在 1/3 的管制限以内 4.6 发现异常及分析原因,可使用排列图及鱼骨图分析异常原因; 4.7 重新计算管制界限,将超出管制界限之点去除后,重新计算管制界限 4.8 当控制图处于统计受控状态,进行制程能力分析
X(平均值) = (X1+X2+X3+......Xn)/n
R(平均移动极差)=( | X1 - X2 |+ | X2 - X3 |+........ | Xn-1 - Xn |)/(n-1)
SPC控制图的判定方法
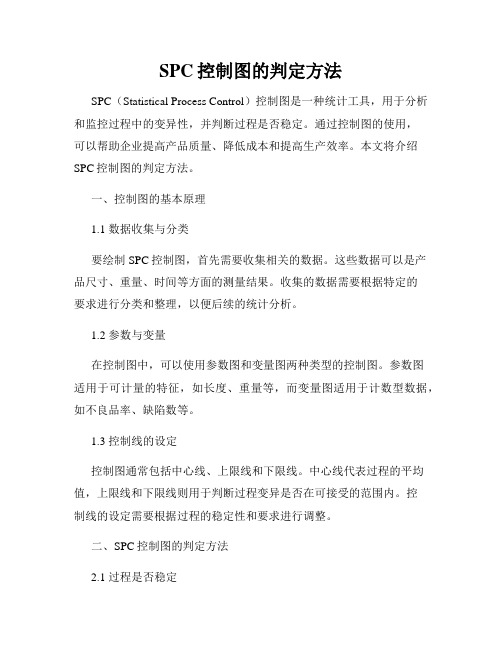
SPC控制图的判定方法SPC(Statistical Process Control)控制图是一种统计工具,用于分析和监控过程中的变异性,并判断过程是否稳定。
通过控制图的使用,可以帮助企业提高产品质量、降低成本和提高生产效率。
本文将介绍SPC控制图的判定方法。
一、控制图的基本原理1.1 数据收集与分类要绘制SPC控制图,首先需要收集相关的数据。
这些数据可以是产品尺寸、重量、时间等方面的测量结果。
收集的数据需要根据特定的要求进行分类和整理,以便后续的统计分析。
1.2 参数与变量在控制图中,可以使用参数图和变量图两种类型的控制图。
参数图适用于可计量的特征,如长度、重量等,而变量图适用于计数型数据,如不良品率、缺陷数等。
1.3 控制线的设定控制图通常包括中心线、上限线和下限线。
中心线代表过程的平均值,上限线和下限线则用于判断过程变异是否在可接受的范围内。
控制线的设定需要根据过程的稳定性和要求进行调整。
二、SPC控制图的判定方法2.1 过程是否稳定在绘制控制图之前,首先需要判断过程是否稳定。
稳定的过程指的是过程产生的变异性仅来自于随机误差,而不是系统性的因素。
判断过程是否稳定可以通过以下几种方式进行:(1)过程能否满足规范要求:通过对过程数据进行规范性能指标的计算与分析,判断过程是否满足要求。
(2)过程的输入是否稳定:观察过程的输入数据,如材料的质量、设备的稳定性等,判断输入是否稳定。
(3)过程是否存在特殊因素:通过了解和分析过程中的特殊因素,如人为因素、设备故障等,判断过程是否稳定。
2.2 控制图的规则绘制了控制图后,可以通过判断数据点的分布情况,在控制图上标示出不同的规则。
常用的规则有以下几种:(1)单点超出控制限:单个数据点超出上限线或下限线。
(2)连续点在中心线同一侧:三个或更多连续的数据点在中心线的同一侧。
(3)多点连续递增或递减:连续五个或更多数据点递增或递减。
(4)趋势:六个或更多连续递增或递减的数据点。
SPC控制图的判定方法

产生原因: 当工序能力不足,为找出符合要求的产品经过全
数检查,或过程中存在自动反馈调整时,常出现这种 形状
E.双峰型:(如附图)
靠近直方图中间值的频数较少,两侧各有一个“峰”.
