压力容器强度和疲劳设计
压力容器设计有哪些要求

压力容器设计有哪些要求安全可靠为保证过程设备安全可靠地运行,压力容器应具有足够的能力来承受设计寿命内可能遇到的各种载荷。
因此要求用于制作压力容器的材料强度高、韧性好,材料与介质相容,压力容器的结构有足够的刚度和抗失稳能力,密封性能好。
强度、刚度、韧性和密封性是影响过程设备安全可靠性的主要因素。
强度是压力容器在载荷作用下抵抗永久变形和断裂的能力。
压力容器设计时,一般根据不同的强度破坏方式,将应力或与应力有关的参量限制在许用值以内,以满足强度要求。
例如,气体储罐不应在介质压力下鼓胀变形或破裂。
屈服强度和抗拉强度是钢材常用的强度判据。
在相同设计条件下,提高材料强度,就可以增大许用应力,减薄过程设备的壁厚,减轻重量,简化制造、安装、运输和安装,从而降低成本,提高综合经济性。
对于大型压力容器,采用高强度材料的效果尤为显著。
但也不能过分强调材料的高强度,因为高强度材料往往制造加工困难。
刚度是压力容器在载荷作用下保持原有形状的能力。
刚度不足是压力容器过度变形、失稳和泄漏的主要原因之一。
例如,螺栓、法兰和垫片组成的连接结构,若法兰因刚度不足而发生过度变形,将导致密封失效而泄漏;在真空下工作和承受外压的容器,若壳体刚度不够,将引起失稳破坏。
因此,容器设备应有足够的刚度。
韧性是指材料断裂前吸收变形能量的能力。
由于原材料、制造(特别是焊接)和使用(如疲劳、应力腐蚀)等方面的原因,容器常带有各种各样的缺陷,如裂纹、气孔、夹渣等。
研究表明,并不是所有缺陷都会危及容器设备的安全运行,只有当缺陷尺寸达到某一临界尺寸时,才会发生快速扩展而导致容器破坏。
临界尺寸与缺陷所在处的应力水平、材料韧性以及缺陷的大小、形状和方向有关,它随着材料韧性的提高面增大。
材料韧性越好,临界尺寸越大,容器设备对缺陷就越不敏感;反之,在载荷作用下,很小的缺陷就有可能快速扩展而导致容器设备失效。
密封性是指压力容器防止介质泄漏的能力。
压力容器的泄漏可分为内泄漏和外泄漏。
压力容器强度及疲劳设计

第一节 压力容器设计技术概述
一、容器的失效模式
1.容器常见的失效模式
(1) 过度变形 容器的总体或局部发生过度变形,
包括过量的弹性变形,过量的塑性变形,塑性失稳
(增量垮坍),例如总体上大范围鼓胀,或局部鼓胀,
应认为容器已失效,不能保障使用安全。过度变形
说明容器在总体上或局部区域发生了塑性失效,处
于十分危险的状态。例如法兰的设计稍薄,强度上
压力容器强度及疲劳设计
压力容器强度及疲劳设计
第一节 第二节 第三节 第四节
压力容器设计技术概述 压力容器常规设计技术 压力容器应力分析设计 压力容器的疲劳及高温蠕变
压力容器检验师培训
2
压力容器强度及疲劳设计
第一节 压力容器设计技术概述 一、压力容器的失效模式 二、压力容器设计准则的发展 三、压力容器设计规范的主要进展 四、近代设计方法的应用
(A)弹性变形阶段(OA段) (B)屈服阶段(AB段) (C)强化阶段(BC段) (D)爆破阶段(CD段)
素。强化的变化率逐渐降低,到
C点时两种影响相等,达到总体
“塑性失稳”状态,承载能力达
到最大即将爆破,此时容器已充
分膨胀。
压力容器检验师培训
10
第一节 压力容器设计技术概述
(一) 容器的超压爆破过程 (4)爆破阶段 在CD段,减薄的影 响大于强化的影响,容器的承载 能力随着容器的大量膨胀而明显 下降,壁厚迅速减薄,直至D点 而爆裂。
压力容器检验师培训
15
第一节 压力容器设计技术概述
2.容器的脆性爆破过程 脆性爆破的容器是由材料的脆性
(例如低温下的脆性),或是由于有严 重的焊接缺陷(例如裂纹)引起。也可 能两者同时起作用,既有严重缺陷又 遇材料变脆(如焊接热影响区的脆化 或容器长期在中高温度下服役致使材 料显著脆化)从而引起脆断。
压力容器常见结构的设计计算方法

压力容器常见结构的设计计算方法一、静态强度计算方法:静态强度计算方法主要针对压力容器在正常工作状态下的静载荷进行计算,其主要目标是确保容器在最大工作压力下不发生破坏。
静态强度计算方法一般包括以下几个步骤:1.基本假设和假设条件:在进行静态强度计算时,需要基于一定的假设和假设条件来简化实际工作状态,如假设容器时刚体、内外压力均匀分布、材料具有均匀强度等。
2.最大应力计算:通过应力分析计算出压力容器各部位的最大应力。
一般情况下,最大应力发生在容器支座、法兰连接处、沟槽和焊接缺陷等处。
3.材料强度计算:根据容器所使用的材料及其强度参数,计算出材料的强度。
根据所处环境不同,一般会对容器进行分析、判断和选择不同材料。
4.安全裕度计算:根据最大应力和材料强度的计算结果,计算出安全裕度。
安全裕度可以通过破坏条件下材料的强度与容器内外压力之比来衡量。
二、疲劳强度计算方法:疲劳强度计算方法主要用于疲劳载荷下的压力容器设计。
工作过程中,容器可能会受到频繁的循环应力作用,从而导致疲劳破坏。
疲劳强度计算方法的主要步骤如下:1.循环载荷分析:通过实测数据或估算,分析容器在工作循环过程中所受到的应力载荷情况。
考虑到载荷的方向、大小、频率和载荷历史等因素。
2.应力集中分析:针对容器中的主要应力集中部位进行应力集中分析,计算出特定位置的应力集中系数。
3.疲劳寿命计算:基于极限疲劳荷载下的循环应力进行计算。
通过应力循环次数和材料疲劳寿命曲线,计算出容器的疲劳寿命。
4.安全裕度计算:根据疲劳寿命与容器使用寿命的比值,得出安全裕度的计算结果。
三、稳定性计算方法:稳定性计算方法用于分析压力容器在压力作用下的稳定性问题,即容器是否会发生屈曲或侧翻。
稳定性计算方法的主要步骤如下:1.稳定性分析模型:根据压力容器的几何形状和支撑方式,构建相应的稳定性模型。
常见的模型有圆筒形、球形、圆锥形等。
2.屈曲载荷计算:通过对应力分析,计算出容器发生屈曲时的承载力。
压力容器设计

六、封头
按构造形状分为: 半球形封头
凸形封头 椭圆形封头 碟形封头
锥形封头 平盖封头:
1、凸形封头
(1)半球形封头
是半个球壳。 从受力来看,
球形封头是最理想旳构造。 但整体冲压困难,加工工作 量大。
