PI 4410 Tubcoat Product Data Sheet (revamp)
汽车保险杠涂料介绍

项目 原漆外观
不挥发份(%)
粘度
KU/20℃
秒/涂4/20℃ 细度(m)
密度(g/cm3/20℃)
检测标准 JISK 5400 4.1
JISK 5407.4
JISK 5400 4.5.2
GB/T 1723-93
JISK 5400 4.7.1
JISK 5400 4.6.2
FLEX 500 1K塑料底漆 分散均匀,无沉淀结块
30
粘度
KU/20℃ 秒/FC#4/20℃
JISK 5400 4.5.2 GB/T 1723-93
55~65 40
细度(m)
JISK 5400 4.7.1
---
密度(g/cm3/20℃)
JISK 5400 4.6.2
实测值
项目 稀释剂配比
标准涂装条件 备注
FLEX 100罩光清漆 涂装规格书
--25-45
--1.010.05
复合涂层涂膜性能(一)
No.
项目
1
漆膜外观
2
光泽(60)
3
附着力(2mm)
4
铅笔硬度(三菱)
5
耐水性
6
耐湿性
7
耐汽油性
8
耐二甲苯性
9
耐酸性
10
耐碱性
11
耐热变色性
12
耐粘着性
13
冷热存放实验
14
耐冲击性
15
耐弯曲性
耐
污
16
染
性
汽油 机油 润滑油 洗涤剂
17
耐 候性
1500H
附着
外观 附着 外观
外观 附着
RT -30C
Akzo Nobel Coatings Inc. Resicoat R4-ES HJF42R 防腐蚀

Functional Powder CoatingsProduct Datasheet20, Culvert Street T+1 855-294-8934Nashville, TN 37210F+1 615-564-4181USAResicoat ®R4-ESfor Electrostatic Spray Application on Preheated Surfaces Code: HJF42RProduct DescriptionResicoat ® R4 is a high quality thermosetting epoxy powder coating for the corrosion protection of valves and fittings, manufactured from cast iron or steel. The powder coating is available to be applied in one layer on a preheated surface by electrostatic spray application. Typical film thickness achieved is in the range of 250 – 500 µm. The resultant thermoset epoxy has a high mechanical resistance with excellent electrical insulation properties. Drinking water approvals are available to confirm the coatings suitability, as a hygienic and environmental friendly coating. The outstanding adhesion of Resicoat ® R4epoxy powders to the metal substrate provides long term protection of the coated component. It ensures a reliable conservation to the function and value of the parts for the common water and gasdistribution network. The applicator of Resicoat ®R4 benefits from a modern and environmentallyfriendly process. It is possible to overcoat Resicoat ®R4 with polyester powder and liquid coatings to achieve UV protection.Typical valueMethod Powder PropertiesBinder System Epoxy resinDensity1.45 – 1.55 g/cm³ASTM D5965Gel time at 392° F (200° C )25 – 40 sec.ASTM D4217Particle size distribution D10 = 10 – 15 µm D90 = 135 – 160 µm Malvern ISO 8130-1Storage stability 6 months at ≤ 74 °F (23 °C)Safety precautionsSee Material Safety Datasheet (MSDS)Application DataPreheating temperature object 392 – 428 °F (200 – 220 °C) object temperaturePost cure conditions objectThe coating is self curing, if the wall thickness of the steel/cast iron is greater than 8 mm. If the wall thickness of the steel/cast iron is less than 8 mm, additional curing of 3 to 8 minutes at 392 °F (200 °C) object temperature is required.1. Pre-cleaning The surface must be free of oil, grease, salt, and other impurities.2. BlastingMolding sand, rust and sharp edges must be removed with angular steel grit. The graphite from the cast iron must beremoved from the blasting material according NACE No.2/ SSPC-10/Sa 2.5. Recommended anchor profile of ≥60 µm should be stored max. 4 hours before pre-heating (dust-free and dry).3. Pre-heating This form of heating produces a uniform, defined temperature in the component. Any oxidation should be avoided.4. Coating applicationImmediately after preheating, the coating process starts without loosing any object temperature. The coating is done in the shortest possible time in a single pass with no interruptionFunctional Powder Coatings20, Culvert Street T+1 855-294-8934Nashville, TN 37210F+1 615-564-4181USATypical valueMethodCoating Process5. Coating cureCuring is achieved by the heat contained in the object. If the heating capacity of the work piece is sufficient. To confirm fully curing, MIBK is dropped for 30 sec. on the film surface with no visible change.Material PropertiesColorblueRecommended film thickness 10 – 14 mils (250 – 350 µm)Flowsmooth Gloss at 90° angle 70 – 90 units DIN 67530Cross cut test Gt 0DIN EN ISO 2409Impact resistance> 5 Joule > 2.26 Joule > 18 JouleDIN 30677-2ASTM D279420 inchpoundASTM G14 modified1/8 in (3.2 mm) steel plate Abrasion resistance < 40 mg ASTM D4060CS-17, 1000 g, 1000 cycles Dielectric strength≥ 30 kV/mm IEC 60243-1Volume resistivity (DC voltage) 1.1 x 1015ASTM D257Elongation> 5 %DIN 30671Indentation resistance 48 h, 158 °F (70 °C)24 h, 140 °F (60 °C)< 30 %< 10 %DIN 30677-2/DIN EN 14901ASTM G17Compressive strength > 100 MPa ASTM D695Shear adhesion> 35 MPa ASTM D1002Heat aging in air (90 d), water fulfilled DIN EN 14901Thermal stability under heat aging pass AS/NZS 4158:2003Weathering (Xenon test), 100 d pass ASTM D2596-99HardnessF Pencil Strain polarization pass WIS 4-52-01Cathodic disbonding 30 d, 74 °F (23 °C)≤ 10 mm DIN 30677-2, GSK Hot water immersion 90 d, 158 °F (70 °C)pass AWWA C550-05Adhesion> 20 MPa ASTM D4541Adhesion after 7 d,194 °F (90°C)water≥ 16 MPaISO 4624, GSK Tensile strength approx. 500 kg/cm³ASTM D2370Penetration< 5 %ASTM G17Functional Powder Coatings20, Culvert Street T+1 855-294-8934Nashville, TN 37210F+1 615-564-4181USATypical valueMethodMaterial PropertiesDisinfectant resistanceaccording DVGW work sheet W 291(chlorine dioxide, sodium hypochlorite)no change of surface,no chalkingafter 10 test stages à 15 h The following migration test with demineralised water showed no defects of the film. The concentration of the examined parameters in the tested water were below the limits of the epoxy guideline for ancillaries for pipes DN > 300 mm (in main trunks).Water condensation test (Cleveland test), 21 d no changeASTM D4585Salt spray resistance, 2000 h no blistering, no loss of adhesionBS 3900:F4Salt spray test, 4000 hno under-rusting on the cut DIN EN ISO 9227(steel substrate)Water absorption, 100 d, 74 °F (23 °C)pass AS/NZS 3862Chemical resistance (pH 3–13, 23° C)fulfilledEN 598Conformities ·AWWA C116·AWWA C550-05·EN 14901·ISO 12944-2, table 1(standard does not include powder coating systems)It is assumed that Resicoat ® R4 is suitable to meet the high atmospheric corrosivity category C4 (typically in industrial areas and coastal areas with moderate salinity) and the very high atmospheric- corrosivity -categories C5-I (industrial) and C5-M (marine) if applied as a holiday-free coating at a film thickness> 400 µm. A sufficient film thickness is highly required to ensure good edge coverage. For gloss and color stability a UV-resistant polyester topcoat has to be applied.Drinking Water ApprovalsUS: ANSI/NSF 61 Drinking Water System Components – Health Effects, NSF DE: UBA-Coatings Guideline, Approval no.: C-138801-06, Hygiene InstitutDE: DVGW directive work sheet W 270, Approval no. W-211795-11, Hygiene Institut UK: BS 6920, Approval No. 1112500, WRASDate of issue:July 10, 2015Authorized by:GK Revision No.:3Disclaimer: This Product Data Sheet is based on the present state of our knowledge and on current laws. The data referring to Powder Properties, Application Data and Physical Tests is based on lab based samples. Factors such as quality or condition of the substrate may have an effect on the use and application of the product. It remains the responsibility of the user to test thoroughly if the product is applicable for the intended use. The use of the product beyond our recommendation releases us from our responsibility, unless we have recommended the specific use in writing. It is always the responsibility of the user to take all necessary steps to fulfil the demands set out in the local rules and legislation. We are not liable for any application-technological advice. The Product Data Sheet shall be updated from time to time. Please ensure you have the latest version before using the product. All products and Product Data Sheets are subject to our standard terms and conditions of sale (GCS). You can receive the latest copy of GCS via internet or our post address. Brand names mentioned in this Product Data Sheet are trademarks of or are licensed to the AkzoNobel group.Resistance against chemical substances of Resicoat ®R4 at room temperature20, Culvert Street T+1 855-294-8934Nashville, TN 37210F+1 615-564-4181USA Chemical resistanceAugust 01, 2014Page 1 of 3Acetic acid 10 % 2 years no change Ammonia 10 % 2 years no change Ammonia 36 % 1.5 years no change Antifrogen L 50 % 1 year no change Antifrogen N 50 %1 year no change Benzol 1 month no change Bore oil 1 year no change Butanol6 months no change Carbon tetra chloride 1 yearno change Caustic soda solution 10 % 2 years no change Caustic soda solution50 %2 years no change Chlorine cleanser and disinfectant 1.5 years no change Citric acid2 years no change Deicer Safeway KF HOT 1 year no change Deicer Safeway SF (solid) 1 year no change Deicer Safewing MP II 1951 1 yearno change Dichromatic potassium 10 % 1 year no change Diesel2 years no change Engine oil SAE 20 1 year no change Ethanol 1 year no change Ethyleneglycole 1 yearno change Formaldehyde 37 % 6 months no change Formic acid 5 % 2 years no change Formic acid 10 %1.5 years no change Glycerol 1 year no change Glysantin 1 yearno change Hydrochloric acid concentrated1 week no change Hydrochloric acid 10 %2 years no change Hydrochloric acid 25 % 1.5 yearsno change Hydrofluoric acid 1 % 1 day no change Hydrogen peroxide 3 % 1 year no change Hydrogen peroxide10 %1 yearfadedLactic acid10 % 1 week no changeMethanol 1 week no changeMethyl tert-butyl ether (MTBE)100% 6 months softeningNitric acid10 % 1.5 years no changeNitric acid25 % 1 year no changeOxalic acid 5 % 6 months no changePalm oil at 90° C7 days no changePetrol 2 years no changePetroleum 1 year no changePhosphoric acid10 % 2 years no changePhosphoric acid50 % 2 years no changePotassium hydroxide10 % 1 year no changePotassium hydroxide25 % 1 year no changePotassium hydroxide50 % 1 year no changePropanol 1 year no changeSea water 2 years no changeSodium acetate10 % 1 year no changeSodium carbonate20 % 1 year no changeSodium hypochlorite (15 % Cl2)10 weeks no changeSodium chloride 2 % 1 year no changeSodium chloride20 % 1 year no changeSodium formiate10 % 1 year no changeSuds 1 % 1 year no changeSulphuric acid 2 % 2 years no changeSulphuric acid20 % 2 years no changeSulphuric acid50 % 2 years no changeTartaric acid 5 % 1 year no changeToluol 1 year no changeTurpentine oil 1 year no changeUrea10 % 1 year no changeUrine 1 year no changeXylol 1 year no change 20, Culvert Street T+1 855-294-8934Nashville, TN 37210F+1 615-564-4181USA Chemical resistance August 01, 2014Page 2 of 3Our printed literature and technical information Sheets as well as our advisory services are offered to facilitate andsupport decision-making processes. All specifications provided reflect the state of our knowledge at the time of print. Anytechnical data and measured values supplied have been tested for compliance with current applicable standards, ifavailable. The information provided is not legally binding upon the party supplying such information.20, Culvert Street T+1 855-294-8934Nashville, TN 37210F+1 615-564-4181USA Chemical resistance August 01, 2014Page 3 of 3。
