TaRAR1 is Required for Lr24-Mediated Wheat Leaf Rust Resistance
约翰·德尔4045D 4045T 8阀值发动机商品说明书
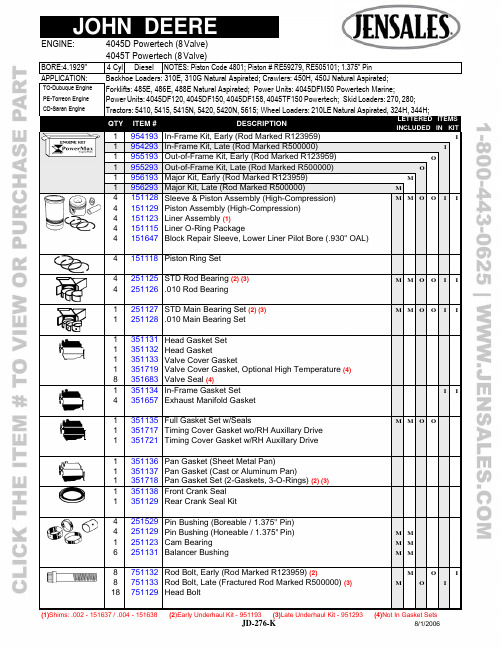
APPLICATION: Backhoe Loaders: 310E, 310G Natural Aspirated; Crawlers: 450H, 450J Natural Aspirated; Forklifts: 485E, 486E, 488E Natural Aspirated; Power Units: 4045DFM50 Powertech Marine; Power Units: 4045DF120, 4045DF150, 4045DF158, 4045TF150 Powertech; Skid Loaders: 270, 280; Tractors: 5410, 5415, 5415N, 5420, 5420N, 5615; Wheel Loaders: 210LE Natural Aspirated, 324H, 344H; (1)Shims: .002 - 151637 / .004 - 151638 (2)Early Underhaul Kit - 951193 (3)Late Underhaul Kit - 951293 (4)Not In Gasket Sets8/1/2006JD-276-K TO-Dubuque Engine PE-Torreon Engine CD-Saran Engine QTY ITEM # DESCRIPTION LETTERED ITEMSINCLUDED IN KIT1 954193 In-Frame Kit, Early (Rod Marked R123959) I1 954293 In-Frame Kit, Late (Rod Marked R500000) I1 955193 Out-of-Frame Kit, Early (Rod Marked R123959) O1 955293 Out-of-Frame Kit, Late (Rod Marked R500000) O1 956193 Major Kit, Early (Rod Marked R123959) M 1 956293 Major Kit, Late (Rod Marked R500000) M4 4 4 4 4 151128 151129 151123 151115 151647 Sleeve & Piston Assembly (High-Compression) Piston Assembly (High-Compression)Liner Assembly (1)Liner O-Ring PackageBlock Repair Sleeve, Lower Liner Pilot Bore (.930" OAL)M M O O I I4 151118 Piston Ring Set4 4 251125 251126 STD Rod Bearing (2) (3) .010 Rod BearingM M O O I I1 1 251127 251128 STD Main Bearing Set (2) (3) .010 Main Bearing SetM M O O I I1 1 1 1 8 351131 351132 351133 351719 351683 Head Gasket Set Head GasketValve Cover GasketValve Cover Gasket, Optional High Temperature (4)Valve Seal (4)1 4 351134 351657 In-Frame Gasket Set Exhaust Manifold GasketI I1 1 1 351135 351717 351721 Full Gasket Set w/Seals Timing Cover Gasket wo/RH Auxillary DriveTiming Cover Gasket w/RH Auxillary DriveM M O O1 1 1 351136 351137 351718 Pan Gasket (Sheet Metal Pan) Pan Gasket (Cast or Aluminum Pan)Pan Gasket Set (2-Gaskets, 3-O-Rings) (2) (3)1 1 351138 351129 Front Crank Seal Rear Crank Seal Kit4 4 1 6 251529 251129 251123 251131 Pin Bushing (Boreable / 1.375" Pin) Pin Bushing (Honeable / 1.375" Pin) Cam Bearing Balancer Bushing M M M MMM8 8 18 751132 751133 751129 Rod Bolt, Early (Rod Marked R123959) (2) Rod Bolt, Late (Fractured Rod Marked R500000) (3) Head BoltM M O O IIAPPLICATION: Backhoe Loaders: 310E, 310G Natural Aspirated; Crawlers: 450H, 450J Natural Aspirated; Forklifts: 485E, 486E, 488E Natural Aspirated; Power Units: 4045DFM50 Powertech Marine; Power Units: 4045DF120, 4045DF150, 4045DF158, 4045TF150 Powertech; Skid Loaders: 270, 280; Tractors: 5410, 5415, 5415N, 5420, 5420N, 5615; Wheel Loaders: 210LE Natural Aspirated, 324H, 344H; (5).015 - 451112 / .030 - 451528 (6).015 - 451114 / .030 - 451529 (7)Oversize Ex Seat - 451121 (8)Oversize In Seat - 451123 JD-276-K 8/1/2006 TO-Dubuque Engine PE-Torreon Engine CD-Saran Engine QTY ITEM # DESCRIPTION LETTERED ITEMSINCLUDED IN KIT1 959333 Basic Valve Kit B1 959133 Valve Train Kit V1 551116 Camshaft w/Gear, Early (Marked R135439) 1 551353 Camshaft w/Gear, Late (Marked R504534)8 551118 Tappet4 451111 STD Exhaust Valve (5) V B4 451113 STD Intake Valve (6) V B4 4 8 8 16 451531 451532 451115 451116 451117 Exhaust Service Repair Valve Guide (.502 OD / 2.390" OAL) Intake Service Repair Valve Guide (.502 OD / 2.209" OAL) Valve Spring Rotator Keeper (Half)V VV BB4 451126 Ex Seat, OEM TO & PE (1.345-T-1.482 x 1.695 x .242) (7)4 451119 Ex Seat, OEM CD (1.345-T-1.482 x 1.697 x .243)4 451127 In Seat, OEM TO & PE (1.550-T-1.650 x 1.857 x .257) (8)4 451122 In Seat, OEM CD (1.550-T-1.650 x 1.859 x .257)8 451128 Rocker Arm1 451129 Rocker Arm Shaft2 451165 Rocker Arm Shaft Plug1 551119 Cam Timing Gear (60 Tooth)1 551121 Crank Timing Gear (30 Tooth)1 551355 Upper Idler Gear Assembly (Gear, Hub, Bolt, Washers)1 551142 Upper Idler Gear Bushing, Late (1.750 ID x .840 Wide)1 551351 Lower Idler Gear, Marked R120636 "Includes Bush - 551352"8 551123 Push Rod (1-Socket 1-Ball / 10.43" OAL)1 651116 Oil Pump1 651118 Oil Cooler: Code 5901 (5 Plate) 1 651119 Oil Cooler: Code 5902 (7 Plate)1 651122 Oil Cooler: Code 5904 (3 Plate)1 751134 Crankshaft, Early (4 Bolt Nose)1 751353 Crankshaft, Late (Single Bolt / Taper Nose)4 751349 Connecting Rod (1.375" Pin)1 751135 LH Balancer Shaft1 751136 RH Balancer Shaft1 851152 Fuel Pump: Codes 3701, 37061 851153 Fuel Pump: Code 37021 851154 Fuel Pump: Code 37071 851369 Fuel Pump: Code 37151 851155 Fuel Pump Push Rod1 851147 Thermostat: Except Marine (180º)1 851187 Water Pump: Except Marine (Cast Iron / STD Flow)1 851148 Water Pump Kit: Except Marine (STD Flow)1 851368 Automatic Belt Tensioner Assembly。
MW 315 系列门安装指南说明书

P.N. 5028 file #g00084 rev. 02/11/2020INSTALLATION GUIDE FOR MW 315 SERIES DOORSBEFORE STARTING:CAUTION: If this product is being installed next to a copper-based wood preservative, a barrier must be installed between the treated lumber and this product to prevent a reaction between the metal and the preservative.1.Read these instructions completely BEFORE starting to install the door. However, re-handing of doors withview lites may require removal and re-installation of the lite so that the fasteners are located on the interior of the door panel. This will result in better security and a better weather seal.2.The rough opening (RO) into which this door is to be installed should be ½” wider and ½” higher thanthe outside measurement of the door frame, excluding the nailing fin. The 2x4s used in the door packaging can be re-used in the RO. (See framing illustration below.) Check the RO to be certain that it is plumb and square. Pre-drilling pilot holes into the wood frame of the RO where the installation screws are to be usedand through the nailing fin will make them easier to install.3.This panel has wooden stiles and is prepped for use with a “drive-in” latch bolt.4.We recommend that fiberglass insulation be placed between the metal door frame and the wood roughopening to prevent possible air infiltration between the components.TOOLS AND SUPPLIES REQUIRED:Tape measure, square, level, drill, drill bits, #2 Phillips-square combo drive bit, hammer, two (2) saw horses, shimming material and appropriate nails for nailing through the nailing fin.DOOR INSTALLATION:1.Remove the door from the carton and place it on the saw horses with what will be the outside ofthe door facing up and the hinges in the proper position for the handing and swing desired.2.Remove the screw pack, containing fifteen installation screws, the weather-stripped header parting stop andthe optional lock set from the carton.3.Set the door assembly into the rough opening with the hinge jamb tight against the wood roughopening.4.Open the door and install one of the #10 x 3½“ wood screws into the center hole of the top hinge.5.Check the aluminum frame to be certain it is square and plumb. If so, install a wood screw through thecenter hole of the bottom hinge and then another through the center hole of the center hinge. Install twoscrews in the holes in the lower surface of the jamb.6.Check the aluminum frame for squareness again and shim if necessary.7. Depending on the actual size of the rough opening, place the appropriate thickness shimmingmaterial between the lock jamb of the metal door frame and the wood rough opening, especiallyin the areas where the four installation screws will be placed and in the lock area. USECAUTION so as to not bow, bend or distort the frame with the shimming material.8. Install one of the installation screws through the top installation screw hole in the lock jamb and thenone through the bottom hole. Proceed with the second hole from the top and then the bottom. Whileinstalling these screws, maintain a uniform space between the door panel and the metal frame (approximately 5/32”). Shim as necessary.9. Install the remaining installation screws in the installation screw holes in the hinge jamb,following the same sequence as those installed in the lock jamb.10. Check the aluminum frame for squareness again and adjust the screws and shim as necessary.11. Install customer-provided nails or screws through the nailing fin on both the lock and hinge jamb, in additionto the previously mentioned installation screws through the jambs. Use at least four (4) equally spaced nails or screws on each fin.12.To install the snap-in header parting stop into the frame header:A.Swing the door completely open to allow sufficient working area.B.Hook the leg of the parting stop containing the weatherstrip into the slot in the frame header.Remember to keep the weatherstrip toward the door, the same as in the jambs.C.Swing the parting stop up and press it against the frame header until the other leg of the partingstop snaps into the other groove in the header. NOTE: Due to Standard AluminumCommercial Tolerances, it may be necessary to gently tap the parting stop into place with ahammer. If so, use either a soft faced hammer or place a block of wood between the hammerand the parting stop to avoid damaging the extrusion or the painted finish. See the illustrationbelow.13.Remove the adhesive backed cardboard spacers from the lock side of the door.14. Install the lockset as per the lock manufacturer’s instructions.15. Apply caulk across each end of the sweep to help prevent water infiltration in this area.。
IATA AHM目录
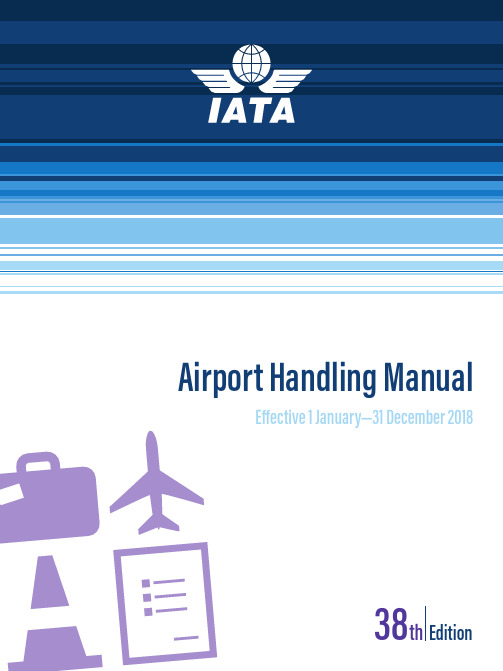
Airport Handling ManualEffective 1 January—31 December 201838NOTICEDISCLAIMER. The information contained in thispublication is subject to constant review in the lightof changing government requirements and regula-tions. No subscriber or other reader should act onthe basis of any such information without referringto applicable laws and regulations and/or withouttak ing appropriate professional advice. Althoughevery effort has been made to ensure accuracy, theInternational Air Transport Association shall not beheld responsible for any loss or damage caused byerrors, omissions, misprints or misinterpretation ofthe contents hereof. Furthermore, the InternationalAir Transport Association expressly disclaims anyand all liability to any person or entity, whether apurchaser of this publication or not, in respect ofanything done or omitted, and the consequencesof anything done or omitted, by any such person orentity in reliance on the contents of this publication.Opinions expressed in advertisements appearing inthis publication are the advertiser’s opinions and donot necessarily reflect those of IATA. The mentionof specific companies or products in advertisementdoes not imply that they are endorsed or recom-mended by IATA in preference to others of a simi-lar nature which are not mentioned or advertised.© International Air Transport Association. AllRights Reserved. No part of this publication maybe reproduced, recast, reformatted or trans-mitted in any form by any means, electronic ormechanical, including photocopying, record-ing or any information storage and retrieval sys-tem, without the prior written permission from:Senior Vice PresidentAirport, Passenger, Cargo and SecurityInternational Air Transport Association800 Place VictoriaP.O. Box 113Montreal, QuebecCANADA H4Z 1M1Airport Handling ManualMaterial No.: 9343-38ISBN 978-92-9229-505-9© 2017 International Air Transport Association. All rights reserved.TABLE OF CONTENTSPage Preface (xv)Introduction (xvii)General (1)AHM001Chapter0—Record of Revisions (1)AHM011Standard Classification and Numbering for Members Airport Handling Manuals (2)AHM012Office Function Designators for Airport Passenger and Baggage Handling (30)AHM020Guidelines for the Establishment of Airline Operators Committees (31)AHM021Guidelines for Establishing Aircraft Ground Times (34)AHM050Aircraft Emergency Procedures (35)AHM070E-Invoicing Standards (53)Chapter1—PASSENGER HANDLING (91)AHM100Chapter1—Record of Revisions (91)AHM110Involuntary Change of Carrier,Routing,Class or Type of Fare (92)AHM112Denied Boarding Compensation (98)AHM120Inadmissible Passengers and Deportees (99)AHM140Items Removed from a Passenger's Possession by Security Personnel (101)AHM141Hold Loading of Duty-Free Goods (102)AHM170Dangerous Goods in Passenger Baggage (103)AHM176Recommendations for the Handling of Passengers with Reduced Mobility(PRM) (105)AHM176A Acceptance and Carriage of Passengers with Reduced Mobility(PRM) (106)AHM180Carriage of Passengers with Communicable Diseases (114)AHM181General Guidelines for Passenger Agents in Case of SuspectedCommunicable Disease (115)Chapter2—BAGGAGE HANDLING (117)AHM200Chapter2—Record of Revisions (117)AHM210Local Baggage Committees (118)AHM211Airport Operating Rules (124)Airport Handling ManualPageChapter2—BAGGAGE HANDLING(continued)AHM212Interline Connecting Time Intervals—Passenger and Checked Baggage (126)AHM213Form of Interline Baggage Tags (128)AHM214Use of the10Digit Licence Plate (135)AHM215Found and Unclaimed Checked Baggage (136)AHM216On-Hand Baggage Summary Tag (138)AHM217Forwarding Mishandled Baggage (139)AHM218Dangerous Goods in Passengers'Baggage (141)AHM219Acceptance of Firearms and Other Weapons and Small Calibre Ammunition (142)AHM221Acceptance of Power Driven Wheelchairs or Other Battery Powered Mobility Aidsas Checked Baggage (143)AHM222Passenger/Baggage Reconciliation Procedures (144)AHM223Licence Plate Fallback Sortation Tags (151)AHM224Baggage Taken in Error (154)AHM225Baggage Irregularity Report (156)AHM226Tracing Unchecked Baggage and Handling Damage to Checked and UncheckedBaggage (159)AHM230Baggage Theft and Pilferage Prevention (161)AHM231Carriage of Carry-On Baggage (164)AHM232Handling of Security Removed Items (168)AHM240Baggage Codes for Identifying ULD Contents and/or Bulk-Loaded Baggage (169)Chapter3—CARGO/MAIL HANDLING (171)AHM300Chapter3—Record of Revisions (171)AHM310Preparation for Loading of Cargo (172)AHM311Securing of Load (174)AHM312Collection Sacks and Bags (177)AHM320Handling of Damaged Cargo (178)AHM321Handling of Pilfered Cargo (179)AHM322Handling Wet Cargo (180)AHM330Handling Perishable Cargo (182)AHM331Handling and Protection of Valuable Cargo (184)AHM332Handling and Stowage of Live Animals (188)AHM333Handling of Human Remains (190)Table of ContentsPageChapter3—CARGO/MAIL HANDLING(continued)AHM340Acceptance Standards for the Interchange of Transferred Unit Load Devices (191)AHM345Handling of Battery Operated Wheelchairs/Mobility AIDS as Checked Baggage (197)AHM350Mail Handling (199)AHM351Mail Documents (203)AHM353Handling of Found Mail (218)AHM354Handling of Damaged Mail (219)AHM355Mail Security (220)AHM356Mail Safety (221)AHM357Mail Irregularity Message (222)AHM360Company Mail (224)AHM380Aircraft Documents Stowage (225)AHM381Special Load—Notification to Captain(General) (226)AHM382Special Load—Notification to Captain(EDP Format and NOTOC Service) (231)AHM383Special Load—Notification to Captain(EDP NOTOC Summary) (243)AHM384NOTOC Message(NTM) (246)Chapter4—AIRCRAFT HANDLING AND LOADING (251)AHM400Chapter4—Record of Revisions (251)AHM411Provision and Carriage of Loading Accessories (252)AHM420Tagging of Unit Load Devices (253)AHM421Storage of Unit Load Devices (263)AHM422Control of Transferred Unit Load Devices (268)AHM423Unit Load Device Stock Check Message (273)AHM424Unit Load Device Control Message (275)AHM425Continued Airworthiness of Unit Load Devices (279)AHM426ULD Buildup and Breakdown (283)AHM427ULD Transportation (292)AHM430Operating of Aircraft Doors (295)AHM431Aircraft Ground Stability—Tipping (296)AHM440Potable Water Servicing (297)AHM441Aircraft Toilet Servicing (309)Airport Handling ManualPageChapter4—AIRCRAFT HANDLING AND LOADING(continued)AHM450Standardisation of Gravity Forces against which Load must be Restrained (310)AHM451Technical Malfunctions Limiting Load on Aircraft (311)AHM453Handling/Bulk Loading of Heavy Items (312)AHM454Handling and Loading of Big Overhang Items (313)AHM455Non CLS Restrained ULD (316)AHM460Guidelines for Turnround Plan (323)AHM462Safe Operating Practices in Aircraft Handling (324)AHM463Safety Considerations for Aircraft Movement Operations (337)AHM465Foreign Object Damage(FOD)Prevention Program (340)Chapter5—LOAD CONTROL (343)AHM500Chapter5—Record of Revisions (343)AHM501Terms and Definitions (345)AHM503Recommended Requirements for a New Departure Control System (351)AHM504Departure Control System Evaluation Checklist (356)AHM505Designation of Aircraft Holds,Compartments,Bays and Cabin (362)AHM510Handling/Load Information Codes to be Used on Traffic Documents and Messages (368)AHM513Aircraft Structural Loading Limitations (377)AHM514EDP Loading Instruction/Report (388)AHM515Manual Loading Instruction/Report (404)AHM516Manual Loadsheet (416)AHM517EDP Loadsheet (430)AHM518ACARS Transmitted Loadsheet (439)AHM519Balance Calculation Methods (446)AHM520Aircraft Equipped with a CG Targeting System (451)AHM530Weights for Passengers and Baggage (452)AHM531Procedure for Establishing Standard Weights for Passengers and Baggage (453)AHM533Passengers Occupying Crew Seats (459)AHM534Weight Control of Load (460)AHM536Equipment in Compartments Procedure (461)AHM537Ballast (466)Table of ContentsPageChapter5—LOAD CONTROL(continued)AHM540Aircraft Unit Load Device—Weight and Balance Control (467)AHM550Pilot in Command's Approval of the Loadsheet (468)AHM551Last Minute Changes on Loadsheet (469)AHM561Departure Control System,Carrier's Approval Procedures (471)AHM562Semi-Permanent Data Exchange Message(DEM) (473)AHM564Migration from AHM560to AHM565 (480)AHM565EDP Semi-Permanent Data Exchange for New Generation Departure Control Systems (500)AHM570Automated Information Exchange between Check-in and Load Control Systems (602)AHM571Passenger and Baggage Details for Weight and Balance Report(PWR) (608)AHM580Unit Load Device/Bulk Load Weight Statement (613)AHM581Unit Load Device/Bulk Load Weight Signal (615)AHM583Loadmessage (619)AHM587Container/Pallet Distribution Message (623)AHM588Statistical Load