精加工论文1doc
机械设计制造及其自动化毕业设计论文(完整版).doc
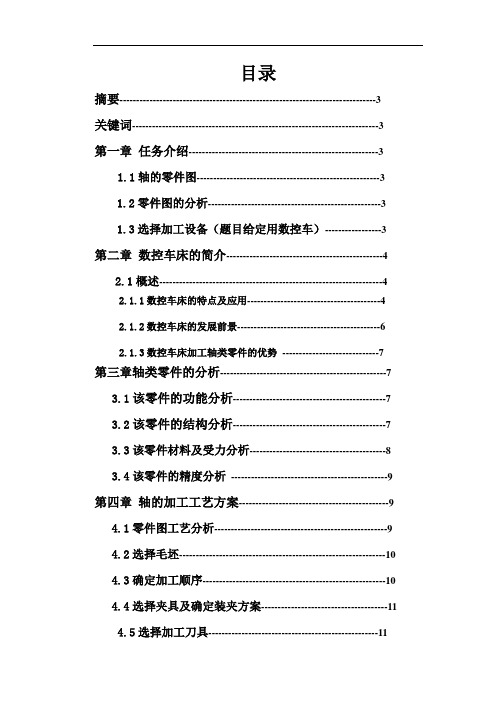
目录摘要-----------------------------------------------------------------------------3关键词--------------------------------------------------------------------------3 第一章任务介绍---------------------------------------------------------31.1轴的零件图-------------------------------------------------------31.2零件图的分析----------------------------------------------------31.3选择加工设备(题目给定用数控车)-----------------3 第二章数控车床的简介-----------------------------------------------42.1概述-------------------------------------------------------------------42.1.1数控车床的特点及应用----------------------------------------42.1.2数控车床的发展前景-------------------------------------------62.1.3数控车床加工轴类零件的优势-----------------------------7 第三章轴类零件的分析--------------------------------------------------73.1该零件的功能分析----------------------------------------------73.2该零件的结构分析----------------------------------------------73.3该零件材料及受力分析-----------------------------------------83.4该零件的精度分析-----------------------------------------------9第四章轴的加工工艺方案---------------------------------------------94.1零件图工艺分析----------------------------------------------------94.2选择毛坯--------------------------------------------------------------104.3确定加工顺序-------------------------------------------------------104.4选择夹具及确定装夹方案--------------------------------------114.5选择加工刀具---------------------------------------------------114.6确定进给路线---------------------------------------------------124.7合理选着切削用量---------------------------------------------124.8 编写工艺卡------------------------------------------------------134.9 编写加工程序---------------------------------------------------144.10调试模拟运行程序,无误后加工----------------------164.11完成零件加工并进行精度检测--------------------------16第五章总结------------------------------------------------------------------17参考文献------------------------------------------------------------------------18致谢--------------------------------------------------------------------------------18摘要数控加工制造技术正逐渐得到广泛的应用,对零件进行编程加工之前,工艺分析具有非常重要的作用。
数铣技师论文--2.doc
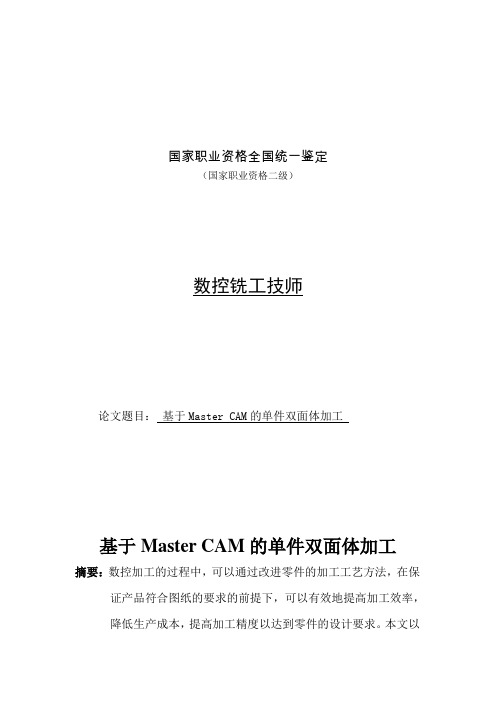
国家职业资格全国统一鉴定(国家职业资格二级)数控铣工技师论文题目:基于Master CAM的单件双面体加工基于Master CAM的单件双面体加工摘要:数控加工的过程中,可以通过改进零件的加工工艺方法,在保证产品符合图纸的要求的前提下,可以有效地提高加工效率,降低生产成本,提高加工精度以达到零件的设计要求。
本文以较为复杂的带椭圆凸台的工件为研究对象,主要通过MasterCAM介绍使用一些优化方法去保证或改进产品的加工精度、质量和生产效率等。
关键词:加工工艺,效率,精度,加工质量,切削参数一、引言在数控自动编程加工时不仅要使工件的外形和尺寸达到图纸要求,而且还要达到好的经济效益。
数控程序编制的方法不同,将直接影响工件的加工质量、效率和经济性,所以应首先做好工艺分析和刀路规划,使工艺内容具体化,具有高的严密性,同时注重加工的适应性,选择正确的加工方法和加工内容。
将保证零件的加工精度和表面粗糙度要求放在首位,力求使编程所得的加工路线构成简单,而且行程最短,减少空行程时间,提高加工效率。
在满足零件加工质量、生产效率等条件下,尽量简化数学处理的数值计算工作量,以简化编程工作。
本文以一个凸台零件数控铣削加工的实例来说明。
二、零件结构工艺分析图1零件图图2零件建模正面 图3零件建模反面这个零件由正反两面组成,正面中间是一个椭圆台,椭圆台正中有通孔,围绕着椭圆台的是一个曲面内凹槽,其中曲面的外边界与凸台不同心,内凹槽左边是2个连接的半圆槽,零件左下角和右上角各有一通孔。
零件的反面是由一圈1.5mm 薄壁围起来的一个回转样式的凸台,而通孔处各有一个不封闭槽。
从零件的实体图形可以看出,这个零件可以用虎钳装夹,并且应曲面凹槽椭圆凸台半圆槽薄壁回转样式凸台不封闭槽先加工正面,否则不能保证1.5mm的薄壁不被损坏,装夹时应选椭圆凸台的短轴方向,从而保证加工反面装夹时,曲面凹槽与圆柱型凹槽的交界边发生变形。
三、零件加工工艺过程分析零件的毛坯为100*90*30mm长方体,材料是45号钢件,铣削性能好。
浅析发动机零部件加工中的珩磨技术

浅析发动机零部件加工中的珩磨技术论文导读:珩磨工艺是磨削加工的一种特殊形式,又是精加工中的一种高效加工方法。
发动机汽缸体缸孔珩磨是平台珩磨最典型的应用。
平台珩磨后可在缸孔(或缸套)表面形成一种特殊的结构,这种结构由具有储油功能的深槽及深槽之间的微小支承平台表面组成。
铰珩工艺是在传统珩磨工艺的基础上发展起来的新工艺,其加工过程中融入了铰孔的特点,目前在缸体曲轴孔、连杆大小头孔的精整加工中广泛应用。
发动机缸孔表面的微观质量,决定了发动机运转时的磨合性能、运转可靠性和润滑油消耗,通过刷珩工艺可以缩短发动机的磨合时间和显著降低润滑油消耗。
在这种情况下进行的珩磨称作模拟珩磨,工件的珩磨质量可显著提高,工件的宏观形状精度可提高五至十倍。
