塑炼工艺3—塑炼方法及影响因素31页PPT
第8章 塑炼工艺

辊速和速比
• 辊距一定,提高开炼机的辊速或速比会增 大胶料的机械剪切作用,从而提高机械塑 炼效果。
• 开炼机的速比一般在1.15-1.27之间。 • 速比过大,升温加快,又会降低塑炼效果。
辊温
• 辊温低,塑炼效果好。辊温过低容易造成 设备超负荷而受到损害。
• 塑炼温度与生胶胶种有关,NR通常控制前 辊温度在45-55℃,后辊温度在40-50℃ 为宜。
• 缺点:劳动强度大,生产效率低。
包辊塑炼法
• 特点:把胶片包在前辊上,让其自然地反复过辊 塑炼,直至达到规定的可塑度要求为止。
• 优点:劳动强度低。 • 缺点:散热慢,塑炼时间长,效率低,最终获得
的可塑度也较低。不适于可塑度要求高的。 • 分段塑炼:先将胶料包辊塑炼一定时间,然后下
片冷却4~8小时,再进行第二次塑炼。 • 目的:消除由于温度升高引起的假可塑度,提高
二.塑炼的目的和要求
1.塑炼的目的 (1)减小弹性,提高可塑性; (2)降低粘度,提高胶料的共混性能; (3) 改善流动性,提高胶料的成型性能; (4)提高胶料溶解性和成型粘着性。
2.塑炼胶的质量要求:在能满足后续工艺 要求的条件下可塑度越低越好。 (1)可塑度要适当; (2)塑炼要均匀。
确定适当可塑度的依据
• 加工要求:混炼加工:门尼粘度≤60 压延擦胶:门尼粘度≤40 发泡制品:门尼粘度更低
• 性能要求:不同制品的要求不一样。 如胎面胶和胎侧胶的要求不一样。
可塑度不当易引起的问题
• 可塑度过高 压出半成品挺性不好; 胶料容易粘辊; 胶料容易流失; 强度性能下降。
• 可塑度过低 混炼时配合剂不易加入; 压延时半成品易掉皮,出现漏白; 压延、压出半成品收缩大; 胶料流动性差,产品易有缺陷。
塑炼工艺3—塑炼方法及影响因素
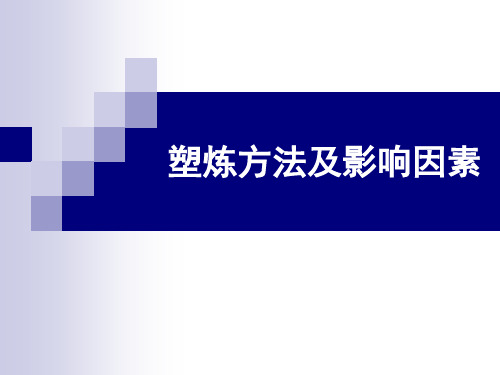
2.喂料速度 . 喂料速度要适当而均匀。速度过快, 喂料速度要适当而均匀。速度过快, 胶料在机筒内的停留时间短,塑炼不均匀, 胶料在机筒内的停留时间短,塑炼不均匀, 出现夹生现象。速度太慢, 出现夹生现象。速度太慢,不仅降低生产 效率。 效率。 3.排胶孔隙大小 . 排胶孔隙大小依胶料塑炼程度要求而 孔隙小,排胶速度和排胶量减小, 定。孔隙小,排胶速度和排胶量减小,胶 料可塑度偏大,生产效率降低。反之, 料可塑度偏大,生产效率降低。反之,出 胶孔隙加大,排胶量大,生产能力提高, 胶孔隙加大,排胶量大,生产能力提高, 但塑炼胶的可塑度偏低且不均匀。 但塑炼胶的可塑度偏低且不均匀。
五.塑炼后的补充加工 1.压片或造粒 . 2.冷却与干燥 . 3.停放 . 干燥后的胶片按规定堆放4~8h以上才 干燥后的胶片按规定堆放 以上才 能恭下道工序使用。 能恭下道工序使用。 4.质量检验 .
