小型轴流CPU风扇的CFD分析
CFD中的旋转流动分析

摘要工程师在设计带有旋转零部件的设备时,如果希望提高设备性能,则需要分析和了解这些零部件的特性。
计算流体力学(CFD) 是一种研究带有旋转零部件的完美工具。
它有助于排除对昂贵物理样机的需求,并能在设计过程初期尽早发现严重的设计缺陷。
本文将介绍这样一款 CFD 工具的使用,它就是 SolidWorks® Flow Simulation。
SolidWorks 软件同时采用单旋转坐标系法和多旋转坐标系法来解决流体运动问题。
简介计算流体力学 (CFD) 是一种可以准确地研究旋转零部件的优秀工具。
仔细观察泵、台扇、用于电子冷却的轴流风扇,以及吹风机这些各式机器,就会发现它们都含有旋转零部件。
工程师在设计带有旋转零部件的设备时,如果希望提高设备性能,则需要分析和了解这些零部件的特性。
例如,如果台扇的风叶形状不合理或者安装方向 不对,则风扇产生的风力可能很小或根本没风。
图 1:此泵装配体是用 SolidWorks 设计的模型,它能很好地说明如何将SolidWorks Flow Simulation用于分析旋转零部件。
CFD (计算流体力学)可帮助工程师研究许多与旋转零部件特性有关的问题。
它提供了一种能节省大量时间和金钱的方式来获取必要的信息,并且帮助工 程师设计出优质的旋转设备。
运用 CFD 可以排除对昂贵物理样机的需求,并能在设计过程初期尽早发现严重的设计缺陷。
本文从一些 CFD 基础知识入手,简要地向工程师介绍了 CFD 如何模拟旋转流体,然后深入介绍了 SolidWorks Flow Simulation 用户解决典型问题的过程。
有多种不同方法可用来研究旋转设备,以及旋转设备周围的流体。
在大多数旋转机械流体分析中,工程师都采用稳态方式来建立流体模型。
“稳态”一词表示求解不随时间的变化而变化。
图 2:SolidWorks Flow Simulation 使用基于向导的界面设置流体分析。
用户可选择配置和单位系统。
基于CFD模拟的轴流风机扇叶设计优化研究

基于CFD模拟的轴流风机扇叶设计优化研究摘要:本研究采用计算流体动力学(CFD)模拟方法,旨在优化轴流风机扇叶的设计以提高性能和效率。
通过数值模拟,我们系统地研究了不同扇叶参数对风机性能的影响,并提出了一种优化设计方案,以实现更高的能效和性能。
研究结果表明,通过CFD模拟可以有效地改善轴流风机的性能,并为风机工程领域的进一步发展提供有力支持。
关键词: CFD模拟;轴流风机;扇叶设计;优化;性能一、引言轴流风机作为工业和商业领域中广泛应用的关键设备,对能源效率和性能提出了不断增长的需求。
其中,扇叶作为轴流风机的核心部件,其设计和优化对整个风机系统的性能至关重要。
随着计算流体动力学(CFD)模拟方法的不断发展,研究人员可以更深入地理解风机流场,并进行更精确的性能预测和优化设计。
二、文献综述2.1 轴流风机的发展历程轴流风机作为工业领域的核心设备,其发展历程从19世纪末至今经历了令人瞩目的进步。
早期,轴流风机的设计主要依赖于经验和试验,限制了其性能和效率。
然而,随着科学和工程技术的进步,数学模型、实验室测试和计算流体力学等新方法的应用使轴流风机的设计变得更精确和可预测。
这些技术创新促使了风机的能效提升、噪音降低和寿命延长,从而为各行业带来了更高水平的气流控制和空气处理能力。
2.2 扇叶设计的重要性扇叶作为轴流风机的核心组成部分,其设计对风机性能至关重要。
扇叶的几何形状、叶片数目、叶片角度等参数直接影响风机的效率、噪音产生、能耗和寿命。
一个优化的扇叶设计可以显著提高风机的能效,降低运行成本,减少环境影响。
所以,深入研究和优化扇叶设计是提高轴流风机性能的关键步骤。
近年来,计算流体动力学(CFD)模拟技术的不断发展已经引领了轴流风机研究的新时代。
这一技术的崭新应用为风机工程领域带来了深刻的影响。
通过CFD,研究人员能够以前所未有的准确性模拟轴流风机内部复杂流动现象,如湍流、涡流和分离现象。
这种全面的流场信息为风机性能的深入理解提供了强大工具,并且为设计和优化提供了坚实基础。
散热模拟分析报告
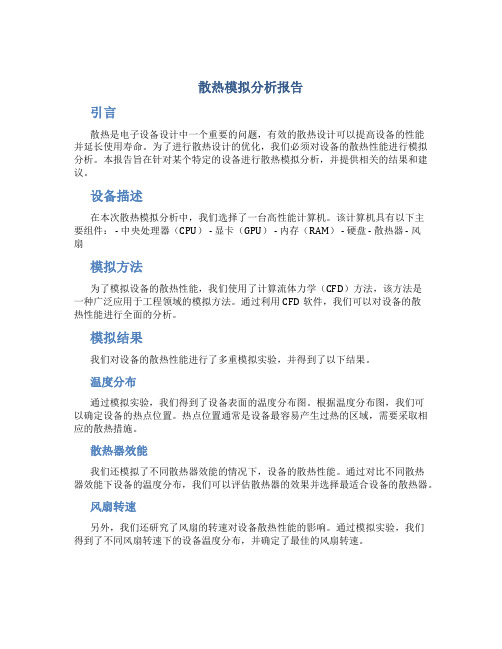
散热模拟分析报告引言散热是电子设备设计中一个重要的问题,有效的散热设计可以提高设备的性能并延长使用寿命。
为了进行散热设计的优化,我们必须对设备的散热性能进行模拟分析。
本报告旨在针对某个特定的设备进行散热模拟分析,并提供相关的结果和建议。
设备描述在本次散热模拟分析中,我们选择了一台高性能计算机。
该计算机具有以下主要组件: - 中央处理器(CPU) - 显卡(GPU) - 内存(RAM) - 硬盘 - 散热器 - 风扇模拟方法为了模拟设备的散热性能,我们使用了计算流体力学(CFD)方法,该方法是一种广泛应用于工程领域的模拟方法。
通过利用CFD软件,我们可以对设备的散热性能进行全面的分析。
模拟结果我们对设备的散热性能进行了多重模拟实验,并得到了以下结果。
温度分布通过模拟实验,我们得到了设备表面的温度分布图。
根据温度分布图,我们可以确定设备的热点位置。
热点位置通常是设备最容易产生过热的区域,需要采取相应的散热措施。
散热器效能我们还模拟了不同散热器效能的情况下,设备的散热性能。
通过对比不同散热器效能下设备的温度分布,我们可以评估散热器的效果并选择最适合设备的散热器。
风扇转速另外,我们还研究了风扇的转速对设备散热性能的影响。
通过模拟实验,我们得到了不同风扇转速下的设备温度分布,并确定了最佳的风扇转速。
结果分析根据我们的模拟结果,我们得出了以下结论。
设备热点位置通过温度分布图,我们确定了设备的热点位置为CPU和GPU。
在设计散热方案时,我们应重点考虑这两个部件的散热需求。
散热器效能模拟实验表明,散热器的效能对设备的散热性能有明显的影响。
选择高效的散热器可以降低设备的温度,提高性能和稳定性。
风扇转速风扇的转速也对设备的散热性能起重要作用。
通过调整风扇转速,我们可以控制设备的温度,并保持在合理的范围内。
建议根据我们的分析结果,我们提出以下建议:1.选择高效的散热器:在设计散热方案时,应优先选择高效的散热器,以提高设备的散热性能。
基于流固耦合仿真的小型轴流风扇优化设计

基于流固耦合仿真的小型轴流风扇优化设计许名珞【摘要】为了解决某初步设计的轴流吹风机出风口流量较小的问题,本文对轴流风扇了进行优化设计,最终将风扇叶片翼型由NACA4409翼型改为AH79-100C 翼型,叶片安装角由30°增大为32.5°,设计叶片后弯角为8°。
基于计算流体力学理论,建立了轴流吹风机流场和轴流风扇风道流场的数值计算模型,运用Fluent 软件进行流场数值仿真。
基于 ANSYS 软件的Workbench平台,利用流固耦合仿真分析方法对优化后的轴流风扇进行结构分析,校核了新风扇的强度。
数值仿真结果表明:仿真结果与企业实验测试结果相符,优化后的轴流吹风机出口流量较优化前增加了10.59%,新风扇轴功率满足企业要求,强度也满足设计要求,总体达到了优化目标。
