含钛铁水脱硫及转炉冶炼实践
KR法铁水预处理脱硫的生产实践浅析

211管理及其他M anagement and otherKR 法铁水预处理脱硫的生产实践浅析张振杰(南京钢铁股份有限公司板材事业部第一炼钢厂,江苏 南京 210035)摘 要:硫对于大部分钢种危害程度较高的一种元素,并且其通常情况下是以硫化物的形式存在于钢中。
在实际的应用过程中倘若钢内的硫含量过高,将会对钢材的加工以及使用方面造成极大程度的影响,因此对展开铁水预处理脱硫的意义重大。
本文主要针对南钢KR 机械搅拌法改造后铁水预处理脱硫的生产实践进行了有效的分析。
关键词:机械搅拌法;铁水;脱硫;生产中图分类号:TF704.3 文献标识码:A 文章编号:11-5004(2020)22-0211-2 收稿日期:2020-11作者简介:张振杰,男,生于1982年,汉族,河北衡水人,本科,工程师,研究方向:钢铁冶炼及其相关。
近些年来,铁水预处理脱硫技术得到了相对较快的发展,至今已出现了多种不同类型的工艺处理方法,然而在具体的应用过程中经常使用广泛的有喷吹法以及KR 搅拌法。
KR 搅拌法在进行铁水预处理脱硫的生产实践过程中消耗相对喷吹法较小,同时在处理的过程中有所产渣量相对较少,反应速度快和效率高等优势。
1 方案选型现阶段,铁水脱硫的主要手段在具体生产过程中经常采用的有以KR 法未代表的机械搅拌法以及喷吹法。
该两种脱硫方法在具体实践过程中,均有一定的优势与特点,从而使其能够在炼钢业内得到相对较为广的应用。
关于KR 法脱硫工艺与喷吹法脱硫工艺主要特点的比较。
(1)关于KR 脱硫法工艺由于其在脱硫的过程中动力条件相对较为充分因此该工艺具有相对较高的脱硫率,同时其重现性与稳定性相对较高。
然而因为喷吹脱硫工艺在具体的实施过程中其角度方面的制约还有脱硫剂不能下沉等方面因素的影响,在脱硫的过程中存在一定的死角区域,从而一定程度上影响铁水动力学条件,且经常出现回硫的情况以及对于脱硫剂的消耗相对较大等不足之处,由于该因素的存在使得喷吹脱硫工艺在重现性与稳定性方面与KR 脱硫法存在一定的差距。
高炉冶炼低钛铁水的生产实践
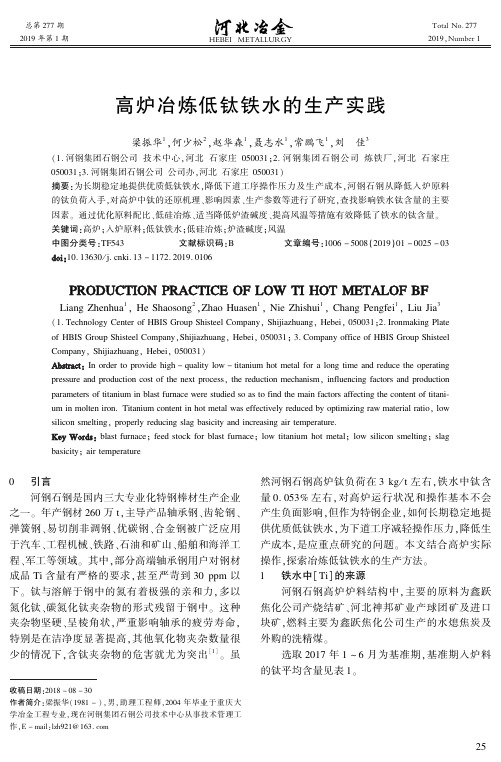
总第277期2019年第1期HEBEIMETALLURGYTotalNo.2772019ꎬNumber1高炉冶炼低钛铁水的生产实践梁振华1ꎬ何少松2ꎬ赵华森1ꎬ聂志水1ꎬ常鹏飞1ꎬ刘㊀佳3(1.河钢集团石钢公司技术中心ꎬ河北石家庄050031ꎻ2.河钢集团石钢公司炼铁厂ꎬ河北石家庄050031ꎻ3.河钢集团石钢公司公司办ꎬ河北石家庄050031)摘要:为长期稳定地提供优质低钛铁水ꎬ降低下道工序操作压力及生产成本ꎬ河钢石钢从降低入炉原料的钛负荷入手ꎬ对高炉中钛的还原机理㊁影响因素㊁生产参数等进行了研究ꎬ查找影响铁水钛含量的主要因素ꎮ通过优化原料配比㊁低硅冶炼㊁适当降低炉渣碱度㊁提高风温等措施有效降低了铁水的钛含量ꎮ关键词:高炉ꎻ入炉原料ꎻ低钛铁水ꎻ低硅冶炼ꎻ炉渣碱度ꎻ风温中图分类号:TF543㊀㊀㊀㊀㊀㊀文献标识码:B文章编号:1006-5008(2019)01-0025-03doi:10.13630/j.cnki.13-1172.2019.0106PRODUCTIONPRACTICEOFLOWTIHOTMETALOFBFLiangZhenhua1ꎬHeShaosong2ꎬZhaoHuasen1ꎬNieZhishui1ꎬChangPengfei1ꎬLiuJia3(1.TechnologyCenterofHBISGroupShisteelCompanyꎬShijiazhuangꎬHebeiꎬ050031ꎻ2.IronmakingPlateofHBISGroupShisteelCompanyꎬShijiazhuangꎬHebeiꎬ050031ꎻ3.CompanyofficeofHBISGroupShisteelCompanyꎬShijiazhuangꎬHebeiꎬ050031)Abstract:Inordertoprovidehigh-qualitylow-titaniumhotmetalforalongtimeandreducetheoperatingpressureandproductioncostofthenextprocessꎬthereductionmechanismꎬinfluencingfactorsandproductionparametersoftitaniuminblastfurnacewerestudiedsoastofindthemainfactorsaffectingthecontentoftitani ̄uminmolteniron.Titaniumcontentinhotmetalwaseffectivelyreducedbyoptimizingrawmaterialratioꎬlowsiliconsmeltingꎬproperlyreducingslagbasicityandincreasingairtemperature.KeyWords:blastfurnaceꎻfeedstockforblastfurnaceꎻlowtitaniumhotmetalꎻlowsiliconsmeltingꎻslagbasicityꎻairtemperature收稿日期:2018-08-30作者简介:梁振华(1981-)ꎬ男ꎬ助理工程师ꎬ2004年毕业于重庆大学冶金工程专业ꎬ现在河钢集团石钢公司技术中心从事技术管理工作ꎬE-mail:lzh921@163.com0㊀引言㊀㊀河钢石钢是国内三大专业化特钢棒材生产企业之一ꎮ年产钢材260万tꎬ主导产品轴承钢㊁齿轮钢㊁弹簧钢㊁易切削非调钢㊁优碳钢㊁合金钢被广泛应用于汽车㊁工程机械㊁铁路㊁石油和矿山㊁船舶和海洋工程㊁军工等领域ꎮ其中ꎬ部分高端轴承钢用户对钢材成品Ti含量有严格的要求ꎬ甚至严苛到30ppm以下ꎮ钛与溶解于钢中的氮有着极强的亲和力ꎬ多以氮化钛㊁碳氮化钛夹杂物的形式残留于钢中ꎮ这种夹杂物坚硬㊁呈棱角状ꎬ严重影响轴承的疲劳寿命ꎬ特别是在洁净度显著提高ꎬ其他氧化物夹杂数量很少的情况下ꎬ含钛夹杂物的危害就尤为突出[1]ꎮ虽然河钢石钢高炉钛负荷在3kg/t左右ꎬ铁水中钛含量0.053%左右ꎬ对高炉运行状况和操作基本不会产生负面影响ꎬ但作为特钢企业ꎬ如何长期稳定地提供优质低钛铁水ꎬ为下道工序减轻操作压力ꎬ降低生产成本ꎬ是应重点研究的问题ꎮ本文结合高炉实际操作ꎬ探索冶炼低钛铁水的生产方法ꎮ1㊀铁水中[Ti]的来源㊀㊀河钢石钢高炉炉料结构中ꎬ主要的原料为鑫跃焦化公司产烧结矿㊁河北神邦矿业产球团矿及进口块矿ꎬ燃料主要为鑫跃焦化公司生产的水熄焦炭及外购的洗精煤ꎮ㊀㊀选取2017年1~6月为基准期ꎬ基准期入炉料的钛平均含量见表1ꎮ52总第277期㊀㊀㊀