误差过大与伺服报警(410#411#报警).
410和411的报警

FANUC 18i系统故障分析及解决2010-3-6 11:07:00 来源:中国设备管理网阅读:743次我要收藏摘要叙述410和411故障现象、原因分析及解决方法。
关键词FANUC系统故障方法中图分类号TP307 文献标识码B1.故障分析为了在机床出现机械、电机、伺服放大器、编码器故障时,尽可能减轻机床的损坏,FANUC 系统从软件上设定了410和411的报警。
410报警:SERVO ALARM:n—TH AXIS-EXCESS ERROR报警解释:①第n轴的停止位置偏差值超过参数1829的设定值。
②在简易同步控制中,同步补偿量超过参数8325的设定值。
411报警:SERVO ALARM:n—TH AXIS-EXCESS ERROR报警解释:第n轴移动时的位置偏差值超过参数1828的设定值。
410和411报警系统处理过程如下图所示:在NC进行伺服控制的过程中,系统的移动指令经脉冲分配处理,由图中的①进入误差寄存器,对误差寄存器的数值递增,通过伺服的速度回路以及电流回路,由伺服放大器驱动伺服电机转动,使安装在电机后面的增量式编码器发出数字脉冲,反馈到伺服放大器,通过FSSB光缆由图中的②进入误差寄存器,对误差寄存器的数值进行递减,正常情况下误差寄存器里的数值始终保持在一定范围以内,伺服停止时,误差寄存器的数值为0。
如果移动指令或编码器反馈两者中有一个没有,就会造成误差寄存器里的绝对数值过大,在移动时,如果误差寄存器里的绝对数值>参数1828里设定的数值,机床就会出现411报警,在停止时如果误差寄存器里的绝对数值>参数1829里设定的数值,机床就会出现410报警。
误差寄存器的数值可以在FANUC系统的诊断300号看到。
机床在停止的时候,垂直轴(V轴)因为伺服放大器不良下滑,之后就出现410V轴报警。
伺服参数设置画面中V轴误差寄存器的值为-17894,其绝对值超过了参数1829的设定值。
2.故障原因(1)410报警:①机床在停止状态如果遭到碰撞,导致某一轴的位置偏移超过参数1829的设定值时。
伺服故障报警及处理方法
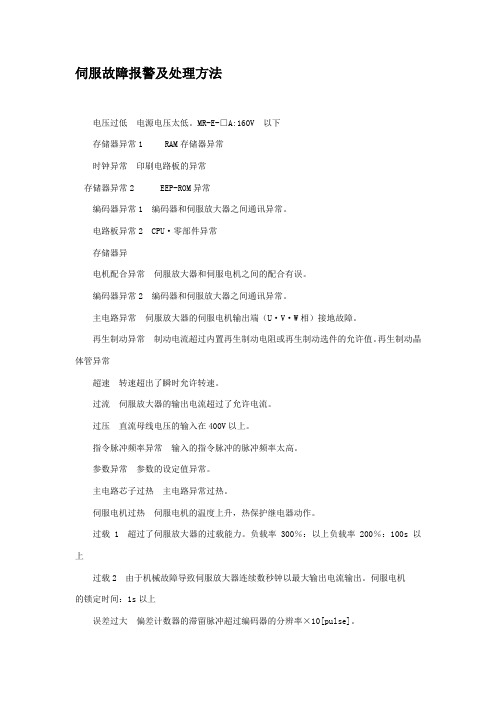
伺服故障报警及处理方法电压过低电源电压太低。
MR-E-□A:160V 以下存储器异常1 RAM存储器异常时钟异常印刷电路板的异常存储器异常2 EEP-ROM异常编码器异常1 编码器和伺服放大器之间通讯异常。
电路板异常2 CPU·零部件异常存储器异电机配合异常伺服放大器和伺服电机之间的配合有误。
编码器异常2 编码器和伺服放大器之间通讯异常。
主电路异常伺服放大器的伺服电机输出端(U·V·W相)接地故障。
再生制动异常制动电流超过内置再生制动电阻或再生制动选件的允许值。
再生制动晶体管异常超速转速超出了瞬时允许转速。
过流伺服放大器的输出电流超过了允许电流。
过压直流母线电压的输入在400V以上。
指令脉冲频率异常输入的指令脉冲的脉冲频率太高。
参数异常参数的设定值异常。
主电路芯子过热主电路异常过热。
伺服电机过热伺服电机的温度上升,热保护继电器动作。
过载 1 超过了伺服放大器的过载能力。
负载率300%:以上负载率200%:100s以上过载2 由于机械故障导致伺服放大器连续数秒钟以最大输出电流输出。
伺服电机的锁定时间:1s以上误差过大偏差计数器的滞留脉冲超过编码器的分辨率×10[pulse]。
串行通讯超时RS-232C通讯的时间超过参数的设定值。
串行通讯异常伺服放大器和通讯设备(计算机等)之间出现串行通讯错误。
CPU·部件异常再生制动电流过大警告可能会超出内置再生制动电阻或外部再生制动选件的制动能力。
过载警告可能发生过载1,过载2报警。
伺服紧急停止警告EMG-SG之间断开。
主电路OFF警告主电路电源断开时,伺服开启信号(SON)为ON。
伺服报警代码及处理欠压电源电压过低。
MR-E-□A:160V 以下<主要原因><处理方法>·电源电压太低。
→检查电源系统·控制电源瞬间停电在60ms以上。
→检查电源系统·由于电源容量过小,导致启动时电源电压下降。
FANUC伺服报警

l 伺服报警的详细信息#7(OVL):发生过载报警。
#6(LV): 伺服放大器中发生低电压报警。
#5(OVC):数字伺服内部发生过电流报警。
#4(HCA):伺服放大器发生异常电流报警。
#3(HVA):伺服放大器中发生过电压报警。
#2(DCA):伺服放大器中发生再生放电回路报警。