产生原因: 当有两种不同的平
均值相差大的分布混 在一起时, 常出现这 种形状。
F.离岛型:(如附图)
UCL A B C
XC B
LCL A
判定准则7: (15C) 连续15点在中心线上下两侧的C 区
UCL A B
XC C B
LCL A
判定准则8: (1界外) 有1点在A区以外
UCL A B C
XC B
LCL A
二、柱状 图的判定方法
直方图常见的形态: • A.正常型:(如附图)
B.锯齿型:(如附图) 产生原因:
等级
Cp制程精密度 Capability precision
处置建议
A
1.33≤ │ Cp│ 此一制程甚为稳定,可以将规格
许容差缩小或胜任更精密之工作。
B
1.00 ≤ │ Cp│ ≤ 有发生不良品之危险,必须加以
1.33
注意,并设法维持不要使其变坏
及迅速追查原因
C 0.83 ≤ │ Cp│ <1.00 检讨规格及作业标准,可能本制 程不能胜任如此精密之工作。
• 图示判定准则:
• 当控制图中的点出现下列情况之一,说明生产过程存在特
殊原因,需立即采取措施予以消除以确保生产过程处于稳
定状态。
判定准则1:(2/3A)
判定准则2: (4/5B)
3点中有2点在A区或A区以外 5点中有4点在B区或B区以外
UCL A
SPC控制图的种类及判异方法48页课件

计数值:由计数而得的数据或将之转换成百分率,例如不良数、由不良数转换而成的不良率、 缺点数、由缺点转换而成的单位缺点数或百万件缺点数,为一可分割之量值。 计量值:不可分割之量值。实际量测产品或过程质量特性所得的尺度量值,这类量测的量测不 是真值而只是近似值而已,例如长度、直径、压力、强度等,为连续数据。
步骤7:确定控制限是否能经济地满足要求; 步骤8:运用控制限进行控制;
SPC统计过程控制
四、计量型数据控制图
均值-极差控制图( x R控制图 )
最常用;最基本; 控制对象为计量值; 适用于n ≤9的情况; 均值图用于观察和分析分布的均值的变化,即
过程的集中趋势; 极差图观察和分析分布的分散情况,即过程的
LCL x 3 x 2.66MR d2
相当于n=2时的均值控制图
各常数值如下:
MR控制图
CL MR
UCL D4MR 3.267 MR LCL D3MR 0
相当于n=2时的极差控制图; n=2时,D4=3.267,D3=0
n
2
3
4
5
6
7
8
9 10
D4 3.27 2.57 2.28 2.11 2.00 1.92 1.86 1.82 1.78
离散程度。
SPC统计过程控制
四、计量型数据控制图
均值-极差控制图 -控制限
均值控制图
CL x UCL x A2R LCL x A2R
极差控制图
CL R UCL D4R LCL D3R
SPC统计过程控制
4、X bar-s图
计算各样组的平均数
四、计量型数据控制图
计算这些组平均数的平均数
频数分布在进行调整期间已经完成,分析结果表明进 行一段时期加工生产的开端是可以令人满意的。
SPC中控制图的原理、制作和分析方法
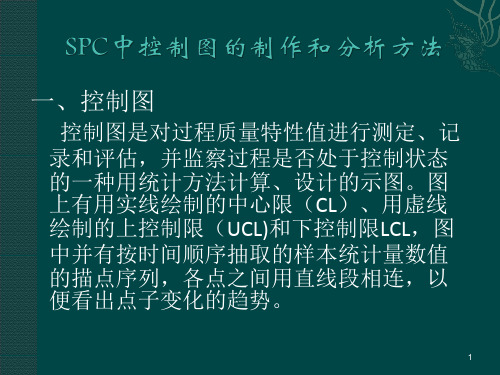
UCL A
B
CL
C C
B
LCL A
如图九-9
27
十、如何作休哈特控制图
例: 我公司生产轴颈产品,工序冷轧
占 R1.8
+0.07 +0.03
轴颈不合格项的比例比较大,由于是关健质
量特性 ,故决定应用控制图对此工序(85 )
进行过程控制。
分析:此质量特性是计量特性值,故可选用正态分布 图。又由于本例是大量生产,不难取得数据,决定 选用均值X-R极差控制图。
б=
R d2
=
0.019 2.326
= 0.008
32
Cp =
Tu-TL 6б
=
1.87-1.83 6×0.008
=
0.816
由于X=1.843,与容差中心M=(Tu+TL)/2=
(1.87+1.83)/2=1.85不重合,有必要计算偏移 过程能力指数
33
计算有偏移的过程能力:
K
=
|m-μ| T/2
16
九、判异准则 判异准则有两类:①点子出界应判异;②
界内点排列不随机判异。关于判异准则, 常规控制图的标准GB/T4091-2001有8种准则, 将控制图等分为6个区、每个区宽1σ。这6 个区的编号为A、B、C、C、B、A。(如图 九-1)其中两个A区、B区及C区对于中心 线C对称; 需要指明的是这些判异准则主要 适用X均值图,且假定质量特性值服从正态 分布。
步骤1:取预备数据,然后将数据合理分成25组。
28
步骤2:计算各子组样本平均数X,例如第一 组样本的平均值为1.840.
