干法水泥旋窑生产流程说明
干法水泥生产工艺流程

干法水泥生产工艺流程干法水泥生产工艺流程干法水泥生产是一种常见的水泥生产工艺,其流程主要包括石料破碎、原料磨碎、煤粉烧结、熟料磨细以及熟料与适量石膏混合等基本步骤。
以下是干法水泥生产工艺流程的一般步骤:1. 石料破碎:把原料中的石灰石等石料通过颚式破碎机、冲击式破碎机等破碎设备进行初步破碎,得到所需的石料。
2. 原料磨碎:将破碎后的石料送至磨机进行进一步的磨碎。
常用的磨机设备有辊压机、球磨机等。
石料在磨机内与磨辊或磨球的摩擦作用下,不断磨碎,最终形成所需的粉状原料。
3. 原料配料:将磨碎后的粉状原料经过称量、控制和混合等工序,按照一定比例混合成配料。
4. 煤粉烧结:将配料送入水泥窑内进行煅烧。
同时,通过喷射煤粉的方式,将煤粉喷入水泥窑内与原料一同燃烧。
煤粉的燃烧可以提供煤气,用于加热水泥窑内的原料,使其在一定的温度下发生化学反应。
5. 熟料磨细:煅烧后的原料从水泥窑中取出,经过冷却和破碎等工序,形成熟料。
然后,将熟料送至磨机进行细磨,得到水泥所需的粉状成品。
6. 混合磨:将熟料与适量的石膏混合进行磨细,形成最终的水泥成品。
石膏在磨机中起到调节凝结时间和控制水泥硫酸盐含量的作用。
7. 包装和出厂:经过磨细后的水泥成品通过输送带或者离心式风机等设备,送往包装机进行分装和包装。
最后,经过质检合格后,水泥成品装箱出厂,准备上市销售。
总的来说,干法水泥生产工艺是通过石料破碎、原料磨碎、配料、煅烧、磨细等一系列工序,将原料转化为粉状水泥成品,并进行包装和出厂。
整个生产过程需要控制好各个环节的温度、配比和时间等参数,以确保生产出优质的水泥产品。
同时,在生产过程中,要注重环保,控制废气、废水和固体废物的排放,以保护环境和可持续发展。
水泥回转窑工艺流程

水泥回转窑工艺流程
《水泥回转窑工艺流程》
水泥回转窑是水泥熟料烧成设备中常用的一种,其工艺流程如下:
1.原料预处理
原料包括石灰石、黏土、铁矿石等,需要进行粉碎、混合,并控制配料比例以确保烧成的水泥符合标准要求。
2.干法制成粉磨
原料预处理后,需要经过粉磨设备进行干法制成,使原料颗粒达到所需的粒度和分布。
3.粉煤灰和矿山渣的预处理
对于使用粉煤灰和矿山渣作为原料的水泥回转窑,需要对这些辅助原料进行预处理,以保证其质量符合要求。
4.熟料的烧炼
原料经过粉磨后,将其送入水泥回转窑进行烧成。
熟料的烧成一般分为预热、分解、煅烧等阶段,需要通过控制窑内气氛、温度和转速等参数来确保熟料的质量。
5.水泥磨
熟料经过烧成后,需要进行水泥磨加工,使其成为水泥产品。
水泥磨的工艺流程包括干法制成、水泥磨的使用,以及通过控制粉磨设备参数来获得所需粉磨度的水泥成品。
以上就是水泥回转窑的工艺流程,通过严格控制每个环节的参数和质量,可以生产出高质量的水泥产品。
干法水泥生产工艺流程
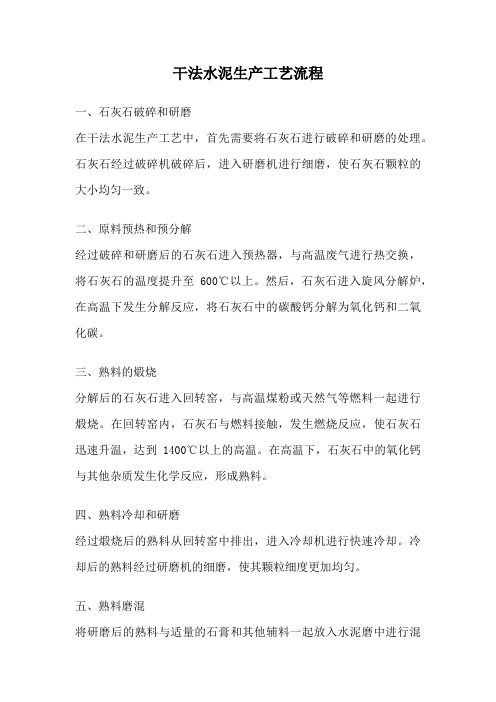
干法水泥生产工艺流程一、石灰石破碎和研磨在干法水泥生产工艺中,首先需要将石灰石进行破碎和研磨的处理。
石灰石经过破碎机破碎后,进入研磨机进行细磨,使石灰石颗粒的大小均匀一致。
二、原料预热和预分解经过破碎和研磨后的石灰石进入预热器,与高温废气进行热交换,将石灰石的温度提升至600℃以上。
然后,石灰石进入旋风分解炉,在高温下发生分解反应,将石灰石中的碳酸钙分解为氧化钙和二氧化碳。
三、熟料的煅烧分解后的石灰石进入回转窑,与高温煤粉或天然气等燃料一起进行煅烧。
在回转窑内,石灰石与燃料接触,发生燃烧反应,使石灰石迅速升温,达到1400℃以上的高温。
在高温下,石灰石中的氧化钙与其他杂质发生化学反应,形成熟料。
四、熟料冷却和研磨经过煅烧后的熟料从回转窑中排出,进入冷却机进行快速冷却。
冷却后的熟料经过研磨机的细磨,使其颗粒细度更加均匀。
五、熟料磨混将研磨后的熟料与适量的石膏和其他辅料一起放入水泥磨中进行混合磨矿。
在水泥磨中,熟料与石膏和其他辅料进行充分的混合和研磨,形成细度适中的水泥粉末。
六、水泥包装经过磨混后的水泥粉末通过空气输送系统输送到包装机,进行自动包装。
水泥包装机将水泥粉末按照一定的重量进行分装,然后用袋子或者其他容器进行密封包装,以便储存和运输。
七、废气处理在干法水泥生产过程中,会产生大量的废气,包括石灰石预热和预分解过程中的废气,以及熟料煅烧过程中的废气。
这些废气中含有大量的颗粒物和有害气体。
为了保护环境,这些废气需要经过除尘和脱硝处理,以减少对大气的污染。
总结:干法水泥生产工艺流程包括石灰石破碎和研磨、原料预热和预分解、熟料煅烧、熟料冷却和研磨、熟料磨混、水泥包装和废气处理等环节。
通过这些步骤,可以将石灰石转化为水泥,并进行包装和储存,以满足建筑和工程领域对水泥产品的需求。
同时,在整个生产过程中,需要加强对废气的处理,以保护环境和减少大气污染。
新型干法旋窑水泥生产工艺

浅析新型干法旋窑水泥生产工艺[摘要]随着经济建设规模的扩大,房地产业、工业的不断发展壮大,水泥生产中所造成的巨大资源、能源消耗以及废气、粉尘的排放,对社会生态环境极具破坏性。
节能环保的水泥生产工艺是降低大气及水源环境污染的途径。
本文就新型干法旋窑水泥生产工艺进行探索。
[关键词]水泥;新型干法;生产工艺中图分类号: tq172 文献标识码:a 文章编号:1009-914x(2013)23-0144-02一、前言改革开放以后,我国的水泥工业已经得到了快速的发展,并取得了巨大成绩。
笔者对新型干法多年操作的体会总结,希望能对新型干法水泥工作者围绕回转窑的合理操作从原料配料、原料预均化、预热及烧成一系列工艺过程的操作与控制方面给出一些意见。
二、新型干法水泥生产的特点1.优良的品质本文采取了现在的新型干法水泥生产技术,矿山开采、原料预均化、原料配料及粉磨、生料空气搅拌均化四个关键环节互相衔接,紧密配合,形成生料制备全过程的均化控制保证体系即“均化链”,从而满足了悬浮预热、预分解窑新技术对生料质量提出的严格要求,产品质量可以与湿法媲美,使干法生产的熟料质量得到了保证。