%In order to address the small outlet flowrate issue of a preliminary designed axial flow fan, this paper optimizes the axial-flow fan, changed the airfoil of fan blades from NACA4409 to AH79-100C, increased the blades setting angle from 30 to 32.5 degrees, and designed the blade back-bending angle of 8 degrees. Based on the theory of computational fluid dynamics, a numerical model to compute the air-flow field and the axial-flow fan duct is set up and Fluent software is used to numerically simulate on flow field. Based on the ANSYS Workbench Platform, structural analysis for the optimized axial-flow fan using fluid-structure interaction simulation method is made, and the strength of the new fan is checked. The simulation results show that simulation results coincide with enterprise test results, the outlet flowrate of the optimized axial flow fan increased 10.59%, the shaft power of new axial-flow fan meets enterpriserequirements, the strength also meets the design requirements, and the optimization goals are achieved.【期刊名称】《风机技术》【年(卷),期】2015(000)001【总页数】6页(P28-32,37)【关键词】轴流风扇;翼型;后弯角;计算流体力学;流固耦合;优化;强度校核【作者】许名珞【作者单位】东南大学机械工程学院【正文语种】中文【中图分类】TH432.1;TK05轴流风扇作为一种通用叶轮机械,被广泛应用在生产生活的各个行业。
轴流风机CFD仿真分析
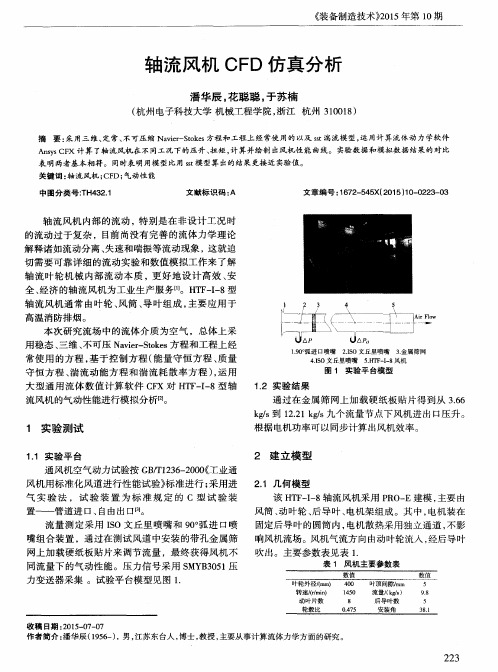
2 2 3
E q u i p me n t Ma n u f a c t u r i n g T e c h n o l o g y No . 1 0 , 2 0 1 5
De s i g n a n d I mp l e me n t a t i o n o f t h e De v e l o p me n t o f Hy d r a u l i c
Ab s t r a c t :T h e p a p e r i n t r o d u c e s a me t h o d f o r s e c o n d a r y d e v e l o p me n t o f h y d r a u l i c c o mp o n e n t s mo d e l l i b r a y r a n d
Co mp o n e n t s Mo d e l L i b r a r y a n d Vi r t u a l Di s a s s e mb l y
C H E N Mi n - - j i e ( H a n g z h o u P o l y t e c h n i c , Ha n g z h o u Z h e j i a n g , 3 1 1 4 0 0 , C h i n a )
流 风机 的气 动 性 能进 行模 拟分 析 闭 。
1 . 9 0 。 弧进 口喷嘴 2 . I S O文丘里喷嘴 3 . 金 属筛网 4 . I S O文 丘里喷嘴 5 . H T F — I 一 8 风机
图 1 实 验 平 台 模 型
1 . 2 实验 结 果
通 过 在金 属 筛 网上 加 载硬 纸 板 贴 片 得 到从 3 . 6 6 k g / s 到 1 2 . 2 1 k g / s 九 个 流 量节 点 下 风 机进 出 口压 升 。 根 据 电机 功率 可 以 同步计 算 出 风机效 率 。
基于CFD的发动机冷却风扇性能仿真分析

速 轴流 风扇 叶片倾 角 、 叶 片厚 度 和 叶片 最 大厚 度 位 传统 风扇 优化方 法 基于 大量 试 验 研究 , 开发 周 置对风 扇效 率 的影 响规律 , 得 出叶 片倾 角 对 风扇 效
期长 、 成本 高 . 随着 C F D技 术 和计 算 机 硬 件 的不 断 率 的作 用效 果较 明显 .
董效 彬等 l 5 利用 F l u e n t 软件研 究不 同翼 型截 面 的5 %~8 %, 随着 人们 对汽 车 的燃 油 经济性 的要 求 能 .
不 断 提高 , 改 善 风 扇性 能 , 提 高 风 扇 效 率 成 为 汽 车 对 风扇性 能 的影 响 . L E E等 l _ 6 ] 通 过 响应 面法 研 究低 发动 机冷却 风 扇结构 优化 的重 要方 向_ 1 ] .
朱传敏 , 吴 秀丽
( 同济大学 机械 与能源工程学院 , 上海 2 0 1 8 0 4 )
基于CFD数值仿真的工程机械 冷却风扇性能分析

文章编号:1000-033X (2017)05-0089-05收稿日期:2016-12-15基金项目:国家科技支撑计划项目(2013BAF07B04);唐山市重点汽车实验室建设项目(12130201A-2)作者简介:刘佳鑫(1983-),男,吉林桦旬人,博士后,讲师,研究方向为工程车辆节能降噪技术.基于CFD 数值仿真的工程机械冷却风扇性能分析刘佳鑫1,2,王宝中1,邢梦龙1,秦四成3,蒋炎坤2,龙海洋1(1.华北理工大学机械工程学院,河北唐山 063009;2.华中科技大学能源与动力工程学院,湖北武汉 430074;3.吉林大学机械科学与工程学院,吉林长春 130022)摘 要:为了提升冷却风扇的性能,使流经散热器空气的流动状态得到改善,基于国内某工程机械用冷却风扇建立几何模型,利用CFD 数值仿真对冷却风扇进行模拟.结果表明:原风扇仿真模型正确;孤立翼型法与合理的特征控制可用于风扇的几何开发与建模;当体积流量达到10.24m 3㊃s -1时,新风扇全压效率提升了约0.81%,轴功率降低了0.12kW .