关键词:珩磨,平台珩磨,铰珩,刷珩,模拟珩磨,缸孔珩磨工艺是磨削加工的一种特殊形式,又是精加工中的一种高效加工方法。
这种工艺不仅能去除较大的加工余量,而且是一种提高零件尺寸精度、几何形状精度和表面粗糙度的有效加工方法,在发动机零部件的制造中广泛应用。
珩磨加工原理珩磨是利用安装于珩磨头圆周上的一条或多条油石,由涨开机构(有旋转式和推进式两种)将油石沿径向涨开,使其压向工件孔壁,以便产生一定的面接触。
同时使珩磨头旋转和往复运动,零件不动;或珩磨头只作旋转运动,工件往复运动,从而实现珩磨。
在大多数情况下,珩磨头与机床主轴之间或珩磨头与工件夹具之间是浮动的。
这样,加工时珩磨头以工件孔壁作导向。
因而加工精度受机床本身精度的影响较小,孔表面的形成原理基本上类似两块平面运动的平板相互对研而形成平面的原理。
珩磨加工特点加工精度高:中小型的通孔加工,其圆柱度可达0.001mm 以内。
一些壁厚不均匀的零件,如连杆,其圆度能达到0.002mm。
对于大孔(孔径在200mm以上),圆度也可达0.005mm,如果没有环槽或径向孔等,直线度可达到0.01mm/m以内。
表面质量好:珩磨速度低(是磨削速度的几十分之一),且油石与孔是面接触,因此每一个磨粒的平均磨削压力小,这样珩磨时,工件的发热量很小,工件表面几乎无热损伤和变质层,变形小,珩磨加工面几乎无嵌砂和挤压硬质层。
车工高级技师技术论文范文

车工高级技师技术论文范文车工作为一项专业的技能,车工技师这个队伍正在发展壮大。
下面是由店铺整理的车工技师论文范文,欢迎大家阅读。
车工技师论文范文篇一:《浅析车工的技能》【摘要】随着工业的发展,与工业相关的技术也不断的得到完善,对技术工人的要求也不断地提高,其中,车工在我国的行业中担任着不可或缺的角色,车工的技能也在不断地增加,本研究就车工中的工艺技巧与如何学好车工工艺进行了研究。
【关键词】车工;技能0.前言作为一项专业的技能,车工工艺正以前所未有的速度在发展壮大,学习车工工艺,培养新一代的车工工人已成为众人瞩目的事情。
掌握好这项技能不仅仅对于自身的发展是有利的,还会促进相关技术的发展,应当得到足够的重视。
1.车工工艺中的车工技巧1.1对刀对刀的方式有很多种,其中,z 向对刀与o向对刀较为常见。
Z向对刀相比于其他的常规对刀并没有什么不同,刀尖与主轴中心调在同一水平高度;而0 向对刀稍有差异,在对刀的时候首先调整刀尖到刀轴回转中心的距离,大约等于工件半径,然后在卡盘上装一对刀圆环,内环半径等于工件半径,刀体与中滑板导轨平行,慢慢调整中滑板位置,当刀尖旋转碰到a点时说明刀体回转中心在主轴中心线位置。
1.2加工对车工而言,除了对刀之外,还必须对器械进行加工,加工时先用圆弧刀自由加工,留2mm 余量再用转刀精加工,精加工走刀用手转动刀柄实现轨迹加工,吃刀量由床鞍控制,每次进刀量为0.5mm。
1.3浇帽口的补偿金属模型在实际生产过程中发现铸造出的圆球打断浇帽口时经常破坏圆球体,使圆球在浇帽口方向减少3mm左右。
因此在车上模时中滑板向前移4mm,刀回转半径也增加4mm,车出的纺棰体圆弧和理论上的圆弧比较接近,补偿了打浇帽口的损失,铸造出的零件稍经打磨可以达到使用要求。
用转刀加工圆球面,操作简单,刀具装卸简便,节约成本;精度较高;加工范围广,通过调整车刀的长度和调整车刀的回转中心位置可以加工不同直径的内圆球面,整个系列的圆球模型加工只需要一套刀就可以了,这种加工方法的工装成本不到靠模法工装的30%。
超精密加工技术论文【精选文档】
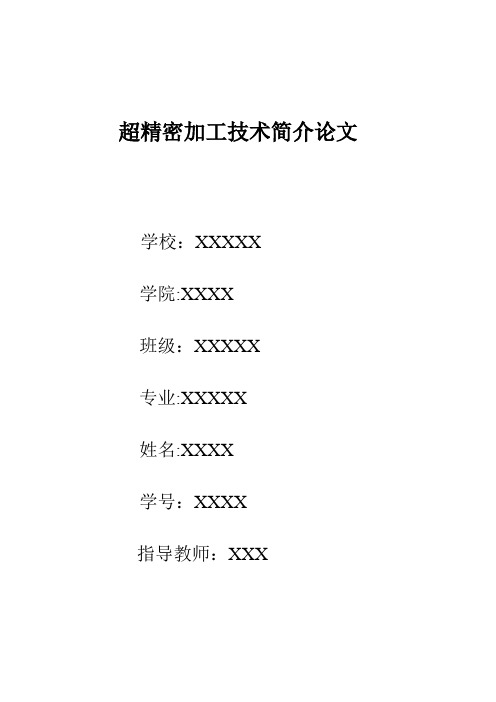
超精密加工技术简介论文学校:XXXXX学院:XXXX班级:XXXXX专业:XXXXX姓名:XXXX学号:XXXX指导教师:XXX目录目录 .......................................................................................................................................... - 1 -一、概述................................................................................................................... - 0 -1、超精密加工的内涵...................................................................................... - 0 -2。
、发展超精密加工技术的重要性................................................................ - 0 -二、超精密加工所涉及的技术范围....................................................................... - 1 -三、超精密切削加工............................................................................................... - 2 -1、超精密切削对刀具的要求.......................................................................... - 2 -2、金刚石刀具的性能特征.............................................................................. - 2 -3、超精密切削时的最小切削厚度.................................................................. - 2 -四、超精密磨削加工............................................................................................... - 3 -1、超精密磨削砂轮.......................................................................................... - 3 -2、超精密磨削砂轮的修整.............................................................................. - 3 -3、磨削速度和磨削液...................................................................................... - 4 -五、超精密加工的设备........................................................................................... - 4 -六、超精密加工的支撑环境................................................................................... - 5 -1、净化的空气环境.......................................................................................... - 5 -2、恒定的温度环境.......................................................................................... - 