DFMEA - 车身附件 - 铰链
DFMEA--白车身
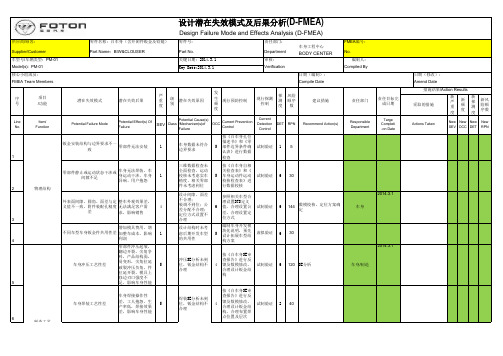
新 严 重 度
新 频 度
新 探 测 度
新风 险顺 序数
Actions Taken
New New New New SEV OCC DET RPN
制造工艺 7
车身涂装工艺性差
车身电泳底漆厚度 不均匀、部分区域 未充分覆盖底漆、 5 车身锈蚀、影响整 车寿命
按《白车身SE审
涂装SE分析未到 位,钣金结构不 合理
查报告》进行反
4
馈及数模修改, 合理设计钣金结
试制验证
2
构,保证涂装效
40
果
按《白车身SE审
总装件无法安装;
查报告》进行反
车身总装操作性
总装SE分析未到
馈及数模修改,
车身总装工艺性差
差,工人抱怨、生 5
位
未分 4 合理设计钣金结 试制验证 2 40
产率低;零部件维
析可维修性
构,合理考虑安
修操作性差
装操作空间,进
5
块化说明,预先 设计拓展车型结
虚拟验证
6
构方案
30
冲压SE分析未到 位,钣金结构不 合理
按《白车身SE审 查报告》进行反 4 馈及数模修改, 试制验证 6 合理设计钣金结 构
120 SE分析
车身焊装工艺性差
车身焊接操作性
差,工人抱怨、生 产率低,焊接效果
5
差,影响车身性能
按《白车身SE审
焊装SE分析未到 位,钣金结构不 合理
压要求
能销售
10
材料选择不对或 结构不合理
按法规要求指标 4 指标进行设计, 试制验证 6
240
按法规要求设计,进行 CAE分析确认
车身/性能 2014.3.1
DFMEA-底盘-行车制动系各零件
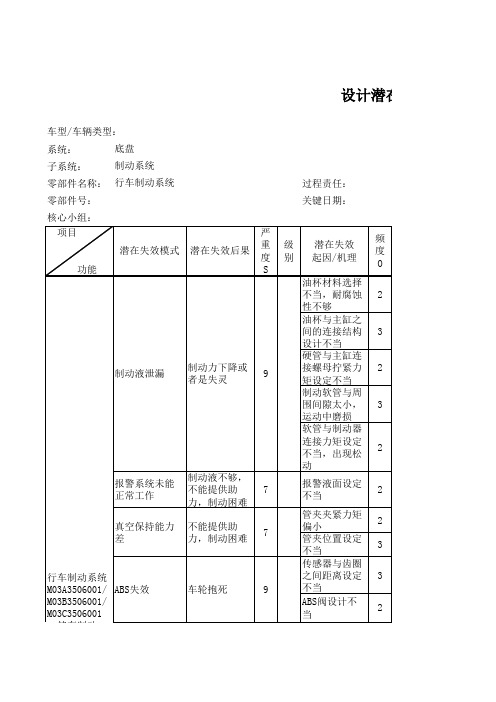
系统:子系统:零部件名称:过程责任:零部件号:关键日期:核心小组:液;·监控制动液液面高度;·辅助人力制动;行车制动系统设计潜在失(车型/车辆类型:底盘制动系统M03A3506001/M03B3506001/M03C3506001设计潜在失(系统:子系统:零部件名称:过程责任:零部件号:关键日期:核心小组:车型/车辆类型:底盘制动系统制动器系统:子系统:零部件名称:过程责任:零部件号:关键日期:核心小组:·向制动盘提供制动力·配合制动其提供制动力制动盘设计潜在失(车型/车辆类型:底盘制动系统系统:子系统:零部件名称:过程责任:零部件号:关键日期:核心小组:M03A3501011/号给制动尾灯车型/车辆类型:底盘制动系统制动踏板总成设计潜在失(系统:子系统:零部件名称:过程责任:零部件号:关键日期:核心小组:构中人力的直接作用对象;·提供制动信号给发动机ECU;·调节管路压力,分配制动力。
避免在制动时后轮先抱死侧滑,同时尽可能充分地利用附着条件,产生较大的制动力。
漏比例阀设计潜在失(车型/车辆类型:底盘制动系统系统:子系统:零部件名称:过程责任:零部件号:关键日期:核心小组:M03B3540100/M03C3540100/M03D3540100/M03E3540100·储存制动液;·提供助力辅车型/车辆类型:底盘制动系统带主缸真空助力器总成设计潜在失(比例阀比例阀进出油系统:子系统:零部件名称:过程责任:零部件号:关键日期:核心小组:制动主缸设计潜在失(车型/车辆类型:底盘制动系统带主缸真空助系统:子系统:零部件名称:过程责任:零部件号:关键日期:核心小组:车型/车辆类型:底盘制动系统真空助力器设计潜在失(系统:子系统:零部件名称:过程责任:零部件号:关键日期:核心小组:总成M03A3561130真空助力软管总成设计潜在失(车型/车辆类型:底盘制动系统·提供助力,辅助人力制动系统:子系统:零部件名称:过程责任:零部件号:关键日期:核心小组:ABS支架M03A3550210·安装固定ABS总成车型/车辆类型:底盘制动ABS支架设计潜在失(系统:子系统:零部件名称:过程责任:零部件号:关键日期:核心小组:M03A3561110/M03A3561150/M03B3561150·供油制动软管总成设计潜在失(车型/车辆类型:底盘制动系统:子系统:零部件名称:过程责任:零部件号:关键日期:核心小组:灵车型/车辆类型:底盘制动制动硬管总成设计潜在失(FMEA编号:编制人:修订人:第 1 页共 12 潜在失效模式及后果分析(DFMEA)附件6潜在失效模式及后果分析(DFMEA)附件6FMEA编号:编制人:修订人:第 2 页共 12FMEA编号:编制人:修订人:第 3 页共 12 潜在失效模式及后果分析(DFMEA)附件6FMEA编号:编制人:修订人:第 4 页共 12 潜在失效模式及后果分析(DFMEA)附件6FMEA编号:编制人:修订人:第 5 页共 12 潜在失效模式及后果分析(DFMEA)附件6FMEA编号:编制人:修订人:第 6 页共 12 