Chemlok 6108 封面料数据表说明书

Chemlok® 6108 Technical Data SheetChemlok® 6108 is a covercoat used to affix a variety of elastomers to various metals. It is composed of a mixture of polymers, organic compounds and mineral fillers dissolved or dispersed in an organic solvent system. Chemlok 6108 is a non-chlorinated solvent surface treatment that provides strong resistance to harsh environments. In some applications, it may be used as a one-coat.Features and Benefits:Versatile – affixes a variety of elastomers and metals when used in combination with Chemlok 205 or 207.Non-Chlorinated Solvent System – suitable for solvent incineration.Environmentally Resistant – provides superior resistance to heat, oils and salt spray. Elastomers:• Natural Rubber (NR) • Polychloroprene (CR)• Polyisoprene (IR) • Nitrile (NBR)• Styrene-butadiene (SBR) • Butyl (IIR)• Polybutadiene (BR) • EPDM Polymers• Chlorinated Polyethylene (CPE)• Chlorosulfonated Polyethylene (CSM)Application:Surface Preparation – Thoroughly clean metal surfaces prior to primer application. Remove protective oils, cutting oils and greases by solvent degreasing or alkaline cleaning. Remove rust, scale or oxide coatings by suitable chemical or mechanical cleaning methods.Allow primer to thoroughly dry before applying Chemlok 6108.For further detailed information on surface preparation of specific substrates, refer to Chemlok application guide. Mixing – Thoroughly stir Chemlok 6108 before use, and agitate sufficiently during use to keep dispersed solids uniformly suspended. If dilution is needed, use xylene or toluene. Note proper dilution for the various application methods is best achieved by experience. Give careful attention to agitation since dilution will accelerate settling. Applying – Apply Chemlok 6108 by spray, brush or dip methods.Regardless of application method, the dry film thickness of Chemlok 6108 should be 17.8-25.4 micron (0.7-1.0 mil). Curing – Chemlok 6108 cures during the rubber vulcanization process.Cleanup – Use solvents such as xylene and MEK to remove Chemlok 6108 before heat is applied. Once cured, removal by solvent is not possible.Shelf Life/Storage:Shelf life is one year from date of shipment when stored by the recipient at 21-27°C (70-80°F) in original, unopened container. Do not store or use near heat, sparks or openflame.Chemlok 6108 — Technical Data SheetParker LORDEngineered Materials Group 111 LORD DriveCary, NC 27511-7923USAValues stated in this document represent typical values as not all tests are run on each lot of material produced. For formalized product specifications for specific product end uses, contact the Customer Support Center.Information provided herein is based upon tests believed to be reliable. In as much as Parker LORD has no control over the manner in which others may use this information, it does not guarantee the results to be obtained. In addition, Parker LORD does not guarantee the performance of the product or the results obtained from the use of the product or this information where the product has been repackaged by any third party, including but not limited to any product end-user. Nor does the company make any express or implied warranty of merchantability or fitness for a particular purpose concerning the effects or results of such use.WARNING — USER RESPONSIBILITY . FAILURE OR IMPROPER SELECTION OR IMPROPER USE OF THE PRODUCTS DESCRIBED HEREIN OR RELATED ITEMS CAN CAUSE DEATH, PERSONAL INJURY AND PROPERTY DAMAGE.This document and other information from Parker-Hannifin Corporation, its subsidiaries and authorized distributors provide product or system options for further investigation by users having technical expertise.The user, through its own analysis and testing, is solely responsible for making the final selection of the system and components and assuring that all performance, endurance, maintenance, safety and warning requirements of the application are met. The user must analyze all aspects of the application, follow applicable industry standards, and follow the information concerning the product in the current product catalog and in any other materials provided from Parker or its subsidiaries or authorized distributors.To the extent that Parker or its subsidiaries or authorized distributors provide component or system options based upon data or specifications provided by the user, the user is responsible for determining that such data and specifications are suitable and sufficient for all applications and reasonably foreseeable uses of the components or systems.©2021 Parker Hannifin - All Rights ReservedInformation and specifications subject to change without notice and without liability therefor. Trademarks used herein are the property of their respective owners.OD DS6010CE 07/21 Rev.2Cautionary Information:Before using this or any Parker LORD product, refer to the Safety Data Sheet (SDS) and label for safe use and handling instructions.For industrial/commercial use only. Required to use under organized emissions. Must be applied by trained personnel only. Not to be used in household applications. Not for consumer use.Chemlok® 6108技术说明书Chemlok® 6108作为面涂可以帮助和促进各式各样的弹性体附着至各种金属。
阿克苏诺贝尔粉末涂料产品数据表 - Interpon ACE 2010 YN106G 黑色中光泽平滑

Akzo Nobel Powder Coatings BVProduct Data SheetAkzoNobel Powder CoatingsInterpon ACE 2010YN106G Black Medium Gloss SmoothProduct Description Interpon ACE 2010is a series of superior UV and weather resistant TGIC-free polyester powdercoatings designed for exterior exposure and for use as a decorative and/or functional coating foragricultural and construction equipment and components. These coatings also provide significantlyimproved gloss retention and resistance to color change and possess outstanding transfer efficiencyand faraday cage penetration.Powder Properties Chemical type Polyester super-durable (TGIC-free)Area of usage Exterior parts for agricultural machinery or construction equipmentParticle Size Custom manufacturedAppearance Smooth, Medium glossColour BlackGloss (60°)60 ± 5 GUDensity (g/cm3)1,25 ± 0,10Stoving schedue15-30 minutes at 180°C, 10-25 minutes at 190°C, 8-20 minutes at 200°C(time at object temperature)Recommended DFT DTM: 70μm min - 110μm max; On Primer: 50μm min - 90μm max;On e-coat 45μm min - 90μm maxFailure to observe the correct curing and DFT conditions may cause adifference in color, gloss and the deterioration of the coating propertiesApplication ElectrostaticStorage Stability Under dry, cool (<25°C) conditions, at least 12 months from productiondate.Test Conditions The results are based on mechanical and chemical tests which (unless otherwise indicated) have been carried out under laboratory conditions and are given for guidance only. Actual product performance willdepend upon the circumstances under which the product is used.Substrate Cold Rolled SteelPretreatment Iron phosphate pretreated panels (ACT BonderiteÒ1070 DIW Panels)Film Thickness76-90 µmCure Schedule15 minutes at 190°CMechanical Tests Elongation ASTM-D522(conical mandrel)No crack at max elongationAdhesion ASTM-D3359(2 mm crosscut)5BHardness ASTM D3363(Gouge)3HCorrosion and Chemical Tests Cyclic Corrosion SAE J233440 days corrosion creep ≤ 3,5 mm fromscribeChemical resistance Good resistance to DI water, diesel fueland engine oilDurability Tests Exterior durability SAE J25272000h, excellent color and glossretention performanceColor stability atelevated temperatureGoodAkzoNobel Powder Coatings B.V. T +31 (0)71 308 6981Rijksstraatweg 31 (building 24) F +31 (0)71 318 6924PO Box 2170BA SassenheimThe NetherlandsPretreatment Aluminum, steel or Zinc surfaces to be coated must be clean and free from grease. Iron phosphate andparticularly lightweight zinc phosphating of ferrous metals improves corrosion resistance.Aluminum substrates may require a chromate or non-chromate conversion coating.Application Interpon ACE 2010 YN106G powders can be applied by manual or automatic electrostatic sprayequipment.It is recommended that for consistent application and appearance product be fluidized duringapplication. Unused powder can be reclaimed using suitable equipment and recycled through the coating system.Safety Precautions This product is intended for use only by professional applicators in industrial environments and shouldnot be used without reference to the relevant health and safety data sheet which Akzo Nobel has provided to its customers.DisclaimerIMPORTANT NOTE: The information in this data sheet is not intended to be exhaustive and is based on thepresent state of our knowledge and on current laws: any person using the product for any purpose otherthan that specifically recommended in the technical data sheet without first obtaining written confirmationfrom us as to the suitability of the product for the intended purpose does so at his own risk. It is always theresponsibility of the user to take all necessary steps to fulfill the demands set out in the local rules andlegislation. Always read the Material Data Sheet and the Technical Data Sheet for this product if available. Alladvice we give or any statement made about the product by us (whether in this data sheet or otherwise) iscorrect to the best of our knowledge but we have no control over the quality or the condition of the substrateor the many factors affecting the use and application of the product.Therefore, unless we specifically agree in writing otherwise, we do not accept any liability whatsoever for theperformance of the product or for any loss or damage arising out of the use of the product. All productssupplied and technical advices given are subject to our standard terms and conditions of sale. You shouldrequest a copy of this document and review it carefully. The information contained in this data sheet issubject to modification from time to time in the light of experience and our policy of continuousdevelopment. It is the user's responsibility to verify that this data sheet is current prior to using the product.Brand names mentioned in this data sheet are trademarks of or are licensed to AkzoNobelAkzoNobel Powder Coatings B.V.T +31 (0)71 308 6981 Rijksstraatweg 31 (building 24) F +31 (0)71 318 6924 PO Box 2170BA SassenheimThe Netherlands。
百格测试——精选推荐
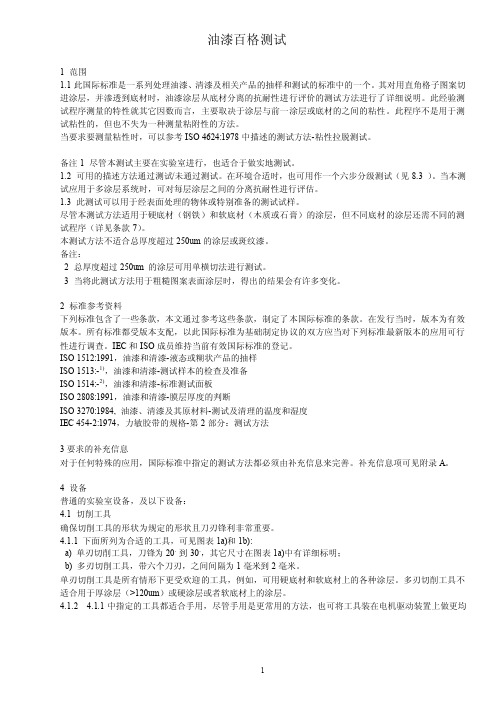
油漆百格测试1 范围1.1此国际标准是一系列处理油漆、清漆及相关产品的抽样和测试的标准中的一个。
其对用直角格子图案切进涂层,并渗透到底材时,油漆涂层从底材分离的抗耐性进行评价的测试方法进行了详细说明。