Summary (628)AHM590Load Control Procedures and Loading Supervision Responsibilities (631)AHM591Weight and Balance Load Control and Loading Supervision Training and Qualifications (635)Chapter6—MANAGEMENT AND SAFETY (641)AHM600Chapter6—Record of Revisions (641)AHM610Guidelines for a Safety Management System (642)AHM611Airside Personnel:Responsibilities,Training and Qualifications (657)AHM612Airside Performance Evaluation Program (664)AHM615Quality Management System (683)AHM616Human Factors Program (715)AHM619Guidelines for Producing Emergency Response Plan(s) (731)AHM620Guidelines for an Emergency Management System (733)AHM621Security Management (736)AHM633Guidelines for the Handling of Emergencies Requiring the Evacuation of an Aircraft During Ground Handling (743)AHM650Ramp Incident/Accident Reporting (745)AHM652Recommendations for Airside Safety Investigations (750)AHM660Carrier Guidelines for Calculating Aircraft Ground Accident Costs (759)Airport Handling ManualChapter7—AIRCRAFT MOVEMENT CONTROL (761)AHM700Chapter7—Record of Revisions (761)AHM710Standards for Message Formats (762)AHM711Standards for Message Corrections (764)AHM730Codes to be Used in Aircraft Movement and Diversion Messages (765)AHM731Enhanced Reporting on ATFM Delays by the Use of Sub Codes (771)AHM780Aircraft Movement Message (774)AHM781Aircraft Diversion Message (786)AHM782Fuel Monitoring Message (790)AHM783Request Information Message (795)AHM784Gate Message (797)AHM785Aircraft Initiated Movement Message(MVA) (802)AHM790Operational Aircraft Registration(OAR)Message (807)Chapter8—GROUND HANDLING AGREEMENTS (811)AHM800Chapter8—Record of Revisions (811)AHM801Introduction to and Comments on IATA Standard Ground Handling Agreement(SGHA) (812)AHM803Service Level Agreement Example (817)AHM810IATA Standard Ground Handling Agreement (828)AHM811Yellow Pages (871)AHM813Truck Handling (872)AHM815Standard Transportation Documents Service Main Agreement (873)AHM817Standard Training Agreement (887)AHM830Ground Handling Charge Note (891)AHM840Model Agreement for Electronic Data Interchange(EDI) (894)Chapter9—AIRPORT HANDLING GROUND SUPPORT EQUIPMENT SPECIFICATIONS (911)AHM900Chapter9—Record of Revisions (911)AHM901Functional Specifications (914)AHM904Aircraft Servicing Points and System Requirements (915)AIRBUS A300B2320-/B4/C4 (917)A300F4-600/-600C4 (920)A310–200/200C/300 (926)A318 (930)A319 (933)Table of ContentsPageChapter9—AIRPORT HANDLING GROUND SUPPORT EQUIPMENT SPECIFICATIONS(continued) AHM904Aircraft Doors,Servicing Points and System Requirements for the Use of Ground Support Equipment(continued)A320 (936)A321 (940)A330-200F (943)A330-300 (948)A340-200 (951)A340-300 (955)A340-500 (959)A340-600 (962)Airbus350900passenger (965)AIRBUS A380-800/-800F (996)ATR42100/200 (999)ATR72 (1000)AVRO RJ70 (1001)AVRO RJ85 (1002)AVRO RJ100 (1003)B727-200 (1004)B737–200/200C (1008)B737-300,400,-500 (1010)B737-400 (1013)B737-500 (1015)B737-600,-700,-700C (1017)B737-700 (1020)B737-800 (1022)B737-900 (1026)B747–100SF/200C/200F (1028)B747–400/400C (1030)B757–200 (1038)B757–300 (1040)Airport Handling ManualPageChapter9—AIRPORT HANDLING GROUND SUPPORT EQUIPMENT SPECIFICATIONS(continued) AHM904Aircraft Doors,Servicing Points and System Requirements for the Use of Ground Support Equipment(continued)B767—200/200ER (1041)B767—300/300ER (1044)B767—400ER (1048)B777–200/200LR (1051)B777–300/300ER (1055)Boeing787800passenger (1059)BAe ATP(J61) (1067)Bombardier CS100 (1068)Bombardier CS300 (1072)CL-65(CRJ100/200) (1076)DC8–40/50F SERIES (1077)DC8–61/61F (1079)DC8–62/62F (1081)DC8–63/63F (1083)DC9–15/21 (1085)DC9–32 (1086)DC9–41 (1087)DC9–51 (1088)DC10–10/10CF (1089)DC10–30/40,30/40CF (1091)EMBRAER EMB-135Regional Models (1092)EMBRAER EMB-145Regional Models (1094)Embraer170 (1096)Embraer175 (1098)Embraer190 (1100)Embraer195 (1102)FOKKER50(F27Mk050) (1104)FOKKER50(F27Mk0502) (1106)Chapter9—AIRPORT HANDLING GROUND SUPPORT EQUIPMENT SPECIFICATIONS(continued) AHM904Aircraft Doors,Servicing Points and System Requirements for the Use of Ground Support Equipment(continued)FOKKER70(F28Mk0070) (1108)FOKKER100(F28Mk0100) (1110)FOKKER100(F28Mk0100) (1112)IL-76T (1114)MD-11 (1116)MD–80SERIES (1118)SAAB2000 (1119)SAAB SF-340 (1120)TU-204 (1122)AHM905Reference Material for Civil Aircraft Ground Support Equipment (1125)AHM905A Cross Reference of IATA Documents with SAE,CEN,and ISO (1129)AHM909Summary of Unit Load Device Capacity and Dimensions (1131)AHM910Basic Requirements for Aircraft Ground Support Equipment (1132)AHM911Ground Support Equipment Requirements for Compatibility with Aircraft Unit Load Devices (1136)AHM912Standard Forklift Pockets Dimensions and Characteristics for Forkliftable General Support Equipment (1138)AHM913Basic Safety Requirements for Aircraft Ground Support Equipment (1140)AHM914Compatibility of Ground Support Equipment with Aircraft Types (1145)AHM915Standard Controls (1147)AHM916Basic Requirements for Towing Vehicle Interface(HITCH) (1161)AHM917Basic Minimum Preventive Maintenance Program/Schedule (1162)AHM920Functional Specification for Self-Propelled Telescopic Passenger Stairs (1164)AHM920A Functional Specification for Towed Passenger Stairs (1167)AHM921Functional Specification for Boarding/De-Boarding Vehicle for Passengers withReduced Mobility(PRM) (1169)AHM922Basic Requirements for Passenger Boarding Bridge Aircraft Interface (1174)AHM923Functional Specification for Elevating Passenger Transfer Vehicle (1180)AHM924Functional Specification for Heavy Item Lift Platform (1183)AHM925Functional Specification for a Self-Propelled Conveyor-Belt Loader (1184)AHM925A Functional Specification for a Self-Propelled Ground Based in-Plane LoadingSystem for Bulk Cargo (1187)Chapter9—AIRPORT HANDLING GROUND SUPPORT EQUIPMENT SPECIFICATIONS(continued) AHM925B Functional Specification for a Towed Conveyor-Belt Loader (1190)AHM926Functional Specification for Upper Deck Catering Vehicle (1193)AHM927Functional Specification for Main Deck Catering Vehicle (1197)AHM930Functional Specification for an Upper Deck Container/Pallet Loader (1201)AHM931Functional Specification for Lower Deck Container/Pallet Loader (1203)AHM932Functional Specification for a Main Deck Container/Pallet Loader (1206)AHM933Functional Specification of a Powered Extension Platform to Lower Deck/Container/ Pallet Loader (1209)AHM934Functional Specification for a Narrow Body Lower Deck Single Platform Loader (1211)AHM934A Functional Specification for a Single Platform Slave Loader Bed for Lower DeckLoading Operations (1213)AHM936Functional Specification for a Container Loader Transporter (1215)AHM938Functional Specification for a Large Capacity Freighter and Combi Aircraft TailStanchion (1218)AHM939Functional Specification for a Transfer Platform Lift (1220)AHM941Functional Specification for Equipment Used for Establishing the Weight of aULD/BULK Load (1222)AHM942Functional Specification for Storage Equipment Used for Unit Load Devices (1224)AHM950Functional Specification for an Airport Passenger Bus (1225)AHM951Functional Specification for a Crew Transportation Vehicle (1227)AHM953Functional Specifications for a Valuable Cargo Vehicle (1229)AHM954Functional Specification for an Aircraft Washing Machine (1230)AHM955Functional Specification for an Aircraft Nose Gear Towbar Tractor (1232)AHM956Functional Specification for Main Gear Towbarless Tractor (1235)AHM957Functional Specification for Nose Gear Towbarless Tractor (1237)AHM958Functional Specification for an Aircraft Towbar (1240)AHM960Functional Specification for Unit Load Device Transport Vehicle (1242)AHM961Functional Specification for a Roller System for Unit Load Device Transportation on Trucks (1245)AHM962Functional Specification for a Rollerised Platform for the Transportation of Twenty Foot Unit Load Devices that Interfaces with Trucks Equipped to Accept Freight ContainersComplying with ISO668:1988 (1247)AHM963Functional Specification for a Baggage/Cargo Cart (1249)AHM965Functional Specification for a Lower Deck Container Turntable Dolly (1250)AHM966Functional Specification for a Pallet Dolly (1252)Chapter9—AIRPORT HANDLING GROUND SUPPORT EQUIPMENT SPECIFICATIONS(continued) AHM967Functional Specification for a Twenty Foot Unit Load Device Dolly (1254)AHM968Functional Specification for Ramp Equipment Tractors (1256)AHM969Functional Specification for a Pallet/Container Transporter (1257)AHM970Functional Specification for a Self-Propelled Potable Water Vehicle with Rear orFront Servicing (1259)AHM971Functional Specification for a Self-Propelled Lavatory Service Vehicle with Rear orFront Servicing (1262)AHM972Functional Specifications for a Ground Power Unit for Aircraft Electrical System (1265)AHM973Functional Specification for a Towed Aircraft Ground Heater (1269)AHM974Functional Specification for Aircraft Air Conditioning(Cooling)Unit (1272)AHM975Functional Specifications for Self-Propelled Aircraft De-Icing/Anti-Icing Unit (1274)AHM976Functional Specifications for an Air Start Unit (1278)AHM977Functional Specification for a Towed De-Icing/Anti-Icing Unit (1280)AHM978Functional Specification for a Towed Lavatory Service Cart (1283)AHM979Functional Specification for a Towed Boarding/De-Boarding Device for Passengers with Reduced Mobility(PRM)for Commuter-Type Aircraft (1285)AHM980Functional Specification for a Self-Propelled Petrol/Diesel Refueling Vehicle forGround Support Equipment (1287)AHM981Functional Specification for a Towed Potable Water Service Cart (1289)AHM990Guidelines for Preventative Maintenance of Aircraft Towbars (1291)AHM994Criteria for Consideration of the Investment in Ground Support Equipment (1292)AHM995Basic Unit Load Device Handling System Requirements (1296)AHM997Functional Specification for Sub-Freezing Aircraft Air Conditioning Unit (1298)Chapter10—ENVIRONMENTAL SPECIFICATIONS FOR GROUND HANDLING OPERATIONS (1301)AHM1000Chapter10—Record of Revisions (1301)AHM1001Environmental Specifications for Ground Handling Operations (1302)AHM1002Environmental Impact on the Use of Ground Support Equipment (1303)AHM1003GSE Environmental Quality Audit (1305)AHM1004Guidelines for Calculating GSE Exhaust Emissions (1307)AHM1005Guidelines for an Environmental Management System (1308)Chapter11—GROUND OPERATIONS TRAINING PROGRAM (1311)AHM1100Chapter11—Record of Revisions (1311)AHM1110Ground Operations Training Program (1312)Appendix A—References (1347)Appendix B—Glossary (1379)Alphabetical List of AHM Titles (1387)IATA Strategic Partners..............................................................................................................................SP–1。
Infoprint 250 導入と計画の手引き 第 7 章ホスト
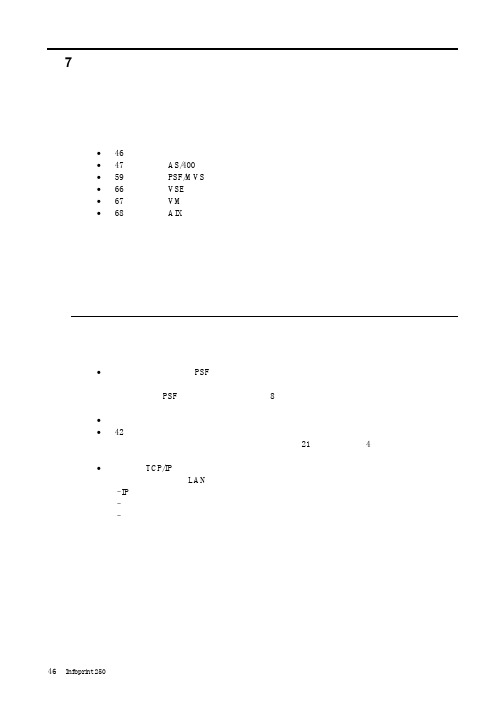
SUBNETMASK
255.255.255.128
Type of service...............: TOS
*NORMAL
Maximum transmission unit.....: MTU
*LIND
Autostart.....................:
AUTOSTART
*YES
: xx.xxx.xxx.xxx
: xx.xxx.xxx.xxx
*
(
)
IEEE802.3
60 1500
: xxxx
48 Infoprint 250
31. AS/400
IP
MTU
1
1
IPDS TCP
CRTPSFCFG (V3R2)
WRKAFP2 (V3R1 & V3R6)
RMTLOCNAME RMTSYS
MODEL
0
Advanced function printing............:
AFP
*YES
AFP attachment........................:
AFPATTACH
*APPC
Online at IPL.........................:
ONLINE
FORMFEED
*CONT
Separator drawer......................:
SEPDRAWER
*FILE
Separator program.....................:
SEPPGM
*NONE
Library.............................:
lr常见报错及解决的办法
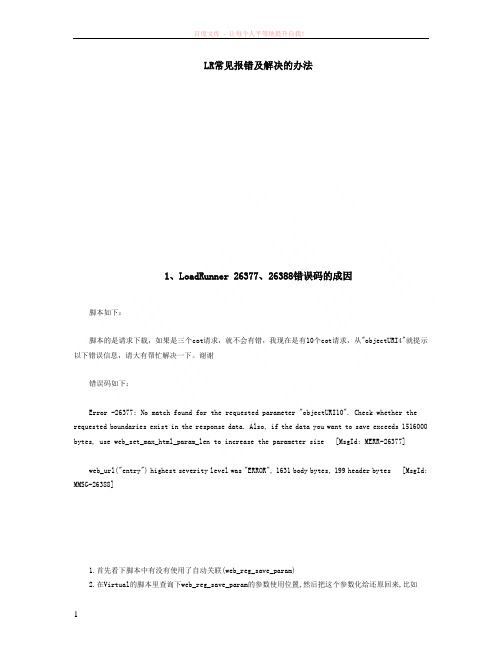
LR常见报错及解决的办法1、LoadRunner 26377、26388错误码的成因脚本如下:脚本的是请求下载,如果是三个cot请求,就不会有错,我现在是有10个cot请求,从"objectURI4"就提示以下错误信息,请大有帮忙解决一下。
谢谢错误码如下:Error -26377: No match found for the requested parameter "objectURI10". Check whether the requested boundaries exist in the response data. Also, if the data you want to save exceeds 1516000 bytes, use web_set_max_html_param_len to increase the parameter size [MsgId: MERR-26377]web_url("entry") highest severity level was "ERROR", 1631 body bytes, 199 header bytes [MsgId: MMSG-26388]1.首先看下脚本中有没有使用了自动关联(web_reg_save_param)2.在Virtual的脚本里查询下web_reg_save_param的参数使用位置,然后把这个参数化给还原回来,比如web_reg_save_param("Siebel_Analytic_ViewState2",............然后就在全文查询Siebel_Analytic_ViewState23,至于修改成什么东西要看几个地方,如果是启动了自动关联,一般在脚本上面会有一段被自动注释掉的:关联变量名="值"比如上面的Siebel_Analytic_ViewState2大概就是// {Siebel_Analytic_ViewState2}= "/wEPDwUKMTI5Nzk1OTc3NmRkikSkNLllgC5BL8dbmU5bHIwtt4I="那么这里的/wEPDwUKMTI5Nzk1OTc3NmRkikSkNLllgC5BL8dbmU5bHIwtt4I=就是要找的值了,这个也可以在"View Tree"里找到4.把"View script"里的被关联的那部分参数改成/wEPDwUKMTI5Nzk1OTc3NmRkikSkNLllgC5BL8dbmU5bHIwtt4I=就好了(不是修改web_reg_save_param里的参数,要把它注释掉,从下面正文里查询另一个带Siebel_Analytic_ViewState2的东东,把它改掉)把web_set_max_html_param_len(50000)值加大这个函数要放在所有参数化前面。
诺瓦科技LED同步控制系统MCTRL R5用户手册英文版

H C E
T L ., CO
. D
M CT R L R 5 Use r Mau al
1 Appearance
Front Panel
① : indicates status of R5 indicators: Blue indicator keeps on → normal; Red indicator keeps on → alarm; Orange indicator keeps on → No signal; Blue breathing light keeps on → standby. ② :OLED, A liquid crystal display and an operation screen
X
N A I'
N
O
S A V
R A T
T
H C E
T L ., CO
. D
Table of Contents
1 Appearance������������������������������������������������������������������������������������������������� 1
Front Panel���������������������������������������������������������������������������������������������������������������������� 1 Back Panel����������������������������������������������������������������������������������������������������������������������� 1
Netra 1290服务器设置指南说明书

Shipping Kit ContentsYour shipping kit should contain the following items:■Netra 1290Server Getting Started Guide (this document)■Rackmount kit:■Slide assemblies with mounting brackets (2)■No.10-32UNF screws with washers (8)■M6screws with washers (8)■Cable management arm (CMA-800)■Lite cable management arm (CMA-Lite)■Ethernet/serial cables (4)■Antistatic wrist strap and snap-on converter ■RJ-45to DB-25male adapter ■RJ-45to DB-9female adapter ■Unpacking tools:■13mm wrench■8mm wrenchSetting Up the Netra 1290ServerThe following list summarizes the tasks to set up your Netra 1290server:1.Verify power,air conditioning,and floor area requirements.2.Set up the Sun™Rack and connect the power cables.Refer to the Sun Rack Installation Guide.3.Unpack the Netra 1290server and install it into the rack.Refer to the Netra 1290Server Installation Guide ,819-4372.4.Power on the Sun Rack.Refer to the Sun Rack Installation Guide.5.Connect an administrative console to access the system controller and power on the Netra 1290server.Refer to the Netra 1290Server Installation Guide ,819-4372.6.Allow the server to run through POST and ensure there are no errors,then power off the server.Refer to the Netra 1290Server System Administration Guide ,819-4374,if there are errors.7.(Optional)Install options and storage devices.Refer to the Netra 1290Server Service Manual ,819-4373,and documentation that came with the option or storage device for details.8.Power on the Netra 1290server,and configure the system.Refer to the Netra 1290Server System Administration Guide ,819-43749.(Optional)Create additional domains.Refer to the Netra 1290Server System Administration Guide ,819-4374.a.Install the Solaris™software on each domain.Refer to the Solaris Installation Guide.b.Boot the Solaris software on each domain.Refer to the Netra 1290Server System Administration Guide ,ra ™ 1290 Server Getting Started GuidePart No. 819-4378-10, Rev. A May 2006Sun Microsystems, Accessing Netra 1290Server DocumentationThe Netra 1290server documentation is available online at the following URL:/documentationContacting Sun Technical SupportIf you have technical questions about this product that are not answered in the Netra 1290server documentation,go to:/service/contactingSun Welcomes Your CommentsSun is interested in improving its documentation and welcomes your comments and suggestions.You can submit your comments by going to:/hwdocs/feedbackPlease include the title and part number of your document with your feedback:Netra 1290Server Getting Started Guide ,part number 819-4378-10.Copyright 2006Sun Microsystems,Inc.All rights e is subject to license terms.Third-party software,including font technology,is copyrighted and licensed from Sun suppliers.Portions may be derived from Berkeley BSD systems,licensed from U.of CA.Sun,Sun Microsystems,the Sun logo,Netra,and Solaris are trademarks or registered trademarks of Sun Microsystems,Inc.in the U.S.and in other countries.All SPARC trademarks are used under license and are trademarks or registered trademarks of SPARC International,Inc.in the U.S.and in other countries.ernment Rights—Commercial ernment users are subject to the Sun Microsystems,Inc.standard license agreement and applicable provisions of the FAR and its supplements.Copyright 2006Sun Microsystems,Inc.Tous droits réservés.Distribuépar des licences qui en restreignent l’utilisation.Le logiciel détenu par des tiers,et qui comprend la technologie relative aux polices de caractères,est protégépar un copyright et licenciépar des fournisseurs de Sun.Des parties de ce produit pourront être dérivées des systèmes Berkeley BSD licenciés par l’Universitéde Californie.Sun,Sun Microsystems,le logo Sun,Netra,et Solaris sont des marques de fabrique ou des marques déposées de Sun Microsystems,Inc.aux Etats-Unis et dans d’autres pays.Toutes les marques SPARC sont utilisées sous licence et sont des marques de fabrique ou des marques déposées de SPARC International,Inc.aux Etats-Unis et dans d’autres pays.。
verilator reference guide

