来料检验规范及流程
来料检验流程

来料检验流程来料检验是在制造企业采购原材料和零部件后,对供应商提供的产品进行质量检验的过程。
来料检验的目的是确保所采购的产品符合企业的质量要求,以避免因使用不合格的原材料和零部件而导致生产问题。
来料检验流程包括以下几个环节:1. 接受来料:收到供应商发来的原材料和零部件后,由检验员验收入库,并录入系统。
2. 制定检验标准:根据企业的质量要求和相关标准,制定来料检验的标准和方法。
可以使用抽样检验和全检验的方式进行。
3. 取样检验:根据检验标准,从接受来料的批次中取样进行检验。
采取随机抽样和代表性抽样的方法,确保样品具有代表性。
4. 实施检验:根据检验标准和方法,对样品进行检验。
包括外观检验、尺寸检验、功能性检验等。
使用各种设备和工具,如显微镜、测量工具、测试仪器等。
5. 检验结果评判:根据检验结果和检验标准,对样品进行评判。
判断是否合格、不合格或待定,并记录检验结果。
6. 处理不合格品:如果样品检验不合格,需要进行不合格品处理。
包括退货、返修、报废等。
7. 管理记录:对每个批次的来料检验进行记录。
包括样品编号、检验员、检验日期、检验结果等。
建立来料检验的档案,方便追溯和管理。
8. 问题分析与改进:对不合格品进行问题分析,找出原因,并采取相应的改进措施。
与供应商进行沟通,提高产品质量和交付准时率。
9. 审核与验证:定期对来料检验流程进行审核和验证,确保检验结果的准确性和可靠性。
对检验标准和方法进行更新和改进。
10. 持续改进:不断改进来料检验流程,提高效率和准确性。
通过培训和学习,提升检验员的技能和知识。
来料检验流程的目标是确保所采购的原材料和零部件符合质量要求,降低生产过程中的质量风险。
通过严格的检验和管理,可以提高产品质量和顾客满意度,构建供应链的稳定性和可靠性。
来料检验作业指导书

来料检验作业指导书一、背景介绍来料检验是指对供应商提供的原材料进行检验,以确保其质量符合企业的要求,从而保证产品质量稳定。
本作业指导书旨在提供来料检验的操作规范和流程,以确保检验工作的准确性和一致性。
二、检验标准1. 外观检验- 外观要求:检查原材料的表面是否有划痕、变色、气泡等缺陷。
- 尺寸要求:测量原材料的长度、宽度、厚度等尺寸是否符合要求。
- 颜色要求:比对原材料的颜色与标准样品的颜色是否一致。
2. 化学成分检验- 根据原材料的种类和用途,确定需要检测的化学成分。
- 采用适当的化学分析方法,对原材料进行化学成分分析。
- 比对化学成分检测结果与标准要求,判断原材料是否合格。
3. 物理性能检验- 根据原材料的用途,确定需要测试的物理性能指标,如强度、硬度、密度等。
- 使用相应的测试设备和方法,对原材料进行物理性能测试。
- 比对测试结果与标准要求,判断原材料的物理性能是否符合要求。
4. 包装检验- 检查原材料的包装是否完好,有无损坏、破损、渗漏等情况。
- 检查包装标识是否清晰、准确,与实际原材料相符。
三、操作流程1. 接收原材料- 由仓库人员接收供应商送来的原材料,并填写相应的接收记录。
- 检查原材料的外包装是否完好,有无破损。
- 将原材料送至来料检验区域。
2. 样品取样- 根据来料检验标准和抽样计划,从原材料中取出代表性样品。
- 确保样品的数量和取样方法符合要求,避免取样误差。
3. 检验操作- 根据检验标准,对样品进行外观检验、化学成分检验、物理性能检验等。
- 使用准确、可靠的检验设备和方法,确保检验结果的准确性。
- 记录检验结果和检验过程中的相关信息,如检验员、日期、检验设备等。
4. 检验结果判定- 将检验结果与标准要求进行比对,判断原材料的合格与否。
- 若原材料符合要求,填写合格记录,并将原材料送至仓库进行存储。
- 若原材料不符合要求,填写不合格记录,并通知供应商进行处理。
5. 检验报告和记录- 根据检验结果,编制检验报告,详细记录检验的过程和结果。
来料检验规范
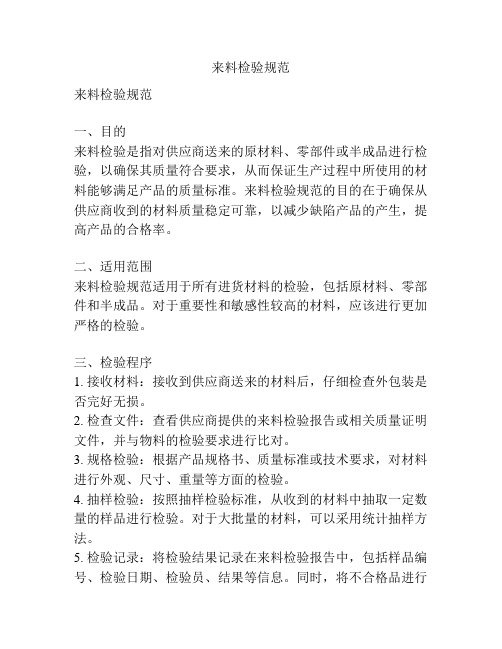
来料检验规范来料检验规范一、目的来料检验是指对供应商送来的原材料、零部件或半成品进行检验,以确保其质量符合要求,从而保证生产过程中所使用的材料能够满足产品的质量标准。
来料检验规范的目的在于确保从供应商收到的材料质量稳定可靠,以减少缺陷产品的产生,提高产品的合格率。
二、适用范围来料检验规范适用于所有进货材料的检验,包括原材料、零部件和半成品。
对于重要性和敏感性较高的材料,应该进行更加严格的检验。
三、检验程序1. 接收材料:接收到供应商送来的材料后,仔细检查外包装是否完好无损。
