Synchronous Motors
永磁同步电机效率计算方法

永磁同步电机效率计算方法英文回答:Efficiency Calculation Methods for Permanent Magnet Synchronous Motors.Permanent magnet synchronous motors (PMSMs) are highly efficient electric motors that are widely used in various applications. The efficiency of a PMSM is an important parameter that indicates its performance and energy consumption. Several methods can be employed to calculate the efficiency of a PMSM.Direct Measurement Method.The most direct method for determining the efficiency of a PMSM is through direct measurement. This involves measuring the input electrical power and output mechanical power of the motor under specific operating conditions. The efficiency can then be calculated as the ratio of outputpower to input power.Loss Separation Method.The loss separation method breaks down the losses in the PMSM into individual components. These losses include:Stator copper losses.Rotor eddy current losses.Hysteresis losses.Mechanical losses (friction and windage)。
电气英语翻译

电气英语翻译电气工程英语复习资料Fleming's left-hand rule: Place the thumb and the first and second finger of the left hand so that all three are mutually perpendicular to each other. With the first finger in the direction of the field and the second finger in the direction of the current, the thumb indicates the direction of the force.弗莱明左手定则:伸出左手大拇指、食指以及中指并使它们相互垂直。
使食指指向磁场的方向,中指指向电流的方向,那么拇指所指的方向是力的方向。
The air gaps of turbine generators usually are much longer than in other types of machines. A long air gap reduces the reactance of the armature winding and improves voltage regulation and stability. It is also necessary for ventilation. An obvious disadvantage of a long air gap is that it necessitates a greater field mmf to produce a specified air-gap flux.汽轮发电机的气隙通常比其它类型的电机大得多,这么大的气隙使电枢绕组的电抗减小并增大了电压调节范围和稳定性。
对于通风来说它也是必要的。
Synchronous Motors - Part 1

SYNCMTR1
Synchronous Motor Characteristics
Copyright 2004 Kilowatt Classroom, LLC.
Sync Motors
Synchronous Motors are three-phase AC motors which run at synchronous speed, without slip.
• Synchronous motors are often direct-coupled to the load and may share a common shaft and bearings with the load.
• Large synchronous motors are usually started acrossthe-line. Occasionally, reduced voltage starting methods, such as autotransformer or part-winding starting, may be employed.
• When the motor speed reaches approximately 97% of nameplate RPM, the DC field current is applied to the rotor producing Pull-in Torque and the rotor will pull-in -step and “synchronize” with the rotating flux field in the stator. The motor will run at synchronous speed and produce Synchronous Torque.
上海电器 TDBS系列悬挂式矿井提升机用交流调速同步电动机 说明书

一、概述上海电气集团上海电机厂有限公司从90年代初成功开发了矿井提升机用同步电动机,同时与国外著名电机制造公司开展合作,生产制造了TDBS系列悬挂式矿井提升机用交流调速同步电动机,积累了先进的设计和制造技术。
并在此基础上于20世纪初自主开发了当时国内最大的TDBS 4400千瓦24极交流调速同步电动机,用于安徽铜陵有色金属公司冬瓜山矿。
近年来,随着国际变频器厂商推出1140V级、3300V级及6000V级交直交变频装置,我公司相应开发、生产了匹配相应电压等级变频装置的交流调速同步电动机。
打破了该领域进口产品的长期垄断,是目前国产化最大的TDBS 5500千瓦16极交直交变频调速电动机,用于淮南矿务局谢桥矿。
本系列同步电动机与传统直流电机相比,具有更优良的调速性能,它不受换向限制,过载能力大,在整个调速过程中,都能输出最大转矩,效率比直流电机提高5%~8%,节能显著。
此外,交流调速同步电动机还具有转动惯量小,重量轻,结构简单(定子为整体结构),可突破直流电机结构限制,制作输出更大转矩的单台电机,并且可靠性高,维护量和维护费用低。
所以交流调速同步电动机有着良好的技术、经济指标,是理想的提升机驱动设备。
本公司有着数十年生产矿井提升电机的历史,在电机与提升机的衔接配合上,有着成熟的设计技术,积累了丰富的制造经验。
本系列同步电动机可全面匹配目前市场上已有的变频装置,为客户提供性能优良、结构合理、质量可靠、效率提高、外形美观动力源。
二、型号说明三、产品性能1. 电机适用海拔高度小于1000米,大于1000米时请事先告知;2. 电机为负载—转速非周期变化工作制S9;3.变频装置为交直交时,电机功率因数cos 变频装置为交交时,电机功率因数cos ≈1;4. 电机正反向双向运行,为连续工作方式;5. 电机定子瞬时过电流为2倍额定电流,时间60秒;6.电机过载要求不同时,需事先告知;1. General IntroductionShanghai electrical machinery from starting in the early 1990 of the 20th century, followed by the world-leading, successful development of a mine hoist AC synchronous electric motor, while cooperating with foreign famous motor manufacturing company, produced Ac synchronous motor for Hegang Mining Bureau TDBS 3500-12 1500V 0~82r/min, Huinan Xieqiao Mining TDBS 3200-16 1460V 0~68r/min, accumulation of advanced design and manufacturing technology. And, on that basis, developed in early 2000 and at that time the largest AC speed synchronization of mine hoist TDBS 4400-24 1500V 0~51r/min, used in Anhui Tongling Nonferrous Metals Inc Dongguashan Mining. In recent years, with international and domestic frequency converter manufacturer 1140V level, 3300V 6000V and AC-DC converter, I plant development, production matching the corresponding voltage AC synchronous motor of variable frequency devices.Compared to DC motors, cycloconverter-fed synchronous motors have good performance in speed regulation and also large capacity of overload without limit in commutation, the largest torque output is always possible within the whole speed range. This type of motors can also save on electricity because the efficiency is 3%-5% higher than that of DC motors. Featuring low moment of inertia, light weight, simple structure, high reliability and good convenience for installation and maintenance, the motor is an ideal driving equipment for mine hoists with good technical and economical specifications.SEMC has a history of tens of years in manufacturing motors for mine hoists and have got abundant design experience in linking up motors with hoists, all of this can be applied to cycloconverter-fed induction motors, cyclonconverter-fed synchronous motor of TDBS series is the latest model with good performance and appearance, reasonable structure and reliable quality.3. Motor Performance1.Motor applies for altitudes less than 1000m, more than 1000m prior notice required;2.The duty type for motor load-speed non-cyclic variation is S93.Power factor of the motor:AC-DC-AC cos =1、AC-AC cos ≈1;4.Motor of bidirection continuous work;5.Motor stator instaneous over current as twice as rated current can reach 60 sec;6.If motor over-load requirement is different please in form in advance.四、设计分析手段全面采用Solid Edge、Ansys等先进的设计软件,通过模态化,分析电机的电磁、发热、振动等问题,优化电机振动、噪声磁共振,避免了电磁力与结构产生共振的可能。
同步电动机滑差检测原理

