基于磨损行为的单晶硅片化学机械抛光材料的去除特性
硅的cmp抛光技术

硅的cmp抛光技术
硅的CMP抛光技术,全称为化学机械抛光技术,是半导体晶片表面加工的
关键技术之一。
这种技术利用化学腐蚀和机械力对加工过程中的硅晶圆或其它衬底材料进行平坦化处理。
CMP设备包括抛光、清洗、传送三大模块,
其作业过程中,抛光头将晶圆待抛光面压抵在粗糙的抛光垫上,借助抛光液腐蚀、微粒摩擦、抛光垫摩擦等耦合实现全局平坦化。
此外,单晶硅片制造过程和前半制程中也需要多次用到化学机械抛光技术。
与先前普遍使用的机械抛光相比,化学机械抛光能使硅片表面变得更加平坦,并且还具有加工成本低及加工方法简单的优势,因而成为目前最为普遍的半导体材料表面平整技术。
由于目前集成电路元件普遍采用多层立体布线,集成电路制造的前道工艺环节需要进行多层循环。
在此过程中,需要通过CMP工艺实现晶圆表面的平
坦化。
集成电路制造是CMP设备应用的最主要的场景,重复使用在薄膜沉
积后、光刻环节之前。
以上信息仅供参考,如有需要,建议查阅CMP技术相关论文或咨询专业人士。
单颗磨粒超声辅助磨削SiC陶瓷材料去除机理

第32卷第19期中国机械工程V o l .32㊀N o .192021年10月C H I N A M E C HA N I C A LE N G I N E E R I N Gp p.2331G2339单颗磨粒超声辅助磨削S i C 陶瓷材料去除机理丁㊀凯㊀李奇林㊀雷卫宁㊀徐铭洲㊀王㊀许江苏理工学院机械工程学院,常州,213001摘要:为研究不同磨削速度下超声振动作用对S i C 陶瓷磨削过程中材料去除机理的影响,采用钎焊单颗金刚石磨粒工具,基于连续变磨削深度试验方法,在S i C 陶瓷抛光表面开展了超声辅助磨削与普通磨削对比试验.结果表明,随着单颗磨粒磨削深度的逐渐增大,S i C 陶瓷超声辅助磨削与普通磨削时的材料去除机理均经历了 塑性去除ң脆G塑转变ң大尺寸脆性断裂 的变化;在磨削速度为1m /s 时,相比于普通磨削,单颗磨粒超声辅助磨削可显著增大S i C 陶瓷的脆G塑转变临界切厚及相应的磨削划痕横截面积,并减小切向磨削力与磨削比能;而随着磨削速度的增大,超声辅助磨削与普通磨削在单颗磨粒磨削划痕尺寸㊁磨削力之间的差异逐渐减弱.关键词:单颗磨粒;超声辅助磨削;S i C 陶瓷;磨削划痕形貌;材料去除机理中图分类号:T G 580D O I :10.3969/j .i s s n .1004 132X.2021.19.008开放科学(资源服务)标识码(O S I D ):M a t e r i a lR e m o v a lM e c h a n i s md u r i n g UA Go f S i CC e r a m i cw i t haB r a z e dS i n gl eA b r a s i v eG r a i nT o o l D I N G K a i ㊀L IQ i l i n ㊀L E IW e i n i n g ㊀X U M i n gz h o u ㊀WA N G X u S c h o o l o fM e c h a n i c a l E n g i n e e r i n g ,J i a n g s uU n i v e r s i t y o fT e c h n o l o g y ,C h a n g z h o u ,J i a n gs u ,213001A b s t r a c t :T o s t u d y t h e e f f e c t s o f u l t r a s o n i c v i b r a t i o n s o n t h em a t e r i a l r e m o v a lm e c h a n i s md u r i n gg r i n d i n g o f S i Cc e r a m i c su n d e r d i f f e r e n t g r i n d i n g s p e e d s ,ab r a z e d s i n gl e a b r a s i v e g r a i n t o o lw a s u s e d t o c o n d u c t c o m p a r i s o n t e s t s f o rU A Ga n d c o n v e n t i o n a l g r i n d i n g(C G ).I n a d d i t i o n ,t h e t e s t sw e r e c o n Gd u c t e do n t h e p o l i s h e d s u r f a c e s b a s e do n t h e c o n t i n u o u s v a r i a b l e g r i n d i n g d e pt hm e t h o d s .T h e r e s u l t s s h o wt h a t t h em a t e r i a l s f o r b o t hU A Ga n dC Go f S i Cb o t h e x p e r i e n c e t h e f o l l o w i n g c h a n g i n g s t a ge s ,i .e .,p l a s t i cr e m o v a l ңb r i t t l e Gp l a s t i ct r a n s i t i o nңl a r g es c a l eb r i t t l ef r a c t u r e ,w i t hi n c r e a s i n gg r i n d i n g d e p th s o f t h e si n g l e a b r a s i v e g r a i n .C o m p a r e d t oC G ,U A G m a y e f f e c t i v e l y e n l a r g e t h e c r i t i c a l d e pt h o f b r i t t l e Gp l a s t i c t r a n s i t i o n f o rS i Cc e r a m i c sw h e n g r i n d i n g s p e e d i sa s1m /s ,a n d m a y a l s o p r o d u c e l o w e r t a n g e n t i a l g r i n d i n g f o r c e sa n ds p e c i f i c g r i n d i n g e n e r gi e s .H o w e v e r ,t h ed i f f e r e n c e sb e t w e e n U A Ga n dC Gf o r t h ec r i t i c a ld e p t ho fb r i t t l e Gp l a s t i ct r a n s i t i o na n d g r i n d i n g f o r c e sw i l lb e g r a d u a l l y w e a k e n e dw i t h i n c r e a s i n gg r i n d i n g s pe e d .K e y wo r d s :s i n g l ea b r a s i v e g r a i n ;u l t r a s o n i ca s s i s t e d g r i n d i n g (U A G );S i Cc e r a m i c ;g r i n d i n g s c r a t c hm o r p h o l o g y;m a t e r i a l r e m o v a lm e c h a n i s m 收稿日期:20210210基金项目:国家自然科学基金(51805231,51905234)0㊀引言先进陶瓷材料(如碳化硅(S i C )㊁氮化硅(S i 3N 4)等)具有低密度㊁高强度与优异的耐高温㊁耐磨损等性能[1G2],在航空航天[3]㊁医学[4]等领域的应用日趋广泛.先进陶瓷构件一般需经过机械加工以达到其较高的表面质量及尺寸形状精度要求[5].现阶段,先进陶瓷材料加工最常用的方法是采用金刚石砂轮进行磨削,但往往存在砂轮磨损速度快㊁表面/亚表面损伤较严重等问题.而研磨和抛光虽可有效改善加工表面的损伤状况,但效率低㊁成本高[6],因此,先进陶瓷加工困难始终是其应用中的突出阻碍.超声辅助磨削(u l t r a Gs o n i c a s s i s t e d g r i n d i n g,U A G )是集超声加工与磨削于一体的高性能复合加工技术[7G8],国内外诸多研究表明,相比于普通磨削(c o n v e n t i o n a l g r i n d Gi n g,C G ),超声辅助磨削可显著改善加工质量,非常适合加工先进陶瓷材料[9G12].先进陶瓷材料加工过程中的材料去除机理直接决定了其加工表面质量.对于普通磨削,B I F A N O 等[13]提出了塑性域磨削理论,即当最大单颗磨粒切厚小于脆G塑转变临界切厚时,陶瓷材料将主要发生弹塑性变形,进而在磨削加工中实现塑性去除.同时,B I F A N O 等[13]采用显微压痕法在静态缓慢加载条件下建立了适用于先进陶瓷普通磨削时的脆G塑转变临界切厚模型.但在超声辅助磨削过程中,工具㊁工件间的接触状态与相1332 Copyright©博看网 . All Rights Reserved.对运动状态均发生了显著变化,磨粒与工件间存在高频变化的强冲击作用,相应地材料去除机理也必将受到影响.对此,一些学者开展了相关的研究.梁志强等[14]基于光滑质点流体动力学法对不同冲击速度下A l2O3陶瓷材料内部裂纹产生与扩展情况进行了仿真研究,结果表明超声效果越强侧向裂纹越易于产生,但扩展速度降低㊁尺寸减小,工件材料塑性域去除范围变大.Z HO U 等[15]采用金刚石压头对B K7及J G S1玻璃开展了超声辅助刻划试验,认为超声振动作用可显著增大玻璃材料的脆G塑转变临界切厚,因此超声辅助磨削更易于实现塑性域磨削.L I A N G等[16]研究了单颗金刚石磨粒椭圆振动超声辅助刻划单晶蓝宝石材料的划痕微观形貌及横截面深度㊁宽度尺寸,同样认为超声振动作用可显著增大脆G塑转变临界切厚.C A O等[17]采用单颗金刚石磨粒工具对S i C陶瓷进行了普通刻划及超声辅助刻划试验,通过两种方法所获得的划痕微观形貌及横截面尺寸的对比分析,得到了和文献[15G16]相似的结论.郑非非等[18]采用金刚石压头对反应烧结S i C进行了超声辅助划擦试验,研究了这一过程中超声振动作用对材料去除行为的影响,结果表明超声振动的高频冲击作用增强了切削能量的输入,加剧了微裂纹的扩展.上述研究均表明超声振动作用会对脆性材料磨削过程中的材料去除机理产生显著的影响,对脆性材料超声辅助磨削机理的研究具有良好的借鉴意义.但现有研究中磨粒刻划速度较小,仅在1.67ˑ10-4~3.6m/s之间,与实际磨削时工具运动形式㊁速度范围差别较大.另外,振动作用的方向均垂直于磨削表面,此时磨粒与工件间以锤击作用为主,不同于振动方向平行于磨削表面时的磨粒运动轨迹重叠作用,难以反映后者形式下超声振动作用对材料去除机理的影响.针对这一现状,本文采用钎焊单颗金刚石工具,在超声振动方向平行于工件表面状态下,开展了S i C陶瓷超声辅助磨削与普通磨削试验,通过单颗磨粒划痕形貌特征及其尺寸㊁磨削力与磨削比能的对比分析,研究了超声振动作用㊁磨削速度对S i C磨削过程中材料去除机理的影响.1㊀单颗磨粒超声辅助磨削运动学分析图1为单颗磨粒超声辅助磨削示意图.超声刀柄沿轴向(Z向)实现纵向振动,并且在做旋转运动的同时沿X方向做进给运动.在图1所示的坐标系中,单颗磨粒在超声辅助磨削过程中的图1㊀单颗磨粒超声辅助磨削示意图F i g.1㊀I l l u s t r a t i o no f a s i n g l e a b r a s i v e g r a i n f o rU A G运动方程可表示为X=R c o sωt+v w tY=R s i nωtZ=A s i n2πf t}(1)式中,R为杯形金刚石砂轮半径;A为超声振动振幅;ω为角速度;v w为进给速度;f为超声振动频率;t为时间.根据式(1),采用MA T L A B绘制得到单颗磨粒在超声辅助磨削过程中的运动轨迹为空间正弦曲线,如图2所示.图2㊀单颗磨粒普通磨削与超声辅助磨削运动轨迹F i g.2㊀M o t i o n t r a j e c t o r y o f a g r a i nd u r i n g C Ga n dU A G2㊀试验2.1㊀试验设备单颗磨粒超声辅助磨削试验与普通磨削试验均在D MG U l t r a s o n i c20L i n e a r立式超声高速加工中心上进行,但进行超声辅助磨削试验时不采用其自身的超声振动模块,而是采用由南京航空航天大学研制的超声振动装置,该超声振动装置主要包括超声电源㊁原边供电系统(含初级线圈)㊁超声刀柄三部分.原边供电系统固定在机床主轴上,通过电源线与超声电源相连.超声刀柄的最大转速为30000r/m i n.试验系统如图3所示,单颗磨粒工具采用弹簧夹头,螺帽安装在超声刀柄上,抛光试样采用石蜡粘接在粘板上,并通过夹2332中国机械工程第32卷第19期2021年10月上半月Copyright©博看网 . All Rights Reserved.具与测力仪相连接.进行普通磨削试验时,关闭超声电源即可.图3㊀单颗磨粒超声辅助磨削试验装置F i g .3㊀E x p e r i m e n t a l s e t u p o f u l t r a s o n i c a s s i s t e d g r i n d i n gf o r a s i n gl e a b r a s i v e g r a i n 2.2㊀单颗磨粒工具与试样试验所用的单颗磨粒工具采用钎焊工艺制作,如图4所示.