PFMEA2
PFMEA评分标准
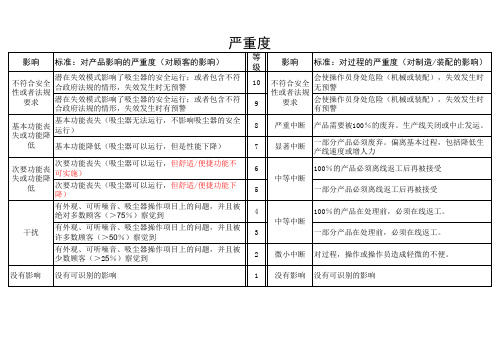
影响
标效模式影响了吸尘器的安全运行;或者包含不符 不符合安全 合政府法规的情形,失效发生时无预警 性或者法规 潜在失效模式影响了吸尘器的安全运行;或者包含不符 要求 合政府法规的情形,失效发生时有预警 基本功能丧失(吸尘器无法运行,不影响吸尘器的安全 基本功能丧 运行) 失或功能降 低 基本功能降低(吸尘器可以运行,但是性能下降) 次要功能丧失(吸尘器可以运行,但舒适/便捷功能不 次要功能丧 可实施) 失或功能降 次要功能丧失(吸尘器可以运行,但舒适/便捷功能下 低 降) 有外观、可听噪音、吸尘器操作项目上的问题,并且被 绝对多数顾客(>75%)察觉到 干扰 有外观、可听噪音、吸尘器操作项目上的问题,并且被 许多数顾客(>50%)察觉到 有外观、可听噪音、吸尘器操作项目上的问题,并且被 少数顾客(>25%)察觉到 没有影响 没有可识别的影响
会使操作员身处危险(机械或装配),失效发生时 不符合安全 无预警 性或者法规 会使操作员身处危险(机械或装配),失效发生时 要求 有预警 严重中断 显著中断 产品需要被100%的废弃。生产线关闭或中止发运。 一部分产品必须废弃。偏离基本过程,包括降低生 产线速度或增人力 100%的产品必须离线返工后再被接受
严重度
影响 标准:对产品影响的严重度(对顾客的影响) 等 级
10 9 8 7 6 中等中断 5 4 中等中断 3 2 1 微小中断 没有影响 一部分产品在处理前,必须在线返工。 对过程,操作或操作员造成轻微的不便。 没有可识别的影响 一部分产品必须离线返工后再被接受 100%的产品在处理前,必须在线返工。
PFMEA
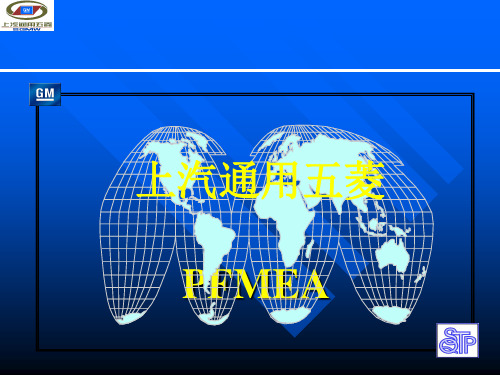
PFMEA
FMEA是一种用来确认分析方法,它包含:
▲确认潜在的失效模式并评价其生产的效应; ▲确认失效模式对客户所产生的影响; ▲确认潜在的产品/过程失效原因; ▲确认现有控制产品/过程失效的方法; ▲确认排除或降低失效改善方案; ▲设计之前预先进行风险分析,确保设计水平。
PFMEA
设计阶段的FMEA(DFMEA-Design FMEA):
10、潜在失效模式——所谓潜在失效模式是指过程可能发生的不满 足过程要求/或设计意图的形式是对某具体工序不符合要求的描述 (假定提供的零件/材料是合格的) 列出每一个潜在失效模式。假设这种失效可能发生但不一定非得 发生——以Plow Chart为主线
PFMEA
FMEA就是这样一个工具: ◆控制工具;
◆风险性分析工具; ◆管理工具;
识别和评估潜在的失效模式及其影响; 确定能够消除或减少潜在的失效发生的改善措施。
确保在前期已考虑并记录了过程可能产生的 所有失效模式以降低缺陷的发生风险
PFMEA
失效模式
Hale Waihona Puke 原因发生的概率控制
后果 严重度
发现的概率
RPN = O × S × D
如新工序的设计,我们可以预先进行DFMEA,尽可能周全的考 虑产品规格,工序操作水平、工序能力诸多因素,使工序符合规 定的要求。
■ 生产过程的FMEA(PFMEA-Process FMEA):
针对工序间的不合格品,可运用PFMEA作量化分析,在影响 不合格产品产生的诸多因素中,那一个系统原因影响最大?是否 主要原因….其它,如PPM值高、CPK低、生产过程异常等等都可 以通过采用PFMEA直观的找出主要原因,进行改善达到应有的效 应。
3、确保对高RPN项目已制定了行动计划 4、确保供应商评审分供方PFMEA
pfmea评分标准

pfmea评分标准PFMEA(Process Failure Mode and Effects Analysis)是一种用于识别和评估过程中潜在失效模式及其影响的方法。
在进行PFMEA评分时,通常会使用一个评分标准来确定失效模式的严重性、频率和检测能力。
下面是一种常见的PFMEA评分标准:1. 失效严重性评分(Severity):评估失效对产品质量、安全性和客户满意度的影响程度。
常见的评分标准包括:- 10分:失效会导致严重的安全问题、法律问题或产品完全无法使用。
- 8分:失效会导致严重的质量问题、客户满意度下降或产品需要修复。
- 6分:失效会导致一些质量问题、客户满意度下降或产品性能降低。
- 4分:失效会导致一些次要的质量问题或产品性能略有影响。
- 2分:失效会导致一些很小的质量问题或产品性能几乎不受影响。
- 0分:失效对产品质量、安全性和客户满意度没有任何影响。
2. 失效频率评分(Occurrence):评估失效在过程中发生的概率。
常见的评分标准包括:- 10分:失效在每次过程中都会发生。
- 8分:失效在大部分过程中都会发生。
- 6分:失效在一些过程中会发生。
- 4分:失效在很少的过程中会发生。
- 2分:失效在极少的过程中会发生。
- 0分:失效在过程中几乎不会发生。
3. 检测能力评分(Detection):评估当前控制措施对失效模式的检测能力。
常见的评分标准包括:- 10分:当前控制措施可以完全检测到失效模式。
- 8分:当前控制措施可以大部分检测到失效模式。
- 6分:当前控制措施可以一些检测到失效模式。
- 4分:当前控制措施可以很少检测到失效模式。
- 2分:当前控制措施几乎不能检测到失效模式。
- 0分:当前控制措施无法检测到失效模式。
根据以上评分标准,可以计算出PFMEA的风险优先指数(Risk Priority Number,RPN),RPN=Severity × Occurrence × Detection。
五大工具培训考试题答案知识讲解

五大工具培训考试题卷部门姓名得分一、产品质量先期策划和控制计划部分(100分)一填空题:(每栏1分,共50分)1、APQP是指用来确定和制订使产品满足顾客要求所需步骤的结构化方法,是针对具体产品项目。
