浅析汽车铝合金铸造的工艺性能
汽车铸铝轮毂低压铸造技术分析

汽车铸铝轮毂低压铸造技术分析低压铸造技术是目前用于汽车铸铝轮毂制造的主要工艺之一,本文将对汽车铸铝轮毂低压铸造技术进行深入分析,探讨其工艺原理、优势以及发展趋势。
一、低压铸造技术的工艺原理低压铸造是一种通过在铸造过程中施加较小的压力来使熔融金属充满模具腔体并凝固成型的铸造工艺。
在汽车铸铝轮毂的制造中,低压铸造技术的工艺原理主要包括以下几个步骤:1. 模具准备:首先需要制备好轮毂的模具,模具的设计和制造对最终产品的质量和性能有着至关重要的影响。
2. 熔炼铝合金:选用合适的铝合金材料,并将其熔化成为熔融状态,以备后续的铸造过程使用。
3. 注射压力控制:将熔融的铝合金注入模具腔体中,并在注入的过程中施加一定的低压力,以确保熔融金属充分填充模具并凝固成型。
4. 凝固成型:在注入过程中施加的低压力有助于减少气孔和缩松等缺陷的产生,最终得到成型完好的铸铝轮毂产品。
二、低压铸造技术的优势相比传统的重力铸造和高压铸造技术,低压铸造技术在汽车铸铝轮毂的制造中具有诸多优势:1. 产品质量稳定:低压铸造技术可以有效地减少气孔、缩松等缺陷的产生,从而得到质量更加稳定的铸铝轮毂产品。
2. 生产效率高:低压铸造技术可以实现自动化生产,生产效率高,可大大降低生产成本和加工周期。
3. 节能环保:低压铸造技术在铸造过程中能够有效地降低能耗,减少废料和排放物的产生,符合现代节能环保的要求。
4. 成本低廉:低压铸造技术相对于高压铸造技术而言,生产设备和工艺要求相对简单,生产成本更加低廉。
5. 制造复杂性零部件能力强:低压铸造技术适用于复杂结构的铸件制造,因此能够满足汽车铸铝轮毂各种复杂结构的制造需求。
三、低压铸造技术的发展趋势随着汽车工业的不断发展和铸造技术的不断创新,低压铸造技术在汽车铸铝轮毂制造中的应用也在不断推进,并呈现出以下发展趋势:1. 自动化程度提高:随着自动化设备和智能制造技术的发展,低压铸造技术在汽车铸铝轮毂制造中的自动化程度将不断提高,生产效率将进一步提升。
汽车铸铝轮毂低压铸造技术分析
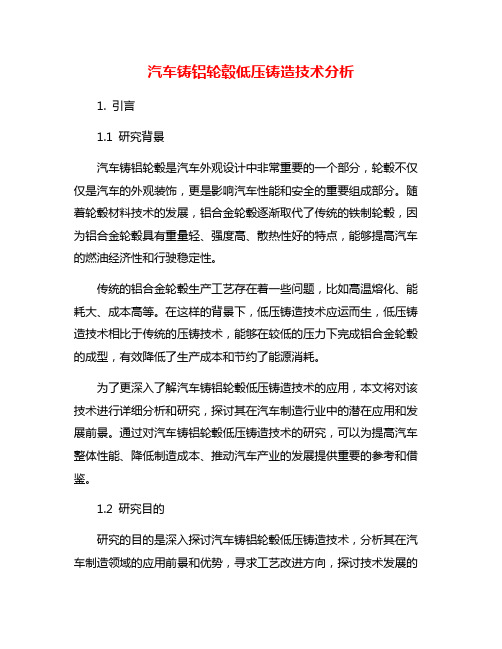
汽车铸铝轮毂低压铸造技术分析1. 引言1.1 研究背景汽车铸铝轮毂是汽车外观设计中非常重要的一个部分,轮毂不仅仅是汽车的外观装饰,更是影响汽车性能和安全的重要组成部分。
随着轮毂材料技术的发展,铝合金轮毂逐渐取代了传统的铁制轮毂,因为铝合金轮毂具有重量轻、强度高、散热性好的特点,能够提高汽车的燃油经济性和行驶稳定性。
传统的铝合金轮毂生产工艺存在着一些问题,比如高温熔化、能耗大、成本高等。
在这样的背景下,低压铸造技术应运而生,低压铸造技术相比于传统的压铸技术,能够在较低的压力下完成铝合金轮毂的成型,有效降低了生产成本和节约了能源消耗。
为了更深入了解汽车铸铝轮毂低压铸造技术的应用,本文将对该技术进行详细分析和研究,探讨其在汽车制造行业中的潜在应用和发展前景。
通过对汽车铸铝轮毂低压铸造技术的研究,可以为提高汽车整体性能、降低制造成本、推动汽车产业的发展提供重要的参考和借鉴。
1.2 研究目的研究的目的是深入探讨汽车铸铝轮毂低压铸造技术,分析其在汽车制造领域的应用前景和优势,寻求工艺改进方向,探讨技术发展的新方向。
通过对低压铸造技术的概述和分析,全面了解其在生产工艺中的具体运用,探究影响因素及其优势与劣势的比较,为提升铸铝轮毂质量和生产效率提供技术支持。
结合行业发展现状和需求,探讨汽车铸铝轮毂低压铸造技术的未来发展前景,为汽车制造业的技术升级和转型提供支持和推动。
通过本文的研究,旨在为相关领域的专业人士和研究者提供参考和借鉴,促进汽车铸造工艺的创新和提升,推动行业发展和技术进步。
1.3 研究意义研究汽车铸铝轮毂低压铸造技术的意义在于提高产品质量和生产效率,降低生产成本,延长产品使用寿命,提升汽车行驶安全性和舒适性。
通过深入研究汽车铸铝轮毂低压铸造技术,可以促进技术的进步和产业的发展,推动我国汽车制造业向更高水平迈进。
研究汽车铸铝轮毂低压铸造技术还将为相关领域的研究提供参考和借鉴,推动汽车零部件制造工艺的不断创新和完善。
铝合金铸件的铸造工艺分析

铝合金铸件的铸造工艺分析摘要:随着我国汽车工业的迅猛发展,一方面对汽车用压铸件的需求量日益提升;另一方面为了应对环境污染以及资源紧张的发展现状,对汽车用压铸件的质量要求及应用范围提出了更高的要求。
本文从高压铸造的角度探讨铝合金铸件几种关键的高圧鋳造工艺。
关键词:铝合金铸件;铸造工艺压力铸造是近代金属加工工艺中发展较快的一种少无切削的特种铸造方法,具有生产效率高、经济指标优良、铸件尺寸精度高和互换性好等特点,在制造业,尤其是规模化产业得到了广泛应用和迅速发展。
压力铸造是铝、镁和锌等轻金属的主要成形方法,适用于生产大型复杂薄壁壳体零件。
压铸件已成为汽车、运动器材、电子和航空航天等领域产品的重要组成部分,其中汽车行业是压铸技术应用的主要领域,占到70%以上。