5 -3、较好的抗振动干扰环境.............................................................................. - 6 -七、超精密加工的运用领域................................................................................... - 6 -八、超精密加工的现状及未来发展....................................................................... - 6 -1、超精密加工的现状...................................................................................... - 6 -2、超精密加工的发展前景.............................................................................. - 7 - 总结:....................................................................................................................... - 8 - 参考文献: ................................................................................................................. - 8 -超精密加工技术一、概述超精密机械加工技术是现代机械制造业最主要的发展方向之一,已成为在国际竞争中取得成功的关键技术。
超精密制造技术论文
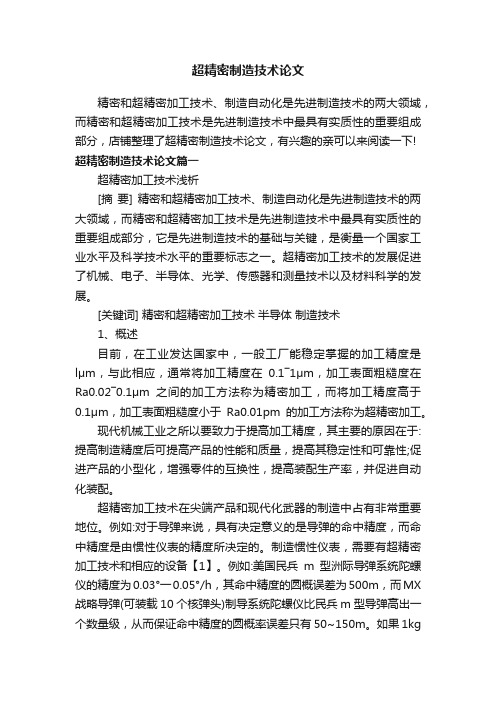
超精密制造技术论文精密和超精密加工技术、制造自动化是先进制造技术的两大领域,而精密和超精密加工技术是先进制造技术中最具有实质性的重要组成部分,店铺整理了超精密制造技术论文,有兴趣的亲可以来阅读一下! 超精密制造技术论文篇一超精密加工技术浅析[摘要] 精密和超精密加工技术、制造自动化是先进制造技术的两大领域,而精密和超精密加工技术是先进制造技术中最具有实质性的重要组成部分,它是先进制造技术的基础与关键,是衡量一个国家工业水平及科学技术水平的重要标志之一。
超精密加工技术的发展促进了机械、电子、半导体、光学、传感器和测量技术以及材料科学的发展。
[关键词] 精密和超精密加工技术半导体制造技术1、概述目前,在工业发达国家中,一般工厂能稳定掌握的加工精度是lμm,与此相应,通常将加工精度在0.1―1μm,加工表面粗糙度在Ra0.02―0.1μm之间的加工方法称为精密加工,而将加工精度高于0.1μm,加工表面粗糙度小于Ra0.01pm的加工方法称为超精密加工。
现代机械工业之所以要致力于提高加工精度,其主要的原因在于:提高制造精度后可提高产品的性能和质量,提高其稳定性和可靠性;促进产品的小型化,增强零件的互换性,提高装配生产率,并促进自动化装配。
超精密加工技术在尖端产品和现代化武器的制造中占有非常重要地位。
例如:对于导弹来说,具有决定意义的是导弹的命中精度,而命中精度是由惯性仪表的精度所决定的。
制造惯性仪表,需要有超精密加工技术和相应的设备【1】。
例如:美国民兵m型洲际导弹系统陀螺仪的精度为0.03°一0.05°/h,其命中精度的圆概误差为500m,而MX 战略导弹(可装载10个核弹头)制导系统陀螺仪比民兵m型导弹高出一个数量级,从而保证命中精度的圆概率误差只有50~150m。
如果1kg重的陀螺转子,其质量中心偏离其对称轴0.5nm,则会引起100m的射程误差和50m的轨道误差。
惯性仪表中有许多零件的制造精度都要求达到小于微米级。
发动机曲轴毕业论文

成都工业学院毕业设计(论文)设计(论文)题目:发动机曲轴工艺设计及钻中心孔夹具和钻斜油孔夹具设计系部名称:机电工程系专业:数控技术专业班级:09423学生姓名:学号:指导教师:二O一二年五月摘要曲轴是发动机上的一个重要的旋转机件,装上连杆后,可承接活塞的上下(往复)运动变成循环运动。
曲轴主要有两个重要加工部位:主轴颈和连杆颈。
主轴颈被安装在缸体上,连杆颈与连杆大头孔连接,连杆小头孔与汽缸活塞连接,是一个典型的曲柄滑块机构。
发动机工作过程就是:活塞经过混合压缩气的燃爆,推动活塞做直线运动,并通过连杆将力传给曲轴,由曲轴将直线运动转变为旋转运动。
而曲轴加工的好坏将直接影响着发动机整体性能的表现。
曲轴的材料一般为35、40、45钢或球墨铸铁QT600-2,曲轴有两个重要部位:主轴颈,连杆颈。
本次采用45钢,设计的主要就是这两方面的在数控机床的加工。
集合多种的曲轴加工后,深入分析了曲轴的加工工艺。
关键词:曲轴主轴劲夹具连杆劲数控加工AbstractThe crankshaft is an important engine rotating parts, fitted with linking, you can undertake up and down the piston (reciprocating) motion into circular motion. The crankshaft main two important processing areas: the main journal and rod neck. Spindle neck to be installed on the cylinder block, connecting rod journal and connecting rod hole connection, connect the connecting rod small end hole and the cylinder piston, is a typical slider-crank mechanism. Engine working process: the piston after the blasting of the mixed compressed gas pushes the piston linear motion and force to the crankshaft through the connecting rod, the linear motion into rotary motion by the crankshaft. The crankshaft processing will directly affect the overall performance of the engine performance. The material of the crankshaft is made of carbon structural steel or ductile iron, there are two important areas: the main journal rod neck. This paper introduces the fixture design of the engine crankshaft process design of the two processes. Ensure product quality, increase productivity, reduce costs, make full use of the existing production conditions to ensure workers have designed