FMEA失效模式及后果分析(PPT共 52张)
FMEA培训资料潜在失效模式及后果分析

Potential Failure Mode and Effects Analysis
潜在失效后果
• 是指失效模式对系统功能的影响 • 要根据顾客或经理可能发现的情况来描
述失效的后果(顾客可以是内部或外部)
• 应记住不同级别系统、子系统和零件之
间还存在系统层次上的关系
潜在失效的后果
考虑以下方面: 对完成功能的影响 对上级系统和系统内其他零件的影响 对所有顾客的影响(包括使用成本) 对法规的影响 对营销方案/的影响 对可制造性/可装配性的影响
Potential Failure Mode and Effects Analysis
级别
• 是指产品特性分级 • 应用适当的方式进行标识 • 每一个在DFMEA中标识的特性均应在
PFMEA中有特殊的过程控制
级别—特殊特性
特性:产品或零件的尺寸、性能、外观、 重量等可定义的固有的特征。
特殊:一种是与安全和/或法规有关,即该特 性影响安全和/或法规;一种是该特性的波动 会影响到产品或零件的基本性能,但不会影响 到安全和/或法规。
FMEA小组应对评价准则和分级规则达成一致意见。 组织可对准则进行修改,不推荐修改9和10的准则。 严重度的定级可以通过修改设计、使之补偿或减轻失
效的后果来降低。如:“瘪胎”可以减轻突然爆胎的 严重度,“安全带”可以减轻车辆碰撞的严重程度。 “车辆/项目”在用于其他产品时,可理解为“最终产 品/生产产品”。如电视机/显示器、电脑/接线端子等。 9~10:与安全/法规有关,5~8:与性能/功能有关 2~4:与外观和感觉有关 严重度为1的失效模式不应进行进一步的分析。
的SFMEA,也可能没有SFMEA。 针对自行车(系统)、车架(子系统)
功能的DFMEA就是SFMEA,针对“下部 前车管”功能的则是DFMEA。
FMEA潜在失效模式及后果分析(PPT 77张)
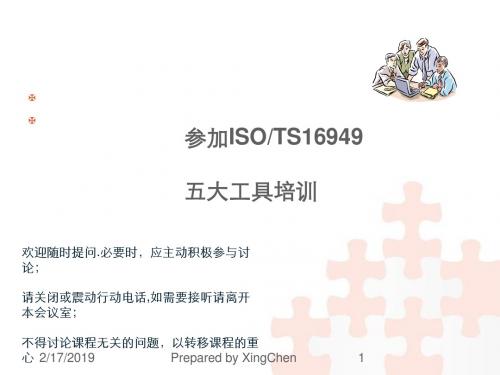
后果是 什么? 功能、特 性或要求 是什么?
有多 糟糕 ? 起因是 什么? 发生的频 率如何?
能做些什么? -设计更改 -过程更改 -特殊控制 -标准、程序或 指南的更改
会是什么问题? -无功能 -部分功能/功能 过强/功能降级 -功能间歇 -非预期功能
2/17/2019
怎样能得到 预防和探测? 该方法在 探测时 有多好?
2/17/2019
Prepared by XingChen
10
2/17/2019
Prepared by XingChen
11
下图描述了进行 FMEA的顺序。这并不是简单地填写一下表
格,而是要理解FMEA的过程,以便消除风险并策划适宜的 控制方法以确保顾客满意。
2/17/2019
Prepared by XingChen
24
8)核心小组 列出有权确定和/或执行任务的责任部门的名称和个人的姓名(建议所 有参加人员的姓名、部门、电话、地址等都应记录在一张分发表上。) 9)项目/功能 填入被分析项目的名称和其他相关信息(如编号、零件级别等)。利 用工程图纸上标明的名称并指明设计水平。在初次发布(如在概念阶 段)前,应使用试验性编号。用尽可能简明的文字来说明被分析项目 满足设计意图的功能,包括该系统运行环境(规定温度、压力、湿度 范围、设计寿命)相关的信息(度量/测量变量)。如果该项目有多种 功能,且有不同的失效模式,应把所有的功能单独列出。
16
DFMEA考虑的内容:
设计 FMEA 针对设计意图并且 假定该设计将按此意图进行生 产/装配。 制造或装配过程中可能发生的 潜在失效模式和 / 或其原因 / 机 理不需、但也可能包括在设计 FMEA当中。 当这些未包含在设计 FMEA 当 中时,它们的识别、后果及控 制应包括在过程FMEA当中。
过程FMEA失效模式及后果分析PPT培训课件

评估失效模式的 后果
确定失效模式的 严重程度…
制定预防和探测 措施
食品加工过程,包括原料 采购、加工、包装和储存 等环节。
例如,原料可能存在农药 残留、微生物污染等问题 ;加工过程中可能出现烘 烤不均匀、切割尺寸不对 等;包装过程中可能出现 标签错误、密封不严等。
例如,农药残留可能导致 消费者健康问题;烘烤不 均匀可能导致食品口感和 质量下降;标签错误可能 导致消费者对产品的误解 。
THANKS FOR WATCHING
感谢您的观看
跟踪实施效果
对改进措施的实施情况进行跟 踪和效果评估,持续改进。
02 过程FMEA的实施过程
确定分析范围和边界
确定分析对象
明确过程FMEA的分析对象,如产品、服务或系统 等,并定义其边界和范围。
确定分析阶段
确定失效模式可能发生的阶段,如设计、制造、 运输、安装等。
确定分析重点
根据分析对象和阶段,确定失效模式分析的重点 和关注点。
如何制定有效的改进措施和行动计划?