此经验测试程序测量的特性就其它因数而言,主要取决于涂层与前一涂层或底材的之间的粘性。
此程序不是用于测试粘性的,但也不失为一种测量粘附性的方法。
当要求要测量粘性时,可以参考ISO 4624:1978中描述的测试方法-粘性拉脱测试。
备注1 尽管本测试主要在实验室进行,也适合于做实地测试。
1.2 可用的描述方法通过测试/未通过测试。
在环境合适时,也可用作一个六步分级测试(见8.3 )。
当本测试应用于多涂层系统时,可对每层涂层之间的分离抗耐性进行评估。
1.3 此测试可以用于经表面处理的物体或特别准备的测试试样。
尽管本测试方法适用于硬底材(钢铁)和软底材(木质或石膏)的涂层,但不同底材的涂层还需不同的测试程序(详见条款7)。
本测试方法不适合总厚度超过250um的涂层或斑纹漆。
备注:2 总厚度超过250um 的涂层可用单横切法进行测试。
3 当将此测试方法用于粗糙图案表面涂层时,得出的结果会有许多变化。
2 标准参考资料下列标准包含了一些条款,本文通过参考这些条款,制定了本国际标准的条款。
在发行当时,版本为有效版本。
所有标准都受版本支配,以此国际标准为基础制定协议的双方应当对下列标准最新版本的应用可行性进行调查。
IEC和ISO成员维持当前有效国际标准的登记。
ISO 1512:1991,油漆和清漆-液态或糊状产品的抽样ISO 1513:-1),油漆和清漆-测试样本的检查及准备ISO 1514:-2),油漆和清漆-标准测试面板ISO 2808:1991,油漆和清漆-膜层厚度的判断ISO 3270:1984, 油漆、清漆及其原材料-测试及清理的温度和湿度IEC 454-2:1974,力敏胶带的规格-第2部分:测试方法3要求的补充信息对于任何特殊的应用,国际标准中指定的测试方法都必须由补充信息来完善。
规格书

操作条件 OPERATING CONDITIONS Crude product Dried product ATM 35 3000 885Kg/m
3
Organics ATM AMB 1200
3
FV 25 800 880~1040Kg/m
850Kg/m3
变送器规格 TRANSMITTER SPECIFICATION 型号 MODEL 测量范围 MEAS.RANGE 精度 ACCURACY 输出信号 OUTPUT SIGNAL 测量元件材质 SENSOR MATERIAL 本体材质 BODY MATERIAL 工艺接头规格 PROCESS CONN.SIZE 电气接口尺寸 ELEC.CONN.SIZE 防爆等级 EXPLOSION-PROOF CLASS 防护等级 ENCLOSURE PROOF 安装形式 INSTALLATION TYPE 安装图号 HOOK-UP DWG.NO. 附件 ACCESSORIES 输出指示表 OUTPUT INDICATOR 毛细管长度 CAPILLARY LENGTH 毛细管材料 CAPILLARY MATERIAL 毛细管填充材料 CAP.FILL FLUID 密封膜片材质 DIAPHRAGM MATERIAL 法兰标准及等级 FLANGE STD.& RATING 法兰尺寸及密封面 FLANGE SIZE & FACING 法兰材质 FLANGE MATERIAL 延伸长度 EXTENSION LENGTH (mm) 制造厂 MANUFACTURER 备注 REMARKS 0~26.55 Kpa 0.2 4~20mA 316L 1/2NPT iaⅡBT3 IP67 法兰 YES 316L HG20592-97 PN1.6 DN80 300? 位号 牌/tag plate
多乐士工业专用高耐化学清洁地面漆技术参数表说明书

DULUX TRADE HI-CHEM EPOXY ENAMELTECHNICAL DATA SHEETVersion 3 – 2019 AUGUSTTHIS ISSUE SUPERSEDES ALL PREVIOUS PUBLICATIONSPRODUCT DESCRIPTIONSemi-gloss epoxy enamel for interior industrial and home use (e.g. garage floors, etc.)PRODUCT USES·Can be applied on walls, floors and suitably primed metal surfaces.FEATURES AND BENEFITS·Good resistance to a wide range of chemicals and most solvents.·Cures to a hard film with good adhesion and abrasion resistance.·Provides an economical alternative to tiling in bathrooms, showers, kitchens, toilets and low cost housing.·Suitable for surfaces that require frequent cleaning with solvents, detergents or alkaline cleaners.·The cured film is non-toxic. When properly applied and cured, the product is completely safe for direct or accidental food contact on floor and wall applications.PRODUCT INFORMATIONAppearance Semi- glossColour White, Light Grey, Dark Grey and Brilliant GreenBinder Type Polyamide cured EpoxyDensity at 23°C Approx. 1.30Solids Content By weight: Approx. 60%By volume: Approx. 44%Packaged Viscosity Viscosity at 23°C: Approx. 70 KUSpreading Rate at 35µm DFT Brush: Approx. 9 m² per litre, depending on surface porosity,profile and application methodRecommended DFT per coat Min. 50µm. Max. 60µm.Recommended WFT per coat Min. 110µm. Max. 140µm(Higher film build will increase resistance)Flash Point25ºCDULUX TRADE HI-CHEM EPOXY ENAMELAPPLICATION INFORMATIONMixing Stir the Base and Curing Agent separately untilhomogeneous with a flat paddle. Then add the Curing Agentto the Base and stirring until homogeneous with a flat paddle Mixing Ratio 4 parts Base to 1 part Curing Agent by volume.Application Surface conditions Surface Temperature between 10 - 35°C. Relative Humiditybetween 10 - 85 % OR 2ºC above dew point minimum. Application methods Dulux Trade Hichem Epoxy Enamel is packaged in twocomponents in the proper proportions which must be mixedtogether until homogenous before use. See MixingAirless Spray: Ready for use after induction period of 30minutes.Air Spray: After mixing, thin 10% by volume and allowinduction period of 30 minutes.Brush: Can be used on small areas where joining is not aproblem e.g. signs, pipes, colour bands, etc.Roller: Short nap roller may be used on tanks and silostaking precautions to pick up the wet edge to avoid “window-paning”.Self-Priming on porous masonry: The product can only beover coated with itself. If a primer is required,Dulux TradeHichem Epoxy Enamel thinned 10% by volume can beutilised as a primer coat.N.B. Mix the paint first, then stir in the thinners.Thinner Dulux Trade Heavy Duty Thinners for spraying tomaximum of 10% of product volume and should only beadded after mixing the Curing Agent with the Base andstirred homogeneous with a flat paddle.Induction Period30 minutes at 25°C (i.e. do not paint immediately aftermixing).Pot Life to gelation Approx. 8 hours at 25°CDrying Time Dry to handle: 24 hours at 25ºC.Recoating Time 6 hours minimum; up to 7 days maximum at 25°C. (Dryingtimes will be extended during cold, wet or humid conditions.)APPLICATION INFORMATIONCleaning of equipment After use, remove as much product as possible, and thenclean immediately with Dulux Trade Heavy Duty Thinners. Substrates Correctly prepared cement plaster, concrete and correctlyprepared and primed mild steel and ironDULUX TRADE HI-CHEM EPOXY ENAMELAPPLICATION INFORMATIONPrecautions:Do not apply during cold (below 10°C) or wet weather.Do not apply directly to bare metal surfaces.Recommended for interior surfaces only, as the film willchalk on exterior exposure.Cure is slow at low temperatures; below 15°C it takes somedays to reach handling and recoating hardness.The pot life is short above 35°C; shield pressure pots andfluid lines from direct sun.Equipment and brushes must be cleaned immediately.Heat resistant to + 120°C (continuous) although someyellowing occurs above 100°C.Not suitable for direct application to powdery or friablesurfaces whether previously painted or not.Coats Required Apply two to three finishing coats to new surfaces to achievea minimum continuous film of 70µm microns to produceclosed film and solid colour.For non-skid pedestrian areas, three full coats will berequired. See “SURFACE PREPARATION”.SURFACE PREPARATIONEnsure that surfaces are sound and free from dust, oil, grease, dirt, and debris. Surfaces must be thoroughly dry - no more than 12% moisture content.NEW SURFACESCement Plaster, Concrete (non-friable)·Freshly rendered concrete should have dried/cured for a minimum of 6 weeks, the moisture content of the concrete should be below 12% before any preparation andpainting is attempted.·It is recommended that fresh plaster should be allowed 1 week drying for every 5mm thickness; and longer in cold or damp weather.·Ensure the entire surface is sound and clean. Remove any plaster spills, and all loose debris from the surface, ensuring an even and clean surface.·Acid etch the surface with a solution of hydrochloric acid to remove laitance, uncured cement, etc. as follows: On steel or power floated concrete (very smooth), use onevolume hydrochloric acid to two volumes water. More than one application may benecessary to achieve a paintable surface. On wood floated concrete (rough), use one volume hydrochloric acid to four volumes water.N.B. Hydrochloric acid is corrosive -please wear protective clothing, gloves, masks and eye goggles against splashes.·Allow the acid solution to react for 15 minutes and then wash away all acid with copious amounts of clean water.·Remove excess water and allow thorough drying–no more than 12% moisture content.DULUX TRADE HI-CHEM EPOXY ENAMELSURFACE PREPARATIONNEW SURFACESFloors Concrete – NON-SKID Pedestrian areas (walkways and passages)·Follow the cleaning and etching instructions under surface preparation, new surfaces, Cement Plaster, Concrete (non-friable)·Coat 1 – Apply and, while it is still wet, sprinkle dry, silica sand over the surface. (The silica sand should be sifted through a 250µm sieve and retained on a 210µm sieve. A practical spreading rate is 500 grams of sand per square meter of painted floor.)·Coat 2 - The following day, sweep off any excess sand and apply a further coat to seal the surface. Allow overnight drying again·Coat 3 – Apply 3rd coat·Observe chemical curing times as stated in this technical data sheet.Mild Steel and Iron·Remove all shop-primer and corrosion products from the steel. Sand blast steel to achieve a bright metal condition, and a cleanliness standard of Sa2½ minimum.·Clean bare steel with a solvent wash (rags dipped in lacquer thinner). Change rags frequently.·Apply one or two coats Dulux Trade Corrocote 1 Metal Etch Primer, depending on the severity of the conditions. Two coats are preferred for coastal conditions. PREVIOUSLY PAINTED SURFACES·The existing coating system should be dry and free of contaminants such as oil, grease and loose paint.·Test that the surface will accept epoxy by allowing a cloth soaked with Dulux Trade Heavy Duty Thinners to rest on it for 15 minutes - it must not lift or wrinkle. If lifting or wrinkling occurs, the paint must be removed with paint stripper or any other suitable means.·Abrade damaged or failed areas back to a sound substrate and treat as new.·Aged or weathered epoxies or urethanes must be well sanded to a matt finish to providea profile for adhesion.DULUX TRADE HI-CHEM EPOXY ENAMELHEALTH AND SAFETY INFORMATIONSolvent based paints are flammable.This product contains no added lead. Avoid contact with skin or eyes. Keep out of reach of children. If accidently swallowed, seek medical advice immediately and show this container to the doctor. Dry sanding, flame cutting and/or welding of the dry paint film will give rise to dust and/or hazardous fumes. Wet sanding should be used wherever possible.If exposure cannot be avoided by the provision of local exhaust ventilation, suitable respiratory protective equipment should be used. Do not empty into drains or watercourses. Ensure good ventilation during application and drying. It is recommended to use suitable protective clothing and equipment. To avoid the risk of spillage, always store and transport containers in a secure upright position. Refer to Material Safety Data Sheet for complete information.ADDITIONAL INFORMATIONPackaging 5 Litre (4L base in large tin, 1L curing agent).Storage Conditions Store under cool dry conditions away from direct sunlight,heat and extreme cold.Disclaimers Colour references are as accurate as modern printing willallow. Please refer to colour cards for an accuraterepresentation of the colour.Among others, the following factors may affect final colourappearance: product sheen and texture, colour and lightreflections, application, surface texture and preparation.For best colour and sheen consistency, it is advisable to usecontainers of the same batch number, to mix differentbatches together in a large container, or to finish in a cornerbefore starting a new container.TDS STANDARD DISCLAIMERThe recommendations contained herein are given in good faith and meant to guide the specifier or user in accordance with good painting practices. They are gained from our tests and experiences and are believed to be accurate and reliable. No warranty/guarantee is implied by the recommendations contained herein since the conditions of use; application method, substrate and cleanliness of the substrate are beyond Dulux control.Important Note; Technology may change with time, necessitating changes to this Technical Data Sheet (TDS).It is the responsibility of the user to ensure that the latest TDS is being used for reference. Dulux Technical Data Sheets are available on our website www.duluxtrade.co.za or please contact: Dulux On-Line on 0860 330 111. Email*************************ICI Dulux (Pty) Ltd is part of AkzoNobel. ICI Dulux (Pty) Ltd Reg No.1946/020769/07。