每一个具体产品项目都必须进行。
为保证每项产品的计划达到顾客满意,引导资源实现质量目标,促使早期识别质量问题而采取预防措施,避免后期更改造成的损失,最终达到以最低的成本及时地提供优质产品的目的。
2、APQP参考手册中规定的产品质量策划过程的五个阶段分别是策划,产品设计和开发,过程设计和开发,产品和过程确认,反馈、评定和纠正措施。
3、在APQP的活动中所建立的产品质量先期策划小组、项目管理小组、横向职能小组都是属于多方论证的解决方法性质的小组。
3、在产品设计和开发的输出中属于项目管理小组负责输出的有拟订策划内容,提供顾客要求,确定项目小组,确定项目管理小组,制订APQP进度计划。
它将转化为过程设计和开发的输入。
4在APQP的活动中,在过程设计和开发阶段输出的文件中包括有试生产控制计划、测量系统分析计划和初始过程能力研究计划。
5、场地平面布置图是为了确定检测点的可接受性性、控制图的位置、目视辅具的应用、中间维修站和缺陷材料的贮存区而绘制的,它是由产品质量策划小小组依据“场地平面布置检查清单”来进行评价的。
6、PFMEA是在开始生产以前之前、产品质量策划过程中进行的,它是一个动态文件。
7、产品和过程确认的输出有试生产、测量系统分析、初始过程能力研究、生产件批准、生产确认试验、包装评价、生产控制计划和质量策划认定和管理者支持。
8、试生产的目的之一是用来收集足够的产品质量数据进行初始过程能力研究,测量系统分析,PPAP文件提交,生产确认试验,包装评价,试生产能力和质量策划认定。
9、控制计划的目的是按照顾客的要求生产出合格的优质产品。
它是通过为总体系设计、选择和实施增值性控制方法以提供结构性的途径来达到上述目标的。
潜在失效模式分析(PFMEA)样板-2
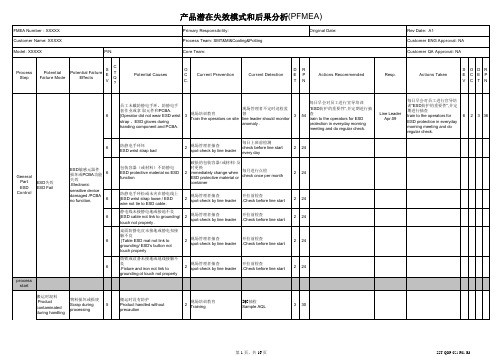
Resp.
Actions Taken
S E V
O D C E C T
R P N
6
பைடு நூலகம்
员工未戴防静电手环、防静电手 套作业或拿 取元件和PCBA. |Operator did not wear ESD wrist strap 、ESD gloves during handing component and PCBA.
2
30
Incorrect P/N of label referenced by SeaStar supplier
wrongly use materials
5
1.Order wrong material
2 Detail description in the PO Spot check PO
3
30
生产用错料,客户 投诉 LED P/N 中的Bin Wrongly use code 错误 materials for Wrong Bin code production within LED P/N ,complianing by customer
2
2
24
6
2
2
24
6
2
现场管理者抽查 spot-check by line leader
开拉前检查 .Check before line start
2
24
6
2
现场管理者抽查 spot-check by line leader
开拉前检查 .Check before line start
2
24
process start 搬运时混料 Product contaminated during handling 物料损坏或报废 Scrap during processing 搬运时没有防护 Product handled without precaution
PFMEA评分表

PFMEA评分表PFMEA评分表》是一种常用的品质管理工具,用于进行潜在失效模式与效应分析(Process Failure Mode and Effects Analysis,简称PFMEA)。
它的目的是识别关键步骤或流程中的潜在失效模式,并评估其对产品或服务质量的影响程度。
PFMEA评分表可以帮助团队全面分析和评估可能发生的失效模式,并制定适当的预防和纠正措施,从而最大程度地降低产品或服务质量风险。
通过对各种失效模式和其效应的评估,可以提前发现潜在问题并采取相应的控制措施,以确保产品或服务质量的稳定和可靠。
在PFMEA评分表中,各个步骤或流程会被列出,并根据其对产品或服务的潜在失效的重要程度进行评分。
评分标准可以根据具体情况进行制定,但通常包括失效模式的严重性、发生频率和检测能力等方面的考量。
评分结果可以帮助团队确定哪些步骤或流程需要重点关注和改进,从而优化生产或服务流程,提高质量稳定性。
综上所述,《PFMEA评分表》是一种重要的品质管理工具,用于识别和评估潜在的失效模式,以确保产品或服务质量的稳定和可靠。
PFMEA评分表是一种用于进行过程故障模式与影响分析的工具。
它由以下几个组成部分构成,并且包含一些必填项。
1.项目信息在评分表的顶部,需要填写一些项目信息,以便对分析的过程进行标识和跟踪。
这些信息可能包括项目名称、项目编号、评分表编制人员等。
2.设计和工艺流程步骤在评分表中,需要列出与该过程相关的设计和工艺流程步骤。
这些步骤可以按照顺序进行排列,并且需要明确指出每个步骤的名称和内容。
3.故障模式与影响分析针对每个设计和工艺流程步骤,需要进行故障模式与影响分析。
这部分需要列出可能的故障模式,并对其进行评估。
评估可以基于指标如严重性、发生频率和可探测性等进行。
4.推理控制计划在评分表中,需要制定推理控制计划,以预防或控制故障模式对产品或过程的影响。
这部分需要明确列出控制措施、控制方式以及执行者。
PFMEA
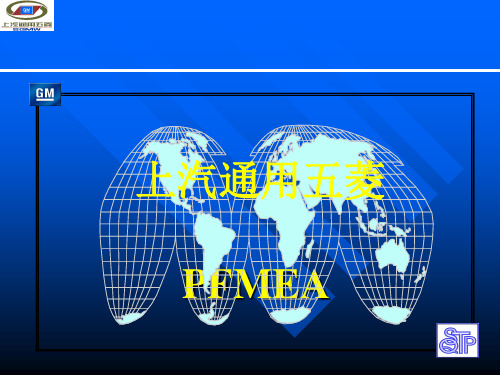
●哪一种失效会发生? ●发生后会造成什么影响 ●其影响的严重性有多大? ●是哪一种原因导致失效? ●失效发生概率? ●当前工序控制方? ●检测失效的能力? ●风险优先指数? ●建议行动?