同步电动机滑差检测原理Synchronous motors are widely used in industrial applications due to their efficiency and reliability. However, it is important to regularly monitor the condition of these motors to ensure they are operating optimally. One key parameter that needs to be monitored is the slip of the synchronous motor.同步电机因其高效和可靠性而被广泛应用于工业领域。
然而,定期监测这些电机的状态以确保其正常运行是很重要的。
需要监测的一个关键参数是同步电机的滑差。
The slip of a synchronous motor refers to the difference between the synchronous speed and the actual speed of the motor. Synchronous speed is the theoretical speed at which the motor should operate based on the frequency of the electrical supply, while the actual speed is the speed at which the motor is operating in real-world conditions. By monitoring the slip of synchronous motors, maintenance professionals can gain valuable insights into the health and performance of the motors.同步电机的滑差是指同步速度与电机实际速度之间的差异。
电机常用英语词汇
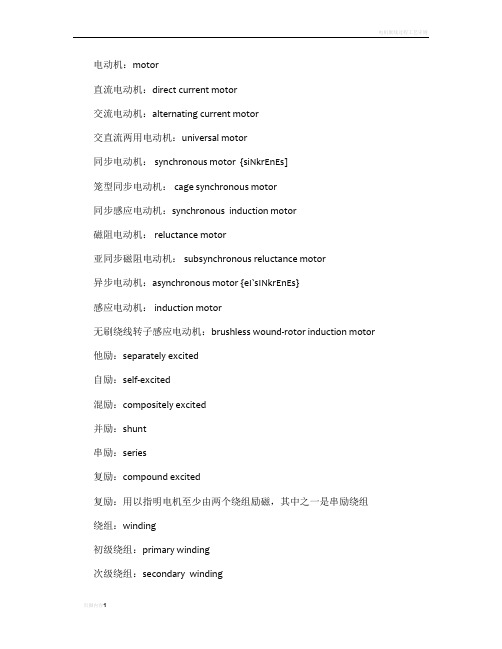
电动机:motor直流电动机:direct current motor交流电动机:alternating current motor交直流两用电动机:universal motor同步电动机: synchronous motor {siNkrEnEs]笼型同步电动机: cage synchronous motor同步感应电动机:synchronous induction motor磁阻电动机: reluctance motor亚同步磁阻电动机: subsynchronous reluctance motor异步电动机:asynchronous motor {eI`sINkrEnEs}感应电动机: induction motor无刷绕线转子感应电动机:brushless wound-rotor induction motor 他励:separately excited自励:self-excited混励:compositely excited并励:shunt串励:series复励:compound excited复励:用以指明电机至少由两个绕组励磁,其中之一是串励绕组绕组:winding初级绕组:primary winding次级绕组:secondary winding主绕组:main winding定子绕组:stator winding转子绕组:rotor winding电枢绕组:armature winding阻尼绕组:damping winding起动绕组:starting winding辅助起动绕组: auxiliary starting winding励磁绕组: excitation winding磁场绕组: field winding试验:性能试验:performance test型式试验:type test重复试验:duplicated test检查试验:routing test 对每台电机在制造完工后所进行的试验,以判明其是否符合标准抽样试验:sampling test验收试验:acceptance test效率:efficiency 输出功率对输入功率之比总损耗:total loss(of a machine) ; power losses(of a machine ) 输入与输出功率之差热量试验:calorimetric test 从电机所产生的热量来推算损耗的试验方法空载试验:no-load test 在电机作电动机运行而轴上无有效机械输出时进行的试验轻载试验:light load test 当电机在驱动或被驱动状态下运行时,做为电动机,仅供给被驱动机械的空载损耗。
电机常用英语词汇
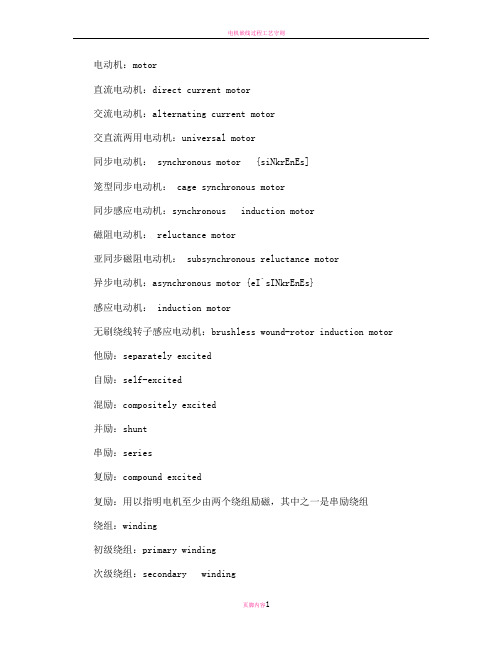
电动机:motor直流电动机:direct current motor交流电动机:alternating current motor交直流两用电动机:universal motor同步电动机: synchronous motor {siNkrEnEs]笼型同步电动机: cage synchronous motor同步感应电动机:synchronous induction motor磁阻电动机: reluctance motor亚同步磁阻电动机: subsynchronous reluctance motor异步电动机:asynchronous motor {eI`sINkrEnEs}感应电动机: induction motor无刷绕线转子感应电动机:brushless wound-rotor induction motor 他励:separately excited自励:self-excited混励:compositely excited并励:shunt串励:series复励:compound excited复励:用以指明电机至少由两个绕组励磁,其中之一是串励绕组绕组:winding初级绕组:primary winding次级绕组:secondary winding主绕组:main winding定子绕组:stator winding转子绕组:rotor winding电枢绕组:armature winding阻尼绕组:damping winding起动绕组:starting winding辅助起动绕组: auxiliary starting winding励磁绕组: excitation winding磁场绕组: field winding试验:性能试验:performance test型式试验:type test重复试验:duplicated test检查试验:routing test 对每台电机在制造完工后所进行的试验,以判明其是否符合标准抽样试验:sampling test验收试验:acceptance test效率:efficiency 输出功率对输入功率之比总损耗:total loss(of a machine) ; power losses(of amachine ) 输入与输出功率之差热量试验:calorimetric test 从电机所产生的热量来推算损耗的试验方法空载试验:no-load test 在电机作电动机运行而轴上无有效机械输出时进行的试验轻载试验:light load test 当电机在驱动或被驱动状态下运行时,做为电动机,仅供给被驱动机械的空载损耗。
永磁同步电机 功率计算

永磁同步电机功率计算英文回答:Permanent magnet synchronous motors (PMSMs) are a type of synchronous motor that uses permanent magnets to create the magnetic field in the stator. This type of motor has a number of advantages over traditional synchronous motors, including higher efficiency, lower torque ripple, and a wider speed range.The power output of a PMSM is determined by the following equation:P = T ω。
where:P is the power output in watts.T is the torque in newton-meters.ω is the angular v elocity in radians per second.The torque produced by a PMSM is determined by the following equation:T = K Φ I.where:K is a constant.Φ is the magnetic flux in webers.I is the current in amperes.The magnetic flux is determined by the design of the motor and the permanent magnets used. The current is determined by the motor controller.The speed of a PMSM is determined by the following equation:ω = (V IR) / KΦ。
脉动转矩研究资料

/
r
[1
(Rs
Rr
) 2np
/
R 4np m
]}
cos(np
)
(np 1)
永磁磁极在均匀气隙中的磁场
• 在气隙中磁密径向分量
Br1(r, )
0M1 r
[1
(Rs
/
r)2
{1 (Rr / Rm )2 (R r / Rm )2 ln(Rm / Rr )2}
{(r 1/ r [(Rs / Rm )2 (Rr / Rm )2 ]
(r 1) / r [1 (Rs Rr )2 / Rm 4 ]} cos( )
(np 1)
磁阻转矩的求解
• 在不计铁心饱和时,气隙的实际磁场=磁极在光滑气 隙内产生的磁场开槽引起的相对气隙磁导分布函数。
• 径向气隙磁场的分布为:
Br1(r, , ) Br1(r, ) ~(r, )
ks s1 )
2
• 第1、2项齿槽转矩是由Br2 ()中各次谐波和定子齿 槽产生的谐波磁密共同作用产生。
• 其周期数为极数、极数和槽数最大公约数的比值。
• 该类齿槽转矩与定子槽数和转子极数的配合有关,可 以通过合理的槽极配合削弱齿槽转矩。
齿槽转矩的分类
4Br0
hm2
B m1
sm
r mz1 z2
dr
永磁体内径 向磁密分布
磁阻转矩的求解
• 能量虚位移法,齿槽定位力矩可表示为
T ( ) dWm ( ) d
削弱磁阻转矩的方法
• 极弧系数不接近1时,移动相邻磁极的位置可有效 减小磁阻转矩的基波分量。
• 极弧系数接近1时,谐波平衡法:齿面加2个辅助 凹槽, 凹槽宽与槽口相等。。
电机及控制技术论文集

电机及控制技术论文集本文基于SVM的直接转矩控制理论,以永磁同步电机数学模型为参考模型,以电机转速为可调参数建立参考模型,满足波波夫超稳定性定理构建合适的自适应率,实现了采用模型参考自适应法来进行永磁同步电机无速度传感器调速控制的方案。
在Matlab-Simulink软件环境下搭建系统的仿真图并进行仿真和分析,结果验证了该方案的可行性。
【关键词】SVM直接转矩控制无速度传感器 MRAS模型参考自适应永磁同步电机PMSM的体积小、噪声低、效率高、功率密度较大,在电力电子技术与现代控制理论迅速发展的大环境下,这些优点使PMSM渐渐得到了广泛的应用。
永磁同步电机的直接转矩控制DTC是在矢量控制发展日渐成熟之后兴起的另一种高性能交流调速技术。
由于拥有控制结构简洁、动态响应较快、对电机参数依赖较少等特点,直接转矩控制已成为学术界研究的热点。
在现代交流调速系统领域中,速度传感器由于存在降低系统可靠性,增加系统成本等问题,已经大大制约了交流传动系统的发展,所以采用无速度传感器的调速方案是当今国内外研究的趋势。
永磁同步电机无速度传感器的研究方法主要有基于磁链位置的估算法、基于反电动势法、滑膜观测器法、扩展卡尔曼滤波法、高频注入法、人工智能估算法、模型参考自适应法MRAS。
因为模型参考自适应法具有控制相对简单而且精度高的优点,所以本文将模型参考自适应法应用到永磁同步电机调速系统当中。
将永磁同步电机本身作为参考模型,将含有转子转速的模型作为可调模型,采用并联型结构进行速度辨识,两个模型的输出量物理意义相同。
利用可调和参考模型输出量所构成的误差,计算出合适的比例积分自适应率,并以此来调整可调模型的参数,满足Popov超稳定性定理,使系统逐渐稳定,最终使可调模型的状态能稳定、快速地逼近参考模型,即让误差值趋近于零,进而使转速估计值逐渐逼近实际值,实现转速的识别。
1 永磁同步电机数学模型建立dq坐标系下的数学模型,可以得到定子电压、电流均为直流的永磁同步电动机的电压方程式,利于分析永磁同步电动机控制系统的瞬态性能和稳态性能。
永磁同步电动机调速范围的优化及性能分析

