加工含硫原油存在问题及防范措施(2021新版)
炼油厂加工高硫高酸值原油遇到的问题及对策
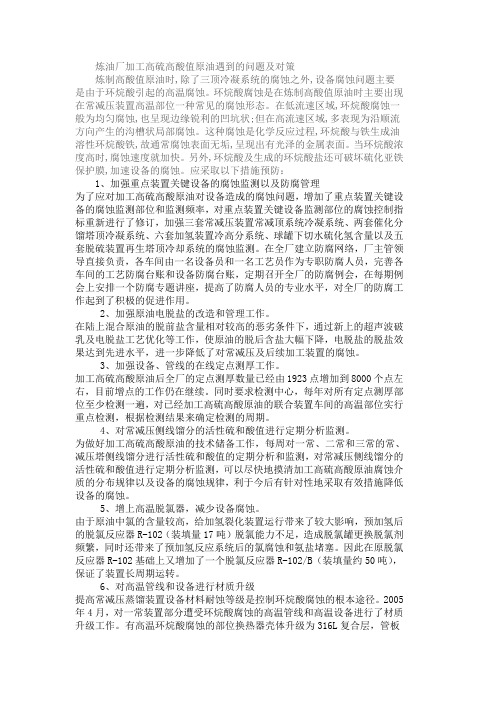
炼油厂加工高硫高酸值原油遇到的问题及对策炼制高酸值原油时,除了三顶冷凝系统的腐蚀之外,设备腐蚀问题主要是由于环烷酸引起的高温腐蚀。
环烷酸腐蚀是在炼制高酸值原油时主要出现在常减压装置高温部位一种常见的腐蚀形态。
在低流速区域,环烷酸腐蚀一般为均匀腐蚀,也呈现边缘锐利的凹坑状;但在高流速区域,多表现为沿顺流方向产生的沟槽状局部腐蚀。
这种腐蚀是化学反应过程,环烷酸与铁生成油溶性环烷酸铁,故通常腐蚀表面无垢,呈现出有光泽的金属表面。
当环烷酸浓度高时,腐蚀速度就加快。
另外,环烷酸及生成的环烷酸盐还可破坏硫化亚铁保护膜,加速设备的腐蚀。
应采取以下措施预防:1、加强重点装置关键设备的腐蚀监测以及防腐管理为了应对加工高硫高酸原油对设备造成的腐蚀问题,增加了重点装置关键设备的腐蚀监测部位和监测频率,对重点装置关键设备监测部位的腐蚀控制指标重新进行了修订,加强三套常减压装置常减顶系统冷凝系统、两套催化分馏塔顶冷凝系统、六套加氢装置冷高分系统、球罐下切水硫化氢含量以及五套脱硫装置再生塔顶冷却系统的腐蚀监测。
在全厂建立防腐网络,厂主管领导直接负责,各车间由一名设备员和一名工艺员作为专职防腐人员,完善各车间的工艺防腐台账和设备防腐台账,定期召开全厂的防腐例会,在每期例会上安排一个防腐专题讲座,提高了防腐人员的专业水平,对全厂的防腐工作起到了积极的促进作用。
2、加强原油电脱盐的改造和管理工作。
在陆上混合原油的脱前盐含量相对较高的恶劣条件下,通过新上的超声波破乳及电脱盐工艺优化等工作,使原油的脱后含盐大幅下降,电脱盐的脱盐效果达到先进水平,进一步降低了对常减压及后续加工装置的腐蚀。
3、加强设备、管线的在线定点测厚工作。
加工高硫高酸原油后全厂的定点测厚数量已经由1923点增加到8000个点左右,目前增点的工作仍在继续。
同时要求检测中心,每年对所有定点测厚部位至少检测一遍,对已经加工高硫高酸原油的联合装置车间的高温部位实行重点检测,根据检测结果来确定检测的周期。
加工含硫含酸原油的腐蚀问题和对策论文

加工含硫含酸原油的腐蚀问题和对策论文加工含硫含酸原油的腐蚀问题和对策论文【摘要】随着近年来国内几大油田都进入了二次和三次采油期,原油酸值和腐蚀性都增加。
而进口原油特别是中东原油的增加,使得加工原油硫含量较高,这给石油的炼制和防腐提出了更高的要求。
【关键词】含硫含酸原油腐蚀问题对策加工高硫原油与加工高酸原油带来的腐蚀问题是不同的,加工高酸原油带来的腐蚀问题主要集中在蒸馏装置,而加工高硫原油时,由于原油中的非活性硫不断向活性硫转变,使硫腐蚀不仅存在于一次加工装置,也同样存在于二次加工装置,甚至延伸到下游化工装置,贯穿于炼油的全过程中。
硫在原油的不同馏分中的含量和存在的形式不尽相同,但都随沸点的升高而增加,并且富集于渣油中。
因此,有必要对炼油装置的腐蚀类型和防护措施做一个简单的综述。
1 几种主要腐蚀类型在原油加工过程中,主要有硫腐蚀和环烷酸腐蚀。
其中,硫腐蚀不是孤立存在的。
硫和无机盐、环烷酸、氮化物、水、氢、氨等其它腐蚀性介质共同作用,形成多种复杂的腐蚀环境。
而环烷酸和硫的相互作用和相互制约、促进使腐蚀问题变得错综复杂。
不同的原油中含有不同类型的硫化物,它们的含量和存在形式既能抑制又能促进环烷酸腐蚀,从而导致硫化物既可增强又可降低含酸原油的腐蚀性。
大致有以下几种腐蚀类型。
1.1湿硫化氢腐蚀原油中存在的H2S以及有机硫化物在不同条件下逐步分解生成的H2S,与原油加工过程中生成的腐蚀性介质(如HCl、NH3等)和人为加入的腐蚀性介质(如有机胺、水等)共同形成腐蚀性环境,在装置的低温部位(特别是气液相变部位)造成严重的腐蚀。
1.2高温硫腐蚀高温硫化物的腐蚀是指240℃温度以上的部位元素硫、硫化氢和硫醇等活性硫形成的腐蚀。
表现为均匀腐蚀,其中以硫化氢的腐蚀性最强。
化学反应如下:H2S+Fe→FeS+H;S+Fe→FeS;RSH+Fe→FeS+不饱和烃。
1.3高温环烷酸腐蚀环烷酸腐蚀经常发生在酸值大于0.5mgKOH/g、温度在270~400℃之间高流速的工艺介质中。
加工高含硫原油防腐工作经验总结归纳

精心整理[资料]加工高含硫原油防腐工作经验总结含硫原油,经验总结,加工,防腐近几年,加工高含硫原油不断增加,大部分装置的原料含硫超过设计值,设备腐蚀加重,给设备安全运行造成威胁。
针对加工高含硫原油造成的设备腐蚀情况,我们应加强设备防腐管理,开展全面的腐蚀调查,采取各种有效的防腐措施,现对近年1、加工高含硫原油存在的腐蚀问题:1.1加工高含硫原油情况1.2加工高含硫原油后设备腐蚀情况含硫油指含硫0.5-2.0%,表2加热炉腐蚀主要发生在对流段冷进料炉管及软化水管。
二蒸馏装置2000年2月,炉1、炉2、炉3对流段软化水管及冷进料管腐蚀穿孔,于同年5月份大修,3台炉对流段整体更换。
主要原因是瓦斯和燃料油含硫较高,烟气露点上升,管子受烟气露点腐蚀减薄。
塔器腐蚀主要发生在常、减压塔碳钢内构件,腐蚀形态为高温段(>300℃)的均匀减薄,低温段(<120℃)的减薄和坑蚀。
三蒸馏装置2000年底大修检查发现常、减压塔碳钢内件腐蚀较重。
常压塔7-26、43-48层塔盘支梁减薄近一半,部分受液盘穿孔。
主要原因是碳钢受高温硫腐蚀和低温H2O+HCL+H2S腐蚀。
冷换设备腐蚀主要发生在:1高温硫腐蚀;21、三蒸馏、四蒸馏常顶冷却器18-8管束2、三蒸馏装置渣油一次换热器(换度由14mm减至9mm 1.7mm/a。
管线阀门1、19979、10)平衡管腐蚀穿孔;减压塔底流控阀及法兰腐蚀穿孔;常压炉(炉-1)转油线低速蒸汽入口腐蚀穿孔;减四线压力表碳钢接管腐蚀穿孔。