#1(FBA):发生断线报警。
#0(OFA):数字伺服内部发生溢出报警。
当诊断数据No.200中的OVL等于1时(发生伺服报警No.400)。
#7(ALD): 0:电机过热1:放大器过热当诊断数据No.200中的FBA等于1时#6(OFS): 数字伺服中发生电流变换错误。
#5(MCC):伺服放大器上的电磁接触器触点熔焊。
#4(LDA): LED指示串行脉冲编码器C故障。
#3(PMS): 反馈电缆故障造成反馈脉冲错误。
如果没能解决您的问题可到留言薄留言以寻求帮助,本文相关问题也可直接在文章后留言.我会尽快回复原创文章,转载请注明:转载自爱数控本文链接地址:.下面的文章可能对您有所帮助与 PMC、I/O Link 相关的系统报警 (SYS_ALM197)今天在群里(群号:33475775)有朋友问到关于ALM197报警的解决方法 解决方法: 在系统报警画面上显示系统报警 197 时,表示这是与 PMC、 Link 相关的系统I/O...FANUC2056报警今天看见有人在群里问到有关于2056报警的问题 首先2000+号报警是各个机床厂自己自己设定的报警号与FANUC系统无关 所以每个机床厂家的2056报警是不同的 对于你这个报警已经写...FANUC 数字伺服参数与维修数字伺服参数设定、主要参数调整及维修 伺服参数的设置 维修过程中主要伺服参数的调整 iB/iC/18i系列FSSB的设置 伺服报警与故障处理 主...368报警 (串行数据错误)上图中368报警以及相关编码器报警的原因有: (1) 电机后面的编码器有问题,如果客户的加工环境很差,有时会有切削液或液压油浸入编码器中导致编码器故障。
伺服报警故障代码大全

伺服报警故障代码大全伺服系统是现代工业自动化生产中常见的一种控制系统,它通过对电机进行控制,实现对机械运动的精确控制。
然而,在使用伺服系统的过程中,我们有时会遇到各种报警故障代码,这些代码代表着不同的故障类型,需要我们及时排查和处理。
下面将为大家详细介绍一些常见的伺服报警故障代码,以便大家在实际工作中能够更好地应对这些问题。
1. E001,伺服系统过载报警。
当伺服系统负载过大时,会触发E001报警代码。
这时需要检查负载情况,可能需要重新调整负载参数或者更换合适的伺服系统。
2. E002,伺服系统过热报警。
当伺服系统工作时间过长或者环境温度过高时,会触发E002报警代码。
此时需要及时停机降温,或者加强散热措施,以确保伺服系统的正常工作。
3. E003,伺服系统电压过高或过低报警。
电压异常会导致伺服系统工作异常,触发E003报警代码。
这时需要检查电源电压情况,可能需要更换稳压器或者调整电源线路。
4. E004,伺服系统编码器故障报警。
编码器是伺服系统的重要传感器,一旦出现故障会触发E004报警代码。
此时需要检查编码器连接情况,可能需要更换或者维修编码器。
5. E005,伺服系统通信故障报警。
通信故障会导致伺服系统无法正常接收指令,触发E005报警代码。
这时需要检查通信线路和通信模块,可能需要重新连接或者更换通信设备。
6. E006,伺服系统电机故障报警。
电机是伺服系统的核心部件,一旦出现故障会触发E006报警代码。
此时需要检查电机连接情况和电机状态,可能需要更换或者维修电机。
7. E007,伺服系统位置偏差报警。
位置偏差会导致伺服系统无法精确定位,触发E007报警代码。
这时需要检查位置传感器和位置控制参数,可能需要重新校准或者调整位置控制系统。
以上是一些常见的伺服报警故障代码,我们在使用伺服系统时,要时刻关注系统的运行状态,及时处理各种报警故障,以确保系统的正常运行。
希望以上内容能够帮助大家更好地理解和应对伺服系统报警故障,提高工作效率和生产质量。
FANUC常见伺服报警及解决方法
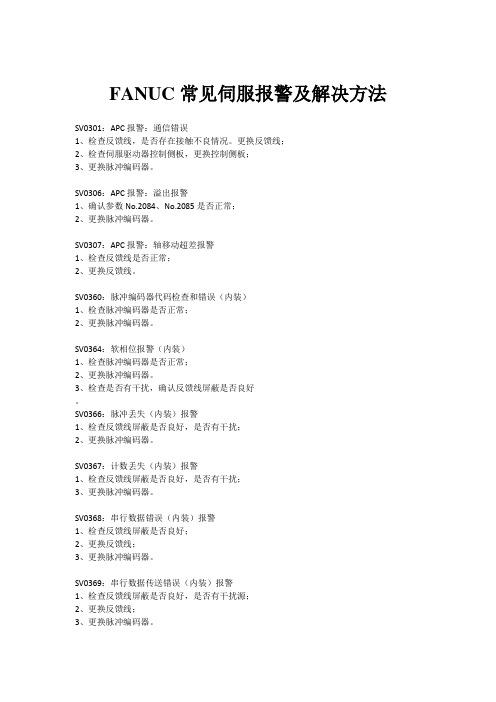
FANUC常见伺服报警及解决方法SV0301:APC报警:通信错误1、检查反馈线,是否存在接触不良情况。
更换反馈线;2、检查伺服驱动器控制侧板,更换控制侧板;3、更换脉冲编码器。
SV0306:APC报警:溢出报警1、确认参数No.2084、No.2085是否正常;2、更换脉冲编码器。
SV0307:APC报警:轴移动超差报警1、检查反馈线是否正常;2、更换反馈线。
SV0360:脉冲编码器代码检查和错误(内装)1、检查脉冲编码器是否正常;2、更换脉冲编码器。
SV0364:软相位报警(内装)1、检查脉冲编码器是否正常;2、更换脉冲编码器。