工具基体材料为304不锈钢,金刚石磨粒(Y K G9)粒径约为300μm ,钎焊磨粒处焊后工具直径为8.32mm .试验所用工件材料为无压烧结S i C 陶瓷,尺寸为50mmˑ10mmˑ10mm ,试验前采用U N I P O L802抛光机将试样的50mmˑ10mm 表面抛光至镜面,如图5所示.试样抛光表面微观形貌如图6所示.可以看出,S i C 陶瓷内部存在一些微孔,其显气孔率μɤ0.5%.图4㊀单颗磨粒工具F i g .4㊀S i n gl e a b r a s i v e g r a i n t o ol 图5㊀工件抛光表面F i g .5㊀P o l i s h e d s u r f a c e o f t h ew o r k pi e c e 2.3㊀试验方法与参数工件抛光表面与机床X O Z 平面成夹角β放置,如图7a 所示.单颗金刚石磨粒与工件抛光表面在切入点接触后,随着单颗磨粒工具沿X 轴方向做进给运动,磨削深度a p 逐渐增大,在切出点时达到最大值.通过对相同工艺参数条件下单颗磨粒超声辅助磨削与普通磨削划痕形貌特征的对图6㊀工件抛光表面微观形貌F i g .6㊀M i c r o t o p o g r a p h y of p o l i s h e d s u r f a c e o f t h ew o r k pi e c e 比分析,可以获得连续变切厚条件下超声振动作用对S i C 陶瓷去除机理转变规律的影响.如图7b 所示,在试样抛光面宽度b ㊁磨削深度a p 最大值㊁切入点切出点连线三者组成的三角形中,β与b 和磨削深度最大值a p m a x 之间的关系如下:b t a n β=a p m a xc o s β(2)试验中所用试样抛光面的宽度b =10mm ,预设定磨粒切出工件时的最大磨削深度a p m a x =20μm ,则由式(2)计算可得βʈ0.114ʎ.D MG U l t r a s o n i c 20L i n e a r 立式超声高速加工中心C轴旋转的最小分度值为0.001ʎ,可以满足要求.(a)三维模型(b)俯视图图7㊀单颗磨粒超声辅助磨削试验方法F i g .7㊀E x p e r i m e n t a lm e t h o do f u l t r a s o n i c a s s i s t e d g r i n d i n gf o r a s i n gl e a b r a s i v e g r a i n3332 单颗磨粒超声辅助磨削S i C 陶瓷材料去除机理丁㊀凯㊀李奇林㊀雷卫宁等Copyright©博看网 . All Rights Reserved.另外,通过前期磨削参数与超声振动参数匹配性研究[19]可知,磨削速度对超声辅助磨削效果的影响较为显著,而进给速度对其影响较小,因此本试验中将进给速度v w固定为20mm/m i n,磨削速度v s分别设置为1,4,7,10m/s.所有试验均在干切削条件下进行.2.4㊀观测方法采用e d d y N C D T3300电涡流位移传感器㊁R&SR T H1002示波器对单颗磨粒工具末端振幅及谐振频率进行测量,其单边振幅为7.5μm,谐振频率为26.35k H z.采用K i s t l e r9129a测力仪及5070电荷放大器对磨削力进行测量,测量时采样频率设置为4k H z.试验后首先对试样表面进行喷金处理,然后采用Z E I S SS i g m a500场发射扫描电镜对磨削划痕微观形貌进行分析,在此基础上采用H I R O X R HG2000三维形貌测量系统对单颗磨粒磨削划痕特征尺寸进行测量.3㊀试验结果与分析3.1㊀单颗磨粒超声辅助磨削与普通磨削划痕形貌图8㊁图9分别为v s=1m/s㊁v w=20m m/m i n 条件下,单颗磨粒超声辅助磨削划痕与普通磨削划痕微观形貌.对比图8b㊁图9b可以看出,单颗磨粒超声辅助磨削划痕形状呈现明显的正弦曲线特征.同时可以看出,在单颗金刚石磨粒刚刚切入工件抛光表面时,无论是超声辅助磨削划痕还是普通磨削划痕均表现为塑性去除特征,同时伴有微小脆性破碎引起的凹坑.对于单颗磨粒磨削划痕周围分布的微孔隙,根据其分布特征及尺寸,由图6可知,这些微孔隙产生于材料制备环节,并非单颗磨粒磨削过程所致.随着磨削深度的增大,两条磨削划痕均出现了明显的脆G塑性去除转变分界线,如图8c㊁图9c所示.在经过图中所示的分界线后,S i C 陶瓷材料去除特征均从塑性去除㊀㊀㊀㊀(a)整体形貌特征㊀㊀㊀㊀㊀㊀㊀㊀㊀(b)塑性去除区域特征㊀㊀㊀㊀㊀㊀㊀(c)脆G塑转变区域特征图8㊀v s=1m/s,v w=20m m/m i n条件下单颗磨粒超声辅助磨削划痕微观形貌F i g.8㊀M i c r o t o p o g r a p h y o f t h e s c r a t c h p r o d u c e db y a s i n g l e a b r a s i v e g r a i nd u r i n g u l t r a s o n i c a s s i s t e d g r i n d i n g i nv s=1m/s,v w=20m m/m i n㊀㊀㊀㊀(a)整体形貌特征㊀㊀㊀㊀㊀㊀㊀㊀(b)塑性去除区域特征㊀㊀㊀㊀㊀㊀㊀(c)脆G塑转变区域特征图9㊀v s=1m/s,v w=20m m/m i n条件下单颗磨粒普通磨削划痕微观形貌F i g.8㊀M i c r o t o p o g r a p h y o f t h e s c r a t c h p r o d u c e db y a s i n g l e a b r a s i v e g r a i nd u r i n g c o n v e n t i o n a l g r i n d i n g i nv s=1m/s,v w=20m m/m i n转变为明显的脆性断裂,然后随磨削深度的进一步增大,材料去除形式完全转变为大尺寸脆性断裂.图10㊁图11分别为v s=10m/s㊁v w=20mm/m i n条件下,单颗磨粒超声辅助磨削划痕与普通磨削划痕微观形貌.同于图8㊁图9,可以看到在此条件下随着单颗金刚石磨粒磨削深度的增大,超声辅助磨削划痕与普通磨削划痕均体现了明显的材料脆G塑性去除机理的转变,即经历了 塑性去除ң脆G塑转变ң大尺寸脆性断裂 变化过程.而对比图8㊁图10也可以看出,随着磨削速度的增大,单颗磨粒运动轨迹曲线趋于平缓,已接近于普通磨削.另外,由图8c㊁图9c可以发现,当磨削速度v s=1m/s时,两种方法得到的磨削划痕均超过脆G塑转变区域分界线后出现了明显的材料脆性断裂去除.而在磨削速度增大到v s=10m/s后,如图10c㊁图11c所示,可看到磨削划痕超过脆G塑转变区域分界线后材料脆性断裂程度均明显减弱,甚至出现小面积因塑性去除特征而产生的光滑区域或塑性沟槽.4332中国机械工程第32卷第19期2021年10月上半月Copyright©博看网 . All Rights Reserved.㊀㊀㊀㊀(a )整体形貌特征㊀㊀㊀㊀㊀㊀㊀㊀(b )塑性去除区域特征㊀㊀㊀㊀㊀㊀㊀(c )脆G塑转变区域特征图10㊀v s =10m /s ,v w =20m m /m i n 条件下单颗磨粒超声辅助磨削划痕微观形貌F i g .10㊀M i c r o t o p o g r a p h y o f t h e s c r a t c h p r o d u c e db y a s i n g l e a b r a s i v e g r a i nd u r i n g u l t r a s o n i c a s s i s t e d g r i n d i n gi n v s =10m /s ,v w =20m m /m i n ㊀㊀㊀㊀(a )整体形貌特征㊀㊀㊀㊀㊀㊀㊀㊀(b )塑性去除区域特征㊀㊀㊀㊀㊀㊀㊀(c )脆G塑转变区域特征图11㊀v s =10m /s ,v w =20m m /m i n 条件下单颗磨粒普通磨削划痕微观形貌F i g .11㊀M i c r o t o p o g r a p h y o f t h e s c r a t c h p r o d u c e db y a s i n g l e a b r a s i v e g r a i nd u r i n g c o n v e n t i o n a l g r i n d i n g i n v s =10m /s ,v w =20m m /m i n 3.2㊀超声振动作用对脆G塑转变临界切厚的影响通过图8~图11中单颗磨粒超声辅助磨削划痕与普通磨削划痕微观形貌的分析,可以观察到随磨削深度的增大,S i C 陶瓷材料去除机理体现出显著的脆G塑性转变过程.其中,由图8~图11所示的脆G塑转变区域特征可知,图中的分界线是脆G塑性转变的临界点,因此本文中取分界线处的磨削划痕深度作为S i C 陶瓷超声辅助磨削及普通磨削时的脆G塑转变临界切厚(h c ).为研究超声振动作用对S i C 陶瓷磨削过程中材料去除机理的影响,对所有试验条件下的单颗磨粒磨削划痕脆G塑转变临界切厚h c 及对应横截面面积进行了测量,测量方法如图12所示.另外,为对比分界线两侧塑性区㊁脆性区磨粒磨削划痕深度的差异,分别对分界线及其两侧相邻处的磨削划痕深图12㊀单颗磨粒磨削脆G塑转变临界切厚测量方法(v s =1m /s ,v w =20mm /m i n)F i g .12㊀M e a s u r i n g m e t h o d f o r t h e c r i t i c a l d e p t ho f b r i t t l e Gp l a s t i c t r a n s i t i o nd u r i n g a s i n g l e a b r a s i v e g r a i n g r i n d i n g(v s =1m /s ,v w =20mm /m i n)度进行了测量.在v s =1m /s ㊁v w =20mm /m i n 条件下,三处的测量结果分别为0.067μm ㊁0.173μm ㊁0.249μm ,进一步表明了随着磨削深度的增大,S i C 陶瓷材料将实现从塑性到脆性的转变.单颗磨粒超声辅助磨削与普通磨削时,磨削速度对磨削划痕脆G塑转变临界切厚的影响如图13所示.可以看出,在v s 为1~10m /s 时,单颗磨粒普通磨削时的脆G塑转变临界切厚h c 值较稳定,变化范围在0.077~0.087μm 之间.而对于单颗磨粒超声辅助磨削过程,当磨削速度为1m /s 时,h c 值为0.173μm ,显著大于普通磨削时的0.077μm ,表明在此工艺参数条件下超声振动作用有助于增大S i C 陶瓷的脆G塑转变临界切厚.当磨削速度增大到10m /s 时,超声辅助磨削时的h c 值下降为0.093μm ,仅略大于普通磨削时的0.084μm ,表明随着磨削速度的增大,超声辅助磨削与普通磨削时h c 值之间的差异将逐渐减小.对于S i C 陶瓷普通磨削㊁超声辅助磨削时的脆G塑转变临界切厚数值,相关文献也进行了报道.L I 等[3]的研究表明:采用赫兹弹性接触理论计算的S i C 陶瓷普通磨削时的脆G塑转变临界切厚约为0.007μm ,而基于单颗磨粒刻划方法获得的测量值为0.076μm .同样基于单颗磨粒刻划方法,C A O 等[17]的研究表明,S i C 陶瓷普通磨削时的脆G塑转变临界切厚约为0.08μm ,而在垂直5332 单颗磨粒超声辅助磨削S i C 陶瓷材料去除机理丁㊀凯㊀李奇林㊀雷卫宁等Copyright©博看网 . All Rights Reserved.图13㊀磨削速度对S i C 脆G塑转变临界切厚的影响(v w =20mm /m i n)F i g .13㊀E f f e c t o f g r i n d i n g s p e e do n t h e c r i t i c a l d e pt ho f b r i t t l e Gpl a s t i c t r a n s i t i o n f o r S i C (v w =20mm /m i n )于工件表面振幅为1.25μm ㊁刻划速度为0.5m /s 条件下,超声辅助磨削时的脆G塑转变临界切厚约为0.125μm .对比本文与上述文献的报道可知,S i C 陶瓷普通磨削时的脆G塑转变临界切厚测量结果非常接近,但均大于理论计算值,而超声辅助磨削时的脆G塑转变临界切厚测量结果因振动施加方向㊁单颗磨粒刻划速度的不同而有所差异.磨削速度对单颗磨粒磨削划痕脆G塑转变分界线处横截面积S 的影响规律如图14所示.可以看出,对于普通磨削而言,其脆G塑转变分界线处横截面积随磨削速度的增大略有减小,而超声辅助磨削时当v s =1~7m /s 时分界线处横截面积相对稳定,但在v s =10m /s 时急剧减小.对比两种加工方法,当磨削速度为1m /s 时,超声辅助磨削划痕的S 值为0.428μm 2,明显大于普通磨削时的0.054μm 2,即在此条件下超声辅助磨削可获得较大的材料去除率.当磨削速度增大到10m /s 时,超声辅助磨削划痕的S 值降低为0.168μm 2,仍大于普通磨削时的0.023μm 2,但总体而言二者之间的差异呈减小的趋势.图14㊀磨削速度对S i C 脆G塑转变区横截面积的影响(v w =20mm /m i n)F i g .14㊀E f f e c t o f g r i n d i n g s pe e do n t h e c r o s s Gs e c t i o n a l a r e a of b r i t t l e Gpl a s t i c t r a n s i t i o na r e a f o r S i C (v w =20mm /m i n )综合上述结果可知:超声辅助磨削时,随磨削速度的增大,S i C 陶瓷脆G塑转变临界切厚逐渐减小,对应脆G塑转变分界线处的横截面积相对稳定,但当v s =10m /s 时分界线处的横截面积急剧减小.而普通磨削时S i C 陶瓷材料脆G塑转变临界切厚及对应的横截面积较稳定,受磨削速度影响较小.