切管机毕业设计
旋管式切管机毕业设计
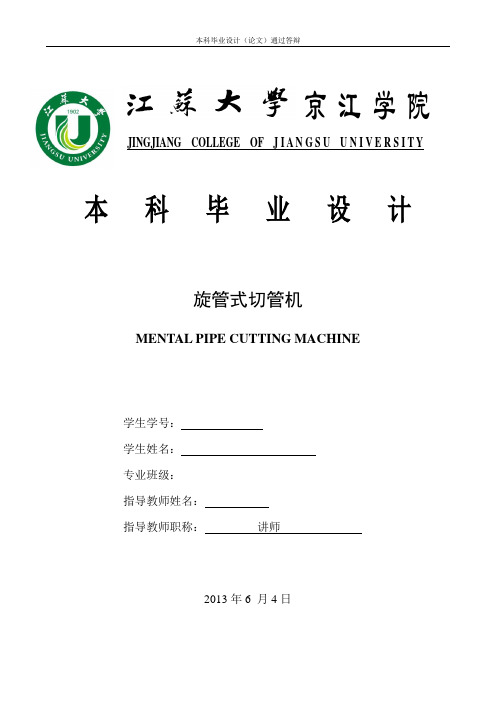
本科毕业设计(论文)通过答辩京江学院JINGJIANG COLLEGE OF J I A N G S U U N I V E R S I T Y本科毕业设计旋管式切管机MENTAL PIPE CUTTING MACHINE学生学号:学生姓名:专业班级:指导教师姓名:指导教师职称:讲师2013年6 月4日江苏大学京江学院本科毕业设计目录引言 (5)第一章旋管式切管机传动方案的选择 (7)1.1传动方案 (7)1.2传动方案的选择 (8)第二章旋管式切管机传动装置设计与计算 (10)2.1传动装置的总体设计与计算 (10)2.1.1电动机的选择 (10)2.1.2电动机功率的选择 (10)2.1.3电动机转速的选择 (11)2.1.4电动机型号确定 (11)2.1.5传动方案的拟定 (11)2.1.6各轴的转速、功率和转矩 (11)2.2进行传动机构设计与计算 (13)2.2.1带轮的设计与计算 (13)2.2.2涡轮蜗杆的传动与计算 (16)2.2.3齿轮的设计与计算 (19)2.3各传动轴尺寸的计算与校核 (27)2.3.1蜗杆轴的计算与校核 (27)2.3.2涡轮轴的校核与计算 (30)2.3.3滚轮轴的校核与计算 (33)第三章滚筒系统和进给系统的设计 (36)3.1滚筒系统的设计 (36)3.2进给系统的设计 (37)第四章绘制设计装配图及零件图 (38)结论 (39)致谢 (40)参考文献: (41)2江苏大学京江学院本科毕业设计摘要金属切管机是一种主要用于车辆,工业或建材生产中的下料工作的机器。
工作对象主要为各种型号各种材料的管材。
此次的设计主要是针对车辆用金属管材进行加工的切管机,完成的工作主要是切管机中滚子,机体和减速箱部分的设计。
包括传动装置的设计和计算,其中有电动机的选择,传动方案的拟订,各轴的转速,功率和转矩的计算。
总体结构的设计,其中有各轴尺寸的设计,各主要传动件的结构尺寸的设计。
《切管机毕业设计》word版
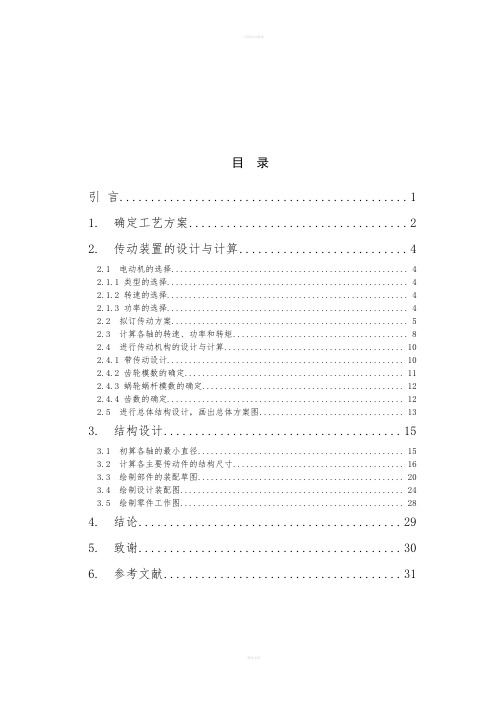
目录引言 (1)1. 确定工艺方案 (2)2. 传动装置的设计与计算 (4)2.1 电动机的选择 (4)2.1.1 类型的选择 (4)2.1.2 转速的选择 (4)2.1.3 功率的选择 (4)2.2 拟订传动方案 (5)2.3 计算各轴的转速、功率和转矩 (8)2.4 进行传动机构的设计与计算 (10)2.4.1 带传动设计 (10)2.4.2 齿轮模数的确定 (11)2.4.3 蜗轮蜗杆模数的确定 (12)2.4.4 齿数的确定 (12)2.5 进行总体结构设计,画出总体方案图 (13)3. 结构设计 (15)3.1 初算各轴的最小直径 (15)3.2 计算各主要传动件的结构尺寸 (16)3.3 绘制部件的装配草图 (20)3.4 绘制设计装配图 (24)3.5 绘制零件工作图 (28)4. 结论 (29)5. 致谢 (30)6. 参考文献 (31)引言中国是一个上下有五千年历史的文明古国,从原始的石器时代到金属时代,我们伟大的祖先就进行了简单的机械加工,但是在当时的生产条件下,其生产的效率和精度都是非常的低下。
随着时代的发展,人们在想方设法改善自己的生存条件和生活水平,正是由于这点,促进了机械制造生产的飞速发展,人们在超着一个精度更高、效率更高、成本更低、更加人性化的方向发展。
中国虽然是一个文明古国,其拥有几千年的历史背景和文化积淀,但是其在工业制造方面和发达国家还是存在较大的差异,其机械制造技术却远远比不上西方等发达国家,众所周知,机械制造技术的先进与否直接与加工的精度,生产的效率,以及生产的成本产生直接关系。
随着机械化生产的速度发展,人们对机械产品的要求也越来越高,其主要表现在实用和经济等方面。
本次设计的目的和要求就是设计一个简单实有的切管机,其目的在于能够高效而廉价的加工出生产所需要的产品,并且要求其生产效率较高,适合大多数不是批量加工管件或者对管件加工要求不高的工厂使用。
在当今这个各项技术飞速发展的时代,尤其的随着计算机技术的高速发展,机械制造行业也得到了飞速的发展,其主要表现在数控加工等方面,生产效率也随着其得到了飞速的发展。
自动切管机毕业设计

自动切管机毕业设计自动切管机毕业设计随着工业自动化的不断发展,各种自动化设备在生产线上的应用越来越广泛。
其中,自动切管机作为一种重要的机械设备,被广泛应用于管道加工和制造行业。
本文将探讨自动切管机的设计原理和实现方法,以及其在工业生产中的应用前景。
首先,自动切管机的设计原理是基于先进的控制系统和切割技术。
通过传感器和电脑控制系统的协同作用,自动切管机能够实现对管材的准确测量和切割。
其核心技术包括图像识别、数据处理和切割控制等方面。
通过对管材的外观特征进行图像识别,自动切管机能够准确地确定切割位置和角度。
同时,通过数据处理和切割控制,自动切管机能够实现高效、精确的切割操作。
在实现自动切管机的设计过程中,需要考虑多个方面的因素。
首先是机械结构的设计。
自动切管机需要具备稳定的结构和高精度的切割能力。
因此,在设计过程中需要充分考虑机械结构的稳定性和刚性,以及切割刀具的选用和切割力的控制。
其次是控制系统的设计。
自动切管机的控制系统需要能够实时监测和控制切割过程,确保切割的准确性和稳定性。
因此,需要选择合适的传感器和控制器,并进行系统的调试和优化。
最后是安全性的考虑。
自动切管机在工作过程中可能会涉及到高速旋转的切割刀具,因此需要采取相应的安全措施,保障操作人员的安全。
自动切管机在工业生产中具有广泛的应用前景。
首先,在管道加工行业中,自动切管机能够实现对各种类型和尺寸的管材的快速、精确切割,提高生产效率和产品质量。
其次,在建筑和制造业中,自动切管机可以应用于各种管道系统的安装和维修,提高工作效率和安全性。
此外,自动切管机还可以应用于汽车制造、航空航天等领域,为相关行业的发展提供支持。
然而,自动切管机的设计和制造并非易事。
在实际应用中,需要考虑到不同管材的特性和切割要求,设计出适用于不同场景的自动切管机。
同时,还需要不断进行创新和改进,提高自动切管机的性能和稳定性。
此外,自动切管机的市场竞争也较为激烈,需要与其他同类产品进行竞争,提供更好的解决方案和服务。
2024切管机设计方案

2024切管机设计方案切管机是一种用于切割金属、塑料、木材等管材的机械设备,广泛应用于建筑、制造业、石化、船舶、轨道交通等领域。
本文将以2024年作为时间背景,设计一款切管机的方案,并对其进行详细的介绍。
1.设计要求:(1)切割管径范围广,满足不同管径的需求;(2)切割精度高,保证切割后的管材的尺寸精度;(3)操作简单,降低操作难度,提高工作效率;(4)设备稳定性好,降低维护成本;(5)安全可靠,防止意外事故的发生。
2.设计方案:基于以上设计要求,本文设计一款全自动切管机。
该切管机的设计理念是将传统的手动操作改为自动化操作,提高工作效率和安全性。
(1)控制系统:采用PLC控制系统,通过编程实现自动化操作。
操作人员只需在人机界面上输入所需管材的直径和长度,机器将自动完成切割工作。
(2)切割刀具:采用高硬度和高耐磨的材料制成的切割刀具。
根据不同管材的材质和直径,选择合适的刀具进行切割,以保证切割质量和刀具的使用寿命。
(3)传动系统:采用伺服电机和精密滚珠丝杠传动系统。
伺服电机提供高精度、高速度的运动,滚珠丝杠传动系统保证了切割刀具的稳定性和切割精度。
(4)安全保护系统:包括急停按钮、光电安全门、过载保护等。
急停按钮可以在紧急情况下立即停止切割操作,光电安全门可以防止操作人员误入危险区域,过载保护可以避免切割过程中因工件太硬或过大而损坏设备。
