垫圈类零件连续冲裁模工艺分析与模具设计
垫圈冲压工艺及模具设计
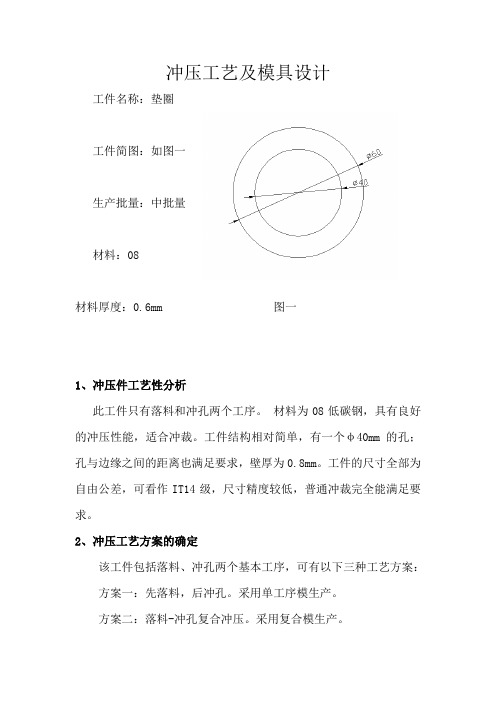
冲压工艺及模具设计工件名称:垫圈工件简图:如图一生产批量:中批量材料:08材料厚度:0.6mm 图一1、冲压件工艺性分析此工件只有落料和冲孔两个工序。
材料为08低碳钢,具有良好的冲压性能,适合冲裁。
工件结构相对简单,有一个φ40mm的孔;孔与边缘之间的距离也满足要求,壁厚为0.8mm。
工件的尺寸全部为自由公差,可看作IT14级,尺寸精度较低,普通冲裁完全能满足要求。
2、冲压工艺方案的确定该工件包括落料、冲孔两个基本工序,可有以下三种工艺方案:方案一:先落料,后冲孔。
采用单工序模生产。
方案二:落料-冲孔复合冲压。
采用复合模生产。
方案三:冲孔—落料级进冲压。
采用级进模生产。
方案一模具结构简单,但需两道工序两副模具,成本高而生产效率低,难以满足大批量生产要求。
方案二只需一副模具,工件的精度及生产效率都较高,且工件最小壁厚20mm远大于凸凹模许用最小壁厚1.8mm,模具强度较好,制造难度小,落料圆和冲孔圆同轴度满足要求。
方案三也只需一副模具,生产效率高,操作方便,但工件同轴度不意满足要求。
通过对上述三种方案的分析比较,该件的冲压生产采用方案二为佳。
3、主要设计计算(1)排样方式的确定及其计算设计复合模,首先要设计条料排样图。
垫圈的形状为圆,直排时材料利用率低,应采用多排,如图二垫圈排样图所示的排样方法,可显著地减少废料。
搭边值查表可得1mm和1.2mm。
冲裁件面积 A=πr²=3.14×30²=2826 mm²条料宽度 B=60×2﹢1.2×2+61×1.7/2=174.2 mm由于冲压常用钢板规格宜选710mm×1420mm的钢板,取B=177.5 mm步距 S=60+1=61 mm一个步距的材料利用率η=nA/BS×100%=3×2826/﹙177.5×61﹚×100%=78.3%故条料宽度为177.5mm,步距离为61 mm,一个步距的材料利用率为78.3%。
垫圈冲压工艺与模具毕业设计

垫圈冲压工艺与模具毕业设计摘要随着工业的发展,冲压技术在各个领域中得到广泛应用,垫圈冲压作为其中的一种重要工艺,具有操作简单、效率高等优点。
本毕业设计以垫圈冲压工艺为研究对象,通过对冲压工艺参数的优化设计,提高了垫圈冲压工艺的质量和效率。
通过对垫圈冲压工艺中一些常见问题的分析,并对模具结构进行优化设计,增加了模具的使用寿命和冲压件的质量。
通过实际工艺测试,验证了优化设计的有效性。
关键词:垫圈冲压;工艺参数;模具结构;优化设计1.引言冲压工艺作为一种常见的金属加工工艺,其应用领域非常广泛。
垫圈冲压作为冲压工艺的一种重要形式,因其形状简单、操作方便等优点,在汽车、机械制造等行业中得到广泛应用。
本毕业设计以垫圈冲压工艺为研究对象,通过对冲压工艺参数的优化设计,提高了垫圈冲压工艺的质量和效率。
2.垫圈冲压工艺参数的优化设计冲压工艺参数的合理选择对于提高冲压件的质量和效率至关重要。
本设计通过对垫圈冲压过程中的几个关键参数进行优化设计,提高了垫圈冲压的质量和效率。
2.1材料选用垫圈通常使用冷轧板材或冷拔优质钢丝作为原材料。
本设计中选择了冷轧板材作为垫圈的原材料,因其成本较低、易于加工等优点。
2.2模具设计垫圈的模具设计是冲压工艺中非常重要的一环。
本设计通过对模具的结构进行优化设计,提高了模具的使用寿命和冲压件的质量。
模具采用硬质合金材料制作,保证了模具的硬度和耐磨性。
同时,对模具的几何形状进行了优化设计,减少了冲压过程中的歪斜和裂纹等缺陷。
2.3工艺参数的优化选择在垫圈冲压工艺中,工艺参数的选择对于冲压件的质量和效率有着重要影响。
本设计通过实验和理论分析,选择了合适的冲压速度、冲裁力和冲压次数等参数,使得冲压件的质量和效率达到最优。
3.结果与分析通过对垫圈冲压工艺中一些常见问题的分析,本设计提出了解决方案,并进行了实际工艺测试。
结果表明,通过优化设计的冲压工艺参数和模具结构,有效地提高了垫圈冲压工艺的质量和效率。
圆垫圈的冲裁模具设计
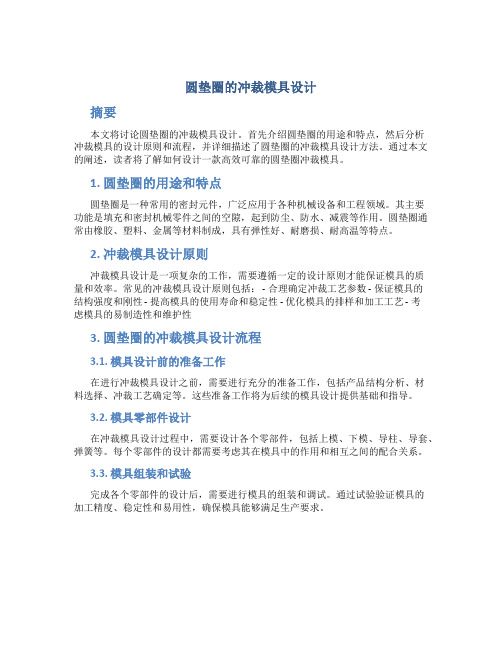
圆垫圈的冲裁模具设计摘要本文将讨论圆垫圈的冲裁模具设计。
首先介绍圆垫圈的用途和特点,然后分析冲裁模具的设计原则和流程,并详细描述了圆垫圈的冲裁模具设计方法。
通过本文的阐述,读者将了解如何设计一款高效可靠的圆垫圈冲裁模具。
1. 圆垫圈的用途和特点圆垫圈是一种常用的密封元件,广泛应用于各种机械设备和工程领域。
其主要功能是填充和密封机械零件之间的空隙,起到防尘、防水、减震等作用。
圆垫圈通常由橡胶、塑料、金属等材料制成,具有弹性好、耐磨损、耐高温等特点。