3、检查是否有干扰,确认反馈线屏蔽是否良好。
SV0366:脉冲丢失(内装)报警1、检查反馈线屏蔽是否良好,是否有干扰;2、更换脉冲编码器。
SV0367:计数丢失(内装)报警1、检查反馈线屏蔽是否良好,是否有干扰;3、更换脉冲编码器。
SV0368:串行数据错误(内装)报警1、检查反馈线屏蔽是否良好;2、更换反馈线;3、更换脉冲编码器。
SV0369:串行数据传送错误(内装)报警1、检查反馈线屏蔽是否良好,是否有干扰源;2、更换反馈线;3、更换脉冲编码器。
SV0380:分离型检查器LED异常(外置)报警1、检查分离型接口单元SDU是否正常上电;2、更换分离型接口单元SDU。
SV0385:串行数据错误(外置)报警1、检查分离型接口单元SDU是否正常;2、检查光栅至SDU之间的反馈线;3、检查光栅尺。
SV0386:数据传送错误(外置)1、检查分离型接口单元SDU是否正常;2、检查光栅至SDU之间的反馈线;3、检查光栅尺。
SV0401:伺服准备就绪信号断开1、查看诊断No.358,根据No.358的内容转换成二进制数值,进一步确认401报警的故障点。
2、检查MCC回路;3、检查EMG急停回路;4、检查驱动器之间的信号电缆接插是否正常;5、更电源单元。
同步控制中SV0407:误差过大报警1、检查同步控制位置偏差值;2、检查同步控制是否正常。
数控机床误差过大故障的分析与处理.

数控机床误差过大故障的分析与处理
数控机床误差过大故障分析与处理
一
定位超调故障的分析与处理
可能原因 加减速时间 设定不当 位置环比例 增益设置不 当
速度环比例 增益设置不 当 速度环积分 时间设置不 当
检查步骤 依次检查数控装置 或伺服驱动器上的 这几个参数的设置 是否与说明书要求 相同
排除措施 依照参数说明书, 正确设置个参数
数控机床误差过大故障分析与处理
项目 超调 1 2 单脉 1 冲精 度差 2 故障原因 加/减速时间设定过小 与机床的连接部分刚性差或连接不牢固 需要根据不同情况进行故障分析 机械传动系统存在爬行或松动
一 加工误差过大故障的分析与处理
检查步骤 检测起、制动电流是否已经饱和 检查故障是否可以通过减小位置 环增益改善 检查定位时位置跟随误差是否正 确 检查机械部件的安装精度与定位 精度 调整速度控制单元扮傻姑娘的相 应旋钮,提高速度环增益 检查定位是位置跟随误差是否正 确 检查机械部件的安装精度与定位 精度 更换位置控制单元板(主板) 检测位置检测器件(编码器、光 栅) 测量不圆度,检查周向上是否变 形,45°方向上是否成椭圆 测量各轴的定位精度与反向间隙 调整控制单元,使同样的进给速 度下各插补轴的位置跟随误差的 差值在±1%以内 在项目3调整后,在45°上成椭圆 检查接口板的调整 测量、重新调整间隙 措施 延长加/减速时间设定 减小位置环增益或提高机 床的刚性 若正确,见第2项,否则 第3项 调整机床机械传动系统
机床反向间隙大、定位精度差 位置环增益设定不当 Nhomakorabea4
5 6
各插补轴的检测增益设定不良
感应同步器或旋转变压器的接口板调整不 良 丝杠间隙或传动系统间隙
CNC常见报警

3n1~3n6(绝对编码器故障)故障原因:编码器与伺服模块之间通讯错误,数据不能正常传送。
恢复方法:在该报警中牵涉三个环节:编码器,电缆,伺服模块。
先检测电缆接口,再轻轻晃动电缆,注意看是否有报警,如果有,修理或更换电缆。
在排除电缆原因后,可采用置换法,对编码器和伺服模块进行进一步确认。
3n7~3n8(绝对脉冲编码器电池电压低)故障原因:绝对脉冲编码器的位置由电池保存,当电池电压低有可能丢失数据,所以系统检测电池电压,提醒到期更换。
恢复方法:选择符合系统要求的电池进行更换。
必须保证在机床通电情况下,执行更换电池的工作。
SV400#,SV402#(过载报警)故障原因:400#为第一、二轴中有过载;402#为第三、第四轴中有过载。
当伺服电机的过热开关和伺服放大器的过热开关动作时发出此报警系统检查原理:伺服放大器有过载检查信号,该信号为常闭触点信号。
当放大器的温度升高引起该开关打开,产生报警,一般情况下这个开关和变压器的过热开关以及外置放电单元的过热开关串联在一起,该信号是当伺服有此报警时,由PWM指令电缆传给NC。
伺服电机过载开关检测电机是否过热,该信号也为常闭触点,当电机过热时,该开关打开产生报警,该信号发出报警通过电机反馈线通知系统。