(5)自动送料系统:将要切割的管材放入送料位置,自动送料装置会将管材按照预设长度推进到切割区域,保证切割的准确性和一致性。
3.设计特点:(1)切割管径范围广泛:该切管机可适用于不同直径的管材,通过更换刀具和调整切割参数,可满足不同管径的切割需求。
(2)切割精度高:采用伺服电机和高精密度的滚珠丝杠传动系统,保证切割精度达到要求,切割后的管材尺寸误差小。
(3)操作简单方便:采用PLC控制系统,通过触摸屏对切割参数进行设定,操作简单易懂。
自动送料装置可以自动将管材推进到切割区域,减少操作人员的劳动强度。
碾压式切管机设计

摘 要碾压式切管机的设计是一项技术革新项目。
切管机主要用于车辆,工业或建材生产中的批量下料工作,用于切割4~8/3''''的金属管。
它的特点是工作平稳、连续、效率高、劳动强度低、能保证尺寸精确度的要求,适应于在各种环境下的连续工作。
碾压式切管机的工用原理是:由电动机经V 带传动,蜗轮减速箱、开式齿轮传动到一对滚子,从而带动(金属管)的旋转,实现切割时的主运动。
与此同时,操纵手轮,通过螺旋传动,将圆盘刀片向下移动进给,并在不断增加刀片对管子的压力过程中,实现管子的切割工作。
原始数据:滚子的转速为1n =70转/分,驱动电动机的型号选择JO2-22-4,其额定功率为电N =1.5千瓦,满载转速电n =1410转/分,切管直径D 为3/8〞~ 4〞本次设计,主要是针对车辆用金属管材进行加工的切割机,完成的工作主要是切管机中的滚子,机体和减速箱部分的设计.包括传动装置的设计和计算,其中有电动机的选择,传动方案的拟定,各轴的转速,功率和转矩的计算.总体结构的设计,其中有各轴尺寸的设计,各主要传动件的结构尺寸的设计.并且针对以上的设计计算进行了详细的校核.最后通过得到的数据,绘制了总体装配图,减速机和滚子部分的装配图.然后又针对各主要基本件,绘制了多张零件图。
为了确定最佳方案,采取了多种方案进行了认真分析、研究和比较。
关键词: 切管机;设计计算;结构设计;批量下料;方案ABSTRACTRolling type pipe cutters design, is a technical innovation projects. Pipe cutters is mainly used for vehicles, industrial or building materials production batch of material work, suitable for cutting metal pipe. Its characteristic is, smooth, continuous, high efficiency, low labor strength, ensuring the dimension accuracy requirement, adapted to various environment in the work continuously Rolling type pipe cutters work by motor with principle is: by v-belts transmission, worm gear reducer, gear to open a roller, thus promote (tube) rotation, realize the main movement during cutting. Meanwhile, manipulate the handwheel, through screw transmission, will move down the disc blade feeding, and increasing the pressure on the pipe blades, realize the pipe in the process of cutting jobs.Raw data: roller speed for = 70 R.P.M., motor model selection JO2-22-4, its ratedpower for = 1.5 kw, carrying speed = 1410 R.P.M., cut tube diameter D for 3/8 "~ 4"This design is mainly for vehicles with metal pipes carry on the processing of cutting machine, completed work, mainly is the pipe cutters, the body and the roller gear box part of the design. Includes transmission device, the design and calculating, including motor driving scheme worked, the choice of the shaft, speed, torque and power calculation. Overall structure design, including the design of each shaft dimension, the main transmission parts. And the design of structure size for above a detailed design calculation of dynamicrigidity. Finally, through the data from the general assembly, mapped the speed reducer and roller part, the assembly drawing. Then in each major basic pieces, painted a detail drawings. In order to determine the optimal scheme took various schemes, carried on the earnest analysis, research and comparison.Key words:Pipe cutters; Design calculation; Structure design; Batch nextmakings; scheme目录第一章方案的选择与论证 (4)1.1 电动机的选择 (4)1.2 拟定传动方案 (6)1.3 总体结构设计 (9)第二章传动装置的设计与计算 (11)2.1 传动比分配 (10)2.2 计算各轴的转速,功率和转矩 (11)2.2.1 各轴的转速 (11)2.2.2 各轴的功率 (11)2.2.3 各轴传递的转矩 (12)第三章进行传动机构的设计与计算 (14)3.1 带传动设计 (14)3.2 齿轮传动设计 (14)第四章结构设计 (17)4.1 初算各轴的最小直径 (17)4.2 计算各主要传动件的结构尺寸 (18)4.3 初定轴承跨距 (21)第五章设计总结 (26)参考文献 (27)致谢 (28)附录 (29)第一章方案的选择与论证几种方案优缺点的比较如下表:经过方案的比较和实际的调查,了解它们之间各自的优、缺点后,经过认真研究分析,认为第四种方案为最佳方案,最后确定采用第四种方案来进行设计。
大型管材相贯线切割机设计 毕业设计
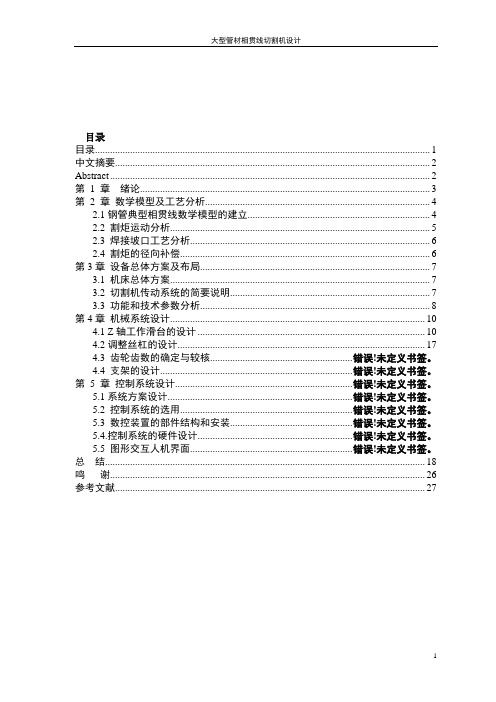