㊀㊀㊀㊀㊀㊀㊀㊀㊀㊀㊀㊀㊀㊀㊀㊀㊀㊀㊀㊀㊀㊀㊀㊀㊀㊀㊀㊀㊀㊀㊀㊀㊀㊀㊀㊀㊀㊀㊀㊀㊀㊀㊀㊀㊀HEBEIYEJIN表1㊀入炉原料钛含量wt%Tab.1㊀Ticontentofchargedrawmaterialwt%物料烧结矿球团矿块矿焦炭煤粉TiO2含量0.1240.1680.1020.1530.08㊀㊀从各类入炉原燃料钛含量角度分析ꎬ焦炭和球团矿中钛含量较高ꎬ入炉烧结矿和块矿中钛含量占比接近ꎮ高炉在同时期炉料结构基本采取65%烧结矿+19%球团矿+16%块矿的方案ꎬ偶尔根据炉况略微调整ꎬ整体变化幅度不大ꎮ2㊀铁水中[Ti]的还原机理㊀㊀钛被认为是一种稀有金属ꎬ这是由于其在自然界中存在状态分散并难于提取ꎮ常见的钛的化合物有钛铁矿(FeTiO3)㊁金红石(TiO2)等ꎮ㊀㊀钛在高温环境中的还原能力极强ꎬ能与氧㊁碳㊁氮等许多元素化合ꎬ还能从部分金属氧化物(如Al2O3)中夺取氧ꎮ钛的还原主要发生在高炉内高温区ꎬ还原方式主要有两种:一是从高价氧化物向低价氧化物逐级进行还原:TiO2ңTi3O5ңTi2O3ңTiOңTiꎬ这主要存在于渣焦界面ꎻ二是渣铁界面的(TiO2)ңTiꎮ研究表明ꎬ用H2还原TiO2ꎬ在700~1000ħ可得到Ti3O5ꎬ1300ħ时可还原成Ti2O3ꎬ1500ħ时可还原成TiOꎮ用CO还原钛氧化物时ꎬ比用H2还原所需温度要高ꎬ钛的低价氧化物只能用碳直接还原[2ꎬ3]ꎮ㊀㊀高炉中TiO2的还原从软熔带开始ꎬ随着炉料的下降ꎬ还原量最大的位置在炉腹高温区和风口之间渣铁界面ꎻ渣铁界面的TiO2易被还原成[Ti]ꎬ扩散至铁水中ꎬ形成溶解钛ꎮTi的还原率较低ꎬ大部分TiO2进入炉渣ꎮ㊀㊀2017年1~6月ꎬ河钢石钢高炉产铁水钛平均含量为0.053%ꎬ处于一个相对稳定的状态ꎬ炉渣中的钛含量在0.60%左右ꎬ属于微钛渣ꎮ3㊀低钛铁水冶炼生产实践3.1㊀优化原料配比ꎬ使用低钛炉料㊀㊀选取2017年7~12月为实验期ꎬ经测算ꎬ烧结矿配矿过程中减少含钛量高的矿粉入烧ꎬ使烧结矿中的TiO2ɤ0.11%ꎬ同时调低高炉原料中球团矿配加比例ꎬ增加烧结矿比例ꎬ将高炉炉料结构调整为72%烧结矿+13%球团矿+15%块矿ꎬ高炉铁水[Ti]可ɤ0.050%ꎮ3.2㊀控制铁水物理温度㊀㊀高炉铁水温度对Ti含量的影响如图1所示ꎮ从图1中可以看出ꎬ高炉铁水温度和Ti含量之间具有规律性的正比关系ꎬ随高炉铁水温度的升高ꎬTi含量同步升高ꎮ高炉铁水温度对Ti含量有着明显影响ꎮTiO2被还原的反应方程式:2C+(TiO2)=[Ti]+2CO㊀㊀ΔG>0㊀㊀该反应为吸热反应ꎬ高炉温度越高ꎬ越有利于反应向右进行ꎬ化学反应生成的[Ti]越多ꎮ因此ꎬ尽可能地降低铁水的物理热ꎬ将有效降低铁水中的[Ti]含量ꎮ实验期将铁水的温度控制在1480~1505ħ之间ꎮ图1㊀铁水物理热对[Ti]的影响Fig.1㊀Effectofphysicalheatofhotmetalon[Ti]3.3㊀采取低Si冶炼㊀㊀高炉冶炼过程中ꎬ高炉炉温的高低ꎬ通常用Si含量来表征ꎮ即ꎬ高炉铁水中[Si]越高ꎬ高炉炉温越高ꎻ反之ꎬ炉温越低ꎮ在高炉铁水[Si]含量超过0.7%之后ꎬ即会呈现高炉炉热现象ꎬ铁水的物理热也会提高ꎮ从氧化物的稳定性看ꎬTi与Si的性质很接近ꎬ在高炉中还原程度应与Si接近ꎬ还原单位重量Ti所消耗的热量比还原Si时高0.14倍[2]ꎮ在高温区域ꎬSi的还原和Ti的还原成正比关系ꎬ如图2所示ꎮ随着铁水[Si]含量的增加ꎬ[Ti]也相应增加ꎻ铁水[Ti]随着[Si]含量的增加离散度变大ꎮ当铁水[Si]ɤ0.50%时ꎬ[Ti]绝大部分在0.050%以下ꎬ即图2中的第三象限ꎮ在实际操作中ꎬ可以采取控制燃料比的方式降低[Si]含量ꎬ提高理论燃烧温度和煤气利用率ꎬ减少炉体热量损失ꎬ进而增加焦炭负荷ꎬ降低滴落带高度ꎬ以尽可能地减少TiO2[4]向铁水转移ꎮ㊀㊀以高炉稳定顺行为前提ꎬ将实验期炉温[Si]控制在0.3%~0.5%之间ꎬ[Si]稳定符合率完成89.8%ꎬ较基准期提高1.16%ꎮ同时ꎬ稳定炉温为稳定煤气流和炉况创造了条件ꎬ也可保证铁水[Ti]的部分降低ꎮ62河北冶金㊀㊀㊀㊀㊀㊀㊀㊀㊀㊀㊀㊀㊀㊀㊀㊀㊀㊀㊀㊀㊀㊀㊀㊀㊀㊀㊀㊀㊀㊀㊀㊀㊀㊀㊀㊀㊀㊀㊀㊀㊀㊀㊀㊀㊀㊀2019年第1期图2㊀铁水中[Ti]与[Si]的关系Fig.2㊀Relationshipof[Ti]and[Si]inthehotmetal3.4㊀选择适宜的造渣碱度㊀㊀炉渣碱度也严重影响[Ti]含量ꎬ当渣中TiO2含量较高(>25%)时ꎬ[Ti]随碱度升高而减少ꎬ主要是由于CaO与TiO2结合ꎬ生成钙钛矿ꎬ降低了TiO2的活度ꎻ而TiO2含量较低(<25%)时ꎬ[Ti]却随碱度升高而增加[5]ꎬ主要是CaO与SiO2结合ꎬ提高了TiO2的活度ꎮ同时ꎬ若过多降低碱度会使铁水硅㊁硫含量上升ꎬ易对下道工序钢水冶炼过程造成负面影响ꎮ所以ꎬ高炉冶炼时ꎬ以满足生铁含硫和渣铁热量等条件为原则ꎬ应选择合理的造渣制度ꎬ维持适宜的炉渣碱度来控制TiO2的还原程度ꎮ实验期调整炉渣碱度在1.25~1.30之间ꎬMg/Al在0.62~0.64之间ꎬ并且尽量靠下限控制ꎮ3.5㊀提高风温ꎬ降低焦比㊀㊀风温是活跃炉缸最经济的重要手段ꎬ热风带入的热量占高炉热量总收入的1/3左右ꎮ高风温改善了煤粉在高炉内的燃烧状态ꎬ可以补偿风口前煤粉分解吸收的热量ꎬ促进煤粉的充分燃烧ꎬ是实现高煤焦置换比的前提ꎮ河钢石钢高炉在实验期将平均风温提升至1181ħꎬ较基准期1177ħ提高了4ħꎮ同时ꎬ由于煤比上升ꎬ焦比下降ꎬ通过焦炭带入铁水中的[Ti]也相应降低ꎮ3.6㊀优化布料矩阵ꎬ精心操作㊀㊀长期稳定顺行的炉况ꎬ不但是高炉高产㊁低耗的必要条件ꎬ也是稳定铁水成分的先决条件ꎮ各种炉况失常现象ꎬ在发生发展和治理过程中ꎬ不可避免地要带来炉缸㊁炉底热负荷的大幅度波动ꎬ使铁水成分波动异常ꎮ㊀㊀河钢石钢高炉在实验期优化布料矩阵ꎬ坚持 以稳定中心气流为主ꎬ控制合理的边缘温度 为原则ꎬ采取以下措施:(1)中心温度控制在550ħ左右ꎬ边缘温度控制在60~80ħ之间ꎮ(2)用多环布料的矩阵焦6矿5ꎬ矿角差7ʎ㊁焦角差10ʎꎮ(3)用等面积布料的方法计算出炉料矩阵形式ꎬ并利用理论与实践相结合ꎬ摸索出合理的基础布料矩阵O38236.53353333312C38236.52352332332312283ꎬ然后根据十字测温边缘和中心温度的趋势进行微调整ꎮ4㊀生产指标情况㊀㊀通过实施调整措施ꎬ高炉铁水的钛含量从0.053%降低到0.046%ꎬ主要成分对比见表2ꎮ表2㊀铁水成分对比wt%Tab.2㊀Comparisonofhotmetalcompositionwt%时间SiMnSPTi2017年1~6月0.4300.4560.0210.1020.0532017年7~12月0.4010.4830.0210.1050.0465㊀结语㊀㊀(1)通过调整原料配比㊁采取低Si冶炼㊁控制铁水温度和炉温㊁选择适宜的炉渣碱度㊁提高风温㊁降低焦比㊁优化布料矩阵㊁精心操作等一系列的强化措施ꎬ实现了高炉铁水中钛含量的降低ꎬ达到了预期的目标ꎮ㊀㊀(2)通过本次生产实践ꎬ积累了生产低钛铁水的经验ꎮ为今后优化下道工序生产组织ꎬ稳定钢材成品质量奠定了基础ꎮ参考文献[1]刘颖ꎬ赵瑞华ꎬ席军良ꎬ等.转炉冶炼低钛轴承钢的生产实践[J].河北冶金ꎬ2011ꎬ(5):10~11.[2]贺友多.炼铁学[M].北京:冶金工业出版社ꎬ1980. [3]黄希祜.钢铁冶金原理[M].北京:冶金工业出版社ꎬ1981. [4]李洪波.冶炼硅钢用高炉铁水中Ti的影响因素分析[J].电工材料ꎬ2016ꎬ(4):13~15[5]杜鹤桂.高炉冶炼钒钛磁铁矿原理[M].北京:科学出版社ꎬ1996.72。
