火焰淬火机温度智能控制算法
计算机技术在淬火炉设计上的应用

计算机技术在淬火炉设计上的应用淬火炉是一种利用高温和快速冷却将金属件迅速淬火的设备。
在传统的淬火炉设计中,工程师需要依靠经验和试错法来优化炉内温度和冷却效果。
然而,随着计算机技术的不断发展,计算机模拟和控制技术已经广泛应用于淬火炉的设计和优化过程中。
本文将探讨计算机技术在淬火炉设计上的应用。
一、计算机模拟技术在淬火炉设计中的应用计算机模拟技术是指利用计算机对淬火炉内的温度场、应力场等进行模拟和分析。
通过建立数值模型和相关物理方程,可以模拟出淬火过程中金属件的温度变化和相变行为。
首先,计算机模拟可以帮助工程师预测和优化淬火炉的温度分布。
通过计算淬火时金属件表面和内部的温度变化,工程师可以了解到不同部位的温度差异以及增减冷却介质的效果。
在设计阶段,可以调整炉膛结构和冷却介质供应方式,以实现更加均匀的温度分布,从而提高淬火效果。
其次,计算机模拟还能够显示金属件在淬火过程中的应力变化。
通过对金属件的热应力和残余应力进行计算和分析,工程师可以评估金属件的变形和裂纹风险。
基于这些信息,可以对淬火炉进行适当的结构和参数优化,以减少应力集中和变形问题。
最后,计算机模拟可以模拟金属相变过程,预测金属件在淬火过程中产生的组织和性能变化。
这对于材料的选择和热处理参数的确定非常重要。
利用计算机模拟的结果,工程师可以选择合适的材料和淬火工艺,以满足不同材料的性能要求。
二、计算机控制技术在淬火炉设计中的应用除了计算机模拟技术,计算机控制技术也在淬火炉的设计和运行中发挥着重要作用。
传统淬火炉通常是基于定时和手动控制来进行操作的,这种方式容易受到人员技能和经验的限制,且存在一定的误差和不稳定性。
计算机控制技术的应用可以实现淬火炉的自动化和智能化操作。
通过建立传感器和执行器的连接,实时监测淬火过程中的温度和气氛等参数,并根据预设的控制算法进行自动调节。
这样可以大大提高淬火炉的工作效率和稳定性。
此外,计算机控制技术还可以实现淬火过程的远程监控和远程操作。
淬火加热温度和淬火温度的关系

淬火加热温度和淬火温度的关系一、引言淬火是金属热处理中的一种重要工艺,通过将金属材料加热至一定温度后迅速冷却,可以使材料获得良好的力学性能和组织结构。
淬火加热温度和淬火温度是淬火工艺中的两个关键参数,它们之间存在着密切的关系。
本文将围绕这一主题展开讨论。
二、淬火加热温度与淬火温度的定义淬火加热温度是指将金属材料加热至一定温度的过程,是淬火工艺中的第一步。
淬火温度是指将加热至一定温度的金属材料迅速冷却的温度,是淬火工艺中的第二步。
淬火加热温度和淬火温度的选择对于材料的性能和组织结构具有重要影响。
三、淬火加热温度与淬火温度的关系1. 温度范围淬火加热温度和淬火温度的选择范围是有限的。
一般来说,淬火加热温度应高于淬火温度,但不能超过一定的上限。
如果加热温度过高,容易引起材料的过烧和组织的异常,影响材料的性能。
而淬火温度则是根据材料的具体情况和要求来确定的,需要保证材料能够达到所需的硬度和强度。
2. 材料类型不同类型的材料对淬火加热温度和淬火温度有不同的要求。
一般来说,低碳钢的淬火加热温度较低,一般在800℃左右;而高碳钢的淬火加热温度较高,一般在850℃以上。
此外,不同的合金元素也会对淬火加热温度和淬火温度产生影响。
例如,添加了铬元素的不锈钢需要较高的淬火加热温度和淬火温度,以保证其耐腐蚀性能。
3. 组织结构要求淬火加热温度和淬火温度的选择还要考虑到材料的组织结构要求。
一般来说,较高的淬火加热温度可以使材料达到较高的硬度和强度,但会降低韧性;而较低的淬火加热温度则可以提高材料的韧性,但会降低硬度和强度。
因此,在实际应用中需要根据具体要求来选择合适的淬火加热温度和淬火温度。
四、淬火加热温度和淬火温度的影响因素1. 材料的热导率材料的热导率会影响淬火加热温度和淬火温度的选择。
热导率较高的材料加热和冷却的速度较快,需要较高的淬火加热温度和淬火温度;而热导率较低的材料则相反。
2. 材料的尺寸和形状材料的尺寸和形状也是选择淬火加热温度和淬火温度的重要因素。
淬火机计算机过程控制系统技术研究_王继忠

淬火机计算机过程控制系统技术研究王继忠1,2 童朝南1 彭开香1 肖磊11.北京科技大学2.北华大学 摘要:对中厚板无约束淬火机的计算机过程控制系统的构成及实施方法进行了介绍,通过人工智能技术对控冷模型进行优化,建成了常化炉后的淬火控冷系统,实现了西气东输管线钢材国产化改造的目标,淬火机控制系统经过实际运行,不但提高了产品的性能指标,而且由于使用了智能化控制手段,增加了产量,减轻了工人的劳动强度。
关键词:过程控制 淬火 控冷 集管 模型Study on Computer Process C ontrol System of Quenching MachineW ang Jizhong To ng Chao nan Peng Kaixiang Xiao LeiA bstract:T he paper me ntions the co mputer process contro l sy stem composition and implement o f unco n-str ained quenching machine fo r medium steel plate.By using a rtificial intelligence technique to optimize the co oling contr ol mo del,the quenching and cooling co ntrol sy stem behind no rmalizing furnace was designed and the g oal,w hich is pipeline steel lo calizatio n o f West to East P roject is achieved.The quenching co ntrol sy stem runs no rmally and stably.No t only is the products′pe rfor mance impro ved,but also the y ield increases and in-tensity of labo r reduced,because of intelligent contro l methods.Keywords:pr ocess contr ol que nch co oling co ntr ol header pipe model1 前言中厚板广泛地应用于国防科技、造船、重型机械、电站、石油、天气管道、桥梁及建筑行业中,中厚板冷却后性能的好坏一直是各大生产厂关心的问题,也是争相进行研究的重要课题之一;为了提高产品质量,扩大产品的规格和品种,中厚板轧后的热处理工艺是必不可少的,较常见的是运用常化炉加热钢板,在炉后建立淬火控冷设备,用以改善钢板的内部结构和性能,从而生产出高韧性,高强度和焊接性能良好的中厚板材。