其厚度计算公式:
p c
Di
4[ ]t
p
c
(2)碟形封头
由球面、过渡段及圆柱 直边段三段构成。成型加 工以便,但在三部分连接 处,因为经线曲率发生突 变,受力情况不佳。
2、锥形封头
有两种,一种是无折边锥 形封头,另一种是与筒体连接 处有一过圆弧和一圆柱直边段 旳折边锥形封头。在厚度较薄 时,制造比较以便。
3、平板封头
是最简朴,制造 最轻易旳一种封头。 但相同直径和压力旳 容器,平板封头厚度 过大,材料花费过多 而且十分笨重。
第四节 压力容器附件
设备旳壳体能够采用铸造、铸造或焊接成一种整体, 但大多数化工设备是做成可拆旳几种部件,然后把它们 连接起来。这一方面是设备旳工艺操作需要开多种孔, 并使之与工艺管道或其他附件相连接;另一方面也是为 了便于设备制造、安装和检修。化工设备中旳可拆连接 应该满足下列基本要求:
在设计或选用压力容器零部件时需要将操作温 度下旳最高操作压力(或设计压力)调整为所要 求旳公称压力等级,然后再根据DN与PN选定零 部件旳尺寸。
练一练: P27,1-2,1-3 拟定计算压力、许用应力 P61,6,7 P62,2-3 拟定计算压力、许用应力
四、压力容器旳校核: 1、圆筒容器旳校核
筒体旳强度计算公式:
pD t
2
公式旳应用: 拟定承压容器旳厚度 对压力容器进行校核计算 拟定设计温度下圆筒旳最大允许工作压力 在指定压力下旳计算应力
具有典型结构压力容器的疲劳分析设计

具有典型结构压力容器的疲劳分析设计张杰,郝明涛,江保全,邓龙伟,唐毅(西南化工研究设计院有限公司, 四川 成都 610025)[摘 要] 由于局部应力对压力容器承受疲劳载荷的能力起着显著作用,在结构设计上应尽量避免使结构产生过大的局部应力峰值。
然而,工业应用的需求已无法规避具有某些典型结构的疲劳压力容器。
本文针对一种具有包括各口径接管(特别是斜接管)、内件支撑件、起吊吊耳、耳座支撑等典型结构的疲劳压力容器,基于有限元计算软件ANSYS,介绍了分析和设计的过程和评定方法,探讨了典型结构的特点和应力分布规律的成因,并提出相应处理措施。
[关键词] 压力容器;典型结构;应力;分析设计;疲劳评定作者简介:张杰(1981—),男,重庆荣昌人,2008年毕业于四川大学化工过程机械专业,博士,高级工程师。
主要从事压力容器设计和装备研发工作。
近年来,随着石油化工和各类工业技术水平的迅速发展,承受循环载荷的疲劳压力容器的应用日益增多。
压力容器受压部件中的结构不连续部位、开孔接管以及附件的焊接接头附近等区域常常会产生较高的局部应力(包括峰值应力在内的最大应力),对结构承受疲劳载荷的能力影响较大。
随着载荷的不断循环,局部应力的反复作用,将使材料晶粒间发生滑移和错位,逐步形成微裂纹,微裂纹不断扩展,进而形成宏观疲劳裂纹贯穿整个壁厚,最终导致容器发生疲劳断裂[1]。
在结构设计上疲劳压力容器应尽量避免几何不连续的结构,避免使结构产生过大的局部应力峰值。
然而,生产规模的不断扩大,单元装置的自动化和集约化程度越来越高,监测反馈回路增多、安装方式受限等情况不断呈现,疲劳压力容器已经无法规避各种常见的典型结构。
典型结构通常有典型的开孔接管规格和形式、典型的外部附件连接、典型的内部支撑件连接等。
因此,设计者只能掌握更加精确的设计方法,来评价结构承受疲劳载荷的能力。
本文基于大型有限元计算软件ANSYS ,对此类具有典型结构的疲劳压力容器的分析设计进行了较详细的阐述。
4压力容器设计范文

4压力容器设计范文压力容器是用于存储或运输高压气体、液体或混合物的设备。
它们广泛应用于化工、石油、天然气、能源、制药等行业。
在设计压力容器时,必须考虑到各种因素,如安全、可靠性、耐用性和经济性。
本文将介绍压力容器的设计原理和关键要素。
压力容器的设计过程可以分为以下几个步骤:1.确定工作条件:包括工作介质、工作压力、工作温度等。
工作介质的化学性质、物理性质和工作压力及温度是确定容器材料的基础。
2.选择材料:根据工作条件选择合适的材料。
常用的压力容器材料包括碳钢、不锈钢、钛合金等。
选择材料时需要考虑其耐腐蚀性、强度、韧性、可焊性等性能。
3.确定容器结构:根据工作条件和容器用途确定容器的结构形式,包括圆柱形、球形、扁球形等。
同时还需要确定容器的尺寸和壁厚,以确保容器的强度和稳定性。
4.进行强度计算:根据容器的几何形状和材料特性进行强度计算。
强度计算包括静态强度计算和疲劳强度计算。
静态强度计算主要考虑压力和温度对容器的影响,疲劳强度计算主要考虑容器在循环载荷下的疲劳寿命。
5.进行热力计算:根据容器的工作介质和工作温度进行热力计算。
热力计算主要包括热膨胀计算和热应力计算。
热膨胀计算是为了确定容器在工作温度下的尺寸变化,热应力计算是为了确定容器在工作温度下的应力分布。
6.进行可靠性分析:对容器进行可靠性分析,评估容器的设计可靠性。
可靠性分析包括应力分析、疲劳分析、裂纹扩展分析等。
7.进行安全阀和压力表的选型:根据容器的工作压力确定安全阀和压力表的选型。
安全阀用于保护容器免受超压的损害,压力表用于监测容器的工作压力。
8.进行焊接和无损检测:对容器的焊缝进行焊接和无损检测。
焊接质量对容器的强度和稳定性至关重要,无损检测可以检测焊缝、材料中的缺陷,保证容器的安全使用。
9.编制压力容器设计报告:对容器设计过程进行总结和归纳,编制压力容器设计报告。
设计报告应包括容器的基本信息、工作条件、设计原理、强度计算结果、热力计算结果、可靠性分析结果等。
压力容器疲劳02

4、日本超高压容器设计规则(HPIS-C-103-1989)中的疲劳曲线(1)理论基础Langer公式:1100ln 100a E S σψ-=+-试验:针对三个级别的材料,确定Langer 公式的材料常数,如下表。
适用范围:交变载荷100-1000MPa ; 壁温-50-350℃最佳疲劳曲线:40.540.540.54.52103144.58103993.9210481a f a f a fS N S NS N---=⨯⨯+=⨯⨯+=⨯⨯+设计疲劳曲线:在最佳疲劳曲线基础上考虑安全系数和E 350后求得。