潜在失效模式及后果分析(DFMEA)附件6FMEA编号:编制人:修订人:第 7 页共 12 潜在失效模式及后果分析(DFMEA)附件6FMEA编号:编制人:修订人:第 8 页共 12 潜在失效模式及后果分析(DFMEA)附件6FMEA编号:编制人:修订人:第 9 页共 12 潜在失效模式及后果分析(DFMEA)附件6FMEA编号:编制人:修订人:第 10 页共 12 潜在失效模式及后果分析(DFMEA)附件6FMEA编号:编制人:修订人:第 11 页共 12 潜在失效模式及后果分析(DFMEA)附件6FMEA编号:编制人:修订人:第 12 页共 12 潜在失效模式及后果分析(DFMEA)附件612 页果件6件6果12 页12 页果件6果12 页件612 页果件6果12 页件612 页果件6果12 页件612 页果件6果12 页件612 页果件6果12 页件6。
DFMEA--汽车白车身开闭件及铰链
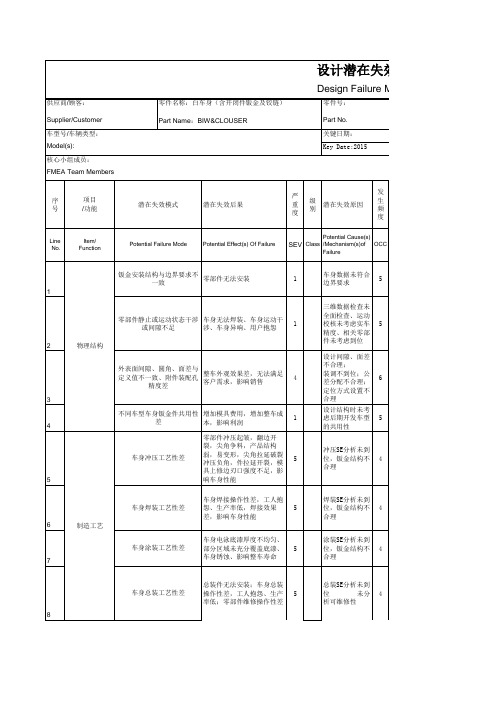
22
车身出现裂纹、松动、变形 损坏、疲劳破坏,影响内部 车身钣金件疲劳性不满足要 安装结构,影响整车寿命, 用户抱怨 求 顶盖雪压工况易出现变形, 影响车身结构,用户抱怨 油箱固定点强度不足,安装 位置结构断裂或变形,影响 整车性能 外挂踏板安装强度不足,安 装位置结构断裂或变形,外 挂踏板使用过程中无法实现 正常功能,客户抱怨 地板局部强度不满足要求, 使用过程中由于乘员踩踏造 成地板局部变形,客户抱怨 三踏板安装点强度不足,三 踏板安装点断裂或变形,影 响整车正常使用,客户抱怨
7
3
23
7
5
24
7
材料选择不对或 结构不合理
5
25
7
材料选择不对或 结构不合理
3
26
7
材料选择不对或 结构不合理
5
27
车身局部工况强度不满足要 求 可靠耐久
28 可靠耐久
29
备胎支架强度不足,支架发 生断裂或变形,影响备胎安 车身局部工况强度不满足要 装,客户抱怨 求 底盘安装点刚度、强度不 足,钣金断裂或永久变形, 影响车辆性能和安全 动力及附件安装点刚度、强 度不足,钣金断裂或永久变 形,影响车辆性能和安全 电子电器安装点刚度、强度 不足,钣金断裂或永久变 形,影响车辆使用和安全
SEV Class /Mechanism(s)of
Failure
OCC
钣金安装结构与边界要求不 零部件无法安装 一致 1
1
车身数据未符合 边界要求
5
零部件静止或运动状态干涉 车身无法焊装、车身运动干 或间隙不足 涉、车身异响、用户抱怨 2 物理结构 外表面间隙、圆角、面差与 整车外观效果差,无法满足 定义值不一致、附件装配孔 客户需求,影响销售 精度差 3 不同车型车身钣金件共用性 增加模具费用,增加整车成 差 本,影响利润 零部件冲压起皱,翻边开 裂,尖角争料,产品结构 弱,易变形,尖角拉延破裂 冲压负角,件拉延开裂,模 具上修边刃口强度不足,影 响车身性能 车身焊接操作性差,工人抱 怨、生产率低,焊接效果 差,影响车身性能
汽车车身饰件DFMEA-机舱盖板装置
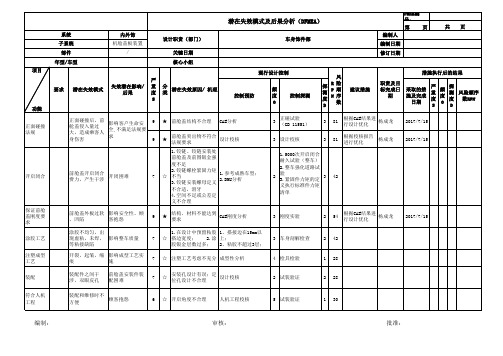
功能 正面碰撞 法规
开启闭合
保证前舱 盖刚度要 求 涂胶工艺 注塑成型 工艺
系统 子系统
部件 年型/车型
内外饰 机舱盖板装置
/
设计职责(部门)
关键日期 核心小组
要求
潜在失效模式
严
失效潜在影响/ 后果
重 度
分 类
潜在失效原因/ 机理
S
潜在失效模式及后果分析(DFMEA)
车身饰件部
现行设计控制
控制预防
、凹陷
客抱怨
9
★
结构、材料不能达到 要求
CAE刚度分析
3
正碰试验 (GB 11551)
3
81
根据CAE结果进 行设计优化
杨成龙
3 设计校核
3
81
根据校核报告 进行优化
杨成龙
1.5000次开启闭合
耐久试验(整车)
2.整车强化道路试
2
验 3.紧固件力矩的定
3
42
义执行标准件力矩
清单
2017/7/15 2017/7/15
频
度
控制探测
O
风
探 测 度 D
R险 P顺 N序
数
建议措施
编制人
FMEA编 号:
第 页
编制日期
修订日期
共页
措施执行后的结果
职责及目 标完成日
期
采取的措 施及完成
日期
严 重 度 S
频 度 O
探 测 度 D
风险顺序 数RPN
正面碰撞后,前 舱盖侵入量过 大,造成乘客人 身伤害
影响客户生命安 全,不满足法规要 求
9 9
前舱盖开启闭合 费力,产生干涉
汽车车身饰件DFMEA-前风挡下装饰板系统
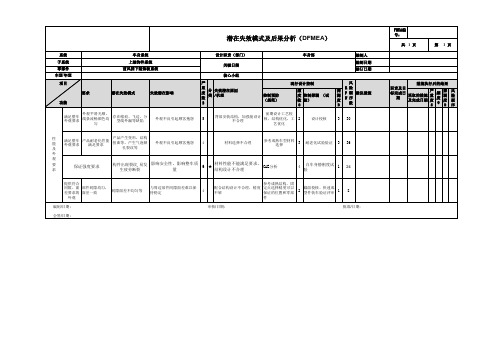
部件间隙均匀, 面差一致
间隙面差不均匀等
外观
编制/日期: 会签/日期:
与周边部件间隙面差难以保 持稳定
4
参考成熟结构,固
配合结构设计不合理,精度 定点选择精度可以