2021年第49卷第3期D设计分析esign and analysis 程献会等 永磁同步电动机调速范围的优化及性能分析17 收稿日期:2020-11-24基金项目:山西省自然基金(2013011035-1);中国博士后科学基金(2018M640250)永磁同步电动机调速范围的优化及性能分析程献会,王淑红(太原理工大学电气与动力工程学院,太原030024)摘 要:根据内嵌式调速永磁同步电动机的弱磁控制特点,以弱磁扩速倍数为优化目标,利用有限元仿真软件,分析了内嵌式调速永磁同步电动机矩形和V 形永磁体尺寸和位置对电机参数和调速范围的影响,通过优化永磁体的位置和尺寸扩大了电机弱磁调速范围㊂计算了优化后电机的参数,对比了优化前后电机调速的范围㊂为内嵌式调速永磁同步电动机的优化和参数计算提供一定的参考㊂关键词:内嵌式调速永磁同步电动机;永磁体尺寸;调速范围;有限元分析中图分类号:TM351 文献标志码:A 文章编号:1004-7018(2021)03-0017-04Optimization and Performance Analysis of Speed Control Range of Permanent Magnet Synchronous MotorCHENG Xian -hui ,WANG Shu -hong(School of Electrical and Power Engineering,Taiyuan University of Technology,Taiyuan 030024,China)Abstract :According to the embedded control weak magnetic control characteristics of permanent magnet synchronousmotor,with weak magnetic speed ratio as the optimization goal,and using finite element simulation software,embedded speed permanent magnet synchronous motor was analyzed rectangle and V the size and position of permanent magnet motor parameters and the influence of the speed range,through optimizing the position and size of the permanent magnet motor weak magnetic speed range had expanded.The parameters of the optimized motor were calculated,and the range of motor speed before and after optimization was compared.It provided a certain basis for the optimization and parameter calculationof the built-in speed-regulating permanent magnet synchronous motor.Key words :built-in speed-regulating permanent magnet synchronous motor,permanent magnet size,speed regulatingrange,finite element analysis0 引 言永磁同步电动机具有结构简单㊁运行可靠㊁效率高等显著优点,其应用范围较为广泛,在航空㊁国防㊁工业生产和日常生活中都可以看到它的身影[1-2]㊂已有许多专家学者对永磁同步电动机进行过优化设计,从而使电机性能更优越,使用更广泛㊂文献[3]采用田口法,以电机的效率和磁钢用量作为优化目标,对内嵌式永磁电动机进行优化设计;文献[4]同样采用田口法对铁耗和转矩脉动进行了优化㊂文献[5-6]对电动汽车用永磁同步电动机进行了电磁设计和弱磁调速分析;文献[7]中搭建了凸极式永磁同步电动机弱磁调速的控制系统;文献[8]从内置式永磁同步电动机的数学模型及弱磁控制方式入手,采用数值计算方法,分析了不同参数对电机弱磁调速的影响;文献[9]讨论了永磁体分段对永磁同步电动机参数和调速范围的影响;文献[10]设置了一种分段Halbach 结构的表贴式永磁同步电动机以降低涡流损耗等;文献[11]对V 形异步起动永磁同步电动机的齿槽转矩进行了优化;文献[12]采用多目标遗传算法对不同类型的电机结构进行优化㊂对于调速永磁同步电动机,在传统的控制方法下,电机受到电源电压和电流的限制,基速以上很难有较大的调速范围㊂为了扩大电机的调速范围,并确保电机的恒功率运行范围和电机性能,不仅要采用带有弱磁控制模块的控制系统,电机本体参数也应与控制系统有较好的配合,满足弱磁调速策略对电机参数的要求㊂永磁同步电动机的励磁由电机转子上的永磁体提供,永磁体在电机制作时已放置好,励磁无法根据实际需要进行调节,所以在电机设计时应考虑永磁体的尺寸和位置,为弱磁调速控制提供合理的永磁体磁链及交直轴电感参数㊂本文在电机设计过程中,以弱磁调速的倍数为电机永磁体尺寸的优化目标,使用有限元仿真软件,对两种不同形状的永磁体电机进行参数化仿真,确定电机永磁体的位置和尺寸对电机调速范围的影响㊂分析了矩形永磁体和V 形永磁体在不同尺寸和位置,对电机参数的影响,给出永磁体的尺寸,完 D设计分析esign and analysis 2021年第49卷第3期 程献会等 永磁同步电动机调速范围的优化及性能分析 18 成对电机调速范围的优化并分析电机性能㊂1 永磁同步电动机弱磁调速的基本原理1.1 永磁同步电动机的数学模型在三相电流对称㊁电机稳定运行且忽略定子绕组电阻㊁铁心饱和㊁铁耗的情况下,永磁同步电动机在d,q坐标轴下的数学模型如式(1)㊁式(2)㊂电压方程:u=u2d+u2q= ω(L q i q)2+(L d i d+ψf)2(1)电磁转矩方程:T em=32p[ψf i q+(L d-L q)i d i q](2)由电压方程可得出:ω=u(L q i q)2+(L d i d+ψf)2(3)式中:p为电机的极对数;L q,L d分别为电机定子的交直轴电感;i q,i d分为电机定子的交直轴电流;ψf 是电机的永磁体磁链;ω为电机角频率㊂由式(3)可以看出,当电机的端电压和电流达到极限值,且电流全部为直轴去磁电流时,电机可以达到理想最大转速:ωmax=u limψf-L d i lim(4) 调速永磁同步电动机的电压和电流的极限值取决于控制系统的逆变器,如果需要更高的转速范围,需要减小永磁体的磁链和增加直轴电感㊂但过小的永磁体磁链会造成电机转矩的下降,在电机优化时应综合考虑,不应为了单纯提高调速范围而牺牲太多的转矩㊂1.2 基于最大转矩电流比控制的弱磁调速性能分析凸极永磁同步电动机采用最大转矩电流比控制时,电机的电流矢量应满足:∂(T em/i s)∂i d=0∂(T em/i s)∂i q=üþýïïïï(5) 定子电流矢量轨迹如图1所示,当电机的端电图1 定子电流矢量轨迹压和电流达到极限值时,经过公式推导可得出此时的转折速度:ωb=u lim(L q i lim)2+ψ2f+(L d+L q)C2+8ψf L d C16(L d-L q)(6)式中:C=-ψf+ψ2f+8(L d-L q)2i2lim㊂ 定义电机的弱磁扩速倍数:k=ωmaxωb(7) 将弱磁率ξ=L d i sψf和凸极率ρ=L qL d代入到式(7)中,可得:k=ωmaxωb= 1+(ρξ)2+116(1-ρ)[(1+ρ)C2f+8C f]1-ξ(8)式中:C f=-1+1+8(1-ρ)2ξ2㊂根据式(8)可得如图2所示的凸极永磁同步电动机弱磁扩速倍数随凸极率和弱磁率的变化曲线,可以看出,电机的弱磁扩速倍数随凸极率和弱磁率的增加而增加㊂对永磁同步电动机的凸极率和弱磁率进行优化,便可以影响电机的扩速范围㊂图2 弱磁扩速倍数k与ξ,ρ的关系2 永磁同步电动机优化分别对原功率为2.2kW,永磁体为矩形和V形的两台内置式永磁同步电动机进行优化,以弱磁率和凸极率为优化目标,使其满足两倍以上的调速范围㊂2.1 建立电机的物理模型样机的基本参数如表1所示,电机的物理模型如图3㊁图4所示㊂在电机基本结构尺寸不变的情况下,对电机的永磁体尺寸㊁位置进行优化,永磁体尺寸主要有永磁体宽度b m,永磁体磁化方向长度h m㊂矩形永磁体的位置主要靠轴心距确定,就是永磁体下边缘距离电机中心的距离,即o2㊂轴心距越大,永磁体离气隙越近,离电机转轴的中心则越远㊂V形永磁体的位置还要依靠永磁体旋转角度来确 2021年第49卷第3期 D设计分析esign and analysis 程献会等 永磁同步电动机调速范围的优化及性能分析19 定,旋转角为θ㊂表1 电机的基本参数参数值参数值定子外径Φso /mm 155定子槽数36定子内径Φsi /mm 98极对数2转子内径Φri /mm 38额定转速n /(r㊃min -1)1500气隙长度δ/mm0.6轴向长度l /mm105图3 矩形永磁体电机模型图4 V 形永磁体电机模型2.2 电机的优化在初步确定电机额定电流的情况下,对永磁体的尺寸范围进行优化设计㊂利用Maxwell 软件,分别建立两种永磁同步电动机的2D 模型,并设置永磁体宽度㊁磁化方向长度和轴心距为参数化变量,求解不同情况下的凸极率和弱磁率,参数化范围如表2㊁表3所示㊂表2 矩形永磁体参数矩形参数范围步长宽度b m /mm30~502磁化方向长度h m /mm4~5.50.5轴心距o 2/mm33~351表3 V 形永磁体参数V 形参数范围步长单片宽度b m /mm 15~242磁化方向长度h m /mm4~70.5轴心距o 2/mm30~351 对在此范围内的所有不同组合进行参数化扫描仿真,并进行最优化求解,最优化算法采用默认的拟牛顿算法,它是求解非线性优化问题最有效的方法之一,收敛速度快㊂最优化求解的目标为ρ≥1.5,ξ≥0.5,由图2可以看出,理论上满足3倍的调速范围㊂经过Maxwell的最优化求解,可得出永磁体宽度㊁永磁体磁化方向长度和轴心距的初选结果㊂2.2.1 永磁体的尺寸确定经过分析和有限元软件的计算,可得到ρ和ξ随电机永磁体尺寸的参数变化规律㊂矩形永磁体和V 形永磁体的变化规律都是随着电机永磁体厚度和磁化方向的增加,ρ增加且ξ下降;永磁体宽度对两个参数的影响更明显,如图5㊁图6所示㊂(a)矩形永磁体电机(b)V 形永磁体电机图5 凸极率和弱磁率随永磁体宽度的变化(a)矩形永磁体电机(b)V 形永磁体电机图6 凸极率和弱磁率随永磁体磁化方向长度的变化两个优化参数变化趋势并不相同,在有限元优化求解给出的结果下,要想达到优化目标,并考虑制作工艺难度㊂最后确定矩形永磁体尺寸确定为宽42mm,厚4mm;V 形永磁体尺寸确定为单片永磁体宽20mm,厚4mm㊂2.2.2 永磁体的位置确定在永磁体尺寸确定的情况下,随着轴心距的增加,如图7所示,矩形永磁体电机的ρ会增加,ξ会下降;V 形永磁体电机的ρ和ξ呈相同变化规律,凸极率增加,弱磁率下降㊂(a)矩形永磁体电机(b)V 形永磁体电机图7 凸极率和弱磁率随轴心距的变化经过优化求解,矩形永磁体电机轴心距选择35mm;V 形永磁体电机轴心距选择33mm㊂V 形永磁体不仅要考虑轴心距,还要考虑永磁体旋转的角度θ对交直轴电感的影响㊂如图8所示,随着旋转角度的增加,凸极率上升,弱磁率下降,最终旋转角选择23°㊂图8 凸极率和弱磁率随旋转角度的变化3 电机参数分析与对比3.1 矩形永磁体电机在永磁体尺寸和位置确定之后,对电机模型进行有限元仿真,电机的直轴电感为0.074H,交轴电感为0.143H,磁链为0.608Wb,仿真得出凸极率为1.93,弱磁率为0.597,满足求解目标㊂ D设计分析esign and analysis 2021年第49卷第3期 程献会等 永磁同步电动机调速范围的优化及性能分析 20 对优化后的电机进行MATLAB仿真分析,采用基于最大转矩电流比的弱磁控制方式,控制框图如图9所示㊂在空载及负载条件下进行仿真分析,对比优化前后电机的调速范围,结果如表4㊁图10所示㊂可以看出,优化后空载条件下调速范围可以达到两倍以上,负载下调速范围也明显提高,达到了优化的目的㊂图9 弱磁控制框图表4 矩形永磁体电机最高转速对比转矩T/(N㊃m)优化前n f/(r㊃min-1)优化后n a/(r㊃min-1)仿真实验仿真020001900310010185018002400(a)空载下电机转速(b)负载下电机转速图10 矩形永磁体电机转速优化3.2 V形永磁体电机对确定永磁体位置和尺寸的电机模型进行有限元仿真,电机的直轴电感为0.073H,交轴电感为0.142H,磁链为0.635Wb,凸极率为1.96,弱磁率为0.56,满足求解要求㊂对优化后的V形永磁体电机,进行基于最大转矩电流比的弱磁调速控制下的空载及负载仿真,结果如表5所示㊂空载可以达到两倍左右的调速范围,负载下速度也有所提高,满足优化目标,如图11所示㊂表5 V形永磁体电机最高转速对比转矩T/(N㊃m)转速n/(r㊃min-1)优化前优化后022003000 1020002450(a)空载下电机转速(b)负载下电机转速图11 V形永磁体电机转速优化4 结 语本文借助有限元仿真软件,以内嵌式永磁同步电动机的调速范围为优化目标,讨论了矩形和V形永磁体不同尺寸和位置对电机参数的影响,结合对调速范围的影响,确定了电机永磁体的尺寸和位置,完成了电机的优化设计㊂以优化完成的电机尺寸,对其进行参数分析和对比,较之前的电机有了明显的转速范围的提升,达到了本次优化的目的㊂优化过程和结果对内嵌式永磁同步电动机的设计和参数提供了一定的参考㊂参考文献[1] 唐任远.现代永磁电机理论与设计[M].北京:机械工业出版社,2015.[2] 王秀和.永磁电机[M].北京:中国电力出版社,2011.[3] 贾金信,杨向宇,曹江华.基于田口法的内嵌式永磁电动机的优化设计[J].微电机,2013,46(6):1-4.[4] 王艾萌,温云.田口法在内置式永磁同步电机优化设计中的应用[J].华北电力大学学报(自然科学版),2016,43(3):39-44.[5] 陈晨.纯电动汽车用永磁同步电动机设计及弱磁扩速分析[D].天津:天津大学,2010.[6] 解志霖.电动大巴车用永磁电机设计[D].沈阳:沈阳工业大学,2017.[7] 郭殿林,陈康,包兵.电动汽车凸极式永磁同步电机弱磁调速的研究[J].煤矿机械,2016,37(7):58-60.[8] 皮秀,王善铭.弱磁调速的永磁同步电机参数的分析设计[J].中国科技论文在线,2010,5(8):585-591.[9] 孙慧芳,高琳,李计亮,等.弱磁调速用永磁同步电机设计分析[J].微电机,2010,43(12):16-20.[10] 高锋阳,齐晓东,李晓峰,等.部分分段Halbach永磁同步电机优化设计[J/OL].电工技术学报:1-14[2021-02-04].ht⁃tp:///10.19595/ki.1000-6753.tces.191554..[11] 李晓峰,高锋阳,齐晓东,等.对称V型异步起动永磁同步电机齿槽转矩优化[J/OL].电力系统及其自动化学报:1-9[2021-02-04]./10.19635/ki.csu-epsa.000497.[12] 刘晓宇,袁彬,戴太阳,等.基于自适应网格及响应面模型的永磁电机多目标优化[J].微特电机,2020,48(7):24-27,30.作者简介:程献会(1995 ),女,硕士研究生,研究方向为电机与电器㊂。
BH系列电动机说明书