常用橡胶的塑炼特性
一.橡胶塑炼难易的原因 1.NR塑炼容易的原因 . 塑炼容易的原因 (1)大分子中存在甲基和双键的共轭效应, )大分子中存在甲基和双键的共轭效应, 键能降低,易断裂; 键能降低,易断裂; (2)分子量大,易断链; )分子量大,易断链; (3)大分子断链后生成的自由基稳定性高; )大分子断链后生成的自由基稳定性高; (4)大分子氧化生成的氢过氧化物分解导致 ) 大分子链断裂破坏。 大分子链断裂破坏。
塑炼方法及影响因素
一.准备工艺 1.烘胶 . NR烘胶温度一般在 烘胶温度一般在50~60℃,时间为 烘胶温度一般在 ℃ 24~36h,冬季加热时间为 ,冬季加热时间为36~72h。 。 CR烘胶温度一般在 烘胶温度一般在24~40℃,时间为 烘胶温度一般在 ℃ 时间为4~6h。 。 烘胶温度不宜过高, 烘胶温度不宜过高,否则会影响橡胶的物理 机械性能。 机械性能。 2.切胶 . 用切胶机将生胶切成小块, 用切胶机将生胶切成小块,每块重量视胶种 而异, 每块 每块10~20kg,CR每块不超过 每块不超过10kg。 而异,NR每块 , 每块不超过 。 3.破胶 . 橡胶块需用破胶机破胶,以便塑炼。 橡胶块需用破胶机破胶,以便塑炼。破胶辊 距一般为2~3mm,辊温控制在45℃以下。 距一般为 ,辊温控制在 ℃以下。
橡胶工艺之塑炼(机理及常见的塑炼方式)
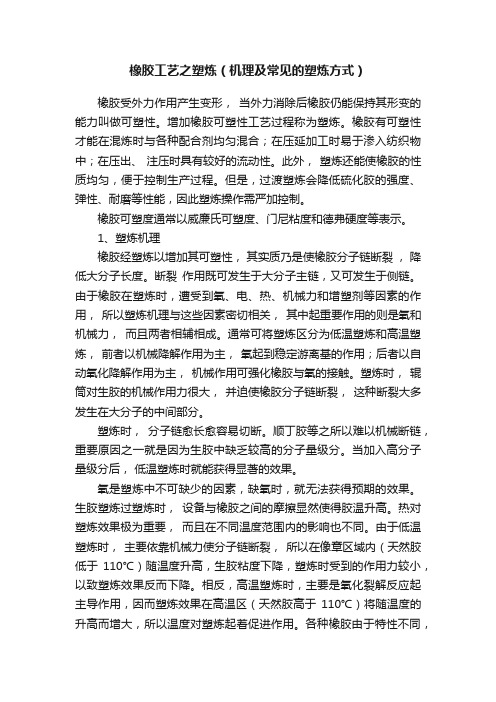
橡胶工艺之塑炼(机理及常见的塑炼方式)橡胶受外力作用产生变形,当外力消除后橡胶仍能保持其形变的能力叫做可塑性。
增加橡胶可塑性工艺过程称为塑炼。
橡胶有可塑性才能在混炼时与各种配合剂均匀混合;在压延加工时易于渗入纺织物中;在压出、注压时具有较好的流动性。
此外,塑炼还能使橡胶的性质均匀,便于控制生产过程。
但是,过渡塑炼会降低硫化胶的强度、弹性、耐磨等性能,因此塑炼操作需严加控制。
橡胶可塑度通常以威廉氏可塑度、门尼粘度和德弗硬度等表示。
1、塑炼机理橡胶经塑炼以增加其可塑性,其实质乃是使橡胶分子链断裂,降低大分子长度。
断裂作用既可发生于大分子主链,又可发生于侧链。
由于橡胶在塑炼时,遭受到氧、电、热、机械力和增塑剂等因素的作用,所以塑炼机理与这些因素密切相关,其中起重要作用的则是氧和机械力,而且两者相辅相成。
通常可将塑炼区分为低温塑炼和高温塑炼,前者以机械降解作用为主,氧起到稳定游离基的作用;后者以自动氧化降解作用为主,机械作用可强化橡胶与氧的接触。
塑炼时,辊筒对生胶的机械作用力很大,并迫使橡胶分子链断裂,这种断裂大多发生在大分子的中间部分。
塑炼时,分子链愈长愈容易切断。
顺丁胶等之所以难以机械断链,重要原因之一就是因为生胶中缺乏较高的分子量级分。