随着汽车、摩托车、内燃机、电子通信、仪器仪表、家用电器、五金等行业的快速发展,压铸件的功能和应用领域不断扩大,从而促进了压铸技术不断发展,压铸件品质不断提高。
本文针对铝合金高压压铸技术进行分析探讨。
1高性能压铸合金技术对于新型高强韧压铸铝合金的开发,主要包括两个方面:一是针对现有传统压铸铝合金的合金成分或添加合金元素进行优化设计;二是开发新型压铸铝合金系。
而新型压铸铝合金一般要求其满足以下几点:①适用于壁厚为2-v4 mm复杂结构压铸件的生产;②铸态下的抗拉强度和屈服强度分别可以达到300 MPa和150 MPa,且具有15%的伸长率;③具有良好的耐腐蚀性能;④可以通过工业上对变形铝合金常用的高温喷漆过程对合金进行一定的强化;⑤可进行热处理强化处理;⑥可回收利用且环境友好。
当前常用的高强韧压铸铝合金有Silafont-36, Magsimal-59, Aural-2及ADC-3等牌号,均为国外开发,其共同特点是Fe含量均比普通压铸铝合金更低;另外其他杂质元素如Zn,Ti等均进行了严格控制。
对于新型压铸镁合金的开发,主要包含三个方面:超轻高强度压铸镁合金;抗高温蠕变压铸镁合金;耐蚀压铸镁合金。
新能源汽车车架用铸造铝合金的生产工艺及性能研究
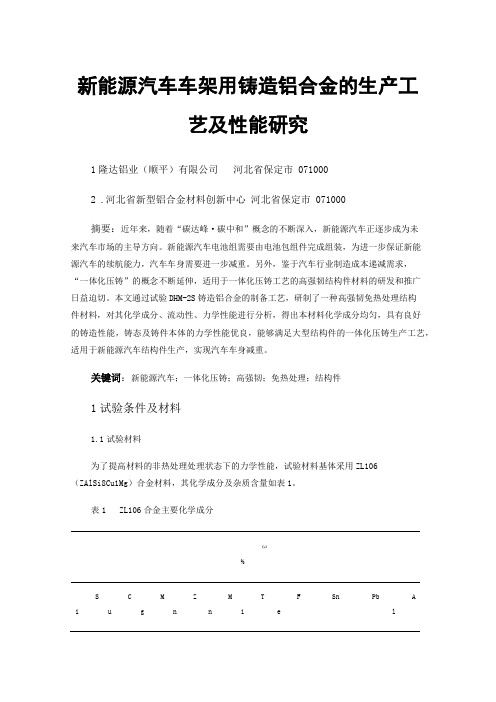
新能源汽车车架用铸造铝合金的生产工艺及性能研究1隆达铝业(顺平)有限公司河北省保定市 0710002 .河北省新型铝合金材料创新中心河北省保定市 071000摘要:近年来,随着“碳达峰·碳中和”概念的不断深入,新能源汽车正逐步成为未来汽车市场的主导方向。
新能源汽车电池组需要由电池包组件完成组装,为进一步保证新能源汽车的续航能力,汽车车身需要进一步减重。
另外,鉴于汽车行业制造成本递减需求,“一体化压铸”的概念不断延伸,适用于一体化压铸工艺的高强韧结构件材料的研发和推广日益迫切。
本文通过试验DHM-2S铸造铝合金的制备工艺,研制了一种高强韧免热处理结构件材料,对其化学成分、流动性、力学性能进行分析,得出本材料化学成分均匀,具有良好的铸造性能,铸态及铸件本体的力学性能优良,能够满足大型结构件的一体化压铸生产工艺,适用于新能源汽车结构件生产,实现汽车车身减重。
关键词:新能源汽车;一体化压铸;高强韧;免热处理;结构件1试验条件及材料1.1试验材料为了提高材料的非热处理处理状态下的力学性能,试验材料基体采用ZL106(ZAlSi8Cu1Mg)合金材料,其化学成分及杂质含量如表1。
表1 ZL106合金主要化学成分ω%S iCuMgZnMnTiFeSn Pb Al7 .5-8.51.0-1.5.3-0.5≤0.2.3-0.5.10-0.25≤0.8≤0.05≤0.05余量向ZL106合金中添加Al-Mo中间合金和少量的AL-Ti-C,以进一步提高其在非热处理状态下的力学性能。
ZL106硅含量7.5-8.5%,在此基础上进一步加大硅成分范围的比例,以提高合金的流动性。
由于“碳达峰碳中和”应对再生金属进行充分利用,所以在材料的选择中应采用大量再生铝金属,在再生铝金属中,Fe 元素成分含量较高,需要对Fe含量进行控制。
Cu元素在铸态下会有明显应力开裂倾向,在大型薄壁结构件铸造过程中,应避免此倾向,所以大幅降低Cu元素的含量。
浅析汽车铝合金铸造的工艺性能

铸件在模 具浇注过程 中会 产生一系列 的问题 。过 快的冷却 速度会 降低熔融 金属 的流动性 ,这使得
薄 壁 铸 件 的 模 具 空 腔 完 全 填 充 之前 金 属 过 早 的凝 固 ,导 致 不 完 全 填 充 和气 孔 的产 生 。 因此 ,薄 壁
铸 件铸造生 产过程 中的主要影 响因素是流动性 ,
型 、结 晶和冷却过程 中表现最为突出的那些性 能 的综合 。流动性 、收缩性 、气密性 、铸造应力 、 吸气性 。铝合金这些特性取决于合金的成分 ,但 也与 铸造 因素 、合 金加 热 温度 、铸 的复杂 程
作者简介 :肖军 ( 1 9 7 0 一),男 ,湖北 十堰人 ,工程师 。
如成分 ,过 热度 ,表 面张力 ;模具铸造变量 ,如 冷却速度 、过热度 、模具材料等 。虽然一直在研
究 影 响铝 合 金 及 其 复 合 材 料 的流 动 性 的 因素 ,然 而 ,到 目前 为止 还 没 有 可 靠 的理 论 模 型 来 解 释 铝 合 金及 其 复合材 料 的流 动性 行为 。 合 金 的 流 动 性 好 ,充 型 能 力 强 ,容 易 获得 形
中图分类号 :T G 3 1 6 文献标识码 :B 文章编 号 :1 0 0 5 — 4 8 9 8( 2 0 1 3 )0 2 — 0 0 4 8 — 1 0
d o i :1 0 . 3 9 6 9 / j . i s s n . 1 0 0 5 — 4 8 9 8 . 2 0 1 3 . 0 2