PFMEA
什么是过程FMEA?
一个系统化的行动团队所开展的工作,目的是: 1、确定和评价过程的潜在失效和后果
2、确定可以消除或减少潜在失效发生机会的措施 3、过程文件化——确定为了使客户满意,一个过程必须 做的事
PFMEA
什么是过程FMEA?
系统化的团队,是指: 由一个制造工程牵头,制造、物流、质量、售后等经验 丰富的人员组成的多功能小组 是一种知识管理的方法,能将经验教训尽可纳入PFMEA PFMEA不能由一个人完成 ※个人的努力可能产生有偏差的结果 ※任何措施应为小组成员的共同决定
PFMEA
FMEA就是这样一个工具: ◆控制工具;
◆风险性分析工具; ◆管理工具;
识别和评估潜在的失效模式及其影响; 确定能够消除或减少潜在的失效发生的改善措施。
确保在前期已考虑并记录了过程可能产生的 所有失效模式以降低缺陷的发生风险
PFMEA
控制 失效模式
原因
后果
发生的概率
严重度
发现的概率
RPN =
PFMEA
如何降低风险?
产品为什么产生缺陷?
-前期没有考虑到所有的可能的失效模式-PFMEA -没有采取有效地措施-CP -措施没有被落实-SOS PPM
过程更改 Process Change 信息反馈 Feedback
PRR CS1/2
控制计划 Control Plan 作业指导书 SOS
流程图 Process Flow
PFMEA-2
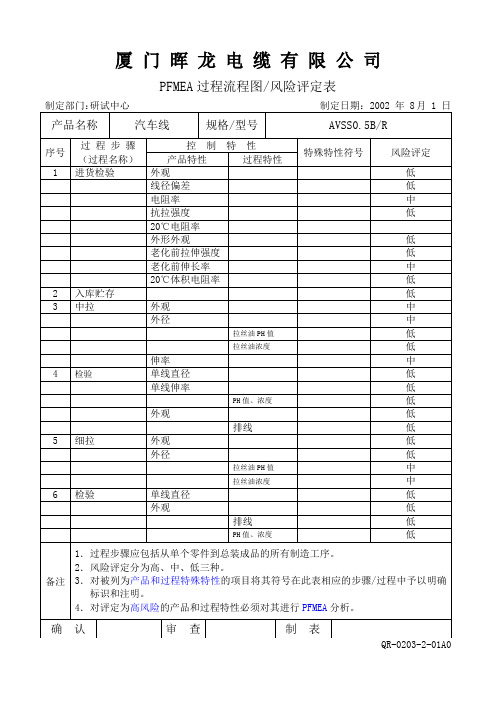
线芯结构
低
挤塑材料
低
12
检验
外观、印字
高
结构、尺寸
中
包装、标志
低
13
包装
低
14
入库贮存
低
1、过程步骤应包括从单个零件到总装成品的所有制造工序。
2、风险评定分为高、中、低三种。
3、对被列为产品和过程特殊特性的项目将其符号在此表相应的步骤/过程中予以明确标识和注明。
4.对评定为高风险的产品和过程特性必须对其进行PFMEA分析。
中
外径
中
拉丝油PH值
低
拉丝油浓度
低
伸率
中
4
检验
单线直径
低
单线伸率
低
PH值、浓度
低
外观
低
排线
低
5
细拉
外观
低
外径
低
拉丝油PH值
中
拉丝油浓度
中
6
检验
单线直径
低
外观
低
排线
低
PH值、浓度
低
备注
1.过程步骤应包括从单个零件到总装成品的所有制造工序。
2.风险评定分为高、中、低三种。
3.对被列为产品和过程特殊特性的项目将其符号在此表相应的步骤/过程中予以明确标识和注明。
厦门晖龙电缆有限公司
PFMEA过程流程图/风险评定表
产品名称
汽车线
规格/型号
AVSS0.5B/R
序号
过程性符号
风险评定
产品特性
过程特性
1
进货检验
外观
低
线径偏差
低
电阻率
中
抗拉强度
低
PFMEA案例(2[1].2)
![PFMEA案例(2[1].2)](https://img.taocdn.com/s3/m/9113fc0e5f0e7cd18425361e.png)
工序号及 加工内容
潜在失效 模式
潜在失 效后果
分 类
潜在失效起 因/机理
频 度 O
R P N
现行控 制措施
建议措施
采取措 施
严 重 度
频 度
探 测 度
R P N
P007 装配
内弧板与 其他弧板 不一致
排壳排 链器无 法在炮 箱上锁 紧
8
零件一致性 差,装配基 准不一致
8
3
19 2
装配前 进行检 查
装配前对 零件进行 检查,统 一装配基 准
排壳排链器工艺潜在失效模式及后果(PFMEA)分析(机加)
措施执行结果 工序号及 加工内容
潜在失效 模式
潜在失 效后果
严 重 度 S
分 类
潜在失效起 因/机理
频 度 O
探 测 度 D
R P N
现行控 制措施
建议措施
责任 和目 标完 成日 期
采取措 施
严 重 度
频 度
探 测 度
R P N
P003 钻/ 钻,扩, 铰孔 φ28+0.21 0, φ29+0.21 0。
增加工序 6A,进行 油压机压 装;指定 专门人员 加工;压 装严格压 力和时间。 增加高精 度设备, 定员,定 机,定切 削。
221车间 2004.01
8
2
2
32
P014/镗/ 镗内孔, 保证尺寸 ,形状公 差和表面 粗糙度要 求。
①尺寸及 形置公差 超差。
后续工序 加工余量 不够。
7
G
①机床精度低。 ②切削速度不 匹配。 ③刀、量具使 用不对。
8
3
19 2