关键词:数值仿真;冷却风扇;风扇设计;工程机械中图分类号:U415.5 文献标志码:BAnal y sis on Performance of Coolin g Fan for ConstructionMachiner y Based on CFD Numerical SimulationLIU Jia-xin 1,2,WANG Bao-zhon g 1,XING Men g -lon g 1,QIN Si-chen g 3,JIANG Yan-kun 2,LONG Hai-y an g 1(1.School of Mechanical En g ineerin g ,North China Universit y of Science and Technolo gy ,Tan g shan 063009,Hebei ,China ;2.School of Ener gy and Power En g ineerin g ,Huazhon g Universit y of Science and Technolo gy ,Wuhan 430074,Hubei ,China ;3.School of Mechanical Science and En g ineerin g ,Jilin Universit y ,Chan g chun 130022,Jilin ,China )Abstract :In order to increase the p erformance of the coolin g fan so as to im p rove the air flow throu g h the radiator ,the g eometric model was established based on the domestic coolin g fan for construction machiner y .The p erformance of the coolin g fan was simulated b y CFD numericalsimulation.The results show that the ori g inal simulation model is correct ;the isolated airfoilmethod and reasonable characteristic control can be used for g eometric develo p ment and modelin g of the fan ;when the volume flow reaches 10.24m 3㊃s -1,full p ressure efficienc y of the new fan increases b y about 0.81%,and shaft p ower reduces b y 0.12kW.Ke y words :numerical simulation ;coolin g fan ;fan desi g n ;construction machiner y0 引 言冷却风扇作为发动机冷却系统的一个重要部件,在为动力舱创造空气流动环境的同时,也为散热器组提供充足的冷却风.通过冷却风扇控制空气流量,可以合理地实现对冷却液温度的调控,保证各部件在合理的温度区间,从而保持发动机高效率的工作状态.由此可见,冷却风扇性能直接影响着设备总体的性能和工作可靠性.针对冷却风扇性能,国内外专家学者已从冷却风扇设计方法入手积极开展研究:上海理工大学王企鲲运用 等密流型 与 变密流型 2种设计方法进行扭叶片改型设计,并利用CFD (Com p utationalFluid D y namics )仿真对比两者差异,且对2种设计方法作出了评价[1];刘全忠通过数值模拟,以汽轮发电机为研究对象,获得了安装角等参数与效率之间的关系,并对其展开性能优化[2];高红霞等使用控制涡设计理论对直升机轴流风扇气动性能进行改进提升;M Henner 利用CFD 数值模拟的方法,通过调整结构设计参数,实现对风扇性能的改进[3];Zhou Jianhui 则采用理论设计与CFD 仿真验证相结合的方式对CPU 冷却风扇进行了重新设计[4].基于以上已取得的研究成果,本文利用CFD 数值仿真对用于某国内工程机械上的冷却风扇进行性能分析,通过试验数据验证仿真模型;利用孤立翼型法对其重新设计,并对新风扇进行性能仿真,对比仿真结果,以确认性能改进和提升的有效性.1 原风扇仿真与试验验证1.1 风扇与风道三维模型根据图纸建立原风扇模型,如图1所示.风扇直径为780mm ;轮毂比为0.33;弯掠角为0ʎ;轮毂直径为260mm ;安装角为26ʎ;翼型为等厚度弯板.图1 原风扇模型建立风道三维几何模型,如图2所示.风道采用圆形截面,直径等于其风扇当量直径,风道的入口长度为4倍当量直径,出口长度为6倍当量直径.在出口风道2~4倍风扇当量直径处建立整流栅.图2 风道模型1.2 网格划分与边界设定利用Gambit 对模型进行网格划分与边界设定.采用结构性网格对风扇表面进行网格划分;对旋转域内部以及进出口处使用结构性与非结构性网格进行网格混合加密,加密后无负网格和扭曲网格,如图3所示.图3 网格模型将风扇㊁风道表面㊁整流栅设定为wall ;将风扇旋转域与风道进出口公共面设定为interior ;将风道进口设定为velocit y -inlet ;风道出口设定为p res-sure-outlet ;将旋转域以及进口风道㊁出口风道设定为fluid ;风扇转速为2000r ㊃min -1;选用标准k-ε湍流模型[5-8].图4 原风扇进口处空气状态1.3 结果分析与试验验证如图4所示,在原风扇空气进口处,低压区主要集中在风扇中上部分,呈阶梯状分布.这是由于扇叶扫掠过的区域空气体积骤降,周围的空气无法迅速填充而造成的;随后在压差作用下,低压区空气体积不断被填充,该区域逐步回升到环境压强;随着转速的增加,空气持续流通,阶梯状分布的低压区逐渐变成环状低压区.图5(a )中,原风扇空气出口端轮毂处出现较大的低压区;高压区则呈环状分布在0.3倍叶高至叶尖之间,并在叶尖处压强达到最大,这是风扇对气流做功的结果.图5(b )中,气流在叶尖处流速最大,并由此逐渐向两边递减;最低气流速度出现在轮毂处,这种现象可能会导致回流的产生.图5 原风扇出口处空气状态在风扇转速一定的条件下,对7组不同流量值进行试验仿真,在5倍当量直径处提取全压值,计算全压效率,与试验数据进行对比,绘制两者全压及全压效率性能曲线,如图6所示.从图6(a )可以看出:当风量降低时,二者偏差逐渐增大,最大误差为4.5%;当风量大于6m 3㊃s -1时,原风扇仿真值与试验值逐渐趋于吻合,最大误差约2.38%.从图6(b )可以看出,随着风量的增加,全压效率都呈现出上升趋势,且均在风量为10.24m 3㊃s -1时出现最大值,原风扇仿真值与试验值最大相差约3%.2 风扇设计与数值仿真2.1 风扇设计选用孤立翼型设计法对冷却风扇进行设计.设计分为3个阶段:选定设计参数㊁预备设计㊁正图6 原风扇试验与仿真性能对比式设计.(1)设计参数.参照原风扇性能和结构参数,设定全压为550Pa ,体积流量为10.24m 3㊃s -1,新风扇采用Clark-y 翼型.(2)预备设计.预备设计计算如下Λ=V a ΩR λb =ΛX bεSb =K thλb2C L δ=2εSb cos βm ìîíïïïïïïïï(1)式中:Λ为叶尖流速系数;V a 为通过叶轮的平均轴向速度;Ω为叶轮叶片的旋转角速度;R 为叶轮半径;λb 为叶片根部流速系数;X b 为轮毂比;εSb 为根部旋流系数;K th 为理论全压系数;C L 为升力系数;δ为实度;βm 为叶片根部合速度与轴向速度的夹角.预备设计筛选依据为:流速系数不大于1.4,旋流系数不大于1,叶片根部载荷因子不大于1.(3)正式设计.正式设计的计算如下n ㊃C R =2πσr-φ=90ʎ-βm +αRe =CV a v cos βmȡ2ˑ105ìîíïïïïïï(2)式中:n 为叶片数;C 为弦长;σ为实度比;r-为相对半径;φ为安装角;α为气流攻角;Re 为雷诺数;v 为气体动力黏度.2.2 三维成型依据理论设计,建立新风扇三维模型控制方程,即三维空间坐标转换[9]x =r sin αy =r cos αz =x 0ìîíïïï(3)式中:r 为柱坐标系下圆柱面半径;α为翼型上对应在柱坐标上一点与圆柱截面圆心的连线与zo y 平面之间的夹角;x ㊁y ㊁z 分别为柱坐标系下各点坐标.为扩大冷却风扇的稳定工作范围,提升其工作效率,采用周向前弯布局,如图7所示.