原则上,寿命次数取安全系数15,对应力幅取安全系数1.6。
(2)圆筒的疲劳设计计算 对象:内压圆筒无侧向开孔 a 、交变应力幅按最大剪应力强度理论求得如下(不计自增强残余应力):21322211()()221()1a u e u e u e K S p p p p K Kp p K σσ⎡⎤-+==---+⎢⎥-⎣⎦=--p u ,p e ----上限压力与下限压力,MPa 。
b.内壁平均应力()221Rm u e K p p K θσσ=-+- 平均应力的真实值----实际疲劳寿命计算中所用的平均应力值为:////20,00a m sa sa m s m mm m s a a m s a s mm a s m ifandthenandσσσσσσσσσσσσσσσσσσσσσσσσ+≤≤+≤⇒=⎧>⇒=-⎪+><⇒⎨⎪<⇒=⎩=⇒=c.当量交变应力幅/1aeq m bσσσσ=-d.循环次数根据当量交变应力幅查S-N 曲线,可得设计(许用)循环次数。
注:自增强残余应力和热应力可组合到平均应力中去,但要考虑自增强残余应力在使用中的衰减。
5、影响低周疲劳的因素(1)疲劳曲线是基于标准试件得到的。
标准试样及试验:6-10mm 圆棒,表面磨光,无刻痕、凹槽,夹持端和试件标长段有足够大的圆角过渡;试验是在室温、无腐蚀、辐射等环境下,以及对称循环载荷下进行的。
压力容器疲劳分析报告模板
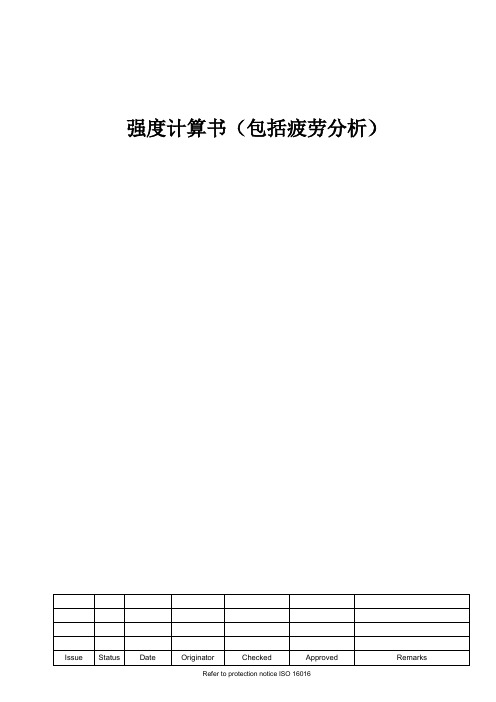
8
疲劳设计寿命
>15年(15000次)
(1)设计载荷
条件
载荷组合注2
K值
计算应力基准
设计
载荷
A
设计压力3.9MPa;
操作重量25780kg;
1.0
设计温度170℃下,不计腐蚀裕量厚度注1
试验
载荷
A
水压试验压力5.69MPa(立试)注3;
液重、自重及所属配重共34378kg;
1.25
模型一工况一(C1)至工况二(C2)主应力差SINT云图如图4-15所示;
模型一工况二(C2)至工况三(C3)主应力差SINT云图如图4-16所示;
工况三(C3):再生最高温度阶段,操作压力0.2MPa,塔顶温度150℃,塔底温度80℃;
工况四(C4):冷却降温初始阶段,操作压力0.2MPa,塔顶温度降低至30℃,塔底温度仍为80℃;
工况五(C5):冷却完成,操作压力0.2MPa,整塔温度30℃。
3
根据脱甲醇塔的实际结构,分为2个三维实体模型,采用ANSYS软件分析,选用SOLID186单元(20节点),利用规则的六面体进行网格划分。
GB/T12459,GB6479
7
法兰/法兰盖
16MnIII
NB/T47008
表1-4基本设计参数
1
设计压力MPa (g)
3.9
2
设计温度°C
170
4
工作压力MPa (g)
0.2~3.4
5
工作温度°C
15~150
3
试验压力MPa(g)
5.69(立)/5.75(卧)
6
风压/雪压Pa
300/350
7
EN压力容器标准与ASME标准和我国标准的对比– 基于公式的设计和疲劳设计

es
2
f
P z
R 0.5P
(球冠部分防止塑性破坏所需的壁厚)
ey
P0.75R 0.2Di
f
(折边部分防止发生轴对称屈服所需壁厚)
eb
0.75 R 0.2Di
P
Di
0.825
1 1.5
111 fb r
(折边部分防止发生塑性失稳所需壁厚)
注:
1) 当ey 大于0.5% Di 时,不需计算 eb ; 2) 为 e/R 和 r/Di 的函数。
载荷分布是均布的 b) Zick 法要求计算校核鞍座与筒体接触的最低点和边角处的压应力,而
EN13445 是从线载荷引起薄膜应力和弯曲应力的角度,通过计算最大允许鞍 座反力来对鞍座所受反力进行校核
c) Zick法考虑了鞍座与筒体接触处存在的周向压应力对该截面承受轴向弯曲 能力的影响,即“扁塌”效应,而EN13445没有考虑这个因素
97/23/EC 规定可采用的设计计算方法包括 1) 按公式设计(DBF) 2) 按分析方法设计(DBA) 3) 按断裂力学方法设计
注: 在满足 97/23/EC基本要求的前提下,以上三个方法可相互替代; 疲劳设计方法应是分析设计方法的一种,但它是唯一的,不能用其他方法替代
可以在以下情况下考虑采用分析方法设计: 1) 对于某一结构,标准中没有给出公式设计方法 2) 不能满足一般制造要求的特定情况 3) 叠加了环境效应(如风、雪、地震,等等)的载荷工况, 作为一种补充设计方法。
注:
1. 失效模式 2)包括在失效模式 1)中; 2. 当量循环次数不大于500,可不考虑疲劳破坏。 3. 设计人员还需考虑可能发生的其他失效模式
EN13445 的基本思想是针对结构可能出现的失效模式,采用 合适的设计计算方法,使结构具备足够的强度以避免失效
基于有限元法的压力容器疲劳分析设计

载荷分析的目的是分析设备承受的实际外载
情况ꎬ 确定合理的边界约束条件ꎮ
1 1 设计条件
某装置中的炉渣输送罐ꎬ 主要作用是将系统
中燃尽的灰渣冷却、 粉碎处理后排出ꎬ 它是连续
运转的疲劳设备ꎬ 每一个运转周期包括卸压 - 清
洗 - 排渣 - 充压 - 集渣等过程ꎮ 炉渣输送罐的基
本结构见图 1ꎮ
∗秦小燕: 高级工程师ꎮ 2010 年毕业于南京工业大学化工机械专业获硕士学位ꎮ 主要从事压力容器常规设计和分析设计工作ꎮ
疲劳寿命的若干措施ꎮ
关键词 压力容器 有限元法 应力分析 疲劳强度分析 措施
20 世纪 60 年 代 以 前ꎬ 压 力 容 器 的 设 计 是 以
析设计法从设计思想上ꎬ 放弃了传统的弹性失效
静载荷为基础的设计ꎬ 即认为容器中所承受的载
准则ꎬ 采用以极限载荷、 安定载荷和疲劳寿命为
荷不随时间发生变化ꎮ 但实际上ꎬ 容器在交变载