含钛铁水脱硫及转炉冶炼实践
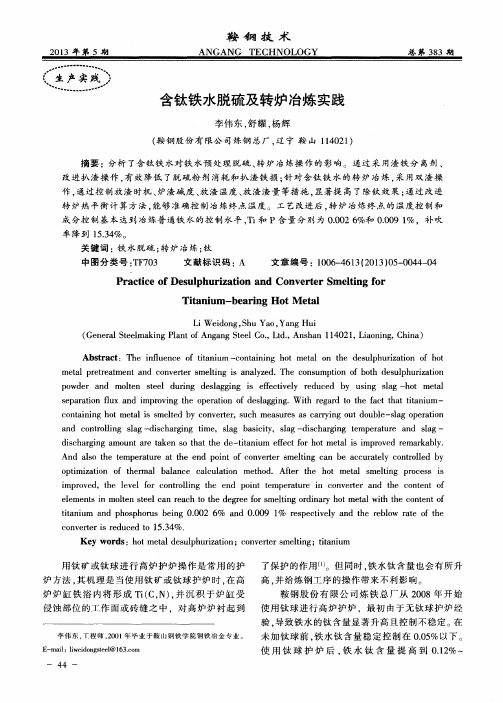
生 一产 ~
~实 一 ~践
\./
鞍 钢 技 术
ANGANC TECHNoLoGY
含钛铁水脱硫及转炉冶炼实践
李 伟东 ,舒 耀 ,杨辉 (鞍钢 股份 有 限公 司炼钢 总厂 ,辽 宁 鞍 山 114021)
总 第 383期
摘 要 :分析 了含钛铁 水 对铁 水预 处理脱 硫 、转 炉冶 炼操作 的影 响 。通 过 采 用渣 铁 分 离剂 、 改进扒 渣操 作 ,有 效降低 了脱 硫粉 剂 消耗 和扒 渣铁 损 ;针 对含 钛铁 水 的转 炉 冶炼 ,采 用双渣 操 作 ,通 过控制 放渣 时机 、炉渣碱 度 、放 渣 温度 、放 渣渣量 等措施 ,显 著提 高 了除钛效 果 ;通过 改进 转炉 热平衡 计算 方法 ,能够准 确控制 冶 炼终点 温度 。工 艺改进 后 ,转 炉冶炼 终点 的温度 控制 和 成分控 制基 本达 到 冶炼普通铁 水 的控 制 水平 。Ti和 P含 量分 别 为 0.002 6%和 0.009 1%,补 吹 率 降 到 15.34%。
关 键 词 :铁 水 脱 硫 ;转 炉 冶 炼 ;钛 中图分 类号 :TF703 文献标 识码 :A 文章 编号 :1006—4613(2013)05—0044—04
Practice of Desulphurization and Converter Smelting for
Titanium -bearing Hot M etal
Key words:hot metal desu1phurization;converter smelting;titanium
用 钛矿 或钛 球 进行 高炉 护 炉操 作是 常用 的护 了保 护的作用 ]。但 同时 ,铁水钛 含量也 会有所 升
高钛高锰铁水冶炼实践
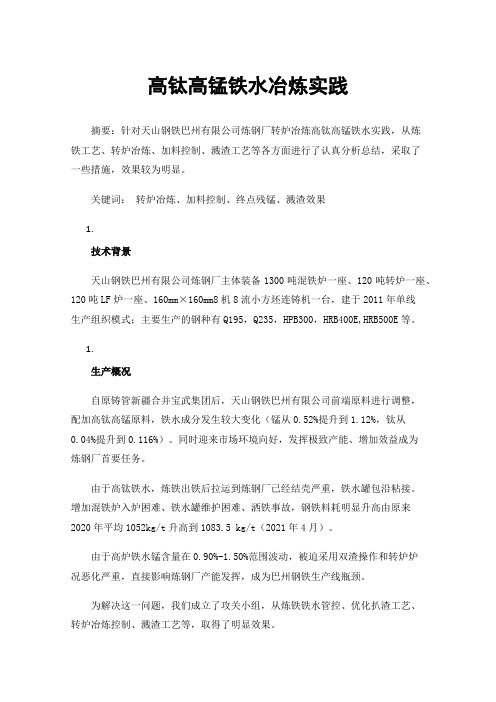
高钛高锰铁水冶炼实践摘要:针对天山钢铁巴州有限公司炼钢厂转炉冶炼高钛高锰铁水实践,从炼铁工艺、转炉冶炼、加料控制、溅渣工艺等各方面进行了认真分析总结,采取了一些措施,效果较为明显。
关键词:转炉冶炼、加料控制、终点残锰、溅渣效果1.技术背景天山钢铁巴州有限公司炼钢厂主体装备1300吨混铁炉一座、120吨转炉一座、120吨LF炉一座、160mm×160mm8机8流小方坯连铸机一台,建于2011年单线生产组织模式;主要生产的钢种有Q195,Q235,HPB300,HRB400E,HRB500E等。
1.生产概况自原铸管新疆合并宝武集团后,天山钢铁巴州有限公司前端原料进行调整,配加高钛高锰原料,铁水成分发生较大变化(锰从0.52%提升到1.12%,钛从0.04%提升到0.116%)。
同时迎来市场环境向好,发挥极致产能、增加效益成为炼钢厂首要任务。
由于高钛铁水,炼铁出铁后拉运到炼钢厂已经结壳严重,铁水罐包沿粘接。
增加混铁炉入炉困难、铁水罐维护困难、洒铁事故,钢铁料耗明显升高由原来2020年平均1052kg/t升高到1083.5 kg/t(2021年4月)。
由于高炉铁水锰含量在0.90%-1.50%范围波动,被迫采用双渣操作和转炉炉况恶化严重,直接影响炼钢厂产能发挥,成为巴州钢铁生产线瓶颈。
为解决这一问题,我们成立了攻关小组,从炼铁铁水管控、优化扒渣工艺、转炉冶炼控制、溅渣工艺等,取得了明显效果。
1.铁水钛含量升高的不利影响1.铁水罐结壳的影响。
由于铁水钛含量较高,含钛铁水表面裸露,铁水中的钛会与空气中的氧迅速反应,生产钛的氧化物TiO2进入渣中,渣熔点升高,形成高熔点渣系物质极易结壳。
2.扒渣工序铁损的影响。
渣黏稠,由于渣黏稠,渣中的铁液被包裹在渣中,造成扒渣工序铁损增加。
3.转炉冶炼终点温度的影响。
钛在转炉冶炼过程中氧化放热,当铁水中钛含量在0.10%~0.20%时,发热量较大,因此在计算热平衡时必须考虑此部分的热量增加,才能准确控制终点温度。
玉钢3#高炉钒钛矿中钛渣冶炼实践
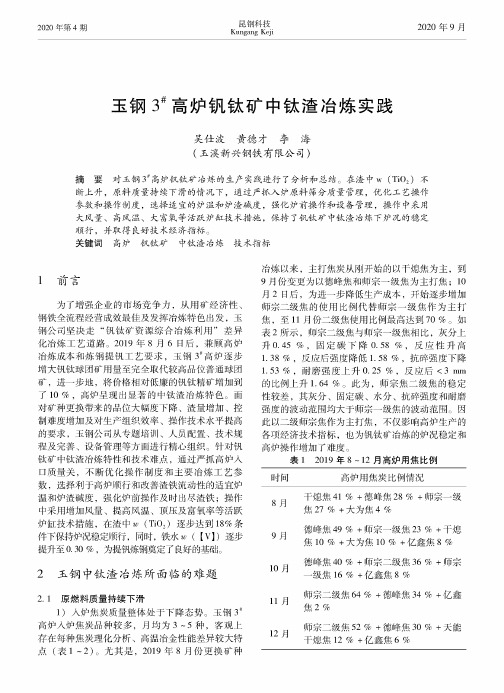
昆钢科技. Kungang Keji 2020920204玉钢3#高炉机钛矿中钛渣冶炼实践吴仕波黄德才李海(玉溪新兴钢铁有限公司)摘要对玉钢3#高炉饥钛矿冶炼的生产实践进行了分析和总结。
在渣中x(T1O)不断上升,原料质量持续下滑的情况下,通过严抓入炉原料筛分质量管理,优化工艺操作参数和操作制度,选择适宜的炉温和炉渣碱度,强化炉前操作和设备管理,操作中采用大风量、高风温、大富氧等活跃炉缸技术措施,保持了饥钛矿中钛渣冶炼下炉况的稳定顺行,并取得良好技术经济指标$关键词高炉饥钛矿中钛渣冶炼技术指标1前言为了增强企业的市场竞争力,从用矿经济性、钢铁全流程经营成效最佳及发挥冶炼特色出发,玉钢公司坚决走“X钛矿资源综合冶炼利用”差异化冶炼工艺道路。
2019年8月6日后,兼顾高炉冶炼成本和炼钢提X工艺要求,玉钢3#高炉逐步增大X钛球团矿用量至完全取代较高品位普通球团矿,进一步地,将价格相对低廉的X钛精矿增加到T10%,高炉呈现出显著的中钛渣冶炼特色。
面对矿种更换带来的品位大幅度下降、渣量增加、控制难度增加及对生产组织效率、操作技术水平提高的要求&玉钢公司从专题培训、人员配置、技术规程及完善、设备管理等方面进行精心组织。
针对X 钛矿中钛渣冶炼特性和技术难点,通过严抓高炉入口质量关,不断优化操作制度和主要冶炼工艺参数,选择利于高炉顺行和改善渣铁流动性的适宜炉温和炉渣碱度,强化炉前操作及时出尽渣铁;操作中采用增加风量、提高风温、顶压及富氧率等活跃炉缸技术措施,在渣中!(TlO)逐步达到18%条件下保持炉况稳行,同时,铁水!(【V】)逐步提升至0.30%,为提X炼钢奠定了良好的基础。
2玉钢中钛渣冶炼所面临的难题2.1原燃料质量持续下滑1)入炉焦炭质量整体处于下降态势。
