XX公司硫酸DCS控制系统简介
DCS系统简介1
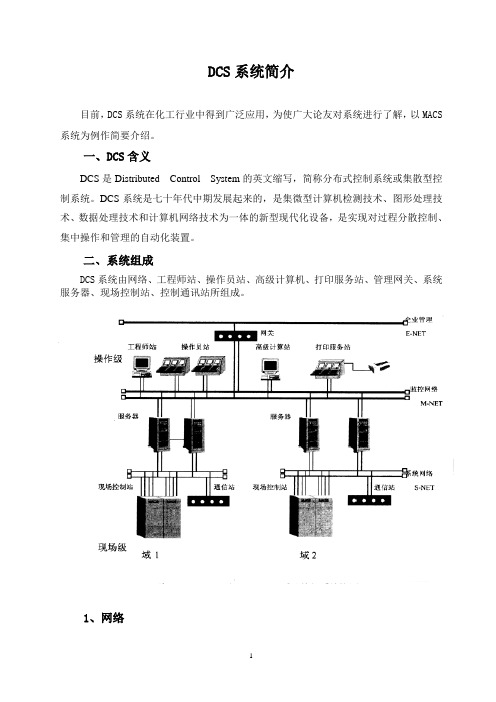
DCS系统简介目前,DCS系统在化工行业中得到广泛应用,为使广大论友对系统进行了解,以MACS 系统为例作简要介绍。
一、DCS含义DCS是Distributed Control System的英文缩写,简称分布式控制系统或集散型控制系统。
DCS系统是七十年代中期发展起来的,是集微型计算机检测技术、图形处理技术、数据处理技术和计算机网络技术为一体的新型现代化设备,是实现对过程分散控制、集中操作和管理的自动化装置。
二、系统组成DCS系统由网络、工程师站、操作员站、高级计算机、打印服务站、管理网关、系统服务器、现场控制站、控制通讯站所组成。
1、网络以MACS系统为例:系统网络由上至下分为三个层次:监控网络、系统网络和控制网络。
①监控网络(M—NET)由10M/100M高速冗余以太网构成,用于系统服务器与现场控制站、通信控制站等的连接。
完成现场控制站、通讯控制站的数据下装,服务器与现场控制站、通讯控制站之间的实时数据通讯。
②系统网络(S—NET)由10M ARCNET网构成,用于连接现场控制站和服务器之间的通信。
③控制网络(C—NET)由PROFIBUS-DP构成,可兼容CAN、FF、MODBUS等多种现场总线网络,用来与现场控制站主控单元和过程I/O(信号输入输出模板)单元的通信,完成实时输入、输出数据传送服务的专用网络系统。
2、工程师站它是由工业PC机和各种组态软件工具组成,主要用以完成以下功能:组态:完成数据库、图形、控制算法、报表的组态;参数配置:简化历史库、事故追忆、变量组定义等;设备组态:实现应用系统的操作员站、服务器、现场控制站及过程I/O模块的配置等;数据下装和增量下装:将组态后的数据下装到服务器、操作员站,在线运行时,还可通过增量下装的形式修改数据库和控制算法。
应用软件:MACS专用组态软件,可选装MACS专用操作员软件。
3、操作员站操作员站是操作人员使用的设备,操作员站的监控软件是最重要的人机交互界面,能使操作人员通过薄膜键盘、轨迹球灵活方便地监控过程。
DCS系统在硫酸制造中的应用
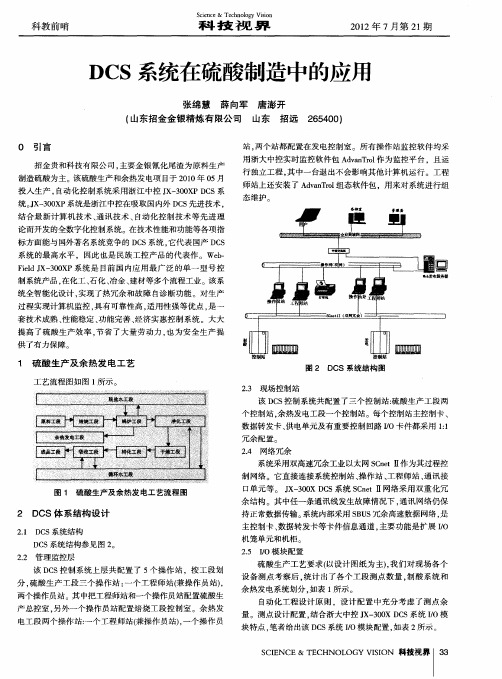
站, 两个站都 配置在发电控制室 。所有 操作站监控 软件均采
用浙 大中控实时监控软件包 A vn r 作为监控 平台 ,且运 daTo l
行独立工 程 , 其中一台退出不会影 响其他 计算机运行 。工程
师站上还安装 了 A vn rl 态软件包 .用来对 系统进 行组 d aTo组
态维护 。
娄 型 P lo t0 ^ , 0i I4 Ia -2 l : ∞n 4 一 ^ 0 疆 D 0
工鞍
埘 料 [
惜 蜘
热电阻
热电■
l 9
( % = 喇)
l O
( 人)
l O
4 ∞t . 一 a g
千^意 蛙 电舟
3
≮| 。 。 _
’ 辕 % 雾零霪霉嚣 毫 ’l
S E E&T C CINC E HNO OG II L Y V SON 科技视 界 l 3 3
l
S in e& Te h oo y V s n ce c c n l g ii o
21 02年 7月第 2 期 l
科 技 视 界
科教前哨
表 1 系统 I 点 统计 / 0
表 2 控 制站 I , 块 配 置 0模
| 0
藏 蹭 黎
掰一# 。 。
净化 千暧
艚 化
3 l 9
l ’ பைடு நூலகம்t :
i 8 2 ,
8
3 8
4
I O 2 6
3 0
枷
F劭 r 作 s
鹰幅
糟 环 球 0 ( } 0
3
I 8
2
O
l 2
l 8
S in e& T eh l g io ce c c noo yV s n i
DCS控制系统介绍
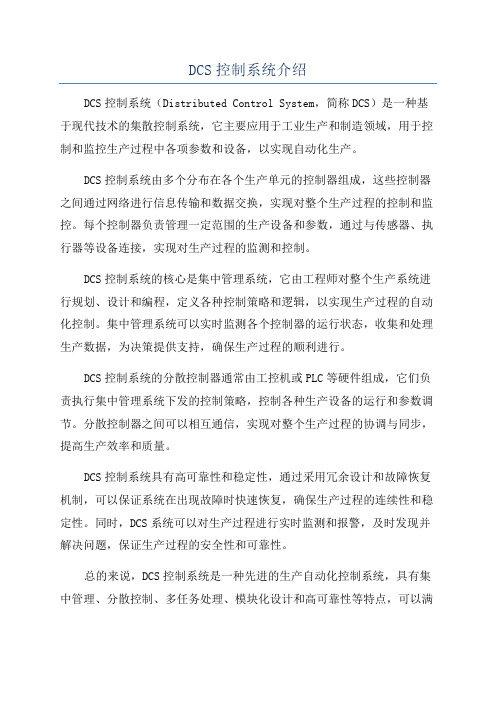
DCS控制系统介绍
DCS控制系统(Distributed Control System,简称DCS)是一种基于现代技术的集散控制系统,它主要应用于工业生产和制造领域,用于控制和监控生产过程中各项参数和设备,以实现自动化生产。
DCS控制系统由多个分布在各个生产单元的控制器组成,这些控制器之间通过网络进行信息传输和数据交换,实现对整个生产过程的控制和监控。
每个控制器负责管理一定范围的生产设备和参数,通过与传感器、执行器等设备连接,实现对生产过程的监测和控制。
DCS控制系统的核心是集中管理系统,它由工程师对整个生产系统进行规划、设计和编程,定义各种控制策略和逻辑,以实现生产过程的自动化控制。
集中管理系统可以实时监测各个控制器的运行状态,收集和处理生产数据,为决策提供支持,确保生产过程的顺利进行。
DCS控制系统的分散控制器通常由工控机或PLC等硬件组成,它们负责执行集中管理系统下发的控制策略,控制各种生产设备的运行和参数调节。
分散控制器之间可以相互通信,实现对整个生产过程的协调与同步,提高生产效率和质量。
DCS控制系统具有高可靠性和稳定性,通过采用冗余设计和故障恢复机制,可以保证系统在出现故障时快速恢复,确保生产过程的连续性和稳定性。