2、1998年减压渣油泵出口Cr5Mo三通腐蚀穿孔。
二蒸馏装置:1、减底渣油线原用20#钢,渣油泵(泵30)出口至换11渣油线腐蚀穿孔,1998年6月和99年5月将泵进出口管更换为Cr5Mo,检查旧管内表面腐蚀严重。
2、渣油泵30出口碳钢弯头腐蚀减薄至3mm,2000年2月7日更换。
三蒸馏装置:1、换13/1C壳程进口短管(20#钢)2000年2月18日因高温硫腐蚀减薄穿孔,测厚为1.5mm。
加工含硫原油设备存在的隐患
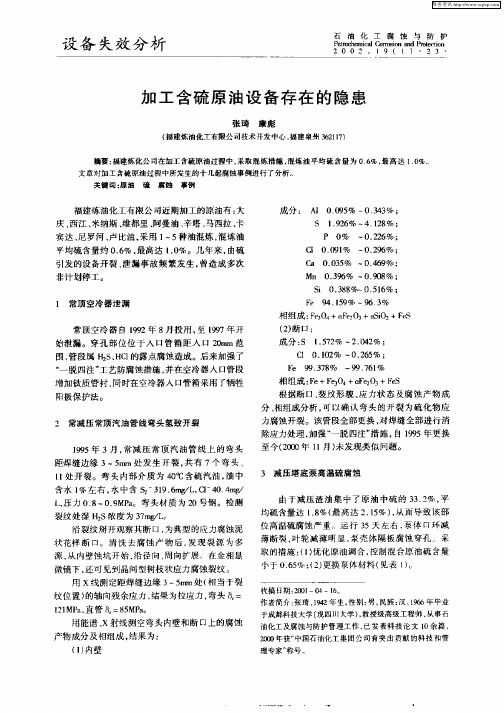
于成都科技大学 ( 现四川大学) 教授 级高级工程师 , 事石 , 从 油化工及腐蚀 与防护管理工作 , 已发 表科 技论 文 l 余 篇 , O
20 年 获 0O 中国石油化工集团 公司有 突出贡献 的科 技和管
用能谱 、 x射线测空弯头内壁和断 口上的腐蚀
产物 成分及 相组 成 , 果为 : 结 () 】 内壁
源 , 内壁蚀 坑开始 . 从 沿径 向 、 向扩展 。在金 相显 周
微镜 下 , 还可 见到 晶问型树 枝状 应力腐蚀 裂纹 。 用 x线 测定距 焊缝边 缘 3 r'处 ( 当 于裂 ~5 n 相 m
纹位置) 的轴向残余应力, 结果为拉应力 , 弯头 =
1 1 P , 管 =8 M a 2 M a直 5 P。
关键词 : 油 原 硫 腐蚀 事 例
福建 炼 油化工有 限公 司近期 加工 的原 油有 : 大 庆、 西江 、 纳斯 、 米 维都 里 、 阿曼 油 、 辛塔 、 马西拉 、 卡 宾 达 、 罗河 、 比油 , 尼 卢 采用 1 5种 油混炼 , ~ 混炼 油
成分 : _ 0 0 5 ~0 3 3 ; A l .9 % . % 4
至今 (0O年 1 月 ) 发现类 似问题 。 20 1 未 3 减 压塔底 泵高温硫 腐蚀 由于 减 压渣 油 集 中 了原 油 中硫 的 3 .% , 3 2 平 均硫 含量达 I8 最 高达 2 1% )从 而导 致 该 部 _%( .5 , 位高 温硫 腐蚀 严 重 。运 行 3 左 右 , 体 口环 减 5天 泵 薄断 裂 , 叶轮 减 薄 明显 , 泵壳 体 隔板 腐 蚀 穿孔 。采 取 的措施 :1优 化原油调 合 , () 控制 混合原 油硫 含量
C1 0. 0 1 2% ~0. 6 2 5% : F 9 3 8 e 9. 7 % ~9 7 % 9. 6l
含硫原油产品的危害及处理
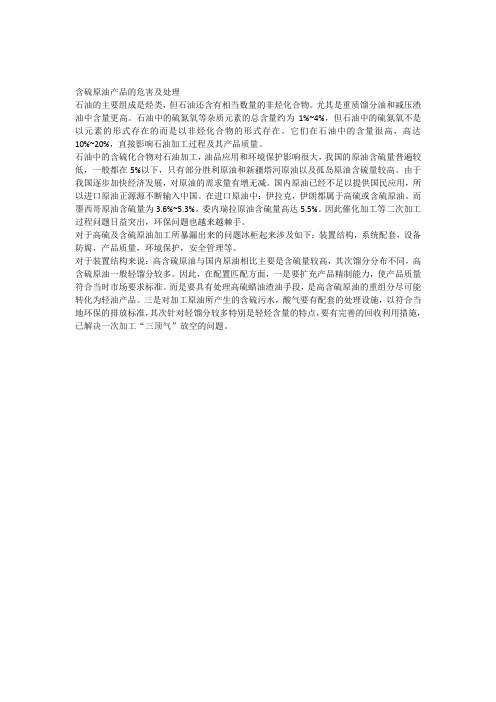
含硫原油产品的危害及处理
石油的主要组成是烃类,但石油还含有相当数量的非烃化合物。
尤其是重质馏分油和减压渣油中含量更高。
石油中的硫氮氧等杂质元素的总含量约为1%~4%,但石油中的硫氮氧不是以元素的形式存在的而是以非烃化合物的形式存在。
它们在石油中的含量很高,高达10%~20%,直接影响石油加工过程及其产品质量。
石油中的含硫化合物对石油加工,油品应用和环境保护影响很大,我国的原油含硫量普遍较低,一般都在5%以下,只有部分胜利原油和新疆塔河原油以及孤岛原油含硫量较高。
由于我国逐步加快经济发展,对原油的需求量有增无减。
国内原油已经不足以提供国民应用,所以进口原油正源源不断输入中国。
在进口原油中:伊拉克,伊朗都属于高硫或含硫原油。
而墨西哥原油含硫量为3.6%~5.3%。
委内瑞拉原油含硫量高达5.5%。
因此催化加工等二次加工过程问题日益突出,环保问题也越来越棘手。
对于高硫及含硫原油加工所暴漏出来的问题冰柜起来涉及如下:装置结构,系统配套,设备防腐,产品质量,环境保护,安全管理等。
对于装置结构来说:高含硫原油与国内原油相比主要是含硫量较高,其次馏分分布不同,高含硫原油一般轻馏分较多。
因此,在配置匹配方面,一是要扩充产品精制能力,使产品质量符合当时市场要求标准。
而是要具有处理高硫蜡油渣油手段,是高含硫原油的重组分尽可能转化为轻油产品。
三是对加工原油所产生的含硫污水,酸气要有配套的处理设施,以符合当地环保的排放标准,其次针对轻馏分较多特别是轻烃含量的特点,要有完善的回收利用措施,已解决一次加工“三顶气”放空的问题。
加工含硫原油的环保问题与对策
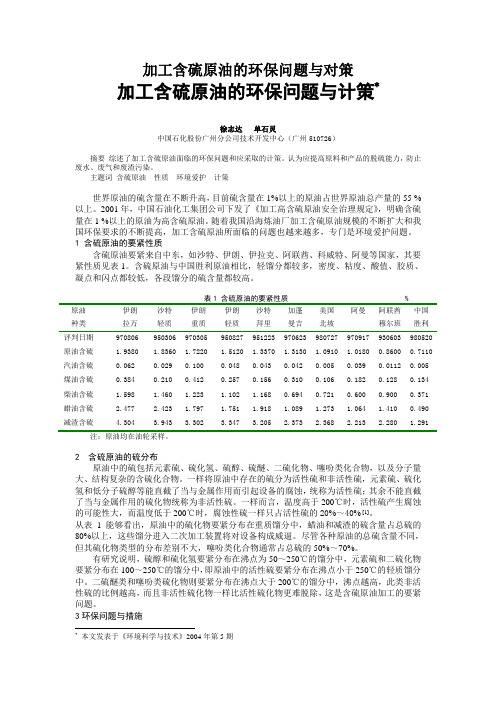
加工含硫原油的环保问题与对策加工含硫原油的环保问题与计策*徐志达单石灵中国石化股份广州分公司技术开发中心(广州510726)摘要综述了加工含硫原油面临的环保问题和应采取的计策。
认为应提高原料和产品的脱硫能力,防止废水、废气和废渣污染。
主题词含硫原油性质环境爱护计策世界原油的硫含量在不断升高,目前硫含量在1%以上的原油占世界原油总产量的55 %以上。
2001年,中国石油化工集团公司下发了《加工高含硫原油安全治理规定》,明确含硫量在1 %以上的原油为高含硫原油。
随着我国沿海炼油厂加工含硫原油规模的不断扩大和我国环保要求的不断提高,加工含硫原油所面临的问题也越来越多,专门是环境爱护问题。
1 含硫原油的要紧性质含硫原油要紧来自中东,如沙特、伊朗、伊拉克、阿联酋、科威特、阿曼等国家,其要紧性质见表1。
含硫原油与中国胜利原油相比,轻馏分都较多,密度、粘度、酸值、胶质、凝点和闪点都较低,各段馏分的硫含量都较高。