目录目录 (1)中文摘要 (2)Abstract (2)第1 章绪论 (3)第2 章数学模型及工艺分析 (4)2.1钢管典型相贯线数学模型的建立 (4)2.2 割炬运动分析 (5)2.3 焊接坡口工艺分析 (6)2.4 割炬的径向补偿 (6)第3章设备总体方案及布局 (7)3.1 机床总体方案 (7)3.2 切割机传动系统的简要说明 (7)3.3 功能和技术参数分析 (8)第4章机械系统设计 (10)4.1 Z轴工作滑台的设计 (10)4.2调整丝杠的设计 (17)4.3 齿轮齿数的确定与较核......................................................... 错误!未定义书签。
4.4 支架的设计............................................................................. 错误!未定义书签。
第5 章控制系统设计....................................................................... 错误!未定义书签。
5.1系统方案设计.......................................................................... 错误!未定义书签。
5.2 控制系统的选用..................................................................... 错误!未定义书签。
5.3 数控装置的部件结构和安装................................................. 错误!未定义书签。
5.4.控制系统的硬件设计.............................................................. 错误!未定义书签。
方形纸筒切管机设计学士学位
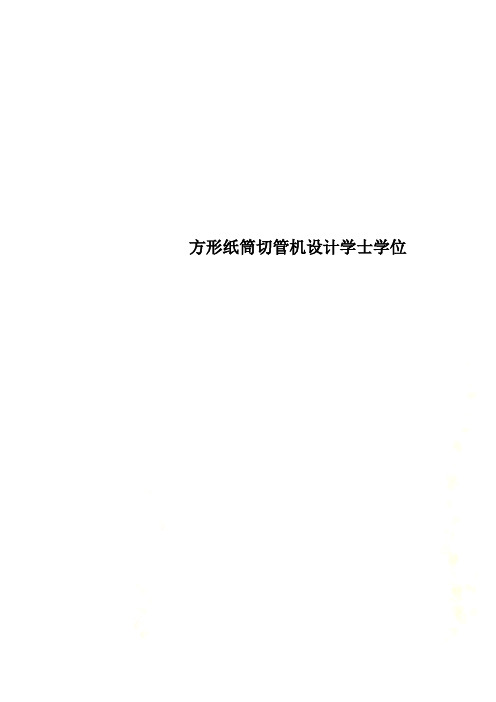
方形纸筒切管机设计学士学位哈尔滨远东理工学院学士学位论文题目:方形纸筒切管机设计姓名:张龙分院:机电工程学院专业:机械设计及其自动化学号:10140435指导教师:马慧良二0 一四年五月二十二日摘要方形纸管切割属于一个新的课题,目前国内尚无类似设备,也未见关于此类设备的论著,本课题研究的目的在于提供一种操作简便、高效率、高精度、成本低的方形纸筒切管机。
本产品可以通过更换仿形凸轮的方式实现对多种规格方形纸管的仿形切割,更换凸轮快速、方便,针对不同规格纸管,使用对应规格的仿形凸轮,使切刀随纸管的转动同步进退,确保切刀对纸管圆周各处切割均匀;该产品具备一副对切刀架,有两把相对的切刀同时对纸管进行切割,可以使纸管的芯轴所受的径向力始终保持平衡而不致于弯曲,切刀的进给与返回采用气缸作为动力源,动作可靠、灵活。
关键词:方形纸管;仿形凸轮;对切刀架;气缸;芯轴AbcstractSquare paper tube cutting belongs to a new problem. At present, there’s no similarity equipment or treatise in our country. The purpose to study this problem is to afford a cheap paper tube machine. It is easy to handle and efficiency and precision.This kind of machine can cut various kinds of paper tube by replace with model cam. And this work is easy and fast. According to the different specifications paper tube, You can use corresponding modeling cam, The paper tube and the knives run in-phase, In order to cut the paper tube to equality. This manufacture have a double knife rest, when the machine works, this pair of knives cut the paper tube at the same time. It can make the axes of pape r tube came under balanceable strength, and cann’t be in bend. The power of knives’ advance and backtrack is cylinder, credibility and agility.Key words: Quadrate Paper Tube;Model Cam;Double Knife Rest;Cylinder;Spindle目录摘要 (I)Abcstract ....................................................................................................................................... I I 第1章绪论. (1)1.1 课题背景 (1)1.1.1 纸制品包装的特点的概述 (1)1.1.2 纸包装的环境性能 (2)1.2 生产现状 (2)1.2.1 切深不均 (2)1.2.2 刀具和芯轴的使用寿命短 (3)1.2.3 芯轴刚度不足 (3)1.2.4 生产效率低下 (3)1.3 解决方案 (3)1.3.1 切深不均的解决方案 (3)1.3.2 刀具进给与返回 (3)1.4 各工艺过程的连锁动作 (3)1.5 立题意义 (4)1.6 本文主要内容 (4)第2章设计说明 (5)2.1 概述 (5)2.2 功能元分解 (5)2.2.1 驱动系统 (5)2.2.2 传动系统 (5)2.2.3 横向行走机构 (6)2.2.4 对切刀架总成 (6)2.2.5 尾座总成 (7)2.2.6 控制系统 (7)2.3 本章小结 (7)第3章动力与结构参数计算 (9)3.1 功能描述 (9)3.2 工艺参数 (9)3.3 工作条件 (9)3.4 动力参数计算 (9)3.4.1 推动力计算 (9)3.4.2 功率计算 (10)3.4.3电机减速器选型 (10)3.4.4 气缸选型 (12)3.5 结构参数确定 (13)3.5.1传动机构齿轮设计 (13)3.5.2弹簧设计 (14)3.5.3仿形凸轮结构设计 (15)3.6主要零件校核 (18)3.6.1主轴齿轮平键校核 (18)3.6.2主轴芯轴平键校核 (18)3.6.3气缸安装螺钉校核 (18)3.7导轨的选择 (19)3.7.1导轨概述 (19)3.7.2导轨的设计程序及内容 (19)3.7.3选择导轨 (19)3.8本章小结 (19)第4章气动回路设计 (21)4.1 气动系统简介 (21)4.1.1气动控制系统的优点 (21)4.1.2气动系统的缺点: (22)4.2 气动回路图 (22)4.2.1 回路组成 (22)4.2.2 回路特点 (23)4.2.3 气动系统主要参数 (23)4.3 本章小结 (23)第5章参考机型 (24)5.1 双刀自动切管机 (24)5.2 多刀切割纸管机 (26)5.3 经济效益 (28)5.3.1 社会效益 (28)5.4 本章小结 (28)结论 (29)致谢 (30)参考文献 (31)第1章绪论1.1 课题背景人类在科学领域的发展下,特别是17世纪的产业革命以来,在自然与经济改造发展方面取得了巨大的成就,但是全球发展迅速的经济文明中也存在着不文明的反面影响,由于处理措施在工业化过程中的不太恰当,尤其是开发利用自然资源的不合理,以及废气、废水、和废物在治理工业化过程中不被重视,所以产生了地球能源日益短缺、环境日趋恶化、资源的日益匮乏,使世界经济的可持续发展和地球的生态空间产生严重的危机。