同时,DCS系统可以对生产过程进行实时监测和报警,及时发现并解决问题,保证生产过程的安全性和可靠性。
总的来说,DCS控制系统是一种先进的生产自动化控制系统,具有集中管理、分散控制、多任务处理、模块化设计和高可靠性等特点,可以满
足各种工业生产领域的自动化控制需求,提高生产效率,节约成本,保证生产质量,是工业生产自动化的重要技术手段。
DCS系统介绍范文
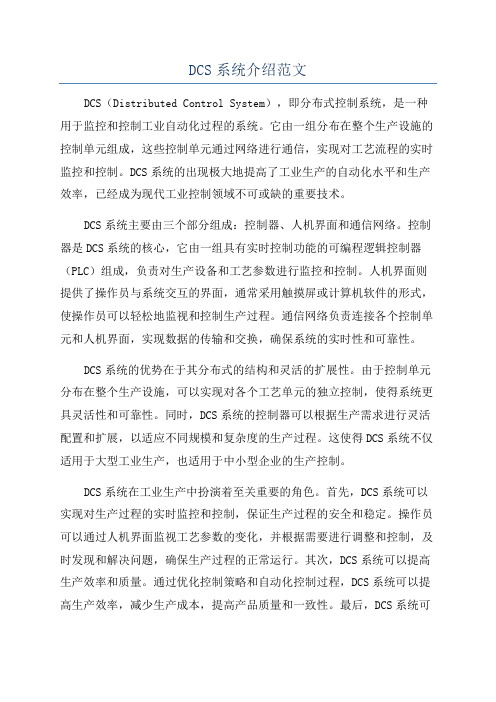
DCS系统介绍范文DCS(Distributed Control System),即分布式控制系统,是一种用于监控和控制工业自动化过程的系统。
它由一组分布在整个生产设施的控制单元组成,这些控制单元通过网络进行通信,实现对工艺流程的实时监控和控制。
DCS系统的出现极大地提高了工业生产的自动化水平和生产效率,已经成为现代工业控制领域不可或缺的重要技术。
DCS系统主要由三个部分组成:控制器、人机界面和通信网络。
控制器是DCS系统的核心,它由一组具有实时控制功能的可编程逻辑控制器(PLC)组成,负责对生产设备和工艺参数进行监控和控制。
人机界面则提供了操作员与系统交互的界面,通常采用触摸屏或计算机软件的形式,使操作员可以轻松地监视和控制生产过程。
通信网络负责连接各个控制单元和人机界面,实现数据的传输和交换,确保系统的实时性和可靠性。
DCS系统的优势在于其分布式的结构和灵活的扩展性。
由于控制单元分布在整个生产设施,可以实现对各个工艺单元的独立控制,使得系统更具灵活性和可靠性。
同时,DCS系统的控制器可以根据生产需求进行灵活配置和扩展,以适应不同规模和复杂度的生产过程。
这使得DCS系统不仅适用于大型工业生产,也适用于中小型企业的生产控制。
DCS系统在工业生产中扮演着至关重要的角色。
首先,DCS系统可以实现对生产过程的实时监控和控制,保证生产过程的安全和稳定。
操作员可以通过人机界面监视工艺参数的变化,并根据需要进行调整和控制,及时发现和解决问题,确保生产过程的正常运行。
其次,DCS系统可以提高生产效率和质量。
通过优化控制策略和自动化控制过程,DCS系统可以提高生产效率,减少生产成本,提高产品质量和一致性。
最后,DCS系统可以实现远程监控和控制,使得操作员可以远程监控和控制生产过程,提高生产的灵活性和效率。
总的来说,DCS系统是现代工业生产中不可或缺的重要技术,其优势在于分布式的结构和灵活的扩展性,可以实现对生产过程的实时监控和控制,提高生产效率和质量,确保生产过程的安全和稳定。
硫酸dcs系统培训

功能符号: I:指示 A:报警 G:监视 R:记录 Q:积算 Z:紧急动作 C:调节 Y:运算 S:联锁 仪表常用符号说明: SP:设定值 RSP:远方设定值 LSP:本机设定值 PV:测量值 OP或OUT:输出值 OPEN:打开 CLOSE或SHUT:关闭 ON:接通 OFF:断开 PC:气开式阀门(有气就开,气大阀门开度大) PO:气闭式阀门(有气就关闭,气大阀门开度小) PV>SP:为正偏差 PV<SP:为负偏差 DA:调节器正作用(当PV>SP时,调节器输出增大) RA:调节器反作用(当PV>SP时,调节器输出减小)
硫酸分厂常用仪表介绍
常用压力测量仪表 常用物位测量仪表 常用温度测量仪表 常用流量测量仪表 常用成分分析测量仪表 阀门
常用压力测量仪表
压力测量是工业生产中测量最为常用的测量参数,比如:炉膛和烟道压力、 锅炉汽包压力。在现场液位测量表中,常用的是液柱式压力计,常以水或 水银为工作液.一般常用于低压,负压和压力差的测量. 根据U型玻璃管中的 工作液不同,实际换算的压力值也不同。U型管压力计的测量原理: 将压力 计的一端接被测压力,另一端与大气相通,此时,可由管内工作液的垂直高度 差测知被测压力的表压值 。在判断控制仪表是否出现故障时,可以在现场 借助U型管压力计所估算值,作为参考。以下是单位换算: 1Mpa=1000000Pa 1毫米水柱(mmH2O)=9.80665Pa 1毫米汞柱(mmHg)=133.322Pa 1工程大气压(kgf/cm2)=98066.5pa 1物理大气压(atm)=101325Pa
压力定义 压力是垂直于作用在单位面积的力,即物理意义上的压强。工程上将 压强称为压力。 由于测压的参考点不同,工程上压力有3种表示:绝对压力Pa、表压P、 真空度或负压Pv。
DCS 控制系统介绍

DCS 控制系统介绍DCS 系统是随着现代大型工业生产自动化的不断兴起和过程控制要求的日益复杂应运而生的综合控制系统,它是计算机技术、系统控制技术、网络通讯技术和多媒体技术相结合的产物,可提供窗口友好的人机界面和强大的通讯功能。
是完成过程控制、过程管理的现代化设备。
DCS 集散系统 : DCS 英文全称 DISTRIBUTED CONTROL SYSTEM , 中文全称为集散型控制系统。
DCS 可以解释为在模拟量回路控制较多的行业中广泛使用的,尽量将控制所造成的危险性分散 , 而将管理和显示功能集中的一种自动化高技术产品。
DCS 系统一般由五部份组成: 1. 控制器; 2.I/O 板; 3. 操作站;4. 通讯网络;5. 图形及编程软件。