不够
保证的位置和零部
2
截面校核、快速成 型件装车验证评审
1
8
件
审核/日期:
批准/日期:
FMEA编 号:
共 1页
第 1页
措施执行后的结果
职责及目
标完成日 期
采取的措施 及完成日期
严 重 度 S
频 度 O
探 测 度 D
风 险 顺 序
分 类
失效潜在原因 /机理
S
控制预防 (规范)
现行设计控制
频 度 控制探测 (试 数 验) O
5
背部安装结构,加强筋设计 不合理
前期设计工艺校 核,结构优化,工
艺优化
2
设计校核
编制人 编制日期 修订日期
风
R险
探 测 度 D
P 顺 建议措施 N序
数
3 30
性 能 及
满足整车 外观要求
产品耐老化性能 满足要求
产品产生变形,结构 扭曲等,产生气泡锁
孔裂纹等
外观不良引起顾客抱怨
4
材料选择不合理
参考成熟车型材料 选择
3
耐老化试验验证
3
36
外
观
要 求
保证强度要求
构件出现裂纹,易发 生疲劳断裂
影响安全性,影响整车质 量
6
★
材料性能不能满足要求, 结构设计不合理
CAE分析
4
白车身静刚度试 验
1
24
新员工培训DFMEA介绍
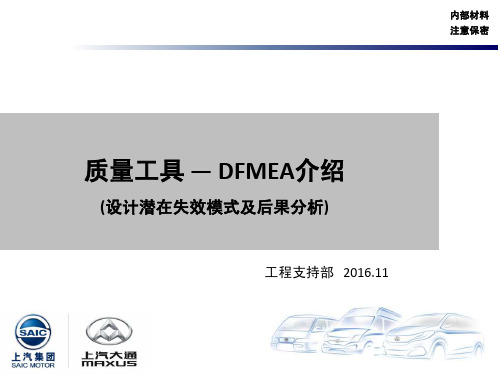
识别与分析零件相关的周边系统。 周围的系统与零件功能相关,后续作为影响因素进行分析。
方法和资源: 方块图 Block Diagram 参数图(P-图) Parameter Diagram 关系矩阵分析 BOM清单 接口图、示意图等
内部材料 注意保密
2014-5
26
二. DFMEA策划及准备
了解这些顾客,有助于更加充分地定义功能范围。
内部材料 注意保密
2014-5
18
一. FMEA发展和介绍
DFMEA在APQP中的角色
设计相关:PDT协同
历史信息 失效记录
设计过程:DRE/供应商负责
价值工程 价值分析
DFMEA
内部材料 注意保密
基于可制造性/ 装配性/维修性
的设计
设计验证计划 ADV
功能
潜在失效模式
严 级 潜在失效 频
潜在失效后果 重 别 起因/机理 度
度
现行设计控制
预防
探测
风
探险
测顺
度序
数
建议措施
措施效果
责任和目标 完成日期
采取的
严 重
频
探 测
R P
措施 度 度 度 N
1
2
3 4 567
8
9
2014-5
10
8
一. FMEA发展和介绍 DFMEA简介 — 5W
What 什么是DFMEA?
内部材料 注意保密
质量工具 — DFMEA介绍
(设计潜在失效模式及后果分析)
工程支持部 2016.11
第一部分:FMEA发展和介绍 第二部分:DFMEA策划及准备 第三部分:DFMEA分析和实施
DFMEA表(新版DFMEA-总装结构)

3L
尺寸链的计算 2 尺寸检验
3L
尺寸链的计算 2 尺寸检验
3L
尺寸链的计算 2 尺寸检验
3L
尺寸链的计算 2 尺寸检验
3L
尺寸链的计算 2 尺寸检验
3L
轴套设计 安装尺寸要 格,客户不满
求
意
6
控制臂总 成
保证产品的 安装尺寸要
求
安装尺寸不合 格,客户不满 意
零部件分析
零部件 要素(项
目/接 口)
零部件的功 能,要求,预 期输出及特性
失效原因
壳体
零件的尺寸设 计满足要求
尺寸设计不当
轴套
零件的尺寸设 计满足要求
尺寸设计不当
控制臂
零件的尺寸设 计满足要求
公司名称: 制造地址: 顾客名称: 车型/项目:
项目: FMEA开始日 FMEA修订日 跨职能团
设计潜在失效模式及影响分析 FMEA编号: 过程职责: 保密级别:
版本号:
页 码:
第
页,共
页
编制者/日期:
批准/日期:
范围定义:(针对具体产品详细说明) 1、产品适用车型: 2、客户针对此项目的特别要求:含技术要求、法律合规性、目录和标准零件 3、明确设计控制权及客户对接部门: 4、FMEA团队及会议机制: 5、FMEA完成步骤时间节点及要求:
尺寸设计不当
压装盖 板
零件的尺寸设 计满足要求
尺寸设计不当
齿环
零件的尺寸设 计满足要求
尺寸设计不当
齿型连 接套
零件的尺寸设 计满足要求
尺寸设计不当
O型圈*2
零件的尺寸设 计满足要求
尺寸设计不当
启动准备工作:(针对具体产品详细说明) 1、顾客要求转化清单: 2、FMEA的边界分析证据:设计框图、边界图、示意图、图纸、3D模型 3、类似设计经验教训:物料清单、风险评估、FMEA、防错要求、可制造性和可装配性设计、质量功能展开、质量/可靠性 历史(内部、零公里、现场失效、保修和索赔) 4、技术新颖性、创新程度、设计复杂性、人员和系统安全、网络物理系统 5、产品设计和使用的工况环境情况说明:
DFMEA案例分析
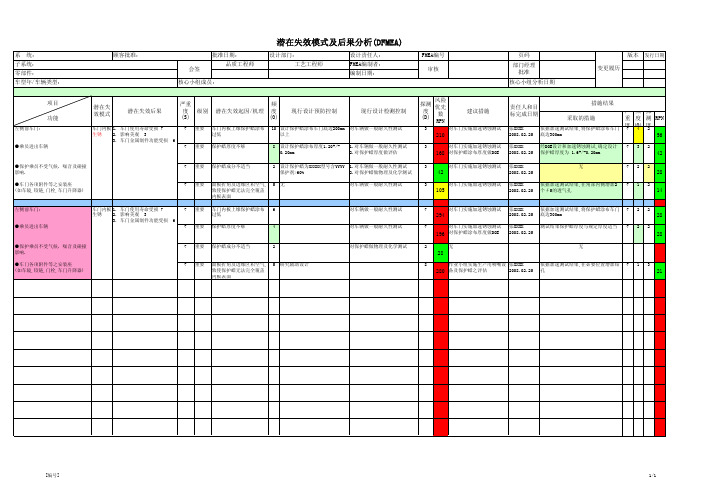
2
对保护蜡做物理及化学测试
2
无
无
影响.