工人现 场控制
pfmea类别
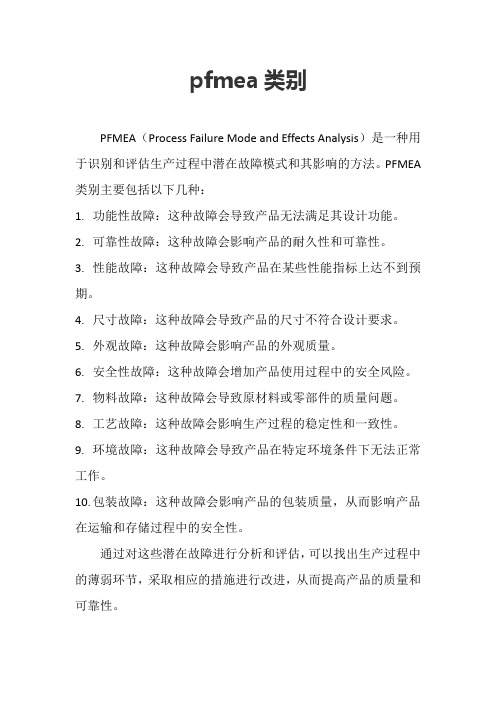
pfmea类别
PFMEA(Process Failure Mode and Effects Analysis)是一种用于识别和评估生产过程中潜在故障模式和其影响的方法。
PFMEA 类别主要包括以下几种:
1.功能性故障:这种故障会导致产品无法满足其设计功能。
2.可靠性故障:这种故障会影响产品的耐久性和可靠性。
3.性能故障:这种故障会导致产品在某些性能指标上达不到预期。
4.尺寸故障:这种故障会导致产品的尺寸不符合设计要求。
5.外观故障:这种故障会影响产品的外观质量。
6.安全性故障:这种故障会增加产品使用过程中的安全风险。
7.物料故障:这种故障会导致原材料或零部件的质量问题。
8.工艺故障:这种故障会影响生产过程的稳定性和一致性。
9.环境故障:这种故障会导致产品在特定环境条件下无法正常工作。
10.包装故障:这种故障会影响产品的包装质量,从而影响产品在运输和存储过程中的安全性。
通过对这些潜在故障进行分析和评估,可以找出生产过程中的薄弱环节,采取相应的措施进行改进,从而提高产品的质量和可靠性。
PFMEA开发教程
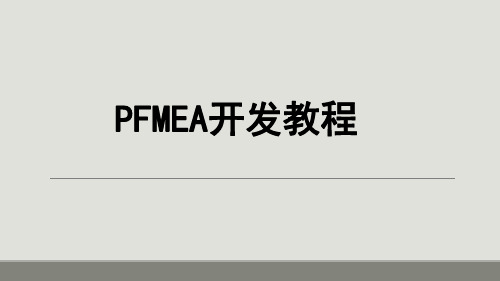
PFMEA开发教程目录•什么是PFMEA1•为什么要做PFMEA2•什么时候做PFMEA3•由谁来做PFEMA4•如何做PFMEA5•PFMEA和APQP的关联6PFMEA 中英文全称:过程失效模式和后果分析-> Process Failure Mode & Effect Analysis失效模式:指制造过程无法达到预定或规定的要求所表现出的现象;如:不合格品、不良设备状况后果:指失效模式在内部、车厂及顾客处(包括后续工序)所造成的不良影响PFMEA定义及其含义:PFMEA是一种分析工具,用于识别出产品或过程的潜在失效,从而可以采取相应的纠正措施FMEA的发展历史:●1949年由美国军方创建用于国防工业●上世纪50年代被航空航天工业采纳●上世纪70年代,汽车工业将FMEA作为在对其零件设计和生产制造的评审项目的重要部分-Ford公司首次应用于汽车工业●上世纪80年代,产品事故责任的费用突升和不断的法庭起诉事件发生,使FMEA成为降低事故的不可缺少的重要工具●1993年美国汽车工业行动集团(AIAG)首次发行了FMEA标准,定义了对OEM和供应商最基本的FMEA要求●2008年AIAG发布FMEA (第四版)FMEA的主要类型:●DFMEA: 在产品正式设计发布之前分析潜在失效—专注于产品由于设计造成的和功能相关的潜在失效●PFMEA: 用于分析制造和装配过程—专注于过程由于设计和操作造成的和功能相关的潜在失效模式0246810类别1类别2类别3110100设计开发过程开发售后阶段010080602040成本($)减少变更成本风险1:10:100设计改起来很麻烦,这个风险等以后有问题再改吧?FMEA评估和减小风险做PFMEA 之后,我们产品不良率能降低多少PPM 呢?M2M3.1M3.2M3.3M3PPAP发布初版u p d a t eu p d a t eu p d a t eu p d a t ePFMEA制作IQC SQEMEDSMT PQOQA评审PMMPPFMEA 是团队的成果过程步骤/功能要求潜在失效模式潜在失效影响潜在失效原因严重度频度控制预防控制探测探测度RPN5、DIETZ的PFMEA分析理论举个例子目前公司内所有的PCB板都会镭雕二维码以及相关信息,小小的二维码在追溯以及防错等方面发挥着重大作用。
PFMEA(潜在失效模式及后果分析)
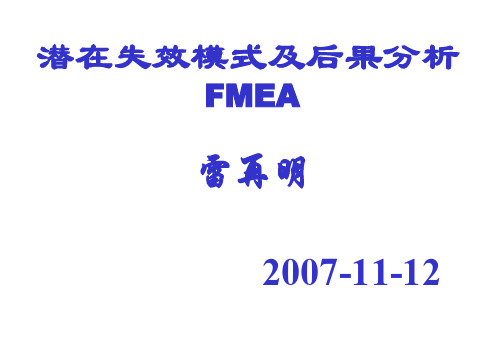
过程失效的潜在影响
1、失效的潜在影响被定义为失效模式对客户 的影响。这里所 说的客户可能是下道操作、以后的操作或场所或者最终 客户(消费者)。在评估失效的潜在影响时每一个都必 须考虑到。
2、根据客户可能注意或经历的问题来描述失效的影响。对于 最终使用者,其影响总会与产品或系统性能相关(例如 噪音、粗糙、不稳定的操作、要求的使用过大力量、不 起作用、异味、不稳定、操作削弱、断续的操作、外观 不良等)
SFMEA
PFM EA
生产
DFMEA
3.3 谁来做FMEA?