当加入高分子量级分后,低温塑炼时就能获得显著的效果。
氧是塑炼中不可缺少的因素,缺氧时,就无法获得预期的效果。
生胶塑炼过塑炼时,设备与橡胶之间的摩擦显然使得胶温升高。
热对塑炼效果极为重要,而且在不同温度范围内的影响也不同。
由于低温塑炼时,主要依靠机械力使分子链断裂,所以在像章区域内(天然胶低于110℃)随温度升高,生胶粘度下降,塑炼时受到的作用力较小,以致塑炼效果反而下降。
相反,高温塑炼时,主要是氧化裂解反应起主导作用,因而塑炼效果在高温区(天然胶高于110℃)将随温度的升高而增大,所以温度对塑炼起着促进作用。
各种橡胶由于特性不同,对应于最低塑炼效果的温度范围也不一样,但温度对塑炼效果影响的曲线形状是相似的。
第三章 塑炼混炼
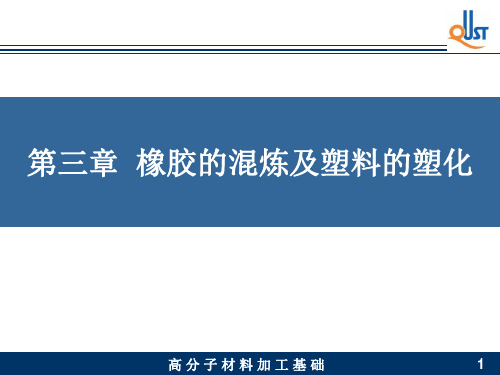
(-)混炼理论
混炼不是生胶和配合剂简单的机械混合过程,混 炼胶也不是生胶与配合剂的简单机械混合物; 混炼的实质是橡胶的改性过程。期间,机械力/化 学反应起着重要作用; 混炼胶是由生胶和各种配合剂组成的一种复合体。
(1)、准备工作
为了便于塑炼 加工,生胶需 要经过烘胶、
切胶和破胶等
塑炼前的准备 工艺。
生胶,长期储存后,粘度很高, 且在冬天常因结晶而硬化。 切胶后的NR、CR一 为便于使用,把烘好的 在切胶和塑炼前把生胶放在烘房 般要在破胶机上进 大胶包用切胶机切成小 中预先对胶包进行加温,便于切 行破胶,以便进行 块 割和进一步的加工。 塑炼。 烘胶的温度和时间视生胶的种类 与季节而定。
高分子材料加工基础 18
2、塑炼的原理
熔体粘度——加工温度、切变速率、分子量。 分子量越小,可塑度越大。生胶经机械塑炼后, 分子量降低,粘度下降,可塑性增加。 生胶在塑炼过程中可塑性的提高是通过分子量的
降低来实现的。
塑炼的实质是使橡胶大分子链断裂,大分子链由
长变短的过程。
高分子材料加工基础
高分子材料加工基础 6
工作原理:
两个辊筒以不同的表面速度
相对回转,物料由于与辊筒
表面的摩擦和粘附作用,以
及物料之间的粘接作用,被
拉入两辊筒之间的间隙之内。
高分子材料加工基础
7
工作原理:
受到强烈的挤压与剪切,使物料在辊隙内形成楔形 断面的料片,从辊隙中排出的料片由于两个辊筒表 面速度和温度的差异而包在一个辊筒上,重新返回 两辊间。
高分子材料加工基础
21
剪切力作用于橡胶时,分子链将沿流动方向伸展;
橡胶塑炼与混炼—塑炼(橡胶加工课件)

保持变形后的形状
降低弹性、增大塑性 塑炼
塑炼
1、塑炼概念与原理
讨论:塑炼、塑炼目的及不利面
分组汇报: 教师点评 1、塑炼: 炼:炼胶、炼胶作业,在炼胶机完成的作业过程。