步骤3:计算各子组样本极差R,例如第一组 样本的极差为0.010.
SPC图的使用方法培训

否
子组均值是否 能很方便的计
否
使用中位数图
算?
是
子组容量是否
是
大于或等于9?
否
是否能方便的
否
计算每个子组
的S值?
是
使用u图
“We make safety product”
四、控制图适用类型选择
区分
基准
Xbar-R (均值-极差控制图)
Xbar-Rs (均值-标准差控制图)
Xmed-R (中位数-极差控制图)
用于控制一部机器、一个部件、一定长度、一定面积或任何一定的单位中(即样本大小不变)所出现的缺陷数目,如 布匹上的疵点数、铸件上的砂眼数、机器设备的缺陷数或故障次数等。
单位缺陷数控制图。当样本大小变化时,不宜用缺陷数控制图,需换算为平均每单位的缺陷数后再使用U控制图。
“We make safety product”
下限规格
Cpl=(x-Sl)/3σ
评价基准
Cp(k)值 Cp(k)≥1.67 1.67>Cp(k)≥1.33 1.33>Cp(k)≥1.0 1>Cp(k)≥0.67 Cp(k)<0.67
评价基准 非常充分
充分 一般 不充分 非常不充分
“We make safety product”
二、Xbar-R管理图作成方法
2.1 工程能力指数定义内容如下:
Cp = T/6σ (其中, T=SU-SL; SU是规格上限,SL 是规格下限)
※ σ: 标准偏差
2.1.1 只给出单边规格的情况(上限或者下限)
Cp = (SU -x) / 3σ (只给出上限规格的情况)
Cp = (x - SL) / 3σ (只给出下限规格的情况)
合计
对于SPC控制图的制作方法和步骤的教程

对于SPC控制图的制作方法和步骤的教程SPC控制图的制作方法和步骤一、控制图法的涵义影响产品质量的因素很多,有静态因素也有动态因素,有没有一种方法能够即时监控产品的生产过程、及时发现质量隐患,以便改善生产过程,减少废品和次品的产出?控制图法就是这样一种以预防为主的质量控制方法,它利用现场收集到的质量特征值,绘制成控制图,通过观察图形来判断产品的生产过程的质量状况。
控制图可以提供很多有用的信息,是质量管理的重要方法之一。
控制图又叫管理图,它是一种带控制界限的质量管理图表。
运用控制图的目的之一就是,通过观察控制图上产品质量特性值的分布状况,分析和判断生产过程是否发生了异常,一旦发现异常就要及时采取必要的措施加以消除,使生产过程恢复稳定状态。
也可以应用控制图来使生产过程达到统计控制的状态。
产品质量特性值的分布是一种统计分布.因此,绘制控制图需要应用概率论的相关理论和知识。
控制图是对生产过程质量的一种记录图形,图上有中心线和上下控制限,并有反映按时间顺序抽取的各样本统计量的数值点。
中心线是所控制的统计量的平均值,上下控制界限与中心线相距数倍标准差。
多数的制造业应用三倍标准差控制界限,如果有充分的证据也可以使用其它控制界限。
常用的控制图有计量值和记数值两大类,它们分别适用于不同的生产过程;每类又可细分为具体的控制图,如计量值控制图可具体分为均值——极差控制图、单值一移动极差控制图等。
二、控制图的绘制控制图的基本式样如图所示,制作控制图一般要经过以下几个步骤:①按规定的抽样间隔和样本大小抽取样本;②测量样本的质量特性值,计算其统计量数值;③在控制图上描点;④判断生产过程是否有并行。
控制图为管理者提供了许多有用的生产过程信息时应注意以下几个问题:①根据工序的质量情况,合理地选择管理点。
管理点一般是指关键部位、关健尺寸、工艺本身有特殊要求、对下工存有影响的关键点,如可以选质量不稳定、出现不良品较多的部位为管理点;②根据管理点上的质量问题,合理选择控制图的种类:③使用控制图做工序管理时,应首先确定合理的控制界限:④控制图上的点有异常状态,应立即找出原因,采取措施后再进行生产,这是控制图发挥作用的首要前提;⑤控制线不等于公差线,公差线是用来判断产品是否合格的,而控制线是用来判断工序质量是否发生变化的;⑥控制图发生异常,要明确责任,及时解决或上报。