制定改进措施和行动计划是FMEA分析的最终目的。
根据风险优先级,选择具有最大潜在改进的失效模式进行改进。这可能包括设计更改、工艺改进、过 程控制强化等。制定行动计划时,应明确责任人、完成时间和检查点,以确保改进措施的有效实施。
如何持续改进FMEA分析?
持续改进FMEA分析可以提高其有效性和可靠性。
明确分析的对象,包括产品、系统、过程等,并对其进行 定义和描述。
列出所有可能的失效模式
全面考虑可能出现的失效模式,并对其进行分类和归纳。
评估失效模式的后果
分析失效模式可能导致的影响和后果,包括对产品、系统 、过程的影响以及对顾客的影响。
确定失效模式的严重程度、发生频率…
FMEA培训ppt课件
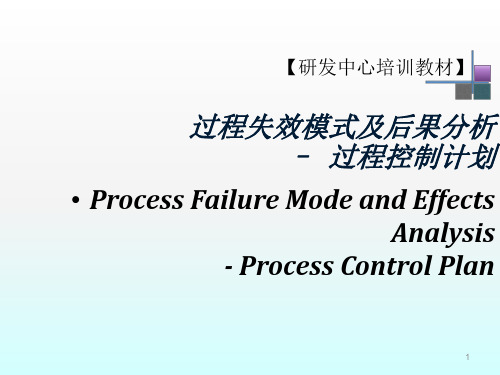
宏观的描述:装护板
将护板取出
微
对护板进行检查
观
的
护板放置到底座上
活
动
操作工拿出5颗螺钉
将螺钉放置到护板上
操作工将螺钉打紧
①
③
⑤
④
②
32
PFMEA -- 过程定义
详细叙述各个流程的作用(用动词+名词的方式)
------进行这样的分析是为后面用头脑风暴的方法来分析失效模式做准备
工步 列出要研究的各个工步 将护板取出 对护板进行检查 护板放置到底座上 操作工拿出5颗螺钉 将螺钉放置到护板上 操作工将螺钉打紧
关键日期—(5) FMEA计划完成日期,APQP进度计 划安排日期。 FMEA编号/版本—(6) 用于追溯FMEA的内部编号与版本 编制人—(7) FMEA编制人的姓名、电话及所属 公司 日期—(8) 原始稿编制日期、修订号和日期
22
製程名稱: 核心小組:
工程放行日期: 製 表 人 員:
措施執行的結果
已采取的 措施
严频探 R
重度测 度数度 (S)(O)(D)ss FMEA 开发思路
团队组建
•多功能小组 •成员来自各个级别的人员,如客户、产品设计、过程设计 、生产 线等 •确定小组组长 • 获得领导支持
过程定义
过程流程图 识别过程中每一工步的目的(采用“动词+名词”形式)
采取降低风险的行动
• 更改产品/过程设计,降低严重度(伤害性风险与设计风险); • 更改产品/过程设计,降低频度数; • 采用防错技术,提高可探测性,降低不可探测度数; • 提高在线检测技术和不合格品控制,提高可探测性,降低不可探测风险; • 变更过程控制计划; • 改进加工工艺、工装刀具。
FMEA失效模式效应分析的描述、类型及展开PPT(44张)

影响 设计 问题
制造 问题 影响
原因
现行控制 (DVP&R)
现行测试
原因
现行控制 20 (DVP&R)
结合DFMEA&PFMEA的实例讲解(附件1、2、3)
★ 建立FMEA活动小组; ★ DFMEA/PFMEA针对每个潜在失效模式及后果确定
潜在危害性(S、O、D); ☆ 列出每个原因的目前控制; ☆ RPN风险优先数量运算; ☆ 严重度、频度、不易探测度
☆一般常用的符号
开始和结束 活动说明 决策
过程流程的流向
9
1.3 例
流程 图
准备
接受文件
输入复印份数
开始
机器是否正 常运行?
否
纠正错误
是
是
装订
装订文件
否
重新开始
整理
复印文件的流程图
结束
10
1.3 因果分析
(其中采用方法之一 :鱼刺图又称特性要因图,石川图)
☆ 用图解法对影响过程或产品质量问题的各种因素 进行全面系统的观察和分析,找出其因果关系
FMEA
失效模式效应分析 Failure Mode & Effects Analysis
1
Unit1 失效模式效应分析(FMEA)的描述
1.1 什么是FMEA、起源、分类和实施原则 1.2 FMEA的要素及实施的前期准备 1.3 流程图与因果分析 1.4 系统与子系统
2
1.1 什么是FMEA?