系统的主要技术概述系统主要有现场控制站( I/O 站)、数据通讯系统、人机接口单元(操作员站OPS 、工程师站 ENS )、机柜、电源等组成。
系统具备开放的体系结构,可以提供多层开放数据接口。
硬件系统在恶劣的工业现场具有高度的可靠性、维修方便、工艺先进。
底层汉化的软件平台具备强大的处理功能,并提供方便的组态复杂控制系统的能力与用户自主开发专用高级控制算法的支持能力;易于组态,易于使用。
支持多种现场总线标准以便适应未来的扩充需要。
系统设计采用合适的冗余配置和诊断至模件级的自诊断功能,具有高度的可靠性。
系统内任一组件发生故障,均不会影响整个系统的工作。
系统的参数、报警、自诊断及其他管理功能高度集中在 CRT 上显示和在打印机上打印,控制系统在功能和物理上真正分散。
整个系统的可利用率至少为 99.9 %;系统平均无故障时间为 10 万小时,实现了核电、火电、热电、石化、化工、冶金、建材诸多领域的完整监控。
“ 域” 的概念。
把大型控制系统用高速实时冗余网络分成若干相对独立的分系统,一个分系统构成一个域,各域共享管理和操作数据,而每个域内又是一个功能完整的 DCS 系统,以便更好的满足用户的使用。
DCS系统介绍
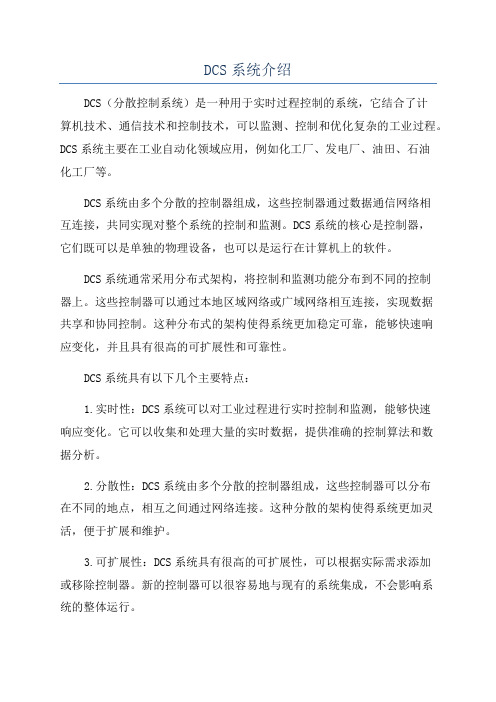
DCS系统介绍DCS(分散控制系统)是一种用于实时过程控制的系统,它结合了计算机技术、通信技术和控制技术,可以监测、控制和优化复杂的工业过程。
DCS系统主要在工业自动化领域应用,例如化工厂、发电厂、油田、石油化工厂等。
DCS系统由多个分散的控制器组成,这些控制器通过数据通信网络相互连接,共同实现对整个系统的控制和监测。
DCS系统的核心是控制器,它们既可以是单独的物理设备,也可以是运行在计算机上的软件。
DCS系统通常采用分布式架构,将控制和监测功能分布到不同的控制器上。
这些控制器可以通过本地区域网络或广域网络相互连接,实现数据共享和协同控制。
这种分布式的架构使得系统更加稳定可靠,能够快速响应变化,并且具有很高的可扩展性和可靠性。
DCS系统具有以下几个主要特点:1.实时性:DCS系统可以对工业过程进行实时控制和监测,能够快速响应变化。
它可以收集和处理大量的实时数据,提供准确的控制算法和数据分析。
2.分散性:DCS系统由多个分散的控制器组成,这些控制器可以分布在不同的地点,相互之间通过网络连接。
这种分散的架构使得系统更加灵活,便于扩展和维护。
3.可扩展性:DCS系统具有很高的可扩展性,可以根据实际需求添加或移除控制器。
新的控制器可以很容易地与现有的系统集成,不会影响系统的整体运行。
4.可靠性:DCS系统具有很高的可靠性,它可以实现冗余配置,以确保系统在控制器故障或通信故障的情况下仍然正常运行。
此外,DCS系统还可以进行故障诊断和预测,及时发现和修复故障,减少停机时间。
5.开放性:DCS系统采用开放的标准和协议,可以与其他系统和设备进行集成。
例如,它可以与企业资源计划(ERP)系统、质量管理系统、人机界面(HMI)等系统相连接,实现数据共享和协同工作。
DCS系统可以实现多种控制策略,例如PID控制、模型预测控制、优化控制等。
它可以对工业过程进行自动化控制,提高生产效率和产品质量,减少能源消耗和废品产生。
DCS系统的介绍
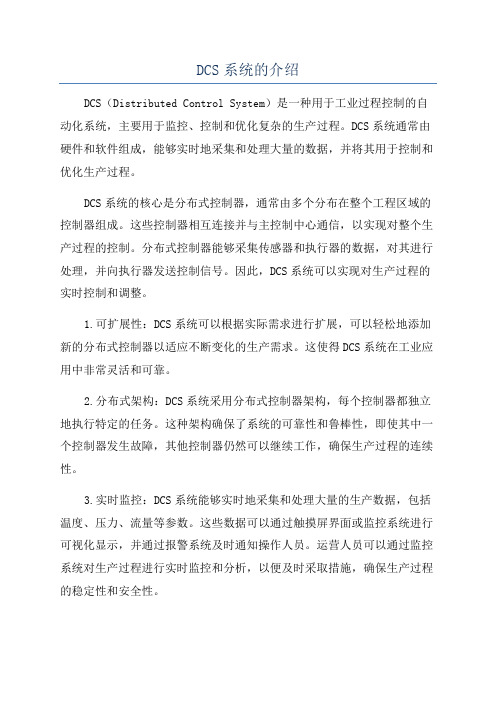
DCS系统的介绍DCS(Distributed Control System)是一种用于工业过程控制的自动化系统,主要用于监控、控制和优化复杂的生产过程。
DCS系统通常由硬件和软件组成,能够实时地采集和处理大量的数据,并将其用于控制和优化生产过程。
DCS系统的核心是分布式控制器,通常由多个分布在整个工程区域的控制器组成。
这些控制器相互连接并与主控制中心通信,以实现对整个生产过程的控制。
分布式控制器能够采集传感器和执行器的数据,对其进行处理,并向执行器发送控制信号。
因此,DCS系统可以实现对生产过程的实时控制和调整。
1.可扩展性:DCS系统可以根据实际需求进行扩展,可以轻松地添加新的分布式控制器以适应不断变化的生产需求。
这使得DCS系统在工业应用中非常灵活和可靠。
2.分布式架构:DCS系统采用分布式控制器架构,每个控制器都独立地执行特定的任务。
这种架构确保了系统的可靠性和鲁棒性,即使其中一个控制器发生故障,其他控制器仍然可以继续工作,确保生产过程的连续性。
3.实时监控:DCS系统能够实时地采集和处理大量的生产数据,包括温度、压力、流量等参数。
这些数据可以通过触摸屏界面或监控系统进行可视化显示,并通过报警系统及时通知操作人员。
运营人员可以通过监控系统对生产过程进行实时监控和分析,以便及时采取措施,确保生产过程的稳定性和安全性。
4.网络通信:DCS系统采用高速稳定的网络通信协议,可以实现控制器之间的快速数据传输和通信。
这使得控制器可以进行实时的数据交换和协作,以实现协调控制和优化生产过程。
5.灵活的编程语言:DCS系统通常提供多种编程语言和开发工具,使控制系统的编程和调整变得更加灵活和方便。
这些编程语言包括基于图形的编程环境、函数块图、状态图等,可根据用户的需求和经验进行定制。
6.故障诊断和维护:DCS系统通常具备自动故障诊断和维护功能。