2. 冲裁模具设计原则冲裁模具设计是一项复杂的工作,需要遵循一定的设计原则才能保证模具的质量和效率。
常见的冲裁模具设计原则包括: - 合理确定冲裁工艺参数 - 保证模具的结构强度和刚性 - 提高模具的使用寿命和稳定性 - 优化模具的排样和加工工艺 - 考虑模具的易制造性和维护性3. 圆垫圈的冲裁模具设计流程3.1. 模具设计前的准备工作在进行冲裁模具设计之前,需要进行充分的准备工作,包括产品结构分析、材料选择、冲裁工艺确定等。
这些准备工作将为后续的模具设计提供基础和指导。
3.2. 模具零部件设计在冲裁模具设计过程中,需要设计各个零部件,包括上模、下模、导柱、导套、弹簧等。
每个零部件的设计都需要考虑其在模具中的作用和相互之间的配合关系。
3.3. 模具组装和试验完成各个零部件的设计后,需要进行模具的组装和调试。
通过试验验证模具的加工精度、稳定性和易用性,确保模具能够满足生产要求。
4. 圆垫圈的冲裁模具设计方法4.1. 模具结构设计圆垫圈的冲裁模具通常采用简单结构,包括上模、下模和冲头。
模具结构设计需要考虑圆垫圈的尺寸和形状要求,确保冲裁后的产品符合设计要求。
4.2. 冲裁工艺分析在进行冲裁模具设计之前,需要进行冲裁工艺分析,包括冲裁力计算、模具开口量确定、模具排样等。
通过冲裁工艺分析,可以确定合理的冲裁参数,提高冲裁效率和产品质量。
4.3. 材料选择和热处理对于圆垫圈的冲裁模具,材料的选择和热处理至关重要。
垫圈冲压成型工艺及模具设计机械加工工艺过程卡
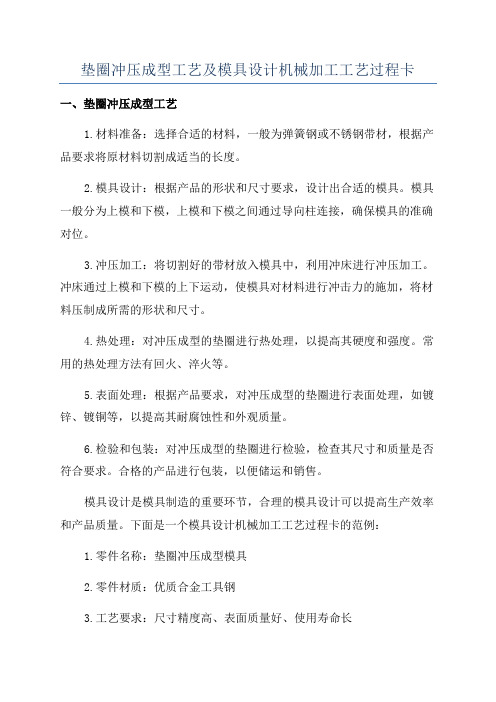
垫圈冲压成型工艺及模具设计机械加工工艺过程卡一、垫圈冲压成型工艺1.材料准备:选择合适的材料,一般为弹簧钢或不锈钢带材,根据产品要求将原材料切割成适当的长度。
2.模具设计:根据产品的形状和尺寸要求,设计出合适的模具。
模具一般分为上模和下模,上模和下模之间通过导向柱连接,确保模具的准确对位。
3.冲压加工:将切割好的带材放入模具中,利用冲床进行冲压加工。
冲床通过上模和下模的上下运动,使模具对材料进行冲击力的施加,将材料压制成所需的形状和尺寸。
4.热处理:对冲压成型的垫圈进行热处理,以提高其硬度和强度。
常用的热处理方法有回火、淬火等。
5.表面处理:根据产品要求,对冲压成型的垫圈进行表面处理,如镀锌、镀铜等,以提高其耐腐蚀性和外观质量。
6.检验和包装:对冲压成型的垫圈进行检验,检查其尺寸和质量是否符合要求。
合格的产品进行包装,以便储运和销售。
模具设计是模具制造的重要环节,合理的模具设计可以提高生产效率和产品质量。
下面是一个模具设计机械加工工艺过程卡的范例:1.零件名称:垫圈冲压成型模具2.零件材质:优质合金工具钢3.工艺要求:尺寸精度高、表面质量好、使用寿命长4.工艺步骤:4.1设计模具结构:根据垫圈的形状和尺寸要求,设计模具的上模、下模、导向柱和定位装置等部件。
4.2绘制模具图纸:根据模具结构设计,绘制模具图纸,包括三视图、剖视图、局部放大图等。
4.3材料准备:选择合适的优质合金工具钢作为模具材料,根据模具图纸将材料切割成适当的尺寸。
4.4粗加工:对材料进行粗加工,包括铣削、车削、钻孔等工艺。
通过粗加工,将材料修整成接近最终形状的毛坯。
4.5精加工:对粗加工后的毛坯进行精加工,包括镗削、磨削、线切割等工艺。
通过精加工,使模具达到精度要求。
4.6热处理:对加工完成的模具进行热处理,以提高其硬度和耐磨性。
常用的热处理方法有淬火、回火等。
4.7组装调试:将经过热处理的零部件进行组装,确保模具的准确配合和正常工作。
圆垫圈的冲裁模具设计论文
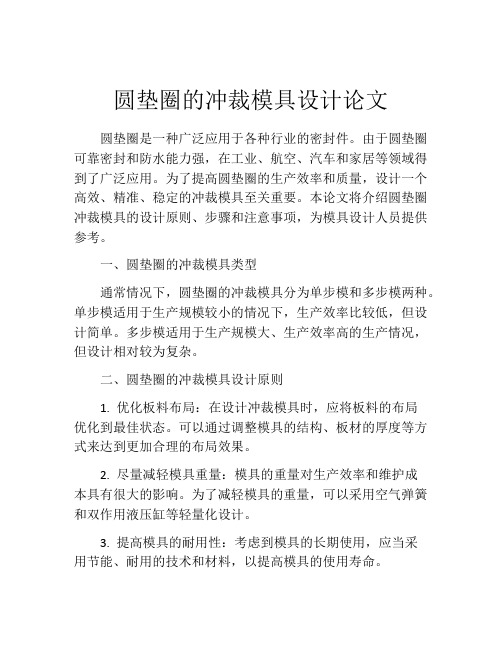
圆垫圈的冲裁模具设计论文圆垫圈是一种广泛应用于各种行业的密封件。
由于圆垫圈可靠密封和防水能力强,在工业、航空、汽车和家居等领域得到了广泛应用。
为了提高圆垫圈的生产效率和质量,设计一个高效、精准、稳定的冲裁模具至关重要。
本论文将介绍圆垫圈冲裁模具的设计原则、步骤和注意事项,为模具设计人员提供参考。
一、圆垫圈的冲裁模具类型通常情况下,圆垫圈的冲裁模具分为单步模和多步模两种。
单步模适用于生产规模较小的情况下,生产效率比较低,但设计简单。
多步模适用于生产规模大、生产效率高的生产情况,但设计相对较为复杂。
二、圆垫圈的冲裁模具设计原则1. 优化板料布局:在设计冲裁模具时,应将板料的布局优化到最佳状态。
可以通过调整模具的结构、板材的厚度等方式来达到更加合理的布局效果。
2. 尽量减轻模具重量:模具的重量对生产效率和维护成本具有很大的影响。
为了减轻模具的重量,可以采用空气弹簧和双作用液压缸等轻量化设计。