失效模式效应分析 Failure Mode & Effects Analysis
☆ 使小组能集中于问题的实质,围绕问题产生集体 智慧和意见
☆ 集体智慧的火花集中于问题的原因而不是问题的 现状
第六单元FMEA失效模式及后果分析手册

现行控制方法几乎确定 X X 可以侦测
当场侦错(有自动停止功能的自动化量具)。缺陷 2 零件不能通过
几乎肯定
现行控制方法肯定可以 X 侦测
PPT文档演模•检板 查类型:A、防错 B、量测 C、人工检查
该项目由过程/产品设计了防错法,不会生产出缺陷 1 零件
第六单元FMEA失效模式及后果分析 手册
•FMEA分析表填写说明
涂以最 小厚度 的蠟,
外 观 不7 满
以延缓
意
腐蚀
* 车
间
内
附
件7
功
能
损
害
PPT文档演模板
人工插
8度 太高 --温度 太低 --压力 太低
因撞击
2
使喷头
变形
每小时进行目 5 测检查一次喷 膜厚度(深度计) 和范围
在开始和 停机后试 验喷雾形 状,按照 预防维护 程序清洗 喷头
•2.预估产品可能发生的制程缺点及衡量该项缺点可能造成的影 • 响,并分析其制程或装配上的可能原因及推测防止或检测该 • 项缺点应改善的制程管制(Process Control)
PPT文档演模板
•3.研究各项缺点的发生机率(Occurrence),发生后的严重程
度
• (Severity),及缺点检测难易度(Detection)计算出“风险优先
建议措 施 (19)
责任和目标 完成日期 (20)
措施执行结果(22)
采取措施(21)
严 发 探 R. 重 生 测 P. 度 率 度 N.
车门内 部人工 涂蠟
在 指 定
车 间 寿 命
7
的 表 面
降 低 导 致:
兔*
蠟 不 足
使 用 一 段
FMEA-潜在失效模式分析(ppt 175页)
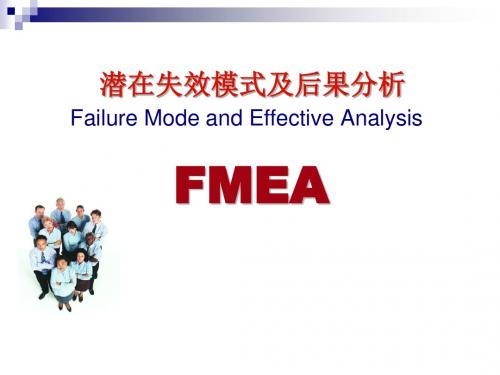
设计FMEA初始阶段的工作
l 在进行设计FMEA开始时,负责设计的工程师应 列出设计希望做什么?不希望做什么?
— 充分理解、明了设计意图 — 顾客要求和需求,其来源如:通过质量功 能展开、车辆要求文件、已知的产品要求和/或制 造、装配、服务、回收利用等要求。 期望特性的定义越明确,就越容易识别潜在的 失效模式,以采取预防防和纠正措施。
评估和分析的部分是关于分析的评估。最重要 的是对有关设计(产品或功能),功能评估和应 用方面的任何更改,以及潜在失效导致的风险进 行讨论。
每一种FMEA都应该确保对在产品或装配中的 每个部件给予关注。与风险和安全相关的部件或 过程应给予更高的优先权。
FMEA程序成功执行的最重要因素之一是及时 性。这意味着它是一种事前行为,而不是一种事 后演习。要取得最大成效,FMEA必须在存在潜 在失效模式的产品或过程执行前进行,适当预先 花时间完成FMEA,产品/过程的更改会在最容易 和最低成本情况下,并且将降低后期更改风险。 FMEA措施将减轻或消除执行更改产生更大关注 点的机会。
*识别和评估风险:
FMEA过程的重要步骤之一是评价风险。风险用三种 方法来评价,严重度、发生率和探测度。
严重度是失效对顾客产生影响的级别一种评估。 发生率是失效的要因可能发生的频繁程度。 探测度是对产品或过程控制探测失效要因会失效模式 程度的一种评价。
*建议措施和结果;
建议措施的意图是降低综合风险和失效模式发生的可 能性,建议措施阐述严重度、发生率和探测度降低。
问题在于: 自觉与不自觉 科学法则与自然法则 注意性与随意性 借鉴型与抛弃型 螺旋提高与闭环解决
FMEA简史
50年代初
60年代中
70年代中
美国Grumman 公司把FMEA思 想用于一种战斗 机操纵系统的设 计分析
培训课件潜在的失效模式及后果分析fmea

协作性:
虽然 FMEA 的编制责任通 常都指派到某个人,但是 FMEA 的输入应该是小组的努力。
小组成员应由知识丰富的 人员组成(如设计、分析/试验 、制造、装配、服务、质量及 可靠性等方面的有丰富经验的 工程师)
7
潜在失效模式及后果分析 FMEA
主观性
FMEA 的特点(3)
31
(22)
过程 FMEA 的開發
5 )車型年/車輛類型
填入將使用和/或正被分析的設計所影響的預期車型年
及車輛類型。 (如果已知的話)
过 程 FMEA
系统
X 子系统 ______部件 01.03/车身密封 (2) 车型年/车辆类型 199X/狮牌 4门/旅行车 (5) 核心小组: T.芬德-轿车产品开发部、切利得斯-制造部、J.福特-总
建議 措施
責任及目標 完成日期
措施結果
采取 的措施
R S ODP
N
功能、特性或 要求是什么?