设计 工艺 制造 生产 服务 质量 试验 可靠性
集体智慧 多方合作
熟悉产品 了解过程 富有经验 掌握信息和资
料
团队: FMEA是系统化的专业活动 多功能小组会议是FMEA的主要活动形式 多功能小组通常有相关专业人员组成,有时包括相关 的工人代表,甚至可包括客户或供应商
—— 失效的表现形式
• 系统、子系统、零件未达到设计意图的形式 • 过程不满足过程要求的形式 • 典型的失效模式: 典型的失效模式可能是(但不仅限于):弯曲、粘连、毛刺、处理 损害、破裂、变形、弄脏、裂纹、变形、松动、泄漏、粘结、 生锈、氧化、断裂……
2.3 失效后果(Failure Effect)
—— 失效给顾客带来的影响
典型的失效后果: 整车无法装配、异常噪声、行走不正常、不良外观、不稳 定、不走直线、无法换向、车子无法打开、无法折叠、刹 车无法锁定……
2.4 失效的起因/机理
——引起失效的原因:物理的/化学的 ——空气弹簧托断裂的机理:晶体开裂、热处理脆性 ……
失效起因/机理、失效模式、失效后果的关系
• 对于最終使用者, 失效的后果經常被指为: 零件断裂、 杂音、不規律的动作、不能操作的、不稳定的、色差、 外观不良、粗糙不平的、操作不顺畅、費力、 令人不 舒服的气味、操作性減弱、刹车不良等等。
PFMEA的评分标准

备注:
1项目:根据过程所属的系统、子系统或零部件进行分类,包括名称和编号。
2年型/车型:汽车的年型或车型(非汽车零件时用产品替代)
3核心小组:过程评估小组名称、部门和电话。
4过程责任:供应商生产部门和责任小组。
5关键日期:过程FMEA完成日期。
6过程的标识:用于追溯过程FMEA的内部编号。
7编制人:过程FMEA编制人的姓名、电话及所属公司。
8日期:原始稿编制日期、修改号和日期。
9过程功能/要求:与工艺流程中的作业编号和说明相同,简明指出过程目的(如:焊接,钻孔等)
10产品特性编号/说明:此栏所需填入的内容与工艺流程文件一致。
11潜在失效模式:所谓潜在失效模式是指过程可能发生的不能满足过程或设计要求的状况。
是对某一作业可能发生的不符合性的描述。
如,太长、太松等。
12潜在失效影响:潜在影响是指失效模式对客户的影响。
客户泛指下步作业、后续作业、组装厂和最终用户。
如,影响美观、不可显示等。
13严重度:是指潜在失效模式对客户影响的严重程度评价。
14级别:分为关键级别、重要级别、一般级别
15潜在失效原因/机理:列出失效模式的潜在原因,如:装备不当、轴承故障、设定不当等。
16频度:是指失效原因/机理预计发生频度,分1到10级。
PFMEA管制程序附件2 PFMEA严重度(S)评价准则
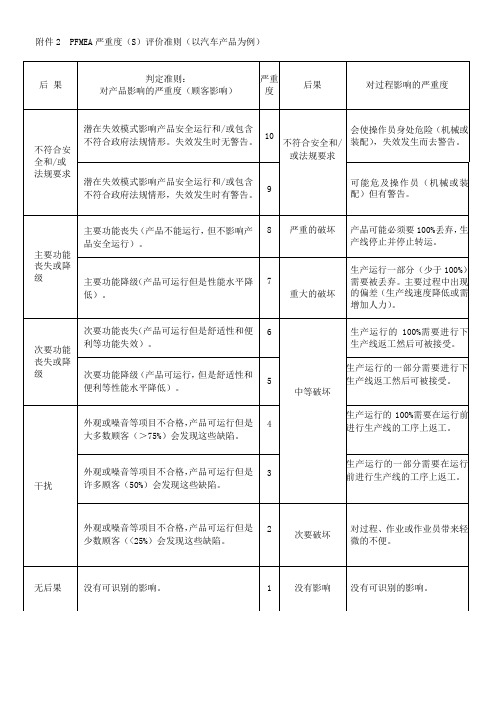
次要破坏
对过程1
没有影响
没有可识别的影响。
附件2 PFMEA严重度(S)评价准则(以汽车产品为例)
后 果
判定准则:
对产品影响的严重度(顾客影响)
严重度
后果
对过程影响的严重度
不符合安全和/或法规要求
潜在失效模式影响产品安全运行和/或包含不符合政府法规情形。失效发生时无警告。
10
不符合安全和/或法规要求
会使操作员身处危险(机械或装配),失效发生而去警告。
生产运行一部分(少于100%)需要被丢弃。主要过程中出现的偏差(生产线速度降低或需增加人力)。
次要功能丧失或降级
次要功能丧失(产品可运行但是舒适性和便利等功能失效)。