28ห้องสมุดไป่ตู้
●车门各项附件等之安装座 (如车镜,铰链,门栓,车门升降器)
7 重要 面板折角及边缘区积空气, 5 研究辅助设计 致使保护蜡无法完全覆盖 内板表面
8
作业小组实施生产用喷嘴设 张XXXX
依据加速测试结果,在必要位置增加钻 7 1 3
280 备及保护蜡之评估
2008.02.25 孔
以上
7 重要 保护蜡厚度不够
8 设计保护蜡涂布厚度1.20+/0.20mm
1.对车辆做一般耐久性测试 2.对保护蜡厚度做评估
探测 度 (D)
风险 优先
数 RPN
建议措施
3
对车门实施加速锈蚀测试
210
责任人和目 标完成日期
措施结果 采取的措施
张XXXX
依据加速测试结果,将保护蜡涂布车门
2008.02.25 底边300mm
7
对车门实施加速锈蚀测试 张XXXX
依据加速测试结果,将保护蜡涂布车门 7 2 2
294
2008.02.25 底边300mm
28
7
对车门实施加速锈蚀测试 张XXXX
测试结果保护蜡厚度与规定厚度适当 7 2 2
196 对保护蜡涂布厚度做DOE 2008.02.25
28
●保护乘员不受气候,噪音及碰撞
7 重要 保护蜡成分不适当
保护剂>60%
2.对保护蜡做物理及化学测试
3
对车门实施加速锈蚀测试 张XXXX
42
2008.02.25
无
722
28
●车门各项附件等之安装座 (如车镜,铰链,门栓,车门升降器)
DFMEA - 车身附件 - 后牌照灯饰板总成
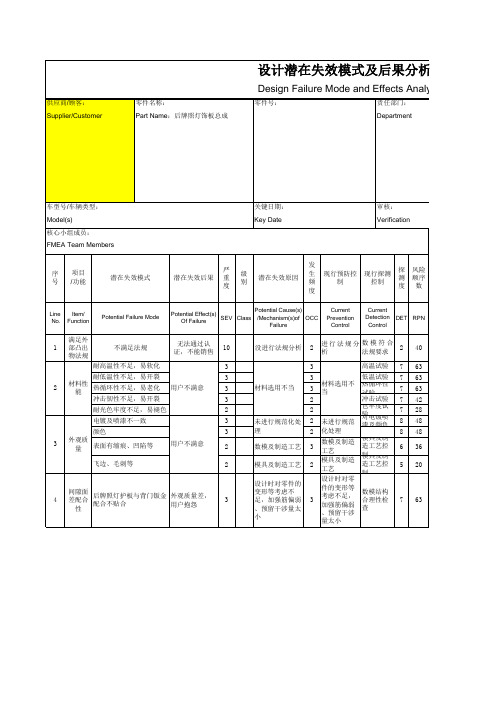
未进行规范 化处理 数模及制造 工艺 模具及制造 工艺 设计时对零 件的变形等 考虑不足, 加强筋偏弱 、预留干涉 量太小
3
外观质 表面有缩痕、凹陷等 量 飞边、毛刺等
用户不满意
2 2
4
间隙面 后牌照灯护板与背门钣金 外观质量差, 差配合 配合不贴合 用户抱怨 性
3
3
7
63
后果分析(D-FMEA)
2
材料性 热循环性不足,易老化 能 冲击韧性不足,易开裂 耐光色牢度不足,易褪色 电镀及喷漆不一致 颜色
耐低温性不足,易开裂 用户不满意
3 3 2 3 3
材料选用不当
3 2 2
未进行规范化处 理 数模及制造工艺 模具及制造工艺 设计时对零件的 变形等考虑不 足,加强筋偏弱 、预留干涉量太 小
2 2 3 2
Potential Cause(s) /Mechanism(s)of OCC Failure
Current Prevention Control
Current Detection Control
DET RPN
1
满足外 部凸出 物法规
不满足法规 耐高温性不足,易软化
无法通过认 证,不能销售
10 3 3
供应商
车身工程中心 FMEA编号: No.
fects Analysis (D-FMEA)
审核:
编制人: Compiled By 日期(编制): Compile Date 日期(修改): Amend Date 措施结果/Action Results 建议措施 责任部门 责任目 标完成 日期 新 严 重 度 新 频 度 新 探 测 度 新风 险顺 序数
设计潜在失效模式及后果分析(D-FMEA)
汽车车身饰件DFMEA-开闭件钣金

设计者
2
36
根据CAE分析报 告进行优化
设计者
2
48
根据CAE分析报 告进行优化
设计者
2
28
根据校核报告进 行优化
设计者
1
28
根据校核报告进 行优化
设计者
2017/9/20
2017/9/20
2017/9/20 2017/9/20 2017/9/20
涂胶工艺
注塑成型 工艺
冲压成型 工艺性
漏液孔
符合人机 工程
致
车门密封
达不到要 防水防尘效果 求,漏风 差,顾客抱怨
6
☆
门下垂导致上密封间 隙过大
、漏雨
CAE分析 设计校核 CAE分析
2
强检试验 (GB15743)
1
18
根据CAE结果进 行设计优化
设计者
2017/9/20
2
淋雨试验
2
24
根据校核报告进 行优化
设计者
2017/9/20
4
强化试验
2
48
根据CAE报告进 行优化
参考成熟车型和满足 GB15743-1995
2
侧撞试验
1 20
设计者 2017/9/20
外板表面 外板共振异响,
刚性差
易变形
6
☆
外板刚度不足;缺少 对外板的支撑
CAE分析
2
刚度实验
2
24
根据CAE结果进 行设计优化
设计者
2017/9/20
内外板过 软
影响安全性
9
★
结构、材料不能达 到要求
侧门到侧围及侧围门 6 ☆ 洞止口密封间隙不一
汽车车身饰件DFMEA-门盖密封系统
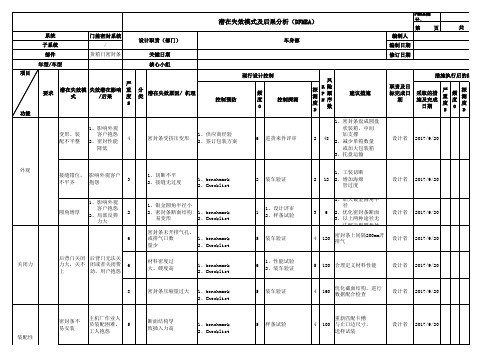
1、benchmark 2、Checklist
系统设计压缩角,压
缩量、密封面宽度定 1、benchmark
义不合理
2、Checklist
密封条压缩量/厚度/ 材料密度/材料硬度 1、benchmark 之间数值关系不匹配 2、Checklist
在功能满足前提下芯 材宽/海绵管高
benchmark
与其他车型断面 相似,无法辨别
批准:
共页
后的结果 风险顺序数 RPN
日期
严 重 度 S