诊断方法:当发生报警时可通过系统的诊断画面确认是哪一个轴发生的报警该诊断指明哪一个轴发生伺服报警720 . 7---X 轴721 . 7---Y 轴722 . 7---Z 轴723 . 7---4 轴该诊断区分是伺服放大器还是电机过热AIDF=0, 说明伺服放大器有问题AIDF=1, 说明伺服电机过热730 . 7---X 轴731 . 7---Y 轴732 . 7---Z 轴733 . 7---4 轴处理方法:当发生报警时,要首先确认是伺服放大器或是电机过热,因为该信号是常闭信号,当电缆断线和插头接触不良也会发生报警,请确认电缆,插头。
如果确认是伺服/变压器/放电单元,伺服电机有过热报警,那么检查:①过热引起(测量IS,IR侧联负载电流,确认超过额定电流)检查是否由于机械负载过大,加减速的频率过高,切削条件引起的过载②联接引起:检查以上联接示意图过热信号的联接。
三菱伺服报警

三菱伺服报警三菱伺服报警是在使用三菱伺服系统时可能会遇到的一种情况。
当系统检测到异常或故障时,会触发报警,提示用户进行相应的处理。
三菱伺服系统广泛应用于工业自动化领域,其稳定性和可靠性备受信赖。
然而,即使是高质量的产品,在长期使用过程中也难免会出现一些问题,报警就是其中之一。
一、三菱伺服系统报警的原因及处理方法1. 供电电压异常:当供电电压超出正常范围时,三菱伺服系统会报警。
此时,应检查电源线路是否连接良好,电压是否稳定,及时修复故障。
2. 电机过载:如果电机工作负荷过大,超出额定范围,也会导致报警。
可以通过降低负载、调整参数等方式解决问题。
3. 温度过高:三菱伺服系统在工作过程中会产生一定的热量,如果散热不良,温度过高,会触发报警。
应保持系统通风良好,控制温度适宜。
4. 控制系统故障:可能是软件问题、通信故障等引起的报警。
需要重新检查参数设置、重新连接通信线路等进行排查。
5. 机械故障:如果机械部件出现故障,也会引起三菱伺服系统报警。
此时需要检查机械结构是否正常,并进行维修或更换损坏部件。
二、如何有效预防三菱伺服系统报警1. 定期检查维护:定期对三菱伺服系统进行检查和维护,保证各部件正常工作,避免因故障引发报警。
2. 合理使用:在操作三菱伺服系统时,要按照使用手册上的要求进行操作,避免因错误操作导致系统报警。
3. 提高操作技能:操作人员应具备一定的技能和经验,能够熟练操作三菱伺服系统,及时处理各种异常情况,降低报警概率。
三、三菱伺服系统报警的处理流程1. 接收报警信号:当三菱伺服系统检测到异常时,会产生报警信号,通知操作人员进行处理。
2. 分析原因:操作人员需根据报警代码或报警信息,分析报警的具体原因,确定故障点。
3. 处理故障:根据故障的具体情况,采取相应的措施进行处理,例如检查线路、调整参数、更换零部件等。
4. 清除报警:在故障处理完成后,重新启动三菱伺服系统,并确认报警已经清除,确保系统正常运行。
误差过大与伺服报警(410#411#报警).
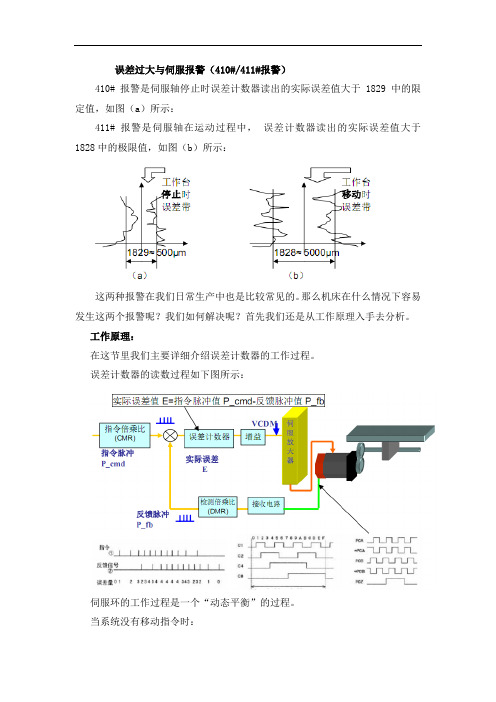
误差过大与伺服报警(410#/411#报警)410# 报警是伺服轴停止时误差计数器读出的实际误差值大于 1829 中的限定值,如图(a)所示:411# 报警是伺服轴在运动过程中,误差计数器读出的实际误差值大于1828中的极限值,如图(b)所示:这两种报警在我们日常生产中也是比较常见的。
那么机床在什么情况下容易发生这两个报警呢?我们如何解决呢?首先我们还是从工作原理入手去分析。
工作原理:在这节里我们主要详细介绍误差计数器的工作过程。
误差计数器的读数过程如下图所示:伺服环的工作过程是一个“动态平衡”的过程。
当系统没有移动指令时:情况1:机床比较稳定,伺服轴没有任何移动情况2:机床受外界影响(如震动、重力等),伺服轴移动。
当系统有移动指令时初始状态——机床待启动电机运行定位完成故障原因:通过上面的分析我们可以看出,每当伺服使能接通时,或者轴定位完成时,都要进行上述的调整。
当上面的调整失败后,就会出现 410#报警——停止时的误差过大。
当伺服轴执行插补指令时,指令值随时分配脉冲,反馈值随时读入脉冲,误差计数器随时计算实际误差值。
当指令值、反馈值其中之一不能够正常工作时,均会导致误差计数器数值过大,即产生411#移动中误差过大。
那么哪个环节会导致上述两种情况发生呢?通过我们维修记录的统计,多数情况是发生在反馈环节上。
另外机械过载、全闭环震荡等都容易导致上述报警发生,现将典型情况归纳如下:⑴编码器损坏⑵光栅尺脏或损坏⑶光栅尺放大器故障⑷反馈电缆损坏,断线、破皮等⑸伺服放大器故障,包括驱动晶体管击穿、驱动电路故障、动力电缆断线虚接等。