3. 提高模具的耐用性:考虑到模具的长期使用,应当采用节能、耐用的技术和材料,以提高模具的使用寿命。
三、圆垫圈的冲裁模具设计步骤1. 确定模具的尺寸和规格:在设计模具前,应当根据生产需求先确定好摸的尺寸和规格。
2. 确立模具结构类型:根据需要,确定单步模或多步模的结构类型。
3. 绘制2D 图:在AutoCAD 等软件中进行2D 图的绘制。
此时应注意模具零部件的结构和相互关系,以确保模具有可行的结构。
4. 绘制3D 图和相关分析:在模具可行性分析和实际使用前,可以进行3D 图的绘制和分析,以确保模具满足生产需求。
5. CNC 加工:根据设计图纸,进行CNC 加工,以确保模具零部件准确无误地加工出来。
6. 装配:在零部件加工完成后,进行模具装配,调整和测试。
四、注意事项1. 模具的设计要尽量考虑到生产量的大小和加工工艺的复杂性,以满足生产效率和质量的要求。
2. 必须保证模具的加工精度和装配精度,以确保部件的精度符合要求。
垫圈级进模冲裁-工艺设计
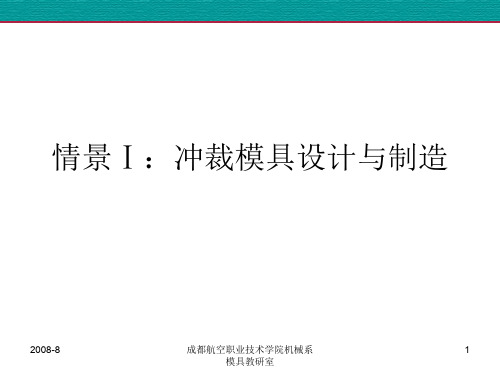
2008-8
成都航空职业技术学院机械系
1
模具教研室
பைடு நூலகம்
成形工艺设计
工作任务:垫圈冲裁工艺设计
零件名称:垫圈 生产批量:大批 材料:Q215 材料厚度:t=1mm
2
冲压工艺性分析
材料:Q215
普通碳素钢,有一定的塑性和强 度,韧性及铸造性均好,适于冲 压和焊接。其力学性能可查相关 材料手册,见下表。
总
nA1 LB
100%
=1564×235.5÷(750×1000)×100%
=49.1%
即每张板材的材料 利用率为49.1%。
10
相关工艺设计计算——步距的控制
该垫圈采用级进工序冲压,对条料的定距要求比较高, 故定距采用安装于凹模面上的固定挡料销和始用挡料销,
结构比较简单、成本较低。
①特点同序号2,且刃口直壁下面的扩大部分可使 凹模加工简单,但采用下漏料方式时刃口强度不如 序号2的刃口强度高。 ②用于冲裁形状复杂或精度要求较高的中小型件, 也可用于装有顶件装置的模具。
α(`) β(°) 刃口高度h(mm) 备注
15
2
≥4
≥5
≥6
18
表 热砸钢板和钢带的规格尺寸(mm)
公称厚度
尺寸精度
经查标准公差表,零件图上尺寸均为自由公差, 一般按IT14级确定工件的公差,普通冲裁均能满 足其尺寸精度要求。各尺寸公差为:φ10+0.36 , φ20-0.52
生产纲领
大批量生产适合冲压加工。
结论
可以冲裁。
5
冲压工艺方案的确定
综上分析,该垫圈形状简单、尺寸精度低,仅有冲孔、落 料两种工序,
垫圈冲压成型工艺及模具设计垫圈冲压成型工艺及模具设计
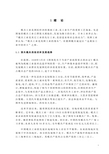
1 绪论模具工业是国民经济的基础工业,是工业生产的重要工艺装备。
先进国家的模具工业已摆脱从属地位,发展为独立的行业。
日本工业界认为:“模具工业是其它工业的先行工业,是创造富裕社会的动力”。
美国工业界认为:“模具工业是美国工业的基石”。
在德国模具被冠以“金属加工业中的帝王”之称。
1.1 国内模具的现状和发展趋势在我国,1998年3月在《国务院关于当前产业政策要点的决定》模具被列为机械工业技术改造序列的第一位,生产和基本建设序列第二位,把发展模具工业摆在发展国民经济的重要位置。
目前,我国冲压模具在产值占模具总产值的40%以上,处于主导地位。
冲压是一种先进的少无切削加工方法,具有节能省材,效率高,产品质量好,重量轻,加工成本低等一系列优点,在汽车,航空航天,仪器仪表,家电,电子,通讯,军工,日用品等产品的生产中得到了广泛的应用。
据统计,薄板成型后,制造了相当于原材料的12倍的附加值,在国民经济生产总值中,与其相关的产品占四分之一,在现代汽车工业中,冲压件的产值占总产值的59%。
但大型多工位级进模、精密冲压模具、大型多型腔精密注塑模、大型汽车覆盖件模具等虽已能生产,但总体技术水平不高,与国外先进国家相比,仍有很大差距。
改革开放以来,随着国民经济的高速发展,市场对模具的需求量不断增长。
近年来,模具工业一直以15%左右的增长速度快速发展,模具工业企业的所有制成分也发生了巨大变化,除了国有专业模具厂外,集体、合资、独资和私营也得到了快速发展。
到目前,中国约有模具生产厂家2万多家,从业人员有50多万人,全年模具产值高达450亿元人民币以上。
中国模具工业的发展在地域分布上存在不平衡性,东南沿海地区发展快于中西部地区,南方的发展快于北方。
模具生产最集中的地区在珠江三角和长江三角地区,其模具产值约占全国产值的三分之二以上。