under the premise of a good and safe working conditions. In process design, the author combines practical theory of design, traditional crankshaft production process improvements, optimizing processes and process equipment, production and processing more economical and reasonable so that the crankshaft. Fixture design part of the collection of processing machine tools, cutting tools and auxiliary tools and other relevant information used based on the workpiece material, structural features, technical requirements and process analysis, in accordance with the fixture design steps to design a line with the crankshaft production process and fixture manufacturing requirements of the fixture.目录摘要 (I)Abstract (II)目录..................................................................................................................................................... 第1章绪论.. (1)1.1 课题研究的意义及现状 (1)1.2 论文主要研究内容 (2)第2章发动机曲轴零件图分析 (3)2.1曲轴的作用分析 (3)2.2曲轴的结构及其特点 (3)2.3曲轴的主要技术要求分析 (4)2.4曲轴的材料和毛坯的确定 (4)第3章工艺规程设计 (5)3.1 计算生产纲领,确定生产类型 (5)3.2 选择毛坯 (5)3.3 工艺过程设计 (5)3.3.1定位基准的选择 (5)3.3.2加工阶段的划分与工序顺序的安排 (6)3.3.3制定工艺路线 (7)3.4 确定加工余量 (10)3.4.1确定机械加工余量 (11)3.4.2设计毛坯图(一)确定毛坯尺寸公差 (12)3.5重要工序设计 (15)3.5.1选择加工设备和工艺装备 (15)3.6 确定切削用量及基本工时 (17)3.6.1曲轴主要加工表面的工序安排 (17)3.6.2确定工时定额 (17)3.6.3粗磨第一主轴颈和齿轮轴颈 (19)3.6.4精车二、三、五、主轴颈、油封轴颈、法兰 (19)3.6.5切槽 (20)3.6.6精车第三主轴颈及过渡圆角 (20)第4章夹具设计 (24)4.1 机床夹具的分类、基本组成和功用 (24)4.2发动机曲轴夹具的设计思路 (24)4.2.1形状复杂 (24)4.2.2刚性差 (24)4.2.3技术要求高 (25)4.3铣曲轴两端面打中心孔夹具 (25)4.3.1零件的工艺性分析: (25)4.3.2零件机械加工工艺路线制定: (25)4.3.3夹具结构方案确定 (27)4.3.4其它装置和夹具体确定 (29)4.3.5定位误差分析计算 (31)4.3.6夹具结构及操作介绍 (33)4.3.7本设计的主要优缺点 (34)总结....................................................................................................................错误!未定义书签。
特种加工技术论文

特种加工技术论文特种加工作为一种有着悠久历史的加工方法,对人类的物质文明和生产活动起到了极大的推动作用。
下面是店铺整理的特种加工技术论文,希望你能从中得到感悟!特种加工技术论文篇一特种机械加工技术摘要:太阳能级多线切割技术是一种特殊的机械加工技术,它是在传统的机械加工的基础上建立起来的。
随着太阳能市场的启动和发展,作为晶体硅太阳能电池制造过程的主要环节,越来越受到人们的重视。
本文介绍了硅片切割的发展史,并从硅片切割的设备、工艺、生产流程和新技术等方面进行了较详细的阐述。
关键词:多线切割技术;硅片生产流程;硅片切割工艺;硅片切割新技术中图分类号: TU74 文献标识码: A太阳能级硅片切割的历史在上世纪80年代以前,人们在切割超硬材料的时候一般采用涂有金刚石粉的内圆切割机进行切割。
然而随着半导体行业的飞速发展,人们对已有的生产效率难以满足,同时由于内圆切割的才来损失非常大,在半导体行业成本的摩尔定律的作用下,人们对于降低切割陈本,提高效率的要求欧越来越高。
多线切割技术因此而逐步发展起来。
多线切割机由于其更高效、更小的切割损失以及更高精度的优势,对于切割贵重、超硬材料有着巨大的优势,近十年来已取代传统的内圆切割成为硅片切割加工的主要方式。
在2003年以前,多线切割主要满足于半导体行业的需求,切割技术主要掌握在欧、美、日、台等国家和地区,国内半导体业务以封装业务为主,上游的晶圆切割技术远远落后于发达国家和地区,相关的设备制造研发也难有进展。
2003年随着太阳能光伏行业的爆发式增长,国内民营企业的硅片切割业务迅速发展起来。
大量引进了瑞士和日本的先进的数控多线切割设备。
这才使切割太阳能级硅片的多线切割机的数量开始在国内爆发式增长,相关的技术交流也开始在国内广泛兴起。
当前国内使用的硅片切割机的种类及特点目前国内各个硅片切割厂家基本使用国际3大多线切割机的设备。
也就是,瑞士的HCT、M+B、日本的NTC,另外近两年日本的TMC(东京制纲)线锯也开始打入国内市场,并取得了不错的销量。
传动轴工艺毕业设计毕业论文
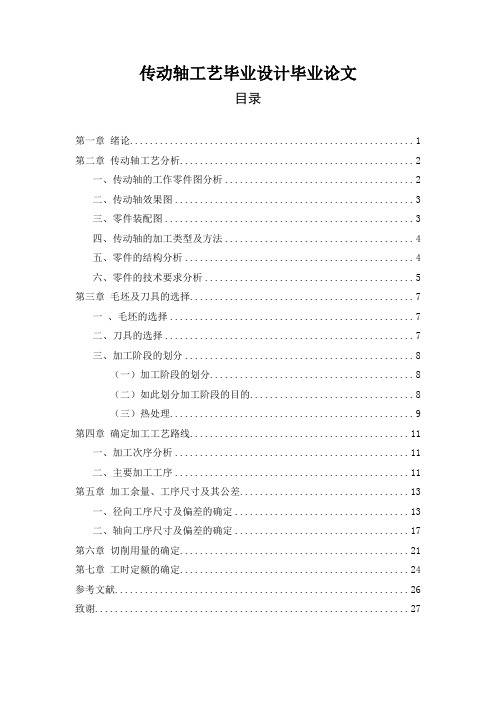
传动轴工艺毕业设计毕业论文目录第一章绪论 (1)第二章传动轴工艺分析 (2)一、传动轴的工作零件图分析 (2)二、传动轴效果图 (3)三、零件装配图 (3)四、传动轴的加工类型及方法 (4)五、零件的结构分析 (4)六、零件的技术要求分析 (5)第三章毛坯及刀具的选择 (7)一、毛坯的选择 (7)二、刀具的选择 (7)三、加工阶段的划分 (8)(一)加工阶段的划分 (8)(二)如此划分加工阶段的目的 (8)(三)热处理 (9)第四章确定加工工艺路线 (11)一、加工次序分析 (11)二、主要加工工序 (11)第五章加工余量、工序尺寸及其公差 (13)一、径向工序尺寸及偏差的确定 (13)二、轴向工序尺寸及偏差的确定 (17)第六章切削用量的确定 (21)第七章工时定额的确定 (24)参考文献 (26)致谢 (27)传动轴工艺分析第一章绪论本设计为传动轴的工艺设计,本文从传动轴的选材、加工方法、加工过程中余量的确定、工艺规程、互换性与公差等方面对传动轴做了细致的分析,针对其肯能在加工中出现的问题通过数据的形式加以强调。
在现代机加工中虽已不用此工艺过程,但作为学习而言,经典的工艺路线的练习对如何去更好的掌握机械加工这一项技术是非常重要的。
故本文虽是用旧的技术加工零件,但其中的原理还是很值得去讨论研究的。
本设计在起草的过程中多次前往工厂与相关技术人员讨论,发现了很多理论与实际有出入的地方,在这些方面会尽力去把理论与实际相结合,力争做到最合适。
