LV8549M-TLM-H;中文规格书,Datasheet资料
TLV2543CN;TLV2543CDBR;TLV2543CDW;TLV2543IDB;TLV2543IDW;中文规格书,Datasheet资料

Terminal Functions
TERMINAL NAME AIN0 – AIN10 NO. 1 – 9, 11, 12 15 I/O I DESCRIPTION Analog input. These 11 analog-signal inputs are internally multiplexed. The driving source impedance should be less than or equal to 50 Ω for 4.1-MHz I/O CLOCK operation and capable of slewing the analog input voltage into a capacitance of 60 pF. Chip select. A high-to-low transition on CS resets the internal counters and controls and enables DATA OUT, DATA INPUT, and I/O CLOCK. A low-to-high transition disables DATA INPUT and I/O CLOCK within a setup time. Serial-data input. A 4-bit serial address selects the desired analog input or test voltage to be converted. The serial data is presented with the MSB first and is shifted in on the first four rising edges of I/O CLOCK. After the four address bits are read into the address register, I/O CLOCK clocks the remaining bits in order. Serial data output. This is the 3-state serial output for the A/D conversion result. DATA OUT is in the high-impedance state when CS is high and active when CS is low. With a valid CS, DATA OUT is removed from the high-impedance state and is driven to the logic level corresponding to the MSB/LSB value of the previous conversion result. The next falling edge of I/O CLOCK drives DATA OUT to the logic level corresponding to the next MSB / LSB, and the remaining bits are shifted out in order. End of conversion. EOC goes from a high to a low logic level after the falling edge of the last I/O CLOCK and remains low until the conversion is complete and data are ready for transfer. Ground. This is the ground return terminal for the internal circuitry. Unless otherwise noted, all voltage measurements are with respect to GND. I Input /output clock. I/O CLOCK receives the serial input and performs the following four functions: 1. It clocks the eight input data bits into the input data register on the first eight rising edges of I/O CLOCK with the multiplexer address available after the fourth rising edge. 2. On the fourth falling edge of I/O CLOCK, the analog input voltage on the selected multiplexer input begins charging the capacitor array and continues to do so until the last falling edge of I/O CLOCK. 3. It shifts the 11 remaining bits of the previous conversion data out on DATA OUT. Data changes on the falling edge of I/O CLOCK. 4. It transfers control of the conversion to the internal state controller on the falling edge of the last I/O CLOCK. Reference +. The upper reference voltage value (nominally VCC) is applied to REF+. The maximum input voltage range is determined by the difference between the voltage applied to this terminal and the voltage applied to the REF – terminal. Reference –. The lower reference voltage value (nominally ground) is applied to REF –. Positive supply voltage.
FTLF8519F2GTL, 规格书,Datasheet 资料

Finisar Corporation October 6, 2005 Rev B
Page 1
芯天下--/
FTLF8519F2xTL 2x5 Pin SFF Product Specification – October 2005
I.
Pin Descriptions
Product Specification
2.125 Gb/s RoHS Compliant Short Wavelength 2x5 SFF Transceiver
FTLF8519F2xTL
PRODUCT FEATURES Up to 2.125 Gb/s bi-directional data links Standard 2x5 pin SFF footprint (MSA compliant) 850nm Oxide VCSEL laser transmitter Duplex LC connector RoHS compliant and Lead Free Up to 500m on 50/125µm MMF, 300m on 62.5/125µm MMF Metal enclosure, for lower EMI Single 3.3V power supply Low power dissipation <750mW Industrial operating temperature range: -40°C to 85°C Finisar’s FTLF8519F2xTL Small Form Factor (SFF) transceivers comply with the 2x5 standard package defined by the Small Form Factor Multi-Sourcing Agreement (MSA)1. They are simultaneously compatible with Gigabit Ethernet as specified in IEEE Std 802.32 and Fibre Channel FC- PI-2 Rev. 7.03. They are RoHS compliant and lead-free per Directive 2002/95/EC4 and Finisar Application Note AN-2038. PRODUCT SELECTION APPLICATIONS 1.25 Gb/s 1000Base-SX Ethernet Dual Rate 1.063/2.125 Gb/s Fibre Channel
L4955中文资料
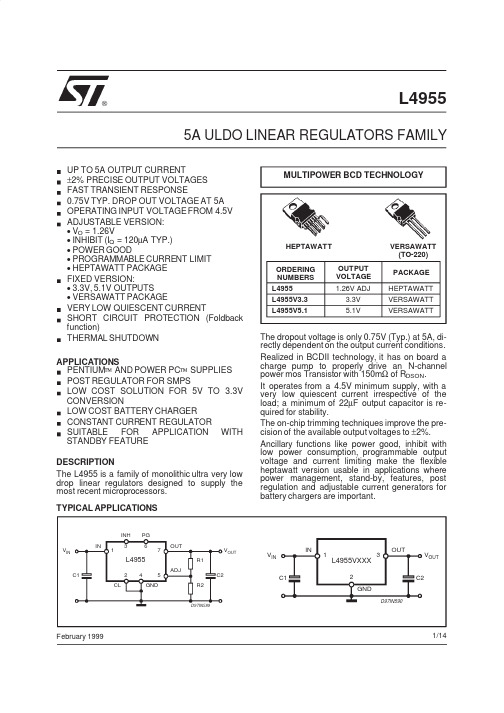
0.2
20
60
0.9 x VO
•
0.2
•
0.1
0.4
60
75
Unit V V V mV mV V V V A A A A mA mA µA V V µA V V V
dB
3/14
元器件交易网
L4955
L4955V3.3 - ELECTRICAL CHARACTERISTICS (Tj = 25°C, Vin = 5V, unless otherwise specified)
2/14
元器件交易网
L4955
PIN FUNCTIONS
HW VW Name
Fun ction
1
1
IN Unregulated input voltage; this pin must be bypassed with a capacitor larger than 10µF.
元器件交易网
®
L4955
5A ULDO LINEAR REGULATORS FAMILY
UP TO 5A OUTPUT CURRENT ±2% PRECISE OUTPUT VOLTAGES FAST TRANSIENT RESPONSE 0.75V TYP. DROP OUT VOLTAGE AT 5A OPERATING INPUT VOLTAGE FROM 4.5V ADJUSTABLE VERSION: • VO = 1.26V • INHIBIT (IQ = 120µA TYP.) • POWER GOOD • PROGRAMMABLE CURRENT LIMIT • HEPTAWATT PACKAGE FIXED VERSION: • 3.3V, 5.1V OUTPUTS • VERSAWATT PACKAGE VERY LOW QUIESCENT CURRENT SHORT CIRCUIT PROTECTION (Foldback function) THERMAL SHUTDOWN
MEMORY存储芯片ADM485ARZ-REEL中文规格书
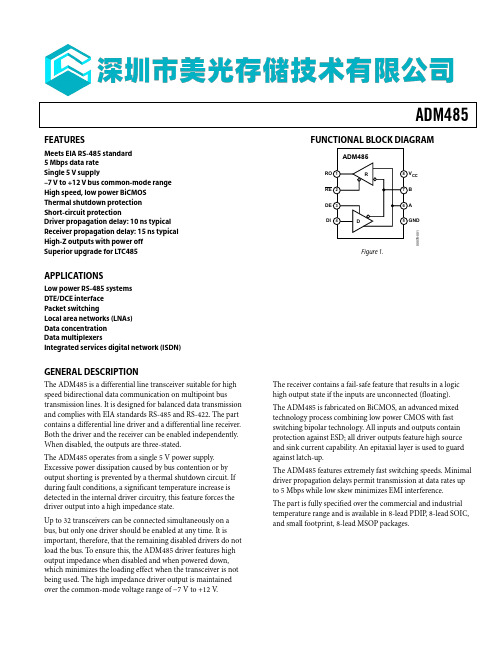
ADM485FUNCTIONAL BLOCK DIAGRAMCC 00078-001FEATURESMeets EIA RS-485 standard 5 Mbps data rateSingle 5 V supply–7 V to +12 V bus common-mode range High speed, low power BiCMOS Thermal shutdown protection Short-circuit protectionDriver propagation delay: 10 ns typical Receiver propagation delay: 15 ns typical High-Z outputs with power off Superior upgrade for LTC485APPLICATIONSLow power RS-485 systems DTE/DCE interface Packet switchingLocal area networks (LNAs) Data concentration Data multiplexersIntegrated services digital network (ISDN)GENERAL DESCRIPTIONThe ADM485 is a differential line transceiver suitable for high speed bidirectional data communication on multipoint bus transmission lines. It is designed for balanced data transmission and complies with EIA standards RS-485 and RS-422. The part contains a differential line driver and a differential line receiver. Both the driver and the receiver can be enabled independently. When disabled, the outputs are three-stated.The ADM485 operates from a single 5 V power supply. Excessive power dissipation caused by bus contention or by output shorting is prevented by a thermal shutdown circuit. If during fault conditions, a significant temperature increase is detected in the internal driver circuitry, this feature forces the driver output into a high impedance state.Up to 32 transceivers can be connected simultaneously on a bus, but only one driver should be enabled at any time. It is important, therefore, that the remaining disabled drivers do not load the bus. To ensure this, the ADM485 driver features high output impedance when disabled and when powered down, which minimizes the loading effect when the transceiver is not being used. The high impedance driver output is maintained over the common-mode voltage range of −7 V to +12 V .Figure 1.The receiver contains a fail-safe feature that results in a logic high output state if the inputs are unconnected (floating). The ADM485 is fabricated on BiCMOS, an advanced mixed technology process combining low power CMOS with fast switching bipolar technology. All inputs and outputs contain protection against ESD; all driver outputs feature high source and sink current capability. An epitaxial layer is used to guard against latch-up.The ADM485 features extremely fast switching speeds. Minimal driver propagation delays permit transmission at data rates up to 5 Mbps while low skew minimizes EMI interference. The part is fully specified over the commercial and industrial temperature range and is available in 8-lead PDIP , 8-lead SOIC, and small footprint, 8-lead MSOP packages.ADM485Rev. F | Page 2 of 16ADM485SPECIFICATIONSV CC = 5 V ± 5%, all specifications T MIN to T MAX, unless otherwise noted.Rev. F | Page 3 of 16ADM485TIMING SPECIFICATIONSV CC = 5 V ± 5%, all specifications T MIN to T MAX, unless otherwise noted.1 Guaranteed by characterization.Rev. F | Page 4 of 16ADM485Rev. F | Page 5 of 16ABSOLUTE MAXIMUM RATINGST A = 25°C, unless otherwise noted.Stresses above those listed under Absolute Maximum Ratings may cause permanent damage to the device. This is a stress rating only; functional operation of the device at these or any other conditions above those indicated in the operationalsection of this specification is not implied. Exposure to absolute maximum rating conditions for extended periods may affect device reliability.Table 4. TransmittingInputsOutputsDE DIB A 1 1 0 1 1 0 1 0 0X 1Z 2Z 21 X = don’t care.2Z = high impedance.1 X = don’t care.2Z = high impedance.ESD CAUTION。