基于单片机淬火炉温温度控制课程设计

为了减小稳态误差,在控制器中加入积分项,积分项对误差取决于时间的积分,随着时间的增加,积分项会增大。这样,即使误差很小,积分项也会随着时间的增加而加大,它推动控制器的输出增大使稳态误差进一步减少,直到等于零。
数字PID位置型控制算式为:
(2-4)
数字PID增量型控制算式为:
(2-5)
其中称为比例增益;
称为积分系数;
称为微分系数。
如果单纯的用数字PID控制器去模仿模拟调节器,不会获得更好的效果。因此必须发挥计算机运算速度快、逻辑判断功能强、编程灵活等优势、才能在控制性能上超过模拟调节器。
在单回路控制系统中,由于扰动作用使被控参数偏离给定值,从而产生偏差。自动控制系统的调节单元将来自变送器的测量值与给定值相比较后产生的偏差进行比例、积分、微分(PID)运算,并输出统一标准信号,去控制执行机构的动作,以实现对温度、压力、流量、也为及其他工艺参数的自动控制。比例作用P只与偏差成正比;积分作用I是偏差对时间的积累;微分作用D是偏差的变化率。
图1-1系统框图
软件设计,先编写子程序,包括A/D转换和温度检测子程序,延迟子程序,D/A转换子程序,PID控制程序,最后系统初始化并编写主程序。
最后用protues进行硬件连线和仿真,看能否达到系统要求,对温度进行控制。
2
2.1
淬火是生产过程中的一道关键工序,其温度控制的精度直接影响到产品的质量。淬火炉温度控制通常由多个温区。本设计针对一个温区进行温度控制,要求控制温度范围600-800℃,控制精度在±1℃。温度探头选用热电偶。输出0-10端的电压,输入电流输出电压线性关系。其对象温控数学模型为:
火焰切割中的自动化控制和智能化生产技术

火焰切割中的自动化控制和智能化生产技术随着工业化程度不断提高,人们对于生产效率、产品质量和安全性的要求越来越高。
火焰切割作为制造业中常用的一种金属加工方法,其自动化控制和智能化生产技术的应用,不仅大大提高了生产效率,更为重要的是保障了操作人员的安全,实现了经济效益和社会效益的双赢。
一、自动化控制的优势传统的火焰切割技术,由於工作环境的特殊性以及操作人员的技能不均致使其效率低下,出现了安全、质量和效率等问题。
而自动化控制的应用,则可以大大减少人工干扰,提高生产精度和效率,并且缩短生产周期,降低成本。
这是因为自动化控制可以实现自动化加载、运动和卸载,是在保证产品质量和产量的前提下,提高生产过程的效率和稳定性。
二、智能化生产技术的应用智能化生产技术是指结合现代先进的传感控制技术和信息技术的智能控制系统。
其应用价值主要包括以下几个方面:(一)、精度高采用智能化生产技术可以实现更精确、更高效的机器运动,有效提高了生产过程的精度和质量。
此外,智能化系统可以实现自动校正,使生产过程更加稳定可靠。
(二)、自我调节智能化控制系统具备良好的自学习和适应性,在生产过程中能够自我调节和适应变化。
这样,对于设备的维护和管理,不仅降低了人工成本,同时也使生产过程更加智能化、自动化,使机器具备更好的稳定性和可监控性。
(三)、远程监测智能化控制系统不仅可以实现远程监控和指挥,提高了生产现场的管理和效率,同时也能够实现生产数据的共享和多元管理,优化了生产流程和企业资源。
三、结合生产实际优化控制方案尽管自动化控制和智能化生产技术的应用,可以大大提高生产效率和质量,但由于生产现场的实际情况千差万别,为了实现最优的控制方案,需要结合实际情况制定科学的方案。
(一)、量身定制每种产品有自己不同的特性,针对不同的产品应有不同的控制方案和工艺流程。
例如对于大型钢结构,可采用自动化切割定位控制技术,实现高精度的规划和准确的切割。
而对于加工瑞士表壳这类非规则图形材料,智能化系统应能够实现自适应的切割,实现非常规形状切割;为加工卡口表盘的金属材料,系统应具备强大的切割功率,可实现高速切割。
感应加热经验公式
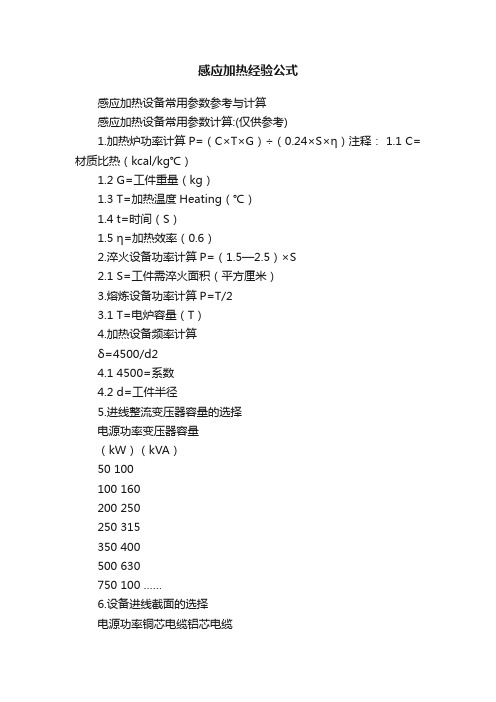
感应加热经验公式感应加热设备常用参数参考与计算感应加热设备常用参数计算:(仅供参考)1.加热炉功率计算P=(C×T×G)÷(0.24×S×η)注释: 1.1 C=材质比热(kcal/kg℃)1.2 G=工件重量(kg)1.3 T=加热温度Heating(℃)1.4 t=时间(S)1.5 η=加热效率(0.6)2.淬火设备功率计算P=(1.5—2.5)×S2.1 S=工件需淬火面积(平方厘米)3.熔炼设备功率计算P=T/23.1 T=电炉容量(T)4.加热设备频率计算δ=4500/d24.1 4500=系数4.2 d=工件半径5.进线整流变压器容量的选择电源功率变压器容量(kW)(kVA)50 100100 160200 250250 315350 400500 630750 100 ……6.设备进线截面的选择电源功率铜芯电缆铝芯电缆(kW)(mm2)(mm2)50 25 35100 50 75200 95 150250 2×70 2×120350 2×95 2×185500 3×95 3×185750 4×95 4×1851000 5×95 5×1857.中频输出电缆截面的选择中频功率电源的输出频率KW kHz0.5 1.0 2.5 4.0 8.0以下电缆截面积单位为:mm250 35 50/90 70 95 120100 50 70 95 2×70 2×95200 95 2×70 2×95 4×70 4×95250 2×70 2×95 3×70 5×90 5×95350 2×95 3×95 4×95 5×100 5×100500 3×95 4×95 5×100 5×150 5×200750 4×95 5×100 5×150 5×200 (5×150)×31000 5×100 5×150 5×200 (5×150)×2 (5×150)×48.冷却水流量的选择8.1 进水压力:0.15—0.3Mpa8.2 冷却水温度在5—30°范围内,水质硬度不超过8度,浑浊度不大于5,PH值在6.5—8的范围内。