而在模具制造领域中占有重要地位的冲压模具生产技术与工业发达国家相比还相当落后,主要原因是我国在冲压基础理论及成形工艺、模具标准化、模具设计、模具制造工艺及设备方面与工业发达国家尚有相当大的差距,导致我国模具在寿命、效率、加工精度、生产周期等方面与工业发达国家的模具相比差距相当大。
垫圈的冲裁模设计

垫圈的冲裁模设计垫圈冲裁模具设计垫圈是一种常用的密封元件,在机械、汽车和建筑行业中广泛应用。
垫圈的冲裁模具设计是实现垫圈生产的重要步骤之一、本文将对垫圈的冲裁模具进行详细设计,以确保垫圈的质量和生产效率。
1.垫圈冲裁模具的构造垫圈冲裁模具通常由上下模板、冲头、导柱、导套和底座等组成。
冲头是用来将材料冲下的部件,它需要与上下模板以及底座等部件相连接。
导柱和导套则用来保证冲头与模板之间的相对位置,以确保冲裁的准确性。
2.垫圈冲裁模具的材料选择垫圈冲裁模具所选用的材料需要具备耐磨、耐冲击和耐腐蚀等特点。
常用的模具材料有合金工具钢、高速钢和硬质合金等。
具体选择材料时需考虑垫圈的形状、尺寸和生产数量等因素。
3.垫圈冲裁模具的设计原则垫圈冲裁模具的设计应遵循以下原则:(1)合理确定冲裁模具的结构和外形尺寸,以适应垫圈的形状和尺寸要求。
(2)采用合理的冲头形状和尺寸,以确保冲裁的准确性和一致性。
(3)冲裁模具的冲裁力要足够大,以确保材料能够完全冲下,并且冲裁过程中不产生过大的变形。
(4)冲裁模具的导柱和导套要设计合理,以确保冲头在冲裁过程中的定位准确。
(5)考虑垫圈的生产数量和使用寿命等因素,设计模具的强度和耐用性。
4.垫圈冲裁模具的制造工艺垫圈冲裁模具的制造过程一般包括以下几个步骤:(1)根据设计图纸,制作上下模板、冲头和底座等模具部件。
(2)加工导柱和导套等配件,保证模具的准确定位。
(3)对模具部件进行硬化处理,以增加其硬度和耐磨性。
(4)将模具部件进行装配,并进行必要的调试,确保各部件之间的配合准确。
(5)进行模具的试产和调整,以确保冲裁的准确性和生产效率。
5.垫圈冲裁模具的维护与保养为了确保垫圈冲裁模具的正常使用和延长其寿命,需要进行定期的维护与保养工作。
主要包括:(1)对模具进行清洁,去除灰尘和油污等杂质。
(2)定期对模具进行润滑,以减小摩擦和磨损。
(3)及时修复或更换损坏的模具部件,以保证模具的正常工作。
垫圈冲裁工艺设计

第3页/共29页
三、相关工艺设计计算
1、冲裁间隙:查表(教材P56)(GB/T16743-1997),初始双面间隙Zmin=0.1mm,Zmax=0.14mm
第4页/共29页
2、冲裁排样设计:垫圈落料的单排排样:B——料宽;待计算;S——步距:条料每次送进的距离。待计算;a,a1——搭边:排样时冲裁件之间及冲裁件与条料侧边之间留下的工艺废料。查表(教材P65表)得a=1.0mm,a1=0.8mm
第26页/共29页
表冲裁凹模刃口型式及主要参数
刃口型式
序号
简图
特点及适用范围
直 筒 形 刃 口
2
①刃口强度较高,修磨后刃口尺寸不变;②凹模内易积存废料或冲裁件,尤其间隙较小时,刃口直壁部分磨损较快;③用于冲裁形状复杂或精度要求较高的零件;
3
①特点同序号2,且刃口直壁下面的扩大部分可使凹模加工简单,但采用下漏料方式时刃口强度不如序号2的刃口强度高。②用于冲裁形状复杂或精度要求较高的中小型件,也可用于装有顶件装置的模具。
2.0
2.2
2.5
2.8
3.0
0.25~0.5
1.2
1.5
1.8
2.0
2.2
2.5
0.5~0.8
1.0
1.2
1.5
1.8
1.8
2.0
0.8~1.2
0.8
1.0
1.2
1.5
1.5
1.8
第23页/共29页
表条料宽度偏差Δ
条料宽度B
材料厚度t
~0.5
>0.5~1
>1~2
~20
0.05
0.08
0.10
第11页/共29页
垫片零件的冲压工艺分析与模具设计说明书(唐金平)-推荐下载

第1章.分析零件的冲压工艺性:冲压工件的工艺性是指从冲压工艺方面来衡量设计是否合理。
一般来讲,在满足工件使用要求的条件下,能以最简单最经济的方法将工件冲制出来,就说明该件的冲压工艺性好,否则,该件的工艺性就差。
当然工艺性的好坏是相对的,它直接受到工厂的冲压技术水平和设备条件等因素的影响。
以上要求是确定冲压件的结构,形状,尺寸等是确定冲裁件工艺实应性的主要因素。
根据这一要求对该零件进行工艺分析如下:(1)材料 Q235是普通碳素钢,具有良好的冲压性能。
(2)工件结构 该零件形状简单。
孔边距远大于凸、凹模允许的最小壁厚,故可以考虑采用复合冲压工序。
(3)尺寸精度零件图(如下图)上尺寸未标注公差,属自由公差,按IT14级确定工件的公差,一般冲压均能满足其尺寸精度要求。
经查公差表,按“入体原则”标注各尺寸为:18、9、30和8。
φ043.0-φ36.00+052.0-03-零件图第2章.冲压工艺方案的确定零件为一落料——冲孔件,可提出的加工方案如下:方案一:先落料,后冲孔。