Spears Schedule 40 PVC
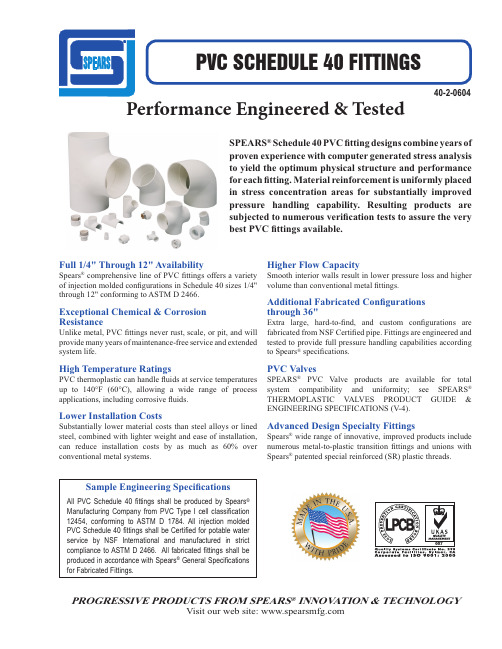
40-2-0604Performance Engineered & TestedSPEARS ® Schedule 40 PVC fi tting designs combine years of proven experience with computer generated stress analysis to yield the optimum physical structure and performance for each fi tting. Material reinforcement is uniformly placed in stress concentration areas for sub stantially improved pressure handling capab ility. Resulting products are subjected to numerous verifi cation tests to assure the very best PVC fi ttings available.Full 1/4" Through 12" Availability Spears ® comprehensive line of PVC fi ttings offers a variety of injection molded confi gurations in Schedule 40 sizes 1/4"through 12" conforming to ASTM D 2466.Exceptional Chemical & Corrosion ResistanceUnlike metal, PVC fi ttings never rust, scale, or pit, and will provide many years of maintenance-free service and extended system life.High Temperature Ratings PVC thermoplastic can handle fl uids at service temperatures up to 140°F (60°C), allowing a wide range of process applications, including corrosive fl uids.Lower Installation CostsSubstantially lower material costs than steel alloys or lined steel, combined with lighter weight and ease of installation, can reduce installation costs by as much as 60% over conventional metal systems.PROGRESSIVE PRODUCTS FROM SPEARS ® INNOV ATION & TECHNOLOGYVisit our web site: Higher Flow CapacitySmooth interior walls result in lower pressure loss and highervolume than conventional metal fi ttings.Additional Fabricated Confi gurations through 36"Extra large, hard-to-fi nd, and custom confi gurations arefabricated from NSF Certified pipe. Fittings are engineered and tested to provide full pressure handling capabilities accordingto Spears ® specifi cations.PVC ValvesSPEARS ® PVC Valve products are available for totalsystem compatibility and uniformity; see SPEARS ®THERMOPLASTIC V ALVES PRODUCT GUIDE & ENGINEERING SPECIFICATIONS (V-4).Advanced Design Specialty FittingsSpears ® wide range of innovative, improved products include numerous metal-to-plastic transition fi ttings and unions withSpears ® patented special reinforced (SR) plastic threads.Sample Engineering Specifi cationsAll PVC Sche dule 40 fi ttings shall be produce d by Spe ars ®Manufacturing Company from PVC Type I cell classifi cation 12454, conforming to ASTM D 1784. All inje ction molde d PVC Schedule 40 fi ttings shall be Certifi ed for potable water se rvice by NSF Inte rnational and manufacture d in strict compliance to ASTM D 2466. All fabricated fi ttings shall beproduced in accordance with Spears ® General Specifi cationsfor Fabricated Fittings.PACIFIC SOUTHWEST1 Gateway Ct . Suite APVC Thermoplastic Pipe Temperature Pressure De-RatingNOT FOR USE WITH COMPRESSED AIR OR GASSpears ® Manufacturing Company DOES N OT RECOMMEND the use of thermoplastic piping products for systems to transport or store compressed air or gases, or the testing of thermoplastic piping systems with compressed air or gases in above and below ground locations. The use of our product in compressed air or gas systems automatically voids any warranty for such products, and its use against our recommendation is entirely the responsibility and liability of the installer.WARNING: DO N OT USE COMPRESSEDAIR OR GAS TO TEST AN Y PVC OR CPVCTHERMOPLASTIC PIPI N G PRODUCT OR SYSTEM, A N D DO N OT USE DEVICES PROPELLED BY COMPRESSED AIR OR GAS TO CLEAR SYSTEMS. THESE PRACTICES MAY RESULT IN EXPLOSIVE FRAGMEN TATION OF SYSTEM PIPIN G COMPON EN TS CAUSIN G SERIOUS OR FATAL BODILY INJURY .PVC Chemical ResistancePVC is generally inert to most mineral acids, bases, salts and paraffi nic hydrocarbon solutions. For more information on PVC chemical resistance refer to the Chemical Resistance of Rigid Vinyls Based on Immersion Test, published by the GEON ® Company.To determine the maximum internal pressure rating at an elevated temperature, simply multiply the pipe pressure rating at 73°F by the percentage specifi ed for the desired temperature.System OperatingTemperature °F (°C)73(23)80(27)90(32)100(38)110(43)120(49)130(54)140(60)PVC100%90%75%62%50%40%30%22%NOTE: Valves, Unions and Specialty Products have different elevated temperature ratings than pipe.PVC Basic Physical PropertiesPropertiesASTMTest Method PVCMechanical Properties, 73°FSpecifi c Gravity, g/cm 3 D 792 1.41Tensile Strength, psi D 6387,200Modulus of Elasticity, psi D 638440,000Compressive Strength, psi D 6959,000Flexural Strength, psi D 79013,200Izod Impact, notched, ft-lb/inD 256.65Thermal PropertiesHeat Defl ection Temperature, °F at 66 psi D 648165Thermal Conductivity, BTU/hr/sq ft/°F/in C 177 1.2Coeffi cient of Linear Expansion, in/in/°FD 696 3.1 X 105FlammabilityLimiting Oxygen Index, % D 286343UL 94 rating94V-0Other PropertiesWater Absorption, % 24 hr. D 570.05Industry Standard Color White / Dark GrayASTM Cell Classifi cation D 178412454NSF Potable Water ApprovedYes。
Perkadox 14-40B-PD-S 产品数据表说明书
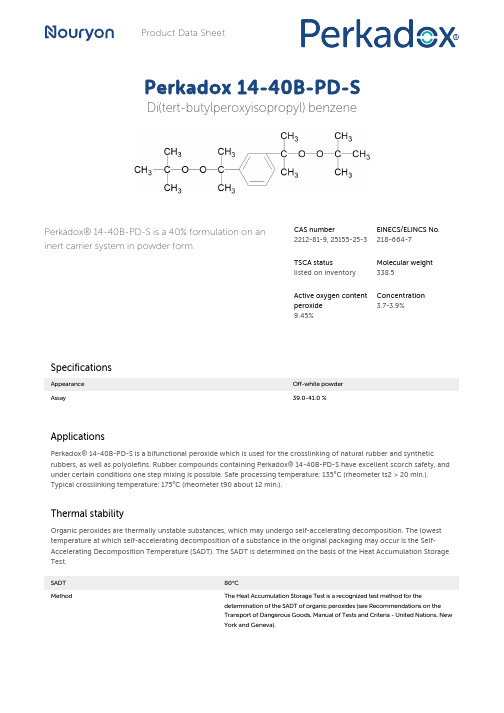
Product Data SheetPerkadox 14-40B-PD-S Di(tert-butylperoxyisopropyl) benzenePerkadox® 14-40B-PD-S is a 40% formulation on an inert carrier system in powder form.CAS number2212-81-9, 25155-25-3EINECS/ELINCS No.218-664-7TSCA statuslisted on inventoryMolecular weight338.5Active oxygen contentperoxide9.45%Concentration3.7-3.9%SpecificationsAppearance Off-white powderAssay39.0-41.0 %ApplicationsPerkadox® 14-40B-PD-S is a bifunctional peroxide which is used for the crosslinking of natural rubber and synthetic rubbers, as well as polyolefins. Rubber compounds containing Perkadox® 14-40B-PD-S have excellent scorch safety, and under certain conditions one step mixing is possible. Safe processing temperature: 135°C (rheometer ts2 > 20 min.). Typical crosslinking temperature: 175°C (rheometer t90 about 12 min.).Thermal stabilityOrganic peroxides are thermally unstable substances, which may undergo self-accelerating decomposition. The lowest temperature at which self-accelerating decomposition of a substance in the original packaging may occur is the Self-Accelerating Decomposition Temperature (SADT). The SADT is determined on the basis of the Heat Accumulation Storage Test.SADT80°CMethod The Heat Accumulation Storage Test is a recognized test method for thedetermination of the SADT of organic peroxides (see Recommendations on theTransport of Dangerous Goods, Manual of Tests and Criteria - United Nations, NewYork and Geneva).StorageDue to the relatively unstable nature of organic peroxides a loss of quality can be detected over a period of time. To minimize the loss of quality, Nouryon recommends a maximum storage temperature (Ts max.) for each organic peroxide product.Ts max.30°CNote When stored under strictly recommended storage conditions, Perkadox® 14-40B-PD-S will remain within the Nouryon specifications for a period of at least 12months after delivery.Packaging and transportThe standard packaging is a cardboard box for 25 kg peroxide formulation. Both packaging and transport meet the international regulations. For the availability of other packed quantities consult your Nouryon representative. Perkadox®14-40B-PD-S is classified as Flammable solid, class 4. 1, UN 1325.Safety and handlingKeep containers tightly closed. Store and handle Perkadox® 14-40B-PD-S in a dry well-ventilated place away from sources of heat or ignition and direct sunlight. Never weigh out in the storage room. Avoid contact with reducing agents (e. g. amines), acids, alkalines and heavy metal compounds (e. g. accelerators, driers and metal soaps). Please refer to the Safety Data Sheet (SDS) for further information on the safe storage, use and handling of Perkadox® 14-40B-PD-S. This information should be thoroughly reviewed prior to acceptance of this product. The SDS is available at /sds-search.Major decomposition productsMethane, Acetone, tert-Butanol, Di(2-hydroxyisopropyl)benzene, Diacetylbenzene, Acetyl 2-hydroxyisopropyl benzeneAll information concerning this product and/or suggestions for handling and use contained herein are offered in good faith and are believed to be reliable.Nouryon, however, makes no warranty as to accuracy and/or sufficiency of such information and/or suggestions, as to the product's merchantability or fitness for any particular purpose, or that any suggested use will not infringe any patent. Nouryon does not accept any liability whatsoever arising out of the use of or reliance on this information, or out of the use or the performance of the product. Nothing contained herein shall be construed as granting or extending any license under any patent. Customer must determine for himself, by preliminary tests or otherwise, the suitability of this product for his purposes.The information contained herein supersedes all previously issued information on the subject matter covered. The customer may forward, distribute, and/or photocopy this document only if unaltered and complete, including all of its headers and footers, and should refrain from any unauthorized use. Don’t copythis document to a website.Perkadox® is a registered trademark of Nouryon Functional Chemicals B. V. or affiliates in one or more territories.Contact UsPolymer Specialties Americas************************Polymer Specialties Europe, Middle East, India and Africa*************************Polymer Specialties Asia Pacific************************2022-12-5© 2022Polymer crosslinking Perkadox 14-40B-PD-S。
Sikaflex-252 粘合剂产品数据表说明书