无刷电机解决方案

Level Shift
OUT1 (NC) (NC) VCC
5 6 7 8
Current Limitter
Duty Controller
12 11 10
High Side Regulator
RD FG PWM
OSC Lock Detection
PWM
RGH
9
TSD
订购及封装信息
ONPN Description LV8861VH-TLM-H FAN MOTOR DRIVER (7.6mmx9.75mmx1.3mm) Pkg HSSOP16
ON Semiconductor Target
19
LB1975/76
三相风扇电机驱动器
独特特性 • 3-Phase Bipolar Drive VMmax46V,Iomax2.5A VMmax60V,Iomax2.5A • Direct PWM Drive • DIP28H Package 优势 应用数据 • High voltage,current 1chip • LB1975 VREG • LB1976 VCC • High Efficiency Reg VCC • Large Power dissipation
+
S/S
F/R
FG1 FG2
LVSD
TSD VM
+
Hys.Amp
VM
• • • •
其它特性 Built-in high side kickback absorbing diodes Built-in current limiter Built-in FG output PWM duty can be controlled by IC input
控制器
BUK136-50L,118;中文规格书,Datasheet资料
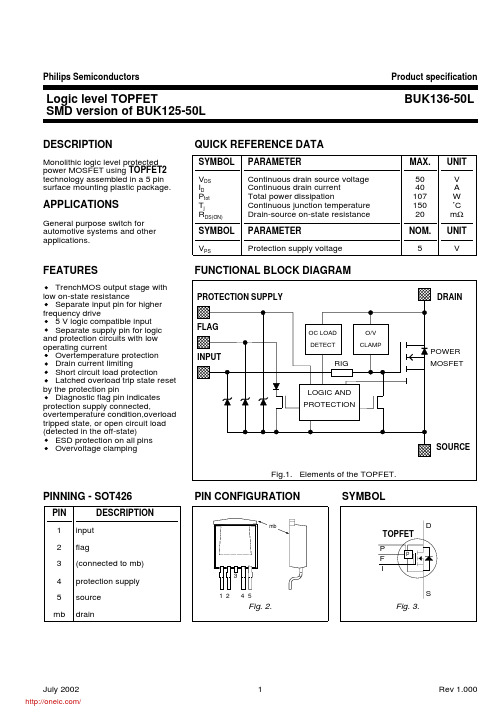
Philips Semiconductors Product specificationLogic level TOPFETBUK136-50LSMD version of BUK125-50LDESCRIPTIONQUICK REFERENCE DATAMonolithic logic level protected SYMBOL PARAMETERMAX.UNIT power MOSFET using TOPFET2technology assembled in a 5 pin V DS Continuous drain source voltage 50V surface mounting plastic package.I D Continuous drain current 40A P tot Total power dissipation107W APPLICATIONST jContinuous junction temperature 150˚C R DS(ON)Drain-source on-state resistance 20m ΩGeneral purpose switch for automotive systems and other SYMBOL PARAMETERNOM.UNIT applications.V PSProtection supply voltage5VFEATURESTrenchMOS output stage with Separate input pin for higher 5 V logic compatible input Separate supply pin for logic Overtemperature protection Drain current limitingShort circuit load protectionLatched overload trip state reset Diagnostic flag pin indicates overtemperature condition,overload tripped state, or open circuit load ESD protection on all pins Overvoltage clampingPINNING - SOT426PIN CONFIGURATIONSYMBOLPhilips Semiconductors Product specification Logic level TOPFET BUK136-50L SMD version of BUK125-50LLIMITING VALUESLimiting values in accordance with the Absolute Maximum Rating System (IEC 134)SYMBOL PARAMETER CONDITIONS MIN.MAX.UNIT Continuous voltageVDS Drain source voltage1VIS= 0 V-50V Continuous currentsI D Drain current VPS= 5 V; Tmb=25˚C-self -AlimitedVPS= 0 V; Tmb=80˚C-40AI I Input current-55mAI F Flag current-55mAIPProtection supply current-55mAThermalPtot Total power dissipation Tmb= 25˚C-107WT stg Storage temperature-55175˚CT j Junction temperature2continuous-150˚CTsoldMounting base temperature during soldering-260˚C ESD LIMITING VALUESYMBOL PARAMETER CONDITIONS MIN.MAX.UNITVCElectrostatic discharge capacitor Human body model;-2kVvoltage C = 250 pF; R = 1.5 kΩOVERLOAD PROTECTION LIMITING VALUEWith an adequate protection supply For overload conditions an n-MOS The drain current is limited to connected, TOPFET can protect transistor turns on between the reduce dissipation in case of short itself from two types of overload -input and source to quickly circuit load. Refer to OVERLOAD overtemperature and short circuit discharge the power MOSFET CHARACTERISTICS.load.gate capacitance.SYMBOL PARAMETER REQUIRED CONDITION MIN.MAX.UNIT Overload protection3protection supplyVDS Drain source voltage VPS≥ 4 V035VOVERVOLTAGE CLAMPING LIMITING VALUESAt a drain source voltage above 50 V the power MOSFET is actively turned on to clamp overvoltage transients. SYMBOL PARAMETER CONDITIONS MIN.MAX.UNITInductive load turn off IDM = 25 A; VDD≤ 20 VEDSM Non-repetitive clamping energy Tmb= 25˚C-550mJEDRM Repetitive clamping energy Tmb≤ 95˚C; f = 250 Hz-60mJ1 Prior to the onset of overvoltage clamping. For voltages above this value, safe operation is limited by the overvoltage clamping energy.2 A higher Tj is allowed as an overload condition but at the threshold Tj(TO)the over temperature trip operates to protect the switch.3 All control logic and protection functions are disabled during conduction of the source drain diode. If the protection circuit was previouslylatched, it would be reset by this condition.Philips Semiconductors Product specification Logic level TOPFET BUK136-50L SMD version of BUK125-50LTHERMAL CHARACTERISTICSYMBOL PARAMETER CONDITIONS MIN.TYP.MAX.UNIT Thermal resistanceRth j-mbJunction to mounting base--0.94 1.17K/W OUTPUT CHARACTERISTICSLimits are for -40˚C ≤ Tmb ≤ 150˚C; typicals are for Tmb= 25˚C unless otherwise specified.SYMBOL PARAMETER CONDITIONS MIN.TYP.MAX.UNIT Off-state VIS= 0 VV(CL)DSS Drain-source clamping voltage ID= 10 mA50-70VIDM= 5 A; tp ≤ 300 µs; δ≤ 0.01506070VI DSS Drain source leakage current1VPS= 0 V; VDS= 40 V--100µATmb= 25˚C-0.110µAOn-state tp≤ 300 µs; δ≤ 0.01; VPS≥ 4 VRDS(ON)Drain-source resistance IDM= 15 A; VIS≥ 4.4 V--40mΩTmb= 25˚C-1520mΩINPUT CHARACTERISTICSLimits are for -40˚C ≤ Tmb ≤ 150˚C; typicals are for Tmb= 25˚C unless otherwise specified.SYMBOL PARAMETER CONDITIONS MIN.TYP.MAX.UNIT Normal operationVIS(TO)Input threshold voltage2ID= 1 mA0.6- 2.6VTmb= 25˚C 1.1 1.6 2.1VI IS Input current VIS= 5 V-16100µAV(CL)IS Input clamping voltage II= 1 mA 5.5 6.48.5VRIGInternal series resistance3to gate of power MOSFET- 1.7-kΩOverload protection latched VPS≥ 4 VI ISL Input current VIS= 5 V1 2.74mA1 The drain current required for open circuit load detection is switched off when there is no protection supply, in order to ensure a low off-statequiescent current. Refer to OPEN CIRCUIT LOAD DETECTION CHARACTERISTICS.2 The measurement method is simplified if VPS = 0 V, in order to distinguish IDfrom IDSP. Refer to OPEN CIRCUIT LOAD DETECTIONCHARACTERISTICS.3 This is not a directly measurable parameter.Philips Semiconductors Product specificationLogic level TOPFETBUK136-50LSMD version of BUK125-50LPROTECTION SUPPLY CHARACTERISTICSLimits are for -40˚C ≤ T mb ≤ 150˚C; typicals are for T mb = 25˚C.SYMBOL PARAMETERCONDITIONSMIN.TYP.MAX.UNIT Protection & detection V PSF Threshold voltage 1I F = 100 µA; V DS = 5 V 2.53.454VNormal operation or protection latched I PS , I PSL Supply current V PS = 4.5 V -210450µA V (CL)PS Clamping voltageI P = 1.5 mA5.56.58.5V Overload protection latched V PSR Reset voltage 1 1.83V t prReset timeV PS ≤ 1 V1045120µsOPEN CIRCUIT LOAD DETECTION CHARACTERISTICSAn open circuit load condition can be detected while the TOPFET is in the off-state. Refer to TRUTH TABLE .V PS = 5 V. Limits are for -40˚C ≤ T mb ≤ 150˚C and typicals are for T mb = 25˚C.SYMBOL PARAMETER CONDITIONSMIN.TYP.MAX.UNIT I DSP Off-state drain current 2V IS = 0 