采用两套单工序模生产。
方案二:落料—冲孔复合冲压,采用复合模生产。
方案三:冲孔—落料连续冲压,采用级进模生产。
方案一模具结构简单,但需两道工序、两副模具,生产效率低,零件精度较差,在生产批量较大的情况下不适用。
方案二只需一副模具,冲压件的形位精度和尺寸精度易保证,且生产效率高。
尽管模具结构较方案一复杂,但由于零件的几何形状较简单,模具制造并不困难。
方案三也只需一副模具,生产效率也很高,但与方案二比生产的零件精度稍差。
欲保证冲压件的形位精度,需在模具上设置导正销导正,模具制造、装配较复合模略复杂。
所以,比较三个方案欲采用方案二生产。
由工件尺寸可知,凸凹模壁厚大于最小壁厚,为便于操作,采用倒装复合模结构及弹性卸料方式。
所以可以采用复合模生产,即采用方案二。
第3章.模具设计计算3.1排样方式的确定及计算3.1.1排样的确在冲压生产中,节约金属和减少废料具有非常重要的意义,特别是在大批量生产中,较好地确定冲件尺寸和合理排样是降低成本的有效措施之一。
垫圈冲压工艺与模具设计
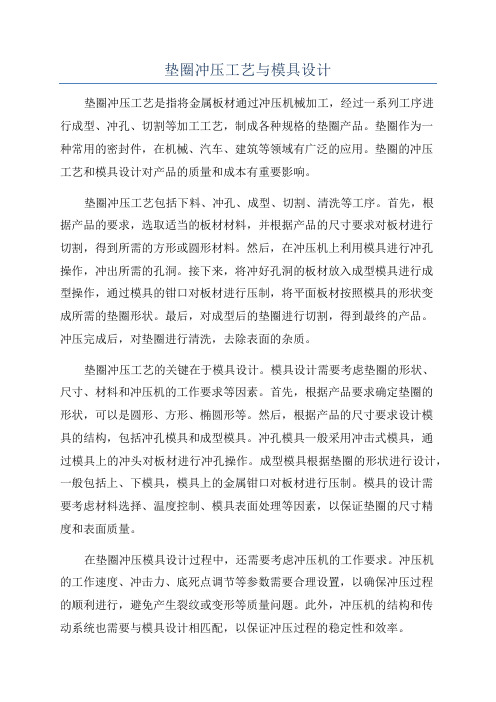
垫圈冲压工艺与模具设计垫圈冲压工艺是指将金属板材通过冲压机械加工,经过一系列工序进行成型、冲孔、切割等加工工艺,制成各种规格的垫圈产品。
垫圈作为一种常用的密封件,在机械、汽车、建筑等领域有广泛的应用。
垫圈的冲压工艺和模具设计对产品的质量和成本有重要影响。
垫圈冲压工艺包括下料、冲孔、成型、切割、清洗等工序。
首先,根据产品的要求,选取适当的板材材料,并根据产品的尺寸要求对板材进行切割,得到所需的方形或圆形材料。
然后,在冲压机上利用模具进行冲孔操作,冲出所需的孔洞。
接下来,将冲好孔洞的板材放入成型模具进行成型操作,通过模具的钳口对板材进行压制,将平面板材按照模具的形状变成所需的垫圈形状。
最后,对成型后的垫圈进行切割,得到最终的产品。
冲压完成后,对垫圈进行清洗,去除表面的杂质。
垫圈冲压工艺的关键在于模具设计。
模具设计需要考虑垫圈的形状、尺寸、材料和冲压机的工作要求等因素。
首先,根据产品要求确定垫圈的形状,可以是圆形、方形、椭圆形等。
然后,根据产品的尺寸要求设计模具的结构,包括冲孔模具和成型模具。
冲孔模具一般采用冲击式模具,通过模具上的冲头对板材进行冲孔操作。
成型模具根据垫圈的形状进行设计,一般包括上、下模具,模具上的金属钳口对板材进行压制。
模具的设计需要考虑材料选择、温度控制、模具表面处理等因素,以保证垫圈的尺寸精度和表面质量。
在垫圈冲压模具设计过程中,还需要考虑冲压机的工作要求。
冲压机的工作速度、冲击力、底死点调节等参数需要合理设置,以确保冲压过程的顺利进行,避免产生裂纹或变形等质量问题。
此外,冲压机的结构和传动系统也需要与模具设计相匹配,以保证冲压过程的稳定性和效率。
总之,垫圈冲压工艺与模具设计是决定垫圈产品质量和成本的重要因素。
通过合理设计冲压工艺和模具,可以提高垫圈的生产效率和产品质量,降低生产成本,满足市场需求。
同时,还需要注重模具的维护和保养,延长模具的使用寿命。
垫圈冲裁模设计

材料厚度t(mm)
KX
KT
KD
≤0.1
0.065~0.075
0.1
0.14
钢
>0.1~0.5 0.045~0.055
0.63
0.08
>0.5~2.5 0.04~0.05
0.55
0.06
注:卸料力系数KX,在冲多孔、大搭边和轮廓复杂制件时取上限值。
27
表2.9.4 冲裁凹模刃口型式及主要参数
刃口 序号 型式 直2 筒 形 刃 口3
36
结束
37
38
39
40
41
连接与固定零件
1、模柄 2、固定板 3、垫板 4、螺钉与销钉
42
模柄
基本要求
压力机滑块上的模柄孔正确配合,安装可靠;
与上模正确而可靠连接。
种类
压入式模柄
旋入式模柄
凸缘模柄
槽型模柄和通用模柄
浮动模柄
推入式活动模柄
材料:Q235(A3钢)、Q275钢
360
450
189
200
240
300
130
150
180
220
60
70
90
110
100
110
130
160
130
150
180
220
150
模柄孔尺寸(直径/mm×深度/mm)
φ30×50
工作台板厚度/mm
29
35
40
50
60
刃口尺寸计算
重要性: 凸模和凹模的刃口尺寸和公差,直接影响冲裁件的尺寸精度。 模具的合理间隙值也靠凸、凹模刃口尺寸及其公差来保证。
25
表2.5.5 导料板与条料之间的最小间隙Cmin
垫圈冲压工艺与模具设计

垫圈冲压工艺与模具设计垫圈是一种常见的紧固件,广泛应用于机械设备和汽车等领域。
常见的垫圈有平垫圈、弹性垫圈等。
垫圈冲压工艺与模具设计对垫圈的质量和生产效率有着重要影响。