另外,在较低的磨削速度条件下超声振动作用可显著增大S i C 陶瓷磨削加工过程中的脆G塑转变临界切厚及其对应位置的横截面积,而随磨削速度的增大,这一特性将逐渐减弱.这一结果为优化硬脆材料的超声辅助磨削工艺提供了依据.3.3㊀磨削力与磨削比能在硬脆材料磨削过程中,磨削比能是综合反映材料去除方式的主要参数[20],与切向磨削力直接相关.单颗磨粒典型超声辅助磨削切向力信号如图15所示,可以看出随着单颗磨粒切厚的增大(即磨削时间的增加),磨削力呈逐渐增大的趋势.为获得单颗磨粒磨削划痕脆G塑转变分界线处切向磨削力的大小,按照下述方法对磨削力信号进行处理:①采用图16所示方法确定单颗磨粒运动至分界线处的直线距离L ;②按照t =L /v w 确定相应的运动时间t ;③在其磨削力原始信号中以首个磨削力信号波形(如图15所示,标记为N o .1)时间为零点,找到时间t 所对应的或距离最近的切向磨削力波形,并取该波形平均值作为最终测量结果.图15㊀单颗磨粒超声辅助磨削S i C 切向磨削力信号(v s =1m /s ,v w =20mm /m i n)F i g .15㊀T a n g e n t i a l g r i n d i n g f o r c e s i g n a l o f a s i n gl e a b r a s i v e g r a i n g r i n d i n g of S i Cc e r a m i c (v s =1m /s ,v w =20mm /m i n )6332 中国机械工程第32卷第19期2021年10月上半月Copyright©博看网 . All Rights Reserved.图16㊀单颗磨粒直线运动距离确定方法F i g.16㊀D e t e r m i n a t i o no f d i s t a n c e o f l i n e a rm o v e m e n t f o r a s i n gl e a b r a s i v e g r a i n 按照上述方法确定的单颗磨粒超声辅助磨削划痕与普通磨削划痕中脆G塑转变分界线处的切向磨削力结果如图17所示,可以看出,超声辅助磨削及普通磨削时的切向磨削力均随磨削速度的增大而减小;相同条件下,超声辅助磨削时的磨削力均小于普通磨削时磨削力;当磨削速度v s =1m /s时,超声辅助磨削力相较于普通磨削力的减小幅度最大,约为17.1%;随着磨削速度的增大,磨削力降低幅度减小为8%~14%.图17㊀磨削速度对S i C 脆G塑转变处切向磨削力的影响(v w =20mm /m i n)F i g .17㊀E f f e c t o f g r i n d i n g s p e e do n t a n g e n t i a l g r i n d i n gf o r c e o f b r i t t l e Gpl a s t i c t r a n s i t i o n (v w =20mm /m i n )依据切向磨削力F t 测量结果,按照下式可以计算得到单颗磨粒磨削划痕脆G塑转变分界线处对应瞬时磨削比能的数值:E =F t v s v w S(3)式中,E 为磨削比能;S 为单颗磨粒磨削划痕脆G塑转变区分界线处的横截面积,测量结果如图14所示.图18所示为不同磨削速度下,单颗磨粒超声辅助磨削与普通磨削划痕脆G塑转变区域分界线处的瞬时磨削比能变化规律.由图18可见,随着磨削速度的增大,两种方法在分界线处的磨削比能均呈增大趋势,其中普通磨削尤为显著.这是因为在磨削速度v s =1m /s 时,单颗磨粒超声辅助磨削划痕与普通磨削划痕在超过脆G塑转变区域的分界线后立即呈现较大尺寸脆性断裂去除特点;而在磨削速度增大至10m /s 后,在分界线邻近区域脆性断裂去除比例降低㊁塑性去除特征有所增加,因此磨削比能增大.同时可以看出,在相同工艺参数条件下,由于超声辅助磨削相比于普通磨削可减小磨削力(图17)㊁增大磨削划痕横截面积(图14),因此超声辅助磨削时的磨削比能小于普通磨削时的磨削比能.当v s =1m /s 时,相比于普通磨削,超声辅助磨削时的磨削比能降低幅度约为90%;当磨削速度增大到10m /s 后,降低幅度略有下降,约为88%.上述结果表明超声辅助磨削可有效减少磨削过程中所消耗的能量.图18㊀磨削速度对S i C 脆G塑转变处瞬时磨削比能的影响(v w =20mm /m i n)F i g .18㊀E f f e c t o f g r i n d i n g s p e e do n i n s t a n t a n e o u s s pe c if i cg r i n d i n g e n e r g y o f b r i t t l e Gpl a s t i c t r a n s i t i o n (v w =20mm /m i n)3.4㊀讨论单颗磨粒超声辅助磨削划痕与普通磨削划痕脆G塑转变分界线处特征参数的测量结果表明,在低磨削速度条件下,超声振动作用可有效增大S i C 陶瓷的脆G塑转变临界切厚,从而更易于促使材料以塑性方式去除以获得更优良的加工表面质量.从金刚石磨粒运动分析的角度来看,一方面,单颗磨粒在超声辅助磨削过程中的运动轨迹为正弦曲线(图2),理论上,此时金刚石磨粒的切削刃区域1㊁2㊁3均可参与切削过程,且区域1㊁3将随磨粒的运动而交替进行切削(图19),而对于普通磨削过程,则是由切削刃区域2持续进行切削.相比较而言,显然在超声辅助磨削过程中金刚石磨粒更易于保持锋利性,使得磨削力得以减小并进而降低磨削比能.另一方面,当超声振动方向平行于磨削表面时,单颗磨粒在工件表面产生的磨削划痕轨迹形状如图20所示.定义其波长为λ[16],则有λ=(v s +v w )/f (4)㊀㊀由式(4)可知:在谐振频率一定的条件下,波长λ随磨削速度v s 的增大而增大,如图21所示.记单颗磨粒在超声振动状态下的振动速度为v U ,7332 单颗磨粒超声辅助磨削S i C 陶瓷材料去除机理丁㊀凯㊀李奇林㊀雷卫宁等Copyright©博看网 . All Rights Reserved.图19㊀单颗磨粒超声辅助磨削切削刃分布F i g .19㊀C u t t i n g e d g e s d i s t r i b u t i o no f a s i n gl e a b r a s i v e g r a i nd u r i n g u l t r a s o n i c a s s i s t e d g r i n d i ng图20㊀单颗磨粒超声辅助磨削划痕轨迹F i g .20㊀M o t i o n t r a j e c t o r y o f a g r a i nd u r i n g UAG 图21㊀磨削速度对波长及切入角的影响F i g .21㊀E f f e c t o f g r i n d i n g s p e e do nw a v e l e n gt h a n d p e n e t r a t i o na n gl e v U 与磨削速度v s 的合速度为v T .定义v U 与v T 的夹角为切入角α,其最小值αm i n 出现在正弦波形的起点处.由图21可知:αm i n 随着磨削速度v s ㊁波长λ的增大而增大.理论上,当v s 增大到一定程度后,正弦波形将趋近于直线即磨粒运动轨迹趋于平直,αm i n 趋近于90ʎ,单颗磨粒的超声辅助磨削运动学特征逐渐消失,这一结果通过对比图8b 与图10b 也可以得到体现;当磨削速度v s 较小时,其数值远低于合速度v T ,因此S i C 陶瓷超声辅助磨削时的h c 值明显大于普通磨削时的h c值,而随着v s 的增大,它与v T 之间的差异将逐渐减小,超声辅助磨削与普通磨削时h c 值的差异也将逐渐减小.上述分析均表明随着磨削速度v s的增大,超声振动作用对磨削过程的影响将逐渐减弱.除了有关塑性域磨削理论及磨粒运动学特性的观点之外,有学者从其他角度对超声辅助加工的特性进行了研究.Y A N G 等[21]认为,在超声辅助加工中,大的切削速度和加速度会增大材料应变率,进而导致材料加工过程中裂纹尖端扩展阻力增大,同时,由于切削速度较大,即使中位裂纹得以形成也难以有足够的时间进一步扩展,因此,相比于普通加工,超声辅助加工可有效降低加工损伤.这一结论对超声辅助磨削的相关理论研究具有重要意义.4㊀结论(1)单颗磨粒超声辅助磨削与普通磨削S i C 陶瓷时,随着磨削深度的增大,两种加工方法对应的材料去除机理均经历了 塑性去除ң脆G塑转变ң大尺寸脆性断裂 的变化过程.(2)在试验条件下,当磨削速度为1m /s 时,S i C 陶瓷超声辅助磨削时的脆G塑转变临界切厚为0.173μm ,显著大于普通磨削时的0.077μm ,即超声振动作用可增大S i C 陶瓷的脆G塑转变临界切厚.但随着磨削速度的增大,两者之间的差异逐渐减小.(3)相比于普通磨削,超声辅助磨削可减小磨削划痕脆G塑转变区域的切向磨削力,其中磨削速度为1m /s 时最大降低幅度约为17.1%.随磨削速度的增大,磨削力降低幅度有所下降.同时,由于切向磨削力较小㊁划痕横截面积较大,因此单颗磨粒超声辅助磨削划痕脆G塑转变区域的磨削比能也低于普通磨削时的磨削比能.参考文献:[1]㊀T U T i a n z h e ,J I A N G G u o ji a n .S i C R e t i c u l a t e dP o r Go u sC e r a m i c s b y 3DP r i n t i n g ,G e l c a s t i n g a n dL i q u i d D r y i n g [J ].C e r a m i c sI n t e r n a t i o n a l ,2018,44(3):3400G3405.[2]㊀Z HA O Z h e n gc a i ,L I N R u i l i n ,D A IM i n m i n ,e t a l .F a c i l e J o i n i n g o fS i C C e r a m i c s w i t hS c r e e n Gp r i n t ed P o l y c a r b o s i l a n ew i t h o u tP re s s u r e [J ].J o u r n a l of t h e E u r o p e a n C e r a m i c S o c i e t y,2021,41(3):2157G2161.[3]㊀L IC h e n ,Z HA N G F e i h u ,M E N G B i n b i n ,e ta l .M a t e r i a lR e m o v a l M e c h a n i s m a n d G r i n d i n g F o r c e M o d e l i n g o fU l t r a s o n i cV i b r a t i o nA s s i s t e dG r i n d i n gf o r S i CC e r a m i c s [J ].C e r a m i c s I n t e r n a t i o n a l ,2017,43(3):2981G2993.[4]㊀D AM B A T T A YS ,S A R HA N A AD ,S A Y U T IM ,e t a l .U l t r a s o n i cA s s i s t e dG r i n d i n g o fA d v a n c e dM a Gt e r i a l sf o rB i o m e d i c a l a n dA e r o s p a c eA p p l i c a t i o n s :a R e v i e w [J ].I n t e r n a t i o n a l J o u r n a l o fA d v a n c e d M a n Gu f a c t u r i ng T e ch n o l o g y ,2017,92:3825G3858.[5]㊀Z HA O B o ,C H E N F a n ,J I A Xi a o f e n g,e t a l .S u r Gf a c e Q u a l i t y P r e d i c t i o n M o d e lo f N a n o Gc o m p o s i t e C e r a m i c s i n U l t r a s o n i c V i b r a t i o n Ga s s i s t e d E L I D8332 中国机械工程第32卷第19期2021年10月上半月Copyright©博看网 . All Rights Reserved.。
单晶硅片化学机械抛光的表面损伤研究(江南大学)

研 创新 计划 项 目( C X Z Z 1 3 — 0 7 3 8) . 收 稿 日期 :2 0 1 3—0 9—2 1
抛光 液 ,而抛光液 中的磨 料磨粒 ,无论 是单个 磨粒尺
寸偏 大时还是 因磨粒 的团聚 现象而 产生磨 粒胶 团时 , 当其在抛光界面上 的相互作用力较大时则会造成抛光 表面 的划伤 ,甚至引起亚表层晶格缺陷 ,从而无法有
使用 ,实 现环 保 型 绿 色抛 光 。 关 键 词 :化 学 机 械抛 光 ;化学 作 用 ;机械 作 用 ;材 料 去 除 ;损 伤 中图 分 类 号 :T H 1 1 7 . 1 文 献 标 识码 :A 文章 编 号 :0 2 5 4 — 0 1 5 0 ( 2 0 1 4 ) 4— 0 1 5— 8
Ch e n Xi a o c h u n Zh a o Yo n g wu W an g Yo n g g u a n g
( S c h o o l o f Me c h a n c i  ̄E n g i n e e r i n g , J i a n g n a n U n i v e r s i t y ,Wu x i J i a n g s u 2 1 4 1 2 2,C h i n a )
。