Verilator-3.810Wilson Snyder 2010-07-10Contents1NAME2 2SYNOPSIS2 3DESCRIPTION2 4ARGUMENT SUMMARY2 5ARGUMENTS4 6EXAMPLE C++EXECUTION14 7EXAMPLE SYSTEMC EXECUTION16 8BENCHMARKING&OPTIMIZATION17 9FILES19 10ENVIRONMENT20 11CONNECTING TO C++21 12CONNECTING TO SYSTEMC22 13DIRECT PROGRAMMING INTERF ACE(DPI)22 14VERIFICATION PROCEDURAL INTERF ACE(VPI)25 15CROSS COMPILATION26 16CONFIGURATION FILES27 17LANGUAGE STANDARD SUPPORT2818LANGUAGE EXTENSIONS29 19LANGUAGE LIMITATIONS35 20ERRORS AND W ARNINGS41 21F AQ/FREQUENTLY ASKED QUESTIONS50 22BUGS55 23HISTORY56 24CONTRIBUTORS56 25DISTRIBUTION57 26AUTHORS57 27SEE ALSO571NAMEVerilator-Convert Verilog code to C++/SystemC2SYNOPSISverilator--helpverilator--versionverilator--cc[options][top_level.v][opt_c_files.cpp/c/cc/a/o/so]verilator--sc[options][top_level.v][opt_c_files.cpp/c/cc/a/o/so]verilator--sp[options][top_level.v][opt_c_files.cpp/c/cc/a/o/so]verilator--lint-only[top_level.v]...3DESCRIPTIONVerilator converts synthesizable(not behavioral)Verilog code,plus some Synthesis, SystemVerilog and Sugar/PSL assertions,into C++,SystemC or SystemPerl code.It is not a complete simulator,just a compiler.Verilator is invoked with parameters similar to GCC,Cadence Verilog-XL/NC-Verilog,or Synopsys’s VCS.It reads the specified Verilog code,lints it,and optionally adds coverage and waveform tracing code.For C++and SystemC formats,it outputs.cppand.hfiles.For SystemPerl format,it outputs.spfiles for the SystemPerl preproces-sor,which greatly simplifies writing SystemC code and is available at . Thefiles created by Verilator are then compiled with C++.The user writes a littleC++wrapperfile,which instantiates the top level module,and passes thisfilenameon the command line.These Cfiles are compiled in C++,and linked with the Verilatedfiles.The resulting executable will perform the actual simulation.To get started,jump down to"EXAMPLE C++EXECUTION".4ARGUMENT SUMMARYThis is a short summary of the arguments to Verilator.See the detailed descriptionsin the next sections for more information.{file.v}Verilog top level filenames{file.c/cc/cpp}Optional C++files to compile in{file.a/o/so}Optional C++files to link in--assert Enable all assertions--autoflush Flush streams after all$displays--bbox-sys Blackbox unknown$system calls--bbox-unsup Blackbox unsupported language features--bin<filename>Override Verilator binary-CFLAGS<flags>C++Compiler flags for makefile--cc Create C++output--cdc Clock domain crossing analysis--compiler<compiler-name>Tune for specified C++compiler--coverage Enable all coverage--coverage-line Enable line coverage--coverage-toggle Enable toggle coverage--coverage-user Enable PSL/SVL user coverage--coverage-underscore Enable covarge of_signals-D<var>[=<value>]Set preprocessor define--debug Enable debugging--debug-check Enable debugging assertions--debugi<level>Enable debugging at a specified level--debugi-<srcfile><level>Enable debugging a source file at a level +define+<var>+<value>Set preprocessor define--dump-tree Enable dumping.tree files-E Preprocess,but do not compile--error-limit<value>Abort after this number of errors--exe Link to create executable-F<file>Parse options from a file,relatively-f<file>Parse options from a file--gdbbt Run Verilator under GDB for backtrace--help Display this help-I<dir>Directory to search for includes--if-depth<value>Tune IFDEPTH warning+incdir+<dir>Directory to search for includes--inhibit-sim Create function to turn off sim--inline-mult<value>Tune module inlining-LDFLAGS<flags>Linker pre-object flags for makefile-LDLIBS<flags>Linker library flags for makefile--language<lang>Language standard to parse+libext+<ext>+[ext]...Extensions for finding modules--lint-only Lint,but do not make output--MMD Create.d dependency files--MP Create phony dependency targets--Mdir<directory>Name of output object directory--mod-prefix<topname>Name to prepend to lower classes--no-pins64Don’t use uint64_t’s for33-64bit sigs --no-skip-identical Disable skipping identical output+notimingchecks Ignored-O0Disable optimizations-O3High performance optimizations-O<optimization-letter>Selectable optimizations-o<executable>Name of final executable--output-split<bytes>Split.cpp files into pieces--output-split-cfuncs<statements>p functions--pins-bv<bits>Specify types for top level ports--pins-uint8Specify types for top level ports--pipe-filter<command>Filter all input through a script--prefix<topname>Name of top level class--profile-cfuncs Name functions for profiling--private Debugging;see docs--psl Enable PSL parsing--public Debugging;see docs--sc Create SystemC output--sp Create SystemPerl output--stats Create statistics file-sv Enable SystemVerilog parsing--top-module<topname>Name of top level input module--trace Enable waveform creation--trace-depth<levels>Depth of tracing--trace-underscore Enable tracing of_signals-U<var>Undefine preprocessor define--unroll-count<loops>Tune maximum loop iterations--unroll-stmts<stmts>Tune maximum loop body size--unused-regexp<regexp>Tune UNUSED lint signals-V Verbose version and config-v<filename>Verilog library-Werror-<message>Convert warning to error-Wfuture-<message>Disable unknown message warnings-Wno-<message>Disable warning-Wno-lint Disable all lint warnings-Wno-style Disable all style warnings-x-assign<mode>Initially assign Xs to this value-y<dir>Directory to search for modules5ARGUMENTS{file.v}Specifies the Verilogfile containing the top module to be Verilated.{file.c/.cc/.cpp/.cxx}Specifies optional C++files to be linked in with the Verilog code.If any C++files are specified in this way,Verilator will include a make rule that generates a module executable.Without any C++files,Verilator will stop at the module__ALL.a library,and presume you’ll continue linking with make rules you write yourself.See also the-CFLAGS option.{file.a/.o/.so}Specifies optional object or libraryfiles to be linked in with the Verilog code, as a shorthand for-LDFLAGS"<file>".If anyfiles are specified in this way,Verilator will include a make rule that uses thesefiles when linking the moduleexecutable.This generally is only useful when used with the–exe option.–assertEnable all assertions,includes enabling the–pslflag.(If psl is not desired,butother assertions are,use–assert–nopsl.)See also–x-assign;setting"–x-assign unique"may be desirable.–autoflushAfter every$display or$fdisplay,flush the output stream.This insures thatmessages will appear immediately but may reduce performance.Defaults off,which will buffer output as provided by the normal C stdio calls.–bbox-sysBlack box any unknown$system task or function calls.System tasks will besimply NOPed,and system functions will be replaced by unsized zero.Argu-ments to such functions will be parsed,but not otherwise checked.This preventserrors when linting in the presence of company specific PLI calls.–bbox-unsupBlack box some unsupported language features,currently UDP tables and thecmos and tran gate primitives.This may enable linting the rest of the designeven when unsupported constructs are present.–binfilenameRarely needed.Override the defaultfilename for Verilator itself.When a de-pendency(.d)file is created,thisfilename will become a source dependency,such that a change in this binary will have make rebuild the outputfiles.-CFLAGSflagsAdd specified C compilerflags to the generated makefiles.When make is run onthe generated makefile these will be passed to the C++compiler(gcc/g++/msvc++).–ccSpecifies C++without SystemC output mode;see also–sc and–sp.–cdcExperimental.Perform some clock domain crossing checks and issue relatedwarnings(CDCRSTLOGIC)and then exit;if warnings other than CDC warn-ings are needed make a second run with–lint-only.Additional warning infor-mation is also written to thefile{prefix}__cdc.txt.Currently only checks some items that other CDC tools missed;if you haveinterest in adding more traditional CDC checks,please contact the authors.–compiler compiler-nameEnables tunings and work-arounds for the specified C++compiler.gccTune for Gnu C++,although generated code should work on almost anycompliant C++compiler.Currently the default.msvcTune for Microsoft Visual C++.This may reduce execution speed as itenables several workarounds to avoid silly hardcoded limits in MSVC++.This includes breaking deeply nested parenthesized expressions into sub-expressions to avoid error C1009,and breaking deep blocks into functionsto avoid error C1061.–coverageEnables all forms of coverage,alias for"–coverage-line–coverage-toggle–coverage-user".–coverage-lineSpecifies basic block line coverage analysis code should be inserted.Coverage analysis adds statements at each codeflow change point,which are the branches of IF and CASE statements,a super-set of normal Verilog Line Coverage.At each such branch a unique counter is incremented.At the end ofa test,the counters along with thefilename and line number corresponding toeach counter are written into logs/coverage.pl.Verilator automatically disables coverage of branches that have a$stop in them, as it is assumed$stop branches contain an error check that should not occur.A/*verilator coverage_block_off*/comment will perform a similar function on any code in that block or below,or/*verilator coverage_on/coverage_off*/ will disable coverage around lines of code.Note Verilator may over-count combinatorial(non-clocked)blocks when those blocks receive signals which have had the UNOPTFLAT warning disabled;for most accurate results do not disable this warning when using coverage.–coverage-toggleSpecifies signal toggle coverage analysis code should be inserted.Every bit of every signal in a module has a counter inserted.The counter will increment on every edge change of the corresponding bit.Signals that are part of tasks or begin/end blocks are considered local variables and are not covered.Signals that begin with underscores,are integers,or are very wide(>256bits total storage across all dimensions)are also not covered.Hierarchy is compressed,such that if a module is instantiated multiple times, coverage will be summed for that bit across ALL instantiations of that module with the same parameter set.A module instantiated with different parameter values is considered a different module,and will get counted separately.Verilator makes a minimally-intelligent decision about what clock domain the signal goes to,and only looks for edges in that clock domain.This means that edges may be ignored if it is known that the edge could never be seen by the receiving logic.This algorithm may improve in the future.The net result is coverage may be lower than what would be seen by looking at traces,but the coverage is a more accurate representation of the quality of stimulus into the design.There may be edges counted near time zero while the model stabilizes.It’s a good practice to zero all coverage just before releasing reset to prevent counting such behavior.A/*verilator coverage_off/on*/comment pair can be used around signals that do not need toggle analysis,such as RAMs and registerfiles.–coverage-underscoreEnable coverage of signals that start with an underscore.Normally,these signals are not covered.See also–trace-underscore.–coverage-userEnables user inserted functional coverage.Currently,all functional coverage points are specified using PSL which must be separately enabled with–psl.For example,the following PSL statement will add a coverage point,with the comment"DefaultClock"://psl default clock=posedge clk;//psl cover{cyc==9}report"DefaultClock,expect=1";-D var=valueDefines the given preprocessor symbol.Same as+define;+define is fairly stan-dard across Verilog tools while-D is an alias for GCC compatibility.–debugSelect the debug built image of Verilator(if available),and enable more internal assertions,debugging messages,and intermediate form dumpfiles.–debug-checkRarely needed.Enable internal debugging assertion checks,without changing debug verbosity.Enabled automatically when–debug specified.–debugi<level>=item–debugi-<srcfile><level>Rarely needed-for developer use.Set internal debugging level globally or on the specified sourcefile to the specified level.+define+var+valueDefines the given preprocessor symbol.Same as-D;+define is fairly standard across Verilog tools while-D is an alias for GCC compatibility.–dump-treeRarely needed.Enable writing.tree debugfiles.This is enabled with–debug, so"–debug–no-dump-tree"may be useful if the dumpfiles are large and not desired.-EPreprocess the source code,but do not compile,as with’gcc-E’.Output is written to standard out.Beware of enabling debugging messages,as they will also go to standard out.–error-limit<value>After this number of errors or warnings are encountered,exit.Defaults to50.–exeGenerate a executable.You will also need to pass additional.cppfiles on the command line that implement the main loop for your simulation.-FfileRead the specifiedfile,and act as if all text inside it was specified as command line parameters.Any relative paths are relative to the directory containing the specifiedfile.Note-F is fairly standard across Verilog tools.-ffileRead the specifiedfile,and act as if all text inside it was specified as command line parameters.Any relative paths are relative to the current directory.Note -f is fairly standard across Verilog tools.–gdbbtIf–debug is specified,run Verilator underneath a GDB process and print a backtrace on exit.Without–debug or if GDB doesn’t seem to work,thisflag is ignored.–helpDisplays this message and program version and exits.-I dirAdd the directory to the list of directories that should be searched for include directories or libraries.Same as+incdir and-y;+incdir and-y are fairly stan-dard across Verilog tools while-I is an alias for GCC compatibility.–if-depth valueRarely needed.Set the depth at which the IFDEPTH warning willfire,defaults to0which disables this warning.+incdir+dirAdd the directory to the list of directories that should be searched for include directories or libraries.Same as-I and-y;+incdir and-y are fairly standard across Verilog tools while-I is an alias for GCC compatibility.–inhibit-simRarely needed.Create a"inhibitSim(bool)"function to enable and disable evaluation.This allows a upper level testbench to disable modules that are not important in a given simulation,without needing to recompile or change the SystemC modules instantiated.–inline-mult valueTune the inlining of modules.The default value of2000specifies that up to 2000new operations may be added to the model by inlining,if more than this number of operations would result,the module is not rger values, or a value<=1will inline everything,will lead to longer compile times,but potentially faster runtimes.This setting is ignored for very small modules;they will always be inlined,if allowed.-LDFLAGSflagsAdd specified C linkerflags to the generated makefiles.When make is run on the generated makefile these will be passed to the C++linker(ld)*after* the primaryfile being linked.Thisflag is called-LDFLAGS as that’s the traditional name in simulators;it’s would have been better called LDLIBS as that’s the Makefile variable it controls.(In Make,LDFLAGS is before thefirst object,LDLIBS after.-L libraries need to be in the Make variable LDLIBS, not LDFLAGS.)–language valueSelect the language to be used whenfirst processing each Verilogfile.The lan-guage value must be"1364-1995","1364-2001","1364-2001","1364-2005",or "1800-2005".This should only be used for legacy code,as the preferable option is to edit the code to repair new keywords,or add appropriate‘begin_keywords. +libext+ext+ext...Specify the extensions that should be used forfinding modules.If for example module x is referenced,look in x.ext.Note+libext+is fairly standard across Verilog tools.–lint-onlyCheck thefiles for lint violations only,do not create any other output.You may also want the-Wall option to enable messages that are considered stylistic and not enabled by default.If the design is not to be completely Verilated see also the–bbox-sys and–bbox-unsup options.–MMDEnable creation of.d dependencyfiles,used for make dependency detection, similar to gcc-MMD option.On by default,use–no-MMD to disable.–MPWhen creating.d dependencyfiles with–MMD,make phony targets.Similar to gcc-MP option.–Mdir directorySpecifies the name of the Make object directory.All generatedfiles will be placed in this directory.If not specified,"obj_dir"is used.–mod-prefix topnameSpecifies the name to prepend to all lower level classes.Defaults to the same as–prefix.–no-pins64Backward compatible alias for"–pins-bv33".–no-skip-identicalRarely needed.Disables skipping execution of Verilator if all sourcefiles are identical,and all outputfiles exist with newer dates.+notimingchecksIgnored for compatibility with other simulators.-O0Disables optimization of the model.-O3Enables slow optimizations.This may reduce simulation runtimes at the cost of compile time.This currently sets–inline-mult-1.-O optimization-letterRarely needed.Enables or disables a specific optimizations,with the opti-mization selected based on the letter passed.A lowercase letter disables an optimization,an upper case letter enables it.This is intended for debugging use only;see the source code for version-dependent mappings of optimizations to-O letters.-o<executable>Specify the name for thefinal executable built if using–exe.Defaults to the –prefix if not specified.–output-split bytesEnables splitting the output.cpp/.spfiles into multiple outputs.When a C++file exceeds the specified number of operations,a newfile will be created at the next function boundary.In addition,any slow routines will be placed into __Slowfiles.This accelerates compilation by as optimization can be disabled on the slow routines,and the remainingfiles can be compiled on parallel ing–output-split should have only a trivial impact on performance.With GCC3.3on a2GHz Opteron,–output-split20000will result in splitting into approximately one-minute-compile chunks.–output-split-cfuncs statementsEnables splitting functions in the output.cpp/.spfiles into multiple functions.When a generated function exceeds the specified number of operations,a new function will be created.With–output-split,this will enable GCC to compile faster,at a small loss in performance that gets worse with decreasing split values.Note that this option is stronger than–output-split in the sense that –output-split will not split inside a function.