自动钢管切割机的毕业设计任务书
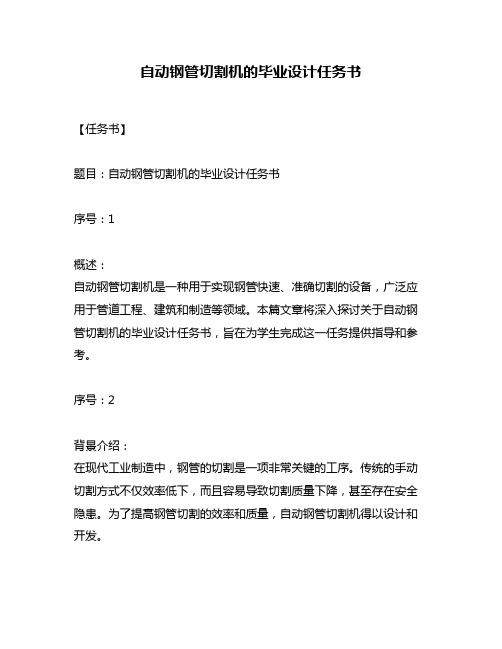
自动钢管切割机的毕业设计任务书【任务书】题目:自动钢管切割机的毕业设计任务书序号:1概述:自动钢管切割机是一种用于实现钢管快速、准确切割的设备,广泛应用于管道工程、建筑和制造等领域。
本篇文章将深入探讨关于自动钢管切割机的毕业设计任务书,旨在为学生完成这一任务提供指导和参考。
序号:2背景介绍:在现代工业制造中,钢管的切割是一项非常关键的工序。
传统的手动切割方式不仅效率低下,而且容易导致切割质量下降,甚至存在安全隐患。
为了提高钢管切割的效率和质量,自动钢管切割机得以设计和开发。
序号:3任务目标:本次毕业设计的任务是设计一个高效、准确的自动钢管切割机。
具体任务目标包括:1. 实现钢管的自动进给和定位功能。
2. 开发切割方案,确保精准切割钢管。
3. 配备适当的安全保护装置,确保操作人员的安全。
4. 考虑到切割机的稳定性和可靠性,进行整体结构设计和动力学分析。
5. 实现人机交互界面,方便操作和监控。
序号:4任务要求:1. 毕业设计需要进行系统性的研究和试验,确保切割机的性能和质量。
2. 需要编制相应的设计方案和设计报告,对设计过程和结果进行详细阐述。
3. 有序、规范地组织整个设计任务,确保按照规定的时间节点完成各项任务。
4. 论文格式应符合学校要求,包括格式、字数、插图、引用标准等方面的要求。
5. 提高设计的创新性,可以考虑引入先进的控制方式、材料、传感器等。
序号:5预期成果:完成毕业设计的学生应该提交以下成果:1. 详细的设计方案和设计报告,包括设计原理、系统结构、电气控制电路图、传动布置等。
2. 完工的自动钢管切割机实物,并进行详细的性能测试和性能分析。
3. 完善的操作手册和维护手册,方便使用和维护人员进行操作。
4. 毕业论文,内容详细且规范,清晰地呈现研究过程、结果和结论。
序号:6观点与理解:自动钢管切割机在现代制造业中发挥着重要的作用,因此其设计与研发具有重要的意义。
通过本次毕业设计任务,学生将不仅锻炼自己的设计与研发能力,还能获得针对自动钢管切割机的系统性理解和掌握,为未来的工作或研究打下坚实的基础。
自动钢管切割机毕业设计任务书

自动钢管切割机毕业设计任务书任务书一、任务背景自动钢管切割机是一种用于切割钢管的机器,可以自动完成钢管的定位、夹紧和切割等工作。
该机器广泛应用于建筑、制造业等领域,具有高效、精度高、安全可靠等特点。
二、任务目标本次毕业设计旨在设计一台自动钢管切割机,实现以下目标:1. 实现自动化控制:通过PLC控制系统实现对整个切割过程的自动化控制。
2. 提高生产效率:通过优化机器结构和控制系统,提高切割速度和准确度,从而提高生产效率。
3. 保证安全可靠:在设计中考虑到人员安全因素,采用多重保护措施确保机器运行时的安全性。
三、任务要求1. 机械结构设计:根据要求设计出合理的钢管夹紧和定位装置,并与电气系统相匹配。
同时考虑到结构强度和稳定性等因素。
2. 控制系统设计:采用PLC进行自动化控制,并实现对整个切割过程的监测与调节。
同时考虑到通信协议、数据传输等因素。
3. 系统集成:将机械结构和控制系统进行集成,实现自动化切割功能。
同时考虑到整个系统的可靠性和稳定性。
4. 安全保护措施:在设计中采用多重保护措施,如安全门、急停按钮等,确保机器运行时的安全性。
5. 编写毕业设计论文:撰写符合规范要求的毕业设计论文,并进行答辩。
四、任务计划1. 第一阶段(1周):熟悉自动钢管切割机的原理和相关技术知识。
2. 第二阶段(2周):进行机械结构设计和控制系统设计,并完成初步方案的制定。
3. 第三阶段(3周):进行系统集成和测试,并对系统进行调试和优化。
4. 第四阶段(1周):编写毕业设计论文并进行答辩准备。
五、任务评估本次毕业设计将根据以下标准进行评估:1. 设计方案合理性及可行性;2. 系统运行效果及稳定性;3. 完成毕业设计论文质量及答辩表现;4. 项目实施过程中的沟通协调能力和团队合作精神。
六、任务分工1. 机械结构设计:XXX同学2. 控制系统设计:XXX同学3. 系统集成和测试:XXX同学、XXX同学4. 毕业设计论文撰写:XXX同学、XXX同学七、任务验收标准1. 设计方案符合要求,机械结构和控制系统相匹配;2. 自动钢管切割机能够实现自动化切割功能,并保证安全可靠;3. 毕业设计论文符合规范要求,答辩表现优秀。
专用管子切割机设计

切割机的设计双夹紧设备结构原理示意图1、夹紧臂;2、压紧块;3、工件;4、V型夹具;5、滑台;6、连杆;7、连架杆;8、液压缸设计评语:内容摘要本设计主要是由3部分组成,驱动部分、压紧部分、切割部分。
驱动部分主要使传递管件向前运动,然后经过夹紧装臵后把工件固定牢固,然后利用切割机把管件根据需要的长度切割下来。
首先是一个1.1KW的电动机通过皮带轮带动减速机运行,然后减速机通过联轴器与下压轮连接进行运转,带动管件向前运动,形成了驱动机构。
根据市场调查和设备自身设计等情况,现在本设计以管直径为40,壁厚5的普通钢管为例,进行设计。
其他规格的管件可以更换对应的模具,使管件的设计范围在10-80,长度基本定在0-345,。
那现在以直径40的管件为例介绍如下。
1.1KW-6电动机带动减速机,其中带轮之间有个传速比为1:2,选取的减速机为ZD15型减速机,传动比为48.57,这样速度传递到下压轮的转速就为960/2/48.57=10转/分,大约为6秒1转。
本驱动中按有槽轮机构,这样就可以根据槽轮机构调整工件的进度,按照1转6秒,那么一转的位移量为3.14*110=345,说明管件最大移动量为345,这样切割的最大长度为345。
下面是加紧机构,根据设备原理采用了上下两块板把工件给加紧的办法,上面加紧板采用自身有浮动的机构,下面加紧板给于固定在设备上,这样就可以实现移动式的加紧,同时考虑到以防碰撞等现象,常用的是力臂机构,采用了杠杆的原理,这样就可以保证加紧机构的另一侧是液压缸,液压缸的力最大可以达到了3吨,这样使工件牢固的加紧在工作台上。
在紧挨着加紧工作台的位臵装有主要部件,那就是切割部分,所谓的切割机,主要是通过切割机中砂轮片的高速运转把工件给切割下来。
考虑到同时切割2件工件,那么切割机的另一侧装有液压缸,可以通过液压缸的移动实现切割。
目录内容摘要---------------------------------4 目录-------------------------------------6第一章引言------------------------------7第二章设计------------------------------82.1选题背景-------------------------82.2方案论证-------------------------112.3过程设计-------------------------132.3.1总体计算及分析-------------132.3.2驱动装臵中传动管件的计算---142.3.3电动机与减速机的选择-------152.3.4槽轮机构-------------------162.3.5带轮分析-------------------192.3.6液压分析-------------------222.3.7夹紧机构设计与计算---------272.3.8齿轮设计-------------------28第三章参考文献---------------------------33第四章致谢-------------------------------35第一章引言本设计主要是加快管件的切割速度,同时实现自动化式的加工,很高兴能在百忙中抽出时间指导本设计。