第二章传动轴工艺分析一、传动轴的工作零件图分析此图对所加工传动轴的各项尺寸及各面形位公差的要求做了详细的说明,对各表面粗糙度做了标注,通过此图可以得知此零件的基本信息和如何进行工艺分析。
二、传动轴效果图此图客观的反应了所加工轴的形状及各面各键槽的布局情况,通过此图可以更直观的认识所加工零件。
三、零件装配图此图对所加工轴在实际工作情况中的配合情况做了详细的说明,通过此图可以让人清楚的知道此传动轴的工作情况,更直观的认识此轴在机器中的作用,从而可以更好的对此轴制定更合理的工艺规程。
论文

第一章前言随着科学技术的飞速发展和经济竞争的日趋激烈,产品更新的速度越来越快,多品种、中小批量生产的比重明显增加。
同时随着航空工业、航天工业、汽车工业和轻工业消费品生产的高速增长,复杂形状的零件越来越多,精度要求越来越高。
此外,激烈的市场竞争要求产品研制、生产周期越来越短,传统的加工设备和制造方法已难于适应这种多样化、柔性化与复杂形状零件的高效高质量加工的要求。
因此,近几十年来,世界各国十分重视发展能有效解决复杂、精密、小批量、多变零件加工的数控技术。
在机械制造业和模具制造业中,大量采用数控机床加工零件,数控技术的应用和数控机床的生产量已成为衡量一个国家工业化程度和技术水平的重要标志。
而加工中心编程是数控技术应用中不可缺的一个重要环节。
专家们曾预言:机械制造的竞争,其实质是数控的竞争。
1.1数控加工技术(Numerical Control Machining Technology)是指高效、优质地实现产品零件特别是复杂零件的加工技术,是自动化、柔性化、敏捷化和数字化制造加工的基础关键技术。
数控加工过程包括由给定的零件加工要求(零件图纸、CAD数据或实物模型)进行加工的全过程,其主要内容涉及数控机床加工工艺和数控编程技术两大方面。
1.2数控机床(Numerical Control Machining Tools)是指采用数字控制技术对机床的加工过程进行自动控制的一类机床。
国际信息处理联盟第五技术委员会对数控机床的定义是:“数控机床是一个装有程序控制系统的机床,该系统能够逻辑地处理具有使用代码、或其他符合编码指令规定的程序。
”它是集现代机械制造技术、自动控制技术及计算机信息技术于一体,采用数控装置或计算机,来全部或部分地取代一般通用机床在加工零件时对机床的各种动作(如启动、加工顺序、改变切削用量、主轴变速、选择刀具、冷却液开停以及停车等)的人工控制,是高效率、高精度、高柔性和高自动化的光、机、电一体化的数控设备。
果蔬加工技术论文范文

果蔬加工技术论文范文果蔬加工主要包括采后预处理、贮藏保鲜和精深加工。
下面是店铺为大家整理的果蔬加工技术论文范文,希望你们喜欢。
果蔬加工技术论文范文篇一果蔬加工的新趋势王希敏孟秀梅刘昌衡刘健敏(山东省科学院生物研究所,山东济南 250014)摘要:对国内外果蔬加工的新趋势,果蔬的营养价值和保健功能作一综述。
关键词:果蔬加工;营养;保健功能;发展前景中图分类号:TS255.2文献标识码:E文章编号:1672-979X(2007)03-0072-03Study on Processing Tendency and Development Prospect of Fruit and VegetableWANG Xi-min, MENG Xiu-mei, LIU Chang-heng, LIU Jian-min (Biology Research Institute, Shandong Academy of Sciences, Jinan 250014, China)Abstract:In this paper, the processing tendency of fruit and vegetable is summarized; nutrition value and healthy function of fruit and vegetable is analyzed.Key words:processing of fruit and vegetable; nutrition; health function; development prospect我国是水果和蔬菜的生产大国,产量居世界第一位。
果蔬加工业已成为果蔬种植业规模化的重要环节。
在日常生活中,人们从粮食和动物性食物中获得碳水化合物、蛋白质、脂肪等,以满足人体生命活动所需的热能;果蔬则是维生素、矿物质和有机酸等营养成分的主要来源。
1 果蔬加工的新趋势果蔬加工主要包括采后预处理、贮藏保鲜和精深加工。
机械制造工艺及精密加工技术论文3篇
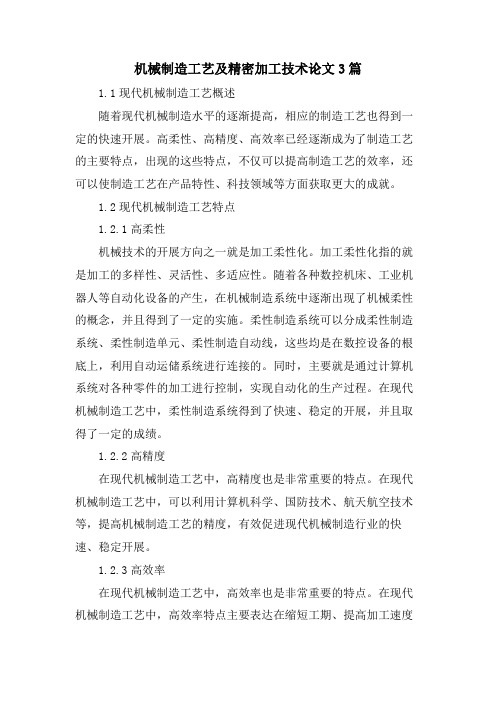
机械制造工艺及精密加工技术论文3篇1.1现代机械制造工艺概述随着现代机械制造水平的逐渐提高,相应的制造工艺也得到一定的快速开展。
高柔性、高精度、高效率已经逐渐成为了制造工艺的主要特点,出现的这些特点,不仅可以提高制造工艺的效率,还可以使制造工艺在产品特性、科技领域等方面获取更大的成就。
1.2现代机械制造工艺特点1.2.1高柔性机械技术的开展方向之一就是加工柔性化。
加工柔性化指的就是加工的多样性、灵活性、多适应性。
随着各种数控机床、工业机器人等自动化设备的产生,在机械制造系统中逐渐出现了机械柔性的概念,并且得到了一定的实施。
柔性制造系统可以分成柔性制造系统、柔性制造单元、柔性制造自动线,这些均是在数控设备的根底上,利用自动运储系统进行连接的。
同时,主要就是通过计算机系统对各种零件的加工进行控制,实现自动化的生产过程。
在现代机械制造工艺中,柔性制造系统得到了快速、稳定的开展,并且取得了一定的成绩。
1.2.2高精度在现代机械制造工艺中,高精度也是非常重要的特点。
在现代机械制造工艺中,可以利用计算机科学、国防技术、航天航空技术等,提高机械制造工艺的精度,有效促进现代机械制造行业的快速、稳定开展。
1.2.3高效率在现代机械制造工艺中,高效率也是非常重要的特点。
在现代机械制造工艺中,高效率特点主要表达在缩短工期、提高加工速度这两方面。
比方,冷加工工艺,主要可以采取三种方法:一是,多重加工方法。
通过对各种设备加工方式的集中整合,利用计算机系统进行一定的控制,保证切削加工程序的高效进行,在一定程度上缩短加工周期和辅助时间。
二是,提高切削速度。
利用TIC硬质合金刀具、金刚石刀具、陶瓷刀具等一些具备高性能的刀具,保证切削线速度能够到达10m/s之上,在一定程度上有效提高切削速度。
三是,强化新加工工艺的运用。
比方,应用激光、电火花、化学腐蚀等加工工艺展开相关的机械制造加工。
除此之外,对于一些加工难度大、性能要求特殊的材料而言,也可以利用一些新加工工艺展开机械制造,保证机械制造加工的有序进行。
典型零件的数控加工与仿真论文.

毕业(设计论文系(部机电工程系专业机械制造与自动化班级08机械制造与自动化一班指导教师姓名学号摘要数控技术及数控机床在当今机械制造业中的重要地位和巨大效益,显示了其在国家基础工业现代化中的战略性作用,并已成为传统机械制造工业提升改造和实现自动化、柔性化、集成化生产的重要手段和标志。
数控技术及数控机床的广泛应用,给机械制造业的产业结构、产品种类和档次以及生产方式带来了革命性的变化。
数控机床是现代加工车间最重要的装备。
它的发展是信息技术(1T与制造技术(MT结合发展的结果。
现代的CAD/CAM、FMS、CIMS、敏捷制造和智能制造技术,都是建立在数控技术之上的。
掌握现代数控技术知识是现代机电类专业学生必不可少的。
本次设计内容介绍了数控加工的特点、加工工艺分析以及数控编程的一般步骤。
并利用CAXA制造工程师软件完成零件的三维造型,进行加工轨迹设计,实现加工仿真。
利用SEMENS仿真软件完成仿真加工。
利用CAD/CAM软件及G代码指令进行手工编程。