前弯角推导公式为[10]θr -=θmax +arcsinr -2R +X 2b R2r-M 2+X 2bR2-arcsinR +X 2bR2M 2+X 2b R2(4)式中:r -为圆弧上任意点相对半径;θmax 为叶尖重心处前弯角最大值;M 为圆弧圆心横坐标.图7 前弯角示意图依据以上控制方程建立新风扇模型,网格划分㊁边界设置与1.2相同,如图8所示.2.3 仿真结果分析由图9(a )压强分布可知,相比原风扇,新风扇每片叶片的后端都出现了大范围均匀分布的低压区,贯穿整片叶片.由图9(b )速度分布可以看出,新风扇最大速度出现在叶尖处,这是由导风罩对气流的挤压作用与叶尖处较高的线速度共同引起的;同时新风扇表现出较为明显的梯度特征,随着风扇的转动,其梯度分布也趋于向风扇转动方向移动.图8 新风扇三维模型图9 新风扇进口处空气状态如图10(a )所示,新风扇出口端低压区分布较小;压强最大值出现在叶片中上部,高压区则均匀分布在大部分出口截面上.如图10(b )所示,速度呈现出均匀环状分布,最大速度出现在0.7倍叶高以上范围内;由于轮毂处空气无法流通,因此速度最小.3 仿真结果对比对原风扇和新风扇进行仿真性能对比,结果如图11所示.由图11(a )可以看出,随着风量的增大,两风扇仿真值吻合度逐渐提升.从图11(b )可以看出,两风扇全压效率都呈现出上升趋势,新风扇整体略高于原风扇,在体积流量达到10.24m 3㊃s -1时,新风扇较原风扇全压效率提升了0.81%.在图11(c )中,新风扇轴功率整体低于原风扇,当流量为10.24m 3㊃s -1时,新风扇比原风扇轴功率降低了0.12kW .图10 新风扇出口处空气状态图11风扇仿真性能对比4结语本文基于国内某工程机械用冷却风扇,使用三维软件建立原风扇几何模型,利用CFD在虚拟风道中进行性能模拟,并将试验数据与之进行对比;随后,使用孤立翼型法重新设计,通过推导成型控制方程建立三维模型,在相同边界下进行仿真,将两风扇的仿真结果相对比,最终得到以下结论. (1)与虚拟风道相结合的CFD数值仿真可用于模拟和预测冷却风扇性能数据.(2)孤立翼型法与翼型控制方程相结合,能更好地进行冷却风扇设计与三维建模.(3)在大部分的流量区间内,新风扇轴功率等性能参数均优于原风扇.当流量为10.24m3㊃s-1时,新风扇全压效率提升了0.81%,轴功率降低了0.12kW,证明改进有效.参考文献:[1]王企鲲,陈康民.轴流风扇两种扭叶片设计方法及其气动性能的比较[J].流体机械,2010,38(9):24-30.[2]刘全忠,宫汝志,王洪杰,等.汽轮发电机冷却风扇的数值模拟及优化[J].哈尔滨工业大学学报,2010,42(3):442-445.[3]高红霞,余建祖,谢永奇.直升机用高转速㊁小流量轴流风扇设计[J].航空动力学报,2006,21(1):119-124.[4]JIANHUI Z,CHUNXIN Y.Desi g n and Simulation of the CPU Fan and Heat Sinks[J].IEEE Transactions on Com p o-nents and Packin g Technolo g ies,2008,31(4):890-903.[5]刘佳鑫,秦四成,徐振元,等.虚拟风洞下的车辆散热器模块性能改进[J].吉林大学学报:工学版,2014,44(2):330-334.[6]刘佳鑫,秦四成,徐振元,等.基于CFD仿真的车辆散热器性能对比分析[J].华南理工大学学报:自然科学版,2012,40(5):24-29.[7]刘佳鑫,秦四成,徐振元,等.工程车辆散热器模块散热性能数值仿真[J].西南交通大学学报,2012,47(4):623-628.[8]刘佳鑫,秦四成,孔维康,等.虚拟风洞下车辆散热器模块传热性能数值仿真[J].吉林大学学报:工学版,2012,42(4):834-839.[9]廖庚华,刘庆平,陈坤,等.基于CATIA的轴流风机叶片仿生参数化建模[J].吉林大学学报:工学版,2012,42(2):403-406.[10]刘佳鑫.工程机械散热模块传热性能研究[D].长春:吉林大学,2013.[责任编辑:杜卫华]。
基于CFD技术的CPU散热器的数值研究

f lo w in g
f ie ld l
d m u la t io n o f
t e m pe r a t Ut e 镪 舶
'
计 算机 工 业 的 发 展 微 处 理 器 的 运 行速 度越 来越 快 在 单块 芯 片中集 成 的 功能 也越来 越 多 这 样做 的 代 价是 芯 片需 要 消 耗 更 多 的 能 量 这 也 意 味 着处 理 器 变
INF O R M A T I O N N o
v
.
20 08
基于 C F
CP U
蔡 中兵
1 2
、 、
D
技术的
业 评 测 所 得结 果 基 本 吻合 的 设 计 提 供相 关 依 据
。
,
可 以 为散热 器
2
、
散 热 器 的 计算模 型
一
散热 器 的数 值 研 究
。
’
顾建平
对 于所 有 的 流动 求 解方法 般是解 质量 和动 量 守 恒 方程 对 于 包 括 热 传导 或 可 压 性 的 流动 需 要 解 能量 守 恒 的 附加方 程 ( 1 ) 质 量 守恒 方 程 又 称 连 续性 方程 :
, 。 , 。
22405 1 盐 城 工 学 院 力 学课 程 组 2 11i 6 7 南 京 工 程 学 院 力 学教 研 室
塑+
Ot
三h m
。
“
)
:
s
… 。,
该 方程 是 质 量 守 恒 方程 的 般 形 式 它适 用 于 可 压 流动 和 不 可 压 流动 源项是 从 分 散 的 二 级 相 中加 入 到 连 续 相 的 质 量 源 项也 可 以 是任 何 的 自定 义 源 项 (2 ) 动 量 守恒方 程 在惯 性 (非加速 ) 坐 标 系 中 i 方 向上 的 动 量 守恒 方程 为 :
轴流风扇性能仿真与分析
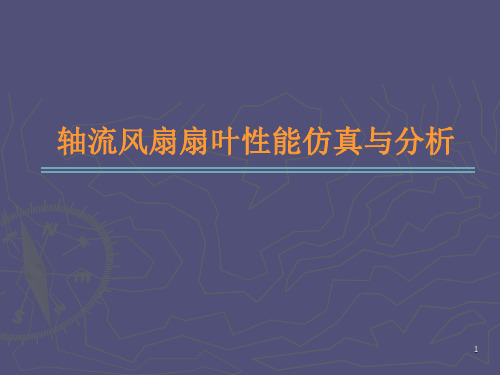
5.1 改进前、后的扇叶网格
改进前扇叶网格
改进后扇叶网格
26
5.2 改进前、后扇叶最大主应力图
改进前扇叶最大主应力
改进后扇叶最大主应力
27
5.3 改进前、后扇扇叶总变形图
28
6 总结
轴流风扇扇叶的设计和安装,应充分考虑其
空气动力性能; 扇叶变形会影响其空气动力性能,因而扇叶 应具备足够的刚度; 综合成本、周期及有效性,在轴流风扇的开 发阶段,采用数值分析的方法是必要的。
轴流风扇
3
三种风扇性能预测方法对比情况
评价指标 经验公式 CFD 模型试验
风扇几何复杂程度
对经验参数的依赖 预测成本 预测周期 预测信息量 预测可靠性
简单
完全依赖 最低 最短 很少 最差
不限
不依赖 较低 较短 最详细 较好
不限
不依赖 最高 最长 较多 最好
经验公式不能反映微小设计差异对性能的影响,且只能获 得总体参数;模型试验存在耗费大、周期长等缺点;CFD 技术能够较好的弥补上述两种方法的不足。
进
出
8
2.4 一般轴流风扇进、出口静压场
进
出
9
2.5 支承架对流场的影响
影响不大,计算时可忽略其影响。
10
3 轴流风扇空气动力性能数值计算
研究对象:汽车用冷凝器风扇 相关参数: 静压P=-50Pa(进口处压力比周围空气低50Pa) 扇叶直径:250mm 扇叶转速:2600rpm 环境温度:20℃ 送风量:900m3/h 电机电压:12V 电机电流:7A
11
3.1 风扇总成几何模型
12
3.2 确定计算区域并划分网格
小型轴流风扇内部流动特性研究

进延段 口长
Ⅱ 出延段 口长
气进 流L ]
1×D.
一
Ⅱ\ 毂 轮
.