玉钢3#高炉入炉焦炭品种较多,月均为3~5种&客观上存在每种焦炭理化分析、高温冶金性能差异较大特点(表1~2)%尤其是,2019年8月份更换矿种冶炼以来,主打焦炭从刚开始的以干熄焦为主,到9月份变更为以德峰焦和师宗一级焦为主打焦;10 2后,为进步生成,开始逐步师宗二级焦的使用比例代替师宗一级焦作为主打焦,至11月份二级焦使用比例最高达到70%%如表2所示,师宗二级焦与师宗一级焦相比,灰分上升0.45%,固定碳下降0.58%,反应性升高1.38%,反应后强度降低1.58%,抗碎强度下降1.53%,耐磨强度上升0.25%,反应后<3mm 的比例上升1-64%%此为,师宗焦二级焦的稳定性,、固定碳、水、抗碎度和耐磨强度的波动范围均大于师宗一级焦的波动范围%因此以二级师宗焦作为主打焦,不仅影响高炉生产的各项经济技术指标,也为X钛矿冶炼的炉况稳定和高炉操作度%表12019年8~12月高炉用焦比例时间高炉用焦炭比例情况8干熄焦41%+德峰焦28%+师宗一级焦27%+大为焦4%9德焦49%+师宗焦23%+干熄焦10%+大为焦10%+亿鑫焦8%10德焦40%+师宗二焦36%+师宗一级焦16%+亿鑫焦8%11师宗二级焦64%+德峰焦34%+亿鑫焦2%12师宗二级焦52%+德峰焦30%+天能干熄焦12%+亿鑫焦6%20204玉钢3#高炉X钛矿中钛渣冶炼实践・5・表2各种焦炭的理化分析项目Aad%Mt%S%Mad%Vad%Fcad%M40%M10%CRI%CSR%师宗一级焦13.64 6.790.570.370.9785.0389.28 4.8527.8365.01师宗二级焦14.09 5.090.520.480.9784.4587.75 5.1029.2163.43德峰焦14.06 5.380.480.290.9884.6890.38 4.7226.9064.70亿鑫焦13.43 5.760.710.880.9684.7387.24 5.6825.8366.69大为焦13.31 4.770.500.300.9685.4389.80 4.3928.5564.76干熄焦13.780.880.650.350.9084.9690.38 4.6128.8963.952)烧结矿品位及物理性能呈现持续下降态势。
首钢第三炼钢厂铁水脱硫捞渣生产实践

h t tl n h r ci e o e u p u iai n a d sa k m c i e i . t ema i g P a t o a ,a d t e p a t fd s l h rz t n lg s i ma h n n No 3 S e l k n l n , me c o
善转 炉操 作 的重要 手段 之一 。当前应 用最 普遍 的
脱硫 剂是 钙基 和镁 基材 料 ,尤其 是镁 基脱 硫 ,由
于其温降小 、 铁损少 、时间短 ,已成为 目前铁水
预处理 的重要方 法 。但是 产 生 回硫 以及 防止 回硫
已成 为镁基 脱硫 研究 和探 讨 的重 点工 作 。
20t 水 鱼雷 罐 运 至 第 三炼 钢 厂一 9 铁 包一 6 铁 0t 脱硫 间一 喷镁 脱 硫一 捞 渣 ( 采用 气 动扒 渣 机 , 原
因铁 损 大而 改为 回转 式捞 渣 机 )一 10 t 车 吊 4 天
至炉 前兑 铁 。
1 工 艺 流程
首钢第三炼钢厂 20 04年前有 3 8 转炉 , 座 0t
为 了满足 市场 对钢 材质 量越 来越 高 的要求 和
的市场竞 争 ,为生 产 出高 质 量 的 方坯 及 矩 形 坯 , 配 合工 艺升 级改 造 ,第 三炼钢 厂对 现有 的铁 水扒 渣 站进行 改 造 。在充 分利 用铁 水扒 渣站 原有 扒渣 设备 的基 础 上 ,改造 原有 的移 动烟 尘罩 ,使 其成 为 移动平 台 ,在 平 台上加 装铁 水脱硫 设 备 ,进行 铁 水预 处理 脱硫 。
J ie g L iz u Z IL p n IJn h HOU Ja b in o
( o 3Sel kn ln) N . t maigPa t e
含钛铁水脱硫及转炉冶炼实践
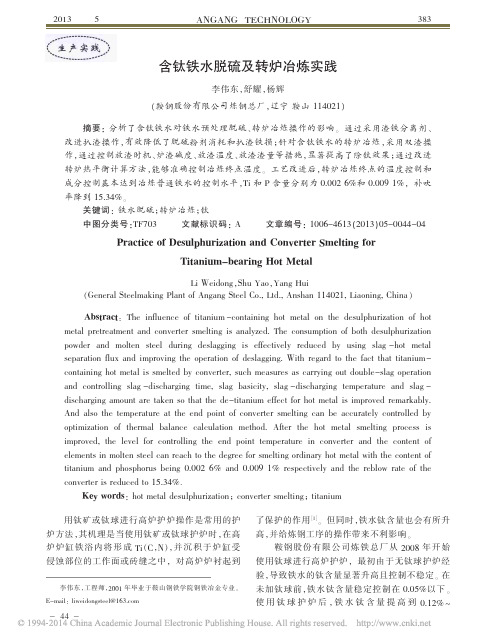
1.1 对铁水预处理脱硫的影响 在对含钛铁水进行脱硫处理时, 采用氮气喷
吹脱硫,氮会与铁水中的钛和碳结合生成 Ti(C,N),且极易与 CaO 结合生成高熔点化合物, 使渣变粘,恶化渣的流动性,降低钙粉的利用率, 增 加 喷 吹 时 间 和 粉 剂 消 耗 [1]; 另 外 , 喷 吹 过 程 中 进 入渣中的铁液被包裹在渣中,不易分离,因此会造 成扒渣工序铁损增加。 1.2 对转炉炼钢的影响
转炉冶炼过程中, 钛的氧化物会与石灰中的 CaO 结合生成高熔点化合物, 使石灰的脱磷硫作 用降低[1],因此会增加渣料消耗。 另外,石灰利用 率的降低增加了转炉脱磷负担, 造成冶炼终点补 吹次数增加,导致终渣 FeO 含量过高,增加转炉冶 炼吹损,同时对溅渣护炉也有不利影响。
2 含钛铁水脱硫工序冶炼实践
实践表明,加入渣铁分离剂后,喷吹过程渣流 动性好,成渣速度快,喷枪、扒渣板粘渣程度得到 改善,渣铁容易分离。 表 1 为分离剂加入前后渣成 分的对比情况。 由表 1 可以看出,渣铁分离剂加入 后,渣中 TFe 显著降低,约降低 15.8%。
项目 加渣铁分离剂 未加渣铁分离剂
表 1 渣成分对Βιβλιοθήκη 情况TFe/%Key words: hot metal desulphurization; converter smelting; titanium
用钛矿或钛球进行高炉护炉操作是常用的护 炉方法,其机理是当使用钛矿或钛球护炉时,在高 炉 炉 缸 铁 浴 内 将 形 成 Ti(C,N),并 沉 积 于 炉 缸 受 侵蚀部位的工作面或砖缝之中, 对高炉炉衬起到
ω[CaO]/%
ω[SiO2]/%
ω[MgO]/%
ω[Al2O3]/%
攀钢含钒钛铁水预处理工艺实践
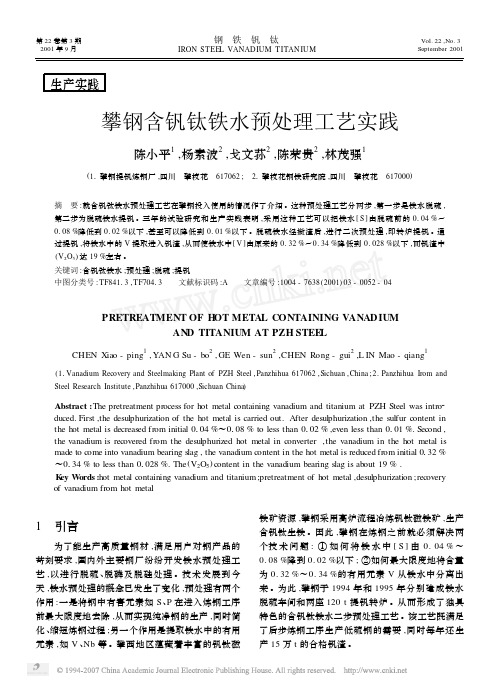
ηS = 11. 14 + 11. 79 W - 0. 416 W 2
(1)
r = 0. 76 , 2. 5 < W < 16 , n = 3581
②ηS 与喷吹速度 Q (kg/ min) 的关系
ηS = 64. 15 + 0. 771 Q - 0. 0045 Q2
(2)
3 撇渣
脱硫后的脱硫渣如果不去除 ,将会造成后步炼
图 4 铁水熔化性温度 、凝固点与含钒量的关系
由表 4 可知 ,攀钢采用 CaC2 基脱硫剂在铁水罐 内进行铁水脱硫 ,能够把铁水 [ S ] 脱到 0. 01 %的水 平 。但由于从高炉送来的铁水包盛铁量波动大 、带
铁水量 t·罐 - 1
90~130
表 2 喷粉脱硫喷吹参数
喷枪头 距罐底/ mm
过程温降/ ℃
3113 20