綴彆岆 妦繫ˋ
衄嗣 媎詹ˋ
岆妦繫ˋ
楷汜腔 ˋ
能做些什么? - ??更改 - ?程更改
特殊控制 - ?准、程序或
指南的更改
?有什么??? - ?功能 - 部分功能/功能
?? /功能降? - 功能?歇 - 非?期功能
2
潜在失效模式及后果分析 FMEA
3
潜在失效模式及后果分析
FMEA
4
潜在失效模式及后果分析 FMEA 什么是 FMEA
FMEA 一組系統化的活動
(a)發現、評價產品/過程中潛在的失效及其後果 (b)找出能夠避免或減少這些潛在失效發生的措施 (c)全部過程形成文件
5
潜在失效模式及后果分析 FMEA
潜在失效模式及后果分析(FMEA)
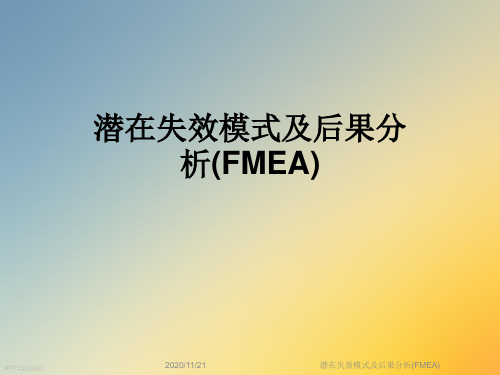
PPT文档演模板
2020/11/21
潜在失效模式及后果分析(FMEA)
•FMEA 在质量体系中
•顾客满意度的改进过程
•获得顾客需求输入
•DFMEA
•PFMEA
•更新PFMEA •控制计划 •反应计划
•过程怎样改变
•控制计划
•过程变量
•产品特性
•数据收集
PPT文档演模板
•进行适当的比较
2020/11/21
潜在失效模式及后果分析(FMEA)
•失效链
•水箱支架断裂
•1 失效原因
•水箱后倾
•1 失效模式
•2 失效原因
•水箱与风扇碰撞
•1 失效后果
•2 失效模式
•水箱冷却水管被风扇刮伤
•2 失效后果
•3 失效原因
•水箱冷却液泄漏
•冷却系统过热
•3 失效后果
PPT文档演模板
•时间
•发动机气缸损坏
2020/11/21
PPT文档演模板
2020/11/21
潜在失效模式及后果分析(FMEA)
•FMEA和FMA、FTA
• FMEA是一种事前行为:
• FMA(Failure Mode Analysis)是一种事后行 为。
• FMA是对产品/过程已经发生的失效模式分析 其产生的原因,评估其后果及采取纠正措施的一 种活动。
潜在失效模式及后果分析(FMEA)
•什么是 FMEA?