1/750 HP1 W 1/125 HP6 W 1/50 HP15 W 1/30 HP25 W 1/19 HP40 W 1/12 HP60 W 1/8 HP90 W1/19-1/8 HP 40-90 W(2-Pole)Induction Motors BH Series200 W (1/4 HP)Frame Size: Ⅺ4.09 in.(Ⅺ104 mm sq.)ⅥFeatures●BH Series motors provide 200W output power and up to 530 lb-in (60 N•m) of torque in a compact 4.09 in. sq. (104 mm sq.) mounting configuration.●Right-angle gearheads are available.●For easy installation, the BH Series motor and gearhead come pre-assembled.✻Motors and gearheads are also available separately.ⅥProduct LineⅷCombination Type◆Right-Angle Shaft◆Parallel Shaft●Enter the gear ratio in the box (Ⅺ) within the model name.●Enter the gear ratio in the box (Ⅺ) within the model name.T: Contains a built-in thermal protector. If a motor overheats for any reason, the thermal protector is opened and the motor stops.When the motor temperature drops, the thermal protector closes and the motor restarts. Be sure to turn the motor off before inspecting.●Details of Safety Standard➝Page G-2●Enter the gear ratio in the box (Ⅺ) within the model name.●The values in the table are for the motor only.(Cable Type,Right-Angle Hollow Shaft)(Terminal Box Type,Parallel Shaft)(Terminal Box Type,Right-Angle Solid Shaft)A-54System Configuration A-15Features A-14Specifications A-54A-55Dimensions A-57Connection Diagrams A-63List of Motor and Gearhead Combinations A-64AC MotorsInduction Motors Synchronous MotorsTorque Motors Watertight Motors Magnetic BrakeClutch &BrakeBrake PackReversible Motors Right-AngleGearheads AccessoriesIntroductionBefore Using a Standard AC MotorⅷRound Shaft Type●Enter the gear ration in the box (Ⅺ) within the model name. A colored background indicates gear shaft ration in the same direction as the motor shaft; a white background indicates rotation in the opposite direction.●Decimal gearheads are not available for the BH Series.●The speed is calculated by dividing the motor's synchronous speed (50 Hz: 1500 r/min, 60 Hz: 1800 r/min) by the gear ratio. The actual speed is 2ϳ20% less than the displayed value, depending on the size of the load.ⅥPermissible Overhung Load and Permissible Thrust LoadMotor (Round shaft type) ➝Page A-11Gearhead ➝Page A-11ⅥPermissible Load Inertia J for Gearhead➝Page A-12v Single-Phase 230 VAC 50 HzⅷParallel ShaftⅥGearmotor — Torque TableⅷRight-Angle Shaftv Single-Phase 115/230 VAC 60 Hz, Three-Phase 230 VAC 60 HzUnit סUpper Values: lb-in/Lower Values: N •m Unit סUpper Values: lb-in/Lower Values: N •m Unit סUpper Values: lb-in/Lower Values: N •mUnit סUpper Values: lb-in/Lower Values: N •m1/750 HP1 W 1/125 HP6 W 1/50 HP15 W 1/30 HP25 W 1/19 HP40 W 1/12 HP60 W 1/8 HP90 W1/19-1/8 HP 40-90 W(2-Pole)ⅥMounting Method for Hollow Shaft GearheadsⅷStepped-Down ShaftⅷStraight Load ShaftThese diagrams show how to mount loads depending on theshape of the shaft.The tolerance of the inner diameter for the hollow shaft isfinished as H8, and "key slot" processing is given to mountthe load shaft. The recommended tolerance of the load shaftis h7. Apply a coating of molybdenum disulfide or similargrease to the inner diameter of the load shaft to preventbinding. Recommended load shaft dimensions are shownbelow.●Replace the safety cover after installing the load shaft.Note:●Be careful not to apply a shock to the hollow shaft when mounting a load. It maydamage the bearing inside the gearhead.Recommended size of inner diameter for thehollow shaft and load shaftA-56System Configuration A-15Features A-14Specifications A-54A-57Connection Diagrams A-63List of Motor and Gearhead Combinations A-64Induction Motors Synchronous MotorsTorque MotorsWatertight Motors MagneticBrakeClutch &BrakeBrake Pack Reversible Motors Right-Angle Gearheads AccessoriesIntroduction Before Usinga Standard AC MotorⅥDimensions Scale 1/4, Unit = inch (mm)Mounting screws are included with the combination type parallel shaft.➝Page A-223Enter the gear ratio in the box (Ⅺ) within the model name.◆Combination Type Right-Angle, Hollow Shaft Cable TypeBHI62F-ⅪRH, BHI62E-ⅪRHWeight: 22 lb. (10.0 kg) including gearhead Motor Model: BHI62F-G2, BHI62E-G2Gearhead Model: BH6G2-ⅪRH d A299ⅷKey (Included) (Scale 1/2)1/750 HP1 W 1/125 HP6 W 1/50 HP15 W 1/30 HP25 W 1/19 HP40 W 1/12 HP60 W 1/8 HP90 W1/19-1/8 HP 40-90 W(2-Pole)◆Combination Type Right-Angle, Solid Shaft Cable Type BHI62F-ⅪRA, BHI62E-ⅪRAWeight: 22 lb. (10.0 kg) including gearheadMotor Model: BHI62F-G2, BHI62E-G2Gearhead Model: BH6G2-ⅪRAdA300Ϫ.1ⅷKey and Key Slot (Included) (Scale 1/2)∗At the time of shipment, a parallel key is inserted on the gearhead's shaft.A-58System Configuration A-15Features A-14Specifications A-54A-59Connection Diagrams A-63List of Motor and Gearhead Combinations A-64Induction Motors Synchronous MotorsTorque MotorsWatertight Motors Magnetic BrakeClutch &BrakeBrake PackReversible Motors Right-Angle Gearheads AccessoriesIntroductionBefore Usinga Standard AC MotorGearhead Model: BH6G2-ⅪRH d A301ⅷKey (Included) (Scale 1/2)ⅷUse cable (VCTF ) with a diameter of 0.24 inch (6 mm)ϳ0.47 inch (12 mm).ⅷDetails of Terminal Box ➝ Page A-2241/750 HP1 W 1/125 HP6 W 1/50 HP15 W 1/30 HP25 W 1/19 HP40 W 1/12 HP60 W 1/8 HP90 W1/19-1/8 HP 40-90 W(2-Pole)Gearhead Model: BH6G2-ⅪRAdA302Ϫ.1ⅷKey and Key Slot (Included) (Scale 1/2)∗At the time of shipment, a parallel key is inserted on the gearhead's shaft.ⅷUse cable (VCTF) with a diameter of 0.24 inch (6 mm)ϳ0.47 inch (12 mm).ⅷDetails of Terminal Box ➝Page A-224A-60System Configuration A-15Features A-14Specifications A-54A-61Connection Diagrams A-63List of Motor and Gearhead Combinations A-64Induction Motors Synchronous MotorsTorque MotorsWatertight Motors Magnetic BrakeClutch &Brake Brake Pack Reversible Motors Right-Angle Gearheads AccessoriesIntroductionBefore Using a Standard AC Motor◆Combination Type, Parallel Shaft Type Cable TypeBHI62F-Ⅺ, BHI62E-ⅪWeight: 18 lb. (8.0 kg) including gearhead Motor Model: BHI62F-G2, BHI62E-G2Gearhead Model: BH6G2-Ⅺd A3030Ϫ0.1ⅷKey and Key Slot (Included) (Scale 1/2)∗At the time of shipment, a parallel key is inserted on the gearhead's shaft.◆Combination Type, Parallel Shaft Type with Terminal BoxBHI62FT-Ⅺ, BHI62ET-Ⅺ, BHI62ST-ⅪWeight: 18 lb. (8.0 kg) including gearheadMotor Model: BHI62FT-G2, BHI62ET-G2, BHI62ST-G2Gearhead Model: BH6G2-Ⅺd A304Ϫ0.1ⅷKey and Key Slot (Included) (Scale 1/2)∗At the time of shipment, a parallel key is inserted on the gearhead's shaft.ⅷUse cable (VCTF ) with a diameter of 0.24 inch (6 mm)ϳ0.47 inch (12 mm).ⅷDetails of Terminal Box ➝ Page A-2241/750 HP1 W 1/125 HP6 W 1/50 HP15 W 1/30 HP25 W 1/19 HP40 W 1/12 HP60 W 1/8 HP90 W1/19-1/8 HP 40-90 W(2-Pole)◆Round Shaft Type Cable TypeBHI62F-A, BHI62E-AWeight: 11 lb. (5 kg)◆Round Shaft Type with Terminal BoxBHI62FT-A, BHI62ET-A, BHI62ST-AWeight: 11 lb. (5 kg)d A308ⅷCapacitor (Included with single-phase motors)●If you need to order a capacitor without a motor, add "-C" to the capacitor model name shown. A capacitor cap is included with a capacitor.●Enter the gear ratio in the box (Ⅺ) within the model name.Conductors: UL Style 3271, AWG 20ⅷUse cable (VCTF) with a diameter of 0.24 inch (6 mm)ϳ0.47 inch (12 mm).ⅷDetails of Terminal Box ➝Page A-224A-62System Configuration A-15Features A-14Specifications A-54A-63Dimensions A-57Connection Diagrams A-63List of Motor and Gearhead Combinations A-64AC MotorsInduction Motors SynchronousMotorsTorqueMotorsWatertight Motors Magnetic BrakeClutch &Brake Brake Pack Reversible Motors Right-Angle Gearheads Accessories Introduction Before Using a Standard AC MotorⅥConnection Diagrams●The direction of motor rotation is as viewed from the shaft end of the motor.●CW represents the clockwise direction, while CCW represents counterclockwise direction.✽1Enter F or E (power supplyvoltage) in the box (Ⅺ) within the model name.✽2Connecting to the terminal block for terminal box typeApplicable lead wire: AWG 24ϳ12(0.2 mm 2ϳ4.0 mm 2)Strip length: 0.31 inch (8 mm)Note :●Change the direction of single-phase motor rotation only after bringing the motor to a stop. If an attempt is made to change the direction of rotation while the motor is rotating, the motor may ignore the reversing command or change its direction of rotation after some delay.●To protect the contact point of switches, connect a CR circuit.Connecting CR circuit, contact capacity ➝Page A-226●For increased safety, provide a breaker or fuse on the power-supply input.●How to Connect a Capacitor ➝Page A-225ⅷInner Connection Diagram for 4-Terminal CapacitorT erminals of the capacitor are connected as shown in the figure. For lead wire connection, use one lead wire per terminal.1/750 HP1 W 1/125 HP6 W 1/50 HP15 W 1/30 HP25 W 1/19 HP40 W 1/12 HP60 W 1/8 HP90 W1/19-1/8 HP 40-90 W(2-Pole)ⅥList of Motor and Gearhead CombinationsⅷCombination Type Right-Angle Shaft●Enter the gear ratio in the box (Ⅺ) within the model name.ⅷCombination Type Parallel Shaft●Enter the gear ratio in the box (Ⅺ) within the model name.A-64System Configuration A-15Features A-14Specifications A-54。
自动化专业英语原文和翻译P1U6
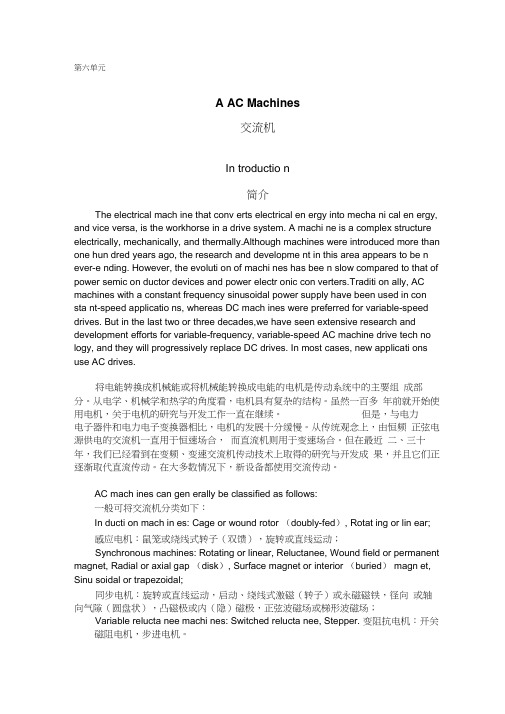
第六单元A AC Machines交流机In troductio n简介The electrical mach ine that conv erts electrical en ergy into mecha ni cal en ergy, and vice versa, is the workhorse in a drive system. A machi ne is a complex structure electrically, mechanically, and thermally.Although machines were introduced more than one hun dred years ago, the research and developme nt in this area appears to be n ever-e nding. However, the evoluti on of machi nes has bee n slow compared to that of power semic on ductor devices and power electr onic con verters.Traditi on ally, AC machines with a constant frequency sinusoidal power supply have been used in con sta nt-speed applicatio ns, whereas DC mach ines were preferred for variable-speed drives. But in the last two or three decades,we have seen extensive research and development efforts for variable-frequency, variable-speed AC machine drive tech no logy, and they will progressively replace DC drives. In most cases, new applicati ons use AC drives.将电能转换成机械能或将机械能转换成电能的电机是传动系统中的主要组成部分。
永磁同步电动机英文翻译