⑹伺服电机损坏,包括电机进油、进水,电机匝间短路等⑺机械过载,包括导轨严重缺油,导轨损伤、丝杠损坏、丝杠两端轴承损坏,连轴节松动或损坏。
作为维修工程师应该通过上述现象看本质,上述的典型故障现象其实说明一个问题,即:指令脉冲与反馈脉冲两者之一出现了问题。
上面⑴~⑷是由于反馈环节不良导致反馈信息不能准确传递到系统。
数控系统跟踪误差过大报警现象及实例分析

图3 数控机床加工过程结构示意图
(1)控制器(数控系统)环节 数控机床的 控制器环节是用数控系统完成的,此环节包含了数 控系统硬件本身和相关的软件控制。
(2)放大驱动环节 放大驱动环节主要由伺 服驱动模块完成,现在的驱动模块也往往有自己的 CPU,所以除了硬件外同样也会有软件参数设置不 合理及错误的故障原因。
1. 相关概念 跟踪误差指的是数控机床在移动过程中的误 差,即在移动过程中,理论移动量和实际移动量的 差值(这里是和位移量“相当”的一个量值,大 多数情况下是一个电量,因为此时经过了反馈环 节),是动态的概念范畴,即E(S)=R(S)-B(S)。 这 里 , 还 要 特 别 提 及 另 外 一 个 概 念 —— 定 位 误差。定位误差指的是数控机床移动停止后产生 的误差,即位移结束后,理论位移量和实际位移 量的差值,是静态概念范畴,即E′(S)= C(S)理论- C(S)实际。 一般通用闭环控制系统结构如图1所示,其中 R(S)为输入信号,C(S)为输出信号,E(S)为输入端 定义的误差信号,G(S)为前向通道传递函数,H(S) 为反馈通道传递函数,B(S)为反馈信号。
(4)故障处理 重新换上同型号的连接电 缆,再次运行,机床故障排除。
(5)心得体会 由于X轴的编码器电缆是通过 Z轴拖动的拖链进入到电气柜的,因为本身接触不
冷加工
85 2013年 第1期
E 设备与维修 quipment and Maintenance
图1 通用闭环控制系统结构 而对于全闭环数控机床,其控制系统框图如图 2所示。 参照图1、图2并进行比对,我们不难发现数学
模型中的各个环节在实际机床内包含的部件和机 构。
图2 全闭环控制数控机床控制结构框图
2. 故障理论根源 跟踪误差过大报警产生的原因是机床在运行过 程中,实际坐标位置与反馈坐标位置不相符,且其 值超过系统规定的允许值,此时,系统便会产生 “跟踪误差过大”报警,即E(S)=R(S)-B(S)≥给 定规定值。图3为数控机床加工过程结构示意图, 从系统的控制回路看,凡是和跟踪误差数学关系表 达式相关的量都有可能成为造成此类报警的原因。 详细来说有以下几个环节:
伺服驱动器报警代码表

伺服驱动器报警代码表硬件型号:伺服MR-JE-A系统版本:伺服驱动器系统伺服驱动器报警代码表:1、AL.E6,伺服紧急停止。
引起此故障的原因一般有两个,一个是控制回路24V电源没有接入,另一个是CN1口EMG和SG之间没有接通。
2、AL.37,参数异常。
内部参数乱,操作人员误设参数或者驱动器受外部干扰导致。
一般参数恢复成出厂值即可解决。
3、AL.16,编码器故障。
内部参数乱或编码器线故障或电机编码器故障。
参数恢复出厂值或者更换线缆或者更换电机编码器,若故障依旧,则驱动器底板损坏。
4、AL.20,编码器故障。
电机编码器故障或线缆断线、接头松动等导致。
更换编码器线或伺服电机编码器。
MR-J3系列发生此故障时,还有一种可能是驱动器CPU接地线烧断导致。
5、AL.30,再生制动异常。
若刚通电就出现报警,则驱动器内部制动回路元件损坏。
若在运行过程中出现,可检查制动回路接线,必要时外配制动电阻。
6、AL.50、AL.51,过载。
检查输出U、V、W三相相序接线是否正确,伺服电机三相线圈烧坏或接地故障。
监控伺服电机负载率是否长时间超过100%,伺服响应参数设置过高,产生共振等原因。
7、AL.E9,主回路断开。
检查主回路电源是否接入,若正常则主模块检测回路故障,须更换驱动器或配件。
8、AL.52,误差过大。
电机编码器故障或驱动器输出模块回路元件损坏,通常油污较多的使用场合此故障较多。
伺服放大器也叫伺服驱动器,是用来控制伺服电机的一种控制器。
其作用类似于变频器作用于普通交流马达。
主要应用于高精度的定位系统。
目前是传动技术的高端产品。
噪声干扰包括二类,一类是从外部进入伺服放大器并可能导制其运行异常,另一类是由伺服放大器辐射出去并可能导致周围设备运行异常。