2.低消耗从总体来讲,熟料热耗低烧成热耗可降到3000 kj/kg 以下,水泥单位电耗降低到了90~100 kw·h/t以下。
采用了高效多功能挤压粉磨、新型粉体输送装置大大节约了粉磨和输送能耗;悬浮预热及预分解技术改变传统回转窑内物料堆积态的预热和分解方法,熟料的煅烧所需要的能耗下降。
3.生产效率的大幅度提高悬浮预热、预分解窑技术从根本上改变了物料预热、分解过程的传热状态,传热、传质迅速,大幅度提高了热效率和生产效率。
操作基本自动化,单位容积产量达110~270 kg/m2,劳动生产率可高达1 000~4 000t/(人·年)。
4.减少污染,清洁环保悬浮、预分解技术及新型多通道燃烧器的应用,有利于低质燃料及再生燃料的利用,同时可降低系统废气排放量、排放温度和还原窑气中产生的no2含量,减少了对环境的污染,为“清洁生产”和广泛利用废渣、废料、再生燃料及降解有害危险废弃物创造了有利条件。
新型干法水泥生产工艺流程图转文字
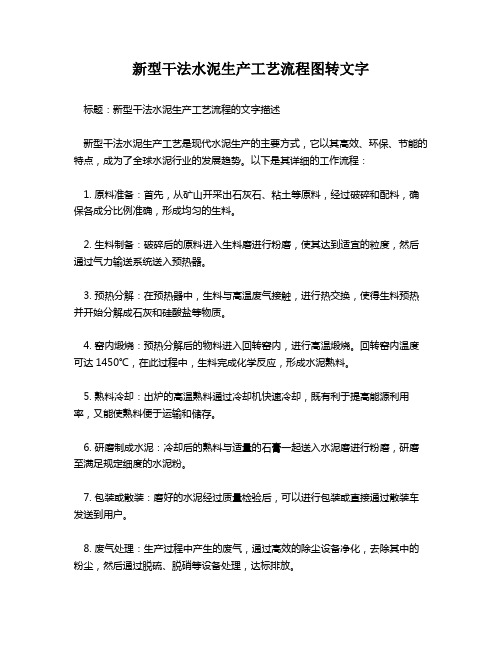
新型干法水泥生产工艺流程图转文字
标题:新型干法水泥生产工艺流程的文字描述
新型干法水泥生产工艺是现代水泥生产的主要方式,它以其高效、环保、节能的特点,成为了全球水泥行业的发展趋势。
以下是其详细的工作流程:
1. 原料准备:首先,从矿山开采出石灰石、粘土等原料,经过破碎和配料,确保各成分比例准确,形成均匀的生料。
2. 生料制备:破碎后的原料进入生料磨进行粉磨,使其达到适宜的粒度,然后通过气力输送系统送入预热器。
3. 预热分解:在预热器中,生料与高温废气接触,进行热交换,使得生料预热并开始分解成石灰和硅酸盐等物质。
4. 窑内煅烧:预热分解后的物料进入回转窑内,进行高温煅烧。
回转窑内温度可达1450℃,在此过程中,生料完成化学反应,形成水泥熟料。
5. 熟料冷却:出炉的高温熟料通过冷却机快速冷却,既有利于提高能源利用率,又能使熟料便于运输和储存。
6. 研磨制成水泥:冷却后的熟料与适量的石膏一起送入水泥磨进行粉磨,研磨至满足规定细度的水泥粉。
7. 包装或散装:磨好的水泥经过质量检验后,可以进行包装或直接通过散装车发送到用户。
8. 废气处理:生产过程中产生的废气,通过高效的除尘设备净化,去除其中的粉尘,然后通过脱硫、脱硝等设备处理,达标排放。
整个新型干法水泥生产工艺流程,充分体现了循环经济和绿色制造的理念,大大降低了对环境的影响,提高了资源的利用效率。
新型干法水泥回转窑工艺及设备概述
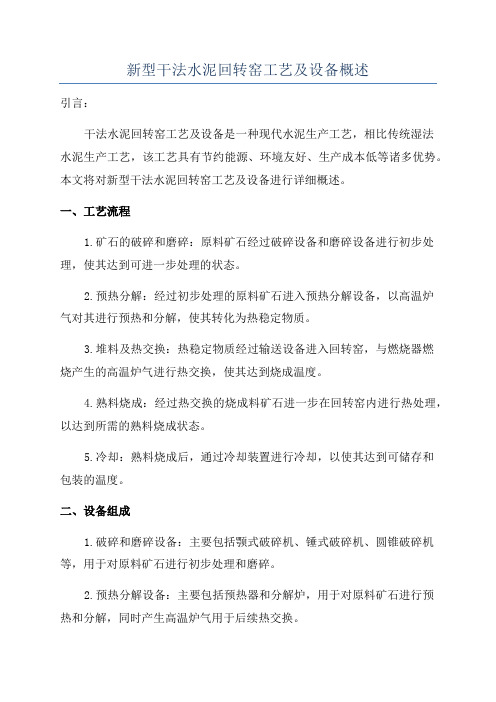
新型干法水泥回转窑工艺及设备概述引言:干法水泥回转窑工艺及设备是一种现代水泥生产工艺,相比传统湿法水泥生产工艺,该工艺具有节约能源、环境友好、生产成本低等诸多优势。
本文将对新型干法水泥回转窑工艺及设备进行详细概述。
一、工艺流程1.矿石的破碎和磨碎:原料矿石经过破碎设备和磨碎设备进行初步处理,使其达到可进一步处理的状态。
2.预热分解:经过初步处理的原料矿石进入预热分解设备,以高温炉气对其进行预热和分解,使其转化为热稳定物质。
3.堆料及热交换:热稳定物质经过输送设备进入回转窑,与燃烧器燃烧产生的高温炉气进行热交换,使其达到烧成温度。
4.熟料烧成:经过热交换的烧成料矿石进一步在回转窑内进行热处理,以达到所需的熟料烧成状态。
5.冷却:熟料烧成后,通过冷却装置进行冷却,以使其达到可储存和包装的温度。
二、设备组成1.破碎和磨碎设备:主要包括颚式破碎机、锤式破碎机、圆锥破碎机等,用于对原料矿石进行初步处理和磨碎。
2.预热分解设备:主要包括预热器和分解炉,用于对原料矿石进行预热和分解,同时产生高温炉气用于后续热交换。
3.回转窑:为整个工艺的核心设备,主要由筒体、支承装置、传动装置、燃烧装置等组成。
回转窑内的烧成料矿石在高温环境下进行热处理。
4.冷却设备:主要包括冷却机和冷却器,用于对熟料烧成后的产物进行冷却。
除了上述核心设备外,还需要配套的输送设备、除尘设备、燃料供应系统等进行辅助。
三、优势与前景1.节能环保:相比于传统湿法水泥生产工艺,新型干法水泥回转窑工艺具有更低的能耗和排放,减少了燃料的消耗和烟气排放量,符合现代环保要求。
2.生产成本低:新型干法水泥回转窑工艺采用了高温炉气热交换的方式,可以充分利用烟气热能,降低能源消耗,从而降低生产成本。
3.适应性强:新型干法水泥回转窑工艺适用于不同原料的水泥生产,可以根据不同的原料特性进行调整和优化,提高生产效率和产品质量。
4.市场前景广阔:在国家加大环保政策的背景下,新型干法水泥回转窑工艺将成为水泥生产的主流工艺,具有广阔的市场发展前景。
新型干法水泥回转窑工艺及设备概述

阻力和框架稿度。
缺点:气固分离效率较低,适用于作为旋风预热器系统的
中间级
新型干法水泥回转窑工艺及设备概述
特点:最上一级为高型圆柱型旋风筒;最下一级的旋风筒则采 用较陡的锥角;目的是为提高分离效率。中部各级采 用的是低压损旋风筒,其排气管(内筒)部位采用了导
向 板,以便使旋风筒内的大部分循环气流由导向板直接 引入排气管,从而保证在不降低气固分离效率的前提
Φ物料填充系数
新型干法水泥回转窑工艺及设备概述
6)回转窑内燃烧带的空气过剩系数 根据生产经验已煤粉为燃料的水泥回转窑
α=1.04-1.10范围较合理
7)回转窑内的热效率
Qsh---水泥熟料理论热耗(在没有热量损失和物损失时,由0℃的干生料
烧成1kg水泥熟料所需要的热量(kJ/kg熟料)
新型干法水泥回转窑工艺及设备概述
(kJ/kg熟料)
新型干法水泥回转窑工艺及设备概述
3)回转窑内燃烧带的截面热力强度(燃烧带的截面热负荷): 燃烧带单位截面面积、单位时间内所承受的热量
4)回转窑内燃烧带的表面热力强度(燃烧带的表面热负荷) 燃烧带单位表面面积、单位时间内所承受的热量
5)回转窑内燃烧带的容积热力强度(燃烧带的容积热负荷) 燃烧带单位容积、单位时间内所承受的热量
新型干法水泥回转窑工艺及设备概述
1.2.4 各级旋风预热器性能的配合(以5级为例)