关键词:数控技术CAXA制造工程师三维造型仿真加工手工编程自动编程目录1 绪论 (11.1 数控加工的特点 (11.2 数控机床 (11.3 数控加工 (21.4 数控编程系统 (31.5 CAD/CAM系统 (42.数控加工步骤 (52.1 自动编程的基本步骤 (52.2 加工工艺的确定 (62.3 加工模型建立 (62.4 刀具轨迹生成 (72.5 后期G代码生成 (72.6 加工代码输出 (73.课题学习目的 (94.可乐瓶底机构分析 (105 凹模型腔的造型 (115.1 绘制截面线 (116型腔造型 (186.1 生成网格面 (186.2 生成直纹面 (187可乐瓶底凹模模型腔加工 (237.1 加工前的准备工作 (237.2 后置设置 (237.3 等高线粗加工 (257.4 参数线精加工 (267.5 轨迹方仿真.检验与修改 (277.6 生成G代码 (297.7 生成工序单 (30参考文献 (33致谢 (341 绪论1.1 数控加工的特点数控加工,也称之为NC(Numerical Control加工,是以数值与符号构成的信息,控制机床实现自动运转。
毕业论文(设计):典型零件加工工艺设计及加工

毕业设计(论文)任务书学生姓名学号所在系部机械工程系所学专业数控技术所在班级E-mail 联系电话毕业设计(论文)题目典型零件的加工工艺设计及加工指导教师职称工作单位及所从事专业联系方式姓名教授讲师本课题是根据高职数控技术专业教学计划选定的,旨在通过本课题的研究,使学生全面理解数控技术专业知识、掌握典型零件的工艺设计、如何确定工序、还有刀具、夹具及数控车床如何的选用。
帮助学生走上工作岗位时能尽快胜任工作。
专业方向、基本理论及设计内容(设计要求和设计步骤要求详细到章节):1、本课题的设立是典型零件的加工;2、基本理论依据是:数控加工工艺、机械基础和机械技术、金属切削原理与刀具、数控机床加工程序的编制;3、设计要求:通过轴类零件加工工艺分析设计设计,使我们在拟定工工艺分析方案过程中,得到方案分析、结构工艺性、机械制图、零件设计、编写技术文件和查阅技术资料的等方面的综合训练,树立正确的设计思想,掌握基本的设计方法,并培养学生具有初步的结构分析、结构设计与计算能力,并阐述了在机械加工实习课中如何对盖板零件进行工艺分析,从而提高工件质量。
5总结总结这次设计所遇到的问题,进一步提高自己的设计能力,动手能力,工艺的编制能力等主要参考文献、资料:1、刘战术主编.《数控机床及其维修》.人民邮电出版社出版2、荣维芝主编.《数控机床加工程序的编制》.机械工业出版社3、焦小明主编.《机械加工技术》.机械工业出版社4、田春霞主编.《数控加工技术》.机械工业出版社5、陈立德主编.《机械设计基础》.高等教育出版社6、周开勤主编.《机械零件手册》高等教育出版社7、刘力主编.《机械制图》.高等教育出版社出版8、《机床设计手册》编写组主编.《机床设计手册之零件设计》.机械工业出版社出版9、《数控机床编程及原理》.机械工业出版社出版10、《金属切削机床设计》.上海科学技术出版社教研室审批意见专业教研室主任签字:(盖章)系部审批意见系部主任签字:(盖章)目录摘要 (1)前言 (2)第一章、零件图样工艺分析1.1零件图的分析 (3)1.2零件结构工艺分析 (4)第二章、选择加工设备与刀、夹、量具2.1加工设备的选择 (5)2.2刀具的选择 (6)2.3夹具的选择 (7)2.4量具的选择 (8)第三章、数控车削加工的对刀3.1对刀的概念 (9)3.2确定对刀点或对刀基准点的一般原则 (10)第四章、加工工艺规程设计4.1加工顺序的安排 (11)4.2装夹方式 (12)4.3定位基准的选择 (13)第五章、切削用量的选择5.1切削深度的选择 (14)5.2进给量的选择 (15)第六章、工艺文件的填写6.1数控刀具卡 (17)6.2数控工序卡 (18)第七章、程序的编制7.1编程方法 (19)7.2编制程序 (22)第八章、心得体会 (25)总结 (25)参考文献 (26)摘要本零件在设计加工过程中分析了轴的特点及作用,介绍了轴的数控加工工艺设计与程序编制。
车工高级技师论文 Doc1
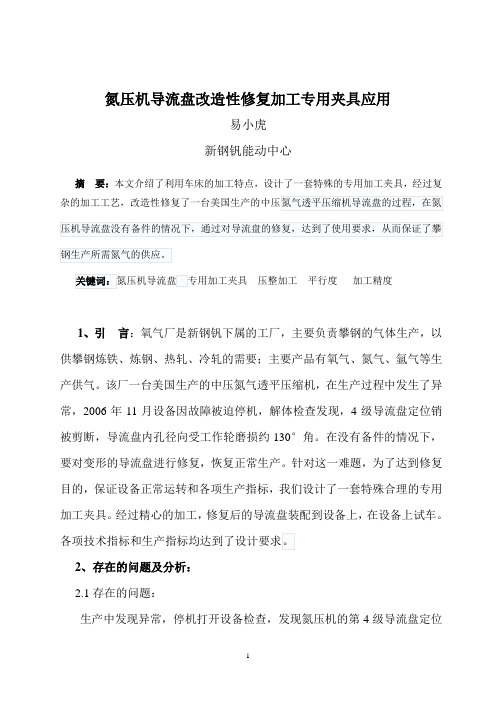
氮压机导流盘改造性修复加工专用夹具应用易小虎新钢钒能动中心摘要:本文介绍了利用车床的加工特点,设计了一套特殊的专用加工夹具,经过复杂的加工工艺,改造性修复了一台美国生产的中压氮气透平压缩机导流盘的过程,在氮压机导流盘没有备件的情况下,通过对导流盘的修复,达到了使用要求,从而保证了攀钢生产所需氮气的供应。
关键词:氮压机导流盘专用加工夹具压整加工平行度加工精度1、引言:氧气厂是新钢钒下属的工厂,主要负责攀钢的气体生产,以供攀钢炼铁、炼钢、热轧、冷轧的需要;主要产品有氧气、氮气、氩气等生产供气。
该厂一台美国生产的中压氮气透平压缩机,在生产过程中发生了异常,2006年11月设备因故障被迫停机,解体检查发现,4级导流盘定位销被剪断,导流盘内孔径向受工作轮磨损约130°角。
在没有备件的情况下,要对变形的导流盘进行修复,恢复正常生产。
针对这一难题,为了达到修复目的,保证设备正常运转和各项生产指标,我们设计了一套特殊合理的专用加工夹具。
经过精心的加工,修复后的导流盘装配到设备上,在设备上试车。
各项技术指标和生产指标均达到了设计要求。
2、存在的问题及分析:2.1存在的问题:生产中发现异常,停机打开设备检查,发现氮压机的第4级导流盘定位销被剪断,导流盘内孔径向被工作轮磨损约130°角,径向深约12mm,轴向深约3mm的月牙槽;导流盘底平面略成波浪式变形;在导流盘圆周均匀分布的导流叶片端面上,冲刷约有1 mm高低不平的伤痕,如图一所示:图12.2问题形成原因:这台离心式氮压机,是整体从美国进口的整体组装设备,由于设计和装配缺陷,装配导流盘的蜗壳上,没有控制导流盘径向自由度的止口,组装导流盘时精度不够,没有紧力,导流盘在径向上形成摆动,完全依靠钟摆式的定位销定位,如图一所示:设备在大致两年高速运行、中压氮气的冲刷和高频振动的工作情况下,造成定位销被剪切,导流盘逐渐往下移动,与高速旋转的离心式工作轮摩擦磨损,导流盘整体材料是铝镁合金,而工作轮是不锈钢,导流盘材质与工作轮材质相比软硬度差别太大,所以导流盘沿内孔圆周130°径向磨损深约12 mm,纵向深约3mm 的月牙槽。
技师论文薄壁零件加工

浅谈薄壁零件的加工方法单位山东技师学院姓名郭尚超考评职称车工技师浅谈薄壁零件的加工方法摘要:薄壁零件已日益广泛地应用在各工业部门,但在薄壁零件的加工中会遇到比较棘手的问题,原因是薄壁零件刚性差,强度弱,在加工中极容易变形,使零件的形位误差增大,不易保证零件的加工质量。
高精度、薄壁腔体类零件金属切除量大、工件壁薄、刚性低,加工中需要解决的主要问题是控制和减小变形,在此基础上,希望尽可能提高切削效率、缩短加工周期。
其加工工艺需要从工件装夹、工序安排、切削用量参数、刀具选用等多方面进行优化。
关键词薄壁零件精度加工方法一.影响薄壁零件加工精度的主要因素影响薄壁零件加工精度的因素有很多,但归纳起来主要有以下三个方面:1.工件的尺寸精度和形状精度。
易受力变形。
因壁薄,在夹紧力的作用下,容易产生变形,从而影响2. 易受热变形。
因工件较薄,切削热会引起工件热变形,使工件尺寸难以控制。
3. 易振动变形。
在切削力(特别是径向切削力)的作用下,容易产生振动和变形,影响工件的尺寸精度和形状,位置精度和表面粗糙度。
二.减少薄壁工件变形的方法主要是减少切削力和切削热,改善或改变夹紧力对零件的作用。
1. 在切削过程中,切削力时必然要产生的,但它的大小时可以改变的,影响切削力的大小的因素很多,主要是被加工件材料、刀具、切削用量和冷却润滑等几个方面。
2. 减少切削力的方法。
在薄壁零件的切削中,合理的刀具几何角度对车削时切削力的大小是至关重要的。
刀具前角大小,决定着切削变形与刀具前角的锋利程度。