伺服放大器是由微弱信号控制的电子设备,因此,通常需要以下的防护措施。
此外,由于伺服放大器是通过高速开关输出电流的,所以会形成噪声源。
当噪声引起周围设备运行异常时,就应采取抗干扰措施。
伺服故障报警及处理方法

伺服故障报警及处理方法伺服系统是现代化自控系统的重要组成部分,广泛应用于机械加工、自动化生产等领域,起到精确控制运动的作用。
然而,偶尔会出现故障,该如何处理这些伺服故障报警呢?下面就来详细介绍一下。
1.温度过高报警温度过高报警是指伺服系统温度超过预设范围时报警。
处理方法如下:-检查风扇是否正常运转,如果风扇不转或转速不足,需要更换或维修风扇。
-检查冷却系统是否正常,如果冷却液不足或污染,需要及时补充或更换冷却液。
-检查散热器是否堵塞,如果堵塞严重,需要清洗或更换散热器。
-检查工作环境温度,如果环境温度太高,需要采取降温措施。
2.过流报警过流报警是指伺服系统运行时电流超过额定值时报警。
处理方法如下:-检查电源电压是否稳定,如果电源电压波动较大,需要采取稳压措施。
-检查伺服驱动器和电机的线路是否接触不良或短路,需要重新连接或更换线路。
-检查伺服电机是否超负荷运行,如果是,需要调整负载,避免超负荷运行。
3.过压报警过压报警是指伺服系统运行时电压超过额定值时报警。
处理方法如下:-检查电源电压是否稳定,如果电源电压波动较大,需要采取稳压措施。
-检查伺服驱动器和电机的线路是否接触不良或短路,需要重新连接或更换线路。
-检查伺服电机的参数设置是否正确,如果参数设置不正确,需要调整参数。
4.过速报警过速报警是指伺服系统运行时速度超过额定值时报警。
处理方法如下:-检查伺服电机的参数设置是否正确,如果参数设置不正确,需要调整参数。
-检查编码器是否损坏或接触不良,需要修复或更换编码器。
-检查伺服驱动器是否工作正常,如果驱动器故障,需要修复或更换驱动器。
5.低电压报警低电压报警是指伺服系统运行时电压低于额定值时报警。
处理方法如下:-检查电源电压是否稳定,如果电源电压波动较大,需要采取稳压措施。
-检查电池是否电量不足,需要及时更换电池。
-检查电路是否有漏电或接触不良现象,需要修复或更换电路。
总结起来,伺服故障报警的处理方法主要包括检查电源电压、检查线路连接、检查电机参数和设备设置等。
FANUC 系统数控机床误差过大报警处理4页
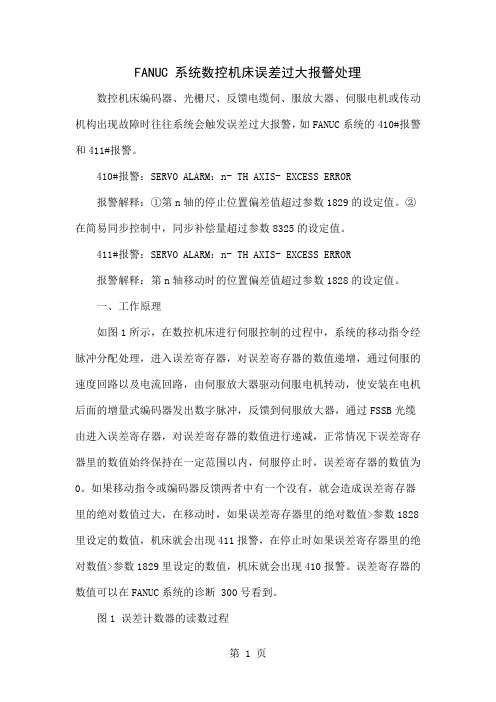
FANUC 系统数控机床误差过大报警处理数控机床编码器、光栅尺、反馈电缆伺、服放大器、伺服电机或传动机构出现故障时往往系统会触发误差过大报警,如FANUC系统的410#报警和411#报警。
410#报警:SERVO ALARM:n- TH AXIS- EXCESS ERROR报警解释:①第n轴的停止位置偏差值超过参数1829的设定值。
②在简易同步控制中,同步补偿量超过参数8325的设定值。
411#报警:SERVO ALARM:n- TH AXIS- EXCESS ERROR报警解释:第n轴移动时的位置偏差值超过参数1828的设定值。
一、工作原理如图1所示,在数控机床进行伺服控制的过程中,系统的移动指令经脉冲分配处理,进入误差寄存器,对误差寄存器的数值递增,通过伺服的速度回路以及电流回路,由伺服放大器驱动伺服电机转动,使安装在电机后面的增量式编码器发出数字脉冲,反馈到伺服放大器,通过FSSB光缆由进入误差寄存器,对误差寄存器的数值进行递减,正常情况下误差寄存器里的数值始终保持在一定范围以内,伺服停止时,误差寄存器的数值为0。
如果移动指令或编码器反馈两者中有一个没有,就会造成误差寄存器里的绝对数值过大,在移动时,如果误差寄存器里的绝对数值>参数1828里设定的数值,机床就会出现411报警,在停止时如果误差寄存器里的绝对数值>参数1829里设定的数值,机床就会出现410报警。
误差寄存器的数值可以在FANUC系统的诊断 300号看到。
图1 误差计数器的读数过程二、故障原因通过以上分析可知,每当伺服使能接通,或者轴定位完成时,都要进行上述误差比较。
当以上误差比较超值后,就会出现410#报警,即停止时的误差过大。
当伺服轴执行插补指令时,指令值随时分配脉冲,反馈值也随时读入脉冲,误差计数器随时计算实际误差值。
当指令值、反馈值其中之一不能正常工作时,均会导致误差计数器数值过大,即产生411#移动中误差多大报警。
FANUC伺服报警SV0401~SV0411(一)