6
中等破坏
生产运行的100%需要进行下生产线返工然后可被接受。
次要功能降级(产品可运行,但是舒适性和便利等性能水平降低)。
5
生产运行的一部分需要进行下生产线返工然后可被接受。
干扰
外观或噪音等项目不合格,产品可运行但是大多数顾客(>75%)会发现这些缺陷。
4
生产运行的100%需要在运行前进行生产线的工序上返工。
外观或噪音等项目不合格,产品可运行但是许多顾客(50%)会发现这些缺陷。
3
生产运行的一部分需要在运行前进行生产线的工序上返工。
外观或噪音等项目不合格,产品可运行但是少数顾客(<25%)会发现这些缺陷。
潜在失效模式影响产品安全运行和/或包含不符合政府法规情形,失效发生时有警告。
9
可能危及操作员(机械或装配)但有警告。
主要功能丧失或降级
主要功能丧失(产品不能运行,但不影响产品安全运行)。
8
严重的破坏
产品可能必须要100%丢弃,生产线停止并停止转运。
PFMEA评分准则
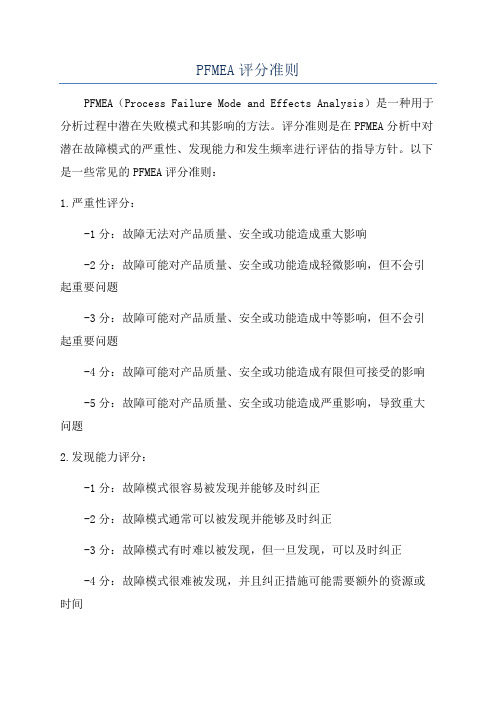
PFMEA评分准则PFMEA(Process Failure Mode and Effects Analysis)是一种用于分析过程中潜在失败模式和其影响的方法。
评分准则是在PFMEA分析中对潜在故障模式的严重性、发现能力和发生频率进行评估的指导方针。
以下是一些常见的PFMEA评分准则:1.严重性评分:-1分:故障无法对产品质量、安全或功能造成重大影响-2分:故障可能对产品质量、安全或功能造成轻微影响,但不会引起重要问题-3分:故障可能对产品质量、安全或功能造成中等影响,但不会引起重要问题-4分:故障可能对产品质量、安全或功能造成有限但可接受的影响-5分:故障可能对产品质量、安全或功能造成严重影响,导致重大问题2.发现能力评分:-1分:故障模式很容易被发现并能够及时纠正-2分:故障模式通常可以被发现并能够及时纠正-3分:故障模式有时难以被发现,但一旦发现,可以及时纠正-4分:故障模式很难被发现,并且纠正措施可能需要额外的资源或时间-5分:故障模式几乎无法被发现或纠正,即使投入大量资源或时间也难以解决3.发生频率评分:-1分:故障模式非常少见,几乎不会发生-2分:故障模式偶尔会发生,但发生频率很低-3分:故障模式有时会发生,但发生频率不高-4分:故障模式经常发生,但有可行且有效的纠正措施-5分:故障模式经常发生,且纠正措施有限或无效根据以上评分准则,可以计算每个故障模式的风险优先指数(Risk Priority Number, RPN),即严重性、发现能力和发生频率的乘积。
RPN 可以帮助确定哪些故障模式应优先处理。
一般来说,RPN越高,意味着故障模式的风险越大,需要优先考虑。
评分准则可以根据具体行业和产品的特点进行调整,以便更好地适应实际情况。
同时,需要有专业人员对每个评分准则进行培训和指导,以确保统一的评分标准和准确的评估结果。
总结起来,PFMEA评分准则是对潜在故障模式的严重性、发现能力和发生频率进行评估的指导方针。
【优质文档】pfmea范例-优秀word范文 (2页)
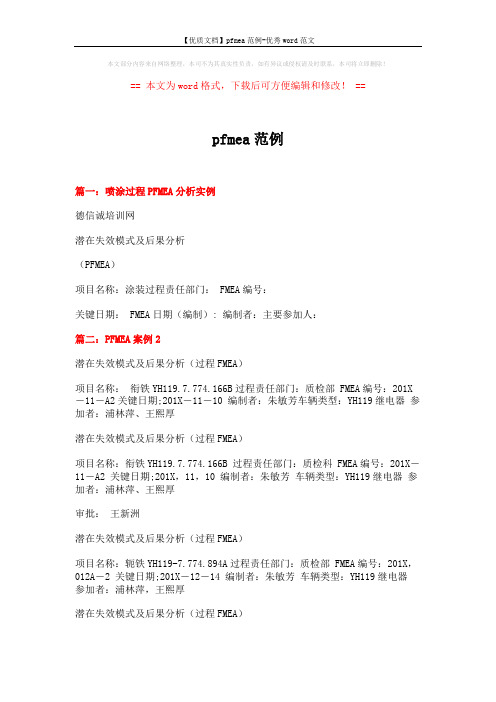
【优质文档】pfmea范例-优秀word范文
本文部分内容来自网络整理,本司不为其真实性负责,如有异议或侵权请及时联系,本司将立即删除!