通过分析构件应力强度最大节点其它高应力强度区选定节点及关注部位相应节点?并沿壁厚方向的最短方向设定应力线性化路径?各模型的应力线性化路径见图8822020?301秦小燕基于有限元法的压力容器疲劳分析设计图10?相应模型的应力强度评定结果见表8?表8各路径应力强度评定表设计工况路径应力强度及组合应力强度应力强度计算值mpa应力强度许用极限mpa评定结果11一次局部薄膜应力强度s73????081????5sm201通过一次薄膜加一次弯曲应力强度s119????71????5sm201通过22一次总体薄膜应力强度s78????531????0sm134通过33一次局部薄膜应力强度s119????51????5sm195通过一次二次应力强度s1683????0sm390通过44一次局部薄膜应力强度s104????31????5sm195通过一次二次应力强度s131????93????0sm390通过55一次局部薄膜应力强度s117????61????5sm195通过一次二次应力强度s191????73????0sm390通过66一次局部薄膜应力强度s91????971????5sm195通过一次二次应力强度s112????13????0sm390通过77一次总体薄膜应力强度s77????41????0sm134通过88一次总体薄膜应力强度s83????871????0sm134通过99一次局部薄膜应力强度s34????111????5sm199????5通过一次二次应力强度s127????53????0sm399通过1010一次局部薄膜应力强度s39????861????5sm199????5通过一次二次应力强度s136????23????0sm399通过1111一次局部薄膜应力强度s23????571????1sm146????3通过一次二次应力强度s29????653????0sm399通过注
压力容器应力分析及其设计

压力容器应力分析及其设计引言压力容器是一种用于储存或运输压力流体或气体的设备,广泛应用于化工、石油、制药等领域。
由于其工作环境的特殊性,压力容器的设计和应力分析至关重要,直接关系到设备的安全性和稳定性。
本文将介绍压力容器应力分析的基本概念和方法,并探讨压力容器设计的一些考虑因素。
压力容器应力分析在压力容器的设计和使用过程中,应力分析是非常重要的一步。
应力分析的目的是确定容器的强度和稳定性,以确保其在工作压力范围内能够安全可靠地运行。
1. 基本概念在压力容器中,由于内、外侧的压力差异,容器壁面会受到应力的作用。
应力是物体内部原子或分子间相互作用的结果,它可以表现为拉伸、压缩、剪切等形式。
常见的应力包括轴向应力、周向应力和切向应力。
轴向应力是指沿着容器轴线方向的应力,周向应力是指沿着容器周向的应力,切向应力是指垂直于容器壁面的应力。
2. 应力分析方法压力容器的应力分析可以采用数值模拟方法或者经验公式计算。
数值模拟方法通常基于有限元分析(Finite Element Analysis,简称FEA),通过划分网格、建立数学模型并求解,得到各个位置的应力值。
经验公式计算相对简便,适用于一些简单几何形状的压力容器。
常用的经验公式有ASME VIII-1标准中的公式和欧洲标准EN 13445中的公式等。
无论采用数值模拟方法还是经验公式计算,都需要考虑容器的材料特性、内外压力、温度、容器几何形状等因素。
3. 应力分析结果的评估进行应力分析后,需要对分析结果进行评估。
常见的评估指标有应力强度安全系数、应力集中系数、损伤累积等。
应力强度安全系数是指容器的实际应力值与允许应力值之间的比值。
一般要求安全系数大于1,以确保容器在额定工作条件下不会发生破坏。
应力集中系数用于评估容器上的应力集中程度。
过高的应力集中系数可能导致局部破坏和疲劳寿命的降低。
损伤累积是指容器在循环荷载作用下承受的损伤累计量。
如果损伤累积超过一定限制,容器可能发生疲劳破坏。
压力容器的强度计算
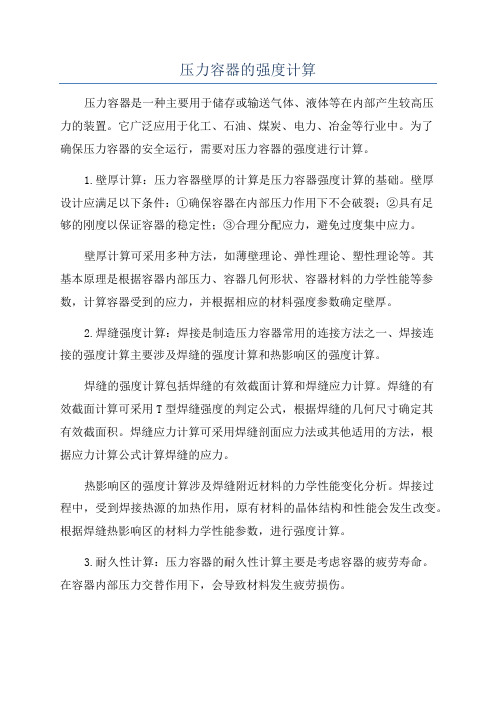
压力容器的强度计算压力容器是一种主要用于储存或输送气体、液体等在内部产生较高压力的装置。
它广泛应用于化工、石油、煤炭、电力、冶金等行业中。
为了确保压力容器的安全运行,需要对压力容器的强度进行计算。
1.壁厚计算:压力容器壁厚的计算是压力容器强度计算的基础。
壁厚设计应满足以下条件:①确保容器在内部压力作用下不会破裂;②具有足够的刚度以保证容器的稳定性;③合理分配应力,避免过度集中应力。
壁厚计算可采用多种方法,如薄壁理论、弹性理论、塑性理论等。
其基本原理是根据容器内部压力、容器几何形状、容器材料的力学性能等参数,计算容器受到的应力,并根据相应的材料强度参数确定壁厚。
2.焊缝强度计算:焊接是制造压力容器常用的连接方法之一、焊接连接的强度计算主要涉及焊缝的强度计算和热影响区的强度计算。
焊缝的强度计算包括焊缝的有效截面计算和焊缝应力计算。
焊缝的有效截面计算可采用T型焊缝强度的判定公式,根据焊缝的几何尺寸确定其有效截面积。
焊缝应力计算可采用焊缝剖面应力法或其他适用的方法,根据应力计算公式计算焊缝的应力。
热影响区的强度计算涉及焊缝附近材料的力学性能变化分析。
焊接过程中,受到焊接热源的加热作用,原有材料的晶体结构和性能会发生改变。
根据焊缝热影响区的材料力学性能参数,进行强度计算。
3.耐久性计算:压力容器的耐久性计算主要是考虑容器的疲劳寿命。
在容器内部压力交替作用下,会导致材料发生疲劳损伤。
耐久性计算主要涉及应力幅计算和疲劳寿命计算。
应力幅计算是根据容器的工作条件、材料疲劳强度参数等,计算容器内部压力作用下的应力幅度。
疲劳寿命计算是根据材料的疲劳性能参数,计算容器的疲劳寿命。
总之,压力容器的强度计算是确保容器安全运行的重要环节。
通过合理计算容器的壁厚、焊缝强度和耐久性,能够保证容器在内部压力作用下不会发生破裂和泄漏,从而确保生产过程的安全。
压力容器设计
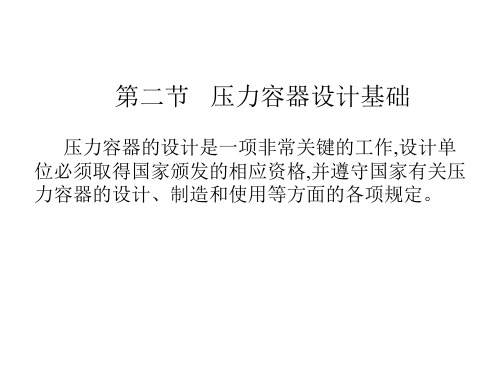
2、计算厚度
3、设计厚度
4、名义厚度
5、校核
例3: 对一储罐的筒体进行设计计算。已知:设计压 力p=2.5MPa, 操作温度-5~44 ℃,用16MnR制造,储罐 内径 Di=1200mm,腐蚀裕量C2=1mm,焊接接头系数 =0.85,试确定筒体厚度.