系统可以自动监测设备状态和性能,如果发现故障,可以发送警报并定位问题所在。
DCS系统的介绍

DCS系统的介绍DCS(分布式控制系统)是一种集成了过程控制、数据采集、通信、运算和显示等功能的自动化控制系统。
它主要应用于诸如发电厂、化工厂、石油化工、冶金、制药、水处理、水电站等领域。
DCS系统通过集中控制器、工作站、输入/输出子系统、通信网络等构成,实现对整个系统的实时监控和自动控制。
1.集中控制器(CPU):集中控制器是DCS系统的核心,负责实时监控和控制系统的各种参数。
它可以处理来自传感器和执行器的输入和输出信号,执行控制算法,并向操作员提供实时数据。
2.工作站:DCS系统通常包括一台或多台工作站,用于操作员监控和操纵系统。
工作站提供了人机界面,使操作员能够查看关键数据、趋势图、报警信息等。
通过工作站,操作员可以对系统进行调整和优化,实现最佳控制效果。
3.输入/输出子系统:输入/输出子系统负责将传感器和执行器与DCS系统进行连接。
它包括模拟输入、模拟输出、数字输入、数字输出等接口模块,用于将各种信号转换为数字信号,以便于集中控制器的处理。
4.通信网络:DCS系统中的各个组件通过通信网络进行连接。
通信网络是实现数据传输和交换的重要一环,它可以是以太网、现场总线、红外线通信等。
通信网络高效稳定的运行是确保DCS系统正常运行的关键。
1.高度集成:DCS系统集成了过程控制、数据采集、通信、运算和显示等功能,可以实现对整个系统的一体化管理,提高工作效率和生产效益。
2.实时监控:DCS系统可以提供实时的数据和趋势图,使操作员对系统状态进行实时监控和分析。
这样,操作员可以及时发现和处理潜在问题,保证生产过程的稳定性和安全性。
3.灵活可扩展:DCS系统可以根据实际需要进行灵活扩展和升级。
用户可以根据生产线的变化进行系统配置和改造,以适应新的生产要求。
4.可靠性高:DCS系统采用了分布式架构,其中集中控制器、工作站和输入/输出子系统等可以实现冗余备份,提高了系统的可靠性和稳定性。
5.易于操作:DCS系统提供了友好的用户界面和操作方法,使操作员能够轻松地操作和管理系统。
DCS控制系统简介
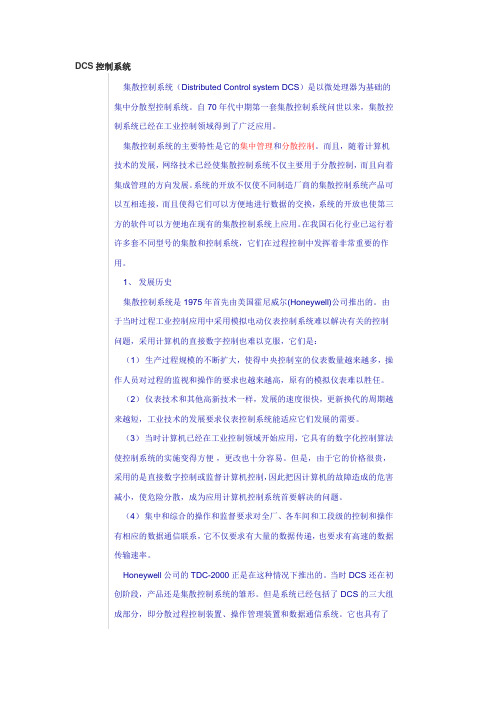
DCS控制系统集散控制系统(Distributed Control system DCS)是以微处理器为基础的集中分散型控制系统。
自70年代中期第一套集散控制系统问世以来,集散控制系统已经在工业控制领域得到了广泛应用。
集散控制系统的主要特性是它的集中管理和分散控制。
而且,随着计算机技术的发展,网络技术已经使集散控制系统不仅主要用于分散控制,而且向着集成管理的方向发展。
系统的开放不仅使不同制造厂商的集散控制系统产品可以互相连接,而且使得它们可以方便地进行数据的交换,系统的开放也使第三方的软件可以方便地在现有的集散控制系统上应用。
在我国石化行业已运行着许多套不同型号的集散和控制系统,它们在过程控制中发挥着非常重要的作用。
1、发展历史集散控制系统是1975年首先由美国霍尼威尔(Honeywell)公司推出的。
由于当时过程工业控制应用中采用模拟电动仪表控制系统难以解决有关的控制问题,采用计算机的直接数字控制也难以克服,它们是:(1)生产过程规模的不断扩大,使得中央控制室的仪表数量越来越多,操作人员对过程的监视和操作的要求也越来越高,原有的模拟仪表难以胜任。
(2)仪表技术和其他高新技术一样,发展的速度很快,更新换代的周期越来越短,工业技术的发展要求仪表控制系统能适应它们发展的需要。
(3)当时计算机已经在工业控制领域开始应用,它具有的数字化控制算法使控制系统的实施变得方便,更改也十分容易。
但是,由于它的价格很贵,采用的是直接数字控制或监督计算机控制,因此把因计算机的故障造成的危害减小,使危险分散,成为应用计算机控制系统首要解决的问题。
(4)集中和综合的操作和监督要求对全厂、各车间和工段级的控制和操作有相应的数据通信联系,它不仅要求有大量的数据传递,也要求有高速的数据传输速率。
Honeywell公司的TDC-2000正是在这种情况下推出的。
当时DCS还在初创阶段,产品还是集散控制系统的雏形。
但是系统已经包括了DCS的三大组成部分,即分散过程控制装置、操作管理装置和数据通信系统。
DCS在硫酸生产和余热发电项目中的应用

DCS在硫酸生产和余热发电项目中的应用1 引言国大黄金冶炼股份有限公司主要以金银冶炼,电解铜,硫酸生产为主。
该硫酸生产和余热发电项目于2005年10月投入生产,自动化工程采用浙大中控JX-300X DCS控制系统。
JX-300X DCS是浙大中控WebField集散控制系统家族重要成员,该系统全智能化设计,实现了热冗余和故障自诊断功能。
对生产过程实现计算机监控,具有可靠性高,适用性强等优点,是一套技术成熟、性能稳定、功能完善、经济实惠控制系统。
大大提高了硫酸生产效率,节省了大量劳动力,也为生产正常进行提供了有力保障。
2 硫酸生产及余热发电工艺硫酸生产及余热发电工艺流程图如图1所示。
图1 硫酸生产及余热发电工艺流程图3 DCS体系结构设计3.1 DCS系统结构DCS系统结构参见图2。