永磁同步电动机英文翻译英文原文Research on Voltage Space-vector Control System of Synchronous Motor Vector control of field oriented control, the basic idea is: through coordinate transformation control method for simulation of DC motor to control the permanent magnet synchronous motor. Three-phase symmetrical windings in three-phase AC can produce a rotating magnetic motive force, two phase symmetrical windings into two symmetric alternating current can produce the same rotating magnet ometive force; therefore the three-phase symmetric winding can be replaced with two phase symmetrical windings equivalent independent of each other, equivalent principle is the constant magnetomotive force produced before and after transformation, transformation and total power constant.In oil field, the power factor was reduced and the reactive power consumption was increased because of the usage of the large number of asynchronous motor, and resulting in a huge waste of energy, which reduced the integrated cost-effective of field. The permanent magnet synchronous motor possess all the advantages of synchronous motor and it has high efficiency and higher power factor. For the advantages of permanent magnet synchronous,it will bring good energy saving results if it is used in pumping unit. As a result,the study on permanent magnet synchronous motor control system is important.In this paper the theory of vector control system on PMSM is first deeply studied,and the idea of coordinate transformation is used to build the mathematical model of PMSM. An in-depth theoretical analysis of voltage space vector control algorithm is done. Secondly,based on the mathematical model of permanent magnet synchronous motor and SVPWM theory,the model of PMSM vector control system is established by of Matlab/Simulink. The simulation result shows the possibility of using the control system.In the paper, the software and hardware of PMSM vector control system is designed core-based TI Company’s motor control DSP chip TMS320LF2407A. Hardware ncludes the main circuit,control circuit and its peripheral circuits;software contains the main program and SVPWM interrupt subroutine,it achieves the implementation of the dual closed-loop current. At last,the motor experiments are carried on under the laboratory,the experimental results verify the correctness of the hardware and control program.Permanent magnet synchronous motor with the advantages of simple structure,high efficiency,wide speed range,widely used in machining,aerospace and electric tractionfields,this paper introduces the structure,control strategy of permanent magnet synchronous motor and its vector torque control research present situation and direction.Based on space vector principle,the three kind of coordinate systems as well as the transformation o f them which usually used in motor’s speed control system are introduced,then,the mathematic models on different coordinate systems are derived,be based on that,the principle of traditional direct torque control system as well as the direct torque control system based on SVPWM are analyzed detailed,meanwhile,the realization process of SVPWM algorithm is derived.Finally,the simulation model of convientional DTC Control system are established in MATLAB/Simulink.Control of permanent magnet synchronous motor mainly in the following1.1 vector controlThe core idea of vector control of three-phase current,voltage,the flux of the motor by coordinate transformation into the rotor flux oriented phase reference coordinate system, control idea according to DC motor, control motor torque.The advantages of the field oriented vector control is good torque response,precise speed control,zero speed can achieve full load.However,the vector control system needs to determine the rotor flux,to coordinate transformation,a large amount of calculation,but also consider the effect of changes in the rotor of the motor parameters,which makes the system more complex,this is the vector control deficiencies.1.2 direct torque controlIt is based on stator flux orientation,implementation of direct control of stator flux and torque.The control is based on the idea of amplitude real-time detection of motor torque and flux are given,and the torque and flux linkage value comparison,the torque and flux adjusting the appropriate stator voltage space vector selection table switch calculated directly from an offline,power switch and control of inverter state.Direct torque control does not need the vector coordinate transformation complex,the motor model is simplified,no pulse width modulation signal generator,control has the advantages of simple structure,motor parameter changes,can obtain good dynamic performance.But there are also some shortcomings,such as the inverter switching frequency is not fixed,large torque ripple current to realize digital control requires high sampling frequency.1.3 direct torque control based on space vector modulation(SVM-DTC)The SVM-DTC control is the vector control and direct torque control together,its theory foundation and DTC control theory,is based on torque angle control.According tothe change of torque angle and flux vector position,get the flux of the next cycle position,which can be the reference voltage vector is required,then the reference voltage vector modulation,PWM wave inverter driving.The SVM-DTC control,the flux changes to determine the next position,so the accurate estimation of flux has great effect on the control system,and the flux estimation depends on motor parameters are stable.In addition,the electromagnetic torque and torque angle is a nonlinear relationship,but in the practical application is approximately linear,using PI regulation,performance so that the PI parameters can also affect the system.1.4 The model reference adaptive control(MRAS)The model system requirements of the control system with a model for the adaptive control,the output response model is ideal,this model is called the reference model.The system always tries to make dynamic consistency can bedynamic reference model and the adjustable model in operation.By comparing the output of reference model and actual process,and through the adaptive controller to adjust some parameters of the adjustable model or generate anauxiliary input,so that the output error between actual output and the reference model as small as possible.In practical application,usually used for speed estimation,to realize the speed sensor less operation.Therefore,the model reference adaptive depends mainly on the accuracy of the adjustable model,the stable operation of the system plays a decisive role in.In addition,the adaptive control law parameters tuning is a difficult problem,the control accuracy of the control system has a great impact.1.5The state observer based controlControl based on state observer is developed based on the modern control theory,observer based on the mathematical model of permanent magnet synchronous motor,used for each observation control system and the state,thus extracting speed control.It is also dependent on the accuracy of the motor model,the appearance of large error will run at low speed or increasing temperature leads to the variation of motor parameters,so as to bring large deviation to control.1.6 intelligent controlThe use of intelligent algorithms,intelligent control of the control system, such as fuzzy control,neural network control,self-tuning parameters and so on,through one or several times after the trial operation, automatic parameter tuning out,to realize the optimization control.Intelligent control has many advantages,especially in the motor is multi variable,nonlinear control system,however,control and its performance depends on the control object,that is to say not every control system can achieve good control,which require sexperience.At the same time,the large amount of computation,but also hascertain requirements for the controller.Synchronous Motor because of having power factor higher run –time efficiency higher , stability good, the revolving speed settles to wait a merit, is extensively been applied to industrial production amid. The starting fault that acquaints with synchronous motor, and debugging in time, all have important meaning to the motor and the production systems . By way of energy in time, accurate debugging and transaction fault, have the familiar fault progress of the synchronous motor in detail analytical!2 Familiar fault2.1 The synchro motor after switching on electricity the incapability startsThe synchro motor after starting the incapability run - time generally has the reason of severals as follows:(1)Power supply voltage over low.Because at the square of voltage, the starting torque direct proportion of synchro motor's the voltage of power supply over make low the starting torque of synchro motor significantly the droop is lower than load troque, can not start thus and want to raise vs this power supply voltage to enlarge the starting torque of dynamo.(2)The fault of motor. Check motor settle, the rotor winding had no short circuit, open circtui, open soldering and link bad etc. fault, these the faults will make the dynamo can not start to create starting of rating of intensity of magnetic field, make thus the dynamo can not start;Checking the motor bearing has already had no failure, the port cap has have no loose, if bearing failure port shroud loose, result in bearing's down sinking, mutually rub with stator iron core, result in thus dynamo's canning not start, vs settle the rotor fault can be shaken table with the low tension, gradually click to check to seek a fault condition and adopt homologous treatment;The countersgaft accepts and carries to shroud a loose condition and all wants a pan car before driving each time and sees motor rotor whether slewing is vivid, if bearing or shaft kiowatt damage and replace in time.(3)The control device breaks down.This kind of faults are mostly the d.c. output voltage of the windings of Li magnetic belt to adjust not appropriate or don't output, result in the stator current of motor over big, cause the motor conduct electricity the run make or the losing of dynamo magnetic belt run - time.Should check whether output voltage current and its waveform that the Li magnetic belt equips is normal at this time, the Rong breaks whether the machine Rong breaks, the contact is bad;Whether circuitboard plug-in puts prison or alignment;Check loop resistance, put out whether crystal gate tube of magnet burns out or brokes through.(4)Mechanical trouble. Such as be dragged along a dynamic machinery to block, result in motor incapability's starting, the rotor that moves motor in response to the pan at this time sees whether the slewing is vivid, machinery burden whether existence fault 2.2The synchro motor incapability leads long into synchronization.Synchro motor in common use law of nonsynchronous starting,throw in Li magnetic belt when the motor rotor revolving speed hits synchronous revolving speed of 95%, make it leads long into synchronization. The synchro motor incapability leads long into synchronous reason as follows:(1)The Li magnetic belt winding short circuit.Because the winding of Li magnetic belt, existence short circuit breaks down, as a result makes motor able to stabilize run - time but incapability and lead long into synchronization while being lower than synchronous revolving speed. Check to seek the Li magnetic belt winding short circuit, can open into low - tension(about the 30 Vs) in the rotor derivation on - line, put on the magnetic poles surface with a hand work steel saw, pursue inspection magnetic poles, if vibrating is violent, explain the magnetic poles to have no short circuit on steel saw of the magnetic poles' surface, if the vibrating of saw blade micro or don't flap, explain the magnetic poles short circuit. After unloading the magnetic poles, check the fault to click,is short-circuit degree, adopt local to mend or re- round to make.(2) Power supply voltage over low. Power supply voltage over low, result in the strong Li link of the device of Li magnetic belt incapability working, make the motor incapability lead long into synchronization thus, the concrete way is to raise power supply voltage appropriately.(3) The fault of Li magnetic belt device. Such as throw Li over speedy(namely throw in Li magnetic belt, motor rotor revolving speed over low), will make the motor can not lead long into synchronization, should check to throw if the Li link exists fault at this time. If Li magnetic belt device fault, the output's current is lower than a rating value, cause the electricity magnetic troque of dynamo over small but can not lead long into synchronization, at this time in response to scrutiny Li magnetic belt device of throw Li link and phase - shifting link, waveform use oscillo graph to check to throw Li link and phase - shifting link, should also check and put out magnetic belt link and put out crystal gate of magnetic belt whether tube discovers a question as usual, handle in time, if the incapability handles in time, by way of the energy quickly restore capacity, should replace to provide for use circuit board.2.3 Brush and compress tightly spring and gather to give or get an electric shock ring fault.The brush leads short and compresses tightly spring press scarcity and make brush and gather to give or get an electric shock ring of indirectly touch badly, thus generate spark or arc electric, arc electric or spark to on the other hand and easily spark short circuit, will make arc electric burn on the other hand shorter, spark open circtui thus, result in Li magnetic belt device only the Li magnetoelectricity press but have no Li magnetoelectricity streaming;Compress tightly spring ageing lapse, make brush and gather to give or get an electric shock ring of indirectly touch badly, effect the starting of motor thus;Gather to give or get an electric shock a ring surface to there is grease stain and scar or slot scar, will make brush and gather to give or get an electric shock ring of indirectly touch badly, generate spark, spark further burn gather to give or get an electric shock ring, will also make gnd short-circuit, the spark effects the starting of motor thus.For gather to give or get an electric shock ring superficial grease stain, can wipe to clean with the acetone; For thin trace, use many fettle shagging rings of sandpapers surface, is ring surface roughness to hit R1.6 ums, if the slot scar obviously needs to get on the car bed transform, truning, enter amount of knife to take every time 1 mm as proper, in the 1-1.5 ms/s, the truning speed control's roughness hits of the ums of R1.5-1.8 and becomes bad anti to finally polish with the sandpaper 2-3 times over the 0.05 mms.2.4 The damper winding breaks down.The damper winding of synchro motor rotor is provided for synchro motor starting to use and wipe - out run - time at the same time amid spark because of loading to change of out of step osc.Start the damper winding in the process to incise the magnetic field of stator revolution but induced very big starting current in the synchro motor, so the big current by all means will result in damping hair thermal expansion, under the normal condition because of starting time short, the damper winding starting is behind soon will cool off, but block up revolution in the motor, lack phase, start the super - in time to length ways wait a condition down, if don't shut down in time, will result in the damping take off soldering to split etc. condition.The damper winding is weaker link in the synchro motor parts, the damper winding familiar fault has:The damping takes off soldering and split, the damping ring discharges wildfire, damping ring the strain is serious.These faults will effect the starting of synchro motor. The damping takes off soldering and chooses silver actinium welding rod and adopts oxyacetylene welding to weld, the dynamo after taking out the core heats into rotor 200 Celsius degrees set rotor vertical inthe oven, after taking out and adopt 750 Celsius degrees to or soly weld temperature, damping and the blind side of of damping ring complete solderings are full, clear a soldering dirt again, ;For split of the damping , after dismantling original damping, choose the material of material homology and adopt the above-mentioned method to weld after packing good damping.Damping ring the wildfire is mainly what damping ring indirectly touches bad or get in touch with area isn't enough to result in. Damping ring the strain seriously is mainly a damping to fix anticoincidence in the slot, the damping plugs into damping ring while welding hole falsely, appear additional stress after welding, at plus damping ring intensity not enough to, treatment is loose open all connectivity bolts of damping rings, vs strain anti big of damping ring, after oxyacetylene welding heating adjust with the exclusive use fixture even, vs strain serious replace a new damping of ring.3 ConclusionWhen the synchro motor appears fault, cautiously analytical possible reason, gradually expel, look into related data when it's necessary, absorb experience, propose corrective actions.Analytical the dynamo fault not only need to have firm theory knowledge and experience of prolific maintenance repairs, but also need to aim at concrete fault, deep consideration, brave creative, the dynamo after ensuring to break down removal can stabilize run - time over a long period of time.中文翻译永磁同步电动机矢量控制系统(中文对照)矢量控制亦称磁场定向控制,其基本思路是:通过坐标变换实现模拟直流电机的控制方法来对永磁同步电机进行控制。
电动车的电机的用途