SPC控制图异常判定资料

01 SPC控制图概述
SPC控制图定义
定义
SPC控制图是一种用于监控、分析和 控制生产过程的工具,通过收集数据 并在控制图上绘制点来评估过程的稳 定性。
THANKS FOR WATCHING
感谢您的观看
如何选择合适的控制图?
不同的控制图适用于不同类型的数据和过程。在选择控制图 时,需要考虑数据的分布、过程的特性以及要监控的过程参 数。常见的控制图包括均值-极差控制图、均值-标准差控制 图、不合格品率控制图等。
选择依据:根据数据类型和过程特性选择合适的控制图,确 保能够有效地监测和控制过程。
如何解读控制图的异常信息?
总结词
累积和控制图通过计算累积和来评估过程的稳定性,适用于监测生产过程的关键特性。
详细描述
当控制图上的点超出上控制限或下控制限,或者点在控制限内但呈持续上升或下降趋势 时,可以判定为异常。此外,如果点在控制限内但出现周期性波动,也可能是异常。
移动极差控制图异常判定实例
总结词
移动极差控制图通过计算移动极差来评 估过程的稳定性,适用于监测数据分布 较为稳定的过程。
目的
控制图用于检测生产过程中的异常波 动,预防不良品产生,并保持产品质 量稳定。
SPC控制图原理
中心线(CL)
控制图的中心线表示过程的预期平均值。
控制上限(UCL)和控制下限(LCL)
这两个界限用于判断数据点是否超出可接受的范围。
判定原则
当数据点超出UCL、LCL或连续7点上升或下降时,判定为异常。
累积和控制图异常判定标准
SPC控制图判异准则最新版

本人将国标中的控制图的8条判异准则,每条总结成2到5个字,总共二十多个 字,可以像背诗一样,很容易记住: 一外、九同、六递、十四交 三二同B外、五四同C外、十五C内、八C外 详细解读及图表可参考下文,图表均摘自国标。
精选2021版课件
1
8条判异准则详解
故障,原料不合格 ➢ 检验方法或标准变化 ➢ 计算错误,测量误差
精选2021版课件
4
六递:连续6点递增或递减
异常原因: 工具逐渐磨损,维护水平逐渐降 低,操作人员技能逐渐提高
精选2021版课件
5
十四交:连续14点中 相邻点交替上下
异常原因: 白夜班交替,交替使用两不同机 台,两个不同供应商查明原因,采取措施,加以消除,不再出现,纳入标准
精选2021版课件
2
一外:一个点落在A区以外
异常原因: ➢ 新操作人员,方法不对,机器
故障,原料不合格 ➢ 检验方法或标准变化 ➢ 计算错误,测量误差
精选2021版课件
3
九同:连续9点落在中心线同一侧
异常原因: ➢ 新操作人员,方法不对,机器
➢一外:1个点落在A区以外 ➢九同:连续9点落在中心线同一侧 ➢六递:连续6点递增或递减 ➢十四交:连续14点中相邻点交替上下 ➢三二同B外:连续3点中有2点落在中心线同一侧的B区外 ➢五四同C外:连续5点中有4点落在中心线同一侧的C区外 ➢十五C内:连续15点落在中心线两侧的C区以内 ➢八C外: 连续8点落在中心线两侧且无一在C区以内(即在C区以外)
精选2021版课件
6
三二同B外:连续3点中有2点 落在中心线同一侧的B区以外
异常原因: ➢ 新操作人员,方法不对,机器
SPC培训教材

SPC培训教材引言SPC(StatisticalProcessControl,统计过程控制)是一种以统计方法为基础的过程控制技术。
它通过对生产过程中收集的数据进行分析,实现对过程稳定性和产品质量的有效监控和控制。
本教材旨在为读者提供SPC的基本概念、原理、方法和应用技巧,帮助读者掌握SPC的实施步骤和技巧,提高生产过程的质量管理水平。