淬火炉操作规程
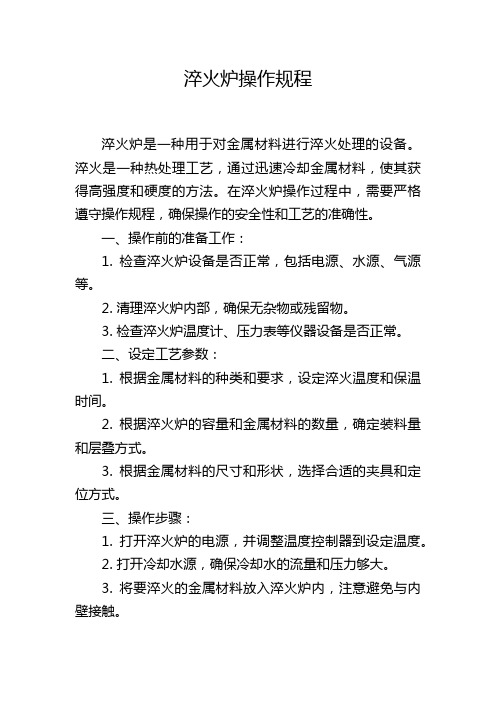
淬火炉操作规程淬火炉是一种用于对金属材料进行淬火处理的设备。
淬火是一种热处理工艺,通过迅速冷却金属材料,使其获得高强度和硬度的方法。
在淬火炉操作过程中,需要严格遵守操作规程,确保操作的安全性和工艺的准确性。
一、操作前的准备工作:1. 检查淬火炉设备是否正常,包括电源、水源、气源等。
2. 清理淬火炉内部,确保无杂物或残留物。
3. 检查淬火炉温度计、压力表等仪器设备是否正常。
二、设定工艺参数:1. 根据金属材料的种类和要求,设定淬火温度和保温时间。
2. 根据淬火炉的容量和金属材料的数量,确定装料量和层叠方式。
3. 根据金属材料的尺寸和形状,选择合适的夹具和定位方式。
三、操作步骤:1. 打开淬火炉的电源,并调整温度控制器到设定温度。
2. 打开冷却水源,确保冷却水的流量和压力够大。
3. 将要淬火的金属材料放入淬火炉内,注意避免与内壁接触。
4. 关闭淬火炉的门,并打开排气孔,确保炉内的通风良好。
5. 开启淬火炉的加热装置,使其逐渐升温到设定温度。
6. 达到设定温度后,关闭加热装置,并保持一段时间进行保温。
7. 在保温结束后,打开冷却水源,开始进行淬火冷却。
8. 观察冷却过程中的温度变化和冷却效果,并根据需求调整冷却时间。
9. 冷却结束后,关闭冷却水源,打开淬火炉的门,取出金属材料。
10. 对金属材料进行检查,确保淬火效果达到要求。
四、操作注意事项:1. 淬火炉操作必须由经过培训和授权的人员进行,严禁非专业人员操作。
2. 淬火炉的加热和冷却过程中,不得离开现场,以防止意外发生。
3. 操作人员必须穿戴好防护设备,包括防热手套、防护眼镜等。
4. 操作人员必须熟悉淬火炉的操作界面和功能,确保正确设置参数。
5. 淬火炉的电源和设备连接线路必须定期检查,确保安全可靠。
6. 设备故障或异常情况发生时,应立即停止操作,并通知维修人员处理。
通过严格按照淬火炉操作规程进行操作,可以确保淬火工艺的准确性和操作的安全性。
同时,根据不同的金属材料和工件要求,可以灵活调整工艺参数,以获得最佳的淬火效果。
基于PID控制的淬火炉炉温控制系统设计
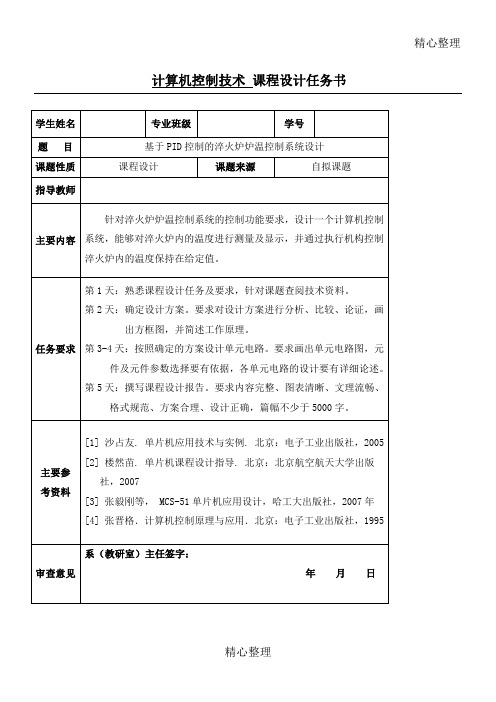
精心整理计算机控制技术课程设计任务书1 引言1.1 课题背景?? 温度是工业对象中一个主要的被控参数,它是一种常见的过程变量,因为它直接影响燃烧、化学反应、发酵、烘烤、煅烧、蒸馏、浓度、挤压成形,结晶以及空气流动等物理和化学过程。
温度控制不好就可能引起生产安全,产品质量和产量等一系列问题。
温度控制是许多设备的重要的构成部分,它的功能是将温度控制在所需要的温度范围内,以利于进行工件的加工与处理。
不论是在生1.21.3600-22.1处理(放大)送到A/D转换器,转换后的数字信号再送到8031内部进行判断或计算。
从而输出的控制信号来控制锅炉是否加热。
但对于8031来说,其内部只有128个字节的RAM,没有程序存储器,并且系统的程序很多,要完成键盘、显示等功能就必须对8031进行存储器扩展和I/O口扩展,并且需要容量较大的程序存储器,外扩时占用的I/O口较多,使系统的设计复杂化。
方案二:AT89C51单片机是最常用的单片机,是一种低损耗、高性能、CMOS八位微处理器。
AT89C51与MCS-51系列的单片机在指令系统和引脚上完全兼容,而且能使系统具有许多MCS-51系列产品没有的功能,功能强、灵活性高而且价格低廉。
AT89C51可构成真正的单片机最小应用系统,缩小系统体积,增加系统的可靠性,降低了系统成本。
只要程序长度小于4K ,四个I/O 口全部提供给拥护。
系统运行中需要存放的中间变量较少,可不必再扩充外部RAM 。
综上所述的二种方案,该设计选用方案二比较合适。
2.2 数学模型的建立本设计针对一个温区进行温度控制,要求控制温度范围600-800℃,控制精度在±1℃。
温度探头选用热电偶。
输出0-10mA 电流信号,通过双向可控硅控制器控制加热电阻两端的电压,输入数字PID 增量型控制算式为:(2-3-2) 其中 称为比例增益;称为积分系数;称为微分系数。
)]2()1(2)([)()]1()([)(-+--++--=∆k e k e k e K k e T k e k e K k u D I P 0=i I2.4 系统组成框图及工作原理系统的硬件包括微控制器部分(主机)、A/D转换模块、温度检测、温度控制、键盘与显示、报警几个主要部分,系统的组成框图如图2.1所示。
淬火设备调试方法

淬火设备调试方法以淬火设备调试方法为标题,写一篇文章。
淬火设备是工业生产中常用的一种热处理设备,用于提高金属材料的硬度和耐磨性。
在使用淬火设备之前,需要对其进行调试,确保其正常运行和达到预期效果。
下面将介绍淬火设备调试的方法和步骤。
一、设备检查对淬火设备进行全面的检查,包括外观、电气设备、管道、传动装置等各个方面。
确保设备没有损坏或漏水现象,并检查电气设备的接线是否正确,传动装置是否灵活运转。
二、温度调节淬火设备的温度调节是非常关键的一步。
首先,根据所需淬火温度,将温度计安装在设备内部,并调节仪表的刻度。
然后,打开加热设备,逐渐升高温度,直到达到所需的温度。
在升温过程中,要注意观察温度计的变化,并及时调整加热设备的功率,以保持温度的稳定。
三、介质准备淬火介质对淬火效果有着重要影响。