后发展的多材料结构轿 车要求连接两种不 同类型 的材料 ( 如铸 铁一 铝 、钢一 铝 、铝一 镁 等 ),对这 些连接技术 以及对材料和零件防腐蚀 的表 面处理 技术 ,是今后扩大铝合 金在汽车上应用 的重要课
汽车用铝合金压铸件

汽车用铝合金压铸件随着汽车工业的快速发展,铝合金压铸件作为一种重要的汽车零部件材料,正逐渐得到广泛应用。
本文将从铝合金压铸件的特点、应用领域、制造工艺以及未来发展趋势等方面进行介绍和分析。
铝合金压铸件是指通过压铸工艺将铝合金熔液注入到模具中,经过凝固和冷却后得到的零部件。
相比于传统的铸造工艺,铝合金压铸件具有以下几个显著的特点。
铝合金压铸件具有较高的强度和刚性。
铝合金本身具有良好的机械性能,经过压铸工艺后,其内部组织更加致密,结构更加均匀,因此能够获得更高的强度和刚性。
铝合金压铸件具有良好的表面质量和尺寸精度。
压铸工艺能够快速、高效地制造出形状复杂的零部件,且表面光洁度高,尺寸稳定性好,能够满足汽车工业对于外观和精度的要求。
铝合金压铸件具有较好的耐腐蚀性和耐热性。
铝合金具有良好的耐腐蚀性,能够适应汽车在各种恶劣环境下的使用要求。
而且铝合金具有较低的熔点和热膨胀系数,能够耐受高温条件下的使用,不易变形和破裂。
铝合金压铸件在汽车工业中有着广泛的应用。
首先,它被广泛应用于汽车车身和车身结构件。
汽车车身需要具备较高的强度和刚性,而铝合金压铸件能够满足这一要求。
其次,铝合金压铸件还广泛用于汽车发动机零部件,如缸盖、曲轴箱等。
铝合金的导热性能好,能够有效地散热,提高发动机的工作效率。
此外,铝合金压铸件还用于汽车悬挂系统、传动系统和制动系统等。
铝合金压铸件的制造工艺主要包括模具设计、合金熔炼、模具注液、凝固冷却、脱模清理等环节。
模具设计是关键,需要根据零部件的形状和尺寸来确定模具的结构和材料。
合金熔炼是将铝合金材料加热熔化,得到熔液的过程。
模具注液是将熔液注入到模具中,并保持一定的压力,使熔液充满整个模腔。
凝固冷却是指熔液在模具中逐渐冷却凝固,形成零部件的过程。
脱模清理是将凝固后的零部件从模具中取出,并进行除渣、修整等工艺处理。
未来,随着汽车工业的不断发展,铝合金压铸件在汽车领域的应用将会进一步扩大。
一方面,随着汽车整车质量的减轻和节能环保的要求,铝合金作为轻质材料将会得到更广泛的应用。
铝合金铸造工艺性能
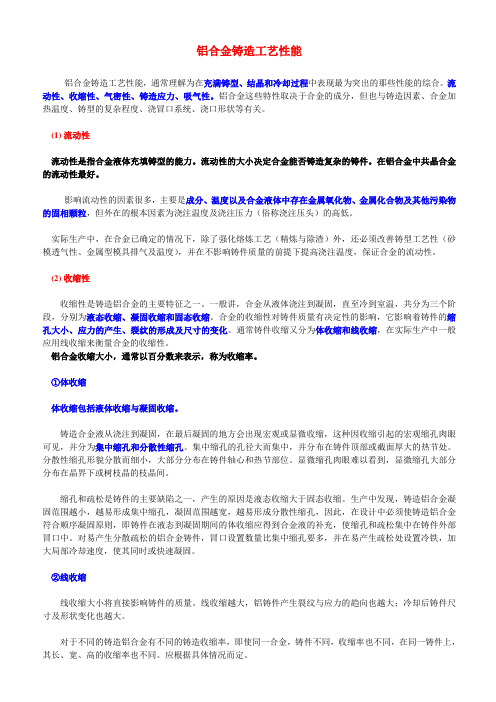
铝合金铸造工艺性能铝合金铸造工艺性能,通常理解为在充满铸型、结晶和冷却过程中表现最为突出的那些性能的综合。
流动性、收缩性、气密性、铸造应力、吸气性。
铝合金这些特性取决于合金的成分,但也与铸造因素、合金加热温度、铸型的复杂程度、浇冒口系统、浇口形状等有关。
(1) 流动性流动性是指合金液体充填铸型的能力。
流动性的大小决定合金能否铸造复杂的铸件。
在铝合金中共晶合金的流动性最好。
影响流动性的因素很多,主要是成分、温度以及合金液体中存在金属氧化物、金属化合物及其他污染物的固相颗粒,但外在的根本因素为浇注温度及浇注压力(俗称浇注压头)的高低。
实际生产中,在合金已确定的情况下,除了强化熔炼工艺(精炼与除渣)外,还必须改善铸型工艺性(砂模透气性、金属型模具排气及温度),并在不影响铸件质量的前提下提高浇注温度,保证合金的流动性。
(2) 收缩性收缩性是铸造铝合金的主要特征之一。
一般讲,合金从液体浇注到凝固,直至冷到室温,共分为三个阶段,分别为液态收缩、凝固收缩和固态收缩。
合金的收缩性对铸件质量有决定性的影响,它影响着铸件的缩孔大小、应力的产生、裂纹的形成及尺寸的变化。
通常铸件收缩又分为体收缩和线收缩,在实际生产中一般应用线收缩来衡量合金的收缩性。
铝合金收缩大小,通常以百分数来表示,称为收缩率。
①体收缩体收缩包括液体收缩与凝固收缩。
铸造合金液从浇注到凝固,在最后凝固的地方会出现宏观或显微收缩,这种因收缩引起的宏观缩孔肉眼可见,并分为集中缩孔和分散性缩孔。
集中缩孔的孔径大而集中,并分布在铸件顶部或截面厚大的热节处。
分散性缩孔形貌分散而细小,大部分分布在铸件轴心和热节部位。
显微缩孔肉眼难以看到,显微缩孔大部分分布在晶界下或树枝晶的枝晶间。
缩孔和疏松是铸件的主要缺陷之一,产生的原因是液态收缩大于固态收缩。
生产中发现,铸造铝合金凝固范围越小,越易形成集中缩孔,凝固范围越宽,越易形成分散性缩孔,因此,在设计中必须使铸造铝合金符合顺序凝固原则,即铸件在液态到凝固期间的体收缩应得到合金液的补充,使缩孔和疏松集中在铸件外部冒口中。
汽车用铝合金铸件技术条件-概述说明以及解释

汽车用铝合金铸件技术条件-概述说明以及解释1.引言1.1 概述概述汽车用铝合金铸件技术条件是指在汽车制造过程中,对于使用铝合金材料进行铸造的要求和标准。
随着车辆轻量化趋势的不断发展,汽车制造商越来越倾向于使用轻质材料来替代传统的钢铁材料。