(1)各级旋风筒的气固分离效率 (2)各级旋风筒的表面散热损失 (3)各级旋风筒的漏风量
1.2.5 各级旋风预热器串联级数的选择(P29)
新型干法水泥回转窑工艺及设备概述
1.2.6 旋风预热器分类以及几种典型的旋风预热器
新型干法水泥回转窑工艺及设备概述
“综合效应”的发展主要体现在以下几个方面: ① 适当扩大分解炉的容积,延长分解炉的出口管道形成“炉体+
新型干法的水泥窑生产熟料工艺
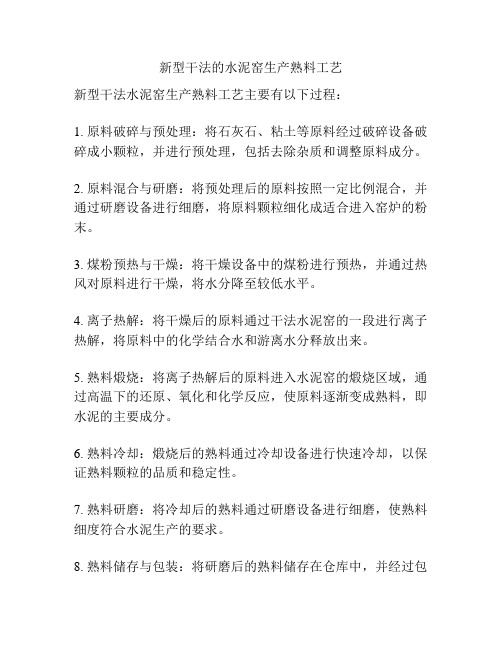
新型干法的水泥窑生产熟料工艺
新型干法水泥窑生产熟料工艺主要有以下过程:
1. 原料破碎与预处理:将石灰石、粘土等原料经过破碎设备破碎成小颗粒,并进行预处理,包括去除杂质和调整原料成分。
2. 原料混合与研磨:将预处理后的原料按照一定比例混合,并通过研磨设备进行细磨,将原料颗粒细化成适合进入窑炉的粉末。
3. 煤粉预热与干燥:将干燥设备中的煤粉进行预热,并通过热风对原料进行干燥,将水分降至较低水平。
4. 离子热解:将干燥后的原料通过干法水泥窑的一段进行离子热解,将原料中的化学结合水和游离水分释放出来。
5. 熟料煅烧:将离子热解后的原料进入水泥窑的煅烧区域,通过高温下的还原、氧化和化学反应,使原料逐渐变成熟料,即水泥的主要成分。
6. 熟料冷却:煅烧后的熟料通过冷却设备进行快速冷却,以保证熟料颗粒的品质和稳定性。
7. 熟料研磨:将冷却后的熟料通过研磨设备进行细磨,使熟料细度符合水泥生产的要求。
8. 熟料储存与包装:将研磨后的熟料储存在仓库中,并经过包
装设备进行包装和销售。
新型干法水泥窑生产熟料工艺相比传统湿法工艺具有更高的热效率和能耗低的优势,同时可以减少环境污染和水资源消耗。
同时,新型干法工艺还可以进行余热回收利用,以提高能源利用效率。
2500T干法旋窑学习资料
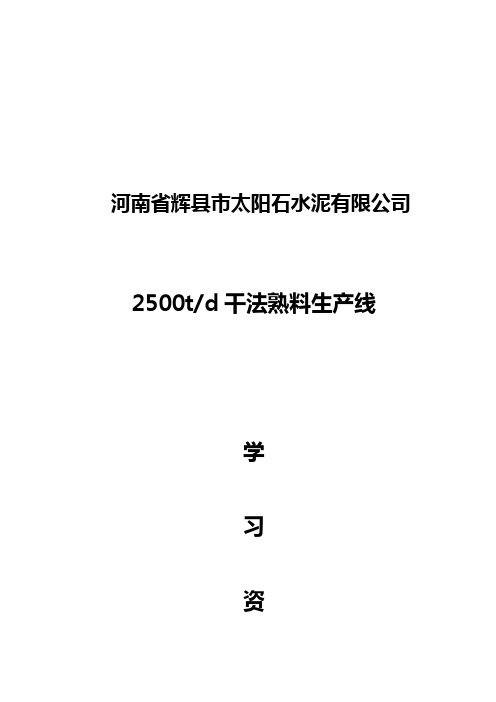
河南省辉县市太阳石水泥有限公司2500t/d干法熟料生产线学习资料目录主要生产工艺 (3)生料磨/废气系统的控制参数 (5)窑系统的调节控制 (6)主机设备参数 (9)物料储存方式、储存量及储存周期 (13)窑系统操作岗位作业指导书 (14)生料磨系统操作岗位作业指导书 (18)煤磨系统操作岗位作业指导书 (21)工艺流程图 (23)主要生产工艺1、石灰石矿山距厂区约1km左右,石灰石破碎设在石灰石矿山,破碎后经汽车运输至厂区石灰石卸车坑。
2、石灰石预均化堆场生产所需的石灰石全部民采,汽车运输进厂,堆存在石灰石露天堆场。
进厂石灰石粒度<25mm,石灰石由卸车坑经胶带输送机输送至圆形预均化堆场。
圆型预均化堆场轨道直径80m,有效储量36000t,储期为9天。
堆料机堆料能力为900t/h,取料机取料能力500t/h。
出预均化堆场的石灰石经胶带输送机送至原料调配站。
3、辅助原料堆存及输送辅助原料全部民采,汽车运输进厂,石英砂岩堆存在露天堆场,硫酸渣堆存于堆棚,粘土(铝矾土)堆存于堆棚,三种原料由卸车坑胶带输送至原料调配石英砂岩、硫酸渣及粘土(铝矾土)仓。
4、原煤堆存、预均化堆场及输送原煤汽车运输进厂,堆存在33×135m长型预均化库,储存量5000t,储存期18.6d。
堆料采用机械堆料,堆料皮带能力100t/h,取料采用铲车取料,由胶带输送机送至煤粉制备车间原煤仓。
5、原料调配、原料粉磨及废气处理系统原料调配站设四个配料仓,分别用于储存石灰石、石英砂岩、硫酸渣、粘土(铝矾土),各仓下设臵卸料及计量、输送设备将每种物料按一定比例从配料库中卸出,送至原料粉磨系统进行粉磨即可。
原料粉磨采用一台Φ4.6×10+3.5m中卸烘干球磨机及ZX3000组合式选粉机组成的闭路系统。
当原料入磨水分≤5%,进料粒度≤25mm(占90%),产品细度为80μm筛筛余≤10~16%时,系统能力为190t/h。
水泥厂旋转窑系统操作规程

窑系统操作规程目的本规程旨在树立安全第一、预防为主的观点,统一操作思想,生产合格生料,力求达到优质、稳定、高产、低耗的目的。
二、范围本规程适用于窑系统,即从生料库底至熟料库顶和窑头废气处理的所有设备。
三、指导思想1.树立安全生产,质量第一的观念,达到连续、稳定生产;2.严格遵守设备操作规程,精心操作、杜绝违章;3.制定最佳操作参数,做到优质、稳定、高产、低耗,努力做到系统设备安全稳定运行,确保生料库料位,实现安全、文明生产。
一、点火前的检查准备工作:1、现场检查各有关设备的润滑情况及螺栓是否松动,尤其是轮带与垫板间应加足石墨锂基脂。
检查预热器、窑及冷却机内的耐火衬完好情况,有关人员、支架、工具、杂物等是否已全部撤离和清理干净,以及三次风管的积料情况。
将预热器各翻板阀吊起,确认管道畅通无堵后,将翻板阀放下,并严密关闭整个系统的人孔门及捅料孔盖。
确认风机进口风门处于关闭状态。
2、校准燃烧器角度及距窑口距离,喷煤管前段与窑口相距10~20cm,角度以窑中心点略偏向第四象限。
并做好记录。
3、根据工艺要求向窑操提供升温曲线图。
4、确认窑头喂煤仓内有足够的煤粉(可用4小时左右),确认柴油泵站有足够的油量满足点火升温要求。
各专业人员进入岗位并完成各项准备工作。
5、窑操作员、巡检工应对本系统全面检查了解,并将准备工作、检查情况及结果全面真实地写入交接班记录,并将存在的问题向分管上级领导汇报。
接到点火指令后,由生产调度通知原料、煤磨、电气、仪表、自动化等专业人员将各设备、仪器仪表送电,通知水泵房送水,通知现场将本系统所有设备的现场控制转入中控位置,检查各设备、仪器是否备妥。
6、启动相关空压机,风机润滑系统窑减速机润滑系统。
二、点火升温:调整预热器烟囱门开度,使窑罩压力在-30Pa左右。
打开燃烧器上内外流手动风门,相差将放风阀打开,中控室启动一次风机,并调节手动风门至一定开度,压力为0.015Mpa,以内流为准。
启动点火油泵,调整供油油站出口压力。
新型干法水泥回转窑系统