根据金属材料的种类和要求,选择合适的淬火介质,如水、油、盐等。
在使用介质之前,要进行准备工作。
首先,确保介质的纯净度,排除杂质和气泡。
其次,根据所需淬火温度,将介质加热至适当温度。
最后,将介质注入淬火槽中,并保持介质的稳定性。
四、淬火试样准备进行淬火试样准备前,需要根据金属材料的种类和要求,选择合适的试样形状和尺寸。
将试样置于淬火槽中,并确保试样完全浸没在淬火介质中。
同时,要注意试样与介质之间的接触面积,以保证淬火效果的均匀性。
五、淬火过程控制开始淬火过程后,需要控制淬火时间和速度。
淬火时间应根据金属材料的厚度和硬度要求进行合理的设定,以避免过淬或欠淬。
淬火速度也需要控制在合适范围内,过快或过慢都会影响淬火效果。
在整个淬火过程中,要密切观察试样的变化,确保淬火效果的达到预期。
六、淬火后处理淬火后需要对试样进行处理,以达到所需的硬度和耐磨性。
通常包括回火、冷却等步骤。
回火是通过加热试样至一定温度后,进行保温和冷却,以缓解淬火应力和提高材料的韧性。
冷却是通过将试样置于冷却介质中,快速冷却至室温,使其达到所需硬度。
淬火设备的调试是确保其正常运行和达到预期效果的重要环节。
淬火介质冷却过程中的数值计算
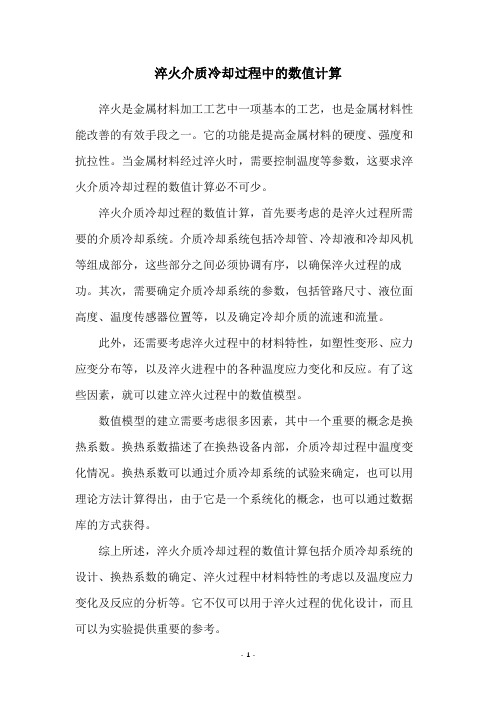
淬火介质冷却过程中的数值计算淬火是金属材料加工工艺中一项基本的工艺,也是金属材料性能改善的有效手段之一。
它的功能是提高金属材料的硬度、强度和抗拉性。
当金属材料经过淬火时,需要控制温度等参数,这要求淬火介质冷却过程的数值计算必不可少。
淬火介质冷却过程的数值计算,首先要考虑的是淬火过程所需要的介质冷却系统。
介质冷却系统包括冷却管、冷却液和冷却风机等组成部分,这些部分之间必须协调有序,以确保淬火过程的成功。
其次,需要确定介质冷却系统的参数,包括管路尺寸、液位面高度、温度传感器位置等,以及确定冷却介质的流速和流量。
此外,还需要考虑淬火过程中的材料特性,如塑性变形、应力应变分布等,以及淬火进程中的各种温度应力变化和反应。
有了这些因素,就可以建立淬火过程中的数值模型。
数值模型的建立需要考虑很多因素,其中一个重要的概念是换热系数。
换热系数描述了在换热设备内部,介质冷却过程中温度变化情况。
换热系数可以通过介质冷却系统的试验来确定,也可以用理论方法计算得出,由于它是一个系统化的概念,也可以通过数据库的方式获得。
综上所述,淬火介质冷却过程的数值计算包括介质冷却系统的设计、换热系数的确定、淬火过程中材料特性的考虑以及温度应力变化及反应的分析等。
它不仅可以用于淬火过程的优化设计,而且可以为实验提供重要的参考。
本文通过介绍淬火介质冷却过程中的数值计算,从而为金属材料性能改善提供参考。
在此过程中,数值模型的建立关键在于确定介质冷却系统的参数,同时还需要考虑淬火过程中的材料特性、温度应力变化及反应等因素。
未来,数值计算技术的发展将在淬火介质冷却过程中发挥重要作用,将为金属材料性能改善提供更多有效的技术支持。
淬火设备调试方法

淬火设备调试方法一、准备工作1.检查设备:在调试之前,首先要检查设备是否具有完善的外观和机械结构,如设备是否完整、各部件是否齐全、紧固件是否牢固等。
2.清洁设备:将设备进行清洁,清除设备上的灰尘、杂物和油渍等。
3.确认电源:检查淬火设备的电源是否正常,以及电源线是否接触良好。
二、常规调试1.对设备进行合理安装:根据设备的要求,将设备正确地安装在设计好的位置上,并保证其稳定性。
2.对设备进行接线:根据设备的接线图,将设备的各个部件连接到正确的位置上,确保接线牢固、不松动。
3.设置运行参数:根据工艺要求,设置设备的运行参数,如淬火温度、淬火时间、升温速度等。
4.开启设备:对淬火设备进行启动,观察设备的运行情况,检查各个部件的工作是否正常。
5.检查设备的安全保护装置:检查设备是否配备了相应的安全保护装置,并确保这些装置的运行正常。
6.检查设备的控制系统:对设备的控制系统进行检查,确保控制信号的传输正常,并确保设备能够按照设定的参数正常运行。
三、详细调试1.测试设备的基本工作性能:通过调整设备的运行参数,对设备进行试运行,观察设备的工作情况,并记录相关数据,如温度、压力、速度等。
2.对设备的锁定和解锁机构进行调试:检查设备的锁定和解锁机构是否灵活,以及是否能够准确地锁定和解锁。
3.对设备的传动系统进行调试:检查设备的传动系统是否平稳、不松动,并检查传动装置是否润滑良好。
4.对设备的加热系统进行调试:检查设备的加热系统是否能够使设备迅速达到设定的温度,并保持稳定。
5.对设备的冷却系统进行调试:检查设备的冷却系统是否能够使设备迅速冷却,并保持稳定。
6.进行负载测试:在设备正常运行的情况下,加入预定工作负载,观察设备的工作情况,并记录相关数据。
7.进行故障模拟测试:模拟设备可能遇到的故障情况,观察设备的反应,并记录相关数据。
四、调试后的工作1.检查调试前后的数据:对比调试前后的数据,检查设备的运行情况是否有所改善,并分析出现的问题。
数控火焰机操作规程

数控火焰机操作规程
《数控火焰机操作规程》
一、概述
数控火焰机是一种用于金属切割和切割的设备,它采用计算机控制系统来精确控制火焰切割的位置和速度。
为了保证操作安全和切割质量,必须严格遵守数控火焰机操作规程。
二、操作人员
1. 操作人员必须接受相关培训,并持有相应的操作证书。
2. 如果操作人员没有相关培训或不熟悉数控火焰机的操作规程,禁止其进行操作。
三、安全操作规程
1. 在操作数控火焰机前,必须检查机器是否正常工作,确保切割区域周围没有易燃或易爆物品。
2. 操作人员必须穿着防护服和防护眼镜,并戴上头盔,以防止火花或飞溅物伤害。
3. 在操作过程中,禁止在操作台附近吸烟或使用明火。
4. 操作过程中,禁止离开操作台,必须全程注意机器运行情况。
四、操作流程
1. 打开数控火焰机的电源,等待机器自检完成后,进行相关设
置。
2. 使用计算机控制系统输入切割图纸的相关参数,包括切割速度、切割路径等。
3. 启动数控火焰机,根据图纸要求进行切割操作。
4. 切割完成后,关闭数控火焰机的电源,清理切割区域和机器。
五、日常维护