PRODUCT DATA SHEET Sikaflex®-252Version 03.01 (04 - 2023), en_NZ012001212520001000PRODUCT DATA SHEETSikaflex®-252Elastic adhesive for vehicle assembly bondingTYPICAL PRODUCT DATA (FURTHER VALUES SEE SAFETY DATA SHEET)Chemical base 1-component polyurethane Color (CQP001-1)WhiteCure mechanism Moisture-curing Density (uncured)depending on color1.2 kg/l Non-sag propertiesGood Application temperature ambient10 ─ 35 °C Skin time (CQP019-1)40 minutes A Open time (CQP526-1)35 minutes A Curing speed (CQP049-1)(see diagram 1)Shore A hardness (CQP023-1 / ISO 48-4)50Tensile strength (CQP036-1 / ISO 527) 3 MPa Elongation at break (CQP036-1 / ISO 527)400 %Tear propagation resistance (CQP045-1 / ISO 34)7 N/mm Tensile lap-shear strength (CQP046-1 / ISO 4587) 2.5 MPa Service temperature (CQP509-1 / CQP513-1)4 hour 1 hour-40 ─ 90 °C 130 °C 150 °CShelf life12 months BCQP = Corporate Quality ProcedureA) 23 °C / 50 % r. h.B) storage below 25 °CDESCRIPTIONSikaflex®-252 is an elastic 1-component poly-urethane adhesive especially designed for bonding large components in vehicle as-sembly. It is suitable for bonding coated met-al, GRP, ceramic materials and plastics.PRODUCT BENEFITSBonds well to a wide variety of substrates ▪Capable of withstanding high dynamic stresses▪Good gap-filling properties ▪Can be painted ▪Vibration-damping▪Electrically non-conductive▪AREAS OF APPLICATIONSikaflex®-252 is suitable for assemblies that are subject to dynamic stresses. Suitable sub-strate materials are timber, metals, particu-larly aluminum (including anodized compon-ents), sheet steel (including phosphated, chromated and galvanized components), met-al primers and paint coatings (2-component systems), ceramic materials and plastics.Seek manufacturer’s advice before using on plastics that are prone to stress cracking.This product is suitable for professional exper-ienced users only. Tests with actual substrates and conditions have to be performed to en-sure adhesion and material compatibility.1 / 2CURE MECHANISMSikaflex®-252 cures by reaction with atmo-spheric moisture. At low temperatures the water content of the air is generally lower and the curing reaction proceeds more slowly (seediagram 1).Diagram 1: curing speed Sikaflex®-252CHEMICAL RESISTANCESikaflex®-252 is generally resistant to fresh water, seawater, diluted acids and dilutedcaustic solutions; temporarily resistant to fuels, mineral oils, vegetable and animal fats and oils; not resistant to organic acids, glycol-ic alcohol, concentrated mineral acids and caustic solutions or solvents.METHOD OF APPLICATIONSurface preparationSurfaces must be clean, dry and free from grease, oil, dust and contaminants.The surface treatment depends on the specif-ic nature of the substrates and is crucial for a long lasting bond. Suggestions for surface pre-paration may be found on the current edition of the appropriate Sika® Pre-treatment Chart. Consider that these suggestions are based on experience and have in any case to be verified by tests on original substrates.ApplicationSikaflex®-252 can be processed between10 °C and 35 °C (climate and product) butchanges in reactivity and application proper-ties have to be considered. The optimum tem-perature for substrate and adhesive is between 15 °C and 25 °C.Consider that the viscosity will increase at low temperatures. For easy application, condition the adhesive at ambient temperature prior to use. To ensure a uniform thickness of the bondline it is recommend to apply the adhes-ive in the form of a triangular bead (see figure1).Figure 1: Recommended bead configurationSikaflex®-252 can be processed with manual, pneumatic or electric driven piston guns as well as pump equipment. The open time is significantly shorter in hot and humid cli-mates. The parts must always be installed within the open time. Never join bonding parts if the adhesive has built a skin.Tooling and finishingTooling and finishing must be carried out within the skin time of the product. Finishing agents must be tested for suitability and com-patibility prior to use.RemovalUncured Sikaflex®-252 can be removed from tools and equipment with Sika® Remover-208 or another suitable solvent. Once cured, the material can only be removed mechanically. Hands and exposed skin have to be washed immediately using hand wipes or a suitable industrial hand cleaner and water.Do not use solvents on skin.FURTHER INFORMATIONThe information herein is offered for general guidance only. Advice on specific applications is available on request from the Technical De-partment of Sika Industry.Copies of the following publications are avail-able on request:Safety Data Sheets▪Sika Pre-treatment Chart For 1-componentPolyurethanes▪PACKAGING INFORMATION Unipack600 mlBASIS OF PRODUCT DATAAll technical data stated in this document are based on laboratory tests. Actual measured data may vary due to circumstances beyond our control.HEALTH AND SAFETY INFORMATION For information and advice regarding trans-portation, handling, storage and disposal of chemical products, users shall refer to the ac-tual Safety Data Sheets containing physical, ecological, toxicological and other safety-re-lated data.DISCLAIMERThe information, and, in particular, the re-commendations relating to the application and enduse of Sika products, are given in good faith based on Sika's current knowledge and experience of the products when prop-erly stored, handled and applied under nor-mal conditions in accordance with Sika's re-commendations. In practice, the differences in materials, substrates and actual site condi-tions are such that no warranty in respect of merchantability or of fitness for a particular purpose, nor any liability arising out of any legal relationship whatsoever, can be inferred either from this information, or from any writ-ten recommendations, or from any other ad-vice offered. The user of the product must test the product's suitability for the intended application and purpose. Sika reserves the right to change the properties of its products. The proprietary rights of third parties must be observed. All orders are accepted subject to our current terms of sale and delivery. Users must always refer to the most recent issue of the local Product Data Sheet for the product concerned, copies of which will be supplied on request.PRODUCT DATA SHEET Sikaflex®-252Version 03.01 (04 - 2023), en_NZ012001212520001000Sika (NZ) Limited85-91 Patiki RoadAvondale, Auckland 1026New Zealand 0800 745 2 / 2。
AZ 100 Remover 正向工作Photo仿真剂去封封面数据表说明书

Technisches Datenblatt AZ 100 RemoverStripper for positiveworking PhotoresistDescriptionAZ 100 Remover is especially designed for stripping positive working photoresists like the AZ Photoresists. The stripper is free of phenols, chromates, chlorinated hydrocarbons or metal ions. The remover can be mixed with water in any ratio.Table 1Physical and Chemical Properties_____________________________________________________________ Density (at 25°C) 0.955 kg/lColor (Alpha) max. 20Flashpoint (AP) 72 °CNormality (potentiometric) 3.1 mol/lBoiling range 159 – 194 °C_____________________________________________________________ProcessingBath Make-upAZ 100 Remover is a ready to use solution. A 1 : 1 mixture with water is possible. On thin films like aluminum the use of the undiluted AZ 100 Remover is recommended.Process SequenceRemoval of the resist occurs most adequately in a two tank system. In the first bath the majority of the resist is stripped; in the second tank the resist residues are removed.As indicated in table 2, the total immersion time depends on the bath temperature and the thermal treatment of the resist structures. Use mechanical or nitrogen burst agitation.After stripping, the substrates are rinsed in deionized water, followed by drying in a rinse dryer.Technisches DatenblattTable 2Stripping Capability of AZ 100 RemoverBake temperature of resist °CRemoverTemperature °CStripping time min.120 21 5140 21 10150 50 5180 80 5190 80 10Determination of NormalityProcedurePut about 1,5 g of the remover, weighed to an accuracy of 0.001 g, into an Erlenmeyer flask and immediately add approximately 90 ml deionized water. The titration is performed by an automatic potentiometric titrator (i.e. Titroprocessor 672, Metrohm) or by manual titration. In the latter case add 3 drops of the indicator (i.e. 0.1% aqeous solution of Methyl red and titrate to endpoint with Hydrochloric acid (HCl) 0.5 N.(ml HCl)Normality of AZ 100 Remover = 0.477 x ___________________(g AZ 100 Remover)Waste DisposalAfter acidification with hydrochloric acid (3.5%) to pH = 8.5, AZ 100 Remover is bio-logical degradable. At all times local regulations should be observed!Handling PrecautionsWarningBefore using refer to safety data sheet and technical bulletin. Open container only after adjustment to room temperature.Technisches DatenblattFirst aidIf eye contact:Flush with water for at least 15 minutes.Contact physician.If skin contact:Wash affected areas with soap and water.If inhaled (mist):Move into fresh air.Equipment CompatibilityAZ 100 Remover is up to temperatures of 40 °C compatible to polyvinylchloride and to polypropylene up to 55 °C. For elevated temperatures material like quartz, stainless steel and PTFE are recommended.StorageKeep in sealed original containers.Store between 0 – 35 °C.Shelf life is limited. The expiration date is printed on the label of every bottleWe advise our customers regarding technical applications to the best of our knowledge within the scope of the possibilities open to us, but without obligation. Current laws and regulations must be observed at all times. This also applies in respect of any protected rights of third parties. Our suggestions do not relieve our customers of the necessity to test our products, on their own responsibility, for suitability for the purpose envisaged. Quotations from our literature are only permitted with our written authority, and the source must be stated.。
Product Specification sheet

3. Abbreviations
ADSL Asymmetric Digital Subscriber Line CO Central Office CPE Customer Premise Equipment POTS Plain Old Telephone Service RT Remote Terminal ADSL-NT Network termination of ADSL
Product Specification sheet
Cat # K2320 ADSL Filter/Splitter
Table of Contents Item 1. 2. 3. 4. Description Introduction References Abbreviations Technical 4.1 Schematic 4.2 Electrical specification 4.3 HP-r Definition 4.4 DC characteristic 4.5 Test method 4.5.1 Insertion loss 4.5.2 Return loss Environmental 5.1 Resistibility to over-voltage & over-currents 5.2 Climatic conditions 5.2.1 Operating Temperature 5.2.2 Storage and transport 5.2.3 Operating humidity Reliability 6.1 Thermal shock 6.2 Temperature and humidity exposure 6.3 Vibration test Mechanical 7.1 Dimensions 7.2 Rating plate Page 2 2 2 3 4 5 5 6 7 8 8 8 8 8 8 8 9 9
西门子 SITOP模块式电源 产品说明书

Startup delay, max.
1s
Voltage rise, typ.
50 ms
Rated current value Iout rated
5A
Current range
0…5A
• Note
> 60 °C Derating
delivered active power / typ.