铝合金作为一种重要的轻质材料,在汽车行业中得到了广泛的应用。
汽车用铝合金铸件技术条件的重要性不容忽视。
正确的技术条件可以保证铝合金铸件的质量和性能,同时也能提高生产效率和降低成本。
对于汽车制造商来说,汽车用铝合金铸件的质量和性能直接影响到车辆的安全性和可靠性。
因此,制定合适的技术条件对于保证汽车的品质至关重要。
本文将从以下几个方面对汽车用铝合金铸件技术条件进行详细的探讨。
首先,我们将介绍车辆轻量化趋势,解析为什么轻质材料在汽车制造中的应用越来越广泛。
其次,我们将深入探讨铝合金铸件在汽车行业中的应用,介绍铝合金材料在汽车制造中的优势和挑战。
最后,我们将重点关注汽车用铝合金铸件技术条件的重要性,分析如何制定合适的技术条件以保证铸件的质量和性能。
通过对这些内容的探讨和分析,我们将总结出汽车用铝合金铸件技术条件的关键要点,展望未来该技术的发展前景。
我们希望本文能够帮助读者更好地理解汽车用铝合金铸件技术条件的重要性,并为汽车制造商提供实用的指导和建议。
让我们一起深入研究这一重要的汽车制造技术,为推动汽车工业的发展做出贡献。
1.2 文章结构本篇文章主要分为引言、正文和结论三个部分。
在引言部分,首先概述了本文要讨论的内容——汽车用铝合金铸件技术条件。
接着介绍了文章的结构和目的,以让读者了解本文的整体安排和写作意图。
正文部分分为三个小节。
首先,讨论了当前车辆轻量化趋势,即汽车行业中越来越重视车辆的减重问题,并探讨了轻量化的重要性和影响。
接着,阐述了铝合金铸件在汽车行业中的应用情况,展示了铝合金铸件在解决车辆轻量化问题上的优势以及其在汽车制造中的广泛应用。
最后,重点讨论了汽车用铝合金铸件技术条件的重要性,介绍其对于铸件质量、性能、成本和可靠性的影响,以及对整个汽车制造工艺的重要作用。
铸造铝合金的性能定性分析
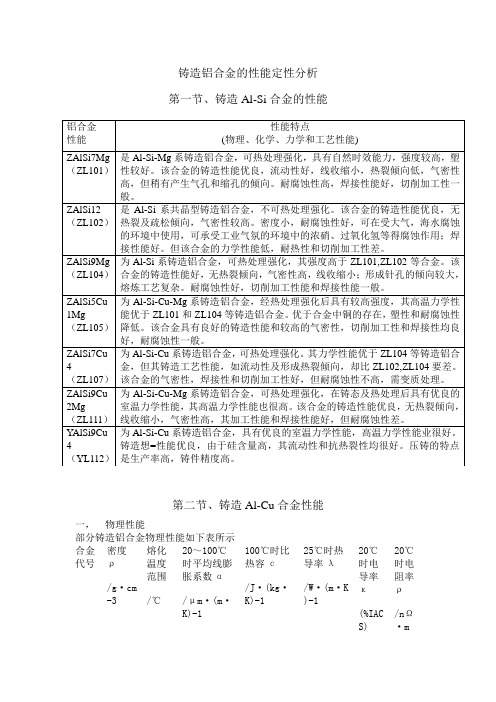
铸造铝合金的性能定性分析第一节、铸造Al-Si合金的性能第二节、铸造Al-Cu合金性能一,物理性能部分铸造铝合金物理性能如下表所示合金代号密度ρ/g·cm-3熔化温度范围/℃20~100℃时平均线膨胀系数α/μm·(m·K)-1100℃时比热容с/J·(kg·K)-125℃时热导率λ/W·(m·K)-120℃时电导率κ(%IACS)20℃时电阻率ρ/nΩ·m铝合金性能性能特点(物理、化学、力学和工艺性能)ZAlSi7Mg (ZL101)是Al-Si-Mg系铸造铝合金,可热处理强化,具有自然时效能力,强度较高,塑性较好。
该合金的铸造性能优良,流动性好,线收缩小,热裂倾向低,气密性高,但稍有产生气孔和缩孔的倾向。
耐腐蚀性高,焊接性能好,切削加工性一般。
ZAlSi12 (ZL102)是Al-Si系共晶型铸造铝合金,不可热处理强化。
该合金的铸造性能优良,无热裂及疏松倾向,气密性较高。
密度小,耐腐蚀性好,可在受大气,海水腐蚀的环境中使用,可承受工业气氛的环境中的浓硝、过氧化氢等得腐蚀作用;焊接性能好。
但该合金的力学性能低,耐热性和切削加工性差。
ZAlSi9Mg (ZL104)为Al-Si系铸造铝合金,可热处理强化,其强度高于ZL101,ZL102等合金。
该合金的铸造性能好,无热裂倾向,气密性高,线收缩小;形成针孔的倾向较大,熔炼工艺复杂。
耐腐蚀性好,切削加工性能和焊接性能一般。
ZAlSi5Cu 1Mg(ZL105)为Al-Si-Cu-Mg系铸造铝合金,经热处理强化后具有较高强度,其高温力学性能优于ZL101和ZL104等铸造铝合金。
优于合金中铜的存在,塑性和耐腐蚀性降低。
该合金具有良好的铸造性能和较高的气密性,切削加工性和焊接性均良好,耐腐蚀性一般。
ZAlSi7Cu 4(ZL107)为Al-Si-Cu系铸造铝合金,可热处理强化。
论汽车铝合金缸体缸盖铸造工艺研究现状
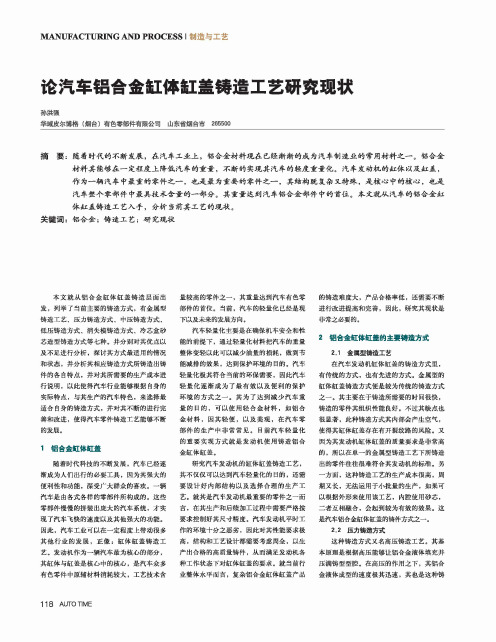
MANUFACTURING AND PROCESS I卸造与工艺论汽车铝合金缸体缸盖铸造工艺研究现状孙洪强华域皮尔博格(烟台)有色零部件有限公司山东省烟台市2655〇〇摘要:随着时代的不断发展,在汽车工业上,铝合金村料现在已经渐渐的成为汽车制造业的常用材料之一。
铝合金材料其能够在一定程度上降低汽车的重量,不断的实现其汽车的轻度重量化。
汽车发动机的缸体以及缸盖,作为一辆汽车中最重的零件之一,也是最为重要的零件之一,其结构既复杂又特殊,是核心中的核心,也是汽车整个零部件中最具技术含量的一部分。
其重量达到汽车铝合金部件中的首位。
本文就从汽车的铝合金缸体缸盖铸造工艺入手,分析当前其工艺的现状。
关键词:铝合金;铸造工艺;研究现状本文就从铝合金缸体缸盖铸造层面出发,列举了当前主要的铸造方式,有金属型 铸造工艺、压力铸造方式、中压铸造方式、低压铸造方式、消失模铸造方式、冷芯盒砂 芯造型铸造方式等七种。