2. 检查文件:查看供应商提供的来料检验报告或相关质量证明文件,并与物料的检验要求进行比对。
3. 规格检验:根据产品规格书、质量标准或技术要求,对材料进行外观、尺寸、重量等方面的检验。
4. 抽样检验:按照抽样检验标准,从收到的材料中抽取一定数量的样品进行检验。
对于大批量的材料,可以采用统计抽样方法。
5. 检验记录:将检验结果记录在来料检验报告中,包括样品编号、检验日期、检验员、结果等信息。
同时,将不合格品进行标注和处理。
6. 不合格处理:对于不合格的材料,及时通知供应商,并要求其退换或重新提供合格的材料。
并且要对不合格品进行分类、封存和处理,以防止误用。
四、监督和改进1. 监督:建立来料检验数据的统计和分析系统,对不合格品进行整理和分析,找出常见的问题和缺陷,并采取措施加以改进。
2. 持续改进:与供应商保持良好的沟通和合作关系,定期进行供应商评估,并对不合格品的原因进行深入调查和分析,以减少不合格品的数量和频率。
3. 记录和归档:保留所有的来料检验记录和相关文件,便于日后的追溯和参考。
五、操作注意事项1. 检验人员应经过专业培训,具备相关的技能和知识,并严格按照检验标准和操作规程进行检验工作。
2. 检验仪器和设备应定期校准和维护,确保其准确性和可靠性。
3. 对于质量较为关键的材料,可以借助第三方检验机构进行确认和验证,以提高检验结果的准确性。
来料检验管理控制规范

来料检验管理控制规范引言概述:来料检验是一个重要的质量管理环节,对于确保产品质量具有重要意义。
来料检验管理控制规范是指在来料检验过程中,制定一系列的规范和控制措施,以确保来料的质量符合要求。
本文将从四个方面详细阐述来料检验管理控制规范的内容。
一、来料检验前的准备工作1.1 来料检验计划的制定来料检验计划是来料检验的基础,应根据产品特性和质量要求制定。
该计划应包括检验的项目、方法、标准和检验频率等内容,以确保检验的全面性和准确性。
1.2 检验设备和环境的准备在进行来料检验前,需要准备好相应的检验设备和环境。
检验设备应符合相关标准和要求,并定期进行校准和维护。
同时,检验环境应保持整洁、干净,避免有害物质的污染。
1.3 来料检验人员的培训和资质要求来料检验人员应具备相关的专业知识和技能,能够熟练操作检验设备和使用检验方法。
同时,应定期进行培训,了解最新的检验标准和方法,以提高检验的准确性和可靠性。
二、来料检验的方法和标准2.1 抽样检验方法抽样检验是来料检验中常用的一种方法,通过从整批来料中抽取一部份样品进行检验,以判断整批来料的质量状况。
常用的抽样方法包括正态抽样、双抽样和加权抽样等。
2.2 检验项目和标准的确定来料检验项目和标准的确定应根据产品的特性和质量要求进行。
检验项目包括外观、尺寸、物理性能、化学成份等,标准可以是国家标准、行业标准或者企业内部标准。
2.3 检验记录和报告的编制来料检验过程中应及时记录检验结果,并编制检验报告。
检验记录和报告应包括检验项目、检验结果、判定依据和处理意见等内容,以便于后续的质量跟踪和问题解决。
三、来料检验的流程控制3.1 来料接收和登记来料接收时应核对送货单和物料清单,确保所收货物与定单一致。
同时,应及时登记来料信息,包括供应商、批次、数量等,以便于后续的追溯和管理。
3.2 样品的取样和标识在来料检验过程中,需要从整批来料中取得样品进行检验。
样品的取样应符合相关的标准和要求,并进行标识,以避免混淆和错误。
来料检验制度

来料检验制度一、引言来料检验是企业在采购原材料、零部件或成品时,对供应商提供的货物进行质量检验的重要环节。
通过检验可以确保所采购的物料质量符合企业的要求,为生产制造提供良好的基础。
本文将介绍来料检验制度的重要性、目的、流程以及常见的检验方法。
二、重要性和目的1. 保证产品质量:通过对来料进行检验,可以及时发现和排除不合格品,降低不良品率,保证产品质量的稳定性和一致性。
2. 控制采购成本:通过来料检验,可以避免采购低质量物料导致生产中出现的问题,减少返工和报废的成本,提高资源利用率。
3. 维护供应商关系:通过对来料的合格供应商进行检验,可以及时发现并辅导供应商进行质量改进,促进供应链的稳定和顺畅。
三、流程1. 接收:当供应商送达货物时,由来料检验部门接收,并记录到货时间、数量、包装等信息。
2. 采样:在接收到货物后,按照一定的规则和要求,从货物中抽取样本进行检验。
3. 检验:对采样得到的样本进行各项检验,包括外观检验、尺寸检验、性能检验等。
4. 判定:根据检验结果,对货物进行合格或不合格的判定,并及时通知供应商和相关部门。