频 度 O
探 测 度 D
设计者 2017/9/20
外观 关闭力
接缝错位, 影响外观客户
不平齐
抱怨
3
1、影响外观
圆角增厚
客户抱怨 2、局部反弹
2
力大
6
后背门关闭 后背门无法关
力大,关不 闭或者关闭费 6
上
劲,用户抱怨
1、切断不平 2、接缝无过度
1、benchmark 2、Checklist
3
与其他车 型混用
零部件误用, 增加工时,产 6 品报废
与本车其他 密封条混用
零部件误用, 增加工时,产 品报废
6
阻燃性不满 影响安全,不
足法规
满足法规
2
有害气体物 影响健康不满
质超标
足法规
4
断面结构导 致拔出力低
1、benchmark 2、Checklist
密封条自身反弹力/
厚度/材料密度/材料 硬度之间数值关系不 匹配
1、工装切断 2 12 2、增加海绵
管过度
设计者 2017/9/20
1、加大钣金圆角半 径
3 6 2、优化密封条断面 3、以上两种途径无 法解决则圆角处
汽车车身饰件DFMEA全套资料
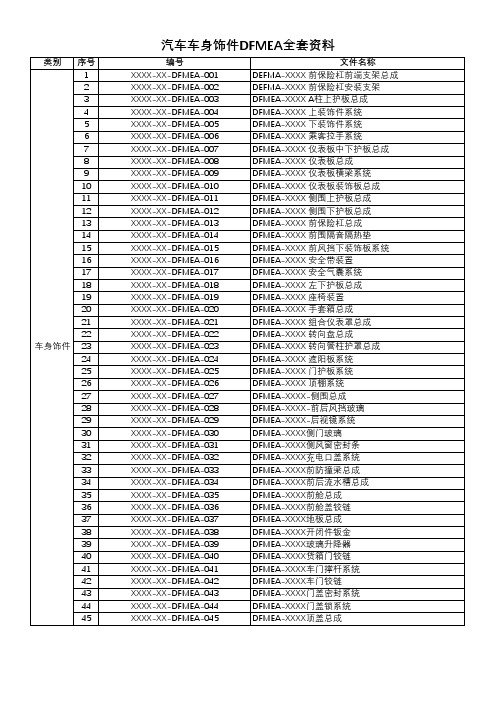
类别序号编号文件名称1XXXX-XX-DFMEA-001DEFMA-XXXX 前保险杠前端支架总成2XXXX-XX-DFMEA-002DEFMA-XXXX 前保险杠安装支架3XXXX-XX-DFMEA-003DFMEA-XXXX A柱上护板总成4XXXX-XX-DFMEA-004DFMEA-XXXX 上装饰件系统5XXXX-XX-DFMEA-005DFMEA-XXXX 下装饰件系统6XXXX-XX-DFMEA-006DFMEA-XXXX 乘客拉手系统7XXXX-XX-DFMEA-007DFMEA-XXXX 仪表板中下护板总成8XXXX-XX-DFMEA-008DFMEA-XXXX 仪表板总成9XXXX-XX-DFMEA-009DFMEA-XXXX 仪表板横梁系统10XXXX-XX-DFMEA-010DFMEA-XXXX 仪表板装饰板总成11XXXX-XX-DFMEA-011DFMEA-XXXX 侧围上护板总成12XXXX-XX-DFMEA-012DFMEA-XXXX 侧围下护板总成13XXXX-XX-DFMEA-013DFMEA-XXXX 前保险杠总成14XXXX-XX-DFMEA-014DFMEA-XXXX 前围隔音隔热垫15XXXX-XX-DFMEA-015DFMEA-XXXX 前风挡下装饰板系统16XXXX-XX-DFMEA-016DFMEA-XXXX 安全带装置17XXXX-XX-DFMEA-017DFMEA-XXXX 安全气囊系统18XXXX-XX-DFMEA-018DFMEA-XXXX 左下护板总成19XXXX-XX-DFMEA-019DFMEA-XXXX 座椅装置20XXXX-XX-DFMEA-020DFMEA-XXXX 手套箱总成21XXXX-XX-DFMEA-021DFMEA-XXXX 组合仪表罩总成22XXXX-XX-DFMEA-022DFMEA-XXXX 转向盘总成23XXXX-XX-DFMEA-023DFMEA-XXXX 转向管柱护罩总成24XXXX-XX-DFMEA-024DFMEA-XXXX 遮阳板系统25XXXX-XX-DFMEA-025DFMEA-XXXX 门护板系统26XXXX-XX-DFMEA-026DFMEA-XXXX 顶棚系统27XXXX-XX-DFMEA-027DFMEA-XXXX-侧围总成28XXXX-XX-DFMEA-028DFMEA-XXXX-前后风挡玻璃29XXXX-XX-DFMEA-029DFMEA-XXXX-后视镜系统30XXXX-XX-DFMEA-030DFMEA-XXXX侧门玻璃31XXXX-XX-DFMEA-031DFMEA-XXXX侧风窗密封条32XXXX-XX-DFMEA-032DFMEA-XXXX充电口盖系统33XXXX-XX-DFMEA-033DFMEA-XXXX前防撞梁总成34XXXX-XX-DFMEA-034DFMEA-XXXX前后流水槽总成35XXXX-XX-DFMEA-035DFMEA-XXXX前舱总成36XXXX-XX-DFMEA-036DFMEA-XXXX前舱盖铰链37XXXX-XX-DFMEA-037DFMEA-XXXX地板总成38XXXX-XX-DFMEA-038DFMEA-XXXX开闭件钣金39XXXX-XX-DFMEA-039DFMEA-XXXX玻璃升降器40XXXX-XX-DFMEA-040DFMEA-XXXX货箱门铰链41XXXX-XX-DFMEA-041DFMEA-XXXX车门撑杆系统42XXXX-XX-DFMEA-042DFMEA-XXXX车门铰链43XXXX-XX-DFMEA-043DFMEA-XXXX门盖密封系统44XXXX-XX-DFMEA-044DFMEA-XXXX门盖锁系统45XXXX-XX-DFMEA-045DFMEA-XXXX顶盖总成车身饰件汽车车身饰件DFMEA全套资料。
DFMEA_-_车身附件_-_铰链
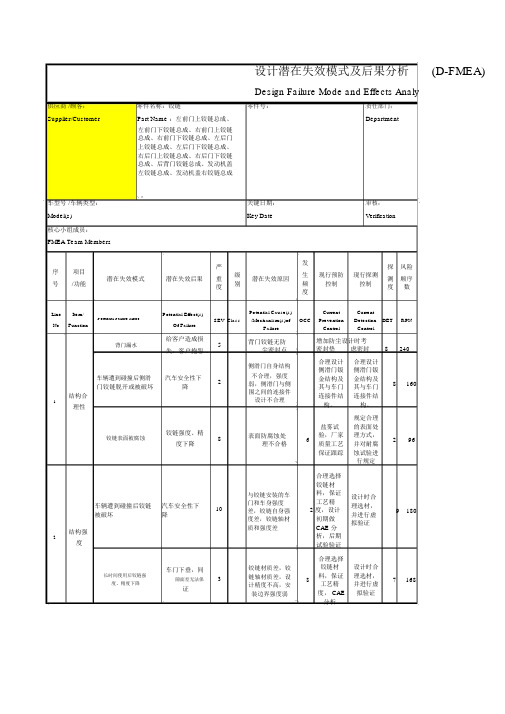