电动车的电机的用途英文回答:Electric Motor Applications in Electric Vehicles.Electric motors play a pivotal role in electric vehicles (EVs), serving as the driving force that propels the vehicle forward. Unlike conventional vehicles powered by internal combustion engines, EVs rely on electric motors to convert electrical energy from the battery into mechanical energy. This innovative technology offers numerous advantages, including improved efficiency, reduced emissions, and enhanced performance.Types of Electric Motors in EVs.There are several types of electric motors used in EVs, each with unique characteristics and applications. The most common types include:Permanent Magnet Synchronous Motors (PMSMs): PMSMs are widely used in EVs due to their high efficiency and compact design. They rely on permanent magnets fixed to the rotor, eliminating the need for a field winding and reducing energy losses.Induction Motors (IMs): IMs are a simple and robust type of electric motor commonly used in industrial applications. They are characterized by their ability to operate at variable speeds, making them suitable for EVs with regenerative braking systems.Switched Reluctance Motors (SRMs): SRMs offer high torque at low speeds and are relatively inexpensive to manufacture. They are particularly suited for EVs used in urban areas where frequent stops and starts are common.Axial Flux Motors (AFMs): AFMs are unique in their design, with the stator and rotor arranged in an axial configuration. This allows for a more compact and lightweight motor, which can be beneficial for EVs with limited space constraints.Functions of Electric Motors in EVs.Electric motors in EVs perform the following essential functions:Propulsion: The primary function of the electric motor is to provide motive power to the vehicle. It converts electrical energy into mechanical energy, which is then transmitted to the wheels through a gearbox.Regenerative Braking: During braking, the electric motor acts as a generator, converting the kinetic energy of the vehicle into electrical energy. This energy is stored in the battery, extending the vehicle's range.Hill Climbing: Electric motors provide high torque at low speeds, enabling EVs to climb hills efficiently. The instant torque delivery provides a responsive and smooth driving experience.Noise Reduction: Compared to combustion engines,electric motors operate quietly, reducing noise pollution and enhancing the overall driving comfort.Advantages of Electric Motors in EVs.The adoption of electric motors in EVs offers several advantages, including:Efficiency: Electric motors are inherently more efficient than combustion engines. They convert over 90% of electrical energy into mechanical energy, compared to around 30% for gasoline engines.Emissions Reduction: EVs produce zero tailpipe emissions, contributing to improved air quality and mitigating climate change.Performance: Electric motors deliver instant torque and can accelerate quickly and smoothly. They also have a wider operating range, allowing for more efficient and responsive driving.Maintenance Costs: Electric motors have fewer moving parts than combustion engines, resulting in reduced maintenance costs and increased reliability.Conclusion.Electric motors are the heart of electric vehicles, enabling them to deliver efficient, emission-free, andhigh-performance transportation. As the technology continues to evolve, we can expect even more advanced and innovative electric motor designs that will further enhance the driving experience and accelerate the adoption of EVs.中文回答:电动汽车中电动机的用途。
关于电动机的创作文献