FANUC伺服报警SV0401~SV0411(一)SV0401伺服准备就绪信号断开报警原因:伺服放大器伺服准备就绪信号(VRDY)尚未被置于ON时,或在运行过程中被置于OFF时发生此报警。
相关链接:FANUCSV0401报警诊断方法及案例介绍SV0403硬件/软件不匹配报警原因:轴卡与伺服软件组合不正确,可能的原因有:1)没有提供正确的轴卡;2)闪存中没有安装正确的伺服软件。
解决方法:软件或硬件异常,请直接联系北京发那科维修部门。
SV0404伺服准备就绪信号接通报警原因:伺服放大器的伺服准备就绪信号(VRDY)一直为ON时发生此报警。
解决方法:1)某些特殊情况可以使用参数P1800#1=1进行屏蔽;2)因放大器或者轴卡损坏引起,更换放大器与轴卡。
SV0409检查的扭矩异常报警原因:系统开启异常扭矩负载功能之后,检测到异常负载导致。
解决方法:1)如果不适用异常负载检测,请设定参数P2016#0=0;2)如果使用异常负载检测功能,请确认是否存在异常负载现象,例如机械异常卡住,或者异常加工状态;3)如果使用异常负载检测功能,同时加工状态正常,请重新调整该功能的相关参数。
SV0410停止时误差过大报警原因:伺服轴停止时误差过大引起报警。
解决方法:1)排查动力线、反馈线是否接错;2)排查伺服电机初始化参数是否有误;3)正确设定不同状态下伺服轴停止时误差报警水平参数P1829、P5312等;4)如果伺服电机使用过程中出现抖动等现象,请先排查抖动问题,SV0410为附加报警;5)Cs轴控制时出现此问题,请检查主轴编码器相关参数。
SV0411运动时误差过大报警原因:伺服轴运动时误差过大引起报警解决方法:1)排查动力线、反馈线是否接错;2)排查伺服电机初始化参数是否有误;3)正确设定不同状态下伺服轴停止时误差报警水平参数P1828、P5310等;4)如果伺服电机使用过程中出现抖动等现象,请先排查抖动问题,SV0410为附加报警;5)Cs轴控制时出现此问题,请检查主轴编码器相关参数。
伺服电机位置偏差过大的原因

伺服电机位置偏差过大的原因
1. 传感器故障:伺服电机的位置控制依赖于反馈传感器,如编码器或霍尔传感器,如果传感器故障或损坏,则会导致位置误差。
2. 机械结构问题:伺服电机的位置控制是通过机械结构来达成的,如果机械结构出现问题,例如轴承损坏、机械传动装置松动或磨损等,都会导致位置误差。
3. 电气问题:伺服电机的电力输出和控制电路也可能会出现问题,例如电源电压不稳定、电机驱动器工作不正常、控制信号干扰等,都可能导致伺服电机位置控制误差过大。
4. 温度变化:由于温度的变化,机械结构和电气装置的性能会发生变化,从而导致伺服电机位置控制误差过大。
5. 控制器设置错误:错误的控制参数设置,例如PID控制参数选择不当、速度和加速度的设置过大或过小等,会导致伺服电机位置控制误差过大。
- 1、下载文档前请自行甄别文档内容的完整性,平台不提供额外的编辑、内容补充、找答案等附加服务。
- 2、"仅部分预览"的文档,不可在线预览部分如存在完整性等问题,可反馈申请退款(可完整预览的文档不适用该条件!)。
- 3、如文档侵犯您的权益,请联系客服反馈,我们会尽快为您处理(人工客服工作时间:9:00-18:30)。
误差过大与伺服报警(410#/411#报警)
410# 报警是伺服轴停止时误差计数器读出的实际误差值大于 1829 中的限定值,如图(a)所示:
411# 报警是伺服轴在运动过程中,误差计数器读出的实际误差值大于1828中的极限值,如图(b)所示:
这两种报警在我们日常生产中也是比较常见的。
那么机床在什么情况下容易发生这两个报警呢?我们如何解决呢?首先我们还是从工作原理入手去分析。
工作原理:
在这节里我们主要详细介绍误差计数器的工作过程。
误差计数器的读数过程如下图所示:
伺服环的工作过程是一个“动态平衡”的过程。
当系统没有移动指令时:
情况1:机床比较稳定,伺服轴没有任何移动
情况2:机床受外界影响(如震动、重力等),伺服轴移动。
当系统有移动指令时
初始状态——机床待启动
电机运行
定位完成
故障原因:
通过上面的分析我们可以看出,每当伺服使能接通时,或者轴定位完成时,都要进行上述的调整。
当上面的调整失败后,就会出现 410#报警——停止时的误差过大。
当伺服轴执行插补指令时,指令值随时分配脉冲,反馈值随时读入脉冲,误差计数器随时计算实际误差值。
当指令值、反馈值其中之一不能够正常工作时,均会导致误差计数器数值过大,即产生411#移动中误差过大。
那么哪个环节会导致上述两种情况发生呢?通过我们维修记录的统计,多数情况是发生在反馈环节上。