5. 处置:对不合格的货物,可以要求供应商调整或重新供货;对合格的货物,可以放行或送往下一道工序。
四、常见的检验方法1. 外观检验:通过观察货物的外形、色泽、表面处理等方面,判断是否符合要求。
2. 尺寸检验:通过测量货物的尺寸,判断是否满足设计要求。
3. 功能检验:通过对货物进行试验、操作等,验证其功能是否正常。
4. 化学检验:使用化学分析方法,检测货物中的元素含量、化学成分等。
5. 物理检验:使用物理测试仪器,检测货物的硬度、耐磨性、强度等物理性能。
五、建立和改进来料检验制度的建议1. 明确责任:明确来料检验制度的责任主体,制定相关的岗位职责和工作流程。
2. 审核供应商:建立供应商审核制度,确保选择和认证的供应商有一定的质量保证。
3. 设定检验标准:根据产品设计和要求,制定相应的来料检验标准。
来料检验及异常处理流程

来料检验及异常处理流程一、来料检验流程:1.接收原材料:当供应商将原材料送到公司时,接收人员负责接收原材料。
他们会核对送货单和实际接收数量,确保一致性。
如果发现数量不一致,则会与供应商协商解决。
2.样品收集:接收人员从接收的原材料中抽取一定数量的样品,确保样品能够全面代表整批原材料。
3.检验依据:根据公司的检验标准和规定,制定检验计划和检验依据,明确要求的检验项目和标准。
4.检验方法选择:根据检验项目的不同性质和要求,选择合适的检验方法,如外观检查、物理性质测试、化学成分分析等。
5.执行检验:根据检验计划和检验依据,实施相应的检验活动。
检验员按照检验方法和标准,对原材料进行检验,并记录检验结果。
6.检验结果评定:根据检验结果和标准,评定原材料是否合格。
如果原材料符合要求,则通过;如果不符合要求,则判定为不合格。
7.合格原材料处理:对于合格的原材料,将其进行封存,并进行标识。
符合要求的原材料可以进入下一道工序使用。
8.不合格原材料处理:对于不合格的原材料,根据具体情况,采取以下措施:返回供应商、报废、返工等。
同时,需要记录不合格原材料的情况并进行归档,以便后续处理。
二、异常处理流程:1.异常检测和发现:在来料检验过程中,如果发现原材料存在异常情况,如外观缺陷、超出标准范围的物理性质、化学成分分析结果与标准不符等,应立即停止检验过程,将异常情况进行记录和报告。
2.异常情况分类:根据异常情况的性质和严重程度,将异常情况进行分类。
如严重影响生产的异常、有风险的异常、可修复的异常等。
3.处理方案制定:根据异常情况的分类和具体情况,制定相应的处理方案。
对于严重影响生产的异常,需要立即停止生产并与供应商协商解决;对于有风险的异常,需要进行风险评估并采取合适的措施进行处理;对于可修复的异常,需要返工或者重新采购原材料。
4.异常情况解决:根据制定的处理方案,采取相应的措施解决异常情况。
如与供应商协商解决问题、制定修复方案并进行返工、重新采购原材料等。
来料质量检验标准规范
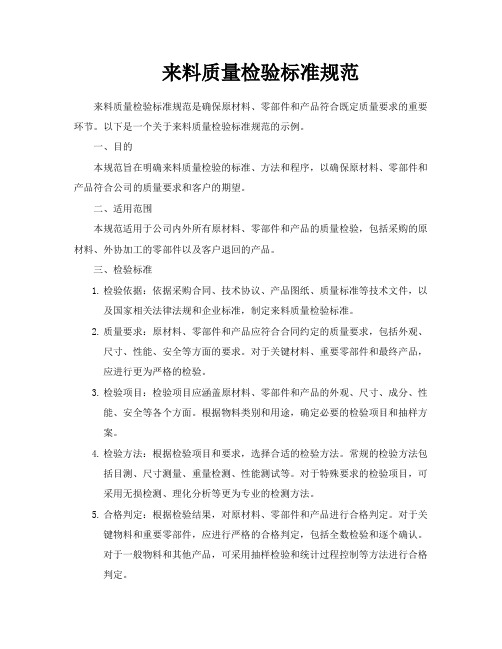
来料质量检验标准规范来料质量检验标准规范是确保原材料、零部件和产品符合既定质量要求的重要环节。
以下是一个关于来料质量检验标准规范的示例。
一、目的本规范旨在明确来料质量检验的标准、方法和程序,以确保原材料、零部件和产品符合公司的质量要求和客户的期望。
二、适用范围本规范适用于公司内外所有原材料、零部件和产品的质量检验,包括采购的原材料、外协加工的零部件以及客户退回的产品。
三、检验标准1.检验依据:依据采购合同、技术协议、产品图纸、质量标准等技术文件,以及国家相关法律法规和企业标准,制定来料质量检验标准。
2.质量要求:原材料、零部件和产品应符合合同约定的质量要求,包括外观、尺寸、性能、安全等方面的要求。
对于关键材料、重要零部件和最终产品,应进行更为严格的检验。
3.检验项目:检验项目应涵盖原材料、零部件和产品的外观、尺寸、成分、性能、安全等各个方面。
根据物料类别和用途,确定必要的检验项目和抽样方案。
4.检验方法:根据检验项目和要求,选择合适的检验方法。
常规的检验方法包括目测、尺寸测量、重量检测、性能测试等。
对于特殊要求的检验项目,可采用无损检测、理化分析等更为专业的检测方法。
5.合格判定:根据检验结果,对原材料、零部件和产品进行合格判定。
对于关键物料和重要零部件,应进行严格的合格判定,包括全数检验和逐个确认。
对于一般物料和其他产品,可采用抽样检验和统计过程控制等方法进行合格判定。
6.不合格处理:对于检验不合格的原材料、零部件和产品,应及时进行处理。