第一章:SPC基本概念1.1质量管理的发展1.2SPC的定义和作用1.3SPC的基本原理1.4SPC与全面质量管理的关系第二章:SPC的基本工具2.1控制图2.1.1控制图的类型和用途2.1.2控制图的绘制方法2.1.3控制图的判读规则2.2直方图2.2.1直方图的绘制方法2.2.2直方图的分析和应用2.3过程能力指数2.3.1过程能力指数的定义和计算方法2.3.2过程能力指数的应用和分析第三章:SPC的实施步骤3.1数据收集和整理3.1.1数据的类型和来源3.1.2数据的收集方法3.1.3数据的整理和表示3.2控制图的绘制和应用3.2.1控制图的绘制步骤3.2.2控制图的判读和应用3.3过程分析和改进3.3.1过程分析的方法和工具3.3.2过程改进的策略和实施第四章:SPC的应用案例4.1制造业中的应用案例4.2服务行业中的应用案例4.3公共事业中的应用案例第五章:SPC的推广和持续改进5.1SPC的推广策略5.2SPC的培训和效果评估5.3SPC的持续改进和优化结论通过对本教材的学习,读者应该能够掌握SPC的基本概念、原理、方法和应用技巧。
然而,SPC的实施需要结合实际情况进行具体的分析和应用,因此读者需要在实践中不断探索和总结,不断提高自己的质量管理水平。
希望本教材能够为读者提供有用的指导和帮助,促进SPC在各个领域的应用和发展。
重点关注的细节:控制图的绘制和应用控制图是SPC(统计过程控制)中最重要的工具之一。
它通过图形化的方式,直观地展示了生产过程中的数据变化,帮助工作人员及时发现问题,采取相应的措施,从而实现对生产过程的有效控制。
SPC控制图的绘制方法及判断方法

备数据如表6所示。该铸件重量规格要求为13 ±2(公斤),并希望
工序能力在1~1.33
解:
2021/10/10
11
解: (1)由表 3的计算公式 6中计 的算 每表 个样本 xi及 的极 平 Ri。 差 均如 值:
5
x1j
x1
j1
5
14.012.613.213.112.113.00 5
R1maxx1j mixn1j 14.012.11.9
中。
如
L1=14.0
S1=12.1
……
……
• 计算最大值平 L、 均最 值小S、 值平均极 R和 差范围中 M: 值
k
k
Li
L i1
34.1913.68 i1 Si
30.8112.32
k 25
k 25
RLS 13.6812.321.36
MLS 13.6812.3213.00
2021/10/10
2
(4) 做出 图x 及R图的坐标系,并将横坐标样本号单位对齐,将 表6中各样本的 、x i Ri在图上打点,联结点成平均值、极差
波动曲线,图5即为分析用控制图。
14
x图13
12
UCL=13.719 CL=12.940 LCL=12.161
4
R图 3
UCL=2.86
2 1
0
5
10
15
20
25
CL=1.35 样本号
依此类推,并 的xi将 、Ri计 记算 入6中 后 表。
(2)由表 4的计算公式计算总平均 x和极差平均 R 。
25
x
xi
i 1
13.00 12.94 12.72
323 .50
SPC分析图及控制限的确定

暂无
按照控制图不同用途可分为:
分析用控制图(判稳)
控制用控制图(判异)
他们之间的联系: 分析用控制图通过 判稳准则分析过程 的稳定性,并得出 过程控制限应用到 控制用控制图,通 过判异准则预测过 程的稳定性
分析用控制图与控制用控制图的区别: 分析用控制图
初始过程研究时用分析用 控制图 管理者用分析用控制图 分析用控制图先采集数据, 画控制限 对过程进行研究,了解过 程的稳定性和能力,是对 过程的事后了解; 分析用控制图没有预防性
计数值 控制图
选定质量特性
选定控制图种 类
收集数据
计算和验证正 态分布
计算控制图中 心线及控制线
画图