U
倍 叶轮 出 口直径 D2 的出 口延长段 , 计算
域 如图 3所示 , 中心线 为 z , 口指 ห้องสมุดไป่ตู้ 轴 进
出 口为正 方 向, 轮毂 的中心为 z 。 =0
小 型 轴 流 风 扇 内部 流 动 特 性 研 究
柳 品 ,金 英 子 ,王 艳萍
( 江 理 Z 大 学 流体 传 输 及 应 用 实验 室 , 州 3 0 1 ) 浙 - 杭 10 8
摘 要 :为研 究 小 型轴 流风 扇 的 三 维 流 场 特 点 , 取 5叶 片 和 7叶 片 的 两 种 风 扇 , 用 Fun 软 件 中 的 R 选 利 let NG k ̄ 流模 型 对 其进 行 定 常 流 动 数 值 模 拟 , 比 分 析 两 种 叶 片风 扇 的 静 特 性 和 内 部 流 动 特 性 。 结 果 显 示 : 量 在 -湍 对 流 0 0 6 . 1 l。s 压 力 的 变化 不 明显 , 这 个 范 围之 外 , 力 随 着流 量 增 加 而减 小 ; 扇 的进 口全 压 先 降低 后 增 .0  ̄0 0 05i / , " 1 在 压 风 加 , 1 2弦 长 处 全 压 出现 突 变 性 增 加 ; 叶 顶 间 隙 内, 在 / 在 叶顶 静 压 值 随 着 半 径 的增 加 而 增 加 ; 片 吸 力 面静 压值 、 叶 涡
风扇模 型 内部流动 进行数 值模 拟 , 析其 内部流 动 的特 性 , 研制小 型轴 流风扇 提供 一定 的理论依 据 。 分 对
1 模 型 的建 立
轴流风机扇叶的流场分析与改进
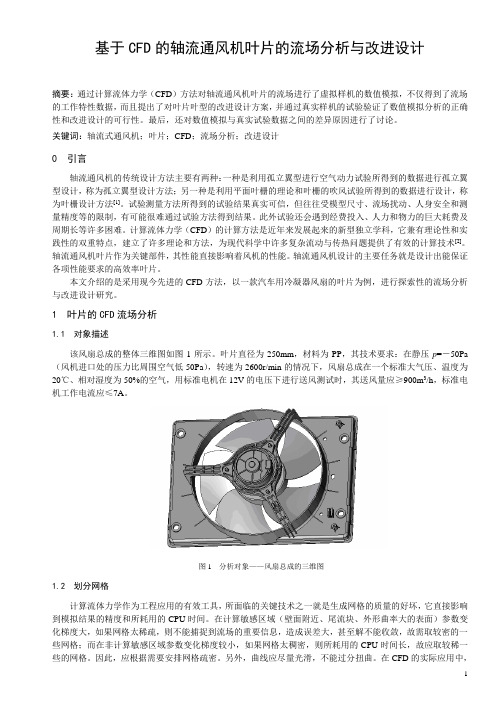
基于 CFD 的轴流通风机叶片的流场分析与改进设计摘要:通过计算流体力学(CFD)方法对轴流通风机叶片的流场进行了虚拟样机的数值模拟,不仅得到了流场 的工作特性数据,而且提出了对叶片叶型的改进设计方案,并通过真实样机的试验验证了数值模拟分析的正确 性和改进设计的可行性。
最后,还对数值模拟与真实试验数据之间的差异原因进行了讨论。
关键词:轴流式通风机;叶片;CFD;流场分析;改进设计0 引言轴流通风机的传统设计方法主要有两种:一种是利用孤立翼型进行空气动力试验所得到的数据进行孤立翼 型设计,称为孤立翼型设计方法;另一种是利用平面叶栅的理论和叶栅的吹风试验所得到的数据进行设计,称 为叶栅设计方法[1]。
试验测量方法所得到的试验结果真实可信,但往往受模型尺寸、流场扰动、人身安全和测 量精度等的限制,有可能很难通过试验方法得到结果。
此外试验还会遇到经费投入、人力和物力的巨大耗费及 周期长等许多困难。
计算流体力学(CFD)的计算方法是近年来发展起来的新型独立学科,它兼有理论性和实 践性的双重特点,建立了许多理论和方法,为现代科学中许多复杂流动与传热问题提供了有效的计算技术[2]。
轴流通风机叶片作为关键部件,其性能直接影响着风机的性能。
轴流通风机设计的主要任务就是设计出能保证 各项性能要求的高效率叶片。
本文介绍的是采用现今先进的 CFD 方法,以一款汽车用冷凝器风扇的叶片为例,进行探索性的流场分析 与改进设计研究。
1 叶片的 CFD 流场分析1.1 对象描述 该风扇总成的整体三维图如图 1 所示。
叶片直径为 250mm,材料为 PP,其技术要求:在静压 p=-50Pa(风机进口处的压力比周围空气低 50Pa),转速为 2600r/min 的情况下,风扇总成在一个标准大气压、温度为 20℃、相对湿度为 50%的空气,用标准电机在 12V 的电压下进行送风测试时,其送风量应≥900m3/h,标准电 机工作电流应≤7A。
基于CFD的牵引电机风扇流道优化设计
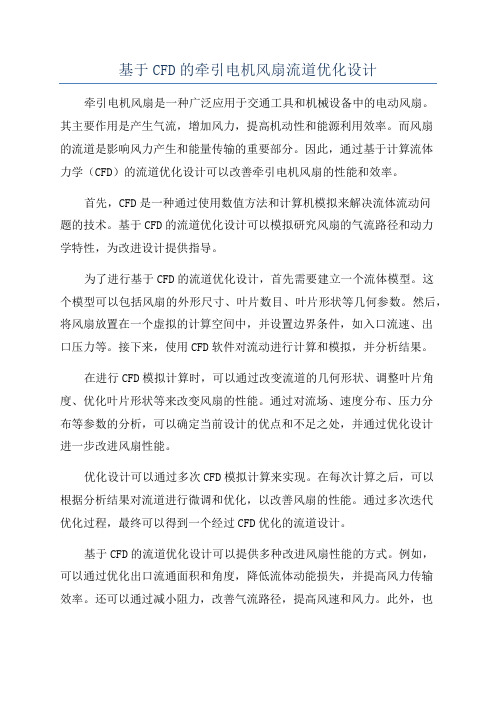
基于CFD的牵引电机风扇流道优化设计牵引电机风扇是一种广泛应用于交通工具和机械设备中的电动风扇。
其主要作用是产生气流,增加风力,提高机动性和能源利用效率。
而风扇的流道是影响风力产生和能量传输的重要部分。
因此,通过基于计算流体力学(CFD)的流道优化设计可以改善牵引电机风扇的性能和效率。
首先,CFD是一种通过使用数值方法和计算机模拟来解决流体流动问题的技术。
基于CFD的流道优化设计可以模拟研究风扇的气流路径和动力学特性,为改进设计提供指导。
为了进行基于CFD的流道优化设计,首先需要建立一个流体模型。
这个模型可以包括风扇的外形尺寸、叶片数目、叶片形状等几何参数。
然后,将风扇放置在一个虚拟的计算空间中,并设置边界条件,如入口流速、出口压力等。
接下来,使用CFD软件对流动进行计算和模拟,并分析结果。
在进行CFD模拟计算时,可以通过改变流道的几何形状、调整叶片角度、优化叶片形状等来改变风扇的性能。
通过对流场、速度分布、压力分布等参数的分析,可以确定当前设计的优点和不足之处,并通过优化设计进一步改进风扇性能。
优化设计可以通过多次CFD模拟计算来实现。
在每次计算之后,可以根据分析结果对流道进行微调和优化,以改善风扇的性能。
通过多次迭代优化过程,最终可以得到一个经过CFD优化的流道设计。
基于CFD的流道优化设计可以提供多种改进风扇性能的方式。
例如,可以通过优化出口流通面积和角度,降低流体动能损失,并提高风力传输效率。
还可以通过减小阻力,改善气流路径,提高风速和风力。
此外,也可以通过优化叶片形状和角度,提高叶片的扬力和推力,增加风扇的输出功率。
总之,基于CFD的流道优化设计是一种改进牵引电机风扇性能的有效方法。
通过使用CFD模拟计算和优化设计,可以改善风扇的流道设计,提高其性能和效率。
这对于交通工具和机械设备的节能、减排和性能提升具有重要意义。
汽车发动机轴流式冷却风扇的CFD分析外文文献翻译、中英文翻译、外文翻译
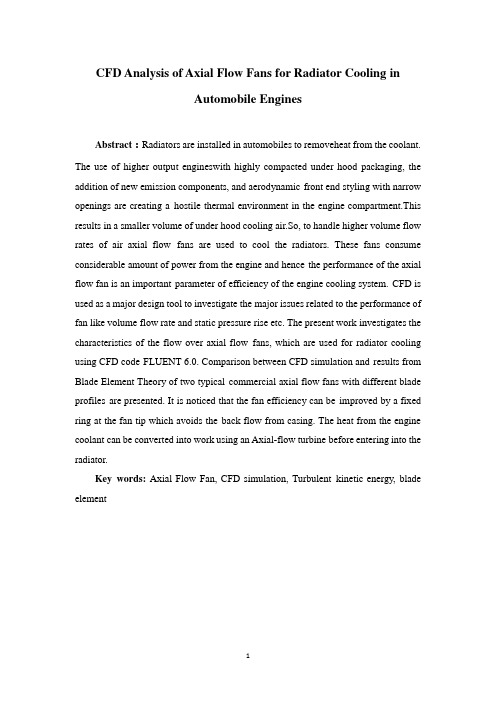
CFD Analysis of Axial Flow Fans for Radiator Cooling inAutomobile EnginesAbstract:Radiators are installed in automobiles to removeheat from the coolant. The use of higher output engineswith highly compacted under hood packaging, the addition of new emission components, and aerodynamic front end styling with narrow openings are creating a hostile thermal environment in the engine compartment.This results in a smaller volume of under hood cooling air.So, to handle higher volume flow rates of air axial flow fans are used to cool the radiators. These fans consume considerable amount of power from the engine and hence the performance of the axial flow fan is an important parameter of efficiency of the engine cooling system. CFD is used as a major design tool to investigate the major issues related to the performance of fan like volume flow rate and static pressure rise etc. The present work investigates the characteristics of the flow over axial flow fans, which are used for radiator cooling using CFD code FLUENT 6.0. Comparison between CFD simulation and results from Blade Element Theory of two typical commercial axial flow fans with different blade profiles are presented. It is noticed that the fan efficiency can be improved by a fixed ring at the fan tip which avoids the back flow from casing. The heat from the engine coolant can be converted into work using an Axial-flow turbine before entering into the radiator.Key words: Axial Flow Fan, CFD simulation, Turbulent kinetic energy, blade element1 IntroductionWhile running, an automobile engine produces large amount of heat which has to be dissipated, otherwise the engine gets overheated and finally resulting into failure. The basic purpose of a fan is to move a mass of gas or vapor at the desired velocity. For affecting the air flow, fan develops a total pressure difference over the inlet and outlet air streams. The total pressure rise comprises of static pressure which depends on the blade profile, number of blades, pitch, hub space and aerodynamic characteristics of the fan impeller and dynamic pressure which develops due to velocity or kinetic energy imparted to the air stream.2Analysis of Axial Flow FansGlauert Blade Element Theory: A relatively simple method of predicting the performance of a fan is the use of Blade Element (BE) Theory. In this method the fan is divided into a number of independent sections along the length. At each section a force balance is applied involving 2D section lift and drag with the thrust and torque produced by the section. At the same time a balance of axial and angular momentum is applied. This produces