设计潜在失效模式及后果分析(D-FMEA)Design Failure Mode and Effects Analy供应商 /顾客: 零件名称:铰链零件号:责任部门:Supplier/CustomerPart Name :左前门上铰链总成、 Department左前门下铰链总成、右前门上铰链 总成、右前门下铰链总成、左后门 上铰链总成、左后门下铰链总成、 右后门上铰链总成、右后门下铰链 总成、后背门铰链总成、发动机盖 左铰链总成、发动机盖右铰链总成车型号 /车辆类型: 关键日期: 审核: Model(s)Key DateVerification核心小组成员: FMEA Team Members序 项目 潜在失效模式潜在失效后果号/功能Line Item/ Potential Effect(s)No.FunctionPotential Failure ModeOf Failure严发探 风险级生 现行预防 现行探测重 潜在失效原因测 顺序别频 控制 控制度度 数度Potential Cause(s)Current CurrentSEV Class /Mechanism(s)ofOCCPrevention Detection DETRPNFailureControlControl给客户造成损 背门漏水失,客户抱怨车辆遭到碰撞后侧滑 汽车安全性下门铰链脱开或被破坏降结构合 1理性铰链强度、精铰链表面被腐蚀度下降车辆遭到碰撞后铰链 汽车安全性下 被破坏降结构强 2度车门下垂,间长时间使用后铰链强隙面差无法保度、精度下降证52810 3背门铰链无防尘密封点侧滑门自身结构 不合理,强度弱,侧滑门与侧围之间的连接件设计不合理表面防腐蚀处理不合格与铰链安装的车门和车身强度差,铰链自身强度差,铰链轴材质和强度差铰链材质差,铰链轴材质差,设计精度不高,安装边界强度弱增加防尘设计时考 密封垫 虑密封 8 240合理设计 合理设计 侧滑门钣 侧滑门钣金结构及 金结构及 8160其与车门 其与车门连接件结 连接件结 构。
DFMEA判定标准

没有现行控制,无法探测或并未分析
在任何阶段 不易探测
探测能力很弱,虚拟分析与预期的实际操作没有关联
在设计定稿后,设计发布之前,使用GO/NG试验对产品确认。
在设计定稿 后,设计发 布前
在设计定稿后,设计发布前,通过试验到失效的试验对产品确认(直 到故障发生)
在设计定稿后,设计发布前,通过老化试验对产品进行确认,(在耐 久性试验后进行测试,如功能检查)
严重度DFMEA
影响
标准:对顾客的影响
不符合 安全性 或法规
要求
基本功 能丧失 或降低
次要功 能丧失 或降低
潜在的失效模式影响了汽车的安全运行;或者包含不符合政府法规的情形, 失效发生时无预警。 潜在的失效模式影响了汽车的安全运行;或者包含不符合政府法规的情形, 失效发生时有预警。 基本功能丧失(汽车无法运行,但不影响安全)。
≥1/10000
4
几乎相同设计,或者在设计模拟/测试时,仅有个别失效。
≥1/100000
3
低 几乎相同设计,或者在设计模拟/测试时,没能 觉察到失效。 ≥1/1000000 2
很低 通过预防控制消除失效。
通过预防控制消
除失效。
1
探测度DFMEA
探测几率
标准:设计控制可能探测出来的可能性
没有探测机 会
在设计定稿前对产品进行确认(可靠性试验、开发确认试验)使用 GO/NG的试验来验证(如性能接受标准、功能有检查等)。
在设计定稿 在设计定稿前对产品进行确认(可靠性试验、开发确认试验)使用试
之前
验到失效的试验来验证(如直到有泄露、弯曲、破裂等现象)。
在设计定稿前对产品进行确认(可靠性试验、开发确认试验)老化的 试验来验证来确认。
DFMEA-车身各结构钣金部分及其他
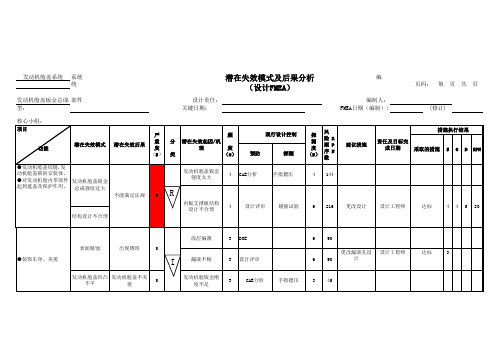
6 90
计
3 45
达标
3
(O)
现行设计控制
预防
探测
●发动机舱盖铰链.发
动机舱盖锁的安装体。 ●对发动机舱内零部件 发动机舱盖钣金
发动机舱盖钣金 强度太大
4 CAE分析
起到遮盖及保护作用。 总成强度过大 不能满足法规
9
R
手指摁压
内板支撑板结构 设计不合理
4
设计评审
碰撞试验
结构设计不合理
探 测 度 (D)
风 险R 顺P 序N 数
发动机舱盖系统 系子统系 统
潜在失效模式及后果分析 (设计FMEA)
FMEA 编
页码: 第 页 共 页
发 年动 度机 车舱型盖/车钣辆金类总成 部件 型:
设计责任: 关键日期:
编制人: FMEA日期(编制):
(修订)
核心小组: 项目
功能
潜在失效模式
严பைடு நூலகம்
频
潜在失效后果
重 度
分 潜在失效起因/机
理
度
(S) 类
4 144
6 216
建议措施
措施执行结果
责任及目标完
成日期
采取的措施 S O D RPN
更改设计 设计工程师
达标
4 4 5 80
●装饰车身、美观
表面腐蚀
出现锈斑
5
发动机舱盖凹凸 发动机舱盖不美
不平
观
5
涂层偏薄
3 DOE
I
漏液不畅
3 设计评审
发动机舱钣金刚 度不足
3
CAE分析
手指摁压
6 90
更改漏液孔设 设计工程师
DFMEA_-_车身附件_-_门锁总成

测试
2 18 5 60 3 54 5 45 4 48