判断过程是否 处于稳态
判断过程能力 是否满足要求
转化为控制用 控制图
连续25个点都在控制限内
(显著性水平为0.0654)
连续35个点至多一个点落在控制限外 (显著性水平为:0.0041)。 连续100个点至多两个点落在控制限外 (显著性水平为:0.0026)。
• 随机抽出样品50pcs以上,测出样品的数据,计算控制限,做出控制图;
一
• 观察控制图是否在控制(稳定)状态,如果点全部在控制界限内,而且点的排 列无异常,则可以转入下一步;
二
三
• 如果异常状态,或虽未超出控制界限,但排列有异常,则需要查明异常的原因, 并采出有效的措施消除异常使之处于控制状态, • 然后再重新取数据计算控制界限,转入下一步
FUC
唐孝华2016/03/14
控 制 图
• 是对过程质量加以测定、 记录从而进行控制管理的 一种用科学方法设计的图 • 图上有中心线(CL), 上控制界限(UCL)、下 控制界限(LCL),并有 按时间序列抽取的样本统 计量数值的描点序列。
- 1、下载文档前请自行甄别文档内容的完整性,平台不提供额外的编辑、内容补充、找答案等附加服务。
- 2、"仅部分预览"的文档,不可在线预览部分如存在完整性等问题,可反馈申请退款(可完整预览的文档不适用该条件!)。
- 3、如文档侵犯您的权益,请联系客服反馈,我们会尽快为您处理(人工客服工作时间:9:00-18:30)。
计算各组不合格品率pi
计算各样本的平均缺陷数 c
计算各样本的单位缺陷数ui
计算公式
1n
x i
n
xij
j 1
Ri max xij min xij
x j x n1 n为奇数 i
2
xi
1 2
x
i
n 2
x
i
n1 2
n为偶数
Ri max xij min xij
(1)计算各样本参数(见表3) (2)计算分析用控制图控制线(见表4) 5 作分析用控制图并判断工序是否处于稳定状态 6 与规格比较,确定控制用控制图 7 控制用控制图制好后,即可用它控制工序,使生产过程保持 在正常状态。
4
作控 程制 序图
绘 制 的 一 般 工
确定受控质量特性 选定控制图种类 收集预备数据 计算控制界限 作分析用控制图
ni——第i样本的样本容量(各样 本样本容量可以不等) ci——第i样本的缺陷数(各样本 样本容量相等)
6 各样本样本容量不等
3 收集预备数据
收集预备数据的目的只为作分析用控制图以判断工序状态。 数据采集的方法是间隔随机抽样。为能反映工序总体状况,数 据应在10~15天内收集 ,并应详细地记录在事先准备好的调 查表内。数据收集的个数参见表2。
max(xij)——第i样本中最大值;
min(xij)——第i样本中最大值。
x
i
n
ห้องสมุดไป่ตู้
1
——n为奇数时,第i样本中按大
2
小顺序排列起的数据列中间位置的数据
1 2
x i
n
2
x i
n1
2
——n为偶数时,第I样 本 中按大小顺序排列起的
数据列中中间位置的两个数据的平均值
(pn)i——第i样本的不合格品数 (各样本样本容量皆为n)
X~ 图 用 M3A2 1.880
-
2.575
1.187
-
2.282
0.796
-
2.115
0.691
-
2.004
0.549
0.076
1.924
0.509
0.136
1.864
0.432
0.184
1.816
0.412
0.223
1.777
0.363
X图用 E2
2.660 1.772 1.457 1.290 1.184 1.109 1.054 1.010 0.975
Li max xij Si min xij
L
1 k
k i 1
Li
S
1 k
k i 1
Si
RLS M LS
2
Rsi xi xi1
p pn n
k
pn i
p n i1 k
pi
pn i
ni
k
ci
c i1 k