–pins64Backward compatible alias for"–pins-bv65".Note that’s a65,not a64.–pins-bv widthSpecifies SystemC inputs/outputs of greater than or equal to width bits wide should use sc_bv’s instead of uint32/uint64_t’s.The default is"–pins-bv65".Versions before Verilator3.671defaulted to"–pins-bv33".The more sc_bv is used,the worse for performance.–pins-uint8Specifies SystemC inputs/outputs that are smaller than the–pins-bv setting and8bits or less should use uint8_t instead of uint32_t.Likewise pins of width9-16will use uint16_t instead of uint32_t.–pipe-filter commandRarely needed and experimental.Verilator will spawn the specified command as a subprocess pipe,to allow the command to perform custom edits on the Verilog code before it reaches Verilator.Before reading each Verilogfile,Verilator will pass thefile name to the sub-process’stdin with’read_verilog"<filename>"’.Thefilter may then read the file and perform anyfiltering it desires,and feeds the newfile contents back to Verilator on stdout with’Content-Length’.Output to stderr from thefilter feeds through to Verilator’s stdout and if thefilter exits with non-zero status Verilator terminates.See the t/t_pipe_filter test for an example.To debug the output of thefilter,try using the-E option to see preprocessed output.–prefix topnameSpecifies the name of the top level class and makefile.Defaults to V prepended to the name of the–top-module switch,or V prepended to thefirst Verilog filename passed on the command line.–profile-cfuncsModify the created C++functions to support profiling.The functions will be minimized to contain one"basic"statement,generally a single always block or wire statement.(Note this will slow down the executable by˜5%.)Fur-thermore,the function name will be suffixed with the basename of the Verilog module and line number the statement came from.This allows gprof or oprofile reports to be correlated with the original Verilog source statements.–privateOpposite of–public.Is the default;this option exists for backwards compati-bility.–pslEnable PSL parsing.Without this switch,PSL meta-comments are ignored.See the–assertflag to enable all assertions,and–coverage-user to enable functional coverage.–publicThis is only for historical debug ing it may result in mis-simulation of generated clocks.Declares all signals and modules public.This will turn offsignal optimizations as if all signals had a/*verilator public*/comments and inlining.This will also turn offinlining as if all modules had a/*verilator public_module*/,unless the module specifically enabled it with/*verilator inline_module*/.–scSpecifies SystemC output mode;see also–cc and-sp.–spSpecifies SystemPerl output mode;see also–cc and-sc.–statsCreates a dumpfile with statistics on the design in{prefix}__stats.txt.-svSpecifies SystemVerilog language features should be enabled;equivalent to"–language1800-2005".This option is selected by default,it exists for compati-bility with other simulators.–top-module topnameWhen the input Verilog contains more than one top level module,specifies the name of the top level Verilog module to become the top,and sets the default for if–prefix is not used.This is not needed with standard designs with only one top.–traceAdds waveform tracing code to the model.Verilator will generate additional {prefix}__Trace*.cppfiles that will need to be compiled.In addition veri-lated_vcd_sc.cpp(for SystemC traces)or verilated_vcd_c.cpp(for both)must be compiled and linked in.If using the Verilator generated Makefiles,these will be added as source targets for you.If you’re not using the Verilator makefiles, you will need to add these to your Makefile manually.Having tracing compiled in may result in some small performance losses,even when waveforms are not turned on during model execution.–trace-depth levelsSpecify the number of levels deep to enable tracing,for example–trace-level1 to only see the top level’s signals.Defaults to the entire ing a small number will decrease visibility,but greatly improve runtime and tracefile size.–trace-underscoreEnable tracing of signals that start with an underscore.Normally,these signals are not output during tracing.See also–coverage-underscore.-U varUndefines the given preprocessor symbol.–unroll-count loopsRarely needed.Specifies the maximum number of loop iterations that may be unrolled.See also BLKLOOPINIT warning.–unroll-stmts statementsRarely needed.Specifies the maximum number of statements in a loop for that loop to be unrolled.See also BLKLOOPINIT warning.–unused-regexp regexpRarely needed.Specifies a simple regexp with*and?that if a signal name matches will suppress the UNUSED warning.Defaults to"*unused*".Setting it to""disables matching.-VShows the verbose version,including configuration information compiled intoVerilator.(Similar to perl-V.)-vfilenameRead thefilename as a Verilog library.Any modules in thefile may be used toresolve cell instantiations in the top level module,else ignored.Note-v is fairlystandard across Verilog tools.-WallEnable all warnings,including code style warnings that are normally disabledby default.-Werror-messageConvert the specified warning message into a error message.This is gener-ally to discourage users from violating important site-wide rules,for example-Werror-NOUNOPTFLAT.-Wfuture-messageSuppress unknown Verilator comments or warning messages with the givenmessage code.This is used to allow code written with pragmas for a laterversion of Verilator to run under a older version;add-Wfuture-arguments foreach message code or comment that the new version supports which the olderversion does not support.-Wno-messageDisable the specified warning message.-Wno-lintDisable all lint related warning messages,and all style warnings.This is equiv-alent to"-Wno-CASEINCOMPLETE-Wno-CASEOVERLAP-Wno-CASEX-Wno-CASEWITHX-Wno-CMPCONST-Wno-IMPLICIT-Wno-LITENDIAN-Wno-SYNCASYNCNET-Wno-UNDRIVEN-Wno-UNSIGNED-Wno-UNUSED-Wno-WIDTH"plus the list shown for Wno-style.It is strongly recommended you cleanup your code rather than using this option,it is only intended to be use when running test-cases of code received from thirdparties.-Wno-styleDisable all code style related warning messages(note by default they are alreadydisabled).This is equivalent to"-Wno-DECLFILENAME-Wno-DEFPARAM-Wno-INCABSPATH-Wno-SYNCASYNCNET-Wno-UNDRIVEN-Wno-UNUSED-Wno-VARHIDDEN".-Wwarn-messageEnables the specified warning message.-Wwarn-lintEnable all lint related warning messages(note by default they are alreadyenabled),but do not affect style messages.This is equivalent to"-Wwarn-CASEINCOMPLETE-Wwarn-CASEOVERLAP-Wwarn-CASEX-Wwarn-CASEWITHX-Wwarn-CMPCONST-Wwarn-IMPLICIT-Wwarn-LITENDIAN-Wwarn-UNSIGNED-Wwarn-WIDTH".-Wwarn-styleEnable all code style related warning messages.This is equivalent to"-Wwarn-DECLFILENAME-Wwarn-DEFPARAM-Wwarn-INCABSPATH-Wwarn-SYNCASYNCNET -Wwarn-UNDRIVEN-Wwarn-UNUSED-Wwarn-VARHIDDEN".-x-assign0-x-assign1-x-assign fast(default)-x-assign uniqueControls the two-state value that is replaced when an assignment to X is en-countered.-x-assign=fast,the default,converts all Xs to whatever is best forperformance.-x-assign=0converts all Xs to0s,and is also fast.-x-assign=1converts all Xs to1s,this is nearly as fast as0,but more likely tofind resetbugs as active high logic willfire.-x-assign=unique will call a function to de-termine the value,this allows randomization of all Xs tofind reset bugs and isthe slowest,but safest forfinding reset bugs in code.If using-x-assign unique,you may want to seed your random number generatorsuch that each regression run gets a different randomization e thesystem’s srand48()or for Windows srand()function to do this.You’ll probablyalso want to print any seeds selected,and code to enable rerunning with thatsame seed so you can reproduce bugs.-y dirAdd the directory to the list of directories that should be searched for includedirectories or libraries.Same as+incdir and-I;+incdir and+y are fairlystandard across Verilog tools while-I is an alias for GCC compatibility.6EXAMPLE C++EXECUTIONWe’ll compile this example into C++.mkdir test_ourcd test_ourcat<<EOF>our.vmodule our;initial begin\$display("Hello World");\$finish;endendmoduleEOF。
Indradrive 系列 故障代码
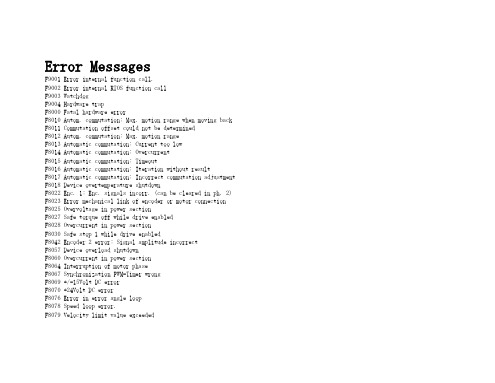
Error MessagesF9001 Error internal function call.F9002 Error internal RTOS function callF9003 WatchdogF9004 Hardware trapF8000 Fatal hardware errorF8010 Autom. commutation: Max. motion range when moving back F8011 Commutation offset could not be determinedF8012 Autom. commutation: Max. motion rangeF8013 Automatic commutation: Current too lowF8014 Automatic commutation: OvercurrentF8015 Automatic commutation: TimeoutF8016 Automatic commutation: Iteration without resultF8017 Automatic commutation: Incorrect commutation adjustment F8018 Device overtemperature shutdownF8022 Enc. 1: Enc. signals incorr. (can be cleared in ph. 2) F8023 Error mechanical link of encoder or motor connectionF8025 Overvoltage in power sectionF8027 Safe torque off while drive enabledF8028 Overcurrent in power sectionF8030 Safe stop 1 while drive enabledF8042 Encoder 2 error: Signal amplitude incorrectF8057 Device overload shutdownF8060 Overcurrent in power sectionF8064 Interruption of motor phaseF8067 Synchronization PWM-Timer wrongF8069 +/-15Volt DC errorF8070 +24Volt DC errorF8076 Error in error angle loopF8078 Speed loop error.F8079 Velocity limit value exceededF8091 Power section defectiveF8100 Error when initializing the parameter handlingF8102 Error when initializing power sectionF8118 Invalid power section/firmware combinationF8120 Invalid control section/firmware combinationF8122 Control section defectiveF8129 Incorrect optional module firmwareF8130 Firmware of option 2 of safety technology defectiveF8133 Error when checking interrupting circuitsF8134 SBS: Fatal errorF8135 SMD: Velocity exceededF8140 Fatal CCD error.F8201 Safety command for basic initialization incorrectF8203 Safety technology configuration parameter invalidF8813 Connection error mains chokeF8830 Power section errorF8838 Overcurrent external braking resistorF7010 Safely-limited increment exceededF7011 Safely-monitored position, exceeded in pos. DirectionF7012 Safely-monitored position, exceeded in neg. DirectionF7013 Safely-limited speed exceededF7020 Safe maximum speed exceededF7021 Safely-limited position exceededF7030 Position window Safe stop 2 exceededF7031 Incorrect direction of motionF7040 Validation error parameterized - effective thresholdF7041 Actual position value validation errorF7042 Validation error of safe operation modeF7043 Error of output stage interlockF7050 Time for stopping process exceeded8.3.15 F7051 Safely-monitored deceleration exceeded (159)8.4 Travel Range Errors (F6xxx) (161)8.4.1 Behavior in the Case of Travel Range Errors (161)8.4.2 F6010 PLC Runtime Error (162)8.4.3 F6024 Maximum braking time exceeded (163)8.4.4 F6028 Position limit value exceeded (overflow) (164)8.4.5 F6029 Positive position limit exceeded (164)8.4.6 F6030 Negative position limit exceeded (165)8.4.7 F6034 Emergency-Stop (166)8.4.8 F6042 Both travel range limit switches activated (167)8.4.9 F6043 Positive travel range limit switch activated (167)8.4.10 F6044 Negative travel range limit switch activated (168)8.4.11 F6140 CCD slave error (emergency halt) (169)8.5 Interface Errors (F4xxx) (169)8.5.1 Behavior in the Case of Interface Errors (169)8.5.2 F4001 Sync telegram failure (170)8.5.3 F4002 RTD telegram failure (171)8.5.4 F4003 Invalid communication phase shutdown (172)8.5.5 F4004 Error during phase progression (172)8.5.6 F4005 Error during phase regression (173)8.5.7 F4006 Phase switching without ready signal (173)8.5.8 F4009 Bus failure (173)8.5.9 F4012 Incorrect I/O length (175)8.5.10 F4016 PLC double real-time channel failure (176)8.5.11 F4017 S-III: Incorrect sequence during phase switch (176)8.5.12 F4034 Emergency-Stop (177)8.5.13 F4140 CCD communication error (178)8.6 Non-Fatal Safety Technology Errors (F3xxx) (178)8.6.1 Behavior in the Case of Non-Fatal Safety Technology Errors (178)8.6.2 F3111 Refer. missing when selecting safety related end pos (179)8.6.3 F3112 Safe reference missing (179)8.6.4 F3115 Brake check time interval exceeded (181)Troubleshooting Guide | Rexroth IndraDrive Electric Drivesand ControlsI Bosch Rexroth AG VII/XXIITable of ContentsPage8.6.5 F3116 Nominal load torque of holding system exceeded (182)8.6.6 F3117 Actual position values validation error (182)8.6.7 F3122 SBS: System error (183)8.6.8 F3123 SBS: Brake check missing (184)8.6.9 F3130 Error when checking input signals (185)8.6.10 F3131 Error when checking acknowledgment signal (185)8.6.11 F3132 Error when checking diagnostic output signal (186)8.6.12 F3133 Error when checking interrupting circuits (187)8.6.13 F3134 Dynamization time interval incorrect (188)8.6.14 F3135 Dynamization pulse width incorrect (189)8.6.15 F3140 Safety parameters validation error (192)8.6.16 F3141 Selection validation error (192)8.6.17 F3142 Activation time of enabling control exceeded (193)8.6.18 F3143 Safety command for clearing errors incorrect (194)8.6.19 F3144 Incorrect safety configuration (195)8.6.20 F3145 Error when unlocking the safety door (196)8.6.21 F3146 System error channel 2 (197)8.6.22 F3147 System error channel 1 (198)8.6.23 F3150 Safety command for system start incorrect (199)8.6.24 F3151 Safety command for system halt incorrect (200)8.6.25 F3152 Incorrect backup of safety technology data (201)8.6.26 F3160 Communication error of safe communication (202)8.7 Non-Fatal Errors (F2xxx) (202)8.7.1 Behavior in the Case of Non-Fatal Errors (202)8.7.2 F2002 Encoder assignment not allowed for synchronization (203)8.7.3 F2003 Motion step skipped (203)8.7.4 F2004 Error in MotionProfile (204)8.7.5 F2005 Cam table invalid (205)8.7.6 F2006 MMC was removed (206)8.7.7 F2007 Switching to non-initialized operation mode (206)8.7.8 F2008 RL The motor type has changed (207)8.7.9 F2009 PL Load parameter default values (208)8.7.10 F2010 Error when initializing digital I/O (-> S-0-0423) (209)8.7.11 F2011 PLC - Error no. 1 (210)8.7.12 F2012 PLC - Error no. 2 (210)8.7.13 F2013 PLC - Error no. 3 (211)8.7.14 F2014 PLC - Error no. 4 (211)8.7.15 F2018 Device overtemperature shutdown (211)8.7.16 F2019 Motor overtemperature shutdown (212)8.7.17 F2021 Motor temperature monitor defective (213)8.7.18 F2022 Device temperature monitor defective (214)8.7.19 F2025 Drive not ready for control (214)8.7.20 F2026 Undervoltage in power section (215)8.7.21 F2027 Excessive oscillation in DC bus (216)8.7.22 F2028 Excessive deviation (216)8.7.23 F2031 Encoder 1 error: Signal amplitude incorrect (217)VIII/XXII Bosch Rexroth AG | Electric Drivesand ControlsRexroth IndraDrive | Troubleshooting GuideTable of ContentsPage8.7.24 F2032 Validation error during commutation fine adjustment (217)8.7.25 F2033 External power supply X10 error (218)8.7.26 F2036 Excessive position feedback difference (219)8.7.27 F2037 Excessive position command difference (220)8.7.28 F2039 Maximum acceleration exceeded (220)8.7.29 F2040 Device overtemperature 2 shutdown (221)8.7.30 F2042 Encoder 2: Encoder signals incorrect (222)8.7.31 F2043 Measuring encoder: Encoder signals incorrect (222)8.7.32 F2044 External power supply X15 error (223)8.7.33 F2048 Low battery voltage (224)8.7.34 F2050 Overflow of target position preset memory (225)8.7.35 F2051 No sequential block in target position preset memory (225)8.7.36 F2053 Incr. encoder emulator: Pulse frequency too high (226)8.7.37 F2054 Incr. encoder emulator: Hardware error (226)8.7.38 F2055 External power supply dig. I/O error (227)8.7.39 F2057 Target position out of travel range (227)8.7.40 F2058 Internal overflow by positioning input (228)8.7.41 F2059 Incorrect command value direction when positioning (229)8.7.42 F2063 Internal overflow master axis generator (230)8.7.43 F2064 Incorrect cmd value direction master axis generator (230)8.7.44 F2067 Synchronization to master communication incorrect (231)8.7.45 F2068 Brake error (231)8.7.46 F2069 Error when releasing the motor holding brake (232)8.7.47 F2074 Actual pos. value 1 outside absolute encoder window (232)8.7.48 F2075 Actual pos. value 2 outside absolute encoder window (233)8.7.49 F2076 Actual pos. value 3 outside absolute encoder window (234)8.7.50 F2077 Current measurement trim wrong (235)8.7.51 F2086 Error supply module (236)8.7.52 F2087 Module group communication error (236)8.7.53 F2100 Incorrect access to command value memory (237)8.7.54 F2101 It was impossible to address MMC (237)8.7.55 F2102 It was impossible to address I2C memory (238)8.7.56 F2103 It was impossible to address EnDat memory (238)8.7.57 F2104 Commutation offset invalid (239)8.7.58 F2105 It was impossible to address Hiperface memory (239)8.7.59 F2110 Error in non-cyclical data communic. of power section (240)8.7.60 F2120 MMC: Defective or missing, replace (240)8.7.61 F2121 MMC: Incorrect data or file, create correctly (241)8.7.62 F2122 MMC: Incorrect IBF file, correct it (241)8.7.63 F2123 Retain data backup impossible (242)8.7.64 F2124 MMC: Saving too slowly, replace (243)8.7.65 F2130 Error comfort control panel (243)8.7.66 F2140 CCD slave error (243)8.7.67 F2150 MLD motion function block error (244)8.7.68 F2174 Loss of motor encoder reference (244)8.7.69 F2175 Loss of optional encoder reference (245)Troubleshooting Guide | Rexroth IndraDrive Electric Drivesand Controls| Bosch Rexroth AG IX/XXIITable of ContentsPage8.7.70 F2176 Loss of measuring encoder reference (246)8.7.71 F2177 Modulo limitation error of motor encoder (246)8.7.72 F2178 Modulo limitation error of optional encoder (247)8.7.73 F2179 Modulo limitation error of measuring encoder (247)8.7.74 F2190 Incorrect Ethernet configuration (248)8.7.75 F2260 Command current limit shutoff (249)8.7.76 F2270 Analog input 1 or 