V; 2 V ≤ V DS ≤ 40 V 0.9 1.8 2.7mA V DSF Drain threshold voltage 3V IS = 0 V 0.212V V ISFInput threshold voltage 4I D = 100 µA0.30.81.1VOVERLOAD CHARACTERISTICST mb = 25˚C unless otherwise specified.SYMBOL PARAMETERCONDITIONS MIN.TYP.MAX.UNITShort circuit load protection V PS > 4 VI DDrain current limiting 5V IS = 5 V;-40˚C ≤ T mb ≤ 150˚C 406284A P D(TO)Overload power threshold for protection to operate 90220330W T DSC Characteristic timewhich determines trip time 6250500700µs Overtemperature protection V PS = 5 VT j(TO)Threshold temperaturefrom I D ≥ 4 A or V DS > 0.2 V150170-˚C1 When V PS is less than V PSF the flag pin indicates low protection supply voltage. Refer to TRUTH TABLE.2 The drain source current which flows in a normal load when the protection supply is high and the input is low.3 If V DS < V DSF then the flag indicates open circuit load.4 For open circuit load detection, V IS must be less than V ISF .5 Product specification will include curve showing output characteristics.6 Trip time t d sc varies with overload dissipation P D according to the formula t d sc ~ T DSC / ln[ P D / P D(TO)].Philips Semiconductors Product specificationLogic level TOPFETBUK136-50LSMD version of BUK125-50LTRUTH TABLEFor normal, open-circuit load and overload conditions or inadequate protection supply voltage.Assumes proper external pull-up for flag pin. Refer to FLAG CHARACTERISTICS .CONDITIONPROTECTIONINPUT FLAG OUTPUT Normal on-state 110ON Normal off-state 100OFF Open circuit load 110ON Open circuit load 101OFF Short circuit load 1111OFF Over temperature1X 1OFF Low protection supply voltage 011ON Low protection supply voltage1OFFKEY ‘0’ equals low‘1’ equals high‘X’ equals don’t care.FLAG CHARACTERISTICSThe flag is an open drain transistor which requires an external pull-up circuit.Limits are for -40˚C ≤ T mb ≤ 150˚C; typicals are for T mb = 25˚C.SYMBOL PARAMETER CONDITIONSMIN.TYP.MAX.UNITFlag ‘low’normal operation; V PS = 5 V V FSF Flag voltageI F = 100 µA -0.81V I FSF Flag saturation current V FS = 5 V -10-mAFlag ‘high’overload or fault I FSO Flag leakage current V FS = 5 V -0.110µA V (CL)FS Flag clamping voltage I F = 100 µA5.56.28.5VApplication information R FSuitable external pull-up V FF = 5 V-47-k ΩresistanceSWITCHING CHARACTERISTICST mb = 25˚C; R I = 50 Ω; R IS = 50 Ω; V DD = 15 V; resistive load R L = 10 Ω.SYMBOL PARAMETER CONDITIONS MIN.TYP.MAX.UNIT t d on Turn-on delay time V IS : 0 V ⇒ 5 V- 1.85µs t r Rise time- 3.58µs t d off Turn-off delay time V IS : 5 V ⇒ 0 V -1130µs t fFall time-512µs1 In this condition the protection circuit is latched. To reset the latch the protection pin must be taken low. Refer to PROTECTION SUPPLYCHARACTERISTICS.Philips Semiconductors Product specificationLogic level TOPFETBUK136-50LSMD version of BUK125-50LMECHANICAL DATA1 Epoxy meets UL94 V0 at 1/8". Net mass: 1.5 g.For soldering guidelines and SMD footprint design, please refer to Data Handbook SC18.Philips Semiconductors Product specification Logic level TOPFET BUK136-50L SMD version of BUK125-50LDEFINITIONSDATA SHEET STATUSDATA SHEET PRODUCT DEFINITIONSSTATUS1STATUS2Objective data Development This data sheet contains data from the objective specification forproduct development. Philips Semiconductors reserves the right tochange the specification in any manner without noticePreliminary data Qualification This data sheet contains data from the preliminary specification.Supplementary data will be published at a later date. PhilipsSemiconductors reserves the right to change the specification withoutnotice, in order to improve the design and supply the best possibleproductProduct data Production This data sheet contains data from the product specification. PhilipsSemiconductors reserves the right to make changes at any time inorder to improve the design, manufacturing and supply. Changes willbe communicated according to the Customer Product/ProcessChange Notification (CPCN) procedure SNW-SQ-650ALimiting valuesLimiting values are given in accordance with the Absolute Maximum Rating System (IEC 134). Stress above one or more of the limiting values may cause permanent damage to the device. These are stress ratings only and operation of the device at these or at any other conditions above those given in the Characteristics sections ofthis specification is not implied. Exposure to limiting values for extended periods may affect device reliability. Application informationWhere application information is given, it is advisory and does not form part of the specification.Philips Electronics N.V. 2002All rights are reserved. Reproduction in whole or in part is prohibited without the prior written consent of the copyright owner.The information presented in this document does not form part of any quotation or contract, it is believed to be accurate and reliable and may be changed without notice. No liability will be accepted by the publisher for any consequence of its use. Publication thereof does not convey nor imply any license under patent or other industrial or intellectual property rights.LIFE SUPPORT APPLICATIONSThese products are not designed for use in life support appliances, devices or systems where malfunction of these products can be reasonably expected to result in personal injury. Philips customers using or selling these products for use in such applications do so at their own risk and agree to fully indemnify Philips for any damages resulting from such improper use or sale.1 Please consult the most recently issued datasheet before initiating or completing a design.2 The product status of the device(s) described in this datasheet may have changed since this datasheet was published. The latest information isavailable on the Internet at URL .分销商库存信息: NXPBUK136-50L,118。
华硕主板

数字家庭主板M2NDH-支持AMD®SocketAM2Athlon64FX/Athlo64X2/Athlon64/Sempron -AMDLive!™Ready-强大扩充能力:1xPCI-Ex16、2xPCI-E、3xPCI-华硕WiFi-APSolo-华硕DHRemote™-华硕MP3-In™-华硕Q-Connector-高保真音频中央处理器支持AMD®SocketAM2Athlon64FX/Athlo64X2/Athlon64/Sempron 支持AMDCool'n'Quiet™技术AMD64架构,同时兼容32位和64位计算AMDLive!™Ready芯片组NVIDIAnForce®430MCP前端总线2000/1600MT/s内存双通道内存架构4x240-pinDIMM内存插槽,支持最大容量高达8GB的DDR2800/667/533ECC和non-ECC、un-buffered内存扩充插槽1xPCI-Expressx16插槽2xPCI-Expressx1插槽3xPCI2.2插槽存储装置/RAID-1xUltraDMA133/100/66/33-4xSerialATA3.0Gb/s-NVIDIAMediaShield™RAID通过SerialA TA设备支持RAID0、1、0+1、5和JBOD网络功能NVIDIAnForce®430内建GigabitMAC,支持externalAttansicPHY无线局域网:54MbpsIEEE802.11b/g(华硕WiFi-APSolo)音频功能ADI6声道高保真音频CODEC背板S/PDIF数字音频输出USB高达8个USB2.0/1.1接口M2N-VMDH-AMDSocketAM2-NVIDIAGeForce6100/nForce430-双通道DDR2800/667/533-1xPCIExpressx16+1xPCIExpressx1+2xPCI-双VGA:DVI-D和D-Sub-8声道高保真音频-2x1394a接口中央处理器支持AMD®SocketAM2Athlon64X2/Athlon64FX/Athlon64/Sempro nAMDCool'n'Quiet™技术AMD64架构,兼容32位和64位计算AMDLive!™Ready芯片组NVIDIAGeForce6100/nForce430前端总线2000/1600MT/s 内存双通道内存架构4x240-pinDIMM插槽,支持最大容量为8GB的DDR2800/667/533non-ECC,un-buffered内存显卡集成GeForce6100GPU高清晰视频处理,最高分辨率可达1920x1440(@75Hz)支持RGB显示;UXGA1600x1200(@60Hz)支持DVI-D显示支持双VGA输出:DVI-D和RGB注意:DVI-D不能用来输出RGB信号至CRT。
M5839中文规格书
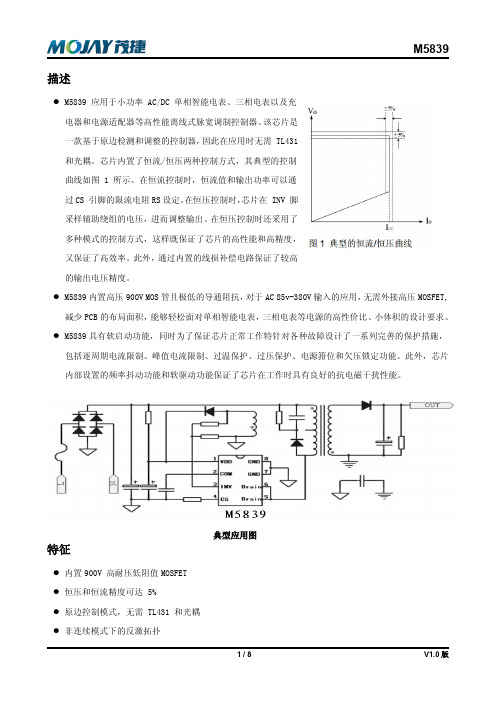
恒流工作
M5839 的恒压/恒流特征曲线如图 1 所示。M5839 被设计应用于工作在非连续模式下的反激式系统中。
在正常工作时,当 INV 电压低于内部 2.0V 的基准电压好时,系统工作在恒流模式,否则系统工作在恒压
模式。当次级输出电流达到了系统设定的最大电流时,系统就进入恒流模式,并且会引起输出电压的下降。
M5839 在 CS 端设计了一个约为 540ns 的前沿消隐时间用来防止在开关导通时刻错误的过流保护被 触发。因此,不需要在 CS 端在增加额外的 RC 滤波电路。采样电流的输入信号 CS 和误差放大器的输出 COM 共同决定开关的占空比,稳定输出. EMI 特性的改善