图2 DCS系统结构图3.2 管理监控层该DCS控制系统上层共配置了5个操作站,按工段划分,硫酸生产工段三个操作站:一个工程师站(兼操作员站),两个操作员站。
其中把工程师站和一个操作员站配置硫酸生产总控室,另外一个操作员站配置焙烧工段控制室。
余热发电工段两个操作站:一个工程师站(兼操作员站),一个操作员站,两个站都配置发电控制室。
所有操作站监控软件均采用浙大中控实时监控软件包AdvanTrol作为监控平台,且运行独立工程,其中一台退出不会影响其他计算机运行。
工程师站上还安装了AdvanTrol组态软件包,用来对系统进行组态维护。
3.3 现场控制站该DCS控制系统共配置了三个控制站:硫酸生产工段两个控制站,余热发电工段一个控制站。
每个控制站主控制卡、数据转发卡、供电单元及有重要控制回路I/O卡件都采用1:1冗余配置。
3.4 网络冗余系统采用双高速冗余工业以太网SCnet Ⅱ作为其过程控制网络。
它直接连接系统控制站、操作站、工程师站、通讯接口单元等. JX-300X DCS系统SCnet Ⅱ网络采用双重化冗余结构。
其中任一条通讯线发生故障情况下,通讯网络仍保持正常数据传输。
DCS控制系统介绍
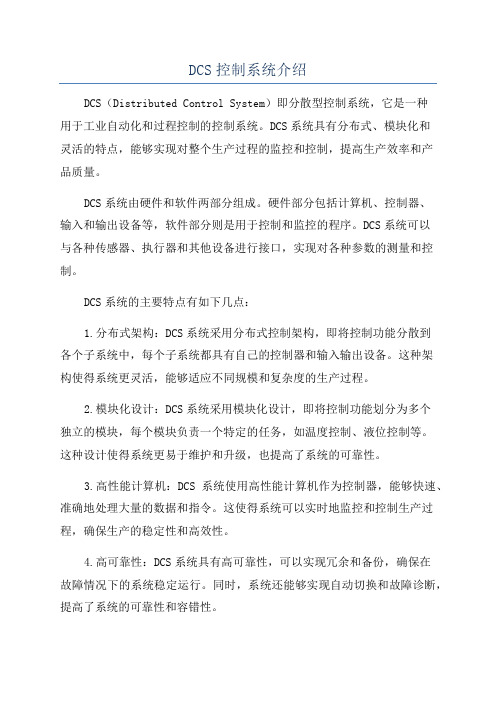
DCS控制系统介绍DCS(Distributed Control System)即分散型控制系统,它是一种用于工业自动化和过程控制的控制系统。
DCS系统具有分布式、模块化和灵活的特点,能够实现对整个生产过程的监控和控制,提高生产效率和产品质量。
DCS系统由硬件和软件两部分组成。
硬件部分包括计算机、控制器、输入和输出设备等,软件部分则是用于控制和监控的程序。
DCS系统可以与各种传感器、执行器和其他设备进行接口,实现对各种参数的测量和控制。
DCS系统的主要特点有如下几点:1.分布式架构:DCS系统采用分布式控制架构,即将控制功能分散到各个子系统中,每个子系统都具有自己的控制器和输入输出设备。
这种架构使得系统更灵活,能够适应不同规模和复杂度的生产过程。
2.模块化设计:DCS系统采用模块化设计,即将控制功能划分为多个独立的模块,每个模块负责一个特定的任务,如温度控制、液位控制等。
这种设计使得系统更易于维护和升级,也提高了系统的可靠性。
3.高性能计算机:DCS系统使用高性能计算机作为控制器,能够快速、准确地处理大量的数据和指令。
这使得系统可以实时地监控和控制生产过程,确保生产的稳定性和高效性。
4.高可靠性:DCS系统具有高可靠性,可以实现冗余和备份,确保在故障情况下的系统稳定运行。
同时,系统还能够实现自动切换和故障诊断,提高了系统的可靠性和容错性。
5. 开放性:DCS系统是一个开放系统,可以与其他系统进行连接和通讯,如MES(Manufacturing Execution System)、ERP(Enterprise Resource Planning)等。
这种开放性使得系统更加灵活,可以实现工厂级别的集成和管理。
DCS系统主要应用于工业生产过程控制,如化工、电力、石油、制药等行业。
它可以实现对生产参数的实时监测和调节,确保产品的质量和安全,提高工艺的稳定性和效率。
总之,DCS控制系统是一种分散型、模块化和灵活的控制系统,能够实现对工业生产过程的监控和控制,提高生产效率和产品质量。
DCS系统介绍范文
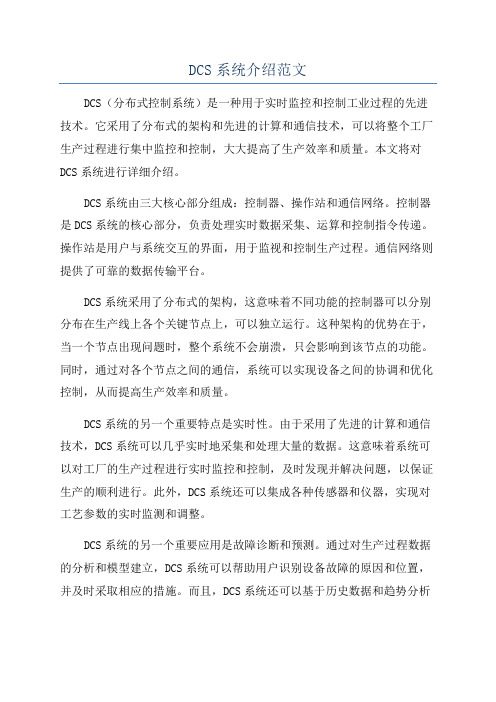
DCS系统介绍范文DCS(分布式控制系统)是一种用于实时监控和控制工业过程的先进技术。
它采用了分布式的架构和先进的计算和通信技术,可以将整个工厂生产过程进行集中监控和控制,大大提高了生产效率和质量。
本文将对DCS系统进行详细介绍。
DCS系统由三大核心部分组成:控制器、操作站和通信网络。
控制器是DCS系统的核心部分,负责处理实时数据采集、运算和控制指令传递。
操作站是用户与系统交互的界面,用于监视和控制生产过程。
通信网络则提供了可靠的数据传输平台。
DCS系统采用了分布式的架构,这意味着不同功能的控制器可以分别分布在生产线上各个关键节点上,可以独立运行。
这种架构的优势在于,当一个节点出现问题时,整个系统不会崩溃,只会影响到该节点的功能。
同时,通过对各个节点之间的通信,系统可以实现设备之间的协调和优化控制,从而提高生产效率和质量。
DCS系统的另一个重要特点是实时性。
由于采用了先进的计算和通信技术,DCS系统可以几乎实时地采集和处理大量的数据。
这意味着系统可以对工厂的生产过程进行实时监控和控制,及时发现并解决问题,以保证生产的顺利进行。
此外,DCS系统还可以集成各种传感器和仪器,实现对工艺参数的实时监测和调整。
DCS系统的另一个重要应用是故障诊断和预测。
通过对生产过程数据的分析和模型建立,DCS系统可以帮助用户识别设备故障的原因和位置,并及时采取相应的措施。
而且,DCS系统还可以基于历史数据和趋势分析对设备的未来故障进行预测,以提前进行维护和保养,避免生产中断和不必要的损失。
DCS系统在工业生产中起着至关重要的作用。
它可以监控和控制各种生产过程,如化工生产、电力生产、制造业等,提高生产的自动化程度和控制精度。