关于电动机的创作文献英文回答:Electric Motors: A Comprehensive Overview.Electric motors are electromechanical devices that convert electrical energy into mechanical energy. They are widely used in a variety of applications, ranging from industrial machinery to consumer electronics.Principle of Operation.The basic principle of operation of an electric motor is electromagnetic induction. When an electric current flows through a coil of wire, it creates a magnetic field. If this magnetic field interacts with another magnetic field, it will cause the coil to rotate.Types of Electric Motors.There are many different types of electric motors, each with its own unique characteristics and applications. Some of the most common types include:DC motors: DC motors are powered by direct current (DC). They are relatively simple to operate and can provide a wide range of speeds and torques.AC motors: AC motors are powered by alternating current (AC). They are more efficient than DC motors and can operate at higher speeds.Synchronous motors: Synchronous motors rotate at a constant speed that is synchronized with the frequency of the AC power supply. They are used in applications where precise speed control is required.Induction motors: Induction motors are the most common type of AC motor. They are relatively simple to manufacture and can operate at a variety of speeds.Stepper motors: Stepper motors rotate in discretesteps. They are used in applications where precise positioning is required.Applications of Electric Motors.Electric motors are used in a wide variety of applications, including:Industrial machinery: Electric motors are used to power industrial machinery such as conveyors, pumps, and fans.Consumer electronics: Electric motors are used to power consumer electronics such as refrigerators, washing machines, and air conditioners.Transportation: Electric motors are used to power electric vehicles, such as cars, buses, and trains.Renewable energy: Electric motors are used to generate electricity from renewable energy sources, such as solar and wind power.Advantages of Electric Motors.Electric motors offer a number of advantages over other types of motors, including:High efficiency: Electric motors are very efficient at converting electrical energy into mechanical energy.Low maintenance: Electric motors require very little maintenance.Long lifespan: Electric motors have a long lifespan, especially when properly maintained.Quiet operation: Electric motors are relatively quiet in operation.Compact size: Electric motors are relatively compact in size, making them ideal for use in a variety of applications.Disadvantages of Electric Motors.Electric motors also have some disadvantages, including:High cost: Electric motors can be expensive topurchase and install.Limited torque: Electric motors can have limited torque, especially at low speeds.Heat generation: Electric motors generate heat when they operate, which can be a concern in some applications.Overall, electric motors are versatile and efficient devices that are used in a wide variety of applications. They offer a number of advantages over other types of motors, but they also have some disadvantages. Whenselecting an electric motor for a particular application,it is important to consider the specific requirements ofthe application and the advantages and disadvantages of different types of electric motors.中文回答:电动机,全面概述。
211167870_SINAMICS_S120在驱动大功率直驱永磁同步电机中的应用