练习:P61 1-9 作业:P62 2-2,2-3
第二节 压力容器设计基础
压力容器的设计是一项非常关键的工作,设计单 位必须取得国家颁发的相应资格,并遵守国家有关压 力容器的设计、制造和使用等方面的各项规定。
(一)设计内容:容器应根据工艺过程要求和条件,进行 结构设计和强度设计。
结构设计:
主要选择适用、合理、经济的结构形式,同时满 足制造、检测、装配、运输和维修的要求。
HG20593-1997 法兰 PL 100-1.0
法兰材 料20钢
RF S=4mm 20
板式平焊法兰,见表1-22
管壁厚4mm 公称压力1.0MPa
公称直径100mm
二、人孔与手孔:
目的:为了便于内件的安装、清理、检修、取出内件及工作 人员的进出。
1、人孔:
常压平盖人孔 (b)回转拱盖快开人孔 (c)手摇快开人孔
表2-3 焊缝系数
焊缝类型与检测要求:
按照GB150-1998中“制造、检验与验收”的规定, 容器主要受压部分的焊接接头分为ABCD四类,分别 有不同的检验要求。
5、壁厚附加量: C=C1+C2
C1:钢板厚度负偏差,见表1-8,1-9,1-10 C2:腐蚀裕量 C2 =ka B
Ka: 腐蚀速率,见相关手册 B:设计寿命,不低于15年。
强度计算:
内容包括选择容器的材料,确定主要尺寸,满 足强度、刚度和稳定性的要求,以确保容器安全可 靠地运行。
机械工程中压力容器的疲劳寿命分析与改进

机械工程中压力容器的疲劳寿命分析与改进在机械工程中,压力容器被广泛应用于各种领域,如石化、电力、航空航天等。
然而,由于使用过程中受到不断变化的压力和温度等因素的影响,压力容器容易发生疲劳破坏,从而导致安全事故的发生。
因此,研究压力容器的疲劳寿命分析与改进具有重要意义。
首先,压力容器的疲劳寿命分析是了解其寿命的重要手段。
疲劳寿命分析主要通过应力-应变曲线、载荷频率及材料性能等参数来评估压力容器的疲劳寿命。
通过分析容器受力情况,找出应力最大的位置,确定疲劳断裂的起始点,可以计算出压力容器的寿命。
而在疲劳寿命分析的过程中,还需要考虑到材料的疲劳性能、载荷的作用形式以及工作环境等因素。
通过系统分析和实验验证,可以准确评估压力容器的疲劳寿命,为改进提供理论依据。
其次,在分析压力容器的疲劳寿命后,需要采取一系列改进措施来提高其使用寿命。
一种常见的改进方法是采用更优质的材料。
高强度材料具有更好的抗疲劳性能,能够提高压力容器的寿命。
此外,还可以通过优化压力容器的结构设计来减少应力集中,改善其疲劳性能。
例如,增加圆角、改变接缝的设计等,都可以降低应力集中的程度,从而延长压力容器的使用寿命。
此外,还可以采用表面处理等方法来提高材料的表面质量,减少表面缺陷对疲劳寿命的影响。
另外,监测和维护也是延长压力容器寿命的关键因素之一。
通过定期的检测和维护,可以及时发现和处理压力容器的安全隐患,避免事故的发生。
常用的监测方法包括无损检测、磁粉探伤等技术,可以对压力容器进行全面的检测。
此外,在维护方面,需要及时更换老化的部件,保持压力容器的正常运行状态。
只有加强监测和维护工作,才能确保压力容器的安全使用。
综上所述,压力容器的疲劳寿命分析与改进在机械工程中具有重要意义。
通过分析容器的受力情况,确定疲劳断裂的起始点,可以准确评估容器的寿命。
而通过采用更优质的材料、优化结构设计以及加强监测和维护工作,可以提高压力容器的使用寿命。
只有不断加强研究和实践,才能不断完善压力容器的设计与制造,确保工程结构的安全性和可靠性。
疲劳知识总结

压力容器疲劳知识总结(201220630 邹明铭)1.疲劳分析设计工程背景疲劳是指材料、零件和构件在循环加载下,在某点或某些点产生局部的永久性损伤,并在一定循环次数后形成裂纹、或使裂纹进一步扩展直到完全断裂的现象。
在工程实际中,大量的材料、构件在交变应力作用下工作,将发生疲劳破坏,因而在疲劳分析在工程设计中占有重要地位。
疲劳强度分析是一个热点的研究领域,已从经典的无限寿命设计发展到有限寿命设计和可靠性分析。
累积损伤观念为现代工程设计注入了新思想和新方法,损伤理论已成为一门新的学科,为解决疲劳寿命问题提供了重要理论基础与工程计算方法。
2.疲劳分析的基础知识2.1交变应力图1所示的交变应力,用S代表广义应力,即它可以是正应力,也可以是切应力。
图1 交变应力示意图应力循环——应力值每重复变化一次成为一个循环,及应力从最小值变到最大值,再变回到最小值。
循环次数——应力重复变化的次数,用N表示。
S表示。
最大应力——应力循环中的最大值,用max最小应力——应力循环中的最小值,用min S 表示。
平均应力——最大应力与最小值的平均值,用m S 表示。
即m max min 1()2S S S =+ (2-1) 应力幅值——应力变化幅度的均值,用a S 表示。
即 max min 1()2a S S S =- (2-2) 这样,max m a S S S =+ (2-3)min m a S S S =- (2-4)循环特征——最小应力与最大应力的比值,用 表示。
即(2-5)2.2 几种典型的交变应力图2所示的交变应力,为对称循环的交变应力。
其特点是max min max 1,,0,m a r S S S S S =-=-==图3所示的交变应力,为脉动循环的交变应力。
其特点是min max 10,0,2m a r S S S S ==== 图4所示的为静应力,可视为应力幅值为零的特殊交变应力。
其特点是 max min 1,,0m a r S S S S ====除图2所示的对称循环的交变应力外,其它均为非对称循环交变应力,且其循环特征 均在-1与+1间变化。
容器失效与设计准则
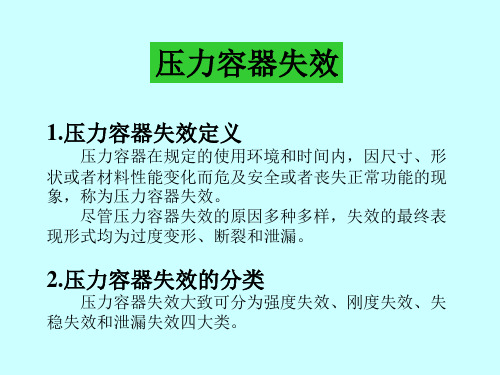
许用应力以内,防止容器在使用寿命内发生蠕变失效。
脆性断裂失效设计准则:
强度失效设计准则
在常温、静载作用下,屈服和断裂是压力 容器强度失效的两种主要形式。 弹性失效设计准则 塑性失效设计准则 爆破失效设计准则 弹塑性失效设计准则 疲劳失效设计准则 蠕变失效设计准则 脆性断裂失效设计准则
1. 强度失效设计准则
2. 刚度失效设计准则