根据不合格的性质和严重程度,与供应商协商退货、换货或进行生产调整。
对不合格品进行有效控制,防止非预期使用。
7.记录保存:质量检验记录是来料质量的重要凭证,应按规定进行保存。
记录应清晰、完整,便于查阅和分析。
四、检验流程1.来料接收:供应商将物料送达企业后,仓库管理员应核对物料的品种、规格、数量等信息,确保与采购合同一致。
2.初步检验:仓库管理员应对物料进行初步检查,包括外观、尺寸等基本项目的检查。
来料检验作业指导书

来料检验作业指导书一、背景介绍来料检验是指对供应商提供的原材料、零部件或成品进行质量检验的过程。
通过来料检验,可以确保所采购的物料符合公司的质量要求,减少不良品流入生产线,保证产品质量和客户满意度。
本作业指导书旨在规范来料检验的流程和方法,以提高检验效率和准确性。
二、检验流程1. 接收物料1.1 确保物料标识清晰可读,包括物料名称、规格、批次号等信息。
1.2 核对物料清单,确保所接收的物料与订单一致。
1.3 确保物料包装完好无损,无明显变形、破损或污染。
2. 样品抽取2.1 根据采购数量和抽样标准,确定抽样数量和抽样方法。
2.2 从接收的物料中随机抽取样品,确保样品具有代表性。
2.3 根据需要,将样品进行标识和记录,以便后续处理。
3. 检验方法3.1 根据物料的特性和质量要求,选择适当的检验方法,如外观检验、尺寸测量、物理性能测试等。
3.2 使用合适的检验设备和工具,确保检验结果准确可靠。
3.3 遵循相关标准和规范,进行检验操作,记录检验结果。
4. 检验结果评定4.1 将检验结果与规定的质量标准进行比较,判断样品是否合格。
4.2 根据不同的检验项目和要求,对不合格样品进行分类和处理,如返工、退货等。
4.3 将检验结果记录在检验报告中,并及时通知相关部门和供应商。
5. 数据分析和改进5.1 定期统计和分析来料检验的合格率和不良率,发现问题和趋势。
5.2 根据数据分析结果,制定改进措施,提高来料检验的效率和准确性。
5.3 定期评估供应商的质量绩效,与供应商合作改进。
三、注意事项1. 检验人员应具备相关的技术和知识,熟悉检验方法和操作规程。
2. 检验设备和工具应定期校准和维护,确保准确可靠。
3. 检验记录应完整、准确,并按照规定进行保存和归档。
4. 与供应商之间应建立良好的沟通和合作关系,及时解决质量问题。
5. 定期进行培训和学习,提高来料检验的专业水平和技能。
以上是来料检验作业指导书的内容,通过严格按照指导书的要求进行来料检验,可以确保所采购的物料质量符合要求,提高产品质量和客户满意度。
来料检验规范
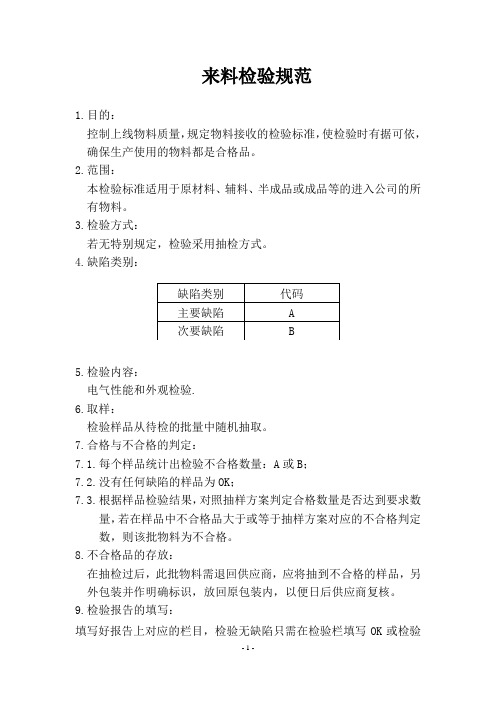
来料检验规范
1.目的:
控制上线物料质量,规定物料接收的检验标准,使检验时有据可依,确保生产使用的物料都是合格品。
2.范围:
本检验标准适用于原材料、辅料、半成品或成品等的进入公司的所有物料。
3.检验方式:
若无特别规定,检验采用抽检方式。
4.缺陷类别:
5.检验内容:
电气性能和外观检验.
6.取样:
检验样品从待检的批量中随机抽取。
7.合格与不合格的判定:
7.1.每个样品统计出检验不合格数量:A或B;
7.2.没有任何缺陷的样品为OK;
7.3.根据样品检验结果,对照抽样方案判定合格数量是否达到要求数
量,若在样品中不合格品大于或等于抽样方案对应的不合格判定数,则该批物料为不合格。
8.不合格品的存放:
在抽检过后,此批物料需退回供应商,应将抽到不合格的样品,另外包装并作明确标识,放回原包装内,以便日后供应商复核。
9.检验报告的填写:
填写好报告上对应的栏目,检验无缺陷只需在检验栏填写OK或检验
无不良,有缺陷就在品质状态栏填写缺陷原因。
来料检验流程
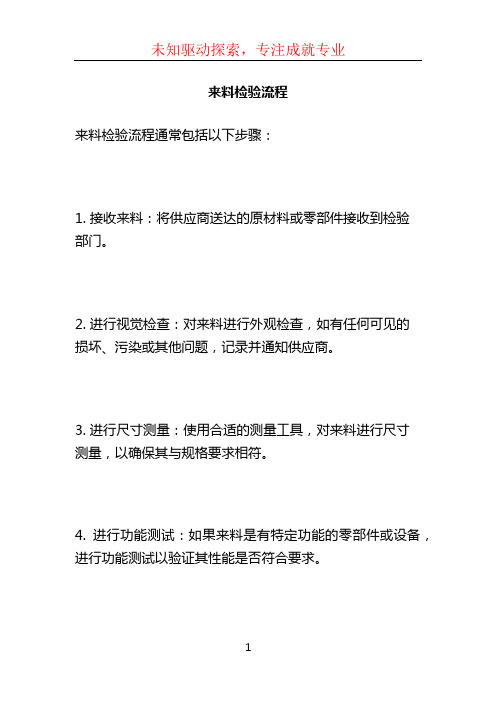
来料检验流程
来料检验流程通常包括以下步骤:
1. 接收来料:将供应商送达的原材料或零部件接收到检验
部门。
2. 进行视觉检查:对来料进行外观检查,如有任何可见的
损坏、污染或其他问题,记录并通知供应商。
3. 进行尺寸测量:使用合适的测量工具,对来料进行尺寸
测量,以确保其与规格要求相符。
4. 进行功能测试:如果来料是有特定功能的零部件或设备,进行功能测试以验证其性能是否符合要求。
5. 进行化学分析:有需要的情况下,对来料进行化学成分分析,以确保其成分符合要求。
6. 制作检验报告:将检验结果记录在检验报告中,包括检验日期、检验员、检验方法、结果等信息。
7. 判断是否合格:根据检验结果和规定的标准,判断来料是否合格。