120 W
constant overload current / at short-circuit during run-up / typical
Built-in incoming fuse
T 3.15 A (not accessible)
Protection in the mains power input (IEC 898)
Recommended miniature circuit breaker at 1-phase operation: from 6 A (10 A), characteristic C (B); required at 2-phase operation: circuit breaker 2-pole connected or circuit breaker 3RV2011-1EA10 (setting 3.8 A) or 3RV2711-1ED10 (UL 489) at 230 V; 3RV2011-1DA10 (setting 3 A) or 3RV2711-1DD10 (UL 489) at 400/500 V
AZ_PR光刻胶的数据资料

DUV光刻胶系列 AZ DX3200P系列 应用于通孔图形的KrF正型光刻胶
KrF Excimer Laser Positive-tone Photoresist for Contact Hole
12
AZ DX5200P系列 应用于沟槽及通孔图形的超高分辨率KrF正型光刻胶 厚膜光刻胶系列
KrF Excimer Laser Positive-tone Photoresist for Contace Hole and Trench
目录
G线/I线/G线I线通用光刻胶系列
AZ 1500系列
高感光度标准G线正型光刻胶
High Sensitivity Standard g-line Positive-tone Photoresist
5
AZ 6100系列 AZ 3100系列
高感光度高耐热性G线正型光刻胶 高感光度高附着性G线I线通用正型光刻胶
27
AZ CTP系列
应用于有机电致发光显示器阴极隔离的负型光刻胶
Negative-tone Resist for Cathode Separator on Organic EL Display
28
辅助化学品系列
显影液及其他相关化学品
Developers,and other ancillary chemicals
High Sensitivity & High Heat Stability g-line Positive-tone Photoresist
6
High Sensitivity & High Adhesion g/i Cross-over Positive-tone Photoresist
7
Sikaflex
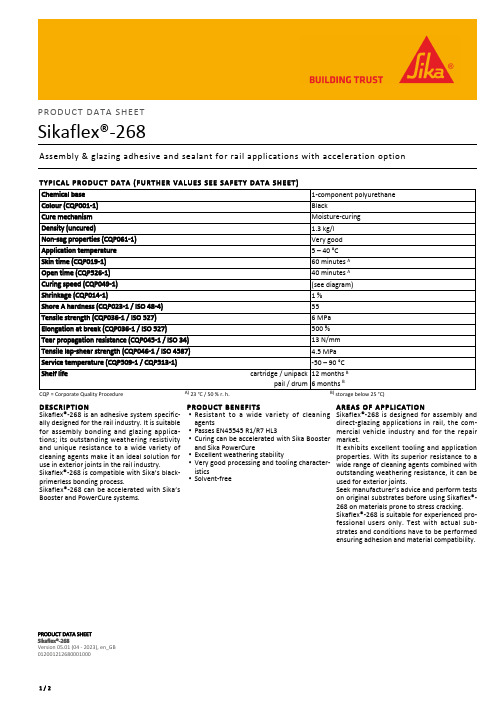
PRODUCT DATA SHEET Sikaflex®-268Version 05.01 (04 - 2023), en_GB012001212680001000PRODUCT DATA SHEETSikaflex®-268Assembly & glazing adhesive and sealant for rail applications with acceleration optionTYPICAL PRODUCT DATA (FURTHER VALUES SEE SAFETY DATA SHEET)Chemical base 1-component polyurethane Colour (CQP001-1)BlackCure mechanism Moisture-curing Density (uncured)1.3 kg/l Non-sag properties (CQP061-1)Very good Application temperature 5 ─ 40 °C Skin time (CQP019-1)60 minutes A Open time (CQP526-1)40 minutes A Curing speed (CQP049-1)(see diagram)Shrinkage (CQP014-1)1 %Shore A hardness (CQP023-1 / ISO 48-4)55Tensile strength (CQP036-1 / ISO 527) 6 MPa Elongation at break (CQP036-1 / ISO 527)500 %Tear propagation resistance (CQP045-1 / ISO 34)13 N/mm Tensile lap-shear strength (CQP046-1 / ISO 4587) 4.5 MPa Service temperature (CQP509-1 / CQP513-1)-50 ─ 90 °CShelf lifecartridge / unipack pail / drum 12 months B6 months BCQP = Corporate Quality ProcedureA) 23 °C / 50 % r. h.B) storage below 25 °C)DESCRIPTIONSikaflex®-268 is an adhesive system specific-ally designed for the rail industry. It is suitable for assembly bonding and glazing applica-tions; its outstanding weathering resistivity and unique resistance to a wide variety of cleaning agents make it an ideal solution for use in exterior joints in the rail industry.Sikaflex®-268 is compatible with Sika’s black-primerless bonding process.Sikaflex®-268 can be accelerated with Sika’s Booster and PowerCure systems.PRODUCT BENEFITSResistant to a wide variety of cleaning agents▪Passes EN45545 R1/R7 HL3▪Curing can be accelerated with Sika Booster and Sika PowerCure▪Excellent weathering stability▪Very good processing and tooling character-istics▪Solvent-free▪AREAS OF APPLICATIONSikaflex®-268 is designed for assembly and direct-glazing applications in rail, the com-mercial vehicle industry and for the repair market.It exhibits excellent tooling and application properties. With its superior resistance to a wide range of cleaning agents combined with outstanding weathering resistance, it can be used for exterior joints.Seek manufacturer’s advice and perform tests on original substrates before using Sikaflex®-268 on materials prone to stress cracking.Sikaflex®-268 is suitable for experienced pro-fessional users only. Test with actual sub-strates and conditions have to be performed ensuring adhesion and material compatibility.1 / 2CURE MECHANISMSikaflex®-268 cures by reaction with atmo-spheric moisture. At low temperatures the water content of the air is generally lower and the curing reaction proceeds somewhatslower (see diagram 1).Diagram 1: Curing speed Sikaflex®-268CHEMICAL RESISTANCESikaflex®-268 is generally resistant to fresh water, seawater, diluted acids and diluted caustic solutions; temporarily resistant to fuels, mineral oils, vegetable and animal fats and oils; not resistant to organic acids, glycol-ic alcohol, concentrated mineral acids and caustic solutions or solvents.It is resistant to a wide range of rail cleaning agents if used according to the guidelines of the manufacturer. Some rail cleaning agents contain aggressive chemicals such as phos-phoric acids which may influence the durabil-ity of Sikaflex®-268 significantly. Therefore it is of highest importance to limit the exposure time to a minimum, observe correct dilution of cleaning agent and to perform a thorough rinsing after the cleaning process. Test newly introduced cleaning agents.The above information is offered for general guidance only. Advice on specific applications will be given on request.METHOD OF APPLICATION Surface Preparation Surfaces must be clean, dry and free from grease, oil and dust. Surface treatment de-pends on the specific nature of the substrates and is crucial for a long lasting bond. All pre-treatment steps must be confirmed by pre-liminary tests on original substrates consider-ing specific conditions in the assembly pro-cess.ApplicationSikaflex®-268 can be processed between 5 °C and 40 °C (climate and product) but changes in reactivity and application properties have to be considered. The optimum temperature for substrate and sealant is between 15 °C and 25 °C.Consider the viscosity increase at low temper-ature. For easy application, condition the ad-hesive at ambient temperature prior to use. To ensure a uniform thickness of the bondline it is recommend to apply the adhesive in formof a triangular bead (see figure 1).Figure 1: Recommended bead configurationSikaflex®-268 can be processed with hand, pneumatic or electric driven piston guns as well as pump equipment. The open time is significantly shorter in hot and humid climate. The parts must always be installed within the open time. Never join bonding parts if the ad-hesive has built a skin.For advice on selecting and setting up a suit-able pump system, contact the System Engin-eering Department of Sika Industry.Tooling and finishingTooling and finishing must be carried out within the open time of the adhesive. We re-commend the use of Sika® Tooling Agent N. Other finishing agents must be tested for suit-ability and compatibility.RemovalUncured Sikaflex®-268 can be removed from tools and equipment with Sika® Remover-208 or another suitable solvent. Once cured, the material can only be removed mechanically.Hands and exposed skin have to be washed immediately using hand wipes such as Sika® Cleaner-350H or a suitable industrial hand cleaner and water. Do not use solvents on skin.FURTHER INFORMATIONThe information herein is offered for general guidance only. Advice on specific applicationsis available on request from the Technical De-partment of Sika Industry.Copies of the following publications are avail-able on request:Safety Data Sheets ▪General GuidelinesBonding and Sealing with 1-component Sikaflex®▪PACKAGING INFORMATION Cartridge 300 ml Unipack 600 ml Pail 23 l Drum195 lBASIS OF PRODUCT DATAAll technical data stated in this document are based on laboratory tests. Actual measured data may vary due to circumstances beyond our control.HEALTH AND SAFETY INFORMATION User must read the most recent correspond-ing Safety Data Sheets (SDS) before using any products. The SDS provides information and advice on the safe handling, storage and dis-posal of chemical products and contains phys-ical, ecological, toxicological and other safety-related data.DISCLAIMERThe information, and, in particular, the re-commendations relating to the application and end-use of Sika products, are given in good faith based on Sika's current knowledge and experience of the products when prop-erly stored, handled and applied under nor-mal conditions in accordance with Sika's re-commendations. In practice, the differences in materials, substrates and actual site condi-tions are such that no warranty in respect of merchantability or of fitness for a particular purpose, nor any liability arising out of any legal relationship whatsoever, can be inferred either from this information, or from any writ-ten recommendations, or from any other ad-vice offered. The user of the product must test the product's suitability for the intended application and purpose. Sika reserves the right to change the properties of its products. The proprietary rights of third parties must beobserved. All orders are accepted subject toour current terms of sale and delivery. Usersmust always refer to the most recent issue ofthe local Product Data Sheet for the product concerned, copies of which will be supplied on request.PRODUCT DATA SHEET Sikaflex®-268Version 05.01 (04 - 2023), en_GB 012001212680001000SIKA LIMITED WatchmeadWelwyn Garden City Hertfordshire, AL7 1BQ Tel: 01707 394444Web: Twitter: @SikaLimited2 / 2。
A4 系列压料、自动抬压脚分组件说明书
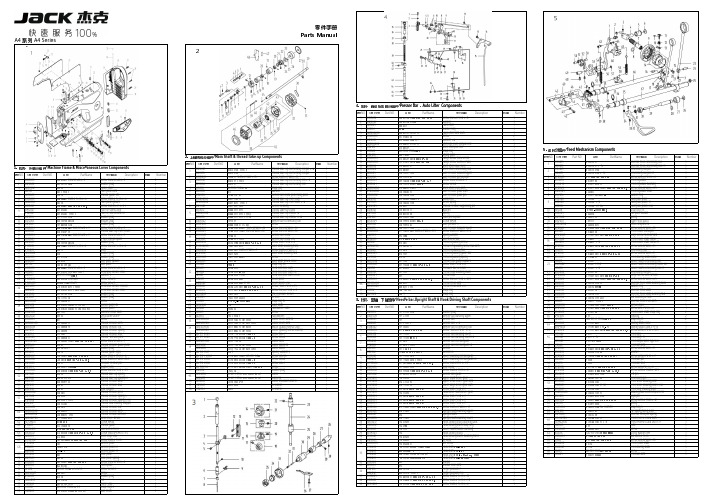