定 ,反应空间大 ,喷枪插入深度稳定 ,在脱硫剂消耗 为 7. 18~10. 40kg/ t Fe 时 ,铁水 [ S ]均在 0. 005 %以 下。
通过试验 ,还得出了脱硫率 (ηS) 与脱硫剂单耗
W 、喷吹速度 Q 的关系如下 : [2 ]
①ηS 与脱硫剂单耗 W (kg t Fe) 的关系
第 22 卷第 3 期 2001 年 9 月
钢 铁 钒 钛
IRON STEEL VANADIUM TITAN IUM
Vol. 22 ,No. 3 September 2001
生产实践
攀钢含钒钛铁水预处理工艺实践
陈小平1 ,杨素波2 ,戈文荪2 ,陈荣贵2 ,林茂强1
800
N2 流量 Nm31h - 1
120~150
喷粉速度 kg. min - 1
铁水脱硫预处理技术及其在炼钢的应用

铁水脱硫预处理技术及其在炼钢的应用摘要铁水预处理是指铁水在进入炼钢炉进行冶炼前,为除去某种有害成分或回收某种有益成分的处理过程。
铁水预处理是现代化炼钢厂的重要工序之一,其主要目的是降低铁水中的有害元素,如硫、硅和磷等的含量,为炼钢炉提供合格的铁水。
我国虽然是钢铁生产大国,但在生产工艺、装备、钢材品种、质量、成本、高附加值产品方面与发达国家相比还存在很大的差距,还不能称为钢铁生产强国。
国际钢协技术调查中的大部分被调查者都认为加强成本竞争能力和质量竞争能力是钢厂具有竞争力的重要因素,并认为为了加强成本竞争能力,降低原料成本比减少二次加工成本更重要。
铁水预处理工艺已经经过近四十年的发展,在一些发达国家的钢铁厂中,几乎100%的铁水都进行了预处理。
而本文主要介绍铁水预脱硫技术及在炼钢中的应用。
通过比较,分析几种脱硫剂和喷吹方式的特点,介绍炼钢铁水脱硫工艺及处理效果,并提出了铁水脱硫站存在的问题和改进意见。
关键词:铁水预处理,脱硫,喷吹目录1绪论 (1)2脱硫剂的选择 (2)2.1常用的脱硫剂 (2)2. 2如何选择脱硫剂 (2)3脱硫喷吹方式的选择 (4)3.1脱硫预处理喷吹方式的选择 (4)3.2脱硫预处理方法 (4)4铁水脱硫预处理工艺在炼钢的应用 (6)4.1工艺流程 (6)4.2主要设备及工艺参数 (6)4.2.1主要设备 (6)4.2.2工艺参数 (7)4.3脱硫剂 (8)4.4脱硫处理效果 (8)4.5脱硫处理能力及脱硫处理比 (9)结束语 (10)致谢 (11)参考文献 (12)1 绪论铁水预处理用以满足用户对超低硫、磷的要求,发展高附加值的钢种如船板钢、油井管钢等钢种,要求[S]、[P]<0.005%,管线钢、Z向钢、IF钢等钢种要求[S]≤0.002~0.004%。
通过铁水预处理,可以减轻高炉脱硫负担,放宽对硫的限制,提高产量,降低焦比。
采用低硫铁水炼钢,可减少渣量和提高金属收得率。
转炉钢水炉外脱硫剂成分优化及应用实践
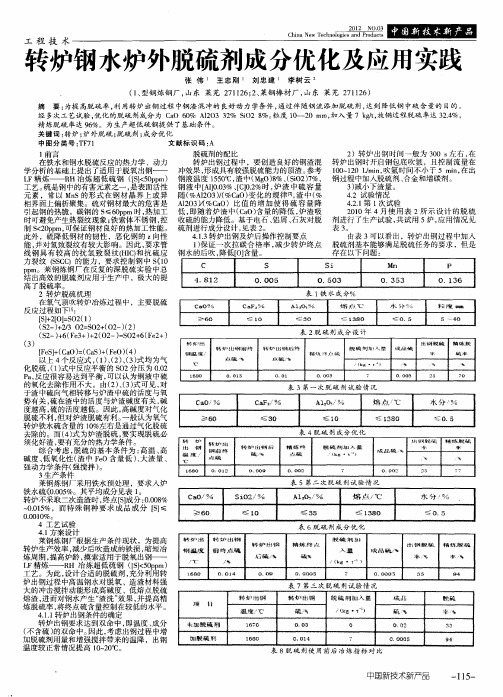
Ci w enoea o. ha e T h li nP dt nN c ogs drus c
转炉钢水炉外脱硫剂成分优化及应用实践
张 伟 王忠 刚 刘 忠建 李树 云
(、 1 型钢炼钢厂 , 山东 莱芜 2 12 ; 、 7 16 2 莱钢棒材厂 , 山东 莱芜 2 12 ) 7 16
摘 要: 为提 高脱硫 率 , 用转 炉 出钢 过程 中钢 渣 混冲 的 良好动 力 学条 件 , 过 伴 随钢 流添加 脱 硫 剂 , 利 通 达到 降低 钢 中硫 含 量 的 目的 。 经 多次 工艺试 验 . 化的 脱硫 剂成 分为 C O 6 % A2 3 3 % S 2 8 粒度 1 一 2 l, 优 a 0 10 2 i %。 O O 0 mT 加入 量 7 k/ 放 钢过 程脱 硫率 达 3 . , l g, t 2% 4 精 炼 脱硫 率达 9 %。 为生产超 低硫 钢提 供 了基础 条件 。 6 关键 词 : 炉 ; 转 炉外脱 硫 ; 脱硫 剂 ; 分优化 成
雌 越 德 瓣姆 鸱髓 { 崎
敝 一
, 糯
如 睁 0I 4 ☆ ∞ 杜.1005 。
巍糍 , 堍
氟 敝%
《 k t 柚
稿. 0 0 3 9 4
涨 噶
r 霉
袁 7第三 次脱硫 剂 试验情 况
鞯 炉 蝴
# 《 i t
麟
镧
黼 煳 蜘 辙
() 3
存 在 以下 问题
e l 嚣 l S i f啦 1 l O 0 l O 0 8 ,5 .3 2 0 5
表 1铁 水 成 分 %
O5 3 3
p O1 3 6
表 2脱 硫 荆 成 分 设 计
铁水脱硫渣铁替代废钢在转炉冶炼的实践
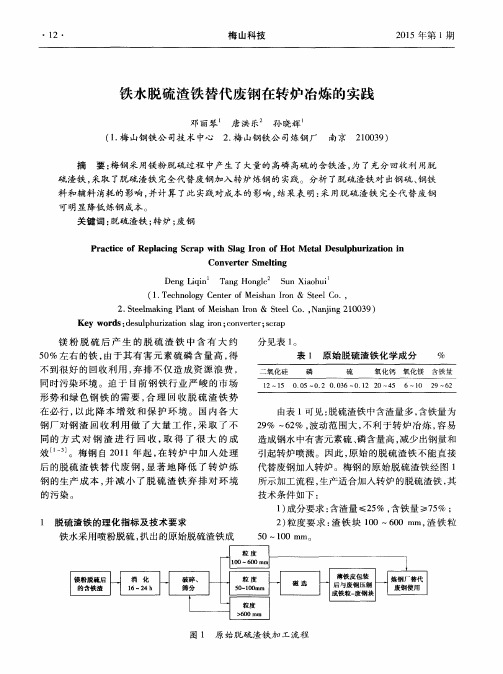
梅钢 的产 品结 构 中 , 大部 分 产 品 的硫 含 量 ≤
0 . 0 2 0 %。脱硫渣铁的使用采用集 中使用方式 , 即 转 炉 加入 的废 钢全 部采 用脱 硫渣 铁代 替 。为 了充
分 合 理 的利用脱 硫 渣 铁 , 避 免 因脱 硫 渣 铁 的使 用 导 致 出钢硫 含量 偏 高 , 造 成硫 含 量超标 , 选 择 了要 求过 L F精 炼炉 的钢 种 试 验 。试 验 的钢 种 为 S P A
由表 1可见 : 脱硫 渣铁 中含渣 量 多 , 含 铁量 为 2 9 %~ 6 2 %, 波动 范 围 大 , 不利于转炉冶炼 , 容 易 造成钢 水 中有害 元素硫 、 磷 含量 高 , 减少 出钢 量和 引起转 炉 喷溅 。 因此 , 原 始 的脱 硫 渣铁 不 能直 接
后 的脱 硫 渣 铁 替 代 废 钢 , 显 著 地 降 低 了 转 炉 炼
硫 渣铁 , 采取 了脱硫 渣铁 完全代 替废 钢加 入 转炉 炼钢 的 实践 。分 析 了脱硫 渣铁 对 出钢 硫 、 钢铁
料和 辅料 消耗 的影 响 , 并计 算 了此 实践 对成 本 的影 响 , 结 果表 明 : 采 用 脱硫 渣铁 完全 代 替废 钢
可 明显 降低 炼钢 成 本 。 关键词: 脱硫 渣铁 ; 转炉 ; 废 钢 P r a c t i c e o f R e p l a c i n g S c r a p wi t h S l a g I r o n o f Ho t Me t a l D e s u l p h u r i z a t i o n i n
钢厂对钢渣 回收利 用做 了大量 工作 , 采 取 了 不 同的方 式 对 钢 渣 进 行 回 收 , 取 得 了 很 大 的 成 效_ J l 。梅钢 自 2 0 1 1年 起 , 在 转 炉 中加 人 处 理
转炉高硅高钛铁水冶炼工艺优化
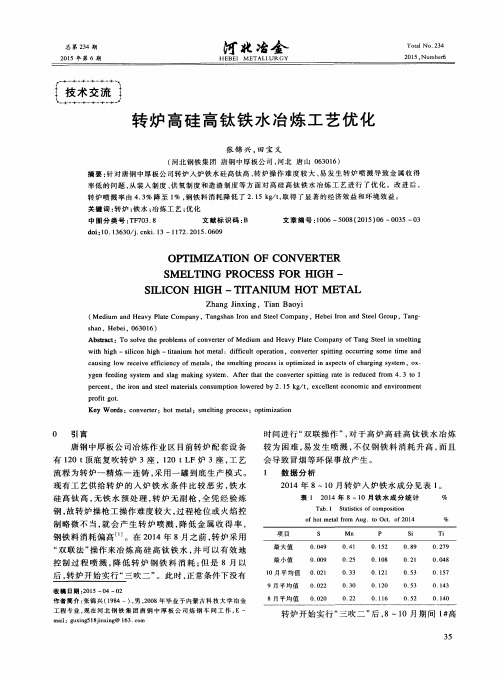
O王 Ⅱ I ZATI ON 0F C0NVERTER
S M ELTD G PROCESS F OR HI GH —