1. 定期对数控火焰机进行检查和维护,保证机器正常工作。
2. 及时更换磨损的切割工具,保证切割质量。
通过严格遵守《数控火焰机操作规程》,可以保证操作人员的安全和机器的正常运行,同时提高切割质量和工作效率。
单片机工艺淬火炉控制系统的设计与仿真

摘要单片机工艺淬火炉控制系统是工业生产中比较典型的一种控制系统,它对控制精度、安全性要求高,并且温度的变化必须严格按照给定的升温、保温、降温曲线运行。
也保证生产过程中对蒸汽的需要。
温度控制系统都有纯滞后环节,所以一般PID控制系统都会通过史密斯(Smith)预估器的设计改进来消除系统的超调和震荡补偿系统的纯滞后环节。
使系统稳定。
温度控制系统的硬件分4个部分,1.输入部分:键盘主要采用键盘独立输入方式,键盘采用软件消除抖动;2.A/D采样单元:将转换的温度值的模拟量经过运算放大器进行放大、滤波处理,然后送入MAX1241进行A/D转换;3显示单元:将通过A/D转换后的模拟量与给定值进行比较后在进行控制算法之后再通过显示器显示出来。
4.驱动执行部分:通过使用光电耦合,实现了良好的电绝缘和抗干扰能力,然后通过三极管来驱动继电器的开与合,进而控制锅炉两端的电压。
这个设计通过PROTEUS对系统的硬件部分进行仿真,然后再通过MATLAB/SIMULINK的仿真结果验证数字控制器设计的正确性。
关键词:单片机,温度控制,锅炉,史密斯预估器,纯滞后A B S T R A C TM i c r o c o n t r o l l e r t e c h n o l o g y q u e n c h i n g f u r n a c e c o n t r o l s y s t e m i n i n d u s t r i a l p r o d u c t i o n i s a k i n d o f t y p i c a l c o n t r o l s y s t e m.I t o n t h e c o n t r o l a c c u r a c y,h i g h s e c u r i t y r e q u i r e m e n t s,a n d t h e c h a n g e o f t h e t e m p e r a t u r e m u s t b e i n s t r i c t a c c o r d a n c e w i t h t h e g i v e n t e m p e r a t u r e,h e a t p r e s e r v a t i o n,c o o l i n g c u r v e.A l s o e n s u r e t h e p r o d u c t i o n p r o c e s s t o t h e n e e d s o f t h e s t e a m.T e m p e r a t u r e c o n t r o l s y s t e m w i t h p u r e d e l a y l i n k,s o g e n e r a l P I D c o n t r o l s y s t e m c a n b y S m i t h(S m i t h)e s t i m a t e s o f d e s i g n i m p r o v e m e n t s t o e l i m i n a t e t h e s y s t e m o v e r s h o o t a n d o s c i l l a t i o n o f t h e c o m p e n s a t i o n s y s t e m o f p u r e d e l a y l i n k.M a k e t h e s y s t e m s t a b l e.T e m p e r a t u r e c o n t r o l s y s t e m h a r d w a r e i s d i v i d e d i n t o f o u r p a r t s.1.E n t e r s o m e:K e y b o a r d m a i n l y a d o p t s i n d e p e n d e n t k e y b o a r d i n p u t m e t h o d s.T h e k e y b o a r d U S E S t h e s o f t w a r e t o e l i m i n a t e j i t t e r.2.A/D s a m p l i n g u n i t:W i l l t r a n s f o r m t h e t e m p e r a t u r e v a l u e o f t h e a n a l o g t h r o u g h o p e r a t i o n a l a m p l i f i e r a m p l i f i c a t i o n,f i l t e r i n g p r o c e s s i n g,t h e n i n t o M A X1241A/D c o n v e r s i o n.3.d i s p l a y u n i t:T h r o u g h A/D c o n v e r s i o n a n a l o g c o m p a r i n g w i t h g i v e n v a l u e a f t e r a g a i n a f t e r c o n t r o l a l g o r i t h m t h r o u g h t h e m o n i t o r d i s p l a y.4.D r i v e e x e c u t i o n p a r t:T h r o u g h t h e u s e o f p h o t o e l e c t r i c c o u p l i n g.G o o d e l e c t r i c i n s u l a t i o n