表1 含硫原油的要紧性质 %原油种类伊朗拉万沙特轻质伊朗重质伊朗轻质沙特拜里加蓬曼吉美国北坡阿曼阿联酋穆尔班中国胜利评判日期970806 950306 970305 950827 951223 970623 980727 970917 930603 980520 原油含硫 1.9380 1.8360 1.7220 1.5120 1.3370 1.3130 1.0910 1.0180 0.8600 0.7110 汽油含硫0.062 0.029 0.100 0.048 0.043 0.042 0.005 0.039 0.0112 0.005 煤油含硫0.384 0.210 0.412 0.257 0.156 0.310 0.106 0.182 0.128 0.134 柴油含硫 1.598 1.460 1.223 1.102 1.168 0.694 0.721 0.600 0.900 0.371 蜡油含硫 2.477 2.423 1.797 1.751 1.918 1.089 1.273 1.064 1.410 0.490 减渣含硫 4.304 3.943 3.302 3.347 3.205 2.373 2.368 2.213 2.280 1.291 注:原油均在油轮采样。
加工高含硫原油的防范措施

加工高含硫原油的防范措施
随着工业化的加速以及对能源依赖的不断增加,对于能源需求
的供应也在逐渐增加,因此精炼工厂对于高含硫原油的需求也在逐
渐增加,然而这也带来了一些新的挑战和问题,比如高含硫原油的
加工会产生大量的污染物,造成环境的污染,同时也会对工人的身
体健康产生负面影响,因此在加工高含硫原油的过程中需要采取一
系列的防范措施来降低影响。
首先,应该进行原油的预处理。
在加工之前,应该对原油进行
预处理,包括脱水、脱盐、脱蜡等等,以提高原油质量,并且减少
其中的杂质含量,从而降低加工过程中的环境污染,同时也可以减
少设备的磨损和腐蚀。
其次,在加工过程中应该采取先进的技术和设备,比如应用渣
油催化裂化技术,可以降低生产中的硫排放,从而减少对环境的影响。
此外,使用一些先进的化工技术,如高温加氢裂化技术,也可
以在加工高含硫原油的过程中有所帮助。
第三,提高废气处理的技术水平。
在生产过程中,废气是产生
最多的污染物之一,因此需要采取先进的废气处理技术,比如采用
尾气净化器、吸附器等设备,降低硫酸盐等有害气体的含量,从而
使产生的废气满足环境保护要求。
最后,加强生产过程的监管。
在加工高含硫原油的过程中,需
要对生产过程进行全方位的监测和管理,比如加强生产过程的现场
安全监测,加强技术培训和环保意识教育,严格控制硫含量的排放,降低对环境的影响。
加工高含硫原油是一个挑战性很大的任务,在这个过程中需要采取一系列的防范措施,从而降低对环境的影响,提高加工质量,保护生产工人的身体健康,达到可持续发展的目标。
浅析炼制高硫原油的危险性及对策(2021版)
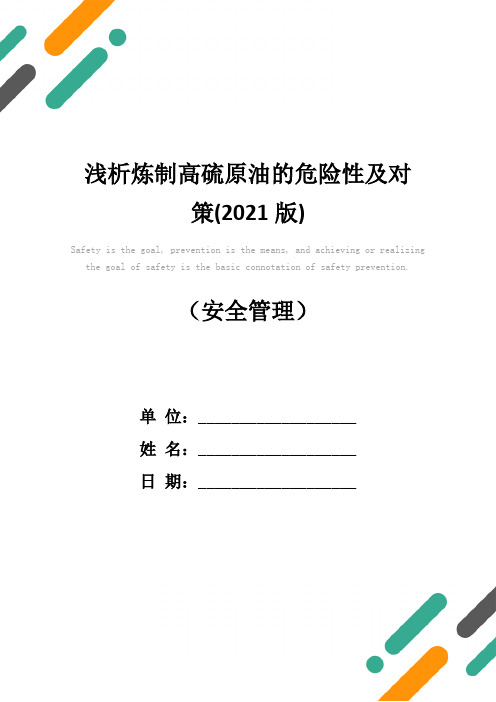
Safety is the goal, prevention is the means, and achieving or realizing the goal of safety is the basic connotation of safety prevention.(安全管理)单位:___________________姓名:___________________日期:___________________浅析炼制高硫原油的危险性及对策(2021版)浅析炼制高硫原油的危险性及对策(2021版)导语:做好准备和保护,以应付攻击或者避免受害,从而使被保护对象处于没有危险、不受侵害、不出现事故的安全状态。
显而易见,安全是目的,防范是手段,通过防范的手段达到或实现安全的目的,就是安全防范的基本内涵。
1前言长岭分公司原油车间担负着各生产装置原料油的供给任务。
随着分公司加工原油中含硫量的增加,使得车间各罐区内外的硫化氢含量严重超标的现象时有发生。
同时,分公司为追求效益最大化而实施的蜡油加氢、掺炼粗苯等一系列技改措施,也使得罐区储存高含H2S原料油的时间和次数越来越多。
因此,罐区发生硫化氢中毒事故的几率也随之增加,针对高硫原油的危险性制定相应的防治对策是保证罐区安全生产的必要工作。
2H2S危害分析高硫原油在一次加工和后续加工工艺过程中产生的硫化氢不仅对催化裂化、加氢裂化、催化重整、加氢精制、焦化、减粘等生产装置设备的腐蚀十分明显,而且对储运设施的腐蚀也不容忽视。
加工过程中,储运设施中的轻油、污油和液态烃系统的气相腐蚀最为突出。
各种硫化物在加氢脱硫反应中生成的硫化氢,其腐蚀主要表现在气相腐蚀。
硫化氢与设备接触,生成金属硫化物,常见为硫化铁,常温下硫化铁与空气中的氧气接触,会发生氧化放热反应,发生自然事故。
如1998年2月20日某石化总厂油品车间1座2000m3的焦化汽油罐在送料过程中,因罐内壁硫化铁自然而发生油罐火灾。
常减压蒸馏装置加工含硫原油的主要问题及对策
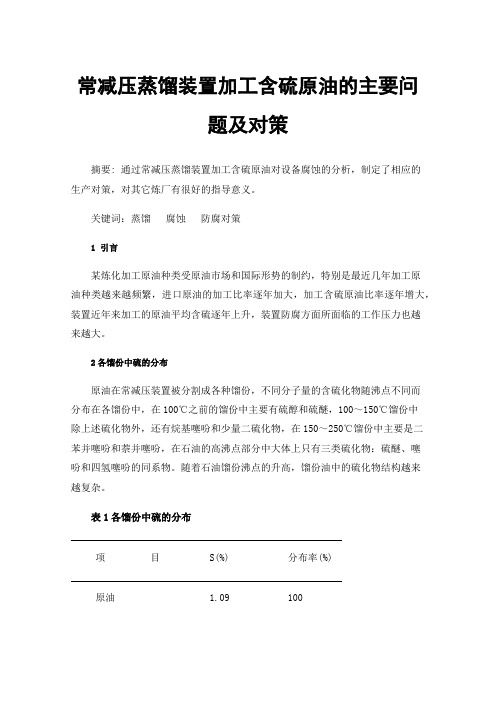
常减压蒸馏装置加工含硫原油的主要问题及对策摘要: 通过常减压蒸馏装置加工含硫原油对设备腐蚀的分析,制定了相应的生产对策,对其它炼厂有很好的指导意义。
关键词:蒸馏腐蚀防腐对策1引言某炼化加工原油种类受原油市场和国际形势的制约,特别是最近几年加工原油种类越来越频繁,进口原油的加工比率逐年加大,加工含硫原油比率逐年增大,装置近年来加工的原油平均含硫逐年上升,装置防腐方面所面临的工作压力也越来越大。
2各馏份中硫的分布原油在常减压装置被分割成各种馏份,不同分子量的含硫化物随沸点不同而分布在各馏份中,在100℃之前的馏份中主要有硫醇和硫醚,100~150℃馏份中除上述硫化物外,还有烷基噻吩和少量二硫化物,在150~250℃馏份中主要是二苯并噻吩和萘并噻吩,在石油的高沸点部分中大体上只有三类硫化物:硫醚、噻吩和四氢噻吩的同系物。
随着石油馏份沸点的升高,馏份油中的硫化物结构越来越复杂。