== 本文为word格式,下载后可方便编辑和修改! ==
pfmea范例
篇一:喷涂过程PFMEA分析实例
德信诚培训网
潜在失效模式及后果分析
(PFMEA)
项目名称:涂装过程责任部门: FMEA编号:
关键日期: FMEA日期(编制): 编制者:主要参加人:
篇二:PFMEA案例2
潜在失效模式及后果分析(过程FMEA)
项目名称:衔铁YH119.7.774.166B过程责任部门:质检部 FMEA编号:201X -11-A2关键日期;201X-11-10 编制者:朱敏芳车辆类型:YH119继电器参加者:浦林萍、王熙厚
潜在失效模式及后果分析(过程FMEA)
项目名称:衔铁YH119.7.774.166B 过程责任部门:质检科 FMEA编号:201X-11-A2 关键日期;201X,11,10 编制者:朱敏芳车辆类型:YH119继电器参加者:浦林萍、王熙厚
审批:王新洲
潜在失效模式及后果分析(过程FMEA)
项目名称:轭铁YH119-7.774.894A过程责任部门:质检部 FMEA编号:201X,012A-2 关键日期;201X-12-14 编制者:朱敏芳车辆类型:YH119继电器
参加者:浦林萍,王熙厚
潜在失效模式及后果分析(过程FMEA)。
PFMEA判定准则
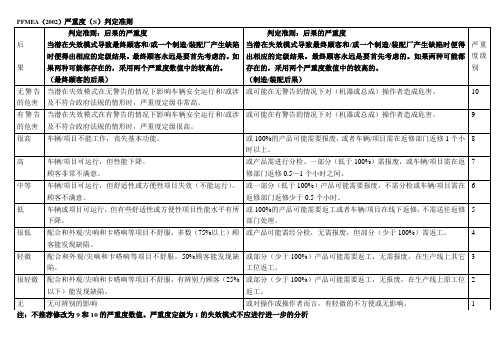
微小
控制有微小机会能探测出
X
只通过目测检查来实现控制
8
很小
控制有很少机会能探测出
X
只通过双重目测检查来实现控制
7
小
控制可能能探测出
X
X
用控制图的方法,如SPC(统计过程控制)来实现控制
6
中等
控制可能能探测出
X
控制基于零件离开工位后的计量测量,或者零件离开工位后100%的止/通测量
5
中上
控制有较多机会可探测出
0.5个,每1000件
≥1.20
3
0.1个,每1000件
≥1.30
2
极低:失效不太可能发生
≤0.01个,每1000件
≥1.67
1
探测度(D)判定准则
探测性
评价准则:
检查类别
探测方法的推荐范围
探测度
A防错
B量具
C人工检验
几乎不可能
绝对肯定不可能探测
X
不能探测或没有检查
10
很微小Hale Waihona Puke 控制方法可能探测不出X
只能通过间接或随机检查来实现控制
7
中等
车辆/项目可运行,但舒适性或方便性项目失效(不能运行)。
顾客不满意。
或一部分(低于100%)产品可能需要报废,不需分检或车辆/项目需在返修部门返修少于0.5个小时。
6
低
车辆或项目可运行,但有些舒适性或方便性项目性能水平有所下降。
或100%的产品可能需要返工或者车辆/项目在线下返修,不需送往返修部门处理。
检査类别探测方法的推荐范围探测c人工检验几乎不可能绝对肯定不可能探测不能探测或没有检杏10很微小控制方法可能探测不出微小控制有微小机会能探测出只通过n测检查来实现控制很小控制有很少机会能探测出只通过双重bl测检杏来实现控制川控制图的方法如spc统计过程控制来实现控制中等控制可能能探测
pfmea评价标准
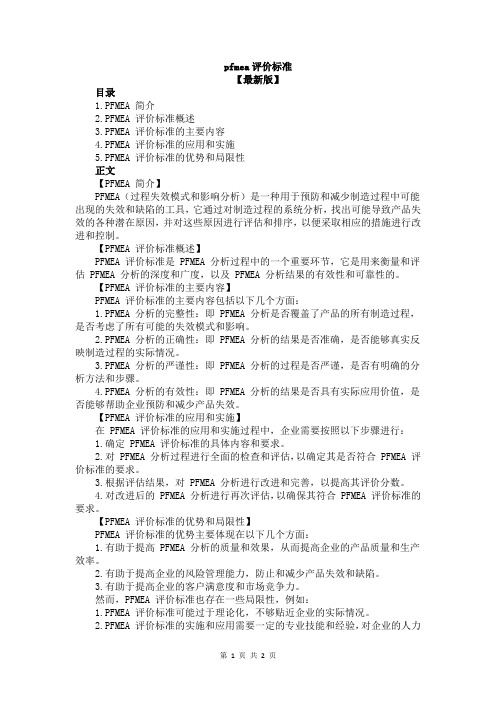
pfmea评价标准【最新版】目录1.PFMEA 简介2.PFMEA 评价标准概述3.PFMEA 评价标准的主要内容4.PFMEA 评价标准的应用和实施5.PFMEA 评价标准的优势和局限性正文【PFMEA 简介】PFMEA(过程失效模式和影响分析)是一种用于预防和减少制造过程中可能出现的失效和缺陷的工具,它通过对制造过程的系统分析,找出可能导致产品失效的各种潜在原因,并对这些原因进行评估和排序,以便采取相应的措施进行改进和控制。
【PFMEA 评价标准概述】PFMEA 评价标准是 PFMEA 分析过程中的一个重要环节,它是用来衡量和评估 PFMEA 分析的深度和广度,以及 PFMEA 分析结果的有效性和可靠性的。
【PFMEA 评价标准的主要内容】PFMEA 评价标准的主要内容包括以下几个方面:1.PFMEA 分析的完整性:即 PFMEA 分析是否覆盖了产品的所有制造过程,是否考虑了所有可能的失效模式和影响。
2.PFMEA 分析的正确性:即 PFMEA 分析的结果是否准确,是否能够真实反映制造过程的实际情况。
3.PFMEA 分析的严谨性:即 PFMEA 分析的过程是否严谨,是否有明确的分析方法和步骤。
4.PFMEA 分析的有效性:即 PFMEA 分析的结果是否具有实际应用价值,是否能够帮助企业预防和减少产品失效。
【PFMEA 评价标准的应用和实施】在 PFMEA 评价标准的应用和实施过程中,企业需要按照以下步骤进行:1.确定 PFMEA 评价标准的具体内容和要求。
2.对 PFMEA 分析过程进行全面的检查和评估,以确定其是否符合 PFMEA 评价标准的要求。
3.根据评估结果,对 PFMEA 分析进行改进和完善,以提高其评价分数。
4.对改进后的 PFMEA 分析进行再次评估,以确保其符合 PFMEA 评价标准的要求。
【PFMEA 评价标准的优势和局限性】PFMEA 评价标准的优势主要体现在以下几个方面:1.有助于提高 PFMEA 分析的质量和效果,从而提高企业的产品质量和生产效率。
- 1、下载文档前请自行甄别文档内容的完整性,平台不提供额外的编辑、内容补充、找答案等附加服务。
- 2、"仅部分预览"的文档,不可在线预览部分如存在完整性等问题,可反馈申请退款(可完整预览的文档不适用该条件!)。
- 3、如文档侵犯您的权益,请联系客服反馈,我们会尽快为您处理(人工客服工作时间:9:00-18:30)。
1
Suppier's storage doesn't meet reqirement. Be affected with damp in the storage which reduce the material performance. Materail less than the quantity in the PO. (B) Failed to receive the products timely and affect the production. (C)1. Affect the normal production and disturb the production plan. 2. Be claimed by the customer because of failed to provide the products on time. 3. Increase the extended freight. (B) Failed to receive the products timely and affect the production. (C)1. Affect the normal production and disturb the production plan. 2. Be claimed by the customer because of failed to provide the products on time. 3. Increase the extended freight. Incorrect dimension unable to assembly (C) Dimension incorrect unable to assembly performance reduced and hard to (A)Product be discovered. (B) Receive the ineligible products.The performance reduced and hard to be discovered. (C) 1.Product performance reduced and hard to be discovered. 2.Send the ineligible products to custome. Rejected or be claimed by customer. 3.Purchase again and affect the normal production. 5 Deficient supplier production capacity.PoteΒιβλιοθήκη tial Failure Mode