为了改善 M5839 系统的 EMI 特性,芯片内部采用了两种方式。其中一种方式是采用频率抖动,即在 M5839 正常工作频率的基础上叠加一个微小的扰动。也就是说,内部振荡器的频率被调制用来分散谐波干 扰能量,分散的能量能够最小化 EMI 带宽。另一种方式是软驱动,即逐渐打开功率 MOSFET。当提供给功 率 MOSFET 的栅驱动太强时, EMI 特性会变差;当提供给功率 MOSFET 的栅驱动太弱时,开关损耗又会 加大,因此需要在 EMI 特性和开关损耗之间寻求折衷来提供合适的栅驱动。M5839 采用了软驱动和图腾柱 输出结构,既获得了很好的 EMI 特性,又降低了开关损耗。频率抖动和软驱动的综合应用使系统的 EMI 特 性获得了很大的改善。 保护控制
4/8
V1.0 版
M5839
流/恒压控制,系统必须工作在反激式系统的非连续模式。(参照典型应用电路)在非连续模式的反激式转 换器中,输出电压能够通过辅助绕组来设定。当功率 MOSFET 导通时,负载电流由输出滤波电容 CO 提供, 原边电流呈斜坡上升,系统将能量存储在变压器的磁芯中,当功率 MOSFET 关断时,存储在变压器磁芯中 的能量传递到输出。
APT50M50L2LL 500V 89A 0.050
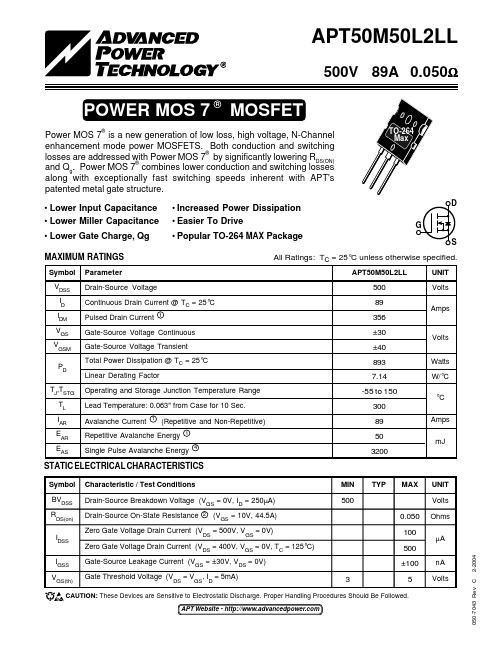
050-7043 R e v C 2-2004MAXIMUM RATINGSAll Ratings: TC = 25°C unless otherwise specified.CAUTION: These Devices are Sensitive to Electrostatic Discharge. Proper Handling Procedures Should Be Followed.APT Website - •Lower Input Capacitance •Increased Power Dissipation •Lower Miller Capacitance •Easier To Drive•Lower Gate Charge, Qg•Popular TO-264 MAX PackageAPT50M50L2LL500V 89A 0.050ΩPower MOS 7®is a new generation of low loss, high voltage, N-Channel enhancement mode power MOSFETS. Both conduction and switchinglosses are addressed with Power MOS 7®by significantly lowering R DS(ON)and Q g . Power MOS 7®combines lower conduction and switching losses along with exceptionally fast switching speeds inherent with APT's patented metal gate structure.Characteristic / Test ConditionsDrain-Source Breakdown Voltage (V GS = 0V, I D = 250µA)Drain-Source On-State Resistance 2 (V GS = 10V, 44.5A)Zero Gate Voltage Drain Current (V DS = 500V, V GS = 0V)Zero Gate Voltage Drain Current (V DS = 400V, V GS = 0V, T C = 125°C)Gate-Source Leakage Current (V GS = ±30V, V DS = 0V)Gate Threshold Voltage (V DS = V GS , I D = 5mA)Symbol V DSS I D I DM V GS V GSM P D T J ,T STG T L I AR E AR E ASParameterDrain-Source VoltageContinuous Drain Current @ T C = 25°C Pulsed Drain Current1Gate-Source Voltage Continuous Gate-Source Voltage Transient Total Power Dissipation @ T C = 25°C Linear Derating FactorOperating and Storage Junction Temperature Range Lead Temperature: 0.063" from Case for 10 Sec.Avalanche Current 1 (Repetitive and Non-Repetitive)Repetitive Avalanche Energy 1Single Pulse Avalanche Energy4UNIT Volts AmpsVolts Watts W/°C °C Amps mJSTATIC ELECTRICAL CHARACTERISTICSSymbol BV DSS R DS(on)I DSS I GSS V GS(th)UNIT VoltsOhms µA nA VoltsMINTYPMAX5000.050100500±10035APT50M50L2LL50089356±30±408937.14-55 to 15030089503200DYNAMIC CHARACTERISTICS050-7043 R e v C 2-2004APT50M50L2LLZ θJ C , T H E R M A L I M P E D A N C E (°C /W )RECTANGULAR PULSE DURATION (SECONDS)FIGURE 1, MAXIMUM EFFECTIVE TRANSIENT THERMAL IMPEDANCE, JUNCTION-TO-CASE vs PULSE DURATION0.160.140.120.100.080.060.040.020Characteristic / Test Conditions Continuous Source Current (Body Diode)Pulsed Source Current 1 (Body Diode)Diode Forward Voltage 2 (V GS = 0V, I S = -89A )Reverse Recovery Time (I S = -89A , dl S /dt = 100A/µs)Reverse Recovery Charge (I S = -89A , dl S /dt = 100A/µs)Peak Diode Recovery dv /dt 5UNIT Amps Volts ns µC V/nsMINTYPMAX893561.368017.08Symbol R θJC R θJAMINTYPMAX0.1440UNIT °C/WCharacteristic Junction to Case Junction to AmbientSymbol I S I SM V SD t rr Q rrdv /dtSymbol C iss C oss C rss Q g Q gs Q gd t d(on)t r t d(off)t f E on E off E on E offCharacteristic Input Capacitance Output CapacitanceReverse Transfer Capacitance Total Gate Charge 3Gate-Source Charge Gate-Drain ("Miller") Charge Turn-on Delay Time Rise TimeTurn-off Delay Time Fall TimeTurn-on Switching Energy 6Turn-off Switching Energy Turn-on Switching Energy 6Turn-off Switching EnergyTest ConditionsV GS = 0VV DS = 25V f = 1 MHz V GS = 10VV DD = 250VI D = 89A @ 25°C RESISTIVE SWITCHINGV GS = 15VV DD = 250V I D = 89A @ 25°CR G = 0.6ΩINDUCTIVE SWITCHING @ 25°CV DD = 333V, V GS = 15V I D = 89A, R G = 3ΩINDUCTIVE SWITCHING @ 125°CV DD = 333V, V GS = 15V I D = 89A, R G = 3ΩMINTYPMAX1055020601052005010524225681490165021051835UNITpFnC nsµJSOURCE-DRAIN DIODE RATINGS AND CHARACTERISTICSTHERMAL CHARACTERISTICS1Repetitive Rating: Pulse width limited by maximum junction temperature2Pulse Test: Pulse width < 380 µs, Duty Cycle < 2%3See MIL-STD-750 Method 34714Starting T j = +25°C, L = 0.81mH, R G = 25Ω, Peak I L = 89A5dv /dt numbers reflect the limitations of the test circuit rather than the device itself. I S ≤ -89A di /dt ≤ 700A/µsV R ≤ 500VT J ≤ 150°C 6 Eon includes diode reverse recovery. See figures 18, 20.APT Reserves the right to change, without notice, the specifications and information contained herein.050-7043 R e v C 2-2004APT50M50L2LLTypical Performance CurvesR D S (O N ), D R A I N -T O -S O U R C E O N R E S I S T A N C E I D , D R A I N C U R R E N T (A M P E R E S )I D , D R A I N C U R R E N T (A M P E R E S )(N O R M A L I Z E D )V G S (T H ), T H R E S H O L D V O L T A G E B V D S S , D R A I N -T O -S O U R C E B R E A K D O W N R D S (O N ), D R A I N -T O -S O U R C E O N R E S I ST A N C EI D , D R A I N C U R R E N T (A M P E R E S )(N O R M A L I Z E D )V O L T A G E (N O R M A L I Z E D )255075100125150V DS , DRAIN-TO-SOURCE VOLTAGE (VOLTS)FIGURE 2, TRANSIENT THERMAL IMPEDANCE MODEL FIGURE 3, LOW VOLTAGE OUTPUT CHARACTERISTICS V GS , GATE-TO-SOURCE VOLTAGE (VOLTS)I D , DRAIN CURRENT (AMPERES)FIGURE 4, TRANSFER CHARACTERISTICSFIGURE 5, R DS(ON) vs DRAIN CURRENTT C , CASE TEMPERATURE (°C)T J , JUNCTION TEMPERATURE (°C)FIGURE 6, MAXIMUM DRAIN CURRENT vs CASE TEMPERATUREFIGURE 7, BREAKDOWN VOLTAGE vs TEMPERATURE T J , JUNCTION TEMPERATURE (°C)T C , CASE TEMPERATURE (°C)FIGURE 8, R DS(ON) vs. TEMPERATUREFIGURE 9, THRESHOLD VOLTAGE vs TEMPERATURE90807060504030201001.151.101.051.000.950.900.850.0191F0.209F RC MODELJunction temp. (°Case temperature. (°050-7043 R e v C 2-2004APT50M50L2LLV DS , DRAIN-TO-SOURCE VOLTAGE (VOLTS)V DS , DRAIN-TO-SOURCE VOLTAGE (VOLTS)FIGURE 10, MAXIMUM SAFE OPERATING AREA FIGURE 11,CAPACITANCE vs DRAIN-TO-SOURCE VOLTAGE Q g , TOTAL GATE CHARGE (nC)V SD , SOURCE-TO-DRAIN VOLTAGE (VOLTS)FIGURE 12, GATE CHARGE vs GATE-TO-SOURCE VOLTAGEFIGURE 13, SOURCE-DRAIN DIODE FORWARD VOLTAGE V G S , G A T E -T O -S O U R C E V O L T A G E (V O L T S )I D , D R A I N C U R R E N T (A M P E R E S )I D R , R E V E R S E D R A I N C U R R E N T (A M P E R E S )C , C A P A C I T A N C E (p F )30,00010,0001010I D (A)I D (A)FIGURE 14, DELAY TIMES vs CURRENTFIGURE 15, RISE AND FALL TIMES vs CURRENT I D (A)R G , GATE RESISTANCE (Ohms)FIGURE 16, SWITCHING ENERGY vs CURRENTFIGURE 17, SWITCHING ENERGY VS. GATE RESISTANCES W I T C H I N G E N E R G Y (µJ )t d (o n ) a n d t d (o ff ) (n s )S W I T C HI N G E N E R G Y (µJ )t r a n d t f (n s )050-7043 R e v C 2-2004APT50M50L2LLTO-264 MAX TM (L2) Package OutlineDimensions in Millimeters and (Inches)APT’s products are covered by one or more of U.S.patents 4,895,810 5,045,903 5,089,434 5,182,234 5,019,5225,262,336 6,503,786 5,256,583 4,748,103 5,283,202 5,231,474 5,434,095 5,528,058 and foreign patents. US and Foreign patents pending. All Rights Reserved.Figure 18, Turn-on Switching Waveforms and DefinitionsFigure 19, Turn-off Switching Waveforms and DefinitionsDrain CurrentGate VoltageDrain VoltageT J= 125 C 90%90%td(off)10%t fSwitching EnergyT J = 125 CDrain CurrentDrain VoltageGate VoltageSwitching Energy10 %t d(on)90%5 %10 %t rAPT60DF60V DD。
H5084NL;H5084NLT;中文规格书,Datasheet资料
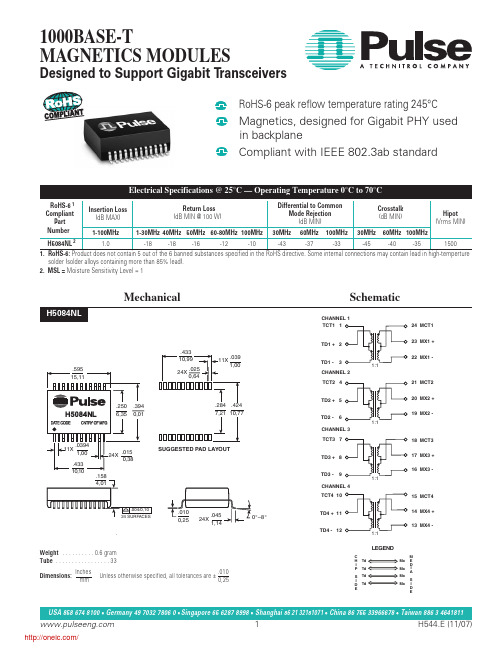
Differential to Common Mode Rejection (dB MIN)
30MHz 60MHz 100MHz
Crosstalk (dB MIN)
30MHz 60MHz 100MHz
Hipot (Vrms MIN)
Tel: 65 6287 8998 Fax: 65 6280 0080
Pulse North Asia No. 26, Kao Ching Rd. Yang Mei Chen Taoyuan Hsien Taiwan R. O. C.