•2.术语定义
(影响的)严重度( Severity )- 影响对顾客要求 的重要程度 - 如果失败发生,也可以和安全及其他 风险相关(1=不严重,10=非常严重)
(要因的)发生率( Occurrence )- 给定要因发
FMEA培训教材ppt完整版

FMEA培训教材ppt完整版•FMEA概述与基本原理•失效模式识别与评估方法•故障原因分析技巧与工具应用•风险等级划分标准与应对措施制定目录•FMEA在产品设计阶段应用实践•FMEA在生产过程监控和持续改进中作用•总结回顾与展望未来发展趋势01FMEA概述与基本原理FMEA定义及发展历程FMEA定义故障模式与影响分析(FailureModes and Effects Analysis)发展历程起源于军事领域,后广泛应用于航空、汽车、电子等各个行业FMEA核心思想与目标核心思想预防性分析,识别潜在故障模式及其对系统的影响,提前采取措施降低风险目标提高产品可靠性、减少维修成本、增强客户满意度032. 功能分析识别系统或部件的功能及潜在故障模式01适用范围产品设计、生产过程、服务流程等各个环节021. 定义范围明确分析对象及目标评估故障模式对系统性能、安全、经济等方面的影响3. 故障影响分析综合考虑故障发生概率、严重度及可检测性,对故障模式进行风险等级排序4. 风险等级评估针对高风险故障模式,制定预防措施和应急计划5. 制定措施定期回顾FMEA 结果,更新措施并持续改进6. 跟踪与持续改进02失效模式识别与评估方法产品无法实现设计功能或性能不达标,如电子设备无法开机、机械部件卡滞等。
功能性失效安全性失效可靠性失效产品存在安全隐患,可能导致人身伤害或财产损失,如汽车刹车失灵、电器短路引发火灾等。
产品在规定条件下和规定时间内无法完成规定功能,如电池寿命短、设备频繁故障等。
030201常见失效模式类型介绍失效模式识别技巧与工具技巧了解产品工作原理及结构特点分析历史故障数据及维修记录•运用头脑风暴等方法集思广益工具故障树分析(FTA)事件树分析(ETA)因果图(Cause-Effect Diagram)01020304•方法选择:根据失效模式的性质和影响程度选择合适的评估方法,如风险矩阵、风险指数等。
实施流程1. 明确评估目标和范围2. 收集相关数据和信息3.选择合适的评估方法并建立评估模型4.对失效模式进行定量或定性评估5.根据评估结果制定相应的改进措施并跟踪验证03故障原因分析技巧与工具应用故障树分析法概述故障树的建立故障树的定性分析故障树的定量分析故障树分析法(FTA )原理及应用01020304介绍FTA 的基本概念、原理、作用及适用范围。
FMEA失效模式及后果分析

概念
初始设计
设计完成
样件制造
设计/过程 确认
生产开始
DFMEA 开始早于过程,完成时间在早期的图样完成但任何工具 的制造开始之前 PFMEA 开始于基本的操作方法讨论完成时,完成时间早于生产 计划制定和生产批准之前
9
FMEA 的益处
改进产品的质量、可靠性与安全 提升企业的形象和竞争力 降低成本 减少浪费 降低保证成本 书面规定并跟踪减少风险所需的措施
失效
在規定条件 下, 产品参 数值不能维 持在規定的 上下限之间
5
FMEA 的起源
FMECA
•Failure Mode Effects and Criticality Analysis
•1950’s 起源于宇航和美国军方
•对关注的问题加以分类和排列
•将评定结果作为预防的目标
•坚持安全的观点
6
FMEA 的起源 FMEA (Failure Mode Effects Analysis)
14
头脑 风暴 四大原则
4个原则(会议前向成员解释) • 暂缓下结论 不要批评其他人的观点,更不要嘲笑人
或其观点
• 自由 鼓励参与者梦想或遐想,鼓励大胆及愚蠢的建议,
但不提议无任何建议或离座闲逛
• 数量 要求大量的建议
• 交叉培养 鼓励一个小组的建议被其他小组的成员扩
展或开发,将所有人的建议写在题板上以便被全部人都 能够看到,同时编号。但建议减少或小组成员感到空洞 时,千万不要说丧气话
13
头脑风暴 Brainstorming
头脑风暴是一种技法,可以激发小组成员 产生大量的有创意的点子,。 由纽约广告代理的老板Alex F Osborn在 1930年发明,其前提是在一般的讨论中,人们 害怕别人批评而约束自己,因此而不能产生有 创意的点子。 脑力风暴包括创造一种氛围,让人们感到 无拘无束,此时人们可能提出在平时认为不太 可能提出的解决方案,但往往收到意想不到的 效果。
AFMEA失效模式与后果分析

•FMEA 实施
FMEA与FTA
FMEA是具有质量分析的事先分析工 具,自下而上分析
FTA是事后的失效模式分析,即失 效树自上而下分析
类似的产品的FTA是其FMEA的重要 输入
PPT文档演模板
AFMEA失效模式与后果分析
FMEA 分类
SFMEA---系统失效模式分析 DFMEA---设计失效模式分析 PFMEA---过程失效模式分析
目运行的环境信息。如果该项目有多种功能,且
有不同的失效模式,应把所有功能单独列出。
PPT文档演模板
AFMEA失效模式与后果分析
•設計FMEA表填写说明
10、潛在的失效模式
没有达到设计意图的形式,假定失效可能發生,但不一定發 生;
突发型:断裂、开裂、碎裂、弯曲、塑性变型、失稳、短路、 断路、击穿、泄漏、松脱等等。
6 关键日期
填入FMEA初次预定完成日期,不超过APQP计划中的日 期
PPT文档演模板
AFMEA失效模式与后果分析
設計FMEA表填写说明
• 2 系统 • 2 子系统 • 2 零组件: 2 •年型/车型: 5 •核心小组: 8
7
设计责任: 3 关键日期: 6
FMEA编号: 1 页次: of 编制人: 4
AFMEA失效模式与后果分析
10、潛在的失效模式(续)
失效模式可能是高一级子系统、系统的潜在失效 模式的起因,也可能是它低一级的零部件潜在失 效模式的后果。
•零件失 效模式
•后 果
PPT文档演模板
•被分析的项目 失效模式
•(子系统)
•系统失 效模式
•起 因
AFMEA失效模式与后果分析
•設計FMEA表填写说明
失效模式及后果分析(FMEA)简介

什么是FMEA?