5零件手册Parts ManualA4 系列 A4 Series14. 压料、自动抬压脚分组件/Presser Presser Bar Bar ,Auto Auto Lifter Lifter Components公司件号 Part NO.名称 PartName零件描述 Description压脚扳手螺钉SM9/64"x40 L=11Screw SM9/64"x40 L=11压脚扳手螺钉垫圈Washer 压脚扳手Hand lifter O 型圈Rubber ring 压脚扳手凸轮分部件Hand lifter cam asm.前杠杆螺纹销Screw 螺纹销橡胶垫圈(厚)Washer (H )抬压脚前杠杆分部件Lift front lever component 抬压脚拉杆Knee lifter pull rod 5. 送料分组件/Feed Feed Mechanism Mechanism ComponentsGB/T896-1986挡圈 5Snap ring Main Shaft & Thread Take-up Components压脚升降板Lifting plate序号NO.公司件号 Part NO.名称 PartName零件描述 Description数量 Number抬压脚拉杆螺钉SM3/16"x32Hinge Screw SM3/16"x32Part NO.名称 PartName零件描述 Description后杠杆轴位螺钉SM15/64"x28Hinge screw SM15/64"x28111405015倒送料连杆Reverse feed connecting rod 11. 机壳、外装分组件/Machine Frame & Miscellaneous Cover Components抬压脚后杠杆Knee lifter back lever 11305015倒送料连杆(-7)Reverse feed connecting rod(-7)1挑线连杆销 (厚料)Thread take-up connecting rod pin (抬压脚顶杆Knee lifter connecting rod 211426021倒送料连杆销Connecting rod pin 1公司件号 Part NO.名称 PartName零件描述 Description挑线连杆销Thread take-up connecting rod pin 松线导管上支架Wire release bracket upper 11326011倒送料连杆销(-7)Connecting rod pin(-7)1上轮螺钉 SM15/64"x28 L=15Screw SM15/64"x28 L=15松线导管压板Wire release press plate 3101S11005螺钉 SM9/64"x40 L=6Screw SM9/64"x40 L=66101S11001后窗板螺钉SM3/16"×28 L=9Screw SM3/16"×28 L=9挑线连杆(厚料)Thread take-up connecting rod (H)油管压板螺钉SM3/16"x28 L=7Screw SM3/16"x28 L=7410101053送料调节器Feed regulator 110122003面板调节孔螺塞Rubber plug 挑线连杆Thread take-up connecting rod 松线导管压板螺钉M4x8Screw M4x8511403043送料调节器轴套Feed regulator bushing 113837002商标牌Head card GB/T896-1986挡圈Snap ring 抬压脚前杠杆组件Knee lifter lever asm 6101S11023送料调节器轴端螺钉SM3/16"x28 L=6.5Screw SM3/16"x28 L=6.51302591面板(喷漆)Face plate asm 垫片washer713826005标盘螺柱Feed regulator stud 113813005左线钩Thread guide left 针杆曲柄护板Needle bar crank protecting plate 810122016送料调节螺钉O形圈Rubber ring 1101S11007右线钩螺钉SM11/64"×40 L=6Screw SM11/64"×40 L=6挑线杆分组件Thread take-up lever asm.913811008固定表盘Fixing dial plate 113822006面板垫Face plate gasket 挑线杆组件(厚料)Thread take-up lever asm.(H )13811008固定表盘(-7)Fixing dial plate(-7)1101S11027防油板螺钉SM1/8"×44 L=3.4Screw SM1/8"×44 L=3.4挑线杆滚针轴承Needle bearing 13811013固定表盘(H-M )Fixing dial plate(H-M)110412007面部防油板Face oil shield asm.挑线曲柄分部件Thread take-up crank 10H05018GB/T896-1986挡圈3.5Snap ring 3.5111412082面部防油板(厚料)Face oil shield asm.(H)挑线曲柄分部件(厚料)Thread take-up crank (H )1113811009标盘按钮Dial plate button 110122013针杆上衬套孔塞Rubber plug 挑线曲柄分部件(H-M )Thread take-up crank (H-M )1213827002按钮复位簧Spring110122005挑线连杆销螺孔塞Rubber plug 针杆连杆Needle bar connecting rod 1313812010上限位片Upper limit patch 110122004针杆曲柄螺孔塞Rubber plug挑线曲柄螺钉(左旋)Screw141381100700标盘旋钮组件Knob component 1101S11004挑线杆护罩螺钉SM3/16"×28 L=7Screw SM3/16"×28 L=7针杆曲柄紧固螺钉 SM9/32"x28 L=16Screw SM9/32"x28 L=1615101S11022送料距旋钮螺钉SM3/16"x28 L=18Screw SM3/16"x28 L=181********挑线杆防护罩Thread take-up lever cover 针杆曲柄定位螺钉SM9/32"x28 L=16Screw SM9/32"x28 L=16101S11004挑线杆护罩螺钉SM3/16"×28 L=7Screw SM3/16"×28 L=7针杆曲柄Needle bar crank 13512004三孔线勾3-hole thread guide 针杆曲柄(厚料)Needle bar crank (H )10122005挑线连杆销螺孔塞Rubber plug送料轴挡圈螺钉SM1/4"x40 L=6Screw SM1/4"x40 L=6114S11015割线刀螺钉SM9/64"×40 L=6Screw SM9/64"×40 L=6上轴前轴套组件Main shaft bushing front 11419001割线刀Knife 夹线器螺钉SM15/64"x28 L=7Screw SM15/64"x28 L=720722002油塞Rubber plug 主轴中轴套Main shaft bushing mid 13822001操作屏孔塞Rubber plug 上轴中套挡圈螺钉Screw13822007后窗板垫Side plate gasket 上轴挡圈Main shaft thrust collar 302592后窗板(喷漆)Side plate挡圈20Snap ring 20101S11001后窗板螺钉SM3/16"×28 L=9Screw SM3/16"×28 L=9送料偏心轮 Feed eccentric cam 13811031一体机电控罩壳(鲍麦克斯)Electronic control box 送料偏心轮(厚料)Feed eccentric cam (H)W01009GB/T97.1-1985垫圈 5Washer 5送料偏心轮(H-M)Feed eccentric cam (H-M)114S13001直驱电机螺钉M5×20Screw M5×20送料偏心轮盖板Cover plate 114S30001螺栓(内六角)M5×25Screw M5×25送料偏心轮盖板(H-M)Cover plate(H-M)13833010一体机电控组件(琦星)Electronic control box(Q)送料偏心轮螺钉 SM1/4"x40 L=13Screw SM1/4"x40 L=1313833013一体机电控组件(鲍麦克斯)Electronic control box 护针片螺钉 SM9/64"x40 L=5Screw SM9/64"x40 L=510122006送料调节器孔塞Rubber plug 上轴后轴套The rear axle sleeve 10122007下轴工艺孔塞Rubber plug 上轴后套挡油油封Oil seal 138S05001操作面板螺钉ScrewGB/T894.1-1986挡圈15Snap ring 1513833012一体机电控面板组件(琦星)Control panel(Q)上轴Main shaft 13833015一体机电控面板组件(鲍麦克斯)Control panel 手轮贴条Handwheel lable 101S12001底板支柱Machine head stud 螺钉Screw 13822002装饰条Decorative article 手轮(喷漆)Handwheel 101S11004螺钉Screw电机罩壳组件(配琦星)Motor cover asm(Q)1381300400小夹线器组件Thread tension asm.电机罩壳组件(配鲍麦克斯)Motor cover asm138S16019小夹线器螺母Thread tension nut 电机光栅组件(配鲍麦)Motor grating sensor asm 11227001小夹线弹簧Thread tension spring6`12. 机头附件(1)-线架组件/Machine Head Accessories(1)-Thread Stand Components公司件号 Part NO.名称 PartName零件描述 Description8. 润滑、油量检测组件/Oil Oil Lublication 、Oil Oil Measuring Measuring Components20131019线架杆顶防护橡皮Spool rest rod rubber cap 公司件号 Part NO.名称 PartName零件描述 Description数量 S04050 十字槽凹穴六角头螺栓 M5 L=16 Screw M5 L=16 W01047垫圈M5Washer M5油窗Oil sight window N01034 螺母 M5Nut M510122019油窗O形圈Rubber ring 13831022上线架过线杆 Spool rest arm upper 上轴供油管Main shaft oil tube 10113011过线圈(内)Thread guide ring 112S30005油泵连接螺柱Oil pump connecting stud 10113010过线圈(外) Thread guide ring 11329010开口挡圈10Snap ring 1013831019线架杆上节Spool rest rod upper 6. 切线装置部件/Thread Trimmer Components供油管Hook oil tube13831021线架杆接头 Spool rest rod joint 10112020油泵安装板Oil pump installing base 13831020线架杆下节Spool rest rod lower 序号NO.公司件号 Part NO.名称 PartName零件描述 Description数量 NumberW03002弹垫Spring washer10122106橡胶垫圈Spool rest rod rubber ring 209S12001压脚螺钉SM11/64"×40 L=10.5Screw SM11/64"×40 L=10.5W01048垫圈M16Washer M161113S15002定刀调节螺钉SM1/8"x44 L=9.5Screw SM1/8"x44 L=9.5110103022油泵体衬套Oil pump bushing N02008六角薄螺母 M16Spool rest rod nut M16211319001定刀Secant knife 1101S30007柱塞螺钉Plunger Screw 10. 绕线器组件/ Bobbin ComponentsS04051十字槽凹穴六角头螺栓 M5Spool rest arm lower screw M53113S17001螺钉SM9/64"x40Screw SM9/64"x40110127013柱塞簧Plunger spring N01034 螺母 M5Nut M5411312003护针片Needle guard patch 110122018回油柱塞Plunger 公司件号 Part NO.名称 PartName零件描述 Description数量 W03002弹簧垫圈 5Spring washer 55201S11009螺钉SM9/64"x40 L=5.5Screw SM9/64"x40 L=5.5110120001油泵体Oil pump 6113S11001螺钉SM11/64"x40 L=12Screw SM11/64"x40 L=122油泵螺钉Screw1383103900绕线器组件Bobbin winder asm.油泵叶轮Oil pump impeller 114S11008螺钉M4x6Screw M4x6油泵叶轮托板Oil pump impeller cover GB/T97.1 垫圈4Washer油泵盖Lubricating oil pump cover 10113030压线控制板Thread press control plate 101S30006螺钉Screw10111120绕线衬垫Winding pad 1012000100油泵分部件Lubricating oil pump component 13831101绕线器装置主座Bobbin winder bed116S30003抬牙叉固定螺钉SM15/64"×28 L=14.5Screw SM15/64"×28 L=14.5GB/T 896-1986 开口挡圈5Snap ring 10136001供油管接头Rubber joint 10127061复位板拉簧Spring13812110调节板Regulating plate 10110030绕线凸轮Bobbin winder cam S09045螺钉Screw1380510600绕线器连杆组件Bobbin winder connecting rod 13827103满线复位簧spring 10127060弹簧Spring GB/T 896-1986开口挡圈4Snap ring13802111绕线器主轴Bobbin winder mian shaft 13802026绕线凸轮轴Bobbin winder cam shaft S09103绕线轮螺钉Screw13831102绕线轮Bobbin winder wheel O01110O 型圈Ring 11422062密封垫Washer114S11003螺钉SM3/16"×28 L=10Screw SM3/16"×28 L=101381300600底线夹线器Bobbin thread tension asm.13811004夹线螺母Thread tension nut 11427006小夹线弹簧Spring10112005夹线板Thread tension disk 11413022夹线过线板Thread tension guide plate 112S13004夹线螺钉Screw114S16001螺母SM11/64"×40Nut SM11/64"×4012. 机头附件(2)/Machine Head Accessories(2)公司件号 Part NO.名称 PartName零件描述 Description数量 1011203100机头连接钩部件 Hinge component10122060机头连接钩座 Head connecting rubber cushion 10117021机针(14#)Needle (14#)10117022机针DP×5#21(厚料)Needle (H)101S30010 机头连接钩座钉 Nail 10118003梭心 Bobbin机头支柱 Machine head rest pin 20731047螺丝刀(大)Screw driver10131003螺丝刀(中) Screw driver,medium9. 自动倒送料开关、感应抬压脚组件/Automatic Automatic Reverse Reverse Feed Feed ComponentsNO.公司件号 Part NO.名称 PartName零件描述 Description数量 NumberS05254GB/T70.1-2000螺钉M2.5×4Screw M2.5×411383004600下感应探头Lower sensor1201S11012螺钉SM9/64"×40 L=7.7Screw SM9/64"×40 L=7.7113813022过线压板Screw M4x8113822030橡皮塞(单孔)Rubber plug1101S11004挑线杆护罩螺钉SM3/16"×28 L=7Screw SM3/16"×28 L=711403003600双开关组件Auto reverse feed switch asm 1116S30003抬牙叉固定螺钉SM15/64"×28 L=14.5Screw SM15/64"×28 L=14.52W02004GB/T93-1987弹垫M6Spring washer M621011628005抬牙叉固定螺钉垫圈Washer2杰克缝纫机股份有限公司杰克缝纫机全球销量遥遥领先1383003400自动倒送料电磁铁Auto reverse feed solenoid 111. 油盘、膝抬压脚分组件/Oil Ceservoir,Knee Lifter Components1383003500自动倒送料电磁铁(-7)Auto reverse feed solenoid(-7)11211326005销子Pin 1序号NO.公司件号 Part NO.名称 PartName零件描述 Description数量 Number110122022油盘座垫Oil reservoir rubber cushion 1213801020油盘Oil Reservoir 1公司地址(Address of Company):310111005抬压脚顶杆Knee lifter push rod 1台州市椒江区机场南路15号410122020油盘垫Oil Reservoir gasket 1No.15 Rd Airport South,Jiaojiang District Taizhou City,Zhejiang,P.R.C 7. 自动抬压脚组件/Auto Lifter Components510122021O 型圈Rubber ring1邮编( Zip Code ):3180006101S11028排油孔螺钉SM5/16"×24 L=7Screw SM5/16"×24 L=72国内销售部(Domestic Trade Department):Part NO.名称 PartName零件描述 710131001油盘磁铁Oil reservoir magnet 1电话(TEL):0086-0576-******** 88177789810122023油盘支架Oil reservoir rubber cushion 1传真(FAX):0086-0576-********销子Pin 910112027抬压脚双向曲柄Knee lifter crank 1国贸部(International Trade Department):开口销 GB/T91 2×14Cotter pin电话(TEL):0086-0576-******** 88177774电磁铁接头Solenoid connector 传真(FAX):0086-0576-********法兰螺母M8Flange nuts M8服务热线:400-8876858电磁铁组件Solenoid asm.2018.12后窗板螺钉SM3/16"×28 L=9screw SM3/16"×28 L=9资料如有更改,恕不另行通知,以实物为准。
中国_44140010_辐射松木制的画框,相框,镜框及类似品(2003-2013)出口量及出口额

—— —— 689354.00 美元 797954.00 美元 1467848.00 美元 1589230.00 美元 1808432.00 美元 1984795.00 美元 2493206.00 美元 1754502.00 美元 1011788.00 美元 1387304.00 美元 1686800.00 美元 1919647.00 美元 1572806.00 美元 1706146.00 美元 1882370.00 美元 1383060.00 美元 1681365.00 美元 1912599.00 美元 2521060.00 美元 1190954.00 美元 1081230.00 美元 1166581.00 美元 1287669.00 美元 1185499.00 美元
—— —— —— —— —— —— —— —— —— —— —— —— —— —— —— —— —— —— —— —— —— —— —— —— —— ——
—— —— —— —— —— —— —— —— —— —— —— —— —— —— —— —— —— —— —— —— —— —— —— —— —— ——
机构简介: 如果您对本产品其它相关进出口相关数据感兴趣,欢迎登陆中国产业洞察网官方网站查询并来电咨询。 我们致力于成为您身边的决策咨询专家顾问!