2, wire break (249)8.7.77 F2802 PLL is not synchronized (250)8.7.78 F2814 Undervoltage in mains (250)8.7.79 F2815 Overvoltage in mains (251)8.7.80 F2816 Softstart fault power supply unit (251)8.7.81 F2817 Overvoltage in power section (251)8.7.82 F2818 Phase failure (252)8.7.83 F2819 Mains failure (253)8.7.84 F2820 Braking resistor overload (253)8.7.85 F2821 Error in control of braking resistor (254)8.7.86 F2825 Switch-on threshold braking resistor too low (255)8.7.87 F2833 Ground fault in motor line (255)8.7.88 F2834 Contactor control error (256)8.7.89 F2835 Mains contactor wiring error (256)8.7.90 F2836 DC bus balancing monitor error (257)8.7.91 F2837 Contactor monitoring error (257)8.7.92 F2840 Error supply shutdown (257)8.7.93 F2860 Overcurrent in mains-side power section (258)8.7.94 F2890 Invalid device code (259)8.7.95 F2891 Incorrect interrupt timing (259)8.7.96 F2892 Hardware variant not supported (259)8.8 SERCOS Error Codes / Error Messages of Serial Communication (259)9 Warnings (Exxxx) (263)9.1 Fatal Warnings (E8xxx) (263)9.1.1 Behavior in the Case of Fatal Warnings (263)9.1.2 E8025 Overvoltage in power section (263)9.1.3 E8026 Undervoltage in power section (264)9.1.4 E8027 Safe torque off while drive enabled (265)9.1.5 E8028 Overcurrent in power section (265)9.1.6 E8029 Positive position limit exceeded (266)9.1.7 E8030 Negative position limit exceeded (267)9.1.8 E8034 Emergency-Stop (268)9.1.9 E8040 Torque/force actual value limit active (268)9.1.10 E8041 Current limit active (269)9.1.11 E8042 Both travel range limit switches activated (269)9.1.12 E8043 Positive travel range limit switch activated (270)9.1.13 E8044 Negative travel range limit switch activated (271)9.1.14 E8055 Motor overload, current limit active (271)9.1.15 E8057 Device overload, current limit active (272)X/XXII Bosch Rexroth AG | Electric Drivesand ControlsRexroth IndraDrive | Troubleshooting GuideTable of ContentsPage9.1.16 E8058 Drive system not ready for operation (273)9.1.17 E8260 Torque/force command value limit active (273)9.1.18 E8802 PLL is not synchronized (274)9.1.19 E8814 Undervoltage in mains (275)9.1.20 E8815 Overvoltage in mains (275)9.1.21 E8818 Phase failure (276)9.1.22 E8819 Mains failure (276)9.2 Warnings of Category E4xxx (277)9.2.1 E4001 Double MST failure shutdown (277)9.2.2 E4002 Double MDT failure shutdown (278)9.2.3 E4005 No command value input via master communication (279)9.2.4 E4007 SERCOS III: Consumer connection failed (280)9.2.5 E4008 Invalid addressing command value data container A (280)9.2.6 E4009 Invalid addressing actual value data container A (281)9.2.7 E4010 Slave not scanned or address 0 (281)9.2.8 E4012 Maximum number of CCD slaves exceeded (282)9.2.9 E4013 Incorrect CCD addressing (282)9.2.10 E4014 Incorrect phase switch of CCD slaves (283)9.3 Possible Warnings When Operating Safety Technology (E3xxx) (283)9.3.1 Behavior in Case a Safety Technology Warning Occurs (283)9.3.2 E3100 Error when checking input signals (284)9.3.3 E3101 Error when checking acknowledgment signal (284)9.3.4 E3102 Actual position values validation error (285)9.3.5 E3103 Dynamization failed (285)9.3.6 E3104 Safety parameters validation error (286)9.3.7 E3105 Validation error of safe operation mode (286)9.3.8 E3106 System error safety technology (287)9.3.9 E3107 Safe reference missing (287)9.3.10 E3108 Safely-monitored deceleration exceeded (288)9.3.11 E3110 Time interval of forced dynamization exceeded (289)9.3.12 E3115 Prewarning, end of brake check time interval (289)9.3.13 E3116 Nominal load torque of holding system reached (290)9.4 Non-Fatal Warnings (E2xxx) (290)9.4.1 Behavior in Case a Non-Fatal Warning Occurs (290)9.4.2 E2010 Position control with encoder 2 not possible (291)9.4.3 E2011 PLC - Warning no. 1 (291)9.4.4 E2012 PLC - Warning no. 2 (291)9.4.5 E2013 PLC - Warning no. 3 (292)9.4.6 E2014 PLC - Warning no. 4 (292)9.4.7 E2021 Motor temperature outside of measuring range (292)9.4.8 E2026 Undervoltage in power section (293)9.4.9 E2040 Device overtemperature 2 prewarning (294)9.4.10 E2047 Interpolation velocity = 0 (294)9.4.11 E2048 Interpolation acceleration = 0 (295)9.4.12 E2049 Positioning velocity >= limit value (296)9.4.13 E2050 Device overtemp. Prewarning (297)Troubleshooting Guide | Rexroth IndraDrive Electric Drivesand Controls| Bosch Rexroth AG XI/XXIITable of ContentsPage9.4.14 E2051 Motor overtemp. prewarning (298)9.4.15 E2053 Target position out of travel range (298)9.4.16 E2054 Not homed (300)9.4.17 E2055 Feedrate override S-0-0108 = 0 (300)9.4.18 E2056 Torque limit = 0 (301)9.4.19 E2058 Selected positioning block has not been programmed (302)9.4.20 E2059 Velocity command value limit active (302)9.4.21 E2061 Device overload prewarning (303)9.4.22 E2063 Velocity command value > limit value (304)9.4.23 E2064 Target position out of num. range (304)9.4.24 E2069 Holding brake torque too low (305)9.4.25 E2070 Acceleration limit active (306)9.4.26 E2074 Encoder 1: Encoder signals disturbed (306)9.4.27 E2075 Encoder 2: Encoder signals disturbed (307)9.4.28 E2076 Measuring encoder: Encoder signals disturbed (308)9.4.29 E2077 Absolute encoder monitoring, motor encoder (encoder alarm) (308)9.4.30 E2078 Absolute encoder monitoring, opt. encoder (encoder alarm) (309)9.4.31 E2079 Absolute enc. monitoring, measuring encoder (encoder alarm) (309)9.4.32 E2086 Prewarning supply module overload (310)9.4.33 E2092 Internal synchronization defective (310)9.4.34 E2100 Positioning velocity of master axis generator too high (311)9.4.35 E2101 Acceleration of master axis generator is zero (312)9.4.36 E2140 CCD error at node (312)9.4.37 E2270 Analog input 1 or 2, wire break (312)9.4.38 E2802 HW control of braking resistor (313)9.4.39 E2810 Drive system not ready for operation (314)9.4.40 E2814 Undervoltage in mains (314)9.4.41 E2816 Undervoltage in power section (314)9.4.42 E2818 Phase failure (315)9.4.43 E2819 Mains failure (315)9.4.44 E2820 Braking resistor overload prewarning (316)9.4.45 E2829 Not ready for power on (316)。
lr中错误解决方法19种

lr中错误解决⽅法19种⼀、Error -27727: Step download timeout (120 seconds)has expired when downloading resource(s). Set the“Resource Page Timeout is a Warning” Run-Time Setting to Yes/No to have this message as a warning/error, respectively处理⽅法:Run-Time Setting ------ Internet Protocol ------ Preferences ------Option ------ Step download timeout(sec)改为32000A、应⽤服务参数设置太⼤导致服务器的瓶颈 B、页⾯中图⽚太多 C、在程序处理表的时候检查字段太⼤或多⼆、错误现象:Action.c(16): Error -27728: Step download timeout (120 seconds) has expired when downloading non-resource(s)。
错误分析:对于HTTP协议,默认的超时时间是120秒(可以在LoadRunner中修改),客户端发送⼀个请求到服务器端,如果超过120秒服务器端还没有返回结果,则出现超时错误。
解决办法:⾸先在运⾏环境中对超时进⾏设置,默认的超时时间可以设置长⼀些,再设置多次迭代运⾏,如果还有超时现象,需要在"Runtime Setting">"Internet Protocol:Preferences">"Advanced"区域中设置⼀个"winlnet replay instead of sockets"选项,再回放是否成功。
五线接收器控制器说明书

5-Wire Relay ReceiverCat. Nos. WSP02-R10, WSP12-010, WSP12-020, WSP02-080, WST02-R10, WST12-010, WST12-020 & WST12-080International versions availableINSTALLATIONOPTION B: Hardwired/Wireless Combo 3-Way Switch (1 hardwired 3-way switch, 1 wireless switch) 1. W ARNING: To avoid risk of fire, shock, or death, TURN OFF POWER at circuit breaker or fuse and verify that it is OFF before installation begins. Make sure that it remains OFF until installation is complete. Please be aware that with some versions of the product, it is possible to have multiple branch circuits feeding the Relay Receiver. 2.R ead the WARNINGS AND CAUTIONS section before beginning these installation options. Read all steps for this option before taking any action to install receiver.3. I f hardwired switch is currently a single pole switch, the switch will need to be replaced with a hardwired 3-way switch. For best performance use a plastic wiring box. When a 5-Wire RelayReceiver is used with a hardwire 3-way switch, the maximum load rating is reduced(see specifications).4. C onfirm that both neutral and hot wires are present at wall switch location. Connect wires as shownin Figure E . Twist wire nuts on clockwise making sure no bare wires show. Wrap connections withelectrical tape.5. R estore power and follow programming instructions for appropriate programming mode (see“Programming” below). For this installation, Toggle Mode is recommended.6. T est receiver. (If receiver is not working, review wiring and programming instructions).7. Stow all wires in wiring box. Finish any installation of hardwired 3-way switch.OPTION C: Hardwired/Wireless Combo 4-Way Switch (1 hardwired 4-way switch, 1 hardwired 3-way switch, 1 wireless switch) 1. R ead the WARNINGS AND CAUTIONS section before beginning these installation options. Readall steps for this option before taking any action to install receiver.2. W ARNING: To avoid risk of fire, shock, or death, TURN OFF POWER at circuit breaker or fuseand verify that it is OFF before installation begins. Make sure that it remains OFF until installationis complete. Please be aware that with some versions of the product, it is possible to have multiplebranch circuits feeding the Relay Receiver.3. I f both hardwired switches are currently 3-way switches, one of the switches will need to be replacedwith a hardwired 4-way switch. For best performance use a plastic wiring box. When a Leviton 5-Wire Relay Receiver is used with a hardwire 3-way switch, the maximum load rating is reduced (see specifications). 4. C onfirm that both neutral and hot wires are present at wall switch location. Connect wires as shownin Figure F . Twist wire nuts on clockwise making sure no bare wires show. Wrap connections withelectrical tape. 5. R estore power and follow programming instructions for appropriate programming mode (see “Programming” below). For this installation, Toggle Mode is recommended. 6. T est receiver. (If receiver is not working, review wiring and programming instructions).7. Stow all wires in wiring box. Finish any installation of fixture or wall switch.PROGRAMMING:The receiver must be powered when programming. After programming, settings are retained when power isdisconnected. The receiver sensitivity is reduced when in Learn Mode to prevent unintentionally associatingunwanted transmitters with the receiver. Transmitters should be within 15 feet (5 meters) of the receiver when programming. Program the receiver in any of the modes below.Rocker Mode (default): In Rocker Mode the receiver responds only on a transmitter press and not on the release. For example, one side of the rocker on a wireless light switch will activate the relay (turn the light ON) when pressed and the opposite side of the same rocker will deactivate the relay (turn the light OFF)when pressed.Momentary Mode: In Momentary Mode, each end of the rocker on a wireless light switch acts as a separatebutton. Each end of the rocker programs separately to 1 or more receivers. When a rocker is pressed the output on the receiver will activate (turning the electrical load ON). When the rocker is released the output will deactivate (turning the electrical load OFF).Toggle Mode: In Toggle Mode, each end of the rocker acts as a separate button. Each end of the rockerprograms separately. When the rocker is pressed the output of the receiver will always change state (if OFF,it will turn ON; if ON, it will turn OFF). Like Rocker Mode, the output status only changes when a button ispressed and is ignored on the release.Follow the instructions below for the desired programming mode:Rocker Mode (default) Programming Instructions 1. R ead all Rocker Mode programming steps before taking any action to program receiver in Rocker Mode.2. A ctivate Rocker Learn Mode by pressing and holding the LRN button for 1 second (See Figure A). The electrical load connected to the receiver will begin turning ON and OFF in a slow pattern.3. W hen associating a wireless light switch with the receiver, press one end of a switch rocker (See FigureB). When associating a transmitter other than a wireless light switch, press the LRN or TCH button on the Leviton transmitter (see appropriate transmitter starter guide). The load will stay ON for about 3 seconds indicating that the receiver has stored the transmitter’s unique ID in its memory.4. N OTE: If only one transmitter is desired then skip Step 4 and exit Learn Mode by following Step 5. To associate a second transmitter with this receiver, wait until toggling of the load resumes. Repeat the instructions in Steps 3 and 4 until the unique IDs of all desired transmitters are stored in the memory of the receiver.WARNINGS AND CAUTIONS:• DISCONNECT POWER AT CIRCUIT BREAKER OR FUSE WHEN SERVICING, INSTALLING ORREMOVING FIXTURE.• TO BE INSTALLED AND/OR USED IN ACCORDANCE WITH ELECTRICAL CODES ANDREGULATIONS.• IF YOU ARE NOT SURE ABOUT ANY PART OF THESE INSTRUCTIONS, CONSULT AN ELECTRICIAN.• RELAY RECEIVERS ARE INTENDED ONLY FOR USE INDOORS, IN DRY LOCATIONS, AND WITHPERMANANTLY INSTALLED FIXTURES.• SUITABLE FOR USE ON A CIRCUIT CAPABLE OF DELIVERING NOT MORE THAN 15 RMSSYMMETRICAL AMPERES MAXIMUM.• RELAY RECEIVERS SHOULD NOT BE INSTALLED IN LOCATIONS WHERE THE UNITS WILL BE INCLOSE PROXIMITY TO THE LIGHT BULB(S) OR OTHER SOURCES OF HEAT, SUCH AS ABOVE ACEILING HUGGER FIXTURE, PARTICULARLY WITH HIGHER WATTAGE LOADS.• WHEN USING RELAY RECEIVERS TO SWITCH A MOTOR, OVERLOAD AND OVER-CURRENTPROTECTION SIZED FOR THE MOTOR LOAD SHOULD BE PROVIDED AT THE BRANCH CIRCUITFEEDER SUPPLYING THE MOTOR IN ACCORDANCE WITH THE NEC OR CEC, AS APPLICABLEFOR THE INSTALLED LOCATION.• THE MAXIMUM OVER-CURRENT PROTECTION REQUIRED FOR THE BRANCH CIRCUIT SUPPLYING THIS PRODUCT IS 15 AMPS. WHEN ONE OR MORE MOTORS ARE INSTALLED AND NOT INTERNALLY PROTECTED THEN AN OVERLOAD PROTECTIVE DEVICE SIZED AT NOT MORE THAN 115% OF THE MOTOR FULL LOAD AMPS (FLA) SHOULD BE INSTALLED FOR EACH MOTOR.• WHEN USING DEVICES TO CONTROL MOTORS AND HVAC EQUIPMENT WHICH DO NOT RESPOND WELL TO THE ON/OFF CYCLING WHICH OCCURS IN THE LEARN MODE, ITIS ADVISED TO CONFIGURE THE RECEIVER’S WITHOUT THE MOTOR OR HVAC LOADCONNECTED AND INSTEAD PROGRAM THE PRODUCTS IN ADVANCE BY CONNECTING THEMLIGHT OR OTHER LOAD THAT IS SAFE TO TOGGLE ON AND OFF.DESCRIPTION:The 5-wire Relay Receiver provides fast and simple installation of remote controls for lighting, HVAC, motor, and other loads. The receiver responds to radio signals from selfpowered wireless light switches and other compatible transmitters. The relay receiver can be used in single pole, 3-way, or 4-way switch applications. The receiver mounts in ceiling junction boxes, wall switch boxes, and wiring cavities. The threaded versionmounts through standard 1/2" knock-out holes (See Figure I).COMPATIBLE DEVICES:• Self Powered Light Sensor (WST models only)• Single Rocker Self-powered Wireless Light Switch • Dual Rocker Self-powered Wireless Light Switch• Handheld Self-powered Wireless Light Switch• Key Card Access Switch• SLT Wireless Sensor • Self-powered Wireless Occupancy Sensor• More transmitters availableTOOLS NEEDED FOR INSTALLATION:• Non-conductive probe (pencil or ballpoint pen)• Electrical tape • Wire nuts • Screwdriver TO INSTALL:To install the 5-Wire Relay Receiver, select your application from the options below. Follow the instructions for that application. For transmitter installation instructions, see appropriate installation guide(s).SELECT 1 OF THE FOLLOWING COMMON APPLICATIONS:OPTION A: Single Pole or Multi-way Wireless Switch (1 or more wireless light switches)1. W ARNING: To avoid risk of fire, shock, or death, TURN OFF POWER at circuit breaker or fuseand verify that it is OFF before installation begins. Make sure that it remains OFF until installation iscomplete. Please be aware that with some versions of the product, it is possible to have multiple branchcircuits feeding the Relay Receiver.2. R ead the WARNINGS AND CAUTIONS section before beginning these installation options. Readall steps for this option before taking any action to install receiver.3. F or in-wall installation, a wiring box must be used. For ceiling installation make wire connections insidea junction box. Ensure that the temperature in the ceiling box will not exceed 50 degrees C (seespecifications). For best wireless signal performance install receiver in plastic box away from floor andaway from metal objects. 