cmp(化学机械抛光)技术发展优势及应用【最新】
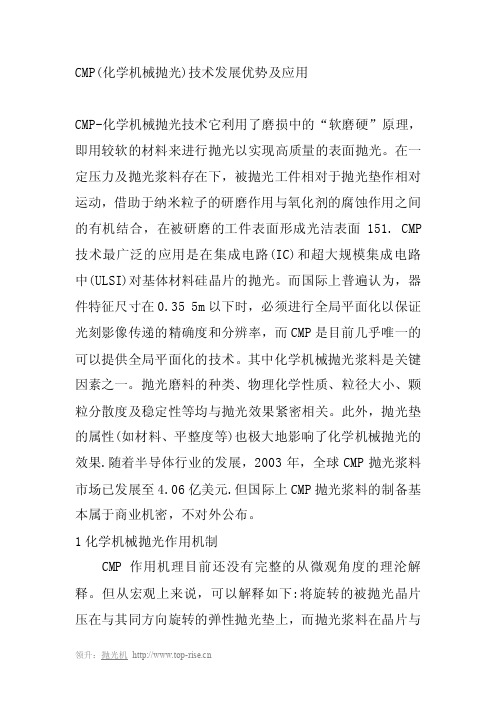
CMP(化学机械抛光)技术发展优势及应用CMP-化学机械抛光技术它利用了磨损中的“软磨硬”原理,即用较软的材料来进行抛光以实现高质量的表面抛光。
在一定压力及抛光浆料存在下,被抛光工件相对于抛光垫作相对运动,借助于纳米粒子的研磨作用与氧化剂的腐蚀作用之间的有机结合,在被研磨的工件表面形成光洁表面151. CMP 技术最广泛的应用是在集成电路(IC)和超大规模集成电路中(ULSI)对基体材料硅晶片的抛光。
而国际上普遍认为,器件特征尺寸在0.35 5m以下时,必须进行全局平面化以保证光刻影像传递的精确度和分辨率,而CMP是目前几乎唯一的可以提供全局平面化的技术。
其中化学机械抛光浆料是关键因素之一。
抛光磨料的种类、物理化学性质、粒径大小、颗粒分散度及稳定性等均与抛光效果紧密相关。
此外,抛光垫的属性(如材料、平整度等)也极大地影响了化学机械抛光的效果.随着半导体行业的发展,2003年,全球CMP抛光浆料市场已发展至4.06亿美元.但国际上CMP抛光浆料的制备基本属于商业机密,不对外公布。
1化学机械抛光作用机制CMP作用机理目前还没有完整的从微观角度的理沦解释。
但从宏观上来说,可以解释如下:将旋转的被抛光晶片压在与其同方向旋转的弹性抛光垫上,而抛光浆料在晶片与底板之间连续流动。
上下盘高速反向运转,被抛光晶片表面的反应产物被不断地剥离,新抛光浆料补充进来,反应产物随抛光浆料带走。
新裸露的品片平面又发生化学反应,产物再被剥离下来而循环往复,在衬底、磨粒和化学反应剂的联合作用下,形成超精表面,要获得品质好的抛光片,必须使抛光过程中的化学腐蚀作用与机械磨削作用达到一种平衡。
如果化学腐蚀作用大于机械抛光作用,则会在抛光片表面产生腐蚀坑、桔皮状波纹;反之,机械抛光作用大于化学腐蚀作用则表面产生高损伤层.为了进一步了解CMP作用的本质,近年来国内外有很多关于CMP作用微观机理的研究.清华人学王亮亮、路新春的研究表明:CMP中主要是低频、大波长的表面起伏被逐渐消除,而小尺度上的粗糙度并未得到显著改善;当颗粒直径在10^-25 nm的范围时,粒径和粗糙度不存在单调的增减关系;桔皮的产生主要是抛光浆料中碱浓度过高所致。
单晶硅滑动磨损性能及其相变研究
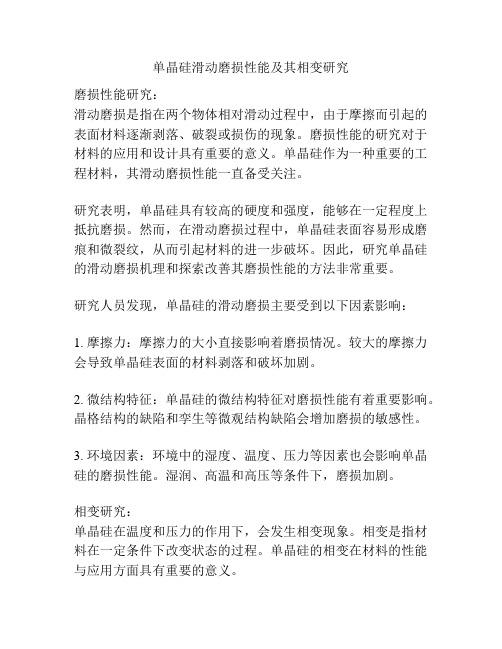
单晶硅滑动磨损性能及其相变研究磨损性能研究:滑动磨损是指在两个物体相对滑动过程中,由于摩擦而引起的表面材料逐渐剥落、破裂或损伤的现象。
磨损性能的研究对于材料的应用和设计具有重要的意义。
单晶硅作为一种重要的工程材料,其滑动磨损性能一直备受关注。
研究表明,单晶硅具有较高的硬度和强度,能够在一定程度上抵抗磨损。
然而,在滑动磨损过程中,单晶硅表面容易形成磨痕和微裂纹,从而引起材料的进一步破坏。
因此,研究单晶硅的滑动磨损机理和探索改善其磨损性能的方法非常重要。
研究人员发现,单晶硅的滑动磨损主要受到以下因素影响:1. 摩擦力:摩擦力的大小直接影响着磨损情况。
较大的摩擦力会导致单晶硅表面的材料剥落和破坏加剧。
2. 微结构特征:单晶硅的微结构特征对磨损性能有着重要影响。
晶格结构的缺陷和孪生等微观结构缺陷会增加磨损的敏感性。
3. 环境因素:环境中的湿度、温度、压力等因素也会影响单晶硅的磨损性能。
湿润、高温和高压等条件下,磨损加剧。
相变研究:单晶硅在温度和压力的作用下,会发生相变现象。
相变是指材料在一定条件下改变状态的过程。
单晶硅的相变在材料的性能与应用方面具有重要的意义。
研究发现,当单晶硅受到高温或高压的作用时,会发生相变现象。
相变会导致单晶硅的晶格结构发生改变,进而影响材料的强度、硬度和导电性等性能。
相变的研究可以通过实验和模拟方法进行。
实验可以通过提供不同的温度和压力条件,观察单晶硅的相变行为。
而模拟方法可以利用计算机模型,模拟材料在不同条件下的相变过程,从而揭示相变机理。
研究人员希望通过对单晶硅滑动磨损性能和相变的研究,提高单晶硅的材料性能,并拓展其在微电子器件、光学器件等领域的应用。
此外,研究人员还探索了改善单晶硅的滑动磨损性能的方法。
一种常用的方法是通过改变材料表面的涂层来提高硬度和抗磨损性能。
例如,利用化学气相沉积等技术在单晶硅表面覆盖薄膜,可以增加材料的硬度和抗磨损性能。
此外,通过表面处理和改善材料的晶格结构也可以有效改善单晶硅的滑动磨损性能。
化学机械抛光技术

精密表面加工。因而可以获得高精
度 、低表 面粗糙度值和 无损伤的工
次通过性的生产运转 ,因而开发
件表面。用这种方法可以真正使被
抛光工件表面实现全局平坦化。
实用的在线检测工具是必须的;另 外,抛光后工件表面残留浆料的清 除是 C MP 后清洗工艺的的主要课 题,在实际生产中,片子表面残留
出来,再进行氧化反应,这样在化
学作用过程和机械作用过程的交替
' 26 秘 o 年第3 o 钢
● ⅦC 琨代霹部件
维普资讯
澎
进行 中完成工件表面 抛光。两个过
0 : 朋C 盘: 应用
理, 包括纳米两相流的基本问题、 纳
化学机械抛光装置
完美的表面 ,又可以得到较高的抛 光速率,得到的平整度比其他方法 高两个数量级 ,是能够实现全局平 坦化的惟一方法。
工表面具有纳米级型面精度和亚纳 米级表面粗糙度,同时表面和亚表
面无损伤, 已接近表面加工的极限。
广泛应用在集成电路、 计算机磁头,
硬磁盘等超精密表面加工,如化学 机械抛光应用在半导体工业中的层 间介电介质, 镶嵌金属w、 lc 、 A 、 u A ,多晶硅,导体,绝缘体, u 硅氧 化物等的平坦化加工;薄膜存储磁
致产品报废,因而探索它们的形成 机理 ,揭示微观损伤、微接触和微
力作用在夹持头上,将被抛光工件
赖磨粒尺寸,但化学机械抛光加工 中却独立于磨粒尺寸。 传统抛光单个磨粒承受工作载
荷, 被挤进工件表面 , 向上拔出, 耕 犁一个犁沟去除工件材料,表面粗 糙度取决于压痕尺寸和磨粒大小 ,
机械作用力
中的磨粒浓度。
抛光去除速率须遵守Pe o 方 r tn s 程
硅晶片化学机械抛光材料去除机制与模型

2 Sho o a r dE g er gJ ns n e i ,h na gJ gu2 2 1 , hn ; .c ol f t i a n ne n ,i guU i rt Z ej a s 10 3 C ia M e an l i i a vs y i n i n 3 Sh l f c ai n ne n , i guP leh i U i r t,C aghuJ gu23 1 C i ) . o h c E g er g J ns o c n n e i c o Me n a l i i a t y c vs y h zo i s 106,hn n n a a
陈
( .江 苏 工 业 学 院 材 料 系 1
杨 陈志刚 李 霞章 陈爱莲
江 苏常 州 2 3 1 106;2 .江 苏 大 学材 料 学 院 江苏常. 23 1) 州 10 6 江 苏 镇 江 2 2 1 10 3
3 .江苏 工业 学 院机 械 系
摘 要 :通过 分 析 软质 层 的 形成 、作 用 以及 纳 米磨 料 的 自身 变 形对 材 料 去 除 的影 响 ,改 进 了 C MP过 程 的接 触 力 学 模 型 ;分 析 了纳 米 磨料 自身 变 形量 对 磨 料嵌 入 硅 晶 片基 体 材 料 的 深 度 的 影 响 ,以 及 纳 米 磨 料 硬 度 对 抛 光 表 面 粗 糙 度 的影 响 。结 果表 明 :软质 层 的 存在 增 加 了单个 纳 米 磨料 所 去 除材 料 的 体 积 ,且 对 基体 材 料有 保 护 作用 ,减 小 了纳 米 磨料 嵌 入 基体 材 料 的深 度 ;纳 米 磨 料 的 自身 变 形抵 消 了 纳米 磨 料嵌 入 基 体材 料 的切 削 深度 ,从 而也 决 定 了抛 光 表 面 的粗糙 度 ;纳 米磨 料 的 自身变 形量 与纳 米磨 料 的 硬 度有 关 ,硬度 低 的 纳米 磨 料 自身变 形 量 大 , 因而 切削 深 度小 ,抛 光后 表 面 的粗 糙 度
纳米ceo2磨料对硅晶片cmp的效果与机理研究
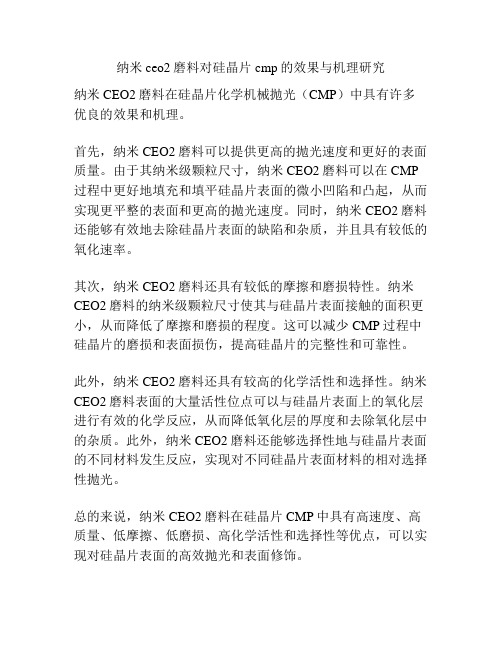
纳米ceo2磨料对硅晶片cmp的效果与机理研究
纳米CEO2磨料在硅晶片化学机械抛光(CMP)中具有许多优良的效果和机理。
首先,纳米CEO2磨料可以提供更高的抛光速度和更好的表面质量。
由于其纳米级颗粒尺寸,纳米CEO2磨料可以在CMP 过程中更好地填充和填平硅晶片表面的微小凹陷和凸起,从而实现更平整的表面和更高的抛光速度。
同时,纳米CEO2磨料还能够有效地去除硅晶片表面的缺陷和杂质,并且具有较低的氧化速率。
其次,纳米CEO2磨料还具有较低的摩擦和磨损特性。
纳米CEO2磨料的纳米级颗粒尺寸使其与硅晶片表面接触的面积更小,从而降低了摩擦和磨损的程度。
这可以减少CMP过程中硅晶片的磨损和表面损伤,提高硅晶片的完整性和可靠性。
此外,纳米CEO2磨料还具有较高的化学活性和选择性。
纳米CEO2磨料表面的大量活性位点可以与硅晶片表面上的氧化层进行有效的化学反应,从而降低氧化层的厚度和去除氧化层中的杂质。
此外,纳米CEO2磨料还能够选择性地与硅晶片表面的不同材料发生反应,实现对不同硅晶片表面材料的相对选择性抛光。
总的来说,纳米CEO2磨料在硅晶片CMP中具有高速度、高质量、低摩擦、低磨损、高化学活性和选择性等优点,可以实现对硅晶片表面的高效抛光和表面修饰。
第二十二届中国磨粒技术学术会议主题报告速览

第二十二届中国磨粒技术学术会议主题报告速览Quick review of topic reports on 22nd Chinese Conference of Abrasive Technology马宇昊,尹韶辉,刘 坚,李明泽,索鑫宇(湖南大学)9月22日至24日,第二十二届中国磨粒技术学术会议在江苏无锡召开,参会专家、学者近500人。
本次会议共邀请到12位专家学者进行主题报告,分别展示了磨粒技术领域的最新发展和学术成果。
华侨大学徐西鹏教授报告了一种金刚石衬底的高效低损伤反应磨削加工中活性磨料选择方法。
通过第一性原理计算、真空热处理实验、激光诱导等离子体刻蚀实验等方式遴选适宜辅助研磨金刚石的活性金属元素,然后通过添加活性金属微粉和将活性金属镀覆在磨粒表面等方法制备出含活性金属的磨削砂轮,分别采用恒进给切入式磨削和恒载荷端面磨削两种方式研究了含活性金属砂轮反应磨削金刚石的磨削机理、磨削质量和磨削效率。
华中科技大学陈学东教授针对超精密运动工作台超稳结构设计、超精运动控制及超静环境减振等问题,介绍了纳米精度运动系统多物理场耦合动力学仿真与设计、超精密宏微主从-双台交叉同步控制以及准零刚度减振-稳姿等技术的研究进展,并介绍了这些技术在IC制造装备研制中的实际应用。
澳大利亚昆士兰大学黄含教授在报告中对硬脆材料延性域加工的前期工作进行了系统回顾,并重点介绍了脆性材料延性域加工的理论依据,以及阈值破坏机理对脆性材料去除模型的影响。
最后介绍了半导体晶体材料加工去除机理和磨削工艺开发的一些案例,根据自己的研究经验提出未来脆性材料延性域加工领域需要解决的关键问题。
南方科技大学张璧教授的报告聚焦磨削加工过程中复合材料的去除机理、加工表面完整性和先进磨削技术等,汇报国内外研究机构在各类复合材料的磨削加工研究方面的最新进展,首次提出复合材料磨削加工过程中的四大效应,即尺寸效应、各向异性效应、界面效应和热效应,这四大效应可能会共同影响复合材料的磨削加工结果。
MEMS的主要工艺类型与流程

MEMS的主要工艺类型与流程MEMS(微机电系统)是一种将微型机械结构与微电子技术相结合的技术,具有广泛的应用前景,在传感器、加速度计、微流体器件等领域有重要的作用。
MEMS的制备过程包括几个主要的工艺类型和相应的流程,本文将详细介绍这些工艺类型和流程。
1.半导体工艺半导体工艺是MEMS制备中最常用的工艺类型之一、它借鉴了集成电路制造的技术,将MEMS结构与电路结构集成在一起。
半导体工艺的制备流程主要包括以下几个步骤:(1)硅片准备:选择高纯度的单晶硅片作为基底材料,通常使用化学机械抛光(CMP)等方式使其表面光滑。
(2)掩膜和光刻:使用光刻胶将掩膜图形转移到硅片表面,形成所需的结构图案。
(3)蚀刻:使用干法或湿法蚀刻技术去除光刻胶外部的硅片,仅保留需要的结构。
(4)沉积:在蚀刻后的硅片表面沉积不同材料,如金属、氧化物等,形成MEMS结构的各个层次。
(5)光刻:重复进行掩膜和光刻步骤,形成更多的结构图案。
(6)终结:最后,进行退火、切割等步骤,完成MEMS器件的制备。
2.软件工艺软件工艺是MEMS制备中的另一种主要工艺类型。
与半导体工艺不同,软件工艺使用聚合物材料作为主要基底材料,并采用热压、激光加工等方式形成MEMS结构。
软件工艺的制备流程主要包括以下几个步骤:(1)选择聚合物材料:根据应用需求选择合适的聚合物材料作为基底材料。
(2)模具制备:根据设计要求制作好所需的模具。
(3)热压:将聚合物材料放置在模具中,通过加热和压力使其形成所需的结构。
(4)取模:待聚合物冷却后,从模具中取出完成的MEMS结构。
3.LIGA工艺LIGA(德语为"Lithographie, Galvanoformung, Abformung"的首字母缩写)工艺是一种利用光刻、电沉积和模具制备的工艺方法,主要适用于高纵深结构的制备。
LIGA工艺的制备流程主要包括以下几个步骤:(1)光刻:使用光刻胶将掩膜图形转移到聚合物或金属表面,形成结构图案。
化学机械抛光技术研究现状与展望

第24卷第2期2009年4月 山东建筑大学学报JOURNAL OF SHANDO NG J I A NZ HU UN I V ERS IT Y Vol .24No .2Apr .2009收稿日期基金项目国家自然科学基金重点项目(U 635);山东省自然科学基金重点项目(Z F 6)作者简介张健(),女,山东东营人,山东建筑大学机电工程学院在读硕士,主要从事硬盘盘片的化学机械抛光研究文章编号:1673-7644(2009)02-0168-07化学机械抛光技术研究现状与展望张健,史宝军,杜运东,杨廷毅(山东建筑大学机电工程学院,山东济南250101)摘要:化学机械抛光技术几乎是迄今唯一可以提供全局平面化的表面精加工技术,可广泛用于集成电路芯片、计算机硬磁盘、微型机械系统(M E M S )、光学玻璃等表面的平整化。