下面将详细介绍垫圈冲压工艺与模具设计的相关内容。
一、垫圈冲压工艺垫圈的冲压工艺包括材料选择、工艺参数的确定以及模具的设计。
首先是材料选择。
常见的垫圈材料有碳钢、不锈钢、铝合金等。
根据垫圈的使用环境和要求,选择合适的材料是保证垫圈质量的关键。
其次是冲压工艺参数的确定。
冲压工艺参数包括冲压力、冲床的选型、冲头的尺寸以及冲床的运行速度等。
冲压力的大小直接关系到垫圈的形状和尺寸精度。
冲床的选型要考虑到最大冲压力和垫圈的尺寸范围。
冲头的尺寸要适合垫圈的外径和内径,以保证冲出的垫圈尺寸合适。
冲床的运行速度也是影响冲压效率和垫圈质量的重要因素。
最后是模具的设计。
模具的设计要满足垫圈的形状、尺寸和生产效率要求。
垫圈的形状决定了冲模的形状,冲头的尺寸和冲压力的大小也要考虑在内。
模具的设计要合理布置冲头、辅助装置和导向装置等,以保证冲压过程中的稳定性和垫圈的尺寸精度。
二、垫圈模具设计垫圈模具主要由上模、下模、冲头和导向装置等组成。
下面将对其中几个关键部件进行具体介绍。
1.上模:上模包括上模座和上模块。
上模座用于固定上模块,上模块用于固定垫圈的边缘。
上模的设计要满足垫圈的形状和尺寸要求,并考虑到冲头的尺寸和冲压力的大小。
2.下模:下模通常是一个扁平的平面,用于支撑材料,以避免冲压过程中的材料撕裂。
下模的设计要满足垫圈的外径和内径要求,并考虑到冲压力的大小。
3.冲头:冲头是直接对材料进行冲压的部件。
冲头的设计要适合垫圈的外径和内径,并考虑到冲床的选型和冲压力的大小。
4.导向装置:导向装置用于保证上模和下模的正确对位。
导向装置的设计要合理布置,并考虑到冲压过程中的导向和稳定性。
垫圈模具设计的目标是提高生产效率和垫圈质量。
因此,在模具设计过程中,要考虑到垫圈的形状、尺寸和材料选择等因素,并结合冲床的选型和冲压力的大小,合理布置冲头、导向装置和辅助装置等,以提高生产效率和垫圈质量。
圆垫圈冲裁模具设计
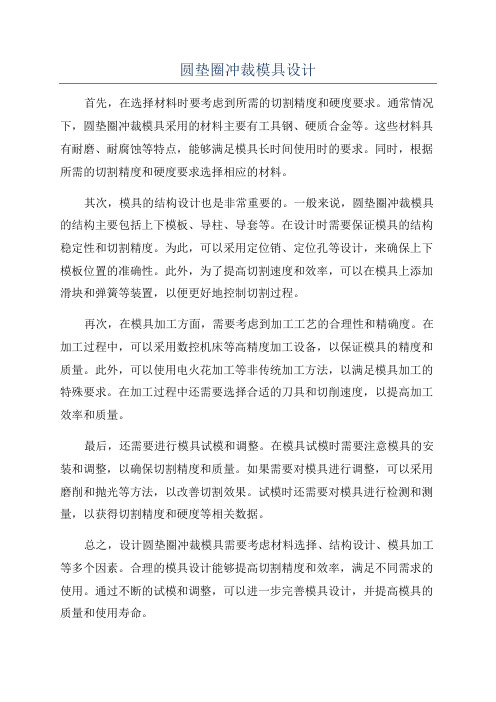
圆垫圈冲裁模具设计
首先,在选择材料时要考虑到所需的切割精度和硬度要求。
通常情况下,圆垫圈冲裁模具采用的材料主要有工具钢、硬质合金等。
这些材料具有耐磨、耐腐蚀等特点,能够满足模具长时间使用时的要求。
同时,根据所需的切割精度和硬度要求选择相应的材料。
其次,模具的结构设计也是非常重要的。
一般来说,圆垫圈冲裁模具的结构主要包括上下模板、导柱、导套等。
在设计时需要保证模具的结构稳定性和切割精度。
为此,可以采用定位销、定位孔等设计,来确保上下模板位置的准确性。
此外,为了提高切割速度和效率,可以在模具上添加滑块和弹簧等装置,以便更好地控制切割过程。
再次,在模具加工方面,需要考虑到加工工艺的合理性和精确度。
在加工过程中,可以采用数控机床等高精度加工设备,以保证模具的精度和质量。
此外,可以使用电火花加工等非传统加工方法,以满足模具加工的特殊要求。
在加工过程中还需要选择合适的刀具和切削速度,以提高加工效率和质量。
最后,还需要进行模具试模和调整。
在模具试模时需要注意模具的安装和调整,以确保切割精度和质量。
如果需要对模具进行调整,可以采用磨削和抛光等方法,以改善切割效果。
试模时还需要对模具进行检测和测量,以获得切割精度和硬度等相关数据。
总之,设计圆垫圈冲裁模具需要考虑材料选择、结构设计、模具加工等多个因素。
合理的模具设计能够提高切割精度和效率,满足不同需求的使用。
通过不断的试模和调整,可以进一步完善模具设计,并提高模具的质量和使用寿命。
垫圈类零件连续冲裁模工艺分析与模具设计

0引言垫圈类零件在工业领域有着非常广泛的应用,其结构形式往往比较多。
在实际进行设计的过程总,需要首先对垫圈的结构形式进行分析,然后确定模具的基本结构,然后再确定排样方案,最后进行凸模、凹模尺寸的计算,最后对冲裁力、卸料力、推料力、顶件力、压力机公称压力进行计算,然后进行模具相关零件的设计工作,压力机的选择应该有公称压力来进行,在这些都确定完成之后,就可以进行相关模具结构和零件的绘制工作。
1冲裁模的工艺方案选择在本次生产设计的过程中,所要冲的是三个相互嵌套的垫圈零件,其最大尺寸在50毫米左右,最小尺寸为14毫米,每套垫圈由三个小垫圈所组成,材料的厚度为0.5毫米,属于大批量生产零件,需要根据以上条件来进行合模的设计[1]。
为了保证模具制造的精度,将工料选择在了3毫米做左右,这样容易保证复合模的平整性,相关模工件的平整性稍微差一点,在加工过程中,容易出现弯曲变形的现象,在实际开展设计的过程中,应该考虑以下的一些因素。
由于一次加工需要加工成3个相互嵌套的零件,为了达到该目的,就需要使用三个凹凸模,一个落料模和一个凸模。