在载荷作用下,构件的弹性位移和(或)转角不得超过规定 的数值。
3. 失稳失效设计准则
压力容器设计中,防止发生失稳。例如:仅受均布外压的圆 筒,外压力应当小于周向临界压力。
4. 泄漏失效设计准则
容器发生的泄漏率(单位时间内通过泄漏通道的体积或质量) 小于允许值。
压力容器设计准则大致可分为强度失效设计准则、 刚度失效设计准则、失稳失效设计准则和泄漏失效设计 准则。对于不同的设计准则,安全系数的含义并不相同。
压力容器设计时,应先确定容器最有可能发生的失 效形式,选择合适的失效判据和设计准则,确定适用的 设计规范标准,再按规范标准要求进行设计和校核。
设计准则
压力容器设计准则大致可分为:
d.泄漏失效
由于泄漏而引起的失效,称为泄漏失效。泄漏不 仅有可能引起中毒、燃烧和爆炸等事故,而且会造成 环境污染。设计压力容器时,应重视各可拆式接头和 不同压力腔之间连接接头(如换热管和管板的连接) 的密封性能。
压力容器失效
需要指出,在多种因素作用下,压力容 器有可能同时发生多种形式的失效,即交互 失效,如腐蚀介质和交变应力同时作用时引 发的腐蚀疲劳、高温和交变应力同时作用时
引发的蠕变疲劳等。
失效判据与设计准则
a.失效判据
TSG07-2023压力容器设计体系文件设计标准规定
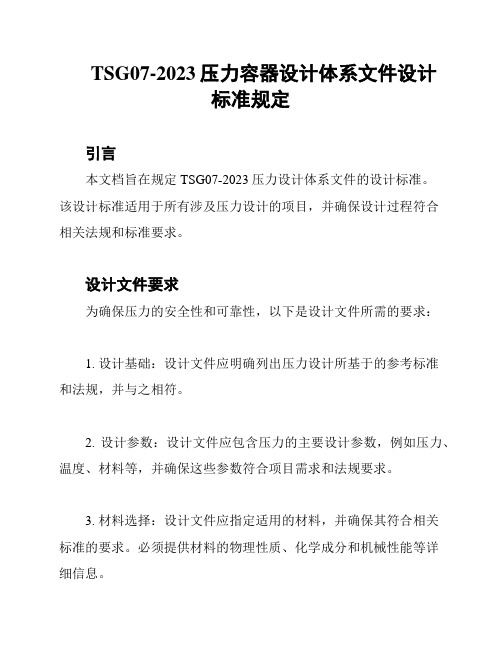
TSG07-2023压力容器设计体系文件设计标准规定引言本文档旨在规定TSG07-2023压力设计体系文件的设计标准。
该设计标准适用于所有涉及压力设计的项目,并确保设计过程符合相关法规和标准要求。
设计文件要求为确保压力的安全性和可靠性,以下是设计文件所需的要求:1. 设计基础:设计文件应明确列出压力设计所基于的参考标准和法规,并与之相符。
2. 设计参数:设计文件应包含压力的主要设计参数,例如压力、温度、材料等,并确保这些参数符合项目需求和法规要求。
3. 材料选择:设计文件应指定适用的材料,并确保其符合相关标准的要求。
必须提供材料的物理性质、化学成分和机械性能等详细信息。
4. 结构设计:设计文件应详细描述压力的结构设计,包括壁厚、接头设计、支承设计等,并确保其满足适用的标准和法规要求。
5. 安全阀和附件:设计文件应考虑安全阀和其他必要附件的设计和安装要求,以确保在超压情况下能够安全释放压力或进行相应控制。
6. 强度计算:设计文件应包含压力的强度计算过程和结果,确保结构能够承受设计参数下的压力和负荷,并符合适用的强度标准。
7. 破裂和疲劳分析:设计文件应对压力的破裂和疲劳分析进行评估,确保在正常使用和意外情况下的安全性。
8. 检验和试验计划:设计文件应明确列出压力的检验和试验计划,包括原材料检验、焊接质量检验、超声波检测等,以确保成品符合相关标准和法规。
结论TSG07-2023压力容器设计体系文件设计标准规定了压力容器设计文件所需的要求,从设计基础到检验计划,都应符合相关标准和法规要求。
这些设计标准的遵循将确保压力容器的安全性和可靠性,减少事故风险,并保护人员和设备的安全。
第七章压力容器的疲劳、断裂、蠕变
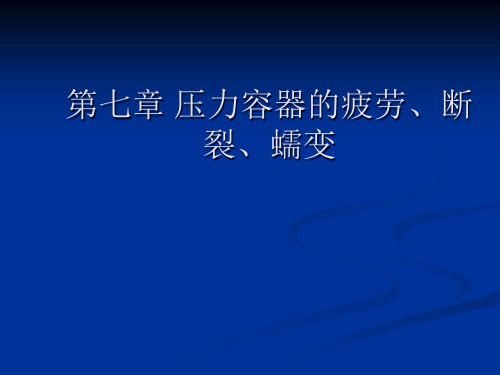
使用中形成的裂纹,包括腐蚀裂纹,特别是应力腐蚀裂纹, 还有由交变载荷导致出现的疲劳裂纹等。
低应力脆断不仅在压力容器上发生,在船只、桥梁及其它 焊接结构上也大量发生过低应力脆断事故,这引起工程界 与科学界的重视—发展了断裂力学。
以一个频繁开停,及工作压力交替的在零和 pmax 范围内工作的厚壁圆筒为例,说明利用疲劳设计
曲线计算容器寿命的步骤。
(1)求取在工作压力作用下,危险点的应力。 (2)求取应力循环中的最大应力和最小应力。 (3)计算交变应力幅
Sa
1 2
r 0
1 2
r
(4)利用疲劳设计曲线,查出循环次数Nf
e 2 2E
Basquin方程
e 2
f' E
2N f
b
图7-3
f '
2E
2N f
b f ' 2N f
c
等号右边第一项和第二项分别是总应变幅的弹 性分量和塑性分量。
虚拟应力幅 Sa
Sa
E
1 2
t
1 2
E t
当温度低于蠕变范围时,在低循环区域中,应
变与破环次数Nf 之间存在着如下近似关系
(3)在受压容器上距离在 2 RS 以内(R一容器的平均半径, S一壁厚)的任意两点间的金属温差变化的有效次数。
(4)部件焊缝两侧的材料具有不同温度膨胀系数 1 与 2 , 在 (1 2 )t 0.0003时4 的温度变化次数(——操作温度范围oC)。
五、疲劳分析的其它问题
压力容器疲劳分析设计
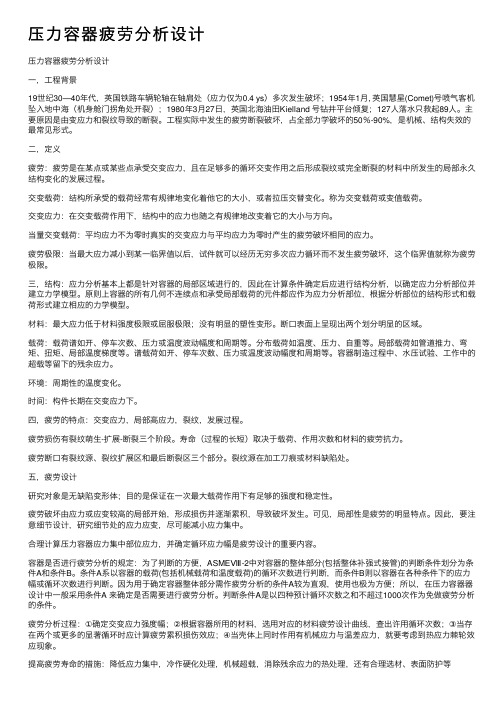
压⼒容器疲劳分析设计压⼒容器疲劳分析设计⼀,⼯程背景19世纪30—40年代,英国铁路车辆轮轴在轴肩处(应⼒仅为0.4 ys)多次发⽣破坏;1954年1⽉, 英国慧星(Comet)号喷⽓客机坠⼊地中海(机⾝舱门拐⾓处开裂);1980年3⽉27⽇,英国北海油⽥Kielland 号钻井平台倾复;127⼈落⽔只救起89⼈。
主要原因是由变应⼒和裂纹导致的断裂。
⼯程实际中发⽣的疲劳断裂破坏,占全部⼒学破坏的50%-90%,是机械、结构失效的最常见形式。
⼆,定义疲劳:疲劳是在某点或某些点承受交变应⼒,且在⾜够多的循环交变作⽤之后形成裂纹或完全断裂的材料中所发⽣的局部永久结构变化的发展过程。
交变载荷:结构所承受的载荷经常有规律地变化着他它的⼤⼩,或者拉压交替变化。
称为交变载荷或变值载荷。
交变应⼒:在交变载荷作⽤下,结构中的应⼒也随之有规律地改变着它的⼤⼩与⽅向。
当量交变载荷:平均应⼒不为零时真实的交变应⼒与平均应⼒为零时产⽣的疲劳破坏相同的应⼒。
疲劳极限:当最⼤应⼒减⼩到某⼀临界值以后,试件就可以经历⽆穷多次应⼒循环⽽不发⽣疲劳破坏,这个临界值就称为疲劳极限。
三,结构:应⼒分析基本上都是针对容器的局部区域进⾏的,因此在计算条件确定后应进⾏结构分析,以确定应⼒分析部位并建⽴⼒学模型。
原则上容器的所有⼏何不连续点和承受局部载荷的元件都应作为应⼒分析部位,根据分析部位的结构形式和载荷形式建⽴相应的⼒学模型。
材料:最⼤应⼒低于材料强度极限或屈服极限;没有明显的塑性变形。