———————————————————————作者简介:马进(1982-),男,河南信阳人,硕士研究生,电气工程师,研究方向为工业自动化与智能控制。
0引言永磁同步电动机以永磁体提供励磁,使电动机结构较为简单,降低了加工和装配费用,且省去了容易出问题的集电环和电刷,提高了电动机运行的可靠性;又因无需励磁电流,没有励磁损耗,提高了电动机的效率和功率密度。
本文重点介绍采用SINAMICS S120变频器作为变频电源驱动2000kW 直驱永磁同步电机的应用。
1系统拓扑结构采用SINAMICS S120变频器作为变频电源驱动2000kW 直驱永磁同步发电机,该发电机作为电动机使用为另外一台被测2000kW 直驱永磁同步发电机提供动力驱动,被测发电机输出电能经过被测变流器回馈到SINAMICS S120变频器交流供电侧从而实现电能闭环、达到节能目的;SINAMICS S120整流单元连接24脉动整流变压器,达到较少谐波,降低谐波对其他设备干扰的目的,如图1所示。
2系统硬件说明2.12000kW 直驱永磁同步电机2000kW 直驱永磁同步电机技术参数见表1。
2000kW 直驱永磁同步电机如图2所示。
2.2SINAMICS S120变频驱动器该项目中直驱永磁同步电机的额定频率只有10Hz ,在实际测试过程中永磁同步电机的运行频率区间范围是2Hz~15Hz ,电机的运行频率较低需要参考西门子工程师手册结合变频器低频降容系数来进行变频器的选取工作。
IGBT 模块和逆变器功率单元的功率周期能力:“功率周期能力”是指元器件(例如熔断器或IGBT 模块)承受温度的波动的能力,这个温度波动是在运行过程中由变化的负载引起的、不致使元器件过早老化或损坏的SINAMICS S120在驱动大功率直驱永磁同步电机中的应用Application of SINAMICS S120in Driving High-power Direct-drive Permanent Magnet Synchronous Motors马进MA Jin(索提斯云智控科技(上海)有限公司,上海201806)(Sothis CIC Tech (Shanghai )Co.,Ltd.,Shanghai 201806,China )摘要:本文介绍西门子SINAMICS S120系列变频器在驱动2000kW 直驱永磁同步电机中的变频器选型配置和调试过程处理,通过对2000kW 直驱永磁同步电机的相关参数的设置调试以及功能校验,使得SINAMICS S120驱动大功率永磁同步电机得到了实际性的验证。
同步电动机的失磁保护
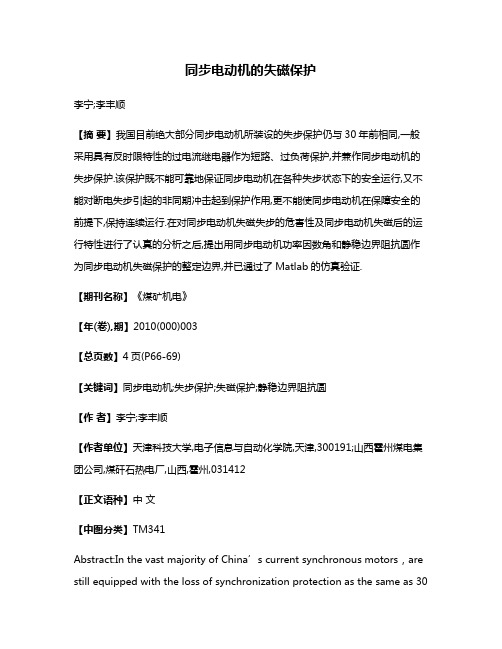
同步电动机的失磁保护李宁;李丰顺【摘要】我国目前绝大部分同步电动机所装设的失步保护仍与30年前相同,一般采用具有反时限特性的过电流继电器作为短路、过负荷保护,并兼作同步电动机的失步保护.该保护既不能可靠地保证同步电动机在各种失步状态下的安全运行,又不能对断电失步引起的非同期冲击起到保护作用,更不能使同步电动机在保障安全的前提下,保持连续运行.在对同步电动机失磁失步的危害性及同步电动机失磁后的运行特性进行了认真的分析之后,提出用同步电动机功率因数角和静稳边界阻抗圆作为同步电动机失磁保护的整定边界,并已通过了Matlab的仿真验证.【期刊名称】《煤矿机电》【年(卷),期】2010(000)003【总页数】4页(P66-69)【关键词】同步电动机;失步保护;失磁保护;静稳边界阻抗圆【作者】李宁;李丰顺【作者单位】天津科技大学,电子信息与自动化学院,天津,300191;山西霍州煤电集团公司,煤矸石热电厂,山西,霍州,031412【正文语种】中文【中图分类】TM341Abstract:In the vast majority of China’s current synchronous motors,are still equipped with the loss of synchronization protection as the same as 30years ago,commonly use the over-current relay with the characteristics of inverse-time as the short-circuit and over-load protections,and doubles as the loss of synchronization protection for synchronous motor.The protection cannot guarantee synchronous motor`s working safety under the conditions in variety of loss synchronizations,also cannot provide the fundamental protection for the non-simultaneous impact caused by the loss synchronization of power-off,furthermore,cannot keep the working continuity of synchronous motors under the premise of safety to maintain continuous operation.After the careful analysis on the harmfulness of the loss of excitation and the loss of synchronization to synchronous motor,and the operating characteristics after the loss excitation of synchronous motor,proposes to use synchronous motors’power factor angle and static impedance circle as the setting boundaries to the loss excitation protection of synchronous motor,and it has proved by Matlab simulation. Keywords:synchronous motor;loss of synchronization protection;loss of excitation protection;static stability boundary impedance circle同步电动机的励磁绕组失去励磁或严重欠励磁,转子磁场按指数规律消失,导致同步电动机反电势E0按同样规律消失。
同步电动机和异步电动机的无功

同步电动机和异步电动机的无功Synchronous and asynchronous motors are two types of electric motors that differ primarily in their operation and characteristics. Both motors require reactive power, but the way they utilize and handle it differs significantly.同步电动机和异步电动机是两种主要的电动机类型,它们在运行和特性上有所不同。
两种电动机都需要无功功率,但它们利用和处理无功功率的方式存在显著差异。
Synchronous motors, as their name suggests, operate in sync with the alternating current (AC) supply. They have a rotor that rotates at the same speed as the rotating magnetic field generated by the stator. This synchronization allows the motor to produce both active and reactive power, making it particularly suitable for applications that require precise speed control and power factor correction.同步电动机如其名所示,与交流电源同步运行。
它们的转子以与定子产生的旋转磁场相同的速度旋转。
这种同步性使得电动机能够同时产生有功功率和无功功率,因此特别适用于需要精确速度控制和功率因数校正的应用。
- 1、下载文档前请自行甄别文档内容的完整性,平台不提供额外的编辑、内容补充、找答案等附加服务。
- 2、"仅部分预览"的文档,不可在线预览部分如存在完整性等问题,可反馈申请退款(可完整预览的文档不适用该条件!)。
- 3、如文档侵犯您的权益,请联系客服反馈,我们会尽快为您处理(人工客服工作时间:9:00-18:30)。
Introduction (cont’d)
ECE 8830 - Electric Drives
Topic 14: Synchronous Motors Spring 2004
Introduction
The stator of a synchronous motor is identical to that of an induction motor. However, unlike an induction motor, a magnetic field is created by the rotor either through the use of permanent magnets or through a rotor winding with slip rings and brushes. The presence of the magnetic field on the rotor allows the rotor to move at synchronous speed with the stator field.
Equivalent Circuit of Non-Salient Pole Wound Rotor Motor
A simple per-phase equivalent circuit for a round rotor synchronous motor can be developed in a manner similar to the perphase equivalent circuit of the induction motor.
In addition to the field winding, the rotor of a wound field synchronous motor usually also contains a second winding. This armortisseur, or damper winding, is like the short-circuited squirrel cage bars in an induction motor.
Non-salient pole synchronous generators are used in high-speed applications such as steam-power stations to match the high-speed steam turbines.
ห้องสมุดไป่ตู้
Introduction (cont’d)
The figure on the next slide shows a transformer-coupled circuit linking the stator and the moving rotor winding.
Equivalent Circuit of Non-Salient Pole Wound Rotor Motor (cont’d)
A comparison of a 6MW induction motor and a wound field synchronous motor is shown on the next slide.
Introduction (cont’d)
Introduction (cont’d)
Salient pole synchronous generators are used in low speed applications, such as in hydroelectric power stations where they are used to match the low operating speed of the hydraulic turbines.
Introduction (cont’d)
Synchronous motors are more expensive than induction motors but offer the advantage of higher efficiency, an important advantage at high power. Thus, synchronous motors are used for power generation and large motor drives.
The de-axis is aligned with the North pole of the rotor and the qe-axis is aligned orthogonally to the de-axis.
Note: In Ong’s book the qe-axis leads the de-axis whereas in Bose’s book the qeaxis lags the de-axis.
The rotor is supplied with a current If produced by a voltage Vf.
Equivalent Circuit of Non-Salient Pole Wound Rotor Motor (cont’d)
The rotor circuit can be replaced by an ac current source whose amplitude is If’(=nIf) and frequency is e. That results in the equivalent circuit below:
Introduction (cont’d)
The rotor shape of a synchronous motor may be salient or non-salient, i.e. the airgap may be non-uniform or uniform, respectively.