简要:提高橡胶塑性的炼胶
详细:将橡胶经过机械加工、热处理或加入某些化学助剂,使其由强韧的弹性状态转变为柔 软而便于加工的塑性状态的工艺过程称之为塑炼。
塑炼
1、塑炼概念与原理 2、生胶塑炼前的准备 3、塑炼的工艺方法 4、影响塑炼的工艺因素 5、开炼机塑炼实训 6、常见塑炼胶质量分析
1、塑炼概念与原理
引入新课 F 塑性
F 弹性
F 刚性
1、塑炼概念与原理
引入新课 橡胶具有高弹性 优点:
缓冲、减震、柔软
缺点:
产品加工过程是受力变形并定型,如发生弹性回复,尺寸形状不能保持
2、生胶塑炼前的准备-烘胶
目的
对象
“两保证两可以” (1)保证切胶机的安全操作和
工作效率; (2)保证炼胶机的安全操作和
工作效率; (3)可以烘去水份; (4)可以解除结晶(对结晶橡
胶) 。
(1)硬橡胶 如:硬NBR等 (NBR3606)
(2)结晶橡胶 如:NR、CR 等
实物展示 ( NBR 、NR、CR、 EPDM、SBR、BR)
2、生胶塑炼前的准备-破胶
使块状的橡胶变为碎胶 (1)便于称量; (2)便于塑炼; (3)保护设备; (4)提高效率(塑
炼)。
用于开炼机塑混炼的大块橡胶, 如:NR和CR。 说明: ❖ 1、用密炼机塑混炼的NR和CR, 一般无需破胶而直接进行塑混炼。 ❖ 2、其它合成橡胶,一般无需破 胶而直接进行塑混炼。
6、常见塑炼胶质量分析
之二PPT-如何用薄通法塑炼橡胶

如何用薄通法塑炼橡胶
内容
1. 适用范围
薄通法
2. 操作技术要素
3. 实操
橡胶 让生活更美好
如何用薄通法塑炼橡胶
一、适用范围
开炼机塑炼 √
1、薄通法适用范围
密炼机塑炼
×
螺杆机塑炼
×
橡胶 让生活更美好
如何用薄通法塑炼橡胶
剪切力
2、原理
机械塑炼
挤压力
橡胶 让生活更美好
如何用薄通法塑炼橡胶
二、薄通法操作技术要素
橡胶 让生活更美好
如何用薄通法塑炼橡胶
2、操作 步骤:五步
调节辊距
1) 调节辊距
2) 第一次投胶
投胶
薄通
3) 薄通 4) 旋转胶料
旋转胶料
5) 再次投胶循环
橡胶 让生活更美好
如何用薄通法塑炼橡胶
第一步:调节辊距
辊距:0.5mm
注: 1).空载 2).空转或停车 3).一致 4). 同调
橡胶 让生活更美好
如何用薄通法塑炼橡胶
第二步:第一次加胶
注: 1).位置 2).借力 3).分离 4).安全 a. 手 b. 投进 c. 停车处理
橡胶 让生活更美好
如何用薄通法塑炼橡胶
第三步:薄通
注: 仔细观察
橡胶 让生活更美好
如何用薄通法塑炼橡胶
第四步:旋转胶料
旋转90度
注: 左旋右旋
橡胶 让生活更美好
如何用薄通法塑炼橡胶
1. 低 2. 薄 3. 通 4. 90
橡胶 让生活更美好