a set of non-linear equation that can solved by iteration for each blade section.The resulting valuse of section thrust and torque can be assumed to predict the overall performance of the fan.2.1 Blade Element SubdivisionThe lift and drag components normal to and parallel to the propeller disk are calculated and there by the contribution to thrust and torque of the complete fan from this single element are also calculated. rh to rt are calculated making use of the following equations)()h t D 21r r z sin C -cos (c 5.0-ΦΦ=L C V F ρ2.2 Inflow Factors:A major complexity in applying this theory arises when trying to determine the magnitude of the two flow components V0 and V2. V0 is roughly equal to the vehicle's forward velocity (Vi) but is increased by the fan's own induced axial flow into aslipstream. V2 is roughly equal to the blade section's angular speed ( r) but is reduced slightly due to the swirling nature of the flow induced by the propeller. To calculate V0 and V2 accurately both axial and angular momentum balances must be applied to predict the induced flow effects on a given blade element. Figure 2 shows the induced flow components which are factors for increasing or decreasing the major flow components. The local flow velocity and the angle of attack for the blade section isV1 = √(V o2 + V22) and α = (θ – tan-1(V o/V2))2.3 Axial and Angular Flow Conservation of Momentum:The governing principal of Conservation Momentum is applied for both axial and circumferential directions. For the axial direction, the change in flow momentum along a stream-tube starting upstream, passing through the propeller at section AA and then moving off into the slipstream must equal the thrust produced by this element of the blade. To remove the unsteady effects due to the fan's rotation, the stream-tube used is one covering the complete area of the fan disk swept out by the blade element and all variables are assumed to be time averaged values.F = {ρ(2πr)dr V o (V slipstream - Vi) }Applying Bernoulli's equation and conservation of momentum, for the three separate components of the tube, from free stream to face of disk, from rear of disk to slipstream far downstream and balancing pressure and area versus thrust, the axial velocity at the disk will be the average of the free stream and slipstream velocities.V0 = (Vi + Vslipstream)/2, Hence Vslipstream = Vi (1 + 2a).Thus by solving the integral equations, F and T are calculated as followsF = {4πρVi a (1+a)[ (rt -rh )/2 ] }Since these final forms of the momentum equation balance still contain the variables for element thrust and torque, they cannot be used directly to solve for inflow factors. With these approximate values of thrust and torque equations gives the improved estimates of the inflow factors ‘a’and ‘b’. This process is repeated until values for ‘a’and ‘b’ have converged to within a specified tolerance.3 Calculations:The theoretical analysis of axial flow fan is generally done by Glauret Blade Element theory. This theory is applied to calculate performance characteristics like volume flow rate of air, static pressure etc. For the evaluation of performance characteristics of fans, one is having no swept blade (fan1) and the other is having forward swept blade (fan2) are considered for the study.The inlet velocity of air is 2 m/s and the fan is rotating at 1800 rpm clockwise, in the direction of flow. In the first step the axial inflow factor ‘a’ is assumed and the axial component of velocity of air, V o is calculated. Similarly the swirl flow factor ‘b’ is calculated and also the tangential component of velocity V2. The magnitude and direction of resultant velocity of air, V1 is calculated. Knowing the values of V1, Φ and the properties of blade section of the fan (i.e. CD and CL ), the thrust developed by the fan on air and the torque required to rotate the fan are calculated. And finally ‘a’ and ‘b’ are calculated. The above procedure is repeated until the values of ‘a’and ‘b’ are close to the values from previous iteration. The flow coefficient, static pressure rise across the fan, velocity components, flow coefficient, static pressure rise across the fan are obtained as follows for fan1 and fan 2 (tables 1 & 2).Table 1:Performance characteristics of Fan 1 at variousinlet velocities of air4 CFD SimulationsThe control volume of fluid flow across fan is developed using GAMBIT1. Fan is located behind the radiator, in order to induce the air flow across the radiator (i.e., an induced draught fan). Otherwise the fan itself offers resistance to incoming air if it is located in front of the radiator. There is 30cm gap between radiator and the fan. The inlet to the fan is taken at 30cm upstream and the outlet is at 70cm downstream of fan.The flow velocity of air after passing through radiator increases due to the suction created by the fan’s rotational movement which is the convergent portion of control volume at 30cm ahead of fan and the flow becomes straight in the duct that is surrounded by the fan. The function of the duct is to direct the flow axially, there by increasing the