表1各馏份中硫的分布项目S(%)分布率(%)原油 1.09100石脑油(初馏点-0.020.30180℃)轻柴(180-260℃)0.13 1.16柴油(260-360℃)0.46 6.60蜡油(360-500℃) 1.0221.20渣油(>500℃) 2.0254.00其它16.743加工含硫原油产生的主要影响3.1硫化氢对人身安全的威胁硫化氢是一种无色有臭蛋味的气体,相对密度为1.198g/cm3,易溶于水生成氢硫酸,也易溶于原油及石油产品,易在地表面及低洼处积聚而不易飘散。
且是一种强烈的神经毒物,吸入后对人体有很大的危害,易导致硫化氢中毒。
3.2硫对产品质量的影响硫含量是直馏份油产品中的一个重要质量指标,由于硫及其衍生物的存在,易导致产品中的硫含量及铜片腐蚀试验不合格。
3.3硫对设备的腐蚀主要部位在加热炉烟气露点腐蚀、常顶冷凝相变区、减顶油气腐蚀、高温部位硫腐蚀、塔内器件硫腐蚀和馏份油管道腐蚀等。
4含硫原油腐蚀机理分析4.1低温部位的露点腐蚀常减压装置低温部位露点腐蚀部位主要是加热炉低温烟气管道低点;“三塔顶”油气线的H2S-HCl-H2O低温露点腐蚀。
高含硫原油接卸与储运过程的危害及防范措施

高含硫原油接卸与储运过程的危害及防范措施
高含硫原油是指硫含量较高的原油,其硫含量超过了一定的限制。
高含硫原油的接卸和储运过程中,存在一定的危害和隐患。
为了保障运输安全和环境保护,我们需要采取一系列的防范措施。
1.危害环境:高含硫原油接触到土地和水源时,会导致土地污染和水污染,影响环境质量。
2.危害人员健康:高含硫原油接卸时会产生有毒气体,如硫化氢气体等,如果工人没有正确佩戴呼吸器,会导致中毒甚至死亡。
3.火灾爆炸:由于高含硫原油易燃易爆,如果在接卸过程中出现泄漏和火花,极易引起火灾爆炸事故。
1.压力容器漏气:高含硫原油在储存过程中会产生一定的气体,如果气体无法及时排放,会导致压力容器漏气。
2.管道泄漏:由于高含硫原油的酸性,容易腐蚀管道,在运输过程中出现泄漏,会污染周边环境和威胁工人安全。
3.挥发性污染:高含硫原油的挥发性比较大,储存过程中引入空气或有机物,会导致挥发性污染,污染空气和环境。
1.工作场所需通风良好,防止聚集的有毒气体不易排除,导致不安全和有害。
2.操作人员必须戴防毒面具、脚套、手套等防护装备,防止有毒气体和有害物质对身体造成伤害。
3.运输车辆必须符合安全标准,具备阻燃、防爆、漏油等装置,确保车辆安全运输。
4.储存容器需定期进行保养和清理,检查容器是否有漏洞和物理损坏,同时要防止灾害性事故的发生。
5.储存环境需防水、防火、防静电。
容器周围需要设立报警器、灭火器、紧急处理装置等安全设施。
总之,对于高含硫原油接卸和储运过程,需要加强管理和监管,制定详细的规章制度和应急预案,进行相应的安全培训和技术指导,如此才能确保环境和人员安全,实现资源的安全高效利用。
高含硫原油接卸与储运过程的危害及防范措施
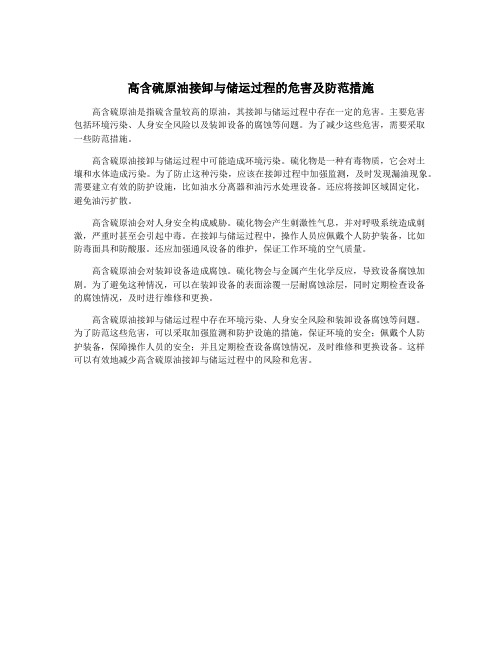
高含硫原油接卸与储运过程的危害及防范措施
高含硫原油是指硫含量较高的原油,其接卸与储运过程中存在一定的危害。
主要危害
包括环境污染、人身安全风险以及装卸设备的腐蚀等问题。
为了减少这些危害,需要采取
一些防范措施。
高含硫原油接卸与储运过程中可能造成环境污染。
硫化物是一种有毒物质,它会对土
壤和水体造成污染。
为了防止这种污染,应该在接卸过程中加强监测,及时发现漏油现象。
需要建立有效的防护设施,比如油水分离器和油污水处理设备。
还应将接卸区域固定化,
避免油污扩散。
高含硫原油会对人身安全构成威胁。
硫化物会产生刺激性气息,并对呼吸系统造成刺激,严重时甚至会引起中毒。
在接卸与储运过程中,操作人员应佩戴个人防护装备,比如
防毒面具和防酸服。
还应加强通风设备的维护,保证工作环境的空气质量。
高含硫原油会对装卸设备造成腐蚀。
硫化物会与金属产生化学反应,导致设备腐蚀加剧。
为了避免这种情况,可以在装卸设备的表面涂覆一层耐腐蚀涂层,同时定期检查设备
的腐蚀情况,及时进行维修和更换。
高含硫原油接卸与储运过程中存在环境污染、人身安全风险和装卸设备腐蚀等问题。
为了防范这些危害,可以采取加强监测和防护设施的措施,保证环境的安全;佩戴个人防
护装备,保障操作人员的安全;并且定期检查设备腐蚀情况,及时维修和更换设备。
这样
可以有效地减少高含硫原油接卸与储运过程中的风险和危害。
高含硫原油接卸与储运过程的危害及防范措施
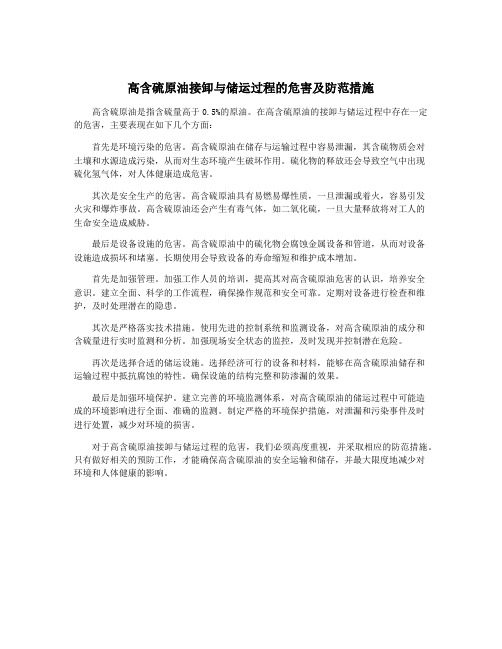
高含硫原油接卸与储运过程的危害及防范措施高含硫原油是指含硫量高于0.5%的原油。
在高含硫原油的接卸与储运过程中存在一定的危害,主要表现在如下几个方面:首先是环境污染的危害。
高含硫原油在储存与运输过程中容易泄漏,其含硫物质会对土壤和水源造成污染,从而对生态环境产生破坏作用。
硫化物的释放还会导致空气中出现硫化氢气体,对人体健康造成危害。
其次是安全生产的危害。
高含硫原油具有易燃易爆性质,一旦泄漏或着火,容易引发火灾和爆炸事故。
高含硫原油还会产生有毒气体,如二氧化硫,一旦大量释放将对工人的生命安全造成威胁。
最后是设备设施的危害。
高含硫原油中的硫化物会腐蚀金属设备和管道,从而对设备设施造成损坏和堵塞。
长期使用会导致设备的寿命缩短和维护成本增加。
首先是加强管理。
加强工作人员的培训,提高其对高含硫原油危害的认识,培养安全意识。
建立全面、科学的工作流程,确保操作规范和安全可靠。
定期对设备进行检查和维护,及时处理潜在的隐患。
其次是严格落实技术措施。
使用先进的控制系统和监测设备,对高含硫原油的成分和含硫量进行实时监测和分析。