4. C onnect wires as shown in Figure D . Twist wire nuts on clockwise making sure no bare wires show.Wrap connections with electrical tape.5. R estore power and follow programming instructions for appropriate programming mode (see“Programming” below). For this installation, Rocker Mode (the default programming mode) isrecommended.6. T est receiver. (If receiver is not working, review wiring and programming instructions).7. Stow all wires in wiring box. Finish any installation of fixture or wall switch.5. T o complete programming, just wait; the receiver automatically exits Learn Mode after 30 seconds.Alternatively, press and hold the LRN button for 1 second to exit Learn Mode.Momentary Mode Programming Instructions1. Read all Rocker Mode programming steps before taking any action to program receiver in Momentary Mode.2. While the receiver is in Rocker Learn Mode, press and hold the LRN button for 3 seconds (See Figure A).The electrical load connected to the receiver will begin turning ON and OFF in a fast pattern. The receiver is now in Momentary Learn Mode.3. Follow Steps 3-5 of "Rocker Mode Programming Instructions."Toggle Mode Programming Instructions1. Read all Rocker and Momentary Mode programming steps before taking any action to program receiverin Toggle Mode.2. While the receiver is in Momentary Learn Mode, press and hold the LRN button for 3 seconds(See Figure A). The electrical load connected to the receiver will continue turning ON and OFF in a fast pattern. The receiver is now in Toggle Learn Mode.3. Follow Steps 3-5 of "Rocker Mode Programming Instructions."Selective Deleting: Follow the Program Mode steps above to delete a transmitter from a receiver’s memory. Upon pressing the LRN button on a transmitter (See Rocker Mode Programming Instructions, Step 3) which has previously been associated with the receiver, the electrical load connected to the receiver will stay OFF for 3 seconds indicating that the receiver has removed the transmitter’s unique ID from its memory.Clear All: If the CLR button is pressed and held for 2 seconds (See Figure C), the entire memory of the receiver will be deleted. The receiver will instantly enter the default programming mode (Rocker Mode) indicated by the electrical load turning ON and OFF.Automatic ON / Automatic OFF. If the receiver learns a wireless motion sensor, the load will turn OFF after no occupancy has been detected for 15 minutes. If learned in the Rocker Mode, the output will be Manual ON / Automatic OFF. If learned in Momentary Mode, the output will be Automatic ON / Automatic OFF.ADDITIONAL PROGRAMMING OPTIONSInverted Output Mode: The receiver supports the Inverted Output Mode of operation. In the defaultconfiguration, the N.O. relay contact is open (not connected) when not active, and closed (connected) when active. When the outputs are in Inverted Output Mode, the N.O. contact is closed when not active and open when active. Inverting the outputs may be used to emulate a normally closed relay that opens when a switch is activated.One common use for this mode is for magnetic door release controls. The output is ON and the door-hold electromagnet is active until a Momentary switch is activated, deactivating the electromagnet and allowing the door to close. The magnet is reactivated as soon as the switch is released.Inverted Output Mode Programming Instructions 1. Turn the power to the receiver OFF.2. Press and hold the CLR button for 5 seconds while turning on the power. The load will blink twice toindicate activation of Inverted Output Mode.To change back to normal operating mode, repeat Steps 1 and 2. The load will blink once to indicatenormal (non-Inverted) mode. The state of this mode is stored in non-volatile memory and is maintained even if the power is removed.Repeater Function (WST models only): The default setting for the receiver is Repeater-ON. A repeater re-transmits a copy of every signal received, and many repeaters also function as receivers. It isrecommended that no more than two repeaters are active within range of any LevNet RF transmitters or receivers. Repeaters should be installed high above the floor in a central location, minimizing the number of walls or other obstructions through which the wireless signal must travel.Repeater Programming Instructions:1. Turn the power to the receiver OFF 2. P ress and hold the LRN button for 5 seconds while turning on the power. The load will blink twice toindicate activation of the repeater mode. T o change back to normal operating mode, repeat Steps 1 and 2. The load will blink twice indicate therepeater is ON and blink once to indicate the repeater is OFF.PK-93717-10-00-0B ARN1401For Technical Assistance Call: 1-800-824-3005 (U.S.A. Only)LIMITED 5 YEAR WARRANTY AND EXCLUSIONSLeviton warrants to the original consumer purchaser and not for the benefit of anyone else that this product at the time of its sale by Leviton is free of defects in materials and workmanship under normal and proper use for five years from the purchase date. Leviton’s only obligation is to correct such defects by repair or replacement, at its option, if within such five year period the product is returned prepaid, with proof of purchase date, and a description of the problem to Leviton Manufacturing Co., Inc., Att: Quality Assurance Department, 201 North ServiceRoad, Melville, New York 11747. This warranty excludes and there is disclaimed liability for labor for removal of this product or reinstallation. This warranty is void if this product is installed improperly or in an improper environment, overloaded, misused, opened, abused, or altered in any manner, or is not used under normal operating conditions or not in accordance with any labels or instructions. There are no other or implied warranties of any kind, including merchantability and fitness for a particular purpose , but if any implied warranty is required by the applicable jurisdiction, the duration of any such implied warranty, including merchantability and fitness for a particular purpose, is limited to five years. Leviton is not liable for incidental, indirect, special, or consequential damages, including without limitation, damage to, or loss of use of, any equipment, lost sales or profits or delay or failure to perform this warranty obligation . The remedies provided herein are the exclusive remedies under this warranty, whether based on contract, tort or otherwise.ARN141FCC COMPLIANCE STATEMENT: Contains FCC ID: SZV-TCM2XXC. Contains IC (Canada): 5713A-TCM2XXCThe enclosed device complies with Part 15 of the FCC Rules. Operation is subject to the following two conditions: (i.) this device may not cause harmful interference and (ii.) this device must accept any interference received, including interference that may cause undesired operation.ETL (US) - Conforms to UL STD 244A. This device was tested according to and was found to comply with UL 244A Solid State Controls for Appliances.ETL (Canada) - Certified to CAN/CSA STD C22.2 No. 14-05. This device was tested according to and was found to comply with CAN/CSA STD C22.2 No. 14-05.Leviton is a registered trademark of Leviton Mfg. Co. in the United States, Canada, Mexico, and other countries. Other trademarks herein are the property of their respective owners.。
NNM 7.5安装指南(HP-UX 11i v2系统)说明书

Installation Instructionsfor NNM 7.5 on an HP-UX 11i v2 SystemYou can install NNM 7.5 on an HP-UX 11i v2 system, and then run NNM 7.5 in Aries Dynamic Translation mode.Note: This is recommended only if you want to run NNM AdvancedEdition on an HP-UX 11i v2 system. If you want to run NNM StarterEdition on an HP-UX 11i v2 system, HP recommends you use theNNM 7.5 for the HP-UX 11.23 operating system product instead,which runs in native mode.For general information about installing NNM, review the NNM Quick Start Installation Guide for the HP-UX Operating System.To run NNM 7.5 AE in Dynamic Translation mode on an HP-UX 11i v2 system, you must install the software from a special depot. Use the following instructions to obtain and install the required depot:1.Log in to the system with super-user privileges (typically, as user root).2.Run the following commands:mkdir /tmp/DEPOTcd /tmp/DEPOT3.Follow the instructions on the download page (accessible from/products/nnm/download.html) to downloadthe NNM.HPUX11iv2_IPF32.tar.gz file to the /tmp/DEPOT directory.4.To extract and uncompress the depot, run the following command:gunzip -c /tmp/DEPOT/NNM.HPUX11iv2_IPF32.tar.gz | tar xvfYou can normally find the gunzip command in /usr/contrib/bin/gunzip.If gunzip is not available on your system, you can download it from.5.Run the following commands:cd /tmp/DEPOT/disk1./pre-installThe pre-install script is required for the rest of the installation to succeed. It replaces the system uname command with a script, and creates the /.ariesrcfile.6.After pre-install script is run, make sure that system uname is replaced by unamescript which emulates HP-UX11.11 behaviour. Check /usr/bin/uname and/sbin/uname. This can be done by running following commands:/usr/bin/uname/sbin/unameoutput of both commands should look like:HP-UX <hostname> B.11.11 U 9000/785 2013808516 unlimited-user licenseAlso check that /.ariesrc file is created with following line:/ -pa_os_cpu7.Run the following command:./installLet the installation wizard guide you through the initial NNM installation.8.When the previous step completes, run the following commands:cd /tmp/DEPOT/disk2./installLet the installation wizard guide you through the final portion of the NNMinstallation.9.Look in the /var/adm/sw/swagent.log file for ERROR or WARNINGstrings.10.Download the Aries cumulative patch, PHSS_32502 or higher. It is availableat /service/patch/mainPage.doApply the patch by following the instructions included with the patch.11.Install Perl package version D.5.8.0.D (By default HP-UX 11i v2 will have Perlversion B.5.8.0.B). The required Perl depot is named as follows:HPOvPerlA-05.06.012-HPUX11.0-release.depotIt is available at this URL:/cpe/patches/nnm/7.50/s700_800_11.X.jsp Follow the instructions at that web site to install the package.12.Install NNM patch PHSS_32124. It is available at this URL:/cpe/patchesApply the patch by following the directions given at that web site.Important: In the step where you run the swinstall command, include this additional switch in the command line:–x allow_incompatible=trueThis means the command you execute will be as follows:swinstall -x autoreboot=true -x patch_match_target=true \ –x allow_incompatible=true –s PHSS_32124.depot13.After installation is complete, replace back the uname script with system uname.pre-install script leaves a copy of original system uname at /usr/bin/uname.orig and /sbin/uname.orig. Restore them by running following commands:mv /usr/bin/uname.orig /usr/bin/unamemv /sbin/uname.orig /sbin/uname14.It is recommended that uname command should be replaced by uname script toemulate HP-UX 11.11 behaviour for running other configuration scripts, such as setupExtTopo.ovpl and setupSyslog.ovpl. This can be done by following step 5,6 followed by the configuration script. Then restore the system uname by following step 13.。
LR代码错误及解决方法

LR代码错误及解决方法在进行机器学习模型的开发过程中,我们可能会遇到各种各样的问题,其中之一就是出现错误的代码。
这些错误可能是由于语法错误、模块缺失、数据异常、模型参数不合适等原因导致的。
下面我将给出一些常见的LR (逻辑回归)代码错误及解决方法。
1.语法错误:这是最常见的错误之一,可能是由于拼写错误、括号不匹配、缩进错误等导致的。
解决方法是仔细检查代码,确保语法正确,尤其是拼写和括号的使用。
可以使用IDE提供的语法检查功能来寻找错误。
2. 缺少必要的模块:在使用LR模型之前,我们需要导入相应的模块,例如numpy、pandas和sklearn等。
如果缺少这些模块,我们在导入时会遇到ImportError。
解决方法是确保这些依赖模块已经正确安装,并在代码中使用import语句导入它们。
3. 数据异常:LR模型通常对于数据的特征处理有一些要求,例如数据应该是数值型的,而不是文本型的。
如果数据中存在缺失值、异常值或者数据类型不匹配等问题,我们在进行训练时会遇到ValueError或TypeError。
解决方法是进行数据预处理,例如填充缺失值、处理异常值、进行类型转换等。
4.模型参数不合适:LR模型有一些重要的参数,例如学习率、正则化参数等。
如果这些参数不合适,我们可能会遇到收敛速度慢、过拟合或欠拟合的问题。
解决方法是进行参数调优,可以使用交叉验证等方法来选择最佳的参数。
5. 代价函数错误:LR模型使用的是逻辑损失函数(Log Loss),在实现时需要注意代价函数的选择和实现是否正确。
如果使用了错误的代价函数或者实现有误,我们可能会遇到训练错误或预测结果不准确的问题。
解决方法是参考LR模型的代价函数定义,确保正确地实现代价函数。
6.训练过程错误:LR模型的训练过程通常需要迭代多次,通过梯度下降或其他优化算法来更新模型参数。
如果迭代次数不够或者优化算法实现有误,我们可能会遇到训练错误或模型参数无法收敛的问题。
Windows7安装常见的二十四中错误提示原因分析及解决方法参考
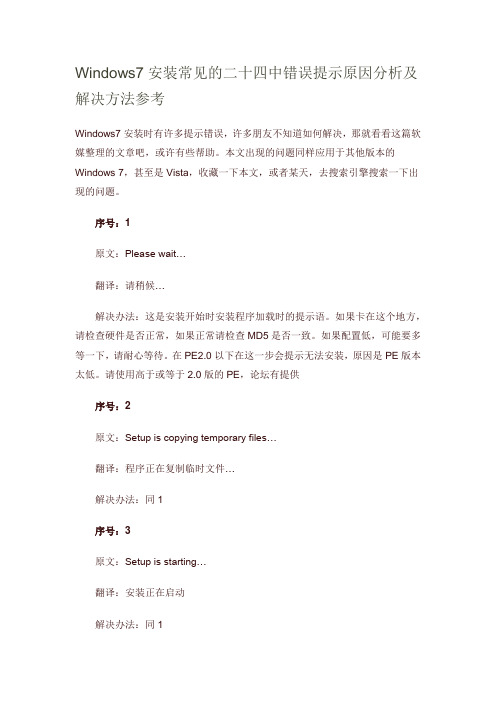
Windows7安装常见的二十四中错误提示原因分析及解决方法参考Windows7安装时有许多提示错误,许多朋友不知道如何解决,那就看看这篇软媒整理的文章吧,或许有些帮助。
本文出现的问题同样应用于其他版本的Windows 7,甚至是Vista,收藏一下本文,或者某天,去搜索引擎搜索一下出现的问题。
序号:1原文:Please wait…翻译:请稍候…解决办法:这是安装开始时安装程序加载时的提示语。
如果卡在这个地方,请检查硬件是否正常,如果正常请检查MD5是否一致。
如果配置低,可能要多等一下,请耐心等待。
在PE2.0以下在这一步会提示无法安装,原因是PE版本太低。
请使用高于或等于2.0版的PE,论坛有提供序号:2原文:Setup is copying temporary files…翻译:程序正在复制临时文件…解决办法:同1序号:3原文:Setup is starting…翻译:安装正在启动解决办法:同1序号:4原文:Windows installation cannot be started from the current operating system. To install Windows, boot from the installation media, or upgrade to Windows XP or later and restart the installation.翻译:无法从当前操作系统启动Windows安装。
若要安装Windows,请从安装介质启动,或升级到Windows XP或更高版本,然后重新启动安装。
解决办法:已经说得很清楚了,如果你是从2000系统安装,那是不行的。
请在XP或者2003、Vista升级或安装。
序号:5原文:Install Windows翻译:安装Windows解决办法:同1序号:6原文:Windows could not load required file. The file may be corrupt. To install Windows, restart the installation. Error code: 0x%2!X!翻译:Windows无法加载所需的文件。
Matriarch Firmware Update V1.2.0说明书

MATRIARCH FIRMWARE UPDATE V1.2.0 Sept 23, 2020Firmware version 1.2.0 for the Matriarch contains a number of new features as well as some bug fixes.HOW TO UPDATE YOUR FIRMWARE1. Connect a USB cable from Matriarch to your computer.2. Open your SysEx sending software.NOTE: We recommend downloading Bome SendSX for Windows or SysEx Librarian for Mac.3. In the SysEx software, select Matriarch as your MIDI output device.NOTE: In SysEx Librarian, this is located in the drop-down menu at the top of the application window.In Bome SendSX, this is located in the MIDI OUT menu on the menu bar.4. Select the SysEx file “Matriarch_FIRMWARE_INVALIDATE.syx” included with this downloadand click Send. On the Matriarch, the Arp Rate LED will start blinking red/green.5. In the SysEx sending software, re-select Matriarch as your MIDI output device (Matriarchreboots and needs to be re-selected after INVALIDATE).6. Select the SysEx file “Matriarch_FIRMWARE_ERASE.syx” included with this downloadand click Send. On the Matriarch, the Arp Rate LED will blink green. Matriarch is now ready for new firmware.7. Select the new firmware file “Matriarch_Firmware_v1_2_0.syx” included with this downloadand click Send. The Matriarch Arp Rate LED will blink yellow-orange while receiving.8. You’re done! Matriarch will reboot to the new firmware when done.TROUBLESHOOTINGIf the Matriarch Arp Rate LED is still blinking yellow-orange after the firmware has finished sending,or if the Arp Rate LED stops blinking and the unit does not reboot automatically once firmware hasfinished sending, you should try again.Turn the Matriarch power off and on again, disconnect and reconnect the USB cable, andthen start over at step 1.You can retry as many times as necessary and it will not hurt the hardware. If it doesn’t work after twoor three tries, you should contact Moog Technical Support for further assistance.**********************************************************************************.CHANGES SINCE V1.1.0:• Synchronization and Timing Engine update - Analog Clock in/out and MIDI Clock all remain tightly in phase now, eliminating the possibility of drift between these clocks which was present in earlier firmware.• New function when step recording: hold SHIFT + press the TIE button to duplicate the current step. This function copies the note(s) from the current step to the next step and ties them together, advancing the sequence by one step for each SHIFT + TIE press. This makes it easy to program longer notes and chords into your sequences.• New Global Parameter (5.1) “Arp/Seq CV Out Mirrors KB CV”: If ON, then the Arp/Seq CV OUT, GATE OUT, and VEL OUT jacks on the front panel will output the same voltages as the rear-panel KB CV OUT, KB GATE OUT, and KB VEL OUT jacks, whenever the Arp/Sequencer is not running.• New Behavior: HOLD button acts like a Sustain Pedal (KB Hold) when Arp/Seq is not running.• The default setting for CLOCK INPUT PPQN and CLOCK OUTPUT PPQN was changed from expecting/outputting a clock every 8th note, to expecting/outputting a clock every 16th note (changed from 2 PPQN to 4 PPQN).• Arp/Sequencer Gate Length can be adjusted using MIDI CC 106. Value 64 = 50% gate length (default).• Matriarch no longer outputs unexpected streams of MIDI CC/NRPN data.• PPQN In/Out settings now match documentation in manual.• External Analog Clock overrides MIDI Sync.• Arp/Seq PLAY button does not output MIDI CC 73 (can still respond to it if necessary).• Improves compatibility with other Grandmother/Matriarchs.• Changed MIDI Clock Output default setting to “Off”.• Fix for stuck envelopes (was due to retriggering faster than a certain minimum, easy to do in multi-trig mode).• Can now edit global parameters via MIDI SysEx messages (documented below).NEW GLOBAL PARAMETERS & FUNCTIONS:4.8 MIDI OUT Filter - Panel Knobs (off, on)4.9 MIDI OUT Filter - Pitch/Mod Wheels (off, on)4.10 MIDI OUT Filter - Keys (off, on)5.1 Arp/Seq CV OUT Mirrors KB CV10.1 Reset Global Settings (function)10.2 Show Firmware Version (function)GLOBAL SETTINGSMost Matriarch front-panel controls relate to creating sound. Below the surface, there is another level of parameters known as the Global Settings, which determine how the instrument operates, and howit can connect and interact with other electronic instruments and audio equipment.To access Matriarch’s Global Settings, simultaneously press and hold the HOLD [SHIFT] buttonlocated in the Left-Hand Controller and the SYNC ENABLE button located in Oscillator 1 until theSYNC ENABLE button begins to blink. This indicates that Matriarch is in the Global Settings edit mode. Now you can use the keyboard commands listed below to make any needed changes to the Global Settings. The SYNC ENABLE button will blink a specific number of times to indicate which Global Setting is currently selected. When you have finished making any changes, simply press the SYNC ENABLE button to exit the Global Settings edit mode.Once you are in the Global Settings edit mode, you can freely select different groups and parameters using the black keys, and can switch the value of the selected parameters by using the white keys, until you press the SYNC ENABLE button to exit. Double-tapping on a white key will both update the setting and exit the Global Settings edit mode simultaneously.NOTE: Global Settings are retained even when the power has been turned off.HERE’S HOW IT WORKS:Global Settings are organized in groups of ten. An individual parameter in the chosen group is selected using one of the lower 10 black keys, starting with C#0. The white keys, starting with C0, are used to set the value of the chosen parameter. The first 10 parameters are in the default group, and no group selection is required. Additional groups are selected using one of the upper black keys, starting with C#2. To access these additional parameters, hold down the Group Select key while pressing the individual Parameter Select key.NOTE: Tuning scales are imported into Matriarch via MIDI, and can be sent from tuning software such as Scala,or the Moog Phatty Tuner. Matriarch supports the following MIDI TUNING STANDARD message types:· Bulk Tuning Dump (128-note scales)· Single-Note Tuning (retunes notes individually)· Scale/Octave Types 5, 6, 8, 9 – 1-Byte and 2-Byte formats.The official MIDI Tuning Standard description is part of The Complete MIDI 1.0 Detailed Specification PDF document, available free of charge at . You will be required to register at the site in order to access this document, and other information related to MIDI.FUNCTIONS WITHIN THE GLOBAL EDIT MODEThis firmware version introduces a couple of useful functions which are launched from within the Global Edit system. They are selected like other global parameters, but the functions activate immediately upon being selected, since there is no need to set any additional parameter value for them.EDITING PARAMETERS USING MIDI SYSEX MESSAGESYou can edit the global and some panel parameters using MIDI System Exclusive (SysEx) messages. The template for these SysEx messages is shown below.TO SET A PARAMETER TO A VALUE:F0 04 17 23 [Parameter ID], [value MSB], [value LSB], 00 00 00 00 00 00 00 00 [Unit ID] F7• Values above are shown in hexadecimal format.