Tel: 886 3 4641811 Fax: 886 3 4641911
Inches
.010
Dimensions:
Unless otherwise specified, all tolerances are ±
mm
0,25
Schematic
CHANNEL 1 TCT1 1
24 MCT1
TD1 + 2
TD1 - 3
1:1
CHANNEL 2
TCT2 4
23 MX1 + 22 MX1 -
C H Td I P Td
S Td
I D
Td
E
LEGEND
M Mx E
D Mx I
A Mx
S Mx I
D E
USA 858 674 8100 • Germany 49 7032 7806 0 • Singapore 65 6287 8998 • Shanghai 86 21 32181071 • China 86 755 33966678 • Taiwan 886 3 4641811
TPCF8304(TE85L,F);中文规格书,Datasheet资料

Drain power
(Note 3a)
dissipation
(t = 5 s) (Note 2b) Single-device value at
dual operation (Note 3b)
Single-pulse avalanche energy (Note 4)
Avalanche current
TPCF8304
TOSHIBA Field Effect Transistor Silicon P-Channel MOS Type (U-MOS IV)
TPCF8304
Notebook PC Applications Portable Equipment Applications
Unit: mm
• Low drain-source ON resistance: RDS (ON) = 60 mΩ (typ.) • High forward transfer admittance: |Yfs| = 5.9 S (typ.) • Low leakage current: IDSS = −10 μA (max) (VDS = −30 V) • Enhancement model: Vth = −0.8 to −2.0 V (VDS = −10 V, ID = −1 mA)
Note 4: VDD = -24 V, Tch = 25°C (initial), L = 0.2 mH, RG = 25 Ω, IAR = -1.6 A Note 5: Repetitive rating; pulse width limited by max channel stemperature
Switching time
Turn-on time Fall time
L165V,L165H, 规格书,Datasheet 资料
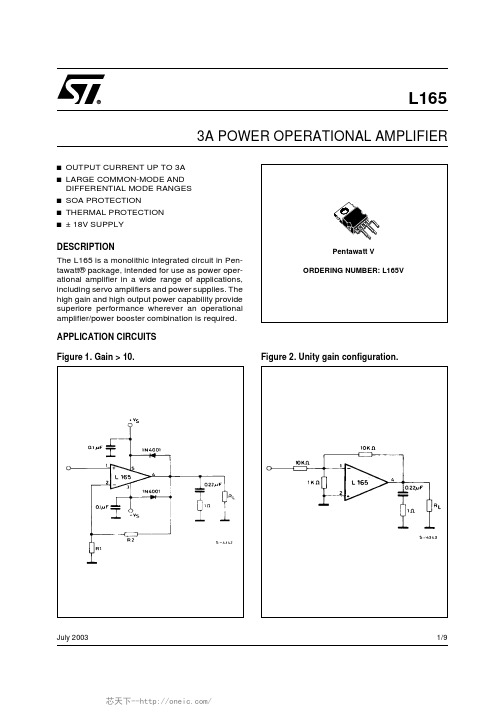
1/9L165July 2003 s OUTPUT CURRENT UP TO 3A s LARGE COMMON-MODE AND DIFFERENTIAL MODE RANGES s SOA PROTECTIONs THERMAL PROTECTION s± 18V SUPPLYDESCRIPTIONThe L165 is a monolithic integrated circuit in Pen-tawatt® package, intended for use as power oper-ational amplifier in a wide range of applications,including servo amplifiers and power supplies. The high gain and high output power capability provide superiore performance wherever an operational amplifier/power booster combination is required.3A POWER OPERATIONAL AMPLIFIERAPPLICATION CIRCUITS Figure 1. Gain > 10.Figure 2. Unity gain configuration.L1652/9ABSOLUTE MAXIMUM RATINGSPIN CONNECTION (Top view)SCHEMATIC DIAGRAMTHERMAL DATASymbol ParameterValue Unit V S Supply voltage± 18V V 5 V4Upper power transistor V CE 36V V 4V 3Lower power transistor V CE 36VV i Input voltageV S V j Differential input voltage± 15V I o Peak output current (internally limited) 3.5A P tot Power dissipation at T case = 90°C 20W T stg , T jStorage and junction temperature-40 to 150°C Symbol ParameterValue Unit R th-j-caseThermal resistance junction-casemax3°C/WL165ELECTRICAL CHARACTERISTCS (V S = ± 15 V, T j = 25 °C unless otherwise specified)Symbol Parameter Test Condition Min. Typ.Max.Unit V S Supply Voltage± 6± 18VI d Quiescent Drain Current V S = ±18 V4060mAI b Input Bias Current0.21µAV os Input Offset Voltage± 2± 10mVI os Input Offset Current± 20± 200nASR Slew-rate G v= 108V/µsG v = 1 (°)6V o Output Voltage Swing f = 1kHzI p = 0.3AI p = 3A 2724V ppf = 10kHz I p = 0.3A I p = 3A 2724V ppR Input Resistance (pin 1) f = 1 KHz100500KΩG v Voltage Gain (open loop)80dB e N Input Noise Voltage B = 10 to 10 000 Hz2µV i N Input Noise Current f = 1 KHz100pA CMR Common-mode Rejection R g≤ 10 KΩ; G V = 30 dB70dB SVR Supply Voltage Rejection R g = 22 KΩ; V ripple = 0.5 Vrmsf ripple = 100 HzG v= 10G v= 1006040dBdBEfficiency f = 1 kHz; R L = 4ΩI p = 1.6 A; P o = 5W I p = 1.6 A; P o = 18W 7060%%T sd Thermal Shut-down Case Temperature P tot = 12 W110°CP tot = 6 W130°C3/9L1654/9Figure 3. Open loop frequency response.Figure 4. Closed loop frequency response(circuit of figure 2).Figure 5. Large signal frequency response.Figure 6. Maximum output current vs. voltage[VCE] across each output transistor.Figure 7. Safe operating area and collectorcharacteristics of the protected power transistor.Figure 8. Maximum allowable powerdissipation vs. ambient temperature.5/9L165Figure 9. Bidirectional DC motor control with TTL/CMOS/µP compatible inputs.Figure 10. Motor current control circuit with external power transistors (I motor > 3.5A).Must be V S2 ≥V S1; E1, E2 = logic inputs; V S1 = logic supply voltageD1 to D4:V F ≤ 1.2 @ I = 4At rr ≤ 500nsNote : The inputvoltage level is compatible with L291 (5-BIT D/A converter).The transfer function is: IM V i-----R4Rx R3------------------=L1656/9Figure 11. High current tracking regulator.Figure 12. Bidirectional speed control of DC motor (Compensation networks not shown).A: for ± 18 ≤ Vi ± 32Note: V z must be chosen in order to verify2 V i - V z ≤ 36V B: for V i ≤ ±18VD1 to D4:V F ≤ 1.2 @ I = 2At rr ≤ 500ns7/9L165Figure 13. Split power supply.Figure 14. Power squarewave oscillator with independent adjustments for frequency and duty-cycle.P1 : duty-cycle adjustP2 : frequency adjust (f = 700 Hz with C1 = 10 nF , P2 = 100K Ω, f = 25 Hz with C1 = 10 nF , P2 = 0)L1658/9L165 Information furnished is believed to be accurate and reliable. However, STMicroelectronics assumes no responsibility for the consequences of use of such information nor for any infringement of patents or other rights of third parties which may result from its use. No license is grantedby implication or otherwise under any patent or patent rights of STMicroelectronics. Specifications mentioned in this publication are subject to change without notice. This publication supersedes and replaces all information previously supplied. STMicroelectronics products are notauthorized for use as critical components in life support devices or systems without express written approval of STMicroelectronics.STMicroelectronics acknowledges the trademarks of all companies referred to in this document.The ST logo is a registered trademark of STMicroelectronics©2003 STMicroelectronics - All Rights ReservedSTMicroelectronics GROUP OF COMPANIESAustralia - Brazil - Canada - China - Finland - France - Germany - Hong Kong - India - Israel - Italy - Japan -Malaysia - Malta - Morocco - Singapore - Spain - Sweden - Switzerland - United Kingdom - United States.9/9。
A4989SLDTR-T;中文规格书,Datasheet资料

Selection Guide
Part Number A4989SLDTR-T Packing Tape and reel, 4000 pieces per reel
Absolute Maximum Ratings
Characteristic Supply Voltage Logic Supply Voltage Logic Inputs and Outputs SENSEx pins Sxx pins LSSx pins GHxx pins GLxx pins Cxx pins Operating Ambient Temperature Junction Temperature Storage Temperature TA TJ(max) Tstg Range S Symbol VBB VDD Notes Rating –0.3 to 50 –0.3 to 7 –0.3 to 7 –1 to 1 –2 to 55 –2 to 5 Sxx to Sxx+15 –2 to 16 –0.3 to Sxx+15 –20 to 85 150 –55 to 150 Units V V V V V V V V V ºC ºC ºC
The above-supply voltage required for the high-side N-channel MOSFETs is provided by a bootstrap capacitor. Efficiency is enhanced by using synchronous rectification and the power FETs are protected from shoot-through by integrated crossover control and programmable dead time.
414H;中文规格书,Datasheet资料

/
414 H
DC axial compact fan
Technical features
General description Particular design features: Compact fan with low power consumption. Some models suitable for use at high ambient temperatures. General features: Material: fibreglass-reinforced plastic. Impeller PA, housing PBT. Electronic commutation completely integrated. Protected against reverse polarity and locking. Connection via single strands AWG 28, TR 64, bared and tin-plated. Air exhaust over bars. Direction of rotation counter-clockwise seen on rotor. Masse: 17 g. 0.027 kg 40 x 40 x 20 mm Fiberglass-reinforced PA plastic Fiberglass-reinforced PBT plastic Air exhaust over bars Left, looking at rotor Sintec sleeve bearing 45000 h 15000 h Single strands AWG 28, TR 64, bared and tin-plated. Protected against reverse polarity and locking. VDE, CSA, UL
50V64-743 Integrated Furnace Control 安装说明书
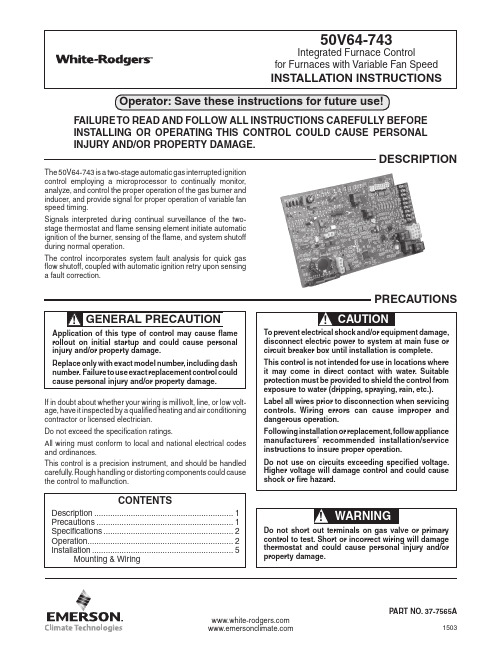
If in doubt about whether your wiring is millivolt, line, or low volt-age, have it inspected by a qualified heating and air conditioning contractor or licensed electrician.Do not exceed the specification ratings.All wiring must conform to local and national electrical codes and ordinances.This control is a precision instrument, and should be handled carefully. Rough handling or distorting components could cause the control to malfunction.FAILURE TO READ AND FOLLOW ALL INSTRUCTIONS CAREFULL Y BEFORE INSTALLING OR OPERATING THIS CONTROL COULD CAUSE PERSONAL INJURY AND/OR PROPERTY DAMAGE.CONTENTSDescription .............................................................1Precautions ............................................................1Specifications .........................................................2Operation ................................................................2Installation ..............................................................5 Mounting & WiringThe 50V64-743 is a two-stage automatic gas interrupted ignition control employing a microprocessor to continually monitor, analyze, and control the proper operation of the gas burner and inducer, and provide signal for proper operation of variable fan speed timing.Signals interpreted during continual surveillance of the two-stage thermostat and flame sensing element initiate automatic ignition of the burner, sensing of the flame, and system shutoff during normal operation.The control incorporates system fault analysis for quick gas flow shutoff, coupled with automatic ignition retry upon sensing a fault correction.PART NO. 37-7565A1503 DESCRIPTIONPRECAUTIONS2SPECIFICATIONSOPERATIONOPTION SWITCHESSwitches on the 50V64-743 control are used to control functions of the circulator blower. Switches labeled SW3 and SW4 control the circulator blower speed. Switch labeled SW2 controls the heat delay-to-fan-off period. The following table shows the time periods that will result from the various switch positions.50V64TIMING SPECIFICATIONS(All times are in seconds, unless noted otherwise)PRE-PURGETRIAL FOR IGNITION PERIODIGNITION ACTIVATION PERIOD RETRIESVALVE SEQUENCE PERIOD INTERPURGE POST-PURGE LOCKOUT TIMEHEAT DELAY-TO-FAN ON HEAT DELAY-TO-FAN OFF*COOL DELAY-TO-FAN OFF*ELECTRONIC AIR CLEANER HUMIDIFIER0522 times 156052584560/100/ 140/180N/A YES YES* These times will vary depending on option switch position. See OPERATION section for further information.ELECTRICAL RATINGS [@ 77°F (25°C)]:Input Voltage: 25 VAC, 60 HzMax. Input Current @ 25 VAC: 525mA + MV Relay Load Ratings:Gas Valve Relay: 1.5 amp @ 25 VAC, 60 Hz, 0.6 pf Ignitor: 2.0 amp @ 80VAC, 60 Hz - resistive Humidifier Relay: 1.0 Amp @120 VAC, 60 Hz.Electronic Air Cleaner Relay: 1.0 Amp, @ 120 VAC, 60 Hz Flame Current Requirements:Minimum current to insure flame detection: 1 µA DC*Maximum current for non-detection: 0.1 µA DC*Maximum allowable leakage resistance: 100 M ohms *Measured with a DC microammeter in the flame probe lead OPERATING TEMPERATURE RANGE:-40° to 175°F (-40° to 80°C)HUMIDITY RANGE:5% to 95% relative humidity (non-condensing)Timing Specs: (@ 60 Hz**) maximumFlame Establishing Time: 0.8 sec Flame Failure Response Time: 2.0 secGases Approved: Natural, Manufactured, Mixed, LiquidPetroleum, and LP Gas Air Mixtures are all approved for use.SW1 SWITCH POSITIONS Set switch # SW1-2Off On Off OnTIME SW1-1Set switch #On Off Off On1/2 Min 5 Min 10 Min 15 MinOPTION SWITCH POSITIONS HEAT delay-to-fan-off (SW2):Set switch #1On On Off Off 2Off On On Off60 sec.100 sec.140 sec.180 sec.The dip switch settings for this control may be different from thecontrol being replaced. Please set the switches for the delay period according to the chart above.If W1 and W2 are tied together, the time delay of second stage is based on the switch settings of SW1, per the following table.HEAT MODEIn a typical system, a call for first stage heat is initiated by closing the W1 thermostat contacts. The Humidifier output is energized and the inducer blower is enabled at low speed. The control waits for the stage 1 