加强现场安全状态的监控,及时发现并控制潜在危险。
再次是选择合适的储运设施。
选择经济可行的设备和材料,能够在高含硫原油储存和运输过程中抵抗腐蚀的特性。
确保设施的结构完整和防渗漏的效果。
最后是加强环境保护。
建立完善的环境监测体系,对高含硫原油的储运过程中可能造成的环境影响进行全面、准确的监测。
制定严格的环境保护措施,对泄漏和污染事件及时进行处置,减少对环境的损害。
对于高含硫原油接卸与储运过程的危害,我们必须高度重视,并采取相应的防范措施。
只有做好相关的预防工作,才能确保高含硫原油的安全运输和储存,并最大限度地减少对环境和人体健康的影响。
高含硫原油接卸与储运过程的危害及防范措施

高含硫原油接卸与储运过程的危害及防范措施高含硫原油是指硫含量在0.5%以上的原油,属于中低硫原油。
高含硫原油的接卸与储运过程中存在着多种危害,对环境和人身安全造成潜在威胁。
制定有效的防范措施至关重要。
本文将从高含硫原油的危害、接卸与储运过程中的风险以及相应的防范措施等方面进行论述。
一、高含硫原油的危害1. 环境污染:高含硫原油在接卸和储运过程中,若发生泄漏、挥发或溢出,会对周围环境造成污染。
硫化物与空气中的水分、氧气结合生成二氧化硫,对大气造成污染;硫化物还会污染土壤和地下水,对植被和生态环境造成危害。
2. 健康危害:高含硫原油中的硫化氢是一种无色有毒气体,对人体呼吸道及消化系统有较强的刺激作用,严重时还会导致窒息、中毒甚至死亡。
接触高含硫原油的工作人员容易受到健康威胁。
3. 爆炸危险:高含硫原油中的硫化氢易燃易爆,一旦遇到明火或高温,容易引发爆炸、火灾事故,对周围区域和人员安全构成威胁。
1. 接卸过程中的危害:高含硫原油在接卸时,如管道、储罐或运输设备发生泄漏或溢出,会导致硫化氢等有毒气体释放,对接触人员造成威胁。
三、防范措施1. 接卸过程的防范措施:加强原油接卸工作人员的安全培训,提高其对高含硫原油的认识和防范意识;使用适当的个人防护装备,如防毒面具、防护服等;定期对接卸设备和管道进行检查和维护,及时消除潜在的泄漏隐患。
2. 储运过程的防范措施:严格遵守储运设施操作规程,如定期检查储罐、管道等设施,及时消除漏点和破损;使用先进的监测设备,对储运设施进行实时监控,及时发现异常情况;设立安全防护区域,对储运区域进行安全隔离,确保人员安全。
3. 应急处理措施:建立完善的应急处理预案,对高含硫原油泄漏、泄露等突发情况进行预案演习和应急处置演练,提高工作人员的应急处理能力;配备应急处理装备和药品,在发生事故时能够及时采取有效的应急处理措施。
高含硫原油接卸与储运过程中存在着多种潜在危害,需采取有效的防范措施来保障环境和人身安全。
高含硫原油接卸与储运过程的危害及防范措施
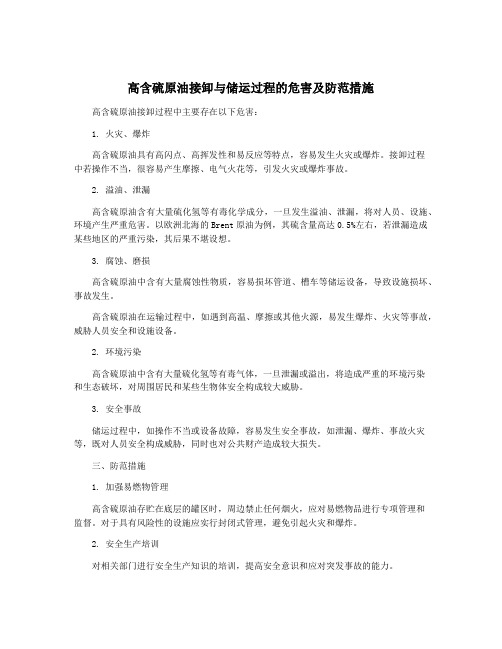
高含硫原油接卸与储运过程的危害及防范措施高含硫原油接卸过程中主要存在以下危害:1. 火灾、爆炸高含硫原油具有高闪点、高挥发性和易反应等特点,容易发生火灾或爆炸。
接卸过程中若操作不当,很容易产生摩擦、电气火花等,引发火灾或爆炸事故。
2. 溢油、泄漏高含硫原油含有大量硫化氢等有毒化学成分,一旦发生溢油、泄漏,将对人员、设施、环境产生严重危害。
以欧洲北海的Brent原油为例,其硫含量高达0.5%左右,若泄漏造成某些地区的严重污染,其后果不堪设想。
3. 腐蚀、磨损高含硫原油中含有大量腐蚀性物质,容易损坏管道、槽车等储运设备,导致设施损坏、事故发生。
高含硫原油在运输过程中,如遇到高温、摩擦或其他火源,易发生爆炸、火灾等事故,威胁人员安全和设施设备。
2. 环境污染高含硫原油中含有大量硫化氢等有毒气体,一旦泄漏或溢出,将造成严重的环境污染和生态破坏,对周围居民和某些生物体安全构成较大威胁。
3. 安全事故储运过程中,如操作不当或设备故障,容易发生安全事故,如泄漏、爆炸、事故火灾等,既对人员安全构成威胁,同时也对公共财产造成较大损失。
三、防范措施1. 加强易燃物管理高含硫原油存贮在底层的罐区时,周边禁止任何烟火,应对易燃物品进行专项管理和监督。
对于具有风险性的设施应实行封闭式管理,避免引起火灾和爆炸。
2. 安全生产培训对相关部门进行安全生产知识的培训,提高安全意识和应对突发事故的能力。
3. 安全设备投入使用为降低事故发生的概率,必须配备足够的安全设备,如消防设备、监测系统等,并且保持这些设备的正常使用和维护。
4. 安全生产责任落实要将安全生产纳入到企业的日常经营中,建立安全生产管理体系,明确责任,并在应急响应机制上进一步扎实化工厂的安全保障工作。
5. 实施全球标准企业应该始终关注全球的安全标准,并及时采取相应措施,以确保其贸易合法性,并保持其好的企业形象。
同时,企业应对现有设施断面进行识别和风险评估,确定风险等级,建立风险预警和应急响应机制。
加工含硫原油的安全防腐技术

加工含硫原油的安全防腐技术背景原油是一种宝贵的能源资源,其加工过程中需要多道工序。
其中,含硫原油是现代工业生产过程中的一种现象,由于其含硫量高,加工过程中易产生腐蚀,对工业设备的安全稳定运行带来威胁。
因此,研究开发加工含硫原油的安全防腐技术迫在眉睫。
含硫原油的相关问题含硫原油的性质含硫原油是指硫含量在0.5%以上的石油。
含硫原油是一种多组分原油,杂质、酸值、水份等影响因素很多,且油品复杂。
合理使用含硫原油的安全防腐技术,对于工业生产的顺畅进行至关重要。
含硫原油带来的工业危害含硫原油是一种多酸化物质,容易对工业设备构成腐蚀威胁,引发易燃、易爆、环境污染等安全问题,制约了工业客户的经济效益的提高。
安全防腐技术防腐涂料技术目前工业上使用的最广泛的防腐技术之一是防腐涂料技术。
其主要原理是通过对含硫原油生产装置内腐蚀的防止来保障装置的运行。