对它自身,FMEA不是一个 万能问题解决的工具,它需要 与其它解决问题的工具联合使 用。
FMEA提供一个机会 但它不能解决问题。
1949年11月
60年代中期 1976年
70年代末 80年代初期
FMEA的历史
美国军方运用在战斗机 操作系 统; 美国航空APOLLO登月计划;
正式纳入美国军标MIL-STD1629A;
对每个过程开发FMEA表要素 从风险特性开发控制计划
TQM中适合FMEA的情况
� 顾客要求 � 工程规范 � 系统和部件的规范 � 过程和供应商要求和控制 � 开发系统设计和过程FMEA � 消除潜在的失效 � 改善设计和过程 � 设计是一个吹毛求疵的要素
FMEA问题
FMEA自身也会失败!!
哪些情况导致FMEA失败?
QS 9000推荐十级。
FMEA技术研究的内容
综合考虑三要素 严重度 频度 探测度
计算风险顺序数RPN=S*O*D
什么时候做FMEA?
QS 9000推荐的FMEA时间表
DFMEA
PFMEA
概念
设计 进程
设计 完成
样件 制造
工程/制造 确认
开始 生产
技术文件的展开
开发过程流程图 从过程流程图到FMEA表进入每个主要过程
产品:冲压开裂、涂附性差、不耐腐蚀、断丝、 螺纹粘扣 过程:温度不合、夹渣、表面划伤 安全:中毒、火灾 环境:粉尘、污水
FMEA技术研究的内容
出现上述问题所造成的后果 (潜在的失效后果)
局部影响 高一层影响 最终影响 度
本工序、本厂 后工序、下个生产厂
用户使用、用户满意
FMEA技术研究的内容
制造和装配过程潜在失效模式及后果分析(PPT 51张)

FMEA编号: 共 页,第 页
编制人 :
FMEA日期(编制) (修订) 等
措施结果 采取的 措施 S O D R P N9Biblioteka 附录G:过程 FMEA的标准表
系统 子系统 部件 项目 核心小组 子系 统 功能 要求
潜在 失效 模式 潜在 失效 后果 严 重 度 S 级 别 潜在 失效 起因/ 机理 频 现行 度 过程 O 控制 -预防 现行 过程 控制 -探测 探 R 建议 测 P 措施 度 N D 责任及 目标完 成日期
8
附录G:过程 FMEA的标准表
系统 子系统 部件 项目 核心小组 子系 统 功能 要求
潜在 失效 模式 潜在 失效 后果 严 重 度 S 级 别 潜在 失效 起因/ 机理 频 现行过程 度 控制 O -预防 -探测 探 R 建议 测 P 措施 度 N D 责任及 目标完 成日期
潜在失效模式及后果分析 (过程FMEA)
6
过程FMEA的开发
• 负责过程的工程师掌握一些有益于过程FMEA准备工作的文件
是有帮助的。FMEA从列出过程期望做什么和不期望做什么的 清单,即过程图开始。 • 过程FMEA应从一般过程的流程图开始。这个流程图应明确与 每一工序相关的产品 / 过程特性。如果有的话,相应的设计 FMEA中所明确的一些产品影响后果应包括在内。用于FMEA 准备工作的流程图的复制件应伴随着FMEA。 • 为了便于潜在失效模式及其后果分析的文件化,编制了过程 FMEA表,见附录G 。 FMEA准备工作中所有的框图的复制件应伴随FMEA过程。
á Ï Ö ò ³ ß ´ ç £ ¬ ¾ ¶ Ï ò ³ ß ´ ç â ¹ Í Û Ö ò á Ï ³ ß ç ´ £ ¬ â Í Ô ² ß ³ ´ ç £ ¬ Ö Ð Ð Ä ¿ ׳ ß ´ ç £ ¬ ¸ ÷± í æ ´ Ã Ö Ú ² ¶ È ¬ £ Ì ×µ ³ ³ ¤È ¶ Ö Ï á ò ß ³ ´ ç ¬ £ Í â ² Ô ³ ß ç ´ £ ¬ ä Æ Ó à ¸ ÷² ¿ ³ ß ´ ç £ ¬ ¸ ÷ í à ± æ ´ Ö Ú ² ¶ È ¬ £ Í â ² Ô ¼ °Ë ¶ Ã æ ø Ì ¶ ¯ Ö Ï á ò ß ³ ´ ç ¬ £ Í â ² Ô ³ ß ç ´ £ ¬ Æ ä Ó à ¸ ÷² ¿ ³ ß ´ ç £ ¬ ¸ ÷ í à ± æ ´ Ö Ú ² ¶ È ¬ £ ¸ ÷¿ ² Î » ø Ì ¶ ¯ Ö Ï á