S I LI CON HI GH —TI TANI U M HOT M ETAL
Zh a n g J i n xi ng,Ti a n Ba o y i
。+
+
,
转 炉 高 硅 高钛 铁 水 冶 炼 工艺 优 化
张锦 兴 。 田 宝 义
( 河 北 钢 铁 集 团 唐 钢 中厚 板 公 司 , 河北 唐山 0 6 3 0 1 6 ) 摘要: 针 对 唐 钢 中 厚板 公 司 转 炉 入 炉 铁 水 硅 高 钛 高 、 转炉 操作难度 较大 、 易 发 生 转 炉 喷 溅 导 致 金 属 收 得 率低 的问题 , 从装 入制度 、 供 氧制 度 和 造 渣 制 度 等 方 面 对 高 硅 高 钛 铁 水 冶 炼 工 艺 进 行 了优 化 。 改 进 后 , 转 炉喷溅率 由 4 . 3 %降至 1 %, 钢 铁 料 消 耗 降低 了 2 . 1 5 k g / t , 取 得 了显 著 的经 济 效 益 和环 境 效 益 。
y ge n f e e di ng s y s t e m a n d s l a g ma ki ng s y s t e m . Af te r t h a t t h e c o nv e r t e r s p i t t i n g r a t e i s r e du c e d f r om 4. 3 t o 1 p e r c e nt ,t he i r o n a nd s t e e l ma t e r i a l s c o ns umpt i o n l o we r e d by 2. 1 5 kg /t ,e xc e l l e nt e c o no mi c a n d e nv i r on me n t p r of i t g ot . Ke y W or d s:c on v e r t e r ;ho t met a l ;s me l t i ng pr o c e s s ;o p t i mi z a t i on
含钛铁水脱硫及转炉冶炼实践
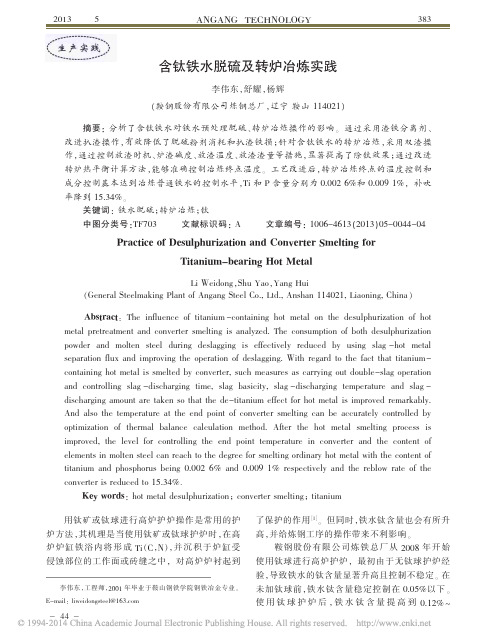
图 1 碱度和钛制在 2.4~2.6 时,钢中的钛含量基本在 0.005%以下,此时放渣基 本可以满足除钛要求。 3.4 放渣前熔池渣量控制
2013 年第 5 期
鞍钢技术
ANGANG TECHNOLOGY
总第 383 期
0.20%,有时甚至超过 0.20%。 铁水钛含量的升高 给炼钢工序带来的不利影响主要体现在铁水脱硫 工序扒渣铁损增加, 转炉冶炼工序石灰熔剂消耗 增加,溅渣护炉效果变差。 另外,许多钢种要求钢 中不能有残余的钛元素。 因此,采取相应的措施, 减轻或消除含钛铁水对脱硫扒渣和转炉炼钢操作 的影响,对减少铁损和冶金辅料的消耗、降低生产 成本、保证钢水成分等具有重要意义。
项目
工艺
镁粉 钙粉 扒渣铁损
普通铁水
正常工艺
0.856 3.456 28.36
含钛铁水
原工艺
1.023 4.218 55.82
新工艺
0.924 3.786 35.38
比较
新工艺比原工艺减少 新工艺比正常工艺增加
0.099 0.068
0.432 0.330
20.44 7.02
《鞍钢技术》2013 年第 5 期 总第 383 期
关键词: 铁水脱硫;转炉冶炼;钛
中 图 分 类 号 :TF703
文献标识码: A
文章编号: 1006-4613(2013)05-0044-04
Practice of Desulphurization and Converter Smelting for
Titanium-bearing Hot Metal
正常双渣法冶炼, 放渣时机一般在冶炼过程 进 行 到 中 期 进 行 ,放 渣 渣 量 为 1/2~2/3,然 后 加 入 渣料重新造渣。 据文献[3]介绍,在含钛铁水的吹炼 过 程 中 , 钛 元 素 选 择 氧 化 的 转 化 温 度 为 1 340~ 1 400 ℃。 鞍 钢 180 t 转 炉 吹 炼 时 间 达 到 1/4~1/3 时,钢水熔池温度平均在 1 400 ℃以上,此时钛的 氧化基本完成,是倒渣除钛的有利时机。 3.3 放渣前炉渣碱度控制
含钛铁水转炉冶炼及其预脱钛行为研究
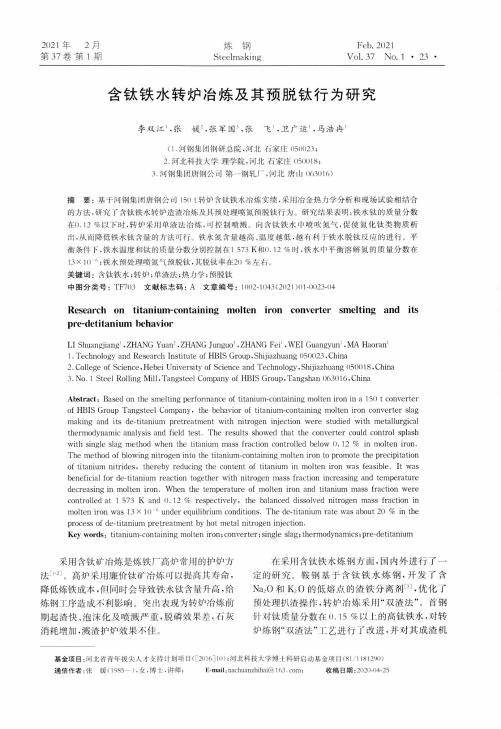
2021 年 2 月炼钢Feb.2021第 37 卷第 1 期Steelmaking Vol.37 No. 1•23 •含钛铁水转炉冶炼及其预脱钛行为研究李双江1,张媛2,张军国3,张飞1 ,卫广运1,马浩冉1(1.河钢集团钢研总院,河北石家庄05U023;2.河北科技大学理学院,河北石家庄()5()m8;3.河钢集团唐钢公司第一钢轧厂,河北唐山063016)摘要:基于河钢集团唐钢公司150 t转炉含钛铁水冶炼实绩,采用冶金热力学分析和现场试验相结合的方法,研究了含钛铁水转炉造渣冶炼及其预处理喷氮预脱钛行为。
研究结果表明:铁水钛的质量分数在0.12 %以下时,转炉采用单渣法冶炼,可控制喷派。
向含钛铁水中喷吹氮气,促使氮化钛类物质析出,从而降低铁水钛含量的方法可行。
铁水氮含量越高、温度越低,越有利于铁水脱钛反应的进行。
平衡条件下,铁水温度和钛的质量分数分别控制在1573 K和(>.12 %时,铁水中平衡溶解氮的质量分数在13 X 1()^ ;铁水预处理喷氮气预脱钛,其脱钛率在2() %左右。
关键词:含钛铁水;转炉;单渣法;热力学;预脱钛中图分类号:T F703文献标志码:A文章编号:1002-1043(2021)01-0023-04Research on titanium-containing molten iron converter smelting and itspre-detitanium behaviorLI Shuangjiang1, ZHANG Yuan2, ZHANG Junguo3, ZHANG Fei1, WEI Guangyun1 ,MA Haoran11. Technology and Research Institute of HBIS Group.Shijiazhuang 050023,China2. College of Science,Hebei University of Science and Technology,Shijiazhuang 050018,China3. No. 1Steel Rolling MilUTangsteel Company of HBIS Group,Tangshan 063016,ChinaAbstract:Based on the smelting performance of titanium-containing molten iron in a 