本文综述了C M P 的技术原理和C M P 设备及消耗品的研究现状,指出了C M P 急待解决的技术和理论问题,并对其发展方向进行了展望。
关键词:化学机械抛光;平整化;表面微加工;无颗粒抛光中图分类号:T H117 文献标识码:AAdvances and pr oble m s of che m i ca l m echan i ca l poli sh i n gZHANG J ian,SH IB ao 2jun,DU Yun 2dong,et a l .(School of Mechanica l and Elec tric Enginee ring,Shandong J ianzhu University,Jinan 250101,China )Ab stra ct :Chem ical m echanica l polishing (C MP )is the only finish m achining technique up t o date f or sur face gl obal p lanarization,which has been w idely used f or the p lana rizing of integrated c ircuits(I C)chip,hard disk,m icr o 2e lectr om echanica l syste m s (MEMS ),op tica l gla ss,e tc .I n this pape r,we re 2vie w the technical principle,equi pm ents and expendables used in C MP,and outline the technical and theor e tical pr oblem s which are p ressed f or s oluti on and give a f uture pr ospect of C MP .Key wor ds:chem ical m echanical polishing;p lana rization;surface m icr om achining;abrasive 2fr ee pol 2ishing0 引言在计算机硬盘技术中,存储密度从2003年以每年60%的速度快速上升,计算机磁头的飞行高度已降低到10nm 左右,并有进一步下降的要求,这就要求磁头及硬盘表面都必须超光滑,磁头、磁盘的表面粗糙度、波纹度和纳米划痕会影响磁头的飞行稳定性和表面抗腐蚀性,其中下一代磁盘要求表面划痕深度≤1n m ,粗糙度≤0.1nm 。
硅片化学机械抛光表面材料去除非均匀性实验_苏建修

第22卷第5期 超 硬 材 料 工 程V ol.22 2010年10月SU PER HA RD M A T ERI AL EN GI NEER IN G Oct.2010硅片化学机械抛光表面材料去除非均匀性实验苏建修1,陈锡渠1,杜家熙1,宁欣1,康仁科2(1.河南科技学院,河南新乡453003;2.大连理工大学精密与特种加工教育部重点实验室,辽宁大连116024)摘 要:化学机械抛光技术已成为超大规模集成电路制造中实现硅片全局平面化的实用技术和核心技术。
CM P的最大问题之一是硅片材料去除的非均匀性,它是集成电路对硅片表面平坦化需求的一个重要指标。
文章提出了硅片表面材料去除非均匀性计算公式,在CP-4实验用抛光机上进行了硅片化学机械抛光实验,并用美国A DE公司生产的Wafer Check-7200型非接触式电容厚度测量设备对单晶硅片的厚度进行高精度检测,经过计算,得出了不同抛光速度下硅片表面材料去除非均匀性的数据,为理解硅片CM P材料去除非均匀性形成机理,进一步揭示硅片CM P材料去除机理提供了理论依据。
关键词:化学抛光;材料去除;非均匀性中图分类号:T Q164 文献标识码:A 文章编号:1673-1433(2010)05-0001-04Experiment of material removal un-uniformity in chemicalmechanical polishing of silicon waferSU Jian-x iu1,CHEN Xi-qu1,DU Jia-x u1,NING Xin1,KANG Ren-ke2(1.H enan I ns titute of Science and T echnology,X inx iang453003,China;2.K ey L abor atory f or Pr ecision and N on-T raditional M achining T echnology of M inistry ofEducation,D alian Univers ity of T echnology,D alian116024,China)Abstract:Chemical mechanical polishing(CMP)has becom e an operative and key technol-og y in pr oduction of super-large-scale-integ ratio n to achiev e co mplete planarization.Oneof the key po ints o f CM P is material rem oval un-uniform ity of the silicon w afer;it is a keyfactor of planarization r equired in integ rated circuit pro duction.The for mula o f calculatingeliminating un-unifo rmity of the silicon wafer w as first proposed in this article,CMP ex-periment w as taken out on a CP-4laboratory po lishing machine,and thickness of the sili-co n w afer w as highly precisely m easured w ith WaferCheck-7200pr oduced by ADE Cor p,U SA.M aterial remo val un-uniform ity at differ ent po lishing speed w as calculated and the-ory evidence w as pr ovided for understanding the fo rmation and further revealing themechanism of m aterial remo val un-unifo rmity o f silico n w afer CM P.Keywords:CM P;material remov al;un-unifor m收稿日期:2010-08-20作者简介:苏建修(1966-),男,河南博爱人,博士研究生,从事宝石级金刚石的合成研究。
硅单晶损伤层对抛光去除量的影响研究

硅单晶损伤层对抛光去除量的影响研究
引言:
硅单晶作为一种重要的半导体材料,在电子、光伏、通信等领域有着广泛的应用。
在硅单晶的生长、切片、抛光等过程中,不可避免地会产生损伤层,其厚度和性质对硅单晶的性能和加工效率有着重要的影响。
因此,研究硅单晶损伤层对抛光去除量的影响具有重要的实际意义。
实验方法:
本实验采用了一种新型的硅单晶生长方法,生长得到的硅单晶表面光滑、无损伤层。
实验中,将硅单晶切割成不同厚度的片材,采用不同速度的机械抛光机进行抛光处理。
在抛光过程中,记录抛光去除量,并对抛光去除量与硅单晶损伤层厚度的关系进行分析。
结果与讨论:
实验结果表明,硅单晶损伤层对抛光去除量的影响显著。
随着硅单晶损伤层厚度的增加,抛光去除量逐渐增大。
这是因为损伤层会影响硅单晶表面的平整度和光滑度,导致抛光剂无法均匀地分布在硅单晶表面,从而增加了抛光去除量。
此外,实验还发现,损伤层的厚度对抛光去除量的影响较大,因此在实际生产中需要控制损伤层的厚度,以保证硅单晶的性能和加工效率。
结论:
本实验研究了硅单晶损伤层对抛光去除量的影响,实验结果表明,硅单晶损伤层对抛光去除量的影响显著。
碳化硅化学机械抛光中材料去除非均匀性研究进展
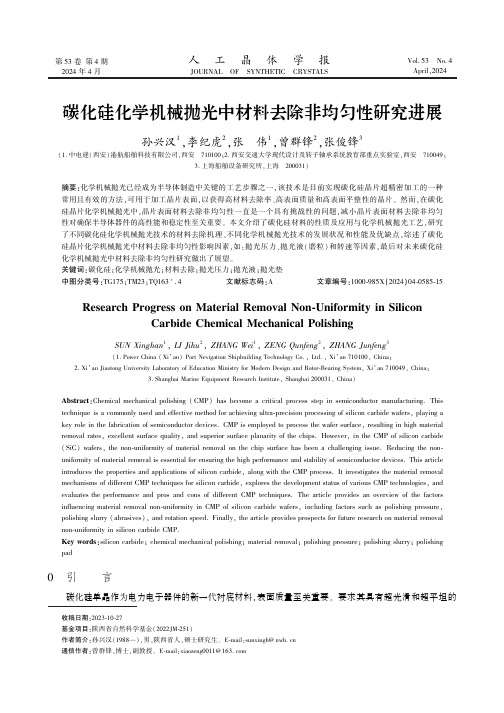
第53卷第4期2024年4月人㊀工㊀晶㊀体㊀学㊀报JOURNAL OF SYNTHETIC CRYSTALS Vol.53㊀No.4April,2024碳化硅化学机械抛光中材料去除非均匀性研究进展孙兴汉1,李纪虎2,张㊀伟1,曾群锋2,张俊锋3(1.中电建(西安)港航船舶科技有限公司,西安㊀710100;2.西安交通大学现代设计及转子轴承系统教育部重点实验室,西安㊀710049;3.上海船舶设备研究所,上海㊀200031)摘要:化学机械抛光已经成为半导体制造中关键的工艺步骤之一,该技术是目前实现碳化硅晶片超精密加工的一种常用且有效的方法,可用于加工晶片表面,以获得高材料去除率㊁高表面质量和高表面平整性的晶片㊂然而,在碳化硅晶片化学机械抛光中,晶片表面材料去除非均匀性一直是一个具有挑战性的问题,减小晶片表面材料去除非均匀性对确保半导体器件的高性能和稳定性至关重要㊂本文介绍了碳化硅材料的性质及应用与化学机械抛光工艺,研究了不同碳化硅化学机械抛光技术的材料去除机理㊁不同化学机械抛光技术的发展状况和性能及优缺点,综述了碳化硅晶片化学机械抛光中材料去除非均匀性影响因素,如:抛光压力㊁抛光液(磨粒)和转速等因素,最后对未来碳化硅化学机械抛光中材料去除非均匀性研究做出了展望㊂关键词:碳化硅;化学机械抛光;材料去除;抛光压力;抛光液;抛光垫中图分类号:TG175;TM23;TQ163+.4㊀㊀文献标志码:A ㊀㊀文章编号:1000-985X (2024)04-0585-15Research Progress on Material Removal Non-Uniformity in Silicon Carbide Chemical Mechanical PolishingSUN Xinghan 1,LI Jihu 2,ZHANG Wei 1,ZENG Qunfeng 2,ZHANG Junfeng 3(1.Power China (Xi an)Port Nevigation Shipbuilding Technology Co.,Ltd.,Xi an 710100,China;2.Xi an Jiaotong University Laboratory of Education Ministry for Modern Design and Rotor-Bearing System,Xi an 710049,China;3.Shanghai Marine Equipment Research Institute,Shanghai 200031,China)Abstract :Chemical mechanical polishing (CMP)has become a critical process step in semiconductor manufacturing.This technique is a commonly used and effective method for achieving ultra-precision processing of silicon carbide wafers,playing a key role in the fabrication of semiconductor devices.CMP is employed to process the wafer surface,resulting in high material removal rates,excellent surface quality,and superior surface planarity of the chips.However,in the CMP of silicon carbide (SiC)wafers,the non-uniformity of material removal on the chip surface has been a challenging issue.Reducing the non-uniformity of material removal is essential for ensuring the high performance and stability of semiconductor devices.This article introduces the properties and applications of silicon carbide,along with the CMP process.It investigates the material removal mechanisms of different CMP techniques for silicon carbide,explores the development status of various CMP technologies,and evaluates the performance and pros and cons of different CMP techniques.The article provides an overview of the factors influencing material removal non-uniformity in CMP