为了保证毛坯的布放质量,对毛坯采用了销定位的方式,通过内连接销将两个顶块直接连接起来,这样可以在摸底弹顶器的作用下,将垫圈顶出来[2]。
在上下模的导向过程中,采用了导柱导向的方式,模架采用了后侧导柱导向模架。
2冲裁件的工艺性本次冲裁的工件形状为圆形垫圈,其结构相对比较简单,切左右、前后对称。
该材料的材料为8号钢,其厚度在0.5毫米左右。
为了满足实际加工的需要,将悬臂和凹槽的宽度选择在了0.6米,悬臂和凹槽的深度选择在恶劣3毫米。
为了保证加工的顺利进行,需要合理设计裁件孔与孔之间,孔和边缘之间的距离,该距离不应该过小。
冲裁件的精度和断面粗糙度的要求。
在本次工件设计的过程找那个,经常冲裁件的公差设定在了11级,冲裁孔的公差等级为IT9级,孔到边尺寸公差等级也是IT9级。
由于冲裁件实际工作中,与相邻零件接触部位的不同,需要根据这些接触面实际的用处,对其表面粗糙度进行合理选择,一般可以将表面粗糙度选择为3.2-12.5之间,毛刺实际高度应该由查表可知。
垫圈类零件连续冲裁模工艺分析与模具设计
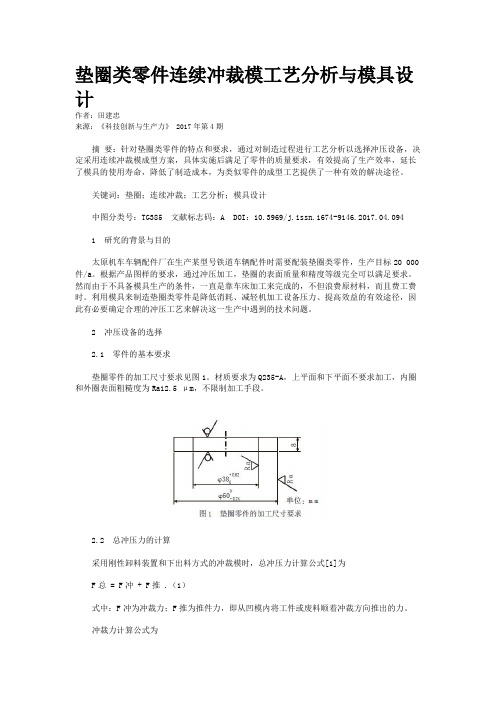
垫圈类零件连续冲裁模工艺分析与模具设计作者:田建忠来源:《科技创新与生产力》 2017年第4期摘要:针对垫圈类零件的特点和要求,通过对制造过程进行工艺分析以选择冲压设备,决定采用连续冲裁模成型方案,具体实施后满足了零件的质量要求,有效提高了生产效率,延长了模具的使用寿命,降低了制造成本,为类似零件的成型工艺提供了一种有效的解决途径。
关键词:垫圈;连续冲裁;工艺分析;模具设计中图分类号:TG385 文献标志码:A DOI:10.3969/j.issn.1674-9146.2017.04.0941 研究的背景与目的太原机车车辆配件厂在生产某型号铁道车辆配件时需要配装垫圈类零件,生产目标20 000件/a。
根据产品图样的要求,通过冲压加工,垫圈的表面质量和精度等级完全可以满足要求。
然而由于不具备模具生产的条件,一直是靠车床加工来完成的,不但浪费原材料,而且费工费时。
利用模具来制造垫圈类零件是降低消耗、减轻机加工设备压力、提高效益的有效途径,因此有必要确定合理的冲压工艺来解决这一生产中遇到的技术问题。
2 冲压设备的选择2.1 零件的基本要求垫圈零件的加工尺寸要求见图1。
材质要求为Q235-A,上平面和下平面不要求加工,内圈和外圈表面粗糙度为Ra12.5 μm,不限制加工手段。
2.2 总冲压力的计算采用刚性卸料装置和下出料方式的冲裁模时,总冲压力计算公式[1]为F总 = F冲 + F推 .(1)式中:F冲为冲裁力;F推为推件力,即从凹模内将工件或废料顺着冲裁方向推出的力。
冲裁力计算公式为F冲= 1.3Ltτ= 1.3×(πD + πd)tτ =1.3×(3.14×60+3.14×38)×8×343N=1097698.8N.(2)式中:L为刃口周长;t为材料厚度;τ为材料的抗剪强度。
对于Q235-A钢,τ的取值范围为304~373 MPa,选取τ = 343 MPa。
垫圈类零件连续冲裁模工艺分析与模具设计
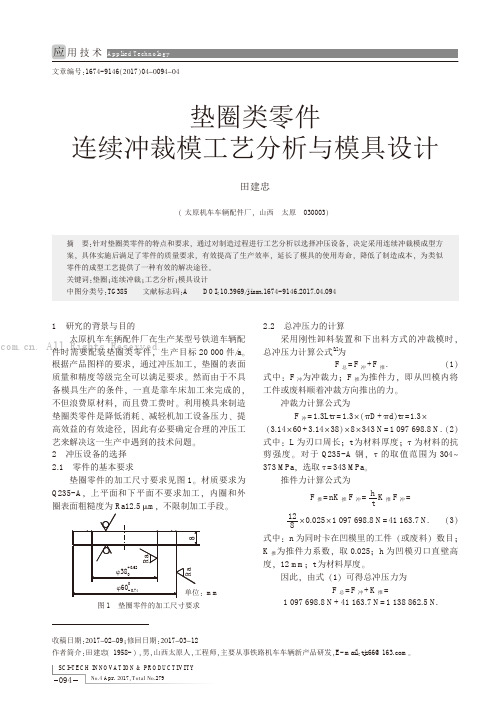
冲裁间隙是直接关系到冲件断面质量尧 尺寸精 度尧 模具寿命尧 力量和能量消耗的重要工Байду номын сангаас参数袁 因此必须依据一定的原则来选取合理的间隙值袁 从 而满足对使用性能的要求遥
094
晕燥援4 A pr.圆园17袁栽 燥贼葬造 晕燥援279
相应的质量为 m = F 总/g= 1 138 862.5 N /9.8 m窑s-2= 113.9 t. 渊4冤 因此袁 选用 200 t四柱液压机袁 型号为 Y A 32-200遥 3 模具压力中心的确定 为了保证压力机和模具正常工作袁 必须使冲模 的压力中心与压力机滑块中心线相重合袁 否则在冲 压时会使冲模与压力机滑块歪斜袁 引起凸凹模间隙 不均和导向零件加速磨损袁 造成刃口和其他零件的 损坏袁 使冲出的产品不能满足使用要求遥 由零件图知该零件具有一定的厚度袁 若采用一 次成形的落料要冲孔复合模袁 则退料问题不好解 决袁 并且模具的强度亦成问题袁 因此笔者决定采用 连续冲裁模的形式遥 在连续冲裁模的结构中袁 大冲 头和小冲头的落料规格不统一袁 因而必须正确确定 压力中心的位置遥 图 2 为采用连续冲裁模时压力中 心确定示意图遥
式中院 n 为同时卡在凹模里的工件 渊或废料冤 数目曰
K 推为推件力系数袁 取 0.025曰 h 为凹模刃口直壁高 度袁 12 m m 曰 t为材料厚度遥
因此袁 由式 渊1冤 可得总冲压力为
F 总=F 冲+K 推= 1 097 698.8 N + 41 163.7 N = 1 138 862.5 N .