如何用薄通法塑炼橡胶
1. 低
温度低
机械力大 P
40~70℃
?? 能不能温度调节很低 T
生胶的塑炼工艺
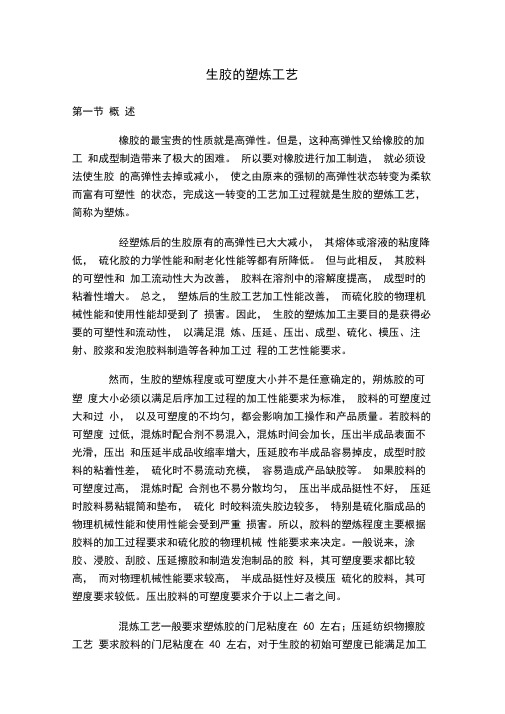
生胶的塑炼工艺第一节概述橡胶的最宝贵的性质就是高弹性。
但是,这种高弹性又给橡胶的加工和成型制造带来了极大的困难。
所以要对橡胶进行加工制造,就必须设法使生胶的高弹性去掉或减小,使之由原来的强韧的高弹性状态转变为柔软而富有可塑性的状态,完成这一转变的工艺加工过程就是生胶的塑炼工艺,简称为塑炼。
经塑炼后的生胶原有的高弹性已大大减小,其熔体或溶液的粘度降低,硫化胶的力学性能和耐老化性能等都有所降低。
但与此相反,其胶料的可塑性和加工流动性大为改善,胶料在溶剂中的溶解度提高,成型时的粘着性增大。
总之,塑炼后的生胶工艺加工性能改善,而硫化胶的物理机械性能和使用性能却受到了损害。
因此,生胶的塑炼加工主要目的是获得必要的可塑性和流动性,以满足混炼、压延、压出、成型、硫化、模压、注射、胶浆和发泡胶料制造等各种加工过程的工艺性能要求。
然而,生胶的塑炼程度或可塑度大小并不是任意确定的,朔炼胶的可塑度大小必须以满足后序加工过程的加工性能要求为标准,胶料的可塑度过大和过小,以及可塑度的不均匀,都会影响加工操作和产品质量。
若胶料的可塑度过低,混炼时配合剂不易混入,混炼时间会加长,压出半成品表面不光滑,压出和压延半成品收缩率增大,压延胶布半成品容易掉皮,成型时胶料的粘着性差,硫化时不易流动充模,容易造成产品缺胶等。
如果胶料的可塑度过高,混炼时配合剂也不易分散均匀,压出半成品挺性不好,压延时胶料易粘辊筒和垫布,硫化时皎料流失胶边较多,特别是硫化脂成品的物理机械性能和使用性能会受到严重损害。
所以,胶料的塑炼程度主要根据胶料的加工过程要求和硫化胶的物理机械性能要求来决定。
一般说来,涂胶、浸胶、刮胶、压延擦胶和制造发泡制品的胶料,其可塑度要求都比较高,而对物理机械性能要求较高,半成品挺性好及模压硫化的胶料,其可塑度要求较低。
压出胶料的可塑度要求介于以上二者之间。
混炼工艺一般要求塑炼胶的门尼粘度在60 左右;压延纺织物擦胶工艺要求胶料的门尼粘度在40 左右,对于生胶的初始可塑度已能满足加工性能要求的生胶,一般不需再行塑炼加:正,可以直接进行混炼。
生胶的塑炼工艺课件(PPT31张)
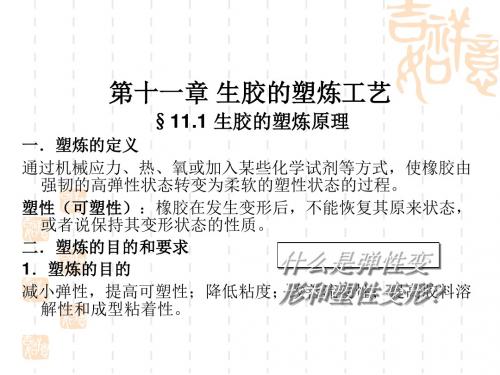
第十一章 生胶的塑炼工艺
(三)开炼机塑炼的影响因素
1.装胶容量 装胶容量取决于开炼机的规格,容量大,散热困难,胶温升高,降低塑炼 效果;容量过小则降低生产效率。 合理的容量根据经验公式计算:
Q K D L