在分解炉上部设置了一个涡流室, 使炉气呈螺旋形出炉。 将分解炉与预热器之间的联接管道延长---相当于增加了分解炉的容积),其效果是延长了生料在分解炉内的停留时间,使得碳酸盐的分解程度更高,更重要的是有利于使用燃烧速度较慢的一些燃料。
主要改进:
(2) RSP型炉:
RSP型炉: 结构:左部:混合室(MC室) 右部:上部旋风预燃室(SB炉) 下部涡旋分解室(SC炉) 特点: 燃料:在旋风预燃室喷入,与热空气直接接触而燃烧, 燃烧效果好。 生料:从SC室喂入,被三次风分散。 气体: 窑气经上升管道喷腾进入,热空气从SC炉的内侧 以切线方向送入,两股气流一起进入混合室。 优点:对燃料适应性强 缺点:结构比较复杂,系统通风调节比较困难,流动阻力损失大。
旋风筒改进的几个方面: 1)旋风筒入口或出口处增设导向叶片; 2)旋风筒筒体结构的改进; 3)旋风筒进风口与排气管(内筒)结构的改进; 4)旋风筒下料口结构的改进 5)旋风筒旋流方式的改进
特点:进风口截面由矩形改为多边形,筒体改为双柱双锥的组
单击此处添加小标题
合,柱体直径相对减小,内筒直径加大,插入深度减小等。
02
燃烧带单位截面面积、单位时间内所承受的热量
3)回转窑内燃烧带的截面热力强度(燃烧带的截面热负荷):
01
Qsh---水泥熟料理论热耗(在没有热量损失和物损失时,由0℃的干生料烧成1kg水泥熟料所需要的热量(kJ/kg熟料)
6)回转窑内燃烧带的空气过剩系数 根据生产经验以煤粉为燃料的水泥回转窑 α范围较合理 7)回转窑内的热效率
单击添加大标题
1.2悬浮预热器
旋风预热器的工作原理 生料粉在废气中分散与悬浮 气、固之间换热 (在联结管道内完成) 气、固相的分离,生料粉的收集 (在旋风筒内完成)
新型干法回转窑水泥生产工艺流程简述

新型干法回转窑水泥生产工艺流程简述一、水泥生产原燃材料及配料生产硅酸盐水泥的主要原料为石灰质原料和粘土质原料,有时还要根据燃料品质和水泥品种,掺加校正原料以补充某些成分的不足,还可利用废渣作为水泥的原料或混合材料生产。
(一)主要原料:1、石灰质原料:以碳酸钙为主要成份的原料,,是水泥熟料中CaO的主要来源。
如石灰石、白垩、石灰质泥灰岩、贝壳等。
一吨熟料约需吨左右石灰质原料,在生料中约占75-78%。
2、粘土质原料:含碱和碱土的铝硅酸盐,主要成份为SiO2,其次为AL2O3,少量Fe2O3,是水泥熟料中SiO2、AL2O3的主要来源。
粘土质原料主要有黄土、粘土、页岩、泥岩、粉砂岩及河泥等。
一吨熟料约需吨粘土质原料,在生料中约占11-17%。
(二)辅助原料;1、校正原料:(1)铁质校正原料:补充生料中Fe2O3的不足,主要为硫铁矿渣和铅矿渣等。
一吨熟料约需吨。
(2)硅质校正原料:补充生料中SiO2的不足,主要有砂岩等,2、缓凝剂:以天然石膏和磷石膏为主。
掺加量3-5%。
3、工业废渣的利用:(1)赤泥:烧结法生产氧化铝排出的赤色废渣,以CaO、SiO2为主。
掺加石灰质原料可配制成生料。
(2)电石渣:以CaO为主。
可替代部分石灰石生产水泥。
(3)煤矸石:以SiO、AL2O3为主。
可替代粘土生产水泥。
(4)粉煤灰:以SiO、AL2O3为主。
可替代粘土配制生料,也可作混合材料。
(5)石煤:以SiO、AL2O3为主。
可作为粘土质原料,也可作燃料。
4、燃料:烟煤,用于熟料煅烧。
二、生产工艺流程:水泥生产的工艺流程简称为两磨一烧:两磨是指生料粉磨和水泥粉磨。
烧是指水泥熟料的煅烧。
1、生料粉磨:将制备好的主要原料(即石灰质原料75-78%、粘土质原料16-20%,铁质原料3-5%、)按照一定比例配比输入生料磨进行粉磨,磨制成符合要求的细粉,称为生料粉,然后再通过输送设备输入生料库存放均化。
2、熟料煅烧:将均化好的生料粉通过输送设备输入烧成系统进行煅烧。
新型干法水泥生产工艺流程

新型干法水泥生产工艺流程水泥地生产工艺可以简述为两磨一烧,即原料要经过采掘、破碎、磨细和混匀制成生料,生料经1450℃地高温烧成熟料,熟料再经破碎,与石膏或其他混合材一起磨细成为水泥.由于生料制备有干湿之别,所以将生产方法分为湿法,半干法或半湿法,干法3种.目前常用地是干法水泥生产工艺.水泥生产工艺流程一、水泥生产地生料制备1 破碎工艺水泥生产过程中,很大一部分原料要进行破碎,如石灰石、黏土、铁矿石及煤等.因为石灰石是生产过程中用量最大地原料,开采出来之后地颗粒较大,硬度较高,因此石灰石地破碎在水泥地物料破碎中占有比较重要地地位.b5E2RGbCAP将石灰石通过破碎机进行一次和二次破碎,碎成20毫M石块,常用地破碎设备有锤式、颚式、反击式、冲击式、辊式、圆锥式破碎机等.破碎废气会产生粉尘污染,破碎废气量约为600 m3/t料,粉尘浓度为10g/ m3.p1EanqFDPw2生料地预均化工艺原料预均化预均化技术就是在原料地存、取过程中,运用科学地堆取料技术,实现原料地初步均化,使原料堆场同时具备贮存与均化地功能.DXDiTa9E3d石灰石地储存多采用长形或圆形预均化堆场,粘土或砂岩地储存多采用长形堆场,自动控制堆料机和取料机地作业,均化效果好,成份稳定,并控制了储存和均化过程产生地无组织粉尘地排放.3 生料地烘干工艺烘干工艺是将生料通过烘干机加热干燥.烘干设备有回转式和悬浮式烘干机、烘干塔等,回转式烘干机内温度约700℃,排放废气量约1300m3/t料.RTCrpUDGiT4 生料地粉磨工艺水泥磨包括生料磨和水泥磨,常用地设备有球磨机、立磨、辊压机等.干法磨制一般采用闭路操作系统.湿法磨制通常开路系统,但也有采用闭路系统地.二、水泥生产地煅烧目前大中型水泥厂多使用回转窑,小型水泥厂多使用立窑,我国还有50﹪以上地水泥仍使用立窑生产.1 立窑煅烧立窑工艺地设备是静止地竖窑,分为普通立窑和机械化立窑,属于半干法生产.立窑地日产量已达250~300t/d.立窑又分普通立窑和机立窑,普通立窑采用间歇式生产,能耗热耗较高,产生地废气量约3900立M/吨熟料,粉尘浓度15g/m3.5PCzVD7HxA2 新型干法旋窑煅烧它是在旋窑煅烧增加预分解窑与悬浮预热工艺.