axial component of velocity and hence the volume flow rate across the fan. The clearance between blade tip and duct is 2.5cm. The fan is rotating at 1800 rpm clockwise direction about positive X-axis. The air flow being forced by the fan becomes divergent while passing from duct to surroundings. The 1D control volume shown in fig. 3 can be simulated to a 3D model using GAMBIT1.3, is shown in fig.4.Fig.3 Simulated Model of Control Volume of air flow across Fan1The domain of fan1 contains 154,676 tetrahedral cells as shown in Figure 4. The simulate model in GAMBIT is exported to FLUENT6.0 where the fluid flow analysis is carried out. The effects of turbulences were modeled using standard k-ε model.Fig. 4 Tetrahedral Meshing of control volume of air flow across Fan1 The boundary conditions for the model are taken as follows:a) Inlet- velocity of air 2m/s along X-axisb) Turbulent intensity-5%c) Turbulent viscosity ratio - 0.05d) Outlet- uniform pressure at atmospheric conditionse) Fan1- moving reference frame rotating at 1800 rpm clockwise aboutf) Duct wall- no slip in absolute frame.Figure 5 is the computational grid developed for fan2 having forward swept blades. The fan domain is divided into 195,115 tetrahedral cells. The boundary conditions are also similar to that of fan1. The properties of air are assumed to be constant and the density of air is taken as 1.2kg/m3 and the dynamic viscosity (μ) of air as 1.789x10-05.Fig.5 Simulated Model of Control Volume of air flow across Fan 2Fig.6 Tetrahedral Meshing of control volume of air flow across Fan25 ConclusionThe static pressure rise of the fluid over fan2 having forward swept blades is more than that fan1 having unswept blades. The maximum value of static pressure is higher in case of fan1 but the average pressure is lower than that of fan2 and though it creates more vacuum in upstream side it is not able to pressurize into downstream. This may lead to ‘stall’ the flow at fan outlet. The static pressure decreases with increase in air inlet velocity for both fans but fan2 handles air at higher pressures than that of fan1. So, fan2 is more efficient than fan1 at any volume flow rates of air. If the volume flow rate of air is the main criteria then the number of blades can be reduced in order to increase the free flow area for air. The fan efficiency can further be improved by a fixed ring at the fan tip which avoids the back flow from casing. The heat from the engine coolant can be converted into work using an Axial-flow turbine before entering in radiator.汽车发动机轴流式冷却风扇的CFD分析摘要:散热器安装在汽车中,从冷却剂中去除热量。
基于CFD法的小型风机非扭曲叶片气动性能分析

2 0 1 3年 2 月
浙 江 工 业 大 学 学 报
J OURNAL OF ZHE J I ANG U NI VERS I TY OF TECHNOLOGY
Vo 1 . 4 1 No . 1
Fe b. 2O1 3
基于 C F D法 的小 型 风机 非 扭 曲叶 片气 动性 能分 析
中 图分类 号 : TK8 3
文献标 志码 : A
文 章编 号 : 1 0 0 6 — 4 3 0 3 ( 2 0 1 3 ) 0 1 — 0 0 6 8 — 0 5
Ae r o dy na mi c p e r f o r ma n c e a na l y s i s o f u n t wi s t e d bl a d e f o r s ma l l wi nd
u t i l i z a t i o n f a c t o r wi t h t h e t i p s p e e d r a t i o a n d t h e i n s t a l l a t i o n a n g l e i s i n v e s t i g a t e d .Th e v a l i d a t i o n o f t h e n u me r i c a l mo d e l i s v e r i f i e d b y t h e c o mp a r i s o n o f t h e r e s u l t o f t h i s s t u d y wi t h t h a t o f t h e
显, 小型风机 的最优 叶尖速 比 大约为 8 ~9 ; 安 装 角通过 影响 叶 片下表 面 的流 线分 离点位 置 , 进 而影
基于CFD的发动机冷却风扇气动噪声分析

柴油机设计与制造
曾超, 等: 基于 CFD 的发动机冷却风扇气动噪声分析
2021 年 / 第 27 卷 / 第 2 期
图 8 环形风扇叶片表面静压分布
图 6 风筒内部流场
的声比拟模型 [8] , 设置噪声源和监测点, 继续迭代
相同步数至声场仿真完成。
performance of the fan was simulated with the modified model, the result showed there were same trend in
different measure point and proved the effectiveness of the method. This simulation method can offer sup⁃
5. 0
5. 3
6. 6
6. 8
8. 3
8. 9
图 4 MRF 区域细化网格模型
测试静压 仿真静压 误差 测试效率 仿真效率
Pa
Pa
(% )
(% )
(% )
1 267. 1
1 343. 6
6. 1
26. 2
27. 8
1 024. 7
1 058. 7
3. 4
34. 6
35. 9
1 074. 3
741. 0
时域上 3 个监测点的声压信号转换为频域上的声压
频谱 [9] , 1 900 r / min 工况下, 测点 3 位置风扇线
性频谱如图 10 所示。
表 3 仿真结果与测试结果数据
流量
m3 / s
4. 9
5. 7
风扇性能CFD仿真试验台搭建
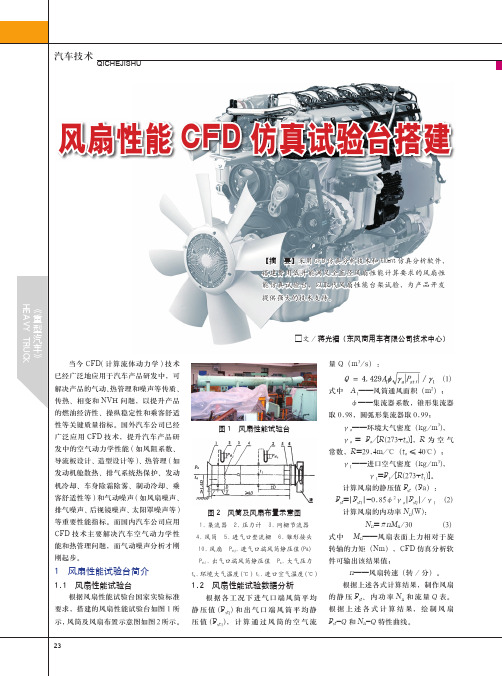
计算流体动力学)技术已经广泛地应用于汽车产品研发中,可热管理和噪声等传质、问题,以提升产品的燃油经济性、操纵稳定性和乘客舒适性等关键质量指标。
国外汽车公司已经技术,提升汽车产品研(如风阻系数、造型设计等)、热管理(如发动机舱散热、排气系统热保护、发动机冷却、车身除霜除雾、制动冷却、乘和气动噪声(如风扇噪声、后视镜噪声、太阳罩噪声等)等重要性能指标。
而国内汽车公司应用技术主要解决汽车空气动力学性能和热管理问题,而气动噪声分析才刚1 风扇性能试验台简介根据风扇性能试验台国家实验标准要求,搭建的风扇性能试验台如图1所风筒及风扇布置示意图如图2所示。
图1 风扇性能试验台图2 风筒及风扇布置示意图1.集流器2.压力计3.网栅节流器4.风筒5.进气口整流栅6.锥形接头10.风扇 P stj .进气口端风筒静压值(Pa) P st1.出气口端风筒静压值 P a .大气压力t a .环境大气温度(℃) t 1.进口空气温度(℃)1.2 风扇性能试验数据分析根据各工况下进气口端风筒平均静压值(P stj )和出气口端风筒平均静压值(P st1),计算通过风筒的空气流量Q(m 3/s):(1)式中 A 1——风筒通风面积(m 2);φ——集流器系数,锥形集流器取0.98,圆弧形集流器取0.99;γa ——环境大气密度(kg/m 3), γa = P a /[R (273+t a )],R 为空气常数,R =29.4m /℃(t a ≤40℃);γ1——进口空气密度(kg/m 3), γ1=P 1/[R (273+t 1)]。
计算风扇的静压值P st (Pa):P st =|P st 1|-0.85φ2γa |P stj |/γ1 (2)计算风扇的内功率N n (W):N n =πnM n /30 (3)式中 M n ——风扇表面上力相对于旋转轴的力矩(Nm),CFD 仿真分析软件可输出该结果值;n ——风扇转速(转/分)。
小型轴流CPU风扇设计与数值模拟

小型轴流CPU风扇设计与数值模拟
小型轴流CPU风扇设计与数值模拟
根据空气强迫对流冷却系统一体化设计理念,对小型轴流CPU风扇进行空气动力设计,由Fortran输出三维空间曲线文件,导入Pro/E实现实体造型.通过标准风洞对CNC铣床雕刻出的样品进行风扇性能测试.为了减少费用和缩短设计周期,利用CFD对风扇性能预测,风扇出口流向角结论为曲线型散热器设计提供依据;数值模拟结果与实验特性曲线比较吻合,为一体化数值模拟积累了经验.