pressure switch to close. When the pressure switch closes the silicon nitride ignitor is powered. This control has an adaptive algorithm that reduces the ignitor temperature to slightly greater than the minimum temperature required to ignite gas in each particular application. The con-trol measures the line voltage and determines an initial ignitor temperature setting based on the measurement. After each successful ignition, the control lowers the ignitor temperature slightly for the next ignition attempt. The control continues to lower the ignitor temperature until ignition does not occur, and the control goes into retry mode. For the second attempt to ignite gas within the same call for heat, the control increases the ignitor temperature to the value it was on the previous successful ignition. After ignition is successful, the control sets the ignition temperature at this value. The control is constantly making adjustments to the ignitor modulation routine to com-pensate for changes in the line voltage. The control will relearn after power interruptions.The Silicon Nitride ignitor manufactured by White-Rodgers must be used. These ignitors are specially designed to operate with the adaptive ignition routine used by the control to ensure the most efficient ignitor temperature.At the end of the ignitor warm-up time, the first stage of the two-stage manifold gas valve is energized (low fire). Flame must be detected within 5 seconds. If flame is detected, the 45 second delay-to-fan-on period begins. After the delay-to-fan-on period ends, the circulator enable, (pin 15 on the 16-pin connector is the “E” output to the circulator) and air cleaner are energized.A call for second stage heat (W1 and W2) after a call for first stage heat will activate a 30-second 2nd stage delay. Following the 30-second delay, the inducer motor is driven at high speed. The control checks the 2nd stage pressure switch. When the pressure switch closes, the 2nd stage gas valve turns on and the circulator is enabled at high speed (“E” remains energized any time the circulator is on).When the second stage of the thermostat is satisfied, the inducer motor is reduced to low speed, and the 2nd stage gas valve and high circulator speed are de-energized.When the first stage of the thermostat is satisfied, the gas valve is de-energized and the heat delay-to-fan-off timing begins. The inducer will postpurge for an additional 5 seconds. When this time is expired, the inducer and humidifier will de-energize. Upon completion of the heat delay-to-fan-off period, the circulator and air cleaner are de-energized.If flame is not detected during the trial-for-ignition period, the gas valve is de-energized, the ignitor is turned off, and the control goes into the “retry” sequence.The “retry” sequence starts with a 60-second interpurge, en-abling the inducer at low speed for 60 seconds following an unsuccessful ignition attempt (flame not detected). After this wait, the ignition sequence is restarted. If this ignition attempt is unsuccessful, one more retry will be made before the control goes into system lockout.If flame is detected, then lost, the control will repeat the initial ig-nition sequence for a total of ten “recycles”. After ten unsuccessful attempts to sustain flame, the control will go into system lockout.During burner operation, a momentary loss of power of 250 milliseconds or longer will de-energize the main gas valve. When power is restored, the gas valve will remain de-energized and a restart of the ignition sequence will begin immediately.A momentary loss of gas supply, flame blowout, or a shorted or open condition in the flame probe circuit will be sensed within 2 seconds. The gas valve will de-energize and the control will restart the ignition sequence. Recycles will begin and the burner will operate normally if the gas supply returns, or the fault con-dition is corrected, before the last ignition attempt. Otherwise, the control will go into system lockout.If the control has gone into system lockout, it may be possible to reset the control by a momentary power interruption of five seconds or longer. Refer to PRECAUTIONARY, SYSTEM LOCKOUT, AND DIAGNOSTIC FEATURES.COOL MODEIn a typical system, a call for cool is initiated by closing the thermostat contacts. This energizes the compressor, circulator “E” output and air cleaner. After the thermostat is satisfied, the compressor is de-energized and the optional cool mode delay-to-fan-off period begins. After the optional delay-to-fan-off period ends, the circulator “E” output and air cleaner are de-energized.MANUAL FAN ON MODEIf the thermostat fan switch is moved to the ON position, the circulator “E” output and air cleaner are energized. When the fan switch is returned to the AUTO position, the circulator “E” output and air cleaner are de-energized. PRECAUTIONARY, SYSTEM LOCK-OUT, AND DIAGNOSTIC FEATURES PRECAUTIONARY FEATURESThe following precautionary features are built into the control.1. If the high temperature limit or flame rollout sensor openat any time, the gas valve is de-energized.2. During a call for heat cycle, if flame is sensed at any timewhen the gas valve is de-energized, the circulation “E” output and inducer fan are energized at low speed in conjunction with system lockout.3. If the high limit (and/or auxiliary limit) switch(es) open atany time during a call for heat, the circulator blower and inducer fan are energized at low speed.SYSTEM LOCKOUT FEATURESWhen system lockout occurs, the gas valve is de-energized, the circulator “E” output and the inducer blower are energized at low speed. The diagnostic indicator light will flash to indicate system status. (System lockout will never override the precautionary features described above.)To reset the control after system lockout, do one of the following:1. Interrupt the call for heat at the thermostat for at least onesecond and less than twenty seconds (if flame is sensedOPERATION34MOUNTING AND WIRINGINSTALLATIONAll wiring should be installed according to local and national electrical codes and ordinances.The 50V64 control may be mounted on any convenient surface using the four standoffs provided.The control must be secured to an area that will experience a minimum of vibration and remain below the maximum ambient temperature rating of 175°F . T he control is approved for minimum ambient temperatures of -40°F .Any orientation is acceptable.Refer to the wiring diagram and wiring table when connecting the 50V64 control to other components of the system.UL approved, 105°C rated 18 gauge min., stranded,²/64" thick insulation wire is recommended for all low voltage safety circuit connections. Refer to 50V64 control specification sheet for recommended terminals to mate with those on the control.UL approved, 105°C rated 16 gauge min., stranded, 4/64" thick insulation wire is recommended for all line voltage connections. Refer to 50V64 control specification sheet for recommended terminals to mate with those on the control.Following installation or replacement, follow appliance manufacturer’s recommended installation or service instructions to insure proper operation.5 flashes, then pause Flame sense when no flame should be present6 flashes, then pause Line reverse polarity or ignitor circuit error7 flashes, then pause Gas valve circuit error 8 flashes, then pause Weak flame9 flashes, then pauseOpen inducer limit errorThe Green and Red LED's will also flash once for 1 second atpower-up.FAULT CODE RETRIEVAL Two seconds after the power ON, the control shall flash the last four error codes that have occurred over the last 14 days on the red LED. The control will flash the newest error first and the oldest error last with a two-second pause between flash codes. Solid LED error codes will not be displayed. The green ST A TUS LED shall remain ON while the red LED flashes the error codes.The last four fault codes can be erased from memory by pow-ering up with G energized and then toggling W1 three times within eight seconds. W1 must be toggled after the power ON reset for approximately one second each time. The control will acknowledge by turning on the red LED and green ST A TUS LED for two seconds.with the gas valve de-energized, interrupting the call for heat at the thermostat will not reset the control).2. Interrupt the 24 VAC power at the control for at least fiveseconds. Y ou may also need to reset the flame rollout sensor switch.3.After one hour in lockout, the control will automatically reset itself.DIAGNOSTIC FEATURESThe control continuously monitors its own operation and the operation of the system. If a failure occurs, the red LED on thecontrol will flash a failure code. If the Red and Green "status"LED's are on solid, the 5 amp replaceable fuse is bad. If the fuse is good or the Red LED is on by itself, the entire control should be replaced, as the control is not field-repairable.If the sensed failure is in the system (external to the control), the red LED will flash in the following flash-pause sequences to indicate failure status (each flash will last approximately 0.25 seconds, and each pause will last approximately 2 seconds).2 flashes, then pause Retries or recycles exceeded 3 flashes, then pause Inducer or pressure switch error4 flashes, then pause Open limit or rollout switchOPERATION550V64 TERMINALTYPE SYSTEM COMPONENT CONNECTIONLINE Input voltage (120 VAC) HOT SIDE XFMR-H spade terminal*24 VAC transformer line voltage neutral side Input voltage (120 VAC) neutral sidespade terminal*24 VAC CommonLow heat speed select, output to circulator blower 24 VAC CommonDelay tap, output to circulator Cool tap, output to circulator YLO, output to circulatorAdjust tap, output to circulator 24 VAC Common O, output to circulatorHumidistat, output to circulator Heat tap, output to circulator 24 VACW2, output to circluator Y, output to circulator G, output to circulator G reen CFM indicator spade terminal*Circulator blower neutral sideCIR-H CIR-N XFMR-N FPHUM - N EAC - N EAC HUM LINE-N spade terminal*24 VAC transformer line voltage hot side spade terminal*spade terminal*spade terminal*spade terminal*spade terminal*spade terminal*spade terminal*4-pin connector 16-pin connectorTYPICAL SYSTEM WIRING TABLECirculator blower hot sideHumidifier hot sideElectronic Air Cleaner hot side Humidifier neutral sideElectronic Air Cleaner neutral side Flame probe**** maximum recommended flame probe wire length is 36 inches.IND 01 (1)IND 02 (2)IND 03 (3)GRND (4)Inducer 01Inducer 02Inducer 03Inducer ground2-pin connector IGN-H IGN-N Ignitor output Ignitor common * Spade terminals are 0.25" x 0.032"W1W2G R B/C YLO Y BK OMVH (3)MV COM (8)HLI (2)HLO (9)TR (11)MV (4)TH (7)GND (5)PS2 (6)PS0 (1)IL1 (10)PS1 (12)E11-1E11-2E11-3E11-4E11-5E11-6E11-7E11-8E11-9E11-10E11-11E11-12E11-13E11-14E11-15E11-16First stage call for heat Second stage call for heat Input for fan operation24 VAC transformer (HIGH side)24 VAC transformer (LOW side)First stage call for cool Second stage call for cool Humidistat enable H/P or cooling modeGas valve second stage Gas valve ground High limit input High limit output24 VAC transformer (low voltage COMMON side)Gas valve first stage24 VAC transformer (low voltage HIGH side)MUST BE RELIABLY GROUNDED TO CHASSIS 2nd stage pressure switch Pressure switch output Inducer limit input1st stage pressure switch12-pin connector9-screw terminal block120 VACHOT NEUTRAL TYPICAL SYSTEM WIRING DIAGRAM7White-Rodgers is a business of Emerson Electric Co.The Emerson logo is a trademark and service mark of Emerson Electric Co. 。
PW-845LVA工业电脑主板 产品说明书

Manual for PW-845LVA