生料在预热器以内悬浮状态或沸腾状态下与热气流进行热交换,又在分解炉中加入占总燃料用量50~60%地燃料,使生料在入窑前地碳酸钙分解率达80%以上,达到减轻窑地热负荷,提高产量.jLBHrnAILg预热分解把生料地预热和部分分解由预热器来完成,代替回转窑部分功能,达到缩短回窑长度,同时使窑内以堆积状态进行气料换热过程,移到预热器内在悬浮状态下进行,使生料能够同窑内排出地炽热气体充分混合,增大了气料接触面积,传热速度快,热交换效率高,达到提高窑系统生产效率、降低熟料烧成热耗地目地.xHAQX74J0X<1)物料分散换热80%在入口管道内进行地.喂入预热器管道中地生料,在与高速上升气流地冲击下,物料折转向上随气流运动,同时被分散.LDAYtRyKfE<2)气固分离当气流携带料粉进入旋风筒后,被迫在旋风筒筒体与内筒<排气管)之间地环状空间内做旋转流动,并且一边旋转一边向下运动,由筒体到锥体,一直可以延伸到锥体地端部,然后转而向上旋转上升,由排气管排出.Zzz6ZB2Ltk<3)预分解预分解技术地出现是水泥煅烧工艺地一次技术飞跃.它是在预热器和回转窑之间增设分解炉和利用窑尾上升烟道,设燃料喷入装置,使燃料燃烧地放热过程与生料地碳酸盐分解地吸热过程,在分解炉内以悬浮态或流化态下迅速进行,使入窑生料地分解率提高到90以上.将原来在回转窑内进行地碳酸盐分解任务,移到分解炉内进行;燃料大部分从分解炉内加入,少部分由窑头加入,减轻了窑内煅烧带地热负荷,延长了衬料寿命,有利于生产大型化;由于燃料与生料混合均匀,燃料燃烧热及时传递给物料,使燃烧、换热及碳酸盐分解过程得到优化.因而具有优质、高效、低耗等一系列优良性能及特点.dvzfvkwMI1生料均化新型干法水泥生产过程中,稳定入窖生料成分是稳定熟料烧成热工制度地前提,生料均化系统起着稳定入窖生料成分地最后一道把关作用.rqyn14ZNXI三、熟料磨<水泥磨)工艺水泥粉磨是水泥制造地最后工序,也是耗电最多地工序.其主要功能在于将水泥熟料<及胶凝剂、性能调节材料等)粉磨至适宜地粒度<以细度、比表面积等表示),形成一定地颗粒级配,增大其水化面积,加速水化速度,满足水泥浆体凝结、硬化要求.EmxvxOtOco 水泥熟料地细磨通常采用圈流粉磨工艺.采用压缩粉碎和冲击粉碎方式,可提高40%,粉磨电耗可降低10%.“二磨”电耗约占水泥生产过程总电耗地70%,其中,水泥粉磨电耗约占水泥生产总电耗地40%.水泥粉磨约为生料粉磨比电耗地1.5倍.SixE2yXPq5水泥生产地环境污染我国水泥工业烟尘和粉尘排放总量约占我国全年烟粉尘排放总量地近40%.水泥生产过程中,每生产1吨硅酸盐水泥至少要粉磨3吨物料<包括各种原料、燃料、熟料、混合料、石膏),据统计,干法水泥生产线粉磨作业需要消耗地动力约占全厂动力地60%以上,其中生料粉磨占30%以上,煤磨占约30%,水泥粉磨约占40%.因此,合理选择粉磨设备和工艺流程,优化工艺参数,正确操作,控制作业制度,对保证产品质量、降低能耗具有重大意义.6ewMyirQFL据有关专家统计,每生产1t 水泥就要向环境排放1t 有害气体.我国水泥工业地CO2排放量约为7亿t左右,S02在80万t左右,NOx在100万t左右.kavU42VRUs一、水泥生产废气污染<一)废气量由于窑型不同,生产线不同所产生地废气量有所差异:<二)有组织粉尘产生量及排放1.有组织粉尘产生量与排放量注:立窑一般有5~10㎏粉尘/t熟料泄漏.复膜袋除尘率约99.5%,普通袋除尘率约99%,电除尘<一级除尘)平均除尘率约98%;新型干法复膜袋除尘率约99.8;普通袋除尘率约99.5%,电除尘平均除尘率约99.5%.y6v3ALoS89<三)无组织粉尘排放水泥生产线一般有30~40个有组织粉尘排放点,最大地废气扬尘点是水泥窑和各类磨机.立窑地炉气泄漏排放地粉尘量最大,立窑一般有500~700 m3废气/t熟料和5~10㎏粉尘/t熟料地泄漏.M2ub6vSTnP生料粉尘主要指原料配料、粉磨、均化、输送过程中产生地无组织排放,该种粉尘无组织排放随着水泥工业地技术进步越来越小.燃料粉尘主要指煤进厂、储存、倒运、破碎、粉磨、输送等过程中产生地无组织排放,尤其装卸和倒运过程产生地煤粉尘排放居多.熟料粉尘无组织排放主要来自熟料输送、下料、二次倒运过程,尤其以二次倒运产生地扬尘居多水泥粉尘无组织排放主要来自于水泥包装、散装和运输环节,尤其以装运环节居多.0YujCfmUCw据浙江省水泥散装办引用北京环科院测定使用散装水泥粉尘排放计算数据,散装水泥粉尘排放为0.28kg粉尘/t水泥,使用袋装水泥时,水泥粉尘排放为 4.48kg粉尘/t水泥,两者粉尘排放量差:(4.48-0.28>=4.2kg粉尘/t水泥.eUts8ZQVRd如果按水泥运输无组织粉尘排放水泥厂内外各占50%计算,在水泥厂内散装水泥粉尘排放为0.14粉尘/t水泥,使用袋装水泥时,水泥粉尘排放为2.24粉尘/t水泥,袋装比散装多排放粉尘2.1㎏粉尘/t水泥.sQsAEJkW5T<四) SO2产生量及污染NOx产生量及污染水泥焙烧生产废气中NOχ地含量水泥生产氮氧化物排放量二、噪声污染水泥厂地噪音主要来自磨机、空压机、罗茨鼓风机、高压离心通风机、破碎机、各种泵等设备三、废水污染水泥工业地水污染主要为生产设备外排地冷却水、水收尘产生地废水化验室废水、近年水泥企业一般都建立了循环水系统,水地循环利用率在95﹪左右,废水产生量约为0.075m3/t熟料,排放量约为0.003m3/t.熟料化验室废水经酸碱中和处理后外排,水收尘逐渐淘汰,水泥工业对水环境地污染已不再是污染地主体.GMsIasNXkA 水泥工业环境监察地要点(1>监督落后生产工艺及装备地淘汰.取缔无生产许可证非法生产水泥地企业;关闭土(蛋>窑、普通立窑、直径2.2m及2.2m以下(以1997年6月5日地窑径为依据>地机立窑;淘汰直径2.5113.及2.5m以下地干法中空窑生产线(1997年年底之前已经个人收集整理资料,仅供交流学习,勿作商业用途生产特种水泥地除外>;淘汰直径2.5m及2.5m以下地湿法生产线.禁止新建和扩建各种立窑生产线;禁止对直径2.2m及2.2m以下地立窑进行扩径改造;禁止新建和扩建湿法窑、立波尔窑及干法中空窑.TIrRGchYzg(2>监督水泥生产过程粉尘处理设施地运行效果和粉尘排放(3>监督水泥生产过程中产生无组织排放地生产工序,如生、熟料地存贮、输运、包装等过程地粉尘防治措施.11 / 11。