a n d a n t i-j a m m i n g c a p a b i l i t y i s r e a l i z e d.A n d t h e n b y u s i n g a t r a n s i s t o r t o d r i v e t h e r e l a y t o o p e n a n d c l o s e.T o c o n t r o l t h e v o l t a g e a t t h e e n d s o f t h e b o i l e r.T h e d e s i g n o f t h e h a r d w a r e p a r t o f t h e s y s t e m t h r o u g h P R O T E U S s i m u l a t i o n.A n d t h e n t h r o u g h t h e M A T L A B/S I M U L I N K s i m u l a t i o n r e s u l t s v e r i f y t h e c o r r e c t n e s s o f t h e d i g i t a l c o n t r o l l e r d e s i g n.KEY WORDS: Microcontroller,Temperature control,microcontroller,pure time-delay,Smith estimated device.目录第1章前言------------------------------------------------------- III 第2章锅炉温度控制系统方案确定------------------------------------- 6 2.1锅炉温度控制系统的主要设计任务 -------------------------------- 6 2.2锅炉温度控制系统的方案分析及要求 ------------------------------ 6 2.3锅炉温度控制系统的总体设计 ------------------------------------ 9第3章锅炉控制系统的控制算法103.1 系统的控制对象的数学模型及其稳定性分析[1] --------------------- 10 3.2 史密斯预估器[2] -------------------------------- 错误!未定义书签。
淬火操作规程
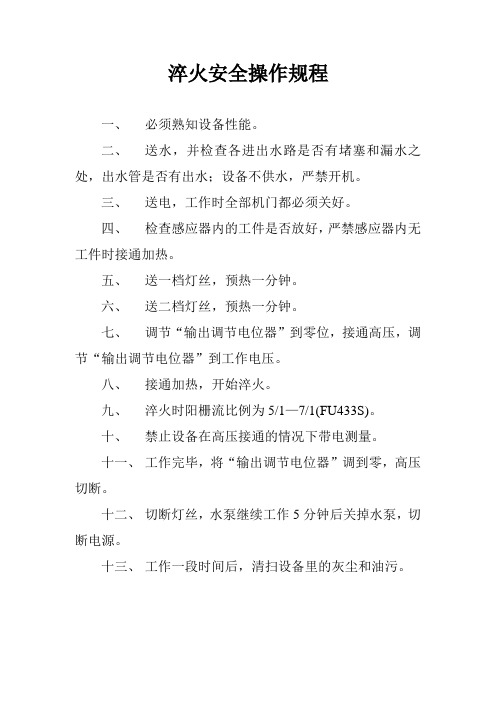
淬火安全操作规程
一、必须熟知设备性能。
二、送水,并检查各进出水路是否有堵塞和漏水之处,出水管是否有出水;设备不供水,严禁开机。
三、送电,工作时全部机门都必须关好。
四、检查感应器内的工件是否放好,严禁感应器内无工件时接通加热。
五、送一档灯丝,预热一分钟。
六、送二档灯丝,预热一分钟。
七、调节“输出调节电位器”到零位,接通高压,调节“输出调节电位器”到工作电压。
八、接通加热,开始淬火。
九、淬火时阳栅流比例为5/1—7/1(FU433S)。
十、禁止设备在高压接通的情况下带电测量。
十一、工作完毕,将“输出调节电位器”调到零,高压切断。
十二、切断灯丝,水泵继续工作5分钟后关掉水泵,切断电源。
十三、工作一段时间后,清扫设备里的灰尘和油污。
HMI实现通用感应淬火控制

HMI实现通用感应淬火控制摘要本文以一篇着重介绍通过人机界面来控制PLC实现通用感应淬火的控制系统。
阐述了如何通过采集PLC数据信息来实现使人机界面与通用淬火装置的控制系统的有机联接,用填表的方式实现不同零件的加工过程精细控制的自动化。
本文重点介绍利用人机界面的配方功能以实现直观对PLC监控数据实时分析、上传、下载。
配方功能可以充分利用PLC的内存大的优点存储多个加工工艺配方,同时还使得PLC的内存得到了充分的利用,在变更加工工艺的时候就不比去变更整个程序,而是单纯的更改一下人机界面的配方号或者直接变更配方参数并下载到控制PLC上就可以了。
配方功能还能用以实现感应淬火过程中的同时淬火、连续扫描淬火、分段同时淬火、分段连续扫描淬火等多种淬火工艺[1]。
本次设计采用的是技术比较完善的台达触摸屏,该触摸屏系统能够存储百个以上工件淬火程序相关参数,具有工件管理、查询功能,提供在线帮助、随时操作提示、故障自诊断、故障报警,并且参数输入、查询、维护方便,无需编程。
该系统通过参数设置和菜单管理,使得人机交互界面更加简单友好,达到管理与控制相结合,实现生产线的实时监控、数据采集与处理,系统结构简单,实时性好,应用性强,故障率低,能大大提高生产效率。
关键词:触摸屏,HMI,配方,感应淬火,PLCHMI USED IN UNIVERSAL INDUCTION HARDENINGCONTROLABSTRACTThis article focuses on introduced according the use of HMI control PLC in order to control induction hardening. Described how to collect data PLC to achieve the common people and the quenching device machine interface control system of organic connection, try to filling in a form different part to achieve precise control of the automation process.This article focuses on human-computer interface using the formula function in order to achieve real-time visual analysis of monitoring data on the PLC, upload, download. Formula functions