机械毕业论文钢管切割机设计
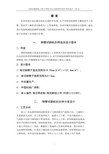
前言在毕业设计选定题目的社会调研中发现,生产中所需的钢管大都使用手工切断,采用手工操作劳动强度大,工作效率低,并存在极其危险的安全隐患,建议设计制造机械化的钢管切割机,当即受到企业欢迎,表示愿意使用设备,我们小组主动承接了此项设计任务。
一、钢管切割机的用途及设计要求1、用途钢管切割机主要是用来切割加工工程所需不同长度的管材,它可以自动适应各种管材横截面直径的大小,对不同材质的钢管均有较好的切割性能,切口平整圆滑为下道工序的顺利加工奠定了基础。
2、设计要求1)被切割管子直径范围为19.05mm(3/4")~101.6mm(4") 。
2)被切割管子壁厚范围为3~5mm。
3)中批量生产。
4)中型机械厂承制。
5)单人操作,每日两班制(每班断续工作,时间≤10小时)。
二、钢管切割机的总体方案设计1、工艺分析原工厂对金属管材的切割采用了弓锯切割及气割的方法。
弓锯的工艺质量因人而异,且工作效率低下,浪费人工工时,不适合批量加工。
气割的方法较弓锯切割工作效率高,节约人工工时,但切割处的金属内部分子结构发生转变,材质性能劣化,并且切口处的金属熔渣严重影响下道工序的加工。
为此,根据加工现场的工艺情况和要求,设计研制了这台钢管切割机,它采用了碾压的方法切割金属管材,对管材的切口加工精度高,并且适合连续切削,节约了人工工时,提高了生产效率。
2、对执行机构的运动要求 2.1 计算总传动比和分配传动比 2.1.1 总传动比计算初步确定滚筒转速:n =70r/min 则总传动比:i 总=—电动机满载转速(nE )滚筒转速(nT ) =140070=202.1.2分配传动比各级传动机构的传动比分配如下: 带传动: i 0=1.67 蜗杆传动: i 1=25齿轮传动: i 2=2 i 3=5/21实际总传动比等于:i 总'=i0i1i2i3=1.67×25×2×521=19.88 2.2 各传动轴传动功率及机械效率的计算带传动: η1=0.96 蜗杆传动:η2=0.7 齿轮传动: η3=0.94 滚动轴承:η4=0.99各传动轴传动特性,见表1轴号功 率 P (KW)电机Ⅰ0P =1.50转 矩 T (N.m)转 速 (r/min)T =95500P 0n 0=95501.51400=10.23=14000轴Ⅰ=ⅠP 0 1.5×0.96 =1.44=×0.96=16.4T 0i 0η1n Ⅰn 0i 0=14001.67=838.3轴Ⅱ =P 1.44×0.78×0.99 =1.11η1 =η2Ⅰη4 =Ⅰ==316.6T i 1η2ⅡⅡⅠη4=16.4×25×0.78n n i 1=838.325=33.53ⅡⅠn==轴Ⅲ =ⅢPⅡ×0.99 =1.03=0n Ⅲn Ⅱi 2=33.52=16.8轴Ⅳ=P 1.03×0.94×0.99 =0.96η3η3Ⅲη4 =Ⅲ=×0.96×T i 2η3ⅣⅣⅡη4=316.6×2× ×0.94n n i 3==70.6ⅣⅢ==η4i 3222521122=61.416.8×4.22T T P 表1轴T P P P 1.11×0.94 ==10.23×1.67T ×0.993 切管工艺方案及传动方案设计和选型3.1 切管工艺方案选择,见表23.2传动方案选择如下图1所示图 1如上图1所示,提供的切管机的三种传动系统方案.若仅满足总传动比要求,可以采用单级蜗杆传动.但综合考虑结构,操作及调整布局等方面的要求,宜采用图中传动系统方案3。
自动切管机结构设计.

第1章绪论(具体的CAD图和计算公式和完整的设计说明书和中英文翻译加q q 聊八零七零六一五七九)1.1课题背景中国是一个拥有上下五千年的历史文明的国家。
我们伟大的祖先从原始的石器时代到金属时代,就能够进行机械加工的简单操作的流程,但是其生产的效率和精度在当时的生产条件下都是非常的低下。
追随着时代不断进步的脚步,人们在变换着方法来提高自己的生活水平和生存条件,就是基于这一点上面,机械制造自动化的快速发展速度越来越快速,一个精度更加高、效率更加高、成本更加低、更加人性化的时代正在向着人们不断靠近。
中国虽然是一个丰厚底蕴的文明古国,但是和西方这些发达的国家比较起来,它在工业制造工艺的方·面和发达国家比较起来还是存在较大的差距,机械制造的技术是也有很大的差距的,从事机械行业的人都晓得,机械制造技术的先进程度与加工的精确度,生产的效率,以及生产的成本多少有着直接的关系。
随着我国工业及民用建筑的迅速增长,国民经济的发展速度也越来越快,金属管材在机械制造、压力容器、民用家电等行业被大量使用,因此切管机在国内很多行业中都被广泛应用,为了满足机械行业的发展需求,我们必须进一步提高切管机的制造技术[1]。
1.2课题研究意义当今这个时代的各项技术的发展速度是很迅速的,尤其是计算机的应用技术的发展速度也是非常快速的,机械制造业的发展速度也随之得到了很大的进步和提高,它主要体现出来的方面有生产效率跟随数控制造这些方面的迅速进步中也得到了快速的提高。
数控加工的高精度对于大多数人来说都是第一个选择,但是使用数控加工等方法来对金属管材进行加工制造对于一些规模不大的工厂和企业来说就有点不太适合,并且对资源的浪费程度也到了一个很高的地步,实在是入不敷出。
因此,本次毕业设计对根据工厂平时的实际情况,对原有的切管技术进行更进一步的改进。
使得本次毕业设计的切管机能够拥有操作不复杂、维护不复杂、生产的成本少、生产效率高,并且能够符合产家要求等优点。
切管机毕业设计

切管机毕业设计切管机毕业设计在工业领域,机械设备的研发和创新一直是推动行业发展的重要动力之一。
而切管机作为一种常见的机械设备,其在管道加工和制造领域中起着重要的作用。
本文将探讨切管机的毕业设计,包括设计目标、设计原理、创新点以及实施方案。
设计目标在进行切管机毕业设计时,首先需要明确设计目标。
切管机的设计目标主要包括提高生产效率、降低人工成本、提高切割精度和稳定性等方面。
通过对目标的明确,可以为后续的设计和实施提供明确的指导。
设计原理切管机的设计原理主要包括切割方式、切割原理和控制系统。
切割方式可以分为手动切割和自动切割两种。
手动切割需要操作人员手动控制切割过程,适用于小批量生产。
而自动切割则通过控制系统实现对切割过程的自动控制,适用于大规模生产。
切割原理主要包括切割刀具的选择和切割方式的确定。
控制系统则负责对切割过程进行控制和监测。
创新点在进行切管机毕业设计时,创新点是非常重要的。
可以通过对现有切管机的分析和改进,提出新的设计方案。
例如,可以引入先进的传感器技术,实现对切割过程的实时监测和控制。
另外,可以优化切割刀具的设计,提高切割精度和效率。
还可以考虑引入机器学习算法,通过对切割过程的数据进行分析和学习,优化切割参数的选择。
实施方案在进行切管机毕业设计时,实施方案是设计的关键。
首先,需要进行详细的需求分析,明确设计目标和技术要求。
然后,可以进行设计方案的选择和优化。
在设计过程中,需要考虑机械结构、电气控制、软件编程等方面的问题。
同时,还需要进行实验验证和性能测试,确保设计方案的可行性和有效性。
最后,可以进行设计报告的撰写和成果展示。