150 t converterof HBIS Group Tangsteel Company, the behavior of titanium-containing molten iron converter slagmaking and its de-titanium pretreatment with nitrogen injection were studied with metallurgicalthermodynamic analysis and field test. The results showed that the converter could control splashwith single slag method when the titanium mass fraction controlled below 0.12 % in molten iron.The method of blowing nitrogen into the titanium-containing molten iron to promote the precipitationof titanium nitrides, thereby reducing the content of titanium in molten iron was feasible. It wasbeneficial for de-titanium reaction together with nitrogen mass fraction increasing and temperaturedecreasing in molten iron. When the temperature of molten iron and titanium mass fraction werecontrolled at 1573 K and 0.12 % respectively, the balanced dissolved nitrogen mass fraction inmolten iron was 13 x i〇~6under equilibrium conditions. The de-titanium rate was about 20 % in theprocess of de-titanium pre t reatment by hot metal nitrogen injection.Key words:titanium-containing molten iron;converter;single slag; thermodynamics;pre-detitanium采用含钛矿冶炼是炼铁厂高炉常用的护炉方 法[w]。
武钢二炼钢KR铁水脱硫生产实践
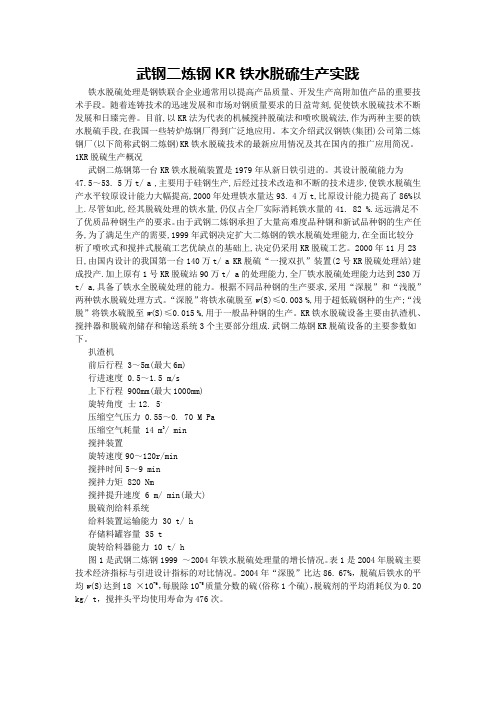
武钢二炼钢KR铁水脱硫生产实践铁水脱硫处理是钢铁联合企业通常用以提高产品质量、开发生产高附加值产品的重要技术手段。
随着连铸技术的迅速发展和市场对钢质量要求的日益苛刻,促使铁水脱硫技术不断发展和日臻完善。
目前,以KR法为代表的机械搅拌脱硫法和喷吹脱硫法,作为两种主要的铁水脱硫手段,在我国一些转炉炼钢厂得到广泛地应用。
本文介绍武汉钢铁(集团)公司第二炼钢厂(以下简称武钢二炼钢)KR铁水脱硫技术的最新应用情况及其在国内的推广应用简况。
1KR脱硫生产概况武钢二炼钢第一台KR铁水脱硫装置是1979年从新日铁引进的。
其设计脱硫能力为47.5~53. 5万t/ a ,主要用于硅钢生产,后经过技术改造和不断的技术进步,使铁水脱硫生产水平较原设计能力大幅提高,2000年处理铁水量达93. 4万t,比原设计能力提高了86%以上.尽管如此,经其脱硫处理的铁水量,仍仅占全厂实际消耗铁水量的41. 82 %.远远满足不了优质品种钢生产的要求。
由于武钢二炼钢承担了大量高难度品种钢和新试品种钢的生产任务,为了满足生产的需要,1999年武钢决定扩大二炼钢的铁水脱硫处理能力,在全面比较分析了喷吹式和搅拌式脱硫工艺优缺点的基础上,决定仍采用KR脱硫工艺。
2000年11月23日,由国内设计的我国第一台140万t/ a KR脱硫“一搅双扒”装置(2号KR脱硫处理站)建成投产.加上原有1号KR脱硫站90万t/ a的处理能力,全厂铁水脱硫处理能力达到230万t/ a,具备了铁水全脱硫处理的能力。
根据不同品种钢的生产要求,采用“深脱”和“浅脱”两种铁水脱硫处理方式。
“深脱”将铁水硫脱至w(S)≤0.003 %,用于超低硫钢种的生产;“浅脱”将铁水硫脱至w(S)≤0.015 %,用于一般品种钢的生产。
KR铁水脱硫设备主要由扒渣机、搅拌器和脱硫剂储存和输送系统3个主要部分组成.武钢二炼钢KR脱硫设备的主要参数如下。
扒渣机前后行程 3~5m(最大6m)行进速度 0.5~1.5 m/s上下行程 900mm(最大1000mm)旋转角度士12. 5。
4-含钛铁水转炉冶炼实践-鞍钢
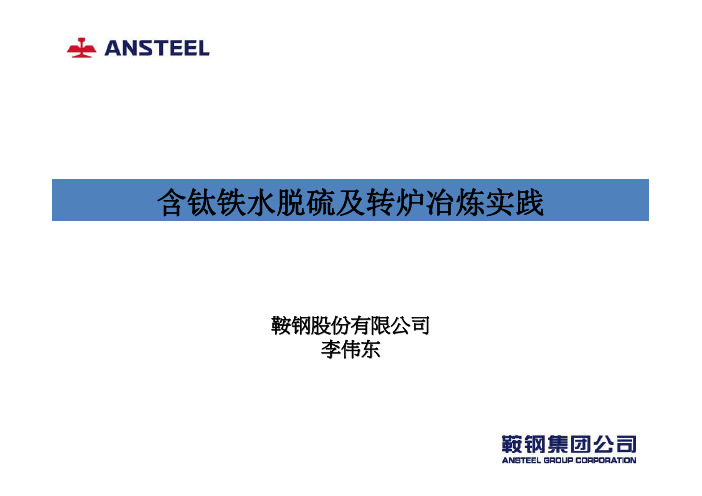
含钛铁水脱硫及转炉冶炼实践
鞍钢股份有限公司
李伟东
2.含钛铁水对冶炼工序操作的影响 含钛铁水
脱硫及转炉
冶炼实践
1.技术开发背景及意义
用钛矿或钛球进行高炉护炉操作已是高炉
操作者常用的护炉方法,其机理是当使用钛矿
护炉时,Ti(C,N)将在高炉炉缸铁浴内形成并沉
积于炉缸受侵蚀部位的工作面或砖缝之中,对
高炉炉衬起到了保护的作用。
但同时铁水钛含
量也会有所升高,并给炼钢工序的操作带来不
利影响。
2008年以后,鞍钢股份炼铁总厂开
始使用钛球进行高炉护炉,由于最初无
钛球护炉经验,导致铁水的钛含量显著
升高且控制不稳定。
在未加钛球前,铁
水钛稳定控制在0.05%以下,使用钛球
护炉后,铁水钛提高到0.12~0.20%之
间,有时甚至超过0.20%。
?
3.含钛铁水脱硫工序冶炼实践
5 结论
1)含钛铁水脱硫时,渣的粘度、脱硫的粉剂消耗和扒渣铁损较高,通过使用渣铁分离料、改进扒渣操作,可大幅度降低粉剂消耗和扒渣铁损。
2)转炉冶炼含钛≤0.20%铁水时,采用双渣操作,放渣前渣量控制在总渣量的1/3,在吹炼进行到1/4~1/3时放出2/3的炉渣,可有效除钛,将钢水中钛含量控制在0.0050%以下。
3)转炉冶炼含钛铁水时,热平衡计算时应将钛的热效应考虑进去,钛的氧化放热基本与硅的氧化放热相同。
4)鞍钢180吨转炉冶炼含钛铁水,采用改进的新工艺后,转炉冶炼终点Ti和P的含量及补吹率均显著降低,基本达到冶炼普通铁水时的控制水平。
谢谢!
敬請批評指正!。
宣钢含钛高炉渣脱硫性能的实验研究
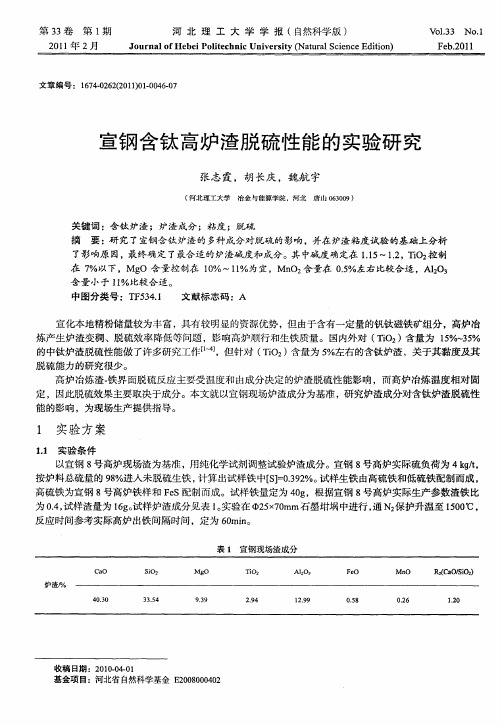
中图分 类号 :T 5 41 F 3.