S e v
6
O c c u r
1
Current Process Controls Prevention
Current Process Controls Detection
100% visual inspection Check the PO more than two people. Visual inspect the label 100% Review supplier quality systerm regularly. Check the package whether affected by damp . Review customer package way and appraise regularly. Supplier provide the quality warranty Test every lot. Check the SPC data according to the annual test data. Have a third party test annually. Audit the supplier quality regularly. Audit the supplier quality regularly.
transportation Move the matrial to the right position by Process effectively and Function/ safely.
Rev Level: Process Responsibility MODEL S Key Date
Rev date:
5
7
168 N/A
5 Audit the moving. Inspect and transit.200% visual inspect.
7
140 N/A
5
7
140 N/A
4
Page 1 of 12
POTENTIAL FAILURE MODE AND EFFECTS ANALYSIS (PROCESS FMEA) Print #: Part name: Model Year(s) / Vehicle(s) Core Team Material
D e t e c
8
R. P. N.
Recommended Responsibility Action Results Actions & Target Actions S O D R. Date Taken e c e P. v c t N.
48 N/A
1
8
48 N/A
1
8
48 N/A
6
72 N/A
POTENTIAL FAILURE MODE AND EFFECTS ANALYSIS (PROCESS FMEA) Print #: Part name: Model Year(s) / Vehicle(s) Core Team MODEL S Rev Level: Process Responsibility Key Date Rev date: Supplier name: FMEA Number Page Prepared By FMEA Date (Orig) 11/18/2010 Potential Effect(s) of Failure C l a s s Potential Cause(s)/ Mechanism(s) of Failure
5
Unreaonale arrangement of the production. Delayed because of traffic or weather. Tools not PM regulation in time Poor package and easy to be damaged. Unreasonalbe method to put the package during transiton and damage the package. Workers don't move the material according to the WI and drop the material from the truck.
Jinyi Automotive Parts Co.,Ltd. QS/NBJY-D-FM-1106 of 12 Page
Mike Yang、Alice Mu、Feng Liping、Jacky Jiang、Gordon Liu
(Rev.) 12/02/2010
No.
Process Function/ Requirements
Note: (A) = End User, (B) = TESLA (C) = JINYI Material performance failed Products easy to distort and aging: to meet customer (A) Customer can't open the car door. requirement. (B)1.Products performance failed to meet the requirement and difficult to be discovered. Send to cusomer as eligible one. 2.Ineligible products send to customer and affect company reputation. 3. Increase the cost (C)1.Customer complaint and affect company reputation. 2.Customer claim and increase the cost.
3 Carry out the security 1 storage.
9
135 N/A
Material failed to arrive on time.
Deficient supplier production capacity.
Audit supplier production capacity regularly. 9 Follow the PO production regularly. Follow the PO transportation regularly. 100% Inspection at time of Material Pick and Material Load at Line (Double verification) Audit the supplier packaging method and appraise it regularly. Inspect and transit.200% visual inspect. Inspect and transit.200% visual inspect. 45 N/A
Wrong materil PO and cause the supplier provide the wrong material. Supplier stick the wrong the label cause they send the wrong material. Material packaging way don't meet the requirement.Because of affecting with damp in the transportation make the material performance changing. Material performance provided by the supplier is not stable. Material receive and inspection. Receive and inspect the mateial according to the PO. Ensure the right quantity and performance. Materail: PC/PBT 553 2