ò ß ³ ´ ç ¬ £ Í â ² Ô ³ ß ç ´ £ ¬ Æ ä Ó à ¸ ÷² ¿ ³ ß ´ ç £ ¬ ¸ ÷ í à ± æ ´ Ö Ú ² ¶ È ¬ £ ¸ ÷¿ ² Î » ø Ì ¶ ¯ Í ² â Ô ³ ß ç ´ £ ¬ Ö á Ï ò ³ ß ´ ç £ ¬ Í â ¹ Û ¡ ¢ ± í Ã æ ´ Ö ² Ú È £ ¶ ¬ ¶ ¾ Ï ò ø Ì ¶ ¯ ² » Ô ¡ ² Û ³ ß ´ ç ,Í â ¹ Û £ ¬ ± í Ã æ ´ Ö ² Ú ¶ È ³ Ï Ï ÷² Î Ê ý (½ ø ¸ ø Á ¿ ¡ ¢ × ª Ë Ù ¡ ¢ ³ Ô µ ¶ Á ¿ ) õ Ê ¹ ½ Ê ä Ë Í ´ ø Ë Ù ¶ È á Ô ° Ë ² ú Æ ·Ö Ø Á ¿ ³ Ï Ï ÷² Î Ê ý ¡ ¢ × ê Ï ÷² Î Ê ý (½ ø ¸ ø Á ¿ ¡ ¢ × ª Ë Ù ¡ ¢ ³ Ô µ ¶ Á ¿ ) õ Ê ¹ ½ Ê ä Ë Í ´ ø Ë Ù ¶ È µ Ï ³ ÷² Î Ê ý (½ ø ¸ ø Á ¿ ¡ ¢ × ª Ë Ù ¡ ¢ ³ Ô µ ¶ Á ¿ ) õ Ê ¹ ½ Ê ä Ë Í ´ ø Ë Ù ¶ È µ Ï ³ ÷² Î Ê ý (½ ø ¸ ø Á ¿ ¡ ¢ × ª Ë Ù ¡ ¢ ³ Ô µ ¶ Á ¿ ) õ Ê ¹ ½ Ê ä Ë Í ´ ø Ë Ù ¶ È µ Ï ³ ÷² Î Ê ý (½ ø ¸ ø Á ¿ ¡ ¢ × ª Ë Ù ¡ ¢ ³ Ô µ ¶ Á ¿ )
FMEA潜在的失效模式及后果分析
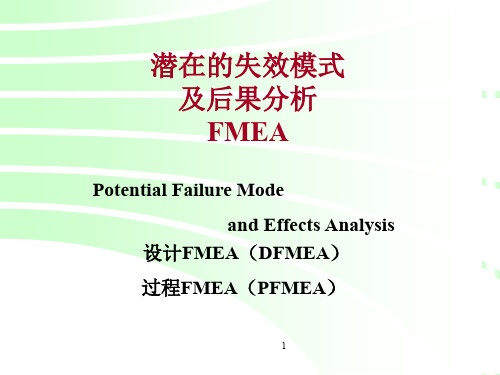
措施结果
项目 功能
潜在失 效模式
潜在失 效后果
严 重 度 S
级 别
潜在失 频 效起因/ 度
机理 O
现行设 计控制
预防
现行设 计控制
探测
探 测 度 D
R P N
建议措 施
责任及目 标完成日
期
采取的措 施
S
O
R DP
N
19
正表 DFMEA(设计)
项目/功能:
1、零部件、编号,修改状态 2、要满足设计意图的功能 3、工作环境
计、分析、试验、可 靠性、材料、质量、 服务、供方、以及高 一层和低一层总成、 系统、零部件设计人
• FMEA应成为促进不 同部门之间充分交换 意见的催化剂,从而 提高整个集体的工作 水平
• 可以邀请一位有 FMEA和团队工作推 进经验的推进员来协 助小组工作。
11
DFMEA是一份动态文件
• DFMEA要在一个设计概念最终 形成之时或之前开始
理效
的师是 一、负 种小责 分组设 析主计 技要的 术采工
用程
)Leabharlann 、9降低失效风险的方式
• 能客观评价设计,包括 功能要求及设计方案
• 为满足生产、装配、服 务和回收要求而评价初 步的设计
• 潜在失效对系统和车辆 运行产生影响在设计和 开发过程中得到考虑
• 为设计、开发、确认项 目的策划提供更多信息
4、其他方法
8
二、DFMEA简介
•
•
•
•
•
和维计体 文过过现 件程程了 化,中工
并正程 规常师 范的在 化思设
(
避 免 可 能 的 出 错
零 部 件 的 设 计 思 想
FMEA失效模式及其影响分析(ppt 63页)

In what way does the key input go wrong
SEV
Potential Causes of Failures (KPIVs)
What causes the key input to go wrong
OCC
Current Process Controls
What are the existing controls & procedures (inspection & test) that prevent with the cause or Failure Mode
prioritization, so the most likely failure modes can be addressed.