• If the intended parameter value is less than 128, then [value MSB] is 0 and [value LSB] is the intended parameter value. If the intended parameter value is 128 or higher, then the value MSB is the intended value divided by 128, and the value LSB is the remainder (intended value modulo 128).• The Unit ID byte must be set to match the Unit ID of the synth you want to edit (all synths are set to Unit ID 0 by default; this value will be 0 unless you change it) or set the Unit ID value to 0x7F to address any Unit ID, or multiple units with different IDs sharing the same MIDI port.• Note:The byte before Unit ID (byte 14 if counting from F0 = 0) must be set to zero or the message will be ignored. This is because the same kind of SysEx message is output by the unit in reply to a request to getthe value of a parameter (see below). Replies output by the unit have the byte before Unit ID set to 1,to avoid getting stuck in a MIDI feedback loop if these messages are echoed back to the unit.TO REQUEST A PARAMETER VALUE:F0 04 17 3E [Parameter ID] 00 00 00 00 00 00 00 00 00 00 [Unit ID] F7• Values above are shown in hexadecimal format.• Unit ID must match the Unit ID of the Matriarch, or set Unit ID = 7F (all).• The Matriarch will reply with a “set parameter” SysEx message for the requested Parameter ID with its current value, with the byte before the Unit ID (byte 14 if counting from F0 = 0) set to 1 to indicate that the message is a reply coming from the Matriarch.Global parameters for sysex editing (values below are shown in decimal format):Global parameters for sysex editing (cont’d):Global parameters for sysex editing (cont’d):Global parameters for sysex editing (cont’d):Matriarch MIDI CC listMatriarch responds to the following MIDI CC messages.Note: All CC Numbers in the range 1-31 can be used at 14-bit resolution (value range 0-16383) by using the CC number shown below in combination with its 14-bit LSB CC, which is the CC number + 32. Example: 14-bit Oscillator 2 Frequency uses CC 16 (MSB) and CC 48 (LSB).Matriarch MIDI CC List (cont’d):。
Fujitsu PRIMERGY服务器注意事项说明书

Important notes for PRIMERGY serversNo.Applicable machines Known issues WorkaroundsH1See the PDF file provided in the "Workarounds" column.Some PRIMERGY models are not supporting the BitLocker feature.See the attached PDF file (51KB) for a list of PRIMERGY models and product IDs thatare not supporting BitLocker.If your PRIMERGY machine is not in this list, the machine can support BitLocker™Drive Encryption. Please refer to caution statements for BitLocker™ Drive Encryptionbefore using the function.If you are required to update your BIOS or firmware, please contact your local supplier or thenearest Fujitsu sales company to obtain details of support and contact information.>> /global/contact/computing/PRMRGY_index.htmlIf you replace a system board, BIOS and the firmware version may go back to the previous versionprior to the update. In that case, please re-install the update.You can check your BIOS version by referring to the BIOS Setup Utility (see the User's Guide).H3TX150 S6On-board LAN on TX150 S6 servers cannot be a team member.H4RX100 S5RX200 S4RX100 S4BX620 S4RX200 S3If your server configuration is not using an internal CD-ROM/ DVD-ROM drive, anunknown error might be recorded in the OS event log.Source: Service Control Manager Eventlog ProviderEvent ID: 7026The following boot-start or system-start driver(s) faiYou can check your BIOS version by referring to the BIOS Setup Utility (see the User's Guide).H5RX200 S4RX300 S4TX300 S4RX600 S4TX120RX100 S4RX200 S3If your server configuration is not using a parallel port and running a 32-bit operatingsystem, an unknown error might be recorded in the OS event log.Source: Service Control Manager Eventlog ProviderEvent ID: 7000The parallel port driver service faType in the following registry keys and disable the parallel port to avoid the given error. If you areusing a parallel port, this setting is not required.If you add a parallel port after applying this setting, you will be required to restore the regisH6RX200 S4RX300 S4TX300 S4Your server might hung up during the OS boot process (while a progress bar is beingdisplayed).You are required to install patches that are provided by Microsoft.For more details, please visit the Microsoft website: /kb/954429/If you have a software support contract, please contact your support counter.H8TX150 S6TX300 S4If you are using an OS installation type, the Device Manager page might displayprocessor names that have not been installed on your computer.This is a matter of Device Manager to display information, and will not affect system operations.(Reference) To display information correctly, try the following procedure.1. Under "Processors" in the Device Manager page, delete all processor entry.H9TX200 S3RX200 S3RX300 S3The Global Array Manager RAID management tool does not operate in a WindowsServer 2008 environment.Please choose ServerView RAID for your RAID management tool. Before using the ServerViewRAID software, please verify the status of tested software products for Windows Server 2008. BIOS and firmware updates are required on some PRIMERGY models.See the "Workarounds" column. H2H10ECONEL 100 A notification alarm for disk failures does not e ServerView Alarm Service to monitor disk failures.H11BX620 S4The listed processors below have not been tested yet for the Hyper-V function.Xeon 5110 (1.60GHz)Xeon 5130 (2GHz)Xeon 5160 (3GHz)Xeon LV5148 (2.33GHz)Xeon E5310 (1.60GHz)Xeon L5320 (1.86GHz)Xeon X5355 (2.66GHz)The listed processors in the left column are not supporting the Hyper-V feature.H12BX620 S4TX120TX150 S6RX100 S5ECONEL100 S2RX600 S4You need to change BIOS settings to use the Hyper-V feature.In the BIOS setup utility, change the following items' settings as shown.BX620 S4[Advanced] -> [CPU Configuration]1) Enable "Vanderpool Technology".2) Enable "Execute Disable Bit".TX120[Advanced] -> [Advanced System Configuration]1) Enable "VirtuH13RX100 S5TX150 S6ECONEL100 S2TX120/ TX120W The Enterprise and Datacenter editions have not been tested yet for guest operatingsystems of the Hyper-V role.Enterprise and Datacenter are not supported for a use of guest OS of the Hyper-V role.。
Sailrite快attan用轻量级缆轮模型SPR 6067 Fastener Selection

DOT® SNAP FASTENERS - LIGNE 24The most common fastener used in marine applications. Great for boat covers, dodgers and tarps or on tabs of fabric or webbing for forestay hanks on sails under 100 sq. ft. Highly resistant to corrosion.P ROFILE: Low profile with smooth, domedbutton top. Looks great and button capsare available in popular canvas colors.STRENGTH: Very easy to fasten with moderate connection strength. The overall shear strength is excellent, but one pull on an angle and the fastener will pop free. Stainless steel snaps and those with hard action sockets have slightly better strength.EASE OF INSTALLATION: A hole cutter and Snap Fastener Installation Tool (#25204) or Sailrite®Snap Fastener Deluxe Installation Tool (#100949)is required for installation. Use the Pres-N-Snap Tool (#109011), the SnapRite® System (#104500)or the W-1 Hand Press (#121274) with properdies for quicker, more efficient installation.SAILRITE® SNAP FASTENERS - LIGNE 24Comparable to DOT snap fasteners and canbe used in all the same applications.P ROFILE: Low profile with smooth, domed button top. Available in a limited color selection.STRENGTH: Very easy to fasten with moderate connection strength. The overall shear strength is excellent, but one pullon an angle and the fastener will pop free. Stainless steel snaps and those with hard action sockets have slightly better strength.E ASE OF INSTALLATION: A hole cutter and Snap Fastener Installation Tool (#25204) or Sailrite®Snap Fastener Deluxe Installation Tool (#100949)is required for installation. Use the Pres-N-Snap Tool (#109011), the SnapRite® System (#104500)or the W-1 Hand Press (#121274) with properdies for quicker, more efficient installation.LIFT-THE-DOT® FASTENERSOften used to secure boat covers and dodgers.P ROFILE: Medium profile and fastener will stick upabove the application. Can stub your toe on it.STRENGTH: Only opens when lifted from oneside. Unlikely to come undone when peeledfrom the other side. Fantastic shear strength.E ASE OF INSTALLATION: Cutting holes forthe sockets and 2-prong studs is best done withspecial hole cutters (#100972, #110012). Foldingthe prongs over by hand can be tedious. EyeletType Lift-the-DOT Fasteners can be installed withthe Pres-N-Snap Tool (#109011) and the Lift-the-DOT® Eyelet Type Base Die Set (#106397).LOXX® PULL IT UP FASTENERSA cleverly engineered, self-locking snap fastenerthat is great for applications where security, mediumprofile and performance are important. Ideal formarine, leather and automotive applications.P ROFILE: Medium height profile but lowenough to be toe friendly and very attractive.STRENGTH: Very positive connectivityand can only be released by liftingup on the spring-loaded cap.E ASE OF INSTALLATION: Requires onlyan inexpensive key (#121357) and 3/8” holecutter. All components screw together.P ULL-THE-DOT®(ONE WAY) FASTENERSUniquely designed, three-sided built-in locking snapfastener that can withstand extreme pressure on threesides without unlocking. Well suited for applicationswhere the strain on the snap is not shear, like on thefront panel of a dodger. Highly resistant to corrosion.P ROFILE: Low profile with smoothdomed button top.S TRENGTH: Strong, positive hold. Pull from theprotrusion side to open. Close the snap by closingthe lip side first and then the protrusion side.EASE OF INSTALLATION: Keeping the sockets andbuttons aligned consistently can be a challenge. Thestud can be installed as normal, but the socket mustbe installed so the protrusion is on the side that is tobe released easily. As with normal snap fasteners, useof the Pres-N-Snap (#109011) with the appropriatedie or the SnapRite System (#104500) is preferred.TWIST-LOCK FASTENERSA quick and secure way to fasten pieces offabric together or to a solid surface. Oftenused to hold covers and enclosures in place.Designed specifically for wet environments.PROFILE: Very high profile stud. Easy to graband locate, but stands high off the application.STRENGTH: Requires a manual twist ofthe fastener stud to lock and release. Twist-Lock fasteners will not come undone.E ASE OF INSTALLATION: Installation of mostparts can be completed without any specialtools but is much quicker and more efficient withthe proper tools. A Snap Fastener InstallationTool (#25204), Sailrite Snap Fastener DeluxeInstallation Tool (#100949) or the SnapRite®Twist Lock Die Kit (#104619) is required to installbuttons, and a #2 hole cutter (#121387) or theSailrite® Twist-Lock Eyelet Hole Cutter (#108001)makes eyelet installation much easier. Install theTwist Lock Barrel Stud with the Pres-N-Snap Tool(#109011) and the Turn Lock Die Set (#104993).F or cloth-to-surface applications, use the Twist-Lock Driver Installation Tool (#120751) or theTwist-Lock Stud Driver for Single Screw Stud tool(#100135) to drill the stud into a hard surface.Fastener Selection Guide2 We stock two brands of snap fasteners: DOT® fasteners and Sailrite®-branded snap fasteners. Use on boatcovers, enclosures, dodgers and tarps, or install on tabs of fabric or webbing and use as forestay hanks forsails under 100 sq. ft. Choose from top quality, nickel-plated brass with bronze springs (surface studs have stainless steel screws) or from 100% stainless steel snap fasteners.All fasteners are highly resistant to corrosion. Installation tools are required. Use either the Snap Fastener Installation Tool (#25204) or the Sailrite® Snap Fastener Deluxe Installation Tool (#100949), or for quicker installation, use the Pres-N-Snap Installation Tool (#109011), the SnapRite® System (#104500) or the W-1Hand Press (#121274) with Snap Fastener 4 Piece Die Set (#120742).fabricC, SSCD, SSDfabricB, SSBORSRA, SRG A, SSAfabricB, SSBORSRA, SRG A, SSA+J+fabricB, SSBORSRJ+J+fabricB, SSBORSRJfabric++C, SSCOR OR OR OR ORE, SSE F, SSF G H I K D, SSDfabricB, SSBORORSRA, SRG A, SSAB, SSBORSRA, SRG A, SSAfabricORORORMBCMBDMBBMBAOR OR OR OR ORE, SSE F, SSF G H I K11/64" or 3/16" - most common barrel lengths for regular thickness fabric assemblies. 1/4" barrel length for fabric assembly thickness of up to 3/16"5/16" barrel length for fabric assembly thickness of up to 1/4" Normal Action – Snaps come apart with normal force.Hard Action – Snaps come apart with additional force.*Complete sets come with the shortest barrel button. DOT Snap Fastener Buttons (nickel-platedbrass only) also available in these colors:Black#333014Navy#333032Blue#333024White#333028Fastener Selection Guide 4CLOTH -TO-CLOTH -TO -CLOTH (C -TWIST-LOCK FASTENERSII+++++fabricCCfabricDDGGfabricSRAGGfabricfabricenclosures in place. Designed specifically for wet environments. All complete sets include an eyelet, stud and all necessary backing plates.Use a 2 screw stud (flat base) with buttons on cloth-to-cloth applications to add a more finished appearance to the back of the stud. Buttons are very strong and eliminate any possibility of chafe. The Snap Fastener Installation Tool (#25204), SnapRite ® Twist Lock Die Kit (#104619), Sailrite ® Snap Fastener Deluxe Installation Tool (#100949) or Pres-N-Snap Installation Tool (#109011) with the Turn Lock Die Set (#104993) is required for installation. The studs used for cloth-to-surface installation screw into any hard surface. Use the Twist-Lock Stud Driver for Single Screw Stud tool (#100135) or Twist-Lock Driver Installation Tool (#120751) with the 5/8" screw stud for easier installation.ORNICKEL-PLATED BRASS XWORAAA+AAfabricBBKKfabricJJORAA+AAfabricBBKKfabricJJOR++AA+AAfabricBBKKfabricJJORAA+AAfabricBBKKfabricJJORFastener Selection GuideCLOTH -TO -CLOTH (C -C)CLOTH-TO-SURFACE (C -S)COMPONENTS (NICKEL-PLATED)A DOT ® Snap Fastener Button Silver 11/64" Barrel AA 1DOT ®Twist-Lock Fastener Eyelet (Standard Legs)AA 2DOT ® Twist-Lock Fastener Eyelet (Extended Legs)BB DOT ® Twist-Lock Washer SSGTwist-Lock Fastener Eyelet (Stainless)SSH3Twist-Lock Fastener 2 Hole Base (Stainless)SSI Twist-Lock Fastener Clinch Plate (Stainless)SSA1 Snap Fastener Button 11/64"COMPLETE SETS*DOT ® 2 Prong Stud Set (4 pc.) - Nickel-plated Brass DOT 2 Button Back Set (5 pc.) - Nickel-plated Brass DOT Button Back Set (5 pc.) - Nickel-plated Brass DOT 5/8" Screw Stud Set (3 pc.) - Nickel-plated Brass = Add one = Add twoUse for up to 3/32" assemblies (up to 5 layers of canvas) Use for 9/64"–3/16" assemblies (6–9 layers of canvas)7/8" between holes*Complete sets always come with the shortest pronged eyeletSSH SSHSSASSI SSI SSGSSG+IIfabricfabricSTAINLESS STEEL(Only sold in kits #777500 and #777600. Not sold individually)KEY COMPONENTS (STAINLESS STEEL)II Screw Flat Head 6 x 1/2" (2 Required)Fastener Selection Guide6fabricfabricfabric++ororororororororCleverly engineered, self-locking snap fasteners that cannot come undone once engaged. Releases instantly by pulling up on the head of the button component. The positive engagement and locking feature is great for applications where security, medium height profile and performance are paramount.Nickel-plated brass fasteners available in a variety of stud styles including screw studs, two-hole plate studs and machine screw studs. Ideal choice for marine, leather and automotive applications. Locking Key required for installation.Note: Loxx Pull It Up Fasteners are compatible with Tenax ® Pull It Up fasteners previously sold by Sailrite ®.LLLLNN NN OOOO PPQQRR SSTTUU IIIIMMMM(LL)(LL)(NN)(OO)(MM)(MM)+ororXX(XX)XXZZ(XX)(ZZ)+orUUWWorYYorLOXX PULL IT UP FASTENERS SPECIALTY FINISHESfabricfabricfabricoror AAACCC (AAA)(CCC)BBBDDD (BBB)(DDD)orAAA(AAA)BBB(BBB)oror (NN)(OO)or ++ororororPPQQRR SSTTUU IIII++orUUWWorYY• = Add one •• = Add two Use for 0.065" – 0.125" (1.65mm – 3.18mm) assemblies (3-6 layers of canvas) Use for up to 0.087" – 0.174" (2.22 – 4.44mm) assemblies (4-8 layers of canvas)Fastener Selection GuideINSTALLATION: Rivet or screw the stud in place as normal but install the socket so the protrusion is on the side that is to be released easily. Pull from the protrusion side to open. Close the snap by closing the lip side first and then the protrusion side. The protrusion will also prevent the snap from turning after installation. Install with the SnapRite ®System (#104500) using the SnapRite button or thePres-N-Snap Tool (additional die required, #109011).RRTfabricfabricSD+fabricSV+ororSRRSRRPull-The-Dot SnapRite PULL-THE-DOT ®(ONE-WAY) FASTENERSFastener Selection Guide KEY COMPONENTS (NICKEL-PLATED)LLift-the-DOT Long Eyelet-Type Base Stud Eyelet-Type Base WasherDouble Height Machine Screw Stud PQ+OorUse for up to 1/8" assemblies (up to 6 layers of canvas)Use for up to 11/64" assemblies (up to 8 layers of canvas) Use for up to 3/32" assemblies (up to 5 layers of canvas)+++fabricOLM orZYVV++NO Ofabric* Installation requires the Pres-N-Snap tool and Lift-the-DOT Eyelet-Type Base Die Set #106397** Complete sets come with standard socket leg lengthCOMPLETE SETS**Lift-the-DOT Cloth-to-Surface (3 pc.) (。