前角大,切削变形和摩擦力减小,切削力减小,所以前角取5-20°,刀具的后角大,,摩擦力小,切削力相应减小,所以后角取4-12°。
主偏角在30-90°范围内,车薄壁零件的内外圆时,取较大的主偏角,副偏角取8-15°。
三.合理地选择切削用量降低切削力切削力的大小与切削用量密切相关,背吃刀量和进给量同时增大,切削力增大,变形也大,对车削薄壁零件极为不利。
加工中心技师专业论文

技师专业论文工种:加工中心操作工(FANUC卧式加工中心TH6580X80型)题目:加工中心结合专用夹具在床头箱体中的应用姓名:888888身份证号:888888888888888等级:技师联系电话:88888888888日期:2009年12月7日加工中心结合专用夹具在床头箱体中的应用摘要床头箱体是机械式车床上的重要零件,其加工质量的好坏将直接影响到机床的使用效果。
其外观参考实物图。
以往床头箱体外侧孔系加工是在镗床和钻床上完成、轴承镗孔和连接孔的加工,生产效率低且加工质量难以保证,为解决上述问题,我们采用本厂制造的TH6580X80卧式加工中心结合精心设计的夹具进行床头箱体加工,取得了很好的应用效果。
不但精度能够保证,而且生产效率也显著提高,为工厂创造了可观的经济效益。
参考实物图关键字:加工中心床头正文1、零件工艺过程分析及工序安排箱体类零件具有以下几个特点:第一是加工内容多,需要频繁更换刀具,而且刀具在选择上也是十分的讲究;第二是生产加工的精度要求高,如果采用普通机床进行加工,质量难以保证,而且由于加工工艺流程长,工件周转次数多,生产效率难以提高;第三是床头箱体孔系位置形状复杂,而且大部分为壳体,体积较大,较难装夹。
如果采用数控加工中心进行箱体加工,凭借加工中心自身的精度高和加工效率高、刚度好和自动换刀的特点。
只要制定好完善的加工工艺流程,设计出合理的专用夹具和选择好加工刀具,编辑出合理完善的加工程序,就完全可以解决上述在加工生产实践中所遇到的问题。
鉴于我们使用的设备为双工作台,因此,我们将该工件分两个工作台交替加工,因为床头箱体六个面都需要加工,所以,在第一组夹具中加工两端面镗孔及各个法兰螺纹孔,还有后背方窗及前端置口,在第二组夹具中加工上面置口螺纹孔及底面钻眼和反划。
这样可以体现加工中心双工作台在加工中的优势,根据上述工序安排,设计相应的专用夹具。
2、毛坯准备工件装夹到加工中心上的前期准备工序由其它设备来完成,如示意图A上底面及外观毛坯面的粗加工,放在普通机床上加工,两端镗孔面和前后两面及上口面由普通铣床统一加工,斜面处由刨床统一刨出,底面由大型数控磨床来统一加工。
镗工技师论文

镗工技师论文镗工技师论文国家职业资格(二)级论文职业(工种):镗工题目:精密镗孔机的现场镗铰孔单位:姓名:身份证号码:等级:二级日期:精密镗孔机的现场镗铰孔()关键词:镗孔机、装夹方式、加工方法、刀具材料、刀具几何参数。
内容摘要随着船舶行业的发展,船东对船舶产品的质量要求越来越高。
原有的手工铰孔的方法已不能满足实际情况的需要,利用镗孔机现场配铰铰制孔的新方法应运而生。
利用镗孔机加工出来的化学品船舶轴系、舵系、轮机部分的铰制孔的质量远远优于手工铰孔的质量,且镗孔机还能提高加工效率、缩短生产周期。
正文随着船舶行业的发展,公司承接的不锈钢特种船舶越来越多,而船东对船舶产品的质量要求越来越高。
原有的手工铰孔方法已不能满足现代船舶产品生产的需要,寻求新的加工方法成了急待解决的问题。
笔者凭着丰富的操作经验,解决了操作空间狭小、施工环境恶劣、主轴太长等困难,通过选择合理的刀具的材料,合理的改进刀具结构,利用精密镗孔机成功的完成中间轴铰制孔的现场镗铰工作。
下边,我从装夹方式、加工方法、刀具材料、机器的应用等多方面综合阐述镗孔机现场配铰铰制孔的方法:一、装夹方式:最初,因没用经验,为方便操作和固定镗孔机,我采用了搭设固定式支架的方法,这种方法虽然稳定,但效率太低,每加工一个孔就需移动一次工装,十分费时,且在校调过程中调整起来非常不便。
通过心细的观察和现场综合分析,我对镗孔机的固定工装进行了改进:我将机座板上的螺栓连接孔做成腰形孔,便于镗孔机的调节,同时用三颗螺钉做主支承再加上两颗螺钉辅助支承,通过调节螺钉上的螺母来实现镗孔机想要的理想高度和水平,调节合适后,将三颗主支承螺钉上的螺母夹紧后,镗孔机的位置也相应固定,起到定心的作用。
二、加工方法:针对手工配铰中出现的问题,我分析后发现,引起手工配铰失败的原因有:1.主机孔与铰孔套错位。
2.铰孔套与机座孔错位。
3.主机孔与机座孔底孔引偏,相对于配合表面倾斜。
4.现场空间狭小,管道纵横交错,影响施工。
- 1、下载文档前请自行甄别文档内容的完整性,平台不提供额外的编辑、内容补充、找答案等附加服务。
- 2、"仅部分预览"的文档,不可在线预览部分如存在完整性等问题,可反馈申请退款(可完整预览的文档不适用该条件!)。
- 3、如文档侵犯您的权益,请联系客服反馈,我们会尽快为您处理(人工客服工作时间:9:00-18:30)。
网络高等教育本科生毕业论文(设计)题目:精密加工技术和超精密加工技术的应用与研究学习中心:重庆酉阳奥鹏学习中心层次:专科起点本科专业:机械设计制造及其自动化年级: 2010 年秋季学号: 101186411523学生:赵奎指导教师:徐磊完成日期: 2012 年 9 月 9 日内容摘要本文主要是通过介绍精密加工技术和超精密加工技术。
了解几种常用的精密加工方法及特点(如砂带研磨,精密切削,超精密磨削,珩磨,精密研磨与抛光)国内外精密加工技术发展现状,以及应用领域。
再对超精密加工技术在军事科技方面应用的介绍,发展现状和趋势,对精密加工技术和超精密加工技术进行对比,了解这两者面临的问题及其研究任务。
最后对这俩种技术的应用,发展现状和趋势进行总结,让我们对这俩种技术有新的认识。
关键词:精密加工,超精密加工技术,发展,应用,研究,探讨目录内容摘要 (I)引言 (4)1 精密加工技术和超精密加工技术简介 52 几种常用的精密加工方法及特点 (6)2.1 砂带研磨 (6)2.2 精密切削 (6)2.3 超精密磨削 (6)2.4 珩磨 (7)2.5 精密研磨 (7)2.6 抛光 (8)3 国内精密加工技术发展趋势 (9)3.1 北京机床研究所 (9)3.2 航天航空工业部三零三部所 (9)3.3 其他研究所 (9)4 超精密加工的发展趋势 (10)4.1 日本 (10)4.2 美国 (10)4.3 欧洲 (10)5 超精密加工的发展趋势 (11)6 精密加工技术和超精密加工技术应用 126.1精确制导武器的大量使用和超视距攻击能力的提高126.2 夜战能力的提高 126.3电子对抗技术的进步 136.4军用卫星系统的发展 136.5军用微型武器系统是未来的发展趋势 147精密加工技术和超精密加工技术二者面临的问题 157.1加工精度 157.2加工效率 158 探讨超精密加工技术的研究任务 168.1超精密加工的加工机理 168.2超精密加工设备制造技术 168.3超精密加工刀具、磨具及刃磨技术 168.4精密测量技术及误差补偿技术 168.5超精密加工工作环境条件 168.6超精密加工技术目前面临的研究任务 169探讨精密加工技术和超精密加工技术的发展思路 209.1开发新的精密加工方法 209.2开发精密的机械机构 209.3开发高精度的测试系统 209.4开发适用于精密加工并能取得高精度、高表面质量的新型材料 219.5超精密加工技术的发展思路 2110 结论 (22)参考文献 (23)引言为了满足现代先进制造与加工技术的需要,提高生产效率和改善零件的加工质量,精密加工技术和超精密加工技术已成为目前高科技技术领域的基础,超精密加工技术已成为社会生产发展的一个重大趋势。
精密和超精密加工技术的发展,直接影响到一个国家尖端技术和国防工业的发展,因此世界各国对此都极为重视,投入很大力量进行研究开发,同时实行技术保密,控制关键加工技术及设备出口。