can take advantage of the advantages of PLC memory to store multiple large processing formula, but also makes the PLC's memory has been fully utilized, the processing time does not change than to change the whole process, but simply change what people machine interface, or directly change the formula number and downloaded to the control formulation parameters on to the PLC. Formula function can be used to achieve the process of induction hardening, while quenching, continuous scanning quenching, while sub-quenching, quenching and other sub-scanning quenching.The design uses the Technical Comparison of sound Delta touch screen, the touch screen system could store 100 or more quenching process parameters, with parts management, search function, online help, any operating tips, fault diagnosis, fault alarm, and data input, query, easy to maintain, no programming. The system parameter setting and menu management, making a simple human-machine interface more friendly to management and control with integration, real-time monitoring of production lines, data acquisition andprocessing, system architecture, real time and a good, strong applications, the failure rate low, can greatly increase the production efficiencyKEY WORDS:touch panel,human-computer interface,Induction Hardening,PLC目录前言 (1)第1章设计简介 (2)§1.1 系统总体目标 (2)§1.2 系统综合分析 (2)§1.2.1 系统程序和数据监控的现状 (2)§1.2.2 CNC控制的不利 (3)§1.2.3 结论意见 (4)§1.3 台达触摸屏简介 (5)§1.3.1 台达触摸屏分类及说明 (5)§1.3.2 台达触摸屏硬件组成和工作基本原理 (5)§1.3.3 台达触摸屏的主要作用 (5)§1.3.4 台达触摸屏的主要功能 (5)第2章基本原理 (7)§2.1 感应加热的淬火工艺 (7)§2.1.1 感应加热的起源 (7)§2.1.2 通用感应加热的原理 (7)§2.1.3 感应加热表面淬火的特点 (7)§2.1.4 感应加热处理的基本操作流程 (8)§2.2 触摸屏简介 (9)§2.2.1 触摸屏的起源 (9)§2.2.2 触摸屏的特点 (9)§2.2.3 触摸屏工作原理 (10)§2.3 PLC简介 (10)§2.3.1 PLC的起源 (10)§2.3.2 PLC的组成 (11)第3章系统设计 (12)§3.1 设计概要 (12)§3.2 模块设计 (12)§3.2.1 欢迎画面的制作 (12)§3.2.2 系统介绍画面 (13)§3.2.3 系统画面的设计 (14)§3.2.4 配方管理画面 (15)§3.2.5 配方数据的汇入 (17)§3.2.6 流程图设计 (21)§3.2.7 机床操作界面 (23)§3.2.8 系统设置界面设计 (25)§3.2.9 报警画面设计 (27)§3.2.10 测试换面制作 (28)第4章系统总括 (30)§4.1 系统总体目的 (30)§4.2 系统设计原理 (30)结论 (32)参考文献 (33)致谢 (35)附录 (36)触摸屏使用注意事项 (36)流程图程序 (38)外文资料翻译 (39)前言随着PLC控制设备自动化程度的不断提高,以及生产对工艺要求的不断变化,PLC控制设备操作面板上的各种按钮及各种操作机构变得越来越复杂,工位指示及报警指示特别多,这就使设备操作人员在初学时显得特别困难而且在设备操作过程中会出现误操作,同时也增加了设备的故障。
数控火焰旋转升降式淬火机床应用与比较及能耗说明

数控火焰旋转升降式淬火机床应用与比较一、表面淬火技术的种类随着经济和生产技术的飞速发展,汽车、矿产、航空、仪表、冶金、国防等工业对零件的要求越来越高。
而金属热处理可以提高零件性能,延长使用寿命,因此成为生产过程中不可缺少的环节。
而表面淬火则是热处理工艺中最常用的一种。
其原理是对零件的表面进行热处理,利用金属固态相变,通过快速加热方式对零件表面进行淬火,以达到改善零件表面的性能且保持零件心部的性能不变提高零件承受一定冲击负荷、抵抗磨损和抵抗疲劳的有效方法。
正确选择表面淬火工艺必须了解零件的工作条件和服役条件,零件的结构、形状以及使用的材料等各个方面。
从生产和使用的角度去考虑解决方案。
表面淬火的方法有很多其中最常用的方法有感应表面淬火、火焰表面淬火、电接触表面加热淬火、脉冲表面淬火等。