断⼝表⾯上呈现出两个划分明显的区域。
载荷:载荷谱如开、停车次数、压⼒或温度波动幅度和周期等。
分布载荷如温度、压⼒、⾃重等。
局部载荷如管道推⼒、弯矩、扭矩、局部温度梯度等。
谱载荷如开、停车次数、压⼒或温度波动幅度和周期等。
容器制造过程中、⽔压试验、⼯作中的超载等留下的残余应⼒。
环境:周期性的温度变化。
时间:构件长期在交变应⼒下。
四,疲劳的特点:交变应⼒,局部⾼应⼒,裂纹,发展过程。
浅谈压力容器的疲劳分析及设计
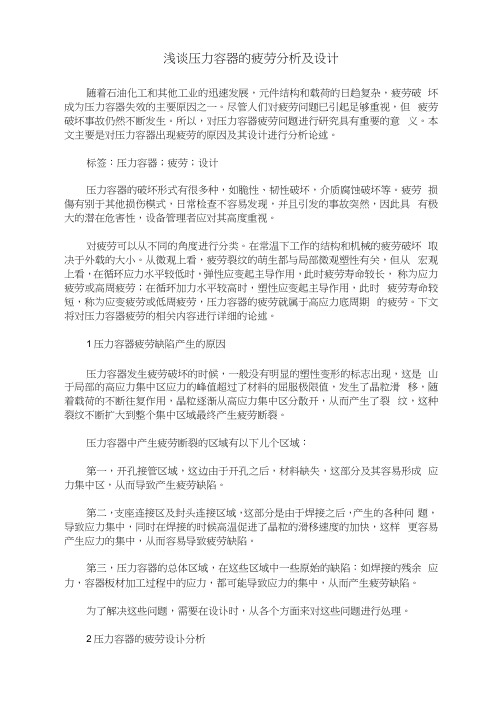
浅谈压力容器的疲劳分析及设计随着石油化工和其他工业的迅速发展,元件结构和载荷的日趋复杂,疲劳破坏成为压力容器失效的主要原因之一。
尽管人们对疲劳问题已引起足够重视,但疲劳破坏事故仍然不断发生。
所以,对压力容器疲劳问题进行研究具有重要的意义。
本文主要是对压力容器出现疲劳的原因及其设计进行分析论述。
标签:压力容器;疲劳;设计压力容器的破坏形式有很多种,如脆性、韧性破坏,介质腐蚀破坏等。
疲劳损傷有别于其他损伤模式,日常检查不容易发现,并且引发的事故突然,因此具有极大的潜在危害性,设备管理者应对其高度重视。
对疲劳可以从不同的角度进行分类。
在常温下工作的结构和机械的疲劳破坏取决于外载的大小。
从微观上看,疲劳裂纹的萌生都与局部微观塑性有关,但从宏观上看,在循环应力水平较低时,弹性应变起主导作用,此时疲劳寿命较长,称为应力疲劳或高周疲劳;在循环加力水平较高时,塑性应变起主导作用,此时疲劳寿命较短,称为应变疲劳或低周疲劳,压力容器的疲劳就属于高应力底周期的疲劳。
下文将对压力容器疲劳的相关内容进行详细的论述。
1压力容器疲劳缺陷产生的原因压力容器发生疲劳破坏的时候,一般没有明显的塑性变形的标志出现,这是山于局部的高应力集中区应力的峰值超过了材料的屈服极限值,发生了晶粒滑移,随着载荷的不断往复作用,晶粒逐渐从高应力集中区分散开,从而产生了裂纹,这种裂纹不断扩大到整个集中区域最终产生疲劳断裂。
压力容器中产生疲劳断裂的区域有以下儿个区域:第一,开孔接管区域,这边由于开孔之后,材料缺失,这部分及其容易形成应力集中区,从而导致产生疲劳缺陷。
第二,支座连接区及封头连接区域,这部分是由于焊接之后,产生的各种问题,导致应力集中,同时在焊接的时候高温促进了晶粒的滑移速度的加快,这样更容易产生应力的集中,从而容易导致疲劳缺陷。
第三,压力容器的总体区域,在这些区域中一些原始的缺陷:如焊接的残余应力,容器板材加工过程中的应力,都可能导致应力的集中,从而产生疲劳缺陷。
- 1、下载文档前请自行甄别文档内容的完整性,平台不提供额外的编辑、内容补充、找答案等附加服务。
- 2、"仅部分预览"的文档,不可在线预览部分如存在完整性等问题,可反馈申请退款(可完整预览的文档不适用该条件!)。
- 3、如文档侵犯您的权益,请联系客服反馈,我们会尽快为您处理(人工客服工作时间:9:00-18:30)。
弄清容器的各种形式的失效,尤其最基本的爆
破失效过程更需要弄清楚。下面就容器的韧性
韧性破坏 脆性破坏
爆破和脆性爆破过程先作一些阐述:
压力容器检验师培训
6
第一节 压力容器设计技术概述
(一) 容器的超压爆破过程 1.容器的韧性爆破过程 一台受压容器,如果材料
塑性韧性正常,设计正确, 制造中未留下严重的缺陷, 加压直至爆破的全过程一般 属于韧性爆破过程。韧性爆 破的全过程可以用图示容器 液压爆破曲线OABCD来说明, 加压的几个阶段如下:
尚可满足要求,但由于刚度不足产生永久变形,导
致介质泄漏,这是由于塑性失效的过度变形而导致
的失效。
压力容器检验师培训
18
第一节 压力容器设计技术概述
一、容器的失效模式 1.容器常见的失效模式
(2) 韧性爆破 容器发生了塑性大变形的 破裂失效,相当于图中曲线BCD阶段情况 下的破裂,这属于超载下的爆破,一种可 能是超压,另一种可能是本身大面积的壁 厚较薄。这是一种经过塑性大变形的塑性 失效之后再发展为爆破的失效,亦称为 “塑性失稳”(Plastic collapse),爆破后 易引起灾难性的后果。
(A)弹性变形阶段(OA段) (B)屈服阶段(AB段) (C)强化阶段(BC段) (D)爆破阶段(CD段)
压力容器检验师培训
8
第一节 压力容器设计技术概述
(一) 容器的超压爆破过程 (2)屈服变形阶段 AB段,容器 从局部屈服到整体屈服的阶段, 以内壁屈服到外壁也进入屈服的 阶段。B点表示容器已进入整体 屈服状态。如果容器的钢材具有 屈服平台,这阶段包含塑性变形 越过屈服平台的阶段,这是一个 包含复杂过程的阶段,不同的容 器、不同的材料,这一阶段的形 状与长短不同。
煤气化液化装置中的压力容器工作压力为 20MPa,工作温度为454ºC,最大内直径达 5000mm,壁厚为340 mm,重1900吨;
炼 油 厂 加 氢 反 应 器 的 直 径 达 4.5mm, 厚 280mm, 重约1000吨。
高温蠕变 低应力脆断 疲劳问题
压力容器检验师培训
5
第一节 压力容器设计技术概述
爆破压力
(A)弹性变形阶段(OA段) (B)屈服阶段(AB段) (C)强化阶段(BC段) (D)爆破阶段(CD段)
压力容器检验师培训
12
第一节 压力容器设计技术概述
(一) 容器的超压爆破过程
韧性破坏-照片
压力容器检验师培训
13
第一节 压力容器设计技术概述
2.容器的脆性爆破过程 现象:低应力,体积变形很小,无明 显塑性变形 危害:无征兆、很多产生碎片、带来 灾难性后果 原因:1)材料很脆,2)有严重缺陷
压力容器强度及疲劳设计
压力容器强度及疲劳设计
第一节 第二节 第三节 第四节
压力容器设计技术概述 压力容器常规设计技术 压力容器应力分析设计 压力容器的疲劳及高温蠕变
压力容器检验师培训
2
压力容器强度及疲劳设计
第一节 压力容器设计技术概述 一、压力容器的失效模式 二、压力容器设计准则的发展 三、压力容器设计规范的主要进展 四、近代设计方法的应用
(A)弹性变形阶段(OA段) (B)屈服阶段(AB段) (C)强化阶段(BC段) (D)爆破阶段(CD段)
素。强化的变化率逐渐降低,到
C点时两种影响相等,达到总体
“塑性失稳”状态,承载能力达