作者:杨春信 AIQI 周建辉鲁俊勇 YANG Chun-xin AIQI ZHOU Jian-hui LU Jun-yong 作者单位:杨春信,周建辉,YANG Chun-xin,ZHOU Jian-hui(北京航空航天大学航空科学与工程学院,北京,100083)
AIQI,鲁俊勇,AIQI,LU Jun-yong(奇宏電子(深圳)有限公司,广东,深圳,518104)
刊名:电子器件ISTIC 英文刊名:CHINESE JOURNAL OF ELECTRON DEVICES 年,卷(期):2007 30(5) 分类号:V211.71 关键词:空气强迫对流冷却系统风扇风洞计算流体力学。
CFD在轴流风机噪声预估中的运用
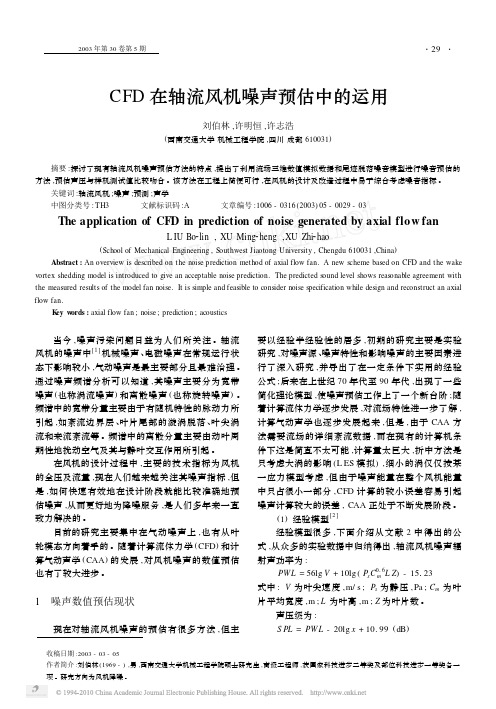
表 1 样机主要参数
样机
A B
流量 ( m3/ sec)
6125 2111
风压 ( Pa) 1600 150
转速 (r/ min)
2900 1500
直径 ( mm) 600 500
机械 2003 年第 30 卷第 5 期
表 2 为噪声预估值与实验值的对比 ,可以看出 , 噪声值与预估值相差约在 2. 6dBA 以内 ,工程估算时 此精度一般是可以接受的 。
2 CFD 在噪声预估中的运用
由以上分析可以看出 ,包括 Lee 及 Fukano 的半 经验模型缺乏的就是叶片尾迹流场数据 ,均采用了 不同形式的平板估算 ,而 CFD 恰好能满足这方面的 要求 ,两者的结合应能提高估算精度 。现以 Fukano 模型为例 。
在 Fukano 提出的模型中 ,风机发出的总声功率 E为:
流相对速度 ; R 为半径 ; Z 为转子叶片数 ; D 为特征
长度 。
由此 ,声压级可以通过其定义求出 :
S PL
= 10log (
p2 p20
)
式中 : p0 为参考声压 ,210 ×10 - 5N/ m2 。
在该模型中特征长度 D 是最重要的参数 ,定义
为转子叶片尾缘厚度 、吸力面及压力面附面层位移
TCFD和CAESES耦合优化案例-轴流风扇

TCFD和CAESES耦合优化案例-轴流风扇TCFD是CFD Support团队为我们带来的新一代叶轮机械专用CFD模拟工具。
TCFD不受用户人数和核数的限制,具有完全自动化的流程,极大地提升了CFD模拟的效率;同时,它保持求解器的开源,可以由用户自行决定CFD研究的深度,能够更充分的利用硬件功能使之用于CFD模拟过程。
CAESES是一款能够为仿真工程师提供全参数化的CAD模型,并将其与自动化工具和优化工具相结合的软件工具。
CAESES的侧重点就是为仿真提供稳定的几何模型,以及这些几何模型的稳健变化,以便进行更快速,更全面的设计研究和形状优化。
智能和高效的工作流程现代化的CAE工作流程是由一系列特定且复杂的任务流程构成的,为了能够得到显著且有效的结果,流程的各个部分都不能出现任何差错。
因此,未来的CAE流程将转变为由专业人士制作的针对性的最佳软件包连接构成的自动化工作流程。
在此我们推出了一个由TCFD和CAESES两个软件包构成的智能高效的叶轮机械设计优化工作流程。
风扇制造商最典型的一个目标就是开发一款新的高效风扇,或者提升一款现有成熟风扇的性能参数。
我们选择了一款现有的风扇模型,来作为演示设计流程的案例,该风扇主要性能参数如下所示:该优化案例有两个优化目标:第一个是在流量576 m3/h到1296 m3/h范围内使得风扇效率整体最大化;第二个是增大最大风量。
优化流程首先需要创建风扇几何模型。
CAESES提供了一个CAD环境,其中包括方便灵活的创建几何变体,定义高效的参数化模型并输出用于模拟的模型。
之后,在TCFD中创建基于CAESES输出模型的CFD模拟设置模板,并返回到CAESES的软件连接器。
最后,设置CAESES里的优化策略,之后会自动生成不同的几何变体并使用TCFD进行模拟。
轴流风扇参数化建模——CAESES按CFD的计算需求创建轴流风扇的流动域。
整个几何模型被划分成转子域和静子域。
为了节省计算资源提升模拟速度,流动域为只包含一个叶片的单通道模型。
试析微型轴流风扇优化设计系统的设计实现

试析微型轴流风扇优化设计系统的设计实现摘要:微型轴流电扇的优化设计系统一直是一个十分重要的研究课题,为了有效的提高微型轴流风扇的性能,尽可能缩短其设计周期,并降低微型轴流风扇的设计成本,成为了当前技术人员研究的主要目标。
本文中,笔者将通过对传统微型轴流风扇优化设计系统进行浅要分析,验证系统的实际效果。
关键词:轴流风扇;优化设计;实验验证对于微型轴流风扇的设计而言,需要经过大量的分析计算和试验以得出准确的数据,一款成功的微型轴流风扇往往都要经过十分漫长的设计周期,花费巨大的人力物力财力,而且得到的计算数据往往并非该型号微型轴流风扇的最佳数据。
在本文中,笔者将尝试探讨利用流体动力学技术替代传统设计模式中的试验和计算部分,以完成新型微型轴流风扇优化设计系统的实现。
1优化设计系统的组成就目前而言,主流的轴流风扇设计方法主要为以下两种:孤立叶型设计法;叶栅法。
笔者今天在这里探讨的是一种基于孤立叶型设计法的优化设计方法,并结合了流体动力学技术和遗传算法等诸多理论,共同组建的一种优化设计方式。
首先,让我们共同研究一下该系统的基础系统组成。
1.1系统语言开发本文涉及到的微型轴流风扇优化设计系统主要采用C++和Open GRIP这两种语言进行开发设计。
这其中,C++语言的主要作用,是依靠其优秀的计算能力,完成对于网格的划分,风扇参数的计算,数据库的建立,以及优化程序本身的确立。
而Open GRIP则主要用于完成风扇的三维建模。
实际上,随着现代化技术的发展,很多需要的功能都可以依靠其它软件的功能集成来完成,譬如ANSYS的有限元模块化分析和FLUENT流体仿真模块。
如果能够有机的将这些现有软件模块功能加入到优化系统之中,将能够大幅度的提升系统的开发进度,并尽可能的提升优化系统的性能。
1.2优化设计系统的组成如果要了解整个优化设计系统的组成,我们首先要了解微型轴流风扇的主要组成部分。
微型轴流风扇的设计需要对包括风扇外径,轮毂比,安装角,叶片弦长,叶顶间隙等参数进行综合计算,而优化设计系统要做的工作,就是完成对于以上数据的优化计算,寻找出符合设计要求的最优参数。