防腐涂料有适合在不同气氛下运行的类型,分为有机涂料和无机涂料两种类型,但目前工业使用中以有机涂料较多。
其他技术随着科技的不断进步,人们对于含硫原油的加工也提出了更高的要求。
一些新技术可以用于对含硫原油进行处理:1.电解法:通过电解等方法处理含硫原油,使其硫含量降低,可有效减少其腐蚀性,保障设备的运行安全。
2.节温降压技术:对于含硫原油加工时,倡导采用节温降压技术,减少传统钢化工艺的使用,以达到节能环保、安全高效的加工目的。
安全防腐技术的应用含硫原油防腐技术,应用范围极广,且已经成功应用于许多工业领域。
它提高了安全性,腐蚀减少,机器寿命得到了保障。
通常情况下,在加工含硫原油时,应注意以下几点:1.防腐涂料的选择及涂布要求。
2.选择合适的工艺进行处理。
3.禁止随意修改处理程序。
4.始终注意安全,以免发生意外事故。
结论含硫原油在工业使用中不可避免,但是在其加工过程中,对工艺流程和防腐技术的研究必不可少。
通过针对性的安全防腐技术措施,可有效的减少含硫原油对设备的腐蚀,保障工业设备的安全稳定运行及经济效益的提高。
高含硫原油接卸与储运过程的危害及防范措施
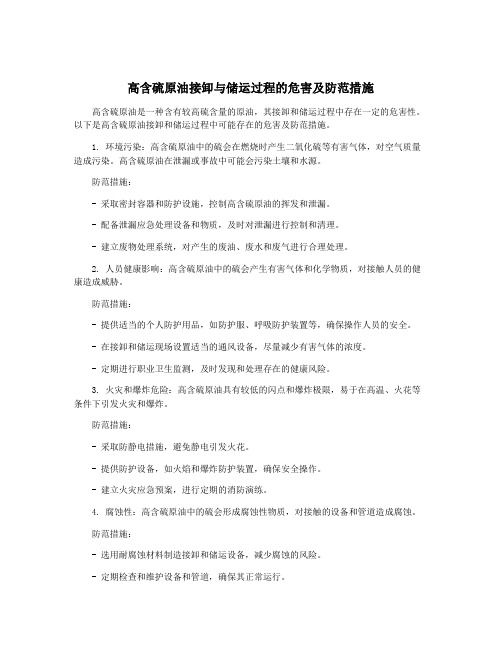
高含硫原油接卸与储运过程的危害及防范措施高含硫原油是一种含有较高硫含量的原油,其接卸和储运过程中存在一定的危害性。
以下是高含硫原油接卸和储运过程中可能存在的危害及防范措施。
1. 环境污染:高含硫原油中的硫会在燃烧时产生二氧化硫等有害气体,对空气质量造成污染。
高含硫原油在泄漏或事故中可能会污染土壤和水源。
防范措施:- 采取密封容器和防护设施,控制高含硫原油的挥发和泄漏。
- 配备泄漏应急处理设备和物质,及时对泄漏进行控制和清理。
- 建立废物处理系统,对产生的废油、废水和废气进行合理处理。
2. 人员健康影响:高含硫原油中的硫会产生有害气体和化学物质,对接触人员的健康造成威胁。
防范措施:- 提供适当的个人防护用品,如防护服、呼吸防护装置等,确保操作人员的安全。
- 在接卸和储运现场设置适当的通风设备,尽量减少有害气体的浓度。
- 定期进行职业卫生监测,及时发现和处理存在的健康风险。
3. 火灾和爆炸危险:高含硫原油具有较低的闪点和爆炸极限,易于在高温、火花等条件下引发火灾和爆炸。
防范措施:- 采取防静电措施,避免静电引发火花。
- 提供防护设备,如火焰和爆炸防护装置,确保安全操作。
- 建立火灾应急预案,进行定期的消防演练。
4. 腐蚀性:高含硫原油中的硫会形成腐蚀性物质,对接触的设备和管道造成腐蚀。
防范措施:- 选用耐腐蚀材料制造接卸和储运设备,减少腐蚀的风险。
- 定期检查和维护设备和管道,确保其正常运行。
- 在可能的情况下,采用防腐涂料或腐蚀抑制剂进行防护。
高含硫原油的接卸和储运过程中存在环境污染、人员健康影响、火灾和爆炸危险、以及腐蚀性等危害。
为了有效防范这些危害,需要采取适当的防范措施,包括控制挥发和泄漏、提供适当的个人防护用品、设置良好的通风设备、采取防静电措施、提供火灾防护装置、使用耐腐蚀材料等。
还需要建立应急预案,并进行培训和演练,以确保在事故发生时能够及时采取应对措施,最大限度减少事故的影响。
加工含硫原油存在问题及防范措施
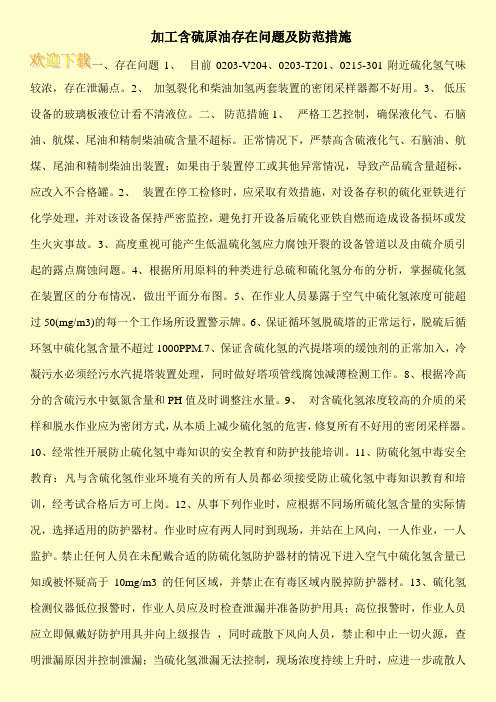
加工含硫原油存在问题及防范措施一、存在问题1、目前0203-V204、0203-T201、0215-301附近硫化氢气味较浓,存在泄漏点。
2、加氢裂化和柴油加氢两套装置的密闭采样器都不好用。
3、低压设备的玻璃板液位计看不清液位。
二、防范措施1、严格工艺控制,确保液化气、石脑油、航煤、尾油和精制柴油硫含量不超标。
正常情况下,严禁高含硫液化气、石脑油、航煤、尾油和精制柴油出装置;如果由于装置停工或其他异常情况,导致产品硫含量超标,应改入不合格罐。
2、装置在停工检修时,应采取有效措施,对设备存积的硫化亚铁进行化学处理,并对该设备保持严密监控,避免打开设备后硫化亚铁自燃而造成设备损坏或发生火灾事故。
3、高度重视可能产生低温硫化氢应力腐蚀开裂的设备管道以及由硫介质引起的露点腐蚀问题。
4、根据所用原料的种类进行总硫和硫化氢分布的分析,掌握硫化氢在装置区的分布情况,做出平面分布图。
5、在作业人员暴露于空气中硫化氢浓度可能超过50(mg/m3)的每一个工作场所设置警示牌。
6、保证循环氢脱硫塔的正常运行,脱硫后循环氢中硫化氢含量不超过1000PPM.7、保证含硫化氢的汽提塔项的缓蚀剂的正常加入,冷凝污水必须经污水汽提塔装置处理,同时做好塔项管线腐蚀减薄检测工作。
8、根据冷高分的含硫污水中氨氮含量和PH值及时调整注水量。
9、对含硫化氢浓度较高的介质的采样和脱水作业应为密闭方式,从本质上减少硫化氢的危害,修复所有不好用的密闭采样器。
10、经常性开展防止硫化氢中毒知识的安全教育和防护技能培训。
11、防硫化氢中毒安全教育:凡与含硫化氢作业环境有关的所有人员都必须接受防止硫化氢中毒知识教育和培训,经考试合格后方可上岗。
12、从事下列作业时,应根据不同场所硫化氢含量的实际情况,选择适用的防护器材。
作业时应有两人同时到现场,并站在上风向,一人作业,一人监护。
禁止任何人员在未配戴合适的防硫化氢防护器材的情况下进入空气中硫化氢含量已知或被怀疑高于10mg/m3的任何区域,并禁止在有毒区域内脱掉防护器材。
加工高含硫原油的防范措施
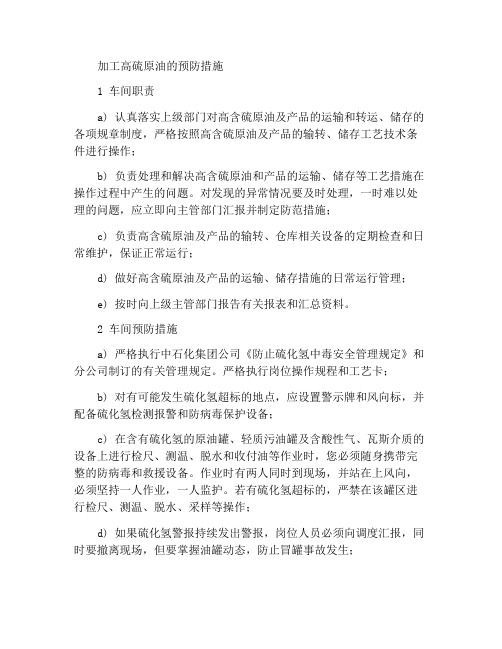
加工高硫原油的预防措施1 车间职责a) 认真落实上级部门对高含硫原油及产品的运输和转运、储存的各项规章制度,严格按照高含硫原油及产品的输转、储存工艺技术条件进行操作;b) 负责处理和解决高含硫原油和产品的运输、储存等工艺措施在操作过程中产生的问题。