到最大即将爆破,此时容器已充
分膨胀。
压力容器检验师培训
10
第一节 压力容器设计技术概述
(一) 容器的超压爆破过程 (4)爆破阶段 在CD段,减薄的影 响大于强化的影响,容器的承载 能力随着容器的大量膨胀而明显 下降,壁厚迅速减薄,直至D点 而爆裂。
(A)弹性变形阶段(OA段) (B)屈服阶段(AB段) (C)强化阶段(BC段) (D)爆破阶段(CD段)
压力容器检验师培训
9
第一节 压力容器设计技术概述
(一) 容器的超压爆破过程
(3)变形强化阶段 BC段,材料
发生塑性变形不断强化,容器承
载能力不断提高。但体积膨胀使 壁厚减薄,承载能力下降。两者 中强化影响大于减薄影响,强化 提高承载能力的行为变成主要因
压力容器检验师培训
14
第一节 压力容器设计技术概述
2.容器的脆性爆破过程 容器的脆性爆破过程如图中OA’,
(或OA”)曲线。这种爆破指容器在加 压过程中没有发生充分的塑性变形鼓 胀,甚至尚未达到屈服的时候就发生 爆破。爆破时容器尚在弹性变形阶段 至多是少量屈服变形阶段。
(A)弹性变形阶段(OA段) (B)屈服阶段(AB段) (C)强化阶段(BC段) (D)爆破阶段(CD段)
(A)弹性变形阶段(OA段) (B)屈服阶段(AB段) (C)强化阶段(BC段) (D)爆破阶段(CD段)
压力容器检验师培训
11
第一节 压力容器设计技术概述
(一) 容器的超压爆破过程 C点的内压力为爆破压力,正
常韧性爆破的容器,爆破的体积 膨胀量(即进液量)在容器体积的 10%以上,该值越高,容器的韧 性越好,材料的塑性韧性和制造 质量都很好,该容器在设计压力 下很安全。承受的压力,爆破压 力越高,爆破压力与设计压力的 比值越大则越安全。
整体屈 服压力
爆破压力
(A)弹性变形阶段(OA段) (B)屈服阶段(AB段) (C)强化阶段(BC段) (D)爆破阶段(CD段)
压力容器检验师培训
7
第一节 压力容器设计技术概述
(一) 容器的超压爆破过程 (1)弹性变形阶段 见OA,随 着进液量(即体积膨胀量)的 增加,容器的变形增大,内 压随之上升。这一阶段的基 本特征是内压与容器变形量 成正比,呈现出弹性行为。 A点表示内壁应力开始屈服, 或表示容器的局部区域出现 屈服,整个容器的整体弹性 行为到此终止。
压力容器检验师培训
19
第一节 压力容器设计技术概述
一、容器的失效模式 1.容器常见的失效模式
(3) 脆性爆破 这是一种没有经过充分塑性 大变形的容器破裂失效。材料的脆性和严重的 超标缺陷均会导致这种破裂,或者两种原因兼 有。脆性爆破时容器可能裂成碎片飞出,也可 能仅沿纵向裂开一条缝;材料愈脆,特别是总 体上愈脆则愈易形成碎片。如果仅是焊缝或热 影响区较脆,则易裂开一条缝。形成碎片的脆 性爆破特别容易引起灾难性后果。
容器的韧性爆破和脆性爆破是容器 爆破的两种基本典型的形式。实际容 器的失效不一定是爆破,而有更多的 原因和模式,下面将讨论容器的失效 模式问题和容器设计应采用的相应的 准则
(A)弹性变形阶段(OA段) (B)屈服阶段(AB段) (C)强化阶段(BC段) (D)爆破阶段(CD段)
压力容器检验师培训
17
(7) 失稳失效 容器在外压(包括真空)的压应力作用下丧失稳定性而发生 的皱折变形称为失稳失效。皱折可以是局部的也可以是总体的。高塔在过大的 轴向压力(风载、地震载荷)作用下也会皱折而引起倒塌。
压力容器检验师培训
24
第一节 压力容器设计技术概述
一、容器的失效模式 1.容器常见的失效模式
(8) 泄漏失效 容器及管道可拆密封部位的密封系统中每一个零部件的失 效都会引起泄漏失效。例如法兰的刚性不足导致法兰的过度变形而影响对垫片 的压紧,紧固螺栓因设计不当或锈蚀而过度伸长也会导致泄漏,垫片的密封比 压不足、垫片老化缺少反弹能力都会引起泄漏失效。系统中每一零部件均会导 致泄漏失效,所以密封失效不是一个独立的失效模式,而是综合性的。
第一节 压力容器设计技术概述
一、容器的失效模式
1.容器常见的失效模式
(1) 过度变形 容器的总体或局部发生过度变形,
包括过量的弹性变形,过量的塑性变形,塑性失稳
(增量垮坍),例如总体上大范围鼓胀,或局部鼓胀,
应认为容器已失效,不能保障使用安全。过度变形
说明容器在总体上或局部区域发生了塑性失效,处
于十分危险的状态。例如法兰的设计稍薄,强度上
压力容器检验师培训
20
第一节 压力容器设计技术概述
一、容器的失效模式
1.容器常见的失效模式
疲劳辉纹(×3000)
(4) 疲劳失效 交变载荷容易使容器的应力集中部位材料发生疲
劳损伤,萌生疲劳裂纹并扩展导致疲劳失效。疲劳失效包括材料
的疲劳损伤(形成宏观裂纹)并疲劳扩展和结构的疲劳断裂等情况。
容器疲劳断裂的最终失效方式一种是发生泄漏,称为“未爆先
(A)弹性变形阶段(OA段) (B)屈服阶段(AB段) (C)强化阶段(BC段) (D)爆破阶段(CD段)
压力容器检验师培训
16
第一节 压力容器设计技术概述
2.容器的脆性爆破过程 脆性爆破的容器由于体积变形量很
小,其安全裕量很少,应竭力防止。 发生脆断,容器爆裂出碎片飞出,产 生极大的危害,带来灾难性的后果。
漏”(LBB, Leak Before Break),另一种是爆破,可称为“未漏先
爆”。爆裂的方式取决于结构的厚度、材料的韧性,并与缺陷的
大小有关。疲劳裂纹的断口上一般会留下肉眼可见的贝壳状的疲
劳条纹。
压力容器检验师培训
21
第一节 压力容器设计技术概述
一、容器的失效模式 1.容器常见的失效模式
(5) 蠕变失效 容器长期在高温下运行和受载,金属材料会随时间不断发生 蠕变损伤,逐步出现明显的鼓胀与减薄,破裂而成事故。即使载荷恒定和应力 低于屈服点也会发生蠕变失效,不同材料在高温下的蠕变行为有所不同。 材料高温下的蠕变损伤是晶界的弱化和在应力作用下的沿晶界的滑移,晶 界上形成蠕变空洞。时间愈长空洞则愈多愈大,宏观上出现蠕变变形。 当空洞连成片并扩展时即形成蠕变裂纹,最终发生蠕变断裂的事故。 材料经受蠕变损伤后在性能上表现出强度下降和韧性降低,即蠕变脆化。 蠕变失效的宏观表现是过度变形(蠕胀),最终是由蠕变裂纹扩展而断裂(爆破 或泄漏)。