y0= l1y1+ l2y2 = l1+ l2
- 1、下载文档前请自行甄别文档内容的完整性,平台不提供额外的编辑、内容补充、找答案等附加服务。
- 2、"仅部分预览"的文档,不可在线预览部分如存在完整性等问题,可反馈申请退款(可完整预览的文档不适用该条件!)。
- 3、如文档侵犯您的权益,请联系客服反馈,我们会尽快为您处理(人工客服工作时间:9:00-18:30)。
要: 针对垫 圈类零件的特点和要 求,通过对制造过程进行工艺分析以选择 冲压设备 ,决定采 用连续 冲栽模成 型方
案 ,具体 实施后满足 了零件 的质量要 求,有 效提 高 了生产效率 ,延长 了模具的使 用寿命 ,降低 了制造 成本 ,为类似
零件的成型工艺提供 了一种有效的解决途径。 关键词 : 垫圈; 连续冲栽 ; 工 艺分析 ; 模具设计
l 09 7 6 98 8 N+4l 1 63 . 7 N= 1 1 3 8 8 6 2. 5 N.
收 稿 日期 : 2 0 l 7 一 O 2 — 0 9 ; 修 回 日期 : 2 0 1 7 一 ( ) 3 一 l 2
作者简介 : 1 日迮忠 ( 1 9 5 8 一) , 男, 山西 太原人 , 工程师 , 主要从事铁路机车车辆新产品研发, F
3 7 3 MP a .选取 r : 3 4 3 MP a
件 的加 r 寸要 求 见l 冬 1 1 、材 质要 求 为
推件 力计算 公 式 为
,
Q 2 3 5 一 A. 1 平 断平 l 卜面 要 求 加 l 1 .内圈 和 外
圈表 而 - 卡 i I 糙度 为 R a I 2 . 5 m,不 限制 J J I 1 T手 段
1, 、
F 推=n K 抻 F 冲=
f
. 十:
I L ×0 0 2 5 ×1 0 9 7 6 9 8 . 8 N= 4 l1 6 3 . 7 N .
.
( 3 )
\
:
。
.
. ’
0 C
式 中 :, 为同时卡
卅
1 模 里的 r 什 ( 或废 料 )数 I l ; 岛
4 . 1 落料 间隙 的确定
因此 ,选 用 2 0 0 t 四柱液 压机 ,型号 为 Y A 3 2 — 2 0 0 。
3 模具 压 力 中心 的确定
落料间隙的确定原则 :落料制件尺寸决定于凹 模尺寸 ,在设计落料模时 ,以凹模为基准 ,间隙取 在凸模上。考虑到冲裁中凸凹模 的磨损 ,所设计的 凹模 基 本 尺 寸 应 取 制 件 尺 寸 公 差 范 围 内 的 较 小 尺 寸 ,这样在凸凹模有一定程度磨损的情况下 ,仍 能 冲出合格制件 。凸凹模的间隙取最小合理间隙值 。 落料凹模刃 口基本尺寸 D 计算公式为
为推 件 力 系数 ,取 0 . 0 2 5 ;h 为【 I J 1 模 J 『 I
¨
¨
度 ,l 2 I I l t n ;t 为材料 度 。
此 ,F } 1 式 ( 1 )r 叮 得总 冲J
亟
c i = ’ 冲 +
“ 【 l 1
图1 垫 圈 零 件 的加 工 尺 寸 要 求
D凹 = ( D一 ) = ( 6 0 - 0 . 5 × 0 . 7 4) = 5 9 . 6 3 mm. ( 7 )
=
I . 3 L t z =1 3×( 盯 D+ 1 T ) , r = 1 . 3 X
( 3 . 1 4×6 0+3 . 1 4×3 8 ) X8×3 4 3 N=l 0 9 7 6 9 8 . 8 N.( 2)
式 巾: 为 口周 长:, 为 材 料 度 ;. r 为 材料 的抗 剪 强 度 对 丁 Q 2 3 5 一 A 钢 ,r的取 值 范 『 书 i 为3 0 4 ~
质量 和 精 等级 完 全 【 I J ‘ 以 满 足要求
式 巾:
为冲 裁 力 ; 推 为 推 件 ,即从 [ I J 】 模I 大 】 将
备模 , { J : 的 条什 , ・ l 是靠 车 r 木l J J l 1 T 来完 成 的 ,
小但 浪 赞 材 料 ,而 f i _ _ T 费时 。利 川模 具 来制 造
太 f J 【 车 辆 配件 J 在生 产某 件 时需 根据 产 装
类 零 件 ,生 产 F ] 标 2 0 0 0 0件/ a 。 然而 由 于不具
总 冲压 力 汁箅 公式 … 为
总 = F冲 + ( 1 )
样 的要求 ,通过 冲乐] J l l q ,垫 圈 的表
{ S CI - TECH I NNOVATI ON & PRODUCTI VI TY
— —
0 9 4— — N o ・ 4 A p r ・ 2 0 1 7 . T o t a l N o ・ 2 7 9
应用技 ■
相应 的质量 为
m= F dg =1 1 3 8 8 6 2 . 5 N / 9 . 8 m・ s =1 1 3 . 9 t . ( 4 )
丁 件或 废料顺 着 冲裁 r 口 】 } 俸 的 I ) j 冲裁 力计 箅 公式 为
’
类 什 是降低 i i l i 牦 、减轻  ̄ J L J J I 】 1 _ 没备 乐 力 、提 高 效 益的 r 效途径。 此 有必 要确 定 合理 的冲 压 f
米解 决这 一牛 产 巾遄 刮 的技 术问题 . 2 冲压 设备 的选 择 2 . 1 岑什的 I 基 本要求
应 用 技 术
文章编号 : 1 6 7 4 — 9 I 4 6 ( 2 0 I 7 ) 0 4 ~ 0 0 9 4 — 0 4
垫 圈类 零件 连续】 ; } I l l 栽 工艺分新与 具设计
田建 忠
( 太原 机 车 车辆 配 件 厂 , 山西 太原 ( ) …) 3)
摘
中图 分 类 号 : T G 3 8 5 文献 标 志 码 : A D OI : 1 0 . 3 9 6 9 6 . i s s n . 1 6 7 4 - 9 1 4 6 . 2 0 1 7 . 0 4 总 冲压 力的 、 f : 铁道 午辆 配 采』 H 刚性 卸 料装 和下 } { 料力 ‘ J = I = = 的 冲裁 { : 5 l 时,