Page 3 of 35
附件清单
请完整的检查你的产品包装,如果发现有损坏或缺失的物件,请与
你的供应商联系。
■
PW-845LVA主板
×1
■
产品说明手册
×1
■
产品保修卡
×1
■
驱动程序光盘
×1
■
miniIDE数据线
×1
■
串口转接线
×1
■
并口转接线
×1
■
音频转接线
×1
Manual for PW-845LVA
Page 2 of 35
2.1.11 miniPCI接口------------------------------------13 2.1.12 miniIDE接口------------------------------------14 2.1.13 CF卡接口---------------------------------------14 2.1.14 鼠标/键盘扩展接口------------------------------15 2.1.15 PC104plus接口----------------------------------15 2.1.16 红外接口---------------------------------------16 2.1.17 SMBUS接口--------------------------------------16 2.1.18 CD-IN接口--------------------------------------17 2.2 跳线设置 2.2.1 清除CMOS跳线-----------------------------------18 2.2.2 COM3/4供电选择跳线-----------------------------18 2.2.3 COM2传输方式选择-------------------------------19 2.2.4 看门狗设置-------------------------------------20 2.2.5 USB供电模式选择--------------------------------20 第三章 BIOS设置 3.1 主菜单---------------------------------------------21 3.2 标准CMOS功能---------------------------------------22 3.3 高级BIOS功能---------------------------------------23 3.4 高级芯片组功能-------------------------------------24 3.5 整合外围设备---------------------------------------25 3.6 电源管理设备---------------------------------------26 3.7 PnP/PCI Configurations-----------------------------29 3.8 PC健康状态-----------------------------------------29 3.9 频率电压控制---------------------------------------30 3.10 载入优化或默认设置---------------------------------31 3.11 设置管理员和用户密码-------------------------------32 第四章 驱动光盘说明--------------------------------------33
M-HL9 LoRa模块硬件设计手册说明书

硬件设计手册M-HL9LoRa模块产品南京仁珏智能科技有限公司地址:南京市浦口高新区星火路20号网址:1/11◆关于本手册本文档描述了M-HL9模块的硬件应用接口,包括相关应用场合的电路连接以及射频接口等。
M-HL9模块的应用十分广泛,本文档将详细介绍M-HL9模块的所有功能。
本文档可以帮助用户快速的了解M-HL9模块的接口定义、电气性能和结构尺寸的详细信息。
结合本文档和其应用文档,用户可以快速的使用M-HL9来设计物联网通讯应用方案。
◆修订历史日期版本发布说明2019.02V1.0◆文档变更通知用户可以通过仁珏官网查看最新技术资料。
◆免责申明和版权公告本文中的信息,包括供参考的URL地址,如有变更,恕不另行通知。
文档“按现状”提供,不负任何担保责任,包括对适销性、适用于特定用途或非侵权性的任何担保,和任何提案、规格或样品在他处提到的任何担保。
本文档不负任何责任,包括使用本文档内信息产生的侵犯任何专利权行为的责任。
文中提到的所有商标名称、商标和注册商标均属其各自所有者的财产,特此声明。
版权归©2019仁珏所有。
保留所有权利。
目录一M-HL9介绍 (4)1.1M-HL9外观: (4)1.2产品特性 (4)1.3应用领域 (4)二.管脚定义 (5)2.1管脚布局 (5)2.2管脚描述: (5)三.电气特性 (6)3.1绝对最大额定值 (6)3.2建议工作参数 (6)3.3直流电气特性 (6)3.4射频参数 (6)四.应用说明 (7)4.1模块系统框图: (7)4.2最小系统 (7)4.3电源部分 (7)4.4GPIO引脚 (8)4.5UART串口 (8)4.6RESETn复位 (8)4.7BOOT启动选择 (8)4.8DIO和CLK调试接口 (8)4.9SDA/TXD和SCL/RXD (9)4.10ADC0和ADC1 (9)4.11wake_up唤醒 (9)4.12AT配置引脚 (9)4.13ANT天线设计 (9)五.封装尺寸 (11)5.1M-HL9模块尺寸 (11)5.2推荐SMT封装尺寸: (11)一M-HL9介绍1.1M-HL9外观:图1-1M-HL9模块图1.2产品特性●采用小尺寸邮票孔封装●支持AT指令配置,简单易操作●采用LoRa扩频调制技术●支持点对点以及SX1301网关模式●发射功率可调,最大20dBm●天线支持IPEX或邮票孔方式●接收灵敏度低至-142dBm●支持低功耗串口,无需唤醒操作●链路预算高达162dBm●采用小尺寸邮票孔封装●支持休眠唤醒,功耗低至2uA●传输距离可达3~5km1.3应用领域自动抄表、水、电计量家庭和楼宇自动化工业监控、无线报警和安全系统二.管脚定义2.1管脚布局M-HL9模块采用邮票孔封装,可以作为一个SMD元件来使用,方便集成到产品之中,而无需射频设计经验。
博士科学家助理说明书

DRSP-I, DRSP-I-DC4-20 mA Isolated Signal SplittersM-5244/1114DescriptionThe DRSP-I series accepts a 4-20 mA current input and provides two optically isolated 4-20 mA current outputs that are linearly related to the input. Typical applications include isolation, output splitting, output device separa-tion, and redundancy (i.e. to prevent failure of the entire loop if one device fails), or a combination of these.Full 4-way isolation makes this module useful for ground loop elimination, common mode signal rejec-tion, or noise pickup reduction.Sink/Source I/OStandard is a 15 VDC loop excitation supply for the input and a 20 VDC loop excitation supply for each output. These power supplies can be selectively wired for sinking or sourcing allowing use with any combination of powered or unpowered milliamp I/O devices.I/O Status LEDsA green input L ED and two red output L EDs vary in intensity with changes in the process input and output signals. These provide a quick visual picture of your process loop at all times.Output TestAn output test button provides a fixed output (inde-pendent of the input) when held depressed. The test output level is potentiometer adjustable from 0 to 100% of output span.Terminals are provided to operate the test functions remotely for each channel. This also allows use as a remote manual override to provide a temporary fixed output.Input Range 4-20 mADC Input Impedance 50 Ω typicalVoltage Burden1.25 VDC max. at 20 mA current inputInput Loop Power Supply 15 VDC ±10%, regulated, 25 mADCMay be selectively wired for sinking or sourcing mA input LED IndicatorsVariable brightness LEDs indicate I/O loop level and status One for input, one for each output Output Range Channel 1: 4-20 mADC Channel 2: 4-20 mADC Output LinearityBetter than ±0.1% of spanOutput Zero and SpanMulti-turn zero and span potentiometers for each output chan-nel to compensate for load and lead variations ±15% of span adjustment range typicalOutput Loop Power Supplies One for each output channel20 VDC nominal, regulated, 25 mADCMay be selectively wired for sinking or sourcing mA output Output Ripple and Noise Less than 10 mV RMSOutput Functional TestFront buttons set each output to test level when pressed Each test level potentiometer adjustable 0-100% of spanTerminals provided for remote switching of each output to test levelResponse Time 70 milliseconds typical Common Mode Rejection 120 dB minimumIsolationFull 4-way isolation: input 1, output 1, output 2, power 1200 V RMS minimumAmbient Temperature Range and Stability –10°C to +60°C operating ambientBetter than ±0.04% of span per °C stabilityPower85-265 VAC, 50/60 Hz or 60-300 VDC, 6 W maximumDC version: 9-30 VDC or 10-32 VAC 50/60 Hz, 6 W maximum HousingIP 40, mounts to standard 35 mm DIN rail ConnectorsEight 4-terminal removable connectors 14 AWG max wire size Dimensions1.78" W x 4.62" H x 4.81"D45 mm W x 117 mm H x 122 mm D Height includes connectorse-mail:**************For latest product manuals:User’s Gui d eShop online atOutput LEDs: Variable brightness red LED indicates output level for each channelTest Cal.: Output test level adjustmentTest: Push to test output. Sets each output to level determined by Test Cal. potentiometer.Span: Output span calibration for each channelInput LED: Variable brightness green LED indicates input level Zero: Output zero calibration for each channelCurrent Sourcing InputDRSP-I provides power to input loop. Typical when using a passive or unpowered transmitter or sensor.Electrical ConnectionsWARNING! All wiring must be performed by a qualified electri-cian or instrumentation engineer. See wiring diagrams.Avoid shock hazards! Turn signal input, output, and power off before connecting or disconnecting wiring.The DRSP-I is factory configured for one 4-20 mA input and two 4-20 mA outputs as indicated on the serial number label.To maintain full isolation, avoid combining power supplies in common with inputs, outputs, or unit power.The power supplies are fuse protected and the unit may be returned for fuse replacement.Signal Input TerminalsPolarity must be observed when connecting the signal inputs. The DRSP-I may be wired for a sinking or sourcing input.Determine if your input device provides power to the current loop or if the loop must be powered by the DRSP-I. Typical voltage may be 9-24 VDC at your device’s terminals if it provides power to the loop.Signal Output TerminalsPolarity must be observed when connecting the signal outputs.The two DRSP-I output channels may be individually wired for a sinking or sourcing output as needed.For each channel determine if your output device provides power to the current loop or if the loop must be powered by the DRSP-I. Typical voltage may be 9-24 VDC at your device’s terminals if it provides power to the loop.The wiring diagram illustrates typical wiring examples. Each channel may be wired as needed.If the output does not function, check wiring and polarity for both inputs and outputs.Module Power TerminalsCheck white model/serial number label for module operating voltage to make sure it matches available power.Connect power last. When using DC power, either polarity is acceptable, but for consistency with similar products, positive (+) can be wired to terminal 13 and negative (–) can be wiredto terminal 16.External Contacts For Test FunctionClosing the contact provides the same function as pressing the Test button for each channel. May be used as a manualoverride.Current Sinking OutputsTypical of some PLCs that have current sourcing inputs.Current Sinking Outputs with Separate Power SuppliesTypical of a system using loop powered displays with external loop supplies.Current Sourcing OutputsDRSP-I provides power to each loop. Typical of a system or PLC using current sinking inputs.Current Sinking InputTypical of a system using a transmitter that is externally pow-ered and provides power to the loop.Current Sinking Input with Separate Power SupplyTypical of a system using a passive transmitter that uses a loop power supply to power to the loop.Module PowerDRSP-I: 685-265 VAC, 50/60 Hz or 60-300 VDC DRSP-I-DC: 9-30 VDC or 10-32 VAC 50/60 Hz2324To maintain full isolation, avoid combining power supplies in common with inputs, outputs, or unit power.DC to DC Isolated Signal SplitterCalibrationFront-mounted Zero and Span potentiometers for each channel can be used to compensate for load and lead variations.1. Apply power to the module and allow a minimum 30 minute warm up time.2. Using an accurate calibration source, provide an input to the module equal to the minimum input required for the applica-tion.3. Using an accurate measurement device for the output, adjust the Zero potentiometer for the exact minimum output desired. The Zero control should only be adjusted when the input signal is at its minimum. This will produce the cor-responding minimum output signal. The Zero control will provide adjustment for the 4 mA or low end of the signal.4. Set the input at maximum, and then adjust the Span pot for the exact maximum output desired. The Span control should only be adjusted when the input signal is at its maximum. This will produce the corresponding maximum output signal. The Span control will provide adjustment for the 20 mA or high end of the signal.5. Repeat adjustments for maximum accuracy.6. Repeat adjustments for second channel.Output Test FunctionWhen the Test button is depressed it will drive the output with a known good signal that can be used as a diagnostic aid during initial start-up or troubleshooting. When released, the output will return to normal.The Test Cal. potentiometer is factory set to approximately 50% output. It can be adjusted to set the test output from 0 to 100% of the output span.Press and hold the Test button and adjust the Test Cal. potenti-ometer for the desired output level.The output test function for each channel may be externally wired for remote test operation or a manual override. See wir-ing diagram.MountingThe housing clips to a standard 35 mm DIN rail. The housing is IP40 rated and should be mounted inside a panel or enclosure. See illustration below.Avoid shock hazards! Turn signal input, output, and power off before installing or removing module.1. Tilt front of module downward and position the lower mounts and spring clips against the bottom edge of DIN rail.2. Push front of module upward until upper mount snaps into place.Removal1. Push up on bottom back of module.2. Tilt front of module downward to release upper mount from top edge of DIN rail.3.The module can now be removed from the DIN rail.Upper Mount OperationThe DRSP-I accepts a 4-20 mA current input and provides two optically isolated 4-20 mA current outputs that are linearly related to the input.The green input L ED provides a visual indication that a signal is being sensed by the input circuitry of the module. It also