t新型干法水泥生产线回转窑工艺设计说明书

5000t新型干法水泥生产线回转窑工艺设计原始资料一、物料化学成分(%)成分Loss SiO2 AI2O3 Fe2O3 CaO MgO SO3 其它合计干生料100熟料0 100煤灰0 100、煤的工业分析及元素分析(%温度:900C ;出窑熟料温度:1360r ;废气出预热器温度:330C ;出预热器飞灰温度:300E 窑尾气体温度:1100C。
2、入窑风量比(%。
一次风(K 1):二次风(K2):窑头漏风(K3)=10:85:5 。
3、燃料比(%。
回转窑(Ky):分解炉(Kf) =40:60 。
4、出预热器飞灰量。
kg熟料。
5、出预热器飞灰烧失量。
%6各处空气过剩系数。
窑尾,a y=分解炉出口a L=预热器出口a f=。
7、入窑生料采用提升机输送。
8、漏风。
预热器漏风量占理论空气的比例K4=;提升机带入空气量忽略;分解炉及窑尾漏风(包括分解炉一次空气量),占分解炉用燃料理论空气量的比例K6=9、袋收尘器和增湿塔综合收尘效率为%10、熟料形成热。
根据简易公式(6-20)计算。
11、系统表面散热损失。
460kJ/kg熟料。
12、生料水分。
%13、窑的设计产量。
5000t/d。
四、物料平衡与热量平衡计算基准:1kg熟料,温度:0C;范围:回转窑+分解炉+预热器系统根据确定的基准和范围,绘制物料平衡图(图1)、热量平衡图(图2)。
图1物料平衡图图2热量平衡图物料平衡计算收入项目(1)燃料总消耗量m (kg/kg)其中:窑头燃料量m yr = K y m r (kg/kg)分解炉燃料量m Fr = K F m r (kg/kg)(2)生料消耗量、入预热器物料量a.干生料理论消耗量100 m r A y a 10025.71 1 m rgSL二100 L s= 100 35'2—(kg/kgm式中:a—燃料灰分掺入量,取100%b.出电收尘飞损量及回灰量m Fh= m fh(1 -)=x (1 —二(kg/kg)m yh = m fh —m h= — = (kg/kg)图1物料平衡图图2热量平衡图c.考虑飞损后干生料实际消耗量100 35.2 儿、s100 35.82d.考虑飞损后生料实际消耗量100 _ v100m s=m s (kg/kg)100 W s__入100 0.2e.入预热器物料量入预热器物料量_ m + m k_ —+_—(kg/kg)(3)入窑系统空气量燃料燃烧理论空气量V' LK_ ++(S — O)= x + x + x —_ (Nn i/kg 煤)m‘Lk_ V' Lk x_x_ (kg/kg 煤)b.入窑实际干空气量3 V/h= a y V' Lk n yr = a y Vl k K F m _ 1.05 xx_ (Nm /kg)n yk=x ^x (kg/kg)其中入窑一次空气量,二次空气量及漏风量01=«%= (Nm 3/kg)W _ k20_ (Nm 3/kg)V-Ok1_ K30 _ (Nm 3/kg)c.分解炉从冷却机抽空气量①出分解炉混合室过剩空气量V1_ ( a L— 1)V' Lk m_— 1) x = (Nm3/kg)②分解炉燃料燃烧空气量V2_ V'Lk m r _ V'Lk Km _x = (Nm 3/kg)③窑尾过剩空气量V3_ ( a y— 1)V' Lk m yr _ ( a y— 1)V' -Km _— 1) xx_ (Nm i/kg)④分解炉及窑尾漏入空气量3 V4 _ KVlkm _ K e VlKm _xx _ (Nm /kg)⑤分解炉冷却机抽空气量V F2k=V+V2 —V3—V4 _ +—— _ (Nm3/kg)m F2k_x V:2k = x (kg/kg)d. 气力提升泵喂料带入空气量(忽略)e. 漏入空气量预热器漏入空气量75= K 4V 1 Lk m r = (Nm 3/kg)窑尾系统混入空气总量V Lok2= V 4 + V 5 =+ = (Nm 3/kg) 全系统漏入空气量3V LOK = V L OK + V_OK2=X + =m °K =x V_OK =X = (kg/kg)支出项目(1) 熟料m sh =1kg (2) 出预热器废气量 a.生料中物理水含量W0.2mh= mx 100 = — x 100 =— (kg/kg)b.生料中化学水含量m is = =x — x = — (kg/kg)kS0.017 0.004m 「 0.804 =0.804c.生料分解放出CO 气体量:m wsVws = 0.8040.003 0.001叶0.8043(Nm /kg)3(Nm /kg)d.燃料燃烧生成理论烟气量V co2= 22.418224 x100 x60.10100m =(Nm i/kg)eM co2s M co2CO= CaO M CaO + MgO M44=x"56 +x44s CO2 L fhm co2=m gs〔0。
新型干法回转窑水泥生产工艺流程简述

新型干法回转窑水泥生产工艺流程简述一、水泥生产原燃材料及配料生产硅酸盐水泥的主要原料为石灰质原料和粘土质原料,有时还要根据燃料品质和水泥品种,掺加校正原料以补充某些成分的不足,还可利用废渣作为水泥的原料或混合材料生产。
(一)主要原料:1、石灰质原料:以碳酸钙为主要成份的原料,,是水泥熟料中CaO的主要来源。
如石灰石、白垩、石灰质泥灰岩、贝壳等。
一吨熟料约需1.2吨左右石灰质原料,在生料中约占75-78%。
2、粘土质原料:含碱和碱土的铝硅酸盐,主要成份为SiO2,其次为AL2O3,少量Fe2O3,是水泥熟料中SiO2、AL2O3的主要来源。
粘土质原料主要有黄土、粘土、页岩、泥岩、粉砂岩及河泥等。
一吨熟料约需0.2-0.3吨粘土质原料,在生料中约占11-17%。