同时,DCS系统还可以更好地适应生产线的变化,并实时调整控制策略,以适应市场变化和对品质要求的提高。
然而,随着技术的不断进步,DCS系统面临着一些挑战。
首先是数据安全和网络安全问题。
由于DCS系统涉及到大量的数据采集和传输,数据泄露和攻击风险也随之增加。
我国硫酸装置自动控制系统介绍

用. 根据我们多 程设 年工 计及现场经 压力测量尤其是在净化、 验, 转化工段 气相压力 测量中 要着重
解决的问 题是,由 于侧压管路及根部阀门腐蚀而造成的堵塞.而解决这一问题的关键则在于根部
取压阀门的 和取压方式的 选型 采用。 对于净化工段应采用PC v 塑料或玻璃 钢球阀 作为根部取样阀 门引 , 压管采用PC 合管, 命近 v复 同时 根部的 测量管线应保证5抽 以 垂直尺寸。 以 . 上的 而转化工段
其中 和卜 m型智能化电 - 磁浓度计便是目 前国内 仪表中 应用厂家广泛且反映较好的一种。该 浓度计是在完成大量理化数据的回归分析后,建立了 溶液浓度与电导率、 温度之间的数学模型, 通过测量溶液的电导率与温度,由微处理器求得溶液的浓度, 具有侧量精度高, 温度补偿范围广
等优点,从而大大地提高了仪表的可靠性。目前产品己形成系列:9 ̄9 肠 氏、1 . ̄ 6 明 5 3 05
! 渐
圣国潇脚疗世雳去三属卒玲萝拜忿纷
2到九十年代初, . 随着计算机可靠性及性/ 价比的不断提高, 在硫酸生产中采用计算机控制是
技术进步的必然趋势。9 年, 1 3 9 宝鸡磷肥厂在国内硫酸行业首次采用非引进设备并具有综合控制、 监测、管理功能的 控制系统。随后葫芦岛锌厂、贵溪冶炼厂、云南云峰化学工业公司、苏州硫酸 厂等几十家硫酸装置均成功采用了以 万控制系统。 现简单介绍如下: 云南云峰化学工业公司 . a 采 用美国 西屋公司的和P I5 F 洲 系统,实现 2 k/ 硫酸装置的自 二 0 a 3t 动控制。该系统由四台D 刊、一台 工程师站 E 二台 璐、 操作站0 一台历史数据报表记录站HR 咫、 D 组成, 整个硫酸生产线的软件组态 修改、 监控、控制操作均可由戊5 完成。 其中二台DU P 作为分散控制单元,另二台作为分散控制 单元,以确保系统的可靠,系统构成图如图 1 所示。 E 提供所有软件工具及硬件设备维护和组态系统, 璐 用它定义过程点,组态数据库, 建立图
(完整版)集散控制系统DCS简介

集散控制系统DCS简介DCS是以微型计算机为基础,将分散型控制装置,通信系统,集中操作与信息管理系统综合在一起的新型过程控制系统。
它是一个由过程控制级和过程监控级组成的以通信网络为纽带的多级计算机系统,综合了计算机(Computer)、通讯(Communication)、显示(CRT)和控制(Control)等4C技术,其基本思想是分散控制、集中操作、分级管理、配置灵活、组态方便。
采用了多层分级的结构,适用现代化生产的控制与管理需求,目前已成为工业过程控制的主流系统。
集散控制系统把计算机、仪表和电控技术融合在一起,结合相应的软件,可以实现数据自动采集、处理、工艺画面显示、参数超限报警、设备故障报警和报表打印等功能,并对主要工艺参数形成了历史趋势记录,随时查看,并设置了安全操作级别,既方便了管理,又使系统运行更加安全可靠。
其特点有:1、基于现场总线思想的I/O总线技术2、先进的冗余技术、带电插拔技术po3、完备的I/O信号处理4、基于客户/服务器应用结构5、WindowsNT平台,以太网,TCP/IP协议6、OPC服务器提供互连7、Web浏览器风格,ActiveX控件支持8、ODBC,OLE技术,实现信息,资源共享9、高性能的过程控制单元。
10、支持标准现场总线11、Internet/Intranet应用支持(1)高可靠性由于DCS将系统控制功能分散在各台计算机上实现,系统结构采用容错设计,因此某一台计算机出现的故障不会导致系统其它功能的丧失。
此外,由于系统中各台计算机所承担的任务比较单一,可以针对需要实现的功能采用具有特定结构和软件的专用计算机,从而使系统中每台计算机的可靠性也得到提高。
(2)开放性DCS采用开放式、标准化、模块化和系列化设计,系统中各台计算机采用局域网方式通信,实现信息传输,当需要改变或扩充系统功能时,可将新增计算机方便地连入系统通信网络或从网络中卸下,几乎不影响系统其他计算机的工作。
DCS在硫酸控制系统中的应用

2 硫酸系统改造
株洲 冶炼 集 团公 司 的硫 酸 系统 于 2000年 正 式投厂 运行 。原系统 采用 英国欧路 TS3500系统 ,由于 投入运 行 时 间较 长 ,系统 内的 许 多硬 件相 对 落 后 ,处 理 效果 较差 。为 了更好 的利用公 司有效 资源 ,提高 生产效 率 ,
行 业 应 用 与交流
ndustrial Applications and Com munications
《自动化技术与应用》 2016年第 35卷第 7期
DCS在硫酸控制系统 中的应用
何飞 勇
(株洲冶炼集团股份有限公司 ,湖南 株洲 412004)
摘 要 :针对 DCS控制系统在我公司制硫酸工艺 中的运用 ,主要从生产工艺 的角度 介绍 DCS控制系统 (集散控制 系统 )的性能及 现场总线技术 ,并从未来现场总线技术的发展的角度简述 FCS控制 (现场总线控制系统 )。