并分别对其优点以 及不足进行分析,探讨其方式最适用的情况 和状态,并分析其相应铸造方式所铸造出铸 件的各自特点,并对其所需要的生产成本进 行说明,以此使得汽车行业能够根据自身的 实际特点,与其生产的汽车特色,来选择最 适合自身的铸造方式,并对其不断的进行完 善和改进,使得汽车零件铸造工艺能够不断 的发展。
1铝合金缸体缸盖随着时代科技的不断发展,汽车已经逐 渐成为人们出行的必要工具,因为其强大的 便利性和功能,深受广大群众的喜欢。
一辆 汽车是由各式各样的零部件所构成的。
这些 零部件慢慢的拼装出庞大的汽车系统,才实 现了汽车飞快的速度以及其他强大的功能。
因此,汽车工业可以在一定程度上带动很多 其他行业的发展,正像:缸体缸盖铸造工艺。
发动机作为一辆汽车最为核心的部分,其缸体与缸盖是核心中的核心,是汽车众多 有色零件中原辅材料消耗较大,工艺技术含量较高的零件之一,其重量达到汽车有色零部件的首位。
当前,汽车的轻量化已经是现下以及未来的发展方向。
铝合金缸体压铸工艺探讨

铝合金缸体压铸工艺探讨一、引言铝合金缸体是内燃机的重要零部件,其质量和性能直接影响着整个发动机的工作效率和使用寿命。
在发动机制造业中,铝合金缸体压铸工艺一直是研究的热点,因为铝合金具有轻质、导热性能好、成型性能好等优点,适合用于发动机零部件的制造。
本文将探讨铝合金缸体压铸工艺的相关内容,希望为相关研究和实践提供一定的参考。
二、铝合金缸体的特点1. 轻质:铝合金密度小,比重仅为2.7g/cm³,比钢材轻很多,因此可以减轻整个发动机的重量,有利于提高车辆的动力性能和燃油经济性。
2. 导热性能好:铝合金的热导率高,热膨胀系数小,因此散热性能优秀,适合用于发动机缸体等需要散热的部件制造。
3. 成型性能好:铝合金易于加工成型,可以通过压铸工艺制作复杂形状的零部件,满足发动机缸体等部件的设计需求。
4. 耐腐蚀性好:铝合金具有良好的耐蚀性能,能够抵御多种化学介质的侵蚀,有利于提高发动机零部件的使用寿命。
由于上述特点,铝合金成为了发动机制造业中不可或缺的材料之一,广泛应用于缸体、缸盖、曲轴箱等部件的制造。
三、铝合金缸体压铸工艺介绍铝合金缸体的制造一般采用压铸工艺,其工艺流程主要包括原料处理、压铸成型、热处理、表面处理等环节。
1. 原料处理:铝合金缸体的原料主要是铝合金材料,需要通过熔炼、合金化等工艺处理成合格的铝合金液态材料,以满足后续压铸成型的需要。
2. 压铸成型:原料处理完成后,将铝合金液态材料注入到压铸模具中,施加一定的压力,使其在模具中形成所需形状的缸体零件。
3. 热处理:通过热处理工艺,对铝合金缸体进行固溶处理、淬火处理等热处理工艺,以提高其硬度、强度和耐热性能。
4. 表面处理:对铝合金缸体进行喷砂、喷丸、阳极氧化等表面处理工艺,以提高其表面质量和耐腐蚀性能。
铝合金缸体的压铸工艺具有生产效率高、成本低、制造成型性能优越等优点,因此被广泛应用于发动机制造领域。
但是在实际应用中,铝合金缸体压铸工艺还存在一些问题,需要进一步研究和改进。
铝合金缸体压铸工艺探讨
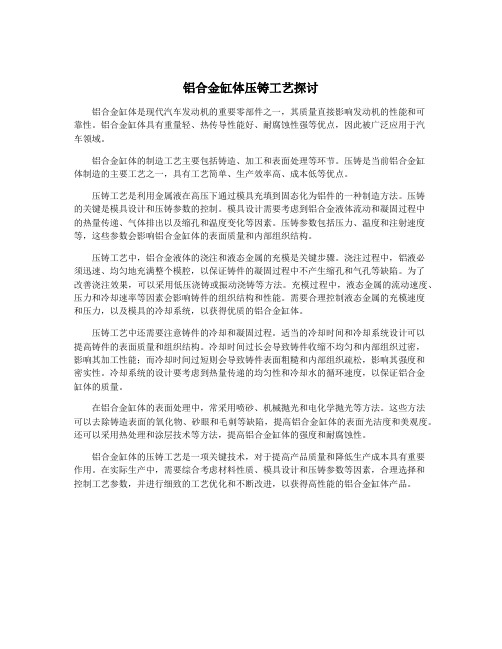
铝合金缸体压铸工艺探讨铝合金缸体是现代汽车发动机的重要零部件之一,其质量直接影响发动机的性能和可靠性。
铝合金缸体具有重量轻、热传导性能好、耐腐蚀性强等优点,因此被广泛应用于汽车领域。
铝合金缸体的制造工艺主要包括铸造、加工和表面处理等环节。
压铸是当前铝合金缸体制造的主要工艺之一,具有工艺简单、生产效率高、成本低等优点。
压铸工艺是利用金属液在高压下通过模具充填到固态化为铝件的一种制造方法。
压铸的关键是模具设计和压铸参数的控制。
模具设计需要考虑到铝合金液体流动和凝固过程中的热量传递、气体排出以及缩孔和温度变化等因素。
压铸参数包括压力、温度和注射速度等,这些参数会影响铝合金缸体的表面质量和内部组织结构。
压铸工艺中,铝合金液体的浇注和液态金属的充模是关键步骤。
浇注过程中,铝液必须迅速、均匀地充满整个模腔,以保证铸件的凝固过程中不产生缩孔和气孔等缺陷。
为了改善浇注效果,可以采用低压浇铸或振动浇铸等方法。
充模过程中,液态金属的流动速度、压力和冷却速率等因素会影响铸件的组织结构和性能。
需要合理控制液态金属的充模速度和压力,以及模具的冷却系统,以获得优质的铝合金缸体。
压铸工艺中还需要注意铸件的冷却和凝固过程。
适当的冷却时间和冷却系统设计可以提高铸件的表面质量和组织结构。
冷却时间过长会导致铸件收缩不均匀和内部组织过密,影响其加工性能;而冷却时间过短则会导致铸件表面粗糙和内部组织疏松,影响其强度和密实性。
冷却系统的设计要考虑到热量传递的均匀性和冷却水的循环速度,以保证铝合金缸体的质量。
在铝合金缸体的表面处理中,常采用喷砂、机械抛光和电化学抛光等方法。
这些方法可以去除铸造表面的氧化物、砂眼和毛刺等缺陷,提高铝合金缸体的表面光洁度和美观度。
还可以采用热处理和涂层技术等方法,提高铝合金缸体的强度和耐腐蚀性。