切管机毕业设计的重要性切管机毕业设计不仅是对所学知识的应用和实践,更是对创新能力和解决问题的能力的考验。
通过进行切管机毕业设计,可以培养学生的工程实践能力和创新思维能力。
同时,切管机作为一种常见的机械设备,其在管道加工和制造领域中的应用广泛,对学生未来的就业和发展也具有重要意义。
自动切管机及送料机构设计毕业设计论文

机械96班姓名刘赞
五、开始及完成日期:
自2012年11月12日至2013年5月25日
六、设计(论文)指导(或顾问):
指导教师签名
签名
签名
教研室主任
〔学科组组长研究所所长〕签名
系主任签名
2012年11月12日
摘
自动切管机主要用于加工各种用途的管件,包括各种材料的金属管件,本次设计的自动切管机及送料机构所加工的管件主要是直径在60~70mm之间。本论文设计的自动切管机及送料机构,能自动切管和送料达到自动加工金属管件的目的。完成的工作主要是自动切管机中圆锥齿轮减速器、切管机棍筒、机架及自动送料机构工作方案的设计。其中,切管机的工用原理是:电动机通过V带传动,圆锥齿轮减速箱、开式齿轮传动到一对棍筒,然后带动金属管的旋转,获得切割时的主运动。同时,圆盘刀片向下移动,实现管子的切割工作。其中包括确定切管机设计方案的制定、传动装置的设计和计算(包括电动机的选择、拟定传动方案、各轴转速、功率和转矩的计算、传动机构的设计与计算等)。根据已有的经验公式,对上述各项进行了详细的计算和强度校核之后,确定了各个零件之间的尺寸位置。最后绘制切管机装配图、部件图以及部分零件图。
某Hale Waihona Puke 车车辆厂,每天都要切割大量50~60 mm材料为Q235的金属管,现需设计制造一台切管机。
1.切管尺寸范围:50~60 mm。
2.切管力:F=3500N。
3.切管时滚筒转速:70r/min。
三、本设计(论文或其他)应达到的要求:
1.通过该设计使学生熟悉机械设计的一般思路。
2.使学生掌握机械设计的方法和技巧。
3.通过设计巩固机械制图、金属材料、机械设计基础等课程的知识。
4.完成自动切管机方案设计、主要部件的参数计算。
切管机设计

图书分类号:密级:毕业设计(论文)切管机设计THE CUTTING PIPE DESIGN学位论文原创性声明本人郑重声明:所呈交的学位论文,是本人在导师的指导下,独立进行研究工作所取得的成果。
除文中已经注明引用或参考的内容外,本论文不含任何其他个人或集体已经发表或撰写过的作品或成果。
对本文的研究做出重要贡献的个人和集体,均已在文中以明确方式标注。
本人完全意识到本声明的法律结果由本人承担。
论文作者签名:日期:年月日学位论文版权协议书本人完全了解关于收集、保存、使用学位论文的规定,即:本校学生在学习期间所完成的学位论文的知识产权归所拥有。
有权保留并向国家有关部门或机构送交学位论文的纸本复印件和电子文档拷贝,允许论文被查阅和借阅。
可以公布学位论文的全部或部分内容,可以将本学位论文的全部或部分内容提交至各类数据库进行发布和检索,可以采用影印、缩印或扫描等复制手段保存和汇编本学位论文。
论文作者签名:导师签名:日期:年月日日期:年月日摘要现在的社会在随着计算机技术高速的发展下,机械制造行业也同样迅速发展起来,同时生产效率也得到了飞快的提升。
切管机它主要运用于加工各种用途的金属管件,它具有降低成本、提高生产效率、节约能源等优点。
这次的切管机毕业设计是加工3/8″~4″之间的钢管。
这次毕业论文设计的是切管机,它主要设计的是切管机的机体、切管机中的减速箱、切管机的滚子部分等。
此中该论文内包含着传动部分的设计与计算(其中有关于切管机电动机容量的选择,切管机各轴的转速、功率和转矩的计算)、切管机的结构设计(其中有切管机各主轴传动件的结构尺寸计算)。
在经过了计算部分的强度校核之后,就可以根据其中的数据与公式来选定零件的尺寸,之后就对下面几种图进行绘图,有切管机的装配草图、切管机的设计装配图、切管机的部分图及切管机的零件工作图等。
此次论文设计所完成的切管机主要的任务是用于车间中对钢管的切削加工,设计该切管机可以在生产中提高生产的效率并且降低劳动的强度。
【精品毕设】机械专业切管机毕业设计论文

第一章绪论在机械制造、工程施工和建筑安装工作中, 钢管的传统切割方法主要是依靠手工锯割、锯床锯割、滚轮挤压、砂轮切割和气焊切割等。
这些钢管切割方法在不同程度上都存在着切割效率低、工人劳动强度大、工作环境差的缺点。
而且, 有的方法还存在着锥形切口(如滚轮挤压)、切口粗糙、凹凸不平(如气焊切割)、切削噪声大(如砂轮切割)、不易在现场施工作业等缺陷。
针对上述问题, 近年工厂来广泛采用高效自动切割机,她效率高、操作简便, 有的还能实现自动化,能够对不同管径、壁厚和材质的钢管进行切割的钢管切割机。
包钢的高效自动切管机是由武汉重型机床厂生产的一种专用钢管切断机床,广泛的应用于工业领域。
它是一种专用的切断机床,适用于大批量、自动或半自动的切断无缝钢管的头部和尾部,紧接着对切断后的两端进行倒角,机床的刚度大,功率大,自动化程度高,生产效率也高,是无缝钢管厂的必要设备,在生产无缝钢管的工艺中起着精整地作用。
其年钢管切头量为40万吨,切断后管子断面可自动倒内角外角或切大坡口。
装上镗孔辅件后也可以镗0、3、5、7、11、14、五种角度及各种规格管径的锥空口。
机床有切头自动定长检测装置,可以完成经冷锯切断后的管端平端面。
倒内角的工作分为手动、半自动、全自动。
该切管机通过机—电—液一体化的设计与综合,能够实现自动化控制,而且在其生产过程中效率高,操作方便、快捷,该设备广泛应用于无缝钢管的生产领域,因此对该设备的性能和生产工艺过程的掌握显得无比重要。
该设备是在原有的半自动切管机的基础上改造而成。
经改造后的切管机的执行元件由液压站提供动力源。
在工作现场除了清理切削铁屑的工人,整个过程可在电气,液压的控制下实现自动切割钢管的动作。
操作方便,快捷,大大提高了生产效率。
如加工直径为102mm的钢管,每小时可达130根;加工直径245mm的钢管,每小时为68根。
该切割机的特点是:该机床的执行元件全部采用液压传动。
由油缸顺序动作来完成切割过程。
切管机的设计

优秀设计毕业设计(论文)题目切管机设计专业名称班级学号学生姓名指导教师填表日期20** 年5 月10 日南昌航空大学科技学院毕业设计(论文)任务书I 、毕业设计(论文)题目: 切管机设计II 、毕 业设计(论文)使用的原始资料(数据)及设计技术要求:设计一切管机,已知该切管机滚子的转速为701=n r/min ,圆盘刀片的直径mm 80=φ ,加工管件的直径范围为4~8/3'''',电机的额定功率KWP 5.1=电,满载转速 m in /1410r n =电,每天工作10小时,载荷变动小。
I I I 、毕 业设计(论文)工作内容及完成时间:1. 收集资料、外文资料翻译,开题报告 第1周—第2周2. 传动方案的确定 第3周—第4周3. 参数确定及设计计算 第5周—第7周4. 切管机装配图设计及零部件图设计 第8周—第15周5. 撰写毕业设计论文 第16周—第17周Ⅳ、主要参考资料:[1] 璞良贵,纪名刚主编.机械设计.第七版.北京:高等教育出版社,2001[2] 孙桓,陈作模主编.机械原理.第六版.北京:高等教育出版社,2002[3] 成大先主编.机械设计手册.北京:化学工业出版社,2004[4] 赵学田主编.机械设计自学入门.北京:冶金工业出版社,1982[5] Ye Zhonghe, Lan Zhaohui. Mechanisms and Machine Theory. Higher毕业设计(论文)开题报告题目切管机设计专业名称班级学号学生姓名指导教师填表日期20** 年3 月16 日一、选题的依据及意义:中国是一个上下有五千年历史的文明古国,从原始的石器时代到金属时代,我们伟大的祖先就进行了简单的机械加工,但是在当时的生产条件下,其生产的效率和精度都是非常的低下。