随着航空航天、高精密仪器仪表、惯导平台、光学和激光等技术的迅速发展和多领域的广泛应用,对各种高精度复杂零件、光学零件、高精度平面、曲面和复杂形状的加工需求日益迫切。
目前国外已开发了多种精密和超精密车削、磨削、抛光等机床设备,发展了新的精密加工和精密测量技术。
1 精密加工技术和超精密加工技术简介目前,精密加工是指加工精度为1~0.1µm,表面粗糙度为Ra0.1~0.01µm 的加工技术,但这个界限是随着加工技术的进步不断变化的,今天的精密加工可能就是明天的一般加工。
精密加工所要解决的问题,一是加工精度,包括形位公差、尺寸精度及表面状况,有时有无表面缺陷也是这一问题的核心;二是加工效率,有些加工可以取得较好的加工精度,却难以取得高的加工效率。
精密加工应该包括微细加工和超微细加工、光整加工等加工技术。
超精密加工技术超精密加工是指被加工零件的尺寸精度高于0.1µm,表面粗糙度Ra小于0.025µm,以及所用机床定位精度的分辨率和重复性高于0.01µm 的加工技术,亦称之为亚微米级加工技术,且正在向纳米级加工技术发展。
我们知道,这个界限是有限的,随着加工技术的进步不断变化,今天的超精密加工可能就是明天的一般加工。
超精密加工技术主要包括:超精密加工的机理研究,超精密加工的设备制造技术研究,超精密加工工具及刃磨技术研究,超精密测量技术和误差补偿技术研究,超精密加工工作环境条件研究。
超精密加工技术是适应现代高技术需要而发展起来的先进制造技术,它综合应用了机械技术发展的新成果以及现代电子、传感技术、光学和计算机等高新技术,是高科技领域中的基础技术,在国防科学技术现代化和国民经济建设中发挥着至关重要的作用,同时作为现代高科技的基础技术和重要组成部分,它推动着半导体技术、光电技术、材料科学等多门技术的发展进步。
超精密加工技术已成为国防工业研制现代化武器装备的关键技术,也是衡量一个国家科学技术水平的重要标志。
2 几种常用的精密加工方法及特点传统的精密加工方法有布轮抛光、砂带磨削、超精细切削、精细磨削、珩磨、研磨、超精研抛技术、磁粒光整等。
2.1砂带磨削砂带磨削是用粘有磨料的混纺布为磨具对工件进行加工,属于涂附磨具磨削加工的范畴,有生产率高、表面质量好、使用范围广等特点。
国外在砂带材料及制作工艺上取得了很大的成就,有了适应于不同场合的砂带系列,生产出通用和专用的砂带磨床,而且自动化程度不断提高(已有全自动和自适应控制的砂带磨床),但国内砂带品种少,质量也有待提高,对机床还处于改造阶段。
2.2精密切削精密切削也称金刚石刀具切削(SPDT),用高精密的机床和单晶金刚石刀具进行切削加工,主要用于铜、铝等不宜磨削加工的软金属的精密加工,如计算机用的磁鼓、磁盘及大功率激光用的金属反光镜等,比一般切削加工精度要高1~2个等级。
例如用精密车削加工的液压马达转子柱塞孔圆柱度为0.5~1µm,尺寸精度1~2µm;红外反光镜的表面粗糙度Ra0.01~0.02µm,还具有较好的光学性质。
从成本上看,用精密切削加工的光学反射镜,与过去用镀铬经磨削加工的产品相比,成本大约是后者的一半或几分之一。
但许多因素对精密切削的效果有影响,所以要达到预期的效果很不容易。
同时,金刚石刀具切削较硬的材料时磨损较快,如切削黑色金属时磨损速度比切削铜快104倍,而且加工出的工件的表面粗糙度和几何形状精度均不理想。
2.3超精密磨削超精密磨削用精确修整过的砂轮在精密磨床上进行的微量磨削加工,金属的去除量可在亚微米级甚至更小,可以达到很高的尺寸精度、形位精度和很低的表面粗糙度值。
尺寸精度0.1~0.3µm,表面粗糙度Ra0.2~0.05µm,效率高。
应用范围广泛,从软金属到淬火钢、不锈钢、高速钢等难切削材料,及半导体、玻璃、陶瓷等硬脆非金属材料,几乎所有的材料都可利用磨削进行加工。
但磨削加工后,被加工的表面在磨削力及磨削热的作用下金相组织要发生变化,易产生加工硬化、淬火硬化、热应力层、残余应力层和磨削裂纹等缺陷,需要合理管控。
2.4珩磨珩磨用油石砂条组成的珩磨头,在一定压力下沿工件表面往复运动,加工后的表面粗糙度可达Ra0.4~0.1µm,最好可到Ra0.025µm,主要用来加工铸铁及钢,不宜用来加工硬度小、韧性好的有色金属。
2.5精密研磨通过介于工件和工具间的磨料及加工液,工件及研具作相互机械摩擦,使工件达到所要求的尺寸与精度的加工方法。
精密研磨与抛光对于金属和非金属工件都可以达到其他加工方法所不能达到的精度和表面粗糙度,被研磨表面的粗糙度Ra≤0.025µm加工变质层很小,表面质量高,精密研磨的设备简单,主要用于平面、圆柱面、齿轮齿面及有密封要求的配偶件的加工,也可用于量规、量块、喷油嘴、阀体与阀芯的光整加工。
但精密研磨的效率较低,如干研速度一般为10~30m/min,湿研速度为20~120m/min。
对加工环境要求严格,如有大磨料或异物混入时,将使表面产生很难去除的划伤。
2.6抛光是利用机械、化学、电化学的方法对工件表面进行的一种微细加工,主要用来降低工件表面粗糙度,常用的方法有:手工或机械抛光、超声波抛光、化学抛光、电化学抛光及电化学机械复合加工等。
手工或机械抛光是用涂有磨膏的抛光器,在一定的压力下,与工件表面做相对运动,以实现对工件表面的光整加工。
加工后工件表面粗糙度Ra≤0.05µm,可用于平面、柱面、曲面及模具型腔的抛光加工。
手工抛光的加工效果与操作者的熟练程度有关。
a超声波抛光是利用工具端面做超声振动,通过磨料悬浮液对硬脆材料进行光整加工,加工精度0.01~0.02µm,表面粗糙度Ra0.1µm。
超声抛光设备简单,操作、维修方便,工具可用较软的材料制作,而且不需作复杂的运动,主要用来加工硬脆材料,如不导电的非金属材料,当加工导电的硬质金属材料时,生产率较低。
b 化学抛光是通过硝酸和磷酸等氧化剂,在一定的条件下,使被加工的金属表面氧化,使表面平整化和光泽化。
化学抛光设备简单,可以加工各种形状的工件,效率较高,加工的表面粗糙度一般为Ra≤0.2µm,但腐蚀液对人体和设备有损伤,污染环境,需妥善处理。
主要用来对不锈钢、铜、铝及其合金的光亮修饰加工。
c 电化学抛光是利用电化学反应去除切削加工所残留的微观不平度,以提高零件表面光亮度的方法。
它比机械抛光具有较高的生产率和小的表面粗糙度:一般可达Ra0.2µm,若原始表面为Ra0.4~0.2µm,则抛光后可提Ra0.1~0.08µm,加工后工件具有较好的物理机械性能,使用寿命长,但电化学抛光只能加工导电的材料。
随着电化学加工技术的发展,还产生了多种新型的复合加工方法,例如超精密电解磨削、电化学机械复合光整加工、电化学超精加工等。
它们主要以降低工件的表面粗糙度值为目的,加工去除量很小,一般在0.01~0.1mm,对于表面粗糙度达到Ra0.8~1.6µm的外圆,平面、内孔及自由曲面均可一道工序加工到镜面,表面粗糙度Ra0.05µm,甚至更低。
电化学机械加工属于一种加工单位极小的精密加工方法,从原理上讲加工精度可以达到原子级,所以加工精度具有大的潜力,但由于左右其加工精度的因素目前还不是很清楚,所以在实际应用中,其加工表现出一定的不稳定性,这在很大程度上限制了它在工业生产中的应用。
3 国内精密加工技术发展现状3.1 北京机床研究所北京机床研究所是国内进行精密加工技术研究院的主要单位之一,研究出了多种不同类型的超精密机床、部件和相关的高精度测试仪器等,如精度达0.025µm的精密轴承、JCS-027超精密车床、JCS-031超精密铣床、JCS-035精密车床、超精密车床数控系统、复印机感光鼓加工机床、红外大功率激光反光镜、超精密振动一位移测微仪等,达到了国内领先、国际先进水平3.2 航天航空工业部三零三部所航天航空工业部三零三部所在超精密主轴、花岗岩坐标量测机等方面进行了研究及产品生产。