indicates the input signal strength by changing in intensity as the process changes from minimum to maximum.If the LED fails to illuminate, or fails to change in intensity as the process changes, check the module power or signal input wiring.The two red output L EDs provide a visual indication that the output signals are functioning. They become brighter as the input and each corresponding output change from minimum to maximum.The red L ED will only light if the output loop current path is complete. Failure to illuminate or a failure to change in intensity as the process changes may indicate a problem with the module power or signal output wiring.Note that it may be difficult to see the LEDs under bright lighting conditions and low I/O levels.It is the policy of OMEGA to comply with all worldwide safety and EMC/EMI regulations that apply. OMEGA is constantly pursuing certification of its products to the European New Approach Directives. OMEGA will add the CE mark to every appropriate device upon certification.The information contained in this document is believed to be correct, but OMEGA Engineering, Inc. accepts no liability for any errors it contains, and reserves the right to alter specifications without notice. WARNING: These products are not designed for use in, and should not be used for, human applications.WARRANTY/DISCLAIMEROMEGA ENGINEERING, INC. warrants this unit to be free of defects in materials and workmanship for a period of 13 months from date of purchase. OMEGA’s WARRANTY adds an additional one (1) month grace period to the normal one (1) year product warranty to cover handling and shipping time. This ensures that OMEGA’s customers receive maximum coverage on each product.If the unit malfunctions, it must be returned to the factory for evaluation. OMEGA’s Customer Service Department will issue an Authorized Return (AR) number immediately upon phone or written request. Upon examination by OMEGA, if the unit is found to be defective, it will be repaired or replaced at no charge. OMEGA’s WARRANTY does not apply to defects resulting from any action of the purchaser, including but not limited to mishandling, improper interfacing, operation outside of design limits, improper repair, or unauthorized modification. This WARRANTY is VOID if the unit shows evidence of having been tampered with or shows evidence of having been damaged as a result of excessive corrosion; or current, heat, moisture or vibration; improper specification; misapplication; misuse or other operating conditions outside of OMEGA’s control. Components which wear are not warranted, including but not limited to contact points, fuses, and triacs.OMEGA is pleased to offer suggestions on the use of its various products. However, OMEGA neither assumes responsibility for any omissions or errors nor assumes liability for any damages that result from the use of its products in accordance with information provided by OMEGA, either verbal or written. OMEGA warrants only that the parts manufactured by it will be as specified and free of defects. OMEGA MAKES NO OTHER WARRANTIES OR REPRESENTATIONS OF ANY KIND WHATSOEVER, EXPRESS OR IMPLIED, EXCEPT THAT OF TITLE, AND ALL IMPLIED WARRANTIES INCLUDING ANY WARRANTY OF MERCHANTABILITY AND FITNESS FOR A PARTICULAR PURPOSE ARE HEREBY DISCLAIMED. LIMITATION OF LIABILITY: The remedies of purchaser set forth herein are exclusive, and the total liability of OMEGA with respect to this order, whether based on contract, warranty, negligence, indemnification, strict liability or otherwise, shall not exceed the purchase price of the component upon which liability is based. In no event shall OMEGA be liable for consequential, incidental or special damages.CONDITIONS: Equipment sold by OMEGA is not intended to be used, nor shall it be used: (1) as a “Basic Component” under 10 CFR 21 (NRC), used in or with any nuclear installation or activity; or (2) in medical applications or used on humans. Should any Product(s) be used in or with any nuclear installation or activity, medical application, used on humans, or misused in any way, OMEGA assumes no responsibility as set forth in our basic WARRANTY / DISCLAIMER language, and, additionally, purchaser will indemnify OMEGA and hold OMEGA harmless from any liability or damagewhatsoever arising out of the use of the Product(s) in such a manner.Servicing North America:USA:One Omega Drive, Box 4047 ISO 9001 Certified S tamford CT 06907-0047Tel: (203) 359-1660FAX: (203) 359-7700e-mail:**************Canada: 976 BergarLaval (Quebec) H7L 5A1, CanadaTel: (514) 856-6928 FAX: (514) 856-6886 e-mail:*************For immediate technical or application assistance:USA and Canada: S ales Service: 1-800-826-6342 / 1-800-TC-OMEGA®Customer Service: 1-800-622-2378 / 1-800-622-BEST ®Engineering Service: 1-800-872-9436 / 1-800-USA-WHEN ® TELEX: 996404 EASYLINK: 62968934 CABLE: OMEGAMexico:En Espan ˜ol: (001) 203-359-7803 e-mail:*****************FAX: (001) 203-359-7807**************.mxOMEGAnet ® Online ServiceInternet e-mail**************Servicing Europe:Benelux:P ostbus 8034, 1180 LA Amstelveen, The Netherlands Tel: +31 (0)20 3472121 FAX: +31 (0)20 6434643Toll Free in Benelux: 0800 0993344e-mail:*****************Czech Republic:Frystatska 184, 733 01 Karviná, Czech RepublicTel: +420 (0)59 6311899 FAX: +420 (0)59 6311114Toll Free: 0800-1-66342 e-mail:*****************France:11, rue Jacques Cartier, 78280 Guyancourt, France Tel: +33 (0)1 61 37 2900 FAX: +33 (0)1 30 57 5427 Toll Free in France: 0800 466 342e-mail:**************Germany/Austria: D aimlerstrasse 26, D-75392 Deckenpfronn, GermanyTel: +49 (0)7056 9398-0 FAX: +49 (0)7056 9398-29 TollFreeinGermany************e-mail:*************United Kingdom: O ne Omega Drive, River Bend Technology CentreISO 9002 CertifiedNorthbank, Irlam, Manchester M 44 5BD United KingdomTel: +44 (0)161 777 6611 FAX: +44 (0)161 777 6622Toll Free in United Kingdom: 0800-488-488e-mail:**************.ukM-5244/1114RETURN REQUESTS / INQUIRIESDirect all warranty and repair requests/inquiries to the OMEGA C ustomer Service Department. BEFORE RETURNING ANY PRODUC T(S) TO OMEGA, PURC HASER MUST OBTAIN AN AUTHORIZED RETURN (AR) NUMBER FROM OMEGA’S C USTOMER SERVIC E DEPARTMENT (IN ORDER TO AVOID PROC ESSING DELAYS). The assigned AR number should then be marked on the outside of the return package and on any correspondence.The purchaser is responsible for shipping charges, freight, insurance and proper packaging to prevent breakage in transit.PATENT NOTIC E: U. S. Pat. No. 6,074,089; 5,465,838 / C anada 2,228,333; 2,116,055 / UK GB 2,321,712 / Holland 1008153 / Israel 123052 / France 2 762 908 / EPO 0614194. Other patents pending.FOR WARRANTY RETURNS, please have the following information available BEFORE contacting OMEGA:1. P urchase Order number under which the product was PURCHASED,2. M odel and serial number of the product under warranty, and 3. R epair instructions and/or specific problems relative to the product.FOR NON-WARRANTY REPAIRS, consult OMEGA for current repair charges.Have the following information available BEFORE contacting OMEGA:1. Purchase Order number to cover the C OST of the repair,2. Model and serial number of the product, and3. Repair instructions and/or specific problems relative to the product.OMEGA’s policy is to make running changes, not model changes, whenever an improvement is possible. This affords our customers the latest in technology and engineering.OMEGA is a registered trademark of OMEGA ENGINEERING, INC.© Copyright 2004 OMEGA ENGINEERING, INC. All rights reserved. This document may not be copied, photocopied, reproduced, translated, or reduced to any electronic medium or machine-readable form, in whole or in part, without the prior written consent of OMEGA ENGINEERING, INC.。
- 1、下载文档前请自行甄别文档内容的完整性,平台不提供额外的编辑、内容补充、找答案等附加服务。
- 2、"仅部分预览"的文档,不可在线预览部分如存在完整性等问题,可反馈申请退款(可完整预览的文档不适用该条件!)。
- 3、如文档侵犯您的权益,请联系客服反馈,我们会尽快为您处理(人工客服工作时间:9:00-18:30)。
LV8549M
Overview The LV8549M is a stepping motor driver IC of low saturation voltage. It is optimal for motor drive in 12V system product a 2-phase bipolar stepping motor.
Functions
• DMOS output transistor adoption (Upper and lower total RON=1Ω typ) • The compact package (MFP-10S) is adopted. • V CC max=20v, I O max=1A • For one power supply (The control system power supply is unnecessary.) • Current consumption 0 when standing by
Specifications
Absolute Maximum Ratings at Ta = 25°C
Parameter Symbol
Conditions
Ratings
Unit
Maximum power supply voltage V CC max -0.3 to +20V Output impression voltage VOUT -0.3 to +20V Input impression voltage V IN -0.3 to +6
V GND pin outflow current IGND For ch 1.0 A Allowable Power dissipation Pd max * 1.05W Operating temperature Topr
-30 to +85°C Storage temperature
Tstg
-40 to +150
°C
*: When mounted on the specified printed circuit board (57.0mm ×57.0mm × 1.6mm), glass epoxy, both sides Caution 1) Absolute maximum ratings represent the value which cannot be exceeded for any length of time.
Caution 2) Even when the device is used within the range of absolute maximum ratings, as a result of continuous usage under high temperature, high current,
high voltage, or drastic temperature change, the reliability of the IC may be degraded. Please contact us for the further details.
Recommended Operating Range at Ta = 25°C
Parameter Symbol
Conditions
Ratings
Unit Power supply voltage V CC
4.0 to 16
V
Input “H” level voltage V IN H
+1.8 to +5.5V Input “L” level voltage V IN L
-0.3 to +0.7
V
Bi-CMOS integrated circuit
12V Low Saturation Voltage Drive
Stepping Motor Driver
Electrical Characteristics at Ta = 25°C, V CC = 12V
Parameter Symbol
Conditions
Ratings
Unit
min typ max
Power supply voltage
I CC 0 Standby mode ENA=L 1μA
I CC 1
ENA=H
1.7
2.3
mA
Input current
I IN
V IN =5V 30
50 65μ
A Thermal shutdown operating temperature
Ttsd Design certification 150
180 210°C Width of temperature hysteria ΔTtsd Design certification 40
°C
Low voltage protection function operation voltage VthV CC 3.3 3.5 3.65V Release voltage Vthret 3.55
3.8 3.95
V
Output ON resistance (Upper and lower total) R ON
I OUT =1.0A 0.7
1 1.25Ω
Output leak current I O leak V O =16V 10μA Diode forward voltage
VD
ID=1.0A
1.0
1.2
V
Package Dimensions
unit : mm (typ) 3086B
Pin Assignment
V CC 12345
109876IN1IN2OUT1OUT2OUT3OUT4GND
LV8549M
ENA NC A l l o w a b l e p o w e r d i s s i p a t i o n , P d m a x -- W
01.5
1.0
Block Diagram
Pin function
Operation explanation
1. STM output control logic
Input Output
State
ENA IN1 IN2 OUT1 OUT2 OUT3 OUT4
L -
- OFF OFF OFF OFF Stand-by
H
L L H L H L Step 1 H L L H H L Step2
H H L H L H Step3 L H H L L H Step4
2. About the switch time from the stand-by state to the state of operation
When ENA pin are "L", this IC has completely stopped operating. After the time of reset (about 7μs of an internal setting) it shifts to a prescribed output status corresponding to the state of the input when the signal enters the ENA pin.
3. Example of current wave type in each excitation mode when stepping motor parallel input is controlled.
IN1100
(%)-100
100-100
IN2I1I2Step1Step2Step3Step4
ENA OUT1OUT3
IN1IN2
(*IN1 and IN2 are
Full-Step input)
(OUT2 is a reverse phase of OUT1)(OUT4 is a reverse
phase of OUT3)
Application Circuit Example
* Bypass capacitor (C1) connected between V CC-GND of all examples of applied circuit recommends the electric field capacitor of 0.1μA to 10μA.
Confirm there is no problem in operation in the state of the motor load including the temperature property about the value of the capacitor.
Mount the position where the capacitor is mounted on nearest IC.
分销商库存信息: ONSEMI
LV8549M-TLM-H。