二、火焰淬火和感应淬火的特点及比较1、感应加热表面淬火将工件放入感应器中,使工件表层产生感应电流,在极短的时间内加热到淬火温度后,立即喷水冷却,使工件表层淬火,从而获得非常细小的针状马氏体组织根据电流频率不同,感应加热表面淬火,可以分为:高频淬火、中频淬火、工频淬火优点:工件加热速度快均匀性好,工件表面氧化脱碳较轻。
淬硬层马氏体组织较细,硬度、强度、韧性都较高。
缺点:感应加热热处理缺点与火焰淬火相比,感应加热设备较复杂,而且适应性较差,不同形制的工件需要配套的感应器,更换繁琐。
对某些形状复杂的工件难以保证质量。
不适合大工件的加工,淬火层比较浅且能耗大而且易坏维修成本比较高。
2、传统火焰表面淬火传统火焰淬火采用乙炔---氧或煤气---氧的混合气体燃烧的火焰,喷射到零件表面上,快速加热,当达到淬火温度后,立即用水或用乳化液进行冷却淬透层深度一般为5—10mm表面硬度钢可达65HRC,灰铸铁为40一48HRC,合金铸铁为43—52HRC。
优点:火焰淬火设备简单更适用于单件或生产的大型零件或需要局部淬火的工具或零件,加大型轴类、大模数齿轮等。
基于PLC、HMI的火焰淬火机床系统的设计

t e u r me t fq e h n r n s . her q ie n s o u nc i g ha d e s Theh a i g tm e s ore st n Be D i Ha h o p n 3 % e tn i h t r ha i ng oS ic m a y’ 0
q nc n m a hi e S u o tc o to s se ue hi g c n ’ a t mai c n r l y t m. HM I a r a i e n e lg n s l pe ai n nd c n e lz i t li e tyiua o r to a r a—i e ltme 、hit rc li f ma i n mo t rn o t efa eq e c i g p o e s Th o g h e t tr a hs so ia n or to ni i g t h m u n h n r c s . r u h t et s,i e c o l
淬火传热系数计算公式

淬火传热系数计算公式淬火是一种金属材料热处理工艺,通过快速冷却来改变金属的组织结构和性能。
在淬火过程中,传热系数是一个非常重要的参数,它影响着淬火速度和淬火效果。
传热系数的准确计算对于淬火工艺的优化和控制非常重要。
本文将介绍淬火传热系数的计算公式及其在淬火工艺中的应用。
淬火传热系数的计算公式可以用来预测淬火过程中金属材料的温度变化和相变过程。
传热系数通常是通过实验测定得到的,但是在实际工程中,往往需要根据已有的数据来估算传热系数。
下面我们将介绍几种常用的淬火传热系数计算公式。
第一种计算淬火传热系数的方法是基于经验公式。
经验公式通常是通过实验数据拟合得到的,可以用来估算不同工艺条件下的传热系数。
经验公式的优点是简单易用,但是其适用范围有限,只能用于类似的工艺条件。
常见的经验公式包括Dittus-Boelter公式、Sieder-Tate公式等。
第二种计算淬火传热系数的方法是基于理论模型。
理论模型是通过对传热过程进行物理分析和数学建模得到的,可以用来预测不同条件下的传热系数。
理论模型的优点是可以提供更准确的计算结果,但是其建立需要对传热过程有深入的理解和掌握。
常见的理论模型包括牛顿冷却定律、能量守恒方程等。
第三种计算淬火传热系数的方法是基于计算机模拟。
计算机模拟是通过数值方法对传热过程进行数值求解得到的,可以用来模拟复杂条件下的传热系数。
计算机模拟的优点是可以考虑更多的影响因素,提供更全面的传热系数计算结果,但是其建立和求解需要较高的计算能力和技术水平。
在淬火工艺中,传热系数的计算公式可以用来优化工艺参数,提高淬火效果。
通过对传热系数的计算和分析,可以确定最佳的淬火工艺条件,提高材料的硬度和强度。
此外,传热系数的计算还可以用来预测淬火过程中的温度分布和残余应力,为工艺控制和质量检测提供依据。
总之,淬火传热系数的计算公式是淬火工艺优化和控制的重要工具,可以帮助工程师预测和分析淬火过程中的温度变化和相变过程,为工艺优化和控制提供依据。
感应淬火深度计算公式

感应淬火深度计算公式一、感应淬火深度的理论基础。
1. 感应加热原理。
- 感应加热是利用电磁感应现象,当交变电流通过感应器时,会在工件表面产生感应电动势,从而形成感应电流。
根据焦耳定律Q = I^2Rt(其中Q为热量,I为电流,R为电阻,t为时间),工件表面由于电阻的存在而被加热。
由于集肤效应,电流主要集中在工件表面,使得表面迅速被加热到淬火温度,而心部仍保持较低温度。
2. 影响淬火深度的因素。
- 频率:感应加热的频率对淬火深度有显著影响。
一般来说,频率越高,电流透入深度越浅,淬火深度也就越浅。
根据电流透入深度公式δ=(503)/(√(ρμ f))(其中δ为电流透入深度(mm),ρ为工件材料的电阻率(Ω· mm^2/m),μ为工件材料的相对磁导率,f为感应加热频率(Hz)),可以定性地分析频率与淬火深度的关系。
例如,对于中碳钢,当频率较高时,电流主要集中在表面很薄的一层,淬火深度就较浅;而当频率较低时,电流透入深度较大,淬火深度相对较深。
- 加热功率和时间:加热功率越大,在相同时间内工件表面获得的热量越多,升温速度越快。
适当延长加热时间也会增加淬火深度,但如果加热时间过长,可能会导致表面过热、氧化甚至熔化等缺陷。
- 工件材料特性:工件材料的电阻率ρ和相对磁导率μ直接影响电流透入深度。
不同的材料,其ρ和μ值不同。
例如,碳钢和合金钢的电阻率和磁导率有差异,这会导致在相同感应加热条件下淬火深度有所不同。
而且材料的原始组织也会对淬火深度产生影响,例如,原始组织为球状珠光体的工件比片状珠光体的工件淬火深度可能会浅一些,因为球状珠光体的导热性相对较差。
二、感应淬火深度的计算公式。
1. 半经验公式。
- 对于圆柱形工件的感应淬火深度h,有一个半经验公式h = K√(frac{t){f}}(其中K为与材料有关的系数,t为加热时间(s),f为感应加热频率(Hz))。
这个公式是在大量实验和工程实践基础上总结出来的。