随着时代的发展,人们在想方设法改善自己的生存条件和生活水平,正是由于这点,促进了机械制造生产的飞速发展,人们在超着一个精度更高、效率更高、成本更低、更加人性化的方向发展。
自动钢管切割机毕业设计任务书

自动钢管切割机毕业设计任务书1. 任务背景随着工业化进程的加快,钢管行业得到了长足的发展。
钢管在许多领域都有广泛应用,包括建筑、交通、能源等。
钢管的生产过程中,切割是其中一项重要的工序。
传统的钢管切割工作依赖于人工操作,效率较低且存在安全隐患。
为了提高钢管切割的生产效率和质量,开发一种自动钢管切割机成为很有必要的课题。
2. 任务目标本毕业设计的目标是设计并制作一台自动钢管切割机,实现对钢管的快速、准确切割。
具体目标如下: 1. 设计一套完整的自动钢管切割方案。
2. 开发一款高效、稳定的控制系统,能够准确控制钢管的切割尺寸和位置。
3. 设计一个合适的夹紧机构,确保钢管在切割过程中的稳定性。
4. 实现自动切割的同时保证切割质量,尽量减少切割面的粗糙度。
5. 考虑钢管不同直径、壁厚的切割问题,具有一定的通用性。
3. 任务内容和方案3.1 自动钢管切割机的设计方案1.确定机床的整体结构和机头设计,使得切割过程中操作方便且机器具有良好的稳定性。
2.设计夹紧装置,保证钢管在切割过程中不发生位移,达到切割精度要求。
3.选择合适的切割工具,根据钢管的材质和直径确定切割方式和参数。
3.2 控制系统的设计与实现1.使用PLC或单片机等控制器作为控制核心,编写相应的控制程序,实现对切割机各个部件的自动控制。
2.设计合适的传感器装置,采集钢管的尺寸和位置信息,作为控制系统的输入信号。
3.通过编程控制切割机的运动轨迹和速度,实现对钢管的精准切割。
3.3 切割质量的保证1.选择合适的切割工具和切割参数,尽量减少切割面的粗糙度。
2.设计优化的切割路径,确保切割的平整度和垂直度满足要求。
3.考虑切割工具的磨损和寿命问题,设计相应的更换机构和预警功能,提前进行维修和更换。
3.4 通用性设计1.考虑钢管不同直径和壁厚的切割问题,设计可调节的夹紧装置和切割参数。
2.提供简单易用的操作界面和切割设定功能,使得适应不同规格的钢管切割。
自动圆管切割机机械设计毕业设计论文
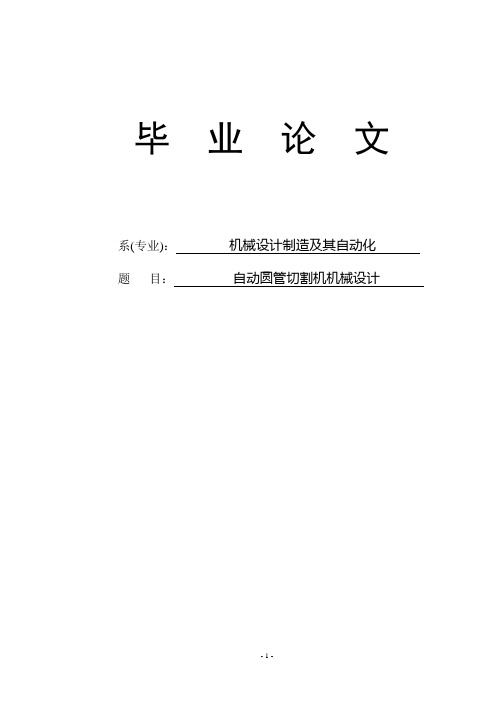
学位论文原创性声明
本人郑重声明:所呈交的论文是本人在导师的指导下独立进行研究所取得的研究成果。除了文中特别加以标注引用的内容外,本论文不包含任何其他个人或集体已经发表或撰写的成果作品。对本文的研究做出重要贡献的个人和集体,均已在文中以明确方式标明。本人完全意识到本声明的法律后果由本人承担。
2)工程设计类题目的图纸,要求部分用尺规绘制,部分用计算机绘制,所有图纸应符合国家技术标准规范。图表整洁,布局合理,文字注释必须使用工程字书写,不准用徒手画
3)毕业论文须用A4单面打印,论文50页以上的双面打印
4)图表应绘制于无格子的页面上
5)软件工程类课题应有程序清单,并提供电子文档
5.装订顺序
1)设计(论文)
7)参考文献
8)致谢
9)附录(对论文支持必要时)
2.论文字数要求:理工类设计(论文)正文字数不少于1万字(不包括图纸、程序清单等),文科类论文正文字数不少于1.2万字。
3.附件包括:任务书、开题报告、外文译文、译文原文(复印件)。
4.文字、图表要求:
1)文字通顺,语言流畅,书写字迹工整,打印字体及大小符合要求,无错别字,不准请他人代写
本次研究需要将铝管切割的整个工作过程实现自动化,其中包括自动上料,夹紧,送料,切割,换工位,去毛刺等一系列工作,即本次研究的目标是完成整个自动化生产流水线。在机械生产过程中广泛的使用自动化生产线,能够很大程度上提高劳动效率以及产品的质量,除此之外还能够改善工人劳动条件、降低能源消耗[4]。
自动生产线是在计算机技术和人工智能技术迅速发展的前提下产生的,自动生产线是将智能设备应用于工业生产中,使得机械生产过程具有一定自适应能力。因此自动生产线是很多工业技术的综合展现,这其中包含了机械装配、气动、传感器和PCL控制等技术,自动化生产线的实践性非常强,对于我国的机械行业发展具有非常重要的意义[5]。
- 1、下载文档前请自行甄别文档内容的完整性,平台不提供额外的编辑、内容补充、找答案等附加服务。
- 2、"仅部分预览"的文档,不可在线预览部分如存在完整性等问题,可反馈申请退款(可完整预览的文档不适用该条件!)。
- 3、如文档侵犯您的权益,请联系客服反馈,我们会尽快为您处理(人工客服工作时间:9:00-18:30)。
切管机毕业设计目录引言 01. 确定工艺方案 (1)2. 传动装置的设计与计算 (3)2.1 电动机的选择 (3)2.1.1 类型的选择 (3)2.1.2 转速的选择 (3)2.1.3 功率的选择 (3)2.2 拟订传动方案 (4)2.3 计算各轴的转速、功率和转矩 (7)2.4 进行传动机构的设计与计算 (8)2.4.1 带传动设计 (8)2.4.2 齿轮模数的确定 (10)2.4.3 蜗轮蜗杆模数的确定 (10)2.4.4 齿数的确定 (11)2.5 进行总体结构设计,画出总体方案图 (12)3. 结构设计 03.1 初算各轴的最小直径 03.2 计算各主要传动件的结构尺寸 (1)3.3 绘制部件的装配草图 (5)3.4 绘制设计装配图 (11)3.5 绘制零件工作图 (15)4. 结论 (18)5. 致谢 (30)6. 参考文献 (31)引言中国是一个上下有五千年历史的文明古国,从原始的石器时代到金属时代,我们伟大的祖先就进行了简单的机械加工,但是在当时的生产条件下,其生产的效率和精度都是非常的低下。
随着时代的发展,人们在想方设法改善自己的生存条件和生活水平,正是由于这点,促进了机械制造生产的飞速发展,人们在超着一个精度更高、效率更高、成本更低、更加人性化的方向发展。
中国虽然是一个文明古国,其拥有几千年的历史背景和文化积淀,但是其在工业制造方面和发达国家还是存在较大的差异,其机械制造技术却远远比不上西方等发达国家,众所周知,机械制造技术的先进与否直接与加工的精度,生产的效率,以及生产的成本产生直接关系。
随着机械化生产的速度发展,人们对机械产品的要求也越来越高,其主要表现在实用和经济等方面。
本次设计的目的和要求就是设计一个简单实有的切管机,其目的在于能够高效而廉价的加工出生产所需要的产品,并且要求其生产效率较高,适合大多数不是批量加工管件或者对管件加工要求不高的工厂使用。
在当今这个各项技术飞速发展的时代,尤其的随着计算机技术的高速发展,机械制造行业也得到了飞速的发展,其主要表现在数控加工等方面,生产效率也随着其得到了飞速的发展。
数控技术加工的精度高,得到了无数人的喜爱,但是对于一些小型的工厂和对管件加工并不频繁的企业来说,应用数控等方法来加工这些管件就有点大材小用,而且严重浪费了资源。
为此,在本次设计中,特根据工厂生产加工的实际情况,对现有的切管技术进行改进。
使本次设计的切管机具备了操作简单、生产成本低、维护简单、生产效率高等优点。
本次设计的切管机主要是针对各种用途金属管材进行加工。
本次设计的任务主要是对切管机中减速箱及有关零件进行的设计。
其中包括传动装置的设计和计算。
总体结构的设计以及对设计计算进行校核。
并且通过得到的数据,绘制总体装配图,减速机装配图,减速箱焊接图等。
然后又针对各主要基本件,绘制了多张零件图本次设计的切管机为减轻工人的劳动强度,提高生产效率有着积极的意义。
1. 确定工艺方案此次的设计任务为设计一简单高效的切管机,为此,对如下几种设计方案进行比较:方案一:用锯弓锯断金属管:需要锯弓往复的切削运动和滑枕摆动的进给与让刀运动。