如果不合格,通知供应商并采取必要的措施,如发起退货、进行返工等。
8. 存档:将检验报告和相关记录存档,以备以后参考和追溯。
9. 处理不合格品:对于不合格的来料,根据公司的质量管理制度,进行相应的处理,如退货、报废、返工等。
10. 维护供应商评估:根据来料检验结果,对供应商的质量表现进行评估,并与供应商进行沟通和改进。
来料检验规范及流程
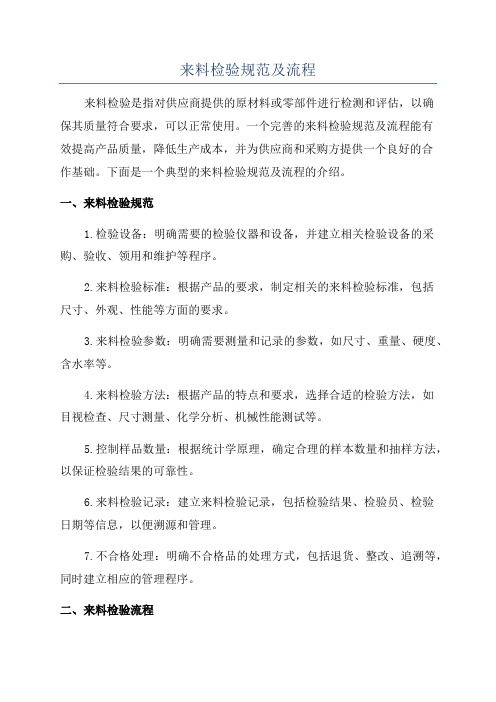
来料检验规范及流程来料检验是指对供应商提供的原材料或零部件进行检测和评估,以确保其质量符合要求,可以正常使用。
一个完善的来料检验规范及流程能有效提高产品质量,降低生产成本,并为供应商和采购方提供一个良好的合作基础。
下面是一个典型的来料检验规范及流程的介绍。
一、来料检验规范1.检验设备:明确需要的检验仪器和设备,并建立相关检验设备的采购、验收、领用和维护等程序。
2.来料检验标准:根据产品的要求,制定相关的来料检验标准,包括尺寸、外观、性能等方面的要求。
3.来料检验参数:明确需要测量和记录的参数,如尺寸、重量、硬度、含水率等。
4.来料检验方法:根据产品的特点和要求,选择合适的检验方法,如目视检查、尺寸测量、化学分析、机械性能测试等。
5.控制样品数量:根据统计学原理,确定合理的样本数量和抽样方法,以保证检验结果的可靠性。
6.来料检验记录:建立来料检验记录,包括检验结果、检验员、检验日期等信息,以便溯源和管理。
7.不合格处理:明确不合格品的处理方式,包括退货、整改、追溯等,同时建立相应的管理程序。
二、来料检验流程1.采购订单及合同:确保来料检验的基础,包括产品规格、质量标准、交货日期等信息。
2.送货接收:接收供应商送来的原料或零部件,并核对送货单和采购订单是否一致。
3.样品抽样:根据抽样方法,从送货中抽取样品,保证样品的代表性和可证据性。
4.检验参数测量:使用合适的检验方法,对样品进行测量和测试,记录测量结果。
5.检验结果评估:根据来料检验标准,评估检验结果是否合格,并记录评估结果。
6.不合格品处理:对于不合格品,根据不合格处理程序进行处理,如退货、整改等。
7.合格品接收:接收合格的原料或零部件,并进行验收,记录接收结果。
8.数据分析及统计:对检验结果进行分析和统计,找出问题的原因,并及时采取改进措施。
9.持续改进:根据统计结果和过程控制,持续改进来料检验规范及流程,以提高产品质量和效率。
以上是一个典型的来料检验规范及流程的介绍,可以根据具体的产品和公司情况进行调整和完善。
来料检验作业指导书

来料检验作业指导书一、引言来料检验是指对供应商提供的原材料、零部件或者成品进行检验,以确保其质量符合公司的要求和标准。
本作业指导书旨在为来料检验人员提供准确的操作指导,以确保检验工作的准确性和一致性。
二、检验准备1. 检验设备准备来料检验需要使用一系列的检验设备,包括但不限于量具、显微镜、试验设备等。
在进行检验前,检验人员应确保所有设备的正常运行,并进行必要的校准和维护。
2. 检验环境准备来料检验应在整洁、璀璨、无风尘、无湿度的环境中进行,以确保检验结果的准确性。
检验人员应定期清洁检验区域,并保持良好的工作秩序。
三、检验流程1. 检验计划制定根据公司的质量要求和标准,制定来料检验计划。
检验计划应包括待检验物料的种类、数量、检验方法、检验标准等内容。
2. 来料接收当供应商送达物料时,检验人员应与供应商的送货员一起进行来料接收。
检验人员应核对送货单上的物料信息与实际物料是否一致,并进行必要的记录。
3. 外观检验外观检验是来料检验的首要步骤,其目的是检查物料的外观是否符合要求。
检验人员应根据标准要求对外观进行检查,并记录检验结果。
4. 尺寸检验尺寸检验是来料检验的重要环节,其目的是检查物料的尺寸是否符合要求。
检验人员应使用适当的量具对物料的尺寸进行测量,并与标准要求进行比对。
5. 功能性检验功能性检验是针对特定物料的功能要求进行的检验。
检验人员应根据标准要求进行相应的功能性测试,并记录测试结果。
6. 化学成份检验对于需要进行化学成份检验的物料,检验人员应采取适当的取样方法,并使用相应的试剂进行化学分析。
检验人员应根据标准要求对化学成份进行检验,并记录检验结果。
7. 特殊检验根据具体物料的特殊要求,进行相应的特殊检验。
特殊检验可以包括但不限于温度测试、压力测试、电气测试等。
检验人员应根据标准要求进行相应的特殊检验,并记录检验结果。
8. 检验结果判定根据检验结果,判定物料是否合格。
合格的物料可以进入下一步的生产流程,不合格的物料应进行相应的处理,如退货、返工等,并进行记录。