关键词 :硫酸工艺 ;现场总线 ;DCS(集散控制 系统 );FCS(现场总线控制系统 );AC 800M ;IFIXlMODBUSIOPC 中图分类号 :TP311.1 文献标识码 :B 文章编号 :1003—7241(2016)07—0099-03
Application of DCS in The Control System of Sulphuric Acid
自动化技术与应用》 016年第35卷第7期
2024年度-DCS控制系统
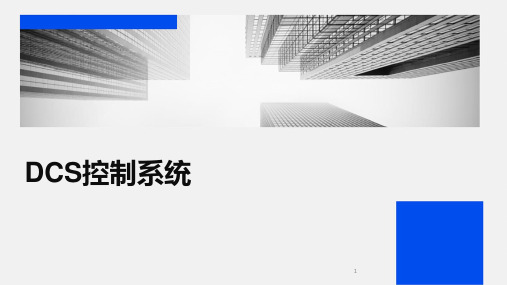
03
软件设计与实现
11
操作系统选择与优化
实时性
选择具有高实时性能的操作系 统,确保控制系统对输入信号
的快速响应。
稳定性
操作系统应具备高稳定性和可 靠性,以减少系统故障和停机 时间。
兼容性
操作系统应与各种硬件设备、 通信协议和编程语言具有良好 的兼容性,以降低开发难度和 成本。
优化资源分配
根据控制系统的实际需求,合 理分配计算资源,提高系统整
13
人机界面设计原则
直观性
界面设计应直观易懂,使用户能够快速了解 系统的运行状态和操作方式。
响应性
界面应对用户的操作做出及时响应,提供友 好的反馈和提示信息。
一致性
保持界面风格、操作方式和信息呈现的一致 性,降低用户学习成本。
可定制性
允许用户根据实际需求定制界面布局和功能 ,提高用户体验。
14
04
DCS控制系统基本概念和原理
深入讲解了DCS控制系统的定义、结构、工作原 理等基本概念。
DCS控制系统软件设计
系统阐述了DCS控制系统的软件设计流程、编程 语言、组态软件等方面的知识。
ABCD
DCS控制系统硬件组成
详细介绍了DCS控制系统的硬件设备,包括控制 器、输入输出模块、通信模块等。
DCS控制系统应用实例
软件设计与开发
采用模块化设计思想,开发适用于化 工工艺流程的控制算法和人机界面; 实现与上层管理系统的数据交互与集 成,提供实时数据监测、历史数据查 询、报警处理等功能。
Hale Waihona Puke 21实施效果评价及改进方向探讨
实施效果评价
通过引入DCS控制系统,化工厂生产过程自动化水平得到显著提升,生产效率提高20% 以上;产品质量更加稳定可靠,降低了不合格品率;同时减少了人工干预程度,降低了
- 1、下载文档前请自行甄别文档内容的完整性,平台不提供额外的编辑、内容补充、找答案等附加服务。
- 2、"仅部分预览"的文档,不可在线预览部分如存在完整性等问题,可反馈申请退款(可完整预览的文档不适用该条件!)。
- 3、如文档侵犯您的权益,请联系客服反馈,我们会尽快为您处理(人工客服工作时间:9:00-18:30)。
XX公司80万吨硫酸DCS控制系统简介
一、系统概述
XX公司80万吨/年硫酸项目中所配置的DCS系统选用了美国HONEYWELL公司最新的知识管理系统(Experior~PKS~System)。
该系统对各装置中现场设备的被测数据进行采集,并可根据用户需要进行数据处理及多种控制。
系统采用工业以太网网络,连接所有人机接口(HMI)、过程控制站以及安全管理控制器等节点,完成高速、容错通讯功能,采用遵循IEEE802.3工业标准协议的冗余实时控制网,通讯速率为10/100MB;下层为I/O网,连接着控制器与I/O模件。
系统按用户要求采用220V, 50Hz交流电源。
系统设置1个工程师站(全装置专用),采用冗余服务器的配置,用于修改控制策略,完成系统功能组态等。
工程师站设置有组态软件保护密码,以防一般人员擅自修改控制策略、应用程序和系统数据库。
全厂共设置5台操作员站(其中硫酸主控制室配置3台操作员站,余热发电控制室配置2台操作员站),对整个工艺流程进行监视、操作,也可组态定义虚拟工作区,实施分区操作。
其基本功能包括显示系统总貌,分组显示、回路显示、报警显示、系统状态显示、用户定义的生产流程动态显示、相关参数显示等。
系统过程控制站采用具有很高性能价格比的混合控制器C200,CPU设计采用 Power PC 603e 100MHz 处理器,每个控制器可带64块I/O模件,可同时完成500个以上回路控制和达到50ms快速逻辑处理(最快可达5ms)功能。
本方案配置的过程控制站及远程I/O站组成过程控制级,分别完成对各装置的数据采集(DAS)、模拟量控制(MCS)、顺序逻辑控制(SCS)等。
输入输出处理器(IOP)和现场接线端子板(FTA)可对现场信号进行扫描和处理。
多种类型IOP包括高电平模拟量输入卡(HLAI)、模拟量输出卡(AO)、开关量输入卡(DI)、开关量输出卡(DO)等,分别对相应信号进行采集和处理。
每个IOP都有CPU,可以独立工作,而与控制功能的处理完全分开。
这样就保证了较高的采样速率,同时发挥控制器最大控制能力。
可对每个通道智能自诊断,输入短路、开路、超量程等进行检查。
所有I/O卡件均为镀膜封装,具有防腐、防尘和防静电特性。
二、PKS系统硬件配置说明
1 、系统配置图:
2、DCS系统配置描述
控制器根据控制器根据I/O点表要求,PKS系统分散处理系统在硫酸控制室、余热发电控制室各配置一对冗余控制器,整个系统电源和通讯接口均为冗余配置。