服务内容: 整合全球各国官方政府的真实、权威贸易数据,支持产品、企业、港口、产地等多条件搜索,
提供全球进出口商之间的最新贸易交易数据,实现对行业、采购商、竞争对手等多角度全方位的分析、评估。
中国_44140010_辐射松木制的画框,相框,镜框及类似品(2003-2013)出口量及出口额
数据样本如下: 出口额_月度_基础 值 单位 2013年12月 2013年11月
预感光乳胶说明书
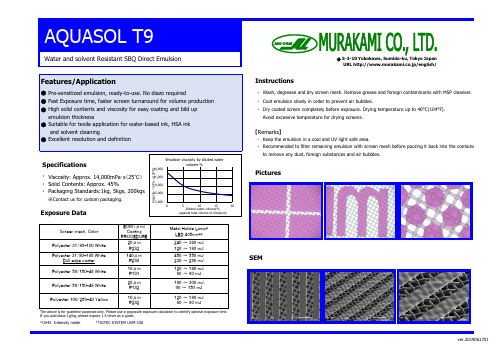
●Pre-sensitized emulsion, ready-to-use. No diazo required・Wash, degrease and dry screen mesh. Remove grease and foreign contaminants with MSP cleanser.●Fast Exposure time, faster screen turnaround for volume production ・Coat emulsion slowly in order to prevent air bubbles.●High solid contents and viscosity for easy coating and bild up ・Dry coated screen completely before exposure. Drying temperature up to 40°C(104°F).emulsion thicknessAvoid excessive temperature for drying screens.●Suitable for texile application for water-based ink, HSA ink and solvent cleaning【Remarks 】●Excellent resolution and definition・Keep the emulsion in a cool and UV light safe area.・Recommended to filter remaining emulsion with screen mesh before pouring it back into the container to remove any dust, foreign substances and air bubbles.・Viscosity: Approx. 14,000mPa ・s (25℃)・Solid Contents: Approx. 45%・Packaging Standards:1kg, 5kgs, 200kgs※Contact us for custom packaging.*UV42 Intensity meter **AITEC SYSTEM UVM-100The above is for guideline purposes only. Please use a grayscale exposure calculator to identify optimal exposure time.If you add diazo 1g/kg, please expose 1.5 times as a guide.10μm P2S2Polyester 100/250-40 YellowScreen mesh, Color Metal Halide Lamp*LED 405nm**EOM (μm)Coating PROCEDURE 20μm P2S210μm P1S1120 ~ 180 mJ 60 ~ 90 mJ 240 ~ 360 mJ 120 ~ 180 mJ Polyester 59/150-48 White InstructionsExposure DataFeatures/ApplicationPolyester 31/80-100 WhiteDull edge coater Polyester 31/80-100 White 140μm P2S8450 ~ 550 mJ 230 ~ 280 mJ SEMWater and solvent Resistant SBQ Direct EmulsionPicturesSpecifications20μm P1S2180 ~ 300 mJ 90 ~ 150 mJ Polyester 59/150-48 White 120 ~ 180 mJ 60 ~ 90 mJ◆5-3-10 Yokokawa, Sumida-ku, Tokyo JapanURL http://www.murakami.co.jp/english/AQUASOL T92,0005,0008,00011,00014,00005101520V i s c o s i t y /mP a ・s(25℃)Diluted water volume/%(against total volume of emulsion)Emulsion viscosity by diluted watervolume %ver.2019061701。
阿克苏油漆施工实用工艺-I670

1. Scope 前言This Painting Technology Specification covers surface preparation and painting specification. This document is organized on basis of International Protective Coatings Products Data Sheets. It is composed of additional regulations and the detail descriptions in the above documents mentioned, and therefore is not to be the substitute of the approved specifications. The specification is prepared with the reference of the Project Contract Specification.本技术工艺涵盖了表面处理及涂料技术规格。
文件根据阿克诺贝尔防护涂料产品手册制定的,不是取代任何该项目的规文件,而是对它们补充说明或细节性描述。
此外,本文件服从于此项目合同技术规中提到的要求。
2. Standards, References, Definitions and Abbreviations 标准和参考文献2.1 Abbreviations 缩写SSPC The Society of Protective Coating 美国防护涂料协会ASTM America Society for Testing and Materials 美国试验和材料协会ISO International Standard Organization 国际标准化组织DFT Dry Film Thickness 干膜厚度WFT Wet Film Thickness 湿膜厚度2.2 Reference and Standards 现行的参考和标准ISO 8501-1 Preparation of steel substrates before application of paints and related products - Visual assessment of surface cleanliness.表面清洁度目测法评估ISO 8502-3 Preparation of steel substrates before application of paints and related products - Test for the assessment of surface cleanliness - Assessment of dust on steelsurfaces prepared for painting, pressure sensitive tape method.表面清洁度测试评估-准备涂漆的钢材表面灰尘评估-压敏胶带法ISO 8503 Preparation of steel substrates before application of paints and related products - Surface roughness characteristics of blast cleaned substrates.喷射清理表面粗糙度特征ISO 11124 Preparation of steel substrates before application of paints and related products -- Specifications for metallic blast-cleaning abrasives -- Part 2: Chilled-iron grit -- Part 3:High-carbon cast-steel shot and grit油漆和相关产品施工前钢材表面处理–金属喷砂清洁磨料的规定ISO 11125 Preparation of steel substrates before application of paints and related products -- Test methods for metallic blast-cleaning abrasives油漆和相关产品施工前钢材表面处理–金属喷砂清洁磨料测试方法ISO 11126 Preparation of steel substrates before application of paints and related products -- Specifications for non-metallic blast-cleaning abrasives油漆和相关产品施工前钢材表面处理–非金属喷砂清洁磨料的规定ISO 11127 Preparation of steel substrates before application of paints and related products -- Test methods for non-metallic blast-cleaning abrasives油漆和相关产品施工前钢材表面处理–非金属喷砂清洁磨料测试方法SSPC SP1 Solvent Cleaning 溶剂清洗SSPC SP10/ISO Sa 2.5 Near White Blast Cleaning 近白级喷射清理SSPC SP3/ISO St3 Power Tool Cleaning 动力工具清理SSPC PA 2 Measurement of Dry Film Thickness 干膜厚度测量方法ISO 2808 Measurements of Film Thickness 漆膜厚度测量法ISO 4624 Paints and varnishes - Pull-off test for adhesion 附着力拉开测试法3. Coating Systems 油漆配套4. Surface Preparation 表面处理4.1 Steelwork preparation 钢结构处理In order to provide surfaces which will ensure optimum paint performance, prior to blast cleaning, weld defects such as pinholes and discontinuities shall be repaired. Sharp edges and flame-cut edges shall be reduced to R=2mm by grinding. Welds shall be smooth and free of all weld slag and weld spatter.为了保证涂料发挥最性能,钢结构表面在喷砂前,电焊缺陷例如气孔和不连续焊等要修正好。
- 1、下载文档前请自行甄别文档内容的完整性,平台不提供额外的编辑、内容补充、找答案等附加服务。
- 2、"仅部分预览"的文档,不可在线预览部分如存在完整性等问题,可反馈申请退款(可完整预览的文档不适用该条件!)。
- 3、如文档侵犯您的权益,请联系客服反馈,我们会尽快为您处理(人工客服工作时间:9:00-18:30)。
PI 4410 TUBCOAT
Clear Peelable coating For Temporary Protection of Bath Tubs, Shower Trays and Screens
1. INTRODUCTION:
PI 4410 - Water based peelable coating that is sprayed onto the Shower Array tray whirlpool and bath Tub. It dries to form a durable temporary
protective peelable coating that protects the shower trays, whirl pool and
bath tub from damage during the construction phase. A water-
based, clear peelable coating,PI 4410 Tubcoat PI 4410 protects
tubs, whirlpools and shower stalls against scratches, abrasions and job
site dirt and grime. Easy-to-apply, the water-based coating cures to a
durable, easy-to-remove "protective skin." One gallon covers
approximately two standard 5' tubs.
Cost effective solution for Bathtub and Shower fixture damage
Virtually eliminates tub and shower repairs
caused during construction
Provides Temporary protection through final inspection
Replaces crude or ineffective liner materials
Value added service for home buyers satisfaction
Professional image for contractor and builder
Use for protecting Showers, Bathtubs, Laminates, Polished stone and Non-Porous surfaces. Protects against scratches, nicks, paint over-spray, miscellaneous damage, provides reliable protection during the construction process. Peels off easily when the surface is no longer subjected to other construction trades.
2. PHYSICAL CHARACTERISTICS
Colour Blue
Weight 1kg/litre
Viscosity Spray viscosity or high
viscosity for brushing
Flashpoint None
3. APPLICATION
Patch Test
Because it is difficult to determine the type and amount of application, perform a small test first. This will determine PI 4410 Tubcoat effectiveness, coverage, and the approximate amount of time required for it to work.
PI 4410 Tubcoat should be used as received. It is applied by spray; brushing, roll coating or dipping. The coating dries to touch in 30 minutes or less, depending on temperature and film thickness. PI 4930 should be applied to form a dry film in the range of 100 – 300 microns (.001" to .003") thick. Application temperature is
ambient to no lower than 10 deg C, as drying times will be affected.
4. CURING
PI 4410 Tubcoat will cure tack-free within 30 minutes after application, dependent upon temperature, humidity and thickness of coating. Deviations from application section will require adjustments in the curing times, as well as in the strip-ability parameters. Forced drying at 43 degrees Celsius for 3 to 7 minutes may accelerate curing. It is imperative that PI 4410 Tubcoat be thoroughly cured and dry (approx 24 hours), with no water being in the film before an attempt is made to strip the coating from the substrate.
5. STORAGE
It is recommended that temperatures of 10°C - 32°C (55°F- 90°F) should be used for storage and the product should be used within one year of purchase. PI 4410 Tubcoat should be stored in the original shipping container in an indoor environment. Containers should be sealed until needed. Protection from freezing is necessary.
6. REMOVAL
Once the home is built and the final cleanup is scheduled, the protective coating is peeled away in one piece to form a bag enclosing
all waste and debris, revealing a tub in showroom condition!
PI 441O Tubcoat is readily removed from surfaces by peeling. Start with one corner of the dried film and peel slowly and carefully away from the protected substrate. Careless, quick removal will invariably cause the film to rip.
Performance statements are based upon representative experience from testing Worldwide; however, actual performance will be
determined by substrate selection and preparation, exposure conditions, and maintenance of the marking.。