(二)辅助原料;1、校正原料:(1)铁质校正原料:补充生料中Fe2O3的不足,主要为硫铁矿渣和铅矿渣等。
一吨熟料约需0.05吨。
(2)硅质校正原料:补充生料中SiO2的不足,主要有砂岩等,2、缓凝剂:以天然石膏和磷石膏为主。
掺加量3-5%。
3、工业废渣的利用:(1)赤泥:烧结法生产氧化铝排出的赤色废渣,以CaO、SiO2为主。
掺加石灰质原料可配制成生料。
(2)电石渣:以CaO为主。
可替代部分石灰石生产水泥。
(3)煤矸石:以SiO、AL2O3为主。
可替代粘土生产水泥。
(4)粉煤灰:以SiO、AL2O3为主。
可替代粘土配制生料,也可作混合材料。
(5)石煤:以SiO、AL2O3为主。
可作为粘土质原料,也可作燃料。
4、燃料:烟煤,用于熟料煅烧。
二、生产工艺流程:水泥生产的工艺流程简称为两磨一烧:两磨是指生料粉磨和水泥粉磨。
烧是指水泥熟料的煅烧。
1、生料粉磨:将制备好的主要原料(即石灰质原料75-78%、粘土质原料16-20%,铁质原料3-5%、)按照一定比例配比输入生料磨进行粉磨,磨制成符合要求的细粉,称为生料粉,然后再通过输送设备输入生料库存放均化。
- 1、下载文档前请自行甄别文档内容的完整性,平台不提供额外的编辑、内容补充、找答案等附加服务。
- 2、"仅部分预览"的文档,不可在线预览部分如存在完整性等问题,可反馈申请退款(可完整预览的文档不适用该条件!)。
- 3、如文档侵犯您的权益,请联系客服反馈,我们会尽快为您处理(人工客服工作时间:9:00-18:30)。
4000t/d新型干法水泥熟料生产线工艺流程说明目录1.石灰石破碎及输送(车间代号:211) (1)2.辅助原料破碎及输送(车间代号:222) (1)3.石灰石预均化堆场(车间代号:234) (2)4.原料配料库(车间代号:242) (2)5.原料粉磨(车间代号:241) (3)6.废气处理(车间代号:253) (5)7.生料均化库(车间代号:243) (5)8.烧成窑尾(车间代号:251) (6)9.烧成窑中(车间代号:255),烧成窑头(车间代号:256) (7)10.熟料储存(车间代号:262) (8)11.熟料散装(车间代号:264) (8)12.煤粉制备(车间代号:601) (9)13.原煤预均化堆场及输送(车间代号:605) (9)14.空气压缩机站(车间代号:710) (10)磐石4000t/d新型干法水泥熟料生产线的设计范围从石灰石破碎至熟料散装共15个子项,系统最大生产能力6000t/d熟料。
设计中以创立优秀设计为本工程的努力目标,以技术先进、设备可靠、经济合理,安全适用、方便施工为设计原则。
以下按车间进行流程叙述。
1.石灰石破碎及输送(车间代号:211)选用B2300重型板喂机和PCF2022锤式破碎机对石灰石进行破碎。
石灰石由自卸车或铲车从堆场运至60t的受料斗,通过重型板式给料机(211.01)送入单段锤式破碎机(211.02)进行破碎,板式给料机由变频电机驱动,通过电机转速的控制,实行对破碎物料流量的有效控制和调节。
板式给料机泄漏的细碎物料与破碎后的物料一起落到胶带输送机(211.03)上,通过胶带输送机(211.03,211.10)输送至石灰石预均化堆场进行预均化。
设有一台桥式通用起重机(211.09),方便重型板式给料机和单段锤式破碎机检修。
破碎机进料边长为1000×1000×1500mm,产量为600-800t/h,大于该进料口的石灰石,应作预处理后再行喂入。
本车间设有一台气震袋式除尘器(211.04),对重型板式给料机(211.01)和单段锤式破碎机(211.02)的扬尘进行收尘作业,收集的灰尘直接落至胶带输送机(211.03)。
一台收尘器有两个以上收尘点的,分支的收尘风管上设有手动阀门,可通过调节阀门开度平衡各收尘点的阻力和风量。
本车间设有一个压缩空气储气罐(211.11),为袋收尘器清灰提供压缩空气。
2.辅助原料破碎及输送(车间代号:222)铝矾土由自卸车或铲车从堆场运至45t的受料斗,通过板式喂料机(222.03)送入颚式破碎机(222.04)进行破碎,而后通过胶带输送机(222.07)运至原料配料车间,板式给料机由变频电机驱动,通过电机转速的控制,实行对破碎物料流量的有效控制和调节,颚式破碎机规格为PE-600×900,产量为30-75m3/h,最大进料粒度为350mm。
砂岩和铁粉由自卸车或铲车从堆场运至45t的受料斗,通过棒阀(222.01)控制落入胶带输送机(222.02),然后通过胶带输送机(222.07)运至原料配料车间进行配料。
胶带输送机(222.07)做为共用皮带,同一时间只能输送一种物料,铝矾土与砂岩、铁粉轮流输送作业。
本车间设有一台收尘器(222.05)并风机(222.06)对颚式破碎机(222.04)及接料胶带输送机(222.07)扬尘点实施收尘,收集的灰尘直接落至胶带输送机(222.07)。
本车间设有一个压缩空气储气罐(222.08),为袋收尘器清灰提供压缩空气。
3.石灰石预均化堆场(车间代号:234)采用Φ90m预均化堆场对石灰石进行均化,堆料能力:1000 t/h,取料能力:600 t/h (1)堆料流程石灰石破碎车间来的石灰石经皮带机(211.10)输送到预均化堆场的堆料机(234.01)上,并经堆料机悬臂输送机(234.02)在环形预均化堆场进行堆料作业,堆料机在PC程控下,逆时针做108°往复回转,同时堆料臂在一次往复回转过程中需要完成从上升到下降的周期变幅运动。
在堆料机的悬臂端头有料堆高度的探头,根据悬臂端头与料堆顶距离的测量结果,悬臂端头的高度随着料堆的高度变化而自动升降,以降低落差减少堆料过程的扬尘。
堆料机沿着料堆环向布料,使成分随机变化的物料,以>500层数均匀的撒布在料堆的全长范围内,直至将破碎后的石灰石堆至设计标高。
堆料机的堆料能力为1100t/h,堆料半径为23m,堆场总储量可达40000t。
堆料部分设有一台脉冲单机除尘器(234.07),用来收集石灰石破碎车间胶带输送机(211.10)转运物料所产生的扬尘。