来料检验规范

5.1来料检验流程图(如附件1)。
5.2点收:依《仓库管制程序》办理。
5.3来料检验
5.3.1.货仓依据送货单核对数量、料号、物料标示正确后签收,并填写〈品质检查报告〉送检,将ROHS物料放在RoHS物料待验区:非ROHS物料放在非ROHS物料待验区,或以“待验”标示管制。其中代工业务客供物料货仓按“套单”开《品质检查报告〉,IQC依BOM单核对料件规格、型号。
5.3.9.检查作出检验结论后,IQC将《品质检查报告》第二联(红联)发到采购,由采购知会供应商、货仓、PMC,生产部,由仓库办理入库或退货手。采购并将不合格《品质检查报告》传真给客户或供应商。第一联(白联)品质部保存,并由品质文员或班组长进行统计汇总。制程来料不良IQC出《纠正预防通知书》反馈给供应商要求改善并回复对策,品质部将《品质检查报告》《纠正预防通知书》表单存档便于追溯。
5.3.10.对于生产急需物料,IQC应进行优先检验或由采购部提出《特采申请单》品质部、工程部确认批准后方可采取特殊放行,并在《品质检查报告》上注明特采放行,对于特采放行的物料IQC应保留适当样品进行检验或对下线之物料进行跟踪,如发现不合格则立即上报部门主管或经理。
5.4.11.免检物料,必须由物料申请部门或PMC开《来料免检申请单》注明免检原因,并由品质、货仓、生产、PUC、工程签名确认,方可免检上线。
程序文件
编写部门
文件编号
制定日期
版本
名称:来料检验规范
修订日期
页数
修改状态
5.3.5.除非客户规定一般使用M11-STD-105E,一般抽样水准II级单次正常检验抽样,特殊抽样S-2,AQ1:电子类(MA0.4/MT0.65);塑胶类、包材类(MAO.4/MI1.0)ROUS:AC:0REJ:1
来料检验流程标准
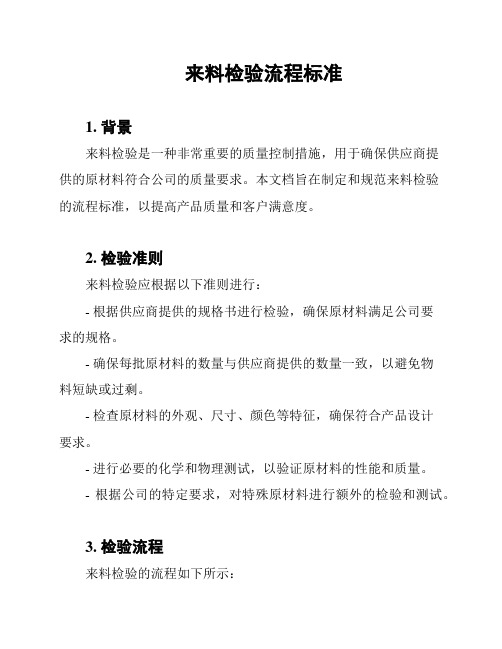
来料检验流程标准1. 背景来料检验是一种非常重要的质量控制措施,用于确保供应商提供的原材料符合公司的质量要求。
本文档旨在制定和规范来料检验的流程标准,以提高产品质量和客户满意度。
2. 检验准则来料检验应根据以下准则进行:- 根据供应商提供的规格书进行检验,确保原材料满足公司要求的规格。
- 确保每批原材料的数量与供应商提供的数量一致,以避免物料短缺或过剩。
- 检查原材料的外观、尺寸、颜色等特征,确保符合产品设计要求。
- 进行必要的化学和物理测试,以验证原材料的性能和质量。
- 根据公司的特定要求,对特殊原材料进行额外的检验和测试。
3. 检验流程来料检验的流程如下所示:3.1 接收原材料- 检查原材料的外包装是否完好,并核对货物与交货单是否一致。
- 将原材料送至来料检验区域,准备进行下一步的检验工作。
3.2 进行检验- 根据公司的检验计划和检验标准,对每批原材料进行检验。
- 根据检验结果,将原材料分类为合格或不合格。
- 对不合格的原材料,进行进一步的分析和调查,并与供应商进行沟通,以解决质量问题。
3.3 记录和报告- 将检验结果记录在来料检验报告中,包括每批原材料的检验日期、数量、检验结果等信息。
- 向相关部门和质量团队提供来料检验报告,以便进行后续的质量控制工作。
3.4 处理原材料- 对合格的原材料,将其移至适当的存储区域,以确保其质量不受损。
- 对不合格的原材料,采取适当的措施,如退货、进行再加工等,以最小化质量损失。
4. 审查和改进每年对来料检验流程进行审查和改进,以确保其持续有效和符合最新的质量标准和要求。
以上是来料检验流程标准的简要描述,旨在帮助组织制定和执行合适的来料检验流程。
具体操作细节和流程步骤应根据组织的实际情况进行调整和优化。
来料检验流程
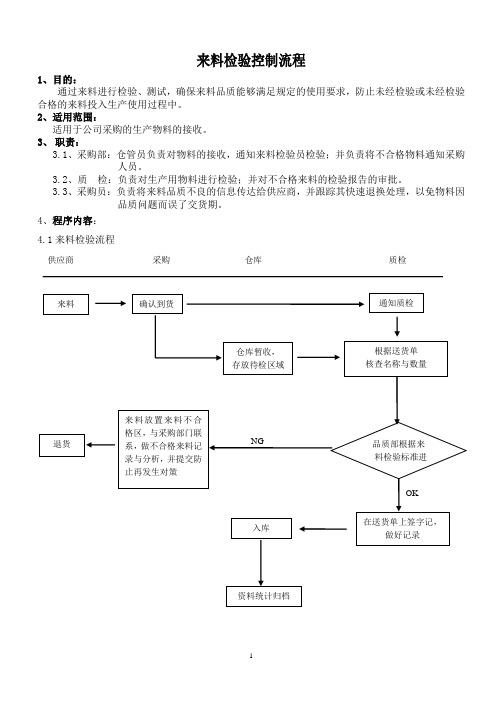
来料检验控制流程
1、目的:
通过来料进行检验、测试,确保来料品质能够满足规定的使用要求,防止未经检验或未经检验合格的来料投入生产使用过程中。
2、适用范围:
适用于公司采购的生产物料的接收。
3、职责:
3.1、采购部:仓管员负责对物料的接收,通知来料检验员检验;并负责将不合格物料通知采购
人员。
3.2、质检:负责对生产用物料进行检验;并对不合格来料的检验报告的审批。
3.3、采购员:负责将来料品质不良的信息传达给供应商,并跟踪其快速退换处理,以免物料因
品质问题而误了交货期。
4、程序内容:
4.1来料检验流程
供应商采购仓库质检
4.2原材料接收
4.2.1材料仓库必须指定固定的区域为待检区,放置待检或已检待判的来料。