of silicon carbide wafers,including factors such as polishing pressure,polishing slurry (abrasives),and rotation speed.Finally,the article provides prospects for future research on material removal non-uniformity in silicon carbide CMP.Key words :silicon carbide;chemical mechanical polishing;material removal;polishing pressure;polishing slurry;polishing pad ㊀㊀收稿日期:2023-10-27㊀㊀基金项目:陕西省自然科学基金(2022JM-251)㊀㊀作者简介:孙兴汉(1988 ),男,陕西省人,硕士研究生㊂E-mail:sunxingh@ ㊀㊀通信作者:曾群锋,博士,副教授㊂E-mail:xiaozeng0011@0㊀引㊀㊀言碳化硅单晶作为电力电子器件的新一代衬底材料,表面质量至关重要㊂要求其具有超光滑和超平坦的586㊀综合评述人工晶体学报㊀㊀㊀㊀㊀㊀第53卷表面,以确保单晶衬底表面粗糙度低于0.3nm,从而满足外延薄膜生长的要求[1-2]㊂然而,碳化硅单晶的高硬度和化学惰性造成了在抛光加工中的困难,因此需要寻求更加适用的抛光技术,这对于确保材料的质量和性能至关重要[3-7]㊂化学机械抛光(chemical mechanical polishing,CMP)技术是半导体晶片表面加工的关键技术之一㊂该技术综合了抛光液的化学腐蚀作用和磨粒及抛光垫的机械去除作用,以实现抛光后工件表面的良好质量㊁无损伤和高面形精度[8]㊂在碳化硅晶片的CMP过程中,研究者尽管控制晶片表面各点的速度相同并施加均匀载荷,实验结果却显示晶片下表面各点的材料去除率(material removal rate,MRR)不同㊂MRR随着从晶片中心到边缘的位置变化而变化,且边缘处的MRR较高,容易导致 过磨(over-grinding) 现象[9-11],即晶片表面材料去除非均匀性现象㊂在碳化硅晶片CMP过程中,晶片表面材料去除非均匀性受抛光头与抛光盘转速㊁抛光压力㊁抛光垫和抛光液特性等因素,以及这些因素相互作用的影响,这给碳化硅晶片CMP中材料去除非均匀性机理及控制方法等方面的研究带来诸多困难㊂对于材料去除非均匀性的问题,许多学者根据不同的理论和实验,对不同参数下的材料去除非均匀性进行了研究,得出了不同的结论㊂在研究过程中,主要关注抛光压力㊁抛光液㊁相对转速㊁温度和抛光头的摆动参数等因素对非均匀性的影响[12-15]㊂目前,关于材料去除非均匀性形成机制的研究还不够深入,由于涉及多个因素和复杂的相互作用,存在争议和不确定性[16-17]㊂尤其是电力电子器件的发展对CMP技术提出了很高要求,研究碳化硅CMP中材料去除非均匀性对提高碳化硅CMP技术水平有重要理论意义和应用价值[18]㊂因此,进一步深入研究材料去除非均匀性的机制是必要的㊂本文将从碳化硅材料的基本性质㊁微观结构特点,以及与材料去除特性之间的关联关系出发,阐述碳化硅CMP技术和材料去除非均匀性的机理,研究碳化硅CMP中影响材料去除非均匀性的因素,最后对未来碳化硅CMP中材料去除非均匀性的研究方向做出展望㊂1㊀碳化硅的性质与应用碳化硅又称金刚砂,分子式为SiC,每一个C原子周围通过共价键形式连接四个Si原子,每一个Si原子周围通过共价键形式连接四个C原子,即:碳化硅是由诸多CSi4单元和SiC4单元彼此穿插组成的四面体结构,这种四面体结构以共边形式连接形成平面层,通过顶点与下一层的四面体相连形成三维结构㊂这种典型的晶体结构如图1所示,因此,碳化硅优越的力学性能与其自身结构密切相关[19]㊂图1㊀碳化硅结构Fig.1㊀Silicon carbide structure碳化硅的物理性质主要表现在高硬度㊁高耐磨性㊁高导热率等方面,且密度为3.211g/cm3㊁莫氏硬度高达9.5㊁显微硬度在3000~3300kg/mm2,其硬度仅次于金刚石,并且当温度在1500ħ时,碳化硅仍能保持优良的硬度和强度[20]㊂此外,碳化硅还具有出色的热导率(达到4.9W/(K㊃cm))㊁高击穿电场和良好的电学性能㊂因此,它在高频㊁高效㊁高温微电子领域被广泛应用作为大功率元器件㊂同时,碳化硅还具有卓越的抗辐射性能(>103W/cm),使其在人造卫星㊁航空航天和核能等领域得到广泛应用㊂碳化硅的物理性质如㊀第4期孙兴汉等:碳化硅化学机械抛光中材料去除非均匀性研究进展587㊀表1所示㊂表1㊀碳化硅的物理性质[1]Table 1㊀Physical properties of silicon carbide [1]Property Value Band gap /eV 2.3~3.3Density /(g㊃cm -3) 3.211Thermal conductivity /(W㊃K -1㊃cm -1)3~4.9Saturated electron drift rate /(107cm㊃s -1) 2.0Breakdown field /(MV㊃cm-1)0.8~3.0Microhardness /(kg㊃mm -2)3000~3300Mohs hardness 9.5Melting point /ħ2700碳化硅具有出色的化学和热稳定性㊂在常温下,它不与酸㊁碱发生反应,表现出良好的化学稳定性㊂在碱性环境且存在氧化剂的情况下,能够生成可溶性硅酸盐,这为碳化硅CMP 提供了关键的化学反应原理㊂此外,碳化硅还具备良好的热稳定性,当加热到1300ħ时,在空气中形成的二氧化硅保护层能够防止碳化硅继续被氧化㊂在空气中加热到1627ħ时,碳化硅表面的保护膜开始被破坏,达到最高工作温度,因此,工业高温使用时,温度一般控制在1600ħ以下㊂2㊀碳化硅CMP 技术简介CMP 技术是半导体制造过程中实现晶片表面平坦化的关键工艺[17,19],该工艺结合传统纯机械和纯化学抛光方法去除晶片表面微米/纳米级不同材料,从而实现晶片表面的高度(纳米级)平坦化㊂根据不同工艺制程要求,每一片晶片都会历经几道甚至几十道CMP 技术步骤㊂CMP 技术中使用的抛光材料包括抛光液㊁抛光垫和清洁剂等,其中占比最大的是抛光液和抛光垫㊂CMP 工作原理示意图如图2所示㊂在碳化硅晶片CMP 技术中,抛光液起到化学去除的作用,抛光液中的化学成分与碳化硅晶片表面进行化学反应,把晶片损伤表面和表面附着物质通过反应转变成更容易抛光的氧化层;抛光垫起到机械去除的作用[21],抛光垫对碳化硅晶片表面研磨,将软化层抛离抛光表面,并使未反应的晶片表面重新暴露出来,从而保证晶片表面化学作用继续进行,如此反复的氧化成膜-机械去除过程可实现有效抛光的目的,其CMP 反应原理如图3所示㊂图2㊀CMP 工作原理示意图[20]Fig.2㊀Schematic diagram of CMP working principle [20]图3㊀CMP 反应原理示意图[22]Fig.3㊀Schematic diagram of CMP reaction principle [22]3㊀碳化硅CMP 中材料去除机理对于碳化硅晶片而言,采用不同的CMP 技术,其MRR㊁加工后表面质量,以及材料去除机理也不相同[23]㊂该部分将从不同碳化硅CMP 技术的材料去除机理出发,研究碳化硅CMP 中材料去除的非均匀性,为后续研究者提供参考㊂588㊀综合评述人工晶体学报㊀㊀㊀㊀㊀㊀第53卷3.1㊀传统CMP在传统CMP 过程中,化学反应和机械磨削相互作用,共同促进碳化硅材料的去除㊂化学反应使表面材料发生溶解或转化,而机械磨削则通过磨料颗粒的切削和磨损作用去除材料㊂同时,通过合理调节抛光液的成分㊁压力和磨料颗粒的特性,可以实现对碳化硅表面的控制去除,获得所需的表面质量和形貌㊂按照磨料的存在状态,碳化硅的传统CMP 分为游离磨粒抛光和固结磨粒抛光[24]㊂图4㊀游离磨粒抛光示意图[24]Fig.4㊀Schematic diagram of free abrasive polishing [24]游离磨料抛光工艺装置主要由旋转工作台㊁工件承载器及研磨液输送装置三部分组成[24],游离磨粒抛光示意图如图4所示,其原理为:将抛光垫固定在旋转工作台上,使组成的部分进行自旋转,同时通过外部承载器给晶片表面施加正压力,使它们能够进行相对运动㊂在传统游离磨料抛光中,通常采用三体摩擦方式对材料进行去除,即晶片表面㊁抛光垫表面和磨料之间的三体相互作用㊂这种三体摩擦方式是实现抛光和材料去除的核心方法,通过控制这三者之间的相互作用,可以实现表面的加工和改进㊂固结磨粒抛光加工装置与游离磨粒抛光装置类似,区别在于抛光垫,即固结磨粒抛光使用的是固结磨粒研磨抛光垫,同时使用树脂结合剂固结磨粒和去离子水及环保的化学试剂作为抛光液㊂该抛光过程的原理为:利用固结磨粒研磨抛光垫表面露出的磨粒尖端对晶片表面实现材料的有效去除㊂固结磨粒加工技术的核心是固结磨粒研磨抛光垫,其结构图如图5所示㊂图5㊀固结磨粒垫结构图[24]Fig.5㊀Schematic diagram of bonded abrasive pad structure [24]游离磨粒抛光和固结磨粒抛光均属于传统CMP 方式,这两种方式均结合了化学反应和机械力的去除作用,实现碳化硅晶片表面的材料去除,但是在碳化硅晶片上,机械力可能在不同区域施加得不均匀,导致材料去除的非均匀性,且抛光效率低,这些因素使传统CMP 在处理碳化硅时面临更大的挑战㊂3.2㊀等离子辅助抛光(plasma assisted polishing ,PAP )PAP 技术由日本大阪大学的Yamamura 于2010年首次提出[26-27]㊂碳化硅PAP 是一种在传统CMP 过程中引入等离子体辅助作用的技术㊂PAP 的材料去除机理主要涉及等离子体化学反应和机械磨削作用,即:通过化学反应实现晶片表面的无损伤加工,同时结合机械磨削作用对材料进行去除,提高晶片表面材料的去除率㊂PAP 技术结合了离子体化学反应和机械磨削作用两者的优势,不会对晶片亚表面造成损伤㊂碳化硅PAP 的原理为[28]:首先,对碳化硅表面改性,即进行等离子体辐照;其次,具有强氧化性等离子体中的自由基与碳化硅表面的原子发生化学反应,生成较软的改性层;最后,使用软磨料对改性层进行抛光,去除该改性层㊂如此交替进行的过程,使晶片的表面逐渐变平整,最终产生无损伤的晶片平坦表面㊂PAP 技术的原理如图6所示㊂PAP 加工装置由以下两个单元组成:等离子体发生单元㊁材料去除单元㊂其中,等射频电源产生离子体,载气使用惰性气体,使用强氧化性自由基团的气体作为反应气体㊂PAP 加工装置示意图如图7所示㊂㊀第4期孙兴汉等:碳化硅化学机械抛光中材料去除非均匀性研究进展589㊀图6㊀PAP技术原理图[28]Fig.6㊀Schematic diagram of PAP technology principle[28]图7㊀PAP加工装置示意图[28]Fig.7㊀Schematic diagram of PAP processing equipment[28]在PAP碳化硅中,材料去除率不仅受活性自由基及氧化层生成速率较低的影响,还受磨料硬度的影响,因此在PAP碳化硅中要解决以上因素的影响㊂另外,PAP设备价格昂贵,加工费用较高,限制了PAP碳化硅晶片的推广㊂3.3㊀催化剂辅助刻蚀(catalyst-assisted reactive etching,CARE)CARE的材料去除原理为:碳化硅在催化剂的作用下,其表面反应生成硬度较低的氧化层,然后在磨料机械去除的作用下,去除晶片表面的氧化层,最终获得高质量的晶片表面㊂Okamoto等[29]以铂作为催化剂,氢氟酸(HF)或水(H2O)作为刻蚀剂,研究CARE工艺对碳化硅晶片表面材料的去除过程㊂在铂催化剂的作用下,刻蚀剂的分解物与晶片反应生成硬度较低的氧化层,其中氧化层与HF反应生成H2SiF6,以形成新鲜的表面,最终获得高表面质量的晶片㊂该技术不需要添加磨料即可实现晶片表面的加工,但是效率较低㊂其加工装置示意图如图8所示㊂3.4㊀紫外线辅助化学机械抛光(ultraviolet-assisted chemical mechanical polishing,UV-CMP)紫外光催化反应是一种强氧化反应,其原理为:在紫外光的作用下,电子捕捉剂与光催化剂发生光催化反应,生成氧化性较强的活性自由基(㊃OH)㊂其次,活性自由基(㊃OH)与碳化硅的表层发生氧化反应生成硬度较低的SiO2氧化层,然后使用磨料进行机械抛光,去除晶片表面的SiO2氧化层,最终获得高质量的晶片表面㊂叶子凡等[30]选取催化剂作为紫外光的吸收剂,催化剂在紫外光的辐射下发生能级跃迁,产生电子-空穴对,并用氧化剂产生的活性自由基对晶片表面进行改性处理,生成硬度较低的氧化层,最后在磨料的机械去除作用下去除氧化层,以实现高质量的晶片表面㊂同时,提出了紫外CMP抛光模型:他认为紫外系统会对碳化硅晶片表面生成的SiO2氧化层厚度有影响,当加入紫外系统,晶片表面的MRR有很大的提高,其抛光模型如图9所示㊂590㊀综合评述人工晶体学报㊀㊀㊀㊀㊀㊀第53卷图8㊀CARE 加工装置示意图[29]Fig.8㊀Schematic diagram of CARE processing equipment [29]图9㊀UV-CMP 抛光模型[30]Fig.9㊀UV-CMP polishing model [30]在UV-CMP 碳化硅中,引入紫外光可进一步提高晶片表面的氧化速度,促进晶片表面材料的有效去除,但是在操作中很难控制紫外光和催化剂生成活性自由基的速率,从而影响晶片表面材料去除的速率与材料去除的非均匀性㊂3.5㊀基于芬顿反应的化学机械抛光(Fenton reaction-based chemical mechanical polishing ,Fenton-CMP )芬顿反应是法国科学家Fenton 最早发现并提出的,该反应为:二价铁离子(Fe 2+)与过氧化氢(H 2O 2)发生反应,生成羟基自由基(㊃OH),以氧化分解有机物[31-32]㊂基于芬顿反应碳化硅CMP 原理为:用芬顿反应生成的含有游离氧气(O 