对发现的异常情况要及时处理,一时难以处理的问题,应立即向主管部门汇报并制定防范措施;c) 负责高含硫原油及产品的输转、仓库相关设备的定期检查和日常维护,保证正常运行;d) 做好高含硫原油及产品的运输、储存措施的日常运行管理;e) 按时向上级主管部门报告有关报表和汇总资料。
2 车间预防措施a) 严格执行中石化集团公司《防止硫化氢中毒安全管理规定》和分公司制订的有关管理规定。
严格执行岗位操作规程和工艺卡;b) 对有可能发生硫化氢超标的地点,应设置警示牌和风向标,并配备硫化氢检测报警和防病毒保护设备;c) 在含有硫化氢的原油罐、轻质污油罐及含酸性气、瓦斯介质的设备上进行检尺、测温、脱水和收付油等作业时,您必须随身携带完整的防病毒和救援设备。
作业时有两人同时到现场,并站在上风向,必须坚持一人作业,一人监护。
若有硫化氢超标的,严禁在该罐区进行检尺、测温、脱水、采样等操作;d) 如果硫化氢警报持续发出警报,岗位人员必须向调度汇报,同时要撤离现场,但要掌握油罐动态,防止冒罐事故发生;e) 凡进入含硫介质的设备、容器内作业时,必须按规定切断一切物料,彻底冲洗、吹扫、置换,加好盲板,经取样分析合格后,落实安全措施,并办理容器作业票,在监督下工作,作业人员一般不超过两人,每人次工作不得超过1小时;f) 未穿戴适当的防病毒设备,任何人不得进入可能发生硫化氢中毒的区域,并禁止在有毒区内脱掉防毒器材。
遇有紧急情况,按应急预案进行处理。
高含硫原油接卸与储运过程的危害及防范措施

高含硫原油接卸与储运过程的危害及防范措施随着石油产量的逐渐增加,高含硫原油的开采和储运工作也在不断展开。
高含硫原油是指其中硫含量超过0.5%的原油,它在开采、接卸和储运过程中存在着一系列的危害和安全隐患。
本文将就高含硫原油接卸与储运过程中可能存在的危害进行分析,并提出相应的防范措施,以期能够有效地减少事故发生的概率,保障工作人员和社会公众的安全。
1. 环境污染高含硫原油在接卸过程中容易产生硫化氢等有毒物质,如果泄漏或者接触到空气,则会对周围的环境造成污染。
为此,在高含硫原油接卸过程中,应该加强对接卸设备和管道的监测,确保其完好无损,避免原油泄漏。
在接卸过程中应该采取适当的防护措施,减少对环境的影响。
2. 工作人员健康受到威胁硫化氢是高含硫原油中常见的有毒气体,其对人体的危害性很大,一旦被吸入或者接触到皮肤,就会对工作人员的健康造成影响。
在高含硫原油接卸过程中,必须配备好相应的个人防护装备,如防毒面具、化学防护服等,以保障工作人员的健康安全。
3. 火灾和爆炸高含硫原油中的硫化氢是易燃易爆的化学品,一旦泄漏并与空气中的氧气混合,就会产生爆炸的危险。
在高含硫原油接卸过程中,必须加强火灾和爆炸的防范措施,如定期检查接卸设备、配备消防器材等,及时处理封堵泄漏点。
1. 储罐漏油高含硫原油储运过程中,储罐漏油是一个常见的安全隐患。
漏油不仅会导致油气污染环境,还可能引发火灾爆炸等事故。
在高含硫原油的储运过程中,需加强对储罐的检修和维护工作,确保其完好无损,同时运用先进的泄漏检测设备,及时发现并处理漏油问题。
2. 人为操作错误在高含硫原油储运过程中,人为操作错误是导致事故发生的主要原因之一。
为了防范这一危险,需要加强对操作人员的培训和教育,提高其安全意识,制定严格的作业规程,明确操作规范,避免因为操作失误造成事故。
3. 化学品混装由于高含硫原油中的硫化氢易燃易爆,如果与其他物质混装,可能产生化学反应,导致火灾或爆炸。
- 1、下载文档前请自行甄别文档内容的完整性,平台不提供额外的编辑、内容补充、找答案等附加服务。
- 2、"仅部分预览"的文档,不可在线预览部分如存在完整性等问题,可反馈申请退款(可完整预览的文档不适用该条件!)。
- 3、如文档侵犯您的权益,请联系客服反馈,我们会尽快为您处理(人工客服工作时间:9:00-18:30)。
( 安全技术 )
单位:_________________________
姓名:_________________________
日期:_________________________
精品文档 / Word文档 / 文字可改
加工含硫原油存在问题及防范
措施(2021新版)
Technical safety means that the pursuit of technology should also include ensuring that people
make mistakes
加工含硫原油存在问题及防范措施(2021
新版)
一、存在问题
1、目前0203-V204、0203-T201、0215-301附近硫化氢气味较浓,存在泄漏点。
2、加氢裂化和柴油加氢两套装置的密闭采样器都不好用。
3、低压设备的玻璃板液位计看不清液位。
二、防范措施
1、严格工艺控制,确保液化气、石脑油、航煤、尾油和精制柴油硫含量不超标。
正常情况下,严禁高含硫液化气、石脑油、航煤、尾油和精制柴油出装置;如果由于装置停工或其他异常情况,导致产品硫含量超标,应改入不合格罐。
2、装置在停工检修时,应采取有效措施,对设备存积的硫化亚
铁进行化学处理,并对该设备保持严密监控,避免打开设备后硫化亚铁自燃而造成设备损坏或发生火灾事故。
3、高度重视可能产生低温硫化氢应力腐蚀开裂的设备管道以及由硫介质引起的露点腐蚀问题。
4、根据所用原料的种类进行总硫和硫化氢分布的分析,掌握硫化氢在装置区的分布情况,做出平面分布图。
5、在作业人员暴露于空气中硫化氢浓度可能超过50(mg/m3)的每一个工作场所设置警示牌。
6、保证循环氢脱硫塔的正常运行,脱硫后循环氢中硫化氢含量不超过1000PPM.