控制站的I/O系统已配置了30%的备用点和10%的插槽空间。
3、系统监视平台
PKS系统用容错以太网架构组成单一的FTE系统网络,所有网络通讯模件,是1:1冗余的,并且可以接受双路外供电以保证其可靠性。
人机接口的配置按招标技术规范要求配置如下:
3.1、工程师站:系统的工程师站采用冗余配置2台服务器,以保证系统的高可靠性,服务器均采用DELL计算机,操作系统为Windows2003。
3.2、操作员站:系统共配置5个操作员站,分别为硫酸主控制室3台,余热发电控制室2台。
3.3、外围设备
系统配置2台UPS电源,分别在硫酸主控制室(5KVA)、余热发电及焙烧控制室(15KVA)。
4、机柜配置
PKS机柜规格为:高×宽×深=2200mm×800mm×800mm,前后开门。
5、通讯网络及设备
5.1、过程控制局域网
ExperionPKS系统的过程控制网络采用FTE控制网络来连接所有的控制站和I/O站。
FTE支持过程管理/过程控制(控制器与HMI之间)、点到点和I/O网络的通信。
通过冗余通讯或非冗余通信介质,数据传输速率最高可达到100/1000Mbits/s。
传输介质是光纤和STP(屏蔽双绞线)铜质电缆。
5.2、网络负荷计算
对每个FTE接口模件的缺省的NUT(网络刷新时间)的设置如下:
NUT Time = 10000 microseconds
Smax = 1
UMax = 20
Number of Repeaters = 0
Cable Length = 1000 Meters
Cable Usage = A+B
5.3 、 PC机接口
ExperionPKS系统配置了一个网络通讯接口ODA (开放数据存取),通过该接口,网络上的其他的计算机可以读取ExperionPKS系统中的数据。
ODA开放式数据存取功能:当第三方应用从ExperionPKS服务器中请求数据时,要使用ODA选项。
例如:
- 通过EXCEL读取数据
- 从ACCESS数据库中执行SQL语言
- 其它的PlantScape系统请求数据
- OPC客户机请求数据
- 用户的程序从PlantScape数据库取得数据
ODA 三个主要的选项如下:
1) ODBC驱动选项: 可以在其它应用,如ACCESS中使用SQL语言获取服务器的数据。
服务器数据库包括只读的ODBC表,包括点,事件历史和过程历史。
其特性包括:
- 开放的实时和历史数据读取
- 数据流量控制,避免影响性能
- 冗余数据源
- 完全的性能
2) OPC服务器:ExperionPKS OPC服务器允许第三方OPC客户应用读/写ExperionPKS点参数。
OPC服务器基于HONEYW ELL的HCI服务器工具,和OPC V1.0。
3) 网络服务器:此选项提供基于网络访问ExperionPKS服务器数据库的应用,
如:EXCEL 数据交换,网络节点接口和网络API选项
- MICROSOFT EXCEL数据交换允许从EXCEL获取ExperionPKS的实时或历史数据。
此选项可以读写一个或多个
ExperionPKS数据库。
且提供报表工具等.
- 网络节点接口允许ExperionPKS服务器可以读写其它ExperionPKS服务器的数据。
通过网络API可以从网络其它应用访问ExperionPKS服务器数据库。
通过C++或VISUAL BASIC获取ExperionPKS系统的数据。
5.4、 PC机接口厂管理网
Experion PKS系统通过以太网络与工厂管理网络互联,通过SQL 语言来查询Experion PKS系统数据库中的数据。
5.5 、电缆及连接配件
FTE控制网络电缆及以太网通讯电缆均随Experion PKS系统一起供货。
Experion PKS系统各设备之间的连接电缆和所用接插件也随Experion PKS系统一起供货,并留有足够的长度。
Experion PKS系统的内部电源系统电缆也随ExperionPKS系统一起供货。
各控制柜之间跨盘线均采用预制电缆。
硫酸主控制室与余热发电控制室的操作站之间采用光纤方式通讯,速率100M。
5.6、交换机及集线器(HUB)配置
硫酸主控制室及余热发电控制室各配置2台交换机用于DCS系统数据采集,交换机采用CISCO品牌产品。
6、软件配置
全部软件采用正版软件。
6.1 操作系统及工具软件
ExperionPKS系统配备有全套的操作系统软件,采用Windows 2003 操作系统。
在系统服务器上(工程师站)配备有数据库管理系统SQL Sever,电子表格Excel、网络管理软件等应用软件及工具软件。
6.2 工程组态软件
ExperionPKS系统配有工程组态软件包括:Control Builder(控制策略组态软件),Quick Builder(数据库管理软件),HMIWeb Display Builder(用户流程画面生成工具),Knowledge Builder(用户资料组态工具)等。
对Control Builder 具备在线修改和下装组态的功能,当一个或部分程序修改和下装时,不影响其他已在控制器的程序的运行。
组态软件除在工程师站上一套外,在其他五套操作员站上也可运行组态软件。
8、子站硬件配置。