FMEA是用来检查潜在
失效和预防它再次发生的系统性方法.它增强了我们预测问题的能力,并提供了一个排序或区分
优先次序的系统,因而使得最可能的失效模式得以确定.
FMEA is generally applied during the initial stages of a process or product design. Brainstorming is used to determine potential failure modes, their causes, their severity, and their likelihood of occurring. In Six Sigma, we apply FMEA to know failure modes. Our main interests are the cause and likelihood of occurrence, for which we have actual data and do not need to rely on brainstorming.
- 1、下载文档前请自行甄别文档内容的完整性,平台不提供额外的编辑、内容补充、找答案等附加服务。
- 2、"仅部分预览"的文档,不可在线预览部分如存在完整性等问题,可反馈申请退款(可完整预览的文档不适用该条件!)。
- 3、如文档侵犯您的权益,请联系客服反馈,我们会尽快为您处理(人工客服工作时间:9:00-18:30)。
6
DFMEA 设计失效模式及后果分析
DESIGN POTENTIAL FMEA BENEFITS 潜在的设计失效模式及后果分析的益处:
• • Helps assure potential failure modes and their effects have been addressed. 可帮助确认潜在失效模式和它们的影响后果. Identifies associated causes/mechanisms 可识别相关的起因/机理 Identifies actions to reduce or eliminate the chance of the failure occurring. 可标识出降低或消除失效出现机会的措施. Aids in objective evaluation of design requirements and alternatives. 有助于在设计要求和选择中的目标评估. Aids in initial design for manufacturing and assembly requirements. 有助于在初始设计过程中满足制造和装配的要求. Increase probability that failure modes and effects have been considered during design phase. 在设计阶段可增加考虑到失效模式及其影响后果的机率. Aids in design test and development programs 有助于实验设计和项目开发.
FMEA 失效模式及后果分析
History 历史
• May 1991-Supplier Quality Requirements Task Force Supplier Advisory Council identified several tools that would benefit from standardization. 在1991年5月, 供应商质量要求行动小组供应商顾问委员会明确了几种工具, 并通过标准化 使大家受益. Supplier Quality Requirements Task Force assessed feasibility and selected several projects for communization, including FMEA. 供应商质量要求行动小组评估了其可行性并选择了几个项目以便沟通, 其中包括FMEA. FMEA Work Group completed Reference Manual in Dec. 1992 在1992年12月, FMEA工作小组完成了参考手册的编写. Early 1993-FMEA Reference Manual approved 在1993年年初, FMEA参考手册被认可. Mid 1993-Training developed 1993年中期, 建立了相关培训. Phased in during 3rd quarter 1993, according to individual customer requirements. 根据个别顾客要求, 在1993年第三季度逐步执行. February 1995 updated and reissued 3 1995年2月更新并再版.
ADDITIONAL ASSISTANCE 其他帮助来源 • Chrysler 克莱斯勒 – Procurement and Supply(Supplier Development) 采购和供应(供应商开发). • Ford 福特 – Customer Division Supplier Technical Assistance(STA) 客户部供应商技术支持. • GM 通用 – Procuring Division Supplier Development contact 采购部供应商开发 For specific technical questions, contact the appropriate responsible engineer (work with your customer). 2 如有特殊问题, 可以与相应的工程师(与你们顾客一起工作的)联系.
FMEA 失效模式及后果分析
OVERVIEW OF THE CHRYSLER/FORD/GM POTENTIAL FAILURE MODE AND EFFECTS ANALYSIS REFERENCE MANUAL 克莱斯勒, 福特,通用的 潜在失效模式及效果分析参考手册 概述
1
FMEA 失效模式及后果分析
•
• • • • •
FMEA 失效模式及后果分析
PLEASE NOTE 请注意 • FMEA training offered by Ford(Fairlane Training & Development Center) is not in conflict with and is in fact complimentary to this standardized FMEA training/ FMEA guideline. 由福特(Fairlane培训和开发中心)提供的FMEA培训与这种标准化的FMEA 培训/FMEA指导并不矛盾, 实际上是一种有益的补充.
5
DFMEA 设计失效模式及后果分析
DESIGN POTENTIAL FMEA 潜在的设计失效模式及效果分析
• Analytical technique and systemized group of activities. 分析技术和系统化的小组活动. • Utilized primarily by Design Responsible Engineer/Team 它主要被具有设计责任的工程师ctives 目的
• Attendance at this overview course should enable participants to : 参加这个概述课程, 将会使与会者学会: – Describe how to prepare FMEAs using the Reference Manual. 运用参考手册, 描述怎样去准备FMEAs. – Understand the format of the Reference Manual. 了解参考手册的格式. – Know where to go to receive additional assistance. 知道到哪里可以得到额外的支持.