7、保证含硫化氢的汽提塔项的缓蚀剂的正常加入,冷凝污水必须经污水汽提塔装置处理,同时做好塔项管线腐蚀减薄检测工作。
8、根据冷高分的含硫污水中氨氮含量和PH值及时调整注水量。
9、对含硫化氢浓度较高的介质的采样和脱水作业应为密闭方式,从本质上减少硫化氢的危害,修复所有不好用的密闭采样器。
10、经常性开展防止硫化氢中毒知识的安全教育和防护技能培
训。
11、防硫化氢中毒安全教育:凡与含硫化氢作业环境有关的所有人员都必须接受防止硫化氢中毒知识教育和培训,经考试合格后方可上岗。
12、从事下列作业时,应根据不同场所硫化氢含量的实际情况,选择适用的防护器材。
作业时应有两人同时到现场,并站在上风向,一人作业,一人监护。
禁止任何人员在未配戴合适的防硫化氢防护器材的情况下进入空气中硫化氢含量已知或被怀疑高于10mg/m3的任何区域,并禁止在有毒区域内脱掉防护器材。
13、硫化氢检测仪器低位报警时,作业人员应及时检查泄漏并准备防护用具;高位报警时,作业人员应立即佩戴好防护用具并向上级报告,同时疏散下风向人员,禁止和中止一切火源,查明泄漏原因并控制泄漏;当硫化氢泄漏无法控制,现场浓度持续上升时,应进一步疏散人员并启动应急预案。
14、硫化氢检测报警仪器的安装率、投用率、完好率应达到100%。
15、硫化氢作业现场急救措施:在接触硫化氢气体的作业场所中,作业人员一旦发生硫化氢中毒,监护人员应立即将中毒人员脱离毒区,在上风口空气新鲜处对中毒人员进行抢救。
窒息者应立即对其施行人工呼吸(禁止用口对口法进行人工呼吸),并通知气防站和医院。
16、需进入有毒区域进行抢救的人员,必须事先自身配戴适用的防毒器材后实施抢救。
17、在含硫烟气环境下,会产生低温硫酸露点腐蚀,应经常分析燃料气和燃料油的硫含量,并监测排烟温度,防止产生低温硫酸露点腐蚀。
三、防硫化氢中毒
1、H2S的理化性质
H2S是无色有臭蛋味的毒性气体。
分子量34.08,比重1.19,沸点-60.2℃,熔点-83.8℃,自燃点260℃,易溶于水,也溶于乙醇、汽油、煤油、原油中
H2S的化学性质不稳定,在空气中容易燃烧。
爆炸极限为4.3—
45.5%(体积)。
能与金属反应生成硫化物
2、H2S的危害
H2S是一种恶臭毒性很大的气体。
国家卫生标准规定,H2S在空气中最高允许浓度是10mg/m3。
人不小心进入含H2S的环境中会引起中毒及死亡
表1H2S对人体的危害
H2S浓度mg/m3
接触时间
毒性反应
0.035
开始闻到臭味
0.4
臭味明显
4—7
感到中等强度难闻的臭味
30—40
臭味强烈
70—150
1—2小时
呼吸道及眼刺激症状。
吸入2—15分钟后嗅觉疲劳,不再闻到臭味
300
1小时
6—8分钟出现眼强烈刺激症状,长期接触引起肺水肿
760
15—60分钟
发生肺水肿、支气管炎及肺炎。
接触时间长时引起头疼、头昏、步态不稳、恶心、呕吐、排尿困难
1000
数秒种
很快出现急性中毒,呼吸加快,麻痹而死亡
1400
立即
昏迷、呼吸麻痹而死亡
3、存在H2S介质的部位
反应系统
循环氢系统
高压分离、脱硫系统
低压分离系统
汽提塔系统
含硫污水系统
富DEA系统
四、H2S的检测方法
1、固定安装的H2S检测报警仪
DCS报警总汇可以将固定式H2S检测报警仪发出的报警提示给操作员:
固定式H2S检测报警仪平面布置图(见附录-图2)
操作员在DCS区域图中可检查固定H2S检测报警仪发出的报警
并可找到发生H2S危害的区域
2、便携式H2S检测报警仪
进入危险区域、危险部位必须携带便携式H2S检测报警仪
便携式H2S检测报警仪可手持,也可配挂在上衣口袋上
注意
不能有物体遮盖住报警仪的检测探头
五、防H2S中毒的防护设施
1、自给正压式空气呼吸器
注意
如果对于维护或使用呼吸器不谨慎或不警惕,可导致使用者伤亡
1.1凡是下列情况下应使用自给正压式空气呼吸器
注意
使用自给正压式空气呼吸器可以抵御因在有害大气环境中作业或停留而产生的风险
进入缺氧场所:O2含量<18%
进入火灾现场
进入有毒有害气体泄漏事故区:有毒气体浓度占总体积的1%以上的地方
进入易挥发性介质泄漏事故区
进入未经置换或置换不合格以及氮封的危险场所
1.2自给正压式空气呼吸器的使用
注意
任何维护、使用空气呼吸器的人员必须接受正确的培训。
1.2.1背戴气瓶
将气瓶阀向下背上气瓶;
通过拉肩带上的自由端(即松紧带)调节气瓶的上下位置和松紧,直到感觉舒适为止
1.2.2扣紧腰带
从腰带扣内向外插入腰带插头;
压下插头伸出带扣的一端,确保扣牢。
1.2.3佩戴面罩
放松面罩下面一根颈带,拉开面罩头网;
先将面罩置于使用者脸上;
将头网从头部的上前方向后下方拉下;
从上向下将面罩戴在头上,调整面罩位置,使下巴进入面罩下面凹形内;
先收紧上面的头带,如果感觉不适可调节头带松紧。
1.2.4检测面罩密封
用手按住面罩接口,通过呼气检查面罩密封是否良好;
否则再收紧头带或重新佩带头罩。
注意
面罩的密封件与皮肤紧密贴合是面罩密封的保证,必须保证密封面与皮肤之间无头发和胡须等
1.2.5佩戴供气阀
将供气阀上的红色旋钮放在12点钟位置,确认其接口与面罩接口啮合
沿顺时针方向旋转90°,当听到咔嚓声时即可
1.2.6检查装具性能
使用前必须完全打开气瓶阀
观察压力表读数,气瓶压力应不小于28MPa
通过几次深呼吸检查供气阀性能,吸气和呼气都应舒畅,无不适感觉
1.2.7使用装具
正确佩戴,认真检查后装具即可投入使用
使用时要注意报警器发出的报警信号,听到报警信号,应立即撤离现场
从发出报警声到压缩空气用完大约可使用8分钟
1.2.8使用结束
先松开面罩颈带,然后松开头带,将面罩从下向上脱下
按下供气阀开关,关闭供气阀
拉出腰带插头伸出端,将插头从带扣中退出
放松肩带,将装具从背上卸下,关闭气瓶阀
六、H2S泄漏处理原则
注意
出现H2S介质泄漏,情况危险时,要疏散现场全部人员。
当嗅到H2S气味时,人员应从现场撤离。
6.1DCS室内H2S报警器报警
主控室操作员
确定报警泄漏相关区域
通知室外操作员
确认报警、报警复位
室外操作员
携带好正压式空气呼吸器到现场
在另一个人的监护下(也要携带好防护用具)查找H2S泄漏原因
班长
指挥人员按照事故处理预案进行处理
报气警讲明,是何种物料泄漏,泄漏具体地点、泄漏程度,有无产生着火爆炸的可能、人员伤亡等情况
气防站
气防站到现场后,车间人员要向气防站人员介绍事故状况,有无人员受伤须抢救,有无重点设备须要保护,有无紧急措施须协助实施
6.2人员H2S中毒的急救
急救原则:抢救别人,保护自己
将H2S中毒人员救离事故现场;迅速切断毒源;尽快把中毒者移至空气新鲜处,松解衣扣和腰带,清除口腔异物;维持呼吸道畅通(平躺后仰头抬额,如颈部受伤,采取抬颌法)
云博创意设计
MzYunBo Creative Design Co., Ltd.。