Eaton Wi-Fi Smart Dimmer EWFD30 用户手册说明书

Control your lights from anywhere with Eaton’s Wi-Fi Smart Dimmer (EWFD30) which replaces standard switches and features ON/OFF and DIM/BRIGHT control. The dimmer can be remotely controlled using the Brightlayer Home App.Eaton’s Wi-Fi Smart Dimmer (EWFD30) has additional features such as low-level and high-level trim settings to help prevent flickering.Bulb ratingsYour Wi-Fi Smart DimmerFeaturesQuick Start Dimmer rating - EWFD30Load TypeSingle Gang 2-Gang 3-Gang INC/ELV/FLR/HAL/MLV 600W 500W/VA 400W/VA CFL/LED450W450W400W/VASingle location installation Operation instructionsLED CFL FLR INC MLV/ELV HALSingle pole & multi-locationWorks with a regular 3-way switch or with Accessory Dimmer (EWACD) for multi-locationTools neededAdditional system requirementsPhillips-head ScrewdriverWire cuttersPrior to installationRequires neutral for installationWARNINGS AND CAUTIONS:• T urn OFF circuit breaker or remove fuse(s) and test that power is OFF before installation process • N ever wire any electrical device with power turned ON Wiring dimmer HOT may cause permanent damage to dimmer and void warranty • I f you are not sure about any part of these instructions, please contact a licensed electrician CAUTION• Use only with 120V/AC 60Hz• Do not exceed maximum rating of dimmer as indicated on the device • M ust be installed and used in accordance with all national and local electrical codes • I f a bare copper or green ground connection is not available in the wallbox, contact a licensed electrician for installation • U se only #14 or #12 copper wire rated for at least 75ºC with these devicesDO NOT USE WITH ALUMINUM WIREIMPORTANT: Wi-Fi Smart Dimmer (EWFD30) will not work or will be damaged if wired incorrectly and warranty will be voided. Refer to wiring instructions provided.NOTE: The Wi-Fi Smart Dimmer (EWFD30) is wired directly to the light fixture.• Press ON button to turn lights ON at previously selected level• Press OFF button to turn lights OFF• The bottom LED indicates the dimmer is turned ON • When lights are OFF, press and hold the ON button for 2 seconds until LED blinks green for full brightness • W hen the lights are ON, press and hold the OFF button for 2 seconds until the LED indicator blinks green After a 10 second delay, the lights will fade off FACTORY RESET: The dimmer can be reset which will exclude the device from its network and restore all factory defaults.• T urn ON the dimmer• P ress and hold the ON button for 30 seconds until the LED indicator blinks red for the fourth time • R elease the button • L ED indicator will start flashing fast while it is being reset • T he LED indicator will then start blinking magenta at a normal rate indicating the dimmer is not part of a Wi-Fi networkScan for more advanced featuresincluding adjusting the brightness level of the LED indicators and additional wiring configurationsFor color change kit installation instructions, see back pageTools required for installation (not included) for the Wi-Fi Smart Dimmer (EWFD30):A 2.4GHz Wi-Fi network with high-speed internetIOS 12.0 or later or Android 8.0 or later mobile device. Note: Must be connected to Wi-Fi and Bluetooth A Brightlayer Home account set-up through the Brightlayer Home AppFor multi-location applications (3-way or 4-way), the Accessory Dimmer (EWACD) or a regular 3-way switch with one Wi-Fi Smart Dimmer (EWFD30) can be used.Neutral is requiredLight level may be adjusted with lights ON or OFF Press to brighten Press to dimWi-Fi Smart Devices offer reliability with unbeatable ease o f setup. Voice controlw ith Alexa and H ey Googleinstallation requiredSet schedules, groups, and scenes/smarthomeEWFSW15EWFTRCR15EWACDEWFFSC15Amazon, Alexa and all related logos are trademarks of , Inc. or its affiliates. Google and Google Play are trademarks of Google LLC. Wi-Fi CERTIFIED logo is a trademark of the Wi-Fi Alliance.by following the instructions on the screen.Select the device type to addNote: Now the user can utilize many features that areavailable such as creating schedules, scenes, presetlight levels and minimum/maximum brightness settingsthrough the Brightlayer Home App.Amazon, Alexa and all related logos are trademarks of ,Inc. or its affiliates. Google and Google Play are trademarks of GoogleLLC. Wi-Fi CERTIFIED logo is a trademark of the Wi-Fi Alliance.Fold in half vertically with page 1 on outside, then Z-fold in horizontal direction to final folded size of 3.4 in. W x 5.5 in. H with part number facing outward.。
无线网卡ra0配置命令

⽆线⽹卡ra0配置命令=================================================================================================== ATE Test Command Format for station driver****** IMPORTANT ******If you are not familiar with hardware, it is recommanded not to modify hardware default value.It may damage hardware.=================================================================================================== Usage:iwpriv ra0 [act] [parameters]=[val]where[act] [parameters] [val] constraints explaination----- ------------- ----------------- --------------------------------=====================================1. Set ATE actions.Value:ATESTART - Start ATE function and stop station function.ATESTOP - Stop ATE function and start station function.TXCONT - Start continuous TX, for power mask.TXCARR - Start carrier test, for frequency calibration.TXFRAME - Transmit frame, for EVM.RXFRAME - Continuous RX, for PER/FER.1.1 ATEDASet ATE frame header destination address.Value:xx:xx:xx:xx:xx:xx ; hex1.2 ATESASet ATE frame header source addr.Value:xx:xx:xx:xx:xx:xx ; hex1.3 ATEBSSIDSet ATE frame header BSSID.Value:xx:xx:xx:xx:xx:xx ; hex1.4 ATECHANNELSet ATE Channel, deimal.Value:802.11b/g: 1 ~ 14 depends on CountryRegion setting1.5 ATETXPOW0Set ATE Tx power for Antenna 1.Value:0 ~ 31 ; 2.4GHz, deimal-7 ~15 ; 5.5GHz, deimal1.6 ATETXPOW1Set ATE Tx power for Antenna 2.Value:0 ~ 31 ; 2.4GHz, decimal-7 ~15 ; 5.5GHz, deimal1.7 ATETXFREQOFFSETSet ATE RF frequency offset.Value:0 ~ 63 ; unit: 2KHz, decimal1.8 ATETXLENSet ATE frame length.Value:24 ~ 2312 ; decimal1.9 ATETXCNTSet ATE frame Tx count.Value:1 ~ ; 32-bit, decimal1.10 ATETXMODE (Refer to TxMode)Set ATE Tx Mode.Value:0: CCK 802.11b1: OFDM 802.11g2: HT_MIX 802.11b/g/n3: Green Field 802.11n1.11 ATETXBW (Refer to TxMode)Set ATE Tx and Rx Bandwidth.Value:0: 20MHz1: 40MHz1.12 ATETXGI (Refer to TxMode)Set ATE Tx Guard Interval.Value:0: Long1: Short1.13 ATETXMCS (Refer to TxMode)Set ATE Tx MCS type.Value:0 ~ 151.14 ATETXANTSet ATE TX antenna.Value:0: All1: Antenna one2: Antenna two1.15 ATERXANTSet ATE RX antenna.Value:0: All1: Antenna one2: Antenna two3: Antenna three1.16 ATERXFERSet ATE to periodically reset and show up RxCount (per-second) and RxTotalCount. Value:0: Disable counter visability1: Enable counter visability1.17 ATESHOWShow all parameters of ATE.Value:11.18 ATEHELPList all commands of ATE.Value:11.19 ResetCounterReset statistic counter.Value:11.20 ATERRFRead all of the RF registers.Value:11.21 ATEWRF1Writethe RF register 1.Value:xxxxxxxx ;32-bit, hex1.22 ATEWRF2Write the RF register 2.Value:xxxxxxxx ;32-bit, hex1.23 ATEWRF3Write the RF register 3.Value:xxxxxxxx ;32-bit, hex1.24 ATEWRF4Write the RF register 4.Value:xxxxxxxx ;32-bit, hex1.25 ATELDE2POverwrite all EEPROM contentsValue:1E.g.iwpriv ra0 set ATELDE2P=11.26 ATERE2PDisplay all EEPROM content.Value:1E.g.iwpriv ra0 set ATERE2P=1=================================================================================================== 2. Examples:=========2.1 Check EVM & Poweriwpriv ra0 set ATE=ATESTARTiwpriv ra0 set ATEDA=00:11:22:33:44:55iwpriv ra0 set ATESA=00:aa:bb:cc:dd:eeiwpriv ra0 set ATEBSSID=00:11:22:33:44:55iwpriv ra0 set ATECHANNEL=1 ; set Channeliwpriv ra0 set ATETXMODE=1 ; set TX-Mode.iwpriv ra0 set ATETXMCS=7 ; set MCS type.iwpriv ra0 set ATETXBW=0 ; set Bandwidthiwpriv ra0 set ATETXGI=0 ; set Long GI.iwpriv ra0 set ATETXLEN=1024 ; set packet length.iwpriv ra0 set ATETXPOW0=18iwpriv ra0 set ATETXPOW1=18iwpriv ra0 set ATETXCNT=100000iwpriv ra0 set ATE=TXFRAMEiwpriv ra0 set ATETXPOW0=19iwpriv ra0 set ATETXPOW0=20iwpriv ra0 set ATE=ATESTART2.2 Check Carrieriwpriv ra0 set ATE=ATESTARTiwpriv ra0 set ATECHANNEL=1 ; set Channeliwpriv ra0 set ATETXMODE=1 ; set TX-Mode.iwpriv ra0 set ATETXMCS=7 ; set MCS type.iwpriv ra0 set ATETXBW=0 ; set Bandwidthiwpriv ra0 set ATETXCNT=200 ; Tx frame count(decmial)iwpriv ra0 set ATE=TXFRAME ; Start Tx Frame(inform BBP to change, modulation mode) iwpriv ra0 set ATE=TXCARR ; Start Tx carrier, Measure carrier with instrumentiwpriv ra0 set ATETXPOW0=05iwpriv ra0 set ATETXPOW1=05iwpriv ra0 set ATETXFREQOFFSET=19iwpriv ra0 set ATE=ATESTART2.3 Check specturm maskiwpriv ra0 set ATE=ATESTARTiwpriv ra0 set ATECHANNEL=1 ; set Channeliwpriv ra0 set ATETXMODE=1 ; set TX-Mode.iwpriv ra0 set ATETXMCS=7 ; set MCS type.iwpriv ra0 set ATETXBW=0 ; set Bandwidthiwpriv ra0 set ATETXCNT=200 ; Tx frame count(decmial)iwpriv ra0 set ATE=TXFRAME ; Start Tx Frame(inform BBP to change, modulation mode) iwpriv ra0 set ATE=TXCONT ; Start continuous TX, Measure specturm mask with instrument iwpriv ra0 set ATETXPOW0=5iwpriv ra0 set ATETXPOW1=5iwpriv ra0 set ATE=ATESTART2.4 Frequency offset tuningiwpriv ra0 set ATE=ATESTARTiwpriv ra0 set ATECHANNEL=1 ; set Channeliwpriv ra0 set ATETXMODE=1 ; set TX-Mode.iwpriv ra0 set ATETXMCS=7 ; set MCS type.iwpriv ra0 set ATETXCNT=200 ; Tx frame count(decmial)iwpriv ra0 set ATETXFREQOFFSET=0 ; Set frequency offset 0(decimal)iwpriv ra0 set ATE=TXFRAME ; Start Tx Frameiwpriv ra0 set ATE=TXCARR ; Start Tx carrier, Measure carrier frequency with instrumentiwpriv ra0 set ATETXFREQOFFSET=10 ; Dynamic turning frequency offset, 10(decimal) iwpriv ra0 set ATETXFREQOFFSET=20 ; Dynamic turning frequency offset, 20(decimal) iwpriv ra0 set ATE=ATESTART ; Stop, Store the tuning result to EEPROM2.5 Rxiwpriv ra0 set ATE=ATESTARTiwpriv ra0 set ATECHANNEL=1 ; set Channeliwpriv ra0 set ResetCounter=1 ; Reset statistic counteriwpriv ra0 set ATETXFREQOFFSET=value ;To use the ¨value〃(decimal) you got in tx calibration iwpriv ra0 set ATETXMODE=1 ; set TX-Mode.iwpriv ra0 set ATETXMCS=7 ; set MCS type.iwpriv ra0 set ATETXBW=0 ; set Bandwidthiwpriv ra0 set ATE=RXFRAME ; Start Rx,iwpriv ra0 set ATERXFER=1 ; show RxCnt and RSSI/per-antenna, Transmit test packetsiwpriv ra0 set ATE=ATESTART ; Stopiwpriv ra0 stat ; get statistics counteriwpriv ra0 set ATERXFER=1iwpriv ra0 set ATERXANT=1iwpriv ra0 set ATE=ATESTARTiwpriv ra0 set ATERXANT=0iwpriv ra0 set ATE=RXFRAME2.6 Show all ate parametersiwpriv ra0 set ATESHOW=1Mode=4TxPower0=0TxPower1=0TxAntennaSel=0RxAntennaSel=0BBPCurrentBW=0GI=0MCS=7TxMode=1Addr1=00:11:22:aa:bb:ccAddr2=00:11:22:aa:bb:ccAddr3=00:11:22:aa:bb:ccChannel=1TxLength=1024TxCount=40000TxRate=11RFFreqOffset=02.7 Online helpiwpriv ra0 set ATEHELP=1ATE=ATESTART, ATESTOP, TXCONT, TXCARR, TXFRAME, RXFRAMEATEDAATESAATEBSSIDATECHANNEL, range:0~14(unless A band !).ATETXPOW0, set power level of antenna 1.ATETXPOW1, set power level of antenna 2.ATETXANT, set TX antenna. 0: all, 1: antenna one, 2: antenna two.ATERXANT, set RX antenna.0: all, 1: antenna one, 2: antenna two, 3: antenna three. ATETXFREQOFFSET, set frequency offset, range 0~63.ATETXBW, set BandWidth, 0:20MHz, 1:40MHz.ATETXLEN, set Frame length, range 24~2312.ATETXCNT, set how many frame going to transmit.ATETXMCS, set MCS, reference to rate table.ATETXMODE, set Mode 0: CCK, 1: OFDM, 2: HT-Mix, 3: GreenField, reference to rate table. ATETXGI, set GI interval, 0: Long, 1: Short.ATERXFER, 0: disable Rx Frame error rate. 1: enable Rx Frame error rate.ATERRF, show all RF registers.ATEWRF1, set RF1 register.ATEWRF2, set RF2 register.ATEWRF3, set RF3 register.ATEWRF4, set RF4 register.ATELDE2P, load EEPROM from .bin file.ATERE2P, display all EEPROM content.ATESHOW, display all parameters of ATE.ATEHELP, online help.2.8 Display Rx Packet Count and RSSIiwpriv ra0 set ATERXANT=0 ==> Enable All Three Rx Antennasiwpriv ra0 set ATERXFER=1 ==> Enable Rx Frame Error Rate: RxCnt/RxTotaliwpriv ra0 set ATE=RXFRAME ==> Start RxMlmePeriodicExec: Rx packet cnt = 2/4MlmePeriodicExec: Rx AvgRssi0=-88, AvgRssi1=-80, AvgRssi2=-91MlmePeriodicExec: Rxpacket cnt = 2/6MlmePeriodicExec: Rx AvgRssi0=-86, AvgRssi1=-77, AvgRssi2=-89iwpriv ra0 set ATERXANT=1 ==> Enable Three Rx Antenna-1iwpriv ra0 set ATERXFER=1 ==> Enable Rx Frame Error Rate: RxCnt/RxTotaliwpriv ra0 set ATE=RXFRAME ==> Start RxMlmePeriodicExec: Rx packet cnt = 0/7MlmePeriodicExec: Rx AvgRssi=-87MlmePeriodicExec: Rx packet cnt = 7/14MlmePeriodicExec: Rx AvgRssi=-90=================================================================================================== 3. Hardware Access=======================================================3.1 iwpriv ra0 bbp [parameters]=[Value]Read/Write BBP registers by ID number.BBPID3.1.1 Read BBP register, BBPID only, no ¨=〃 symbol.BBPID:0 ~ xx ; decimal, 8-bitBBPID=Value3.1.2 Write BBP register.BBPID:0 ~ xx ; decimal, 8-bitValue:00 ~FF ; hexdecimal, 8-bit=====================================3.2 iwpriv ra0 mac [parameters]=[val]Read/Write MAC registers by offset.MAC_OFFSET3.2.1 Read MAC register, MAC_OFFSET only, no ¨=〃 symbol.MAC_OFFSET:0000 ~ FFFF ; hexdecimal, 16-bitMAC_OFFSET=Value3.2.2 Write MAC register.MAC_OFFSET:0000 ~ FFFF ; hexdecimal, 16-bitValue:0000 ~FFFF ; hexdecimal, 32-bit=====================================3.3 iwpriv ra0 e2p [parameters]=[val]Read/Write EEPROM content by address.EEP_ADDR3.3.1 Read EEPROM content, EEP_ADDR only, no ¨=〃 symbol.EEP_ADDR:00 ~ FF ; hexdecimal, 16-bit alignment (0, 2, 4, 6, 8, A, C, )EEP_ADDR=Value3.3.2 Write EEPROM content.EEP_ADDR:00 ~ FF ; hexdecimal, 16-bit alignment (0, 2, 4, 6, 8, A, C, )Value:0000 ~FFFF ; hexdecimal, 16-bit=====================================3.4 Example3.4.1 Hardware accessiwpriv ra0 bbp 0 # read BBP register 0iwpriv ra0 bbp 0=12 # write BBP register 0 as 0x12iwpriv ra0 mac 0 # read MAC register 0iwpriv ra0 mac 0=1234abcd # write MAC register 0 as 0x1234abcdiwpriv ra0 e2p 0 # read E2PROM 0iwpriv ra0 e2p c=12ab # write E2PROM 0xc as 0x12ab3.4.2 Statistic counter operationiwpriv ra0 stat # read statistic counteriwpriv ra0 set ResetCounter=0 # reset statistic counterSuggestion:1. To turn on ATE functionality, you have to add compile flag "RALINK_ATE" to Makefile2. Before doing ATE testing, please stop AP function3. If you want to test another ATE action, prefer to stop AP & ATE function4. All ATE function settings will lose efficacy after reboot.5. Before hardware register access, please reference hardware spec.Note.In ATE mode, the channel must set via "ATECHANNEL"=================================================================================================== 4. ated=======4.1 IntroductionThe ated is an optional user space component for RT28xx Linux driver.When Windows GUI starts, AP enters ATE mode (i.e.,ATESTART) immediately.It behaves as a proxy between Windows GUI and RT28xx Linux driver when ATE process proceeds.The ated will be killed automatically when Windows GUI is closed.You can kill it manually, too(for example, type '$killall ated').RT28xx linux driver will leave ATE mode either ated is killed or Windows GUI is closed.4.2 Environment setup1. Connect the platform you want to test directly with a Windows host by ether network line.2. In the Windows host, run WinPcap_4_0.exe for the QA GUI or ./RT2880_ATE/RaUI.exe(please unrar "RT2880_ATE.rar" to get it).4.3 How to use ated for ATE purpose0. First you should set both "HAS_ATE=y" and "HAS_QA_SUPPORT=y" in the file ~/Module/os/linux/config.mk and compile the driver.1. Modify the Makefile according to our target "PLATFORM".2. Change the path of "CROSS_COMPILE" if needed.3. Then type 'make' command to compile the source code of the daemon.4. After the driver interface has started up, attach both of the wireless interface and the ethernet interface to the bridge interface.5. If you have no bridge interface, please give an IP address to the ethernet interface.(for example : '$ated -beth0')6. After the interfaces have entered forwarding states, manually start ated, type '$ated -bbrX -iraX'.7. If your WLAN interface and Bridge interface is "ra0" and "br0" respectively, just type $ated.(For further usage of options, type $ated -h)8. In the Windows host, run RT28xxQA_ATE.exe or ./RT2880_ATE/RaUI.exe.9. Select the wired network adapter, then press OK and wait for a moment.10.If the Windows host cannot tolerate such a broadcast storm from ated,please run ated with option -u.(for example : '$ated -ira1 -u')11.If your target platform concerns its network security, please run RT28xxQA_unicast.exe instead of RT28xxQA_ATE.exe. Note :a. The names of WLAN interface(default is "ra0") and Bridge interface(default is "br0") must be specified manually(for example : '$ated -bbr1 -ira2') if your WLAN interface or Bridge interface is not "ra0" or "br0" respectively !b. Please make sure no other RaUI is running before you excute ./RT2880_ATE/RaUI.exe.。
failed to initialize a tracing processor

failed to initialize a tracing processor【实用版】目录1.引言:介绍“未能初始化跟踪处理器”的错误信息2.错误原因:分析可能导致该错误的各种原因3.解决方案:提出解决该错误的具体方法4.总结:对全文进行总结,提供避免类似问题的建议正文一、引言当您在使用计算机时,可能会遇到“failed to initialize a tracing processor”的错误信息。
这种错误通常表示某个程序或系统组件在初始化跟踪处理器时出现了问题。
本文将分析可能导致这种错误的原因,并提供相应的解决方案。
二、错误原因1.缺少必要的软件或组件:跟踪处理器可能依赖于某些软件或组件才能正常工作。
如果这些软件或组件没有正确安装或丢失,就可能导致该错误。
2.系统配置问题:系统的某些配置参数可能影响跟踪处理器的初始化。
例如,安全设置可能会阻止跟踪处理器的正常工作。
3.病毒或恶意软件:病毒或恶意软件可能会干扰跟踪处理器的初始化过程,从而导致该错误。
4.软件冲突:某些软件之间的冲突也可能导致跟踪处理器无法正常初始化。
三、解决方案1.检查软件和组件:确保所有必要的软件和组件都已经正确安装,并且是最新版本。
2.检查系统配置:检查系统配置参数,确保跟踪处理器可以正常工作。
例如,可以尝试降低安全设置以允许跟踪处理器访问。
3.清除病毒和恶意软件:使用杀毒软件或反恶意软件工具扫描计算机,确保没有病毒或恶意软件干扰跟踪处理器的初始化。
4.解决软件冲突:查找可能导致软件冲突的程序,并尝试卸载或更新它们,以解决跟踪处理器的初始化问题。
四、总结“failed to initialize a tracing processor”错误可能是由多种原因导致的。
要解决这个问题,需要耐心地检查软件和组件、系统配置、病毒和恶意软件以及软件冲突等方面。
通过排除这些潜在问题,可以恢复正常的跟踪处理器功能。
第1页共1页。