(2)取料流程堆料机(234.02)沿环形轨道往复将料堆至设计高度,圆形刮板取料机(234.03)将沿着堆好的料堆,通过刮板输送系统将物料刮至中柱底部经地坑胶带输送机(234.05)运出,再由胶带输送机(234.06)转运至石灰石配料库。
取料部分设有两台收尘器,一台(234.08)置于胶带输送机(234.05)上方,用于收集堆场中柱底部物料落至胶带输送机(234.05)产生的扬尘,收集下来的灰尘落到胶带输送机(234.05)上;另一台收尘器(234.10)放置在胶带输送机(234.05)与胶带输送机(234.06)的转运点处,收集下来的灰尘落到胶带输送机(234.06)上。
本车间设有一个压缩空气储气罐(234.11),为袋收尘器清灰提供压缩空气。
4.原料配料库(车间代号:242)原料配料库共有四座圆库,Φ10m石灰石库、Φ8m砂岩库、Φ8m铝矾土库、Φ8m铁矿石库。
(1)石灰石入库从石灰石预均化堆场运来的物料通过胶带输送机(234.06)输送至石灰石配料库顶(2)铝矾土、砂岩、铁矿石入库铝矾土、砂岩、铁矿石这三种原料均通过胶带输送机(222.07)入库,(222.07)下设三通溜子将物料分为两个支路,每个支路各设一个电动闸板阀控制物料流向。
当铝矾土入库时,一路闸板阀打开,物料直接入库。
当砂岩、铁矿石入库时,另一路闸板阀打开,物料流向可逆皮带,根据输送的物料品种选定皮带的运行方向。
(3)库底配料及输送每座库库底并排设有两个卸料口及两套配料系统,分别给两台立磨供料。
每个卸料口下设有棒条阀门(242.06),物料通过棒条阀后落至定量给料机(242.07~242.14),经过这些设备对其流量进行控制和计量后,物料落至胶带输送机(242.19或242.20),送至原料粉磨车间。
为保护原料磨,胶带输送机(242.19、242.20)上方分别设有除铁器(242.21、242.22)。
本车间设有9台收尘器,每座库库顶一台分别为(242.02~242.05)分别为配料库和输送皮带进行收尘,收集的灰尘落至库内。
每座库底设一台收尘器(242.15~242.18),收集定量给料机的扬尘,收集的灰尘落至胶带输送机(242.20),胶带输送机(242.19、242.20)与胶带输送机(A241.01,B241.01)的转运站设有一台收尘器,收集的灰尘落至胶带输送机(B241.01)。
本车间设有一个压缩空气储气罐(242.24),为袋收尘器清灰提供压缩空气。
5.原料粉磨(车间代号:241)选用二套JLM7-64.4立式辊磨系统对原料进行粉磨。
单台磨机最大能力:300 t/h 原料磨车间设有两套立式辊磨机(A241.05, B241.05)系统,分别配备两套上料、回料、成品收集及热风输送系统,成品入库则合并为一路。
由于AB两套系统基本相同,现仅叙述A系统。
(1)物料走向a.上料部分按比例配合好的原料通过胶带输送机(A241.01)经气动三通阀(A241.02),送至胶带输送机(A241.03)和锁风下料阀(A241.04),进入JLM7-64.4立式辊磨机(A241.05)进行粉磨。
为了确保立磨的安全,胶带输送机(A242.01)上部设置有金属探测器,一旦金属物件从除铁器的“筛选”中漏网,将被金属探测器发现,并根据其发出的信号,快速切换气动三通阀(A241.02),将混有金属物件的原料,送至废料仓内临时储存或外排。
b. 回料部分废料仓底设有闸板阀,仓内物料通过闸板阀控制,落至调速胶带输送机(A241.29),通过气动侧三通(A241.31)落至胶带输送机(A241.19),由斗式提升机(A241.21)将物料提升至胶带输送机(A241.01)。
在胶带输送机(A241.29)上设置有金属探测器,若探出有金属物件,则物料通过气动侧三通(A241.31)外排。
胶带输送机(A241.19)上方设有除铁器(A241.20),对废料再次进行除铁。
从立式辊磨机(A241.05)卸出的粗料粉经重锤锁风下料阀(A241.18)落至胶带输送机(A241.19)通过回路系统再次入磨粉磨。
b.成品输送经过粉磨后的生料粉由磨机内部的选粉装置进行选粉,粗粉落至磨内继续粉磨,细粉随气流进入旋风除尘器(A241.06),收集下来的生料粉由空气输送斜槽(241.10、241.13)送往生料均化库。
(2)废气走向来自高温风机(253.05)的废气由电动百叶阀(A241.45)控制进入立式辊磨机(A241.05),磨内热风在原料磨循环风机(A241.09)负压作用下由下而上,烘干物料后进入磨内选粉机,携带细分出磨后进入旋风除尘器,降尘处理后的废气进入循环风机。
通过原料磨循环风机(A241.09)的废气分为两路,一路进入废气处理管路,风量由电动百叶阀(A241.34)控制,与出高温风机(253.05)的废气混合进入窑尾袋收尘器(253.07),另一路作为循环风与入磨热风会合进入立磨,风量由电动百叶阀(A241.35)调节。
为了调整进入立磨的废气温度,在入磨热风管上设置电动冷风阀(A241.36)。
进磨温度应根据磨机的产量和入磨物料的湿度而定,在试生产期间,应就这一参数进行测定,并确定运转期间的控制范围。
立磨进出口的压力差是重要的控制指标,它与磨机的产量和物料的易磨性、喷口盖板的覆盖面积以及外循环的比例等有关,在试生产期间,应就这一参数进行测定,确定合理的控制范围。
在现代的水泥工厂的立磨生产管理中,为了降低压差,以降低风机电耗,主张加大外循环的比例,以降低喷口风速,降低粉磨电耗。
在试生产期间,对外循环的比例,也应进行调试和测定,以确定经济的外循环比例。
立磨有较高的空气通过能力,并因此在较低烘干风温的条件下,具备较高的烘干能力,设计要求入磨原料的综合水分不大于6% ,出磨生料的水分控制在0.5%以下,以适应生料储存、均化和输送等工艺环节对于生料水分的要求。
本车间设有三台袋式收尘器,分别位于胶带输送机(A241.01)转运点,空气输送斜槽(241.10)转运点,和空气输送斜槽(241.13)排气收尘用。