Q—塑炼容量,L;K—经验系数,取值一般为0.0065~0.0085,L/cm3; D—辊筒直径,cm;L—辊筒工作部分长度,cm 合成橡胶塑炼时生热大,装胶容量应比NR少。 2.辊距 辊距越小,机械塑炼效果越明显。薄通时实际使用辊距一般为0.5~1mm。
第十一章 生胶的塑炼工艺
2.薄通塑炼法 辊距在1 mm以下,胶料通过辊距后不包辊而 直接落到接胶盘,让胶料返回到辊距上方重新通过 辊距,这样反复数次。 优点:胶料散热快,冷却效果较好,塑炼胶可塑度均 匀,质量高,能达到任意的塑炼程度。 3.化学增塑塑炼法 采用化学塑解剂增加塑炼效果,提高塑炼生产效 率并节约能耗。化学塑解剂应以母胶的形式使用, 并应适当提高开炼机的辊温。
第十一章 生胶的塑炼工艺
2.转速 转速快,塑炼效率高。转速从25转提高到75转,塑炼时间从30min缩短到10min。 转速的提高必然会加速胶料生热升温,因此必须加强冷却。 3.时间 用密炼机塑炼,胶料的可塑度随塑炼时间的增加而增加。使用塑解剂进行塑炼时, 塑炼效果会提高,塑炼时间可缩短30%~50%。 4.上顶栓压力 上顶栓必须加压,以增加转子对胶料的剪切作用。压力过小,不能压紧胶料,但压 力过大,又会造成设备负荷过大。上顶栓压力一般为0.5~0.8MPa。 5.装胶容量 各种规格密炼机的装胶容量为密炼室容积的48%~62%。 6.化学塑解剂 密炼机塑炼温度高,采用化学塑解剂增塑法合理有效,不仅能充分地发挥塑解剂的 增塑效果,而且在同样条件下会降低排胶温度,提高塑炼胶质量。
橡胶塑炼的目的原理及其影响因素

橡胶塑炼的目的原理及其影响因素橡胶塑炼是一种重要的橡胶加工工艺,通过增加橡胶的可塑性和可加工性,使其满足不同行业和产品的需求。
本文将从目的、原理以及影响因素三个方面对橡胶塑炼进行详细介绍。
一、目的:橡胶塑炼是为了改善橡胶的物理性能,提高其加工性能,以满足不同行业和产品对橡胶的需求。
具体目的如下:1.提高橡胶的可塑性:橡胶塑炼可以使橡胶分子链间的键断裂,增加链段间的自由运动性,从而提高橡胶的可塑性。
2.改善橡胶的可加工性:橡胶塑炼可以使橡胶分子链间的键重新结合,提高链段间的交联程度,从而降低橡胶的黏度,提高其可加工性。
3.提高橡胶的物理性能:橡胶塑炼可以改善橡胶的拉伸强度、硬度、变形能力等物理性能,使其满足不同行业和产品的需求。
二、原理:1.热加工:橡胶加热可以提高分子链的运动性,使链段间的键断裂,增加橡胶的可塑性,同时热加工还能提高橡胶的流动性,使其易于加工。
热加工方法主要包括压炼、炼胶机等。
2.机械加工:橡胶通过剪切、挤压等机械力的作用下,可以改变其链段间的交联程度,从而改变其硬度、强度、伸长率等物理性能。
机械加工方法主要包括混炼机、胶研机等。