另外机械过载、全闭环震荡等都容易导致上述报警发生,现将典型情况归纳如下:
⑴编码器损坏
⑵光栅尺脏或损坏
⑶光栅尺放大器故障
⑷反馈电缆损坏,断线、破皮等
⑸伺服放大器故障,包括驱动晶体管击穿、驱动电路故障、动力电缆断线虚接等。
⑹伺服电机损坏,包括电机进油、进水,电机匝间短路等
⑺机械过载,包括导轨严重缺油,导轨损伤、丝杠损坏、丝杠两端轴承损坏,连轴节松动或损坏。
作为维修工程师应该通过上述现象看本质,上述的典型故障现象其实说明一个问题,即:指令脉冲与反馈脉冲两者之一出现了问题。
上面⑴~⑷是由于反馈环节不良导致反馈信息不能准确传递到系统。
⑸~⑺反映的是虽然指令已经发出,但是在执行过程中出现了问题,有可能是在系统内部,也有可能是出在伺服放大器上,还有可能是由于机械负载阻止电机正常转动。
下面我们通过几个实例分析,加深对位置误差控制的理解。
实例分析:
实例 1:某立式加工中心(全闭环),低速运行时无报警,但是无论在哪种方式下高速移动X轴时(包括JOG 方式、自动方式、回参考点方式)出现411#报警。
通过前面的介绍,我们了解到 411#报警是轴移动时,指令值与反馈值的差,超过了1828#参数中设定的极限值(参照第三章3-6 节常用伺服参数设置⑷中说明),在这种情况下一般不要怀疑参数问题,除非人为修改过机床参数。
我们重点需要检查的是①反馈信号②驱动输出。
由于该机床采用的是全闭环控制,考虑光栅尺容易受污染,所以首先采用“排它法”排除光栅尺损坏的可能。
具体步骤,将全闭环修改为半闭环进行试验。
实例进行说明如下:
⑴将参数1815# b2(OPTx)=0 (半闭环控制)
⑵进入伺服参数画面,参见下图
⑶将“初始化设定位”(英文 INITIAL SET BITS)改为 00000000。
⑷将“位置反馈脉冲数.”(英文POSITION PULSE NO.)改为 12500。
⑸计算 N/M 值,具体参照第三章3-4节伺服参数初始化⑺部分说明。
⑹关电,再开电,参数修改完成。
之后先用手抡移动 X 轴,当确认半闭环运行正常后用 JOG 方式从慢速到高速进行试验,结果X轴运行正常。
从试验结果得出结论;半闭环运行正常,全闭环高速运行时411#报警,充分证明全闭环测量系统故障。
后打开光栅尺护罩,发现尺面上有油膜,清除尺面油污,重新安装光栅尺并恢复原参数,包括将 1815# b2=1,恢复修改过的伺服参数N/M 等,机床修复。
实例2:某数控车床FANUC 0i TC数控系统(半闭环控制),Z轴移动时411#报警。
首先我们通过伺服诊断画面观察Z 轴移动时误差值,参见下图:
通过观察,发现Z轴低速移动时“位置偏差”数值可随着轴的移动跟随变化,而Z轴高速移动时,“位置偏差”数值尚未来得及调整完就出现 411#报警。
这种现象是比较典型的指令与反馈不谐调,有可能是反馈丢失脉冲、也有可能是负载过重而引起的误差过大。
由于是半闭环控制,所以反馈装置就是电机后面的脉冲编码器,该机床使用FANUC 0i-TB数控系统,并且X 和Z 轴均配置αi 系列数字伺服电机,所以编码器互换性好,并且比较方便,因此维修人员首先更换了两个轴的脉冲编码器。
但是更换以后故障依旧,初步排除编码器问题。
通过查线、测量,确认反馈电缆及连接也无问题。
视线转向外围机械部分,对此技术人员将电机与机床脱离,将电机从联轴节中卸下,通电旋转电机,无报警。
排除了数控系统和伺服电机有问题。
检查机械,此时最好用手搫丝杠,发现丝杠很沉,明显超过正常值,说明进给轴传动链机械故障,通过钳工检修,修复Z轴机械问题,重新安装 Z轴电机,机床工作正常。
实例3:某立式数控铣床FANUC 0i-MC 数控系统(半闭环),Y轴解除急停开关后数秒钟随即产生410#报警。
410#报警是由停止时误差过大引起的,一般也是由①反馈、②驱动、③外围机械这三种因素引起的。
凡是这类误差过大的报警,我们首先要观察伺服运转(SV-TURN)画面。
通过观察我们发现松开急停开关后“位置偏差”数值快速加大,并出现报警,此时机床攒动一下并停止。
如何简易快速的判断位置偏码器故障,我们可以先按下紧急停止开关,用手或借助工具使电机转动。
此时,如果伺服TURN画面中的“位置偏差”也跟着变化,说明编码器基本没有问题。
使用此方法,通过伺服诊断画面看到反馈脉冲良好,基本排除脉冲编码器及反馈环节的问题。
经过仔细观察发现,通电时间不长,电机温升可达 60~70°C。
通过摇表测量,发现电机线圈对地短路,更换电机后,机床工作正常。