4.2.2原材料到达公司后,材料仓库暂收,并依单据资料与供应商的送货清单对物料进行外
包装、规格型号、数量的初步验证,不符合则通知由采购处理。
4.3来料检验
4.3.1 质检员收到采购知后,核对原材料型号/规格是否符合,并进行来料检验。
4.3.2根据检验标准进行来料检验,填写来料检验记录表,并进行统计分析。
4.4判定及处理
4.4.1经检验为合格的物料,在送货单上签字。
4.4.2经判定为不合格的物料,按《不合格品控制程序》进行处理。
4.5记录报告
4.5.1来料质检员对原材料检验判定后,填写《来料检验记录表》。
4.5.2每月由来料质检员将物料检验情况统计登录到《来料检验月报表》,作为统计供应商品
质水准的依据。
4.5.3检验记录报告由质量部进行归档保存。
编制:审核:批准:。
来料检验流程
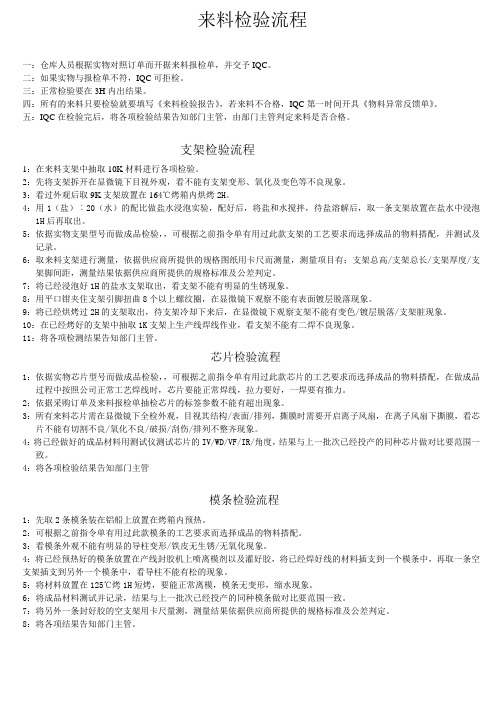
来料检验流程一:仓库人员根据实物对照订单而开据来料报检单,并交予IQC。
二:如果实物与报检单不符,IQC可拒检。
三:正常检验要在3H内出结果。
四:所有的来料只要检验就要填写《来料检验报告》,若来料不合格,IQC第一时间开具《物料异常反馈单》。
五:IQC在检验完后,将各项检验结果告知部门主管,由部门主管判定来料是否合格。
支架检验流程1:在来料支架中抽取10K材料进行各项检验。
2:先将支架拆开在显微镜下目视外观,看不能有支架变形、氧化及变色等不良现象。
3:看过外观后取9K支架放置在164℃烤箱内烘烤2H。
4:用1(盐)︰20(水)的配比做盐水浸泡实验,配好后,将盐和水搅拌,待盐溶解后,取一条支架放置在盐水中浸泡1H后再取出。
5:依据实物支架型号而做成品检验,,可根据之前指令单有用过此款支架的工艺要求而选择成品的物料搭配,并测试及记录。
6:取来料支架进行测量,依据供应商所提供的规格图纸用卡尺而测量,测量项目有:支架总高/支架总长/支架厚度/支架脚间距,测量结果依据供应商所提供的规格标准及公差判定。
7:将已经浸泡好1H的盐水支架取出,看支架不能有明显的生锈现象。
8:用平口钳夹住支架引脚扭曲8个以上螺纹圈,在显微镜下观察不能有表面镀层脱落现象。
9:将已经烘烤过2H的支架取出,待支架冷却下来后,在显微镜下观察支架不能有变色/镀层脱落/支架脏现象。
10:在已经烤好的支架中抽取1K支架上生产线焊线作业,看支架不能有二焊不良现象。
11:将各项检测结果告知部门主管。
芯片检验流程1:依据实物芯片型号而做成品检验,,可根据之前指令单有用过此款芯片的工艺要求而选择成品的物料搭配,在做成品过程中按照公司正常工艺焊线时,芯片要能正常焊线,拉力要好,一焊要有推力。
2:依据采购订单及来料报检单抽检芯片的标签参数不能有超出现象。
3:所有来料芯片需在显微镜下全检外观,目视其结构/表面/排列,撕膜时需要开启离子风扇,在离子风扇下撕膜,看芯片不能有切割不良/氧化不良/破损/刮伤/排列不整齐现象。
- 1、下载文档前请自行甄别文档内容的完整性,平台不提供额外的编辑、内容补充、找答案等附加服务。
- 2、"仅部分预览"的文档,不可在线预览部分如存在完整性等问题,可反馈申请退款(可完整预览的文档不适用该条件!)。
- 3、如文档侵犯您的权益,请联系客服反馈,我们会尽快为您处理(人工客服工作时间:9:00-18:30)。
3
尺寸检查
厚度及允许偏差符合表2的规定
千分尺测量
精度为0.01MM的千分尺
5.表2:
厚度
允许偏差
厚度
允许偏差
0.8~1.5
±0.17
>2.5~3.0
±0.22
>1.5~2.0
±0.19
>3.0~4.0
±0.24
>2.0~2.5
±0.21
>4.0~5.0
±0.26
6.附录A3:
7.1.适用范围:不锈钢冷轧钢板及钢带
规则类别
备注
常规
抽样
39.1
PF2A4-161J
(1)材料名称、牌号
目测
√
40.2
PA-A4-1-5C
(2)材料颜色、规格
41.3 3
PA-A8-1
(3)材料批次、合格证
42.4 4
PA-A6
(4)材料质保书、测试报告,阻燃性能等
用打火机燃烧1分钟,不燃烧
√
√
5
PC聚碳酸酯
43.66
POM聚甲醛树脂
±0.180
20.附录B2:
21.1.适用范围:铜及铜合金带材
22.2.编制依据:GB/T2059-2000;GB/T17793-1999
表1:
序号
检验项目
检验要求
检验方法
检验工具
1
质保书和合格证
有
无质保书或合格证不予验收
目测
2
外观检查
带材的表面应光滑,清洁,不得有裂纹、起皮、毛刺、气泡压折和铜绿(铜锈氧化)斑点凹坑杂物等缺陷.