机器的结构比较复杂,锯切运动也不是连续的。
当金属直径相差较大时,锯片还要调换,生产效率低。
方案二:用切断刀切断金属管:如在车床上切断,但是一般车床主轴不过几十毫米,通不过直径较大的金属管,并且占有一台普通机床,不太经济。
或者用专用的切管机,其工作原理是工件夹紧不动,装在旋转刀架上的两把切断刀,既有主切削的旋转运动,又有进给运动,工作效率高,但是机床结构比较复杂。
方案三:用砂轮切断金属管:需要砂轮旋转的切削运动和摇臂向下的进给运动。
此机构的结构简单,生产效率高,但是砂轮磨损较快费用很高。
方案四:用碾压的方法切断金属管:其需要金属管旋转的切削运动和圆盘向下的进给运动。
这种方法是连续切削的,生产效率高,机器的结构也不太复杂。
但是会使管子的切口内径缩小,一般用于管子要求不高的场合。
本次设计的要求为滚子转速n=70r/min,圆盘刀片直径a=80mm,加工管件的直径为3/8″~4″,电机额定功率i为P=1.5Kw满载转速为N=1410r/min,每天工作10小时,载荷变动小。
根据毕设要求和结合生产实际。
在本次设计中选用方案四。
工艺方案确定后,并根据有关数据,加上其它一些必要的尺寸,得出工艺方案的原理图如图1-1图1-1工艺方案原理图方案四管机的工作原理:动力由电动机→带轮→蜗杆→蜗轮→直齿轮→中间惰轮→滚子轴上小齿轮。
由于滚子的旋转运动,从而带动工件的旋转,实现切削时的主运动。
与此同时,操作手轮,通过螺旋传动,将圆盘刀片向下进给移动,并在不断增加刀片对管子的压力过程中,实现管子的切割工作。
2. 传动装置的设计与计算2.1 电动机的选择要选择电动机,必须了解电动机,出厂的每台电动机都有铭牌,上面标有电动机的主要技术参数。
因此,要合理地选择电动机,就要比较电动机的这些特性。
在进行简单机械设计时,应选择好电动机的类型,转速和功率。
2.1.1 类型的选择工业上一般用三相交流电源,所以选用三相交流异步电动机。
三相交流异步电机具有结构简单,工作可靠,价格便宜,维护方便等优点,所以应用广泛。
在选择电动机的类型时,主要考虑的是:静载荷或惯性载荷的大小,工作机械长期连续工作还是重复短时工作,工作环境是否多灰尘或水土飞溅等方面。
在本次设计中由于其载荷变动较小,有灰尘故选择笼式三相交流异步电机。
2.1.2 转速的选择异步电机的转速主要有3000r/min、1500r/min、1000r/min、750r/min几种。
当工作机械的转速较高时,选用同步转速为3000r/min的电机比较合适。
如果工作机械的转速太低(即传动装置的总传动比太大)将导致传动装置的结构复杂,价格较高。
在本次设计中可选的转速有1500r/min和750r/min。
在一般机械中这两种转速的电机适应性大,应用比较普遍。
2.1.3 功率的选择选择电动机的容量就是合理确定电动机的额定功率,电动机功率的选择与电动机本身发热、载荷大小、工作时间长短有关,但一般情况下电动机容量主要由运行发热条件决定。
故根据电动机的额定功率大于所需功率10%来选择电动机。
综上所述,本次设计的切管机电机额定功率为P=1.5Kw满载转速为N=1410r/min,每天工作10小时,载荷变动小用于多尘场合。
选用Y90L-4型电动机,其额定功率P电=1.5Kw,满载转速n电=1400r/min,同步转速1500r/min(4极),最大转矩为2.3N·m。
电动机确定后,计算出切管机的传动比为:i总=nn电工=140070=20 (2-1)2.2 拟订传动方案传动方案的拟定,通常是指传动机构的选择及其布置。
这是彼此相联系的两个方面。
其运动形式大致分为;(1)传递回转运动的有:带传动,链传动,齿轮传动,蜗轮传动等;(2)实现往复直线运动或摆动的有:螺旋传动,齿轮齿条传动,凸轮机构,曲柄滑块机构等;(3)实现间歇运动的有棘轮机构和槽轮机构等;(4)实现特定运动规律的有凸轮机构和平面连杆机构等。
传动机构的选择就是根据机器工作机构所要求的运动规律,载荷的性质以及机器的工作循环进行的。
然后在全面分析和比较各种传动机构特性的基础上确定一种较好的传动方案。
机器通常由原动机、传动装置和工作机等三部分组成。
传动装置位于原动机和工作机之间,用来传递运动和动力,并可以改变转速、转矩的大小或改变运动形式,以适应工作机功能要求。
传动装置的设计对整台车的性能、尺寸、重量和成本都有很大影响,因此需要合理的拟定传动方案。
在本次毕业设计中,已知切管机的i总=20,若用蜗杆,一次降速原本可以达到,其方案如图2-1。
但是由于切割的管子最大直径为4″,如图1-1故两个滚筒的中心距不能小于108mm,因此带动两个滚筒的齿轮外径不能大于滚筒的直径(Ø100mm)。
若取蜗杆z1=2,蜗轮z2=40,m=4,则蜗轮分度圆直径d2=160mm,比同一轴上的齿轮大,按图2-2-1的布置,蜗轮将要和滚筒相撞,为此,应该加大两轴之间的中心距。
这样就要加上一个惰轮,才可以解决这个问题,如图2-2-2。
在本次设计中,取蜗轮齿数为z2=50,模数m=4。
由于带传动具有缓冲和过载打滑的特性,故可将最为在电机之后的第一级传动,此外开式齿轮传动不宜放在高速级,因为在这种条件下工作容易产生冲击和噪音,故应将齿轮传动放在底速级。
一个好的传动方案,除了首先应满足机器的功能要求外,还应当工作可靠、结构简单、尺寸紧凑、成本低廉以及使用维护方便。
经比较各种传动方案,在本次设计中确定采用带传动、蜗杆传动、齿轮传动等机构组成的传动方案。
并初步画出其传动系统图,如图2-2-3。
图2-2-1蜗轮蜗杆传动方案图图2-2-2蜗轮蜗杆加中间惰轮传动方案图在传动方案确定后,根据i总=i1·i2……的关系分配传动比.下面对个机构的主要特性进行比较,如表2-2-1:图2-2-3带传动、蜗轮蜗杆、中间惰轮、齿轮方案图表2-2-1几种主要传动机构的特性比较特性类型带传动齿轮传动蜗杆传动主要优点中心距变化范围较大,结构简单,传动平稳,能缓冲,起过载安全保护作用外廓尺寸小,传动比准确,效率高,寿命长,适用的功率和速度范围大外廓尺寸小,传动比大而准确,工作平稳,可制成自锁的传动单级传动比,i 开口平型带:2~4,最大值≤6,三角带型: 2~4, 最大值≤7有张紧轮平型开式圆柱齿轮:4~6,最大值≤15.开式圆柱正齿轮:3~4,最大值≤10.闭式: 10~40,最大值≤100开式: 15~60,最大值≤100带:3~5最大值≤8闭式圆柱齿轮:2~3,最大值≤6外廓尺寸大中,小小成本低中高效率η平型带0.92~0.98三角带0.9~0.96开式加工齿0.92~0.96闭式0.95~0.99开式0.5~0.7闭式0.7~0.94自锁0.40~0.45考虑到传动装置的结构,尺寸,重量,工作条件和制造安装等因素,必须对传动比进行合理的分配.根据公式T=9550Pn(N·m)可知:当传动的功率P(Kw)一定时,转速n(r/min)越高,转矩T就越小.为此,在进行传动比的分配时遵循”降速要先少后多”.V带传动的传动比不能过大,否则会使大带轮半径超过减速器的中心高,造成尺寸不协调,并给机座设计和安装带来困难,又因为齿轮在降速传动中,如果降速比较大,就会使被动齿轮直径过大,而增加径向尺寸,或者因小齿轮的齿数太少而产生根切现象.而其在升速传动中,如果升速比过大,则容易引起强烈的震动和噪音,造成传动不平稳,影响机器的工作性能.为此,各机构的传动比分配情况如下:i1=1.2;i2=50;i3=1.5;i4=14.5(2-2)i总= i1i2 i3i4=1.2⨯50⨯1.5⨯14.5=20 (2-3)注:传动系统只大齿轮是个惰轮,它不改变传动比只起加大中心距,改变滚筒旋转方向的作用.2.3 计算各轴的转速、功率和转矩此处省略NNNNNNNNNNNN字。