3.化学加工:橡胶塑炼过程中,可以添加助塑剂、稳定剂、促进剂等化学物质来改善橡胶的塑炼效果,提高其加工性能和物理性能。
常见的化学加工方法有添加法、表面活性剂法等。
三、影响因素:1.原料的选择:不同类型的橡胶树脂、填料以及添加剂的选择,对橡胶塑炼的效果有很大的影响。
例如使用不同种类和粒度的填料可以调整橡胶的硬度、强度等物理性能。
2.加工条件的控制:包括加热温度、加热时间、剪切速度等加工条件对橡胶塑炼效果有直接影响。
较高的加热温度和长时间加热可以提高橡胶的可塑性,但过高的温度和过长时间加热会导致橡胶老化、劣化等问题。
3.添加剂的使用:添加剂的种类和用量对橡胶塑炼的效果有显著影响。
例如使用助塑剂可以改善橡胶的可塑性和加工性能,使用稳定剂可以防止橡胶老化等。
总之,橡胶塑炼通过改善橡胶的可塑性和可加工性,提高其物理性能,满足不同行业和产品对橡胶的需求。
橡胶塑炼之十:塑炼工艺实施PPT优秀文档

LOGO
3.10 塑炼工艺实施
3.10 塑炼工艺实施
塑炼工艺方法按使用设备分为开炼机塑炼法、密炼机塑炼法、螺杆塑炼 法等三种方法,本课程主要介绍开炼机塑炼法,开炼机塑炼有薄通塑炼和包 辊塑炼两种方法。 1、薄通塑炼法
将辊距调至1~,让胶料通过辊缝,任其落入接料盘中,待胶料全部通 过辊缝后,再将落盘的胶料扭转90°再进行薄通。如此反复进行到规定次数。
在过辊过程中,可以配以多次割胶翻炼,以利于散热及获得均匀的可塑性。 如此反复进行到规定次数。 将辊距调至2~8mm,让胶料通过辊缝,包前辊,保证堆积胶量适当,连续过辊进行塑炼,直至规定时间为止。
塑炼工艺3—塑炼方法及影响因素共33页文档
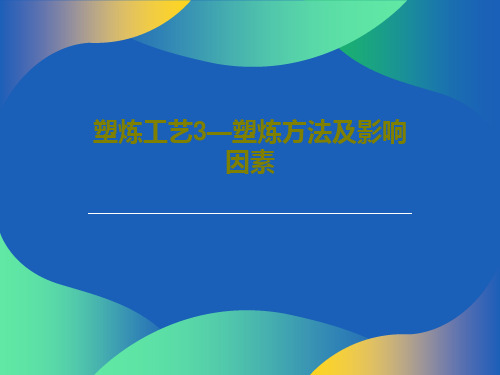
16、业余生活要有意义,不要越轨。——华盛顿 17、一个人即使已登上顶峰,也仍要自强不息。——罗素·贝克 18、最大的挑了使别人过得更美好。——雷锋 20、要掌握书,莫被书掌握;要为生而读,莫为读而生。——布尔沃
塑炼工艺3—塑炼方法及影响 因素
41、实际上,我们想要的不是针对犯 罪的法 律,而 是针对 疯狂的 法律。 ——马 克·吐温 42、法律的力量应当跟随着公民,就 像影子 跟随着 身体一 样。— —贝卡 利亚 43、法律和制度必须跟上人类思想进 步。— —杰弗 逊 44、人类受制于法律,法律受制于情 理。— —托·富 勒
END
塑炼工艺3—塑炼方法及影响因素33页PPT

谢谢你的阅读
❖ 条道路,那么,任何东西都不应妨碍我沿着这条路走下去。——康德 72、家庭成为快乐的种子在外也不致成为障碍物但在旅行之际却是夜间的伴侣。——西塞罗 73、坚持意志伟大的事业需要始终不渝的精神。——伏尔泰 74、路漫漫其修道远,吾将上下而求索。——屈原 75、内外相应,言行相称。——韩非