铝合金缸体的压铸工艺是一项关键技术,对于提高产品质量和降低生产成本具有重要作用。
在实际生产中,需要综合考虑材料性质、模具设计和压铸参数等因素,合理选择和控制工艺参数,并进行细致的工艺优化和不断改进,以获得高性能的铝合金缸体产品。
汽车铝合金轮毂铸造工艺研究分析
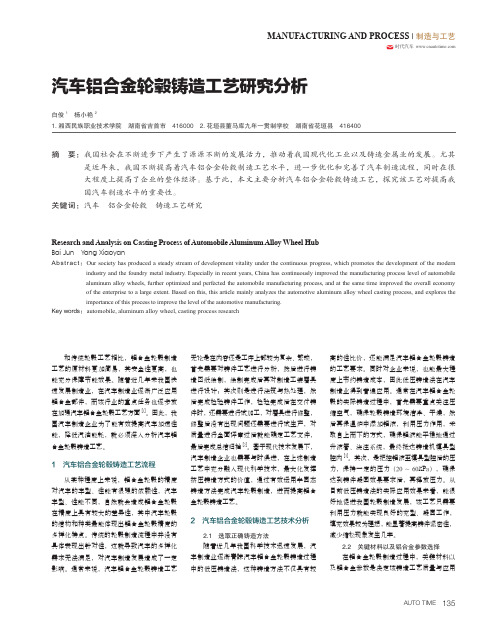
MANUFACTURING AND PROCESS | 制造与工艺时代汽车 汽车铝合金轮毂铸造工艺研究分析白俊1 杨小艳21.湘西民族职业技术学院 湖南省吉首市 4160002.花垣县董马库九年一贯制学校 湖南省花垣县 416400摘 要: 我国社会在不断进步下产生了源源不断的发展活力,推动着我国现代化工业以及铸造金属业的发展。
尤其是近年来,我国不断提高着汽车铝合金轮毂制造工艺水平,进一步优化和完善了汽车制造流程,同时在很大程度上提高了企业的整体经济。
基于此,本文主要分析汽车铝合金轮毂铸造工艺,探究该工艺对提高我国汽车制造水平的重要性。
关键词:汽车 铝合金轮毂 铸造工艺研究和传统轮毂工艺相比,铝合金轮毂制造工艺的原材料更加简易,其安全性更高,也能充分保障节能效果。
随着近几年来我国快速发展制造业,在汽车制造业逐渐广泛应用铝合金部件,而该行业的重点任务也逐步放在加强汽车铝合金轮毂工艺方面[1]。
因此,我国汽车制造企业为了能有效提高汽车加速性能,降低汽油能耗,就必须深入分析汽车铝合金轮毂铸造工艺。
1 汽车铝合金轮毂铸造工艺流程从某种程度上来说,铝合金轮毂的精度对汽车的车型、性能有很强的依赖性,汽车车型、性能不同,自然就会造成铝合金轮毂在精度上具有较大的差异性,其中汽车轮毂的结构和种类最能体现出铝合金轮毂精度的多样化特点。
传统的轮毂制造流程中并没有具体表现出针对性,这就导致汽车的多样化需求无法满足,对汽车制造发展造成了一定影响。
通常来说,汽车铝合金轮毂铸造工艺无论是在内容还是工序上都较为复杂、繁琐,首先需要对铸件工艺进行分析,然后进行铸造图纸绘制,绘制完成后再对制造工装磨具进行设计;其次则是进行浇筑与热处理,然后完成检验铸件工作,检验完成后在交付铸件时,还需要进行试加工,对磨具进行修整,修整后没有出现问题还需要进行试生产,对质量进行全面评审过后就能确定工艺文件,最后完成总结归档[2]。
基于现代技术发展下,汽车制造企业也需要与时俱进,在上述制造工艺中充分融入现代科学技术,最大化发挥挤压铸造方式的价值,通过有效运用半固态铸造方法完成汽车轮毂制造,进而提高铝合金轮毂铸造工艺。
汽车铝合金轮毂低压铸造工艺分析

汽车铝合金轮毂低压铸造工艺分析发表时间:2019-09-11T16:42:59.423Z 来源:《基层建设》2019年第17期作者:蒋才坚[导读] 摘要:随着我国制造业、汽车行业的快速发展,对汽车铝合金轮毂铸造技术工艺的应用提出较高要求。
广东肇庆动力金属股份有限公司 526020摘要:随着我国制造业、汽车行业的快速发展,对汽车铝合金轮毂铸造技术工艺的应用提出较高要求。
特别以往工艺应用下,多采用钢制轮毂,整体性能较差,所以考虑引入安全性、轻便性特征明显的铝合金材料,但如何在铝合金轮毂铸造工艺水平上提高,成为目前需考虑的主要问题。
为了实现汽车铝合金轮毂铸造工艺的更好发展,本文对汽车铝合金轮毂铸造工艺进行简要分析,通过阐述汽车铝合金轮毂铸造的重要性,加强汽车铝合金轮毂铸造工艺的关键技术,提出几点参考性建议,为促进汽车制造发展献力。
关键词:汽车轮毂;铝合金轮毂;铸造工艺近年来,汽车行业处于快速发展时期,国内外的整车供应商不但在供货量上稳步提升,还在车型的设计、结构的改进以及材料的使用等方面不断的推陈出新,由此也带来了汽车零部件产业的发展与繁荣时期。
轮毂作为汽车整体结构中的一个重要组成部分,在汽车的安全性和外观美化方面有不可估量的作用。
因此,一直以来轮毂的设计与开发都得到了广大研发人员的关注和重视。
随着全球资源的日益紧张,以及人们节能环保观念的日益加深,汽车轻量化已经成为时代的主题。
要实现轻量化有三种途径:第一种是结构的改进优化;第二种是使用新材料;第三种是改进现有工艺技术。
对于汽车轮毂来讲,多年以来对其结构的改进优化已经做了很多工作,在这个基础上进行轻量化设计的提升空间不大。
近年来,汽车轮毂中开始大量使用铝合金、镁合金等质量轻、强度高的材料来替代以往的钢质材料,取得了不错节能减排效果。
在车轮的成形工艺方面,目前以低压铸造工艺为主要生产方式,利用这种方式生产的轮毂占到了市场总额的80%左右。
该工艺在实现大规模的自动化生产和提高材料的利用率等方面具有很大的优势,因此,在业内被广泛的采用。
汽车铝压铸件研究报告

汽车铝压铸件研究报告
【摘要】
汽车铝压铸件是一种重要的汽车零部件,对于提高汽车性能和降低汽车重量具有重要意义。
本研究通过对汽车铝压铸件的制造工艺、性能以及应用进行了详细的研究和分析,旨在深入了解汽车铝压铸件的相关知识,并为其在汽车制造领域的应用提供参考。