2)的㊃OH 溶液,对SiC 表面进行氧化处理,使其表面生成硬度较低且结合力小的SiO 2氧化层[33],然后在磨料的机械作用下去除该氧化层,最终获得高质量的晶片表面㊂其化学反应为Fe 2++H 2O 2ңFe 3++OH -+gOH (1)SiC +4gOH +O 2ңSiO 2+2H 2O +CO 2ʏ(2)Fe 3++H 2O 2ңFe 2++H ++gOOH (3)由以上反应可以发现:羟基自由基(㊃OH)是基于芬顿反应碳化硅CMP 的关键,且Fe 2+在反应中仅起催化的作用㊂从式(3)的化学反应可以看出:生成的㊃OH 浓度越高,晶片表面的化学反应速度越快,促使更多的高硬度晶片表面转化为更多软质的SiO 2氧化层,进而促使机械去除过程更容易[34]㊂因此,芬顿反应生成的㊃OH 浓度对晶片表面材料的高效去除至关重要[35]㊂碳化硅Fenton-CMP 技术材料去除过程示意图如图10所示㊂图10㊀碳化硅Fenton-CMP 技术材料去除过程示意图[34]Fig.10㊀Schematic diagram of the material removal process in silicon carbide Fenton-CMP technology [34]在Fenton-CMP 碳化硅中,无法控制羟基自由基(㊃OH)的产生量,且在操作过程中耗时,使晶片表面的氧化效率较低,从而影响晶片表面材料去除的速率与材料去除的非均匀性㊂3.6㊀电化学机械抛光(electrochemical mechanical polishing ,ECMP )ECMP 技术的原理为:利用电化学改性原理促使碳化硅表面的改性层硬度降低,即生成氧化层,然后在氧化铝等磨粒的机械作用下去除该氧化层,最终获得高质量的晶片表面[36]㊂其加工装置示意图如图11所示㊂㊀第4期孙兴汉等:碳化硅化学机械抛光中材料去除非均匀性研究进展591㊀图11㊀电化学机械抛光装置[36]Fig.11㊀Electrochemical mechanical polishing device [36]王磊等[37]使用ECMP 技术对碳化硅晶体的材料去除进行了研究,对比了三种电解液(NaOH㊁NaNO 3和H 3PO 4)对碳化硅晶体的电化学氧化效果,并选择了浓度为0.6mol /L 的NaNO 3作为电解液,同时使用金刚石-氧化铝混合磨粒的机械去除作用对碳化硅晶体进行了表面处理,得到了高质量的晶体表面,混合磨粒的去除机理示意图如图12所示㊂Murata 等[38]开发了一种环保高效的碳化硅ECMP 方法,该方法不需要含有催化性化学物质,并使用由固体聚合物电解质和CeO 2组成的复合垫,实现了约15μm /h 的高MRR,几乎是传统CMP技术获得的碳化硅晶片的10倍㊂在ECMP 碳化硅中,通过外加电场和化学作用使晶片表面氧化层硬度降低,可进一步快速提高晶片表面MRR,同时通过控制电流强度可提高晶片表面精度㊂另外,控制好晶片表面的氧化速率和材料去除率是高效获得光滑表面与解决材料去除非均匀性问题的关键㊂图12㊀混合磨粒去除机理示意图[37]Fig.12㊀Schematic diagram of the hybrid abrasive material removal mechanism [37]3.7㊀化学机械磁流变复合抛光(chemo-mechanical magnetorheological finishing ,CMMRF )碳化硅CMMRF 是一种先进的表面加工技术,可实现对碳化硅材料的高效材料去除㊂通过梁华卓等[39]的研究,碳化硅CMMRF 材料去除机理可总结为:通过使用抛光液与碳化硅表面的改性层发生化学反应,生图13㊀CMMRF 材料去除模型[40]Fig.13㊀CMMRF material removal model [40]成硬度较低的氧化层,然后在磁流变抛光垫和磨粒的机械作用下对氧化层进行去除,以实现晶片表面材料的高效去除㊂同时,他们还发现了磁性粒子电离出来的二价铁与抛光液中的过氧化氢发生芬顿反应[40],生成具有超强氧化性的羟基自由基(㊃OH),然后㊃OH 与晶片表面的改性层发生反应,生成硬度较低的SiO 2层,最终在磨料和磁流变抛光垫的作用下进行机械去除,如此重复的过程可实现高质量的晶片表面㊂碳化硅CMMRF 的材料去除模型如图13所示㊂在CMMRF 碳化硅中,该工艺的磨料为半固着状592㊀综合评述人工晶体学报㊀㊀㊀㊀㊀㊀第53卷态,相比于游离磨料工艺,该工艺材料去除高,但加工过程较复杂,还需进行工艺优化㊂通过以上机理及现状研究,不同CMP技术下碳化硅材料去除非均匀性的研究显示了各种方法的潜在优势㊂其中,ECMP和CMMRF对碳化硅材料的去除率较高,可进一步提高晶片表面材料去除的均匀性,但是CMMRF过程复杂,还需进行工艺优化以提高晶片表面材料去除的均匀性㊂不同CMP技术性能及优缺点如表2所示㊂表2㊀不同化学机械抛光技术性能及优缺点Table2㊀Performance and advantages/disadvantages of different chemical mechanical polishing technologies CMP技术晶片表面质量最大MRR优缺点传统CMP RMS<0.8nm(Si面)Ra<0.1nm<1000nm/h(Si面)表面质量好且加工损伤小,但抛光效率低PAP RMS>0.1nm<200nm/h软磨料将因活性自由基生成的氧化层去除且加工损伤小,但抛光效率最低CARE RMS<0.08nmRa<0.1nm<492nm/h㊃OH直接作用于晶片,不需添加磨料就能实现基晶片加工,但抛光效率低UV-CMP Ra>0.0539nm<400nm/h引入紫外光作用,可实现超精密加工,但受紫外光和催化剂影响且抛光效率低Fenton-CMP Ra>0.0965nm<200nm/h反应设备简单,但反应过程复杂且抛光效率低ECMP Ra>0.23nm<4000nm/h电化学作用且效率高,加工过程可控CMMRF Ra>0.42nm<6000nm/h磨料为半固着状态,突破了游离磨料对晶片的加工,材料去除高,但加工质量还需进行工艺优化综上所述,对于碳化硅晶片而言,不同的CMP技术具有特定的材料去除机理,CMP技术的选择要根据具体的应用情况来定㊂PAP㊁CARE㊁UV-CMP和CMMRF等技术均结合了化学反应和机械去除作用,可实现高质量的晶片表面,同时也可以减少纯机械作用对晶片表面的损伤㊂ECMP技术利用电化学改性和机械磨削相结合,能够实现高效抛光㊂然而,每种技术都有其适用的特定应用场景,选择合适的技术需要考虑加工要求㊁材料特性和设备条件等因素㊂4㊀碳化硅CMP中材料去除非均匀性影响因素分析在碳化硅CMP中,材料去除的非均匀性是指在抛光过程中不同位置或不同晶面的材料去除速率不同㊂通过文献调研,发现影响碳化硅CMP材料去除非均匀性的主要因素有:抛光压力㊁抛光液(磨粒)和转速㊂该部分将综述影响碳化硅CMP材料去除非均匀性的主要因素,分析不同因素对碳化硅晶片表面平整性的影响㊂4.1㊀抛光压力对材料去除非均匀性的影响抛光压力是碳化硅材料去除非均匀性的一个重要因素㊂如果抛光压力不足,可能导致磨料与碳化硅表面之间的接触不充分,减少了磨料对材料的切削作用㊂这会导致材料去除速率不均匀,表现为一些区域的材料去除较慢,而其他区域的材料去除较快㊂非均匀的材料去除可能导致晶片表面粗糙度和平坦度的不一致性㊂与压力不足相反,过大的抛光压力可能会导致磨料对碳化硅表面的切削过度㊂这可能引起表面的过度去除,形成凹陷或坑洞,导致表面不平整和不均匀的去除㊂过大的压力还可能引起磨料的堵塞或过度磨损,进一步影响材料去除的均匀性㊂为了实现材料去除的均匀性,抛光过程中需要实现压力均匀分布㊂压力均匀分布可以确保磨料在整个表面上均匀切削材料,从而获得一致的材料去除速率㊂因此,在碳化硅晶片CMP过程中,适当的抛光压力对实现均匀地材料去除非常重要㊂确保适当的压力水平,并实现均匀的压力分布,有助于获得表面平整度高㊁表面质量一致的抛光结果㊂庞龙飞等[1]基于CMP不同接触状态模型,研究了碳化硅晶片在抛光压力分别为160㊁220㊁280和340g/cm2下Si面的粗糙度,发现抛光后的晶片表面粗糙度会随着抛光压力的增大而变差,并对造成该现象的原因进行了分析:抛光压力的增加导致抛光垫压缩量变大,降低了抛光垫表面储存抛光液的能力,进而导致晶片与上下抛光盘之间的摩擦力增大,同时也导致晶片表面的粗糙度增大,晶片表面材料去除出现不均匀现象㊂晶㊀第4期孙兴汉等:碳化硅化学机械抛光中材料去除非均匀性研究进展593㊀片Si面在不同抛光压力下的粗糙度如图14所示㊂图14㊀不同抛光压力下晶片Si面粗糙度[1]Fig.14㊀Surface roughness of the Si face of chips at different polishing pressures[1]甘琨等[41]将抛光盘和抛光头转速分别固定为30和50r/min,控制抛光液的速率为4.2mL/min,抛光时间为10h,分析抛光后晶片表面粗糙度随抛光头压力变化的影响,也发现晶片表面粗糙度受抛光压力影响;通过实验对比分析,发现抛光压力为200N时,抛光后晶片表面材料去除均匀,且其表面质量最好,抛光压力对晶片表面粗糙度影响如图15所示㊂图15㊀不同抛光压力情况下碳化硅晶片表面粗糙度[41]Fig.15㊀Surface roughness of silicon carbide wafers at different polishing pressures[41]哈尔滨工业大学陈浩[9]通过理论和实验分析了碳化硅CMP后的平整性,其建立的SiC与抛光垫的有限元接触模型如图16所示㊂通过有限元仿真,得出了晶片表面接触应力云图,如图17(a)所示,并对不同压力下晶片表面接触应力进行分析,发现:随着下压力的增加,边缘处的接触应力随之增加,导致晶片边缘区域出现 过抛 现象,即导致晶片表面出现材料去除非均匀性现象,降低了晶片表面的平整性㊂郭钰等[6]研究了抛光压力和pH值共同作用对晶片表面材料去除的影响,发现抛光压力为200g/cm2㊁pH值为8.5时,抛光压力为300g/cm2㊁pH值为9.5时,抛光压力为400g/cm2㊁pH值为9.5时,晶片表面的材料去除逐渐增大,之后再增加pH值也不能有效提高晶片表面材料的去除率㊂因此,抛光压力越大,需要匹配的抛光液的pH值越高,从而达到更大的去除速率,促使晶片表面材料去除更加均匀㊂。
单晶硅表面机械划痕和氧化层在湿法刻蚀中的掩膜行为对比研究

单晶硅表面机械划痕和氧化层在湿法刻蚀中的掩膜行为对比研究单晶硅是一种广泛应用于半导体工业及太阳能光伏领域的重要材料。
在制备过程中,单晶硅的表面往往需要进行湿法刻蚀处理,以便获取高质量的晶片。
然而,在湿法刻蚀过程中,单晶硅表面的机械划痕和氧化层对掩膜的行为有很大影响。
因此,本文通过对单晶硅表面机械划痕和氧化层在湿法刻蚀中的掩膜行为进行对比研究,探讨了其影响机理和掩膜效果。
单晶硅表面机械划痕和氧化层对掩膜的行为是由于它们在湿法刻蚀过程中的化学反应和物理作用引起的。
机械划痕是指单晶硅表面被硬物刮擦或者切削后留下的凹槽和凸起。
这些划痕和微观的表面缺陷会影响湿法刻蚀过程中的化学反应动力学和反应区域。
划痕较深时,反应物难以进入到划痕底部,导致反应区域的扩散限制和反应速率的减缓。
因此,在刻蚀过程中,机械划痕会导致掩膜被腐蚀掉而形成缺陷,影响晶片的品质。
与机械划痕相比较,单晶硅表面氧化层对掩膜的行为更加复杂。
氧化层是由空气或水分对单晶硅表面反应生成的一层厚度相对较厚的氧化物,其主要成分是SiO2。
湿法刻蚀过程中,氧化层的存在会导致两个不同反应区域的形成。
氧化层下的区域称为氧化物区(也称为湿法反应区),而氧化层上方则称为氧化层上的表面区域,又称干法反应区。
在氧化物区,刻蚀液会与单晶硅反应生成气体或固体产物,导致氧化物区的体积不断缩小。
在干法反应区,由于氧化层的存在,氧分子的扩散是十分困难的,因此,与氧化层上方的气体接触的单晶硅表面与刻蚀液接触的表面之间会形成一层很薄的水层。
这种水层会妨碍刻蚀液与单晶硅表面的接触,减慢反应速度,甚至阻碍刻蚀完整进行。
在单晶硅表面机械划痕和氧化层对掩膜的行为中,划痕会影响反应质量和掩膜的完整性,而氧化层,则会减缓反应速率和导致表面抛光不理想等问题。
为了提高单晶硅的质量和晶片的制备效率,需要针对划痕和氧化层分别采取不同的措施。
针对单晶硅表面机械划痕,可以采用化学机械抛光(CMP)或者热氢处理等方法来去除划痕。
磨削速度和压力对单晶硅去除特性的影响

磨削速度和压力对单晶硅去除特性的影响于月滨;王紫光;周平;高尚;郭东明【摘要】为研究单晶硅磨削损伤,使用金刚石磨块在不同磨削速度和压力下对单晶硅表面进行高速划擦试验,金刚石的粒度尺寸为38~45 μm.通过测量硅片表面粗糙度、亚表面损伤深度和材料去除率,研究磨块的磨削速度和压力对材料去除特性的影响规律.结果表明:相同压力时,材料去除率随磨削速度增加呈先增大后减小的趋势,亚表面损伤深度逐渐变小;随法向压力增大,亚表面损伤深度变化不明显;在5N压力下,表面粗糙度值Ra变化明显,由6.4 μm减小到3.2μm;而10 N压力下,Ra无明显变化.【期刊名称】《金刚石与磨料磨具工程》【年(卷),期】2016(036)003【总页数】6页(P1-5,10)【关键词】单晶硅;磨削速度;法向压力;粗糙度;去除率;亚表面损伤【作者】于月滨;王紫光;周平;高尚;郭东明【作者单位】大连理工大学,精密与特种加工教育部重点实验室,大连116024;大连理工大学,精密与特种加工教育部重点实验室,大连116024;大连理工大学,精密与特种加工教育部重点实验室,大连116024;大连理工大学,精密与特种加工教育部重点实验室,大连116024;大连理工大学,精密与特种加工教育部重点实验室,大连116024【正文语种】中文【中图分类】TG74;TQ164作为一种性能优异的基底材料,单晶硅在集成电路、光电及国防科技等领域中被广泛应用。
为保证器件性能,单晶硅衬底加工要满足极高的表面几何精度和完整性要求。
使用金刚石磨粒砂轮进行超精密磨削加工是获得高性能硅衬底表面的主要方法[1-2]。
这种加工方法的实质是,嵌入在砂轮结合剂中的金刚石磨粒压入并划擦单晶硅表面,使材料的表面发生脆/塑性变形直至形成磨屑然后剥落,从而实现材料的去除[3]。