2 24
没进行法规分析 1
进行法规 分析
法规校核
1
10
材料耐老化性能 差
6
定义材料 的耐老化 试验验证
性要求
3
54
外把手制造质量 差
6
严格要求 供应商按 外观检查 色板加工
2
60
1、转动机构设 计时无缓冲
2、回位弹簧自 身有异响
1、采用缓
冲设计
2、控制采
褪色、变形
用户抱怨
3
外观
26
外观不良,车身有色 外观质量差,
差
引发顾客抱怨
5
27 在正常 使用, 无异 响,无 卡滞现 象
28
异响 卡滞
手感重,导致 顾客报怨
5
手感重,导致 顾客报怨
5
29
扣手位置在不人手方 便操作区域
引发顾客抱怨
4
插接件松动,引 发接触不良,导 4
致无法通电
设计采用 防松插接
件
检测
OCC
Current Prevention
Control
Current Detection
Control
DET
RPN
1
外观质 量
外壳破裂、漏水
引发顾客不满 3
制造工艺及材料
差,门锁塑料表 面存在气泡、变
5
形、表面不平整
跟进追踪 厂家制造 外检检测 工艺情况
5
75
制造工艺差,锁
体上铆接、焊点
跟进追踪
2
磨损、松动、热
验验证
熔、碎裂等
线束卡子设计缺
陷,材质不合 适,线束端子脱
车门的DFMEA
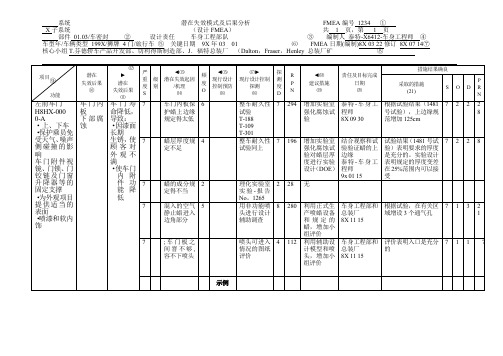
责任及目标完成 日期 ⒇
措施结果确良
采取的措施 (21)
P S ODR
N
左前车门
H8HX-000 0-A ·上、下车 ·保护乘员免 受天气、噪声 侧碰撞的影
车门内 板 下部腐 蚀
车门寿 7 命降低, 导致: ·因漆面 长期 生锈,使 7 顾客对
车门内板保 6 护蜡上边缘 规定得太低
蜡层厚度规 4 定不足
系统
潜在失效模式及后果分析
FMEA 编号 1234 ①
X 子系统
(设计 FMEA)
共 1 页,第 1 页
部件 01.03/车密封 ②
设计责任 车身工程部队
③ 编制人 泰特-X6412-车身工程师 ④
车型年/车辆类型 199X/狮牌 4 门/旅行车 ⑤ 关键日期 9X 年 03 01
⑹ FMEA 日期(编制)8X 03 22 修订 8X 07 14⑦
核心小组 T.芬德轿车产品开发部、切利得斯制造部、J.福特总装厂 (Dalton,Fraser,Henley 总装厂矿
⑧
项目 ⑨
功能
潜在 失效后果
⑩
⑿
► 潜在 失效后果 ⑾
严 重 度
级 别
◄⒀ 潜在失效起因
/机理
频 度
◄⒂ 现行设计 控制预防
⒄► 现行设计控制
探测
探 测 度
S
⒁
O
⒃
⒃
D
R P N
◄⒅ 建议措施
设计(DOE) 程师
在 25%范围内可以接
9x 01 15
受
理化实验室 2 28 无
实验-报告
No。1265
用非功能喷 8 280 利用正式生 车身工程部和 根据试验,在有关区 7 1 3 2
汽车制动系统设计DFMEA案例分析
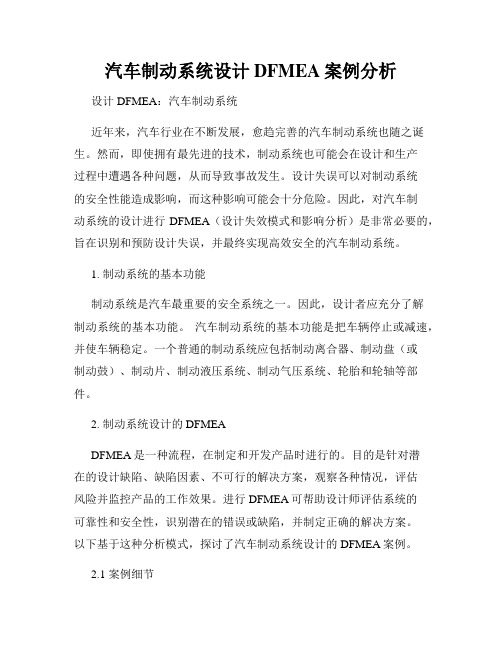
汽车制动系统设计DFMEA案例分析设计DFMEA:汽车制动系统近年来,汽车行业在不断发展,愈趋完善的汽车制动系统也随之诞生。
然而,即使拥有最先进的技术,制动系统也可能会在设计和生产过程中遭遇各种问题,从而导致事故发生。
设计失误可以对制动系统的安全性能造成影响,而这种影响可能会十分危险。
因此,对汽车制动系统的设计进行DFMEA(设计失效模式和影响分析)是非常必要的,旨在识别和预防设计失误,并最终实现高效安全的汽车制动系统。
1. 制动系统的基本功能制动系统是汽车最重要的安全系统之一。
因此,设计者应充分了解制动系统的基本功能。
汽车制动系统的基本功能是把车辆停止或减速,并使车辆稳定。
一个普通的制动系统应包括制动离合器、制动盘(或制动鼓)、制动片、制动液压系统、制动气压系统、轮胎和轮轴等部件。
2. 制动系统设计的DFMEADFMEA是一种流程,在制定和开发产品时进行的。
目的是针对潜在的设计缺陷、缺陷因素、不可行的解决方案,观察各种情况,评估风险并监控产品的工作效果。
进行DFMEA可帮助设计师评估系统的可靠性和安全性,识别潜在的错误或缺陷,并制定正确的解决方案。
以下基于这种分析模式,探讨了汽车制动系统设计的DFMEA案例。
2.1 案例细节应用DFMEA对新型汽车制动系统进行评估。
制动系统的开发人员已确定了一系列的模式,包括安装端口、材料、制动系统的阀门、抽吸和压力泵、筒和活塞,以及几个不同的操作组件。
同时,汽车制动系统设计还考虑了传动控制、电子系统和机械系统等方面,以确保高效安全的设计。
2.2 评估模式评估模式是DFMEA的重要组成部分。
为了进行制动系统的评估,需要确定系统中的各个子部件,并评估每个子系统的失效模式。
失效模式是指系统中可能发生的错误模式或缺陷,例如材料错误,设备质量问题或人员操作不当等。
每个失效模式都伴随着一个或多个潜在的后果,因此,准确评估失效模式是必要的。
2.3 评估影响对于每种失效模式,需要评估其潜在的影响。
DFMEA经典案例
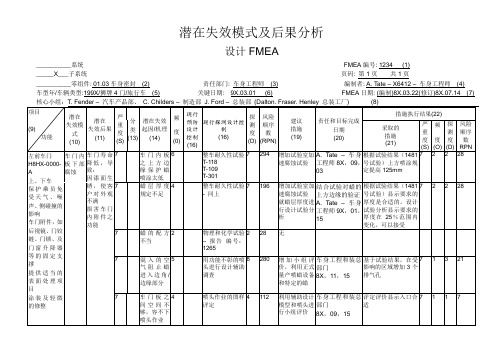
物理和化学试验–报告编号:1265
2