【正文】
1. 汽车铝压铸件的制造工艺
汽车铝压铸件的制造工艺包括铸型设计、熔炼铸造、铸型填充、凝固收缩、冷却、去毛刺、机械加工等环节。
其中,铸型设计是关键步骤,合理的铸型设计能够提高铝压铸件的质量和性能。
2. 汽车铝压铸件的性能
汽车铝压铸件具有优良的力学性能和耐磨性能,可以满足汽车在高速行驶过程中对零部件强度和稳定性的要求。
同时,铝压铸件重量轻、成本低,并且易于加工和制造,具有良好的成型性和可塑性。
3. 汽车铝压铸件的应用
汽车铝压铸件广泛应用于汽车发动机、车身和底盘等部位。
例如,汽车发动机缸体和缸盖、转向机壳、变速箱壳体等都是由铝压铸件制造而成。
这些铝压铸件具有优良的耐热性和抗腐蚀性能,在汽车制造中起到关键作用。
【结论】
汽车铝压铸件作为一种重要的汽车零部件,在提高汽车性能和降低汽车重量方面具有重要意义。
本研究通过对汽车铝压铸件的制造工艺、性能以及应用的研究和分析,对于深入了解和推动汽车铝压铸件的发展具有重要意义。
建议在今后的研究中继续加强对汽车铝压铸件的材料和制造工艺的探索,进一步提高其质量和性能,推动其在汽车制造领域的广泛应用。
汽车铝合金轮毂铸造技术探讨
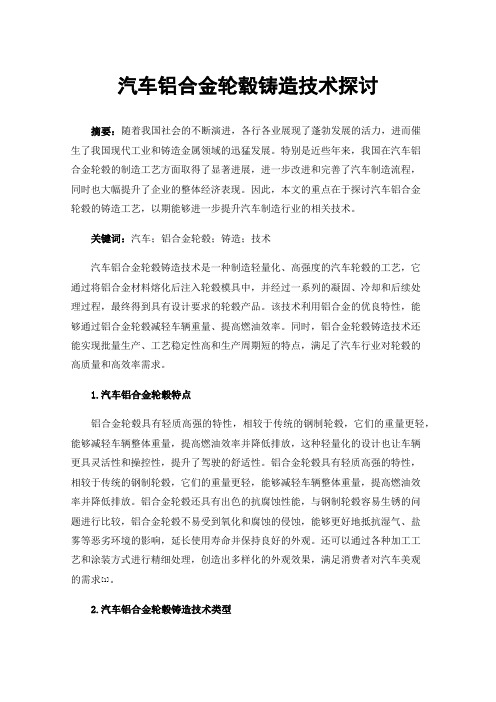
汽车铝合金轮毂铸造技术探讨摘要:随着我国社会的不断演进,各行各业展现了蓬勃发展的活力,进而催生了我国现代工业和铸造金属领域的迅猛发展。
特别是近些年来,我国在汽车铝合金轮毂的制造工艺方面取得了显著进展,进一步改进和完善了汽车制造流程,同时也大幅提升了企业的整体经济表现。
因此,本文的重点在于探讨汽车铝合金轮毂的铸造工艺,以期能够进一步提升汽车制造行业的相关技术。
关键词:汽车;铝合金轮毂;铸造;技术汽车铝合金轮毂铸造技术是一种制造轻量化、高强度的汽车轮毂的工艺,它通过将铝合金材料熔化后注入轮毂模具中,并经过一系列的凝固、冷却和后续处理过程,最终得到具有设计要求的轮毂产品。
该技术利用铝合金的优良特性,能够通过铝合金轮毂减轻车辆重量、提高燃油效率。
同时,铝合金轮毂铸造技术还能实现批量生产、工艺稳定性高和生产周期短的特点,满足了汽车行业对轮毂的高质量和高效率需求。
1.汽车铝合金轮毂特点铝合金轮毂具有轻质高强的特性,相较于传统的钢制轮毂,它们的重量更轻,能够减轻车辆整体重量,提高燃油效率并降低排放,这种轻量化的设计也让车辆更具灵活性和操控性,提升了驾驶的舒适性。
铝合金轮毂具有轻质高强的特性,相较于传统的钢制轮毂,它们的重量更轻,能够减轻车辆整体重量,提高燃油效率并降低排放。
铝合金轮毂还具有出色的抗腐蚀性能,与钢制轮毂容易生锈的问题进行比较,铝合金轮毂不易受到氧化和腐蚀的侵蚀,能够更好地抵抗湿气、盐雾等恶劣环境的影响,延长使用寿命并保持良好的外观。
还可以通过各种加工工艺和涂装方式进行精细处理,创造出多样化的外观效果,满足消费者对汽车美观的需求[1]。
2.汽车铝合金轮毂铸造技术类型2.1重力铸造这种铸造技术主要通过重力作用,将熔化的铝合金材料注入到预先制作好的铸型中,然后在自然重力的作用下,使铝液充分填充整个模具腔体,最终形成轮毂的形状。
它不需要高压力或复杂的设备,只需利用重力即可完成铝液的充填过程,因此生产成本相对较低,适用于大规模生产,由于铝液在注入过程中没有额外的压力作用,可以避免气体和杂质的夹杂,从而提高轮毂的密度和强度。
- 1、下载文档前请自行甄别文档内容的完整性,平台不提供额外的编辑、内容补充、找答案等附加服务。
- 2、"仅部分预览"的文档,不可在线预览部分如存在完整性等问题,可反馈申请退款(可完整预览的文档不适用该条件!)。
- 3、如文档侵犯您的权益,请联系客服反馈,我们会尽快为您处理(人工客服工作时间:9:00-18:30)。
浅析汽车铝合金铸造的工艺性能
作者:林润琛
来源:《环球市场》2017年第20期
摘要:随着轻量化发展的要求,汽车工业广泛采用铝合金代替钢铁部件以减轻整车重量,从而降低排放,节约材料。
铝合金铸造工艺性能,通常理解为在充满铸型、结晶和冷却过程中表现最为突出的那些性能的综合。
铝合金材料可以用来减轻汽车重量,实现汽车轻量化。
汽车发动机的缸体缸盖是汽车所有零件中最重的,而且最重要,结构也很复杂。
基于此,文章就汽车铝合金铸造的工艺性能进行简要的分析。
关键词:汽车;铝合金铸造;工艺性能
1.汽车铝合金铸造的工艺性能
1.1铝合金铸造工艺的流动性
流动性是指合金液体充填铸型的能力。
流动性的大小决定合金能否铸造复杂的铸件。
在铝合金中共晶合金的流动性最好。
常见铝合金铸造时流动性的影响有:充型能力首先取决于金属液体本身的流动能力(即流动性),同时又受铸造工艺隐身(如:铸型性质、浇筑条件及铸件结构等)的影响。
影响流动性的因素很多,主要是成分、温度以及合金液体中存在金属氧化物、金属化合物及其他污染物的固相颗粒,但外在的根本因素为浇注温度及浇注压力(俗称浇注压头)的高低。