由于磨削过程主要是通过机械力作用实现材料去除,在加工后的单晶硅亚表面不可避免地会产生非晶层、相变甚至裂纹等损伤,直接影响元器件的性能[4]。
基于分子动力学的SiC化学机械磨削材料去除机理研究

基于分子动力学的SiC化学机械磨削材料去除机理研究龚福潜;吴柯;朱博恩;章博阳;许荣滨【期刊名称】《机械制造》【年(卷),期】2024(62)4【摘要】为了研究SiC化学机械磨削的材料去除机理,采用Lammps分子动力学仿真软件建立O_(2)环境中SiO_(2)磨料化学机械磨削加工SiC的原子模型进行分析。
仿真结果表明,O_(2)分子在磨粒的机械作用下和SiC表面的Si原子发生化学反应,生成SiO_(2)和SiO,并与C原子反应生成CO_(2)和CO。
当磨削温度低于1200K时,磨削温度提高对SiC的表面活化能和O_(2)扩散速率影响较小,O_(2)消耗量约为300个,Si-0键生成数量约为370个。
随着磨削温度提高到1600K,O_(2)扩散速率和化学反应速率提高,O_(2)消耗量超过340个,Si-0键生成数量超过440个。
O_(2)浓度增大能够加快化学反应速率,Si-0键生成数量从376个增加到598个。
当磨削深度从2A增大到6A时,原子去除数量从98个增加到265个,摩擦力增大2倍,同时磨削速度的提高能够提高材料去除率。
基于分子动力学对O_(2)环境下SiC化学机械磨削的材料去除机理进行研究,发现SiC会和O_(2)发生化学反应,生成Si-O氧化膜和C-O气体,为SiC的化学机械磨削提供理论依据。
【总页数】8页(P38-45)【作者】龚福潜;吴柯;朱博恩;章博阳;许荣滨【作者单位】宁波大学机械工程与力学学院;浙江五洲新春集团股份有限公司【正文语种】中文【中图分类】TH145.1【相关文献】1.超高速磨削切屑去除机理的分子动力学仿真研究2.纳米磨削过程中加工表面形成与材料去除机理的分子动力学仿真3.基于单分子层去除机理的芯片化学机械抛光材料去除模型4.单颗磨粒超声辅助磨削SiC陶瓷材料去除机理5.基于分子量级的化学机械抛光材料去除机理因版权原因,仅展示原文概要,查看原文内容请购买。
硅片化学机械抛光中表面形貌问题的研究

图 1 化学机械抛光示意图
软, 粘贴在刚性的主盘上, 主盘和晶片同向转动, 抛 光液以一定的流量加在抛光垫的中心。
抛光中的设备型号以及实验参数为: 抛光机: Polish M od el 3800; 抛光垫: R odel Suba 600; 抛光液: DANM MAZ IN SR310或自制抛光液; 主盘转速: 60 r/m in; 压力: 0 16 M Pa; 抛光液流速: 0 3 L /m in。 腐蚀后的硅片经去离子水冲洗后进行抛光。粒径
样品编号
1234567
去除厚度 / m 2 0 4 0 5 3 7 7 9 7 14 2 19 4
1 4 观测方法 使用非接触式厚 度仪测 量样品 厚度, 按 照 GB /T
6618 1995标准取 5 点 厚度 的平 均值; 利 用扫 描电 镜 观察样品腐蚀状 态的 表面形 貌; 利 用 WYKO MHT 型光干涉形貌仪测量粗糙度数值以及判断是否有桔皮
果。工业上对抛光过程的控制往往基于经验, 与实验 室研究有较大差别。本文作者通过实验手段对实际抛
光中的表面形貌问题进行了研究, 包括: 抛光过程中 硅片形貌及粗糙度的变化; 硅溶胶粒径对粗糙度的影 响; 抛光液中碱浓度和抛光桔皮现象的联系等。 1 实验部分 1 1 样品
样品为 直径 为 152 4 mm 的 n 型 ( 100 ) 单 晶硅 研磨片。在进行抛光之前首先进行化学腐蚀, 以去除 在研磨中 造 成的 损伤 层, 获 得完 美 的无 机械 损 伤表 面。 1 2 抛光液制备
貌的改善作用。
未经滤波的粗糙度曲线和经过低通滤波之后的曲
线的偏 差逐 渐增 大, 说 明随 着抛 光 时间 的 延 长, 低 频、大波长的形貌信息对样品表面粗糙度的影响逐渐
- 1、下载文档前请自行甄别文档内容的完整性,平台不提供额外的编辑、内容补充、找答案等附加服务。
- 2、"仅部分预览"的文档,不可在线预览部分如存在完整性等问题,可反馈申请退款(可完整预览的文档不适用该条件!)。
- 3、如文档侵犯您的权益,请联系客服反馈,我们会尽快为您处理(人工客服工作时间:9:00-18:30)。
© 1994-2010 China Academic Journal Electronic Publishing House. All rights reserved.
3. Key Laboratory for Precision and Non2Traditional M achining Technology of M inistry of Education, Dalian University of Technology, Dalian 116024, China)
材料去除率 ,则有
ΔM =ΔM a +ΔM p
(2)
ΔM a =ΔMm_a +ΔM c_a
(3)
ΔM p =ΔMm_p +ΔM c_p
(4)
2 硅片 CM P材料去除率实验
2. 1 实验设备及实验条件 取直径为 5. 08 cm (2英寸 )的单晶硅研磨腐蚀片
试样若干 ,在美国 CETR公司的 CP24抛光机上进行实 验. 该实验设备可在线测量抛光系统的摩擦力 、摩擦系 数以及声发射信号等 ,抛光机放置在 1 000 级超净室 中 ,环境温度控制在 22 ℃左右. 抛光垫为 Rodel公司 生产的 IC21000 / Suba IV 平抛光垫 ,实验用水为 18124 MΩ的去离子水. 实验所用的 3 种抛光液由天津晶岭 电子材料科技有限公司提供 , S1号为 FA /O 标准单晶 硅抛光液 ; S2号为纯磨粒抛光液 (即标准抛光液中所 用的磨粒加去离子水配制 ,含量与 S1号标准抛光液相 同 ) ; S3号为无磨粒抛光液 (为去除磨粒的 S1 标准抛 光液 ). 2. 2 实验参数的选择
第
7卷 第 3期 2009年 5月
纳 米 技 术 与 精 密 工 程 Nanotechnology and Prec ision Eng ineer ing
Vol. 7 No. 3 M ay 2009
基于磨损行为的单晶硅片化学机械抛光材料的去除特性
苏建修 1 , 高 虹 2 , 陈锡渠 1 , 宁 欣 1 , 郭东明 3
表示由抛光垫 、磨粒的机械作用所增强的化学作用材
料去除率 ;ΔMm_p和 ΔMm_a分别表示由化学作用所增强
的抛光垫 、磨粒的机械作用产生的材料去除率.
设 ΔM 为 CM P时的机械与化学交互作用去除率 ,
ΔM p 为抛光垫的机械与抛光液的化学交互作用材料 去除率 ,ΔM a 为磨粒的机械与抛光液的化学交互作用
(1. School of M achinery and Electricity, Henan Institute of Science and Technology, Xinxiang 453003, China; 2. College of Vocational Education, Guizhou University, Guiyang 550025, China;
Abstract: In order to understand the behavior of material removal in the p rocess of chem ical m echanical polishing (CM P) , the model of form ing elem ent of material removal rate (MRR ) has been built based on friction and abrasion behaviors in wafer CM P p rocess. D ifferent CM P slurries were designed for CM P test of MRR. According to the test results, the MRR p roduced by mechanical action, chem ical action and interaction between the m echanical action and the chem ical action, respectively, has been obtained. The test results show that the interaction rate between the m echanical action and the chem ical action is 8517% —9911% , the action rate of the abrasive is 6915% —9410% and the interaction rate between the mechanical action of the abrasives and the chem ical action of slurry is 5511% —9311%. It is concluded that the mechanical action p roduced by the abrasive is the main mechanical action in wafer CM P p rocess and the MRR m ainly results from the interaction between the m echanical action of the abrasives and the chem ical action of slurry. These results p rovide a theoretical guide for further understanding of the m ate2 rial removal mechanism in wafer CM P.
交互作用去除率 ,则总的材料去除率为
M =M c +Mm_p +Mm_a +ΔM c_p +ΔM c_a &
(1)
式中 : M 为总的材料去除率 ; M c为抛光液化学腐蚀作
用引起的材料去除率 ; Mm_p和 Mm_a分别表示只考虑抛 光垫 、磨粒的机械作用材料去除率 ;ΔM 和 c_p ΔM c_a分别
(1. 河南科技学院机电学院 , 新乡 453003; 2. 贵州大学职业技术学院 , 贵阳 550025; 3. 大连理工大学精密与特种加工教育部重点实验室 , 大连 116024)
摘 要 : 为了掌握化学机械抛光 (CM P)过程中硅片表面材料的去除行为 ,根据 CM P过程中硅片表面材料的磨损行 为 ,建立了硅片 CM P时的材料去除率构成成分模型 ,设计了不同成分的抛光液并进行了材料去除率实验 ,得出了 机械 、化学及其交互作用所引起的材料去除率. 结果显示 ,机械与化学的交互作用率为 8517% ~9911%. 磨粒的机 械作用率为 6915% ~9410% ,磨粒的机械与化学交互作用率为 5511% ~9311%. 由此可见 ,磨粒的机械作用是化学 机械抛光中的主要机械作用 ,磨粒与抛光液的机械化学交互作用引起的材料去除率是主要的材料去除率. 研究结 果可为进一步研究硅片 CM P时的材料去除机理提供理论参考依据. 关键词 : 化学机械抛光 ; 材料去除机理 ; 材料去除率 ; 磨损行为 中图分类号 : TN30511 文献标志码 : A 文章编号 : 167226030 (2009) 0320265205
笔者根据 CM P过程中硅片表面材料的磨损行为 , 建立了硅片 CM P时的材料去除率构成成分模型 ,并通 过材料去除率实验 ,得出了各机械 、化学及其交互作用 所引起的材料去除率 ;最后通过对材料去除率实验结 果进行分析 ,认为磨粒的机械作用是化学机械抛光中 的主要机械作用 ,磨粒的机械与抛光液的化学交互作 用引起的材料去除率是主要的材料去除率.
© 1994-2010 China Academic Journal Electronic Publishing House. All rights reserved.
· 266·
纳 米 技 术 与 精 密 工 程
第 7卷 第 3期
Keywords: chem ical mechanical polishing; m aterial removal mechanism; material removal rate; abra2 sion behavior
CM P过程的精确控制在很大程度上取决于对其 材料去除机理的认识和理解 ,但是 ,目前对 CM P的材 料去除机理 、材料去除非均匀性形成机理 、CM P过程 变量和技术等许多问题还没有完全弄清楚. 随着芯片 特征尺寸的不断缩小和芯片集成度的不断提高 ,对 CM P技术提出了更高的要求 ,目前的 CM P 技术水平 已不能满 足 下 一 代 IC 芯 片 制 造 的 工 艺 要 求 , 探 索 CM P机理是提高 CM P 技术水平的重要基础研究工 作 [4].
在超大规模集成电路 ( ultra large scale integrated circuit, ULSI) 制 造 中 , 化 学 机 械 抛 光 ( chem ical me2 chanical polishing, CM P) 技术被认为是不可或缺的实 用技术 ,它不仅在材料制备阶段被用于超光滑无损伤 单晶硅衬底的加工 ,而且也是多层布线金属互连结构 工艺中实现局部和全局平坦化的理想方法. 目前 , CM P 技术已成为 ULSI时代最广泛使用的平坦化技术 [ 123 ].
收稿日期 : 2008212216. 基金项目 : 国家自然科学基金重大资助项目 (50390061) ;河南科技学院高学历人才启动基金资助项目 ; 河南省教育厅自然科学研究计划项目 (2008B460007). 作者简介 : 苏建修 (1963— ) ,男 ,博士 ,教授. 通讯作者 : 苏建修 , jxsu2008@peop le. com. cn.