ui
ci ni
备注
xij——第I样本中的第j个数据i=1,2…k;
j=1,2…n;
数据如表6所示。该铸件重量规格要求为13 ±2(公斤),并希望工
序能力在1~1.33
解: 11
解:(1)由表3的计算公式计算表6中的每个样本的平均值xi 及极差Ri。如:
5
x1
x1 j
j 1
5
14.0 12.6 13.2 13.1 12.1 13.00 5
R1 max x1 j min x1 j 14.0 12.1 1.9
判断工序是否处 于稳定状态
NO
结束
YES
与规格比较,确定 控制用控制图
应用控制图控制工
5
序
图名称 X R图
X~ R 图
L—S图
X—Rs图 Pn图 P图 C图 U图
步骤 (1)计算各样本平均值 xi (2)计算各样本极差Ri
(1)找出或计算出各样本 的中位数 X~i (2)计算各样本极差Ri
(1)找出各组最大值Li和最 小值Si (2)计算最大值平均值 L 和最小值平均值 S (3)计算平均极差 R (4)计算范围中值M
“ x ”R 控制图是通过 图和x R图的联合使用,掌握工序质量
特性分布变动的状态。它主要适用于零件尺寸、产品重量 、
热处理后机械性能、材料成分含量等服从正态分布的质量特性
•
的控制。 例1 某铸造厂决定对某铸件重量采用
x 图 R进行控制,每天
抽取一个样本,样本容量n=5,共抽取样本k=25个,测取的预 备
✓ 在坐标图上画出三条控制线,控制中线一般以细实线表示,
控制上下线以虚线表示。
✓ 将预备数据各样本的参数值在控制图中打点。 ✓ 根据本节介绍的控制图的判断规则判断工序状态是否 稳定,
若判断工序状态不稳定,应查明原因,消除不稳定因素,重 新收集预备数据,直至得到稳定状态下分析用控制图;若判 断工序处于稳定状态,继续以下程序。
L—S图用 A9
2.695 1.826 1.522 1.363 1.263 1.914 1.143 1.104 1.072
9
各类控制图作法举例
10
1 x R控制图(平均值——极差控制图)
• 原理:
❖ x图又称平均值控制图,它主要用于控制生产过程中产品质量
特性的平均值;
❖ R图又 称极差控制图,它主要用于控制产品质量特性的分散。
6 与规格比较,确定控制用控制图
✓ 由分析用控制图得知工序处于稳定状态后,还须与规格要求 进行比较。若工序既满足稳定要求,又满足规格要求,则称 工序进入正常状态。此时,可将分析用控制图的控制线作为 控制用控制图的控制线;若不能满足规格要求,必须对工序
✓ 所谓满足规格要求,并不是指上、下控制线必须在规格上、
下限内侧,即UCL>TU;LCL< TL。而是要看受控工序的工
序能力是否满足给定的Cp值要求。
8
样本大小
2 3 4 5 6 7 8 9 10
X 图用 A2
1.880 1.023 0.729 0.577 0.483 0.419 0.373 0.337 0.308
表5 控制图系数表
R图用
D3
D4
-
2.267
控制图的绘制与判断
1
主要内容
➢ 绘制程序 ➢ 各类控制图作法举例 ➢ 控制图的观察与判断
2
绘制程序
3
1 确定受控质量特性 即明确控制对象。一般应选择可以计量(或计数)、技术上可控、 对产品质量影响大的关键部位、关键工序的关键质量特性进行
2 选定控制图种类 3 收集预备数据 4 计算控制界限
各种控制图控制界限的计算方法及计算公式不同,但其计算
表2 控制图的样本与样本容量
控制图名称
样本数k
样本容量n
备注
X R 图 X~ R 图
L—S图 X—Rs图 pn图、 p 图
C图、U图
一般k=20~25
一般3~6
X~ 图的样本容量常取3或5
K=20~30 一般k=20~25
1
1/p~5/p
尽可能使样本中缺 陷数C=1~5
7
5 作分析用控制图并判断工序是否处于稳定状态