44.77
DMC团状模塑料
45.88
阻燃ABS
(5)材料性能测试:
a.绝缘电阻≥0.5M欧;
b.工频耐压测试符合对应产品技术参数及要求
安秒特性测试台,兆欧表,耐压测试仪
√
46.99
PBT
47.110
MBS
48.111
尼龙1013B
49.附录C2:
50.1.适用范围:绝缘导线(RV)450/750V,(BV)450/750V
序号
检验项目
检验要求
检验方法
检验工具
1
质保书和合格证
有
无质保书或合格证不予验收
目测
2
外观检查
钢板和钢带不得有分层,表面不允许有裂纹、结疤、折叠、气泡和杂物。允许有轻微的擦伤和氧化色
目测
3
尺寸检查
厚度及允许偏差符合表2的规定
千分尺测量
精度为0.01MM的千分尺
4.表2:
厚度
允许偏差
厚度
允许偏差
≤0.40
批量在100卷及以上时按每100卷抽检2卷抽检。从被抽中的每卷中至少相隔1M的3处各取一段电线作为试样。
4.检验项目及要求
4.1检查合格证或质保书,无合格证和质保书的不予接收。
4.2检查产品外观质量,绝缘层应无气泡,裂痕等缺陷。色泽均匀一致符合样品要求。
4.3用精度为0.01MM的卡尺测量材料定值(材料内径,外径)
>0.30~0.40
±0.020
>1.20~2.00
±0.050
>0.40~0.50
±0.025
>2.00~3.00
±0.060
24.附录B3:
25.1.适用范围:铜及铜合金拉制棒 2.编制依据:GB/T4423-1992
文件名称
原材料检验规则及要求
文件编号
JYQE2011C001
产品型号及名称
原材料
>4.0~5.0
允许偏差
±0.15
±0.17
±0.18
±0.20
±0.22
±0.24
文件名称
原材料检验规则及要求
文件编号
JYQE2011C001
产品型号及名称
原材料
共 6 页
第 4 页
1
附录B1:
1.适用范围:铜及铜合金板材
2.编制依据:GB/T2040-2002,GB/T17793-1999
表1:
30.3.检验规则:检验项目分常规检验和定期抽样检验两种
31.3.1常规检验作为绝缘材料进厂检验的依据。
32.3.2定期抽样检验在常规检验合格的材料中,每12个月不应少于一次,同时材料供方能提供相关的绝缘材料
33.的质保书或检测报告,报告内容应包括材料的主要特性参数。定期抽样材料的耐高温性能,耐燃性能,电器
34.绝缘性能,关键尺寸(线材的内外径)及工频耐压测试等项目在产品上体现。测度过程中,在规定时间内绝
35.缘材料外观不应有明显的变化(允许有轻微的发黄),并能承受承载电路或用电设备的温度;通电测试完成
36.后其绝缘性能、耐压测试应满足标准要求。
37.4.检验项目及要求
38.序号
材料名称
技术要求
试验方法及设备
12.2.编制依据:GB/T708-2006;YB/T5058-2005
表1:
序号
检验项目
检验要求
检验方法
检验工具
1
质保书和合格证
有
无质保书或合格证不予验收
目测
文件名称
原材料检验规则及要求
文件编号
JYQE2011C001
产品型号及名称
原材料
共 6 页
第 3 页
续表1:
序号
检验项目
检验要求
检验方法
检验工具
>0.20~0.30
±0.025
>1.20~2.00
±0.060
>0.30~0.40
±0.030
>2.00~3.00
±0.080
>0.40~0.50
±0.035
>3.00~5.00
±0.100
>0.50~0.80
±0.040
>5.00~8.00
±0.130
>0.80~1.20
±0.050
>8.00~12.00
表1:
序号
检验项目
检验要求
检验方法
检验工具
1
质保书和合格证
有
无质保书或合格证不予验收
目测
2
外观检查
钢带表面应光滑,不得有裂纹、拉裂、气泡、折叠、杂物、结疤和压入氧化铁皮和分层现象
目测
3
尺寸检查
厚度及允许偏差符合表2,表3的规定
千分尺测量
精度为0.01MM的千分尺
17.表2: (MM)
厚度
3.0~5.0
>5.0~8.0
>8.0~15
>15~25
>25~40
>40~60
允许偏差
+0.55
+0.65
+0.70
+0.85
+0.90
+1.05
-0.30
-0.35
-0.40
-0.45
-0.50
-0.55
18.:
表3: (MM)
厚度
0.8~1.5
>1.5~2.0
>2.0~2.5
>2.5~3.0
>3.0~4.0
文件编号
JYQE2011C001
产品型号及名称
原材料
共 6 页
第 2 页
1式 附录A2:
1.适用范围:热轧薄钢板及钢带(Q235-A)
2.编制依据:GB/T709-2006,GB912-1989
表1:
序号
检验项目
检验要求
检验方法
检验工具
1
质保书和合格证
有
无质保书或合格证不予验收
目测
2
外观检查
钢板和钢带不得有分层,表面不允许有裂纹、结疤、折叠、气泡和杂物。允许有轻微的擦伤和氧化色
51.2.编制依据:GB/T5023.1-2008额定电压450/750V及以下聚氯乙烯绝缘电缆第一部分一般要求。
52.GB/T5023.2-2008额定电压450/750V及以下聚氯乙烯绝缘电缆第二部分试验方法。
文件名称
原材料检验规则及要求
文件编号
JYQE2011C001
产品型号及名称
原材料
共 6 页
GB/T2040-2002 铜及铜合金板材
GB912-1989 碳素结构钢和低合金结构钢热轧薄钢板及钢带
GB711-1988 优质碳素结构钢热轧厚钢板和宽钢带
GB/T3280-2007 不锈钢冷轧钢板和钢带
GB/4423-1992 铜及铜合金拉制棒
GB/T5023-2008 额定电压450V、750V及以下聚氯乙烯绝缘电缆
3.技术要求:
3..1外观检验:
口面毛刺不得大于0.1MM,折弯成型部位不得有裂痕,断层等缺陷。
3.2尺寸检验:
说明:如公司没零件技术图纸,供应商必须提供。
3.3性能及插拔力定期委外验证并提供检验记录或质保书。
来料检验操作程序及流程
供应商来料
通知检验
共 6 页
第 5 页
续表1:
序号
检验项目
检验要求
检验方法
检验工具
1
质保书和合格证
有
无质保书或合格证不予验收
目测
2
外观检查
棒材的表面应光滑,清洁,不得有裂纹、起皮、毛刺、气泡压折和铜绿(铜锈氧化)斑点凹坑杂物等缺陷.
目测
3
尺寸检查
厚度及允许偏差符合表2的规定
千分尺测量
精度为0.01MM的千分尺
26.表2:
序号
检验项目
检验要求
检验方法
检验工具
1
质保书和合格证
有
无质保书或合格证不予验收
目测
2
外观检查
板材的表面应光滑,清洁,不得有裂纹、起皮、毛刺、气泡压折和铜绿(铜锈氧化)斑点凹坑杂物等缺陷.