1、不要轻言放弃,否则对不起自己。
2、要冒一次险!整个生命就是一场冒险。走得最远的人,常是愿意 去做,并愿意去冒险的人。“稳妥”之船,从未能从岸边走远。-戴尔.卡耐基。
梦 境
3、人生就像一杯没有加糖的咖啡,喝起来是苦涩的,回味起来却有 久久不会退去的余香。
塑炼工艺3—塑炼方法及影响因素 4、守业的最好办法就是不断的发展。 5、当爱不能完美,我宁愿选择无悔,不管来生多么美丽,我不愿失 去今生对你的记忆,我不求天长地久的美景,我只要生生世世的轮 回里有你。
任务三 塑炼工艺
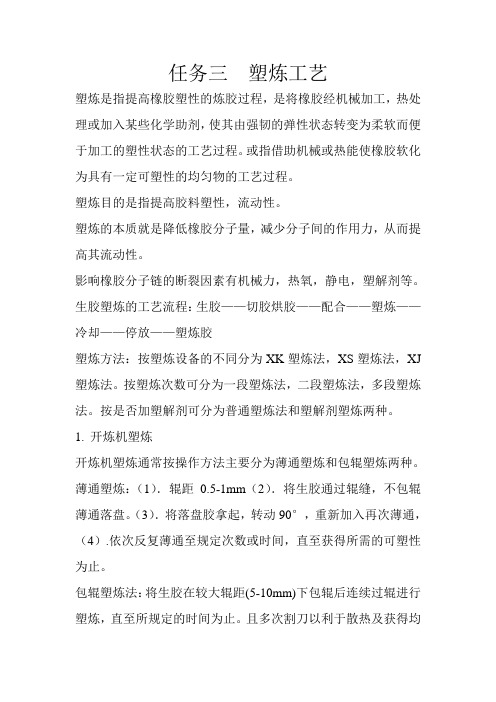
任务三塑炼工艺塑炼是指提高橡胶塑性的炼胶过程,是将橡胶经机械加工,热处理或加入某些化学助剂,使其由强韧的弹性状态转变为柔软而便于加工的塑性状态的工艺过程。
或指借助机械或热能使橡胶软化为具有一定可塑性的均匀物的工艺过程。
塑炼目的是指提高胶料塑性,流动性。
塑炼的本质就是降低橡胶分子量,减少分子间的作用力,从而提高其流动性。
影响橡胶分子链的断裂因素有机械力,热氧,静电,塑解剂等。
生胶塑炼的工艺流程:生胶——切胶烘胶——配合——塑炼——冷却——停放——塑炼胶塑炼方法:按塑炼设备的不同分为XK塑炼法,XS塑炼法,XJ 塑炼法。
按塑炼次数可分为一段塑炼法,二段塑炼法,多段塑炼法。
按是否加塑解剂可分为普通塑炼法和塑解剂塑炼两种。
1.开炼机塑炼开炼机塑炼通常按操作方法主要分为薄通塑炼和包辊塑炼两种。
薄通塑炼:(1).辊距0.5-1mm(2).将生胶通过辊缝,不包辊薄通落盘。
(3).将落盘胶拿起,转动90°,重新加入再次薄通,(4).依次反复薄通至规定次数或时间,直至获得所需的可塑性为止。
包辊塑炼法:将生胶在较大辊距(5-10mm)下包辊后连续过辊进行塑炼,直至所规定的时间为止。
且多次割刀以利于散热及获得均匀的可塑性2.工艺条件及其对塑炼效果的影响开炼机塑炼时需要在低温进行,因此降低炼胶温度和增加机械作用力是提高开炼机塑料效果的关键。
(1).辊温:低温塑炼时,温度越低塑炼效果越好。
当温度低时,橡胶的弹性大,所受的机械力越大,塑炼效率高。
反之,温度升高,则橡胶变软,所受到得机械作用力小,塑炼效率低。
天然橡胶温度的一般掌握在45-55℃,合成橡胶一般掌握在30-45℃.(2).辊距:当辊筒的速度恒定时,辊距减小会使生胶通过辊缝时所受的摩擦、剪切力、挤压力增大,同时胶片变薄易于冷却,冷却后的生胶变硬,所受的机械剪切力作用力增大,塑炼效果随之提高。
(3).辊速及速比;塑炼时,辊筒转速快,即单位时间内生胶通过辊缝次数多,所受机械力的作用大,塑炼效果好。