文 献标志 码 :A
宣 化本地 精粉储 量较 为丰 富 ,具有 较 明显 的资源优 势 ,但 由于含 有一定 量 的钒 钛磁 铁矿组 分 ,高炉冶 炼产 生 炉渣 变稠 、脱硫 效率 降低 等 问题 ,影 响高炉 顺行 和生 铁质量 。国 内外对 ( i )含量 为 1% ̄ 5 TO2 5 3% 的中钛炉 渣脱硫 性能做 了许 多研 究工作 ,但 针对 ( i2 TO )含量 为 5 右 的含 钛炉 渣 ,关 于其 黏度及 其 %左 脱硫 能力 的研究 很少 。 高炉 冶炼 渣. 铁界 面脱 硫 反应 主要 受 温度 和 由成分 决定 的炉 渣脱硫 性 能影 响 ,而高 炉冶 炼温 度 相对 固 定 ,因此脱硫 效果 主要取 决于 成分 。本 文就 以宣 钢现场 炉渣成 分 为基准 ,研 究炉 渣成分对 含钛 炉渣 脱硫性 能 的影 响 ,为现 场生产 提供指 导 。
十C O,离 子理 论 的炉 渣脱 硫反 应为 :[] ( )=O] ( ) 因此 ,炉渣 中 的 C O是 主要 的脱硫 剂 , S+ O 一 [ + S 。 a 在其 他 因素不 变 的条 件下 ,随着 炉 渣碱 度 ( a / i 2 C O SO )的提 高 ,C O 的 含量会增 加 ,使渣 中的 o 活度 a 一 的 提高 ,随着 O 的活度 提高 ,脱 硫反 应 的 L 和速度 都会 增 大 ,炉渣脱 硫 能力增 强 【 丌 s 5 。从 动力 学 角度 分 析 , ~
图1 实验装置示意图
装 置 设备包 括二 硅化 钼 电炉 ,自动 控温 柜 ,变压 器 ,氮气 罐等 。二 硅化 钼 电炉 由六 根 U 型二 硅化钼 棒
- 1、下载文档前请自行甄别文档内容的完整性,平台不提供额外的编辑、内容补充、找答案等附加服务。
- 2、"仅部分预览"的文档,不可在线预览部分如存在完整性等问题,可反馈申请退款(可完整预览的文档不适用该条件!)。
- 3、如文档侵犯您的权益,请联系客服反馈,我们会尽快为您处理(人工客服工作时间:9:00-18:30)。
含钛铁水脱硫及转炉冶炼实践
用钛矿或钛球进行高炉护炉操作已是高炉操作者常用的护炉方法。
其机理是当使用钛矿护炉时,Ti(C,N)将在高炉炉缸铁浴内形成并沉积于炉缸受侵蚀部位的工作面或砖缝之中,而Ti(C,N)的沉积或团聚物被认为起到了保护炉衬的作用。
2008年以后,鞍钢股份炼铁总厂开始使用钛球进行高炉护炉,由于最初无钛球护炉经验,铁水的钛含量显著升高且控制不稳定。
在未加钛球前,铁水钛稳定控制在0.05%以下,使用钛球护炉后,铁水钛提高到0.12%~0.20%,最高时甚至超过0.20%。
铁水钛含量升高,对炼钢工序的操作产生诸多不利影响,主要体现在:脱硫工序扒渣铁损增加,转炉冶炼工序熔剂消耗增加,溅渣护炉效果变差。
因此,研究针对含钛铁水的冶炼技术,对降低冶炼成本、减轻或消除铁水钛含量升高对炼钢操作的影响具有重要意义。
铁水钛含量升高的不利影响
对铁水预处理脱硫工序的影响。
在铁水预处理脱硫时,如果钛含量较高,镁钙复合喷吹的载气氮气与铁水中的碳、钛极易结合生成Ti(C,N),且易与CaO结合,恶化钙粉的脱硫效率,并使得脱后渣黏稠,增加喷吹粉剂消耗;同时由于渣黏稠,喷吹时进入渣中的铁液被包裹在渣中,造成扒渣工序铁损增加。
对转炉炼钢的影响。
在转炉冶炼过程中,钛的氧化物与石灰中的CaO 结合使得白灰利用率降低,转炉势必增加渣料消耗,造成熔剂成本增加。
同时渣量增加,直接导致转炉冶炼吹损增加,并且白灰利用率的降低增加了转炉脱磷负担,冶炼终点补吹次数增加,造成终渣FeO含量高,在增加铁损的同时恶化溅渣护炉效果。
含钛铁水脱硫工序冶炼实践
目前国内外针对含钛铁水脱硫的应对策略。
德国等欧洲国家钢厂对采用加钒钛矿护炉的铁水,采取的办法是将冰晶石(K3AlF6)作为铁水熔剂制作成粉末与流化石灰粉混合后,通过脱硫喷枪喷入铁水中。
由于冰晶石熔点仅为600℃ ,能显著降低脱硫渣的熔点。
为防止氮化物的生成,可将脱硫载气氮气用氩气代替。
由于国内冰晶石资源贫乏,进口或国内人造冰晶石的价格过高,而鞍钢的氩气资源不足,因此须要研究新的方法以降低或彻底杜绝高钛铁水对铁水脱硫的影响。
渣铁分离剂的开发和使用。
为了减少扒渣铁损,鞍钢开发了一种渣铁分离材料。
该材料是通过添加适量的钠盐和钾盐来改善铁渣成分,可以通过喷枪喷入铁水中,也可在喷吹前加在铁水表面或折铁前加在铁水罐底,通过喷吹或折铁的动力学作用使其与铁水渣充分反应,生成低熔点物质,从而降低脱硫渣熔点,使得渣中的铁珠顺利下落至铁水融池,最后减少扒渣铁损。
采用渣铁分离料后,铁水渣流动性提高,
喷枪、扒渣板粘渣程度得到改善,渣铁容易分离,渣中TFe含量显著降低。
扒渣操作的改进。
含钛铁水的扒渣不同于普通铁水(wTi≤0.05%,下同),扒渣操作不当,会造成铁损增加。
鞍钢经过生产实践,确定对含钛铁水的聚渣和扒渣操作可固定为聚渣两次、扒渣三次。
首先扒除固态渣;然后第一次聚渣,第一次聚渣必须做到全覆盖,通过渣耙子的搅动促进聚渣剂融化和结膜;之后进行第二次扒渣操作;扒渣操作结束后进行第二次聚渣操作,第二次聚渣操作也要做到全覆盖,但不必用渣耙子搅动助融;接着进行第三次扒渣操作即可。
含钛铁水表面裸露后,铁水中的钛会与空气中的氧迅速反应,形成新的渣层,因此聚渣和扒渣操作的关键点是聚渣剂加入要快,同时聚渣和扒渣要交叉进行。
每次扒渣结束前即投入聚渣剂,防止铁水裸露造成钛氧化,造成扒渣终点难以判断,误导操作者增加聚渣和扒渣次数,导致扒渣铁损增加。
工艺改进效果。
采用渣铁分离料并改进扒渣操作后,脱硫粉剂消耗及扒渣铁损显著降低,但其生产指标与普通铁水相比仍然较高。
因此含钛铁水在硫磺含量满足钢种要求或可以通过LF等精炼手段脱硫时,一般不进行喷吹脱硫,而采用直接兑入转炉冶炼的方式,必要时在炉外精炼完成脱硫任务。
含钛铁水转炉工序冶炼实践
在转炉冶炼过程中,钛优先于硅氧化,形成钛的氧化物进入渣中,有研究发现,在TiO2含量低于20%时,TiO2含量越低,渣熔点越高。
含钛铁水冶炼时,渣中含有一定量的TiO2,使得炉渣熔点降低,黏度增加,且TiO2易与CaO结合,导致白灰利用率降低,冶炼终点磷硫超标频次增加,造成补吹炉次增多,钢水过氧化,转炉炉渣中FeO 含量高,恶化了溅渣护炉效果。
因此,对于含钛铁水,转炉冶炼操作须要进行改进。
造渣方式的改进。
为了保证炉渣的脱磷脱硫效果,应将含有钛氧化物的炉渣放出,避免冶炼后期影响磷硫的去除,即采用双渣操作。
由于钛优先于硅氧化,冶炼前期钛即完全氧化,待钛完全氧化后,将含有钛氧化物的炉渣排除,重新造渣,即可避免钛氧化物增加炉渣的黏度、降低白灰利用率的问题。
放渣时机的选择。
正常双渣法冶炼,放渣时机一般选择在冶炼过程进行到1/2~2/3的时刻进行,放渣渣量选择为倒出总渣量的1/2~2/3,然后加入渣料重新造渣。
有研究显示,在含钛铁水的吹炼过程中,钛氧平衡常数随着温度的升高而增加,温度升高,氧对钛的氧化能力降低。
而铁水中钛元素选择氧化的转化温度为1340℃~1400℃,因此,在转炉冶炼过程中,吹炼前期是去除钢中钛的有利阶段。
对于180吨转炉而言,在吹炼1/4~1/3的时刻放渣,倒炉温度平均在1370℃左右,落在1340℃~1400℃温度区间内,因此放渣时机选择在1/4~1/3
的时刻。
为了最大量地去除炉渣中的钛氧化物,倒炉放渣时尽量多放,放渣量至少要达到2/3~3/4,以炉口不见钢为宜。
放渣前操作改进。
放渣前,钛和硅已经完全氧化,为了保护炉衬,炉渣须要保持一定的碱度,同时为了炉渣发泡,便于放渣,须要控制一定的渣量,从而有利于放渣操作的进行。
但碱度控制不易过高,石灰等造渣料加入过多,随放渣操作的进行而损失掉,增加了熔剂消耗。
加入量过大,炉渣不易起泡,放渣困难;加入量过少,也达不到放渣去除钛的目的,因此应控制合适的碱度和渣量。
碱度控制在2.3~2.6的范围内基本可以满足去除钛的要求。
现场实际操作时,控制一次造渣总量占总渣量的1/3、放渣比在2/3为宜。
为了达到最佳的放渣效果,放渣前枪位控制原则是低—高,即放渣前2min内应提高枪位化渣,炉内渣发泡后稳定控制30秒以上,然后放渣。
放渣后的操作优化。
放渣后碱度应控制在3.0~3.5,根据钢种磷含量要求适当调整,低磷钢按照上限控制。
白云石加入量按终点炉渣中MgO含量为8%~12%控制,从而满足溅渣护炉要求。
后期冶炼操作的重点是化渣。
炉渣中SiO2含量低,因此在二次吹炼初期就要配加适量的含铁化渣剂提高渣中FeO含量,辅助白灰和白云石融化,提高炉渣的脱磷脱硫能力,而且枪位按高—低控制。
热平衡计算方法的改进。
钛在转炉冶炼过程中氧化放热,当铁水中钛含量在0.10%~0.20%时,发热量较大,因此在计算热平衡时必须考虑此部分的热量增加,才能准确控制终点温度。
现场操作时,可按钛
和硅在转炉冶炼过程放热量一致进行对待,在热平衡计算时应综合考虑铁水中的钛和硅含量,在装入制度上做适当调整,即调整废钢和冷却剂的使用量,同时兼顾前期放渣对温度的影响,才能准确控制冶炼终点温度。
工艺改进效果。
优化造渣制度和热平衡计算后,冶炼终点Ti、P、补吹率显著降低,基本达到正常使用普通铁水时的控制水平。