28
无
7
混入的空气阻止蜡进入边角/边缘部分
5
用功能不彰的喷头进行设计辅助调查
8
280
增加小组评价,利用正式量产喷蜡设备和特定的蜡
车身工程和装总部门
8X,11,15
基于试验结果,在受影响的区域增加3个排气孔
7
1
3
21
7
车门板之间空间不够,容不下喷头作业
4
喷头作业的图样评定
7
2
2
28
7
蜡层厚度规定不足
4
整车耐久性试验
-同上
7
196
增加试验室加速腐蚀试验
就蜡层厚度进行设计试验分析
结合试验对蜡的上方边缘的验证
A. Tate –车身工程师9X,01,15
根据试验结果(1481号试验)显示要求的厚度是合适的。设计试验分析显示要求的厚度在25%范围内变化。可以接受
7
2
2
28
7
蜡的配方不当
现行探测设计控制
(16)
探测
度
(D)
风险
顺序
数
(RPN)
建议
措施
(19)
责任和目标完成日期
(20)
措施执行结果(22)
采取的
措施
(21)
严重
度(S)
频
度
(O)
探测度
(D)
风险
顺序
数
RPN
左前车门
H8HX-0000-A
上、下车
保护乘员免受天气、噪声、侧碰撞的影响
车门附件,如后视镜、门铰链、门锁、及门窗升降器等的固定支撑
- 1、下载文档前请自行甄别文档内容的完整性,平台不提供额外的编辑、内容补充、找答案等附加服务。
- 2、"仅部分预览"的文档,不可在线预览部分如存在完整性等问题,可反馈申请退款(可完整预览的文档不适用该条件!)。
- 3、如文档侵犯您的权益,请联系客服反馈,我们会尽快为您处理(人工客服工作时间:9:00-18:30)。
采取的措施
Recommend Action(s)
Responsible Department
Targe Completi -on Date
Actions Taken
New New New SEV OCC DET
增加防尘密封垫
参考成熟结构合理设计 零件结构
合理选材和合理的结构 设计
合理选材和合理的结构 设计
Item/ Function
Potential Failure Mode
Potential Effect(s) SEV Class Of Failure
Potential Cause(s) Current /Mechanism(s)of OCC Prevention Failure Control
Current Detection Control
DET RPN
背门漏水
给客户造成损 失,客户抱怨
5
背门铰链无防尘 密封点 侧滑门自身结构 不合理,强度 弱,侧滑门与侧 围之间的连接件 设计不合理
增加防尘 设计时考 密封垫 虑密封 8 合理设计 侧滑门钣 金结构及 其与车门 连接件结 构。 盐雾试 验,厂家 质量工艺 保证跟踪 合理选择 铰链材 料,保证 工艺精 2 度,设计 初期做 CAE分 析,后期 试验验证 合理选择 铰链材 料,保证 工艺精 度,CAE 分析 合理设计 侧滑门钣 金结构及 其与车门 连接件结 构。 规定合理 的表面处 理方式, 并对耐腐 蚀试验进 行规定
9
180
长时间使用后铰链强 度、精度下降
车门下垂,间 隙面差无法保 证
3
铰链材质差,铰 链轴材质差,设 计精度不高,安 装边界强度弱
8
设计时合 理选材, 并进行虚 拟验证
7
168
及后果分析(D-FMEA)
车身工程中心 FMEA编号: No.
Effects Analysis (D-FMEA)
编制人: Compiled By 日期(编制):2014 Compile Date 日期(修改): Amend Date 措施结果/Action Results 建议措施 责任部门 责任目 标完成 日期 新 严 重 度 新 频 度 新 探 测 度 新风 险顺 序数
240
车辆遭到碰撞后侧滑 门铰链脱开或被破坏 1 结构合 理性
汽车安全性下 降
2
8
160
铰链表面被腐蚀
铰链强度、精 度下降
8
表面防腐蚀处理 不合格
6
2
96
车辆遭到碰撞后铰链 汽车安全性下 被破坏 降 2 结构强 度
10
与铰链安装的车 门和车身强度 差,铰链自身强 度差,铰链轴材 质和强度差
设计时合 理选材, 并进行虚 拟验证
设计潜在失效模式及后果分析(D-FMEA)
Design Failure Mode and Effects Analysis (D-FMEA)
供应商/顾客: Supplier/Customer 零件名称:铰链 Part Name:左前门上铰链总成、 左前门下铰链总成、右前门上铰链 总成、右前门下铰链总成、左后门 上铰链总成、左后门下铰链总成、 右后门上铰链总成、右后门下铰链 总成、后背门铰链总成、发动机盖 左铰链总成、发动机盖右铰链总成 零件号: 责任部门: Department
车型号/车辆类型: Model(s) 核心小组成员: FMEA Team Members
关键日期: Key Date
审核: Verification
ቤተ መጻሕፍቲ ባይዱ
序 号
项目 /功能
潜在失效模式
潜在失效后果
严 重 度
级 别
潜在失效原因
发 生 频 度
现行预防 控制
现行探测 控制
探 测 度
风险 顺序 数
Line No.