1.2铝合金铸造工艺的收缩性
收缩性是铸造铝合金的主要特征之一。
一般讲,合金从液体浇注到凝固,直至冷到室温,共分为三个阶段,分别为液态收缩、凝固收缩和固态收缩。
合金的收缩性对铸件质量有决定性的影响,它影响着铸件的缩孔大小、应力的产生、裂纹的形成及尺寸的变化。
通常铸件收缩又分为体收缩和线收缩,在实际生产中一般应用线收缩来衡量合金的收缩性。
铝合金收缩大小,通常以百分数来表示,称为收缩率。
1.3铝合金铸造工艺的热裂性
铝铸件热裂纹的产生,主要是由于铸件收缩应力超过了金属晶粒间的结合力,大多沿晶界产生从裂纹断口观察可见裂纹处金属往往被氧化,失去金属光泽。
裂纹沿晶界延伸,形状呈锯齿形,表面较宽,内部较窄,有的则穿透整个铸件的端面。
1.4铝合金铸造工艺的气密性
铸铝合金气密性是指腔体型铝铸件在高压气体或液体的作用下不渗漏程度,气密性实际上表征了铸件内部组织致密与纯净的程度。
不同铸铝合金气密性不同,它与合金的性质有关,合金凝固范围越小,产生疏松倾向也越小,同时产生析出性气孔也少,则合金的气密性也越高。
1.5铝合金铸造工艺的铸造应力
铸造应力一般包括:铸造热应力、相变应力和收缩应力三种。
各种应力产生的原因不尽相同。
它们在铝铸件中的残余应力降低了合金的力学性能,严重影响了铸件的加工精度。
当然铝铸件中的残余应力也可以通过退火处理预以消除。
一Si合金因导热性好,冷却过程中无相变,只要铸件结构设计合理,铝铸件中的残余应力就较少。
2.以汽车铝合金缸体缸盖铸造工艺为例分析
研究发动机的缸体缸盖材质和铸造工艺,一方面可实现汽车轻量化,另一方面还涉及到发动机内部复杂的结构和工艺。
2.1主要的铸造工艺分析
2.1.1金属型铸造工艺。
在汽车发动机缸体缸盖主要铸造方法中,有比较先进的方法,也有传统的方法,比如金属型铸造工艺就是一种典型的传统铸造方法。
其优点在于铸造时间快,铸造零件组织紧密,性能良好。
但是缺点也很明显,其所生产的铸件内部有空气,有开裂的纹路等。
由于对于发动机缸体缸盖质量要求很高,因此单一的金属型铸造工艺所生产的零部件不一定符合发动机要求。
金属型铸造工艺的成本高,周期长,不适合小批量生产,关于缸体缸盖的制造方面,可针对外形采取该工艺,内腔采用砂芯,二者结合就会起到事半功倍的效果。
2.2.2中压铸造工艺。
中压铸造工艺具有高压铸造不能替代的优势,比如可以使用砂芯。
其主要是经由高压铸造改造的。
改造后的重压铸造工艺可以进一步满足要求越来越高的发动机功率和日益复杂的缸体结构,而且,可以使用砂芯是中压铸造工艺的突破点。
其主要原理就是通过比高压要低的压力进行铸造,同时可以使用砂芯,适用于复杂内腔结构的缸体。
2.2.3低压铸造工艺。
低压铸造工艺结合了上述铸造工艺的优势,使用的压力更低,可以充分利用铸造材料,铸造出更加牢固、密闭的缸体。
其利用了较低的压力,使铝合金液体由下而上的对型腔进行填充。
低压铸造工艺的有点是显而易见的,比如金属液体充型的速度可以方便调节,铸件质量更高。
其不仅可以使用砂芯,适合更加复杂的结构,还能够以较低的压力实现铸造。
缺点是铸造时间长,效率低,成品率低。
2.2铸件低压铸造工艺设计
2.2.1加工余量与收缩率。
铸造工艺设计中,在满足产品要求基础上,采用增大起模斜度、调整机械加工量及增加工艺余量等措施,与铸造工艺条件相满足。
缸体铸件机械加工余量:小平面为(1.5±0.5)mm,大平面为(2.5±0.5)mm,根据7级精度对铸件尺寸差进行控
制。
在汽车发动机缸体低压铸造过程中,依照产品结构特征与铸件材料AC4B,设置模具收缩率为0.7%。
2.2.2模具中铸件位置。
低压铸造模具中,对铸件位置予以确定时,禁止违背顺序凝固原则,应对汽车发动机缸体结构特性进行分析的基础上,对低压铸造过程中液体金属补缩铸件所需的条件予以充分利用,创建一个由底壳结合面至发动机缸体结合面,以安装在缸体的螺栓孔处为实际浇注位置。
2.2.3模具结构形式设计。
为达到顺利开模的目的,应采用多分型面的方式从6大方向对模具进行开模,具体为:顶模、底模、左模、前模、右模、后模。
2.2.4模具冷却系统设计。
工艺过程中热量向模具传入与从模具中传出应该保持平衡,所以要在模具中对水冷系统进行设置,以保证及时传出模具中的热量。
设计中通过调整通入模具冷却水流量与时间,对模具温度进行控制,实际生产中,铸件与浇道相远离的水泵孔凸台厚大部位,容易出现铸造缺陷,所以应注意通过局部水冷对模具温度进行控制,先凝固厚大部位,保证该部位组织细密。
综上,铝是绿色环保材料,易回收,可循环回收。
采用铝所节省的能量是生产该零件所用原铝耗能的6~12倍。
我国车用铝合金市场的发展前景非常广阔。
在汽车中扩大铝合金的应用将会产生巨大的经济效益和社会效益。
参考文献:
[1]李晓强.铝合金轮毂,汽车轮胎材料建设的新方向——针对汽车铝合金轮毂的铸造工艺研究[J].黑龙江科技信息,2016,27:124.。